
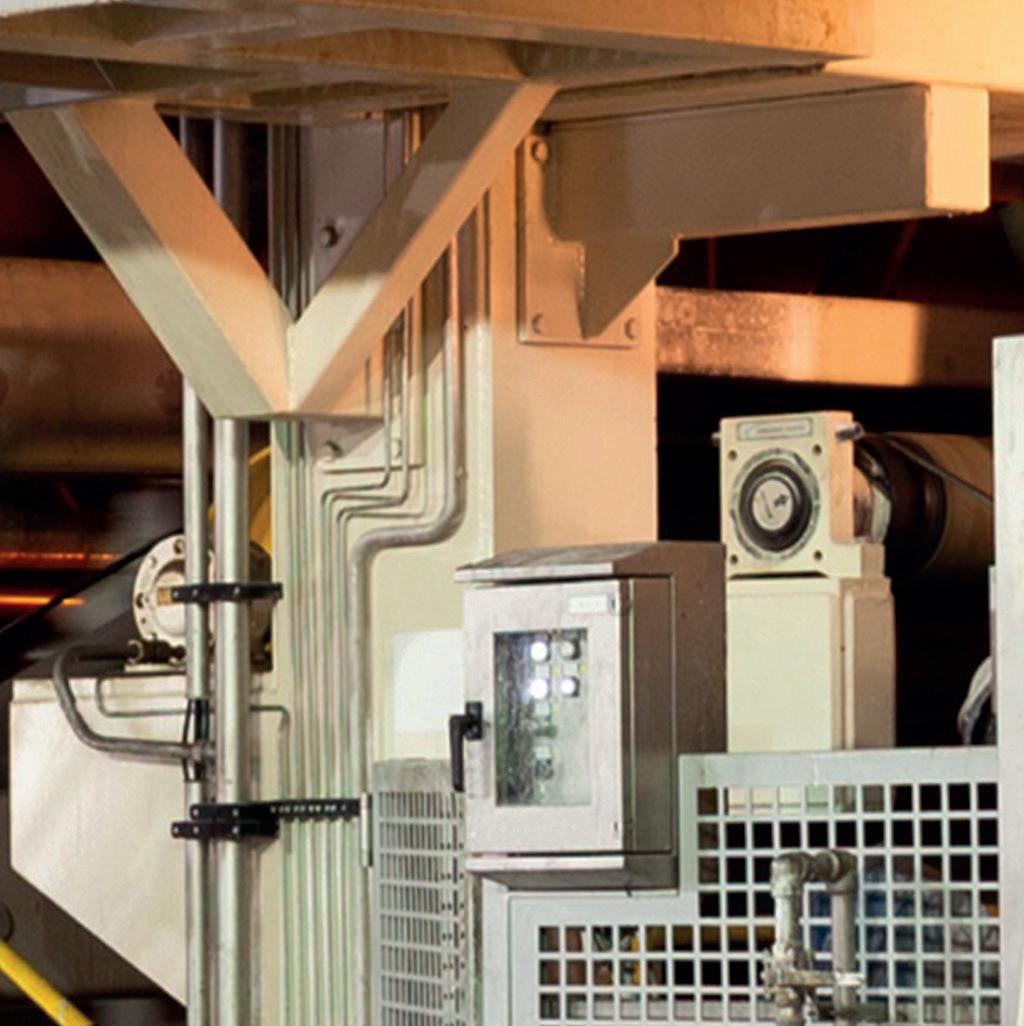
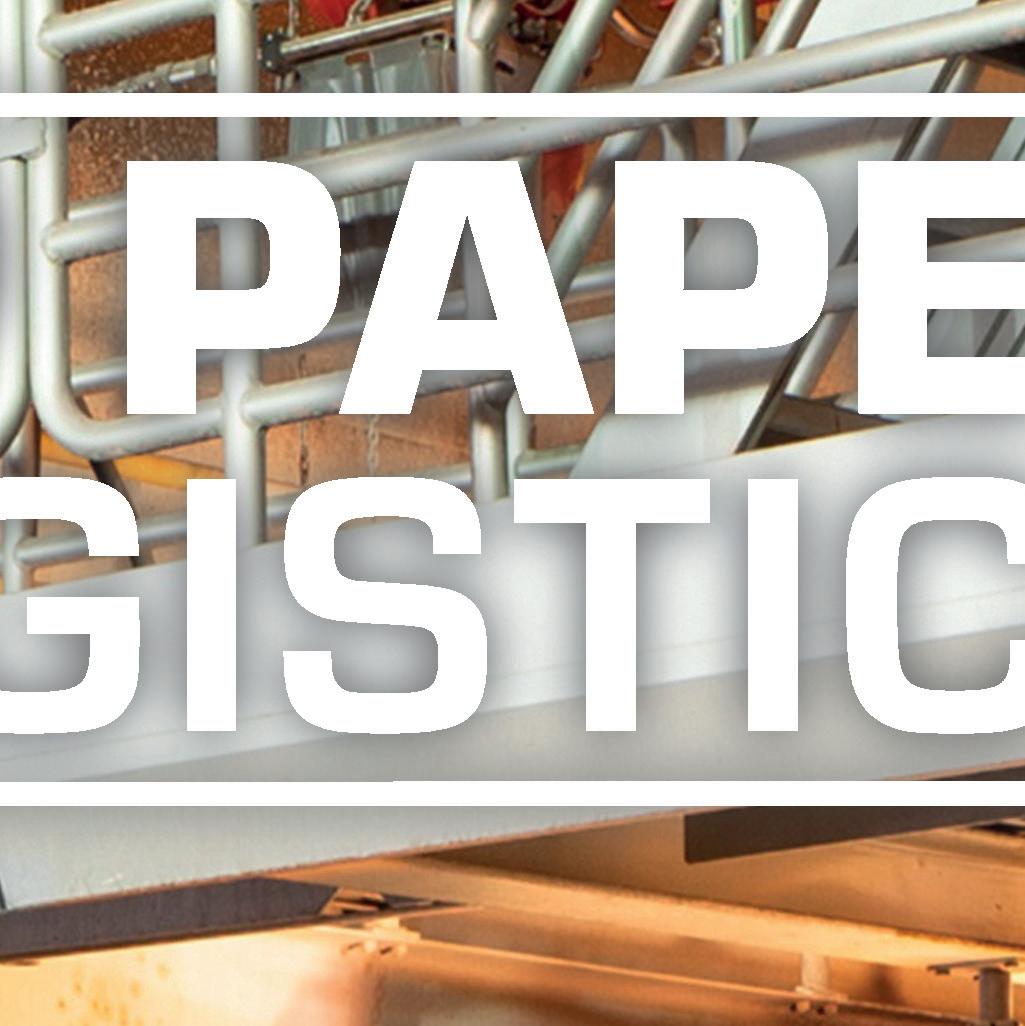
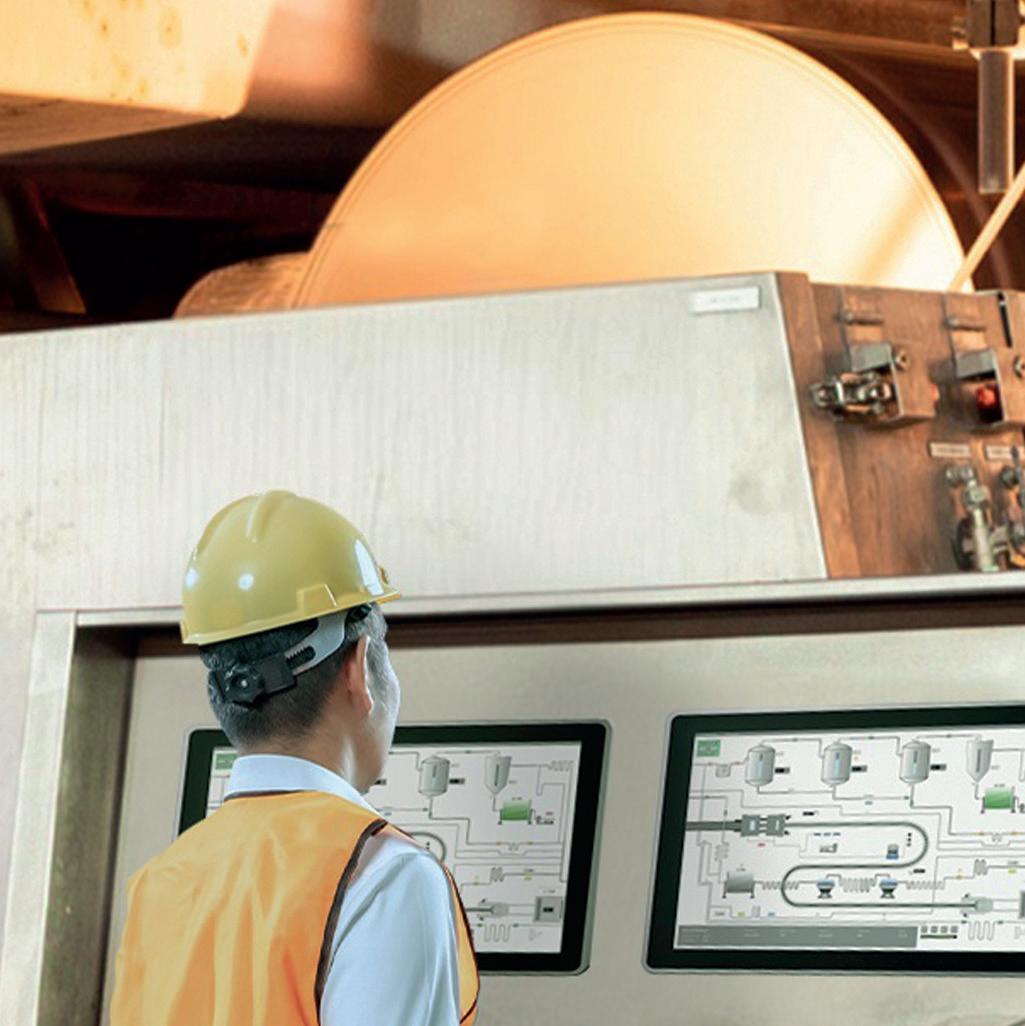


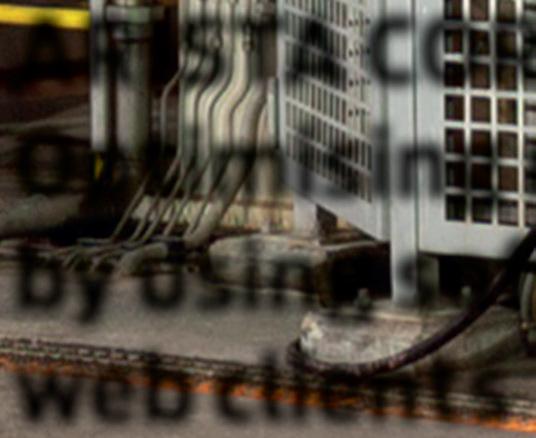
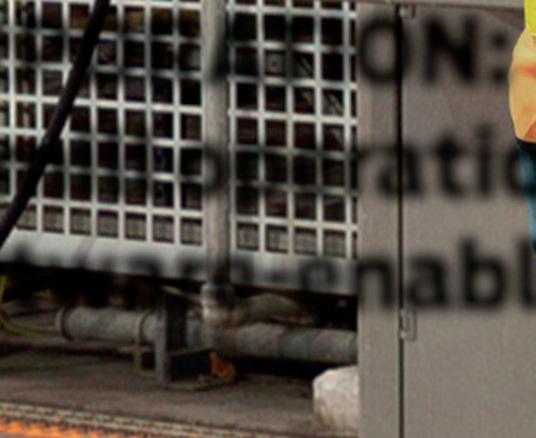
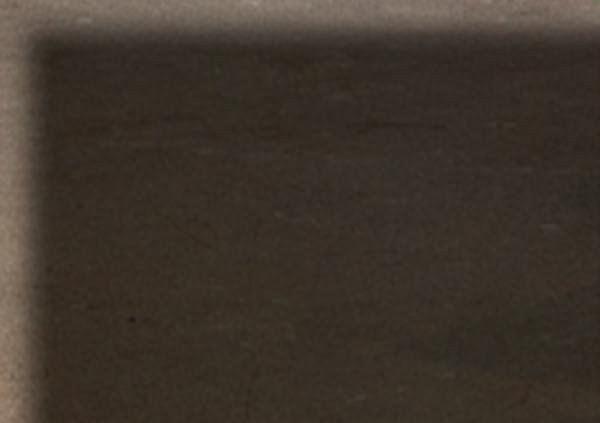

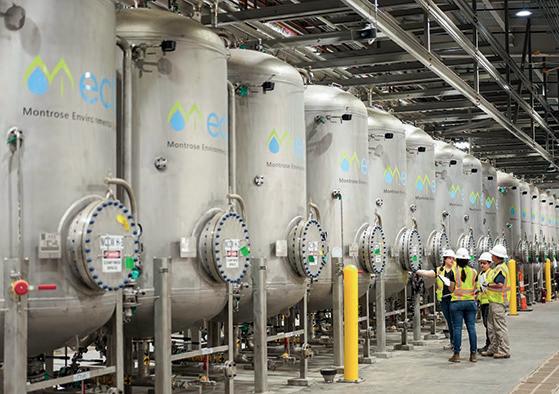

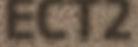




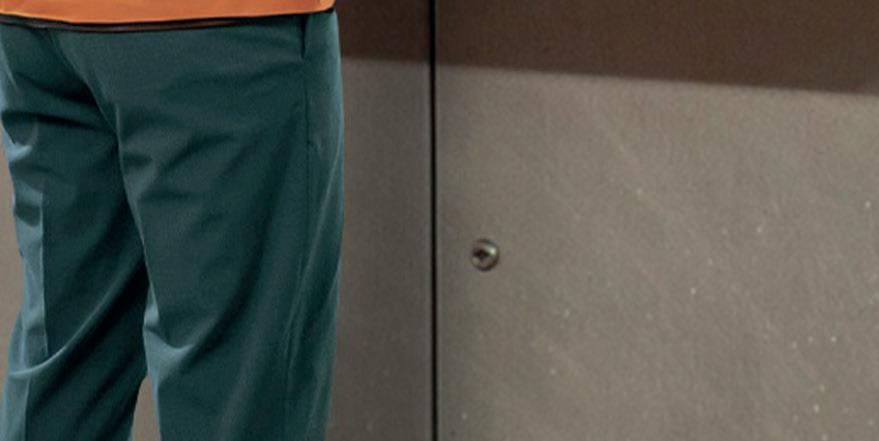
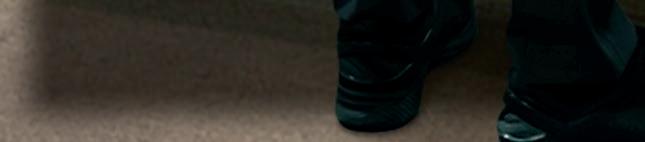

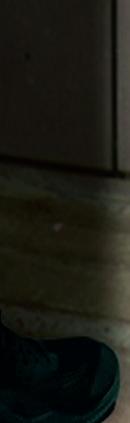

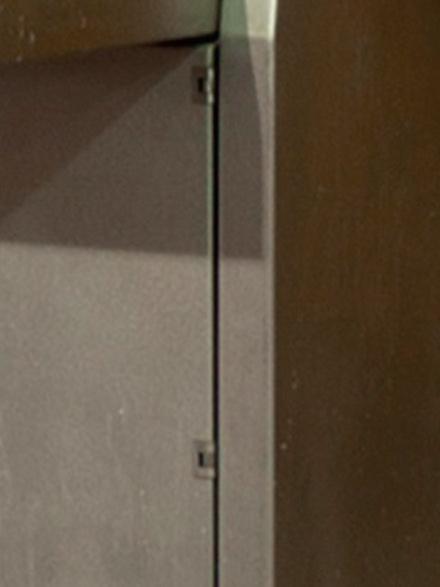
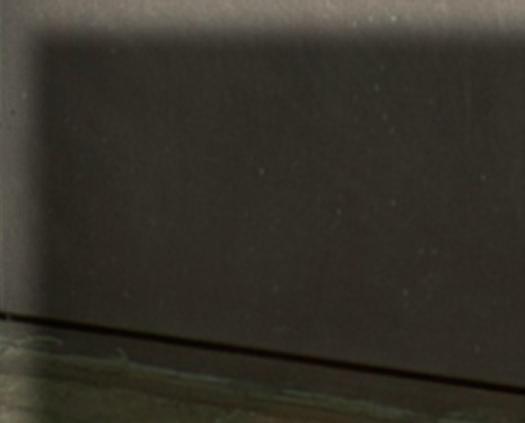

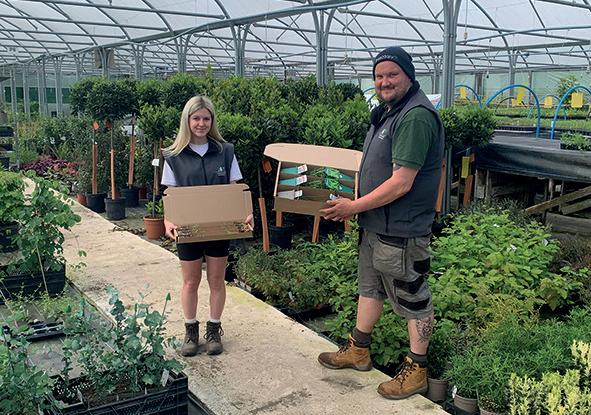

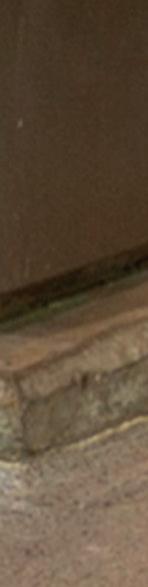
Valmet DNAe is a next-generation distributed control system. As a fully web-based platform, it delivers an industry-leading user experience and cybersecurity by design.
