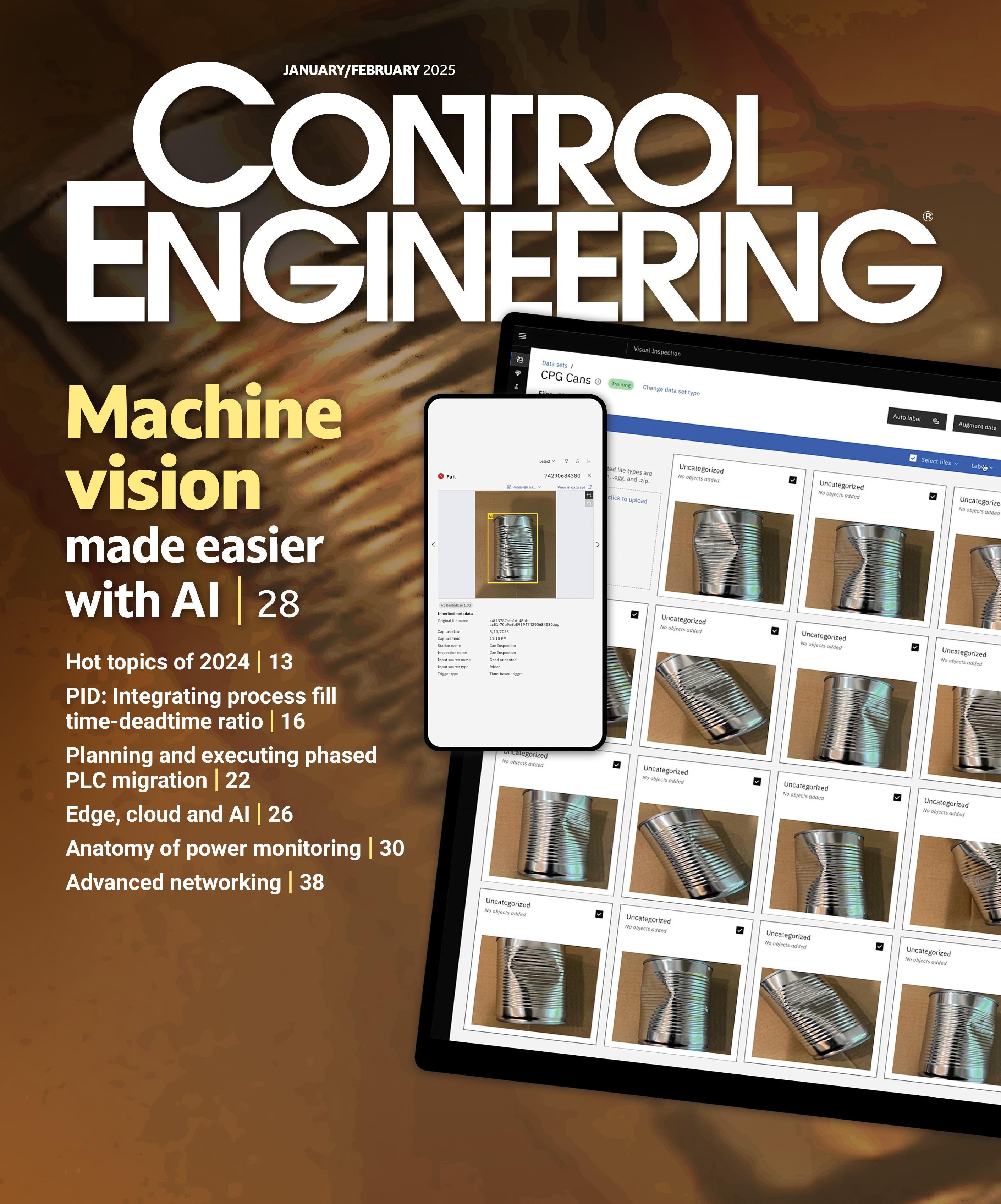

AutomationDirect carries a full line of AC and DC motors from trusted brands like Toshiba®, U.S. Motors®, WEG®, Leeson®, IronHorse® and Marathon®, at some of the best prices in the industry. In-stock motors are shipped quickly with free shipping on orders over $49*.
Starting at $370.00
• 230/460 VAC 3-phase from 1/4 - 20 hp
• 1200 and 1800 RPM
• Models with pre-mounted Avtron encoder
• Constant torque operation; zero to base speed on vector drives
• 5000:1 speed range
• Constant horsepower operation to 2X base speed
WEG S-Series Rolled Steel Motors and Brake Motors
Starting at $194.00
• Three-phase 208- 230/460 VAC from 1/4 to 20 hp
• Single-phase 120/240 VAC from 1/4 to 3 hp
• 1200, 3600 and 1800 RPM
• TEFC enclosure with IP55 rating
• Premium and Standard Efficiency available
• 230/460 VAC 3-phase from 1/2 - 100 hp
• 1200, 1800, 3600 RPM
• Inverter duty
• Optimized for operation with variable speed drives (VFDs)
• Compatible with encoder installation
• NEMA premium efficiency ratings on certain models
• 3-year warranty
• Certified Class I, Div 2, Groups A,B,C,D
• Brake motors include spring set, solenoid actuated AC brake with manual release lever
• UL, CSA
• 18 month warranty
Toshiba EQP SD (Severe Duty Motors)
Starting at $376.00
• TEFC enclosure with IP55 protection
• Class I, Division 2, Groups A, B, C, D
• NEMA premium efficiency
• UL, UR, CSA
IronHorse MTS Stainless Steel Washdown-Duty
Starting at $417.00
• Three-phase 208-230/460 VAC from 1/3 to 20 hp
• 1200, 3600 and 1800 RPM
• TEFC or TENV enclosure
• IP69K protection
• Premium Efficiency (EISA Compliant)
• BISSC Certified
• TEFC enclosure
• 304 stainless steel frame, end bracket, junction box and hardware
• Class I, Div 2 hazardous locations
• In accordance with NEMA, CSA, UL, and CE
• 2 year warranty
IronHorse MTRJ Series Jet Pump Motors
Starting at $167.00
• 3600 RPM
• Class F winding insulation
• Single-phase 120/230 VAC from 1/3 to 2 hp
• Built-in thermal protection on single-phase models
• Oversized 300-series bearings
• Heavy-duty cast iron construction
• 3-year warranty
• Three-phase 208- 230/460 VAC from 1/3 to 3 hp
• 56J frame with threaded shaft for connection to a jet pump
• 2 year warranty
No matter how many “ings” your process has, Productivity PLCs can handle them all while providing substantial cost savings. Whether you’d prefer a single controller for complete end-to-end control or a segmented control system with multiple controllers, the scalable Productivity PLC family has what you need for less.
This family offers three series of PLCs each with different I/O capacities but all using the same FREE advanced programming software, so you can easily scale your control hardware up or down depending on the application.
NEW! More discrete and relay I/O expansion modules have been added to the Productivity PLC family for even more affordable control options.
For the Productivity1000 PLC series:
• A 4-channel, high current relay output module with up to 7A/point and four Form C contacts, perfect for applications with higher current loads
For the Productivity2000 PLC series:
• A 6-channel, high current (7A/point) relay output module with both Form A and Form C contacts
• A 16-point low voltage discrete input module and 16-point low voltage discrete output module, ideal for devices that utilize transistor-transistorlogic (TTL) and voltage levels ranging from 3.3 to 5 VDC
7 | January and February online article sampling from www.controleng.com, more headlines, authors, companies, links
43 | New Products for Engineers, www.controleng.com/products
HMI has advanced display, low-side MOSFET gate drivers, machine controller, magnetic sensors, turbine flowmeter, wireless differential pressure sensor, high-precision non-contact displacement sensors, robotic programming system, modular PLC with I/O expansions, self-learning 3-phase soft starters.
Product of the Year voting begins in March! https://www.controleng.com/events-and-awards/product-of-the-year
47 | Back to Basics: How industrial AI deepens sustainability in 3 ways
Benefits include cleaning and contextualizing data, managing many data streams and continuously optimized supply chain strategies.
CE Edge & Cloud Computing Newsletter
• How edge computing improves operations, sustainability
• Machine connectivity and edge computing advances for manufacturers
• Seven open-source interconnection strategies for empowering Industry 4.0
IIoT Process Control & Automation Newsletter
• How to use AI-informed advanced analytics to fill the skills gap
• How to unlock design efficiency, standards for P&ID development
• Generative AI benefits for asset lifecycle management
Go to www.controleng.com/subscribe and select newsletters.
u Global System Integrator Report
Did you see the November/December 2024 edition included with your November/December issue? If not, catch up here: www.controleng.com/global-system-integrator-report
Control Engineering eBook series, now available: Winter Edition
u PID Tuning eBook Winter edition
Featured articles include:
How to enhance plant performance using controls PID spotlight, part 4: How to balance PID control for a selflimiting process
Three ways big data can realize sustainability, digital transformation initiatives
Learn more at: www.controleng.com/ebooks
u Mechatronics and Motion Control eBook Winter edition
Articles include:
New AI-powered closed-loop tools can revolutionize manufacturing in 9 ways
Sustainable machine design offers real-world benefits
How vector and servo drives deliver savings More topics at: www.controleng.com/ebooks
u Control Engineering digital edition
Five digital edition advantages: 1. Useful links throughout. 2. Click on headlines to see online version with more text and often more images and graphics. 3. Download a PDF version. 4. Cover page faces a wide selection of topical eBooks. 5. Sustainability. www.controleng.com/ magazine
uLatest automation mergers, January 2025: Motion, process controls; visionClint Bundy is managing director, Bundy Group.
u Video interview: Take precise measurements, bravely apply results –Mark T. Hoske, editor-in-chief, Control Engineering (A)
u PID spotlight, part 12: What does good and bad level controller tuning look like?- Ed Bullerdiek, process control engineer, retired (B) https://www.controleng.com/pid-spotlight-part-12-what-does-good-and-bad-level-controller-tuning-look-like
u How to drive visibility through centralized monitoring techniquesSean Saul, vice president of the DeltaV platform at Emerson https://www.controleng.com/how-to-drive-visibility-through-centralized-monitoring-techniques
u To drive improved digital transformation, don’t forget about the process - Erik Lindhjem, vice president and general manager of Emerson’s Reliability Solutions business (C)
u Cut engineering time 70%, boost operational efficiencyJohn Oskin, senior vice president, SmartSights
u The challenge and opportunity for AI at the industrial edgeOliver Wang, product marketing manager for IPC at Moxa
uTwo benefits to new remote robotic monitoring, controlFredrik Ryden, CEO, Olis Robotics (D)
uHow to use Ethernet to improve high-density monitoringBob Myles, director of engineering, Moore Industries-International Inc.
uCANbus technology helps industrial applications 5 ways - Raymond Chiu, product marcom specialist, Moxa, and Tiffany Lin, product manager, Moxa (E)
uHow new automation technologies shape industrial networking trendsFelipe Sabino Costa, MSc, MBA, PMP, CCNA, CISA-US DHS, senior product marketing manager at Moxa Americas https://www.controleng.com/how-new-automation-technologies-shape-industrial-networking-trends
uNew Products for Engineers on www.controleng.com/products.
uProcess automation continues to evolve with the integration of advanced technologies such as artificial intelligence (AI), digital twins and robotics. This dynamic transformation holds significant implications for distributed control systems (DCSs) and their applications in modern industries. These innovations are increasing operational efficiency, while paving the way for sustainable solutions and more resilient industrial processes. Recent strides in AI have enabled autonomous control of intricate systems, such as distillation columns, in chemical plants.
‘AI learns by itself in simulations and then generates highly robust control models that cannot be achieved with conventional control models to achieve advanced control.’
Reinforcement learning algorithms like factorial kernel dynamic policy programming (FKDPP) showcase the potential to create self-learning systems.
Mitsuhiro Yamamoto, vice president and executive officer of the systems business division, digital solutions headquarters, Yokogawa Electric Corp., noted, “With regard to the realization of autonomy through AI, an important milestone is autonomous control using FKDPP. This algorithm learns by itself in simulations, and then generates highly robust control models that cannot be achieved with conventional control models to achieve advanced control. Beyond that, we believe that generative AI will open new possibilities in plant operations. Yokogawa will support digital transformation in the OT [operational technology] domain by providing data analysis, abnormality prediction and decision support to operators using generative AI.”
Digital twins are expanding the scope of process automation by creating virtual models that provide predictive analytics and enhanced measurement capabilities. Engineers can utilize these models to anticipate issues and optimize performance. These virtual representations of physical systems enable better planning and simulation, leading to significant cost savings and reduced downtime.
“We believe that advances in digital twin technology are an enabler of autonomous operations,” Yamamoto said. “The digital twin will make it possible to measure things that cannot be measured in reality, and to predict the future, expanding the scope of the twin, which in turn will broaden the scope of its application for autonomous operations.”
Integrating robotics with the DCS is a critical advancement. Robots conduct site inspections, can respond to alarms and feed real-time data into control systems. This enhances situational awareness and allows for immediate corrective actions.
“With regard to robotics, Yokogawa has realized the integration of DCS and robots through the Robot Management Core, which provides a single-user interface for different robots from multiple suppliers,” Yamamoto said. “We envision a future where DCSes and robots work together. For example, the alarm triggered by the DCS can be used to trigger the robot to inspect the site and address the problem. Also, data collected by the robot during its rounds of inspection can be reflected in DCS operations in real time.”
IT/OT convergence helps
IT/OT convergence bridges operational technology with information technology (IT) to unify plant operations with enterprise systems. This integration facilitates efficient collaboration and opera-
tional transparency, unlocking innovative opportunities for process management. By breaking down traditional silos, IT/OT convergence fosters a holistic approach to operational excellence.
Key platforms for IT/OT convergence ensure secure handling of OT data, while enabling comprehensive analysis and collaboration. Yokogawa was recently selected as main automation contractor for Shell’s Holland Hydrogen I project, and it is providing the integrated control system and the energy management system for the Yuri Green Hydrogen project in Australia. The company provided a remote operation/monitoring system and a video monitoring solution for the Ishikari Bay New Port Offshore Wind Farm, the largest wind farm in Japan. These projects use Collaborative Information Server (CI Server), critical for implementing IT/OT convergence. ce
Gary Cohen is senior editor and product manager at Control Engineering and WTWH Media, gcohen@wtwhmedia.com.
