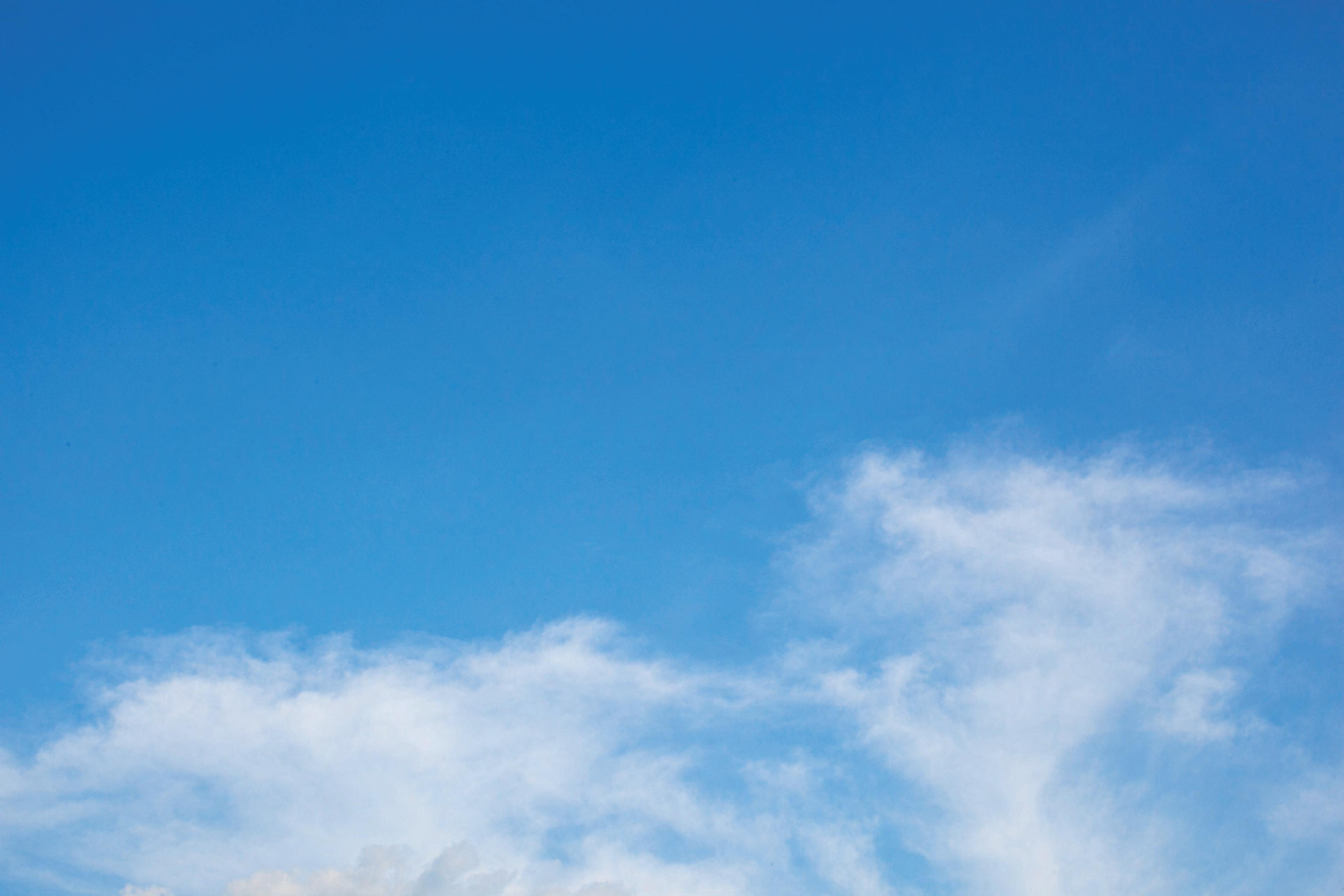
45 minute read
CASE Wheel Loader G-Series Evolution
from Plant & Civil Engineer 2021
by 4SMNI
CASE WHEEL LOADER G-SERIES EVOLUTION BRISTLES WITH NEW INNOVATIONS
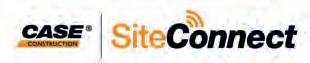
Feedback from operators who have been able to trial CASE Construction Equipment’s new G-Series Evolution Wheel Loader range has been highly favourable, as Plant & Civil Engineer’s David Stokes found out during a oneto-one interview with members of the manufacturer’s European team.
The impressive new range enjoyed a recent virtual launch, the first time CASE Construction Equipment has staged such an event in Europe; such was its success, it may not be the last, especially if the pandemic continues. CASE Business Director for Europe Joseph O’Grady told us that initial reaction from customers, the dealer network and others who joined online was very encouraging. “Although not physically present in person as we would have been in the past, we were able to successfully get across all of the unique features of the new G-Series, so yes, all were very impressed,” says Joseph. And adds Crispin Turner, Marketing Manager for Northern Europe: “Living in unprecedented times, a virtual launch was our only option. It was a challenge, but using online platforms like WhatsApp we were still able to interact with those who joined the event, and having that dialogue with customers and dealers worked fantastically well. “That said, customers do like to get up close to machines to feel and see for themselves what the latest technology can offer, so depending on how the easing of lockdown measures progresses over the next few months that may be possible at a local level through our dealerships; we will just have to wait and see.” However, he revealed: “Not to give too much away, but we have had some of the new machines out with customers already ahead of the launch and feedback has been very positive; everything we are claiming about the new G-Series is proving to be true, according to those operators who have tried the machine, the first deliveries of which will be taking place in a matter of weeks.”
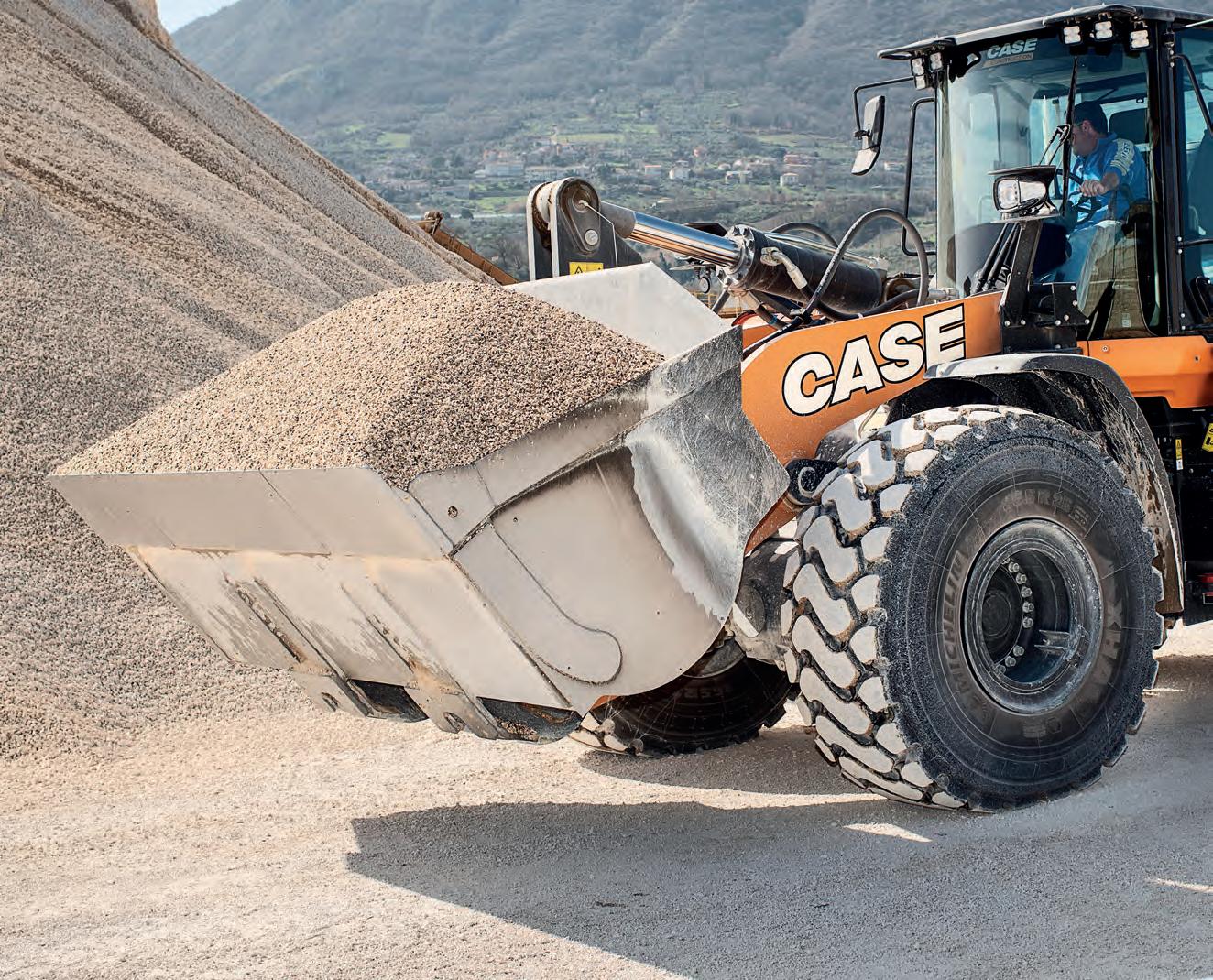


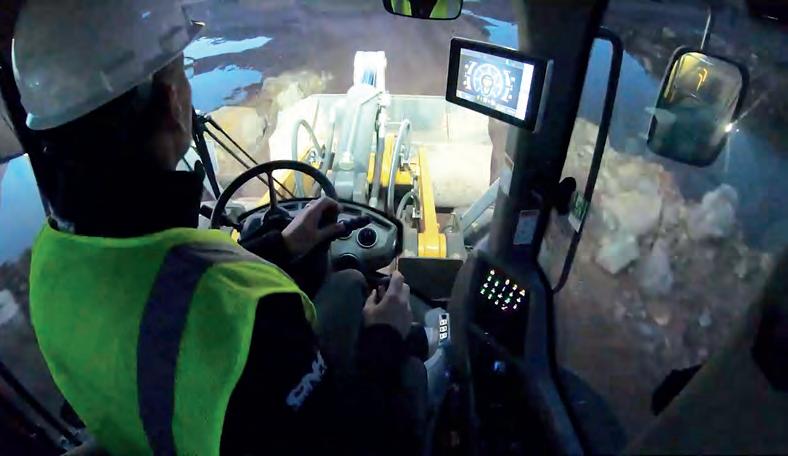
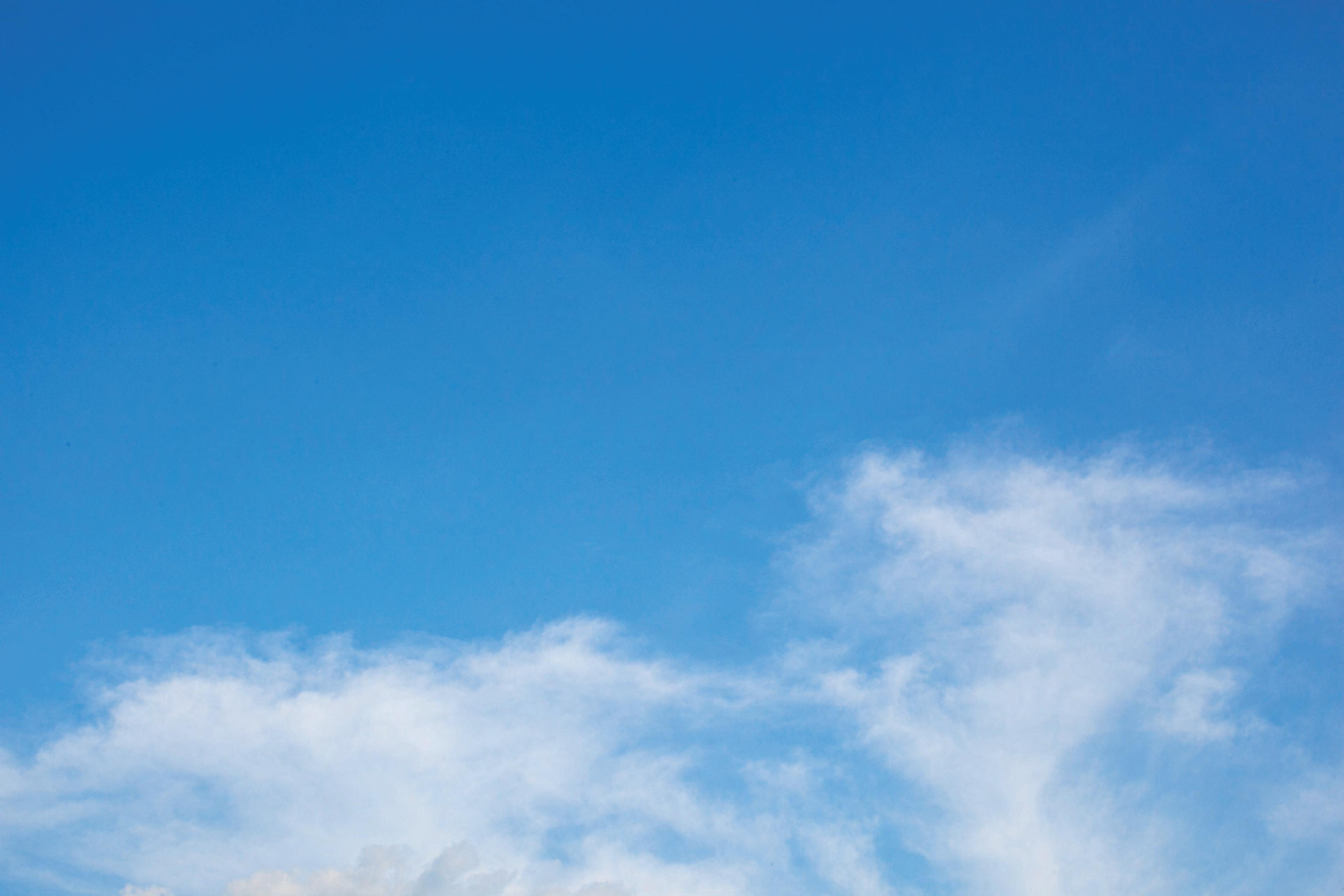
New Innovations
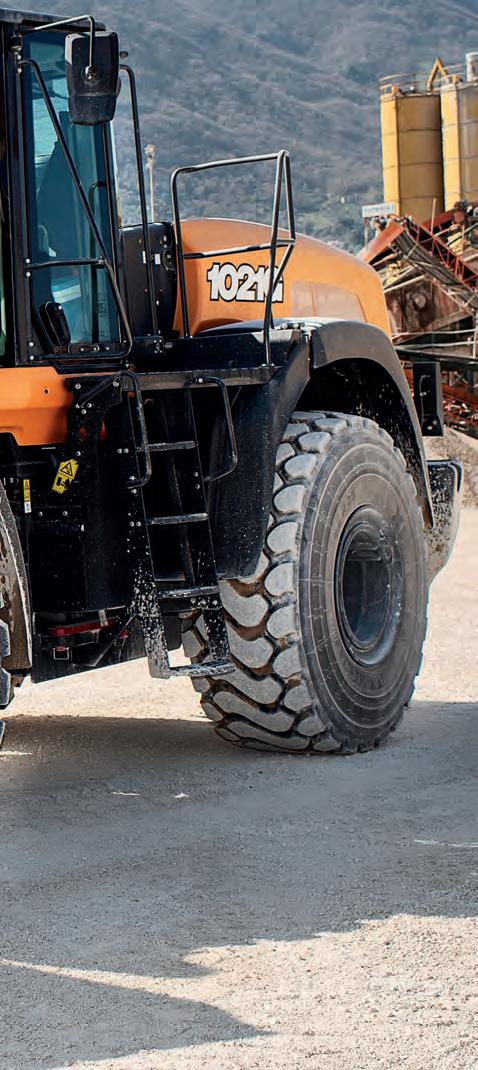
So what can customers expect to see in the new G-Series, which features a host of new innovations: over to Egidio Galano, Product Management Director, CASE Construction Equipment, Europe. “All of these new features have been driven by direct feedback from customers and dealers - from the tyres to the bucket to the engine and to the controls - to provide comprehensive connectivity and systems improvement.
