ONE-OF-A-KIND REFINERY
Come by Chance Renewable Diesel
Plant Starts Operations
Page 16

Plus
Biodiesel Industry
Workforce
Survey Results
Page 26 Pacific
Biodiesel's Continued
Evolution
Page 20
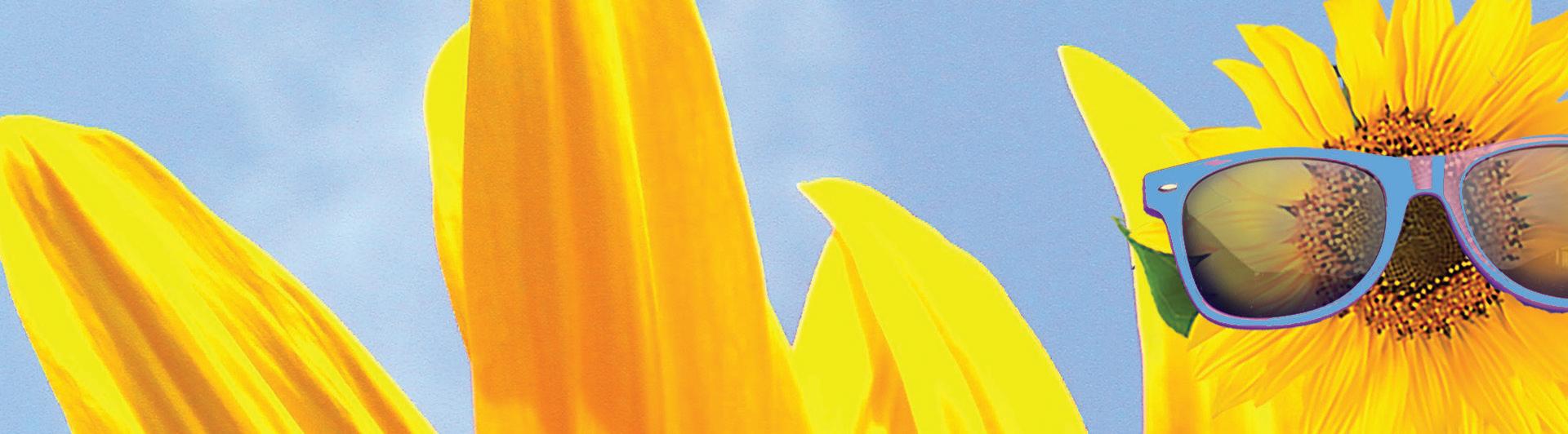

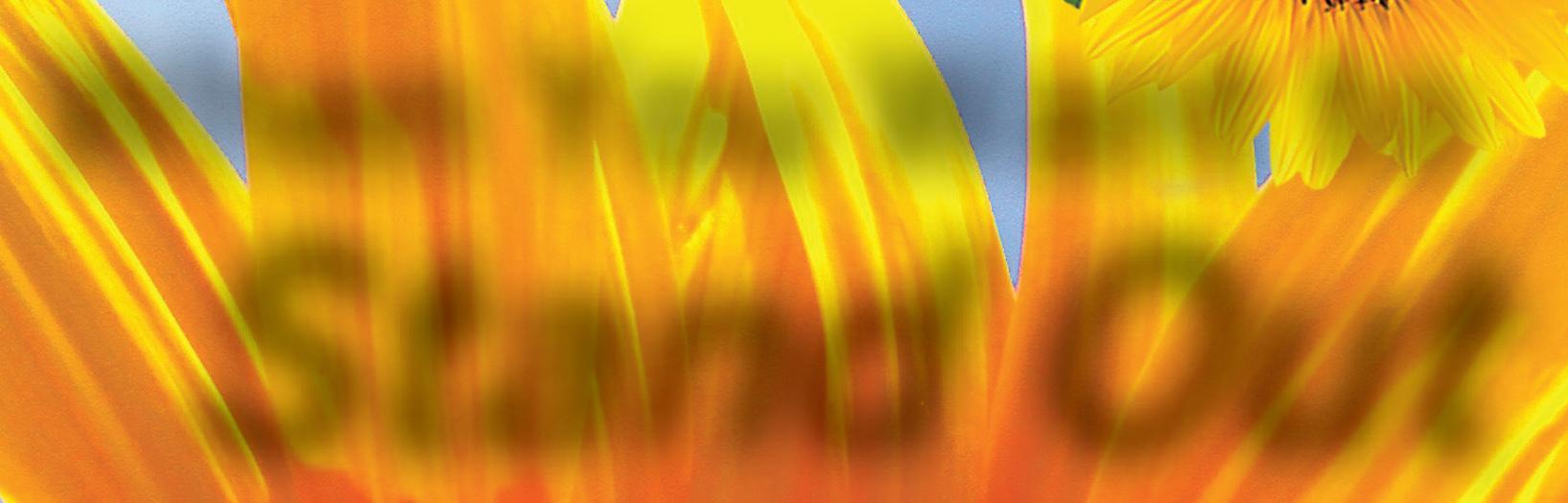
Come by Chance Renewable Diesel
Plant Starts Operations
Page 16
Plus
Biodiesel Industry
Workforce
Survey Results
Page 26 Pacific
Biodiesel's Continued
Evolution
Page 20
16 CONVERSION
A converted Canadian renewable diesel facility
Is leveraging its unique geographic location for logistical and carbon reduction benefits.
BY KATIE SCHROEDER20 PRODUCTION Pacific Pioneer
Operating for nearly 30 years, Pacific Biodiesel’s commitment to sustainability extends far beyond biofuel production.
BY KEITH LORIA26 INDUSTRY
Survey results indicate overall job satisfaction is very high in the biodiesel industry, current growth is modest and the workforce is diverse when it comes to age, gender and longevity in the industry.
Through audits and supplier capacity building, Neste promotes sustainable supply chain practices.
Loamist's Biomass Explorer platform provides real-time mapping and detailed data visualization, enabling efficient locating and evaluation of biomass resources.
BY ANDY MILLER AND PETE CHRISTENSEN2024 North American SAF Conference and Expo 2025
Biodiesel Summit: Sustainable Aviation Fuel & Renewable Diesel
Biodiesel Jobs
Biodiesel Magazine
Carbis Solutions Group, LLC
Clariant Corp.
Clean Fuel Alliance America
Crown Global Companies-Crown Iron Works
Dallas Group of America, Inc.
Desmet Ballestra North America
DSM-Firmenich
Filtration Technology Corporation
Helle Engineering, LLC
Oil-Dri Corporation of America
PFT-Alexander Service, Inc.
Pick Heaters, Inc.
United Color Manufacturing
Inc.
Minneapolis Convention Center | Minneapolis, MN (866) 746-8385 | www.fuelethanolworkshop.com
Celebrating its 40th year, the FEW provides the ethanol industry with cutting-edge content and unparalleled networking opportunities in a dynamic business-to-business environment. As the largest, longest running ethanol conference in the world, the FEW is renowned for its superb programming—powered by Ethanol Producer Magazine—that maintains a strong focus on commercial-scale ethanol production, new technology, and near-term research and development. The event draws more than 2,000 people from over 31 countries and from nearly every ethanol plant in the United States and Canada.
Minneapolis Convention Center | Minneapolis, MN (866) 746-8385 | www.fuelethanolworkshop.com
Capturing and storing carbon dioxide in underground wells has the potential to become the most consequential technological deployment in the history of the broader biofuels industry. Deploying effective carbon capture and storage at biofuels plants will cement ethanol and biodiesel as the lowest carbon liquid fuels commercially available in the marketplace. The Carbon Capture & Storage Summit will offer attendees a comprehensive look at the economics of carbon capture and storage, the infrastructure required to make it possible and the financial and marketplace impacts to participating producers.
