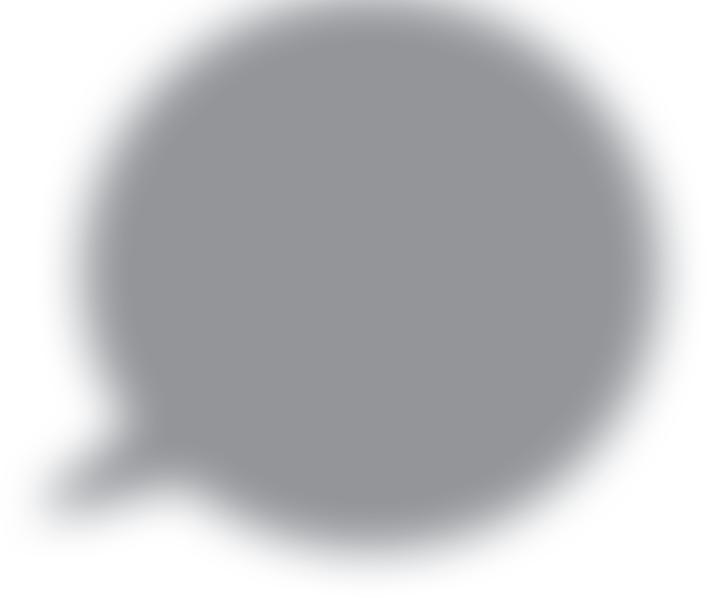
2 minute read
Berkeley space team has “Eureka” moment with 3D printing
The Space Enterprise Berkeley (SEB) team launched their first-ever liquidfueled rocket, Eureka-1, which reached 11,024-ft in December last year. The collegiate team partnered with Protolabs to create parts for Eureka-1’s plenum and complex parachute system using selective laser sintering (SLS).
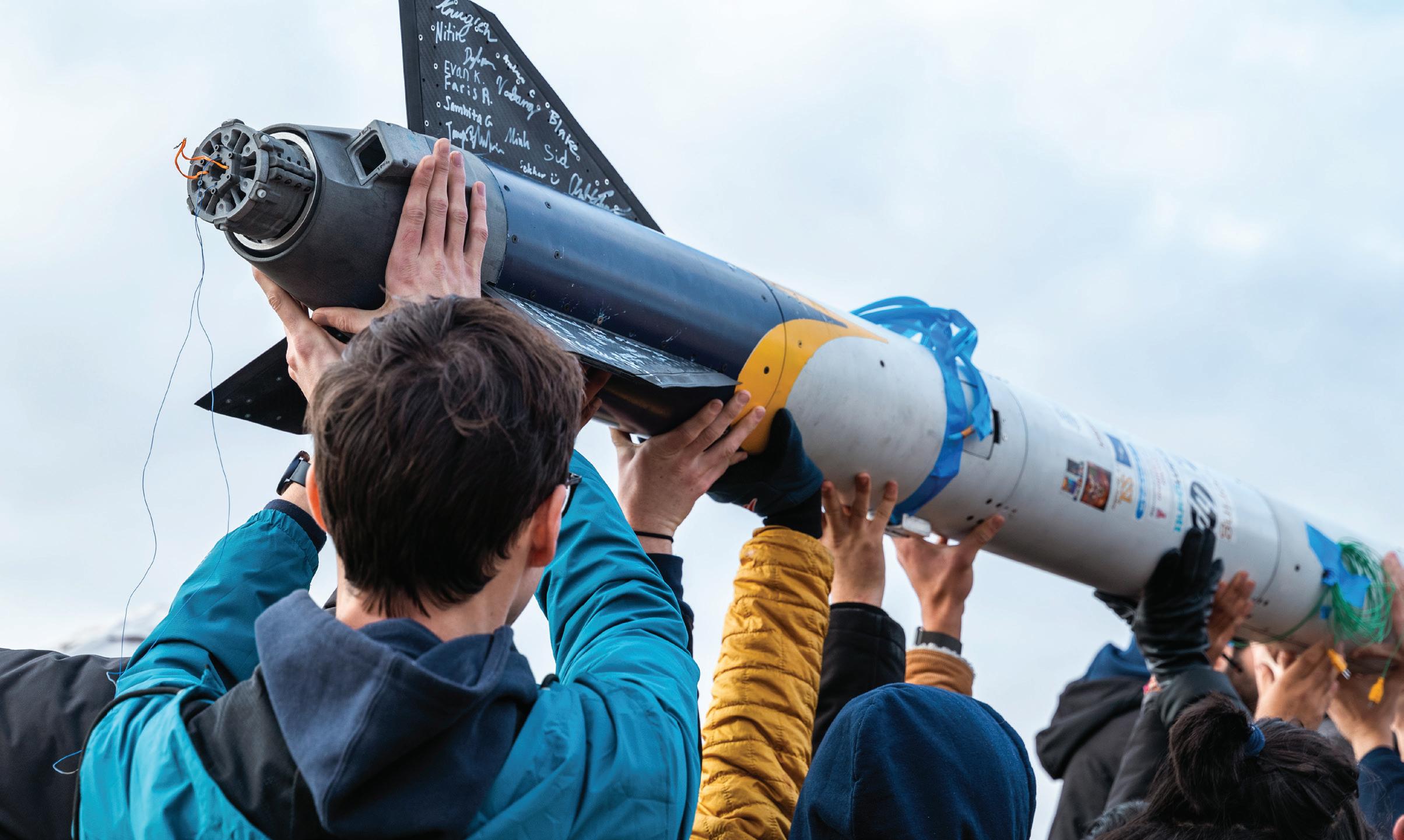
“3D printing made sense for creating a part that could combine functionalities. It had to mount a parachute swivel, secure the avionics bay, and integrate a camera. That would’ve been a complex part with traditional manufacturing,” said Asa Garner, structures lead for SEB.
Garner used CAD to create the assembly design. He made a block diagram to show where the parts should be, and sub-teams with di erent requirements agreed on a general layout. Then, each team designed its individual parts in CAD to develop the general geometries. Garner knew that 3D printing would be the best solution for many parachutes and outer plenum components.