That’s what our customers wanted and that’s what we are giving them with this new G-Series,” he tells us. Complete with comprehensive enhancements across its entire line, the new G-Series Evolution Wheel Loader is said to improve performance and productivity by increasing uptime as well as empowering operators with greater control and understanding of the machine and its capabilities, resulting in increasing profitably. “Wheel loaders that are designed to work in the most extreme working environments benefit from improved performance and profitability when you shorten cycle times, by simplifying operations and increasing uptime,” explains Egidio. “Each of the enhancements included in the new CASE G-Series Evolution loaders drive those incremental improvements that lead to big gains in productivity and efficiency.” Designed to be reliable and save time, the all-new payload system is integrated directly into the wheel loader’s primary display and provides bucket-weight, pass counts, accumulated/running weight, job tracking data and more, for high-volume loading and production environments. Operators benefit from the ability to precisely load each truck and reduce under/overload situations by accurately weighing each bucket, whilst cumulatively tracking the total weight of material loaded into each truck. The improved payload system helps operators track total loads including the total volume of material moved over a specific time, load history by customer, ticket or material, as well as providing a comprehensive ticket history. CASE SiteConnect and SiteWatch also come as standard for three years on each CASE G-Series Evolution Wheel Loader. CASE SiteWatch telematics is a solution designed to gather critical information about the machine’s performance and location and make that data quickly available.
CONTINUES ON NEXT PAGE
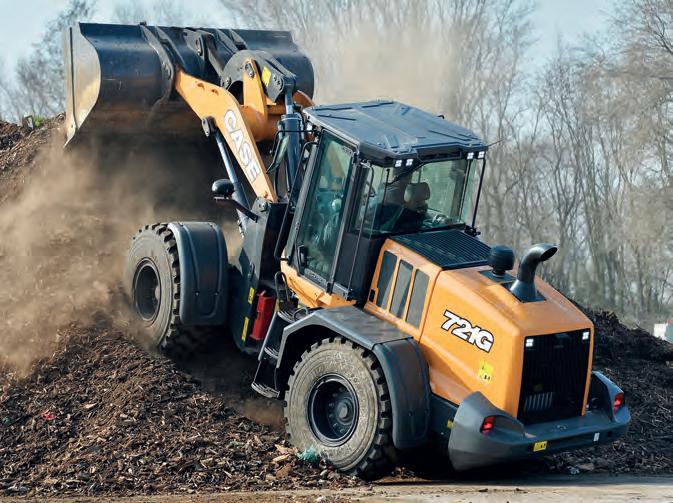
CONTINUED
Featuring a new dashboard, SiteWatch is designed for intuitive navigation that clearly identifies issues without requiring operators and fleet managers to be physically present. “The new G-Series Evolution includes a new integrated payload scale that lets operators read and log every single bucket load. Once the truck target load is set, the system can show if the last bucket exceeds the target load and, in this case, the “tip-off” mode can be activated, helping the operator to partially release the material in the bucket until the target load is achieved. This means no more unproductive time wasted on long loading and wheel loader weighing operations, and more time profitability,” comments Egidio. Tyre health and performance, of course, has a significant impact on overall machine performance, including fuel efficiency. The all-new Tyre Pressure Monitoring System features individual sensors that mount to the valve stem of each tyre along with a receiver module that communicates the pressure for each tyre onto the display and alerts the operator when the tyre pressure is outside of a set range.
Keeping it Simple
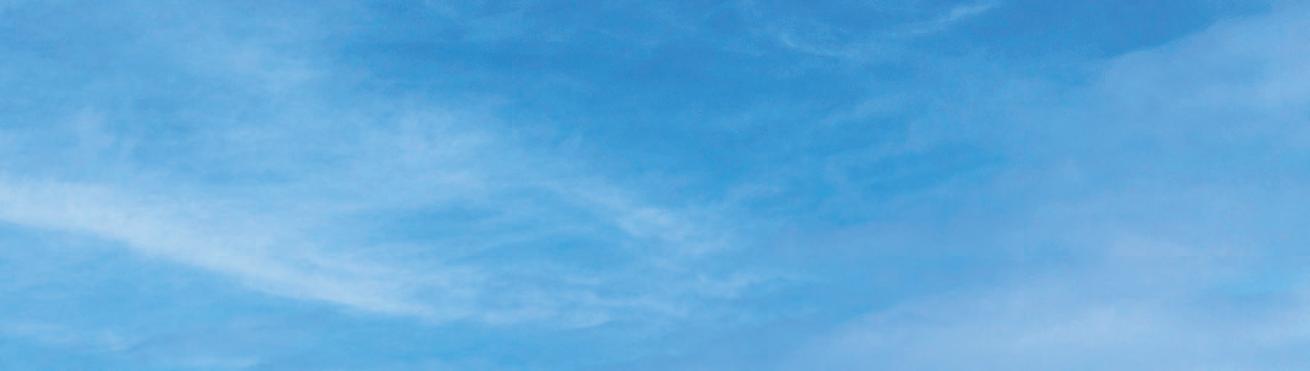
With each new technological advance, of course, comes the challenge of being able to master the machines, a task that could be daunting for the ‘older’ operator who, if they are anything like me, may be inclined to resist change, but by all accounts that shouldn’t be the case with this new G-Series; we are assured that it is no different than managing a smartphone! The G-Series Evolution Wheel Loader range features an all-new touchscreen display that provides tablet-like performance for accessing all critical machine settings and operational data, allowing operators to anticipate and react more quickly to real-time changes in conditions. This includes all-new electro-hydraulic controls that enable the operator to independently set lift (boom) and tilt (bucket) responsiveness to match operator preference and loading situations. Each function can be independently set with a choice of three responsiveness modes: smooth, moderate and aggressive. CASE has simplified the previous engine power management operating mode offering with two new ones: Smart and Max. Max mode is chosen when the operator wants to work with maximum engine performance in tough conditions, while the new Smart Mode delivers high performance and an enhanced operating experience through improved communication between the engine and transmission on jobsites that are less challenging. Operators can take advantage of the new parallel lift functionality across all boom configurations that assist in material retention and smooth loading by automatically maintaining the angle and position of the bucket or forks. To further simplify usability, CASE has introduced three new colour-coded configurable buttons on the right armrest enabling the operator to react quickly, with minimal movement, whilst being able to interact with pre-programmed machine settings. These settings are determined by the operator and can include critical functions/displays such as the all-new payload screen, rear-view camera, differential lock or declutch, and strobe activation. “These advances, combined with the ergonomic design of the joysticks and the operator station, centralise total operation of the loader for improved operator performance and focus, and reduced fatigue,” says Egidio.
Uptime & Responsiveness
Uptime and responsiveness, of course, are primary drivers for users when it comes to buying heavy construction equipment and the advances brought to the new CASE G-Series Evolution with remote diagnostics combined with the ability to update software and cancel inactive faults remotely will significantly shorten any downtime events experienced by the owner/operator. This technology is powered through the new telematics enabled 4G SiteConnect Module installed on the machine that can be accessed via the new SiteManager App (available on iOS and Android devices). “This platform was built with customers in mind,” says Egidio. “With SiteConnect, we are enabling two-way communication between machines and CASE dealers, who can run remote diagnostics and best advise operators on any issues identified without even visiting the site. Algorithm-driven proactive analysis of potential failures and reduced time to fix issues means more uptime and productivity. If a potential problem is detected, an alert is sent to the CASE dealer with specific recommendations and actions to fix issues before they become problems.”
Service intervals
Thanks to extended service intervals from 500 to 1000+ hours the total cost of maintenance has been reduced by up to 20% when compared to the current Wheel Loader range. In addition, CASE has developed CASE Care, a standard planned maintenance programme with genuine parts and lubricants available in Germany and the UK, with Europe-wide availability planned. The programme is underpinned by the support, logistics and technical expertise of the wide-reaching CASE dealer network. CASE Care can be selected as part of a bundle of CASE Service Solutions, alongside the CASE Protect Warranty extension, with a range of options for total peace of mind.
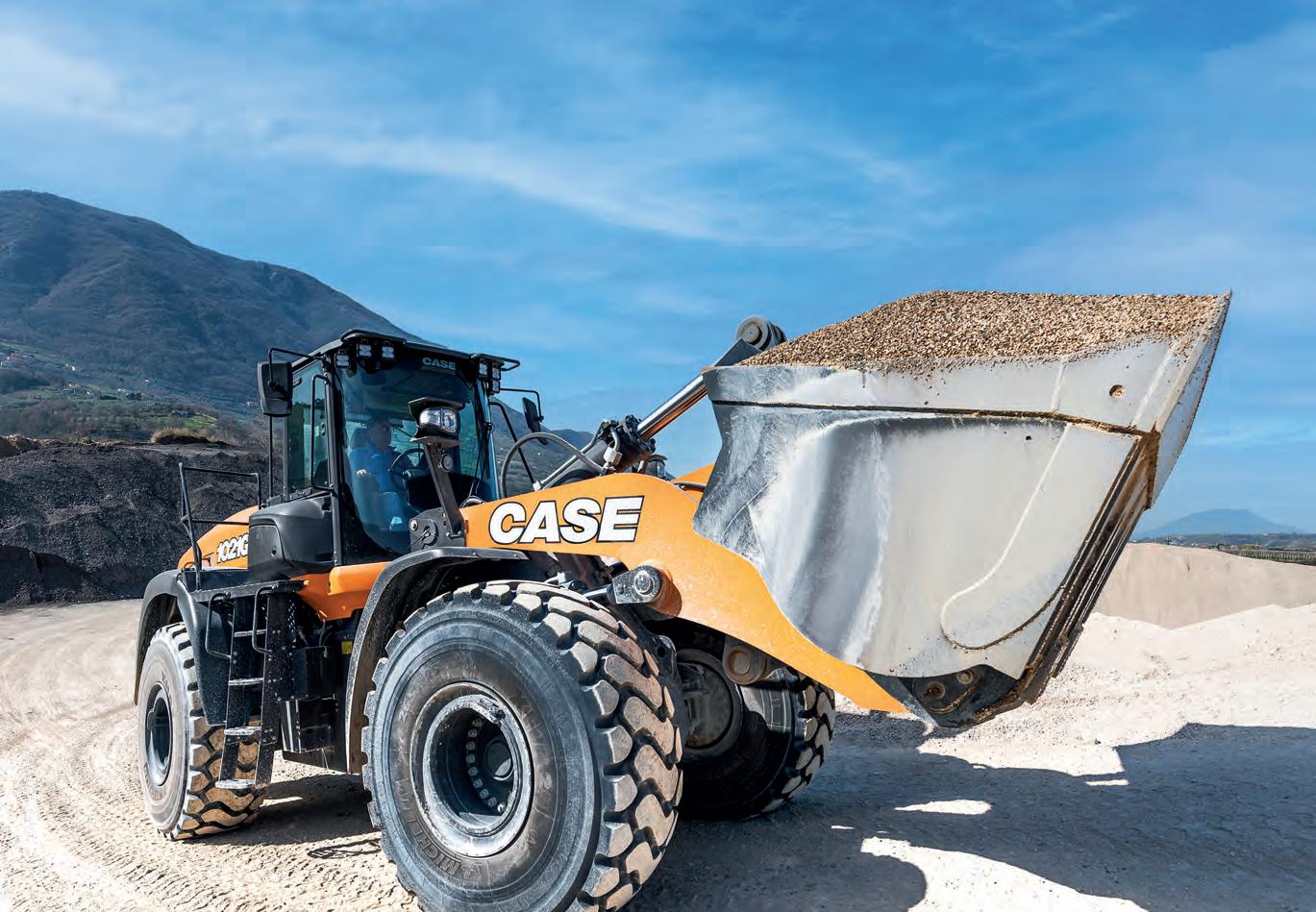
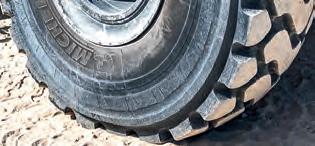
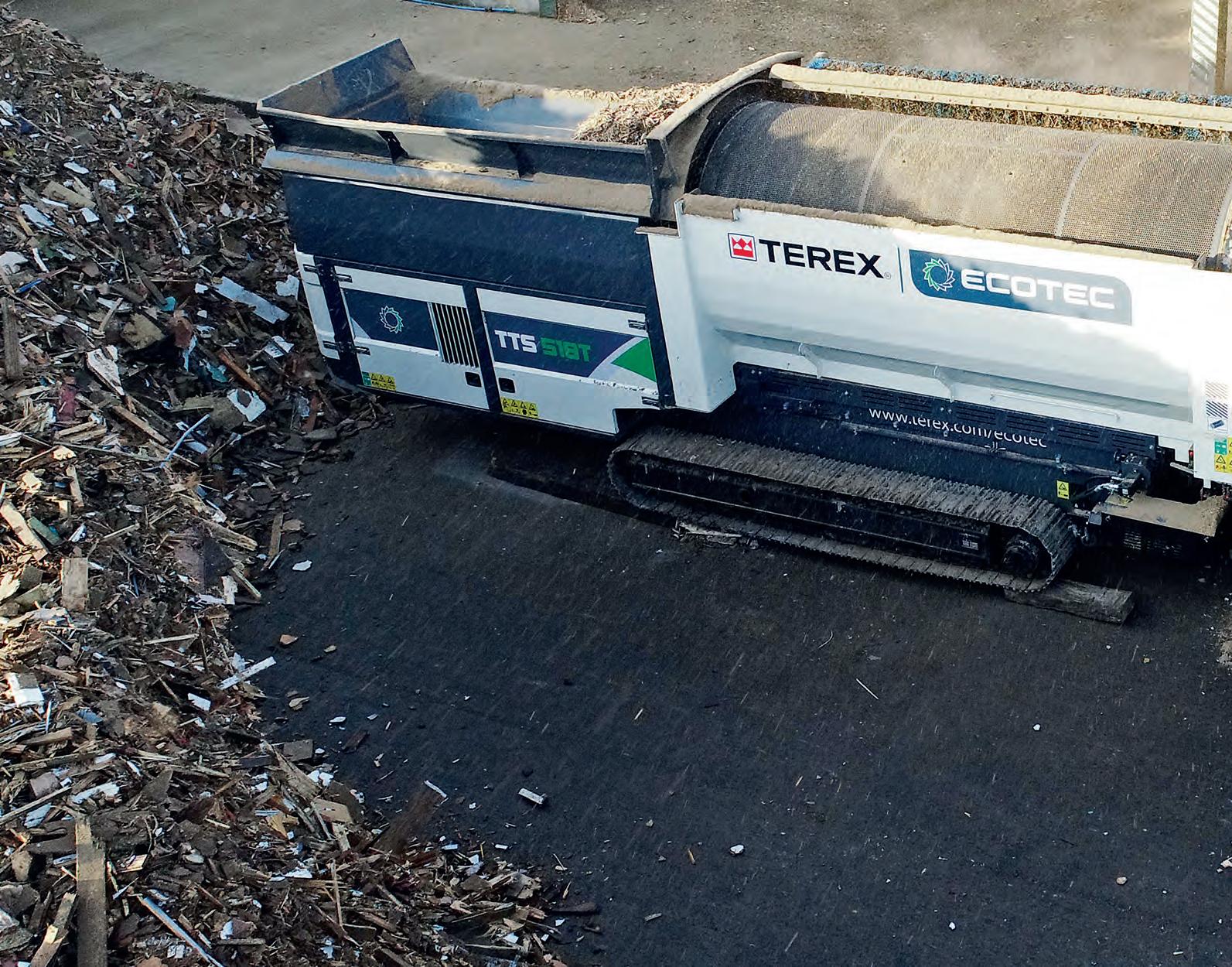
TEREX ECOTEC’S NEW TTS 518T TROMMEL MAKES BIG IMPACT AT R. HEATRICK LTD
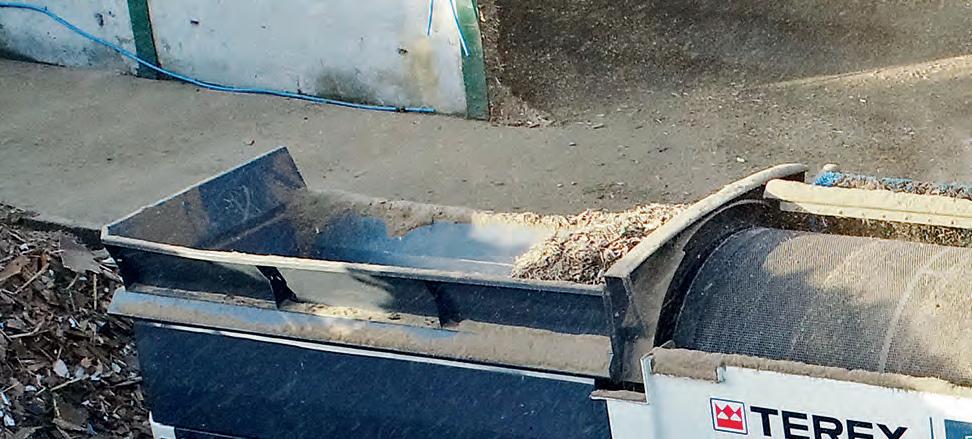
When Terex Ecotec launched their new TTS 518T Trommel earlier this year, it had undergone extensive testing with Portadown, County Armagh based recycling and demolition contractors R. Heatrick Ltd who were so impressed by its performance they bought it!