Saint Paul RiverCentre | Saint Paul, MN (866) 746-8385 | www.safconference.com
The North American SAF Conference & Expo, produced by SAF Magazine, in collaboration with the Commercial Aviation Alternative Fuels Initiative (CAAFI) will showcase the latest strategies for aviation fuel decarbonization, solutions for key industry challenges, and highlight the current opportunities for airlines, corporations and fuel producers. The North American SAF Conference & Expo is designed to promote the development and adoption of practical solutions to produce SAF and decarbonize the aviation sector.
Cobb Galleria | Atlanta, GA (866) 746-8385 | www.biomassconference.com
Now in its 18th year, the International Biomass Conference & Expo is expected to bring together more than 900 attendees, 160 exhibitors and 65 speakers from more than 25 countries. It is the largest gathering of biomass professionals and academics in the world. Powered by Biomass Magazine, conference provides relevant content and unparalleled networking opportunities in a dynamic business-to-business environment. In addition to abundant networking opportunities, the largest biomass conference in the world is renowned for its outstanding programming, maintaining a strong focus on commercial-scale biomass production, new technology, and nearterm research and development. Join us at the International Biomass Conference & Expo as we enter this new and exciting era in biomass energy.
As we were thinking about the cover of the Summer Issue of Biodiesel Magazine, we didn't envision the wintry image that we ended up with, but it was such a compelling story and cool photo that we ultimately decided that it was our winner. It represents our page-16 feature, “Jumping at the Chance,” which details the opportunity, driving force, strategy behind and ultimate result of an oil refinery-to-renewable diesel conversion in Come By Chance, Newfoundland, Canada. In the story, Associate Editor Katie Schroeder interviews majority stake owner Cresta Fund Management’s Chris Rozzell, as well as Todd O’Malley, CEO of Braya Renewable Fuels, the owner and operator of the refinery. Both speak of the allure of the project, challenges faced during the conversion process, the state of the current marketplace, near-term goals and priorities of the facility, as well as future ambitions. The project was quite an undertaking and the owners are proud of what they’ve done, eager to show the industry. Says O’Malley, “The main goal the end of the day is to be a leader, and I think a blueprint for future facilities around the world.”
That summery image you’re looking for will appear as the lead image for our page-20 feature, “Pacific Pioneer,” another producer-focused feature. Sunflower crops are just one of the many components of Pacific Biodiesel, Hawaii’s lone biodiesel producer. Though the company is solely focused on its operations in the island state, it has actually designed and constructed 13 biodiesel plants across the U.S. and Japan. It has been about four years since we lasted visited with the company, but this time we chat with cofounder Kelly King, who tells contributing writer Keith Loria her version of the journey Pacific Biodiesel has embarked on since 1995, and how she and husband Bob King have gotten to where they are now, which is laser-focused on zero waste, innovation, community-based agriculture and energy, and running a full-circle system. As I mentioned above, one part of that is farming sunflowers and other biofuel crops on Maui, which they began doing in 2017. She has some updates on new projects they’re involved in, and adds that though at one time they expected to be retired by now, they actually hope to build another refinery on the island.
Finally, it has been quite a few years since we’ve conducted an industry jobs and salary survey, and the results of our most recent one are on page 28. While we don’t separate the data by specific position (yet), overall, we’re confident of the picture this paints of the industry in terms of job satisfaction, benefits and other aspects.
When this article is published, the Biodiesel, Renewable Diesel and Sustainable Aviation Fuel Summit will be just around the corner. Colocated with the International Fuel Ethanol Workshop & Expo in Minneapolis from June 10-12, we have a full agenda that we’re confident will not disappoint. Learn more or register at few.bbiconferences.com.
Joe Bryan
Tom Bryan
John Nelson
Anna Simet
Katie Schroeder
Chip Shereck
Bob Brown
Jessica Tiller
Marla DeFoe
Jaci Satterlund
Raquel Boushee
CEO jbryan@bbiinternational.com
President tbryan@bbiinternational.com
Vice President of Operations/ Marketing & Sales jnelson@bbiinternational.com
Editor asimet@bbiinternational.com
Associate Editor katie.schroeder@bbiinternational.com
Senior Account Manager cshereck@bbiinternational.com
Account Manager bbrown@bbiinternational.com
Circulation Manager jtiller@bbiinternational.com
Marketing & Advertising Manager mdefoe@bbiinternational.com
ART
Vice President, Production & Design jsatterlund@bbiinternational.com
Graphic Designer rboushee@bbiinternational.com
Subscriptions Subscriptions to Biodiesel Magazine are free of charge to everyone with the exception of a shipping and handling charge for any country outside the United States. To subscribe, visit www.biodieselmagazine.com or you can send your mailing address and payment (checks made out to BBI International) to: Biodiesel Magazine Subscriptions, 308 Second Ave. N., Suite 304, Grand Forks, ND 58203. You can also fax a subscription form to 701-746-5367. Reprints and Back Issues Select back issues are available for $3.95 each, plus shipping. Article reprints are also available for a fee. For more information, contact us at 701-746-8385 or service@bbiinternational.com. Advertising Biodiesel Magazine provides a specific topic delivered to a highly targeted audience. We are committed to editorial excellence and high-quality print production. To find out more about Biodiesel Magazine advertising opportunities, please contact us at 701-746-8385 or service@bbiinternational.com. Letters to the Editor We welcome letters to the editor. If you write us, please include your name, address and phone number. Letters may be edited for clarity and/or space. Send to Biodiesel Magazine Letters, 308 Second Ave. N., Suite 304, Grand Forks, ND 58203 or email asimet@bbiinternational. com. TM
Please recycle this magazine and remove inserts or samples before recycling
Give your hydrotreater catalyst more
Crown technology delivers maximum contaminant removal to extend hydrotreater catalyst life.
Get the cleanest possible feedstock delivered to your hydrotreater and achieve up to double catalyst life with Crown technology. Our rugged, robust RD Ready ™ Pretreatment System is guaranteed to meet product specs for all common contaminants and drastically improve plant uptime by reducing the need for catalyst changeovers. Backed by the construction of 50+ biodiesel plants, design of 10+renewable diesel pretreatment plants, and a propriety database of feedstock specs and results, Crown RD Ready ™ Pretreatment System protects your investment now, and in the future. Protect your hydrotreater and your Renewable Diesel operation with CPM and Crown.
Phillips 66 reported that its Rodeo biorefinery in San Francisco is projected to produce 50,000 barrels per day of renewable fuels by the end of second quarter. The facility began renewable diesel production during the first quarter and is expected to begin producing sustainable aviation fuel (SAF) components soon. The converted facility, referred to as the Rodeo Renewable Energy Complex, is now processing only renewable feedstocks.
The U.S. exported 45,891 metric tons (mt) of biodiesel and biodiesel blends of B30 and greater in March, according to data released by the USDA Foreign Agricultural Service on May 2.
Exported volume was up in March compared to both the 30,040 mt exported the previous month and the 36,718 mt exported in March of last year. The U.S. exported to eight countries in March, with Canada being the top destination at 40,066 mt, followed by Peru at 5,560 mt and Singapore at 134 mt. The value of U.S. biodiesel exports reached $65.7 million in March, up from $42.5 million in February and $61 million in March 2023. Total biodiesel exports for the first quarter of this year reached 93,149 mt at a value of $132.7 million, compared to 68,203 mt exported during the same period of last year at a value of $116.1 million.
While exports were up in March, imports were down. Approximately 116,141 mt of biodiesel and biodiesel blends of B30 or greater were imported during the month, down from 180,488 mt imported in February and 146,427 mt imported in March 2023. The U.S. imported biodiesel from approximately eight countries in March. The
During a first quarter earnings call held April 26, Phillips 66 President and CEO Mark Lashier said the biorefinery is currently producing 30,000 barrels per day of renewable fuels. “We're on track to increase production capability to full rates of approximately 50,000 barrels per day by the end of the second quarter,” he said. “Once complete, we'll have the ability to produce renewable jet, a key component of sustainable aviation fuel.”
top source of U.S. biodiesel imports was Canada at 37,465 mt, followed by Italy at 29,984 mt and Spain at 14,927 mt. The value of U.S. biodiesel imports was at $164.4 million in March, down from $245.29 million the previous month and $256.78 million in March of last year.
