
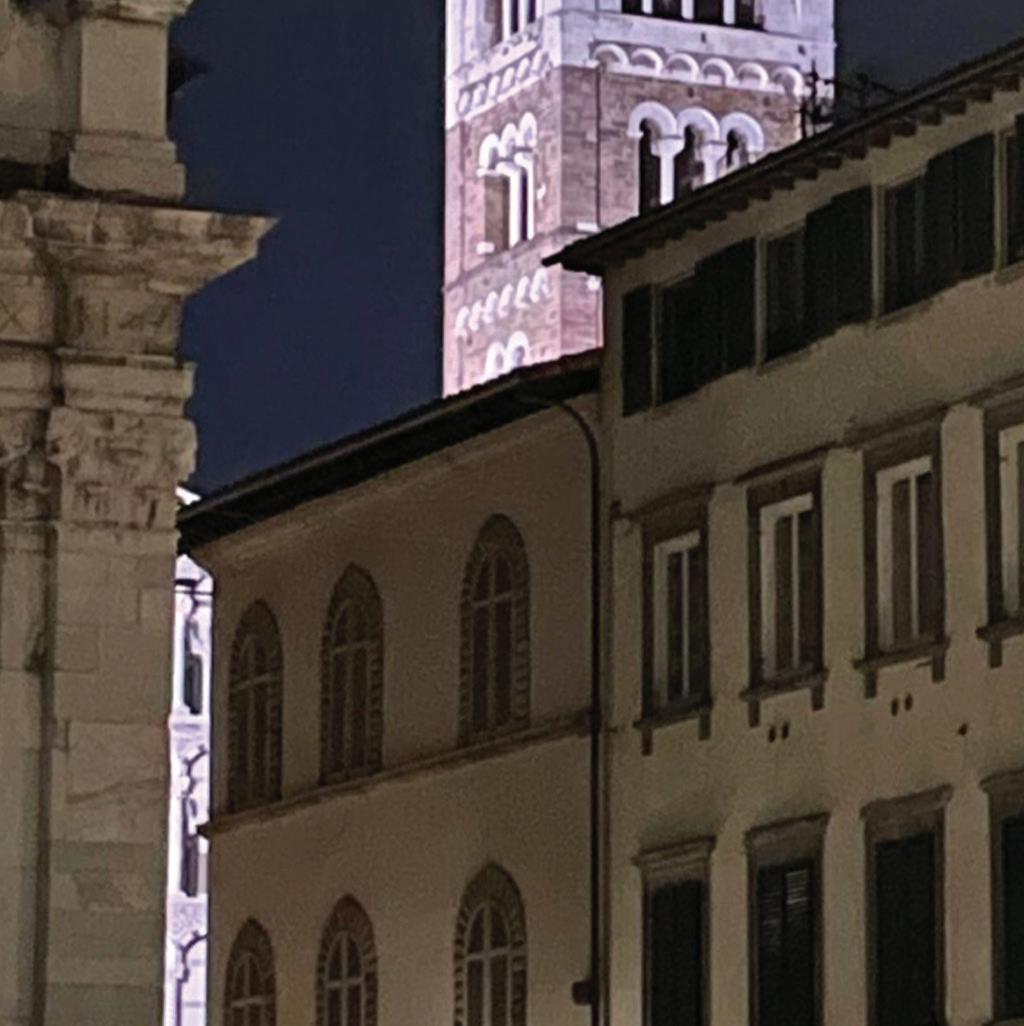


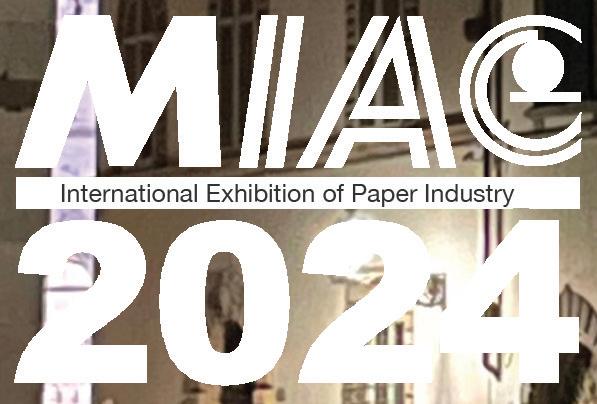
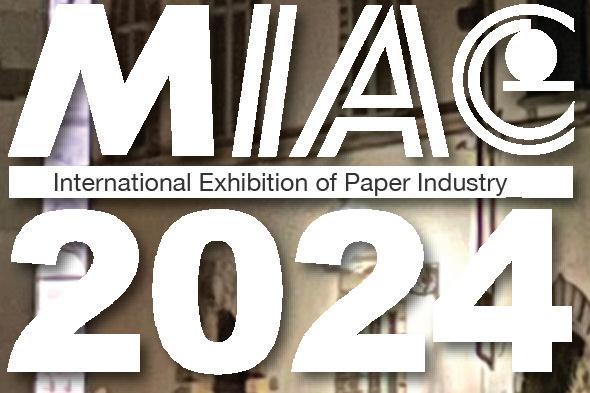
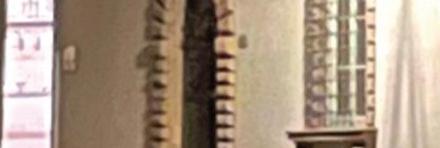
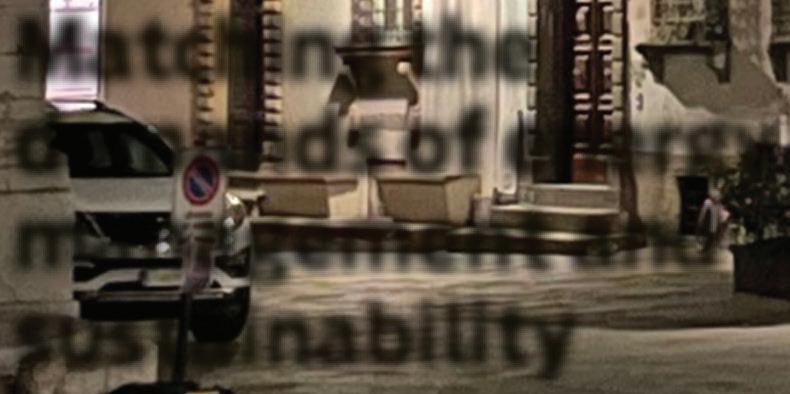
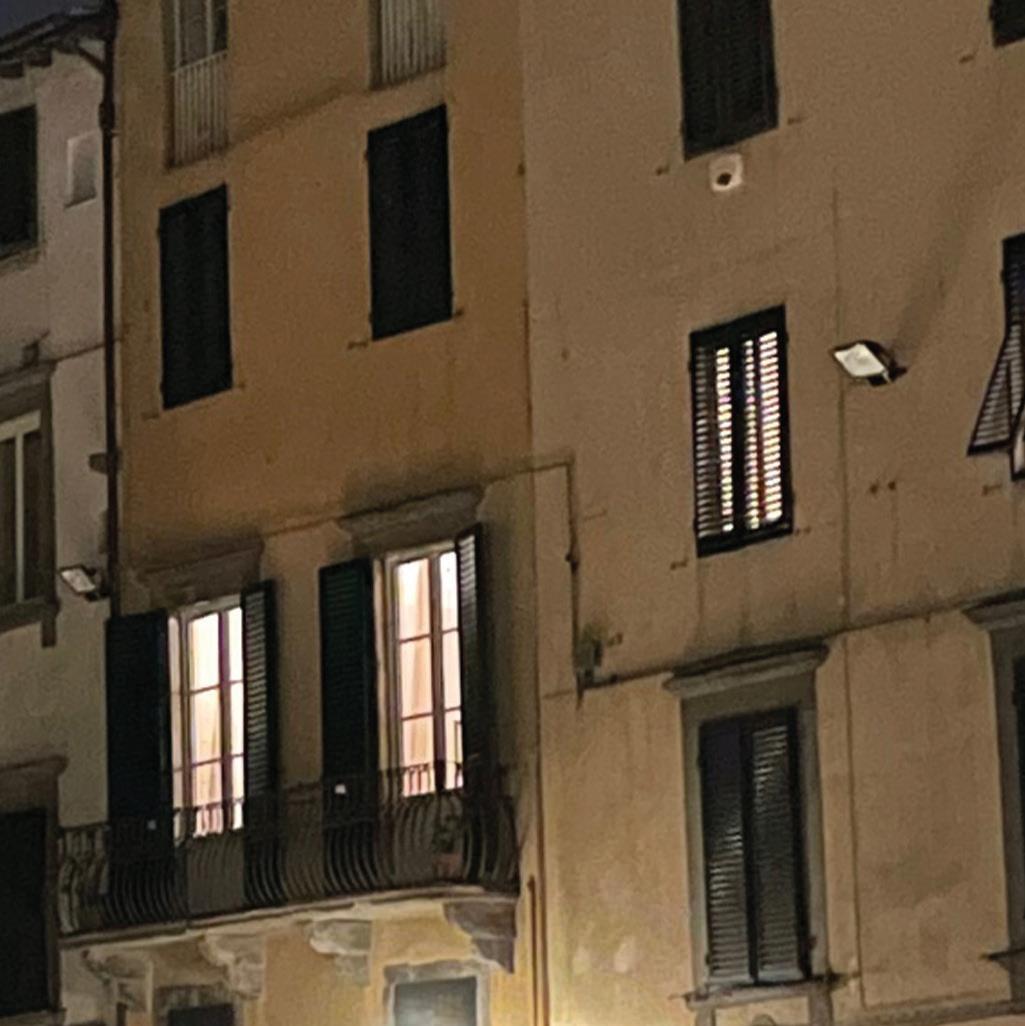
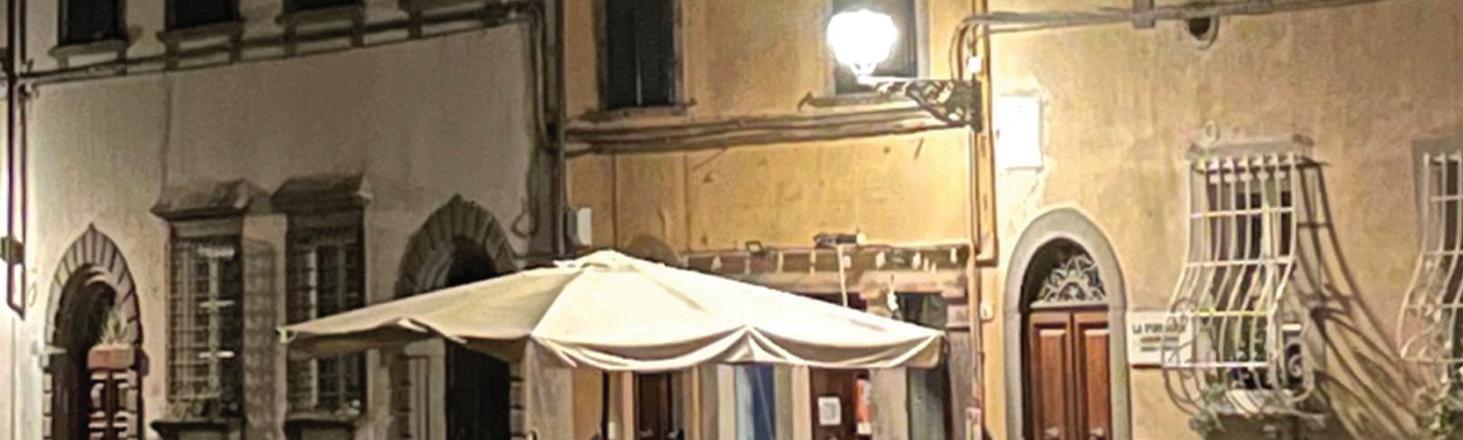
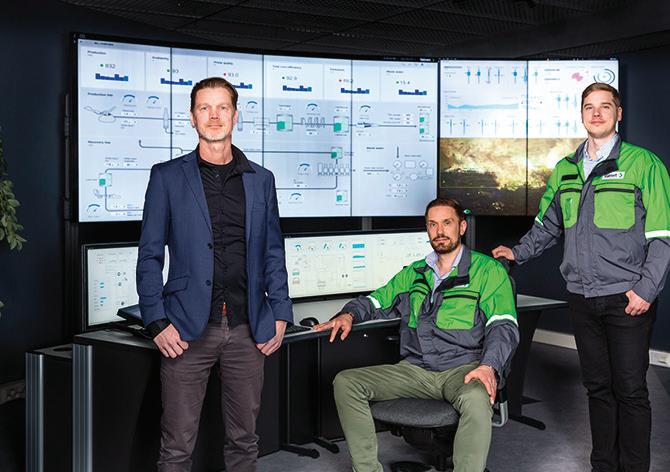
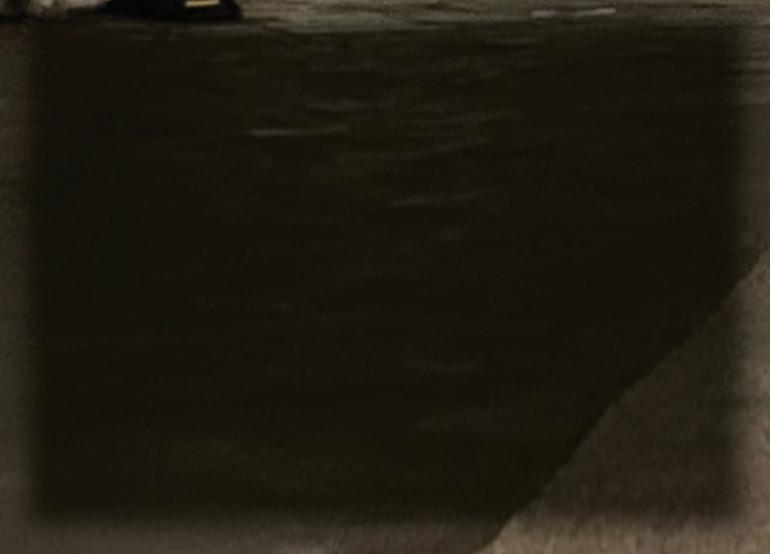


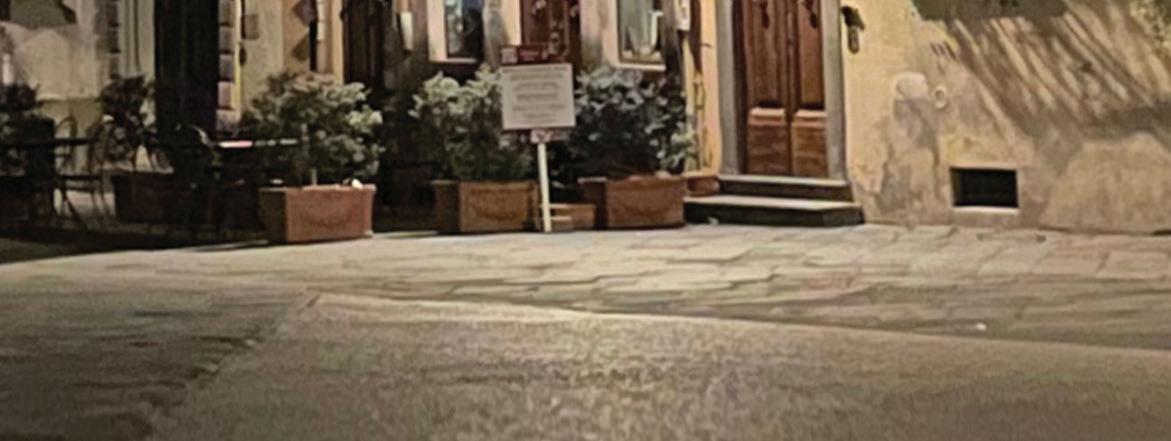
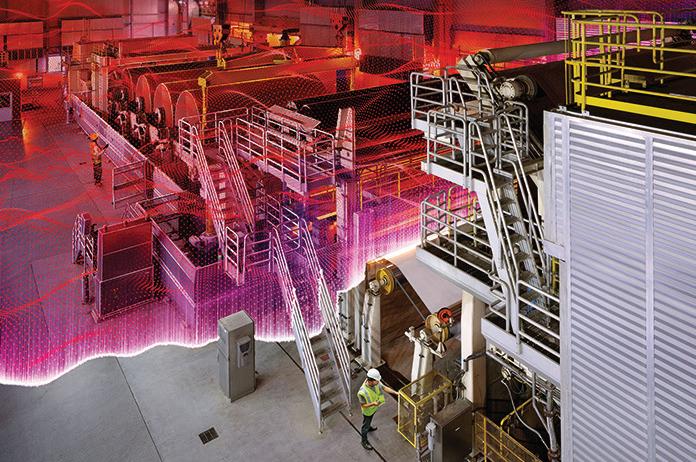
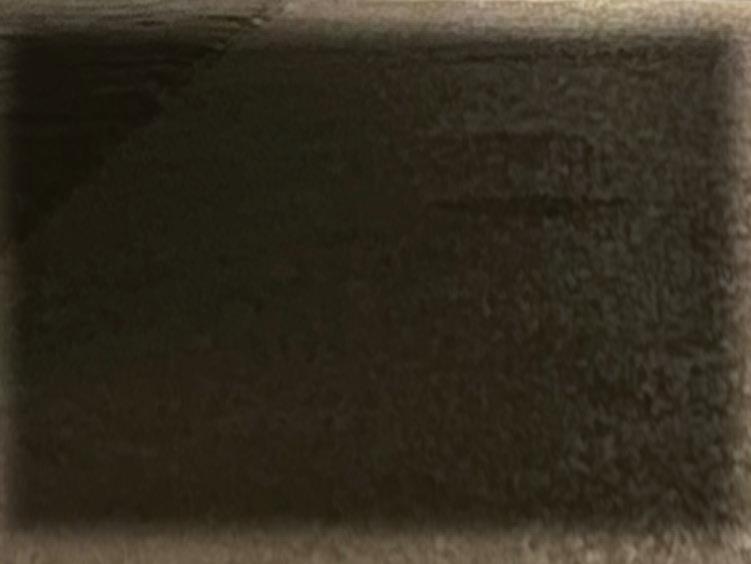


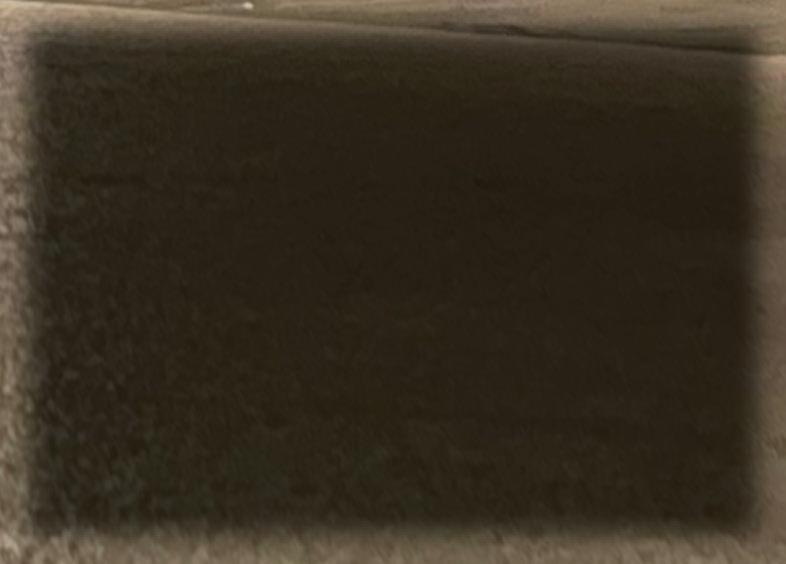

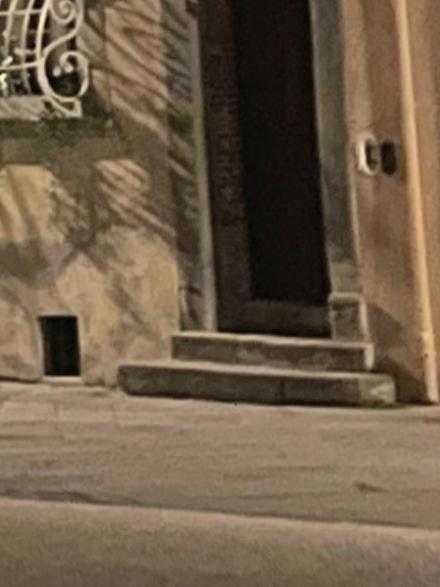
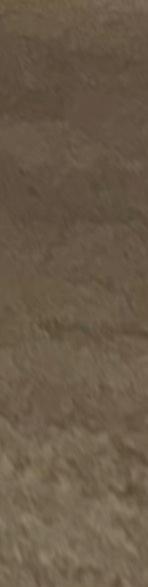
Valmet DNAe is a next-generation distributed control system. As a fully web-based platform, it delivers an industry-leading user experience and cybersecurity by design.
The system brings the process know-how of the world’s leading experts directly to your control applications and improves efficiency. It provides unique data collection and utilization capabilities, enabling informed decision-making.
Valmet DNAe is a catalyst for sustainable practices, and it sets the stage for autonomous operations and a digitalized future. Empower people to perform at their best, reach and exceed your targets, enable path to autonomous operations and evolve throughout the lifecycle with the new DCS. Are you ready to evolve?
For more information, visit valmet.com/dnae
Welcome to the September-October issue of Pulp Paper & Logistics, which includes Green Packaging International covering developments in fibrebased packaging. In this issue you’ll also find a preview of the MIAC show being held at Lucca in Italy which this year celebrates 30 years serving the tissue and paper industries.
Here at Pulp Paper & Logistics, we thank all those readers who took the time to complete their re-registration, so that they continue to receive the magazine. I’m pleased to say that the number has increased to more than 24,000 decision makers in the pulp and paper industry, proving that the magazine’s content is both informative and relevant to today’s mill owners and manufacturing specialists.
Looking forward, we have also taken into account the feedback on the features and subjects that are of importance to our readers. Where possible these will be included in the 2025 schedule.
For the coming November-December issue we invite submissions relating to the following subjects: logistics and handling; paper packaging production technology; and mill safety and security. The deadline for receipt is 15 November and items should be sent to me by email at pulppaperlogistics@virginmedia.com
Vince Maynard, Publisher and Editorial Director
Front cover: Night scene from Lucca, the venue for MIAC 2024. See page 18
Vol. 15 Issue No. 88, September/October 2024
ISSN 2045-8622 (PRINT)
PUBLISHER &
EDITORIAL DIRECTOR
Vince Maynard
Tralee, Hillcrest Road, Edenbridge, Kent, TN8 6JS, UK
Tel: +44 (0) 1732 505724
Mobile: +44 (0) 7747 002286
Email: pulppaperlogistics@virginmedia.com
EDITOR
John Nutting
Tel: +44 (0) 1732 868071
Mobile: +44 (0) 7860 221486
Email: johnnutting47@gmail.com
CONSULTANT EDITOR
David Young
Tel: +44 (0) 1737 551687
Mobile: +44 (0) 7785 796826
PRODUCTION
Anthony Wiffen
Tel: +44 (0) 1460 261011
Mobile: +44 (0) 7851 612799
Email: anton_print_1@mac.com PRINTER
KNOCK OUT PRINT
+44 (0) 1892 823540
Unit 2 The Coppice, Petteridge Lane, Matfield, Kent TN12 7LP
info@knockoutprint.co.uk
http://www.knockoutprint.co.uk
The world’s first tissue machine to operate solely with electricity at 2,000 metres per minute is on course to start up by the end of this year.
First revealed in June, the machine is at tissue manufacturer Fortissue, which is working with Italian engineering firm Toscotec on what is described as a ground-breaking project on PM1 at its Viana do Castelo mill in northern Portugal.
Started up by Toscotec in 2015 as PM1, the Ahead line is being upgraded by the Italian company to run with electrical power.
Equipped with Toscotec’s TT NextPress shoe press, the machine is being upgraded after nine years of operation to meet the goal of making tissue production more sustainable.
Toscotec will install a fully electrically-powered air system including an e-powered TT Hood with several stages of heat recovery. TT Swing will ensure maximum flexibility by giving the choice of the operation modes from full cascading to hybrid depending on the specific production needs. A TT Turbodryer will harness the heat
and Toscotec
recovered from the air system to improve the shoe press dewatering effect and increase post-press dryness.
Finally, the new e-powered TT SteamBooster will generate 100 percent of the steam necessary for the TT SYD Steel Yankee Dryer by recovering the heat present in the hood’s exhaust air together with electric steam generation.
The mill will be able to take electrical power from the local grid in Portugal or by using 100 percent renewable energy taken from its solar and wind plants.
The corresponding greenhouse gas (GHG) emissions will be cut by 20 percent when the tissue line operates from the grid, and net-zero GHG emissions if it runs on renewable energy both for its electric and thermal requirements.
Nuno Ribeiro, owner of Fortissue, said: “At Fortissue we are proud to be spearheading the energy transition of the tissue industry. This groundbreaking project will pave the way for a new generation of production lines with top
performances that also meet the sustainability requirements put forth by tissue consumers in the European market and beyond.”
Gabriele Romanini, sales manager at Toscotec, added:
“Toscotec’s partnership with Fortissue has come a long way in the past 10 years and we are delighted that they selected us for this pioneering project. PM1 was state-of-art when it came on line, and we are now working to take it to a whole new level to become the first high-performance tissue line in the world to run on green electricity.”
Founded in 2015, Fortissue has capacity to produce around 35,000 tons of tissue products. It is part of the Ghost Group, which also includes Suavecel and Nunex Worldwide. With more than 20 years of experience in the personal hygiene market, the Ghost Group employs more than 300 staff and says it focuses its investments on the best available technology worldwide, enabling the delivery of high quality products, while optimising energy and water consumption and guaranteeing zero waste of raw materials.
UPM Communication Papers has been proceeding with the closure of its Hürth newsprint mill and the permanent shutdown of a fine paper machine at Nordland Papier in Dörpen. Both are in Germany. Graphic paper production at the Hürth mill ceased at the
end of August while the PM3 at Nordland Papier was to be shut at the latest by the end of 2024, resulting in annual capacity reductions of 330,000 tonnes of newsprint paper and 280,000 tonnes of uncoated fine paper.
Discussions with representatives of the 338
