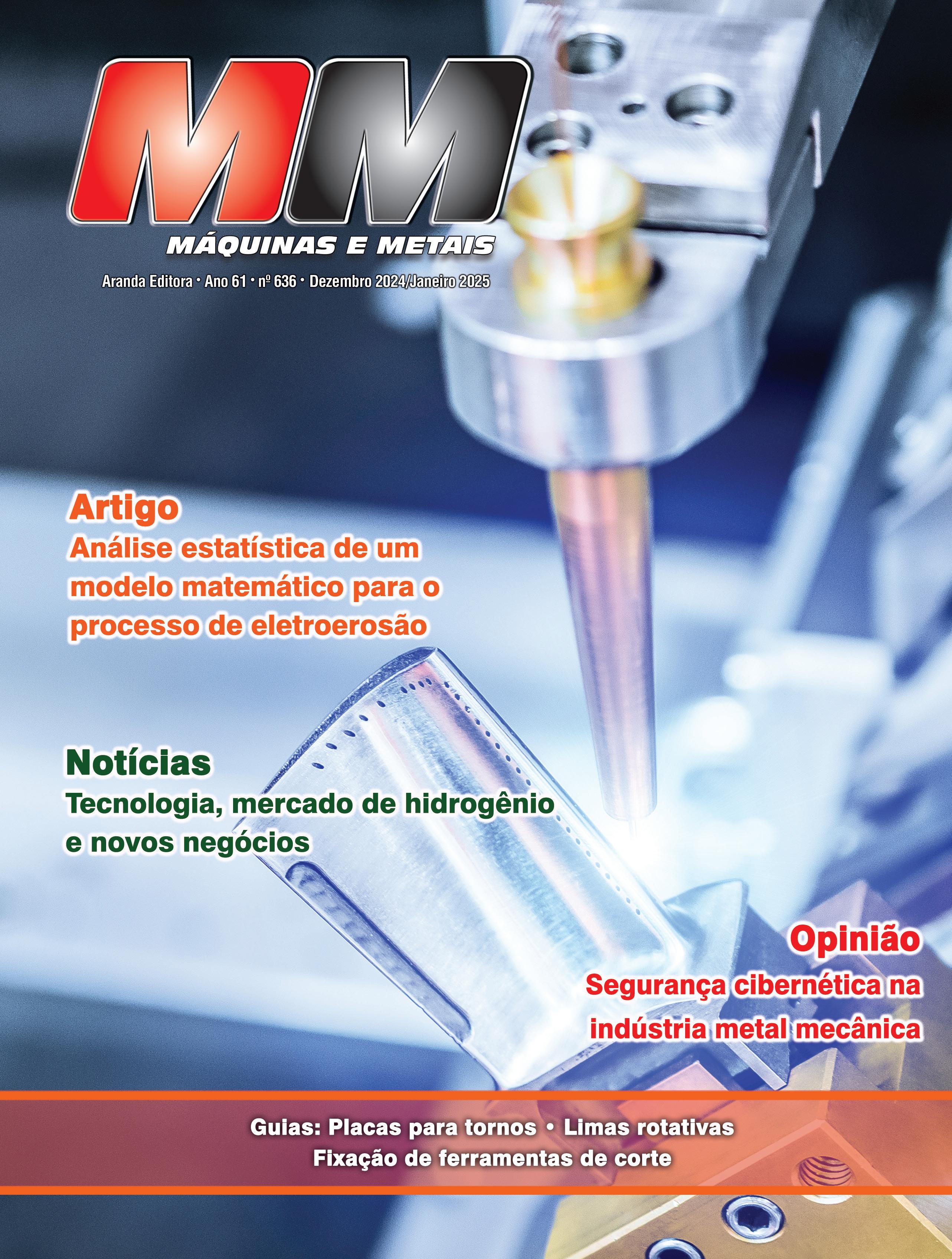
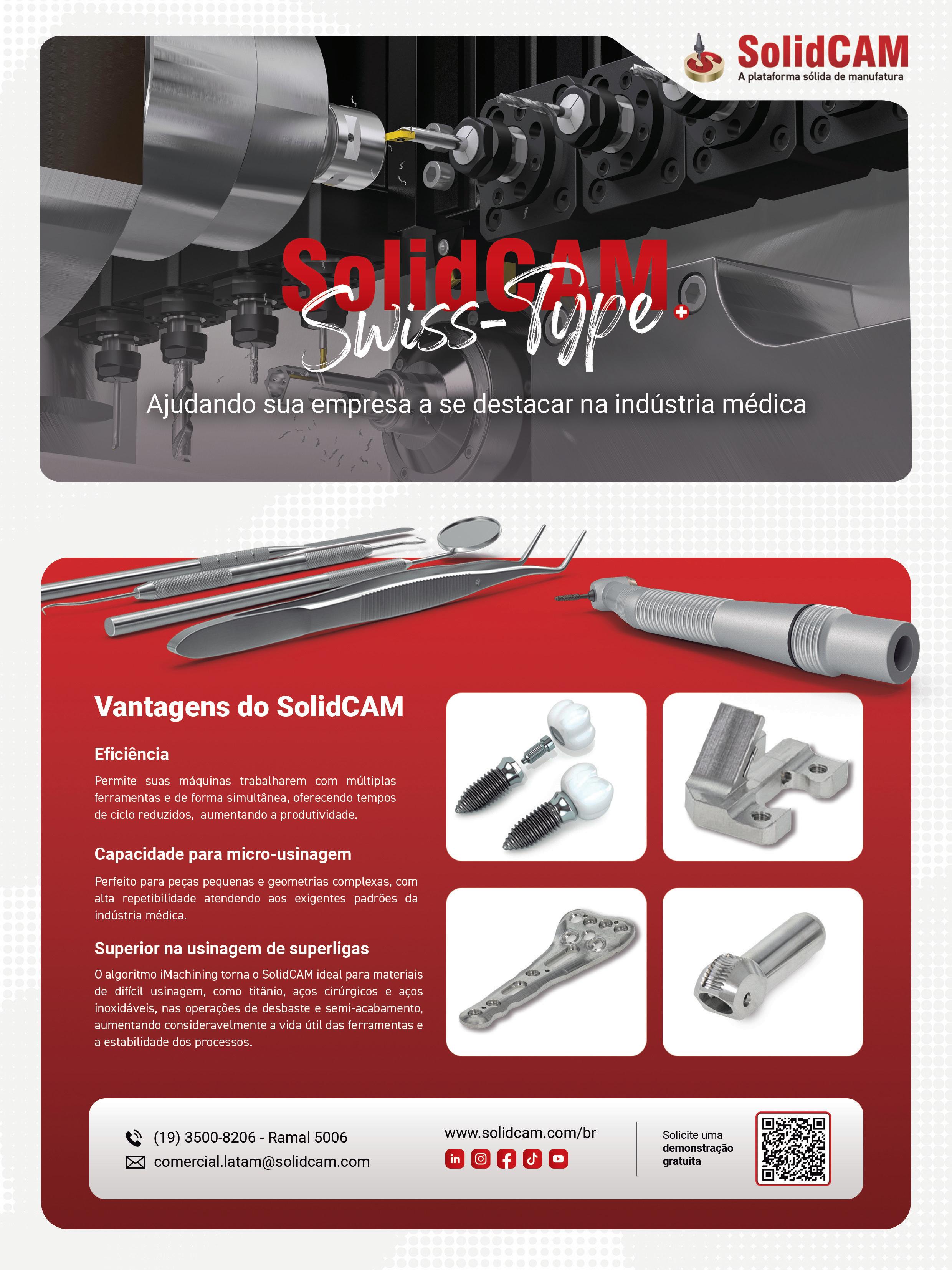

Sistemas de fixação de ferramentas de corte
Pesquisa reúne fornecedores de sistemas que asseguram que as ferramentas de corte se mantenham estáveis durante as operações de usinagem.
28 GUIA II
Limas rotativas
Uma relação de empresas que fabricam ou comercializam as ferramentas que são usadas na remoção de material e em diversos trabalhos de acabamento de peças metálicas.
31 GUIA III
Fornecedores de placas para tornos
Quais são as empresas que ofertam no mercado as placas que garantem a fixação e a estabilidade das peças a serem usinadas, evitando movimentos indesejados que podem comprometer a precisão do trabalho.
Análise estatística de um modelo matemático para o processo de EDM
Pesquisadores apresentam um modelo teórico das grandezas físicas envolvidas no processo de usinagem, tais como corrente elétrica, tensão elétrica, características do material, geometria da região de ação da corrente e calor gerado. O objetivo é compreender os fenômenos termofísicos do processo, visando seu aprimoramento.
Capa: Operação de eletroerosão (EDM). Imagem: Pixel B/Shutterstock
Layout da capa: Vanessa C. Silva
O cenário para o setor de usinagem em 2025 pode ser visto como promissor, com importantes segmentos consumidores de peças sinalizando um período de demanda estável.
As projeções para o setor automotivo indicam um crescimento moderado, com a Associação Nacional de Veículos Automotores (Anfavea) prevendo um aumento de 7,8% na produção de veículos em 2025, chegando a 2,75 milhões de unidades, a despeito do avanço das importações dos modelos elétricos. Embora inferior ao observado em 2024, esse possível desempenho assegura, no mínimo, a continuidade dos contratos de fornecimento dos componentes essenciais para a indústria automobilística.
Já o segmento de eletroeletrônicos projeta um crescimento de 6% no faturamento do setor, de acordo com a
Associação Brasileira da Indústria Elétrica e Eletrônica (Abinee), impulsionando o consumo de componentes usinados de precisão, especialmente em áreas como automação e tecnologia 5G.
No setor de energia, a transição para fontes renováveis e a modernização da infraestrutura elétrica também criam novas oportunidades, as quais se estendem ainda para a produção de componentes para turbinas eólicas, painéis solares e sistemas de armazenamento de energia, que demandarão peças usinadas de alta qualidade.
E na tecnologia médica a tendência também é de aumento da demanda por dispositivos personalizados e de alta precisão, os quais requerem capacidade da indústria para usinar peças com elevados padrões de qualidade e em materiais desafiadores.
A competição global que pressiona os preços e a escassez de mão de obra qualificada, porém, continuam sendo obstáculos a serem transpostos pelas empresas do setor, que se vêem diante da necessidade de investir em maquinário de última geração para permanecerem competitivas, o que nem sempre é possível. Assim, o sucesso dessa indústria – que é também o maior indicador da saúde industrial do País –dependerá de sua capacidade de inovar, investir em tecnologia e desenvolver uma força de trabalho qualificada, ainda que nem sempre disponha dos recursos financeiros necessários. Buscar conhecimento e informação pode ser uma forma de contornar essas adversidades. Um bom ano!
