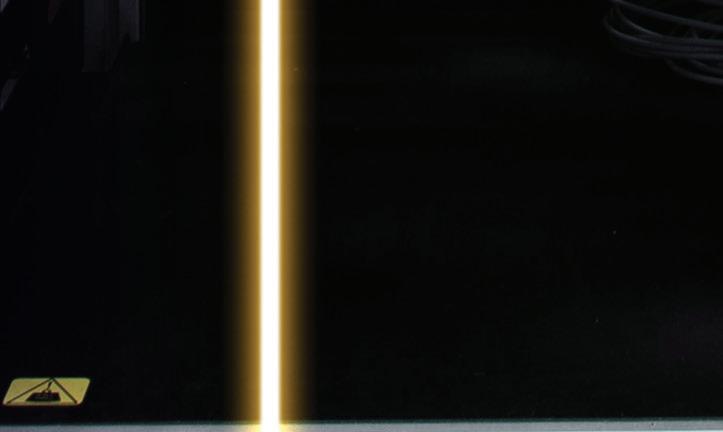
1 minute read
Move over AI: shops pave digital journeys with actionable data
As manufacturers seek more unified operations with greater visibility, many jump at the chance to gather data only to find themselves buried in meaningless and costly information. Renishaw Central aims to capture the right information and reveal hidden machine data that improves process control and quality.
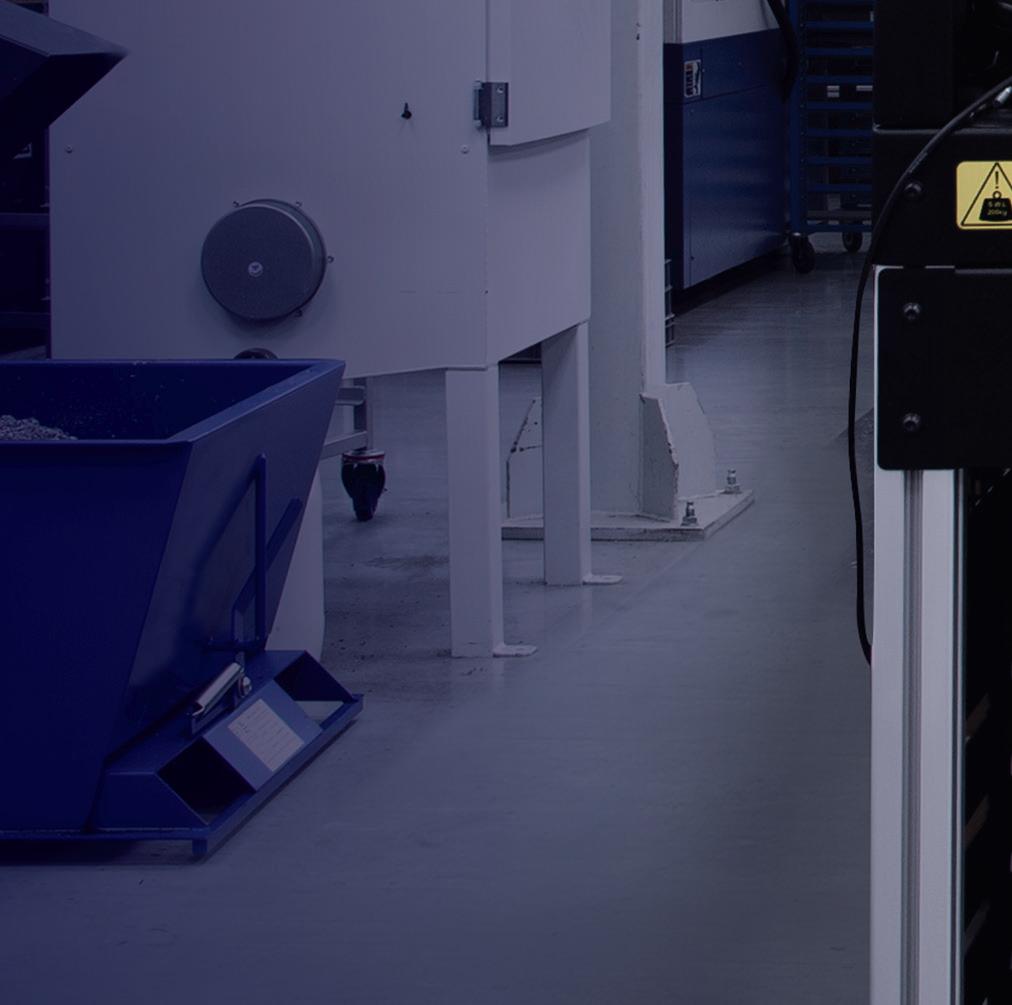
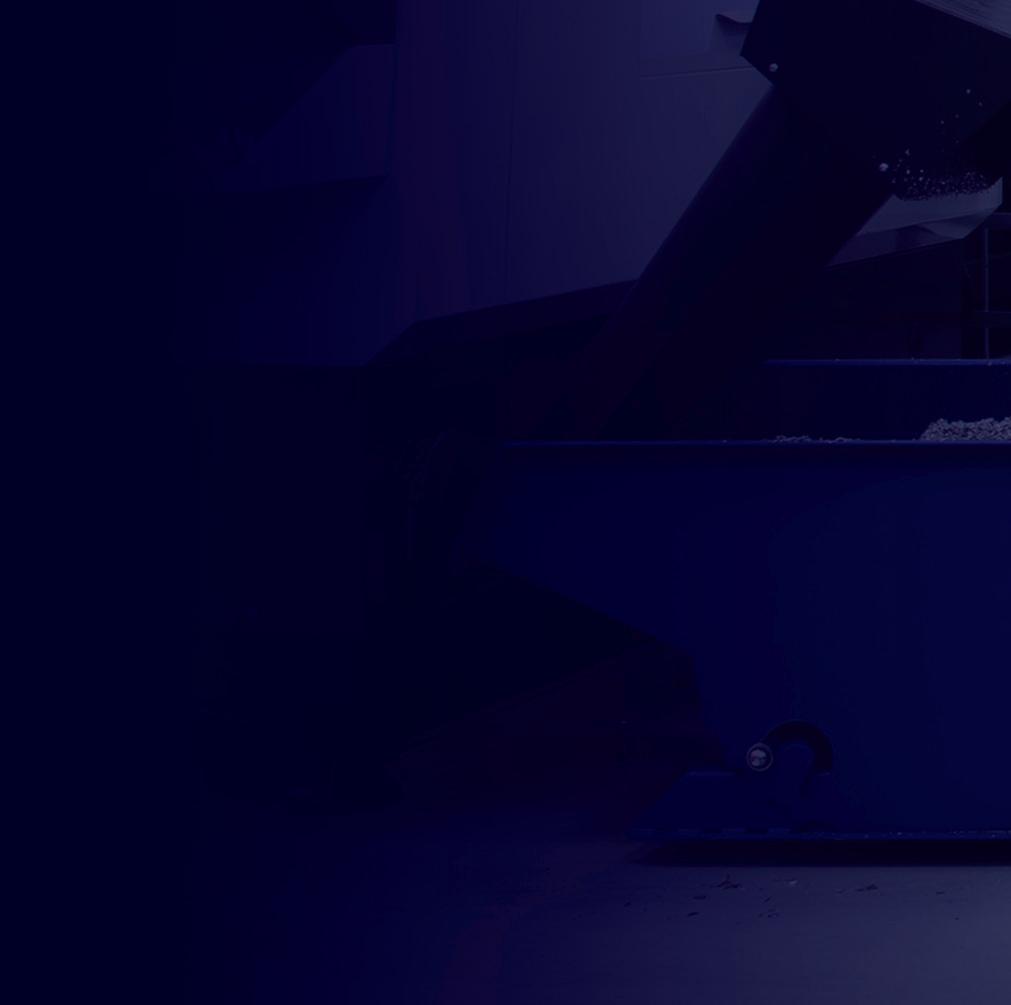
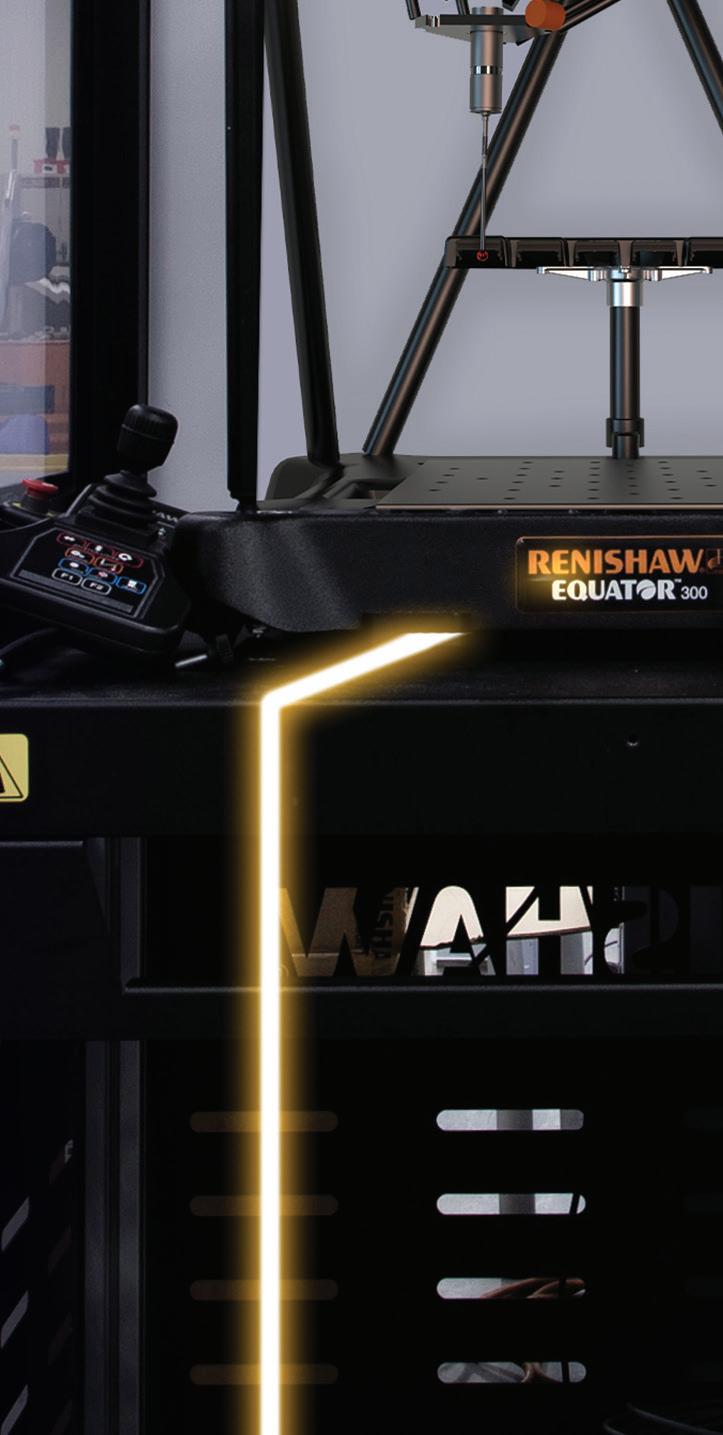
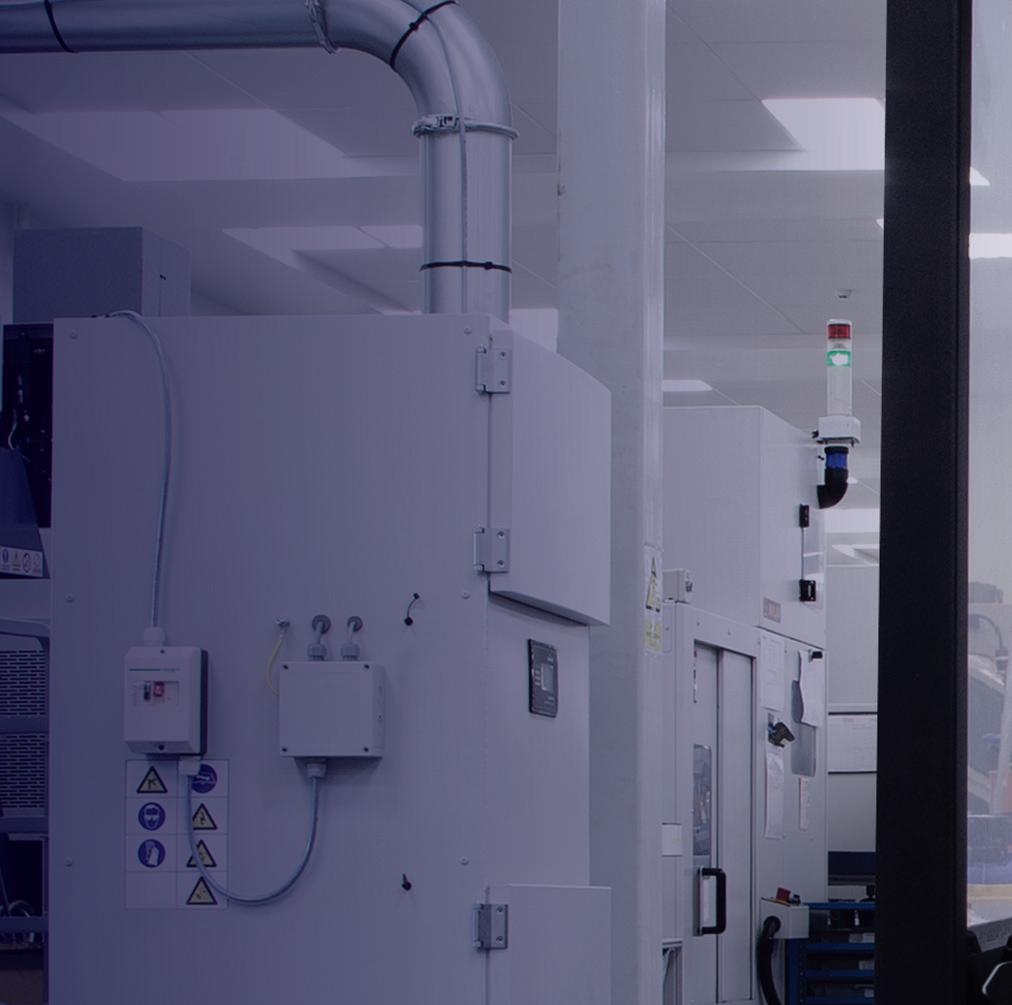
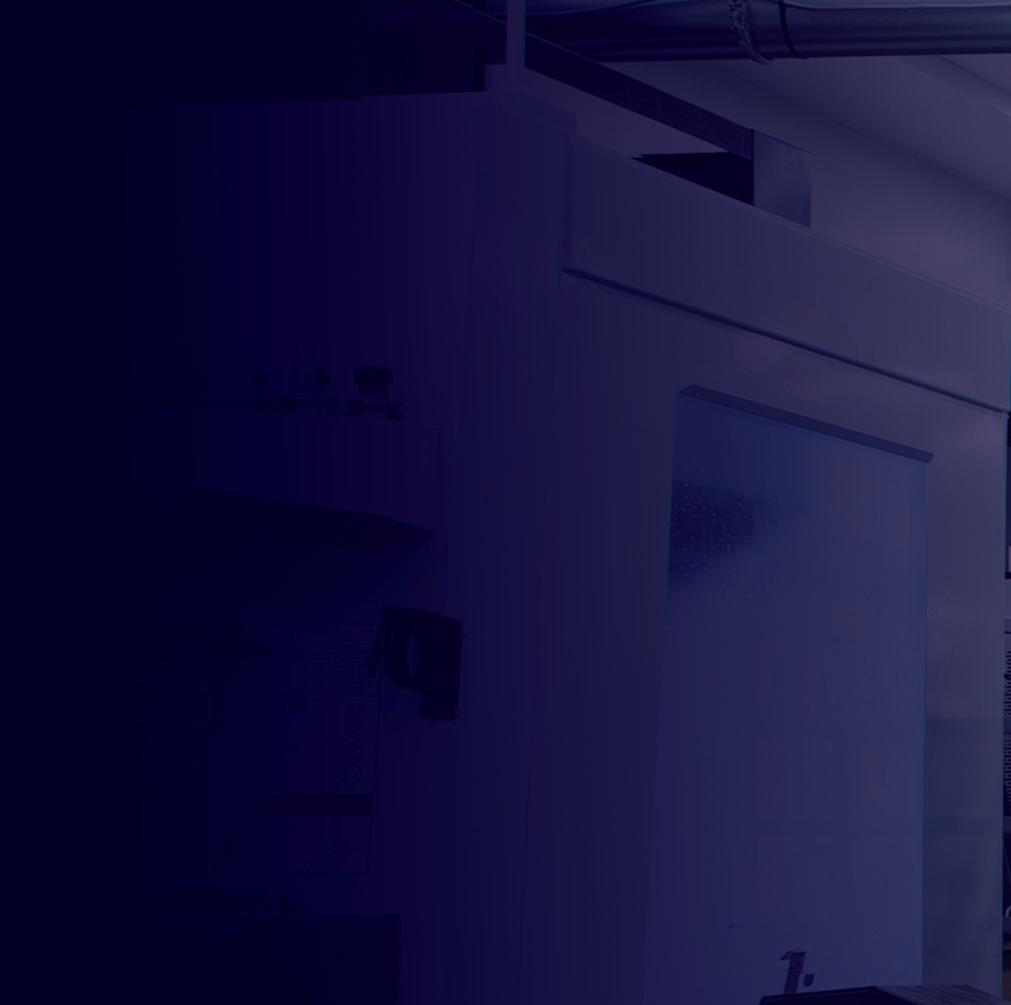
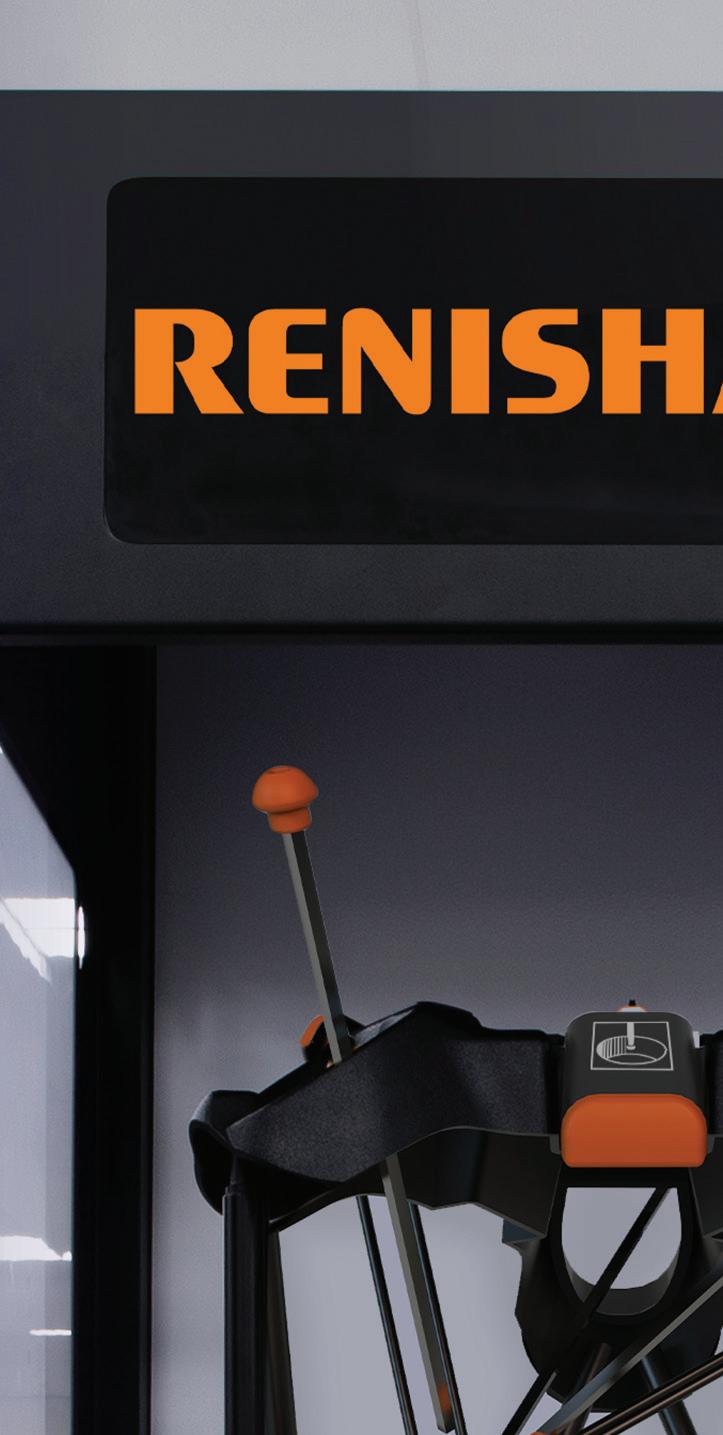

