KÉRAMICA
revista da indústria cerâmica portuguesa
MELHORIA CONTÍNUA NA INDÚSTRIA CERÂMICA
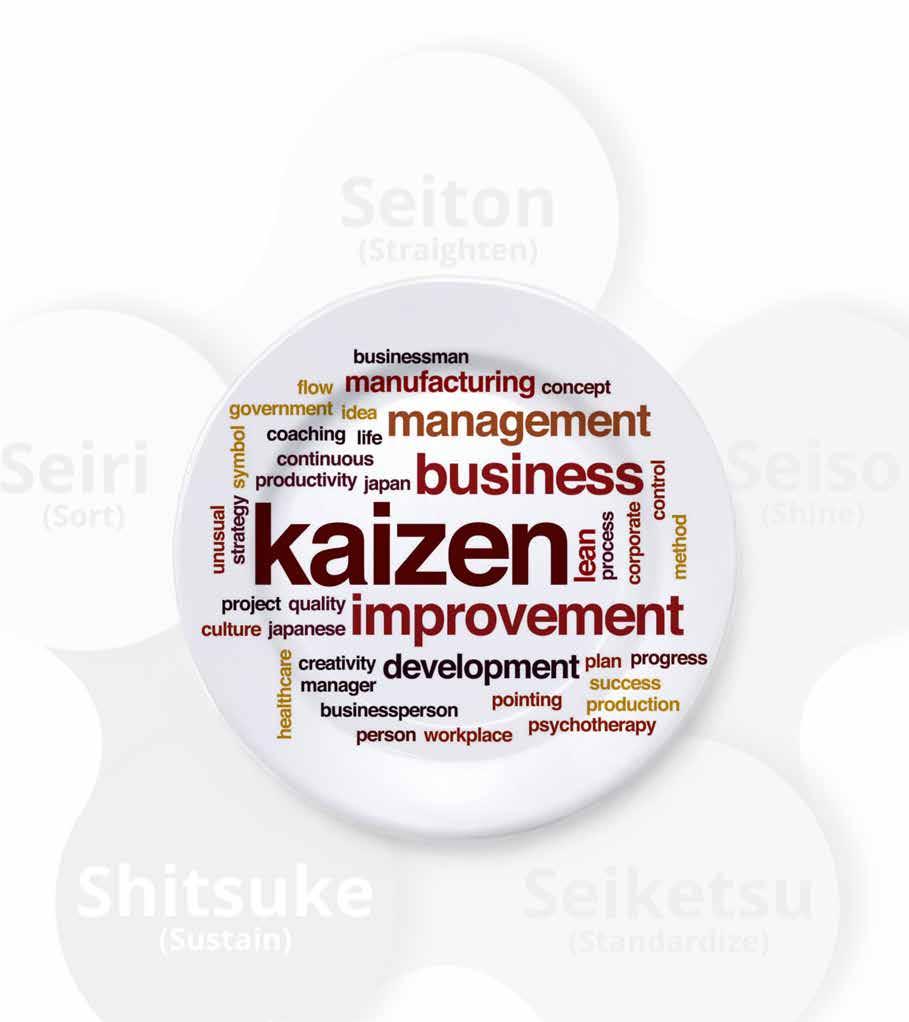
revista da indústria cerâmica portuguesa
Acreditada pelo IPAC como organismo de certificação de produtos (incluindo Regulamento dos Produtos de Construção), serviços e sistemas de gestão
Destaque . 05
A melhoria contínua e a sustentabilidade na Indústria
Lean . 10
Lean Management na Indústria Cerâmica
Secção Jurídica . 22
Prevenção da Corrupção: As novidades do Regime
Novidades das Empresas Cerâmicas
Notícias & Informações . 36 04
Melhoria Contínua . 13
Melhoria Contínua na Indústria Cerâmica
O Papel da Digitalização na Melhoria Contínua
A Evolução da Indústria Cerâmica: De Kaizen à Indústria 4.0 e a
Transformação do Mercado
Melhoria Contínua na Indústria Cerâmica: Estudo de Caso
Portuguesas na Feira Cersaie 2024 . 38
Novidades das Empresas Cerâmicas Portuguesas na Feira Cersaie 2024
Associativismo . 32
“Ceramic Days 2024” – Jornadas Europeias da Cerâmica 2024 31ª Reunião anual do Fórum Mundial do Pavimento e Revestimento Cerâmico
Novidades das Empresas Cerâmicas Portuguesas 13 16 19 24 29
A Melhoria Contínua como Motor de Inovação na Indústria Cerâmica
Calendário de Eventos . 40
Propriedade e Edição APICER - Associação Portuguesa das Indústrias de Cerâmica e de Cristalaria NIF: 503904023
Direção, Administração, Redação, Publicidade e Edição Rua Coronel Veiga Simão, Edifício Lufapo Hub A - nº 40, 1º Piso 3025-307 Coimbra [t] +351 239 497 600 [f] +351 239 497 601 [e-mail] info@apicer.pt [internet] www.apicer.pt
Tiragem 500 exemplares
Diretor Marco Mussini
Editor e Coordenação Albertina Sequeira [e-mail] keramica@apicer.pt
Conselho Editorial Albertina Sequeira, António Oliveira, Cristiana Costa Claro, Marco Mussini e Martim Chichorro. Capa Nuno Ruano
Colaboradores Albertina Sequeira, André Guimarães, Cristiana Costa Claro, Daniel Gaspar, Filipa Pereira Silva, Henrique Marçal, João Paulo Pinto, Mariana Bem-Haja, Mickael Osório Lopes Monteiro, Nádia Rodrigues, Odete Monteiro Lopes, Rui Ferreira, Samuel Messias, Tiago Costa Dias, Tiago Sacchetti
Paginação
Nuno Ruano
Impressão
Gráfica Almondina - Progresso e Vida; Empresa Tipográfica e Jornalística, Lda Rua da Gráfica Almondina, Zona Industrial de Torres Novas, Apartado 29 2350-909 Torres Novas [t] 249 830 130 [f] 249 830 139 [email] geral@grafica-almondina.com [internet] www.grafica-almondina.com
Distribuição
Gratuita aos associados e assinatura anual (6 números); Portugal €42,00 (IVA incluído); União Europeia €60,00; Resto da Europa €75,00; Fora da Europa €90,00
Versão On-line https://issuu.com/apicer-ceramicsportugal
Notas
Proibida a reprodução total ou parcial de textos sem citar a fonte.
Os artigos assinados veiculam as posições dos seus autores. Esta edição vem acompanhada da Revista Técnica da Indústria 2024 #26 Novembro . Dezembro | Bimestral
Índice de Anunciantes CERTIF (Verso Capa) • GOLDENERGY (Contra-Capa) • INDUZIR (Pag 1) • ISH (Verso Contra-Capa) • SMARTENERGY (Pag 37)
Conteúdos conforme o novo acordo ortográfico, salvo se os autores/colaboradores não o autorizarem
Publicação Bimestral nº 392 . Ano XLIX . Novembro . Dezembro . 2024
Depósito legal nº 21079/88 Publicação Periódica inscrita na ERC [Entidade Reguladora para a Comunicação Social] com o nº 122304 ISSN 0871 - 780X Estatuto Editorial disponível em http://www.apicer.pt/apicer/keramica.php
Melhoria Contínua na Indústria Cerâmica
KAIZEN ™ – Management methodology./ melhoria contínua.
MUDA; MURA; MURI – Desperdícios vários.
5S – do japonês seiri (Triar) seiton (Organizar), seiso (Limpar), seiketsu (Normalizar), shitsuke (Sustentar).
TPS – Toyota ProductionSystem.
TL – Team Leader.
KPI – Key Performance Index.
OEE – Overall Equipment Effectiveness.
FIFO – First In First Out.
JIT – Just in Time.
LT – Lead Time.
MTO – Make to Order.
MTS – Make to Stock.
SMED – Single Minute Exchange of Die.
SIPOC – Supplier Input Process Output Costumer.
TPM – Total Productive Maintenance.
VSM – Value Stream Mapping.
WIP – Work in Progress.
Estes conceitos (apenas alguns exemplos), são familiares às empresas, aos gestores, aos quadros técnicos e de forma geral aos colaboradores-chave? Os gestores e os quadros das empresas sabem como são calculados estes indicadores?
Se sim , a empresa está no caminho do sucesso, da sustentabilidade e da procura do desafio permanente e da sua reinvenção enquanto organização.
Se não , será por certo necessário parar um pouco o turbilhão diário e perceber porque é que ainda não se está a fazer este caminho.
Nunca como hoje, o tema melhoria contínua na indústria se coloca, não só como uma urgência, mas como uma inevitabilidade. Reduzir o desperdício e eliminar as atividades sem valor acrescentado, é a chave da rentabilidade dos capitais investidos e quiçá da própria sobrevivência da empresa.
No final da Segunda Guerra Mundial, o Japão devastado levou a que quadros da TOYOTA visitassem os Estados Unidos da América, para avaliar e estudar os métodos de organização da produção, utilizados pelos americanos para reconstruir o país. Decidiram: produção em massa, não!Grandes lotes, geravam grandes stocks, aumentando custos e defeitos, e impediam a variabilidade na procura.
Destas reflexões e análises nasceu o que mais tarde se tornaria o Toyota Production System (TPS), que o Ocidente acolhe em 1990 como sistema LEAN.
Se fizermos uma tradução simples do inglês, LEAN em português significa magro, esguio. A gestão baseada no pensamento LEAN, será uma gestão sem gorduras, sem excessos, um sistema limpo.
Quando falamos de um sistema LEAN falamos de quê?
Falamos de identificar valor, de mapear a cadeia de valor, de criar fluxo, de estabelecer sistemas pull e evitar o desperdício. Estas, sem menosprezo por outras, são a chave do sucesso de qualquer empresa.
Mas será que um sistema nascido na indústria automóvel se aplica a todas as indústrias, e em particular à indústria cerâmica e da cristalaria?
A resposta é sem hesitação, sim. Os problemas são equivalentes e transversais. As indústrias cerâmicas e da cristalaria, têm desenvolvido processos cada vez mais complexos, tanto do ponto de vista da inovação, da tecnologia, da organização da gestão, em tudo idênticos à restante indústria. Contudo temos de ser muito realistas, em Portugal as metodologias LEAN na indústria cerâmica, são pouco utilizadas.
A APICER, Associação Portuguesa da Indústria Cerâmica e Cristalaria, desenvolveu um Guia de Ferramentas LEAN, com o Projeto CER++, com o objetivo de dar a conhecer as potencialidades destes instrumentos. Recomendo que voltem a reler.
O pensamento e as ferramentas LEAN, a adotar nas empresas, não devem ser olhados como uma receita milagrosa, mas sim integradas e enquadrados em con-
textos de reorganização e apoiados por especialistas, envolvendo toda a organização do topo ao chão de fábrica, sob pena de fracasso e descrédito.
Voltando ao primeiro conceito deste Editorial, “KAIZEN ™ significa melhoria continua. Este conceito significa também melhoria contínua na vida pessoal, social e profissional. Quando aplicado ao local de trabalho, KAIZEN ™ significa melhoria contínua envolvendo todos _ administradores, restantes colaboradores” como defineMasaakiImai, fundador do Instituto KAIZEN e se pode ler no site do Instituto Kaysen.
Pode ser encontrada, uma síntese feliz, no referido site, dos princípios-base da melhoria continua.
Conhecer o Cliente. Colocar sempre o cliente em primeiro lugar.
Criar fluxo. Otimizar os processos para um fluxo de trabalho contínuo.
Ir ao gemba. Observar os locais para compreender os desafios.
Capacitar as pessoas. Incentivar a participação ativa de todos os colaboradores.
Os concorrentes da indústria cerâmica e da cristalaria são todos os agentes económicos que produzem bens e serviços, onde os nossos clientes gastam o seu dinheiro. Por isto o nosso mindset terá de ser, sempre, continuo usimprovement para lutar contra a concorrência.
José Cruz Pratas (Presidente da Direção da APICER)
por Rui Ferreira, Professor adjunto convidado na Escola Superior de Tecnologia do Instituto Politécnico de setúbal
Introdução
Desde muito cedo tomei contacto com o sistema de gestão Lean , mais concretamente a partir de 1998, ao integrar a João de Deus e Filhos, empresa de fabrico de componentes para automóveis. Esta empresa, na época pertencente à multinacional Magneti-Marelli, do grupo Fiat, mostrou-me o novo paradigma da gestão do “chão de fábrica”, onde mais tarde vim a encontrar semelhanças com o TPS (Toyota Production System) . Percebi desde então, que era necessário alterar a cultura de toda a empresa. A mudança foi transversal ao nível da hierarquia,
sendo que este novo paradigma exigia maior planificação, estruturação, padronização e estabelecimento de rotinas. Consistia numa nova forma de trabalhar, muito mais profissional, organizada e que fazia todo o sentido. Para a implementar, exigia-se um líder, um tutor, um mentor e um motivador de equipas. Recordo o Eng. Giovanni Polosa como a pessoa certa para esta mudança de paradigma na gestão.
