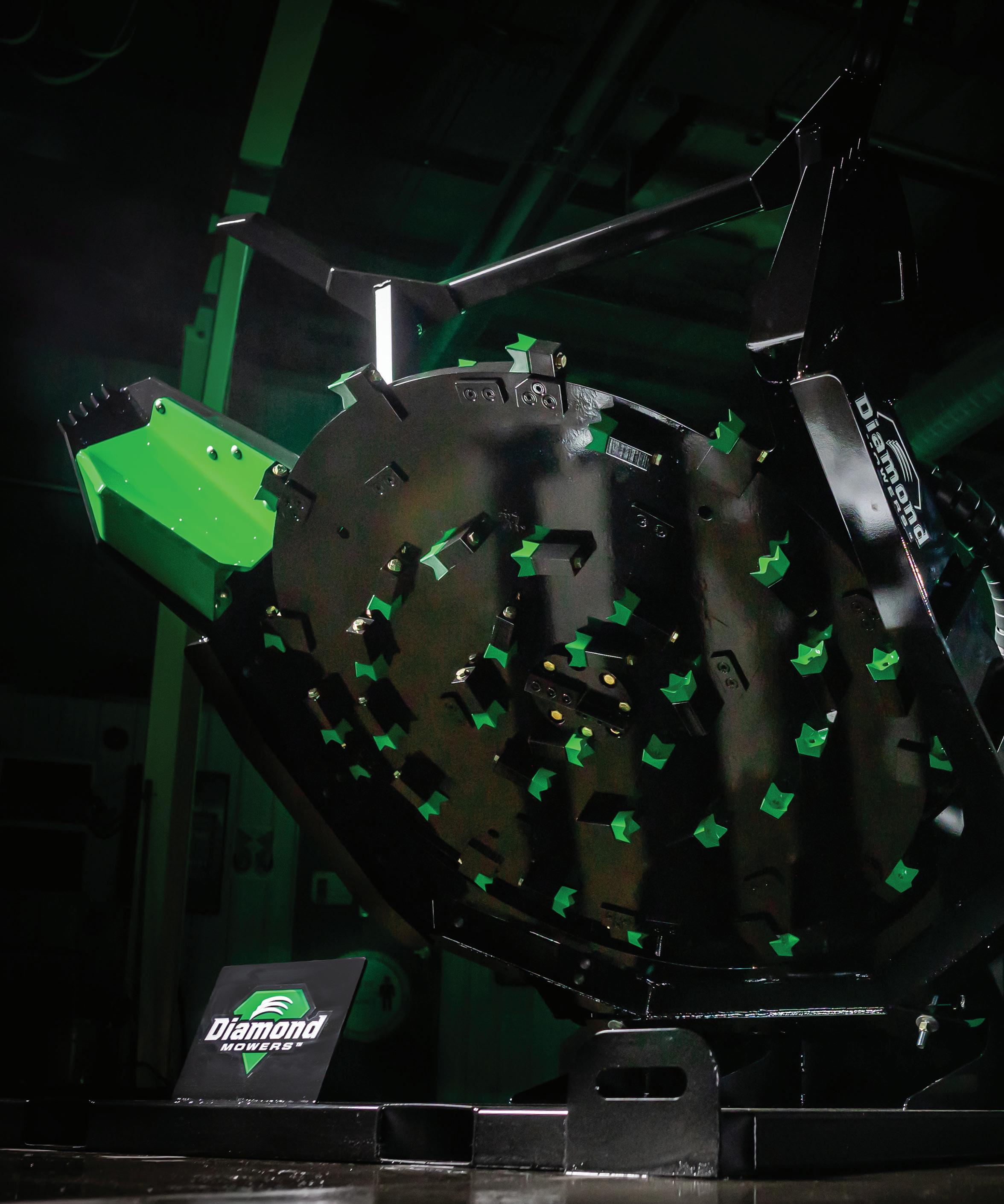

Get your safety and other automation components from AutomationDirect, a trusted supplier in the industry for over 25 years. We offer high-quality safety products at great prices, so you can afford to protect even the simplest systems.
Safety Relays
Starting at $126.00 (LG5924-02-61-24)
Safety relay modules are a simple and reliable method of controlling a safety system that uses positive guided contacts and redundancy for fail-safe systems. Available models include E-stop, two-hand, safety gate, safety mat, light curtain, and speed safety relays.
Safety Light Curtains
Starting at $540.00 Sender/Receiver Pair (YBES-30K4-0170-P012)
Safety light curtains use an array of photoelectric beams to sense intrusion into a plane of detection. Type 4/Category 4 curtains achieve high fault tolerance through redundancy/ monitoring, have a tighter field-of-view, and are less susceptible to optical short circuits.
Safety Controllers
Starting at $353.00 (MOSAIC-M1)
Safety controllers use monitoring logic, overvoltage / short-circuit protection, redundant relays, and positive guided contacts to provide a high level of fail-safe operation.
Safety Switches
Starting at $17.00 (SP2K61X11)
Safety switches are interlocking devices used to monitor (and sometimes lock) machine guards, doors, gates or windows.
Trapped Key Systems
Components starting at $210.00 (800000-CS-A101)
A trapped key system uses a series of mechanical locks and keys to control the access to running equipment or machines, ensuring safe access to those machines. These systems rely on the transfer of keys between a power isolation switch (or control switch) and a mechanical locking mechanism fixed on a guard.
Earlier this year, both my middle school daughters had opportunities to see fluid power in action — and build their own devices powered by it. It was truly an eyeopening experience for them, and they were excited to be enmeshed in my world in a tiny way.
Upon returning from IFPE in March, my 7th grader reported excitedly that she had built a hydraulic arm as her courses in science, health, and math collaborated to teach about prosthetic devices. I have never seen her so thrilled by her science and health classes and she was eager to share how they used syringes and water to power the movement of the device. No matter how many times I have showed her a cylinder in action on a mobile machine or pneumatics powering amusement park rides, she didn’t seem interested. But giving her the power to make her own device brought home what I write about every day.
A few days later, I drove my 5th grader and her friend to the Science Olympiad at John Carroll University, near Cleveland. There, she and her friend built a rocket ship powered by water and compressed air (a 2-liter bottle and a bike pump). Although they didn’t win the competition, they quickly learned that the right amount of water and more pumps of air shot those rockets higher. Again, it was delightful to see how they worked out the necessity of the right force to create higher power.
Fast forward to this past month, as the NFPA Fluid Power Vehicle Challenges were held at Danfoss in Ames, Iowa, and Norgren in Littleton, Colo. These year-long competitions between college students give students a real-life opportunity to build fluid power machines, something that classroom learning cannot replicate. (Read more about the winners on page 10.)
While most of the students participating were seniors, the Milwaukee School of Engineering put forward a team of underclassmen, whose experiences with fluid power were limited. I received comments from two of those students, Jeffrey Kaas, CFPHS, a freshman, and Daniel Cantu, a sophomore at the time of the competition, sharing some thoughts on what the challenge was like.
“NFPA’s Fluid Power Vehicle Challenge was pivotal in helping me to understand fluid power principles. While I had spent the last few months preparing for the Hydraulic Specialist Certification test, study guides and online courses don’t even compare to hands-on experience,” Kaas said. “I think that hands-on experiences like the vehicle challenge are crucial to anyone interested in learning fluid power at the university level, and I hope that over time, more and more universities begin to create FPVC teams, whether for seniors or for a fluid power club, like MSOE did this year.”
Cantu added that he joined the MSOE Fluid Power Club hoping to learn some basics and network with industry specialists.
“When I was given the opportunity to work on the Fluid Power Vehicle Challenge, things really changed. I went from not having any background in fluid power to understanding how hydraulic circuits work, different types of pumps work, and the overall functionality and purpose fluid power holds,” he said. “I truly recommend participating in a Fluid Power Vehicle Challenge because you will gain knowledge that is not only found in a textbook, you’ll be able to apply yourself, and it is simply rewarding to start and finish something that you knew nothing about beforehand.”
One thing I tell anyone new to the industry is that they will fall in love with the technology and the people moving fluid power forward. But to get new folks into the industry, we first must let them experience it. It will be exciting to see more NFPA Fast Track to Fluid Power Hubs form and introduce whole new generations to this industry. I encourage you to get involved in new ways as well. Keep the conversations and hands-on experiences going from young elementary school students all the way up to universities. FPW
Mary C. Gannon • Editor-in -ChiefOOne of the things I love about the triennial IFPE Show in Las Vegas is that I always get new insights on component manufacturers, even ones I thought I knew well. Such was the case this year in talking to Matt Grussing, Director of Sales – Western Region & Key Accounts, at Bailey International. I’ve assumed that the company was solely a manufacturer of hydraulic cylinders, pumps valves, etc., but when I asked Grussing about how their supply chain was these days, he surprised me with his answer. Bailey, he said, is a good blend of a manufacturer and a distributor, and that has greatly helped their customers with the supply chain situation.
“We take the manufacturer’s mentality of the quality, the on-time delivery, all of the different aspects of that, and blend it in with our distribution mentality that allows us to do inventory management systems for people,” he said. “We do a lot of pre-planning. We’ve got an intuitive inventory management software that we utilize. And when customers partner with us on a contracted inventory basis, that system then takes over and watches their ebbs and flows of the inventory pools and automatically adjusts our inventory loads in our production. That allows us to be at the right place at the right time.”
According to Grussing, Bailey was a distributor back when the company first started. It evolved into a manufacturing company about three decades ago. But as it grew, the family that owned the
company (until 2012) evolved into the manufacturing mentality, but never lost the distributor mentality.
“So, in 2020 when COVID happened — when that cliff dropped — a lot of our customers who were on this contract manufacturing were in good shape, because Bailey has its inventory bulked up. They didn’t get in a cash-tight situation; they weren’t forced to take the inventory,” said Grussing. “And when things rebounded in August, we had all that inventory piled up for them, so they were able to be in the market faster. We really view that as a huge part of our business. This is an augmentation to the mentality of serving customers both as a manufacturer and a distributor, to be able to serve that rapid nimble way that a distributor does, but with the manufacturing scale and mentality.”
I’d not previously given a lot of thought to the companies that blend the manufacturing and distributor roles, but at least in this supply chain instance, it seems that the setup could be the best of both worlds for end customers. FPW
Paul J. Heney VP, Editorial Director pheney@wtwhmedia.com On Twitter @wtwh_paulheney Position sensors for stroke measurement in hydraulic cylinders
Compact safety rotary encoders for position and speed measurement
Dynamically compensated inclination sensors for precise angle measurement
AUTOMATE 2023, Detroit, Booth #121
STRONG – SAFE – EFFICIENT SENSORS FOR MOBILE AUTOMATION
Tank top semiimmersed returnsuction filter. Working pressure to 145 psi, and flow rates up to 79.5 gpm.
ELIXIR
LPM 211
pressure filter.
Working pressure up to 6029 psi, flow rates up to 66 gpm.
Tank top semiimmersed filter. Working pressure up to 116 psi, flow rates up to 198 gpm.
In-Line suction, return, and delivery filters with working pressure to 232 psi, and flow rate up to 60 gpm.
In-line low & medium pressure filter. Working pressure up to 870 psi, flow rate up to 87 gpm
Closed-loop feedback opens up possibilities
Manufacturers across all industries seek ways to electrify, digitize, and automate their systems to decrease costs and increase efficiency. Electro-pneumatic pressure regulators and valves enable such efforts while improving pressure and flow rate accuracy.
HYDRAULIC EFFICIENCY
Raising the efficiency of hydraulic pumps
Adding shuttles to axial piston pumps can substantially increase overall efficiency.
Sustainable mobile machines take shape
The latest “green” machines come in all types and sizes.
Mechanical wear: what you can’t see can hurt you
Tiny particulates in lubricants that are invisible to the naked eye can have costly consequences in hydraulic systems.
