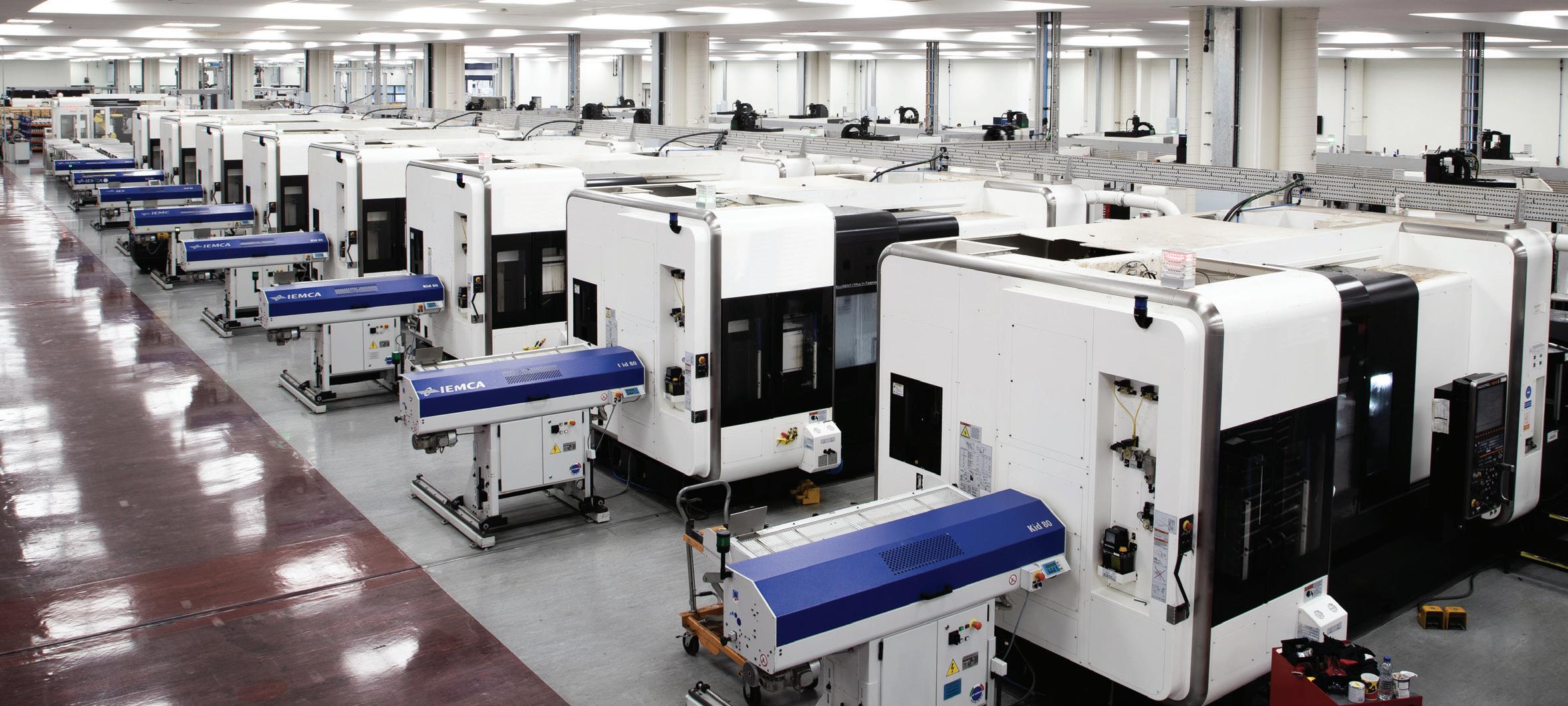
4 minute read
Digital Manufacturing
time and not at the end of the line. With patented Intelligent Process Control (IPC) software, it can also capture nearline quality information from an Equator gauging system, for instance, and send information such as tool-offset updates back to the machine to improve consistency and control.
“If someone manually changes a tool offset or if a tool offset is wrong, the process is inaccurate, and the quality can go haywire. So, we’ve paid just as much attention to the collection of toolsetting data as we have for workpiece setup or inspection,” said Hartley.
Digital journeys evolve from their problems
The engineering company Renishaw is known for its metrology, measurement, motion control, and manufacturing technologies. The supplier also develops advanced analytical instruments and machines for healthcare. As a manufacturer of its own products, company engineers deeply understand the end-to-end challenges that OEMs face and how data visibility can improve process control.
In fact, such control is the core of Renishaw Central. The platform connects a range of new and legacy equipment to help operators understand what’s happening at the machine level.
