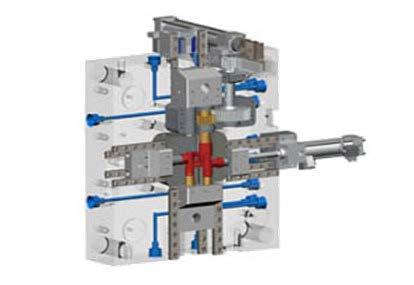
20 minute read
E. Meurisse, I. Schruff ......................................................................................................................... pag
CONCLUSIONS In this work, uniaxial constant amplitude fatigue tests with stress ratio R = 0.1 were performed on AlSi11Cu2(Fe) diecast specimens and the effect of sand-blasting in improving the fatigue behaviour of the alloy was evaluated. Regardless of the surface finishing, the results show a similar statistical dispersion in fatigue life, even though the amplitude strength and S-N slope for sand-blasted specimens resulted higher than the corresponding ones for the as-diecast specimens. Microstructural investigations confirmed that crack initiation sites in as-diecast specimens are preferentially localised on the surface or on sub-cortical defects, while in sand-blasted ones also internal defects provide sites for fatigue crack initiation. FUNDING This work was partially funded by the European Project NADIA (New Automotive components Designed for and manufactured by Intelligent processing of light Alloys, NMP-2004-SME 3.4.4.5, contract n.026563-2) and by FIR 2018, Prot. n. 117696 of the University of Ferrara (Italy)
[1] Avalle M et al. Casting defects and fatigue strength of a die cast aluminium alloy: a comparison between standard specimens and production components. Int. J. Fatigue; 2002;24:1-9 [2] Linder J at al. The influence of porosity on the fatigue strength of high-pressure die cast aluminium. Fatigue Fract. Engng, Mater. Struct.; 2006;29:357-363 [3] Nourian-Avval A et al. Fatigue design with high pressure die casting aluminum including the effects of defects, sectin size, stress gradient, and mean stress. Mater. Today Commun.; 2020;25:101567 [4] Lattanzi L et al. Effects of microstructure and casting defects on the fatigue behaviour of the high-pressure die-cast AlSi9Cu3(Fe) alloy. 3rd International Symposium on Fatigue Design and Material Defects (FDMD). 2017 Sept 19-22; Lecco, Italy. Structural Integrity Procedia. 2017;7:505-512
Micro Spray technologies for an efficient die spraying in HPDC
a cura di: M. Lutz
The potential for savings in an HPDC process is getting smaller and smaller. The areas where it is still possible to make significant improvements are thermoregulation and die spraying (which are closely related and interlocked). Nowadays, all foundries are able to implement effective spraying, but is this spraying efficient? Effectiveness shows the ability to achieve the set goal, while efficiency shows the ability to achieve the set goal with the least amount of resources. As far as die spraying is concerned, new release agents (oils or concentrates) are now available on the market that change the spraying philosophy: Whereas in the past spraying was used to cool the die surface, today spraying is used only to create the release film between the die and the casting. In this case, the differentiator is the technology used to apply these products: To achieve maximum results, the release agents must be micro-dosed. The precision and repeatability of micro-spraying is crucial and can only be achieved with appropriate technologies. WOLLIN's ECO spraying technology can reach the goal in different ways, adapting to the different needs of the foundry (long-term production or frequent die changes): the experience developed in recent years allows to successfully manage a wide range of projects. The objectives are multiple: reduction of cycle time; reduction of release agent, water and air consumption; longer life and higher availability of the die; better quality of castings and reduction of scrap.
KEYWORDS: ECOSPRAY, MICROSPAY, EFFICENCY, QUALITI, COST-SAVING
INTRODUCTION: EFFICIENCY IN DIE CASTING The die casting process has been established for many years and itself offers little potential for further savings. It is essentially the periphery that continues to offer opportunities for optimization. In addition to more efficient furnaces, explicit mention should be made here of die tempering, as well as the spraying process. The development of multi-circuit temperature control units in which each individual cooling channel can be controlled, the use of jet cooling systems, the use of 3D printing in die production, and new, more temperature-resistant release agents are resulting in new approaches to the spraying process. This is significantly improved when it only has to ensure good release properties and good demouldability.
REQUIREMENTS PROCESS TECHNOLOGY It should not be concealed that a conversion of the casting processes requires a lead time of one to two years and ties up capacities in process technology. Those who Martin Lutz
Wollin GmbH; Germany
take this on will be rewarded with more stable processes, a reduction in the scrap rate and better casting surfaces.
DIE TEMPERATURE CONTROL The use of effective water- and oil-based multi-channel die temperature control systems enables a casting process that is much more thermally stable than in the past. This means that the temperature difference of the die between the filling phase and the solidification phase is significantly lower. Thanks to die temperature control channels close to the die and the use of jet cooling systems for squeezers and hotspots, cooling of the die by the spraying process is no longer necessary today.
