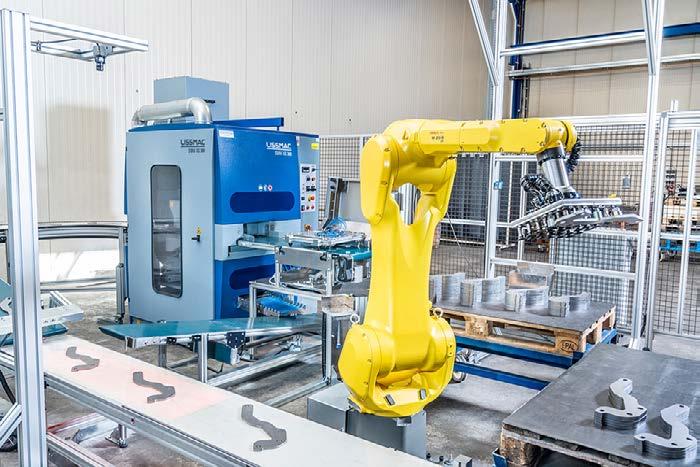
5 minute read
Kantenafronding is de basis voor kwaliteitsdelen
De robot herkent zelfstandig de te bewerken delen, neemt ze van de pallet, en legt ze op de invoerband. Na bewerking door de Lissmac SBM-XS 300 neemt hij de delen op van de uitvoerband en legt ze op een andere pallet. (Foto’s: Kuipers Technologies)
Door toenemende kwaliteitseisen wordt het afronden van kanten, het verwijderen van walshuid en het ontbramen steeds belangrijker in de plaatbewerking. De Duitse toeleverancier Kuipers Technologies in Meppen, vlak over de grens bij Emmen, heeft daarom geïnvesteerd in een geautomatiseerde installatie van Lissmac.
Met ongeveer 330 medewerkers in een drieploegendienst produceert Kuipers onderdelen en samenstellingen voor onder andere de regeneratieve energiesector, trailers, algemene machinebouw en winkelinrichtingen. Het is een hightech plaatwerkbedrijf, dat hoge kwaliteitsstandaarden hanteert. Zo is het machinepark altijd ingericht op de eisen die de markt stelt. Onlangs is er geïnvesteerd in een SBMXS 300 van Lissmac, een installatie voor het dubbelzijdig ontbramen en kanten afronden van geponste en lasergesneden werkstukken in slechts één bewerking.
Natslijpproces voldeed niet
De hechting van de coating en de daaruit resulterende corrosiebescherming zijn belangrijke kwaliteitscriteria voor klanten en oppervlaktebehandelaars. Daarom was het voor Kuipers onvermijdelijk om te investeren in een op maat gemaakt systeem. Directeur Michael Kuipers vertelt: “Aanvankelijk dachten we dat een universele machine met het natslijpproces de goede oplossing was voor alle delen die we produceren. Zo’n machine was dan ook al enkele jaren bij ons in bedrijf. Maar de resultaten waren niet optimaal. Zo begon de zoektocht naar een installatie die aan al onze eisen voldoet.” Vooral bij het slijpen van staal traden corrosieproblemen op. Er bleven vochtige restanten achter op de delen. En ook het onderhoud van de natslijpmachine was intensief. De nieuwe ontbraammachine zou een snellere doorlooptijd van de te bewerken artikelen moeten garanderen, zodat de klanten al op korte termijn konden worden bediend met de door hen gewenste levertijden. Terwijl de oude installatie nu wordt ingezet voor de bewerking van RVS en aluminium, kan Kuipers met de nieuwe Lissmac installatie stalen onderdelen dubbelzijdig ontbramen of afronden, parallel aan de productie. Door de nieuwe investering zijn de processen verbeterd en uitgebreid, gezien de verschillende te bewerken materialen. Bovendien kan het proces beter worden gestuurd met het oog op de logistiek.
Automatisering
De Lissmac SBM-XS 300 is een compacte machine, die aan beide zijden kan werken. Bij kleine delen staat dit garant voor een snelle doorlooptijd en een hoge flexibiliteit in de bewerking. De standaard uitvoe-
De ontwikkeling en implementatie van de automatisering was een grote uitdaging omdat de de cyclustijd twee tot drie keer tijdens het proces verandert.
