Preview pages 14 - 17
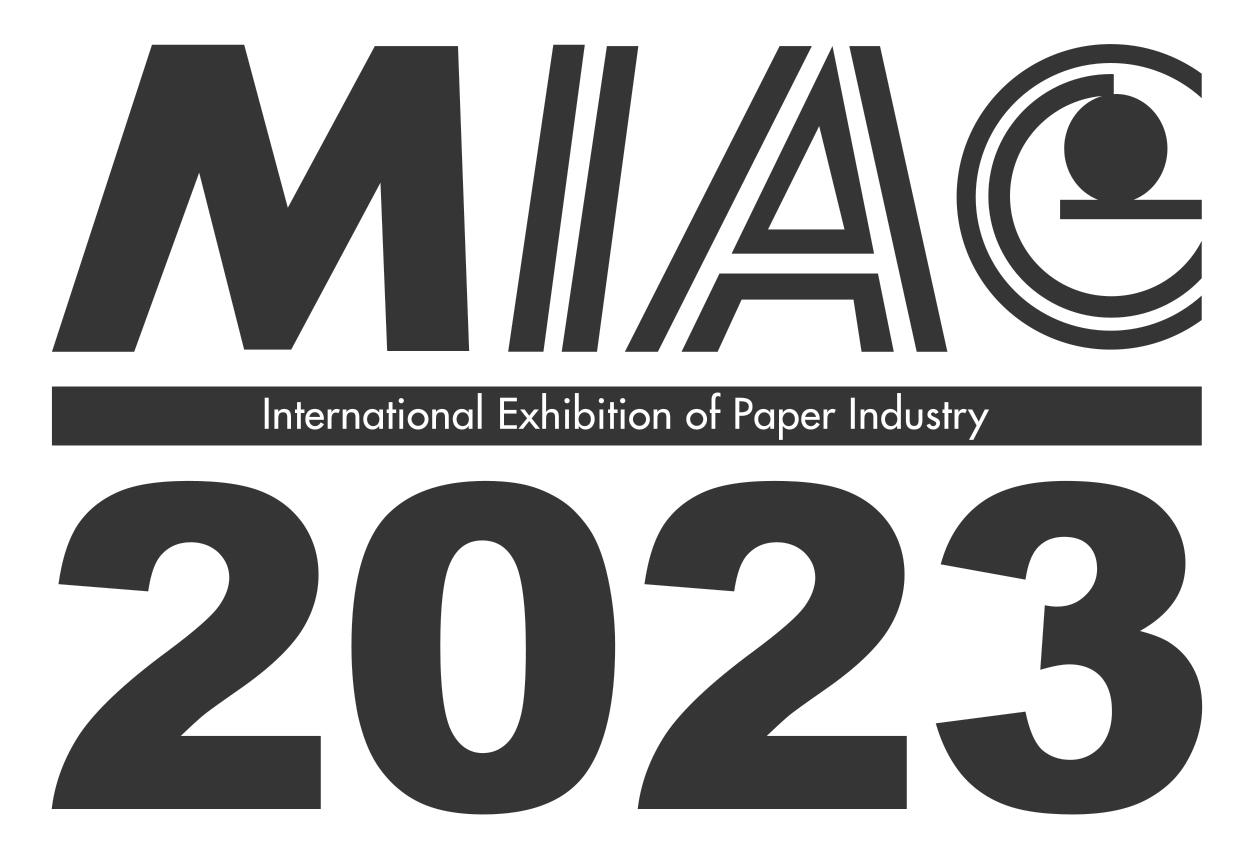
ANDRITZ: Tailor-made system for steam recovery
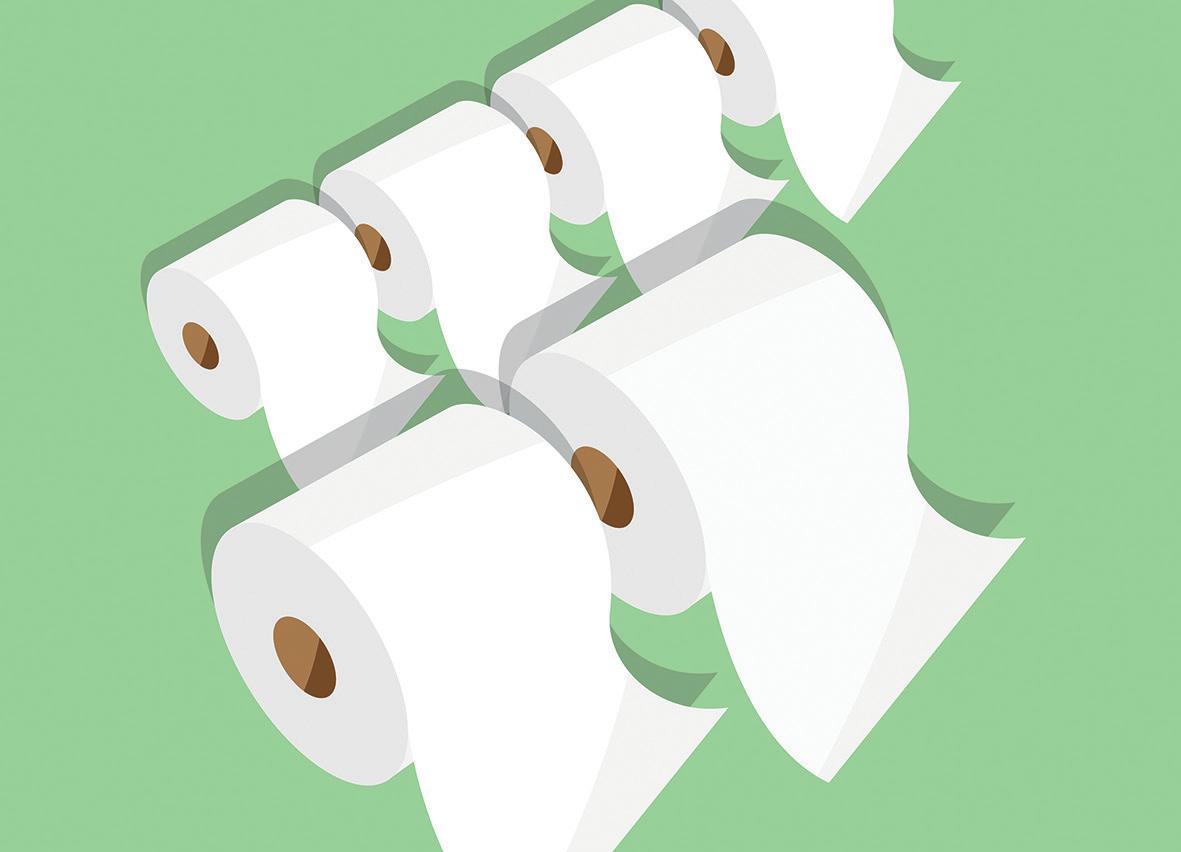
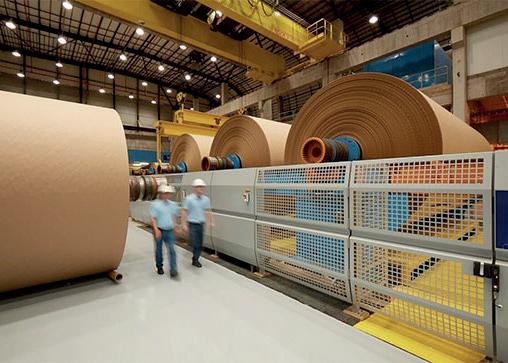

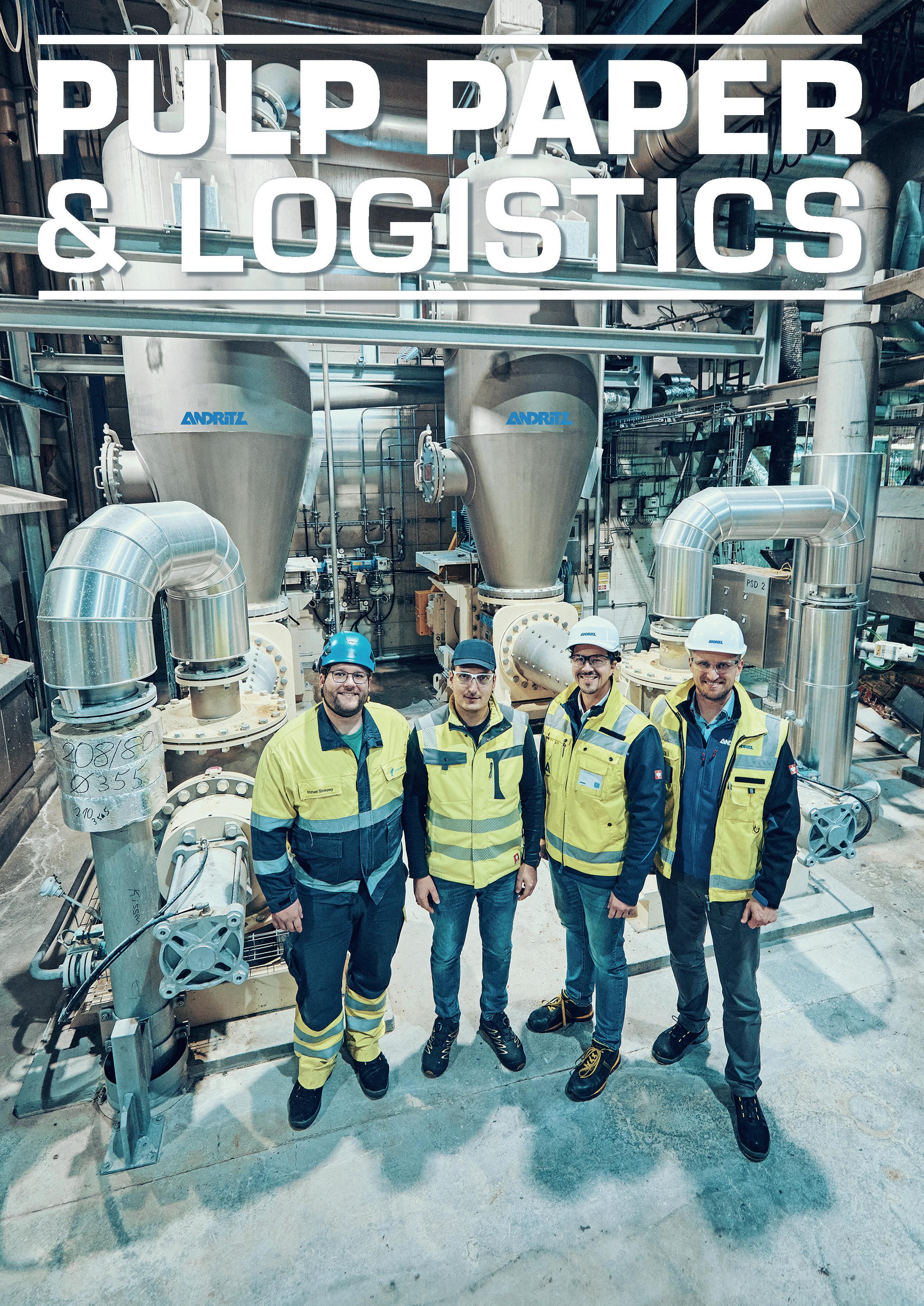
Preview pages 14 - 17
Bearing in mind environmental sustainability and the cost of energy, Prime Dry Hood E uses the same air system as gas- or steam-heated hoods, but with electric heaters replacing gas burners or steam heaters. The result is a system capable of achieving air temperatures of 400 - 450°C while increasing energy efficiency and reducing carbon dioxide emissions. To optimize energy cost and
energy security, a hybrid system is feasible. This can switch between gas and electric heating for hood air and enables a mill to select the fuel source which is most suitable for prevailing climatic conditions, the time of day, or changing tariffs for gas and electricity over a 24-hour period. For further information, please contact us at tissue@andritz.com
Welcome to the September-October issue of Pulp Paper & Logistics. With preparations for the MIAC tissue show in Lucca in full swing for three days from 11-13 October, within this issue we have included an overview of both the exhibitors and the conference schedule.
