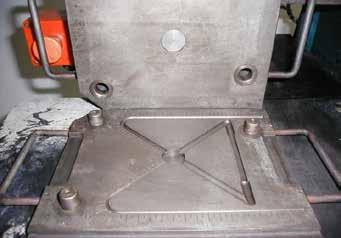
12 minute read
MATÉRIA TÉCNICA
from Ed153
by Aspa Editora
DESMOLDANTE SEMI-PERMANENTE: DESMOLDANTE OU AUXILIAR DE FLUXO?
Autor: Marcos Aurélio Rufato – Chem-Trend
Advertisement
Introdução
Ao longo dos anos, o uso de desmoldantes semi-permanentes vem crescendo a passos largos nas empresas de artefatos de borracha ao redor do mundo. Porém, muitas vezes, há uma necessidade real de que o desmoldante, além de facilitar a extração dos artefatos produzidos do molde (função básica e principal de qualquer agente desmoldante), também auxilie na formação dos artefatos, trabalhando como um verdadeiro auxiliar no fl uxo do composto de borracha. Esta caracterís� ca dos desmoldantes semi-permanentes está sendo cada vez mais explorada pelos engenheiros de processo e químicos das empresas, pois já é possível trabalhar com compostos mais nobres - onde o uso dos auxiliares de fl uxo clássico pode alterar alguma caracterís� ca � sica do composto ou onde o desenho do molde exige que a borracha escoe por caminhos muito sinuosos -, sabendo que o desmoldante semi-permanente irá contribuir para que este composto fl ua com facilidade e a formação do artefato seja completa e sem defeitos. Há, também, a possibilidade de economia de energia elétrica que se consegue com a diminuição da pressão de injeção, pois com o uso de semi-permanentes é possível injetar, com pressão menor, a mesma quan� dade de composto de borracha na qual seria necessária uma pressão maior, caso não houvesse um agente desmoldante no molde. O intuito deste trabalho é demostrar, com os resultados ob� dos em testes experimentais, em laboratório, e prá� cos, em injetora de produção que, na realidade, os desmoldantes semi-permanentes são, ao mesmo tempo, agentes desmoldantes e auxiliares de fl uxo.
1) Ensaios em laboratório
Nestes ensaios, foram feitas várias vulcanizações de um composto preparado em quan� dade sufi ciente para todos os testes, variando-se o tratamento na super� cie do molde. Iniciamos com o molde virgem, sem tratamento algum, para termos como resultado base, a fl uidez real do composto. Após obtermos este resultado, iniciamos os tratamentos, primeiramente com emulsão de silicone e em seguida com três � pos diferentes de desmoldantes semi-permanentes.
1.1) Molde Nos ensaios em laboratório foi u� lizado o método de medição de fl uidez chamado “Método Du Pont”, ou mais conhecido como Teste no Molde Aranha:uma quan� dade defi nida de composto de borracha (30 +/- 1 grama) é transferida por ori� cio de 4,8 mm de entrada e 1,3 mm de saída a uma pressão de 150 Kgf. O molde é fechado, sem degasagem, aguardando-se a vulcanização do artefato. Após a vulcanização, visualiza-se a fi gura formada e também se calcula a porcentagem de massa transferida. Este é um método ainda não norma� zado, mas que se tem demonstrado efi caz no obje� vo de avaliação compara� va da fl uidez de compostos.
Figura 1: Molde Aranha.
1.2) Composto: O composto usado para os ensaios tem a seguinte fórmula:
Borracha Natural GEB-1 100,0 phr N – 339 55,0 phr ZnO 4,0 phr 6 PPD 2,0 phr TMQ 1,0 phr Ácido Esteárico 1,0 phr Enxofre 2,5 phr TBBS 0,6 phr
Podemos notar que o composto não possui plas� fi cante nem auxiliares de fl uxo, fato que o torna di� cil de transferir e de fl uir na super� cie do molde. O composto foi feito em misturador interno � po Banbury, homogeneizado em misturador aberto e apresentou a seguinte curva reométrica:
Toque (lb-in) Chem Trend
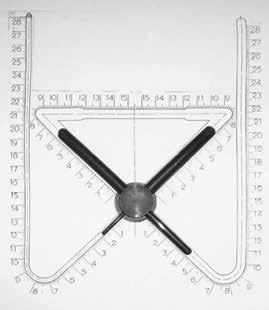
Figura 2: Curva Reométrica.