workers at the mills have been concluded. Antti Hermonen, SVP of operations at UPM Communication Papers, said: “In cooperation with the workers council, we have engaged in a constructive dialogue with the aim of developing responsible solutions for our employees.
The thoughtful and collaborative approach taken by all parties during the consultations resulted in socially responsible solutions for our people.”
The financial impact of the closures is said by UPM to remain materially unchanged from the announcement in May.
What is being described as a milestone development in press section steam savings, Smurfit Westrock has started up a Voith HighPerformance Press at its Roermond Papier mill in The Netherlands. The success of the project could lead to others at Smurfit Westrock mills.
Installed on the mill’s PM1 line in a rebuild that took 38 hours, the line started up again smoothly and production was subsequently “fully ramped up again”, said Voith.
In a statement, Voith added that the advantages of the new press became immediately clear: The HighPerformance Press increases the dry content of the paper web after the press section and enables Smurfit Westrock to make significant steam savings in the dryer section. As a result, energy consumption and carbon dioxide emissions can be significantly reduced.
Furthermore, the increased dry content after the press section enables an increase in production speed. This in turn can lead to higher production quantities with consistent quality.
Sjon Vrieze, technical operations manager at Smurfit Westrock Roermond Papier, explains:
“Thanks to the innovative HighPerformance Press solution from Voith, we can save 7,500 tons of steam and 1,113 tons of CO2 per year. This is an important contribution to our decarbonisation roadmap and shows the potential for converting other Smurfit Westrock paper machines.”
Voith continues to support Smurfit Westrock with
optimisation measures that exploit the maximum potential of the new press.
Bas Noldus, production manager at Smurfit Westrock Roermond Papier, commented: “We were delighted when Voith approached us with its new HighPerformance Press solution. From the very beginning, there was a trusting relationship and close cooperation. It quickly became clear that it was important for Voith to respond to our needs and enable us to achieve
In a move to reduce pulp output to meet ‘market conditions’ UPM is temporarily cutting production at its Kaukas and Kymi pulp mills in Finland.
The move follows negotiations with staff held in March.
“We are adjusting our production as a normal measure in line with market and cost developments, focusing on profitability,” says Marko Sundqvist, vice president of UPM’s Pulp Operations in Finland.
The shutdown of the Kaukas pulp mill started on 9 September and of the Kymi pulp mill on 23 September, and lasted for about three weeks. Maintenance work will be carried out during part of the shutdown period, but
significant production benefits with the HighPerformance Press.”
The press upgrade is the latest of a number of recent improvements made to PM1. These included the installation of a shoe blade gap former, a rebuild of the inrush flow system and an extension of the machine room.
Following the completion of the final phase, the 5-metre wide PM1 was capable of producing 85-135gsm recycled fluting and testliner at a speed of 1,200 metres per minute.
temporary layoffs are possible.
UPM’s pulp mills in Pietarsaari in Finland and at Paso de los Toros in Uruguay will continue to run at full capacity. Deliveries to customers will continue normally during the shutdowns.
UPM Pulp operates four pulp mills worldwide, three in Finland and one in Uruguay, with annual pulp capacity of 3.7 million tonnes.
The chief executive of paper maker DS Smith has called for the new UK government to help make the country a more attractive place to invest, and to align with EU regulations to support trade.
Miles Roberts shared industry insights on trade, investment and what is needed to support UK manufacturing.
Speaking on the Wake Up to Money and Today programmes, Roberts said:
“Support for a vibrant, growing, UK manufacturing base will in turn support economic growth, and right now there is an excellent opportunity to reset and realign with the EU to help make that a reality.
“A failure to maintain the standards of our biggest trading bloc presents a cost, but if we can make sure that standards are common, it will reduce cost to British business, and in turn, the consumer. Unless something is demonstrably not in the UK’s own interest, then we should be asking why we aren’t aligning with EU rules.
“Aside from the need for regulatory alignment, British
businesses need a long-term national industrial strategy that will support higher levels of investment and growth.
“For manufacturers, energy sources are critical – we need to understand the source and cost of energy, how we connect to it, if the power supply is sufficient, and how the grid will support it, before any planning to invest in new technologies or factories can happen.
“For our part, DS Smith has already invested into lower-carbon facilities in Italy and Poland, and into greener technologies
in Germany, France and Spain, because we have ambitious decarbonisation targets and the industrial and energy policy frameworks in those countries are made clear. With a clear plan, the UK can underscore why it is an attractive place to invest, and growth can follow.”
Points that Roberts made during the broadcasts included: Regulatory alignment:
● It is an excellent moment for the new government to reset the relationship with the EU to support trade.
● The EU is developing new
legislation, but the UK is not keeping pace with the new standards which creates automatic divergence with our biggest trading partner, and generates avoidable costs to business.
● We need regulatory alignment –unless something is demonstrably not in the UK’s own interest, then we should be considering aligning with EU rules, so that we have less friction.
Supporting UK manufacturing and making the UK a more attractive place to invest:
● A vibrant, growing, UK manufacturing base could have a very significant and positive effect on the economy.
● Alongside regulatory alignment with the EU, it is crucial that the government set out a longterm plan for infrastructure and energy solutions.
● The UK will be a more attractive option for investment into manufacturing if a clear energy plan is set out.
● Understanding the energy sources and connections, and how the grid’s capacity will be enhanced to accommodate this, is critically important.
Metsä Group’s pulp and sawmill business has again achieved EcoVadis’s highest level of recognition, the Platinum rating, for its sustainability efforts. Since 2019, Metsä Fibre has consistently been among the top one percent of pulp, paper, and cardboard manufacturers evaluated by EcoVadis. The company received particularly
high marks (90 out of 100 points) for its responsible sourcing practices.