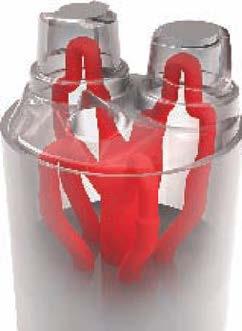
Fig.1 -Die tempering.
The significantly lower cooling of the die saves energy, since the die has lost much less heat energy after the part has been removed and sprayed, so it does not have to be supplied again.
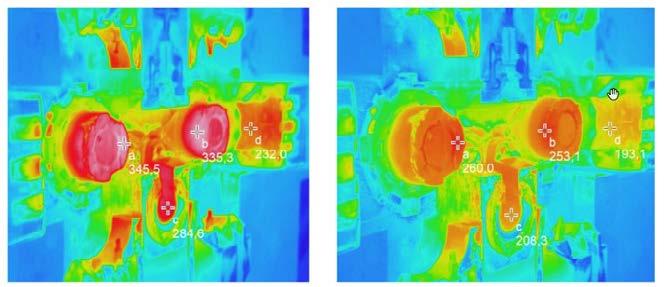
Fig.2 -Die temperature before and after Spraying.
SEPARATING AGENT The new water- or oil-based release agents developed in recent years allow a significantly wider temperature spread of up to 400 °C. Depending on the application, wax-containing, wax-free or even wax-reduced release agents are offered. What they all have in common are very good release properties. Wax-reduced release agents additionally offer improved demoulding lubrication, as well as a significant improvement in surface quality, low machine contamination, clean surfaces and reduced scrap rates.
SPRAY PROCESS For an optimal result in micro spraying, a few things are helpful. Ideally, a spraying machine with a high payload is used, which can support a mask spraying tool adapted to the die. Separate pressure control for blowing and spraying air is also advantageous for a good result, as is a booster station for control air pressures of up to 8 bar; Wollin also offers retrofit solutions for this. When the spraying tool is moved into the die, the two die halves are blown out at high pressure. The masking tool, which is adapted to the die and equipped with DDV nozzles, ensures uniform release agent application during spraying. Patented dosing nozzles are used for micro-spraying, which are offered with different dosing volumes so that a suitable release film is achieved for each part of the die.
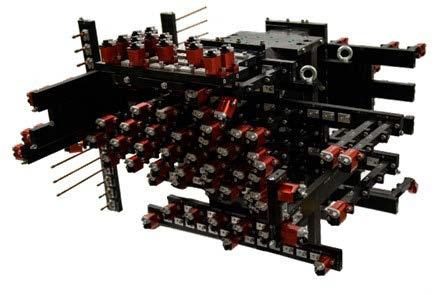
Fig.3 -Mask spray tool.
Experience shows that the release agent concentrates available on the market have excellent flow properties, so that even areas of the die that are difficult to reach receive sufficient release agent. The release agent is applied in a pulse by which the release agent in a chamber of the spray nozzle is sprayed into the die under high pressure in very fine atomized form. The air pressure must not be set too high so that the release agent is sprayed onto the die and does not evaporate without effect. Contrary to initial assumptions, ionization of the release agent and die is not only not necessary, but in many cases rather a hindrance. Due to the course of the field lines, most of the release agent is deposited in the foremost area of the die. Due to the fine atomization of the release agent, there is practically no Leidenfrost effect with microspraying. Another advantage of applying only the amount of release agent required for the release effect is that only very small amounts of substances are measured in the air. Afterblowing after spraying is unnecessary, since no excess water was sprayed. The formation of cracks due to thermal shock during conventional spraying is avoided, resulting in a significant extension of the die service life.
QUALITY The lack of water during spraying enables a more even distribution of the release agent in the die, which contributes to a significant improvement in part quality. The surface and the microstructure become significantly more homogeneous, practically no blowholes are formed, and porosity is reduced to a minimum.
ENVIRONMENTAL ASPECT Significant savings can be achieved through the contemporary form of spraying using EcoSpray. Today, awareness of environmentally compatible and resource-saving production is greater than ever. The aluminum industry already has a major advantage here thanks to the very good recyclability of die castings. However, the classic casting process has a not inconsiderable impact on the environment, which is also reflected in the costs. These include the energy costs incurred by cooling and reheating the dies, and the enormous consumption of water and compressed air during spraying. With microspraying, on the other hand, only very small quantities of the release agent are evaporated, no fresh water is required and, crucially, no waste water is produced. The consumption of energy-intensive compressed air is reduced enormously. This makes the die casting process much better in terms of its climate footprint.
Tab.1 - Saving.