Terex Ecotec’s smallest trommel to date, compact yet uncompromised, the TTS 518T has been intuitively designed; they say it offers operators ‘unrivalled application flexibility, production rates and serviceability,’ and that’s exactly what the team at R. Heatrick’s has discovered, as Plant & Civil Engineer’s David Stokes reports. R. Heatrick Ltd was established over 50 years ago in 1969 by Robert Heatrick after investing in a Ford backhoe loader to undertake drainage contracts for local businesses in the Armagh area, and as the company grew it began to diversify into civil engineering completing many projects throughout Northern Ireland. Today, the company remains a family business with hard work and dedication to quality at its core; acquiring Skipway Waste Management & Recycling in 2012, it has grown into a major player in the recycling and demolition sectors, securing countless contracts across the UK. Operating from depots in Belfast and Portadown and quarries in Moira and Lisburn, the Group’s impressive and growing fleet of almost 60 trucks and skip loaders, as well as specialist tipping, ejector and walking floor trailers are a familiar sight on our roads. How it came to acquire Ecotec’s latest TTS 518T trommel is a story long in the making, beginning when the company put a prototype of the new model through its paces over quite a few months. “During our testing we used a variety of materials including stone, timber and other waste,” says Trevor Heatrick, “and we never ceased to be amazed at its efficiency and performance. We can change the drum very quickly, in a matter of minutes compared to maybe two days work on a competitor’s trommel; the drum simply lifts out with the aid of a forklift and can be replaced by a different sized one from another manufacturer, so we can easily integrate it into our existing trommel fleet. “Another major benefit of the Terex Ecotec trommel is being fitted with tracks as opposed to wheels, so manoeuvrability is better. It can be packed up in 10 minutes and tracked on to a low loader to transport it to another of our sites – we use it in our quarries, in our waste facility in Belfast and in the yard at Portadown where it can be offloaded and put to use in next to no time. “It is a very versatile and compact machine that is very easy on fuel; running it for 12 hours a day I reckon we are using just 10 gallons of diesel.”
A QRS ‘First’
The TTS 518T was supplied and delivered by Terex Ecotec’s new Northern Ireland dealer, Quarry & Recycling Solutions (QRS), headed up by Dougie Watt; it was his first sale since being appointed just a few days previously! “We have dealt with Dougie in the past, before his appointment by Terex Ecotec, so we had every confidence that he would continue to support us going forward with the new trommel. When we had the machine on testing we recommended some changes

and refinements to improve its performance; they took those suggestions on board and the modifications were implemented in due course, so we knew exactly what we were investing in,” says Trevor. Adds Dougie: “I have had a long standing working relationship with Trevor for many years, having looked after all his maintenance and repairs, so when I took on the Terex Ecotec dealership I approached him about this new trommel, knowing that a more compact machine would suit his requirements, and I was delighted we were able to secure the deal.” Fully equipped with a Stage V/Tier 4 engine and the latest intelligent screening technology, the TTS 518T delivers a superior and cost-efficient end-product, as Trevor Heatrick has discovered. And as Dougie commented, the machine, available in both tracked and wheeled variants, is ideal for operations where space may be limited. Highly versatile, it can screen a variety of material including compost, biomass, soil, gravel and waste.
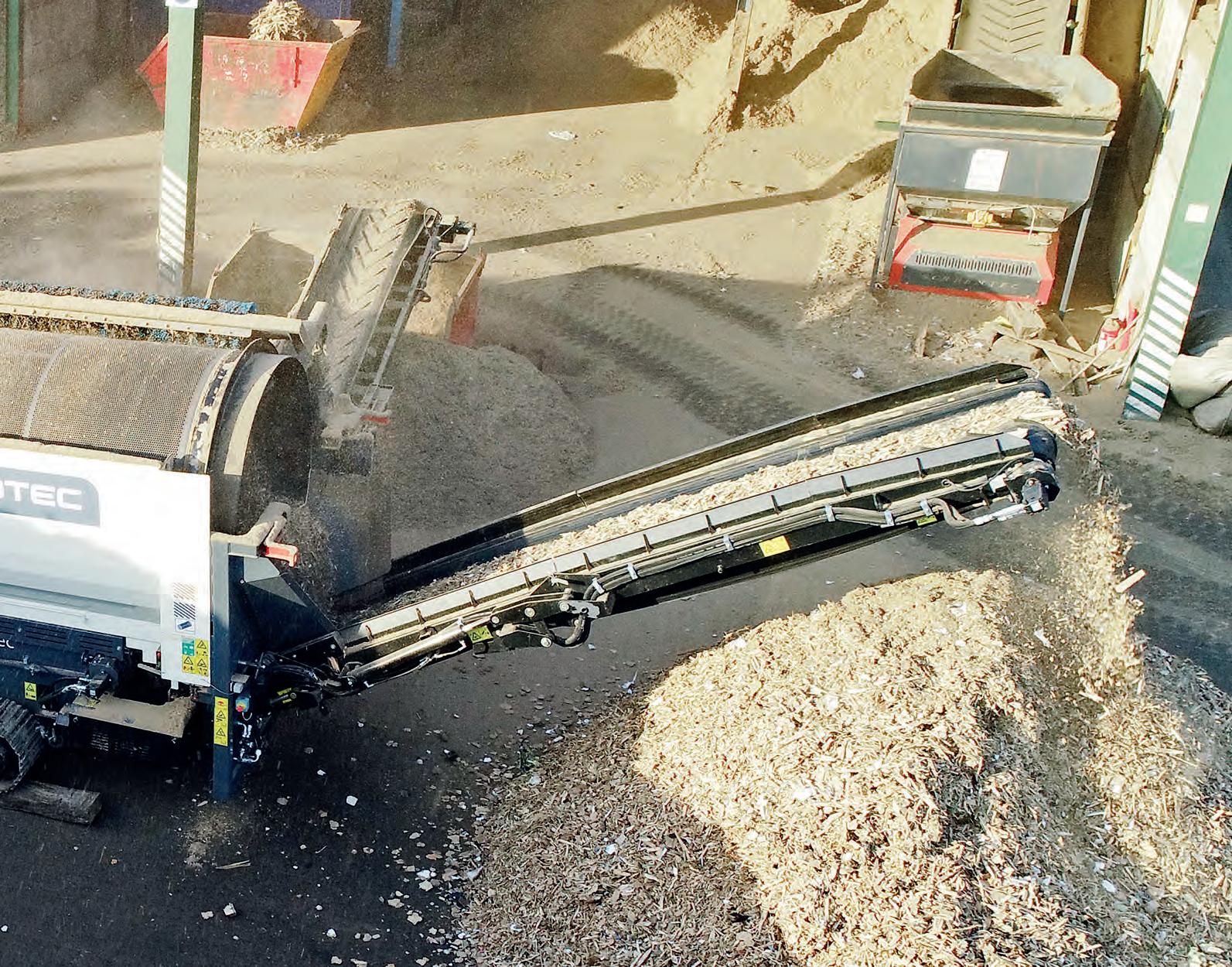
(L-R) Trevor Heatrick, R. Heatrick Ltd, David Sproule & Dougie Watt, Quarry & Recycling Solutions Ltd (QRS).
Optimal Performance
Providing a total screening area of 23m² the TTS 518T is fitted with a 1.8m x 4.7m horizontal drum with spiral design. It shares the same intuitive control system and ‘push to start’ buttons used on the TTS 620, allowing the operator to effortlessly configure the machine to suit the required application. The intelligent feed control system continually monitors the machine adjusting the feeder speed to optimise screening performance and throughput. Being driven at the head, the feeder provides an excellent and continuous feed rate, reducing slippage in difficult applications. The feeder has also been designed as a slide out cassette which allows for easy maintenance and quick and simple belt changing. The clear tunnel area underneath the feeder prevents material build up and allows any material in this area to drop directly onto the ground. With double-sided drum access via 180 degrees opening side doors, maintenance can be carried out with ease. The swing out engine cradle provides unprecedented service access enabling daily checks and maintenance to be carried out safely from ground level. All the conveyors are fully modular allowing each to be removed independently, with the fines and oversize also lowering to ground level for maintenance.
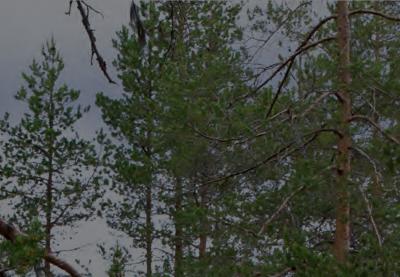
news New Range of Small Articulated Loaders (SALs) from Bobcat
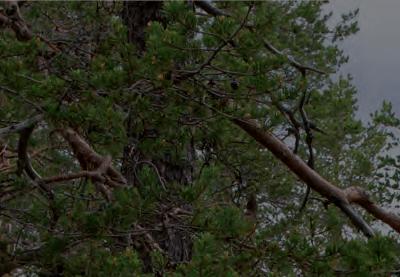

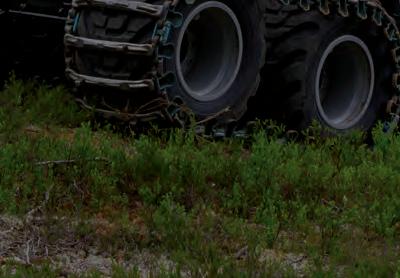
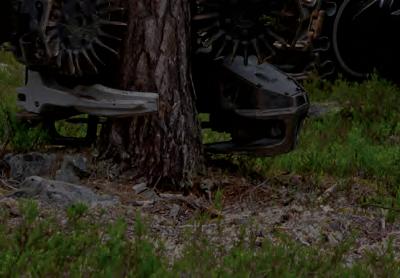
Bobcat has launched the company’s new L23 and L28 small articulated loaders (SALs), offering high lift capacities in confined spaces, ease-of-use with simple intuitive controls and low ground disturbance for working on any terrain.
The new SALs offer impressive stability and tipping loads of up to 1.39 tonne. It is therefore easy to place loads with the SALs over trenches and pavements, a task that is further enhanced by the excellent all-round visibility on both machines. The high lift capacities compared to machine weight are ideal for heavy lift and carry operations in confined areas. The extendable boom on the L28 provides more options for easy placement of loads and counterweight options allow the user to customize the capacity to the application. The machines’ compact size, with a width of just over one metre combined with a tight turning radius, allow Bobcat SALs to work easily even in tricky and hard to reach areas. Despite their robust construction, the SALs are also built to be light enough for easy transportation. John Chattaway, Loaders Product Manager at Bobcat, said: “SALs pack a serious punch in a compact, lightweight package that’s wonderfully easy to operate, making them a powerful and handy multi-purpose tool for a wide range of applications. Both the L23 and L28 are 25 HP machines with intuitive controls that make them ideal for almost any user to operate, appealing to an even wider customer base and extending the reach of Bobcat loader products. “The key attributes that SAL users are looking for are a high lifting capacity coupled with stability and low ground disturbance as these machines are mainly used in load and carry applications. Bobcat brings to this market the company’s years of experience in the loader business enabling us to build machines that are safe, reliable and very durable. This adds up to a quality of machine not matched by our competitors.” Bobcat SALs are available with canopy and cab versions, both specially designed to provide extra space where needed for easy entry, exit and operator comfort. The controls are intuitive for all levels of operator experience and an enclosed cab and heated seat are available for colder climates. A simple, intuitive twin-pedal design on the SALs enables quick and easy direction changes: one pedal moves the machine forward, the other puts it into reverse. These travel controls are easy for operators to master, making the SAL a great choice for seasonal employees or rental customers. It is also convenient and simple for operators who need to master controls for multiple machines.
