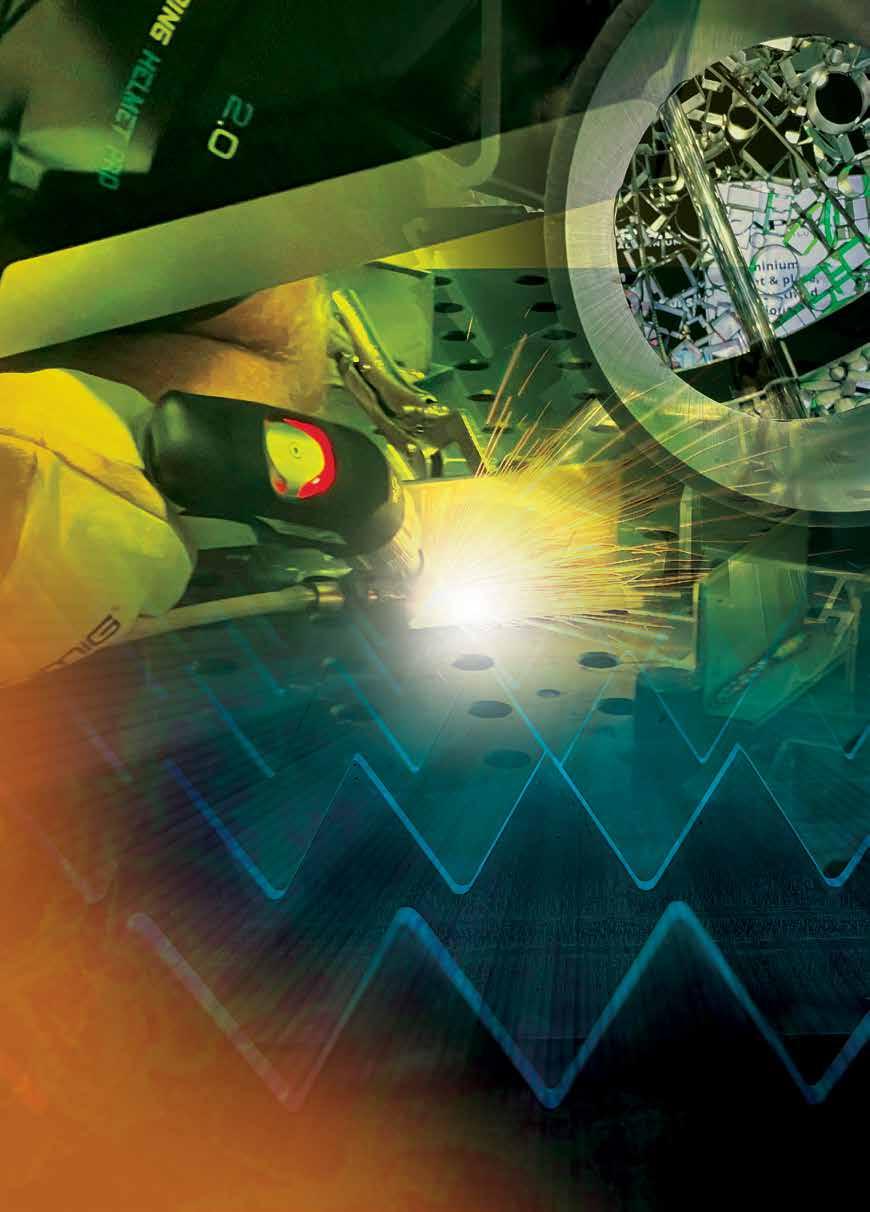
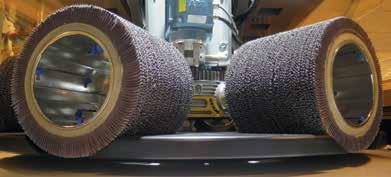

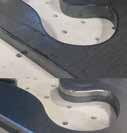
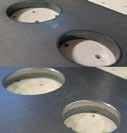
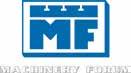

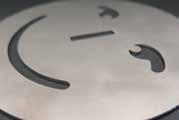

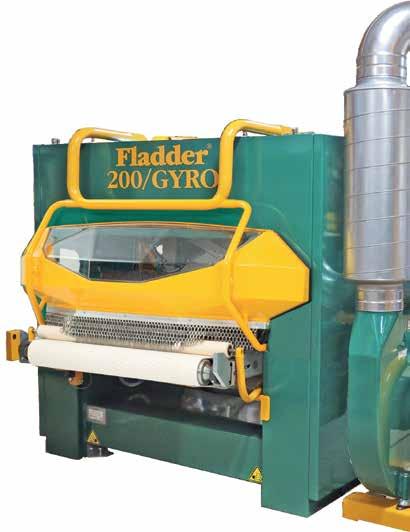
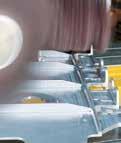
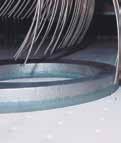

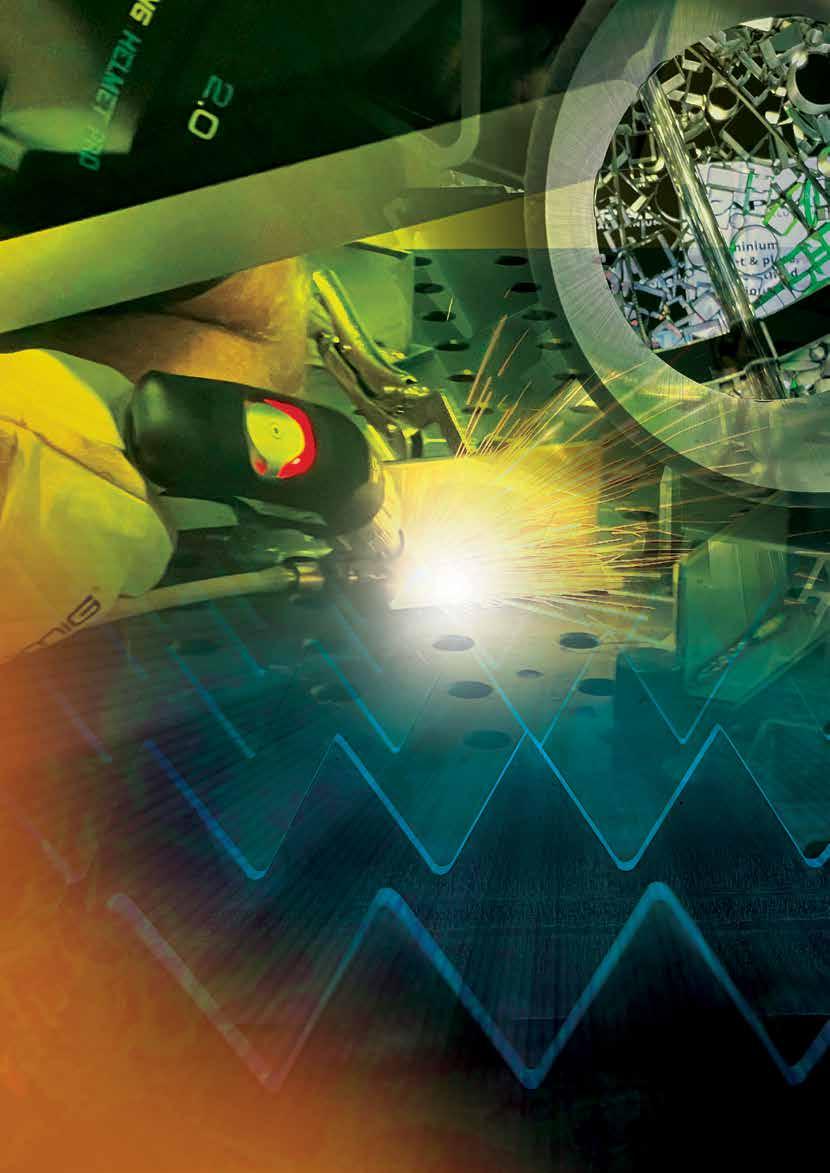
AUSTRALIA’S PREMIER MANUFACTURING SOLUTIONS EVENT




























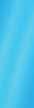






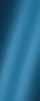
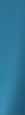


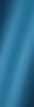

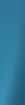













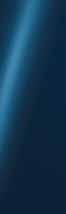




































MCEC MELBOURNE
10,900SQM OF EXHIBITION SPACE





348 EXHIBITORS




4DAYS









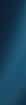













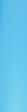




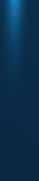
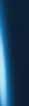


