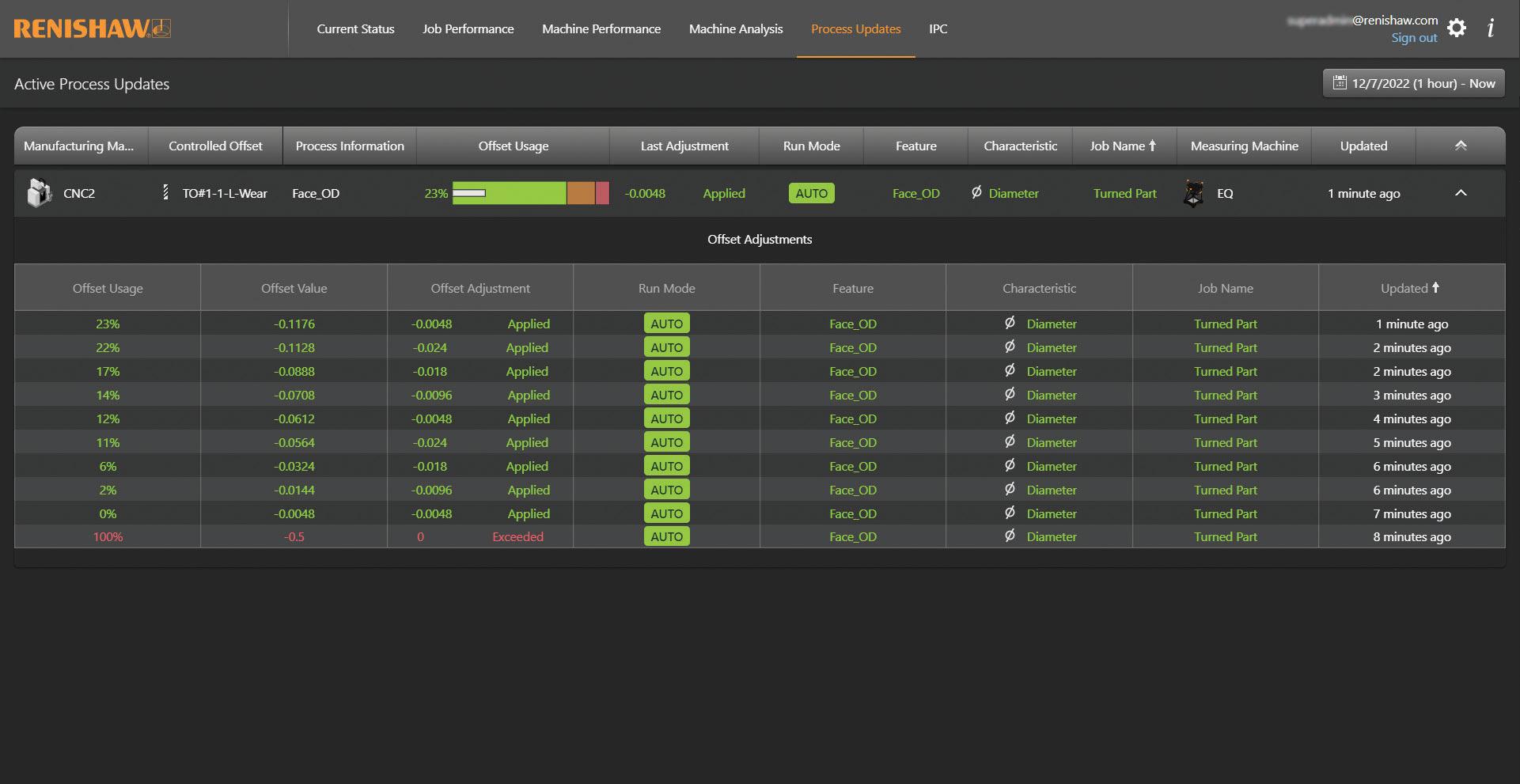
The intention is to limit variability and monitor quality in real
While collecting data is one task, acting on it is quite another. In the 1980s, Renishaw printed most measurement results for backup with dot matrix printers. But the information typically sat dormant unless they found a quality problem and referenced it in a post-mortem investigation. Though Renishaw pioneered on-machine process control, even they weren’t actively using the data.
Then, in the 1990s and early 2000s, a shop floor data collection system worked over the DNC system that could push up programs to the machines, take down measurement results, and store the data centrally. The data was still not mined or analyzed for any purpose other than figuring out quality control issues after they occurred.
“We collected a lot of data and never went back to look at it. It was just kept for historical purposes — for traceability reasons — but filed away and not really addressed,” said Brown. “A very small portion was functional and worked with the kitting stations, but 90% of the data just sat there.”
In the 2010s, they implemented an external Industry 4 platform to connect more equipment, but it didn’t collect metrology or measurement data and required user input in many cases. So, the system depended on the quality of manually inputted information.
Now, in the 2020s, they have Renishaw Central to build upon previous efforts and add a real-time data analysis piece — but not just for data analysis’ sake. Renishaw Central extracts and reveals actionable data that would otherwise remain hidden and unshared.
“We started asking, ‘Why do machines stop? Why are things not quite what we expect them to be? What have we missed? What are the unknown unknowns?’” said Brown. “And we wondered how we could use the data day by day to transition from a reactive to a proactive position.”
To test its own product, the company deployed the platform in the U.K. at its low-volume, high-variety manufacturing facilities in Miskin and Stonehouse. The platform connected 67 machines across both facilities, revealing that two error types were responsible for 82% of automation stoppages. After remedial action, automation stoppages decreased by 69%. Additionally, using the IPC set-up feature, set-up times on sliding-head lathes decreased by more than 85%.
A global selection of pilot customers also confirmed that Renishaw Central provided the right data and insights to improve their processes and performance.
Bringing machine data to life
The Renishaw Central platform is machine-agnostic and uses APIs to connect different machines to a unified, on-premises network.