Hellen Corina de Oliveira e Souza Diretora de redação hellen.souza@arandaeditora.com.br
* Cadastre-se para receber a newsletter quinzenal da Máquinas e Metais no link: https://bit.ly/3uzxCua
Ou via QR Code:
ISSN 0025-2700
REDAÇÃO
Diretor: José Roberto Gonçalves
Diretora de redação: Hellen Corina de Oliveira e Souza
Redator: Adalberto Rezende
Pesquisa: Milena Venceslau
PUBLICIDADE
Luci Sidaui - Tel.: (11) 3824-5300 luci@arandaeditora.com.br Ariane Ribeiro - Cel. (11) 99101-5045 ariane.ribeiro@arandaeditora.com.br
Dora Bandelli - Cel.: (11) 95327-6608 / Tel.: (11) 4194-2448 dora.bandelli@arandaeditora.com.br
Consultor de marketing: Sérgio Massis
REPRESENTANTES Minas Gerais: Oswaldo Alípio Dias Christo Rua Wander Rodrigues de Lima, 82, cj. 503 30750-160, Belo Horizonte, MG Tel./Fax: (31) 3412-7031, Cel.: (31) 9975-7031 oadc@terra.com.br
Paraná/Santa Catarina: Romildo Batista
Rua Carlos Dietzsch, 541 cj. 204 bloco E CEP 80330-000, Curitiba, PR Tel.: (41) 3501-2489, Cel.: (41) 9728-3060 romildoparana@gmail.com
Rio Grande do Sul: Maria José da Silva Tel.: (11) 2157-0291, Cel.: (11) 98179-9661 maria.jose@arandaeditora.com.br
INTERNATIONAL ADVERTISING SALES REPRESENTATIVES
China: Mr. Weng Jie, Media Manager Hangzhou Oversea Advertising Ltd. 55-3-703 Guan Lane, Hangzhou, Zhejiang 310003, China Tel: +86 571 870-63843, Fax: +1 928 752-6886 (retrievable worldwide). Email: ziac@mail.hz.zj.cn
Germany: IMP InterMediaPartners GmbH, Mr. Sven Anacker
Beyeröhde 14, 42389 Wuppertal, Tel.: +49 202 271 69-0 fax: +49 202 271 69-20, sanacker@intermediapartners.de
Italy: QUAINI Pubblicità, Ms. Graziella Quaini Via Meloria 7 -20148 Milan
Tel.: +39 2 39216180, fax: +39 2 39217082, grquaini@tin.it
Japan: Echo Japan Corporation, Mr. Ted Asoshina Grande Maison Room 303, 2-2, Kudan-kita 1-chome, Chiyoda-ku, Tokyo 102-0073, Japan
Tel.: +81-(0)3-3263-5065, fax: +81-(0)3-3234-2064
aso@echo-japan.co.jp
Korea: JES MEDIA INC, Mr. Young-Seoh Chinn 2nd Fl., Ana Blsdg, 257-1, Myeongil-Dong, Gangdong-gu Seoul 134-070, Tel.: +82 2 481-3411, fax: +82 2 481-3414 jesmedia@unitel.co.kr
Switzerland: Rico Dormann, Media Consultant Marketing Moosstrasse 7, CH - 8803 Rüschlikon
Tel.: +41 44 720 8550, fax: +41 44 721 1474 dormann@rdormann.ch
Taiwan: WORLDWIDE Services Co. Ltd., Mr. Erin King 11F-B, nº 540, Wen Hsin Road, Section 1, Taichung, 40848
Tel.: +886 4 2325-1784, fax: +886 4 2325-2967 global@acw.com.tw
UK, Belgium, Denmark, Finland, Norway, Netherlands, Sweden: Mr. Eddard J. Kania
Robert G Horsfield International Publishers Daisy Bank, Chinley, Hig Peaks, Derbyshire SK23 6DA
Tel.: +44 1663 75-0242, Cel.: +44 797416-8188 ekania@btopenworld.com
USA: Ms. Fabiana Rezak, 2911 Joyce Lane, Merrick, NY 11566
Tel.: +1 516 858-4327, Fax: +1 516 868-0607 Cel.: +1 516 476-5568 - arandausa@gmail.co ADMINISTRAÇÃO
Diretor: Edgard Laureano da Cunha Jr. Gerente: Rosilene de Paiva Branco Circulação: Clayton Delfino – Tel.: (11) 3824-5300
Produção: Vanessa Cristina da Silva e Talita Silva Projeto gráfico: Lobo Artes
MÁQUINAS E METAIS, MÁQUINAS E METAIS, revista brasileira de tecnologia de usinagem e automação da manufatura, é uma publicação de Aranda Editora Técnica Cultural Ltda. O acesso à revista digital e o download no formato pdf são gratuitos em nosso site www.arandanet.com.br/revista/MM Redação, Publicidade, Administração e Correspondência: Alameda Olga, 315 - 01155-900 - São Paulo - SP - BRASIL Tel.: +55 (11) 3824-5300 - info@arandanet.com.br www.arandanet.com.br
A Index Brasil, empresa especializada no desenvolvimento de tornos e centros de torneamento, integrante do grupo homônimo com matriz na Alemanha, inaugurou em sua sede na cidade de Sorocaba (SP) um centro tecnológico de serviços para empresas do setor de usinagem.
A companhia também desenvolveu um sistema automatizado para tornos universais da linha IT600, que já está disponível para comercialização. Este sistema pode ser adquirido junto a novos tornos e também separadamente, para casos em que o cliente requer uma atualização de máquinas operantes no chão de fábrica, por exemplo.
O objetivo da empresa com a inauguração do centro tecnológico, conforme foi comentado por Alexander Sadowskij, diretor geral da Index Brasil, e Rafael Rodrigues dos Santos, gerente comercial da companhia, em entrevista concedida à Máquinas e Metais , é proporcionar aos clientes uma análise aprofundada de fatores no que se refere à produtividade. Nas palavras dos executivos, os principais fatores que serão analisados
são a demanda dos clientes e como eles podem obter maior produtividade investindo em tecnologia, visando à otimização de processos de usinagem. “Muitas vezes, é necessário saber qual é a ‘dor’ do cliente, em um primeiro momento, para a partir daí buscar a melhor solução em torneamento que vai atender às suas necessidades”, comentou Alexander. Ele também disse que instituições de pesquisa e ensino ligadas à área de usinagem são bem-vindas à nova unidade. No centro tecnológico serão realizados trabalhos que vão desde consultoria para melhoramentos em operações em parques fabris, customização de sistemas automatizados para usinagem e simulação de processos. Além disso, conforme explicou Rafael, os custos de produção de peças por torneamento também poderão ser analisados. “A pergunta que fazemos para nossos clientes é: ‘Você sabe o quanto você deixa de ganhar em produtividade por não investir em automação?’. Percebemos que muitas vezes os fatores relacionados ao custo por peça não são observados de uma maneira aprofundada. Mudar isso é um dos nossos objetivos”, disse o executivo.
A Index oficializou o início das operações do centro tecnológico e o lançamento do sistema automatizado integrado aos tornos universais IT600 em um evento comemorativo, em que foram celebrados os 55 anos de presença da empresa no Brasil. Na ocasião, foram realizadas apresentações nas quais foram abordadas as oportunidades para o setor de usinagem em diferentes ramos de atividade, dentre eles o setor aeroespacial, indústria automotiva, setor médico-hospitalar e o agronegócio. O contato com a Index Traub pode ser feito pelo endereço eletrônico www.index-group.com.
de eletrolisadores. Mais demanda para o setor metal mecânico.
A Neuman & Esser (NEA), empresa global de origem alemã, anunciou a ampliação de sua fábrica de geradores para usinas de hidrogênio de baixo carbono, também chamado de hidrogênio verde. Localizada em Belo Horizonte (MG), a unidade teve sua capacidade quadruplicada, atingindo uma produção capaz de gerar 70 MW/ano de hidrogênio verde.
As instalações passam a ocupar uma área de 3.500 metros quadrados, e a expectativa da empresa é aumentar a produção em até sete vezes em relação aos níveis atuais, além de expandir a capacidade de empacotamento de compressores de gases industriais, tais como H 2 e CO 2 e movimentar uma parte importante do segmento metal mecânico. “Nossa estratégia de fortalecimento abrange quatro frentes de atuação: fabricação de unidades compressoras para gases, sistemas de moagem e classificação de materiais sólidos, geradores de hidrogênio e serviços especializados”, afirmou o diretor-presidente da NEA Brasil, Marcelo Veneroso.
Eletrolisadores
Os eletrolisadores são o coração dos sistemas de geração de hidrogênio e são produzidos pela NEA sob rigorosas especificações. São dispositivos que convertem água em hidrogênio e oxigênio utilizando eletricidade. Seus componentes mecânicos são projetados para resistir a ambientes corrosivos e suportar altas pressões. São fabricados por usinagem, corte, estampagem, dobra e caldeiraria, o que deve aumentar a demanda por estes serviços, visto que a empresa adquire boa parte desses itens de fornecedores locais.
Flanges usinadas em aço carbono, componentes para placas confeccionados em aço inoxidável ou revestidos para resistir à corrosão, além de carcaças diversas moldadas em plásticos de engenharia, são alguns dos itens necessários à montagem dos eletrolisadores.
Para armazenar e movimentar o hidrogênio a ser comercializado são necessários vasos produzidos com aços de alta resistência ou inoxidável, além de tubulações às quais são conectadas as flanges. A necessidade de montagem rápida desses sistemas representa uma demanda por processos mais eficientes e materiais mais resistentes, aumentando a demanda por aços especiais e plásticos de engenharia.
Os vasos de pressão para armazenamento e transporte do hidrogênio (foto acima) podem ser produzidos em aços especiais ou por enrolamento filamentar (filament winding), que combina o uso de resinas termofixas e fibras de alta resistência. Esses materiais são escolhidos com base na sua resistência química, condutividade elétrica, durabilidade e custo, podendo variar em função das especificidades de operação.
Descarbonização em vista
A Neuman & Esser é a única empresa produtora de eletrolisadores na América Latina e mantém atualmente uma parceria com a Universidade Federal de Itajubá (MG), onde está instalada uma planta operacional de hidrogênio verde em pequena escala. Além de fortalecer a aliança com a academia, os investimentos anunciados vão promover a criação de 200 novos postos de trabalho diretos e indiretos, empregando uma mão de obra qualificada e bem remunerada. “Vamos promover também a multiplicação do conhecimento de produção de eletrolisadores, pois não há no mercado mão de obra qualificada ou sequer estrutura para qualificá-la”, comentou Rafael Serpa, gerente de vendas e aplicação da Neuman & Esser no Brasil. Rafael explicou ainda que há dois perfis para a clientela das usinas de hidrogênio verde: o mercado de exportação, que visa suprir a demanda de países que atualmente enfrentam restrição da oferta devido a problemas climáticos ou geopolíticos, a exemplo da Alemanha e Japão; e o mercado interno, movido pela necessidade de descarbonização de atividades industriais.
As empresas locais podem tanto se interessar por iniciar ações neste sentido quanto substituir o chamado hidrogênio cinza, produzido a partir do gás natural e com maior pegada de carbono, pelo hidrogênio verde, obtido por eletrólise da água. “A produção a partir do gás gera de 10 a 12 quilos de CO2 para cada quilo de hidrogênio, enquanto a eletrólise zera totalmente as emissões”, explicou Rafael.
A agenda ESG na indústria, que implica a descarbonização de processos produtivos, também deverá favorecer o ciclo econômico ligado ao hidrogênio, com a estruturação de um parque fabril que vai movimentar toda a cadeia de fornecedores e ferramentas de
financiamento, além de promover a formação de mão de obra qualificada.
A Sandvik Coromant anunciou uma parceria estratégica com o Serviço Nacional de Aprendizagem Industrial de São Paulo (SENAI-SP) para promover a reciclagem de resíduos de metal duro gerados pelas escolas da rede no Estado de São Paulo.
A iniciativa visa reduzir o impacto ambiental das operações das escolas, ao mesmo tempo em que equipa os alunos com as ferramentas e o conhecimento para adotar práticas sustentáveis em suas futuras carreiras. De acordo com os termos da parceria, a Sandvik fornecerá ao SENAI-SP pastilhas de metal duro de sua fabricação.
Claudio Camacho, vice-presidente de vendas para América do Sul e Central da Sandvik Coromant, comentou que a parceria representa um avanço significativo, especialmente na área de reciclagem. “Ao combinar a expertise educacional do SENAI-SP com a liderança tecnológica da Sandvik Coromant, impactaremos positivamente o aprendizado dos alunos e o meio ambiente”.
A parceria promoverá o gerenciamento dos resíduos de forma responsável, mas também garantirá que os materiais reciclados sejam reintegra-
dos ao ciclo de produção, retornando como ferramentas novas a serem utilizadas pelos alunos do SENAI-SP em seu treinamento.
Carlos Kenji Takeuti, gerente do Value Center da Sandvik Coromant, detalhou o processo: “Estamos entregando caixas para as escolas do SENAI em todo o Estado de São Paulo para a coleta de metal duro. Uma vez que os alunos descartem os resíduos, nós os coletaremos e transportaremos para nosso centro de distribuição. De lá, os resíduos serão enviados para nossa instalação certificada na Áustria, onde serão processados de volta em matéria-prima. Esses materiais retornarão às nossas linhas de produção e serão transformados em novas ferramentas, que eventualmente voltarão para os alunos do SENAI-SP usarem em seus estudos”.
A GWM iniciou o processo de habilitação de fornecedores para a nacionalização de peças em sua nova fábrica em Iracemápolis (SP), entre os quais estarão empresas do setor metal mecânico e de usinagem. O anúncio foi feito durante uma apresentação no Sindicato Nacional da Indústria de Componentes para Veículos Automotores (Sindipeças), quando a montadora chinesa revelou ainda a inclusão de mais dois modelos – um SUV e uma picape –na linha de produção que vai fabricar o modelo Haval H6 (imagem acima).
A montadora anunciou também a nomeação de Marcio Alfonso como o novo diretor de produção, que acumulará a responsabilidade pelas áreas de Engenharia e PDI (Pesquisa, Desenvolvimento e Inovação). “Estamos dando mais um passo importante para fortalecer nossa operação no Brasil.
A apresentação no Sindipeças foi uma oportunidade única de envolver nossos futuros fornecedores e parceiros, alinhando expectativas e reforçando o compromisso da GWM com o desenvolvimento local”, afirmou.
Componentes nacionalizados
O chamado “Programa de Localização” da GWM terá diversas fases, incluindo o estabelecimento de contratos de confidencialidade, workshops para identificação de peças para fornecimento local, desenvolvimento de capacidade técnica e a fase comercial, na qual será firmado o contrato e feita a nomeação do fornecedor. Como parte de seu compromisso com a nacionalização, a GWM já desenvolveu uma lista de mais de cem componentes para serem produzidos localmente. O objetivo é alcançar um índice de nacionalização superior a 60%, o que permitirá à montadora exportar seus veículos para a América Latina.
A produção na nova fábrica de Iracemápolis está programada para o primeiro semestre de 2025 com o SUV híbrido Haval H6, inicialmente em regime de pré-produção, para testar e ajustar os novos equipamentos da linha de montagem e verificar os processos de manufatura e de controle da qualidade. A produção em série inicia no segundo semestre. Com a modernização e ampliação da capacidade instalada, a fábrica da GWM poderá atingir a produção de 50 mil unidades dentro de três anos. A previsão da marca para 2025 é de cerca de 10 mil
veículos e mais de 40 mil em 2026 com dois turnos em operação e três produtos em linha.
O início da produção faz parte da primeira fase do projeto de investimentos da GWM no mercado brasileiro, que totaliza R$ 10 bilhões até 2032. Nessa primeira fase, que vai até 2026, o aporte será de R$ 4 bilhões. As empresas interessadas em atuar como fornecedores da GWM podem estrar em contato pelo e-mail alexandre. cinacchi@gwmmotors.com.br.
