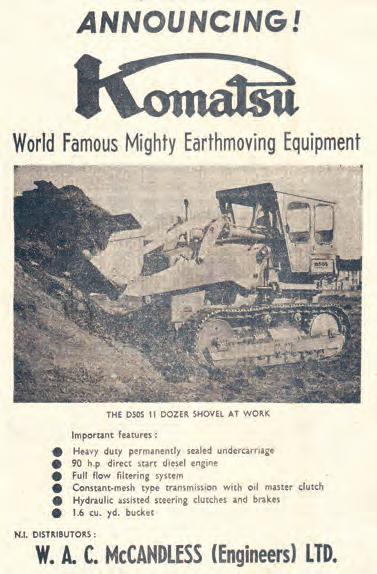
32 minute read
Komatsu 100th Anniversary
from Plant & Civil Engineer 2021
by 4SMNI
DOUBLE CELEBRATION FOR WAC McCANDLESS & KOMATSU
This year marks a double celebration for construction equipment manufacturer Komatsu and its Northern Ireland dealers WAC McCandless.
While Komatsu is marking its 100th anniversary with a number of activities throughout the year, WAC McCandless is also looking back with some well deserved pride on 60 years as a Komatsu dealer, making it one of the manufacturer’s longest established dealers in Europe. With a focused eye on future growth and success, the Belfast based dealership has many positives to reflect on the past, with a proud company history dating back to brothers Rex and Cromie McCandless and a small motorcycle repair shop in Belfast’s Fulton Street in 1943. In 1975 the Gibson Family took over the company with Will and Marie Gibson spending many years working in and growing the business, which today is now managed on a day to day basis by Ciaran and Gerald Carvill, supported by a dedicated team of sales, service, parts and accounts staff, all of whom continue to contribute to the success of the company. Sixty years ago, motorcycles and light engineering spawned an interest in construction equipment, but the acquisition and subsequent growth of famous brands like NCK-Rapier, Rob Roy, Yale and Ingersoll Rand soon necessitated a move to larger premises on the Limestone Road in Belfast, acquiring the Komatsu agency in 1961. As the sole distributor in Northern Ireland for Komatsu construction equipment and among the manufacturer’s longest established dealers in Europe, the name of WAC McCandless (Engineers) Ltd is now firmly established as one of the major distributors of Construction & Quarry Equipment in Ireland. Over the past 60 years, the Komatsu range of products has rapidly expanded from track shovels and bulldozers to tracked, wheeled and mini excavators, rigid and articulated dump trucks, wheeled loaders, backhoe loaders, and motor graders. The range of other products offered by McCandless has also grown to include Atlas Copco compressors, lighting towers, water pumps and generators since 2014, covering All Ireland, Dynapac asphalt pavers and rollers, soil compactors and a range of light compaction equipment since 2013, again covering All Ireland, and Epiroc hydraulic attachments since 2016 covering All Ireland, and Esco Wear Parts covering NI since 1978.
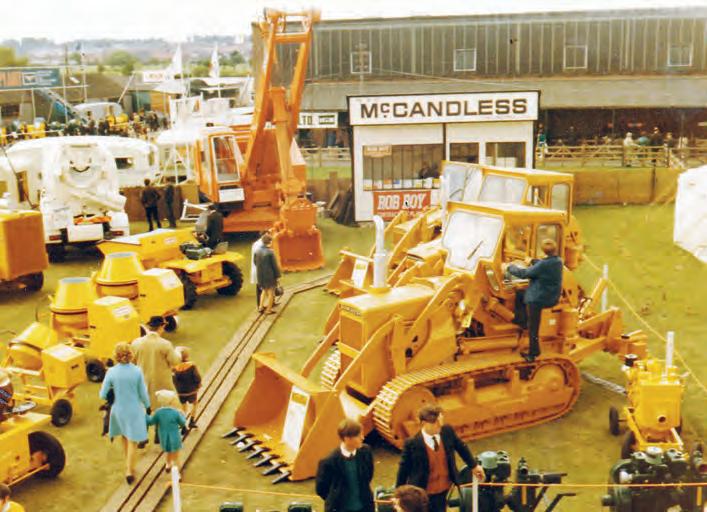
The original advertisement promoting the launch of Komatsu at the 1961 Balmoral show.
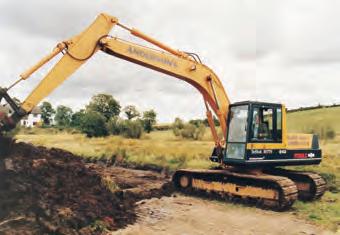
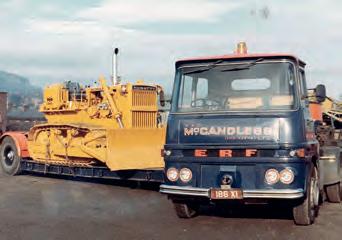
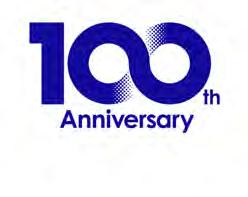
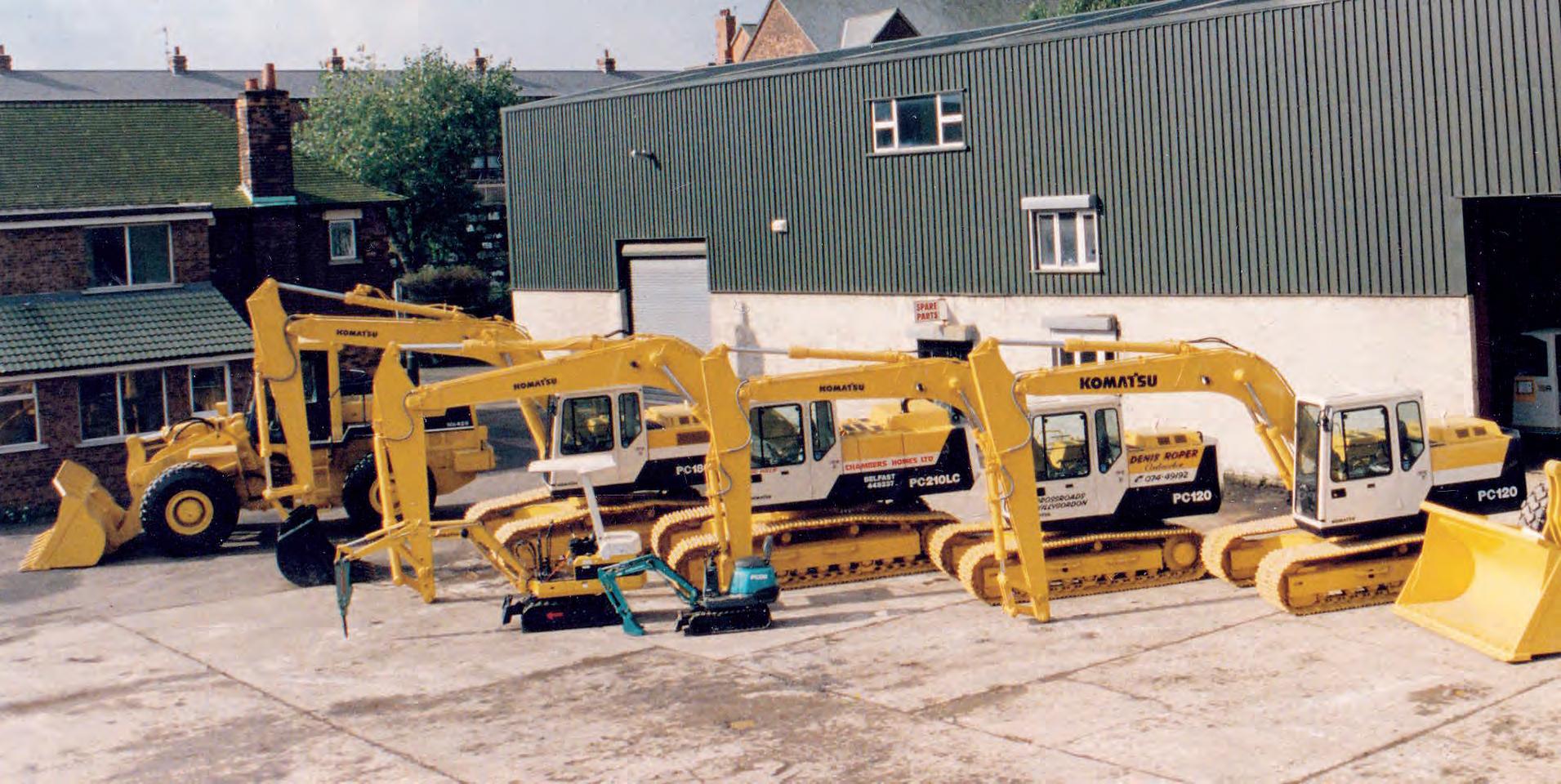
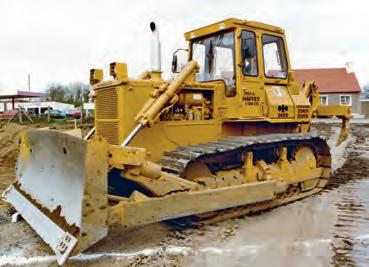
WAC McCandless remains one of Ireland’s fastest growing dealerships, with the company holding market leading shares of the excavator, bulldozer and rigid dump truck sectors. So, to what does WAC McCandless’s Managing Director Ciaran Carvill attribute the company’s success over the past six decades? “It’s all down to hard work from a good team around us and a focus on customer service and after sales support, coupled with the fact that in the Komatsu brand we have an excellent range of products. “Sixty years is an anniversary worth celebrating, but alas the Covid-19 pandemic and social distancing restrictions have made that virtually impossible.” Adds Ciaran: “Over the years we have built up a loyal customer base; indeed many of the customers we deal with today have been with us since the early Sixties when we took on the Komatsu agency. Quite a few of them are still running Komatsu machines. They have become more like friends than customers.” Those loyal customers include Whitemountain Quarries, who have just purchased their 3rd Komatsu Rigid Dump Truck in 18 months (covered elsewhere in this issue). Their Operations Manager Glenn Henry says they have dealt with WAC McCandless for a large part of their history, adding: “We are pleased they have reached this significant milestone and we wish them every success for the future. We have an excellent relationship with the dealership and a good experience of the Komatsu brand in terms of reliability and operating costs.”