Wollin Eco Spray savings: Energy savings (tempering of die cast mould) Compressed air (vol.) Fresh water
Waste water Acronimo
50-70%
50-70%
100%
100%
COST FACTOR The environmentally friendly process of micro-spraying also has the advantage that it achieves significant cost benefits with only slightly higher investment costs for the dies and their temperature control. The energy savings in die temperature control often achieve a return on investment in just a few months, the generation of compressed air is very expensive, a saving of 50-70% offers enormous financial savings. The costs for fresh water treatment are eliminated, the release agent mixing in the foundry is no longer necessary. In addition to cost savings, the risk of bacterial contamination is significantly minimized. The expensive disposal of waste water is completely eliminated. New foundries are already being designed without the equipment for waste water disposal. By eliminating the need for afterblowing during the spraying process, up to 10 seconds or more of cycle time can be saved. The extension of the die service life also provides significant savings for the maintenance or renewal of the dies.
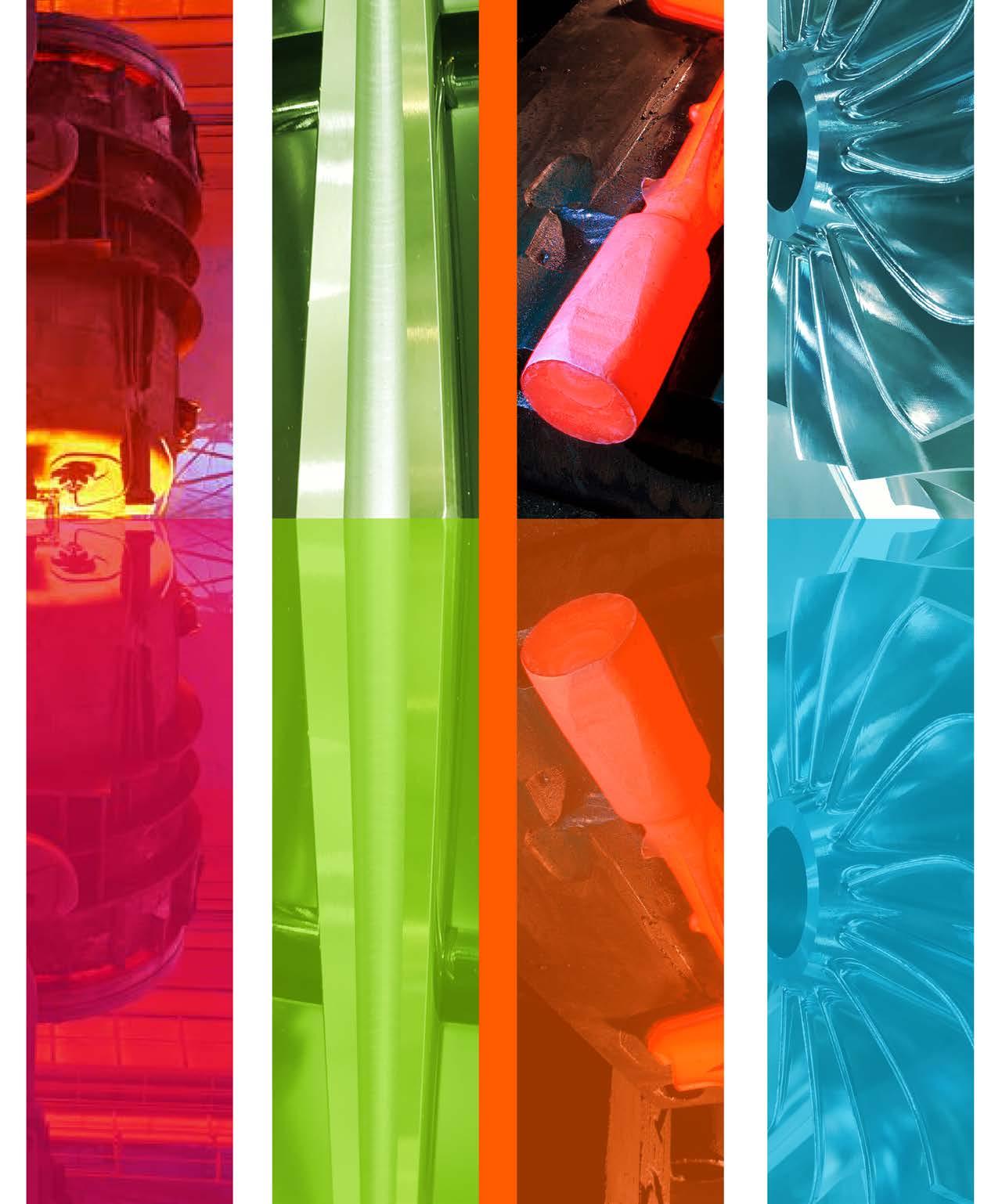
Tab.2 - Example Cost Savings.