A GAC, fabricante de veículos chinesa, assinou um acordo de cooperação com universidades brasileiras para o desenvolvimento local de peças para motores flex que vão equipar automóveis híbridos a partir de 2025.
A Universidade Estadual de Campinas (Unicamp), Universidade Federal de Santa Catarina (UFSC) e a Universidade Federal de Santa Maria (UFSM) são as instituições que vão colaborar com a empresa asiática.
Elas vão atuar na coordenação de pesquisas e projetos voltados para a fabricação de autopeças, desenvolvimento de materiais para aplicações na indústria automotiva e novas tecnologias para otimização de processos
produtivos, assim como capacitação de profissionais para essas áreas.
O investimento nesse consórcio será de R$ 5,8 bilhões nos próximos cinco anos, de acordo com informações divulgadas à imprensa. “Juntos vamos desenvolver novas tecnologias que poderão ser aplicadas em escala industrial, promovendo a competitividade global do mercado automotivo brasileiro”, comentou Alex Zhou, CEO da GAC Brasil.
Um material supostamente frágil poderá revolucionar a fabricação de moldes e ferramental para a indústria
de plásticos. Este é o objetivo de um esforço que está sendo empreendido por três empresas alemãs: a BCE Special Ceramics GmbH, a Kramski GmbH e a fabricante de fresas Zecha Hartmetall-Werkzeugfabrikation GmbH. Juntas, elas estão pesquisando o uso de elementos cerâmicos na confecção de um molde de 16 cavidades, em um projeto a ser concluído em 2025.
De acordo com comunicado divulgado pela Zecha, fabricante de ferramentas de corte que desenvolveu as fresas para usinagem dos materiais cerâmicos, os três parceiros do projeto estão convencidos de que a fabricação de moldes com este material oferece vantagens significativas em relação ao aço.
A Kramski, fornecedora global de ferramental para estampagem
e moldagem por injeção, já utiliza revestimentos cerâmicos, entre outros recursos, para aprimorar moldes para o setor de plásticos, tendo em vista especialmente evitar a adesão do material a ser moldado, assim como o desgaste das cavidades ocasionado principalmente pelos plásticos reforçados com fibra de vidro. “Mesmo quando usamos aços na faixa acima de 54 HRC, muitas vezes há um desgaste enorme, especialmente na área dos pontos de injeção. Isto leva ao aparecimento de rebarbas no componente, que devem ser evitadas a todo custo, principalmente porque acabam por levar a uma manutenção excessiva do equipamento. Para a ferramenta de 16 cavidades que queremos otimizar no projeto atual, planejamos fazer uma cavidade em cerâmica e vamos realizar
testes com ela”, explicou Jörg Carle, diretor técnico da Kramski.
A especialista em cerâmica técnica
BCE Special Ceramics GmbH é a parceira no fornecimento do material para a confecção do molde. A empresa processa cerâmicas de óxido de alumínio (Al2O3) e óxido de zircônio (ZrO2), bem como materiais mistos, e defende a escolha correta do material em relação à aplicação específica do cliente e às opções de fabricação. “Não fabricamos cegamente de acordo com desenhos do cliente, mas questionamos o que se espera da peça e quais serão as condições de trabalho. Se necessário, revisamos a geometria com o cliente e, por fim, sugerimos a cerâmica adequada. O grupo de materiais cerâmicos é tão diverso quanto os plásticos ou os metais. Só nós podemos escolher entre cerca de 20 tipos ou qualidades de cerâmica”, explicou Torsten Prescher, engenheiro de aplicação da BCE.
Processamento de materiais ultraduros
Já a Zecha Hartmetall-Werkzeugfabrikation GmbH desenvolveu a linha de fresas denominada Marlin 3D, especialmente para processamento de cerâmica sinterizada e metal duro, que serão usadas no projeto.
Graças à tecnologia laser de última geração, materiais de corte altamente duros, como PCD e CVD, recebem geometrias de ferramentas que antes eram impossíveis de alcançar. Ao ajustar a geometria com extrema precisão, obtém-se maior eficiência, o que se reflete na formação de arestas, dimensões e formas precisas, bem como na excelente qualidade superficial da peça. “As fresas 3D Marlin também oferecem algumas vantagens para a indústria de materiais cerâmicos: o processamento não se limita mais à retificação. Em vez disso, agora podemos
obter superfícies com brilho espelhado ou contornos delicados na faixa de micra por meio de fresamento”, afirmou Stephen Rapp, gerente de produto da Zecha, enfatizando vantagens como tempos de ciclo reduzidos devido ao resfriamento mais rápido da ferramenta de moldagem por injeção. “Como a maioria dos tipos de cerâmica não são condutores e, portanto, não podem ser processados por eletroerosão, a fresagem no estado sinterizado é um enorme avanço e abre novos mercados, como aplicações na fabricação de moldes”, concluiu.
Foi lançado pela Dassault Systèmes o Solidworks 2025, software em versão atualizada que traz novos recursos para desenvolvedores de peças, moldes, estampos e componentes que serão fabricados por usinagem, por exemplo. A empresa, com matriz na França e filial brasileira na cidade de São Paulo (SP), já está comercializando licenças para uso do novo software para modelamento 3D no Brasil.
As novidades abrangem recursos atualizados que podem ser utilizados em aplicações em projetos de peças usinadas para motores, veículos e máquinas industriais, assim como ferramentas para conformação e estampagem de metais e moldes para plásticos,
Imagem: Dassault Systèmes
entre outros desenvolvimentos do setor metal mecânico.
Mario Belesi, diretor do Solidworks na América Latina, conversou com a reportagem da Máquinas e Metais e comentou sobre os recursos de inteligência artificial (IA) que estão disponíveis no cluster de ferramentas do Solidworks 2025: “A inteligência artificial pode, por exemplo, propor detalhes técnicos que estão em desenvolvimento no projeto de peças que serão fabricadas por usinagem e também fazer sugestões sobre simulações avançadas de processos de torneamento”.
De acordo com informações divulgadas à imprensa, a versão atual do software traz recursos atualizados para aplicações que envolvem o uso de ferramentas de design Solidworks PDM, Simulation, Solidworks Electric Schematic, Electrical Schematic Designer e DraftSight.
A conexão com a plataforma 3DExperience da Dassault Systèmes também é um dos recursos proporcionados pelo Solidworks 2025. Neste sentido, os usuários podem operar em tempo real sistemas voltados para a otimização de tarefas em processos de modelamento 3D – modelamento de chanfros, criação de filetes e bordas, por exemplo –, simulação de operações, notificações sobre o andamento de trabalhos e compartilhamento de informações entre departamentos, além de outros recursos.
Mario também comentou que os clientes podem optar pela aquisição de licença perpétua do software, locação de licença ou pelo uso das tecnologias disponíveis em nuvem. “Os modelos de negócios para uso da licença do Solidworks 2025 seguirão com essas opções e estamos investindo em parcerias com startups e instituições de pesquisa e ensino”, concluiu.
Novo fab lab no interior de SP
Um laboratório voltado para aplicações do software Solidworks em projetos que envolverão empresas e instituições de pesquisa e ensino passou a operar no interior de SP. De acordo com Mario Belesi, as atividades na nova unidade, situada no PIT – Parque de Inovação Tecnológica São José dos Campos –, serão intensificadas ao longo de 2025. A Dassault Systèmes pode ser contatada pelo endereço eletrônico www.3ds.com.
IA é novo recurso em software para diagnóstico de usinagem
Foi lançado pela Mitsubishi Electric (Japão), com filial brasileira em Diadema (SP), um sistema que prevê erros de usinagem a partir de simulação e análise realizadas por inteligência artificial (IA). O novo recurso, denominado “NC MachiningAID”, pode detectar eventuais anomalias em processos de usinagem e, a partir daí, aprender sobre condições ideais de trabalho e também sugerir estratégias. A análise realizada pelo sistema baseado em IA abrange inspeções que podem envolver a previsão de desgaste anormal de ferramentas de corte, erros de geometria e colisão entre a ferramenta e a peça a ser usinada, por exemplo. Conforme explicou Eduardo Miller,
especialista em engenharia de aplicação CNC da Mitsubishi Electric, a tecnologia gera alertas sobre a possibilidade de ocorrência de problemas na usinagem. O sistema realiza uma pré-inspeção a partir da simulação de um processo antes de sugerir os parâmetros corretos de usinagem. “Tudo é calculado de forma temporal. Todos os eixos de usinagem são mostrados em formato de tempo. O sistema processa automaticamente os dados de usinagem, incluindo, por exemplo, a compensação térmica e outros parâmetros. A troca de ferramentas e o histórico de uma determinada ferramenta que poderá ser usada são analisados. Caso seja detectada qualquer informação fora do espectro de processo, gera-se um alarme que interrompe o processo simulado. Assim, a inteligência artificial mostra ao usuário onde está o problema”, comentou. Mais informações podem ser obtidas pelo e-mail e.miller@ mitsubishielectric.com.br.
Indústria alemã de máquinas-ferramentas enfrenta retração
Dados recentes divulgados pela Associação Alemã de Construtores de Máquinas-ferramentas (VDW) apontam que os pedidos recebidos pela indústria alemã de máquinas-ferramentas no terceiro trimestre de 2024 caíram 16% em relação ao mesmo período
do ano anterior. Os pedidos de dentro da própria Alemanha caíram 17%, enquanto os do exterior caíram 15%. Já os pedidos recebidos nos três primeiros trimestres de 2024 caíram 23% em relação ao mesmo período do ano anterior, enquanto os pedidos nacionais caíram 10%. Os vindos do exterior ficaram 28% abaixo do valor do ano anterior. “A situação dos pedidos continua desafiadora”, comentou Markus Heering, diretor executivo da VDW, ponderando que a indústria alemã teve um desempenho comparativamente bom nos primeiros nove meses de 2024, apoiada por uma série de grandes projetos individuais: “Em geral, no entanto, os clientes nacionais estão muito inquietos e não estão dispostos a investir”. Isso está arrastando para baixo o mercado doméstico europeu como um todo, já que a Alemanha é o parceiro comercial mais importante para muitos países. Outras regiões também perderam terreno.
A Ásia é a mais afetada devido à fraca demanda da China, enquanto o menor declínio foi registrado na América. Os Estados Unidos e o México asseguraram a demanda.
“Vimos pouca mudança no estado da indústria desde o primeiro semestre de 2024”, observou Heering. “O fluxo de notícias vindas da indústria automotiva está dando motivo para preocupação. E os níveis gerais de negócios estão baixos em todos os setores, tanto nos mercados quanto nas indústrias de clientes. Vários projetos importantes dos setores aeroespacial, tecnologia médica, energia, construção naval e defesa estão ajudando a manter as atividades. A automação continua sendo um impulsionador essencial do investimento em máquinas-ferramentas no setor”.
De acordo com pesquisas da associação, mais fabricantes de máquinas-ferramentas estão planejan -
do reintroduzir turnos de trabalho de curta duração em um futuro próximo: 35% dos entrevistados estavam considerando isso no segundo trimestre, com o número subindo para 45% no terceiro trimestre. Também há planos para reduzir o número de trabalhadores temporários. No final do primeiro semestre de 2024, o setor empregava cerca de 65.250 pessoas. Assim, a previsão de produção para o ano como um todo permaneceu inalterada: um declínio de 8%.
A fabricante global ESAB Corporation concluiu o processo de aquisição da brasileira Sumig (Caxias do Sul, RS), fabricante de produtos e equipamentos para soldagem. A empresa atua há mais de 40 anos, atendendo clientes ao redor do mundo, em setores como industrial, automotivo e agrícola.
A operação havia sido anunciada no início de 2024 e vai resultar na integração da linha de produtos da Sumig ao portfólio da ESAB, com atuação global em soldagem, corte e controle de gases. “A robótica e a automação continuam impulsionando o crescimento e a produtividade na indústria de fabricação ao redor do mundo, e estamos entusiasmados em complementar nosso portfólio com a aquisição da Sumig”, afirmou Olivier Biebuyck, presidente de tecnologia de fabricação da ESAB Corporation.
A ESAB (Elektriska SvetsningsAktiebolaget) foi fundada em 1904, na Suécia, pelo engenheiro Oscar Kjellberg, que inventou o primeiro eletrodo revestido. Durante a Primeira Guerra Mundial, a empresa se expandiu rapidamente, especialmente na indústria naval, estabelecendo
subsidiárias em locais estratégicos. A partir dos anos 1980, a empresa se consolidou globalmente por meio de aquisições, passando a ter sede nos Estados Unidos na década de 1990. Hoje opera em mais de 147 países, com 26 plantas de fabricação espalhadas por todo o mundo.
A ESAB atua há quase 70 anos operando na América do Sul, com operações e distribuição em mais de 10 países da região. Esta é a terceira aquisição que a empresa concluiu na região somente em 2024. As demais envolveram as empresas Sager S.A.S e Condor.
No dia 17 de julho de 2025 será realizado durante a 15ª edição da Intermach um workshop que terá como tema central a instrumentação. Na ocasião, as demandas do setor metal mecânico e de usinagem serão deba-
Imagem: Intermach/Divulgação
tidas por especialistas em qualidade e instrumentação.