MIAC Lucca offers an insight into the developments being made not only in the production of tissue but also its processing and handling. Lucca is at the heart of tissue production in northern Italy and a base for many of the regional machinery and equipment suppliers.
We can also report that this year’s reader reregistration is well under way and already showing a great response. New reader registrations over the past six months have also shown significant growth and we will report further on this in the November-December issue.
Also in the November-December issue we will be featuring an update of logistics and material handling, environmental monitoring technology plus reeling, winding and wrapping.
Contributions for this issue should be sent to pulppaperlogistics@virginmedia.com and be with us no later than 6 November.
Finally, to arrange a meeting during MIAC please contact me, Vince Maynard, at the same email address. See you in Lucca.
Vol. 14 Issue No. 80, September/October 2023
ISSN 2045-8622 (PRINT)
PUBLISHER & EDITORIAL DIRECTOR
Vince Maynard
Tralee, Hillcrest Road, Edenbridge, Kent, TN8 6JS, UK
Tel: +44 (0) 1732 505724
Mobile: +44 (0) 7747 002286
Email: pulppaperlogistics@virginmedia.com
CONSULTANT EDITOR
David Young
Tel: +44 (0) 1737 551687
Mobile: +44 (0) 7785 796826
EDITOR
John Nutting
Email: johnnutting47@gmail.com
REGIONAL REPRESENTATIVE
Einar Johansson
Tel: +46 8 540 255 15
Mobile: 0046 70 234 80 85
Email: einar.lennart@gmail.com
PRODUCTION
Anthony Wiffen
ASTAC Business Publishing Ltd
Tel: +44 (0) 1460 261011
Mobile: +44 (0) 7557 280 769
Email: anton_print_1@mac.com
PRINTER
Brown Knight and Truscott
Tunbridge Wells, Kent, TN2 3BW
United Kingdom
Tel: +44 (0)1892 511678
The world’s biggest packaging company is being created with the combination of Ireland-based Smurfit Kappa and US-based WestRock, following talks that were first revealed at the beginning of September.
Negotiations between the boards of each company, both leaders in paper-based packaging products, were completed within a week, with a vision to form a “global leader in sustainable packaging with unparalleled scale, quality, product and geographic diversity”.
There was said to be a “compelling strategic, commercial and financial rationale for combining Smurfit Kappa’s and WestRock’s highly complementary paper-based packaging companies”.
With sales last year of US$21.3 billion, WestRock provides the bulk of turnover, while Smurfit Kappa had sales of €12.82 billion ($13.7bn).
But the new company will be called Smurfit WestRock and based in Ireland with equivalent yearly sales of more than $34bn
and adjusted earnings before tax of $5.5bn a year. Next biggest packaging manufacturer after the merger will be International Paper, which reported sales of $21.2bn in 2022.
The rationale of the merger was said to come from the good fit between the operations of each company. Smurfit Kappa is a European leader in corrugated and containerboard along with a largescale pan-regional presence in
the Americas. WestRock is strong in the US and has a broad footprint in Brazil and Mexico, across corrugated and consumer packaging delivering a broad portfolio of packaging products serving diverse, growing endmarkets.
Smurfit Kappa’s chief executive Tony Smurfit will have the same role in the new company with Irial Finan as chair of its board.
Commenting on the combination, Smurfit said:
“This incredibly exciting coming together of our two great companies is a defining moment within the global packaging industry. Smurfit WestRock will be the ‘Go-To’ packaging partner of choice for customers, employees and shareholders.
“We will have the leading assets, a unique global footprint in both paper and corrugated, a superb consumer and specialty packaging business, significant synergies, and
enhanced scale to deliver value in the short, medium and long term.”
In a video interview on CNBC, Smurfit said: “We had a big gap in our portfolio as we were not involved in the United States, and we’ve been figuring out a way to get in there in a way that would reward our shareholders over the long term. Clearly we’ve been talking WestRock for a long time and we identified it as an asset that we can develop with.
“With WestRock we’re combining a company which is at the beginning of its transformation with Smurfit Kappa which is the middle or towards the end of its transformation. We’ve done a lot over the years and we can combine both companies to make a serious player in the world.
About 65 per cent of our revenue will be in the United States and Latin America, and we intend to list there as a primary listing. We’re an unloved sector but we
want to make ourselves loved.”
David Sewell, chief executive of WestRock, also commented on the merger: “We look forward to working with Smurfit Kappa to build a leading global platform that harnesses the strength of WestRock’s consumer portfolio, presents a truly comprehensive offering of packaging solutions for customers and delivers meaningful value to our shareholders today and into the future.
“Smurfit Kappa shares our deep commitment to innovation across the packaging lifecycle, and we are confident that Smurfit WestRock will continue to lead
the industry forward. I’m grateful to WestRock’s team members, whose hard work has made this combination possible, and excited for the many opportunities that will arise from becoming part of the partner of choice in our industry.”
It was not revealed in an agreed statement what role Sewell will have in the new company. The board of Smurfit WestRock will consist of six WestRock directors and eight Smurfit Kappa directors, including Finan, Smurfit and Ken Bowles as chief financial officer.
Operationally, the new company will be run from Dublin and Atlanta, with geographic reach in 42 countries and a significant presence across both Europe and the Americas. With a total of 100,000 employees Smurfit WestRock will, says the release, to be able to improve operating efficiency with increased returns at around 500 converting operations and 67 paper mills.
WestRock has grown through a number of acquisitions since it was created from the merger of Rock-Tenn Company and
Anthony Smurfit was born in Lancashire in 1963 and after studying in Ireland and the US, with a management degree went to Japan to study the packaging industry. He joined his father Sir Michael Smurfit MBE in the family company Jefferson Smurfit & Sons and was later in 1989 appointed a director.
After the merger of Jefferson Smurfit and Kappa in 2005, he worked his way up through the management structure in a number of regional markets, to become operations director in 2009 and chief executive in 2015. He has served on many other
MeadWestvaco Corporation
in 2015 to create a leading global provider of consumer and corrugated packaging with combined net sales at the time of $15.7bn.
Earlier, in 2011, Rock-Tenn had acquired Smurfit-Stone
The recycling rate for cardboard increased to 93.6 per cent in the US in 2022, according to The American Forest & Paper Association (AF&PA).
It meant that the average rate for old corrugated containers (OCC) over three years to 2022 was 91.3 per cent.
For paper, 67.9 per cent was recycled in 2022, about the same as in the previous years, and meaning that the paper recycling
rate has met or exceeded 63 per cent every year since 2019.
The amount of paper recycled totalled almost 50 million tons.
The US paper industry first voluntarily set a goal to help improve paper recycling in the 1990s. The recycling rate has more than doubled since then.
“Paper and cardboard continue to be some of the most-recycled materials in the US,” said AF&PA chief executive Heidi Brock.
“Paper recycling is also one of the best examples of how we, as a society, are working to respect our environment and contribute to a circular economy.”
The paper industry has completed or announced nearly $7 billion in manufacturing investments from 2019-2025 that will use more than 9 million tons of recovered fibre.
“Paper recycling is a success story, and our industry’s
boards such as Cepi and the C&C drinks group. He’s married to actress Sharon Devlin, has four children, and is a horse breeding enthusiast.
Container Corporation.
Smurfit Kappa was formed in 2005 by the merger of Ireland’s Jefferson Smurfit and Dutch-based Kappa Packaging and owned by private equity firms Madison Dearborn Partners, Cinven and its management.
commitment continues,” Brock said. “We’re working to use even more recycled paper in manufacturing and set a goal to increase the use of secondary materials like recycled paper in new paper products to 50 per cent by 2030. These recycled paper products are a key component to our circular value chain.
“The paper industry also has a real ownership stake in the recycling system. AF&PA members own more than 100 material recovery facilities nationwide. They are continuously working to innovate and improve technology, especially when it comes to paper recycling.”
Afibre-based bottle with an interior biodegradable coating has been launched in a bid to replace plastic-based liners made from oil-based sources.
The bottle is the result of collaboration between Asiabased moulded fibre packaging manufacturer RyPax, and Scottishbased CelluComp, the developer of the micro fibrillated cellulose product Curran, made from root vegetable waste.