The U.S. Department of Energy (DOE) has issued a pre-publication Federal Register final rule for electric motors under the Energy Policy and Conservation Act, as amended (EPCA). In this final rule, DOE is adopting amended standards for a subset of electric motors, expanded scope electric motors. It has determined that the standards for this equipment would result in significant conservation of energy, and are technologically feasible and economically justified. Compliance date is Jan. 1, 2029. www.controleng.com/articles/new-rulesets-energy-standards-for-expanded-scopeelectric-motors
uControl system industry leader to step down after decade
The Control System Integrators Association (CSIA) has announced that CEO Jose M. Rivera will be stepping down after a decade of dedicated leadership. Under his guidance, CSIA has seen significant modernization, increased resilience and a strong financial position. Rivera will continue in his role to ensure a successful transition to the next CEO. “As March 2025 approaches, marking 10 years at the helm of CSIA, I reflect on our journey with immense pride,” says Rivera. “CSIA has significantly uplifted the SI industry by empowering members to build stronger businesses. Together, we have navigated critical challenges, including the COVID-19 pandemic, and emerged more resilient.”
CSIA Board of Directors’ Chair Karen Griffin highlights the significant strides made under his guidance, including modernizing the association, introducing alternative revenue sources, and expanding CSIA’s global presence. Griffin emphasized the strong financial position and resilience that Rivera's leadership has fostered. www.controleng.com/articles/controlsystem-industry-leader-to-step-down-afterdecade
The Field Level Communications (FLC) initiative of the OPC Foundation organized a 90-minutes event during SPS show in Nuremberg (Germany) to update OPC UA FX and explain the impact it has on the future of industrial communication. The speakers and the panelists are Matthias Gärtner (Siemens), Paul Brooks (Rockwell Automation), Andreas Pfaff (Mitsubishi Electric), Veli-Pekka Ketonen (B&R), Jochen Weiland (Schneider Electric) and René Hummen (Belden) sharing insights about the OPC UA FX value propositions and how the solution differs from conventional fieldbuses.
Courtesy: OPC Foundation
OPC Foundation announces key updates in governance, elections, joint forces for DPP, cloud, compliance and field-level communications. Developments include:
• The Clean Energy and Smart Manufacturing Innovation Institute (CESMII), the Labs Network Industrie 4.0 (LNI 4.0), the Digital Twin Consortium, the ECLASS e.V., the Industrial Digital Twin Association (IDTA), the OPC Foundation (OPCF), the VDMA, and the ZVEI have joined forced to create a best-of-breed system architecture to support the upcoming Digital Product Passport (DPP) by combining the best aspects of the Asset Administration Shell, OPC UA, and other related technologies. By making use of CESMII’s Smart Manufacturing Profiles, which are modeled with OPC UA, and integrating them with the semantics of the Asset Administration Shell and ECLASS, the rich and existing ecosystem of OPC UA modeling tools can be leveraged to build DPPs. To access the resulting DPPs, the existing REST interfaces of both OPC UA and the Asset Administration Shell can be used.
• Google Cloud and major manufacturers join the OPC Foundation cloud
Initiative. The initiative aims to standardize interoperability by enhancing the integration of IT and cloud applications using OPC UA, developing a cloud reference architecture with best practices, maintaining OPC UA Information Models (Companion Specifications) in the cloud for semantic data models, and creating a new protected identity for OPC UA Cloud eXchange UACX.
• The OPC UA Cloud Initiative steering committee includes prominent cloud suppliers, such as Alibaba Cloud, Amazon Web Services, Google Cloud, Huawei Cloud, Microsoft Azure, and SAP Cloud. Additionally, leading industrial automation companies like ABB, Beckhoff, Honeywell, Mitsubishi Electric, Rockwell Automation, Schneider Electric, Siemens, and Yokogawa are actively participating.
• The OPC Foundation has announced the addition of OPC UA FX (Field eXchange) capabilities to its certification program. OPC UA Certification Program provides a formal testing and certification process for controllers that implement the OPC UA FX specification series.
www.controleng.com/articles/ exciting-2024-opc-governance-updates-dpp-cloud-initiative-certifications
uEtherNet/IP Concurrent Connections now provides CIP Safety for industrial networks
ODVA advanced CIP Safety and process device profiles Specification for EtherNet/IP for RTD and thermocouple temperature sensors.
“The availability of Concurrent Connections for CIP Safety on EtherNet/ IP creates a whole new level of assurance that industrial networks will be both resilient and safe in the face of device failure or communication errors,” according to Dr. Al Beydoun, president and executive director of ODVA. “Concurrent Connections for CIP Safety is a win-win that offers the highest availability and functional safety together to enable the toughest applications to be handled while reducing injuries and increasing output.”
About the sensor profiles, Beydoun said: “The addition of a new temperature process device profiles for EtherNet/IP provides end users with another valuable tool to enable more efficient device commissioning and replacement. All EtherNet/IP process device profiles are aligned with the Process Automation Device Information Model (PA-DIM) and NAMUR NE 107 diagnostics. This allows for easier movement of data from the factory floor to the cloud for analysis and action and quicker identification of maintenance issues through standardization.”
www.controleng.com/articles/ethernet-ip-concurrent-connections-now-provides-cip-safety-for-industrial-networks
uNear-infrared sensor sees planets, is useful in industrial machine vision
A near-infrared-sensitive camera applied in astrophotography to see planets can be used in industrial machine vision applications.
www.controleng.com/articles/ids-cameras-redefine-astrophotography-with-starvis-2-sensors-for-capturing-planets
uTop 10 in digitalization for 2024: Advanced manufacturing institute
MxD, one of 17 U.S. advanced manufacturing institutes, released its top 10 achievements for 2024. (MxD stands for manufacturing times digitalization.)
Watch for coverage on the following events at www.controleng.com.
• The 29th Annual ARC Industry Leadership Forum, “Winning in the Industrial AI Era,” Feb. 10-13, Orlando, Florida, ARC Advisory Group, https://www.arcweb.com/events/arc-industry-leadership-forum-orlando
• Promat 2025, March 17-20, Chicago https://www.promatshow.com/home
• Trihedral SCADAfest, Orlando, March 19-21, https://scadafest.com
• Advanced Automation Forum, Control Engineering, WTWH Media, April 30-May 1 https://www.advancedautomationforum.com
• Automate, A3, Detroit, May 12-15, https://www.automateshow.com
‘New temperature process device profiles for EtherNet/IP provides end users with another valuable tool to enable more efficient device commissioning and replacement. ’ -ODVA
Successes include U.S. Department of Defense 5-year renewal and the MxD “Behind the Firewall: Assessing Cyber Resilience in U.S. Manufacturing” report on cybersecurity preparedness among manufacturers.
www.controleng.com/articles/top-10-in-digitalization-for-2024-advanced-manufacturing-institute
u$3.8M awarded to two multi-university projects for semiconductor energy
The National Science Foundation, as part of its Future of Semiconductors, or FuSe2, program, recently awarded $3.8 million for two projects involving University of Arizona engineers developing solutions for the semiconductor energy dilemma.
www.controleng.com/articles/3-8m-awarded-totwo-multi-university-projects-for-semiconductorenergy
Online new edited by Puja Mitra, WTWH Media, for Control Engineering, from news releases.
The Bundy Group reported 14 automation transactions in its December 2024 summary. Analysis on the acquisitions and reports are highlighted below including transactions from FloWorks International, Control Specialists, DwyerOmega and Revere Control Systems. A sampling follows. See full report online.
Oak Hill Advisors arranged a refinancing for FloWorks, Dec. 11, 2024
FloWorks International LLC, a distributor of critical flow control products and a portfolio company of Wynnchurch Capital, has successfully completed a refinancing. The refinancing, which will support future acquisitions, was arranged with Oak Hill Advisors acting as the Administrative Agent and Lead Left Arranger for the private unitranche facility. On Nov. 22, FloWorks acquired Applied Controls LLC and AC Systems Integration LLC.
Motion & Control Enterprises acquired North East Technical Sales, Dec. 2, 2024
Motion & Control Enterprises has acquired North East Technical Sales Inc., a value-added distributor of instrumentation and control solutions for industrial and municipal customers. Founded in 1973 and based in Harleysville, Pennsylvania, NETS serves customers across multiple states, including New York, Pennsylvania, New Jersey, Delaware, Maryland, West Virginia and Virginia, and will continue under its current name and leadership.
DwyerOmega acquired Process Sensing Technologies, Nov. 21, 2024
DwyerOmega, a portfolio company of Arcline Investment Management, has acquired Process Sensing Technologies (PST), a UK-based provider of measure-
ment instrumentation and monitoring solutions. The acquisition significantly enhances DwyerOmega’s sensing and instrumentation portfolio, strengthens its global market position and broadens its capabilities across key parameters, including moisture, gas, level and flow.
Relevant Industrial, a provider of industrial solutions, has acquired Control Specialists, LLC, a trusted provider of process instrumentation, control systems and specialized industrial services based in Evansville, Indiana. Effective Nov. 6, the acquisition enhances Relevant Industrial’s ability to serve industries such as renewable energy, semiconductor, refining, petrochemical, OEM and food processing.
Revere Control Systems, Nov. 11, 2024
SJE, a provider of control solutions for the water industry, has acquired Revere Control Systems, a premier provider of turnkey controls and automation solutions. Founded in 1980, Revere offers engineering services, including design, networking and programming, with expertise in municipal water and industrial automation. The acquisition enhances SJE’s capabilities and expands its control solutions offerings. ce
Clint Bundy is managing director, Bundy Group, which helps with mergers, acquisitions and raising capital. Edited by Mark T. Hoske, editor-in-chief, Control Engineering, WTWH Media, mhoske@wtwhmedia.com.
THE GLOBAL semiconductor manufacturing industry in the third quarter of 2024 showed strong momentum with all key industry indicators performing positive quarter-on-quarter (QoQ) increases for the first time in two years, SEMI announced in its Q3 2024 publication of the Semiconductor Manufacturing Monitor (SMM) Report, prepared in partnership with TechInsights. The growth is fueled by seasonal factors and strong demand from investments in AI data centers; the consumer, automotive, and industrial segments are experiencing a slower pace of recovery. Growth is expected to continue into fourth-quarter 2024.
After declining in the first half of 2024, electronic sales rebounded in Q3 2024, growing 8% QoQ, with a projected QoQ increase of 20% in Q4 2024. IC
sales rose by 12% QoQ in Q3 2024 and are expected to grow another 10% in Q4 2024. Overall, IC sales are forecasted to increase over 20% in 2024, primarily driven by memory products due to price improvement across the board and strong demand for data center memory chips. Semiconductor capital expenditures (CapEx) decreased in the first half of 2024, but the trend is turning positive starting in Q3 2024. Memory-related CapEx is surging 34% QoQ and 67% year-on-year (YoY) in Q3 2024 reflecting improvement in the memory IC market compared to the same period of the last year. ce
Edited
by
Puja Mitra, WTWH Media,
from a SEMI news release. Read more online.
As the world’s first ESV, we solve motion control challenges with ingenuity. Evolution Motion Solutions combines over 80 years of industry expertise in controls to deliver technically superior solutions for battery EV, fast-moving consumer goods, automotive, and oil & gas industries. We may not manufacture your systems or machines, but we help them run more efficiently and reliably with custom-built control solutions that optimize production time and enhance performance.
(888) 565-5479
evolutionmotion.com
Factory Automation • Heavy Industrial • Mobile/Off-Highway
®
1111 Superior Avenue, 26th Floor, Cleveland, OH 44114
Content Specialists/Editorial
Mark T. Hoske, editor-in-chief
847-830-3215, MHoske@WTWHMedia.com
Sheri Kasprzak, managing editor, engineering, automation and control, SKasprzak@WTWHMedia.com
Stephanie Neil, vice president, editorial director engineering, automation and control, 508-344-0620 SNeil@WTWHMedia.com
Emily Guenther, webinar coordinator EGuenther@WTWHMedia.com
Amanda Pelliccione, marketing research manager 978-302-3463, APelliccione@WTWHMedia.com
Gary Cohen, senior editor GCohen@WTWHMedia.com
Anna Steingruber, associate editor ASteingruber@WTWHMedia.com
Chris Vavra, senior editor
Suzanne Gill, Control Engineering Europe suzanne.gill@imlgroup.co.uk
Agata Abramczyk, Control Engineering Poland agata.abramczyk@trademedia.pl
Lukáš Smelík, Control Engineering Czech Republic lukas.smelik@trademedia.cz
Aileen Jin, Control Engineering China aileenjin@cechina.cn
Editorial Advisory Board www.controleng.com/EAB
Doug Bell, president, InterConnecting Automation, www.interconnectingautomation.com
David Bishop, chairman and a founder Matrix Technologies, www.matrixti.com
Daniel E. Capano, senior project manager, Gannett Fleming Engineers and Architects, www.gannettfleming.com
Frank Lamb, founder and owner Automation Consulting LLC, www.automationllc.com
Joe Martin president and founder Martin Control Systems, www.martincsi.com
Rick Pierro, president and co-founder Superior Controls, www.superiorcontrols.com
Eric J. Silverman, PE, PMP, CDT, vice president, senior automation engineer, CDM Smith, www.cdmsmith.com Mark Voigtmann, partner, automation practice lead Faegre Baker Daniels, www.FaegreBD.com
WTWH Media Contributor Guidelines Overview
Content For Engineers. WTWH Media focuses on engineers sharing with their peers. We welcome content submissions for all interested parties in engineering. We will use those materials online, on our Website, in print and in newsletters to keep engineers informed about the products, solutions and industry trends.
* Control Engineering Submissions instructions at https://www.controleng.com/connect/how-to-contribute gives an overview of how to submit press releases, products, images and graphics, bylined feature articles, case studies, white papers and other media.
* Content should focus on helping engineers solve problems. Articles that are commercial in nature or that are critical of other products or organizations will be rejected. (Technology discussions and comparative tables may be accepted if nonpromotional and if contributor corroborates information with sources cited.)
* If the content meets criteria noted in guidelines, expect to see it first on the website. Content for enewsletters comes from content already available on the website. All content for print also will be online. All content that appears in the print magazine will appear as space permits, and we will indicate in print if more content from that article is available online.
* Deadlines for feature articles vary based on where it appears. Print-related content is due at least three months in advance of the publication date. Again, it is best to discuss all feature articles with the content manager prior to submission. Learn more at: https://www.controleng.com/connect/how-to-contribute
Think Again about the top industrial automation, controls and instrumentation article topics of 2024, the most-viewed industrial automation-related webcasts and videos and the top Control Engineering magazine covers of 2024, part of Control Engineering’s 2025 look at the State of Automation.
In the Control Engineering annual tally of hot topics in industrial automation, controls and instrumentation for articles posted during 2024, the following topics ranked highest based on Google Analytics for www. controleng.com. See top 3 covers below from 2024 and the top 10 Control Engineering articles posted before 2024. See the most-viewed industrial automation webcasts and videos. 2024 was Control Engineering’s 70th year of publication.
ed earlier in the year naturally have an advantage; only one article among the following 10 were posted after midyear. Below these top 10, see to articles popular in second-half 2024, July through December 2024.