Fiz também o meu primeiro workshop Kaizen ¹, que tal como se verifica na Figura 1, significa do japonês, "melhoria" ou "mudança para melhor". Apliquei a conhecida metodologia SMED² (Single Minute Exchange of Die) , numa prensa progressiva de 200t, com ferramenta de corte e estampagem de 7 estações. Os resultados foram excelentes, com um tempo médio de setup de cerca de 4 horas e após a implementação de algumas melho -
2 • Os 10 pilares do WCM que representam um tempo; Fonte: Elaborado pelo próprio
rias organizacionais, sem qualquer tipo de CAPEX, a troca de fabrico passou para cerca de 90 minutos. Com isto pretendo animar e motivar os leitores, para os resultados rápidos da implementação do Lean Manufaturing e ainda para o facto de a melhoria ser mais fácil de implementar inicialmente, quando tudo está por fazer.
Seguiram-se muitos outros workshops , onde estratégias e metodologias como o Kanban³, Hoshin⁴ e grupos de resolução de problemas foram elaborados, promovendo o trabalho em equipa, o raciocínio lógico e científico, as decisões com recurso a dados e o registo estruturado de todas as ações, possibilitando lições aprendidas e a divulgação do conhecimento.
Em 2001 mudo de sector, para a transformação do vidro, a convite do meu amigo Eng. José Pacheco, passando a fazer parte dos quadros técnicos da Covilis, e mais tarde, em 2007, dos quadros do Grupo Francês ao qual a Covilis pertence.
No setor do vidro percebi o significado de “indústria de consumo intensivo de energia”, onde as prioridades de gestão não se limitam aos custos de mão de obra, transportes ou não qualidade; passando os custos de energia a fazer parte da lista de prioridades de gestão, pois podem representar 30-50% do custo de produção.
Nesta minha experiência, tomei contacto com a metodologia WCM⁵ (World Class Manufacturing) , que tem por base 10 pilares para alcançar a excelência de nível mundial, conforme se pode verificar na Figura 2.
Esta metodologia já foi desenvolvida mais tarde, na década de 1980, também por um japonês, Hajime Yamashina⁶, tendo por base o TPS e o Lean Manufacturing . Foi implementado em 2005 pela FCA (Fiat Chrysler Automobiles) , tendo ganho notoriedade como metodologia estruturada e sendo hoje globalmente aplicada.
Em projetos Lean manufacturing ou WCM , defendo a ideia da implementação se efetuar passo a pas -
3.- Kanban: Na década de 1960, a empresa Toyota criou o sistema Kanban para abastecimento e controlo de stocks O sistema movimenta e fornece itens de acordo com o consumo, fazendo com que não haja abastecimento de materiais sem solicitação.
4.- Hoshin: O Hoshin assenta numa metodologia de procura da eficiência e da produtividade no posto de trabalho, sendo o balanceamento de mão de obra uma vertente importante do Hoshin, por estar diretamente ligado à procura da eficiência e capacidade produtiva de uma unidade de fabrico.
so em áreas bem delimitadas, para não correr riscos de insucesso e maus resultados. Os bons resultados, serão o elixir de motivação para as próximas etapas da implementação global.
Também ao nível da definição estratégica, encontrei algumas semelhanças entre as duas metodologiascom que contactei, apostando muito na utilização de metodologias estruturadas de decisão ao processo participativo Hoshin-Kanri⁷
Em resumo, a grande diferença que identifiquei entre o WCM e o sistema de gestão Lean Manufacturing está ao nível do método e estrutura de implementação, pois o WCM implementa-se definindo os pilares de implementação e por área, enquanto o sistema de gestão Lean se foca apenas na priorização das áreas.
Com esta partilha de experiências, pretendo passar ao leitor alguns dos fatores-chave para o sucesso da implementação de um sistema de gestão Lean Manufacturing em qualquer organização, nomeadamente:
• Liderança da direção;
• Promotor Lean ou Lean Manager;
• Constituir a(s) equipa(s);
• Ter espírito Kaizen (de melhoria);
• Investir em formação;
• Definir indicadores e rotinas de gestão;
• Ter por base o trabalho padronizado;
• Trabalhar, passo a passo, em áreas restritas e não procurar abarcar todas as áreas, porque acabará por não terminar.
Eficiência Energética e Produtividade: Um Caminho Indissociável para a Excelência
Durante a gestão de projetos de melhoria, entendi que não se deve dissociar a eficiência energética da produtividade. Muitas vezes fui confrontado com as dificuldades de visualizar à priori os ganhos de grandes e promissores projetos de eficiência energética. No final, constatou-se que não era possível visualizar os ganhos nas métricas de gestão, pois estavam impactados pela performance de produtividade. Esta situação é tanto ou mais importante, quanto maior a intensidade de consumo das instalações; assim, faz todo o sentido que nas reuniões de fábrica se comuniquem e discutam os consumos de energia de uma forma rotineira. Na Figura 3, podemos ver um exemplo de uma área de reunião de equipas, onde assuntos como segurança, qualidade, produtividade e consumos são abordados, numa base diária ou de turno, conforme o regime de trabalho.
5.- WCM: É uma filosofia estratégica de gestão integrada que tem como objetivo levar uma organização ao estado mais elevado de classe mundial – com processos extremamente eficientes e produtivos e produtos rigorosamente livres de defeitos. Esta filosofia de gestão assenta em 10 pilares;
6.- HajimeYamashina: Professor japonês da Universidade de Kyoto;
7.- Hoshin-Kanri: Processo participativo e negocial entre a administração e as equipas operacionais, sobre novas metas e objetivos e consequentes projetos necessários;
Na minha experiência profissional na SGS Portugal, tive a oportunidade de realizar 18 diagnósticos Ex-ante, a convite da Helena Santos e do Miguel Trindade (HS Consultores), no âmbito do Aviso de Descarbonização da Indústria. Tive também a oportunidade de implementar vários projetos com base em sistemas de gestão Lean . Este trabalho consolidou a visão de que um projeto de eficiência energética só será eficaz se for sustentado por um conjunto de Key Drivers para a Excelência, que incluem: Fatores contratuais, fatores de produtividade e das boas Práticas aplicáveis (Ex. ISO 50001, Energias renováveis, motores de alto rendimento, entre outros).
Casos de estudo
Neste espaço, partilho convosco alguns casos de estudo; projetos que refletem a aplicação de alguns dos
exemplos anteriores, e que apresentam resultados relevantes. Contudo, o foco não está em iniciativas complexas, mas sim em soluções simples, que frequentemente são o cerne de uma gestão Lean . A simplicidade, aliada a uma execução bem estruturada, revela-se muitas vezes mais eficaz do que estratégias excessivamente sofisticadas. Estes exemplos não só demonstraram resultados tangíveis, como também proporcionaram a todos um enorme prazer na sua implementação, provando que pequenas mudanças podem ter grandes impactos.
• Redução de potência contratada
Uma empresa industrial alcançou uma poupança significativa ao otimizar a sua potência contratada. Após analisar as faturas de energia de 2014 e 2015, constatou-se uma redução no maxímetro, devido ao encerramento de uma linha de produção antiga. Foram realizadas simulações baseadas no histórico de consumos e na legislação sobre excessos de potência, ajustando a potência contratada de 19500 kW para 16000 kW, em cada período tarifário.
Esta mudança gerou uma poupança anual de 170 mil euros e promoveu uma cultura de análise contínua das faturas energéticas.
• Reutilização de águas industriais
Este projeto ilustra como é possível otimizar o uso da água na indústria sem a necessidade de grandes investimentos. A estratégia adotada consistiu na divisão da água em grupos, com base na sua qualidade ou
condutividade, aproveitando-a de forma mais eficiente em processos industriais com diferentes exigências. Por meio de simples ligações em tubo PVC, foi implementado um sistema de “descargas em cascata”, que permitiu a reutilização da água em três processos distintos, antes de ser descartada no coletor municipal. Um esquema de princípio encontra-se apresentado na Figura 4.
Essa abordagem não gerou custos significativos, além das ligações necessárias, mas resultou numa importante economia de água, com uma redução de 100m³ mensais (equivalente a 1.200m³ anuais). Além de ser uma solução de baixo custo, a ação contribuiu para a melhoria da qualidade da água utilizada, aumentando a sua durabilidade e estabilidade em termos de condutividade, pH e sólidos em suspensão.
• Regulação de Pressão: Simplicidade e Eficiência em Ciclos de Autoclave
A eficiência energética na indústria não exige, necessariamente, investimentos elevados ou soluções complexas. Um exemplo claro disso é a implementação da “Regulação de Pressão” nos ciclos de autoclave, que demonstrou ser uma solução prática, acessível e de alto impacto. Antes da mudança, o sistema mantinha a pressão ao longo de todo o ciclo, resultando num desperdício energético significativo, conforme se pode verificar na Figura 5 (registo da pressão em azul e temperatura em vermelho).
Esta medida baseia-se na interrupção da injeção de ar comprimido após a fase de manutenção de temperatura e pressão (130ºC e 13 bar), eliminando consumos desnecessários durante o arrefecimento, conforme se pode ver na Figura 6 (registo da pressão em azul e temperatura em vermelho).
Com um custo de implementação praticamente nulo, esta ação reduziu o consumo de energia por ciclo de 300 kWh para 150 kWh, gerando uma poupança de
150 kWh por ciclo. Considerando a realização de 10 ciclos diários, durante 300 dias por ano, o impacto anual foi de menos 450.000 kWh em consumo de energia, que corresponde a uma redução de custos de 33.750 € (a 0,075 €/kWh).
• Otimização de processos com standby mode
A aplicação do conceito de “Standby Mode” em equipamentos industriais demonstra como estratégias simples e inteligentes podem trazer significativas poupanças energéticas e financeiras. Este princípio baseia-se na redução ou eliminação do consumo de energia de equipamentos durante períodos de inatividade, sem comprometer a produtividade.
Um exemplo prático é o túnel de lavagem Klopper, conforme se pode verificar na Figura 7, onde foram implementados dispositivos como electroválvulas e caudalímetros, para controlar o consumo de água desmineralizada e ar comprimido. Além disso, foi desenvolvido um sistema de hibernação para diversos componentes, ativado automaticamente após 120 segundos de inatividade nos transportadores. Os resultados esperados são impressionantes: uma redução de 127 kW durante as paragens, o que corresponde a 137.160 kWh/ano e cerca de 10.287 €/ano em custos energéticos, considerando uma taxa de paragem de 15%.
Sobre o autor
Tenho mais de 20 anos de experiência em empresas multinacionais, onde trabalhei em áreas como produção, manutenção, engenharia e eficiência energética. Ao longo da minha carreira, liderar projetos que reduziram consumos energéticos e emissões de CO2 tornou-se uma paixão, pois acredito que a sustentabilidade é essencial para o futuro da indústria e do planeta.
Atualmente, leciono no Instituto Politécnico de Setúbal e tenho o privilégio de partilhar o meu conheci-
mento com futuros profissionais em disciplinas ligadas à produção e tecnologia. Paralelamente, estou a realizar o doutoramento em Engenharia Industrial, explorando a forma como a inovação tecnológica e a sustentabilidade podem transformar a gestão industrial. Acredito no poder das pessoas e na transformação dos processos para o alcance de resultados. Aposto em ferramentas digitais como o Power BI e em metodologias como o Lean Manufacturing para desenvolver soluções práticas e impactantes.
por
Introdução ao lean em cerâmica
A indústria cerâmica é um sector-chave na economia portuguesa pelo seu impacto económico contribuindo significativamente para o PIB¹ e o emprego, especialmente em regiões do centro e norte do país. Portugal é um dos principais produtores e exportadores da Europa, marcando posição na cerâmica de construção, louça sanitária e de mesa, cerâmica técnica e peças decorativas.
Esta indústria apoia sectores relacionados como a extração de minério, embalagem e transporte, enquanto impulsiona a inovação tecnológica e práticas sustentáveis. Também contribui para o turismo através de oficinas e museus temáticos.
Os principais desafios que o sector enfrenta incluem o aumento dos custos de energia e a concorrência
asiática, embora o sector continue estrategicamente importante para o desenvolvimento industrial português. Para dar resposta a estes desafios, a indústria cerâmica apresenta-se como um sector fascinante para aplicar os princípios de gestão magra (lean management) . Aquilo que normalmente se designa por“produção magra (lean) ”teve as suas origens na indústria automóvel nos anos 1940s, contudo a aplicação dos princípios e ferramentas lean cedo se alastrou a outros sectores de actividade económica. No caso do sector da cerâmica, a eliminação dos desperdícios (muda) e da melhoria contínua (kaizen) representam um território de oportunidades para o sector.
Entender como estes princípios se traduzem nos desafios específicos da indústria da cerâmica exige que pensemos sobre as operações e a produção de novas maneiras.
