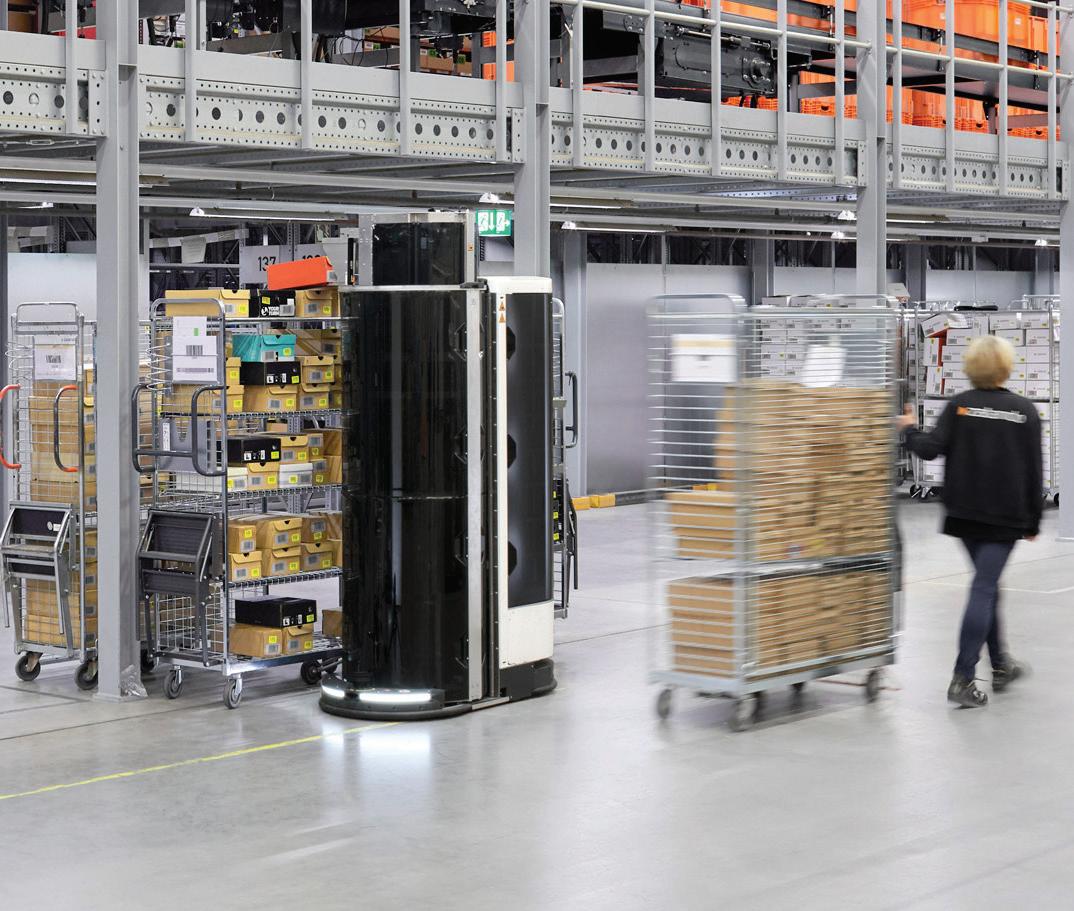
Rohlik installed Brightpick Autopickers in a Prague fulfillment center without changing its process significantly. The robots almost eliminated picking labor and dramatically reduced costs.

Rohlik installed Brightpick Autopickers in a Prague fulfillment center without changing its process significantly. The robots almost eliminated picking labor and dramatically reduced costs.
A er a successful pilot in Prague, Brightpick’s AI-powered warehouse robots will automate order picking, consolidation, and dispatch for Rohlik Group, one of Europe’s largest e-grocers.
The human hand is said to have 27 degrees of freedom — and as any robot designer will tell you, that’s not an easy thing to replicate cost-e ectively.
“Replacing the human hand is extremely di cult,” said Jan Zizka, CEO of Brightpick. “I think some companies tried, and it ended up costing €50,000. You would need to sell billions of those hands to get to a reasonable price.”
Human evolution has granted us attributes that enable survival and advance our capabilities, such as picking and holding objects of irregular shapes and various textures. Though robots and automation technology have yet to catch up, e-grocery warehouses can usually get away with simpler motion — with vacuum grippers, for example — but not without challenges.
“In e-grocery, there’s a well-defined portfolio of items, but they’re still quite diverse. There are bags and boxes of di erent thicknesses. Some materials are porous and don’t work well or at all with a suction cap,” said Zizka. “Throughout our company’s history, we’ve probably designed around 200 grippers, not only for grocery, but also for very specific items in automotive, and some for as general of use as possible.”
