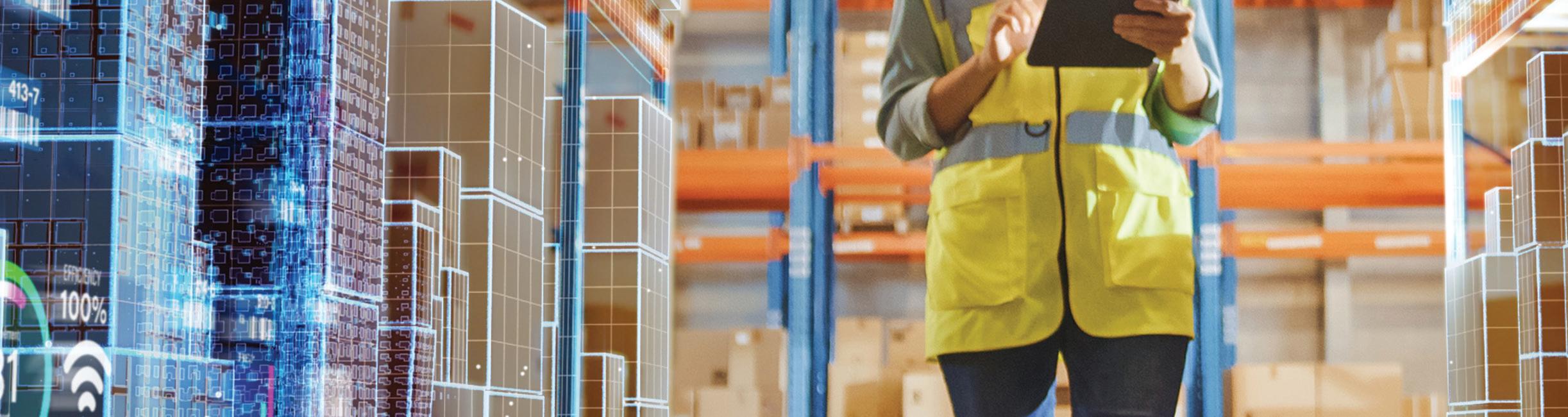
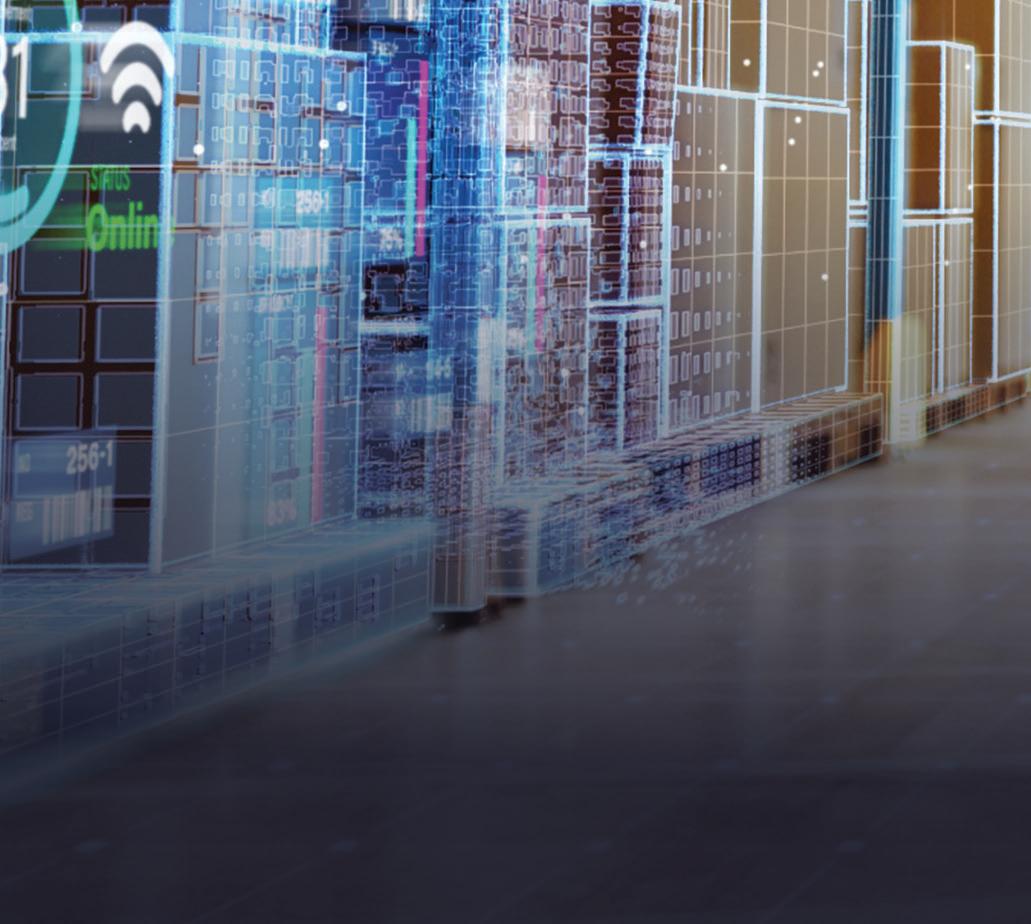

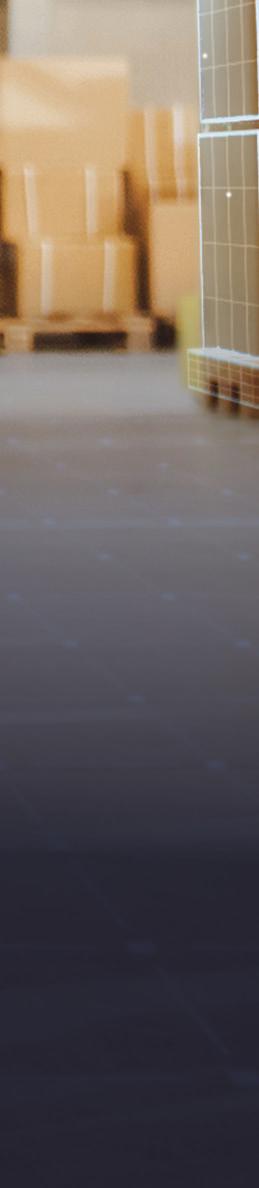

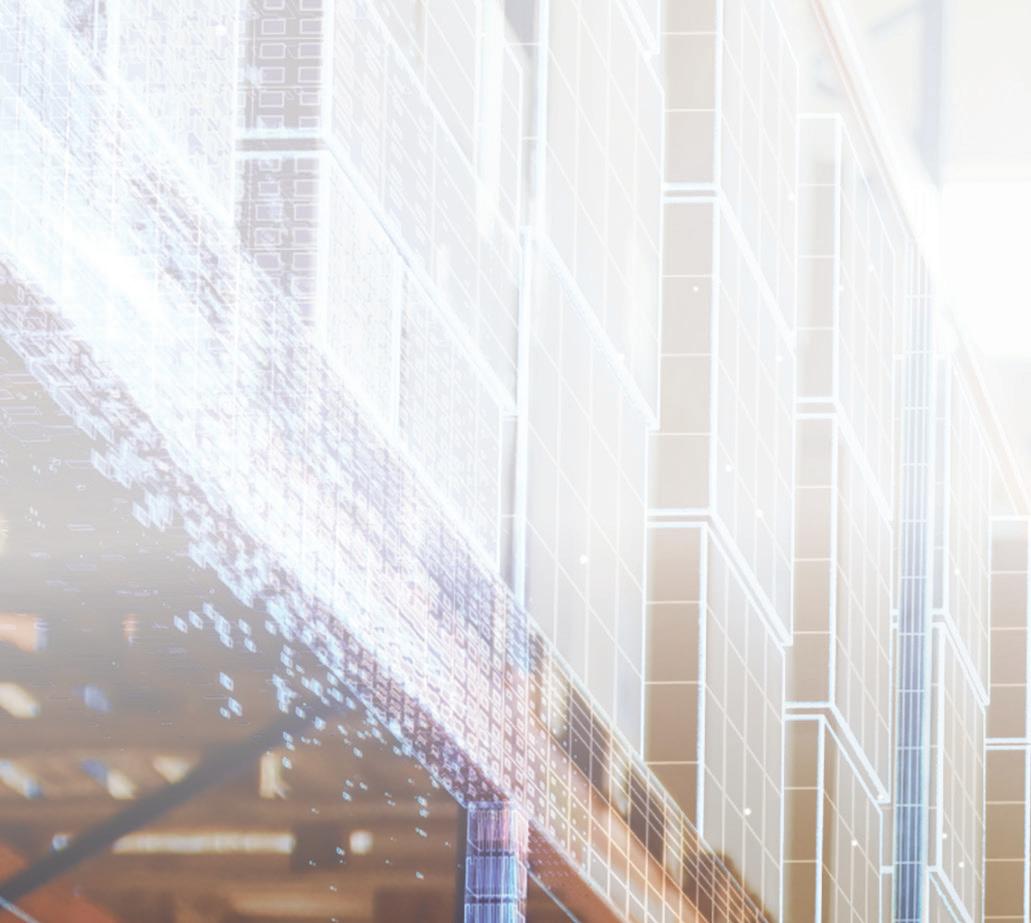
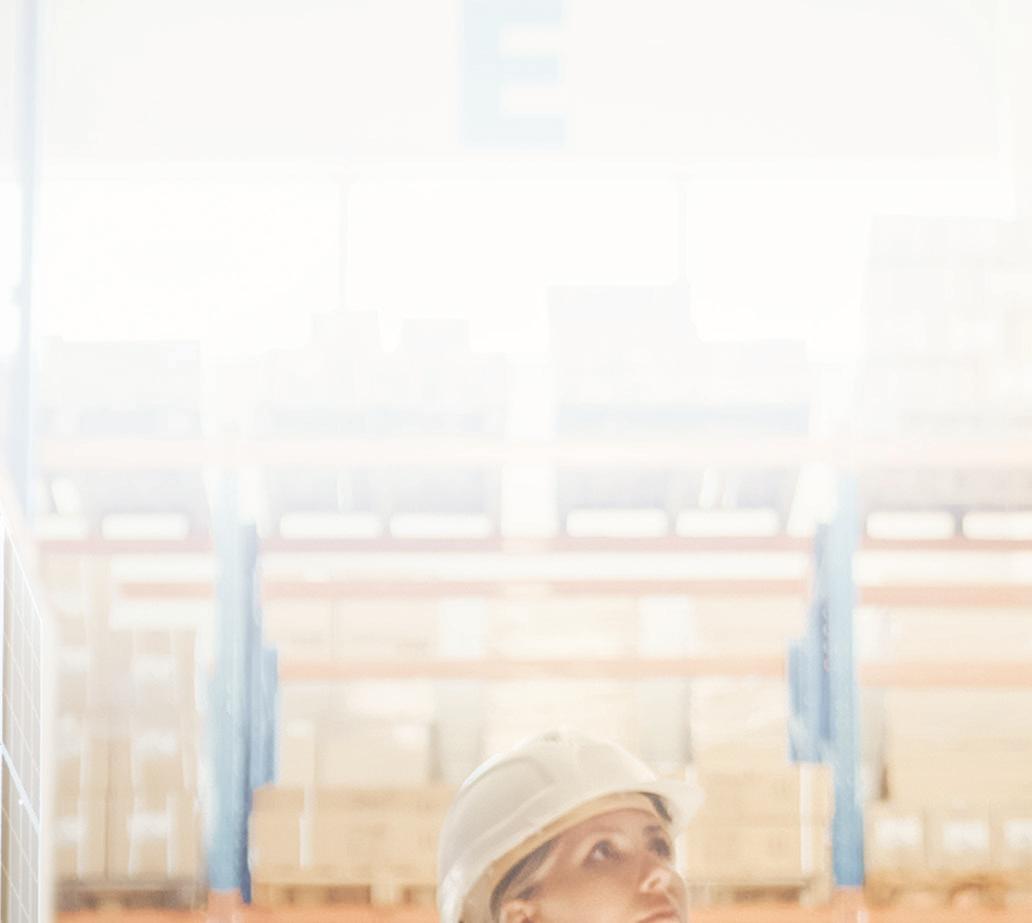
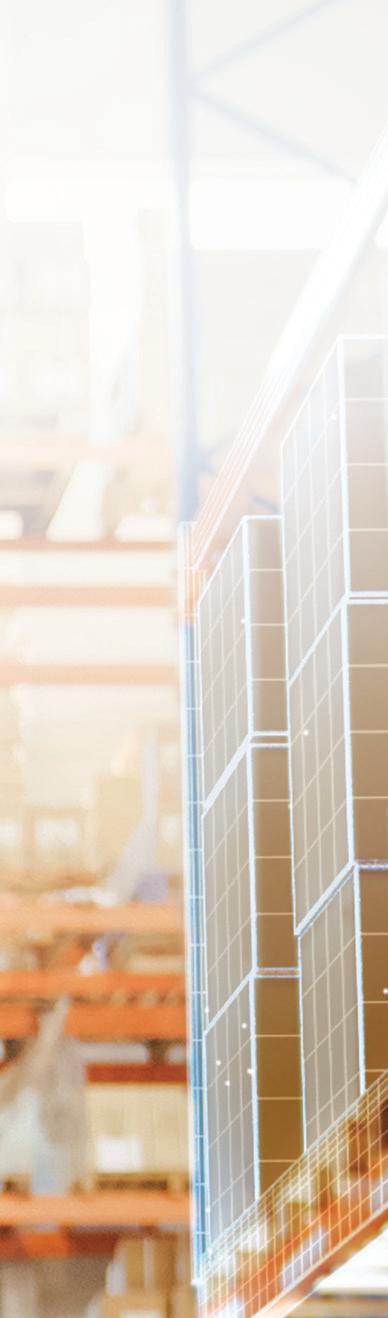





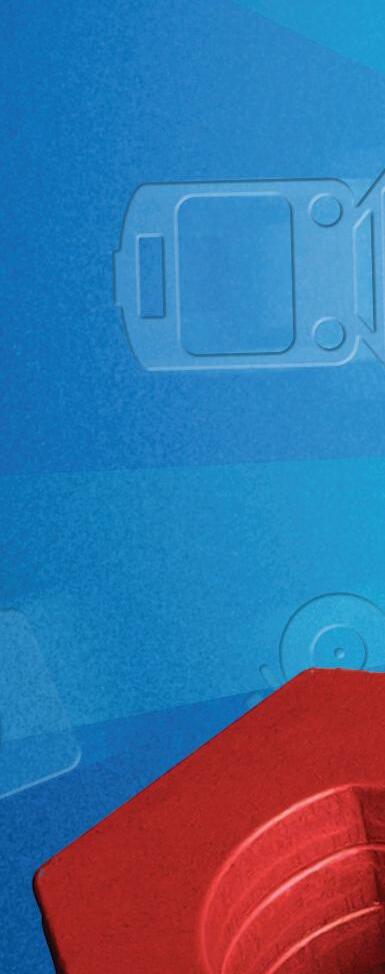
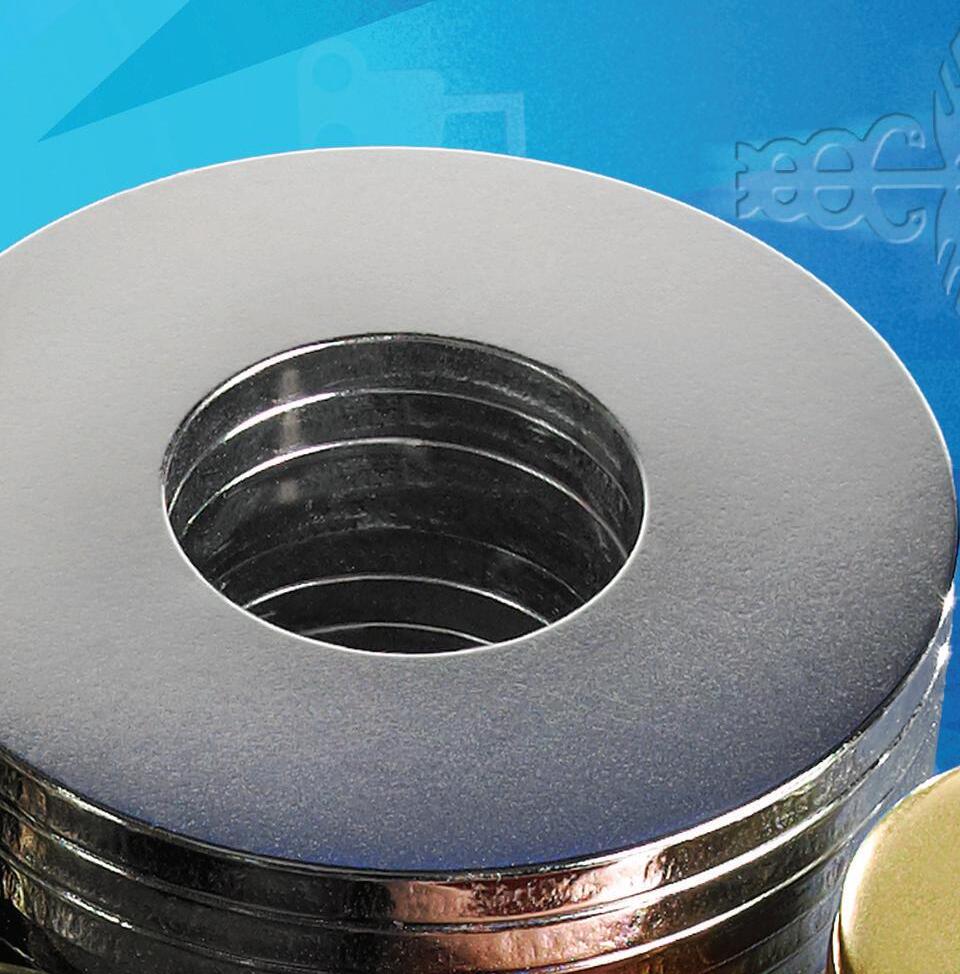
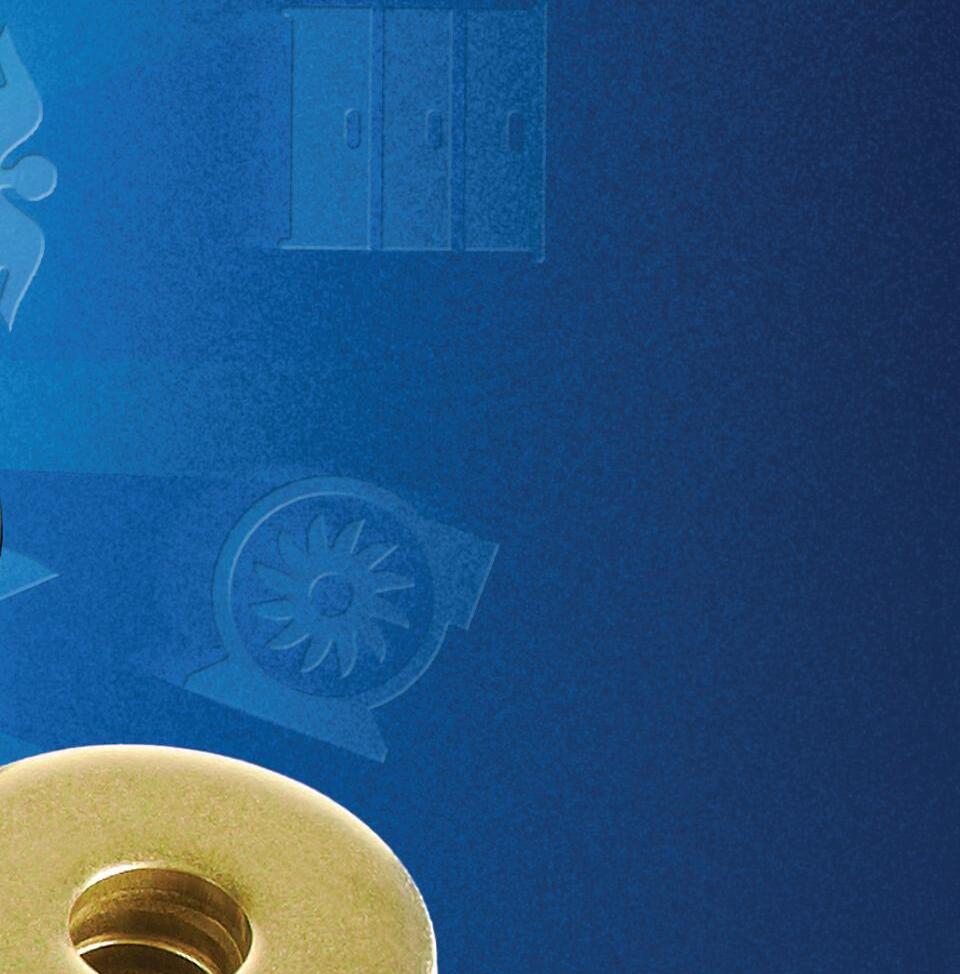
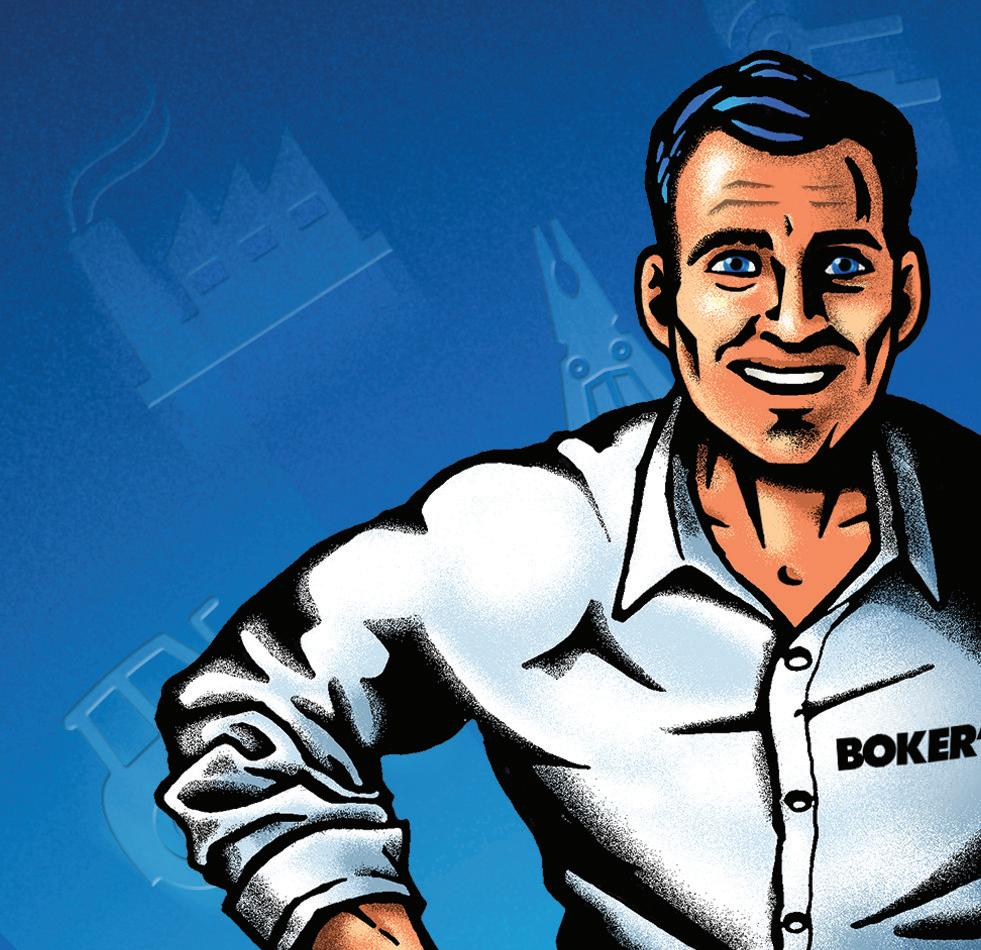
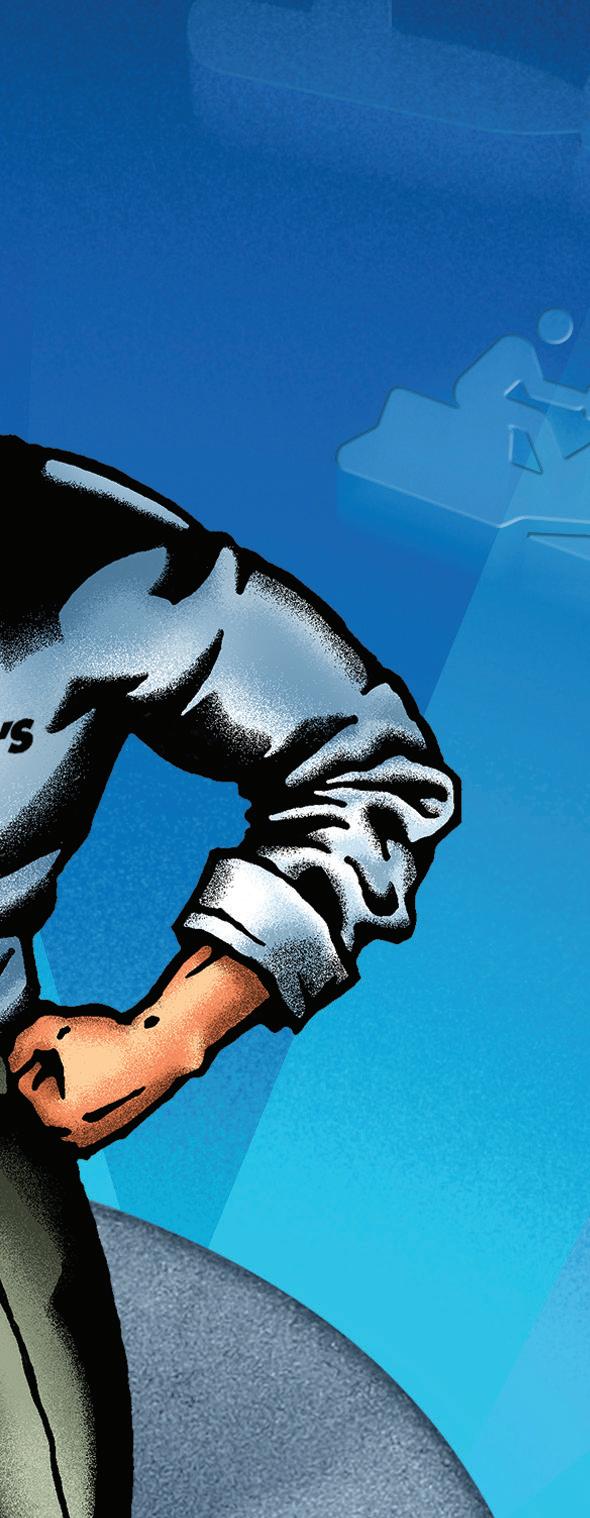
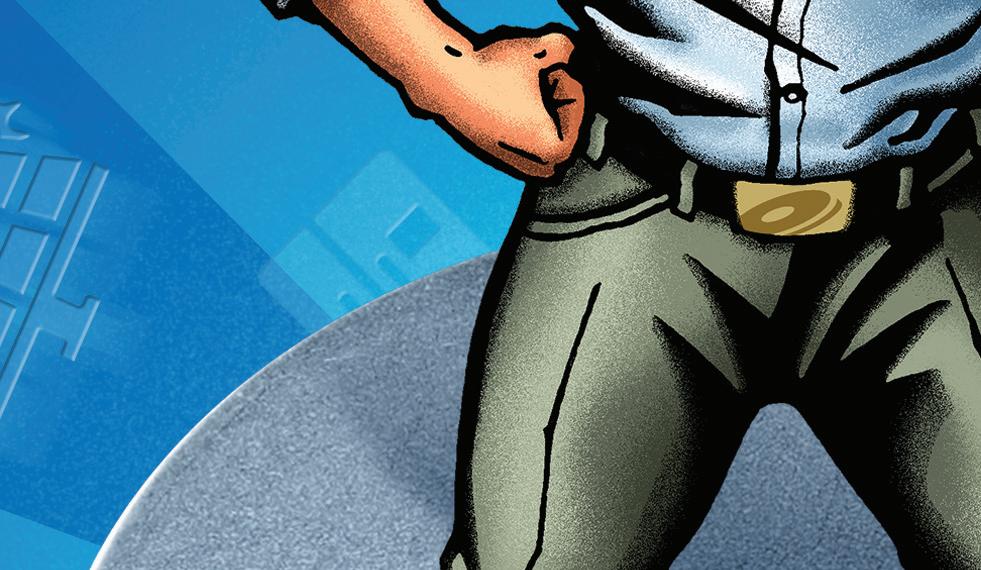

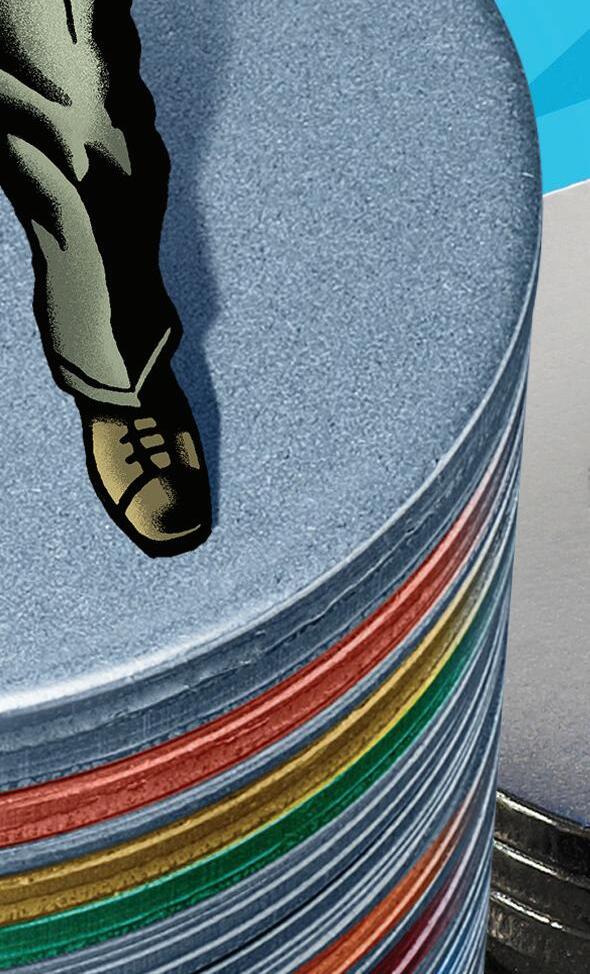
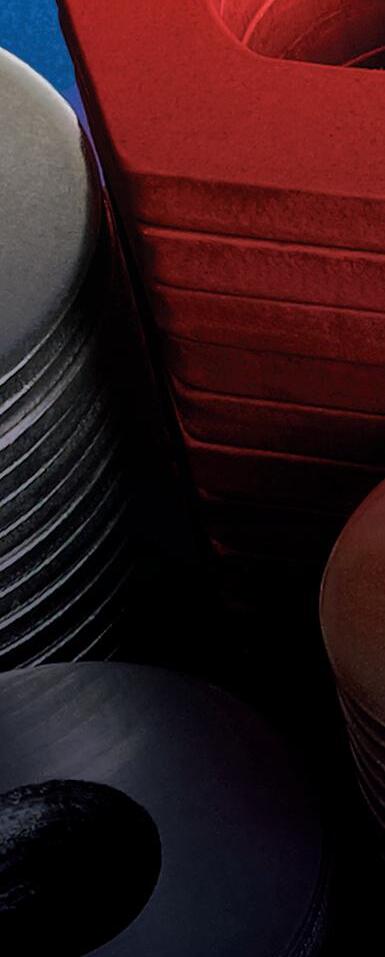
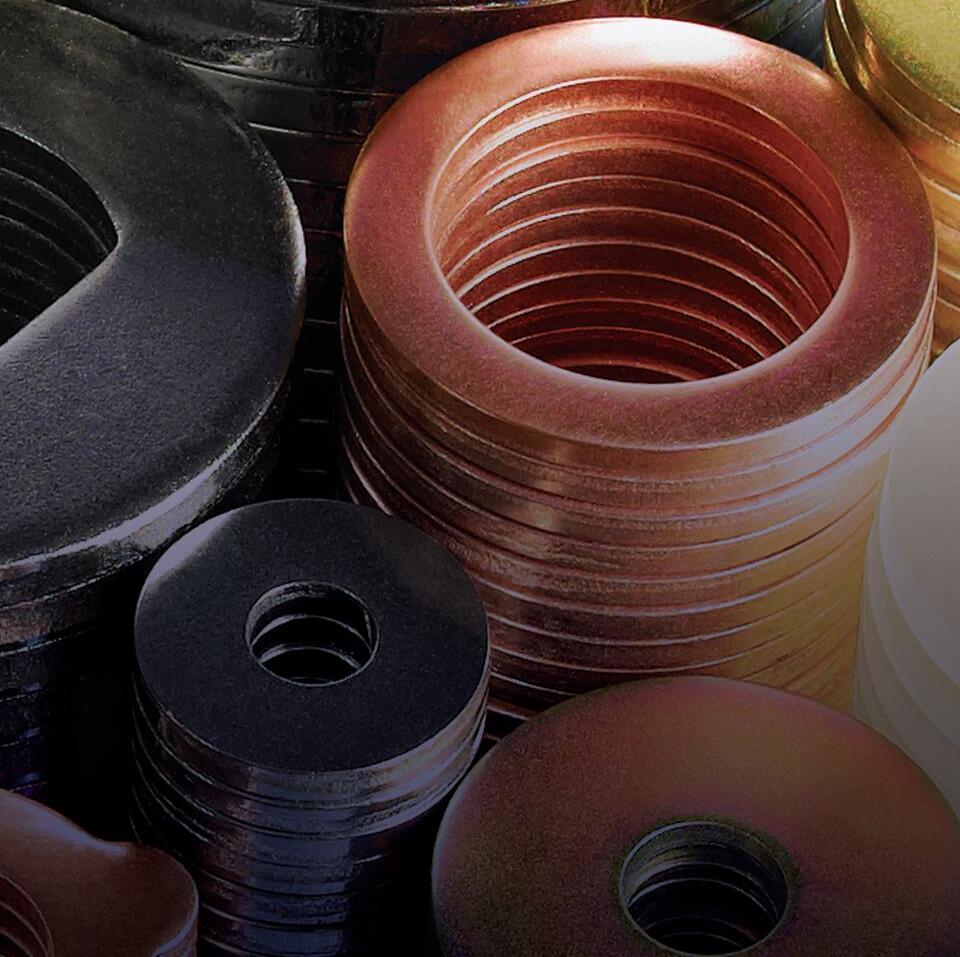
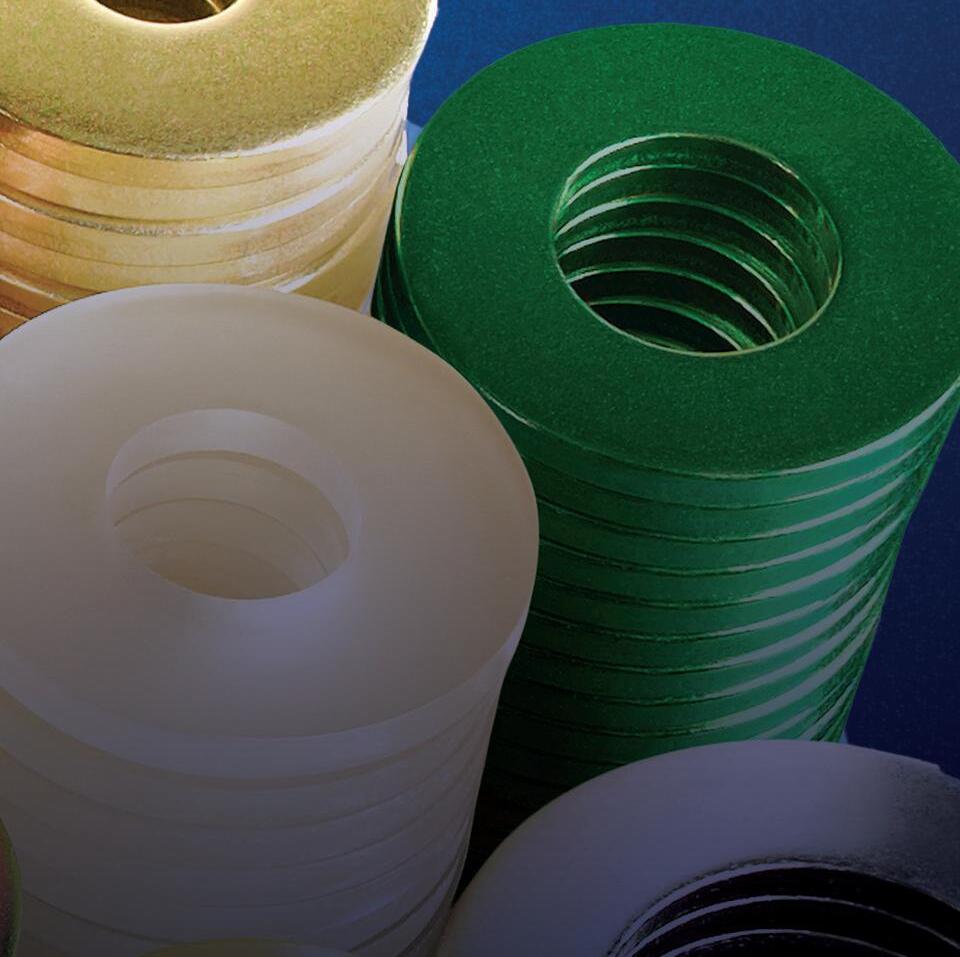

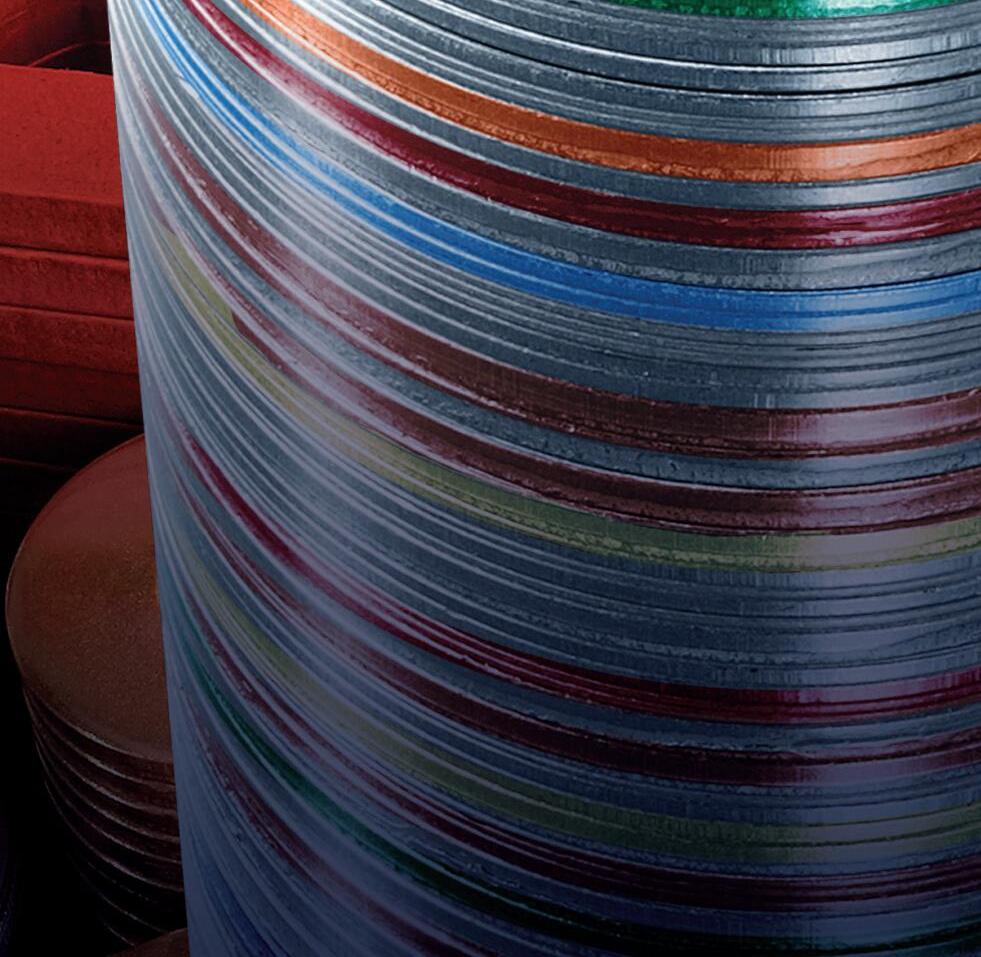
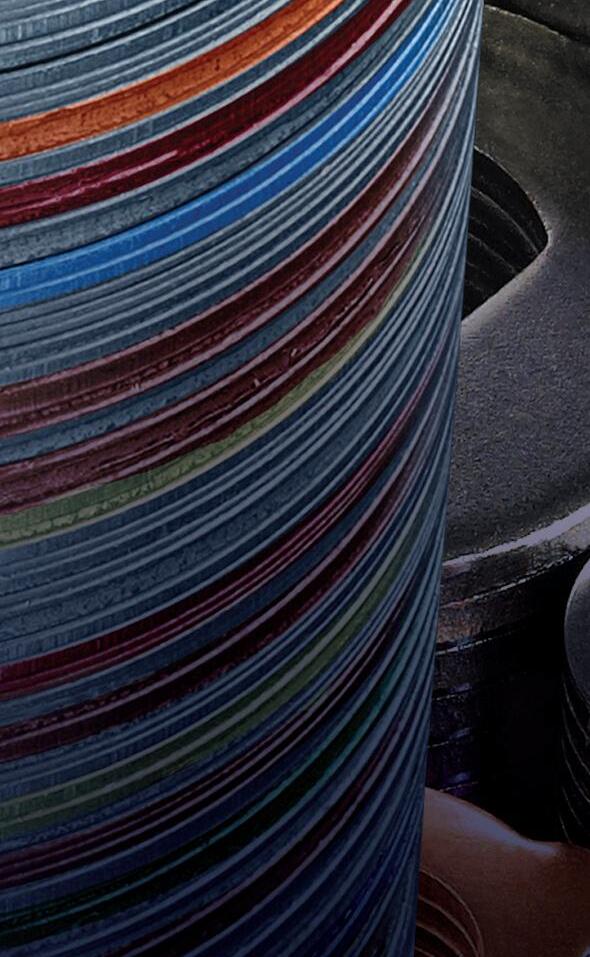
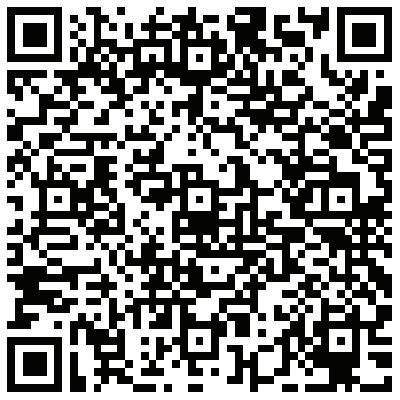

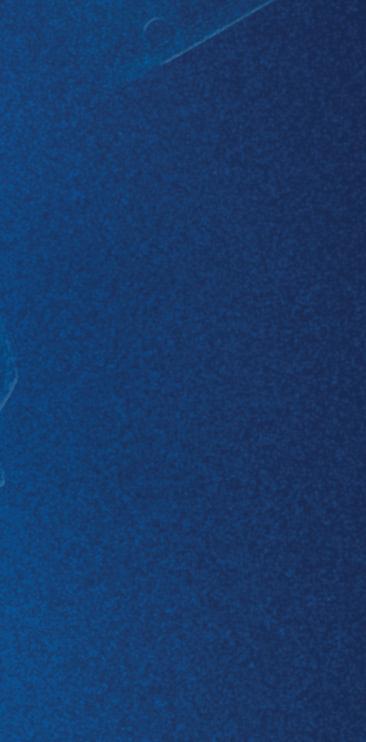
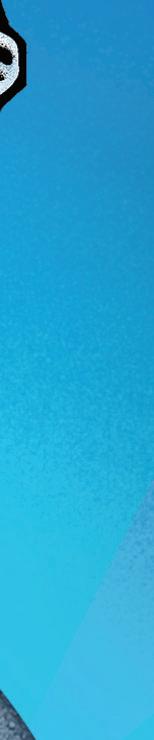