Compreender os benefícios
Quando implementado corretamente, a gestão lean transforma o fabrico de cerâmica em múltiplas dimensões. Pense nisto como uma sincronização fina de uma orquestra onde cada secção deve desempenhar seu papel perfeitamente para que o todo alcance a harmonia. Em termos de eficiência operacional, as empresas normalmente reportam reduções do tempo de ciclo de produção entre 30% a 40%. Esta melhoria resulta do repensar os métodos de trabalho (normalmente dominados pelo paradigma dos grandes lotes). Imagine um processo tradicional de carregamento de forno onde os
operadores esperam para encher por completo o forno antes de iniciar o ciclo. De acordo com os princípios lean , podemos optimizar a carga com base na procura do mercado (não mais com base em previsões), executando ciclos menores e mais frequentes e que melhor respondam às necessidades reais dos Clientes.
A melhoria na qualidade manifesta-se por múltiplos canais. Considere o processo de esmaltar ou de acabamentos, caracterizados por métodos tradicionais que dependem muito da experiência do operador: a abordagem lean fomenta a implementação de procedimentos de trabalho padrão e ferramentas de gestão visual. A padronização reduz as taxas de defeitos em 40% a 50%. É semelhante a um mestre oleiro a ensinar aprendizes dividindo movimentos complexos em pequenas etapas e de fácil aprendizagem.
A redução de custos resulta naturalmente destas melhorias. O consumo de energia geralmente diminui em 20% a 30% graças à melhor utilização dos equipamentos de grande consumo energético (ex. Fornos). O desperdício de matéria-prima cai em 25% a 35% através da melhoria de processos como o manuseio e a mistura. Algo semelhante a um chefe de cozinha que reduz o desperdício através da correcta preparação, medição e uso eficiente de recursos.
Desafios da implementação
A implementação lean nos processos de fabrico cerâmico enfrenta obstáculos únicos que exigem soluções criativas. Considerem-se estes dois exemplos:
• Os tempos de secagem e queima nos processos de fabrico cerâmico não são tão previsíveis quanto as operações de outras indústrias. Variáveis como a humidade, temperatura e composição do material afetam os tempos de processamento. Esta variabilidade torna desafiador implementar conceitos lean como o takt time ou o nivelamento de processos;
• As propriedades dos materiais apresentam outro desafio significativo. A composição da argila pode variar em consistência e maneabilidade (algo que pode acontecer dentro do mesmo lote). Esta variabilidade torna a padronização difícil, mas não é impossível.
Roadmap de implementação
Atendendo ao que já foi referido anteriormente não é tarefa fácil apresentar um roteiro padrão para o sector da cerâmica. Os passos que seguem, embora tendo como foco esta indústria, são genéricos:
1. Criar as bases (duração de 3 a 6 meses): durante esta fase, concentre-se em conhecer os processos e as práticas actuais através de ferramentas como o mapeamento da cadeia de valor (VSM). Procure implementar os princípios de good house keeping (ou 5S²), começando com mudanças simples, como organizar áreas de trabalho, criar simples padrões e fomentar a gestão visual;
2. Melhorar processos (duração de 8 a 12 meses): nesta fase passa-se à implementação de conceitos e ferramentas mais avançados. Exemplos disso são os procedimentos de trabalho padronizados, métodos de resolução de problemas, revisão de layouts , trabalho em equipa, lean coaching , definição de quadros de planeamento e de indicadores, entre outros;
3. Integração avançada (duração de 1 a 2 anos): nesta fase, implementam-se sistemas como o desdobramento estratégico (hoshin kanri) , pullf low management , desenvolvimento da rede de fornecedores, gestão de projectos em ambiente lean management e programas TPM³ ao nível de equipamentos e instalações.
Estudo de um caso
Para que perceba melhor como o lean management pode transformar radicalmente uma empresa do sector da cerâmica vamos considerar o exemplo de uma empresa da região centro do país. Trata-se de um fabricante de componentes técnicos de cerâmica. Quando a empresa iniciou a sua jornada lean, enfrentou desafios comuns a muitos na indústria: elevados custos de energia, problemas de qualidade e longos prazos de entrega.
A transformação começou com um projecto piloto na linha de produção de maior volume. Em vez de tentar implementar todos os princípios lean de uma só vez, a empresa começou com os 5S e a gestão visual. Isto resultou em melhorias imediatas ao nível da organização do local de trabalho e no fluxo de materiais.
Ao longo de dois anos, a empresa alcançou resultados notáveis:
• Os prazos de entrega diminuíram em 35%;
• Consumo de energia reduziu em 25%;
• Os níveis de stock caíram 40%;
• Defeitos de qualidade diminuíram 50%;
• A produtividade do trabalho aumentou 20%.
A chave para o sucesso desta empresa esteve sempre na abordagem paciente e sistemática. A empre-
2.- 5S – metodologia de organização e asseio dos locais de trabalho desenvolvida no Japão após a 2ª Grande Guerra (seiriseitonseisoseiketsu e shitsuke).
3.- TPM (total productive maintenance): manutenção produtiva total, uma abordagem holística à organização e gestão da manutenção desenvolvida pela indústria nipónica nos anos 1970s.
sa cedo percebeu que uma mudança sustentável e duradoura requer melhorias técnicas e mudança cultural, algo que só se consegue dando tempo às pessoas para que possam assimilar e manter as melhorias. Como se entende, a Toyota não conseguiu alcançar os actuais níveis de desempenho operacional e financeiro nos primeiros anos de implementação do TPS⁴ (sistema que serviu de inspiração ao pensamento magro), mas sim graças a um processo de melhoria contínuo ao longo de várias décadas.
Os factores críticos de sucesso da empresa foram os seguintes:
• Comprometimento da gestão de topo e liderança presente no terreno (gemba) ;
• Programas abrangentes de formação e envolvimento dos colaboradores;
• Abordagem sistemática de implementação com metas claras;
• Abertura para o erro (sim, leu bem. Se cultivarmos
a proatividade nas pessoas, aprende-se mais com o erro do que com o sucesso);
• Monitorização regular do desempenho e ajustes sempre que necessários.
Olhar para o futuro
A aplicação do pensamento lean na indústria da cerâmica reserva-nos oportunidades empolgantes, especialmente quando combinado com as tecnologias que resultam da Indústria 4.0. Por exemplo: a tecnologia sensorial permite monitorizar o teor de humidade em tempo real, garantindo processos de secagem mais exactos. A inteligência artificial pode prever necessidades de manutenção antes que o equipamento falhe tal como pode ser aplicada na análise de dados e nos processos de decisão. Estas tecnologias não substituem os princípios e as ferramentas lean management , mas melhoram-nas.
Conclusão
Implementar os conceitos e as ferramentas lean management neste sector requer uma visão de longo prazo, liderança, paciência, criatividade e comprometimento de todos nas Organizações. Embora os desafios sejam significativos, os benefícios potenciais fazem a jornada lean valer a pena. O sucesso não vem da aplicação cega e/ou isolada de ferramentas, mas da sua adaptação às características singulares dos processos de fabrico no sector da cerâmica.
Deste modo, as empresas deste sector que consideram a implementação lean devem:
• Desenvolver uma estratégia de implementação abrangente alinhada com os objetivos do negócio;
• Investir na formação, treino e desenvolvimento dos seus colaboradores;
• Estabelecer sistemas robustos de monitorização de desempenho;
• Considerar oportunidades de integração tecnológica (ex. Indústria 4.0);
• Manter o foco na melhoria contínua.
Lembre-se, lean management não é um destino, mas uma jornada de melhoria contínua. Cada passo dado cria oportunidades para futuros avanços, levando a empresa a níveis cada vez melhores de eficiência, qualidade e satisfação do Cliente.
Se a sua Empresa precisa de suporte nas fases iniciais da sua jornada lean management , a CLT Services ( www.cltservices.net ) poderá ser o parceiro que precisa.
A Melhoria Contínua é muito mais que apenas um conjunto de ferramentas, métodos e processos. Trata-se de uma cultura, de um hábito, de uma rotina – só desta forma conseguimos resultados sustentáveis e duradouros. A Melhoria Contínua pode e deve ser aplicada em qualquer empresa, seja de produtos ou de serviços. Não existem limites para o que é possível fazer e alcançar com esta forma de encarar e ver o mundo – é uma filosofia que nos permite a busca constante por novas e melhores soluções, por mais pequenas que nos possam parecer. É algo que está presente na nossa vida, no nosso dia a dia mesmo que de forma inconsciente. ‘Isto não é possível aplicar aqui’ é uma frase comum! E na maior
parte das vezes está errada: terá é de ser adaptada à realidade, ao contexto e acima de tudo às pessoas. Pessoas… só funciona mesmo se as pessoas estiverem alinhadas, motivadas e perceberem por experimentação o benefício que isto nos traz a todos.
No que toca à melhoria contínua no setor da cerâmica, nomeadamente em fábricas mais tradicionais e com trabalho manual, a metodologia a adotar pode ser similar a fábricas mais automatizadas e inovadoras, obviamente com as limitações inerentes ao processo, o que não significa que os resultados sejam inferiores. No caso concreto da fábrica da Bordallo Pinheiro, o início da implementação da cultura de Melhoria Continua passou por formação e explicação aos colaboradores, seguindo-se das reuniões diárias e rápidas segmentadas por áreas e em conjunto, todos os dias: reuniões de 15 minutos no máximo com o responsável de secção a liderar envolvendo todos os colaboradores, mostrando os principais resultados do dia anterior e reuniões com a mesma duração com os responsáveis de todas as áreas produtivas e de suporte. Estas reuniões são suportadas com várias ajudas visuais e intuitivas: gráficos com os resultados em formato físico e que são preenchidos diariamente nos quadros existentes e em formato digital para dina-
mizar e consultar rapidamente dados específicos. Estas reuniões não são para resolver problemas, nem para os discutir de forma detalhada - são essencialmente para comunicar, fazer passar informação a todos e para estar em constante alinhamento. Desta reunião podem surgir ações ou a necessidade de reuniões específicas, mas a regra principal é que sejam rápidas, diretas e eficazes. Esta, na minha opinião, é uma das ferramentas mais importantes e que ajuda a suportar todas as outras – inicialmente é preciso forçar a presença de todos, é preciso fazer a reunião mesmo que não estejam todos, é preciso controlar o tempo de forma rigorosa, é preciso muito acompanhamento! Mas por experiência, passado algum tempo, passa a ser natural e rotina e essa é uma das primeiras vitórias.
O passo seguinte foi a aplicação dos 5S – muita organização, muitas ajudas visuais e marcações e constante verificação – aliado a mais formação para que os conceitos se tornassem cada vez mais claros. Esta ferramenta continua a ser uma luta diária para que seja aplicada e seja mantida, mas tem benefícios muito significativos no combate aos demais desperdícios.
Para a Bordallo Pinheiro, sendo uma fábrica onde a componente manual é um dos pontos mais fortes, a necessidade de controlar e acompanhar a produtividade e a qualidade sempre foi uma das maiores preocupações. E conseguimos isso ‘automatizando’ diariamente
os dados e compilando essa informação convertendo em dashboards. Através de cartões com RFID, os colaboradores registam o início e o fim de todas as peças produzidas, o sistema compara com os tempos que estão registados no nosso sistema ERP e dá-nos rapidamente um esquema de cores intuitivo que nos permite avaliar o status atual – verde, amarelo e vermelho. Para além disso, esses cartões acompanham as peças até à etapa final e é possível associar a qualidade das mesmas. Isto para além de nos permitir acompanhar o trabalho feito diariamente e validar o custo real de cada peça, permite-nos perceber a quem e que peças precisamos de reforçar a formação contínua dos colaboradores.
Após o reforço daquilo que consideramos ser a base da melhoria contínua – normalização, gestão vi-
sual e formação – demos continuidade através de projetos direcionados e mais específicos nas mais diversas áreas. Sempre com equipas multidisciplinares e com metodologia associada: A3 de cada projeto com objetivos SMART, planos de ação detalhados e cronogramas definidos.
Finalmente, reforçando o que referi inicialmente, as pessoas são o ponto fulcral para o sucesso destas ferramentas. É preciso explicar, envolver e comprometer as pessoas de forma constante em todas as fases do processo. É preciso que experimentem, é preciso que errem e é preciso que acertem – só assim conseguimos com que acreditem no que estamos todos a fazer. E esta é a parte mais difícil e complexa de todo o processo, mas é aqui que a cultura nasce, se enraíza e se dissemina.
Esta é a metodologia que achamos funcionar na nossa realidade, mas tal como a Melhoria Contínua incita, podemos e devemos sempre questionar o que foi feito até hoje no sentido de perceber o que podemos fazer diferente amanhã. O futuro é imprevisível, mas com
a visão e a cultura certa, temos pelo menos a segurança de que estaremos mais preparados para os desafios que poderão surgir.
A Melhoria Contínua deve ser rigorosa nas etapas a seguir, mas não deve ser quadrada – tudo pode e deve ser adaptado. O rigor é essencial para que perdure.
A adaptabilidade por outro lado é crucial para que as ferramentas funcionem nas mais diversas realidades.
Olhar para tudo com um sentido crítico e construtivo, simplificar o que parece complexo e tornar a informação transparente e transversal a todos, é essencial para se abraçar um projeto de melhoria contínua. Se existir pelo menos uma pessoa da equipa a afirmar que isto fez diferença no seu trabalho já é um sentimento de missão cumprida e um passo em frente rumo à transformação.