Brightpick recently completed a nine-month pilot of its robotic solution in a Prague fulfillment center for Rohlik Group, one of Europe’s largest e-grocers with more than 1.5 million customers and 12 million orders per year. The solution includes autonomous mobile robots (AMRs) that fully automate order picking, consolidation, and dispatch. Rohlik plans to roll out the Brightpick solution across multiple warehouses in 2023 and 2024, starting with Munich in July 2023
and continuing with Frankfurt, Vienna, Prague, and other fulfillment centers. Once fully deployed in the Munich warehouse, the center will be able to dispatch more than 1,000 order totes per hour and 5,000 completed orders per day, where some orders contain multiple totes.
“Brightpick Autopicker is our flagship product with a relatively simple arm, which makes it a cost-effective solution,” said Andrey Bakholdin, VP of marketing and business development at Brightpick. “Even though the arm only has two degrees of freedom, the gripper, or the suction cap, that we designed can grab items at a 60° angle. With our AI and 3D-vision cameras, we can pick most ambient groceries and now chilled groceries.”
Item picking is a major operational challenge, as grocery orders contain an average of 30 items per order. A typical grocery fulfillment center also has various picking zones for ambient, fresh, chilled, and frozen items. Brightpick’s mobile robot solution automates both picking and order consolidation across these different zones. The robots are patented
and powered by proprietary machine vision, AI algorithms trained on more than 250 million picks, and machine learning to improve with each pick.
“We use 3D vision and artificial intelligence to learn how to create better grippers. Our machine learning has seen enough items to generalize unseen items and make the robots smart enough that they don’t need to be retrained. This is the magic and probably the biggest milestone we’ve had thus far,” said Zizka.
Brightpick Autopicker robots are like humans with carts that move around the warehouse, retrieve product storage totes from shelving, and robotically pick items from those totes to consolidate orders directly in the aisles. The robots don’t need to travel back and forth to centralized picking stations. This results in faster picking, and they reliably pick most groceries with 99.9% accuracy. They also include goods-to-person capabilities for items that require human dexterity and autonomously find the nearest human picking station.
In most online grocery fulfillment centers, including Rohlik’s, picked items
are sent via totes on conveyor belts to a central location for consolidation.
Brightpick Dispatcher robots consolidate items arriving from various picking zones into completed orders to dispatch for delivery, curbside pickup, or in-store pickup. These robots can also pre-pick orders and store them in a temporary staging area until they need to be dispatched. This enables warehouses to smooth out picking volumes throughout the day and increase total daily throughput.
Brightpick Intuition software is the AI-powered brain of the solution that guides the robots from picking all the way to dispatch. A typical warehouse will have 15 to 100 robots, which companies can remotely monitor and control, tracking every robot, order, tote, and item in real time.
The fully autonomous, end-toend robotic solution reduces picking labor by 95% and cuts costs for order fulfillment by half. However, humans are still needed in any warehouse regardless of how many robots there are and how much programmable intelligence they have.
“The human element is a huge differentiator for us because we provide an end-to-end solution,” said Bakholdin. “We don’t just do robotic picking — we also do storage, retrieval, consolidation, and so forth. And because we can always go to a human, as a last resort, we always get the order picked. There’s no single point of failure.”
Automated warehouses use many facets of automation, such as autonomous storage and retrieval systems, moving conveyor systems, palletizing and sorting systems, and automated guided vehicles and robots. Found throughout industries such as automotive, machine building, food and beverage, material handling, logistics, and e-commerce, warehouse automation is a fixture in today’s industrial environment. HELUKABEL offers a wide array of flexible and continuous-flex control, data, VFD/servo power and feedback cables, as well as the guidance and protection systems to ensure the transmission of power and data remains constant so materials stay on the move and arrive at the right place in your facility just in time.
Oftentimes, when providers install robotic pickers as a point solution and can’t pick certain items, humans must physically go to the robots to fix them, move the items, or restart the system. In this case, picking issues aren’t handled as part of the process flow and are considered failures.
Contrarily, with so much talk about collaborative robots and humans working efficiently with machines, Brightpick actualizes this concept by designing a robot’s inabilities into the workflow. Humans are included in fallback scenarios that keep operations running, so much so that there don’t appear to be any issues on the floor. And the machine-learning algorithms can collect information to make the robots smarter for next time.
The icing on the cake — and what e-grocers such as Rohlik love to hear — is that the solution takes mere weeks to deploy.
“There are three reasons we can deploy so quickly,” said Bakholdin. “First, we use standard commodity shelving and totes that can be procured anywhere, so they are very easy to assemble. Second, our robots use LiDAR for navigation, which is purely visual, so you don’t need any magnetic tape, QR codes, or fencing around the system. And the third part is probably the most important: All the heavy lifting — designing the solution, simulating it, and ensuring that it works — happens before the installation begins.”
The company uses a warehouse’s
real-life historical data to create a detailed simulation and test the solution extensively to visualize the system’s behavior before installation. The team designs a digital twin of the facility and robot fleet and delivers an animation of the process and a detailed report with metrics. This simulation saves upfront time and costs to ensure the solution meets physical requirements and performance expectations.