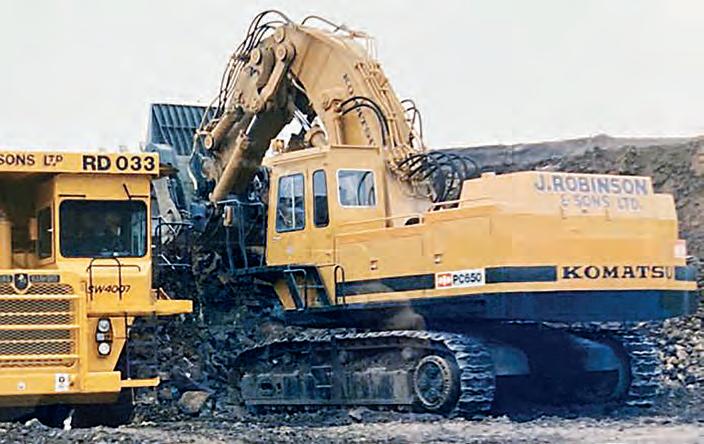
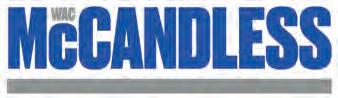
www.wacmccandless.com
McHALE PLANT SALES JOIN THE KOMATSU CELEBRATIONS
Also marking Komatsu’s impressive milestone is its dealer in the south of Ireland, Birdhill and Rathcoolebased McHale Plant Sales.
For close on 30 years, they have been distributor in Ireland for Komatsu equipment – a role that was expanded some years ago with the addition of Komatsu Forest timber harvesting machinery to their portfolio of responsibilities. Comments the company’s Executive Chairman, Michael McHale: “Anyone who has ever viewed a major construction project anywhere in the world – or witnessed rescue efforts resulting from some major tragedy or natural disaster – will have seen Komatsu machinery to the fore such is its presence in international markets. “In Ireland, we are thankful and proud of the contribution Komatsu makes and of the work that Komatsu owners are doing in shaping Ireland’s future through construction, infrastructure, reclamation, restoration, agriculture and utilities projects,” he added.
Early Beginnings
Komatsu Ltd. was established in 1921 from Komatsu Iron Works Ltd, which manufactured mining machines, developed by Meitaro Takeuchi, founder of Komatsu Ltd., for use in the Yusenji copper mine. Based on a firm belief of developing the machinery industry in the rural areas and promoting the growth of industries, as well as a high aspiration of high quality transcending national boundaries, Meitaro Takeuchi began manufacturing at Komatsu Ltd. with an eye to international markets, even when he founded Komatsu. The next year, Komatsu absorbed Komatsu Electric Steel Mills, building the foundation for integrated production from steel castings to machining and assembly, which have resulted in one of Komatsu’s strengths today.
Komatsu UK
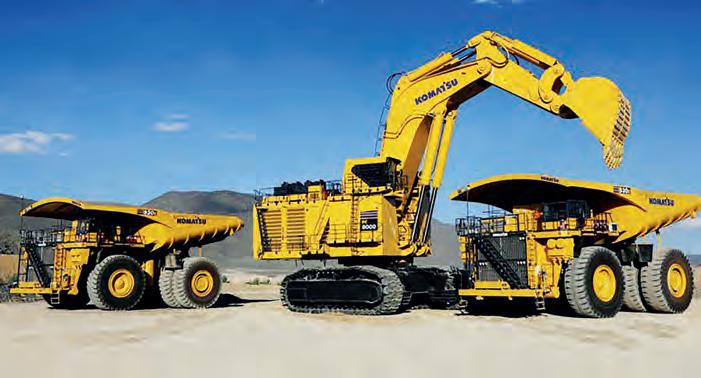
To launch production in the UK, Komatsu UK Ltd. was established. A plant was also purchased from the local authority in Birtley, Tyne and Wear, North England in 1985 and production of hydraulic excavators and wheel loaders began in 1986. The manufacturer’s impressive product portfolio has since expanded significantly, and continuing to meet the challenges of an ever changing marketplace, in 2020 Komatsu launched the PC30E-5 electric mini excavator, an industry-pacesetting model, to promote the widespread use of construction equipment friendly. Based on Komatsu’s accumulated technological expertise of hybrid construction equipment and electric forklift trucks, this electric model offers excavation performance on par with the internal combustion model of the same power output. While achieving zero exhaust gas and an outstanding noise reduction, it also promises extended use in indoor and night-time work. Meanwhile, Komatsu President and CEO Hiroyuki Ogawa has celebrated the manufacturer’s 100th anniversary – that was on May 13 this year – and comments: “All thanks to the support from each of our stakeholders, such as customers,
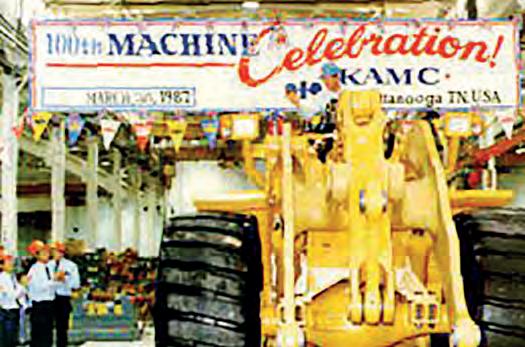

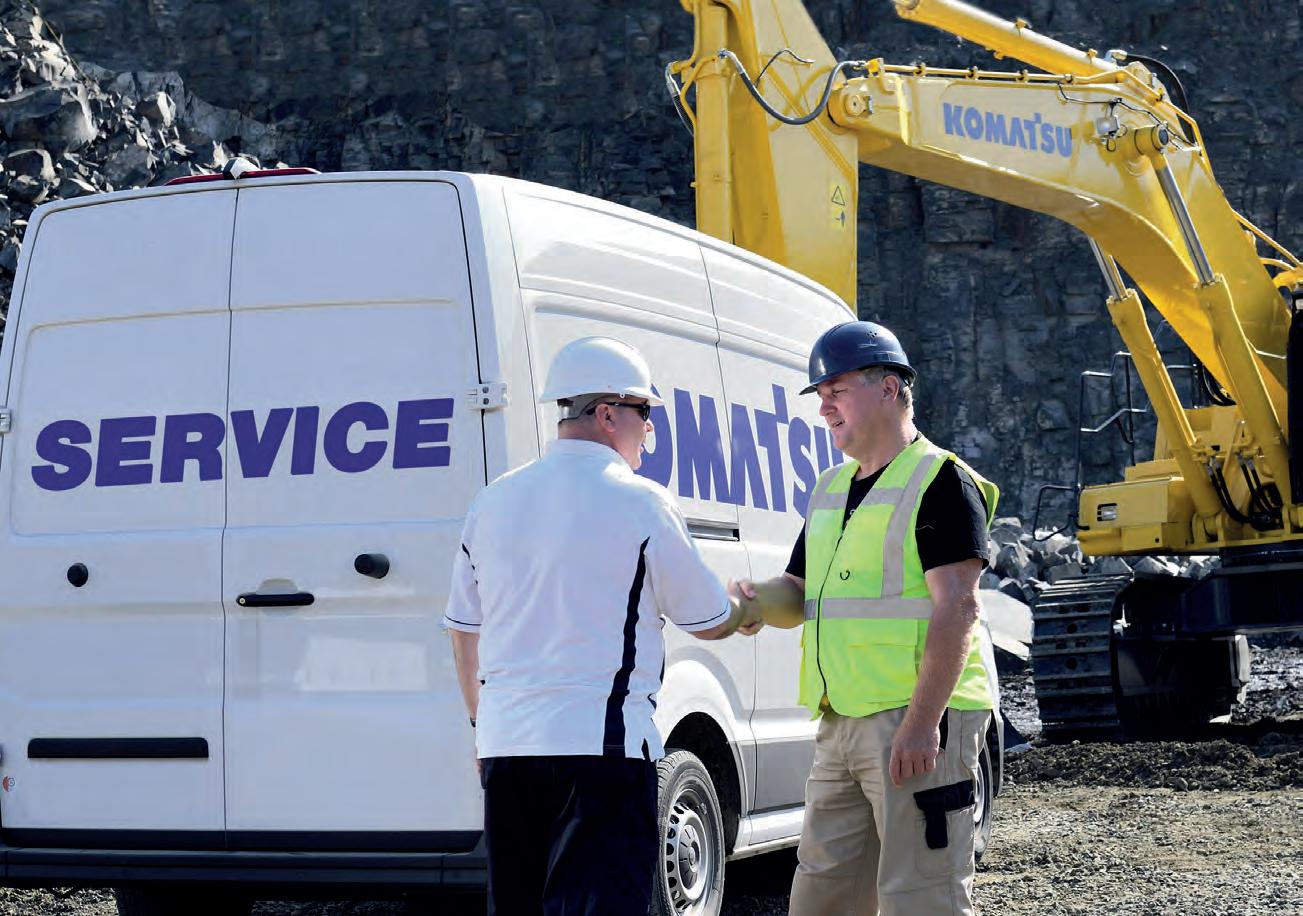
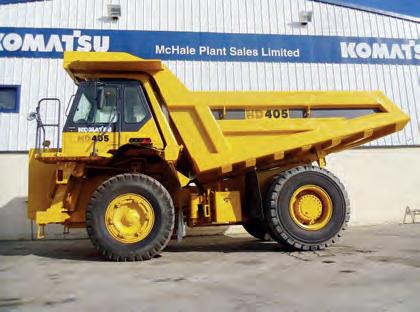
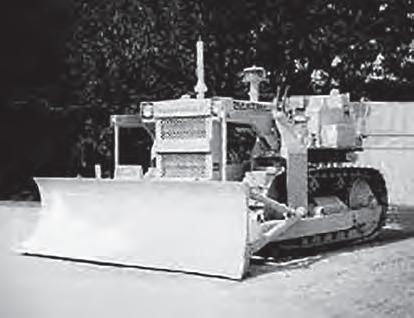
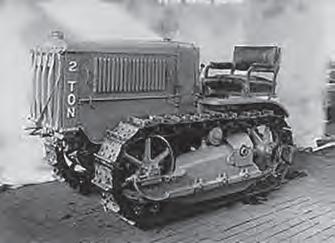
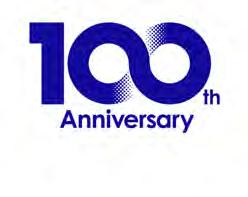
shareholders, distributors, suppliers, and business partners, we are celebrating our 100th anniversary in 2021. I would like to extend our cordial appreciation to them all. “Since its establishment in Komatsu City, Ishikawa Prefecture, Komatsu has worked to maximise its corporate value, i.e., the sum total of the trust given to it by all its stakeholders, as it has remained to commit to Quality and Reliability. “Towards the next 100 years, we will create value through manufacturing and technology innovation to empower a sustainable future where businesses, people, and our planet thrive together. As we look forward, I would like to ask all our stakeholders for their continued support.” Considering its 100th anniversary as a communication opportunity to enhance and disseminate its corporate brand and express appreciation to all stakeholders for their support over the years, Komatsu is going to implement commemorative activities and make efforts for sustainable growth into the future. (For more details, log on to: https://komatsu-100th.com/en/) Among special activities, Komatsu is exhibiting the G40 bulldozer (Komatsu Model 1 Ground Levelling Machine), Japan’s first bulldozer and the only one unit available today, in the lobby of its head office in Tokyo. And to mark what Komatsu call ‘a century of vision, drive and innovation’ – much of which will be broadcast through social media channels at #Komatsu100 – a unique 100th anniversary logo has been designed and will appear on Komatsu communications.