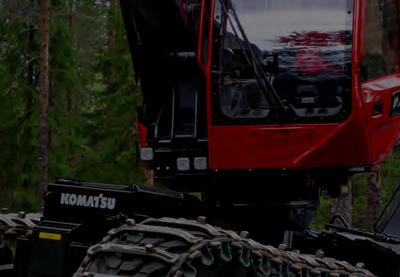
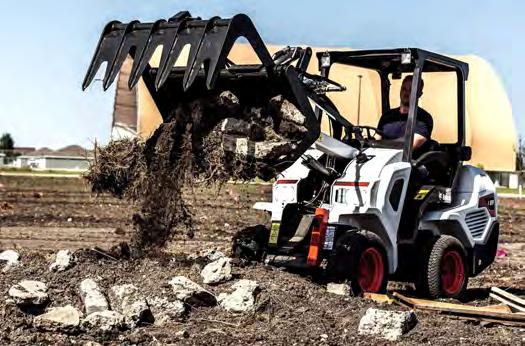
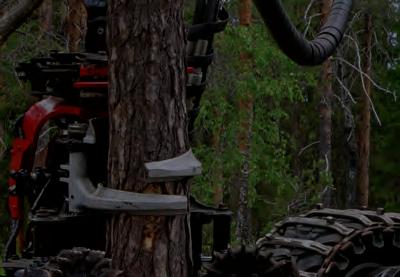
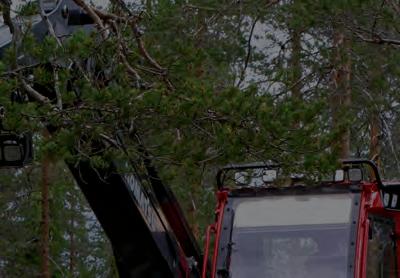
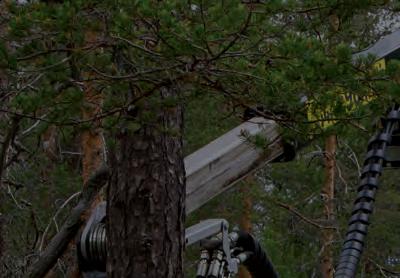
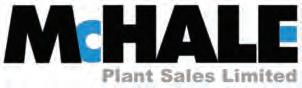
WE HAVE A GREAT OPPORTUNITY FOR A
Email: recruitment@mchaleplant.comEngcon increases www.mchaleplantsales.comits activity in the
FULL TIME SPARE UK and Ireland
PARTS PERSON Streamlining your excavator with a tiltrotator is becoming more common, and so it is the UK. With this, Engcon UK has TO JOIN OUR TEAM IN DUBLIN. hired a new Country manager and a product ambassador.
This is a hands-on role and the successful candidate should have Sam Ryan most recently came from the Quarrying and a flexible approach to the job and be willing to help out in other Concrete industry business and is now looking forward departments. Experience in a similar capacity would be an advantage to participating in Engcon’s continued expansion. and manual handling will be required. “It feels very exciting to be part of a world leader’s continued journey to
The successful candidate will: • Assist in the day to day running of the Spare Parts department change the world of digging,” says Sam Ryan, who will be responsible for all sales in the UK and Ireland. The focus will be on developing its own sales team, customer support and expanding the dealer network.• Deal with customers at the front counter and also handle telephone enquiries “We already have a strong organization and a good dealer network, • Manage goods in/out but there is still work to be done to spread the message about how a • Manage stock control and stock takes tiltrotator increases the excavator’s capacity and flexibility,” says Sam. In connection with Sam’s employment, Derrick Smith was also
The ideal candidate should: hired as a product ambassador. His focus will be to increase • Have a basic mechanical knowledge of the contact with end customers and users of Engcon’s products.
Plant /Construction/Agri Machinery “I am passionate about end customer contacts and have previously • Be computer literate and customer service orientated worked with customers who used the products I worked with, so • Have a full clean Irish Drivers Licence I feel really excited to continue to do so with Engcon’s products”, • Have excellent communication and organisational skills says Derrick Smith, who has already targeted some specially and have the ability to work on own initiative selected products that set Engcon apart from its competitors. • Experience in a similar role an advantage. “EC-Oil Automatic Quick Hitch System that allows excavators Full Time Role: Monday to Friday 08.30-17.30. to connect hydraulic tools without leaving the cab is clearly interesting. The fact that it is also included free of charge Email: recruitment@mchaleplant.com when customers buy our quick hitch, tiltrotator and control www.mchaleplantsales.com system makes the offer unbeatable”, says Derrick Smith. Both Sam and Derrick are already in place at Engcon UK’s office in Tewkesbury and are now ready to take on the tasks ahead.

Landline: 028 30821230 Ross Mine: 0044 754 1318364 Matt Hogg: 0044 789 9911135 Maurice McCrea: 0044 7710 837590

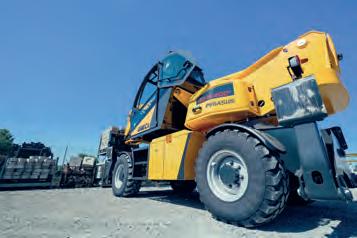
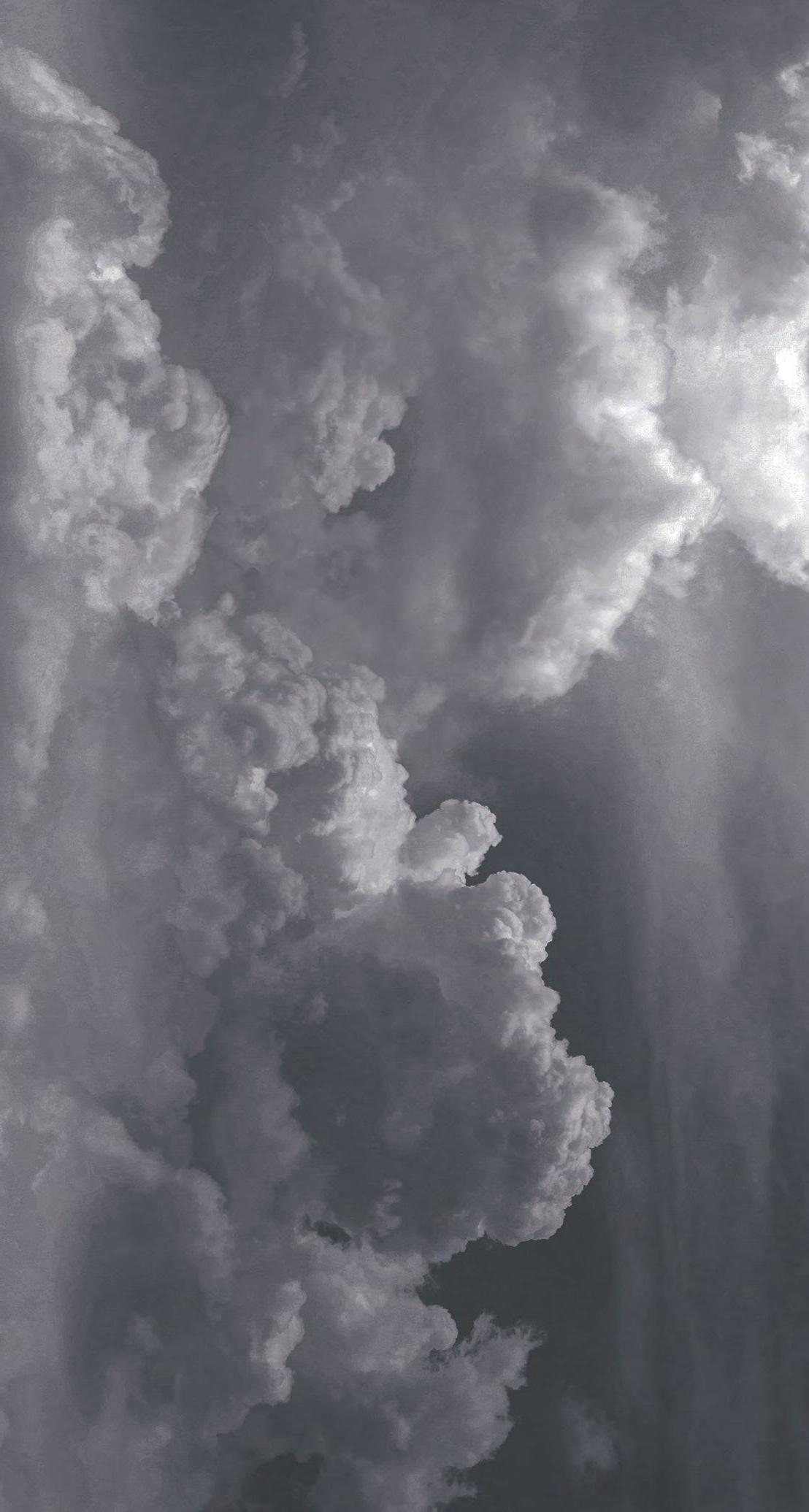

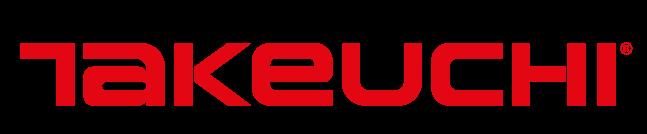

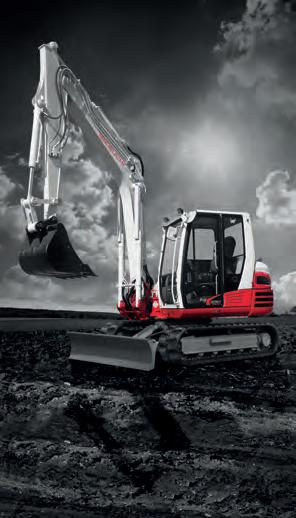

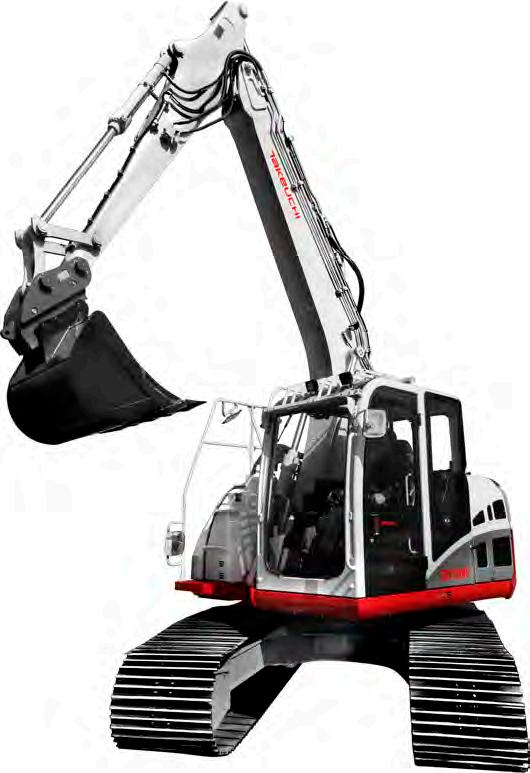
LATEST TAKEUCHI 15 TONNE EXCAVATOR IMPRESSES OPERATORS AT LOWRY CONSTRUCTION
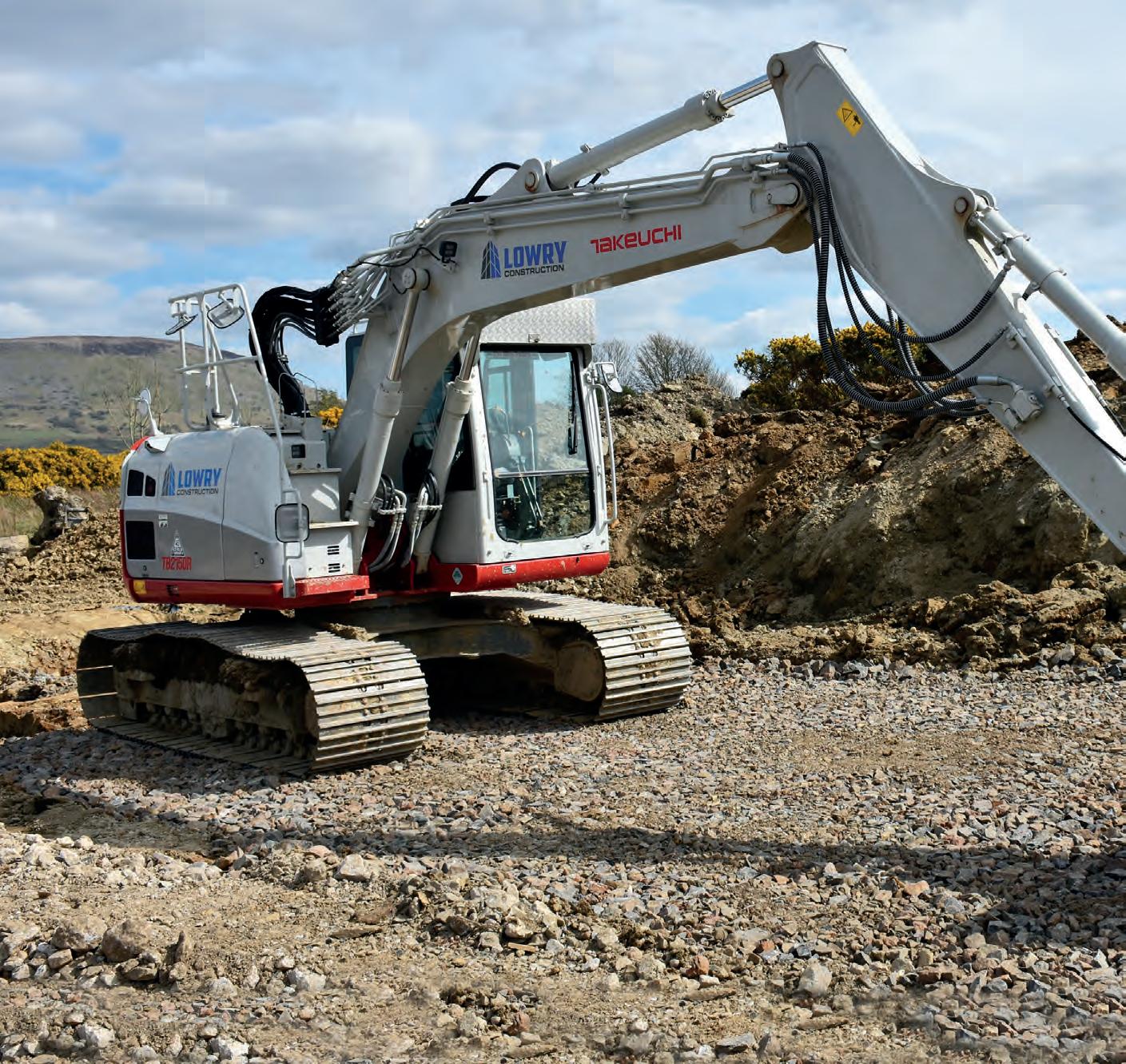
As one of the most compact 15 tonne excavators available, Takeuchi’s TB2150R boasts a host of features that have already made it a firm favourite on the Lowry Construction fleet since it was delivered by Northern Ireland Takeuchi dealers, Newry based Alan Milne Tractors.