“Responsibility and sustainability are integral to our strategy and daily operations. We highly value the Platinum recognition from EcoVadis, which we have now received for the sixth time. We use the feedback from the assessment as a tool for
continuous improvement,” says Ismo Nousiainen, chief executive of Metsä Fibre.
“Metsä Group’s strategic sustainability goals for 2030 pave the way toward a carbon-neutral society. Our objectives include fossil-free factories, 100 percent utilisation of production side streams, and completely fossil-free raw materials by 2030.”
EcoVadis, an organisation that evaluates corporate responsibility, provides a platform for companies to assess their suppliers’ performance in global environmental and social responsibility. The assessment covers four areas: environment, human rights and labour practices, business ethics, and sustainable procurement.
Targeting emissions zero
WE ENABLE OUR CUSTOMERS TO REDUCE CO 2 EMISSIONS
More than €30 million has been invested in solar power systems at Smurfit Westrock’s mills in Spain as part of the paper maker’s mission to cut carbon dioxide emissions by switching from fossil fuels and cutting waste going to landfill.
More than 12,000 solar panels were unveiled at the Sangüesa paper mill. These will augment its biomass and recovery boilers to generate more than half of its annual energy requirements, the equivalent to powering 3,600 homes.
The €6 million photovoltaic system, which is the largest of its kind in the Navarra region, is expected to reduce the mill’s annual carbon dioxide emissions by more than 3,000 tonnes. Since 2005, the Sangüesa paper mill has reduced its carbon dioxide emissions by more than 51 percent.
A €6 million photovoltaic system has been installed at Smurfit WestRock’s Sangüesa paper mill
With a second investment of €27 million, the Nervión paper mill will adopt a fully circular production process involving the biggest landfill reduction project Smurfit has ever undertaken. The project will remove 75,000 tonnes of waste from landfill, and additionally, eliminate around
450,000km per year of road transport.
Javier Rivas, operations chief at Smurfit Kappa Paper & Board Europe, said: “The recent inauguration of both the Sangüesa and the Nervión investments are milestones for the Smurfit Kappa paper division and
Stora Enso is cooperating with the police and other authorities with an investigation into an environmental incident at a wood harvesting site at Kainuu in Finland.
In what was described as an aggravated nature conservation offence, in August forestry machinery crossed a river where there is a population of the highlyendangered freshwater pearl mussels.
Stora Enso said it takes the matter extremely seriously, because the pulp and paper maker adheres to strict responsibility requirements and comprehensive guidelines for the consideration of freshwater pearl mussel in harvesting operations.
“It is evident that our guidelines have not been followed. What has happened is completely contrary to our values and sustainability commitments,” said Seppo Parvi,
country manager for Finland at Stora Enso.
Following its own investigation
Stora Enso said that its guidelines and procedures will be refined to ensure that everyone involved in harvesting in valuable natural areas is aware of them in the future.
“It is our responsibility to ensure that this never happens again. We have taken immediate steps to tighten up our procedures, including forestry planning,
aligned with the EU Green Deal’s transition to climate neutrality through increasing clean energy technologies.”
Chief sustainability officer Garrett Quinn added: “These two projects demonstrate the Group’s continued investment to deliver on its sustainability goals with over €30 million in these two projects alone, delivering reduced emissions, and increasing the circularity of our production process.”
The Sangüesa and Nervión inauguration events were attended by Smurfit WestRock chief executive Tony Smurfit.
Smurfit WestRock’s Nervión mill in Spain where its biggest-ever landfill reduction project has started
environmental training, guidelines and information systems. The police investigation is ongoing, but it is clear that Stora Enso bears its responsibility in this case, both environmentally and financially,” said Parvi.
Stora Enso is supporting the restoration work led by Metsähallitus on site both financially and materially. Stora Enso has also decided to participate in the LIFE Revives programme. “Participation in this programme will not repair the damage already done, but it is the least we can do in this case,” said Parvi.
Despite the continuing threat of missile strikes, a tissue maker in Ukraine has invested in new technology to improve energy efficiency and operational safety.
Kyiv Cardboard and Paper Mill has purchased a TT SYD Steel Yankee Dryer and a high efficiency TT Hood system from Italy’s Toscotec to replace its existing cast iron dryer cylinder and Yankee hoods on PM2 at its Obukhiv mill, south of Kyiv. The project is planned for start-up in 2025.
Ivo Valtchev, vice chief executive
at Kyiv Cardboard and Paper Mill, said, “Despite the war in Ukraine and the current economic situation, we continue to invest in advanced technologies and to modernise production. The new TT SYD and Hood will improve the energy efficiency of PM2, as well as increase our operational safety, which is especially important in this difficult time for the country.”
Compared with the existing cast iron Yankee, the new TT SYD will significantly reduce PM2’s energy consumption and guarantee higher operational safety; the
high-efficiency TT Hood and burner system will considerably optimise the Yankee hoods’ energy consumption. The upshot of the overall project will be substantial energy savings.
Matteo Giorgio Marrano, sales manager at Toscotec, added, “Toscotec is happy to start a new cooperation with Kyiv Cardboard and Paper Mill and we are confident that this technological upgrade will deliver a competitive advantage to drive their market growth. The combination of Toscotec’s key drying equipment – TT SYD and
Atlanta-based Georgia-Pacific has completed the US$550 million expansion of its Green Bay, Broadway mill in Wisconsin, celebrating with an opening event in September.
The expansion included a new through-air-dried (TAD) paper machine and three converting lines that will produce Brawny brand paper towels and other premium private label brands for the retail market.
Construction on the 600,000sqft site began in July 2022, helping to
support Georgia-Pacific’s own retail towel brands, and the growth of premium private label brands. It also reduces manual ‘touches’, a critical part of the new paper machine’s production process, the associated converting equipment, and the overall infrastructure.
With the production process nearly 85 percent automated, the technology-focused jobs as part of this project will manage high levels of automation across the entire product system.
The new TAD machine increases
TT Hood – represents the best available technology in tissue for its value in energy efficiency.”
Founded in 1982, Kyiv Cardboard and Paper Mill is one of the largest producers of full-cycle cardboard and paper products in Eastern Europe. It is part of the Austrian group Pulp Mill Holding.
tissue capacity to the Broadway mill, which already operates seven other paper machines and several converting operations.
“Today is an exciting day for Georgia-Pacific,” said John Nundahl, manufacturing chief at Georgia-Pacific during the opening. “After more than two years, it is wonderful to see the results of this new investment in the form of more than 100 full-time jobs, enhanced levels of technology and automation, and production capabilities that will produce Brawny paper towels
and other premium private-label brands.”
Since 2006, around $1.2 billion has been invested in GeorgiaPacific’s Green Bay facilities, including the Broadway mill. Many of the investments were focused on high-tech equipment and technology, including the latest in automation, laser-guided vehicles, artificial intelligence, and robust data analytics that it says help operations run safely and efficiently. Georgia-Pacific has five facilities in Wisconsin, which provide almost 2,000 direct jobs in the state.
Flow Link Systems (FLS), a Voith subsidiary that supplies customers with valves, strainers and high-quality steel castings, has won an award recognising its commitment to the use of renewable energy in industrial activities.
Efforts to integrate renewable energy into the India-based company’s energy mix include optimising energy consumption and improving energy efficiency through continuous monitoring, measurement, and control.
Commenting on the EQ Solar Award, Dr Nithyanandan Devaraaj, chief executive of Flow Link Systems, said: “FLS is amongst the early users of renewables for its energy needs in India. The recognition has
come in at the right moment for the commitment of the
Compensation of almost US$500 million has been awarded to Smurfit Holdings after its operations were ‘unlawfully expropriated’ by the Venezuelan government in 2018.
The award on 28 August against the Bolivarian Republic of Venezuela was made by the arbitral tribunal of the World Bank’s International Centre for Settlement of Investment Disputes (ICSID).
Smurfit Holdings BV, a wholly owned subsidiary of Smurfit Westrock, will receive compensation in excess of US$468.7 million, plus legal costs of $4.5 million, plus interest from the end of May 2024 until the date of payment.
The case involved the
breaking of the treaty that provided reciprocal protection of investments between the Netherlands and Venezuela.
Following the government occupation in August 2018, Smurfit Kappa Group’s Venezuelan operations were deconsolidated.
By majority, the Tribunal dismissed Venezuela’s objections to its jurisdiction, and held that Venezuela breached the treaty’s protection against unlawful expropriation and Venezuela’s seizure of Smurfit’s business there.
The tribunal concluded that Venezuela’s occupation of Smurfit’s Venezuelan subsidiaries in 2018 “constitutes an expropriation that was not taken
in the public interest and was not compliant with due process of law”.
Smurfit Westrock said it will now pursue the full value of the award from Venezuela.
Tony Smurfit, chief executive of Smurfit Westrock, commented: “We are pleased with the award of the ICSID tribunal. It validates our assertion that our Venezuelan business was unlawfully expropriated in 2018. While the award cannot compensate us for the full loss in relation to our operations in Venezuela, including the significant impact it had on our people and the wider community there, we will now pursue the full value of this award from the Venezuelan government.”
organisation and the team to a small carbon footprint. This award is deemed special given the across-industry competition and FLS specifically belonging to an energyintensive sector. We wish to continue this success journey of decarbonisation in meeting corporate expectations.”
The award is given by EQ International Magazine with the participation across the industry to encourage the adoption of renewable energy sources to decarbonise industrial activities. By striving for low-carbon emissions, companies contribute significantly to ecological sustainability.
The 56th Pulp and Paper International Congress and Exhibition, a gathering of the forest base industry organised by Brazilian Pulp and Paper Technical Association (ABTCP), includes a robust technical programme coupled with an exhibition featuring the latest technological trends in the sector.
It is being held from 1-3 October at the Expo Transamérica, in São Paulo (SP).
“The opening ceremony, which traditionally occurs on the morning of the first day of the congress, always gathers important participants to discuss current issues regarding all players in this extensive production chain, and is definitely worth blocking your calendar to attend it,” says Darcio Berni, executive director of ABTCP.
Swedish analyser and measurement technology company
PulpEye has been acquired by Andritz. The acquisition is said to complement Andritz ’s capabilities by adding the core pulp quality analysers and measurements into the group’s automation and digitalisation portfolio.
PulpEye focuses on online applications and services for the global pulp and paper industry. The Swedish company provides pulp, paper and board producers with a wide range of online pulp analysers, measurements and controls ranging from chip quality,
kappa to fibre properties and more throughout the process. Since 2002, PulpEye products have contributed to stabilised and higher pulp quality, process efficiency and reduced energy consumption in pulp production. Andritz will continue to invest in the further development of the PulpEye product line and will establish a dedicated service network to provide customers with global support. The acquisition complements the extensive portfolio of Smart Series, Andritz Intelligent Instruments, and leverages the group’s position to provide total solutions combining
measurements, analysers, advanced process control and optimisation, as well as a broad range of services.
Stephan Keuschnigg-Zingl, senior vice president for pulp and paper automation and digitalisation at Andritz , says: “We are very pleased to welcome the PulpEye team with its excellent analyser portfolio to Andritz. This acquisition further strengthens our offering in automation and digitalization and allows us to provide reliable analysers to measure all the main quality parameters of pulp processing, as well as new solutions and services leveraging them.“
● In a second acquisition, Andritz has taken over Finnish company Procemex, which specialises in web monitoring and inspection for the pulp and paper industry. The value of the deal was not revealed.
Procemex’s smart camera-based solutions help customers ensure product quality and minimise costly production downtime. With 20 years of industry experience, Procemex has delivered more than 1,000 systems worldwide. It has a team of more than 100 vision systems experts and operates from Finland and subsidiaries in Germany, Japan, and the US.
With the launch of DNAe, Valmet redefines what a distributed control system can be in a connected digital world, particularly in pulp and paper mill operations. Report by Ralf Salonen and Randel Wells
The future holds remarkable prospects for process industries. Every challenge is a catalyst for innovation and growth. The pressures of globalisation and demographic and climate change are reshaping expectations. As technology leaps forward, Valmet is creating solutions that transform complexity into simplicity, enabling a new generation of workers to navigate and excel in a digital landscape.
Transformative times for process industries
“The world around us is changing rapidly. Industrial systems like the DCS need to embrace this digitally-connected world,” explains Jukka Ylijoki, vice president of R&D for Automation Systems at engineering group Valmet.
“Building a truly open yet secure and sustainable DCS that would last for decades required a complete overhaul. No aspect of
our recently launched Valmet DNAe was left untouched. We had to be sure it delivered the reliability, performance, flexibility, and security our customers needed.”
A foundation for digitalisation and autonomous operations
“Compared to 20 years ago, the requirements for a DCS have changed dramatically,” says Harri Mustonen, director of control systems at Valmet. “The primary purpose of a DCS is still to connect field devices to process controls, but over the last few years, digitalisation initiatives everywhere have pushed the DCS toward higher levels of connectivity and automation.”
The common thread is better data utilisation. To enable greater autonomy, the DCS needs to collect, manage, analyse, and share highquality data across operational technology (OT) systems at the facility and the information technology (IT) systems of the back office.
“Valmet DNAe makes this possible as a single
unified system,” says Mustonen. “In addition to real-time process controls, Valmet DNAe brings structured high-quality information
management tools for advanced analytics and reporting to the core of the DCS. This enables customers to improve their digital intelligence at every level to achieve higher targets while reducing production costs.”
Cybersecurity meets open connectivity
Making the digital transformation smooth for customers was a key ingredient in the development of Valmet DNAe. “Customers need to be able to open their DCS in an easily controlled manner to combine systems and data sources,” says Ylijoki.
“Our networking and connectivity goals for Valmet DNAe were far more ambitious than anything we had done before. How do you secure a system designed to be open and adaptable? To answer that, we maintained a laser-like focus on cybersecurity.
“This was perhaps our biggest insight when we started developing Valmet DNAe,” Ylijoki
continues. “The need for a platform that is fundamentally cybersecure is proving itself time and again.”
Valmet DNAe ensures cybersecurity measures from the operating field layer up to IT-level communication. The system’s different network
A common controller and I/O family enables a smooth transition from Valmet DNA to Valmet DNAe over a plant’s lifecycle. Additionally, Valmet has introduced a new modular controller and a single-channel I/O as new hardware options for Valmet DNAe
layers and technical features have been developed based on certified Security Development Lifecycle Assurance (SDLA) methodologies, ensuring security from the first line of code.
At the core of the Valmet DNAe distributed control system is the Trusted Information Framework (TIF), which serves as the backbone for communication and data management. The TIF framework provides a robust foundation for system security and integrity. Built on the TIF foundation, Valmet DNAe architecture is cybersecure by design, and it includes measures such as role-based access control, authentication, encryption, endpoint protection, and comprehensive audit trails. IT security integration helps security teams stay alert to potential threats, and the Valmet DNAe system also enables the implementation of intrusion detection.
Every user counts more than ever “Industries face a silver tsunami of retirement,” says Mustonen.
Attracting new recruits and keeping them is hard, adding to the pressure to optimise and do more with less. Smaller and smaller teams need to be able to run processes in larger, more complex operations.
Valmet DNAe empowers teams to collaborate seamlessly across process areas, sites, departments, and organisations by implementing a design philosophy that focuses on usability. Users get an intuitive holistic view of processes, sites, and fleets for best situational awareness and cross-team collaboration.
more users into the DCS realm is the key to success.
“The most experienced people are leaving the workforce. New recruits lack the expertise from 30-plus years in the same job, and they don’t even want such a career. Changing jobs after a few years is the norm now. Even though the DCS role is bigger, the system needs to be much easier to learn and use to counter high turnover.”
“Valmet DNAe is as much about bringing people together and new ways of working as it is about connecting systems,” says Ylijoki. “We want the best experts to be available for our customers and work seamlessly to analyse data, resolve issues, and optimise process performance.”
