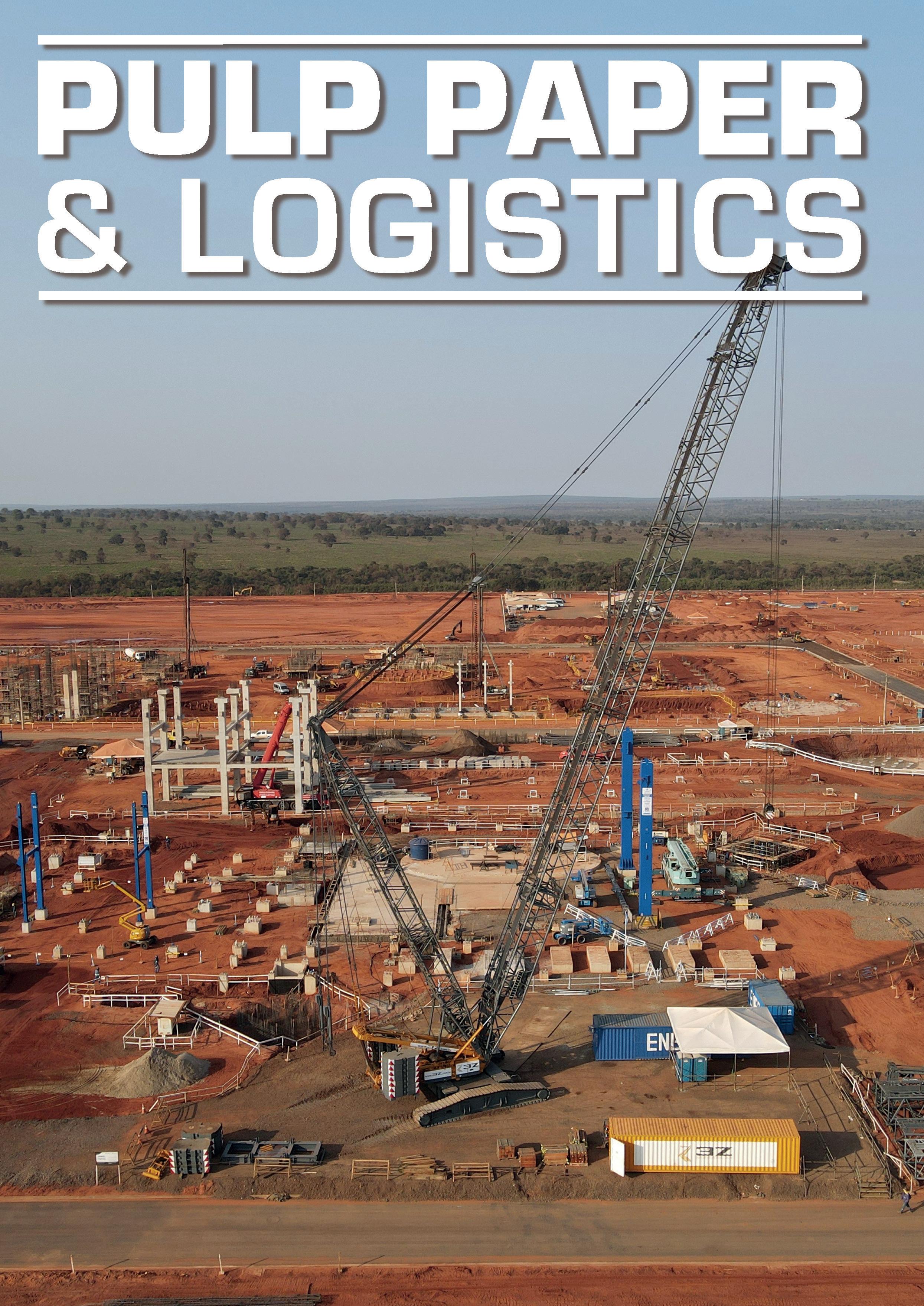
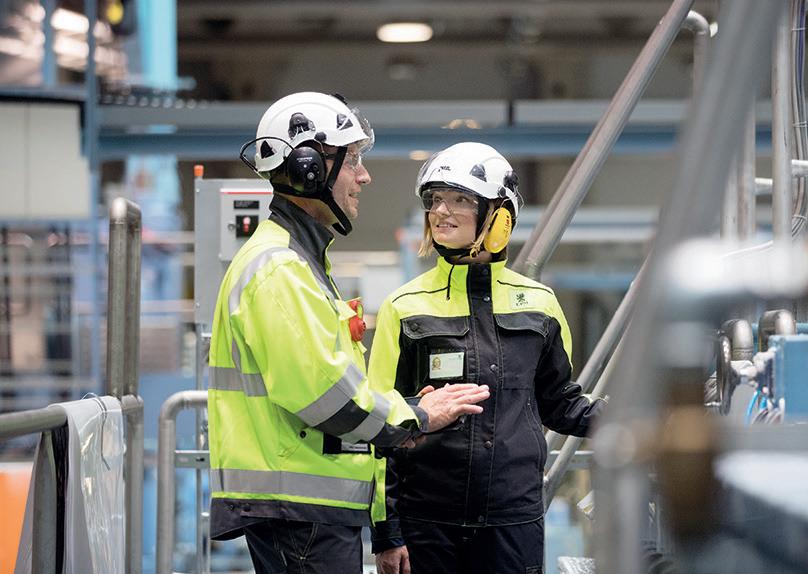
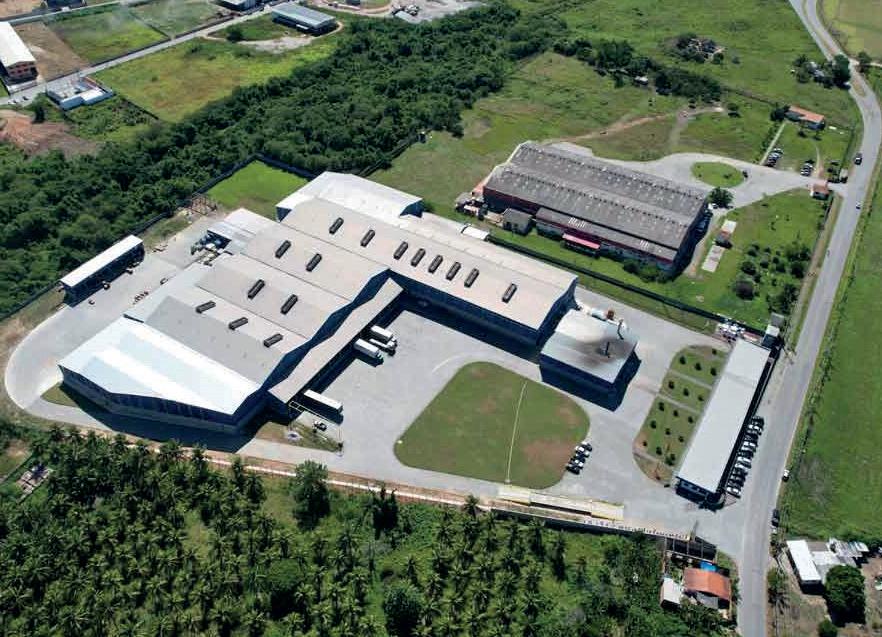
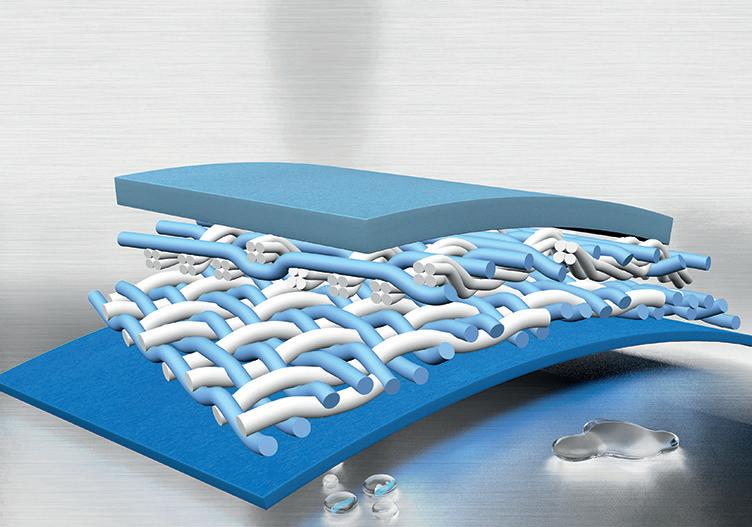
Sustainability isn‘t just about how many times a product can be used. It is also about reducing production waste, curbing energy consumption, and positively impacting both people and profits.
We offer products and services for the entire paper and board production process. From stock preparation to
the paper machine, our competencies incorporate world-class experience and expertise, automation support and technical services, as well as fabrics and rolls. Each solution is crafted to reduce environmental impact and im prove the quality of the end product.
For further information, please contact us at paperboard@andritz.com
Welcome to the September-October issue of Pulp Paper & Logistics.
We are seeing no let-up in the growth of consumer demand for packaging materials and mills are continuing to develop and extend production methods to increase their product offerings to buyers and specifiers.
Manufacturing flexibility in paper mills and the ability to complete quick changeovers of product grades is gaining importance to stay competitive. This makes the most of the mill as an asset, with packaging material production continuing to show where innovation and design helps meet consumer expectations to reduce the volume of single-use plastics.
Looking to the near future, many of us will be heading for Lucca in Italy for the MIAC 2022 show, now back to full strength. In this issue we have included an overview of what visitors can expect, with a comprehensive list of exhibitors and details of the conference programme that outlines the growing importance of the tissue industry. I’ll be there so if you want to set up a meeting during MIAC please let me know.
In our next issue, we plan to cover preventive maintenance, recycling technology and equipment, water management and provide a logistics & handling update. Submissions for the November-December issue should be sent to pulppaperlogistics@virginmedia.com no later than 7 November.
Vince Maynard, PublisherVol. 13 Issue No. 74, September/October 2022
ISSN 2045-8622 (PRINT)
PUBLISHER & EDITORIAL DIRECTOR
Vince Maynard
Tralee, Hillcrest Road, Edenbridge, Kent, TN8 6JS, UK
Tel: +44 (0) 1732 505724
Mobile: +44 (0) 7747 002286
Email: pulppaperlogistics@virginmedia.com
David Young
Tel: +44 (0) 1737 551687
Mobile: +44 (0) 7785 796826
John Nutting
Email: johnnutting47@gmail.com
Einar Johansson
Tel: +46 8 540 255 15
Mobile: 0046 70 234 80 85
Email: einar.lennart@gmail.com
Anthony Wiffen
ASTAC Business Publishing Ltd
Tel: +44 (0) 1460 261011
Mobile: +44 (0) 7557 280 769
Email: anton_print_1@mac.com
Brown Knight and Truscott
Tunbridge Wells, Kent, TN2 3BW
United Kingdom
Tel: +44 (0)1892 511678
Work has started on WestRock’s expansion and modernisation of the woodyard at its containerboard mill in Hodge, Louisiana.
The US$97 million investment in the construction of a new woodyard and new equipment will increase capacity and efficiencies and reduce operating costs at the facility, the company said.
It comes soon after the recently-completed five-year modernisation plan that the company announced in 2017.
“WestRock is committed to delivering on the promise of a sustainable future,” said Patrick Kivits, president of corrugated packaging at WestRock.
“The planned woodyard
improvements are expected to reduce the use of source material by 4 per cent while yielding higher product volume. This makes our planet better and contributes to the long-term operational success of both our facility and the Hodge community.”
WestRock reported in its third
The Feldmuehle GmbH mill at Uetersen in Germany, which manufactures high-quality white coated label papers and packaging papers for domestic and international markets, is switching its steam generation from using gas to light heating oil.
The mill’s management, which is investing €2.6 million in making the conversion, said that the move will ensure the continued operation of the site in the event of a worsening gas shortage. It also said that it would secure the
competitiveness of the mill as gas prices rise sharply.
The investment will be financed by an extraordinary shareholder contribution.
Feldmuehle is working on a plan to make the mill carbon-dioxide neutral in the longer term, including the use of wind, solar and geothermal energy.