NOTE: This article online links to each article.
1. How to choose a VFD for medium-voltage motors – April 1, 2024
Top 5 article topics posted during 2024 were: Selection of variable frequency drives, industrial networking, robotic safety, good and bad controller tuning tutorial, career and salary survey. Top 5 article topics posted during 2023 were: PLC programming, robotic trends, VFD optimization, automation salary and career information and 6G wireless.
These automation and control topics help Control Engineering subscribers do their jobs better. For more value, think again about bookmarking this article to review what you may have missed. For future areas of automation coverage based on subscriber research (and to contribute articles), see the Control Engineering article topic list for 2025.
https://www.controleng.com/articles/control-engineering-reveals-new-2025-topicsfrom-subscriber-research
Top 10 Control Engineering articles posted during 2024
Analytics count the number of visits to articles posting during 2024, so articles post-
Understand the advantages of multi-level output drive topology in medium voltage (MV) motor applications. Motor insulation reliability and reflected waves: What to consider when selecting a variable frequency drive (VFD). (See Figure 1.)
2. Industrial networking 101: Everything you need to know – Feb. 8, 2024
Industrial networking is vital to today’s manufacturing landscape. From different types of networks to key components and best practices, this guide will help you navigate the intricacies of industrial Ethernet networking. See video.
3. Industrial robot safety considerations, standards and best practices to consider –June 6, 2024
As industrial robots become more integral to manufacturing processes, ensuring their safe operation is crucial as well as making sure workers are protected.
4. PID spotlight, part 5: What does good
FIGURE 1: The article, “How to choose a VFD for medium-voltage motors,” posted April 1 was the most-viewed article of 2024 on the Control Engineering website. Author Lucas Paruch is a product manager of medium voltage drives at Yaskawa America Inc., seen here with Figure 1 from the article showing the most common low-voltage drive topology. Courtesy: Yaskawa America, Control Engineering
FIGURE 2: Top three covers of 2024: Michael Smith, Control Engineering creative director, selected these three favorite covers of the year (Figure 2). January/ February cover photo from CC-Link Partner Association (SPLA) Americas, July/August cover photo from CDM Smith and September/October cover about the 2024 Engineering Leaders Under 40 winners were Smith’s favorite covers of 2024.
and bad controller tuning look like? – June 3, 2024
PID controllers have visual cues that you can use to identify performance problems. Improperly set controller gain, integral, and derivative offer unique patterns that you can use to guide your efforts to improve controller performance. See seven takeaways for better PID tuning.
5. Results are in: Control Engineering Career and Salary Survey, 2024 – June 25
Benefits and salaries increased. Leading automation technologies help resolve economic challenges and workforce shortages.
6. PID spotlight, part 2: Know these 13 terms, interactions – March 12, 2024
Learning proportional-integral-derivative (PID) controller tuning begins with the basics: Definition of
terms, the PID equation (multiple forms) and seeing how each of the PID terms functions independently from each other and separated from a process.
7. Back to the future of the PLC – May 2, 2024
Programmable logic controllers (PLCs) are not going away any time soon, and improving technologies combined with user demands will continue their evolution as a foundational automation platform.
8. Generative AI benefits for asset lifecycle management – Aug. 27, 2024
Generative AI is driving rapid improvements in asset lifecycle management, building on previous AI enhancements and unlocking operational efficiency.
9. Improving underground mining safety with millimeter wave technology – June 19, 2024
A professor began a project to design and deploy an emerging imaging and networking technology to improve safety and overcome hazardous conditions of underground mines.
10. Three reasons to tune control loops: Safety, profit, energy efficiency – Jan. 29, 2024
PID Spotlight, part 1: PID controller tuning is a keystone skill for control practitioners that is often given short shrift. What is the justification for investing in this critical skill? Why tune control loops?
One article above was posted after midyear. Because the list above favors article posted earlier in the year, please see the leading articles per month below that are not among those listed above or in a prior month below.
July 2024 - PID spotlight, part 6: Deadtime? How to boost controller performance anyway
August 2024 - Industry 4.0 is the springboard to a holistic automation future
September 2024 - Rising to the challenge: Engineering Leaders Under 40, Class of 2024
October 2024 - Gain critical advice on automation, SCADA from system integrators
November 2024 - More answers: Tips and tricks for next-generation automation programming
December 2024 - Why it’s critical to integrate distributed control systems
Top three covers of 2024: Michael Smith, Control Engineering creative director, selected these three favorite covers of the year (Figure 2). January/February cover photo, from CC-Link Partner Association (SPLA) Americas, highlights synchronized networks benefits for machine controls. July/ August cover photo, from CDM Smith, points to challenges of operational technology cybersecurity. September/October cover provides a sampling of eight faces among the 2024 Engineering Leaders Under 40 winners, arranged by Smith on the cover. Review these and other print/digital editions on the 2024 digital edition page. https://www.controleng. com/control-engineering-magazine
See the top Control Engineering webcasts below, based on the number of registrants, with links to the description pages below. Webcasts are posted for one year, so to view or review any of the following, do so before the following dates in 2025. Top three Control Engineering 2024 webcasts eligible for one RCEP PDH credit for those listening live on the broadcast date were:
PLCs: Programming tips and tricks appropriate for next-generation applications, Sept. 10, 2024
Back to basics: What you need to know about today’s PLCs, Nov. 6, 2024
How to Automate: The Mechanics of Loop Tuning, Aug. 1, 2024
A webcast that didn't offer RCEP credit would have ranked #2, above: Research Review: Control Systems: HMI, SCADA and PLCs, April 22, 2024
Top three 2024 webcasts created by suppliers of industrial automation and controls were:
How to Achieve Operational Excellence in Modern Monitor and Control with Edge Computing, May 16, 2024
Revolutionizing Manufacturing: The Power of Smart Factories, Aug. 13, 2024
Beyond ProcessBook & PI Vision: Exploring Today's Industrial Analytics Tools, March 14, 2024 Webcasts are available here: www.controleng. com using the pulldown menu for webcasts, near the top of the page.
Based on Control Engineering YouTube channel
FIGURE 3: The article, “PLC programming language fundamentals for improved operations, maintenance,” posted July 18, 2023, was the most-viewed article posted on the Control Engineering website among articles posted before 2024. Author Frank Lamb, the founder and owner of Automation Consulting LLC and a member of the Control Engineering editorial advisory board is shown with the function block diagram (FBD) PLC programming Figure 3 from the article.
views, https://www.youtube.com/@ControlEngTV, the following were the three most-popular videos posted in 2024.
• Improving PLC Version Control and Device Backup Using Modern Git Workflows
• Expert Interview Series: Nick Roe, Matrix Technologies: Industrial networking fundamentals
• Automate 2024 Demo: Doosan Robotics' Mixmaster Moodie
The following three YouTube shorts were the most-popular during 2024.
• Robot serving Modelo beer at Yaskawa booth at Automate 2024
• Automate 2024 Demo: ArcWorld HC Collaborative Welding workcell
• Automate 2024 Demo: Robotic parcel induction workcell uses high-speed GP12 robot
Control Engineering also recognizes top articles weekly and monthly. Think Again about how to deliver hot Control Engineering topics to your peers in 2025, appreciated whether recognized among the leading contributions or now, to help expand Control Engineering knowledge. ce
Mark T. Hoske is editor-in-chief, Control Engineering, mhoske@wtwhmedia.com. Traffic ranking and compilation based on www.controleng.com Google Analytics and Control Engineering’s YouTube channel were performed by Anna Steingruber, Emily Guenther provided webcast measurements. Cover analysis was by Michael Smith, all with WTWH Media.
‘Want to make the 2025 hot topic list? Here's how: https:// www.controleng. com/connect/ how-to-contribute’
controleng.com
CONSIDER THIS Bookmark this Control Engineering article so you can refer back to and catch up on the hot topic articles, webcasts, videos and covers you might have missed.
ONLINE
With this article online see the top 10 articles posted in Control Engineering posted before 2024 and top 3 videos posted before 2024. See what was on the 2023 Control Engineering hot topics list.
https://www.controleng.com/ articles/hot-topics-in-controlengineering-for-2023
Ed Bullerdiek, process control engineer, retired
Lengthy deadtime adversely affects the PID control of an integrating process. Knowing the process fill time/deadtime ratio will tell how well a PID controller will work, or if it will work at all. Can your PID controller be a hero? See “Quick-start PID tuning” and 6 graphs to help.
FIGURE 1: Controller stability decreases as the fill time/deadtime ratio decreases, constraining the possible controller gain, which limits controller effectiveness. Below a 1:1 ratio, effective control is no longer possible.
Courtesy: Ed Bullerdiek, retired control engineer
When using proportional-integral-derivative (PID) control for an integrating process, lengthy deadtime can adversely affect control. To tell how well or even if, PID control will work, find and use the process fill-time/deadtime ratio. Also learn from a personal story on PID troubleshooting. In PID spotlight, part 6: [https://www.controleng.com/articles/pid-spotlight-part-6-deadtime-how-to-boost-controllerperformance-anyway/] we discussed the impact of the lag/deadtime ratio on controller tuning for self-limiting processes. We learned that as the lag/ deadtime ratio decreased the controller tuning would become more difficult and controller performance would suffer. In short, excessive deadtime is bad for control. We also learned that for a constant lag/deadtime ratio the controller gain would always be the same whether the lag was 10 seconds and the deadtime 5 seconds (2:1 ratio), or the lag was 10 days and the deadtime 5 days (still a 2:1 ratio, however the integral time constant would be very different in the two cases.)
Integrating processes have the same dynamic, but with one difference. The important ratio isn’t lag/deadtime, but fill time/deadtime. Fill time is the inverse of the process gain:
Tfill = 1 / K p
Fill time is analogous to lag time for a self-limiting process in that both describe how fast the process moves to its final value; in the case of an integrating process to 100% or 0%. Similar to self-limiting processes the slower the integrating process moves toward 100/0% the more tolerant the controller tuning is of deadtime. Intuitively, this should make sense; the bigger the vessel, the longer it takes for the level to overflow/run dry and the longer we have to get the level under control.
Figure 1 shows that as deadtime comes to dominate the integrating process response the maximum stable controller gain decreases (red line), which limits the effectiveness of a PID controller. Figure 1 also shows that the controller gain (blue line) for disturbance rejection PID tuning decreases proportionally to the stability limit. We saw this in figure 1 in PID spotlight part 6 regarding self-limiting processes.
There is a difference between deadtime dominant self-limiting and integrating processes. Deadtime dominant self-limiting processes can still be controlled – poorly. Integrating processes cannot be effectively controlled once the fill time/deadtime ratio drops below 1:1. Self-limiting processes stop on their own, and the controller can eventually drag the process variable back to setpoint. Integrating processes will simply overflow or run dry. (To reiterate prior advice, if you are on a design team make vessels larger, if at all possible, especially if you expect charge rate growth.)
Controller gain is our primary knob for matching output to input (or input to output) and thus stopping an input (output) disturbance from filling/emptying the vessel. If we can make the controller gain larger, we can better limit the impact of an input change on the level. Figure 1 tells us that if we have a bigger vessel relative to any process deadtime the controller will be easier to tune and provide better control.
Figure 2 shows the response of an integrating process with a high fill time/deadtime ratio (10:1) that has the PID controller tuned for disturbance rejection. Similar to the lag dominant self-limiting processes we reviewed in PID spotlight part 6, high controller gain:
• Limits the process variable (PV) deviation from setpoint (SP) to about 2% despite there being a 10% change in inlet flow.
• The controller output (OP) responds very aggressively to a SP change, hitting the OP limit on a 10% SP change. This could be very disruptive to the downstream process. (If you are tuning for disturbance reduction, then the downstream process, if any, must be able to handle wild input flow changes.) The overall response to the SP change is considerably more oscillatory than the response to a 10% change in input flow.
• The controller is easy to tune since the maximum controller gain (the stability limit) is quite high.
Note that the controller output (OP) exceeds the input flow disturbance size by about 75%, or in this case a 10% inlet flow disturbance results in a peak output flow that is 17.5% above the initial output flow. We will see that this remains constant through all of the fill time/deadtime ratio cases.
If aggressive output swings are not tolerable when the setpoint is changed, there are several methods that can be used to limit these swings. In PID spotlight part 6, a setpoint (SP) filter was applied to suppress output swings. This is not available on all systems. Figure 3 shows the response when the controller is set up for integral action only on SP changes.
When we compare Figure 3 to Figure 2 we can see that the controller response to the inlet flow disturbance has not changed. We still have a strong response to the change, which limits the PV disturbance to about 2%.
The response to the SP change is considerably muted since the controller gain contribution is removed. Not surprisingly it takes the PV longer to reach SP, and the controller OP response does not hit the low limit and has less oscillation. While we would not expect level controller setpoints to be changed very often you may want to consider setting up the controller to limit output response on a setpoint change to limit the impact on those rare occasions when it is.
FIGURE 2: Disturbance rejection tuning of an integrating process (10:1 fill time/deadtime); Tuning constants are K = 7.5, Ti = 8.0 minutes/repeat, Td = 0 minutes.
controleng.com
KEYWORDS: Proportionalintegral-derivative, PID tutorial
LEARNING OBJECTIVES
Learn how the fill time/ deadtime ratio tells how well a proportional-integralderivative (PID) controller can respond to setpoint (SP) changes and reject process disturbances.
Understand that PID control of a fill time dominant process performs well and offers flexible tuning.
Know that PID control of a deadtime dominant integrating process is not possible.
FIGURE 3: Disturbance rejection tuning of an integrating process (10:1 fill time/deadtime); Integral only on SP change; Tuning constants are K = 7.5, Ti = 8.0 minutes/repeat, Td = 0 minutes
Figure 4 shows the response of an integrating process with a fill time/deadtime ratio of 5:1 that has the PID controller tuned for disturbance rejection. The controller gain, as is typical of disturbance rejection tuning, is set to roughly one-half the controller gain stability limit.
While controller gain has been considerably reduced, we still have:
• Limited PV deviation from SP at about 4% following the 10% change in input flow. Since the controller gain has been cut in half the deviation has doubled from the 10:1 case above.
• The controller output (OP) responds aggressively to a SP change, moving about 43% before the PV starts moving. The overall response to the SP change is considerably more oscillatory than the response to a 10% change in input flow.
• The controller is easy to tune since the maximum controller gain (the stability limit) is still quite high.
Note that the controller integral constant has not changed.
Figure 5 shows the response of an integrating process with a fill time/deadtime ratio of 1:1 that has the PID controller tuned for disturbance rejection. The controller gain at 0.7 is now considerably constrained by the controller gain stability limit of 1.5.