Time (Min) 12.0 Temperature (ºC) 160.0
S’Max - S’ Min 13.94 lb-in S’Max 13.38 lb-in S’Min 2.44 lb-in TC 50 2.17 Minute TC 90 5.12 Minute Scorch Time (TS 1) 1.03 Minute tan.delta@TC 90 0.16 -
Neste composto ob� vemos as seguintes caracterís� cas � sicas:
PROPRIEDADE: RESULTADO: NORMA: Tensão de Ruptura, Kgf/cm2 219,19 ASTM D412-98 Alongamento, % 405,33 ASTM D412-98 Módulo 100 % , kgf/cm2 31,10 ASTM D412-98 Módulo 300 % , kgf/cm2 151,54 ASTM D412-98 Rasgamento, kgf/cm 106,30 ASTM D624-98 Dureza, shore A 64,0 ASTM D2240-97 Resiliência, % 36,0 DIN 53512 Abrasão, mm3/40 m 117,42 DIN 53516 1.3) Parâmetros de ensaio:
• Tempo de vulcanização: 8 minutos. • Temperatura de vulcanização: 160ºC +/- 5. • Pressão: 150 Kgf / cm2, após o início de transferência a pressão caía, aguardávamos 1 minuto e completávamos a pressão p/ 150 Kgf / cm2. • Temperatura do composto no carregamento do molde: Ambiente. • Não foi efetuada degasagem. • Antes do início de qualquer ensaio, o molde era limpo com tratamento químico e solvente. • Para todas as amostras foram realizadas 10 vulcanizações.
2) Resultados
2.1) Amostra em Branco O composto foi prensado sem nenhum � po de tratamento no molde. • Taxa de transferência: 31,06 %.
AMOSTRA EM BRANCO
Figura 3: Prova em Branco.
2.2) Emulsão de Silicone O composto foi prensado usando-se emulsão de silicone na super� cie do molde (emulsão a 36% de sólidos, diluído 1:36), aplicado a cada duas prensadas. • Produto aplicado com pincel. • Taxa de transferência: 34,46 %. • Melhoria de 9,86 % em relação à prova em branco.
AMOSTRA EM BRANCO EMULSÃO DE SILICONE AMOSTRA EM BRANCO
DESMOLDANTE SEMI-PERMANENTE MONO-COAT® BASE ÁGUA STANDARD
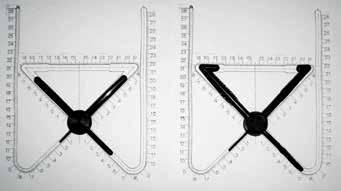
Figura 4: Emulsão de Silicone.
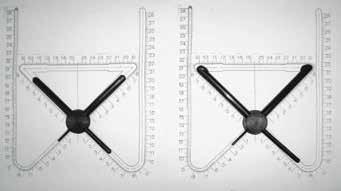
2.3) Desmoldante Semi-Permanente Mono-Coat® Base Solvente O composto foi prensado usando-se desmoldante semi-permanente base solvente na super� cie do molde. Produto em aerosol, aplicado segundo as regras de aplicação dos desmoldantes semi-permanentes. • Taxa de Transferência: 37,10 %. • Melhoria de 16,28 % em relação à prova em branco.
AMOSTRA EM BRANCO
DESMOLDANTE SEMI-PERMANENTE MONO-COAT® BASE SOLVENTE Figura 6: Desmoldante Semi-Permanente Mono-Coat® Base Água – Standard.
2.5) Desmoldante Semi-Permanente MonoCoat® Base Água – Alto Fluxo: O composto foi prensado usando-se um desmoldante semi-permanente base de água, com fórmula ajustada para melhorar o fl uxo do composto, na super� cie do molde. Produto aplicado por spray, segundo as regras de aplicação dos desmoldantes semi-permanentes. • Taxa de transferência: 39,00 %. • Melhoria de 20,35 % em relação à prova em branco.
AMOSTRA EM BRANCO
DESMOLDANTE SEMI-PERMANENTE MONO-COAT® BASE ÁGUA ALTO FLUXO
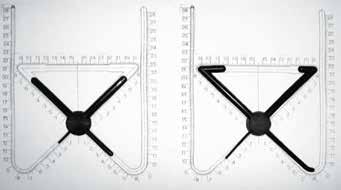
Figura 5: Desmoldante Semi-Permanente Mono-Coat® Base Solvente.
