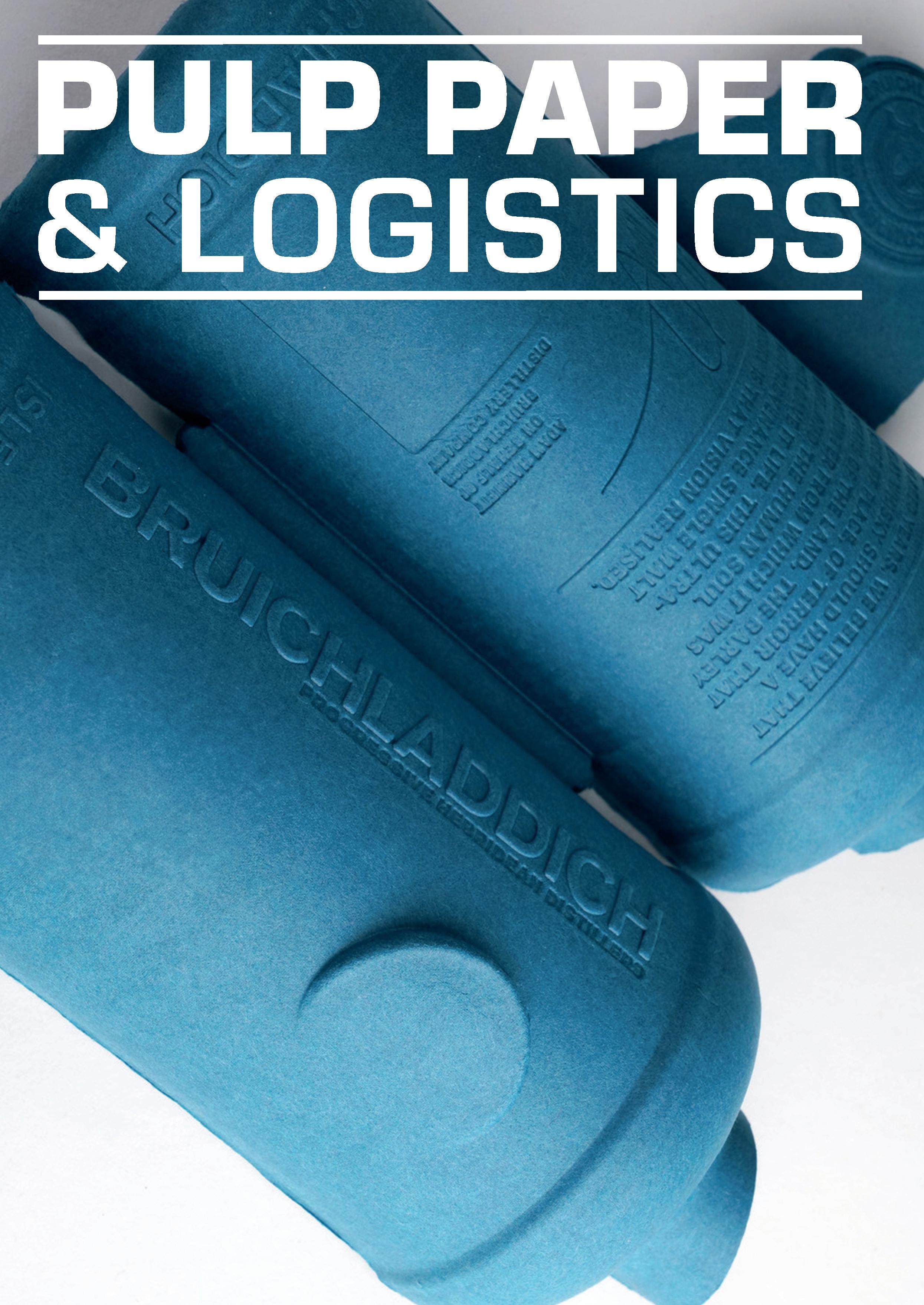
GREEN PACKAGING: First sustainable
coloured wrap for whisky bottles
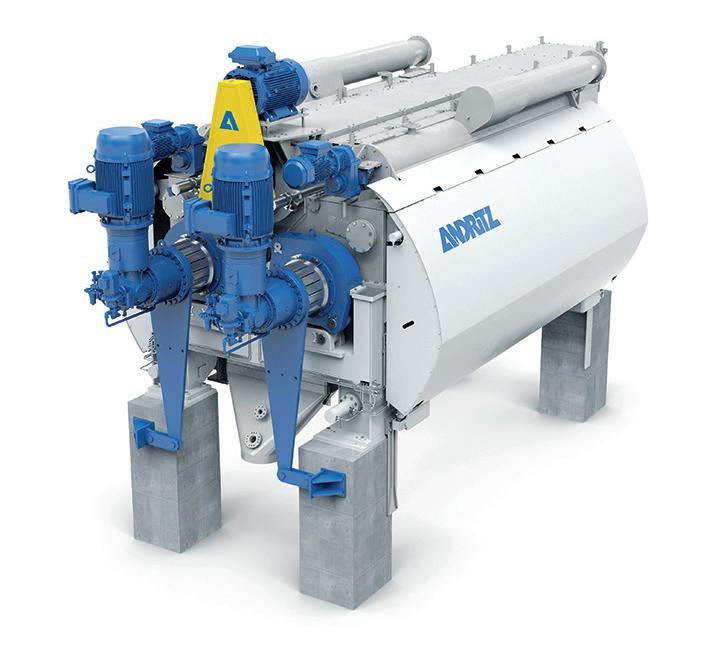

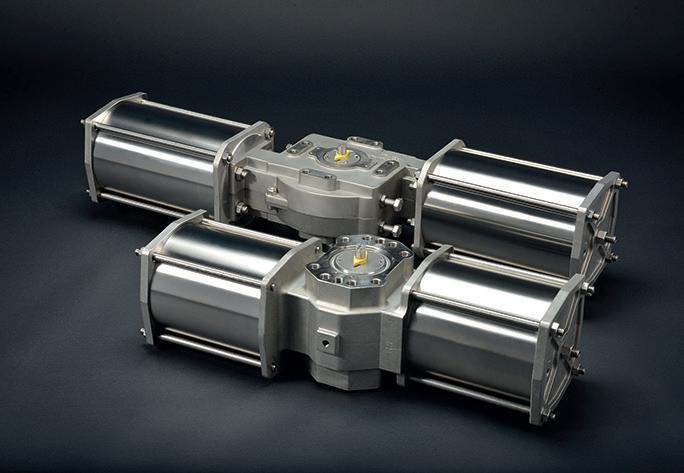
GREEN PACKAGING: First sustainable
coloured wrap for whisky bottles
e most complete and integrated portfolio of process technologies, services and automation systems for the entire tissue value chain.
With a holistic approach, from stock-preparation to tissue machines, rewinders, converting, and packaging, we offer a comprehensive range of technologies and services, for the whole tissue mill.
Valmet offers the most complete and integrated portfolio of process technologies, services and automation systems for the entire tissue value chain.
Explore our comprehensive tissue making and converting solutions at www.valmet.com/tissue
With a holistic approach and extensive know-how, covering stock-preparation, tissue machines, rewinders, converting and packaging, we provide solutions for optimizing the complete tissue making process.
Explore our comprehensive tissue making and converting solutions at www.valmet.com/tissue
e most complete and integrated portfolio of process technologies, services and automation systems for the entire tissue value chain.
With a holistic approach, from stock-preparation to tissue machines, rewinders, converting, and packaging, we offer a comprehensive range of technologies and services, for the whole tissue mill
Explore our comprehensive tissue making and converting solutions at www.valmet.com/tissue
Welcome to the March-April issue of Pulp Paper & Logistics. As I prepare to attend the new Pulp & Beyond trade show, which is being held from 10-11 April at Helsinki in Finland, it will be interesting to see how the event differs from the long-standing PulPaper event format.
Events like this are a great window to the new products and services that are being made available from a wide range suppliers all under one roof, and are also an oppor-tunity to listen to specialists about their views on many aspects of our industry during the conference and panel discussions.
Certainly there will be talk about the impact of the huge mergers and acquisitions happening in pulp and paper, such as the deal involving Mondi and DS Smith, and the even bigger Smurfit Kappa takeover of US-based WestRock that is expected to be completed this summer (see industry news in this issue).
For those readers not able to attend Pulp & Beyond, we will report back in the May-June issue, which will also include our annual shipping, ports, handling and ware-house focus (including cranes and forklifts), mill automation & software, plus the Green Packaging section, which brings news of forest-industry-based alternatives to plastic packaging.
Contributions for the May-June issue should be sent to us no later than 14 May by email at pulppaperlogistics@ virginmedia.com
To arrange a meeting at Pulp & Beyond, email me, Vince Maynard at the above address.
Vince Maynard,Publisher and Editorial Director
Vol.
ISSN
PUBLISHER
Vince
Tralee,
Kent, TN8 6JS, UK
Tel: +44 (0) 1732 505724
Mobile: +44 (0) 7747 002286
Email: pulppaperlogistics@virginmedia.com
EDITOR
John Nutting
Tel: +44 (0) 1732 868071
Mobile: +44 (0) 7860 221486
Email: johnnutting47@gmail.com
CONSULTANT
David Young
Tel:
Mobile: +44 (0) 7785 796826
PRODUCTION
Anthony
Tel:
Mobile:
Email:
Two more paper packaging giants had agreed to merge with Mondi’s £5.1 billion (€6.0bn) bid in March for DS Smith that will create a leader in the pulp and paper making world with sales of around £15bn (€17.5bn) a year.
The news that Mondi had agreed in principle to the consolidation follows rival Smurfit Kappa’s takeover of US-based WestRock in an $11bn (€10.1bn) deal that is expected to be completed in July.
Paper packaging manufacturers have been struggling in the past year as customers have destocked following the boom during the Covid-19 pandemic. Global sales at Mondi in the past year slipped by 18 percent to €7.33bn, and
likewise sales at DS Smith were also down 18 percent at £3.51bn for the half year to the end of October.
In a joint press release, the companies said that there was a compelling and strategic rationale for the merger: “The combination is an exciting opportunity to create a pan-European industry leader in paperbased sustainable packaging solutions, with complementary geographic footprints, leading customer relationships, a strong balance sheet and cash flow profile, and the potential to deliver substantial benefits to respective shareholders, customers, employees and related stakeholders.”
Both UK-based companies have been looking into ways of
making savings, saying the merger “would benefit both shareholders with increased exposure to structural growth trends in sustainable packaging and a highly complementary geographic footprint, creating a leading player in corrugated packaging across Europe”.
The value to Mondi was shown by the size of offer, which was 33 percent more than DS Smith’s closing share price of 281p on 7 February.
If the merger goes ahead, Mondi’s chief executive Andrew King will continue in the same position at the larger company with Mike Powell as financial chief. Current Mondi chair Philip Yea will continue in his position, with DS smith expecting to add three non-executive directors to
the enlarged group’s board.
Commenting on DS Smith’s half-year results, group chief executive Miles Roberts said: “I am pleased with the performance for the first half of the year. Our focus on value-added packaging solutions to predominantly FMCG customers, together with the benefit from our self-help productivity initiatives and flexible supply chain has driven a robust profit performance. Our Q2 volume performance was improved versus Q1 and we expect this trend to continue with H2 volumes stronger than H1, sequentially and on a like-forlike basis, as we continue to win market share.”
Andrew King, group chief executive at Mondi, commented on the company’s year-end results
in February, saying: “In the first quarter of 2024, selling prices are generally lower than the averages achieved in the second half of 2023. However, we are seeing improvements in our order books and are implementing price increases across our range of paper grades. Input costs remain elevated compared to historical levels but have broadly stabilised since the end of 2023. We remain well positioned to capitalise as demand improves with our strong operational leverage and organic growth investment projects.”
Mondi operates in 40 countries worldwide with 22,000 employees, but has no mills in the UK. DS Smith operates in 34 countries with 30,000 employees, and has more than 50 sites in
l Waste recovery firm Biffa has launched a national takeback scheme in the UK for paper cups where collections and processing are cost and carbon-efficient, so 100 percent of a polyethylene lined cup can now be recycled. To increase the recycling of these cups, the answer is to use consistent materials across brands, says Biffa.
Biffa’s waste strategy and packaging manager Roger Wright
the UK.
Mondi must by the end of trading on 4 April either announce a firm intention or not to make an offer for DS Smith.
