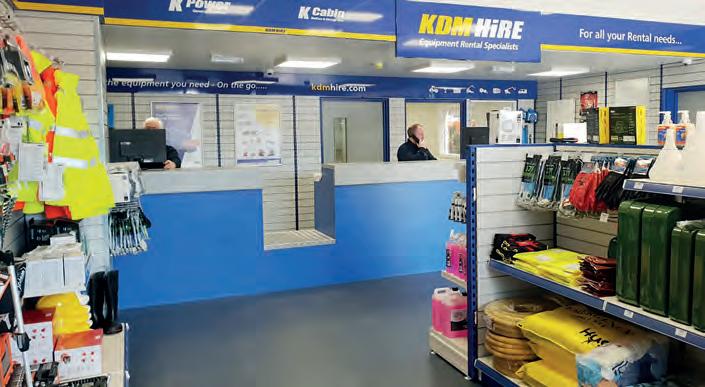
42 minute read
KDM Hire Invests in new Tool & Equipment Hire depot
from Plant & Civil Engineer 2021
by 4SMNI
KDM HIRE INVESTS £1.3 MILLION IN NEW TOOL & EQUIPMENT HIRE DEPOT
Tyrone-based hire firm KDM Hire Ltd continues to expand its offering with the opening of a new depot in Castlereagh in Belfast.
Located on Alexander Road close to the outer ring, the depot is ideally placed to serve greater Belfast, Lisburn and County Down. This tool and equipment hire depot adds to the company’s existing four depots in Mallusk and Dublin alongside a cabin hire yard and headquarters, both based in Cookstown. The new depot has been designed to cater to both trade and domestic customers with a large range of modern equipment available for the construction, industrial and DIY sectors. The £1.3 million invested in the new facility is part of an ongoing strategy to grow the company’s position as one of the country’s leading hire companies; exciting new product offerings are also in the pipeline with some due to be launched in the coming weeks. The company has also recently acquired a three-acre green field site in Ballycoolin Industrial Estate at Blanchardstown, Dublin which should be fully operational later this year. These expansion plans are anticipated to increase staff numbers to over 180 in the coming year from the 155 currently employed. A spokesperson for the company said: “This is an exciting time for KDM Hire, coming out of a tough year brought on by the pandemic. This new depot provides us with a platform to reach new customers while offering existing customers an improved local service when working in the East of the province.”
Largest Range
A professional and dynamic family-run business which has grown to become one of the UK and Ireland’s leading equipment rental companies, KDM Hire offers one the largest ranges of equipment available for hire including a considerable number of specialist products and support services catering to a wide variety of industries and sectors. To guarantee reliability and safety on-site, its hire fleet is maintained to the highest standards by an experienced team of manufacturer trained service engineers. The dedicated team is supported by an unrivalled service and spare parts department.

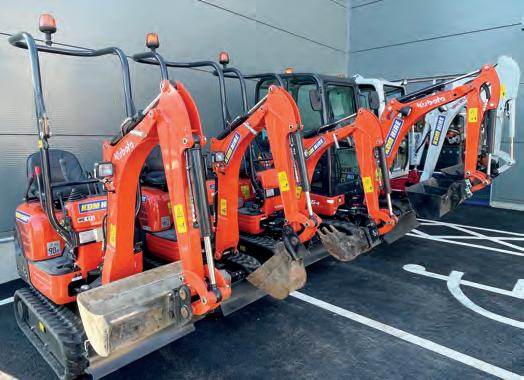
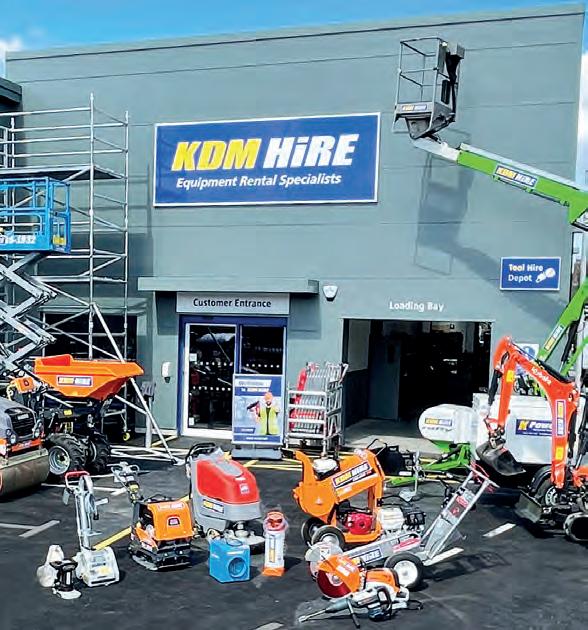
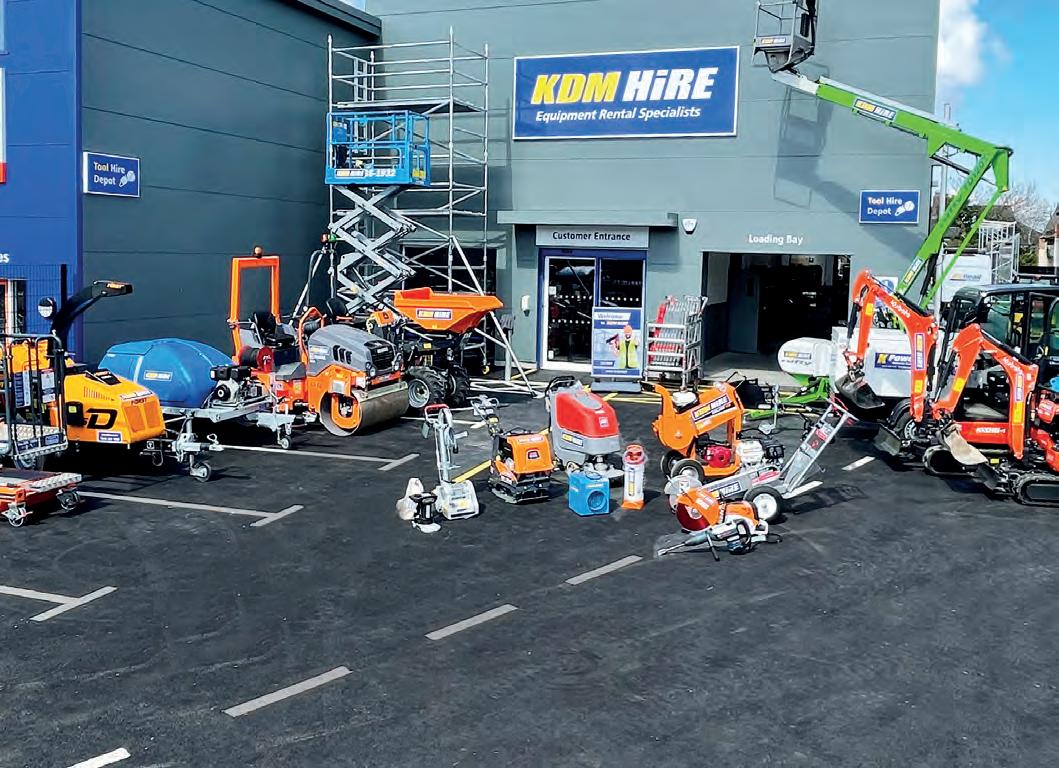
All equipment is examined, tested and certified ensuring compliance with all current regulations and industry criteria. For on-site maintenance and in the unlikely event of a breakdown, its fleet of mobile service engineers is on standby to ensure downtime is kept to an absolute minimum. “Operating since 1990, our team has built up considerable experience in the equipment rental industry so whether it is advice, technical support or simply answering questions on availability, we aim to ensure customers are supported every step of the way.”
Industry Awards
With over 30 years within the industry, KDM Hire’s dedicated staff has been recognised on numerous occasions with various accolades and awards for their passion and tireless commitment to continual improvement and customer care. Awards celebrated include European Rental Company of the year, Northern Ireland Plant Hire Company of the Year and UK Independent Passionate Hire Company of the Year.
0845 338 1388 www.kdmhire.com

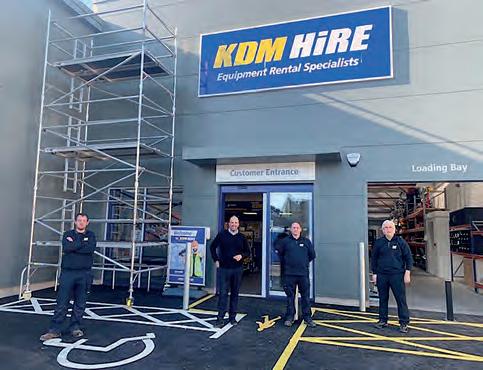
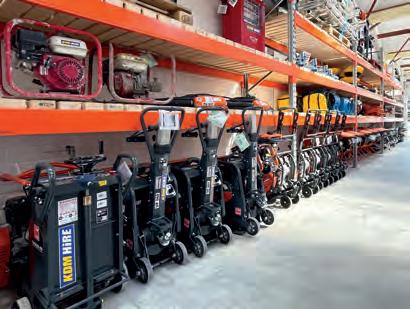
hire news Speedy Begins Major Fleet Expansion Plan with Electric Lift Investment
Hire equipment and services provider Speedy has invested in 130 new electric lifts as it begins a multi-million-pound equipment expansion plan for 2021.