Now that the controller gain has dropped below 1.0:
• PV deviation from SP is about 17% following the 10% change in input flow. The controller will no longer be able to prevent overfill/emptying of the vessel should a large enough disturbance occur. To prevent this feedforward control or other advanced measures may be required.
• As expected because of the lower controller gain the OP has a restrained response to the SP change. The overall response to the SP change is now less oscillatory than the response to a 10% change in input flow as the output overshoot remains 75% of the input flow disturbance.
The constraint on controller gain imposed by the stability limit results in controller tuning that may not meet our needs. We can also see the tradeoff between limiting PV deviation from SP versus minimizing OP movement; as controller gain has decreased PV deviation has risen and OP movement has been reduced.
Figure 6 shows the response of a process we hope to never encounter; one where the deadtime exceeds the fill time. In this case, the fill time/ deadtime ratio is 1:5. The ratio tells us that when a disturbance occurs, the vessel is very likely to overflow/run dry before the controller can begin to respond due to the deadtime. It was possible to construct a scenario where the controller could keep the PV within the vessel, but only if the disturbance is very small (input flow change of 5%). In this case even a SP change results in significant PV overshoot.
This behavior is a marked contrast from deadtime dominant self-limiting processes. It is still possible to control (poorly) a self-limiting process with considerable deadtime because, well, the process is self-limiting. If uncontrolled, they do not run away like an integrating process will.
Finally, note that the output (OP) overshoot is still 75% above the (now smaller) size of the inlet flow disturbance. Controller output overshoot is a function of the integral constant, not the controller gain. Controller gain primarily sets how far the process variable (PV) will deviate from setpoint (SP) on a disturbance. Integral alone sets how fast the PV returns to SP, but the trade-off for faster return to SP is more OP overshoot. Disturbance rejection tuning involves setting the controller gain as high as possible without oscillation, which is about one-half the controller gain stability limit,
and the integral as fast as possible without excess oscillation, which is a function of deadtime and the process gain. This results in the oddity that the controller output response is always the same for disturbance rejection tuning regardless of the controller gain, and thus the process variable’s maximum deviation from setpoint.
Shortly before writing this, I was asked by a friend to review a level controller that had unexpectedly gone unstable. This was a high impact, high consequence controller so it received a lot of attention. The trend showed a slow roll, indicating that the controller gain was probably too small. We looked through the trend to find a place where the operator had placed the controller in manual and stepped the output; we were looking for an unintentional open loop step test so we could estimate some rough tuning constants without taking the time to do a formal test.
We found that the process had an astounding three and a half minutes of deadtime. Those of you with experience know that level controllers rarely have significant deadtime. However, we looked at the loop tuning log and found that over the preceding years there was a constant trend of lowering the controller gain. What this told us is that over the years the deadtime had been slowly increasing, adversely affecting controller stability. Control staff had been lowering controller gain without digging deeper into the probable cause.
In this particular case, the probable cause was plugged taps. The level instrument is mounted on a bridle that is attached to the side of the separator vessel. As the taps between the vessel and the bridle plug, the level in the bridle will start to lag the vessel level, and as the plugging progresses this will become deadtime. This preliminary diagnosis was passed to the operations team for resolution, temporary tuning was left in place, and a note was added to the loop tuning log.
If you haven’t already please consider listening to the Control Engineering webcast, “The mechanics of loop tuning.” This discusses the process of diagnosing issues that can affect control-
4:
rejection tuning of an integrating process (5:1 fill time/ deadtime); Tuning constants are K = 3.5, Ti = 8.0 minutes/repeat, Td = 0 minutes.
5: Disturbance rejection tuning of an integrating process (1:1 fill time/ deadtime); Tuning constants are K = 0.70, Ti = 10 minutes/repeat, Td = 0 minutes.
ler performance. Loop tuning logs can help you identify nascent issues before they become a big problem (as happened here.) The message is that you are not done when you have completed tuning a controller. If you find that you are constantly revisiting a controller or if the tuning just doesn’t look right (experience helps here), there is probably some kind of problem that cannot be fixed by tuning. You may not be able to identify the problem, but you should pass along the message that
FIGURE 6: Disturbance rejection tuning of an integrating process (1:5 fill time/deadtime);
Tuning constants are K = 0.15, Ti = 17 minutes/ repeat, Td = 0 minutes.
there appears to be a bigger problem to someone capable and empowered to do something about it. (Note: There is no implied criticism here. The impact of deadtime is never discussed in a systematic way, therefore it shouldn’t be a surprise that busy practitioners might miss the significance of this trend.)
controleng.com
Link to PID spotlights, parts 1-12 and with this article online, starting with “Three reasons to tune control loops: Safety, profit, energy efficiency.”
https://www.controleng. com/articles/three-reasonsto-tune-control-loops-safetyprofit-energy-efficiency
Aug. 1 RCEP webcast is available for one year: How to automate series: The mechanics of loop tuning
https://www.controleng. com/webcasts/how-to
For integrating processes the fill-time/deadtime ratio gives us important information about how well a PID controller can control that process. If fill time greatly exceeds deadtime (the ratio is high) controller gain can be set quite high without stability problems. If disturbance rejection is required controller gain can be set high enough to sharply limit the impact of a disturbance. However, the use of high controller gain will result in extreme controller output steps when the controller setpoint is changed. If this is not tolerable then some form of setpoint processing will be required.
As the fill time/deadtime ratio falls the maximum stable controller gain falls. As the ratio falls the ability of a PID controller to limit the effect of disturbances declines; process variable maximum deviation to a 10% inlet flow disturbance grows from 2% at a 10:1 ratio to 4% at a 5:1 ratio to 17%
at a 1:1 ratio. Estimated process variable deviation would be 80% at a 1:5 ratio; successful PID control would not be possible. From this it appears that a ratio of 1:1 is about the minimum where successful control is still possible. This is unlike self-limiting processes, which by their nature permit PID control (poorly) at lag/deadtime ratios far below 1:1.
Controller gain is not influenced by the fill time or deadtime individually: Only by the ratio. The controller gain will be the same if the fill time is 100 seconds and the deadtime is 10 seconds, or if the fill time is 100 hours and the deadtime is 10 hours. Integral is proportional to the deadtime plus fill time.
Interestingly, disturbance rejection tuning will always result in the controller output overshooting the inlet flow disturbance by 75% regardless of fill time/deadtime ratio.
tuning for a level controller
My preferred default tuning for a level controller before startup is:
K = 2.0
Ti = 20 minutes/repeat
This will work reasonably well unless there is an unusually low fill time/deadtime ratio (~2:1) or the process gain is less than 0.02 %/minute (fill time > 50 minutes).
A controller gain of 2.0 guarantees that the controller will be able to keep all but the most extreme disturbances from causing the level to overfill/run dry. Unless there is something very unusual about the process, a process gain less than 0.02 %/minute would not be expected. (A process revamp where a large vessel has been repurposed may very well have an unusually low process gain, but you are unlikely to see this on new construction.)
Once startup is complete you should revisit each controller to reset the tuning to better match the desired response (surge control, disturbance rejection, etc.) ce
Ed Bullerdiek is a retired control engineer with 37 years of process control experience in petroleum refining and oil production. Edited by Mark T. Hoske, editor-in-chief, Control Engineering, WTWH Media, mhoske@wtwhmedia.com.
With the ACOPOS P3, B&R is setting new standards for motion control. This 3-axis servo drive offers a power density of 4 amps per liter, making it one of the most efficient servo drives with integrated safety functions on the market. It also offers unrivaled dynamics and precision, with a sampling time of just 50 µs for the entire controller cascade.
• 69% smaller footprint with highest power density
• No additional fans in the control cabinet
• The right solution for every machine
br-automation.com
C. Todd Majors, P.E., Hargrove Controls & Automation
how phased
can minimize downtime, reduce costs and improve system performance with this comprehensive guide to planning and execution.
Consider the process of buying and renovating an older house. Before any renovations can begin, appraisals and inspections are necessary, especially for an aging home. Once the property is purchased, decisions must be made about which renovations to prioritize and the order in which to complete them. Renovating the entire house at once may not be feasible, so the work is often done in phases. Should leaky plumbing be addressed first? Or perhaps the house needs a fresh coat of paint. Determining where to begin is crucial. In many ways, upgrading obsolete PLCs in a facility mirrors this process.
• Learn the key considerations for PLC migrations.
• Discover examples of how a PLC migration can be broken into phases.
• Reflect on what to expect from a partner during the PLC migration process.
As machinery ages, obsolescence and the likelihood of failure increases while options for repairs and direct replacements decreases, leading to downtime, wasted resources and frequent troubleshooting — ultimately causing significant operational headaches. Legacy PLCs can also introduce cybersecurity vulnerabilities.
Additionally, a 20-year-old PLC relying on parts sourced from online auctions can create operational risks. It no longer offers the reliability or performance that facilities need. A PLC migration can help resolve these issues while also providing cost
savings through improved uptime, higher-quality throughput and reduced energy consumption. However, upgrading machines and systems all at once is often too costly and time-consuming for most facilities to manage without causing significant disruptions to production.
A phased PLC migration allows for two key benefits:
1. It spreads the cost over time.
2. It reduces the amount of downtime needed for each stage.
The following factors will help in planning the right phases, determining the upgrade path, and budgeting for a phased PLC migration.
Upgrading a PLC requires considering its role within the broader control system, starting by assessing the current system's network, hardware and communication connections for compatibility and integration with the entire control system. This also includes looking at what the existing documentation reveals about the equipment, which network the PLC is on and what additional components will be required to ensure smooth operation after the update.
Some components to assess for potential impact during the migration include human-machine interfaces (HMI), network, motion controls and software.
Older HMIs typically lack sufficient memory, processing power, and proper communication protocols to keep up with modern PLCs. Therefore, if
the HMIs involved in the migration are also outdated, they typically need to be upgraded along with the legacy PLC. However, newer HMIs are often made backwards compatible, supporting older communication protocols.
The industrial communication network — such as EtherNet/IP, Profinet or Profibus — that the PLC uses to communicate with its I/O cards and other devices plays a crucial role in determining the upgrade path, especially if the network, like the PLC, is also outdated. If the network relies on outdated serial protocols, such as RS-232 or RS-485, the entire network will need to be updated to support modern communication standards like Ethernet/IP or Profinet.
Modern PLCs may not support analog communication directly or may lack the proper interfaces needed to connect with older analog motion control systems. If the system relies on analog motion control, the upgraded PLC may not communicate with it effectively, making it necessary to upgrade the motion control systems as well.
Additional system components — such as the software code — may also need to be upgraded to ensure compatibility with the new PLC. Properly updating the software is crucial to avoid integration issues and fully utilize the capabilities of the modern PLC.
Breaking up a successful PLC migration into phases can help minimize disruption to throughput and provide greater flexibility in managing the upgrade process. In some cases, running simulations before implementing the migration can be highly effective. Performing a full simulation — replicating real-world processes, such as a virtual conveyor system — can help ensure the new software functions correctly before shutting down production for installation. Although this approach involves programming both the simulation and the actual system, it greatly reduces debugging time and lowers the risk of software issues during the migration.
There are several ways to divide the upgrade into phases; here are a few examples of independent phases to jumpstart the project:
• Upgrade smaller areas over time, which allows modernization of smaller sections of the plant, one at a time. After the first area is upgraded, the process can be fine-tuned, implementing lessons learned to improve subsequent upgrades. This approach reduces risk to the entire plant and provides valuable operations feedback on the system for future improvements.
‘Upgrade HMIs first, as they are often compatible with older PLCs, allowing for smoother communication during the transition.’
• Upgrade HMIs first, as they are often compatible with older PLCs, allowing for smoother communication during the transition.
• Lay new network cables in parallel with the existing network to support newer protocols in advance, minimizing downtime. These cables can be connected to the new PLC once installed. Alternatively, the new network can be installed in parallel with the old one, gradually transferring the load to the modern system to reduce disruption.
• Install the new PLC in tandem with the old one, allowing both to receive system inputs. The older PLC can continue handling outputs while the newer is tested and debugged. As the migration progresses, controls are gradually transferred to the new PLC. Another option is using the new PLC only to control migrated equipment until all can be converted.
With numerous interconnected components and potential upgrade paths, creating a detailed, wellinformed plan based on a thorough facility assessment is critical to ensure a smooth and successful migration.
Adequate and thorough planning is often a challenge for PLC migrations, whether phased or all at once. A solid plan must consider every component connected to the upgraded PLC, the project timeline, and the roles and responsibilities of everyone involved. Engineers, project managers, operations, and maintenance teams should collaborate in the planning process to ensure no critical documentation or perspectives are overlooked.
controleng.com
KEYWORDS: Automation upgrades, PLC migration, control systems ONLINE GSIR 2024 expert Q&A: System integration challenges, trends https://www.controleng. com/gsir-2024-expertqa-system-integrationchallenges-trends/ CONSIDER THIS How will you facilitate your next PLC migration project?
‘Overly restrictive budgets or cutting corners often result in lower-quality solutions that may not deliver the expected results.’
It’s also important to remember that adding more personnel doesn’t necessarily speed up the project. Allocating the right resources is essential, but some tasks must occur sequentially.
When choosing a migration partner, it’s important to select one that focuses on finding the best upgrade path for the facility, rather than just pushing a preferred software vendor. While some facilities may prefer to stick with a specific platform, big brand hardware vendors often come with a higher price tag. In many cases, equivalent functionality can be achieved at a reduced cost without solely relying on one specific vendor.
Downtime is always required for a PLC upgrade, but a well-developed plan can significantly minimize its impact. Additionally, budget constraints or underestimating costs can complicate the process, making careful financial planning crucial. While cost management is important, overly restrictive budgets or cutting corners often result in lower-quality solutions that may not deliver the expected results.
A well-developed plan that addresses key components and current performance will lead to a more accurate budget and timeline, while helping calculate ROI. The cost of the project can be justified in several ways, such as through quality improvements, increased throughput and reduced energy usage.
for themselves in as little as three months due to reduced energy costs.
Choosing the right partner for a PLC migration project is crucial to ensuring its success. A good migration partner will conduct a thorough on-site assessment and listen closely to the needs and concerns of the facility, ensuring the best upgrade options are recommended.
The right partner should also have extensive experience and a proven track record in the customer’s specific industry or facility type. This expertise ensures a deep understanding of the unique challenges and requirements of the environment. Beyond this, the partner should provide a "30,000-foot view" of the entire migration project, helping to clarify how all the interconnected aspects fit together rather than focusing solely on isolated components. This perspective is particularly valuable for customers lacking in-house expertise to fully manage the complexities of a PLC migration.