● In other news, DS Smith is installing a £48 million fibre preparation line at its Kemsley mill in the UK to improve efficiencies and reduce emissions and costs.
Kemsley is the UK’s largest recycled papers mill with annual capacity for 830,000 tonnes. The new line will supply recycled fibre to PM3 capable of producing white top test liner, plasterboard liner and other corrugated case materials (CCM) grades.
A state-of-the-art drum pulping and screening system that more efficiently separates contaminants from fibre such as plastics, barriers and coatings will also be installed as part of the project. The new equipment will lower Kemsley mill’s freshwater use by more than 50,000 cubic metres a year.
Niels Flierman, Head of Paper & Recycling at DS Smith commented: “The installation of the new fibre preparation line will ensure that we can continue to make high performing papers more efficiently while delivering on our medium and long-term sustainability goals.”
Stora Enso says that it has finalised the restructuring plan to improve longterm competitiveness and profitability announced in June 2023. Production units have been closed the number of employees reduced by 1,150. The restructuring is aimed at improving Stora Enso’s operational profit by about €110million a year.
These actions weren’t in time to affect Stora Enso’s sales for the full year in 2023 which were 20 per cent down on the year earlier at €9.4 billion, while pre-tax operating earnings fell by €1.55bn to €342m.
Net debt rose by €1.3bn to €3.17bn, with the acquisition of De Jong Packaging Group, the consumer board investment at the Oulu site in Finland, and a proposed dividend payment for 2023 of 10 € cents per share.
such as increasing pulp prices, declining global pulp inventories, less customer destocking, and lower inflation and interest rates.
says that not all takeaway cups are the same. He says that “the biggest myth of all” is that cups with lids and sleeves attached can still be recycled if contaminated.
“A widespread phenomenon of people using their empty cups as ‘mini-bins’. Although the intentions are to compact waste and avoid littering, this habit is contaminating recycling and causing valuable resources to be lost.”
Commenting on the results Stora Enso’s chief executive Hans Sohlström said: “In a world being rapidly reshaped, we must adapt, streamline, and develop our business to meet the evolving needs of our customers. We have faced unprecedented market conditions and focus our efforts on what we can control to improve our competitiveness and prepare for an uncertain future.”
The company said that it expects market conditions to remain uncertain in 2024, with ongoing pressure on demand, prices and margins. However, there are some positive signs
Sohlström continued: “To remain competitive and drive growth, Stora Enso will launch a profit improvement programme targeting an annualised €80 million improvement of our operational EBIT. This could lead to a potential reduction of approximately 1,000 employees. The employee reductions, efficiency improvements and synergy opportunities would impact all divisions and group functions. The majority of these savings would materialise in 2025.
“This plan does not include new production site closures. While difficult, it is necessary for the group’s long-term success. We remain committed to ensuring Stora Enso remains a leader in our industry through our strategy to improve profitability and cash flow.”
Paper packaging manufacturer Mondi – which is in the process of merging with DS Smith – has completed the acquisition of the Hinton Pulp mill in Alberta, Canada, from West Fraser Timber for US$5 million.
The mill has the capacity to produce around 250,000 tonnes of pulp per annum and will provide Mondi with access to local, high-quality fibre from a well-established wood resource as part of a long-term partnership with West Fraser.
Investment in the mill is planned to improve productivity and sustainability performance with
a new kraft paper machine that will integrate Mondi’s paper bag operations in the Americas to support future growth.
UK-based Mondi Group chief executive Andrew King commented on the acquisition, saying: “We are delighted to welcome our new colleagues from Hinton Pulp mill to Mondi and look forward to working together to secure the mill’s future and support Mondi’s growth in North America with our portfolio of sustainable packaging.”
● Mondi recently started up a new slitting and rewinding unit at its Slovak paper mill in Ružomberok. The equipment extends capacity in narrow reels.
“We want to give our customers supply security for their paper needs in folio and various reel widths and for this we needed to
extend our narrow reel capacity,” said Bernhard Cantzler, marketing and sales director at Mondi Uncoated Fine Paper.
Improve your press section efficiency!
SmartScan™ contactless sensor accurately measures paper web dryness after the press section 24 hours a day, 7 days a week. Using a proprietary microwave technology, it is developed to overcome the typical limits of the NIR (near-infrared) sensors.
SmartScan™ is available both for fixed point positions or traversing web scan. To save hundred of thousands of Euros in energy costs, stop collecting samples, choose the safe accuracy of SmartScan™ technology.
In January DS Smith celebrated the 50th anniversary of its Viana do Castelo kraft paper mill in Portugal where a multiyear investment is equipping the facility with the latest technologies to help reduce carbon emissions by 10,000 tonnes a year.
Construction of the mill by the Celnorte group started in 1971 with production starting three years later. The mill was nationalised in 1976 until 2000 and later acquired by Europac. DS Smith bought Europac in 2019 for €1.9 billion, including the Viana mill.
An ambitious upgrade enabled the mill to diversify its products, enter the energy production market and invest in paper for recycling as an important source of raw materials. It is currently the country’s largest paper recycler.
In April 2023, DS Smith initiated a €145 million modernisation process, DS Smith’s largest financial investment in Portugal,
and the largest in the mill’s history.
Mário Amaral, the plant’s manufacturing director, says: “The plant is preparing for the future, to face the next 50 years at ease.”
With its first phase being completed in October last year,
the development programme is still under way, said Amaral: “The project is at cruising speed, with the first phase consisting of refurbishing the paper machine presses, and reinforcing key equipment, with the aim of improving energy efficiency
Brazilian pulp and paper maker Klabin has officially recognised Andritz for its technical expertise and project management performance during the Puma II pulp and paper mill expansion project at Ortigueira.
The Puma II project management team initiated the programme in 2020 to evaluate the performance of its suppliers.
The expansion was the largest investment in Klabin’s history, with a total value of BR12.9 billion (€2.4bn).
Andritz played an important role by delivering key pulp and paper production technologies for a wood processing plant, power and recovery boilers, a white liquor plant, a SulfoLoop sulfuric acid plant, and a biomass gasification plant. A capacity
increase for the bleached pulp fibreline was also part of the order.
Recently, Klabin presented Andritz with an award for superior technical quality in civil construction, excellent technical quality in assembly, timeand house-keeping including organization, work safety, environmental practices and people management.
and reducing environmental impacts. The second phase is the replacement of the recovery boiler, which is scheduled for completion in May 2025. The new top-of-the-range boiler will help make the virgin pulp production line more efficient.”
The Confederation of European Paper Industries (Cepi) has criticised a wild-card ‘Life’ document published by the EU Commission that quantifies the effects on climate of sustainable lifestyles resulting from changes in consumer preferences and circular economy measures.
Cepi, in line with representatives from across the forest sector calls for a careful approach to estimating the share of carbon dioxide absorbed by forests as part of the models devised by the EU Commission. “Climate change has impacted forests’ capacity to act as carbon sinks and it is also important to steer clear from a flawed approach where emissions are compensated by ‘offsets’ from nature,” says Cepi.
Instead, the EU should prioritise emission reductions in the first place. An ‘emission reduction first’ approach that would not be overlying on forests is wrongly associated with the least ambitious of the EU Commission’s proposed scenarios for 2040.
Cepi says the EU energy system needs to be largely decarbonised by 2040, as ambitious targets would require an increase in the supply of affordable fossilfree energy. The pulp and paper sector is already leading the way amongst energy-intensive industries. Its specificity, as it requires lower range levels of heat, makes it an ideal candidate for the early deployment of a large range of existing renewable
Jori Ringman, director general of Cepi: “sustainable forest management, energy decarbonisation, circularity and sustainable consumption should not be neglected”
energy technologies that are often not yet widely used in industrial settings.
Commenting on the latest report, Jori Ringman, director general of Cepi, says: “Over the past decade, the EU has demonstrated leadership on climate policy, setting a clear direction of travel. The Commission should now prioritise incentivising companies to choose Europe as their destination for investments in decarbonisation efforts.
“Next steps should include an indepth assessment, not only of the respective impacts of the different scenarios towards climate neutrality, but also about their feasibility. Input from an industry which systemic role places at the crossroads of sustainable forest management, energy decarbonisation, circularity and sustainable consumption should not be neglected.”
l The brownfield site of the former Androscoggin paper mill at Jay in Maine, USA, is expected to be used by Godfrey Forest Products to construct a new oriented strand board (OSB) production plant. Local reports say that the plant, costing “hundreds of millions”, will take two-and-a-half years to complete and will in 2027 have capacity for 800,000 tons a year of building materials. International Paper built the Androscoggin Mill in 1965 and sold it to Verso Paper in 2006, which sold it to Pixelle Specialty Solutions in 2020. An explosion in the pulp digester in 2020 caused significant damage from which the mill never recovered.
l As Suzano in Brazil prepares to start up its Cerrado project, the world’s largest single-line pulp plant located in Mato Grosso do Sul state, some of the highlights of the company’s latest sustainability report include: R$18.6 billion in investments – the highest in its history; The purchase of Kimberly-Clark’s tissue business in Brazil and the incorporation of the Neve brand; 5.1 million tonnes of carbon removed from the atmosphere, totaling 27.1mt since 2020; 22,250 people lifted out of poverty in 2023, taking the total figure since 2020 to 51,883; and 55,600 hectares connected through ecological corridors, in line with its biodiversity conservation commitment.
l Andritz has won the 2024 Microsoft Intelligent Manufacturing Award in the
category ‘Disrupt!’, which recognises systems that have the potential to fundamentally transform value chains. Andritz received the award for its digital products that enable autonomous operation of pulp mills.
With its Metris digital platform, Andritz has defined a five-level journey towards autonomy, which has been implemented in 39 pulp mills at varying levels. One of these mills has achieved 97 percent autonomous operation as compared with the industry benchmark of 60 to 65 percent. This has led to an 18 percent increase in productivity.
l By the beginning of March, 80 exhibitors had been confirmed their participation at Zellcheming Expo, which is being held from 18-20 June 2024 at the RheinMain CongressCenter (RMCC) in Wiesbaden, Germany. It means that nearly 87 percent of exhibition space had been booked.
“This positive development, which we particularly appreciate in view of the continuing difficult economic situation, gives us a lot of momentum for the final phase of preparations for this year’s event,” said Petra Hanke, managing director of Zellcheming Service GmbH. “At the moment, only about 13 percent of the hall, or about 270 sqm, is still available. Therefore, we are sure that we will not only have a very good and comprehensive range of products on the entire exhibition area, but that we will also be able to further expand our range of topics.”
Smurfit Kappa is planning to invest €54 million to double the capacity of its Ibi Bagin-Box plant at Alicante in Spain.
The Ireland-based paper maker intends to strengthen the sustainability of both the plant’s operations and its product portfolio, with enhanced waste management systems and significant savings in energy consumption. Smurfit Kappa says that its Ibi plant has a strong track record in recycling with several modern systems that identify and separate by-products.
Saverio Mayer, chief executive of Smurfit Kappa Europe, said that the announcement “demonstrates our commitment to the Bag-inBox division and forms part of our multi-country expansion plan. We have invested €90 million in the Ibi plant throughout the last decade which has significantly enhanced our offering”.
Mayer continued: “Our customers know that when
they choose us, they will get everything they need for their product, invariably resulting in a beautifully designed bag-in-box with a reduced carbon footprint.” General manager of the
Smurfit Kappa Ibi plant Pascual Martínez added: “We are proud to be taking Ibi to the next level through this investment and creating a further 200 jobs for the local economy. We have a
talented and very skilled team here that can solve even the most complex challenge. I am excited about embarking on the next chapter for Ibi.”
Bag-in-Box Ibi creates a broad range of products for wine, dairy products, liquid eggs, cooking oils and water. Smurfit Kappa says it is the leading Bag-in-Box provider in Europe.
● Smurfit Kappa has been recognised as a leading ESG performer for the third year running by the research and analytics firm Morningstar Sustainalytics, achieving both Industry and Regional Top-Rated status. Again classified as ‘low risk’ with a score of 10.7, the company was placed first against its paper packaging industry peers, and one of the topranked companies evaluated by Sustainalytics in Europe.
The leading trade association for the UK’s paper-based industries, the Confederation of Paper Industries (CPI), has published a manifesto in anticipation of the coming general election.