7ZONES




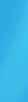
















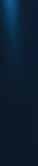








EXTENDED TRADING HRS!
AUSTRALIA’S PREMIER MANUFACTURING SOLUTIONS EVENT
MCEC MELBOURNE
10,900SQM OF EXHIBITION SPACE
348 EXHIBITORS
4DAYS
7ZONES
EXTENDED TRADING HRS!
BEFORE JUNE 30TH TO TAKE ADVANTAGE OF THE $150,000 INSTANT ASSET WRITE-OFF!
*NOW FOR BUSINESS UP TO $500 MILLION TURNOVER!
17TH & 24TH JUNE OPEN TILL 3PM SAT. Contact your accountant or business adviser to discuss your particular circumstance
The Beka Mak BMSY-440DGH Metal Cutting Bandsaw is a dual mitre, semi-automatic bandsaw which is ideal for larger steel fabricators. With a capacity of 600 x 400mm all Beka Mak bandsaws cut to their full capacity. The SemiAutomatic operation includes a full stroke hydraulic vice and dual mitre up to 60 degrees with a hydraulic mitre clamping mechanism that allows the operator to change angles in seconds.
440MM ROUND & 600 X 440MM (WXH) RECTANGULAR CAPACITY
MITRE BETWEEN +60° & -60° WITH DRO ANGLE DISPLAY INVERTER CONTROLLED VARIABLE BLADE SPEED 20-100MPM
WIDE SAW BLADE WITH SENSITIVITY CUTTING PRESSURE ADJUSTMENT.
• PLASMA NITRIDING COATING
• 28MM PRECISION BORED HOLES
• 100MM GRID LINES & PERIMETER RULER ENGRAVING
• 200MM HIGH SIDES WITH INTERLOCKING SOLID STEEL RIBS
• HEAVY POWDER COATED TUBE STEEL LEGS COMPLETE WITH LEVELLING CASTER WHEELS
The Metalmaster M28 Pro Series welding tables feature a fully welded heavy S355 plate steel construction that is CNC machined to achieve a high flatness tolerance of +/- 0.1mm over 1m2. The surface is treated with a plasma nitriding treatment to ensure a hard wearing & spatter resistant surface along with precision bored 28mm holes spaced at an industry standard 100x100mm grid pattern with diagonal style (additional hole in the centre) giving you almost endless possibilities for clamping applications.
METALMASTER ClearAir mobile welding fume bench is a compact all in one downdraft table with 1120 x 825mm work area (with fume shroud closed)
2000 X 1000MM 2400 X 1200MM 3000 X 1500MM
“Setting the standard for Quality & Value”
The METAMASTER Syncro series has been specifically developed to provide reliable & advanced bending features at an affordable price. With a range of machines from 40T to over 200T we have a machine to suit your needs.
ALL MACHINES ARE FITTED WITH THE SWISS DESIGNED CYBELEC TOUCH 12 CNC CONTROLLER WITH INTUITIVE 2D GRAPHICAL TOUCH DRAW PART PROFILE PROGRAMMING AND STANDARD WITH AUTO BEND SEQUENCING
5 CNC CONTROLLED AXIS (Y1, Y2, X, R, V) AS STANDARD
ITALIAN MADE LASERS & MONITORED SAFETY SYSTEM COMPLETE THE MACHINE WITH QUALITY COMPONENTS
The Metalmaster Deburr1380 manual deburring machine is the ultimate cost-saving solution for deburring, grinding, edge rounding and finishing of metal parts.
EDGE-ROUNDING
GRINDING
VARIABLE
The perfect addition to complement our METALMASTER M28 Pro Series welding tables, this starter kit will give you the basics while offering a wide variety of clamps & fixturing elements. The modular design makes it easy to set-up and tear down for your job at hand whether it is big or small. Increase precision & consistency for all your welding tasks to save you time and money.
ORDER
AUSTRALIAN MANUFACTURING WEEK 2023
Looking back at the week that was bigger than we thought it was going to be. A tremendous success for all the exhibitors, bringing manufacturing back into focus.
ONE ON ONE AMT interviews Dr Bronwyn Fox, Chief Scientist at the CSIRO.
56
AUSTRALIAN NATIONAL FABRICATION FACILITY AMT takes a look through the ANFF, and sits down with the CEO Jane Fitzpatrick.
58
SAMSARA EATING PLASTIC AMT finds out how an Australian startup is saving the Earth through a novel sustainable process.
There’s a lot to take in! But Okuma make your choice easy, bringing all the pieces together through innovative technology, quality manufacturing and comprehensive service and support, defining the Okuma experience.
We offer the leading edge of ‘full service’ distribution and lifetime support for Okuma CNC machines. Solution focussed, our team work with our customers to provide machining realities, with exceptional results.
Our team gives you immediate access to decades of industry experience and a network of local and global machine tool experts. We partner with you from the very first meeting, guide you through project planning and support you through implementation, training and after sales care.
CONTACT OKUMA FOR ALL YOUR CNC MACHINE REQUIREMENTS
The global deployment of solar power technology will be critical to the success of the global energy transition. As you’d have heard ad nauseum, digging resources out of the ground just won’t be part of the global energy future equation. When I say resources, I don’t mean coal, gas and oil (any more). By 2050, solar and other renewables will have to be the leading source of energy generation globally. This important energy transition is accelerating at scale and at pace, but geopolitical tensions and the COVID-19 pandemic have highlighted the fragility of Australia’s current supply chains and the risks associated with highly concentrated energy supply chains.
In the March 2023 edition of Resources and Energy Quarterly (REQ), there is an extended five-year outlook highlighting the medium term prospects of the resources industry. This includes industries producing the raw steel, copper, nickel, aluminium and other metals from which we build everything.
Short-term effects on these prospects include flooding of local mines and transport routes, and the fallout from the Russian invasion of Ukraine and a subsequent spike in energy prices, which are expected to boost resources and energy exports to a record $464bn in 2022–23.
Australia has world leading solar resources and a vast land mass that will allow us to facilitate deployment at scale. These advantages must be leveraged to meet Australia’s national targets of cutting emissions by at least 43% by 2030 and reaching net zero by 2050, enable the export of energy to other countries to help achieve their net zero goals and establish a local green hydrogen industry of global significance. It will require a rapid and large scale escalation in solar power installations and there will be challenges ahead.
The Australian Silicon Action Plan, generated by PwC and CSIRO, addresses the need for Australia to improve its standing in locally produced silicon for solar panel manufacturing from the abundant supplies of quartz. Local silicon of course should also be available for the local production of semiconductors and fibre-optics. However, the vast majority of the world’s silicon is produced in China. Renewable technologies will generate 90% of the world’s electricity by 2050, with solar PV the leading technology. The International Renewable Energy Agency (IRENA) has estimated that annual global solar power generation capacity must increase from the current level of one terawatt (TW) to 5.2TW by 2030 and 14TW by 2050 to stay on track to meet the Paris Agreement’s emissions goals. Global demand for thermal coal demand has passed its peak, with most proposed thermal coal-fired power plants now cancelled around the world. Falling prices are expected to reduce thermal coal earnings from $65bn in 2022–23 to $19bn by 2027–28. Australia has a genuine opportunity to emerge as a global superpower in solar PV manufacture, energy generation and export. We have the highest per capita deployment of rooftop solar in the world a great start. We also have world class solar resources and significant areas of land available for large scale solar arrays. However, one of the greatest risks to Australia’s solar ambitions and energy independence is our complete reliance on overseas supply chains for solar cells. Silicon, the critical mineral required for solar cell technology, has a highly geographically concentrated supply chain. This creates significant risks for the cost, reliability, and timeliness of new solar developments.
Editor Paul Hellard phellard@amtil.com.au
Contributors
Carole Goldsmith
William Poole
Drew Turney Ruza Zivkusic
Sales Manager
Nicholas Raftopoulos nraftopoulos@amtil.com.au
Publications Co-ordinator Caroline Robinson publications@amtil.com.au
Publisher Shane Infanti sinfanti@amtil.com.au
Designer Franco Schena fschena@amtil.com.au
Prepress & Print
Printgraphics Australia
AMT Magazine is printed in Australia under ISO140001
Environmental Certification using FSC® Mix certified paper sourced using sustainable tree farming practices.
Contact Details
AMT Magazine
AMTIL Suite 10, 5 Corporate Boulevard Bayswater VIC 3153
AUSTRALIA
T 03 9800 3666
F 03 9800 3436
E info@amtil.com.au
W www.amtil.com.au
Copyright © Australian Manufacturing Technology (AMT). All rights reserved. AMT Magazine may not be copied or reproduced in whole or part thereof without written permission from the publisher. Contained specifications and claims are those supplied by the manufacturer (contributor).
Disclaimer
The opinions expressed within AMT Magazine from editorial staff, contributors or advertisers are not necessarily those of AMTIL. The publisher reserves the right to amend the listed editorial features published in the AMT Magazine Media Kit for content or production purposes.
AMT Magazine is dedicated to Australia’s machining, tooling and sheet-metal working industries and is published bi-monthly. Subscription to AMT Magazine (and other benefits) is available through AMTIL Associate Membership at $190.00 (ex GST) per annum. Contact AMTIL on 03 9800 3666 for further information.
What a show we just experienced. I am pleased to report that this year’s Australian Manufacturing Week exhibition was a great success with most exhibitors reporting it as the best show we have ever run in our 23 year history.
On behalf of the Australian Manufacturing Technology Institute Limited (AMTIL), which owns and operates AMW, I would like to take the opportunity to thank the many organisations and people involved in putting on the event. First and foremost - the 348 exhibitors who put on a fantastic showcase and the 15,914 attendees (an all time record) - from 29 different countries - who came to visit Australian Manufacturing Week. In addition to the visitors we also had over 3,000 exhibitor personnel and over 300 students attend the show, making it almost 20,000 people involved.
I would also like to thank our contractors who largely go unnoticed in the overall scheme of putting on such a large event but are an integral part of making it happen. So at the risk of embarrassing some companies and individuals, I write this article to thank them and give our readers some insight into the mechanics of running our show. Thank you to Roger Motteram and his team at Harry the Hirer, including Igor Kolevski, Corinne Thomas, Leigh Provis, Philip Brightwell and Tim Whelan. The 4-6 months of daily pre-show email communication to ensure every “T” is crossed and every “I” dotted with our team ensured a smooth move in. The Begg trademarked “Sector” plan, which involved five sectors of carpet lay and stand build over five days, was well received by other contractors and certainly gave us a few laughs along the way. Over 15,000 carpet tiles were laid with a fair percentage of them having to be kicked back into place after being run over by fork lifts! Also thanks to the electrical and rigging crew led by Travis Wall and his team including of electricians and riggers, including Carla San Miguel Moreno, Steve Porter, Dan Owen and Derek Jensen. Safety is paramount during our move-in and move-out process and the challenge of having carpet laid, rigging done and crane movements all at the same time (along with everything else) was made easy by the professionalism of the HTH staff. An interesting fact is, that in order to provide power to all the stands and equipment, over 11kms of electrical cable needed to be laid in the carpark prior to the show.
Our logistics contractor GEL Events, ably led by the “Freightman” Michael Stubbs, again did a great job of controlling the logistics of freight, loading dock chaos, fork lifts and crane movements. Special thanks to Michael Barker, Fiona Ganatzos, Heath and Tony for an outstanding effort. To be on-site from 6.00am until 10.00pm most days and be organised and flexible at the same time takes a great deal of management and patience. The nightly debriefs in Sector Six always came with a few laughs too! And of course the L Arthur crew led by Mark Van Namen did an outstanding job coordinating the 210 crane lifts and over 300 lifts in total of machines weighing in excess of 5 tonne. F Wood and Son is our plumbing contractor and well done to Paul Wood and Bryan Campbell on another smooth show. It was great to also see a couple of apprentices also working on our show. Thanks to Alana and Mark behind the scenes for getting the administration done.
Thanks to Derek Metcalfe and the guys at Infrabuild, with some late changes to our schedule being easily accommodated. Another interesting fact is that we recycled over twelve tonnes of swarf and scrap metal generated by exhibitors at the show.
Thanks to our gas suppliers, Peter Kuebler at BOC Technologies and Scott Sutton at Coregas, again accommodating some rushed changes to our schedules and late orders being placed. Interesting fact: On the Thursday prior to the show opening, 55 gas packs were delivered to the venue and each morning of the show a number of stands had to have gas pack changeovers.
Thanks to Christian Wood at Cryocut for supplying and removing over 3,000 litres of cutting fluid and meeting all the exhibitor requirements.
Thanks to Mark Shenoda and his team at AGE Electrical for testing and tagging all the electrical leads.
Thanks to Judith Graham at Monash Tech School and Jack Parr at the Vernier Foundation for pulling the student tours together. Getting our next generation of employees interested in our industry is a significant activity.
Thanks to Jamie McGuiness at IKON Cleaning for being so accessible each and every day. Cleaning is often a thankless task, so good on your team for having our show looking so good at opening time.
Thanks to Christian Cramp and Kevin Alexander and his team at Australian Security Services, including Julie, Kavina, Bill, Muhammad, Walter, Else and Mustafa. Your smiling faces each morning and evening was great to see. Interesting fact: we clocked up 1018 manhours of security during the show.
Thanks to the MCEC venue staff and their Operations Manager Sheldon Fernandes for his appreciation of our efforts. Quite understandingly the MCEC has very strict guidelines and safety considerations and liaising with Sheldon to provide a safe working environment provided an excellent outcome. Thanks to Laura Waples, Miranda Pertzel , Jason Stuckey, Scott Sandilands and to Steve and Mick, working the dock and behind the scenes to help make everything happen.
Thanks to our registration providers, LUP Events. To Jenny Byard and Gemma Stonem in the lead up to the event, thanks to you. Great effort by Joseph Obsioma and his team on site to manage the record number of registrations and help out when we looked like running out of lanyards.
Finally, thanks to my team led by Kim Banks, Anne Samuelsson, George Joshua, Dea Stavar, Julie, Caroline, Paul, Nick, Greg, Franco and Koulla on another outstanding show. Our show plan has 543 task items and each one of them has been managed and ticked off on time on budget. Great effort team and an outstanding result!
One of the great pleasures of my job as Industry Minister is the wide variety of people I meet from across our diverse manufacturing sector.
Their points of view may vary, but their optimism about the sector’s future shines through. It’s also pleasing to see they are strongly committed to a thriving and sustainable manufacturing sector. Australia was left badly exposed by global logistics failures during the COVID-19 pandemic, something the Australian Government wants to rectify by supporting the growth of more extensive domestic value chains. Our manufacturers recognise that too and are boosting R&D spending, commercialising new innovations, upskilling their workforce, and embracing new and advanced technologies. A thriving advanced manufacturing sector is critical to Australia’s future economic prosperity and national security.
One way the Australian Government is enabling that is through our $15 billion National Reconstruction Fund. We expect the fund to become operational in the second half of this year, providing new opportunities for loans, equity investment and guarantees across seven priority areas. In the meantime, we have been advancing other initiatives across government so we can capitalise on emerging opportunities.
One of these is quantum technologies – a field where Australia’s research capabilities are among the world’s best. Quantum technologies will form a $1 trillion industry globally in coming decades. Updated market projections by CSIRO have shown that quantum technologies are forecast to reach $6 billion and generate more than 19,000 jobs in Australia by 2045.
Around Australia, universities and research institutes have nurtured internationally respected figures like Professor Warwick Bowen who, in 2021, led development of the world’s first quantum microscope at the University of Queensland. Incredible Australian companies are also emerging from our research pedigree, from Silicon Quantum Computing and Diraq in quantum computing, to Q-CTRL and Quintessence Labs in quantum software and cryptography, to Nomad Atomics in quantum sensing. And Australian companies and research institutions are collaborating with industry partners to translate their discoveries into practical applications in advanced manufacturing, agriculture, aerospace, defence and biotechnology, to name but some.
The Government has launched Australia’s first National Quantum Strategy so we make good on our competitive advantages. This will set our long-term vision of how we translate our research strength into more concrete businesses that will grow our economy and create jobs, by:
• Guiding the development of industry-relevant applications of quantum technology
• Reaffirming our commitment to quantum technologies and building a sustainable, world-leading quantum economy
• Identifying the areas we need to focus on to support industry growth and capability, and
Through the $1 billion Critical Technology Fund – which is part of the broader NRF – the Government will help to support homegrown innovation and production in quantum and quantum-related areas like engineering, data science, software development, AI, and robotics. Australia also has international collaborations and partnerships in place that will create or boost opportunities for Australia quantum businesses. The Quad agreement with the US, Japan, and India, for example, will accelerate quantum investment and capability. Our trilateral AUKUS security pact will also involve
information sharing and critical technology cooperation. These and other agreements will also help to establish norms and technical standards that support technology interoperability and our shared national and strategic interests.
We want more Australians involved in the standards-setting process – and we’ll upskill Australian industry, researchers and technical experts to enable that to happen. Support for critical technologies is also high on the government’s agenda.
In 2022, we announced a review of the List of Critical Technologies in the National Interest to better capture the opportunities while managing the risks of those current and emerging technologies that will help us reach our long-term economic, social, and environmental objectives. Artificial Intelligence, robotics and clean energy generation and storage are just some of the areas that Australia must prioritise to ensure we are ready for the industries of the future.
The updated List identifies seven key enabling technology fields. The inclusion of clean energy generation and storage technologies recognises not just the imperative to transformation to a low-carbon economy but the economic opportunities this transformation will create.
Australia’s capabilities in clean energy generation and storage are already significant. We are advancing important photovoltaic and renewable energy storage technologies, and we’re continuing to make breakthroughs. We are also a leader in adopting the integration of renewables into the grid.
With our strengths in mining and mineral processing, Australia is well on the way to creating new clean energy-related industries with significant export potential. Accompanying the 2023 Critical Technologies List is a Critical Technologies Statement that will set out the Government’s commitment to the seven key enabling technologies fields.
The statement will provide a national strategy and common vision and ensure all stakeholders are working together and across the research, investment, talent attraction and international collaboration sectors. It recognises that critical technologies industries are essential to Australia’s economic prosperity, as well as our geopolitical and security interests.
The advent of digital and emerging technologies offers us a historic opportunity to supercharge our manufacturing sector.
The Australian Government believes in this opportunity for Australia, and we will back innovative and forward-looking manufacturers to lead the way. Working together, governments and businesses have already achieved a noticeable uptake of digital technologies since COVID-19, particularly in manufacturing.
That optimism I encounter during my interactions with our business owners managers and investors is not misplaced. In its Advancing Prosperity report released in March, the Productivity Commission said taking advantage of the opportunities afforded by quantum, AI and other digital technologies will require (among other things) that governments and businesses continue to adopt and support innovative models.
With appropriate policies, guidance and regulations, the Australian Government intends to do just that. industry.gov.au
Before COVID-19, Australian industry was evolving to adopt Industry 4.0 practices and technologies. One of the most important dimensions is robotics – promising to transform how humans and machines work together in manufacturing.
In our submission to the Government’s National Robotics Strategy consultations, Ai Group highlighted the areas that demand attention for robotics uplift in industry. Assistance with strategy and business model transformation, skills development, research and investment will all prove critical.
Robotics and assistive technologies are an integral component of Industry 4.0 transformation. Smart sensors, additive manufacturing, robotics, mobile connectivity, human-machine interfaces, big data analytics, cloud computing and augmented/virtual reality all work together to enable integration and automation at the systems level. Robotics has already found a place in Australian industry. Data on the uptake of robotics is available from Ai Group’s futuremap® platform, a business diagnostic designed to assist manufacturers and related industries to adopt Industry 4.0 practices. Since its launch in 2018 by the Innovative Manufacturing Cooperative Research Centre (imcrc), nearly 1200 Australian businesses have completed the futuremap® tool.
Using data gathered from futuremap®, Ai Group has identified that:
• 33% of Australian industrial businesses were using robotics and assistive technologies at the time they completed futuremap®;
• 32% of businesses were not currently utilising robotics, but were exploring its use;
• Robotics utilisation rates vary between subsectors – from 21% in chemicals to 54% in petroleum and coal;
• Robotics use is generally higher in industries with greater human involvement in material flows, where robots enable more efficient and safer materials handling; and
• Robotics use is not necessarily correlated with the technology content of the final product. Some less technology intensive products (such as basic metals manufacturing and coal products) have above average rates of robotics use. While robotics has already found a foothold in Australian industry, there is considerable room for growth. For every business currently using robotics and assistive technologies, there is another business exploring their use.
Robotics adoption ‘makes sense’ when it is embedded in a broader set of digital-driven industrial managements practices. To improve the uptake of robotics technology by the one-in-three businesses currently exploring it, policy needs to target the broader adoption of Industry 4.0 practices.
In our submission, Ai Group suggested that businesses exploring robotics should be offered support across a range of Industry 4.0 technologies and practices to update their manufacturing practices. Such support measures should also be appropriately scaled and accessible to SMEs as well as the larger enterprises.
Many SMEs are progressing Industry 4.0 strategies without using the label. Instead, their primary objectives are to better manage their operations, become more energy efficient, improve productivity, lower costs or meet new demands from customers. Robotics should be added to the list of reasons to pursue deeper manufacturing automation.
However, skills needs will be one of our major challenges. Advanced manufacturing needs a mix of technical/specialist, generic and leadership skills. However, robotics will increase the importance of digital skills within the industrial skills mix. Digital connections
are the essence of Industry 4.0, and skills in the digital space will be essential for not just specialist roles but the entire industrial workforce.
Data from Ai Group’s national Skills Survey of 2022 reveals what manufacturers need. The top ranked priority was basic digital skills, which will be required in every role for successful systems integration. Human-machine interface skills – the ability to work effectively, productively and safely with robotics – ranked a close second. Programming and coding skills also ranked highly. Most Australian universities that offer engineering training include robotics in their qualifications. However, as technology evolves at increasingly rapid rates, there is a need to ensure that those studying robotics have access to the workplaces that are using the most up-to-date technology. Work-integrated learning should become the norm for university programs in robotics and related digital engineering fields.
In the VET sector there is some robotics-oriented training on offer, but coverage is far from comprehensive. Some organisations are addressing the gap by developing micro-credentials or short courses to train workers to program or work alongside robots. An investment in the development of nationally available training resources would be a valuable initiative to help workers develop their skills.
Robotics are only an enabler of industry, not an end in themselves. However, they are critical in supporting the scaling of a business and improving international competitiveness. As the economic drivers shift to make the return on investment more attractive for small to medium businesses, more work needs to be done to ensure industry and the workforce are equipped to deploy robots more widely.
aigroup.com.au
On Friday 5 May, the Lake Liddell Recreation Area outside Muswellbrook was the best place to be in the country.
That Friday, power plant workers, union leaders, environmental groups and two federal MPs – Minister for Climate Change and Energy Chris Bowen and Member for Hunter Dan Repacholi –gathered to take in the view across Lake Liddell.
We were there to announce the formation of the National Net Zero Authority (NNZA). The name itself is a bit vague, but the intent is crystal clear. The NNZA will be a federal government authority to oversee a Just Transition for traditional mining and energy workers, their families and their communities.
Two of Australia’s largest power plants back onto the lake. For the past 50 years, Liddell and Bayswater power stations have supplied much of the energy to Australia’s east coast. The energy transition from fossil fuels to renewables has seen Liddell shut down, with Bayswater not long to follow. But their closure doesn’t have to be a bad thing for the workers who kept them running for decades.
The AMWU has been working towards a Just Transition for communities like the Hunter for a very long time. Thousands of our members are employed at places like Liddell and Bayswater. When I started at the union as an organiser, those power stations were part of my patch.
Those power stations weren’t just places to work. For generations of workers in the Hunter, Liddell and Bayswater were their whole working lives. They formed the backbone of entire towns – not just economically, but in terms of identity.
In April, Liddell’s last unit shut down for good. At the moment Bayswater is scheduled to shut sometime between 2030 and 2033, but with energy companies moving closure dates for coalfired power plants closer and closer, the actual date could be much sooner.
For years, workers at Liddell, Bayswater and power plants all over the country watched with fear and alarm as closure dates were announced and began creeping closer. A way of life that had underpinned decades of prosperity and security for local workers was fading away, and in its place was nothing.
Compounding that fear was a feeling that workers were facing this enormous challenge alone. Instead of facing up to the difficult
reality that the world was changing, governments preferred to wage imported culture wars in parliaments and on the front pages of newspapers. Politicians played dress-ups in hi-vis and smeared coal dust on their faces for the cameras while workers wondered how they were going to pay their mortgages and what their kids were going to do when they left school.
While Canberra was wasting time, AMWU members were talking with their workmates about what the hell we were going to do about it all. The writing was on the wall – the shift was on to renewables. If it was up to the energy and mining companies, they would shut down as soon as their operations became unviable and hang the workers who made their profits out to dry.
Government wasn’t acting, and business didn’t care. So we had to come up with the solutions ourselves.
In mining towns like Collie in Western Australia, that meant bringing people together who had spent a long time facing off. Getting energy and mining workers, unions, environmentalists, local councils and industry in a room together even once was a massive ask. Doing it month in, month out for years to hammer out a plan that would give workers secure, well-paid work in new industries should have been impossible.
Plenty of people said it couldn’t be done – until we went and did it. At the time of writing, the Collie Just Transition Working Group has secured more than $660m in state government investment to retrain and reskill energy and mining workers, diversify the local economy, and attract major projects to town that will create hundreds of good blue-collar jobs.
It’s a remarkable achievement, but Collie’s a town of just under 9,000 people. We want the NNZA to do what the Collie Just Transition Working Group did for every traditional energy and mining community in the country. Backed by federal government funding, with statutory powers to compel energy and mining companies to the table, and with the heft to attract billions in private investment to communities that need it, the NNZA can make sure that not one worker – full-time, part-time, contract or subcontract – is left behind during the energy transition.
amwu.org.au
HG Farley LaserLab Australia - manufacturing Plasma, Laser & Waterjet Machines for 50+ years and now offering both Low and High end machinery - Giving every workshop a solu�on that can start small and grow large.
W.A.L.C FIBER LASER BEVEL MACHINE
up to 30kW FIber Laser Source
up to 4.5m Width
up to 30m Length
up to 40mm MS, SS & AL
Bevel Cu�ng
High Pressure Air Cu�ng
TRUEDGE PLASMA, BEVEL, OXY & BT50 DRILLING Machine
BT50 30 x Auto Tool Changer
Drill up to 100mm Diameter
Tap up to 40mm Diameter
Hypertherm XPR300 Plasma Unit - 40mm MS
ImaTechno Bevel Cu�ng
IHT Auto Gas Oxy/Flame Torch - 200mm MS
Australian Made Machine
Showcased at Austech 2023 - STAND MT500
FARLEY AUSTRALIAN MADE MACHINES:
QuikEDGE Plasma Machine
ELF Plasma Machine
TruEDGE Plasma, Bevel, Drill + Oxy Machine
Op�onal Cut Tables + Parts (in-house fabrica�on)
Farley LaserLab Machinery Range Installed in Australia - Ask for a Local reference for each machine
Queensland Government unlocks $10m of manufacturing grant funding.
Queensland manufacturers have access to $10m in funding, under Round 3 of the Queensland Government’s recently announced Manufacturing Hubs Grant Program.
The MHGP gives local manufacturers a new opportunity to get financial help for business-expanding initiatives, which will create more good jobs and better services in the region.
The funding boost, which was secured in the 2022/23 Queensland Budget, meant even more manufacturers would have financial support as they modernised and transitioned to manufacturing 4.0 processes.
These grants are an opportunity for manufacturers to become more productive, build advanced manufacturing capabilities and create the jobs of the future through:
• technology adoption
• skills and training
• business development
• advanced robotic manufacturing hub services.
Grants between $10,000 and $500,000 are available for eligible manufacturing small to medium enterprises in the Cairns, Townsville, Central Queensland, Mackay and the Gold Coast regions.
To date, the MHGP has awarded more than $13m to co-fund 49 projects in regional areas, including for business development, technology adoption, skills and training across the five eligible regions throughout Queensland.
Following a review of Rounds 1 and 2, the application process for Round 3 has been simplified to ensure as many people as possible can access grant funding.
rdmw.qld.gov.au/regional-development/mhgp
Supporting the growth of Australian quantum jobs and industries.
The Tech Council of Australia (TCA) welcomes the Australian Government’s National Quantum Strategy (the strategy) released by the Hon. Ed Husic MP, Minister for Industry and Science. The strategy outlines a roadmap for the future of quantum technology in Australia. Kate Pounder, TCA CEO, said the strategy is a pivotal step in cementing Australia’s leadership in this critical sector.
“The Tech Council of Australia, home to the Australian Quantum Alliance, welcomes the Government’s release of the National Quantum Strategy. The National Quantum Strategy provides national leadership at a crucial time for Australia’s quantum industry.”
“Quantum technology is at an inflection point. Australia is a leader in the research and development of quantum technology. We have built leading homegrown companies, and attracted some of the world’s leading global companies in quantum to undertake research in Australia. This strategy is an important step for Australia and highlights the significant opportunity for increased commercialisation of quantum technologies.”
“The strategy builds on the momentum from the Australian Government’s $1bn commitment to critical technologies under the National Reconstruction Fund, the recent announcement of a
$3.4bn Advanced Strategic Capabilities Accelerator in response to the Defence Strategic Review, and the Australian Quantum Graduates Program.” “Our challenge is to now become a leader in commercialisation. Early commercialisation will deliver billions of dollars in economic value and thousands of jobs by 2030 globally and in Australia, while supporting our strategic and national security objectives.”
“We welcome the strategy’s focus on improving investment and commercialisation opportunities for quantum in Australia as these are crucial to get right.” “We have strong foundations to build a globally successful quantum sector right here in Australia – we are already home to more than 3% of global quantum start-ups and are attracting 3.6% of global venture capital investment, well above our 1.6% share of global GDP.”
“Our strength in quantum has been the product of strong government support for decades, and we look forward to working with the Government to build on these existing measures and help propel our quantum sector toward an even brighter future.” techcouncil.com.au
Treasurer Jim Chalmers has a $70bn a year budget hole: the Grattan Institute found 13 ways to fill it. Kate Griffith, Danielle Wood and Iris Chan have some ideas in this piece originally published in The Conversation.
No one likes spending cuts and tax hikes, but on our estimate the government will soon need more of them if they are going to make a dent in looming A$70bn a year budget deficits.
A new Grattan Institute report, Back in Black? A menu of measures to repair the budget argues the present combination of low unemployment and high inflation makes this a good time to start to put things in order.
The sooner we do, the sooner we will be well-placed to respond to future economic shocks and avoid pushing costs onto future generations.
The massive government support unleashed during the 2020 and 2021 lockdowns was essential for supporting households and businesses and helped keep unemployment low and Australia’s 2020 recession mild.
It left us with government debt that, at 23% of GDP, set to climb to almost 32% by the end of the decade, is high by historical standards, but low by international standards.
Our real problem is a structural one of spending growing faster than revenues. And it was building long before COVID.
Costs are inexorably growing for three reasons. The first is that our expectations are growing as we age and become more wealthy, pushing up spending on healthcare, disability care and aged care. The second is that many of these services happen to be the hardest to mechanise, meaning there is little we can do to stop them costing more over time.
The third reason is geopolitical and climate developments. The huge AUKUS deal is just the latest manifestation of pressure to ramp up defence spending. Increases in the frequency and severity of natural disasters mean we have no choice but to spend more on emergencies than before.
Combined with higher interest rates that are pushing up the cost of servicing debt, these three forces are set to leave a persistent gap between government revenue and spending of about 2% of GDP according to Treasury calculations. That’s $50bn per year in today’s dollars, each and every year.
Grattan Institute estimates suggest the true structural gap exceeds $70bn per year when extra, largely unavoidable, spending is taken into account – including on AUKUS, overdue wage rises for care workers, more realistic growth in hospital spending, and longoverdue increases in unemployment benefits.
And that’s just the next decade. In the longer term, the budget will come under extra pressure from slower productivity growth, Australia’s ageing population, and climate change.
Higher economic growth and productivity growth would reduce the enormity of the challenge, and Grattan Institute has put forward ideas about how to support this before.
But hoping we will be able to grow our way out of chronic budget deficits is not a prudent approach. While we should try to boost growth, by itself it is unlikely to get the nation’s finances onto a sustainable trajectory.
13 multibillion dollar ideas
The size of the problem, and the political difficulty of budget repair, mean both spending and revenue measures need to be on the table.
Cyclical component includes cyclical movements in commodity and asset prices. Temporary fiscal measures include COVID-related direct economic and health support. Data are for financial year. Source: Treasury, October 2022 Budget.
Solid bars represent projections from the Parliamentary Budget Office, patterned bars represent additions from Grattan Institute analysis.
Spending cuts have been the focus of budget repair efforts for most of the past decade, so a lot of the low-hanging fruit has already been picked. But there are still savings to be had.
The biggest would come from greater discipline in decisions about what to spend on infrastructure and defence. Better decisions upfront based on economic – rather than political – considerations could save several billion each year.
Our report identifies a further $15bn a year of savings measures, including undoing Western Australia’s special GST funding deal, counting more of the family home in the age pension asset test, and improving hospital efficiency and purchasing in health.
Tax breaks and minimisation opportunities are growing. Reining in superannuation tax concessions, reducing the capital gains tax discount, limiting negative gearing, and setting a minimum tax on trust distributions could collectively raise more than $20bn a year.
Reworking the legislated Stage 3 tax cuts so they are less generous at the top end would save another $8bn per year.
Lifting the age at which people could get access to their super from 60 to 65 and freezing compulsory super contributions at their present level (10.5% of salary) would save at least another $8bn.
Other options include lifting the rate of goods and services tax (with a compensation package, and the Commonwealth and states sharing the net revenue), winding back fuel tax credits and beefing up the petroleum resource rent tax.
This article was originally published by The Conversation theconversation.com/au
Value of purchasing locally manufactured vibratory equipment proven again.
Based at the top of Yorke Peninsula in South Australia, Daniel Seed specialises in seed cleaning and grading for a variety of crops, primarily lentils but also wheat, barley, vetch, oats, peas and beans. Seed cleaning and grading has become one of the most important farming practices ensuring that weed seeds, chaff, dirt and other non-seed contaminants are removed allowing for the best seeds to be sown whilst maximising seeding productivity.
The grading process removes only unwanted weeds and poorquality seed from each load ensuring the heavier, better quality seed remains. Larger seeds generally have better vigour and are the best start to greater yield, thereby ensuring maximum returns for the farmer.
Owner Peter Daniel was facing an issue with his production line that was operating two gravity cleaning tables fed by two individual surge hoppers. The issue related specifically to the imported vibratory feeders that were not performing to the level required both in terms of throughput per hour and flow control – both crucial factors to ensure the productivity and smooth running of the lines.
“We were hoping to get 7TPH (tonnes per hour) out of the imported feeders and they were barely managing 4TPH – they didn’t even perform to the factory specs,” Daniel said.
It was a simple Google search that led Daniel to Enmin. For over 40 years, Victorian based Enmin has been a market leader in Materials Handling and Vibratory Equipment for a diverse range of applications with particular expertise in the food and allied industries.
“As soon as I spoke to the people at Enmin I could tell they were very professional and specialised in this area. That gave me the confidence to deal with them and ultimately purchase two vibratory feeders,” said Daniel. The feeders came with Enmin’s LD4 electromagnetic drive (the only drives manufactured in Australia) and a CV6 controller.
“Easy fine tuning to regulate grain flow is critical and this is where Enmin’s controller, with its pinpoint accuracy, comes into its own,” he said.
“Enmin’s product knowledge was excellent; they listened carefully to our needs to ensure we received the right solution. The quality of the product was also excellent and we found their equipment had a very good reputation in the marketplace. Being an Australian manufacturer was also an important factor for us in our purchase decision as we knew that back-up and support was just a quick phone call away,” Daniel added.
“The units were installed in late January and we’re very happy with the performance so far – they’re operating 12-14 hours per day and their output seems well suited to our requirements, having tested them with lentils, wheat and beans to date. The Enmin units will ensure we achieve an 8TPH per feeder throughput, which is higher than we were originally looking for,” he said.
“Enmin’s customer service across both sales, design and manufacturing was outstanding. They delivered on time and did everything they said they would – we’ve been very impressed,” Daniel added.
“Whilst lower cost equipment from overseas may initially seem an attractive proposition, it is ultimately false economy. In the long-term product quality and performance, quick delivery turnaround and the ability to work closely with us during every phase of the project far outweighs any price difference. In terms of return on investment, there is simply no comparison,” Enmin’s Sales Manager, Paul Leahy summed up.
In addition to its vibratory and materials handling products, Enmin also has an extensive range of Industrial vibrators to suit any industry that handles bulk material. The ‘Flow-Easy’ range is specifically designed to suit Australia’s environment and covers a multitude of applications such as mining, quarrying and agriculture. enmin.com.au
Meeting all specifications with diode-laser-based brake disc claddings, a Laserline coating process taking under a minute enables cost-effective mass production
In order to counteract the health hazards posed by particulate matter, the EU has for the first time also included dust from braking systems within the new vehicle emission standard, Euro 7. Diode-laser-clad hard coatings enable reliable compliance with all specifications, reducing brake dust with a maximum particle size of PM10 by up to 90%. The series-ready cladding process developed by Laserline enables cost-sensitive mass production for all market segments. One of the greatest health hazards in urban areas is particulate matter emissions from road traffic. Particulates are suspected of causing allergies as well as respiratory, cancer and cardiovascular diseases. Combustion engine emissions are not the only source of particulates, as disc and pad wear in vehicular braking systems itself generates about a quarter of the total. In the draft Euro 7 vehicle emission standard –due to come into force in 2025 – the EU Commission takes account of this fact and for the first time sets specific limits for particulate emissions from braking systems. These limits equally apply without exception to electric vehicles, the latter thus being affected for the very first time by the EU regulations on pollutant emissions from motor vehicles. Automobile manufacturers are now faced with the universal challenge of significantly reducing particulate emissions from braking systems.
One of the most effective measures for reducing brake dust emissions is to apply hard coatings by using a diode-laser-based cladding process, where said claddings offer long-term protection against abrasion and corrosion. The component of healthendangering particulate matter as generated by vehicle braking –tested at PM10, so 10µm and below –can thus be reduced by up to 90%. The new Euro 7 emission standards are expected to specify an overall average of 7mg/km of PM10 particulate matter, and this can be reliably met. Fortunately, in order to apply these coatings, both the standard gray cast iron material used for brake discs as well as the conventional production processes remain unchanged – a supplementary production step applies the cladding after completion of the original brake disc.
Together with its technology partners, diode laser specialist Laserline has developed the process setup of this procedure to series maturity and has additionally ensured integration suitability within Industry 4.0 production environments. Using diode lasers with OPC UA interfaces and up to 22kW output power, powder-based highspeed cladding processes are utilized, and in some cases leading to a process time of less than one minute per brake disc. Coupled with appropriate use of materials to yield very effective and at the same time cost-effective claddings, mass production of brake disc cladding becomes affordable for all automotive market segments, even for vehicles in the medium and lower segments. Lastly, further cost considerations indicate specifying a higher power laser in order to achieve a higher throughput, which saves on production space by reducing the space requirements and in turn ultimately significantly reduces the relative investment per disc. raymax.com.au
•
Harness the power of automation to deliver value – but nurture human co-operation to make it work, by Anthony Wong,
Director, South Pacific, Rockwell Automation.
Automation industry analysts sometimes observe that, just like invention, innovation is 1% inspiration and 99% perspiration. However, nothing useful happens without that 1% spark. Both inspiration and innovation require fertile and nurturing environments where they can grow and thrive, despite the stresses and scarcity imposed by today’s tumultuous times.
To achieve optimisation, it is not enough to just introduce technology to an environment and expect it to thrive. It is necessary to establish systems that enable people and devices to collaborate effectively, and therefore make a significant impact in their specific application. Users need to acknowledge that there are various situations where innovation is required, but the speed and complexity of these scenarios are affecting the way we innovate. As a result, there is a growing demand for open, interoperable, and adaptable systems that can help users achieve flexible and optimised manufacturing. New technologies have been emerging for 100 years, but what’s changed are the levels of speed and complexity. The difference now is users asking, “Why can’t I get the same complicated data and intelligence in my plant that I get from my consumer technologies?”
Given the continued upheaval caused by COVID-19 and its remote work and supply chain aftershocks, it’s hard for engineers and managers to maintain the relative equilibrium they need to innovate and improve operations performance.
Lately, they have to rethink and revise everything they do. Plus, they’re facing demands that return on investment (ROI) happen sooner, too. In addition, large manufacturers are facing production challenges, including corporate directives intended to solve them, which can cause friction between formerly isolated departments. For instance, IT previously focused on computing infrastructure and what software was put into plants, but now they’re dealing with users who want to add software containers, artificial intelligence (AI) and models, and are worried they’ll lose control of their processes. Such aid is often directed to smaller and emerging technology manufacturers, such as makers of electric vehicle (EV) batteries and life sciences systems. For example, in the US we’re partnering with the Advanced Regenerative Manufacturing Institute (ARMI), which is a consortium of companies we helped co-found that brings technical startups together.
One of its startup labs is working on growing skin, tendons, and other tissue, and we’re participating to help them conduct experiments that will enable them to move from the lab to industrialscale operations.
Beyond applying helpful technologies, innovation must also be nurtured with human cooperation. Maximising production means finding optimisation scenarios. However, they can’t happen in silos, so everyone must be empowered to work together.
Building systems that let individuals and devices work together can make a big difference in optimisation. These systems are characterised by open architectures and ecosystems that follow open standards and extend their capabilities into optional architectures. These include every industry segment and vertical we target, including major local verticals such as food and beverage, medical and pharmaceutical, water and wastewater, resources and energy and sustainability in all things.
Information needs to be used in the right way, so it can take manufacturing to new levels, and enable co-innovation to help shape the future. A key here is to combine data science with plantfloor expertise. These systems need to integrate the personas of their users.
By harnessing the power of the cloud, companies can simplify software management while increasing productivity, speeding time to market, and designing systems that cost less to build and provide more value over their lifetime.
Technology shouldn’t add complexity and block performance – it should instead provide a good production environment that makes it easier and less risky to innovate.
Rockwell Automation’s FactoryTalk® Design Hub software provides the simplicity and reusability that users can take advantage of to optimise their operations now, facilitating collaboration across automation design teams with software and project content that is always up-to-date and with powerful tools that scale as needed. rockwellautomation.com/en-au
Innovators in commercial e-Mobility technology SEA Electric is proud to announce the expansion of its existing business relationship with Hino Trucks.
The move follows in the footsteps of earlier supply agreements, which included the sale of SEA Electric branded class 5 trucks. This latest announcement paves the way for SEA Electric’s proprietary SEA-Drive® power-system to be fitted to both the Hino Trucks’ M and L Series. SEA Electric’s SEA-Drive® 120a powersystem was part of Project Z, Hino Trucks’ first advancement into zero-emission vehicles in the medium-duty space. Further details of the SEA Electric-Hino Trucks’ arrangement will be unveiled in due course.
“This is another monumental day for SEA Electric in our quest to electrify the world’s commercial fleets, and move to a zero emissions future,” said Tony Fairweather, SEA Electric CEO and Founder.
“Hino Trucks’ products are renowned the world over for their dependability and reliability, and we are proud to be a part of the next chapter of that story. “SEA Electric has committed to building a business that is sustainable both environmentally and economically and we welcome the opportunity to expand our relationship with a global leader such as Hino Trucks to further develop and advance our technological offerings.
“Cultivating a diverse ecosystem of partners, such as Hino Trucks, enables SEA Electric to work with different customers simultaneously, including upfitters, suppliers, and more, creating an opportunity to extend beyond our current markets.” For Hino Trucks, the announcement expands its range in a growing market.
“We are pleased to add SEA Electric’s SEA-Drive® power-system to our M and L series product offering. As our industry introduces
electric options, Hino Trucks can now offer an option for all the markets affected by ACT mandate," said Glenn Ellis, President of Hino Trucks.
The SEA-Drive® powered Hino Trucks M5e and L6e models recently featured prominently at Work Truck Week, in Indianapolis, IN, with the M5e made available for sampling in the Ride and Drive activity.
hino.com/electricvehicle.html
sea-electric.com
When fast, precise and synchronised linear motion is required, our Lifgo rack and pinion gear units have proven to be reliable in many industry sectors around the world.
businesses need to re-think digital to survive and thrive.
Kim Clarke, General Manager - Enterprise, MYOBIt’s been a difficult few years and further economic tightening is predicted. Australian business owners are concerned about a recession and face rising taxes and inflation, alongside the skills and labour shortages that are set to continue.
These are uncontrollable forces that manufacturers must manage through to survive. To meet the challenges coming their way, manufacturers across the country will need to optimise productivity and efficiency, ensuring they perform at their best while saving time and money where possible.
It’s a war cry the mid-market, including thousands of manufacturers, knows only too well. Research commissioned by business management platform MYOB shows mid-sized businesses have weathered the economic storm particularly effectively to date.
The latest mid-market snapshot – a survey of 510 mid-sized Australian businesses (20-500 employees and over $5m annual revenue) – revealed 69% of respondents saw revenue increase for the 2022 calendar year, compared to 2021. That increases to 77% for respondents in manufacturing or wholesale.
But despite emerging from last year with strong results, the MYOB survey also indicates mid-sized businesses have been planning for a difficult 2023. Heading into the year, 82% were concerned about a global recession, and for respondents in manufacturing or wholesale that rises to 90%. In terms of potential impacts, 44% of those polled believe a global recession will mean decreased demand for goods and services offered, and one in four (25%) believe a recession will result in reduced cashflow.
Already feeling the economic pinch, 75% of respondents indicated they will increase their prices in the short term (3-6 months). The top factors contributing to this include skills shortages putting pressure on wages and salaries (52%), increasing production costs (51%), and increasing supply costs (44%).
Pricing is however just one lever businesses can pull and will only alleviate tensions temporarily. A factor essential for mid-market success in any economic climate is employing and maximising the use of intelligent digital tools to drive efficiency and adaptability. Unfortunately, many are not realising these benefits – relying on outdated systems as they strive to succeed in a modern world. MYOB’s insights show that for 91% of mid-market business decision-makers, each of their employees are wasting at least 1-2 hours each week on manual or repetitive tasks due to inefficient or ineffective solutions. This wasted time and effort is not only hampering productivity, but the opportunity to reach their full potential. Almost half of the respondents (49%) report if they had this time back, they would rather their team target new customers, spend more time on strategy and business planning (40%) or on training or upskilling (37%).
The research also shows more than one-in-10 (12%) respondents are using more than ten different tools, apps or online systems to manage their business.
While most mid-sized enterprise leaders say they use an average of five digital solutions/tools to run their business, more than half (54%) of those surveyed admit they’re only using two to four of their applications or online systems regularly (twice a week or more).
Mid-market leaders understand the benefits of connected, modern digital tools, however many struggle to find the right solutions to better operate and grow their business. They often don’t have
the luxury of large IT departments who can pull together complex solutions, or the budgets for customised integrations. Doing the legwork for businesses, MYOB has evolved its platform to streamline key business workflows - from finance and inventory management to employee onboarding and payroll - bringing everything together in one place.
In addition to the rise of SaaS (Software as a service), technology overall continues to change rapidly and when MYOB asked midmarket leaders which technologies would most significantly change their business over the next five years, big data came out on top for 39% of mid-market businesses polled. This was followed by cloud computing (37%), and improvements in connectivity, such as 5G (35%).