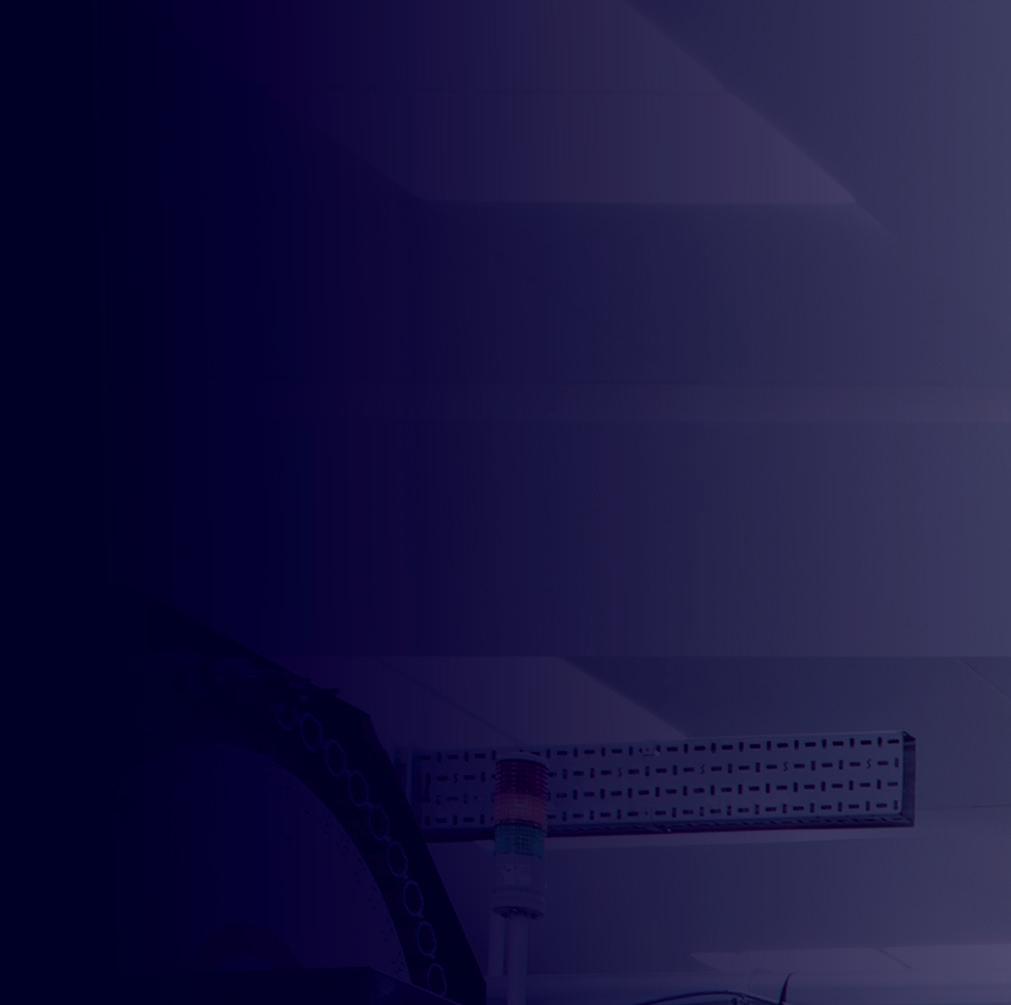
Rachael Pasini
Senior Editor

The cloud is often revered as a sacred watering hole where all data may happily gather and intermingle under the magical governance of AI, which can transform any hopeless datum into a meaningful contrail of predictive knowledge.
But storing mass information doesn’t equate to storing the right information. And sorting through the noise can be costly and unproductive.
Plus, many manufacturers prefer to hold onto now-called legacy systems that still serve their purpose while adding new technology incrementally. Collecting and pooling data from many machines of di erent eras can be a massive undertaking with no guarantee that the information will be helpful.
“They are very much dreaming of the cloud, but when it comes to a 20-year-old controller, the dream can evaporate and become a nightmare,” said James Hartley, applications and marketing manager of Renishaw’s Machine Tool Products Division.
Deciding where to capture information and how to use it to improve processes can be burdensome. Why would anyone waste time collecting data and creating reports if the same manufacturing problems persist? If data isn’t doing anything useful to improve production times, scrap rates, or quality metrics, then it just wastes more time and money, adding to ine ciencies.