The document highlights what the next Government must do to ensure the UK’s paper-based industries have a practical policy and regulatory framework to facilitate investments in UK manufacturing, promote recycling, achieve resource efficiency, and manufacture world-class, sustainable, and indispensable paper-based products within the UK.
Director general of the CPI Andrew Large said: “This is a critical juncture for the UK’s paper-based Industries. The UK must move on from the economic and social upheavals of the recent past and establish a firm foundation for green industrial growth.”
CPI has also been taking aim at proposed amendments to the EU Packaging and Packaging Waste Regulation (PPWR) that could potentially lead to a massive surge in plastic consumption at the expense of the circular economy and decarbonisation initiatives.
It has called upon European decision makers to “stand firm” and support the cardboard exemptions in the PPWR. This is crucial to support the UK and wider European economy, protect local jobs, and promote sustainable packaging that have been the cornerstone of the industry’s environmental commitments.
Existing exemptions that apply to cardboard in relation to reuse targets for transport packaging are being supported by the CPI. These exemptions recognise the sustainability of cardboard and the adverse consequences that would arise if cardboard were included under the scope of reuse targets. They also account for the need to regulate different packaging materials uniquely, steering the PPWR away from a one-size-fits-all approach.
The paper-based industries are aligned with the European Union’s goals of climate neutrality and driving transformative change across the economy. Corrugated cardboard plays a critical role in packaging, securing and delivering 75 percent of goods across Europe. An impressive European recycling rate of 82 percent ensures that packaging can be recycled into new cardboard boxes
l Smurfit Kappa has achieved four of its mid-term, Better Planet 2050 sustainability targets. The targets quantify the company’s commitment to delivering a sustainable future through: low-carbon, circular packaging; increasing support for the communities in which it operates; and further enhancing the lives of its employees.
Published in Smurfit Kappa’s 17th Sustainable Development Report, the company achieved its targets on: Waste, with a 35.8 percent reduction in waste sent to landfill, ahead of its 2025 target of 30
repeatedly, resulting in a remarkable recycled content of about 89 percent.
However, the proposed removal of these exemptions, currently under discussion in the EU, presents a significant threat to the industry’s sustainable track record.
The CPI says it is deeply concerned that applying reuse targets to corrugated cardboard transport packaging would be counterproductive, hindering the regulations’ ability to improve the environmental impacts of packaging.
Reuse targets for transport packaging inherently favour plastic packaging over recyclable materials like cardboard, which could flood the market with billions of harder-to-recycle plastic crates. This will also increase the EU’s reliance on fossil resources, worsening the environmental impact of packaging and undermining the primary objective of the PPWR. Reuse targets are also inherently anti-innovation, since they act as a barrier to the introduction of new, better, packaging formats.
Commenting on the proposals in November 2023, Andrew Large said, “A one-size-fitsall approach to packaging regulations risks undermining the well-functioning paper packaging circular economy in favour of an explosion in the numbers of fossil oil-based plastic crates and unproven reuse systems. The revisions to PPWR will have a significant effect on consumers across Europe, and CPI urges the EU to support existing well known and well used recycling systems, such as those for cardboard.”
percent (24 percent in 2022); Forestry, by selling 95.5 percent of its packaging with Chain of Custody certification, ahead of its 2025 target of 95 percent (94.3 percent in 2022); Communities, with €25.6 million donated to support social, environmental and community initiatives, ahead of its 2025 target of €24 million (€18.4 million in 2022); and Diversity, in which 25.1 percent of management positions were held by women at the end of 2023, ahead of its 2024 target of 25 percent (23.5 percent in 2022).
Executives from the global forest products industry will be meeting in Helsinki, Finland, in April for the first Pulp & Beyond 2024 show and conference. What can PPL’s readers expect to see?
Key topics such as climate change, the green transition and the future prospects of the forest products industry will be the focus of Pulp & Beyond 2024, described as the former PulPaper show, but for a new generation. The event will also feature discussions on global economy and politics, as well as the importance of innovation. Pulp & Beyond 2024 will be held on Wednesday and Thursday 10-11 April, at the Helsinki Expo and Convention Centre.
By the end of February, almost 170 exhibiting companies representing the forest products industry and its service and equipment suppliers were confirmed, including ABB, Andritz (main partner), Cargill (a sponsor of the event), Honeywell, Metsä Group, Sappi, Solenis Switzerland, Spooner Industries, Stora Enso, Sulzer Pumps (a sponsor of the event), Tappi, UPM-Kymmene, Valmet and Voith. The main conference programme offers
essential keynote speeches and panel discussions, moderated by André Noël Chaker. The programme for the Speaker’s Corner on the event’s second stage was to be announced in March.
Climate change and the green transition will be the main focus on 10 April, the opening day of the event.
During the opening ceremony at 10am, attendees will hear opening remarks from Katja Metsäranta, chair of the co-organising Finnish Forest Products Engineers’ Association, and a keynote speech from Petteri Taalas, director general of the Finnish Meteorological Institute, regarding the significance of forests in combating climate change.
In a panel discussion “Towards carbon zero pulp & paper industry” at 11am, Michael Carus, founder of Nova-Institute and executive manager of the Renewable Carbon Initiative, and Petri Vasara, vice president of AFRY, will
discuss the zero-carbon emission targets and the opportunities and challenges for the pulp and paper industry in achieving carbon neutrality.
A keynote speech, “Role of EU-policies in global responsibility” at 1pm will be delivered by Paula Lehtomäki, chief executive of the Finnish Forest Industries Federation. It will explore what the EU has achieved in terms of global responsibility and what the EU Commission’s future political priorities are.
A panel discussion, “Green transition from policymakers’ and investors’ point of view” at 3pm, will tackle the role of the forest industry in the green transition and perspectives on investments. Participating in the discussion will be members of the European Parliament MEP Petri Sarvamaa and Sirpa Pietikäinen, director general of Cepi Jori Ringman, and chairman of Häggblom & Partners Ltd and board member of United Bankers Ltd, Rainer Häggblom.
Insights into the global economy and politics will be highlighted on Thursday 11 April at 10am, as Risto E J Penttilä, chief executive of Nordic West Office, delivers his keynote speech on the topic “Prospects on global economy.”
The first panel discussion of the day, part of the World Bioeconomy Roundtable series, entitled “Bioproducts as investments – Drivers and obstacles,” begins at 11am and is organised in collaboration with the World Bioeconomy Forum (WB). Participants include Bernardita Araya, CMPC Ventures Manager; Petri Hakanen, chief technical officer of UPM; Christian Orglmeister, executive director for New Bio-Businesses, strategy and digital tech at Suzano and Peep Pitk, chief executive of OÜ Fibenol. The panel discussion will be introduced with a keynote by Dirk Carrez, executive director of the Bio-based Industries Consortium.
Promoting sustainability and sustainable business growth through innovation will be discussed at 1pm by keynote speaker Michael Strobl, director of Product Development & Technical Services for Innovation at MM Board & Paper GmbH. A panel discussion on the future of the forest industry, entitled “Going beyond the
boundaries: what are the next chapters for forest industry?” will take place at 2.30pm. Participants include Per Tomani, director of business development for Biorefinery & Energy at RISE Research Institutes of Sweden; Åsa Ek, head of innovation at Stora Enso Biomaterials; Kristiina Kruus, Dean, Aalto University, School of Chemical Engineering; and Johan Engström, chief technical officer of Andritz
The Pulp & Beyond 2024 Conference (€450 plus VAT) will be held from Tuesday 9 April at the Helsinki Expo and Convention Centre. The Pulp & Beyond 2024 excursion to Jyväskylä (€250 plus VAT) will be organised for Thursday and Friday from 11-12 April. Concurrently, from 10-11 April, ChemBio Finland 2024 and Helsinki Chemicals Forum 2024 will be held at the Helsinki Expo and Convention Centre.
More information from #pulpandbeyond and www.pulpandbeyond.com
Collaboration between the Finnish paper maker Metsä Board and Soilfood is adding value to fibre-rich side streams which are being transported to farmers for soil improvement. PPL reports
Soilfood, a Finnish circular economy company, is processing the fibre-based side streams generated in the production of paperboard from manufacturer Metsä Board, into various soil improvement fibres for local farms.
Side streams have been previously used by Soilfood from Metsä Board’s board mills at Kemi and Äänekoski. Now the cooperation has been extended to the Tako mill, located in the centre of Tampere.
Metsä Board’s cooperation with Soilfood started with a research project initiated in 2015 by the Natural Resources Institute Finland. The study looked at how wood-based fibre sludge could help reduce erosion and nutrients leaching from fields to water bodies.
The large-scale use of side streams is part of a new circular economy approach, where raw materials are kept in use as long as possible and existing materials are re-used.
The two companies are also working together to develop other new ideas for the beneficial use of
existing production side streams.
Mika Leino, environmental director at Metsä Group, explains:
“Our goal is to have zero landfill waste from the processes of our paperboard mills after 2030. Currently, more than 99 percent of our production side streams are used either as materials or energy. Metsä Board wants to focus on its core competence as a producer of fresh fibre paperboard, but at the same time seek more opportunities for promoting the circular economy. That’s why partners like Soilfood are important to us.”
Soilfood collects fibre sludge from the Tako mill on a weekly basis. “The unique location of the Tako mill in the centre of Tampere
brings with it special challenges as there are no large storage areas on the grounds of the mill,” says Jaakko Ikonen, vice president of Tako Board Mill.
Eljas Jokinen, managing director of Soilfood, explains the journey of the side streams: “Soilfood takes on the responsibility of handling the side stream from its point of origin. In practice, the side stream must be mobilised almost as soon as it is generated. The number of loads varies according to the mill’s production schedules and volumes. The products Soilfood processes from Tako’s fibre-rich side stream are then transported to farmers in the surrounding area as soil improvement products.”
In agricultural use, the soil improvement fibres both increase organic matter content of soil and improve its water retention capacity. At the same time, nutrients of wood are returned to the soil.
The fibres also reduce the environmental impact of farming by increasing soil carbon stocks and reducing the leaching of nutrients into water bodies*.
* Rasa, K, Pennanen, T, Peltoniemi, K, et al. Pulp and paper mill sludges decrease soil erodibility. J. Environ. Qual. 2021; 50: 172– 184. https://doi. org/10.1002/jeq2.20170
More efficient and reliable logistics have been developed for Metsä Group’s new bioproduct mill at Kemi, taking into account sustainability at every stage of operation and minimising environmental impacts.
The Kemi bioproduct mill is said to be the most efficient wood processing mill in the northern hemisphere and the largest ever investment in the Finnish forest industry, worth €2.02 billion.
Pulp bales produced at the bioproduct mill are automatically loaded onto HCT (high capacity transport) trucks. These trucks, powered by biodiesel, transport the bales 15km to a port warehouse. The specially-designed HCT trucks carry up to 72 tons of pulp in each load, about oneand-a-half times more than a standard truck. This, says Metsä, significantly reduces the carbon footprint of transportation.
A specific logistics route, built in collaboration with the city of Kemi, enhances transportation and traffic safety in the area.
At the Ajos port, pulp bales are directed to Metsä Group’s new 37,000 sqm product warehouse, where unloading is automated. Fossil fuels in the port and warehouse have been replaced with electric-powered forklift and
loading equipment. Additionally, the port’s electronic materialhandling crane features an electronic pulp grab, the first of its kind.
Eight new electric forklifts at the port improve environmental efficiency and enhance workplace safety. The elevated cabin, improved visibility, and lower noise levels contribute to a safer
working environment.
For pulp shipments to Asian markets, the mill uses the latest fleet of vessels where the technology enhances environmental efficiency.
“The foundation of the new logistics solution is to ensure safety, delivery reliability, and environmental efficiency. It secures a smooth chain from the mill to customers,” says Pasi Pulkkinen, who was the former logistics director for the Kemi bioproduct mill project.
Teemu Kauppi, director of Kemi Port Operations unit, adds: “The core process of port operations remains the same as before, but with the latest equipment investments, the opportunities to improve operations in every aspect have grown significantly.”
With the new bioproduct mill, the exports abroad from Ajos port in Kemi is expected to increase by more than a million tons a year, says Metsä.
New types of energy recovery systems for electric forklift trucks are able to prolong the operation time and improve the overall efficiency of the machine significantly, says a paper published in the Journal of Physics Conference Series.