The mill at Uetersen has been operating for about 100 years. In June 2018, Feldmuehle became a subsidiary of the Berlin-based Beteiligungsgesellschaft Kairos Industries AG.
quarter fiscal results that sales were up 14.6 per cent up at US$5.5 billion, with net profit up 51 per cent at $378m.
The Atlanta, Georgia-based paper products manufacturer has agreed to acquire the remaining interest it does not own in Grupo Gondi, which operates four paper
mills, nine corrugated packaging plants and six high graphic plants in Mexico. The deal, which is expected to close before the end of 2022, is worth $970 million, plus the assumption of debt, representing an estimated enterprise value of almost $1.8 billion.
At Mitsubishi HiTec Paper in Germany, 18 new apprentices started their training in August.
At the Bielefeld and Flensburg mills, the youngsters are being trained as paper technologists, machine and plant operators, industrial mechanics, electronics technicians for industrial engineering, electronics
technicians for automation technology and cutting machine operators.
The latest influx means that 42 apprentices are now undergoing their training at Mitsubishi HiTec Paper.
The ground-breaking ceremony in Jackson County included Louisiana’s state governorThe Smurfit Kappa paper mill at Nettingsdorf in Austria has launched a district heating project that will benefit 20,000 homes in three communities when completed. The scheme will capture excess heat generated from the mill that will be supplied to local homes, businesses and schools.
Civil works have started on the project with the first trenches excavated and pipes laid in June. The central heat distribution building and equipment will be erected in the coming months and it is planned that a local
elementary school and the kindergarten in Nettingsdorf will be the first to benefit from the scheme early next year.
This follows a recent €134 million programme of investment at the mill which included the installation of a new design of boiler that allows the recovery of biomass generated in paper pulp production. This boosted energy optimisation and cut annual carbon dioxide emissions by 40,000 tonnes.
Once fully operational, the new network will provide heating to households in the neighbouring villages of Kremsdorf, Haid
and Ansfelden and replace the fossil fuels previously used. The production process will generate up to 25 MW of heat that will help save about 21,000 tonnes of carbon dioxide a year.
Garrett Quinn, chief sustainability officer at Smurfit Kappa, commented: “Supporting our local communities is every bit as important as our day-to-day business of creating packaging. We are focused on working in partnership with local people to identify the sustainability projects that will make a positive difference to their lives. The innovative district heating scheme under
way at Nettingsdorf is the latest example of this type of community sustainability initiative and will be a great resource for the area.”
Smurfit Kappa has had success with a similar scheme operated from its Pitea paper mill in Sweden which has been converting excess heat into central heating for domestic and business premises in the local community for more than 40 years.
The remaining civil work in the first phase at Nettingsdorf is due to be completed this year and the project remains on schedule to provide service to the first premises early in 2023.
Amulti-million pound funding package for UK-based Lucart Hygiene to support its growth in the ‘away from home’ tissue paper business has been provided by Santander UK.
The Malvern company – formerly Essential Supply Products – was acquired by Italian paper maker Lucart SpA in March 2021, marking its entrance into the UK market. Lucart group is a familyrun business established in 1953 and is Europe’s seventh-largest tissue paper producer, with capacity to manufacture 390,000 tonnes of tissue a year.
The funding from Santander UK supports the refinancing of Lucart Hygiene’s manufacturing facility at Blackmore Park as well as providing an invoice finance facility to aid the business’ working capital.
Lucart Hygiene manufactures and supplies tissue paperbased products and dispensing systems to businesses, primarily wholesalers spanning a wide range of industries in the UK and
Republic of Ireland. Its products include ‘away from home’ toilet paper, hand towels, face tissues, napkins and industrial rolls for use in restaurants, gyms, factories, offices, cleaning companies, and the healthcare sector.
The business is focused on expanding in the ‘away from home’ tissue market, with its Lucart Professional product range playing a key role in the wider group’s aim to consolidate its position as the second largest company in this market in Europe. This target is supported by the production and commercial
efficiencies that have been created by Lucart Hygiene’s integration into the global Lucart group.
The group has ten production plants and a logistic centre in Italy, France, Hungary, Spain and Germany, as well as the UK, with staff of more than 1,700.
In its first nine months operating as Lucart Hygiene, the business had sales of £21.8m, and is forecast to achieve annual slaes of £37m by the end of this year. Its longer-term goal is to achieve annual turnover of £50m within the next five years, and to eventually invest in a paper mill in
the UK.
Sustainability is a strong focus for Lucart Hygiene and the wider group. Almost 50 per cent of paper manufactured by Lucart group is produced from recycled material.
Jonny Wilks, managing director of Lucart Hygiene, said: “With the ever-changing economic challenges businesses are facing, we took the decision to look for a new finance partner to support us through these uncertain times. We are pleased to now bank with Santander UK as it understands the needs and values of our business, and, with its support, we are extremely confident about our plans.”
In Italy, Lucart group’s target to produce 100 per cent recyclable or compostable packaging was reached four years early. Its 17th sustainability report for 2021 also revealed that it recycled more than 7.6 billion beverage cartons, cut its carbon emissions by 14.9 per cent and started up a 3MW solar array at its Borgo a Mozzano plant.
Mondi is investing around €5 million in a new research and development facility at its Steinfeld mill in Germany to help customers develop products that achieve their sustainability goals.
Work has already started on the facility, which will include pilot lines for both plastic- and paper-based products, from coating, film extrusion and printing to filling lines for a range
of products.
When opened at the end of 2023, it will also bring together experts with extensive knowledge of different materials and packaging types. Extrusion coating, aqueous coating and siliconisation will be available, as well as various printing machines. Filling lines for different materials, including both horizontal and vertical filling, forming and sealing
equipment will allow customers to conduct trials without interrupting their own running production.
Elisabeth Schwaiger, head of R&D and IP Flexible Packaging at Mondi, says: “This R&D centre demonstrates our handson approach to developing sustainable packaging solutions at Mondi. We look forward to working with our customers, combining their knowledge with
ours to meet their sustainable packaging goals. The investment helps to contribute to our own Mondi Action Plan 2030 sustainability goals, specifically our target to make 100% of our products reusable, recyclable or compostable by 2025.”
The R&D centre will complement Mondi’s other centres such as the recycling and food safety laboratories at Frantschach in Austria.
Funding for growth: Lucart Hygiene’s facilities in the UKImprove your press section efficiency! SmartScan™ contactless sensor accurately measures paper web dryness after the press section 24 hours a day, 7 days a week. Using a proprietary microwave technology, it is developed to overcome the typical limits of the NIR (near-infrared) sensors.
SmartScan™ is available both for fixed point positions or traversing web scan. To save hundred of thousands of Euros in energy costs, stop collecting samples, choose the safe accuracy of SmartScan™ technology.
24020
As Stora Enso outlined its strategy and performance during a virtual Capital Markets Day in September, where it outlined its plans in its three key growth areas of renewable packaging, building products and biomaterial innovations, the Sweden-based company reiterated a number of initiatives that demonstrate its changing focus.
It has also revealed a number of acquisitions and divestments while outlining new product initiatives.
By 2030, Stora Enso aims to have a significantly lower exposure to market pulp and reduce its cyclicality.
In renewable packaging, it said it was well positioned to further strengthen its leading positions and capture growth opportunities in consumer board, containerboard and corrugated packaging. The ambition is to generate more than 60 per cent of group sales from renewable packaging by 2030.
In building products, its markets are growing due to increased demand of wood-based material in the construction sector. The company’s ambition by 2030 is to increase the share of building products in the wood sales mix to 40 per cent by growing mainly added value products.
As reported in July, Stora Enso’s sales in the second quarter were 18 per cent up at just over €3 billion while net profit was up 44 per cent at €299 million.
A few days before the Capital Markets Day, Stora Enso acquired De Jong Packaging Group, based in the Netherlands, for about €1 billion
De Jong Packaging Group is one of the largest corrugated packaging producers in the Benelux countries and it will expand Stora Enso’s business in packaging for fresh produce, e-commerce and industrial products.
It will also strengthen Stora Enso’s European market presence in corrugated packaging and provide an entry into the Netherlands, Belgium, Germany and the UK, increasing its corrugated packaging capacity by about 1,200 million sqm to more than 2,000 million sqm.
Chief executive of Stora Enso Annica Bresky commented: “In line with our strategy, we are investing in growing our market share in renewable and circular packaging solutions. De Jong Packaging has a solid presence in the corrugated packaging sector and an impressive customer base. Acquiring their operations supports our future strategic direction to advance renewable packaging solutions within Europe.”
Divestments include the Nymölla paper mill in Sweden to Sylvamo, a US-based global producer of uncoated paper, for €150m, and the Maxau paper mill in Germany, and all related assets to Schwarz Produktion for about €210 million.
This Nymölla deal is part of the earlier announced plan to divest four of Stora Enso’s five paper production sites.
“Following our recent agreement to divest the Maxau site, I am pleased that we found a good, experienced owner in Sylvamo for our Nymölla site. The process to divest the remaining paper assets continues,” said Seppo Parvi, chief financial officer and head of paper division at Stora Enso.
Sylvamo plans to integrate the Nymölla site – which has capacity for 485,000 tonnes of wood-free uncoated office papers, with Multicopy as the leading paper brand – into its global paper business. TreeToTextile, the sustainable textile fibre company, is not part of the transaction and will continue operations at the site.
Schwarz Produktion, part of Schwarz Group, one of the top retailers in the world, is expected to take over the Maxau site in the beginning of 2023. Schwarz’s plan is to continue paper production. Stora Enso will continue to operate the Maxau site and serve its supercalendered paper (SC) customers until then. The move will reduce Stora Enso’s SC paper capacity by 530,000 tonnes a year.
Stora Enso says the divestment process continues for Hylte and Anjala paper sites with no committed timeline for conclusion.
With increasing demand for fibre-based packaging, Stora Enso has started a feasibility study for building a new formed fibre plant in Hylte, Sweden.
The new plant would mainly produce PureFiber – a range of formed fibre products that contain no per- and polyfluoroalkyl chemicals.
According to the LCA-study, these products have an up to 75 per cent lower carbon dioxide footprint compared to alternative packaging materials such as plastics and bagasse.
Mikael Krook, sales and commercialisation chief for Formed Fiber at Stora Enso, commented: “The new plant would serve as a
centre of excellence to produce low-carbon packaging solutions. In addition to producing food service applications, such as lids, bowls and trays, we would offer more advanced solutions such as modified atmosphere packaging that helps extend the shelf life of fresh produce.”
Stora Enso and Huhtamaki have joined forces to launch an “industrial scale” paper cup recycling initiative, The Cup Collective. The programme aims to recycle half a billion paper cups in the first two years.
Initially the programme will be implemented across the Benelux. With the aim of setting new standards for paper cup collection and recycling in Europe, The Cup Collective has issued an open invitation for partners from across the supply chain to get involved in working towards a systemic European solution.
The programme is managed by Co-cre8, a UK-based firm with more than a decade’s experience in designing and implementing recycling programmes in Europe.
Hannu Kasurinen, EVP of Stora Enso’s Packaging Materials division, said: “Stora Enso wants to accelerate the circularity of all packaging materials and we have an excellent foundation to make that happen. The paperboards we make are designed to be recycled and our own production sites, including Langerbrugge in Belgium, can process and recycle paper cups into new fibre-based products. By partnering with Huhtamaki and Cocre8 we will now be able to provide a platform to collect and capture the value of paper cup fibres on an industrial scale.”
Arecyclable, paperbased system to replace plastic shrink wrap for PET bottle multi-packs has been launched by Mondi.
Hug&Hold comprises two elements that provide secure and safe transportation and stacking of bottled drink multi-packs. The first is a patent-pending sleeve made of 100 per cent kraft paper that wraps around the bottles to hold them securely.
Made from Advantage SpringPack Plus, it offers high tensile strength and can withstand enough weight to
strap and stabilise the bottles during transportation. The second element is a corrugated clip that holds the bottles around the neck. An optional integrated handle means a bundle of bottles can be carried and transported easily. Simple separation of single bottles from the pack by the consumer or retail staff adds to the convenience of the design.
Mondi worked with Krones, a specialist in packaging automation technology, to ensure that Hug&Hold packs bottles in a fully automated process.