Key to the design is a proprietary pulp fibre made with a mix of Curran, bamboo, and bagasse. It is said to be strong with low porosity, enabling the application of a thin, impermeable coating to the bottle’s interior.
With a high-quality finish, the bottle is expected to appeal to luxury brands in the beverages, beauty, and cosmetics sectors. It will be supplied with a recyclable aluminium screw cap.
“Integrating RyPax’s and CelluComp’s proven technology,
materials and production expertise to produce the industry’s first all-fibre bottle at scale is a major evolution for the industry,” said Christian KempGriffin, chief executive of CelluComp, which is based in Fife, near Edinburgh.
Alvin Lim, chief executive of RyPax, which is part of The Wing Fat Printing Co with offices and production facilities in Macau, China and the US, commented: “Our unique capabilities and entrepreneurial approach have finally produced a design most packaged goods companies, and their consumers, have been longing for.
“Combining our global expertise in fibre packaging design and production with CelluComp’s innovative ingredient solution, we are making a genuine breakthrough in barrier packaging. This initiative will remove millions of tons of plastic waste from the environment.”
RyPax and CelluComp have been collaborating on the development
of a commercial all-fibre bottle for more than three years. They recently gained validation from the Danish Technological Institute (DTI), which has been an important partner in helping create a viable proof of concept.
“This collaboration and design are something the industry has
Further progress has been made with Stora Enso’s restructuring, as reported in the July-August issue of PPL.
The restructuring, with the objective of making the company more competitive with a decentralised and more customer orientated operating plan, will mean that the job count will be cut by more than 1,000.
In the Biomaterials division, pulp production and lignin extraction will be closed at the Sunila mill in Finland. Production at the site – with annual capacity of 375,000 tonnes of long-fibre and 50,000 tonnes of lignin – has been on hold since May and will not be ‘ramped up’ says Stora Enso. The pilot plant for bio-based battery material will
continue operation.
In the Packaging Materials division, one of Stora Enso’s four containerboard production lines – with capacity for 120,000 tonnes of recycled board – at its Ostrołęka site in Poland was closed down permanently with the loss of 50 jobs.
The Napi sawmill, with annual capacity for 50,000 cubic metres
been waiting to see for a very long time and we’re excited a solution is now available,” said Alexander Bardenstein, business development manager with DTI.
“The RyPax/CelluComp bottle has been through all of our comprehensive testing to earn our endorsement and allows them to start tailoring this technology for the global marketplace.”
The partnership says it is poised to scale up production for a range of industry applications, from beverages, beauty, health, medicine, and food to retail brands.
Fibre-based bottles have been developed by a number of companies, one being brewer Carlsberg in 2019, when it unveiled two research prototypes of its Green Fibre Bottle, which were the first ‘paper bottles’ to contain beer.
A year later British firm Frugalpac was said to be scaling up to meet demand for its Frugal Bottle production facility with Group Roland near Ipswich in the UK.
of sawn timber, 180,000 cubic metres of processed wood products and 25,000 tonnes of pellets, will be closed before the end of the year, with the loss of 90 jobs.
While the changes are expected to cut annual sales by about €380 million, or about 3.3 per cent of last year’s sales of €11.7 billion, yearly earnings before interest and tax are expected to increase by €110m. The cost of restructuring could be up to €190m.
Whether you work in board and paper, tissue, pulp or energy industry, Valmet’s comprehensive service offering helps to lower your environmental footprint significantly – at the same time improving your operational results. The key is a close collaboration and the right combination of services for every stage of the lifecycle. As most of the environmental impact comes from the operational phase, by working consistently in close cooperation with your team, we can offer many concrete solutions.
From energy, water and raw material savings to circularity and lower emissions, together we’ll keep the process reliable, optimized and sustainable to the fullest extent – benefiting both your business and the environment.
Are you ready to succeed with us? Explore how on www.valmet.com/waytoserve
Recyclable paper-based packaging for multipacks of cans will be rolled out across North America by PepsiCo as part of the New York state-based drinks giant’s commitment to ensure that its products don’t become waste.
The paperboard wraps and clips, replacing traditional plastic rings will be adopted by PepsiCo
Beverages North America in a phased, regional approach in the US later this year.
PepsiCo says it will be the first time the use of paperboard for multipacks has been launched by a brand across the whole country.
The conversion to more sustainable packaging will include brands like Pepsi, Pepsi Zero, MTN DEW, Starry, Gatorade, amongst others.
The recyclable wraps and clips, supplied by an undisclosed manufacturer, have already been used in Canada where the transition to paperboard is beginning to roll out with 7Up.
The use of recyclable materials will help drive progress toward PepsiCo’s pep+ goals to reduce virgin plastic from non-renewable sources per serving in its global
beverage and convenient foods portfolio by 50 per cent in the ten years to 2030.
Last year a US Coca-Cola bottler started using paperboard multipack clips to eliminate plastics in its supply chain. Liberty Cola-Cola Bottling in New York adopted Graphic Packaging’s KeelClip for six packs of the canned cola.
British-based paper maker for luxury products and related technologies, James Cropper has launched a production unit for the delivery of hydrogen as a power source.
James Cropper subsidiary TFP Hydrogen has unveiled the TFP Hydrogen Modular Production Unit (MPU), which is said to represent a significant move towards enabling rapid scalability for PEM electrolyser
manufacturing.
Using proprietary coatings technologies developed by TFP Hydrogen, the MPU is designed to operate close to customers and component suppliers, streamlining the supply chain for PEM electrolyser manufacturers.
The MPU can be commissioned and fully operational within six to 12 months.
David Hodgson, managing director at TFP Hydrogen,
commented: “As we confront the undeniable reality of climate change, TFP Hydrogen stands resolute in our dedication to effecting meaningful change through the advancement of PEM electrolysis.
“Green hydrogen holds the promise of reshaping the energy landscape, propelling the world towards achieving crucial net-zero targets by 2050. The TFP Hydrogen MPU
is a tangible manifestation of this commitment, a catalyst for transformative change.”
The coating technology developed by TFP Hydrogen and integrated within the MPU is said to address the material challenges associated with titanium components in PEM Electrolysers.
The range of coatings provided by TFP Hydrogen play a central role in enhancing the durability
in the year to the end of April
of the components, shielding against corrosion, and minimising contact resistance; ultimately improving the overall operational efficiency and extending the lifetime of the electrolyser.
● Group sales at James Cropper for the year to the end of April were 24 per cent up at £129.7million with operating
profits up 4 per cent to £4.8m. Best performing segment was paper with sales up 25 per cent to £88.2million, “despite a challenging cost base”.
Newly appointed managing director of Paper Products, Richard Bracewell said: “Today, the business is transitioning to an advanced materials and paper products group, committed to creating a greater global presence for James Cropper and better serving our existing and new customers.
“In particular, within Paper Products, we are focussing our offer on luxury packaging and premium creative papers where our customers really value our innovation, expertise and quality. The integration of Colourform into James Cropper Luxury Packaging will drive a unique and compelling proposition, building better efficiencies in our operating model and increasing relevance and scale in key markets.”
See People, p32, for more James Cropper news
The sale of the Thunder Bay (Ontario) pulp and paper mill by Resolute Forest Products to an affiliate of Atlas Holdings has been completed, as announced in May.
Resolute, a subsidiary of Domtar Corporation and a part of the Paper Excellence Group, will continue to operate its sawmills and woodlands operations in north west Ontario. Continuing agreements include a long-term woodchip and biomass supply deal in
A commercial carbon dioxidecapture plant that offers potential for companies to mitigate their factory carbon emissions has been installed in Austria by Andritz – a key supplier of process equipment and technologies to the pulp and paper industry.
which Resolute will continue to supply the Thunder Bay mill.
The sale of the Thunder Bay mill was a requirement of the Canadian competition authority following Domtar’s recent acquisition of Resolute.
Based in Montreal, Resolute Forest Products is a leading producer of wood, pulp, tissue and paper products sold in 60 countries. It operates some 40 facilities in the United States and Canada, along with power generation assets.
The plant separates carbon dioxide from the flue gases emitted during steel manufacture using an aminebased process developed by Andritz. The captured carbon dioxide is filled into large industrial gas bottles and delivered to an Austrian energy storage company that is investigating new ways of making it available for re-use in steel production, fostering a sustainable carbon circularity and reducing the need for fossil fuels.
The pilot plant started operating at Voestalpine’s steel mill at Linz in Austria, close to
Andritz ’s headquarters, in the second quarter of this year. With its carbon capture technology, Andritz is supporting companies in decarbonising their operations and creates the basis for storage or further processing and utilisation of carbon dioxide.
Says chief executive of Andritz Joachim Schönbeck: “As the availability of renewable energy and green hydrogen will not be sufficient to meet medium-term climate targets, carbon capture will play a key role in significantly reducing carbon dioxide emissions in this transition phase.”
Even in the pulp and paper industry, in which the trend is towards power systems being based on bio-mass rather than fossil fuels, carbon capture systems could be used as a means of reducing overall carbon emissions.
The transportation from China of two huge sections for the new drum pulper for installation at Norske Skog’s Golbey mill in France presented some logistics challenges.
Technology group Voith, which has been rebuilding the mill’s PM1 line, engaged deugro to manage the project, involving the safe moving of the drums – the largest of which was 32 metres long with a diameter 5.7 metres and weighing 195 tonnes – from Shanghai in China by ship to Antwerp in Belgium, then using 350km of inland waterways to a river port in France. After discharge at the Port of Frouard, the drum sections were delivered a further 80km by road on special trailers to the mill in the Vosges region.
To determine the most suitable road route, several surveys,
including turning simulations and swept path analyses, were conducted by Dteq Transport Engineering Solutions along with local partners on deugro’s behalf.
“The most challenging part of the journey was the manoeuvring through the many traffic circles and tight turns, as well as traversing the town of Lunéville,”
said Ambra Gotsch, project coordinator at deugro Germany.
“To allow for the safe navigation through the extremely sharp turns in Lunéville, we arranged the transfer from conventional THP trailers to self-propelled modular trailers using a jacking/stooling operation. After crossing the most critical turns in the city, the cargo
Australia’s leading tea producer Madura Tea is reducing its impact on the environment by switching its packaging materials from metallised OPP (oriented polypropylene) to flexible packaging paper.
