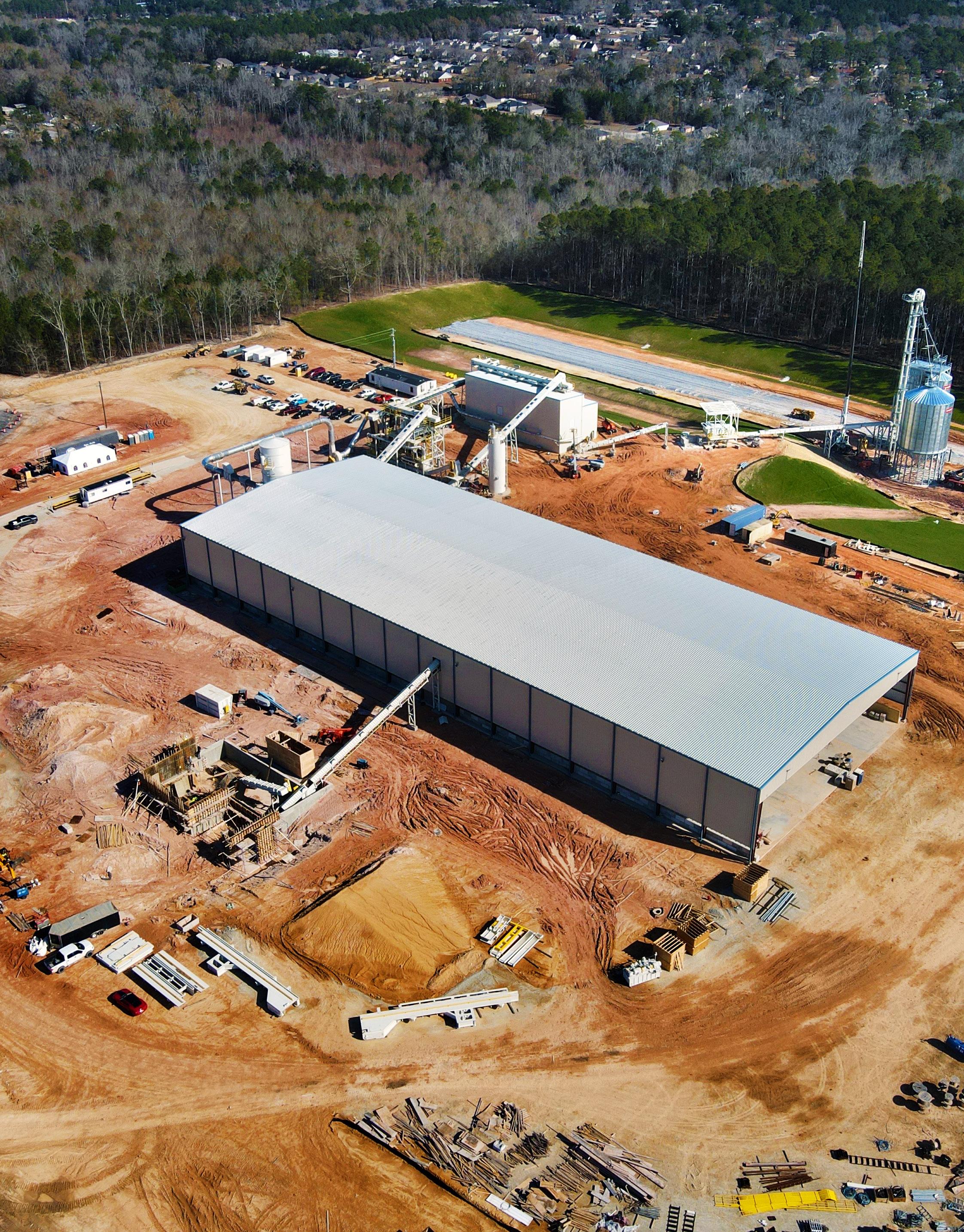
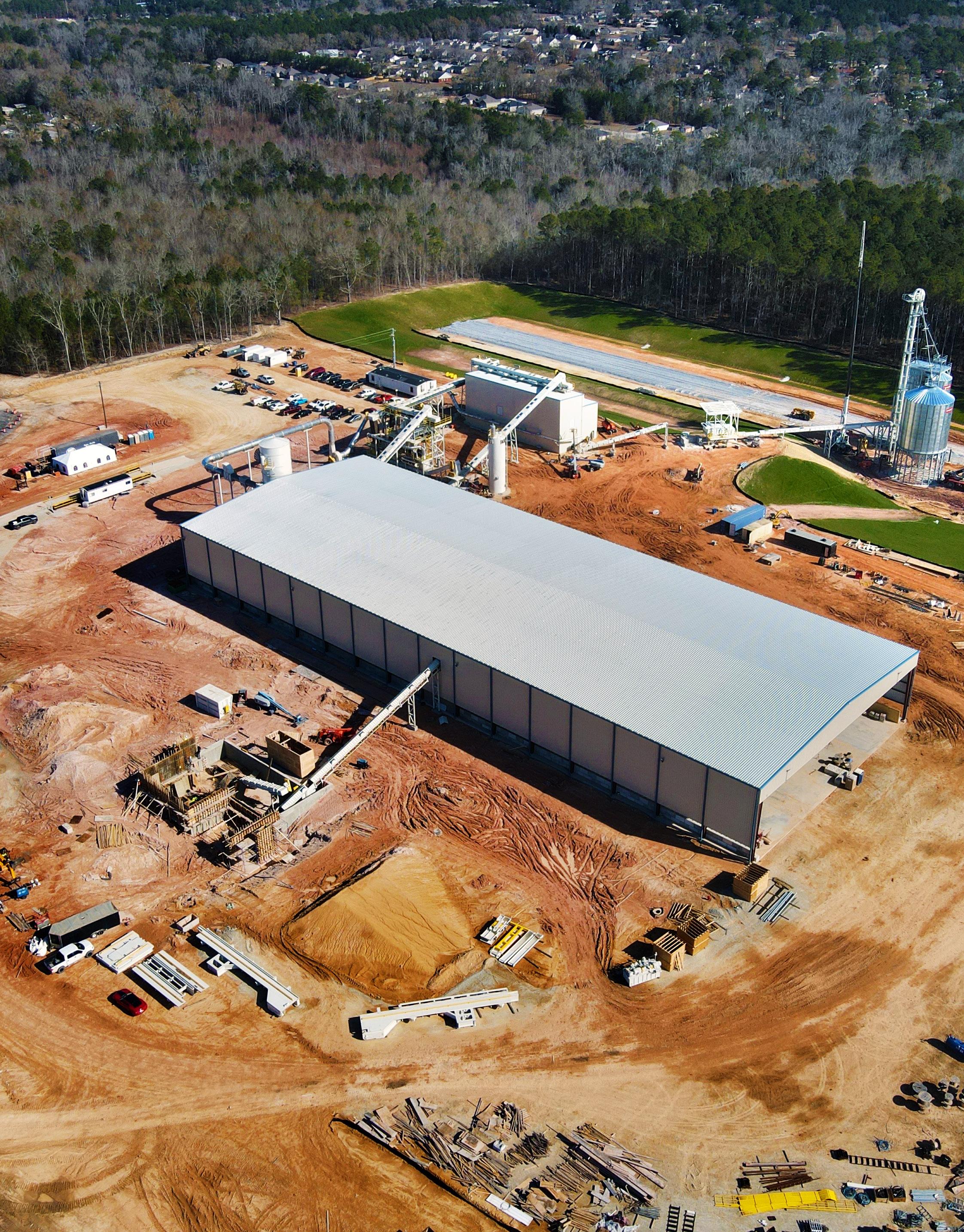