“As soon as we realized we wanted to 3D-print these parts, I looked up all the datasheets for the various Protolabs materials. Then, I simulated options in nTopology and eventually settled on PA12 40% glass-filled nylon,” said Garner. “With PA12 glass-filled, we didn’t have to compromise on strength. We added a little bit more material than we would with metal, but it ended up being about the same weight and way easier.”
Aerospace commonly uses SLS and glass-filled nylon to make lightweight components, especially for rocketry and uncrewed drones. SLS provides material strength and consistency and is helpful for custom and complex parts. By building parts additively, engineers can skeletonize the designs and remove any mass that doesn’t contribute to the part’s functionality.

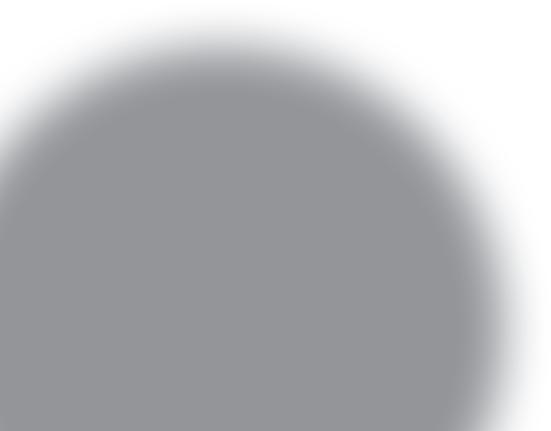

“As a practical measure, you can reduce the number of parts and decrease assembly times,” said Eric Utley, application engineer at

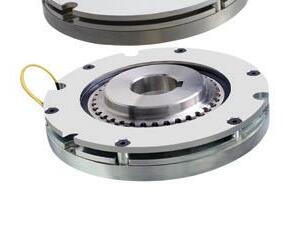
The lattice design made the part lighter, stronger, and able to withstand anticipated stress during flight.