The firm’s Powered Access business has bought 90 scissor lifts and 40 mast boom units, manufactured by Dingli, as part of its strategy to expand its range of hybrid and pure electric lifting models, providing contractors with more choice as they work towards net-zero emissions targets. The new scissor lifts include the JCPT0807DCS and JCPT1008DC models, which deliver a max working height of 7.8 metre and 10 metres respectively. The AMWP8100 mast boom lifts offer a working height of up to 11.2 metres. Each model provides efficient zeroemission battery power, in a compact form-factor, making them suitable for a variety of working at height tasks including maintenance and installation projects. The equipment is available from the firm’s 11 Powered Access Specialist Service Centres, located across the UK. The specialist Powered Access division of Speedy, the UK’s largest hire provider, was launched in November 2020 following the merger of Speedy’s acquired powered access firms Lifterz, Platform Sales & Hire and Prolift. Andy Briggs, managing director at Speedy Powered Access said: “We are continuing to see strong demand for our powered access equipment and this investment will provide our customers with greater availability of our core, versatile models that are supporting them in reducing their environmental impact. “This marks the beginning of what will be another year of significant investment for our business. We have built a strong, UK-wide proposition and look forward to expanding our fleet with the assets our customers need to complete their projects safely, sustainably and efficiently.” Supporting Speedy’s responsibility programme ‘Energise’, Speedy Powered Access provided a brand new Dingli 26’ scissor lift (pictured) for the International Powered Access Federation (IPAF) to use at North Warwickshire & South Leicestershire College’s MIRA Technology Institute campus. The lift was used with the college’s new intake of powered access engineering apprentices.
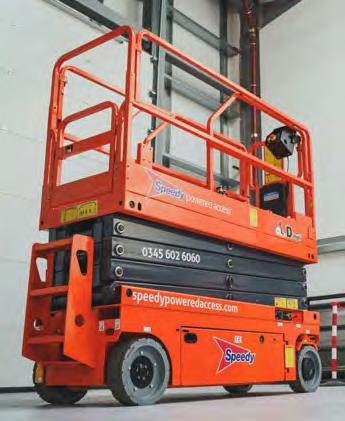
In light of the current status of the roadmap out of lockdown, the Construction Plant-hire Association (CPA) has reviewed the timings and plans for the CPA Stars of the Future Apprentice and Trainee Awards 2021 to ensure that nominees and winners receive the recognition they deserve.
The original plan was to host the Stars of the Future awards ceremony on Thursday 1st July 2021. It has been decided to move the awards ceremony to Tuesday 14th September 2021 so a live physical event can be hosted at the Heart of England Conference and Events Centre in Fillongley near Coventry. To take into account the new timings, the deadline for Stars of the Future nominations has been extended to Monday 31st May 2021. Nomination forms are available on the CPA website at www.cpa.uk.net. The headline sponsor for CPA Stars of the Future 2021 is Sunbelt Rentals UK. Kevin Minton, Chief Executive of the CPA said: “Stars of the Future is now in its ninth year and it has become firmly established as the premier event of the construction plant sector for recognising and rewarding the skills and calibre of the industry’s apprentices and trainees. Even though physical events may well be allowed from 21st June 2021, there is still a great deal of uncertainty and we didn’t want to run the risk of limiting the event to a purely online awards announcement for the second year running. “By holding the awards ceremony a few months down the line, we hope there will no longer be any issues with events and our intention is to hold it as a live event at the Heart of England Conference and Events Centre where winners are able to receive their prizes and receive rightful recognition for their efforts. Sponsors will also have the opportunity to meet and congratulate the nominees and winners face-to-face. “We also realise that colleges have only recently returned to live classes, so by extending the nomination deadline it allows more preparation time in terms of gathering information together for the nomination process. We’d like to urge employers in the construction plant sector to nominate apprentices and trainees who they believe should be recognised as stars in the making,” Kevin continued. For Stars of the Future 2021, several awards can be won and nominations are welcomed from plant-hire and crane companies, manufacturers, contractors, suppliers and others operating in the construction plant sector with apprentices and trainees in their workforce. Stars of the Future is a national awards scheme for apprentices and trainees in the construction plant-hire industry, organised by the CPA, the leading trade association for the plant-hire sector in the UK. The CPA has over 1,700 members who supply 85% of hired plant to the construction industry. Stars of the Future winners will be in contention for a number of prizes, as well as national recognition. Previous prizes have included Snap-on tool kits, iPads and an all-expenses paid trip to Germany to visit a Liebherr crane manufacturing plant.
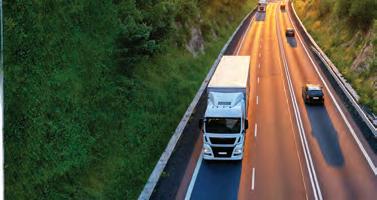
Helping businesses thrive again.
Release working capital from assets, such as machinery, stock and customer invoices.
closecommercialfinance.ie

news TOBROCO-GIANT Unveils Two New G-Series Models
TOBROCO-GIANT has unveiled two new models in the G2300 series, offering higher performance and even more compact dimensions, so that the machines are easy to transport.
The G2300 HD, which is also available as X-TRA-version, is equipped with a 26 hp-Kubota engine with 1500 m3 cubic capacity, four cylinders and high torque and is certified to EU standard level V for clean engines. For driver comfort combined with high performance the machine has got a hydrostatical four-wheel-drive and limited slip on both axles. Due to the 8-tonne planetary axles the machine has got a traction force of 23.000 N, which is required for a lot of different applications on building sites, with earth-moving tasks, on farms or with gardening and landscaping. Tipping loads of 1.595 kg for the G2300 HD or 2.260 kg for the X-TRA version ensure powerful and efficient loading and unloading of materials. Because of the operating weight of 2.300 and 2.350 kg both models can be transported very easily on a car trailer from one working site to the next. All machines are equipped with a safety roof as a standard. Optionally, this can be changed into a foldable safety roof or a complete cabin. All roofs and cabins have been intensively tested by independent controllers and are certified on the international ROPS/FOPSstandard. The curved windscreen and the narrow stacks lead to an excellent 360° view. So the driver is always able to view the whole working area and can work safely and precisely at any time. A sprung and adjustable comfortable seat helps to create a pleasant working condition as well as the spacious and comfortable working environment with control instruments that are easy to use, the smoothly operating joystick and the tilting and adjustable steering column - this comfort equipment prevents exhaustion and leads to comfortable and efficient work during long hours. TOBROCO-GIANT offers more than 200 different attachments so that the G2300 models can be used all year round.
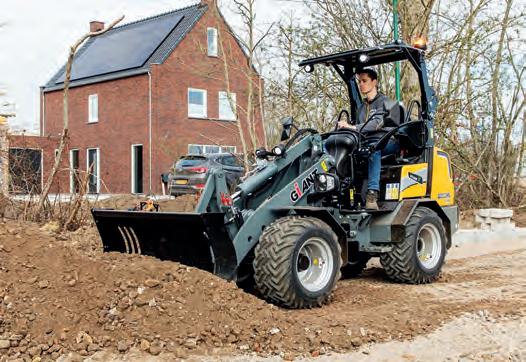
The exhibition industry, like all corners of the event world has suffered during the Covid-19 pandemic and with events being cancelled, organisers have been forced to explore alternative routes to continue operating.
Virtual webinars and online networking were once a very niche area of the events sector; however, many companies have embraced the technology as they explore new ways to engage and do business in this new way of living. But can a digital event really replace the real thing? The sights, the smells and the face-to-face interaction is what makes an exhibition enjoyable, exciting and successful. So, as we take a look back at Hillhead Digital, we ask… was it worth the effort? Hillhead is the UK’s largest quarrying, construction, and recycling exhibition which attracts nearly 20,000 unique visitors biannually. Usually held in a limestone quarry in Buxton, Derbyshire, this event has been postponed until next year due to ongoing Covid restrictions. In its place, the organisers made the decision to present a virtual exhibition, Hillhead Digital which was held on 30-31 March. Through multifaceted, stateof-the-art streaming, a huge technological operation and delivering truly novel and interactive content, Hillhead Digital connected more than 5,000 participants across the globe. Attachment manufacturer Miller UK used this year’s Hillhead Digital virtual platform to showcase its new range of quick couplers, and with more than 100 visitors from 16 different countries, the event proved to be a useful platform. During the show, visitors had the opportunity to virtually meet with the team from Miller via video or web chat. In addition, visitors could download Miller collateral and watch promotional videos. Firmly in the spotlight was the GT Series of quick couplers which look set to herald a new era of unrivalled power and cuttingedge intelligent coupler technology for excavators increasing job site safety, machine versatility and productivity. Normally at a trade show Miller would have a number of live demonstration units working for customers to get close to the product to understand its key features and benefits. To assist prospective customers product qualification journey at the digital show, Miller created an exclusive virtual product demo of the new GT quick coupler series with the support of industry journalist and vlogger, Peter Haddock from Content with Media. “It is great to see Miller recognising the importance of digital events and hosted content, I really enjoyed working with the team over the past couple of weeks, creating exciting content and video interviews for the Hillhead Digital virtual exhibition,” said Peter. “During my visit to Miller HQ, I got to see first-hand the unabated research, design and development that has gone into The GT Series quick couplers and it’s seriously impressive,” he added. Barry Robison commented, “We were disappointed when we heard the news that Hillhead was to be postponed until next year as it’s such an important show for us. It’s a sign of the times and people have to adapt to move forward, and Hillhead Digital has proven to be very valuable for us. The GT series is bringing innovation to the excavator industry like never before. It’s exciting and we can’t wait to show our visitors in real life at next year’s show.” As cities around the world begin to re-open, the events industry is more eager than ever to get back to some sense of normal. So, while digital shows could now part of the ‘new normal’, and have provided essential business opportunities in a Covid world, we all look forward to the future where the industry can deliver safe and successful exhibitions and drive game-changing opportunities.