PEAK POSITIONING
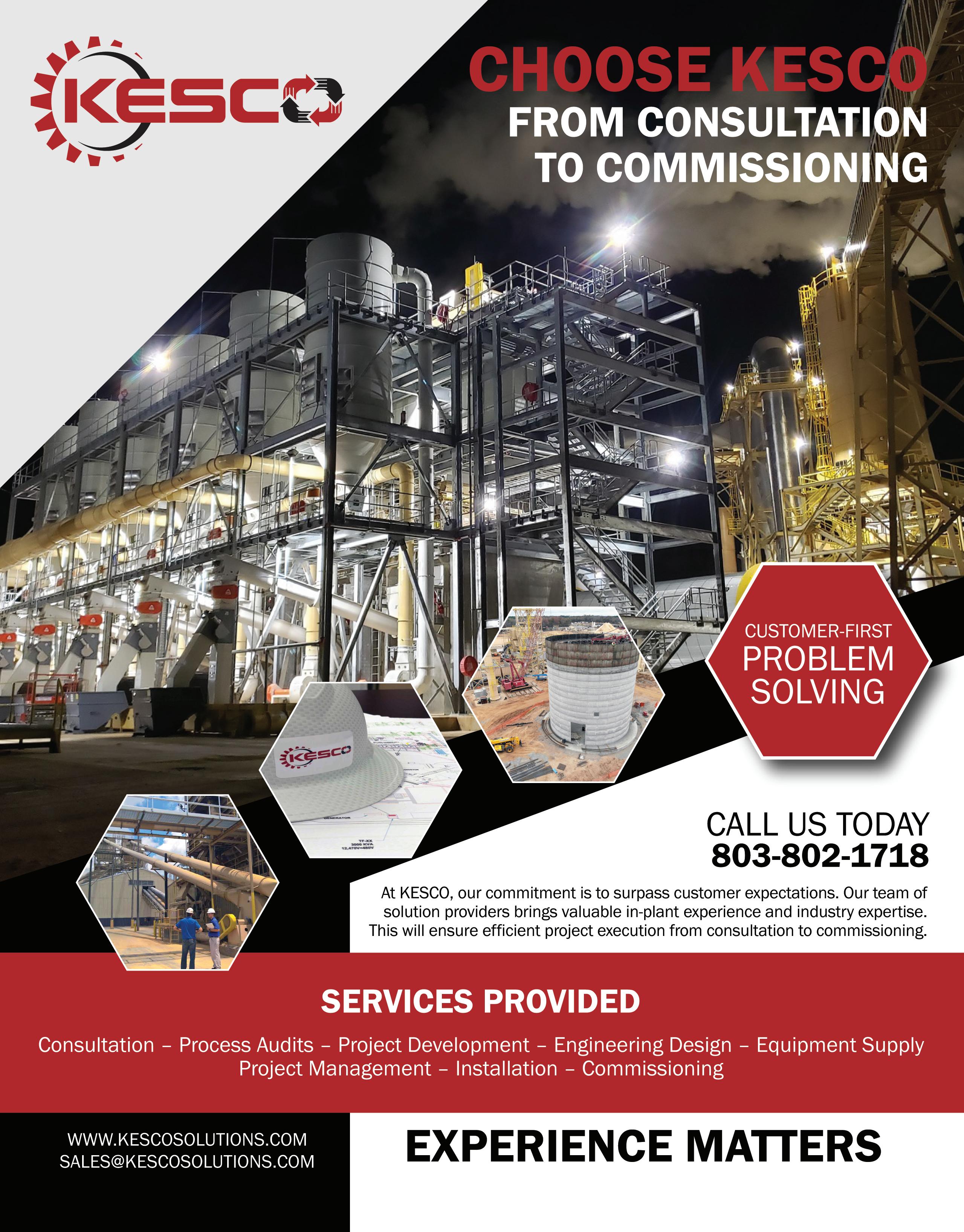
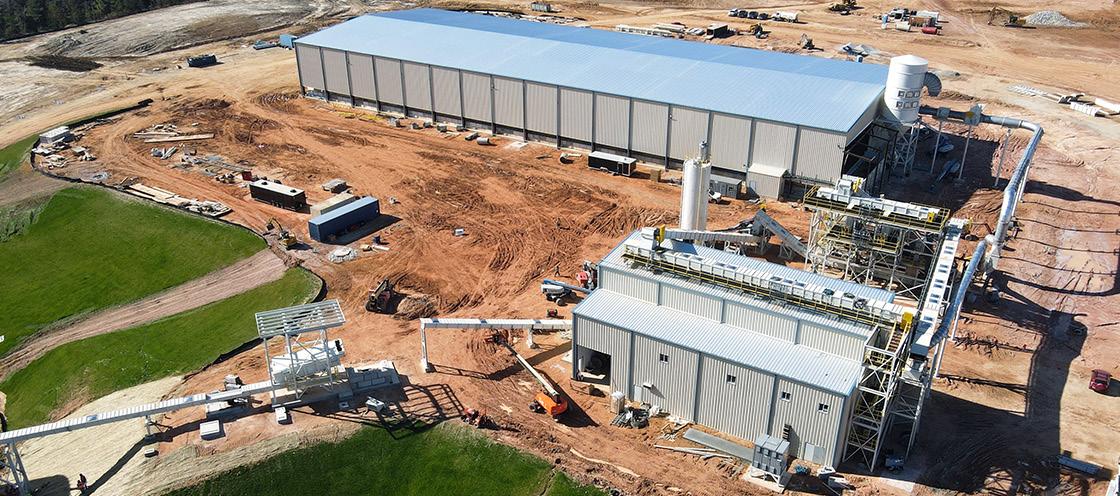
