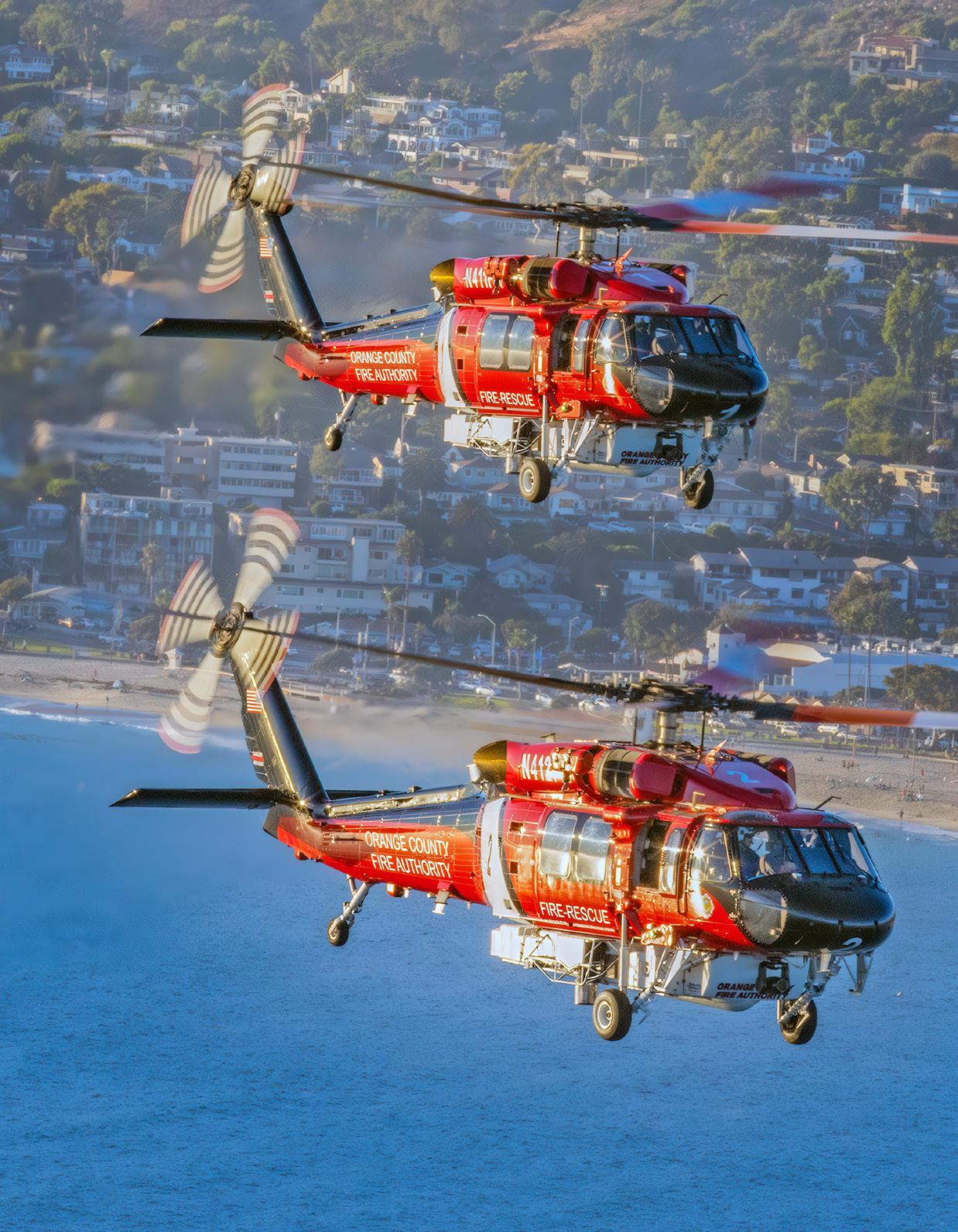

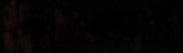


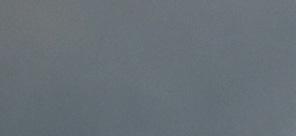
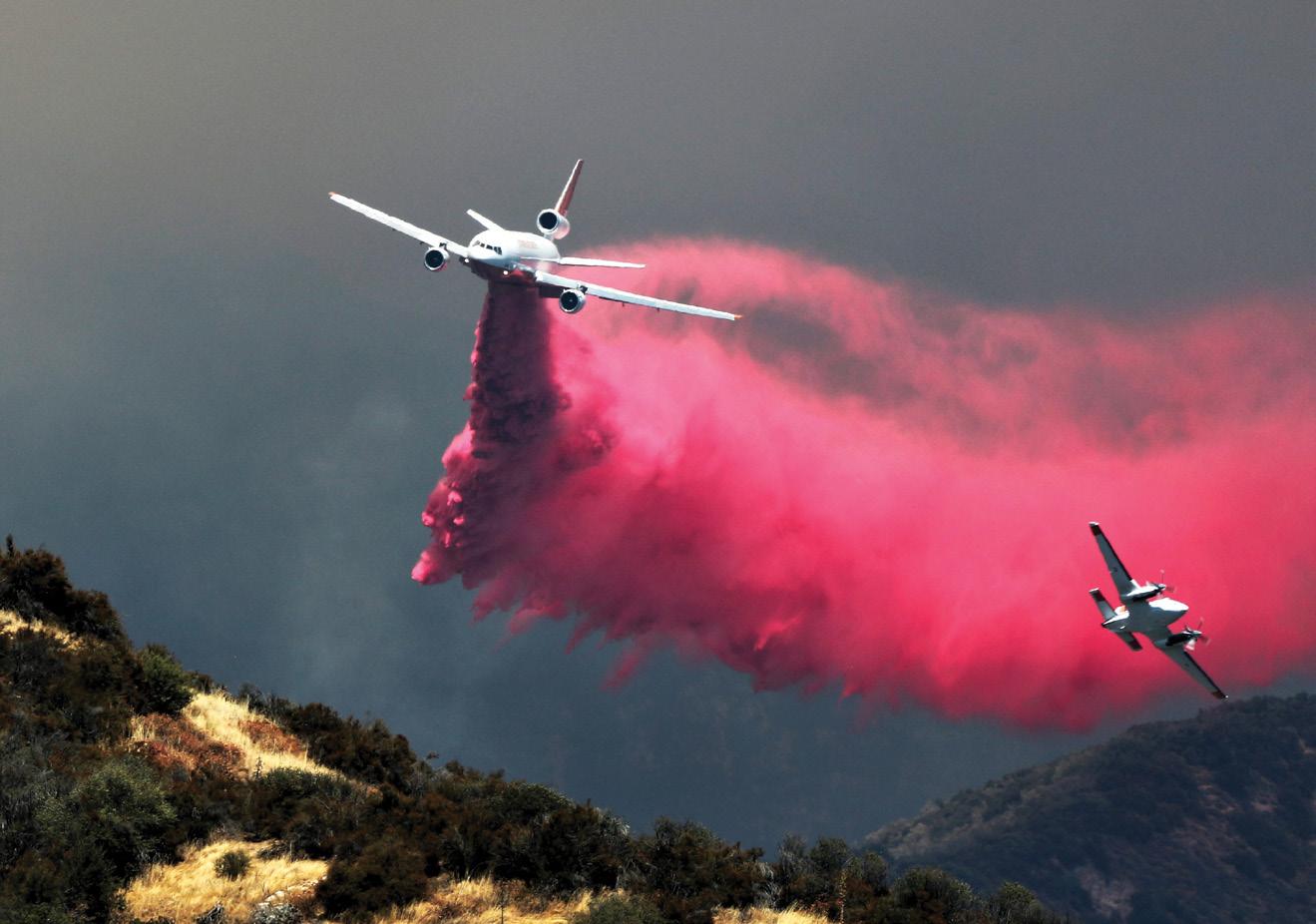
Performance, Experience and Value You Can Count On.
With more than 60 years of experience working alongside the firefighting community, Perimeter Solutions offers the most comprehensive set of fire retardant solutions on the market today – featuring field-proven products, infrastructure, equipment and logistics services. We’re the partner you want when you’re up against the challenge of fighting wildfires.
When you choose PHOS-CHEK® you’re getting more than just retardant. You’re getting a company that understands your mission-critical needs and how to deliver them – every day. At Perimeter Solutions, we want to be your best firefighting partner.
Trusted. Solutions That Save.
WHAT YOU GET WITH PERIMETER SOLUTIONS
• Experience
• Performance
• Fire Support Infrastructure
• Resilient Response
• Knowledge Base
• Innovation
• Reliable, 24/7 Response
DISPLAY ADVERTISING: Melanie Woodley melanie@marsaylmedia com
EDITOR
Ryan Mason ryan@marsaylmedia com
ACCOUNTING/ADMINISTRATION: Casey Armstrong casey@marsaylmedia com
CONTRIBUTING WRITERS: Igor Bozinovski bozinovski igor@gmail com
Robert Craymer robertc@covingtonaircraft com
Dan Reese dan@intwcg com
Paul Seidenman avwriter@sbcglobal net
Dave Soderstrom davesoda727@hotmail com
Babak Taghavee babaktaghvaee@gmail com
PRODUCTION: Felicia (Lisa) Pannell lisa@marsaylmedia com
CIRCULATION: Mary Jane Virden maryjane@marsaylmedia com
CONTRIBUTING PHOTOGRAPHERS:
Kane Arlow
Igor Bozinovski
Marissa Fortney
Aaron Maurer
Jeff Serpa
Dave Soderstrom
Marty Wolin © COPYRIGHT 2024 AerialFire retains all rights for reproduction of any material submitted, to include but not limited to articles, photographs, emails and bulletin board posts. All material remain the copyright of AerialFire. No part of this publication may be reproduced, in part or whole, without the written consent of the publisher. Editorial published do not necessary reflect the views of the publisher. Content within AerialFire is believed to be true and accurate and the publisher does not assume responsibility for any errors or omissions. Unsolicited editorial manuscripts and photos are welcomed and encouraged. We cannot be responsible for return unless submissions are accompanied by a stamped, self-addressed envelope. Advertising deadline is 12 noon, on the 1st of the month preceding the month of publication.
PROUD MEMBER: FIND US ON:
AerialFire is Published bi-monthly by Marsyal Media P.O. Box 850, Perry, GA 31069 USA 475 Myrtle Field Rd., Perry, GA 31069 USA Phone / Fax: 478-987-2250
info@marsaylmedia.com
Ryan Mason | ryan@aerialfiremag.com
The last few months have been rough for the aerial firefighting industry, with the loss of several aviators and aircraft.
The recent incidents are tragedies, and one, at this stage, appears to be attributed to catastrophic equipment failure, which underscores the importance of learning from past incidents and our industry’s unwavering commitment to safety.
As we reflect on these incidents, it’s clear that not all maintenance issues or part degradation are visible to the human eye. This reality prompts us to ask: Are we, as an industry, effectively fostering the next generation of more modern aircraft to protect the public and the lives of our aerial firefighters from dangers they may be exposed to that they shouldn’t have to be? It’s a question that requires our collective effort and collaboration.
While aircraft age isn’t the sole cause for every aircraft accident, it doesn’t take an expert to look at the median age of the global fleet of aircraft fighting fires to realize we are not doing enough to foster the development of next-gen aircraft that will keep the industry operating 20, 30, or even 40 years from now when we see operators, through no fault of their own, operating aircraft that can be up to 50 years old.
One of the main complaints I hear of current contractors, at least in the North American segment, is agencies’ willingness to look at the bottom line only and the lowest price they want to pay for aerial firefighting service from private industry.
The sad reality is that the thought process of using this mindset on the government level only provides the barest minimum for companies. By that, the cost offered currently
factors in operational expenses and a razor-thin profit margin. The Federal Government is basing its payment structure on what they are willing to provide contractors with solely on putting out the flames, without looking at the big picture and looking forward at the long-term life cycle of the industry and what it will take financially to allow operators to develop new aircraft and new ways to attack fires safely.