26 31 36 40
EDITORIAL
VP, Editorial Director Paul J. Heney pheney@wtwhmedia.com @wtwh_paulheney
Editor-in-Chief Mary Gannon mgannon@wtwhmedia.com @dw_marygannon
Technology Editor Ken Korane kkorane@wtwhmedia.com @fpw_kenkorane
Senior Editor Rachael Pasini rpasini@wtwhmedia.com
Associate Editor Heather Hall hhall@wtwhmedia.com @wtwh_heathhall
Contributing Editor Josh Cosford @FluidPowerTips
Contributing Editor Carl Dyke @carlindustry
Contributing Writer Robert Sheaf rjsheaf@cfc-solar.com
PRINT PRODUCTION
VP, Creative Services Mark Rook mrook@wtwhmedia.com @wtwh_graphics
VP, Creative Services Matthew Claney mclaney@wtwhmedia.com @wtwh_designer
Art Director Allison Washko awashko@wtwhmedia.com @wtwh_allison
Senior Graphic Designer Mariel Evans mevans@wtwhmedia.com @wtwh_mariel
Graphic Designer Shannon Pipik spipik@wtwhmedia.com @WTWH_Shannon
Director, Audience Development Bruce Sprague bsprague@wtwhmedia.com
MARKETING
VP, Digital Marketing Virginia Goulding vgoulding@wtwhmedia.com @wtwh_virginia
Digital Marketing Manager Taylor Meade tmeade@wtwhmedia.com @wtwh_taylor
Digital Production/ Marketing Designer Samantha King sking@wtwhmedia.com
Marketing Graphic Designer Hannah Bragg hbragg@wtwhmedia.com
Marketing Graphic Designer Nicole Johnson njohnson@wtwhmedia.com
Webinar Manager Matt Boblett mboblett@wtwhmedia.com
Webinar Coordinator Dan Santarelli dsantarelli@wtwhmedia.com
ONLINE DEVELOPMENT & PRODUCTION
Web Development Manager B. David Miyares dmiyares@wtwhmedia.com @wtwh_webdave
Senior Digital Media Manager Patrick Curran pcurran@wtwhmedia.com @wtwhseopatrick
Front End Developer Melissa Annand mannand@wtwhmedia.com
Software Engineer David Bozentka dbozentka@wtwhmedia.com
Digital Production Manager Reggie Hall rhall@wtwhmedia.com
Digital Production Specialist Nicole Lender nlender@wtwhmedia.com
Digital Production Specialist Elise Ondak eondak@wtwhmedia.com
VIDEO SERVICES
Videographer Garrett McCa erty gmccafferty@wtwhmedia.com
Videographer Kara Singleton ksingleton@wtwhmedia.com
PRODUCTION SERVICES
Customer Service Manager Stephanie Hulett shulett@wtwhmedia.com
Customer Service
Representative Tracy Powers tpowers@wtwhmedia.com
Customer Service Representative JoAnn Martin jmartin@wtwhmedia.com
Customer Service Representative Renee Massey-Linston renee@wtwhmedia.com
Customer Service Representative Trinidy Longgood tlonggood@wtwhmedia.com
IN-PERSON EVENTS
Events Manager Jen Osborne jkolasky@wtwhmedia.com @wtwh_jen
Events Manager Brittany Belko bbelko@wtwhmedia.com
Event Marketing Specialist Olivia Zemanek ozemanek@wtwhmedia.com
FINANCE
Controller Brian Korsberg bkorsberg@wtwhmedia.com
Accounts Receivable Specialist
Jamila Milton jmilton@wtwhmedia.com
SALES
Ryan Ashdown 216-316-6691 rashdown@wtwhmedia.com
Jami Brownlee 224.760.1055 jbrownlee@wtwhmedia.com
Mary Ann Cooke 781.710.4659 mcooke@wtwhmedia.com
Jim Powers 312.925.7793 jpowers@wtwhmedia.com @jpowers_media
www.nfpa.com
WTWH Media, LLC 1111SuperiorAve.,Suite2600,Cleveland,OH44114 Ph: 888.543.2447 • Fax: 888.543.2447
Courtney Nagle 440.523.1685 cseel@wtwhmedia.com @wtwh_CSeel
2011- 2020
FLUID POWER WORLD does not pass judgment on subjects of controversy nor enter into dispute with or between any individuals or organizations. FLUID POWER WORLD is also an independent forum for the expression of opinions relevant to industry issues. Letters to the editor and by-lined articles express the views of the author and not necessarily of the publisher or the publication. Every effort is made to provide accurate information; however, publisher assumes no responsibility for accuracy of submitted advertising and editorial information. Noncommissioned articles and news releases cannot be acknowledged. Unsolicited materials cannot be returned nor will this organization assume responsibility for their care.
FLUID POWER WORLD does not endorse any products, programs or services of advertisers or editorial contributors. Copyright© 2023 by WTWH Media, LLC. No part of this publication may be reproduced in any form or by any means, electronic or mechanical, or by recording, or by any information storage or retrieval system, without written permission from the publisher.
SUBSCRIPTION RATES: Free and controlled circulation to qualified subscribers. Non-qualified persons may subscribe at the following rates: U.S. and possessions: 1 year: $125; 2 years: $200; 3 years: $275; Canadian and foreign, 1 year: $195; only US funds are accepted. Single copies $15 each. Subscriptions are prepaid, and check or money orders only.
SUBSCRIBER SERVICES: To order a subscription please visit our web site at www.fluidpowerworld.com
FLUID POWER WORLD (ISSN 2375-3641) is published eight times a year: in January, February, April, June, July, August, October, and December by WTWH Media, LLC; 1111 Superior Ave., Suite 2600, Cleveland, Ohio 44114.
OH
2600, Cleveland, OH 44114
As a natural-born tree-hugger, some wonder why I’m an editor for fluid power and manufacturing publications. Wouldn’t a person who values environmentalism participate in more “green” efforts? Yet, I cover mobile machines that cut down trees, hydraulic systems that rely on oil rigs, and automation equipment that expedites manufacturing (and subsequently creates more stuff that often ends up in landfills and oceans.)
I’ve questioned it myself and wondered if my values and choices are misaligned. But the truth is, the more I learn, the more I understand the complexity of our evolution and how deeply our daily lives intertwine. I truly appreciate how hard it is to fulfill so many conflicting goals while being conscious of everything else.
Regarding sustainability and environmental impacts, it’s easy to focus on the negative aspects and shun all of humanity’s mistakes. But there’s still so much to celebrate, and those of us with
engineering mindsets see every challenge as an opportunity to improve.
Coincidentally, as I pondered all this, the Association of Equipment Manufacturers (AEM) released a study on the “Benefits of Construction Equipment Technologies and Their Impact on Society.” It noted that modern engines and drivetrains are more efficient than they were 27 years ago when the EPA instituted non-road engine regulations. Today’s tier 4 engines are roughly 11 to 15% more fuel efficient per machine hour and do more work per gallon of fuel consumed. Though the statistic may seem underwhelming, it’s a significant improvement when scaled up across all machines in use today. AEM compares this to permanently removing 1,350,000 cars — the amount registered in New Hampshire — from the road. That certainly helps visualize the impact.
The study also noted that construction equipment produces 96% less NOx and particulate emissions per gallon of diesel consumed and 13% less CO2 emissions per machine hour than it did 30 years ago. It would take 25 modern wheel loaders to produce the same emissions that one wheel loader from 1990 would release.
This demonstrates that we live in a world that strives to mitigate environmental impacts from past decisions and continuously innovate for more environmentally conscious futures. Of course, there’s plenty more work to do, but it’s important to take a step back from time to time and acknowledge the work done thus far.
Globally, companies are adopting more solutions to improve air quality, reduce waste, and conserve energy. Innovation abounds and accelerates next-generation technology that builds upon all our lessons learned. It’s not an overnight change, but change is happening. And as long as we stay on this path, we’ll surely see continued improvements — and have so much more to celebrate — for years to come. FPW
Rachael Pasini Senior Editor rpasini@wtwhmedia.comEvery year, the NFPA holds a Fluid Power Vehicle Challenge for engineering students who attend universities around the U.S. The competition combines two technology platforms not normally associated with one another — human-powered vehicles and fluid power. Teams are tasked with designing and building their own fluid power vehicles over the course of a school year. The program culminates in final competitions at two separate locations.
In April, schools competed in four races during the final competitions and were judged by fluid power industry professionals. In addition to the races, students gave presentations on their vehicle construction, testing, and lessons
learned. Each team also met individually with the industry judges to assess their vehicle design. Specific awards were given to highlight the use of pneumatics and electronics in the teams’ designs.
Texas A&M University (TAMU) was named Grand Champion at the 2023 Fluid Power Vehicle Challenge Final Competition hosted by Norgren in Littleton, Colorado, held April 12-14. Purdue University earned second place, and the University of Alabama at Birmingham took home third. The prize for Best Use of Pneumatics, sponsored by Norgren, was taken home by California Polytechnic State University. The prize for Innovative Use of Electronics, sponsored by IFP Motion Solutions, was awarded to Texas A&M.
Students of the University of Louisville at Lafayette team raved about their experience and how the competition sparked a passion for the fluid power industry.
| Courtesy of the NFPA
“Designing a complete hydraulic system was a learning experience that required not only knowledge about hydraulics but also about associated mechanical and electrical systems,” said Mark Finley, TAMU Fluid Power Club president. “We applied what we learned in our fluid power classes directly to our project, including designing our circuit in Automation Studio and using the fluid power lab in Thompson Hall to build and test our circuit before ordering components. We also expanded our knowledge of fluid power by becoming familiar with industry-grade systems and components different from those found in our lab, and we found this breadth of experience and knowledge to be valuable.”
The team’s fluid-powered bicycle used a hydraulic circuit instead of a chain to transfer power from the rider to the wheels. They built the design with Fusion 360, a computer-aided design software, so they could see the finished bike before they had their parts.
“We were able to talk to and be mentored by a lot of great people involved in the competition through the NFPA,” said Finely. “One thing I really enjoyed was how open-ended the project was. We had a set end goal, but we had nearly complete freedom of design. After we came up with ideas and documented them, we could then take them to experienced people for advice on how to modify our systems, specifically to ensure safety. From there, we could make changes and move forward into the fabrication and assembly process, where we learned a lot of lessons that you wouldn't necessarily learn in a classroom.”
Two weeks later, the University of Louisiana at Lafayette was named Grand Champion at the 2023 Fluid Power Vehicle Challenge Final Competition hosted by Danfoss Power Solutions in Ames, Iowa, held April 26-28.
“Working with the National Fluid Power Association has been an incredibly enriching and transformative experience for me, both personally and professionally. The competition provided a platform to not only deepen my understanding of fluid power systems, but also to interact and
engage with some of the brightest minds from industry,” said Michael Tonore, member of the Mechanical Engineering (MCHE) Fluid Power Vehicle Team for the University of Louisville at Lafayette. “The collaborative environment fostered a sense of camaraderie and allowed for the exchange of ideas, as well as constructive criticism. In addition to technical growth, the social interactions during the competition introduced me to potential mentors and future collaborators.”
South Dakota State University earned second place at the Iowa competition, and Cleveland State University came in third. The prize for Best Use of Pneumatics, sponsored by Norgren, was taken home by Murray State University. The prize for Best Use of Electronics, sponsored by IFP Motion Solutions, was awarded to Purdue University Northwest. FPW
IFPS announced that its highly sought-after Inperson Hydraulic Specialist Review Training is now available in two new locations. Professionals can join IFPS in Memphis, Tennessee, August 21-25, or Windsor, Ontario, Canada, November 6-10, to gain the confidence needed to ace the certification test and take their careers to the next level.
A Hydraulic Specialist (HS) applies fluid power theory and related knowledge to analyze power transmission and motion control requirements. An HS also designs industrial or mobile hydraulic systems to perform required tasks. This specialist sizes and selects components, designs or modifies complete circuits, prepares Bills of Materials, and specifies fluids, prime movers, and fluid conductors.
An HS also designs appropriate instrumentation and control systems (hydraulic and electronic) for industrial and mobile machinery. The HS may become involved in sales activities, product warranty claims, evaluation of prototype machinery, and instructional activities for Fluid Power Technicians and Fluid Power Mechanics concerning principles of hydraulics.
The HS in-person training program is designed for review, so test preparation before the session is still essential. During the program, 34 hours of training will be conducted Monday to Thursday, and the testing will be held on Friday.
Limited seats are still available, so register today and take the first step toward becoming a Hydraulic Specialist: www.ifps.org/in-person-certification-review-training FPW
Mobile hydraulics is often called on for tough forestry jobs, and Diamond Mowers’ new Belt Drive Disc Mulcher is suited for contractors and mulching professionals who specialize in land clearing, vegetation and forestry management, and pasture reclamation. It features increased torque to obliterate anything in its path without slowing down, recovers twice as fast as other mulchers, and boasts an efficient design that promotes lower hydraulic temperatures for maximum uptime and carrier life.