The system brings the process know-how of the world’s leading experts directly to your control applications and improves efficiency. It provides unique data collection and utilization capabilities, enabling informed decision-making.
Valmet DNAe is a catalyst for sustainable practices, and it sets the stage for autonomous operations and a digitalized future. Empower people to perform at their best, reach and exceed your targets, enable path to autonomous operations and evolve throughout the lifecycle with the new DCS. Are you ready to evolve?
For more information, visit valmet.com/dnae
elcome to the July-August issue of Pulp Paper & Logistics, which arrives at an exciting moment for the industry. The recent completion of the deal to create Smurfit WestRock means that the pulp, packaging and paper business has a leader that is truly massive on a global scale with annual projected sales of $32 billion, 63 mills, more than 500 converting sites, and 100,000 plus staff in 40 countries.
With the pending acquisition of DS Smith by International Paper (see the details in the news section), competition is hotting up, and key to having an edge is the use of innovative technology.
Innovation takes many forms with increasing complexity of offering and cost. But at the end of the day innovation is led by our industry and the goal is to manufacture products as cost effectively as possible while protecting the environment and cutting fossil fuel sourced energy consumption.
The industry has been meeting the challenge of market changes with the decline in demand for newsprint being matched by a rise in the need for sustainable and recyclable packaging and tissue products.
These developments are highlighted with the inclusion of Green Packaging International in every issue of Pulp Paper & Logistics.
For those of you visiting or exhibiting at MIAC in Lucca in Italy I will be available for meetings for the duration of the show to discuss any new products or ideas for forthcoming issues. Appointments should be booked in advance where possible at my email address below.
Looking forward to the next issue, September-October 2024, we will be featuring the 30th anniversary MIAC 2024 show preview; tissue handling and processing plus mill carbon capture and emissions management.
Contributions for the issue should be with me no later than 17 September at pulppaperlogistics@virginmedia.com.
Vince Maynard, Publisher and Editorial Director
ISSN 2045-8622 (PRINT)
PUBLISHER & EDITORIAL
Vince Maynard
Tralee, Hillcrest Road, Edenbridge, Kent,
TN8 6JS, UK
Tel: +44 (0) 1732 505724
Mobile: +44 (0) 7747 002286
Email: pulppaperlogistics@virginmedia.com
John Nutting Tel: +44 (0) 1732 868071 Mobile: +44 (0) 7860 221486 Email: johnnutting47@gmail.com CONSULTANT
David Young Tel: +44 (0) 1737 551687
+44 (0) 7785 796826 PRODUCTION
Anthony Wiffen
Tel: +44 (0) 1460 261011 Mobile: +44 (0) 7851 612799 Email: anton_print_1@mac.com
The world’s biggest packaging company was created in July with the approval by shareholders of WestRock to accept the US$11 billion offer by Smurfit Kappa that was originally made in September 2023.
Smurfit Westrock is based at Dublin in Ireland and has projected sales of $32 billion, 63 mills and more than 500 converting sites worldwide, employing more than 100,000 people. It will consume yearly about 15 million tons of recycled fibre and have capacity to produce around 24 million tons of paper.
With sales in 2022 of US$21.3 billion, WestRock provides the bulk of turnover, while Smurfit Kappa had sales of €12.82 billion ($13.7bn).
Smurfit Kappa’s chief executive
Tony Smurfit has the same role at Smurfit Westrock, with Irial Finan as chair of its board.
The arrival of Smurfit Westrock creates a new global order in the pulp and paper industry. Two years ago in 2022, WestRock rivalled US-based International Paper with sales each of $21.2bn, making them leaders ahead of Texas-based Kimberley-Clark with
sales of $20.0bn; Smurfit Kappa with $13.7bn, Finland’s UPM with $12.5bn; Stora Enso, also in Finland and with $12.5bn; Japan’s Oji Holdings with $12.2bn; the UK’s Mondi with $9.5bn; Hong Kong’s Nine Dragons Paper Holdings with $7.5bn and Japan’s Nippon Paper Holdings with $7.5bn.
Now, Smurfit Westrock is well ahead of International Paper (IP)
World leading pulp producer
Suzano has expanded its presence in North America with the acquisition of the assets of US-based Pactiv Evergreen for $110 million.
The deal includes two mills, at Pine Bluff, Arkansas and Waynesville, North Carolina that manufacture liquid packaging board and cupstock.
Subject to regulatory approval later this year, the mills will add about 420,000 tonnes of integrated paperboard to Suzano’s production capacity. Alongside the acquisition, Suzano has signed a long-term supply
deal with Pactiv Evergreen to provide liquid packaging board for its converting business. Suzano is currently the largest supplier of hardwood market pulp in North America, with US offices in Fort Lauderdale, Florida, and a research and innovation campus close to Vancouver, Canada. Already a major producer of materials for food and beverage packaging in Latin America, Suzano will work alongside Pactiv Evergreen’s team, using its operational knowledge and experience to enhance the competitiveness and profitability of the mills, which are already
by revenue. But that could change with the continuing negotiations between Tennessee’s IP and UK-based DS Smith, who were expecting to complete a $7.8 billion deal – which had overtaken an acquisition offer by Mondi (see PPL March-April 2024) – by the final quarter of 2024, creating a pulp and paper giant that could match Smurfit Westrock.
With most of IP’s operations in the Americas and DS Smith’s in Europe, the combination of the two papermakers – sales of $18.9bn a year from IP and $8.9bn from DS Smith – is expected to generate combined sales of almost $28bn.
Those negotiations were interrupted by a counter offer of $15bn for DS Smith by Brazil’s Suzano. But just as Smurfit Westrock announced that its own
well-positioned in the North American packaging industry.
Fabio Almeida, executive vice
of paper and packaging
acquisition is in line with our strategy. We
creation was complete at the beginning of July, IP rejected the offer by Suzano, which declined to rebid (story below).
Next stage in the merger between IP and DS Smith is gaining approval from the European Commission. But with their geographic operations being mostly complementary, only minor changes may be required. Chief executive of the combined firm would be Andrew Silvernail. Formerly executive adviser at New York City-based global investment firm KKR & Co, he was elected as chief executive of IP from the beginning of May, succeeding Mark Sutton who has been with the company for 40 years and remains as chairman.
Following the completion of the Smurfit Westrock deal and its listing on the New York stock exchange, Tony Smurfit commented: “Combining Smurfit Kappa and WestRock creates a world-leading sustainable packaging player, bringing
are entering the North American market as a competitive producer of paperboard, taking on quality assets that are strategically welllocated from an operational and logistical perspective, and opening new opportunities for growth.”
“As a business with 100 years of history behind us, we see this deal as an investment into our future and we look forward to building a longlasting and positive relationship with the teams at Pine Bluff and Waynesville, as well as the local communities around both facilities.”
The acquired assets benefit from high availability of wood in the region, low energy costs, and good access to railways, ports, and highways, says Suzano.
Commenting on the sale,
Tony Smurfit, chief executive of Smurfit Westrock
together a tremendous depth of experience and expertise from both companies. We believe that this combination has created the ‘go-to’ leader and partner of choice in sustainable packaging. I’m proud to be chosen to lead this great team of people.”
The board of Smurfit WestRock will consist of six WestRock directors and eight Smurfit Kappa directors, including Finan, Smurfit and financial chief Ken Bowles.
Operationally, the new company will be run from Dublin and Atlanta, with geographic reach in 40 countries and a significant presence across both Europe and
Michael King, chief executive of Pactiv Evergreen, said: “The sale of Pine Bluff and Waynesville concludes the strategic alternatives review process. This transaction is consistent with our disciplined focus on value creation, and we expect it to reduce the capital intensity of our business, improve our cash flow profile and further strengthen our balance sheet.
“We put considerable thought into positioning Pine Bluff and Waynesville for the future and believe this agreement serves the best interests of our stakeholders and our local communities. I want to thank our Pine Bluff and Waynesville employees for their significant contributions to Pactiv Evergreen and continued dedication to our customers.”’
WestRock has grown through a number of acquisitions since it was created from the merger of RockTenn Company and MeadWestvaco Corporation in 2015 to create a leading global provider of consumer and corrugated packaging with combined net sales at the time of $15.7bn.
Earlier, in 2011, Rock-Tenn had acquired Smurfit-Stone Container Corporation.
Smurfit Kappa was formed in 2005 by the merger of Ireland’s Jefferson Smurfit and Dutch-based Kappa Packaging and owned by private equity firms Madison Dearborn Partners, Cinven and its management.
Smurfit Kappa’s final quarterly results, posted just before its merger with WestRock on 5 July showed that sales were only slightly down at US$2.97 billion, but net profit was halved at $132 million.
Chief executive Tony Smurfit, who took over the same role at Smurfit Westrock, commented: “I am pleased to report a strong set of results, and continued delivery of quality and service for our
customers. This has been driven by our performance-led culture, together with the continuing benefits of our prior year capital allocation decisions.
“These results were also achieved against a backdrop of significantly higher recovered fibre costs and lower corrugated box prices. We expect these increased costs will be recovered through increased box pricing with the customary time lag.”
A giant in the South American pulp industry, Suzano withdrew its attempt to thwart International Paper’s bid for DS Smith at the beginning of July. IP reportedly rejected the bid as being too small, so Suzano pulled out, bringing the IP bid for DS Smith back into the frame.
In a statement to Packaging Insights, Suzano said: “After some negotiations with the IP company regarding a potential transaction between the companies, [Suzano] has reached what it believes to be the maximum price for the
transaction to generate value for Suzano, without engagement from the other party.
“Suzano formalises that it will not pursue a transaction involving the acquisition of IP.”
Reason, says Suzano, is that it wanted to maintain its ‘capital discipline’, indicating that it didn’t want to increase its net debt.
Meanwhile, Suzano has expanded its operations in North America with the $110 million acquisition of Pactiv Evergreen and in Brazil has started up the world’s largest pulp mill (see news elsewhere).
Spain-based Saica Group is to acquire Schumacher Packaging’s Polish subsidiary, including two stateof-the-art corrugated board plants at Bydgoszcz and Wroclaw, two paper mills at Grudziadz and Myszków, one of which was completely modernised in 2023, and three service centres.
Based in Ebersdorf near Coburg in Bavaria, the Schumacher Packaging Group is one of the largest family-owned producers of customised corrugated and solid board packaging in Europe, recognised as an industry leader in innovation and technology, it has also pioneered high performance digital printing for corrugated board.