All users can now easily access and leverage process data to improve and accelerate datadriven decision making. Bringing
With the DCS taking on an increasingly important role, high availability is a must for a fully digitalised DCS. “System reliability is critical because the primary function of a DCS is to secure continuous, trouble-free production,” notes Mustonen. Fault tolerance and redundancy have been at the core of Valmet DNAe development, ensuring continuous availability of real-time high-quality data. This enables precise control of the process and faster response times to both unexpected disturbances and planned changes.
“You can eliminate process variability and run at the optimal operating point to produce the targeted production and quality with the minimum input,” says Mustonen. “This is critical for long-term sustainability. Valmet DNAe delivers the controls, data, analytics, and diagnostic
intelligence to confidently towards more efficient use of resources and lower emissions.”
The future starts now Valmet keeps its lifetime systems compatibility promise to customers with Valmet DNAe. Existing Valmet DNA customers can benefit now from the latest
Valmet DNAe is inherently cybersecure by design. The innovative system core and architecture provide multi-layered protection to shield operations from cyber threats.
Developed following the industry-leading IEC 62443-4-1 standards and independently verified with Security Development Lifecycle Assurance (SDLA) certification, Valmet DNAe delivers hardened defenses against cyber threats.
Valmet DNAe was developed with a design philosophy that empowers people to perform and collaborate better across their organisation. The system provides a common user interface for controls, analytics, configuration, and maintenance. Intuitive workflows simplify operations and enable users to manage larger process areas with less effort. With role-based access control and support for global
technology and innovations in Valmet DNAe.
“We have well-defined upgrade paths for existing Valmet DNA customers to transition to Valmet DNAe on a timeline that best fits their production and investment plans,” says Mustonen.
“Whether it’s a hydrogen production or power plant, paper
expert networks, Valmet DNAe also enables global collaboration and multisite operations to increase operational flexibility and ease recruitment. The new user interface enables significantly easier onboarding for the new generation of DCS users.
Process insight is included in Valmet DNAe and can be run onpremise in an edge server or fully in the cloud. Easy-to-use trending, analysis, and filtering allow users to follow, study, and troubleshoot processes, while powerful reporting and self-service data visualisation help cross-team collaboration.
Advanced analytics and reporting solutions provide actionable insights to all users from control room personnel to analytics teams and office stakeholders. The easyto-use dashboarding and analysis tools and advanced monitoring and prediction applications are specifically designed for industrial data and provide a comprehensive
machine, or whiskey distillery, tremendous process expertise has gone into those applications,” adds Ylijoki. “They’re the strongest foundation to build on. We introduce innovative technology while securing customers’ existing assets by migrating control functions without changing their behaviour.”
view of production processes or sites.
Valmet DNAe is a scalable automation system that grows with a business. It adapts to evolving operational needs and technological advancements. Valmet’s commitment to lifetime system compatibility guarantees that there’s always an upgrade path available.
Predictable lifecycle costs and long-term commitment are ensured through lifecycle plans. Service agreements provide performance guarantees and expert support for continuous performance improvement.
Upgrading an existing Valmet DNA can be started smoothly through the user-friendly Valmet DNAe User Interface.
Since the 1960s, Valmet has been pioneering digital solutions for industrial customers. Valmet’s first DCS arrived in 1978, one
Customers are able to jump-start optimisation and performance enhancement through a library of industry-specific applications for Valmet DNAe. Valmet also provides a reference network with ready-made templates to significantly reduce project times and ensure the final Valmet DNAe network design adheres to cybersecurity requirements.
Securing the present is as important as securing the future.
“One of the key advantages of the Valmet DNAe system is that it can evolve. This is pivotal to our customer promise,” says Ylijoki. “More than that, though, our system is designed to adapt and remain competitive in the future.”
of the very first on the market. Since then, all its distributed control system generations have had industry-leading release compatibility.
Valmet’s controllers and I/Os are built for reliable real-time operation, ensuring uninterrupted performance. The adaptable hardware family offers a wide range of options to perfectly fit to specific needs, regardless of the current system.
● Common hardware family between Valmet DNA and Valmet DNAe
● A new modular controller and a single-channel I/O as new hardware options for Valmet DNAe
● Easy migration from existing DCS or PLC systems
● Open connectivity to third party systems and devices
● Scalability to expand the system’s size and functionality
● Redundancy options maximise uptime in mission-critical processes
ABB is calling on process industries, and especially pulp and paper, to evolve their operations by leveraging advanced solutions that bridge digital gaps and is drawing on expert teams assembled across five disciplines to deliver insights to build on successes in energy management, process safety, skills retention and process performance results. PPL reports
Global technology leader ABB has launched Do
More With Digital, a global campaign that highlights the opportunities for process industries to realise their full potential through digital transformation.
Leveraging its deep ties across pulp and paper, mining, metals and cement, ABB recognises a significant opportunity to continue equipping these sectors with advanced industryspecific solutions, driving their digitalisation journey and allowing
them to accelerate their adoption curve in a shorter timeframe. While these industries will continue to be enhanced through technology development using the likes of generative artificial intelligence (Gen AI), data analytics, machine learning (ML),
cloud and edge computing, they are also considered hard-to-abate due to the volume of production, location of operations, energy and heat chemistry, and many other factors.
The World Economic Forum reports that digital solutions can
accelerate efforts to reach net zero in high-emission industries, delivering up to 20 percent of the total reduction that the International Energy Agency says is needed by 2050. ABB is leveraging its experience of previous energy transitions, its recent record in industrial software development, and its 140 years of heritage across a range of industries to guide customers on their digitalisation journeys. ABB has worked with customers
ABB’s advanced suite of digital offerings is empowering mills to overcome its most pressing challenges by enabling datadriven decision making
within the process industries for decades, supporting with the deployment of digital solutions such as advanced process control (APC), energy management systems (EMS), and manufacturing execution systems (MES).
These have evolved from original packages to become variations used for distinct industries, with their own tools and libraries, and remain the foundation for advanced technology progression.
Customers recognise that they are at different stages of their digitalisation journey, often with starters (those embedding digital for the first time), stallers (those piloting a new advanced solution, often with a start-up) or scalers (those moving to the next level, perhaps with a technology company). ABB is currently working across this ecosystem to jointly design and develop new solutions for current and future needs.
“Adoption of advanced digital technologies is still much slower than one might expect in the process industries,” says Sanjit Shewale, global business line manager for digital at ABB Process Industries. “Customers are facing new challenges in proving and scaling up solutions that will drive real, transformative change.
“However, there are opportunities for all parties to use technologies to retain knowledge of processes in their business as people retire or move on in shorter timeframes than was typical in the past. Through co-creation, there is the chance to show more and do more for positive investment decisions that quickly result in unprecedented
levels of energy management, efficiency, sustainability, safety and service.”
ABB reports that it is also working with fellow global technology companies to integrate the likes of Gen AI capabilities into the ABB Ability suite of industrial software, supporting industrial companies to improve data collection, unlock insights hidden in operational data, and enable significant gains in efficiency and productivity. Partnerships also exist for initiatives to accelerate the adoption of digital solutions to help industries meet their goals on net-zero emissions. One such example is real-time data transmission using cloud-based software integrated with ABB systems.
In the pulp and paper industry, ABB’s advanced suite of digital offerings is empowering mills to overcome its most pressing challenges by enabling data-driven decision making. A holistic view of operations, leading to reduced waste, minimised downtime, and stable production profiles for mills, ensures that ABB can deliver exceptional results to meet its customers’ expectations.
Alongside Jujo Thermal in Finland, part of the Nippon Paper Group, ABB’s team was able to transform the thermal paper maker’s operations by understanding its complex production needs and implementing ABB Ability Manufacturing Execution System (MES) for pulp and paper. Jujo Thermal achieved reduced production costs within just six months through improved utilisation of overproduction, while also improving overall efficiency with more integrated workstreams.
“The significance of the pulp and paper industry in our everyday
lives cannot go understated, nor can the problems that the industry is currently facing,” says Stefano Cinquina, global business line manager for pulp and paper at ABB Process Industries. “Working to tighter margins than ever, incremental gains in productivity and efficiency make a huge difference. For decades, we have been a trusted advisor to the pulp and paper industry. This deep domain expertise, coupled with our expertise in implementing digital solutions at scale, allows us to co-create a digital roadmap that unlocks a new era of efficiency for the industry.”
ABB’s team embraces what it refers to as five key pillars –operational excellence, process performance, asset performance, sustainability, connected workforce – all with embedded cyber security. ABB considers such a framework when advising industries that need to keep up the rapid pace of innovation, optimise efficiency and, in turn, minimise energy waste and reduce costs.
ABB’s Process Automation business automates, electrifies and digitalises industrial operations that address a wide range of essential needs – from supplying energy, water and materials, to producing goods and transporting them to market. With around 20,000 employees, along with leading technology and service expertise, the company helps customers in process, hybrid and maritime industries improve performance and safety of operations, enabling a more sustainable and resourceefficient future.
More information from: go.abb/ processautomation
As markets demand more environmentally-friendly raw materials, mills need to be able to change between producing kraft and dissolving pulp. This is how Andritz makes the process more accessible. PPL reports
Cellulose fibres are becoming increasingly important to the textile industry as the world moves away from fossil-fuel derived products and seeks more environmentally-friendly raw materials. Andritz has developed the A-ConFlex continuous cooking method for bleached dissolving pulp production to simplify the process for pulp producers switching between dissolving pulp and kraft pulp according to market demand.
Andritz says it has made it easy for pulp producers to switch between producing kraft and dissolving pulp, but adds that it is by no means a simple process. There are major differences between the two pulps when it comes to qualities and production processes. However, with the A-ConFlex concept, Andritz has taken a complex challenge and transformed it into a user-friendly and reliable solution.
A-ConFlex is the only potential system available on the market for continuous dissolving pulp production and is already a proven technology with 10 systems delivered to Andritz customers around the world.
Key changes to a kraft mill fibre line
There are a number of differences in the production of kraft pulp and dissolving pulp. Viscosity is the main one as it needs to be much lower in dissolving pulp than in kraft pulp. Another difference is
that the pulp needs to be much cleaner. All hemicellulose has to be removed along with all traces of metals and impurities, such as sand. The third main difference is that the water supply needs to be changed to purified waters, to ensure purity of the final pulp.
“Basically the quality of the dissolving pulp needs to be at a much higher quality level, when compared to kraft pulp,” says Michael Bloder, head of product and technology management for wet end at Andritz
To address these differences, a number of adaptations need to be made on a kraft pulp fibre line to enable the production of dissolving pulp. Sampsa Laakso, technology manager for fibre line cooking, explains: “The most important change to the fibre line is the installation of a pre-hydrolysis vessel before the digester; this is for the removal of hemicellulose. This is carried out by adding steam and heat to the chips with the reaction, then hydrolysing the hemicellulose.”
When it comes to lowering the viscosity, the process has been adapted to reduce the level by up to half at the oxygen delignification stage. Taneli Alajoutsijärvi, technology specialist for fibre line washing and bleaching at Andritz, says: “In dissolving pulp we want to have a low viscosity, around 400-500 ml/g, whereas in kraft pulp we want as high viscosity as possible, around 800-850 ml/g. So, we have to significantly reduce the viscosity
levels. This we do in various ways on the fibre line, including the possibility of introducing an ozone stage, which gives more flexibility to the control of viscosity.
“The viscosity issue is very important as, if it is too high, the dissolvability of the pulp is reduced.”
Andritz DD-Washers in the fibre line are also put to good use in the production of dissolving pulp, Alajoutsijärvi says: “Production rates are higher for kraft pulp and lower when it comes to producing dissolving pulp, so we use DD-Washers more efficiently
by adding more washing stages for dissolving pulp production. For example, there can be two washing stages per DD-Washer for kraft and three for dissolving pulp due to the lower production level. These changes can be flexible according to quality parameters and are carried out by the operators on the run.”
difference is that the drainability is far higher as the dissolving pulp is cooked for longer and does not hold as much water as in the kraft process. Also, adaptations can be made to ensure that the pulp is as clean as possible with minimised traces of metals or foreign particles such as sand.
removes heavy particles such as sand and silicates in a very efficient way.”
drying line
When it comes to pulp drying, much of the drying machine remains unchanged with just some minor adaptions. The main
“The biggest change we need to make in the drying area is to replace the post screening installed for the kraft process with a pure cleaner plant to ensure that silicates and any other heavy impurities are removed,” says Bloder. “The cleaner plant
Cleanliness of the pulp before drying is further ensured by adding a hot shower in the forming section, as well as a final berol surfactant spray. Bloder explains: “In kraft pulp production, we usually add steam to the pulp to heat it up in the forming section. However, when switching to dissolving pulp, we usually add a hot water shower instead, again to make sure that remaining metals such as magnesium and calcium can be removed properly.”
Just before the sheet enters the dryer, a berol spray is added which produces a chemical reaction with the fibre itself. This is important when it comes to the production process of dissolving pulp end user products.
Due to the changes in properties and conditions when operating with dissolving pulp, the risk of creating dust increases. The dryer is designed for minimum dust creation including, for example, the blow boxes, which are from the beginning designed and manufactured for optimum performance and runnability for different types of fibres.
When it comes to the bale finishing, the duo wrapper is usually replaced or bypassed and a so-called ‘paper wrapper’ is installed.
Once the pre-hydrolysis vessel is heated, and the chip feeding and transfer lines are in dissolving mode, the switch from producing kraft pulp to producing top quality dissolving pulp takes place. The time taken during this part of the process is dependent on the grade of dissolving pulp required. “First, we fill up the pre-
hydrolysis vessel with chips while making room in the digester,” says Laakso. “Pre-hydrolysis chip filling is the only time when the digester blowline is closed. After the pre-hydrolysis vessel is full of chips, we then start transferring the chips to the digester. At the same time the digester blowline is opened again. It depends on the digester size, but normally it takes a couple of hours before dissolving pulp comes out of the digester.”
Alajoutsijärvi continues:
“Transition from the cooking plant drying machine takes about 24 hours. It takes some time to fine-tune the process to meet the prime quality properties of the dissolving pulp. However, with the A-ConFlex concept, you can continuously control the reaction degree of the hemicellulose hydrolysis, adjust the viscosity of the pulp, and ensure cleanliness of the pulp to meet the highest criteria of dissolving pulp, such as Lyocell grade which can be produced with the Andritz concept.”
In the drying process, there are only minor adjustments to be carried out. Bloder confirms: “In the pulp drying area, there are only small adjustments, such as adapting the production and basis weight, to be made, which are usually done within the few hours before the dissolving pulp arrives in the pulp drying area.
“This is not a totally easy process, but with the A-ConFlex technology we have developed a solution that works really well,” concludes Alajoutsijärvi. “Most importantly, we can continuously make a change from kraft to dissolving pulp and back, without stopping the process.”
More information from Taneli Alajoutsijärvi by email: taneli. alajoutsijarvi@Andritz.com
The paper and tissue industries meet at Lucca in Italy in October for the annual MIAC exhibition and conferences. Pulp Paper & Logistics will be there
This year the MIAC show – the premier event in the tissue industry –celebrates 30 years of being held in the centre of the business at Lucca in northern Italy.
See the following pages for the list of exhibitors – this year they number 254 companies at the time of publication – and the floor plan for the show at the Lucca Exhibition Centre from 9 to 11 October, which offers the latest in technologies and services for those working in the paper and cardboard sectors and the tissue manufacturing world.
The show and conferences are free to participating professionals provide that they register. They will find that there will be networking opportunities for discussing the significant changes in the global paper industry.
The tissue industry has shown resilience facing these challenges by responding to customers’ needs by optimising its processes and products. These needs and the industry’s responses will be addressed in the two MIAC Tissue Conference mornings where new technology and innovation that supports the industry will be showcased.
Meeting the demand of a new industry that operates with higher standards of sustainability and lower carbon emissions requires a range of approaches, from energy saving to efficient energy production from renewable sources. In MIAC Energy these new technological approaches will
be explored.
Visiting MIAC 2024 provides a complete overview of the technology and equipment available to the paper industry sector, from the production of paper and cardboard to the converting of tissue.