A programação do workshop também contará com sessões sobre tecnologias e inovações em instrumentação para a indústria metal mecânica, e terá espaço para discussões sobre máquinas e sistemas industriais usados para a fabricação de peças metálicas, inspeção e controle da qualidade, entre outros tópicos.
A Intermach acontece de 15 a 18 de julho de 2025 no Centro de Convenções e Exposições Expoville, em Joinville (SC). A feira está sendo promovida pela Messe Brasil. Mais informações podem ser obtidas pelo site da Intermach.
O Grupo United Grinding anunciou a assinatura de um acordo de aquisição da Divisão de Soluções para Usinagem (GF Machining Solutions Division, GFMS), da suíça Georg Fischer AG, que desenvolve tecnologias de manufatura de alta precisão e tem unidade brasileira em São Paulo (SP).
A fusão tem foco na integração de tecnologias voltadas para a usinagem de precisão, especialidade de ambas as empresas. A transação está sujeita a aprovações regulatórias e foi avaliada entre 630 e 650 milhões de francos suíços, devendo ser concluída até o segundo trimestre de 2025.
O United Grinding Group é um dos principais fabricantes mundiais de máquinas-ferramentas para retificação, eletroerosão e medição, além de manufatura aditiva. Estão sob comando do grupo marcas como Mägerle, Jung, Studer, Walter e Ewag, assim como centros de competência nas Américas e na Ásia. O acionista majoritário do grupo é a Patinex AG, uma holding suíça.
Os suportes para fixação de ferramentas de corte têm grande relevância no processo de usinagem, pois asseguram que elas sejam mantidas estáveis durante a operação, o que é importante para a qualidade da usinagem e para a durabilidade da ferramenta. Além disso, evitam acidentes, ao mesmo tempo em que facilitam a troca rápida de uma ferramenta. Conheça neste guia a oferta desse tipo de produto.
Alcede (41) 3327-3730 vendas@alcede.com.br
AWW (11) 4479-3122 aww@aww.com.br Walter, Alemanha
Blacktools (54) 3218-7810 blacktools@blacktools.com.br
Boehlerit (11) 5546-0755 vendas@boehlerit.com.br
BTfixo (54) 9999-6074 vendas@btfixo.com.br
Cedifer (11) 3329-3700 fabio@cedifer.com.br
Ceratizit (19) 3115-9500 vendas@ceratizit.com
Dormer Pramet (11) 5660-3000 renato.brandao@dormerpramet.com
Gühring (11) 2842-3069 vendas@guhring-brasil.com
Korloy (11) 4193-3810 pedido@korloybrasil.com
Mansfer (11) 99524-2608 comercial@mansfer.com.br
MB (19) 98805-1893 mb@mbferramentas.com.br
Sanches Blanes (11) 4824-2900 atendimento@sanchesblanes.com.br
Sandvik (11) 46803536 marketing.coromant@sandvik.com
Sanposs (011) 4126-6711 sanposs@sanposs.com.br
Schunk (11) 4468-6888 info@br.schunk.com
Boehlerit, Horn e Bilz, Alemanha
HQT e ACC, Taiwan
Laip, Espanha
Ceratizit, Alemanha
Gühring, Alemanha
Korloy, Coreia do Sul
Union Carbide, Coreia do Sul
Albrecht, Diebold, Dümmel, Gewefa, Hobe e Utilis; Alemanha e Suíça
Suportes Brasil (11) 99156-6525 suportesbrasil@suportesbrasil. com.br
Vitor e Buono (11) 3376-7777 contato@vitorbuono.com.br
YG-1 (11) 4496-2170 vendas@yg1.solutions
Zoller (11) 98209-1019 comercial@zoller-br.com
Vertex, Taiwan
YG-1, Coreia do Sul
Zoller, Alemanha
Obs.: Os dados constantes deste guia foram fornecidos pelas próprias empresas que dele participam, de um total de 84 empresas pesquisadas. Fonte: Revista Máquinas e Metais, dezembro de 2024 / janeiro de 2025.
Valdemir Martins Lira e Jeverson Teodoro Arantes
A usinagem de peças na indústria metal mecânica requer constante aprimoramento e desenvolvimento, seja por meio da modernização das máquinas operatrizes, da evolução das ferramentas de usinagem ou da análise do processo em si. Para esse último, uma alternativa é analisar as grandezas físicas fenomenológicas que ocorrem durante a usinagem via eletroerosão por penetração (EDM, de electrical discharge machining). O conhecimento das grandezas físicas, tais como corrente elétrica, tensão elétrica, características do material, geometria da região de ação da corrente, calor gerado, entre outras, contribui para a realização da erosão de uma quantidade determinada de massa de material e que resulta na boa qualidade superficial da peça de trabalho e, consequentemente, na boa qualidade do produto final. Este artigo apresenta um modelo teórico físico das grandezas que envolvem o processo de eletroerosão por penetração. Os resultados das simulações do modelo teórico mostram que o mesmo pode ser utilizado para analisar a quantidade de calor gerada e a quantidade de massa de material a ser erodida e consequentemente ser uma ferramenta para entender os fenômenos termofísicos que consideram como variáveis as características do material, forma geométrica da região a ser erodida e a energia para realizar tal usinagem.
O“acaso” possibilitou que cientistas russos (Lazarenko, Lazarenko, 1964), por volta de 1943, descobrissem que a erosão de contatos elétricos podia ser aplicada como processo para usinar outro material de maneira controlada e precisa. Mais adiante, em 1950, o inglês Dagobert William Rudorff patenteou nos Estados Unidos da América do Norte um dispositivo de descarga elétrica e um método para corte de material com uso de um fluido dielétrico (Lima, 2008) e ainda nos anos de 1950 surgiram as máquinas com comando mais preciso (Witte, 1998) e que possibilitaram melhora da técnica recente de usinagem por meio da eletroerosão. A popularização comercial do processo ocorreu nos anos 70. Desde então o processo por eletroerosão vem agregando tecnologias ao seu processo, a exemplo do Comando Numérico Computadorizado (CNC), que per-
mite obter formas geométricas mais complexas.
A figura 1 mostra uma visão básica do equipamento para realizar a eletroerosão por penetração (EDM, de electrical discharge machining) (Riffei, 1992). As peças usinadas por penetração são fixas sobre uma mesa que se move verticalmente e horizontalmente (Lira, 2017). Há ainda a utilização de líquido não condutor de eletricidade –denominado de dielétrico, como óleo mineral, hidrocarbonetos sintéticos ou querosene (Lima, 2008).
Figura 1 – Representação básica do equipamento para realizar a eletroerosão por penetração (Wertheim, 1975).
A ferramenta para a usinagem por pe -
Os autores são professores associados do Centro de Engenharia, Modelagem e Ciências Sociais Aplicadas (CECS) da Universidade Federal do ABC (UFABC) São Paulo. Reprodução autorizada.
netração é um eletrodo, cujo material pode ser grafite, cobre, bronze, liga de alumínio e latão, entre outros (Singh, Maheshwari, Pandey, 2003) (Lee, Hsu, Tai, 2004) (Norliana, Solomon, Bahari, 2007). Tais materiais têm como característica a condutividade elétrica (Lynch, 1974). Há na figura 1 um injetor de líquido dielétrico (exemplo: óleo)
utilizado para a refrigeração e remoção de partículas soltas de sobremetal do metal a ser usinado.
Na usinagem via eletroerosão não há contato físico entre a ferramenta de trabalho (eletrodo) e a peça (Wurzel, 2015) (Benedict, 1987). Assim, a atuação como elemento de trabalho é a descarga elétrica como meio de transformação da matéria (figura 2). Essa descarga elétrica gera calor intenso na região bombardeada da peça (Yue, et al ., 2018) (Shen, et al ., 2018) e
resulta na fusão do material. Partículas de material são removidas, o que classifica esse processo como um processo com remoção de material. Em suma, a usinagem por meio da eletroerosão é um processo térmico (Zhang, et al., 2018) (Guitrau, 1997) (Fuller, 1990) de fabricação caracterizado pela remoção de material via descargas elétricas (figura 2). Logo, a eletroerosão é indicada para usinar materiais condutores de eletricidade, ou seja, metal ou cerâmica (Bilal, et al., 2019).
Características elétricas do processo de eletroerosão
As grandezas que agem nesse processo são: a tensão, a corrente elétrica e a pausa do impulso (Jeswani, 1980) e, em termos de polaridade, têm-se as seguintes condições: o eletrodo pode ser carregado negativamente ou positivamente. Mas esclarece as seguintes situações de trabalho: no caso de ligação positiva do eletrodo, ocorre pouca queima do mesmo na usinagem de desbaste, mas com longa duração do pulso (Casanueva et al., 2000) (Lee, Yur, 2000) e baixa frequência. Para a duração do pulso, veja a figura 4. No caso de ligação negativa o eletrodo consegue erodir com pequena duração do pulso e alta frequência.
Na figura 3 o fluxo de corrente que percorre o eletrodo pode variar de 0,5 A até 80 A (Medeiros, 1981) (Guitrau, 1997) (Fuller, 1990). Com esses valores as superfícies da peça e do eletrodo são fortemente aquecidas até 12.000 graus (Ho, Neewman, 2003), valor de temperatura que pode ser semelhante ao verificado no processo de plasma (Meek, Craggs, 1978). Com tal intensidade de temperatura, o metal é fundido e parte dele evapora. Simultaneamente a isso ocorre uma
explosão e partículas sólidas do metal são soltas (Guitrau, 1997) (Fuller, 1990). Nessa situação ainda ocorre em menor grau o desprendimento de partículas do eletrodo (Hockenberry, Williams, 1967).
Conforme estudo de Patel (2014), o valor baixo da corrente proporciona menor desgaste do eletrodo e menor poder de erosão. Isso ocorre para o eletrodo de cobre devido às características desse material, caso contrário aos eletrodos de grafite (ValentinVCiV , Bissacco, Tristo, 2021). Já o alto valor de corrente proporciona baixo desgaste do eletrodo de grafite com alto rendimento na erosão.
Ainda na figura 3 há um gerador de pulsos que gera uma sequência de pulsos. As pausas entre um e outro pulso podem ser controladas (figura 3) e a duração dos pulsos pode ser ajustada. Isso pode incorrer em algumas variáveis do processo, como: na ocorrência de pequena duração do pulso, estando o eletrodo positivo, aumento do desgaste do eletrodo, e, consequentemente, pequeno volume de material erodido (Casanueva, et al. , 2000). Com uma grande duração do pulso diminui o desgaste do eletrodo e ocorre maior taxa de erosão (Lee, Yur, 2000).
A variável intervalo de faísca é influen -
ciada pela distância entre o eletrodo ao redor da peça de trabalho (GAP) (figura 3) e quanto menor a geração de centelha, mais precisa fica a região atuada pelo eletrodo na eletroerosão por penetração. Por outro lado, a área superficial de remoção depende da área do eletrodo, do material da peça e do eletrodo (Guitrau, 1997) (Fuller, 1990).
No gráfico, figura 4, inicialmente tem-se a aplicação da tensão (região “A” do gráfico) e nesse intervalo não há passagem de corrente, ocorrendo assim a ionização entre a região do eletrodo e a peça. Por meio de tal ionização ocorre uma reação química quando um fluido reagente proporciona a formação de íons não existentes em substâncias moleculares (Lima, 2008). O resultado é a formação de
soluções eletrolíticas que conduzem corrente elétrica (Lima, 2008).
Na região “B” do gráfico (figura 4) ocorre a fase de ignição com passagem de corrente elétrica e queda da tensão entre peça e eletrodo. Surge um canal virtual com passagem de íons carregados positivamente para a peça e com íons carregados negativamente para o eletrodo (Bruyn, 1978) (Kuneida, Lauwers, Rajurkar, 2005).
A fase de queima inicia na região “C” do gráfico e nela há grande concentração de energia entre peça e eletrodo, e isso derrete uma porção focada da superfície da peça. Nessa região a temperatura pode atingir a de sublimação (Descoeudres, 2006) (Grigoriev, et al. , 2019). Na fase final da região “C” ocorre o colapso (explosão) do canal virtual de descarga (Bruyn, 1978) de forma a cavitar a região da peça que estava concentrada de energia e também em menor proporção a do eletrodo (Tseng, Chung, Chang, 2017).
Após essa fase começa a pausa e em seguida o sistema da máquina move o eletrodo para cima para que ocorra a dissipação do calor das partículas. E no gráfico reinicia-se a fase de duração do pulso.
Modelamento teórico físico do processo de eletroerosão por penetração
Pelo exposto no item 2 nota-se que a eletroerosão é um processo térmico resultante da ação da corrente elétrica, da tensão e da duração do pulso,
e que ainda considera os materiais da peça e o eletrodo. O modelamento básico irá considerar, na sua formulação, grandezas físicas da termodinâmica (Jenkins, 2008) (Reddy, Gokcen, 1996) (Hudson, 1996) que ocorrem na região afetada na peça pela corrente e tensão elétrica, e também a influência destas na geração de calor, pois Van Dijck (1973) e Eubank et al . (1993) sugerem que o principal mecanismo responsável pela remoção de material está associado ao fenômeno de superaquecimento do material fundido. E na geração de calor devem ser consideradas as características e a forma geométrica do material a ser erodido. Para tanto iremos analisar, por meio da figura 5, as etapas durante o ciclo de eletroerosão.