Total biodiesel imports for the first three months of 2024 reached 464,342 mt at a value of $653.6 million, compared to 402,766 mt imported during the same period of 2023 at a value of $737.4 million.
Vertex Energy Inc. on May 9 announced it will cease renewable diesel production at its refinery in Mobile, Alabama, and return the previously converted hydrocracker unit to fossil fuel production later this year. During a first quarter earnings call, Vertex CEO Benjamin Cowart explained that the company designed the renewable diesel conversion project to allow it to redeploy the facility’s renewable equipment back into conventional production if its strategy required readjustment. Cowart cited current market conditions as the reason Vertex has elected to pause renewables production.
The U.S. Department of the Treasury and Internal Revenue Service on April 30 released updated guidance on the sustainable aviation fuel (SAF) tax credit. As part of that guidance, the SAF Interagency Working Group released the 40BSAF-GREET 2024 model, which incorporates a pilot program to encourage the use of climate-smart agriculture practices for SAF feedstocks.
The SAF tax credit, established by the Inflation Reduction Act in 2022, aims to incentivize SAF production that achieves a lifecycle greenhouse gas (GHG) reduction of at least 50% when compared to petroleum-based jet fuel. The tax credit starts at $1.25 per gallon for SAF that achieves a 50% GHG reduction. An additional 1 cent per gallon is available for each percentage point by which the lifecycle GHG emission of the fuel exceeds 50%, with a cap of $1.75 per gallon. Language included in the IRA specifies that the GHG reduction threshold can be calculated using the most recent Carbon Offsetting and Reduction Scheme for International Aviation model that has been adopted by the International Civic Aviation Organization, or by a “similar methodology” to the most recent CORSIA model. The use of the European-based CORSIA model has been criticized by the U.S. agriculture and biofuel industries for failing to accurately account for U.S. agricultural practices and preventing crop-based fuels from participating in the SAF market.
The Treasury Department and IRS on Dec. 15, 2023, released initial guidance on the SAF tax credit, announcing that taxpayers will be able to use an updated version of the Energy Department’s Greenhouse Gases, Regulated Emissions and Energy Use in Transportation (GREET) model to calculate lifecycle GHG reductions for the purposes of the SAF tax credit. As part of that guidance, the U.S. EPA, Transportation Department, USDA and DOE announced the formation of the SAF Interagency Working Group to support the development of the updated GREET model, referred to as 40BSAFGREET. The working group committed to release the updated model by March 1, 2024, but failed to meet the deadline. Agriculture Secretary Tom Vilsack on March 1 announced the short-term delay, citing the need to get calculations for climate-smart agriculture right. The updated guidance issued April 30 provides clarity around eligibility for the SAF credit, including release of the 40BSAF-GREET 2024 model. According to the agencies, the 40BSAF-GREET 2024 model incorporates new data, including updated modeling of key feedstocks and processes used in aviation fuel and indirect emissions. The model also integrates key GHG emission reduction strategies, such as carbon capture and storage, renewable natural gas and renewable electricity.
The notice released April 30 also, on a pilot basis, incorporates a USDA pilot program to encourage the use of certain Climate Smart Agriculture practices for SAF feedstocks. For corn ethanol-to-jet, the pilot provides a GHG reduction credit if a “bundle” of certain CSA practices (no-till, cover crop and enhanced efficiency fertilizer) are used. It would allow a similiar GHG reduction credit for soybean-tojet if the soybean feedstock is produced using a “bundle” of applicable CSA practices (no-till and cover crop). This is a pilot program specific to the 40B credit, which is in effect for 2023 and 2024.
Within the notice, the IRS also provides a safe harbor provision that can ultimately allow a SAF synthetic blending component pro-
duced from CSA corn or CSA soybean to be eligible for an additional proxy reduction (CSA reduction) in the calculation of the emissions reduction percentage. The notice includes specific equations for calculating this emissions reduction percentage, and offers an example of a registered SAF producer that produces a SAF synthetic blending component via the ethanol-to-jet production pathway using 100% CSA corn, indicating the resulting fuel would achieve a 53% GHG reduction.
To credit CSA practices in the Clean Fuel Production Credit (45Z), which becomes available in 2025, the agencies will do further work on modeling, data and assumptions, as well as verification. A new 45Z-GREET will be developed for use with the 45Z tax credit.
Total U.S. biofuels operable production capacity fell slightly in February, but renewable diesel capacity increased more than half a billion gallons from the same time last year, according to data released by the U.S. Energy Information Administration on April 30. Biodiesel capacity was at 1.98 billion gallons per year in February, down 89 MMgy when compared to January and down 79 MMgy when compared to February of last year. Capacity for renewable diesel and associated fuels, including renewable heating oil, renewable jet fuel, renewable naphtha, renewable gasoline and other biofuels and biointermediates was at 3.85 billion gallons per year in February, a level of capacity that has held steady since October 2023. When compared to February 2023, renewable diesel capacity was up 597 MMgy.
PBF Energy Inc. announced that its St. Bernard Renewables facility operated well during the first quarter of year, producing an average of 18,000 barrels per day of renewable diesel. The SBR biorefinery is colocated at PBF Energy’s Chalmette oil refinery in Louisiana. The 320 MMgy facility primarily produces renewable diesel and is jointly owned by PBF Energy and Eni Sustainable Mobility Spa. PBF and Eni closed on the 50-50 partnership in St. Bernard Renewables in mid-2023.
The SBR facility’s renewable diesel unit began operations in June 2023, and a feedstock pretreatment unit was brought online the following month. Karin Davis, chief financial officer of PBF Energy, discussed the biorefinery’s operations during the company’s first quarter earnings call, held May 2.
In May, Iowa passed a bill that boosts funding for the state’s renewable fuel infrastructure program. According to the Iowa Biodiesel Board, HF 26914 increases annual funding for the Iowa Renewable Fuel Infrastructure Program from $10 million to $14 million, effective July 1. The bill specifically allocates the funding for biodiesel and ethanol products. According to the IBB, the revised program guidelines include an increase in the cap for retail biodiesel projects, now set at $1.75 million compared to the previous $1.25 million. This adjustment results in an additional $500,000 annually allocated to retail biodiesel projects.
Tremendous growth in the biomass-based diesel industry should be celebrated by producers and farmers, as well as those who enjoy breathing cleaner air and lower greenhouse gas emissions. However, that growth coupled with disappointing Renewable Fuel Standard volumes set by the U.S. Environmental Protection Agency have put stress on the industry. Despite the current storm created by these conditions, new markets rapidly coming online provide a sunnier outlook for the years ahead.
In 2023, biomass-based diesel (BBD) consumption reached just under 4.6 billion gallons. Out of total diesel fuel consumed in the United States in 2023, BBD accounted for around 8%, a significant growth from recent years (approx. 5.5% in 2022). The U.S. Energy Information Agency’s most recent data, which is current through February, shows biodiesel production capacity has remained relatively steady at 2.1 billion gallons per year (BGY), while renewable diesel capacity has expanded up to 3.9 BGY (from 2.2 BGY as recent as October 2022). The main driver for this growth continues to be states with a Low Carbon Fuel Standard. California’s market remains strong, with consumption making up approximately 60% of its entire diesel pool.
Looking forward, renewable diesel capacity expansions and greenfield projects are continuing well into 2024 and parts of 2025. Currently, around 1.65 BGY of renewable diesel production capacity is expected by the end of 2025 in the U.S., with an additional 300 million gallons per year (MMgy) sanctioned in Canada. Sustainable aviation fuel (SAF) projects also continue apace, with an approximate 600 MMgy of production capacity expected by the end of 2025, with the majority of near-term growth coming from the familiar hydroprocessed esters and fatty acids (HEFA) production pathway.