As a media sponsor Pulp Paper & Logistics will be at Lucca and publisher Vince Maynard will be pleased to meet exhibitors and industry professionals alike. Email Vince at pulppaperlogistics@ virginmedia.com to make an appointment.
Located in central Italy, Tuscany is one of the world’s most popular regions for tourists with beautiful landscapes, artistic heritage and key cities. Places to see after MIAC Exhibition should include a visit to Lucca and other cities such as Pisa, Viareggio, Montecatini Terme, Forte dei Marmi and Florence.
The city of Lucca is one of the major tourist destinations in Italy, and well known worldwide for the unique Walls of Lucca that surround its historical centre.
Another famous symbol of the city of Lucca is the charming Anfiteatro Square built on the ruins of the Roman amphitheatre. Within walking distance there is the medieval Fillungo street, which is the main thoroughfare of the town centre and heart
of the city’s shopping. Other architectural and cultural attractions in Lucca include the Church of San Michele and the famous San Martino Cathedral. Lucca is rightly called ‘The city of 100 churches’.
In Europe, Lucca is the leading area for tissue production (24 per cent); Italy is also one of the leading countries in the corrugated cardboard sector.
The paper industry in Italy has 165 paper mills, producing nine million tons of paper products a year, and employs 20,000 people. Italy is one of the top four producers in Europe with annual sales of almost €7 billion.
Lucca itself is home to a number of leading companies in the paper industry that have total sales of
€2.6 billion with more than 8,000 employees.
How to get to Lucca
MIAC 2023 is located at the Lucca Exhibition Centre, Via della Chiesa XXXII 237, 55100 Lucca, Italy.
To reach the free parking of MIAC Exhibition it is advisable to look on your satnav for ‘Vitricaia street – Lucca’.
Activities covered at MIAC 2024
l Machinery and plant for the production of paper and board
l Components and part of paper machines
l Converting machines for tissue
l Instruments and systems to measure, test, control and manage plants
l Machinery and plants for water treatment
l Plants, machinery and electrical control
l Chemicals, additives and raw materials
l Machinery and plant for drying, filtration and energy recovery
l Laboratory, diagnostics, logistics, services and plant optimisation
Three conferences are offered at MIAC covering tissue in two sessions, paper and board in another and finally on the third day an energy conference. Participation is free to all conference sessions although online pre-registration recommended. A simultaneous translation service is provided.
Conference programme
Session 1.
Wednesday 9 October, MIAC Conference room
14.00: Massimo Rammuni –Assocarta
Opening remarks
14.10: Francesco Pasquini –Lucart
The tissue overview in Italy and Europe
14.30: Denny Di Vita – A.Celli Paper
Smarnip-T – The Shoe Press Excellence
14.50: Mickey Lindevall – Valmet Real results. Reel innovation. New generation Valmet Advantage SoftReel
15.10: Stefan Federling – Andritz Revolutionising tissue production. Advanced automation and digitalization in Brazil’s most autonomous plant
15.30: Sebastiano Goddi –Toscotec Digital technologies for sustainability. Innovative upgrade of TT Brain DCS
15.50: Mika Suojärvi – Trimble Forestry Europe Finding answers to questions by using process data
16.10: Dominik Stempfle – Voith Paper
Successes at Saica with predictive and AI-based monitoring
Session 2.
10.00: Massimo Rammuni –Assocarta Opening remarks
10.10: Christoph Euringer – Afry Tissue industry trends –opportunities and challenges for value creation
10.30: Giovacchino Giurlani –Valmet Tissue Converting The state-of-the-art in tissue converting technology
10.50: Alessandro Viani – Futura
Setting a goal of 1000m/min for the Away-From-Home/ Professional sector
11.10: Alberto Colombo – Omet New boundaries in the world of interfolding
11.30: Andrea Rodolfi – IBS Papertech
Advancing Tissue OOE with AIbased web inspection and unwind automation technology
11.50: Veljko Zlatanović— Stax Technologies
Folded tissue packaging solutions
12.10: Matteo Giardini – Plusline
The end-of-line revolution using Plusline’s solutions
MIAC Energy Conference
Thursday 10 October
14.00-16.30 MIAC conference room
Energy efficiency and decarbonisation paths for the paper industry
The challenges of decarbonisation for the paper sector start from energy saving and efficiency, as well as the use of renewable
sources. During the conference the latest technological advances and the most innovative solutions will be discussed.
14.00: Alessandro Bertoglio –Assocarta Opening remarks
14.10: Arne Kant – Afry
Towards climate neutrality – a plan for the Italian paper industry: a talk with paper mill representatives
14.50: Paolo Della Negra –Valmet
Is a fully electrified mill a utopian idea? It is not!
15.10: Chiara Spinelli and Giuseppe Bonforte – Renovit Technical feasibility and economic benefits in considering the New ETS2
15.30: Erika Sboarina – ANDRITZ
Revolutionizing efficiency. An approach system rebuild delivering major environmental and economic advantages
15.50: Paolo Masiero – Solar Turbines
Digital Twins – the contribution of AI for a more efficient, flexible and sustainable energy future
16.10: Francesco Del Medico –Glayx
Pshave Platform. The optimisation of energy assets in real-time
9.Septembar – Tissue Converting stand B63
ACE Tissue Technologies stand A18
A.Celli Paper stand B88/B108
Acquaflex stand B83
Aermec stand A5
Aerothermic stand B67
Africa Pulp&Paper stand MP
AFT Aikawa Fiber Technologies stand B82
Officine Airaghi stand C21
Albany International stand B107
Amotek stand B37
ANDRITZ stand B29/B43
A. Piovan stand B87/B109
A-SAFE Italia stand C34
AstenJohnson stand C7
Atlas Copco Italia stand B100
Axchem Group stand B91
Azmec stand B89
Babbini stand A21
Baosuo Paper Machinery Manufacture stand B5
Baroncini Nello stand A6
Bellmer stand B23/B49
B.F.G. Rapp.ze Ind.li stand B83
BHM Ingenieure – Engineering & Consulting stand C30
BIM Kemi Sweden stand C23
BM Group Polytec stand C49
Böttcher Italiana stand B56
Bolzoni stand A1
Bretting Manufacturing stand B2/B3/B4
BTG stand B64/B72
Buckman stand B84
Calpeda stand A5
Camozzi stand B100
Cannon Artes stand A20
Cannon Bono Energia stand A20
Carta&Cartiere stand MP
Cascade Italia stand A8
Cellwood Machinery stand B10
Centrax Gas Turbines stand C29
Centro Aria Compressa stand B100
CHT Germany stand C26
Coincart stand A14
Comertek stand B27
CPS Company stand B38
S.A. Giuseppe Cristini stand B83
CTP stand B86
Daxing Paper-Making Machinery stand C39
Henan Dazhi Paper Machinery stand C38
De Iuliis Carlo & Alfonso stand B33/B40
Debem stand A22
Deublin Italiana stand B73
Devasol stand B19
Di Marco stand B65/B71
D.M. Progetti stand C3
Dystar stand B83
E80 Group stand B58
Ecol Studio stand B66
Ecoverde stand B23/B49
Effebi stand A5
Eigenmann & Veronelli stand C6
EIL stand B24/B48
Elettromar stand B14
Elio Cavagna stand B45
El Papel stand MP
emtec Electronic stand C22
Enfasi stand C19
Enrico Toniolo stand B16
EOC Group
stand A2
Eurofins Lamm stand C44
Euroimpianti stand C2
Euroincis stand B21
Eurotronix stand B31
Euwid stand MP
Fan Separator stand B32/B41
Fife-Tidland stand B25
Filtereco stand C18
Firefly stand B98
Fis Impianti stand B111
FMW Förderanlagen stand B82
Food Contact Center stand A24
For-Tech stand C8
FPZ stand B55
F.lli Frediani stand B32/B41
Futura stand B44
Gambini stand B74
Ghetti 3 stand A10
Giotto Technologies stand B5
Giuliani stand B87/B109
Glayx stand C32
GTK Timek Group stand C20
Hannecard Tissue & Paper stand B113
Henkel stand A19
HERGEN – Máquinas e Equipamentos stand C16
Hoerbiger Italiana stand B73
IBS Austria stand B32/B41
ICM Makina Ve Muh. stand B52
IFP Packaging stand C2
IM Converting stand B22
Indexa Italia 2 stand B57
Infinity Machine & Engineering stand B15
Ingersoll Rand stand B9
Inox BF stand A15
Intecom stand C35 ipw stand MP
Italmatic Presse Stampi stand B69
Italprogetti stand B47
Jaeger stand B32/B41
Julia Utensili stand B99
Jungheinrich stand A13
Kadant Group stand B116
Kairos stand B42
Kansan Materials stand C33
Kapp-Chemie stand B23/B49
Kappa stand C14
Kawasaki Gas Turbine stand B32/B41
Kemira stand B79
La Papeterie stand MP
Lario Energy stand B28
L.B.Z. Lavorazioni Meccaniche stand C21
Le Maitre Papetier stand MP
Linde Material Handling Italia stand A3
L&M Pumps stand C25
Lotus stand C4
Maanshan Songlin Doctor Blade&Saw Manufacture stand C13
MacDue stand B117
Maflex stand B12
MAN Energy Solutions stand A26
Mapro International stand C9
Mare stand B18/B53
Mario Cotta – Zincometal Group stand B114
Martin Lohse stand B82
Gruppo Martinelli Industriale stand A5
Maxima stand B85
Metissue
Mevas
Microline
Mingazzini
Mink Bürsten
Movingfluid
Multipack
MWN
Zhejiang Onepaper Smart Equipment stand C37
Oradoc MTK stand B120
Organik Kimya stand C27
Overmade stand B1
Paper Advance stand MP
PaperAsia stand MP
Paper Desk stand MP
Paper Market stand MP
Paper Market.eu stand MP
Paper Middleast stand MP
Paper Technology – PITA stand MP
Paper360 stand MP
Paper First stand MP
Papnews stand MP
Parason Machinery stand B87/B109
PastaePapel stand MP
Paul Wegner stand B82
PCHEM stand C10
PCMC – Paper Converting Machine Company stand B112
Petrofer stand B83
Pfannenberg Italia stand C28
Plastylenia stand B76
PL di Lazzari stand A22
Plusline stand B6
Pneumax stand C24
PNR Italia stand A25
Polimek stand B87/B109
Powermade
stand B1
Proxitalia stand C15
Pulp Paper & Logistics stand MP
Pulsar Engineering stand B39
Foshan New PURUI Industrial Textile stand C41
Renova stand B103
Renovit stand A16
Replus Tissue stand B24/B48
RIF stand B59
Robopac stand B75
Robuschi stand B9
Rolco Europe stand B46
Rotocalco Mediterranea stand B97
Runtech Systems stand B9
Rynek Papierniczy stand MP
SABA Automation stand B95
Sadas stand B122
Sael stand B80
Safem stand C17
Sauer stand B30
Saueressig stand B13
S.B.R. Solutions stand C14
SchäferRolls stand B78
SDF stand B50
Sei Sistemi stand B36
Senning stand B2/B3/B4
Service AMS stand C46
serv-o-tec stand C43
Sicem Saga stand B35
Sicma stand B81
Sinergy-SL stand B80
Slittec stand C45
Solar Turbines stand B20
Solenis stand B23/B49
Shanghai Soontrue Machinery Equipment stand C42
Sorgato stand C36
Sotemapack stand B75
Spares Service & Machinery stand B90
ST Macchine stand B106
STAX Technologies stand B112
Stiavelli Irio stand A4
STILL stand A6
S.TO.R.I. stand B92/B104
Sulzer Pumps stand B32/B41
Svecom-P.E. stand C1
Tamburini stand C5
Tasowheel stand B87/B109
Tau Machines stand B118
Techno Paper stand B82
Technowrapp stand B51
Techpap stand C47
Tec.Mec. stand B17
TC Rolls & Covers stand B101
Tecnofer Ecoimpianti stand C48
Tecno Paper stand B54
Tip95 stand B119
Tissue Tec Sales & Service stand B26
Tissue360 stand MP
TissueMAG stand MP
Tissuenet stand B34
TKM stand B11
IMA TMC stand B68
Toscana Spazzole Industriali stand A12
Toscotec stand B92/B104
Toyota Material Handling Italia stand A11
Trimble stand C11
Tubicom stand B62
Turkiye Kagit Sanayii stand MP
Unimatec stand B121
Vakuo – vacuum pumps and systems stand B110
Valmet stand B93/B102
Ve.Car stand A3
VEGA
Mondi has been recognised with a number of awards at this year’s Crescents and Stars for Packaging competition in Turkey.
Commenti ng on the successes, Markus Gärtner, chief executi ve of Mondi Corrugated Packaging, said: “We are incredibly proud of our team’s achievements and the recogniti on we have received at the Crescents and Stars for Packaging 2024. These awards are a testament to our relentless pursuit of excellence and our commitment to providing our clients with sustainable, innovati ve packaging soluti ons that not only meet, but exceed their expectati ons.
Mondi’s winners are: Koala Display, Mondi Adana; Corrugated Packaging for Premium Umbrellas, Mondi Ansbach; Doorbell Guard,
Koala Display is a pioneering corrugated packaging solution for potted flowers, the Koala Display is 100 percent recyclable and provides a visually appealing, practical alternative to traditional wooden stands
British packaging and equipment
manufacturer Antalis is offering MetsäBoard Prime FBB EB, a recyclable and compostable barrier board for fresh food packaging.
Using a dispersion barrier, the coated paperboard is a costefficient replacement for singleuse plastic packaging. Easily recyclable in paper or paperboard waste streams. MetsäBoard Prime FBB EB is ideal for premium packaging, especially in food and food service uses, where a medium grease and moisture barrier is needed.
Prime FBB EB is a bright OBAfree board that is lightweight, strong and has excellent printability. It is made without fluorochemicals and optical brighteners (OBA), making it suitable for direct food contact.
MetsäBoard Prime FBB EB is biodegradable and can be composted. The industrial compostability certification complies with DIN EN 13432 and ASTM D6400 standards, while the home compostability certification complies with NF T 51-800 – all DIN CERTCO certificates. It accelerates
Mondi Bad Rappenau; Eco Cage Paper Basket, Mondi Bupak; Plate Protector, Mondi Eschenbach; TopLock Box, Mondi Gebze; Beer Arena, Mondi Grünburg; Bott le Protector, Mondi İzmit; Display Guard, Mondi Tire; 3-in-1 Separator, Mondi Tire; and Beer Cool Box, Mondi Warsaw.
Operati ons chief at Mondi Corrugated Soluti ons Armand Schoonbrood added: “Each of our award-winning products refl ects our strategy to integrate customer feedback into our design process, ensuring that we address both the practi cal and environmental challenges our clients face. This recogniti on fuels our drive to conti nue innovati ng and leading the industry towards
Designed to resemble a football stadium, ‘Beer Arena’ is distinctive packaging for beer cans and bottles, created for football fans
more sustainable and effecti ve packaging soluti ons.”
The winners will be presented with gold, silver and bronze trophies at the Crescent and Stars for Packaging 2024 awards ceremony to be held in Istanbul later this year.
More informati on from www. mondigroup.com
MetsäBoard Prime FBB EB from Antalis is biodegradable and can be composted
from www. antalis.com
To help drinks brands eliminate plastic from their supply chains, James Cropper has launched tops and bases for inner bottle packaging made from moulded fibre.
Specifically designed for the champagne and whisky market, the tops and bases are made from Colourform. Using bespoke moulds, the tops and bases fit the
bottle shape and are placed within rigid boxes to ensure product protection.
Replacing traditional plastic and foam parts, the fibre products have been developed to support brands in their efforts to meet the European Commission’s proposal to regulate packaging waste, which states that (a) all packing shall be recyclable by 2030 and (b) weight and volume of packing
are reduced to the minimum necessary while still ensuring functionality.
The Colourform inserts help brands reduce, or even eliminate, non-sustainable materials from their supply chain, and are said to be five times lighter than the alternatives, thus helping reduce carbon emissions in transit.