Enhanced forward visibility ensures that contractors won’t accidentally hit obstacles and can better position vegetation for optimal performance. The mulcher features a 60-in. cutting width and can slice through trees and brush up to 14-in. in diameter. It also shreds material up to 6-in. in diameter and attaches to most skid-steer and compact track loaders.
The mulchers can be used for clearing land in some unexpected ways. According to Matt Nelson, an engineer with the company, these products are critical for maintaining landscapes. And while the machinery is said to “eat trees,” the goal is generally to help with the environment, not hurt it.
“Out west, say in California or Oregon, defensible space is a really big deal. People need to protect homes and other structures that are built into the forest, from occasional forest fires. You need to remove all that scrub brush, which are often called ladder fuels,” said Nelson. “So, when — not if — a fire comes through, it’s much easier to protect those structures. These mulchers are the perfect solution.”
The skid-steers that Diamond Mowers’ attachments are used with are small and nimble, and thus, they are able to get in between the houses to clear out this type of scrub brush. In addition, in areas like the Midwest, Nelson said that cedar trees are growing at a rapid pace, taking over rangelands.
“If you were to go to areas of the Midwest years ago, it’d be nothing but grass,” Nelson said. “But today, if you go to Oklahoma, Kansas, or Nebraska, you’ll see a lot of cedar trees. And those cedar trees are drinking 20 to 30 gallons of water each day. That rancher obviously, is making money on raising cows. If you can’t have as many cattle on a particular piece of property, it’s impacting your bottom line in a really big way. This equipment is the fastest way to remove those invasive species.”
Nelson also noted that in the eastern half of the U.S., you’ll see their products in residential site development, for irrigation canal maintenance, or anywhere that trees aren’t wanted.
Historically, a disc mulcher has used a fixed displacement motor. Nelson said that’s akin to running on a single speed bicycle. When a user turns the high flow on, it’s going to take almost a minute for the large wheel to come up to speed. That wheel, using all of that stored energy, is really how these machines work. With the old designs, you just had to be patient. Diamond Mowers incorporated a variable displacement motor, running through a belt drive with a roughly three to one reduction system. And they’ve taken
that former minute of waiting for the spool uptime and reduced it down to 13 seconds.
“What that gives the customer is a measurable 20% to 30% base increase in productivity,” said Nelson. “Plus, cooler hydraulic temperatures, because the machine itself is spending less time in relief, and we are not wasting all that energy. It’s designed specifically for that customer who’s using these disc mulchers for profit, and we’re really excited about the new design.”
Nelson noted that the design improvement is an adaptation of the company’s related line of drum mulchers. With those devices, a variable displacement belt driven system has been used for many years, but the concept had just never made its way over to the disk space.
“So even though it’s new to the industry and it’s delivering all this performance, it’s using components that we have a long and successful history with,” he said.
Nelson stressed that their customers are first and foremost concerned with uptime.
“Uptime first, and then productivity and performance. I lump those things into the same bucket as their second concern. And then ease of use, and ease of maintenance is their third concern,” he said.
Diamond uses a Rexroth A6107 variable motor as the prime mover, the same motor
they are using in the drum mulchers. Nelson believes it is probably the most prominent motor in the mulcher space. A Kevlar stranded poly chain belt is used in the drive system for durability.
One long frustration has been that hose protection and routing can be difficult on these types of attachments. The hoses are constantly getting pushed and pulled, and they’re also getting scraped and twisted. Thus, protecting those hoses is really important. Hose leaks aren’t something that anyone wants to deal with (especially in the field), so all of the Parker Hannifin hydraulic hoses that are used are wrapped for additional protection. But there was one more new solution with the hoses that’s been a big success.
“Especially in the mulching space, these hoses are constantly getting pulled and pulled — and it’s particularly hard on the couplers,” said Nelson. “The flat face couplers just don’t hold up. So, what we did is we incorporated swivels from Super Swivels. Because of that, we’re able to use a much shorter hose length, which really limits the amount of push and pull. And we’re seeing a lot better hose life, because of the incorporation of these swivels.” FPW
DiamondAfter 10 years of research, Gefran, an Italian sensor and control company, has launched its Twiist contactless linear position transducer to the North American market. The transducer not only measures position but can also measure temperature, velocity, acceleration, and tilt angle
“There are several products on the market that measure position and Gefran has them as well, but only Twiist can measure position, acceleration, speed, vibration, and three spatial angles (x, y, and z axes) all at the same time,” said Edoardo Zilioli, Gefran’s Marketing Manager, Sensors Division. “And if desired, Twiist can also monitor the ambient temperature inside the transducer. Readings and data processing happen simultaneously.”
This multi-variable position transducer is in the Hall effect category, but what truly sets it apart is its unique helical magnetoelectronic design, its ability to take multiple measurements simultaneously, and its focus on improving operator safety. This patented technology is the result of a decade-long partnership between Gefran’s internal R&D department and the University of Brescia’s engineering department in Brescia, Italy.
“Gefran offers a complete bundle of electrical products — sensors, controls, instrumentation, etc. — for industrial machinery, but the Twiist is perfect for mobile and industrial hydraulic applications,” said Ron Akers, Gefran’s Business Development Manager for fluid power. “It allows for multiple types of measurement in one component. Signals for linear and angular positioning and temperature readings are all communicated at the same time. Furthermore, with the onboard
electronics, Twiist provides real-time velocity, acceleration, and tilt angle measurements to keep operators safer.”
The compact design is not limited to 250 mm stroke ranges like traditional Hall effect sensors, said Zilioli. “Measuring linear displacement with a Hall effect chip encapsulated by a magnetic helix is an innovative and ingenious idea. It revolutionizes the classic Hall effect sensor in the range of 5 mm, which among other things is limited to strokes of up to 250 mm,” Zilioli said. “Not only does Twiist reduce the number of expensive components needed for a project, but it is a redundant position transducer with a more useful electrical stroke of 50 to 900 mm.”
Twiist’s compact, air-tight design has a steel barrel with a diameter of 5/8 in. (16 mm) and it comes with a choice of two types of connection points — ball joints for swivel connections and rod ends with eyes for pivot connections. Available in full-scale (FS) strokes from 50 to 900 mm, it has typical linearity of 0.15% FS and typical repeatability of 0.05% FS. It can operate in a temperature range from -40°F to 185°F (-40°C to 85°C).
The Twiist has an IP67 environmental protection rating as well, offering complete protection against dust and airborne particles, as well as protection against water and other liquids when submerged up to 39 in. (1 m) deep. This resistance to contamination makes it ideal for fluid power applications and extends the life of the part and equipment.
Applications could include many in mobile hydraulics. For example, when steering a vehicle, while using spatial inclination and acceleration, the Twiist verifies, at each millisecond, if the ground is stable underneath the construction equipment and it can alert the operator if there is a danger of unstable ground, Zilioli noted. All of this is directly on the steering axis, without any mechanical interference, or worse, mechanical play.
Other applications include: control of stabilization footings in area platforms (extension and subsidence), monitoring position and vibration for mining, fracking, and drilling, and measuring position and inclination for phytochemical sprayer arms on agricultural sprayers. Practically all medium-complex vehicles could use a Twiist multivariable transducer, Zilioli said.
Available outputs are both analog and digital. With the CANopen fieldbus and IO-Link output capabilities, measurements related to process variables, such as position, speed, and inclination are digitally transmitted up to 1,000 times per second. With its integrated CPU, the Twiist collects and analyzes operational data and provides a feedback loop to ensure equipment performance is optimized and operators are kept safe. These magnetoelectronic signals can also monitor process information related to vibration peaks, hours of operation, distance traveled, and more.
To measure inclination signals with high accuracy (three axes: x, y, and z), Gefran uses MEMS chips and proprietary algorithms that are both sophisticated and immune to microvibrations. Gefran has successfully used this technology since 2015 in many of its products and customers use it in applications from mobile hydraulics (mining vehicles, mobile aerial work platforms, etc.) to geotechnics in civil engineering (checking for rocks and soil makeup to plan for tunnels, bridges, reservoirs, etc.). Designed with industry in mind, the Twiist offers substantial benefits across the supply chain. OEMs can use one component while providing the same levels of input and output information.
Zilioli noted that the biggest challenge developing one component to measure multiple
Intelligent, multifunctional Twiist position encoders record not only the position but also many other process variables and set them in relation to each other.
data points was the need to make a metrologically accurate sensor. It had to be manufactured with high-quality materials, be well protected from the environment, be compact in size, and provide consistent and reliable results.
“Gefran has an R&D department that is enviable, and we invest heavily in research through an ever-increasing headcount, annual financial investments, and academic partnerships,” Zilioli said. “Gefran is also a multi-project and multientity company, and for as long as I can remember (since 1968 actually), we’ve operated with agility in terms of projects and operations. For example, in one year alone, I worked on a position sensor, next a wireless force transducer, and then an ultracompact, Lilliputian pressure transducer. In practice, this kind of flexibility and versatility is part of Gefran’s DNA, and to be honest, we enjoy solving complicated problems.”
Zilioli added that accuracy was a challenge within a challenge. “Already a small transducer with a 16-mm diameter housing and a 5 mm wide by 900 mm long internal electronic circuit, the Twiist was a unique enterprise,” he said. “While evaluating strategic redundancy, we knew there were only a couple of suppliers who would make a small multi-layer
circuit board. We knew it was a great opportunity and after years of research, we arrived at the final design.
“Gefran has another hidden and little-known talent. We own and operate several surface-mounting technology (SMD) machines and we use them for assembling our chips and electronic components,” Zilioli concluded. “Gefran does not rely on external suppliers to do this work, so we can control production and maintain the quality of our products.”
Controllers can reduce the number of line items on the bill of materials, the number of parts needed, and costs for purchasing. With fewer failure points and the robustness of the Twiist’s design, engineers and warranty departments benefit alike. For the end user, Twiist offers a simplified proportional system that is easier to use and maintain. Furthermore, in keeping up with the changing pace of technology, if new firmware features and enhancements enter the market, Gefran will provide version updates that can be made onsite.
“The future for Twiist is wide open. As we partner with more engineers and industrial designers, they will think of new ways to apply Twiist technology to their own products,” said Tapan Mody, General Manager at Gefran. “This is an innovative and exciting product.”
The analog version of the rod-shaped Twiist sensor is characterized by an extremely low parameterization effort. It offers a direct standard signal and allows contactless measurement at a very low cost. Additional amplifiers, such as those required for potentiometric transducers, are completely unnecessary. A Gefran customer takes advantage of this to control the hydraulics at the outlet flap of his concrete mixer. The concrete flow from the mixer into the transport vehicle is controlled via the opening of the flap. In the case of very dry concrete, which behaves like granular sand, the flap can be opened completely. Moist, rather liquid concrete, on the other hand, would burst uncontrollably out of the mixer if the outlet flap were completely open and end up anywhere but in the tank wagon. For a controlled flow into the vehicle, the flap must only be opened very slowly and partially.
The position sensor originally mounted on the hydraulic cylinder had to be replaced every four to six months. When the concrete mixer was flushed out with water, the concrete-water mixture attacked the seal between the push rod and the guide tube over time. This allowed water to penetrate the sensor and destroy the measuring element. For the Twiiist sensor, which has IP67 protection as standard,
penetrating water is no problem. Its Hall chip measuring element sits in a hermetically sealed square steel tube that is moved back and forth by the helical magnetic field applied to the outer steel tube (diameter of 16 mm) with the help of a sliding bush. This benefits the operator of the concrete plant, for whom the time-consuming and costintensive sensor changes are no longer necessary.
In addition to the analog version of the rod-shaped displacement transducer (model LS-A), a redundant ratiometric version is available to support safety applications, as well as variants with CANopen (model LM-C) or IO-Link (model LM-L). The sensor models with digital interfaces facilitate integration into the respective machine and control architectures and allow the acquisition and transmission of additional process variables at a transmission rate of up to 1,000 times per second. The acyclic information that the digital sensors process and make available includes the kilometers traveled by the cursor — i.e., how often the push rod has moved back and forth — the maximum temperature reached, and working hours. FPW
Twiist’s compact, air-tight design has a steel barrel with a diameter of 5/8 in. (16 mm) and it comes with a choice of two types of connection points, ball joints for swivel connections and rod ends with eyes for pivot connections.