The group has enjoyed international growth over the years, with 26 sites in Germany, Poland, the Czech Republic, United Kingdom, Italy and the Netherlands. In Poland, it has developed a portfolio of customers with capacity for 440,000 tonnes of paper and 535 million sqm of corrugated board. With 1,540 employees in Poland, Schumacher Packaging had sales of €327 million in 2023.
Commenting in the deal, the value of which was not revealed, Björn Schumacher, chief executive of Schumacher Packaging, said:
“We are very happy that we came to this agreement with Saica – for our employees and our customers. There is a cultural proximity between the two family-owned companies, which will allow for rapid integration. The two companies’ products and services are complementary in Poland.
“Saica fills a gap in its already extensive geographic coverage by expanding into Europe’s sixth largest economy. This is an important step for Schumacher Packaging, as well, to lead our successful and healthy medium-
sized company into a long-term future. The spin-off of the Polish subsidiary will not cause any complications for the rest of the Schumacher Packaging Group. This is because the Polish organisation works almost independently of the other country organisations with its own management.”
Susana Alejandro, president of Saica Group, added: “This will be a very important milestone. Not only this is a step forward in Saica’s business growth strategy, but it also aims to further develop our infrastructure and services in Eastern Europe. We are eager to welcome the Schumacher people in Poland, and further
Italian paper machinery
manufacturer A.Celli celebrated 80 years of business with an event held at its Lucca headquarters at the end of June. It was attended by the group’s executives, representatives from local authorities and prominent personalities from the district and the region.
During the celebration, the group’s years of history were retraced, highlighting achievements and future challenges. Memories and recollections illustrated the stages of a steady journey that has seen the company emerge
in an Italy grappling with postwar reconstruction to evolve its technological value, expanding its business beyond the borders of Italy and beyond its own sector. “Reaching 80 years of activity is a milestone that testifies to the solidity, innovation, and adaptability of the A.Celli Group,”
develop our culture and values with them, caring for the future, valuing people and accepting the challenges we have ahead.”
In 2011, Saica entered the Polish market through a joint venture with Thimm Group, acquiring a corrugated cardboard packaging plant in Tychy, named Top Thimm (with 51 percent of shares and Saica Group with 49 percent). In 2022, Saica Group acquired 76% of shares of Fox Recykling, a waste management company in Gdynia. Saica Group makes paper for the manufacture of corrugated cardboard and packaging, promoting circularity in waste management. With more than 10,300 employees and a presence in Spain, France, Italy, Portugal, the United Kingdom, Ireland, Turkey, Luxembourg, the Netherlands, Poland, and the United States, Saica Group has four business lines: the production of recycled paper for corrugated cardboard (Saica Paper), waste management and environmental services (Saica Natur), the production of corrugated cardboard packaging (Saica Pack), and flexible packaging (Saica Flex). The group’s sales in 2023 were €3.62 billion.
said Alessandro Celli, owner of Italia Technology Alliance. “With the inauguration of the new plant, scheduled for mid-2025, the group is preparing to complete the year of celebrations and write new chapters of its history, continuing to represent made-in-Italy excellence around the world.”
The world’s largest single pulp production line has been started up by Suzano at Ribas do Rio Pardo, in Brazil’s Mato Grosso do Sul state.
Marking the completion of one of the country’s largest ever private-investment projects, the facility has an annual capacity for 2.55 million tonnes of eucalyptus pulp, increasing Suzano’s total capacity by more than 20 percent to 13.5 million tonnes a year.
Investment in the Cerrado Project totalled R$22.2 billion (US$4.3 billion), which included construction of the mill, the planting base and outbound logistics.
Suzano also has capacity at
The world’s largest pulp mill was recently started up in Brazil by Suzano with capacity of 2.55m tonnes a year
the mill to produce 1.5 million tonnes of paper per year, including sanitary paper, printing and writing and packaging lines, among other products that use pulp as raw material.
“The successful completion
of the Cerrado Project reflects the dedication and execution capability of each person involved in this grand and transformative project. It also attests to the culture of excellence that permeates the entire
organization, masterfully led by Walter Schalka during his 11-year tenure here,” said Beto Abreu, newly-appointed chief executive of Suzano.
“His vision and ambition have proven key in delivering a worldclass mill within the planned budget. Crucially, this is also a project which has, at every stage, adhered to Suzano’s core focus on supporting sustainability and having a positive impact on local communities.”
The site has been purposebuilt to meet global demand for sustainably produced eucalyptusbased products. The mill will use renewable biomass to produce, on average, 180 MW of surplus power a month.
Koehler Paper’s Greiz mill hosted a visit by the Minister-President of Thuringia, Bodo Ramelow, and Holger Steiniger, chairman of the Greiz City Council, in July.
Talks centred on local and national needs of the paper manufacturer, which sells its highquality recycled paper worldwide from the site. The company’s climate strategy was also a subject of discussion.
Ramelow was enthusiastic about Koehler’s sustainable corporate policy: “We need companies like Koehler that are committed and courageous. I’m pleased that Koehler has helped to boost Thuringia’s status as a sustainable business location.”
During a tour of the site, the
Minister-President was able to get an impression of the production process. In addition to paper recycling, the plant also uses advanced colour technology that allows high-grade recycled paper with a wide range of colours to be produced. Products made in Greiz
bear the ‘Blue Angel’ ecolabel.
“With your work, you are making Greiz known in the world and that makes us very proud,” added Ramelow.
Recycling and recovery of recyclable materials are key issues in many sectors due to
Sappi Europe has invested in a new barrier coating machine at its Alfeld mill in Germany to support the company’s advances in flexible packaging papers.
In recent years, the Belgiumbased paper manufacturer has made strategic investments to strengthen its position as an innovator in flexible packaging. Notable milestones include the conversion of the PM2 line at Alfeld in 2014 from a graphic to a packaging paper machine, as well as the acquisition of the Cham Paper Group in 2018. The latest milestone was the introduction of a cutting-edge barrier coating machine in 2023. These investments are said to highlight
the company’s dedication to evolving along with market demand and to further enhancing production capabilities. The cost of the new machine
wasn’t revealed by Sappi.
Designed to produce barrier papers that meet increasing demand from the market, the latest coating machine is also
the scarcity and increasing prices of raw materials. That is why the Koehler Paper site in Greiz is supporting the new research group seRo.inTech.
“Becoming a member of research group SeRo.inTech, both as a practice partner and on the advisory board, provides us with an important platform for exchanging ideas with other project partners about the latest secondary raw materials trends, and for expanding our sustainable alignment even further. Koehler is demonstrating in impressive fashion how even energyintensive companies can make a major contribution to achieving climate neutrality in Germany,” said Udo Hollbach, managing director of the Koehler Paper site in Greiz.
key to the development of new barrier chemistries. It is said to be equipped with an extremely high level of automation and is capable of coating a wide range of materials and barriers.
The barrier coating machine is said to be unique in that it represents a far-reaching development concept – from raw materials all the way through base and functional paper grades.
“The future belongs to innovative speciality papers. Our new coating system is the key to new markets, innovative products and sustainable solutions,” said Thomas Rajcsanyi, mill director and managing director of Sappi Alfeld GmbH.
Ahigh-end digital printer has been installed by DS Smith to serve its customers in the Iberian region.
The Nozomi 14000 AQ singlepass digital printer supplied by EFI is operating at the paper maker’s Torrelavit packaging facility in Spain.
The 1.4 metre-wide printer is set up to print high-resolution
images up to 1,200dpi directly onto corrugated cardboard and is providing customers in the Iberian region with reduced lead times and less waste, in contrast to offset litho techniques, said DS Smith.
In addition, the printer will enable DS Smith customers to create multiple designs and variations in a single production run without compromising quality.
International tea and herbal drinks producer Twinings & Co has chosen Sonoco’s all-paper EnviroCan for a new powdered drink, Twinings Thé Latté, which was launched in France in May.
The container is designed with recycled paper fibre, water-based inks and adhesives and, while maintaining durability, performance and product freshness, is fully recyclable.
The project team of Twinings & Co, which manufactures a wide range of drinks including tea, herbal infusions and other powder drinks, said it was “delighted” to be using the
container for Thé Latté, which comes in a range of flavours and can be consumed hot or cold.
“At DS Smith, we are driving greater sustainability and efficiency in packaging by implementing the most advanced high-speed digital printing technologies in our plants. The new technology not only ensures low energy consumption and
maximum production efficiency, but also allows us to deliver high print quality with stateof-the-art printheads and maximum accuracy,” Albert Forcadell, operations director for packaging in South Europe at DS Smith, said.
E-commerce giant Amazon has replaced 95 percent of the plastic air pillows from delivery packaging in North America with paper fillers, and aims completely remove plastic by the end of 2024.
Amazon said it is “constantly inventing and thinking big to make our packaging small”, and wants to use as little packaging as possible to “avoid waste, and prioritising recyclable materials”.
The move is part of Amazon’s objective to avoid and reduce packaging, a multi-year effort to remove plastic in delivery packaging from fulfilment centres in North America, where more than two billion packages are shipped every year.
It will avoid the annual use of nearly 15 billion plastic air pillows.
Pat Lindner, vice president of mechatronics and sustainable packaging at Amazon, said: “I’m proud of the cross-Amazon collaboration to make a positive impact on the customer delivery experience with easier to recycle materials. It’s a great example of how we thoughtfully test and
scale new solutions to protect our customer experience. We are working towards full removal in North America by end of year and will continue to innovate, test, and scale in order to prioritise kerbside recyclable materials.”
Amazon didn’t say where the kraft paper being used is sourced but is expected to come from a number of companies. The paper filler is made from 100 percent recycled content and can be easily further recycled through kerbside collection programmes.
Staff at fulfilment centres are said to be assisted by artificial intelligence (AI) systems for optimising the size of the packages and the amount of filler required for each.
More paper-based packaging news in Green Packaging International, pages 20-27.
The world’s largest producer of market pulp, Suzano has begun testing the first high-capacity electric truck in Brazil at its Aracruz mill in the state of Espírito Santo.
The Atlas truck, capable of towing up to 120 tons, was developed VIX Logística, part of the Águia Branca Group which specialises in logistics, and has the potential to save up to 8,300 litres of diesel per month while reducing carbon dioxide emissions by about 21 tons. Suzano’s ambition is to reduce emissions by 20 percent on the route between the mill and the port of Portocel – where products from Suzano’s Aracruz Unit are exported around the world.
The partnership marks a significant step in accelerating the energy transition of Suzano’s pulp transportation fleet, allowing it to integrate more sustainable transportation practices
throughout its operations, and reinforcing the company’s commitment to sustainability at all stages of the supply chain.
The implementation supports Suzano’s Commitments to Renewing Life – its long-term targets aligned with the UN Sustainable Development Goals, in building a better world for people and the planet. Using the Atlas truck in Suzano’s transportation fleet will help Suzano in its goal of removing 40 million tonnes of carbon dioxide from the atmosphere by 2025.
“The partnership with VIX Logística is an important strategic marker for us, representing a significant milestone in our efforts to implement new technologies at all stages of our operations to help us deliver cleaner and more efficient transportation solutions,” says Beatriz Nalevaiko Venturini, operations chief at Suzano.
The 120 ton capacity of the Atlas truck is a significant improvement on conventional trucks, which weigh around 40 tons including the vehicle and load. Developed from a
Kollmorgen, a pioneer in automated guided vehicle (AGV) technology has launched a flexible automation system for dynamic warehouse environments: NDC Flex.
NDC Flex merges the efficiency of AGVs with the adaptability of autonomous mobile robots (AMRs). This hybrid approach ensures peak site productivity while mitigating risks related to potential disruptions. Whether end-users are facing a specific logistic challenge or aiming to
optimise their operations, NDC Flex is designed to meet their needs.
Part of the system is Cirrus, a cloud-based system that is said to enable efficient collaboration between employees stationed on-site and employees located in the office. Cirrus simplifies tuning and verification of layouts during commissioning, which significantly reduces setup time and accelerates deployment.
NDC Flex vehicles are equipped with obstacle avoidance
technology. This capability supports uninterrupted operation by allowing the vehicle to manoeuvre around unexpected objects and seamlessly continue along its designated path.
With the integration of U-Zone’s Dynamic Docking, NDC Flex vehicles are able to adjust their paths dynamically during the ‘last mile’ of their journey.
The vehicle adjusts to the realworld load position, ensuring maximum system throughput.
Mercedes-Benz Axor 3344 chassis, Atlas operates with electric propulsion powered by lithium iron phosphate batteries, so is tailpipe emission free.
Elias Alves, director of VIX and responsible for VIVA - VIX Autonomous Vehicles – said the partnership aligns with the company’s innovative culture:
“Having an innovation drive within the company allows us to test creative and bold solutions. The adoption of efficient and sustainable technologies is a major trend in the market, and VIX stands out in this movement, remaining at the forefront of the logistics sector.”
Suzano and VIX Logística started testing Atlas in May this year. The vehicle’s operational performance will be carefully monitored by Suzano during the first months of its use, with the intention of further deploying the alternative to other operations of the company.
Kollmorgen-based vehicles include natural navigation capabilities. Comprehensive training and established best practices, simultaneous localisation and mapping (SLAM) survey, and improved configuration ensure sustained, high performance over time. NDC Flex empowers end-users to modify the layout using the Cirrus tool, which enables system providers to easily synchronise and validate end-user changes, simplifying collaboration without sacrificing performance or quality.
More information from www. kollmorgen.com/agv
Rethink Reduce Reuse
ENABLING SUSTAINABILITY IN PULP & PAPER MILLS’ ENTIRE LIFECYCLE
A family of robust chemicals used across a wide number of industries including pulp and paper present significant health threats and are the subject of new regulatory controls. So-called PFAS, they can however be prevented from entering the environment. Jeffrey Lewis* outlines the background and the processes required
PFAS, or per- and polyfluoroalkyl chemicals, include more than 4,500 different compounds present in numerous industrial and commercial goods. Termed ‘forever chemicals’, they resist degradation due to their strong carbon-fluorine bonds, persisting in the environment for extended periods, even centuries.
Since the 1940s, PFAS have been widespread in everyday products, prized for their water and fat repellences. Their usage spans industries like food processing, firefighting, coatings, and cosmetics, and exposing workers across sectors such as construction, electronics, automotive, aerospace, and chemicals.