This unprecedented growth eclipsed what the EPA forecasted, greatly exceeding the set rule for 2023. When the set rule was released in June 2023, it was readily apparent that BBD would easily outpace the D4 volume.
LCFS credit prices across the West Coast are also down from recent highs. Recently, there has been huge growth in credit generation, led by BBD, renewable natural gas and electrical vehicle adoption. Looking at the California LCFS, there is currently over 23 million metric tons of LCFS credits in the California credit bank. This is significantly pulling LCFS credit prices down. This is not only occurring in California but in all LCFS states, just not to the same degree.
Although these lower credit prices are concerning for producers, there is reason for hope with growing demand. New markets have been developing in recent years, due to many corporate initiatives to reduce greenhouse gas emissions and lower their collective carbon footprint. Both the rail and maritime industries are primed and ready to begin their transition to lowercarbon fuel sources. Both biodiesel and renewable diesel fit perfectly into their corporate structures, as they can be used as drop-in fuels.
An estimated 80% of the world’s goods are transported by sea, making low-carbon fuel critical for corporations that have made aggressive carbon reduction commitments. Biodiesel sales in marine markets are growing rapidly throughout the world, with B24 blends being sold in high quantities in Singapore and high quantities of B30 blends being sold in northwest Europe.
These companies would like to increase their uptake in biodiesel and renewable diesel blends in the U.S., a 7-billion-gallon market, but there are some hurdles— namely, the inability for ocean-going vessels to get the benefits of renewable identification numbers (RINs). Reps. Mariannette Miller-Meeks, R-Iowa, and John Garamendi, D-California, have introduced legislation aiming to increase the use of renewable biofuels used by sea vessels. By designating renewable fuel used in ocean-going vessels as an “additional renewable fuel” under the RFS, the Renewable Fuel for Ocean-Going Vessels Act would enable companies to preserve RINs in the program. U.S. Sens. Pete Ricketts, R-Nebraska, and Sherrod Brown, D-Ohio, introduced a similar version of the bill in the Senate, and thus far, the bill has shown signs of bipartisan support.
Railroads are another difficult-to-decarbonize sector with dreams of a cleaner future. The rail market is 4 billion gallons in the U.S., and we project that more than 20% will be BBD before the end of the decade. Multiple Class I railroad companies have been setting lofty goals for biodiesel use in their engines as early as 2030. Union Pacific, BNSF and Canadian National, along with other Class I railroads, are already making strides, successfully testing up to 100% BBD.
While there are near-term headwinds for our industry as discussed above, long-term tailwinds are right around the corner. Demand for BBD fuel is going to continue to grow as existing markets expand, and the benefits of these fuels continue to reach new markets.
Having developed and patented a unique direct steam injection (DSI) system in 1945, Pick Heaters has more than 15,000 installations in the food, chemical, pulp and paper, power, oil and gas, biomass, biodiesel and other industries, remaining an industry leader by continuously refining and innovating its DSI products.
Pick offers a range of DSI heater models, the fit depending on application needs. For example, a Pick BX Steam Injection Heater offers precise heating of starch and water-miscible slurries. “It’s a great choice for viscous slurries like wastewater heating, waste grease, fats, oils and grease (FOG) sludge or oil extraction,” explains Mark Brueggemann, president of Pick. “We will fabricate steam injection heaters for special materials of construction or for pipe size outside the norm—we have the engineering and manufacturing skills to meet a customer’s exact requirements and specifications.”
As for how they work, DSI heaters can be used wherever medium- to high-pressure steam is available and an unlimited supply of industrial hot water is needed, or to heat liquids or slurries in-line. “The Pick System injects steam into the liquid through hundreds of small orifices across
a steam injection tube,” Brueggemann explains. “A fine mist of steam is instantly absorbed by the liquid, resulting in 100% heat transfer with all steam condensed within the heater body. A unique spring-loaded piston rises or falls as more or less steam is required. This prevents pressure equalization between steam and water pressure, thus eliminating steam hammer. Helical flights in the chamber promote thorough mixing prior to discharge.”
Advantages include but are not limited to energy efficiency (savings of up to 28% in fuel costs), exceptional temperature control (plus or minus one degree Celsius), a wide operating range, no steam hammer, low noise, compact design and low maintenance costs.
As for what differentiates Pick from competitor systems, Brueggemann points to the steam mixing chamber and internal injection tube of the Pick System as being the key performance features. “The injection tube smoothly injects steam into the process flow,” he says. “It eliminates shock, hammer, noise and vibration. The heater body is designed around low velocity mixing action, providing negligible liquid side pressure drop, low sound
level and no downstream piping requirements for condensing of steam.”
As for the most active segments in the bioenergy industry, biogas and biodiesel are frontrunners. Brueggemann says Picks systems are commonly used in animal waste operations, particularly in the manure-to-fuel sector. “Introducing heat to the process enhances the breakdown and conversion for the production of biogas,” he explains. “Equally prevalent has been separation of FOG in waste treatment. Adding heat to this process maximizes the separation of these byproducts, resulting in not only savings in waste treatment costs but also providing a valuable source of added revenue.”
Brueggemann emphasizes the company’s goal of providing systems that are engineered to each unique application. “Off-the-shelf equipment only works if the customer’s process exactly fits with the supplier’s model,” he adds. “With industrial equipment, it’s not like selling shoes. At Pick, we gather all the facts, the application conditions to select and size the equipment, as well as an understanding of the complete process. This approach offers the best chance for success.”
Temperature control in wastewater heating requires absolute precision, and only Pick direct steam injection heaters can provide it. That ’s because Pick ’s exceptional temperature control automatically holds discharge temperatures to extremely close tolerances while providing rapid response to changing process conditions.
Pick o ers 100% energy e ciency. This alone can save you up to 28% in fuel costs Pick ’s compact design along with its ease of maintenance saves valuable space. Liquid side pressure drop is the lowest in the industry. With all steam throughly condensed within the heater body, there are no downstream straight-run piping requirements.
Pick – the right choice for heating:
• Starches • Oils and Fats
• Livestock O al • Grease
• Suspended Solids
Biofuels are becoming increasingly prevalent in the transportation industry as global production climbs to around 175 billion liters (approximately 46.2 billion gallons) per year. As data provided by the International Energy Agency suggests, manufacturers are rapidly increasing capacities to meet insatiable demand. However, they are facing multiple challenges, especially regarding feedstocks. To overcome these hurdles, it is crucial for producers to be strategically located to access a greater variety of biobased feedstocks. Additionally, production facilities must include pretreatment units and possess the expertise to process more difficult feedstocks when producing renewable fuels.
The pretreatment unit is a critical addition to biofuel manufacturing plants because it ensures safe, stable and more economically viable operations. The pre-
treatment process involves multiple tasks, such as removal of gums, phosphorus, metals and other impurities to prevent fouling, corrosion, unexpected downtimes and catalyst deactivation. Ultimately, pretreatment protects the core of the fuel production process, whether it’s hydro processing for renewable diesel and sustainable aviation fuel or transesterification for biodiesel. The return on investment in the pretreatment process can be measured in the extended life of the catalyst and maximized production yields.
Manufacturers are learning that multiple oil types, whether blends or wastetype feedstocks commonly used in biofuel production, often do not offer the same quality and stability as crude vegetable oils. Their compositions can change daily, affecting impurity levels and the complexity of their removal. To tackle the broadest
range of critical impurities, various physical or chemical pretreatment technologies like degumming and adsorption can be utilized as standalone or best in combination.
Clariant’s TONSILTM series offers an effective solution to these production challenges by efficiently removing impurities from various feedstocks, including fresh vegetable feedstock to agricultural byproducts or waste oils and fats. This ensures the feedstock meets the standards required by catalyst and equipment manufacturers, and that it is thoroughly purified before undergoing further processing. Using TONSIL enables operators to adapt to changing conditions, fine-tune their production processes, uphold reliability across their operations and reduce the total cost of ownership.
