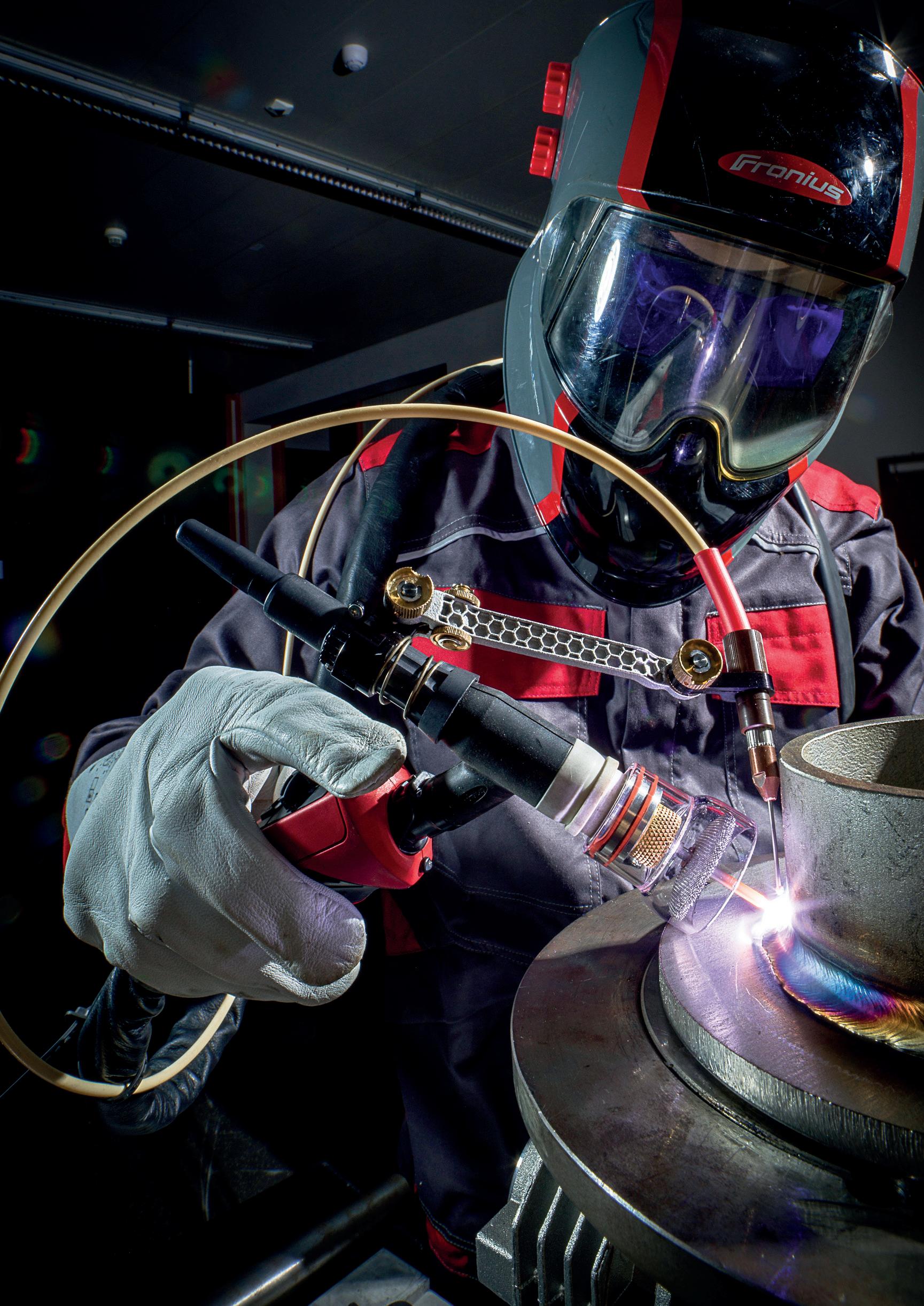
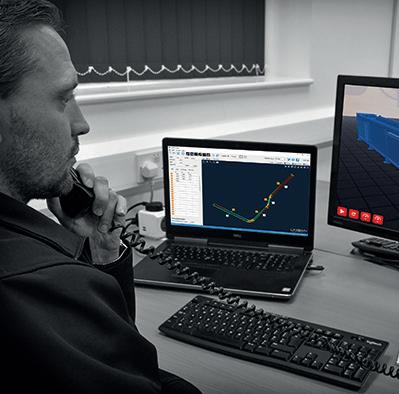

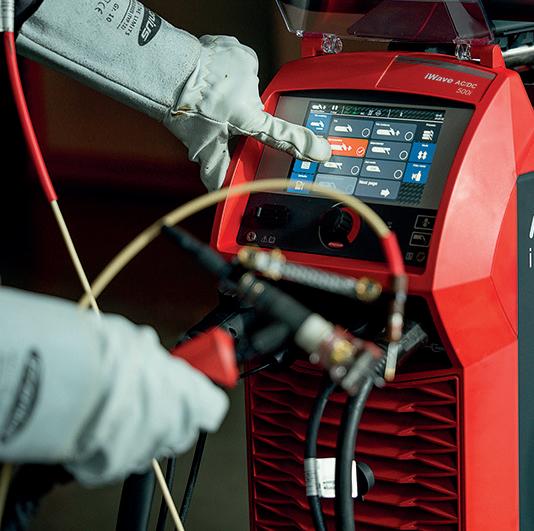
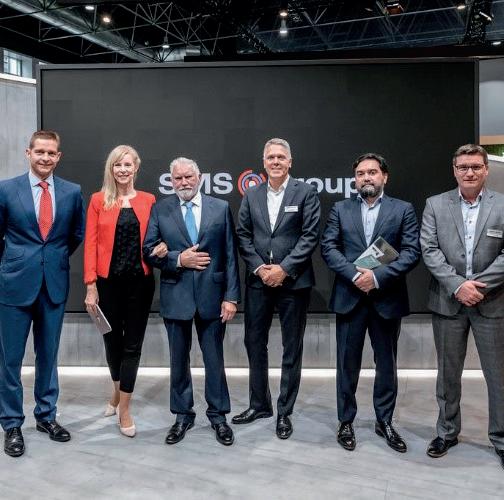
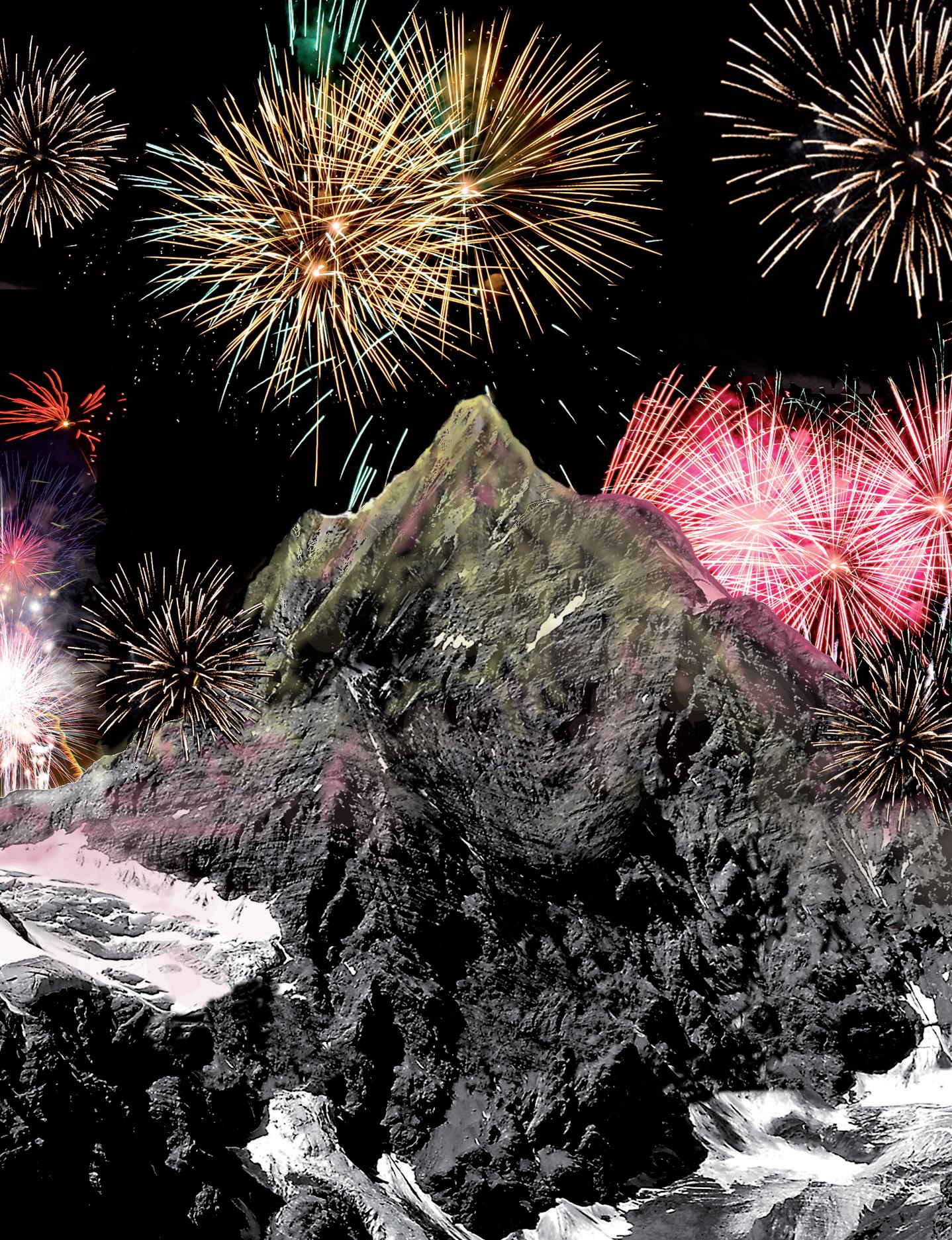
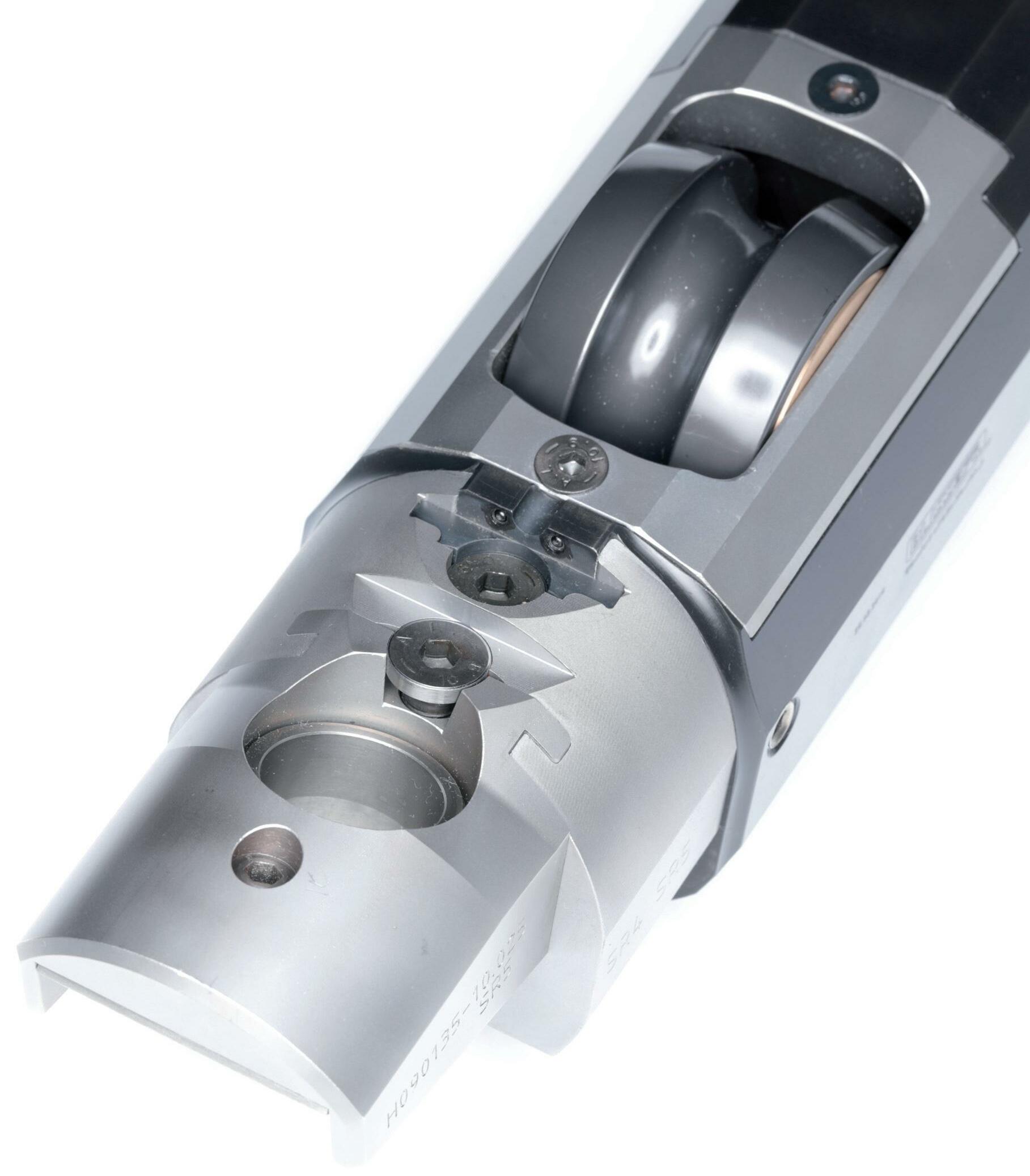
include for the coming year. The Metals production and processing industry we serve, is facing many challenges in the coming years and PIM Metals
When we look at the industry as a whole, energy consumption reduction must play a key role in the long term strategy for not only meeting environmental targets but also profitability, this will be a top down process from those producing raw metal materials to processing machinery
We are all aware of the recyclability of metals but recycling rates have to increase to reduce raw material reliance, recycling also has a cost basis but with ongoing developments from technology providers the return on investment has shown this to be a positive one if adopted.