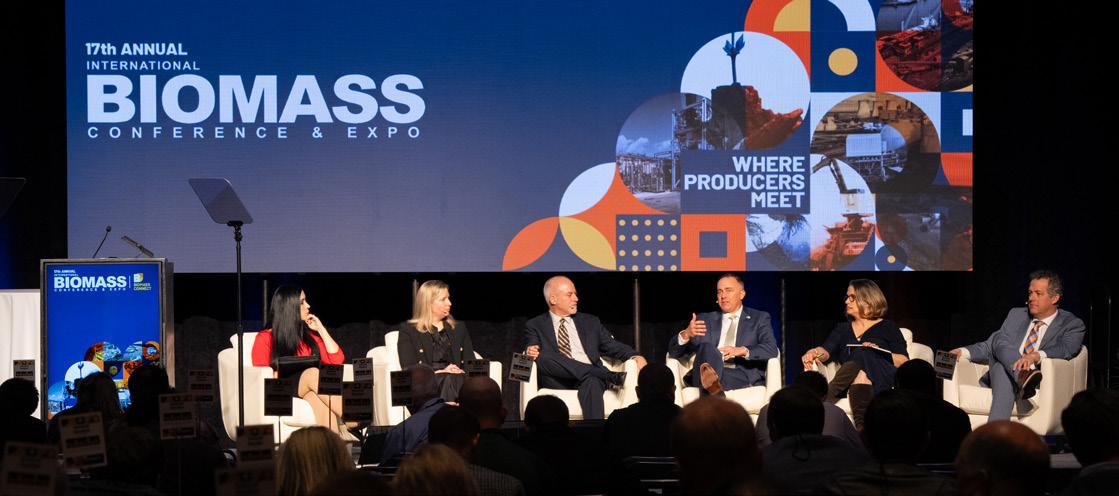
New
products company Peak Renewables has fired up its first pellet plant in Dothan, Alabama, with more projects in the works.