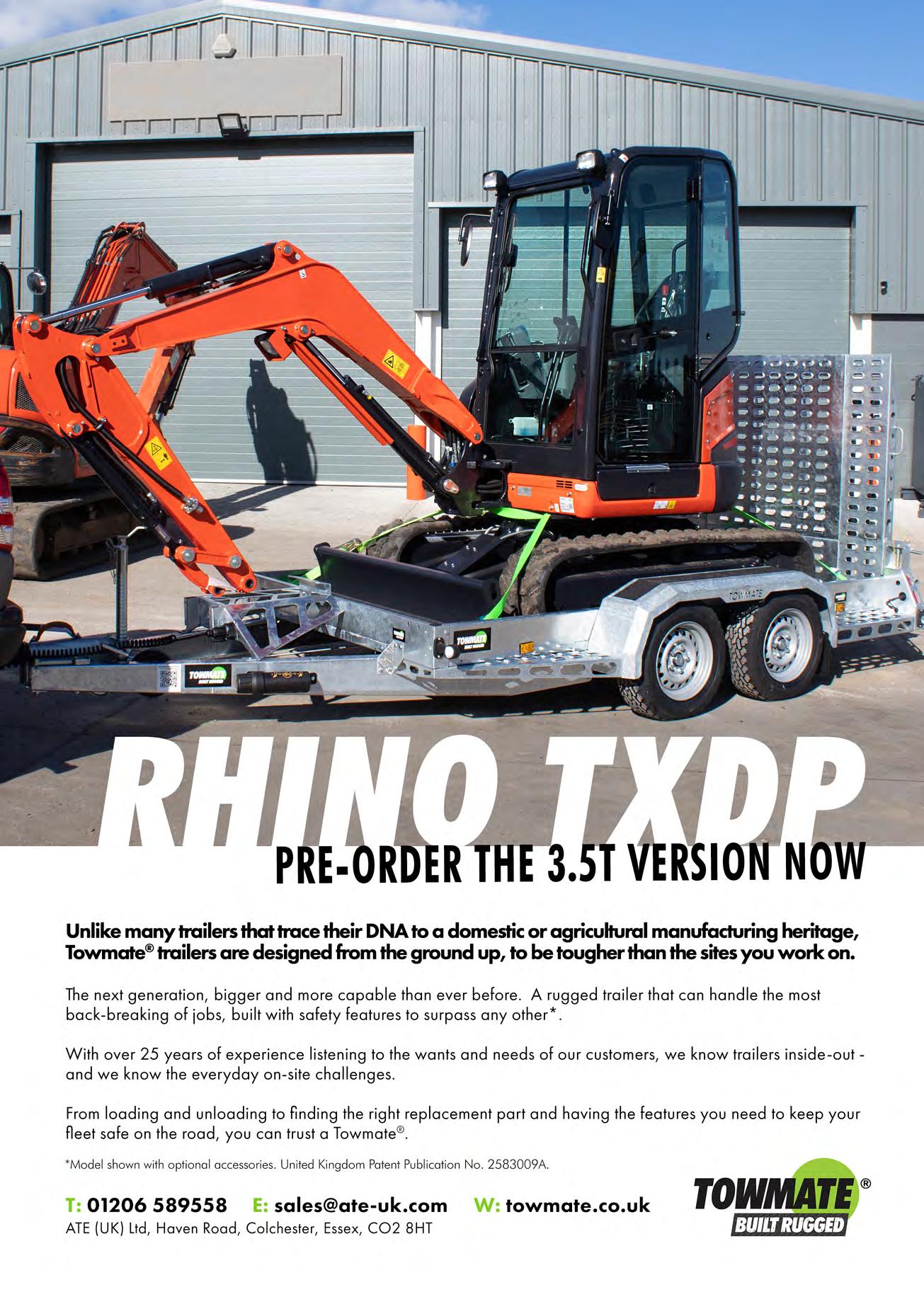
NEW CAT 816 LANDFILL COMPACTOR IMPROVES UPTIME RELIABILITY
Building on a nearly 50-year legacy of delivering maximum compaction performance and rugged durability, the new Cat 816 Landfill Compactors features improved guarding and structure engineering to optimise uptime availability.
New grouping of service points reduces time spent on maintenance, while the compactor’s updated cab design increases operator comfort and productivity. Alleviating potential damage, new frame deflectors divert trash away from the frame and hood enclosure. A new captive hinge on the service doors prevents them from opening unintentionally to protect interior components from contamination. These new deflectors and doors ensure fewer failures resulting from the severe nature of landfill applications. The new 816 compactor features improved airflow technology to reduce cleaning and maintenance. A new radial air filter lasts four times longer than the previous filter, and operators are alerted to airflow blockages by an electronic air inlet restriction indicator. A screened air inlet deflects trash from entering the radiator area to help maintain proper airflow, while an auto-reversing fan with manual activation capability purges debris buildup. Sight gauges for the coolant, transmission oil and hydraulic system provide quick inspection with reduced contamination risk. Grouped hydraulic oil, cooler, fuel cooler and condenser service points, along with centralised grease points, help to further minimise maintenance time. The emergency shutdown, battery disconnect and jump start are quickly and conveniently accessed from ground level. The heavy-duty main structures of the new 816 are built to be rebuilt, offering multiple life cycles. Reusing and rebuilding machine components offers significant savings compared to the cost of buying new and helps to lower total cost of ownership.
Advancing productivity
The compactor’s cab delivers greater comfort and easier machine control for higher operator productivity. Machine controls include membrane switch panels, keyed ignition and electrohydraulic parking brake control switch to increase efficiency. Updates to the single Cat STIC™ system allow for shorter, faster cycles to reduce operator fatigue and increase performance. The STIC system combines steering, gear selection and other functions into a single lever. The cab sits on isolation mounts and features a new Premium Plus seat with leather finish, forced air heating and cooling, two-way thigh adjustment, power lumbar and back bolster adjustment, and dynamic end dampening for total comfort throughout the workday. Pressurized to lower interior sounds levels and keep contamination and odors out, the cab features an automatic climate control system that maintains the operator’s preferred temperature settings. Operators are kept informed about machine operating conditions via a 3G touchscreen with user-friendly interface for viewing the Vital Information Management System (VIMS™) to optimise machine uptime. Fleet management is further improved through Cat Link technology that provides online access through VisionLink® to critical machine data such as machine location, hours, fuel consumption, idle time and diagnostic codes. Cat Compact saves on fuel and machine wear and allows the operator to achieve higher compaction densities through in-cab guidance, machine position reporting and completed pass count. The machine’s standard review camera elevates safety for operators and workers onsite.
Proven powertrain
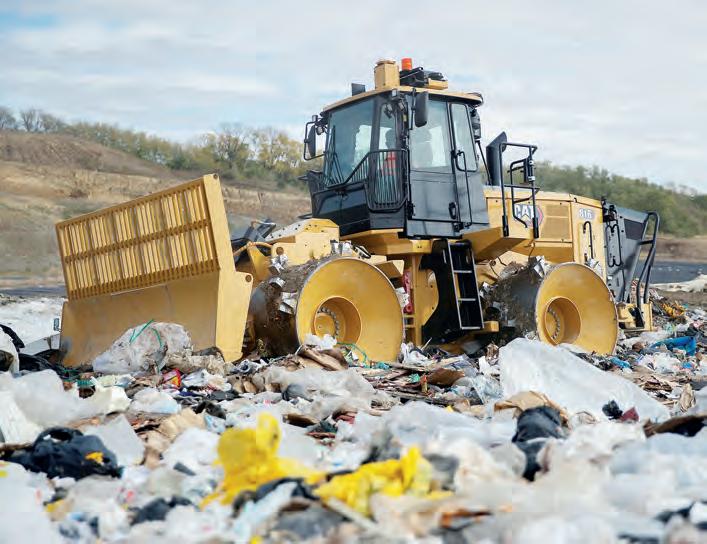
The new purpose-built Cat 816 Landfill Compactor is powered by the field-proven Cat C7.1 engine designed for maximum fuel economy and increased power density. Two engine package options are available – U.S. EPA Tier 4 Final/EU Stage V and Tier 3/Stage IIIA equivalent – for meeting local market emission standard requirements. Its Advanced Productivity Electronic Control System (APECS) transmission control delivers improved shifting performance, achieves greater momentum on grades and saves on fuel by carrying that momentum through shift points. Designed specifically for Cat compactors, Paddle and Plus wheel tips deliver high compaction performance and traction. Striker bars and available cleaner fingers help to keep wheels free of debris, so compaction is more efficient and yields higher densities.