Silvia Hanzelova, sales director for speciality kraft paper at
Mondi, says: “Leveraging Mondi’s team of kraft paper and corrugated specialists, we were able to develop a fully paperbased solution with minimal material usage. Following thorough testing with Krones and a global beverage brand, Hug&Hold has been confirmed in terms of runnability and viability.”
● Mondi has also collaborated with Essity and Dow to create recyclable secondary packaging for Essity’s feminine care products, using renewable materials and post-consumer recycled content that reduces use of fossil-based materials.
Smurfit Kappa has agreed acquire PaperBox, a packaging plant located in Saquarema, 70km east of Rio de Janeiro. The deal, the value of which was not revealed, is expected to be completed at the end of October.
Brazil is the largest corrugated cardboard market in Latin America, with 7.4 billion sqm produced a year, and the south east region, where PaperBox is located, provides to almost half of this. Smurfit Kappa currently operates in three other states: Minas Gerais, Rio Grande do Sul and Ceará.
Laurent Sellier, chief executive of Smurfit Kappa in the Americas, says: “We are very proud to expand our footprint in Brazil to meet the growing
demand for innovative and sustainable packaging. This acquisition will broaden and strengthen our presence in the country, improve our production capabilities and enable us to continue to create new opportunities and
form new partnerships with customers.”
In Mexico, Smurfit Kappa recently invested US$23.5 million to upgrade its Nuevo Laredo sheet mill to become a fully-integrated corrugated plant.
Mondi’s paper-based wrap for PET bottle multipacks replaces plastic film
An estimated 8,000 tons of paper and cardboard bales were lost in a fire at Smurfit Kappa’s SSK paper mill the UK’s Midlands in July.
The paper maker said that high winds carried the fire from adjacent premises into the mill’s recovered fibre yard. West Midlands Fire Service said that at the height of the incident, 110 firefighters with more than 30 appliances attended.
Smurfit Kappa told local media that “the paper mill itself is unaffected and we do not expect any material impact on production”.
In a statement, the corrugated packaging producer added:
“Smurfit Kappa would like to thank both West Midlands Fire Service staff and the SSK team for their swift and professional response in controlling the fire within a few hours and ensuring the safety of all.”
The PaperBox packaging mill in Brazil, which is being acquired by Smurfit KappaUS paper maker WestRock has supplied its paper-based ClusterPak EvoTech secondary packaging in a joint partnership between leading Czech Republic brewer Budějovický Budvar and Mattoni 1873.
The packaging system has been used for multi-packed cans of Birgo, a non-alcoholic beer developed by Mattoni in partnership with Budějovický Budvar.
responsibly managed forests is key to establishing circularity on the Birgo production line, says WestRock.
Amethod for producing three-dimensional cellulose products from an air-formed blank structure in a rotary forming mould system, developed by PulPac, could soon be patented in Europe.
Sweden-based PulPac has been developing its already-established Dry Molded Fiber technology, and the rotary forming system will pose a viable alternative for some products, replacing single-use plastics.
Peter Ekwall, chief intellectual property officer at PulPac explains:
“We continue to use the alreadyestablished air-formed cellulose blank structure, but now it is fed to the rotary-forming mould and we apply a forming temperature in the range of 100 to 300 deg C and a forming pressure of at least 1 MPa, preferably 4-20 MPa.”
Dry Molded Fiber is a forming technology that can replace singleuse plastic with sustainable fibrebased alternatives at low cost.
Cluster-Pak EvoTech features easy, repeatable pastern changes along with an optimised use of water, heat and electricity to improve both energy and operating efficiencies on high speed lines. Its use of recyclable fibre-based packaging made from materials sourced from
“At WestRock, we are driving sustainability by working with customers to develop and implement eco-friendly packaging and machinery solutions that help them to advance their sustainability goals,” said Patrick Kivits, president of Consumer Packaging at WestRock.
“Introducing our Cluster-Pak EvoTech solution to the Czech Republic beverage industry is an exciting example of our efforts. We look forward to helping Mattoni and its partners continue to further their sustainability goals.”
Suzano, the world’s largest hardwood pulp producer, has purchased more than 2,000 square kilometres (206,000 hectares), of eucalyptus forests in Brazil for US$667 million.
The land represents an area similar to the size of Tokyo and brings into Suzano’s
direct ownership a number of eucalyptus plantation forests it currently manages under a longterm leasing agreement in the states of Bahia, Espírito Santo, Mato Grosso do Sul and São Paulo. These forests are located close to Suzano’s existing mills.
Marcello Bacci, financial chief at
Suzano, said: “We are currently in a fortunate position financially, with a competitive cost of debt and good availability of cash, which allows us to invest for the long-term. Securing our wood supply allows us to focus efforts on driving growth with innovability – pursuing sustainable
solutions through innovation –and developing sustainable bioproducts from eucalyptus.”
● Interview with Aires Galhardo, executive officer of pulp operations at Suzano, who is project managing the Cerrado pulp mill project in Brazil: see pages 10-14.
The Birgo packaging line at Budějovický Budvar is using WestRock fibre-based materialsLids made using the Dry Molded Fiber process – examples of applications for the fibre forming technology developed by PulPac
Your paper machine certainly has a lot of potential, it‘s a question of getting it out: Start up faster, dewater more and run your clothing for longer - with our New-Tech fabrics you can increase performance and cost efficiency. Are you looking for process optimisation? Our experts can support you in reaching your goals with a combination of high-tech equipment and know-how. Learn more at: www.heimbach.com
Already a leader in Brazil’s pulp industry, Suzano is aiming to improve its competitiveness with the construction of a massive new fossil-fuel-free mill in the central region of Mato Grosso do Sul.
Suzano is well-established in the region with two large mills at Três Lagoas but is advancing on the technologies used there to provide it with an edge in the pulp markets. The pulp and paper maker is also building the new mill on the back of strong results.
In the second quarter, revenue was R$11.5 billion, up by 17 per cent on the same period a year earlier, with pulp volumes up five
per cent at 2.66 million tonnes and paper volumes up 10 per cent to 324,000 tonnes.
Walter Schalka, chief executive of Suzano, commented: “These excellent second-quarter results
are not only testament to higher pulp prices and positive market demand, as well as the continued efforts of our various teams to ensure Suzano boosts operational efficiency. With this firm financial and operational footing, Suzano is intent on expanding our capacity to create, and share, value with our stakeholders.”
Currently, Suzano operates several pulp mills in Brazil including two at Três Lagoas in Mato Grosso do Sul that together produce 3.2 million tons a year.
In the state of São Paulo, it has three units: Suzano, Limeira, and Jacareí, with capacity of 170,000, 400,000 and 1.1 million tons of pulp, respectively; in Maranhão, the Imperatriz unit (1.5 million tons); in Espírito Santo, the Aracruz unit (2.3 million tons); in Bahia, the Mucuri unit (1.4 million tons) and the Veracel mill (560,000 tons). The Veracel mill is jointly owned by Suzano with Stora Enso of Finland. Suzano’s mills produce pulp that goes to more than 50 countries around the world.
“Suzano is already at the upper end of the most competitive companies in the pulp industry, and this investment will allow the business to produce its lowest cost pulp with the lowest environmental impact.”
It’s not just the mill’s technology that’s key. How the mill more easily accesses its raw forest materials will be an important differentiating factor, says Galhardo.
“The average structural forest radius is only 65 km, which is less than half of Suzano’s current structural average supply radius of 156 km.”
He describes the project as a global cutting-edge industrial sustainability project, producing more energy than it needs for use by the surrounding communities.
“This project will be producing 180 MW of surplus renewable energy and operating on a
fossil-free basis under ordinary conditions. We are pleased to be partnering with major suppliers to the industry to make this happen, including Andritz, Veolia, Suez, Siemens, and Hitachi Energy.”
Galhardo, who took over as executive officer of Pulp Operations at Suzano soon after its merger with Fibria, where he worked up to being appointed chief operating officer responsible for forests, industrial operations, and engineering, is being supported on the by project manager Maurício Miranda.
Before Fibria, Galhardo held leadership positions at Votorantim Celulose e Papel and the brewer AmBev. He played a key role in the construction of Suzano’s largest industrial complex at Três Lagoas, also in Mato Grosso do Sul.
Miranda, who has been with Suzano for 28 years, was also involved with Suzano’s first mill
at Três Lagoas, and its second, eventually managing both from 2017 to 2019.
The Ribas do Rio Pardo mill’s capacity will be 2.55 million tons a year. “That will make it the world’s largest single-line pulp mill,” says Galhardo. “This volume represents about 20 per cent of Suzano’s current total pulp production capacity of 10.9 million tons.
Part of the reason for locating the Cerrado Project at Ribas do Rio Pardo in Mato Grosso do Sul is that Suzano already has other mills in the state, says Galhardo.
“Our relationship with Mato Grosso do Sul is strong and dates back a long time,” he added. “We have our largest pulp production operation in Três Lagoas, with the two mills having a total annual production capacity of 3.25 million tons of bleached eucalyptus pulp.
“So it was only natural that the company looked for a town that was best suited to various technical, logistical, financial, climate and even HDI studies, among others. Ribas do Rio Pardo was the town best suited for setting up our new unit.
“During construction works, the Cerrado Project will create a peak of 10,000 direct jobs and thousands of indirect jobs in the region. Currently we have worked more than five million manpower hours and are very pleased to say that there have not been any accidents throughout this period.
“At the point at which it is ready to go operational, the new Suzano mill will employ 3,000 people directly and indirectly in its industrial and forestry operations. Each one of these people will play a key role in the success of the project. We are also making significant
investment into increasing access to healthcare, training, teaching, increasing local jobs and investing in infrastructure such as strengthening roads and access to rail stations so that the Cerrado Project is helping the local communities in the area.”
The Cerrado Project is one of the biggest private investments currently under way in Brazil. The project represents a total investment of R$19.3 billion, spread out over four years with three quarters of that being spent in 2022 and 2023. Galhardo says that the industrial investment is estimated at R$14.7 billion. “The company plans to invest the remaining R$4.6 billion in areas including forestry, logistics and the construction of a chemical plant.”
Paper prices have been increasing along with other commodities around the world, with Suzano reporting in its first quarter 2022 results that they rose by 28 per cent in the three months to the end of March. But so have the costs of raw materials and energy, which is why Suzano must stay competitive.
“Investments in the Cerrado Project increase Suzano’s competitiveness and make our operations more sustainable,” says Galhardo. “Greater production also opens up new opportunities for growth from the increasing demand for sustainable bio-products made from trees. We are already seeing strong customer and consumer demand for renewable raw materials to displace fossil-based products and we expect this trend to accelerate.”
The new pulp mill at Ribas do Rio Pardo will also be more competitive than other mills because it features advanced management controls and power
systems, says Galhardo.
“We are using state-of-theart technology, including asset management and control tools from Industry 4.0,” he says.
“Another difference that the
new mill has is new biomass gasification plant to replace fossil fuel in the lime kilns, which will make it more technically, economically and environmentally competitive.”
The plan is that the Ribas do Rio Pardo mill will be more than selfsufficient in energy production, with 180MW available to supply the local grid.
“Suzano already meets most of
Austrian engineering group Andritz will be supplying Suzano with technologies for all main process islands in the fibre production and chemical recovery plant for the Cerrado project which is expected to start up in 2024.
Key process equipment, as announced in November 2021 is:
● A complete Wood Processing Plant with five chipping lines
– each including the world’s biggest horizontally fed HHQChipper with a capacity of 500 cubic metres of solid-under-bark per hour. The HHQ-Chipper is said to ensure the highest
and most uniform chip quality, thus increasing fibre yield in both woodyard and fibreline operations. The order also includes two 360-degree stackerreclaimers, the chip screening system and bark handling with two BioCrushers, as well as preparation of biomass for both gasification and the power boiler.
● The world’s largest singleline Fibreline (capacity of more than 8,000 adt/d), including LoSolids continuous cooking for high pulp yield, efficient heat recovery and washing and bleaching technology based on DD-Washers – all contributing
towards high-quality pulp, longest operating times, and low chemical consumption, thus minimising environmental impact.