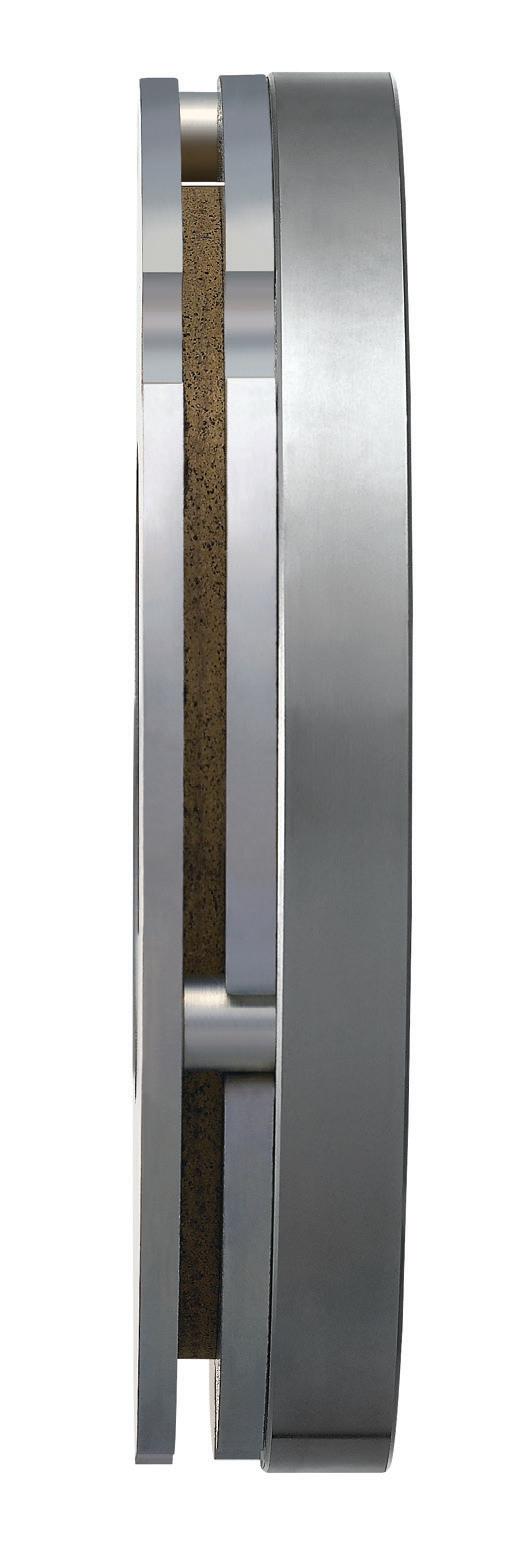
Protolabs. “Initially, I thought people used 3D printing to save on CAD work and assembly. But once it scales up to a production setting, it also saves administrative time. For example, if an aerospace customer has a 13-piece component, they have 13 di erent purchase orders and must keep track of the 13 di erent vendors and their quality certifications. Extrapolate that to a larger product like a rocket. If you can go from 100,000 pieces down to 5,000 pieces, it’s tremendously less supply chain management.”
With 3D printing, design engineers can also accelerate product development by quickly creating parts, collecting feedback, and iterating on the design.