In the pulp and paper industry, PFAS is employed to create grease- and water-repellent products, notably in food packaging, such as plates, popcorn bags, and pizza boxes, as well as in other materials like cartons, containers, and masking paper.
These commonly used compounds do not degrade in natural environments. In addition to public concern regarding the spread of PFAS as pollutants, there’s also worry about their link to a range of serious health risks such as cancer, liver damage, infertility, immune system dysfunction and thyroid disease. Furthermore, it has been estimated that PFAS impose a financial burden ranging from €52 to €84 billion
on European health systems each year.
Contamination trends in Europe
PFAS isn’t limited to products and industrial procedures; it permeates our soil, food, water, and bloodstream. Detected in almost every corner of the globe, PFAS exposure affects most of the world’s population, according to the European Environment Agency. Recent research highlights PFAS contamination in the drinking water of millions of Europeans, while the European Food Safety Authority (EFSA) discovered that part of the European population exceeds the acceptable weekly intake for certain PFAS compounds.
The Forever Pollution Project
brings together journalists and media outlets from across Europe to uncover the extent and nature of PFAS pollution. It has revealed a concerning statistic about PFAS contamination in Europe. Out of the 38,000 sites where there is known or presumed PFAS contamination, more than 1,400 are either pulp, paper and paperboard manufacturing sites, or factories that manufacture products out of paper and/or paperboard. Furthermore, a 2022 study from Örebro University revealed contamination of water and sediment at 13 Swedish paper production sites included in the research. Five of these were classified as low contamination while the remaining eight sites were clearly affected by a PFAS point source.
Some PFAS are already banned in parts of Europe, and there’s discussion about the EU potentially banning certain or all PFAS. A complete ban would impact paper companies using PFAS in their products, necessitating a search for alternatives, which could prove to be more expensive or less suitable.
In Sweden, manufacturers, including those from the pulp and paper industry, seeking to expand production facilities must acquire a new environmental permit and conform to a checklist of environmental requirements. A crucial aspect of this involves agreeing to new limits on the presence of PFAS in wastewater. Companies that ECT2 works with in Sweden report that if PFAS is detected in groundwater or released from a plant, they must
address the issue, outline their remediation plan to the council, and adhere to the agreed-upon strategy.
The PFAS concern could also potentially tarnish the reputation of paper companies as public awareness increases. With PFAS chemicals linked to severe health concerns spreading throughout our environment, heightened negative publicity will mount, compelling the industry to address the issue.
PFAS contamination
As awareness of the risks grows, European governments are taking action to limit PFAS exposure and safeguard public health. This involves restrictions on PFAS usage, bolstering detection efforts, and implementing remediation measures. Aligned with the Stockholm Convention, the EU has long placed restrictions on
certain types of PFAS including perfluorooctanesulfonic acid (PFOS), banned perfluorooctanoic acid (PFOA) in 2020, and is likely to ban perfluorohexane sulfonate (PFHxS) in the near future. Recently, the European Commission issued a regulation establishing maximum levels for select PFAS in food. Moreover, the EU’s Drinking Water Directive, enacted in January 2023, mandates new PFAS limits in drinking water, with member states given two years to comply. Additionally, five EU nations have proposed PFAS restrictions under the Registration, Evaluation, Authorisation and Restriction of Chemicals (REACH) regulation to the European Chemicals Agency.
Transformative technologies in PFAS remediation
To address new regulations on the concentrations of PFAS allowed in water, governmental and private
entities are partnering with companies, such as ECT2, which offer a range of treatment options suitable for various water sources. More conventional methods of PFAS removal involve technologies such as granular activated carbon (GAC), which uses porous carbon particles in granular form to filter and purify water or air. GAC is commonly used in water treatment processes to remove organic pollutants, chemicals, odours and other impurities by trapping them within the porous structure of the carbon particles and is generally considered to be an effective method for improving water quality.
However, employing GAC filtration methods for contaminated water can present certain challenges. Considerable amounts of filtration material are required and businesses find themselves replacing it several times per week. This ongoing
process results in the disposal of thousands of tonnes of PFASladen carbon, which requires incineration to manage effectively. A more efficient approach is to use technology that combines adsorption and specialised ion exchange resin to attract and capture PFAS molecules, reducing concentrations below detection levels. Such a process has been estimated to be 13 times more effective than other technologies such as GAC. An advantage of using ion exchange resin, instead of carbon, is that it uses just a fraction of the volume of material needed to remove the same amount of PFAS.
Furthermore, users can now regenerate PFAS-saturated resin on-site for repeated usage. Unlike alternative systems, this method eliminates the need for users to extract and dispose of
the resin. Instead, a specialised solution is employed to extract PFAS from the resin, rendering it suitable for reapplication. Additionally, the system distils this solution, enabling both the resin and the solution to be reused. Companies using this system are reducing their carbon footprint and generating considerably less waste, equating to one litre of waste per million litres of water treated.
These cutting-edge technologies hold immense promise in significantly mitigating the waste and expenses linked with PFAS remediation efforts in the pulp and paper industry. The widespread adoption of regenerative technology for PFAS treatment is likely to increase with the implementation of new regulations aimed at safeguarding public health.
The urgency is palpable, with time running out for EU Member States to address both the mounting legislative requirements aimed at purifying their drinking and industrial wastewater, and the increasingly evident dangers posed to the health of our citizens.
As each day passes, the need for swift and effective action becomes more pressing, highlighting the importance of prioritising comprehensive and more efficient solutions to mitigate the risks posed by PFAS contamination. Failure to act promptly not only jeopardises environmental sustainability but also undermines public health and safety, underscoring the imperative for immediate and concerted efforts to tackle these challenges head-on.
* Jeffrey Lewis is General Manager in Europe for ECT2, a global leader in technologies for removing challenging contaminants from water and vapour. The company specialises in PFAS and offers a comprehensive suite of services for understanding and managing its impacts. More information from www.ect2.com
Although pulp and paper mill processes vary broadly, in any plant dusts, grease, slag, metals, residues, and cementitious particulates generated during manufacturing can make their way into the wastewater stream, accumulate, and even harden in underground pipelines.
As a result, pulp and paper mills conduct periodic maintenance to flush debris and sediment from pipes, including breaking up hardened obstructions, to prevent blockage and protect downstream wastewater treatment equipment from excessive loading.
“Many plants were built 40 to 80 years ago with most of the pipes underground, so they are old, hard to access, and can accumulate excessive, hardened
Contractors can dramati cally speed up pipe cleaning and prevent process disrupti ons and downti me in pulp and paper mills using a variety of high-performance, stainless-steel hose nozzles. PPL reports
debris that must be removed,” says Bill Benner, senior project manager for Ventilation Power Cleaning (VPC), a Seattle, Washington-based firm that provides vacuum truck services to remove various industrial debris in the form of solids, liquids, sludges, and slurries.
“If this kind of debris is transported by pipe to onsite clarifiers, digesters, sewer vaults, or treatment plants, it can disrupt and overburden the process as it collects and hardens,” Benner adds. “A similar problem occurs when rain washes debris in outdoor processing or storage areas into basins, ponds, or reservoirs prior to transport
through pipes for further treatment.”
The task of pipe cleaning in pulp and paper mills typically falls to third-party cleaning companies like VPC, which come to facilities with a vacuum truck and perform the work periodically, unless emergency debris removal is required.
According to Benner, most wastewater pipes are typically 100 to 150 metres long and 30 to 120cm in diameter. Special nozzles are used to propel a hose connected to a vacuum truck down the pipeline and back using water jets. The nozzle must supply enough force to dislodge any debris and carry it back using
The most effective high efficiency nozzles have tight water patterns that efficiently clean the pipe floor/wall and create a powerful water stream that not only moves debris long distances but also propels the nozzle
water pressure to be suctioned out by the vacuum truck.
“Industrial plants cannot afford production downtime, so we rely on high-performance nozzles to get the job done quickly and reliably. Using the right nozzle and technique can be the difference between cleaning out a pipe within 20 minutes or having it take hours, days, or fail completely,” says Benner.
Fortunately, an assortment
of high-performance, stainless steel hose nozzles is available to expedite the removal of any debris buildup in the pipes of facilities such as pulp and paper mills, steel mills, refineries, chemical plants, or cement plants. This can help to prevent a range of problems including regulatory fines, process disruption, and unscheduled downtime.
As known in the industry, there are tiers of nozzles rated for performance and water efficiency: Tier 1 (about 30 percent efficient), Tier 2 (50-60 percent efficient), and Tier 3 (75-98 percent efficient). Low-performance Tier 1 nozzles tend to use only 30 percent of the available energy, wasting the remainder due to excessive turbulence. Tier 2 nozzles are more efficient but still inadequate for
tougher jobs. In contrast, the mosteffective Tier 3 nozzles have tight water patterns that efficiently clean the pipe floor/wall. In addition, the units create a powerful water stream that not only moves debris over long distances but also propels the nozzle.
“We rely on the highestefficiency Tier 3 nozzles by KEG because they provide the two most important things we need: the ability to move the hose and nozzle down the entire length of pipe to the debris location, along with the ability to push the debris out of the line with water pressure so we can remove it with the vacuum truck,” says Benner.
KEG Technologies, a manufacturer of industrial, sewer and storm lines products including Tier 1 to Tier 3 nozzles, floor cleaners, and chain cutters, is a member of NASSCO, the National
Association of Sewer Service Companies.
What sets the most efficient Tier 3 nozzles apart from others in the category is fluid mechanics engineering on a par with the aerodynamics of race cars or jet fighters. In the case of KEG’s Tier 3 nozzles, the high-performance fluid mechanics design leaves little room for power losses and excessive turbulence.
“We use their Tier 3 nozzles essentially everywhere we go. They have a large repertoire of high-performance nozzles that has reliably met our need in every industrial application,” says Benner. VPC originally purchased about a dozen assorted nozzles from the industrial, sewer and storm line product manufacturer.
For wastewater applications, VPC prefers floor cleaner and spinning style nozzles. As the name
suggests, these nozzles travel along the floor of large diameter pipe – instead of just the centre – and focus high-pressure water from hoses through an assortment of jets. The directed, high-pressure water is ideal for removing sludge, mud, compacted materials, and heavy debris (rocks, bricks, broken concrete, etc.) from industrial pipes, storm lines, and sanitary lines.
“Floor cleaner nozzles are designed to ride on the bottom third of pipe so have the most dynamic effect for removing heavy debris, sand, and rock that has accumulated there,” says Benner. For example, KEG’s Torpedo Nozzle utilises two different water jet angles to ensure superior sand, mud, and debris transport from the pipe floor in diameters from 15cm to 40cm. The company also offers a variety of floor cleaner
sizes designed for pipe diameters from 10cm to 185cm. One unique floor cleaner model, called the Twins, utilises two floor cleaners with high-performance fluid mechanics that work in tandem with a Y-connector, for pipes up to 2.1 metres in diameter.
According to Benner, VPC also uses a unique rotating nozzle to remove stubborn debris from pipes. The Duce Nozzle utilizes water driven rotation and vibration to create a ‘jackhammer’ action to remove grout and mortar residue, scaling, tuberculation, or other deposits that have hardened to the pipe floor or wall. This approach is more efficient than cutting and milling out the material but is not recommended for clay pipes.
“We have found that the KEG Technologies’ Duce Nozzle works extremely well to break up hardened debris,” he says.
When a severe blockage is identified, chain cutter nozzles are designed to cut through difficult obstructions and thick root masses. When high-pressure water enters the chain cutter nozzle chamber, it is directed to spin the cutting chains at high velocity with enough torque to avoid seizing.
Although the high-performance
Tier 3 nozzles cost more than lower performing nozzles, Benner has found this acceptable because his work crew completes jobs much faster by using them. He notes that there is no substitute for having the right tools and experience to clear industrial pipes quickly, whether for routine maintenance or an emergency.
“We will not use inferior nozzles because they just don’t work when industrial pipes and
lines must be efficiently cleaned and cleared of any debris. This commitment to quickly getting the job done right has earned us repeat business and helped to keep plants running without incident or downtime,” says Benner.
Having used high-performance nozzles for years, he emphasises that the units are designed to last.
“We originally bought some KEG Tier 3 nozzles 15 years ago, and
they still perform reliably,” says Benner.
As a final thought Benner concludes, “You really need to understand the products you use, and KEG will go the extra mile to help you understand the product.” • More information from KEG Technologies Inc, 6220 N. Pinnacle Drive, Spartanburg, South Carolina 29303, USA. Tel: 1 866 595 0515. Website: www.kegtechnologies. net
Loss of efficiency in the recovery boiler systems of pulp mills is often due to fouling and corrosion of pipework. Andritz has a system to remove the harmful contents from the ash while keeping the valuable chemicals. PPL reports
Recovery boiler efficiency is often reduced by corrosion and fouling as chlorides and potassium from the kraft recovery cycle accumulate in pipework. Andritz has become the market leader in systems for the removal of these chlorides and potassium using ash recrystallisation (ARC) chloride removal plant of the type recently started up by pulp giant Suzano at its Aracruz mill in Brazil.
The main function of the ARC chloride removal plant in pulp mill operations is to treat the ash that is collected from the electrostatic precipitators (ESP). The plant removes harmful chloride and potassium from the ESP ash and returns valuable chemicals to the chemical recovery cycle. In the case of Suzano at Aracruz, the plant supplied has been designed to handle 550 tons of ash daily.
Rafael Silva Pinto, project manager at the Suzano Aracruz Unit, says, “At Suzano Aracruz we have three recovery boilers, and the role of the ARC is to remove the components that are harmful to the process, namely chloride and potassium. These two components are responsible for clogging the lines and cause corrosion of equipment, leading to low efficiency.”
The accumulations of compounds such as chloride and potassium often lead to significant increases in the frequency of the recovery boiler shutdowns due
to plugging of the heat exchanger passages. Furthermore, the corrosion of the heat exchanger surfaces causes expensive material damage.
“The ARC removes these components, taking care not to lose the sulphate and sodium that are important to return to the system,” continues Silva. “It processes the ash that has been diverted to the plant by removing the harmful components and returning the uncontaminated part of the ash. Previously, the falling ash was returned to the process still containing the chloride and potassium. This means the encrustation of the boilers is now reduced, which allows us to extend our campaigns.”