Thank You, Richmond
Earlier this month, our team at Biomass Magazine and BBI International traveled to Richmond, Virginia, to hold the annual International Biomass Conference & Expo. About 950-plus other people from around the world (25 countries) attended the event. While we might be somewhat biased, based on the feedback we’ve received, the show was a resounding success. We’re adding new features to our shows every year, and I’d be remiss if I didn’t mention two new standouts this year: live podcasts on the trade show floor and “Pitch Day,” which allowed a select number of startups to present to and speak with investors behind closed doors. As for what’s in this issue of Biomass Magazine, be sure to check out Associate Editor Katie Schroeder’s page-18 review of the event, “Beacon of Biomass.” While it’s just a snapshot of the very thorough three-day conference, she includes the general session’s industry association updates, and you might find some interesting details in there regarding your respective biomass sector, whether it’s domestic or industrial wood pellets, biogas or renewable natural gas, biomass-based diesel or biomass power. A sincere thanks to all of our exhibitors, moderators, presenters and attendees for making the trip to Richmond.
Our second feature article, “Peak Positioning,” by freelance author Maria Church, profiles pellet producer Peak Renewables. The company is in late commissioning stages of its first manufacturing plant in Dothan, Alabama, which is a joint venture project with Rex Lumber. In the article, Church chats with Peak Renewables’ CEO Corey Woolard as well as General Manager Mark Cunningham. One thing that Woolard emphasizes is Peak’s plan to diversify its portfolio with other wood product projects, which he says aligns with the company’s goals and is in its best long-term interests. “We’re currently focused on our next project, which is OSB-related and will have excellent positioning to deliver jobs and economic performance in the southeast U.S.,” he says. “Our focus isn’t just in one area of bioenergy and wood products, but in several areas to ensure the longevity of our company.”
The final article I’ll mention is our page-24 contribution, “Decarbonizing Wood Pellet Production via Moving Bed Heating Exchange Technology,” by Solex Thermal Science’s Jill Caskey. In Caskey’s words, decarbonizing—although absolutely necessary—is often associated with barriers including high capital costs, regulatory approvals and long implementation timelines. “In the meantime, operators need access to low-cost, high-ROI, carbon-reducing solutions now. The wood pellet industry is no exception,” she says. The article takes a deep dive into plate-based moving bed heating exchangers and how they may be able to provide wood pellet producers with needed solutions.
Since I began this note discussing an event, I’ll end on a similar note: We just finished up the agenda for the International Fuel Ethanol Workshop, which is being held concurrently with the Biodiesel, SAF & Renewable Diesel Summit, as well as the Carbon Capture & Storage Summit, from June 10 to June 12 in Minneapolis. As usual, producers receive complimentary registrations—hope to see you there!
EDITORIAL
EDITOR
Anna Simet asimet@bbiinternational.com
ONLINE NEWS
EDITOR
Erin Voegele evoegele@bbiinternational.com
STAFF WRITER
Katie Schroeder katie.schroeder@bbiinternational.com
ART
VICE PRESIDENT OF PRODUCTION & DESIGN
Jaci Satterlund jsatterlund@bbiinternational.com
GRAPHIC DESIGNER
Raquel Boushee rboushee@bbiinternational.com
PUBLISHING & SALES
CEO
Joe Bryan jbryan@bbiinternational.com
PRESIDENT
Tom Bryan tbryan@bbiinternational.com
VICE PRESIDENT OF OPERATIONS/MARKETING & SALES
John Nelson jnelson@bbiinternational.com
SENIOR ACCOUNT MANAGER/ BIOENERGY TEAM LEADER
Chip Shereck cshereck@bbiinternational.com
ACCOUNT MANAGER
Bob Brown bbrown@bbiinternational.com
CIRCULATION MANAGER
Jessica Tiller jtiller@bbiinternational.com
MARKETING & ADVERTISING MANAGER
Marla DeFoe mdefoe@bbiinternational.com
2024 Int’l Fuel Ethanol Workshop & Expo
JUNE 10-12, 2024
Minneapolis Convention Center, Minneapolis, Minnesota
Now in its 40th year, the FEW provides the ethanol industry with cutting-edge content and unparalleled networking opportunities in a dynamic business-to-business environment. As the largest, longest-running ethanol conference in the world, the FEW is renowned for its superb programming—powered by Ethanol Producer Magazine—that maintains a strong focus on commercial-scale ethanol production, new technology, and near-term research and development. The event draws more than 2,000 people from over 31 countries and from nearly every ethanol plant in the United States and Canada.