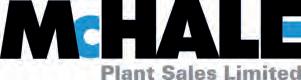
Yanmar this year celebrates the 50th anniversary of the YFW500D, the world’s first tracked carrier equipped with a Yanmar diesel engine.
The original carrier used the undercarriage of a Yanmar rubber crawler combine harvester and added a cargo box to enable it to transport materials on soft ground. Created in 1971, the YFW500D was the world’s first tracked carrier. The carrier was the first in a long line of quality products from Yanmar developed to meet the needs of the times. Yanmar, a pioneer in compact construction equipment, will mark the celebration of this 50th anniversary of the tracked carrier by renewing the company’s commitment to the development of high-performance products and solutions that offer premium reliability and value for customers. Through Yanmar’s contributions to urban development, including housing construction and infrastructure development, they aim to realize a society where everyone can live with peace of mind. MAJOR MODELS
YFW500D-1971
By adding a cargo box to the undercarriage of a combine harvester, Yanmar created the YFW500D, the world’s first Tracked carrier. The YFW500D was powered by a Yanmar diesel engine and could transport materials on soft ground where trucks and dump trucks could not enter
YFW26D - 1978
The YFW26D had a large loading capacity of 3 tons and was equipped with a 17-horsepower Yanmar vertical water-cooled three-cylinder diesel engine that enabled it to run quickly on slopes. The tough steel crawler made it a favorite of worksites.
YFW35WA - 1984
In the late 1970s, the market for wheel carriers was growing, and Yanmar launched the YFW35WA articulated wheel carrier. Equipped with super flat special low-pressure tires for soft ground, the 27 inch (700mm) wide, 38 inch (945mm) diameter tires were an unprecedented development among conventional carriers.
YFW25R - 1985
Yanmar developed a rubber crawler that achieved a speed of 11 km/h, about twice the speed of conventional crawlers. The high-speed YFW25R carrier was a hit product that also featured the industry’s first reverse seat and was the prototype for the C30R model that is still sold today.
YFW40R - 1985
Equipped with a 64-horsepower Yanmar vertical water-cooled four-cylinder diesel engine, the YFW40R was launched in pursuit of not only running speed and power, but also comfort and used a large rubber crawler to reduce operator fatigue in a highly maneuverable HST. This model was the prototype for the C50R, which is still sold today.
YFW8R - 1988
Yanmar released the YFW8R, a compact carrier with a width of only 950mm built tough to work hard on construction sites. Until the YFW8R, tracked carriers had their driver’s seats mounted to one side or the other. But with the YFW8R, for the first time in the industry, the seat was placed in the center making it easy to get on and off from both sides and provided better visibility. This model was the prototype for the C12R, which is still on sale today.
C6R - 1990
The C6R was a 790mm wide mini carrier specially designed for civil engineering and suitable for urban renewal in densely populated residential neighbourhoods and narrow alleys. With the power and sturdy design of a construction machine, it was used for a wide range of tasks from civil engineering work to landscaping and forest road work in narrow areas where small pick-up trucks could not go.
C120R -1996
The largest Tracked carrier in Yanmar’s history, the C120R is a 240-horsepower, 11-ton load, large carrier that combines power and speed to meet the expectations of professionals. The C120R emphasizes strength, durability and operability from its basic structure through to every detail of the undercarriage.
30R-3 - 2000s
Yanmar launched a series of products equipped with environmentally friendly engines that met the strict emission regulations of Europe, the U.S. and Japan. Among them, the C30R-3 adopted a two-pump, two-motor hydraulic system, which enabled much smoother running and spin turns than before, and also incorporated the latest technology such as a GPS remote monitoring system.
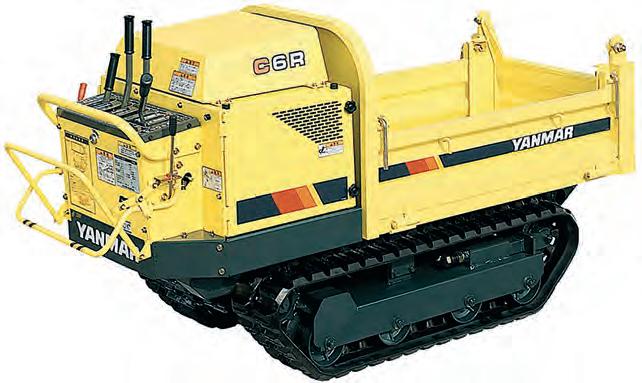
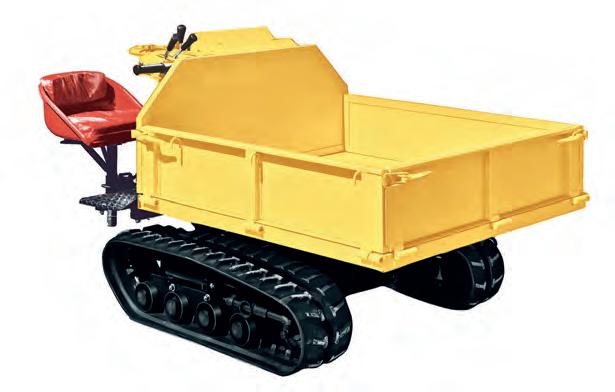
news
Investing in tomorrow: Kubota on tackling the skills gap
Even before the onset of the Coronavirus, the construction industry was facing up to a widening skills gap; something that has only been exacerbated by the pandemic and subsequent measures to supress it.