Digital phobia is a real phenomenon characterized by a discomfort or avoidance of technology and the digital era in general. More seriously known as technophobia or technofear, these digital-laden anxieties are more common than one might think.
Although the exact numbers are unknown, research suggests up to one-third of the general population is a ected, and between 45 to 60% of those aged 45 to 60 years.
Why should this matter? Because in the maturing fastener industry, there’s a decent chance this might be you or someone in your organization reluctant to share their insecurities.
In the workplace, digital fears might include angst about learning and incorporating new computer programs, automated systems, or more advanced processes that integrate artificial intelligence or the Internet-of-things (the network of connected devices that share data).
It’s also easy to rationalize such fears, neatly placing them under the umbrella of security or incompatibility concerns — after all, we’ve all heard horror stories about hacking and data breaches. And we’ve all likely experienced network delays or glitches with our smartphones or even the debit machines at our local grocery.
Truth be told, the biggest obstacle to safe and successful digital transformation is rarely the technology. It’s about supporting users to overcome their fear of change or reluctance to adopt new processes. This is worth considering when making a tech leap in the workplace because the bigger truth is that the digital era is only advancing.
As Paul Przyby of Optimas Solutions shares in the article on page 170, “Although there is something to be said for a legacy business, success is rarely granted to those who refuse to evolve. Optimizing routines and processes is particularly critical and easier in the digital era.”
So, how can you support your team or colleagues (and yourself) in this ever-expanding digital world? Unfortunately, no one solution will dissipate every worry, but there are a few steps to consider.