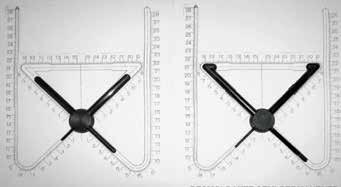
2.4) Desmoldante Semi-Permanente Mono-Coat® Base Água - Standard O composto foi prensado usando-se desmoldante semi-permanente base de água, com fórmula standard, na super� cie do molde. Produto aplicado por spray, segundo as regras de aplicação dos desmoldantes semi-permanentes. • Taxa de transferência: 37,97 %. • Melhoria de 18,19 % em relação à prova em branco.
Figura 7: Desmoldante Semi-Permanente Mono-Coat® Base Água – Alto Fluxo.
Faça parte você também das nossas publicações e fique sempre bem informado! www.borrachaatual.com.br
3) Interpretação dos resultados de laboratório
Podemos verifi car que o fl uxo do composto é melhorado sempre que fazemos algum � po de tratamento na super� cie do molde. Os desmoldantes semi-permanentes melhoram o fl uxo de um composto de borracha, em média, 18,27% em relação ao molde limpo e em até 8,83%, em relação à emulsão de silicone. Ao adicionar a operação de degasagem subimos a taxa de transferência para 51,74%, em média, para os desmoldantes semi-permanentes.
DEGASAGEM
Figura 8: Degasagem.
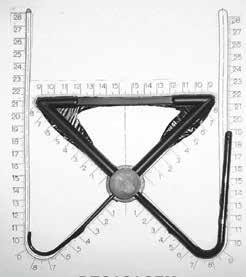
Estes resultados de melhoria de fl uxo se devem ao fato do desmoldante semi-permanente se fi xar na super� cie do molde, através de interações � sico-químicas, e criar uma camada que cobre as micro-ranhuras e micro-depressões que existem na super� cie de qualquer metal. Esta camada deixa a super� cie dos moldes mais lisa e menos porosa, fazendo com que a área superfi cial diminua, bem como reduzindo a tensão superfi cial e, portanto, reduzindo também o contato entre a borracha e a super� cie do molde, deixando que o composto fl ua com mais facilidade e que a desmoldagem fi que muito mais leve e fácil. Abaixo, ampliações da super� cie de um molde feito em microscópio eletrônico demonstrando a camada ancorada.
Você acessa de qualquer lugar e do modo que quiser. Computador, tablet ou celular.
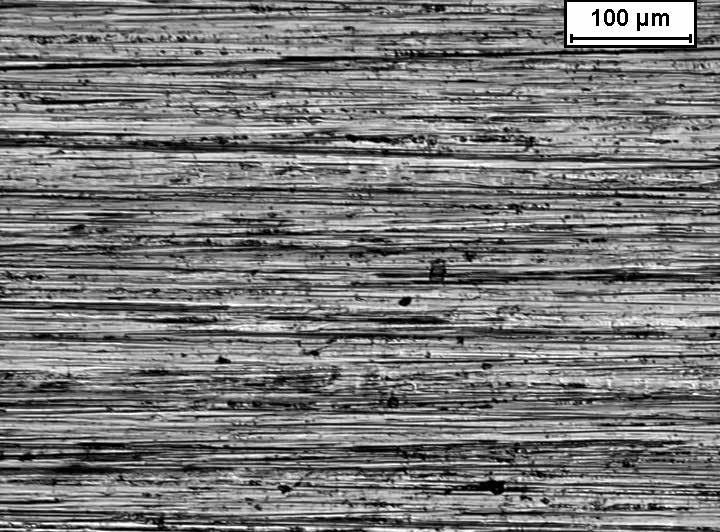
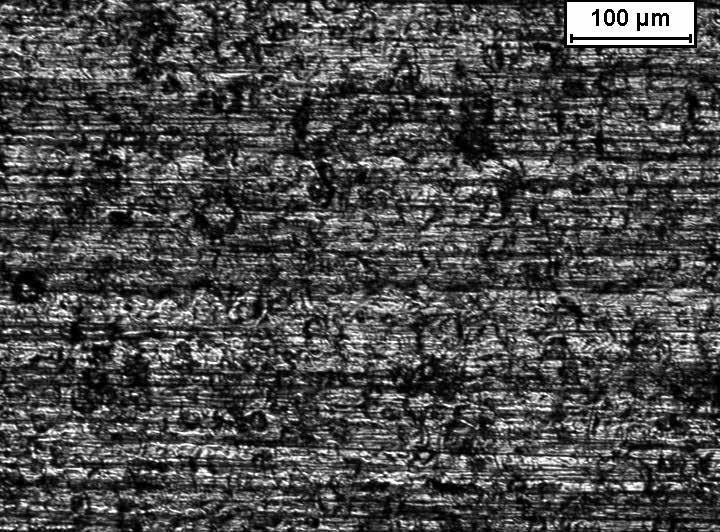
Figuras 9: Superfície virgem X Superfície com desmoldante semipermanente Mono–Coat® Base Solvente (aumentada 100 vezes).