“All the robots are standalone, selfsufficient, and equal,” said Zizka. “The entire idea is that there’s no single point of failure. If someone turned off or removed all the robots in the warehouse for some reason, the system would still work. Performance would be lower, but it would work exactly as before. We’d bring the robots, connect them to the Wi-Fi, and they’d run. It’s like plugging a USB stick into a laptop.”
Brightpick Autopickers were designed for e-commerce and grocery retailers and are suitable for large, small, and micro-fulfillment centers. They work with standard warehouse shelving and totes, enabling fast deployment and easy integration with any warehouse environment, including existing operations and mezzanines. l WH
Brightpick brightpick.ai
Brightpick Autopickers were designed for e-commerce and grocery retailers and are suitable for large, small, and micro-fulfillment centers.
Warehouse workers use headsets and wearables with voice-directed AI technology that synchronizes humans and machines.
By Rachael Pasini • Senior EditorThe sudden pandemic-related labor shortage was an eye-opener that forced companies to rethink operations and plan for more changes. As employee populations shi toward “digital natives,” companies can leverage such workers’ tech skills to increase e ciency and throughput.
Before Siri or Alexa, there was Jennifer — a voicedirected technology that links humans and machines to orchestrate warehouse operations. She’s an AI workhorse that provides comfort and confidence in people-occupied facilities.
“Jennifer can manage several hundred workers simultaneously, constantly recalculating orders and line items,” said Ken Ramoutar, CMO at Lucas Systems. “She does all kinds of smart things that workers don’t see, but they feel the results. For example, a warehouse worker might walk six or eight miles daily. Jennifer helps them get the job done in half that distance.”
These days, automation technology such as AGVs and AMRs get the spotlight for solving labor issues, reducing costs, increasing throughput, and making operations more efficient. But there’s still a sizable number of warehouses depending solely on people.
“We’ve been around 25 years, and more than ever, warehouse workers have become recognized as a huge asset,” said Ramoutar.
COVID-19 taught the world the value of distribution center labor. To prepare the industry for another wave of change — with Generation Z entering the workforce — warehouses need to consider the role of technology in employee retention.
“It’s hard work. It’s stressful work. So, if you want to attract the younger workforce, you better have good tech that helps them, trains them, and gives them information — all things that group expects,” said Ramoutar.
Gen Z grew up with smartphones, tablets, and voice-directed watches. Digital interfaces are as intuitive to them as operating a kitchen faucet. They have quick learning curves for modern gadgets and devices that occupy their daily lives and expect workplaces to supply them with what they need to do their jobs.
But it’s not just Gen Zs. Across the board, employees expect operations to include technologies that make their jobs better and safer.
According to market study insights from Lucas Systems, people value technology so much that they are willing to take a pay cut and switch jobs to use tech that helps them work.
The study polled 500 U.S. onfloor warehouse workers in May 2022 to examine their relationships with technology and their fears, expectations,
and perceptions about their daily jobs. Developed as the “Voice of the Warehouse Worker,” the study was conducted by Wakefield Research for Lucas Systems.
In the study, nearly 3 out of 4 (74%) on-floor workers said they would consider a pay cut at another company for an opportunity to use technology if it helps them in their job. Workers also said they are physically spent, spending over a third of their day walking, and would welcome tech’s help in the form of robots or other tech tools.
Other market study insights included:
• 75% of workers said physical strain in their jobs takes a larger toll on them than mental strain. The leading cause of physical strain is carrying or lifting, followed by walking or traveling.
• Top causes of mental strain include meeting performance or incentive goals and objectives (25%) and safely maneuvering around the warehouse (20%).
• Workers see robots as productive allies
but fear increased quotas. More than two in five believe robots will reduce physical stress (46%) or help them achieve better speed in item picking (44%) or better accuracy (40%).
• In the study, workers perceived their company’s technology as an investment in them. Lucas Systems says this is meaningful in an industry already facing a labor shortage.
“We’re in 400 warehouses across the globe, and there aren’t too many robots in any of them. Many people are thinking about robots and might install a couple to see where they make sense. Then, they might add a few more. We believe this ecosystem of people and robots will be the end game,” said Ramoutar.
Warehouse leaders agree that helping humans and machines get along is critical for automation success. They also understand that AI-embedded technology is the link for efficient
human-machine interactions, but many feel unsure of how to make AI work in their facilities.
According to another Lucas study released in 2021, executives are optimistic about AI — counting on quick and generous returns from their investment and expecting an average ROI of more than 60% within five years of implementation. Despite this optimism, 99% of organizations face challenges using AI e ectively.