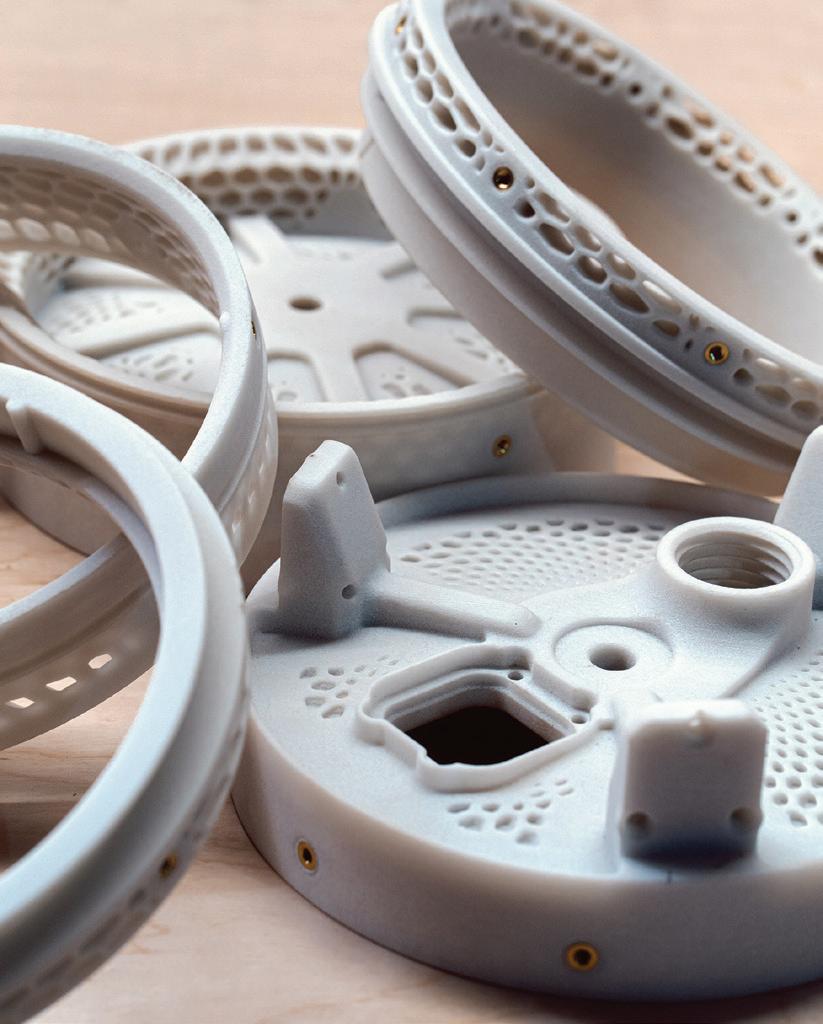
“Software developers started the mindset where you can roll out a product and it doesn’t have to be perfect. You get it out there in people’s hands, then iterate and improve it. That mindset is trickling into hardware,” said Utley.
The SEB team used nTopology to simulate forces on the 3D-printed part and how the part would respond when the parachute opened. They assessed how it would handle stress and