The tops and bases are 100 percent recyclable, with no
dismantling required, making it easy to dispose of the product quickly and correctly with household recycling.
As with all James Cropper Colourform products, the tops and bases are offered in white, black or bespoke shades on request. Customers can also choose to emboss or deboss a logo.
More information from www. jamescropper.com
A partnership between kraft paper maker Mondi and Italy’s CMC Packaging Automation is aiming to meet growing demand for sustainable eCommerce paper and packaging.
By building synergies between CMC’s packaging on-demand technology and Mondi’s expertise in sustainable kraft paper products, the partnership says it is primed to change the market with innovative packaging alternatives.
“We are thrilled to join forces with Mondi, a company that shares our unwavering commitment to sustainability and innovation,” said Luigi Russo, general manager of CMC Packaging Automation.
“This partnership enhances our machine performance and enables us to provide our customers with responsible and sustainable eCommerce packaging solutions that meet the highest performance requirements and standards.
After successful trials with Mondi kraft paper on our machines, we are confident in its exceptional runability, ensuring our customers receive a seamless and efficient solution.”
Mondi’s wide range of paper products (such as Advantage eCom Kraft, EcoVantage eCom Mailer Pro and EcoVantage eCom Mailer) is produced to operate on CMC’s machines.
“It’s an honour to become CMC’s preferred paper partner,” said Silvia Hanzelova, sales
director for speciality kraft paper at Mondi. “Our joint efforts will focus on creating innovative kraft paper solutions that support the circular economy and meet the needs of the eCommerce sector. Together, we can drive significant positive change in the packaging industry, combining our in-depth technical kraft paper knowledge power and our partner CMC’s long history of machine expertise.”
More information from www. cmcsolutions.com
Fibre-based, e-commerce packaging has been developed by DS Smith with an innovative secondary use for Funzy, a manufacturer of modular play sofas for children. The Funzy packaging, intended for online retail, has been designed with a range of secondary uses for consumers. While corrugated cardboard provides a protection for the customer’s products during transportation and storage, and it can also be converted into a shelf and toys for children.
The bottom flap of the packaging is comprised of diecuts for children to assemble into plug-in figures, including rockets and rocking horses, and the craft-friendly material can then be personalised with paint and stickers.
Furthermore, the compact corrugated cardboard packaging can be transformed into a shelf for a child’s bedroom or play area. Overall, the packaging design is intended to create a learning process for both children and adults as they are exposed to the possibilities
provided by this simple concept in upcycling.
Christian Emeka, supply chain manager at Funzy, said: “We are impressed by the initiative, the high-quality advice and creative solutions that the team at DS Smith have given us. We finally have beautiful fibre-based and recyclable packaging, and this embodies our core brand values. Our customers will also be thrilled and after successful test shipping, the DS Smith packaging is ready for series production”. More information from www. dssmith.com
‘Pre-commercialisation’ of Muoto, the three-dimensional wood-based packaging developed by Metsä Spring, has started for a small number of pilot customers.
Suitable for a range of applications Muoto packs can be used for anything from takeaway food to industrial packing. Its fibre composition ensures safety and non-toxicity, while being lightweight, durable and sturdy.
Muoto products have been made at a demo plant operated by the innovations arm of Metsä Group and Valmet at Äänekoski in Finland since May 2022 and if the results of pre-commercial sales are successful, in 2025, Metsä Group will be in a position to evaluate investing in a commercial manufacturing plant.
“We have been extremely pleased with the early results of Muoto. In wood-based product development, it’s quite rare to have a product ready after only a few years of development. Designed for durability and safety,
Muoto is ideal for a wide range of uses, from serving dishes to food containers, so we are ready to expand co-operation with pilot customers,” said Jarkko Tuominen, vice-president of projects at Metsä Spring.
A key benefits of Muoto production process is that it removes many of the supply chain steps that are required for other types of packaging. In the Muoto process, pulp slurry is fed into a mould, formed, dried and cut, thereby making products for shipping directly
to customers, ready to be used in food packaging. The process also requires a minimal amount of water and other resources on one production line; it is largely automated and uses machine learning in multiple touchpoints, making it safe and reliable.
“By offering early access, we aim to gather valuable feedback and insights from customers to further refine our product. Together, we can explore new applications based on the market and customer needs,” explained Tuominen.
Due to the EU directive on single-use plastics, food packaging manufacturers in Europe are searching for affordable and more sustainable alternatives to current packaging solutions. In addition, the European Commission’s proposal for the Packaging and Packaging Waste Regulation (PPWR), when accepted, will force companies to promote circularity and reduce packaging’s environmental impact.
“At Metsä Group, we are constantly looking into potential innovations that could bring more wood-based alternatives into everyday products, thus replacing, among others, various fossil-based products. With Muoto, we can offer an alternative to the plasticdominated market, proving that functionality, responsibility, profitability and design can go hand-in-hand,” added Niklas von Weymarn, chief executive of Metsä Spring.
More information from www. metsaspring.com
Cardboard and paper packaging maker DS Smith is developing a corrugated board collator for beverage and food cans that it says will offer better recycling and security properties than other secondary packaging options. The product is being developed at the company’s research and development facility at Redditch in the UK.
DS Smith’s Paper Hood will be able to pull together multiples of up to 24 cans, says Ashwin Moorthi, head of design and innovation. The manufacturer is in discussions with its equipment engineering partners to build machinery to apply the system.
The Paper Hood will be made from one type of corrugated board, enabling it to be
recyclable in a single waste stream without having to be broken down, as is said to be the
case with collators made from multiple materials. It will also be stronger and hold cans more securely in transport and on shop shelves.
DS Smith’s decision to make the ‘Paper Hood’ was driven by its brand customers’ needs to meet imminent regulations that will put more emphasis on the recyclability and recycled content of products and packaging. It recently launched new packaging in Eastern Europe for Carlsberg’s bottles with rounded corners that were less prone to damage (as pictured).
More information from www. dssmith.com
Mark Your Calendars
In time for Christmas, Celebration Packaging has launched a range of EnviroWare doublewall paper cups for hot drinks featuring green and red designs.
“New for Christmas, 2024, and available to order now, these new designs are perfect for serving up festive takeaway hot drinks,” said Nick Burton, managing director of Celebration Packaging, which is based at Burton-on-Trent in the UK. “Customers can choose from classic Holly Green and vibrant Santa Claus Red colours with white Christmas icons.”
Delivering superior insulation and hand comfort, the cups are available in 8oz and 12oz sizes, with optional CPLA and bagasse sipper domed lids.
Made from FSC certified paper, the double-wall cups are lined with a PLA plant starch moisture barrier. They are commercially compostable (DIN EN 13432:200012) and certified recyclable in standard paper mills.
“When we created the EnviroWare brand, over 17 years ago, our declared mission was to seek out more sustainable packaging solutions,” added Burton. “We have always believed that when sourcing sustainable
The highest accolade in packaging – an Oscar – was awarded to DS Smith at Agra, the 62nd International Fair of Agriculture and Food in Slovenia held in August.
A jury of experts selected DS Smith’s ‘Protection for Car Wheel Carriers’ as the winning entry for its properties as a sustainable pack using fibre-based corrugated cardboard. The product is designed to replace protective expanded polystyrene inserts for the storage, transportation, and delivery of heavier industrial products. The design optimises space utilisation, offers easy assembly and the possibility of reuse or recycling after use.
In addition to the winning entry, DS Smith’s ‘Universal Protection for Household Blenders’ packaging design
was nominated for an award. Replacing polystyrene inserts with corrugated cardboard, it also uses less materials and enables
packaging, the provenance of the raw materials is paramount, but ensuring that it can be properly disposed of at its end-of-life is equally important.
“Through certification by respected and established companies, we can confirm that the products we sell are: suitable for direct contact with food and drink; made from sustainable resources where applicable; suitable for recycling and/or can be composted either industrially or at home.
“Hot drinks are takeaway best-sellers during the Winter, so adding some festive cheer, while at the same time making a sustainable choice, is really heartwarming,” he concluded.
More information from www. packagingfood2go.co.uk
an increase in the volume of products that can be transported, with an overall reduction in CO2 emissions for the supply chain process.
Gabriel Balogh, managing director of DS Smith Slovenia, said: “We are extremely proud to receive the Slovenian Packaging Oscar award and to have two of our packaging solutions among the top five Oscar nominees. This is a testament that we are on the right path in developing sustainable packaging solutions from renewable sources and following circular economy principles.”
More information from www. dssmith.com
Arange of ‘natural’ plant-based food products has been launched by London-based Marigold Health Foods in the UK using Sonoco’s latest recyclable paper-based packaging.
Marigold’s range includes Engevita nutritional yeast, bouillon, gravy, stock cubes, sauces and plant-based meat and fish alternatives.
The packaging matches Marigold’s commitment to offering high-quality ingredients free from artificial additives and palm oil, catering to healthconscious consumers who value sustainability and ethical production.
Sonoco’s packaging is said to exemplify Marigold’s commitment to sustainability and innovation, setting a new standard in the market.
The EnviroCan, designed by Sonoco with a cardboard bottom, is easily recycled by consumers at their kerbsides while maintaining
the original functionality to preserve and protect the food.
Following a two-year development process, the new pack is said to represent a significant advance in recyclable packaging technology. The previous packaging featured a cardboard body with a tinplate base that presented recycling challenges.
By investing in new machinery, Marigold has been able to replace the metal end with a paper-based alternative developed by Sonoco,
resulting in a next-generation, allpaper body and base. This change not only enhances the packaging’s environmental footprint, it also meets the requirements for key UK and European packaging and recycling regulations.
Marigold’s new packaging, made primarily from paperboard with secondary materials such as an aluminium seal and a removable plastic LDPE lid, integrates innovative technology in material design and production. The EnviroCan’s paper bottom, part
of the new design, ensures food safety and optimum shelf-life by providing an oxygen and moisture barrier.
With more than a 20 percent reduction in packaging weight, Marigold has been able to dramatically reduce its transport fuel consumption. The packaging also boasts a lower environmental footprint than other rigid packaging types, while being produced from sustainablysourced, recyclable materials.
Marigold’s transition to a paper base aligns with its commitment to environmental stewardship. The can body is made from 95 percent paper and primarily sourced from recycled materials (60 percent post-consumer recycled fibre). The new packaging supports the circular economy and can be recycled in the UK’s paper waste stream. The remaining 5 percent of the packaging consists of an inner liner, which is essential for protecting the product.
More information from www. sonoco.com
Algro Volume, a premium paperboard, said to be ideal for demanding and durable packaging, and graphic products, is the latest addition to Sappi Europe’s Algro paperboard family.
Produced the Sappi’s Maastricht mill in The Netherlands, Algro Volume has a full-coated top side and lick-coated reverse side. It features odour neutrality, purity of toy safety (heavy metal content) and suitability for direct
food contact according to BfR XXXVI, FDA, and Austrian food legislation. Made of 100 percent virgin fibres, it is fully recyclable and can be supplied as FSC Mix Credit or 100 percent PEFCcertified upon request.
Luis Mata, director of packaging & dye sublimation at Sappi Europe, emphasised the potential of the new product:
“Algro Volume is an outstanding board that delivers against every challenge, expertly designed
to fulfil the rigorous physical demands typically reserved for solid bleached boards (SBB). The multiform base composition optimises stiffness and bulk, and together with Sappi’s unrivalled coating capability ensures exceptional printing and finishing performance for your applications.”
Available in both sheets and reels, Algro Volume supports a variety of finishing techniques, including embossing, varnishing
and foil lamination. End uses include promotional material, covers, cards, tags and tickets, and packaging for pharmaceutical, confectionary, food and beverage, as well as beauty and personal care products.
Algro Volume is available in a range of weights ranging from 220 to 380 g/sqm and is suitable for offset, flexo and screen printing processes.
More information from www. sappi.com
With consumption of ready-todrink (RTD) beverages growing by more than 100 percent in 2023, according to NielsenIQ research, now is the time to capture consumers’ attention with creative, eye-catching, and planet-friendly packaging, says Suzy Gedney, UK marketing manager at paper maker Smurfit Westrock.
Suzy
Gedney
Refreshing a company’s beverage packaging has the potential to boost sales and brand loyalty, especially among the increasing number of ecoconscious consumers.
Smurfit Westrock has explored four key ways to craft captivating drinks packaging that it says will ‘wow’ customers. It also highlights examples of stand-out beverage companies that have successfully revamped their packaging to maximise their appeal in the market.
Here are the four ways to create captivating drinks packaging:
1. Cater for convenience-craving consumers
With busy lives to contend with, consumers increasingly want convenience, which has led to the rise in RTD products. Around 37 percent of adults enjoyed RTD alcoholic drinks in 2022 (Simpson Beverages), particularly those aged 18-34, highlighting their rising popularity. Consumers want to enjoy a premium and delicious drink, but with the convenience of it being easy to carry and enjoy on the go. With the right packaging, RTD products are able to meet this need, offering a simple drinking experience without the need for preparation beforehand, multiple ingredients or an abundance of packaging waste.
2. Align with consumer attitudes
Consumers increasingly prioritise the environment when they shop and drinks packaging needs to reflect that changing attitude. 94 percent of consumers think it is a brand’s responsibility to create products that are not harmful to the earth and 75 percent of consumers are more likely to purchase from brands that offer green or sustainable products (Deloitte Global).
Consumers are actively choosing brands that align with their ecoconscious values, opting for products with eco-friendly packaging made from recyclable, biodegradable or reusable materials. If a manufacturer’s drinks packaging isn’t kind to the planet, it risks being overlooked by eco-conscious consumers, who now expect sustainability when shopping. Switching to environmentally-friendly packaging is essential to remain part of the competitive market and give consumers what they want.
3. Stand out with simple but striking designs
Beverage packaging has a huge impact on consumers’ purchasing behaviour. Striking packaging designs that stand out not only grab a customer’s attention, even when a product is hidden amongst other RTD products, but also boosts the product’s perceived value.
“Now is the time to capture consumers’ attention with creative, eye-catching, and planet-friendly packaging,” says Suzy Gedney, UK marketing manager at paper maker Smurfit Westrock
This ‘premiumisation’ encourages consumers to choose it rather than other options on the shelf. Premium packaging can elevate a drink from a simple beverage to a luxurious, refreshing experience.
An attractive drinks packaging design also enhances the unboxing experience, especially if it is a limited-edition design or a promotional pack.
With consumers looking for refreshing and exciting beverages to enjoy, visually appealing packaging can help drive sales and create brand loyalty. This is even more important now that unboxing experiences are often shared on social media, which has led to a massive 82 percent of people stating that they are persuaded to buy a product or service by watching a video online.
4. Keep messaging consistent
There are a lot of packaging trends out there, but consistency cannot be overlooked.
Clear, consistent and minimalist messaging and designs are essential elements in drinks packaging. Using consistent packaging helps establish a strong brand identity, making it easier for consumers to recognise and trust an RTD product.
It makes sure that a company’s message is obvious and unmistakable, showing consumers it is a familiar brand they can rely on time and time again.
Some 72 percent of shoppers are influenced by a product’s packaging design (Ipsos) and a minimalist design helps a product to stand out without overwhelming the consumer. This is particularly effective in grabbing the attention of busy shoppers, who have to make quick purchasing decisions based on only seeing a product for a moment or two.
Instead of trying to add a whole host of different features to packaging drinks design, it is best to keep things simple by focussing on the value of the product and its benefits.
After all, 31 percent of consumers are interested in purchasing premium soft drinks with additional functional benefits such as ingredients that provide mood-boosting, immune-strengthening qualities (The Grocer) and displaying this information on packaging could help to drive important sales.
More information from www.smurfitkappa.com
Chilean health food producer Soy Silvestre has adopted compostable, flexible packaging to protect Wheatgrass shots, a novel drink with special nutritional content.
Wheatgrass shots constitute an important part of Soy Silvestre’s range and were previously packaged in 30ml plastic pots, wrapped by hand. This is a significant step as liquid products are notoriously difficult to pack, particularly in compostable packaging.