Como referiu Fujio Cho, presidente honorário da Toyota Motor Corporation, ‘Primeiro construímos pessoas, depois construímos carros’!
5Ss – é uma metodologia que deriva de 5 palavras japonesas que se traduzem em Segregar, Organizar, Limpar, Normalizar e Sustentar (5 etapas);
A3 – ferramenta para estruturar e fazer seguimentos de projetos onde normalmente se concentra tudo num papel de tamanho A3;
Dashboard – forma de expor de uma forma visual e intuitiva num só local diversas informações relevantes para o negócio.
ERP – sistema de software utilizado pelas empresas para gestão das suas atividades;
RFID – radio frequency identification / identificação por radiofrequência para captura de dados;
SMART – Specific/Específicos, Measurable/Mensuráveis, Achievable/Atingíveis, Relevant/Relevantes e Time-bound/Prazo definido
por Tiago Sacchetti, Diretor da Bosch
Industry Consulting para a Ibéria
Longe vão os dias em que todas as iniciativas de digitalização de operações eram aprovadas apenas pelo seu brilho próprio. Manutenção preditiva baseada em mineração de dados históricos, quadros digitais de monitorização do estado de inventário em trânsito externo com alarmística incorporada, Kanbans eletrónicos a gerir a movimentação de materiais no chão de fábrica, sistemas de gestão de frotas de agv’s com posicionamento em tempo real, os projetos e as oportunidades eram aliciantes. Ora esta forma de digitalizar motivada pelas possibilidades está a morrer. E ainda bem pois acabou
por criar a perceção errada de que o real valor da digitalização é relativamente baixo, pois o esforço é grande e os benefícios parcos. Em contraponto, os mais otimistas dirão que pelo menos contribuiu para remover aquela inércia inicial que sempre se faz sentir quando tentamos mudar formas de trabalhar.
Na última década, a indústria tem vivido tempos desafiantes provocados não só por fatores externos como a pandemia, disrupções nas cadeias de fornecimento, evolução dos custos energéticos, mas também por iniciativas estratégicas de diferenciação e otimização críticas para manter ou melhorar a competitividade. Neste último caso incluem-se os projetos que fazem uso das tecnologias digitais frequentemente apontadas como sendo as ferramentas adequadas para potenciar ganhos tanto na diferenciação como na otimização.
Depois de uma fase inicial onde, além de um deslumbramento com os potenciais benefícios, houve uma certa confusão sobre o significado e a fronteira inferior da i4.0, várias empresas iniciaram os famosos projectos-piloto na esperança de um dia os verem escalar. Infelizmente um corolário desta estratégia é que os benefícios (e as dificuldades) da solução escalada têm uma visibilidade muito reduzida quando se avalia apenas o impacto do projecto-piloto. Vários continuam no seu purgatório, cumpriram alguns objetivos, mas não todos e com valor insuficiente para justificar uma decisão de investimento para toda a organização.
É aqui que entra a melhoria contínua, de facto o norte verdadeiro do chamado lean não mudou nas últimas décadas (arriscaria até a dizer séculos): os clientes continuam a querer o produto que imaginaram, querem-no de imediato e de preferência com um custo próximo de zero. Este tem sido o motor da melhoria contínua e uma das lições que aprendemos após mais de uma década de i4.0. Sempre que o fazemos surgem programas de digitalização estruturados, que potenciam as sinergias entre projetos (por exemplo partilha de dados e de informações), que se focam nos temas mais importantes para as cadeias de valor, que têm objetivos realísticos relacionados com os indicadores principais do negócio da empresa e que não se centram apenas na tecnologia, incluindo também as dimensões das pessoas (cultura, liderança, organização) e dos processos. Ora se substituirmos na frase anterior a palavra “digitalização” por “melhoria contínua”, a afirmação continua a ser verdadeira. De facto, a digitalização e a melhoria contínua, são muito semelhantes na forma correta de realizar.
A expressão “forma correta de realizar” pode ser percebida como evidente, mas o que a prática nos diz é que utilizar apenas o sentido comum não é suficiente.
Por exemplo, na definição de um processo de planeamento e controlo da produção, não é senso comum desacoplar dois processos com performance distintas (tempo de ciclo, qualidade, disponibilidade) utilizando um supermercado intermédio controlado por um número finito de cartões kanban . Esta é uma solução potencialmente adequada que dificilmente sairia de uma sessão de trabalho com apenas senso comum. O mais normal é o chamado “planear e acender uma vela” onde planeamos sequencialmente cada um dos processos de acordo com a sua performance histórica e depois esperamos que o dia de amanhã siga esse padrão. Normalmente a realidade ataca e terminamos o dia a agradecer às equipas pela capacidade de resolução de problemas urgentes e pela excecional e diferenciadora flexibilidade. No dia seguinte repetimos. Para quebrar este ciclo é importante conhecer métodos e ferramentas adequados para cada desafio e aprender com os erros dos outros.
Com isto não quero dizer que não devamos ter em atenção a velocidade de transformação nos projetos de digitalização. A dimensão pessoal tem uma importância enorme na taxa de sucesso dos projectos de digitalização. Por exemplo, se forçarmos uma solução digital num processo industrial complexo cujos parâmetros são ajustados por operadores especializados com muitos anos de experiência, o mais provável é criarmos um conflito e uma diminuição drástica da tolerância aos erros da tecnologia durante a fase de arranque. Depois de meses a estudar e a criar a solução digital, esta será “encostada” porque de vez em quando faz um ajuste errado. Esta decisão de cancelar está correta, mas melhor que a ter de tomar é organizar o processo de digitalização para que a probabilidade desta situação acontecer seja muito baixa. Estamos, pois, novamente a evidenciar uma semelhança entre as metodologias de digitalização e de melhoria contínua: importa trabalhar a cultura da empresa, adequando o estilo de liderança para empoderar todos na organização a serem os dinamizadoras da melhoria utilizando a dimensão digital.
Já falámos nas semelhanças e vamos agora abordar a complementaridade entre digitalização e melhoria contínua. Os últimos anos têm enfatizado que de facto estas duas metodologias são excelentes parceiros no chão de fábrica. A digitalização (bem feita) permite por exemplo libertar pessoas da tarefa de recolher dados permitindo centrar a sua atenção na sua análise e na tomada de decisões fundamentada. Abro aqui um parêntesis para explicar que adicionei o termo “bem feita”
na frase anterior porque não raras vezes deparamo-nos com “exemplos” de digitalização onde o antigo processo manual é replicado de forma penosa no novo sistema digital. Por exemplo, um cartão kanban que continha todas as informações para permitir a reposição de um componente no bordo de linha é substituído por uma máscara de pedidos de material onde é necessário introduzir penosamente todos os dígitos alfanuméricos do componente necessário. Não só o tempo necessário para esta operação aumentou como a probabilidade de erro do novo processo é elevada. Este é um exemplo a que os escansões da digitalização chamariam digitação (e bem). Em resumo: nem tudo o que é digital é bom.
A complementaridade entre estas metodologias não se esgota neste exemplo, há de facto muitas outras situações onde isto se verifica. A obrigatoriedade de ter um processo bem definido para que possa ser digitalizado implica essa padronização da forma de fazer, pelo que a digitalização funciona aqui como uma espécie de guia durante o processo de desenho e de poka-yoke já na fase de produção. Outro exemplo é a confirmação automática de processos. Um sistema melhorável ne-
cessita: padrão (definição de como realizar determinada operação); confirmação (ou observação); plano de reação rápida (no caso de ser detetado um desvio); resolução eficaz de problemas e comunicação estruturada (novamente dando ênfase à dimensão pessoal da melhoria e da liderança no chão de fábrica). O passo da confirmação de processo, é hoje possível ser realizado de forma digital e com muita frequência, libertando as pessoas para as tarefas de maior valor acrescentado como a resolução dos problemas. Além disso, dado que o custo de realizar confirmações de processo digitais é agora quase nulo, a informação recolhida é assim muito mais completa permitindo análises e conclusões de melhor qualidade.
Não posso concluir sem também referir o benefício significativo que a digitalização e a melhoria contínua têm na sustentabilidade das empresas industriais. É muito frequente verificarmos o alinhamento dos objetivos de melhoria da qualidade e produtividade com os objetivos de redução dos impactos ambientais e o consumo racional de recursos. Por exemplo, os dados da disponibilidade técnica dos equipamentos podem ser utilizados para calcular índices de consumo energético por unidade produzida e para definir de forma mais detalhada o plano de ação para reduzir o consumo energético. A digitalização e a melhoria contínua estão, portanto, no mesmo palco das operações industriais. Não só partilham semelhanças na forma de desenhar e executar os seus programas transformadores como se complementam e reforçam mutuamente em variadíssimas situações das cadeias de valor. É por estas razões que continuamos a abordar estas duas dimensões de forma integrada nas organizações com quem trabalhamos.
por Tiago Costa Dias, Sénior Diretor Kaizen Institute Western Europe
Introdução
Nos últimos anos, a indústria cerâmica tem passado por transformações profundas e estratégicas. Um setor historicamente associado à produção artesanal e a processos manuais está agora a abraçar novas tecnologias e práticas que prometem elevar a eficiência, melhorar a qualidade dos produtos e reduzir os desperdícios. Apesar do crescimento no volume de negócios acumulado nos últimos cinco anos, a indústria enfrenta desafios significativos, como o aumento das importações, que pressionam a competitividade das empresas nacionais. Para se posicionarem de forma mais sólida no mercado global, as indústrias cerâmicas precisam de reforçar a eficiência operacional e apostar em soluções inovadoras.
No centro desta evolução estão duas abordagens complementares que têm transformado a indústria: o Kai-
zen, focado na melhoria contínua, e a Indústria 4.0, que integra tecnologias avançadas para digitalizar e otimizar processos. A convergência destas duas abordagens é crucial para o setor cerâmico alcançar novos patamares de competitividade e sustentabilidade.
Este artigo explora como a metodologia Kaizen, conhecida pelo seu foco na melhoria contínua de processos, pode ser integrada com as tecnologias avançadas da Indústria 4.0 para impulsionar uma verdadeira revolução na indústria cerâmica.
1. O Conceito “Kaizen” e o Modelo de Melhoria
Contínua
Kaizen é uma filosofia de gestão originária do Japão que visa a melhoria contínua de processos, produtos e serviços, promovendo a participação ativa de todos os níveis da organização. O termo, que significa "mudança para melhor" em japonês, reflete a ideia de que pequenas melhorias, implementadas de forma consistente e sistemática, podem resultar em impactos significativos a longo prazo.
Tradicionalmente, a abordagem Kaizen inicia com uma fase de diagnóstico e definição de visão, onde são identificados os problemas existentes e são estabelecidos os objetivos a alcançar. As organizações mais desenvolvidas têm práticas de gestão Kaizen nas suas rotinas diárias, mensais e de revisão estratégica anual, garantindo-lhes uma vantagem competitiva sustentável.
O modelo de melhoria Kaizen pode ser aplicado a diversas áreas dentro de uma empresa cerâmica, incluindo:
• Melhoria da produtividade: através da identificação de gargalos e ineficiências nos processos de produção, aumentando a eficiência operacional e a dos equipamentos, desde os mais importantes, ao nível de Capex como os fornos, até pequenos elementos de acabamento.
• Otimização de recursos energéticos: implementação de projetos para otimização de curvas de fornos, criação de processos de resolução estruturada de problemas, como perdas energéticas, redução de desperdícios de materiais e energia e mitigação de emissões de CO2.
• Aumento da qualidade: identificação e correção de falhas no processo produtivo, com foco na causa raiz e melhoria da percentagem de primeiras.
• Melhoria dos processos de desenvolvimento de produtos: com redução de lead time e desenho de produtos mais alinhados com o consumidor, acelerando o lançamento de coleções, e ganhando vantagem competitiva.
• Melhoria da estratégia e gestão da força de vendas: Modelos, dimensionamento e gestão de equipas, marketing e vendas, dinâmicas de visitas comerciais, integrando equipas físicas e digitais em mercados B2B e B2C.
2. Indústria 4.0: O Impacto das Tecnologias Avançadas no Setor Cerâmico
A Indústria 4.0 e a transformação digital estão a revolucionar o planeamento e controlo da produção, proporcionando maior eficiência e flexibilidade. Tecnologias como Inteligência Artificial (IA), Internet das Coisas (IoT), Big Data, Machine Learning (ML), Robótica Industrial e móvel, Digital Twins e Visão Computacional estão a redefinir as operações empresariais. Estas tecnologias permitem integrar dados em tempo real, automatizar tarefas, programar dinamicamente, prever a procura e planear a capacidade de forma mais eficiente.
A integração de IA no planeamento e sequenciamento da produção otimiza a análise de dados, gera insights acionáveis e melhora o processo de tomada de decisão. Esta nova era transcende os processos tradicionais de planeamento da produção ligando modelos de linguagem (Large Language Models - LLM) a dados operacionais, permitindo decisões baseadas em dados em tempo real. Para a indústria cerâmica, estas tecnologias representam uma oportunidade única de integrar sistemas de produção, monitorização e gestão com maior inteligência e eficiência.