Biodiesel and renewable diesel can lower greenhouse gas and particulate matter emissions today in your marine fleet’s existing fueling systems.
Bet ter. Cleaner. Now.®
cle anfuels.or g
Having recognized the potential in a shuttered petroleum refinery, the owners of the now Come by Chance renewable diesel plant haven't looked back.BY KATIE SCHROEDER
Calling Braya Renewable Fuels’ Come by Chance Refinery a unique facility would be an understatement. Located on the island of Newfoundland, Canada, in a town called Come by Chance and situated on one of the few deep water harbors in North America, there is a long list of factors that make the facility stand out.
Built in the 1970s, the 135,000-barrel-perday Come by Chance Refinery was converted from a petroleum refinery to a renewable diesel (RD) facility in 2023, starting RD production this past February. Cresta Fund Management purchased a majority stake in that the facility in November 2021, well aware of its many distinctive attributes. Chris Rozzell, managing partner of Cresta, explains how the company recognized the incredible potential the facility held for a conversion. When the COVID-19 pandemic hit, the facility was shuttered and became unprofitable. “They imported most or all their crude from distant markets, putting them at a disadvantage to other North American refineries,” Rozzell says. “It was very expensive, and ultimately they just weren’t able to operate profitably.” John Skrinar, a partner at Cresta, had a preexisting relationship with the prior owners—who are still minority owners—and knew that with Cresta’s focus on the low-carbon molecule, the refinery made an ideal candidate for conversion to renewable fuel production.
Braya’s Come by Chance Refinery is positioned at the crossroads of maritime Atlan-
tic trade routes, allowing the facility to easily access feedstock from North America, South America and Europe, explains Todd O’Malley, CEO of Braya. “We have the ability to take various feedstocks, again because of our geographic location, [which is] kind of a corner of regular trade routes throughout the Atlantic Basin. [This includes] soybean oil, used cooking oil, tallow, other waste fats and distillers corn oil, and we bring them in by vessel ... and ultimately run them through the facility to manufacture renewable diesel, and then load that diesel out to oceangoing vessels,” he says.
One of the structural factors that made this facility a great option for a conversion project was its huge hydrocracker, Rozzell explains. “The refinery was already configured to make diesel and jet, so we did not have to convert, for example, a naphtha unit into a diesel unit, which other people have had to do,” he says. “It also had a highly skilled, unionized workforce that, in some cases is multigenerational. We have people who are the third generation of their family working at this facility, and that [history] was very attractive to us.” A significant portion of the refinery’s preexisting workforce stayed with the facility through the conversion, and Braya employs most of its staff locally in Come by Chance.”
All of Braya’s feedstock is shipped in by tanker, and all of the fuel is shipped out the same way. Railcars and trucks are not a viable transportation option for the facility because of its island location. However, access to feed-
stocks via ship has helped keep the carbon intensity (CI) score of Braya’s RD low due to efficient transport, O’Malley explains..
Having feedstock shipped in has also advantaged Braya’s profits despite the decrease in renewable identification number (RIN) values under the U.S. Renewable Fuel Standard, according to Rozzell. That profitability allows for Cresta’s potential to expand to buy some of the struggling biodiesel plants across the U.S. “We see these cyclical industries move up and down because of the way they’re designed,” he says. “When prices are low, facilities shut in. When facilities shut in, we run out of product and prices go up. So, this could be an investment time for us.”
The process of conversion was fairly straightforward, Rozzell explains. One of the main changes that needed to be made to pro-
duce RD was replacing the existing catalyst that was intended for refining crude oil with one that handles fatty acids such as animal fats and vegetable oils. “We’ve chosen HaldorTopsoe as our partner,” he says. “Their catalyst is very flexible, it’s very efficient, and you can take a wider range of feedstocks. That flexibility is very important when you’re thinking about long-term operations.”
One of the challenges faced by Braya in the conversion was the overall impact of COVID on the supply chain. This was coupled with the spike in nickel prices and supply chain issues caused by Russia’s invasion of Ukraine, impacting Braya’s purchase of new steel piping. “The nickel market went a little crazy the past couple of years because Russia is one of the larger exporters of nickel in the world, so that created some supply chain challenges,” Rozzell says.
The newly installed pipes also need to be constantly heated because the biobased feed-
stock may gel up in a way that crude oil does not. In an area where temperatures can sink to negative 20 degrees Celsius, electrical heat tracing and robust insulation was vital. O’Malley also emphasizes the importance of ensuring that employees are not exposed to the brutal temperatures and 40 mile-per-hour winds. “A
close partnership with the technology providers and engineering firms that we use, as well as having that highly experienced local knowledge workforce, allowed us to work through and overcome any issues that did arise,” he says.
Challenges such as unexpected costs or extra work needed to bring the facility up to date regarding safety infrastructure were handled with resilience and flexible financing. Overall, startup of the facility in February went well, and the plant was able to operate at its current capacity within 30 days, according to Rozzell. In spite of challenges in the conversion process, he sees Braya as worth the effort. “It’s one of a kind—we could never build another Braya,” he says. “There is no other facility in the world that has its unique combination of logistics and scale advantages.”
Less than three years after Cresta gained ownership, the facility now produces up to 18,000 barrels per day of renewable diesel and SAF. Currently, Braya does not sell SAF, instead leaving it in with the renewable diesel for sale. “In today’s market, it’s not that profitable to make SAF, and the [customers] of SAF are executing offtake agreements, but they are buying very small amounts,” Rozzell says. “So, we just need a bigger market. But our firm believes that in the long term, all of this product will ultimately become SAF. I don’t see any
other alternatives for the airlines. They’re not going to put batteries in 777s—it’s just not happening.”
The catalyst used in the facility makes around 70%-80% RD and 20%-30% SAF; however, these percentages could be flipped with a “moderate follow-on investment,” Rozzell explains. One of the short-term goals that the company plans to pursue is increasing the percentage of SAF to roughly 40%, which involves installing separate tanking infrastructure to divide the SAF and RD product streams.
When that future arrives, Braya is ideally located to easily transport fuel to New York Harbor, going from Come by Chance to New York City’s La Guardia and JFK airports in only a couple of days. All the fuel produced at Braya’s refinery is currently exported internationally. O’Malley explains that this is partially due to Canada’s market dynamics, regulatory environment and the Coasting Trade Act in Canada, which requires ships selling into Canada to be Canadian made and staffed, as well as flying a Canadian flag. “I would anticipate that
as the CFR continues to develop in Canada, that there will be incremental opportunities for us to supply Canadian markets,” O’Malley says.
Moving forward, one near-term goal is to get the plant running beyond its current 18,000 bpd capacity. Rozzell explains that the hydrocracker is capable of processing 41,000 bpd and, with some investment, that volume is achievable. The limiting factor in maximizing production capacity is hydrogen. “We don’t
produce enough hydrogen to run at full capacity,” he says. “We’re looking at either restarting some of the other refinery units to help create more hydrogen or building out [green] hydrogen [infrastructure].” Braya is involved in assessing the potential of a green hydrogen project that would utilize Newfoundland’s excellent wind resources and abundant hydropower to increase the amount of hydrogen available and decarbonize the refinery’s processes.
Green hydrogen is not the only decarbonization strategy that Cresta plans to explore. Rozzell references a variety of technologies that could serve as alternatives to fuel gas and boilers, which would help reduce the carbon intensity of Braya’s products. “Our priorities right now are primarily tactical,” he says. “For example, let’s get the plant to full capacity and reduce our carbon intensity as much as possible. Then, we can move to the more strategic areas such as horizontal or vertical expansion.” Investment in aggregation and logistics to streamline the feedstock pipeline are two vertical expansion strategies that have been considered, Rozzell explains.
An exciting development for the industry that Rozzell recognizes is the opportunity to use the GREET model in the U.S. for evaluating the CI of RD and SAF. This opens up many feedstock options, he says. “The regulators seem to understand that if we create artificial barriers to producing SAF, we just will likely never have enough feedstock available to make a serious impact.”