Na figura 5, em “A” não há passagem de corrente elétrica entre a região do eletrodo e a peça. O fluido reagente forma íons nas substâncias moleculares (ionização). O resultado é a formação de soluções eletrolíticas que conduzem corrente elétrica.
Em “B” o eletrodo avança em direção à superfície da peça e é iniciada a fase de ignição com passagem de corrente elétrica e queda da tensão entre peça e eletrodo. Nessa etapa surge um canal virtual (Zingerman, 1956) (Snoeys, Van Dijck, 1972) (Bruyn, 1978), com passagens de íons carregados positivamente para a peça e com íons carregados negativamente para o eletrodo. Com as grandezas como entradas de tensão elétrica e de corrente elétrica em um intervalo de tempo relativamente curto, obtém-se a energia elétrica que é a grandeza física de entrada no sistema que sobremaneira influencia a remoção de material (Ramasawmy et al . 2005). A etapa final do ciclo ocorre em “C”: início de queima com grande concentração de energia entre peça e eletrodo. Uma porção de material da superfície da peça derrete (Lee, 2003) e a temperatura é maior que a de fusão do material. Conforme o calor gerado,
ela pode ser mensurada por meio da entalpia (Lide, 2005). Por fim, ocorre o colapso (explosão) do canal virtual de descarga gerando radiação e colisão com a superfície da peça (figura 5 – C), de forma a erodir a região concentrada de energia e também em menor parte a do eletrodo. Nessa etapa, tal concentração de energia gera radiação e energia térmica (radiação, convecção e condução) (figura 5 – C). Em “D” tem-se o fim do ciclo com o recuo do eletrodo e a região erodida. De posse das informações comentadas até aqui, pode-se estabelecer inicialmente o equilíbrio de grandezas como segue:
Por meio da figura 4 inicialmente supõe-se que há a ocorrência dos seguintes fenômenos: B (corrente e tensão) (figura 4: B+C) gera grandezas termofísicas (convecção e condução) e termoquímica (entalpia) indicadas em “III” ( figura 5: III). As grandezas em “B” (figura 4) serão analisadas considerando o tempo do pulso (B → C) e pelos princípios físicos da energia elétrica (Eq. 02) temos que a energia de entrada do sistema é a energia de descarga, que é a energia transformada durante a descarga da faísca. Sua formulação segue abaixo (König, 1979) (Werthheim, 1971)(Richtline, 1976).
Em “III” (figura 5) observa-se grande quantidade de calor e que, em grande parte, pode ser atribuída à entalpia (Lide, 2005) que é constituída por características do material conforme a equação (Eq. 03). Tal calor pode ser considerado como a energia plasma, pois ao término do pulso gera-se um canal de plasma e tal grandeza pode ser considerada no cálculo da energia de calor.
Ainda em “III” (figura 5) ocorre o fenômeno da condutividade térmica que é uma propriedade de cada material e que depende de sua estrutura molecular, de sua densidade e também da temperatura. O valor da condutividade térmica de cada material é definido experimentalmente, aplicando-se a própria definição da Lei de Fourier e as taxas de transferências de calor por convecção e condução são determinadas pelas equações 04 e 05:
Dessa forma a equação 01 resulta em:
Onde:
U = tensão (Volts), I = corrente elétrica (Ampère), Δt pulso = tempo do pulso (s), Csol. = calor específico (Estado sólido) (KJ/Kg.K),
C liq. = calor específico (Estado líquido) (KJ/Kg.K) ,
T fusão = temperatura de fusão (K),
T trab. = temperatura de trabalho (K), Tebulição = temperatura de ebulição (K), Δhfusão = variação da entalpia de fusão (KJ), Δ hevaporação = variação da entalpia de vaporização (KJ),
m = massa (kg): corresponde ao total da quantidade de massa de material erodida por pulso,
A troca = área de troca de calor na superfície sólida (m²),
A fluxo = área do sólido na direção do fluxo térmico considerado (m²) = comprimento atingido pelo calor x
profundidade atingida pelo calor = valor a ser determinado,
L = profundidade erodida (mm),
T sup. = temperatura da superfície (K),
T fluid. = temperatura do fluido (K), h = coeficiente de troca de calor por convecção (W/m².K),
KT = condutividade térmica (W/mK),
T ext. = temperatura na superfície externa da região atingida (K): considerada a temperatura de ebulição,
T int. = temperatura na superfíci e interna da região atingida (K).
Metodologia para simulação do modelo teórico físico do processo de eletroerosão por penetração
Na figura 6 tem-se o fluxo de informações gerais das simulações computacionais de forma que as interações numéricas serão realizadas por meio de entradas de dados e tendo como respostas a quantidade de calor e massa erodida (Joshi, Kothiya, 2012). Nas simulações, os dados de entrada (tensão elétrica, corrente elétrica) são oriundos da pesquisa realizada por Patel (2014) e os dados dos materiais podem ser modelados de diferentes maneiras e em função de parâmetros variados (Puertas, Perez, 2003). Assim, o sucesso da simulação é fortemente dependente das características mecânicas do material da peça (Eq. 06). Nesse sentido, os dados das características físicas dos materiais utilizados no modelo usado são os dos catálogos de fabricantes de materiais e pesquisas publicadas em revistas científicas, de modo que durante a etapa de interações entre variáveis (figura 6) contidas na equação 06 podem resultar respostas consistentes e aderentes ao mundo real (experimentos empíricos), ou seja, quantidade de calor gerada e massa erodida.
Utilização e características químicas do material
Para a realização da simulação computacional utilizou-se o aço inox AISI
6 – Fluxograma de informações em termos de entradas de dados, interações e análise dos resultados (Adaptada de Dauw et al., 1995).
304, pois ele foi objeto de estudo do processo de eletroerosão realizado por Patel (2014), em que visou-se à obtenção do volume de material erodido. A composição química do material está na tabela 01.
O aço inox AISI 304 tem muitas aplicações, tais como em equipamentos para a indústria aeronáutica, ferroviária, naval, petroquímica, papel e celulose, têxtil, frigorífica, hospitalar, alimentícia, de utensílios domésticos, eletrodomésticos, destilarias, tanques em geral, instalações criogênicas, tubos, estampagem geral e profunda (Fischer et al. , 2005).
Na tabela 2 estão os dados de entalpia do AISI 304. Cabe destacar que essa
grandeza termoquímica corresponde à energia interna que as moléculas de uma substância possuem, pois a variação dessa grandeza está intrinsicamente ligada ao calor fornecido, pois comportam-se em função da variação de temperatura que influencia a capacidade calorífica do sistema sob pressão constante.
Dados da forma geométrica da peça e ferramenta
As informações da forma geométrica da peça e da ferramenta são importantes na simulação, pois no modelamento físico proposto do fenômeno da eletroerosão há necessidade de
Tabela 1 – Composição química do aço inox AISI 304 (Patel, 2014)
Elementos químicos
C Si P S Mn Cr Ni N Fe
Porcentagem (%)
0,08 0,75 0,045 0,03 2,00 20,00 10,5 0,10 66,50
Tabela 2 – Dados das características de entalpia de fusão e vaporização do aço inox AISI 304
Dados característicos do material
C Si P S Mn Cr Ni N Fe
Massa (g/mol) (Patel, 2014)
12 28 30 32 54 51 58 14 55
Entalpia de fusão (Kj/mol) (Yaws, 1999) (Lide, 2005)
50,55 0,657 1,7175 12,91 21 13,8 0,3604 13,8
Entalpia de vaporização (Kj/mol) (Yaws, 1999) (Lide, 2005)
entrada de dados na equação 06. Desta forma, no modelamento matemático, considera-se a área da secção transversal do eletrodo (figura 7) dada por: A e = A troca = área de troca de
calor na superfície sólida: π.R 2. Supõe-se que a região erodida corresponde aproximadamente ao volume de material erodido (figura 7) que, por sua vez, considera a área da secção
Quantidade
experimentos
transversal do eletrodo pela profundidade erodida, dada por: A fluxo = área do sólido na direção do fluxo térmico considerado = comprimento atingido (π.R) pelo calor x profundidade atingida pelo calor (L).
As informações da área de troca de calor na superfície sólida (A troca) e da área do sólido na direção do fluxo térmico (Afluxo) serão utilizadas durante a simulação na determinação da quantidade de calor (Q total) (Equação 06).
Software utilizado na simulação: Crystal ball®
As simulações numéricas computacionais foram realizadas no software comercial Excel (Empresa: Microsoft) com uso da ferramenta Crystal ball® da Oracle – versão: 11.1.3.0.0. Por meio do Crystal ball é possível utilizar o método Monte Carlo de análise de dados aleatória. Com essa estratégia de simulação será possível inserir as variáveis de entradas e obter respostas, de modo a verificar quais variáveis influenciam a quantidade de calor e as massas erodidas.
Dados de entrada e saída: grandezas elétricas e massas erodidas
Na tabela 3 estão dispostos os valores dos parâmetros de entrada, como corrente, tensão e duração do pulso. Tudo isso de acordo com o estudo realizado por Patel (2014). Tais dados serão utilizados como entrada na simulação do modelo teórico.
Ainda na tabela 3 estão dispostos os valores das massas erodidas que foram obtidos por Patel (2014) e que serão utilizados como parâmetros de comparação das respostas das massas obtidas por meio de simulações do modelo físico teórico. E por último foram calculadas as energias – parte inferior da tabela 3 –, tendo como base os dados dos experimentos de corrente elétrica, voltagens e duração dos pulsos.
Tabela 4 – Parâmetros de entrada das variáveis para a simulação por meio do Crystal ball Variáveis Min. Máx. Observações
Csol. (KJ/Kg.K) 0,001 0,600
Cliq. (KJ/Kg.K) 0,001 0,01
Ttrabalho (K) 873,15 1873,15 Temperatura ambiente até ebulição
Tfluid. (K) 298,15 673,15 Temperatura ambiente até ebulição
Tfusão (K) 1573,15 1873,15
Tebulição (K) 2500 6000
T sup. (K) 673,15 1873,15 É a temperatura da superfície [K] ≈ Tebulição (K) = Valor a ser determinado
Tint. (K) 1573,15 6000 (0,95 a 0,99)*Text., Text.= Tebulição até Tambiente
Text. (K) 1573,15 6000
h (W/m².K) 50 70 Coeficiente de troca de calor por convecção
KT (W/mK) 45 65
SDhfusão (J) Tabela 02 Somatória da variação da entalpia de fusão
SDhevaporação (J) Somatória da variação da entalpia de vaporização
r (kg/m3) 6000 8500 Densidade do aço inox AISI 304 = 8000 kg/m3
Dt (s) 0,05 0,20
m (kg) 0,0001 0,001
L (m) = 0,0001 0,01
Atroca (m2) 0,000078
Afluxo (m2) 0,00001 0,01
É a massa total da quantidade de material erodido = volume x peso específico = V. r = Atroca.L.r
É a profundidade que resultou de material erodido (mm), (calculado partindo da massa retirada – tabela 3)
Corresponde à área do eletrodo, área de troca de calor na superfície sólida
Área do sólido na direção do fluxo térmico considerado = perímetro x comprimento da região atingida pelo calor (L)
Tabela 5 – Resultados das simulações no Crystal ball visando apurar o nível de certeza da equação 6
Caso Energia (J) (Tabela 03)
1
Nível de certeza (%) Intervalo (J)
Erro padrão da média
Massa erodida (g) (Tabela 03)
Dados de entradas e de saídas do modelo teórico físico
Ao lado, na tabela 04, estão listadas as variáveis de entradas das simulações com valores máximos e mínimos para serem simuladas de forma aleatória e obter as respostas dos valores de quantidades de calor gerado e de massas erodidas. E com isso analisar quais variáveis afetam mais a obtenção daquelas grandezas.
Resultados e discussão
Os gráficos (figura 8) da simulação por meio do Crystal ball do primeiro caso (tabela 3) indicam que para a quantidade de calor gerada o nível de certeza é de 99,69% de possibilidade de ocorrer quantidade de calor dentro do previsto. Para tanto foi utilizado o intervalo de 11,25 J (tabela 3) a 10.000 J e o caso-base tem valor de 11,25 J (tabela 03). O erro padrão da média é de 12,64, isso após 50.000 avaliações (tabela 5).
Já no resultado, primeiro caso da tabela 03, relativo à massa erodida (figura 8), temos que o nível de certeza é de 87,41% de possibilidade de ocorrer a massa erodida dentro do previsto e o erro padrão da média é de 0,0419. Todos os resultados das simulações, tanto das quantidades de calor quanto
Nível de certeza (%)
Intervalo (J)
Erro padrão da média
das massas erodidas, estão na tabela 5. Para a simulação da quantidade de calor (equação 6), o nível de certeza (tabela 5) está acima de 99%. Já para os valores das massas erodidas, o nível de certeza (tabela 5) em cinco casos foi superior a 80% e nos demais casos ficaram acima de 73%. Ressalta-se que o intervalo tanto para a simulação das quantidades de calor quanto para as massas erodidas foram ajustados tendo como base os valores mínimos dos experimentos realizados por Patel (2014) (tabela 03).