Here, Glen Hampson, Construction Division Manager at Kubota UK, takes a closer look at some of the steps being taken to bridge the skills gap - and considers why a sectorwide approach is needed to attract the talent of tomorrow. Generating almost £90bn annually and representing 6.7% of the UK’s GDP, the construction sector is one of the most important facets of the British economy. Key to a thriving and productive construction industry is, of course, the highlyskilled workforce that power it, with the sector currently supporting around 10% of all employment in the UK. Such seemingly robust statistics belie the looming skills shortage that has long been hanging over the industry. This is no small part due to the construction sector’s workforce being among the oldest-skewing out of any industry nationwide. At last count, 22% of all construction professionals are currently aged 50 or over, with a further 15% in their 60s. With such a significant chunk of the sector heading towards retirement over the coming decade, the industry stands to lose a great deal of accrued knowledge, acumen and know-how. The COVID-19 pandemic, and the ensuing (albeit temporary) disruption to further education and apprenticeships, has disrupted an already fragile pipeline of fresh talent – all at a time when the industry needs new blood the most.
Investing in talent
Indeed, the Government’s recently unveiled COVID-19 recovery plans put construction at the heart of rebuilding the country’s beleaguered economy. The Prime Minister’s promise to ‘build, build, build’ has led to the announcement of major infrastructure projects and a pledge to build 180,000 affordable homes between 2021 to 2026 – fantastic opportunities for the sector but ones that will require thousands of new recruits if these plans are to be realised. But how can the industry go about attracting fresh talent? An October 2020 report by the Construction Industry Training Board (CITB) argued that government investment will be the single biggest weapon in preventing a generation of skilled workers from being lost. The report argued for further investment into the recently launched National Skills Fund, alongside reform to the Apprenticeship Levy to allow employers to pass on unspent vouchers in bulk. At Kubota, we have long recognised the importance of meaningful apprenticeships in encouraging more young people to start a career in construction. Apprenticeships offer a vital way into the sector, affording those undertaking the schemes the chance to gain valuable experience in a real world setting, all while earning money.
The Kubota way
As a business, Kubota has always placed great focus on our engineering apprenticeship programmes, recognising that investing in the apprentice of today helps create the expert of tomorrow. Our scheme sees apprentices based at one of our nationwide dealerships, blending practical experience with theory delivered by one of our partner colleges. At the end of the programme, each apprentice will leave with a valuable, industry-recognised qualification in engineering for their chosen machinery product area, alongside the opportunity to attend continual technical training at one of Kubota’s industry-leading training facilities. Our apprenticeship schemes have been especially tailored to be reflective of the wider construction industry, ensuring those completing the programme have all the skills they need to thrive in an industry as fast-paced and quickly evolving as construction. After all, the requisite skills for a career in construction today differ from those needed thirty years ago – and are likely to change again in the next thirty. Since the turn of the Millennium, the role of technology in construction work has grown exponentially; not just in terms of machinery, but design and manufacturing too. Concepts such as AI, virtual reality and 3D printing are a growing part of construction work, and proficiency in using these will, one day, be essential – and that’s something apprenticeship schemes have to take into account.
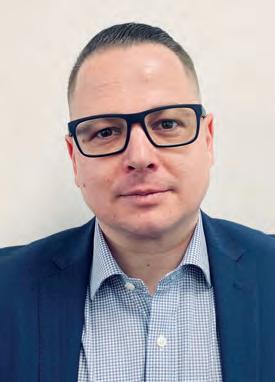
Glen Hampson
Looking ahead
It isn’t unfair to say that the past few years have been incredibly challenging for the construction sector. The turbulence of Brexit and the seismic impact of the Coronavirus have both impacted the sector’s skill gap, but we should rest assured that there are significant opportunities waiting for us. As we look ahead to life beyond the pandemic, it’s clear that tackling the skills shortage should be our sector’s number one priority. Bridging the gap won’t be easy, and will require buy-in from the government and collaboration across the supply chain, but if we invest now in meaningful schemes that harness tomorrow’s talent, we’ll be well positioned to ensure the sector is thriving for decades to come.
Rototilt broadens QuickChange programme to encompass compact sector
Rototilt is expanding its line of nextgeneration quick coupler systems with three additional new sizes: QC45-4, QC 45-5 and QC60-4, with delivery beginning May 2021.
QuickChange can now be provided on tiltrotator models R3 to R8, as well as on QuickChange machine couplers in the 6–32-tonne range. And with the awardwinning SecureLock safety solution™ as standard, the risk of accidents associated with improperly coupled quick couplers is reduced thanks to continuous monitoring of the quick coupler locking function in the machine coupler and tiltrotator. “We’re seeing a clear increase in interest among users of compact machines in using fully automatic quick coupler systems. We can now offer the latest technology for these machines too, with the launch of QC45-4 and QC45-5,” says product manager Sven-Roger Ekström. With Rototilt QuickChange for machine couplers, tiltrotators and tools, you can change hydraulic and electronic tools without even leaving the cab. QuickChange is based on the S standard, which is compact and very robust. QuickChange is part of the common Open-S standard, which ensures compatibility between different manufacturers for the hydraulic interface between machine couplers, tiltrotators and tools. With Rototilt QuickChange, you can quickly disconnect your tiltrotator when the job doesn’t require tiltrotator functionality. Your excavator becomes a full-fledged tool carrier that lets you work faster, smarter and with more precision.
EDGE INNOVATE STOCKPILER CUTS COSTS FOR MOBILE CRUSHING & SCREENING SPECIALIST BRICK & BLOCK
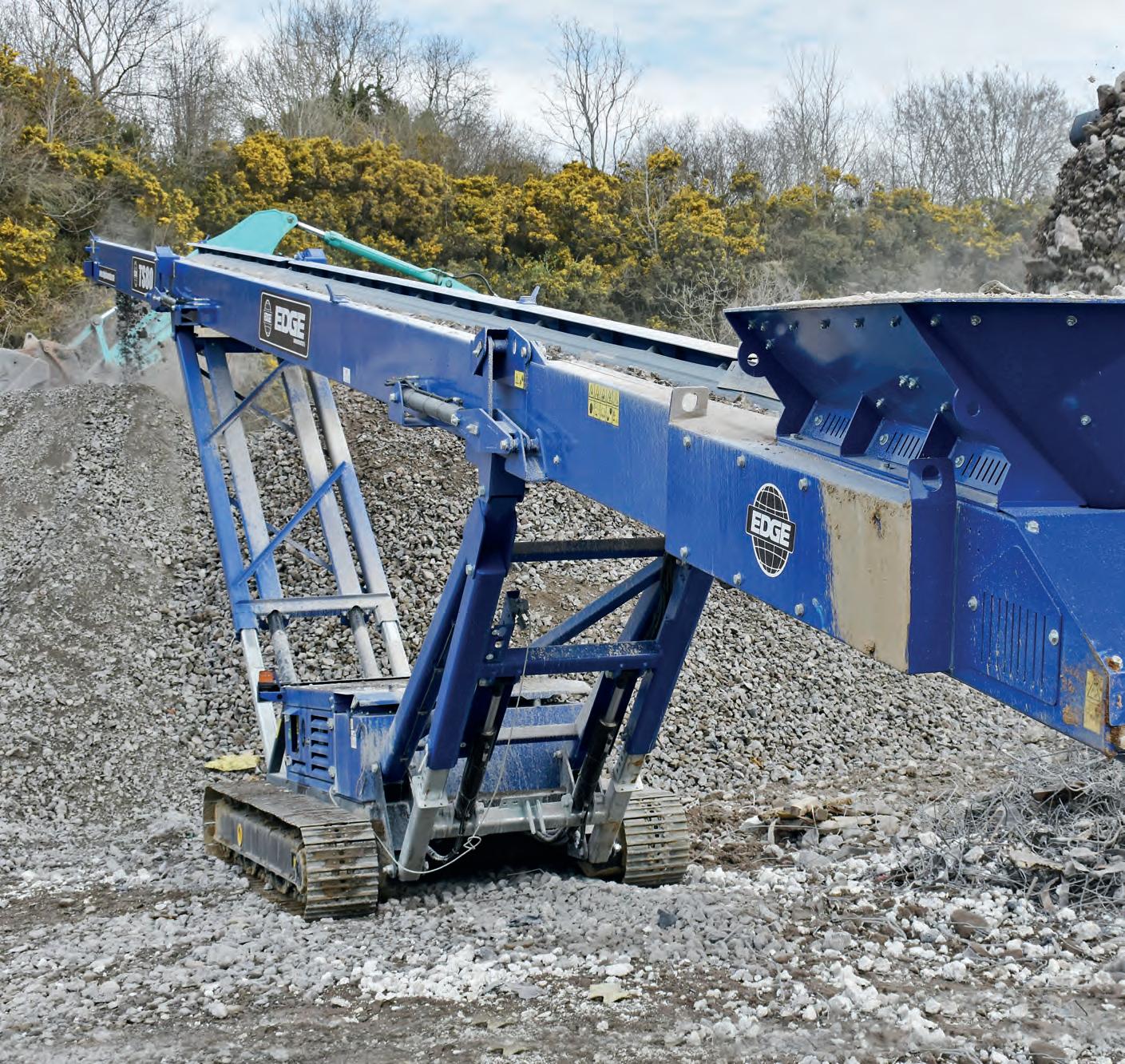
Operating throughout the island of Ireland, Brick & Block has built up a widely respected reputation as a dedicated specialist offering a range of services - from contract crushing and demolition to site clearance and excavation.