Most importantly, the right partner will take the time to understand specific needs, constraints, and timelines, working collaboratively to develop tailored solutions instead of relying on generic approaches. Transparency is key—an ideal partner will clearly explain their approach and the reasons behind it, leaving no ambiguity. Strong communication and a commitment to building a solid working relationship are essential for a successful project that aligns with long-term goals.
u
Improve your PLC migration
uTackle the project in phases.
uBuild out a plan.
uSavings can make the investment in time and money worth the investment.
PLC migrations can reduce operational expenses by improving system accuracy, reliability, and performance. Upgrading to modern PLCs enhances process control, leading to fewer errors, defects, and less rework. This improvement aligns with increased throughput, as reducing errors and defects allows more efficient production and a higher volume of quality output from the facility. Additionally, older equipment often relies on pneumatics for automation, which is costly in terms of energy consumption. Replacing pneumatics with electric actuators or servo systems can result in significant cost savings. Energy consumption savings are a common way to help justify the budget for a PLC migration, with projects often paying
Simultaneously upgrading machines and systems can be costly, time-consuming, and a disruption to production. An assessment of your current system's network, hardware, and communication connections, along with the proper division of phases and allocation of the right resources, are all components needed to execute a successful phased PLC migration so you can minimize downtime, reduce costs and improve your system’s performance. ce
C. Todd Majors, is C&A discrete manufacturing industry leader, Hargrove Controls & Automation. Edited by Sheri Kasprzak, managing editor, engineering, automation and control, skasprzak@wtwhmedia.com.
Emerson’s real-time, actionable data from measurement instrumentation devices ensures you’re not always learning from hindsight. Leverage the power of robust and reliable measurement instrumentation to transform your operations and reach peak performance.
Learn more at www.Emerson.com/MeasurementInstrumentation
Claudio Fayad, Emerson
mobility, and to bridge the IT/OT and cloud/edge gaps—while managing data, computational resources and security as data flows across an new pipeline.
Edge, cloud, and hybrid architectures will be used to deploy artificial intelligence solutions. AI for process modernization projects automatically converts up to 70% of configuration, saving up to 15%.
AKEYWORDS: AI, edge, process manufacturing.
LEARNING OBJECTIVES
Explore many artificial intelligence (AI) opportunities for process manufacturing.
Understand how new workloads bring new needs for AI in process manufacturing.
Examine AI advantages at the edge and future potential.
CONSIDER THIS
Are you seeing advantages in AI process manufacturing applications and preparing for more?
ONLINE
See more with this article online. Also learn more: https://www.controleng. com/articles/why-its-criticalto-integrate-distributedcontrol-systems Online controleng.com u
rtificial intelligence (AI) applications are widely expanding, and process manufacturers have taken notice. Organizations are already planning how to perform powerful AI-based analytics, improving operations and unlocking adaptive advanced process control to drive more autonomous operations and competitive advantage. Greater use of AI means securely freeing contextualized data from the silos built into the different automation layers and disciplines and moving it up into the cloud where AI tools can put it to good use. Such a strategy, in turn, requires teams to design architectures with a boundless automation vision of seamless data mobility. Efficient movement of data to feed data lakes, data scientists, analytics applications, enterprise resource planning systems and other areas becomes more critical with each emerging AI innovation.
A boundless automation vision becomes even more important as AI tools consuming critical plant data will not be exclusively cloud or edge tools, nor will they be limited to one plant or the corporate office. As a result, AI will redefine the way organizations look at their operational technology (OT) and information technology (IT) architectures.
New applications of AI will need to straddle onpremises and cloud technology, and the OT/IT convergence. This will require edge environment solutions as a tool to drive seamless integration and data
People involved in process manufacturing are seeing a significant increase in potential real-world AI use cases. Much of the work today is in augmenting large language models (LLMs) and private LLMs with proprietary data. New, private LLMs inspire a lot of exciting use cases. Companies are developing tools to help modern operators (many digital natives) to improve decisions. Chat bots and embedded advisers, driven by LLMs, support operators and technicians of every experience level with real-time guidance in response to natural language questions.
AI tools are speeding project design and execution. Teams are using AI to perform 3D plant designs faster and easier, with software that can respond to natural language commands to design and edit plant layouts on the fly, while providing multiple design examples in minutes, rather than days or weeks.
Cloud-based modernization software is using AI to better understand legacy code and support engineers as they convert legacy control systems into new systems. AI modernization tools can automatically convert up to 70% of configuration to cut initial capital costs of modernization projects by up to 15% (Figure 1).
Among AI complexities will be variable infrastructure needs. Some AI tools will need to run on the edge; others will require cloud capabilities. Applications that require extremely low latency, such as closed-loop and advanced control solutions, will need to operate on-premises, close to the associated equipment to ensure optimal performance. Many organizations will need to maintain on-premises control of AI tools for better data governance. A pharmaceutical company needing to combine unstructured data from documents with real-time data might not want to put that data in the cloud due to regulatory or intel-
FIGURE 1: AI tools in cloud-based modernization software can dramatically reduce the time and cost of projects to update control systems. Images courtesy: Emerson
lectual property concerns. A smaller, localized language model can bring many of the same benefits and avoid primary risks. Some AI tools are too computing resource intensive for on-premises implementation. Any AI tool that requires continual training to generate probabilistic answers will demand this level of computational power. In most cases, such tools will be implemented in the cloud, where computational power scales quickly and dramatically to handle the fluctuating needs of AI processing.
Because of this wide variation in potential needs, the different applications of AI (reliability, process control, decision making, operational autonomy, operator support, and more) will likely require the ability to run on the edge and in the cloud. To close that gap, many organizations will employ a fit-forpurpose edge environment solution. An edge environment provides the infrastructure teams need to safely connect OT assets to the IT environment on-premises and in the cloud. The resulting seamless data mobility forms the foundation for a secure data pipeline designed to combine real-time, historical and unstructured data to feed AI tools in the enterprise.
An edge environment provides teams with a way to deliver operational data to AI applications on the edge or in the cloud. Using a simplified, secure connection architecture, an edge environment reduces network complexity by providing one, unidirectional data flow from the control layer outward. Trapped data becomes available, without the risk of access into the control layer (Figure 2).
The value of a modern edge environment goes beyond data access as it empowers operations teams to run AI tools using optimized hardware which may not be part of their OT infrastructure. Today, most applications built for OT have fixed resource consumption. As AI tools advance and learn and adapt organically, this will no longer be the case. The more popular AI applications are used, the more computing resources they will be likely to consume.
The most advanced edge environments provide a data sandbox with containerized application tools to encourage varied execution and experimentation— the perfect incubator for the AI tools that will capture competitive advantage in coming years. As edge envi-
ronments advance, they will leverage this containerization to provide the dedicated, optimized compute power and the secure connectivity to data to orchestrate AI workloads, ensuring they are assigned to the appropriate platform. Edge environments will help teams provide the right resources at the right time to drive better business outcomes. They bring data securely to AI systems in the cloud and at the edge and likely will have the ability to observe and dynamically allocate compute power to AI as needed. ce
Claudio Fayad serves as vice president of technology of Emerson’s Process Systems and Solutions business. Edited by Mark T. Hoske, editor-in-chief, Control Engineering, WTWH Media, mhoske@wtwhmedia.com.
FIGURE 2: Edge environment solutions help teams navigate the complexity of OT infrastructure, bringing data from the control layer up to cloud systems.
Kendra DeKeyrel, IBM
Advances in computer vision have been an integral part of the industrial engineering workflow. Software and edge computing are adding efficiency and precision to inspection.
Icontroleng.com
KEYWORDS: Visual inspection, Artificial intelligence (AI), Edge computing
LEARNING OBJECTIVES
Learn how AI and computer vision enhance defect detection, improve quality control and make inspections more efficient.
Discover how edge computing enables flexible, mobile and remote inspections while improving safety and reducing latency.
Gain insights into how AI and edge computing streamline inspections, reduce downtime and drive smarter, faster processes.
CONSIDER THIS
How can integrating AI and edge computing into inspection processes improve efficiency, quality and safety?
ONLINE
With this article online, see another image, more on "Smarter, faster inspections."
nspection has always played an outsized role in industrial engineers’ workflow. It is the critical stage that reveals whether the systems, machines and processes an engineer has been wrangling will come together to produce a high-quality output — or, alternatively, if an upstream problem is causing defects at the end of the line. The inspection stage is integral across industries, whether it is a manufacturing plant floor or public infrastructure like bridges and roads.
Visual inspection technology has evolved significantly in the digital era. It has transformed inspections from time-consuming, manual ordeals into automated processes that can “see” and report anomalies or product defects in under a second. The upshot is a better experience for businesses and consumers alike: fewer defects, less downtime and safer, higher-quality goods. Gone is the era of hand-written reports and the associated tedium and errors.
But modern inspection is not a simple binary. It is not as if processes are either manual or automated, with nothing in between. Visual inspection technology is always evolving, and what was considered innovative just one decade ago — like certain Internet of Things (IoT) tools — can quickly become dated. These days, industrial engineers who want the best-in-class inspection processes need to harness two key emerging technologies: artificial intelligence (AI) and edge computing.
AI has been a boon for further automating and improving inspections, enabling accelerated defect detection and worker safety at scale.
One branch of AI in particular has had an outsized impact on visual inspections: computer vision, a type of machine learning that enables computers to identify and analyze objects. Computer vision does not replace human vision in the inspection process — it augments it, providing acceleration and scale. All comprehensive inspections must have a human subject matter expert “in the loop.” Computer vision makes those humans even more capable.
More manufacturers are relying on computer vision to continuously improve quality control. Software and hardware powered by computer vision allows technicians to ensure parts are in the right location; that individual components are the correct shape, color, size and texture; and that modules are not scratched, dented or otherwise damaged. These AI vision models allow meticulous inspection to occur in real time and across the production line, alerting engineers to defects immediately and enabling them to confront the problem with minimal downtime, thus saving considerable time and resources. Beyond real-time defect detection, AI tools also empower manufacturers to analyze captured defect data and uncover the root causes of recurring issues. This actionable insight enables targeted process improvements, preventing repeated defects and driving sustained enhancements in product quality.
Computer vision is becoming easier for technicians to wield, bridging the technical skills gap. “No-code” models allow technicians to train and deploy computer vision models without having a background in computer or data science. Users can simply upload training images that inform the model without having to roll up their sleeves and wrestle with lines of code and complex algorithms.
Emerging capabilities are making this no-code training process even more seamless. Researchers are helping equip visual inspection software with “anomaly models,” which allow the AI to learn exclusively from images without defects, thus lowering
FIGURE 1: see also COVER:
A no-code-required training interface — like the one powering IBM Maximo Visual Inspection, above — enables a wide spectrum of technicians to leverage AI for inspection, without having a background in computer or data science. Courtesy: IBM Maximo Visual Inspection.
the barrier for building models for products where defects are rare. Visual prompting allows users to build computer vision models in a matter of minutes by providing visual cues within a few example images. Once all this is done, cameras can be pointed at the production line and begin analysis.
But it is not just manufacturers who are benefiting from no-code computer vision tools. Energy and utility companies use the technology to identify metal corrosion and leaks, public works rely on it to detect cracked concrete on infrastructure and it is even being used to track and protect elephants.
A high-tech inspection process is only useful if engineers can easily deploy it. Even when computer vision requires significant processing and training data, these systems can still be used across a range of devices and locations, like smartphones on a factory floor. This is enabled by edge computing frameworks.
Workers can run visual inspection tools on their mobile devices and other lightweight hardware, unlocking flexibility and agility so that quality control can happen just about anywhere, both on-site and remotely, with limited latency. An edge approach allows AI models to run on everything from drones to high-resolution cameras to on-vehicle cameras (which are especially useful for physical infrastructure inspections). It also allows staff to easily capture images on their phones, which can then be used to further train the algorithms. Edge computing capabilities have proven invaluable to manufacturers like Ford Motor
Co., to leverage the combination of computer visionpowered insights and edge-enabled portability for vehicle inspections.
Another benefit of edge computing is worker safety and compliance. Traditionally, humans had to physically insert themselves in the production process to carry out inspections, exposing them to dangerous machinery, chemicals and other hazardous conditions. Edge computing enables devices like drones and stand-alone cameras to serve as a proxy, allowing workers to inspect and analyze from afar and with increased insights, not fewer. ce
Kendra DeKeyrel is vice president ESG and asset management product leader, IBM; edited by Gary Cohen, senior editor, Control Engineering, WTWH Media, gcohen@wtwhmedia.com.
2: A screenshot showcasing the visual inspection capability of IBM Maximo Application Suite. Courtesy: IBM
Peter Galan, retired control system designer
Understanding how power monitoring devices work helps with designing and specifying power monitoring modules or transducers with automation and other applications. Reference appropriate ANSI standards related to power monitoring.
Commercially available power metering devices/modules may fit your automation and control application, or you might want something different, which would suit better to your (your customers’) needs. I’ve designed several such power monitoring (or transducer) modules/devices, which have been successfully manufactured and sold (currently by Emerson Electric Co.) Understanding the anatomy of power monitoring devices can help good engineers to improve their design of a perfect power monitoring device (PMD) , which would fit the automation and control application even for the distributed energy resources.
Introduction: What is a power-monitoring device?
So, what is a power monitoring device? A simple answer, it is an electronic device/instrument capable of measuring of the electrical parameters (voltages, currents, powers) of 3-phase electrical grids. Who needs such a device? Any industrial company may need to measure such parameters/powers for its own use, for example, to detect (and avoid) a poor power factor. Or, if your company manufactures electric motors and/or generators, such a PMD unit could accompany your products. A more sophisticated power monitoring module can be used as a ground fault relay, or even as a synchronizing device for connecting electric generator to the public grid.
FIGURE 1: Diagram shows 3-phase four-wire (WYE) system with three potential transformers (PTs) and three current transformers (CTs).
Images courtesy: Peter Galan, a retired control software engineer
A basic PMD needs to measure phase voltages and currents of a 3-phase electric grid and provide them to the user. To measure and then to process such high voltage and current values, suitable transformers usually are needed. Transformers reduce the measured parameters to the acceptable amplitudes for the processing and isolate the dangerous, high voltage system from electronic instru-
ments (and personnel in the area). Figure 1 shows a schematic of such a 3-phase four-wire (WYE) system with three potential transformers (PTs) and three current transformers (CTs).