The paper by Wen Gong from the Shanghai Institute of Special Equipment Inspection and Technical Research and presented at the 2nd International Conference on Energy and Power Engineering
held in Xi’an in China last year proposes a new energy recovery system with dual hydraulic motors and permanent magnet synchronous motors. The system has two work modes, single and dual modes. The system operates in the single mode for a low flow rate and the dual mode for a high flow rate.
Typically, an energy recovery system has a large flow range, and the system of a single hydraulic motor-permanent magnet synchronous motor
cannot meet the actual working needs of the heavy electric forklift.
Experimental research on energy recovery efficiency and dynamic characteristics has been carried out. The results show that power generation efficiency is above 50 percent within a certain speed range.
Energy recuperation systems for forklifts that combine hydraulics and electrical systems were proposed by Parker Hannifin four years ago using proprietary
EcoReach technologies.
EcoReach also features an integrated hydraulic unit with the motor, pump and hydraulic valves all incorporated into a single housing – this minimises the number of components, enhancing reliability and reducing installation size.
The system is said to offer increased battery life, productivity, load handling capabilities and operational speed plus a significant reduction in energy consumption.
Pulp mills looking for highly-efficient washers but with limited space are the target for the latest offering from Andritz. This is how they work
Along with its well-known DDWasher, the introduction of the Compact Press now means Andritz covers the complete range available for effective and efficient pulp washing for all capacities of pulp mills, from the very small to the very large.
The Compact Press has been named for a good reason; it has a small footprint and is compact in design, making it the perfect retrofit washer for all sizes and capacities of pulp mills, including those with limited space in the fibre line. The presses are available in nine different sizes starting from a capacity of 400 tons per day (t/d) up to 6,000 t/d and are designed to suit all pulping processes, including kraft, semi-chemical, and mechanical pulp. The latest development at Andritz has seen the introduction of a press for the dewatering of mechanical pulp, which is based on the same technology.
spread across the perforated drum. This even distribution is ensured by unique, speciallydesigned screws that are speed controlled so the transport capacity is adjusted to meet the needs of the pulp fed into the machine.
The Compact Press enables high consistency, starting at the dewatering phase where consistency of the pulp is increased by a converging gap between a perforated drum and the static sliding surface of the press. When the consistency has been increased, the wash liquor is then added in two zones. The benefit of the increased consistency means there is less free liquid in the pulp to displace and the wash liquor is used more efficiently, thus saving on chemical costs.
Along with its small footprint, the Compact Press is said to offer many advantages, including highly-efficient washing for producing clean pulp, and uses made-to-last durable components with a long-life cycle, and low cost of ownership due to easy maintenance
The presses have a number of proven advantages that set them apart from other wash presses, including a highly-efficient process with high discharge consistency, tough, durable components, and easy maintenance. More than 150 Compact Press units have been sold to date with the first one, delivered in 2000, still operating successfully.
Depending on the applications, the presses can be fed from 2 percent up to 10 percent feed consistency. Andritz says that what is unique about the Compact Press in its washer range is the high discharge consistency –around 30 percent from the machine, which is beneficial when separating mill waters, from the acidic stage to the alkaline stage.
Uniformity of pulp is very important when creating an efficient process, and it is essential to have distribution of pulp evenly
The second phase of the washing takes place when the pulp is distributed across the full width of the perforated drum and the wash liquor is distributed through a large number of nozzles in two zones to ensure maximum displacement.
The final pressing is carried out between the two drums where the pulp is pulled by the perforated drum through the press nip where the free liquid is squeezed out.
Another unique feature of Compact Press is said to be the integration of the dilution screw into the press itself, which eliminates the need for a separate dilution screw or device and makes the layout more compact and efficient.
The main component of the Compact Press is the MaxDrum, which has been developed with a solid support structure. The drum is built to last, with some examples already having been in operation for more than 20 years. The main feature of the drum is the screen plate, which is more than 4mm thick,
and the support structure underneath, which is 70mm in depth giving maximum strength and support. Along with added strength, this means the drum is highly fatigue resistant.
The MaxDrum also comes with several safety features, including an overload protection system that allows both drums to move
should a foreign object enter the process. When it comes to maintenance, the Compact Press has been designed with maximum efficiency in mind. The press is fitted with a service hydraulic system that allows the opening of the machine for access to the drum surface and seals. The
vat can be lowered to get access underneath the press, so there is no need to use a powered crane, and full maintenance can be carried out with the minimum of operator hours.
More information from Anders Lindström by email from anders.lindstrom@andritz.com
More than 150 Compact Press units have been sold to pulp mills worldwide
Thousands of tons of paper machine clothing and filter fabrics are produced by Valmet each year. To reduce its environmental impact, the engineering firm has consistently worked to reduce waste generation and to re-use side streams in fabrics production. Report by Marianne Valta
Valmet has an extensive research and development programme that works towards circularity in the production of clothing and filter fabrics used in the paper making
industry. Its targets are aligned with Valmet’s Climate Programme. Katriina Markkula, R&D manager for paper machine clothing at Valmet says: “We believe in minimising waste and reusing materials for as long as possible.
Building a closed loop economy isn’t easy, but it’s the ultimate motivation in everything we do –whether it’s product development, exploring more sustainable raw materials, developing our own operations, or innovating ways to
recycle paper machine clothing and filter fabrics at the end of their lifecycle.”
Excellent results in waste reduction
Valmet has recognised waste
Valmet has succeeded with the industrial-scale pilot recycling of used press felts. During the recycling process the press felts are turned into plastic pellets
reduction and material efficiency as one of the key areas for promoting sustainability in its fabrics operations. Every fabric production unit has developed its own waste reduction programme to identify, quantify and reduce waste. Over the past three years, the amount of waste has been reduced by 30 percent.
Many successful initiatives have also already been taken to reuse and recycle the waste that cannot be reduced.
Markkula continues: “At our production unit in Tampere, Finland, the press felt production sidestreams have been recycled for years, and the polyamide is used as raw material for new plastic products.
”We have also installed two new balers, and with other activities, their use has already increased the recycling rate of press felt production waste to 84 percent. In Tianjin, China, close to 100 percent of dryer fabric and forming fabric waste is delivered to a partner who recycles it mechanically into plastic granules to be used in the production of plastic canisters and small plastic drums.”
Of course, the most sustainable way to handle excess material is to find ways to utilise it as it is.
“An example of such an innovation is the pulling clamps that are used to install shoe press belts on paper and board machines – we now manufacture them by utilising belt production sidestreams. Based on customer feedback, they work better than the ones we used before,” Markkula adds.
Significant steps taken in recycling used press felts
The quest to recycle used paper machine clothing and filter fabrics is something for which
the industry has striven for years.
Valmet is currently cooperating with some of
and recycling technology
developers to see how the collection, handling and logistics of used fabrics can be carried out in an environmentally and
financially sustainable way.
So far, Valmet has successfully undertaken industrial-scale pilot recycling of used press felts.
During the recycling process, the felts are turned into plastic pellets.
Says Markkula: “The pellets are of high quality and can be used in demanding applications such as electronics enclosures, furniture parts and vehicle components. The recycling process is also very energy efficient, leading to pellets with a really low carbon footprint that are a very interesting raw material for various industries. Many advanced recycling technologies are already available, and based on our good experiences, we’re encouraged to develop how we operate further.”
In 2022, Valmet launched a new R&D and innovation programme, Beyond Circularity, to transform waste and emissions into valuable resources for sustainable growth.
For fabrics production, the programme offers an opportunity to work with many national and international partners within the field of recycling, expanding competences and opening new possibilities.
“I believe circularity will be the next big thing among our customer industries, and it is also at the core of our R&D. I also believe that no one can succeed alone when it comes to building a more sustainable future. At Valmet, we’re open to new partnerships in this area and therefore welcome everyone to participate in the work,” Markkula concludes.
More information from Katriina Markkula, R&D manager for paper machine clothing at Valmet. Tel: 358 44 5923181
Email: katriina.markkula@ valmet.com
The life of valve actuators is tough in a pulp and paper mill, requiring long-term reliability in challenging conditions. Here’s how their design for low maintenance and extended life is achieved. PPL reports
High-cycle actuators are often seen as having a short lifespan, with costly installation and maintenance requirements. However, many leading processors are realising that well-designed actuators can offer reliable performance for years with minimal maintenance or repair.
In pulp and paper mills, as in manufacturing plants around the world, processors often operate around the clock. To achieve this, high-speed, high-cycle actuators open, close, or throttle valves to regulate, direct, or control the flow of gases, liquids, fluidised solids, or slurries.
Regrettably, many processors today have become accustomed to the idea that high-cycle actuators have a short lifespan and necessitate regular maintenance to replace parts prone to wear, such as O-rings, springs, cylinders, and others. In some facilities, this task can consume a technician’s entire work schedule.
However, many leading processors are beginning to reassess this expectation, given the high costs for installation and maintenance.
The truth is that a well-designed actuator should be able to provide reliable performance for many years beyond the warranty period. If maintenance or repair is needed, it should be infrequent and simple enough for a single technician to handle, using
reduce costs
common tools. For maintenance or repair purposes, the actuator should be easily accessible without the need to remove it from the valve. This is a crucial factor, as valve manufacturers will invalidate warranties if the actuator is detached from its mount.
Actuator usage and stress are often linked to the frequency of valve opening and closing cycles. The cycle count often varies based on the environment or application. Some actuators are
seldom used, while others operate regularly. High cycle, high-speed valve actuators – often found in processor operations – can fire rapidly and repeatedly many times per hour, non-stop throughout the year.
The core issue lies in the high utilisation and demand placed on the actuator.
Actuators come in different styles based on the mechanical action required, such as linear or rotary, but all involve moving parts that experience considerable force, wear, and stress. In processing plants, actuators are
also installed in highly-corrosive industrial settings. Many designs fail to account for these factors and are poorly engineered, leading to excessive side loading, wear on non-wearing parts, and various other issues.
High reliability is another crucial factor that holds significance for Scott Howard of NewGen Products, a specialist in valve automation.
For critical applications, Howard often recommends a top-of-theline actuator, purpose built for the application. Although there may be a higher initial cost, these
actuators are designed to perform reliably in challenging and harsh environments. Even within this category, however, many actuators are not expected to last. “Many of the higher end actuators are rebuilt every three to four years,” says Howard.
There are exceptions, including what Howard refers to as the ‘Ferrari’ of actuators from QTRCO, which is based at Tomball in Texas. Founded in 1998, QTRCO has innovated designs specifically for high-cycle, high-speed, highreliability applications.
The actuators are built with a robust mechanical design that eliminates common failure points like sliding parts, side load forces, and multiple seals. This makes them perfect for demanding applications in extreme temperature, corrosive, or submerged environments.
Among the more innovative designs from QTRCO is its answer to the common aluminium ‘lunchbox’ actuator and its inherent design limitations.
The actuator, which gets its name from its one-piece aluminium extruded body and cylinder that resembles a lunchbox, is popular because it is compact, inexpensive, and works well. Aluminium lunchbox actuators are not very reliable and often fail in more demanding environments or applications.
To resolve many of these issues, QTRCO designed an actuator with an internal ‘rack and gear’ mechanism as an alternative to its traditional rack and pinion design.
The actuators are designed with offset cylinders that align the piston axis with the pinion gear pitch circle diameter, eliminating cantilever forces and friction.
QTRCO also replaced the sliding
blocks, wear pads, and bushings with specialised rollers. As a result, the rack-and-gear actuators have extremely low internal friction. The new design also eliminates one of the primary causes of failure of a lunchbox actuator: the O-rings on the shaft. In a lunchbox actuator, air is forced through ports in the body. The air pushes the piston outwards, and springs push the piston back in. Each cycle pressurises the shaft, which typically has two O-rings, one at the top and one at the bottom. As the shaft cycles back and forth 90 degrees, the reciprocating motion places significant stress on the O-rings.
In QTRCO’s design, this action is reversed, and the air is forced inward through the end cap. The spring return applies no pressure to the shaft seals, which prevents premature O-ring wear. This configuration also has benefits when valve throttling is required. Due to the design of the company’s Q Series and because the piston is located close to the end cap, much less air fill volume is required, and the actuator responds much quicker and is easier when throttling.
QTRCO took a similar approach as an alternative to Scotch yoke actuators. Also known as a slotted link mechanism, the Scotch Yoke is
a simple and effective mechanism that has been used for a long time. However, with typical Scotch Yoke actuators, the force applied to the piston rod is also applied to the shaft and shaft bushings, resulting in friction and bushing wear.