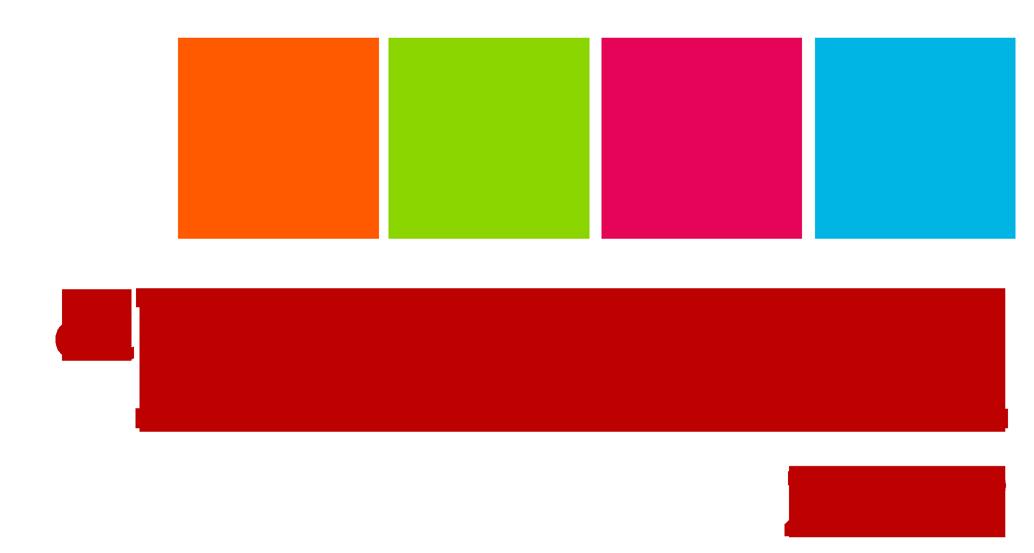
Oil pan for automotive industry Water based medium EcoSpray with concentrate Weight of the casting (complete) 15.000 g 15.000 g Cycle time 82 sec 77 sec Medium 1,8 l/cycle 5 ml/cycle Reject Parts 4 % 0,9 %
Waste water 100% 100%
Cost Savings total / year
Water/Waste water
Die life time (+50%)
Cycle time
Reject parts 197.000,- €
14.000,- €
77.000,- €
25.500,- €
80.500,- €
Bardolino · Verona · Italy, 15-17 June 2022
Organized by
Patronized by
In cooperation with
siderweb
THE ITALIAN STEEL COMMUNITY
Eventi AIM / AIM events
FaReTra (Fair Remote Training) - FORMAZIONE E AGGIORNAMENTO A DISTANZA
Modalità Asincrona (registrazioni)
Giornata di Studio PRESSOCOLATA IN ZAMA Giornata di Studio LA SFIDA DELLA NEUTRALITÀ CARBONICA Corso itinerante METALLURGIA SICURA Corso modulare TRATTAMENTI TERMICI Corso modulare I REFRATTARI E LE LORO APPLICAZIONI Corso GLI ACCIAI INOSSIDABILI 11ª edizione Corso FAILURE ANALYSIS 11a edizione Giornata di Studio PERFORMANCE E DEGRADO DEI MATERIALI METALLICI UTILIZZATI IN CAMPO EOLICO: CAPIRE PER PREVENIRE Giornata di Studio DIFETTI NEI GETTI PRESSOCOLATI: POROSITA’ DA GAS Corso PROVE MECCANICHE Corso di base LEGHE DI ALLUMINIO Giornata di Studio GREEN ECONOMY E ASPETTI AMBIENTALI PER L'INDUSTRIA DEI RIVESTIMENTI Giornata di Studio IL CICLO DI FABBRICAZIONE DI UNA VALVOLA. NORMATIVE, PROGETTO, ACCIAIO, FUCINATURA COLLAUDO Corso CORROSIONE PER NON CORROSIONISTI Giornata di Studio TECNOLOGIE DI FORMATURA DELLE ANIME IN SABBIA PER GETTI IN LEGA LEGGERA
FORMAZIONE E AGGIORNAMENTO IN PRESENZA (con possibilità di collegarsi da remoto)
Giornata di Studio IL RUOLO DEI MATERIALI NELL’ECONOMIA DELL’IDROGENO – Milano, 27 gennaio Corso modulare FONDERIA PER NON FONDITORI (F) – aprile/maggio Corso ADDITIVE METALLURGY (MFM-ML-MP) – marzo / aprile Giornata di Studio LO SVILUPPO TECNOLOGICO DEGLI IMPIANTI DI PRODUZIONE A CALDO DELLE VERGELLE ALTO CARBONIO E ALTO LEGATE E PER FILO SALDANTE (LPM) – marzo/aprile, Lecco c/o Caleotto Giornate di Studio GETTI STRUTTURALI (P) – Brescia, aprile Seminario TRASMISSIONI NELL’AUTOMOTIVE: DALL’ACCIAIERIA AL PROCESSO DI PALLINATURA (TTM) – 16-17 giugno, Modugno (Bari) c/o Magna Corso TRIBOLOGIA INDUSTRIALE (RIV) – 22-23 giugno webinar, 29-30 giugno, Modena Corso MICROSCOPIA ELETTRONICA IN SCANSIONE - SEM - III Edizione (MFM) – giugno Giornata di Studio RACCORDERIA E PRESSATURA. GLI ASPETTI METALLURGICI (LPM) – giugno, Suzzara c/o Intertraco Italia Giornata di Studio TRATTAMENTI PER LA RIMOZIONE DEL PIOMBO PER IL RICICLO DEGLI OTTONI (MTA) – primavera Corso di base SOLIDIFICAZIONE (MFM) –primavera Corso itinerante MACCHINA FUSORIA (A) - primavera / estate Corso MASTER PROGETTAZIONE STAMPI (P) – itinerante, 13 settembre-ottobre-novembre-dicembre
CONVEGNI
27° Convegno Nazionale Trattamenti Termici – Genova, 26-27 maggio 2022 http://www.aimnet.it/tt.htm
ESSC & DUPLEX 2021 - 11th European Stainless Steel Conference Science & Market & 8th European Duplex Stainless Steel Conf. & Exhib. – Lago di Garda, 15-17 giugno 2022 http://www.aimnet.it/essc.htm