Looking to the December issue, please send your news to us on any of the following subjects no later than December 7th. Tube and pipe production & processing, Welding technology and Robotics for production & processing. Email: imtmagazine@virginmedia.com
Corinth Pipeworks has been awarded a contract by Saipem S.p.A for the development of an offshore and onshore natural gas pipeline by Gastrade. The Floating Storage and Regasification Unit (FSRU) will be connected to the National Natural Gas Transmission System of Greece, through a 28 km long pipeline, through which the gasified LNG will be transmitted to Northeastern Europe, with the prospect of also supplying Ukraine.
Corinth Pipeworks’ proposal was evaluated as the most advantageous, providing a both technically and economically feasible solution. The offer
consists of 28 km of 30” SAWL steel pipes, which also includes anti-corrosion coating and
concrete weight coating. The entire quantity of pipes will be manufactured and externally
coated at the Company’s plant in Thisvi, Viotia, Greece. Deliveries are scheduled to begin in 2023.
The development of the pipeline plays a decisive role in the energy security of Greece, the Northeastern Europe and contributes decisively to the smooth energy transition and heterogeneity of supply to this extremely sensitive region.
The pipeline’s construction and operation will strengthen the strategic role of Greece, as an energy hub for the wider region of Northeastern Europe and will offer alternative sources and routes of natural gas supply, strengthening security of supply and energy autonomy, in a challenging period.
Leading material handling solutions provider Linde MH has delivered a specially adapted forklift truck for a new customer in the Midlands whose business operates in the most demanding conditions.
Corbetts The Galvanisers, the largest independent galvaniser in the UK, has been dipping steel into molten zinc for 160 years and continues to supply a wide range of manufacturing and engineering businesses from its site in Telford.
It is such a harsh working environment that the firm’s previous fleet of forklifts, supplied by a competitor, lasted just three years into a five-year lease contract.
“Those forklifts just weren’t up to the job,” says Mark Stephenson, Corbetts’ Procurement Manager. “They were falling apart.”
Looking for a forklift that could satisfy the firm’s desire for durability as well as reliability, Mark approached Linde Material Handling.
Industrial applications of this kind are about as tough as it gets for a forklift, and the solution could not be supplied straight ‘off the peg’.
Dan Wood, business development manager at Linde, called in his product support team to find a way of ensuring that the trucks would go the distance and still be financially viable.
The answer was to devise a bespoke galvanised specification that gives the trucks a longer life. The six-strong fleet of counterbalanced 1202s are already in operation at the Telford site.
Standard paint cannot withstand the acidic conditions in which these trucks operate so Linde applies a special coating to the paint to ensure longevity, The heavy-duty mast bearings and rams are also coated in this way to protect them from the corrosive environment.
The 1202 range of forklifts from Linde are perfectly suited to intense operating environments because their
robust construction and hydrostatic drive, coupled with a tough industrial engine, make them the perfect workhorse.
Corbetts uses the trucks to transport bulky items such as truck bodies and lampposts.
For safety, vehicles in the new fleet are fitted with an awareness system which uses advanced technology to warn operators of pedestrians working in the vicinity.
Mark added: “The package that Dan put together was an additional investment but in the long run it will save us money. The constant downtime of a fleet that just wasn’t up to the job, together with the repair bills, was just not sustainable.”
Wipro Limited (NYSE: WIT, BSE: 507685, NSE: WIPRO), a leading technology services and consulting company, and Outokumpu, a leading multinational stainless steel manufacturer, have announced a strategic deal to accelerate Outokumpu’s cloud transformation for applications. This is yet another win for Wipro in Finland, resulting from Wipro’s renewed focus and investments across the Nordics and in Finland.
The deal will help Outokumpu reach its goal of becoming an agile, datadriven, sustainability-focused organization by delivering next-generation applications and building a Microsoft Azure powered platform for Outokumpu’s corporate and
factory applications. As a result, Outokumpu will be able to respond faster to changing business needs, as well as improve productivity, reliability, and the cost-effectiveness of IT services. In addition, this on-demand platform will reduce consumption of power, lowering the carbon footprint associated with Outokumpu’s IT infrastructure.
Stefan Erdmann, Chief Technology Officer, Outokumpu, said, “Our 2025 vision for growth sees us concentrating on three priorities: sustainability, growth from productivity, and customer-focused steering, strengthening our position as the customer’s first choice in sustainable stainless steel. This partnership with Wipro will expedite this agile, productive, and customer-centric approach, thanks to Wipro’s expertise in delivering digital solutions for
metals and steel companies, and its deep understanding of our mission-critical systems and processes.”
Vinay Firake, Senior Vice President & Managing Director – Nordics, Wipro Ltd, said, “This deal is the latest step in our partnership with Outokumpu to accelerate its digital transformation. Wipro is fuelling the change in how Outokumpu’s IT services are delivered to the business, making them more resilient and responsive to the ever-changing needs of the market and its customers. This long-term relationship has been made possible because of how we partner with customers onthe-ground here in the Nordics. We have accelerated our focus and investments in Finland and continue to build teams locally to drive customer centricity and innovation. We look forward to continuing to bring strategic
value to Outokumpu.”