Antti Frigård, development
manager for evaporation technology at Andritz, adds, “This reduction of incrustation in the boiler will continue to improve in the long run as the ARC operates for longer periods. What generally occurs is that the chloride and potassium are reduced in the recovery cycle and boiler operation is even further improved.”
Andritz was chosen to supply the ARC, the second of its kind to Suzano, as it represented the best cost option for pulp mill. The ARC+ plant was ordered in late 2021, and is complete with the latest improved and more-efficient system when compared with the traditional ARC. The plant replaces ash leaching technology that the mill was using for its ash recovery requirements.
“When we compare the ARC technology with the ash leaching process, there are differing factors as the throughput capacity and efficiency rates are totally different,” says Silva. “Ash leaching has a removal efficiency rate of around 45 percent compared to the ARC at around 95 percent.”
The ARC plant was also chosen by Suzano for its energy efficiency, an important factor for the company. “First and foremost, energy is money, and we are in a period of expensive energy,” Silva says. “The less energy we are consuming, the more we can be selling to the grid. So it is very important to us that we have the most energy efficient technology operating in the mill and the less steam energy the ARC consumes the better.”
The ARC Ash ReCrystallization plant supplied by Andritz removes the harmful chloride and potassium from the electrostatic precipitator (ESP) ash and returns valuable chemicals to the chemical recovery cycle. In the case of Suzano Aracruz, the plant supplied has been designed to handle 550 tons of ash each day
A challenging project, with a fast start-up
The project to install the ARC plant was challenge: it had to be installed in a tight space between a maintenance shop, the sulphate system, and the boilers, which limited the range of crane movements. There were also the usual challenges thrown up by the pandemic to contend with.
Silva explains: “The main challenge was to install the ARC in a tight space with equipment still in operation and work in a corrosive area with a lot of vibration and heat. There was also a lot of scaffolding needed that complicated the task further. All in all, this project was a major challenge for Andritz and the mill team.
“Andritz had sent a designer to the site early on in the
“This
project, and many details of the challenges were already identified at the assembly stage. During the project Andritz spared no
resources, and there were no holidays between Christmas and New Year to affect the productivity of the project. I have
never seen so much commitment for a delivery. All this during the Covid pandemic!”
The plant started up in April 2023 and went into operation immediately. The Andritz commissioning team introduced the ARC plant process in stages with stability being quickly achieved. “We were very impressed at the speed at which the plant went into operation,” says Silva. “We saw the centrifuge running on the first day and we saw chloride coming out right away. As far as we know, this is the first crystalliser with this design installed in the world. We are very pleased and optimistic that we will achieve the expected performance results very quickly.”
Silva concludes, “Suzano has a strong belief in Andritz ’s ability to handle a project like this, and for decades the company has always provided services on time and with top quality.” “This reduction of incrustation in the boiler will continue to improve in the long run as the ARC operates for longer periods.”
l More information from: Antti Frigård. Email: antti.frigard@ andritz.com
Kraft paper bags for cement made from renewable materials that dissolve during the mixing process have been launched in the Balearic Islands of Spain in a collaboration between Mondi and building materials firm Cemex.
The two companies have been working together for 12 years with the SolmixBag making its debut in 2021. Now it is being used in the islands of Ibiza, Mallorca and Menorca, reducing waste and cutting dust on sites, along with meeting legal requirements regarding landfilling and incineration of waste.
SolmixBag is a one-ply paper bag made from 100 percent kraft paper which stores and transports
dry cement, screed and coarse pre-mixes: its design ensures that it disintegrates during the mixing process, eliminating dust and waste on the building site. Strong and durable, the bag is resistant to punctures and dissolves when it comes in contact with water in the cement mixer, where the fibre packaging integrates with the cement.
The SolmixBag packaging comes in a range of sizes and runs on existing filling machines, and is said to provide the same strength and shelf-life as conventional bags. It is easy to carry and store, with great printing capabilities for onshelf standout, says Mondi. Fabio Barbieri, sales director for paper bags at Mondi, says: “This is an exciting step in SolmixBag’s
journey, delivering an easy and convenient solution to use on construction sites. The product launch brings to life our MAP2030 goals by reducing waste so effectively, and also illustrates our collaborative approach.
Working with a well-known and trusted supplier further endorses our product standards from a partner with recognised, genuine additional industry expertise.”
Nadal Mateu Piña, commercial manager for the Balearic Islands at Cemex says: “Mondi has provided the perfect product for our needs: we are now packaging the most sustainable cement in our product portfolio, CEM IV/B –(P) 32,5 SRECO+SR, in Mondi’s SolmixBag.
“Strict legal requirements on the Balearic Islands on landfilling
The carbon footprint of Sappi Europe’s Galerie paper range has been cut by 55 percent, a figure that is expected to be increased to 70 percent by the end of 2024.
Sappi Europe says the milestone was reached in July and is a key step forward in the paper maker’s sustainability journey, contributing significantly to its decarbonisation targets, as well as those of its customers.
In 2023, Sappi Europe’s Kirkniemi Mill at Lohja in Finland successfully switched to using renewable biomass energy, reducing its Scope 1 emissions, direct emissions from Sappi’s own operations, by 90 percent. Building on the significant investment made to Kirkniemi’s energy systems, ‘clean’ electricity is now also being supplied to the mill, eliminating scope 2, indirect emissions. This transformation is among
The SolmixBag, developed by Mondi in collaboration with building materials firm Cemex
and incineration of waste and EPR have initiated this move, and we aim to use this as best practice example to proactively roll out in different regions and countries. The launch not only delivers for the local industry, it also complies with our own sustainability roadmap ‘Future in Action’.”
More information from www. mondigroup.com
Interior view of Sappi’s Kirkniemi Mill where Scope 1 emissions have been cut by 90 percent
nearly 80 projects outlined in Sappi Europe’s decarbonisation roadmap, a blueprint that will see the company’s energy-related sustainability targets through to
2025. This also closely aligns with Sappi’s science-based targets for 2030.
More information from www. sappi.com
UK-based corrugated cardboard packaging producer BoxWay Packaging Group Ltd has utilised its high-tech in-house design capabilities to conceive e-commerce packaging that eliminates the use of plastic for retailer Ashridge Nurseries.
BoxWay worked closely with Somerset-based Ashridge in the design-of cardboard boxes that replace preformed plastic packs to protect their P9 herbaceous pots during their transit to its on-line customers across the UK.
The design team in Exeter devised the cardboard structure by employing an integral flap in a die cut version of an 0427 box, which ensures rigidity, strength and a sustainable choice for the boxes, keeping the pots securely in situ and giving the option of additional space for a variety of plant heights.
Rodney Marsh, fulfilment manager at Ashridge Nurseries, commented: “This clever cardboard box is not only a key ecological development for us as a business to reduce our
carbon footprint and offer our online customers a recyclable, eco-friendly packaging solution, but it also contributes to our considerable efforts to completely remove plastic from our whole supply chain.
“Becoming a plastic-free retailer is a major accomplishment for Ashridge Nurseries. We are now looking forward to rolling out more
cardboard solutions for additional plant lines we sell online to customers across the UK”.
Tom Fooks, new business manager for Boxway Exeter, said: “It was a pleasure to work with Rodney and the Ashridge Nurseries team on this innovative project to devise a concept for a new herbaceous plant cardboard packaging solution that eliminates
Supermarket chain Aldi has introduced paper packaging for its Everyday Essentials Porridge Oats in its UK stores. All the supermarket’s porridge oat products are now free of plastic packaging, including its Everyday Essentials, Organic and Scottish Porridge Oats.
The latest move for Aldi’s Everyday Essentials Porridge Oats is expected to save around
57 tonnes of plastic a year.
It forms part of the supermarket’s target to reduce plastic packaging by 50 percent by 2025 and follows a switch to 100 percent recyclable cardboard packaging on all ownbrand porridge pots last year.
Plastics and packaging director Luke Emery said: “At Aldi, we are committed to reducing the use of plastic across our products
and this latest change is another example of our ongoing progress.
“We know our customers want to make sustainable choices when they shop with us, which is why small steps like this can make a big difference.”
The supplier of the paper bags wasn’t revealed.
More information from www. aldi.com
plastic and I’m thrilled with the result of the new eco-friendly, sustainable structured boxes. I very much look forward to further developing Ashridge Nurseries’ complete range of corrugated solutions, which complements this original design BoxWay Packaging has created”.
More information from www. boxwaygroup.com
UK-based advanced materials and paper products specialist
James Cropper has unveiled a new brand identity, to mark the unification of its Speciality Paper, Colourform and Technical Fibre Products under one name. The new brand will be represented as two market-facing divisions: James Cropper Paper & Packaging and James Cropper Advanced Materials to support the group’s accelerated growth strategy.
Ahead of the company’s 180th anniversary next year, the new branding celebrates James Cropper’s rich heritage, as well as recognising its status as a groundbreaking innovator. To reflect its expertise in colour science, the modern and striking palette of greens has been carefully chosen to balance authenticity with the company’s forward-thinking brand values. The transformation brings to life the brand narrative through photography of its people, stateof-the-art technologies and highend products underpinned by the new brand essence – ‘Making a Material Difference’.
Originally known for papermaking, the group now operates on the global stage with a new brand architecture that reflects its collaborations with the world’s biggest enterprises
and well-known names in energy, aerospace, luxury retail and beyond – from recycled folding box board for Chloe fragrances to bespoke moulded fibre wraps for Bruichladdich whisky bottles, hydrogen fuel cell powered vehicles and even lightweight aircraft materials.
Steve Adams, chief executive at James Cropper, said, “The evolution of the brand identity is the latest milestone in our investment in the future of James Cropper. Building on nearly two centuries of innovation, productivity and efficiency, it’s imperative to recognise how markets have changed and assert our bold ambitions and strategy for growth”.
Since 1988, LuxePack, which is being held at the Grimaldi Forum in Monaco from 30 September to 2 October, has offered participants an immersive experience during the event and beyond, as
the trade show’s venue, hotels, restaurants and more combine to form an interconnected whole. The unique setting has, over the years, helped build strong ties within a creative community and Luxe Pack owes much of its status and
The rebranding follows a major transformation programme, including a streamlined portfolio, operational improvements and several key strategic appointments.
During this time the leadership team has spearheaded a programme of operational modernisation, resulting in higher productivity in paper making with James Cropper on-target to achieve annual cost savings of more than £2 million, alongside investment in a new CRM to better serve customers. This will achieve accelerated delivery of new projects, notably in wine and spirits, combining paper and packaging products for the luxury market.
appeal to the presence of high-level decision-makers from both brands and suppliers.
The organisers of the 35th holding of premium packaging’s annual headline event have rolled out a new initiative designed to help customers reduce the carbon footprint of their visit while enjoying a more seamless
Adams added, “Our priority remains, as always, providing world class service to our valued customers. The rebrand offers an opportunity to clearly communicate our unrivalled product portfolio and technical capability. We also look forward to collaborating with new partners who share our curiosity and excitement for reinventing materials and pursuing sustainable solutions”.
The new facilities at the company’s site at Kendal in the UK’s Lake District were unveiled by Sir James Cropper, whose greatgreat grandfather James Cropper founded the company in 1845.
More information from www. jamescropper.com
experience to effectively develop and consolidate their professional and interpersonal relationships. Last year’s event recorded a footfall of more than 10,000 visitors, a rise of 10.5 percent and the highest achieved since it was founded. More information from www. luxepackmonaco.com
In response to rising demand for corrugated cardboard in Europe, DS Smith has invested €6 million in its La Chevrolière facility near Nantes in western France.
The investment will enable expansion of the facility by 4,000 sqm with a Bobst Mastercut 2.1 die-cut machine and a cardboard pallet production line. A new 2,500 sqm workshop dedicated to producing Kaypal cardboard pallets will have capacity for 250,000 units, and a potential to produce up to 1.5 million pallets per year.
The Kaypal pallet is beneficial to DS Smith’s customers in that it is said to be fully recyclable, ultra-light weight at 3.5 kg,
ergonomic, hygienic, economical and reusable.
It is said to be ideal for road and air transportation of products, floor and point-of-sale (POS) displays, pallet boxes or order preparation for retail logistics centres (interlayer pallets).
Commenting in the investment, Thibault Laumonier, regional managing director for DS Smith in France, said: “At DS Smith Packaging France, we understand that innovation and respect for the environment go hand-inhand and this is in keeping with our Now and Next sustainability strategy and company-wide
purpose of Redefining Packaging for a Changing World.
“The opening of our new Kaypal cardboard pallet production workshop in La Chevrolière will help our regional customers to move towards a circular economy, with sustainable packaging options that impact positively on the reduction of carbon dioxide throughout the entire supply chain. We are setting new industry standards in sustainable packaging and building a future that is more respectful of the environment that we live in.”
More information from www. dssmith.com
Paper is a product that does far more than simply carry information – it is a sensory experience. So says Marco O. Bölling, finishing expert and owner of Bölling Prägedrucksachen in Bad Soden, Germany, who recently explained how to create a lasting impression with paper. The Bölling Prägedrucksachen print shop only uses the finest paper, with great attention to detail in order to maintain its extremely high standards.
The family-owned company was founded in 1964 by Karlheinz C. Bölling and was originally called Stahlstichdruck Bölling KG. The print shop was taken over by Marco O. Bölling in 2000 and the company, which started out as a relief stamping business, has now become a finishing specialist, which combines traditional techniques with state-of-the-art
processes to produce what it says are small works of art on a par with fine sculpture. The raised blind embossing in particular is reminiscent of relief work from the Renaissance. This allows 3D effects to be created on paper, such as a baby’s footprint on a birth announcement card.
“For work like this, you need extremely high-quality paper
with long fibres so that it does not rupture at the edges of the embossing,” says Marco. Because of this, very few types of recycled paper are suitable for this kind of finishing. The paper fibres are ground in every recycling operation, which makes them shorter each time. Secondary fibres can only withstand complex further processing if they are additionally
refined during production.