Currently, operators have no room to delve into the significantly expensive development of new technology that will not only see the industry through the next half-decade of fires but also to purchase newer aircraft to continue to sustain their business and their service to federal agencies like the DOI, BLM, and USFS.
Instead, operators are sometimes left chasing down parts from OEMs that have long discontinued producing an aircraft type, purchasing from after-market producers of legacy parts, or, in some cases, purchasing entire aircraft to scavenge for parts like a vulture picking off the bones of a carcass. While that may be the way business is done, to someone observing from the outside from a market where aircraft are readily available, new, and with a plethora of parts, it would seem absurd.
The United Aerial Firefighters Association (UAFA) is also delving into how to bridge this gap and how to move the needle forward for operators on an industry level. I believe the work being done for the industry will get us further than ever. Still, as an industry, we have to work together to get behind the association’s efforts and put pressure on those who can help move the needle in the right direction for everyone so that there is a bigger pot from which everyone can draw that allows operators the ability to look forward into their next aircraft and what will be better, more costefficient and safer for everyone.
“ ...operators are sometimes left chasing down parts from OEMs that have long discontinued producing an aircraft type, purchasing from after-market producers of legacy parts, or, in some cases, purchasing entire aircraft to scavenge for parts like a vulture picking off the bones of a carcass... ”
The last few weeks have shown that we all feel the loss of every single member of the community hard. On a larger scale, we still have a lot to do and many hills to climb to move forward in safety, and we need to have a more modern fleet to protect both the public and our pilots in the long term.
Fly Safe,
Neptune’s Tanker 01 departs for a firefighting mission. –
Tiffany Taylor | ttaylor@uafa.org
The United Aerial Firefighting Association (UAFA) recently convened its Board of Directors in Denver for a strategic planning session to expand the association’s reach and enhance member value. As the organization enters its second year, the meeting focused on building upon past successes and charting a course for future growth.
Key topics of discussion included future expansion of membership categories better to serve the diverse needs of the aerial firefighting community, establishing a data analysis committee to harness the industry’s growing data resources, and enhancing communication efforts to inform members, government officials, and the public about the critical role of aerial firefighting. The Board also discussed topics for this year’s annual member meeting in Boise, November 13-14, 2024, and initiated planning for upcoming elections, as two Corporate Director terms are set to expire at the year’s end.
The board welcomed industry leaders to discuss cuttingedge practices and technological innovations to fulfill its commitment to representing the membership. Vince Welbaum, from the Colorado Division of Fire Prevention and Control (DFPC), provided valuable insights into the complexities of wildfire management at the state level.
Welbaum’s experience in federal and state roles provided invaluable context for the industry.
Ben Lawrence, from the Colorado Center of Excellence for Advanced Technology Aerial Firefighting, demonstrated the Colorado Team Awareness Kit (COTAK). It provides mapbased situational awareness to firefighters and other first responders when traditional Internet access is unavailable or unreliable. UAFA members operating in Colorado can contact them for access.
Merle Lyman, former Chief of the Department of Defense (DoD) Commercial Airlift Division, shared his federal contracting and logistics expertise. By drawing parallels between the challenges faced by the aerial firefighting industry and the DoD’s Commercial Airlift Fleet (CRAF) program, Lyman offered potential strategies for improving contracting processes within the aerial firefighting sector.
As the wildfire season intensifies, the UAFA remains dedicated to supporting its members and advocating for the aerial firefighting industry. The Denver meeting served as a critical platform for strategic planning and knowledge sharing, positioning the association to address the evolving needs of the industry effectively.
Robert Craymer
| robertc@covingtonaircraft.com
Unscheduled events are incidents that none of us want or need, but they do happen despite our best efforts. The maintenance manual contains a pretty big list of events that Pratt & Whitney Canada describes as unscheduled events. They cover everything from a prop strike to immersion in water. In this article, let’s look at some exceedances; specifically, we will look at over torque and over temperature.
When either a temperature or torque event occurs, information is going to be key. Knowing the answer to the following questions is extremely important: How far above the redline? How long did it stay above redline? This information helps the engine shop determine the work scope required to return the engine to service. This is where the MVP-50T or any engine monitoring system comes in handy. Recorded data can be downloaded and provide accurate readings on exceedance and duration. When something outside the ordinary happens, the pilot can be busy; the most important thing is to get the airplane safely on the ground. That is why engine monitoring systems are a benefit to an operation.
You may be asked to complete a service information letter Gen-135 when one of these unscheduled events occurs. This is a form describing the circumstances of what occurred. If the engine is still under warranty, Pratt & Whitney Canada may also require a second form to be completed. Ask for help if needed; we always want to ensure you don’t inadvertently cause yourself struggles and pain by not crossing all the t’s. You can also visit about what needs to be done with your Pratt & Whitney Canada field service rep or C-First.
What is the first step if an over-temp event has occurred or is suspected? First, we must ensure the indicating system is functioning correctly. Make sure what the pilot witnessed was accurately reflected in the cockpit. Next, we must discuss the over-temp event. Critical components of this event are peak temperature and duration. The maintenance manual has a chart where you can line up the temperature and time, and the chart will provide the maintenance requirements. There is a limit where no action is required if the event occurs within the range. The next level is to determine and correct the cause of the overtemperature. A visual engine inspection may also be a maintenance requirement after an
over-temp. As temperature and duration go up, so does the level of maintenance. If it cannot be determined how long the event lasted or the peak temperature reached, then one must assume the worst case. Engine removal and engine shop visits are required for all Area C category events. When the temperature cannot be determined, you must indicate “Unknown Temperature” when sending the engine in for inspection. This is the signal to the engine shop on how to proceed. The inspection process can include destructive testing of at least two compressor turbine blades, followed by other inspection requirements in the PT6 manual. These actions are for over-temp events that are not at the start. If you have an exceedance of temperature on startup, there is a separate chart to determine what steps must be taken.
The maintenance manual also discusses inadvertent cut-off and relight of the engine during taxi. This is an event of its own and should be handled as stated in the maintenance manual. We have seen issues directly linked to inadvertent cut-off and relight, including failure of the compressor turbine blades. It is extremely important to follow the inspection criteria when such an event occurs.
Shifting the focus to over torque, like the over-temp event, there is a chart with the duration on one side and maximum torque reached on the other. Maintenance requirements are from no maintenance action to return the engine to the shop. If you fall between those categories, your engine has actions to monitor. First, we want to verify the indicating system is accurate. Next look at the oil system, we are looking for metal and debris in the oil. Rotate the propeller, listening for unusual noise. Pull the chip detector(s), oil strainers and the oil filter and look for debris. Per the maintenance manual, perform a ground run if everything looks and sounds normal. Ensure that nothing has changed in propeller operation, such as acceleration at the start or abrupt deceleration at shutdown. Run the engine to a specified power setting in the manual. Once the engine run is complete, pull filters, strainers, and detectors again to look for debris. Then, follow up on this same round of checks at the prescribed time in the future. For instance, we run the engine at 80% for 10 minutes in one manual and make our checks. Perform the checks again in one week/25 hours minimum.
Suppose you have an over-torque at the top of the chart that requires removal for inspection and servicing. You can be thankful that the PT6A has a modular design. You might be able to remove only the power section and send it in for repair rather than pulling the complete engine.
I always tell everyone to listen to your engine and watch for changes. The PT6A is a solid engine that will tell you when something is wrong. If you see something in your regular operation of the engine that strikes you as odd or different, ask about it. Talk to your mechanic about what is different; it may be nothing or an indication that something more dramatic could be coming. Finally, if you have an exceedance, don’t ignore it. Let’s all hope that we can avoid anything unscheduled.
Robert Craymer has worked on PT6A engines and PT6Apowered aircraft for the past three decades, including the last 25+ years at Covington Aircraft. As a licensed A&P mechanic, Robert has held every job in an engine overhaul shop and is an instructor of PT6A Maintenance and Familiarization courses for both pilots and mechanics. Robert has been elected to the NAAA board as the Allied-Propulsion Board Member.
Robert can be reached at robertc@covingtonaircraft.com or 662-910-9899. Visit us at covingtonaircraft.com.
After the Silverado, Blue Ridge, and Bond Fires in 2020 that burned over 27,000 acres combined and severely damaged parts of Orange County, talks began within Orange County Fire Authority (OCFA) and specifically amongst air operations personnel about how the county was going to deal with fires of that magnitude within the county or fires of an even bigger scale that could cause serious risk and a much larger damage scale than previous fires as wildfires steadily escalate in severity in California.
(Continued on page 18)
Shortly after the arrival of a new, well-regarded chief, Chief Brian Fennessy (formerly the Fire Chief of San Diego Fire & Rescue), along with air operations members and command staff, soon began planning the long-term future of the air unit. After two of the agency’s super Hueys were retired in 2021, the agency was left with just two helicopters—both Bell 412 EPs purchased in 2009.
OCFA air operations staff began planning the unit’s next generation of aircraft in early 2021. The unit opted for the Sikorsky S-70 model, which the Los Angeles County
Fire Department initially made successful as an aerial firefighting aircraft.
United Rotorcraft, which holds the type certificate for the S-70 FireHawk, was engaged early in the project as unit staff began planning out their purchase of two identical aircraft, signing for the purchase agreement in November of 2022, with the aircraft arriving in Orange County on June 22, 2024, when intensive crew training
(Continued on page 20)
was carried out before their eventual entry into service on August 19, 2024.
Unlike some agencies and with the complexity of the systems of the first S-70M, pilots for OCFA are sourced from outside the agency, many coming from former military service. OCFA currently has six pilots in-house that fly in single pilot configuration, forming the pilot cadre for the agency; each has completed initial Flight Safety training in the aircraft type. The chief pilot and one additional training pilot have completed phase two training and maintenance test pilot training through Sikorsky on the S-70. OCFA plans to put each of the remaining four pilots through phase two training by the end of 2024.
The agency’s pilot flight hour minimums and requirements are incredibly steep, keeping the pool of applicants capable of meeting the requirements small but targeted to exactly what the agency is looking for. To be a pilot for OCFA, pilots are required to have 4000 hours total time at a minimum, with 1500 hours of that being mountain time and at least 100 hours at night. The agency also requires applicants to have utility experience and night vision goggle experience to apply for a position.
(Continued on page 22)
of the
Air Operations Section.
The new aircraft’s minimum staffing will be three personnel: one fire pilot, a crew chief, and a paramedic/ rescuer for each aircraft.
“Our initial crew chief training starts with our crew chief academy, which is a three-month academy; all of our crew chiefs are fire captains. They come from our field operations with a minimum of three years of experience as a fire captain. They must complete a set of aviation and aerial firefighting classes to apply. Then, they go through our academy here at our base and complete a task book. Once they complete their final check ride, they become qualified as a crew chief. Our current crew chiefs are transitioning now to be qualified in the FireHawks,” said day-to-day chief Kyle Kuzma, who oversees the day-to-day operations of the OCFA air unit.
OCFA has developed its” FireHawk Academy,” where current crew chiefs and rescuers can cross-train on the FireHawks to learn the differences between the Bell 412 and the FireHawks.
Similar to the crew chief role, OCFA’s firefighter paramedic rescuers are selected from the field where they have worked several years in the field before being allowed to apply for a position in air operations that involves a formal interview and selection process before beginning an intensive three-week training academy that involves formal training and testing in the classroom in addition to real-world scenario training and familiarization on the aircraft before culminating in a formal evaluation and check ride.
The agency and the crews view the role of the paramedic rescuer as an essential member of their aircrew in the FireHawks for all missions to provide advance life support to patients and be the eyes and ears for the pilots in the rear cabin of the aircraft. The firehawks will also be used as a search and rescue aircraft. OCFA completes a significant amount of hoist rescue work for injured and lost hikers, mountain bikers, and even motor vehicle crash victims, averaging numerous monthly rescue incidents.