As governments’ attention shifts away from fossil fuel-derived hydrocarbons and toward a net-zero future, Cresta’s and Braya’s leadership hopes that the facility can serve as an example of what’s possible in the energy transition. “The main goal at the end of the day is to be a leader, and I think a blueprint for future facilities around the world,” O’Malley adds. “This is in terms of how we can transition a very difficult but critical segment of the global economy from traditional petroleum fuels to drop in RD and SAF, and do it at world class scale—safely, reliably and environmentally responsibly.”
Author: Katie Schroeder Katie.schroeder@bbiinternational.comOperating for nearly 30 years, Pacific Biodiesel’s commitment to sustainability extends far beyond biofuel production, and with new projects and future ambitions, the company is showing no signs of slowing down.
BY KEITH LORIAServing as a beacon of sustainability and innovation, Pacific Biodiesel was founded in Maui in 1995 by Bob and Kelly King. Born out of a need to address environmental and health concerns stemming from the dumping of used cooking oil into the Central Maui Landfill, the company emerged as a solution to convert waste into opportunity, even before the biodiesel industry had burgeoned in the U.S. It began when the Kings, then-owners of King Diesel, a generator business that was the Maui County Cummins Engine dealership at the time, became acquainted with a compost company called Maui EKO and saw an opportunity. “One of our contracts was at the Central Maui
Landfill and Bob would go every month and do regular maintenance on it,” [Kelly] King says. “Every time he went, the people from Maui EKO would complain because they were working there on the composting, and the used cooking oil (UCO) was a huge problem for them because there’s so much energy and heat in UCO that it would sometimes just spontaneously combust and create a fire.”
Another issue with UCO being put in the landfill, she explains, is people tend to freeze it, and when it melts, it can potentially leach through the lining of the landfill and into the groundwater, creating a toxic substance in the water table. “These two big issues inspired Bob to start researching what
could be done—this was in the late ’90s when the [information] superhighway became available to the public,” King says. “He remembered something from his earlier days working for Westport Marine in Washington as a journeyman mechanic during the early embargo days of the ’70s, when gas stations were running out of fuel.”
That trade secret was that truckers were being told if they got to a gas station and there wasn’t any fuel, they could go to the nearest grocery store and get a five-gallon container of Wesson Oil, which would get them to the next station. “Knowing there was a connection between cooking oil and diesel fuel, Bob started researching biodiesel,” she says. “At the time, the University of
Idaho was doing a lot of research on this, trying to get to the point of making biodiesel out of UCO, which no one was really doing.” (The first biodiesel processing plant in the world started in Leer, Germany, a few years prior and used rapeseed oil for feedstock).
The Kings ended up collaborating with the U of I researchers to build the first plant in the United States that processed UCO into biodiesel that was available to the public. This visionary idea has helped Pacific Biodiesel, based in Kahului, Hawaii, to become the nation’s longest-operating biodiesel producer. “We are the oldest biodiesel processor and most experienced,” King says.
Legendary performer Willie Nelson and his wife Annie have been customers of Pacific Biodiesel on Maui since 2003, with the couple driving only biodiesel vehicles, including the singer’s tour bus. They were also founding members of the Sustainable Biodiesel Alliance with the Kings.
Pacific Biodiesel’s impact stretches far beyond the shores of Hawaii. In 1997, the company began sharing its innovative multifeedstock process technology with other emerging companies, embarking on a journey to build biodiesel facilities across the mainland U.S. and Japan. “The Maui plant got noticed worldwide, and the sec-
ond plant we built for biodiesel processing was in Nagano, Japan, for the 1998 Winter Olympics,” King says. “Not a lot of people know this, but they actually ran some of the vehicles on B20 during those cold Olympic Games.”
The company built another dozen plants around the U.S., and the Kings thought that installation would be their mainstay, but as engine technology became more sophisticated, the process had to become more sophisticated. By the late 2000s, climate issues in Hawaii changed their thinking. “A mandate was passed in Hawaii to become 100% renewable in our electric utilities by 2045, so we came back to Hawaii and decided to focus on building a state-of-
the-art refinery here, which we did on Big Island to help fulfill our state’s mandate,” King says.
Today, Pacific Biodiesel’s operations are focused mainly in Hawaii, where its biodiesel refinery is leading the charge in producing the nation’s highest-quality biodiesel. “We’re pretty much getting all the used cooking oil in the state,” King says. “We’ve gone into grease trap research and figured out a process using a centrifuge system to spin the oil out of this abundant material.”
Pacific Biodiesel has grown into a powerhouse of sustainability, employing nearly 100 individuals statewide. The company’s mission has remained steadfast: to promote a clean, sustainable energy future through community-based production of renewable fuels.
Pacific Biodiesel’s commitment to sus-
tainability doesn’t end with biodiesel production. The company tackled the issue of grease trap waste, diverting hundreds of tons from landfills each month and demonstrating its dedication to a zero-waste philosophy.
In 2017, the Kings ventured into farming, cultivating sunflowers and other biofuel cover crops on Maui to support food security, energy security and carbon sequestration. Through the Kings’ company, Maiden Hawaii Naturals, they now produce culinary oils and cosmetic ingredients from locally grown ingredients. “The idea is to create the high-end value with actual cooking oil,” King says, explaining that the company uses sunflower oil and macadamia nut oil, incorporating advice from Smude’s Sunflower Farms in Minnesota. “This was sort of a pipe dream of mine 15 years ago. I used to talk about my vision of creating cooking oil in the state, selling it to restaurants and food
product manufacturers, and then getting it back afterward to process into biodiesel, and that’s where we are now.”
The Kings received federal funding with the help of U.S. Sen. Mazie K. Hirono, D-Hawaii, to expand their biofuel crop project to Kauai Island, which they farm regeneratively on land owned by Gay & Robinson Inc., a well-known former sugar plantation in the state. Sen. Hirono recently toured the facility, which has three large silos, augers and a crushing mill. The tour included a visit to the mill’s bottling room, where guests sampled the company’s premium culinary oils that are sourced from local agriculture, including sunflowers from the Kings’ farm on Maui.
Last year, the company expanded operations to Kauai under a multiyear agreement established with the U.S. Army Corps of Engineers’ Engineer Research and Development Center in collaboration with
its Construction Engineering Research Laboratory. The project aims to showcase the viability of renewable biofuel derived from various locally cultivated oilseed cover crops in Hawaii. Aligned with the U.S. Army Climate Strategy, the new project will deliver a prototype solution for biofuel production alongside an agricultural model tailored for Hawaii’s unique conditions. It serves to validate the feasibility of transitioning to sustainable fuel for military applications, encompassing transportation and power generation facilities. Furthermore, it contributes to the military’s objective of achieving 100% renewable utility power in the state by 2045.
King notes that the project will demonstrate farming at a much larger scale of 1,000 acres or more, and include sunflowers and other crops in rotation with food crops. She says that the project’s initial phase involves evaluating the production
of a prototype fuel composed entirely of virgin oil feedstock utilizing oilseed cover crops cultivated and processed on Kauai. By employing locally sourced feedstock oil
for biodiesel production at the company's refinery on Hawaii Island, they can conduct real-time testing to confirm adherence to ASTM D6751 standards. Subsequently, the
performance of the prototype fuel will undergo validation on military power generation platforms. “Doing this in the state of Hawaii means a more stable feedstock supply and less shipping and greenhouse gas emissions,” she says. “Our state will benefit, as biodiesel has become an essential component in [Hawaii’s] renewable utility goals, providing firm renewable power when the sun doesn’t shine, and the wind doesn’t blow.”
The goal is to eventually get to 10,000 to 15,000 acres. “We are on our way with our community-based biodiesel model, and so far, we have received about $11 million for this federal sustainable agriculture project,” King says. “We hope to continue with funding in the next few years to get to the end game of creating another biodiesel refinery, hopefully on Kauai. The goal is to have all biodiesel made in the state of Hawaii produced from local feedstock.”