It's changes in technology such as these that have led MYOB to expand its platform beyond the standard software and addons model. Over the past few years and with a specific focus on industry needs, MYOB has invested in developing rich integrations, such as CADTALK, to help manufacturing businesses engineering to order, manage the whole process seamlessly.
With economic challenges set to continue and businesses determined to stay responsive to the environment and competitive against their peers, more business owners are looking to intelligent solutions that not only empower them to make better informed decisions – but to keep ahead of the curve and prepared to take on what’s around the corner.
Equipping themselves to do this, isn’t about increasing the number of digital tools - but taking stock of what is currently being used and making sure these solutions are empowering teams to focus on higher value tasks and growing the business, rather than adding more work and more risk.
Mid-market businesses are already batting above their average, ensuring the use of the right digital tools will allow them to catapult to the next level. myob.com/au
Expert Tips: How to scale up your manufacturing capabilities in uncertain economic times.
In the wake of the COVID-19 pandemic and recent financial uncertainty, economies around the world have faced significant challenges, with businesses striving to adapt and recover. Australia is no exception, as businesses across various sectors grapple with the impacts of rising interest rates and inflation. In response to these challenges, the Australian Government has taken a proactive approach to support the nation's economic recovery through the $15 billion National Reconstruction Fund that will provide finance for projects to stimulate Australia’s manufacturing sector.
This comes after the manufacturing industry experienced setbacks during the pandemic, facing supply shortages and workforce reductions, and is now in the process of rebuilding itself in the post-COVID-19 era. With this in mind, numerous manufacturing businesses are actively seeking avenues to expand and advance, even amidst the prevailing economic uncertainties.
“During the pandemic, the manufacturing industry faced several challenges that affected businesses across the country and the world. Now, manufacturers are continuing to be faced with another set of challenges and are wondering how best to scale up their capabilities in these times. As a business grows, it's essential to ensure that every aspect of its operations remains synchronised to prevent disruption and maintain high levels of quality,” continued Vince.
With this in mind, Vince Giovanniello has shared tips on how manufacturers can scale up their business capabilities in the face of current challenges.
Growing to scale, or scaling up, is when a business ensures all aspects of its processes grow in tandem so that one area isn’t left behind. Scaling up entails intensifying efforts and undertaking additional activities to ensure the capacity to handle increased demand in the event of securing a large contract. Hiring additional staff or acquiring new equipment may be required to meet the demands of new contracts. While this might increase your expenses, it is essential for the continued growth of your business. Financial advisers can help you put strategies in place to scale at a pace that works for your business. Their expertise can ensure that your growth is sustainable and financially viable, while also helping you manage potential risks and make informed decisions during the expansion process.
When scaling up you should have a well-defined plan for what you want to achieve. You should know exactly which areas you’re looking to grow and how you will go about doing this. Having clear objectives allows the entire business to pull in the same direction, and reduces instances of unforeseen outcomes.
Maintaining a versatile business model is crucial to prevent compromising product quality, customer satisfaction, or employee morale. This may involve sourcing different or additional materials from suppliers or building new partnerships. It could also mean branching out to new locations or harnessing new technologies.
Implementing advanced technology, including automation, can significantly improve your manufacturing processes, leading to increased efficiency, productivity, and cost savings. Using digital resources can be an enabler to trigger growth in the first place, as they bring about an increase in efficiency. This leads to higher turnover, and ultimately means you have more money to invest in increased marketing or production if necessary.
As your business scales, it's essential to continually evaluate and optimise your production processes. Identify bottlenecks and inefficiencies and implement changes to improve throughput and minimise waste. Regularly monitor key performance indicators (KPIs) to track progress and make data-driven decisions.
There is always great value in seeking professional advice, particularly in times of uncertainty. Although you may have the relevant expertise internally, it is always beneficial for your company to source guidance externally to get a different perspective. Advisory firms like BlueRock can provide valuable advice for manufacturers who are looking to scale up their business with expert financial counsel.
bluerock.com.au
Automation is the ‘space race’ Australia’s auto manufacturing industry needs. Brent Stafford is Executive Director at Directed Technologies. Here he tells why automation, not electrification, will kick-start our auto industry.
It’s been five years since the last Australian designed and made passenger vehicle rolled off the factory floor at Holden in South Australia. Following the fate of Ford, Toyota and Mitsubishi, Holden closed its last plant, ending a pivotal chapter in Australia’s manufacturing industry that spanned more than 100 years. While the impact of those closures was measured in economic impact ($29bn in lost economic output) and jobs (estimated up to 50,000 gone), one of the most significant and lingering side-effects has been the brain drain of high-tech skills.
When the production lines shut, so did the talent pipelines. Siphoned off to SaaS companies, construction, sales and other industries happy to claim a small victory in the talent war. Fastforward five years and Australia’s automotive manufacturing ecosystem is very different. And it’s changing as rapidly as the automotive industry at large.
Electrification is the flavour du jour in the global automotive market. Customer demand is skyrocketing and the charging infrastructure is struggling to keep pace. And unfortunately, as a once proud automotive manufacturing nation, so have we. While we may have missed the opportunity to be a market leader in electrification, there’s a bigger opportunity for Government and the auto sector coming a little further down the road.
Level four automation of passenger and freight vehicles has taken longer to become mainstream than many predicted. But it’s coming in the next two decades, and the window of opportunity for Australia to define our role in this new generation of technology and claim a genuine leadership position that could reignite our talent pipeline is closing by the day. I’m not talking about producing the next Tesla, BYD or Polestar. I’m talking about the high-tech software, platforms and components to support automation of supply chains and the road network.
Australia is transitioning to a knowledge economy. And the wealth of a knowledge economy doesn’t come from mining dirt and manufacturing metal. It comes from mining data and manufacturing algorithms.
The majority of government investment still goes into physical infrastructure: roads, bridges, airports and precincts. Don’t get me wrong, these are critical to support our growing populations and evolving transport needs. The area we really need to fasttrack investment into is building more ‘infostructure’. The digital superhighways of connectivity through LTE, 5G, vehicle connectivity, smart infrastructure, centres of digital excellence. We need to be investing in advanced manufacturing and high-tech companies that are innovating in the digital as well as the physical world. And yes, I do mean actually creating our own technology hardware as well as software.
This next generation of job creation for the infostructure economy will be around well beyond the lifespan of the next rail or roads project. And it has the added benefit of opening up growth opportunities through export to global markets.
Traditionally, auto manufacturing has invested heavily in hardware, such as metal and the manufacturing of hard parts. As a result, the
government has also prioritised investment and regulation in this space. In recent years, however, this has evolved somewhat to focus less on the actual manufacturing of the components for vehicles, towards ensuring the integration of the digital aspects of vehicles within fleets. This is where the Australia’s advanced manufacturing sector has a unique opportunity.
At Directed Technologies our telematics technology has monitored more than 2bn kilometres of road travel, across more than 2,000 fleets. In recent years we’ve seen the fleet data volumes go from megabytes to petabytes, with near-real time video and sensor data available for every vehicle 24/7.
This flow of data and the analytics are completely digitising traditional business models.
Our fleet monitoring systems see an average 90% reduction in driver violations in the first three months. That’s eliminating incidents of harsh breaking and acceleration which comes at a huge maintenance and fuel cost, speeding and other breaches which could otherwise cost lives. And in an industry that operates on knife edge margins, being able to achieve efficiency gains of 5% are significant. If you think cars are expensive to refill with 60 litres of fuel, heavy trucks regularly carry 1,000 litres of fuel, that could mean saving $50 per truck per refill across a fleet of hundreds or thousands of vehicles each day.
The first generation of freight automation is already here. Truck platooning allows heavy vehicles to electronically connect using radar, sensors and vehicle-to-vehicle communications to form and maintain a tight formation, following each other closely to reduce air drag and improve fuel economy. With Government support, through investment in research and development, financial incentives and tax breaks for advanced engineering and manufacturing, rather than a continued focus on finding the next vehicle to manufacture, Australia could reclaim its role as a leader in the automotive sector once again.
Fuelling growth in this sector will plant the seeds of the next generation of skills. Skills like artificial intelligence, machine learning, and advanced robotics will help our economy continue to punch above its weight and move up the knowledge economy rankings. directedtechnologies.com.au
The economy is coming off the boil, but some sectors remain red hot. Anneke Thompson shares what is coming next.
The Australian economy is in the early throes of its necessary slowdown. The risk of the slowdown getting out of the RBA’s control was heightened this month by news of liquidity issues in some US and European banks. With the US Fed and ECB holding their resolve and continuing to increase their rates, the outlook for the global economy gets cloudier every day.
Inflation appears to be stickier in the US than first thought and the US consumer is still spending while the labour market remains strong. However, if/when job shedding begins to spread beyond the tech sector, the slowdown will accelerate and recession becomes a real threat. The good news is that Australian banks are incredibly safe and well regulated, and while issues overseas will tighten credit supply, there is next to no threat to Australian bank deposits.
The inflation rate in February reduced to 6.8%, down from 7.4% in January and 8.4% in December. However, a few categories continue to show elevated price increases, including rent, some food categories and electricity. It is not expected that rents will reduce any time soon, as there is no fix to supply side issues in the short term. Electricity price increases will remain high until at least the middle of this year, and possibly beyond that. Most discretionary items recorded reductions in the rate of price growth, with holiday travel and accommodation inflation reducing from 29.3% in December to 14.9% in February. Overall, inflation is moderating as well as can be expected, and the RBA will be keenly aware that monetary policy tightening is ineffective against rent rises (indeed –it contributes to rent inflation) and the cost of electricity.
Australia’s unemployment rate is holding down near record low levels at 3.5 per cent, although any further falls are now highly unlikely. Job vacancies over the three months to February 2023 were down 1.5%, although still up 3.6% year on year. Combined with monthly data from employment marketplace SEEK, it does appear that we are well and truly past the peak in the employment market.
Steeply rising home loan repayments, rents, food, electricity and other costs are now showing through in retail trade figures. While spend data was understandably lumpy over the Christmas/summer period, February data reveals that spend levels are the same as they were in September last year. Given very high migration levels, and rising costs, it appears that Australians are now purchasing far less, particularly on household and discretionary items.
Consumer sentiment remains near recessionary levels and has been this low for some time. Business confidence, however, is still reasonably strong, and businesses are reporting conditions are at very good levels. This is likely to change over the next six months though, as the impact of lower consumer spending flows through the economy, and also as record levels of construction activity start to tail off towards the end of the year.
We appear to be close to the peak of the monetary policy tightening cycle, although the RBA will still be wary of very tight labour market conditions and business sentiment remaining strong. Inflation and
retail trade, however, are moving in the direction that the RBA wants them to, which is good news for borrowers. The most likely scenario is that the RBA holds the cash rate at restrictive levels for a number of months at least until they are certain we are past full employment and inflation is on a steady march downwards.
Uncertainty in global liquidity markets is now a real threat to economic stability. While Australian banks are deemed amongst the safest in the world, some smaller, regional banks in the USA with large commercial property loan books are being sounded out as the next big risk. Even if bank liquidity is solid, the very threat of it can cause bottlenecks in credit markets and distrust amongst banks. However, slowing credit does act as a further handbrake on inflation, and assuming we don’t see widespread panic, may actually help central banks in their war against inflation.
Anneke Thompson joined CreditorWatch as Chief Economist in April 2022. She is also the Managing Director of Clio Research, which helps commercial property owners, developers, investors and occupiers navigate the rapidly changing Australian markets and make strategic data-driven decisions. She was formerly the National Director and National Head of Research at Colliers International Australia, and has also worked at NAB and Jones Lang LaSalle. creditorwatch.com.au
Researchers from Tokyo University of Science in Japan have developed an inexpensive method for fabricating multi-walled carbon nanotubes (MWNTs) on a plastic film. The proposed method is simple, can be applied under ambient conditions, reuses MWNTs, and produces flexible wires of tunable resistances without requiring additional steps. It eliminates several drawbacks of current fabrication methods, making it useful for large-scale manufacturing of carbon wiring for flexible all-carbon devices.
Carbon nanotubes (CNTs) are cylindrical tube-like structures made of carbon atoms that display highly desirable physical properties like high strength, low weight, and excellent thermal and electrical conductivities. This makes them ideal materials for various applications, including reinforcement materials, energy storage and conversion devices, and electronics. Despite such immense potential, however, there have been challenges in commercializing CNTs, such as their incorporation on plastic substrates for fabricating flexible CNT-based devices. Traditional fabrication methods require carefully controlled environments such as high temperatures and a clean room. Further, they require repeat transfers to produce CNTs with different resistance values.
More direct methods such as laser-induced forward transfer (LIFT) and thermal fusion (TF) have been developed as alternatives. In the LIFT method, a laser is used to directly transfer CNTs onto substrates, while in TF, CNTs are mixed with polymers that are then selectively removed by a laser to form CNT wires with varying resistance values. However, both these methods are expensive and have their unique problems. LIFT requires expensive pulsed lasers and preparation of CNTs with specific resistance values, while TF uses large amounts of CNTs that are not utilised and go to waste.
Scientific Reports
Researchers from the University of Technology Sydney (UTS) have developed biosensor technology that will allow you to operate devices, such as robots and machines, solely through thought control. As well as defence applications, the technology has significant potential in fields such as advanced manufacturing, aerospace and healthcare – for example allowing people with a disability to control a wheelchair or operate prosthetics.
The advanced brain-computer interface was developed by Distinguished Professor Chin-Teng Lin and Professor Francesca Iacopi, from the UTS Faculty of Engineering and IT, in collaboration with the Australian Army and Defence Innovation Hub. As well as
defence applications, the technology has significant potential in fields such as advanced manufacturing, aerospace and healthcare –for example allowing people with a disability to control a wheelchair or operate prosthetics.
A new study outlining the technology has just been published in the peer-reviewed journal ACS Applied Nano Materials. It shows that the graphene sensors developed at UTS are very conductive, easy to use and robust. The hexagon patterned sensors are positioned over the back of the scalp, to detect brainwaves from the visual cortex. The sensors are resilient to harsh conditions so they can be used in extreme operating environments.
The user wears a head-mounted augmented reality lens which displays white flickering squares. By concentrating on a particular square, the brainwaves of the operator are picked up by the biosensor, and a decoder translates the signal into commands.
The technology was recently demonstrated by the Australian Army, where soldiers operated a Ghost Robotics quadruped robot using the brain-machine interface. The device allowed hands-free command of the robotic dog with up to 94% accuracy.
UTS
The supersolid is a very counterintuitive phase indeed. It is made up of particles that simultaneously form a rigid crystal and yet at the same time flow without friction since all the particles belong to the same single quantum state.
A solid becomes ‘super’ when its quantum properties match the well-known quantum properties of superconductors. A supersolid simultaneously has two orders, solid and super: solid because of the spatially repeating pattern of particles, super because the particles can flow without resistance.
Geoffrey Chester, a Professor at Cornell University, predicted in 1970 that solid helium-4 under pressure should at low temperatures display Crystalline solid order, with each helium atom at a specific point in a regularly ordered lattice and, at the same time, BoseEinstein condensation of the atoms, with every atom in the same single quantum state, so they flow without resistance.
However in the following five decades the Chester supersolid has not been unambiguously detected. Alternative approaches to forming a supersolid-like state have reported supersolid-like phases in cold-atom systems in optical lattices. These are either clusters of condensates or condensates with varying density determined by the trapping geometries. These supersolid-like phases should be distinguished from the original Chester supersolid in which each single particle is localised in its place in the crystal lattice purely by the forces acting between the particles.
As for detection, for a superfluid it is well known that this cannot be rotated until it can host a quantum vortex, analogous to a
whirlpool. But to form this vortex requires a finite amount of energy, and hence a sufficiently strong rotational force. So up to this point, the measured rotational moment of inertia (the extent to which an object resists rotational acceleration) will remain zero. In the same way, a supersolid can be identified by detecting such an anomaly in its rotational moment of inertia.
Physical Review Letters
This unprecedented achievement represents an important landmark in the development of quantum technologies. Stimulated light emission, postulated by Einstein in 1916, is widely observed for large numbers of photons and laid the basis for the invention of the laser. With this research, stimulated emission has now been observed for single photons. Specifically, scientists at the University of Sydney and the University of Basel in Switzerland could measure the direct time delay between one photon and a pair of bound photons scattering off a single quantum dot, a type of artificially created atom.
“This opens the door to the manipulation of what we can call ‘quantum light’,” Dr Sahand Mahmoodian from the University of Sydney School of Physics and joint lead author of the research said. Dr Mahmoodian said: “This fundamental science opens the pathway for advances in quantum-enhanced measurement techniques and photonic quantum computing.”
By observing how light interacted with matter more than a century ago, scientists discovered light was not a beam of particles, nor a wave pattern of energy – but exhibited both characteristics, known as wave-particle duality. The way light interacts with matter continues to enthral scientists and the human imagination, both for its theoretical beauty and its powerful practical application.
Whether it be how light traverses the vast spaces of the interstellar medium or the development of the laser, research into light is a vital science with important practical uses. Without these theoretical underpinnings, practically all modern technology would be impossible. No mobile phones, no global communication network, no computers, no GPS, no modern medical imaging. One advantage of using light in communication – through optic fibres –is that packets of light energy, photons, do not easily interact with each other. This creates near distortion-free transfer of information at light speed.
However, we sometimes want light to interact. And here, things get tricky. For instance, light is used to measure small changes in distance using instruments called interferometers. These measuring tools are now commonplace, whether it be in advanced medical imaging, for important but perhaps more prosaic tasks like performing quality control on milk, or in the form of sophisticated instruments such as LIGO, which first measured gravitational waves in 2015.
The laws of quantum mechanics set limits as to the sensitivity of such devices. Different to laser light, quantum light can make more sensitive measurements with better resolution using fewer photons. This can be important for applications in biological microscopy when large light intensities can damage samples and where the features to be observed are particularly small.
The research was a collaboration between the University of Basel, Leibniz University Hannover, the University of Sydney and Ruhr University Bochum.
Nature Physics
Biomedical and electrical engineers at UNSW Sydney have developed a new way to measure neural activity using light – rather than electricity – which could lead to a complete reimagining of medical technologies like nerve-operated prosthetics and brainmachine interfaces. Professor François Ladouceur, with UNSW’s School of Electrical Engineering and Telecommunications, says the multi-disciplinary team has just demonstrated in the lab what it proved theoretically shortly before the pandemic: that sensors built using liquid crystal and integrated optics technologies – dubbed ‘optrodes’ – can register nerve impulses in a living animal body. Not only do these optrodes perform just as well as conventional electrodes – that use electricity to detect a nerve impulse – but they also address “very thorny issues that competing technologies cannot address”, says Prof. Ladouceur. “Firstly, it’s very difficult to shrink the size of the interface using conventional electrodes so that thousands of them can connect to thousands of nerves within a very small area. “One of the problems as you shrink thousands of electrodes and put them ever closer together to connect to the biological tissues is that their individual resistance increases, which degrades the signal-to-noise ratio so we have a problem reading the signal. We call this ‘impedance mismatch’.
“Another problem is what we call ‘crosstalk’ – when you shrink these electrodes and bring them closer together, they start to talk to, or affect each other because of their proximity.” But because optrodes use light and not electricity to detect neural signals, the problems of impedance mismatch is redundant and crosstalk minimised.
“The real advantage of our approach is that we can make this connection very dense in the optical domain and we don’t pay the price that you have to pay in the electrical domain,” Prof. Ladouceur says. UNSW
New eye-tracking technologies being developed by Australian engineers to identify building defects early in the construction process could save companies millions of dollars, time, and resources. The technology, embedded in 3D headsets, is designed to help construction workers undertake more thorough checklists, cutting down on building costs related to fixing mistakes.
Building defects account for up to 60% of construction costs, resulting in significant budget blowouts, but new eye-tracking AR technologies are being developed by the University of South Australia to address the issue. The technology, embedded in 3D headsets, is designed to help construction workers undertake more thorough checklists, cutting down on more than half of building costs related to fixing mistakes.
UniSA
1/2 NPT Hollow Cone Liquid Nozzle for cooling and washing.
EXAIR’s new 1/2 NPT HollowStream™ liquid atomising spray nozzle provides a hollow cone spray pattern for pressurised liquids. They are applied to solve many problems including cooling, cleaning, rinsing and dust suppression applications for industry. The tangential flow design is vaneless, with wide open internal features to resist clogging and work well with liquids containing particulate. These liquid nozzles produce a uniform distribution of liquid in a ring pattern with medium to large droplets. Their right-angle design is compact and can fit in small areas. Liquid operating pressure is up to 250 PSI.
With HollowStream nozzles, the liquid is supplied into the body of the nozzle creating a swirling action within a vortex chamber. This vortex produces the hollow-cone spray pattern when the precision nozzle breaks the liquid surface tension as it exits the orifice and into a controlled spray angle. With an adjustable flow rate, it’s perfect for dust mitigation, pollution scrubbers, foam breaking and more. Available from Compressed Air Australia, the type 303 stainless steel construction of liquid atomising nozzles adds to their durability and corrosion resistance. HollowStream nozzles are CE compliant and available in a variety of flow rates. They complement EXAIR’s large line of other 1/8, 1/4, 3/8 and 1/2 NPT liquid nozzles, which are also available in a variety of liquid patterns and flow rates. caasafety.com.au
Kemppi launches new portable welding machines for Master M series.
Leading international welding equipment manufacturer, Kemppi, has released two new portable and versatile welding machines for MIG/ MAG welding – the Master M 205 and Master M 323. Part of the popular Master M series, the Master M 205 and Master M 323 are perfectly suited for site work, boat building and repair shops, as well as dedicated hobby welders. Their small size and transportability, make them an ideal choice for repair welding. Both models deliver excellent usability, best-in-class welding performance, and a smooth parameter setup. Developed in collaboration with professional welders and manufactured in Finland, the M 205 and M 323 let users weld quickly and easily for quality results.
The Master M 205
The Master M 205 has been created specifically for welding tasks that require lightweight, easy-to-move welding equipment, but also high-quality welds. Highly portable and powerful, the Master M 205 is a MIG/MAG welding machine for manual, synergic, and pulse MIG/MAG welding of stainless and light steel, and aluminum. Delivering true grunt and convenience, the Master M 205’s 200 A, 1-phase power source operates with a 40% duty cycle. Plus, the Master M 205 comes with 17 welding programs for pulse MIG and 20 welding programs for 1-MIG. These include welding programs for Fe, Ss, AlMg5, AlSi5, CuSi3, and CuAl8 filler materials. Very easy to use, the Master M 205 features a large LCD screen that is bright and easy to read. Self-charging LED lights can be turned on to improve safety, particularly in dim and confined spaces, and they work with or without mains power.
The machine is also hassle-free to operate. The new model can be quickly set up thanks to Weld Assist. This feature saves time and makes welding easier with automatic parameter settings. Just select the material thickness, joint type, and welding position, and start welding.
The Master M 323
This model is ideal for sheet metal welding, and thanks to its portable size and versatile accessories, it is also well suited for welding environments with challenging spaces.
A high-performance, portable MIG welding machine, the Master M 323 delivers 320 amps of power at a 40% duty cycle. To help improve welding quality and save time, it comes with 28 built-in welding programs for Fe, Ss, AlMg5, AlSi5, CuSi3, CuAl8, and FCCrNiMo filler materials. Plus, the Master M 323 includes 4 welding programs for the MAX Cool arc welding process.
Equipped with six memory channels, both models also let users save chosen parameters for fast retrieval. The ability to save customised settings means welders do not have to go through an initial setup for every job, saving precious time while helping to boost productivity. Like the Master M 205, the Master M 323 also comes with Weld Assist, a large LCD screen that is easy to read and use, and selfcharging LED lights. For greater convenience, both models also feature a safe-lift handle design. The handle has been reinforced with metal so that it can be lifted by crane.
A powerful, lightweight welding machine that can go anywhere on site, the Master M 323 is perfect for high-performance industrial welding.
kemppi.com
Henkel, a global leader of adhesives, sealants and functional coatings has commenced the production of Loctite PC 7218 Wearing Compound in Australia. The adhesives are produced at the plant in Kilsyth, Australia, for customers in Australia and New Zealand, with the potential to extend the supply to South East Asia. Loctite PC 7218 Wearing Compound is a two-part, grey, epoxybased surface coating for metals that protects against coarse particle abrasion or erosion, or for rebuilding worn parts. The new and improved formula is safer for the environment and for workers to apply in confined spaces. It does not pose a serious health risk from accidental inhalation and will not cause harm to aquatic life.
The Australian-made Loctite PC 7218 Wearing Compound will help customers reduce downtime and improve supply chain reliability. The cardboard packaging of the outer box will no longer be required for deliveries within the country, thus reducing an estimated 10,000kg of paper waste annually.
“As a global leader in the adhesives market, Henkel is continuously developing new and innovative solutions to serve a wide range of industries. Producing Loctite PC 7218 Wearing Compound locally is a key part of our commitment to create value through our operations and supply chain infrastructure, and specifically designed to meet the growing demand of our customers,” shared Matt Greaves, General Manager, General Manufacturing & Maintenance, Henkel Adhesive Technologies Australia & New Zealand.
Loctite PC 7218 Wearing Compound is used in many sectors, such as mining, power, steel and cement. It is a protective coating that can be applied to vertical and overhead surfaces. Additionally, it is suitable for chemical attack applications and renews worn surfaces quickly.
“Now that we have embarked on the local production of Loctite PC 7218 Wearing Compound in Australia, it has opened doors for us to locally produce other adhesives like Loctite PC 9313 High Impact Wearing Compound in the later part of the year. Through the excellent collaboration from our operations, production and supply chain teams, we are able to further expand our capabilities and provide comprehensive solutions for our customers,” added Greaves. henkel.com.au
MAXXDRIVE® XT industrial gear units are tailored to applications where high powers with low speed ratios are required.
High thermal and mechanical load capacities and long service life: With regard to the requirements for conveyor technology drives in the bulk goods and mineral industries, NORD DRIVESYSTEMS specially developed the MAXXDRIVE XT industrial gear unit. It provides output torques of 15 to 75 kNm with speed ratios from 6.3 to 22.4 and is offered in seven sizes for powers from 22 to 2,100 kW.
The power and speed ranges of the two-stage right-angle gear unit have been specially designed for industries in which low speed ranges are required in combination with high powers – such as the bulk goods and mineral industries. Its robust design makes the MAXXDRIVE XT resistant to dirt and reliable in rough operating conditions. A special sealing concept reduces maintenance. Large roller bearings and centre distances increase the load capacity and service life of the components.
As standard, the industrial gear unit is equipped with a heavily ribbed UNICASE housing and an integrated axial fan. Due to the increased surface and the airflow covers, the cooling airflow is optimised and a very high thermal limiting power is achieved. In many cases, additional cooling is not required.
“As with other application areas, our drive solutions for the industry are individually configured for customers according to the modular principle”, emphasises Jörg Niermann, Head of Marketing at NORD DRIVESYSTEMS. This is based on a comprehensive range of frequency inverters, motors and gear units, as well as coupling and brake systems, each with a wide variety of options. Features such
as hydraulic couplings tailored to the particular process or Taconite seals, which effectively protect radial shaft seals against abrasive dust and corrosion, ensure smooth operation.
NORD also offers innovative predictive maintenance concepts for heavy industrial gear units. NORD drives networked via the frequency inverter communicate their status data via the control system or directly into a secure Cloud. With optional vibration monitoring, condition changes can be detected at an early stage and predictive maintenance can be scheduled in good time. Performance data recording also ensures optimal system dimensioning as well as continuous condition monitoring (Condition monitoring) of the drives. nord.com
OpenIIOT.com.au
Australian Manufacturing Week 2023 grew into a tremendous success, truly a celebration of the manufacturing talents here in Australia.
AMW2023 is done and dusted. And what a show it was. It’s been four long years since our last Melbourne Austech show, due to COVID restrictions and lockdowns. Now fully owned and operated by AMTIL, AMW is Australia’s largest manufacturing solutions event, bringing far more sectors of Australian manufacturing in under the same roof. Seven distinct Zones representing differents areas of the manufacturing world including the original Austech Machine Tools Zone, Additive Manufacturing, Robotics & Automation, Australian Manufacturing, Manufacturing Solutions, Plastics Technology and Weld & Air Technology. AMW2023 just about took over all the halls of the MCEC, and filled them to the brim with the very latest technology in manufacturing, filling 10,900 sqm of show floor space.
In fact, 348 companies joined the show, and Exhibitors attended from here and around the planet. People from 46 countries came to the show! All up, 773 individual brands were promoted by the Exhibitors in the Map Your Show digital directory. Around 1535 people downloaded the AMW Mobile App, and all the feedback we’ve had, proves it was very helpful throughout the show. And a total of 19,236 My Show Planner profiles were created by visitors. In preparation for the show, 17kms of electrical cable was laid, 1,500 light fittings were installed, and we had 1,018 hours of security employed. Well over $80m in manufacturing technology was spread out on the floor and demonstrated over the four very full days. For the show, in fact almost 11,000 sqm of floorspace was sold in record time. We had over 500 students from various schools visit the show in organised groups, and we recycled over 12 tonnes of metal during the show.
Visitors
15,194 ATTENDEES
DAY 1: 2757 • DAY 2: 4439
DAY 3: 5953 • DAY 4: 2765
It really was a spectacular celebration of what Australian manufacturing and all associated industries can do here on shore, here in Australia. The feedback from those who took part has been humbling and heartfelt. Thank you all for coming. We already have special plans for a big Sydney show coming up in April for AMW2024.
The success of the Future Solutions Speaker sessions took us all by surprise. Such a successful reaction. Each of the days had a special theme, and the program was filled with great special focus speakers, MC-ed to perfection by Warrick Merry. The immediate reaction was a full deck of filled seats and standing room only.
Day One’s theme was Additive Manufacturing, proudly sponsored by AMHub, celebrate the various innovations and constant developments that are sweeping this particular segment of the manufacturing industry in Australia. AMTIL followed up with a wonderfully raucous networking event down along the Yarra at the Munich Brahaus, supported by AMTIL, open for the Exhibitors to unwind.
Day Two promoted and recognised the various achievements of women in the manufacturing sector in Australia. There were panels from Commonwealth Bank, Geelong Manufacturing Council, William Buck and SEMMA. Later in the day, a special networking event, sponsored by the Queensland Government, was a huge success. The Third day was a celebration of Australian Manufacturing, proudly sponsored by Autodesk. The presentations from Autodesk Australia, Bosch Australia, Adobe, Rigby Cooke, ANCA and the Victorian Government. An even more special networking event was rallied up for the VIPs at the end of the day’s proceedings, sponsored by the Moreton Bay Regional Council.
The final day’s presentations focussed in on Innovation and research occuring here with the view of the future of manufacturing. Sessions with Monash Smart Manufacturing Hub, Geelong Manufacturing Council, Breakthrough Victoria and the ANFF were tremendous opportunities for those present to learn about the long strides happening right now in preparation for the next 30 years of manufacturing in Australia.
Australian Manufacturing Week returns next year in Sydney, 17-19 April 2024 at Darling Harbour.
australianmanufacturingweek.com.au/amw-sydney-2024/
There’s often a moment at trade-shows when a distinct type of fatigue sets in. The crowded aisles and incessant noise, the recycled air and harsh lighting all start to set in, so that at most industry exhibitions you’ll reach a point, usually mid-to-late afternoon, when everything seems to get just a little bit sluggish.
Although that wasn’t the case at AMW2023. Throughout the week the atmosphere remained upbeat and energised all day every day, with consistently high visitor numbers, and a buzz of activity on any stand you looked at.
And of course, nothing adds that little extra spark of energy like closing a sale on your stand.
“We’ve had good numbers, really good leads, and even a couple of sales, which is not all that common at shows,” said Christian Buhagiar, Director – Strategic Operations at Alfex Group. “Shows can sometimes just be about information-gathering, so it’s nice to see people coming here prepared to make a decision. We’ve sold a couple of lasers and a couple of 3D printers, so there’s some happy faces around the Alfex stand.”
Alfex had a substantial presence at AMW, taking two adjoining stands in the Austech Machine Tools Zone to accommodate its three divisions: its CNC machine tool arm Haas Automation; its Alfex Laser division; and its most recent venture, Alfex Additive Manufacturing Technology. Between them they offered a diverse selection of advanced manufacturing equipment. For Buhagiar, the chance to demonstrate this technology live is what makes events like AMW so vital.
“People can compare what they’re looking for and not just read off a brochure. They can find the right machine for what they want to do, where their business is at, and what their application is. And we enjoy it – there’s nothing better than shaking someone’s hand, having a chat and building that rapport, and being able to show them everything you can offer.” alfex.com.au
Austech was undoubtedly the largest zone at AMW. But while the big machining centres and sheet metal equipment might catch the eye and make the most noise, there was a lot more to the Austech line-up, with several exhibitors displaying all kinds of accessories that are essential to modern manufacturing. One such supplier was Dimac Tooling.
“We’re in a niche area,” explained Matthew Williams, Dimac’s General Manager. “We’re interested in workholding, productivity, coolant management, tool presetters, automation... We’ve generally got the solution for the customer, and if we don’t we’ll certainly point them in the right direction.”
Prominent on the Dimac stand was a new machine from Eidos in Italy that compacts swarf into neat briquettes, removing and retaining the coolant, saving costs and labour, and creating a valuable scrap metal product.
“That’s been getting a lot of interest,” said Williams. “It’s unique, and our customers are raving about it. In fact both customers that have them have bought a second one. You only do that if it’s a good device that solves a problem. You’re looking at solving problems, being more efficient, and saving money essentially.”
Williams was pleased with the interest Dimac saw throughout AMW: “I’d say 90% of customers are coming here looking for a solution for a problem. They’re finding challenges in their machine shop, and they come to us saying “How do I solve it?” Challenging us on how to find a solution.”
dimac.com.au
Over at the Applied Machinery stand the team were fielding an extensive line-up of sheetmetal, engineering and recycling equipment. Front and centre was a new Yawei panel folder, which Applied was launching to the Australian market.
“We’ve been waiting to get our hands on this for a while now and we’re really excited to bring it to market,” said Daniel Fisher, Sales & Marketing Manager at Applied. “We’re getting really good responses and feedback from our customers.”
Four years after the last big manufacturing exhibition in Melbourne, Fisher believes AMW was an invaluable opportunity to reconnect with a wide market.
“Getting in front of customers is absolutely paramount. We’ve got customers we talk to throughout the year, but to get them all together under the one roof is really beneficial. We’ve had really positive conversations with new and existing customers on the floor, and the sentiment in general has been very positive.”
All in all, it suggests an optimistic outlook for Australian manufacturing: “There’s a lot of bad news at the moment, with rising interest rates impacting the ability to raise finance. But the majority of our customers are very busy, and they’re looking to invest. The future’s bright.”
appliedmachinery.com.au
Proudly sponsored by Adobe, the Manufacturing Solutions Zone offers optimised solutions to the most common challenges experienced by manufacturers. There were 119 exhibitors in the Manufacturing Solutions Zone alone, from materials handling and warehousing to integrated manufacturing and safety solutions.
The manufacturing industry would not be able to function effectively without a diverse array of ancillary technologies and support services. The Manufacturing Solutions Zone is where you can find answers, incorporating everything from equipment for materials handling and logistics, and safety products, through to the latest software for streamlining manufacturing operations, and specialist service providers in areas such as law, finance, and skills, training, and recruitment. Without the support of these companies, the Australian manufacturing industries would be at the very least, burdened with supporting itself.
Autodesk has been heavily involved in all facets of manufacturing for decades. Since its introduction of AutoCAD software in 1982, Autodesk has continued to develop the broadest portfolio of 3D software for global markets. Customers across the manufacturing, architecture, building, construction, and the Media & Entertainment world where this magazine’s editor comes from, industries have used Autodesk software to design, visualise, and simulate their ideas before they're ever built or created. The work of Autodesk’s 3D software customers is everywhere you look. From blockbuster visual effects and buildings that create their own energy, to electric cars and the batteries that power them.
At the Autodesk stand, I met a fellow who had made his own custom refractor telescope after creating the model in Autodesk’s Fusion software. Diego A. Colonnello from Astroworks fed his models to a local CNC company, and imported some of the required electrical equipment and motor components but everything else, was his to create, refine and construct. It was a sight to behold.
autodesk.com
Elexon Electronics has been delivering some great solutions to challenging industries like defence, mining, medical and automotive manufacturing for the last 17 years or so from the headquarters in Brisbane. At AMW2023, they announced the implementation of deeper Industry 4.0 manufacturing processes and capability, tailored specifically for the defence and aerospace sectors. “Our state-of-the-art’ setup, unique in Australia, positions us as formidable contenders in the global market,” said Elexon’s CEO Frank Faller. “It was a great and super busy show. One of the best ones for us. AMTIL did a great job. We want to use the success of AMW2023 to showcase our enhanced capabilities, demonstrating to international customers that they need not look beyond our shores for cutting edge solutions.”
elexonelectronics.com
Plastic technology is a specialised branch of study which includes the study of diverse types of chemicals that exhibits plasticity. It also involves the study of several methods in which plastics can be utilised for use in markets. This extensive Zone included the latest in plastics machinery, mould-making technologies, recycling materials, and the many plastics manufacturing processes. This area covered injection and blow moulding, extrusion, thermoforming, and compounding, mould making and toolmaking, and plastic technology processes. There were eight exhibitors in the Plastics Zone but it felt like so many more used the tech in their processes.
Melbourne Rotomould – Melro.
Melbourne Rotomould is famous for custom and contract rotational moulding, with all their design, engineering, toolmaking, production and post production done in-house. They use PE, PP, Nylon, PVDF as well as a lot of recycled feedstock. Arriving at Melro’s stand is exciting. Company director, Tim Leed is sitting in a bright blue Rotovelo that looks like a sports car, but it contains foot pedals inside for movement.
Leed explains that Melro roto moulds the plastic shell for Trisled, which builds the Rotovelo mobile, also known as a human powered vehicle. “Trisled came to us at Melro around 10 years ago. The company had been using carbon fibre and fibre glass to make the frames, which was taking around two to three weeks to build. We roto mould the frame in plastic for Trisled in a much shorter time.”
The Rotovelo is mainly used for racing, but Leed adds that it can also be used by people with limited balance ability, as it is easier and more stable than riding a bicycle. Leed points to the large brown
noise wall panel at the back of the stand. “The government has shown interest in this. It’s made out of 80% recycled soft plastics and is used to cut noise on freeways,” Leed adds. He says the AMW2023 has been good so far with a few genuine enquiries. melro.com.au
Managing Director of PPC Moulding Services Pty Ltd, Grahame Aston enthusiastically shows the stand’s visitors PPC’s new innovatiQ silicon 3D printer. “We bought it last October and the German made machine has been shipped out of Europe for its launch here at Australian Manufacturing Week. This machine is the first of its kind in Australia.”
He proudly shows a large diamond shaped silicone piece and then foot orthotics, that have been printed on the machine. The orthotics are very light compared to other more rigid traditional orthotic material. The machine can also print silicon prototypes, seals and bellows. mouldingservices.com.au
While cutting-edge manufacturing technology was unquestionably the main focus at Australian Manufacturing Week, a significant part of the show was dedicated to showcasing the end-users – the manufacturers themselves.
The Australian Manufacturers Pavilion provided a vivid snapshot of the state of manufacturing in Australia today. It featured impressive exhibits from celebrated manufacturers like Marand and Sutton Tools, with stands to rival even those of the big machinery suppliers. There was also a cohort of organisations highlighting their work supporting the industry: for example the Australian Border Force, giving advice on importing and exporting; or the Vernier Society, discussing their efforts to promote manufacturing in schools. Above all, the zone featured an inspiring array of hard-working, innovative, hugely accomplished manufacturing businesses from across Australia. One of them was New Touch Industries, and Managing Director Brad Drury was impressed with the atmosphere at AMW: “The show has been great, there is a real positive mood amongst everyone I have spoken to.”
For Drury, the Australian Manufacturers Pavilion was an opportunity for New Touch to demonstrate its capabilities and gain exposure in the market: “Our main aim has been discovering new leads, meeting customers and suppliers, networking, and getting the brand out there. I think it’s important to attend trade-shows and take advantage of the marketing opportunities. AMW provides the perfect platform to achieve these initiatives.” newtouchind.com.au
Similar aims prompted Catten Industries to take a stand, allowing it to promote its services and solutions in precision sheet-metal manufacturing, but also to make wider connections across the industry.
“Just to have a presence is one of the main things,” said Ian Cubitt, Managing Director of Catten. “The interaction between businesses – it could be competitors, it could be suppliers – is something we don’t get to do during the rest of the year. From day one the numbers have looked really good and we’ve had really good foot traffic.”
Cubitt saw AMW as a vehicle for Australian manufacturing to demonstrate its vitality as an industry and its importance to Australia’s overall prosperity: “I think it’s extremely important. It’s Australian manufacturing. We’ve got to show the skills and capabilities we’ve got. Post-COVID we’ve seen people realise the importance of having a good solid industry here in the country.” catten.com.au
Parish Engineering was using its stand to highlight the breadth of its capabilities and the diversity of the industries it can supply – from defence to woodworking, the trucking industry to interior design. For CEO Nicole Sinclair, the week had been a great success.
“It’s been fantastic,” she said. “The fact people haven’t been to an exhibition like this since 2019 in Melbourne, and that there are so many machines on display, is really attracting a lot of people to the show. They’re walking around and seeing what we’re capable of. For instance, I’ve seen a lot of defence people walking around, because they’re interested in the capabilities in Australia these days, and investing in it.”
Along with the business opportunities for the companies taking part, Sinclair saw the Australian Manufacturing Pavilion as an investment in the industry’s future.
“Obviously there’s what we’re showcasing to customers, but a lot of trade schools and schools have come through here too. Given that we’ve got a skills shortage at the moment, I think it’s really good for young kids to see what the industry’s like and what we can do in terms of technology today. It’s about changing the perception of the industry – from it being dirty and rough, to seeing that it’s secure and safe and sustainable. It’s a great industry.”
parishengineering.com.au
Featuring the latest advances in 3D printing, this Zone includes Additive Manufacturing users, suppliers and supporters. Among the 26 exhibitors was 3D printing equipment supplier TLC Hofmann and Freedspace Thinglab.
With over 50 years of industry experience and understanding of the Australian manufacturing market, TLC Hoffman specialises in the selective laser melting (SLM) process, focusing on the development and distribution of innovative metal additive manufacturing systems.
Business Manager John Whinnen has attended the AMW event for more than 20 years. Impressed by the crowd turnout, he says the event attracts the largest media coverage.
“It’s really great to see some vibrancy in the manufacturing industry, especially here in Victoria,” Whinnen says. “We’ve had a lot of development in our 3D printing products that we offer in regards to materials; there are more applications, faster throughput, so I think a lot of people are looking at it as a replacement for traditional processes and at onshoring their production processes to negate problems that they’ve had over the last few years of supply chain.”
Making it easier to manage visitors, the AMW event has featured a QR code scanning system for attendees, where simply by scanning the QR code with a phone, visitors could collect all the information they needed about a business and products.
Relieved at the thought of no longer having to bring or collect business cards, Whinnen has welcomed the interactive system. “For years you’d come with boxes of business cards; you’d be collecting them so the scanners for me have been the biggest thing,” Whinnen says.
“Having attended a lot of trade shows both in Australia and globally there’s no doubt what so ever that the AMW is the biggest one – it’s the one we always put at the top of our list to attend.” tclh3dprinting.com.au
Grae Scheuber, Freedspace Thinglab Director says additive manufacturing is becoming bigger, faster and cheaper.
As one of Australia’s leading interdependent vendors of 3D print, scan and design technologies, Thinglab provides product sales, services and support for the professional, education and arts sectors.
The company is divided into three business divisions; Thinglab, Tracklab and Vizulab.
Warehoused in Melbourne, Thinglab features a large range of 3D printing materials and includes a comprehensive 3D scanning software from Artec and Geomagic – tools that can help reverse engineering, improve workflow and increase productivity.
“It’s important to showcase the latest and to network otherwise we’re just going to stagnate and do the same thing, so it’s important we don’t fall behind,” Scheuber says.
“It’s about building those networks and with our customers we have connections with other businesses so we can better serve them and have a better idea of what’s going on – to basically become more integrated into the manufacturing community,” he adds.
“We’ve had a lot of customers come in and say hello and we’ve met a lot of new ones as well. There is a shift in mentality for customers; they’re more maturing whereas maybe four manufacturing events ago there was a lot of cheaper stuff.
“People are more about investing and there is a lot more confidence in the technology than it used to be. The additive sector is becoming bigger, faster and cheaper. It’s more precise and easier to use.” thinglab.com.au
The Weld & Air Solutions Zone pointed the spotlight on advanced welding processes and provide high-quality interactive experiences that demonstrate developments and applications in the welding sector.
The stand is buzzing with interested AMW visitors checking out the range of Kemppi’s industrial orange and black welding machines on show. Regional Sales Manager for NSW and Northern Qld, Emil Dela Cruz explains that Kemppi is a family-owned company, based in Lahti, Finland. It has a fully owned Australian subsidiary with its head office in Wetherill Park, in Sydney’s west and distributors across this country.
“Kemppi develops and produces innovative welding solutions in MIG/MAG, TIG and robotic welding,” Dela Cruz says. “This machine at the front is our Master M 358, which is our premium compact MIG/MAG welder. This smaller machine over here is our portable and light weight design Master M 205, which provides a singlephase pulse MIG welding.” All machines have a liquid air cylinder attached.
There’s also a range of black and orange welding personal protective gear on display including welding helmets, respirators and jackets for male and female welders. The helmets protect workers by eliminating the welding fumes and dust, advises Dela Cruz.
“So far, the expo has been good,” says Dela Cruz. “We have contact details of many interested potential buyers, that we can follow up next week and organize a product demonstration.” kemppi.com
What strikes you when you enter Kraftech’s very large stand is the diversity of machines on display. The Kraftech X-Wing Robotic Welding Series is the shining centrepiece, proudly showing the Australian Made logo. The company’s promotional flyer describes the X-Wing Series machine as: ‘Configured for two station operation, this compact welding equipment includes a centre mounted Fanuc robot on a rotating frame.’
Kraftech’s Project Engineer Jessica Leonbrono advises that the X- Wing Series is made at the company’s Revesby (NSW) factory. “This machine is very space efficient and its configuration allows the operator to load and unload on one side, while the robot is welding on the other. Kemppi provides the welding software for the machine’s operation.”