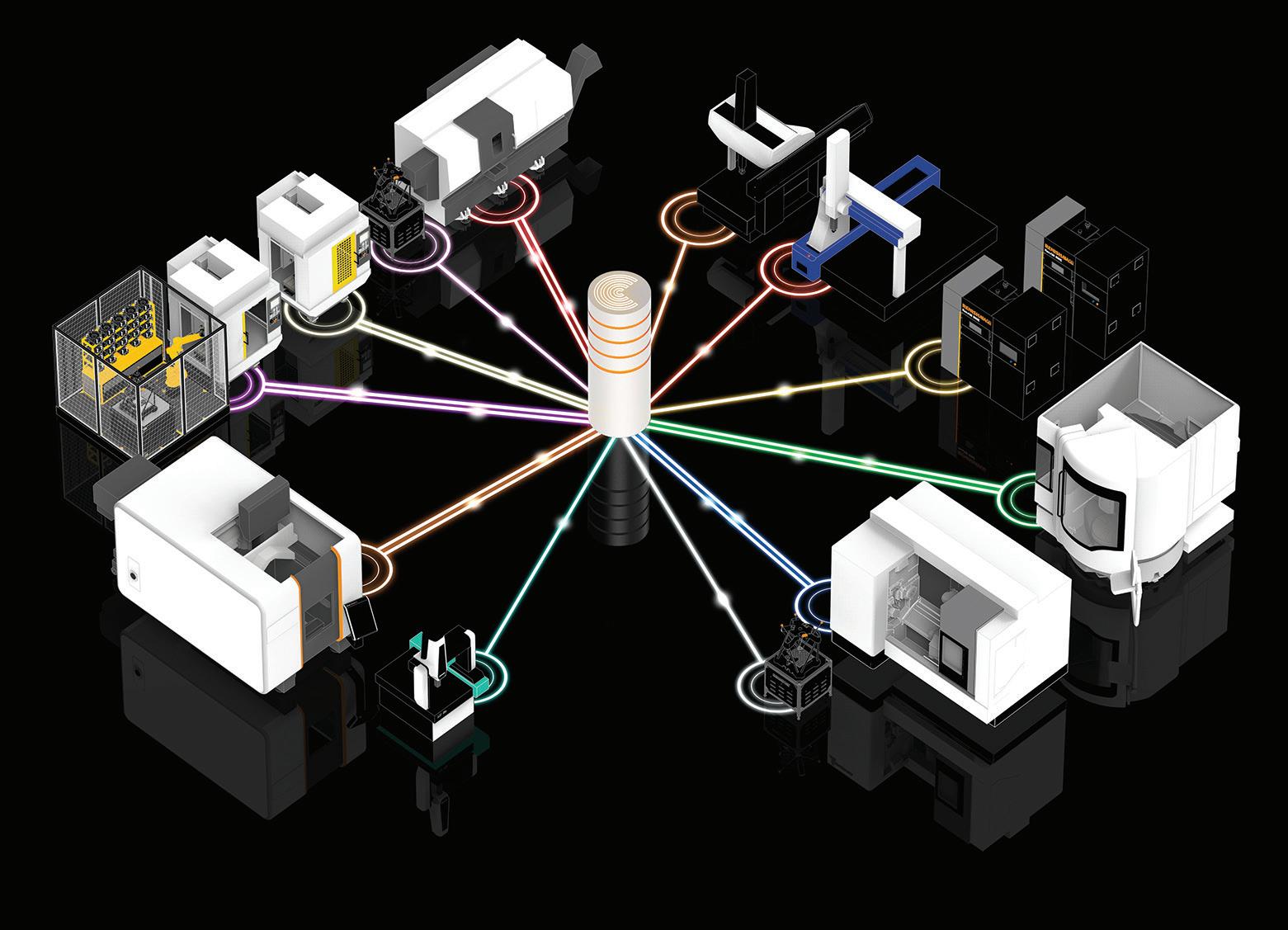
“No one company is going to own Industry 4,” said Hartley. “Therefore, Renishaw is a neutral party, providing all the big controller manufacturers and OEMs with software. We are a licensee for almost all their APIs, which means we can make native connections to those controllers.”
In some cases, data flows one way from machines to Renishaw Central, which collects measurement results, quality metrics, cycle time, status, utilization, warnings, alerts, yield rates, offsets, and other process control information.