The agency has always worked with full-time staff and parttime unit members who fill gaps for vacation and training
when needed. OCFA will transition a seventh pilot to the agency in January and recruit crew chief academy candidates early next year.
“Part-time staff have an assignment out in the field on a fire engine or truck, but they are qualified, so they’re available to fill in here; if somebody is off on vacation or training, or there’s an injury, then we have part-time members that can fill that void. Our part-time members also rotate quarterly to maintain currency and training. So both the full-time and the part-time staff are getting all the same FireHawk training, so all of our part-time staff are qualified on the new aircraft,” said Fire Pilot Joey Heaslet.
The staffing level at optimal standard for the agency will have seven pilots, twelve crew chiefs, and fifteen paramedic rescue staff, which will likely be at full capacity in January 2025.
As an integral part of the firefighting operation, the OCFA air operations are available 24 hours a day, 365 days a year, for both day and night operations. The section operates just like
(Continued on page 26)
all other OCFA fire stations, working a 48/96 schedule for the operational six crew members on each shift, meaning that each crew works 48 hours on, with 96 hours off on a constant rotation. Each flight crew can fly a maximum of 8 flight hours during the day and six at night if required, with the ability to recall off-duty staff in the event of a major response or large fire that may require 24-hour operations until the incident is under control.
The OCFA FireHawks will be available for mutual aid response when needed in surrounding counties and through the state of California. The agency has always worked very closely with CAL FIRE and other agencies in a mutual aid capacity and looks forward to assisting on mutual aid responses once all pilots have completed the carding process, which will allow them to work on fires in other counties in addition to working in their own county.
When asked what differences the S-70M brings to the table for OCFA, the room fills with smiles from satisfied pilots when they talk about the difference the FireHawk brings to the agency.
“It’s obviously a much bigger, more powerful aircraft. So, the ability to have dual engines, which can fly on one engine if needed, is substantial. Yes, the 412 has dual engines, but the capability on one engine (in the 412) is not the same as the FireHawk. The difference of flying with one engine on the FireHawk versus getting you back to safety. So that part is huge, if heaven forbid you were to have a crash landing, not being on skids, but being on wheels that are on suspension gives you more survivability with impact if you have a hard landing,” said Chief Pilot Cody Hamann.
“It’s fantastic. It can carry more water and put more fire out, but it’s a much bigger, safer aircraft. They are proven and tested in battle; that’s why the military uses them because they perform very well,” he continued.
While the new S-70Ms will replace the agency’s primary aircraft, the Bell 412 aircraft will still play a vital role as backup aircraft in the fleet for OCFA. The agency will still rely on them to perform the same duties, keeping both in service to step in when either aircraft is in maintenance or used for training missions as needed where the larger aircraft isn’t required.
(Continued on page 28)
Adapting pilot training and maintenance to a whole new airframe has been a challenge for the crews at OCFA, who have taken an entirely different approach to the safety of the unit and the new aircraft.
The agency has a robust SMS program built up over the last several years as new chief pilot Cody Hamann has taken the reigns. This program has now been adapted to include the complexities of the newer aircraft. In addition, a complete risk assessment is done prior to any mission undertaken by the unit.
“I’ve only been in this position for a couple years now as chief pilot, and we’ve seen that SMS system definitely improve over the years, if you think back to the inception of air ops in Orange County, it was contract pilots from Evergreen that became full time employees here,” said Hamann.
“I’ve been here for eight years now, and it’s changed drastically in that time. It went from that old guard to the new guard, where a lot of the guys here have a 135 background. We don’t operate as 135, but we do some rules in the spirit of things like the evolved SMS, and we’ve been here. The risk assessments force us to look at certain aspects that could change how that day looks like, such as weather and crew rest. So, I picked it up a few years ago and built us a pilot standard. I adopted much of that from the 135 side,” said Fire Pilot Joey Heaslet.
Crews also attribute the ease of tracking as much data as possible to their efforts to keep safety a top priority, from risk assessments to SMS and using systems like Digital Airware. These are all part of the safety systems the agency employs to ensure their operation is at the tip of the spear in safe practices.
There is a saying that was repeated several times during our time at OCFA: “ If you can do it at night, you can do it during the day.”
The agency employs a “crawl, walk, run” approach to starting initial training. OCFA was one of the first agencies in the country to successfully implement night aerial firefighting operations, including filling and dropping on fires in full darkness.
The agency’s training has, since the inception of their night aerial firefighting efforts, had a large component of night operations so that crews are proficient at not only day operations but will have no hesitation at performing the same tasks at night, be it aerial firefighting or rescuing a lost climber from the side of a mountain, putting them a step above many operations that may struggle to perform night operations or to maintain currency at night.
Crews at OCFA attribute their training success to their agency administrators and, in large part, to county commissioners and the agency chief, who give them the latitude to always train as needed to ensure currency so they can provide needed services 24/7 without having to worry about any budgetary burden related to the number of flight hours allowed.
With four in-house maintainers, maintenance crews are kept busy with two aircraft types that need routine maintenance. Since the arrival of the new FireHawks, OCFA maintainers have been learning the new aircraft. OCFA also has a total assurance program through Sikorsky for the FireHawk that has been allocated at 200 hours per year for each aircraft, which staff believe they will hit this year thanks to all of the training and currency being performed in the first year, which will then be reevaluated after the first year to see where the agency sits after the first calendar year of operations.
As with training hours, the staff at the air unit can’t thank the county and agency administration enough for planning the aircraft. “They really gave us the keys to building this aircraft the right way,” said Heaslet.
And by the right way, the unit put more thought into the makeup of the aircraft than many would, not solely focusing on what larger pieces of equipment were needed but also on where things were placed if they were moveable to ensure that they had an aircraft that fit their needs for years to come.
To facilitate this, OCFA staff started putting in their homework, visiting agencies like L.A County Fire Ops, San Diego City Fire, CAL FIRE, Ventura County, and Santa Barbara
County Fire, all of which have flown various previous versions of the S-70 and refurbed versions of HH-60L aircraft that United Rotorcraft fitted. At each location, staff from the unit would fly with the other agencies to see what worked with their aircraft and what didn’t, in addition to meeting many hours with pilots of the other aircraft to find out what their wish list was of things they wish they had or things they wish they had done differently if they had another chance to build an aircraft again.
The result of that research was the aircraft, which has since been completed and features many new or unrealized options on previous FireHawks. It has now become the “gold standard” of what many believe should be the standard configuration of the FireHawk going forward.
Continued on page 30)
The OCFA S-70M features many never-before-seen features in a FireHawk configuration, including 800Mhz radios, fully adjustable front wigwag/pulse lighting, Aerometals particulate filters, multiple in-cockpit viewable cameras covering the belly, tail, and winch camera covering the Goodrich winch system in a top-down view that also records voice comms from the aircraft, a Shotover/Churchill ARS750 mapping system that allows crews to fly direct to incident locations without wasting time finding locations. The aircraft is also already preconfigured to accept a FLIR 380HDc camera system (although the agency is waiting on grant approval funding before acquiring it.)
“So not only did we build it exactly how we wanted it and added things, but we also made it expandable, which was important for us, because you never know in this fire
environment if the FIRIS aircraft could be pulled away, so we definitely made it expandable if we needed that capability,” said Heaslet.
While Heaslet said that ultimately, they believe what the team at OCFA wanted and designed has become the flagship model of what a FireHawk can be, it was not without its challenges to get done. However, the team at United Rotorcraft engaged everyone they needed to get the job done specifically to what they wanted, even if it meant engineers going back to the drawing board with an original idea of theirs to make it happen.
Argentinian Air Tractor AT-802 LC-FBB seen at Sarajevo airport in Bosnia and Herzegovina on 1 August 2024.
If someone told you that South American planes were flying in the Balkans, that might sound strange or out of place, being they are a long way from home.
However, seeing South American AT-802s over the Balkans is very real. It is now a new normal for the Balkans and will remain so through August. So, spotters, if you’re into exotic birds, keep in mind that one Argentinian and one Chilean Air Tractor have just arrived in the Balkans.
SEATs landed at the international airport in Skopje on the afternoon of August 1st, 2024, to help fight the ongoing fires in North Macedonia. On their way to Skopje, they were spotted at Sarajevo airport, where they stopped to refuel and give the pilots a rest.
The planes are a combo of an Argentine aircraft bearing the registration number LV-FBB belonging to Aero Gardian Plan Nacional del Manejo del Fuego, as well as the Chilean-
registered CC-DER, owned by the Helicópteros del Pacífico Chilean Corporación Nacional Forestal (CONAF). Both aircraft were hired by the Spanish company Titan Firefighting Company and are currently working under contract for the Ministry of Interior of the German federal state of Lower Saxony. Their deployment to North Macedonia is part of the German aid to the small Balkan nation of some 2 million citizens.
On their way to Skopje, these two aircraft started from Braunschweig airport and passed through Graz, Austria, and Sarajevo, Bosnia and Herzegovina. Once at their destination, they started aerial fire-fighting operations on August 2nd.
Devastating wildfires are again present in North Macedonia, which has been fighting them for the past few days, again relying on local resources – three Air Tractor AT-802A Fire Boss amphibian firefighting planes and four helicopters: two belonging to the national police (one Bell 412EP and one Mi171E) and two Army (one Mi-8MT and one Mi-17).
Photo by Igor Bozinovski
Since the local capabilities for aerial firefighting are insufficient, the Government in Skopje issued a new call for international assistance on July 30th, 2024. The Ministry of Interior of Serbia immediately reacted by bringing in an Agusta-Bell AB212 helicopter based at Petrovec air base near Skopje from July 31st, 2024. The aircraft was later moved to the Idrizovo police base for the rest of its deployment.
The Czech Republic provided one Slovak-registered UH60A helicopter operated by the Slovak Training Academy, an additional AS-532AL Cougar helicopter was provided by the Slovenian Army, along with two Hungarian military
helicopters, a Mi-17 stationed with EUFOR in Sarajevo, Bosnia and Herzegovina; and Airbus H225M also arrived North Macedonia on August 1. Additionally, two amphibious Air Tractor AT-802 Fire Boss planes from Sweden arrived in Skopje in the early morning of August 2nd coming from Sweden using the route Stockholm/Sweden – Lodz/ Poland-Timisoara/Romania-Skopje/North Macedonia.
This new international effort aims to stop the wildfire tragedy in North Macedonia, which has already this year claimed lives, burned a large number of houses, and set fire to an incredible 1.12% of North Macedonia’s territory.
Montana-based Billings Flying Service announced on June 2nd that the company won Montana’s Department of Natural Resources and Conservation’s first exclusive-use type 1 helicopter firefighting contract.
BFS is providing a tanked CH-47 Chinook helicopter with high-volume precision water drop capability for the summer fire season contract, which started July 1. The aircraft will be based in Montana, however, could be mobilized to surrounding states under a cooperative agreement in place between the US Forest Service and State of Montana.
“As fellow Montanans, our BFS team is particularly honored to support the state’s wildfire preparedness objectives this summer,” said BFS Director of Business Development Katrina Miller. “The CH-47 Chinook’s fire suppression capability is second to none. By contracting this helicopter for exclusive use, the state has secured an asset to work solely for its use at a moment’s notice this season and will have the capability to dispatch initial attack missions as soon as a fire is identified.”
When a wildfire starts, rapid response and precise large water volume drops are imperative to keep it from expanding. By rapidly delivering up to 2,500 gallons per drop with precision at the first signs of a fire, the Chinook gives the state a considerable upper hand in controlling fires before they become serious threats to life and property.
“Montana DNRC prides itself on safe and aggressive initial attack to keep wildfires small, and firefighters and the public safe,” said Deputy State Forester and DNRC Forestry and Trust Lands Deputy Division Administrator Wyatt Frampton. “The addition of this helicopter is made possible through funding from the legislature and will complement our response capabilities to increase the level of service we provide to Montanans.”