Freudenberg Sealing Technologies can now validate the superior performance capabilities of its intelligent seals under development. These seals can handle tasks such as sensor applications and monitoring their state of wear. They enhance machine and system reliability by providing data about their state of performance and safety. That, in turn, helps eliminate mechanical failures and unanticipated downtime. A new feasibility study conducted by the company has verified the benefits of these sealing functions.
Seals prevent contamination, create temperature and pressure safeguards, and protect the external environment from accidental leaks and spills. Maintaining an impervious barrier between the external and internal environments in which they are placed is critical in protecting machinery and systems from temperature and pressure fluctuations, dirt, and grime. They further prevent aggressive fluids and chemicals from polluting their surroundings. In the future, intelligent seals from Freudenberg Sealing Technologies can significantly expand so that the seal is also a sensor and applies built-in functionality via materials and design to become a “smart seal.”
“We deliberately decided to take this route. It promises insights with considerably more information on the seal’s service life than we can get from modeling other usage data in the system,” said Boris Traber, manager of the company’s global Materials Predevelopment. “We’re convinced that future seals will provide us with accurate condition information in real time, which means they can be central elements in predictive maintenance and Industry 4.0 — the systematic digitalization of machines and plants.”
One of Freudenberg’s development efforts is the creation of an intelligent rod seal. This forms a capacitor with outer layers made of an electrically insulating elastomer and an inner
layer of an electrically conductive elastomer with a metallic housing wall. If the successive abrasions of the insulating layer cause the seal to wear down, the distance between the electrically conductive layer to the metallic housing decreases while the capacitance rises. This makes it possible to get a condition measurement at any time, indicating the rod seal’s service life if the wear remains constant. With these intelligent rod seals, maintenance times can be scheduled reliably in advance. Such predictions prevent followup costs caused by leakage damage and lower the risk of contaminating the whole batch. Additionally, the seal is used throughout its entire service life without being replaced prematurely, optimizing operating costs and providing a sustainable solution.
Freudenberg Sealing Technologies has already developed both sealing materials and a smart rod seal that meet all the performance requirements of a conventional rod seal, including those that involve acid and base resistance, standards, service life, and manufacturability.
The smart seal feasibility study proves that the smart seal concept is valid and offers benefits. It confirms that the sensor concept works in real-life situations, and the simulation of the capacitor principle gave the developers important answers.
“The change in capacitance informatively describes the wear of the seal lip. When the seal reaches the limit of its wear and tear, the capacitance increases significantly and approaches an exponential progression. A failure of the seal, and thus an imminent leakage, can be prevented in a timely manner,” said Olaf Nahrwold, development engineer at Freudenberg Sealing Technologies. “To achieve this, we had to tackle several challenges, such as adapting the component geometries and developing the corresponding measurement software, which has proven to be very robust.”
Extensive tests in real application settings were key to the feasibility study. In lab practice, they prove the full function of the seal exactly as intended: Installed in a standard valve, it reliably seals the system in both dry and aqueous environments; at the same time, it continuously provides real-time measurement data about its remaining service life.
The result is substantiated by comparing all capacitive measurements with a real mechanical leakage. To this end, overpressure is applied to the valve. As long as it remains constant, the system is free of leaks. All tests
yielded a rise in capacitance before any measurable leakage: The system accurately captures the state of wear, enabling it to predict when the seal will fail.
“These positive results of the feasibility study are an important condition for the possible everyday use of intelligent seals in
many application scenarios,” said Traber. “We also examined how this concept can be transferred to PTFE seals, such as those used in hydraulic applications with increased requirements for thermal and mechanical resistance at high pressures. These results are also highly encouraging.”
The R&D know-how is reflected in the materials and fundamental structure of the intelligent seal. For smart seals in large-scale series production, this capability also makes it possible for the company to ensure the sensor quality required for the application.
“Given that there are still various unanswered questions, it will probably still take some time before a specific practical application is identified,” said Traber. “The sensor information will also have to be implemented in the plant control systems so that actions can be triggered based on the data. The best way to clear up these questions is through application projects with their specific requirements. We are absolutely convinced of the benefits of our concept in terms of data availability — and that smart seals can create significant advantages in many industrial processes.”
Freudenberg Sealing Technologies fst.comAs it continues to fine-tune its GT Connector line of products, Canfield Connector, a div. of Canfield Industries, has seen the use of its series of molded receptacle and plug connectors replace more traditional Deutsch designs, particularly in mobile machinery. Through investigation and product development, Canfield has come to market with molded versions in 2, 3 and 4 pin selections to address current industrial applications.
“Initially popular within the mobile section of our industrial market, the design has grown acceptance into general industry as this connector offers superior vibration resistance, sealing capabilities and has proven to be judged
as a robust and reliable product,” said Todd Harmon, VP of Canfield. “As many valve and pressure switch manufacturers migrate to this connection option on their products, Canfield is poised to support the mating cord sales with our distribution and sales network.
“The GT connector is growing in popularity within primarily hydraulic (mobile) applications. Many of the hydraulic valve manufacturers now offer this GT (Deutsch) connector as standard on their product lines. It is crossing boundaries from strictly mobile to automation as well,” Harmon continued. “The value of our connection is that we offer a molded solution in place of the hand-wired that requires labor and tools. In addition, we can provide options for indicator lights and surge protection as well. These are both popular options and cannot be achieved with the field wire product.”
The GatorMate GT 2-, 3- and 4-pin series molded connectors are available as either receptacle and plug designs, to enhance the wired section of the connectors accommodating a molded-jacketed cable with indicator lights. They are rated to IP67 and are shock, vibration, moisture, and dust resistant. The design allows users to see that power is applied and holds transient voltage/current within the connector.
The included cables are the Canfield Connector flooded jacketed cable. Special version of the GT connector can include high-flex, media compatible, special use, or high-temperature wire upon request. Along with standard pin configurations, value-added indicator lights and surge protection are available in most configurations. Because of its molded design, added benefits include less labor required than field-wire version, and no special crimping tools needed and a variety of options to boot. FPW Canfield Connector
Hydraulic oil contamination may cause significant damage to hydraulic systems and components, leading to reduced performance and productivity and increased maintenance and repair costs. It’s crucial that you identify the symptoms of hydraulic oil contamination to prevent further damage and ensure optimal hydraulic system operation. Regular readers know how much I preach the importance of hydraulic fluid cleanliness programs, including mitigating contamination. We all know contamination causes excessive and premature wear,
but what are the less common contamination symptoms?
One symptom of hydraulic oil contamination is increased noise and vibration levels. When oil is contaminated, it loses its lubricity, leading to increased friction and wear between the hydraulic components in your system, such as the pump’s rotating group against its housing or wear components. The asperities across the worn parts cause localized noise, chatter, and vibration above and beyond the usual noise generated by pumps and other components.
Although likely noise increases slowly over time as components become worn or scored, sometimes the rapid rise of offensive sounds signals the pump or motor are not long for this world. Awareness of your hydraulic system’s typical sound signature provides you with
an advanced warning to allow maintenance staff to step in before complete failure occurs.
Hydraulic systems rely on clean hydraulic oil to best take advantage of input energy from the prime mover. However, when the oil is contaminated, it causes a reduction in performance as gaps and clearances open up between the precise pistons, spools, vanes, or other parts. The increased clearances result in slower movement, less force, and reduced precision because fluid lost to leakage is wasted as pure heat. Such reductions in efficiency reduce productivity and increase energy consumption while hot oil bypasses to the reservoir rather than the actuators.
Paying attention to your hydraulic oil’s color also provides contamination insight. When hydraulic oil is contaminated with water, it may change color or appear foggy, which are sure signs that excessive saturation has taken hold. However, the oil may also appear darker brown color if oxidation burned the oil or resulted in circulating sludge. If you notice any discoloration, it is essential to have the oil tested to determine the source of the contamination and correct the problem.
Oil contamination can damage internal components, as seen on this gear pump.
| Courtesy of CD Industrial Group/ LunchBox Sessions
even the system components, if left unchecked. Bacterial contamination is more common in water-based fluids, although it may still occur in mineral-based oil highly saturated with water.
If hydraulic oil appears a darker brown color, oxidation may have burned the oil or resulted in circulating sludge. It is essential to have the oil tested to determine the source of the contamination and correct the problem.
| Courtesy of CD Industrial Group/LunchBox Sessions
In addition to color change, contaminated hydraulic oil may emit a foul odor. This odor indicates your oil is contaminated with bacteria, which can cause further damage to the hydraulic oil, or
Hydraulic oil contamination is the number one cause of damage to hydraulic systems and components, leading to reduced performance, increased maintenance and repair costs, and safety hazards. It’s essential to identify the most common symptoms of hydraulic oil contamination and take steps to prevent further damage. If you notice any of the symptoms listed above, it is important to have the oil tested and to take corrective action to address the contamination. In addition, regular oil analysis and maintenance can help prevent contamination and ensure optimal hydraulic system operation. FPW
Abbott Rubber: Hands-on and classroom. Abbott Rubber has been in business since 1951 and serves the OEM and distributor marketplace. They are one of the original members of HSI and they are a source for a broad range of customers around the world. The classroom topic for this visit will be a deep-dive into STAMPED.
NAHAD will host its HSI Hands-On (formerly Regional Training) on October 16-17. This program by the Hose Safety Institute promotes and develops an understanding and adoption of HSI guidelines and best practices in hose design and fabrication. Attendees will participate in a series of interactive presentations, visit distributor locations for hands-on exercises, and tour a manufacturer’s warehouse.
Registration will open the week of August 7.
Attendees will participate in interactive classroom learning and hands-on experiences in a variety of hose types. Training will be conducted in both a manufacturing and distributor environment. Activities at each site will showcase and demonstrate how HSI guidelines are used in practice.
This program is designed for those
newer to the industry, inside and outside sales, and customer support personnel. A full agenda can be found online at nahad.org but includes the following presentations on day one, featuring the following discussions:
• Manufacturers Panel: Emerging Markets and Technologies
• HSI Workshop: Helping End-Users Develop a Safety & Preventative Maintenance Program
• How Its Made — Hose Manufacturing Methods
• Mounting Technology & Line Routing
• Failure Analysis: How and Why
• About the HSI Program: Its Importance to the Industry and to You
Networking opportunities will include lunch and an evening reception.
On day 2, on-site visits will be held offering hands-on training. Participants will be divided into two groups and loaded on buses for a unique experience at each of the following three sites:
Uniflex: Hands-on and classroom. Founded in 1972, Uniflex is a system provider in hose production. They produce innovative, reliable, and durable hose crimpers, cutting machines, pinprick tools, skiving machines, marking tools, test systems, software, and cleaning machines. The classroom topic for this visit will be a presentation by Ultra Clean.
Kuriyama: Warehouse Tour and classroom. The Kuriyama of America group of companies includes eight subsidiaries and six distribution centers, as well as numerous distributors, providing a complete line of thermoplastic, rubber, and metal hose products and accessories including couplings and fittings, for use in industrial and commercial applications. The classroom topic for this visit will be a presentation on new product development and production.
Sponsors for the event include Tribute, PT Couplings and More, and Flexaust. Day one’s presentations will be located at the event hotel, the DoubleTree by Hilton Hotel Chicago O’Hare Airport – Rosemont. Visit nahad.org for more details and to register the week of August 7. FPW
Applications are now being accepted for the Future Leaders in Motion (FLM) Class of 2024 program, which will begin at the 2023 Industry Summit.
The FLM program is designed to develop and enhance the leadership skills of the next generation of professionals who will guide and lead FPDA, the industry, and their companies.
Over 13 months and approximately 60 hours, candidates will:
• work with a mentor and build relationships with their FLM peers,
• participate in self-directed and (virtual) classroom learning,
• complete a series of projects designed to ensure understanding of key concepts to increase performance and the bottom line, and
• enhance natural leadership abilities in positive and productive ways.
Leadership is the art of executing a set of critical skills that encompasses influence, impact, and integrity. Here is a snapshot of what candidates will gain individually and as a team:
• Behavioral Insights: Using the TriMetrixEQ Assessment, candidates will have a clear understanding of their leadership style and tendencies, strengths, and weaknesses.
• Distribution 401: Attend selected advanced UID workshops focused on driving net profit, understanding the cost of mistakes, managing inventory, and building margins. Develop a comprehensive understanding of key facets within the fluid power industry.
• Facets of Leadership: Understand the difference between leadership and management; develop the skill sets to create productive teams and collaborative environments; understand your method of communication to finesse win-win outcomes; improve verbal and written communication, hone your listening skills, and learn to read body language.