Conforme gráfico ao lado (figura 9), para o primeiro caso da tabela 3 relativo à quantidade de calor, a variável duração do impulso (Δt) tem mais de 49,70% de toda a variação das respostas simuladas; é a variável que mais afeta a quantidade de calor gerada. Em seguida, as variáveis que também afetam a geração de calor são: área de troca
Figura 9 – Resultados da simulação para o primeiro caso da tabela 03: influências das variáveis na quantidade de calor gerada (11,25 J) e da massa erodida (0,236 g).
(Atroca) com 23,80 %, temperatura da superfície (Tsup.), 14,3%, profundidade erodida da peça (L) com -6,4%, área de fluxo (Afluxo) com 2 %, temperatura externa (Text.) com 1,1% e temperatura do fluído (Tfluid.) com -0,9%. Tais variáveis com suas porcentagens podem influenciar, de forma quantitativa, os resultados do calor gerado.
Já para as simulações das massas erodidas, para o primeiro caso da tabela 3, a variável calor especifico (- 71,5%) no estado inicial do material, que é o
sólido, é a variável que mais influencia o processo de obtenção da massa erodida. Em seguida têm-se as seguintes variáveis que mais afetam os resultados na simulação das massas erodidas: temperatura da trabalho (Ttrabalho) com 22,3%, profundidade erodida da peça (L) com 6,5%, e a variável duração do impulso (Δt), com 0,60 %.
A tabela 06 apresenta os resultados do 1º caso ao 9º caso relativos às quantidades de calor geradas e massas erodidas.
Tabela 6 Resultado da simulação para o primeiro caso da tabela 3: sensibilidade – quantidade de calor e massas erodidas
Caso Caso
7
Conclusões
As respostas das quantidades de calor geradas apresentam nível de certeza (tabela 5) acima de 99% e isso atesta que a equação 06, por meio da composição das variáveis, representa com robustez o fenômeno que ocorre durante a eletroerosão por penetração. Com relação aos valores das massas erodidas, o nível de certeza (tabela 5), na maioria dos casos, está acima de 80% e nos demais casos acima de 73%. Isso denota que o modelo matemático tende, na maioria dos casos, a ser um modelo robusto. A probabilidade, para esse modelo físico e para as condições impostas, de gerar calor e obter massas erodidas para realizar a operação de erosão por penetração é no mínimo de 99% e de 80% para a massas erodidas, respectivamente. Isso denota que o modelo é constituído de variáveis que estão de acordo com o fenômeno que ocorre durante o processo de eletroerosão por penetração. Cabe destacar que os valores de calor gerados não consideraram na equação a parcela de calor que é gerado pela ferramenta (eletrodo). Isso deve ser objeto de estudo de um modelo mais completo. Das variáveis listadas na tabela 6, a
duração do pulso (Δt) tem em média 51%; a área de troca (A troca) 21%; a temperatura superficial (Tsup.) tem 10 % em média e essa temperatura é aproximadamente a da Tebulição , profundidade erodida da peça (L) (-8,3% em média), área de fluxo (A fluxo) com 4 % em média; e temperatura externa (Text.) com 1,2%, tendo grande impacto na geração da quantidade de calor. Assim, as influências de tais variáveis devem ser investigadas nesse modelo, na esperança de reduzir sua incerteza e, portanto, seu efeito na previsão da quantidade de calor. Em suma, são variáveis que afetam a resposta de forma significativa.
De acordo com os valores obtidos das massas erodidas na simulação resultante (tabela 6), oriundos da equação 06, ao se isolar a massa e utilizando a energia elétrica (E) – informações contidas na tabela 6 e que são compostas por corrente, tensão e duração do pulso –, para os nove casos nota-se que o calor específico (C sol.) para o estado sólido, a temperatura de trabalho (T trab. ) e a profundidade erodida da peça (L) exercem influência significativa na massa erodida.
Com relação ao calor específico (C solid.) (tabela 6), para o primeiro pulso poderá ser considerado o calor específico
no estado sólido, pois a temperatura ainda é a ambiente. Já para os demais pulsos essa temperatura é aumentada e muito, de forma que o calor específico varia até o estado líquido. Assim deveria ser analisada a hipótese de se utilizar um calor específico variando, conforme (C solid. → liq.) ou seja, do estado sólido para o liquido considerando as teorias de Einstein e Debey acerca do calor específico para altas temperaturas (Jenkins, 2008) (Reddy, Gokcen, 1996) (Hudson, 1996) (Hill, 2013).
Com relação à temperatura externa (Text.) (tabela 6), se o material possuir uma condutividade térmica elevada, como é o caso dos metais, e a parede oferecer pouca resistência à transmissão de calor por condução, e a queda de temperatura através da parede for baixa, isto é, se kT → ∞ e T ext. ≈ Tint., ou seja, a temperatura interna (Tint.), tais condições poderão corresponder a 99% da temperatura de ebulição (Tebulição).
Para a temperatura de trabalho (T trab.) (tabela 6) na determinação da massa erodida tem-se que para o primeiro pulso poderá ser considerada a temperatura ambiente. Já para os demais pulsos essa temperatura é aumentada e muito, ou seja, essa grandeza varia. A profundidade erodida da peça (L) pode ser estudada com uma possibi -
lidade de ser entendida como a coordenada Z do sistema CAM (Computer Assisted Manufacture) e ser estimada por meio do valor L, pois o sistema de coordenadas internacional corresponde ao eixo Z (Witte, 1998). Ressalta-se que isso é para realizar o avanço do eletrodo em direção à peça após o primeiro passo. Em suma, o modelo termofísico
teórico estudado joga luz no estudo dos fenômenos físicos envolvidos no processo de usinagem por meio da eletroerosão e permite afirmar que há relação entre a energia gerada pelo calor e a quantidade de material e ser erodida. Consequentemente, pode ser uma ferramenta para entender os fenômenos termofísicos que consideram como variáveis as características
1) Benedict, G. F. Nontraditional manufacturing processes. New York: Marcel Dekker, 1987. p. 207-229.
2) Bilal, A., Jahan, M. P., Talamona, D., Perveen, A. Electro-Discharge Machining of Ceramics: A Review. Micromachines. Vol. 10, 2019, pp.41.
3) Bruyn, H. E. Effect of a magnetic field on the gap Cleaning in EDM. Annais of Cirp, v.27, p.93-95 1978.
4) Casanueva, R., Ochoq, M., Azconod, F.J., Bracho, S. Current mode controlled LCC resonant converter for electrical discharge machining applications. Proceeding of ISIE’ 2000, Mexico.
5) Dauw, D.F.; Van Coppenolle, B. On the evolution of EDM research – part 2: from fundamental research to applied research. In: International Symposium for Electromachining. 11, 1995, Lausanne. Processings. Lausanne: EPFL, 1995.2v.p. 133-142.
6) Descoeudres, A. Characterization of electrical discharge machining plasmas. These (Docteur ès sciences). 2006. 125f. École Polytechnique Federale de Lausanne, Lausanne. Employed in edm. IEEE Trans. Ind. Gen. Appl. 1967, IGA-3, 302–309.
7) Eubank, P.T. et al. Theoretical models of the electrical discharge machining process III: the variable mass, cylindrical plasma mode. Journal of Applied Physics, USA, v.73, n. 11, p. 79007909, jun. 1993.
8) Fischer, U. et al. Tabellenbuch Metall. Verlag: Europa-Lehrmittel, Vollmer GmbH, 2a Edição, pp. 313-314, 2005.
9) Fuller, J. E. Electrical discharge machining. ASM Handbook, v. 16, p. 557-564, 1990.
10) Grigoriev, S.N., Kozochkin, M.P., Porvatov, A.N. Volosova, M. A., Okunkova, A. A. Electrical discharge machining of ceramic nanocomposites: sublimation phenomena and adaptive control. Heliyon. Vol. 5, 2019, pp. 19.
11) Guitrau E. P. The EDM Handbook. USA: Hanser Gardner Publications, 1997, 305 p.
12) Hill,T. An Introduction to Statistical Thermodynamic. Ist Edition, Editora: Dover, 2013.
13) Ho, K. H.; Newman, S. T. State of the Art Electrical Discharge Machining (EDM). International Journal of Machine Tools and Manufacture, Vol. 43, 2003, p. 1287–1300.
14) Hockenberry, T.O.; Williams, E.M. Dynamic evolution of events accompanying the lowvoltage discharges.
15) Hudson, J.B., Thermodynamic. Ist Edition, Editora: John Wiley and Sons, 1996.
16) Jenkins, H. D. B. Chemical Thermodynamics at a Glance. United Kingdom: Blackwell Publishing Ltd., 2008, 202.
17) Jeswani, M.L. Effect of machining area and pulse parameters of EDM performance. Indian Journal of Technology,p.354-356 Sep.1980.
18) Joshi A.; Kothiya, P. Investigating effects of process variables on MRR in EDM. International Journal on Theoretical and Applied Research in Mechanical Engineering (Ijtarme). 2012: p. 6.
do material, forma geométrica da região a ser erodida e a energia para realizar tal usinagem, sendo ainda uma ferramenta de apoio aos estudos empíricos (Medeiros, 1981) (Patel, 2014) (Fischer, et al. , 2005) (Santos, 2010) realizados que visam à obtenção do volume de material removido na usinagem via eletroerosão por penetração.
19) Kansal, H.K., Singh, P, Kumar, P., 2007. Technology and research developments in powder mixed electric discharge machining (PMEDM). Journal of Materials Processing Technology, 184, 32–41.
20) König, W. Fertigunsgsverfahren Band 3. Düsseldorf: VDI-Verlag, 1979.
21) Kuneida, M., Lauwers, B., Rajurkar, K.P., Schumacher, B.M. Advancing EDM through fundamental insight into the process. Annals of CIRP, 54 (2), 2005, 599–622.
22) Lazarenko, B. R., Lazarenko, N. I. Electrospark Machining of Metals. Edited by B. R. Lazarenko (Consulting Bireau), New York, Vol. 2. 1964, p. 1.
23) Lee, H. T., Hsu, F.C., Tai, T.Y. Study of surface integrity using the small area EDM process with a copper-tungsten electrode. Materials Science and Engineering. Ed. Elsevier. Vol.364. 2004 pp. 346-356.
24) Lee, H.T. Tai, T.Y. Relationship between EDM parameters and surface crack formation. J. Mater. Process. Technol., 142 (2003), pp. 676-683.
25) Lee, H.T. Yur, J.P. Characteristics analysis on EDMed surfaces using Taguchi method approach. Mater. Manufact. Process. Vol. 6, 2000, pp. 781-806.
26) Lide, D.R. CRC Handbook of Chemistry and Physics. USA: Editora: ----, 85th edition, 2005, 2661 p.
27) Lima, R.M. Utilização de fluidos dielétricos à base de óleos vegetais na usinagem por
descargas elétricas por penetração. Dissertação (mestrado em Engenharia Mecânica) – Faculdade de engenharia mecânica. Universidade federal de Uberlândia. 2008.
28) Lira, V. M. Princípios dos processos de fabricação utilizando metais e polímeros. São Paulo: Blucher, 2017. 240 p.
29) Lynch, C. T. Handbook of materials science. Volume 1 General Properties. Ohio: Air Force Wright Aeronautical Materials Laboratory, 1974. 752p.
30) Macher, B. Das leitungsverhalten und der Werkzeug-verschleiss bei der funkerosiven Bearbeitung von Stahlmit Speicher und Impulsgeneratoren. Aachen TH, 1966. (Dissertation).
31) Medeiros, J.T. N. Análise de alguns parâmetros tecnológicos da usinagem de aço carbono por eletroerosão. Dissertação (mestrado em Engenharia Mecânica) – Escola de Engenharia de São Carlos. Universidade de São Paulo. 1981.
32) Meek, J.M.; Craggs, J.D. Electrical Breakdown of Gases. John Wiley & Sons: Hoboken, NJ, USA, 1978.
33) Norliana, M.A., Solomon, D.G.,Bahari, Md.F. A review on current research trends in electrical discharge machining (EDM). Int. J. Machine Tools Manufact., vol. 47, 2007, pp. 1214-1228.
34) Patel, K. N. Parametric Optimization of Process Parameters For EDM of Stainless Steel 304. Dissertação (Mestrado) – National Institute of Technology Rourkela, Department of Mechanical Engineering. Odisha, India, 2014.
35) Puertas, I.; Perez, C.J.L. Modelling the manufacturing parameters in electrical discharge machining.
36) Ramasawmy, H. Blunt,L.Rajurkar K.P. Investigation of the relationship between the white layer thickness and 3D surface texture parameters in die sinking EDM process. Precision Eng., Vol. 29, 2005, pp. 479-490.
37) Reddy, R.G., Gokcen, N.A. Thermodynamics. 2nd Edition, Editora: Springer, 1996.
38) Richtline VDI 3400. Elektroerosive
Bearbeitung. Begriffe, Verfahren Anvwendung. Verein Deutscher Ingenieure (VDI), 1976.
39) Richtlline VDI 3402. Elektroerosive Bearbeitung. Definitionen unda Terminologie. Verein Deutscher Ingenieure (VDI), 1976.