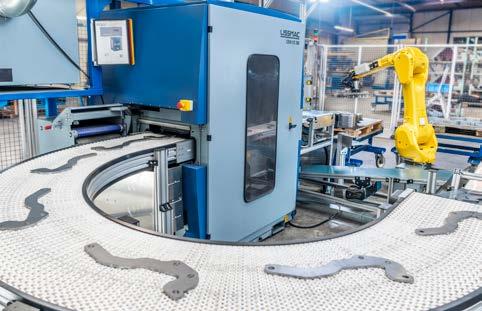
ring is een standalone machine. Omdat de delen bij Kuipers echter parallel aan de productie moeten worden bewerkt, is het systeem geautomatiseerd. “Het bewerken van delen parallel aan de productie functioneert niet bij installaties met zeer korte doorlooptijden. Daarbij komt het aspect dat vakbekwame medewerkers eigenlijk niet alleen maar elke 10 seconden een deel op een lopende band zouden moeten leggen. Dus moest de installatie worden geautomatiseerd - wat iedereen begreep - op een manier dat de volgorde past in onze processen”, verklaart Kuipers. Twee medewerkers uit het robotteam dat Kuipers 3 jaar geleden heeft opgericht en dat samenwerkt met de Hogeschool Osnabrück, hebben ongeveer 2 jaar aan dit project gewerkt. Het resultaat: de robot herkent zelfstandig de te bewerken delen, neemt ze van de pallet, en legt ze op de invoerband. Nadat ze zijn bewerkt door de Lissmac SBM-XS 300 neemt hij de bewerkte delen op van de uitvoerband en legt ze op een andere pallet. Tegelijkertijd belaadt de robot de toevoerband met nieuwe delen. Zijn er verder geen delen meer te bewerken, dan wisselt de robot in afruimmodus en palletiseert de overgebleven, reeds bewerkte delen. Kuiper zegt: “De ontwikkeling en implementatie van de automatisering was een grote uitdaging want de cyclustijd verandert twee tot drie keer tijdens het proces.” Door de automatisering kan de machine nu in een drieploegendienst continu werken. Indien nodig kan hij ook nog steeds standalone werken. Het proces is bovendien eenvoudig opgezet voor de bediener van de installatie, omdat de automatisering hem ontlast van veel instellingen die anders noodzakelijk zijn. Werkorders kunnen zo door iedereen snel en proceszeker worden uitgevoerd.
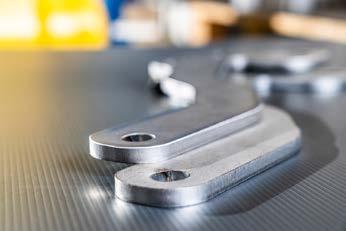
Het gevoel bij afgeronde onderdelen is duidelijk beter, evenals de kwaliteit ervan. Hierdoor bestellen de klanten van Kuipers voor bepaalde toepassingen in toenemende mate afgeronde delen.
Voorwaarde voor goede hechting
Een technisch probleem dat met de nieuwe Lissmac installatie opgelost moest worden, is de hechting van de coating aan delen die later worden gecoat. De kanten uitlijning leidt er toe dat de werkstukken op en rond de snijkanten niet voldoende gecoat worden. Dit kan vooral bij corrosiebeschermende lagen de nagestreefde protectie verhinderen. Een steeds grotere eis van de coaters is bovendien een oxide- en braamvrije snijkant. Bij zuurstof lasersnijden ontstaat echter door het snijgas een oxidelaag aan de snijkant. Door de voorbehandeling kunnen coaters niet garanderen dat deze oxidelaag compleet wordt verwijderd. Om dit probleem uit de weg te gaan, snijden de plaatbewerkers met stikstof als procesgas. Daarbij ontstaat een (micro) braamvorming aan de werkstukken. Hoe groot deze braam is hangt uiteindelijk af van de materiaaldikte. Vast staat evenwel dat de kanten van een lasersnede zeer scherp zijn. Om een betere coatbaarheid of coatinghechting te bereiken rondt Kuipers de kanten daarom af. Over het belang van dit thema zegt hij: “We moeten met onze processen kunnen voldoen aan de verhoogde eisen die worden gesteld aan het oppervlak van delen. Dit zijn corrosiebescherming, ongevallenpreventie en het algemene optische beeld.”
Hechtingsprobleem opgelost
De nieuwe SBM XS 300 heeft zich volgens Kuipers bij alle onderdelen die in de machine passen, bewezen. Bovendien kan na bewerking in de machine elke oppervlaktecoating in verschillende laagdikten worden opgebracht, zoals een KTL-laag, natlak of een poedercoating. Verzinken kan ook. “Door het afronden hebben we het probleem van de hechting verregaand opgelost. Dankzij de kantenafronding hecht de coating beter aan de delen”, zegt Kuipers. “Daar komt bij dat onze klanten de duurzaamheid van de componenten waarderen.” Vast staat: afronden is een extra bewerking en een bewuste investering in gedefinieerde kwaliteit. Het gevoel bij afgeronde onderdelen is duidelijk beter, evenals de kwaliteit van de delen. Hierdoor bestellen de klanten van Kuipers voor bepaalde toepassingen ook in toenemende mate afgeronde delen. De inhoudelijke samenwerking tussen Kuipers en Lissmac bestaat al jaren. Omdat de Lissmac machine eerst manueel werd bediend, ontwikkelde men samen het idee om te automatiseren. Binnen een jaar werd dit geïmplementeerd. “Het ging hand in hand. Terwijl Lissmac zorgde voor de interfaces werd de automatisering compleet door Kuiper Technologies ontwikkeld”, zegt een woordvoerder van Lissmac.