Acknowledge the fear. Expect it, speak it, and clarify that fear of uncertainty is normal. Learning anything new can be intimidating at first or there wouldn’t be a need to learn it. As Lonni Kie er of SmartCert says in the profile on page 178, “Change is hard.” But that’s OK.
Prepare for disruption. Adopting new technologies and processes will inevitably disrupt the status quo — that’s the point. Digital transformations typically aim to reorganize systems in a new, streamlined manner. That means parting with the old ways, even if it’s uncomfortable for a period.
Think process, not revolution. Terms such as digital revolution and the factory of the future can sound daunting. Ultimately, going digital should be about simplifying tasks…and getting there can be divided into small, attainable, and measurable goals.
Seek support and validation. Onboarding new software, automated systems, or new equipment should come with proper training and troubleshooting. Be patient and give yourself and others time to learn. Technology is a tool that, with the ideal features, should enhance and support a business and its employees. Use the digital revolution to your advantage. FE
It’s been said that a bad day in Nashville is better than anywhere else. Soon you’ll have the opportunity to find out as Fastener Fair USA is headed to Music City, Tennessee, from May 16th to 17th.
“It’s our exhibitors who’ve suggested Nashville as a location to us for this event, so we’re listening, and we’re ready,” shares Bob Chiricosta, event director with RX Global, an international B2B trade exhibition organizer. “This year, Fastener Fair will be held at the Music City Center, the convention center downtown, just a block away from Broadway. It’s going to be an exciting show!”
Fastener Fair has been one of North America’s fastest-growing trade shows and conference events for the fastener industry. It’s currently the only local exhibition dedicated to the entire supply chain, which includes mechanical and design engineers, purchasers, wholesalers, distributors, and OEMs.