A green collaborative robot and yellow welding robot are also standing on Kraftech’s stand. “Expo visitors are showing a keen interest in our range of displayed robots,” says Leonbrono. “There’s been a steady flow of traffic today by existing and potential new customers,” says Leonbrono. “All the display machines here are pre-sold already, so we are looking forward to taking future orders.” kraftech.com.au
A crowd is around the Fanuc CRX-10 iA, collaborative welding cobot at Lincoln Electric’s stand. Its Marketing Manager, Paul Smith explains that the cobot uses the Lincoln Electric Power Wave 450, a robotic power source welding system.
“The cobot works alongside operators and if the person gets in its way, then the cobot will stop,” says Smith. “You can see that operator is teaching the cobot where the welding should go. Putting the cobot wire (end part) in position to weld, then that programs it to remember the specific locations to be welded on the metal. So, it’s a ‘point and shoot’ action.”
He says that Lincoln Electric is a supplier of welding equipment and advanced welding robotics and there is a broad selection of its red and black products on the stand. The 126-year-old company’s head office is in Cleveland Ohio and its Australian operations have been here for over 80 years, (now in Padstow, NSW).
“There’s been a good flow of show visitors here with many enquiries and great leads. We are seeing an increased interest in welding automation in answer to the global shortage of welders. Now lesser skilled operators can now work alongside welding robots to get the job done.” lincolnelectric.com
Robots are everywhere here. Like giraffes in the Zoo, happily grazing on boxes and weights behind their cages. But this modern equipment practical technologies with AI software brains, created and designed by engineers to automate and accelerate Australian manufacturing.
Primary among the technologies and capabilities on display at AMW2023 alongside all the very impressive robots and cobots were other Automated Solutions, Instrumentation Control Systems, Measurement, Pneumatics, IOT Solutions, Industry 4.0 and Digitalisation. There were 32 Exhibitors in the Robotics and Automation Zone, situated dead-centre in the middle of the action. Automated Solutions Australia had a presence right in the middle of it all. “The enthusiasm and excitement of Australian manufacturers during the AMW2023 event was contagious, making it a great experience for everyone involved,” said Pat Green, ASA Director. “The exhibition halls were also filled with future STEM students, providing an opportunity to introduce them to automation technology. Attending AMW2023 is truly an enriching experience that leaves you feeling fulfilled, and this year’s event was no different.” One of the most talked-about parts of the ASA exhibit at AMW2023 was the FANUC robots. The FANUC P-250iB/15 Paint Robot was showcased as a versatile robot that could be used for a wide variety of applications, including paint, fibreglassing, and other hazardous dispensing applications. Equally impressive was the R2000iC/270F FANUC Robot, the strongman in the R2000 series with a payload of 270kg. ASA demonstrated this robot’s versatility in handling large and awkward pieces, showcasing its ability to be used for machine tending, part transfer, spot welding, palletising, and many more applications.
This robot was due to fly out to an assignment in New Zealand straight after the show. The ASA crew also took advantage of the networking events outside of the show hours. ASA’s staff and management thrived on this opportunity and were able to connect with other like-minded individuals driving the technological revolution. This year’s AMW was an unforgettable celebration of Australian manufacturing. With record attendance, exciting exhibits, and plenty of networking opportunities, it’s no surprise that everyone left feeling inspired and energised. We can’t wait to see what the future holds for Australian manufacturing and look forward to continuing to be a part of it!
automatedsolutions.com.au
I visited SCHUNK Intec Pty Ltd on their stands, a bit further down. SCHUNK specialises in workholding, gripping tech, toolholding and automation technology. It is such a pleasure to come across these international technology leading companies that are one-by-one, taking the plunge and now opening Australian offices. There are now 3,500 employees in nine plants and 34 directly owned subsidiaries and distribution partners in more than 50 countries throughout the world. The latest addition to the SCHUNK Intec group is now open in Sydney. SCHUNK, a family-owned company, is pushing the agile development and digitalisation of its product and service portfolio in order to make industrial processes more efficient, transparent and sustainable.
The last time I saw a SCHUNK stand was in one of those huge shows in Europe. But with Pete Shepherd as General Manager and Thong Phabmixay in charge of Business Development in Sydney, they will see a lot more movement here at home. “We’re really pleased with the feedback here at AMW. It’s been an incredibly busy few days,” said Shepherd. “The solid interest we’ve had from the visitors has been gratifying. There haven’t been many tire-kickers. People here know what they’re looking at.”
schunk.de.com
CSIRO launches $10m project to build Australia’s first movable hydrogen generator
Australia needs hydrogen to help reach net zero emissions by 2050, and groundbreaking new technology could help reshape the nation’s energy landscape by safely generating hydrogen at off-grid locations.
A new project led by CSIRO, Australia’s national science agency, will develop an easily deployed device to produce hydrogen directly at the point of consumption, in an Australian first.
CSIRO scientists will build a demonstration unit based on patented technology to efficiently generate hydrogen from liquid carriers, supported by a $10m investment over six years from research and innovation provider Advanced Carbon Engineering. The use of a liquid carrier enables hydrogen to be safely and efficiently stored and transported in tanks from where it is produced – like a remote solar or wind farm – to where the energy is to be used.
CSIRO’s Deputy Hydrogen Industry Mission Lead, Dr Vicky Au, said the project will be the first unit using Australian technology to produce hydrogen from a liquid carrier, and addresses some of the key challenges to the growth of the hydrogen sector.
“Australia has the potential to become an energy superpower through hydrogen, but we need to find better methods of safely transporting and storing it at scale,” Dr Au said.
“To get the hydrogen industry moving, we need to be able to get hydrogen where it will be used by the consumer. This generator unit will do just that and will be compact enough to move to where it’s needed – whether that’s a farm, a festival, an industrial facility or, a mine site.
“The power of industry and research coming together cannot be overstated when delivering the solutions needed for a sustainable future.”
CSIRO Researcher Dr John Chiefari said CSIRO’s patented catalytic static mixers would be central to the development of the new hydrogen generator.
“Catalytic static mixers are special tools that mix fluids to speed up and better control chemical reactions without any moving parts. This level of control allows the process to be highly scalable without the technical challenges that this usually entails. This gives us a key advantage over the current packed bed reactor technology,” Dr Chiefari said.
“The technology to add hydrogen to a carrier fluid is already established. Now this hydrogen generation system will enable
hydrogen to be produced locally and on demand from the carrier, with the added advantages of the carrier fluid being safely stored in a similar way to diesel or petrol.”
“This would be a big step forward with a goal to be able to store the fuel in standard tanks and manage it using existing diesel or petrol infrastructure.”
Advanced Carbon Engineering CEO, Mr Jon McNaught, said that the company is building national capabilities by conducting critical research, facilitating innovative discoveries and building new industries.
“Innovation is vital for humanity's future, driving progress and economic growth, solving challenges, creating opportunities, and ensuring a sustainable future for generations,” Mr McNaught said.
The project is being delivered as a part of CSIRO’s Hydrogen Industry Mission, which is dedicated to supporting global decarbonisation through the development of a commercially viable Australian hydrogen industry.
According to Australia’s National Hydrogen Strategy, a clean hydrogen industry will support 16,000 jobs by 2050, plus an additional 13,000 from the construction of related renewable energy infrastructure. Australian hydrogen production for export and domestic use could generate more than $50bn in additional GDP by 2050, and result in avoided greenhouse gas emissions equivalent to a third of Australia’s current fossil fuel emissions by 2050. csiro.au
As stringent hygienic requirements become more relevant in the food, beverage and pharmaceutical industries, the PSH..CM2H.. series guarantees the highest level of cleanliness and protection against contamination.
Developed to withstand high-pressure cleaning, even at high temperatures and with chemical cleaning agents, this series is the ideal drive solution where hygiene is the priority.
Your Benefits:
• Faster cleaning times
• Compact design for your open machine concept
• Suitable for the food and pharmaceutical industry
• Precise and safe positioning
• Fast startup and optimum operation www.sew-eurodrive.com.au
HDR has designed two NEXTDC colocation data centres in Melbourne that are set to house Australia’s largest and most comprehensive cloud ecosystem. Constructed by Kapitol Group, M3 Melbourne, a 100,000m² data centre in West Footscray, and M2 Melbourne, a 16,000m² data centre in Tullamarine, will collectively deliver 210 megawatts of critical IT infrastructure to enterprise and government in a climate of unprecedented digital innovation.
“Designing high-performance, resilient and scalable infrastructure at speed is no easy feat,” said Sam Faigen, project leader at HDR. “Utilising a data-driven design methodology, we have succeeded in delivering two purpose-built facilities, using modular and adaptable solutions, that will accelerate industry growth.”
With Stage 1 of the 150MW masterplan now complete, M3 operates as a colocation facility for retail, enterprise and hyperscale customers, fitted out with HDR-designed administrative offices, collaboration spaces and highly adaptable data halls. Strategically located close to major electricity substations, the campus is situated 10 km from Melbourne’s CBD and resides at the junction between large industrial developments and low-scale residential dwellings.
“Knitted into West Footscray’s semi-residential urban fabric, the building form has been set 20-metres back into the site to respect the neighbours,” Faigen said. “This setback zone features densely plated swales, trees and ‘pocket parks’, as well as a community café along the tree-lined perimeter, that gently transitions the site context from residential to industrial and puts community well-being first.” The rectilinear machine space of the data halls has been wrapped in a faceted façade ribbon that houses active office, lobby and breakout spaces. In contrast, flora ascends the building on engineered trellises, inhabiting the parapets and cascading down the bespoke concrete facade to create a juxtaposition of materiality and form.
Engineered to Uptime Institute’s Tier IV resilient standards by Arup, M3 has achieved an excellent Built Environment Sustainability Scorecard (BESS) and an industry-leading target PUE of 1.29. Planning consultants, Urbis and project managers, Newbridge also played an integral role across the design and construction process. Concurrently, HDR has designed sister facility M2; a 60MW
purpose-built campus and high-grade contemporary workspace strategically located near Melbourne’s Tullamarine airport and its surrounding transport and telecommunications network. Fitted out with HDR-designed commercial office space, meeting rooms, training spaces, an auditorium and customer amenity, the futureproof campus has been designed to transform and scale into a network of interconnected data halls on demand.
“Standing proud as a landmark in its site context, the building’s dynamic form and striking red filigree façade of articulating blades juxtaposes the aluminum structure,” Faigen said. “Not only do these blades respond to the high level of solar exposure and optimise sun shading, but they create a dappled effect on what would otherwise be a rather monolithic structure.”
Generated through emerging data-driven design technologies, HDR has utilised computational and generative design to rapidly evaluate manipulated parameters in real-time and test the specific programmatic needs of the project. Engineered by Aurecon, M2 has achieved Uptime Institute’s Tier IV Gold Certification for Operational Sustainability and a target PUE of 1.29. The project team also included planning consultants, Urbis and project managers, The APP Group.
“With the ever-increasing digitisation of work, life and play, data centres are becoming fundamental infrastructure in our built environment,” said Graeme Spencer, HDR’s national director of education and science. “By thoughtfully integrating deeply technical, data-driven processes, while still maintaining focus on community well-being, we have conceived two resilient, sustainable and highperformance campuses that enable digital transformation.”
In 2022, HDR was ranked No.1 for “Top 30 Data Centre Architecture + AE Firms in the Building Design + Construction’s Giants 400 report. “The Australian digital economy is growing rapidly, accelerating the need for interconnected cloud services, sovereign secured, and sustainable solutions enabled by Tier IV certified facilities to assure business resilience,” said Craig Scroggie, NEXTDC CEO and MD. “As a market leader, NEXTDC is responding to market demand by expanding our digital infrastructure platform.” hdrinc.com
Held on Friday 5th May at Deakin University’s Waurn Ponds Estate, the second Advanced Manufacturing Showcase was an incredible success thanks to its three co-hosts and support from industry and government.
With a 138% increase in registrations, a 30% increase in delegates, nine additional speakers and 19 more exhibitors than last year, the regional showcase event is proving to be an incredibly relevant and valuable gathering of manufacturing and engineering industry professionals, researchers, and innovators.
The theme of the 2023 showcase was ‘Sovereign Capability through Advanced Manufacturing in Victoria’ emphasised by the quality of speakers secured and the four topics discussed throughout the day: Learning and Adopting Manufacturing 4.0 and Building the EcoSystem, Industry 4.0 - Driving Manufacturing Excellence, Advanced Manufacturing Innovations - Pathway to Sustainability and Australian Advanced Manufacturing - The Roadmap.
Each topic was covered by 3-4 incredible presenters, such as Victorian Defence Industry Advocate John O’Callaghan who also MC’d the Welcome session with Cr Trent Sullivan, Mayor of Geelong. Other speakers included: Richard Merjan, Australian Industry Capability Manager of Programs from Hanwha Defense, Jonas Jeyraj Anthony from Panasonic Malaysia, Bradley Trewin, National Sales and Business Development Manager from Bosch Australia Manufacturing Solutions, Jennifer Conley from Geelong Manufacturing Council and Neil Mulcahy from Farmers2Founders.
Diverse exhibitors presented unique innovations and demonstrations of cutting-edge technologies and capabilities to delegates. Guarda Systems conducted the first-ever live demonstration of their
trailblazing masonry-cutting dust suppression technology. Guarda's revolutionary masonry cutting saws and related products are patented and proven in real-world scenarios to reduce respirable crystalline silica (RCS) dust on Australian construction sites by between 87% and 99% compared to conventional saws.
Deakin’s School of Engineering Solar Car project team, led by Lecturer in Mechanical Engineering Matt Jennings, allowed Deakin engineering students to present their progress in designing and building a solar-powered vehicle to compete in the 2023 Bridgestone World Solar Challenge – a 3000km race from Darwin to Adelaide. A live stream of the workshop and drive line assembly was shown alongside students detailing their project learnings.
The 2023 event was supported by AMTIL, Hanwha Defense Australia, Geelong Manufacturing Council, Bosch Australia Manufacturing Solutions, City of Greater Geelong, Regional Partnerships Barwon and Farmers2Founders. “AMTIL is proud to support the Advanced Manufacturing Showcase as an event partner. AMS aligns with the mission of our own Australian Manufacturing Week: celebrating manufacturing in Australia,” said Greg Chalker, Corporate Services Manager at AMTIL.
The AMS organising committee are already looking to next year’s showcase and what opportunities 2024 has in store. manufutures.deakin.edu.au memko.com.au 3ds.com
Email: integratransform@integrasystems.com.au
Website: www integratransform com au
Phone: +61 3 9359 3133
The talk around Industry 4.0 and smart factories has been dominating the manufacturing sector for several years now. However, as recent reports show, adoption is largely still in its infancy. Gregg Ostrowski, Executive CTO at Cisco AppDynamics, talks us through it.
The shift from partial to fully automated factories is incredibly complex, and this explains why most organisations are currently making slower progress than they would like. Some manufacturers are still trying to work out exactly how this new concept can best be applied within their operations, while others are facing cultural resistance. As with all digital transformation programs, there are also difficulties in integrating information technologies (IT) and operational technologies (OT) alongside legacy equipment.
Despite these challenges, there is still a huge amount of excitement about the potential benefits that Industry 4.0 transformation can deliver. From semiconductors and electronics, through to pharmaceuticals, automotive and aerospace, manufacturers recognise the opportunities for increased speed to innovation, agile business models and streamlined operations. However, with economic conditions likely to be challenging throughout 2023, there is little doubt that these transformation initiatives will increasingly come under the spotlight. Whereas organisations had little choice but to invest heavily (and sometimes indiscriminately) in innovation programs to get them through the pandemic, they are now taking a far more rigorous and selective approach to investment decisions. As McKinsey has reported, data is critical to the success of Industry 4.0 initiatives. Transformation leaders depend on data to monitor and improve on performance within the context of their business goals and to enable insight-driven decision-making. Cloud native observability is critical to optimise application performance and end user experience, and to validate investment in any innovation initiative.
The World Economic Forum describes Industry 4.0 as the fusion of technologies blurring lines between physical, digital and biological spheres, and that it will “herald the transformations of entire systems, production, management, and governance” for organisations across the world. And the move to smart factories is expected to grow by 20.6% year on year over the next three years, reaching more than $165bn by 2026. Technologies that assist and enable Industry 4.0 are evolving fast, including interconnected, shared digital platforms that support and accelerate all aspects of industrial processing. Alongside ‘internet-connected everything,’ we are also seeing rapid advancements in technologies relating to compliance monitoring, product design and innovation, time-to-market, waste reduction, pre-production testing and modifications, and distribution and logistics.
It’s important to recognise that the essential foundation for much of this transformation is the wholesale adoption of cloud native technologies which we’re seeing right across the manufacturing sector. Modern application architectures, built on technologies such as microservices and Kubernetes, are enabling manufacturers to innovate at speed while delivering greater operational and technical agility and resilience. IT departments are surging ahead with their transformation programs, using cloud native, low-code and no-code platforms to accelerate release velocity and build more dynamic applications.
However, the shift to cloud native technologies is causing significant challenges for the IT teams responsible for managing and optimising
the availability and performance of new applications. The issue is that they’re unable to monitor these environments and, in particular, they’re struggling to get visibility into applications and underlying infrastructure for large, managed Kubernetes environments running on public clouds.
Unfortunately, many IT departments simply don’t have the tools to cut through this overwhelming bombardment of data that is coming at them from every corner of their IT estate. Indeed, our Agents of Transformation 2022 report found that 65% of technologists feel overwhelmed by soaring data noise and spiraling complexity.
This lack of visibility into cloud native environments significantly increases the risk of applications failing and end users (customers, suppliers and staff) suffering poor digital experiences - something that manufacturers can ill afford. But beyond that, it also means that business and IT leaders have very limited data and insights into the impact that their innovation programs are delivering. They’re unable to connect IT performance within business outcomes and therefore they can’t validate their Industry 4.0 investments.
In order to overcome this issue, manufacturers need to implement a modern cloud native observability solution, which simplifies the complexity of cloud native application architectures and provides observability into highly dynamic and distributed applications, landscapes and architectures.
Manufacturers should also be leveraging the power of AIOps and business intelligence and infusing these capabilities into their cloud environments. This will enable them to automate issue detection and diagnosis using machine learning and provide insights for faster troubleshooting. Ultimately, it allows technologists to understand more quickly what really matters and enables them to prioritise their actions accordingly.
Perhaps most crucially however, where Industry 4.0 transformation is concerned, manufacturers need to be able to monitor the health of key business transactions distributed across their entire technology landscape. If an issue is detected, they need to follow the thread of the business transaction’s telemetry data, so they can quickly determine the root cause of issues, with fault domain isolation, and triage the issue to the correct teams for expedited resolution.
This ability to generate business transaction insights in realtime, and then to view them in business-level dashboards, is essential for leaders within manufacturing organisations to quickly understand the value that their innovation programs are delivering. It means they can make rapid but informed decisions on where to focus investments based on what will have the biggest benefit for customers, employees, and ultimately, the business. And this in turn will enable them to validate their Industry 4.0 investments and achieve their transformation objectives. appdynamics.com
Manufacturers have always been under pressure from different factors, especially time constraints, resource allocation, and managing costs.
Manufacturing planning tools have come a long way and simulation, like digital twin technology, has come a long way. They provide manufacturers with more insight than ever before to help identify, plan, optimise, and seek approval for manufacturing projects. If manufacturers want to succeed, they need to evolve their manufacturing operations and management architecture to take advantage of digital twins. The power of these modern tools is endless.
At Bosch Australia Manufacturing Solutions (BAMS) a digital twin is a physics-enabled virtual replica of a real machine that can be commissioned with the same controllers and the same programs as the real machine, communicating bi-directionally, in real-time, and vastly speeding up the development time and the quality of the final product. If a programmer plugs their PC into a machine in another room, obscured from view, they should not be able to tell whether they are plugged into the real system or the Digital Twin. The objectives of using digital twins at BAMS is to validate the complete machine (debug Robot, PLC, and HMI code) and connect all the sensors, PLC, robot controllers, and HMI to make sure everything interfaces together properly. Digital twins provide open interfaces for connecting controllers which is an invaluable development tool with huge benefits during the commissioning phase. When problems are found on a screen, updating the code, and resetting the system can be a matter of minutes. On the shop floor on the other hand, a simple clearing of the line and reset could take hours, or even days depending on the complexity of the system. When that is coupled with the possibility of a physical change or the code having new bugs in it, these lost hours can compound into huge losses for a project.
The benefits of digital twins compound the most when customers order more than one of the same machine or manufacturing line, since all of the models and controllers used in a digital twin are reusable. If one cell or machine has been constructed in the virtual world, multiplying that out to multiple can be a matter of a few hours. This is game-changing when it comes to commissioning multiple lines at massive customer sites because most of the code can be validated offsite, decreasing time spent on customer sites and reducing disruptions to a customer’s factory.
The use of a digital twin does not stop after the development phase. It exists alongside the real machine as a stress-testing platform, with the ability to predict some niche failure modes by iteratively cycling through countless what-if scenarios that cannot be done in reality. Because BAMS’ digital twin simulations are physicsenabled, not only does BAMS have the capability to stress-test their machines, but they can also help cycle through all sorts of defects and variations with the customer’s products as well and see how that affects the overall system.
After the full system is developed and delivered to the customer site, operators are trained on the machine’s standard operating procedures. The Digital Twin gives BAMS the ability to quickly replicate a lot of error and emergency scenarios and guide the operators through the recovery procedures via a simulated HMI and Teach Pendant, which is not always possible in reality.
BAMS services customers all over Australia, and sometimes outside of Australia. Having a digital twin on hand means that if a customer runs into any issues at their site, BAMS can simulate the failure on the digital twin and remotely service or guide the customer through potential error recovery steps. Even in the final stages, if a service engineer needs to go to a site to make physical changes, having a digital twin to implement the change offline and validate it before pushing it to the real machine can be very powerful.
Simulation as a tool gives BAMS and its customers more ability to control project cost and lead times (including during the quotation phase) and can also help better define scope. In addition to being much more efficient to find and fix problems on the screen before the build phase, digital twins also enable advanced Revision and Documentation Control since all the changes are done to a Common Engineering Model. With accurate data in the model and real parameters as inputs, digital twins can provide a single source of truth for all virtual datasets.
BAMS is leading by innovation with its digital twin simulations and constantly inventing solutions to support local manufacturers. Confidence and risk management are vital in manufacturing and digital twin technology provide this like never before. BAMS can help manufacturers save costs, and time, and improve their efficiency from the initial concept to the site installation and commissioning, in a resource-effective manner. boschmanufacturing.au
Automation industry analysts sometimes observe that, just like invention, innovation is 1% inspiration and 99% perspiration. However, nothing useful happens without that 1% spark. Both inspiration and innovation require fertile and nurturing environments where they can grow and thrive, despite the stresses and scarcity imposed by today’s tumultuous times.
To achieve optimisation, it is not enough to just introduce technology to an environment and expect it to thrive. It is necessary to establish systems that enable people and devices to collaborate effectively, and therefore make a significant impact in their specific application. Users need to acknowledge that there are various situations where innovation is required, but the speed and complexity of these scenarios are affecting the way we innovate. As a result, there is a growing demand for open, interoperable, and adaptable systems that can help users achieve flexible and optimised manufacturing. New technologies have been emerging for 100 years, but what’s changed are the levels of speed and complexity. The difference now is users asking, “Why can’t I get the same complicated data and intelligence in my plant that I get from my consumer technologies?”
Given the continued upheaval caused by COVID-19 and its remote work and supply chain aftershocks, it’s hard for engineers and managers to maintain the relative equilibrium they need to innovate and improve operations performance.
Lately, they have to rethink and revise everything they do. Plus, they’re facing demands that return on investment (ROI) happen sooner, too. In addition, large manufacturers are facing production challenges, including corporate directives intended to solve them, which can cause friction between formerly isolated departments. For instance, IT previously focused on computing infrastructure and what software was put into plants, but now they’re dealing with users who want to add software containers, artificial intelligence (AI) and models, and are worried they’ll lose control of their processes. Such aid is often directed to smaller and emerging technology manufacturers, such as makers of electric vehicle (EV) batteries and
life sciences systems. For example, in the US we’re partnering with the Advanced Regenerative Manufacturing Institute (ARMI), which is a consortium of companies we helped co-found that brings technical startups together.
One of its startup labs is working on growing skin, tendons, and other tissue, and we’re participating to help them conduct experiments that will enable them to move from the lab to industrialscale operations.
Beyond applying helpful technologies, innovation must also be nurtured with human cooperation. Maximising production means finding optimisation scenarios. However, they can’t happen in silos, so everyone must be empowered to work together.
Building systems that let individuals and devices work together can make a big difference in optimisation. These systems are characterised by open architectures and ecosystems that follow open standards and extend their capabilities into optional architectures. These include every industry segment and vertical we target, including major local verticals such as food and beverage, medical and pharmaceutical, water and wastewater, resources and energy and sustainability in all things.
Information needs to be used in the right way, so it can take manufacturing to new levels, and enable co-innovation to help shape the future. A key here is to combine data science with plantfloor expertise. These systems need to integrate the personas of their users.
By harnessing the power of the cloud, companies can simplify software management while increasing productivity, speeding time to market, and designing systems that cost less to build and provide more value over their lifetime.
Technology shouldn’t add complexity and block performance – it should instead provide a good production environment that makes it easier and less risky to innovate.
rockwellautomation.com/en-au
Rockwell Automation introduces it’s own cloud-based manufacturing platform
Plex, which Rockwell Automation acquired in 2021, is a Software as a Service (SaaS) Smart Manufacturing Platform that connects people, systems, machines, and supply chains. It is a digital system of record that automates business processes, tracks data from the shop floor to the top floor, and delivers analytics to improve visibility, quality, and control.
Rockwell Automation recently released its 2023 State of Smart Manufacturing Report, which comprised data from thousands of manufacturers globally, including 75 in Australia. Rockwell found that more than 45% of Australian manufacturers say that they lack the innovation, skilled workforce, and technology to outpace the competition over the next 12 months.
“Although smart manufacturing is key to Australia’s success, only 25% of the country’s manufacturing industry leaders said they were extremely familiar with the technologies,” said Anthony Wong, regional director – south pacific, Rockwell Automation.
“Using Plex for food and beverage manufacturers and processors is like moving from DVDs to a streaming service. It opens up these technologies to smaller players, who don’t have to invest in large up-front costs. The good news is that solutions exist and can be quickly implemented. Plex, for instance, does not require major investment in hardware or IT infrastructure. Plex is modular and scalable – it grows with you,” said Wong.
“Using Plex for manufacturers and processors is like moving from DVDs to a streaming service,” said Wong. “It opens up these technologies to smaller players, who don’t have to invest in large up-front costs.”
This is positive news for a sector that, in Australia, is largely made up of Small and Medium Enterprises.
“Being cloud-based makes it easier to keep software like Plex updated. New functionality is regularly being added, and because it’s a modular system, it doesn’t take everything else offline to perform an update,” said Wong.
The Plex stand will feature demonstrations of the software, and how it can benefit manufacturers of any scale.
“I encourage manufacturers of all sizes to come and speak with our experts on the stand to see how a modular SaaS platform like Plex could help grow their business,” concluded Wong.
rockwellautomation.com/en-au
Digitised mechanical and environmental performance of recycled short glass-fibre reinforced PP compounds supports the transition to more sustainable vehicles
Hexagon’s Manufacturing Intelligence division and Sumika Polymer Compounds Europe (SPC Europe), a leading manufacturer of thermoplastic compounds, have partnered to digitise the performance of new sustainable automotive-grade polypropylene (PP) compounds, enabling engineers to design components that are more recyclable and offer a lower carbon footprint for future vehicles.
Sumika Polymer Compounds’ short glass-fibre polypropylene (GF-PP) THERMOFIL HP and recycled polypropylene (GFrPP) THERMOFIL CIRCLE materials benefit from sustainable manufacturing and recycling processes and offer carmakers performance equivalent to incumbent engineering plastics, but with an up to 60% lower carbon footprint. A growing proportion of today’s PP components are recovered and recycled compared to polyamides (PA), of which up to 70% are utilised in waste-to-energy initiatives or finish up in landfill, but there remains substantial room for improvement. These new Sumika recycled PP compounds are designed for the circular economy, contributing to plastic waste reduction at vehicle end-of-life.
Plastics can contribute up to 20% of the total weight of a car, and their application is escalating with the continuing replacement of metals. The automotive industry’s shift to eMobility has increased the need for lightweighting components to maximise the energy efficiency of vehicles and mitigate the considerable weight of battery packs, but their environmental performance throughout the lifecycle must also be considered by product development teams.
“Limited material behaviour data is a barrier to sustainable eMobility innovations because automotive engineering teams have not been able to put new materials through the rigorous virtual durability and safety tests required for automotive endorsement,” said Guillaume Boisot, head of the Materials Centre of Excellence at Hexagon.
“Our unique multiscale material modelling technology accelerates the adoption of SPC Europe’s ground-breaking recycled materials by making it possible for product development teams to accurately simulate a component and subject it to established automotive engineering test and validation.”
This vital engineering data is the result of a long-term partnership between the two companies, providing product development teams the ability to evaluate the suitability of GF-PP compounds in new designs to address carbon-neutral targets by replacing traditional engineering plastics.
“Our THERMOFIL short glass-fibre reinforced polypropylene compounds offer equivalent performance to traditional engineering plastics while providing a much lower carbon footprint, which makes them highly suitable to meet design challenges that sustainable eMobility brings,” said Bruno Pendélio, marketing manager for SPC Europe. “Combining our efforts with Hexagon allows us to support the race towards carbon neutrality by further lightweighting our customers’ automotive components, reducing physical material testing and prototyping.”
Hexagon conducted a detailed and rigorous testing and physical validation programme with SPC Europe to produce highly accurate multi-scale behavioural models of its THERMOFIL® HP grades and THERMOFIL CIRCLE™ portfolio of recycled PP grades. Each material grade has a model that simulates the materials’ mechanical and environmental performance throughout a component’s lifecycle. The encrypted proprietary material models can be accessed by SPC Europe customers through Hexagon’s Digimat software. Digimat is interoperable with popular computer-aided engineering (CAE) software tools, such as MSC Nastran, Marc, and third-party software, empowering engineers to perform accurate analyses using established digital engineering workflows. hexagon.com/solutions/material-modelling sumikaeurope.com
MathWorks and Universal Robots ecosystem offer robotics engineers AI and autonomy capabilities in cobot programming.
MathWorks, the leading developer of mathematical computing software, joins the UR+ program, the industry’s largest and most comprehensive ecosystem of products certified to integrate seamlessly with cobots from Universal Robots (UR). MathWorks received the UR+ certification for MATLAB, a programming and numeric computing platform that provides software tools and algorithms for designing, simulating, testing and deploying robotics applications, including those for Universal Robots’ cobots.
Robotics engineers use MATLAB for specialised or sophisticated cobot applications that are difficult to program using the UR teach pendant or graphical-based programming tools, including applications that incorporate machine learning, deep learning, computer vision, optimisation, sensor fusion, and advanced signal processing. MATLAB provides AI capabilities for cobots to move more efficiently and productively by perceiving dynamically changing workspaces and sophisticated robot algorithms. Engineers can verify their UR cobot applications by connecting MATLAB to URSim, a simulation software for robot programs, or UR hardware. MATLAB support for Universal Robots is compatible with the entire e- and CB- series of Universal Robots.
"We are delighted to welcome MathWorks to our UR+ solutions ecosystem and look forward to seeing this partnership help simplify the more complex cobot deployment for robotics engineers," said Christopher Savoia, Universal Robots UR+ ecosystem manager. Offline cobot programming and simulation within MATLAB enables users to minimise downtime when programming using robots onsite. Robotics engineers can also deploy robotic algorithms and AI models by generating C++ codes directly on embedded targets, such as GPU boards, using MATLAB Coder™ and Simulink Coder™
for standalone, accelerated execution with UR hardware. "With Universal Robots’ market leadership and MATLAB and Simulink's ability to accelerate the pace of innovation, integrators and end users will now have the ability to solve more complex automation workflows," said Dominic Viens, Director, Design Automation Marketing at MathWorks. “The UR hardware support package reduces the time to market for advanced cobot applications that require the integration of multiple complex technologies. This enables the small- and medium-sized manufacturers to adopt deep technology stacks at a fraction of the cost of hiring external consultants.” mathworks.com universal-robots.com
Fresh food manufacturer Beak and Johnston tracks production with Fortude to ease waste.
Beak and Johnston, an Australian family-owned fresh food manufacturer that produces innovative, value-added meal solutions, has partnered with Fortude, a global digital technology solutions company, to transform the manufacturing operations at its Greenacre plant.
While Beak and Johnston is no stranger to Infor M3 having previously adopted it at their Arndell Park Facility, the manufacturer chose to partner with Fortude for the Greenacre plant roll-out because of the firm’s deep domain expertise and strong implementation track record in the food and beverage industry.
“Our investment in Infor M3 is a strategic move towards becoming the top convenient meals provider of choice for all Australians. Fortude's food and beverage industry implementation experience coupled with its extensive suite of extensions and integrations has enabled us to boost the performance of Infor’s core solution. With Fortude’s support, we have been able to streamline our operations and minimise food waste through effective master demand forecasting and inventory management. We also have been able to establish complete traceability which enables us to ensure compliance and food safety in our operations. We are delighted to have a partner like Fortude that understands our industry and growth ambitions very well,” said Ben Taboada, Group IT Manager, Beak and Johnston. Fortude’s implementation has helped the Australian food manufacturer boost its inventory visibility, overcome integration issues, simplify the stock valuation process, and eliminate supply chain inefficiencies. Fortude also introduced the Infor Manufacturing
Execution System (MES) to support Beak and Johnston's core manufacturing activities through complete traceability and accurate shelf-life management capabilities for its fresh food products.
“The growing consumer demands for convenient and healthy meal solutions points to a booming frozen food industry. However, limited product shelf-life and dynamics of the fresh food industry, pose serious challenges for fresh food manufacturers,” explains Cameron Greening, Senior Vice President (Sales) ANZ, Fortude. “The robust Infor M3 solution equips Beak and Johnston with the tools and realtime insights to overcome these pressing challenges and position itself as the regional leader in the convenience food space. The Fortude team is excited to be part of their transformation journey.”
The Fortude team currently works with Beak and Johnston on continuous enhancements that align the Infor solution with the manufacturer’s strategic business goals. beakandjohnston.com.au fortude.co
AMT: Professor Bronwyn Fox. What is Quantum Technology?
Prof. Bronwyn Fox: Quantum technology uses the building blocks of nature (subatomic particles) to improve our lives. Quantum Technologies will revolutionise the way we use sensing, computing and communications systems. These technologies will cut across a number of industry sectors including energy, secure communications, computer simulations and manufacturing.
It was evident from the conference that Australia has a vibrant research and start-up ecosystem, the result of over two decades of concentrated effort. It was wonderful to see Australian science being translated to create new companies, that are attracting investment and working with customers to solve complex problems.
Australia’s Chief Scientist, Dr Cathy Foley, who was a key-note speaker at the conference today, has been working on Quantum Technology for many years. When Cathy was at CSIRO, she was leading a team that developed Superconducting Quantum Interference Devices (SQUIDs) which are used to measure minute changes in magnetic fields.
Cathy commercialised that technology over a decade ago and it’s been used to discover more than $6bn in mineral deposits. Quantum technologies are being used in industry now. It's clear that the next stage of evolution will be the broader application of quantum technologies to solve the challenges we are facing globally around energy and the environment. That's what we've been discussing today.
AMT: What are quantum sensors and how could they be used manufacturing?
BF: Quantum sensors have unprecedented precision and a unique ability to detect very small changes, for example in magnetic fields. Industry is interested in how these sensors can be used to manufacture high precision medical imaging equipment, battery management systems for vehicles and precision timing to allow better machine to machine communication. This will improve the efficiency of automation and robotics in manufacturing.
AMT: Your first job was at CSIRO, 30 years ago? What were you researching?
BF: My first job after graduating from university was at the Cooperative Research Centre (CRC) for Polymers at the very beginning of the CRC program. I was one of the first employees at one of the first CRCs and I worked on a number of different projects simultaneously. The most significant one for me was recycling Polyethylene Terephthalate (PET), used to make drink bottles. We did a lot of work on understanding how to break down this polymer in a way that meant that it could be re-used.
AMT: Tell me about your current job as CSIRO’s Chief Scientist.
BF: I started this role in October 2021. One of the things I'm most proud of, is our Impossible Without You program to recruit 200 early and mid-career researchers. We are committed to training the next generation of science leaders and thrilled to give this group opportunities for additional professional development and to come together as a cohort. I’ve known first-hand the power and potential of this program, when I joined CSIRO 30 years ago, as there was an influx of younger scientists and it led to a wonderful, vibrant, creative atmosphere.
We have called the recruitment campaign Impossible Without You because it is! We’re saying that CSIRO is focused on solving Australia's and the world’s greatest challenges and we can't do it without you, the best and the brightest.
We have also deliberately recruited for diversity in this cohort. To that, we’ve trained our recruitment panels on unconscious bias, on the power of diversity in delivering the type of innovation we need. True innovation is about creating completely new ways of working as well as products and solutions. We need new and diverse thinking, if we’re going to do that. We've made sure we are mindful of every single facet of diversity and we’ve attracted some fantastic people. For me, it's really amazing to be part of CSIRO again and I really feel that connection to a sense of purpose that you have when you're here. It’s an organisation where you feel like you are truly making a difference in solving challenging problems and creating new industries.
AMT: What are these new industries?
BF: In the past year, I've been to the launch of many different spinouts from CSIRO, one example is Chrysos Corporation.
The Adelaide-based Chrysos is a fascinating company. In partnership with CSIRO, they are using a CSIRO-developed photon assay to measure the concentration of gold in mineral deposits. In the past, that measurement took up to three weeks, now we can get that data almost instantly.
Traditional methods of measuring gold concentration also required high temperatures and the use of nasty analytical reagents. This was to check if the rock sample was viable, contained gold and really to answer the question of whether you should continue to be spending energy, time and money on it.
Where once that process took up to three weeks, the PhotonAssay allows for faster decision-making across the value chain. It uses powerful x-ray analysis and offers mineral analysis data in minutes. The technique uses high powered x-rays to bombard rock samples and activate atoms of gold and other metals. A highly sensitive detector then picks up the unique atomic signatures from these elements to determine their concentrations.
Chrysos was listed on the Australian Stock Exchange (ASX) in May 2022. CSIRO’s Chief Executive, Larry Marshall was there to ring the ASX bell and CSIRO remains Chrysos’ largest shareholder.
There’s also another benefit. By using the photon assay instead of the traditional method of measuring gold concentration, Chrysos has reduced CO2 emissions by 2600.9 tonnes and cut 1752.8 tonnes of hazardous waste materials from the gold mining companies that it works with.
AMT: Can you tell us about two manufacturers that you have done projects with?
BF: We’ve worked extensively with Titomic, an additive manufacturing company that uses cold spray technology, software and robotics in its automated metals manufacturing. The fundamentals of cold spray technology were developed at CSIRO, many years ago. We are currently working with Titomic creating 3D tools for manufacturing, as the company has one of the largest 3D printers in the Southern Hemisphere.
Tooling is incredibly complicated. It's very expensive and you often need quite complex structures to 3D print tools. 3D printing is such an amazing advancement in manufacturing. Titomic is an Australian company with its head office in Mount Waverly, Victoria, as well as operations globally. CSIRO and Titomic are both in the Monash Precinct along with many other Australian manufacturers. We recently went to Titomic for help on a challenge with a partnership that CSIRO has with Swinburne University of Technology. We are building a 3D printed satellite dish and we needed support from Titomic with the tooling and parts of the structure. Another manufacturer that we have worked with recently is Magnium Australia, also a spin out from CSIRO technologies. Magnium is developing its low carbon magnesium manufacturing technology and it’s constructing the world’s first decarbonised magnesium metal plant in Notting Hill, also in the Monash Precinct. Its technology combines Australian feedstock with renewable energy to produce zero carbon Magnesium metal ingots of greater than 99.8% purity. The seeds of this technology were sown in a CSIRO laboratory 20 years ago.
AMT: Are you personally working on any advanced manufacturing innovation?
BF: I am an adjunct Professor at Swinburne University where I’m supervising three PhD students. They are working on the automation of carbon fibre composite manufacturing and the recycling of these materials. The aim is to use robotics and automation to increase the efficiency of the manufacturing process and to reduce the environmental impact and cost of these materials.
AMT: What did you study and which organisations are you proud to be a member of?
BF: As a materials scientist and engineer, I was the founding Director of Swinburne’s Manufacturing Futures Research Institute, with a mission to support the transition of Australia’s manufacturing sector to Industry 4.0. After completing a Bachelor of Science with Honours at Melbourne University, I went on to complete a PhD in Engineering at the Australian National University.
More broadly, I am very honoured to be a Fellow of the Academy of Technological Sciences and Engineering (ATSE), a Fellow of the Royal Australian Chemical Institute (RACI) and a Graduate of the
Australian Institute of Company Directors (GAICD). I’m also the President of the Australian German Chamber of Commerce and serve on the board of Museums’ Victoria, which plays such an important role in inspiring people of all ages to learn more about science.
AMT: You are always busy at work but how do you relax in your leisure time?
BF: I love to start my day by working out at a gym at least three times a week. I get so much power and strength for the day from those workouts and it makes a difference to how clearly I think during the day. I'm also learning German, because for me, it's really important to do something to challenge my brain that isn’t associated with my scientific work. I've been learning German for five years and do two on-line classes a week. I’ve led successful collaborations with industry and universities in Germany since 2006.
I love learning anything new. In 2021, I had the opportunity to take some flying lessons which was fantastic. What I loved about it, was that when you focus on flying a plane you cannot think about anything else at all. It’s exhilarating and terrifying in equal measures. Live music has been a life-long passion. I’m a frustrated ex-musician who used to play saxophone and bass guitar, until science took over. I recently bought a new turntable and I’m enjoying playing old and new vinyl records.
AMT: What are your plans for the future?
BF: It might sound a bit counter-intuitive, but I’ve never had a specific plan for myself, but I’ve always been very ambitious for the outcomes of the work I’m doing. What I mean by that is, that I’ve always focused on the work at hand and doing it well. I recently read a fantastic interview with Alan Finkel, Australia’s former Chief Scientist, and he said “at no stage in my career did I ever have a long-range view of my next career step. Instead, I focussed on doing what I was doing well. Eventually, the doors of opportunity opened and I stepped through.” Then I thought, thank you, Alan, that's given me permission to remain focussed on my current mission. In doing this, focussing on the outcomes rather than your own achievements, you can bring others along with you and nurture and mentor the next generation of science leaders.
Providing access to micro- and nanofabrication services to enable Australia’s innovation agenda.
Starting in 2007 within the Federal Department of Education’s National Collaborative Research Infrastructure Strategy (NCRIS), the Australian National Fabrication Facility (ANFF) provides access to world class micro- and nanofabrication-related facilities and expertise in a simple open access model.
In April last year, the Commonwealth Government released the 2021 National Research Infrastructure Roadmap (NRI) outlining the Research Challenges to be faced by Australia, which included Frontier Technologies and Modern Manufacturing. With a national recognition of the importance of fabrication technologies ability to address these challenges, ANFF continues to support a broad spectrum of R&D.
Frontier Technologies and Modern Manufacturing (FTMM) is one of the eight research challenges identified in the 2021 NRI roadmap. The others are: Food and Beverage, Medical products, Recycling and Clean Energy, Defence, Space, and Environment & Climate. ANFF facilitates cutting-edge discovery and product development in all of these areas.
ANFF is a nationalenterprise, with 500 tools and over 130 experts spread across 21 institutions in a network of eight Nodes. The ANFF network achieved the following annual outcomes in 2022 despite COVID restrictions affecting normal operations. There were 25,189 supplies manufactured, 2,745 clients helped and a total of 185,321 hours of tool use.
AMT spoke with ANFF CEO Dr Jane Fitzpatrick about the scope of the Nodes within the ANFF network. Previously holding positions within the MedTech start-up space and industry-focused research entities, Dr Fitzpatrick holds a PhD in Applied Immunology and a degree in Biotechnology, and she has added technical expertise in many areas, including micro and nanofabrication, throughout her career. Dr Fitzpatrick explained how the Australian National Fabrication Facility is set up as a coordinating body to ensure value for money of Australia’s investment in micro and nanofabrication technologies and expertise, putting the right tools in the right locations, to support Australian priorities.
“What fabrication does is allow you to create structures,” adds Fitzpatrick. “We're creating those structures at the scale of micro and nanometres. These tool sets are very specific and detailed, so they’re expensive and complex and fabrication is not a one-step process. These processes start from patterning, then you're usually taking something away or you're adding bits on, to end up with the required structure. ANFF is dedicated to ensuring that we provide complete process train (the ability to do all the required steps) at our facilities, so new devices can be built in a single place.”
“So depending on what your application is, you may need very similar tools, but they won't be exactly the same set of tools,” Fitzpatrick continued. “The process train will be very specific for what you're trying to do. This is what we've tried to do across the country so that you've got the right process trains in the right places to support the kind of research and development being done in those areas.
In our Melbourne Centre for Nanofabrication at Monash University, it has the most different types of tooling. It's kind of the Swiss Army knife. ANFF can do a lot of different things, whereas a lot of the other nodes have more specificity in their application focus.”
“Around the country, we have split our capabilities into nodes of specific expertise. Several of our nodes have a particular focus of fabrication technologies,” said Dr Fitzpatrick. “Just for instance, we have our Optofab node; and they specialise in devices that manipulates light. So optical fibres, laser technology, laser engraving and welding. Also production of precision optics, mirrors and low transmission coatings can be accessed.”
“At that scale of nanotechnology, we’re able to manipulate light. Visible light has a wavelength in the hundreds of nanometres. Being able to manipulate these physically is what you can do with nanoscale structures. Another area that uses control of items at the nanoscale is quantum technologies. You’re literally taking parts of an atom, holding them in place and manipulating them.”
The ANFF also has a Materials node. They produce materials as well as manipulating those materials for applications such as smart conveyor belts or 3D printed bioscaffolds.