With a wide variety of clients, including landowners, developers and quarry operators, and fully insured through Constructionline and CSR registered, the company was first established by John Minish in 1988. Its core business is mobile crushing and screening, with the capabilities to crush up to 1,500 tonnes per day and can handle any size of task - from 200 tonnes up to 200,000 tonnes. It is also able to deliver crushed stone or concrete and aggregate to sites for reuse or recycling. As its business expanded, the company, which is based at Scarva in County Down, has invested heavily in plant and machinery, the latest acquisition being an EDGE TS80 tracked stockpiler which is earning its keep on a variety of projects across the country. It has been a great investment, as John explains: “We are very happy with the design and build quality; it was also competitively priced which made it even more attractive. “As a growing business, investing in new plant and machinery is an ongoing process,” says John, who takes a fully focused ‘hands on’ no nonsense approach to the business. “Providing a service that meets and exceeds our customers’ requirements is our top priority, so having the right equipment to do so is essential.” So, what’s he like about his new acquisition? “There were three things that influenced my decision to buy the stockpiler – to cut our fuel bill, to become more competitive as it eliminates the need for a loading shovel and to reduce manpower,” says John, whose attention was drawn to EDGE
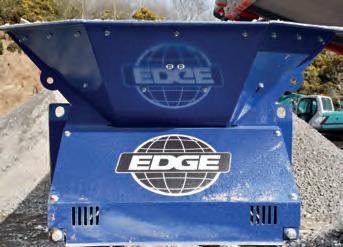
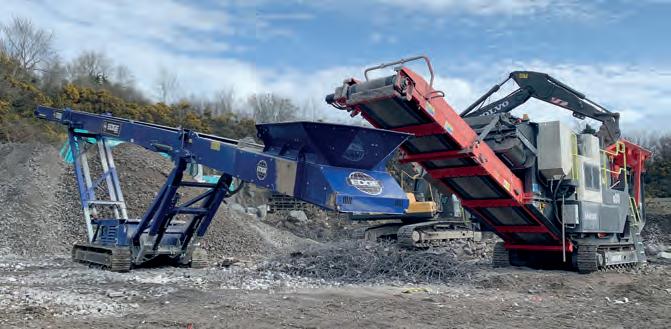
“It has made my operation much more productive, efficient and cost effective. With the Edge Innovate stockpiler I can, on my own, do a week’s crushing work – up to 7,000 tonnes – using less than half the diesel that a shovel could burn through a day.” John uses the EDGE Innovate stockpiler along with a small Sandvik mobile crusher. “The two pieces of equipment perfectly complement each other on many of the projects I am involved in. The stockpiler is easily transportable; it simply folds up and can be moved on a low loader, which is ideal as our work regularly takes us to various sites up and down the country.” Taking a closer look, the EDGE TS80 tracked stockpile, a versatile conveyor that can be used in a wide range of applications, boasts an array of design features including a highly efficient hydraulic drive system with variable belt speed, low fuel consumption, adjustable feed height and variable discharge height. Designed to work in the harshest of environments, it can be continually fed by any crusher, screener or shredder with a rapid set-up time and impressive stockpiling capacities. As John mentioned, moving it around the work area is easy thanks to its hydraulic driven crawler tracks, while its hydraulic head and tail fold for quick and efficient transport between sites. Other notable features include: • Hydraulic adjustable feed height reduces impact and dust creation • Eliminates material segregation and ensures stockpile meets required specification • Discharge height of up to 10.8m (35’9”) • Create conical stockpiles of up to 742m³ (970yds³) • Power source options available: Diesel /
Hydraulic, Direct Electric, Diesel Genset “The new stockpiler is a significant investment for us, but it is already paying dividends,” says John, who adds that being able to deal direct with EDGE Innovate was a bonus. “The whole process was hassle-free and delivery was made earlier than originally stated. The service and support could not be faulted.”
info@edgeinnovate.com www.edgeinnovate.com

Innovate last year when Plant & Civil Engineer ran a feature on the EDGE TSR80, an 80ft long track mounted conveyor with radial stockpiling functionality.
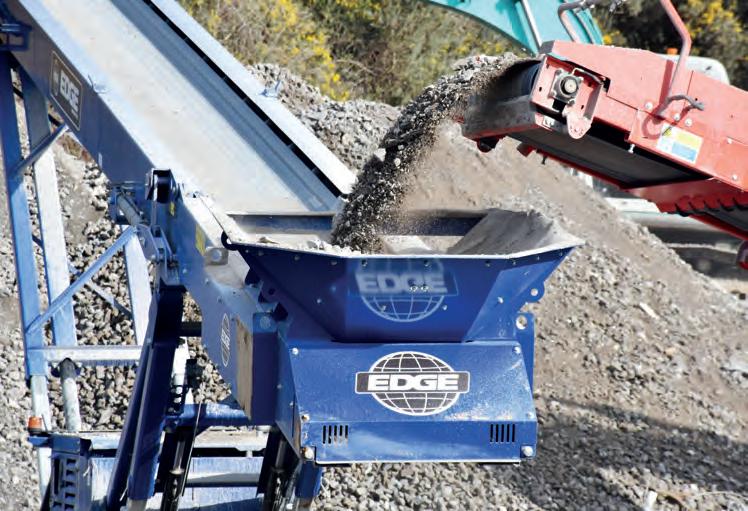

in profile GIBSON BROS LTD IMPRESSED WITH NEW SANDVIK CRUSHERS
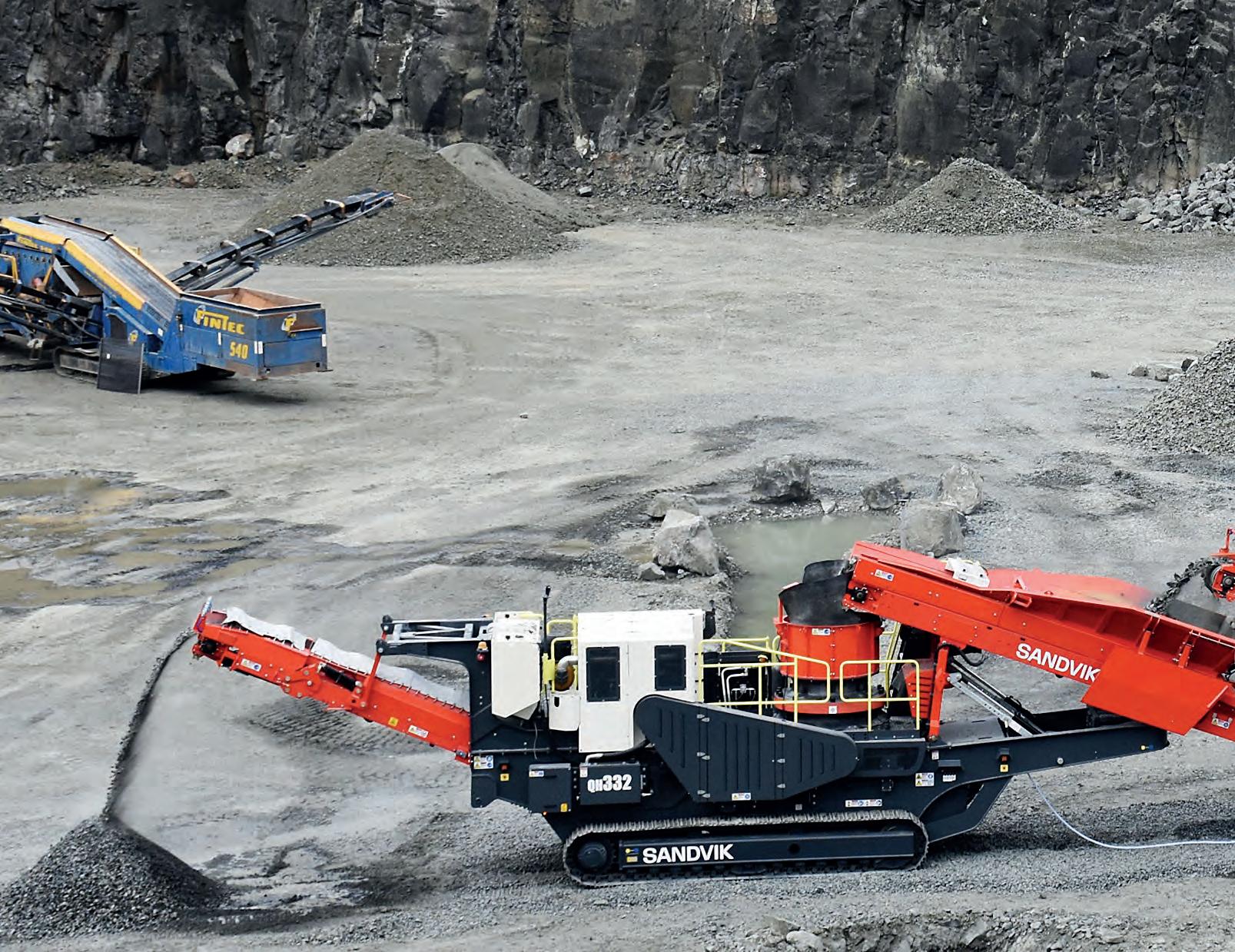
When Gibson Bros Ltd invest in new equipment they like to keep it ‘local’ if at all possible, and that’s been the case when they recently acquired two new machines from Sandvik, whose factory at Ballygawley is known as one of the world’s premier manufacturing facilities for mobile crushers and screens; it also is home to the manufacturer’s first class Centre of Excellence.