Figura 10: Superfície com desmoldante semi-permanente Mono-Coat® Base Solvente (aumentada 200 vezes).
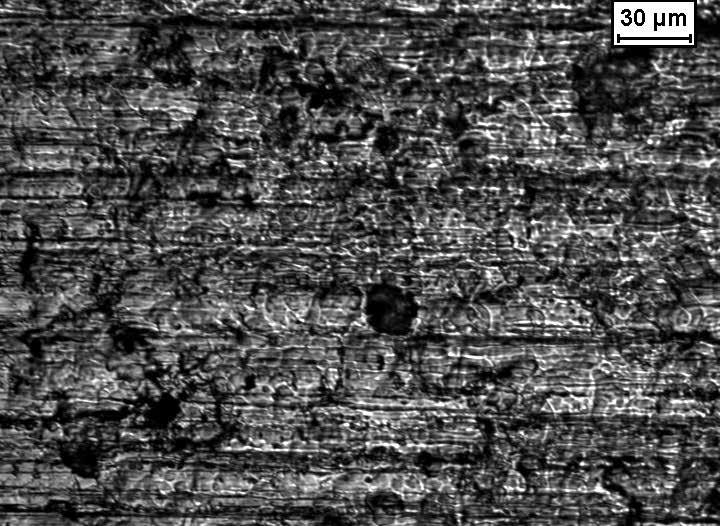
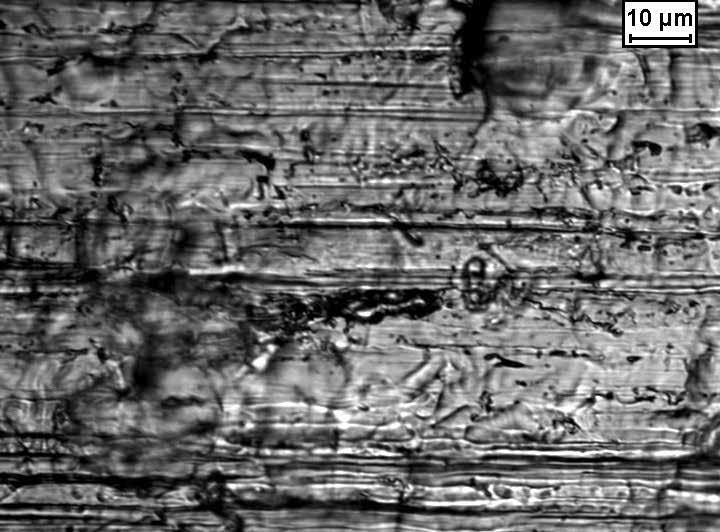
Figura 11: Superfície com desmoldante semi-permanente Mono-Coat® Base Solvente (aumentada 500 vezes).