Many suitable potential and current transformers are available on the market. You need to select such transformers, which will provide safe output voltages (and currents), for further processing. For example, a PT with the ratio 100:1 will be suitable to measure voltages in the range of 480V, as the output of 4.8V is perfect for the further (TTL) processing. However, such a nominal 480VAC voltage, when sampled, it will reach up to √2 [sqrt(2)] times higher value (a peak value). In addition, those sampled values will be positive and negative as well, so a further voltage reduction (and offsetting) will have to be applied to match the input requirements of used analog-to-digital (A/D) converter. The current transformers are of a donut-type where the primary winding is the phase line conductor which passes through the center of the CT. Their output still can be a significant current value (~ Amps), so
your device will need to use additional transformers to further reduce those current values.
A configuration shown in Figure 1 is fully suitable for the voltage/current and power (power factor) monitoring of such a load/appliance like a 3-phase electric motor. If you added another CT, which would measure the neutral current, you could even monitor any ground fault (current leakage) of the load, as the total current flow to/from the load has to be zero if there is no fault.
More powerful 3-phase loads (like motors) are usually configured in the delta connection. It means that the neutral (N) line is not used. It may not be even available for your power monitoring device. In such a case, a so called “two wattmeter method” can be used, as it is shown in Figure 2. In the pictured case as a “common” phase, the phase B (Line 2) has been used.
While such a three-wire delta system with two PTs and tw s (two wattmeter method) is a perfect method for any load power consumption monitoring, it will not be able to detect any current leakage (ground fault). Just add the third CT (on the common line L2) and by calculating the sum of all three line currents, you can detect such a ground fault as well.
The math behind 3-phase power monitoring is explained below. The voltage, V, and the current, I, calculations are based on the root-mean-square (RMS) calculation:
where individual xi values are samples taken from the monitored voltage, vi or the current, ii . The power calculation is based on a similar formula, just the square root is omitted:
Regarding the power calculation, equation 2 provides the phase active power value. Why it is so? Because the voltage sample value, v i is multiplied by the current sample value, ii as it is present at a given sampling time (it has to be the same time). Any phase shift between the voltage and current cycle is automatically taken into account.
‘More powerful 3-phase loads (like motors) are usually configured in the delta connection.’
controleng.com
KEYWORDS: Power monitoring, power sampling, power distortion
LEARNING OBJECTIVES
Understand what a power monitoring device (PMD) is along with principles, challenges, engineering and some ANSI standards that will help.
Review voltage and current sampling considerations for PMDs.
Examine PMD features, such as power demand and total energy.
CONSIDER THIS
Are you using best practices and ANSI standards appropriately for power monitoring?
ONLINE
For other Control Engineering tutorial articles from Peter Galan, see the following article and links in it.
Tutorial: How to find the best controller https://www.controleng. com/articles/tutorial-how-tofind-the-best-controller/
‘The two-wattmeter method is based on the measurement of just two (phaseto-phase) voltages and two-line currents.’
So, how we can calculate the apparent or total power value? There are two options. One is based on a simple multiplication of already calculated V and I values. The other option is through the calculation of the reactive power, Q. Reactive power can be calculated similarly like the active power, just in Formula 2 use the current samples, which are one quarter of the period (that is n/4) shifted. For example, if you use 128 samples per cycle, calculate products of v i * Ii+32 .
Once you have the active and reactive power values calculated per each phase, add them (calculate P act = PA + PB + PC , Q = QA + QB + Q C ) and the apparent (or total, Ptot) power value of the entire 3-phase load can be found as:
And the three-phase power factor, PF, will be:
When you apply the two-wattmeter method (if your load is configured in a delta connection and the neutral line is not available), situation is a little bit different. Figure 3 shows the phase diagrams of the WYE and delta configurations.
A mathematical comment regarding the vectors denotation: Strictly speaking, the voltage and the current vectors should be denoted as VNA , VNB , … INA (in the WYE configuration) but for simplicity, if the vector originates on the neutral line, N, the N symbol is usually omitted. The line current vectors, I a , IB , IC (in the delta configuration they should be named as IL1 , IL2 , IL3 *) depend on both surrounding branches/impedances, so to use the second symbol wouldn’t make sense. And the phase-to-phase voltage vectors may have the vector tail and head swapped, like instead of VBA, VBC in this article you can find Vab, Vcb. In both cases those vectors denote the phase-to phase voltage vectors, which have the phase B (L2) as common, because the letter B (b) is present in both vectors. The phase A (L1) is never used as a common phase, however the phase C (L3) can be common as well.
*Please note that in this article the term “phase” and “line” may not be strictly observed. While in the WYE configuration they have actually identical meaning, in the delta configuration they are not identical.
FIGURE 3: is a phase diagram of WYE and delta configuration.
Figure 3 shows all the relations among the voltage and current vectors for both, the WYE and delta configuration.
As we already know the two-wattmeter method is based on the measurement of just two (phase-tophase) voltages and two-line currents. If we select as a common phase the phase B, our measured voltages will be VBA , VBC and the measured currents IA and IC .
So, what is the total 3-phase power of such a system? Using Formula 2, where the vi values represent the sampled VBA voltage and the ii values are the sampled IA current, you will get the first part of the active power of the entire 3-phase system. Adding the second result of the same calculation where the vi values represent the sampled VBC voltage and the ii values are the sampled IC current, you will get the total 3-phase active power. Now, to calculate the total 3-phase apparent power, P tot, you will either calculate at first the reactive power, Q, (similarly like described above for the WYE configuration) and then you will use Formula 3. Or, much simpler way is to calculate it
directly from already calculated RMS voltage and current values. The formula for the total 3-phase system, active power calculation is:
However, omit the voltage-current phase shift, φ, (we don’t even know this value, as we don’t calculate it), and what you will get is the total apparent power, P tot .
While the three-wire delta system with two PTs and two CTs (two wattmeter method) is a perfect method for the total 3-phase power consumption measurement, you can’t find precisely the power consumption of each individual phase. This is very rarely important, but if yes, just make an estimation by a simple division of the total power by 3.
As it was mentioned before, one nice feature of such a PMD would be the ability to detect the ground fault. What is actually ground fault? Briefly, ground fault is a situation when your power load (motor) exhibits any kind of the current leakage due to deteriorating isolation. As such power appliance (its chassis) has to be grounded, any such current leak would end up into ground.
Please note: This is a safety precaution, but it doesn’t mean that a faulty device or appliance with a ground fault can be used. It must be removed from the grid.
But can such a faulty (deteriorating) load be detected? Do you remember Kirchhoff's current law? It states that the current flowing into a node (or a junction) must be equal to the current flowing out of it. And this is what your PMD can easily do. Use Formula 1 (RMS calculation) to calculate the ICOM current where, as the individual xi values use a sum of all the current samples. In the case of 4-wire (WYE) configuration you need to measure/sample and sum all four current samples: xi = iai + ibi + ici + ini .
In the case of the 3-wire (delta) configuration the line currents have to be added, but all three of them, even the current flowing along the common line.
And how to use such a non-zero leakage (common - ICOM ) current value? Usually very small values can be tolerated, but as the leakage current reaches a certain level, such faulty device should be
immediately disconnected. Your PMD can do that via a suitable relay.
What else can be useful for such a 3-phase electric system monitoring? You might calculate a DC component of the 3-phase voltage. However, in the configurations as shown in Figure 1 and 2, you can’t detect any DC offset of the monitored 3-phase system as the primary and secondary windings of the PTs are completely independent, so you will read permanently zero. However, there is a way to design PMD, which won’t use any PT, and then such a DC voltage monitoring/calculation will be extremely important. Figure 4 shows a simplified diagram how to sample directly all 3 line voltages (and the neutral voltage, V n , available in the WYE configuration) without using any potential transformer. Of course, all the voltages have to be scaled down by suitable resistors. And “suitable” doesn’t mean just having the correct ratio (like 1000:1), but they have to be precise, and, especially very stable toward the temperature changes, that is you will have to use resistors with a small ppm/°C (parts per million per degree centigrade) coefficient. Their precision might not be as important as their temperature stability, because your PMD device, once fully assembled and tested, it will have to be calibrated anyway.
In Figure 4, the voltmeter with the switch represents an analog-to-digital converter with a multiplexer, which is a standard arrangement of a multi-channel scanning/digitizing device.
So, how the direct voltage measurement can be practically implemented? All those voltages are actually “floating,” meaning the ground potential of their 3-phase grid is not connected with the PMD ground, so how it will work? The answer is pretty
FIGURE 4: Direct sampling of all 3-phase voltages plus neutral voltage is shown, a standard arrangement of multi-channel scanning and digitizing.
‘While more samples generally provide better precision, a practical number of samples is around 100/cycle.’
simple as all the grounds are actually interconnected, just any two ground points may have a different (relative) potential. At first you will need to calculate the DC offset of that (remote) 3-phase grid. In the case of the WYE configuration, you can sample just the neutral voltage, V n . Take those n samples, and, instead of the RMS calculation, just add all those samples and divide by their number (n) to get the average value. And this is your voff value. This value is not in volts, it is still in term of your samples value, that is, in counts or bits (that’s why the capital V is not used). So, how high can such a VCOM (converted voff value into volts) be? If your PMD device is not far from the monitored load (like a 3-phase motor), then those separated grounds should have a very close potential, the difference can be in the order of volts at maximum.
However, occasionally, like during the thunder storm, this voltage can momentarily reach hundreds of volts. So, a rigorous protection of your device against such voltage surges (even if you employ PTs) is essential.
In the delta configuration, you can use samples of all three phase voltages (delta even doesn’t provide V n.). So, to calculate the voff value, add those 3*n samples together and divide by a 3*n value.
Now, once you have the voff value (it has to be calculated as a first value), you can calculate the RMS values of the phase (or phase-to-phase) voltages. You just have to subtract this voff value from each voltage sample. For example, the phase A voltage, VA , will be calculated as:
Or the phase-to-phase voltage, VAB, (with the common phase B) will be calculated as:
Notice that the phase-to-phase RMS voltage calculation formula doesn’t use voff offset, as we are interested only into a relative voltage. So, do we need to calculate voff in the delta configuration at all? The answer is yes, as it might be important information, for example, for the auxiliary generator connection to the public grid and in some other special situations.
All the voltages, currents and powers should be reported in the standard units (volts [V], amps [A] and watts [W]/volt-amps[VA]). They will be obtained after conversion of their RMS values (in counts/bits). Their conversion coefficients need to be calculated based on the A/D converter range and the range of the measured parameters (voltages, currents and powers).
A first question might be, how many samples have to be used? There are more options. At first, those samples have to be taken from one (or several) full power cycle. So, your PMD device has to be able to detect a beginning of a power cycle, for example, as a zero crossing of a phase A voltage. Two consequent zero crossing then give you information about half of the power cycle duration/period. So, every second zero crossing in the North America grid should occur every 1/60 of second (16.666 ms); in Europe it will be every 1/50 of second, that is, every 20.0 ms. But generally, this line power frequency can (though very little) vary, so you can’t rely on those constants, you need to measure them.
Now you need to decide how many samples of a monitored variable you are going to use in the calculation formulas. While more samples generally provide better precision, a practical number of samples is around 100/cycle, so to take 128 samples (it has advantage of selecting such a power of 2 value) can be optimal.
Once you have taken (and saved) all samples of all the measured variables, you can process them. However, the results (voltages, currents and powers) might be a little bit “noisy,” as there are always certain variations in the zero-crossing detection, for example, and the A/D converters as well have a limited precision/resolution. For the practical use, it is good idea to put those calculated results through a (moving window) filter, for example, 8 cycles long. Here you can save a lot of calculations, if, instead you take samples of 8 cycles, and only then process them. Doing so provides similarly filtered results. But yes, you will have to save those 1024 samples of each measured variable. And the results can’t be reported/updated more often than once per 8 cycles. That decision belongs to you or your customer.
Your processor should be able to save the digitized samples alternatively in two memory sections. While you are processing samples from one memory section, currently digitized samples are being stored into the second memory section and so on. This is required because the total processing time of all samples/channels can take up to half of a power cycle (~ 10ms), but the sampling has to run continuously without any interruption.
A great importance has the sequence of the individual channel sampling. You need to sample up to 4 voltage channels and 4 current channels. You might need to sample periodically other parameters as well, like the reference voltage, so you could make a periodical calibration.
Important note: For a precise power calculation, it is important that the corresponding voltage-current channels are sampled simultaneously, as any time shift may be wrongly interpreted as a phase shift between the voltage and the current of a given phase! It is recommended to use two A/D converters, which would sample those corresponding voltage and current channels simultaneously.
5: Samples time (phase) shifts are shown (fourth channel omitted for simplicity).
But even the phase voltages (and currents) among themselves ought to be sampled so that that the sampling will not introduce any additional phase shift. Obviously, you would not use a separate A/D converter for each channel. You will be sampling them sequentially, using an analog multiplexer in front of one A/D converter. Such sampling inevitably produces a time shift, which will grow with each following sampled channel. Can you
somehow eliminate this time (actually phase) shift?
Yes, you can, but before you take the sample for processing, you need to apply interpolation. Figure 5 explains the need for such interpolation. Of course, not all the samples need to be interpolated. For example, when you calculate RMS values of the individual phase voltages (equation 6), no interpolation is needed. But equation 7 definitely requires all samples to be properly adjusted for any sampling time shift. For simplicity, Figure 5 shows just 4 channels sampling 3-phase voltage (the fourth channel not shown). So, the analog multiplexer continuously is switching – connecting the input of a monitored channel to the A/D converter in the order as shown in Figure 5. It is evident that the vbi , vci (and the following, not shown sample) is taken later than the vai sample, so to avoid any error in the samples processing, we need to know their values, which would be there if taken exactly at the same time. By selecting a certain channels number (4, 8,..) such an interpolation can be calculated very fast, as it will require just few shifts (to the right), which every processor (usually a digital signal processor) can calculate very fast.
FIGURE 6: Simulated PMD results (with interpolation) are show.
‘When you calculate RMS values of the individual phase voltages (equation 6), no interpolation is needed.’
The last question is whether or not it is worth dealing with the (rather complicated) interpolation at all. How much error would we introduce, if we don’t apply it? Here is the answer. Compare the results shown in Figure 6 and Figure 7. While not “tragic,” the error is visibly present. The PMD
simulator calculates those results by taking 128 samples from a full power cycle with 8 scanning channels. It means that the phase shift between any two adjacent channels is roughly one thousandths of a full cycle (360˚). If using just four channels (as shown in Figure 5), the error would be roughly twice as high.
So far, we’ve learned how to calculate the basic, 3-phase power parameters. Again, they are:
• Power line frequency (from the zero crossing period)
• Phase (phase-to-phase) Voltages
• Phase (line) currents
• Current leakage (ground fault)
• Phase active and total powers
• Power factor.
There are two additional items very useful for every customer, and it is a power demand and the total energy:
• Power demand
• Total energy.