(866) 746-8385 | www.FuelEthanolWorkshop.com
2024 North American SAF Conference & Expo
SEPTEMBER 11-13,
2024
Saint Paul Rivercentre, Saint Paul, Minnesota
The North American SAF Conference & Expo, produced by SAF Magazine in collaboration with the Commercial Aviation Alternative Fuels Initiative (CAAFI), will showcase the latest strategies for aviation fuel decarbonization, solutions for key industry challenges, and highlight the current opportunities for airlines, corporations and fuel producers. The North American SAF Conference & Expo is designed to promote the development and adoption of practical solutions to produce SAF and decarbonize the aviation sector. Exhibitors will connect with attendees and showcase the latest technologies and services currently offered within the industry. During two days of live sessions, attendees will learn from industry experts and gain knowledge to become better informed to guide business decisions as the SAF industry continues to expand.
(866) 746-8385 | www.SAFConference.com
2025 International Biomass Conference & Expo MARCH 18-20, 2025
Cobb Galleria Centre, Atlanta, Georgia
Now in its 18th year, the International Biomass Conference & Expo is expected to bring together more than 900 attendees, 160 exhibitors and 65 speakers from more than 25 countries. It is the largest gathering of biomass professionals and academics in the world. The conference provides relevant content and unparalleled networking opportunities in a dynamic business-to-business environment. In addition to abundant networking opportunities, the largest biomass conference in the world is renowned for its outstanding programming—powered by Biomass Magazine–that maintains a strong focus on commercial-scale biomass production, new technology, and near-term research and development. Join us at the International Biomass Conference & Expo as we enter this new and exciting era in biomass energy. (866) 746-8385 | www.BiomassConference.com

Improving California’s Air Quality
BY KYLE WILLARDCalifornia’s dairy industry injects more than $21 billion into the state’s economy and supports 189,000 jobs while accounting for around half of California’s total methane emissions. This presents a conundrum: How do we balance economic prosperity with environmental responsibility?
Anaerobic manure digesters offer one promising answer to this question. Anaerobic digesters address the environmental impact of flush dairies, where manure-laden water is stored in ponds. As the manure is naturally digested by bacteria, methane and other gases are emitted as a byproduct. By creating sealed ponds (covered lagoons) lined with high-density polyethylene and installing gas filtration equipment, dairy farmers can transform these emissions into marketable renewable natural gas (RNG).
Anaerobic digesters do not create new emissions. They are designed to capture and use existing pollutants. For instance, raw biogas contains hydrogen sulfide (H2S), which causes a pungent odor at an uncovered lagoon. Covering and filtering out H2S significantly mitigates this issue. Additionally, turning captured methane into renewable transportation fuel helps displace carbon-intensive diesel and gasoline-driven transportation, further enhancing air quality in California.
Low Carbon Fuel Standard Credits: Incentives for Progress
The state of California, recognizing the value of reducing greenhouse gas emissions, operates the Low Carbon Fuel Standard credit program. Approved in 2009 and implemented in 2011, the incentive system rewards farmers for installing dairy digester projects by generating credits for each metric ton of carbon dioxide equivalent reduced by the digester. Methane that would have previously been emitted into the atmosphere is instead captured and used to make RNG. This program also allows out-of-state projects to participate if the RNG produced would serve to displace more carbon-intense fuels in California. These credits, once generated, can be sold through a regulated market exchange to producers of carbon-intense vehicle fuels, providing crucial financial incentives that offset the costs and risks of investing in renewable energy technologies like RNG.
Stakeholders such as farmers, investors, operators and developers are actively engaged in the dairy digester sector because they are financially motivated by the LCFS system. The prospect of earning LCFS credits drives enthusiasm and innovation, and California leads the nation in new dairy digesters built by families embracing the program.