39° Convegno Nazionale AIM – Padova, 21-23 settembre http://www.aimnet.it/nazionaleaim
ROLLING 2022 - 12th International Rolling Conference - ottobre 2022
L’elenco completo delle iniziative è disponibile sul sito: www.aimnet.it
(*) In caso non sia possibile svolgere la manifestazione in presenza, la stessa verrà erogata a distanza in modalità webinar www.aimnet.it
RAIDMAP 2021 Relazione finale
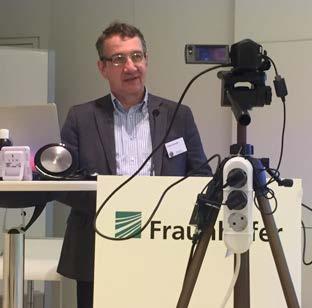
Si è tenuto il 4 e il 5 novembre 2021, presso la sede del Fraunhofer Forum allo SpreePalais di Berlino, l’evento conclusivo di RAIDMAP 2021. RAIDMAP (RAw IDeas for MAterials Projects) è un'iniziativa di formazione avanzata, supportata da EIT – Raw Materials, che consiste nel promuovere la collaborazione tra giovani studenti di ingegneria e professionisti del mondo delle imprese, per lo sviluppo di idee innovative riguardanti progetti di ricerca nel campo dei nuovi materiali e del riciclo e della sostituzione dei materiali. Partner universitari del Progetto sono la Scuola di Ingegneria dell’Università di Padova, il Royal Institute of Technology (KTH) di Stoccolma e il Norwegian University of Science and Technology (NTNU) di Trondheim, mentre i referenti tecnologici sono il Fraunhofer Institute e il Centro Ricerche Fiat. L’evento finale è stato organizzato in collaborazione con l’Associazione Italiana di Metallurgia.
All’interno del progetto RAIDMAP gli studenti di ingegneria, i rappresentanti delle imprese (sono state coinvolte le aziende Norsk Hydro, Enginsoft, SINTEF, Boliden Group e FerroSilva) e i tutor accademici hanno affrontato problemi tecnologici reali, attraverso un percorso che si basa su eventi opportunamente studiati per far incontrare le idee degli studenti con l’esperienza dei professionisti d’impresa, su questioni industriali attuali e su temi come l’economia circolare, il riuso e la sostituzione dei materiali.
Gli studenti seguiti dai tutor accademici e aziendali hanno sviluppato la loro idea progettuale, sottoponendola ad un evaluation board, composto da esperti di estrazione accademica e professionale. L’evaluation board di RAIDMAP 2021 era composto da Beate Brede (Fraunhofer Institute – Germania), Roberto Montanari (Università di Roma 2 – Italia), Fabio Ferri (EIT RM, CLC-S – Italia), Ferdinand Bulmer (EIT RM – Germania), Robert Eriksson (Jernkontoret – Svezia), Massimo Malaguti (Consulente – Italia), Lucia Protopapa (ENEA – Italia), Claudio Testani (APRE – Italia). Il coordinamento operativo dell’evaluation board è stato effettuato dalla Prof.ssa Lisa Biasetto dell’Università di Padova.
Nel corso dell’evento finale le idee selezionate sono state ulteriormente sviluppate ed elaborate, con particolare attenzione agli aspetti di fattibilità e di budget. Le idee progettuali sono state quindi presentate in un contest internazionale per verificarne il potenziale a diventare veri e propri progetti di ricerca, o startup nell'ambito dei bandi EIT – Raw Materials.