Nanotechnology, while amazing, is also very accessible. Think about emulsions, or sunscreen, and you see nanofabrication. Modern day cosmetics have nanoparticles in them, but they’re manufactured in a fully chemical setting. “When you’re talking about nanofabrication, this is creating structures that have a function at that scale,” Fitzpatrick describes.
Clean room characteristics
Deep within many ANFF facilities are specialised environments with their own foundations: rooms built within rooms. With filtered air, light, sound and power. Basically, cut off from the outside. These are the clean rooms.
In here, a huge range of processes might be run. Patterning of nanostructures using an electron beam lithography system or coating a new device with a metallic coating.
“These teams are working at the level of micro and nanostructures,” explained Dr Fitzpatrick. “The more dust you have, the more chance you have dust landing on your project and ruining it. We have to eliminate dust. So, to enter these rooms we have to put on what we call bunny suits, a full coverall made of very low-shedding material. Hair is covered, beards are covered and the mouth is covered because your mouth is a terrible source of contamination. The air in these rooms is cycled at very high rates through very small pored filters to remove as much dust as possible. Depending on the work being done, different classes of dust free is needed. ANFF have Class 100, 1,000 and 10,000 rooms. This number refers to the number of dust particles you can measure in the air. Class 1,000 has less than 102,000 particles of 300nm or greater per cubic metre.
As a key facility in the NCRIS system, ANFF is tasked not only with supporting research excellence in FTMM, but also to promote
innovative, world-first technologies that solve real-world problems in diverse fields such as health care, communications, clean energy and climate change. Users rely on ANFF for open access to Australia's world-class micro- and nanofabrication infrastructure and the key expertise to make it work.
ANFF is well positioned to meet the three key strategies laid out in the NRI Roadmap. First, the launch of ANFF’s commercialisation arm ANFF-C will help increase the commercial impact of Australia's science research and technological innovations. Second, ANFF is taking the initiative to develop a highly skilled workforce in the science sector. It has partnered with TAFE-SA, South Australia's largest vocational education and training provider, to define technician-level courses in micro- and nanofabrication. In addition, ANFF is designing nanofabrication short courses to be delivered in its open-access, online learning platform, ANFF Enlightened. Third, ANFF’s Client Engagement Facilitator Team is smoothening the engagement pathway for industry clients.
“Stable Commonwealth funding over the last five years has allowed ANFF to start moving into areas it wasn’t capable of working in
before because we were so busy worrying about the next cheque,” says Dr Fitzpatrick. “We’ve managed to stabilise and consolidate what we do and how we’ll be doing it over the next five years is the extension of that. We are asking questions; what are the other things that the ANFF can support? What are the other things that our cohort industry and academics are looking for? How can ANFF further push research infrastructure and what is it capable of doing? How do we define and provide translational research infrastructure.” “In the immediate future, we've got a five-year funding cycle and the NCRIS 2023 Guidelines will provide us with capital investment. We now need to look at the next steps. Where do we tweak our model, to provide more services that are required so that we get more innovations to translate into real benefits. We will always stay at the cutting edge of fabrication infrastructure because that’s what we do. If we don’t have that, we don't have anything. So that’s where the baseline is. Then it’s down to what we can enhance on top of that to ensure that Australia is developing great ideas and actually being able to produce them here. That's kind of the next step.” anff.org.au nanomelbourne.com
Diraq, the recently incorporated start-up company from the Dzurak Group at UNSW, are the global leaders in developing silicon metal-oxide-semiconductor (SiMOS) quantum-dot qubit devices for quantum computing.
In 1964, Richard Feynman, Nobel Laureate and the father of nanotechnology, said, “I think I can safely say that nobody really understands quantum mechanics.” However, he later proposed harnessing it to build a more powerful kind of computer.
These computers are machines that use quantum phenomena to store data and perform computations. Quantum computers are predicted to solve many currently intractable problems, such as drug design and climate modelling. Long dismissed as science fiction, today we are in a race to build the hardware that will make quantum computers a reality. Traditional transistors composed of silicon metal oxide semiconductors (SiMOS) control tiny currents of electrons. An applied gate voltage either allows current to flow from source to drain or not. Thus, a transistor acts as a binary switch in a circuit, existing in a charged or un-charged state. A charged state is considered a ‘0’, and an un-charged state a ‘1’. The processors in mobile phones and tablets contain billions of transistors on a single chip.
Innovative technology developed by the Dzurak Group Silicon Quantum Dot Qubit research programme at UNSW has successfully created the world’s first SiMOS-based quantum processor. Their quantum transistor controls a single electron – forming the fundamental unit of quantum information, the qubit.
By manipulating the surface gate voltage, a single electron is confined within a quantum dot. The spin of the electron, a property comparable to rotation, creates a small magnetic field. The binary nature of electron spin – clockwise (spin-up) or counterclockwise (spin-down) – makes spin an ideal candidate for the encoding of information. Within an applied magnetic field, the energy of the spin-up state becomes higher than spin-down. This energy
difference enables read-write memory. We can verify the electron’s energy level, thus ‘reading’ the current state of spin (spin-down is 1; spin-up is 0) and can ‘write’ by flipping the electron’s spin state with a microwave signal of sufficient energy.
If you place two quantum bits side by side, microwave and voltage signals control the qubits and make them interact. In addition, the state of one qubit depends on the state of its neighbour. Letting these qubits interact creates logic gates capable of performing basic Boolean operations (AND, OR, NOT, etc.).
In the recent years, the Dzurak Group has achieved high fidelity single-qubit and two-qubit gates in silicon. More recently, they have explored the potential of ‘global’ spin qubit control in SiMOS quantum dot arrays to scale up the number of qubits to billions. Their revolutionary technology is compatible with the existing semiconductor manufacturing techniques – the only viable approach to scale up the number of qubits to billions for useful commercial applications.
The involvement of ANFF has been crucial to the creation of the first SiMOS quantum computing chip. The fabrication of silicon qubit devices is performed fully in-house in the ANFF-NSW cleanrooms. Without access to ANFF’s suite of state-of-the-art equipment and processes, the Dzurak Group’s cutting-edge research and output rate would not be possible. In particular, the capability to grow highquality silicon dioxide in high temperature furnaces plus access to nanometre-precision electron beam lithography has enabled them to construct world-class qubit devices.
This article has been republished with the kind permission of ANFF, originally appearing in the 2022 ANFF Casebook. Diraq.com.au anff.org.au
How an Australian startup is saving the Earth through a novel sustainable process. Drew Turney digs into the detail.
A pioneering group of Canberra chemical engineers is putting a hefty round of funding into the recycling science of tomorrow, and it might spell the end of one of our biggest environmental headaches. We know about microplastics in the oceans. We've given up plastic shopping bags and drinking straws and we separate rubbish and recycling every week when we put the bins out.
Would it surprise you to learn it's not nearly enough? It might be time not just for doing more of what we're already doing but a new approach altogether. There are 8.3 billion tonnes of plastic waste in the world, and only about 10% of the plastic we discard is recyclable simply because of its chemical properties.
There's simply no way to recycle polymer plastics in textiles, for instance, and Professor Colin Jackson (who we'll hear more from later) calls the amount of textile waste 'massive'. "Clear plastic bottles. We can recycle them pretty well but that's about it," he adds. Even among the material we can recycle, we seldom get more than a handful of new generations out of it, after which it's burnt for energy (releasing more greenhouse gases) or buried in dumps – and that's without accounting for the CO2 we pump into the atmosphere when we manufacture it in the first place.
When it comes to plastic we're not really recycling, we're just delaying landfill. If we're serious about reducing plastic waste we need to change the way we make, use and discard it, and infinite recycling might be the best idea around right now.
Recycling company Samsara Eco, where Jackson is the Chief Science Officer, is determined to halt the production of new plastic in its tracks. It wants to reclaim and endlessly reuse the plastic we already have using synthetic enzymes which break it down to constituent parts and let us remake it into new plastic far more sustainably than traditional recycling.
Jackson had been running a protein engineering and design lab at the Australian National University, engineering synthetic enzymes, a field with wide industrial applications including breaking down pesticides, therapeutic proteins in medicines and more.
One day in 2020, two of his lab students, bioinformatician Matt Spence and protein researcher Vanessa Vongsouthi approached
Jackson with an exciting scientific paper about an enzyme that could break down plastics. Company founder Paul Riley had already been developing the business case, and Samsara Eco was born. Late last year it raised $54m, including funding from Woolworth's venture capital and retail funding body W23.
"It's like building a building with recycled bricks," is how Jackson explain circular recycling. "We knock it down and use the bricks to make another building. You're taking a bottle and breaking it down to its molecular building blocks." The first key piece is the polymer, a chemical containing a large number of repeating molecules. As well as the basis for biological material like DNA, the polymer is the perfect building block for plastics. Those smaller repeating molecules are called 'monomers' and in plastics they're manufactured chemically using fossil fuels. Recycling polymers is a scattershot affair. "Reform it five or six times and you start to get real quality issue," Jackson says. "It involves high temperatures and every time it goes through that you get more side products and the quality deteriorates."
The next lynchpin is the enzyme, a chemical that catalyses chemical reactions. You might know them them as the messenger proteins in biological cells, but it's possible to make synthetic enzymes that do the same job in industrial processes.
Just one is degrading the polymers in plastics down to constituent monomers. To stretch the above building metaphor further, current recycling technology means you might be able to isolate a fireplace hearth you can reinstall somewhere else, but you can't take it back to the individual bricks to make into whatever you need.
The inspiration for Samsara Eco's technology came from a 2016 Japanese study where scientists discovered a bacteria called Ideonella sakaiensis at a bottle recycling facility in Osaka that metabolised PET plastic. "Our enzymes are related to that one, but they're all designed using a machine learning design algorithm. They're unlike
anything you see in nature but they're certainly inspired by nature," Jackson says. A crucial attribute in the process is in only taking the building blocks back so far. If a plastic is eaten by a biological organism that does the same thing it will be remade into carbon dioxide, and releasing all the greenhouse gas locked up in that 8.3 billion tons of plastic waste is obviously a terrible idea.
But Samsara Eco's process takes plastics back to their monomer molecules – particles big enough to retain their CO2 rather than release it. In theory, it means we can endlessly remake plastics and keep the carbon used in their manufacture sequestered indefinitely. But while it sounds like a miracle solution, there's still work to be done – there are plastics and there are are plastics, and they all need different enzymes applied. Soft plastics (anything you can scrunch into a ball in your hand) and coloured materials are hard to recycle, and as mentioned, there's currently no recycling technology that works with textile polymers.
But it's even more complicated. The enzymes created to attack different forms is fast and efficient, but Samsara Eco has its work cut out for it because of what Jackson calls the 'mixed ball' problem. Plenty of applications merge more than one type of plastic together in layers, often with other materials like foils or aluminium as well. Traditional recycling involves heating and reforming plastic, but you can't do that if it contains a layer of metal (or most other materials), rendering an entire class of products unrecycleable altogether. But if Samsara Eco keeps at it, Jackson and colleagues can develop an enzyme for each layer of material, letting them loose to break down only specific targets. "As the technology develops and you get more of a loop, the materials that are more recyclable become more popular and cheaper and it'll make more economic sense," he says.
But there's a difference between an exciting environmental academic study and systemic change. As Jackson stresses more than once, circular recycling will only come when it benefits (or at least doesn't hurt) household and corporate incomes. He states the company's goal as being; '[making] sure the quality is as good as virgin plastic and doing it economically.'
But Samsara Eco (and the rest of us) are facing a harder problem than the science or manufacture of plastic-eating enzymes; culture. Jackson points to Europe, where government regulations around recycling are robust, and Japan, where doing so is seem as a social good that benefits everyone. He goes on to mention a few US states that don't recycle at all. He thinks both carrots and sticks are needed. "Bottle collections – where you get 10c for each empty – is having a really good effect in Australia and incentivising people to recycle," he says. "Community minded messaging about recycling works, and then you can also mandate behaviours, especially when it comes to industry."
CEO Paul Riley agrees. "Legislation will help jumpstart the supply chain cycle and help move us towards our climate change goals," he says. "We have the ideas, talent and drive to solve the problem, but we need government support and corresponding investment to achieve the goals set out in climate roadmaps."
But sustainability has had a rocky road since the early days of the environmental movement. The Redcycle scandal – where soft plastics taken to supermarkets around the country were stacked in warehouses instead of processed – is just the latest regulatory/ commercial failure that's made many consumers wonder why we bother at all. "I worry that it damaged the credibility of the research in Australia and people might be more cynical about it," Jackson laments. "But you need the technology and you need the goodwill." Samsara Eco is working hard on the technology. The rest is up to us...
samsaraeco.com
Stay ahead of your competition with Topsolid CAD and CAM.
IDW CAD/CAM SOLUTIONS
Official Australian Value Added Reseller.
Whether you’re a solo engineer looking for mechanical CAD only, or a high tech manufacturing facility looking to explore the world of industry 4.0, TopSolid has modules to suit your needs, all wrapped up in a PDM system to manage your data securely and efficiently.
Full featured stand-alone CAD
• Intuitive and powerful 3D modelling
• Surface modelling
• Mechanisms and motion simulation
• 2D drawings
• Bills of materials
• Steel structures
• Realistic rendering
• Injection mould tool design
• Progression tool design
• Timing/lead screw design
Advanced CAM
• 100% native inside application; not a third party plugin
• 2½ thru 5-axis milling
• Multifunction mill/turn
• Accurate tool and machine simulation
• Impeller/blade machining
• Cylinder head porting
• Lead/Timing screw machining
• Swiss turn
• G-code verification
A few of our customers who are already benefitting from working with TopSolid and IDW CAD/CAM:
1300 439 223
info@idwcadcam.com.au
The world has a waste challenge, none bigger than that posed by plastics. Professor Veena
Centre Director speaks truth to plastic.
Australia is one of the most wasteful developed nations, second only to the US in terms of per capita plastic bag consumption. On average, each Australian consumes over 24kg of plastic and uses over 230 plastic bags every year.
In 2020, only 12% of the plastic waste was actually recycled and 81% went into landfills, with a lot of it ending up in waterways and the oceans. The 2021 The National Plastics Plan (NPP) also says over one million tonnes of single-use plastics goes straight to landfill and about 130,000 tonnes of plastic leaches into Australian waterways and oceans every year. This is equivalent to 1,280kgs of plastic being dumped every hour in Australia’s ocean.
National Geographic estimates there are 5.25 Trillion pieces of plastic debris in the ocean and of that mass, 269,000 tonnes float on the surface, while some four billion plastic microfibres per square kilometer litter the deep sea.
Various waste technology solutions are emerging, and some behavioural changes are taking place, but is enough being done and at a quick enough speed?
The SMaRT Centre at UNSW has developed a range of MICROfactorieTM Technologies that can reform various wastes usually not subject to traditional recycling methods into value added materials and products, such as filament for 3D printing and Green Ceramics made from textiles, glass and other wastes. While society first needs to prevent plastic and other wastes from getting into our oceans and waterways, we need innovative technical solutions to deal with existing and future wastes. This includes having stronger ‘product stewardship’, where producers of products and users of products are more accountable for when they come to their so-called end of life, and better collection and recycling, using new technologies to extract and reform the valuable elements they contain.
Better behavioural responses are also needed, including awareness campaigns for the public and industry. A range of new and emerging regulatory standards have been introduced by all levels of government, including national waste export bans and prohibition of single use plastic bags. But what do we do with all the waste that used to be shipped offshore and is still being landfilled?
The first independently and commercially operated UNSW SMaRT Centre designed Plastics and Green Ceramics MICROfactorieTM modules are being operated by collaborators Shoalhaven City Council and Kandui Technologies in regional NSW.
The council’s plastics module aims to remanufacture around many tonnes of waste plastics into filament for 3D printing per year, and its Green Ceramics MICROfactorieTM module also being built expects to reform hundreds of tonnes of glass and mattresses per year into green ceramic tiles and other forms of furnishings in the council’s operated facility. Climate change narratives often overlook the need for more sustainable manufacturing and waste management practices, where waste is used as a resource.
Manufacturing that aligns with innovative waste management, recycling and materials circularity are central to helping address the globe’s biggest challenges, including waste plastics. There is growing appetite in industry and society to tackle these issues more swiftly.
Australia has world-leading scientific research and development institutions and leaders, but many feel progress on delivering practical outcomes to our big sustainability challenges has been lacking.
Sahajwalla, UNSW SMaRTCollaboration through co-investing and nurturing pathways to innovation and economic success must be our focus if we want to realise that “waste is a resource” that can be used in so many new, innovative ways. As we develop new and transformative approaches to what needs to be a new era of ‘green manufacturing’, we need to build new and localised supply chains that are laterally integrated. The lateral integration of supply chains of green materials and products is needed to ensure we connect different sectors across our regions.
This integration would build interconnectivity between and across markets, sectors and logistics networks, enabling decentralised, localised and regional pathways to new national and global opportunities. This can be done for micro to macro materials and manufacturing opportunities, eventually leading to mega solutions, depending on the volumes and values associated with the waste materials concerned. Such an approach will boost our sustainability and sovereign capacity.
A recent important breakthrough by the UNSW SMaRT Centre, where carbon and hydrogen needed to make steel come from various wastes, including plastics, found waste materials can actually improve the efficiency of steel making.
This represents the next generation of SMaRT Centre’s patented Polymer Injection Technology, known as Green SteelTM, with steel industrial partner, Molycop, which started out as the Commonwealth Steel Company over 100 years ago. The first 1.0 generation of Green SteelTM is well known for using millions of waste rubber tyres destined for landfill as an alternative source for partial replacement coke and coal in electric arc furnace steel making.
But the next generation of Green SteelTM research now shows waste plastics and bio-waste like coffee grounds are also effective and contain hydrogen which improves the efficiency of steel making. This technology locks the carbon from waste resources into the steel, hence causing no emissions and delivers a form of carbon capture. With the right will, society can find a purpose for most waste types by understanding the elemental value inherent in it. This can only be done through rigorous scientific analysis and active collaboration with industry, the community and governments to ensure innovations are taken up and used. By better valuing our waste materials and creating circularity for their reuse, we can help the world be more sustainable and tackle our big global challenges. unsw.edu.au
smart.unsw.edu.au/technologies-products/microfactorietechnologies
Great Wrap, a Melbourne-based material science company, launches the world's first Compostable Pallet Wrap, made with food waste, to combat the global reliance on petroleum-based pallet wrap and plastic pollution. Tullamarine facility home to what will soon be the largest stretch wrap manufacturer in the country.
Great Wrap’s 10,000sqm facility in Tullamarine is home to state-of-the-art machinery that will make 5,000 tonnes of compostable stretch wrap in 2023 and 20,000 tonnes by 2025 — which will make them Australia’s largest stretch wrap manufacturer and significantly decreasing our need to import stretch wrap from other parts of the world.
In this country alone, we send over 100,000 tonnes of stretch wrap to landfill each year, including cling wrap, catering wrap, silage wrap and pallet wrap. Pallet wrap, the connector of all businesses, is a critical part of the global supply chain. Every day millions of pallets are wrapped to transport goods to their eventual consumer. Unfortunately, very few facilities can recycle petroleum-based pallet wrap — meaning more than 90% goes to landfill.
Great Wrap is home compostable, and when it is composted and returned to soil then it can decrease Australia’s carbon footprint by over 100,000 tonnes every year by lowering our dependence on fossil fuels. This latest innovation can solve the plastic pollution problem as it can be composted or repurposed to create new materials and returned to the soil to add microbial value to agricultural land.
Jordy Kay, Co-founder of Great Wrap, says, “We’ve completed commercial trials with major Australian retailers, food and beverage manufacturers and household name brands, and their feedback is consistent — Great Wrap performs as well as petroleum-based pallet wrap. We’re calling on all Australian business owners to switch because the high-quality product means the only shift is where they purchase it.”
Julia Kay, Co-founder of Great Wrap, says, “We’ve had a huge demand building over the past three years from businesses far and wide. Most businesses, whether you know it or not, are using petroleum-based pallet wrap to send and receive their goods. This product is unavoidable, it is essential, and it's a global problem that we are solving.”
Great Wrap's vision continues beyond creating a compostable and planet-friendly alternative to industrial plastic wrap. In addition to manufacturing Compostable Pallet Wrap, Great Wrap is working on its own pallet wrap collection service.
While currently targeting Australian plastic waste, Great Wrap also launched its direct-to-consumer line in the US in 2022. Their international demand is growing as businesses and governments understand they need to support climate-positive innovations. By 2025, Great Wrap plans to open a biorefinery that will convert local potato waste into 20,000 tonnes of PHA. PHA is a marine degradable material made from microorganisms metabolising potato waste. greatwrap.com.au
SQP Engineering is a family-owned and operated business providing industrial manufacturing solutions. team's CNC machines, allowing them to instead manufacture other valuable production parts. SQP owner David Miller determined that the FX20 is the best fit to accommodate his shop’s needs.
Founded in 2006 and located in Perth, the bulk of SQP’s business has historically been supplying precision-machined products for mining equipment. However, Industry 4.0 technologies (such as robotics and additive manufacturing) and ISO 9001-certification have now allowed SQP to expand into customers in the oil, maritime and defence industries.
The owner of SQP Engineering, David Miller understands that training local talent is critical to the industry’s future success and takes pride in employing three apprentices, two of whom are his sons.
SQP’s core specialty is machining. However, SQP frequently fields request for specialised parts that are either too expensive or outright impossible to be machined. These requests represented lost business opportunities for the shop, so SQP sought a solution.
SQP’s team needed to produce a specialized production part for their customer: wireline counter cover for mining equipment systems. However, the team was unable to produce the required result in the needed time frame using their existing equipment. The team discovered that machining the part was not cost effective and would not produce an accurate part fit for the purpose. Furthermore, the existing polymer 3D printer was not powerful enough to allow SQP to meet acceptable lead times: each cycle took nine hours. The older technology also produced a suboptimal finish.
After struggling to produce this key piece of equipment for customers, SQP determined that a larger and faster composite 3D printer could quickly and efficiently produce these specialized parts. This would not only unlock production for components that can’t be machined — it would also decrease the load on the
“The FX20 was a no-brainer for me,” says Miller. “The platform, the build size, the enhanced additive manufacturing technologies — it gives me an edge above a lot of the competition.”
“Printed parts from the FX20 look 10 times better than the ones we printed before. Customers are completely blown away when they see the surface finish. Once I showed our customer the new and improved part he was blown away as well. His products now look a hell of a lot better.”
SQP also brought the Markforged Metal X system in-house to round out additive capabilities. With the FX20 and Metal X in tandem, SQP can be the one-stop shop its customers need. They can now manufacture a wide range of production-grade parts that no one can machine — while delivering with better pricing and turnaround times.
For SQP, the FX20 and Metal X system will continue to enable better solutions for customers. The ability to quickly print a wide array of production-quality parts will allow SQP’s customers to easily get challenging parts that otherwise cannot be easily procured — and give the option to get machinable parts cheaper and faster without compromise in quality.
With a long list of potential applications, Miller is excited for the new doors the FX20 and Metal X system will open for his business.
“We’re planning on using the FX20 to expand into medical, aviation, and agriculture. It’s allowing us to expand the horizon a little bit and manufacture more of what Western Australia needs,” he adds.
Taking pride in being an early adopter of industry 4.0 and having a technologically advanced machine shop, SQP embraces the cutting edge. David believes that now and, in the future, it’s necessary to embrace additive manufacturing to stay competitive.
“My two boys work for me, they’re in their first and second years of apprenticeship. I want to continue being more technically advanced than the competition. This technology is evolving as we speak. If I don’t get involved with it, and if I don’t get my boys involved with it, I'll be letting them and SQP Engineering down at the same time,” Miller concludes.
sqpengineering.com.au
Markforged.com
Advanced Navigation unveils Australia’s largest subsea robotics centre in Western Australia.
Advanced Navigation has announced the largest subsea robotics facility in Australia, located in Balcatta, Western Australia (WA). The high-tech manufacturing and R&D facility will accelerate the production of the company's revolutionary subsea technologies, including autonomous underwater robot Hydrus, and the growth of its underwater artificial intelligence division. The company’s in-house design and vertical integration has ushered in many innovations, including extreme miniaturisation of pressure-tolerant electronics, sophisticated sonar technologies and AI-based autonomous systems. The new centre also includes full testing facilities with several marine simulation environments to ensure reliable performance and the highest quality production.
“Now more than ever, there is a need to open up the earth's oceans, to make data and knowledge more accessible to global communities, research institutions and governments. Western Australia has always been an exploration hub for ocean discoveries. The new subsea centre will help Advanced Navigation meet the growing demand for high-grade underwater data, bringing new and existing solutions to market far more quickly and efficiently. With the goal to grow our subsea team threefold, we are confident this investment will deepen and advance our understanding of the oceans,” said Xavier Orr, CEO and co-founder, Advanced Navigation.
The subsea centre is located on a massive 5.5 acre site. The facility is split between development and manufacturing for high volume production and continued research and expansion of subsea navigation and robotics technologies. This includes the growth of its underwater artificial intelligence division. Advanced Navigation is a proud stalwart for independent, inhouse design and vertical integration that has ushered in many innovations, including extreme miniaturisation of pressuretolerant electronics, sophisticated sonar technologies and AI-based autonomous systems. The new centre also includes full testing facilities with several marine simulation environments to ensure reliable performance and the highest quality production.
Advanced Navigation's break-through underwater navigation and robotic technologies are utilised across the blue
economy, supporting research, aquaculture, offshore renewable energy, transportation, surveillance, biotechnology and high-tech services.
The company's recent autonomous underwater robot Hydrus continues to revolutionise undersea research, survey and exploration by making data capture far simpler and vastly more accessible. The Hydrus design synthesises numerous cutting-edge navigational, sonar, propulsion and data capture technologies with highly developed and sophisticated artificial neural network (ANN) intelligence.
With support from prominent research institutions including the University of Western Australia, Curtin University and philanthropic organisation Minderoo, Advanced Navigation continues to establish sustainable technologies to foster the growth of the blue economy, nationally and internationally.
“It’s exciting to see Advanced Navigation continue to grow its team of engineers in Western Australia. At UWA we are researching how natural and artificial reef structures can protect coastlines by dissipating wave energy - Hydrus is a key tool in mapping and surveying these underwater structures. The technology makes more efficient use of our funds and ultimately scales up our ability to collect high-resolution data,” said Justin Geldard, Coastal and Ocean Researcher, University of Western Australia Ocean Institute.
The subsea centre is just one of several investments made by Advanced Navigation
as it continues to expand its global reach and capabilities. The company has established headquarters in Sydney with research centres throughout Australia, including Brisbane for aerial drone technology, Canberra for photonic and laser technology and Newcastle for quantum sensing.
In addition to novel autonomous subsea robotics, Advanced Navigation delivers AI-enhanced navigation technologies for land, sea, air and space applications. The company is committed to developing innovative products and systems that will be catalysts of the autonomy revolution.
Advanced Navigation was founded in Sydney in 2012 by engineers Xavier Orr and Chris Shaw to commercialise university research on AI-based inertial navigation. Since 2012, the company has experienced great success and has progressed into several deep and new technology fields. This includes underwater acoustics, GNSS antennas and receivers, radio frequency systems, inertial sensors, robotics, and quantum-enhanced inertial navigation.
Today, Advanced Navigation is a supplier to some of the biggest companies in the world, including Airbus, Boeing, Google, Apple, and General Motors. Advanced Navigation is headquartered in Sydney, with other research facilities throughout the country and sales offices around the world. Advanced Navigation is an Australian manufacturer exporting globally while maintaining carbon-neutral operations. advancednavigation.com
Intellect Systems’ end-to-end capabilities bridge the gap in project quality and compliance.
A company that specialises in end-toend operational technology solutions for Australian and international projects, Intellect Systems, is using its breadth of expertise to advance cost-efficiencies, quality, safety, and compliance essentials. The company – which has handled some of Australia’s biggest mining and infrastructure projects – is vigorously expanding its focus on renewables and transport electrification infrastructure benefitting from smart, practical and effective use of technology to improve and streamline and processes including electrical and control systems.
“Intellect Systems’ end-to-end process means we have the capability to tailor a complete turnkey Operational Technology solution for our clients. Our process bridges the gap between the designer and manufacturer, ensuring the final assets will achieve compliance requirements and suit the desired application,” says Jason Monzu, Managing Director, Intellect Systems.
“In projects where the designer and manufacturer are separate entities, we’ve witnessed ambiguity in the product design and the ownership of the product meeting regulatory standards, with responsibility being passed back and forth. Compliance requirements are often changing, and those requirements need consideration during the design phase.”
“Our advantage is by having both the product design and manufacture handled in-house, we have skin in the game all the way through the project. This guarantees to our clients that both engineering and manufacturing are in unison when it comes to compliance and regulation adherence.”
Intellect has invested in autonomous processing and production optimisation, to minimise waste, maximise efficiency, ensure consistency, and deliver cost savings which we then pass on to our clients.
“We want to make sure that our industry is protected. Sub-par products can produce a dangerous scenario which then sets the industry back as a whole. Good governance and quality assurance are key focuses at Intellect Systems, which is why, along with being a NESMA member, we
are also ISO 9001 and ISO 45001 certified. Being a NESMA member is a signal to prospective clients that they are engaging with a credible company who is achieving best practice,” says Jason Monzu.
“When customers are engaging a NESMA member, they are guaranteed to be engaging a credible business that puts quality, compliance and best practice at the forefront. Engaging a NESMA member also supports the local industry and supply chain.”
“We partner with reputable vendors that produce the best products available, and, due to our buying power and relationships with these vendors, we can leverage their support to end users. As a NESMA member we are playing a part in helping to advance and safeguard our industry.
“One of our ongoing objectives is to continue to implement innovations and optimised practices, particularly in our manufacturing process that can save our clients’ money while assuring a quality product.”
“There’s a lot of overlap between Intellect’s own values and NESMA’s key objectives. Our values of safety, quality, trust, agility,
commitment, and innovation are about providing a product at the highest level of quality, while taking ownership of the process and project drivers, safely.”
While Intellect Systems has an established reputation in the mining industry, its capabilities span a diversified growing range of industries.
“We’ve been engaging in assessment when it comes to EV infrastructure,” says Jason Monzu. “We know that we need infrastructure to support EVs in the future and that’s all part of our business strategy to ensure we have enough exposure in that market. Our State Government is also improving and modernising some of their ageing assets, and we’ve been called upon to play our expanding part in ongoing projects.”
Founded in 2005 and proudly Western Australian owned, Intellect Systems is a specialist provider of End-to-End Operational Technology solutions to the domestic and international markets. As an ISO 9001 and 45001 certified organisation, the company is committed to continuous improvement and holding itself accountable to the highest level of quality and safety. intellectsystems.com.au
The future of Recreational Vehicles manufacturing for Apollo, with Markforged 3D printers.
Apollo Motorhome Holidays, a leading manufacturer of Recreational Vehicles (RV), is pleased to announce its partnership with Markforged, the industry leader in industrial 3D printing solutions. By integrating Markforged 3D printers into its manufacturing process, Apollo is taking a significant step towards revolutionising the caravan industry. Apollo has been at the forefront of the RV industry, offering highquality, luxury motorhomes, campervans and caravans to customers around the world. Now, with the addition of Markforged 3D printers to its manufacturing process, Apollo is set to take its craftsmanship to the next level. Markforged 3D printers are designed to produce functional, high-strength parts using a range of materials, including carbon fiber, stainless steel, and Onyx. With the ability to create custom parts quickly and easily, Apollo can solve supply chain issues, reduce lead times and costs while maintaining its high standards of quality.
"We are thrilled to be partnering with Markforged," said Edney Ferreira /Engineering Manager of Apollo. “Their 3D printing technology is cutting-edge and will allow us to create high-quality, custom parts that are essential to the motorhomes, campervans and Caravans we produce. The addition of Markforged 3D printers to our manufacturing process will streamline our production and provide us with the ability to create custom designs quickly and efficiently.”
To overcome material shortages that added delays to production, Apollo began printing small components and connectors. Over time, they found more uses for the printer, including new tools they could make and iterate to make the process of building RVs easier and faster.
A game changing way to get industrial-grade parts in hours, not weeks — the X7 carbon fibre 3D printer enables engineers and designers to fundamentally improve manufacturing operations at light speed. Now, Apollo is also able to quickly print miniatures of caravan chassis and motorhome cabinetry to show the concepts before starting the final stages of design, and can also be used to
test lean concepts in an assembly line. In the future, they plan to utilise the miniatures to simulate concepts for training new assembly workers as well as to print spare parts on demand for their rental business.
Markforged 3D printers have already been implemented in a variety of industries, including aerospace, automotive, and defence. By incorporating this technology into the caravan industry, Apollo is leading the way in innovation and efficiency. markforged.com
Tapping additive manufacturing for innovation in spinal cord injury assistive technologies.
ARM Hub worked with the Hopkins Centre, Spinal Life Australia (SLA) and Advanced Queensland Fellow Dr Camila Shirota, a Lecturer at Griffith University, to provide our expertise in design, additive manufacturing, and robotics for the Increasing remote care solutions for the people with disability (Spinal Injury) project.
ARM Hub built prototypes and undertook testing of 3D printed hand grippers for wheelchair. The Spinal Life Australia project helped establish an innovation process including online consultation and workshop with end-users to prioritise 3D production for prototypes. This project piloted the translation and implementation of a priority solution into practice.
We participated in four multi-disciplinary innovation workshops at the SLA Healthy Living Centre in Cairns, Far North Queensland, to co-design solutions for people living with spinal cord injury. The co-design workshops involved people with lived experience of spinal cord injuries, allied health practitioners, designers and manufacturers from across Australia.
Our work on this project was made possible by the Queensland Government’s Essential Goods and Supply Chain Program support for manufacturers to make essential goods, consumables, and devices.
An estimated 250,000 to 500,000 people globally suffer a spinal cord injury. In Australia alone, the lifetime cost of care and lost economic activity for someone with quadriplegia is $9m and the total current cost to the community for all spinal cord injuries exceeds $2bn annually. A therapy or equipment that gives people back or increases their independence will also save our community enormous costs.
In addition, COVID-19 significantly disrupted the delivery of healthcare, especially in areas that require physical interaction, such as disability and rehabilitation.
This project uses a co-design process to develop pertinent solutions of AT (assistive technology) and helps to document the areas of rehabilitation and disability services that are vulnerable to disruption. Through the innovation workshops a range of challenges were identified with the targeted design being the development of individually customised weather safe hand grippers for wheelchair. This is a critical issue for wheelchair users, who can push their hand rims 2000-3000 times per day and RSI injuries are common. Matching the hand rim profile to the user can increase efficiency.
We participated in an eighteen-month multi-stakeholder project providing expert advice for manufacturing healthcare solutions that involved automation, industrial design, and additive manufacturing technologies. We recruited manufacturers in relevant areas to participate – one in all-terrain robotics, one in furniture, and two in 3D printing – and our design representatives worked with clinicians, people with a spinal injury and a family member, and members of the research team.
Using feedback from the workshops, we developed a range of 3D printed hand grippers which were tested with a wheelchair user and refined. During this process we developed seven different designs comprised of different materials such as silicon, PLA, ABS and Carbon fibre filament. In the fourth workshop all designs were trialled by wheelchair users at SLA Cairns in a collaborative workshop to assess and evaluate and inform future development.
Based on user feedback, recommendations were made for future product development and wheelchair users expressed a clear interest for the product. Users especially liked being involved in the process and being able to tailor much needed products to their custom requirements.
We built prototypes and undertook testing of 3D printed hand grippers for wheelchair.
This project helped establish an innovation process including online consultation and workshop with end-users to prioritise 3D production for prototypes.
The project piloted the translation and implementation of a priority solution into practice. qut.edu.au
ARM Hub is an agile robotics, AI and design for manufacture industry hub. We are at the forefront of industrial transformation, building strong local supply chains and preparing companies for success in global markets.
ARM Hub was established as a not-for-profit innovation hub on 20 March 2020 by founding partners Queensland University of Technology (QUT) and UAP (previously Urban Art Projects), and attracted investment from the Queensland Government, Commonwealth Scientific and Industrial Research Organisation (CSIRO), Innovative Manufacturing Cooperative Research Centre (IMCRC). We also have partnership support from Germany’s Fraunhofer IAO and the World Economic Forum. Headquartered in Advanced Manufacturing Precinct in Northgate, Brisbane, the ARM Hub provides access to the most tightly woven network of research institutions, facilities and commercial companies across Australia.
Being geographically centred in the fast-growing SouthEast Asia region, and with access to global supply chains, a highly skilled global workforce and quality universities, we are uniquely positioned to service all major industries.
Skyzer is an Australian company specialising in product lifecycle solutions, focusing mainly on electrical devices. Skyzer has built its reputation on highly customised assembly lines, with the utmost data and IP security. Raise 3D Printers has provided Skyzer the tools to offer its clients customised fixtures, jigs and assemblies; electrical housings for small run productions; replacement parts for clients’ products for refurbishing and repairs; and highly customised assembly lines.
Prior to the incorporation of 3D Printing Skyzer could simply not offer some of the services that they offer today before 3D Printing. They used to rely on toolmakers or injection moulding houses to get tooling made up or CNC up parts, which was massively prohibitive. “It could cost upwards of USD$10,000 for moulds, so was only viable on very large scale projects,” explains Troy Sneddon, CEO Skyzer.
The product is required to be assembled at a steep angle, with circular geometries at different heights. This was otherwise extremely difficult and time-consuming without the tailor made mechanical assembly jig that Skyzer designed for their client and print on the Raise3D printers in-house. Both decreasing clients costs, protecting their IP and confidentialities, and allowing rapid production and as such a much shorter cheaper path to market for their client.
"We have always prided ourselves on being early adopters of technology that can help our clients,” says Sneddon. “We initially invested in 3D Printing technologies in 2012 with a Makerbot Replicator 2. Today we run a fleet of Raise 3D Pro 3 printers in both our Sydney and Melbourne facilities.”
The Raise 3D ecosystem offers Skyzer a more professional solution for mass production; coupled with cloud management for seamless supervision and sharing between their sites. “In addition, the power behind the Ideamaker software and the machines themselves has taken us a huge step forward from the Makerbot machines we started with,” Sneddon explains.
Skyzer made the decision to invest in their first Raise3D Printer to increase production capabilities. Now they own a fleet of Raises', allowing them to get product design timelines down for their clients (in one case from three months down to two weeks) through 3D printed fit checks and design iterations.
“The reliability of the machines means we can print with confidence throughout the night and the Pro 3 edition snap in extruders are a real improvement on previous models and will definitely decrease maintenance-based downtimes.” Skyzer managers also heavily rely on the high-resolution camera on the Pro 3 models to supervise printing remotely, and across multiple sites.
"Naturally we have seen labour cost and parts wastage savings," explains Sneddon, “however there are also the substantial cost savings in comparison to alternative tooling and mould costs.” Generally, Skyzer have found that 3D Printing provides them a higher value offering to clients, driving further company growth.
In addition, Sneddon believes that 3D Printing has “inspired even higher levels of creativity throughout our whole team. Even our Finance team have asked for 3D printing of their solutions to officebased problems!"
bilby3d.com.au skyzer.com.au
Talk to our team about your aluminium processing requirement including, profile cutting simple or complex custom shapes, milling, holes, material labelling and coding, and much more!
For more information visit bluescopedistribution.com.au
KARI optimises and converts 3D lattice design with the DfAM process and Materialise 3-matic.
With the recent developments in aviation structure weight reduction technology, Korea Aerospace Research Institute (KARI) required a software solution that gave them complete control over their new lattice design — while enabling them to print the STL file without disrupting the lattice’s structural integrity.
Materialise‘s Design for Additive Manufacturing (DfAM) knowledge and Materialise 3-matic helped KARI to optimise the part’s topology for a smoother surface. And concurrently, print a structurally stable lattice file to verify the model's simulation results. This led to the production of a lightweight, reliable metal 3D-printed part.
Create a topology-optimized lattice structure and make it printable in the design stage
Dr. Kim Tae-wook from KARI researched ways to reduce the weight of parts used in landing gear, aiming for higher accuracy and reliability. Previously, Dr. Kim converted the test results from the Altair® OptiStruct simulation technology into a topology-optimised 3D model and successfully printed the part with an external service bureau. The following study involved weight reduction, where he used advanced features in OptiStruct software to reduce the weight even further, based on the previous set of results.
The new model utilised a lattice structure to minimise material usage and consequently, lower the overall weight of the part. However, Dr. Kim ran into two issues when he wanted to repeat the simulation of this converted model to verify the reliability of the design's new lattice feature. The first was optimising the topology, smoothening the overall surface while retaining the new lattice structure. And the second was creating a printable STL file.
KARI's first metal aerospace part was reliable, but the team wanted to reduce the weight by incorporating a lattice structure.
To change the lattice-inspired raw data into a refined, printable file, Dr. Kim needed a software solution that gave him full control of the lattice structure. He also required a DfAM process to support him, normally recommended by a 3D printing (3DP) design expert. But handling the data with conventional CAD software was not possible in its current state, and the service bureau was unable to provide a solution.
DfAM and Materialise 3-matic training on AM's optimisation processes
When Dr. Kim discussed his requirements with Materialise, he thought it would be possible to print out the new lattice structure
designed in OptiStruct and convert it into STL format. However it was impossible to print an incomplete or rough topology-optimised STL design with an open-volume mesh structure. The exposed lattice framework would converge with the support structures needed to produce the part, increasing the likelihood of fractures during the support removal process. This was the main concern of the service bureau and the company’s reluctance to accept this print job. However, throughout the consultation, Kim Dongho, a Design Engineer at Materialise, explained the DfAM process and advised him of the importance of AM's editing and modeling optimisation processes.
Dongho, Materialise 3-matic’s product expert, solved the printing issue by enhancing the design while considering the build orientation and calculating the surface area of the lattice using 3-matic. He advised Dr. Kim to create a thin, solid layer in the downfacing areas of the part. This approach ensures that only a minimal amount of material is added to the part while solving the printability issue. Dr. Kim purchased 3-matic with dedicated training sessions, and he quickly went through the initial learning curve and focus on the task at hand.
An AM-optimised and print-ready lattice design – resulting in a reliable, lightweight 3DP part for landing gear Using Materialise 3-matic, Dr. Kim successfully converted the data and avoided the risk of lattice breakage by generating downfacing surfaces to protect the lattice structure. And to prevent the support material from fusing with the lattice. As a result, Dr. Kim and the KARI team could realise the simulation into a genuine part with DfAM.
KARI's metal 3D-printed aerospace part with lattice structure is lighter and more reliable than the previous versions.
Using a dedicated 3D modeling tool and technical support from our AM experts enabled KARI to reduce unnecessary experimentation via trial and error and establish a more straightforward design approach. Materialise’s knowledge in metal 3DP helped KARI enhanced the part — with a design optimised for AM — increasing its printability.
The KARI team was so impressed with the results that it's now conducting another project using 3-matic. Dedicated 3D modeling software is an accessible tool for various applications. And combined with DfAM expertise, 3DP is a desirable solution in aerospace, demonstrating qualities that improve reliability and weight reduction for many user cases.
materialise.com
Conflux Technology partnering with Rocket Factory Augsburg to develop aerospace heat exchangers as part of Australian Space Agency’s Moon to Mars Initiative.
Conflux Technology an Australian metal additive manufacturing (AM) innovator of heat exchangers, and German-based Rocket Factory Augsburg (RFA) are entering into a partnership to embed the Conflux heat exchanger into a gas duct of an orbital rocket. This project is part of the Australian Space Agency’s Moon to Mars Initiative: Supply Chain Capability Improvement Grant Program. The million dollar grant funding is being used to develop and manufacture this 3D printed heat exchanger.
“Conflux is partnering with RFA to embed next generation heat exchange technology into a rocket engine. At Conflux we are establishing ourselves as leaders in the development and commercialization of 3D printed thermal solutions and relevant materials for extreme applications. With support from the Australian Space Agency’s Moon to Mars Grant Supply Chain Capability Improvement grant, we are now applying it to the rapidly expanding space industry,” Dan Woodford, Chief Commercial Officer, Conflux Technology.
The Supply Chain Capability Improvement Grant Program is part of the Australian Space Agency’s Moon to Mars Initiative. The initiative supports Australian organisations with projects that could contribute to NASA’s inspirational endeavor to go to the Moon and on to Mars. This initiative is also an important element of the Agency’s goal to transform and grow the Australian space industry. Conflux is proud to be one of the innovative Australian businesses to be awarded funding under this initiative. confluxtechnology.com/
The smallest space invaders fly through millions of cycles for lean electronics process and handling applications.
Tiny pneumatic actuators with profiles typically 80 per cent lower than conventional hydraulic and pneumatic pancake cylinders open up new installation and automation possibilities for materials handling, processing, manufacturing and packaging applications of delicate items such as electronic components.
Firestone Airstroke® Polyactuator pneumatic actuators from Air Springs Supply can exert forces of more than .45kN @ 3.5 bar yet last for millions of cycles in demanding environments where space conservation is important, including cleanliness and hygienesensitive manufacturing and materials handling applications, including electronics and food and beverage.
The cylinders – which have been laboratory tested to five million cycles to ensure performance quality – can also be used in conveyor transfer sections, roller brakes or heat sealing applications requiring just 15mm clearance.
Manufactured as an alternative to conventional pneumatic and hydraulic cylinders, the range includes three models, all of which can be daisy-chained, including 50P (50mm diameter), 70P (70mm) and 120P (120mm), the last of which can lift loads up to 45kg with a 12.7mm stroke at 3.5 bar.
Compact air springs such as these Polyactuators have a starting height down to under 15mm
“These tough but tiny actuators open up a whole new range of possibilities for production engineers,” says air Springs Supply Technical Product Manager James Maslin. “They are just as reliable as the Air Springs range of Airstroke® actuators in capacities up to 40,000g, but miniaturised for applications involving very small spaces and light forces.” Benefits of these small but mighty solutions include affordability, cleanliness, compact installation, and trouble-free performance:
• Corrosion-resistant polyurethane composition
• Compliance with FDA food-contact regulations 21 CFR 177.1680 (Polyurethane Resins) and 177.2600 (Rubber Articles Intended for Repeated Use)
• No maintenance required because they keep their structural integrity, flexibility, and shape over extended periods of service