The packaging is provided by Green Heart Solutions, a Chilean packaging converter, which offers
a range of compostable packaging products. The high-performance pack for Soy Silvestre includes a high barrier cellulose NatureFlex film layer sourced from Futamura,
laminated to a biofilm for hermeticity. It enables Soy Silvestre to produce small flexible sachets.
The pack allows for automated filling and effectively protects the fragile drink through its life cycle: from the wrapping of the liquid product to the freezing stage, through distribution and then the defrosting process. Not only is the product protected for its four-month shelf life, but being compostable, the impact of the packaging on the environment is greatly reduced.
Wheatgrass shots from Chile’s Soy Silvestre now come in compostable, flexible packaging
Bottle caps using Dry Molded Fiber technology are now being tested with the Bottle Collective. This innovative packaging PulPac and PA Consulting (PA), the global innovation and transformation consultancy, marks a significant advance for fibre-based packaging, offering brandowners a sustainable alternative that meets consumer demands for environmentally-friendly products.
The introduction of fibre-based caps is said to be a game-changer for the packaging industry, supporting the transition to higher fibre content in packaging. By replacing traditional plastic
caps with those made from Dry Molded Fiber, companies are able to significantly reduce their environmental footprint while providing consumers with a more sustainable choice. This marks the first stage of innovative developments in fibre-based caps and closures from PulPac and PA, with an upcoming range to be unveiled in the near future.
The Bottle Collective, including members such as Diageo, Logoplaste, Haleon and Sanofi, is a collaborative initiative founded by PulPac and PA Consulting, which aims to bring Dry Molded Fiber bottles to market at scale by 2025.
Soy Silvestre has been offering quality health supplements based on natural ingredients for eight years, with an ethos to promote its connection with nature and healthy habits.
More information from www. futamuragroup.com
A range of shock-proof mailing envelopes launched by Mondi has been developed in collaboration with eCommerce giant Amazon.
Mondi Group’s eCommerce director Nedim Nisic said:
information from www.pulpac. com
The mailer is fully paper-based, made from renewable resources, recyclable in the paper waste stream, and has a feature that eliminates the need for plastic bubble inlays
The Protective Mailers are made from Mondi’s strong and lightweight kraft paper and a fibre-based open-flute material.
Commenting on the launch,
“eCommerce customers are constantly looking for protective, sustainable packaging in which their products are safely delivered to their consumers.
“We have risen to this customer challenge with our new fully paper-based solution – the Protective Mailer. This solution can handle any product, both fragile and bulky, from small electronics to books to fashion accessories and much more.”
US-based speciality chemical producer
Solenis is collaborating with German printing technology leader Heidelberger Druckmaschinen AG to develop more cost-effective ways of integrating barrier coatings for paper packaging directly within existing flexographic printing processes.
Barrier coatings are used to repel hot and cold liquids, oils, greases, and water vapour in paper packaging.
With this innovation, packaging manufacturers will be able to use the Heidelberger portfolio of flexographic machines to printapply Solenis’ barrier coatings. This expands the possibilities for flat sheet paper and inline web-fed flexo applications with improved product performance and better production efficiency.
Specialised print-applied coatings from Solenis include barrier coatings for board material, flexible packaging and cupstock production, as well as anti-slip technical coatings for industrial, shipping and
Barrier coatings that increase the functionality of paper-based packaging are being applied using flexography, replacing plastics films such as PE
container applications.
For fresh food and e-commerce corrugated packaging, barrier coatings can be print-applied to avoid the use of traditional polyethylene (PE) lamination and paraffin wax, making the material easier to recycle.
For cupstock production, floodcoating barrier protection on cold and hot cups is carried out on current equipment and eliminates the need for polyethylene (PE) film lamination to improve resistance.
For a registered print approach, Solenis’ patented heat-sealing
coating can be applied easily on conventional cup converting lines to reduce materials and lower costs.
The collaboration addresses the growing demand for more sustainable paper packaging that reduces the use of plastics through environmentally-friendly alternatives with improved barrier functionality.
“Packaging companies face increasing pressure to optimise processes while meeting ambitious sustainability goals,” said William Kuecker, Senior
Director of Strategic Marketing at Solenis. “Our collaboration with Heidelberger pushes the boundary of what’s possible for packaging manufacturers. With this combination of cutting-edge printing technology and innovative, high-performance specialty coatings, packaging manufacturers can enhance operational efficiency and product performance while meeting the rising demand for sustainable products and processes.”
Dr David Schmedding, board member responsible for technology and sales at Heidelberger added: “With our Boardmaster web flexo technology, we are expanding our reach into the high-volume flexible paper segment, targeting the food industry with solutions focused on efficiency and sustainability. This collaboration with Solenis allows us to optimize application processes and technology together to better serve our customers.”
Solenis offers a broad portfolio of barrier coatings, including environmentally friendly PFASfree oil and grease resistance technology.
The provision of advanced water treatment systems for paper and pulp mills has been enhanced by an agreement signed between Valmet and Flootech, which is based at Järfälla in Sweden. Lack of fresh water supply is becoming a challenge for
many pulp and paper producers worldwide, which emphasises the need of water saving and water treatment equipment. Re-using and/or recycling process effluent is essential today for most companies. Through the partnership
Flootech will provide technical and commercial expertise to Valmet’s customers. The offering will include water treatment and recycling solutions, process water treatment, effluent treatment and reuse as well as sludge dewatering.
“Water scarcity and efforts to reduce environmental footprint are driving the need for more advanced solutions to reduce, re-use and recycle effluents from the pulp and paper industry.
The partnership with Flootech enables us to deliver cost
Stop collecting paper samples!
Improve your press section efficiency! SmartScan™ contactless sensor accurately measures paper web dryness after the press section 24 hours a day, 7 days a week. Using a proprietary microwave technology, it is developed to overcome the typical limits of the NIR (near-infrared) sensors. SmartScan™ is available both for fixed point positions or traversing web scan
To save hundred of thousands of Euros in energy costs, stop collecting samples, choose the safe accuracy of SmartScan™ technology.
competitive and efficient water treatment solutions to our board, paper, and tissue customers. It is a good strategic fit with Valmet’s climate program, and we are happy extend the collaboration to a partnership with the leading provider of water expertise and technologies across the globe,” says Petri Rasinmäki, president of the paper business line at Valmet.
Mikko Siivonen, chief executive of Flootech, commented: “There is a growing requirement for more advanced solutions to enhance clean water quality,
process water recycling and fibre recovery, to treat and extract energy from wastewater, as well as to champion the reuse of water. Costs associated with the environmental impact and regulation, sourcing fresh
water, and the growing price of energy have all increased the importance of optimising pulp and paper mills’ water cycle and water footprint. We are pleased to strengthen our long and successful cooperation with
Software that was developed by Körber to improve shopfloor manufacturing performance and productivity is now controlled by Valmet after the completion of an agreement in August.
Valmet holds the majority of the shares and FactoryPal will continue operating as an own legal entity under the existing brand. The addition of FactoryPal will further strengthen Valmet’s offering of advanced Industrial Internet solutions and digital services to support customers in the tissue industry. The agreement follows Valmet’s acquisition of Körber Business Area Tissue in November 2023.
FactoryPal is said to enable paper mill teams to achieve seamless operations by generating and utilising high-quality data combined with a state-of-the-art user experience and advanced artificial intelligence (AI). Acting as an AI ‘co-pilot’, the application uses data and AI to transform operational challenges into
Valmet by forming a partnership agreement that enables us to provide complete water treatment solutions to close water loops together.”
Flootech is a subsidiary of Nijhuis Saur Industries and offers a range of water treatment technologies, process solutions and services for industrial and municipal sectors and has more than 50 years’ experience.
A typical project was the installation by Flootech of a water treatment plant at Metsä Group’s Kemi Bioproduct mill, which was completed in 2023.
opportunities, optimising many aspects of production.
“FactoryPal is an excellent complement to Valmet’s Industrial Internet solutions and digital services. With the addition of extensive competence and advanced digital services we can support tissue producers to further improve production efficiency and preventive actions. We are eager to take the next step in digitalization of tissue mills,” says Samppa
Ahmaniemi, VP in the tissue converting business unit at Valmet.
Nadja Hatzijordanou, chief executive of FactoryPal, commented: “Our partnership with Valmet marks a significant step towards becoming the leading AI co-pilot for shop floors. By harnessing our combined expertise in machinery, process, and advanced digital and AI solutions, we are committed to delivering unparalleled customer value in
“FactoryPal is an excellent complement to Valmet’s Industrial Internet solutions and digital services,” says Valmet’s Samppa Ahmaniemi
Tissue and beyond.”
Dr Christian Schlögel, Körber Group Executive Board member and responsible for the Business Area Digital, added: “We are very proud of the successful development of FactoryPal as one of Körber’s digital ventures so far. The agreement with Valmet will open additional market and growth opportunities. I am looking very much forward to the future collaboration.”
Suzano’s new pulp mill in Brazil was successfully started up by Andritz in July.
When fully operational, the mill at Ribas do Rio Pardo, Mato Grosso do Sul state, will be the world’s largest single-line eucalyptus pulp mill with an annual production capacity of 2.55 million tons.
It will also be one of the few pulp mills in the world to run without fossil fuels, using as raw material 100 percent of planted trees. It will be energy self-sufficient, producing surplus ‘green’ power for its local suppliers and the national grid.
Commenting on the start-up of the Cerrado project, Maurício Miranda, director of engineering at Suzano and responsible for the construction of the mill, said: “This new pulp mill will increase our production capacity while significantly reducing our environmental impact, supporting our financial and environmental goals. The cuttingedge technologies applied are in line with our commitment to sustainability and innovation.
Trust and reliability are essential in a project like this, and we found both in our partnership with Andritz.”
Andritz has revealed the full specification of the mill’s processes. It supplied leading technologies for fibre production and chemical recovery on an EPCC basis (engineering, procurement, construction and civil works). The process equipment included a complete wood processing plant with five chipping lines,
the world’s largest single-line fibreline (with a capacity of more than 8,000 adt/d) with washing and bleaching technology based on DD-Washers, a pulp drying system with two lines, a black liquor evaporation plant, a Herb recovery boiler to maximise steam production for power generation, a biomass power boiler based on the high-performance EcoFluid bubbling fluidized bed technology, and a complete white liquor plant with causticizing plant and two
lime kilns.
To enhance the mill’s environmental performance, Andritz is also supplying gasification plants to enable fossil-free operation of the lime kilns and a SulfoLoop sulphuric acid plant to produce commercial grade sulphuric acid from the mill’s concentrated odorous gases and elemental sulphur. This will recycle sulphur from the waste streams and make the mill completely selfsufficient in sulphuric acid.
South Korea’s Moorim Paper, has streamlined the procurement processes at its three mills –Moorim Ulsan, Moorim Jinju and Moorim Daegu – utilising Voith Paper Webshop’s ordering process.
“The easy order management provided by Voith has significantly streamlined our procurement
process. We are pleased with the efficiency and reliability of the platform,” said Se-hwan Cheon, purchasing manager at Moorim Paper.
The order from Moorim Paper also includes a range of fabrics and sleeves, underscoring the platform’s capability to facilitate complex orders across a number
of mills, enhancing operational efficiency and customer satisfaction.
Al Choi, sales representative for Voith, commented: “Voith is committed to providing innovative solutions that meet the evolving needs of our customers. The successful execution of this order for Moorim Paper demonstrates
the effectiveness of our Webshop in enabling seamless transactions and driving operational excellence.”
The Voith Paper Webshop offers what it describes as a user-friendly e-commerce platform for easy order management, providing customers with a convenient and efficient procurement experience.
Work has started on the conversion at Mondi’s recentlyacquired paper mill at Duino in Italy of a paper machine to produce high-quality recycled containerboard.
The €200 million investment followed the mill, near Trieste, being bought from Burgo in January 2023.
The investment is said to be part of Mondi’s €1.2 billion of investments in organic growth projects aimed at meeting the growing demand for sustainable packaging, enhancing its product offering, and reducing its environmental impact.
Following the machine’s expected start up in 2025, it will be capable of producing 420,000 tonnes of recycled containerboard and will be Mondi’s widest
recycled paper machine at 8.5 metres. Where possible, the mill will source materials locally to contribute to the local economy, reduce greenhouse gas emissions through shorter transport distances and strengthen supply chain resilience.
“We are excited about the progress of the Duino investment project and the opportunity this
provides our growing packaging business,” says Andrew King, chief executive of Mondi Group. “This containerboard machine will strengthen our backward integration and provide us with security of supply to better serve our customers.”
Markus Gärtner, chief executive of Mondi Corrugated Packaging, added: “Our investment in Duino
Xuan Mai Paper Co in Vietnam reports that the tissue rewinder supplied by A.Celli Paper at the beginning of 2024 is running in line with its expectations.
The E-Wind T100 rewinder – equipped with a winding shaft extractor, a dust removal system and a function for using 12-inch cores – has been used since the start up to process 2.85m-wide tissue paper with basis weight from 13 to 45 gsm at an operational speed of 1,900 metres per minute.
Luong Nhu Huynh, director of
Xuan Mai Paper Co, said: “We are satisfied by the results achieved thanks to the A.Celli team and to the rewinder itself: we produced the first roll in mid-June and its quality was already really good. We are looking forward to work again with A.Celli in the future.”
Founded in 2004, Xuan Mai Paper manufactures medium board and testliner for packaging in Ho Chi Minh City. In 2020 Xuan Mai entered the tissue paper business, producing its new products under the Adomi and Van An brands.
allows us to meet the increasing demand for sustainable solutions across Central Europe, the Mediterranean area, and the local Italian market. The project team is currently preparing for the upcoming construction works, with a new recycled fibre plant, wastewater treatment plant and the associated infrastructure and warehousing.”
Astrategic partnership has been formed between DS Smith and ABB to upgrade the automation systems at the paper maker’s Lucca Mill at Porcari in Tuscany, Italy, which is being expanded with a third tissue line.
ABB describes itself as an electrification and automation technology leader enabling a more sustainable and resourceefficient future, a philosophy shared with DS Smith that is being applied in the manufacture at the mill of a range of packaging grades, serving food, ecommerce, retail and industrial sectors.
The Lucca Mill operates two paper machines, with a third machine under construction. A market leader in containerboard,
it is the biggest mill of its kind in Italy, and uses recovered fibre as its feedstock.
“It’s gratifying to work for a company that sees that we can make a great contribution both to customers and to society, by applying our know-how to societal challenges,” said Fabrizio Sodini, power plant manager at DS Smith.
“At DS Smith, sustainability is integral to our circular business model. We are taking action to lead the transition to a low carbon, circular economy by designing out waste, keeping
materials in circulation, improving energy efficiency, investing in new technologies and switching to renewable energy solutions. Working with likeminded companies, such as ABB, is a massive help in achieving our ambitious Now & Next sustainability goals.”
When the mill needed to upgrade the automation systems in the power plant, which provides energy for the paper production as well for the national grid, management asked ABB to make a proposal. ABB’s process
Specialist Japanese paper
manufacturer Kami Shoji Co has taken delivery of ABB’s automated L&W Fiber Tester Plus, which is said to offer quick and easy measurement of fibre quality as well as advanced analysis of fibre morphology.
Kami Shoji will use the process to conduct defibration testing on its cellulose nanofiber (CNF) paper production to find suitable production conditions.
Defibration is the process of separating wood fibres prior to entering the paper machine.
Kami Shoji’s production method for CNF paper is known to be more cost-competitive than conventional production. The company developed its own press method which enables faster dewatering time in the production of amorphised CNF paper. It results in a product with the same strength and environmental resistance as chemical CNF paper in oily environments.
Kami Shoji’s CNF paper has good elastic deformation to alter the material’s shape, which is not possible with regular chemical CNF
paper. The paper, with specific strength properties, is expected to be used for structure, insulation and soundproofing material.