Cada vez mais, os projetos Kaizen na indústria cerâmica incluem soluções 4.0 como modelos com softwares de otimização de planeamento da cadeia de valor, nomeadamente aumentando a ocupação dos fornos com otimização
das sequências de vidragem contribuindo para melhorar os níveis de serviço e reduzir o consumo de vidro. Outro exemplo é aplicação de Visão artificial para deteção de defeitos ou controlo online e integrado de todos os equipamentos. Estas implementações têm possibilitado às empresas alcançar melhorias de desempenho que frequentemente ultrapassam os dois dígitos por ano, reforçando a competitividade e a sustentabilidade operacional.
Ao adotar tecnologias avançadas e fomentar uma cultura de inovação contínua, a indústria cerâmica atinge maior agilidade, eficiência e nível de serviço. Sistemas inteligentes e resilientes de suporte à decisão acompanham de forma holística todas as etapas de produção, rastreando e automatizando operações que vão desde a entrada de matérias-primas, passando pela alimentação das linhas de produção, até ao controlo de qualidade e à embalagem do produto final.
3. Tendências de Mercado na Indústria Cerâmica e como Kaizen-Indústria 4.0 pode ajudar
O mercado global de cerâmica tem enfrentado rápidas mudanças, impulsionado por fatores como novas exigências dos consumidores, pressões económicas, questões ambientais e avanços tecnológicos. Em Portugal, o setor enfrenta desafios significativos, com os custos energéticos elevados, escassez de mão de obra qualificada e a forte concorrência de outros mercados europeus e emergentes. Nestas condições, alcançar ganhos de eficiência não é apenas desejável, mas essencial para a sobrevivência e crescimento das empresas do setor.
Por outro lado, oportunidades promissoras surgem em áreas ainda pouco exploradas, como a sustentabilidade e a economia circular, em resposta à crescente procura por produtos mais sustentáveis e à necessidade de reduzir a pegada ambiental da produção.
A incorporação de práticas alinhadas com os critérios ESG (Ambientais, Sociais e de Governo) tem ganho relevância na indústria da cerâmica, promovendo sustentabilidade, responsabilidade social e eficiência operacional. Apesar dos desafios, a adoção destas práticas reforça a resiliência do setor, promove inovação e contribui para um futuro mais sustentável.
Em paralelo, o uso de Tecnologias como gestão de energia inteligente, uso de materiais recicláveis e a redução de desperdícios em processos de produção contribuem para esta tendência de sustentabilidade.
Nos últimos anos, no setor cerâmico, temos visto a consolidação de uma tendência de implementação de
processos focados na otimização de séries mais curtas, alinhando-se às exigências de personalização crescente e flexibilidade do mercado. Este modelo permite produzir artigos customizados, reduzindo os custos unitários e minimizando sobras de lotes, enquanto otimiza os recursos produtivos.
Modelos de desenho e gestão de armazéns para otimização de processos de picking têm sido desenvolvidos e implementados, assim como algoritmos de otimização de gestão de stocks de matérias-primas, consumíveis e stocks de produto acabado, permitindo às empresas libertação de cash-flow tão importante nos últimos anos com o aumento do custo do capital.
Além disso, temas como a redução de desperdícios de matérias-primas, incluindo vidragem, pastas e outros materiais, tornaram-se cada vez mais cruciais na indústria cerâmica. O aumento dos preços nos mercados internacionais tem intensificado a necessidade de melhorias, transformando estes tópicos numa tendência clara de otimização, reforçando a importância de projetos de melhoria para otimização, desde a ocupação de fornos, e vários outros processos operacionais com peso substancial na estrutura de custos, nomeadamente energéticos, OPEX e CAPEX.
4. Desafios na Implementação de Kaizen e Indústria 4.0 na Indústria Cerâmica
Apesar dos benefícios, a adoção das metodologias Kaizen junto com as tecnologias da Indústria 4.0 traz desafios naturais às organizações.
Um dos princípios centrais do Kaizen é o envolvimento das pessoas nos processos de mudança, reconhecendo-as como o maior ativo das organizações. Sem o seu compromisso e participação, nenhuma transformação pode ser concretizada. Como tal, a implementação de dinâmicas de melhoria, que promovam uma verdadeira mudança cultural, representa um grande desafio. Para superar isso, é essencial o envolvimento e compromisso da gestão a todos os níveis da organização, desde a validação do caminho a seguir até à criação de boas práticas para validar as mudanças implementadas.
Este alinhamento é fundamental no que a literatura define como confirmação de processo. Processos consistentes geram resultados consistentes, uma máxima antiga, mas que orienta a abordagem de um projeto de transformação Kaizen.
5. Conclusão e Resultados
A integração de Kaizen com a Indústria 4.0 está a proporcionar uma transformação radical na indústria ce-
râmica. Com a crescente adoção de tecnologias avançadas como Machine Learning, IoT e Visão Computacional, as empresas cerâmicas podem melhorar continuamente os seus processos e aumentar a eficiência reduzindo custos nomeadamente nas operações de escolha.
Além disso, as tendências de mercado, com maior personalização dos produtos, maior exigência dos clientes e procura por níveis de serviço mais elevados, estão a impulsionar a necessidade de inovação em sustentabilidade, personalização e qualidade, e a Indústria 4.0 fornece as ferramentas essenciais para responder a estas exigências de forma eficaz, permitindo uma produção mais flexível, eficiente e alinhada com as novas expectativas dos consumidores.
A combinação destas duas abordagens — Kaizen e Indústria 4.0 — impulsiona melhorias em todos os aspetos da produção e posiciona as empresas cerâmicas para um futuro mais competitivo e sustentável. Ao integrar a melhoria contínua com tecnologias avançadas, as empresas estão mais preparadas para enfrentar os desafios e aproveitar as oportunidades de um mercado global cada vez mais dinâmico e tecnológico. Garantindo melhores resultados e acima de tudo a sustentabilidade dos mesmos ao longo do tempo.
Mesmo as organizações com resultados robustos e processos estáveis devem reconhecer que o sucesso do passado não garante o sucesso futuro. É fundamental cultivar uma busca incessante por fazer mais e melhor, questionando todos os paradigmas e práticas estabelecidas. Só assim será possível identificar oportunidades valiosas de melhoria, que permitem realizar mais com menos esforço e recursos.
Os projetos Kaizen desenvolvidos com clientes do setor cerâmico têm conduzido a uma melhoria de resultados impactantes para o seu negócio. Ao longo dos últimos 20 anos, com uma atuação em diversas vertentes dessa vasta indústria, destacamos os seguintes resultados médios:
• Produtividade (output/hora): +20 a 25%
• Eficiência Fornos: +15%
• Quebras (% 1ª): -15 %
• Redução Stocks: -35 %
• Nível Serviço: +20 %
• Redução desperdício de Vidro: - 15%
• Redução de quebra: -10%
• Vendas (B2B e B2C): +15%
• Lead Time Desenvolvimento produto: -40 %
O processo de mudança cultural Kaizen nunca termina, apenas se inicia. Os pequenos desafios de hoje, serão os grandes desafios de amanhã…
por Filipa Pereira Silva e Mariana Bem-Haja FAF Sociedade de Advogados
No âmbito da Estratégia Nacional Anti-corrupção 2020-2024 foi aprovado, pelo Decreto-Lei n.º 109-E/2021, de 9 de dezembro, o Regime Geral de Prevenção da Corrupção (doravante, RGPC), que entrou em vigor no dia 7 de junho de 2022, e cujo regime sancionatório vigora desde 7 de junho de 2023.
A obrigatoriedade de disponibilização de canais de denúncia que assegurem a confidencialidade, exaustividade, integridade e a conservação das denúncias – porventura a face daquele Regime mais visível para as empresas – encontra-se em vigor desde o dia 18 de junho de 2022.
Nesta confluência, a Portaria n.º 185/2024/1, de 14 de Agosto – que entrou em vigor 180 dias após a sua publicação, i.e., em 10 de Fevereiro – aprovou o modelo de declaração de inexistência de conflitos de interesses destinada aos membros dos órgãos de administração, dirigentes e trabalhadores das entidades públicas abrangidas pelo Regime Geral da Prevenção da Corrupção.
Ora, o âmbito de aplicação do decreto-lei suprarreferido, previsto no seu artigo 2.º engloba (i) as pessoas coletivas com sede em Portugal que empreguem 50 ou mais trabalhadores e as sucursais em território nacional de pessoas coletivas com sede no estrangeiro que empreguem 50 ou mais trabalhadores; (ii) os serviços e pessoas coletivas da administração direta e indireta do Estado, das regiões autónomas, das autarquias locais e do setor público empresarial que empreguem 50 ou mais trabalhadores, e ainda as entidades administrativas independentes com funções de regulação da atividade económica dos setores privado, público e cooperativo e ao Banco de Portugal. E, por outro lado, obriga ainda aquelas entidades suprarreferidas que não sejam consideradas entidades abrangidas – por não empregarem 50 ou mais
trabalhadores – a adotar instrumentos de prevenção de riscos de corrupção e infrações conexas, de acordo com a sua dimensão e natureza, por forma a promover a transparência administrativa e a prevenção de conflitos de interesses (cfr. n.º 5 do artigo 2.º do RGPC).
Concretamente, a declaração de inexistência de conflito de interesses, elaborada nos termos do artigo 13.º do RGPC, é uma medida destinada “(...) a assegurar a isenção e a imparcialidade dos membros dos respetivos órgãos de administração, seus dirigentes e trabalhadores e a prevenir situações de favorecimento (...)”, considerando-se
conflito de interesses “(...) qualquer situação em que se possa, com razoabilidade, duvidar seriamente da imparcialidade da conduta ou decisão do membro do órgão de administração, dirigente ou trabalhador, nos termos dos artigos 69.º e 73.º do Código do Procedimento Administrativo (...)”.
Deste modo, sendo a implementação da declaração de inexistência de conflitos de interesses obrigatória para as entidades abrangidas pelo RGPC, que empreguem 50 ou mais trabalhadores, o seu uso (ainda que adaptado a cada realidade) configura, ainda, uma boa prática para aquelas entidades que não atinjam o referido número de trabalhadores, porquanto promove transparência e imparcialidade, nos termos do n.º 5 do artigo 2.º do RGPC, permitindo, no mais, evitar situações de favorecimento.
Aquela declaração deverá ser assinada quando estejam em causa matérias de contratação pública, concessão de subsídios, subvenções ou benefícios, licenciamentos urbanísticos, ambientais, comerciais e industriais e procedimentos sancionatórios.
Volvidos dois anos desde a entrada em vigor do Regime Geral de Prevenção da Corrupção, foi disponibilizada, em novembro do presente ano civil, a Plataforma RGPC, gerida pelo MENAC (Mecanismo
Nacional Anticorrupção) na qual se devem registar todas as entidades abrangidas, passando a fazer, por essa via, a inserção de todos os documentos relativos ao cumprimento do Decreto-Lei n.º 109-E/2021, nomeadamente a comunicação dos planos de prevenção de riscos de corrupção e infrações conexas (PPR) e respetivos relatórios, dos códigos de conduta e relatórios de infrações, com identificação das regras violadas, das sanções aplicadas e das medidas adotadas ou a adotar, no âmbito do sistema de controlo interno, que deve ter por base modelos adequados de gestão dos riscos, de informação e de comunicação em todas as áreas de intervenção.
Desde a entrada em vigor do RGPC, Portugal desceu uma posição no índice de perceção de corrupção mundial – o que indica que a opinião geral da população sobre a prática de corrupção por parte de funcionários públicos e políticos piorou – o que não é de estranhar, considerando que a Estratégia Nacional Anticorrupção considerada, à data, um dos objetivos fundamentais do Governo em funções, apenas agora se encontra plenamente funcional.
Estes são, com certeza, mecanismos cuja boa aplicação permitirá distinguir as empresas com procedimentos mais rigorosos e adequados.
NA INDÚSTRIA CERÂMICA: ESTUDO DE CASO
por Odete Monteiro Lopes e Daniel Gaspar, Docentes na ESTGV¹ - Mickael Osório Lopes
Monteiro, Mestrando no ESTGV - Samuel Messias, Mestrando no ISEC² - e André Guimarães, Investigator no CISE³
Introdução
Este estudo de caso aborda a aplicação da metodologia Lean na secção de embalamento de uma indústria cerâmica em Portugal, com foco na melhoria da produtividade e na redução de desperdícios. Foram utilizadas ferramentas Lean , concretamente o 5S, o Diagrama de Spaghetti e o SMED, para reorganizar e otimizar o ambiente de trabalho, aumentando a eficiência operacional e promovendo um espaço mais organizado e seguro.