With a history stretching back more than half a century, Lowry Construction Ltd has grown to become one of our most successful contractors in the private and public sectors, with construction projects extending from social and private housing, demolition and civil engineering, to community, education & healthcare throughout the north and south of Ireland. Operating out of Castlederg in County Tyrone, the company prides itself in providing high quality workmanship, applying innovative techniques and efficient methods to successfully satisfy the needs of a wide variety of clients, no matter how formidable or challenging the project may be – which is why it only employs the most reliable and robust plant and machinery available, hence its latest acquisition of the Takeuchi TB2150R, the largest excavator in the Takeuchi line up. It’s the company’s second Takeuchi and they’ve since invested in a smaller machine – and considering another from the dealership, so clearly Lowry Construction are a fan of the brand. As for the new TB2150R, says Stephen Lowry: “The operators like the fact that there’s plenty of room in the cab, providing an excellent working environment, with smooth and responsive controls.” He adds: “It is a very stable and solid machine considering it is almost a zero tail swing; it hardly moves when the boom is at full stretch over the side of the tracks.” The excavator is currently being utilised on a new social housing site in Dungiven, where 22 properties are being built, so it’s busy with lots going on, and safety is a priority. “The operator has excellent all round visibility from the cab which is further enhanced by the provision of a good camera system, important for the safety of other workers and tradesmen on the site.” Featuring a fixed boom for greater stability, the machine couldn’t be more operator friendly; indeed, when we spoke to the driver he told us he was ‘thoroughly impressed’ with its smooth and powerful performance, and easy to master controls.
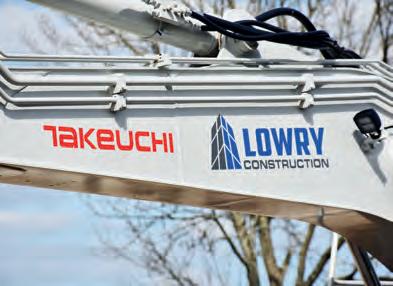
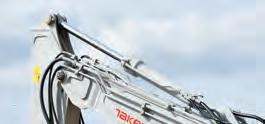

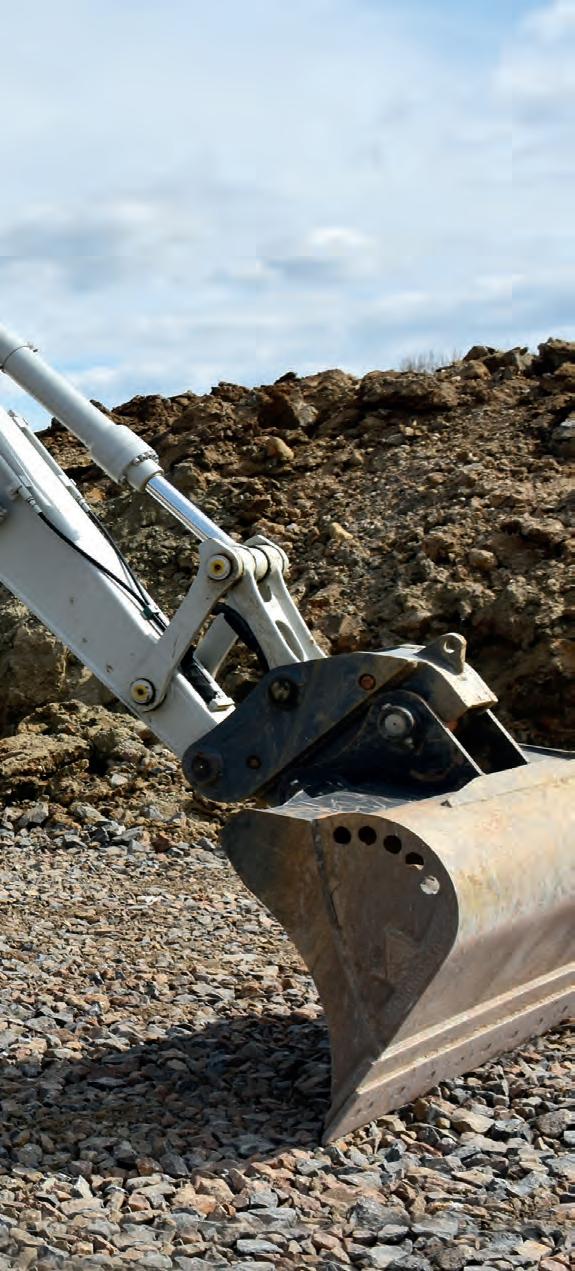
A redesigned operator’s station features a 7” colour intuitive multi-informational display, radio with Bluetooth capabilities, easy to reach rocker switches and precision touch hydraulic joystick controls that are smooth and responsive. A comfortable suspension seat features weight adjustment along with fore and aft movement and is also equipped with a two inch retractable seat belt; an optional deluxe high back air suspension seat is available. The floor of the cab is sufficiently spacious to allow the operator to be comfortable throughout the workday, and the large foot pedals fully support the operator’s feet when using the travel function, while automatic climate control enables the operator to choose a preferred temperature for maximum comfort throughout the year. Regarded as a high specification machine with plenty of value added features, the TB2150R has a large wraparound counterweight, a side / rear view camera, and multiple LED working lights located on the boom, cab, and front cover, providing, as Stephen highlighted, exceptional all round visibility – and with a compact track footprint of just 2690 x 3750mm and a short tail swing, the TB2150R gets to work in spaces other conventional machines can’t go. Powered by a Deutz 85 kW engine, this machine has three auxiliary hydraulic circuits that make it the perfect attachment platform that will provide the operator the power and durability needed to complete the toughest jobs; a fourth auxiliary hydraulic circuit is optional. As Stephen mentioned, operators enjoy the smooth performance and powerful digging force of the TB2150R. The isolation mounted cab provides all day operating comfort essential for rugged tough terrain and groundwork.
Servicing & Support
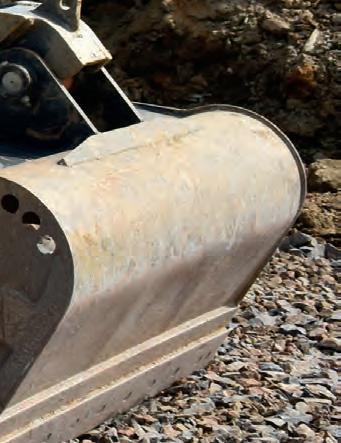
Routine servicing and maintenance is made simple, with a right rear opening panel that allows access to the pilot line and fuel filter, pump group and coolant expansion tank, while a left side access cover brings into reach the dual element air cleaner, batteries and DEF tank and refueling hose; the oil filter, and dipstick are also conveniently positioned for easy access. Working to tight schedules and deadlines means unnecessary and avoidable downtime can be expensive for any operator, so a good back up service is essential if ever it is needed, and says Stephen: “We have no complaints about the support we get from Alan Milne and the team; it has been excellent so far.”
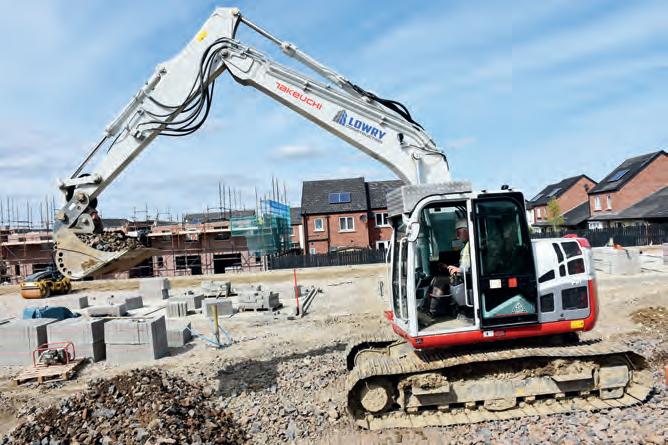
news SDG announce strategic partnership with German construction specialists
Northern Ireland company SDG, a leading supplier of essential products to the construction industry across Ireland and the UK, has announced a £1,000,000 strategic partnership agreement with the German company B.T. Innovation GmbH.
As a result, SDG will now become the UK and Ireland distribution partner of the specialist manufacturer of shuttering magnets, formwork and connecting systems to the construction industry. B.T. Innovation GmbH is an internationally recognised company providing innovative solutions for precast concrete plant and on-site construction, creating products which simplify and accelerate the production and precasting process. The range of bespoke products improve the quality of the final work, reduce the cost of manufacturing, and increase efficiency during installation. Commenting on the partnership, Oliver Phelan, Head of Sales at SDG said: “This collaboration means SDG can offer a full suite of products and systems encompassing all aspects of the precast concrete process from start to finish to clients. The systems and expertise offered from SDG & BT Innovation is unique in the UK and Ireland marketplace, and can be tailored to the specific requirements of the client. It is truly innovative and designed to increase efficiency for them.” Johannes Klose, Key Account Manager, BT Innovation GmbH added: “The partnership with SDG provides an excellent opportunity to further enhance our reach and customer loyalty in the UK and Ireland markets. We always focus on the needs of our customers by constantly providing them with new, innovative, and specialised problem solutions across the construction industry. The team at SDG have the technical skills and expertise required to support our products to clients, and we are confident that in SDG we have found a partner who will successfully deliver all of that.” And said Louise Skeath, SDG’s CEO: “This partnership allows SDG to increase our offering to clients, and further positions us as a key partner to industry. As a company it is essential that we are not merely a supplier of products to construction, but a trusted advisor and innovator of change and new thinking in the industry here and for the future.”
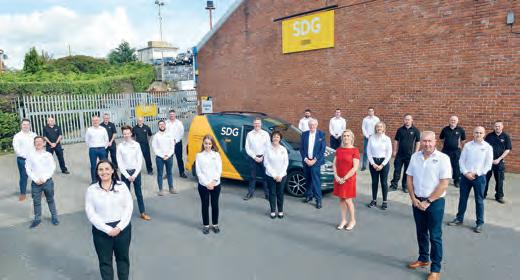
During difficult times it seems easier to ‘’just get on with it’’, trying to adjust to accommodate the way we always did things. But last year has taught everyone to adapt, which inevitably led to embracing changes.
This brings us to the two completely different job sites we witness. They took on MB Crusher attachments and in a very short amount of time they changed their way of work, for the better. In the case of Legarza Exploration & Construction, they’ve specialized in remote locations job-sites since 1992. With nearly 29 years of expertise under their belt, they know exactly how to tackle a site without roads, they are well aware of the struggle of bringing their equipment in, the time and energy it takes to build the road to reach the actual site. Their meticulous planning had helped them succeed in the past, even if it hasn’t been always full proof or cheap. And then they reached a point when waiting for the material to arrive at their remote site made them lose money: that dreadful moment when the price increase in purchasing aggregate has forced them to turn down some jobs. Costs and time have a huge impact on pricing a job and when you have always done the job in a certain way you can easily do the math and realise if you are no longer earning as much as you used to. Instead of assuming that the good old ways would come back and carry on as they were doing, they realised they needed tools, a crusher and a screener with portability so that it could reach the site easily, even where the roads are not yet made. They needed MB Crusher’s units! When we talked to Bill Arthur, the company’s owner, he was quick to admit that they still were “pretty new to the bucket”. But, he has already seen the benefits it’s brought to their job site. He told us the buckets have helped them “save time and money, primarily on [their] budget” by eliminating material purchasing and handling expenses. So how long does it take to break a habit? As long as the moment you decide to improve! Legarza is now using what’s available to create soft roads to reach their jobs site. With MB’s BF80.3 crusher bucket they reduce the larger stones and river rock from the bank to either a ¾ minus or a 3 in minus, and the MB-S18 screening bucket is used to separate the fine portion laying around, faster and cheaper process.
Need for Speed
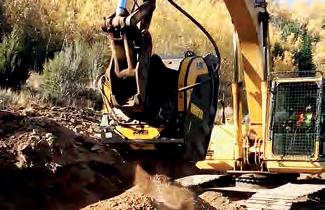
The other job site we viewed didn’t have a huge distance to travel or the lack of roads, quite the opposite in fact as it is located in one of the largest commercial port in India. Get the job done quickly is the requirement here, and the MB Crusher screening bucket is the ideal machine to help to keep clear the loading dock from materials while reducing the number of machinery and operators. As they had the backhoe that was previously used just to move the material around, they installed the MB’s attachment and instantly upgraded their BHL into a screening plant. Now, when the material is mixed in wrong ratios during the unloading process or when lumps forms due to moisture penetration, they just use the screening bucket and in a matter of minutes, the material is processed and reclaimed. Moreover, the screening bucket can be easily moved from one place to another, once the job is finished, to allow the continuous passage of lorries, trucks and containers coming and going from the port area. How long does it take to change the way you operate? Just the realisation that the job is done a lot faster! At the port now they ensure maximum productivity, faster than before, and the job is done better.