The process of making mechanical defibration CNF paper is considered challenging and depends on efficient, accurate visual inspection of the fibres to assess the degree of defibration and the optimum refiner conditions. Using ABB’s automated fibre morphology analysis device, the customer can observe an average of 20,000 fibres in just ten minutes –something that is impossible
automation systems enable innovation while preserving continuity and protecting investments by allowing users to continuously and seamlessly evolve their existing control system to meet future needs.
In the case of the Lucca power plant, ABB replaced an outdated IMMFP12 controller with a new SPC810ev controller, part of the new ABB Ability Symphony Plus SDe Series, the next step for Harmony Rack Control and I/O. The project, booked in November 2023, and scheduled for execution in August 2024, is the first SDe Series project in Italy and Europe, and among the first in the world.
For the same power plant in Lucca, ABB will be also involved in a new project with the aim to upgrade the HMI software from Symphony 2.1 to 3.3.
with manual inspections using an optical microscope – and produce multiple measurements including the fibril perimeter.
“Kami Shoji has used L&W Fiber Tester Plus extensively for the criteria of fibre conditions required for research and development of CNF paper,” said Shosaku Kashiwada, PhD, acting general manager of the Development Plan Section at Kami Shoji Co. “We are very satisfied with the device, which provides extremely valuable measurement results during CNF research.”
As part of a technical upgrade of Cartiera del Vignaletto’s tissue mill at Zevio near Verona in Italy, Toscotec will be improving the cogeneration plant and air systems on the PM4 and PM5 lines.
The tissue maker is aiming to substantially increase the energy efficiency of its operations by installing energy generation equipment designed for cost savings.
The mill’s management commented, “Toscotec demonstrated a high degree of
flexibility in putting forward a customised implementation plan that would allow us to efficiently integrate the installation phase with our production shutdown programme.”
Brazil’s Munksjo Caieiras Ltda, which is dedicated to producing decor paper, has taken delivery of a ropeless tail threading system from Runtech Systems.
The equipment includes Runshooter technology with engineering and startup support.
The upgrade enables the Caieiras mill, north of São Paulo, to achieve faster tail threading with improved operator safety.
“Safety issues are getting more and more important in Brazilian markets as well as everywhere else. With our ropeless tail threading system Munksjo is not only lowering significantly the risk of injuries, but at the same time increasing efficiency on the paper machine by reduced downtime,” says Lari Lampila,
sales and aftermarket manager at Runtech Systems, which is based at Kolho in Finland.
Ropeless tail threading technology provides numerous benefits. It improves operator safety while also shortening tail threading time during web breaks by up to 80 percent to increase production. In many cases, the technology enables mills to increase machine speed, which would not be possible with manual tail threading without increasing the risks to operators.
Munksjö has 11 paper machines and a production capacity of 250,000 tons per year. The Caieiras mill produces more than 46,000 tons of decor paper a year.
Domenico Ventura, application engineer at Toscotec, added: “We are very happy to begin a cooperation with an important Italian producer such as Cartiera del Vignaletto. The
new cogeneration plant is state-of-the-art for energy efficiency and the installation of Toscotec’s TT Hydrogen Burner with a customised design for cogeneration provides the mill with a wide range of operation options in the future.”
Founded in 1966, Cartiera del Vignaletto produces around 140 tons of tissue a day as jumbo and rewound rolls in grades ranging from 15 to 45 gsm, covering the complete range of tissue products, including facial, bath, handkerchief, napkins and kitchen rolls.
Key equipment has been provided by Andritz for a new hardwood Neutral Sulfite Semi-Chemical (NSSC) production line and for a woodyard upgrade to packaging and paper producer Mondi at its Kuopio containerboard mill in Finland. The upgrade is part of Mondi’s expansion at the mill, which produces high-quality semichemical fluting, primarily for food packaging.
“Mondi’s purpose is to be
sustainable by design, and investments like this support our MAP2030 sustainability commitments which include a focus on circular-driven packaging and paper solutions,” said Juha Koukka, managing director of Mondi Kuopio. “The equipment and process improvements will increase production capacity by 55,000 tonnes per annum while enhancing efficiency and improving environmental performance.”
l China’s Zhejiang Jiding New Material Technology has ordered an E-Wind P100 paper rewinder from Italy’s A.Celli for its decoration paper production line at Huzhou City in Zhejiang Province. The rewinder will be used to process master rolls with a width of 3,860 mm, a diameter of 2,800 mm and basis weights from 60 to 110 gsm, at a design speed of 2,000 m/min. The delivery is scheduled for October 2024. Founded in 1991, Zhejiang Jiding produces more than 110,000 tons of high-quality decorative base paper a year, with sales exceeding CNY1.2 billion.
Anew recovery boiler, an ash crystallization plant, and an odorous gas handling system is being supplied by Valmet to Klabin’s Monte Alegre pulp and paper mill as part of a modernisation project.
The equipment, which would typically be valued at €100 million, includes automation and flow control systems, and is expected to be operational by the end of 2026.
The delivery is part of Klabin’s investment of BRL1.7 billion (about €285 million) that expects to extend the operation of the Monte Alegre mill.
The order from Valmet includes a Recovery Boiler with a capacity of 1,950 tonnes of dry solids per day (tDS/d); an Ash Crystallization Plant; and NCG solutions, covering the collection and handling of the mill’s odorous gases.
The new equipment will be
enhanced with automation that will optimise its performance with a comprehensive combination of advanced monitoring and prediction applications, such as a boiler diagnostic camera system, an ash analyser, and Valmet Industrial Internet applications, including a complete package of advanced process controls, a Recovery Boiler Optimiser and Valmet Training Simulators. They will provide continuous operation,
autonomous controls, and highperformance predictability.
Commenting on the order, Edemilson Schroeder Pagano, general project and engineering manager at Klabin, said: “Klabin Monte Alegre’s mill modernisation project aims to increase the efficiency, competitiveness, and sustainability of the mill, the largest paperboard producer in Brazil. We strategically chose Valmet because of its technology,
suitable interface with the recovery plants, and a good plan for implementation and assembly.”
Klabin is the largest producer and exporter of packaging paper in Brazil and produces softwood, hardwood, and fluff pulp to the domestic market. Founded in 1899, Klabin has 23 sites in Brazil and one in Argentina, with annual production of 4.6 million tons of market pulp and paper.
A new drum displacer washer has been started up by Andritz at the Tanigawa pulp mill of Hyogo Pulp Industries, a leading Japanese unbleached kraft pulp producer. The installation of the DD-Washer is a key upgrade to the mill’s high-kappa brown stock washing line.
Naoki Ikawa, representative executive director of Hyogo Pulp Industries, said: “We decided to install a new Andritz DD-Washer because of its flexibility to accommodate higher production rates and its environmental performance, which aligns with our sustainability goals.”
The Tanigawa pulp mill of Hyogo Pulp Industries where an Andritz DD-washer has been started up
The DD-Washer is said to ensure maximum washing efficiency and excellent pulp
quality while optimising water usage, thus improving the mill’s environmental footprint. It has a multi-stage design that enables operators to adjust the washing
stages to the production needs in run mode.
As part of its investment to improve sustainability, Hyogo Pulp Industries also ordered a multi-effect evaporation plant and a methanol liquefaction plant – the first of its kind in the Japanese pulp industry – from Andritz in 2023.
Hyogo Pulp Industries produces about 200,000 tons of unbleached softwood pulp per year for customers in Japan and Southeast Asia. The company also supplies ‘green’ electricity generated from biomass.
Ahigh-capacity chemimechanical pulp production line is being supplied by Andritz to Zhanjiang China Paper Co in Guangdong Province, China.
The new line will fill the gap in the company’s chemi-mechanical pulp supply and end its dependence on market pulp.
Zhao Guohong, chief project director at Zhanjiang China Paper, which is a subsidiary of Guangdong Guanhao High-Tech Co of which Guohong is deputy general manager, said: “Our dependence on market chemimechanical pulp has led to certain limitations in our high-end white cardboard production. The new line from Andritz will enable us to produce our own pulp, reducing raw material risks and enhancing competitiveness.”
The new P-RC APMP (PreConditioning Refiner Chemical Alkaline Peroxide Mechanical Pulp) line, with an annual capacity of 400,000 tons, will produce high-
quality pulp for premium white cardboard.
Andritz will supply the complete line, including systems for wood chip washing, impregnation, highconsistency refining, bleaching, washing, low-consistency refining, screening, and rejects treatment.
The line combines high-quality pulp production with minimal energy consumption and environmental impact based on
Leading Italian manufacturer of recycled cardboard, Cartiera Fornaci, has ordered ABB’s L&W Autoline paper testing equipment for use at its board mill at Fagnano Olona. The compact version of the equipment will automate Cartiera Fornaci’s paper testing process, enhancing efficiency, accuracy and sustainability.
The mill, which produces 55,000 tons of recycled cardboard a year in weights between 360 and 1000gsm, will use L&W Autoline to replace its current manual testing processes, a time-consuming process prone to human error. Automated paper testing is typically 10 times faster than manual testing, with complete results available in less
the following key equipment:
l PrimeMSD Impressafiner for wood chip maceration enabling optimum chemical impregnation l TX68 HC refiner ensuring optimum refining efficiency for maintaining stable pulp quality l Compact Press units for high outlet dryness and superior washing efficiency after bleaching
than 10 minutes.
Benedetta Cattaneo, managing director at Cartiera Fornaci, said: “We were captivated by L&W Autoline from the first demonstration and can clearly see the value it will deliver to our mill as we move away from manual, time intensive processes into a new age of automated insights.”
The scope of the testing modules include Bendtsen Roughness, Thickness, Moisture, Burst P, Bending 50 mm and Grammage.
l PrimeScreen X screens for top energy efficiency and screening performance l Two PrimeFilter D disc filters ensuring advanced thickening and best fiber recovery Guangdong Guanhao HighTech Co is a leading Chinese manufacturer of white cardboard, carbonless copy paper, thermal paper, and other specialty papers.
In brief
l Runtech Systems and Turkish tissue maker Levent Kâğıt have signed a five-year RunCare Agreement. The agreement for the PM2 line at Kemalpasa, Izmir, includes all maintenance activity and an extended warranty for the recently commissioned RunEco Vacuum System with EP600 Turbo Blower, EcoDrop water separator and EcoFlow multi dewatering measurement.
Global hygiene and health company Essity has ordered a PrimeDry YES (Yankee Eco Steam System) from Andritz for a tissue machine at its Stubbins mill in the UK. Startup is scheduled for the fourth quarter of 2024.
The PrimeDry YES generates high-pressure steam, providing up to 25 percent of the steam required for the Yankee by using exhaust air from the Yankee hood. This significantly reduces the boiler’s gas consumption, overall energy costs, and carbon dioxide emissions. The standalone system is integrated into the machine’s DCS and operates completely independently of the machine’s production, allowing for easy operational control. Being classified as a heat exchanger
rather than a boiler, the PrimeDry YES does not require special inspections, maintenance by certified personnel, or system certifications at the customer’s expense.
A high-temperature PrimeDry Hood HT and air system supplied for the rebuild of a tissue machine at Kartogroup España’s mill in Burriana, Spain, has been started up by Andritz Pascual Gómez, operations chief at Kartogroup, said: “The rebuild will significantly reduce gas and steam consumption and lower emissions at our mill, making our production more sustainable and cost-effective. Thanks to the seamless collaboration and personalised approach of the Andritz team, the entire project went smoothly and was completed on schedule.”
The new equipment installed on the PM4 tissue machine features an optimised impingement distribution of the hood nozzle boxes, a heat recovery system,
Phillip Kenyon, organisation improvement manager at the Stubbins mill, said: “The state-ofthe-art PrimeDry YES perfectly meets our requirements for energy saving, thermal recovery
and overall machine efficiency optimisation. We look forward to continuing our collaboration with our trusted partner Andritz on new efficiency projects.”
a state-of-the-art burner management system and Yankee head insulation. These features maximise the hood drying performance while reducing the specific energy consumption, says Andritz. They also result in increased safety and a significant reduction of carbon dioxide emissions.
Kartogroup España SL, a member of the Cominter Group, has more than 40 years’ experience in the tissue business. Its mills, at Burriana and Hernani in Spain, produce high-quality tissue for household and industrial applications.
l Voith is supplying a MasterJet Pro F/B headbox for an undisclosed leading paper manufacturer in North America. Voith says new headbox with ModuleJet dilution technology will enable optimisation of paper production and ensure greater efficiency and optimised production quality. Installation is expected to be completed in May 2025. “The new headbox will enable our customer to improve key paper properties such as formation, cross direction basis weight variation, fibre orientation and smoothness,” said Mitch Kilmer, director of applications at Voith Paper.
Andreas Koronai has joined A.Celli Paper’s team in the technical and sales department to carry out technical audits on existing winders.
A highly regarded and wellknown professional in the paper industry, Koronai’s extensive experience will help provide technical sales support to the customer service department, new winder sales, and in product development.
Koronai graduated in Mechanical Engineering, and started his paper
Lana Wilhelm has received the prestigious Women in Forestry Award of Excellence from the Forest Products Association of Canada (FPAC).
Wilhelm, who is Paper Excellence Group’s director of Indigenous relations, commented: “I’m honoured that my work bridging incredibly diverse communities and interests within the forest products industry has been recognised in this way.
“I wholeheartedly believe that
industry career in 1990 with Beloit GmbH in Germany.
Over the past 15 years, Koronai has been Technical Director and Technologist for rewinding machinery, and established detailed audits for winder upgrades to precisely match the demands of the customer needs from technological and production point of view as well as for safety.
Commenting on his new role, Koronai said: “Rebuilding a machine is a real challenge, especially at paper winders. During the lifetime of a machine in many
the business of forestry has an important role and responsibility in our nation’s Truth and Reconciliation journey.”
The Women in Forestry Award of Excellence recognises the contributions and leadership of women in the forest sector. Recipients must demonstrate leadership, innovation and a commitment to the forest industry.
“We are proud to have team members like Lana Wilhelm, a forester who has spent over 20 years deeply involved in promoting a sustainable and collaborative forest products industry that meaningfully includes Indigenous communities,” said Richard Tremblay, president of pulp and tissue at Paper Excellence Group.
Doug Schwartz has been appointed as president of Billerud North America and member of the company’s group management team.
cases numerous suppliers – or the customer himself – has made modifications of all kinds.
“It’s necessary to know about both, the history of the winder as well as the targets for the future in terms of technology, production and safety, to finally fulfil the customer demands and expectations. Everyone can imagine that this needs a completely different approach to a project compared to a new winder installation.
“I am very pleased to pass on my experience of more than
Schwartz replaces Kevin Kuznicki, who left the company in June to pursue other ventures.
With extensive experience in the US forest and paper industry, Schwartz has held key leadership roles at Sonoco Products Company, International Paper and Champion International Corporation. He was most recently general manager for Rigid Paper Containers at Sonoco.
“I am very happy that Doug, with his proven track record, will now lead our North America operations, which are integral to Billerud’s business and growth strategy,” said Ivar Vatne, chief executive of Billerud, which is based in Sweden.
three decades in rebuilds and technology of winders as well as in development of new two-drumwinders to this enthusiastic A.Celli team. For the future we want to play an even more important role in the Winder rebuilding and upgrade Business and provide interesting alternatives for our customers.”
Timi Hyppänen has been appointed as Metsä Fibre’s senior vice president for business development. Currently Hyppänen works as senior vice president for supply chain at Metsä Fibre. In Hyppänen’s new position, he reports to chief executive Ismo Nousiainen and is a member of Metsä Fibre Management Team.
Metsä Fibre’s previous senior vice president for business development, Kaija PehuLehtonen has been appointed the director of Metsä Group’s carbon capture project.
Do more with digital. Like make your pulp and paper process more sustainable.
It may be surprising, but the key to doing more with paper lies in doing more with digital. Doing more with digital means drastically reducing emissions, chemical usage, and water consumption, paving the way for a more sustainable future. Doing more with digital means stabilizing production, improving on-spec results, and reducing downtime, ensuring you meet and exceed customer expectations. With innovations designed for the challenges of paper making, ABB can be trusted to make your paper process even more efficient. Do more with digital, and achieve more than you thought possible.