• Mentoring and Coaching: Work with a mentor in the industry and participate in small group and one-on-one meetings with a professional career coach.
• University of Innovative Distribution. Participate in this concentrated educational program focused on the unique needs of the wholesale distribution industry.
Candidates will be required to participate in about five hours of prescheduled programming a month. They will also attend UID one week in
March, and spend three days attending the Industry Summit over two consecutive years.
Key event dates include October 1-4, 2023 for the 2023 Industry Summit in Tucson, Arizona; March 11-14 at the 2024 University of Innovative Distribution in Indianapolis; and October 1-3 at the 2024 Industry Summit in Forth Worth, Texas.
Cost for participation is $5,000, as well as all travel and hotel fees for in-person events. The program fee includes two consecutive registrations to the Industry Summit at the beginning and end of the program ($1,800); one registration for UID ($1,295); three team and one-on-one coaching sessions; and virtual presentations and workshops.
Note: The program fee does not include the cost of travel, accommodations, and incidental costs of travel to attend program segments. This will be the employer’s responsibility.
In addition to candidates, the FPDA is also looking for mentors to pair with FLM participants and sponsors of the program. Sponsorships are available for $2,500. Sponsors receive year-round recognition as described below:
• Linked logo on FPDA’s home page and the FLM webpage
• Acknowledgment of support in all FLM marketing materials
• Linked logo in FPDA’s e-newsletter InMotion
• Recognition of sponsorship in all FLM e-seminars and workshops
• Acknowledgment of sponsorship at the 2023 Industry Summit in Tucson, Arizona including podium recognition, signage at the Industry Summit FLM program honoring the first graduating class, and recognition in the Summit agenda FPW
Learn more at FPDA.org.
A routine audit of a wood products company has turned up some surprising results on a system that was thought to be very efficient. The system is simple — one compressor, a 100-hp variable speed drive controlled (VSD) screw compressor, and a heatless desiccant air dryer. Data loggers were placed on the system by a compressed air auditor to measure pressure, power, and flow and found that, in reality, the system is running quite inefficiently compared to a normal optimized configuration, with system specific power (kilowatts consumed per 100 cfm produced) reaching very high levels during light system loading.
We can see from the system profile, Figure 1, that at higher system loads, the specific power drops to 22 kW per 100 cfm. However, during the weekend, the efficiency is very poor, hitting highs of greater than 42 kW/100 cfm. The auditor verified that this compressor is producing air at normal specific power of about 18 kW/100 cfm, so the question is: what is going wrong?
The answer lies in the placement of the flow meter in this system. It is located after the desiccant dryer because it is a thermal mass style that can only measure dry air. The purge flow into the dryer is therefore not measured and causes the reported system efficiency to be low. The dryer is an uncontrolled heatless desiccant style that consumes the same 80 cfm of rated purge flow constantly — even though the average flow through the dryer is about 160 cfm, much lower than its 500-cfm rating. The air dryer purge is the problem here. To add to the challenge, desiccant dried air is not required at this plant as there are no pipes that are exposed to freezing temperatures (and no special requirement for super-dry air in the production processes).
The solution to this efficiency problem is the replacement of the dryer with a more efficient style. The best solution would be to dry the air with a cycling refrigerated unit and save about 12 kW equivalent in purge flow. Savings for this would be roughly $9,000 per year. And if it turns out that a desiccant dryer must be used, purchasing a new one that has dewpoint control and uses an external heater — rather than straight compressed air to regenerate the desiccant — would save an estimated $5,000 per year.
It is best not to let an uncontrolled desiccant air dryer rob the system of its efficiency! FPW
MANUFACTURERS ACROSS ALL INDUSTRIES SEEK WAYS TO ELECTRIFY, DIGITIZE, AND AUTOMATE THEIR SYSTEMS TO DECREASE COSTS AND INCREASE EFFICIENCY.
ELECTRO-PNEUMATIC PRESSURE REGULATORS AND VALVES ENABLE SUCH EFFORTS WHILE IMPROVING PRESSURE AND FLOW RATE ACCURACY.
RACHAEL PASINI, SENIOR EDITORTHE QB3 ELECTRO-PNEUMATIC PRESSURE CONTROL VALVES IN THIS MANIFOLD HAVE INTEGRATED VOLUME BOOSTERS TO PROVIDE HIGH FLOW TO MULTIPLE PROCESSES. COURTESY OF PROPORTION AIR
, there were only manual pressure regulators that relied on the skill and precision of the human hand. With a delicate touch and some trial and error, the correct setting was found and never to be adjusted again. Then came electricity, which prompted I/P and E/P regulators that converted current and voltage to pneumatic pressure to achieve more control within a system. But in time, engineers recognized that not all systems had consistent supply pressure and that complex applications required variable pressure ranges. As such, the electro-pneumatic pressure regulator was born to provide real-time feedback and more accurate, automated control.
Here are five applications in which electro-pneumatic pressure regulators and valves improve accuracy and control in pneumatic systems.
Pneumatic testing is used to ensure functionality and determine the limitations of equipment, such as pipelines. It can also be used for quality control to check for leaks in closed-system devices. Whether using pressure decay, vacuum decay, pressure cracking, chamber, burst, or bubble testing methods, pressure regulators are essential to control the amount of pressure applied to the system or device being tested.
For instance, in medical manufacturing, IV bags must undergo accurate leak testing, especially around the seams and ports, to ensure the fluid inside is contained. Manufacturers often use two devices for this process: one for positive pressure and one for vacuum. However, pressure regulators such as Proportion Air’s QB3 are designed as a single unit that performs both functions.
As shown in Figure 1, the controller sends a signal to the QB3 to command the air pressure applied to the bag. Then, the regulator applies positive pressure to fill the bag with test gas. A small valve isolates the bag, and the system monitors pressure for a set period to verify that no leaks
exist. Once the test is complete, the controller sends a signal to the QB3 to apply a vacuum, and the gas is voided. This same principle can apply to any leak test where an item needs to be filled and then fully exhausted.
“Filling the bag to an accurate pressure and evacuating to an accurate flow is important,” said James Spence, business development manager at Proportion Air. “A separate pressure sensor is not required to verify pressure when using a proportional electronic pressure controller for applications with extremely tight tolerances. Pressure is held at the necessary level and actively measured by a flow transducer.”
Gas-assisted injection molding is another example that works similarly for glass or plastic parts. The process partially fills a mold with material, then injects an inert gas to push the material into the mold’s voids and create hollow areas in the part, reducing part weight without compromising strength. This application benefits from a double-loop pressure control assembly, where output pressure
measurements can be returned to the regulator to ensure the correct pressure.
For example, in Figure 2, the double-loop assembly consists of a QB2X electronic pressure regulator, air volume booster, and DSTY pressure transducer to ensure tight regulation. The QB2X regulator pilots the air volume booster, allowing additional gas flow to the application. The DSTY transducer measures the output pressure of the air volume booster and delivers second-loop feedback to the QB2X, which adjusts the air volume booster pressure accordingly.
“While an assembly may look complicated, they’re basically plug and play,” said Spence. “Ours are closed-loop devices with no PID loop required. The units come from the factory calibrated and ready to hook into a system without complicated programming. They also aren’t prone to drift. If you see drift, check the system for plumbing leaks, wiring, and electronic signal levels. Always verify measuring equipment before recalibrating.”
An electro-pneumatic regulator’s output pressure is easier to control when its supply pressure is close to its desired output. When there is a high-pressure differential between supply and output, the inlet valve may not operate fast enough to prevent significant setpoint overshoot and instability. And repeated or sustained over-pressure can lead to sensor damage.
Over-pressure is a concern in sensitive applications that require precise pressure regulation to fill small volumes. Such applications benefit from an additional miniature regulator that controls the supply air before it reaches the electro-pneumatic pressure regulator. This is especially true when dealing with inches of water column or other small values.
Figure 3 illustrates the SaveAir miniature regulator lowering the air pressure into the QB1X electropneumatic regulator to a preset limit, protecting the internal sensor from over-pressurization and reducing overshoot or instability.
Miniature regulators are also helpful for compact and mobile systems. As the trend for smaller-but-stronger equipment persists, design engineers seek solutions that ensure accuracy while decreasing the equipment’s footprint.
Pressure resolution is the smallest change in command that will result in a change in output pressure. It can also be described as the ability of the transducer to resolve an output signal in the units of the output device scale. High resolution means that a finer scale is used, and the amplitude of the full scale is divided into smaller increments.
“When you have smaller increments to work against, it becomes easier to offer specific and even minute results or work at the cellular level,” said Ron Hibbler, applications manager at Proportion Air. “We achieved this high-resolution pressure control using a true proportional solenoid valve coupled to a unique analog PID control circuit. The true proportional valve eliminates digital stepping.”
A common use for high-resolution devices is microfluidic applications, where small amounts of gas must move through tiny channels. Highly accurate and high-resolution devices provide stable and repeatable pressure control, which results in stable and repeatable flow through the microfluidic channel. Industrial groups and researchers find microfluidics attractive because it dramatically reduces sample and reagent consumption, shortens experiment time, and allows multiple tests to run simultaneously.
“The need for a fast response isn’t only for microfluidic applications,” said Hibbler.
“Products in our electronic regulator category offer a pneumatic response of less than 1 sec and an electronic response in under 10 msec.”
Many applications require differential pressure control, which requires precise pressure control relative to a different pressure in the same process. For example, Figure 4 shows a dispensing application where two QPV highresolution pressure regulators work in tandem
to dispense a sample-solution combination. A counting sensor gathers information at the dispensing point and sends it to the PLC, which calculates the required pressure and sends corresponding signals to both QPVs.
Each QPV is calibrated with respect to an atmospheric reference point to constantly maintain a specific differential pressure from solution to sample. The solution-dispensing QPV’s atmospheric reference point port is tied to the output of the sample-dispensing QPV through the differential sense line. This means that the solution-dispensing QPV will use the pressure controlled by the sample-dispensing QPV as the baseline, ±1 psi. For instance, if the sample-dispensing QPV is set at 15 psi, the solution-dispensing QPV will be 14 to 16 psi.
“The SPV is another product that trims all unnecessary size and weight while maintaining the high performance of the larger, more rugged QPV series,” said Hibbler. “This compact high-resolution valve does not exhaust downstream pressure, only fill and control during constant flow conditions.” FPW
•
Check
•
• Industrial
• Mining
• Forestry
• Medical
• Aerospace
• Factories
• Mobile Equipment
• Defense
• Machine Tool
• Testing Equipment
• Ocean Depth Technology
• Automotive
• Food Processing
• Agriculture
• Industrial
• Aviation
• Petrochemical
• Marine
• Subsea
Giventoday’s push to limit global warming and embrace a carbon-neutral future, there is a heightened focus on improving the efficiency of industrial and mobile equipment and their underlying fluid power systems. One area of keen interest involves minimizing the losses in hydraulic pumps and motors.
Part of the losses of hydrostatic devices are commutation losses, sometimes called compression losses, that result from the unavoidable and continuous process of compressing and expanding oil in the displacement chambers of a pump or motor. Commutation losses are strongly pressure related, but also depend on other factors like the type of oil, the pump construction, and the design and sizing of any silencing grooves. Depending on the operating conditions, commutation losses can amount to 50% of the total losses of a pump.
Researchers are investigating shuttles as a means to reduce or maybe even eliminate these losses. Shuttles are small connections between the individual and neighboring cylinders or displacement chambers. Each shuttle consists of a small cylinder which has two seats, one at each end, and contains a small ball. The shuttle ball can move back and forth inside its cylinder and, while the ball moves, oil flows in and out of the shuttle. Shuttles were first introduced for hydraulic transformers and, in 2021, were presented as a solution in pumps and motors.
Engineers at INNAS recently examined the effects of shuttles on efficiency in a fixeddisplacement slipper type pump from Bosch Rexroth, which was tested with and without shuttles. Results show that adding shuttles to the pump substantially increased both average and peak efficiency over a wide range of speeds and pressures.
Hydrostatic pumps operate between two pressure levels: a low pressure level at the supply side and a high pressure level at the delivery side of the pump. For example, a nine-piston axial piston pump switches 18 times per revolution from one pressure level to the other: from low to high pressure in the bottom dead center (BDC) and from high to low pressure in the top dead center (TDC). At 3,000 rpm, this amounts to 900 switches per second.