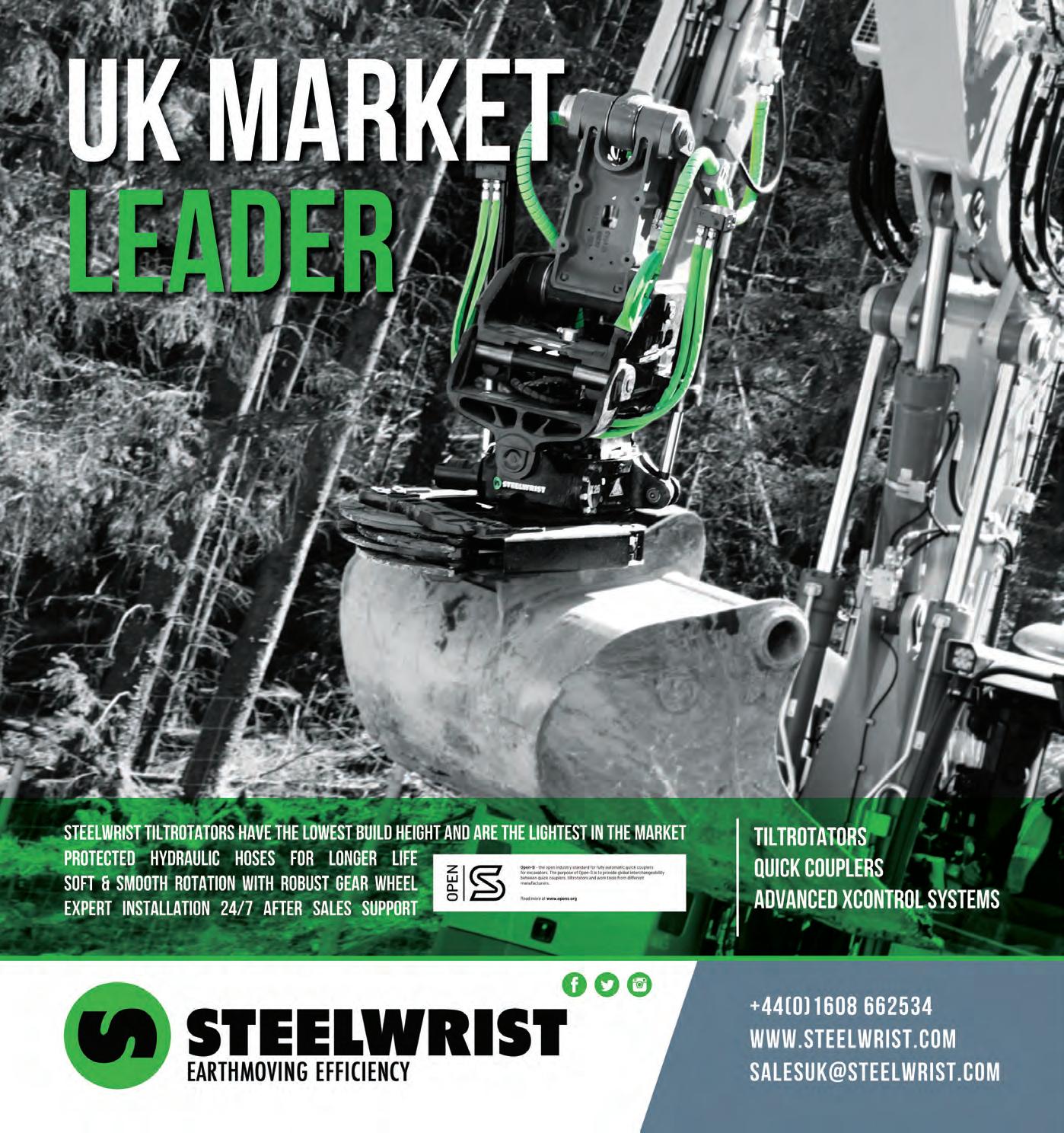

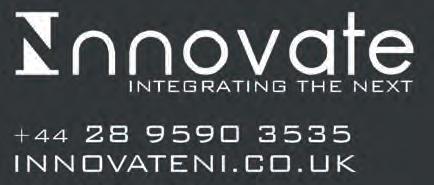
TILTROTATOR SPECIALISTS STEELWRIST UK SET FOR FURTHER GROWTH
Tiltrotator specialists Steelwrist UK’s move to larger and more modern premises couldn’t have been better timed and it is already paying big dividends, as Plant & Civil Engineer’s David Stokes has been finding out during an interview with Managing Director Pat Bulcock.
The company had outgrown their facilities just over three years ago when the search for a new site was launched, eventually settling for premises just outside Banbury in Oxfordshire.
“It was a struggle to find something that was right for our purpose,” says Pat, “but we finally found what we were looking for – and it is a site with a long and interesting history.” He is not wrong there; originally an old mill, latterly it was occupied by a leading interior design company, and before that it was home to Aston Martin – they designed and built the XJ220 there. “We are now well settled into the building after having refurbished it to suit our own operation. It is in a prime location close to the M40 motorway so is easily accessible. Not only do we enjoy a nice office environment, but we also have a spacious warehouse and parts department, as well as a conference room where we can carry out training sessions,” explains Pat. Significant investment was also made to create a fully equipped workshop, complete with new hose making equipment, a tiltrotator test rig and extra strong racking. “The move to these larger premises enabled us to stock up on products and parts ahead of the UK leaving the European Union, meaning we were well placed to continue serving the needs of our customers without any interruption to supplies; it has also helped us to cope with the challenges of the Covid19 pandemic and subsequent lockdowns. “We were pretty cramped in our old building – it was just 1400 sq ft. These new premises extend to over 10,000 sq ft, which is more than five times bigger, so our day to day operation is much more efficient and productive. Had it not been for this move, we would have had to acquire extra warehousing elsewhere, and that would have caused some logistical issues, but now we have everything under one roof.” Steelwrist UK was originally set up as an independent dealership, but has since become part of the Steelwrist Group and continues to go from strength to strength;
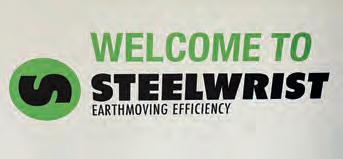
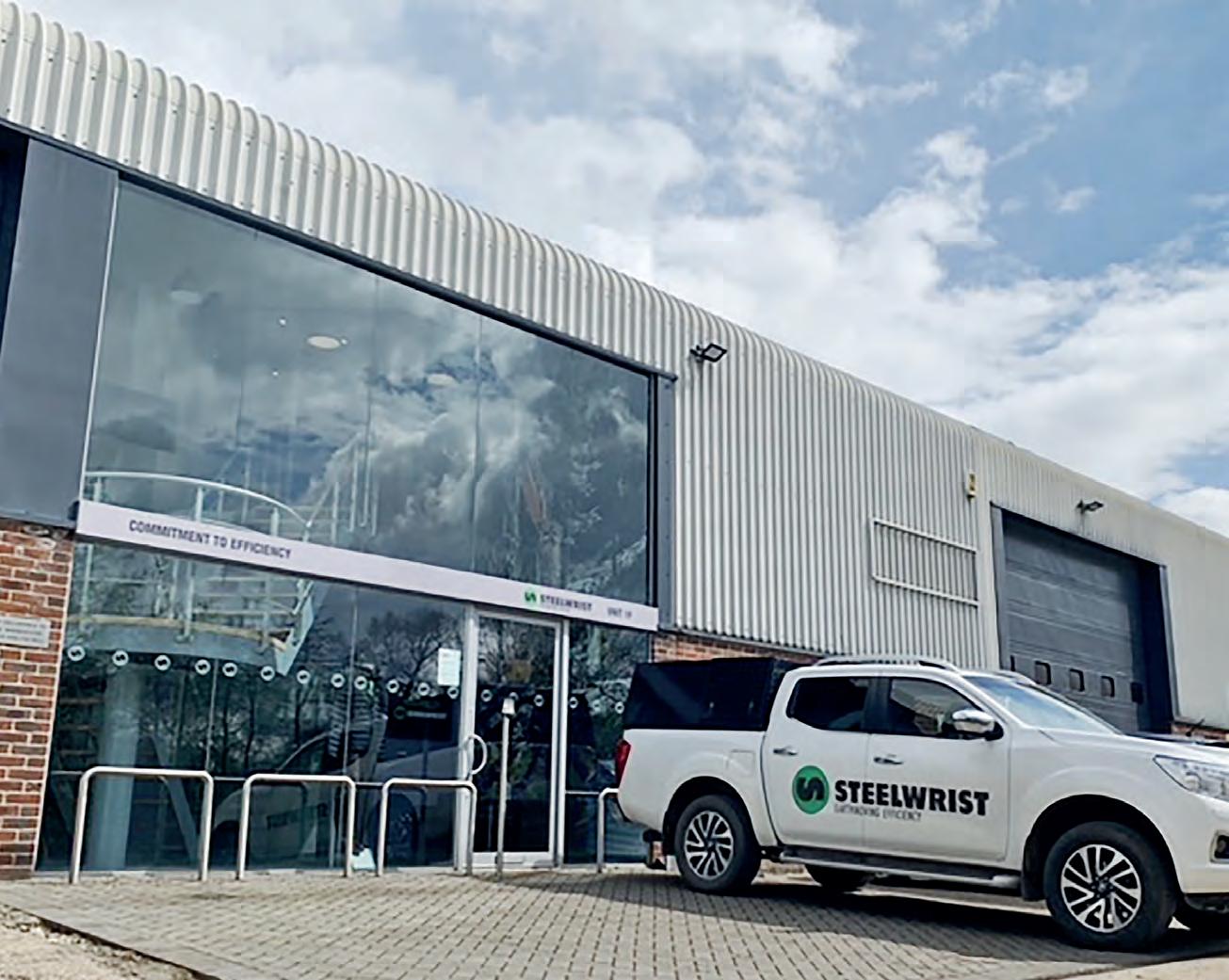
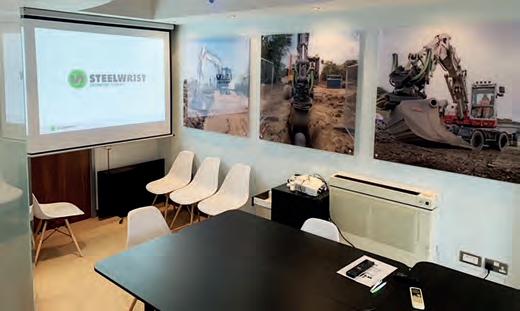

indeed, the new premises is operating at almost full capacity. The company not only supplies the Steelwrist product range, but also offers a comprehensive installation service.
Product Training
Now with a conference room at its disposal, the company has been able to stage classroom product training sessions; the first was recently organised for seven engineers from Hitachi and the aim is to attract other excavator manufacturers and dealerships. Before the move, such events would have been staged in local hotels. “Ideally, we would like to train up at least one ‘champion’ of the Steelwrist product in each dealership, so customers can avail of the best possible service no matter where they are in the country.” While Steelwrist UK has no actual sales people on the road, it does have three full time engineers and four service partners to provide customers with a high level of support. Supporting Pat in the business is his wife Claire whom he describes as ‘the backbone’ of the Steelwrist UK operation. Claire joined the company over four years ago and has certainly proved her worth! “There’s nothing she can’t turn her hand to – from driving a forklift, checking goods in and out, organising transport and events, to running Admin and selling the equipment itself,” says Pat. “She is indispensible and it would be great to see more women in our industry.”
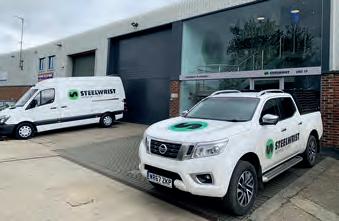
Future Growth
The potential for future growth is quite remarkable when you consider the figures. In 2019, sales of excavators in the UK reached around the 24,000 mark, and says Pat: “At least 45% of those machines – some 10,000 - would have benefitted from having a tiltrotator. “While the Steelwrist product is world class, as is our market leading control system, I like to also focus on the actual concept; I’ve been ‘preaching’ about tiltrotators now for some 16 years, but it is only in the past few years that contractors have come to appreciate the benefits.” Indeed, tiltrotators are now a desired piece of equipment, making an excavator more versatile and an operator more flexible in the work that he can do, and more time efficient. The more complicated the job, the higher the productivity when using a Steelwrist tiltrotator; jobs can be done faster, new types of jobs can be taken on and less manpower is required compared to conventional work with an excavator. As for Steelwrist UK, despite the stiff competition from other brands and current trading conditions, business, in Pat’s words, is ‘booming’. Year to date, sales have increased by 118%, that’s over double what the company did this time last year, and that’s despite the impact on businesses from Brexit and the global pandemic – all of which speaks volumes about the ever growing popularity of the Steelwrist product.
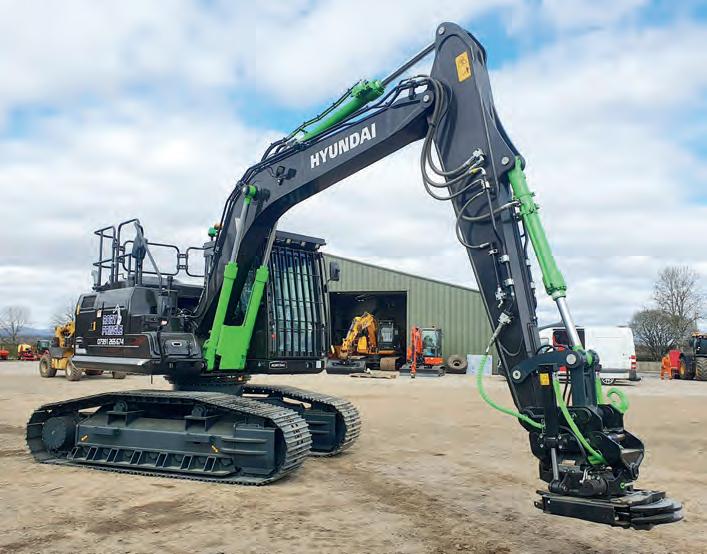
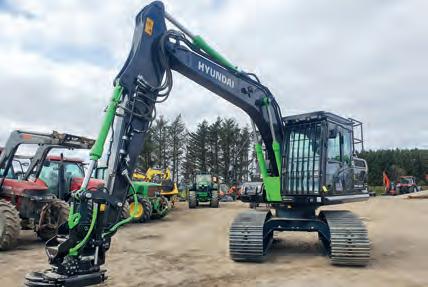
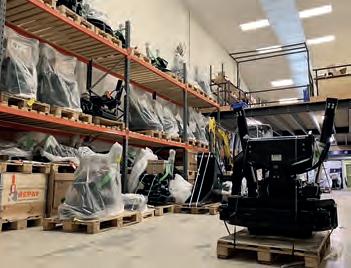
news Topcon Positioning GB appoints new UK Business Manager and Regional Director
Topcon Positioning GB and EMEA have promoted two senior managers to head up the development of its UK and Ireland subsidiaries.