Together with Gundlach Packaging Group and Koehler Paper, Madura Tea is using Koehler NexPlus Seal Pure MOB, which has a mineral oil barrier and offers protection against MOSH/MOAH. After promising tests, the tea
products are now available on the Australian market.
Koehler’s uncoated NexPlus Seal Pure MOB offers strong barrier properties and consists of 100 per cent certified virgin fibre pulp.
During the packaging’s development, Gundlach Packaging Group and Koehler Paper provided Madura Tea with a range of test materials from the NexFlex product range.
“Koehler NexPlus Seal Pure MOB is suitable for contact with
food, [and] impressed everyone involved thanks to its outstanding barrier properties,” explains Yevgen Zolotkovski, sales manager for Flexible Packaging Papers at Koehler Paper.
The paper is heat-sealable, and its strength properties make it ideally suited for further processing on all commercially available packaging machines.
“Madura Tea has made the right decision in demonstrating its environmental responsibility
was transferred back onto the THP trailers for the remaining oncarriage.”
Project manager for operations
Ulf Langner added: “Another operational challenge was the crossing of a railway bridge near the Village of Méhoncourt. Six additional axle lines had to be mounted to the modular trailer to stay within the allowable bridge capacity, then dismantled after passing the bridge.”
Announced in 2021 as a €250 million investment, the rebuilt Golbey PM1 line will produce 550,000 tons of containerboard per year with a wire width of 9,300mm. The pulping drums are to be used as part of a stock preparation system processing up to 2,100 tons of recovered paper a day.
More information from https:// deugro-group.com/companies/
by using recyclable materials from sustainable sources,” says Carsten Loemker, engineering and technology chief at Madura Tea, explaining the tea producer’s motivation.
Improve your press section efficiency! SmartScan™ contactless sensor accurately measures paper web dryness after the press section 24 hours a day, 7 days a week. Using a proprietary microwave technology, it is developed to overcome the typical limits of the NIR (near-infrared) sensors. SmartScan™ is available both for fixed point positions or traversing web scan. To save hundred of thousands of Euros in energy costs, stop collecting samples, choose the safe accuracy of SmartScan™ technology.
Perlen Papier in Switzerland wanted more capacity for steam recovery but space was at a premium. Andritz came up with a tailor-made system that doubled output and exceeded expectations. PPL reports
Perlen Papier is Switzerland’s only producer of newsprint and magazine papers.
Part of CPH Chemie + Papier Holding, the mill near Lucerne operates two paper making lines including one of the largest, fastest and most modern newsprint machines in Europe. Highly focused, the mill makes only publication papers, with capacity of 360,000 tons per year of newsprint and 200,000 tons per year of LWC magazine papers.
Andritz has been working with the company since 1995, when it installed Perlen’s thermomechanical pulp (TMP) plant: a 100,000-ton per year, 100 per cent spruce-based line that feeds both paper machines. Since then, Andritz has carried out upgrades every couple of years, although the TMP plant’s high-speed RTS refiner line had been soldiering on for 27 years with its original Cyclone and Swept Orifice Discharge units.
Operations engineer Michael Stokowy explains: “We operators wanted to upgrade [the units] because they were no longer in the best shape, and it was difficult to get spare parts. The mill management wanted to increase the steam recovery.” This would reduce costs and prepare for any future increase in TMP capacity.
Perlen decided to replace the old units with a pair of new Cyclones and Plug Screw
Dischargers (PSD). The mill wanted maximum steamseparation capacity for the available space, and as Robert Pfeiffer, head of project management for refining systems service at Andritz Pulp & Paper,
explains, “it had to fit in the existing building, otherwise it would have been too expensive”. Unfortunately, this meant that the Austrian engineering group’s existing PSD 600 and 800 models were too big, while the PSD 400
was smaller than desired. So, with instructions to deliver maximum capacity in the limited space, Andritz agreed to design and manufacture a unique new model – just for Perlen.
To make the best use of the
available space, the new PSD 500L is wider than the 400 and narrower than the 600, but also longer than all the standard models, increasing the compression zone by 50 per cent. This ensures optimum fibre compression and density on the screw, while also treating the fibres as gently as possible. Meanwhile, the new standard Cyclone CYS1400 that feeds into the PSD effectively separates the steam and feeds it into the Heat Recovery system to be used for a range of different purposes, which saves money and benefits the environment.
Installing such precisely tailormade equipment into such a tight space would normally take at least several weeks. But in this case, the installation had to take place in the five days of downtime that were already planned for the mill’s annual maintenance. Nevertheless, Andritz and Perlen worked fast and efficiently and succeeded in
meeting the very tight deadline. Perlen placed the order in January 2022 and the tailor-made new equipment arrived just six months later. The pre-installation work took place in August and installation and startup in September 2022.
Keeping the installation on schedule was helped by good collaboration between Andritz and Perlen. As Michael Stokowy explains: “It wasn’t easy – it was
a nervous week. We couldn’t do everything at the same time, because there’s not enough space. It was fairly complicated, but we planned it by the hour, with 24-hour working days. The electrics were a particular challenge, because they could only be hooked up and tested from day three. But we had the site really well under control, with daily updates.”
Pfeiffer notes that, “we solved
problems together” and in that context, Michael Stokowy was especially pleased with the support from Heinz Wiedenhofer, Andritz ’s assembly supervisor. “He is very customer-friendly and did very, very good work. He turned up early, he was always available, very prepared to work a few more hours and he always found a solution for any problem. Identifying problems was half of my role during the installation, so
Heinz made things very pleasant for me, because I personally didn’t have much problem-solving to do.”
The new units were still in the optimisation phase just a couple of months after startup, but even so, Perlen had already considerably exceeded some of its process-related targets. For example, the aim was to increase
steam recovery volumes from six to nine tons per hour, but the new units are already operating consistently at 14.5 tons per hour. This means more steam for use, such as in the paper machine dryer section and for heating the paper machine hall, which saves Perlen money that would otherwise be spent buying steam from the local waste-powered energy plant.
It also lowers the temperature
of the refined fibres in the latency chest, and once optimised, that should improve fractionation efficiency in downstream screening, easing the load on the reject circuit, resulting in even more energy savings. The lower temperature should also limit fibre yellowing and reduce consumption of bleaching chemicals, as well as minimizing wear on thickening units.
Perlen’s TMP line manager Zoran
Jovanovic also adds that the new units are running far more cleanly: “Instead of having to be cleaned every three days, taking threequarters of an hour each time, now it’s only once every 10-11 days, at least.”
Exceeding the project goals also means a faster return on the investment than Perlen had planned. The target was 1.7 years, but it is now expected to be less than one year. “It’s saving us quite a lot of money,” Stokowy confirms. More than that, “It’s saving our nerves. It’s working well and we have fewer worries
about maintenance.”
Robert Pfeiffer explains that this project reflects Andritz ’s philosophy of focusing on the papermaker’s day-to-day reality, along the whole production line. “We believe in ‘small steps, big success’. It’s not all about just getting a one-time sale, but on continuing a long-term partnership. So, we want to provide what will help them the most, within their budget.”
It also demonstrates that an innovative Andritz upgrade can help save both money and the environment.
It’s September so for the paper industry it’s the time to meet at Lucca in Italy for the annual MIAC exhibition and conferences. Pulp Paper & Logistics will be there
Consolidating on MIAC’s success last year, when the paper industry was recovering from the impact of the Covid pandemic, the show and conferences being held in the centre of the business in Italy provide a forum in which new challenges are being faced.
More than 250 exhibitors – see the next pages for a list and floor plan – will be at the Lucca Exhibition Centre from 11 to 13 September, offering the latest in technologies and services for those working in the paper and cardboard sectors and the tissue manufacturing world.
The show and conferences are free to participating professionals provided they register. They will find that there will be networking opportunities for discussing the great changes in the paper world which are happening more quickly with increasingly profound effects.
The tissue industry has shown resilience facing these challenges by responding to customers’ needs by optimising its processes and products. These needs and the industry’s responses will be addressed in the two MIAC Tissue Conference mornings where new technology and innovation that supports the industry in this journey will be showcased. Meeting the demand of a new industry that operates with lower carbon emissions requires a multiplicity of approaches and solutions, from energy saving to efficient energy production. In MIAC Energy new technological
approaches will be explored. The requirements of the new packaging directive in Europe should be achievable through sustainability and energy efficiency in paper production, a subject that will be discussed in the MIAC Paper & Board Conference.
Visiting MIAC 2023 provides a complete overview of the technology and equipment available to the paper industry sector, from the production of paper and cardboard to the converting of tissue.
As a media sponsor Pulp Paper & Logistics will be at Lucca and publisher Vince Maynard will be pleased to meet exhibitors and industry professionals alike. Email Vince at pulppaperlogistics@ virginmedia.com to make an appointment.
Located in central Italy, Tuscany is one of the world’s most popular regions for tourists with beautiful landscapes, artistic heritage and key cities. Places to see after MIAC Exhibition should include a visit to Lucca and other cities such as Pisa, Viareggio, Montecatini Terme, Forte dei Marmi and Florence.
The city of Lucca is also considered one of the major tourist destinations in Italy, and well known worldwide for the unique Walls of Lucca that
surround its historical centre. Another famous symbol of the city of Lucca is the charming Anfiteatro Square built on the ruins of the Roman amphitheatre. Within walking distance from this corner of the city there is the medieval Fillungo street, which is the main thoroughfare of the town centre and heart of the city’s shopping. Other architectural and cultural attractions in Lucca include the Church of San Michele and the famous San Martino Cathedral. Lucca is rightly called ‘The city of 100 churches’.
In Europe, Lucca is the leading area for tissue production (24 per cent); Italy is also one of the leader countries in the corrugated cardboard sector.
The paper industry in Italy has 165 paper mills, producing nine million tons of paper products a year, and employs 20,000 people. Italy is one of the top four producers in Europe with annual sales of €6.8 billion.
Lucca itself is home to a number of leading companies in the paper industry that have total sales of
€2.6 billion with more than 8,000 employees.