Surprisingly, one of the biggest challenges the Kings have run into are birds. “We didn’t have any problems with the first crops we grew on Maui because the birds hadn’t found it, but once they did ... even the local hunters who came to our fields
and claimed they had taken almost 70,000 doves, it hasn’t seemed to have made a dent,” King says. “We know we are going to lose 10 to 15 percent of the crop to the birds. One of the ways we are addressing this challenge is with equipment to dry the seeds so we can harvest earlier, and stem the bird loss without having to spray pesticides.”
In May, Pacific Biodiesel hosted its third annual Sunflower Farm Music Festival on Maui, with musicians from Steely Dan, the Beach Boys, Doobie Brothers and Stray Cats taking part. This year’s event was produced by multiplatinum music producer, artist manager and event producer Kerry Brown, owner of Licorice Pizza Records and a Maui resident. “We only do it as a
benefit; the last two have raised money for local nonprofits addressing food security in our island state,” King says. “Our focus as a biodiesel company has been on sustainable food and fuel, and we are also educating the public while raising funds.”
The three organizations benefiting from this year’s event are Maui Hub, Grow Some Good and Common Ground Collective. Next year, the company will celebrate
its 30th anniversary, and although the Kings thought they would be retired by now, Kelly King shares that it’s such interesting and important work, they don’t plan to stop anytime soon. “Locally produced biodiesel and the added-value products that come from our regenerative agriculture ventures help create our circular economy, support local agriculture and promote healthy eating,” she says. “Our model provides jobs
and revenue in our communities much better than hydrogen or electric, because we can do this within our community under local control.”
With each drop of biodiesel produced and every innovative solution implemented, Pacific Biodiesel proves that sustainability isn’t just a goal—it’s a way of life.
Survey results indicate that overall job satisfaction is very high in the biodiesel industry, current growth is modest, and the workforce is diverse when it comes to age, gender and longevity in the industry.
BY ANNA SIMETTo better understand and report on workforce compensation and job satisfaction trends, Biodiesel Magazine conducted a esurvey of U.S. industry employees. Although a small amount of collected data was kept confidential to protect identities, most is shared in this story. Questions focused on topics including salary, benefits, hours, job retention and satisfaction, experience and education. Although this survey has variables to consider (i.e., does not currently separate salary by job title) it may help gauge where the industry stands in terms of competitiveness to related sectors, as well as highlight potential areas for improvement.
Respondents were asked about the average size of the plant/plants they work at, oversee or manage at their company. The range varied considerably, with most respondents working at plants between 40 MMgy and 50 MMgy, or less than 5 MMgy (see Figure 1).
To better understand the position facilities were in during the past 12 months, they were asked the average capacity per-
cent at which their plant/s operated. Over 65% of respondents reported operating at 90%-100% of capacity, with 19% operating at 80%-89% of capacity. Approximately 7% indicated they operated at an average somewhere between 70 and 79% of capacity over the past year, with less than 4% between 60% and 70% of capacity (See Figure 2).
To gain an idea of the longevity respondents had in the industry, they were asked how long they have been employed by their present facility/at their company, even if there was a break in employment.
Responses were quite varied, with 7-9 years being the most common length of time in the industry at 24%, followed by 10-14 years at 20% (see Figure 3).
In a follow-up question that asked how many different plants or companies the respondent had worked at during their careers, nearly all respondents—84%—said they had only worked at only one.
As for the type of role respondents were in, approximately 26% were in positions including president, CEO, COO, CFO or other executive roles. Categories of plant manager, environmental, health
90-100% 65 % 80-90% 19%
70-80% 8% 60-70% 4%
30-60% 0% Less than 30% 4%
and safety manager, and operations manager each consisted of 12.5% of respondents. Other positions included: maintenance manager; commodities, procurement, sales manager/team member; human resources; office assistant and accounting analyst.
The majority of companies/facilities find filling open positions a struggle some of the time, at just under 35%. Approximately 22% of respondents report that most of the time it is difficult to find new employees, and just over 30% said positions are typically filled quickly and easily. About 13% indicated that turnover is extremely low (see Figure 4).
As a follow-up question, respondents were asked which methods are used to fill open positions. Most indicated that word of mouth is the most effective method, with 80% reporting it to be either very or sometimes effective. Promoting from within was reported as the next most effective, being either very or sometimes effective approximately 74% of the time, followed by internet job sites (65% very/sometimes effective. Approximately 59% of respondents reported having succession planning in place for management positions at their respective plants, and 75% said they had been contacted by a headhunter or recruiter within the past 12 months.
Nearly half of respondents reported that COVID-19 is still having effects on their facility, whether operations or staffing, at least to some degree.
When asked to characterize whether their plant was in a growth or transformation stage—i.e., expanding, taking on new projects or actively hiring—18% of respondents said that they were. An additional 55% said they were seeing growth at least to some degree, with the remaining 27% indicating that they were not currently seeing any kind of growth. Respondents were asked to elaborate on their selection if they answered no to growth. One remarked a change in ownership and resulting focus on dividends as being detrimental to growth. Another stated that the Inflation Reduc-
tion Act favoring low-carbon-intensity feedstocks was detrimental to growth being that the facility uses virgin oils, as well as the elimination of the Blenders Tax Credit, as it “will impact buyers willingness to purchase biodiesel that isn’t made with animal fats or used cooking oil.” The respondent also remarked that “the California Low Carbon Fuel Standard has incentivized the fuel to move to California, and the BTC becoming a producer credit will cause market shift in profitability for both the buyer and seller.”
For those who said their facility is in a growth or transformation stage at least to a degree, approximately 50% expected to hire one to four employees. More than 13% said they will likely need five or more additional employees, and 36% said they do not see any new hires at this point.
When asked about their current outlook regarding their facility right now, 32% said it is positive and that they perceive it to be in a strong position. About 55% said their feelings are neutral; things are business as usual and generally seem fine. Just under 14% said their outlook is negative or worrisome; their facility does not currently seem to be in a strong position.
Nearly half of respondents reported workweeks of 45 or more hours, with approximately 34% working 50 to 59 hours. About 45% indicated their typical workweek is from 40 hours to 44 hours.
As for job satisfaction, the survey results indicate that it is high. Regardless of compensation, 100% of respondents reported being satisfied or very satisfied with their current position in the biodiesel industry. When asked if they were looking for a new job, 100% said that they were not, though 24% said they were consider-
ing searching. Approximately 14% said they may consider a new job if the right opportunity came along, and about 62% said they would not consider leaving their current position.
Regarding the top three job qualities most important to respondents, by highestranked, they were: challenging and exciting work, opportunities to advance and job security, with competitive salary as a close fourth.
When asked about compensation, most respondents (56%) reported making between $75,000 and $100,000 per year, with approximately 48% receiving over
$100,000 per year. (See Figure 6 for additional salary data.) Most were not eligible for overtime compensation (86%), with 9.5% receiving time and a half, and 5% taking PTO in exchange for overtime hours. No respondents reported getting paid hourly. As for their opinions regarding their pay, close to two-thirds (62%) agreed that they were compensated about right, with 38% saying they were compensated too little.
Respondents were also asked about their overall benefits packages, and to answer yes or no to any benefit they knew that was offered or included at their company, to the best of their knowledge. Results are indicated in Figure 5.
As for pay increases, most respondents said they generally receive annual performance reviews along with raises (71%), with 14% indicating they receive annual reviews often without a raise. Within the past 12 months, 81% of respondents have received raises, with 6%-9% being the most common increase (25% of respondents), followed by 5% (20% of respondents) and 3% (25% of respondents). Both categories of 10%-14% raises and 4% raises consisted of 10% of respondents.
As for bonuses, 76% of respondents reported receiving them within the past year. Of those, 25% said they were paid between $25,000 and $50,000, with 10%
of respondents reporting bonuses in each of three ranges, which were $1,000-$2,499, $5,000-$7,499 and $10,000-$14,999.