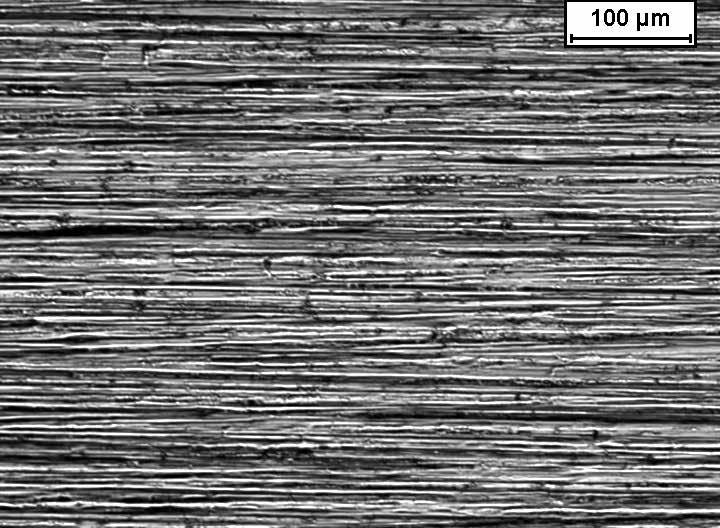
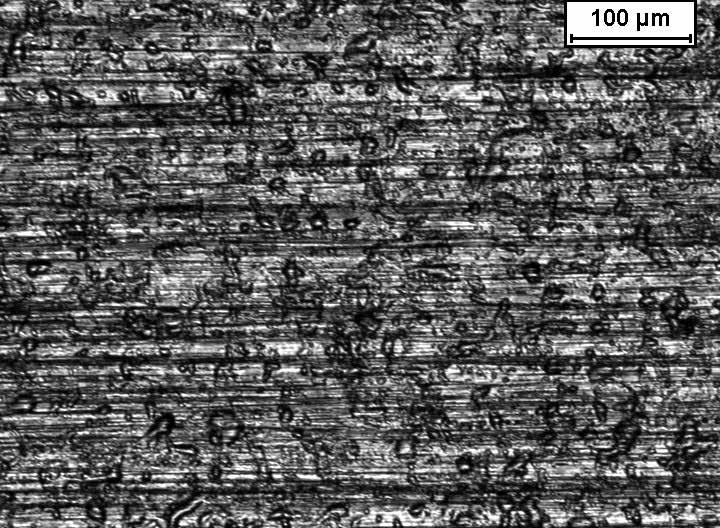
Figuras 12: Superfície virgem X Superfície com desmoldante semi-permanente Mono-Coat® Base Água – Alto Fluxo (aumentada 100 vezes). Figura 13: Superfície com desmoldante semi-permanente MonoCoat® Base Água – Alto Fluxo (aumentada de 200 vezes).
Figura 14: Superfície com desmoldante semi-permanente Mono-Coat® Base Água – Alto Fluxo (aumentada 500 vezes).
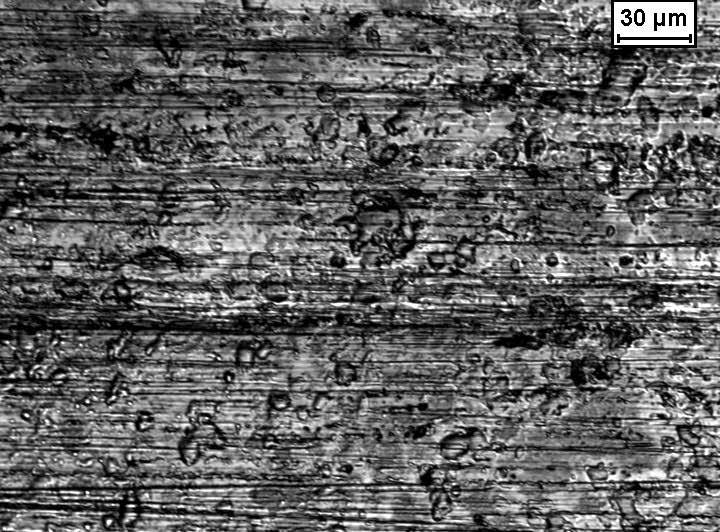
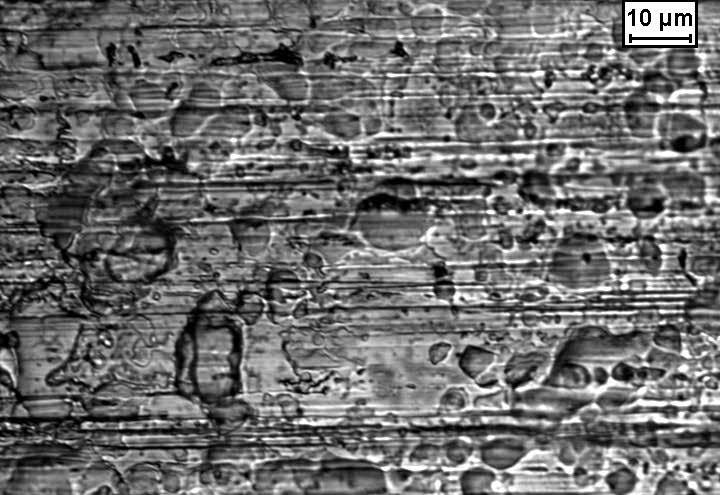
4) Ensaio em Injetora de Produção (Parte Prática)
Neste ensaio, visamos uma avaliação compara� va do comportamento na moldagem por injeção, sem e com a aplicação de um desmoldante semi-permanente no molde, verifi cando a diminuição da pressão mínima de injeção para preenchimento completo das cavidades do mesmo, incluindo canais de escape, a diferença da rugosidade da super� cie do molde nos dois casos e a variação no esforço humano para abrir e sacar as peças do molde.