“The only recycled paper that behaves virtually like new paper is the one made by Koehler Paper and which is produced at the site in Greiz. It behaves almost identically to virgin fibre paper during embossing,” says Marco. Greenium creative board, creative print, COLORline IQ and Koehler Eco paper products made of 100 percent secondary fibre are intended as a sustainable and premium alternative in the area of top-quality printed products, among others. No matter how much the company is dedicated to the art of finishing – it is never an end in itself. Says Marco, “Aesthetics and quality pay off. If you hand a high-quality business card to a new contact, it immediately shows you are serious and trustworthy”. More information from www. koehler.com
With the goal of reducing the carbon footprint of its packaging, French sugar brand Cristalco has re-thought the design of its icing sugar sprinkler container in collaboration with paper packaging giant Sonoco.
Previously made from a polyethylene (PEHD) body covered by an oriented polystyrene (OPS) sleeve and a polypropylene (PP) lid, and after five years of work, six technical studies and a number of life cycle analyses, the new 500g Daddy Sugar container uses 80 percent less plastic.
Sonoco Container Europe’s cardboard container, using 68 percent recycled fibre, comes with a PE film inner liner to preserve the contents and reduce sugar caking by protecting it from humidity. The PP lid (produced by Rovip) has two openings, one with six small holes
for sprinkling, while the other has a wider opening for pastry-making.
“We’ve improved the sprinkler so that the icing sugar pours out better,” explained Julie Moréac, packaging development chief at Cristalco. “We wanted the lid to be as eco-designed as possible, while still retaining its core functionalities. It needed to offer easy dispensing, opening and closing, and a tamper-evident seal. The lid, meanwhile, had to retain its shape and not ‘ovalise’ despite us reducing the amount of material used to form it. These posed significant challenges to overcome.
“In addition, the lid is held in the can without glue, to prevent potential contamination and to keep the amount of materials used to a minimum. The challenge here is securing the lid securely into the cardboard body, the diameter of which can change by as much as a few tenths of a millimetre”.
The new Sonoco containers became available on supermarket shelves under the ‘Daddy’ and ‘Erstein’ brands from June 2024.
Sebastien Fabre, strategic account manager at Sonoco Consumer Europe, said: “We’re always delighted to help companies reach their sustainability goals by
With sushi increasing in popularity as an on-the-go lunchtime meal, a range of paper-based trays with lids has been launched by Sabert Corporation Europe.
Tray2Go comprises a tray made from Forestry Stewardship Council FSC certified paper, while the lids are made from rPET, with a minimum of 50 percent recycled plastic.
Demand for sushi continued to surge during the pandemic, driven by delivery services such as Just Eat, Deliveroo and Uber Eats. In August, 2023, Tesco announced that sushi had overtaken the
traditional sandwich as the UK’s fastest growing premium lunchtime main meal.
“Sushi is vibrant, colourful, attractive and appetising,” said Alex Noake, managing director and commercial director for Europe at Sabert. “It’s more than a food, it’s a form of art, and eating it is an experience balanced between taste, texture and presentation.
“As a developer and manufacturer of practical and easy-to-use food service packaging, Sabert’s mission has always been to make food look great – and that is part of the
rationale behind the development of our new Tray2Go range –but the other driving force is sustainability.
“Tray2Go is made using sustainable materials and is fully-recyclable. The board bases, manufactured in the UK, are made with Forestry Stewardship Council FSC certified material, while the lids are made from rPET at our facility in Belgium, and comprise a minimum of 50 percent recycled material.”
Practical to use, the new multifunctional and versatile Tray2Go range features a double-wall tray, coupled with a secure fitting
reducing non-recyclable materials in their packaging and helping them to find an alternative solution. We’re pleased to have been part of that solution for Cristalco and look forward to working with them into the future”. More information from www. sonoco.com
click-lock lid. Tray2Go is available in four sizes, with the remaining three sizes following soon. Custom sizing is also an option. Available in kraft, black, or white, which is ideal for bespoke printing and customisation, the tray has an inner PE varnish and a GR coating on one side for additional oil and grease resistance. The recessed (footed) base also offers added protection from wet food preparation conveyor belts and manufacturing processes whilst still providing nestability.
More information from www. sabert.eu
Paper-based packaging manufacturer DS Smith this year won Procter & Gamble Excellence Awards in two categories – Baby Care and Home Care packaging solutions. This year, only ten suppliers globally reached the final stage, with DS Smith becoming the first ever to achieve a double win at the event.
Every two years, P&G evaluates its extensive supplier network, choosing a select group for its Excellence Awards. The P&G Supplier Excellence Award selection criteria encompass four key themes: Commercial,
Operations, Innovation and Sustainability, and Citizenship. Winners are chosen based on a comprehensive assessment that considers quantitative and qualitative data across key performance metrics, highlighting consistent excellence throughout the supplier relationship.
The wins align with DS Smith’s company-wide purpose of ‘Redefining Packaging for a Changing World’ and ‘Now & Next’ sustainability strategy. Francesco van Westrenen, global customer business unit director in the packaging
are thrilled to be recognised for excellence in not just one, but two business categories for sustainable fibre-based packaging solutions for both Feminine & Baby Care as well as Fabric & Home Care and by two different procurement organisations within P&G. This is an unprecedented achievement and highlights the outstanding performance and commitment that our company has demonstrated across various aspects of our partnership and DS Smith is the only supplier to ever win simultaneously in two categories.”
More information from www.
DS Smith has provided “pioneering” cardboard multi-packs for brewer Carlsberg in Poland to reduce the volume of shrink-film on pallets.
Using Arcwise technology, DS Smith’s Round Wrap features curved corners and is designed to protect and keep products intact during transportation while using less energy in its fabrication when compared to standard corrugated multi-packs.
Being recyclable, it is anticipated to save up to 224 tons of carbon dioxide a year for Carlsberg in Poland.
A survey conducted by DS Smith and Toluna highlighted that consumers prefer Round Wrap as an ‘enhanced wrap around design’ compared to other packaging designs with ‘stand out on the shelf’ appeal.
The DS Smith design team used the company’s Circular Design Metrics (CDM) tools to measure the impact of the new packaging for Carlsberg Poland. The process involves the use of eight key
indicators including carbon footprint, design for reuse, supply chain optimisation and materials use. The indicators reveal the performance of a packaging design and allow DS Smith design teams to measure its sustainability
performance with enhanced accuracy and insight.
Reinier Schlatmann, managing director for East Europe in DS Smith’s Packaging Division, said: “We are proud to partner with Carlsberg Poland for a trial launch of the DS Smith Round Wrap. This sustainable packaging innovation was developed using our Circular Design Metrics, offering durability, supply chain advantages and branding opportunities. This is aligned with our company wide commitment to Redefining Packaging for a Changing World and our Now & Next Sustainability strategy and mission as we help our customers to design out waste and move towards a circular economy.”
Carlsberg Poland is trialling Round Wrap for Carlsberg, Garage and Somersby beer product ranges.
PulPac and the Matrix Pack Group are partnering to deliver a more cost-effective and environmentally-friendly alternative to traditional singleuse plastic and wooden cutlery.
The collaboration involves PulPac, Matrix Pack and PA Consulting. PulPac and PA Consulting will lead the development of the cutlery, with Matrix Pack acting as a codeveloper in the industrialisation of the post-processing system. Matrix Pack will be the first producer to introduce Dry Molded Fibre Cutlery to the market, with a commercial cutlery set expected to be available by early 2025.
“Our goal within this partnership is to develop a consumer-friendly solution that not only meets market standards for functionality, but also emphasises cost-efficiency,” said Sanna Fager, commercial chief at PulPac. “It’s an honour to work with a front-runner like Matrix Pack. By combining the strengths of PA Consulting, PulPac and Matrix Pack, we can accelerate development and industrialisation, bringing innovative, sustainable products to market.”
Emphasising the significance of this partnership, Fager said, “We are excited to deepen our strong partnership with Matrix Pack and
Dry Molded Fibre Cutlery – “A consumer-friendly solution that meets market standards for functionality and cost-efficiency”
this collaboration underscores PulPac’s commitment to continuously supporting licensees with new product solutions.”
The Dry Molded Fibre technology offers significant advantages over traditional
fibre-forming, including a substantial reduction in cost and environmental impact due to its minimal water and energy consumption.
More information from www. pulpac.com
Packaging and paper specialist Mondi is collaborating with advanced biomaterial engineers Traceless to develop a new coating based on byproducts from the agricultural industry. The bio-circular coating is said to be the first of its kind and will be able to replace traditional fossil-based plastic coatings.
With increasing demand for plastic alternatives in packaging the new coating responds to the demand directly: it is made from renewable plant-based materials based on agricultural residues, it eliminates the need for fossilbased raw materials.
A life-cycle assessment by Traceless showed that the provision of its material to the market leads to overall greenhouse gas savings of 76 percent from sourcing to disposal, if the material is used as a replacement for virgin PET. If
only the production and disposal phase is considered, these savings add up to 95 percent. The material is also home compostable.
The joint work of Mondi and Traceless started in 2021 and brought world-leading expertise together: Mondi’s knowledge in paper coating and packaging, and Traceless’ expertise in materials based on natural polymers. The coating granulates are produced in Traceless’ pilot plant and are applied to Mondi’s kraft paper in its R&D centre for further testing of the coated paper in its laboratories. Eventually, production on an industrial scale will take place at a dedicated plant in Hamburg. Various products require different barriers in their packaging and the coated kraft paper is tested thoroughly for a range of packaging purposes, to ensure it is applicable across a number of end-markets: the
trials have confirmed that kraft paper coated with Traceless is able to resist water, oxygen and fat, while offering good printing capabilities. At the same time, the goal is to develop packaging that is also recyclable in existing streams throughout Europe. Currently, the properties of the bio-based coating are being further optimised to make it fit for different packaging applications for various endmarkets such as e-Commerce, frozen food, fatty and non-fatty food.
Barrier coatings sourced from agricultural waste are being developed by Mondi and Traceless
Marko Schuster, operations chief for functional paper and films at Mondi, said: “We are always looking at what the next steps are in creating truly circular packaging, following our customers’ demands, as well as our own innovative spirit. This is a fantastic example of how we can combine our R&D forces to be one step ahead in the sustainable packaging game, contributing to a circular economy.”
Anne Lamp, chief executive and co-founder of Traceless, added: “Our mission is to make pollution and waste history, by using materials that impact positively. The journey so far has been exciting and insightful, teaching us valuable lessons to ensure our packaging delivers excellent protection.
“By working with Mondi – its team, its machines and its products and processes – we are adapting our existing expertise in innovative biomaterials to reduce plastic barrier coatings in packaging. The goal is to create a truly fit-for-purpose product that works for as wide a range of applications and industries as possible”.
More information www. mondigroup.com
Flexible web client computers specifically designed for pulp and paper mill environments act as human machine interfaces to web-enabled devices and HMI/SCADA applications. Del Williams* reports
Operators in pulp and paper mills have long depended on humanmachine interfaces (HMIs) to offer a visual summary of process systems that simplify the monitoring of crucial status and control data.
A well-crafted graphical user interface enhances situational awareness, reduces workload, and empowers operators to oversee the entire process – facilitating their focus to quickly address any abnormal scenarios.
Most HMI/SCADA software runs on a dedicated computer system. “Today, sophisticated web server technology facilitates access to HMI screens and the viewing of SCADA systems. Newer PLCs and RTUs frequently incorporate web servers that allow diagnostics and monitoring via browsers as well,” says Paul Shu of Arista Corporation, a leading provider of computing platforms and visualisation display products for manufacturing environments across all industrial sectors.
Facilitating implementation of web-based HMIs
Historically, HMI/SCADA client software has run on a dedicated computer with a compatible operating system installed that exhibited slow loading times during start-up and restart procedures. This reduced productivity on a routine basis, cutting into valuable production time. Updating
and maintaining software on individual PCs resulted in higher cost of ownership and even more downtime.
Fortunately, web-based applications have revolutionised accessibility by enabling connectivity from any location using a web browser. Still, for pulp and paper mill operators, the integration of the HMI presented several challenges. When standard web browsers are used, operators must open a
browser and type a long website address to be routed to a specific program. Users have the liberty to explore various unrelated websites as well, but this only exposes the system to potential risks inherent in online browsing activities.
Now pulp and paper mills are able to optimise operations by utilising software-enabled web clients to streamline web-based HMI implementation. The best involve touchscreen displays that
serve up HMI pages on multiple monitors, in multiple split screen configurations, or at cloned workstations to streamline the management of equipment across the production line.
Arista, for example, has introduced a web client computer called Q8 Edge that is designed to serve as the display or control panel for web-enabled PLCs, HMI systems, and IP cameras. In the case of the Q8 Edge web client, Arista designed the
interface to automatically connect with the assigned web pages without opening a browser and entering an address.
“After initial setup, the browser automatically launches with the assigned web link after turning on the PC’s power or restarting the system, so the operator gets to needed information much faster,” says Shu.
Hybrid remote desktop services (RDS) and web-based applications can also be launched simultaneously, when needed. The web client supports clones, duplicate screens, and multi-screens. Touch screens are supported as well. The applications can be displayed one by one by toggling a hot key, or all applications can be displayed by split screen. For data security, the USB drive function is disabled automatically after the system boot up. No external USB drive can be used to download or upload data.
In addition, Arista prevents access to other sites or browser features. “The operator can only see what is displayed on the screen and cannot change anything beyond the intended HMI pages,” says Shu.
When troubleshooting is necessary, the Q8 Edge can be securely accessed using interactive remote mirroring by an administrator.
The approach facilitates installation of a wide range of ruggedised computers, panel PCs, monitors, and KVM. To promote efficient use in space-constrained areas, various types of mounts are available, including pendant arm, wall, pedestal, ceiling, and VESA.
When web-client computers, panel PCs, or mobile workstations must be customised to the manufacturer’s process, this can
be accommodated as well.
“If there are unique requirements such as space constraints, we can meet with the manufacturer to fully understand the situation and design a solution,” says Shu. “In six to eight months, we can deliver the first articles for approval, and begin production of the equipment.”
As pulp and paper
manufacturing facilities continue to actively explore new avenues to enhance productivity, the utilisation of web-based HMIs on industrial-grade computers can significantly boost efficiency. This innovative solution, characterised by streamlined and adaptable display features as well as improved security measures, promises to enhance
the profitability and productivity of plant operations in the years ahead.