Approximately 25% said they did not receive any bonuses during the past 12 months.
The ages of respondents were fairly spread out. Out of all survey takers, 38% were female. The most common age range of all respondents was 45 to 49 years old, at 24% of respondents. An equal 19% of respondents were in both the age ranges of 40-44 and 60-64, 19% were also between the ages of 50 and 59, and nearly 15% were from 25 to 35 years old.
Respondents were also asked about their education. The majority reported having a college/university degree (38%), with nearly a quarter having post-graduate degrees. Nearly 90% had at least some education beyond high school.
*Totals in this survey are rounded to the nearest percent Contact: Anna Simet Editor, Biodiesel Magazine
Production of renewable fuels and biofuels is increasing to meet growing demand. For instance, in 2023, 60% of California’s fossil diesel was displaced by biomass-based diesel, according to the California Air Resources Board. As the world’s leading producer of renewable diesel for road, marine and offroad applications, as well as sustainable aviation fuel (SAF) and renewable feedstock solutions for various polymers and chemicals industry uses, Neste has set for itself internal corporate targets for three interlinked areas: climate, biodiversity and human rights.
BY HELENE DIECKIn this article, we outline some specific diligence measures Neste has implemented pertaining to these three target areas.
Neste uses a variety of globally sourced raw materials to produce its renewable products. The majority of these are waste and residues. In 2023 alone, waste and residues accounted for 92% of our renewable raw material inputs globally. To ensure our products are not contributing to forced labor or deforestation for instance, Neste subjects raw material suppliers to due dili-
gence. This includes reviews to verify that suppliers meet environmental, social, governance (ESG) requirements, including a commitment to adhere to Neste’s Supplier Code of Conduct (or equivalent) and Responsible Sourcing Principle. The reviews encompass a comprehensive range of topics that include governance, labor standards and practices, human rights, the environment, as well as health and safety.
Additionally, we conduct periodic audits to evaluate compliance with Neste’s Supplier Code of Conduct and Responsible Sourcing Principle. Suppliers are expected
CONTRIBUTION: The claims and statements made in this article belong exclusively to the author(s) and do not necessarily reflect the views of Biodiesel Magazine or its advertisers. All questions pertaining to this article should be directed to the author(s).
to remediate significant open issues within a specified timeframe. The audits are conducted either by our own local specialists or a third party.
Neste sources raw materials from more than 60 countries on five continents. We conduct a raw material and country risk assessment with an industry-leading subject matter expert. The assessment allows Neste to effectively prioritize activities by identifying risks in certain countries or geographical areas.
We maintain an up-to-date country risk categorization based on specified indices, such as ethical business practices, human and labor rights, and health and safety.
In addition to the diligence processes and audits, Neste engages regularly in capacity-building with suppliers, and works
closely with industry bodies to effect positive change.
As an example, Neste is an active member of the Consumer Goods Forum, Forest Positive Coalition and Human Rights Coalition. For instance, the Forest Positive Coalition brings together more than 20 global consumer goods manufacturers and retailers to leverage collective action and remove deforestation, forest degradation and conversion from key commodity supply chains. As part of this coalition, members are committed to advancing landscape initiatives.
Another example of collaboration is in advancing regenerative agriculture practices. These practices can help sequester more carbon in the soil and improve soil health, promote biodiversity and reduce emissions from agriculture, while increasing farm productivity. No-tilling and using cover crops are common regenerative practices. With over 60 field trials across the globe, working
with farmers, other value chain partners and research institutions, we have been studying a variety of crops and regenerative agriculture management practices for both annuals and perennials to identify the most promising concepts for scale-up.
The production of renewable fuels is a complex process involving diligence and collaboration. Neste utilizes responsible sourcing to mitigate risks like forced labor and deforestation. Through audits and supplier capacity building, Neste promotes sustainable supply chain practices. Active involvement in industry coalitions and regenerative agriculture initiatives highlights Neste’s commitment to global positive change. As demand for renewable energy rises, Neste's measures and partnerships are an important aspect of a sustainable future.
Author: Helene Dieck Senior Sustainability Manager, Neste www.neste.comLoamist's Biomass Explorer provides real-time mapping and detailed data visualization, enabling efficient location and evaluation of biomass resources.
BY ANDY MILLER AND PETE CHRISTENSENDespite its abundance, low cost and widespread utility, waste biomass is hard to access. Being able to locate, validate and transact feedstocks quickly and repeatedly is critical to scaling the bioeconomy. Addressing these challenges, Loamist developed a platform to simplify location, validation and transaction of waste biomass, ultimately reducing feedstock risk.
With a combined 40 years of experience and background in circular economy
research and traceable supply chains, the cofounders of Loamist decided to focus full time on accelerating the bioeconomy. Quickly, waste biomass was identified as the most expedient path to realizing a scalable, circular bioeconomy. Unlike liquid crude oil feedstocks, biomass is almost always in solid form with low density (i.e., wood chips, corn stalks, grasses, etc.), making it costly and inefficient to transport large distances. At least for now, biomass supply chains will remain local to the sources, so the hurdle is identifying the location of these best sourc-
es to locate near them. Loamist was formed to tackle this challenge head-on: How do we enable the bioeconomy by increasing access to local waste biomass resources?
Feedstock risk is a significant hurdle for companies operating in the biofuel and bioenergy sectors. Biomass feedstock supply can be notoriously unpredictable; availability and consistency can fluctuate due to factors like seasonality, geographic distribution and competition from other uses. For
CONTRIBUTION: The claims and statements made in this article belong exclusively to the author(s) and do not necessarily reflect the views of Biodiesel Magazine or its advertisers. All questions pertaining to this article should be directed to the author(s).
bioeconomy projects, which rely on consistent feedstock supply, these variables can make or break the economic feasibility of new projects.
The intention behind the Loamist Biomass Explorer platform is to reduce feedstock risk by providing instant feedstock analyses for any location in the United States by considering over 50 data layers. These cover essential aspects such as feedstock availability, land attributes, local infrastructure and competitive demand for feedstocks, thus reducing the time and cost associated with choosing an ideal, low-risk site selection. This is done through integration of the following features.
GIS tool for strategic site selection: A purpose-built GIS platform was developed, which, as aforementioned, integrates over 50 data layers to provide instant feedstock analysis at any point location in the U.S. This tool allows project developers to evaluate potential sites for biomass projects quickly. Analysis tools allow users to do instant feedstock basket analysis around a
specific point, as well as instant transportation distance and estimated cost analysis.
Connection with reliable suppliers: Beyond identifying where the biomass is, users can get it consistently by being connected through a network of verified suppliers. This network is crucial for maintaining a stable supply chain and mitigating risks associated with biomass sourcing. By building a robust network of prequalified suppliers, we ensure that clients have access to consistent and reliable biomass sources.
Compliance and certification tools: Loamist also tackles the regulatory landscape of the bioeconomy. A suite of tools helps users navigate the complexities of low carbon fuel standards and the U.S. Renewable Fuel Standard renewable identification numbers. Compliance is simplified by prequalifying biomass for these standards through the use of artificial intelligence to facilitate supplier verification with automated attestation forms. Loamist also partners with testing labs to manage test data results so users can measure feedstock variance over time and quickly qualify supply.
Track and trace system: Finally, Loamist offers a track and trace system that
validates the supply chain, ensuring transparency and accountability. This system is essential not just for operational efficiency, but also for proving and improving carbon intensity scores, a critical measure for environmental impact in the bioeconomy.
In conclusion, Loamist believes its platform represents a significant leap forward in managing one of the most challenging aspects of bioenergy and biofuel production. As the bioeconomy continues to evolve, tools like the Biomass Explorer Platform will be crucial in ensuring its growth is sustainable and impactful. These technologies not only promise to streamline operations, but also to facilitate a more sustainable future, turning the potential of waste biomass into a cornerstone of a greener economy.
Authors: Andy Miller and Pete Christensen www.loamist.com
andy@loamist.com
pete@loamist.com