4.1) Molde: Para os ensaios em injetora, foi u� lizada uma máquina standard, ver� cal, com capacidade de medições de tempo de injeção e tempo de recuo e possibilidade de pressão variável nos estágios de injeção.
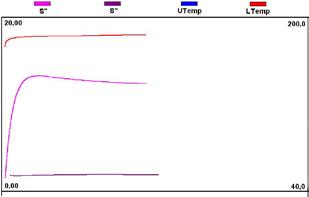
Figura 15 : Injetora.
Molde de aço 1045 de quatro cavidades, com acabamento liso temperado e um ponto de injeção, conforme fi gura abaixo foi fi xado nos platôs da injetora, sendo a abertura intermediária realizada manualmente.
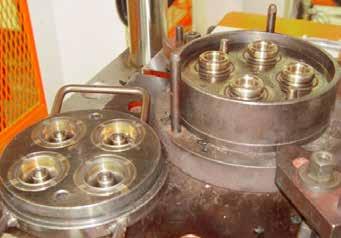

Figuras 16 e 17: Molde Injetor. 4.2) Composto: Composto à base de EPDM, com a seguinte curva reométrica:
SUBTESTE 1 OF 1: CURE
Toque (lb-in) Temperature (ªC)
0,00 Time (m.m) 30,00
Subtest 1 of 1: Cure Time 30,00 m.m Frequency 100,0 cpm Temperature 190,0 ºC Strain 0,50 deg
Propriedades Originais:
PROPRIEDADE: RESULTADO: NORMA: Tensão de Ruptura, MPa 11,1 ASTM D412-98 Alongamento, % 430 ASTM D412-98 Módulo 300 % , kgf/cm2 7,5 ASTM D412-98 Dureza, shore A 58,0 ASTM D2240-97
Parâmetros de ensaio: • Tempo de vulcanização: 1,7 minuto. • Temperatura do composto na região de plas� fi cação e transferência: 60ºC. • Temperatura nos platôs: 190ºC. • Volume de injeção: Fixado de modo a garan� r uma pequena sobra. • Velocidade de injeção: 1º estágio = 50%; 2º estágio= 70%, em relação à velocidade máxima. • Tempo de injeção: 15 segundos. • Tempo de recuo: 35 segundos. • Pressão de injeção: 1º estágio: variável; 2º estágio: variável • O molde foi limpo por ultra-som e posterior jateamento com par� culas poliméricas, antes de cada ensaio. • Foram realizadas 20 vulcanizações para cada situação. • A aplicação do desmoldante seguiu as regras de aplicação para desmoldantes semi-permanentes.
4.3) Resultados:
• Injeção sem uso de desmoldante:
Pressão mínima requerida para preencher as cavidades: 1º estágio: 48 bar | 2º estágio: 53 bar Abertura do molde: Apresentou difi culdade, exigindo uso de ferramentas. Remoção das peças/rebarbas: Apresentou difi culdade, requerendo uso de ar comprimido e escovas.
• Injeção com uso de desmoldante semi-permanente
Mono-Coat® Base Solvente:
Pressão mínima requerida para preencher as cavidades: 1º estágio: 44 bar | 2º estágio: 49 bar Abertura do molde: Não apresentou difi culdade. Remoção das peças/rebarbas: Não apresentou difi culdade.
A tabela abaixo relaciona as massas das peças vulcanizadas (peças + rebarbas) por ordem sequencial de injeção.
Injeção nº Massa (g) Sem Desmoldante
Massa (g) Com Desmoldante
1 2 3 4 5 6 7 8 9 10 11 12 13 14 15 16 17 18 19 20 20,5 20,5 20,5 20,5 20,6 20,6 20,6 20,6 20,5 20,5 20,2 20,5 20,3 20,5 20,4 20,4 20,4 20,5 20,0 20,4
20,5 20,6 20,6 20,4 20,7 20,2 20,4 20,5 20,4 20,1 19,9 19,9 (*) 19,8 20,3 20,4 19,8 20,1 19,6 20,0 20,0
* Aplicação de nova camada de desmoldante semi-permanente Mono-Coat® Base Solvente para a moldagem seguinte. OBS.: É importante notar que a quan� dade de material transferido foi rela� vamente similar, indicando que o ajuste da máquina foi adequado para salientar a variável pressão. Este conjunto de resultados mostrou que o uso da amostra propicia uma moldagem com menor pressão.