The contract’s funding comes from Montana’s House Bill 883, passed last year. The bill allows state lawmakers to roll unused fire suppression fund monies forward for wildfire preparedness activities, including securing helicopter support.
AMars completed its final flight after a flight that took in several sights and provided multiple flybys on its final flight from its base at Port Alberni in British Columbia to its final stop in Patricia Bay, where it will then move on to its final resting place, the British Columbia Aviation Museum.
In the final portion of the flight around Victoria, the Hawaii Mars was joined by the Canadian Snow Birds from the 431 Demonstration Squadron, flying nine CT-114 Tutors in formation with the Martin Mars over several locations near the final landing site at Patricia Bay.
Crowds lined various locations along the route, with the crowd number estimated to be over 10,000 people who witnessed the final arrival of the Martin Mars aircraft as it touched down for the final time at 7 PM Canadian time (10 PM EST) to the roar of the appreciative crowd that lined the foreshore and gathered in hundreds of boats in the bay waiting to witness the arrival of the 79-year-old aircraft that served as an iconic firebomber.
Crews waved to the many onlookers from the nose entry point and roof windows as the aircraft taxied to the boat ramp for the final time as the Snow Birds gave a final salute overflight to celebrate the arrival of the historic aircraft before it moved to the BC Aviation Museum at a later date.
The BC Aviation Museum thanked Minister Popham and Coulson CEO Wayne Coulson and the many hundreds of people who assisted in bringing the Hawaii Mars home to its original location where it was fitted for aerial firefighting. Wayne
and his family to have the Hawaii Mars preserved at the BC Aviation Museum for generations to come.
“We are grateful to Coulson Aviation and thrilled to offer a home for the largest aircraft on display on Vancouver Island,” said Richard Mosdell, project lead on the museum’s Save the Mars Team. “Once the aircraft is settled in the museum’s BC Wildfire Aviation Exhibit, the BC Aviation Museum plans to offer a unique open format that allows visitors to experience the Hawaii Mars up close and personal, including the opportunity to sit in the 4-story cockpit.“
This final landing in Victoria marks the end of an 80-year storied history for the Hawaii Mars. One of only two remaining Martin JRM-3 Mars waterbombers, the Hawaii Mars flew cargo between Hawaii and the Pacific Islands during World War II. It later supported the Korean War with medical transport between Hawaii and California before transitioning to cargo operations between the two states. The four-aircraft surviving fleet was sold to a consortium of BC timber companies in 1958 and converted into the world’s largest waterbombers to fight forest fires, carrying 27,000 liters (7,200 US gallons) per drop.
Coulson purchased the two Mars aircraft in 2007, marking the beginning of the BC company’s fixed-wing air tanker operations for aerial wildfire support. After using the aircraft for several years of successful wildfire suppression support, Coulson retired its Mars waterbombers in 2015. Its second Mars, the Philippine Mars, will be heading to the Pima Air and Space Museum in Tucson, Arizona.
Aero-Flite Inc. announced on May 9th, 2024, that the company had increased its aerial firefighting capacity to suppress wildfires with the addition of another Dash 8-400AT airtanker. This is the third Dash 8-400AT airtanker added to Aero-Flite’s fleet.
The organization’s Next Generation fleet now includes four CL415 amphibious airtankers, seven RJ85 Type 1 airtankers, and three Dash 8-400AT Type 2 airtankers. As a Type 2 large airtanker, the Dash 8-400AT has a tank capacity of 2,462 US gallons. “The Dash offers a large payload, just shy of the 3,000 US gallon tank capacity of a Type 1 large airtanker while using significantly less fuel than a similarly sized Type 1.
It can land at bases with shorter runways and at higher elevations, allowing firefighting support access to more locations and basing closer to remote communities that are more prone to wildfire activity,” shares Chris Niemann, Aero-Flite’s General Manager. The Dash 8-400AT’s versatility is a benefit to government agencies looking to enhance their fleet response.”
The current generation of land-based airtankers are converted from used military or commercial aircraft. Many of these airtankers are reaching the end of their operational life and are faced with limited or no available parts. This increases airworthiness concerns, especially in the face of the demanding flight environment they are exposed to on missions. With hundreds of Dash 8-400 airliners still in operation worldwide, the Dash is one of the most modern airtankers available in the market today. Supply, parts, and maintenance expertise will be available for decades to come.
The manufacturer of the airtanker, Conair Aerial Firefighting in Canada, recently completed their 20th Dash 8-400 airtanker, which was delivered to Aero-Flite. Conair converts the airliner into both the airtanker-only variant and the multi-role
variant. Saskatchewan, Canada, also recently announced an order of four aircraft, 2 Dash 8-400ATs (air tanker-only) and 2 Dash 8-400MREs (multi-role airtanker), with the first to be delivered in 2025. The multi-role version of the aircraft can be operated year-round to transport personnel and cargo and can also be used for medical transport.
“This addition to our fleet marks another achievement towards expanding our services to meet the increased demand across the US for large modernized airtankers,” continues Chris. “Our Dash 8-400AT aircraft are the newest additions to our fleet. Two Dash 8-400AT arrived in 2022 and are contracted to Washington State. Our third Dash 8-400AT arrived at the end of April and will be available to other agencies to support firefighters throughout the country. We plan to continue expanding our fleet with additional aircraft in the future to help state and federal agencies as they work to increase their capacity to respond to wildfires.” Aero-Flite will perform heavy maintenance on their expanded fleet during the winter months in their Spokane, Washington hangars and at their newly acquired facility in Chico, California.
Lane Aviation, Inc., an Air Tractor dealer in Rosenberg, TX, recently welcomed Patrick Humphrey as its Operations Manager.
Originally from South Georgia, Patrick attended the University of West Georgia, Middle Georgia State Aviation Program, and AgFlight in Bainbridge, GA. He started his career at Souther Field Aviation in Georgia, progressing from loader to aerial applicator, working in maintenance, representing the company at trade shows and managing aircraft ferrying.
“I am truly excited and eager to bring my background and experience to Lane Aviation. It’s an honor to
be part of this incredible family. They’ve built an outstanding operation, and I’m committed to serving this company and its customers to the best of my ability,” comments Humphrey.
Lane Aviation will celebrate its 80th year in business in 2025. Located in Rosenberg, TX, Lane Aviation is now in its third generation of ownership, with Logan Lane serving as its President.
“We are excited to welcome Patrick to the team at Lane Aviation. Being able to draw on his personal experience in aerial application, aircraft sales, and
Patrick Humphrey (L) and Lane Aviation President Logan Lane (R)
customer experience will be a great asset for our operations and, most importantly, our customers. We look forward to a bright future with Patrick being involved,” said Lane Aviation President Logan Lane
Patrick and his wife Alexa have relocated to the Houston, TX, area with their children, Fletcher (5), McCartney (4) and Fowler (1). They look forward to calling Texas home.
Milestone Aviation Group Limited, together with Australian firefighting equipment designer and manufacturer Helitak Firefighting Equipment, announced on August 6th, 2024, that the U.S. Federal Aviation Administration (FAA) has certified the FT5000 fire tank for the Sikorsky S-92A helicopter, granting a Supplemental Type Certificate.
This industry-first firefighting platform combines the unique capabilities of the S-92A with Helitak’s lightweight, carbon fiber FT5000 system. The system includes a retractable bellymounted fire suppression tank with a 5,000-liter (1,320 US gallons) capacity.
The first S-92A helicopter equipped with an FT5000 fire tank was recently delivered to launch customer VIH Aviation Group (“VIH”), a Canadian helicopter operator. Once in service, it will be deployed on firefighting missions across Western Canada.
“We are delighted to earn certification for this unique fire tank and introduce a new mission to the S-92A as a nextgeneration, multi-purpose firefighting platform. The Milestone and Helitak teams have worked tirelessly to create a solution that harnesses the advanced capabilities and versatility of the S-92A, combined with Helitak’s innovative tank design,” said Pat Sheedy, President & Chief Executive Officer of Milestone. “I would like to thank our partners at Helitak for their dedication and collaboration on this important project. Furthermore, we’re very pleased to work with VIH to immediately deploy
this pioneering firefighting solution to enhance their ability to fight wildfires greatly.”
“The S-92A presented some unique design challenges for the Helitak team, but after working with our project partner, Milestone, we believe we have delivered a world-class firefighting solution. With older S-92As coming out of the offshore market, the addition of the Helitak FT5000 system will allow S-92A operators to capitalize on the aircraft’s versatility by operating it as a standard category aircraft,” said Jason Schellaars, Founder & CEO of Helitak.
Jen Norie, VIH’s Chief Operating Officer, said, “We are very pleased to introduce the first utility-configured Sikorsky S-92A helicopter into the Canadian commercial market, with the launch phase specifically intended to support government agencies in wildfire suppression. We believe that this aircraft’s dependability, speed, and advanced technological capabilities, paired with the Helitak FT5000 tank and VIH’s extensive operational experience, will significantly enhance the service VIH can provide to customers and position VIH for its next phase of growth.”
Specifically designed for the S-92A, the tank can be installed or removed in minutes and is equipped with a hover pump that achieves a fill time of 48 seconds. Utilizing the S-92A’s advanced avionics and dynamic cabin layout, the aircraft will be capable of transporting crews of up to 19 firefighters to the front lines of wildfire events.
Perimeter Solutions announced on July 10 that the company donated a 260-gallon tote of PHOS-CHEK® LCE20-Fx long-term fire retardant to the Logan Lake Fire Department in British Columbia, Canada. Located in the Highland Valley, Logan Lake is at risk of wildfire, surrounded by forests that incur frequent lightning storms. The fire department can apply the PHOS-CHEK fire retardant as active wildfires are approaching to protect property. It can also be used proactively at the beginning of the season to protect homes from wildfire for months at a time until a significant rain event.
In 2013, Logan Lake became the first community in Canada to be designated as a FireSmart™ Community. That means that the community has taken critical steps to reduce their vulnerability to the impact of wildfire. Similar to the FireWise USA® program organized by the National Fire Protection Association, the FireSmart program encourages residences to clear their gutters and area around their homes of debris, to harden their homes against wildfire with non-flammable or low-flammability materials, and to take other steps to safeguard properties.
Logan Lake was put to the test in 2021 when the Tremont Creek Fire took aim at the community. Residents of Logan Lake were evacuated as the fire approached, not knowing if they would be able to return home. Before being fully contained, the Tremont Creek Fire burned 63,548 hectares (157,031 acres) of land. Logan Lake, however, emerged largely unscathed, a testament to the effectiveness of the community’s commitment to FireSmart principles.
When vegetation and other surfaces are treated with PHOS-CHEK LCE20-Fx, a chemical fire break is formed. The solution creates a coating, and as the fire approaches the water contained within the retardant evaporates. The fire retardant component of the solution then reacts with cellulose present in the woody material, grass, needles, and other matter to prevent it from providing fuel for fire, making it a valuable addition to Logan Lake’s efforts to prevent the spread of wildfire.
Representatives from the Logan Lake Fire Department recently attended a session that Perimeter Solutions hosted in Kamloops on the use of ground-applied fire retardant to help protect communities from wildfire. After hearing Peter de Bruijn, Wildland Fire Prevention & Protection Specialist at Perimeter Solutions, present on the technology, they asked Peter to deliver the same talk at their FireSmart Community Day.
“After hearing what PHOS-CHEK fire-retardant could do, Fire Chief Doug Wilson said he would like to use it for the upcoming wildfire season, and we are proud to make this donation to help in their ongoing fire protection efforts,” says de Bruijn. “By combining Logan Lake’s FireSmart practices with the use of PHOS-CHEK LCE20-Fx, they can create a strong defense against wildfires.”