40) Riffei. G. Influência da fenda de trabalho e da lavação nas condições de operação da eletroerosão por faísca. Santa Catarina, 1992. 127 p. Dissertação (Mestrado)- Universidade Federal de Santa Catarina.
41) Santos, I. Análise dos parâmetros de entrada na eletroerosão por penetração na liga de titânio TI-6AL-4V. Curitiba: UTFPR, 2010. 126 p. Dissertação (Mestrado) – Universidade Tecnológica Federal do Paraná, Curitiba, 2010.
42) Shen, Y., Chen, ,J. Yang, Y., et al. Study on the characteristics of plasma channel based on multi-spark pulse discharge machining effect. Int. J. Adv. Manuf. Technol. Vol. 97, 2018, pp. 1745. siliconized silicon carbide. Proc. Inst. Mech. Eng. Part B J. Eng. Manuf. 2003, 217, 791–803.
43) Singh, S., Maheshwari, S., Pandey, P.C. Some investigations into the electric discharge machining of hardened tool usinag different electrode materials. Journal of Materials Porcessing Tecnhology. Ed. Elsevier. Vol.149. 2003. Pp. 272-277.
44) Snoeys, R., Van Dijck, F. Plasma channel diameter growth affects stock removal in EDM. Annals of the CIRP, 21, 1972, 39-40.
45) Sodré, D.A. Influência do tratamento térmico na usinagem em eletroerosão por penetração nos aços ABNT NM 122 grau 01. Dissertação (Mestrado) Universidade Santa Cecília, Programa de pós-graduação em Engenharia Mecânica. 2017.
46) Tseng, K.H., Chung, M. Y., Chang, C.Y. Parameters for fabricating nano-Au colloids through the electric spark discharge method with micro-electrical discharge machining. Nanomaterials. Vol. 7, 2017, pp. 133.
47) ValentinˇCiˇc, J., Bissacco, G., Tristo, G. Uncertainty of the electrode wear on-machine measurements in micro EDM milling. Journal of Manufacturing Processes, 2021, pp. 153–160.
48) Van Dijck, F. et al. Some results of physical research in EDM. In: International Symposium for Electromachining, 4, 1974, Bratislava. Proceedings. Bratislava: (1974?). 1v. p.68-85.
49) Wertheim, R. Untersuchung der energetisher Vorgänge bei der funkerosiven Bearbeitung als Grundlage für eine Vierbes serung des Prozessablaufs. Aachen, FWTH März ,1975 (Thesis).
50) Wertheim, R. Untersuchung der energetischen Vorgänge bei der funkenerosiven Bearbeitung als Grundlagen für eine Verbesserung des Prozessablauf. Dissertassion – Technischen Hochschule Aachen, Aachen, 1971.
51) Witte, Horst. Máquinas-ferramenta: elementos básicos de máquinas e técnicas de construção: funções, princípios e técnicas de acionamento em máquinas ferramenta. São Paulo: Hemus, 1998. 395 p.
52) Wurzel, C.A. Estudo para a fabricação de eletrodos por metalurgia do pó e desenvolvimento de parâmetros de eletroerosão com ligas de cobre-nióbio. 2015. 109 f. Dissertação (Mestrado) – Engenharia de Minas, Metalúrgia e de Materiais, Universidade Federal do Rio Grande de do Sul, Porto Alegre, RS.
53) Yaws, C. L. Chemical Properties Handbook Ist Edition, Editora: McGraw-Hill Education, 1999, pp.779 .
54) Yue, X., Yang, X., Tian, J., et al. Thermal, mechanical and chemical material removal mechanism of carbon fiber reinforced polymers in electrical discharge machining. Int. J. Mach. Tool Manuf. , vol. 4, 2018, pp. 133.
55) Zhang, Z. Yu, H., Zhang,Y., et al. Analysis and optimization of process energy consumption and environmental impact in electrical discharge machining of titanium superalloys. J. Clean. Prod. Vol. 198, 2018, pp. 833.
56) Zingerman, A.S. Propagation of a discharge column. Soviet Physics-Technical Physics, 1(1), 5, 1956, 992-996.
Utilizadas geralmente em operações de rebarbação em geral, desbaste de cordões de solda ou abertura de trincas e talhas para soldagem, entre outras, as limas rotativas são ferramentas essenciais para operações de usinagem, oferecendo diversos recursos para a remoção de material, usinagem em ângulos agudos e trabalhos em contornos. Executam também o acabamento de perfis, furos, entalhes e chanfros. Neste guia são listados os fornecedores desses produtos, os quais assinalam o tipo de material, entre aço rápido e metal duro, e as aplicações possíveis, tais como metais ferrosos, não ferrosos e/ou compósitos, e também informam se elas possuem revestimento. Além disso, cada modelo é classificado de acordo com seu formato e tem descritas as suas dimensões.
Empresa Telefone E-mail Fabricante País
Disflex (19) 3846-7001 disflex@disflex.com.br
Dormer Pramet (11) 5660-3000 renato.brandao@dormerpramet.com
GDS (11) 95556-1861 vendas@gdsindustria.com.br
RS Tools (51) 3779-1162 vendas@rstools.com.br
Speed Cut (12) 99102-7693 alexandre.almeida@speedcut.com.br
Tungaloy (19) 3826-2521 vendas@tungaloybrasil.com.br
Wolf (11) 4082-0300 vendas@wolfbrasil.com.br
Japão
rápido
Para alumínio/metais não ferrosos Metais ferrosos Para materiais compósitos Cilíndrica com topo reto Cilíndrica com corte no topo Cilíndrica com topo esférico Esférica Oval Árvore arredondada Árvore com ponta Chama Cônica com ponta arredondada Cônica pontiaguda Cônica invertida Outras
Faixa de diâmetros das limas (mm)
Faixa de comprimentos das limas (mm)
Faixa de diâmetros da haste (mm)
Obs.: Os dados constantes deste guia foram fornecidos pelas próprias empresas que dele participam, de um total de 31 empresas pesquisadas. Fonte: Revista Máquinas e Metais, dezembro de 2024 / janeiro de 2025.
A Avoti , com sede no município paulista de Bady Bassitt, está intensificando seus serviços de desenvolvimento de placas para tornos CNC e equipamentos de fixação para usinagem. A empresa fabrica equipamentos sob encomenda e realiza consultoria para projetos, assistência técnica e reposição de peças, entre outros serviços.
Entre os recursos que podem ser integrados ao projeto das placas para tornos estão sistemas de alívio de peso, curso mais longo em comparação a placas convencionais, compensação de força centrífuga e porta-castanhas mais reforçados.
Um dos recentes desenvolvimentos da Avoti levou à fabricação de uma placa mista (hidráulica e pneumática) que possui sistema de centragem pneumática radial e fixação hidráulica axial. A placa (foto acima) é ideal para a fabricação de produtos que deformam ou ovalizam durante a fixação externa para usinagem. Avoti – Tel. (17) 9.8206-0105, www.avoti.com.br.
A Microdrilling , empresa especializada no desenvolvimento de máquinas CNC para furação profunda,
que integra o Grupo Honge Precision Industries Corp. (Taiwan), comercializa os equipamentos da linha XE, que possuem as versões 500, 1000 e 1500.
As máquinas operam em até 4 eixos simultaneamente e podem fazer furos com diâmetro de 3 a 25 mm, e com profundidade que varia de 500 a 1.500 mm no eixo Z. A velocidade máxima de trabalho do spindle é de 6.000 rpm, ao passo que a velocidade de furação pode chegar a até 150 mm/min.
Os equipamentos contam com motor de alta pressão com potência máxima, dependendo do modelo, de 3 a 7,60 cavalos, aproximadamente. Também são equipados com bomba de alta pressão, com vazão de até 150 litros por minuto e pressão máxima de 150 kg/cm².
Esta série de máquinas conta ainda com bomba de refrigeração de alta pressão e sistema de lubrificação automático. Como itens opcionais podem ser fornecidos separadores magnéticos, dispositivo de fixação especial e transportador de cavacos, entre outros.
O contato com a empresa pode ser feito pelo e-mail sales@gundrill.com.tw.
A Seco Tools, com matriz na Suécia e unidade brasileira em Sorocaba (SP), lançou duas novas versões de pastilhas de fresamento divisoras de cavacos, com recursos para reduzir o estresse na máquina e na ferramenta de corte, conferindo mais estabilidade ao processo de fresamento.
Os divisores de cavacos (chip splitters) são um recurso usado para dividir ou direcionar os cavacos de forma controlada, evitando que eles se acumulem e causem problemas no processo de produção. São projetados para controlar o comprimento do cavaco e ao mesmo tempo promover o bom acabamento superficial da peça usinada. Já os quebradores de cavacos (quebra-cavacos, ou chip breakers), embora também fragmentem os cavacos, são usados quando o acabamento superficial é realizado posteriormente.
As pastilhas divisoras de cavacos da linha Turbo 12 e 18 da Seco foram desenvolvidas para a linha Turbo de fresas da empresa e estão disponíveis em cinco classes, para fresas de ombro quadrado e helicoidais. Elas incorporam ranhuras em ambas as arestas de corte para minimizar o tamanho do cavaco e reduzir as forças sem reduzir parâmetros de corte. Seco Tools – Tel. (15) 2101-8600, www.secottols.com.
Está disponível para comercialização o livro “Metalurgia do pó – Produtos sinterizados e manufatura aditiva”, de autoria de Daniel Rodrigues, publicado pela Editora Blucher. A obra, lançada pela Associação Brasileira de Metalurgia, Materiais e Mineração (ABM) possui 206 páginas e está disponível para comercialização em versão física e digital.
A publicação traz uma introdução sobre a fabricação de pós metálicos, além de uma seção dedicada aos processos que envolvem o uso de materiais desse tipo, abrangendo ainda os parâmetros de operações e a caracterização dos pós metálicos. Estes últimos tópicos fazem parte do conteúdo dos capítulos 2 e 3, respectivamente.
A conformação de pós metálicos é o tema principal do quarto capítulo e o processo de sinterização tem destaque no capítulo 5. Os capítulos seguintes trazem informações sobre a manufatura aditiva (impressão 3D) de metais e exemplos de peças que podem ser produzidas por metalurgia do pó.
Um panorama dos trabalhos realizados pelo setor de metalurgia do pó é mostrado na obra, trazendo, por exemplo, informações sobre os processos de atomização, os tipos de
componentes e as etapas envolvidas em processos de sinterização a laser O livro pode ser adquirido pelo site da Editora Blucher (www.blucher.com.br) pelo preço sugerido de R$ 80,00.
O livro “Siderurgia, uma visão geral”, lançado pela Associação Brasileira de Metalurgia, Materiais e Mineração (ABM) e pela Editora Blucher, tem como autores Antonio Augusto Gorni, Antonio Malynowskyj, Eduardo Emery Cunha Quites, Marcelo Carboneri Carboni, Marcos Alexandre Stuart Nogueira, Rubens José Faco e Valdir Anderson Silvério. Desenvolvida com a coordenação de José Roberto Bolota, sócio-diretor da ABM, a publicação é escrita em português e possui 570 páginas. O conteúdo é distribuído em 11 capítulos, nos quais são abordados temas que vão desde os tipos de matérias-primas usadas para a produção de aços, e em que formato os aços são comercializados, até as características de processos produtivos. Em alguns capítulos o leitor vai encontrar informações sobre a produção de aço verde e o uso de hidrogênio no setor siderúrgico.
A obra foi configurada de uma maneira que permite ao leitor fazer consultas rápidas sobre assuntos específicos que se encontram em capítulos diferentes. O lingotamento contínuo de aços, processo pelo qual o material fundido é transformado em um bloco que será submetido à usinagem posteriormente, por exemplo, é o tema do capítulo 9. Aqui, as informações incluem dados sobre os tipos de equipamentos de lingotamento de aços e as fases envolvidas em cada processo, entre outros temas.
Nos capítulos 1 e 2 estão informações sobre os tipos de aços e os formatos que eles
apresentam como, por exemplo, barras, tarugos, blocos, blanques, chapas e tubos, entre outros. O terceiro capítulo é voltado para as matérias-primas siderúrgicas, no qual serão encontradas informações que abrangem as propriedades de materiais e os critérios envolvidos na seleção de cada material e nas aplicações em que serão utilizados.
A redução de minério de ferro em altos fornos é abordada no capítulo 4, assim como no capítulo 5, que é intitulado “Redução de minérios de ferro por redução direta, processos emergentes e produção do aço verde”. Nessa parte, além de informações sobre as etapas dos processos mencionados acima, que são complementadas com ilustrações, a temática da produção de aço verde é abordada.
Nos capítulos 6, 7, 8, 9 e 11, a obra traz, respectivamente, informações sobre a fabricação de aço líquido em conversor a oxigênio, aciaria elétrica, refino secundário de aços, lingotamento contínuo do aço e processo de controle termomecânico (TMCP, Thermo mechanical control process).
O livro possui versões com formato físico e digital. Pode ser adquirido pelo site da Editora Blucher (www.blucher.com.br) pelo preço sugerido de R$ 200,00.
Disponíveis em versões hidráulicas, pneumáticas, universais, especiais, indexáveis ou independentes, as placas para tornos são componentes essenciais no ambiente metal mecânico, desempenhando um papel crucial na precisão e eficiência das operações de usinagem.