How to get to Lucca
MIAC 2023 is located at the Lucca Exhibition Centre, Via della Chiesa XXXII 237, 55100 Lucca, Italy. To reach the free parking at the MIAC Show it is advisable to look on your satnav for ‘Vitricaia street – Lucca’.
Activities covered at MIAC 2023
l Machinery and plant for the production of paper and board
l Components and part of paper machines
l Converting machines for tissue
l Instruments and systems to measure, test, control and manage plants
l Machinery and plants for water treatment
l Plants, machinery and electrical control
l Chemicals, additives and raw materials
l Machinery and plant for drying, filtration and energy recovery
l Laboratory, diagnostics, logistics, services and plant optimisation
Three conferences are offered at MIAC this year covering tissue in two sessions, paper and board in another and finally an energy conference.
Participation is free to all conference sessions although online pre-registration recommended. A simultaneous translation service is provided
MIAC Tissue Conference –first session
11 October 2023 from 13.40 to 16.50 in the MIAC Conference Room
Tissue paper production – beyond any obstacle
We live in a period of great changes, even more profound and accelerated. The tissue industry has demonstrated its great resilience through its ability to face challenges, respond to people’s needs and optimise processes and products. During MIAC Tissue, we will see how technology and innovation supports the industry in this journey.
14.00 Massimo Ramunni, Assocarta: opening remarks
14.10 Guido Pasquini, Lucart
l Challenges and opportunities of the tissue sector
14.30 Elena Troia & Elisa Bertolucci, Toscotec
l Toscotec ramps up Water and Energy Reduction in Tissue Paper Making
14.50 Massimiliano Scaccia, Andritz
l Impulse Shoe Press Belts enhancing Shoe Press
Performance
15.10 Denny Di Vita, A.Celli Paper
l A.Celli E-Wind paper winder
– Enhancing efficiency and productivity in paper production
15.30 Jonas Johansson, Valmet & Matteo Notoni, Sofidel
l Valmet Industrial Internet for on-line real-time tissue quality prediction
15.50 Graziano Buttiglione, Kadant Johnson Systems International
l Efficient, intelligent and connected. Kadant’s DMS control system for the modern paper industry
16.10 Maurizio Tomei, Oradoc
l Drain and maintain. Vacuum systems and dewatering best practices
16.30 Leonardo Cavirani, Runtech Systems
l Efficient paper machine vacuum system rebuilds and optimisation
MIAC Tissue Conference –second session
12 October 2023 from 09.40 to
12.50 in the MIAC Conference
Room
10.00 Massimo Ramunni, Assocarta: Opening remarks
10.10 Eduardo de Almeida, Afry
l Challenges and opportunities for the paper industry. The road to 2030
10.30 Simone Barsanti, Körber
l Sustainability. Challenges, strategies, and solutions for the tissue industry
10.50 Alberto Colombo, Omet
l Omet’s sustainable philosophy
11.10 Giacomo Bianchi, Northern Engraving
l The new Embossing Centre of Excellence & Tissue product development in Europe, home of reliable innovation
11.30 Frank Kretschmer, Schäfferolls
l SchäferRolls Management System (SRMS), the efficient digital management of roll systems
11.50 Gionata Mazzoni, Futura
l The new converting landscape
12.10 Veljko Zlatanovic, Stax Technologies
l Diversa – an absolute excellence in packaging
12.30 Martin Kyles, Maflax
l Devices and practices to guarantee safety and efficiency in modern tissue converting plants
MIAC Energy Conference
12 October 2023 from 13.40 to
16.30 in the MIAC Conference Room
Preparing for the Green New Deal
The decarbonisation challenge requires a multiplicity of approaches and solutions, from energy saving to efficient energy production. In MIAC Energy new technological approaches will be explored.
14.10 Speaker from GST to be confirmed
14.30 Eugenia Famiglietti, Baker Hughes
l How the Italian Paper industry is approaching decarbonisation
14.50 Tiziano Pieretti, Sofidel
l How to cope with climate challenges and competitiveness in the Italian Paper Industry
15.10 Ville Piikkkilä, Valmet
l Hidden opportunities in stock preparation and the wet-end on tissue machines, to gain benefits in lower energy costs, better runnability, a more stable wet end, and improved creping
15.30 Maria Knauer, Voith Paper
l How to save energy with the help of digitalisation
15.50 Paolo Masiero, Solar Turbines
l In the beginning was the Vacuum. Enhanced Vacuum Efficiency with Integrated Cogeneration
16.10 Giuseppe Bonforte, Renovit
l Electrification of consumption in the paper industry. Two case
studies on the implementation of high temperature heat pumps and thermal storage
MIAC Paper & Board Conference
13 October 2023 from 09.40 to 12.10 in the MIAC Conference Room
Efficient production for a better life cycle
The challenge posed by the proposed packaging directive can be won with sustainability and energy efficiency in paper production to ensure a better life cycle compared with reusable solutions. New technological solutions for packaging paper production will be discussed at the MIAC Paper & Board Conference.
10.00 Massimo Ramunni, Assocarta. Opening remarks
10.10 Massimo Ramunni, Aticelca
l The recyclability challenge in the light of the new Packaging and Packaging Waste Regulation
10.30 Eduardo de Almeida, Afry
l Roadmap to net zero water consumption for the pulp and paper industry
10.50 Winifred Wolf, Andritz
l Andritz Occasion: maximise the performance of your OCC stock preparation
11.10 John Schulz, BTG
l Novel solution concept to increase effectiveness in processing and more efficient in board production
l Tradition meets Innovation – the new InfibraFiner digital generation
11.50 Eugenio Ciucani, Holmen
Iggesund Paperboard
l Online data analysis for process optimisation
& Co stand 16
Food Contact Center stand 41
FPZ stand 105
F.lli Frediani stand 118
Futura stand 116
Gambini stand 87
Ghetti 3 stand 23
Giotto Technologies stand 167 Giuliani stand 75
GTK Timek Group stand 163
Hannecard Tissue & Paper stand 60
Henkel stand 34
HERGEN – Máquinas e Equipamentos stand 152
HWK – Hüttenwerke Königsbronn stand 166
IBS Paper Performance Group stand 118
ICM Makina Ve Muh. stand 108
IM Converting stand 175
Indexa Italia 2 stand 103
Infinity Machine & Engineering stand 4
Ingersoll Rand stand 10
Inox BF stand 38
Intecom stand 170
Italberta stand 145
Italmatic Presse Stampi stand 92
Italprogetti stand 113
Jagenberg Paper stand 118
Johnson-Fluiten stand 50
Julia Utensili stand 46
Jungheinrich stand 20
Kadant Johnson Systems International stand 50
Kadant Lamort stand 50
Kairos stand 133
Kapp-Chemie stand 111
Kappa stand 179
Kemira stand 82
Klüber Lubrication stand 132
Körber Tissue stand 69
Lamm stand 151
Lario Energy stand 129
L.B.Z. Lavorazioni Meccaniche stand 162
Linde Material Handling Italia stand 30
L&M Pumps stand 159
Logos Automation stand 123
Lotus stand 140
MacDue stand 51
Maflex stand 7
MAN Energy Solutions stand 39
Mare Dynamics stand 107
Mario Cotta – Zincometal Group stand 61
Martin Lohse stand 79
Gruppo Costante Martinelli – Div. Ind.le stand 28
Maxima stand 77
Mercurio Group stand 118
Mevas stand 91
Microline stand 66
Mingazzini stand 26
Mink Bürsten stand 24
Movingfluid stand 149
Multipack stand 11
MWN Niefern Maschinefabrik stand 83
Nalco stand 36
NASH stand 10
NCR Biochemical stand 99
Nema Automazione stand 121
Northern Engraving Machine Company stand 59
stand 83
SDF stand 110
Sei Sistemi stand 123
Senning stand 17
serv-o-tec stand 148
Sicem Saga stand 124
Sicma stand 80
Sinergy-SL stand 81
Slittec stand 154
Solar Turbines stand 135
Solenis stand 111
Sorgato stand 169
Sotemapack stand 86
Spares Service & Machinery stand 72
ST Macchine stand 64
STAX Technologies stand 59
Stiavelli Irio stand 29
STILL stand 27
S.TO.R.I. stand 70
Sulzer Pumps stand 118
Svecom stand 1
Tasowheel stand 75
Tau Machines stand 52
Techno Paper stand 79
Technowrapp stand 109
Tec.Mec. stand 2
Tec.Mec. Service stand 155
Tecno Paper stand 102
TC Rolls & Covers stand 48
Tecnofer Ecoimpianti stand 157
Termotecnica Industriale stand 173
TIP95 stand 53
Tissue Tec Sales & Service stand 131
Tissuenet stand 125
TKM stand 8
IMA – TMC stand 93
Enrico Toniolo stand 3
Toscana Spazzole Industriali stand 21
Toscotec stand 70
Toyota Material Handling Italia stand 22
Trimble stand 146
Tubicom stand 97
UNIMATEC stand 55
VAKUO – vacuum pumps and systems stand 58
Valmet stand 89
Ve.Car stand 30
VEGA Italia stand 12
Villforth Siebtechnik stand 65
Voith stand 14
Vorwald – Neuenhauser Maschinenbau stand 153
Weingrill stand 84
Winkler+Dünnebier stand 59
Correct as of 24 July
One of the challenges when you want to start up a new tissue production line is selecting the appropriate technology for your requirements. To make the right decision, you need to understand the specific quality demands for your market and then decide on the product strategy. However, in today’s competitive market, there are additional influential factors such as the importance of
How can you use the optimum combination of energy and fibre to reduce the environmental impact of tissue production? In this article, we discuss what hybrid technology can offer in sustainability, cost-effectiveness and quality to achieve an optimal product. Anna Boström Mora reports
caring for the environment by reducing emissions, the increasing demand for raw materials, and the recent rise in energy prices. How can a tissue producer consider all this and still be profitable? Valmet’s hybrid technology* allows you to
optimally meet a combination of targets.