This switching process, called commutation, occurs not only in hydrostatic pumps but also in motors and hydraulic transformers — in both fixed and variable displacement versions. A few pumps use valves to facilitate and enable the switching process, but the vast majority of hydrostatic machines uses a distributor, similar to the function of a commutator in directcurrent electric motors with brushes. In axial piston devices, the valve plate or port plate acts as the distributor. Similar components are found in radial piston pumps and motors, vane pumps, gerotor and geroler motors, and even in gear pumps.
Adding shuttles to axial piston pumps can substantially increase overall efficiency.
The drawing shows three of the nine pistons and cylinders of the A4FO28-pump. Each cylinder is connected to two shuttles, as is shown for the middle cylinder. In total, the revised pump has nine shuttles applied.
In an ideal machine, for example an ideal axial piston pump, piston movement compresses and expands the oil. For instance at BDC, the piston and its cylinder move from the low pressure kidney (the kidney-shape port machined through the valve plate) to the high pressure kidney. In between these two kidneys is the sealing land. When the barrel port is closed off by the sealing land, it has (for a short time) no connection to either the low or the high pressure side of the pump. In that case, the ongoing piston movement will result in compression of the oil inside its cylinder, since the barrel port of the cylinder is closed by the sealing land.
In this ideal pump, the sealing land around BDC needs to be dimensioned such that compression stops precisely at the moment when the pressure level in the barrel cylinder reaches the pressure level of the high pressure kidney. If the sealing land is too short, compression will not be enough and oil in the cylinder will open prematurely to the high pressure kidney. If the sealing land is too long, high pressure spikes will occur. Also in the commutation zone of TDC, the sealing land needs to be dimensioned exactly right (that is, not too long or too short) to avoid short circuiting or cavitation.
The problem is that the valve plate’s geometry and dimensions are fixed after production, whereas the ‘ideal’ timing of commutation cannot be defined as a constant. The amount of compression and expansion strongly depends on parameters like the pump pressure, the bulk modulus of the oil, the amount of leakage (and hence the oil temperature) and even the rotational speed of the pump. In current pumps and motors, manufacturers accept that commutation can’t be ideal. Instead, as a compromise, most commutation conflicts are softened by means of silencing grooves or pressure relief grooves.
The design of the valve plate and its silencing grooves has been a subject of numerous studies because it determines the noise, pressure pulsations, torque variations, and compression and expansion losses (commutation). Most of these concepts are meant to reduce noise in pumps, not power losses.
In 2021, INNAS presented a more general solution for applying shuttles in hydrostatic pumps and motors. Shuttles can, in theory, completely eliminate commutation losses and strongly increase overall efficiency. The solution can be applied in any hydrostatic machine which uses a distributor or valve plate and is applicable for both fixed and variable displacement machines.
To demonstrate the effects of shuttles on pump efficiency, INNAS specialists first tested a standard 28 cc Bosch Rexroth A4FO28/32R, fixed-displacement axial piston pump with no modifications, across a wide range of operating conditions. Efficiency plots at various speeds and pressures are shown in the nearby graphics.
After that, the pump was adapted to incorporate shuttles:
• Connections (shuttle pathways) were made between each pair of neighboring barrel cylinders;
• A new valve plate was designed and manufactured, without silencing grooves but with larger sealing lands;
• The spherical bearing surfaces of the new port plate and the barrel were lapped together to match both surface profiles.
Aside from the new valve plate and adaptation of the barrel, all other components were unchanged. This way, any effects measured can only be attributed to the shuttles and the new valve plate.
As the original A4FO28 is not designed for shuttles, fitting them into the existing barrels was a challenge. The shuttles had to be positioned to use the pressure difference across the barrel ports, and the shuttle volume needed to be large enough for any pump operation between 0 and 400 bar. Finally, the shuttles must be positioned such that centrifugal forces don’t influence the movement and positioning of the shuttle balls. Each barrel cylinder connects to two shuttles: one leading the direction of rotation and one following. The shuttle balls are 4.5 mm diameter ceramic balls with a mass of 0.37 gm. The shuttle chamber has a 4.9 mm diameter. The shuttle balls make a stroke of 6 mm inside the shuttle cylinders and, in the end positions, the balls push into a conical seat and act as a check valve.
The adapted barrel was also designed so that the shuttles could be altered, permitting a change in the size, mass or material of the shuttle balls. It was a compromise solution in which one end of the shuttles has a 90° angled connection to the cylinder, which results in a larger flow restriction and, thus, in higher pressure differences than preferable.
A new valve plate design is also needed. The new plate does not rely on silencing grooves. Instead, the sealing lands around the top and bottom dead centers (TDC and BDC) are increased. The length of the sealing lands is determined by the maximum pump pressure and should be at least large enough to allow for a full compression (after BDC) and full expansion (after TDC). The sealing lands may even be larger, as long as the shuttles are large enough to compensate for any differences or mismatches.
In operation, the barrel ports move across the port plate. In the new plate design, the sealing lands have a length much larger than the arc length of the barrel port. The difference allows for full compression and expansion of the oil in the barrel cylinder, even when the pump operates at maximum
pressure. The distance between the end of the low pressure kidney and BDC, and between the end of the high pressure kidney and TDC, is half the arc length of the barrel port. Consequently, the barrel ports close exactly at the TDC and BDC positions of the pistons. Immediately after reaching one of the two dead centers, piston movement starts the compression (BDC) or expansion (TDC) of the oil contents of the cylinder.
If the pump operates at a lower pressure than maximum, the compression or expansion will stop after the pressure in the barrel cylinder has reached the pressure level of the next kidney. At that point, the shuttle ball of the leading shuttle will start to move, thus avoiding any overpressure or cavitation.
Contrary to the positive overlap of the new valve plate, the old valve plate has a negative overlap with respect to the silencing grooves. Consequently, there is some degree of short-circuiting. Further, the barrel ports
are immediately connected to the next kidney, which results in an extremely fast compression or expansion with high pressure-change rates. Silencing grooves limit these rates to some extent, but nevertheless the rates are very high, resulting not only in dissipative losses across the silencing grooves, but also in strong pressure and flow pulsations, noise, and possibly cavitation and wear.
The pump was tested in the INNAS lab following Bosch Rexroth pump specifications. All tests were performed with Shell Tellus Oil S2 MX46 at a supply temperature of 50°C (±0.5°C). In order to measure at a maximum allowable rotational speed of 3,750 rpm, the supply pressure needed to be 1 bar above atmospheric pressure.
The A4FO28 was tested in 104 different operating points, ranging between 50 and 400 bar and between 10 and 3,750 rpm. All operating points were measured at steady state conditions
The barrel ports, which move across the port plate, have an arc length of 30.2°. In the new valve plate design, the sealing lands have a length of 15.1 + 28.1 = 43.2° in the TDC and of 15.1 + 37.1 = 52.2° in the BDC. This is much larger than the arc length of the barrel port. The difference allows for full compression and expansion of oil in the barrel cylinder, even when the pump operates at maximum pressure. The distance between the end of the low pressure kidney and the BDC, and between the end of the high pressure kidney and the TDC is 15.1°, which is half the arc length of the barrel port. Consequently, the barrel ports close exactly at the TDC and BDC positions of the pistons. Immediately after having reached one of the two dead centers, piston movement starts compression (BDC) or expansion (TDC) of oil in the cylinder.
micrometers. More research is needed to fully explain the results. But the measured data shows unequivocally the positive effects of shuttles on pump efficiency.
for a period of 10 seconds with 0.05 seconds interval between the individual measurement points. These data are averaged in postprocessing. A run-in procedure was performed before each test, for the original and the adapted pump.
At low rotational speeds, pump leakage can become larger than the flow that the pump can deliver. In those cases, the pump is not capable of maintaining the desired pressure, and an additional supply pump is used to maintain the desired pressure level. In such cases, it was no longer possible to measure and define the overall efficiency.
Results show that shuttles and the complementary new valve plate have significantly improved pump performance. Peak efficiency increased from 91.9% to 96.4%. In the range between 500 and 3,000 rpm, and 100 and 400 bar, average overall efficiency has increased from 90.8% to 94.3%.
The contour plots shown nearby represent the measured overall efficiency of the A4FO28, without and with shuttles. Only at 50 bar and speeds ≥ 3,500 rpm was there no improvement of the overall efficiency. In all other cases the overall efficiency increased, especially at pump pressures above 200 bar. This was expected, as shuttles reduce the commutation losses which are strongly pressure dependent.
The most remarkable results are at operating speeds below 1,000 rpm. In this area, overall
efficiency increased by more than 30%. For instance at 100 rpm and 400 bar, the shuttles have increased the overall efficiency from 49.6% to 75.3%, an increase of 33.5%.
The experiments have proven the shuttles substantially increase overall efficiency. Total losses are reduced by 41% on average, and up to 60% at high pump pressure and low rotational speeds.
The improvement is largely due to a reduction in hydromechanical losses. Part of the improvement is a result of lower commutation losses, which was the reason for developing the shuttle solution. But measurements show that, on top of the reduced commutation losses, the shuttles also cut friction losses in the pump itself, especially at low rotational speeds. The shuttles also reduce
The table summarizes the main effects of shuttles on the overall efficiency and losses.
the volumetric power losses by 56% and the drain leakage by about 70% on average. The reason for the reduction of the volumetric loss is uncertain.
One “guess” is that leakage between the slippers and swash plate is reduced. During the suction stroke, the pistons and slippers are pulled away from the swash plate. The retainer plate keeps the slippers close to the swash plate, thereby limiting the gap to about 20 µm. When the piston passes the BDC, the piston and slipper return to the swash plate. This takes time, but since the commutation is almost instantaneous, oil at a high pressure leaks via the gap between the slipper and swash plate to the case, while the slipper is returned to the swash plate and the gap height is reduced again to a few
It should be noted that this is the first test result of shuttles in a conventional pump. We expect that the shuttles can be improved even further when shuttles are integrated in the design of new pumps, instead of adapting conventional pumps.
According to the design principle, the shuttles also work in hydrostatic motors, and in twoquadrant pump/motors. In theory, the shuttles might also work in variable displacement machines. In these pumps and motors, the detrimental effects of the dead volume is much more important than in fixed displacement machines. It is therefore expected that the shuttles could result in even higher efficiency improvements than in fixed displacement machines. Further development work and testing are needed in this direction. FPW
INNAS innas.comThese plots show the overall efficiency of the A4FO28 with and without shuttles.
How shuttles affect efficiency
The latest “green” machines come in all types and sizes.
Ken Korane, Technology Editor
The MT 625e compact lift truck is designed for rough-terrain and suited for work on confined job sites.
of Manitou Group
Mobileequipment manufacturers large and small continue to jump on the electrification bandwagon, touting the benefits of zero emissions, quiet operation and low long-term maintenance costs. Most of the attention to date has been on relatively light-duty equipment like mini excavators and walk-behind compactors and track loaders. In reality, OEMs are expanding their electromobility focus across a diverse range of equipment and applications. Here’s a quick look at some new machines we spotted at Conexpo 2023 in Las Vegas.
The Manitou Group has introduced a new line of electric rotative telehanders that include the MRT 2660e, part of the recently announced VISION+ range. The 100% electric unit is viewed as a versatile tool for handling operations with zero emissions, low noise levels and reduced fuel consumption. It has a loading capacity of 13,000 lb, lifting height of 85 feet and a maximum outreach of 71 ft.
The model performs as well as similar internal combustion models and even allows simultaneous boom movements, thanks to intelligent hydraulics. A 700 V/65 kWh lithium-ion battery ensures optimum use even in cold climates, according to company officials. If needed, customers can add a second 700 V/65 kWh battery to boost the range by an additional four hours. Users also have a third option with a hybrid version of these models that serves as a range extender.
Several charging mode options give operators wide flexibility. An on-board 11 kW charger permits charging in 4 hours 30 minutes, and an on-board 22 kW charger brings recharging time down to just 2 hours 15 minutes. An even quicker solution is an on-board charger that allows charging in less than an hour — although the power source must be 400 Vac.
The MRT 2660e has a 107 kW drive motor and an 84 kW electric motor powering the hydraulics. The hydraulic pump is a fixed displacement piston type that offers 46 gpm flow. System pressure is rated at 5,076 psi.
Manitou is also adding to its range of compact lift trucks with the commercial launch of its first 100% electric compact telehandler. The MT 625e has a capacity of 5,500 lb, a lifting height of more than 19 ft, and a maximum outreach of 11 ft.