O projeto iniciou-se com a identificação das causas da baixa produtividade, incluindo a análise do layout e dos fluxos de produtos e colaboradores. O método 5S ajudou a organizar e limpar o espaço de trabalho, en-
quanto o Diagrama de Spaghetti revelou e reduziu movimentos desnecessários, melhorando os fluxos internos. Já o SMED foi aplicado para diminuir os tempos de setup , aumentando a agilidade da linha de embalagem para responder às encomendas dos clientes.
Os resultados foram significativos, com melhorias notáveis na produtividade e na qualidade do trabalho. Este caso demonstra o impacto positivo da metodologia Lean na transformação dos processos industriais, criando valor para a empresa e incentivando uma cultura de melhoria contínua entre os colaboradores.
Visão Geral da Empresa
A empresa, situada na região centro de Portugal, é especializada na produção de loiça de mesa e de forno em cerâmica, destacando-se pela elevada capacidade produtiva e pelo compromisso com a inovação contínua. Com uma produção superior a 30.000 peças diárias, a maior parte destinada à exportação, a empresa tem uma forte presença no mercado internacional.
Com a visão de se consolidar como líder na fabricação de loiça de grés fino em Portugal, a empresa foca-se na qualidade dos produtos e na eficiência dos processos. O compromisso centra-se em satisfazer as exigências dos clientes e em garantir uma produção sustentável. Para alcançar estes objetivos, investe na flexibilidade dos processos produtivos, assegurando elevados padrões de qualidade e eficiência, e incentiva o envolvimento ativo dos colaboradores em iniciativas de melhoria contínua.
Funcionamento da Secção de Embalagem e Desafios
A secção de embalagem é a que encerra o fluxo de produtos, integrando áreas para armazenamento de
produto acabado, materiais de embalagem, três linhas de embalagem e uma zona de expedição. Nesta seçcão, cada produto é preparado, embalado, paletizado e disponibilizado para expedição. O processo começa com a receção do produto acabado da linha de produção; daqui, ou é imediatamente direcionado para uma das linhas de embalagem ou armazenado temporariamente, antes do embalamento.
O layout da secção foi concebido para otimizar o espaço e facilitar o acesso aos materiais necessários. No entanto, desafios como o excesso de materiais e as especificações variadas dos clientes, como tamanhos de
caixas e posições de etiquetas, complicam o fluxo de trabalho. Estas exigências requerem uma gestão eficiente e rigorosa para assegurar o cumprimento dos requisitos de cada encomenda.
A Figura 1 ilustra o layout da secção de embalagem, com as zonas organizadas pela respetiva função. O armazém de produto acabado (área amarelo torrado) é usado para armazenar temporariamente os produtos à espera de embalamento. O armazém de embalagens (área amarela) concentra os materiais necessários para o processo. A zona de embalagem (área vermelha) inclui as três linhas onde os produtos são acondicionados e paletizados, sendo depois encaminhados para a zona de expedição (área verde), que integra o armazém e a área de cargas e descargas.
As exigências específicas dos clientes em relação às embalagens, etiquetas, caixas e acessórios exigem rigor para evitar reclamações. Uma gestão eficiente da equipa e do fluxo de informações e materiais é essencial para assegurar a correta execução do processo, ajustando-se à especificidade de cada cliente:
O processo de embalagem divide-se em quatro fases: (1) selecção de linhas; (2) separação e preparação de material; (3) embalagem e (4) registo e arrumação do material embalado.
Problemas identificados
Os requisitos dos clientes têm vindo a ser cada vez maiores, não apenas na inclusão de peças com um design mais moderno e inovador, mas também com o uso de caixas e acessórios numa embalagem complexa e elaborada. Assim, a quantidade e variedade de material necessário para a embalagem, tanto de caixas, acessórios e peças, está constantemente a crescer. Deste modo, é importante uma boa gestão do material e, acima de tudo, rentabilizar todo o processo de embalagem, no sentido de conseguir um fluxo de produção constante e sem quebras. Assim, tornou-se fundamental analisar todo o processo de embalagem, no sentido de recolher informação em todas as fases do processo e identificar os principais problemas.
Para a identificação das causas, recorreu-se à construção de um diagrama de Ishikawa. Como se pode verificar no diagrama representado na Figura 2, o grande problema identificado trata-se da baixa produtividade, estando aquém do desejado.
As causas, descritas a seguir, encontram-se organizadas em cinco eixos, a saber: ambiente de trabalho, mão de obra, método, material, máquina:
• Ambiente de trabalho – verificava-se um espaço de trabalho lotado, com paletes de produto acabado e produto embalado ao longo da secção, que dificultava a circulação do material necessário à embalagem e a chegada às mãos dos funcionários. O armazém, embora apresentasse áreas satisfatórias para o armazenamento dos produtos e materiais, encontrava-se com uma taxa de ocupação superior a 100%, havendo sempre a necessidade de usar acessos de algumas zonas ou colocar o material em zonas que não são dedicadas ao armazenamento.
• Mão de obra – a secção tem duas funcionárias com a responsabilidade de fazer o abastecimento das três linhas de embalagem, sendo que uma delas era responsável por abastecer peças do produto acabado a entrar em cada linha, e outra para abastecer com material de caixas e acessórios necessários para referência da peça a embalar. Dado à falta de organização da secção com os espaços lotados, esta tarefa de abastecimento causava por vezes atrasos em colocar o material necessário no abastecimento de cada linha, havendo a necessidade de efetuar maiores deslocações dentro do espaço da fábrica e com tempos de procura da palete do material elevados.
A área de preparação/separação de material de cada
linha de embalagem não era respeitada, o material não chegava em tempo útil aos operadores de cada linha, levando muitas vezes a paragens da linha com necessidade dos operadores saírem do seu posto de trabalho em busca do material necessário à embalagem. Ainda relativo à mão de obra, era visível que as três linhas de embalagem se encontravam desequilibradas em relação ao número de trabalhadores.
• Método – verificava-se a falta de organização no que respeitava à disponibilização do material necessário para a peça ou quando havia necessidade de efetuar a troca de peça a embalar, levando assim a paragens prolongadas da linha. Os tempos de setup eram demorados pois não havia uma instrução ou preparação para quando estas ocorriam, sendo que toda a fase de mudança de referência da peça acontecia apenas quando terminava a referência anterior e com a linha completamente parada.
• Material – um dos problemas mais visíveis era a falta de separação deste na área de preparação das linhas. De facto, verificava-se uma área totalmente ocupada com paletes de peças a embalar, paletes de caixas e acessórios sem qualquer tipo de organização e orientação, ocorrendo muitas vezes a necessidade de retirar algumas paletes para se poder aceder a outras.
• Máquinas – relativamente às linhas de embalagem, estas apresentavam alguma falta de afinação para manter um fluxo constante. O que se verificava com alguma frequência era que peças de menor dimensão, quando se deslocavam ao longo do tapete, iam perdendo o seu alinhamento, acabando por embaterem nas laterais de entrada da máquina da lixadeira e polimento. Em consequência, a linha ficava obstruída, levando a paragens constantes e à necessidade de repor a posição das peças.
Propostas de melhoria
Para resolver os problemas identificados, foi analisada a necessidade de reorganizar os processos de embalagem, tornando-os mais simples, rápidos e eficazes. Algumas das soluções encontradas para os problemas identificados, foram as seguintes:
Melhoria no transporte das peças ao longo do tapete nas linhas de embalagem
Para otimizar o fluxo de produção, foram instaladas guias que evitam desalinhamentos e reduzem paragens frequentes (Figura 3), sobretudo no início do tape-
te, onde o movimento é intermitente. Após esta etapa, o tapete opera a uma velocidade constante, assegurando o alinhamento das peças e um fluxo eficiente.
Reforço da mão de obra e novas funções para os operadores
Foram adicionados novos operadores às linhas de embalagem, sendo designado um chefe de linha para cada uma. O chefe de linha ficou responsável por garantir a disponibilidade de materiais, comunicar avarias e preparar setups. Estas mudanças reduziram paragens, otimizaram os tempos de preparação e aumentaram o fluxo de produção.
Adaptação do posto de trabalho
A antiga bancada de trabalho foi substituída por um modelo mais funcional, com áreas específicas para caixas, fita-cola, resíduos e acessórios, conforme ilustra a Figura 4. Após testes, os operadores aprovaram o novo design, que foi validado como padrão para todas as linhas.
Ferramentas Lean Aplicadas
Para enfrentar os desafios da secção de embalagem, foram implementadas três ferramentas Lean com impacto significativo na organização e produtividade:
• 5S : Esta metodologia, composta por cinco etapas (Utilização, Arrumação, Limpeza, Padronização e Disciplina), foi aplicada para organizar o espaço de trabalho, reduzindo desperdícios e melhorando a acessibilidade aos materiais. A implementação do 5S resultou num ambiente mais seguro e organizado, otimizando o fluxo de trabalho e diminuindo o tempo gasto na procura de materiais. Esta abordagem criou um espaço onde os colaboradores realizam as suas tarefas de forma mais eficiente e produtiva (ver Figura 5).
• Diagrama de Spaghetti : Esta ferramenta foi usada para mapear o fluxo de movimentação de operadores e materiais na secção de embalagem, identificando e eliminando trajetos desnecessários que dificultavam o trabalho. A análise revelou áreas com movimentação excessiva, permitindo ajustes que reduziram o tempo de deslocação em cerca de 69%, melhorando o layout e a logística interna da secção (ver Figura 6).
• SMED (Single Minute Exchange of Die): Esta metodologia foi aplicada para reduzir o tempo de setup na máquina de carimbar, minimizando paragens e aumentando a flexibilidade nas trocas de produto. Com técnicas de simplificação e padronização, o tempo de setup foi reduzido de 13 minutos para cerca de 4 minutos e 50 segundos, uma melhoria de 60%, permitindo maior agilidade na adaptação às variações de produção e aos requisitos dos clientes (ver Figura 7).
Resultados e Impactos das Melhorias Implementadas
A aplicação das metodologias Lean na secção de embalagem gerou melhorias significativas em vários indicadores de desempenho:
• Redução do Tempo de Setup : Com a implementação do SMED, o tempo médio de setup foi reduzido em cerca de 60%, passando de 13 minutos para aproximadamente 4 minutos e 50 segundos. Esta eficiência trouxe maior flexibilidade nas trocas de produtos, facilitando adaptações na produção e minimizando paragens.
• Aumento da Produtividade : A otimização dos processos resultou num aumento médio de 15% na quantidade de peças embaladas, conforme os dados mensais de produção, evidenciando um melhor aproveitamento dos recursos.
• Otimização do Espaço de Trabalho : A aplicação do 5S e a reorganização do layout criaram um ambiente mais limpo, organizado e funcional. A localização estratégica dos materiais reduziu o tempo de deslocamento dos operadores, promovendo um fluxo de trabalho contínuo, seguro e eficiente.
As ações implementadas aumentaram a produtividade, melhoraram a eficiência no embalamento e reduziram desperdícios e paragens. A organização dos espaços e o
abastecimento direto de consumíveis tornaram os processos mais dinâmicos, enquanto a padronização minimizou erros e reclamações.
Conclusão e Recomendações Futuras
Este estudo de caso evidencia o impacto da metodologia Lean na melhoria da produtividade e eficiência de uma secção industrial. Ferramentas como o 5S, o Diagrama de Spaghetti e o SMED, aplicadas na secção de embalagem, geraram resultados significativos. Estas iniciativas organizaram o ambiente de trabalho, reduziram desperdícios, otimizaram processos e aumentaram a capacidade produtiva, contribuindo para a satisfação dos colaboradores.
Os resultados mostram que a eliminação de desperdícios e a melhoria contínua são eficazes para enfrentar desafios operacionais, promovendo uma cultura de eficiência e responsabilidade. O 5S ajudou a organizar o espaço de trabalho e a melhorar o fluxo de materiais, enquanto o SMED reduziu o tempo de setup, aumentando a flexibilidade e a capacidade de resposta às exigências do mercado.
Para manter os ganhos alcançados e assegurar a melhoria contínua, é fundamental investir na formação dos colaboradores. A construção de uma cultura Lean requer o envolvimento de toda a organização e uma compreensão sólida dos princípios de melhoria contínua. Auditorias regulares de 5S e outras práticas Lean são recomendadas para garantir a adesão aos processos padronizados e identificar novas oportunidades de melhoria. Além disso, a empresa deve continuar a explorar novas ferramentas e métodos Lean, em toda a fábrica, que complementem as práticas existentes, adaptando-se às necessidades do mercado e dos clientes. Este compromisso com a filosofia Lean e a melhoria contínua permitirá à empresa manter os resultados obtidos, estimular a inovação e reforçar a sua competitividade no setor cerâmico.
por Henrique Marçal , CEO na TheLeanSix Sigma Company Portugal e Brasil
A melhoria contínua é um modo de vida. Desconheço uma melhor descrição para este “ mindset ”que é verdadeiramente fundamental para a evolução das empresas.
Praticar melhoria contínua é essencial para a competitividade das empresas dos mais variados setores, sendo que para a indústria cerâmica não é diferente.
O avanço da tecnologia, juntamente com a crescente pressão por eficiência, inovação e sustentabilidade, faz com que as empresas do setor da cerâmica precisem adotar boas práticas de melhoria contínua, não apenas para manter a sua posição no mercado, mas também para conseguir reagir e antecipar mudanças, através da melhoria constante dos seus processos.