Perimeter Solutions made the donation of PHOS-CHEK LCE20-Fx earlier this month. The Logan Lake Fire Department will familiarize themselves with the product to incorporate it into their firefighting strategy for the coming months.
Coastal Air Strike’s agile, forward-attack SEAT (single engine air tanker) and Single Engine Scooper aircraft are your best chance to contain small wildfires, to prevent them from becoming big wildfires. Their ability to operate from virtually all airports, ranging from large tanker bases to remote airstrips – even reloading at portable retardant bases – along with the Single Engine Scooper’s ability to scoop nearby water sources, proves them invaluable.
Whelen Aerospace Technologies (WAT) announced on July 23, 2024, at the EAA AirVenture show, the signing of an agreement to acquire substantially all the assets of AeroLEDs, LLC. This strategic acquisition will expand WAT’s product portfolio and solidify its leadership in the aerospace lighting industry while remaining true to the aligned values and culture that both companies hold dear.
WAT and AeroLEDs share a profound commitment to aviation, consistently placing high value on producing innovative, high-quality products that enhance aviation safety. This deal represents more than just a business transaction; it signifies the union of two like-minded entities dedicated to understanding and prioritizing the needs and values of the aviation community.
“Our brands have consistently aligned in our mission to continuously enhance products for the betterment of the aviation community,” said Tyler Wheeler, CEO of WAT. “AeroLEDs has built a remarkable reputation for reliability and innovation, and together, we will continue to deliver high-quality, durable, and efficient lighting solutions that our customers trust and rely on.”
AeroLEDs will maintain its brand and manufacturing operations in Boise, ID, while working closely with
WAT to ensure a seamless integration. The combined strengths of both companies will drive significant advancements in aviation LED lighting technology, benefiting pilots, aviation professionals, and enthusiasts worldwide.
“We are thrilled to join forces with WAT,” said Nate Calvin, CEO of AeroLEDs. “This combination is a testament to our shared commitment to excellence and innovation. With WAT’s resources and our combined expertise, we will push the boundaries of what is possible in aviation lighting, always with the goal of enhancing safety and performance for our community. Importantly, AeroLEDs will continue to provide the same exceptional products and customer service that our customers know and love.”
Both WAT and AeroLEDs are dedicated to delivering top-tier lighting solutions that enhance the safety, efficiency, and overall experience of the aviation community. Customers can look forward to new product developments with a range of pricing options, improved technologies, and an unwavering commitment to exceptional service. The core values that have made AeroLEDs a trusted name in aviation lighting will remain unchanged.
●
●
Entrol, the manufacturer of EASA and FAA-certified FNPT, FTD, and FFS flight simulators, announced on July 24th, 2024, the sale of a second AT-802 FTD 2 flight simulator to Titan Firefighting, the Spanish leader in aerial firefighting training. This state-of-the-art simulator, based on the AT-802 aircraft, is designed to provide a highly realistic training experience for pilots.
This flight simulator boasts real avionics and a replica configuration of the AT-802 operated by Titan Firefighting, ensuring seamless knowledge transfer from the simulator to the actual aircraft.
The unit features a 200ºx40º cylindrical visual system powered by Entrol’s Envision and supported by Unreal
Engine. This system not only provides a high-resolution database of Spain but also offers realistic firefighting scenarios for comprehensive training. The simulator includes the latest vibration system to enhance the training experience further.
The AT-802 FTD 2 flight simulator will be used for various purposes, including type rating, proficiency checks, and specialized firefighting training. Its installation and certification are expected to be completed this summer.
“We are thrilled to continue our partnership with Titan Firefighting and support their mission to upgrade firefighting training with our advanced flight simulators,” said Juanjo Lechosa, Business Manager at Entrol.
Our commitment to exceptional quality and personalized service aligns with our full range of services, all while keeping your budget in mind.
ADVERTISING AND PROMOTIONS:
Creation of niche publications, digital advertising, web development, and commercial printing
DESIGN & MARKETING SERVICES:
Graphic Design, Web Development, Ad Creation, Media Marketing, Digital Marketing
CUSTOM PRINTING:
Printing services for Brochures, Magazines, Business Cards, Postcards, and more!
California’s peak wildfire season is here, and it’s significantly more active than the last five years.
So far this year there have been more than 3,500 wildfires across California, with 207,415 acres burned and 128 structures damaged or destroyed. That’s compared to just 10,080 acres at this time last year – and the five-year average of 38,593 acres burned.
The state continues to expand its aerial firefighting force, which is the largest in the world. California also continues to leverage new technologies to support its firefighting capabilities.
Governor Gavin Newsom joined state fire and emergency officials in Sacramento at CAL FIRE McClellan Air Tanker Base to provide an update on California’s wildfire response and readiness.
“The last couple years brought welcome relief for California as we saw historically low levels of wildfire. This season is shaping up to be very active, bringing the threat of dangerous wildfire to many parts of our state. California is ready with the world’s largest aerial firefighting fleet and new technology that helps us fight fire smarter – and we’re already seeing our investments pay off,” said Governor Gavin Newsom.
The recently signed 2024 budget agreement maintains $2.6 billion through 2028 to protect Californians from wildfires
and improve forest health. This is in addition to $200 million per year for healthy forest and fire prevention programs, including prescribed fire and other fuel reduction projects. The administration is implementing shorter workweeks for state firefighters and aims to bring on more than 2,400 additional firefighters over five years to augment staffing levels.
Some of the highlights of the 2024 plan include:
• Expansion of helitack bases
- Five additional helitack bases are operational, after personnel completed. training, bringing the total to eight bases equipped for night operations.
- Night-flying aircraft have been activated in response to many wildfires this year.
• Contracted aircraft add to CAL FIRE’s permanent fleet of over 60 aircraft
- 20 additional helicopters and 4 airplanes, including five night-flying capable helicopters.
• Drone deployment
- CAL FIRE currently operates 159 unmanned aerial systems, representing a doubling in CAL FIRE’s use of UAS for aerial ignition, support of prescribed burns, and wildfire containment.
• Ongoing transfer and outfitting of seven C-130 aircraft from the federal government.
Kirtland Air Force Base, with over 100 mission partners, forms a vital defense hub in Albuquerque. From disaster relief to fighting insurgencies, continued collaboration ensures success that impacts New Mexico and beyond. This includes hosting the USDA Forest Service’s Albuquerque Air Tanker Base, a partnership that dates to 1977.
Earlier this year, the air tanker base completed a gamechanging upgrade. With a brand-new ramp designed to accommodate very large air tankers , this facility is poised to increase the efficiency and pace at which the agency responds to wildfires.
“It’s like trading your tried-and-true running shoes in for a brand-new pair that promises peak performance,” says Matt Rau, Cibola National Forest and National Grasslands fire staff officer. Rau compares the world of aerial wildland firefighting to the agility and finesse of an elite athlete, where speed and precision are everything. That desired speed and precision inspired the re-evaluation of the Albuquerque air tanker base’s capabilities after the aerial firefighting organization, 10 Tanker, moved its headquarters to New Mexico 10 years ago.
Project Alpha-Ramp was completed April 22. With the alpha ramp upgrade now complete, full-time access is now available for DC-10s, C-130s, RJ85s, BAE146s, and 737s.
“When we talk about the air tanker base’s target operational ability—the completion of the ramp project is it,” says Rau.
Very large air tankers are the largest air tankers currently used by the Forest Service to carry fire retardant, with a 9,400-gallon capacity compared to the 3,000-4,000-gallon capacity of large air tankers. However, to provide very large air tankers access to the Albuquerque air tanker base, a
new ramp, graded to handle the heavier payload of these larger aircraft, was needed. That need has been realized and achieved after two years of renovation work.
An earlier phase of the air tanker base revamp, which will aid with quicker response times, includes increased pumping capabilities, new piping and plumbing in the retardant plant— all of which fall under the more than $15 million in funding New Mexico Senator Martin Heinrich helped secure. Before this upgrade, it would take approximately 90 minutes to fill an aircraft with fire retardant only. That number has decreased to approximately 45 minutes for both a fuel and retardant fill and as little as 10-15 minutes if only a retardant fill is needed. The air tanker base is now one of only two bases in the country that can fill two very large air tankers simultaneously.
The increased efficiency of the air tanker base is further amplified by four new fire retardant tanks that hold 25,000 gallons of retardant each. One tank is dedicated to mixing, two to holding and one to loading, meaning 75,000 gallons of mixed fire-retardant are always available on the air tanker base.
With expanded capabilities, this air tanker base will undoubtedly prove to be a regional and national asset. The air tanker base can respond to fires in the Southwestern Region, as well as the Rocky Mountain, Intermountain and Southern regions. The Forest Service staffs the air tanker base with full-time and seasonal employees. There can be up to 30 individuals working at the air tanker base during fire response operations, including contractors and pilots.
With these valuable upgrades, the Albuquerque air tanker base is ready to usher in a new era of speed, efficiency and precision in wildland firefighting efforts. The sky’s the limit as this base takes off toward a future where every second counts.
One complex challenge in fighting fire from the ground and the air is integrating the rapid growth in available technology into firefighting operations. The Center of Excellence for Advanced Technology Aerial Firefighting (CoE), the research and development section of Colorado’s Division of Fire Prevention and Control (DFPC), is attempting to do just that with its latest offering, “COTAK.”
AerialFire recently spent time with Brad Schmidt, DFPC’s Deputy Director of Spatial Projects and the program lead on the COTAK Program, to learn more about what the state is doing to aid in wildfire technology.
The U.S. Military initially developed the Tactical Assault Kit (TAK) program for tactical operations, which was recently released to state agencies after it was surmised that the technology used on the battlefield could also be used on a state and federal basis for assisting in wildland firefighting and other public safety operations. The civilian version of TAK, known as the Team Awareness Kit, was adopted by Colorado as one of the first states to try and integrate the technology into the wildfire world; the Colorado version of the program was branded as COTAK as a method initially to track wildfire growth, bringing
in more than the currently available GIS mapping, and making the product mobile, able to be used by ground units via mobile phones also to track their position in the field.
What the product, thanks to several years of development, has become is an industry-leading piece of technology that allows crews on the ground to not only view the real-time location of first responders but also fire apparatus, fire mapping data, and drone traffic in the area and thanks to the addition of ADSB input, the location of incoming air attack and firebombing aircraft to the firefight in real-time, changing the game of how we view and fight fires on the ground and in the air. COTAK allows users to see what was previously held between computer programs, mobile apps with limited data, paper maps, and radio communication.
“TAK “ came from military research and development efforts, which happened to be similar to what we were looking for. We looked at creating a real-time wildfire map beyond just having the GIS data on where the fire is burning. We wanted to add real-time information on the location of aircraft, the location of vehicles, and the locations of firefighters and create that real-time map. And so that’s where we identified TAK as a technology that does that, and it was free of charge for us to adopt on the civilian side,” said Schmidt.
Unlike many other agencies, Colorado’s DFPC comes under the control of the state Department of Public Safety, so in addition to firefighting operations, COTAK is also used to support law enforcement operations, specifically being of great assistance during search and rescue operations to show the location of search parties and areas already covered when searching for missing persons.
With the initial success of COTAK and the need for further development, the TAK program has also extended to the federal firefighting side with the introduction of WFTAK (pronounced WOOFTAK), branded as the Wildland Fire Team Awareness Kit, being deployed to the USDA Forest Service. DPFC’s technology and knowledge are also being tapped to assist in developing the same product on a federal level to assist on a national level.
Part of the complexity of designing, updating, and managing a system like this is deciding what to monitor and ensuring that all resources responding to a fire are online within the system. One of the major advancements
the team at DFPC’s Center of Excellence is aiming to address is weaving all of the contracted aircraft into the system so that all people using either COTAK or WFTAK in the future have a complete picture of both ground and aerial assets available to fight the fire.