Founded in 1950 by William and Jack Gibson, Gibson Brothers Ltd has developed into one of Ireland’s most recognised family owned businesses operating in the Quarrying / Civil Engineering and Surfacing sectors. The business has grown, diversified and continues to develop in delivering innovative engineering solutions to a host of public and private sector clients. Gibson Bros operate several quarrying facilities throughout Ireland, providing high PSV aggregates for use in civil engineering, road construction, road maintenance and concrete manufacture. The company recently added a QJ341 jaw crusher, one of the largest in the Sandvik Q-range and the flagship of the mobile range, and a Sandvik QH332 cone crusher. “Local knowledge is very important, and Sandvik really know the needs of their ‘local’ market, which is one of the reasons we opted to deal with them,” says Gibson Bros Ltd Quarry Manager Mark Poots. “The QJ341 is replacing an older Extec C12 which has been working in the quarry since the early 2000s, while the QH332 cone is additional and is linked to a mobile crushing train to help us cope with an increasing demand for our quarry products.” Adds Mark: “The new equipment is performing efficiently at our quarry in Portadown; the QH332 cone in particular has a great reduction ratio with good cubical shaping which is crucial when put in train for aggregate production.” He also praised the load control system for the feeder drive and jaw level sensor on the QJ341. “It’s a great help in maintaining a steady feed to the jaw to maximise tonnage per hour.” Gibson Bros are currently in the process of setting up Sandvik My Fleet on the new equipment, and says Mark: “It will give us remote access to the Sandvik machines and will help us pick up on possible production problems and mechanical issues more quickly, as well as enabling us to organise servicing well in advance. My Fleet is clearly a big bonus.”
Best Selling
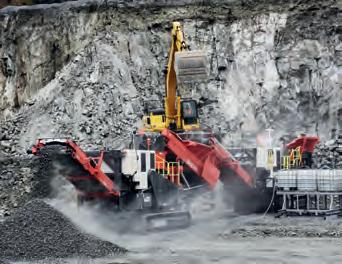
Utilising Sandvik’s unrivalled design and manufacturing expertise, the QJ341 is one of the best-selling track mounted mobile jaw crushers in the world today, designed for quick set-up and ease of operation. Equipped with a C12 jaw crusher, and a powerful and fuel-efficient engine, it features a 1,200 x 750mm (47 x 29 in.) jaw opening, built to tackle the most difficult applications with ease. It has been designed to meet the needs of the operator seeking a high performance mobile jaw crusher which is both reliable and durable. With a large feed opening and unique high crushing speed it is capable of delivering high outputs with excellent reduction ratios. In addition to this, the equipment can start under load, which enables maximum uptime and productivity.
The powerful jaw crusher is capable of a variety of tasks with its large underbelt clearances, and is equipped with a hydraulic raise and lower facility on the main conveyor as standard. There are a number of features to minimise operator intervention whilst maximising their safety, such as the self-locking hopper and jaw level sensor which controls feed rate with minimal input from the user. The hydraulically adjustable jaw setting can be tailored to your application and the reversible crushing action can relieve blockages and deal with sticky problematic materials. The improved load control system for the feeder drive ensures continuous, uninterrupted crushing, keeping productivity levels consistently high, as Gibson Bros have discovered. Fitted with Optitooth jaw plates for extended life, increased throughput and reduced fuel consumption, the Sandvik QJ341 mobile jaw crusher is also as user-friendly as it is productive. Full PLC control system and Danfoss colour screen allow visual data output of all plant operating parameters, contributing to complete control of material flow. Extensive use of steel pipework gives superior heat dissipation whilst providing a maintenance free sealing solution. Easy access to the engine compartment and in-built automatic central lubrication system reduces maintenance time, and with wear resistant liner plates fitted as standard you can keep your crusher working even on the most challenging applications.
Cone Crusher
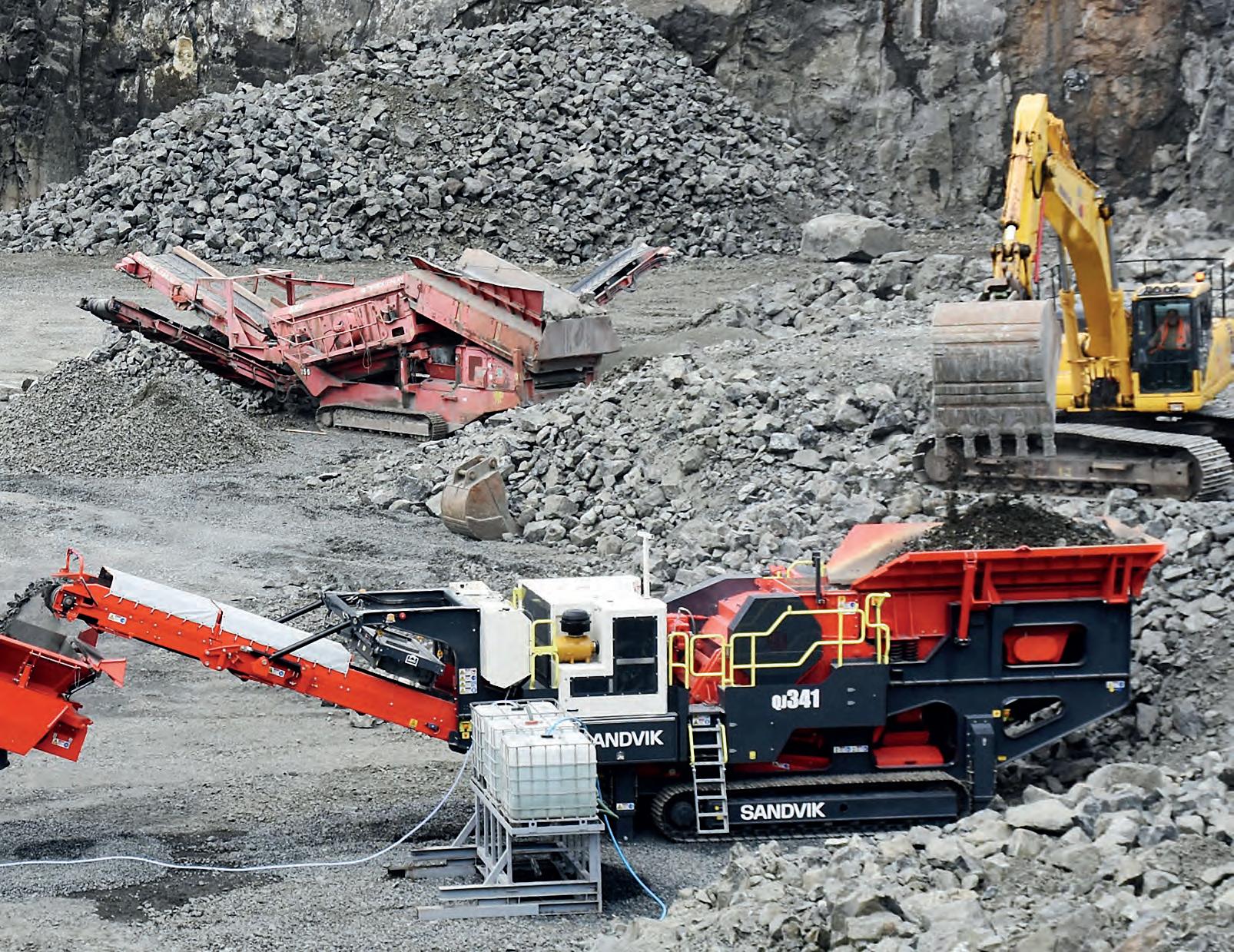
Sandvik QH332, meanwhile, features the Sandvik Hydrocone crusher and comes with a number of features to ensure maximum uptime and minimum operator intervention. At the heart of this machine is the Sandvik CH430 cone crusher; this advanced piece of crushing technology comes equipped with a hydroset system, which puts the user first by providing both safety and setting adjustment functions. In addition, the automatic setting regulation system will not only optimise production but will also keep track of liner wear. The cone comes with a choice of six different crushing chambers and a number of different bush settings, making it the ideal choice for a huge variety of crushing jobs. This machine is powered by a 261kW (350hp) engine and a fuel efficient direct drive system to ensure maximum production capacity and maximum power transfer. Remote camera viewing of the crushing chamber ensures full visibility without the need to access the machine, while there is superb access around the crusher for easy maintenance, especially during liner changes. Other safety features include audible and visual warning for safe operation whilst tracking and start-up / shut down, emergency stop buttons and conveyor pull stop cords around the plant for easy access during operation, and a wireless radio handset and proportional speed control for safe tracking onsite. Spacious platforms provide safe access for service and maintenance, with dust suppression spray bars and an onboard water pump to minimise dust.