Andrew Flood has been promoted to UK Business Manager and David Bennett to UK and Ireland Regional Director. Andrew’s new role will see him responsible for Topcon GB Business whilst David willoversee the UK and Ireland Subsidiaries. Andreas Strunk, European Subsidiaries Vice President, said: “I am extremely proud of the team and all they have achieved so far. These changes will further contribute to strengthening the European Subsidiaries organisational structure. I look forward to more great results and I wish both Andrew and David the best in their new roles.” Andy has more than 15 years of experience in sales in the UK Survey and Construction business. Andy joined Topcon in 2013 starting as Regional Account Manager and developing his experience and skills in construction and distribution sales. During his time, Andy has taken on the responsibility of managing the UK distribution sales for the full Topcon offering and increasing distribution sales which led to his promotion to Sales Manager. Dave joined Topcon in 2013 as the Business Manager for Topcon Great Britain’s positioning business with responsibility for expanding the business and increasing Topcon market share in Great Britain. Following successful business growth, the positioning business separated from the eyecare business in 2018, and Topcon Positioning Great Britain was established as a limited company. This resulted in Dave’s promotion to the role of Managing Director. Dave has helped develop a strong team who have raised the profile of Topcon in Great Britain and increased market share.
Zutec achieves BSI Kitemark for BIM software
Zutec, the Irish construction software company, is one of the first organisations to achieve certification to the new BSI Kitemark™ for Building Information Modelling (BIM) software.
This Kitemark is a global benchmark in supporting BIM compliance, and the company achieved the certification following extensive, independent assessments. Zutec had to prove that its software met high quality, data security and usability benchmarks, and that it supported its clients in achieving BIM standardisation with ISO 19650 compliance, in order to secure the Kitemark. Zutec had to also show its datasafe approach, with the company being certified to ISO 27001. This is the only international standard that defines the requirements of an information management system to demonstrate that an organisation has put in place best-practice information security processes. Beyond this, the business also had to demonstrate its customercentricity with independent evidence of client satisfaction. Tom Boland, Global Head of Digitalisation at Zutec, says, “This new Kitemark is a significant moment for the construction industry. As digital rapidly becomes the norm, there is an increasing need for software tools that add real value to construction workflows. Zutec has been at the forefront of digital construction for over 20 years, so when an opportunity arose to prove just how good our software is, we were keen to achieve Kitemark certification. This mark of trust allows new and existing customers to be confident that Zutec will support them in their BIM journey, shows them that it is easy to use, and allows their teams to collaborate seamlessly on one platform.” He adds, “Our software supporting BIM standards also offers customers peace of mind that their data will be managed properly and be secure. Security is part of our company culture and ensures resilience against cyber threats to protect customer information and data, thus reducing business and project risks.” Andy Butterfield, Managing Director of Built Environment at BSI, comments, “As the demand for digital transformation in architecture, construction and asset management continues to grow, and the number of potential software support tools escalates, it is becoming increasingly difficult for organisations to identify appropriate software to support their needs. “Zutec has become one of the first organisations globally to achieve this mark of trust and I would like to congratulate them all for their commitment to encouraging a collaborative approach across the life cycle of a built asset.”

Tom Boland
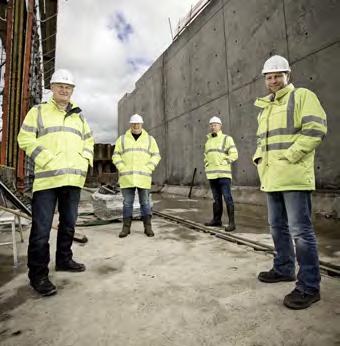
Work is progressing well on a £10m programme of work at Belfast Wastewater Treatment Works, Duncrue, to construct two new treatment tanks, equivalent in volume to six Olympic-size swimming pools – to cope with current and short-term future wastewater requirements.
The two new treatment tanks will provide much-needed additional capacity and enhance the existing process to ensure that the discharge to Belfast Lough remains compliant with Northern Ireland Environment Agency standards. The new assets will also facilitate essential improvements within the associated sewerage networks and will enable maintenance works to be undertaken at the other treatment tanks at a future date.
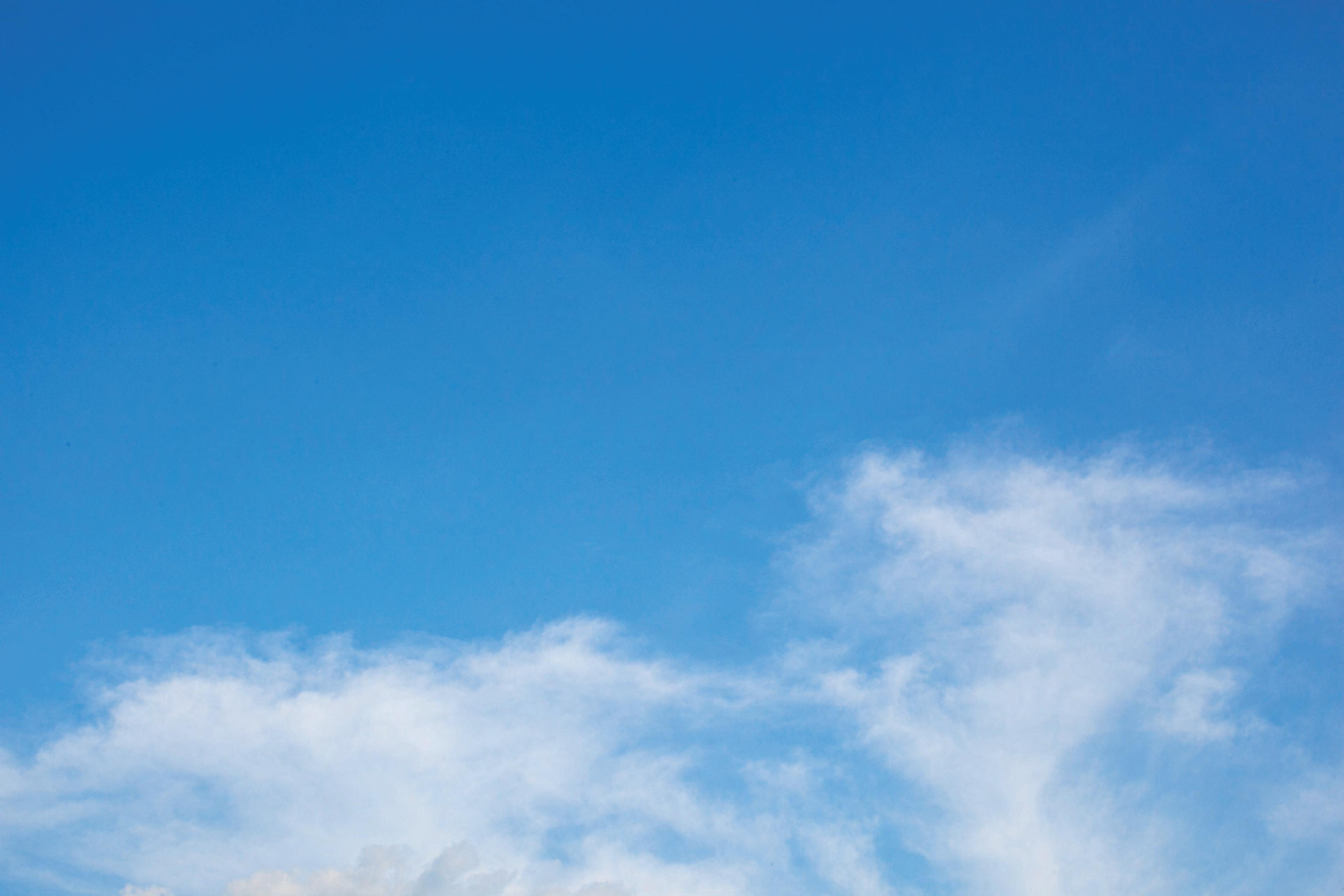
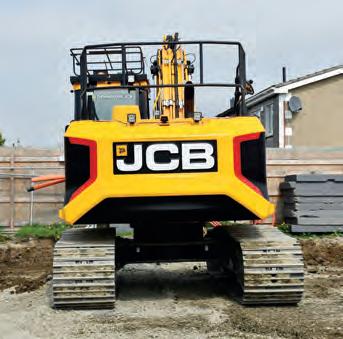
OPERATORS IMPRESSED WITH FIRST JCB’S TO JOIN FLEET AT BRANNIFF CONSTRUCTION
When Ballynahinch based Branniff Construction invested in their first JCB excavator, a 220X, a while back, they were so impressed with its reliability and performance they recently decided to add a second - a new JCB150XHD - to the company’s growing fleet. As Plant & Civil Engineer’s David Stokes reports, it was a big decision for the contractor whose fleet up until then had solely consisted of another well known brand.
Branniff Construction have been operating across the island of Ireland for almost two decades, delivering multiple high quality construction services that include civil engineering and groundworks such as concreting, drainage, kerbing, utilities and fencing. They run a 19-strong fleet of diggers – from three tonne up to 25 tonne – all of which are busily earning their keep on a variety of projects in both the north and south of the country. “When the need arose for another 20 tonne digger, we decided we wanted a change, so we opted for the JCB 220X which we initially took out on trial to see how it performed,” says Seamus Branniff, who heads up the company. “Our operators were very impressed, so we took the plunge and haven’t looked back since.” With a bigger undercarriage which other machines in its class just don’t have to offer more stability and greater ground clearance, the new 15 tonne JCB 150XHD joined the fleet just a couple of months ago and is currently working on a housing project at Tallaght in Dublin, while its bigger brother, the 220X, is being utilised on a flood prevention scheme in Belfast. “The operator is well pleased with the new 150XHD machine; like the 220X it is comfortable, driver friendly, smooth to operate and is very fuel efficient,” adds Seamus. “It is well spec’d, with LED lights, side and rear cameras and GPS ready.” Another prime reason for opting to the new 150XHD was the service they got when they first dealt with Dennison JCB, as Seamus explains: “When we acquired the 220X the service Dennison JCB offered was excellent, absolutely first class, which encouraged us to go back to them for the new machine. “Unnecessary downtime costs money, but we have found that the team at Dennison JCB are very focused on customer support; their response times cannot be faulted, second to none.”
Spacious & Comfortable Cab
Looking closer at the JCB150XHD, Seamus mentioned how comfortable the spacious JCB CommandPlus cab was, so let’s start there. It features an industry-leading Grammer reclining seat with wide, adjustable arm rests. Joystick and switch controls are mounted to pods which are suspended from the seat and move with the operator for optimum control and less fatigue. There is an industry standard isolator lever that prevents accidental activation when exiting the cab, while a powerful new HVAC features 11 targeted vents for optimum performance in either hot or cold environments, and improved cab isolation using the latest double cushion viscous mounts reduces vibration and noise into the cab. A cool/heat box comes as standard as does a spacious luggage tray behind operator’s seat with three independent 12V power supplies. Another handy storage space can be found at the back of the cab in the roof liner, including a hanger for the operator’s protective gear. A Bluetooth radio, fitted as standard, is fully integrated into the control screen. Roof, front, rear and side window blinds also come as standard providing full cab coverage.
Smooth & Powerful Performance
Seamus also highlighted how driver friendly and smooth performing the machine was, and that is in part, due to its well proven Japanese hydraulics that deliver precise and efficient control. Auto-stop and Auto-idle on the JCB Dieselmax Stage V engine provides significant fuel savings, while customisable proportional controls allow for the setting of individual choice of speed and control of attachments.

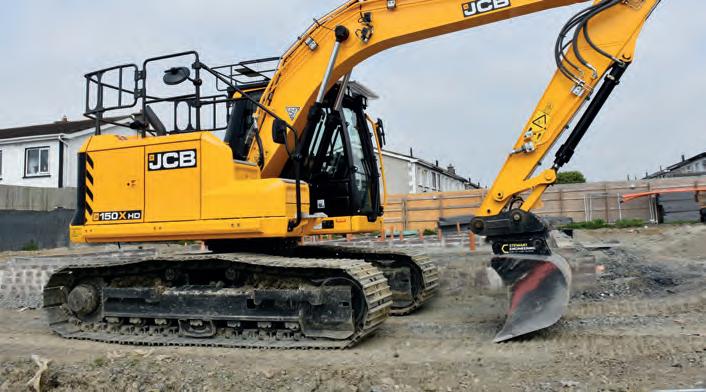
Tracking speed can be found on the joystick for ‘on the move’ tracking change, whilst a convenience button lets you configure a range of functions such as radio mute, camera cycle, or front screen wash; slew drive provides high torque on acceleration and braking for greater controllability and refinement. The machine also has a start-stop button for ease of start-up, which means the operator doesn’t have to turn the key to start it back up again. The start sequence also allows you to start digging within two seconds. Pipework shut-off taps have been added as standard with SAE fittings, to enable quick connection of any attachments, while an advanced tool select system improves attachment handling by monitoring hydraulic pressure and flow – and an easy quick hitch provides simplified operation with an override for removing large breakers or fork attachments.
Simple servicing
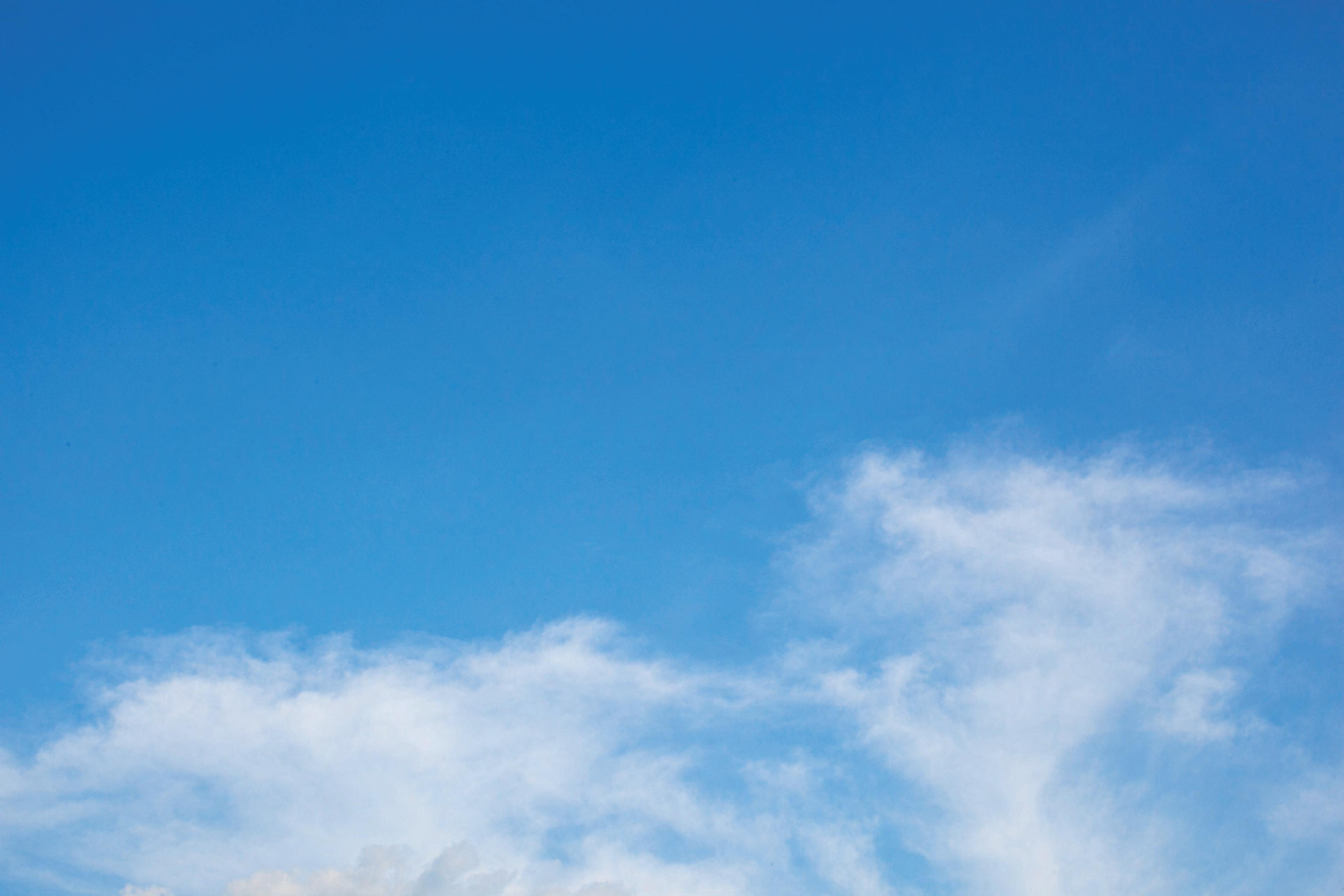
Grouped greasing points make regular maintenance easier and quicker, while there is ground level access to the hour meter, HVAC filter, cab air filter and single fuse box.