I gruppi selezionati per partecipare all’evento finale dell’edizione 2021 sono stati SLAM, ODD-W e FerroSilva.
Il Gruppo SLAM (Sustainable Lightweight Automotives with safe and economic Materials), che è risultato vincitore, ha presentato un progetto nel settore dell’automotive per la produzione industriale sostenibile di autoveicoli più leggeri, attraverso l’impiego di nuovi materiali e di tecnologie manifatturiere affidabili ed economiche.
Gli obiettivi di SLAM, che corrispondono alle sfide affrontate dal gruppo nella fase di sviluppo del progetto, fanno riferimento sostanzialmente alla riduzione del peso delle parti assemblate, e quindi dei veicoli, alla riduzione del carbon footprint del processo industriale e alla ottimizzazione dei parametri di progetto e produzione dei veicoli.
L’evaluation board di RAIDMAP 2021 ha ritenuto il progetto di particolare interesse sia per le ampie e positive ricadute in termini di sostenibilità ambientale ed economica
dei processi produttivi e del ciclo di vita del prodotto, sia per la formulazione attenta e chiara di obiettivi, metodi e costi del progetto.
Il Gruppo ODD-W (The On-Demand Digital Wharehouse) ha presentato una soluzione progettuale per l’introduzione della manifattura additiva nella gestione dei pezzi di ricambio di parti e componenti industriali.
I pezzi di ricambio infatti vengono spesso consegnati da punti di riordino che possono essere anche molto lontani dalla destinazione finale, con una logistica spesso scadente e scarse strutture di stoccaggio. Esiste quindi la necessità di ridurre i costi per il trasporto e lo stoccaggio dei pezzi di ricambio in molti siti produttivi.
Il progetto ODD-W propone una soluzione basata sull’impiego della manifattura additiva e di altri metodi dell’industria metallurgica per riparare le parti di ricambio danneggiate, attraverso tecnologie di reprint/repair/resurface.
Le ricadute positive del progetto ODD-W sono ampie e riguardano principalmente, per quanto riguarda direttamente lo stoccaggio, la diminuzione del capitale impiegato per l’immagazzinamento dei pezzi, la minor necessità di luoghi dedicati allo stoccaggio e del relativo personale, la riduzione dell’obsolescenza dei pezzi stoccati in cattive condizioni. Si riduce inoltre la footprint carbon per la minore attività di trasporto dei pezzi di ricambio, e il rischio di costi indotti dovuti al fermo di produzione per mancanza di un pezzo. Il Gruppo FerroSilva ha infine proposto una soluzione per produrre DRI (Direct Reduced Iron) utilizzando biomassa gassificata.
Gli obiettivi di aumento della produzione dell’acciaio, in considerazione dell’aumento della domanda globale, e di contemporanea riduzione delle emissioni di CO2 sono attualmente incompatibili senza l’individuazione di nuove soluzioni “green”.
La produzione di DRI utilizzando biomassa gassificata offre l'opportunità di una sensibile riduzione delle emissioni di CO2. Le industrie siderurgiche di un Paese produttore di acciaio come la Svezia, che ha costituito il contesto di riferimento di questo progetto, hanno inoltre il vantaggio della disponibilità di grandi quantità di biomassa da residui forestali, in presenza di un prezzo più alto per il gas naturale.
Il progetto ha una valenza di carattere strategico su scala europea, e può rivestire un interesse significativo all’interno dei futuri piani si sviluppo sostenibile basati sull’impiego di tecnologie green.
A conclusione dell'evento si sono quindi tenute le premiazioni di tutti i gruppi partecipanti e gli interventi finali di Franco Bonollo, Presidente della Scuola di Ingegneria dell'Università di Padova, di Beate Brede del Fraunhofer Institute, di Ferdinand Bulmer di EIT RawMaterials e di Lars Arnberg, docente del Royal Institute of Technology – KTH.
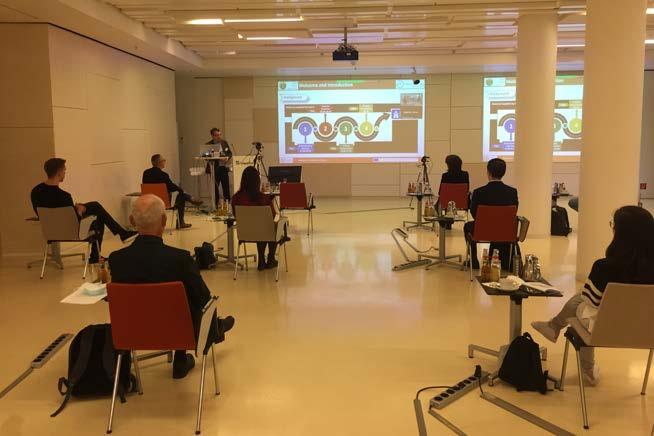
Metallurgia 2040
LA METALLURGIA E IL CONTESTO INDUSTRIALE E MANIFATTURIERO ITALIANO
È certamente ben noto il ruolo centrale del settore metalmeccanico nell’industria manifatturiera italiana, a cui contribuisce in misura del 47,7% in termini di valore aggiunto. È peraltro molto ben intuibile (a partire da banali considerazioni semantiche) come la Metallurgia giochi un ruolo chiave per l’industria metalmeccanica e manifatturiera, sia in maniera diretta (produzione di metalli e leghe, con una incidenza del 35,5%) che indiretta (attrezzature e macchinari per numerose filiere produttive).