Aftersales Support
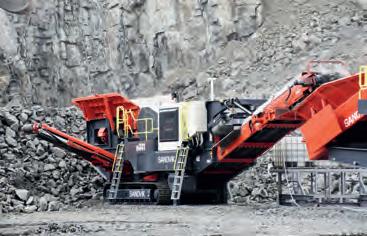
Aftersales service and support, of course, is always an essential ingredient to keep the potential for unnecessary downtime at a minimum, and Gibson Bros Ltd have no complaints in that area. “Sandvik have provided us with an excellent level of service to date; any issues or queries have been dealt with promptly,” says Mark, who also revealed that a third Sandvik machine – a CH430 static cone crusher – is to join the fleet.

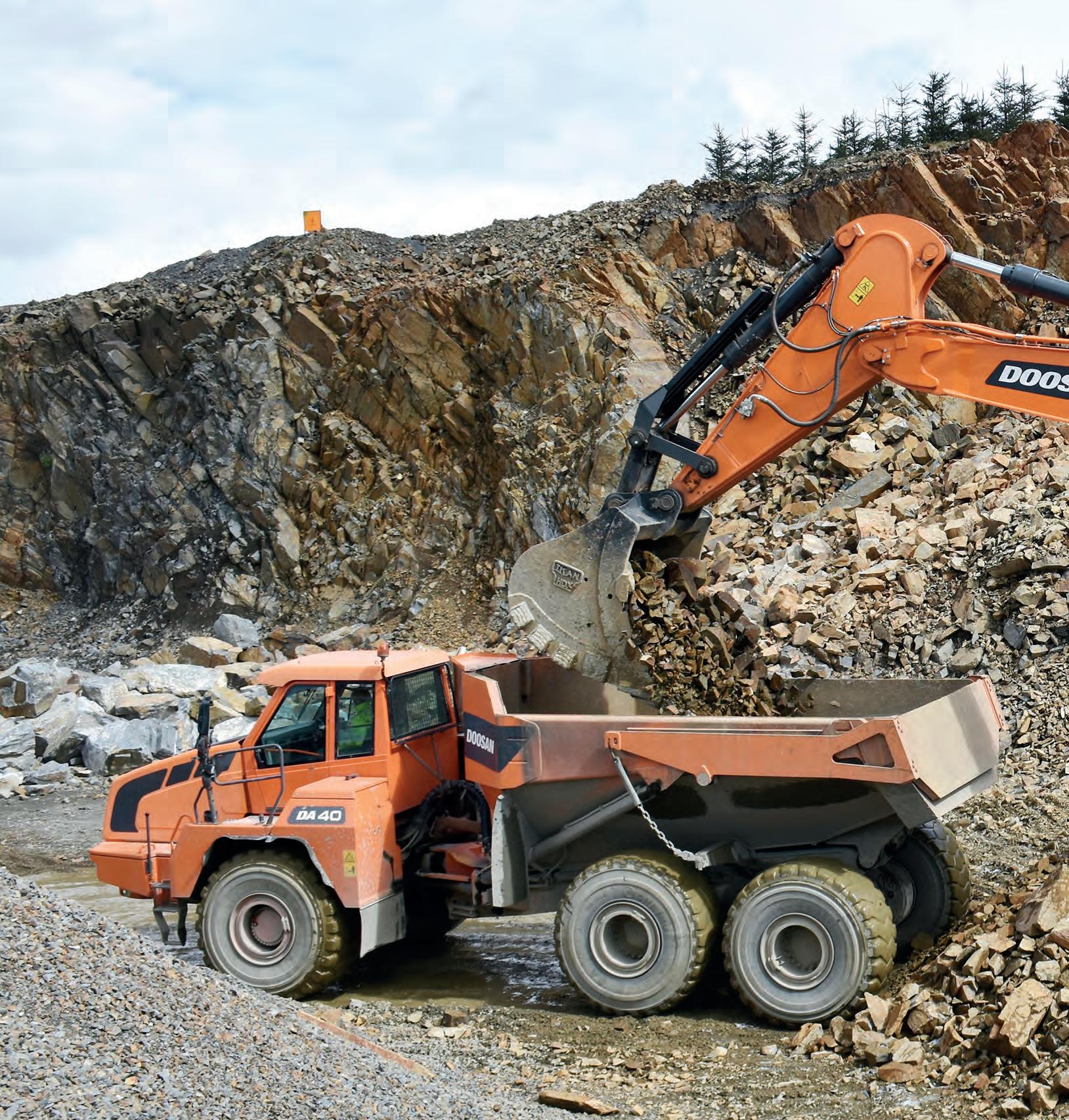

Excavator attachment specialists Hill Engineering have realised the three Bs for Irish neighbours Loughran Rock Industries.
The Newry, Co Down-based manufacturer has produced its Biggest Bespoke Bucket to date – a 4.9-tonner strengthened with 20, 30, 40 and 50mm Hardox - for the Co Armagh aggregates supplier 19 miles away. Loughran Rock Industries, who produce 3,000 tonnes of greywacke a day from their 40-hectare quarry at Mowhan, required a dedicated bucket for a new heavy-duty Dooson 800 excavator – the manufacturer’s biggest excavator, and Loughran’s, to date. Colin Loughran, quarry manager of the family owned business, had heard about Hill’s awardwinning Tefra Tilt hydraulic quick coupler and approached William McIntosh, their business development manager, to quote for and design a bucket to their rock specification. The result is a 2,250mm wide (narrowing to 1,769mm at the back) monster which features six FC600 teeth, six F40 heel shrouds and six side cutters. Weighing in at 4,882kg itself, it has a cutting edge of 70mm and capacity of 4.9m3– slightly larger than the 4.6m3 bucket that would normally be supplied by Doosan. The design and build by Hill Engineering took a month and the bucket has now been in operation, digging greywacke for PSV chips, tar and concrete, for 10 hours a day, six days a week, for two weeks. “We were using an old bucket while the Hill one was being built but there is no comparison,” said Colin. “There are some poor-quality attachments out there in the marketplace but this isn’t one of them. The new Hill bucket is strengthened with
HILL ENGINEERING DELIVER ON LOUGHRAN’S BUCKET LIST
Hardox and is eating through our greywacke at an unprecedented rate. We were happy with the price and are very happy with the product, and the fact it was delivered on time, which is a crucial factor.” William said: “We pride ourselves on providing the highest quality of finished goods and were more than happy to work with Loughran Rock Industries on the design of a bucket that would suit their requirements. “We have the skills and experience needed to produce special attachments, not only for the quarrying sector but also a wide range of other industries where extreme duty performance is essential.” Established in 1985, Loughran Rock Industries have become one of Northern Ireland’s foremost excavators of quarry aggregates, and providers of high grade, ready mix concrete, blocks, stones and hard materials for the construction and agricultural industries. The company’s ongoing policy of investment and reinvestment in modern plant, machinery and delivery fleet, which it also hires out, puts it among the best equipped quarrying operations in the country.