North American & International Power Cords With 1-Week Lead-Times!
Need a power cord supply chain with 1-week lead-times? Let Interpower® worry about manufacturing your cords and cord sets while offering its industry-unique 1-week lead-times.
Our cord sets and accessory power systems ship straight from the factory. Want the cords hanked, coiled, tied, bagged and boxed? Need 1-D or QR barcodes for easier warehousing? Customize cord lengths and colors for countryspecific cords configured and ready to use right out of the box!
• World-class customer service 7 a.m. to 6 p.m. CST
• In-stock cords ship the same day
• No minimum orders
• Value-added options such as colors, lengths, labeling and packaging
®
®
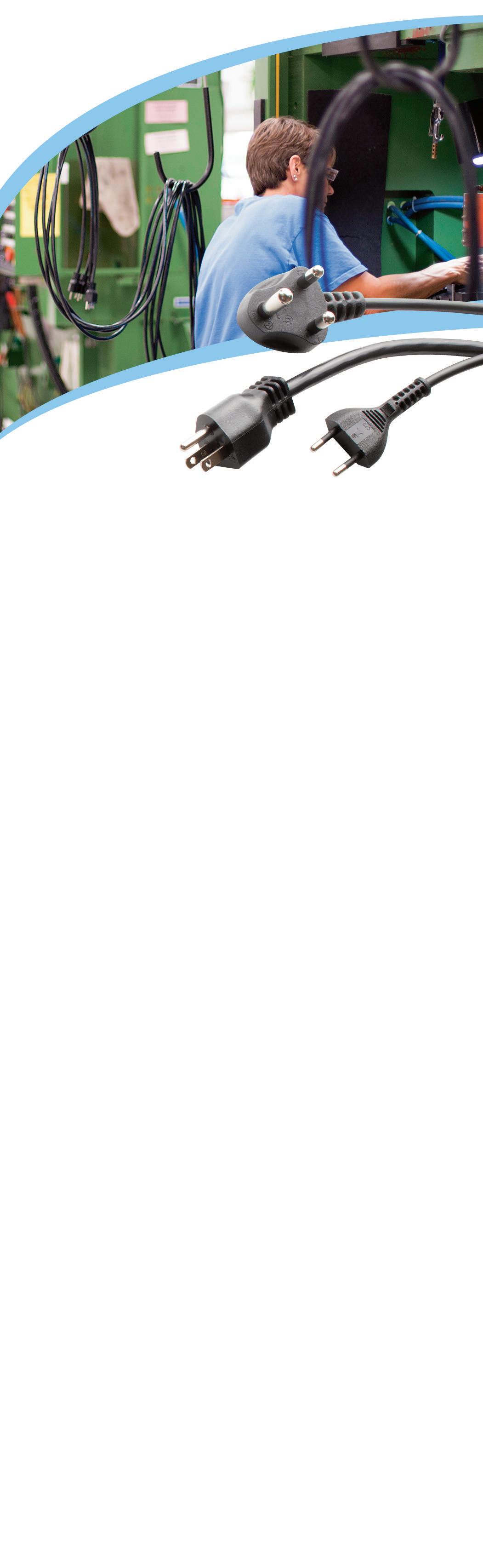
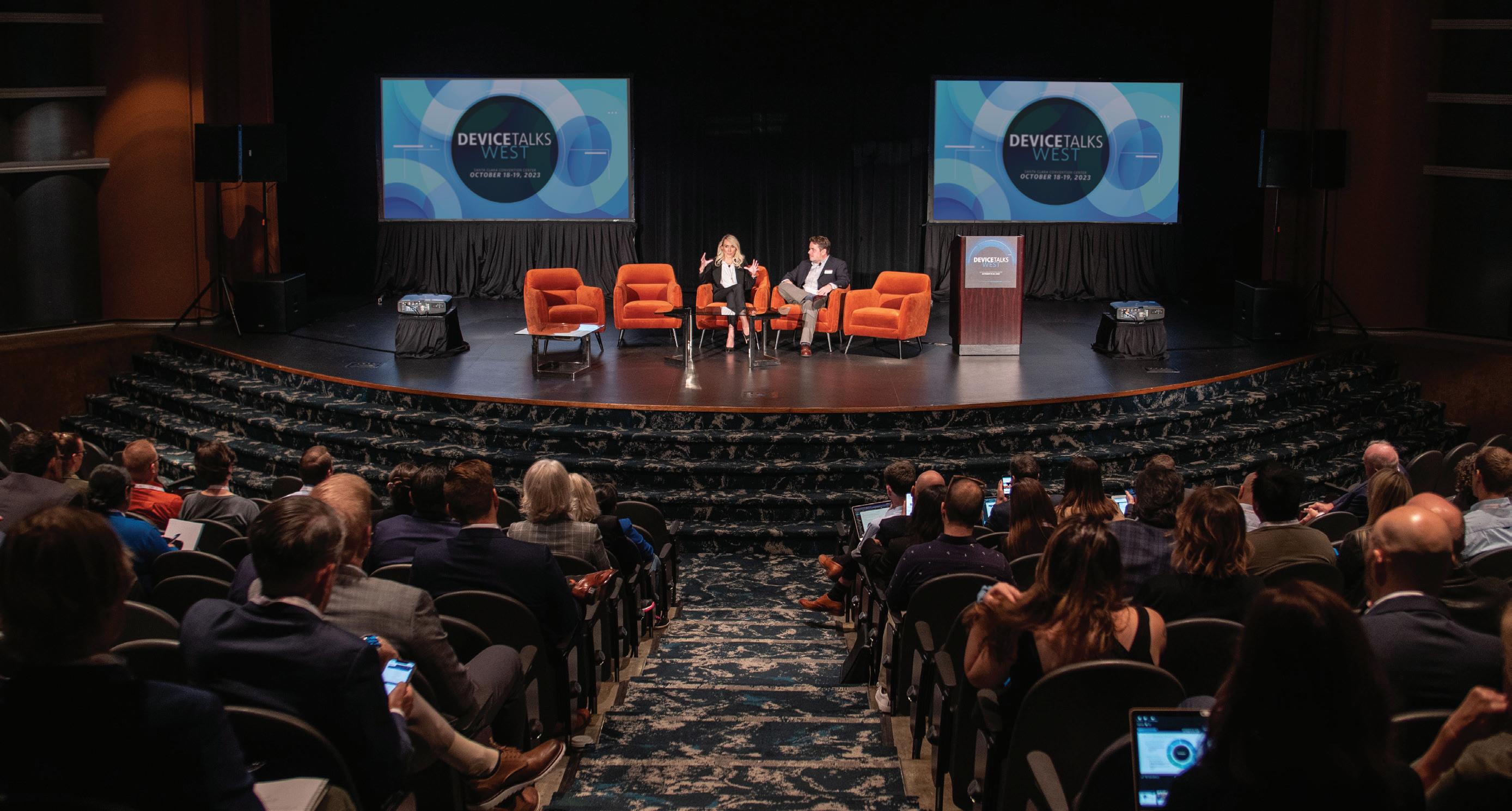
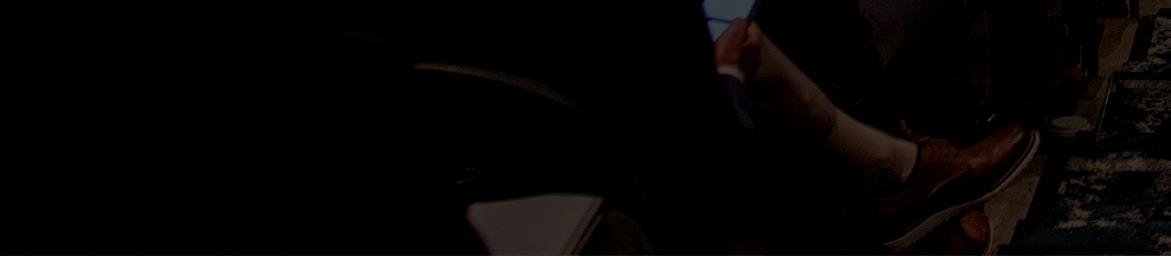
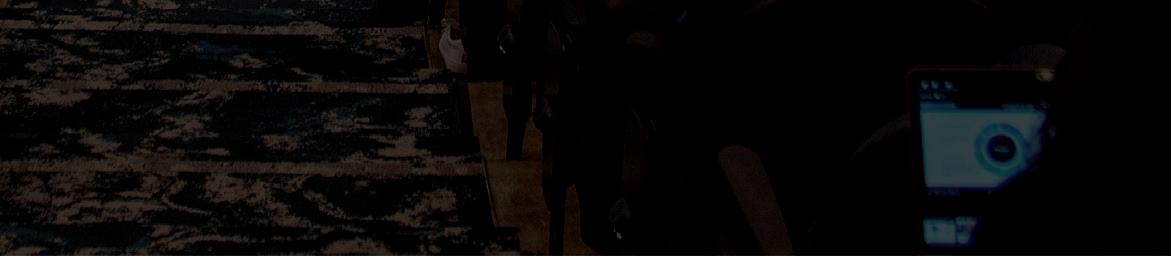
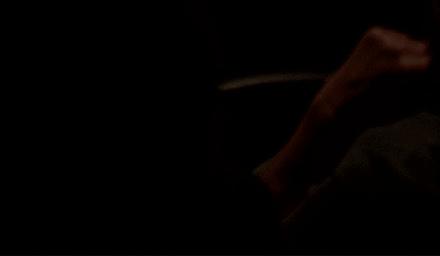
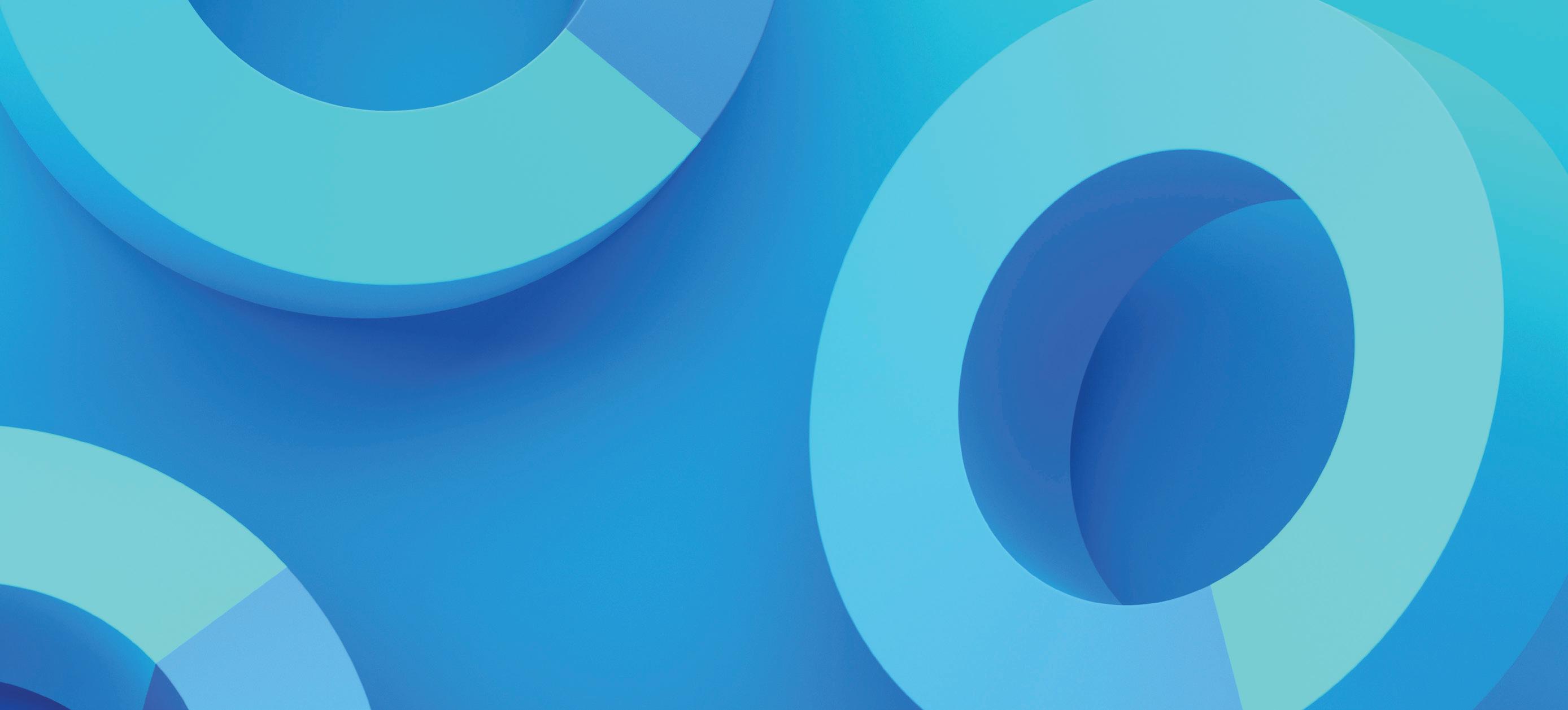
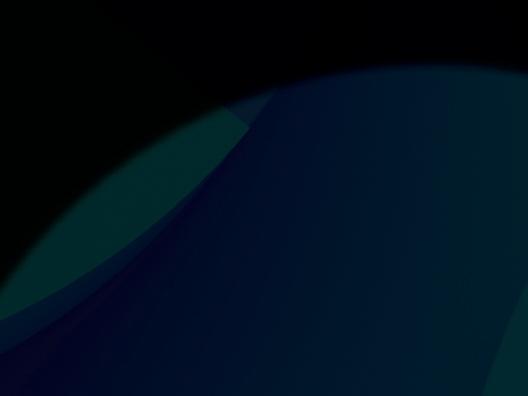
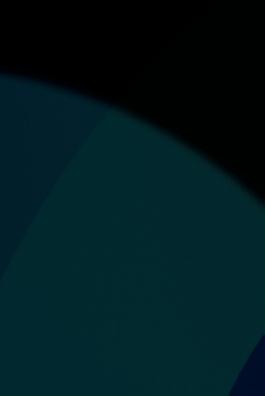
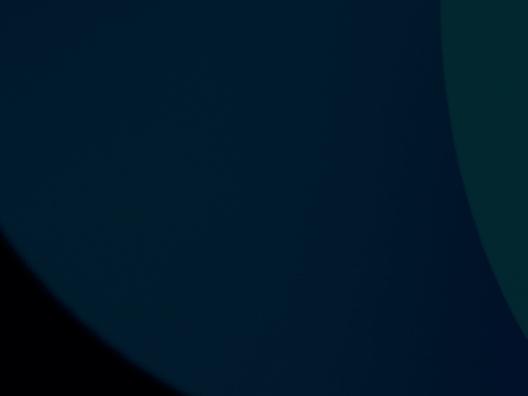