→ Le leghe metalliche sono i materiali strutturali più diffusamente utilizzati nell’Ingegneria, in ragione della peculiare combinazione di resistenza, tenacità, costo e sostenibilità ambientale. → L’inter-settorialità della Metallurgia, e il suo impatto diretto e indiretto sulle varie filiere produttive è ben illustrato in termini generali nella Fig. 1 [1]. → La produzione italiana di metalli e leghe è essenzialmente basata sui processi di riciclo e rifusione del rottame, sempre più strategici in un’ottica di economia circolare.
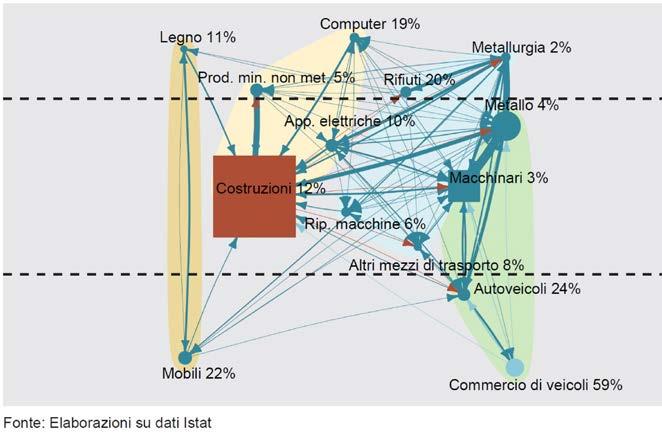
Fig.1 -Ruolo inter-settoriale della metallurgia nelle principali filiere industriali italiane [1].
Tra i materiali metallici essenziali per la produzione industriale, vi sono l’acciaio e le leghe di alluminio. → L’acciaio ha come principale settore di utilizzo quello delle costruzioni con una quota pari al 36,5%, comprensivo delle nuove costruzioni intese sia come investimenti del genio civile che nuove costruzioni private, oltre alle attività di manutenzione. Tra gli altri settori utilizzatori si ritrovano: la meccanica (20,2%), i prodotti in metallo (18,7%), l’automotive (17,1%), gli elettrodomestici (3,2%), gli altri mezzi di trasporto (2,7%) [2]. → Le leghe di alluminio sono sempre più strategiche nel settore della mobilità (39%), delle costruzioni (24%), del packaging, alimentare e sanitario (17%), della meccanica ad alto valore aggiunto (13%) e dei beni di consumo (7%), come illustrato in Fig. 2 [3].
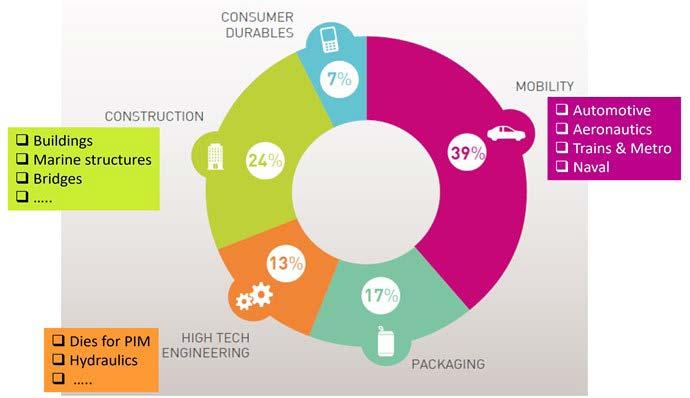
Fig.2 - Utilizzi industriali delle leghe di alluminio.