● An EvoDry Pulp Drying System with two energy-efficient pulp drying lines (each with a working width of 10,005 mm and capacity of 4,000 adt/d) based on the high-capacity Twin Wire Former technology. Both lines are equipped with a fully automatic, hands-free tail threading system. The drying plant is designed for a specific plant capacity of around 400 adt/m, and the final pulp bales are produced in six
Suzano’s Cerrado Project is in the same Brazilian state as its two pulp mills at Três Lagoas, parts of which are shown, including the fibrelineits energy needs from renewable sources and generates a surplus, which will be increased further when the Cerrado Project is complete,” says Galhardo. “This will allow us to contribute even more to the Brazilian power grid, which could reach an average of 220MW after the installation. This is enough to power a city of 1.34 million inhabitants.”
To supply the Cerrado Project at full capacity, about 250,000 hectares of planted forests will be required, says Galhardo. “This will ultimately come from the company’s own forest areas, leased forests and partnerships, in addition to the purchase of wood from third parties. Suzano has already secured around 85 per cent of its wood needs for the initial operating years and is currently defining the structural framework for the new forest base.”
Pulp production by Suzano in Brazil is seen as sustainable because it is made from eucalyptus grown specifically for
complete, high-capacity baling lines.
● An energy-efficient black liquor Evaporation Plant with a capacity of 2,650 t/h, which has advanced energy integration with the cooking plant and the Ash Recrystallization Plant (ARC).
Easy-to-clean lamella heating surfaces ensure high availability and easy operation of the plant. The integrated ARC chlorine removal plant provides high availability and energy efficiency of the recovery boiler, with a high rate of removal for nonprocess elements in the ESP ash.
● A Herb Recovery Boiler with a firing capacity of 11,150 tds/d black liquor, with steam values of 515 deg C and 100 bar(g) at the turbine, features
the process, and is continuously replaced.
Galhardo explains: “The Cerrado Project, like all other Suzano projects, is supplied from eucalyptus plantations that were specifically planted for pulp production, in a growth cycle that on average lasts six to seven years.
“To meet this demand, Suzano currently plants more than 650,000 eucalyptus seedlings every day. Moreover, the final
energy-efficient flue gas cooling and feed water preheating technologies to maximise steam production for power generation.
● A biomass Power Boiler with 120 t/h steam production capacity based EcoFluid Bubbling Fluidised Bed (BFB) technology. This also includes a biomass-fired boiler with flue gas cleaning and other auxiliary equipment. The fuels used are bark, debarking wood losses, screening rejects, harvesting residues, and sludges from the mill’s wastewater treatment plant. In addition, the new Power Boiler is combined with the Recovery Boiler to form a ‘Boiler Island’, and some of the auxiliary equipment is shared between the two boilers.
scope of the project indicates that this will be our most eco-efficient mill in terms of low carbon emissions, especially due to the significant reduction in the use of fossil fuels.”
A key environmental issue is the impact of a monoculture like eucalyptus plantations on the local species of both plants and animals.
Galhardo explained how Suzano is managing this. “Suzano has in
This provides savings in both investment and operating costs.
● A complete White Liquor Plant with gasification plants, enabling full fossil-free operation of the lime kilns with an optimised pulp mill carbon footprint. The new recausticising plant (25,100 cubic metres a day white liquor production) includes efficient green liquor filtration with LimeGreen filters – producing clean green liquor and minimising waste to landfill. This new plant comprises two lime kilns (940 t/d each) with high-efficiency LimeCools and LimeFire multifuel burners. The supply also includes two CFB gasification reactors with biomass handling equipment and two belt dryers.
place a strict zero deforestation policy,” he says. “All of Suzano’s plantations are located on land that had already been cleared for other purposes, such as degraded pastureland or cropland. As a result, these are places where planting eucalyptus in fact helps recover the land’s capacity to absorb carbon from the atmosphere and offers comparatively better opportunities for biodiversity.
“But we know that we can continue to improve. Studies with our wood suppliers show that it is possible to diversify activities alongside planted eucalyptus, and to enhance soil management. Suzano also monitors land use and proactively supports the diversification of activities in its operating areas, such as silvopastoral systems to raise cattle and honey production that supports pollination.
“Suzano’s biodiversity and sustainability commitments are part of its 15 long-term goals, known as the Commitments to Renewing Life. These include the goal of connecting half a million hectares of priority preservation areas in the Cerrado, Atlantic Forest and Amazon biomes through ecological corridors by 2030.”
After the interruptions resulting from the Covid pandemic, the MIAC tissue industry show is being held again in its unrestricted form in Lucca. PPL previews the event
It’s been three years since the last MIAC tissue industry show attracted the world’s paper professionals to Lucca, in Italy, without restrictions. On-line and limited offerings were provided in line within the limitations of the Covid pandemic, but they couldn’t match the scope of the original show.
Now MIAC is back in full force at the Lucca Exhibition Centre over three days from Wednesday 12 October to Friday 14 October, with industry professionals allowed free entry to meet around 250 exhibiting companies.
Exhibitors will be covering the key technologies in paper and paperboard manufacturing and converting in what has become a world of new demands.
The MIAC show has exhibitors –see a full list with a show plan on the following pages – covering all sectors of the paper, cartonboard and tissue industry, in product and service categories such as:
● Machinery and plant for the production of paper and board
● Components and parts of paper machines
● Converting machines for tissue
● Instruments and systems for measurement, test, control and management
● Machinery and plant for water treatment
● Plant, machinery and electrical controls
● Raw materials, chemicals and additives
● Machinery and plant for drying, filtration and energy recovery
● Laboratory, diagnostics, logistics, services and plant optimisation.
As a media sponsor Pulp Paper & Logistics will be at Lucca and publisher Vince Maynard will be pleased to meet exhibitors and industry professionals alike. Email Vince at pulppaperlogistics@ virginmedia.com to make an appointment.
Lucca is the only officially acknowledged ‘paper district’ in Europe with more than 140 paper mills and converters, 6,500 workers, two million tonnes of tissue paper and corrugated cardboard produced each year, and with a turnover of around €3.5 billion.
Lucca is also home to major companies that supply technologies, machinery and services to the paper industry sector, with a turnover of more than €2.6 billion and more than 8,000 workers.
Three conferences are offered at MIAC that cover the key issues affecting the industry’s future
success. There are two sessions for tissue making, one for paperboard manufacturing and one for energy.
Participation is free, but online pre-registration is recommended. Simultaneous translation is provided.
MIAC Tissue Conference –first session Wednesday 12 October 2022 from 13.30 to 16.30 in the MIAC Conference Room
Sustainable and competitive tissue manufacturing, moderated by Arne Kant of AFRY Group
A range of sustainability requirements are being placed on the industry by both customers and regulators. To respond to this, tissue producers are addressing performance and efficiency in all steps of the supply chain, and in turn adding requirements and expectations on the machinery suppliers. Topics regarding reduced emissions, sustainability in drying, data integration, improved control and diagnostics and many other themes impacting the competitiveness of the industry will be discussed in this session.
14.40 Elena Troia, energy & environment sales manager, Toscotec
c Breakthrough tissue innovations for sustainable drying
15.00 Tommi Leander, business manager, Valmet Automation
c Data integration and analytics for tissue web inspection
15.20 Frencesco Furzi, sales manager, A.Celli Paper
c Data integration in reel packaging: advantages and solutions
15.40 Daniel Schoeps, tissue global product manager, Voith and Gernot Nicht, tissue solutions team manager, BTG Eclépens
c How to keep your Yankee healthy: operational services review
16.00 Maurizio Tomei, sales & customer service manager, Oradoc
c OraCrepe Next: WEPA witnesses the future of flexible Yankee doctoring
14.00 Hampus Mörner, manager, Afry Management Consulting The European competitive landscapeThursday 13 October 2022 from 09.40 to 13.00 in the MIAC Conference Room
End-to-end line integration and digitalisation in tissue converting, moderated by Arne Kant, AFRY Group
Converting machine suppliers are increasingly offering integrated lines from jumbo reel to finished, packed, and palletised product. Digitalisation, automated and remote-control systems is another area of development focus. In this session the benefits of complete and automated offerings will be discussed. What will be the next expectations from converting machine suppliers or respond to?
10.10 Hampus Mörner, manager, AFRY Management Consulting
c Evolving expectations from converting machinery suppliers
10.30 Luca Frasnetti, chief technology officer, Körber Business Area Tissue
c The Körber ecosystem
10.50 Francesco Pelaia, customer care director, Futura
c 360° sustainable innovation
11.10 Michele Renai, sales manager area, Maflex
c Pegaso: Smart Supervision System
11.30 Paolo Lazzareschi, technical director, Gambini, and Massimo Bertuccio, sales director tissue & robot division, E80 Group
c Efficiency and safety of the new automatic unwinders
11.50 Stefano Spinelli, director of product management, tissue, PCMC
c ONE global team and the future of technology
12.10 Andrea Germani, key account manager, IMA TMC
c Destination Zero Impact: tracing the future of tissue manufacturing lines through integration and digitalisation processes to sustainability and high efficiency of machines
12.30 Alberto Colombo, project & key account manager, OMET
c Flexibility, innovation and sustainability to develops new technologies
MIAC Paperboard Conference Friday 14 October 2022 from 09.40 to 12.40 in the MIAC Conference Room
Evolving packaging landscape: plastic substitution, other sustainability measures and case studies of improvements, moderated by Arne Kant, AFRY Group
Fibre based solutions being sustainable is a non-brainer for the industry. But regulations and requirements from society are evolving, and paper industry has room for improvements. This session will provide a high-level view on latest developments and requirements from stakeholders in the field.
Machinery suppliers and producers will then showcase examples how the industry is adjusting.
10.10 Christoph Euringer, principal, AFRY Management Consulting
c Developments from European regulatory framework, plastic versus fibre competition and what it means for paper and board producers
10.30 Laura Puustjarvi, head of sustainability, Valmet c Enabling carbon neutral paper and board making processes
10.50 Fabio Lucariello, sales & technical area manager, Cannon Artes
c Experimental results of membrane processes for the reuse of wastewater in the paper mill
11.10 Massimiliano Listi, managing
director, Smurfit Kappa ANIA, and Mario Battiston, sales manager, Runtech Systems
Forming and Press section optimisation concept – a case study of full improvement package for vacuum system, dewatering, and doctoring
11.30 Giancarlo Gianlorenzi, sales manager, Toscotec, and Oliver Thomas, sales manager, Voith
c Papierfabrik Niederauer Mühle’s rebuild case study
11.50 Flavio Granito, global product manager PM4.0, Voith Paper
c OnView. DigitalEye – Camera based detection of waste paper quality and trash content on pulper feed and reject conveyor
12.10 Thomas Nager, machine safety manager, Andritz
c Production – make it safe!
MIAC Energy Conference Thursday 13 October 2022 from 13.30 to 17.10 in the MIAC Conference Room
Diversified energy sources and improved control systems for improved sustainability, moderated by Arne Kant, AFRY Group
The importance of efficient energy consumption within paper industry has significantly increased due to cost inflation and sustainability challenges. To tackle this new sources of energy, improved control systems and overall energy efficiency in the processes are being implemented. This session will provide examples of recent developments.
14.00 Antonio Michelon, director, office head Italy, AFRY
c Energy procurement in a disruptive scenario
14.20 Ulf Johnsson, concept manager mill technology, Valmet c What does a sustainable business mean?
14.40 Caterina Dentoni Litta, head of consulting and innovation, Renovit
c Decarbonising paper mills’ processes and increasing their energy efficiency to improve the sector resilience facing the global energy scenario
15.00 Federico Spinelli, proposal engineer, Lario Energy
c Standardised system for plant’s evaluation
15.20 Roberto Buzzi, sales engineer Italy, Voith Paper
c Towards improved sustainability of stock preparation systems
15.40 Paolo Masiero, program manager strategic growth, Solar Turbines
c New governance models: Use big data to make your strategic choices
16.00 Gianluca Bartolini, senior product manager, Novalt
c Hydrogen-blended fuel gas in CHP applications for pulp & paper industry
16.20 Peter McCaig, project manager, Centrax Gar Turbines
c The Hyflexpower innovation project
MIAC 2022 address: Lucca Exhibition Centre – Via della Chiesa XXXII, 237 – 55100 Lucca – Italy.
Dates: Wednesday, 12 October to Friday 14 October 2022. Opening times, 9am to 5pm, Wednesday and Thursday, and 9am to 3.30pm Friday.