• Easy to clean – no rods or seals to absorb grit and wear or break
• Not prone to leaking compressed air due to wear in seals and rods
• 80% lower profile than typical pancake cylinders*
• A fraction of the cost of traditional pancake cylinders
• Easily customisable to meet specific size and shape requirements
Firestone Industrial Products (for which Air Springs is exclusive Australian national distributor) manufactures the world’s best-selling air spring range. Its Airstroke® actuators and Airmount® isolators are used in materials handling applications worldwide.
The broad range of Airstroke® actuators and complementary Airmount® isolators are supported by Air Springs Supply’s longestablished national sales and technical support network. They are available as OEM equipment or as replacement parts to replace similar components incorporated globally by OEM manufacturers. airsprings.com.au
Power Integrations’ new 3300V IGBT Module Gate Driver reports telemetry data for observability, predictive maintenance and lifetime modeling.
Power Integrations has announced a new, single-channel, plug-andplay gate driver for 190mm x 140mm IHM and IHV IGBT modules up to 3300V. The 1SP0635V2A0D combines Power Integrations’ proven SCALE-2 switching performance and protection features with a configurable isolated serial output interface, which augments driver programmability and provides comprehensive telemetry reporting for an accurate lifetime estimation. Multiple sensing circuits including thermal and device and bus condition information are incorporated, simplifying system design and enhancing observability, control and reliability. Application areas are rail traction inverters, power grid and medium-voltage drives.
Thorsten Schmidt, product marketing manager at Power Integrations, commented: “The serial status output protocol incorporates critical real-time measurements, facilitating advanced operational verification and dramatically increasing overall visibility of the inverter’s health, reliability and efficiency. Engineers may adapt monitoring and control systems to the PI standard plugand-play protocol or request custom adjustments by PI engineers during their project’s development phase.”
Telemetric data available from the 1SP0635V2A0D gate driver includes accurate temperature measurement, which simplifies thermal management and eliminates the need for external
temperature sensors. DC link voltage measurement is also incorporated, minimizing external circuitry, reducing system complexity and cost. Closed-loop gate voltage, gate status and short-circuit monitoring ensure that modules are operated within set limits, improving efficiency and avoiding catastrophic failures. Other features include a status monitor for the fibre-optic interface to ensure that switching commands are received correctly. Similarly, gate monitoring ensures switching commands have been executed correctly and that the power module is in the appropriate operating condition. Short-circuit monitoring provides accurate control, directing the gate driver to respond appropriately in the event of a short circuit.
power.com/1sp0635-digital
New Boson+ CZ 14-75 camera-sensor with a 5x continuous zoom lens maximises performance, simplifies development and streamlines manufacturing supply chain.
Teledyne has announced the first Boson+ thermal camera module with its factory-integrated, high-performance 14mm to 75mm continuous zoom (CZ) lens. With seamless optomechanical integration, the new Boson+ CZ 14-75 reduces development and operational risk and costs, all with an industry-first warranty that is not available when using multiple suppliers. The reliable Boson+ CZ 14-75 is ideal for unmanned aerial vehicles, perimeter surveillance, light armored vehicle situational awareness and targeting, and soldier sighting systems.
“The Boson+ CZ 14-75 camera and lens are factory-designed and integrated to optimize performance and reliability,” said Dan Walker, VP of product management, OEM cores, Teledyne FLIR. “Thanks to flexible and advanced lens control electronics, industry-leading 20 milliKelvin (mK) thermal sensitivity, and integration support, the Boson+ CZ 14-75 streamlines development for applications requiring high-performance infrared zoom capability.”
By completing the factory alignment at Teledyne FLIR, integrators receive a thermal zoom solution calibrated for maximum performance that eliminates boresight wander and other image artifacts while zooming. Critical to dynamic missions, Teledyne FLIR’s advanced lens control electronics provide thermal gradient compensation to maintain focus across the full operational temperature range while object range compensation maintains focus through zoom, even for near targets. Built-in tests (BIT) run at startup, continuously, or are commanded to provide real-time notification of issues and maximize operational reliability.
This Boson+ CZ 14-75 features the latest 12-micron pixel pitch 640x512-resolution thermal detector offering enhanced detection, recognition, and identification (DRI) performance, especially in lowcontrast and low-visibility environments.
The Teledyne FLIR Boson+ CZ 14-75 is available for purchase globally from Teledyne FLIR and its authorised dealers. flir.com/bosonpluscz
Technologies
Teledyne Technologies is a leading provider of sophisticated digital imaging products and software, instrumentation, aerospace and defense electronics, and engineered systems. Teledyne's operations are primarily located in the United States, the United Kingdom, Canada, and Western and Northern Europe. teledyne.com
Engineers show that a jellybean-shaped quantum dot creates more breathing space in a microchip packed with qubits.
The silicon microchips of future quantum computers will be packed with millions, if not billions of qubits – the basic units of quantum information – to solve the greatest problems facing humanity. And with millions of qubits needing millions of wires in the microchip circuitry, it was always going to get cramped in there.
But now engineers at UNSW Sydney have made an important step towards solving a long-standing problem about giving their qubits more breathing space -- and it all revolves around jellybeans. Not the kind we rely on for a sugar hit to get us past the 3pm slump. But jellybean quantum dots –elongated areas between qubit pairs that create more space for wiring without interrupting the way the paired qubits interact with each other.
As lead author Associate Professor Arne Laucht explains, the jellybean quantum dot is not a new concept in quantum computing, and has been discussed as a solution to some of the many pathways towards building the world’s first working quantum computer. “It has been shown in different material systems such as gallium arsenide. But it has not been shown in silicon before,” he says. Silicon is arguably one of the most important materials in quantum computing, A/Prof. Laucht says, as the infrastructure to produce future quantum computing chips is already available, given we use silicon chips in classical computers. Another benefit is that you can fit so many qubits (in the form of electrons) on the one chip. “But because the qubits need to be so close together to share information with one another, placing wires between each pair was always going to be a challenge.”
In a study published today in Advanced Materials, the UNSW team of engineers describe how they showed in the lab that jellybean quantum dots were possible in silicon. This now opens the way for qubits to be spaced apart to ensure that the wires necessary to connect and control the qubits can be fit in between.
In a normal quantum dot using spin qubits, single electrons are pulled from a pool of electrons in silicon to sit under a ‘quantum gate’ – where the spin of each electron represents the computational state. For example, spin up may represent a 0 and spin down could represent a 1. Each qubit can then be controlled by an oscillating magnetic field of microwave frequency.
But to implement a quantum algorithm, we also need two-qubit gates, where the control of one qubit is conditional on the state of the other. For this to work, both quantum dots need to be placed very closely, just a few 10s of nanometres apart so their spins can interact with one another. (To put this in perspective, a single human hair is about 100,000 nanometres thick.)
But moving them further apart to create more real estate for wiring has always been the challenge facing scientists and engineers. The problem was as the paired qubits move apart, they would then stop interacting. The jellybean solution represents a way of having both: nicely spaced qubits that continue to influence one another. To make the jellybean, the engineers found a way to create a chain of electrons by trapping more electrons in between the qubits. This acts as the quantum version of a string phone so that the two paired qubit electrons at each end of the jellybean can continue to talk to another. Only the electrons at each end are involved in any computations, while the electrons in the jellybean dot are there to keep them interacting while spread apart.
The lead author of the paper, former PhD student Zeheng Wang says the number of extra electrons pulled into the jellybean quantum dot is key to how they arrange themselves.
“We showed in the paper that if you only load a few electrons in that puddle of electrons that you have underneath, they break into smaller puddles. So it's not one continuous jellybean quantum dot, it's a smaller one here, and a bigger one in the middle and a smaller one there. We’re talking of a total of three to maybe ten electrons.
“It’s only when you go to larger numbers of electrons, say 15 or 20 electrons, that the jellybean becomes more continuous and homogeneous. And that's where you have your well-defined spin and quantum states that you can use to couple qubits to another.”
A/Prof. Laucht stresses that there is still much work to be done. The team’s efforts for this paper focused on proving the jellybean quantum dot is possible. The next step is to insert working qubits at each end of the jellybean quantum dot and make them talk to another.
“It is great to see this work realised. It boosts our confidence that jellybean couplers can be utilised in silicon quantum computers, and we are excited to try implementing them with qubits next.” unsw.edu.au
New remotely monitored switch-mode cathodic protection system installed on Swanson Dock helps company save millions in cabling costs.
Swanson Dock is a container shipping port facility in the Port of Melbourne, which is Australia’s largest container and cargo port. When the Port of Melbourne undertook major rehabilitation works on the port’s structures, including Swanson Dock, the consulting firm engaged cathodic protection specialist Omniflex to help safely deliver the project.
Because Swanson Dock is an active container wharf, with lots of cranes and trucks moving on top of it on an ongoing basis, there was no space to safely run cables or install T/R boxes along the 900 m long wharf. This meant the only viable option was to opt for a distributed cathodic protection (CP) system mounted under the wharf itself. The ongoing operational nature of Swanson Dock meant that the only viable option was to install a switch-mode distributed CP system mounted under the wharf itself and use remote monitoring technology to collect ongoing system performance data. This would limit the need for engineers to conduct manual inspections under the wharf itself.
Switch-mode technology is better suited to smaller currents driving more individual zones or protection, as found more often in concrete ICCP systems and distributed steel CP systems. Small, compact switch-mode T/R modules are also well suited for use in distributed CP systems, where locating T/R’s closer to the anodes provides significant savings in installation costs, due to reduced cabling, and lower operating costs.
Omniflex provided Swanson Dock with the solution in the form of a PowerView CP system comprising of 20 IP68-rated stainless steel
enclosures mounted under the wharf, delivering a total of 4000 Amps of CP to 80 water anodes, protecting the steel piles and sheet steel wall. The concrete decking is protected by 98 individually controlled concrete zones supplied by switch-mode T/R’s and 400 reference electrodes, resulting in a fully remotely monitored and controlled ICCP system that provides protection for the 900 m long wharf. The distributed CP system Omniflex provided significantly reduced the need for divers to regularly visit and inspect the system, leading to a decrease in downtime and ongoing labour costs. This is in addition to the increased convenience provided by the remote monitoring technology, as it meant system data could be accessed whenever required instead of relying on divers’ availability to conduct manual inspections.
As well as energy savings made as a result of installing a CP system based on modern up-to-date technology, Omniflex’s system also resulted in substantial cabling cost savings, amounting to more than $1m.
Ian Godson, the lead consultant on the project, commented, “The savings of millions of dollars would not have been possible without the Omniflex technology.”
For more information on how Omniflex can help you overcome any challenges with remote monitoring CP systems or to learn more about the benefits of switch-mode CP systems, download the company’s new cathodic protection industry overview.
omniflex.com
Injectronics Industrial offer a unique service to business owners, manufacturing line managers and service repair agents alike - a fault analysis and repair service for many applications including difficult to source and obsolete items.
Introducing a new, time sensitive and cost-effective option when it comes to making a decision on your industrial repair.
The range of repairs available include:
• Human Machine Interface (HMI)
• Variable Frequency Drive (VFD)
• Servo Drive
• Servo Valves
• Spindle Drives
• Stepper Drives
• PLC
• Timer and Counters
1300 646 948
• Power Supplies
• HV Generator
• Industrial Computer
• Motherboards
• CNC Boards
• Industrial Control Panels
• Preventative Maintenance
New analyst report details how SYSPRO embedded analytics increases enterprise visibility and productivity while reducing IT costs. Isaac Gould, Research Manager at Nucleus Research, notes that this new functionality in latest SYSPRO release enables non-technical users to analyse ERP data without burdening IT.
SYSPRO, a global provider of industry-built ERP software, has been recognised for its significant new Embedded Analytics capability in a Nucleus Research report. Released as part of SYSPRO 8 2022, SYSPRO’s new Embedded Analytics functionality empowers everyday manufacturing and distribution business users to conduct sophisticated analyses on ERP data to gain insights, all without involving IT.
“Most companies still lack a modern data analytics ecosystem, and instead rely on Excel spreadsheets that prove too slow and cumbersome to be effective in informing day-to-day operations.
SYSPRO’s introduction of Embedded Analytics functionality within its ERP platform serves to enable typical business users to leverage and visualise real-time data within their ERP systems. With a centralised analytics solution, organisations can propagate analytics to the individual employee level within their workspace while maintaining security and access controls.”
The Nucleus report outlines three expected benefits for users: Improved Organisational Visibility: Out-of-the box, SYSPRO
embedded Analytics can combine multiple sources of data from sales, operations, finance, workforce and other sources from inside SYSPRO ERP so users can gain a complete, up-to-date view of the organisation. Interactive dashboards and visuals enable users to drill down and expand visuals to provide business users with quick access to relevant information.
Improved Employee Productivity: With embedded analytics, SYSPRO users can avoid involving and waiting on IT or data science teams to generate the insights they need. SYSPRO’s wizard enables business users to build custom dashboards and analyse data on their own.
Reduced operational costs: Embedded Analytics enables SMBs and mid-market companies to analyse data without having to hire expensive data scientists to support a separate BI tool. Additionally, because analytics is built-into SYSPRO ERP, there’s no need to spend time and money on integrations between the BI solution and various data sources.
nucleusresearch.com syspro.com
The benefits of repairing electronics: saving money, reducing waste, and extending the product lifespan.
In today's manufacturing industry, electronics play an essential role in the operation of machines, assembly lines and much more. From control panels to power supplies, these components are the backbone of modern manufacturing, providing critical functions such as control, feedback, and monitoring. However, when these parts fail, it can lead to significant downtime, which can be both costly and time-consuming to repair.
One of the primary difficulties in replacing these parts is the constant evolution of technology. As newer and more advanced machines and components become available, older parts become obsolete, making them harder to find and difficult to replace. This is especially true for Human-Machine Interfaces (HMI), which often have customized software and are unique to each machine. Control panels and power supplies also have specific requirements, making finding suitable replacements challenging.
Replacing these components can be costly, with downtime being one of the main factors. Every minute a machine is not running costs a company money in lost production and reduced efficiency. In addition, finding replacement parts can take time, especially if the original manufacturer is no longer in business or no longer produces that particular part. Furthermore, replacing electronics often requires specialized knowledge and expertise, adding to the cost and time required for repairs.
One company that is tackling this issue is Injectronics Industrial. They offer a solution to the problem of obsolete electronics in manufacturing machines. They specialize in reverse engineering electronic components, including HMI, control panels, and power supplies. By reverse engineering, they are able to create replacement components that match the original specification, ensuring that the machine operates correctly.
Their process involves examining the original component to identify its specifications, features, and functions. They then use
this information to repair the component to the specifications of the original. This allows them to produce replacements or repair obsolete parts that are no longer available from the original manufacturer.
The services not only save time and money, but they also extend the life of existing machinery. Rather than replacing entire machines or production lines, companies can simply replace obsolete components, allowing them to continue using their existing equipment for years to come. This reduces waste and promotes sustainability in the manufacturing industry.
Injectronics also offer a diagnostic service. Our electrical engineers aim to inspect and diagnose the fault with industrial electronic controllers within 48 hours. Coupled with our express repair service, we help businesses avoid unnecessary downtime. im-group.com.au
03 9314 9888
PASS Stanztechnik AG is a quality German manufacturer and worldwide leader in standard and special tooling solutions for various turret punching systems.
System : Thick Turret® Tooling
Thick turret tooling experts
A > E Station guide assemblies
Prima Power and Finn Power indexable multi-tools
Amada® ABS and Alpha tooling systems
System : Salvagnini® Tooling
HPM® Powdered steel punches
Special tooling experts
Tool cassettes for S2 and S4 machines
400 & 500mm shear blades
System : Trumpf® Tooling
HPM Powdered steel punches as standard Adjusting Rings
RTC Cartridges
Special tooling experts
Will Jim Chalmers’ budget drive up inflation? Peter Martin, a Visiting Fellow at the Crawford School of Public Policy at ANU says it is not likely – and here’s why.
The proposition that cutting prices will stoke inflation is a hard one to get your head around, even if you are an economist. Yet it has been seriously put forward as a critique of this month’s budget; the one in which Treasurer Jim Chalmers announced measures that will take the edge off electricity and gas prices, the price of prescriptions and some visits to the doctor, and the out-of-pocket costs faced by low-income renters.
And childcare. Although announced in last year’s budget, measures to take effect in July are set to save a typical family with one child in care about $1,780 per year. Some of the critics of these measures were participants in this year’s Economic Society of Australia postbudget survey.
What they said was that cutting these prices will give people more free money to spend on other things, pushing up prices elsewhere, and putting more pressure on inflation and the Reserve Bank, which might have to push interest rates higher.
As one of them put it, subsidising bills is “not really all that different” to giving people cash payments that they can use to bid up prices and push up inflation.
As I said, it’s a hard argument to get your head around. It makes sense in theory, but in practice I don’t think it makes much sense at the moment, given the measures actually in the budget.
Here’s how it might make sense. Imagine a big expense that households had no choice but to pay. If the government introduced measures that increased it by $1,000 a month, those households would be forced to spend a good deal less per month on other things, and would put a good deal less upward pressure on prices.
Actually, we don’t need to imagine. It’s partly why the Reserve Bank has just ramped up interest rates – to increase mortgage payments by up to $1,000 per month, and in doing so take up to $1,000 a month from household budgets to take pressure off prices.
And it’s partly why the Reserve Bank cuts interest rates – to lower mortgage payments and free up money households can use to bid up prices. The argument is that if a cut in the price of paying off a mortgage can be inflationary, so too can cuts in other prices. Except that other price cuts are hardly ever anything like as big.
When the price of petrol (and diesel) jumped 40 cents per litre after Russia invaded Ukraine in 2022, few people doubted it was inflationary. It pushed up the price of nearly everything.
So when the price per litre fell 22.1 cents after the Morrison government temporarily cut fuel excise, few doubted that the measure restrained inflation as it was meant to, even though if the price had been cut by much more the cut might well have fed inflation.
In his post-budget address to Australian Business Economists last week, Treasury Secretary Steven Kennedy revealed the government’s calculations on the budget’s effects on inflation. He said the changes to rent assistance, the price of prescriptions and bulk billing were small and would put only “small downward pressure on prices”, which he conceded might theoretically be offset by a boost to spending. But he said that offsetting effect would be “largely immaterial”, meaning it would be too small to measure. The energy price measures will do much more. Kennedy’s department reckons they will cut inflation by three quarters of a percentage point in 2023-24, producing an inflation rate of 3.25% rather than 4% in the year to June 2024.
It says the caps on wholesale prices will do most of the work, cutting the inflation rate by half a per cent, with the consumer and business rebates cutting inflation by a further quarter of a per cent. When the rebates end in mid-2025 their effect will be unwound.
The department says the offsetting effect from extra spending will be measurable but “small”, and will work “with a lag”. So by the time it has had much of an effect, inflation itself should be a good deal lower.
And Kennedy identified three things that should help offset the offsetting effect:
• lower energy prices and inflation will lower the indexation of payments that are linked to inflation, putting less money into the economy to add to inflation
• the expected 0.75 point cut in inflation should help restrain inflationary expectations, making it harder for high inflation to become self-sustaining
• the cuts in the profits of energy companies brought about by the energy price caps will themselves remove money from the economy.
Australia is well placed to fight inflation in other ways. All of the budget measures taken together, including the cost-of-living measures, should add just $20bn to the amount the government pumps into the economy over the next four years – a mere fraction of $11T that Australians will spend and earn over that time.
Australia’s very, very low unemployment rate has pushed the proportion of the population in paid employment to record highs, making Australia better able than ever to call upon workers to respond to shortages as prices rise.
While you can never know what’s around the corner, I’m yet to see a credible argument that inflation won’t do as predicted in the budget: come down swiftly from here on. It’s forecast to fall from 7% to 6% by the middle of this year, and to 3.25% by the middle of next year. Rather than making inflation worse, it seems to me that by cutting prices for many of us, the budget will help bring down inflation sooner.
Republished with kind permission from The Conversation theconversation.com
Directed Technologies has opened a $15m global connected vehicle and IoT technology hub in Melbourne.
Directed Technologies has officially opened its $15m Connected Mobility Innovation Centre, set to fuel the rapid growth of connected vehicle technology and IoT solutions that save lives, reduce emissions, and enhance productivity.
The Centre will advance Australia’s capabilities in next generation fleet vehicle digitisation and electrification, while providing a foundation for Directed Technologies to scale its APAC class-leading solutions to global markets.
A Victorian-owned and operated company, Directed Technologies is known for its cutting-edge factory-fit connected solutions for a variety of fleet and passenger vehicles including trucks, trailers, cars, motorbikes, and electric delivery vehicles.
The Connected Mobility Innovation Centre currently manages 200Tb of data, processing 20 billion probe data points a day, including live video feeds, vehicle and driver behaviour alerts and efficiency measures and vehicle fault codes. It provides customers with a live view and advanced analytical insights of their people, vehicles, and assets across the global road network to support fleet optimisation and driver assistance programs that reduce congestion, cut carbon emissions through fuel savings and, most importantly, save lives.
The new Connected Mobility Innovation Centre will double Directed Technologies’ local manufacturing capabilities in both telematics and IoT, allowing it to meet an ever-increasing demand for its hightech products.
The company's telematics devices, manufactured locally, are already used in over 2,500 vehicle fleets globally, including Australia Post and Ambulance Victoria, as well as leading truck brands like HINO, Mercedes-Benz, Kenworth, DAF, and IVECO. Directed Technologies has also been selected by renowned brands like Ford to export locally designed hardware solutions to the global passenger vehicle market. The company has seen rapid growth in Australia and New Zealand, with the homegrown technology now exported throughout 15 APAC countries including Japan, South Korea, Malaysia, Thailand, Singapore, Guam, Indonesia, and Vietnam.
Backed in part by the Victorian Jobs and Investment Fund, the $15m dollar state-of-the-art centre will place Victoria at the centre of global connected vehicle opportunities, driving the growth of digital skills and manufacturing capability by providing hundreds of jobs for high-skilled workers across design, production, engineering and manufacturing.
“You don’t need to look to the Silicon Valley or Europe for cutting edge automotive technology,” Steve Siolis, CEO of the Directed Group (pictured) said. “The idea that we don’t make great technology products in Australia is simply not true. We’ve built a world-class facility and developed innovative solutions for the world’s biggest transport companies that have allowed us to compete against global competitors – and win. “This facility is the only one of its kind nationally and one of the few full-stack solution centres of its kind globally. With all telematics solutions designed and built right here on site, there will be significant local employment opportunities as we scale around the globe.”
Brent Stafford, Executive Director of Directed Technologies said, “The reinvigoration of the automotive industry in Victoria is accelerating with data-driven solutions along with innovations in electric and hydrogen vehicle development and advanced materials manufacturing. The opportunities in connectivity, data analytics and machine learning are right here on our doorstep and will help to diversify the economy but will also solidify Victoria’s position as the centre of automotive manufacturing in Australia.”
Directed Technologies’ global team design, manufacture and manage tailored end-to-end solutions for automotive, transport and logistics and other organisations on a digital transformation journey. I spoke to Mark Whitmore, the Global Sales Director at Directed Technologies. His passion for the market was palpable. Directed Technology went out to look for the biggest companies out there constantly managing lots of data. "When a client wants to start tracking the vehicle, it's like the first step in the journey. They'll then need to track what's happening in the cargo-space, so that could include PTO or temperature. Ambulances need so many item-tracking. Essentially you've digitised their external plant so they know where everything is, and we're only just scratching the surface. That's our story of growth."
directedtechnologies.com.au
A new report reveals Australia’s battery industry could support 61,400 new local jobs by 2030.
Australia’s battery opportunity has doubled in the last 18 months, driven by demand, says a report released today by the Future Battery Industries Cooperative Research Centre (FBICRC). The report, referenced by Minister for Industry and Science, Hon Ed Husic MP in an address to the National Press Club, reveals the battery industry could provide $16.9bn per annum in value-add and support 61,400 local jobs by 2030.
The report, Charging Ahead – Australia’s Battery Powered Future, analysed global and geopolitical influences on the potential growth of Australia’s battery industries, as a major supplier of battery minerals. When implemented, and with the support of the $15bn National Reconstruction Fund and the $1bn value add in resources sub-fund, its recommendations, could result in Australia’s battery industry becoming a global leader.
The report, spanning Australia’s resource, energy, industrial, foreign affairs and international trade policies, highlights the impressive growth of Australia’s battery industry, across the supply chain and commercialisation spectrum. It makes key recommendations to harness Australia’s opportunities from the significantly increased and accelerated demand.
FBICRC CEO Shannon O’Rourke welcomed the report findings. “In light of recent geopolitical developments, our report, Charging Ahead – Australia’s Battery Powered Future, has shown Australian policy-makers should explore more aggressive industry policies, target markets that are looking to diversify their supply chains, and partner with geopolitical allies to enable and enhance the potential growth of Australia’s battery industry. The challenge is to help build the Australian manufacturing ecosystem and get it to scale. Measures like the National Reconstruction Fund are essential to give Australian business an opportunity to compete at world scale,” he said.
“FBICRC stands ready to provide our research expertise and analysis to support Governments across Australia to leverage our battery industry’s competitive advantage and make the most of the recent and significant global economic, industrial and political shifts.”
“Since the release of Future Charge, the battery industry has taken off,” Shaun Chau, author of the report and Sustainability Services Managing Director at Accenture in Australia said. “We are seeing
huge interest in battery technologies as part of the energy transition. “The opportunity for Australia to grow its role in the battery supply chain is large. However, other nations have also woken up to the prospect. To capitalise, Australian industry, government and universities need to move decisively and quickly to create the right enabling environment, attract and develop the appropriate capabilities and ready a coordinated industry for action.”
Batteries are manufactured through a complex value chain from mining and then refining of raw materials, through to the manufacturing of cells then battery packs, and finally integration and end-of-life.
FBICRC comprehensively assessed the opportunities for Australia’s battery industry to leverage its competitive advantages as a major supplier of battery minerals and expand its role within a growing global industry, finding:
• The growth of the global battery industry has accelerated rapidly, and the opportunity for Australia is now more than double previous forecasts.
• Major global economies are now vying for greater shares of the battery value chain, creating opportunities and challenges for Australia’s battery industries.
• Australia is cost competitive but will need to lean into its comparative advantages of mineral diversity, reliability, security and ESG credentials to capture the opportunity across the value chain.
• Governments must act quickly and decisively to capture mid and downstream value in the global battery industry. To expand its presence across the battery value chain, findings within the report suggest Australia should rapidly pursue substantial policy initiatives to attract global industry investment; consider more aggressive industry policies in the face of increased foreign economic nationalism; reposition the export focus for batteries and battery material supply on countries seeking to diversify their supply chains; and pursue partnerships with geopolitical allies, in order to capitalise on the opportunities at hand.
FBICRC’s report, Charging Ahead – Australia’s Battery Powered Future, can be downloaded from the FBICRC site. fbicrc.com.au
Two out of three SMEs have been negatively impacted by late customer payments. workers and generate more than $700bn of the economy’s output, this is cause for concern for many of the Australian workforce. With further analysis into the location of the SMEs, the survey also reveals that NSW has the highest proportion (73%) of businesses that have experienced the negative effects of late payments. This is followed by 64% of West Australian, 62% of Victorian, 56% of Queensland and 53% of South Australian SMEs.
With a potential recession looming for Australia, savvy SMEs are keeping a close eye on their cash flow. Even with more stringent spending and cost-cutting, businesses are still at risk of financial hardship if their customers fail to pay on time. Recent research reveals 64% of Australian SMEs have been negatively impacted by late payments, with almost a quarter (22%) of business owners struggling to pay themselves and 15% struggling to pay staff when customer payments are late.
These numbers were revealed in a recent independent survey commissioned by business loan comparison site Small Business Loans Australia. Respondents surveyed were 210 owners and senior decision-makers across the full SME spectrum: micro (1-10 employees), small (11-50 employees) and medium-sized (51-200 employees), as well as a small percentage of larger businesses (more than 200 employees).
Late customer payments were reported to have a negative effect on the following for SMEs:
• Business owners’ salary
• Cash flow to pay supplier invoices
• Staff salaries
• Ability to pay business purchases
• Size of workforce
• Payments on business loans
• Business credit score
The survey revealed that two-thirds (64%) of respondents have been negatively impacted by late payments. Negative consequences included 22% who occasionally did not pay themselves, an equal 15% who didn’t have enough cash flow to pay their own suppliers on time or occasionally struggled to pay staff, 8% who had to postpone or cancel business purchases due to lower cash flow, 6% who had to reduce workers in their business, 5% who were making late payments on a business loan, 4% who had their business credit score negatively impacted and 11% who were impacted negatively in another unspecified way.
Almost a third (30%) of medium-sized businesses occasionally struggled to pay their staff due to late customer payments, closely followed by 27% of small businesses and 8% of micro businesses (which tend to have significantly less employees). Considering there are 2.4m SMEs in Australia which employ more than 7.4 million
Business owners in NSW are also most likely to occasionally sacrifice their own salaries when customer payments are late, chosen by a quarter (25%) of NSW respondents, followed closely by 24% of West Australian, 23% of Queensland, 22% of Victorian and 16% of South Australian respondents.
Small Business Loans Australia discovered that a quarter (26%) of businesses received more late payments in 2022 than in 2019, while 21% had seen no change in the number of late payments since 2019. Over a third (35%) of business owners expected to see an increase of late payments this year compared with 2022 due to the rising threat of recession.
From a State perspective, businesses in NSW are again most likely to have experienced an increase in late payments from 2019 to 2022, chosen by 35% of respondents, followed by 32% of West Australians, 26% of South Australians, 22% of Victorians and 21% of Queenslanders. Victorian business owners are most pessimistic about late payments in 2023, with 39% expecting to see an increase in late payments this year, followed by 37% of South Australians, 36% of NSW business owners, 32% of West Australians and 29% of Queenslanders.
“With so many economic risks on the horizon, it is a concerning time for small business owners – who need to forecast their cash flow for the 2024 financial year,” says Alon Rajic, Founder and Managing Director of Small Business Loans Australia. “Late customer payments can cause frustrations and great impact on a business. Businesses that are struggling with a cash flow problem due to late payments may take out a business loan to assist. If so, SMEs should ensure they are getting the best deal on their loan including low interest and other low fees such as early-payout and sign-up fees.”
The full survey results are here: smallbusinessloansaustralia. com/late-customer-payments/
“Our people appear to be fully engaged because they are satisfied with their jobs”
So many times, companies lessen their chances of achieving desired results due to overlooking staff engagement. There are a multitude of problems that may be overlooked spanning from customer complaints, workplace stress, lowquality products, and missed deadlines. All these issues may not be evident immediately costing you time and money that you didn’t even realise you were losing.
This is the ICEBERG that many organisations fail to see.
Everything looks fine on the surface, so it’s easy to assume there’s nothing to worry about. Your people reassure you that they’re satisfied; they are not complaining, they comply with your policies, and they reach their targets. The message you get is this:
“I’m Clearly Engaged, Because Everything’s Really Good”
Knowing that your people are happy and performing at an acceptable level is a great start, but that’s all it is—a start. The key point that I want to share with you is: employee satisfaction isn’t the same as employee engagement. True engagement comes when your people are actively involved in the success of the business.
There are a number of barriers that prevent this from happening.
To discover whether you’re missing what’s going on beneath the surface, there are several questions you can ask to find out if you or other members of the team are building barriers to engagement: Are employees aware of the company’s purpose, vision and objectives?
The whole essence of this question is to ensure everybody can clearly see the bigger picture. The boardroom may have come up with a wonderful plan, but has this been passed throughout the company?
Are you, as a company, clear about your purpose, vision, and objectives? If the company’s purpose, vision or objectives are not being lived, there are two kinds of gaps that can exist— defined or undefined.
In both instances, there is no meaning or connection. There is no way for employees to resonate with the business.
Purpose talks about why you are in business: what drives you, as a leader, to be passionate about the reasons for your business’ existence, which you can then pass on to your employees, so they can share your passion for your products or services.
For example, if we make a product that makes life easier for our customer, then that is our purpose.
Vision talks about where your company wants to head. If your people are being led blindly, then they will not be able to fulfil their roles properly or effectively because they will see no connection with what the company wants to achieve in the future.
Objectives define the specific outcomes that you need to attain in order to achieve your vision. These objectives are the ammunition for the vision and represent how you can translate thought into action. They usually comprise specific tasks and outcomes; if these tasks are not defined or unclear, then there is a disconnection between the outcome and the vision.
So it’s important to clearly communicate your purpose, vision, and objectives, along with the strategies you intend to use to attain them. If you have communicated this information, has it been done in a way that captures your people’s attention and imagination? If your people have no interest in your message, they are unlikely to remember or relate to what the company’s purpose, vision, and objectives are.
The lack of understanding of the bigger picture may demotivate your people. If your people aren’t clear about the bigger picture, they are likely to feel far less connected with why the company exists, where it is going, and what the strategies are to attain these goals.
When leaders set the standards for procedures, do they involve the people who actually do the work? It is important to remember that your leaders still have the final say, but, if employees are left out of the loop, it can lead to difficulties.
You don’t have to involve your employees every time you make a change or set a new standard. However, if there is no opportunity for employees to be involved, consulted or contribute, this can lead to a lack of engagement.
If your employees don’t have much of a chance to share their concerns or their positive experiences, then this can be both a source of frustration and disappointment to them and a missed opportunity for your company. If there is no system in place for your people to have a voice, you will have a hard time knowing where the problems are. If your leaders are unaware of issues, then those issues don’t get resolved. Your people may be used to just doing what they’re told—they may even be comfortable with that arrangement—but this can create a scenario where there is constant reworking or duplication of work.
If there is poor communication, with no clear systems in place to ensure messages and memos get passed on in an efficient or effective way, it can create an environment where there’s a steady stream of low-level problems that get overlooked or ignored.
Teaching young people the value of a skilled trades career. Andrew Downes gives some SAGE advice.
As Australia grapples with a critical skills shortage, many are now encouraging young people to embrace a career in the trades, where a wealth of opportunities awaits. When we ask our children what they want to be when they grow up, we hope they will dream big, and pursue a career of enjoyment and meaning. Many young people are overtly steered towards university, and led to believe the skilled trades are only an option for those not sharp enough to aim higher. The truth however, is that the trades offer an exciting career path that is rich with possibilities, and critical to Australia’s social and economical goals.
Australia is in the grip of a skilled labour shortage, which has been exacerbated by the COVID-19 pandemic. In 2022, nearly 50% of trade and trechnical jobs were in shortage, according to the National Skills Commission. This represents a golden opportunity for young people, who can enter their training confident they are gaining specialised skills that are in high demand; demand that will only rise as the nation grows. They will achieve stability and secutiry in an uncertain world. A trades career also offers the chance to earn as you learn. Unlike university, where most graduates enter the real world with debt hot on their heels, trade workers make an income from the get-go. Many go on to enjoy above average wages; some salaries rival those of doctors and lawyers. They grow their own businesses. They thrive.
A trade occupation can unlock diverse opportunities and experiences, and foster an upward mobility that reaches beyond the tools. My own career illuminates this.
I started out as an apprentice electrician, before running the electrical department for Bridgestone. I was constantly disappointed with the poor service on offer from contractors. I knew a company with the right attitude could do better for its customers. This belief led me to found SAGE Group in 1994.
The company had humble beginnings. Our first project was a small domestic wiring job that a mate and I charged $140 for. Within a year we had seven people working in my backyard shed; today SAGE has approximately 700 employees with revenue of $180m and offices around the country and overseas.
It wasn’t always easy, but the skills I acquired in my youth as a trades apprentice– collaboration, communication, problem-solving, curiosity– provided a solid foundation for success. There is no limit to where a trade may take you. I love what I do. When I come into work, I don’t feel like I’m walking into a job. I am walking into my passion. What more could we want for the next generation?
Parents, carers, teachers, and mentors need to champion the skilled trades as an invigorating career option as they guide young people towards tomorrow. It is important and valuable work. When our children, or grandchildren – tell us that when they grow up they want to be an electrician, a carpenter, a plumber, a builder, a mason, a welder, or any other tradesperson, we must recognise this for what it is: a big dream; one that is worthy of our encouragement, and our pride.
See the third link below for access to the free video produced by NFP, The Institute of Patent and Trade Mark Attorneys of Australia (IPTA). IPTA is the nation’s peak professional body representing Australian patent and trade mark attorneys. sage.com/en-au/ innovation-intelligence.com
issuu.com/bpts/docs/nobel_iii-digital-book/653
Why make upskilling with Outsource Institute (AUS) a part of your strategic plan.
Education enables upward socio-economic mobility, and the message has never been clearer. Companies should start reskilling their workforces now!
Outsource Institute (AUS) has been involved in the education sector for several decades, which is why they have strong knowledge around what funding businesses may be eligible for to upskill their workforces, to subsequently increase their competitiveness, something that has never been more vital given the current landscape.
Carl Spruce, Director of Outsource Institute is someone who has been involved in the vocational education sector for several decades. “I have witnessed many government-backed initiatives aimed at driving economic outcomes,” said Spruce. He is passionate about sharing information on the various funding options and incentives available to businesses to upskill their workforces and increase their competitiveness. “Despite these resources,” he continued, “it has become clear to me that many in the industry remain unaware of their existence, particularly given the current landscape where upskilling is more vital than ever to address skill shortages in Australia.”
An article titled ‘The Importance of Upskilling During Economic Downturns’ really strikes a chord with Spruce, as it shared the following; When the Economy Is Down, Choose to Look Up, Upskilling is a definitive comment on a company’s belief in and commitment to a better future. Seeing an economic downturn for the opportunities it affords is difficult. But choosing to find those opportunities is a winning strategy for businesses and their workforces.
“One of our clients and a fellow defence industry member shared their experiences and how they partnered with Outsource Institute (AUS) to take advantage of upskilling opportunities that have provided a winning strategy for their businesses and their workforces,” Spruce said.
Carl Quarterman (Managing Director) at Queensland Gaskets, gained knowledge of the government funding available to Queensland Gaskets through AIDN meetings with Outsource Institute which then eventuated into a training relationship being formed between both organisations. Quarterman chose Outsource Institute (AUS) to upskill his workforce, because the support provided and the steady
understanding that Outsource Institute (AUS) had of Queensland Gaskets’ requirements. Quarterman was aware that the defence sector requires high-quality products manufactured with precision. To ensure all staff had the required skills to meet project requirements to maintain Queensland Gasket’s high-quality standard expected of defence suppliers he invested in the training of his team. Queensland Gasket has a reputation of retaining staff for many years, some have been with the company for 30+ years. As some recently transitioned into retirement, they were at risk of losing their skills. Quarterman once again identified that training was needed to upskill their younger staff to maintain a multi-skilled workforce.
Quarterman stated that the government funding available has helped Queensland Gaskets to take the time to train their staff and back fill where required and or spend the money for appropriate supplies for training. Quarterman concluded by saying that training has always been a part of their commitment to employees and is embedded in future plans for Queensland Gaskets. Lean Manufacturing, Environmental Standards and material and products training are of particular interest for the further upskilling of their workforce.
If like Queensland Gaskets, you are ready to commit to a better future and are interested in learning about what funding and training opportunities exist to get you there, please contact Outsource Institute (AUS )Training and Development Specialists on 1300 136 904.
Outsource Institute is experienced in the training of advanced trade apprentices and has state and federal government funding approvals across multiple states in Australia. We also have several pathways into universities with the University of Queensland, Griffith University, University of Southern QLD, and Southern Cross University ensuring our students have the option to continue with their lifelong learning.
Outsource Institute specialise in recognising and enhancing the skills and knowledge of existing tradespeople in the Metal and Engineering sector, many of the students we provide our training services to have basic trade qualifications already but are performing tasks at a higher level and in more diverse fields than a basic trade and therefore need the underpinning knowledge and qualification to advance.
Some examples of Advanced Trade Training in Engineering that Outsource Institute have provided to upskill workforces and individuals in trade and technical skills to enhance Australia's and organisational Sovereign capability include:
1. Austal Services: Certificate IV in Engineering - currently delivering a FluidPower outcome stream onsite.
2. ASC Shipbuilding: we are currently delivering - Advanced Diploma of Engineering (online) and Diploma of Engineering Technical qualifications to add develop the skills required to meet current and future ship building qualification requirements relevant to the participants job role.
3. BAE Systems: Certificate IV in Engineering- we delivered to 35 students face to face onsite Maintenance /welding /welding supervisors in line with their ship building requirements (AS1796 certificate 10 & AS2214). Our Lead Engineering Trainer was able to conduct training and Welding Supervisor Program (WSP) examination onsite and online to reduce down time. We also worked with inhouse personal to validate their Quality procedures and perform assessment.
At Outsource Institute, we have extensive experience in advanced trade apprenticeship training, and have been approved for state and federal government funding across several Australian states. We also have established pathways with prestigious universities such as the University of Queensland, Griffith University, University of Southern QLD, and Southern Cross University, to ensure that our students have the option to pursue lifelong learning.
Our training services aim to recognise and enhance the skills and knowledge of existing tradespeople in the Metal and Engineering sector, to help them advance their careers. Many of our students already possess basic trade qualifications but require further underpinning knowledge and qualifications to perform tasks at a higher level and in more diverse fields.
We've worked with several organisations and individuals to provide upskilling opportunities that enhance Australia's and organisational Sovereign capability, such as Austal Services, ASC Shipbuilding, and BAE Systems. Our Managing Director, Stephen Love, shares, “We've delivered FluidPower outcome stream onsite for Certificate IV in Engineering for Austal Services. At ASC Shipbuilding, we're providing Advanced Diploma of Engineering (online) and Diploma of Engineering Technical qualifications to develop the skills required to meet current and future ship building qualification requirements relevant to the participants' job roles. At BAE Systems, we delivered Certificate IV in Engineering to 35 students face to face onsite for Maintenance/welding/welding supervisors in line with their shipbuilding requirements. Our Lead Engineering Trainer conducted
training and Welding Supervisor Program (WSP) examination onsite and online to reduce downtime. We also worked with inhouse personnel to validate their Quality procedures and perform assessment.”
By undertaking our Certificate IV in Engineering course, participants can further enhance their skills and knowledge within their current trade. Depending on the specialisation chosen, they can develop advanced skills in the design, assembly, manufacture, installation, modification, testing, fault finding, commissioning, maintenance, and service of equipment and machinery. Additionally, they may also gain skills in the fabrication of structures and assemblies, manufacture of sheet metal work, and use of relevant machinery, equipment, and joining techniques.
To retain good employees, businesses should focus on training and offer clear pathways for ongoing learning and development through workforce planning. For instance, completing the Certificate IV in Engineering can lead to recognition as a Higher Engineering Tradesperson or a Special Class Engineering TradespersonLevel II. Those who want to upskill further can take the Diploma of Engineering - Advanced Trade [MEM50119], which is the final step before a Technical Qualification.
At Outsource Institute, we're committed to providing the best training and assessment outcomes for our clients, and we continually challenge ourselves to improve and achieve. “We've gained ISO 9001:2015 certification, which demonstrates our ability to consistently provide products and services that meet customer and regulatory requirements, and to achieve continual improvement within our Quality Management System.”- Joe Spruce, General Manager.
If you are interested in learning about what funding and training opportunities exist please contact Outsource Institute (AUS) Training and Development Specialists on 1300 136 904.
Welding requires a steady hand, focus and attention to detail. Welders or Boilermakers are in high demand as Australian companies in every industry scale up, export more or re-shore their manufacturing. Production welding can be a difficult job - demanding hours of repetitive motion, sometimes awkward ergonomic positioning and high levels of concentration.
Having a Fanuc ARCMate welding robot is like having your best welder on the job, all day, every day. By automating your welding process, you can expect high quality welds, completed at a consistent production rate all while reducing the OH&S risk to your business. By employing a welding robot on your highly skilled welders are now available for those more precise or intricate jobs, requiring the human eye, dexterity and years of welding experience.
Robotic welding technology has significantly improved in recent time thanks to smart and high-speed communication with the welding power source and wire feeder. Gone are the days of misplaced welds, limited part access and difficult programming.
Robots are extremely good at doing what they are told – but what happens when a joint doesn’t fit quiet as well as it once did? Or the fixture isn’t holding the parts as perfectly as it could? This used to be the Achilles heel of welding robots! To overcome this issue, Fanuc ARCmate MIG welding robots feature two distinct technologies 1. Touch Sensing and 2. Through Arc Seam Tracking.
The robot is able to detect and offset its taught positions by utilising a Touch Sense function. When performing the Touch Sensing function, the robot and weld power source work together, the welder applies a low voltage to the weld wire and waits for contact to be made with the part or fixture as the robot moves towards the direction of the part. Once contact is made, the position data is saved to the robot and the deviation to the taught position is calculated automatically by the robots software. This deviation is then used to shift or offset the robots weld path to ensure an accurately placed weld.
The touch sensing function is able to detect and account for displacements and rotations in all six axis. Meaning it can find a part that has shifted in any direction and rotated in any direction. This powerful feature is able to find the position of Fillet welds, V-Groove Butt welds as well as inside and outside diameters of circular items such as sockets or bosses. A similar function can also be achieved with an external laser sensor if the application demands it.
Through Arc Seam Tracking (or TAST for short) enables the robot to modify its taught weld path on-the-fly, accurately following a weld path that may deviate in position due to imperfect joint fitment or distortion in the part. TAST is a feature that must be supported by the weld power source and coupled with the Fanuc TAST software feature.