Fitted with a 25 or 33 kWh lithium-ion battery, this model reduces maintenance costs by 56% and significantly lowers the total cost of ownership for the user, according to company officials. With a 13 in. ground clearance and quick combined hydraulic movements, the MT 625 e is suited for rough-terrain and a first choice for work on confined job sites requiring low emissions, such as urban areas, renovation of historical buildings, and indoor applications.
The unit is designed with an on-board charger, and users can install additional batteries for more autonomy on site. Electric drive motor power is 14 kW and hydraulic motor power is rated at 25 kW. The hydraulic gear pump provides flow of 21 gpm. System pressure is 3,408 psi.
Liebherr has expanded its portfolio of piling and drilling machines for deep foundation applications with the LB 30 “unplugged” drilling rig. The battery-powered drive concept offers the same performance as the conventional diesel version and with the advantage of zero emissions.
While the diesel LB 30 is rated at 320 kW (429 hp), the battery-electric unit includes an electric drive motor rated at 390 kW, with energy storage in high-performance Li-Ion NMC (nickel manganese cobalt) batteries.
During operation the drilling rig can be connected to a conventional electric supply (mains voltage is 400 Vac) or powered by a battery without a cable, therefore “unplugged.” The battery is designed for a working time of four hours in normal operations. Whether in battery or plugged-in operation, drilling performance remains unchanged.
The drilling rig handles all common deep-foundation operations, such as Kelly drilling (a standard procedure for installing large-diameter piles), double rotary drilling, full displacement drilling, continuous flight auger drilling, soil mixing, and applications with a vibrator or hydraulic hammer. The machines can be deployed for drilling diameters of up to 11.2 ft (3.4 m). Both electric and diesel LB 30s can be lowered for transport and are designed for fast set-up at the jobsite.
The hydraulics-intensive machine includes double axialdisplacement pumps (2 × 71 gpm) in an open-loop system for attachments and a 34 gpm pump for kinematics. The set-up allows all operations to run simultaneously. Fixed axialpiston hydraulic motors handle the travel drive and swing functions. In addition to drilling, travel and swing operations, other hydraulic functions include powering the lift cylinders, winches, chain tensioning on the track crawlers, and hydraulic release of travel and swing brakes. Hydraulic tank capacity is 158 gal, with electronic monitoring of all filters. Maximum working pressure is 5,584 psi (385 bar) and maximum drilling torque is nearly 300,000 ft lbf.
With growing interest from municipality customers for quieter, cleaner solutions that meet intensifying sustainability demands and regulations, Gradall has unveiled an electrified concept model of its multipurpose, highway speed wheeled excavator, powered by Volvo Penta’s electric driveline. The zero-emissions machine, named EL41H4, is an electrified version of the OEM’s XL 4100 V highway speed wheeled excavator.
The concept machine is powered entirely by two Volvo Penta batteries, matched to the duty cycle of the excavator,
which fit into the existing engine bay. The electric driveline system from Volvo Penta also includes the complete high voltage system — electric motors, gearboxes, inverters, junction boxes, and cabling.
Unlike a traditional hydraulic excavator, Gradall’s product features a telescopic boom mounted next to a separate cab sitting to the rear of a road-going chassis that allows the machine to be independently dispatched to many locations throughout the workday, rather than requiring a low loader for transport.
With a hydraulic system powered by an electric machine power take-off (EM PTO), this concept machine can effectively use battery power to transport its own excavator. The system will deliver 94 kWh of energy and, with the likelihood of the EL41H4 operator returning to the yard between jobs or for lunch, the potential is high for opportunity charging, or reaching full capacity
in under 45 minutes from a 150 kW charger.
For comparison, the conventional diesel-powered XL 4100 is rated at 228 hp (168 kW) @ 2,200 rpm. Its hydraulic system includes a load-sensing axial piston pump delivering a maximum 77 gpm flow and a gear pump (for pilot and cooling) supplying 11 gpm.
Four double-acting cylinders handle boom, hoist and tool functions; and three hydraulic motors power the swing, tilt and remote-drive functions. Pressurecompensated, load-sensing valves with circuit reliefs are used in all circuits. The machine also has integral hydraulic power steering via a gear-type pump. Operating pressures are up to 4,800 psi. Rated boom force is 21,940 lb and rated bucket breakout force is 24,900 lb.
The unique highway speed design — and its suitability for work in environments where knuckle boom models may not be the ideal fit for operation, such
as under overhead obstructions like power lines — means the concept has huge potential for application to other equipment in the Gradall portfolio. Currently, the EL41H4 is still a concept machine, and extensive testing and development is required to move toward commercialization.
The fully electric DT6 articulated dump truck from Hydrema, based in Støvring, Denmark, marks the company’s first foray into the electric vehicle segment. The completely new design combines an electric direct drive with ondemand hydraulics. Among the key features: quiet operation and zero emissions.
The machine has an articulated chassis with a center pivot point, along with two double-acting hydraulic stabilizers that ensure firm control when driving and tipping. Carrying capacity is 5,500 kg (12,100 lb).
The DT6’s new purpose-built electric platform offers maximum efficiency with minimal losses and an exceptionally low noise level, according to the company. The system is based on a liquid-cooled 96 V ZF eTrac motor, transmission and axles. Power ratings are 29 kW continuous and 69 kW peak. Three different drive modes, Power, Normal and Eco, let the operator adjust for different loads, accelerations and energy recovery situations.
Enhancing system efficiency is on-demand hydraulics. A separate electric drive powering an ultralow-noise hydraulic pump supplies tipping and other auxiliary functions. The pump only runs when necessary to minimize losses. Hydraulic power is 14 kW. A second electric motor drives the hydrostatic load-sensing
articulated steering, which includes two double-acting cylinders with damping, priority valves, and integrated emergency steering. Another electrohydraulic feature is the 180° MultiTip. This compact body-swivel system lets the operator dump the load continuously over a 180° slew range. The robust system is mounted on a large slew bearing, and tipping function is via two powerful double-acting cylinders.
Liquid-cooled 63 kWh lithium ion batteries with an integral Thermal Management System help ensure optimum battery life, with expected battery lifetime of 8 to 10 years. The Hydrema DT6 comes with a powerful 18 kW integrated onboard charger. Under normal
working conditions (8 hours), it only needs to charge during work breaks to ensure maximum uptime throughout the day.
John Deere showcased new E-Drive (hybrid-electric) and E-Power (battery-electric) machines to help address the growing market for alternatively powered products. By 2026, the company aims to offer more than 20 electric and hybrid models that will help reduce the carbon footprint of the construction industry.
E-Drive machines feature an electrified drivetrain with a combustion engine as the primary power source. The product line enables better fuel economy, improved powertrain component life and stronger pushing power on the job versus traditional models, said the company. Available versions include the 644 X-Tier and 944 X-Tier wheel loaders; and the 850 X-Tier dozer, which features a less-complex drivetrain that powers each track with an electric motor to maintain the maneuverability and control of a traditional hydrostatic dozer.
John Deere will also offer several E-Power machines that rely on battery systems from Kreisel Electric, which reportedly provide lower
supplies 8.7 gpm. Implement circuits are rated to 4,975 psi and travel hydraulics to 5,047 psi. An available power boost function raises pressure when needed to 5,265 psi.
John Deere is also developing an electrification infrastructure to address challenges faced by battery electric vehicles in off-road production environments. The system will address needs for charging, data and connectivity, machine support, and will include a range of solutions for overnight and fast charging. It will also help customers monitor usage remotely and manage work while charging their equipment. All John Deere machines and charging stations will use common automotive-style charging connections, helping to simplify the recharge process for electric equipment.
Clean and compact Wacker Neuson aims to help construction contractors meet job-site challenges whether the task demands conventional equipment or alternative-powered battery electric machines. Case in point is the EZ17e 1.7-ton battery-powered mini excavator, essentially an electric analog of the company’s proven dieselpowered EZ17 excavator.
the power and performance needed for digging or breaking efficiently and is an excellent zeroemission solution for indoor applications and in areas where noise and exhaust are a concern, such as construction sites in urban areas and those operating at night.
The battery in the EZ17e offers all-day run time (typical battery run time is 420 minutes) and it can be recharged using a common 240 V, single-phase outlet. Charge time is between five and six hours. In addition, the machine can continue to operate in a stationary position while connected to a power source. The
daily operating costs, lower jobsite noise, and zero tailpipe emissions. The company first began testing the 310 X-Tier E-Power electric backhoe in 2021, and the machine will enter the next phase of development in 2023 based on customer feedback. The 244 X-Tier compact wheel loader is suited for a variety of material handling applications.
The 145 X-Tier E-Power mid-size excavator concept was displayed at the 2023 Consumer Electronics Show and at Conexpo. While no specs have been announced for the 145 X-Tier, the similar-size conventional 135 P-Tier excavator has a 101 hp diesel engine powering open-center, pilot-operated hydraulics. Two variable-displacement axial-piston main pumps supply 28 × 2 gpm flow; and a pilot gear pump
The EZ17 has an effective power rating of 13.8 kW (@2,200 rpm) and, with no rear overhang, is well-suited for working directly alongside walls and obstructions. The drive system combines with a load-sensing hydraulic system (load-independent flow distribution) to deliver quick working cycles, wide application flexibility, and straightforward control for comfortable and fatigue-free operation of the excavator. Thanks to hydraulic pilot control, regardless of the load, the control movements on the joystick stay the same, which increases operating performance while reducing fuel consumption.
A variable-displacement pump delivers flow of 39.6 lpm (10.3 gpm) with operating pressure of 240 bar (3,480 psi). Up to four additional control circuits can be factoryinstalled to suit a variety of attachments.
The tracked EZ17e offers the same features and performance but is powered by a 16.5 kW synchronous reluctance motor and 23.4 kWh lithium ion battery. Thus, the machine provides
battery includes an integrated heater that allows charging regardless of the ambient temperature, and the unit can be charged from various power sources (100 to 415 V).
The EZ17e offers a simple intuitive operating concept that enables simple and comprehensive control of the excavator. The machine is operated using a joystick, jog dial and keypad with all the information needed in the easy-to-read, 7-inch display — for example the charge level of the battery or settings for auxiliary control circuits. It has a maximum digging depth of 97.7-in., a breakout force of 4,608 lb. and the ability to run auxiliary attachments such as hydraulic breakers.
The zero-emission excavator has been a success in the European market and will launch in North America in late 2023 or early 2024. FPW
The John Deere145 X-Tier E-Power Excavator is shown loading materials into an articulated dump truck. Courtesy of John DeereTiny particulates in lubricants that are invisible to the naked eye can have costly consequences in hydraulic systems.
In the world of mechanical maintenance, machinery breakdowns are a reality. Mechanical wear occurs constantly, and moving parts erode in quality over time. According to a study from the STLE and the National Research Council of Canada, 82% of mechanical wear is caused by particle contamination, making contamination one of the leading causes of hydraulic system failure. Additionally, it is common for machinery maintenance teams to ignore fluid cleanliness despite it being one of the major causes of breakdowns, leading to excessive downtime and lost profits.
The particles that damage system components the most are too small for humans to see with their naked eye — somewhere in the one to 10-micron range, or less than 10 times smaller than a grain of salt. These clearance-size particles enter the lubrication zone between machine parts and generate wear. Additionally, dirt and contaminants cause as much as 80% of hydraulic system failures, which can cost up to $100,000 per year.
Since many of these tiny particles are invisible to humans and exist within machinery, it can seem like a mission impossible to prevent them from causing damage to a system. However, there are plenty of ways to slow and mitigate mechanical wear in complex machinery, including routine maintenance and proper lubrication of the mechanical systems. Let’s explore how these particles cause damage to mechanical systems and best practices for avoiding them.
Many machinery operators assume that any new oil they purchase will meet both the performance and cleanliness requirements set by the equipment manufacturer, but that’s usually not the case. End users often focus only on the performance specifications of new oil but do not examine how that oil will perform in a given component application. To achieve maximum component life, starting with new oil that meets the cleanliness specifications set by the original equipment manufacturer (OEM) is important.
Each time an oil is transferred, the oil can pick up more contaminants. In fact, it’s common for a lubricant to increase two to four ISO Cleanliness Codes — a measure of allowable contaminant particle size in a lubricant — during the distribution process. Typical new oil could contain up to
32 times more particles than the acceptable level. That’s because most typical new oil is not certified to meet a specific cleanliness level from the oil manufacturer or distributor at the point of delivery. Bulk oil can be transferred up to eight times on average before it reaches equipment, significantly raising the possibility of contamination in that lubricant.