For free parking at the MIAC Exhibition set your car’s satnav to ‘Vitricaia street – Lucca’.
While Covid continues to affect Europe, some safety requirements for exhibitors and visitors are being specified. Refer to the MIAC website for these at www.miac. info
A.CELLI PAPER SPA 1
A.PIOVAN SRL 114
ACE DUST REMOVAL 38
ACQUAFLEX S.R.L. 113
AERMEC SPA 31
AEROTHERMIC SRL 77
AIKAWA FIBER TECHNOLOGIES OY 90
ALBANY INTERNATIONAL 119
ALFA LAVAL ITALY S.R.L. 73
ALSITER SRL 134
ALVAREZ ULTRA TISSUE MACHINERY 164
AMOTEK SALES & SERVICE SRL 122
AMYLUM BULGARIA EAD A 100% SUBSIDIARY
OF ADM ARCHER DANIELS MIDLAND COMPANY 66
ANDRITZ 72
ARIVENT ITALIANA SRL 88
ATLAS COPCO SPA 127
AXCHEM ITALIA SRL 110
AZMEC SRL . 112
B.F.G. RAPPRESENTANZE INDUSTRIALI SRL 113
BABBINI SPA 46
BAKER HUGHES 70
BAOSUO PAPER MACHINERY MANUFACTURE CO, LTD 150
BARONCINI NELLO SRL 30
BELLMER KUFFERATH MACHINERY GMBH 66
BETT SISTEMI SRL 44
BIM KEMI 159
BM GROUP POLYTEC SPA 156
BOETTCHER ITALIANA SPA 87
BOLZONI ITALIA SRL 35
BONETTI SPA
BRIGHT TREES CONSULTANTS 166
BTG ECLEPENS S.A. 114
BUCCI INDUSTRIES 130
BUCKMAN 41
C. G. BRETTING MANUFACTURING CO., INC. 18
CALPEDA POMPE SPA 31
CAMOZZI SPA 127
CANNON ARTES S.P.A. 36
CCS – CLAREN SRL 111
CELLWOOD MACHINERY AB 12
CENTRAX LIMITED 174
CENTRO ARIA COMPRESSA SRL 127
CHT GERMANY GMBH 177
COINCART SRL 22
COLDWATER JOCELL AB
A DIVISION OF VALMET INC. 114
COMERTEK S.R.L. 55
COSTRUZIONI MECCANICHE
WEINGRILL ING. ZENO SRL 96
CPS COMPANY SRL 76
CROSS WRAP 57
CTP GMBH 114
CTP GMBH 92
D.M. PROGETTI SRL 141
DE IULIIS CARLO & ALFONSO SPA 74
DEUBLIN ITALIANA SRL 100
DEVASOL 61
DI MARCO SPA 102
DM PACK SRL 47
DOSEURO SRL 88
DYSTAR ITALIA S.R.L. 113
E80 GROUP 99
EAGLEBURGMANN ITALIA SRL 52
ECOL STUDIO SPA 78
ECOVERDE SPA 66
EFFEBI S.P.A. 31
EIGENMANN & VERONELLI S.P.A. 144
EIL SRL REPLUS TISSUE RENERGY 67
ELETTROMAR SPA 8
EMTEC ELECTRONIC GMBH 160
ENGRAVING SOLUTIONS S.R.L. 140
ENRICO TONIOLO SRL 6
EOC GROUP 34
EUROINCIS SRL 59
EUROTRONIX S.R.L. 147
EVONIK 145
F.LLI FREDIANI SRL 73
FAN SEPARATOR GMBH 73
FASTPAP OY 114
FIFE-TIDLAND GMBH 50
FILCON EUROPE SARL 114
FILTERECO SRL 152
FIREFLY AB 125
FIS IMPIANTI SRL 114
FIS IMPIANTI SRL 118
FMW FÖRDERANLAGEN GMBH 90
FOCKE & CO 19
FOOD CONTACT CENTER 171
FPZ SPA 88
FRANKLIN ELECTRIC 170
FRANK-PTI GMBH 73
FREIRIA 141
FUTURA SPA 71
GAMBINI S.P.A. 99
GARDNER DENVER SRL – DIVISIONE ROBUSCHI 13
GAW TECHNOLOGIES GMBH 73 GEL SPA. 31
GHETTI 3 SPA 26
GIOTTO TECHNOLOGIES SRL 150
GIUGNI S.R.L. 69
GIULIANI SRL 114
GOGAS GOCH GMBH 114
GRAVION GMBH & CO. KG 73
GRUPPO MARTINELLI SPA 31
GRUPPO TECNOFERRARI S.P.A. CON SOCIO UNICO 4
GTK TIMEK GROUP SA 162
HANNECARD TISSUE & PAPER 132
HENKEL AG & CO. KGAA 37
HERGEN PAPER MACHINERY 143
HOERBIGER ITALIANA SPA 100
HORST SPRENGER GMBH SPEZIALWEKZEUGE 73
HÜTTENWERKE KÖNIGSBRONN GMBH 165
IBS PAPER PERFORMANCE GROUP (IBS-PPG) 73
ICHIKAWA EUROPE GMBH 66
ICM MAKINA 63
IDROELETTRICA SPA 31
IM CONVERTING S.R.L. 173
IMA TMC – AMS DIVISION 104
INDEXA COMPANY 86
INFINITY MACHINE & ENGINEERING 7
INGERSOLL RAND 13
INNIO JENBACHER GMBH & CO OG 68
INTERGEN S.P.A. 73
ISRA VISION 169
ITALMATIC PRESSE STAMPI S.R.L. 103
ITALPROGETTI SPA 3
JAEGER GMBH 73
JAGENBERG PAPER GMBH 73
JOHNSON-FLUITEN S.R.L. 129
JULIA UTENSILI SRL 163
JUNGHEINRICH ITALIANA SRL 23
KADANT JOHNSON SYSTEMS
INTERNATIONAL SRL 129
KADANT LAMORT S.A.S. 129
KAIROS SRL 28
KAPP-CHEMIE GMBH 66
KARBERG & HENNEMANN SRL 154
KEMIRA ITALY SPA 94
KONICA MINOLTA SENSING EUROPE B.V. ITALY
BRANCH OFFICE 4
KÖRBER TISSUE 108
KROHNE ITALIA S.R.L. 102
KUMERA DRIVES OY 73
L.B.Z. LAVORAZIONI MECCANICHE SRL 161
L.C.Z. S.R.L.
MIA AZIENDA 999999
LAMM SRL 149
LANEX A.S. 114
LANGENPAC – MPAC GROUP 49
LARIO
Valco Melton Buckman TensostructureCOLLAREDA SRL 81
OCME 98
OFFICINE AIRAGHI S.R.L. 161
OMET SRL 107
ORADOC SRL 136
OVERMADE SRL 21
P.T.S. FIBRE BASED SOLUTIONS 114
PARASON MACHINERY (I) PVT. LTD. 114
PAUL WEGNER GMBH & CO. KG 90
PCHEM 148
PCMC SPA 133
PETROFER CHEMIE 113
PIMATIC OY 126
PITTERI VIOLINI S.P.A. 168
PL DI LAZZARI SRL 45
PLASTYLENIA SPA 97
PNEUMAX SPA 158
PNR ITALIA 43
POLIMEK SRLS 114
POWERMADE S.R.L. 21
PPI PUMPS PVT. LTD. 90
PROVA1 200
PROXITALIA PRODOTTI CHIMICI SRL 172
PTA GROUP SAS 114
PULSAR ENGINEERING 75
RAGAZZINI SRL 114
RECARD S.P.A. 89
RENOVA SRL 117
RENOVIT 40
RIF SPA 83
ROBOPAC 98
RÖCHLING INDUSTRIAL OEPPING GMBH & CO. KG 2
ROLCO EUROPE B.V. 84
ROTOCALCO MEDITERRANEA SRL 124
RUNTECH SYSTEMS 13
S.A. GIUSEPPE CRISTINI SPA 113
S.TO.R.I. 109
SABA AUTOMATION SRL 106
SAEL SRL 93
SAMSON SRL 157
SAUER S.R.L. 51
SCHÄFER MWN GMBH :CCOR 95
SCHÄFERROLLS GMBH & CO. KG 95
SDF GMBH 65
SENNING GMBH 20
SICEM SAGA SPA 16
SICIT SRL 48
SICMA SPA 91
SINERGY SRL 93
SLITTEC GMBH 153
SOLAR TURBINES SWITZERLAND SAGL 60
SOLENIS ITALIA SRL 66
SOMAS INSTRUMENT AB 102
SOTEMAPACK 98
ST MACCHINE SPA 1 20
STARK S.P.A. 167
STAX TECHNOLOGIES 133
STIAVELLI IRIO SRL 32
STILL S.P.A 30
SULZER PUMPS FINLAND OY 73
SVECOM PE SRL 113
T I P 95 D.O.O. 137
TASOWHEEL SYSTEM OY 114
TAU MACHINES SRL 138
TEC.MEC. SRL 5
TECHNO PAPER SRL 90
TECHNOFLOW SRL 102
TECHNOWRAPP SRL 64
TECNICART SAS DI ING. PERUCCHINI&C 4
TECNO CAUCHO ROLLS & COVERS 123
TECNO PAPER SRL 85
TECNOFER ECOIMPIANTI S.R.L. 151
TECNOFLUOR SRL 45
TEST ZZ EDIPAP PROVA 200
TEST02 200
TISSUE TEC SALES & SERVICE GMBH 56
TISSUENET GMBH 49
TKM GMBH 11
TMC SPA 104
TOPJET S.R.L. 176
TOSCANA SPAZZOLE INDUSTRIALI S.R.L. 24
TOSCOTEC SPA 109
TOYOTA MATERIAL HANDLING ITALIA SRL
RenovaManufacturing comes with its own set of hazards. Controlling those hazards to keep employees safe on the job can be challenging. Each year worldwide, nearly three million workers die due to occupational accidents and diseases, and hundreds of millions more suffer non-fatal injuries at work, according to the latest report of the UN agency in the occasion of World Day for Safety and Health at Work 2022.
The disruption caused by Covid-19 catapulted businesses and managers into unknown territories. It has therefore become critical to keep an eye on the future and develop a strong safety culture now, so that we are able to face tomorrow’s challenges.
Everyone must be on board Workplace safety is extremely important for every industry because employees both desire and are entitled to work in a safe and well protected environment. It is an integral part of any operational system. Ultimately, it is essential for all industries
to adapt and prioritise health and safety principles in order to promote the well-being of both employers and employees.
However, ensuring that rules and regulations are followed to protect your workers is sometimes easier said than done. At UPM Communication Papers, we as
We live in an unstable world, which brings more challenges to those charged with improving safety in the workplace. Anu Ahola* details how safety should be embedded in manufacturing operations
employers are asking a lot from our workers: they have to place safety first and at the same time, efficiency.
And safety is an every-day job: the bottom line is being relentless in pursuing flawless operations. We all have to follow a lot of standard operating procedures that require a great dose of discipline from every worker involved. And everyone must be on board, otherwise it won’t work. We know that if one employee alone doesn’t follow one of the safety rules, it can affect the
entire team and potentially have disastrous repercussions on the whole operational chain.
That’s why having a strong safety culture is so important. Building a resilient safety culture within an organisation is one of the biggest challenges which Safety Managers have to contend with, but if you can get your workers on board and actively involved with health and safety, it will not only enable you to meet your legal obligations effectively, but also lower injury and fatality rates and improve employee wellbeing. Prioritising it as a company-wide effort can certainly be an ongoing effort, but it’s a policy that can reap huge rewards and successes when it becomes part of a company’s DNA.
The importance of a positive approach to safety The mission is to achieve zero accidents, but I believe it can only happen with a positive approach to safety. Companies have to shift away from a safety culture of blame and avoidance, where workers behave safely only if they’re made to feel like they have to, to a culture where employees are encouraged to take personal ownership over safety and understand the importance of choosing to engage in safe behaviours – a culture where safety practices, observations and innovation in the area of safety is celebrated.
We know that encouraging a positive safety culture starts with strong employee leadership roles, who can then present these practices in a concise and thorough way to ensure
all workers apply policies in a consistent way throughout the company. This, in turn, can ensure good industrial relations within a team. It is a group responsibility to help protect our people and environment. By putting good practices in place to manage safety, it will help reduce the number of injuries in the workplace.