Just 10 checks are required for a 500 hour service. The main hydraulic filter service interval has been extended to 2000 hours from 1000 hours and new fuel filter service intervals are 1000 hours.
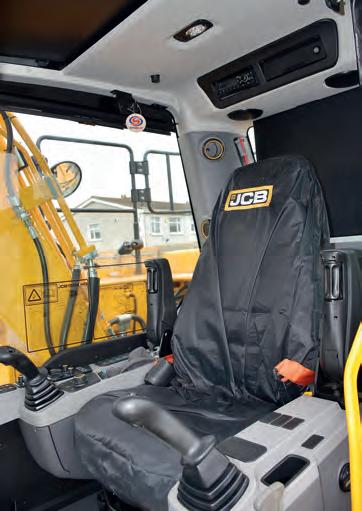
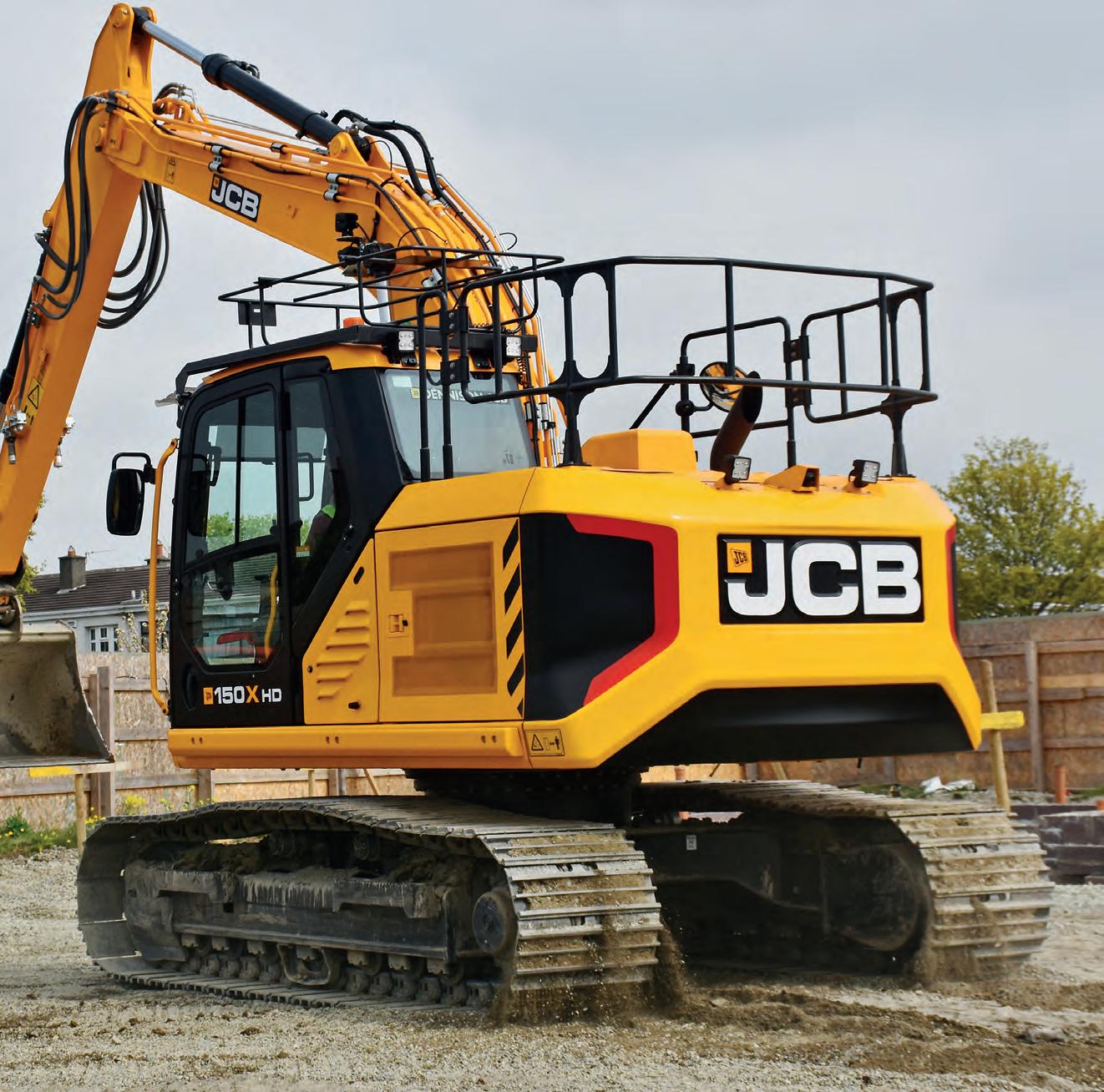
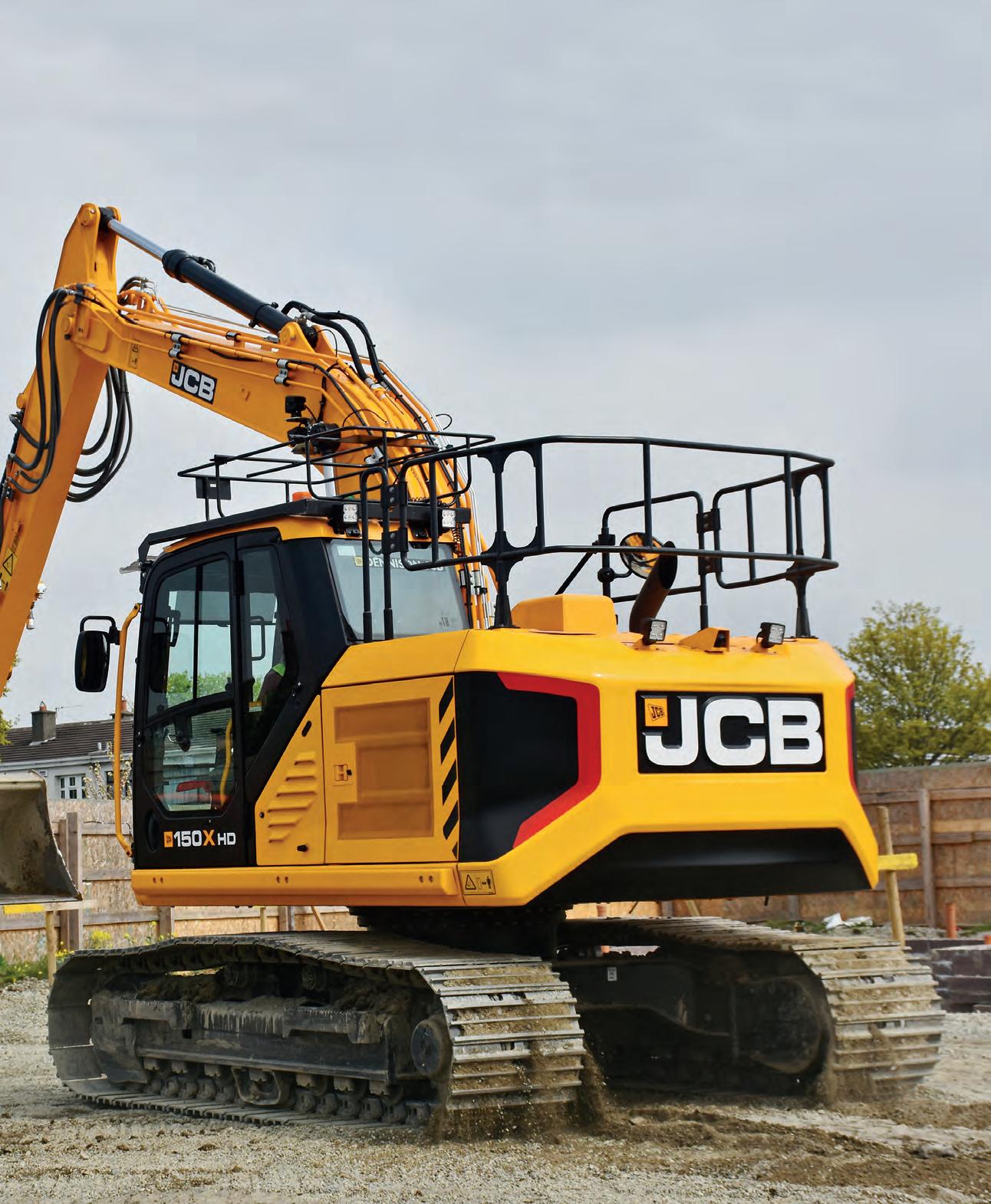
news
National Tyre Distributors Association to launch Responsible Repairer Group
The National Tyre Distributors Association (NTDA) has announced that it is launching a new Responsible Repairer Group for companies providing major repairs for TBR, OTR, Agricultural and Plant & Equipment tyres.
From 1989 until 2009, the NTDA ran an active Tyre Repair Advisory Committee within the Association, which determined the accreditation criteria for its Approved Repairer Group which at its peak, had circa 60 member companies across the UK. Although the formal activities of the Approved Repairer Group ceased in 2009, many repairers remained in NTDA membership and more recently the team in Aylesbury has seen an influx of new membership enquiries and applications from such specialist tyre repairers. Commenting on this area of the trade the NTDA’s Chief Executive Stefan Hay said: “Obviously the world has moved on significantly since 2009 and most repair companies now have upgraded equipment and products, repairing well within BS AU 159 requirements and many are trained and audited by some of our leading aftermarket supplier members and trade partners, but to add a more up-to-date rationale for this group, it’s clear the UK Government remains committed to moving towards a more circular economy which will see us keeping resources in use as long as possible, extracting maximum value from them, minimising waste and promoting resource efficiency. “This, combined with the growing demand from fleet operators and construction and mining companies for tyre distributors to demonstrate that major repairs are carried out by trained and quality assured specialists, provides us with a very solid platform from which to launch the group.” The NTDA believes that having a more sustainable and recognised UK Responsible Repairers Group will demonstrate: • Organised and structured professionalism; • Environmental compliance; • Health & Safety compliance; • Customer credibility; • Kudos on tender document submissions; • A commitment to staff training and development. The NTDA’s National Chairman Martin O’Brien of Lodge Tyre Co. Ltd is also very enthusiastic about the group and added: “The REDUCE, REUSE, REPAIR, REPURPOSE & RECYCLE messages are more important than ever as resources are, without a doubt, finite and there is a growing need for industries to care more for the environment and demonstrate responsibility and what they are doing to maximise available resources. Tyre repair is a discipline that supports every aspect of this, especially when it comes to the high value products such as truck and bus, OTR plant machinery, industrial and agricultural tyres. There is still a network of major repairers, but without proper representation and formal monitoring, which makes a living out of repairing the tyre injuries and damage which most distributors would consider irreparable. They do this fully within the limitations of BS AU 159 and have an enviable reputation for the quality and reliability of their work. It is this network that the NTDA wishes to formally bring together, represent and promote with the Responsible Repairer Group and I encourage such companies to join the Association as soon as possible and get involved.”
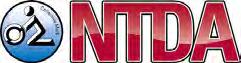
Award Honours Green Credentials of JCB’s Electric Teletruk
JCB has lifted a top award honouring the environmental benefits of its new all-electric telescopic forklift.
The JCB Teletruk was launched in 1997 and remains the world’s only telescopic lift truck to offer users the benefit of forward reach thanks to its telescopic boom. Now the new electric version of this popular machine – the JCB 30-19E – has won The Environment Award from the Fork Lift Truck Association (FLTA), Europe’s leading trade body for the materials handling industry. Judges said the machine - the world’s first electric telescopic forklift - was “ideal for urban environments” thanks to its zero emissions and low noise levels. JCB has received a statuette - known as an ‘Archie’ - to mark the success. JCB Chief Innovation and Growth Officer Tim Burnhope said: “It’s always an enormous thrill to be recognised by your industry peers and we are delighted to win the Environment Award from the Forklift Truck Association. The opportunities for the new electric Teletruk are immense both in terms of benefitting the environment in a very big way and reaching into new markets.” Because it is battery powered, the JCB 30-19E is supremely quiet and produces zero emissions – making it suited to multiple tasks inside buildings. Power is provided by an 80-volt lead acid battery and it can work a full eight hour shift on a single charge.
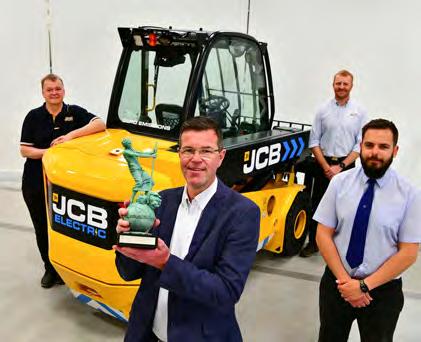
(L-R) JCB’s Rod Scott with the award, Paul Wild, Sam Wilkinson and Lee Harper.
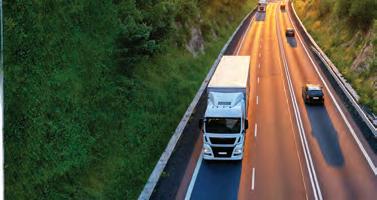
Helping businesses thrive again.
Release working capital from assets, such as machinery, stock and customer invoices.