“It is a very complex system with a lot of players in it, so currently, we’re testing WFTAK with the Federal Forest Service in the Pacific Northwest, but we are looking to expand that testing to start figuring out how we’ll bring cooperative and contractor resources into it as well. In some cases, it may create accounts in the system for them to use, similar to how they can access other federal software. And then, in other cases, it may be integrating with third-party tracking systems to bring information in automatically,” said Schmidt.
The COTAK system is primarily a cloud-based technology, with its technology stored in a cloud-based server, which protects it from technology outages suffered by hardwired systems, such as the system chaos caused by the recent
(Continued on page 56)
Cloudstrike outages, which caused massive issues throughout many industries.
From a user perspective, the COTAK and WFTAK systems can be run on iOS—and Android-based mobile devices in the field and on a Windows-based application via laptop computers. A Linux/Mac app is currently being developed to make the COTAK system available on almost any platform for use in the field.
Once deployed on a device, COTAK users with approved credentials issued by the DFPC CoE can then access a server to obtain the real-time fire information needed on the fireground that will display fire mapping, personnel and fire apparatus information and the location of incoming aerial assets to a specific fire location.
The COTAK system relies on cellular technology to provide location data through repeater stations and cell towers, which in remote areas can be a challenge as service can sometimes be less than optimal. The CoE team is currently working on further solutions to improve connectivity to the system that include the installation of remote cell
technology repeaters and, in the long term, the hopeful addition of satellite compatibility that may consist of the use of the StarLink system in the future to make the system truly able to work in any remote location with no service or transmission delays based on lack of connectivity.
The COTAK system brings to the fireground a staggering amount of previously unavailable information in a single application, which for certain aspects of the firefight may seem to be “drinking from a firehose” regarding the amount of information available. In an aerial firefighting application, at least from the CoE application perspective, COTAK is also even capable of providing near real-time fire perimeters from one of DFPC’s next-gen aircraft fleet of PC-12 aircraft equipped with full-motion video cameras that can provide fire detection, mapping, and video feeds if needed for a specific aspect of fighting the fire, especially useful to initial attack and retardant dropping aircraft.
While the amount of data available could seem daunting, Schmidt stated that information is easily accessible and
(Continued on page 58)
easy to drill down. Like common aviation programs like Foreflight, COTAK also allows for scaling information availability up or down based on the user’s needs by providing layers of information that can be switched on or off based on the end user’s requirements and needs.
TAK software is an open-source program initially provided by the military; however, other state and even international agencies have already made use of the TAK technology in addition to DFPC, and while the Center of Excellence has spent considerable time and resources developing the technology now branded as COTAK, they are also open to assisting other agencies who are either looking to create their version or offering assistance in how to go about building their own or sharing some of the development that their team has made, as they are doing on the federal level with WFTAK.
Users outside the United States include the South Australian Fire Service, which also utilizes the technology to provide real-time monitoring of Australia’s ever-growing fire risk.
Providing the core technology to run and monitor COTAK is one of the challenges the DFPC CoE faces in the long term, but it is being looked at in several different forms. While the ability to run the core location software through app-based technology on a cell phone seems easy, monitoring needs other options when that task is moved to the non-human element, such as fire apparatus on the ground or aircraft. Aircraft are easier to solve as almost every aircraft can provide ADSB-Out technology as
standard. Older aircraft can now be fitted with inexpensive (in relative aviation terms) technology, such as a stratus device providing the needed ADSB-Out signal. Progress is still being made for a reliable and cost-effective fixedbased communication device that will enable ground assets to be monitored effectively on a larger scale at a low price point. Still, the C oE is confident this will soon be a relatively easily solved problem.
The Center of Excellence has no plans to stop the continued improvement of COTAK and continues to evaluate the needs and wants of those who fight wildfire. One of the most recent developments underway involves the reporting via ADSB of prescribed burn helicopters, which will also include their tracking data that will show areas that have already had a prescribed burn conducted, helping those planning the firefight from the ground and the air, valuable information on areas that have already had ground fuel eradicated as yet another essential piece of information in the jigsaw that is fighting wildfire.
Colorado’s DFPC and the Center of Excellence have been at the forefront of developing technology for the aerial firefighting industry since its inception. The ongoing development of COTAK and their ongoing involvement in the development of the national WFTAK product that will benefit aerial and ground firefighters for years to come continue to demonstrate the value of the forwardthinking of the state of Colorado for the benefit of the rest of the country and the citizens of Colorado. COTAK will likely save the lives of firefighters and citizens through advanced technology in the coming years.
•
•
•
by Ryan Varjassy
After the test program was finished on NACL, Vic began the same – 65 conversion on NACM followed by NACN. Andrew had made arrangements with Desmond to have Vic use his old factory hangar at Sandown as well as hiring a previous worker from the Cardiff factory to help in the conversion of the two aircraft. The engine transplant went smoothly with Andrew and Desmond making sure all the parts that were needed were delivered to Sandown. Flight tests were completed again by Neville Duke who described the performance of the – 65 as “a box full of birds” and “homesick angel” referring to it’s lift and speed capabilities. The Firemaster 65’s were ready for the summer firefighting season again in Cannes, France and also in Portugal...and with the new engines, the planes performed exceptionally well according to the pilots. The aircraft was proving to be extremely capable and Andrew was believing that he could get production up and running again based on the new Firemaster 65. NACO and NACP were left as -34’s and were never converted to the more powerful -65.
In 1991 the three -65 Firemasters again went to France for firefighting and NACP worked for Heyboer BV in Lelystad, Netherlands in August of that same year. NACO appeared to have not have worked at all that summer in 1991.
From 1988 to 1992, Andrew would change the corporate name and transfer assets multiple times. Croplease Ltd, Croplease PLC, Croplease Enterprises and eventually EPA Aircraft Company were all owners of the Fieldmaster assets and its production rights all under Andrew MacKinnon’s ownership and direction. Early 1992 saw the
Fieldmaster project begin it’s decline. The Utva Aviation plan that Desmond had originally cultivated (and which Andrew inherited) was dead due to war and political sanctions in Yugoslavia. The summer firefighting contracts in France had not come through for the 1992 season and despite taking the aircraft to numerous airshows, Andrew was unable to secure any future orders and sales. This was essentially the end of Desmond’s dream ag aircraft and Andrew’s business venture.
Andrew had been hemorrhaging money for the past few years and he had finally had enough. He decided to try and recoup some of his losses by parking the aircraft and selling off whatever he could. All of the engines, propellers and instruments were removed, sold... and the airframes were parked and left for years.
NACM Firemaster 65 (TTAF 1403 hrs), NACN Firemaster 65 (TTAF 1280 hrs) and NACO Fieldmaster -34 (TTAF 279 hrs) were parked at Bournemouth Airfield and NACL Firemaster 65 (TTAF 814 hrs) and NACP Fieldmaster -34 (TTAF 543 hrs) were placed at Sandown, alongside the already dismantled NRDC and the engineering sample outside of Desmond’s old hangar. It was an extremely sad and ironic ending that these aircraft returned to the home of their conception only to be left for dead. 1995 saw Andrew once again try to sell the Fieldmaster and NACM and NACN were put back into flying condition with -65 engines.
They performed some promotional demonstrations around the UK and went to a few airshows, but nothing became of
Andrew’s efforts and the planes were once again mothballed and it appeared that the Fieldmaster was dead for good.
By 1995 the Fieldmaster program was essentially over. Owner Andrew MacKinnon and the current company he headed, EPA Aircraft, had found himself with a product he could not produce nor sell. Andrew had also run out of working contracts for the aircraft so they had been parked and all the valuable parts were stripped and sold in an attempt to recoup some of the losses he had incurred.
But in a strange twist of fate, the Fieldmaster was about to get a second chance at life from an extremely unlikely source. Turk Hava Kurumu (THK), based at Etimesgut Airfield in Ankara, Turkey, was that apparent saviour of the abandoned Fieldmasters. They had an extremely long and proud history within Turkish aviation and had wanted to get back into aircraft production in 1992. The Turkish government was in desperate need of newer and more capable firefighting aircraft so it was decided that THK would take up the reigns and build their own aircraft for the role. THK was also the agency that actually did the aerial firefighting, so it kept everything centralized at one location.
It is unclear how THK and EPA Aircraft managed to meet, but a deal was made for THK to acquire the liquid assets and a production licensing agreement from Andrew Mackinnon and his EPA Aircraft Company in 1996. This procurement included all 5 of the production aircraft, the unfinished airframes from Utva Aviation in Yugoslavia, all the manufacturing, production and assembly jigs, all of the paper documents
from engineering plans to blueprints. However, none of the aircraft were in a completed condition so they were disassembled, crated and trucked from the UK to Turkey in the summer of 1997. NACM, NACN and NACO left from Bournemouth and only NACP from Sandown. NACL was left behind until it suddenly disappeared late in 1999. According to Utva, the trucks showed up and all the materials were hastily loaded and very quickly they were off, as stated in an email that was received in 2023 from Utva.
The story out of Turkey can be quite confusing depending on what documentation you read and choose to believe. What is clear is that THK paid between 5 and 6 million British Pounds for what they received but their appears to be some confusion around whether they had purchased all the rights to the aircraft or just a licensing agreement. The issue did make it into a London court but no results of the hearings were released publicly. It was also rumoured that THK was seeking 1.5 million Pounds from NDN aircraft but again there have not been any public records released about this demand. The entire purchase and subsequent issues plagued this program from the start. THK’s president at the time was Atilla Tacoy and he had made the decision to buy the Fieldmasters unilaterally, which annoyed many of his THK employees, not to mention his government superiors. A production plan was proposed that would see TAI Aviation partner with THK which would help spread the cost among both agencies but Tacoy would not budge insisting that THK would carry out the production on it’s own.
(Continued on page 62)
A team of engineers was assembled but when they arrived at an old hangar at the Etimesgut Airfield they expected to find the beginnings of a production line, but sadly this was not the case. They were met with hundreds of moulds, parts and thousands of technical drawings. There were crates containing fuselages and parts and they came to the conclusion that this entire project had been rushed and nothing had been organized. The engineers got to work and it was decided that they would start by building 2-65 Taysu aircraft, which is what they would be known as moving forward. Some reports suggest that THK built these 2 aircraft from scratch, but in reality they were NACM and NACN that were originally built in Cardiff, Wales then converted to -65’s at Sandown by Vic Osborne. THK acquired 2 Pratt -65’s and 2 Hartzell 5 blade propellers and on October 29, 1998...NACM (now TC-ZBC) flew once again for the Republic Day Ceremonies at the Etimesgut Airfield. There was much fanfare around this first flight and it was announced that THK would be making it’s own firefighting aircraft which at the time was the main source of revenue for THK. TC-ZBD (NACN) would fly the next year in 1999 but THK was under increasing pressure to produce aircraft quickly. There were plans in the works for the initial 9 airframes to be made flight worthy, the 5 from the UK and the 4 airframes from Yugoslavia and future plans saw the fleet grow to close to 30 aircraft over the next 2 years giving THK the means to fight fires for years to come.
But things started to unravel quickly. Atilla Tacoy could not shake his critics and was forced to resign under the slanders
he was facing. The Minister of the Interior was forced to act and a lawsuit was filed against Tacoy for acquiring the aircraft of a failed company and for damaging the business and reputation of THK. Tacoy would pass away from cancer in 2001 but his court case continued for three more years after his death which resulted in his acquittal. The government was in desperate need of firefighting aircraft and made the decision to buy a fleet of 12 M18B Dromaders from PZL in Poland. Turkey had also made the decision to ban aerial spraying due to environmental concerns which was the number one source of income for THK followed by aerial firefighting. This government ban dealt the final blow to the Fieldmaster and the entire project was completely eliminated. The program was irreversibly thrown away and the Minister if the Interior stated that “the resources of our country were saved”. Behind the scenes there were cost over-runs, unorganized factory space, accusations of corruption, lawsuits and severe mismanagement with much of this remaining quiet and kept behind closed doors in order to avoid further embarrassment to both THK and the Turkish government.