Intelligent Machine Control to Fore in New Komatsu Excavators
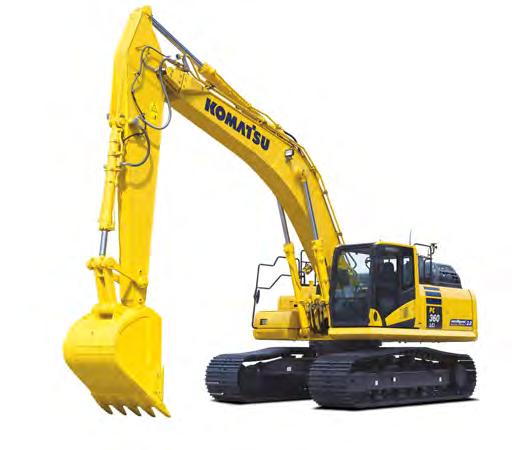
Two new Komatsu excavators, both with latest generation iMC 2.0 intelligent machine control, have been introduced on the European market.
In Ireland – where Komatsu is distributed by McHale Plant Sales of Birdhill and Rathcoole and in Northern Ireland by WAC McCandless – focus will fall on the PC360LCi-11 version, the second model offering being its PC360NLCi-11 stable mate. Singularly one of the most valuable advances in machine operation, the intelligent machine control offered in the PC360LCi-11 is said by Komatsu to offer high productivity earthmoving and precision grading in a single complete package. Representing what they call ‘a step change in machine utilisation’, the newcomer builds on the success of Komatsu’s pioneering fully factory-integrated machine control in a way that McHale Plant Sales director, John O’Brien says “will allow more customers to experience the benefits that intelligent machine control offers”. Key features are operating weights ranging from 35,770kg to 36,850kg; maximum recommended bucket capacity of 2.66m3; and power output of 202kW / 271HP @ 1950rpm from a fuelefficient, EU Stage V Komatsu engine. Others include new Auto Tilt Control and Bucket Angle Hold features. Using Auto Tilt, operation on slopes and ditches is easier. Automatically, the bucket tilts to the design surface with no need for the operator to manually intervene. Under-digging is limited automatically and bucket fill increased. With Bucket Angle Hold, once selected the bucket is automatically held at the desired angle through a grading pass as the arm moves in. Slimmer (36%), lighter (38%) and more compact, the iMC 2.0 monitor – with its ‘smartphone-like’ screen navigation features – comes with increased memory capacity and lightning-fast processing speed. A new IMU sensor facilitates the use and integration of a variety of tilting buckets. Additionally, connection can be made remotely and project design files transferred through a Smart Construction Remote subscription. Other intelligent machine control features carried over into the new PC360LCi-11 and PC360NLCi-11 models are Auto Stop Control, Auto Grade Assist and Minimum Distance Control. Commenting, McHale’s John O’Brien said: “Using an iMC equipped machine for grading purposes alongside its other functions, customers can redeploy their other equipment in order to better optimise fleet usage on the jobsite” “Now, with their availability in Ireland, models factory-fitted with the new iMC 2.0 technology are available to an even wider body of customers who can gain advantage from the benefits that intelligent machine control brings,” he added.
Latest Topcon Construction and Survey Software Now Available
Topcon Positioning Group says its newest release of its suite of software for construction and survey professionals is now available.
MAGNET 7 is designed to utilise the strength that cloudbased connectivity can play in streamlining workflows through GNSS receivers, total stations, and other positioning tools and instruments, and addresses common needs to increase productivity, efficiency, and profitability levels across the job site spectrum. The software is also designed to improve accuracy while efficiently managing data and collaboration -in real-time - with the project team. The new release is particularly timely. On a global scale, COVID19-related demands placed on construction and survey professionals underscore a real need for comprehensive, integrated, software solutions to meet those challenges head on, according to Alok Srivastava, senior director, product management. “The push to ramp up production levels and increase efficiency, while operating profitably, has never been greater,” he said. “Our suite, made up of field software, cloud services, tightly integrated office software and third-party integrations, is a key component of our digital ecosystem, all designed to enhance productivity in the field while helping the office efficiently manage the project dataset. It does so by tapping the power of integrated solutions to provide end-to-end workflows, superior data exchange and a far better level of collaboration. “We’ve long recognised that many of the basic needs and challenges of today’s survey and construction disciplines are similar. With that in mind, this solution provides compatible, comprehensive, connected answers to many of those shared issues.” Enhancements in the field version of the software were made to improve 3D model support, reporting, and interactivity in working directly on a visual map. Additionally, there are improvements in data handling for large and complex 3D projects. Productivity-driven features within the upgraded office solution include an ability to connect to the newest version of the Sitelink3D job site monitoring and management system. Among other benefits, this will enable office personnel to send machine models via the web portal directly to machines on site. This new connection also allows access to the Haul Truck app, which dramatically improves efficiency in the mass-haul environment by sending real-time data - including haul volumes and truck locations - directly to the master schedule. Additional benefits in the office include a new capability for calculating International Roughness Index (IRI), a valuable “key-performance indicator” for resurfacing projects. For added efficiency, IRI data exports directly to ProVAL formats, commonly used in the paving industry, to report and validate road surface smoothness against guidelines set by government transportation departments. Enhanced terrain modelling capabilities for surveyors and an overall increase in file-type capability for all users are also valued additions to the solution.

in profile NEW PRODUCTS & UPGRADES LAUNCHED BY JCB

JCB has recently launched a number of new products and updated others in the manufacturer’s impressive portfolio.
It includes a new 55kW 3CX ECO backhoe loader with EU Stage V compliant engine, taking the backhoe loader into a new decade, with a smart new look that features a revised Command Plus cab. There are four LED beacons integrated into the cab roof as standard, removing the need for magnetic beacons or drilling of the machine. The beacons can be clearly seen from all angles, improving site safety, while there is no requirement for the operator to have to climb up in the cold and wet to install beacons at the start of the day. The Command Plus cab features yellow grab handles, for a clear touch point and there are larger mirrors for an improved view behind the machine when manoeuvring around site or when roading. Revised square worklights offer increased adjustment and the LED option now includes up to 10 lights, providing maximum illumination of the working area. The cab interior provides a new level of comfort and usability, while a revised three-spoke steering wheel provides an improved view of the new front display screen, which comes as standard on the latest 3CX. The screen shows the speedometer, all warning lights and the selected gear on Powershift models. For the first time JCB will also supply a factory-fit radio with Bluetooth telephone compatibility and USB, AUX card capabilities. The radio is integrated into the headliner, but can be controlled by a rotary switch in the side console. Audio and telephone functions are also displayed in the new 7” side display screen. This side screen provides the operator with increased functionality and increased information. The display is controlled by an automotive-style rotary switch that provides quick access to the various operating menus. The 55kW Stage V 3CX ECO introduces a range of advanced automation features, designed to reduce operator fatigue and to boost productivity. This includes Auto Stop, which automatically detects when the machine is no longer in use and shuts down the engine. Auto Stop eliminates engine idling, reducing fuel consumption and cutting emissions. The shutdown delay can be pre-set or adjusted by the operator through the side screen in the cab. Auto Seat Select is available on machines equipped with servo lever control and
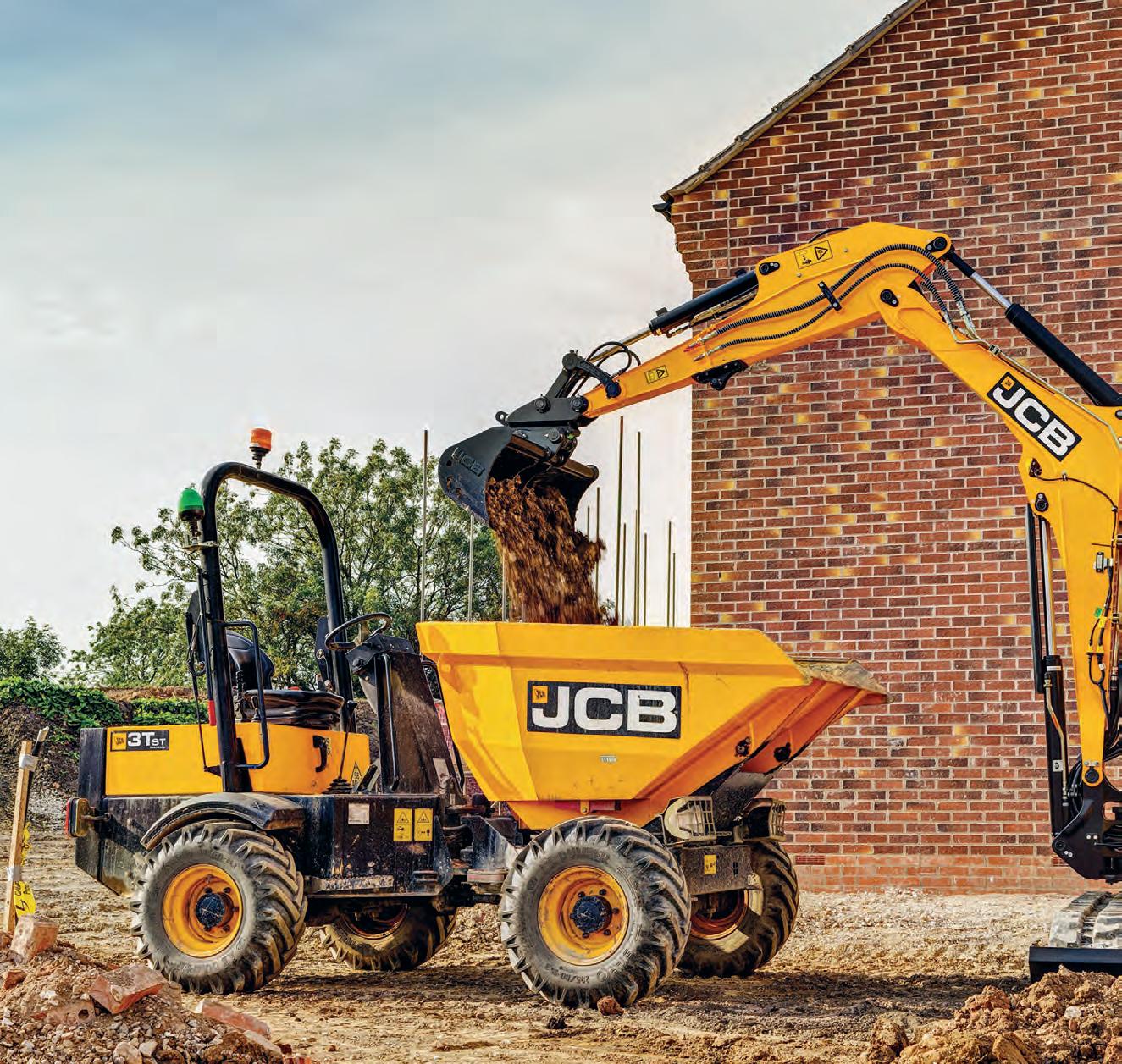
The totally new 36C-1 model. The revised Teletruk telescopic lift truck.