This year represents a couple of firsts for this American-based event: a new location and its largest show — ever.
“The event is shaping up to be the biggest one held in the U.S. to date,” he said. “This includes some of the largest booths we’ve ever offered, with more domestic and international companies exhibiting than ever before.”
Chiricosta expects well over 200 exhibitors, alongside a curated show floor with leading technical and strategic education sessions, and plenty of
Fastener Fair USA is headed to Music City Center in Nashville, Tennessee, from May 16th to 17th, 2023. A few pre-show events — including the Fastener Training Institute’s Fastening 101 course — begin on May 15th. Visit fastenerfairusa.com to learn more and register.
networking opportunities.
“It’s going to be a full schedule. For those interested in attending early, it’ll be worth your while,” he added. “There’s a fastener training opportunity, a golf tournament, followed by a preshow get-together at a place called, Tequila Cowboy.”
Fastener Fair has always been about supporting organizations to “learn, discover, and connect.”
This begins on Monday, May 15th, as the Fastener Training Institute
presents Fastening 101, a one-day course covering fastener engineering basics, including product and design fundamentals. Attendees will learn about different market segments where threaded fasteners are used and their cost differences. The class also delves into fastener engineering, with information on torque, stress, tightening strategies, bolt strength, tension control, and several other elements.
For those interested in testing their swing, the Mid-West Fastener Association — one of the oldest
connections outside of the office.”
This year, the Fastener Fair is partnering with the Fastener Industry Coalition (FIC), which includes 13 key fastener associations, to promote and participate in the Nashville show. FIC is an unincorporated association made up of regional and national fastener associations concerned with the distribution, manufacture, and importation of fasteners.
Show visitors can expect a comprehensive display of product innovations and demonstrations, technical sessions, and opportunities to connect with peers and industry experts.
fastener associations in the U.S. — in cooperation with the North Coast Fastener Association, will also host a golf tournament before the show.
Then, after the first day of the Fastener Fair on May 16th, get ready for its annual networking party — at the Country Music Hall of Fame. It’s home to the Hall of Fame Rotunda and worldclass exhibitions.
“You won’t want to miss this party,” said Chiricosta. “Expect food, an open bar, plenty of networking opportunities, plus live music. In fact, singer and songwriter Tommy O’Keeffe will play live for us.”
This year, Fastener Fair USA is partnering with the Fastener Industry Coalition (FIC) to promote and participate in the event. The FIC comprises regional and national fastener associations supporting the industry. Learn more at fastenercoalition.org.
Attendees might recognize him as Tim O’Keeffe’s son. Tim is the CEO of Huyett, an ISO 9001-certified manufacturer, master distributor, and importer of non-threaded fasteners.
“It’s interesting because we’ve learned that 45% of Fastener Fair USA attendees only go to our event. They don’t attend other shows, so it’s extremely important for us to prepare an event that’s educational, interactive, and fun. It’s not every day that everyone gets to travel or make in-person
“They’ll be presenting some of the talks and panel discussions that will take place,” he said. “We plan to have educational content focused on technology, supply chains, and sales. We also want to offer insight to those new to the industry, including young professionals. We’ll be announcing the conference line-up shortly.”
According to Chiricosta, Fastener Fair USA also brings in 36% of new firstyear attendees to the show each year. And so far, they’ve already received a large and favorable response to this year’s event.
“The companies and exhibitors we’ve talked to so far cannot wait for the show this year,” he said. “They want to be involved and connect with more people. Nashville is great for this because there’s so much nearby manufacturing in the
Kentucky and Tennessee areas. There are international auto plants, and manufacturing facilities for appliances, furniture, and other components toward the coast.”
You can check out the exhibitor list at tinyurl.com/FastenerFairExhibitors.
“Aside from being a fun location in the center of honky tonk bars and non-stop music, Nashville is a place of opportunities,” added Chiricosta. “We expect this year’s Fair will be a not-tobe-missed event.”
As for next year, Fastener Fair USA will be returning to Cleveland, OH.
“Ohio is somewhat of a hub for the fastener world in the United States,” he says. “Sometimes I’m surprised how many international companies have a branch in the state. So, we’ll
probably always return to Cleveland for certain years. But we’re hoping to add Nashville to the rotation, and we’re really looking forward to seeing those in the fastener industry there soon!” FE
Connect and discuss this and other engineering design issues with thousands of professionals online
Vendor-managed inventory (VMI), or inventory management, has been around since the ’80s when companies such as Walmart used it to revolutionize their supply chains. In the 30-plus years since then, inventory management has evolved to become more sophisticated and accessible, allowing companies of all sizes to benefit.
Conventional inventory management systems track when parts are ordered, delivered, stored, and replenished. With today’s tech advances in the Internet of Things (IoT) and artificial intelligence (AI) — which can work together to collect, manage, analyze, and learn from data — it’s possible to expect more from a program than just “managed parts.”
An optimized and automated end-to-end inventory management program will continually work to innovate and improve the entire supply chain management cycle.
Inventory management is a rapidly evolving solution that supports a streamlined supply chain. Advanced programs increase the visibility and forecasting of parts’ consumption, leading to cost savings and greater workflow and productivity.
In simple terms, VMI employs a partner (think full-service distributor) to manage inventory. The resource develops a custom program to ensure the right parts go to the right places at the right times.
However, a modern inventory management program does more than manage parts. Ideally, it’s capable of:
• Understanding and adapting to changes in demand
• Ensuring quality requirements are always met
• Establishing and managing efficient delivery logistics
• Leveraging technology to automate replenishment
• Offering visibility into consumption patterns, inventory quantities, and locations
• Providing data to optimize quantity and delivery decisions
Such tech-enabled functionality streamlines supply chains, elevating productivity and profitability.
One study found that most companies devote 20 to 40% of their overall working capital to inventory alone. Hard and soft costs can be saved with an advanced inventory management program. Additionally, workflow and productivity can be redefined, and human resources reallocated from slow, repetitive, and errorprone work to higher-value (i.e., profitable) activities.
The key to such advanced features: going digital.
It’s no secret that familiarity breeds comfort. Most of us stick to routines because it feels safe and secure. Although there is something to be said for a legacy business, success is rarely granted to those who refuse to evolve. Optimizing routines and process is particularly critical and easier in the digital era. Digitized inventory management is the next level of VMI. Such automated programs ensure accurate and current inventory numbers, meaning an organization is less vulnerable to errors from human calculations or multiple data sources.
Digital inventory management now o ers AI features that can forecast demand changes and adapt stock levels for more accurate supply chain planning of engineered fasteners and C-Class parts — ultimately leading to cost savings and a more secure supply chain.
Advanced inventory management allows organizations to lower on-hand inventory. This can lead to less waste, greater accuracy, and more strategic use of time and resources. Plus, on the ordering side, placing a single PO with one full-service distribution partner can reduce hidden soft costs that add up over many parts and many orders.
So, what does modern inventory management o er that makes it worth the switch? Here are just a few benefits of going digital…
• The ability to work smarter, not harder. Thanks to the analytic technology available today, it’s possible to capture and use data and modeling based on an organization’s real-time and historical consumption patterns. Quality forecasting uses a mix of quantitative (such as past numerical insights and current market demand) and qualitative data (market trends, product lifecycle, competitive landscape, etc.) to guide more accurate inventory management decisions.
Additionally, by integrating RFID technology to manually or automatically
The first step is identifying core pain points a digitized system can help resolve. Here are the top five questions to ask to get started:
• On a scale of 1-10 (with 10 being the best), how accurate are your part counts?
• How long does it take to go from count to replenishment?
• Have stockouts occurred in the last 12 months?
• Has excess and obsolete inventory negatively impacted your company’s balance sheet in the last two to three years?
• Is your current supplier doing anything to support your inventory management process?
The answers to these questions can indicate the need for an inventory management solution.
Digitized inventory management is the next level of VMI. Such automated programs ensure accurate and current inventory numbers, meaning an organization is less vulnerable to errors from human calculations or multiple data sources.
A step-by-step representation of a digital end-to-end inventory management system.
submit replenishment orders, inventory can be monitored in real-time. (RFID or Radio Frequency Identification uses radio waves to identify a tagged object.) Data can be used to create more accurate forecasts about future demands. As a result, it’s easy to modify production plans and inventory levels. Plus, cash flow benefits from this level of accuracy.
• A supplier reduction, also known as vendor consolidation, moderates the number of suppliers within a specific supply market to save costs. Some experts suggest adding just 10 extra suppliers every five years is more than $1 million in additional soft costs. The parts make up only 15% of those costs, while the human resources required to select, manage, and process those suppliers is another 85%. A digital VMI program can make a big impact here.
• A refocused workforce typically leads to greater productivity overall. Thanks to an automated replenishment system, it takes less time, personnel, and processes to maintain accurate
inventory levels. These productivity gains drive soft cost reduction and offer an opportunity to reallocate team members to roles that ensure a greater impact on production.
Digitized inventory management can make supply chains more efficient and resilient to disruptions, offer higher visibility of parts’ consumption, improve forecasting, and support the reallocation of resources to ensure better productivity. It’s about spotting potential issues before they start. FE
Self-adhesive die-cut parts are increasingly working alongside or replacing conventional mechanical fastening methods for affixing, sealing, or leveling certain assemblies. And for good reason: these ultra-sticky solutions are true “lightweight heavyweights,” providing manufacturers with exceptionally flexible design and processing possibilities.
However, there are several subsets within this genre of adhesives, which are important to understand before choosing the ideal fastening solution. Generally speaking, a distinction can be made between simple and complex laminates for die-cut parts, which can permanently or removably bond to a portion or all of a component’s surface.