During this transformation journey, Wipro will conduct application cloud discovery; assess, design and right-size the Microsoft Azure platform; migrate and modernize applications; and build an agile and DevSecOps-based IT operating model – increasing the availability of applications in addition to eliminating downtime.
The services will be delivered through Wipro FullStride Cloud Services, which brings more than 1,000 blueprints and over 40 solution accelerators together, acting as an integrated workbench to plan, create, design, develop and manage the entire transformation journey-enabling Outokumpu to fasttrack its cloud adoption and accelerate modernization at scale.
Recently, the Aluminum Association released updated environmental product declarations (EPDs) that show reductions on the environmental impact of aluminum product types including primary aluminum ingot, recycled aluminum ingot, aluminum extrusion products and aluminum sheet products. An EPD is a comprehensive, internationally harmonized report that describes the potential environmental impact of a particular product through its life cycle. EPDs are
widely used in the building and construction industry to help companies make decisions on which products to use in their projects.
Sustainability advancements – like the increased use of renewable energy for primary aluminum smelting, improved efficiency in downstream manufacturing processes and reduced direct process emissions – since the EPDs were first released in 2014 have led to improved environmental performance across all aluminum
product types.
When used in buildings, aluminum supports innovative designs that optimize energy efficiency and support renewable energy use. The declarations enable aluminum end users in the building and construction industry to make informed choices about using the metal. Specifically, EPDs are used to help earn LEED (Leadership
in Energy & Environmental Design)® credit points for green building certification under LEED® V4.
The EPD reports are based on industrywide survey data and represent the average production performance in the United States and Canada. The reports were certified by UL Solutions – a widely respected program operator and the leading firm in verifying EPDs in North America – and developed in accordance with ISO 14025:2006 reporting standards.
Engineering Solutions, based in Redruth, has invested over £420k in a new top of the range CNC milling machine as a consequence of new market growth, expanding their 24/7 machine running capabilities by 200%.
James Gazzard, Group Commercial Director confirms: “2021 was a huge success for us. We grew our client base by 20%, developed new products and expanded our order book by 50%. With a forecasted 43% growth across the group for 2022/23, this latest investment is in direct response to customer demand.”
In the last year, the precision engineering firm has fought against the weakening
automotive sector - which has been historically core to their product line - and strategically focused on expansions in the subsea, nuclear, oil and gas markets. This vision has not only delivered greater sector infiltration in these markets but also led to an evolvement of the company’s manufacturing strategy as they migrate more into the ‘big batch’ engineering field.
Gazzard continues: “We’ve worked so hard to achieve our new high volume order books but despite a fleet of advanced machinery and a brilliant, highly skilled and experienced workforce, we simply couldn’t keep up with demand. This is where the new CNC machining centre steps in - solving production volumes, shortening on time delivery and opening
up new opportunities. This latest investment allows us to manufacture on a constant cycle as the Matsuura CNC H-Plus 300 enables us to double our lights out running capabilities, halves our running times and significantly enhances our commercial and production efficiencies.”
Reducing the reliance on skilled personnel, through advanced machinery automation is an ongoing solution to the limited skilled recruitment pool the manufacturing sector so commonly experiences.
Gazzard concludes: “We’re huge ambassadors of skills training and apprenticeships. In fact, the new cell leader for the expanded milling section was one of our former apprentices.
We really value our staff and have a number of skilled
mechanical engineer positions available. However, accessing the talent is a key concern for the industry. So, we grow our people from the ground up. Our apprentice programme thrives in our low to medium volume, precision engineering manufacturing departments and we’re looking forward to expanding with at least a further three new apprentices this year.”
With WES’s sister company, British Classic Cars (BCC) having also grown, achieving new routes to market across Europe as well as the development of new brake caliper products for Landrover, Porsche, Mercedes and Datsun, WES Engineering Solutions has streamlined its group’s structure to improve efficiencies across all its businesses.
SMS group and Spanish aluminum manufacturer
LatemAluminium have announced their partnership to bring about sustainable aluminum production in the province of Castilla y León in northern Spain. During the Aluminium trade fair in Düsseldorf, Macario Fernández, CEO of LatemAluminium, and Michael Schäfer, Executive Vice President Flat Products of SMS group, jointly presented the circular economy project for aluminum.
For the ambitious newcomer project on the aluminum market, SMS supplies a state-of-theart aluminum cold rolling mill including ancillary facilities for environmentally friendly and sustainable plant operation.
The cold rolling mill is part of LatemAluminium’s major investment project to install plants for recycling aluminum and aluminum alloys and production facilities for aluminum products in the region of northern Spain. A melting plant for aluminum scrap that the Spanish manufacturer recently acquired has already started operation. A total of about 2,000 new jobs are expected to be created. The new cold rolling mill, coupled with expertise from SMS, will support LatemAluminium in
From left to right: Max Boogen, Boogen / Representative of SMS group; Claudia van Veen, Presenter; Macario Fernández, CEO, LatemAluminium; Michael Schäfer, Executive Vice President Flat Products of SMS group; Macario F. García, General Sales Director, LatemAluminium; Markus Fischer, Technical Sales Aluminum Rolling Mills, SMS group
bringing tailor-made aluminum products to market. The six-high mill, equipped with SMS group’s developed CVC®plus technology (Continuous Variable Crown) for work roll and intermediate roll shifting, combined with further actuators for flexible and precise roll gap setting, will be fully capable of producing cold strip in widths of up to 2,200 millimeters. The mill comes with fully automatic coil and spool handling for efficient operation. SMS group supplies a fully harmonized mechatronic plant solution, incorporating the mechanical equipment and the proven modules of
the X-Pact® electrical and automation systems that are specifically dedicated to the process of aluminum rolling. The scope of supply further includes auxiliaries such as the rolling oil recovery system and the CO2 fire extinguishing system.
The advanced rolling technology is in line with LatemAluminium’s commitment to the environment. SMS group will supply a Multiplate® filter to clean the used rolling oil. An Airwash™ system that recovers rolling oil for economic and ecological reuse cleans the exhaust air.
The first coil is scheduled
to be produced on the new aluminum cold rolling mill in April 2024.
Macario Fernández, CEO of LatemAluminium: “We can always count on SMS group’s technology and are looking forward to the production process.”
Michael Schäfer, Executive Vice President Flat Products at SMS group, stresses: “Europe is a key market for SMS group. Besides our long-term customers, we support newcomers like LatemAluminium with our expertise and economical and sustainable solutions for their successful market entry.”