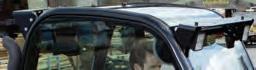
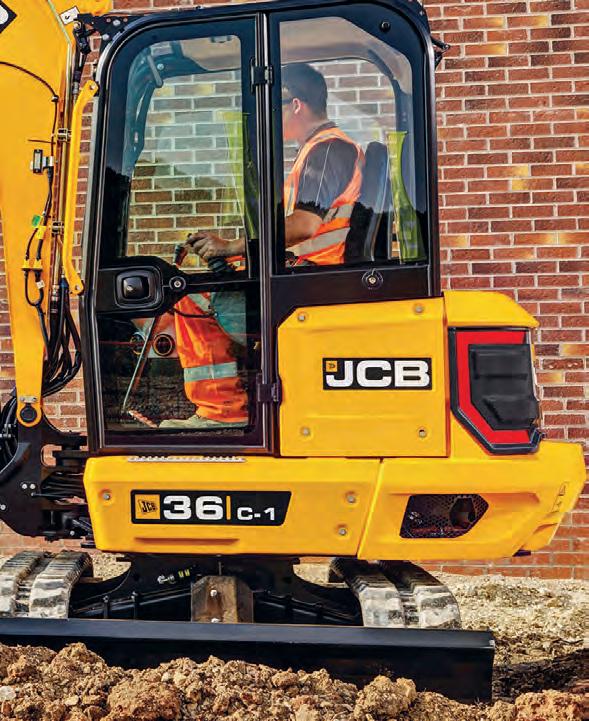
automatically recognises which direction the seat is facing, eliminating the need to select functions as the operator changes from front to rear facing positions.
Compact Excavators
JCB is also launching a 3.5-tonne zero tailswing compact excavator and a new 3.6-tonne conventional model, expanding its ‘Next Generation’ lineup to meet customer demand. While the new 35Z-1 zero tailswing model is a replacement for the previous generation 8035ZTS, the conventional rear-end 36C-1 is a totally new model in the JCB range. The zero tailswing model is ideal for working in confined areas, providing greater protection as the counterweight rotates within the width of the machine. Both machines are powered by a three-cylinder Stage V/T4 Final Perkins engine, delivering 18.4kW (24.6hp). A programmable auto-idle function (2-30 secs) reduces engine speed to 1,400rpm when the levers have not been used for a pre-set time. When the left-hand control pod is lifted, isolating the machine’s hydraulics, the engine speed falls again, to 1,100rpm, reducing fuel consumption and noise levels. A large engine canopy provides easy access to daily checks, with a scalloped counterweight providing easy changing of the engine oil filter. A hinged air conditioning radiator (where fitted) swings out to provide access to the main radiator for cleaning. The two machines use the latest Bosch-Rexroth variable displacement, load-sensing, electro-proportional hydraulic pump. This new technology eliminates stalling, making it possible to utilise all of the engine’s output. A closed-centre valve block provides improved flow, for smoother, more precisely controlled operation, particularly when multi-functioning. The valve block is easy to access, beneath a removable floor plate, where engineers can also find the slew motor. The 35Z-1 and 36C-1 share the same new ROPS/TOPS cab and canopy structure. Flat glazing is used throughout, to minimise replacement costs and an optional FOPS Level 1 guard is offered for further protection. The front screen has a 70/30 split, for maximum visibility to the working area and the lower glass section can be removed and stored inside the rear left-hand window. Slim cab pillars provide excellent visibility all around the machine.
Upgrades
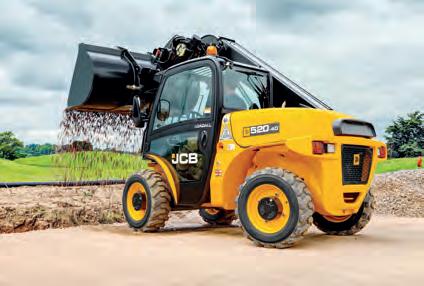
Meanwhile, JCB has upgraded its 4-6 tonne compact excavator line-up with the launch of three Series 2 Stage V models. The zero-tailswing 50Z-2 replaces both the previous 48Z-1 and 51R-1 models, the 56Z-2 takes over from the 55Z-1 and the conventional tailswing 60C-2 replaces the 57C-1. All three of the new machines are powered by a 1.7-litre, turbocharged three-cylinder common-rail Perkins diesel engine, delivering 34kW (45.6hp). The engine is perfectly matched to the hydraulic system and now comes with programmable auto stop, programmable auto idle and one-touch idle functions. The three machines benefit from a new JCB cab, with a revised front screen design to improve forward visibility, particularly when truck loading. Standard LED working lights feature a follow-me-home function, for added safety on site and there is an improved door latch design along with bolt-on grab handles that can be painted in hi-viz colours if preferred. Inside the cab, the layout has been improved, now including the portrait 7” colour screen already seen on the larger 8-10 tonne range. Operators can programme auxiliary hydraulic flows, in both low and high-flow settings, for up to 10 attachments, reducing downtime when swapping between work tools. An integrated rear-view camera can also be routed through the main screen, removing the need for a secondary monitor in the cab.
Loadall telescopic handler now with Stage V engines.
Revised Teletruks
In addition, JCB has introduced a revised range of Teletruk telescopic boom lift trucks with a 46kW (62hp) JCB by Kohler Stage V compliant engine, new styling and a Command Plus cab, which includes fully proportional single lever electrohydraulic controls, leading to improved safety and increased productivity. The machines boast uprated lift capacities at full reach, further increasing performance. The ROPS/FOPS Command Plus cab delivers a 12% increase in space, with the latest JCB next generation styling providing a comfortable working environment. The machines benefit from a single lever control, with luxury Grammer seating in a choice of vinyl or fabric covering. A heated air suspension seat is also available as an option. The seat has an operator presence interlocking seatbelt function and there is a new arm rest pod for improved comfort. The revised seating position increases forward visibility by 13% to deliver exceptional fork tip vision, with angled ROPS roof bars allowing increased visibility when loading at height. A one-piece Command Plus control panel is situated to the right of the seat, providing easy access to all control functions through a rotary controller and membrane switch pad. There is a new eye-level headup display, to provide the operator with easy-to-read information without taking their eyes away from the working area.
Probackhoe Loaders
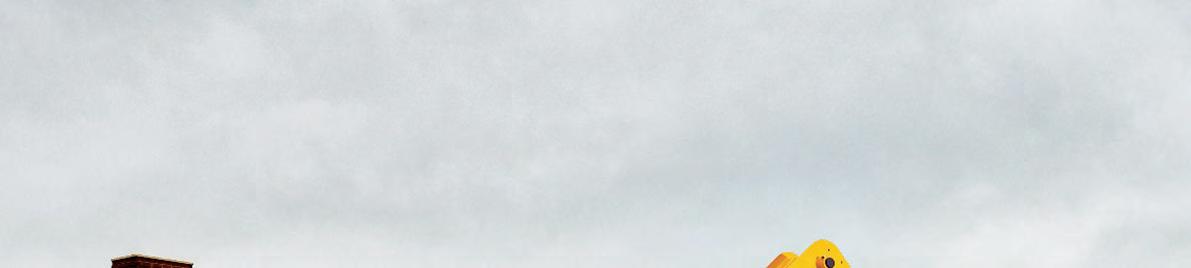
JCB is also introducing the 3CX, 4CX and 5CX PRObackhoe loaders, with the adoption of Stage V compliant engines on all models.