The top reasons are:
• Perceptions of high costs compared to benefits
• Concerns about risks and control of operations decisions
• Cost and time for training and a lack of understanding of implementation
Nearly 90% of respondents, regardless of industry, admitted they need more expertise and information regarding implementation and use.
“There’s a belief that AI is a heavy lift — that it’s di cult to use and risky or expensive. This thinking prevents widespread adoption in the warehouse and the ability to tap AI’s true potential,” said Ramoutar.
Lucas believes the key to driving transformational impact in the warehouse is providing AI where users or IT sta don’t
have to be experts to leverage AIembedded technologies, such as voice, dynamic slotting, and in-warehouse travel optimization solutions.
For example, earlier this year, the company announced its rollout of new technologies promising productivity, comfort, and ease of use for the future Gen Z workforce.
The technologies — built to serve the new “iGeneration” of workers born between 1997 and 2012 — promise to reduce worker stress, provide a less physically-taxing work experience, and help on-floor supervisors be more agile. New technologies include:
• An all-new supervisor management console that provides leadership with a high degree of flexibility and agility to customize data, dashboards, and analytics specific to their operation and needs. Supervisors and managers can get actionable information in a way that’s easy to understand and use through fully customizable consoles.
• New algorithms and machine learning intelligence that reduce walking by up to 50% by showing workers optimal navigation paths.
• The ability for on-floor workers to use the smallest wearables for scanning. Lucas Systems certified its voice-enabled
optimization suite, Jennifer, to run on a Zebra WS50, the world’s smallest all-inone Android enterprise-class wearable mobile computer.
These insights were released in the company’s “Competing for the Warehouse Workforce of the Future” guide, which includes recommendations for attracting and retaining labor. One insight is that most Gen Z workers (73%) say robots will help them achieve greater accuracy and speed in their jobs.
“It’s a competition, and it’s not going to get better,” said Ramoutar. “Baby Boomers and Gen X don’t necessarily expect a super automated place. It’s the Gen Zs who are asking, ‘Where’s the good tech that I need to do my job?’ So, if a warehouse looks outdated and hasn’t been modernized, they won’t work there.”
It’s clear that no matter how many robots are deployed worldwide, warehouses will still need people for quite some time. That means the industry will continue needing AI-embedded tech to synchronize operations for future hybrid — and diverse — workforces.
For instance, Jennifer understands and speaks 34 languages, removing communication barriers that make expansion, hiring, and training easier and faster. Workers can also adjust Jennifer so that she speaks slower or louder, accommodating a broader range of people.
“We have places in the U.S. where Jennifer works in multiple languages in the same warehouse. Individuals speaking Spanish work alongside others speaking Arabic. And the supervisors are probably speaking another language or English. They all can work better and faster with less stress without a common language,” said Ramoutar. “Having this tech for people matters.” ● WH
Jennifer has a natural human voice that workers can adjust, enabling diversity and inclusion in the warehouse.| Courtesy of Lucas Systems
Supercharge your production efficiency, simplicity, and connectivity with our extensive portfolio of linear and rotary mechanical systems, servo drives and motors, control solutions, and I/O systems.
Automate everything that moves on a single, unified platform Install and commission all elements of the automation chain more quickly Integrate solutions into your automation concepts with minimal risk
Explore what’s possible with Electric Automation Solutions by Festo.
Talk to us today.
Modern intralogistics technologies place high demands on drive systems. In many instances, drives must release tremendous force in confined spaces and perform precise positioning tasks in continuous or stop-and-go operations. Speed is also essential, as many thousands of orders must be processed daily.
To speed up warehouses, automatic storage and retrieval machines, driverless transport systems, and intelligent logistics robots are taking over an increasing number of work steps in storing, retrieving, and preparing items for dispatch. Flexible systems that work reliably around the clock keep operations moving cost-e ectively and are often driven by high-performance micromotors. Small motors are crucial for controlling robot movements, enabling them to navigate environments, manipulate objects, and perform various tasks. Examples of how motors are used in warehouse robots include:
• Wheel propulsion: Mobile robots employ motors to drive their wheels or tracks. By controlling the speed and direction of the wheel motors, the robot can move forward, backward, turn, or navigate in di erent directions.
• Steering: Motors are used for steering mechanisms in robots with multidirectional capabilities. By controlling the rotation of the steering motors, the robot can change its direction of motion or perform complex maneuvers.
• Actuation: Motors can act as actuators to perform various tasks. For example, they can be used in robotic arms for grasping, lifting, or manipulating objects. They can also extend or retract appendages, open and close doors, or operate other mechanical components.
Fast-paced warehouse operations demand extensive automation, which is inconceivable without micromotors.
Faulhaber weighs in on intralogistics robots and how drive system capabilities influence their design.Mobile robots require compact, lightweight, high-torque drive systems to improve warehouse autonomy and accuracy. | Courtesy of FAULHABER
• Sensors and feedback control: Encoders or other position sensors can be attached to the motors to provide feedback on their speed, position, or torque. The control system uses this feedback to adjust and regulate the motor’s behavior, ensuring accurate and precise movement.