• Interpretação dos resultados:
Notamos que há uma diminuição na pressão requerida para preenchimento das cavidades do molde da ordem de 9% no primeiro estágio e de 7,5% no segundo, quando se usa uma camada de desmoldante semi-permanente na superfície do molde. Isto demonstra que o uso do desmoldante semi-permanente auxiliou o fluxo do composto preenchendo com mais facilidade as cavidades, exigindo menos esforço da máquina usada e facilitando a operação humana, demandando menos esforço do operador e, consequentemente, deixando a operação mais rápida e segura.
5) Conclusão
De acordo com os resultados ob� dos nos testes realizados, tanto em laboratório como em máquina de produção, podemos concluir, com segurança, que o desmoldante semi-permanente é também um excelente auxiliar de fl uxo para compostos de borracha. Além de trabalhar como desmoldante e auxiliar de fl uxo, os resultados mostram que o semi-permanente também oferece uma economia no consumo de energia, uma vez que reduz o esforço dos equipamentos usados na indústria de borracha durante os processos de injeção, transferência e prensagem. Proporciona maior conforto ao operador dos equipamentos, facilitando a operação de abertura e descarregamento dos moldes, melhorando a produ� vidade dos indivíduos e diminuindo a incidência de LER/DORT (Lesões por Esforço Repe� � vo/Distúrbios Osteomusculares Relacionados ao Trabalho). Fica evidente que o uso dos desmoldantes semi-permanentes pode auxiliar os engenheiros de processo e químicos das empresas de borracha na produção de peças com conformação complicada, longo caminho a ser percorrido pela borracha e onde um composto, que por necessidade de especifi cação ou limitação de processo, tenha viscosidade alta e necessite cura rápida.

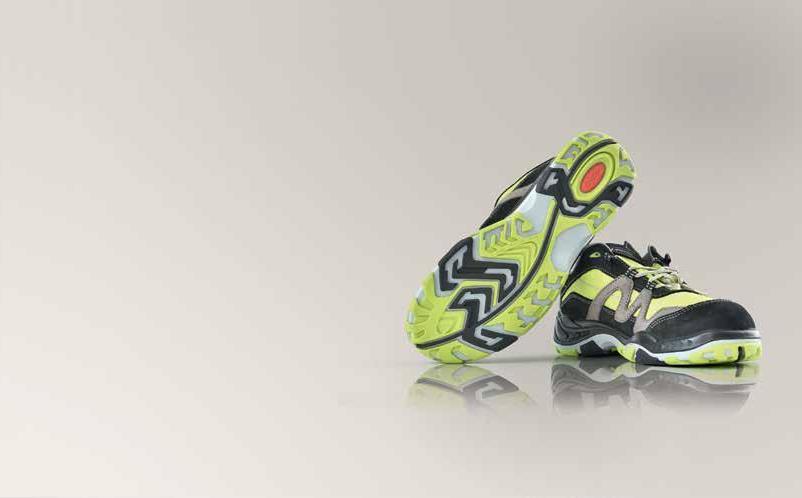
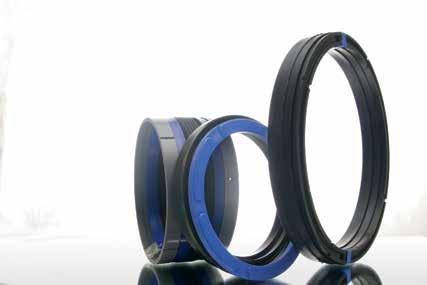
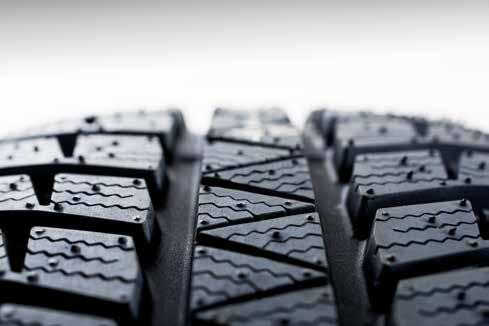