Balancing Business and Regulation
The looming possibility of regulatory changes replacing these incentives with compulsory compliance underscores the delicate balance we navigate. Regulatory compulsion can be a powerful tool in shaping industry behavior. However, it is not without its drawbacks. Take landfills, for instance. Like digesters, landfills also produce methane gas as waste decomposes. Regulations mandate the capture and control of methane emissions in these facilities. Since these facilities are required by law to implement systems to capture this gas, they are ineligible for LCFS credits. This absence of economic incentives can result in this unfiltered gas being combusted in on-site flares rather than being utilized as fuel. In contrast, dairy gas is much more valuable due to incentives, and the industry works hard to find it, capture it and deliver it to users. When an industry pivots from merely burning off methane to actively capturing it, a wave of creative energy is unleashed. This approach not only motivates investors to back projects, but also drives developers to get their projects online quickly, ensuring rapid deployment.
The benefits of incentives for dairy digesters represent a catalyst for innovation and environmental responsibility that is working in our industry.
Author: Kyle Willard Senior Permitting Specialist Maas Energy Works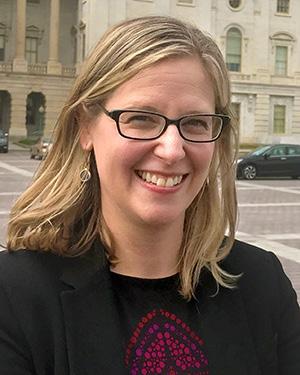
Introducing the American Biomass Energy Association
BY CARRIE ANNANDIf you attended the annual International Biomass Conference and Expo in Richmond, Virginia, last month, you were among the first to learn that the Biomass Power Association has changed its name to the American Biomass Energy Association. We also unveiled an updated version of our longtime logo featuring a leaf and a lightning bolt—images that we feel well convey that we are turning low-value wood and ag byproducts into renewable, reliable and responsible energy.
Although we have a new name and a new and improved logo, very little else is changing. ABEA still has its dedicated team, including Bob Cleaves, Markus Videnieks and myself. We continue to do everything we can to build awareness about U.S.-based biomass energy and the benefits our members bring to their communities and to the nation.
The rebranding is the result of a project we undertook with a Washington, D.C.-based public relations firm, Seven Letter, to understand how Americans feel about biomass. Seven Letter led two focus groups of reliable voters, with one group composed of demographically and geographically diverse regular voters and one group composed of self-described “climate-concerned” voters.
Somewhat surprisingly, few participants of either focus group had much prior knowledge of biomass. One question asked participants about their impressions of solar, wind, oil and gas, geothermal, coal, nuclear and biomass. Respondents could choose favorable, unfavorable, neutral or “I don’t know about this source of energy.” Biomass had by far the most “I don’t know” responses, with about a quarter of the group indicating they did not know anything about biomass.
The good news that came out of our study was that, once focus group participants learned about biomass, they were very supportive and appreciated the need to utilize forest and ag byproducts. They liked that our fuels are organic or plant-derived. And when focus group leaders used the “5 Rs”—recover, recycle, repurpose, renewable and reliable—participants reacted very favorably. They especially liked the “reliable” aspect of biomass, since renewable baseloads are a critical component of an electric grid that is transitioning away from fossil fuels.
We decided to adopt the word “American” into our name as well. This wasn’t only because our focus group subjects liked it, although they very much did. We want our name to reflect that we represent American-based biomass energy. The fuel used by our member facilities is nonmerchantable and locally derived, typically coming from within 75 miles of a facility, and its utilization benefits the local community environmentally and economically.
After all, there is more than enough biomass available here in America that can and should be utilized. The Department of Energy’s Billion-Ton Annual Report, which came out this month, says that 65 million tons of biomass are going unused annually. Many of those tons of unused biomass represent wildfire risk. Many more of those tons are constantly emitting methane, a gas that is at least 28 times as potent as carbon dioxide at trapping heat in the atmosphere, according to the U.S. EPA.
Going forward, ABEA will continue to focus our efforts on getting electricity included in the U.S. Renewable Fuel Standard (aka eRINs), emphasizing the carbon and forest benefits of biomass, incentivizing the industry through tax credits and finding ways to use biomass byproducts like biochar and carbon capture and storage.