The Swedish Steel Prize recognizes those who fully utilize the potential of steel to improve not only their business or industry, but also society. Attracting entries from across the world, the Swedish Steel Prize is meant to inspire engineers, designers and inventors to further explore the unlimited potential of steel. The competition and its gathering promote the sharing of innovative solutions that leads to a better world.
“The Swedish Steel Prize is a celebration of innovation and good engineering,” explains Eva
Petursson, Chair of the Swedish Steel Prize Jury and Head of SSAB’s Research and Innovation.
“We are looking for solutions that really push the limits of steel and with a sustainable or digital twist.”
The Swedish Steel Prize is open to any individual, company or institution and is awarded to the method or product that best displays how the properties of the chosen grade of steel has contributed to a significant innovation.
All entries are assessed by an independent jury. Together they review each entry based on its level of innovation, creativity,
sustainability, performance and competitiveness. Entries addressing the environment, digital solutions and new trends in the economy are especially encouraged.
The winner of the Swedish Steel Prize receives a diploma, a statuette by the sculptor Jörg Jeschke, and intense media exposure. In conjunction with the Swedish Steel Prize event, SSAB will also make a SEK 100,000 donation to charity. The prize will be announced in Stockholm, Sweden as part of the Swedish Steel Prize 2023 event, May 10–11, where peers from around the world come to learn, network
and be inspired by new steel technologies and their innovative applications.
For the full rules, to read about previous finalists and to apply, applicants can go to www.steelprize.com/apply. All applications must be received before the deadline of January 18, 2023 for consideration.
For further information, please contact: Linda Petersson Chair of the Application Nominating Committee
Swedish Steel Prize
linda.petersson@ssab.com
Anna Rutkvist, Project Manager, Swedish Steel Prize, anna. rutkvist@ssab.com
Industrial process heating equipment and solutions specialist Babcock Wanson has launched the TwinPack range of twin-furnace firetube boilers for steam outputs from 30 t/h to 58 t/h, providing maximum efficiency with very low CO² and NOx emissions.
With energy efficiency top of the agenda, Babcock Wanson has designed its Burner Management System and matched combustion head for precise control of excess air throughout the modulating range, and non-degraded operation at very low load. The simultaneous operation of the burners guarantees an exact thermal load distribution while ensuring maximum flexibility in operation and burner turndown ratios of up to 30:1 on natural gas (mixed and dual fuel firing options are also available).
Efficiency can be further enhanced by up to 105% when a TwinPack boiler is specified in conjunction with a Babcock Wanson economiser and heat recovery system.
This precise match between the boiler and burners not only ensures optimal combustion, but also impacts emissions levels with TwinPack boilers boasting the lowest practicable CO² emissions. The specialist burner technology employed by TwinPack boilers also ensures very low NOx emissions to readily meet and often exceed environmental regulations.
A further environmental benefit to the TwinPack range of boilers is their long life.
Featuring a tubular construction flue gas reversal chamber, unique to Babcock Wanson, TwinPack boilers do not require furnace tube tie rods which require regular replacement,
and minimises boiler refractory requirements. This design allows high variations of steam demand whilst minimising mechanical stress on the pressure body for a long, reliable
operational life.
When maintenance is required, TwinPack boilers provide easy tubeplate and furnace tube access via large, easy use doors on the boiler
SMS group announced today that Hindalco, one of the world’s largest aluminium companies, has placed an order for the supply of a highperformance cold rolling mill for wide aluminium strip. The new mill will be constructed within the periphery of Hindalco’s Aditya Aluminium Unit in Lapanga in Odisha, India. The facility is located near another FRP division of Hindalco in Hirakud, where the company is operating a hot rolling mill.
Hindalco Industries Limited supplies the local and international markets with its aluminium products, which cover a whole alloy spectrum from soft to very hard aluminium grades. The new cold rolling mill is part of Hindalco’s strategy to expand its value-added product portfolio and serve the growing demand for sustainable aluminium solutions.
The new cold rolling mill will feature the well proven interplay of the mill builder’s
front and lateral openings. A rear inspection port also provides enhanced access. An in-built upper platform provides safe access to boiler mountings and ease of maintenance and operation.
TwinPack boilers are fitted with comprehensive instrumentation and controls for easy and economic operation. These include the Navinergy system which allows local
CVC® plus (Continuously Variable Crown) technology and other comprehensive actuators, ensuring highest product quality of strips up to 2.2 meters width and as thin as 0.1 millimeters. In addition the
advanced rolling technology aligns with Hindalco’s focus on green technologies. For cleaning the rolling oil, SMS group will supply two of their Multiplate®-filters. The exhaust air will be cleaned by an
Airwash™-system that reclaims rolling oil for economic and ecological re-use.
The first coils will be produced on the new aluminium cold rolling mill in end-2024. With this new mill, Hindalco’s FRP (Flat Rolled Products) capacity will increase by 170,000 tons, cementing its leadership position in aluminium downstream. The new facility will enable Hindalco to serve the packaging, beverage can, and building & construction industries. This project is the biggest aluminium downstream project in India.
Hindalco Industries Limited is the metals flagship company of the Aditya Birla Group and an industry leader in aluminium and copper. In India, Hindalco’s aluminium units across the country encompass the gamut of operations from mining, alumina refining, captive power plants and aluminium smelting to downstream rolling and extrusions. Hindalco ranks among the global aluminium majors with a manufacturing a footprint spanning ten countries.
operation via the boiler HMI plus remote monitoring through a web interface, plus Babcock Wanson’s exclusive unattended operation modes (three days, seven days and even 30 days of continuous operation within authorised limits).
Highly versatile, TwinPack boilers come with a range of options including economisers, combustion air pre-heaters, O2 and CO trim and even
superheater variants.
The TwinPack range of twin-furnace firetube boilers is the latest addition to Babcock Wanson’s range of firetube boilers. In addition to these, Babcock Wanson offers a complete range of products and services for boiler houses and other process heating needs, including coil type steam generators, thermal fluid heaters, hot water boilers, VOC
and odour treatment by thermal oxidation, water treatment and process air heating solutions. The company aims to help optimise customer’s energy production with high quality products and efficient service.
For more information, please contact Babcock Wanson on 020 8953 7111 or info@babcockwanson.com or go to www. babcock-wanson.com/products/ steam-boilers/twinpack/
TIGcold-wire components are available now for Fronius iWave.