During welding, the robot is commanded to weave in a Sine wave motion, during this weaving the welder is constantly monitoring the change in welding current and reporting the deviation from nominal back to the robot. Using this information, the robot then dynamically modifies its taught path to keep the deviation in welding current to a minimum. This feature is able to accommodate major deviations of the part, sometimes as much as 20mm or more.
Automated Solutions Australia (ASA) are able to integrate a range of FANUC welding robots. FANUC robots provide the industry with the largest selection of industrial robots and collaborative or cobots for arc, spot and laser welding. FANUC have welding robots for every task size, reach, and payload to meet your individual requirements. Fanuc ARCMate welding robots are specifically designed for a variety of industrial welding applications, including MIG and TIG welding as well as laser and spot welding. They can even be deployed for laser and plasma cutting. Different versions are available to fulfil a range of needs, and they all have a number of accessories to enhance their flexibility, including automatic torch neck changers as well as a multitude of external part positioning systems including 7th axis linear rails, rotary stages and 2-axis positioners. The FANUC ARC Mate series of welding robots ranges in payload capacity from 7kg to 25kg and in reach from 911mm to 3123mm.
The collaborative Arc welding robots or cobots, include the brand-new FANUC CRX and come with FANUC's tried-and-true, user-friendly ARC Tool Software, which is intended to increase your profitability by decreasing programming time. The simple-toprogram interface enables basic applications, but also gives you access to FANUC's sophisticated capabilities, including Weaving, Seam Tracking/TAST and Multi-pass. The Fanuc CRX robot is capable of hand-guided teaching, which significantly reduces programming time as well as making smaller volume production robot welding more economic. Automated Solutions Australia are capable of supplying and integrating all popular welding brands to meet your shops standards. Major brands supported are Lincoln Electric, Kemppi, Fronius and Abicor Binzel. automatedsolutions.com.au
Kemppi welds stoves for Ukraine in cooperation with companies in the Lahti region.
On 4 January 2023, Kemppi organised a stove welding day, where companies from Lahti region in Finland were invited to weld together stoves for the civilians in Ukraine. By organising this welding day, Kemppi responds to the challenge of LUT University (Lappeenranta-Lahti University of Technology) to help Ukrainians get through their days. Stoves can be used to heat apartments and cook food. The purpose is to help Ukrainians suffering from energy shortages and the lack of piped gas or other fuels. Many Ukrainians have no electricity or heat distribution after the Russian bombings.
“In the end, more than 500 stoves were shipped,” said Emma Naukkarinen of Kemppi Oy. “So our stove welding day was a great success, and the welders were eager to help the Ukrainians. Our shipment left for Ukraine last week, and we packed also axes and lighters with the stoves because we heard there was a need for those as well. The stoves will be handed over to the Institute of Welding in Kiev and they will take care of the distribution there.”
Companies VS-Welding Oy, Speweld Service Oy, Halton Marine Oy, Peikko Finland Oy and Kouvola Vocational Institute Ltd., Eduko responded to Kemppi’s invitation to participate in the welding day. More than thirty companies from all over Finland have already participated in LUT University’s challenge.
“The situation in Ukraine is very challenging because of the destruction caused by the Russian attacks. Electricity and heating disruptions are significant. By making stoves, we can make people’s lives a bit easier in the midst of war. This is a unique project, and we are honored to be part of,” says Aarno Laine, Director, Domestic Sales, Kemppi Oy.
● Beautiful Quality Spot Welds
● Eliminate Distortion & Misalignment
● Minimise Sanding & Grinding
● Reduce Setup & Process Time
● Achieve Weld Position Accuracy
LUT University’s mechanical engineering laboratories are now harnessed to manufacture stoves for Ukrainians suffering from power outages. The stove project and Rector Juha-Matti Saksa’s appeal on social media last weekend inspired a great many to help and attracted new partners in cooperation. Due to the extensive interest, LUT now has the resources to build 105 stoves instead of the original 20–40. The number of stoves symbolises the number of years Finland has been independent.
“The stove project has gotten out of out of hand, but in a good way. Masses of people have reached out to us, wanting to help the Ukrainians,” Saksa relates.
Stoves are being made as part of the University course exercises. Kemppi, which organised the welding day, also participated in the project by sending a welder to Lappeenranta in Finland for two days. Being in nearby northern Europe, Kemppi in Finland is in the right spot to assist in any way they can. kemppi.com
● No Burn on Stainless Steel Welds
● “Easy Setting” Touch Screen Control
● Select Material Type
● Select Material Thickness
● Start Welding with Confidence
Models to Suit most Applications including Aluminium
Manufactured in Japan by Koyo Giken Co., Ltd
MySpot® is produced in a variety of sizes and configurations, including pedestal style. Please visit www.koyogiken.co.jp/en/ for detailed information & latest technology
Authorised Sales & Service Agents Australia and New Zealand
The role of automation to solve the imminent squeeze for infrastructure.
Australia and New Zealand will soon be facing a demand for infrastructure. According to Weld Australia, ANZ has a $237bn pipeline of infrastructure spend, and it is predicted that by 2030, Australia will be short 70,000 skilled welders to deliver the critical energy, defence, rail & infrastructure required to fuel this growth. Fabrication shop capacity restraints; issues resulting from supply chain shortages; competition from overseas; and declining profit margins are all contributing factors. Fabrication shops serving a number of industries are looking at robotic welding to help solve this challenge, and are searching for a path to automation.
Before a fabrication shop can proceed on making a decision on an automation solution, fabrication shops need to examine key issues such as production mix, infrastructure needs, human resource requirements and ultimately, the return on investment. They need to choose pipe welding automation systems for their fabrication shops that will help them achieve consistent, high-quality welds, while increasing their shop productivity and helping them get ahead in an increasingly competitive market.
“The fabrication shop owner should consider how they are going to win more projects, and grow their business while facing shortages of parts and labour, especially in the context of a potential recession ahead,” said CEO Soroush Karimzadeh, of Novarc Technologies Inc. (North Vancouver, Canada.), a full-stack robotics company specialising in the design and commercialisation of cobots and A.I. systems for robotic welding applications.
Novarc’s Spool Welding Robot (SWR) is a welding cobot (collaborative robot) designed specifically for pipe, small pressure vessels and other types of roll welding, that provides pipe fabrication shops with a smart solution to promote safety, reduce costs, increase productivity and improve the weld quality.
An example of a fabrication shop that has benefited from Novarc’s SWR is Metropolitan Mechanical Contractors (MMC) which has been providing services to design complete mechanical systems including HVAC, chiller and boiler systems, plumbing, sheet metal fabrication, and service/maintenance to a number of commercial facilities located throughout the USA (specifically, Minnesota, Iowa, North Dakota, South Dakota and Wisconsin). In business since 1963, the company has completed projects for the Mall of America, Target Center, Target Field and the Xcel Energy Center.
“The projects we work on vary a lot. Specific jobs typically require a percentage for x-ray and ultrasound testing. Sometimes a job is 100% X-Ray, and sometimes 10%. What was important for us was to improve the quality and consistency of our welds,” said Corey Hagerty, Pipefitting Shop Foreman at MMC.
MMC purchased one Novarc SWR in 2022 and this move to automation has made a world of difference in weld quality and capacity.
“Before implementing the SWR, we typically had three to four guys welding, depending on the project, and we averaged from 6080 Factored Diameter Inches (FDI) a day. Currently, we’re doing 200-250 FDI a day on the SWR, and we even achieved 290 in one day,” says Hagerty. “The SWR has helped with our capacity on the larger projects, and that’s definitely where we have shone.”
Since bringing the SWR into the fabrication shop, MMC has been able to realize significant productivity gains: achieving 250 Factored Diameter Inches per shift; increasing their pipe welding capacity; achieving 0% repair rates; and, reducing the dependency on highly skilled welders.
Besides improving weld quality, the SWR reduced MMC’s dependency on highly skilled welders due to the global labor shortage.
But Novarc’s SWR doesn’t abandon the human operator. Instead, it works alongside the welder, allowing those with less skill and experience to successfully take on a
job that only senior welders could perform previously. And the results? Welds with greater precision, accuracy and speed, and a never before achieved balance of quality and productivity.
“We have an individual that was a pretty skilled welder in the field of stick welding, and he didn’t have a significant amount of experience in wire, but he just obtained a certification with wire and we’ve been able to put him on the SWR. It’s been pretty seamless to be able to put a junior-level welder on the SWR, and achieve highquality welds,” says Hagerty.
MMC appreciated the technical support to the welders as well. “The Novarc Academy was also a great help. I had walked through the training sessions myself, and I think that it took out a lot of the unknown and the pessimistic views that a lot of welders can have towards it. The fact that you can override it, interact with it, and make adjustments on the fly is a huge benefit. I fully believe that’s the benefit to Novarc over the other semi-automatic processes,” says Hagerty. NovarcTech.com
Studying for an Arts degree, Rowena Kilbourne dream was to sculpt steel into works of art. Today she welds the great trailers that carry the needs of a nation.
Rowena Kilbourne is close to finishing a welding apprenticeship with MaxiTRANS at the company’s Ballarat manufacturing facility. There is no doubt she loves her work, forging molten metal to her will, connecting, joining, finishing the main rails that, in their lifetime, will carry a million tonnes of freight on Australian highways. Her career began when she enrolled in a TAFE course for welding to further the creative side of her arts degree. With her husband Nathan, the couple learned the craft and process of welding. A Cert II qualification opened the door to employment with MaxiTRANS for the couple.
And to keep life interesting, partway through her apprenticeship, Rowena fell pregnant and today she is a proud mother of Colt, her 19-month-old son. She is on the cusp of completion of her apprenticeship after seven years with MaxiTRANS.
As a welder, Rowena works mostly on the main chassis rails for MaxiTRANS trailer brands, Freighter and Maxi-CUBE. These foundations of a trailer’s long life are fabricated from flat plate steel and are processed through an automated welder. They are then inspected and finished off by the welding team.
Rowena works on the wide spectrum of trailers that are built at the Ballarat plant: Semi-trailers, T-Liners, Vans for refrigerated and dry goods logistics, as well as roll-back lead trailers.
“We also fabricate the main rails for our Hamelex White tipper products produced at our Ballarat site, whether they go through the automatic welder or if they are off-set. For off-set tipper rails we have a jig we use to tac-weld them, before they are fully welded down the line.”
When she fell pregnant, Rowena says MaxiTRANS supported her through 18 weeks of maternity leave and the opportunity to extend the leave for a further 12 months.
Rowena took ten months of the leave and returned to work. “They were happy to have me when I was ready. They never pushed or anything, which was really nice.”
Balancing motherhood and work is definitely a learning challenge, Rowena says, finding a balance can be difficult.
“But it’s something I enjoy,” she says, “having time to watch Colt grow on my off-days is really good. It’s all working out well so far.” Working three days a week at present, Rowena has trade school on
Rowena Kilbourne has been with MaxiTRANS for seven years, closing in on completing her apprenticeship with the Company.
Friday, so the flexibility of shifts afforded by MaxiTRANS works for her. “I only have two units to complete. I’m pretty close to finishing and that’s really exciting.”
Rowena’s husband Nathan worked for some years with MaxiTRANS and he then completed a Cert 4 Training and Assessment course and now teaches welding at the Federation University TAFE in Ballarat.
Rowena says the workplace culture is great and continues to change for the better since Australian Trailer Solutions Group (ATSG) took over the MaxiTRANS business in September 2021.
“I really enjoy working for the company. The new MaxiTRANS under ATSG is continuing to make improvements and creating a very supportive environment for its staff.” Rowena says she has always been treated with respect in the workplace. “It’s quite moving to see the growth that has happened so far,” she says.
Rowena says she would definitely recommend MaxiTRANS as a place to work.
“They care about staff, they (management) will go the distance to support you. It’s a
stable workplace, it’s good work. They really try to look after you.” Rowena says there are career paths open to MaxiTRANS workers.
“I’d like to become a Welding Inspector or even go down the training route. Be a mentor even, I’d love to go there. I’m excited about it, but I have to get confidence in myself first.”
Just listening to Rowena Kilbourne talk, there is so much excitement in her outlook. A young mother, a MaxiTRANS worker who loves the art and craft of industrial welding and at the weekend plays baseball for her local Alfredton team.
And as the finished trailers roll out of the manufacturing facility, it is not hard to imagine Rowena taking a second for a proud smile as the result of her hard work, and all the MaxiTRANS team at Ballarat, leaves for a long working life on the rugged highways of Australia.
MaxiTRANS is the largest supplier of locally manufactured, heavy duty road transport trailer solutions, including trailer repairs and service in Australia.
maxitrans.com
ANCA has been providing a wide range of automation solutions for many years.
The tool manufacturing industry embraces automation solutions at an unprecedented pace. This is a worldwide trend driven by several factors - labour shortage, increasing labour costs, the need for maximising uptime, push for 24/7 machine availability and customers demanding shorter lead times. Manufacturers need to be more flexible and responsive than ever before.
ANCA has been providing a wide range of automation solutions for many years. One of the recent offerings in this space is our ANCA Integrated Manufacturing System, or AIMS for short. AIMS is an ecosystem of individual modules – or building blocks - which could be configured to build a tailored automated tool manufacturing system. Modularity and flexibility mean that it caters to both small and large enterprise type manufacturers. The system could be designed to be very simple, using a trolley for manual pallet and tool transfer with basic ERP connectivity. It could also be a complex, fully autonomous production solution which requires minimal human intervention.
One of the most noticeable components of a fully automated AIMS cell is AutoFetch – the AMR robot responsible for transferring pallets between the setting station called AutoSet, to the tool grinder. It also automatically transfers single tools for spot check measurements outside of the grinder. As you can imagine there’s a lot of traffic and the AutoFetch can get very busy. An AIMS cell is typically configured within a footprint of the existing factory with adjoining areas where standard, manual operations are taking place. This is a great flexibility feature but also raises many questions about how autonomous operation can function alongside the traditional production plant with frequent foot traffic.
There’s no need to fence off the AIMS area thanks to unique technology used with the AutoFetch robot. There are generally two types of automatic vehicles used on the factory floor – AGV and AMR. AutoFetch is an AMR (Autonomous Mobile Robot) which is different to AGV (Automatic Guided Vehicle). The main difference is the way both units navigate their way around the factory. An AGV always follows a predetermined route which is defined by using
various guiding aids like strips embedded in the floor, or reflectors fitted to the walls around the route. The AMR on the other hand, travels from one location to another using its array of sensors and initially scanned map of the area. It doesn’t require any additional infrastructure to transfer material from A to B. You just scan and map the relevant area during AutoFetch setup, mark the load and unload positions and then the robot, using sophisticated algorithms, will find the optimal way from one point to the other.
One of the most common questions we’re being asked is related to safety of the AutoFetch. This is understandable since AutoFetch operates alongside personnel in the factory. The good news is the AutoFetch AMR is designed to safely operate in a factory environment where people are present. The AMR moves from one station to another using an optimised route, and it constantly scans the immediate area for unexpected objects. When an object is detected, the AutoFetch will stop and navigate around it. An array of sensors - laser scanners, 3D cameras and proximity sensors - is used for this purpose. For extra security, an AMR prohibited area could be defined on the map to exclude autonomous traffic altogether. In addition, the AutoFetch could be programmed to reduce speed in certain areas and warn nearby staff with audio warnings such as beeper, horns, or pre-recorded spoken messages. 72% of manufacturers report accidents related to using traditional means of material transport like pallet jacks, trolleys or forklifts. The use of AMRs contributes to increased safety in the factory and reduced accidents due to the elimination of human factors like fatigue, lack of focus or awareness. machines.anca.com
Cemented carbides are in fact the foundation of many modern machine tools. Department Manager Rickard Sundström recaps the rich history of cemented carbide and what the future might hold.
Many notable periods in history are characterised by the material of the time — the Stone Age, the Iron Age, and so on. Labelling these periods based on tool materials demonstrates how integral they were to society, as well as our human drive to constantly improve and find better methods. The applications and sophistication of tools has changed significantly over the centuries, but they’re still just as crucial to keeping our world running today.
The development of the first commercial steel alloy is often credited to Robert Forester Mushet, who discovered in 1868 that adding tungsten to steel increased its hardness even after air cooling. This finding formed the basis of alloy development, leading to the use of tool steels. In the early 1900s, forming and machining metals was still very much a skill; highly skilled craftsmen used tool steel as a cutting tool material.
But as demand for mass production began to increase, particularly with sectors such as the automotive sector starting to take off, it became clear that tool steel wouldn’t be able to keep up. Its limited heat resistance results in softening at higher temperatures, particularly at the cutter-workpiece interface, making high-speed cutting difficult.
As a result, high speed steel was developed, containing more cobalt than tool steel. The additional cobalt gave high speed steel an improved hot hardness, enabling access to much higher cutting speeds. Faster cutting led to a boost in productivity, dropping overall product cost and ultimately was one of the factors that helped to make vehicles more accessible and affordable to the public.
The success of high-speed steel led the industry to develop further, resulting in the invention of cemented carbide. On March 30, 1923, Karl Schröter, the then head of R&D at Osram filed the first patent. The material was originally intended for drawing dies in the light bulb industry, but later cemented carbide was developed and tested for cutting tools. As such, it was introduced at an exhibition in Leipzig in 1927. Fine carbide particles are cemented into a composite with a metal binder to produce cemented carbide. The most common carbides include tungsten carbide (WC), titanium carbide (TiC) and tantalum carbide (TaC), with cobalt and nickel often used as the binding metals In the same way that the introduction of high-speed steel revolutionised the manufacturing market, the invention of cemented carbide allowed for even faster machining. Steel cutting speeds of up to 150 metres per minute became possible, almost four times faster than high-speed steel.
It’s here that Sandvik began developing cemented carbide tools. The Sandvik Coromant brand name was established in 1942, with its sole aim to offer modern cutting tools using cemented carbide as the base. Sandvik Coromant’s first cemented-carbide tools for metal cutting were manufactured the following year, and as industrialisation took off in the fifties and sixties, demand only continued to grow.
In 1969, Sandvik Coromant became the first in the world to offer ceramic-coated cemented carbide inserts. The ceramic ‘Gamma Coating’ greatly improved both the wear and heat resistance of the tools, increasing metal-cutting performance by as much as 50%.
Coromant continued to develop its cemented carbide offering, developing new grades and drills for a variety of industries, with its GC 4225 cemented-carbide grade becoming the world’s bestselling grade in 2005.
But what about the future of cemented carbides? Central to the production of cemented carbides are metals like tungsten and cobalt, but these resources are in limited supply. Cobalt, for example, is a common component in lithium-ion batteries, valuable in extending battery life. But soaring demand combined with mining challenges means we could see shortages as soon as 2028.
To protect these finite resources, it’s imperative that manufacturers and suppliers play their part in working sustainably. This could be through repairing and refurbishing old tools to give them a second, or even a third life. Tools that are completely unusable can be sold through buy-back programmes, with the scrap being recycled into new material. Here at Sandvik Coromant, we offer both services, with our latest line of steel turning grades containing at least 40 per cent recycled material. Considering issues like supply and sustainability right from the tool’s design also help to ensure that no more material is being used than necessary.
The availability of the raw materials will be a factor in the future of cemented carbides. At Sandvik Coromant, continuing to improve and make the most of sustainability schemes will be a focus. In particular, the sorting aspect of our recycling process is likely to be a key area of development, as this is still a challenge in terms of the energy resources it demands.
Despite big leaps in innovation, older cutting tool materials like high speed steel still play an important part in the overall market. It’s clear that even in its 100th year, cemented carbide is still a vital cutting tool material for many industries. But there’s always room for improvement and as applications change and new ones arise, we’ll always be challenged to come up with new and better solutions. sandvik.coromant.com
Five-axis machining is the way to go, says Jason Allen, ISCAR Managing Director.
It is apparent that five axis machining is becoming increasingly popular in modern metal cutting. Five-axis machining provides significant advantages such as machining complex-shaped parts by use of one set-up without changing the location of the workpiece, high machining accuracy, and reduced cycle time.
Advanced technology of workpiece fabrication has led to increased capabilities of precise forging, casting, and mainstreaming additive manufacturing (AM). This has resulted in the increased complexity of workpiece geometry, decreasing machining allowance and material by cutting operations and achieving end results which reflect the final shape of the workpiece. The requests for high-performance cutting tools intended for finishing and semi-finishing geometrically complex surfaces are now vitally important.
Ball-nose milling cutters are considered traditional tools for machining 3D surfaces. Ball-nose cutters are the most common tools for semi-finishing and finishing profile in milling operations. Progress in the field of five-axis machining centers, and a significant step forward in modern CAM systems have emerged tools with a different cutting geometry, referred to as segment or barrel-shape endmills. Even though these tools are well known to machinists, they remain ignored. Five-axis machining combined with CNC software and computer modeling of complex tool configurations has reemerged the use of circular segment endmill applications. The cutting edge of these endmills is an arc that represents a segment of a circle with a radius larger than the nominal radius of a tool. For comparison purposes, in ball-nose cutters the tool radius is the radius of the cutting edge. Machining surfaces using 'passes technique' segment-type endmills enables a substantially increased step size compared to ball-nose cutters, thus reducing the cutting time. A three-axis CNC controlled cutting process cannot guarantee the correct position of a barrel-shaped cutting tool when machining complex surfaces. The five-axis machining concept allows taking full advantage of segment endmills.
Depending on the orientation of the cutting edge relative to the tool axis, segment endmills possess various configurations such as pure barrel, tapered barrel, lens, and oval or parabolic shapes. The form of the tool cutting edge determines the tool application.
For example, lens-shaped tools are suitable for both five and threeaxis machines, while endmills with a tapered barrel profile are intended for five-axis machines. Segment cutter designs appear in multi-flute solid endmills that deliver ultimate tool accuracy and maximize the number of teeth on the cutting tool.
The ISCAR NEOBARREL tool line includes several tool families. These are solid carbide endmills (SCEM) in a diameter range of 8-12 mm (Fig. 1). The 10 mm oval-shaped solid carbide endmill has an arcuated peripheral cutting edge in a radius of 85 mm. This endmill quadruples the step size repeatability compared to a 10 mm ballnose cutter and provides the same machined surface finish quality.
ISCAR MULTI-MASTER tool line refers to assembled tools that mount exchangeable carbide heads. This line offers new barrelshaped heads that feature the same cutting geometry and diameter range as SCEM and provide a wide array of options within the MULTI-MASTER line for five-axis machines (Fig. 2). The exchangeable head concept featured in the MULTI-MASTER tool line guarantees rational use of cemented carbide with a true economical advantage. Diverse tool bodies, extensions, and reducers enable the customization of a modular tool assembly for complex machining projects.
Recently, ISCAR unveiled a new family of segment endmills which utilize the single insert tool design principle (Fig. 3). It is a known fact that the accurate parameters of a single-insert tool are lower when
compared to a cutter with exchangeable carbide heads, not to mention the solid carbide endmill. Precision can be compromised if we analyze how a single insert tool, with two teeth, can compete against a multi-flute SCEM or carbide head tool.
To dissipate the arisen doubts about the reasonability of the single insert segment tool design, we should consider several aspects. The single-insert tool concept facilitates cost-effectiveness by expanding the diameter range of segment mills. These cutters feature nominal diameters of 16-25 mm. A durable insert structure and highly rigid insert clamping enable increasing the feed per tooth in comparison with the feed values that are recommended for solid carbide endmills and exchangeable heads. This ensures an appropriate level of feed and speed to machine productively. When operational stability is poor, decreasing the number of teeth contributes to vibration control. Inserts mounted on the BALLPLUS tool family can transform the tool to a segment endmill by use of inserts only. ISCAR BALLPLUS tools include a diverse choice of tool bodies, adapters, and extensions, which greatly simplify tool customization. Choosing a single-insert segment tool design is now more logical and justified.
In modern manufacturing, barrel-shaped mills have good prospects. The metalworking industry has found many uses for applying a multitude of cutting barrel designs. These include solid carbide endmills, cutters with exchangeable heads, and single-insert tools (Fig. 4), all of which have formed a complete segment of profile milling tools with a challenging future.
iscar.com
Güdel offers a wide range of linear tracks & multi-axis gantries to suit the most demanding applications for robots, logistics,
Gantries with modular design are available in 2-Axis (ZP) & 3-Axis (FP & CP) configurations with optional rotary axes. Maximum flexibility & performance with the capability of manage payloads up to 3,000kg.
CNC Design Pty Ltd, 137-145 Rooks Rd, Nunawading, VIC 3131, (03) 9417 2820 https://www.cncdesign.com.au/gudel-modules-components gudel@cncdesign.com
A new generation turning grade has been launched by Dormer Pramet offering one of the highest levels of productivity and versatility in the market today.
The Pramet T9415 is the most advanced MT-CVD grade launched by Dormer Pramet in almost ten years. This fourth-generation grade covers a broad application range, replacing the previous T9310 and T9315. In addition, it also partly overlaps with grade T9325, giving T9415 one of the widest range of applications in steel turning. With a 30% thicker coating than the previous generation, the Pramet T9415 significantly improves tool durability by increasing resistance to wear and offers higher productivity by allowing for higher cutting speeds. Several testing users of the new grade have reported that their productivity has doubled while machining carbon and structural steels.
Additionally, a new post-treatment process improves toughness and stability of the cutting edge resulting in improved reliability in interrupted cuts and unstable conditions, but the T9415 is still suitable for high cutting speeds.
T9415 inserts have optimised cutting-edge geometry which reduces cutting forces and enhances performance.
The T9415 significantly improves tool durability and offers higher productivity by increasing resistance to wear.
The insert seating area has been ground to improve stability and enhance heat transfer away from the cutting edge. This further helps to improve tool life, reducing the plastic wear on the cutting zones. Also, a gold TiN coating allows operators to better detect wear along the flank of the inserts.
Using the latest technologies, the Pramet T9415 inserts have optimised cutting-edge geometry which reduces cutting forces and enhances performance. Along with saving energy, the inserts themselves are manufactured using the latest production technologies and raw materials which support a more sustainable and environmentally friendly offer.
dormerpramet.com algratooling.com.au
A new assortment of Pramet LNEX 12 negative tangential inserts, with four cutting edges, provides a highly productive solution for a wide range of applications.
The LNEX 12 is a robust insert designed for shoulder milling with a maximum depth of cut up to 10mm. It features a positive rake angle and narrow T-land to provide a smooth cutting action with lower demands on spindle torque.
The peripherally ground insert offers improved wall accuracy and straightness and creates a true 90° corner. The LNEX12 also featuring a patented U-groove segment on all four cutting edges which provide a good surface finish and expand its application range to low-power machines and small depths of cut.
In addition, the two-sided design supports performance by making ramping possible.
The insert comes in two different geometries, F for machining of various workpiece materials in light and medium applications. While M is suited for medium to semi-roughing in steels and cast irons. Alongside the new insert is a line of perfectly matched cutters. The Pramet SLN12X series is available in Cylindrical, Weldon and Shell styles, with all featuring internal coolant systems for improved surface quality.
Its improved body strength and thick core offers enhanced rigidity, giving a reliable cutting process with low vibrations and long tool life for both the insert and cutter. Easily accessible large clamping screws provide simple indexing and handling of inserts.
The combination of the Pramet LNEX 12 inserts and the SLN12X cutters give operators a smooth cut with a clean finish, reducing the need for additional operations, such as deburring. dormerpramet.com algratooling.com.au
Simply Reliable.
Just a short distance from Silverstone, the JRM Group specialises in the design and bespoke manufacturing of solutions for the automotive, motorsport, aerospace, marine and medical industries. The Daventry company also has a prestigious racing division that has progressed through rallying, FIA GT1 and the GT3 endurance competition. It was in 2017 when the ISO: 9001 manufacturer invested in its first 5-axis machine tool that it realised that a high-end CAM system was a necessity. The current plant list at the JRM Group includes a range of manual and CNC turning and milling centres and more recent investments include a DMG MORI LaserTec 30 SLM additive machine and a CLX450 turning centre, but it was the arrival of its first of three DMU 75 monoBLOCK 5-axis machining centres that demanded an equally prestigious CAM solution. This is where OPEN MIND Technologies entered the fray with its industry-leading hyperMILL CAM system.
Discussing the introduction of 5-axis machine tools and hyperMILL, CNC machinist and programmer Mike Sutton from the JRM Group says: “The company needed to progress its machining capabilities into 5-axis machining and simultaneously realised the existing CAM package was limited to 3-axis machining. Undertaking due diligence with a complete review of the marketplace, we opted for hyperMILL and this decision was influenced by the realisation that a lot of our motorsport customers and F1 teams use hyperMILL. It was a fantastic move as our experience of hyperMILL has been fantastic.”
The 40-employee company manufactures everything from prototypes and small batches for the motorsport, aerospace and defence industries to jigs, fixtures and 3D printed components, processing a complete array of materials. The closest the JRM Group gets to production machining is a 5-part wishbone assembly for a high-performance sports car customer in Germany that requires several hundred assemblies a year.
Looking at the wishbone components produced on a 5-axis DMG MORI machine, Mike continues: “We are currently using a cycle in hyperMILL called arbitrary stock removal, machining 25Cr 04 steel with a 40mm high feed face mill. The tool is running at an 8m/min feed rate with 0.5mm cuts and 50% of the tool diameter, which is pretty fast. We have the machine running at 80% rapid and feeding at 8m/min. The 0.5mm cut was recommended by the tool manufacturer as the way to machine with high feed cutters is to take small depths of cut at high speed. This is different to trochoidal milling where you take larger depths of cut with a smaller radial value.”
When programmed with an alternate CAM system, one of the wishbone components had a cycle time of 4 hours. By adopting strategies such as arbitrary stock removal in hyperMILL, JRM has
improved the machining strategy and cut the cycle time from 4 hours to 3 hours and 5 minutes. The 25% saving per part is impressive, especially when considering the company produces hundreds of wishbone parts a year. The savings are significant.
This is just one example of how machining cycles within hyperMILL are making a huge impact on productivity at the JRM Group. As Mike continues: “We have two seats of hyperMILL and we have the flexibility to programme parts from home, the office or on the machine. The strategies are excellent and before joining the JRM Group, I hadn’t used CAM for almost 20 years – now I’m using hyperCAD-S for designing all the jigs and fixtures we produce and then all the strategies in hyperMILL to reduce my programming and cycle times. I can create models, jigs and fixtures by creating the geometry, surfaces and lines in hyperCAD-S. It may be a challenging thought process to design and clamp some of the parts that we have to machine, but with hyperCAD-S, at least we know the drawing and creation of the jigs and fixtures is a straightforward process.”
At the JRM Group, producing jigs and fixtures is a significant role. For example, the company has recently won an order to 3D print a family of up to 30 motorsport components, which will need finish machining. To undertake this, JRM will 3D print the parts on its metal printer, but it also has to use hyperCAD-S to design the fixtures for clamping the non-uniform parts for subtractive finish machining - a process that will be undertaken with hyperMILL.
“hyperMILL was new to me when I joined the company, but now I am using strategies such as Z-Level Finishing, Optimised Roughing,
Drilling
With impressive levels of support from OPEN MIND and an everimproving level of experience, JRM is maximising the machining strategies within hyperMILL to significantly reduce cycle times, programming times, machine setup times and reduce secondary finishing operations - all whilst improving tool life and spindle longevity. One example is the 3D Advanced Milling/Complete Finishing cycle, as Mike adds: “We frequently machine large aluminium clutch covers that require a high-quality surface finish. The clutch covers incorporate a lot of flat and round surfaces in different directions and to get the optimal surface finish, the tool path needs to move in the right direction with an optimised step-over. By applying the Complete Finishing cycle, we don’t have to pick individual surfaces or create tool paths that need optimising, we can just select the optimal step-over rate – and hyperMILL does the rest. On the clutch covers, we select a small step-over rate of 0.1mm and the machining strategy will automatically determine the tool path directions for the best surface finishes. This may take longer to machine, but we allocate such cycles to lights out machiningreturning to the impeccably finished components that require no secondary hand finishing, the following day.”
3D Optimised Roughing is another strategy within hyperMILL that further enhances machining performance. As Mike adds: “When we use the 3D Optimised Roughing cycle in high-performance mode, we can plunge the tool to a large depth and then remove the material radially. This strategy reduces the stress and forces placed upon the tool and spindle. By plunging to the full depth, we can use the full tool flute length. By setting a metric step-over value, hyperMILL will automatically calculate the percentage of the step-over based on the tool diameter and the volume of material to be removed. This enables us to achieve maximum material removal rates whilst prolonging tool life.”
Concluding on the company’s experience of hyperMILL, Mike says: “It is difficult to quantify the savings that we are achieving with hyperMILL, as our production is predominantly low volume work. However, it is evident that our business is enjoying success and continuous growth and throughout this period, our tool life is improving, as is our spindle utilisation and throughput. Additionally, our programming times are continually falling as our experience with hyperMILL grows, and the ongoing development of the CAM system yields greater efficiencies. Essentially, we are continually increasing our productivity and simultaneously, our programming and machining times and our tooling costs are not escalating in line with output – this is a credit to an extremely efficient CAM system.” johnhart.com.au openmind-tech.com
Medical component manufacturing requires the right machine technology and service support.
Headland Technology has been providing all-around solutions to ADVATEK for more than 15 years. When ADVATEK entered to manufacture components for the medical industry they required 2 crucial things, high precision, reliable machines technology, and a reliable partner to provide them with the right knowledge and service to keep the production going 24/7. They found both in Headland Technology.
ADVATEK was founded in 1995 and has since been a leader in the manufacturing of high-end CNC machined components. Their facility is equipped with 11 Makino machines. Their focus is on providing topquality parts at competitive prices and efficient delivery. Located in Bayswater, Victoria, ADVATEK has supplied components to a variety of industries including medical, telecommunications, and aerospace. Their facility has grown to include a 600sqm factory that operates 24 hours a day. The team at ADVATEK is composed of industry experts who have remained committed to the same level of passion and vision since the company's launch over 25 years ago. With many familiar faces at ADVATEK spanning decades, their team is unified, efficient, communicative, focused on quality, and ready to deliver. They are continuously striving to improve and modernise their operations by helping their team to acquire more advanced manufacturing skills. The company not only provides high-quality parts but also highly reliable customer service. They believe that both are equally important to deliver the best possible results to their customers.
With new contracts to manufacture medical components ADVATEK knew they needed to invest in the best machine technology to stay reliant and efficient. It also meant a steep learning curve, requiring precision, reliability, and high-quality repetitive output with a solid process to trace every step of production and even serialise every individual piece. Together with our machine experts, ADVATEK found the right technology to be able to successfully enter the medical industry and can now manufacture over 40,000 units of special medical components per year.
In fact, ADVATEK directors found that Makino machines were the perfect machine technology to manufacture medical components. “We were satisfied with our first Makino machines because of their performance in reliability, accuracy, and ease of operation,” Gary McBean, Marketing Director and co-owner said.
“So, it was only natural to stay with Makino machines to enter the medical component manufacturing industry.”
Investing in the new F3 Makino vertical machine centre did not disappoint in anyaspects of the operation. “It just made sense to stay with Makino since the small machines had the same performance and newer software,” added McBean. “For us, the machine needed to be an allrounder from being user-friendly, efficient PClike capability for data management and editing, and the networking and storage capability of a data centre to be able to provide us with a continuous serialised production process.”
The Makino machine and service reliability was crucial to ADVATEK’s success.
“Our Makino’s run 24/7, lead by a small team, some of whom have been with the company 25 years,” said John MacDonald, Production Supervisor. “We only run one shift a day (Mon-Fri), and on weekends the machines are run unmanned. The finished parts can be picked up on Monday morning. The Makino machines and their reliability are a piece of mind for our production.”
Manufacturing medical components is an around-the-clock operation. Even ADVATEK’s older Makino machines can keep up with the newer Makino machines. Together they were able to manufacture over 400,000 medical housings over the past ten years without sacrificing quality. This demonstrates the reliability of Makino machines and shows how well these machines can handle a high volume of production while still maintaining the highest output quality.
The ADVATEK team is very passionate about Makino machines due to their precision and accuracy which are essential for even the most demanding jobs. Their technologies provide high-speed, high-performance spindles that deliver the highest repeatable metal-removal rates. Kevin Edmonds, ADVATEK’s Production Director and coowner, explains another important aspect.
“In order to be successful you have to have two major components in your day-to-day operation,” said Edmonds. “One is to have consistency in your processes and the right machine technology. The Makino F3 machine gave us exactly what we needed to successfully fulfil the needs to manufacture specialised medical industry components. And Headland Technology as our reliable partner in service and machine technology. Without these two components, it would be difficult for us to be where we are today.”
“The top machine tool suppliers all have similar products. What separates Headland Technology from the rest is their ongoing commitment to service excellence,” said Managing Director Gary McBean, in summing up what ADVATEK values most in the partnership with Headland. advatek.com.au headland.au
Volgren is innovating, driving a sustainable future.
In the intensely competitive world of manufacturing, innovation is essential. Accordingly, Australia’s largest bus body manufacturer Volgren has made its name with innovative, sustainable and efficient public transport solutions.
The company built its first bus in 1979 with the promise of creating a more reliable, comfortable and longer-lasting vehicle with lower operating costs than others then available.
Today, Volgren designs, manufactures and assembles public transport buses of all types across multiple technologies, including zero-emission vehicles. Thanks to its 400-strong manufacturing, operations and aftersales support teams across NSW, Victoria, Queensland and WA, its bus bodies are close to 90% locally produced and offer the lowest lifetime cost of any bus in Australia.
Since 2018 Volgren has delivered dozens of hybrid and electric buses to Australian operators and is now fast-tracking delivery of Australia’s first European hydrogen fuel cell buses.
Volgren’s E-bus, the Optimus E-Bus, is one of its class’s lightest zero-emission bus bodies and operates successfully in Melbourne, Sydney, Brisbane and Perth. The body has been effectively engineered to suit multiple electric chassis and complies with Australia’s highest safety and flammability standards for buses.
Although Volgren officially began trading in the 1970s, its story started in 1940s Dandenong, when local milk carrier George Grenda moved into buses. His business thrived as Dandenong grew, and by the 1970s, Grenda Bus Services was a hugely successful route bus and coach company. In 1977 Swedish vehicle manufacturer Volvo partnered with Grenda to create Volgren and introduced extruded aluminium, rather than steel, for bus body construction and the Swiss Co-Bolt system.
Leading global bus body manufacturer, Marcopolo SA, acquired full ownership of Volgren in 2017, strengthening Volgren’s local capability with its technology, buying power and international experience.
Volgren national purchasing manager Andrew Costello says Volgren is still one of only few Australian companies manufacturing bus bodies from aluminium, rather than steel, despite aluminium’s clear advantages.
“Most buses are still built from fully welded steel. Aluminium is much lighter, resistant to corrosion, and recyclable.
“Moreover, the lighter a bus is, the more people you can fit in the bus.” The CoBolt process is also critical to Volgren’s production; Andrew says this system uses bolted gusseted joints.
“This avoids the risk of continuous bus vibrations fracturing welds. Our system requires no welding and results in a much longer joint life. Our joints are locktightened with very little chance of anything loosening over time. For operators it means far superior reliability than a traditional steel bus and is one of the main reasons why we can offer a 15-year warranty on our buses’ aluminium structures.”
Quality, explains Andrew, is paramount in Volgren’s business. Volgren operates rigorous quality systems and builds quality into its products through its suppliers, logistics and production.
Capral has been Volgren’s principal aluminium supplier for at least 15 years and meets Volgren’s ethos of quality, local input and innovation, Andrew notes.
“We build buses and want our supplies priced at construction-type costs, but we also want an architectural look and finish to our products. Capral has always achieved both for us.”
The supply partnership continues to drive new value for both businesses; where Capral once purely supplied extrusions, it now also machines parts. This advance means Volgren’s teams can focus on faster assembly and minimising customer costs.
Capral’s size and capability are also crucial to Volgren, Andrew says.
“Our whole roof structure is a sheet with aluminium extrusion bows across the roof and main cant rails extending the entire
bus length. Capral is one of the few players in Australia with presses large enough to extrude our parts.”
Andrew says bus body manufacturers must tailor bodies to the requirements of individual bus chassis and operators.
“Our variation is big and requires a large engineering team.
“When Australia used to build cars, Ford would build a Falcon and a Territory here, and that would be it. Whereas we build the equivalent of a Territory, a Commodore, a Ferrari, an electric BYD and a Tesla all on the same production line.”
Even though Volgren’s ownership is now multinational, Andrew says the Volgren team remains family-focused, with experienced people providing a family-style influence.
“The teams here are always looking to improve themselves. They’re not too scared to ask if we can look at doing something better. It’s the way it’s always been at Volgren; we know what the operators are after and work hard to give them what they need.”
Andrew emphasises that Volgren is well placed for future success and to continue contributing to Australia’s environmental sustainability.
The Volgren team are currently exploring Capral’s LocAl™ Lower carbon aluminium offer to further reduce the environmental impact of their builds by reducing the embodied carbon in the Aluminium products they use.
“It’s great to be part of the biggest bus manufacturer in Australia, which is leading the way for zero-emission transport.” volgren.com.au capral.com.au
As part of Automated Solutions Australia’s (ASA) commitment to delivering tomorrows solutions today, ASA has been completing a lot of lab trials using a robotic solution for the application of Cerakote.
For those who aren’t familiar with this product, Cerakote is a thin ceramic coating that is applied as a resin and forms a 3D ceramic matrix as it cures. This makes it possible to protect surfaces that are not made of metal. The formulation of this technology makes it possible for the coating to withstand extremely high temperatures (sometimes as high as 1100 degrees Celsius) without altering its appearance. Once cured, the coating is a becomes very hard and extremely scratch and abrasive resistant.
A Cerakote coating also provides excellent protection against corrosion, thermal stress, and thermal barriers for applications that are sensitive to temperature changes. This type of coating continues to exhibit outstanding performance over an extended period of time. Because of this, Cerakote is ideal for use in defence and military applications as well as on exhausts, pistons and other components that will be exposed to high temperatures. Cerakote has been carefully engineered to provide maximum substrate protection and improved coating performance when compared to traditional powder coating and solvent or waterbased painting applications.
Once cured, products coated with Cerakote typically have a smooth, sleek finish. Although the application of Cerakote is traditionally a simple process, this does not mean it is easy. Dry spray is a common application mistake leaving a scratchy texture, similar to that of sandpaper which is often a result of insufficient solvent transfer during the spraying process. It is necessary to "Wet Out" the coating before beginning the application process in order to prevent any dry spray from occurring. On the other hand, because Cerakote is such a thin liquid, it is very difficult to apply to a surface without runs. Application requires greater control of the thickness when compared to other coatings, usually 8 – 25 microns.
Recently, Automated Solutions Australia (ASA) have been fielding more enquiries about the automation of the Cerakote application process. Automation allows digital flow rate control and consistency of applicator tip speed, as well as being able to program a constant gun-to-target distance. Using FANUC paint robot systems, ASA can far exceed the transfer efficiency and material utilization when compared to traditional spray guns and spray systems. Cerakote can be delivered to the robot in a more efficient manner thanks to in-arm process control. Because the FANUC robot is equipped with integrated fluid handling
capabilities, the substance may be blended to the appropriate proportions and delivered to the applicator in an effective manner. This means the coating process can be more tightly controlled and given the hefty price of Cerakote per litre, a real competitive advantage with minimal waste. Using a FANUC paint system to apply Cerakote means increased operational time. Robots rarely need breaks and when managed right, never have to stop to mix additional paint. The system is programmed to mix the exact amount of solvent to Cerakote ratio required for optimal performance. These systems provide results that are consistent and reproducible across parts with stability.
FANUC painting systems lower the risk of occupational health and safety hazards to the work force and provide increased protection for workers in potentially dangerous areas. These systems are designed to be intrinsically safe, which
means they may operate in potentially hazardous areas. This combined with a drop in emissions volumes of volatile organic compounds (VOC) are some of the benefits companies can experience with a FANUC painting system.
The reliable nature of robotic applications, means there is a decrease in the frequency of rework and repair which may have been caused by errors in manually applying the coating. FANUC paint robots have the ability to make on the fly adjustments to a variety of application parameters, resulting in improvements to film and aesthetic appearance. All of these benefits make automation of Cerakote a great investment. If you’re looking to automate your Cerakote application, call us today on 1800 ROBOTS (1800 762 687).
The whole range of FANUC paint robots are available on the ASA website: automatedsolutions.com.au
Precision meets miniature: NS Tool's innovations in micro machining.
Micro machining is a specialised process used to manufacture small parts with extreme precision and accuracy. NS Tool has gained popularity in the micro machining industry with a series of cutting tools designed specifically for micro machining applications.
With a focus on sub-Ø6mm endmills, they offer an impressive selection of high-quality endmills ranging in size from Ø6mm down to 10 microns! One of the key benefits of NS Tool is its ability to machine materials with high hardness, such as stainless steel, titanium, and hardened steel. The tool's advanced coating technology and design enable it to withstand the high temperatures and stresses associated with cutting these materials, resulting in precise and accurate machining.
Another benefit of NS Tool is their range of tools developed to have the ability to achieve extremely fine surface finishes, with surface roughness values as low as Ra 0.02µm. This makes it ideal for applications that require high-quality surface finishes, such as mold and die manufacturing, the medical industry, and the production of electronic components.
An Australian company, NH Micro is pushing the limits of micromachining. They focus on ultra precision manufacturing capable of producing parts with high levels of complexity and high precision requirements (below 0.5 µm!). They are dedicated to exploring and optimizing the techniques and technologies of precision machining.
With tiny tools, they are leading the way in complex and micro manufacturing.
NS Tool's precision and accuracy have made it a popular choice in the aerospace, medical, and electronics industries, where tight tolerances and high-quality finishes are essential.
livetools.com.au/pages/ns-tool nhmicro.com
Rigby Cooke Lawyers has been advising manufacturers on their commercial needs for decades. And, that’s why we are the ‘go-to’ legal advisors for AMTIL members and the manufacturing industry.
At Rigby Cooke Lawyers, we can assist with all your business legal needs and have the expertise to advise on the following:
> Commercial transactions
> Business structuring (companies, joint ventures and partnerships)
> Commercial contracts
> Employment and workplace relations
> Occupational health and safety
> Succession planning and family business
> Personal property securities law
> International trade (import and export)
> Intellectual property
> Privacy and data protection
> Property sales, purchases and leasing
> Planning and environment
> Building and construction
> Litigation and dispute resolution
> Insolvency, asset protection and reconstruction
> Tax
For more information on how we can assist you and our exclusive benefits for AMTIL members, please contact Julia Cameron, Lead Partner of our Manufacturing practice, on +61 3 9321 7807 or JCameron@rigbycooke.com.au.
AMT gets a look behind the success of Kuebler systems and finds out more about the monitors and sensors, central to their brand.
Kuebler is a leading global specialist for position and motion sensors (including encoders), slip rings and transmission technology, as well as for counters and process devices. Based in Villingen-Schwenningen, Germany, Kuebler now has a presence in 50 countries around the globe. The latest addition to the Kuebler subsidiaries is in Australia, located in southeast Melbourne. The company supplies products and solutions for industries such as elevator technology, drive technology, wind power, mobile automation as well as intralogistics and mechanical engineering. Part of the innovation strategy is also very intensive cooperation with universities and institutes.