The latest UN report on the topic, titled ‘Enhancing social dialogue towards a culture of safety and health’, found that during the pandemic, governments that prioritised active participation of employers’ and workers’ organisations in OSH governance, were able to develop and implement emergency laws, policies, and interventions. Collaboration and communication are crucial to ensuring new measures are both acceptable to, and supported by, employers and workers, meaning they are more likely to be effectively implemented in practice.
At UPM, we actively involve all employees in every aspect of safety with company-wide efforts,
but also locally at the mills and offices, where safety is an integral part of the daily work.
Prioritising safety not only prevents injuries, but also builds morale and improves overall employee health. Many studies show that it also helps attract and recruit the best employees. A good health and safety record is a source of competitive advantage: it attracts partnerships, builds trust in your reputation and brand and secures long-term benefits for you, your business and the wider community.
However, companies need to understand that while success must be celebrated, there is always room for some improvement. Putting in place systems for continuous development will not only ensure the safety of employees, but also enhance organisations’ resilience in an unstable world.
*Anu Ahola is senior vice president operations at UPM Communication Papers
UPM’s Kaukas paper mill in Lappeenranta, Finland, where safety is part of the culture, as it is in all of the company’s operations
“Employees both desire and are entitled to work in a safe and well protected environment,” says Anu Ahola
Paper makers are able to mitigate against rising energy costs by using the latest developments in felt technology. PPL reports
Because of steeply rising energy prices, the challenge of keeping production costs as low as possible is increasingly more acute for paper makers. Lower energy consumption and higher productivity are still the guiding principles.
This means again pushing paper machines to their performance limits: The focus is on highest machine productivity, best runnability and maximum speed. And one of the top priorities is the maximum dry content after the press.
Press felts must support
this important requirement.
Heimbach’s NewTech family of press felts – Atromaxx and Atromaxx.Connect – are said to meet this need.
The Atromaxx concept is based on multi-axially arranged base modules providing a highly incompressible structure. Firstly, this maintains the void volume throughout the running time, and, secondly, a huge amount of water is handled through open drainage channels. The result, says Heimbach, is outstanding dry content.
Due to its structure based on modules, Atromaxx is versatile for the types of paper produced, production speeds and,
combined with suitable batt modules, has been qualified for all machines and press nips.
At higher speeds (more than 500 m/min) nip dewatering is often desired, which makes it possible to reduce or even completely avoid uhle box vacuum, meaning that considerable energy savings are achievable.
However, this requires precisely matched press felts such as Atromaxx, which makes it possible to obtain high dry contents, better runnability and good start-up performance. Numerous references confirm that, says Heimbach.
The efficient dewatering behaviour is significantly influenced by the production speed, the pressure impulse and the degree of felt saturation.
At low speeds of less than 500 metres per minute the dewatering in the nip is usually barely possible, but even in these conditions high dry content values can be achieved with Atromaxx.
Heimbach says that this ‘multitalented’ felt is convincing on machines where, depending on the paper grade, there are large speed variations and thus changes in dewatering behaviour between nip and uhle box.
The Atromaxx felt is based on multi-axially
base
providing a highly incompressible
The outstanding characteristics claimed for Atromaxx felt extends to the seamed version. Atromaxx.Connect can be installed safely and quickly with few personnel. And, says Heimbach, it scores with dewatering values that conventional seam felts are unable to match. The seam and seam zone are designed also for high speeds, guaranteeing the freedom of marking and problem free runnability.
Multi-axial felt Atromaxx: its key features
c Modular system. Combination of totally different base properties
possible within one felt
c Outstanding compaction resistance due to multiaxial structure
c Brilliant void volume retention
c Uptake of huge amount of water
c Excellent dewatering during complete running time
c High stability
c Operation modes for nip and uhle-box dewatering
c Applicable for all paper grades
What’s needed for efficient nip dewatering?
The principle:
The amount of water being pressed from the sheet should be taken up directly in the nip – as
completely as possible - by the storage volume of the roll; water should not be transported with the felt to the UHLE box!
c With a high level of nip dewatering overall dewatering increases as a rule and the dry content after the press rises. As a result runnability improves significantly (e.g. fewer sheet breaks, reduction in edge problems); moreover, steam is saved in the dryer section and production is increased.
c This type of dewatering is the most effective method to keep press felts clean and open.
c In addition, uhle boxes can be operated with a low vacuum – or even shut off, resulting in enormous energy savings.
c Sufficient storage volume in the press roll covers and shoe press belts so that water exiting into the nip can be absorbed.
c Save-alls with sufficient capacity to collect accumulated water.
c Efficient doctoring to avoid water rings.
Finally, Heimbach advises paper maker to only use selected felt designs that are custom-made for nip dewatering.
The seamed version – Atromaxx.Connect – offers the same dewatering performance with safe and fast installation The seam join of Atromaxx.Connect is designed for reliable high-speed operationChemical and biological detection technology specialist Eluceda has launched a quantitative and portable test for hydrogen peroxide in water – with results given in 60 seconds.
The new technology is the latest in a range of tests that uses Eluceda’s E-Sens handheld detectors and is capable of detecting hydrogen peroxide in water at concentrations between 1 and 1,000 parts per million (ppm).
Eluceda was approached by a leading supplier in the paper and pulp industry to design an accurate and easily-repeatable test method that could detect hydrogen peroxide at the necessary concentrations within the paper manufacturing process.
The handheld detectors are used in combination with specialist electrochemical sensors to provide a simple ‘dip and read’ approach. A key feature is the ability to analyse hydrogen peroxide levels in the water even in the presence
The ability to be more precise with hydrogen peroxide usage reduces wastage and saves costs
of pulp, providing an advantage over existing colorimetric analysis.
The ability to be more precise with hydrogen peroxide usage reduces wastage and saves costs while still ensuring the chemical works effectively as a bleaching and biocidal agent.
“As a science and technology-led business, we’re always excited
when are able to use our collective expertise to devise a novel solution to a particular problem an industry is experiencing,” says Dr Ian Eastwood, chief technology officer at Eluceda.
“We are proud of what we’ve been able to achieve with our hydrogen peroxide test, both in terms of the technical
Described as a breakthrough for digital printing on corrugated packaging, Idera print engines have been launched by Flint Group Packaging.
The Idera range was shown alongside Luxembourg-based Flint’s range of sustainable ink and coating technologies at the Corrugated Week 2022 show, held at San Antonio, Texas, in September.
Idera combines Flint subsidiary Xeikon’s digital printing expertise with Flint Group’s corrugated know-how and manufacturing footprint is said to deliver brandnew digital post-print technology, making corrugated printing easy, adaptable and sustainable.
Sebastien Stabel, market segment manager for carton packaging at Xeikon, explains:
“Idera is the perfect choice for
industrial, food-safe, regulatorycompliant and water-based post-print inkjet printing. Idera is a scalable investment model which offers a wide range of productivity and print quality modes with Xeikon on-site ramp-up support. Crucially, we control every aspect of Idera, which helps converters control their running cost and stay competitive.
achievement and effectiveness of it in driving efficiencies and reducing waste in the manufacturing process.”
More information from Eluceda, Unit 3, Caroline Court, Billington Road, Burnley BB11 5UB, United Kingdom. Tel: 44 7816 833661. Email: richard.burhouse@eluceda. com
“As a fully integrated and comprehensive digital platform, Idera makes corrugated packaging easy, adaptable and sustainable, so converters can future-proof their operations and be ready for the inevitable disruption of the market structure.”
More information from www. flintgrp.com or email deanna. klemesrud@flintgrp.com
Anew range of carbon dioxide laser coders have been launched by UK-based Domino Printing Sciences as an additive-free system for food manufacturers utilising NatureFlex compostable cellulose films.
Domino has collaborated with global packaging film producer Futamura to assess the suitability of laser coding for NatureFlex compostable film products. Following initial suitability testing, Domino’s D-Series CO2 laser was used to code the NatureFlex compostable film and achieved a clean, crisp, white code. There was no impact on film integrity or chemical composition, and moisture barrier properties were unaffected.
“We are very pleased to be able to offer Futamura’s food packaging customers an additivefree laser coding solution for their product packaging,” says Dr Stefan Stadler, team leader at the Domino Laser Academy. “We predict that in the coming years, requests for compostable solutions will become more
prominent – and we are ready and willing to work with any brand exploring these new materials to help find the right coding solution for their individual requirements.”
NatureFlex films have been developed for use in food packaging applications to meet the growing demand for
A digital tool that in real time displays losses in stock preparation to further increase the sustainability and efficiency of paper production has been launched by Voith.
Using the newly-developed OnView.MassBalance an operator is able at a glance to locate the specific areas with optimisation potential on the screen. For this purpose, a Sankey diagram maps each feed, accepts and rejects at each process step.
As soon as a critical value is reached, OnView.MassBalance reports this to avoid high losses. In this way, standardized
processes can be established that can be quickly and easily performed by operators across different shifts. Suitable countermeasures can be, for example, checking the pressure drop or the feed consistency of the last screening stage.
“The solution is already being used very successfully, for example in an OCC mill in France with an annual capacity of 250,000 tons,” says Flavio Granito, global product manager for Fiber System 4.0 at Voith Paper. “After the optimisation phase, 600 tons of rejects, including raw material, could be saved per month. This
corresponds to a two per cent improvement in yield.”
Because there are fewer rejects to dispose of and at the same time more paper can be produced with the same amount of raw materials, the system is said to pay for itself in less than a year.
Granito continues: “OnView. MassBalance is another example of how digitalisation can strengthen more sustainable and cost-efficient papermaking. As part of our major sustainability programme, Papermaking for Life, we have set the goal of optimising recycling processes and minimising fibre losses. We aim
environmentally-responsible packaging. The films are designed to meet all the global standards for industrial composting, including BS EN13432, and are certified as home compostable under the OK Compost Home standard.
“Brand owners are always looking at ways to communicate with their consumers on their packaging,” says Amaia Cowan, business development manager for the EMEA region at Futamura UK. “All of our NatureFlex films are certified to prove their suitability for industrial and home composting. Many of our customers want to show the final packaging’s certification and additional disposal information on the film to help inform end consumers.”
to achieve a 90 per cent recycling rate by 2030.”
To calculate the mass balance in stock preparation, the tool uses the signals from the sensors installed in the stock preparation plant. Voith experts identify the sensors required for this and develop a suitable concept together with the customer. Voith also separately offers the OnPerformanceLab (OPL) service. This is said to provide support in analysing losses, defining and implementing new countermeasures, and preparing monthly reports in close coordination with the respective paper technologists.
More information from J. M. Voith SE & Co, St Pöltener Straße 43, 89522 Heidenheim, Germany. Tel: 49 7321 37 2209.
Domino’s D-Series CO2 laser was used to code the NatureFlex compostable film to achieve an additive-free white codeTypically, many paper making inspection systems are set up for the light source to transmit through the product into the sensor, detecting defects such as holes, light and dark spots, and formation errors. However, for many coating applications, a reflection setup – combining bright-field and darkfield views with a sensor detecting reflected light – is more suitable.
Ametek Surface Vision has developed more advanced configurations for coating processes with SmartView, which is said to provide the ideal front-end arrangement to ensure reliable data acquisition, combining a suitable light source with the best-fit sensor technology as well as image processing hardware and software.
For example, the streak threshold algorithm takes a single-line scan signal and averages it over several
lines to generate a so-called averaged signal. This will average out any random background noise. A strong signal ratio from this process allows a background dynamic and a streak defect to be clearly distinguished.
Monochrome cameras make it
difficult to distinguish differentlycoloured defects. For instance, a red spot may need to be identified differently from a black spot in quality assessments but will appear the same to a monochrome camera. Monochrome cameras also find it difficult to detect peel-off defects on
Mondi has opened its first laboratory dedicated to test the recyclability of paper and paper-based packaging which use non-paper components such as coatings.
The laboratory at Mondi’s Frantschach mill in Austria will conduct recycling tests in-house to speed up the process for developing sustainable packaging.