• Simple laminates are ideal when the purpose is bonding. Typically, self-adhesive die-cut parts are used, consisting of two-sided tapes or transfer adhesives.
• Complex laminates, which often have multilayer structures, are the preferred choice when one component must perform several functions — such as any combination of bonding, height compensation, damping, temperature compensation, or dust protection.
Pressure-sensitive adhesives are particularly efficient because they require no drying time. For manufacturers, this means significantly shorter processing times and lower energy consumption.
The portfolio of available sizes and shapes of die-cut parts ranges from miniature formats, a few millimeters in size, to large dimensions with complex geometries.
The assembly and delivery forms are nearly as varied as the products they help assemble. For example, the packaging of die-cut and formed parts are commonly available on rolls, sheets, stacks, and as individual parts. The shape of the finished product is determined by a manufacturer’s distinct production process.
The so-called base liner is the carrier for self-adhesive products, but it can also perform additional functions. At the very
Self-adhesive die cuts provide manufacturers in several sectors with a flexible, lightweight bonding solution that ensures durability.
least, the base liner should include perforations to simplify the separation of the die-cut parts — an e cient and convenient alternative to bulk material.
“Locating holes” serve as positioning aids in the application process, and the poka-yoke principle (the practice of error-proofing) ensures an accurate fit and ideal positioning. In this step, it’s important to ensure double-sided adhesive products are covered on the top side for protection before use. Many cover liners are suitable for die-cut parts: endless cover liners are typically used in fully automatic assembling processes. The term “endless” is used because they have
An assembly machine in operation. The “endless” cover liner is removed before dispensing the double-sided adhesive tape.
no set boundaries, meaning they can cover the entirety of an object. Die-cut cover lines are used for manual or semiautomatic dispensing.
The automotive industry heavily relies on self-adhesives for fastening di erent components, protecting invehicle devices, and providing height compensation. For example, rain sensors are bonded to the inside of windshields by means of a UV-stable, double-sided adhesive die-cut part. Trim strips in the interior are attached by a foam die-cut part with a practical grip tab, which also compensates for height.
For in-vehicle sound systems, a double-sided adhesive die-cut part typically serves to fasten and protect sensitive components.
In addition, self-adhesive die-cut parts o er considerable ease and e ciency to automotive production lines as processing, assembly, and positioning aids. For instance, shaped die-cut variants use individual adhesive dots to help position and precisely
Adhesive joints are increasingly performing certain bonding duties, typically accomplished with screws. The decision to “glue, not screw” can provide benefits, depending on the application. These include:
• An ability to bond to a variety of substrates
• A reduced assembly weight
• An even distribution of stress on the load (while resisting vibration)
• Protection from corrosion
• Optimized e ciencies and reduced costs (compared to drilling or other bonding processes like soldering, crimping, or welding)
affix components as an assembly aid in the welding and soldering process. This selective bonding ensures that sufficient solder can later penetrate between components, joining them securely and permanently.
Adhesive applications are providing a key function in the manufacturing of electronics and Industry 4.0.
In advanced process and automation, intelligent RFID (radio frequency identification) data carriers are an essential building block. RFID transponders are typically attached to components and trays; however, this must be done with extreme care. Metal screws could adversely affect the readability of a tag’s chip. As a result, self-adhesive solutions have become the method of choice.
There are several application techniques available for stamped and formed parts, depending on the assembly. For die-cut parts, it’s important to consider the processing, dispensing, and inspection methods.
In advanced production, automated production cells that employ robotics offer clear advantages here: robotic arms are quicker and more consistent than humans, resulting in more accurate and efficient production. However, users should always be mindful that manufacturing cells — robotically controlled or otherwise — should be modular in design (e.g., equipped with an exchangeable vacuum stamp). Only then are minimal adjustments necessary if, for example, new production variations are introduced that require additional processing steps.
Self-adhesive die-cut parts are no longer a simple alternative for minor joining challenges. These varied and versatile solutions provide significant support for the types of manufacturing efficiencies and line optimizations in a range of engineering environments. FE
Most would agree that paperwork is a necessary nuisance for any business, and the fastener industry is no di erent. Quality assurance means certifications and technical documentation are essential, particularly for critical parts in critical assemblies.
“In the fastener industry, there are several required documentation that varies from the supply chain for raw materials to OEM parts certifications and tracking reports,” shares Lonni Kie er, co-founder of SmartCert. “Paperwork is nothing new for this industry. But what’s been missing until now is a universal digital platform that streamlines this process.”
This is what SmartCert — a company developed by Kie er and her business partners in 2021 — delivers. The industry’s first, cloud-based, self-service platform that lets fastener buyers and sellers digitally manage and exchange required quality certs. It connects every company in a supply chain and automates inbound and outbound documentation, allowing for real-time updates.
“The platform creates greater e ciencies, traceability, and sustainability while removing the risk of missing paperwork,” she explains. “Though it’s definitely not where I thought my history in marketing would lead, I’ve absolutely fallen in love with working in and with the fastener industry.”
Kie er went to the University of Wisconsin for journalism, with an emphasis on advertising and PR. She gained experience working for advertising agencies and, prior to entrepreneurship, spent about halfa-dozen years working for the media company, Gannett.
“Gannett owns several small-city newspapers across the country,” she says. “My job there was primarily focused on digital advertising, where I helped companies analyze their customer base and make decisions on how to best spend their marketing dollars with di erent media to make the biggest impact.”
Although this might seem like a world apart from fasteners and document tracking, the skills Kie er gained continue to support her e orts today.
“The translation in skills for me relates to supporting customers in navigating the ideal path to success,” she shares. “My passion begins after someone says, ‘yes.’ Then, I get to help companies with onboarding and training to ensure they make the wisest decisions and expenditures for the best business outcomes. It’s so rewarding to experience the impact of those decisions.”
To use Kie er’s words, it boils down to “change management.” In this sense, SmartCert not only o ers an automated
solution for managing documents and creating supply-chain e ciencies, but it also supports companies with this digital transformation to ensure success. Given the advancing digital era, going paperless and embracing technology is quickly becoming a must for companies.
“Essentially, we’re competing with the status quo and the way things have been done for decades…and change is hard,” she shares. “I get to support companies in meeting their goals for e ciency and sustainability. Paper is expensive. There’s currently a job shortage. Digitalization done right saves a lot of manual steps.”
SmartCert launched at an ideal time, given the increase in online and remote
work since the pandemic. It’s a web-based platform o ering built-in security and redundancy, with no servers to manage. Users can access documents via a mobile device or desktop computer and quickly connect with their supply chain. It can also be integrated into existing ERP (enterprise resource planning) systems.
“The workforce is a changing landscape,” says Kie er. “More people are working from home and others are nearing retirement. It’s important to o er the tools and technology that will attract someone out of college who is simply not going to be excited about paper. It’s just not their world.”
Perhaps somewhat ironically, SmartCert developed the way many start-ups do, with a pen and napkin. The initial idea was that of Kie er’s husband and business partner, Lyndon Lattie. He’s worked in the fastener industry for 20 years, on both the manufacturing and distributing sides of the business.
“What’s interesting is he worked at Century Fasteners, a distributor, before leaving to start SmartCert, which they fully supported and are now one of our customers,” says Kie er. “But over the years, he experienced first-hand the frustration of waiting on documents that
delayed parts and created bottlenecks. He dealt with this as a salesperson and saw how it repeatedly a ected supply chains — you’re always at the mercy of how manufacturers or vendors are sending in certs and the same goes with customers.”
When Lattie shared his idea with Kie er and his long-time friend and colleague, Paul Decker, both agreed it was brilliant. Decker, who has years of experience running industrial technology companies, joined SmarCert as a third founder.
“At first, I worked the sidelines, but once the beta went live, I joined fulltime to help onboard our customers and ensure their success in using the platform,” says Kie er. “And I love that we have smaller mom-and-pop shops, testing labs, as well as massive fastener corporations with multiple companies under their umbrella.”
SmarCert’s goal is to become the industry standard for the aerospace and fastener industries and to work with other critical supply chains. The company is already making headway in the automotive, electronics, and food sectors.
“Fasteners have become a quick favorite of mine though,” she says. “It’s such a unique and tight-knit community, yet so welcoming. We were recently at the Mid-West Fastener Show and despite a room full of competitors for many of these companies, everyone came together to support each other. I’ve never seen anything like it, and I’m proud of what we do and to be a part of it.”
Kie er adds: “We’re taking companies from paper to digital and helping automate processes. That’s a huge leap forward and an exciting one for the future of fasteners.” FE
“The workforce is a changing landscape,” says Kieffer. “More people are working from home and others are nearing retirement. It’s important to offer the tools and technology that will attract someone out of college who is simply not going to be excited about paper. It’s just not their world.”
PRICING & AVAILABILITY
Get real-time pricing and stock info from authorized distributors and manufacturers.
View and download product data sheets and technical speci cations.
Compare options from suppliers and buy direct from distributors and manufacturers.
DesignFast is a search engine for nding engineering components and products. With DesignFast, engineers and sourcing professionals can quickly search for products, compare prices, check stock, view data sheets and go direct to the supplier for purchase.
DesignFast aggregates product data from thousands of suppliers and distributors and makes it available for searching. DesignFast provides pricing, availability and product data sheets for free download.
designfast.com
As World War II slowly came to an end, Adolf Würth knew two things: he needed to support his family and he wanted to work independently. With a post-war focus on new construction and rebuilding, a wholesale business focused on fasteners made sense.
So, in the summer of 1945, Würth o cially set up his own business — Adolf Würth GmbH & Co. KG, which became the parent company of today’s Würth Group — selling screws in Künzelsau, BadenWürttemberg (Germany). But this took some perseverance.