More than 500 dedicated people are employed worldwide, the export share is 75%, and the turnover in the group was around 90m€ in 2022 (in 2023 it is planned to break the 100m€). In Germany, about 15% of the employees work in R&D. Additionally, Kuebler has set up an incubator team focused on digitalisation and Industry 4.0 solutions. Ten international subsidiaries, two production plants in Germany, one in Pune (India), an assembly in Charlotte NC (USA). This coupled with agencies in more than 50 countries, are all part of the spectrum of the growing global player today. Finally, an Engineering Solution Center has existed in Berlin for several years, especially for specific software, innovative magnetic sensor technology and customer-oriented applications.
“A pillar of success for Kuebler remains the close customer dialogue. Developing new things together and continuously improving the existing is the motto here.”
Kuebler has recently released a swathe of new products in the Measurement, Transmission and Evaluation ranges. According to Kuebler, this business field, which is still quite young, is developing very dynamically. A new portfolio of measuring wheel systems and further bearingless encoders with IlOT functions for preventive maintenance as well as the new slip-ring product family further expands their application solution offer.
Kuebler expects many influencing factors in 2023, making it somewhat difficult to plan for the year. Overall, Kuebler expects continued growth, despite still some partial material shortages, energy cost surcharges and increased raw material prices as influencing factors. At the same time, topics such as climate change and sustainability, as well as digitalisation are advancing, offering enormous development potential. Here, agility and speed of response will be important factors for success.
At the opening of the Australia distribution centre, AMT first asked Lothar Kuebler about the beginnings of the company. His father Fritz Kuebler constructed the world’s first continuously readable short time meters back in Germany in 1960. “My father was quite a genius engineer, I would say,” states Lothar. “He had good ideas with very much a technical focus. I put it down to his entrepreneurship, which made the company grow, starting with short time meters for relay measurement, then he started producing electromechanical counters for the various European markets.” By the time Lothar and his brother Gebhard started in the family business around 1996/1997, the focus was on pushing the range out internationally as they could see the future trend of automation. Sensors were more and more required for motion control, speed control in a lot of new industries as well. “This focus on technical understanding was combined with the quality product, which of course, as a German company, is a must,” Lothar said. “As a customer focused company, I think these were factors which kept pushing us.”
Lothar Kuebler lists the many industries where motion control, drives and motors are all crucial parts of the assembly cluster. Mining systems, both open cut and underground. The elevator industry requires encoders, sensors and motor controls for their drives. “We also now have a linear shaft copy system, and we’re also taking the next step of having an electronic overspeed governor possibility so that you don't need this mechanical overspeed requirement,” says Lothar. “There is now food processing, packaging and the logistics of moving multiple products quickly but precisely and safely into a sellable state. This is where encoders and slip rings operate to assist in the control of the movement of parcels of stock. Then there are the renewable energy industries of wind turbines and solar cells. Precision and monitoring are key to the successful generation of electricity. Monitoring this is key to the success of the whole sector.”
“That fitted quite nicely with our strategy,” explains Lothar. “About seven years ago, we hired a specialised engineering team out of Berlin to make bearing-less solutions, magnetic-based turbines, and software-based signal processors.
“These are very smart sensors we produce now. They give very precise information, but they can also give additional information, on vibrations, accelerations, and velocity information. This can be used, in an example of a windmill, to measure what's happening now. If there's a sudden gust wind coming and that's at the same
time, they must control the plate to optimise the blade. By having perfect signals, you can really enhance the performance of the wind turbine by a couple of percent,” adds Lothar. “If you calculate those over years, then this is a very good sensor, paid off immediately. This is real Industry 4.0 engineering. Data collection and analysing that data in real-time. Condition monitoring and protective maintenance.”
Nowadays there’s a lot of integration of Kuebler’s encoders inside for example, the gear motors. “Kuebler started this trend and they have made this magnetic-based bearing-less systems,” describes Lothar. “You use the bearing in the motor, which is already there. We include quite sophisticated magnetic analysing software so we can simulate all the magnetic fields during operations. Quite special technology. And if we get the data from our customers about these motors, we can integrate it and simulate how the gear motors are operating during their work. That's where this customisation is very important. On the engineering level, cooperation with our customers is most important.” Another area Kuebler is looking into is the logistics industry. Lothar Kuebler describes their ready solutions for this sector. “There are so many warehouses and airports being built, and these large warehouse solutions require automated guided vehicles. There you need to have integrated solutions. This is something we are working on because it's such a growing market. And we also don't need to invent everything new. We can take from our portfolio which is more and more like a Lego system that we can put things together quickly.”
“On the other side,” added Lothar, “Kuebler has quite a big engineering team with about 70 people now worldwide. And a lot of new products are also on the roadmap.”
The major advantage for Kuebler opening up a subsidiary here in Australia is for them to be closer to the customer, and with the addition of Australia, Kuebler now provides a global footprint bringing this support to fruition. Direct contact with the customer is
key to ensure we give them what they need from quick availability, local technical and logistical support and understanding the needs of the Australian market better.
“The Australian market can now take advantage of dealing directly with the manufacturer,” said Kuebler Australian Managing Director, Jason Bouyer. “This is whether it be from the standard portfolio or utilising the R&D department to develop solutions specific to the customer requirements, leading to an improved customer outcome regardless.”
Position measurement products from an array of encoders will continue to be relevant across major industries on mining, packaging, food and beverage, mobile automation and energy, however the supporting product for transmission of data signals and power through sliprings is an additional exciting solution offer. Again, having direct contact with the manufacturer can benefit in achieving the correct solution. kuebler.com/products kuebler.com/encoders kuebler.com/slip-rings kuebler.com/industries kuebler.com/iiot
components.
Agricultural equipment is constantly exposed to tough climate and weather. For this reason optimal paint preparation is essential for the equipment to hold up under such tough conditions. A customengineered continuous feed spinner hanger blast machine RHBD-K 22/27-HD, installed in a new factory of a globally active manufacturer, is making a significant contribution towards this goal. The shot blast machine is integrated into a fully automated manufacturing line. It allows the blast-cleaning of a variety of complex weldments, weighing up to two tons, prior to painting.
This Brazilian manufacturer supplies innovative agricultural machinery for a wide range of applications. For example, it is used for harvesting coffee beans and sugar cane as well as for seeding and cultivating all kinds of agricultural crops. The company is active in more than 100 countries. Reasons for this success are the excellent productivity and quality of the equipment as well as the continuous improvement of the manufacturing operation. It is not surprising that the new factory in Brazil is equipped with a fully automated, digitized manufacturing line. There, steel plates and profiles are cut, welded into complex constructions, shot blasted and painted in continuous flow operation. Based on the tailormade equipment concept, the technical implementation and the high equipment quality, the company had decided to purchase the continuous feed spinner hanger blast machine RHBD-K 22/27HD made by Rösler. The work pieces are transported through the shot blast machine by the power & free conveyor system of the manufacturing line. This required optimal coordination of the various interfaces in the manufacturing line. But thanks to the help by the colleagues at Rösler Brazil the whole project went very smoothly.
After the welding operation the components are transported through an inlet chamber into the actual blast chamber equipped with 12 Gamma 400G turbines, each with a drive power of 11 kW. These innovative Rösler high-performance turbines contain curved throwing blades in “Y” design. Compared to conventional turbines the special blade design with optimal curvature increases
the throwing speed significantly. This results not only in an up to 20 % higher blasting performance but also in significantly shorter cycle times.
Because of the enormous work piece diversity the shot blast machine was designed to handle welding assemblies with dimensions of up 10,000 x 2,000 x 2,500mm (LxWxH) and weights of maximum 2,000kg. Some of the weldments have thick walls and are very sturdy, whereas others have thin walls and are delicate. To account for these differences and to consistently achieve the required preparation grade of Sa 2,5 as well as the specified surface roughness values, the turbine RPM is controlled by frequency inverters. This ensures optimal paint adhesion and prevents warping of the thin-walled components. The variable turbine speed and the automatic control of the media flow allows precise adaptation of the blast-cleaning process to the different welding assemblies. Selection of the workpiece-specific shot blast programs is done at the master computer of the manufacturing line.
Behind the outlet chamber of the shot blast machine is a blast room that allows the manual touchup blasting of geometrically complex assemblies with undercuts and internal passages. Augers below the blast room floor transport the thrown blast media to the central media cleaning system. This eliminates the need for a separate media transport and cleaning system for the blast room.
The customer was also impressed by the wear-resistant design of the Rösler equipment. For example, the blast chamber is made from manganese steel and is protected by easily replaceable 10mm thick wear liners, also made from manganese steel. Another plus is the fact that both sides of the throwing blades can be used, which practically doubles their usable life. The throwing blades can be replaced with a quick-change system without having to take the turbine apart. rosler.com
What type of expenditure could be eligible?
Salaries & wages (including oncosts)
— Contractor or consultant costs
Materials used in trials, including freight costs
Depreciation of assets
Overhead costs attributable to R&D activities
Laser systems remove corrosion, grease, residue, and existing coatings from metal surfaces quickly, with less preparation and mess than traditional techniques.
Most manufacturers understand the value of pretreating metal surfaces of parts to remove corrosion, grease, residue, old coatings, or to roughen the surface of metals prior to coating. By ensuring the items are cleaned down to bare metal, manufacturers can avoid costly warranty issues that result when coatings peel, flake, bubble, or otherwise fail prematurely.
Unfortunately, the traditional techniques used for this purpose –such as sandblasting, dry ice blasting, and chemical stripping – are messy and require expensive consumables, as well as substantial time for preparation and cleanup. These methods are also drawing scrutiny from regulators like the EPA and OSHA since they can pose risks to the environment and applicators.
Today, a more effective alternative is utilizing industrial-grade, precision laser-based systems that can remove paint, contaminants, rust, and residues with a high-energy laser beam that leaves the substrate unaffected. Preparation and cleanup time are minimal, and the low-maintenance equipment can last decades.
According to Vincent Galiardi, owner of Galiardi Laser Clean, a surface cleaning operator based in St. Charles County, Missouri, many people are surprised to learn that clean technology lasers are the most cost-effective, efficient, and safest method of industrial surface preparation.
“Many people are unfamiliar with the use of lasers to pretreat metal surfaces,” says Galiardi. “When I do a demonstration, at first the people in attendance are skeptical. But after I use the laser to treat a small area, everyone starts talking and getting excited. By the end, when I let them try the equipment, everyone is having a good time and saying how great the laser works.”
Given its effectiveness pretreating metal surfaces, industrial laser systems are increasingly being used in manufacturing facilities. The systems can be integrated into automated inline processing lines, or technicians can use mobile handheld units. With significant advantages in safety and efficiency, laser cleaning is poised to disrupt the surface pre-treatment market across more sectors.
There are many applications in manufacturing that require pretreatment of metal surfaces prior to coating. To improve coating adhesion, residue, oil, or grease must be removed before coating application. In some cases, a manufacturer may seek to further enhance coating adhesion by roughening the surface.
When defective metal parts are produced, instead of discarding the product, manufacturers can strip the paint and re-coat the component.
To refurbish existing metal parts or recoat industrial infrastructure, removing the previous coating along with any corrosion is usually required to facilitate the new coating’s adhesion to the surface. To pretreat metal surfaces, sandblasting, dry ice blasting, or chemical stripping are traditionally used as industrial cleaning processes.
Abrasive sandblasting involves forcefully projecting a stream of abrasive particles onto a surface, usually with compressed air or steam. The silica sand used in abrasive blasting typically fractures into fine particles and becomes airborne, which can cause serious or fatal respiratory disease.
When workers inhale crystalline silica, the lung tissue reacts by developing fibrotic nodules and scarring around the trapped silica particles, causing a fibrotic lung condition called silicosis. Estimates indicate that more than one million US workers are at risk of
developing silicosis and that more than 100,000 of these workers are employed as sandblasters. In addition, particles are generated during abrasive blasting that further contribute to respiratory problems and other harmful health effects.
“When sand or any other media is used to knock off particles from a substrate, there is always a byproduct that has the potential to become airborne and inhaled,” says Galiardi. “Besides the sand, this could be the particles you’re removing – the coatings, plating, anodizing, corrosion, and even lead paint.”
“Industry has needed a cleaner, safer surface pre-treatment solution for a very long time,” adds Galiardi. “Sandblasting is inherently unsafe for operators. The silica glass used in sandblasting is toxic. An operator must wear a full HEPA suit when sandblasting to avoid breathing in particulates.”
Sandblasting also is time-consuming to clean up since the sand essentially scatters everywhere, even though it is usually considered a “fast” cleaning method.
With dry ice blasting, dry ice pellets are used as the abrasive. The challenge is that dry ice blasting is often not abrasive enough to sufficiently remove paint or corrosion from the surface of metals. Since dry ice is an expensive consumable, the costs can escalate when cleaning metal surfaces in higher volumes.
With chemical stripping, harsh, even toxic chemicals are used to strip metal-based objects of paint, rust, and other contaminants to bare metal. However, for operators, exposure to corrosive acids and noxious chemical fumes is inherently dangerous. The process can also be time-consuming to prepare the proper chemical bath, achieve the required level of cleaning, and dispose of the waste. In addition, disposing of toxic chemicals is costly and closely regulated by agencies like OSHA and the EPA.
Laser-based systems have significant advantages over these traditional methods, including ease of use in which an operator simply points and clicks a high-energy laser beam at the surface. The substrate is not affected by the laser, and the systems do not create any mess or byproducts. The approach is eco-friendly, energy-efficient, and completes the job in half the time of traditional methods when preparation and cleanup are considered.
“In our experience, laser cleaning is as fast at removing rust or old coatings as other methods, but without the same amount of cleanup,” said Galiardi. “When we treat a surface with lasers, any fumes or dislodged particulate is extracted into a HEPA filter and the job is done. There is no media [sand, dry ice, chemicals] to replenish or clean up.”
Galiardi Laser Clean uses laser systems made by Orlando, Floridabased Laser Photonics, a leading provider of patented industrial grade CleanTech® laser systems for cleaning and surface conditioning. The American-made systems function either as mobile standalone units or can be integrated into production lines.
The laser systems are available in portable and stationary models ranging from 50 to 3,000-watts (a 4,000-watt version is in development) with chamber sizes from 3’ x 3’ in size to 6’ x 12’. The systems can also be installed in manufacturing lines in cabinets or operated by a robotic arm.
Galiardi says that laser pre-treatment of metal surfaces can be used to streamline various manufacturing processes. Corrosion, for example, can begin to accumulate within a very short time on new parts, depending on the material and environmental conditions, and should be removed prior to coating.
For one major auto manufacturer, Galiardi Laser Clean was asked to remove rust from conveying system components used to transport cars through the manufacturing process. The components were corroded due to being left outside during a 6-month delay in the project. When it was time to install the items, the provider wanted to first treat the surfaces and return the components to a “like new” appearance.
In another example, Galiardi was asked to remove rust from over 400 transmissions in a couple of days. The laser systems are particularly effective when reaching into tight spaces that are hard to reach by hand. By masking the area to protect vulnerable parts, the laser can be applied without affecting the rest of the assembled product.
“No other parts [of the transmission] had to be removed and nothing had to be cleaned afterwards,” he says. Galiardi’s company also utilized the laser system to remove cleaning oils from truck chassis. “We used the laser to remove the oil right before painting so it was a bare metal object going with nothing on it that would affect the coating,” he says.
Industrial plants that need to recoat existing metal structures also need to remove rust before painting. According to Galiardi, he removed corrosion from a very large storage tank using the CleanTech laser system in about half the time of the alternative being considered, an abrasive disc grinder.
“Disc grinders basically just chip off [the rust] and it becomes airborne and makes a mess. Grinders can also be dangerous because sparks or debris can shoot off the wheel or catch an article of clothing,” he says. With clean laser technology, there is now an environmentally friendly alternative to abrasive blasting and chemical stripping for surface pretreatment. The approach is safer for operators and highly adaptable to a wide range of manufacturing and industrial applications.
“As people become more aware of laser-based systems and compare them to traditional methods, they need to factor in prep and cleanup time, which can significantly impact project cost. When the improved operator safety, equipment longevity, and lower maintenance of laser systems are also considered, the clean laser technology has a much higher ROI,” says Galiardi. The longevity of low-maintenance laser systems further adds to their value, increasing ROI, and making replacement unnecessary for decades.
“CleanTech laser systems can last for 50,000 to 100,000 hours. That’s many decades working eight-hour days. After purchase, there’s virtually no maintenance necessary,” concludes Galiardi. laserphotonics.com
Manufacturers lift investment in tech-driven efficiencies and productivity.
Manufacturers are seasoned experts when it comes to navigating disruption. After all, despite the swings in demand, talent shortages, rising costs and supply chain issues that have tested manufacturers in recent years, the sector remains resilient and robust. In fact, manufacturers are more optimistic about their prospects than they were a year ago. The newly released CommBank Manufacturing Insights report shows that most manufacturing decision-makers forecast higher revenues, production volumes, and profits in the next 12 months.
The research also highlights broadly recognised challenges. The vast majority expect operating costs to increase further, and persistent supply chain issues are constraining capacity, cash flow and growth. As a result of these objectives and hurdles, manufacturers are increasing investment in making their businesses leaner, more productive, and more sustainable. This includes a large majority planning to increase investment in new technologies—the highestranked strategic priority for the year ahead.
CommBank’s Head of Manufacturing, Maria Christina says manufacturers are deploying digital solutions to streamline processes, strengthen customer experiences, and tackle supply chain issues.
“In the current operating and economic environment, we’re seeing a sharper focus on efficiency and creating capacity to support higher production volumes. Technology has a significant role to play, particularly amid ongoing talent shortages and to optimise supply chain management,” Maria says.
According to CommBank’s previous Manufacturing Insights Report released in early 2022, 72% of manufacturers had accelerated their digital transformation during the pandemic. That built on the long-standing focus on technology in the sector that’s set to step up again. Over the next 12 months, 87% of decision-makers are expecting to increase technology budgets. One in two are planning for technology spending to rise significantly, and 37% expect a moderate increase.
Manufacturers are also earmarking investment across a diverse range of technologies, with the top areas characterised by their potential to aid operational efficiency, collaboration and engagement with customers and supply chain partners.
This includes just over one in three investing or upgrading technologies related to manufacturing and process controls, followed by implementing cloud-based applications among 28%.
The biggest annual mover is expected investment into improving the customer experience and new digital channels, jumping from 18% of manufacturers in 2022 to 27% in 2023. That is now on par with digital supply chain and logistics solutions, with 27% also intending to lift budgets in that area.
Continuing a sustained trend in the uptake of innovative technologies across the industry, many manufacturers are planning further adoption of emerging digital solutions in the next two years. Efficiency gains are the top driver, as well as meeting corporate social responsibility objectives and enhancing customer utility. Looking at the fastest-growing areas also confirms a focus on better systems integration and productivity. Over the next two years, the most widely adopted technologies are set to be next-generation
enterprise resource planning (ERP) systems and autonomous systems, machines, or vehicles (both to be adopted by 31%).
Many manufacturers are also targeting artificial intelligence and machine learning (30%) and advanced analytics capabilities (29%). Rounding out the top five is the 28% intending to introduce nanotechnology into their operations in the next two years.
Maria says that by 2025 many innovative technologies, from 3D printing to blockchain and digital twins, will be commonplace. However, given data is underpinning their functionality, cyber security vigilance is required. “The research shows that the most widespread process to mitigate cyber threats is a rigorous access and password policy, and that’s only in place among 36% of manufacturers. Far fewer regularly update their systems or conduct training for their teams, which are cornerstone activities often recommended by cyber experts,” Maria says.
“The incidence of breaches, frauds and scams is only rising, and manufacturers should consider establishing processes and policies and ensuring they are regularly updated and that teams are aware and equipped.” commbank.com.au
On the 9th of May 2023, the Australian Federal Treasurer delivered the Australian Federal Budget for 2023-24. Below is a summary of the significant measures announced in relation to manufacturing and trade.
The government will support the development of the Australian critical minerals sector through a package of international commercial engagement and project facilitation. The measure is estimated to cost $80.5m over the forward estimates and will be offset through redirecting funds from other DISER portfolio program. Industry Growth Program (IGP) and Entrepreneurs’ Programme
The government will retire the Entrepreneurs’ Programme and replace it with a new IGP. Administered by the Department of Industry, Science and Resources, it will employ commercialisation advisers to support the growth of small and medium business in areas of strategic policy focus. The intention is to get those businesses ready for participation in the National Reconstruction Fund. Grants will be available to businesses participating in the IGP.
The government will provide $2bn to accelerate development of Australia’s hydrogen industry, ‘catalyse’ clean energy industries, and help Australia connect to new global hydrogen supply chains.
The government will allocate $1.3bn over five years from 2022–23 from $1.9bn provided in the 2022–23 October Budget to support the decarbonisation of existing industries, develop new clean energy industries and support sovereign manufacturing capacity essential to the energy transition.
Resourcing for the Department of Foreign Affairs and Trade (DFAT)
The government has committed:
• $80m over four years to enhance the strategic capability of the DFAT;
• $18.5m in 2023–24 for border agencies to undertake design and planning work for operations; and
• almost $2bn on improving relations with Pacific Island nations (on top of an extra $900m in Pacific aid announced in the October budget). This will include $1.4bn over the next for years to expand security infrastructure and criminal justice cooperation in the Pacific, as well as an increase in the numbers of Pacific islanders migrating to Australia.
The government will provide $210m over four years from 2023–24 to expand the EMIIF from $40m to $250m.
The EMIIF will continue to provide financing for small and medium enterprises operating in the Indo-Pacific and support the mobilisation of private and multilateral finance for development outcomes, including women’s economic empowerment and climate action. However, the government has elected to cut the Export Markets Development Grants Scheme (EMDG) by $61m to $554m over the forward estimate period which will disappoint those who have used and intended the use the EMDG.
The government will provide $31.9m over four years from 2023–24 to deliver technical assistance and capacity building support to Indo-Pacific nations to participate in the IPEF.
The IPEF is a regional arrangement with Indo-Pacific members to build cooperation and economic integration in the Indo-Pacific region. The arrangement does not reduce tariffs or enhance market access outcomes but works on four main ‘pillars’ including facilitating trade and eliminate corruption
We also understand that the federal government will continue to provide funding and resources to support the implementation of the Australia-United Kingdom Free Trade Agreement (AUKFTA), which is due to come into effect on 31 May 2023.
The 2023–24 Budget estimates also continue to include provision for the Australia European Union Free Trade Agreement, which has not yet been finalised as negotiations with our European partners are ongoing.
The government will provide an additional $23.8m in 2023–24 to continue initiatives to modernise and improve Australia’s international trade system, including delivering the simplified trade system reforms and continuation of the Trade Information Service.
Funding will be extended for the National Centre for Asia Capability (AsiaLink Business), to develop an Asia capable workforce and grow business in Asia. This measure will cost $14.7m over the forward estimates.
The government will provide $5.6m over two years commencing from 2022–23 to establish a panel to undertake an independent assessment and consultation process to inform the phase out of live sheep exports by sea.
The government has committed $8m over four years from 202324 to establish an Anti-slavery Commissioner. The Commissioner will work across government, industry and civil society to support compliance with the Modern Slavery Act 2018 (Cth), improve transparency in supply chains, and help address modern slavery in Australia and abroad.
If you would like to discuss the announced manufacturing and trade measures in greater detail, please contact our Customs & Trade team at Rigby Cooke. rigbycooke.com.au/expertise/customs-trade/
Cash management forecasting is the key to a sustainable business.
Jeffrey Luckins, a Director in the Audit & Assurance Division at William Buck, gives his guidance.Failure to properly manage cash flows is the key reason for business liquidations and indeed within the first five years, most businesses will indeed cease to exist.
Speaking as a company auditor, one of the key procedures we perform to conclude our opinion on financial reports and address the going concern basis is devoted to determining whether the company can pay their debts as and when they fall due, which is a key solvency requirement for businesses looking forward one year ahead. Indeed, we take the forecast cash flows and we flex them to address locked-in commitments, potential (new) sources of cash inflows and any other potential movements of cash over the next year. We want to know in a worst-case scenario, how it is possible for the business to survive? All business owners should adopt the same philosophy that we do to survive and to thrive.
Surprisingly, our observations are that cash flow management has a low priority in businesses or where it is implemented, the quality, timing and usefulness of the reporting is negligible at best.
Here’s the problem, forecasting is an inexact science and even when it is conducted, the quality of information supporting assumptions in the modelling can be weak or inconsistent with reality where insufficient research and due diligence is conducted. The result being that businesses owners place low reliance and faith in forecasting, preferring to address cash management issues on an ad hoc as needs or weekly basis. Your first goal should be determining the going concern basis is supportable to enable the business to survive in the short-term (i.e., the next year). This exercise may lead you to increase banking facilities, inject new equity, factor trade receivables, reduce short-term commitments or realise assets to enable sufficient working capital to be employed in the business.
Medium term thinking should be about investing in the business to build its critical mass and profitability making a stronger business which is resilient to short-term term challenges. This forecasting may enable you to focus upon proactively implementing incentives and promotions which build a consistent loyal client base, improved decision-making around decisions to replace equipment or indeed to extend the life of existing equipment, acquiring a new business, negotiating with suppliers, and refinancing or communicating with your financiers.
There is now more choice than ever for cashflow forecasting tools. Some software programs appear quite impressive in terms of their visual outputs however the pros and cons of each solution can be difficult to weigh up. Many software tools have limitations, so it is important to ask the right questions before buying. For example, some forecasting software does not interface with popular accounting systems or exports only hardcoded numbers to other programs such as Microsoft Excel.
Like other software programs, Microsoft Excel has limitations and potential issues when it comes to using it as your key forecasting tool. These issues include the risk of accidental errors and reusing templates that are no longer fit for purpose. However, the risk of errors can be minimised through well designed spreadsheets with the appropriate checks and balances. Excel is still probably one of the best options for small-to-medium business in the following cases:
• Deciding on whether to finance a specific project. Starting a new product line or taking on a new contract that requires investment.
• Preparing for an acquisition. When preparing for an acquisition it is important to understand the cashflows of the target business to determine an appropriate offer price and to understand the combined value of your business and the target by modelling expected synergies.
• Preparing for sale or a partial divestment. As the value of a business is based on its future cashflows, both the potential buyers and you will want to see and understand the forecast cashflows to determine an appropriate price.
• Deciding whether to replace equipment or extend the life of existing equipment. Both scenarios can be modelled out over a specific period and compared based on net present value (NPV).
• Valuing your business. Forecast cash inflows and outflows are a key input for a valuation based on the discounted cashflows (DCF) method of valuation.
• Simple monthly, quarterly, or yearly forecasting. Spreadsheets are very useful for setting up forecasting at regular intervals regardless of what interval you choose. The chosen intervals can then be easily rolled up into a yearly overview.
Once a forecast is prepared in Excel, different scenarios can be built in to allow the end user to see and compare the result of these scenarios in the one table. One scenario may include what would happen to the profit and cashflow if the sales volume of a product line increased by say 10%.
The more complex the forecasting becomes due to multiple locations, business units, foreign locations and currencies, and high levels of assumptions or sensitivities, the more it becomes apparent to implement a dedicated forecasting software solution.
Failure is not an option for forecasting cash flows; consider outsourcing this task if you lack the in-house skills to develop the modelling and interpret the results. Your survival as a business is on the line and assuming you have covered this risk, the opportunity to build your business and maximise profitability becomes the key objective. Whichever way you consider it, cash management forecasting is not negotiable for your business.
Jeffrey Luckins is a Director in the Audit & Assurance Division at William Buck – a leading firm of accountants and advisors. williambuck.com
Maybe we should have filed for that patent a little earlier? BRM Principal Patent Attorney Ben Mott navigates that vexxed question.
Australian Manufacturing Week is the "ONE event that showcases the latest innovations, technologies and equipment in the advanced manufacturing sector" but of course you know that, you were there showing your innovations. And you can't believe how well it went! Customers swarmed about your display and you're looking forward to taking a deep breath and getting a return on your R&D. But will you get that return? How long before competitors release their versions of your product and you’re back to competing on price? Perhaps you wish you had invested in Intellectual Property? Well, it may not be too late.
Australia, New Zealand, the US, Canada and Japan have 12-month grace periods that allow you to patent after you have gone public with your invention
These grace periods excuse information published by you (e.g. published on a website or by showing a product) in the 12 months prior to filing a suitable patent application. The grace periods are useful if you publish prematurely or perhaps simply change your mind about patenting after you publish.
Whilst they have their uses, it's best not to rely on the grace periods if you don't have to. Grace periods are not available in most countries and won't help if someone else goes public with relevant information before you file your initial patent application.
What good are patents in Australia, New Zealand, the US, Canada and Japan if your competitors manufacture elsewhere?
Patents aren't just about making. Rather, patents give you the right to stop others doing a long list of things (such as using, importing and/or selling), e.g. the Australian legislation provides that:
"a patent gives the patentee the exclusive rights, during the term of the patent, to exploit the invention and to authorise another person to exploit the invention" and
"exploit, in relation to an invention, includes:
(a) where the invention is a product—make, hire, sell or otherwise dispose of the product, offer to make, sell, hire or otherwise dispose of it, use or import it, or keep it for the purpose of doing any of those things; or
(b) where the invention is a method or process—use the method or process or do any act mentioned in paragraph (a) in respect of a product resulting from such use".
So:
• an Australian patent that covers a product can be used to stop others importing, regardless of where the product is made; and
• an Australian patent that covers a method can be used to stop others importing products made using a version of the method, regardless of where the method is performed. … but the competitors will just change it by 10% Rules of thumb such as a “10% change avoids patent infringement” are myths. Some patents are easily worked around whereas others make it impossible to produce a commercially acceptable alternative.
How close others can get to your patented invention depends on:
• the point(s) of difference between your invention and what was publicly known before your first patent application; and
• how well the wording of your patent captures those points of difference.
The quality of the wording has a lot to do with the skill of your patent attorney. It also has a lot to do with what you know about the relevant publicly-known technologies when preparing the initial patent application. Searching for relevant technologies is always a good first step towards patent protection.
Searching often leads to better patents and/or lower overall costs
A search might reveal that your invention is not new and therefore is not patentable. That would be disappointing, but it would also be a cheap way to get the bad news.
Searches often reveal technologies that are similar but not the same as the invention. These are valuable search results. It may still be possible to secure valid patent protection focused on the key points of difference but, because you and your attorney have a better idea of what you're aiming for, you can put better wording around the points of difference while you still have complete freedom to choose your wording.
In contrast, if you file the patent application without searching, you may be faced with similar search result in the years to come when they are located by patent examiners. Then you'll have the examiners' objections to deal with (and the associated cost) and will have less freedom to choose your wording.
Registering a design is usually inexpensive and straightforward, but a design registration is not a "poor man's patent". It's a different thing that provides different rights. Australian design registrations cover products that have a "substantially similar" overall look. Imitators can copy functional details without infringing so long as they make cosmetic changes.
Australian copyright is granted automatically when an original work is created. It doesn't cost you anything and you don't have to do anything to get it. Great! What's not to like? Unfortunately, for manufacturers and equipment suppliers, there's plenty not to like – generally speaking, Australian copyright does not protect threedimensional products produced in a manufacturing context.
brmpatentattorneys.com.au
Satisfaction surveys have become an integral part of the business landscape, providing organisations with valuable insights into customer experiences and overall satisfaction. These surveys offer a structured method for gathering feedback, enabling companies to understand their customers better, identify areas for improvement, and make informed decisions to enhance their products or services. In this article, we will delve into the significance of satisfaction surveys and explore their key benefits.
Satisfaction surveys serve as a powerful tool for measuring customer satisfaction levels. By collecting data directly from customers, organisations gain insights into their perceptions, preferences, and expectations. The surveys typically consist of a series of questions that assess various aspects of the customer experience, such as product quality, customer service, ease of use, and overall satisfaction. Through these surveys, companies can gauge how well they are meeting customer needs and identify any gaps or areas for improvement.
One of the primary advantages of satisfaction surveys is their ability to provide actionable feedback. By analysing survey responses, companies can identify specific issues or pain points that customers may be facing. This feedback can then be used to drive improvements in products, services, or processes, ultimately leading to enhanced customer satisfaction and loyalty. For instance, if a significant number of respondents express dissatisfaction with a particular feature of a product, the company can prioritise addressing that issue in future iterations or updates. Surveys also play a crucial role in customer retention. When customers feel their opinions are valued and their feedback is taken into account, they are more likely to develop a sense of loyalty towards the brand. By regularly soliciting feedback through surveys, companies can foster a customer-centric culture and demonstrate their commitment to continuous improvement. This, in turn, can help build long-term relationships with customers and reduce churn rates.
Moreover, satisfaction surveys enable benchmarking and performance tracking. By consistently measuring satisfaction levels over time, organisations can track their progress and compare their performance against industry standards or competitors. This benchmarking allows businesses to identify areas where they excel and areas where they may lag behind. It helps set targets for improvement and provides a basis for evaluating the effectiveness of any implemented changes.
Another benefit of satisfaction surveys lies in their ability to uncover hidden insights. Sometimes, customers may not proactively express their concerns or suggestions unless prompted. Surveys provide a platform for customers to voice their opinions, share their experiences, and provide valuable suggestions for improvement. These insights may reveal untapped opportunities, identify emerging trends, or shed light on unmet needs, enabling companies to stay ahead of the competition and make data-driven decisions.
However, it's important to design surveys carefully to ensure their effectiveness. Surveys should have clear objectives, concise and relevant questions, and a user-friendly format. Additionally, organisations must consider the timing and frequency of surveys, as excessive or poorly timed requests for feedback can lead to survey fatigue and diminished response rates.
Satisfaction surveys are invaluable tools for organisations seeking to understand and improve customer satisfaction. By gathering feedback directly from customers, businesses can gain actionable insights, drive improvements, enhance customer loyalty, and track their performance over time. As companies strive to deliver exceptional customer experiences, satisfaction surveys provide a structured and systematic approach to gather and utilise customer feedback effectively.
We are presently undertaking our own survey of exhibitors at the recent Australian Manufacturing Week exhibition to help us strive for an even better show in Sydney for 2024. australianmanufacturingweek.com.au
Here are the AMTIL people without their capes on.
Many people were asking during the show how many people we had at the AMTIL office to prepare for the Australian Manufacturing Week in Melbourne this year. Well, here they are. Eleven of the 12 people we have on staff. Our accountant wasn’t there that day. A show like this takes more than a year to prepare. All the details about the venues, design, sales, legals, risk assessments and insurances.
Services Manager; Julie Lovemore – Communications; Paul Hellard – Editorial; Shane Infanti – CEO; Nicholas Raftopoulos – Publication Sales; George Joshua – Marketing; Franco Schena – Design; Kim Banks – Head of Events; Dea Stavar – Marketing & Events Coordinator. [Not present: Koulla Nicolaou – Finance.]
We are all so happy to see everyone here making our show so amazing. Thank you for everyone who made the AMW2023 such a success.
A number of AMTIL members were visited over the last few weeks, and presented with TEN YEAR plaques, celebrating their memberships. an in-house service division with CNC grinding machines and state of the art PVD coating facility, and they also have a tool management division which provides process planning, stock control, logistics, application support, tool maintenance and process optimisation. guhring.com.au
One facility AMTIL visited to present the ten-year award was Guhring Australia in Melbourne. Guhring Australia was established in 1989, slowly growing into one of Australia’s leading suppliers of precision cutting tools. Guhring has a trade department which imports and distributes the wide range of precision cutting tools from Germany. They have
AMTIL would like to welcome the following companies who have signed up as new members of our association.
ABSS
18 Beckett Avenue
EAST KEILOR, VIC 3033 abss.net.au
AUSTRALIA WIDE ENGINEERING
241 Blackburn Road
MOUNT WAVERLEY, VIC 3149 australiawide.com.au
AXELENT AUSTRALIA
Unit 5-6 34-40 Bennet Avenue MELROSE PARK, SA 5039 axelent.com.au
BRUCE TOWNS ENGINEERING
2-6 Venture Way
BRAESIDE, VIC 3195 brucetownsengineering.com.au
DUROLENZ
15-17 Rosella Street
FRANKSTON, VIC 3199 durolenz.com.au
KUEBLER
21-22 George Street
SANDRINGHAM, VIC 3191 kuebler.com
LINEAR TECHNIK PTY LTD
54-58 Arkwright Drive DANDENONG SOUTH, VIC 3175 lineartechnik.com.au
MAXILOC INDUSTRIAL PTY LTD
14A Sir Laurence Drive
SEAFORD, VIC 3198 maxiloc.com.au
NORMAN G CLARK (A/ASIA) PTY LTD
44 Kylta Road
HEIDELBERG WEST, VIC 3081 ngclark.com.au
NOVASYS GROUP PTY LTD Factory 3, 14 Stephenson Road BAYSWATER NORTH, VIC 3153 novasys.com.au
PIXELSTORM
132 Cremorne Street RICHMOND, VIC 3121 pixelstorm.com.au
Two super coaches of the AFL leave their posts mid-season as the pressure builds to be competitve in the hunt for the ulitmate prize – wishing both Clarkson and Hardwick all the best moving forward. Football wise, we see the mighty Pies still playing exciting football in front of massive crowds – the AFL are rubbing their hands as the brand has never been stronger which ulitmately means more 'cashola' at HQ. The Blues are woeful, the Swans pretty disappointing and Hinkley has seen his team bounce back from a poor start of the season and now eyeing off a top four position. There's a log-jam mid table that will sort itself post bye – who'll be in the top 8 will be anyone's guess. Kangas and Eagles are firmly ensconced at the bottom and described as 'live kills' to anyone who plays them! Till next time… Sanchez
ROUN D 11
11 CraBee1 76 (222)
PROLIM TECHNOLOGIES
16/94-102 Keys Road
MOORABBIN, VIC 3189 prolim.com
2 Shane Infanti 71 (378)
3 Porsche Man 71 (384)
4 Bricky P 70 (288)
5 M. Bontempelli 70 (290)
6 Mottdiggitydog 69 (293)
7 Butcher Bird 69 (298)
8 Pmart9 69 (327)
LASTEK PTY LTD
10 Reid Street
THEBARTON, VIC 5031
lastek.com.au
RITTAL PTY LTD
3 Worth Street CHULLORA, NSW 2190 rittal.com.au
9 Saints21-23 69 (328)
10 MrsBoonzy 69 (371)
Due to the ongoing Coronavirus pandemic, many industry events world-wide have been postponed, rescheduled or cancelled. Readers are advised to check with all event organisers for the latest information. For the latest international travel advice, please visit health. gov.au/health-topics/novel-coronavirus-2019-ncov – For more events, please visit amtil.com.au/events
INTERNATIONAL
WIN EURASIA
TURKEY, Istanbul
7-10 June 2023
win-eurasia.com/tr
DRONE & UNMANNED AVIATION 2023 CONFERENCE
SOUTH AFRICA, Johannesburg
1-2 June 2023
droneconference.co.za
METEC
GERMANY, Dusseldorf
12-16 June 2023
metec.de
THERMPROCESS
GERMANY, Dusseldorf
12-16 June 2023
thermprocess.de
NEWCAST
GERMANY, Dusseldorf
12-16 June 2023
newcast.de
MESSE STUTTGART
GERMANY, Stuttgart
13-16 June 2023
messe-stuttgart.de
M-TECH
JAPAN, Tokyo
21-23 June 2023
manufacturing-world.jp
MANUFACTURING EXPO
THAILAND, Bangkok
21-24 June 2023
manufacturing-expo.com
MTA VIETNAM
VIETNAM, Ho Chi Minh
4-7 July 2023
mtavietnam.com
ALUMINIUM CHINA
CHINA, Shanghai
5-7 July 2023
aluminiumchina.com
VME
VIETNAM, Hanoi
9-11 August 2023
vme-expo.com
LASER TAIWAN
TAIWAN, Taipei City
23-26 August 2023
chanchao.com.tw/laserexpo
FABTECH CHICAGO
USA, Chicago
11-14 September 2023
www.fabtechexpo.com/
SCHWEISSEN & SCHNEIDEN ESSEN
GERMANY, Rhine-Westphalia
11-15 Sept 2023 schweissen-schneiden.com/joining-cuttingsurfacing/
EMO
GERMANY, Hannover
18-23 September 2023 emo-hannover.de
WORLD AVIATION FESTIVAL
LISBON, Portugal
27-28 September 2023 terrapinn.com/conference/aviation-festival/
CMTS
CANADA, Toronto
25-28 September 2023 cmts.ca
MEDICAL FAIR BRAZIL
BRAZIL, Sao Paulo
26-28 September 2023 medicalfairbrasil.com.br
METALEX
VIETNAM, Ho Chi Minh
4-6 October 2023 metalexvietnam.com
3D PRINT CONGRESS & EXHIBITION
FRANCE, Paris
11-12 October 2023
3dprint-exhibition-paris.com
CAMX
USA, Atlanta
30 October-3 November 2023 thecamx.org
WESTEC USA, California
7-9 November 2023 westeconline.com
MACTECH
EGYPT, Cairo
9-12 November 2023
mactech-eg.com/
PLAST IMAGEN
MEXICO, Mexico City
12-18 November 2023
plastimagen.com.mx/en
METAL MADRID
SPAIN, Madrid
15-16 November 2023
MetalMadrid-2023
METALEX
THAILAND, Bangkok
22-25 November 2023
metalex.co.th/
MANUFACTURING INDONESIA
INDONESIA, Jakarta
6-9 December 2023
manufacturingindonesia.com
SEMICON
JAPAN, Tokyo
13-15 December 2023
semiconjapan.org
STEELFAB
UAE, Sharjah
8-11 January 2024
steelfabme.com
EUROGUSS
GERMANY, Nurnberg
16-18 January 2024
euroguss.de/en
IMTEX FORMING
INDIA, Bangalore
19-23 January 2024
www.imtex.in/
ASIAMOLD
CHINA,Guangzhou
4-6 March 2024
https://asiamold-china.cn.messefrankfurt. com/guangzhou/en.html
MMMM
INDIA, New Delhi
29-31 August 2024
https://mmmm-expo.com/en-GB
CONVENTION & EXHIBITION CENTRE
23-26 JULY 2023
Food and beverage industry in the AsiaPacific region – the latest products and ideas for the industry, including food production and technologies to produce beverages.
foodproexh.com
CEMAT SYDNEY OLYMPIC PARK
25-27 JULY 2023
Experience, first-hand, the range of solutions and technology setting the standards and future direction of logistics and warehousing in the Asia Pacific.
Cemat.com.au
AUSTRALIAN WASTE & RECYCLING EXPO
ICC SYDNEY
25-27 JULY 2023
The premier business event for the waste, recycling and resource recovery sector, AWRE is where solutions towards a cleaner, more sustainable future starts. Full circle innovative products and sustainable solutions to collect, process and recycle waste more smartly. Future critical areas include Machinery & Equipment, Software & Services, Bins, Vehicles, Food & Organics and more awre.com.au
IMARC
ICC SYDNEY
31ST OCT – 2ND NOV 2023
The International Mining and Resources Conference (IMARC) is where the mining industry come together, delivering ideas, inspiration and serving as a meeting ground for industry. From ground-breaking technology, world-class content, to a vivid showcase of all the elements that make the mining industry great. www.imarcglobal.com/
PERTH EXHIBITION CENTRE
11-12 OCTOBER 2023
As technology accelerates, it has never been more important for mining companies to connect with suppliers. WA Mining’s exhibition will showcase the latest technical and digital innovations across the entire mining value chain. Meet and do business with leading industry suppliers who are advancing the mining industry in Western Australia. waminingexpo.com.au
WASTE EXPO AUSTRALIA
MELBOURNE CONVENTION & EXHIBITION CENTRE
25-26 OCTOBER 2023
Waste Expo Australia is the country's largest gathering of waste management and resource recovery professionals, which brings together leading solution providers in the waste management, recycling, resource recovery and sustainability sectors. wasteexpoaustralia.com.au/
AUSBIOTECH
BRISBANE, QUEENSLAND
1-3 NOVEMBER 2023
Biotechnology Industry Forum in Australia. AusBiotech is dedicated to the development, growth and prosperity of the Australian Biotechnology Industry. ausbiotech.org/conference-information
AUSRAIL
ICC SYDNEY
13–16 NOVEMBER 2023
AusRAIL Plus has been a highlight on the rail industry calendar and 2023 is set to be bigger than ever as we welcome rail leaders from Australia, New Zealand and the world to discuss the achievements, opportunities and emerging trends in the industry. ausrail.com/
Nicholas Raftopoulos: 0431 753 381
to have a non-obligatory chat on how we can help.
A ‘letter of invitation’ from the Comptroller-General was a bombshell to the entire manufacturing industry.
Ileft Canberra, returning to Melbourne to begin the hectic job of preparing a “Case for an Australian Car”, which I would submit personally to the top executives of General Motors. It would be a selling job, I knew, and a tough one.
Chifley and the Government didn’t waste any time either. Less than three weeks after my talk with Chifley, J.J.Kennedy, ComptrollerGeneral of Trade and Customs, sent a “letter of invitation” to the managing directors of all firms engaged in car assembly and
manufacture, or likely to be interested in such work, in which he called on them to submit proposals to the Government for the manufacture of complete motor vehicles in Australia. This letter was a bombshell to the motor industry. It came so soon after my visit to Chifley that many people, even those in my own organisation, were sure that I had instigated it. I’m sure some of my ‘friends’ even hinted to General Motors in New York that I had drafted the letter. This is why it was a bombshell:
Dear Sir,
5th October, 1944
I have no doubt that you are aware of the desire of the Government to establish the motor vehicle manufacturing industry in Australia including the manufacture of the chassis and the engine.
Following consideration by a special Sub-Committee of Ministers of various major aspects of the matter including a re- examination of measures proposed by the previous Government to achieve a similar objective, Full Cabinet recently approved of recommendations of the special Sub-Committee in the following terms:
1. The Motor Vehicle Agreement be repealed.
2. The Motor Engine Bounty Act be repealed.
3. All interested parties be invited to submit proposals for the consideration of the Government.
4. When considering the proposals received, the question of utilising Government factories for the production of component parts on a scale adequate for the maintenance of the factories as efficient units for future defence production should be examined.
5. If satisfactory proposals are not received as a result of the invitation to interested parties, the Government should set up a Corporation to manufacture a complete car.
6. With a view to decentralisation financial assistance be given to enable freight equalisation to be effected.
The purpose of this letter is to inform you (as one who has previously shown interest in this matter) of the objectives and most recent decision of the Government, and to ascertain whether you are interested in the matter of submitting manufacturing proposals to the Government for consideration. In the latter event, I am directed to invite you to submit proposals to me in such detail as you find it possible or convenient. All information will be treated as strictly confidential and will be submitted to the Cabinet by my Minister. I should welcome an early acknowledgement of this letter together with an indication of whether you contemplate the submission of proposals at a later date.
Yours faithfully,
J.J. KENNEDY Comptroller-General.The sentence which caused the biggest stir was, of course, the one which read: “If satisfactory proposals are not received as a result of the invitation to interested parties, the Government should set up a Corporation to manufacture a complete car.” That was interpreted as a threat aimed directly at everyone in the motor industry. I, for one, was certain it was no idle threat. Chifley was so determined that an Australian car should be made that he would most certainly manufacture cars as a national project if the industry did not take up his request. Now, with the game on–with all our competitors taking the matter seriously for the first time–it was essential that my recommendations to General Motors should be accepted, and that I should present the strongest possible case.
I had a very strong feeling that if no concern came forward with a constructive plan, the Government would ask me to head up the national project. That would mean resigning from General Motrors and going out in opposition to them. I knew, too, that any proposition the Government made me would be a very attractive one. But my duty was to do my utmost for the firm by which I was employed. So I pushed on with the preparation of the case for New York.
To be continued…