• Del Williams is a technical writer based in Torrance, California.
More information from Arista Corporation, 48460 Lakeview Blvd, Fremont, California 94538, USA. Tel: 1 510 226 1800. Email: sales@ goARISTA.com
Aimed at overcoming the paper stress and wrinkling that are common challenges for folded tissue producers, Valmet has launched MTC Wizard, which the engineering group describes as a gamechanger for folded products in the away-from-home market.
The vacuum-assisted mechanical fold system (VAM) system replaces traditional methods by gently pulling the paper into the clamp through vacuuming, eliminating the wear and tear usually caused by mechanical grippers and tuckers. This, says Valmet, leads to reduced maintenance downtime, increased reliability, and performance for single-ply, low-bulk products.
Moreover, the lack of contact between mechanical components minimises wear, enabling for higher operating speeds of 600 meters per minute for three and four panels and 16 cycles per minute. This results in a daily production of up to 55 tons, paving the way in the interfolded
MTC Wizard’s design enables easy access, speeds up maintenance operations, and facilitates cleaning, ultimately increasing operator safety
household towels market. High efficiency is also ensured by an innovative overlap system that provides several benefits: it eliminates speed differences between moving elements for precise overlap and allows controlled sheet positioning up to the folding rolls without stressing the paper.
Additionally, the added value of this technology includes two of Valmet’s SAM (self-adjusting machine) offerings, namely SAM Vacuum and SAM Cut. These solutions offer significant
advantages to customers such as enhanced monitoring of the production process and waste reduction, ensuring seamless operation with minimal manual intervention.
“The MTC Wizard elevates the production of multi-panel, Z and W fold, away-from-home products such as hand towels. It guarantees high-speed performance, through an innovative folding process, boosting production capacity and overall efficiency.” says Giovacchino Giurlani, director of technology for the tissue
converting business unit at Valmet.
“Our primary goal in this project is to optimise the price per ton of multifold away-from-home products. Furthermore, the MTC Wizard’s design enables easy access, speeds up maintenance operations, and facilitates cleaning, ultimately increasing operator safety.
“This technology undoubtedly enhances return on investment for clients by reducing production costs and increasing line production capacity by 30 per cent.”
Contaminant-laden stock flows in pulping systems for recovered paper can be conveyed reliably and largely blockage-free with a newlydeveloped pump from Voith.
Whether in the LC or HC system, the new IntensaPump is said to reliably pump critical contaminants to the next machine in both systems.
“Compared to its predecessor,
the Contaminex CM, the IntensaPump combines a wide range of benefits for our customers, such as higher throughput with reduced energy requirements, lower maintenance requirements and improved runability,” says Wolfgang Müller, global product manager for pulping at Voith.
“These advantages make the IntensaPump a new addition
to our comprehensive BlueLine portfolio and the Intensa family.”
Voith’s BlueLine portfolio includes modern machines and products for stock preparation that are characterized by efficient energy and other raw material consumption as well as gentle fibre treatment.
Large debris easily passes through the pump housing, as
the large nozzle and housing space, as well as the recessed vortex impeller, prevent the IntensaPump from clogging. A frequency converter enables optimised pump speed with reduced energy consumption for discontinuous pump operation. During pumping pauses, when no medium is being pumped, sediment and wear-promoting parts are
An optimized LC (low-consistency) pulping system for recycled paper has been launched by Voith. BluePulpLC is a development of Voith’s TwinPulp system, which has undergone extensive further development, with the focus on improving efficiency and reducing costs.
Following the optimisation of the IntensaPump after the IntensaPulper IP-R, the IntensaMaXX and the IntensaScreenDrum, the revisions of all main components have been successfully completed. The high-performance OCC dissolution system, which meets the latest technological standards, is now available under the name BluePulpLC.
“We are proud that we have been able to further develop our TwinPulp pulping system into the BluePulpLC, a product of the proven BlueLine product family,” says Wolfgang Müller, global product manager for pulping at Voith. “It now
deposited in the horizontal nozzle and prevent further circulation in the pump housing. The pump has been provided benefits at paper maker Modern Karton in Turkey. “By installing the IntensaPump on our OCC 3, we had far fewer blockages in the pump and were able to save a lot of time and maintenance work. At the same time, we need less energy
Energy consumption in the BluePulpLC can be reduced by up to 25 percent with the eccentric IntensaPulper IP-R
combines all the key economic and technological advantages that our BlueLine portfolio stands for: reduced fibre loss; low energy consumption; simple, safe operation; increased runability; and a robust, low-maintenance machine design.”
Voith says that compared with conventional LC pulpers, energy consumption in the BluePulpLC can be reduced by up to 25 percent with the eccentric IntensaPulper IP-R. The improved IntensaPump conveys the highly contaminated stock flow from the IntensaPulper IP-R to the
IntensaMaXX disposal machine largely free of blockages, enabling energy savings of up to 30 percent and reducing wear at the same time. IntensaMaXX allows for maximum contaminant contents, while the special shape of the housing suppresses the formation of spinnings. The IntensaScreenDrum screening drum washes out rejects very efficiently, thanks to sophisticated spray pipes, and minimizes fibre losses.
BluePulpLC can be integrated into existing stock preparation systems as well as newly
configured systems. The response is impressive. For Bulleh Shah Packaging in Pakistan the installation of BluePulpLC has been a valuable step.
“The Voith pulper is outstanding. We get very convincing results. It delivers uniform mixing and separates reliably,” reports Mohammad Asghar, manager in the OCC stock prep area on the PM6 and PM7 paper making lines at Bulleh Shah Packaging.
“After installing the IntensaPump and its back flushing sequence, we are running free of blockage issues and are 100 percent satisfied with the performance.”
The IntensaScreenDrum also receives special recognition: “I have never seen such a highperformance screen in my career. It completely removes plastics and supports us in reaching maximum yield after pulper slushing,” Asghar concludes.
More information from: https://voith.com/corp-en/ papermaking/pulping.html
during operation, which has a positive impact on our carbon dioxide emissions and costs,” says Osman Özkeser, project manager of the OCC 3 rebuild at Modern Karton.
In combination with the IntensaPulper, IntensaMaXX and IntensaScreenDrum, the IntensaPump is part of Voith’s BluePulpLC system, which is likewise designed for the lowest
Voith’s latest IntensaPump is said to reliably pump critical contaminants
fibre consumption, lowest maintenance costs, reduced
energy consumption and best runability.
Spain’s Hinojosa Paper has taken delivery of an industrial blower from Runtech for its mill near Alicante. The blower will be used on the mill’s PM1 machine, which is having its capacity increased.
The delivery includes an EP600 Turbo Blower and EcoSep and EcoDrop water separation.
“We have previously worked together with Hinojosa Paper Alquería with great results. It is a great pleasure to continue our cooperation in this new project. PM1 will benefit from the energyefficient turbo blower technology for many years to come,” says Lari Lampila, sales & aftermarket manager at Runtech Systems.
Runtech says the EP Series Turbo Blowers are the heart of the RunEco paper machine vacuum system and have been delivering significant energy savings to paper mills for more than 20 years. The water-free system ensures reliability while significantly reducing carbon dioxide emissions.
EP Turbo Blowers are advanced blowers equipped with integrated
Runtech’s EP600 blower will help with Hinojosa Paper’s PM1 upgrade
high-speed motors controlled by a frequency converter. This technology enables precise adjustment of speeds and vacuum levels to meet the specific
requirements of the papermaking process.
Hinojosa Paper Alqueria, located in L’Alqueria d’Asnar near Alicante, is a part of Hinojosa Packaging
Group, which has been producing paper products for 75 years. It has 2,900 employees and 24 production plants located in Spain, Portugal, France and Italy.
An undisclosed Asia-Pacific customer of Valmet has ordered a complete new paper making line, and a rebuild of another machine. The orders could be worth up to €160 million.
One order includes a complete paper making line from stock preparation to reel and winders, a comprehensive automation package as well as spare parts and consumables packages. The
other order includes a paper machine rebuild with automation and services. Both will produce uncoated woodfree grades, with
start-ups scheduled for 2026.
Markus Veikkola, director for contracts and customer relations in the board and paper mills
business at Valmet, said: “Our long-term partnership with the customer has resulted in many successful projects, and these orders are continuing our cooperation. The customer was searching for a supplier capable of providing flexible solutions and advanced technology for highspeed paper machines to meet their high quality, production speed and efficiency targets.”
Improve your press section efficiency! SmartScan™ contactless sensor accurately measures paper web dryness after the press section 24 hours a day, 7 days a week. Using a proprietary microwave technology, it is developed to overcome the typical limits of the NIR (near-infrared) sensors. SmartScan™ is available both for fixed point positions or traversing web scan
To save hundred of thousands of Euros in energy costs, stop collecting samples, choose the safe accuracy of SmartScan™ technology.
Cristini S.p.A. Diagnostic Systems Via Bombardieri, 5 – 24020 Fiorano al Serio (BG) Italy Tel +39 035 715 111 Fax + 39 035 711 451 email diagnostic.systems@cristini.it website www.cristini.com
The first commercial kraft lignin plant in Sweden and what is claimed will be the biggest in the world is being set up by forest industry group Södra at its Mönsterås pulp mill.
The plant will be supplied by Andritz and marks Södra’s entry into the lignin market as part of its strategy to make the most of the wood used in pulp production. A by-product of pulp production for paper, kraft lignin is used in pulp mills to generate energy. It is also used as a renewable resource to replace fossil-based materials in the chemical industry or form the basis for new biofuels.
“This investment means a lot for Södra and for our kraft pulp mill in Mönsterås. We will make more out of every tree and strengthen our profitability. This is a big investment for Södra and the green transition,” says Karin Dernegård, mill manager at Södra Cell Mönsterås.
Andritz will supply a system to
recover the lignin contained in the black liquor from the pulping process, making it available to Södra as a saleable product. The project will also include supporting systems that improve the mill’s environmental performance and ensure full integration of lignin recovery into the existing operations.
The system will be based on the Andritz LignaRec lignin recovery process. The lignin drying section, equipped with flash dryer
technology, will further process the kraft lignin, ensuring a highquality product. The integration of the LignaRec process into the Mönsterås pulp mill will be completed by the installation of an Andritz SulfoLoop sulphuric acid plant. This plant enables the closure of the sulphur loop, avoiding the purge of sulphate streams even after lignin recovery is implemented.
Lignin and sulphur recovery systems are part of Andritz ’s
CircleToZero initiative, which aims to maximize the use of side streams in pulp mills, laying the foundation for zero emissions and zero waste production. With the new order, Södra continues its collaboration with Andritz on the reuse of side streams. The company already operates an Andritz Kraftanol biomethanol plant at its Mönsterås mill. This plant is the first of its kind in the world to convert by-products of pulp production into purified biomethanol.
“We are very pleased that Södra has once again placed its trust in us to implement a first-of-itskind solution that supports the green transition and at the same time opens up new business opportunities,” says Joachim Schönbeck, chief executive of Andritz
Södra’s lignin production plant is scheduled to start up in 2027 and is enabled through the Swedish Energy Agency and The Industrial Leap through NextGenerationEU.
Five Continents Special Paper in China has ordered second rewinder from A.Celli for its facility at Hanchuan in Hubei Province.
The Italian-made E-Wind P100 paper rewinder will have a width of 8.66 metres. It will be used to process T-paper and highstrength corrugated paper with basis weights ranging from 70 to 170 grams per square metre at a design speed of 2,600 metres per minute.
Commenting on the order, Zhang Yancheng, vice general manager of Five Continents,
said: “Over the years, A.Celli has provided Chinese customers with
efficient winding and rewinding solutions, thanks to its vast experience and the affordability of its technology; our choice to cooperate with A.Celli again will surely enable us to achieve our goal of improving productivity and creating high-quality products.”
Five Continents is part of Wuzhou Special Paper Group, one of China’s largest food wrapping paper producers which has a listing on the Shanghai Stock Exchange.
India’s Andhra Paper has ordered a tissue line from Valmet for the Kadiyam mill in Andhra Pradesh. With start-up scheduled for the end of 2025, the Advantage DCT100HS line will be set up to improve production and reduce the mill’s environmental impact.
The tissue machine will have a reel width of 2.85 metres, and with a maximum operating speed of 2,000 metres per minute a yearly capacity of 35,000 tons of high-quality tissue grades dedicated for bath, towel, facial and napkin products.
Commenting on the order, Mukesh Jain, executive director at Andhra Paper Limited, said: “This strategic investment proves our commitment to innovation, sustainability, and meeting the evolving needs of our customers.
The decision to invest in cuttingedge technology from Valmet underscores our dedication to enhancing our production capabilities while reducing our environmental footprint.
“The new tissue machine will leverage advanced engineering and design to maximise efficiency and productivity, ensuring that
we continue to deliver highquality products to our valued customers.”
Jenny Lahti Samuelsson, vice president of tissue mill sales in the paper business line at Valmet, added: “It is a privilege to cooperate with Andhra Paper and deliver them world leading Valmet Advantage DCT
Two complete tissue converting lines including packaging systems are to be delivered to Metsä Tissue’s mill at Mariestad in Sweden by Valmet.
Both are part of Metsä Tissue’s expansion and modernisation project ‘The Future Mill’, aiming at world-class environmental and operational performance.
The delivery includes digital services, training and support after the start-up. The order follows an earlier one for delivery of a Valmet Advantage DCT 200 tissue making line to the same mill.
Esa Paavolainen, vice president for projects at Metsä Tissue,
commented: “We have a long history with Valmet and with the addition of converting technologies in their portfolio we clearly see the synergies with Valmet’s end-to-end solution including tissue machine and converting lines. Their cuttingedge technologies and proven
performance will ensure optimal production, a safer working environment and a more efficient tissue production.”
Gianfranco Agnusdei, sales chief in the tissue converting business unit of Valmet, added: “This is one of Valmet’s first projects
technologies. We are looking forward to working together to make the new tissue line successful.”
Along with the Advantage DCT 100HS tissue machine, the line will be equipped with an OptiFlo TIS II headbox and a Steel Yankee Dryer. The machine will feature Advantage technologies such as ReDry, a ViscoNip Press, a gas heated AirCap hood, rewinders and process equipment. In addition, the delivery includes Valmet’s automation with DNA Distributed Control System and IQ Quality Control System.