The pioneering innovation lies in its intelligent control. With the patented new TIG DynamicWire welding package, even amateurs can achieve perfect TIG welds with ease. This is because the dynamic wire control always selects the right travel speed. The process adapts to the welder, not the other way around!
TIG welding represents the top tier of welding processes and demands skill as well as years of practice – or does it? “All the new features that we’ve packed into the iWave cold-wire components as well as the corresponding software solution make TIG welding significantly easier,” explains Manuel Rumpl, Head of Strategic Product Management Industrial Welding Solutions, Fronius International GmbH. “Thanks to TIG DynamicWire, welders can focus all their
The new Fronius cold-wire components for iWave are lightweight and ergonomic, providing a lot more flexibility for TIG welding.
attention on the arc and the welding system regulates the optimal wire speed at all times.”
The iWave power categories
from 300i to 500i can be upgraded to the TIG cold-wire system. The TIG DynamicWire welding package is ready for
use immediately by means of software activation and can also be retrofitted to existing iWave systems at any time.
The innovative advantage of Fronius DynamicWire compared to a conventional continuous wire feed lies in its automatic self-regulation. The welding system actively adjusts the wire speed to the welding behavior, torch position, and current conditions, even automatically compensating for component tolerances of up to 30%. The result? Perfect welds every time.
The patented TFC electrode clamping system (Tungsten Fast Clamp) releases and clamps the tungsten electrode at the touch of a button, allowing it to be changed in a matter of seconds.
Precise and user-friendly
During development of the coldwire system, no detail was too small for Fronius when it came to ensuring that welders could work optimally with minimal steps and adjustments. The wirefeeder is set once and then remains in a stable position. The ergonomic and flexible tungsten holder is particularly lightweight as it is produced using material-saving aluminum 3D printing. There are also no disturbing vibrations at the torch handle, as – unlike with comparable solutions –the mechanical forward and backward motion of the wire has been dispensed with entirely with the new TIG DynamicWire cold-wire welding process.
Change the tungsten electrode at the touch of a button
With the Tungsten Fast Clamp system (TFC), welding expert Fronius is bringing out another new patent. A single touch of
the button releases and clamps the tungsten electrode in the spring-loaded clamping sleeve.
Like the lead of a mechanical pencil, the electrode is changed in a matter of seconds. This
system can now also be mounted on existing torch bodies.
Self-regulating, timesaving, and resourceconserving
In times of skills shortages, iWave complete with cold-wirefeeding and TIG DynamicWire can help all TIG novices and those with less experience achieve a great welding result and fast. Selfregulating parameter settings and characteristics as well as a compensatory active wirefeeder
Self-regulating automatic wirefeed via the TIG DynamicWire welding package. Simply download the software and start welding.
provide the necessary safety and ensure a high level of quality. Since the wire does not continuously move back and forth during intelligent TIG cold-wire welding, even wear parts such as the torch body, torch cap, and clamping sleeve experience reduced abrasion and last longer than comparable solutions.
Fronius iWave equipped with all cold-wire components: intelligent SpeedNet-based TIG cold-wire feeder CWF 25i, TIG cold-wire feed system (CW Feeding), and TFC quickchange electrode system
TIG CW Feeding: the new cold-wire feed system can be mounted on intelligent TIG welding torches with ease and remains in a stable position after a one-time calibration. If gas nozzles need to be changed, it is simply folded away and then put back again.
High quality requirements, sustainability aspects, and safety standards are
driving the demands placed on welding technology ever higher. Nowadays, reproducible welding quality and complete welding data documentation are the state of the art. But if welding takes place manually, these demands cannot be met. The solution is automation – even for small and medium-sized enterprises (SMEs).
Although automated welding processes achieve significantly more consistent welding results, small and mediumsized businesses frequently still struggle with automation. High acquisition costs for welding robots and professional programming expertise are at odds with small batch sizes. The CWC-S Cobot welding cell from Fronius provides a solution to this mismatch.
Consistent welding quality – from batches of just one unit
Thanks to precise torch movements with a repeatability of +/- 0.04 millimeters, weld reproducibility is guaranteed
in the Cobot welding cell every time – even in series if necessary. Intelligent Fronius welding technology controls the welding process and records all welding data as required. The WeldCube data management software –optionally available with the welding cell – serves to store and evaluate these data.
Teach Cobots – with no programming experience
“Programming a CWC-S is intuitive and can be quickly learned by any welding specialist; programming know-how is not required. Components can even be loaded and welding programs started by trainees,” explains Christian Neuhofer, Product Manager at Fronius Welding Automation. “This saves on personnel costs and frees up professional welders for more challenging work – making their job more attractive.” This is an advantage that should not be underestimated when searching for skilled workers to add to the team.
Specify the welding path at the touch of a button
The welding torch is manually guided to the starting points, position points, and end points on the component and these
No programming knowledge is required for teaching the cell – the programming steps are intuitive and easy to learn, allowing the welding specialist to concentrate on more challenging tasks.
are confirmed by pressing a button. The software uses this information to calculate the welding contours and welding sequence, while the required welding parameters can also be selected quickly using predefined characteristics. Motion commands such as “pendulum
parameters” or “weld job” can be inserted by means of dragging and dropping on the touchscreen of the Cobot control.
Before starting the welding process, the operator can simulate the welding sequence once again to detect and correct possible interference
start to finish with the compact Fronius CWC-S Cobot welding cell including rotary unit and optional tailstock.
The welding path is traced point by point on the component. The software then uses these key points to calculate the welding contours and welding sequence.
Amada Weld Tech Europe highlights its industryleading AWS3 Servo Motorised Active Resistance Welding System. The unique system combines the IS-Q inverter power supply with FM series of motorised weld heads, motorised weld pincers, or compacting units.
This integrated solution provides process control, monitoring, and quality analysis in one premium system that enables parameters to be set quickly and precisely. With high stiffness, high speed, electrode impact sensitivity, and exact electrode position control, this cleanroom-proof system can serve in a variety of industry applications. These include electronics, medical engineering, and automotive
contours. Once the CWC-S is fully programmed, it welds component after component with consistent quality and at a regular speed.
The welding cell’s standard equipment includes a Fanuc Cobot CX10 iA with a reach of 1,249 millimeters and a payload of 10 kilograms, and a welding table with a working area of 1,500 x 1,000 x 700 millimeters. Operator safety is ensured by a pneumatic glare shield, sliding side doors with viewing windows, and an extraction hood.