Asseguram a fixação e a estabilidade da peça a ser trabalhada e evitam assim movimentos indesejados que podem comprometer a precisão do trabalho, além de permitirem a realização de cortes precisos e o cumprimento de especificações rigorosas.
Essenciais para a execução de trabalhos que exigem alta precisão e complexidade geométrica, elas fazem com que a peça gire em sincronia com o eixo principal da máquina, mantendo a precisão durante operações como torneamento e faceamento.
Adaptam-se a diferentes formatos e tamanhos de peças, podendo ter duas, três ou quatro castanhas e diâmetros variáveis, conforme a descrição das empresas listadas neste guia, as quais fornecem este produto no mercado nacional.
Empresa Telefone E-mail
Avoti (17) 98206-0105 avoti@avoti.com.br
BTfixo (54) 99999-6074 vendas@btfixo.com.br
Cinco (11) 3763-5543 cinco@kitagawa-cinco.com.br
Davima (11) 99493-1589 davima@davima.com.br
Diber (19) 3869-7348 diber@diber.com.br
Platec (51) 99512-5236 contato@platec.ind.br
Sanposs TSCI (11) 4126-6711 sanposs@sanposs.com.br
Schunk (11) 4468-6888 info@br.schunk.com
Obs.: Os dados constantes deste guia foram fornecidos pelas próprias empresas que dele participam, de um total de 28 empresas pesquisadas. Fonte: Revista Máquinas e Metais, dezembro de 2024 / janeiro de 2025.
Pequenas e médias empresas, inclusive do setor de usinagem, que trocam informações sobre a produção de maneira intensiva, devem estar atentas ao risco de ataques cibernéticos, os quais podem comprometer suas rotinas e resultados. Os antivírus são apenas uma parte da equação de segurança que envolve diversas outras ações.
Nos últimos anos, a segurança cibernética emergiu como um dos pilares essenciais para a sobrevivência e crescimento de empresas de todos os portes, e as indústrias brasileiras não são exceção. Embora o foco das notícias muitas vezes recaia sobre grandes empresas, é fundamental que pequenas e médias empresas reconheçam a importância de proteger seus dados e sistemas, pois o Brasil tem visto um aumento significativo nos ataques cibernéticos. Em 2023, segundo relatórios de segurança publicados por empresas como a Kaspersky, Sophos e IBM Security*, o País foi um dos mais atingidos por incidentes de ransomware, com as pequenas e médias empresas sendo os alvos preferenciais. Isso se deve, em grande parte, à percepção de que essas empresas possuem defesas mais frágeis e menos recursos para investir em proteção cibernética. Ignorar essas medidas pode ser extremamente custoso, tanto financeiramente quanto em termos de reputação. Confira os relatórios:
• Kaspersky Security Bulletin https://www.kaspersky.com/about/ press-releases/ahead-of-the-curve-kasperskys-projections-for-2024s-advanced-threats-landscape
• IBM X-Force Threat Intelligence Index 2024 https://www.ibm.com/ br-pt/reports/threat-intelligence
• Sophos - The State of Ransomware 2024 https://www.sophos.com/en-us/ content/state-of-ransomware
• NetScout Threat Intelligence Report https://www.netscout. com/threatreport/ddos-targets/
Entre os riscos diretos que um ataque cibernético representa, podemos listar:
• paralisação dos sistemas de uma empresa, impossibilitando-a de processar pedidos, emitir notas fiscais, fazer pagamentos e realizar outras operações críticas, o que pode comprometer gravemente a continuidade dos negócios e impactar diretamente o relacionamento com clientes e fornecedores;
• interferência nos dados de controle de processo, causando interrupção da produção;
• vazamento de dados sensíveis como projetos de clientes, processos e documentos internos da empresa, dados financeiros;
• perda de documentos e histórico de informações.
Um ataque de ransomware, que é o mais comum, é um tipo de ciberataque em que os hackers utilizam um software malicioso (malware) para bloquear o acesso aos arquivos ou sistemas da vítima, por meio de criptografia. Após o bloqueio, os atacantes exigem um pagamento (geralmente em criptomoedas) como resgate para liberar o acesso. E obviamente não há garantias que o acesso seja liberado ou que os dados não sejam divulgados mesmo após o pagamento do resgate, podendo ocorrer novas extorsões. Recentemente, uma das maiores empresas da indústria moveleira dos Estados Unidos, a Bassett Furniture Industries, anunciou que teve sua linha de produção paralisada em função de um ataque de ransomware, assim como a fabricante suíça de máquinas e sistemas de soldagem Schlatter Industries, em agosto último, entre outros exemplos.
*Paulo Henrique Pires é engenheiro de software e empresário
GERAÇÃO ARMAZENAMENTO DE ENERGIA GESTÃO DE ENERGIA USO DE ENERGIA
Intersolar South America
Fotovoltaica
Tecnologias termossolares
Usinas de energia solar
ees South America
Tecnologias de armazenamento de energia
Sistemas de armazenamento de energia
Hidrogênio verde
Eletrotec+EM-Power South America
Engenharia elétrica
Eficiência energética
Gestão de energia
O B R A S I L L I D E R A A R E V O L U Ç Ã O E N E R G É T I C A G L O B A L :
Power2Drive South America
Infraestrutura de carregamento
Baterias de tração
Mobilidade elétrica
T H E S M A R T E R E S O U T H A M E R I C A E N F O C A I N O VA ÇÕ E S E M E N E R G I A
R E N O VÁV E L E E L E T R OM O B I L I DA D E
Na vanguarda global da transição energética, o Brasil utiliza seus vastos recursos de energia renovável com soluções avançadas de armazenamento de energia, tecnologias inovadoras de rede e um crescente setor de eletromobilidade. A abundância de seus recursos solares, eólicos e hidrelétricos permite que o país expanda expressivamente sua capacidade de energia renovável, de modo a reduzir a dependência de combustíveis fósseis e diminuir as emissões de carbono, ao passo que a incorporação de sistemas avançados de armazenamento de energia aprimora a estabilidade da rede, resultando em um aumento na confiabilidade do fornecimento de energia a par tir de fontes renováveis intermitentes O aproveitamento desse potencial permitirá que o Brasil alcance a sustentabilidade energética, estimulando o crescimento econômico e criando um poderoso exemplo para outros países The smar ter E South America – a maior plataforma latino-americana para a nova realidade energética e de mobilidade – se dedica a explorar toda questão da nova realidade energética,
abrangendo energia renovável, armazenamento de energia, redes inteligentes e eletromobilidade
Nossa missão é inspirar e facilitar a troca de ideias, tecnologias e práticas que definirão o futuro da energia Realizamos evento mais abrangente para o setor latino-americano de energia renovável, reunindo inovadores, especialistas e líderes do mundo todo para fazer avançar a pauta da energia sustentável. Os quatro congressos deste ano prometem ser um evento marcante, tendo como pano de fundo o dinamismo de um setor energético em rápida evolução: Intersolar South America – O congresso para o setor solar latino-americano ees South America – O congresso para baterias, sistemas de armazenamento de energia e hidrogênio verde Power2Drive South America – O congresso para eletromobilidade e infraestrutura de recarga Eletrotec+EM-Power – O congresso para infraestrutura de eletricidade e gestão de energia
O custo da inação e a negligência comum
Empresas de pequeno porte frequentemente negligenciam a segurança cibernética. O investimento muitas vezes é adiado ou minimizado porque não é percebido como uma prioridade, especialmente em um ambiente onde a produtividade e a eficiência operacional são cruciais para a competitividade e sobrevivência da empresa. No entanto, essa negligência pode ter consequências desastrosas. A implementação de um simples antivírus é frequentemente vista como suficiente para proteger a empresa, mas a realidade é muito mais complexa. Antivírus, embora importantes, são apenas uma parte da equação de segurança. Eles não são capazes de proteger contra ameaças mais sofisticadas, como ataques de phishing, ransomware ou vulnerabilidades em sistemas não atualizados. Depender exclusivamente de antivírus pode deixar a empresa exposta a uma série de ameaças que exigem medidas mais abrangentes e proativas.
A realidade da certificação CMMC e sua relevância
Nos Estados Unidos, empresas que fazem parte da cadeia de fornecimento de defesa enfrentam a exigência de obter a certificação CMMC (Cybersecurity Maturity Model Certification). Essa certificação é um modelo de maturidade de segurança cibernética que visa proteger informações sensíveis dentro da cadeia de suprimentos da defesa. O CMMC define diferentes níveis de maturidade, com requisitos específicos que as empresas devem atender para poderem trabalhar com o governo americano. Embora essa exigência seja particular do contexto americano, estar ciente de tais modelos e preparar-se para eventuais exigências similares no futuro pode ser uma estratégia inteligente. Mesmo que o Brasil ainda não tenha um nível de
exigência equivalente, a adoção de boas práticas de segurança cibernética é fundamental para manter a competitividade.
Medidas práticas para melhorar a segurança cibernética
Dado o cenário desafiador, seguem aqui algumas dicas sobre o que as indústrias brasileiras podem fazer para proteger suas operações sem comprometer seu orçamento.
1. Mapeamento e identificação de vulnerabilidades:
• Mapeamento físico e digital: o primeiro passo para um mapeamento eficaz é realizar um levantamento detalhado de todos os dispositivos conectados à internet, tanto os físicos quanto os digitais. Isso inclui máquinas CNC, servidores, estações de trabalho, impressoras, sistemas de controle e até mesmo dispositivos móveis utilizados na empresa. Cada dispositivo que pode se conectar à rede deve ser registrado. Isso ajudará a criar uma visão clara de todos os pontos de entrada que poderiam ser potencialmente explorados por cibercriminosos. Uma prática recomendada seria garantir que essas máquinas estejam conectadas por meio de uma rede isolada ou utilizar firewalls robustos que limitem o acesso externo.
• Classificação de vulnerabilidades: após o mapeamento, é necessário classificar as vulnerabilidades de acordo com o seu potencial de risco. Por exemplo, um servidor desatualizado que armazena dados sensíveis de clientes pode ser uma prioridade alta, enquanto uma impressora de escritório com acesso limitado à rede pode ser uma prioridade menor. Ferramentas como scanners de vulnerabilidades (ex: OpenVAS) podem ser usadas para identificar falhas de segurança nos sistemas.
2. Treinamento contínuo dos funcionários: os funcionários são a primeira linha de defesa contra ataques cibernéti-
cos. Treinamentos regulares sobre como identificar e responder a ameaças, como phishing e outras formas de engenharia social, são essenciais. Em muitas empresas, a falta de conscientização entre os funcionários é uma das principais brechas exploradas pelos atacantes.
3. Planejamento e resposta a incidentes: ter um plano de resposta a incidentes cibernéticos é crucial. Esse plano deve incluir procedimentos claros sobre como reagir em caso de uma violação, desde a contenção do incidente até a comunicação com as partes envolvidas e a recuperação dos sistemas. No Brasil, a ausência de um plano desse tipo pode resultar em maior tempo de inatividade e perdas financeiras significativas.
4. Escolha de parceiros confiáveis: para pequenas empresas que não têm recursos para manter uma equipe de TI dedicada, a escolha de parceiros confiáveis para auxiliar na segurança cibernética é vital. Associações industriais e redes de contatos podem ser fontes valiosas de recomendações sobre serviços e ferramentas de segurança.
5. Atualização e manutenção regular dos sistemas: a segurança cibernética não é uma tarefa que pode ser “configurada e esquecida”. Atualizações regulares de software e a aplicação de patches de segurança são essenciais para proteger os sistemas contra as ameaças mais recentes. Além disso, considerar a contratação de seguros cibernéticos pode ser uma boa estratégia para mitigar riscos.
Casos e exemplos dos Estados Unidos
Nos Estados Unidos, grandes empresas como a Mazak estão na vanguarda da segurança cibernética ao se unirem a institutos de inovação, como o Cybersecurity Manufacturing Innovation Institute (CyManII). Essa parceria visa impulsionar a segurança cibernética em toda a cadeia de suprimentos, desenvolvendo tecnolo -
gias avançadas para proteger dados e infraestruturas críticas. Embora essas iniciativas sejam específicas do contexto americano, elas oferecem lições valiosas que podem ser adaptadas para o Brasil. Por exemplo, o aumento dos ataques de ransomware nos EUA serve como um alerta para as empresas brasileiras. Especialistas americanos recomendam a adoção de práticas como a autenticação multifator (MFA) e a implementação de soluções de detecção e resposta a endpoints (EDR). Essas práticas, embora ainda emergentes no Brasil, são cruciais para proteger os sistemas contra ameaças sofisticadas e cada vez mais frequentes.
Para que a segurança cibernética seja eficaz, ela deve ser incorporada à cultura organizacional da empresa. Isso significa que a segurança deve ser vista não como um custo, mas como um investimento estratégico que protege o negócio e garante sua continuidade. As indústrias brasileiras, em particular, precisam adotar uma postura proativa em relação à segurança cibernética, antecipando-se às ameaças e implementando medidas que fortaleçam suas defesas. A realidade é que, no cenário atual, a pergunta não é se uma empresa será atacada, mas quando. Portanto, estar preparado é essencial. A implementação de boas práticas de segurança cibernética não apenas protege a empresa contra ataques, mas também pode proporcionar uma vantagem competitiva, especialmente em um mercado cada vez mais exigente em termos de segurança.