With hybrid technology, you can reduce the amount of fibre for the same volume because increasing
your roll bulk equates to fibre savings. Increased roll bulk is achieved by creating higher sheet caliper for the same or lower basis weight, therefore roll bulk is inversely related to roll density; as roll bulk increases, the density of fibres decreases. The product
strategy optimises product specifications and operating costs. You can reduce the length, lower the basis weight and work with product quality. And the beauty of it is that you don’t have to choose one or the other: the options can be combined.
However, before a decision is made, we have to consider that each region has a different product strategy. A quick overview of toilet tissue in various regions reveals the following:
l North America. TAD/structured products have been developed mainly in North America, where the basis weight has been increasing over time, typically above 22 gsm, with only two plies. This combines softness with more fibre per ply and fewer plies than in conventional products worldwide for an increased roll bulk. It also generates better machine efficiency during production
l South America. In Brazil, the required length on the market is either 20 or 30 metres. With a bulkier product produced with a hybrid machine, for example, there
is an opportunity to produce a two-ply instead of a threeply product and still achieve a length of 20 metres and make huge fibre savings. It is also possible to migrate your conventional economy two-ply product to a premium product – still two-ply and the same
length, but softer and with less fibre.
l Europe. In Europe, private labels are strong and dictate the market. 15-20 gsm and ply are important. But is the number of plies good for production efficiency and sustainability? Probably not.
l Asia. Dominant in the facial market, surface softness is more important than bulk in Asia. 15 gsm or lower is the standard basis weight, utilizing more plies to increase product quality. The trend is to move to structured products of higher quality with a decreased ply strategy instead.
There’s a lot of information to digest when deciding on which tissue machine to invest in. We asked Jenny Lahti-Samuelsson, vice president of Tissue Mills Sales at Valmet, to briefly comment on the terminology we so often use in connection with tissue production. With hybrid in mind, this is her summary:
Length
With hybrid technology, reduced length is easily achieved for the same volume, which can create the perception of a premium bulk product among consumers.
Diameter
The consumers feel they are getting more value for the product, even if the amount of fibre is the same. TAD products in the US
usually have a larger diameter. With hybrid technology, you can match that size.
The weight of fibres per area is the easiest way for the producer and consumer to refer to fibre saving. With a lower basis weight in the product but still the same volume, the consumer will experience better conformability in a bulkier product.
Quality
Higher quality enables a higher end product price. In the US, for example, the price of TAD quality is more than twice that of conventional products. Producers can achieve more profit with less fibre use per case.
More information from Jenny Lahti-
Shifting to the premium segment Sustainable production efficiency is achievable with fewer plies or reduced total basis weight. For example, with a hybrid machine, it’s possible to produce a bulky product with fewer plies yet at an equal
“With a hybrid machine, it’s possible to produce a bulky product with fewer plies yet at an equal or higher level of softness”, says Jenny Lahti-Samuelsson, vice president of Tissue Mills Sales at Valmet
Samuelsson by email: jenny.lahtisamuelsson@valmet.com
or higher level of softness. As always, the trade-off is between bulk, softness and tensile strength.
Comparing the average conventional and hybrid numbers, you can reduce the basis weight for a hybrid bath tissue product at higher caliper and comparable tensile levels. Hybrids have better fibre efficiency, resulting in higher roll bulk with a better quality output. The end product will have almost 30 per cent more roll bulk than a conventional embossed product, which means an average of around 22 per cent less fibres with up to 10 per cent better softness quality.
Moving on to towels, a global look reveals that a hybrid towel – even taking into account
the smaller property gap for a heavier embossed kitchen towel product – will have less fibres with more caliper, generating an average of 44 per cent more water absorption than in a similar conventional product. The roll geometries
are comparable, but with 12 per cent less fibre at higher quality. With hybrids, you can migrate your light dry creped product from the value segment to the premium or ultrapremium levels. Reducing fibre consumption with more roll bulk provides the end product with a lighter basis weight and fewer sheet counts (reduced roll length), but still at a higher quality.
What about the environmental footprint of production on hybrid machines? In our studies, we have compared the fibre, water and carbon footprints with an average conventional reference bath tissue product of 115 grams. In the roll case, we can decrease fibre use by 22 per cent, resulting in a reduction of
carbon emissions at equal water use compared to the DCT case.
If you want to move closer to the premium quality level, transferring a conventional machine to a hybrid concept results in a softer and more water-absorbent product. More than this, you will have lower variable operating costs for a roll or case. And with less fibre and less energy, you’ll have a more sustainable product.
* Valmet hybrid technologies consist of the Valmet Advantage NTT, Advantage QRT and Advantage eTAD technology. All figures listed in this article are related to an average for all three machine technologies.
The beauty is that you don’t have to choose one or the other – the options can be combined
Conservation of resources, reduction of energy consumption, carbon dioxide (CO2) reduction, closed-loop circular economy – these are all firmlyestablished cornerstones of Andritz ’s sustainability strategy. Bringing its economic, environmental, and social objectives in line with the major challenges of a raw material and energy environment going through radical changes globally is an urgent task faced by the company. Andritz ’s R&D specialists explore
and develop new technologies to make the valuable resources used in paper production sustainable during unprecedented climate change.
The R&D project ‘Tex2Mat’ for the recycling of waste materials in the production of press felts at the main site in Gloggnitz, which has received funding and been awarded a national prize for environmental technology
in recent years, shows how seriously the company takes its responsibility to ensure a futureproof, sustainable transformation.
This results in the production of paper machine clothing that mitigates climate change. As a result of the consistently-positive feedback from customers who have used felts made from a mixture of new and recycled
material for the first time, the proportion of recycled material in press felt production is continuously being increased –thus promoting a circular economy that is sustainable in the long term.
Based on this success, Andritz is now pursuing its next recycling
Progress is being made by Andritz with a research project that could result in the management and reuse of the materials used to produce forming fabrics in the paper making process. PPL reports
primary and secondary shredding as well as for fine granulation of composite materials.
Andritz also has a polymer sorting process at its disposal that is characterised by high separation performance, especially when high-purity products are required and when polymer mixtures with a wide range of different particle sizes and shapes are also present.
The core unit of this process is the CENSOR ACZ, a sorting centrifuge that separates, washes, and dewaters the raw material simultaneously. As a result, tests are possible with very different waste streams and complete recycling processes can be replicated.
The same site also accommodates the newly-opened Digital Waste Research Lab of the University of Leoben – a research center for waste processing and waste management.
The cooperation between Andritz and the Montanuniversität Leoben creates synergies between research and business, leading to the development of technologies and products needed to meet the future requirements of the recycling industry.
Circulyzer GmbH – a start-up and spin-off of Montanuniversität Leoben’s Department of Process Engineering for Industrial Environmental Protection – is also a vital part of the research project and supports the project with its separation technology. As the separation of the two main components of the forming fabric, (PA) and (PET) mixtures, is much more difficult than with PA synthetics exclusively used for press felts, special attention is given to this process.
So far, there have been no processes for this that make separation worthwhile in terms of economics and the environment. This shows that well-founded basic research is necessary as a starting point for the entire recycling process, so that real future-oriented technologies can be developed rather than just striving to achieve quick, superficial results that then fail to achieve a closedloop recycling economy when implemented.
This joint research initiative, combining science and industry, is all the more valuable when the aim is to meet the longterm requirements in polymer recycling. This may become
Paper Machine Clothing (PMC) for forming fabrics that are made from polyamide (PA) and polyethylene terephthalate (PET).
The main aim of the new research project named ‘ReFibreValue’, which is funded by the FFG (Bridge2 funding programme No. 895423) following the EU Green Deal Waste Framework Directive 2008/98 and the EU Circular Economy Framework. Directive 2018/851 is the research and development of
a completely carbon-neutral material cycle. From the transport of the used forming fabrics from paper production sites and the following recycling processes, including cleaning and separation of the PA and PET, to the subsequent return of the recycled material to the production of new monofilaments and production of new forming fabrics, there should ultimately be a continuous, closed-loop, resource-saving and energysaving cycle, with the up to now usual thermal disposal of material waste associated with high CO 2 emissions being reduced to zero in the long term. Together with partners from the paper industry and MUL - Montanuniversität Leoben, including its departments for Polymer Processing, Materials Science and Testing of Polymers, Resources Innovation Center, Waste Processing Technology and Waste Management, as well as Mineral Processing, the R&D team at Andritz ’s Reutlingen production site is now starting the research project and in order to achieve a positive result similar to the outcome achieved by their colleagues in press felt production at Gloggnitz.
The new Andritz Recycling Technology Center – known as the ART Center – enables recycling trials to be conducted under real production conditions with industrial-sized equipment. The units can be used for
even more important, given the sharp rise in energy prices and availability of raw materials and the need for sustainable CO2 reduction in the future based on legal requirements, for example,
through the introduction of mandatory recycling quotas for industrial waste.
Jan Freudenberg, director of R&D for global forming fabrics, who is in charge of the research
cooperation at Andritz, and his team are convinced that at the end of the research and development phase, involving intensive analysis work and extensive tests, a recycling
technology will have been created that is both economically and environmentally sustainable.
More information from Jan Freudenberg by email at jan. freudenberg@andritz.com
Aimed at manufacturing companies using heating and drying systems, such as in the pulp and paper industries, a 100 per cent hydrogen fed duct burner has been launched by French-based industrial combustion specialist Fives.
The Hy-Ductflam burner is described as a key step towards the decarbonisation of heating and drying processes worldwide as hydrogen emits no carbon dioxide when burnt. Designed for new installations or to replace standard duct burners, the system can be easily implemented by manufacturers with very limited process modification, says Fives. Hy-Ductflam enables its customers to easily switch fuels
going from 100 per cent natural gas (NG) to 100 per cent hydrogen (H2) without any changes made to the equipment.
Typically, by using Hy-Ductflam set for 100 per cent hydrogen, a paper mill will emit 170 kg less of CO2 per ton of paper produced,
A third E-Wind P100 paper rewinder has been started up by Italy’s A.Celli at Maanshan Huawang’s plant at Anhui in China. The rewimder has been installed on its PM16 line to process decorative speciality paper Jumbo rolls at 2,200 mpm.
This rewinder joins the other two P100 rewinders provided by A.Celli in 2019 and 2021. A contract for a fourth P100 was signed in June.