No contexto da indústria cerâmica, a melhoria contínua pode ser aplicada a diversas áreas, nomeadamentea produção, o controlo de qualidade, a gestão de resíduos e a sustentabilidade ambiental.
Vantagens da Aplicação da Melhoria Contínua na Indústria Cerâmica
i. Melhoria no Processo de Produção
A produção cerâmica envolve várias etapas complexas, desde a preparação das matérias-primas até a queima final dos produtos. A melhoria contínua pode ser aplicada em diversas fases do processo produtivo, com foco na redução de desperdícios, aumento da eficiência e melhoria da qualidade do produto.
• Redução de Desperdícios: A indústria cerâmica é, por natureza, um setor que gera uma quantidade considerável de resíduos, seja em forma de matéria-prima não utilizada, seja devido a defeitos nos produtos. Através de ajustes nos processos de mistura de materiais ou de melhorias no controlo de temperaturas e do tempo de queima pode-se melhorar substancialmente o processo produtivo.
• Aumento da Eficiência Energética: A queima de cerâmica é um dos processos mais intensivos em termos de consumo energético de uma unidade industrial. Neste sentido, o aumento da eficiência energética ganha uma importância vital no processo produtivo. A monitorização e controlo em tempo real da temperatura, humidade e pressão são algumas das
técnicas que permitem a otimização do consumo de energia nos fornos e secadores.
ii. Melhoria no Controlo de Qualidad e
O controlo de qualidade é uma área crítica e sensível em qualquer indústria. Na indústria cerâmica, com toda a sua componente mais artesanal e de exclusividade, um produto defeituoso pode gerar grandes perdas financeiras e, principalmente, causar danos reputacionais irreversíveis para as empresas. A melhoria contínua desempenha um papel muito importante no aperfeiçoamento dos processos de controlo de qualidade, garantindo que os produtos finais vão ao encontro dos padrões e requisitos exigidos pelos clientes, garantindo também o cumprimento da legislação aplicada. São bons exemplos, o trabalho padronizado, ou “normalização”, assim como a autonomação (Jidoka) de processos críticos.
Também escutar a Voz do Cliente (VoC – Voice of the Customer) sobre a qualidade dos produtos cerâmicos é uma excelente forma de impulsionar melhorias. As equipas de gestão de cliente e de produção devem trabalhar juntas na resolução de problemas e na melhoria contínua dos seus produtos.
iii. Sustentabilidade e Impacto Ambiental
A indústria cerâmica enfrenta uma crescente pressão no sentido de se adaptar a normas ambientais mais rigorosas e adotar práticas sustentáveis. Nesse contexto, a melhoria contínua tem também um papel vital na transformação das operações, reduzindo o seu impacto ambiental. A utilização de tecnologias mais limpas, como fornos mais eficientes e sistemas de captura de carbono podem ajudar a reduzir significativamente a emissão de gases poluentes. Também ao nível da gestão de resíduos as empresas se podem tornar mais eficientes e sustentáveis, através da reutilização de argilas e/ou outros subprodutos resultantes do processo de fabrico.
iv. Inovação e Desenvolvimento de Produtos
A inovação é um fator crucial para a indústria cerâmica, especialmente com o aumento da competitividade e das constantes mudanças nos padrões de consumo. Também aqui a melhoria contínua desempenha um papel fundamental, trabalhando em sinergia direta com as áres de I&D, na pesquisa e desenvolvimento de novos produtos cerâmicos.
À semelhança do impacto que criou na indústria automóvel na sua génese, também na indústria cerâmi-
ca a melhoria contínua se tem mostrado altamente relevante ao nível da customização e personalização dos produtos. Através do desenvolvimento de sistemas que permitam uma produção mais flexível e adaptada às necessidades dos clientes, não comprometendo lead times de entrega ou a qualidade do produto.
O Papel das Pessoas na Melhoria Contínua
A verdadeira essência da melhoria contínua reside nas PESSOAS.
Embora a tecnologia e os processos sejam elementos fundamentais, são as pessoas que identificam problemas, sugerem soluções, implementam as melhorias, e têm a verdadeira capacidade de fazer a transformação acontecer. A mudança cultural dentro de uma organização, promovida por pessoas motivadas e capacitadas, é o que sustenta verdadeiramente a melhoria contínua.
1. Cultura de Colaboração e de Engagement
Na indústria cerâmica, a melhoria contínua não pode ser vista apenas como uma responsabilidade da gestão ou dos setores de produção. Todos os níveis da organização precisam estar comprometidos com o objetivo de melhorar continuamente. Isso significa criar uma cultura de colaboração, onde as pessoas se sintam incentivadas a compartilhar ideias, identificar fragilidades nos processos e sugerir melhorias.
• Participação ativa: Envolver os trabalhadores na solução de problemas e na busca por inovações é crucial. As pessoas que estão diretamente no chão de fábrica, por exemplo, têm uma visão absolutamente
crucial sobre o que pode ser melhorado nos processos diários.
• Engagement : A liderança deve promover uma comunicação aberta e incentivar os colaboradores e a fomentar o seu envolvimento no processo de melhoria, mostrando que as suas contribuições são altamente valiosas para o sucesso da empresa.
2. Capacitação e Formação Contínua
Investir nas pessoas é fundamental para que a melhoria contínua seja bem sucedida. Os colaboradores devem ser capacitados para identificar áreas de melhoria, aplicar novas técnicas e adotar tecnologias emergentes. Programas de formação contínuos, e bem estruturados ajudam a garantir que os trabalhadores se mantêm atualizados com as melhores práticas do setor.
• Desenvolvimento de Skills : As empresas cerâmicas devem oferecer oportunidades constantes de desenvolvimento, através de cursos, workshops e outras formações técnicas mais específicas, estimulando a criatividade e capacidade das suas equipas para a implementação de boas práticas de melhoria contínua.
• Empowerment: Ao dar autonomia aos colaboradores para tomarem decisões informadas sobre como melhorar os processos, a empresa fortalece o sentimento de pertença e de responsabilidade.
3. Inovação Através das Pessoas
A capacidade de inovação é uma parte essencial da melhoria contínua. As pessoas são fonte de novas ideias e de soluções criativas, sendo o seu envolvimento no processo de inovação essencial para que a empresa se consiga adaptar às novas exigências do mercado, garantindo assim uma maior competitividade.
Muitas inovações vêm de colaboradores que observam as rotinas de trabalho no “Gemba” (expressão japonesa que significa o “local real”, ou seja, o lugar onde as coisas acontecem”), e percebem de que forma as podem tornar mais eficientes. Programas de sugestões de melhoria , onde os colaboradores podem apresentar as suas ideias, são uma excelente forma de fomentar a inovação e a melhoria contínua.
Melhoria Contínua é Trabalho Duro
Atenção! Desengane-se quem pensa que melhoria contínua é fácil. Melhoria contínua é trabalho duro, e exige visão, estratégia, estrutura, liderança, e uma boa dose de resiliência.
Sabemos que os recursos são cada vez mais limitados. Sabemos também que os recursos para a melhoria contínua, são ainda mais limitados. Isto significa que, tudo o que fazemos em melhoria contínua tem de estar orientado à estratégia da organização. Por outras palavras, deve estar diretamente ligado às “dores da gestão”, pois quando a dor é grande os recursos acabam eventualmente por aparecer.
Não há uma fórmula de sucesso “ one fits all ” para a implementação com sucesso da melhoria contínua. Ainda assim, através de uma combinação de abordagens Bottom Up e Top Down , acredito que estaremos sempre mais perto de obter bons resultados.
Na abordagem Bottom Up , pequenos problemas são identificados diariamente “no terreno” pelas pessoas que trabalham diretamente nos processos, e são posteriormente levados à gestão para tomada de decisão e priorização. Muita gente envolvida em pequenas melhorias feitas diariamente, levando à criação de uma cultura de melhoria contínua.
Na abordagem Top Down os desafios e/ou problemas são identificados pela gestão de topo e são posteriormente desdobrados pela organização através de projetos estratégicos de elevado impacto para a organização.
Em suma, a melhoria contínua é um dos pilares estratégicos fundamentais para a competitividade e sustentabilidade de qualquer indústria, e em particular para a indústria cerâmica.
Presente em 35 países, o Grupo The Lean Six Sigma Company é a empresa líder na Europa em formação, certificação, coaching e deployment na área da melhoria contínua, em particular nas áreas do Lean e do Six Sigma Em Portugal desde 2020, e fazendo parte do Grupo Reshape Solutions , a The Lean Six Sigma Company Portugal já teve a oportunidade de dar formação para mais de 15000 pessoas, certificar mais de 5000 profissionais, e colaborar com várias empresas de diversos setores nas áreas da formação e consultoria em Melhoria Contínua.
O nosso propósito é: Inspirar Pessoas, Transformar Processos e Desafiar Resultados! Rumo a um futuro de excelência!
por Cristiana Costa Claro, Técnica Especialista de Ambiente, Sustentabilidade e Assuntos Europeus
As Jornadas Europeias da Cerâmica, organizadas pela Associação Europeia Cerame-Unie (CU),realizaram-se de 2 a 4 de dezembro, em Bruxelas.
Este foi um evento de excelência com diferentes reuniões setoriais, a Assembleia Geral e um Conselho de Presidentes da Cerame-Unie, bem como reuniões plenárias do Fórum de Cerâmica do Parlamento Europeu (EPCF) e uma Conferência Pública.
A sessão plenária do EPCF, organizada no dia 3 de dezembro pela Presidente do EPCF, Elisabetta Gualmini, contou com a participação de membros do Parlamento Europeu, funcionários da UE e dos Estados-Membros, bem como executivos representantes da indústria. Esta sessão foi composta por dois painéis de debate centrados em temas críticos como o Clean Industrial Deal (Acordo Industrial Limpo), o comércio da UE, a competitividade global e o futuro do setor da construção da UE.
No primeiro painel do EPCF destacou-se a importância das políticas comerciais da UE como ferramenta de reforço para a indústria transformadora europeia. Fo -
ram discutidas estratégias para aumentar a competitividade da UE através de instrumentos comerciais tradicionais e outros mais inovadores que sejam adaptados aos novos desafios económicos e regulamentares.
O segundo painel discutiu as estratégias da UE para enfrentar esta crise, destacando a promoção da construção sustentável e acessível. Os palestrantes avaliaram as ferramentas financeiras e regulamentares disponíveis e sugeriram soluções para melhorar as condições de vida dos europeus, promovendo simultaneamente a sustentabilidade na construção.
Estas reuniões foram seguidas pelo cocktail e jantar EPCF, durante o qual Heimo Scheuch foi formalmente apresentado como novo presidente da Cerame-Unie para o mandato de 2025-2027. Neste momento, foi oferecida uma chave simbólica feita em cerâmica através de impressão 3D gentilmente desenvolvida e oferecida pelo CTCV (Centro Tecnológico da Cerâmica e do Vidro).
No discurso do atual Presidente da Cerame-Unie, Alain Delcourt afirmou que apesar dos esforços do setor
Associativismo
para descarbonizar os seus processos “a competitividade da indústria cerâmica é fortemente prejudicada pelos elevados preços de energia e pelo aumento dos custos de carbono, sem ter acesso a fontes de energia e redes descarbonizadas dentro dos prazos impostos pelos regulamentos da UE, como o CELE.”
A indústria cerâmica europeia apelou à consideração sobre a transição nas indústrias heterogéneas e de elevada intensidade energética, no âmbito do Clean Industrial Deal.
O Clean Industrial Deal será conhecido no final dos primeiros 100 dias de mandato da nova Comissão Europeia, ou seja, final de fevereiro de 2025. Espera-se que este acordo reflita e aborde necessidades adaptadas aos setores heterogéneos.
Durante a Conferência Pública os oradores discutiram sobre a competitividade em toda a cadeia de valor na Europa,destacando-se alguns desafios, tais como:
► Necessidade de condições de concorrência justas a nível global
► Simplificação da regulamentação
► Diminuição dos encargos administrativos
► Escassez de recursos com competências adequadas às necessidades
► Necessidade de assegurar preços de energia competitivos
► Apoios para a descarbonização da indústria
Destaca-se ainda a tomada de posse do novo presidente da Federação Europeia CET (EuropeanCeramic Tiles), dos pavimentos e revestimentos cerâmicos, Graziano Verdi.
A indústria cerâmica portuguesa esteve representada neste evento através da técnica da APICER, Cristiana Costa Claro.
por Cristiana Costa Claro, Técnica Especialista de Ambiente, Sustentabilidade e Assuntos Europeus
Enquadramento
O WCTF - World Ceramic Tiles Forum (Fórum Mundial do Azulejo Cerâmico) foi criado em 1994 e é o encontro anual dos fabricantes de pavimento e revestimento cerâmico a nível mundial . O WCTF é uma plataforma aberta a todos os fabricantes de pavimento e revestimento cerâmico do mundo.
O WCTF é composto por membros que representam mais de 30 países de 5 continentes.