Users can choose between the tried-and-tested Fronius Welding Packages Standard, Pulse, LSC (Low Spatter Control), PMC
applications, to name a few. Operators will find the system intuitive, intelligent, and highly interactive.
The operating panel is distinguished by its ease-
of-use, with a single knob operation to push and turn and a touch screen also available. The multilingual user interface and operating concept are both also incredibly intuitive,
with an intelligent design, status line, menu bar, and interactive user guide.
The AWS3 Servo Motorised System comes in basic and advanced options. Static monitoring, remote service capabilities, ethernet communication, force and speed control, and measurement for force or displacement are all available in the basic version. The advanced version also includes additional dynamic process motoring and offers graphical waveform, SPC, and CAN open, and options for profibus or Ethernet/IP.
For more information about the AWS3 Servo Motorised, visit: https://www. amadaweldtech.eu/products/ resistance-welding/op-aws3active-welding-system-andcomponents/aws3-servomotorised#tab-overview
The
(Pulse Multi Control), and CMT (Cold Metal Transfer) depending on the intended area of use, while the TPS 320i or TPS 400i welding systems are available for
in the CWC-S: cuboid 1,500 x 1,000 x 700
the Cobot, subject to the package selected.
The standard equipment can of course be supplemented with special starter packages or the
user-friendly WeldConnect app, for example. Further options include an extraction system, a rotary unit including tailstock, or the option of crane loading.
Intuitive, intelligent, interactive system combines process control, monitoring, and quality analysis
Extremely reliable quick connection technology is warranted to last longer than any other conventional method
QuickFitting, a leading manufacturer of quick connection technology for plumbing, electrical, industrial, municipal, and OEM applications, is proud to stand behind its extremely reliable push-toconnect fittings with the industry’s best warranty. With 54 U.S. patents, the innovative and proven pipe connection technology is warranted to last 75 years, longer than any other conventional method and covering product replacement, labor and damage.
“Reliability is all important for
plumbers, connections behind walls and underground must be trouble free for decades. Plumbers recognize the laborsaving advantages of our products, but they are sometimes apprehensive about the reliability when the technology is unfamiliar,“ according to Matt, CEO. “We know how reliable our products have proven to be. That’s why we offer this warranty, giving plumbers confidence and peace of mind.”
Quick Fitting offers a full range of high-quality plumbing fittings and valves for Copper, CPVC, and PEX plumbing, heating, compressed air, inert
gas and fluid applications. The fittings are reusable, durable plumbing connections, and get the job done 75% faster than traditional methods, including soldering.
The fittings can be installed wet or dry, unlike many other connections, and still delivers a water-tight seal. The fittings greatly simplify installation in wet conditions and in emergency conditions. Plumbers can work more safely and efficiently without having to use chemicals or open flames.
Quick Fitting’s special grip ring technology is manufactured in the US and provides the
right combination of flexibility, strength, and shape memory to enable users to remove and reuse a fitting multiple times without losing any connecting capability. The fittings are guaranteed to make a perfect, permanent connection every time.
All Quick Fitting products are professional-grade, and the 75-year warranty covers their full range of Quick Fitting Brass, Quick Fitting Copper, and Quick Fitting Stainless Steel fittings and valves purchased through an authorized supplier.
For more information visit www.quickfitting.com/.
To allow manufacturers to meet customer demand for lower part prices, the new Seco Helical SN813 milling system features double-sided helix inserts with eight cutting edges that significantly lower cost per edge to boost slotting, side milling and circular rough milling efficiency.
Built for difficult applications involving ISO P, M, K and S materials, the cutters offer applicationspecific sub- family designs featuring left or right-hand helixes, half- or full-effective teeth options, two front insert and many radii choices for
long tool life and maximum chip evacuation.
Reliable and user-friendly, the Helical SN8-13 also eliminates incorrect indexing of front and helix inserts, reducing operator error.
“The demand for price reductions is ongoing and forces shops to economize production operations wherever possible while still maintaining part quality and profit margins,” explained Benoît Patriarca, Global Product Manager Helical Milling at Seco Tools.
“With the Helical SN8-13 system’s design combined with high performance insert geometries and grades, they
can achieve all these goals with one tool.”
Perfect insert indexing Incorrectly indexed inserts can lead to machine downtime, quality issues and scrap.
To eliminate the risk of mistakes, the SN8-13 milling system cutters are specifically designed to make mounting of front and helix inserts easy and foolproof, especially for inexperienced operators.
As an economical alternative to milling products for depths-ofcut from 50 mm up to 100 mm (inch range from 2” up to 3”), Seco offers the Helical SN8-13 in a range of subfamilies built
with its SN13 helix inserts. Those subfamilies include:
R217/220.82: XO16 lead insert for standard use
R217/220.82-H: AC15 lead insert for heavy duty applications
R217/220.81: AC15 lead insert for low power situations
R217/220.81-K: AC15 lead insert for weak fixturing situations
The range is designed with arbor style connections that match most standard holders as well as Seco Weldon, Weldon and Capto interfaces. For more information on the features and specifications of the Seco Helical SN8-13 milling system, please contact a local Seco representative or visit www.secotools.com/ milling.
integrates the technology function directly in the controller, and therefore offers additional process advantages.
The cross-cutting function is always used in mechanical engineering when defined material lengths must be cut or machined. In metalworking, for example, this can be a pipe cut, or a paper or foil cut in other areas. Printing via stamps, for example, is also an area of use. In addition to its cross-cutting library in the control unit, the drive and automation specialist Baumüller offers a newly developed drive-based solution for these applications. The function is integrated directly in the servo controller and
therefore achieves even faster response times and greater precision.
The converters of the Baumüller b maXX 5000 family are equipped with the integrated highperformance control platform b maXX-softdrivePLC. This enables control functions to be loaded directly onto the drive. Programs can therefore run highly synchronized with the controller clock at cycle times up to ≤125 μs. Baumüller has now used this intelligence in the drive in its new cross-cutting solution and lets the function run directly in the servo drive. Once transferred into the drive,
this intelligence forms its own, lean system with numerous advantages. Separate control hardware is therefore not necessary for a large number of applications or can be reduced, saving effort and costs.
The control circuit runs in the fast converter cycle, which means higher dynamics and process accuracy. The process quality is also ensured at a slower clock rate of the field bus. Since Baumüller converters provide a large number of fieldbus interfaces, the drivebased solution can be integrated as a subsystem in the higherlevel systems with little effort.
If the solution is used as an autonomous subsystem and, for example, diagnosis or parameterization by the user is
required, it is also possible to link a separate HMI.