While paper packaging offers many sustainability benefits, it also has certain barrierfunctionality limitations for products like perishable food. To enhance its functionality,
non-paper components such as barrier coatings may need to be added, which in turn can impact recyclability. The data collected at the laboratory can be used to improve existing products and provide reliable information about their environmental impact. Mondi says it will also use the results to determine how the design of new packaging can be improved as well as how best to improve the circularity of its material flows. The tests are carried out on various paper and paper-based packaging products developed by Mondi and are able to
determine whether the packaging can be efficiently recycled. The laboratory works in a similar way to industrial recycling facilities, but on a smaller scale. Results generated provide evidence that the material can be recycled.
paper, which are much more easily detected by colour cameras.
The best colour information is obtained by means of reflection setups. Based on the product colour, the system needs to have the flexibility to white balance the signal.
The SmartView system measures values for hue, saturation, and intensity for each defect, enabling it to be clearly distinguished from surface colours.
Volker Koelmel, global manager for plastics, nonwovens and paper, says: “Colour camera installations provide the best defect identification for pulp applications in the paper industry, delivering the information that image processing and classification systems need to provide automated surface inspection that ensures a highquality product.”
More information from ameteksurfacevision.com
Data collected at Mondi’s new recycling laboratory can be used to improve existing products and provide reliable information about their environmental impact
Mondi’s head of R&D Elisabeth Schwaiger says: “The ability to provide our customers with information on the recyclability of our products will be a key enabler in our efforts to develop more sustainable solutions and enhance our value proposition for customers. Currently, 78 per cent of Mondi’s group wide portfolio is already either reusable, recyclable or compostable. This recycling lab enables us to move closer to our MAP2030 goals of making 100 per cent of our products fulfil these requirements by 2025.”
Coating defects are better identified with Ametek Surface Vision’s SmartViewKlabin, Brazil’s largest producer and exporter of packaging paper, has appointed ABB to provide the management and power distribution system (PDS) for its Puma II project, supporting production target of 920,000 tons per year.
ABB will also supply the drives and motors for the project through Valmet.
The PDS will manage the electrical power to two new paper machines at the Ortigueira mill, in Paraná, with the aim of increasing production. ABB will apply its automation expertise through an Energy Management System (EMS), an arm of the ABB Ability systems that uses the ABB Ability System 800xA distributed controls.
Operating in the power plant, the EMS enables efficient use of electrical power and organises data under one umbrella, before making it available to preventive
maintenance teams. This will enable the mill to generate excess electricity for sale back into the grid on a spot basis, taking advantage of the best tariff.
The collaboration with Puma II is an expansion of the previous ABB system provided in the Puma I project in 2014. Klabin is able to take advantage of the same planning, and part of the existing Puma I infrastructure, by completing a
systematic interweaving in power management.
The first phase of the Puma II Project was completed with the start-up of PM27, which produces the world’s first kraftliner paper made 100 percent from eucalyptus fibre, providing the market with 450,000 tons a year.
The second phase of the Puma II Project involves the construction of PM28, a paperboard machine that will increase production to
Two large rewinders are to be installed by A.Celli downstream of Sichuan Huaqiao Fenghuang Paper’s PM6 line at its Guanghan mill in Sichuan province, China.
The E-Wind P100 rewinders, with a width of eight metres, are the largest of their type offered by A.Celli and will be used to process fluting, testliner and kraftliner paper with basis weights ranging from 70 to 170 gsm at a speed of 2500 m/min.
meet the growing market demand for packaging papers. Scheduled for delivery in 2023, PM28 will have an annual production capacity of 460,000 tons and will consolidate Klabin’s position as a global producer of paperboard for liquid foods such as milks and juices and processed products.
“The continuation of Puma I to Puma II reflects our long-standing and successful partnership with ABB and is an important step in reaching our production target of 920,000 tons of Kraft paper and paperboard per year,” said Gabriel Alves Lemes, Electrical, Instrumentation & Automation Manager at Klabin. “The automation of ABB’s electricity management will deliver both cost and space savings and reduce the mean time between power supply interruptions which means that, with regular preventive maintenance, corrections from failures are rare.”
Huaqiao Fenghuang Paper
Mr Yang said: “We are very pleased to have chosen A.Celli’s rewinders: there is no doubt that their technology is first class. We hope this project is the beginning of a long-term cooperation between our two companies”
Sichuan Huaqiao Fenghuang Paper Industry, founded in 2003, is the branch of Huaqiao Fenghuang Group which manufactures paper and paper products.
Controls from ABB will manage the power to two paper machines at Klabin’s Ortigueira mill, in Brazil Both will also be equipped with parking stations for Jumbo rolls and spools, using a web-in Slittomatic for the automatic positioning of the slitting units. Project director of Sichuan Two A.Celli eight-metre-wide rewinders are being installed at the Guanghan mill of Sichuan Huaqiao Fenghuang PaperAndhra Paper Limited (APL), one of India’s largest integrated pulp and paper manufacturers, is using an ABB advanced process control (APC) system at its Rajahmundry mill to better control the lime production process.
To help reduce the energy requirements of the interactive process in the lime kiln, ABB has integrated its OPT800 Lime APC into APL’s existing Ability System 800xA distributed control system (DCS).
In the kraft recovery process, lime mud is calcined into quick lime which is then further processed to create white liquor. Being endothermic, lots of energy is necessary in the calcination process and is one of the leading
contributors to mill’s costs.
Basically, OPT800 Lime utilises a model of the kiln process to accurately predict process variable interactions and make real-time adaptions to changes. This, says ABB, leads to smooth and
stable pulp mill operation and uniform lime quality, while also reducing energy consumption and emissions, increasing reburned lime availability and decreasing residual carbonate variations.
“We are committed to
Yuen Foong Yu Consumer Products, which is claimed to operate the largest paper mill in Taiwan, has ordered a PrimeLineCompact M1600 tissue line for its Chingshui mill from Andritz .
With start-up scheduled for the last quarter of 2023, the PM10 tissue machine will have a design capacity of 112 admt/d, a width of 3.65m and a maximum operating speed of 1,650 m/ min. Producing household paper, such as toilet paper, napkins, handkerchiefs, and facial tissue, the line will be equipped with the latest PrimePress XT Evo
shoe press for high-quality tissue with excellent bulk and an 18-ft PrimeDry Steel Yankee with PrimeDry Canopy Hood for energy-efficient drying and steam savings.
The project also comprises the stock preparation system, processing a mixture of needlebleached and leaf-bleached kraft pulp , the latest approach flow and broke system as well as a PrimeControl DCS System. Andritz will also supervise installation, commissioning, start-up, and training.
Mingfa Tang, vice president at Yuen Foong Yu Consumer
Products, says: “We are sure that Andritz ’s superior technology will perfectly meet our requirements, enabling us to produce products at best quality while keeping operating costs and energy consumption low.”
environmentally and socially responsible business practices, and by using ABB’s APC solution, we are able to optimize the lime kiln operations,” said M Sura Reddy, senior vice president of mill operations at APL. “We have worked with ABB’s team for more than 15 years, and they understand the specifics of our business very clearly. We look forward to benefiting from the ongoing results.”
The mill, in the East Godavari district of Andhra Pradesh state, produces a range of products from high-quality papers used in writing and printing and speciality boards.
Since 2006, APL has been using ABB’s Ability System 800xA DCS which integrates electrical and safety systems to enable plant operators to make more accurate and timely decisions.
Yuen Foong Yu Consumer Products was founded in 2007 as subsidiary of Yuen Foong Yu Group. It is a leading supplier of household products in Taiwan with brands such as ‘Mayflower’, ‘Tender’ and ‘Delight’.
Vajda-Papír in Hungary has started up the double-width tissue machine supplied by Toscotec at its Dunaföldvár mill.
The complete tissue PM2 line, including an Ahead 2.2L machine was supplied in a turnkey project including installation operations at the mill.
The project included the entire stock preparation system and Toscotec’s patented TT Short Approach Flow fitted with a double dilution system to maximise energy savings. It comprised the electrification and controls, dust and mist removal systems, boiler plant, bridge cranes, air compressor station, roll handling and wrapping systems, and hall ventilation with conditioning system.
Toscotec’s scope included a complete service package with detailed mill engineering, erection, training, commissioning, and start-up assistance. The installation
of the double-width tissue line required a substantial erection team of more than 190 technicians over a period of around 200 days.
The Ahead 2.2L machine features a net sheet width of 5.6m, a maximum operating speed of 2,200 m/min, and a production capacity of more than 80,000 tons per year. It is equipped with Toscotec’s hydraulic TT Headbox-MLT, an upgraded design TT NextPress shoe press, a third-generation TT SYD Steel Yankee Dryer, and TT Hood system designed for maximum energy recovery.
Attila Vajda, managing director of Vajda-Papír, says: “This new Toscotec line constitutes our flagship investment at Dunaföldvár site. We have a vision for VajdaPapír’s expansion to be in harmony with the environment, and that is why we chose the most energy efficient technology available on the market. Throughout the entire project, the whole Toscotec team
demonstrated their extensive expertise and great passion for tissue making. The successful start-up of PM2 represents a key achievement and an important step forward for Vajda-Papír’s sustainable growth.”
For the mill’s PM1, Toscotec had also supplied an Optima 2600 slitter rewinder equipped with automatic shaft puller and dust
removal system that came online in February 2022.
Founded in 1999, Vajda-Papír is based in Budapest and operates three sites. The integrated tissue mill at Dunaföldvár is Hungary’s biggest and most modern integrated tissue mill and manufactures 115,000 tons/year of toilet tissue, handkerchiefs, towels, and napkins.
China’s Guangxi Sun Paper Co has ordered four stock preparation systems from Andritz for tissue machines at its Beihai mill in Guangxi Province for start-up before the end of 2022.
For use on four lines, PM9 to PM12, the stock preparation systems have an aggregate design capacity of 360 tons per day and process needle-bleached and leaf-bleached kraft pulp to
produce tissue. Andritz will install the
complete process technology from pulping to refining,
including fibre recovery. The project also comprises erection, commissioning, start-up, training, and service.
Guangxi Sun Paper was established in 2019 to build an integrated pulp and paper mill in Beihai. The mill is being built in two phases over about five years. When completed, it will have a total annual capacity of 3.5 million tons of pulp and paper.
The staff at the Dunaföldvár mill in Hungary celebrate the first reel off the new Toscotec lineManagement of the technical information about the Toscotec tissue machine newly-installed at Vajda-Papír in Hungary will be provided through Voith’s digital documentation platform OnCare. eDoc.
The Ahead 2.2L tissue machine was installed in July on a turnkey basis including the complete production line and all auxiliary systems (see page 27).
Zoltan Pataki, operations director at Vajda-Papír, says: “The OnCare.eDoc platform contains the entire scope of supply of our new line. It is very easy to pull any type of technical document such as manuals, drawings, and process flow diagrams. Easy access
to specific information allows us to increase operation and maintenance efficiency. With this flexible platform we can finally say goodbye to hours spent searching
for documents and data”.
OnCare.eDoc is said to provide clear user guidance and easy-to-use structure both from desktop and from portable devices. A key benefit
Forest products manufacturer
Arauco has ordered remote supervision systems from ABB for its pulp mills in Chile to ensure higher reliability and monitoring throughout all of its processes.
ABB supported Arauco in the setup of an operations room for remote supervision in central Concepción, Chile, the installation of remote monitoring infrastructure and ongoing service. ABB will establish connections from the operations room to the respective Ability System 800xA distributed control system (DCS) in the Arauco and Licancel mills. Other mills
at Constitución, Nueva Aldea and Valdivia were supported by another DCS as part of the Arauco project.
ABB will also supply seven of its Extended Operator Workplace (EOW) control room consoles and
manage the configuration and installation of these in each of the mills.
“This project with ABB is an important step forward for the company and supports our strategy to focus on the
is that it includes all the technical documentation of the entire paper mill, so that any equipment supplied by Toscotec and Voith can be sourced in one single point. Due to the large amount of collected data, OnCare.eDoc also offers an effective search function for all kinds of documentation needs.