• Balance and stabilization: By controlling the torque and movement of the motors, robots can maintain balance and stability while navigating uneven terrain.
• Obstacle avoidance: Motors can be combined with sensors to prevent collisions. The sensors detect obstacles or proximity to objects, and the motors are controlled to steer the robot away from potential hazards.
“Intralogistics robots work in dynamic environments where they must recognize and avoid obstacles and ensure safe
to “Intralogistics 4.0.” They are used for storage, removal, and dispatch preparation to optimize material flow, relieve employees, and replace conventional lift or pallet trucks.
For example, autonomous picking robots allow precise handling of individual objects. A typical picking robot comprises a lifting column, gripper, and a drive unit — perhaps a Faulhaber BX4 series brushless dc servomotor with an integrated motion controller and planetary gearhead. When used in the gripper, this combination ensures precise positioning during storage or retrieval, all during continuous operation with constant load changes. Yet the complete drive unit weighs only about 300 g and doesn’t require a counterweight even when the gripper fully extends.
cooperation with other robots and human workers. They need to be flexible and adapt to changing processes and the goods they handle,” said Kevin Moser, business development manager at Faulhaber.
Faulhaber engineers address challenges that modern warehouses face by evolving drive systems to match the industry’s shrinking need — the need for smaller, more powerful motion control components that reduce weight and improve speed.
The brushless dc servomotors are compact, with a diameter of only 32 mm and a length of 85.4 mm. This small size makes it possible to design a very flat gripper that can pick up packages stored just above the ground, making optimal use of expensive storage areas. With the brushless commutation system, the motors are long-lasting, deliver high torques, and run quietly with a balanced rotor. Integrated current control limits torque demands and protects the drive against overload.
“Robot design needs to be robust, lightweight, and very compact, resulting in low maintenance, low power consumption but high efficiency for
The BX4 series of brushless dc servomotors are designed for high-precision, start-stop operations in confined spaces.
| Courtesy of FAULHABER
extended battery life and minimum downtime,” said Moser. “Modularity is also important: As operations expand in a modular system, it is easy to add additional robots.”
Graphite-commutated dc micromotors of the CXR series combined with matched gearheads have also proven themselves in handling tasks. Their commutation system is well suited for dynamic, high-performance applications with fast start-stop operations required in many handling systems and automatic sorting, such as where switches are used to change routes on transport paths.
With their linear characteristics, the dc motors are easy to control. Combined with high-resolution encoders, they are ideal for precise positioning tasks. High-quality neodymium magnets and Faulhaber winding ensure high-power density in a compact design. The motors can be installed directly in handling elements and lift considerable weight despite their small size.
“As the degree of automation of intralogistics processes throughout the entire value chain increases, robots must be more autonomous, intelligent, and interconnected. Requirements regarding the speed and dynamics of the systems are increasing as well. This requires the robots to have reliable, safe, and smart
sensor and drive system technology to adapt to these changing conditions,” said Moser.
Warehouses often choose automated guided vehicles (AGVs) for flexible transport within a facility. Availability, speed, flexibility, and small size are essential requirements for these transport systems’ drives. Current consumption also plays a role in ensuring that AGV batteries are as long-lasting as possible. For example, brushless dc servomotors of Faulhaber’s BP4 series drive the wheels, whereby the motor power transfers to the wheels via planetary gearheads and drive belts. High-efficiency motors with innovative winding technology allow for a high copper content that minimizes losses.
Encoders of the IE3-1024 series are built right onto the servomotors for precise position detection. The magnetic incremental encoders feature an indexing channel for referencing a drive shaft revolution and a standardized, electronic encoder interface. The resolution, direction of rotation, index width, and index position can be adapted to the application, and a motion controller controls the servomotors. Such drive systems are also used for mobile robot platforms, which move autonomously in facilities without preinstalled guidance systems.
Warehouse robots continuously become more autonomous in navigating complex environments, adapting to dynamic surroundings, and making
The BXT series are brushless flat motors for compact wheel drives that move mobile robots around the warehouse.
| Courtesy of FAULHABER
real-time decisions. Improved motion control and sensing systems, advanced algorithms, and artificial intelligence enhance their independence, increasing efficiency and productivity. And as the trend of micro-fulfillment increases, so will demand for even more compact but powerful drive systems.
For example, high-torque flat motors of the BXT series are useful for wheel drives when installation space is limited in the axial direction. These motors are 14, 16, and 21 mm long but deliver torques up to 134 mN-m within diameters of 22, 32, and 42 mm, respectively. For precise speed control or strict positioning accuracy requirements, diameter-compliant magnetic encoders or speed controllers are fully integrated into the housed motor variants, expanding the drive by a mere 6.2 mm.