Power demand is an average (like over a 15-minute time period) total/active power consumed by a monitored load. PMD can continuously calculate and remember the highest found value. Such infor-
mation is very important to your power provider to know the highest (peak) power demand.
Total energy is an accumulated total power over the time of monitoring. You can accumulate and report the total consumed energy or the total active energy or both. While this information can’t be used for the billing purposes (as your PMD would have to be certified for this purpose), it is still useful information for your customer.
However, there are more parameters very useful (even mandatory in some cases) to monitor. In North America, they are known as the ANSI standards. Here is a list of the most important ANSI parameters (functions), which your PMD could monitor:
ANSI 27 – Under-voltage protection
ANSI 32 – Reverse power protection
ANSI 46 – Negative Ssequence protection
ANSI 50 – Instantaneous over-current protection
ANSI 59 – Over-voltage protection
ANSI 60 – Voltage (current) imbalance protection
ANSI 81U – Under-frequency protection
ANSI 81O – Over-frequency protection.
All the information alarms should be reported (and cleared) only if a given parameter is out of (or back to) the “normal” range for a certain time. Don’t report any momentarily detected abnormality, as it could be just a false “glitch” caused by many possible factors. Allow the user to set the alarm thresholds levels and the “debounce” times.
All those parameters can be monitored/measured concurrently on two separated 3-phase grinds. Why would we need to do so? Imagine, your PDM has to facilitate connection of an external 3-phase power generator to the public grid. Then, of course you need to monitor both grids, as the generator can be connected only when all the important parameters of both grids are identical.
And what are those “important” parameters? At first it is the ANSI 32 - Reverse power protection function/alarm. This alarm is based on the detection of a reverse current flow to the generator, that is, detection of a lower-than-nominal generated power.
The most important addition is the ANSI 25 functionality, which is needed for a generator-grid
connection to the public grid. Improper connection of a generator to the main system may result in damage to the generator step-up transformer and damage of any part of a generating unit.
The damage incurred may be slipped couplings, increased shaft vibration, a change in bearing alignment, loosened stator windings, loosened stator laminations and fatigue damage to shafts and other mechanical parts. Just ask an expert!
Your PMD, if used as the generator synchronizer, will have to be responsible for the monitoring three basic conditions, known as:
ANSI 25/1 – Grid-to-grid phase shift
ANSI 25/2 – Grid-to-grid phase voltage difference
ANSI 25/3 – Grid-to-grid frequency difference.
If and only if no ANSI alarms are present, and all the ANSI 25 conditions are satisfied, may the external generator be connected to the public grid. How this can be implemented? Figure 8 shows a basic schematic drawing of such a system. It is a relatively complex (multi-parameter) control system, in which PMD plays an important part.
In this tutorial article, you have learned the power monitoring principles and challenges as well, because, as in any “engineering” task, there is a space for the further improvement. Those improvements can be made on the hardware and on the software side. For example, on the hardware side, a modern digital signal processor (DSP) can easily monitor two power gids. Such a processor, using the single instruction multiple data (SIMD) architecture, allows you to apply the user’s code to two independent data sets. For some simpler applications, an integrated power monitoring device may suffice. On the software side of such power monitoring devices, there are still few interesting functionalities worth implementing. For example, your PMD could monitor the 3-phase power quality as well. What does it mean? As many powered devices, like motors, transformers are actually non-linear (meaning their impedance is non-linear), the current flowing through them becomes distorted.
And the same applies to the secondary voltages. How can such transformer distortion be detected? If you remember the Fourier Transform, you have the answer. It is relatively easy to implement such a spectral analysis of the monitored variables (voltages, currents) using the fast Fourier transform algorithm (FFT). If taking 128 samples from the power cycle, you can calculate up to 64 “harmonics” (actually a DC component plus 63 harmonics), which represent the monitored variable quality. There are devices, which can be used to improve such distortion, but you need to know which harmonic and how much correction is required.
If you are a software designer, you would benefit if you start your PMD S/F (or firmware) design with a suitable simulation. This article uses my simulation system (see Figure 7 and 8). It consists of two applications, one (shown in those pictures) is a graphical user interface (GUI), which allows the user to select the operation mode and all parameters for the simulation and further processing. It receives and displays the reported results. The second application is actually such a simulator – 3-phase signal generator, and, most importantly, the processing application. Its code is written entirely in the C language, so it can be very easily ported to any digital signal (or other) processor. Those two applications communicate through the network socket, which can be again useful for the final PMD implementation as your device needs to communicate with the user and/or other devices. ce
Peter Galan is a retired control system designer and engineer; edited by Mark T. Hoske, editor-in-chief, Control Engineering, WTWH Media, mhoske@wtwhmedia.com.
FIGURE 8: Drawing of the PMD used for the external generator connection is shown. [Note: A modern digital signal processor (DSP), like an Analog Devices Sharc processor, can monitor two power grids; using the single instruction multiple data (SIMD) architecture allows you to apply the user’s code to two independent data sets. For some simpler applications, Analog Devices offers integrated power monitoring devices, like ADE9430.]
Felipe Sabino Costa, MSc, MBA, PMP, CCNA, CISA-US DHS, Moxa Americas
The foundation of modern automation is a strong networking infrastructure. Advanced networking strategies can help ensure resilience, minimize downtime, enhance security and prepare for future automation demands
In industrial environments, automation applications are essential for optimizing processes, improving efficiency, reducing human error and ensuring reliability in mission-critical operations. The foundational element that makes all these benefits possible is robust networking infrastructure. Reliable networking enables seamless communication between devices, systems and controllers, serving as the bedrock of automation success.
A well-designed network is fundamental to industrial automation. Neglecting this crucial element can lead to significant operational issues. It's important to understand key networking strategies, including segmentation, quality of service (QoS), redundancy and cybersecurity, and examine how they can optimize automation applications, mitigate common challenges like latency and data loss and prepare for future demands driven by new technologies such as AI and the industrial Internet of Things (IIoT).
Understanding industrial networking
Networking infrastructure is often overlooked in industrial automation; however, it’s the crucial element that connects every aspect of an operation, from machinery to control systems. In environments where downtime can cost thousands per
minute and operations rely on real-time data, the role of a reliable network cannot be overstated.
Automation systems handle vast amounts of data exchanged between sensors, controllers and supervisory systems, and any delay or data loss can directly impact operational efficiency. For instance, a manufacturing facility might deploy real-time sensors that monitor equipment health. If the network cannot handle this data with minimal latency, there’s a higher risk of failing to detect critical issues in time, leading to unexpected downtime. With advances in automation, new technologies are pushing the limits of traditional networking infrastructures. The following strategies can help ensure that networks not only support but also enhance automation capabilities:
• Network segmentation: Dividing a network into smaller segments to reduce unnecessary traffic and isolate sensitive data pathways.
• Quality of service (QoS): Prioritizing data types to ensure critical communications are delivered promptly.
• Redundancy: Creating backup paths in the network to safeguard against disruptions.
• Cybersecurity: Protecting network integrity with security measures that prevent unauthorized access or data tampering.
Network segmentation is a method of dividing a network into isolated sub-networks to improve both security and performance. By segmenting networks, industrial environments can reduce unnecessary
data traffic and confine sensitive communications to specific areas of the network, creating a more secure, streamlined communication channel.
In automation, network segmentation allows businesses to isolate key operational segments, such as production lines, from the broader enterprise network. This means that if there’s an issue in one segment, it doesn’t impact the entire operation, enabling a faster response and reducing the risk of downtime. Segmenting networks also helps secure sensitive data, such as intellectual property or critical process data, by isolating it from other areas that may have higher vulnerability to threats.
Additionally, segmentation minimizes latency by reducing congestion, a benefit especially critical in high-speed manufacturing and assembly line environments where even slight delays can compromise output quality. By reducing the number of devices on each segment, networks become more responsive, allowing automation systems to operate with greater precision. It is possible to segment the network using both physical and logical means. Physically, firewalls, layer 3 switches and routers are the most common options, although other solutions exist, often at a higher cost. Logically, VLANs and subnets are widely used; however, specifically with a cybersecurity mindset, these technologies are not designed to protect the network. Unlike physical options that include specific cybersecurity functions, their primary intent is to support network information segmentation and broadcast domain performance.
QoS is a network feature that prioritizes certain types of data, ensuring that critical communications receive bandwidth first. QoS is particularly valuable in automation, where multiple devices and systems may compete for network bandwidth. In such environments, QoS assigns priority to data flows critical for operations, such as control signals or alerts, allowing them to be delivered promptly.
For example, in a scenario where both operational data from machinery and non-critical data (like camera feeds) are transmitted on the same network, QoS settings would prioritize the control data to prevent disruptions in machine operations. This is essential in real-time environments, where any delay could lead to costly errors or even accidents.
QoS implementation in industrial networking ensures that critical data, such as equipment health indicators or emergency shutdown signals,
‘Automation applications rely on secure, high-performance networks to ensure real-time data communication.’
can always be delivered without interruption, even in periods of high network usage. As automation technologies become more data-intensive, ensuring that the most crucial data reaches its destination will only become more critical to overall performance. New protocols, such as TSN (time-sensitive networking), are being developed to elevate QoS in industrial applications, where prioritization begins at the protocol level. This approach differs from other forms of QoS, which, while effective, may not fully meet the future needs of automation. TSN is designed with QoS by design. This topic will be covered in a separate article.
Redundancy is crucial element of a resilient industrial network. By creating multiple pathways for data, redundancy ensures that even if one path fails, another can carry the traffic, maintaining network reliability. In mission-critical environments, where unplanned downtime can result in substantial financial losses and safety risks, redundancy is essential.
In an automation setting, redundant networking often includes features such as ring topologies or dualhoming. These designs create alternate routes for data flow, preventing a single point of failure from impacting operations. For instance, in a chemical plant, if a network path carrying sensor data from critical equipment fails, a redundant path can take over instantly, avoiding disruptions in monitoring and control.
Redundancy offers flexibility in network maintenance. With redundant paths in place, maintenance can be performed on one path without halting production, a critical for environments where stopping equipment can be costly or logistically challenging.
There are open and proprietary redundancy pro-
controleng.com
KEYWORDS: Networking infrastructure, industrial automation, cybersecurity LEARNING OBJECTIVES
Learn how robust networking infrastructure supports seamless communication, real-time data exchange and operational efficiency in mission-critical environments.
Gain insights into implementing segmentation, QoS, redundancy and cybersecurity to enhance network performance and resilience.
Discover how advanced networking can support the adoption of IIoT, AI-driven applications and scalable systems for evolving industrial needs.
CONSIDER THIS
Is my current networking infrastructure equipped to handle the demands of modern automation, including IIoT, AI integration and the need for enhanced security and resilience?
‘
Proper network design, including segmentation, cybersecurity and redundancy, is key to ensuring system reliability in mission-critical environments.
tocols. At a high level, open protocols offer the advantage of allowing customers to work with different vendors while providing redundancy. However, the downside is often the recovery time (i.e., the time it takes for the network to detect a failure, make a decision to change the path and start transmitting on the new path), which can reach several seconds and may be unacceptable in some cases. Proprietary protocols for use in ring or chain topologies achieve recovery times in the range of 20 to 50 milliseconds, even in large networks with up to 250 switches. For greenfield applications, where the network can be built with the same vendor’s switches, this requirement is generally not an issue, and proprietary protocols are commonly used. In brownfield environments, open protocols are typically preferred, as they allow the integration of different vendors into an existing network topology
As more devices and systems become interconnected, industrial networks are increasingly vulnerable to cyber threats. A security breach can have devastating consequences, including data loss, operational disruption, financial impacts and even serious safety risks for surrounding populations. In automation, where system availability, integrity and safety have always been foundational, cybersecurity is now an essential element, creating a new “DNA” for modern automation needs.
Advanced networking insights
uReliable networks enable seamless communication, critical for efficiency and reliability in automation.
uSegmentation, QoS, redundancy and cybersecurity optimize performance and mitigate risks.
uAdvanced networks support IIoT, AI, scalability and resilience for evolving industrial demands.
Network segmentation and redundancy enhance network security by limiting access points and providing failover options. New switches with security by design, certified by IEC 62443-accredited labs, are becoming increasingly popular. However, advanced security measures — including firewalls, intrusion detection systems (IDS) and real-time monitoring — are essential to protect industrial networks from evolving cyber threats. These systems detect and prevent unauthorized access attempts, ensuring that only authorized personnel can interact with critical systems. Importantly, adopting a cybersecurity standard or framework, such as IEC 62443, enables companies to strategically plan their cybersecurity approach, from budgeting needs to specific requirements and phased implementations. A proactive cybersecurity strategy not only defends against attacks but also improves resilience, allowing systems to recover more quickly if a breach occurs. In a mission-critical environment, even a few minutes of downtime due to a
security incident could cost lives. By implementing strong cybersecurity measures, industrial operations can protect their physical assets and the users.
The future of automation will see even greater integration of IIoT devices and AI-driven applications, placing new demands on industrial networking. IIoT devices generate large volumes of data, much of it requiring real-time processing to be actionable. This surge in data not only increases network bandwidth requirements but also necessitates faster, more intelligent data routing and processing.
Artificial intelligence (AI) and machine learning (ML), a subset of AI, are already finding applications in predictive maintenance, quality assurance, process optimization and cybersecurity. However, these technologies depend on the ability to gather and analyze data at speed, meaning networks must evolve to support these demands. AI-driven applications in automation also require scalable, flexible networks that can handle dynamic data flows and adapt to changing conditions in real time.
Industrial networks will need to support both edge computing architectures, where data is processed closer to the source and to a central server. To support these emerging applications, future industrial networks will require greater bandwidth, improved scalability and sophisticated cybersecurity. Investments in these areas will prepare companies to harness the full potential of IIoT and AI, enabling them to stay competitive in an increasingly digital landscape.
Automation advancements and the demands of new technologies mean that networking infrastructure will continue to play a pivotal role in the success of industrial operations. By implementing advanced networking strategies, industries can enhance automation reliability, efficiency and security for sustainable growth. Preparing networks for IIoT and AI, will help leverage the next generation of automation technology, and stay competitive and resilient. ce
Felipe Sabino Costa, MSc, MBA, PMP, CCNA, CISA-US DHS, is senior product marketing manager at Moxa Americas; edited by Gary Cohen, senior editor, Control Engineering, WTWH Media, gcohen@wtwhmedia.com.
Italian machine builders are set to showcase their cutting-edge ‘Breaking Necks’ solutions and technologies
Italian machine builders are the key to unlocking your strategic business potential.
How are end users leveraging Italian machinery to advance their operational goals and address significant industry trends? Machines Italia’s Spring 2025 issue will explore key trends across various sectors utilizing Italian machinery, including advancements in automation, environmental sustainability, and the increasing demand for flexible and adaptable machinery. For more details, visit machinesitalia.org.