“Efficiency and digitalisation go together. In the future Toscotec’s technical documentation will be delivered on OnCare.eDoc. Our goal is to provide customers with a clear and easy-to-manage digital documentation platform. On a large supply such as Vajda-Papír’s turnkey project, we are confident that OnCare.eDoc will make the difference,” comments Lorenzo Melani, documentation technical coordinator at Toscotec.
technological and sustainable development of our plants and advance our position as a relevant player within Industry 4.0,” said Marcelo Silveira, Arauco’s deputy manager of process reliability. “It will allow us to centrally monitor all of our operations in our Pulp and Energy business and offer a competitive edge on quality, response time, operational stability and cost reduction.”
Arauco has five pulp mills in Chile and seven in South America. In 2020, it produced 3.7 million tons of bleached and unbleached pulp, long-staple and short-staple bleached cellulose of eucalyptus, textile pulp and fluff cellulose.
Information partners: Zoltan Pataki, Vajda-Papír operations director (right) and Lorenzo Melani, Toscotec documentation technical coordinator at Vajda-Papír’s tissue mill in Hungary Remote supervision systems are “an important step forward” for AraucoWith a rising population and employment, Florida is a prime market for tissue sales, which is why South Florida Tissue Paper, a third-generation company founded in Miami in 1997, is aiming to become the main player in both the away-from-home (AFH) sector by consolidating its positioning, and expanding its work in new business areas such as retail tissue.
The tissue maker ordered a Perini Myline from Körber, which has been designed for the production of toilet and kitchen paper rolls up to 200mm in diameter, and is capable of handling parent rolls up to 2,500 mm in diameter at a speed maximum of 600m/min and a production of 40 logs/min.
“We were looking for a strategic partner able to understand the logic of the American market, able to offer not only advanced and competitive technologies but 360-degre consultancy that anticipates the needs of the tissue sector. We found all these characteristics in Körber,” says Juan Corzo III, VP of operations at
South Florida Tissue Paper. The Perini Myline technology is described as well-established, with more than 60 lines sold worldwide since 2016. It is based on the established Sincro exchange phase system and is said to offer a balance between cost and OEE to maximise return on investment, with guarantees for simplicity of operation and
easy maintenance. Says Körber: “The line is also equipped with a laminator-embosser with 409mm diameter steel rollers, and it is water-lamination capable, utilising Körber’s Aquabond technology which eliminates the use of glue, making it greener, more efficient, and less expensive.”
Corzo adds: “With the view of developing our business, we had two different requirements: to select a line that would increase our production capacity and to identify a trustworthy partner
capable of providing careful and timely technical support. With Körber’s Perini Myline we are convinced that we have found the reliable, efficient solution to help us consolidate not only our role in the AFH sector but also to be able to compete in the retail sector. In addition, with Körber Business Area Tissue’s local assistance we can be sure of relying on an experienced partner who is available at any time to provide personal assistance for every need.”
Pulp producer Paracel SA in Paraguay is investing US$1.5 billion in a new pulp mill that will be constructed in Concepción.
All the process and production equipment for the new 1.8 million tonnes per year pulp mill will be supplied by Andritz.
South Florida Tissue is moving into retail products with the help of Körber rewindersFollowing the fire that damaged RDM’s Blendecques recycled cartonboard mill in France, A.Celli Paper will help production to restart with the delivery of an E-Wind P100 paper rewinder.
Although the main production line at the 140,000 tons per year mill was unaffected, the fire involved part of the warehouse and the sheeting and finishing department, including the rewinders.
After the fire, A.Celli Paper sent its specialist team on site to plan a strategy with the RDM Group. The first result of this is the quick delivery of a new rewinder for the restart of production for early 2023.
Blendecques in France, which was hit by a fire in March that affected the sheeting and finishing department
The rewinder, designed to process coated and uncoated paper with basis weights from 250 to 550gsm at a speed of 1,800 m/min, will feature an in-line unwinder, a spool parking station, automatic core feeding and gluing and automatic in-line slitter with a patented Slittomatic system.
Michele Bianchi, chief executive of RDM Group, commented: “The fire at our Blendecques mill has been a shock for all our workforce, impacting the continuity of the business and customer service in an already tight market.
“I’m impressed by the way in which A.Celli reacted and
partnered with us in finding the best fit-for-purpose solution with short implementation times. We are living in challenging times and it is a pleasure seeing how positively our colleagues reacted as well as how supportive, competent and responsible suppliers like A.Celli embraced the challenge to give new future to our mill. We are looking forward to restart the mill and to turn a new page.”
Based in Milan, RDM Group operates nine cartonboard mills in Italy, France, the Netherlands and in the Iberian peninsula.
The Blendecques mill is the sole producer of GD–GT in France and is located in an area with a rich history of papermaking, with eight paper/board machines.
Asia Symbol Group in China has ordered a manufacturing execution system (MES) for a new paper making line at its Guangdong mill from ABB. The expansion will help Asia Symbol to optimise the production processes across all lines at its Guangdong mill, providing better oversight for planning, scheduling and continuously improving efficiency and reducing waste. The application will give operators greater real-time visibility throughout the manufacturing process, creating a ‘visual factory’ to ensure the delivery of products of the right quality at the right time.
Designed to enable pulp and paper producers achieve operational excellence and maximum performance, ABB’s MES helps optimise storage,
energy and raw material usage, in turn improving product output and quality.
Liang LiFu, IT Manager at Asia Symbol’s Guangdong mill
commented: “ABB has been our trusted MES partner due to high competency and clear focus on the entire pulp and paper operation, from mill floor to enterprise level planning. We have benefited from their approach to convert digital data into world-class business results and are looking forward to the expanded use of ABB’s MES over our entire mill.”
Last year, ABB secured another MES upgrade project from April Group for its Kerinci mill in Indonesia, which is also part of RGE Group. The order covers three paper machines delivered in the first quarter of 2022 with annual production of 1.5 million tons.
Cardboard manufacturer KMK Paper has selected Toscotec for the complete rebuild of PM1 at its Kahramanmaraş paper mill in Turkey. Scheduled for the first quarter of 2023, the project will increase the machine’s production capacity and significantly improve paper quality. PM1 produces packaging paper grades, including fluting, testliner, kraft paper, and gypsum board.
The rebuild encompasses the complete paper machine from the forming section to the reel, incorporating leading technology from both Toscotec and Voith. It includes a DuoShake unit in the wet section to ensure optimum formation at a low MD/CD tensile ratio, and a NipcoFlex high-load shoe press that reaches 1,600 kN/m to achieve higher paper quality and dryness. After the size press, the installation of a CB-Turn unit stabilises the sheet on an air cushion and avoids roll contamination. In the dryer section, Toscotec will install new
TT SteelDryers operating at the maximum pressure of 10 bar(g), and DuoCleaner Express for the effective cleaning of the dryer fabrics. A complete tail threading system is also included.
Bekir Yemşen, general manager of KMK Paper, says: “This is a
strategic investment for KMK Paper where we will realise an extensive upgrade of PM1, and we are happy to have reached an agreement with Toscotec. We support the strong synergy between Toscotec and Voith, which perfectly matched the
A thin stock approach system is being supplied by AFT to the Papeles y Conversiones de Mexico (PCM) containerboard mill at Monterrey in Nuevo Leon.
PCM is Mexico’s leader in the manufacture, conversion and marketing of high-quality printing and packaging products.
The project will consist of two
POMp degassers, two POM Dynamix static mixers, two POMlock seal tanks, two POM headers, and two POM head tanks for PCM’s twoply PM2, along with accompanying spare parts and system engineering.
The POMp degasser provides a compact and efficient system at the beginning of the white water handling process, requiring
fewer and smaller silos and tanks downstream. By removing air before the paper machine headbox, the short circulation system will promote better machine runnability with fewer sheet breaks, faster start-ups and grade changes, reduced chemical and water use, and greater system cleanliness, says AFT.
needs of our project.”
Cihangir Hakan Oba, project manager of KMK Paper, adds: “We pursue continuous improvement and development through the adoption of the latest technological innovations. We have a tight schedule on this rebuild, but we got off to a good start and are cooperating well with Toscotec.”
Fabrizio Charrier, sales manager of Toscotec’s Paper & Board division, says: “I am very glad that KMK Paper has placed its trust in Toscotec for this important project, where we’ll manage a complete technological rebuild that incorporates Voith’s key components. This project strengthens Toscotec’s position in a very important market for paper machine rebuilds.”
Established in 1988, KMK Paper operates two paper machines at Kahramanmaraş (PM1 & 2) and one in Kütahya (PM3), manufacturing 240,000 tons/year of kraft paper, gypsum board, coreboard, grey and corrugated cardboard, testliner, and fluting.
“We appreciate our continued partnership with PCM and look forward to a successful start-up later this year,” says Sven Girschner, regional manager – Americas, Process & Equipment Solutions at AFT.
AFT, now part of the Aikawa Group, originated in 1903 as the Union Screen Plate Company in Canada, and subsequently provided the global pulp and paper industry with screen design, manufacturing and applications experience.
PM1 rebuild is a “a strategic investment for KMK Paper”Essity, the Swedenbased global producer of consumer tissue, professional and personal hygiene and health products, will be changing its structure and executive management team from the beginning of 2023.
In the new structure Essity will comprise four business units: Consumer Goods Americas, Consumer Goods EMEA, Professional Hygiene, and Health & Medical.
Consumer Goods Americas will include consumer tissue, baby care, feminine care and incontinence products retail in the United States, Canada and Latin America. Andres Gomez, currently
Sales and Marketing Hygiene Andean and Caribbean within Essity, will be appointed president of Consumer Goods Americas.
The Consumer Goods business unit headed by Volker Zöller
remains unchanged but will be renamed Consumer Goods EMEA.
The Professional Hygiene business unit will also include the Latin America Professional Hygiene business. Pablo Fuentes, current president of Essity Latin America, will take over as president for this business unit.
The business unit Health & Medical Solutions will also include the Latin America medical business and be renamed Health & Medical, headed by Ulrika Kolsrud.
The Global Operational Services unit will be changed to Digital and Business Services. This unit will be headed by a chief digital officer. Global Procurement, currently part of global unit Global
Operational Services will be integrated into Global Supply Chain, and headed by Donato Giorgio.
Robert Sjöström, currently president of Global Operational Services, will take up a new role within Essity and leave the executive management team. He will continue to report to Essity’s president and chief executive Magnus Groth as Senior Advisor for Strategic Projects.
“These changes will streamline our organisation which will increase our efficiency and capability to leverage innovation and digitalization across Essity and strengthen the focus on our consumer products categories in the Americas,” said Groth.
Swedish engineering and design group AFRY has appointed Bo Sandström as its chief financial officer at executive vice president level.
AFRY was formed in 2019 from Sweden’s ÅF and Finland’s Pöyry and has extensive expertise in the construction and management of pulp mills, amongst a range of manufacturing competencies.
The company has more than 60 years of experience and more than 400 major design projects, including the involvement in 90 per cent of the world’s largest pulp mill designs, designed for paper production, and specialities like dissolving and fluff pulps.
Swedish born Sandström has experience from leading positions in several companies, most recently as chief financial officer at ICA-handlarnas Förbund, where he was also a director at ICA Gruppen AB.
Previously, Bo was chief financial officer at Telia Sweden and SATS Group. He holds an MSc in Engineering Physics and a BSc in Management & Economics. Jonas Gustavsson, chief executive of AFRY, commented:
“I’m delighted to welcome Bo Sandström to AFRY. Bo’s extensive financial experience and leadership skills makes him a valuable addition to AFRY and the group executive management team. As CFO, Bo will play a key role in the development of AFRY and I’m looking forward to our collaboration.”
Sandström succeeds Juuso Pajunen as chief financial officer. “It has been a pleasure to work with Juuso Pajunen and during the recent years he has made a substantial contribution to the development of AFRY, including the integration of ÅF and Pöyry in 2019. I would like to thank Juuso for his invaluable commitment, leadership and collaboration, and wish him all the best with his future plans,” said Gustavsson.
ABB’s new High-Performance Infrared Reflection (HPIR-R) sensor gives you more accurate edge-to-edge moisture measurements, at any machine location, so you know the exact real-time CD moisture profile. This means you can target drying energy specifically where needed, cutting excess steam usage and flattening the profile, while at the same time improving sizing and coating pickup. The result is lower operating costs for energy and chemicals, and more saleable tons with better profiles.
To learn more, go to: abb.com/pulpandpaper