The two -65’s were once again stripped of all their useful parts and the 4 aircraft were placed in the boneyard behind a hangar on the south end of the airfield at Etimesgut. NACM, NACN, NACO and NACP were once again destined to be discarded and forgotten. But after sitting for a few years, it was decided that these aircraft should be celebrated as an accomplishment and should therefore be put on display.
(Continued on page 64)
For some though, these wonderful aircraft were destroyed for nothing and to quote Turkish reporter Sedat Halac, “they were placed in front of the THK museum as an exemplary lesson for those who try to do useful work for this country.”
The first aircraft was put on display at the THK Ankara Aviation Museum. This Fieldmaster is painted with TC-ZBC on the tail but it is clearly not the ZBC that was built and was flown. The display aircraft is a -34 Fieldmaster as noted by 4 distinctive differences. The -34’s had a short front wheel mudguard, an angled air filter inlet, three mesh covered vents on the left side cowling and a small air inlet under the propeller on the nose cowling. The other -34 was taken 150 miles (240 KM) south to the Aksaray Bilim Science Center. One of the -65’s made its way 290 miles (465 km) to a Technical Aviation High School in Istanbul and the fourth aircraft remains at THK Etimesgut airfield to this very day, or so it was thought.
The Fieldmaster Resurrection Project was started in July 2023 from a chance online meeting between Vic Osborne of Wales, UK and Ryan Varjassy from Saskatchewan, Canada. The two were a world apart but quickly realized they both had a passion for the lost Fieldmaster. Vic had worked on the aircraft personally and Ryan saw one in a magazine in the mid 1980’s and had a fascination with the aircraft ever
since. Ryan’s dad, Joe Varjassy, was a well known crop duster for over 30 years and Ryan worked with him in the ag industry for many years starting as a young boy. This time spent around ag flying made Ryan develop a love for ag aircraft which he still carries today at age 50. Vic at 75 has a few years on his younger cohort but shares the same enthusiasm for the elusive Fieldmaster.
The two men quickly developed a plan save one of the airframes in order to have it displayed back in the United Kingdom where it was originally born. The search began for any information they could find. Countless hours scouring the internet, sending letters and emails and starting a FaceBook page dedicated to the cause began to show results. Vic still had contacts from his days as an engineer on the Fieldmaster and after the FB launch, more people came out of the woodwork. Former employees, aviation enthusiasts, some Fieldmaster experts and Desmond’s son Roddy Norman are all involved with the project.
The research seemed to raise more questions than it answered for a few months but the more interaction with the online contacts, the more the pieces began to fall into place. The tracking of the production, engine conversions, foreign spraying and firefighting all came from the online searches
and contacts that were made. Information came in from all over the UK, Europe and from as far away as Australia.
One of the most important tasks was tracking down all 6 of the airframes. There was much speculation and false information that needed to be proved or disproved and after much reading and consulting they believed that they had accounted for all of the minus one...NACL...the first production Fieldmaster and the first of the fleet to be converted from a -34 to a -65. The sale of all the assets to THK was supposed to include all 5 production aircraft but NACL remained at Sandown till late 1999, some 2 years after the other 4 aircraft had been shipped and also after the THK production program was canceled. So where was it? The 4 aircraft in Turkey were accounted for but NACL seemed to have vanished. One of our group experts, Martin Forster, had said that he had spoken directly to someone who helped load NACL onto a truck bound for Ankara, Turkey. There was no reason to doubt Martin but there was absolutely no evidence that NACL was actually there. The project group has acquired almost every published photograph of the aircraft as well as a massive amount photos from private collections. They searched Google Earth Historical Images and had found satellite images of all the Fieldmasters in various locations they were known to be. However, Ryan came across some photos that he had not seen before and they were dated Sept 12, 2023 . It was NACL, still in the France Aviation livery she had when she was last seen at Sandown some 24 years ago. And she was at the THK Etimesgut Airfield. Ryan contacted the publisher of the small article that featured the photos and he did confirm that NACL is still at the Etimesgut Airfield and was sadly going to be sent for scrap at some point in the future. But this has now raised another question. It is now a fact that all five aircraft made it to Etimesgut but only 4 are accounted for with the missing aircraft being NACM (TC-ZBC). It was assumed that the last aircraft seen on the Satellite photos at Etimesgut was NACN, but it turns out that it was NACL which means that NACN is still there somewhere. The current theory is that it is inside an old hangar at the airfield with all of the parts, fuselages, jigs and papers from Yugoslavia.
The Fieldmaster Resurrection Project is currently trying to acquire NACL from THK to have it shipped back to the UK, but this is proving to be a difficult task. Our proposal to obtain NACL has finally reached the desk of the correct people at THK after months of emails, letters and phone calls begging for any information on who could help us. Apparently our request will need to go before the Board of Trustees for THK but currently we have no information regarding that timeline.
Additionally, Martin Forster has also obtained the location of the original prototype NRDC which never left the UK and
(Continued on page 66)
was abandoned at Sandown for the better part of 21 years. After moving through a few locations NRDC would end up near Wainfleet along the eastern coast of the UK. She was supposed to become part of a crop dusting museum collection but those plans never materialized due to poor health of the owner. Martin is handling the negotiations on the possibility of also acquiring NRDC for display.
The group was in discussions with the Wight Aviation Museum at the Sandown Airfield about having a Fieldmaster airframe displayed at their facility as Sandown is the obvious choice for NRDC to be displayed as she was born there and was laid to rest in the exact same spot. Unfortunately the Wight Aviation Museum has since reversed their interest in the aircraft so the search is on for a new location. The South Wales Aviation Museum seems like it would be a good fit as it is only 6 miles from the production factory at Cardiff but nothing has been discussed with them at this time.
The Fieldmaster’s ultimate demise was the product of a multitude of issues and failures and not just one singular problem. Firstly, the program suffered from mismanagement essentially from it’s inception resulting in financial constraints throughout it’s entire existence. Second, the cost of the Fieldmaster was wildly expensive for the time. The purchase cost of a production line aircraft was rumoured to be between $450,000 to $500,000 in the mid to late 1980’s which for the time was a huge financial commitment for an unproven aircraft that was so different from the ag planes of the day. Thirdly, because it was so different it was going to be difficult to convince established operators to switch to an unknown platform from their traditional tail-draggers. Drawings and design concepts had been developed for a tail-dragger version of the Fieldmaster but it was never developed beyond that stage.
Fourth, it would have been almost impossible for the Fieldmaster to break into the American market which at the time was arguably the largest ag plane market in the world. Turboprop conversions were already in use in America and factory production of turboprop ag planes had begun. Also there were many options already in existence for operators: Air Tractor, Thrush, Ag-Cat, PZL Dromader, Cessna, Piper and Weatherly. The American market already had a full plate of aircraft to choose from. The world market would have provided more opportunity for sales as an aerial firefighter with the ability to also do pest control as well with the main target areas being Australia and New Zealand but they were also set in their aircraft choices just as the Americans were. And lastly, the Fieldmaster was conceived at a time when aerial spraying was being banned throughout Europe which undoubtedly hurt the possibility of sales. Even in the UK where she was built, aerial spraying and aerial firefighting were already being phased out at the time the Fieldmaster
was in production. So it was a combination of timing, changing laws and poor corporate decisions that really stopped the Fieldmaster from being a commercial success.
The Fieldmaster Resurrection Project has come a long way in their short nine months of existence. They have amassed quite possibly the worlds largest collection of data, photos, videos and an overall clear picture of the Fieldmasters existence. The project has now reached it’s most difficult phase so far, acquisition of these airframes before they are lost again or destroyed. The project group is on the verge of obtaining the original aircraft NRDC which will be the first major milestone completed.
The Fieldmaster Resurrection Project is currently seeking donations to help with the fundraising for this project in order to save these aircraft from destruction and being
erased from existence. The Fieldmaster aircraft were an important part of ag and aerial firefighting aviation history, albeit a failed story that deserved a better outcome than it had. We now have the chance to rescue two airframes and depending on the success of the fundraising, will determine the extent of the restorations. Private donations and corporate sponsors are not only welcome but required in order to progress with the project.
The Fieldmaster Resurrection Project can be contacted by the following outlets: Email: fieldmasterresurrectionproject@gmail.com Facebook: https://www.facebook.com/groups/1483419635727874 or search for NDN/NAC Fieldmaster Resurrection
by Dan Reese
As wildfires continue to grow in severity and frequency across the globe, the need for innovative and effective suppression strategies has become increasingly urgent. The Congressional Wildfire Commission and other stakeholders have advocated adopting emerging technologies like drones and advanced aerial platforms to bolster wildfire response capabilities. However, the current contracting models employed by state and federal agencies pose significant challenges to the sustained growth and implementation of these new-generation technologies. Additionally, the sporadic and inconsistent application of the
current “Call When Needed” contracting model hinders the maturation and proliferation of this technology, placing the entire development burden on the technology vendors.
The United States has access to cutting-edge innovations developed by subject matter experts and tech companies. One example is high-altitude, long-endurance drones that could provide promising solutions to the wildfire crisis when innovative leadership and cultures exist. Yet many of these innovative technologies remain unused despite over two million acres burned in 2024 and represent
a significant missed opportunity to leverage the full capabilities of available resources to respond effectively to the ongoing crisis.
The “Call When Needed” contracting approach, which allows agencies to utilize technologies selectively, often leads to a reliance on familiar legacy systems and forces unrealistic expectations of any new technology. This tendency to revert to comfortable, well-established methods can impede developing and integrating more advanced tools. Without consistent and widespread
adoption, the viability of these innovative technologies is jeopardized, as manufacturers and service providers may not have the necessary market support to sustain their operations and continue improving their offerings.
Examining the critical challenges of engaging new-generation technology for wildfire suppression is essential for the industry’s future. In the future, the industry needs to adopt a more strategic and long-term approach to contracting,
(Continued on page 70)
innovative leadership, and technology adoption. By addressing these obstacles, agencies can unlock the full potential of emerging tools and ensure that the firefighting ecosystem is equipped to meet the evolving demands of wildland fire management.
Wildland fires have become an increasingly pressing global issue, with climate change, land-use patterns, and other factors contributing to their increasing frequency and severity. In response, the firefighting community has been actively exploring and adopting new technologies to enhance its suppression capabilities. However, the current contracting models employed by state and federal agencies have created barriers to the sustained growth and implementation of these new-generation technologies.
It’s a common misconception that people or technology can be pushed to their limits immediately without proper preparation. Just as teams need to warm up before a practice or competition, new technology, systems, and processes require a gradual ramp-up to perform at their best. It can have severe consequences when government officials or other decision-makers demand immediate highintensity usage without allowing for adequate warm-up and testing. This leads to wasted resources, delayed projects, public frustration, and, in some cases, dangerous outcomes. It is often the result when new technology is only engaged in the heat of battle when all other approaches have either failed or been exhausted.
Innovative leadership is crucial for agencies to integrate newgeneration technologies successfully. Leaders who embrace innovation can identify emerging technologies, understand
their benefits, and create the structures to enable effective implementation. Agencies led by those resistant to change risk missing opportunities to enhance capabilities, improve efficiency, and better serve constituents. A lack of innovative leadership can result in an inability to address evolving challenges, a failure to capitalize on technological solutions, and a loss of public trust as agencies struggle to keep pace. Fostering a culture of innovation and empowering leaders to navigate technological transformation is essential for agencies to remain relevant and effective. To achieve this, we need to address some obstacles.
State and federal agencies have long-standing relationships with traditional suppression providers and are often comfortable with the familiar capabilities of legacy systems. This familiarity can create a reluctance to adopt new technologies, even when the potential benefits are clear. Agencies may find it easier to rely on tried-and-true methods rather than invest time and resources into effectively integrating and learning to utilize new-generation tools.