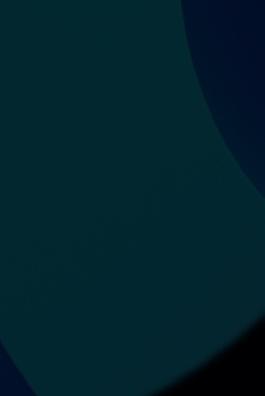
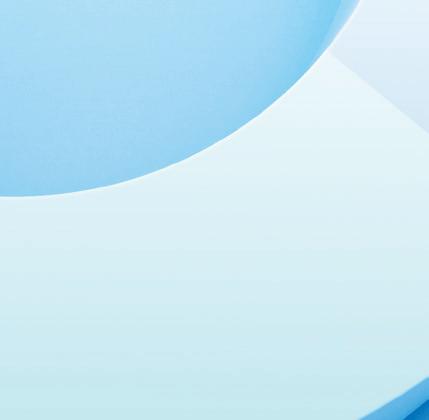
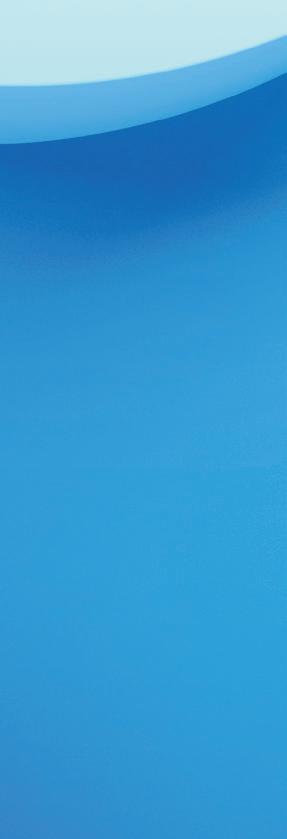

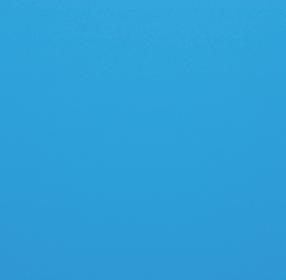
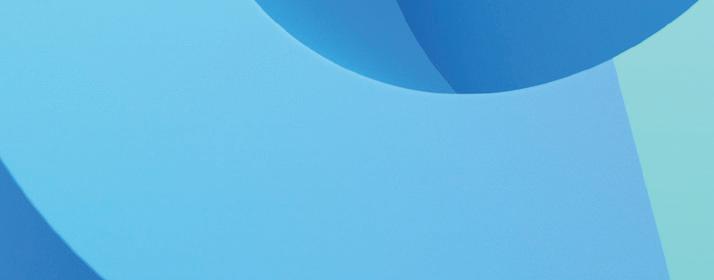
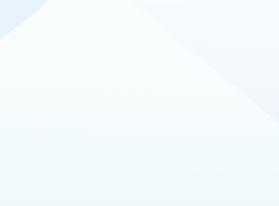

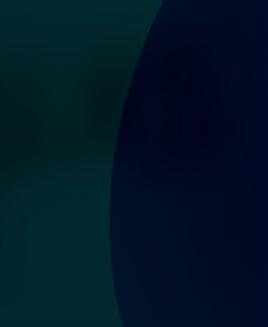
What differentiates the platform is its two-way communication capability. For processes the platform can control, there’s a two-way data exchange in which the system analyzes the data received, makes real-time decisions, and then sends updates back to the machines.