“High efficiency, high power density, and overload capability will be key,” said Moser. “The more compact the drive system, the more space is left for the battery system, and the highest power-to-weight ratio enables increased payload weight per shuttle.” l WH
storage and retrieval.
| Courtesy of FAULHABER
Faulhaberfaulhaber.com/logistics-robot/en
A brushless dc servomotor with an integrated motion controller and planetary gearhead drives this gripper for precise positioning during
WAGO has the interconnect solution for your factory automation devices. With lever-operated termination, the 2734 Series MCS MINI offers a toolfree, easy in-hand wiring of wire-to-board and wire-to-wire configurations. With a pin spacing of 3.5mm and termination of wire up to 14AWG, these are the optimal field connectors for drives and motion controllers. www.wago.com/us/discover-pluggable-connectors/mcs
By standardizing on Festo electric and pneumatic automation solutions, original equipment manufacturers (OEMs) not only gain design symmetry and a sleek, high-tech look for their Intralogistics systems, they can also manufacture more compact, flexible, and high-performance solutions. Through partnership with Festo, OEMs simplify their design and acquisition process for faster time to market.
The Simplified Motion Series (SMS) electric axes feature a motor with integrated servo drive and IO-Link that, for the first time, makes electric axes comparable to pneumatics in terms of cost and installation ease. SMS machine-mounted electric axes offer low energy consumption and the data generation characteristics of mechatronic systems. No other supplier offers a line of electric axes with comparable capabilities, advantages, and price of the SMS.
SMS actuators are ideal for picking and placing, dropping, pushing, lifting, or trapping products on a conveyor line. The series has a simplified form factor and dynamics. SMS adds flexibility to the system while minimizing energy costs and costs per I/O point by utilizing IO-Link communications rather than analog signals.
Axes are available in ball screw, toothed belt, mini slide, electric cylinder, piston rod, and rotary actuator configurations. With onboard push button commissioning, users commission two-position actuation in minutes with no additional software required. Like pneumatics, the system uses two inputs and two outputs to perform controlled pressing, force functionality, and end-to-end positioning.
SMS is designed with economies of scale in mind. SMS decreases costs by high volume standardized production. This eases supply chains issues and means customers receive electromechanical actuators in a variety of form factors quickly and at an industry leading price point.
IO-Link programming through the PLC unlocks infinite
positioning and enables diagnostics, including cycle count, alarm data, and the typical process data experienced with servo systems. IO-Link also delivers operational data for improved quality and predictive analytics ‒ another key differentiator compared to pneumatic actuators. PLC speed control is based on application dependent requirements.
Next generation remote and decentralized I/O
CPX-AP-A is Festo’s next generation modular, lightweight, and flexible remote I/O system with IP65/IP67 protection. CPXAP-A supports flexible placement of Festo’s SMS products. CPX-AP-A remote I/O has a real-time transmission rate of 200 Mbps full duplex. It is parameterizable and scalable to up to 15 modules in one automation system. CPX-AP-A features a complete IO-Link master data storage mechanism, including a device parameterization tool. CPX-AP-A can be adapted to Festo valve terminals.
In addition, CPX-AP-I decentralized I/O with IP65/ IP67 protection seamlessly integrates with Ethernet
communications networks from Rockwell, Beckhoff, Siemens, and other leading PLC manufacturers. CPX-AP-I modules accommodate over 80 digital and analog input blocks, valve manifolds, and IO-Link master modules for extensive control and data acquisition capabilities per interface. CPX-AP-I supports up to 50-meter distance between SMS devices, IO modules, valve terminals, and CPX-AP-A nodes. With 50-meter capabilities, locating valve manifolds close to pneumatic actuators significantly improves performance and lowers energy consumption. The extensive range of compatible Festo and third-party I/O gives OEMs the flexibility to create unique customer solutions.
Festo’s I/O integrates remote I/O and decentralized topology into the PLC. Festo I/O enables a single IP address to connect a fieldbus node and over 80 I/O modules, including valve terminals (which count as one I/O module) into a single networked string. Festo I/O supports device level ring, linear, and star networked topologies. Festo CPX-AP-A and CPX-AP-I support Ethernet/IP, EtherCAT, PROFINET, and Modbus TCP/ IP.
Connect remote and decentralize inputs and outputs to achieve the I/O density the layout requires. For example, place 80 digital inputs plus valve terminals in one location and connect 50 centralized SMS and additional IO-link devices or analog devices. Further downstream and with a singular fieldbus node, the OEM can string together another mixture of 80 modules that are 50 meters apart. These remote and decentralized I/O solutions feature industry leading speeds using a single network and IP address. The only limiting factor is the PLC processing speeds and native communication protocol.
In the current climate where it can be a time-consuming process to find, order, and receive I/O modules, networked valve terminals, and electromechanical actuators with servo control, it makes sense to turn to Festo. Festo provides a one stop shop for rugged, dependable integrated pneumatic, servo-controlled motion, and networked I/O through its always-in-stock Stars of Automation program. (See online catalog for Stars of Automation information.)