To resolve these issues, QTRCO designed a patented Flat Yoke mechanism that can accurately and reliably position any rotary control valve requiring up to 500,000 inch-lbs of torque.
The Flat Yoke is designed with quad body slots that absorb the mechanism’s side loading forces, leaving the piston rod completely free of bending stresses while allowing termination of the rod
at the yoke. Like the Q Series, these F Series actuators also have extremely low internal friction, consume minimal air volume, and can handle the most severe throttling applications.
With an actuator specifically designed for reliable and longlasting performance, processors can save on costs associated with more frequent replacements.
In one processing plant he visited, Howard says the actuator fired twice a minute throughout the entire year, adding up to more than a million cycles per year. Given the usage, the plant would replace the actuator annually during planned outages.
According to Howard, the replacement of an actuator typically requires an entire day for a single technician, often with the help of at least two additional individuals. If the actuator is large enough, a crane is required.
Considering the potential costs for hourly labour rates and rentals, a plant could save thousands of dollars every time it eliminates the need to replace an actuator.
“If a plant doesn’t have to change the actuator every year,
they just saved a fortune,” says Howard.
When preventative maintenance or repair is required, it should be easily conducted using common tools and without removing the actuator from the valve. With large, metal-seated ball valves, it is critical to mount the actuator with extreme precision. A slight misalignment during mounting can result in severe damage to a valve that carries a hefty price tag of hundreds of thousands of dollars. The connection is so crucial that most major valve manufacturers will void
warranties if the actuator is removed.
In rare cases, like with QTRCO designs, the actuators can be easily maintained without removal from the valve. This enables hassle-free removal and replacement of end caps, cylinders, and O-rings, often without special tools.
According to Ross Evans, also with NewGen Products, safety is another concern during preventative maintenance and repair. Actuators of considerable size may require two people for lifting and moving.
“Imagine being in a plant environment and climbing six flights of stairs to a catwalk to service an actuator. With that kind of weight, what does it take to get your cranes and rigging in place to safely take off the actuator? You have to remove all the pneumatic airlines, disconnect the electrical, and you need a couple hands. There’s a lot of cost and time and risk involved,” explains Evans. “The alternative is, I can do maintenance on the valve while it is in place,” adds Evans. “I shut
down the unit, tag it out, take off the end cap, inspect the cylinder, remove an o-ring, grease it, and put it back in place. In about 10 minutes per cylinder, we are back and running.”
The actuator’s design can also contribute to safety concerns. Many Scotch Yoke designs feature a lone piston assembly on one side of the unit. Lifting or rigging an unbalanced, single piston assembly is challenging due to its significant lean on one side.
For high speed, high-cycle processing applications, QTRCO recommends sizing up to a twopiston version of its Flat Yoke design. The two pistons balance the forces on both sides of the shaft, preventing bushing wear. The design also includes the addition of a weight and force balancing second force module diagonally offset from the first.
By balancing the forces, there is less friction and wear and no net force applied to shaft bushings. The balanced weight also makes lifting and handling of the actuators safer and easier, while reducing valve neck stress that can occur in unbalanced Scotch Yoke actuators.
Another issue is the spring set used in many lunchbox actuators, which are under load and must safely be controlled once the end cap is removed. If the spring becomes jammed and the mechanism that contains the spring fails, the force exerted can be equivalent to a shotgun firing.
“In one actuator, the end cap corroded and failed. It discharged the spring out of the actuator across the shop,” says Evans. He says he has personally observed experienced field technicians that regularly work on actuators, who move out of the line of the cylinder to remove the end cap on the actuator.
“Anybody that’s done any type of maintenance on an actuator, they know the potential energy contained in the spring,” says Evans.
With QTRCO, the spring is fully captured using a solid stainlesssteel rod that goes through the spring retainers and there is a safety collar that locks it into place. Replacing the springs simply requires removing the end cap and replacing the cartridge.
“Once they capture those springs, it is designed not to ever come apart again – it remains captured. It is a big safety feature,” says Evans.
Installing actuators that are built to last and require minimal maintenance or repair not only brings significant benefits, but also proves to be more costeffective in the long run, even if the initial cost of ownership is higher. When multiple actuators are installed in a paper mill, the savings can add up.
“If you put a well-designed actuator in one of these demanding applications and rarely
The challenge: The vacuum system on the ‘wet end’ of the paper machine is critical to forming the sheet and providing a quality product. Conditions are corrosive and conventional actuators do not last long in this service.
The solution: Q Series actuator on a valve allows an all stainless steel design for longer service life and precise control.
Results: Customer no longer replaces actuators every two-to-three years and is able to maintain system performance with no degradation in performance.
The challenge: A water canon system is used to clean boiler tubes in a recovery boiler. The area is very wet and actuator corrosion is an ongoing issue.
The solution: The stainless steel L-Series actuator is a direct replacement alternative for the spring and diaphragm actuator offering superior corrosion resistance.
Results: Customer retrofits both soot blower valves with stainless steel actuators to eliminate maintenance issues.
The challenge: High Density (HD) Bleached Pulp Stock Tanks are prone to overflowing and commonly cover the valves and actuators with this highly corrosive material. Due to the corrosive nature of the product, conventional actuators with epoxy coatings continue to rot and fail prematurely.
The solution: Q Series Actuators on V-Ball Valves with remote mount digital Positioner provide the customer with an all Stainless Steel assembly, designed for longer service life and precision control capabilities.
Results: Customer no longer replaces actuators every two-to-three years
The challenge: The steam pressure control valve to the digester is subjected to high vibration and the cast iron actuator yoke legs were fracturing causing unplanned downtime.
The solution: L-Series actuator with a stainless steel yoke was offered on a 6-inch globe control valve. This reduced the total mass and moment arm acting on the actuator eliminating failure.
Results: Customer replaces actuators on all 28 digesters with L-Series to improve pulp mill reliability.
have to do any maintenance or replace it very quickly, the total cost of ownership is far less,” says Evans.
“If you can get an extra three or four years of run time on an actuator, you just made up whatever cost difference you had on the initial price,” notes Evans,
adding that does not even take into consideration the numberone thing that costs the plant money: downtime.
Today, design advancements in high speed, high-cycle actuators make it easier for pulp and paper mills to create high-quality products.
With an actuator specifically designed for reliable and longlasting performance, processors can reduce costs associated with a labour-intensive manufacturing component that today too often requires frequent maintenance, repairs, and replacement.
UK paper maker
James Cropper has partnered with Scotch whisky brand Bruichladdich, bringing the first of its Luxury Redefined range to market with a fully-sustainable outer wrap.
The coloured wrap for Islay single malt The Bruichladdich Eighteen and The Bruichladdich Thirty is the first of its kind for whisky. It is made from recyclable paper pulp with no glue and moulded to the shape of the Bruichladdich optimised, proprietary glass bottle.
Bespoke in colour and shape with specific embossing and debossing features, the design also in-cludes a branded, oversized custom clasp feature. Using 100
Fully-sustainable outer wraps for Bruichladdich’s whisky bottles are made using moulded fibre from James Cropper
percent fresh fibre the wrap is significantly lighter than previous packaging designs without compromising strength or integrity, while significantly reducing Bruichladdich’s carbon dioxide emissions.
James Cropper says it produces the moulded fibre packaging using 100 percent green energy while the wood pulp used in its creation is sourced from sustainably-
managed forests, certified to FSC or PEFC standards.
The launch follows the integration of the award-winning moulded fibre innovation, Colourform, into James Cropper’s broader luxury packaging range.
Aligning with the B Corp distillery’s commitment to reduce its packaging and waste, the latest launches are also housed in the brand’s new decanter-style proprietary bottle, created in collaboration with global creative partner, Thirst. The new bottle contains an average of 60 percent recycled glass content, is lighter in weight and features an elegant glass closure.
More information from www. jamescropper.com
US-based Cardbox Packaging is investing €6.5 million in technology to update the operations at its subsidiary in the Czech Republic.
The move is said to underscore company’s commitment to expand its global footprint and enhance its manufacturing capabilities to meet growing demand for innovative and sustainable cardboard packaging.
The investment will increase efficiency, quality and capacity, and will also be used to move to new production premises.
New equipment includes a Koenig & Bauer Rapida 106 X-8+L printing press and a Bobst Visioncut 106 LER slitting machine.
“We are excited about the expansion of our production plant
in the Czech Republic and the possibilities it brings for better service to our customers,” said Klaus Hockl, chief executive of Cardbox Packaging Holding. “This investment not only strengthens our manufacturing capabilities,
but also demonstrates our commitment to innovation and packaging excellence.”
Cardbox Packaging Group has production facilities in Austria and in the USA, and has been operating in the Czech Republic
since 2012 where it employs 100 of its total of almost 250 employees. Cardbox recently acquired Austrian paper cup manufacturer Valuepap GmbH.
More information from www. cardbox-packaging.com
Mondi is to expand production of its range of paper-based EcoWicketBags. This comes in response to increasing demand for sustainable packaging in the home and personal care (HPC) industry, particularly for products such as diapers and feminine hygiene products.
By expanding the production of EcoWicketBags at its plant in Szada, Hungary, Mondi says it further leverages the group’s integrated value chain, from in-house paper production to coating and converting.
EcoWicketBags bags are made from Mondi’s FunctionalBarrier Paper 95/5, a strong kraft paper
The bags are made from Mondi’s FunctionalBarrier Paper 95/5, a strong kraft paper that can be customised with specific barrier and protective properties to meet a range of product needs. They are available in a range of sizes to meet a variety applications and provide protection from filling to transporting and storage, as well as being ideal for printing customer branding.
The bags are designed to be recycled in European paper mills according to 4evergreen guidelines. According to Statista, paper-based packaging has recycling rate of 82 percent in Europe and Mondi’s EcoWicketBags enable customers in the HPC industry to meet their sustainability goals in a circular economy.
EcoWicketBags add to Mondi’s range of recyclable, monomaterial polymer WicketBags that follow CEFLEX recycling guidelines. The range also includes WicketBags that use a high amount of post-consumer content.
More information www. mondigroup.com
Traditional plastic laminated packaging paper has been replaced by food manufacturer Fazer with a paper-based alternative developed in collaboration with UPM Specialty Papers that is easier to recycle and does not compromise the protection it provides for the Oat Rice Pies.
The packaging has been recognised with awards in the WorldStar, ScanStar and New Wood competitions and is already appearing in the chilled food aisles of Finnish supermarkets.
The new Fazer Oat Rice Pie packaging aligns with both Fazer’s Sustainable Packaging Vision and UPM’s Biofore strategy. The new packaging is the result of more than two years of long-term
development work to ensure the recyclability of the packaging without compromising food safety and product quality.
Food packaging has protective properties that have traditionally been provided by plastic packaging or by laminating plastic
to the surface of paper. The use of plastic has also enabled the package to be sealed with heat. In the packaging paper developed by UPM Specialty Papers, both the barrier and heat seal properties have been incorporated into the packaging
paper without a separate layer of plastic lamination. The barrier properties are designed to protect the product inside the package until the best-before date, while ensuring that, for example, grease in the product cannot penetrate the package.
The new Oat Rice Pies packaging is based on the UPM Confidio barrier paper, which is heat-sealable. In recyclability test, the reject of unprinted Confidio paper is about 1 percent, which means that about 99 percent of the paper can be used to create new, recycled products. The recycling reject of plastic-coated paper packaging is significantly higher.
More information from www. upm.com
ADry Molded Fibre converting line has been successfully installed in the US by Pulpac and its turnkey partner Curt G Joa (JOA).
The Modula machine is being showcased at JOA’s site at Sheboygan Falls in Wisconsin in collaboration with PulPac’s North American sales partner, Seismic Solutions. The converter handles high-volume production of a wide range of Dry Molded Fibre products, while offering freedom and flexibility to make additions and upgrades to the original machine platform concept.
Sweden’s Pulpac has developed a pioneering manufacturing technology for fibre-based products that uses significantly less water and energy than traditional fibre-forming. The dry process is said to reduce the carbon dioxide footprint by up to 80 percent and be up to ten times faster than conventional
fibre-forming, making fibre-based packaging cost-competitive with plastic.
Available through licencing agreements with packaging manufacturers, the technology is supported by a global partner network.