As one tribute from the Würth Group’s historical records points out: “It was not easy to procure goods in the occupation zones. It was hard to find rooms. Finally, a room could be found in an annex of Schlossmühle (castle mill) in Künzelsau: the globally operating Group saw the light of day in an area of just 170 square meters.”
Although today’s Würth Group is an example of a massive and successful global enterprise, it did not start this way. In fact, the first screws were transported with a borrowed ox cart.
Little did Adolf Würth know that this small room in the annex of a mill
would eventually load some 750 tons of ordered parts daily, just for customers in Germany. And he likely never could have imagined that the Würth Group would develop into the largest distributor of fasteners in the world, with more than 125,000 products distributed via more than 400 companies in more than 80 countries — all led by his son, Dr. h. c. mult. Reinhold Würth.
“We actually refer to Dr. Würth as the Professor,” shares Todd Aronson VP, Global and National Sales, Würth Industry North America. “And yes, he still works at the company and is turning 88 this year. He took over the family business at 19, after his father’s
unexpected passing.”
That was in 1954, when Dr. Würth took over with the support of his mother, Alma Würth, making the Würth Group a two-person company. By the early ’60s, he considered expanding, setting up the first subsidiary in the Netherlands in 1962. In 1969, Würth USA Inc. o cially launched in America, and the growth has not stopped since.
“It has truly been his life work,” says Aronson. “Dr. Würth turned a small, family-held company into a global enterprise with more than 83,000 employees. Just this past year, it made more than $20 billion in sales and more than $1.5 billion in profit.”
One part of this global growth includes Würth Industry North America (WINA), now a $1 billion division of the Würth Group. WINA provides customers with an extensive global reach and local knowledge from investments in its distribution centers across the U.S., Canada, Mexico, and Brazil.
WINA has four strategically aligned customer-centric market divisions: Industrial, MRO/Safety/Metalworking, Construction, and Specialty Markets. These divisional companies include Würth Industrial Division, Würth Construction Services, Würth MRO, Safety, & Metalworking, Marine Fasteners, and Würth Additive Group.
“It has been the philosophy of Dr. Würth and the Group to acquire very successful companies, connecting their products and innovations with Würth’s resources and operations,” he explains. “And in the mid90s, Würth Industry North America was launched, representing the first acquisitions in the industrial and OEM markets in the U.S.”
These acquisitions began with Würth Revcar Fasteners in Roanoke, Virginia, a full-service assembly component supplier and an approved Level One fastener distributor to many U.S. Navy and military accounts globally.
“It continued with a succession of acquisitions, including Würth Service Supply, Würth Adams Nut & Bolt, Würth McAllen Bolt & Screw, and several others throughout the years,” adds Aronson. These companies are in several states, including Indiana, Minnesota, and Texas. “And today, WINA covers the entire North American market, including Mexico and Canada.”
With more than 420,000 parts in its international supply chain, WINA works as an industry solutions provider to nearly any industry you can name, including construction, agriculture, energy, MRO and industrial supplies, and the list goes on. Along with fasteners, WINA also o ers
kitting and assembly, safety supplies, vending, as well as engineering assistance, quality control, inventory management, and industrial 3D printing.
“What makes us di erent in today’s world is security. Given the recent supply-chain issues related to the pandemic and current events…well, this is where we excel. Safety and security are the hallmarks of WINA and, of course, the Würth Group overall,” says Aronson. “Through our inventorymanagement programs, technical expertise, and buying power, we’re able to o er reliability. At the end of the day, it’s about securing the supply chain for our customers, and that’s what we do.”
WINA’s success can be attributed to experience and the Würth value system, which has always represented reliability, predictability, and honesty. One of the principles upon which it was built is that a company with “a strong set of values does not have to fear change.” Instead, it learns from economic and market challenges and turns that knowledge into solutions
Here’s one example: “Back in ’07and ’08, when the financial crisis hit, several OEMs faced similar challenges as they do today,” says Aronson. “In response, we developed CPS GLOBAL, a software solution that proactively monitors a customer’s activity. Combined with our VMI programs, CPS enables transparency and analysis of customer usage trends, including forecasting, so we can get ahead of any potential supply-chain changes or challenges.”
VMI is a vendor-managed inventory platform allowing a supplier to manage and optimize inventory for its customers. This program lets the team at WINA analyze customer usage at the individual component level on both a local and an international basis.
“We’ve heard from customers that many feel taken for granted. There hasn’t been a lot of proactive support, so we
With more than 420,000 parts in its international supply chain, WINA works as an industry solutions provider to nearly any industry you can name, including construction, agriculture, energy, MRO and industrial supplies, and the list goes on.
strive to offer pre-emptive measures that can insulate our customers from market changes or delays. Again, it comes down to security,” he says.
The Würth global network certainly has its perks. For one, there are Würth international parts numbers, enabling the quick and easy identification of fasteners and assembly components from around the world. Secondly, it has a team of supplier quality engineers continually auditing and verifying its processes to ensure reliable products and supply chains.
“WINA is extremely customercentric…and, innovative. Würth has always encouraged bringing forth new ideas that could benefit or grow our capabilities.” Aronson adds that the company fosters ideas and strategies that, ultimately, generate greater simplicity and success for its team and customers. One such idea is the Würth Fastener Academy.
“This is a training program that we use to support our customers and the industry, in general, which explains and teaches about all aspects of fasteners — from design and manufacturing to assembly and coatings, including several other technical aspects.”
WINA also launched a YouTube series in 2021, Würth Knowing, which the Fastener Academy inspired. It features two of Würth’s team members: Technical instructor, Randy Lammers, and applications engineer, Aaron Keevan. The duo meets in Lammers’ Texas workshop to discuss and demo
many different topics related to fastener engineering.
“The first season, produced by our director of marketing, Molly Hauer, was based on the topics we routinely get asked by engineers and our customers. It’s quite insightful and fun to watch.”
Another example of an idea that was so successful it turned into its own WINA division is the launch of the Würth Additive Group.
“This started a couple of years ago because one of our managing directors was interested in 3D printing, which he was encouraged to explore. It’s since turned into its own WINA division and is used by our global customers,” says Aronson.
Essentially, additive manufacturing, also known as 3D printing, adds material layer-by-layer to manufacture three-dimensional products without using tools. It allows changes to a virtual model to be quickly transferred to the physical prototype. Manufacturing a prototype is typically time-consuming
and more costly. 3D printing saves on both. Additive manufacturing is also ideal for those parts with complex geometry, such as a uniquely shaped nut or washer.
“Another bonus is the digital inventory capabilities it provides. So, instead of needing to keep an extra part or repair tool on hand, customers can access a digital blueprint and use their in-house machine to print it whenever required,” he says. “We’re really the first movers of this technology as a fastener distributor.”
And that’s one thing the Würth Group, including its divisions such as WINA, has truly mastered. The Group shows no reluctance when it comes to being the first mover in the industry to take a chance, acquire, try new technology, or grow and expand.
“There’s such an entrepreneurial spirit here. When we have an idea, we’re encouraged to see it through. When my team needs the resources to support a customer, it’s provided,” says Aronson. “Würth is heavily invested in its team and our customers, and the feedback and results we get in return prove its success time and time again.” FE
Industrial 3D printing services offer a streamlined and efficient method to reduce the development times of certain parts and simplify supply chains.
Flat: Generally used for load disbursement
Tab/Lock: Designed to effectively lock an assembly into place
Finishing: Often found on consumer products
Wave: For obtaining loads when the load is static or the working range is small
Belleville: Delivers the highest load capacity of all the spring washers
Fender: Distributes a load evenly across a large surface area
Shim Stacks: Ideal for simple AND complex applications
NBK’s history and craftsmanship date back to 1560 when the company first began. Our predecessors were proud to offer their advanced knowledge, state-of-the-art technology and using this today, we have developed various products.
One of NBK’s strengths in the high-tech sector is our Specialty Screws such as vacuum application screws, anti-galling screws, specialty metal screws such as Inconel and Hastelloy, and more.
Furthermore, NBK deals with unique functional screws like low-profile screws, small head diameter screws, captive screws, miniature screws (less than M2), ball transfer screws, ball plungers, clamping screws, and more. We are proud to support our customer’s projects with NBK’s Specialty Screws and their unlimited matching applications. We also offer customized screws!
Boker’s Inc.
3104 Snelling Avenue
Minneapolis, MN 55406-1937
Phone: 612-729-9365
TOLL-FREE: 800-927-4377 (in the US & Canada) bokers.com
NBK America LLC
307 East Church Road, Suite 7
King of Prussia, PA 19406
Phone: 484-685-7500
https://www.nbk1560.com/en-US/
The SLIC Pin™ from Pivot Point is a pin and cotter all-in-one. An excellent alternative to installing e-clips and secondary cotters, the patented SLIC Pin features a spring-loaded plunger which acts as an automatic cotter pin. SLIC installs faster and more consistently than two-piece combinations – increasing productivity, cutting labor costs, and reducing risk of mis-installation and accidental disengagement. Simply depress the plunger with your finger or a tool in order to remove the pin. Use our “removable” style plunger if removing through small gaps. SLIC Pins can be made in virtually any material and finish. Millions of SLIC Pins are installed every year across all industries. Contact Pivot Point for free samples and information.
This area has long been one of the most read and sought after by our engineering audience! From screws to bolts and adhesives to springs, these critical but often overlooked components are the key to every successful design.
FastenerEngineering.com will serve readers in the mechanical design engineering space, providing news, product developments, application stories, technical how-to articles, and analysis of engineering trends. This site will focus on key issues facing the engineering markets around fastener technology, along with technical background on selected components.
ADDITIONAL RESOURCES:
• Special print section in select issues of Design World
• Fastener Engineering monthly newsletter LEARN