General manager of Maanshan
Huawang, Wu Hai Biao said: “We relied in the past on A.Celli’s rewinders for our decorative paper production lines and we couldn’t have made a better choice. This third order confirms our trust in these machines performance and reliability.”
which significantly reduces its carbon footprint (by about twothirds) says Fives.
Providing high efficiency and mechanical reliability, the HyDuctflam is suitable for any duct configuration. This means it can be installed both in new facilities and
as a replacement of standard duct burners, thus limiting costs for manufacturers.
“Fives is at the forefront of hydrogen development and offers the largest range of hydrogen compatible burners on the market. We are proud to provide a new solution that answers the need for decarbonisation of our customers and are exited for new innovations to come,” said Francesco Giudici, general manager at Fives ITAS.
Fives claims to have more than 40 years of experience in the burning of high hydrogen content fuels, and strongly invests in R&D to offer the largest range of hydrogen-compatible burners on the market.
More information from www.fivesgroup.com/energycombustion
Maanshan Huawang New Material Technology Limited, located in Maanshan City, was founded in 2020 by Hangzhou Huawang Industrial Group, a producer of building materials and decorative paper products. Sales in 2022 were 1.19 billion
Key technologies, automation and services have been ordered from Valmet by Naini Papers for a cooking and fibreline rebuild and its new PM3 speciality paper machine at its Kashipur mill in India.
Scheduled for delivery in the first quarter of 2025, the project is expected to cost about €50 million.
The cooking and fibreline rebuild is expected to increase the capacity from the current 300 bone-dry tonnes per day (bdt/d) to 370 bdt/d. The delivery includes key process equipment, such as a SuperBatch digester, a TwinRoll Press, a bleach plant upgrade, and other auxiliary equipment.
Basic engineering, detailed process engineering and site services are included. The automation package includes analysers and measurements for the fibreline, such as Kappa number, brightness, residual chemical, white liquor to cooking and residual alkali, as well as pulp consistency. A spare parts package includes critical spares and consumables for the start-up of the equipment.
Managing director of Naini Papers Ltd Pawan Agarwal commented: “We have been successfully collaborating with
Valmet in many projects, including pulp mills, and decided to choose them again for this rebuild expanding our pulp production capacity. The additional pulp will be used in the upcoming PM3. We see big potential for speciality coated paper in the Indian market and are eyeing the environmentfriendly flexible packaging segment. The paper produced by the PM3 can replace plastics in packages.”
Varun Jain, director for the India region of the Asia Pacific for Valmet, added: “We’re
● An Advantage DCT 100TS tissue production line is to be supplied to Papel San Francisco in Mexico by Valmet. The new TM10 machine will be installed at PSF’s mill at Mexicali in Baja California with start-up planned for the second quarter 2025.
Papel San Francisco currently has five Valmet lines in operation, started up between 2006 and 2020. TM9 is currently under delivery and will start up in 2024. The upcoming delivery of TM10 in 2025 will include the 100th ViscoNip press that Valmet has delivered.
delighted that Naini Papers chose Valmet again as the supplier of their project. Our sustainable technologies, references, local presence and trust built through the projects and various pilot trials at the Valmet R&D centre were the keys to win the order. India is a growing market for speciality grades and Naini Papers has taken the right step forward to be a leading player in this segment.”
The PM3 speciality coated paper machine is the first of its kind in India, with a design speed of 1,200 m/min, producing mainly
woodfree coated and uncoated grades with a basis weight range of 40-170 g/sqm. The raw material used will be mainly hardwood pulp, with an option to mix bale softwood and precipitated calcium carbonate as filler.
Naini Papers Limited, founded in 1995, offers high quality writing and printing papers with improved physical and optical properties. It is a market leader in the production of single layer stock for making paper cups and saturating kraft for laminates.
● Andritz has received the ninth order for a PrimePress X shoe press from China’s Lee & Man Paper Manufacturing for its Best Eternity Recycle Technology mill at Banting in Malaysia, with startup planned for the end of 2024.
The newly ordered shoe press will be installed in the PM26 containerboard machine that runs at a design speed of 1,000 m/ min and produces high-quality Testliner in basis weights from 70 to 160 gsm.
US-based Shawano Specialty Papers has started up a TT SYD Steel Yankee Dryer supplied by Toscotec at its Shawano paper mill in Wisconsin, USA.
Replacing an existing cast-iron dryer on the PM3 tissue machine, the new TT SYD is said to have significantly increased the line’s capacity, is ensuring higher operational safety and reducing the overall operating costs.
Michael Bogenschutz, general manager of Shawano Specialty Papers, a division of Little Rapids Corporation, says “Toscotec provided excellent technical support throughout the entire project. Start-up of the new Yankee went smoothly, and the
dryer is performing well. We are experiencing lower energy consumption and are seeing the potential for increased production efficiency.”
Thailand’s United Paper has started up an OCC (old corrugated containers) line supplied by Andritz at its Prachinburi mill, its second Andritz OCC line at the site.
The new line – complete from pulping to the storage tower –has a capacity of 550 bdmt/d and processes a mixture of AOCC and LOCC for the production of highquality linerboard grades.
The LC pulping system, with FibreSolve FSR pulper and Detrasher, ensures superior slushing of the raw material with minimum fibre loss, as well as efficient separation and removal of rejects. In combination with PrimeScreen X screen baskets, energy savings of up to 25 per
cent compared to conventional systems are said to have been achieved.
Wachara Chinsettawong, managing director of United Paper, says: “Together with the Andritz fibre experts, execution of the entire project was smooth, fast and of highly professional. The two lines from Andritz are equipped with separate drum and LC pulpers, which gives us more flexibility in the use of raw materials. We can’t wait to expand our business with our new premium grades.”
Founded in 1994, United Paper Public Company Limited is a key producer of kraft paper grades for liner board and corrugated medium.
Michael Drage, president of Toscotec North America added, “Our latest-generation design Steel Yankee delivers the highest possible drying efficiency in the
tissue industry, which is of course a deal breaker for any tissue producer. We are happy to see that with this TT SYD, Shawano Specialty Papers has gained a key competitive advantage to support their growth in North America.”
Founded by Charles Egan in 1947, Shawano Specialty Papers remains a family-owned business with product lines serving the medical and beauty market segments, flexographic printing for a variety of packaging markets, and tissue, MG paper, and wet crepe paper for the speciality paper market. It has two mills in Wisconsin, at Green Bay and Shawano, with 450 employees. Based in Italy, Toscotec has sold 260 TT SYD Yankee dryers worldwide since they were first developed in 2000.
The first fibres have been produced by a new highperformance pressurised refining system installed by Andritz at the Vadodara mill of Greenply Industries in India.
The refining system has a design capacity of 35 bdmt/h and processes wood chips for producing various types of medium-density fibreboard (MDF) products. It is equipped with an S1056M single disc refiner ensuring efficient presteaming, low electrical and thermal energy consumption, along with excellent dewatering in the 20-inch (50.8cm) plug screw feeder.
Joint managing director of Greenply Sanidhya Mittal said:
“The pressurized refining system from Andritz is highly efficient and energy saving, which is in line with our environmentally friendly production process. We would like to thank Andritz and its team for their assistance during the installation and the high level of professionalism throughout the whole project.” Greenply Industries Limited, founded in 1984, is one of India’s largest manufacturers of high-quality interiors and produces a broad range of MDF products, such as plywood, decorative veneers, doors, and related products. Greenply holds the FSC certification in forest management.
Metsä Group organised a maintenance and connection shutdown at the Kemi mill in advance the start-up of the largest-ever investment in the forest industry in Finland –the new bioproduct mill and paperboard mill expansion.
The shutdown was due with the aim of starting up the mills on 20 September.
Metsä Group warned the local community that during shutdown, odours could occur, with temporary traffic congestion
around the mill area. It said that odours could also occur before the shutdown due to preparations for the start-up of the bio-product mill.
The work carried out prior to start-up was to ensure that the mills came online smoothly and safely. During the shutdown, the existing pulp mill was to be safely shut down, the paperboard mill’s new investments brought on line, and the connections between the new bio-product mill and the paperboard mill finalised.
The new Kemi bio-product mill has been designed to yearly
produce about 1.5 million tonnes of softwood and hardwood pulp and many other bio-products, including 2 terawatt-hours of renewable electricity.
The mill features world-class production, environmental and energy efficiency, and despite the considerable increase in production capacity, the mill’s emissions were to be lower than the limits specified in the currently valid environmental permit for the existing Kemi pulp mill.
At the Kemi paperboard mill, renewal and bottleneck investments have been carried out
to increase the annual production capacity of white top kraftliner by some 40,000 tonnes. The investments will reduce the mill’s water consumption by 40 per cent and energy use by 5 per cent per tonne of paperboard produced.
Metsä Group said the investments are a major step towards its 2030 sustainability targets and will support its customers’ sustainable business.
An electrostatic precipitator (ESP) for the recovery boiler at Shandong Huatai Paper’s 700,000 tonnes chemical pulp project in Shandong province, China, has been ordered from Valmet, with delivery is scheduled for January 2025.
“Green is our mission, sustainability is our way,” said Houyue Ma, vice general manager of recovery boiler and power generation at Shandong Huatai Paper. “This is one more activity for Huatai to introduce Valmet’s technology to implement the goal of low energy consumption, no pollution, and zero emissions. We look forward to Valmet’s technology and services to further
support our green manufacturing and circular economy.”
Valmet’s delivery includes all mechanical parts of the ESP as well as electrification, instruments, and automation
control equipment for the recovery boiler which has a capacity of 3,200 tonnes dry solids per day (TDS/D). The ESP will collect recovered alkali ash, with a guaranteed emission value
below 10 mg per cubic metre (N).
Igor Panassol, vice president of pulp and energy for the China Area at Valmet, added: “We are very happy to continue our excellent cooperation with Huatai Group in this strategic investment. In addition to previous pulp, paper, and automation technology deliveries, we also have extensive services cooperation with the customer.
“The ESP project further develops our cooperation both in scope and depth. It is an important milestone for both companies and a good example of Valmet’s latest technology supporting customers to reach near-zero emissions through an environmentally friendly solution.”