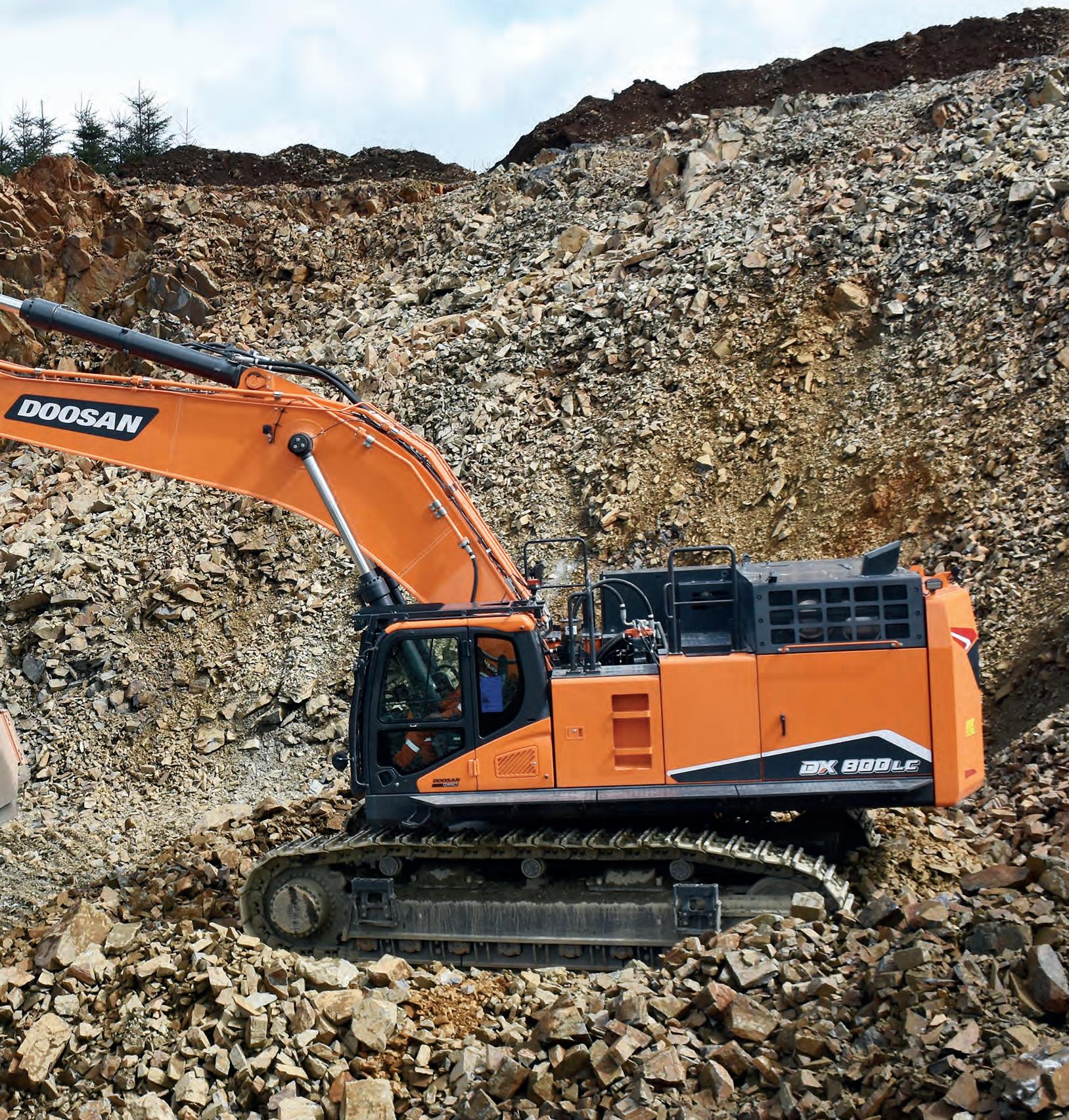
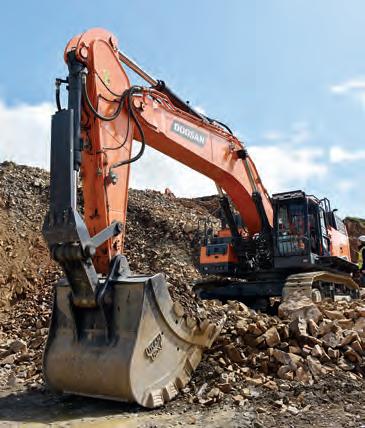
news New Mobile App Launched for DoosanCONNECT Telematics
Doosan has launched a new mobile app for Apple and Android devices for its successful DoosanCONNECT TMS2.0 fleet and asset management system, now covering over 80,000 of the company’s excavators, wheel loaders and articulated dump trucks worldwide.
As well as the standard functionality offered by the DoosanCONNECT system, the mobile app offers new functions such as directions to machines; call service, whereby the app connects the customer directly with the Doosan dealer’s service operation and a Chat option to send messages to the service provider. Cellular support for the DoosanCONNECT TMS2.0 system is offered only in areas where a 2G/3G network service is available. The next generation DoosanCONNECT TMS3.0 system will be available for new Doosan ‘-7’ machines later this year. The DoosanCONNECT system is designed to increase efficiency in site management and equipment operation through real-time data monitoring to check engine and hydraulic system parts of Doosan machines and other construction equipment and to provide information, mapping and visuals on their location and availability. Doosan customers receive a monthly report on equipment operations to ensure efficient equipment deployment with detailed information on service hours and fuelconsumption and timely responses to filter and oil replacement. Doosan plans to further expand the types of equipment covered by DoosanCONNECT and develop various services based on the telematics system to manage consumables and provide enhanced maintenance packages. The DoosanCONNECT system provides comprehensive information about machine performance in a dual mode (satellite, Mobile network). As such, it is the only tool of its type capable of providing this level of information, delivering insightful and cost-saving data about equipment to help customers work more effectively. The DoosanCONNECT telematics system allows fleet managers to compile a number of reports, including fleet status; machine details; machine location; operating hours; fuel usage; engine idle time vs work time; machine error codes; engine warning system; maintenance history and utilisation reports. According to Doosan, the DoosanCONNECT telematics system provides significant benefits for customers through the use of operational data that help improve efficiency, such as altering machine idle times based on fuel usage, machine security and safety. The system can support multiple Doosan machines in different locations, helping customers to monitor machine utilisation rates to assess that the right mix of machines is being used; it can also guide drivers to help them to operate equipment with higher efficiency and to locate replacement machines in the event of maintenance work or breakdowns, all under the umbrella of vigorous anti-theft and theft recovery protection systems. Customers can monitor the physical location of their Doosan machines, ensuring they are where they are supposed to be, which helps prevent equipment theft. Operational data also gives owners insight into monitoring the machine’s fuel efficiency and the selected power mode in different applications. This is helpful to determine if an operator can make adjustments in order to do the same work with less diesel fuel. Doosan machines provide operators with various power modes to help them best match the power needed for specific applications. If a problem does arise, the DoosanCONNECT system alerts owners to help reduce machine downtime. The website reports fault and warning codes, and owners or their dealers are better prepared to fix the problem when they respond because they will have more data about what is wrong with the machine. Doosan dealers can view the problem on the DoosanCONNECT website to help diagnose an issue, without physically being in the same location as the machine. With all of the information available from the DoosanCONNECT system, business owners can make better estimates when completing job bids and planning for jobs. Accurate machine usage reports, such as the number of hours a machine was used for a particular job, help owners respond to new business opportunities.

Kubota wins prestigious Red Dot Award
Kubota’s market leading 5-tonne mini-excavator range has won a globally renowned award for product design excellence. The manufacturer has been awarded a Red Dot Award in recognition of its range of mini-excavators, specially designed to deliver maximum comfort, safety and performance.
The Red Dot Awards celebrate genuine innovation across a multitude of sectors, with a coveted ‘Red Dot’ now an internationally recognised quality mark of design excellence. This year’s event was held on 30th March, in an online ceremony that saw awards handed to some of the world’s most iconic brands. The 5-tonne mini-excavator range consists of three models, the KX060-5, U56-5 and U50-5. Each model combines a compact design with advanced performance capabilities, with newly developed interiors and exteriors designed to provide the ultimate handling experience for operators. Glen Hampson, Division Manager for Construction at Kubota, commented: “We’re absolutely delighted to be named among the winners at this year’s Red Dot Awards ceremony. Indeed, ‘Red Dot’ is a byword for quality and innovation, key tenets that inform the design process across our entire business. “We’re incredibly proud of our 5-tonne mini-excavator range and believe it represents a truly game changing solution for operators, with recognition from Red Dot bearing further testament to the strength of the range.”
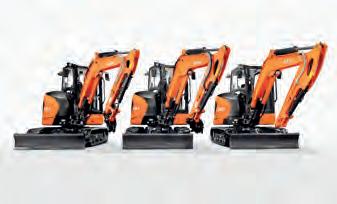