Resistance to change, lack of innovative leadership, and uncertainties about the reliability and capabilities of emerging tools can result in a cautious approach to adopting new-generation technologies. Agencies may hesitate to fully commit to these innovations, fearing they may not perform as expected or require significant training and infrastructure
investments. This hesitancy can lead to slow and piecemeal adoption of innovative solutions, limiting their overall impact and effectiveness.
The lack of a dedicated wildfire training environment for developing and testing emerging technologies significantly hampers their maturation in a controlled manner. Without such an environment, these systems cannot be reliably tested and refined, leading to distrust among decision-makers deploying these technologies. Consequently, the inherent risk associated with untested systems must be transferred to real-life wildfire scenarios, which is far from ideal.
The “Call When Needed” contracting model, which allows agencies to utilize newer technologies as required selectively, can create a sporadic and unpredictable demand for these tools. This inconsistent demand makes it difficult for manufacturers and service providers to maintain a stable business model, leading to challenges in sustaining their operations and investing in research and development. Systems can break down, technology with great potential and processes may fail, and people may become overwhelmed or make mistakes. This frequently occurs with call-when-needed contracts in government that fail to account for the need to exercise and optimize systems before full deployment.
Wildfire suppression agencies often face tight budgetary constraints and must balance various priorities, including personnel, equipment, and infrastructure maintenance. Investing in new-generation technologies may be perceived as a lower priority than maintaining and upgrading legacy systems, mainly when the newer tools’ long-term cost savings and operational benefits are not quantified or understood.
A more strategic and coordinated approach is required to overcome the challenges of engaging new-generation technology for wildfire suppression. This may involve the following measures:
• Developing Long-Term Contracting Strategies Agencies should explore alternative funding and contracting models, such as long-term agreements or exclusive-use contracts, to provide manufacturers and service providers with the stability and market certainty needed to sustain their operations and continue investing in technology improvements.
• Conducting Comprehensive Evaluations and Pilot Programs Agencies should prioritize comprehensive evaluations and well-designed pilot programs to assess newgeneration technologies’ reliability, capabilities, and cost-effectiveness. These assessments should inform strategic decision-making and help overcome the reluctance to adopt unfamiliar tools.
• Fostering a Culture of Innovation and Empowering Leaders to Navigate Technological Transformation Agencies need to cultivate an organizational culture that is open and receptive to innovation. This involves leadership actively encouraging experimentation, risktaking, and the exploration of new technologies.
(Continued on page 72)
• Develop a Representative Training Environment Agencies should establish a funded and representative wildfire training environment for emerging technologies if not accomplished on emergency incidents. Much like how baseball teams utilize Spring Training to hone skills and strategies before the regular season, this dedicated environment would allow new technologies to be thoroughly evaluated and refined in a controlled setting. This approach ensures that systems are “warmed up” and ready for deployment, fostering trust among decision-makers and reducing the inherent risks of implementing untested solutions in real-life wildfire scenarios. By simulating various wildfire conditions and challenges, this training ground will enable technology vendors to improve technologies iteratively, leading to more reliable and effective tools for wildfire management.
• Fostering Interagency Collaboration and Standardization Agencies should work together to develop common standards and protocols for integrating and using new-generation technologies, facilitating interoperability and encouraging widespread adoption across the firefighting ecosystem.
• Quantifying the Benefits and Cost Savings Agencies should invest in research and analysis to demonstrate new-generation technologies’ costbenefit and operational ratio benefits, which will help justify the necessary investments and overcome budgetary constraints.
• Prioritizing Training and Capacity Building Agencies should dedicate resources to training and capacity-building initiatives, ensuring that personnel have the knowledge and skills to utilize new-generation technologies and realize their full potential effectively.
By addressing these challenges through a comprehensive and coordinated approach, agencies can unlock the transformative potential of new-generation technologies and strengthen their ability to respond to the increasing threat of wildfires.
Conclusion
The challenges associated with engaging new-generation technology for wildfire suppression are significant but not insurmountable. By adopting a more strategic and long-term approach to contracting and technology adoption, agencies can overcome the reliance on legacy systems, address the uncertainties surrounding emerging tools, and maintain a consistent demand for innovative solutions. Through innovative leadership, collaborative efforts, comprehensive evaluations, and targeted investments, agencies can foster the growth and integration of new-generation technologies, ensuring that the firefighting ecosystem is equipped to meet the evolving demands of wildland fire management. By doing so, agencies can enhance their suppression capabilities, improve the safety and effectiveness of their operations, and make significant strides in mitigating the devastating impacts of wildfires.
Cascade Pressure Cowl Delivers!
u Increase in Clean Air Volume to PT6 engine
u Decrease up to 32⁰ ITT Temps
u Decrease up to 1.5% NG
u Easy Access to Service
Air Filter System ( Filter swap - 20 min)
Fuel Nozzles
Chip Detectors
Pilot Report: “Before the Cascade Pressure Cowl, this FIREBOSS was always at the back of the pack. Cascade Pressure Cowl installed, it’s always at the front with our best performing FIREBOSS! Performance is everything! ”
Story by Ryan Mason; Images by Conair
In the arena of aerial firefighting, responders are focused on one mission, slowing the spread of the flames. This focus accomplishes the singular goal of buying time. Crews are buying time for ground firefighters to arrive on scene and work towards containment. They are there to cool its intensity and slow its path. They are there to give people time to evacuate homes.
For over 60 years the industry has designed and deployed an arsenal of air assets to perform this service, including a diverse array of airtankers, each successful in its own right. Some built specifically for aerial firefighting, some converted. Some that skim, some that don’t. Some delivering water, some retardant. All offering varying degrees of speed, fuel burn, maneuverability, avionic sophistication, drop effectiveness, reach, reliability, and, of course, payload size. And each offering its own level
of response. All with one purpose, to buy time, protecting people, communities and resources.
Looking to the future, there are benefits to assessing the value of modern airtankers designed to perform more than the one role of aerial firefighter. In addition to performing drops, teams of ground firefighters could be moved between fires rapidly, traveling comfortably and safely, sometimes long distances, with essential equipment packed into cargo holds. After crews unload, the tanker fills and takes off to the fire, ready to respond. If the fire prevails and surges, fanned by changing wind, the tanker evacuates neighborhoods to safety. Or transports patients from hospitals or nursing homes with air ambulance capability. On its return, it carries a full load of freight, filled with critical
supplies needed for sustained support. At night, when not on mission, it uses ISR software and sensors to capture data on wildfires, mapping perimeters.
The frequency and intensity of wildfires will continue to grow but wildfire isn’t the only worry for emergency management responders. Natural disasters are increasing in frequency and severity – floods, hurricanes, tornados, earthquakes, snowstorms, landslides, heat domes – the list goes on.
Investing in an airtanker is a costly endeavor. To be able to maximize return on investment it would be beneficial to select a specialized aircraft that can operate year-round, a multi role all hazard aircraft that could dispatch to disasters of all kinds. Cities trapped or destroyed could be helped
using the aircraft, working alongside partners such as the military, transporting in crews, equipment, medical aid, and life sustaining support. Or a multi role airtanker could convert into a mobile urgent care facility, delivering medical treatment to injured citizens. Or, in critical instances, populations could be airlifted rapidly to safety, removing them from threatened regions.
Everyday the world is faced with challenges requiring the ability to quickly adapt, responding to adversity using versatile tools that can perform with certainty. This multi role aircraft could transport supplies to isolated villages facing shortages. It could serve as a mobile medical clinic
(Continued on page 76)
to communities with no health care facility, offering a variety of exam opportunities or immunization clinics. Critically ill patients from pandemic or war zones can be medically evacuated to safety. Humanitarian aid could be shipped to countries in crisis. Or intelligence using ISR capabilities could be gathered for a wide range of missions including search & rescue, maritime security, fisheries monitoring, smuggling, immigration patrol, and pollution control. The airtanker could be customized, giving agencies the power to select the roles they need, optimizing readiness and improving efficiencies, reducing risk for all emergencies.
Deploying the multi role aircraft mitigates damage and prevents catastrophe. The cost associated with disasters runs into the billions, with the price of an aircraft being a small fraction of that cost. The multi role offers functions which benefit a wide variety of branches including public safety,
emergency management, natural resources, health, and civil protection. As has been done for years in the airtanker-only world, the aircraft could be deployed on loan during times of need, with operational costs offset through interagency agreements, lowering the owner’s annual financial commitment. Alaska is one example of success in sharing the Dash 8-400AT with both domestic and international agencies in need, loaning its contracted airtankers to British Columbia, Alberta, and Montana in recent years. And in Australia, Queensland and New South Wales have a shared Dash 8-400AT, with each state contracting its own multi day period set up such that the airtanker, overall, reaches an extended annual contract period, providing both states the opportunity to secure an exclusive-use airtanker, reaping improved response ability as well as financial benefits. Similar tactics could be applied to a multi role, both as an aerial firefighter, and as an emergency response aircraft.
The time to design, engineer, and certify a specialized aircraft is lengthy, often taking years. And the time required from setting up a production facility to celebrating a first delivery is equally time consuming. But this is not an obstacle and there is no need to wait years for a solution. A multi role airtanker already exists and is in production, a proven platform operating for over a decade in France, built by Conair Aerial Firefighting. It’s the Dash 8-400MRE. Its airtanker-only variant, the Dash 8-400AT, has been operating on since 2020, through Conair and Aero-Flite Inc. Over twenty of this airtanker type (AT/MRE) are operating around the world, a number growing steadily every year. Most recently, Saskatchewan Public Safety Agency (Canada), after retaining FPInnovations to produce a study on next generation airtanker types to replace the province’s aging airtanker fleet, announced the purchase of two multi role and two airtanker-only variants, with deliveries starting in 2025.
Saskatechwan’s action not only modernizes their airtanker fleet, but also offers the ability to adapt and dispatch to a wide range of emergencies throughout the region, covering over 250,000 square miles. With this platform, Conair, as the OEM, provides full-service support with safety being top of mind, engineering custom features, providing ongoing technical support, and training mechanics and crews, including offering the capability of training pilots in industry-leading simulators. Open to flexible solutions, the company and its subsidiary Aero-Flite in the US, will consider nontraditional agreements to accommodate individual agency needs and can provide full-service crewing, maintenance, and operations for purchased aircraft on long-term contract.
Disasters can’t be stopped but can be anticipated and prepared for. A resilient future can be achieved by taking action today, continuing to improve effectiveness and adaptability in response to escalating challenges, performing in more than one capacity. Those facing catastrophe, depend on it.
This year’s installment of APSCON from the Airborne Public Safety Association, held in Houston, Texas, was one for the record books. A record number of fourteen helicopters entered the George R. Brown Convention Center show floor and over 1500 attendees and 154 vendors attended the exhibit portion of the show.
The show was treated to the best of Texas weather, which kept skies clear for the entire duration of the show. This made for a seamless setup and fly-out for the large contingent of helicopters on display, which included a Leonardo Helicopters AW139 for the first time this year.
As with each APSCON show, classes covering every aspect of public safety, including aerial firefighting, were held over the first several days and during the convention’s show floor portion.
(Continued on page 80)
The show floor was abuzz with attendees and exhibitors showcasing their products and services to the industry for another year. The offerings covered everything from training to helicopters, rescue equipment, aerial firefighting technology, avionics, and more.
Next year’s show is scheduled to return to the Grand Canyon State, returning to Phoenix, Arizona, for the first time since 2014.
SUBARU BELL 412EPX
The most reliable work trucks are transformed and reborn year after year for decades. When you’re fighting wildland fires from the sky, critical moments require experienced and renewed solutions. The upgraded transmission of the new Subaru Bell 412EPX provides 11% more shaft horsepower at takeoff, resulting in a 15% boost in the hot and high hover. Add in an unprecedented increase for internal, external and cargo hook with 1,100 pounds/499 kg payload added. Proven operational readiness now with more payload, more firemen and women, more water…and more power to fight fire.
bell.co/fire