It also doesn’t take much to contaminate clean oil. As little as
one teaspoon of dirt in 55 gallons of oil could equate to as many as one billion particles that are four microns and larger. This level of contamination can be a double negative by generating wear and restricting the oil from protecting parts. Additives in the oil can be consumed by trying to manage the level of contaminants, which can lead to shortened oil life and equipment life.
The two leading types of contamination in oil are
particulates and water. Particles typically enter a lubricant or oil after floating in the air, traveling through water vapor, or when transferring a lubricant. Catalysts for oil contamination, such as wear metals, water, and high oil temperature, all lead to oil degradation. The result is dirty oil, acid, sludge, and varnish formation within a machine’s component.
The most common causes of particle contamination within a machine are abrasion, erosion, and fatigue — all of which are caused by a combination of particulates or water breaching into a machine’s lubrication zone and adding pressure to that machine’s mechanical functions. Once they enter into a lubricant, these microscopic contaminates create wear, lead to costly equipment failures, and result in unstable operation.
While the sources and causes of machine decay are numerous and hard to protect against, there are still many ways to proactively defend systems against these damaging particles.
With uncertainty around an oil’s contaminant levels, many resort to pre-filtering oils themselves. However, this is a bad idea for several reasons. First, pre-filtering new oil can be expensive and a risk to the machinery. Consider the fact that purchasing and operating new filtration equipment spends additional budget. Add to that the costs for additional manpower to perform tasks that should be handled by a supplier. If someone unfamiliar with the process attempts to filter oil, they can over-filter it and remove important additives necessary for equipment success, so filtering should always be handled by a technical expert.
Often, companies purchase filtration equipment that is not designed for their applications, or their filtration systems are not properly maintained. Filtration results are also typically not measured or logged before or after the process when conducted on site. The end result is that oil filtration targets are rarely met, equipment suffers, and more contaminants are added to the oil.
Ensuring that any filtration is done by a technical expert is critical, but still, filtration can only do so much. Filters on equipment will remove some, but not all, contaminants — and in most cases, the damage is already done. By the time you recognize that oil is contaminated, the oil has likely already caused damaging wear to machinery. Many systems are not properly balanced or sized to exclude and remove the most critical clearance-sized particles, so even when oil is filtered, it can still carry damaging contaminants. Starting with clean new oil that meets the OEM specifications will ensure harmful particles are not introduced to the system and ease the tension for onboard filtration.
Keeping hydraulics as clean as possible is the key to maximizing productivity and component life. To ensure a long, productive lifespan from components, pay close attention to the OEM’s machine component parts’ ISO Cleanliness requirements. A component’s sensitivity to contamination determines the maximum allowable particulate size in the lubricant, which in turn determines how clean the oil needs to be.
A good rule of thumb is that the oil should comport with a cleanliness level protecting the tightest machine clearance on the equipment. So, if a proportional control valve on a hydraulic system is the tightest clearance on a piece of equipment, then the ISO Cleanliness Code that the component requires would be the target level for new oil.
In addition to selecting the most appropriate oil for your component, you can
ensure proper lubrication of your system by starting with clean oil and monitoring that cleanliness as it functions. Additionally, to ensure that oil remains clean, routinely replace dust caps on lubrication valves and oil filters to reduce contaminants and use certified oil transfer containers to keep oil clean and dry during transfer.
What matters most is that the system is healthy enough to function both currently and in the future. Avoiding breakdowns and managing a fully functional system starts by ensuring that oils and lubricants are appropriately graded and clean enough for their applications. FPW
Chevron Lubricants chevronlubricants.com
The Italian Trade Agency, in cooperation with UCIMU-SISTEMI PER PRODURRE, is pleased to announce this one-day forum
YOU ARE INVITED TO JOIN US TO LEARN AND NETWORK WITH:
Leading Italian suppliers to industry and how each contributes to a more scalable, resilient, and secure manufacturing environment.
Scalable, resilient, and secure manufacturing principles are important for businesses to ensure that they can handle growth or changes. These principles can be applied to build greater resilience into supply chains, structure organizations and decision processes for resilience, build resilient and scalable machinery and technologies, and build more secure and resilient next-gen U.S. supply chains and manufacturing ecosystems.
MORE INFO & REGISTRATION: www.italtradeusa.com/vitruv-2023
Thought leaders delivering Manufacturing Market Outlook and Smart Manufacturing Trends presentations.
Proposition:
Reducing maintenance time and expense is important, especially today with limited resources and lower budgets. If a hydraulic hose can last longer, your productivity increases, and you see savings in parts and
Parker’s Critical Protection (CP) hose cover establishes a new standard for preventing hose failure. CP prevents damage to the hose cover by incorporating a patent pending technology. Other less effective options are used today, but they limit hose flexibility, increase the labor needed to build and install the hose, make routing difficult, and add weight to the hose. In addition, CP is also effective against abrasion damage. If you’re faced with a demanding application, Critical Protection cover can assist in preventing hose failure, and extending hose life.
Parker Hannifin Corporation
Fluid Connectors Group
Hose Products Division
30240 Lakeland Blvd.
Wickliffe, OH 44092
phone 440 943 5700
fax 440 943 3129
HPD.Support@support.parker.com
www.parkerhose.com
Hägglunds Quantum hydraulic motor range does away with established barriers, combining torque and speed with previously unthinkable efficiency. It offers a top speed of over 150 rpm, yet it provides a sustainable maximum torque of more than 350 kNm. At corner power, where the two extremes meet, users can achieve a massive 3 MW – without sacrificing compactness or efficiency. The massive wattage comes in the form of a massive motor — Quantum weighs about 400 kilos.
Hägglunds Quantum is the new name for the Hägglunds CB, which has evolved so significantly over time that it can no longer be considered the same motor.
Adding more power to the Quantum is done via four connection ports, allowing the motor to simply be made longer with additional cam rings and pistons. This allows Hägglunds to increase efficiency by increasing flow with more connections.
for extra labor and material expense due to the design of its patent-pending cover. In addition, CP is also effective against impact and abrasion damage, thus preventing hose failure, and extending hose life.
• Patent pending hose cover protects from external damage
• Excellent abrasion resistance
technology significantly improves hydraulic fluid cleanliness which can extend hydraulic component life, decrease downtime, and lower the cost of equipment ownership. It features a first-of-its-kind fine-fiber layer to trap and lock particles during frequent flow-rate changes, delivering
• Hose retains flexibility
• Maintains hose performance
• Available on select GlobalCore hoses
Available on select GlobalCore hoses and offering a consistent crimp solution, this cover is rated for –40° to 257° F operating temperature and is MSHA approved. The CP cover complements the ToughCover (TC) and SuperTough (ST), providing different levels and types of protection.
• Consistent crimp solution
• -40°F to +257°F operating temperature
• MSHA approved
Smart PowerPack S
transformational improvement in hydraulic equipment protection. The Alpha-Web was designed to meet the industry’s latest and most stringent test standard, ISO 23369, and can be used in everything from low to medium to highpressure applications.
The Smart PowerPack S (SPP S) for utility vehicles is an intelligent electrified power unit that offers greater control and efficiencies over traditionally diesel-powered hydraulic systems. It has 24 pistons and is specially designed for variable-speed applications. A wide speed range from 0 to 3,600 rpm allows full performance of the electric drive across a wide range of demands. The unit has an operating flow range of 2.27 to 14.38 lpm (0.6 to 3.8 gpm) and an operating pressure range of 17.2 to 230 bar (250 to 3,300 psi) with an integrated five-liter fluid reservoir. The Smart PowerPack is available in various sizes. In addition to the AX pump for high performance, the modular system also includes various external and internal gear pumps, thus covering a wide range of tasks.
Uniflex
uniflex.com
The new Uniflex EM 120 is a hose-cutting machine for hydraulic and industrial hoses with up to 135 mm outside diameters. It has a width of 2,291 mm, a depth of 993.5 mm, and an ergonomic height of 1,274.5 mm for convenient operation.
Thanks to its heavy weight of 637 kg and a design that places the motor close to the cutting blade, the EM 120 guarantees precise cuts with its low level of vibration. It is the first fully electric cutting machine on the market. All users need to do is enter the diameter through IPC for Industry 4.0 or IoT, and the machine will automatically set itself and adapt the cutting speed through a sensor. This way, users get an optimized flat cut without tear marks.
Modularity is the signature trait of the LH30VO family of swashplate-type axial piston pumps, with nominal sizes of 28, 45, 85 and now the new 100 cc nominal size unit. The LH30VO100 consists of a modular system of eight controllers with a variety of combination options. This includes an electric proportional pressure control with a negative or positive characteristic curve, a load-sensing control, and a remote pressure control. The electrically-operated controllers have been supplemented by a 12V solenoid variant with or without cable breakage detection. The controllers cover most applications in mobile hydraulics — for example steering pumps, fan drives and drives for equipment cylinders. Nominal pressure rating is up to 280 bar (4,061 psi).
CPX valve manifold configuration for Emerson DeltaV DCS systems provides fast, simple, and effective programming, commissioning, and validation of Festo-based pneumatics for skids and machines. Fast commissioning enables system integrators to speed up time to market, lower engineering overhead, and design new, innovative, and unique distributed control solutions. Simple CPX configuration commissioning is available for the Rockwell ecosystem as well. Engineers use the CPX Festo Maintenance Tool to build the pneumatic system configuration manually or read it online from the CPX terminal. Using imported configuration files from the CPX, the DeltaV DCS seamlessly commissions Festo-based pneumatics.
A common problem with logic valves is the failure of one of the seals, usually located on the outer side of the sleeve where it contacts the drilled hole in the manifold. Many times, they are difficult to remove. I use a two-toed wheel type puller and a sliding hammer to remove them. The seal on the 25MM logic sleeve had failed. I always replace them with 95 durometer Viton O-rings, which are extremely resistant to extrusion failures. The failure cause should always be investigated, such as manifold tolerances and/ or excessive pressure spikes. FPW
The attached circuit was a standard and is still used by some manufacturers that build concrete trucks. It is a simple and inexpensive circuit compared to the latest technology available using pressurecompensated, load-sensing pumps and pressure filters on the charge pump outlet.
A concrete supplier had a small fleet of older concrete trucks that used the attached circuit shown. His recent problem came when the drum on one of the trucks would not rotate in the direction needed to dispense the mixed concrete. From his experience with past problems, he would check the charge circuit pressure in neutral and compare it to turning the drum. It should drop about 50 to 60 psi,
indicating the hot oil shuttle relief was working. He then exchanged the two circuit relief valves and switched the two pilot circuit check valves. Everything still seemed to be fine. He then removed the hot oil shuttle valve and did not see anything visible that could be causing the problem. He then assumed the pump controls must be faulty and sent it to a repair house who advised him that there was nothing wrong with the pump or its controller.
Can you identify what he should do next? We welcome responses of all kinds directly to Robert Sheaf at rjsheaf@cfc-solar.com or to mgannon@wtwhmedia.com. The solution will be provided in conjunction with our August 2023 issue. FPW
What are your machine challenges? You’ll find the answers with HydraForce –the world leader in precision hydraulic motion controls for mobile and industrial applications. Partnering with HydraForce, you’ll have access to unmatched engineering expertise; the industry’s broadest range of cartridge valves; custom integrated-circuit manifolds, and best-in-class remote-management solutions. Now you have the power to build a better machine. Visit HydraForce.com HydraForce.com.
• Resolution ≤5 mV
• Accuracy ±0.25% of full scale
• Real-time adjustable PID control
• Integrated 0 to 10 VDC, 4-20 mA signal, or 3.3 VDC serial communication
• 0 to 10 VDC feedback pressure monitor
• Virtually silent
• No integral bleed required
• Multiple pressure ranges from vacuum to 150 psig
• 2.7 to 65 l/min flow control
The future of proportional control has arrived— and it’s digital. The Clippard Cordis is a revolutionary microcontroller primed for escape velocity from a proportional control market that has grown stagnant.
With unparalleled performance and flexibility not possible with current analog proportional controllers, the Cordis makes everything from calibration, to sensor variety, to future development opportunities more accessible and less complicated.
Contact your distributor today to learn more about how the Cordis can provide precise, real-time control for your application, or visit clippard.com to request more information.
877-245-6247