Founded in 1964, Andhra Paper Limited produces writing, printing and copier papers for export and domestic markets. Its two mills at Rajahmundry and Kadiyam have a total capacity of 240,000 tons per year.
implementing the complete value chain, combining a Valmet tissue making line and converting technologies. It’s a unique offering in the market. With it, we have developed a one-stop solution to actualize the integrated factory concept. We are proud to be part of Metsä Tissue’s expansion journey.”
The delivery comprises of two Valmet Perini Constellation tissue converting lines and the packaging machinery needed for the production of rolled tissue. The machinery represents latest technology for efficiency, flexibility, and low energy consumption.
Packaging and paper maker
Mondi celebrated the completion of upgrades at its Kuopio containerboard mill in Finland in June with an inauguration event attended by local politicians and partners.
The US$125 million investment included upgrades to the wood yard, fibre line, evaporation plant, and paper machine producing ProVantage Powerflute, a high-performance fluting predominantly used for fresh fruit and vegetable trays and boxes. The project is said to have increased capacity of the mill by 55,000 tons per year and improved product quality along with environmental performance by reducing greenhouse gas emissions per tonne of paper and improving resource and energy efficiency,
Mondi said in a statement.
Commenting on the upgrades at the mill, Andrew King, chief
executive of the Mondi Group, said, “We are delighted to celebrate the completion of
this significant investment and the opportunity it gives us to continue providing high-quality, sustainable products to our customers. It also demonstrates our commitment to supporting economic growth in the region and securing the long-term viability of the Kuopio mill.”
Markus Gärtner, chief executive of Mondi Corrugated Packaging, added, “Mondi’s purpose is to be sustainable by design, and investments like this support our MAP2030 sustainability commitments around circulardriven packaging and paper solutions, created by empowered people, taking action on climate. The local community will benefit from a modernised mill, including improvements in safety and environmental performance.”
Smurfit Kappa is having one of its largest corrugated board machines in Mexico modernised by ABB, with controls, drives and motors, along with ongoing expert services.
ABB describes the project, the first collaboration between the two companies in the region, as a “landmark contract”.
The project at Smurfit Kappa’s Cerro Gordo mill near Mexico City involves the PM5 machine being upgraded with ABB’s Ability 800xA distributed control system (DCS), accompanied by a comprehensive paper machine drives system, all designed to optimise the machine’s performance.
Smurfit Kappa – now part of the larger Smurfit Westrock group – is one of the leading providers of paper-based packaging worldwide, with operations spanning 35 countries. It has operated in Mexico since
1957 and has been increasing production capacity in the country, investing more than US$350 million since 2018.
ABB says the technology embedded in the drives, complemented by the control system, will help secure optimum speed and torque control of the paper machine’s sectional drives. This is achieved through a combination of factors such as a
Direct Torque Control algorithm, which ensures precise control and allows for consistent quality and minimised waste over time. ABB guarantees a system uptime of 98.5 percent during the threemonths following the machine’s startup in 2025. This translates to a maximum downtime of just 33 hours within that period.
“We are impressed by ABB’s deep understanding of the
Wuzhou Special Paper in China has ordered a two-drum base winder from Valmet for its PM19 paper machine at Quzhou City. The OptiWin Drum winder has been ordered to enable one winder to handle the high quality and capacity targets of the high-speed paper machine. The winder includes a Valmet Perforating Splicer, a new innovation to support the fast parent roll change. Start-up is scheduled for 2025.
The winder will handle parent rolls with a width of 8.21 metres at a design speed of 3,000 metres per minute and a capacity of 830 tonnes per day. The PM19 paper machine produces uncoated woodfree grades with a basis weight from 55 to 100 g/sqm.
Commenting on the project, Zhang Yanchen, deputy general manager at Wuzhou Special Paper, said: “Valmet winders are equipped with technologies necessary for high-speed printing
paper machines. Also, the collaboration between Valmet and Wuzhou has been good in the past years: Valmet has actively participated in Wuzhou’s projects and always tried to respond to our needs. We are willing to take this opportunity to establish a long-term cooperation.”
Ze Fan, vice president of capital sales in China for Valmet, added: “Wuzhou Special Paper was searching for a supplier capable
industry and their commitment to exceeding expectations,” said Mario Olvera, engineering and project director at Smurfit Kappa Mexico. “We are confident that their expertise will be instrumental in maximising the performance and efficiency of PM5. This project represents a significant step forward for Smurfit Kappa in Mexico, and we look forward to a successful collaboration with ABB.”
Diego Navas, regional sales manager at ABB Pulp and Paper in North America, added: “Partnering with Smurfit Kappa on this momentous project will help ensure optimal equipment design, control performance, and seamless commissioning. A dedicated team of ABB specialists will work alongside our customer on the machine to deliver significant benefits, including increased production, improved efficiency, and reduced operational costs.”
of providing a single winder solution. Our OptiWin Drum two-drum base winder together with the new Valmet Perforating Splicer solution helps them reach their long-term investment targets.”
The order includes an OptiWin Drum two-drum base winder with automatic functions such as set change with core and tail gluing and slitter positioning. To meet the high-capacity targets reliably with only one winder, it is additionally equipped with Valmet Perforating Splicer which will improve capacity with fast parent roll change.
Rizhao Huatal Paper in China has ordered a second paper rewinder from Italy’s A.Celli as part of its PM8 rebuild.
Huatai’s PM8, with a wire width of 5.00 metres and a design speed of 900 metres per minute, will be upgraded and relocated with the goal of producing high porosity sack paper with 100 percent virgin fibre and other grades with a portion of OCC.
In addition to the Ewind P100 rewinder, A.Celli will supply an ÆGO Stream S headbox, capable of managing slice flow up to 180.000 l/min and equipped with a Smarpro dilution water control system for automatic regulation of the sheet basis weight profile.
Jinming Sui of Rizhao Huatai Paper said: “When it came time to rebuild our PM8, we were looking
Rizhao Huatai Paper Industry Co manufactures and distributes a wide range of paper products for the domestic market in China
for an experienced supplier with a history of success for this type of intervention. A.Celli Paper and PMT had the right credentials, and this, along with their proposal, convinced us that they were the best partner we could ask for. We look forward to starting this new project together.”
Rizhao Huatai Paper Industry Co
manufactures and distributes kraft paper, tape base paper, envelope paper, wet paper, food wrapping paper, electrostatic copy paper, and sanitary paper products in the domestic market.
The company is a wholly-owned subsidiary of the Huatai Group, a large listed domestic paper producer located at the port city
of Rizhao City in in Shandong Province.
Rizhao Huatai currently has five special paper lines, a conifer pulp production line, a self-sufficient power plant, a wastewater treatment station and a lignin deep processing plant.
With capacity to produce 500,000 tons of pulp a year, Huatai claims to be the largest speciality paper producer in northern China. Its main products include natural colour chemical needle leaf pulp, refined kraft paper, film original paper, composite kraft paper, tape original paper, envelopes and archival bag paper, wet curtain paper, food packaging paper, highgrade white kraft paper, colour cardboard, kraft paper, transfer printing original paper, release original paper and bag paper.
Leading producer of thin MG papers in Europe for flexible packaging and hygiene products in tissue and airlaid, Lucart Group reports that it has increased its production capacity by 15 percent following the installation of four Perini MyLine systems from Valmet on its converting lines in Europe particularly in France, Hungary and Italy.
“The Perini MyLine is a system that perfectly meets our needs to set up different product changes,” says Gabriele Coli, engineering manager at the Lucca-based Lucart Group. “Thanks to the
“The Perini MyLine is a system that perfectly meets our needs to set up different product changes,” says Gabriele Coli, engineering manager at Lucart Group
flexibility, reliability and high performance that characterise Valmet’s technology, we can diversify our production to
effectively respond to market demand. The multiple benefits already observed with the first line have led us to continue our
collaboration with Valmet as our trusted partner in every aspect.”
Among the many advantages for the company, Coli points to the quick start-up of the Perini MyLine, coupled with a simplified operator interface. Another plus is the laminator-embosser, which enables quick changes in embossing without requiring specific skills from operators.
For customers who need to modify embossing during production, the line offers high flexibility and optimum alignments with processing times. Additionally, the joint research by
C&S Paper in China has ordered two Andritz PrimeLineCompact tissue machines from for its Suqian City mill in Jiangsu Province.
The machines, with a width of 3.50 metres and a design speed of 1,650 metres per minute, will produce tissue for household paper, napkins, handkerchiefs, facial tissues, and toilet paper, each with a capacity of 94 tons per day.
Vice president of C&S Paper Lin Tiande said: “Increasing consumer health awareness and improved living standards are driving the demand for superior tissue qualities. We have been looking for the best available technologies that enable highquality and sustainable tissue production, and we are convinced
Valmet’s Engraving Solutions and Lucart’s technical team, over the years, a series of embossings have been developed and customised, leading to a significant improvement in the various product categories in terms of quality, finish and aesthetics.
Ivo Cataldi, sales manager at Valmet, says, “Lucart is very attentive to the constant upgrading of the final product quality. In this regard, the services offered by Engraving Solutions perfectly reflect the care the company invests in this area. In particular, our facility is equipped with pilot lines dedicated to testing various embossings with Lucart’s paper, in order to optimise the quality of the product to be offered on the market.”
that Andritz is the right partner for us.”
Both machines will be equipped with suction pressure rolls with innovative roll covers and PrimeDry Steel Yankees. Other equipment includes undermachine pulpers and flow and consistency transmitters for both lines, as well as PrimeControl
automation systems for efficient control and monitoring of the entire production process.
Shi Wei, vice president of Paper & Textile APAC at Andritz commented: “Innovative and sustainable solutions have become the driving force in the tissue industry. With our PrimeLine technologies, we
Ultimately, with the installation of Acquabond water-based lamination technology, developed by Valmet, Lucart is said to have reduced consumption of glue for sheet adhesion, also benefiting
from a general simplification of maintenance, plant cleaning and generating eco-friendly products such as the Tenderly brand. Due to the excellent results achieved with the Perini MyLine
are able to help our customers achieve their goals of efficient, sustainable, and high-quality tissue production. We are proud that Asia’s leading paper producers like C&S trust in us.” C&S Paper is one of China’s largest household paper producers, with C&S and Sun as its two main brands.
technology, Lucart Group also uses Perini Proxima lines, which are specifically used for production of away-from-home products.
“If we need steel rollers for embossing at a certain location, we can transfer them seamlessly from one facility to another on all lines, as the laminating units are 100 percent compatible. Moreover, our technicians, trained by Valmet, become in-house trainers who are able to share the know-how they have acquired on the field with colleagues from other plants,” says Coli, who concludes: “Also, if a spare part is not available in our factories in Italy, we can quickly source it through Valmet or from our overseas locations, minimising downtime.”
As Suzano celebrates its centennial year and completed construction in Brazil of the Cerrado Project, the world’s largest single-line pulp mill, Beto Abreu took over as chief executive from the beginning of July.
With more 30 years of experience, Abreu, 53, who is married and a father of three, has held senior executive postions at companies including Rumo, Shell, and Raízen. He is recognised for
his ability to balance delivering strategic transformation with exceptional people-based leadership. He has extensive experience in leading M&A transactions.
Abreu’s appointment was annouced in February, and he succeeds Walter Schalka, who served as Suzano’s chief executive for 11 years, and who now joins the Suzano board.
Commenting on his appointment, Abreu said: “I am honoured and excited to assume
Gunnar Eberhardt has been appointed executive vice president at UPM Communication Papers. He will be a member of UPM’s group executive team and report to chief executive Massimo Reynaudo, starting in October 2024.
Eberhardt, born in 1977, joins UPM from Henkel AG & Co, where he worked as corporate vice president at the Adhesives Automotive OEM Business since April 2022. Prior to his current role he has held several sales, marketing, business unit and region head roles at Henkel and Osram since 2000.
He has a diploma in industrial engineering and an executive master’s degree in Innovation & Technology Management. He is a German citizen, and will be based in Augsburg, Germany.
Commenting on the appointment, Massimo Reynaudo said: “I’m very pleased
Eberhardt,
to welcome Gunnar to UPM and the Group Executive Team. He brings a wealth of international experience from a range of industries, a commercial mindset and strong leadership track record. With Gunnar, the UPM Communications Paper team will get an inspiring leader, and I look forward to our collaboration.”
the role of chief executive officer at Suzano, a company I have always admired for its positive impact on society and strong focus on sustainability, a track record which was extended under Walter’s visionary leadership.
“As we expand into new markets and grow Suzano, we will continue to be a leader on sustainable business and driving forward positive environmental and social transformation. Importantly, we will double down on investing in innovation and strengthening our
strategic partnerships, both of which we regard as key to helping us plant a more sustainable future.”
Iain Cunningham has been appointed by Antalis as its new head of packaging in Ireland.
With more than 20 years of experience at Antalis, Iain brings a wealth of knowledge and expertise to this new role. He will be instrumental in expanding the company’s market share across Ireland’s packaging sector.
Since joining Antalis, Iain has held several key positions, including sales operation manager, operations manager and office papers sales manager. These roles have provided him with an in-depth understanding of the company’s operations and a comprehensive insight into customers’ needs and expectations. His extensive experience makes him exceptionally well-suited to drive growth in the packaging sector.
The appointment comes at a key time for Antalis Packaging due to the company’s ambitious growth plans for its packaging business.
“I am excited to take on this new challenge and to help Antalis continue to increase its presence in the packaging market,” said Cunningham. “I am looking forward to working with our team to deliver exceptional service and innovative packaging solutions to our customers across Ireland.
“Antalis Packaging already supports customers across the UK and Ireland; we can work with anyone who wants help packing, protecting, storing, dispatching or transporting goods.”
Do more with digital. Like make your pulp and paper process more sustainable.
It may be surprising, but the key to doing more with paper lies in doing more with digital. Doing more with digital means drastically reducing emissions, chemical usage, and water consumption, paving the way for a more sustainable future. Doing more with digital means stabilizing production, improving on-spec results, and reducing downtime, ensuring you meet and exceed customer expectations. With innovations designed for the challenges of paper making, ABB can be trusted to make your paper process even more efficient. Do more with digital, and achieve more than you thought possible.