The 3CX PRO is a two-wheel steer machine, the 4CX PRO boasts allwheel steer for increased all-terrain performance and the four-wheel steer 5CX PRO delivers the ultimate backhoe loader specification for bulk earthmoving. All three models benefit from a range of advanced automation features, designed to boost productivity and ease of use. This includes Auto Stop, which detects when the machine is no longer being used and shuts down the engine to reduce fuel consumption and unnecessary engine wear. The time period prior to shut-down can be set by the operator. Auto Seat Select and Auto Stabilisers are standard on servo models, with the seat now recognising which way it is facing and automatically switching between loader and excavator modes. As well as existing Auto-up stabilisers, the system can now automatically extend and stop when the feet reach the ground. Auto Level, on AEC models, automatically levels the machine to a horizontal position on uneven ground. The PRO range also features the ECOROAD six-speed Autoshift transmission that can cut travel time and fuel use by up to 25%, for operators that spend a lot of time on the road. All powershift transmissions are now standard with JCB’s TorqueLock system. The cab also comes with a factoryfit Bluetooth radio, with USB and Aux compatibility that can be controlled from the rotary switch on the side console, no matter which way the operator is facing. In addition, the heating and ventilation controls have been repositioned to the B-pillar, again making them easier to reach whichever way the seat is positioned. The side screen is updated, with a new 7” LCD display. This allows for more information to be displayed and the various menus, including help files and ‘How To’ videos on key functions, can be toggled through using the rotary switch below. Additional secure storage has been located next to the radio, with a lockable compartment for smaller items.
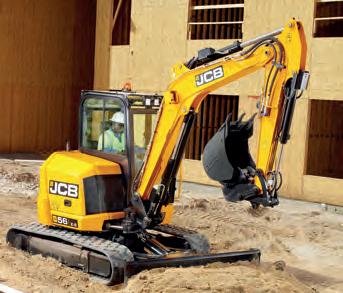
The upgraded 56Z-2 compact excavator
Engine Upgrades
In other developments, JCB has introduced Stage V compliant versions of its popular 140X, 150X and 220X crawler excavators. All three machines will use the JCB DieselMax 448 engine. For the 140X and 150X this will result in substantial rise in torque. Meanwhile, JCB’s construction range of Loadall telescopic handlers for European markets are now also available with Stage V compliant engines. From the 531-70 through to the 540-200, the full line of machines can be powered by the JCB 448 DieselMAX engine, delivering 81kW (109hp).
The new 55kW 3CX ECO backhoe loader.
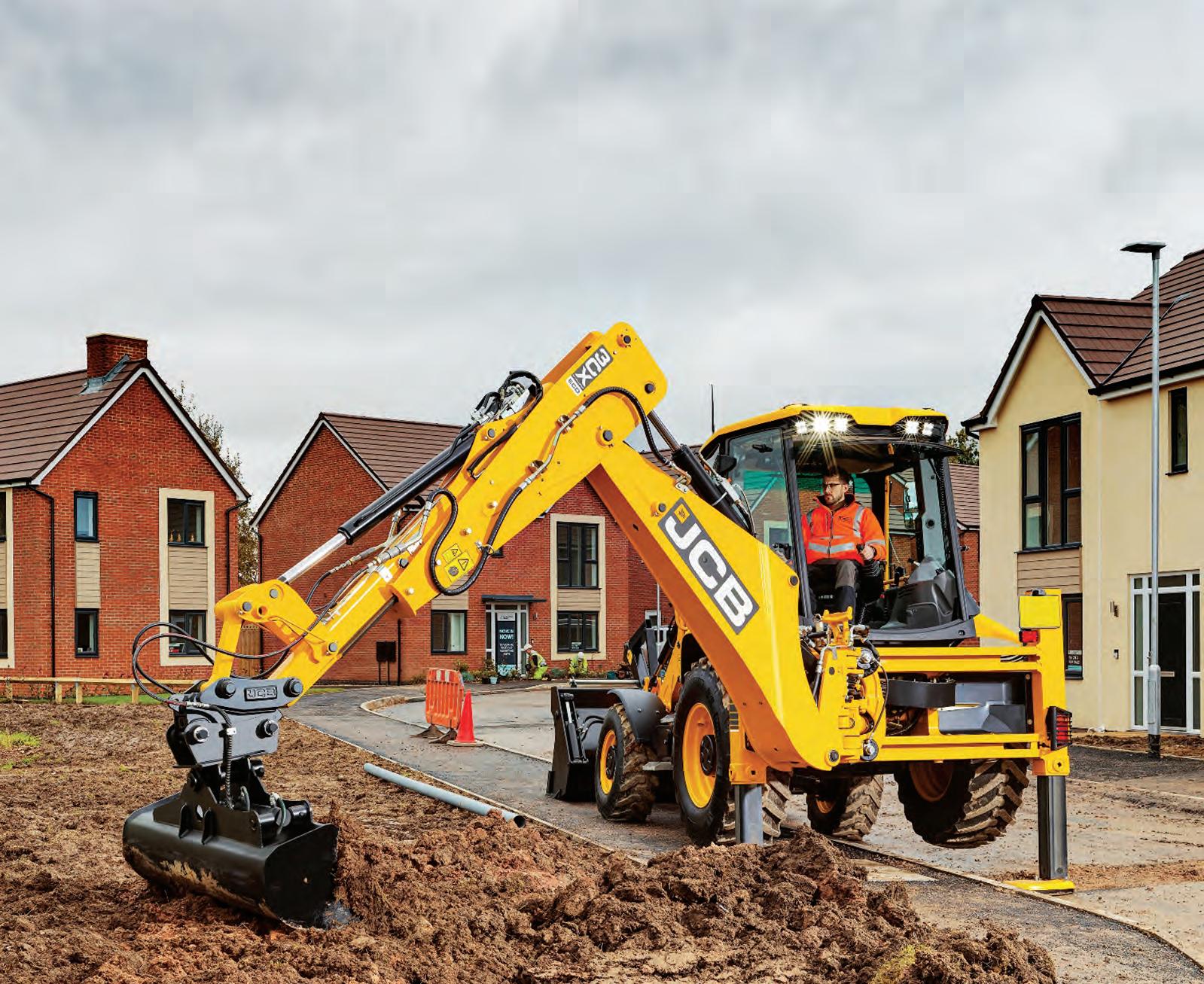
news
Sandvik Mobile Crushing and Screening celebrate My Fleet 1,000th unit milestone
Purpose designed to help customers get the very best out of their investment, Sandvik Mobile Crushing and Screening are now offering their Premium data subscription on new equipment and retrofit packages complimentary for seven years. This marks the celebration of the 1,000th mobile unit to leave the factory with My Fleet connected!
Digitalization has never been more important than it is in today’s climate and it has positively changed the way of working for many people over recent months. Sandvik Mobile crushing and screening have invested heavily into its online distributor portal and My Fleet telematics systems over the past two years. Every new machine within the Q- and U-440i range of mobile crushers and screens is equipped with a My Fleet telematics device and fully connected the moment it leaves the factory. “It’s an exciting time to hit this major milestone of 1,000 units now connected to My Fleet,” said Jesper Persson, Vice President Life Cycle Services. “We are proud of the progress we have made
L-R: Marty Waldorf, Sales Representative, and Dan Soley, Executive VP Sales & Marketing at Miller-Bradford & Risberg Inc.
in digitalization and automation, and how the technology supports our customers. This investment will enable them to learn more about their operation and how best to improve it by tracking their fleet and the health of it. Alerts and notifications will proactively help to resolve issues before they become critical, whilst also enabling remote support wherever possible, saving on time, cost and thereby generating the desired uptime in a sustainable way. “The unit delivered is a Sandvik QI442 impact crusher and the customer to take ownership in February is our US Distributor in Wisconsin, Miller-Bradford & Risberg Inc.” Dan Soley, Executive VP Sales & Marketing comments: “We are delighted to hear the news that our QI442 is the 1,000th unit. My Fleet is a really beneficial tool as it gives great insight into machine utilization and location. The ability to offer remote support means we don’t always need to visit the customer to assist them in their operations. “Customers will be able to benefit from enhanced levels of technical support. Whether through Sandvik, or from our trained distributor network, technical support specialists will be able to view the same operational data and view notifications of any alerts or machine faults via the system, and thereby be able to offer remote support without necessarily needing to be on site. This immediate assistance increases uptime, whilst at the same time providing a safer working operation as the operator doesn’t need to physically climb on the machine, as well as supporting the drive to a more sustainable business.” All Sandvik machines that are already fitted with My Fleet and working out in the field will automatically be granted the extended seven-year data subscription. This includes customers who have purchased the My Fleet retrofit kit which can be fitted to all Sandvik 1 Series models onwards.
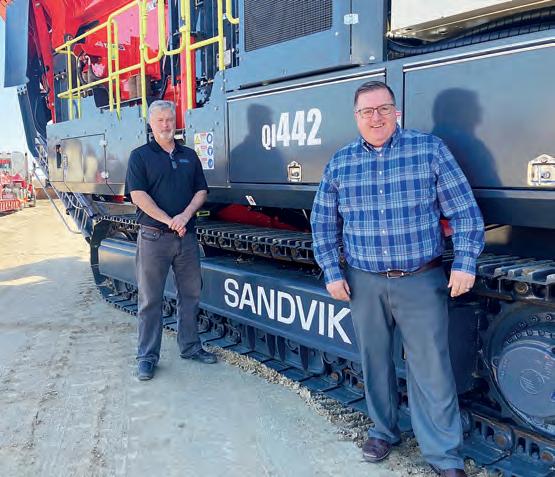
New Options for Proven Terex MPS Screen Modules
Terex MPS has introduced new options for the popular MHS6203 and MHS8203 screen modules including a wash plant option and a feed box and support structure.