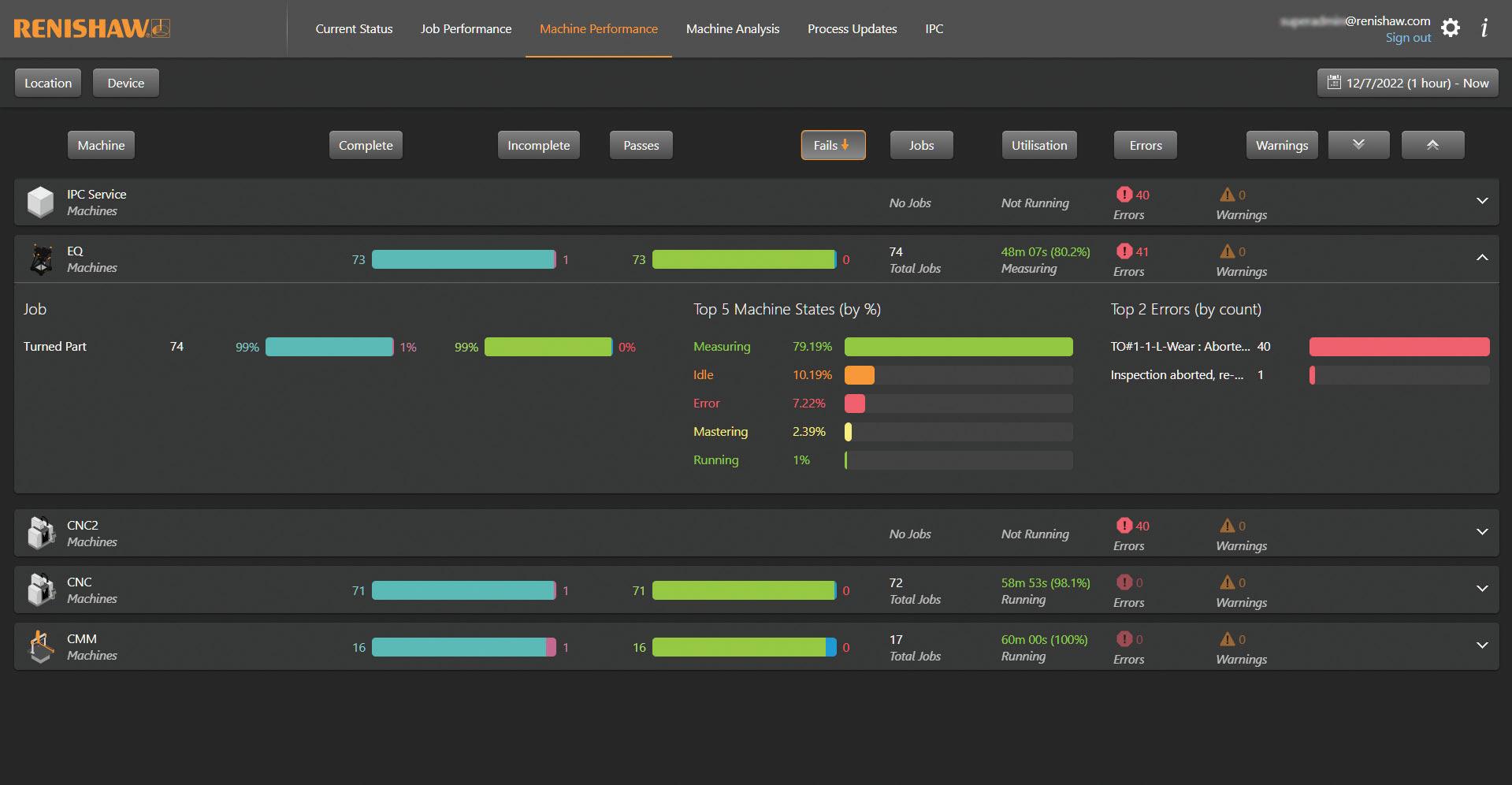
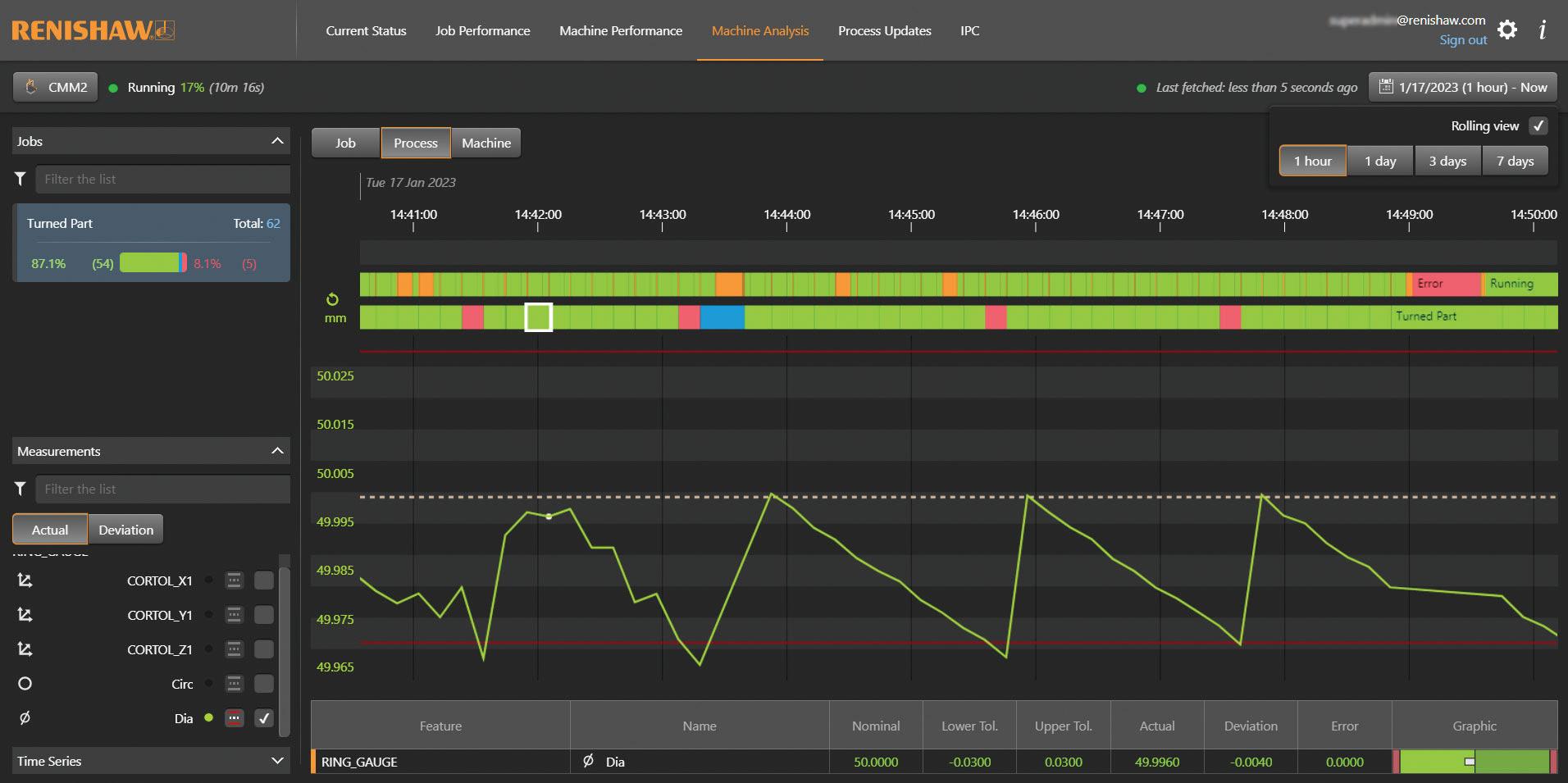
“Data is not enough,” said Brown. “The data itself is just values, and those values by themselves can often mean nothing. It’s only when you start to put thresholds around data and add context that it becomes informative and actionable. If you can’t perform an action at the end of it, what’s the point?”
During Renishaw’s pilot program, Brown noticed that the data showed
North American & International Cords
Shipped in 1 Week!
Interpower North American and international cords and cord sets provide the correct country-specific amperages and voltages, ensuring the end user has the correct connections to the local mains power. Interpower manufactures reliable state-of-the-art electrical cord sets for global markets, cords manufactured in Lamoni and Oskaloosa, Iowa.
lots of little stoppages, yet when he walked over to the machines, they all seemed to be working fine. He learned that operators adapted to the machines’ behavior