Festo engineering productivity tools for electrics and pneumatics include SMS solutions finder, Electric Motion Sizing, and Pneumatic Sizing for error free sizing of linear and rotary systems. Festo features Automation Suite for simplified
electrics commissioning. The Festo configuration tool for the CMMT-ST motor controller saves considerable time and ensures accuracy. Using PartdataManager, OEMs receive CAD data in 2D/3D for the entire catalog of 33,000 products. These and other productivity tools are free and accessible online.
Festo Didactic – the educational arm of Festo ‒ takes lifelong learning and mechatronic technical training to a new, higher level. Festo Didactic assesses levels of mechatronic knowledge and prepares a learning curriculum based on individual needs. The Festo Learning Experience (Festo LX) is a new online portal to make it easier to create individual learning experiences for personnel.
Electrics, pneumatics, seamless connectivity, productivity tools, an AI/machine learning platform for predictive analytics with integrated maintenance functionality, and training make Festo the partner of choice for top-flight Intralogistics systems. Because it is more than a supplier of diverse and high-quality products, Festo lowers engineering overhead, boosts engineering productivity, and brings systems to market faster.
In today’s automated warehousing industry, Amazon and Walmart have distinctly established themselves as the household names of global consumers. How did they achieve such a demand of consumer usability and market share? They designed an infrastructure so that their customers at the push of a few buttons, could quickly purchase and receive almost anything they want or need without having to step outside their house, except maybe to grab the package they ordered just a few days earlier.
The brilliance of this application is its simplicity and ease of access to its users. What is not so simple is the actual infrastructure itself. Warehouse automation involves so many moving and programmable components that if any of those components are not functioning properly, it disrupts the entire flow of the automated process. From the automated storage and retrieval system and the conveyor system down to the pick and place center, getting inventory sorted, packaged, labeled and shipped properly is a very complex process. Even the cable and electrical system solutions being specified for these components add another level of complexity to ensure the longevity of the system itself and safety for its users. Designing a robust, efficient and competitive automated system is a delicate balance for everyone involved. Once the system is commissioned, the facility operations become almost completely self-sufficient with just ongoing routine maintenance and control station monitoring oversight.
As conveyors and automation components require significant technical aptitude and focus from both designer and supplier, pairing artificial intelligence and robotics with your warehouse automation moves things to another level. Automated guided vehicles can interoperate algorithms, and independently move inventory to and from dedicated areas around the clock. Traditional multi-axis robots pick, sort and place products as well as handle heavier products that employees can’t manage without assistance. This improves not only efficiencies but safety as well.
Amazon has over 520,000 robots working in unison with their automated warehouses and have added over one million jobs worldwide to transform their business. Walmart recently partnered with Symbotic to deploy and retrofit all 42 of its regional distribution centers over the next 10 years with robots. These industry leaders are paving the way in industrial automation, which is starting to see smaller type companies with sizeable warehouses follow suit as it relates to warehouse automation and efficiencies just to stay competitive. The importance of factory floor space,
fulfillment process flow, reducing idle and/or downtime, and improving employee safety and efficiencies is critical to these types of business models.
With these factors in play and more within the infrastructure of an automated facility, you also have to be fully prepared to respond to any electrical, mechanical or software issues that can create significant delays to consumers or end users and revenue loss. Robust and sustainable cable systems are key to the life of the automated warehouse, so qualifying and selecting the right component manufacturer and/or electrical system supplier becomes more important than ever. Suppliers who control not only the design quality and manufacturing of their products, but also provide the added value of complete component and electrical system solutions for automated applications quickly rise to the top.
HELUKABEL is a global cable system solutions provider specializing in the production of cables, wires, accessories, cable assemblies, and guidance and protection systems found in equipment used throughout today’s automated warehouses. HELUKABEL offers a wide array of flexible and continuous-flex control, data, network and bus, VFD/servo power and feedback cables to reliably transmit power and data to keep materials on the move.
Our ability to provide cable solutions from bulk cable to complete, plug-and-play cable sub-assemblies makes us the one-stop shop for complete electrical system solutions within the automated warehouse ecosystem.
Where there is e-commerce, there is inevitably logistics management. After all, what could be more efficient than a network-connected fleet of AGVs to travel around huge warehouses and find the required product in record time? These automated guided vehicles have enabled the automation of all these internal transport tasks. They are able to retrieve goods at height in vertical warehouses before transporting them to the conveying chain. In order to meet the high productivity requirements of order preparation, these AGVs must:
• Be compact and offer high power density. The robots must occupy as little space as possible in order to adapt to the confined spaces. Therefore, they need compact motors without compromising on power.