The screen modules feature the proven TSV Series horizontal screens, combining the efficient, high g-force El-Jay oval stroke action and a large blending chute for a range of discharge options. The new wash plant option includes a feed box with two spray bars and support structure, screen spray system with manifold and under screen flume. Outfitted as a wash plant, the module can produce high value washed stone products and can be paired with a sand screw or other sand processing and fines recovery equipment. The new Rock Box Style material feed box allows for the conveyor to feed from either side or over the back of the screen, allowing additional flexibility for placement of the module on a compact site or as part of a multi plant system. The MHS6203 screen module features a 6 ft x 20 ft 3 deck TSV screen, while the MHS8203 features a 8 ft x 20 ft 3 deck TSV screen. All Terex MPS modular crushers and modular screens bolt together on site and require minimal on-site wiring. Designed with logistics in mind, the screen modules ship in two 40’ shipping containers; the screen ships separately.
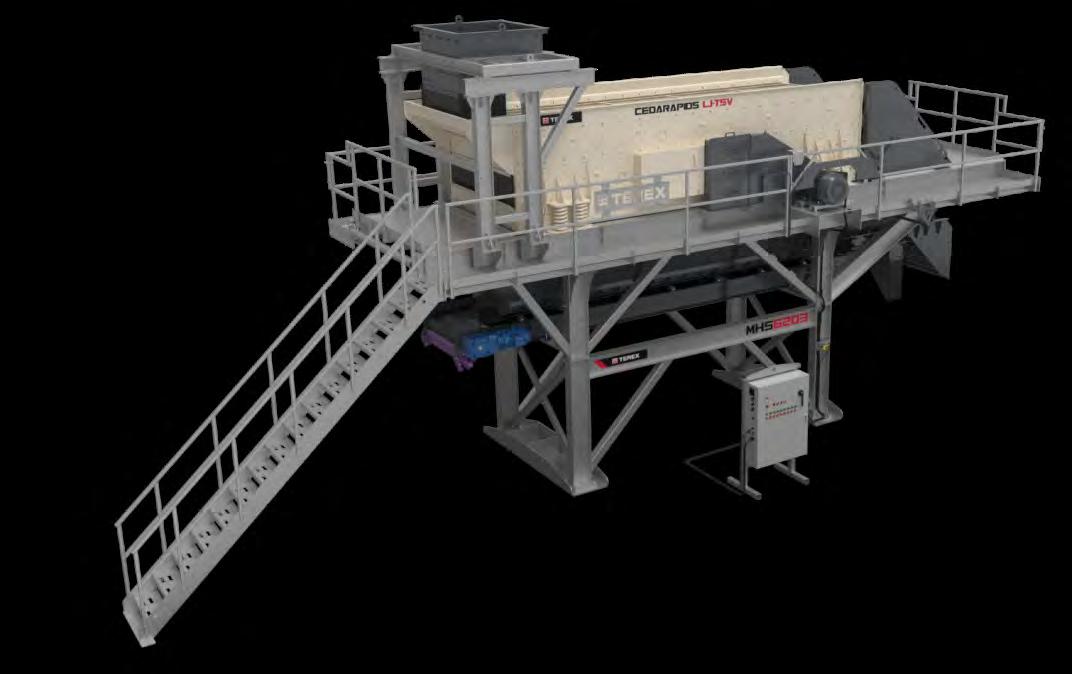
SPECIALIST CONTRACTOR OPTS FOR LATEST LONG REACH HIDROMEK
Specialist contractor Alaska Ecological Contracting Ltd take on ‘problem’ sites that others might consider too steep, too wet and too remote, so the equipment they use has to be more than fit for purpose, which is why they have opted for another Hidromek excavator, as Plant & Civil Engineer’s David Stokes reports.
The latest Hidromek to join the fleet at this Dorset based ecological and environmental contractors is a long reach H4 Series HMK 310 LC; it works along with a Hidromek 220LC and a specially adapted Hidromek 220 amphibious machine. The machine was supplied by TJC Plant Group who have worked closely with Nat Bond and the Alsaka team over a number of years. The company enjoys a close working relationship with many of the UK’s topflight consultant ecologists, and has an enviable reputation for producing innovative solutions to apparently insurmountable technical difficulties, leading where others have followed. Much of its work is in National Parks, on Sites of Special Scientific Interest, Special Areas of Conservation and Areas of Outstanding Natural Beauty, but it also takes on problem sites that other contractors might shy away from. “Our real strength is in our workforce: we take the best machine operators that we can find, and we train them to be even better - to meet our, and exceed our client’s, exacting standards of workmanship.” The new 30 tonne machine is employed on digging silt out of a lagoon at a quarry at Wareham in Dorset operated by Holme Sand & Ballast who produce fine sands for the construction industry, sports amenity market and leisure sectors. Alaska Ecological Contracting’s Nat Bond says it was primarily purchased for that particular task and he expects it to be on site there for some considerable time. “There’s a large lagoon at the quarry where silt and fine clay from the sand washing process is continually settling in the various cells on the way down, so the long reach Hidromek is perfect for digging it out before we haul it away from the site.” He adds: “It has a very comfortable cab that is well laid out, with good all round visibility, while responsive, easy to reach controls provide a smooth performance in comparison to some other machines. Our operator tells us that he prefers grading with this long reach machine rather than what he has been used to.” The company’s other two 20 tonne machines, one mounted on an amphibious tracked frame, the other fitted with a long reach kit, are both serviced in-house, but adds Nat: “We also get good support from local Hidromek dealers TJC Plant Group.”
Safe & Efficient
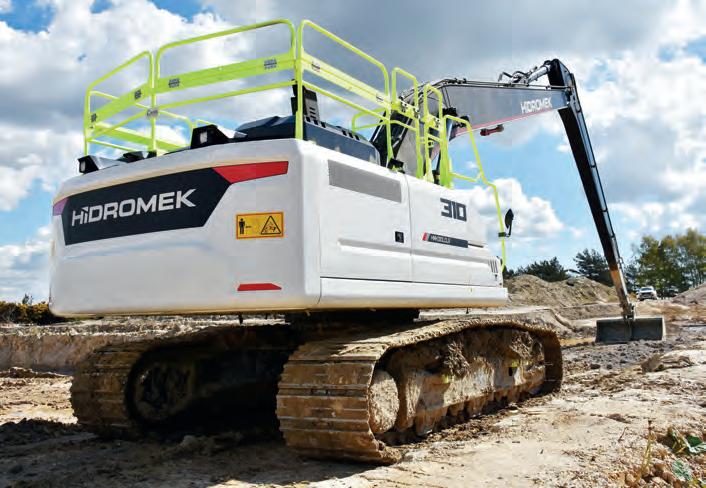
Ideal for working in challenging areas, the H4 Series HMK 310 LC comes with a series of safety features, including an automatic starting horn, swing warning system and travel warning system, while rear and side view cameras help eliminate blind spots. It is a fuel efficient machine, too, with an automatic stop system through configurable idling and stopping times that provides fuel
saving by stopping the engine after the machine is on idle; this automatic stop system helps to decrease the operational costs to minimum, and contributes to saving the environment. The comfortable and spacious cab features an 8 inch touch control panel which is positioned ergonomically at a point where the operator can easily reach it; a large screen easily enables the operator to control the machine features and gives ready access to machine information. The cab’s heated, air suspended seat with adjustable backrest enables the operator to work comfortably and without getting tired for long working hours. Other features to enhance the working environment include proportional control pedals and joysticks, throttle control dial, interior light, cup holder and heating-cooling box, while an air conditioning system which can automatically adjust itself according to the ambient heat located in the redesigned cabin is said to provide ‘the best cooling performance in its class by 30%.’
Opera Interface
The machine comes with Hidromek’s
Opera Control System, an easy to use interface that facilitates communication between the operator and the machine. The operator can easily switch between menus in Opera, change settings, such as hydraulic flow, and check the status of the machine, including pressure, temperature and engine load. The information and warnings on the instrument panel are always easy to see and control, thanks to the positioning of the Opera interface. Other features of the system include automatic powerboost switch-on switch-off, automatic electric power-off and automatic powershift to improve performance. It even tells you when the next service is due. Routine servicing and maintenance is made easy, with fast access to hydraulic and engine equipment, while an automatic greasing system ensures that all parts of the machine can be lubricated from one single centre – and most of the maintenance can be easily carried out without getting on the machine, which shortens the service time and thereby increases machine work time.