Machine builder JOA is part of PulPac’s growing Dry Molded Fibre network and delivers the ‘Modula’ as a turnkey system. It works closely with Seismic Solutions and TetPak, PulPac’s tool-ing partner in North America.
While the Modula machine is adapted to the North American Market, it is available to all customers licensing the Dry Molded Fibre technology from PulPac.
More information from www. pulpac.com.
Smurfit Kappa has created a buzz amongst bee-keepers with sustainable packaging to transport bumblebees for Biobest, a leader in biological crop protection and pollination.
Biobest was founded in 1987 when veterinarian Roland De Jonghe started breeding bees in his garage to organically pollinate tomatoes. Growers were quick to see the advantage of using bumblebees over chemical pesticides and the company flourished.
Smurfit Kappa was approached by Biobest to design an insulated and weather-resistant box to replace the EPS pack it was using to transport live bumblebees.
It also had to be robust enough to withstand long periods of exposure as the boxes are used for outdoor pollination of fruit and vegetables.
From the paper maker’s Better Planet Packaging portfolio, a design made from water-resistant AquaStop paper was used, including hexacomb fitments inside to protect and insulate the insects. Tests were conducted to see if the new pack could survive outside for six to eight weeks, which it did, keeping the bees safe and ready to pollinate.
Peter van Leent, sustainability manager at Biobest, said: “As
providers of organic pest control, sustainability is a core value for us. It was clear throughout our collaboration that Smurfit Kappa has the same deep commitment to sustainability and fully understood the brief.
“We wanted to get a fully recyclable solution to replace the Styrofoam box we were previously using, but needed to ensure that it would perform on several fronts. We’re looking forward to rolling this out for use with other live insects and mites.”
More information www. smurfitkappa.com
Metsä Board has achieved home compostability certification for all its white kraftliners and folding boxboards (excluding PE-coated grades). The certification was issued by DIN CERTCO based on the compliance with standard NF T 51-800.
“All our paperboards can be recycled, which is the preferable option when the packaging or food service container has served its purpose. However, sometimes the packaging material can be stained by food and then composting with biowaste is a good choice,” said Helena Moring-Vepsäläinen, product safety manager at Metsä Board.
“Our paperboards have had industrial compostability certification for several years now and home compostability is one
step further, which is certainly welcomed by consumers.”
All Metsä Board paperboards are made of fresh wood fibres and are
safe to use for sensitive end-use applications. They are lightweight and made using mainly fossil-free energy, thereby contributing to a
Leading Spanish chocolatier Chocolates Valor has converted the packaging for some of its cocoa products to Sonoco’s Greencan packaging.
Founded in 1881, family-owned Valor has a network of chocolate shops and produces more than 22,900 tonnes of the confection every year. It specialises in chocolate bars with high percentages of cocoa, sugar-free chocolate, cocoa powder and snacks among other products.
It also takes pride in being innovative, which is why it
chose to use Sonoco’s Greencan recyclable paperboard tubular package which is made of 92-98
percent paper and features a wide range of barrier properties. Available in a range of shapes
carbon footprint throughout the whole packaging value chain.
More information www. metsagroup.com/metsaboard
and sizes from round, square or rectangular to oval, oblong or triangular, it is a ‘designed to recycle’ paper can, providing a highly recyclable packaging solution, with robust barrier properties.
The Greencan also features an integrated paper lid, so when empty, the whole package will pass through the household recycling stream without any need to take it apart, as with earlier composite packaging.
More information from www. sonoco.com
The largest independent supplier of custom corrugated and other value-added packaging, equipment and packaging-related services in the US, SupplyOne is currently promoting its custom corrugated board products as the ideal sustainable packaging.
The company provides costeffective and versatile designs that minimise packaging waste and emphasise the use of recyclable materials, empowering businesses to reach their sustainability goals.
Pennsylvania-based SupplyOne’s design expertise enables it to achieve great packaging performance with less material. With custom designs, it can produce packaging that is an exact fit to the product, reducing wasted material. This provides more sustainable packaging, both
for the environment and for customers. It also means a smaller and lighter total package, reducing storage space, shipping costs and
transport emissions. By saving fuel and space in the supply chain, SupplyOne’s custom corrugated packaging is cost-effective and
The findings of a European consumer packaging perceptions study has revealed that climate change (68 percent), cost of living (66 percent) and warfare (56 percent) are the three largest issues affecting consumers. In parallel, despite these significant global concerns, 62 percent of European respondents claimed that a sustainable lifestyle has become ‘more important’ or ‘very much more important’ over the last two years.
The survey – commissioned by Pro Carton, the leading European
association for carton and cartonboard manufacturers and conducted by Perspectus Global – surveyed more than 5,000 consumers across five European countries (Germany, France, Italy, Spain and the United Kingdom) to explore their attitudes towards the environment and packaging perceptions.
In Italy (77 percent), Spain (72 percent) and France (70 percent), climate change ranked as the most significant issue for consumers, while the UK reported the cost of living as the most
severe (75 percent). Germany, with one million refugees from Ukraine in the country, expressed warfare as its greatest concern (66 percent) and for the older generations, climate change was their greatest concern, with 60+-year-olds surpassing the European average at 71 percent. Although a substantial portion of European consumers expressed willingness to pay more for ecofriendly packaging, the study revealed mixed perceptions of retailers’ and brand owners’ efforts in this area. While 58.2
environmentally-friendly.
Traditional packaging materials can be wasteful and negatively impact animals, people and the environment. SupplyOne’s custom corrugated team is able to reengineer packaging components to eliminate non-renewable materials and enhance re-usability and recyclability. In addition, the company’s extensive selection of stock corrugated options for corrugated pads, rolls, fan-folds and more means that traditional plastic padding can be replaced with recyclable materials without sacri-ficing safety in transport.
SupplyOne recently bought Crownhill Packaging, a Canadian packaging distributor based in Toronto, the latest in a number of acquisitions.
More information from www. supplyone.com/products/ corrugated-packaging
percent of consumers across the EU believe companies are doing enough and 41.8 percent indicating there is more to be done, Italy stands out the most, with 66 percent of consumers feeling that businesses are on the right track, followed by UK (63 percent), Germany and Spain (56 percent), and France less optimistic (50 percent).
This presents an opportunity for retailers and brand-owners to address consumer concern, communicate their sustainability initiatives effectively and offer more eco-friendly packaging options to bridge the gap and gain trust.
More information from www. procarton.com
Jimmy’s Iced Coffee, a brand long committed to sustainability and environmental responsibility, has completed trials for secondary packing its aluminium bottles in Zero Tree fibre-based cartons, which are now used in its entire e-commerce product line.
The initiative aligns with Jimmy’s B Corp status and demonstrates its dedication to reducing deforestation, minimising carbon emissions and appealing to a broader audience through sustainable practices. B Corps are companies verified by B Lab to voluntarily meet the highest standards of social and environmental performance, transparency and accountability.
Zero Tree packaging uses
fibre sourced from crop waste, a process developed by UKbased Raw Packaging. By using agricultural by-products that would otherwise go to waste, the packaging is said to help mitigate deforestation.
Ben Nethersole, head of operations at Dorset, UK-based Jimmy’s, commented: “By switching to packaging made from crop waste, we are helping to change the mindset of where materials are sourced from, a critical step in conserving our planet’s vital ecosystems. Furthermore, this environmentallyconscious approach significantly lowers carbon emissions, playing an integral role in combating climate change.”
More information from www. raw-packaging.co.uk
Following Sanofi’s Consumer Healthcare (CHC) business joining PA Consulting (PA) and Pul-Pac’s Bottle Collective last year, it is now part of the Blister Pack Collective, enabling the better use of PA and Pulpac’s Dry Molded Fibre technology for pharmaceutical products.
The Blister Pack Collective brings together pharma, consumer health and FMCG businesses to accelerate progress towards a world with more sustainable blister packaging, free from problem plastics like PVC. PA and PulPac have seeded the collective and developed the underlying technology needed to bring a functioning Dry Molded Fibre tablet blister pack to market. Its adoption provides an opportunity to cut back on the 100,000+
tonnes of plastic medicine packaging used every year.
As a founding member of both the Blister Pack and Bottle Collectives, Sanofi CHC is investing in the development of Dry Molded Fibre packaging to help build a healthier, more resilient world, it says.
The blister packs and bottles
are designed to be recycled in the same way as paper packaging and will reduce or eliminate Sanofi CHC’s single-use plastic packaging, significantly improving the environmental profile of the company’s future product portfolio.
The use of Dry Molded Fibre packaging minimises carbon
dioxide emissions, with up to an 80 percent lower carbon dioxide emission footprint than plastic and wet moulded fibre, and requires minimal water usage. It enables the production of versatile tablet packs that are comparable to PVC packs in design and tablet count.
France Depaix, global head of design, product sustainability and packaging innovation at Sanofi Consumer Healthcare, commented: “We are proud to be a part of the Blister Pack Collective as we take significant steps to reduce our environmental footprint and contribute to a healthier planet. By fostering collaboration and adopting innovative solutions, we aspire to set new benchmarks for sustainability, inspiring our peers and partners to join us in this transformative journey”.
More information from www. pulpac.com
Belgian brewer and co-packer BeerSelect was searching for an end-to-end system to pack cans at its new greenfield brewery in Ghent. The system had to be plastic-free, aligning with the brewer’s sustainability goals, be versatile enough to pack different configurations of cans and affordable for a business of its size.
Smurfit Kappa reviewed every aspect of BeerSelect’s operations and proposed its cardboard TopClip packing system. A paperbased alternative for shrink wrap, TopClip uses minimal material and is glue-free.
This design was combined with the installation of a tailor-made automated
cost of the machine met all of BeerSelect’s requirements and enable the brewer to offer its customers packing flexibility. It handles 30,000 cans per hour with the versatility to bundle four-, six- and eight-packs of cans.
TopClip is 100 percent renewable, recyclable and biodegradable with a 30% lower carbon footprint than shrink wrap. The product also provides excellent visibility of the product, showcasing the cans in a retail setting.
More information from www. smurfitkappa.com
DS Smith has been working with Filir, a distributor of confectionary products based in Croatia, to redesign packaging for the brand’s Easter product portfolio.
The traditional plastic packaging for Easter snacks and candies was updated with fibre-based and 100 percent recyclable packaging to replace the plastic bag that was previously used.
The new packaging is designed by DS Smith experts to contain less material and minimise waste, and it has an extended lifecycle for reuse as a gift bag. Key features include a locking system that is intended to prevent the chocolate
boxes from being opened before use.
The Filir product is part of a novel ‘unboxing’ experience whereby the contents inside are intended to be a surprise.
In addition, the green-coloured artwork on the new packaging makes for a striking product
differentiation from competitor brands. The chocolate boxes are easy to assemble and fitted with a corrugated cardboard carry handle for additional versatility and usability.
Jasmina Cuković, Cluster Innovation Specialist at DS Smith Packaging in Croatia said: “We
have been delighted to participate in this plastic replacement project and the primary challenge was to develop a creative packaging solution to maintain and build on the functionality of this popular Easter gift, while maintaining an arresting and recognisable shelf presence for the supermarkets and vendors. It was also vital to ensure the fun-based reuse options and repurposing opportunities for customers after purchase.
“We applied our DS Smith Circular Design Principles and approach to eliminate even the smallest amounts of plastic in the packaging and apply rigorous testing of its sustainable strengths and weaknesses.”
The Fishbone C-Clip, is an improved curbside-recyclable multi-pack carrier for cans or bottles launched by Atlantic Packaging.
C-Clip is the second-generation paperboard Fishbone carrier and is designed with a second carrier layer to support potential cases of lost tension or exposure to moisture, making it better for withstanding refrigerated conditions. Bannerdisplay branding is provided to meet the needs of a range of customers.
The product is part of Atlantic Packaging’s continued commitment to eliminating single-use plastics from the packaging supply chain.
With the United Nations
Environment Program estimating that plastic debris kills more than a million seabirds and 100,000 marine mammals each year, Atlantic is keen to help.
“Traditional plastic ring beverage carriers have long
been problematic for our natural world and contribute to direct entanglement or ingestion threats to land and water-based species,” said president of Atlantic Packaging Wes Carter.