As manufacturing cybersecurity attacks grow more sophisticated and network security for industrial systems is top priority, Skkynet provides secure data communication software and services that allow companies to securely acquire, monitor, control, visualize, network, and consolidate live process data in-plant or in the cloud.
Skkynet software and services are being used in every industrial sector, with over 29,000 installations in 86 countries, including by the top 10 automation providers worldwide.
Skkynet’s unique Cogent DataHub™ technology is secure by design, adhering to guidelines from NIST, ISA, and the European Union’s NIS 2 Directive for segmenting networks—using DMZs to completely isolate OT systems and data. Unmatched tunnel/mirror capabilities allow outbound data connections through a DMZ to IT or cloud services without opening any inbound firewall ports.
Working in combination or separately, these tools provide full capabilities for any company looking for a hybrid and/or cloud implementation. Engineers and managers can securely network industrial data to and from multiple locations, consolidate information from remote plants and devices, share data for predictive maintenance, or use a real-time HMI to view data from around the globe.
Because they are secure by design, these solutions require no security hardware, no VPNs, and no changes to IT policies. Yet plant systems remain invisible to the internet.
Skkynet maintains OEM relationships with hardware and software providers and is a certified AVEVA technology partner. Skkynet customers include Microsoft, Siemens, AVEVA, Caterpillar, ABB, Gamesa, GE, Equinor, Goodyear, BASF, and the Bank of Canada.
This core technology also powers the Cogent DataHub service for Azure, providing secure connectivity on the cloud to hundreds of 3rd party tools available at the Microsoft Azure Marketplace. At the device level for IoT applications, Skkynet offers an Embedded Toolkit (ETK) for securely streaming embedded data.
Skkynet software and services are being used in every industrial sector, with over 29,000 installations in 86 countries, including by the top 10 automation providers worldwide.
Skkynet.com
Idec Corp. expanded its operator interface (OI) family with its new HG1J Series touch screen. It provides vivid visualizations and responsive multi-touch operation in a compact form factor. The HG1J Series is the successor of the HG1G Series HMIs, and it provides an upgrade path for existing installations. The HMI’s projected capacitive touch panel (PCAP) advanced technology (like what is used for smartphones and tablets), saves space and improves performance. It is water- and scratch-resistant, very responsive and resists false signals when dirt or water droplets are present on the HMI face. Fewer touchscreen layers and better light transmission ratings mean less backlight power is needed, and the display provides a 500 cd/m² brightness level featuring 16 million colors and a 480×272 display resolution with a 50,000-hour-rated backlight. Idec Corp., https://lp.idec.com/HG-J-Series-US.html
Littelfuse Inc. launched the IX4341 and IX4342 dual 5 ampere low-side MOSFET gate drivers. These gate drivers are designed for driving MOSFETs and complete the existing IX434x driver series by adding the remaining two logic input versions. The IX434x series has dual non-inverting, dual inverting and non-inverting and inverting input versions. The IX4341 and IX4342 drivers’ short propagation delay times of 16 nanoseconds and brief rise and fall times of 7 nanoseconds make them ideal for high-frequency applications. Electronics designers can parallel the two channels to form one 10 A driver. Littelfuse, www.littelfuse.com
Motion-PLC from Trio Motion
Mencom, a provider of industrial connectors, added a new line of magnetic sensors designed to meet the diverse needs of modern industrial environments such as automation, manufacturing and process control, automotive, medical and aerospace, in many applications. The sensors are available in reed and GMR types and are designed for easy installation using either a clamp or screw system. They operate within a voltage range of 10 to 100V and 5 to 30V, respectively, and perform optimally in temperatures from -25°C to +90°C. The reed sensors have a maximum load capacity of 10 W DC and a switching current of up to 400 mA at 25°C, while the GMR sensors can switch up to 150 mA and detect field strengths of 2.8 mT. They have an IP67 protection rating, resistant to dust and water and have a yellow LED operating indicator for easy status monitoring. Mencom, www.mencom.com/magnetic-sensors.html
Technology is a new class of machine controller that combines motion, robotics and logic. The controllers combine advanced motion control performance with the functionality and simplicity of a PLC to reduce the cost and complexity of machine design. The new controller combines multi-axis motion control and IEC language programming with the company’s new MS I/O system with a slice interface for flexible I/O expansion. Six models can control a range of stand-alone machines, from two to 16 axes, including robotics integration. Motion control and machine logic applications include gantries, packaging and glue laying. I/O slices connect to the controllers, allowing up to 16 I/O slices that combine digital and analogue inputs and outputs. Trio Motion, https://www.triomotion.com
AW-Lake, flow instrumentation manufacturer, launched the TN Turbine Flow Meter, said to be a cost-effective solution for measuring light viscosity fluids, including glycol, water and solvents. It can be used for liquid flow measurement on or off the oil field and serves as easy dropin replacements for other brands of flow meters. With flow ranges from as low as 0.3 gallons per minute (GPM) to as high as 5,500 GPM, it is accurate to within ±1% of reading and offers repeatability of ±0.1% across the full range. Available in a wide range of sizes, the turbine flow meter provides multiple process connections and can work with various existing electronics. Its all-stainless-steel construction and precise machining tolerances ensure excellent durability. AW-Lake, www.aw-lake.com
Sensocon DataSling wireless differential pressure sensors are high-precision devices engineered for accurate monitoring of pressure changes across various environments. With an IP65 weatherproof housing, the sensors suit indoor and outdoor installations, for reliable performance in a wide range of conditions. With LoRaWAN wireless technology, the sensors offer long-range, low-power communications. Sensocon, https://sensocon.com
The Measuring Division of Kaman Precision Products Inc., offers an Advanced Magnetic Sensing (AMS) family of high-precision non-contact displacement sensors, specifically designed for the materials research and development market. These sensors are engineered to deliver high precision with root mean square (RMS) resolution down to 1 micron, providing extremely accurate measurements essential for research applications. This system’s non-contact measurement capability is crucial for maintaining the integrity of delicate materials. Kaman Precision Products Inc., www.kamansensors.com
Carlo Gavazzi’s new RSGT Series Soft Starters are easy-to-use product range for AC 3-phase induction motors up to 75HP / 55kW. To maximize the ease of use without compromising performance, only three settings are required (FLC, ramp-up, ramp-down). The self-learning algorithm adjusts the soft starter’s parameters to work with different applications and varying load conditions. The integration of a Class 10 electronic overload provides advanced motor protection and results in more space savings in the electrical panel. Carlo Gavazzi, www.carlogavazzisales.com
• Unmanaged 10/100/1000 Mbps Ethernet switches
• Single mode and multimode ber optic switches and media converters
• Diagnostic switches for network troubleshooting
• PoE switches, mid-span splitters and injectors
• Wired and wireless IP routers for secure remote access
• Custom con gurations and outdoor-rated options available
ArtiMinds Robot Programming Suite (RPS) makes it easy to create complex robot programs in just a few steps, independent of robot hardware manufacturers. The programming software automatically generates native robot code that runs on the standard controller of the robot manufacturer. The typically high programming effort for integrating cameras, forcetorque sensors, electric grippers and PLCs is replaced by the much simpler selection,
Eaton’s XControl micro PLCs, XC104/ XC204, offer machine and system builders compact, powerful and flexible PLCs for implementing lean and modern automation concept – especially if used in combination with the modular I/O expansions XN300 and the innovative touch panels of the XV series. The PLCs and gateways are simple, flexible and can be expanded with the I/O slice modules of the XN300 system to form a control configuration tailored to the solution. Ethernet interfaces with individual network adapters paired with the standard CAN and RS485 interfaces expand the features of the devices to a universal control and communication point of the networked plant. Eaton, https://www.eaton.com
combination and parametrization of predefined function templates. The software provides an extensive library of templates covering a wide range of tasks from pickand-place to camera-based detection and force-sensitive assembly of components. The user is supported with various assistance functions.
02012025_Control_Engineering_EtherCAT_Ad_(5.25x8).pdf 1 1/2/2025 1:11:08 PM
ArtiMinds Robotics GmbH, www.artiminds.com
EVENT OVERVIEW:
The Advanced Automation Forum (AAF) is a two-day event designed to accelerate digital transformation in manufacturing through collaboration between system integrators, end users and product manufacturers. Taking place on April 30th and May 1st, 2025, this forum will offer hands-on, practical insights into the future of manufacturing, focusing on real-world strategies, successful case studies, and actionable solutions. During the event, we will recognize the important contributions of top system integrators.
KEY FOCUS AREAS:
• The practical implementation of smart manufacturing
• Data-driven decisions
• Securing connected devices through collaborative cybersecurity
• IT/OT alignment
• Upskilling the workforce
• Overcoming integration challenges
• The tools required to support sustainability initiatives
Benefits include cleaning and contextualizing data, managing over 200 production facilities and 3 million data streams; and helping refineries to grow revenues by 38 times.
At present, in the rapidly changing global market full of opportunities and challenges, artificial intelligence (AI) technology, especially industrial AI, has become an important tool to help enterprises meet various challenges in economy, supply chain, energy transformation and other areas. AspenTech is among providers of industrial software using industrial AI. Rob Howard, senior director of global enterprise solutions consulting at AspenTech, and Chen Jie, senior director of solutions consulting at AspenTech Greater China, recently discussed industrial software innovation, markets, sustainable development strategy and industrial AI with Control Engineering China
ASPEN HYBRID Models combine AI data with first principles models and 40 years of industry expertise to create a more predictive model. Three advantages of industrial AI are flexibility, tighter advanced process control (APC) and automation. Courtesy: Control Engineering with AspenTech information
Applications of industrial AI are continuing to expand, with opportunities to help transform and upgrade traditional manufacturing, especially with intelligent production, predictive maintenance, quality inspection and supply chain optimization. Howard said AI has demonstrated three major advantages in the industrial sector: 1) flexibility, enabling quicker and more accurate decision-making and adapting to change; 2) tighter focus for advanced process control and intelligent suggestions to enhance operational understanding; and 3) automation, which rapidly scales technology and reduces operator specialization requirements. Due to its ability to create enormous value, in recent years, traditional automation manufacturers and industrial software companies have been actively expanding. Howard said, “AspenTech has over 40 years of leading experience in industrial solutions. Our product portfolio covers everything from chemical databases and industrial process control apps to a variety of innovative software. In addition, AspenTech has over 20 years of experience in industrial AI, continuously integrating neural networks, generative AI and deep learning into solutions
and achieving significant results.”
Underground image pixel visualization, multivariable adaptive control technology and parallel engineering workflow are among applicable AspenTech innovations. Howard added that between 2005 and 2010, AspenTech integrated neural networks into Mtell (AI predictive analytics field). AspenTech Hybrid Models and AspenTech Virtual Advisor help to increase waste heat recovery, improve reliability and maximize return on investment.
Arithmetic, algorithms and data are the three major difficulties and pain points that manufacturing enterprises and technology providers will commonly face when implementing AI technologies. Data is the most challenging area, and industrial AI needs to combine specific knowledge, experience and engineering insights to adapt AI to industrial scenarios. Helping with industry data asset deposition, AspenTech's chemical modelling database has 34,000 compounds, with more than 8,000 industrial process control applications and a wide range of software. Data governance is a key element for enterprises to fully use data. Production environments include structured and unstructured data; AspenTech can provide enterprises with efficient data aggregation capabilities to help with data governance and cybersecurity. ce
Stone Shi is executive editor-in-chief, Control Engineering China; edited by Mark T. Hoske, editor-in-chief, Control Engineering, WTWH Media, mhoske@wtwhmedia.com.
Onlineu controleng.com
KEYWORDS: AI, manufacturing optimization, sustainability CONSIDER THIS Is AI helping to optimize operations and advance sustainability efforts? ONLINE
How to use a lifecycle digital twin for carbon capture www. controleng.com/articles/ how-to-use-a-lifecycle-digitaltwin-to-streamline-carboncapture-processes
VP,
Sales Account Manager
MWaddell@WTWHMedia.com 312-961-6840
Brian Gross BGross@WTWHMedia.com 847-946-3668
Sales Account Manager
Richard Groth RGroth@WTWHMedia.com 774-277-7266
Sales Account Manager
Robert
Sales Account Manager
RLevinger@WTWHTMedia.com 516-209-8587
Dean Morris DMorris@WTWHmedia.com 513-205-9975
Sales Account Manager
Judy Pinsel 847-624-8418 JPinsel@WTWHmedia.com
Patrick Lynch, Senior Vice President, Sales & Strategy 847-452-1191, PLynch@WTWHMedia.com
Patrick Lynch, Senior Vice President, Sales & Strategy 847-452-1191, PLynch@WTWHMedia.com
McKenzie Burns, Marketing Manager MBurns@WTWHmedia.com
McKenzie Burns, Marketing Manager MBurns@WTWHmedia.com
Courtney New, Program Manager, Content Studio CNew@WTWHMedia.com
Courtney New, Program Manager, Content Studio CNew@WTWHMedia.com
Paul Brouch, Operations Manager 708-743-5278, PBrouch@WTWHMedia.com
Paul Brouch, Operations Manager 708-743-5278, PBrouch@WTWHMedia.com
Rick Ellis, Director, Audience Growth
Rick Ellis, Director, Audience Growth 303-246-1250, REllis@WTWHMedia.com
Michael Rotz, Print Production Manager
Michael Rotz, Print Production Manager 717-422-3622, mike.rotz@frycomm.com
Custom reprints, print/electronic:
Custom reprints, print/electronic: Matt Claney, 216-860-5253, mclaney@wtwhmedia.com
Information: For a Media Kit or Editorial Calendar, go to https://www.controleng.com/advertise-with-us.
Information: For a Media Kit or Editorial Calendar, go to https://www.controleng.com/advertise-with-us.
Letters to the editor: Please e-mail us your opinions to
Letters should include
Letters to the editor: Please e-mail us your opinions to company, and address, and may be edited.
Remote wireless devices connected to the Industrial Internet of Things (IIoT) run on Tadiran bobbin-type LiSOCl2 batteries.
Our batteries offer a winning combination: a patented hybrid layer capacitor (HLC) that delivers the high pulses required for two-way wireless communications; the widest temperature range of all; and the lowest self-discharge rate (0.7% per year), enabling our cells to last up to 4 times longer than the competition.
Looking to have your remote wireless device complete a 40-year marathon? Then team up with Tadiran batteries that last a lifetime.
At SEW-EURODRIVE, we engineer the highest quality drive automation solutions. What truly sets us apart is our unwavering commitment to customer support, long after the sale. We go above and beyond to ensure your business stays on the move with exceptional service at every turn. Upgrade everything.