No programming knowledge whatsoever is needed for the finished technology solution, the movements merely have to be parameterized. All parameters, e.g. transmission factor, distance from the measuring point or roll circumference are adjustable.
Major advantages in using the Baumüller technology solutions include the non-existent programming work due to simple parameterization, the shorter time to market, and the lower costs. The customer can therefore conveniently fall back on validated and tested technology experience.
Aspart of its commitment to driving operational excellence and manufacturing efficiencies, leading welded steel mesh manufacturer Siddall and Hilton Products has invested in two innovative automation projects designed to further streamline its processes and accelerate the company’s journey to being recognised as a world-class manufacturer.
The Yorkshire-based business, which is the UK’s largest manufacturer of industrial welded mesh and perimeter fencing panels, partnered with Sewtec, a global market leader in bespoke machinery and automation, to
develop a robot to automate the process of packaging and banding its finished product – it is believed to be the only robot of its type in the UK.
The innovation follows the commissioning of Siddall and Hilton Products’ EVG-LGR102 welding machine in August 2021 which has a significantly faster throughput than other production lines on site, causing subsequent ‘bottle necks’ in the process as conventional product handling methods were simply not quick enough, resulting in inefficiency and unnecessary downtime of around 10%. Sewtec was identified as an automation partner and, together, the two businesses developed a technical solution to the issue with a fully
integrated pallet de-stacking device introducing pallets into the production line automatically.
A five axis robot has also been integrated into the production line to ‘pick & place’ and rotate if necessary the mesh after welding and automatically stack on to a pallet; once the pallet is fully assembled, it is automatically transferred to an in-line automatic banding machine where edge protection is applied and the product banded, presenting a complete pallet/package at the end of the production line for either warehouse and or dispatch.
Having started the automation project in June 2021, it passed the factory acceptance stage and was installed into the
production line in summer 2022. It is now fully operational.
Andy Dawson, operations director at Siddall & Hilton Products, explains: “We’re well aware that automation will play an important role in helping us realise our determination to be a world-class business with these projects marking our first significant step into robotics.
Following the commissioning of our newest £2m welding machine last year, the need for a swifter, automated stack and wrap palletiser came into start relief – in some instances the line is 90% faster than conventional mesh welding machines when producing standard panels, and our operators have needed to keep stopping the line whilst
they unload and pack the products.
“Having looked at different automation companies, we were really impressed by Sewtec in terms of their concept, level of know-how and communication. They have more than lived up to our expectations and, all being well, this is only the beginning of what we can achieve together.
“By investing in this sophisticated technology, we have been able to recover the efficiency losses of around 10% whilst also improving the overall health and safety of our employees through a reduction in manual handling. It is forwardlooking projects such as this which will help make us more competitive globally and form a vital part of our ambitious growth plans.”
Andy Perks, head of sales at Sewtec, commented, “We’re really pleased to be working with Siddall & Hilton Products. The
two businesses align perfectly and we’re off to a great start on this automation journey.
With so much scope for future endeavours together, we are confident there will be further exciting projects ahead.”
Processing over 22,000 miles of wire a month, Siddall and Hilton Products is the UK’s largest manufacturer of industrial welded steel mesh for highsecurity fencing, general fencing and industrial mesh panels. With
a heritage stretching back 127 years, the company is continuing to grow its workforce with the recruitment and training of new mesh operators as well as a range of development programmes to upskill its team.
Visitorsto FABTECH Booth C10217 will be able to discover so much more than the latest allelectric and hybrid tube bending machines from Unison Ltd., the inventors of all-electric tube manipulation. That’s because Unison, a company renowned globally for its user-friendly control systems and advanced tube simulation software, will use the event to launch Opt2Sim Tube – the latest addition to its Opt2Sim software suite. Delegates visiting Unison’s FABTECH booth will also have the chance to win one of several Opt2Sim Tube software licenses.
“In developing Opt2Sim Tube, our goal was to offer a tube simulation product that would make it simpler and more straightforward than ever before to create virtual parts ready for bending data to be uploaded to the bending machine,” comments Unison Ltd.’s joint managing director, Alan Pickering. “In Opt2Sim Tube, we give users the ability to drag and drop STEP files into the software program and extract tube data instantly. Parts can also be drawn by simply entering XYZ or YBC coordinates and viewed in 3D. Bend data is quickly converted into printable reports and individual tube data can also be extracted. An exceptional piece of tube simulation software, Opt2Sim Tube is incredibly intuitive.”
Unison’s new Opt2Sim Tube software sits within the company’s wider Opt2Sim suite of 3D simulation software programs. Perfected for ‘Design to Manufacture’ production
strategies, Opt2Sim tube bending simulation software uses machine and component data to provide a precise, virtual insight into the tube bending process before a single part is bent.
Enhanced collision detection Products within the Opt2Sim software suite include a version where both CAD modelling capability and control engine are used to not only provide accurate simulation, but also enhanced collision detection. Believed to provide unique capabilities for enhanced batch processing, simulated bending takes place on an exact CAD representation of the Unison Breeze or Synergy machine that will be used.
Additional options include:
Selecting Opt2Sim AI provides advanced Artificial Intelligence that will always aim to find a solution to even the most
complex tube geometry, or whenever a potential collision between tube and machine is simulated. The AI feature is particularly useful with right/ left machines and when assisting in the development of highly complex parts, such as those used in the oil & gas industry.
Opt2Sim WPS (Work Processing System) allows multiple users to batch process multiple parts at once. Widely used in the aviation and shipbuilding sectors, Opt2Sim WPS offers rapid ROI, by enabling many hundreds of different tube profiles to be processed in a matter of hours.
Finally, there is Opt2Sim Tube Scan. Possibly the most advanced tube measurement tool on the market, Opt2Sim Tube Scan provides rapid scanning of physical tube geometry and extraction of tube data, and
incorporates ‘Compare to Master’ and intuitive functions in the event corrections are required.
“We are confident we now offer the most comprehensive suite of tube simulation software available,” adds Alan Pickering. “Unison Opt2Sim makes importing and extracting tube data easy and offers stepped software enhancements that take simulating the bending process, creating batch files and scanning tube coordinates to the next level. Opt2Sim provides users with a complete end-to-end solution, from taking 3D STEP files to bending tube within a single software suite. Opt2Sim Tube Scan takes the functionality of measurement software further than ever before – and is competitively priced when compared to scanning arm technologies.”
Unison will be exhibiting at FABTECH Atlanta, GA, USA
-10