“The Fishbone C-Clip provides
a sustainable alternative and technical design that is both reliable and durable. We are excited to bring this innovation to market as we seek to deliver solutions and advocate for the transition away from problematic direct-to-consumer, single-use plastics to fibre-based, lifeaffirming solutions.”
C-Clip comes in a variety of in-stock and customised options while communicating the values of environmental sustainability. In-stock design options are available for fourpacks and six-packs and sold in quantities of 1,000 in the event that purchasers are not ready to commit to custom printing.
More information from www. atlanticpkg.com
Forest industry group UPM has taken delivery of its biggestever investment, the Paso de los Toros pulp mill in Uruguay, from technology group Andritz, which supplied and commissioned the US$3 billion project to be the most energy-efficient with the highest environmental standards.
With a capacity to produce 2.1 million tons of eucalyptus pulp per year, the mill is the biggest in Uruguay and the world’s biggest single-line mill in operation. It will also contribute around 1 TWh (1 billion megawatt hours) of surplus biomass-generated electricity per year to the Uruguayan power network.
“Our new world class mill boosts our pulp production capacity by over 50 percent. It represents the latest and best available technology that ensures highest performance at minimal environmental impact and optimised maintenance,” said Aki Temmes, executive vice president
of UPM Fibres Business Area. “Our collaboration with Andritz throughout the project was excellent.”
UPM will use the pulp from the Paso de los Toros mill to meet the rising demand of existing customers, particularly in China, but also to target new markets. Having successfully established itself as a reliable pulp supplier in the Asia-Pacific region and in Europe during the last decade,
UPM is now using this experience, as well as the increased capacity, to develop the North American market.
Andritz supplied the complete mill, with core equipment manufactured at its production facilities in Finland, Sweden, Austria and China. The project included a wood processing plant, a fibreline, a pulp drying system, an evaporation plant, a white liquor plant, a HERB recovery boiler to maximise steam production for power generation, a biomass power plant, a biosludge drying system and all the process pumps for the mill. UPM also concluded a maintenance contract with Andritz for the entire mill process areas.
The quality of project management was underlined by the fact that despite the challenging restrictions due to the Covid-19 pandemic, the project is said to have experienced only minor delays.
“We are very happy that UPM
entrusted us with this milestone project and look forward to continuing our support in maintaining the mill. Our goal is to assist customers in maximising the performance of their plants throughout the entire life cycle,” said Joachim Schönbeck, chief executive of Andritz
The Paso de los Toros pulp mill was first proposed in 2017, ten years after UPM’s mill at Fray Bentos started up. Uruguay developed the rail and road network which was necessary to enable the establishment of efficient logistics infrastructure in the inland with a total government investment of around $1 billion. The Government also promoted concession for a specialist terminal for pulp in the port of Montevideo with rail access in order to secure reliable and competitive outlet to export markets.
In addition to the new pulp mill, UPM’s overall investment included the deep-sea port terminal, a new eucalyptus tree nursery and investments in the local facilities.
South American tissue manufacturer Softys Peru is the first to install a hybrid hood heating system developed by Andritz.
It is the industry’s first system that enables a combination of electric and natural gas powered heating. Installation and start-up of the technology the mill in Lima, was completed in December 2023.
The system uses a patented air mixing plenum that enables the combination of heat sources that are used according to the mill’s specific needs.
Softys operates the system in
one of three ways: an electric heating mode, using only the electric heater assembly; a natural gas heating mode, using the burner; or hybrid mode, with a freely adjustable portion of electric and natural gas heating.
This provides Softys with maximum flexibility in choosing heat sources with a view to emissions reduction and energy cost optimisation. The system has been installed in a tissue machine with a design speed of up to 2,000 metres per minute and a paper width of 2.8 metres.
Reinaldo Uribe, director of processes and corporate projects
“Part of our ESG strategy to reduce the greenhouse gas emissions from our tissue machines”: Reinaldo Uribe, director of processes and corporate projects at Softys Peru
at Softys, and inventor of the system, explains: “We invited Andritz as a partner to develop this R&D project as part of our ESG strategy to reduce the greenhouse gas emissions from our tissue machines in Latin America, and we are happy to see that our efforts are now contributing to more sustainable mill operations. In George Nowakowski I found the perfect counterpart to implement this project – from conjoint R&D works, up to the successful patent application and start-up.”
George Nowakowski,vice
president for Tissue Drying America, and inventor of the system from the Andritz side, adds: “Collaborating with a partner like Softys gives us the great opportunity to use our mutual know-how in order to swiftly develop, extensively test and efficiently implement valuable innovations that are beneficial both for the environment and operational efficiency.”
Softys, part of the CMPC group, is one of South America’s largest tissue producers. The mill in Lima has an annual production capacity of around 100,000 tons.
Shandong Huatai Paper successfully started up its PM11 line in the eastern Chinese province of Shandong in January after it was rebuilt by Voith Paper to produce high-quality graphic paper.
With a web width is 10.2 metres and a design speed 1,800 metres per minute the rebuilt line’s annual capacity has been increased from 400,000 to 520,000 tons.
“After the rebuild of PM10 from newsprint to writing paper in 2016, the successful start-up of PM11 represents a significant milestone in Huatai’s transformation process to high-quality graphic paper,” said Wei Lijun, general manager of Shandong Huatai Paper. “The rebuild has not only transformed the almost 20-year-old paper machine into a modern paper machine but has also significantly improved the machine’s stability and capacity. We look forward to writing more success stories with Voith in the future.”
The customised rebuild included a variety of technologies with a focus on stability, reliability and efficiency with a view to extending the line’s service life and providing more sustainable and cost-efficient operation.
This involved upgrading the MasterJet Pro G headbox and implementing the optimisation
of dilution water technology to improve paper quality while reducing energy costs. The Voith experts upgraded the forming section similar to the DuoFormer concept for optimum formation and higher throughput. In addition, the ParaSlice nozzle concept and the EdgeModule system were integrated to stabilize the fibre orientation profile (CD profile). The newly-installed ProRelease+ HighEnd boxes in the pre-dryer section significantly increase the vacuum level to 3000 Pa, ensuring the stability of the paper web at high speeds and minimising the risk of paper breaks.
In addition, a SpeedSizer AT with its uniform film application is said to ensure even and high-quality paper profiles. The CombiDuoRun dryer concept and an efficient new dryer section hood are used in the after-dryer section. Voith’s roll covers ensure optimum sheet
release and reduce paper breaks.
By installing digital systems from the Papermaking 4.0 portfolio, in particular the OnQuality quality management system (QCS) and the OnControl automation technology (MCS), Voith says that PM11 has been brought up to date, resulting in a significant increase in operating convenience and control stability.
With an annual production capacity of 1.5 million tons, Shandong Huatai Paper is one of the world’s leading manufacturers of newsprint.
It is part of the Huatai Group which has an annual production capacity of four million tons of paper and four million tons of chemical and papermaking auxiliary materials. With more than 15,000 employees, the Huatai Group exports to more than 60 countries and regions around the world.
The Navigator Company in Portugal has ordered an Optima 1800 slitter-rewinder for installation at its Aveiro tissue mill with start-up planned for the second half of this year.
The Toscotec slitter-rewinder will be equipped with tension and nip control for high quality winding, processing parent reels with a width of almost 2.8 metres using two unwind stands. Toscotec will also supply the associated roll handling and trim removal system designed to feed the rewinder’s trim paper back to the tissue machine to maximise fibre savings throughout the whole production line. The service package includes full onsite erection, as well as supervision, training, commissioning, and
start-up assistance.
The Navigator Company and Toscotec have been collaborating since 2015, when the tissue maker acquired fellow tissue producer AMS which operated two highspeed Toscotec Ahead tissue machines at its Vila Velha De Ródão mill, PM1 and PM2, started up respectively in 2009 and 2015.
Aveiro mill manager Paulo Santos says, “We are looking forward to continuing our partnership with Toscotec, which has proved in the past to be a reliable supplier for its state-of-the-art technology, flexibility, and expert services. This new rewinder line will support our growth in the international markets as a leading manufacturer of premium quality tissue.”
An integrated producer of forest, pulp and paper, tissue, and
energy, The Navigator Company operates four mills in Portugal: Cacia, Figueira da Foz, Vila Velha de Ródão, and Setúbal. Its total annual production capacity is about 1.6 million tons of paper, and 1.5 million tons of pulp, of which about 80 percent is
German board manufacturer
WEIG is having the BM6 line at its Mayen mill upgraded by Voith with a control system to stabilise production quality.
Voith will be installing a quality control system (QCS) comprised of scanners, actuators and controls with integration into a PCS7 environment.
“The in-depth know-how of the Voith experts, the modular structure of the solution and the very good references in already installed systems were factors in our choice of Voith’s QCS,” says Bernd Stibi, managing director of WEIG Technical Liner.
“In the future, we want to
go even further with Voith in the development of system digitalisation. Voith’s leading digital expertise and broad product and service portfolio were critical factors for us.”
The BM6 project includes the supply, installation and commissioning of a customised
package. The main objectives include increasing dry content, improving moisture profiles, delivering faster grade changes and ensuring long-term service, and the supply of spare and wear parts.
“We are proud to support WEIG in this pioneering project. Our QCS solutions set new standards in
integrated into paper production. The Navigator Company is also a leading operator in the biomass energy sector, where it produces more than 50 percent of all power generated in Portugal from biomass, and 5 percent of all electricity in Portugal.
the industry and offer clear added value in terms of quality, efficiency and total cost of ownership,” says Ernst Jäger, regional sales manager at Voith Paper.
The core elements are the measuring frames made of stainless steel and the ModuleSteam steam blow box in the wire section with intelligent Profilmatic cross-profile control to increase the dry content and improve moisture profiles. Mayen does not require any additional interfaces meaning that the operator uses one control station. This enables efficient work, saves time and simplifies the operator’s tasks.
Guangdong Hengan Paper has successfully started up the two new Andritz tissue machines at its Yunfu mill in China. The machines are the 14th and 15th to be installed by the Austria-based technology group.
The two PrimeLineCompact M1600 machines, designated TM27 and TM28, have a design
speed of 1,700 metres per minute and a working width of 3.65m. They produce top-quality tissue for facial, toilet, handkerchief, and napkin grades from virgin market pulp.
The project included undermachine pulpers, proven PrimeFlow step diffusor headboxes, and 18-foot PrimeDry Steel Yankees with high-load
suction pressure rolls with Polysoft PU-covers and canopy hoods for high drying capacity at lowest energy consumption.
Wang Xiangyang, vice president of the Hengan Group, said: “Hengan and Andritz have been working together for more than 25 years. We have already had 13 Andritz tissue machines in operation and are convinced that the two new ones will perform just as successfully, producing
Film size press and suction press rolls for the new PM1 line operated by Fengsheng Paper Technology at Leshan City, in the Sichuan province of China, are being supplied by Italy’s A.Celli Paper/PMT Solutions.
The paper making line will be equipped with an Ægotm Sizer film size press which features a heads cinematic design developed by PMT to ensure the optimum application of starch across a range of operational conditions.
Also included in the order are two suction press rolls equipped with forged shells to give more durability.
The PM1 will specialise in the production of 30-90 gsm kraft packaging paper with a width at pope reel of 5.66 metres at a design speed of 1,100 metres per minute.
Yang Chao Lin, president of Sichuan Fengsheng Paper, commented: “We’re looking forward to collaborating with A.Celli Paper/PMT: their expertise and innovative solutions give us
high-quality tissue while enabling environmentally friendly production.”
Xie Zhengba, chief engineer at Guangdong Hengan Paper, added: “From the very beginning of this project to the start-up, we have been deeply impressed by Andritz ’s professional team. Each time when needed, they responded very fast and in a perfect manner. We really appreciate our partnership.”
confidence for the success of this project. We are sure that the film size press and suction press rolls provided will be able to meet our needs and enhance our operational capabilities.”
Founded in 1958, Sichuan Fengsheng Paper Technology is located in QianWei, Lingang Industrial Park (Leshan City). It is one of the top five bamboo pulp production companies in China and the leader in Sichuan by capacity, producing 180,000 tons per year of bleached/natural bamboo pulp household paper and 30,000 tons per year of finished product.
Anew highcapacity chemithermomechanical pulping system supplied by Andritz to Wuzhou Special Paper (Jiangxi) Co at Jiujiang City in the Jiangxi Province of China is said to be the largest fibreline worldwide using only one high-consistency refiner at the heart of the process.