and pressed a button to resume the process whenever it stopped. The practice became routine and unnoticed until Renishaw Central revealed each occurrence.
“These somewhat hidden stoppages were accepted, and the solution was to quickly check something and press cycle start,” said Brown. “This is a problem when you’re running lights out.
If you step out of the factory at 10:00 pm on a Friday and a machine stops five minutes later, you’ve lost the whole weekend.”
Interpower cords and components are manufactured in accordance with Interpower’s product quality plan: hipot testing, continuity testing, ground testing, and inspections after each process. Interpower also offers value-added options such as custom lengths, colors, packaging and labeling with no minimum order requirements, and expert customer service from 7 a.m. to 6 p.m. CST.
®
®
Toll-Free Phone: (800) 662-2290
E-mail: info@interpower.com
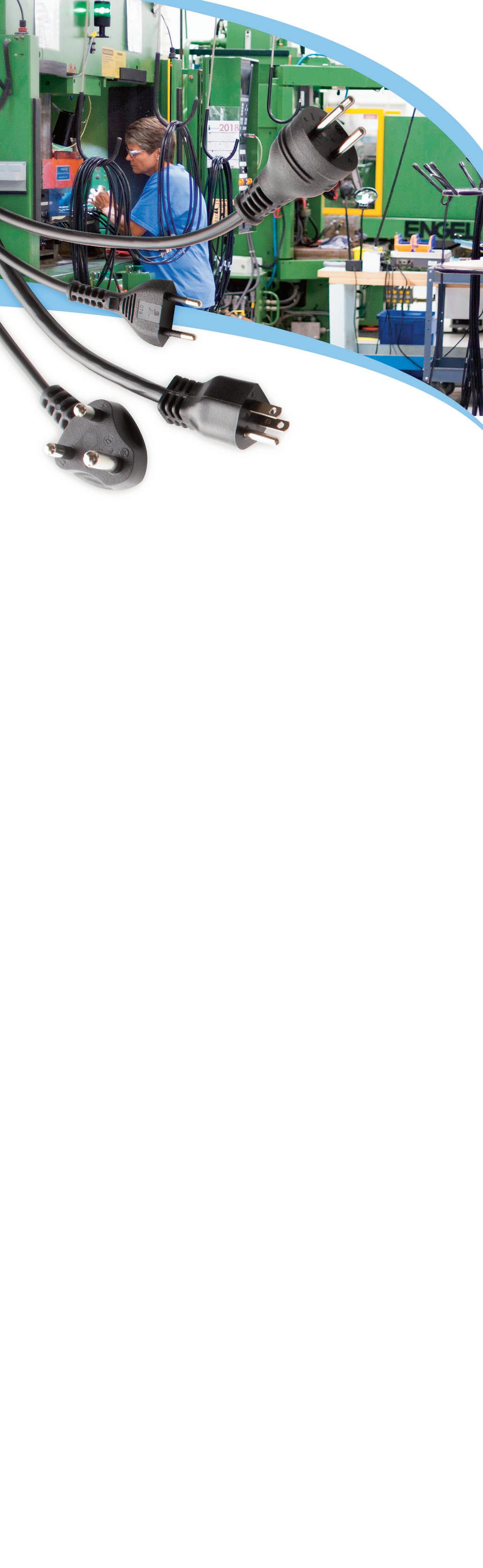
Business Hours: 7 a.m.–6 p.m. CST
Order Online! www.interpower.com