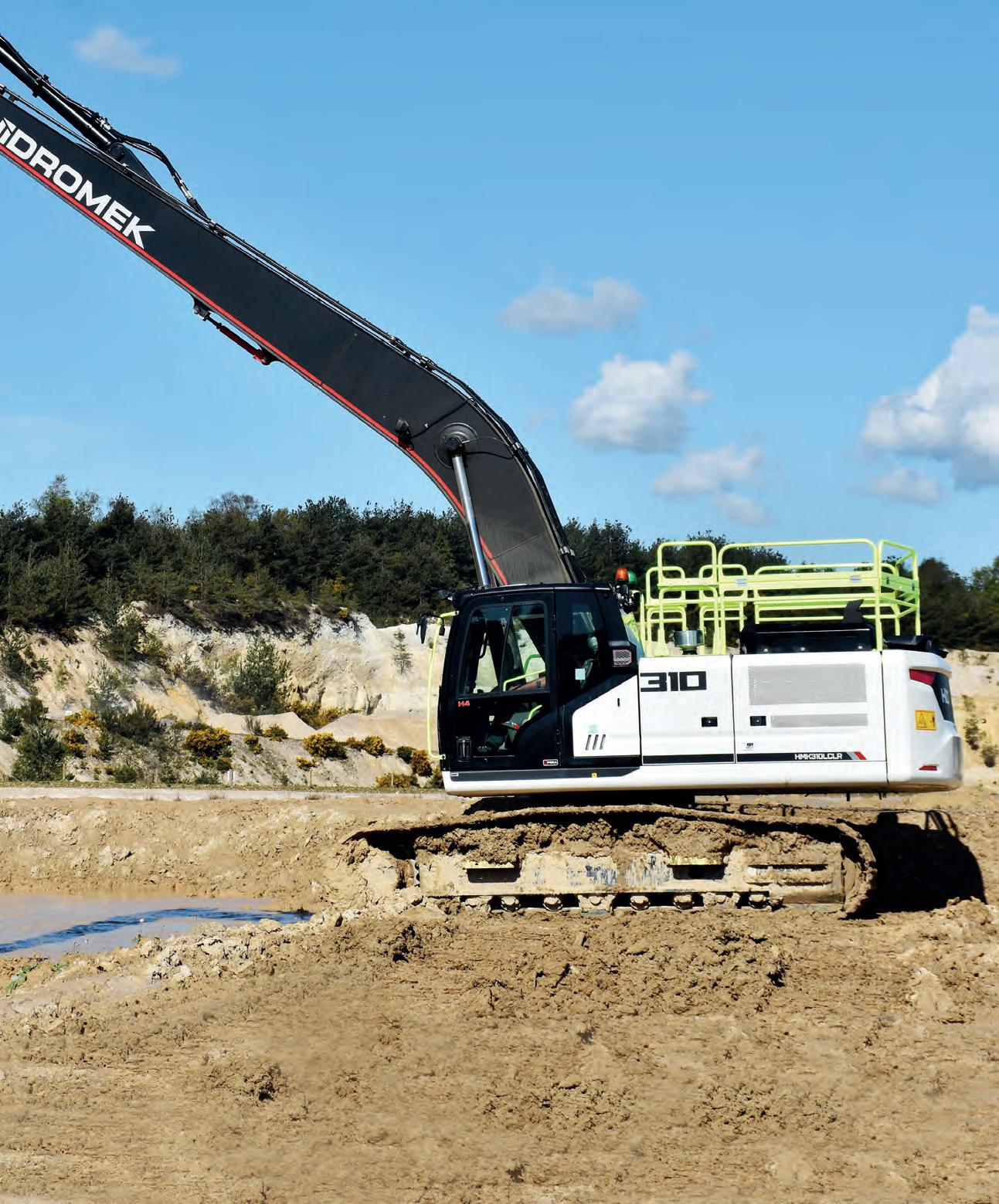
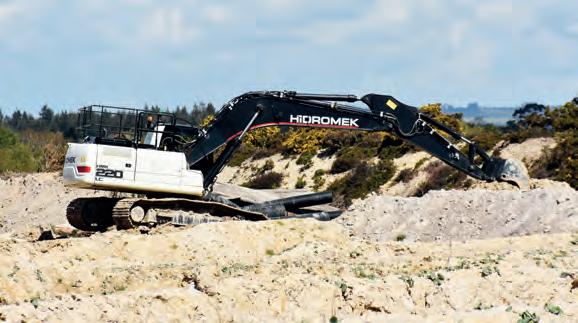
news Alternative fuels - making the switch
A genset is a common sight on many construction and industrial projects, working hard to keep equipment, machinery and welfare running. But do you know what fuel is powering the system behind the scenes?
While traditionally the answer would be easy - diesel - alternative fuels are becoming much more popular. Here Barry Hughes, Applications Manager at leading Cat generator rental company Energyst UK & Ireland, shares insight into alternative fuels for temporary gensets. The environment is a compelling reason to switch from diesel to an alternative fuel. For companies that have made a commitment to become carbon neutral, moving away from diesel is a natural step. But this is not the only reason, businesses may be looking to reduce the impact on the local area by reducing the amount of smoke or smell the genset emits. Alternative fuels also require fewer logistical and operational preparations compared with diesel, as using biodegradable fuels means that operators do not need to make contingencies for spillages. The Red Diesel Tax reduces the cost of diesel in many applications and has been a challenge for alternative fuels, but it does not offer security for the long term. In line with the UK Government’s net zero by 2050 target, some companies are concerned they will be penalised in the future for diesel use, though there will of course be exemptions. In London, the Non-Road Mobile Machinery (NRMM) Low Emissions Zone is now stipulating and policing better environmental practices, such as adopting Stage V engines or improved solutions including early, including the approved use of alternative fuels. As other cities follow suit, it will contribute further to the uptake of alternative fuels. For companies already committed to carbon neutrality, alternative fuels can reduce the requirement to offset at the end of the year, such as by planting trees if they do not achieve their own commitments to the environment, impacting on the business’s operational costs. There are also opportunities to reduce maintenance costs compared with diesel. For this mixture of reasons, we are seeing a huge rise in the number of people looking for alternative fuels.
Types of fuel
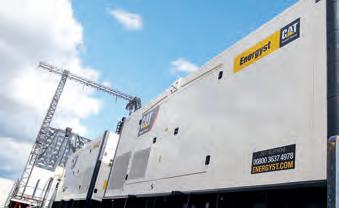
Over the years, biodiesel has had bad press, mainly due to difficulties with quality control. While it is typically the first fuel that comes to mind when the topic of alternative fuels is brought up, it is not something we advocate the use of. There are several other fuel options in the UK and Ireland that offer better performance and reliability, such as hydrotreated vegetable oil (HVO) and gas to liquid (GTL). HVO is a direct ‘drop-in’ replacement for diesel and is not comparable to biodiesel. It does not require engine modifications to gain the maximum benefits from the start, you simply clean the fuel tank and system and add HVO and start the engine. Watch the exhaust emit no smoke, even on start-up! It also requires no change to servicing schedules, is odourless when burnt, is 100 per cent renewable and, because it is biodegradable, brings no concerns about spills or bunding. It results in a large decrease in emissions, up to a 90 percent reduction of carbon footprint, a 10 to 30 percent reduction in nitrogen dioxide (NOx), up to 100 per cent reduction in sulphur oxides (SOx), up to a 35 per cent reduction in particulate matter (PM) and a 20 per cent reduction in hydrocarbons. Its cold filter plugging point is -32°C, lower than both biodiesel (-5°C) and diesel (-12°C). Another option is gas-to-liquid (GTL), which is currently available in the UK and mainland Europe. Named after the process it is made by, GTL offers similar savings to HVO, other than carbon as it is a fossil fuel. GTL is often used with diesel as a blend, which offers some exhaust emissions and operational savings and can be a steppingstone to reducing emissions further in the long run. Though you might assume that heavy fuel oil (HFO) is similar to HVO initially, the two are very different. HFO is a heavy, tar-like fuel used in vessels and ships, offering no environmental benefits - it is important not to get them confused!
Considerations
While HVO is marginally more expensive per litre than diesel, there are more factors in the equation. Firstly, purchasing in bulk can make the prices much more comparable - on a long-term generator hire, the costs may be very close or even the same.. In addition, because HVO contains no carbon, it does not have many of the downsides associated with blends that include diesel, such as water contamination or fungal growth affecting fuel quality. Diesel fuel related problems like lack of testing, treatment and fuel polishing are common reasons for breakdowns that HVO can avoid. For example, it helps overcomes the breakdown risk associated with sizing a generator incorrectly. If sized too large for the application, the generator will run inefficiently, produce smoke and buildup carbon, meaning the operator will need to load bank test it and perform other maintenance activities to prevent a breakdown. While oversizing will still mean companies are paying more for a larger generator than they need, HVO does mean they don’t have to worry about carbon build up causing a breakdown. HVO can therefore reduce maintenance costs, as well as provide operators with peace of mind that unexpected downtime is not about to hit. Alternative fuels are growing in popularity as an environmentally friendly, reliable and financially justifiable option. In line with this, our entire generator fleet is suited to HVO and GTL, helping to keep your environmental conscience clear, and your equipment running.
Manufacturer Launches Patented Vandal Guards For Excavators
Digger Guard®, a patented new range of protective guards developed for leading construction machinery manufacturer Hitachi Construction Machinery UK, has been launched.
Plastics manufacturer, Norplast Ltd, developed the innovative Digger Guard product range in response to a project brief from Hitachi inviting the company to design a new vandal guard to overcome problems with existing systems used to protect excavator cabs. Newcastle-based Norplast’s design and development team achieved innovative improvements which merited a patent for Digger Guard. With industry giant Hitachi as its first major customer, Norplast is overseeing the roll out of its Digger Guard products on models of excavator across the UK. “The existing products on the market had a number of problems that Hitachi Construction Machinery wanted to improve upon: they were difficult to install and remove, heavy and prone to wear, noisy and not watertight when stored,” said Norplast’s Managing Director, Dave Smith. “It was clear to us that there was considerable room for improvement, and we delivered on that for Hitachi with Digger Guard. “Construction industry machinery is exposed to extensive risk of costly damage both accidentally and through vandalism. With Digger Guard we have achieved improvements that we’re confident will save operators time on the job, and reduce both down-time and insurance costs.” A Hitachi Construction Machinery spokesperson commented: “Norplast successfully addressed every problem we originally set out for them to tackle. They’ve designed vandal guards for various models of our excavators and fit-test them at our sites as part of the service. We’re pleased to pass on the benefits of the Digger Guard system to our customers and end-user operators.”