• Implement SS1 safety regulations to avoid obstacles and collisions with human operators. In terms of the drive, this involves using integrated temperature sensors in the motor as well as electronics to prevent the risk of overheating.
• Be connected to the other AGVs in the fleet, in order to be maneuvered simultaneously within the same space. This connectivity is enabled by EtherCAT, CANopen or I/O bus communication.
• With or without electronics, the IDX 56M motors meet all the criteria, whether used for a traction, lifting or steering system.
Whether rollers or belts, conveyors take care of transporting goods to the operations area, where they are scanned, for instance. During this stage, maintenance challenges are decisive, as the slightest breakdown would result in huge losses. Choosing a reliable, connected drive system to minimize maintenance operations is therefore key. This way, motors with integrated electronics can be controlled remotely and perform diagnostics or an update without having to be near the machine.
• With its communication buses, the range of IDX 56L motors can be controlled remotely, simplifying all your maintenance operations.
To arrive safely at their destination, goods need to be correctly packaged and labeled. Depending on the size and shape of the product, the packaging machines take care of this stage using multi-axis systems. Generally equipped with several independent motors, these machines require a master controller to synchronize all the operations in the chain. There are also major challenges here in terms of compact size, maintenance, and connectivity.
The ZUB master controller from maxon allows IDX 56M or 70 motors to operate in complete harmony: while one retrieves a box, the other is already preparing the tape to seal the parcel.
For more info:
Growth in automation in e-commerce - drive.tech
In true WAGO fashion, the manufacturer is continually innovating and improving its product offering. WAGO’s 221 Series Lever Nuts are an excellent example of this, representing the company’s answer to the twist-type splicing wire connector. This termination device quickly and easily connects different wire sizes and types, using 2, 3, and 5-wire connectors.
“A few years ago, WAGO developed the original 222 Series LEVER-NUTS®, which has been effective and successful,” shares Evan Syens, Product Manager, Electrical Splicing Connectors with WAGO Corporation. “However, innovation doesn’t stop for us just because a product has hit the market. We never settle for ‘good enough’ and are always striving for better. WAGO is all about ongoing advancements.”
To this end, WAGO created their newest version wire-connector solution, the 221 Series LEVER-NUTS®— and they’ve quickly become one of the company’s top-grossing products.
“The biggest difference between the original 222 and the latest 221 Series is the size, as the newest version is smaller,” says Syens. “But, perhaps, the most notable feature of our 221 Series LEVERNUTS® products is their transparent housing, which is significant.”
This is because with a typical twist-type connector, it’s impossible to know how secure the wire connections are for each terminal, which is a maintenance and safety concern.
“The clear housing completely takes the guesswork out of the installation process,” Syens explains. “Without it, how would you know how many twists are ideal for a secure connection? There’s room for error. In fact, installers will often secure wires with electrical tape to maintain the twist-type connection. But that’s unnecessary, thanks to WAGO’s innovation. Simply pull the orange lever up, insert a stripped conductor (according to the strip-length gauge on the side of the 221) and push the lever back down. That’s it. You’re done.”
Since every 221 Series LEVER-NUTS® also includes CAGE CLAMP® technology (the spring-pressured connection technology that WAGO pioneered back in the ’50s), installers can also ensure a secure a reliable connection. The CAGE CLAMP® is starting to become the industry standard for electrical interconnection technologies.
What’s more, is WAGO has incorporated test slots in the LEVERNUTS® Series for additional safety — one in the direction of wire insertion and one on the opposite side. This allows an installer to insert a test probe into the slots to determine if a wire is live.
“Another unique feature about these products is that they’re reusable, without any added steps. For example, there’s no need to re-strip the wires. Simply lift the lever and connect the new wires,” he says. “Again, it’s that simple.”
WAGO offers two different versions of the 221 Series:
• The original variant: 24-12 AWG
• The 10 AWG variant: 20-10 AWG
“The 20 to 10-gauge version also has three variants — a 2, 3, and 5-conductor, which goes up to 600 volts and 30 amps. And, as for the operating temperature, each variant is approved to 105° C,” says Syens.
Along with these innovative connectors, WAGO also offers a line of mounting carriers that can be mounted onto a DIN Rail or chassis, easily cleaning up your cabinet, panel, or junction box.
“It’s really about peace of mind because with CAGE CLAMP® technology, you can be confident in a secure connection for your application,” says Syens.
Whether for an electrical contractor, DIY home projects, lighting applications or use in hazardous locations, WAGO’s 221 LEVER-NUTS® Series offers fast, safe, and dependable connection technology.
“Now when people see the orange lever, they associate it with WAGO and know the product can be trusted.”
• Terminate conductors from 24–10 AWG (with two models: 24-12 AWG and 20-10 AWG)
• Connect solid, stranded, and fine-stranded conductors
• Combine different wire sizes and types
• Install devices with higher levels of power consumption
• Save time connecting wires without the use of tools