All too common, data flows are visible until they get to the machine shop. Machine shop personnel hold valuable knowledge about what makes each machine work. They know which machines perform the best for specific jobs or need more frequent servicing. This knowledge remains at the shop level, and people learn to adapt to the machines.
But reliance on personnel know-how creates a data vacuum and counters more unified facility control systems. To plant engineers, there seems to be an invisibility cloak over the shop until quality data pops up later. And without visibility, they can’t make real-time data-driven recommendations on the process.
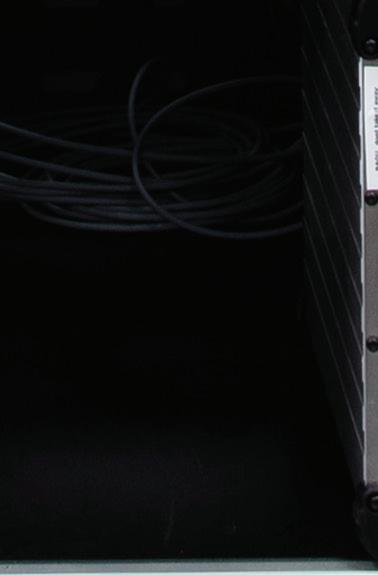
“Many people have the hardware, skills, and technology, but they just don’t have a grip on what’s really going on behind the scenes,” said Guy Brown, development manager of Renishaw Central.
Renishaw’s Equator gauging system captures near-line quality information and sends it to Renishaw Central, which sends updates to the machine to improve part consistency and quality.
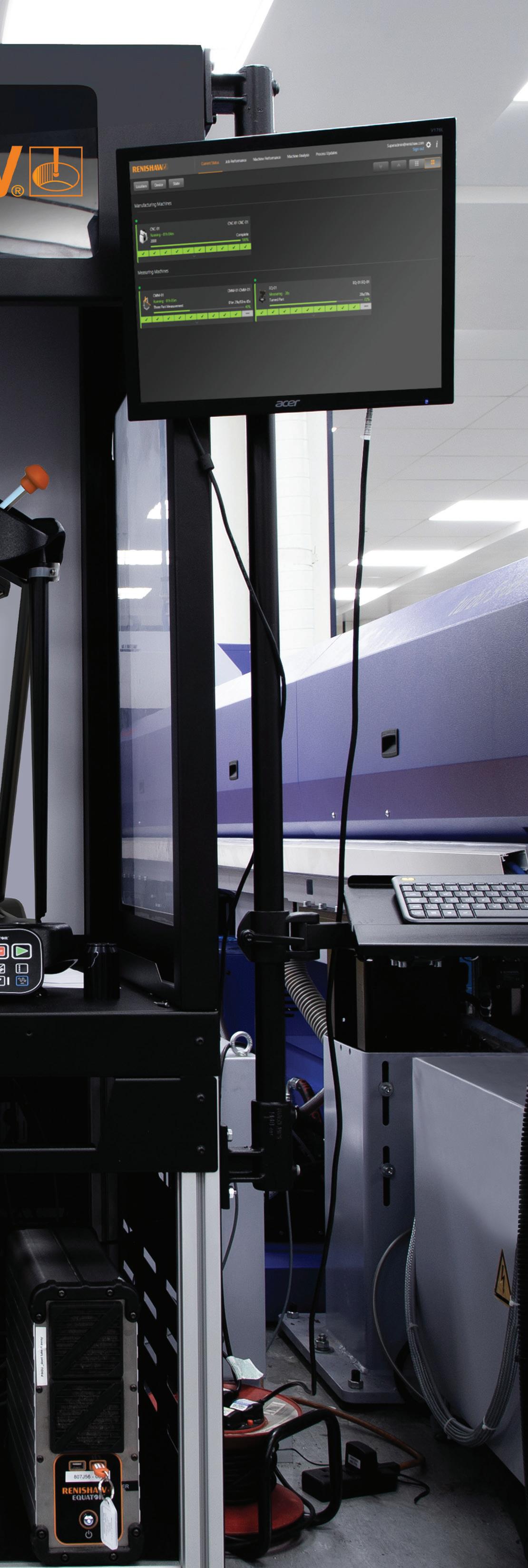
But what if there was a way to extract hidden information from the machines? What if real-time data exchange could provide a holistic view of the machine shop so it’s no longer a data vacuum?
Renishaw Central, an on-premises connectivity and data platform that connects machines and extracts actionable data, aims to do just that — and more.