La metallurgia è anche un attore fondamentale delle sfide globali della trasformazione digitale e della sostenibilità, ambientale ed economica: → La digitalizzazione (simulazione, controllo, monitoraggio) dei processi può trovare validazione (e quindi reale implementazione industriale) solo se strettamente connessa alle interazioni tra struttura e proprietà delle leghe metalliche → Un settore ad elevatissimo livello di innovazione, come l’Additive Manufacturing, è necessariamente legato alla disponibilità di materie prime metalliche di elevatissima qualità e alla necessità di una conoscenza metallurgica di base per lo sviluppo e l’ottimizzazione di prodotti e processi (con particolare riguardo allo sviluppo di trattamenti termici e superficiali dedicati). → La sostenibilità ambientale e una reale concretizzazione del concetto di economia circolare, fortemente auspicate dalla comunità internazionale, non possono prescindere dai metalli, sia in termini di produzione di leghe ad elevate prestazioni a partire da rottame (le leghe metalliche sono gli unici materiali che, riciclati, non presentano un decadimento delle loro prestazioni e vengono riutilizzati per le medesime applicazioni), sia in termini di lightweight design, cioè di progettazione di strutture leggere e resistenti in grado di minimizzare i consumi energetici nel settore della mobilità, sia per quanto attiene all’ottimizzazione dei processi siderurgici e metallurgici (da rendere meno energivori e in grado di ridurre o re-impiegare le scorie generate); → La gestione delle terre rare, bene strategico (anche in termini politico-economici) per l’intero settore delle materie prime per le batterie e la mobilità sostenibile, richiede un accresciuto bagaglio di conoscenze sia di metallurgia estrattiva che di processi di recupero e riciclo. → Le criticità legate alla disponibilità e alla variabilità di prezzo dei semilavorati rendono necessaria, per le varie tipologie di aziende ed operatori coinvolti, una conoscenza di base dei processi metallurgici di trasformazione.
LA METALLURGIA NEL PIANO NAZIONALE INDUSTRIA 4.0. E NEL PNRR
È certamente utile esaminare gli esiti del Piano Nazionale Industria 4.0. Gli investimenti in beni strumentali per la trasformazione digitale delle imprese (strumento dell’iper-ammortamento, Fig. 3) sono stati nell’ordine dei 10 miliardi di euro, utilizzati prevalentemente dall’industria manifatturiera. All’interno della manifattura, il settore in cui l’investimento è stato maggiore è quello dei prodotti in metallo (26% del totale degli investimenti iper-ammortizzati) [4].
Numerosi sono anche, nel PNRR, gli ambiti in cui la Metallurgia può collocarsi a pieno titolo: - MISSIONE 1: DIGITALIZZAZIONE, INNOVAZIONE, COMPETITIVITÀ, CULTURA E TURISMO
Digitalizzazione, Innovazione e competitività nel sistema produttivo - MISSIONE 2: RIVOLUZIONE VERDE E TRANSIZIONE ECOLOGICA
Energia rinnovabile, Idrogeno, Rete e Mobilità sostenibile
Efficienza energetica e riqualificazione degli edifici - MISSIONE 3: INFRASTRUTTURE PER UNA MOBILITÀ SOSTENIBILE
Investimenti sulla rete ferroviaria
Intermodalità e logistica integrata - MISSIONE 4: ISTRUZIONE E RICERCA
Dalla Ricerca all’Impresa È peraltro significativo che nel PNRR l’acciaio venga menzionato un numero di volte confrontabile con quello di “Intelligenza Artificiale” e “Internet of Things”.
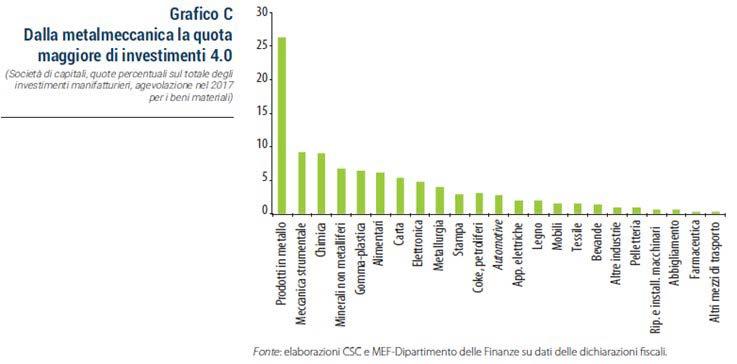
Fig.3 - Ruolo dell’industria metallurgica nel Piano Nazionale Industria 4.0.
GLI SCENARI FUTURI PER LA DIDATTICA IN METALLURGIA
Le principali analisi sulle professioni del futuro evidenziano un ruolo sempre più pervasivo, anche nell’industria manifatturiera e metallurgica, dell’Intelligenza Artificiale, dei Big Data e dell’Internet of Things [5]. È chiaro che queste tecnologie contribuiranno fortemente ad ogni futuro sviluppo industriale, ma non può essere sottovalutato il fatto che: → Serviranno nuovi profili professionali per gestire adeguatamente tali tecnologie, → Questi profili dovranno avere un ampio background metallurgico, proprio per garantire un utilizzo cosciente e consapevole (e non a-critico e ottuso) delle suddette tecnologie.
La formazione universitaria, nel settore metallurgico, è quindi chiamata ad alcune sfide: → Trasmettere, a tutti i livelli e nei vari contesti, una nuova visione della Metallurgia, sostenibile in termini ambientali ed economici, “pulita” e sicura, in grado di implementare l’innovazione digitale e “trasversale” rispetto a qualsiasi produzione industriale.