Este Fórum foi criado para facilitar e promover a discussão de questões de interesse comum, nomeadamente:
► Tendências nacionais e globais de consumo e produção de pavimento e revestimento cerâmico;
► Questões de normalização nacional ou internacional (ISO TC 189);
► Principais desenvolvimentos regulatórios que afetem a competitividade do sector;
► Estatísticas comerciais, barreiras ao comércio, revisão dos códigos SH/alfandegários;
► Sustentabilidade, desempenho ambiental, iniciativas regionais que promovem pavimento e revestimento cerâmico;
► Aumentar o conhecimento e a visibilidade mundial do pavimento e revestimento cerâmico.
O Fórum anual discute as tendências globais na produção e consumo de pavimentos e revestimentos cerâmicos. Além das análises globais e europeias, os países participantes do WCTF partilham ainda informações sobre as tendências nacionais e os quadros regulamentares que afetam o setor.
WCTF 2024
O “ World Ceramic Tile Forum 2024 ” (WCTF) realizou-se de 18 a 20 de novembro, no Hotel Montebelo da Vista Alegre, em Ílhavo, evento promovido pela associação europeia da indústria cerâmica, a Cerame-Unie, e organizado pela APICER em colaboração com o CTCV (Centro Tecnológico da Cerâmica e do Vidro).
O evento contou com a presença de representantes de 12 países (Portugal, Austrália, Brasil, China, Indonésia, Itália, Japão, México, Espanha, Turquia, Ucrânia, Estados Unidos da América) e 1 representante da União Europeia. A indústria nacional esteve representada pela APICER, empresários e fabricantes deste subsetor.
O WCTF 2024 foi um evento de excelência, que permitiu aos participantes discutirem as tendências globais do comércio dos revestimentos cerâmicos , bem como os desenvolvimentos comerciais , a monotorização da implementação dos códigos aduaneiros do Sistema Harmonizado (HS) revistos para os revestimentos cerâmicos (em vigor, desde 2017).
Foi ainda discutida a relevância da informação dada ao consumidor sobre a origem dos revestimentos,
nomeadamente através de rotulagem, tendo sido considerada uma ferramenta essencial para cumprir os requisitos de sustentabilidade da UE e internacionais.
Durante o evento foram ainda temas de discussão os desenvolvimentos e tendências atuais da Inteligência Artificial (IA), das tecnologias de descarbonização e circularidade , da saúde e segurança , e do clima e energia face ao contexto atual de esforços para a sustentabilidade social, ambiental e económica mundial.
No âmbito do WCTF 2024 os participantes tiveram ainda a oportunidade de visitar a Primus Ceramics e conhecer o primeiro secador de impacto zero. Este secador é alimentado 100% com eletricidade produzida a partir de fontes renováveis, funcionando tanto em modo full eletric , como em modo metano, ou em modo “híbrido”.
Durante o Fórum, José Luis Lanuza, presidente do WCTF desde 2014, foi congratulado pela excelência, empenho e liderança. A partir de 2025, o WCTF será presidido pelo novo presidente do CET (Federação Europeia dos Pavimentos e Revestimentos Cerâmicos), Graziano Verdi, CEO do grupo ITALCER.
O WCTF foi organizado em parceria com as reuniões da ISO TC 189, evento onde foram discutidas questões de normalização técnica, nos diferentes grupos de trabalho.
O próximo WCTF e as reuniões da ISO CT 189 terão lugar na Malásia, em novembro de 2025, com data e local a serem anunciados brevemente. Associativismo
por Albertina Sequeira, Vice-Presidente Executiva da Apicer
PORCEL
Celebração do 37º aniversário da Porcel com Inauguração especial
No dia 19 de novembro a Porcel celebrou o seu 37º aniversário, uma data especial que coincide com o nascimento do seu fundador, o Comendador Eng. Adolfo Roque. A ocasião foi marcada por um momento único: a apresentação de uma obra de arte no jardim da empresa, intitulado Panteão da Porcelana , Esta peça, criada pela renomada artista alemã Regina Frank, é o resultado de meses de colaboração criativa, simbolizando a dedicação e o espírito inovador que definem a história de Porcel.
A peça é uma expressão de respeito pela herança da porcelana, simbolizando tradição e inovação — valores fundamentais que orientam a marca Porcel, e que estão cada vez mais direcionados para os ideais de sustentabilidade.
A obra homenageia a durabilidade e o valor da porcelana ao longo de várias gerações, reforçando a importância de manter viva a cultura e o valor das experiências partilhadas. Assente numa saia composta por pratos de porcelana, a figura feminina é adornada com flores brancas e douradas e linhas azuis. Inspirada pela história do artesanato e pela mesa-redonda do Rei Artur,
“Panteão da Porcelana” sugere democracia, partilha e igualdade, conceitos intrínsecos ao círculo. Remete ainda para momentos de celebrações familiares onde a porcelana desempenhava um papel central, promovendo uma reflexão sobre a importância de objetos duradouros num mundo cada vez mais descartável.
Sobre a Artista: Regina Frank (n. 1965, Alemanha) trabalha com tapeçaria, pintura, escultura, instalação, filme, fotografia e performance e tem exposto em várias instituições globais como o MAAT, o Pavilhão do Conhecimento e a Web Summit em Lisboa e em outras cidades como Londres no Serpentine Gallery, New York no New Museum, Los Angeles no MOCA e Tóquio no Wacoal Art Center.
O projeto é um reflexo da trajetória da empresa e um tributo a todos os que contribuíram para o crescimento da Porcel ao longo dos anos.
RECER
A escolha natural para projetos elegantes Inspirada na sóbria elegância do estilo escandinavo, Opal é uma coleção com efeito de madeira, que alia tonalidades suaves e o aspeto de carvalho limpo, sem veios demasiado expressivos. Oferece uma base
rica, mas uniforme, ideal para projetos que privilegiam uma estética minimalista, criando espaços harmoniosos e envolventes.
Espaços Originais com Opal
A coleção é complementada por um revestimento decor 3D que apresenta um jogo original de volumetrias geométricas, criando efeitos de luz e profundidade que acrescentam conforto e distinção aos espaços.
Notícias & Informações
SAINT-GOBAIN
Saint-Gobain em Portugal expande universo digital com novo website integrado que reforça sustentabilidade e presença do Grupo no país
Com um design renovado, novos conteúdos e uma navegação friendly, interativa e completa a Saint-Gobain em Portugal dá mais um importante passo na sua transformação digital com o lançamento de um novo website que agrega o universo corporativo, com informação do Grupo e das diferentes marcas presentes em Portugal. O novo website já está disponível em saintgobain.pt
Com o objetivo de reforçar a sua presença num mundo cada vez mais global e digital, a Saint-Gobain em Portugal investe num novo website com um espaço dedicado a promover áreas em que aposta afincadamente, como o employer branding e a sustentabilidade, e onde os utilizadores poderão encontrar conteúdos como ofertas de emprego, a importância e o caminho que a empresa está a percorrer no que à sustentabilidade diz respeito, informação sobre o Concurso de Estudantes de Arquitetura Saint-Gobain e, ainda, todas as empresas e marcas que fazem parte do Grupo em Portugal.
A nova plataforma disponibiliza ainda uma área dedicada às soluções do universo de marcas da Saint-Gobain Portugal S.A. – Isover, Placo®, Weber – e, ainda, às soluções Climalit® da Saint-Gobain Glass. Nesta secção, os profissionais poderão aceder a um novo calculador de consumo nas páginas de produto que oferece resultados ainda mais precisos sobre as quantidades de produto necessárias para os diferentes projetos.
Com um design renovado, novos conteúdos e uma navegação friendly, interativa e completa, este novo website reflete a identidade da marca, as suas ambições e o seu posicionamento no mercado.
"Na Saint-Gobain em Portugal temos investido cada vez mais no ambiente digital, acreditando que este canal é essencial para fortalecer a nossa relação com diferentes públicos, incluindo clientes e parceiros. Este investimento também apoia o posicionamento que procuramos no mercado, onde nos destacamos pela inovação ", afirma Magali Gagliano, Diretora da Saint-Gobain Solutions.
Além de um design modernizado que mantém a identidade corporativa do Grupo Saint-Gobain, cada detalhe é cuidadosamente pensado para transmitir com clareza o propósito e os valores da multinacional francesa, oferecendo uma navegação intuitiva e otimizada. Notícias &
BAU’2025 (Materiais de Construção)
Anual – Munique (Alemanha) De 13 a 18 de Janeiro de 2025 bau-muenchen.com/en/
MAISON & OBJET’2025 (Cerâmica Utilitária e Decorativa)
Bianual – Paris (França) De 16 a 20 de Janeiro de 2025 maison-objet.com
THE INTERNATIONAL SURFACE EVENTE 2025 - (Ladrilhos cerâmicos)
Bianual – Las Vegas (EUA)
De 27 a 30 de Janeiro de 2025 https://www.intlsurfaceevent.com/
SURFACE DESIGN SHOW’2025 (Ladrilhos Cerâmicos)
Anual – Londres (R.U.)
De 4 a 6 de Fevereiro de 2025 surfacedesignshow.com/
AMBIENTE’2025 (Cerâmica Utilitária e Decorativa)
Anual – Frankfurt (Alemanha) De 07 a 11 de Fevereiro de 2025 ambiente.messefrankfurt.com
CEVISAMA’2025 (Ladrilhos Cerâmicos)
Anual – Valencia (Espanha) De 24 a 28 de Fevereiro de 2025 cevisama.feriavalencia.com
NKBA|KBIS’2025 (Cerâmica Sanitária e Ladrilhos Cerâmicos)
Anual – Las Vegas (USA)
De 25 a 27 de Fevereiro de 2025 https://kbis.com/
THE INSPIRED HOME SHOW’2025 (Cerâmica Utilitária e Decorativa)
Anual – Chicago (EUA) De 2 a 4 de Março de 2025 theinspiredhomeshow.com
EXPOREVESTIR’2025 (Ladrilhos Cerâmicos)
Anual – São Paulo (Brasil) De 11 a 14 de Março de 2025 exporevestir.com.br/
ISH’2025 (Cerâmica Sanitária)
Bianual – Frankfurt (Alemanha) De 17 a 21 de Fevereiro de 2025 ish.messefrankfurt.com/frankfurt/en.html
HIP HORECA PROFESSIONAL EXPO’2025 (Restauração)
Anual – Madrid (Espanha) De 10 a 12 de Março de 2025 expohip.com/en/
The New York Tabletop Show´2025 (Cerâmica Utilitária e Decorativa)
Bianual – New York (EUA)
De 8 a 11 de Abril de 2025 tabletopassociationinc.com
TEKTONICA’2025 (Construção)
Anual – Lisboa (Portugal)
De 10 a 12 de Abril de 2025 tektonica.fil.pt/
SALONE DEL MOBILI’2025 (Design/Tendências)
Anual – Milão (Itália) De 18 a 13 de Abril de 2025 salonemilano.it
COVERINGS’2025 (Ladrilhos Cerâmicos)
Anual – Orlando (USA) De 29 de Abril a 02 Maio de 2025 coverings.com/
THE HOTEL SHOW’2025 (Cerâmica Utilitária e Decorativa)
Anual – Dubai (EAU)
De 27 a 29 de Maio de 2025 thehotelshow.com/
The National Restaurant Show.com’2025 (Cerâmica Utilitária )
Anual – Chicago (USA) De 17 a 20 de Maio de 2025 nationalrestaurantshow.com
CONSTRUMAT’2025 (Construção)
Anual – Barcelona (Espanha) De 20 a 22 de Maio de 2025 construmat.com
3DAY´S OF DESIGN’2025 (Design/Tendências)
Anual – Copenhaga (Dinamarca) De 18 a 20 de Junho de 2025 3daysofdesign.dk/
MAISON & OBJET’2025 (Cerâmica Utilitária e Decorativa)
Bianual – Paris (França) De 04 a 08 de Setembro de 2025 maison-objet.com
CERSAIE’2025 (Ladrilhos Cerâmicos)
Anual – Bolonha (Itália)
De 22 a 26 de Setembro de 2025 cersaie.it
HOST MILANO’2025 (Restauração)
Anual – Milão (Itália)
De 17 a 21 de Outubro de 2025 host.fieramilano.
DECOREX’2025 (Design/Tendências)
Anual – Londres (UK) De 12 a 15 de outubro de 2025 decorex.com
UNICERA ‘2025 (Materiais de Construção)
Anual – Istanbul (Turquia) De 03 a 11 de Novembro de 2025 unicera.com.tr
MAIS CONCRETA’2025 (Construção / Tendências para arquitetura e interiores)
Anual – Porto (Portugal) De 06 a 07 de Novembro de 2025 concreta.exponor.pt/
LONDON BUILD ‘2025 (Materiais de Construção)
Anual – Londres (UK) De 19 a 20 de Novembro de 2025 londonbuildexpo.com
BIG 5 SHOW´2025 (Materiais de Construção)
Anual – Dubai (EAU) De 24 a 27 de Novembrode 2025 www.thebig5.ae/