India’s Andhra Paper Limited has ordered a recovery boiler upgrade and sustainable technologies from Andritz to increase capacity and reach environmental goals at its Rajahmundry mill.
The order also includes an ash leaching system which will remove non process elements, minimise chemical loss in the recovery cycle and improve runnability and life of the recovery boiler, and a lime kiln that will reduce solid wastes and gaseous emissions.
Sura Reddy Mallidi, senior vice president of mill operations at Andhra Paper says: “With this
Nageswara Rao, vice president of projects, and Sura Reddy Mallidi, senior vice president of mill operations of Andhra Paper at an Andritz event
investment, we will be using Andritz proven technologies to improve reliability and efficiency at our Rajahmundry mill.”
The Andritz order includes:
l The recovery boiler capacity upgrade from 1,300 tds/d to
1,500 tds/d on EPC basis, which is to be installed and startedup during the planned mill shutdown. The key delivery includes air system upgrade and super heater modification.
l A new ash leaching plant that removes the non-process elements chloride and potassium from the electrostatic precipitator ash while recovering sodium and sulphate to the chemical recovery cycle. The plant is designed to handle 95 tons of ash per day.
l A new lime kiln with a capacity of 190 tons per day of burnt lime on EPC basis, including a LimeDry lime mud washing and dewatering filter, an LMD
LimeKiln feeding system, a LimeCool and a LimeFire multi fuel burner. Efficient lime mud washing with a LimeDry filter provides high-quality lime mud to minimise lime kiln emissions.
Andhra Paper Limited was founded in 1964 and is today one of the largest integrated paper and pulp manufacturers in India, with two mills at Rajahmundry and Kadiyam and total production capacity of 240,000 tons per year. The company offers a wide range of papers suitable for writing, printing, photocopying and speciality applications for both the domestic and international markets.
Ahuge order for pipework and vessels for installation at Stora Enso’s Oulo mill expansion in northern Finland has been received by Butting Anlagenbau in Germany.
As previously reported, the Oulo mill’s former PM6 paper machine is being converted into a packaging board line with annual production of 750,000 tonnes of high-quality coated primary fibre board with a white or brown reverse side, which Stora Enso says will make it the largest machine of its kind in Europe when it starts up early in 2025.
Butting’s Schwedt site will be supplying 128 container positions for the BCTMP and BM6 areas, including process and storage
tanks with volumes of up to 700 cubic metres, which will be manufactured, delivered, and assembled on site.
With responsibility for the piping in the pulp preparation system,
Butting will lay more than 23 km of pipelines in diameters from DN 15 to DN 1,000. The total weight for container and pipeline construction will be more than 1,000 tonnes of stainless steel,
including primary and secondary supports.
Commenting on the project, Marko Busse and Mario Kulow, joint managing directors of Butting Anlagenbau, said: “The challenge for us is the narrow time frame for assembly. Container construction will start as early as August this year, with pipeline construction following shortly afterwards in October.
“From today’s perspective, a total of at least 100 fitters will be employed on site by September 2024.
“We are delighted to be part of this huge project. Together with our team, we gladly accept the challenge. This will give us another chance to demonstrate our capabilities in Europe’s pulp and paper industry.”
HKB-Hoa Lu Paper has started up an OCC (old corrugated containers) line and a reject treatment system at its Nho Quan District mill in the Ninh Binh Province of Vietnam.
The new line, delivered by Andritz, processes OCC with a capacity of 500 tons per day to produce high-quality testliner and corrugated medium for the local and Chinese markets.
Ngo Huu Phuong, vice chairman of HKB-Hoa Lu Paper, says: “Thanks to the excellent cooperation between our team and Andritz, the line has started up successfully as scheduled. We expect this line will perform excellently and produce highly
competitive products.”
The project comprised the complete stock preparation
equipment including the approach flow, fibre recovery, and reject treatment systems,
detailed engineering and supervision of erection and commissioning as well as operation and maintenance support.
The technology, including PrimePulping LC system, PrimeScreen X, dispersing system, ModuScreen HBE, as well as a Saveall DiscFilter, ensures high efficiency and superior final stock quality paired with excellent fibre properties. Minimum fibre losses and low specific power consumption are further benefits of the new system, says Andritz.
HKB-Hoa Lu Paper Joint Stock Company was founded in 2020 and focuses on the production of a range of board products.
Leading manufacturer of premium papers and self-adhesive materials, Fedrigoni has contracted ABB to install its L&W Lab Management System (LMS) at a new RD&I facility at Verona in Italy to improve efficiency and reduce lab procedure times.
The 3,000 sqm Fedrigoni Innovation Center will be officially opened at the beginning of 2024, comprising four complementary areas: the RD&I department, the FedLab (incubator of new ideas), the Customer Experience Centre and the Customer Academy (internal and external training).
ABB’s LMS has been purposebuilt for paper testing labs, with
automated lab reporting that is specifically tailored to workflow practices. This enables the operator to quickly and accurately complete measurements by sample or instrument and know which test is to be performed for every sample.
Data from the lab instruments is automatically aggregated and captured in the database, eliminating the risk of errors and significantly reducing data collection time. Results become immediately available to the user who can use the web-based application to view historic data, quality reports, product quality limits, trends, and key performance indicators (KPIs) in
on what is described as ‘intuitive dashboard’.
“The Innovation Center aims to be the home of innovation for both our worlds of special papers for packaging and creative communication and premium selfadhesives,” said Marco Nespolo, chief executive of the Fedrigoni Group.
“It will be a physical space where we can bring together the best talents, inside and outside Fedrigoni, and the most advanced technological solutions to develop projects, new products and applications that support our customers. ABB’s lab management system met all of our requirements and will be
instrumental in helping us to roll out new developments more quickly in the future.”
Part of ABB Ability, the LMS is scalable, connecting a range of benchtop lab testing instruments, as well as automated paper testing systems such as the L&W Autoline, into one database and interface.
Founded in 1888, Fedrigoni specialises in labels, self-adhesive materials and high value-added papers for luxury packaging, with more than 5,000 employees in 28 countries and 25,000 products. The Paper division includes the Cordenons Group, the Fabriano brand, and recent acquisitions Éclose, Guarro Casas and Papeterie Zuber Rieder.
Ivar Vatne has been appointed as acting chief executive of Swedishbased global fibre products manufacturer Billerud, following the departure of president and chief executive Christoph Michalski, who had served in both positions since November 2020.
Vatne was financial chief from May 2019 and deputy chief
executive from 2022 at Billerud, joining the paper maker from a number of senior positions such as at Arla, Fiskars and Procter & Gamble.
“The board is confident that Ivar Vatne can quickly step into the role of acting CEO and that he can lead the implementation of our established strategy,” said Jan Svensson, chairman of Billerud.
“The board would like to thank
Richard Bracewell has been appointed as managing director of the Paper Products division of UK-based creative and luxury packaging maker James Cropper. Bracewell will be bringing together the established Speciality Paper business with production of Colourform, the award-winning moulded pulp innovation.
He has most recently served as the business transformation lead for Speciality Paper, where he has been instrumental in repositioning the organisation to ensure longterm differentiation and market competitiveness.
Chief executive of James Cropper Steve Adams commented: “We are thrilled to welcome Richard Bracewell as our new managing director for Paper Products. His leadership, expertise, and deep understanding of our business will undoubtedly drive us towards greater achievements.”
The company says that Bracewell brings a wealth of experience from both within and outside the organisation, having held senior leadership positions at Shell before joining James Cropper
as marketing director for the Speciality Paper Business in 2017. Bracewell commented: “I’m delighted to have been asked to lead James Cropper’s Paper Products business and to continue to build upon our unique and significant capabilities as a leading innovator in the Creative Papers and Luxury Packaging sectors. The changes that we are making within the business, will help us to accelerate our growth strategy in the manufacturing of bespoke papers and moulded fibre packaging, ensuring that we continue to provide our customers with the highest quality products and solutions.”
Christoph Michalski for his significant contribution to Billerud. In the three years he has led the
company together with the CFO, the company has introduced a new strategy, laid the foundation for a future Norwegian BCTMP factory in close cooperation with Viken Skog, and completed the strategically vital acquisition of Verso in North America”, says Jan Svensson, chairman of the board in Billerud.
The recruitment of a new chief executive started in September.
Two appointments have been made in Metsä Fibre’s management structure.
Mikko Antsalo has been appointed as senior vice president for sales and customership, and becomes a member of Metsä Fibre’s management team from the beginning of March 2024. He will report to chief executive Ismo Nousiainen.
Antsalo joins Metsä Fibre from Stora Enso, where he is currently working as head of the paper segment, in packaging materials. Antsalo has a long experience in sales management positions in various forest industry companies.
Ari Harmaala, current sales and customership chief at Metsä
Fibre, will continue to work for the company as senior vice president of sales and marketing development. He will continue to report to the chief executive and remains a member of the company’s management team.
In the second management change Mikko Nieminen has been appointed senior vice president for pulp production and will become a member of Metsä Fibre’s management team also from March 2024. He also will report to chief executive Ismo Nousiainen.
Nieminen also joins Metsä Fibre from Stora Enso where he works as mill director at Imatra mills. Jari Tikkanen, the previous senior vice president for pulp production, has left Metsä Group.
10–11 April 2024 | Messukeskus
Helsinki Expo and Convention Centre
Pulp & Beyond is the leading forum bringing together the latest forest-based bioeconomy innovations, products, services and technologies as well as key people throughout the ecosystem.
Pulp & Beyond offers new encounters, inspiration, networking and business possibilities for marketing global and sustainable solutions, products and services within the forest-based bioeconomy. The event provides the widest available showcase on the latest trends and innovative new products within the forest-based bioeconomy, supporting learning, employer branding and competence development.
If you need a versatile solution to better manage your software lifecycle, look no further than Automation Software Maintenance (ASM). ABB’s newest lifecycle management program removes the complexity and cost of accessing new software releases and features, corrections and enhancements between major system upgrades. ASM is available for DCS, QCS, Paper Machine Drives and Pulp and Paper Process Control Library.
Learn more: abb.com/pulpandpaper