President of Wuzhou Special Paper, Zhao Lei said: “In collaboration with Andritz, we have set a world record by achieving a capacity of 1,500 admt/d using just one HC refiner in our new production line. With this cutting-edge system, we will be self-sufficient in pulp production, guaranteeing topquality products without having to rely on outsourcing.”
Vice general manager Zhang Yancheng added: “Andritz ’s
proven technology, coupled with its team of domestic and international experts, has greatly supported our production line start-up. We’re very satisfied with the high fibre quality and the low energy consumption.”
The new system produces pulp for premium folding boxboard using eucalyptus and acacia chips
as raw material. The patented pre-conditioning refiner chemical alkaline peroxide mechanical pulp (P-RC APMP) process is said to ensure optimum pulp quality at minimum operating cost and lowest environmental impact. Andritz delivered key equipment from the chip washing to the storage tower stage, including:
l A PrimeMSD Impressafiner for wood chip maceration enabling optimum chemical impregnation
l A TX68 twin refiner – the world’s largest of its type –including an advanced feeding system for continuous high throughput and pulp quality at the lowest energy consumption
l Three Compact Press units enabling high pulp discharge consistency and superior washing efficiency after bleaching
l PrimeScreen X screens with an innovative PrimeRotor for top energy efficiency and screening performance
Wuzhou Special Paper (Jiangxi) Co was founded in 2014 as part of Wuzhou Special Paper Co, one of China’s leading food packaging paper manufacturers and one of the largest glassine paper and tracing paper manufacturers.
South Korea’s Moorim P&P is having an evaporation plant at its Ulsan mill, which produces bleached kraft pulp and different types of high-quality paper, upgraded by Andritz. The refurbishment, scheduled for start-up in April 2025, is expected to help to increase the mill’s efficiency and reduce consumption of resources.
Kim Sangwoo, project director at Moorim P&P, says, “We have set ambitious energy saving targets for our Ulsan mill. This upgrade will increase the capacity of our evaporation line no1 and the final dry solids content of the black liquor, which supports these targets. Andritz ’s efficient technologies will contribute to water and energy savings.”
The upgrade is designed to produce a stable, high-solids
black liquor stream for efficient combustion in the recovery boiler. All condensates generated in the evaporation plant will be re-used in other mill areas, reducing the need for raw water.
The project includes: an HD concentrator that will ensure that the evaporation plant sends firing liquor with higher dry solids content to the recovery boiler; an upgrade of the evaporation plant by adding a new effect 6 and an MVR pre-evaporator that will increase the evaporation capacity; and a foul condensate treatment system that will allow the condensates to be reused inside the mill instead of sending them to an effluent treatment plant. This has the double effect of reducing the consumption of freshwater and the need for treating wastewater.
Taiwanese tissue producer Yuen Foong
Yu Consumer Products has successfully started up a new Andritz tissue production line at its mill in Chingshui.
Vice general manager Tang Mingfa said: “The start-up went smoothly and precisely to schedule. This new line is of utmost importance to us as it increases both the quantity and quality of our household paper production and strengthens our competitiveness on the global market. It perfectly aligns with our vision of high quality and sustainable, low-emissions production.”
The PrimeLineCompact tissue machine, with a width of 3.65
metres and a maximum operating speed of 1,650 metres per minute, produces high quality household grades, including toilet paper, napkins, handkerchiefs, and facial tissue.
Key features of the line include:
a PrimeFlow 2-layer headbox that minimises slice deflection to achieve best cross-profile quality; a PrimePress XT Evo shoe press including Impulse shoe press
Construction of an enlarged wastewater treatment plant at Koehler Paper mill in Kehl was completed in January
The plant needed to be expanded following the commissioning of PM8 at the mill in 2019, which produced a higher volume of wastewater.
As a temporary measure, Koehler Paper had to divert some of its wastewater to the municipal treatment plant in Auenheim. To ensure that all production water could be treated in-house at Kehl, new tanks and sand filter systems were installed.
To ensure
In addition, some of the existing tanks were modified to ensure that there was no disruption to the production process.
Joachim Uhl, Kehl’s mill director,
says: “The work to extend the wastewater treatment plant ran really smoothly thanks to the
sleeves to ensure top quality paper with excellent bulk and high post-press dryness; and an 18-foot diameter PrimeDry Steel Yankee and a canopy hood for energyefficient drying and significant steam savings.
The project also included a stock preparation system with Papillon refiners for processing up to 112 admt/d of pulp, an approach flow and broke handling system, and a DCS. The machine is equipped with Andritz forming fabrics, press felts and an Impulse shoe press belt.
Yuen Foong Yu operates the largest mill for consumer paper in Taiwan and is a leading supplier of household products in Taiwan with brands such as Mayflower, Tender and Delight.
excellent work of our project team. The excellent cooperation between different departments and the authorities of the city of Kehl enabled the project to be completed successfully and on schedule. The extended treatment plant offers greater flexibility and capacity, which will allow us to respond more quickly to future demands.”
As a result, all of the treated production water can be reintroduced into the natural water cycle. The renovation project is said to make an important contribution to achieving Koehler’s sustainability goals in the area of resource efficiency.
Acomplete tissue line – Valmet’s first to include both a tissue making line and converting equipment – a has been ordered by Suzano Papel e Celulose, the world’s largest pulp producer and Brazil’s leading tissue manufacturer.
Also including a biomass boiler, it is the first combined order for Valmet since its acquisition of the Korber tissue converting business in 2023.
The tissue making line, converting equipment and the biomass boiler will be installed at the Aracruz mill at Espírito Santo, to meet increasing domestic demand for high-quality tissue
products with low environmental impact. With start-up scheduled for the first quarter of 2026, the line will have a production capacity of 60,000 tons a year.
Commenting on the order, Jean Moraes, Suzano’s corporate engineering executive, said: “Valmet’s state-of-the-art solutions will allow us to expand our tissue products capacity with a new production line in Aracruz mill. This meets our needs in terms of business strategy, production capacity, cost efficiency, and sustainability.”
Rogerio Berardi, director of the paper business line for Valmet in South America added: “It’s an honour to have been chosen by
Suzano for this strategic project in Brazil. The combination of Valmet’s tissue making line, converting equipment, mill engineering, automation systems, and flow control is ensuring high product quality while being the most efficient production line on the market today.”
The Valmet bubbling fluidised bed boiler, which is scheduled to start operating in the final quarter of 2025, will use biomass to produce steam, which in turn is used in the cellulose process and in the generation of electrical energy. Valmet says the boiler will increase the mill’s energy efficiency, contributing to operational stability, and will provide
A new digester top separator has been ordered from Valmet by Södra Cell for its Mönsterås Mill in Sweden.
Södra Cell made the decision after Valmet carried out a mechanical lifecycle analysis on the mill’s digester 4 during the annual shutdown in 2022. The new digester top separator will lengthen the lifespan of the digester, originally installed in 1979.
“Keeping our machine line in good condition is the key to creating a safe work environment for our employees and further improving our performance.
Thanks to Valmet’s lifecycle analysis, the digester top separator will now be renewed on time, contributing to the
safety and reliability of the machine line,” says Johan Carlstroem, maintenance engineer at Södra Mönsterås.
“We are very happy that Södra Cell’s Mönsterås Mill chose Valmet as a supplier for this top separator replacement. Renewing parts that have reached the end of their lifecycle improves
the safety of the mill, and in this case, it also simplifies the daily maintenance as the modern design of the new top separator enables using the same spare parts for the mill’s both digesters,” said Mattias Carlsson, product sales manager for pulp in the EMEA region at Valmet.
One of the world’s leading producers of paper pulp and dissolving pulp, Södra Cell’s three pulp mills have a combined annual capacity of 1.9 million tons. The Mönsterås Mill is Södra’s largest with a capacity of 750,000 tonnes per year of softwood and hardwood pulp. The mill’s core business is pulp production, but it is also an important source of ‘green’ electricity.
significant environmental benefits by reducing particle emissions.
The line will be comprised of an Advantage DCT 200 tissue machine with OptiFlo headbox and Yankee cylinder, ViscoNip press, ReDry, AirCap hood with Air system, WetDust systems and a SoftReel reel.
Also included will be detailed mill engineering, stock preparation equipment as well as automation, including Valmet DNA Distributed Control System (DCS) with built-in machine condition monitoring, Valmet IQ Quality Control System (QCS) and Softness sensor.
Valmet will also supply its converting lines, based on four rolls rewinder technology.
l A second Andritz fibre production line has been started up by Pavatex, which manufactures insulation board at its Golbey plant in France.
The line, which includes a chip handling and pressurised refining system, complements a similar line supplied by Andritz in 2013.
With a capacity of seven tons per hour the new line processes a mixture of spruce and pine wood chips used for board in the building, construction and renovation sectors. Pavatex is part of the Soprema Group.
Andrew Silvernail has been elected as International Paper’s new chief executive, following an extensive evaluation process.
From the beginning of May, Silvernail will succeed Mark Sutton, who will continue in his role as chairman of the company’s board of directors to ensure a smooth and successful transition.
Silvernail has two decades of experience leading global companies in the manufacturing and technology sectors. He joins International Paper (IP) from KKR & Co, a global investment firm, where he served as an executive advisor. Silvernail served as chairman and chief executive of Madison Industries, one of the world’s largest privately held companies. Prior to that, Silvernail served as chairman and chief executive of IDEX Corporation from 2011 to 2020. He previously held
executive positions at Rexnord Industries, Newell Rubbermaid and Danaher Corporation and currently serves on the board of Stryker Corporation.
Sutton, current chief executive and chairman, said, “The board’s succession process was comprehensive, and I’m confident that Andy’s experience paired with the industry expertise of our senior leadership team will amplify the company’s success going forward. It’s been a privilege to work with the IP team for the past 40 years and to lead the company for the past decade.”
Commenting on his selection, Silvernail said, “I want to thank the board for their confidence in me. I look forward to working closely with the board, Mark and our more than 39,000 employees worldwide as we continue to fulfil our vision of being among the most successful, sustainable and responsible companies in the world.”
International Paper’s Santiago Arbelaez has been appointed as chairman of the Paper and Packaging Board (P+PB) board of directors. The appointment was made by USDA Secretary Tom Vilsack and marks a pivotal moment for the organisation.
As chairman, Arbelaez will collaborate closely with the P+PB leadership team and the eight-member board of directors responsible for funding the ‘Paper & Packaging – How Life Unfolds’ campaign. The campaign is a national promotion programme centred around sustainability within the paper and packaging sectors.
In addition to the P+PB appointment, Arbelaez will continue as vice president of Strategy for International Paper’s industrial packaging business Arbelaez commented: “We look forward to further sharpening the uniqueness of our industry’s sustainability story while collaborating widely with other industry partners to drive greater awareness and reinforce the value
and benefits of the board.”
The appointed officers and board members for 2024 include:
Vice-Chair – Alpa Sutaria, senior vice president of strategy and sustainability, WestRock; SecretaryTreasurer – Richard Bennett, vice president of paperboard sales and marketing, Pactiv Evergreen; An Boon, vice president of global marketing, Graphic Packaging International; Beth Cormier, vice president of research, development and sustainability, Sappi; Steve Henry, chief executive, Domtar; Tonie Meyers, senior vice president of paperboard and sheeting operations, Billerud; and Juan Pablo Perez Chavez, chief executive for North America, Smurfit Kappa.
A number of managers have been newly appointed by Metsä Group for its mills in Finland. Janne Rantanen will become manager of the Äänekoski bioproduct mill from the beginning of April, moving from the same post at the Rauma pulp mill.
Ari-Pekka Vanamo, the current manager of the Äänekoski bioproduct mill, will move to the role of VP, HR projects from April and then in 2025 will become VP,
employment relations.
Jaakko Ikonen will become manager of the Rauma pulp mill from April, moving from the Tako paperboard mill in Tampere.
Timo Ahonen becomes manager of the Tako paperboard mill from April, moving from the Kemi paperboard mill.
Tomi Seppä moves up to be manager of the Kemi paperboard mill from April from being project director.
Real Progress is harnessing data to optimize pulp and paper production.
Our quality management and automation solutions harness data, optimize performance, and implement efficiencies in real-time. With the ability to adjust dynamically, reduce variability and waste, and optimize performance, mills can run tighter operations and achieve their circularity goals faster. solutions.abb/realprogress
Be part of Real Progress. —