located stress concentrations or peaks. Using a lattice design, they could smooth out such peaks, dissipating stress across the part and leveraging the material e ciently.
Design for 3D printing and Additive Manufacturing


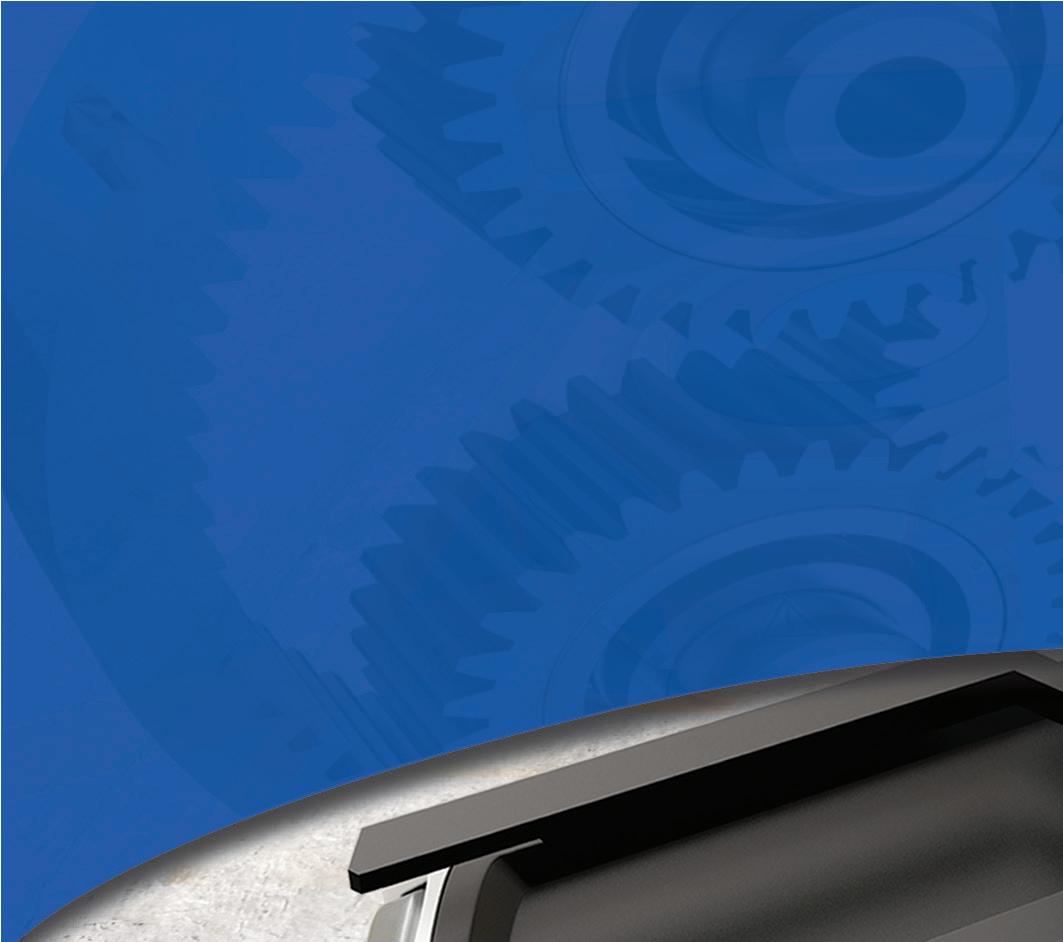
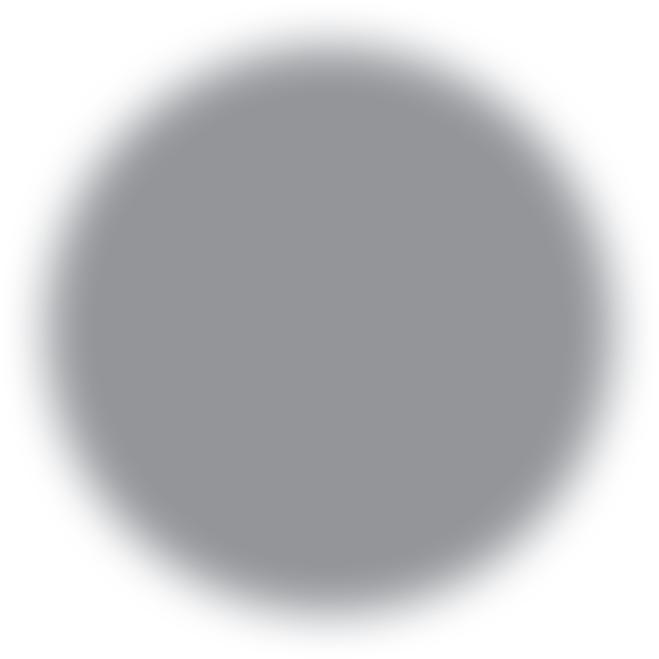
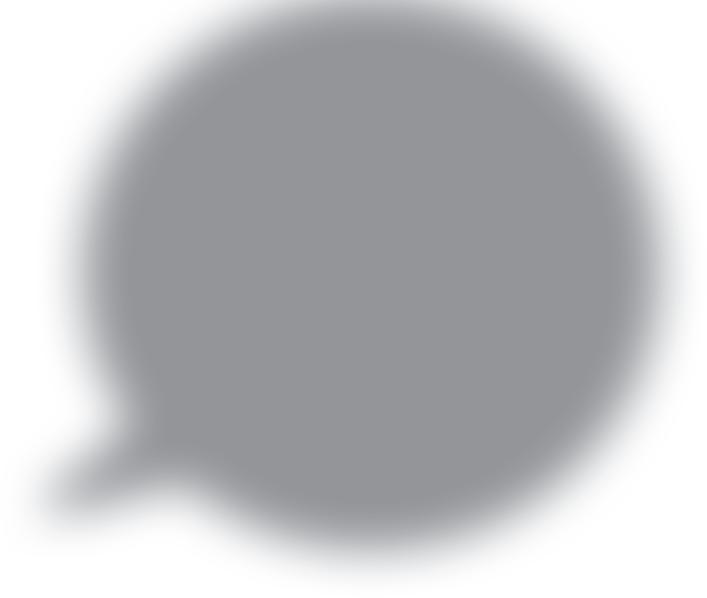
Garner used nTopology to simulate how the 3D-printed parts would respond to stress during flight.