If you’re interested in joining ABEA, we look forward to meeting you. Please contact me with questions or to find out more.
Author: Carrie Annand Executive Director, America Biomass Energy Association carrie@usabiomass.orgBiomass News Roundup
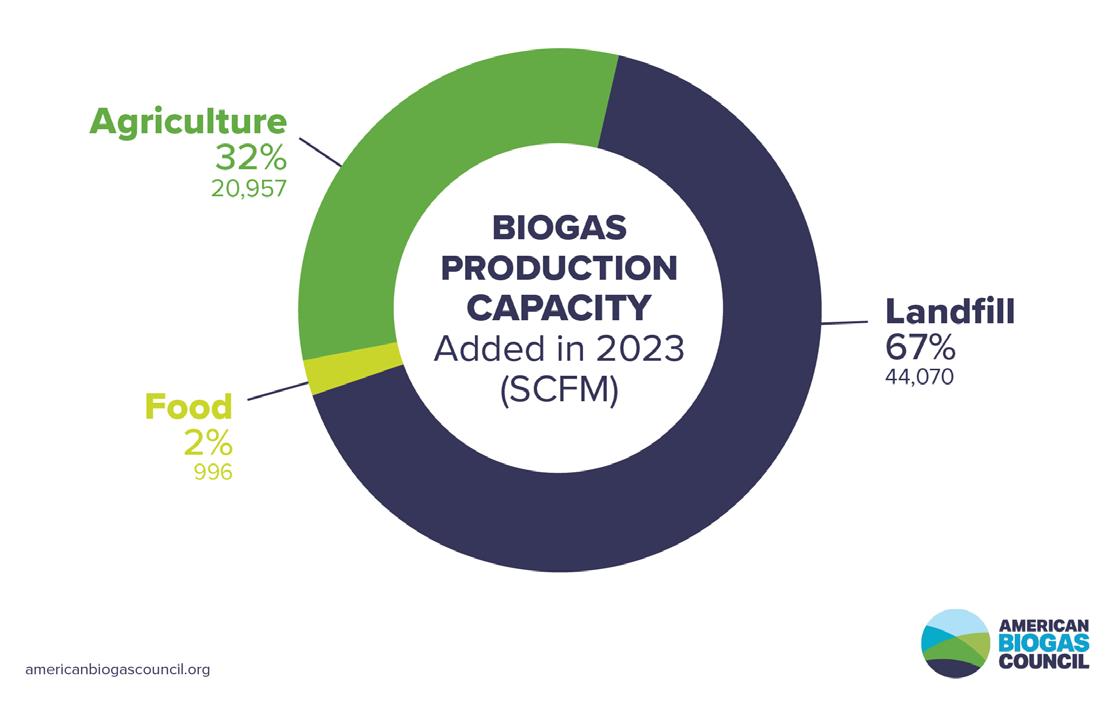
Newly released data from the American Biogas Council indicates that 2023 was the third consecutive year of record growth across the United States biogas industry with nearly 100 new projects coming online, representing $1.8 billion in capital investments. ABC expects this growth to continue into 2024, with more than 100 new projects already projected to go into operation this year. In 2023, 96 new biogas projects became operational in the U.S., pushing the total number of active biogas projects to 2,251, which represents $39 billion in capital investments. The new projects produce 66,000 standard cubic feet per minute (SCFM) of biogas—an electricity equivalent to 4,000 football fields of solar panels, powering 600,000 homes or eliminating 600,000 gasoline cars from the road. Landfill gas (LFG) continues to dominate in terms of both total investment and biogas output. The U.S. currently has 566 LFG projects, including 23 new projects added in 2023. This growth accounts for 57% of capital investments made in 2023 and 67% of new biogas production capacity, according to the ABC. While the growth of the LFG sector was voluminous in terms of both dollars and biogas, 2023 saw only 4-5% growth. In comparison, growth in the agricultural sector was 13.4%, nearly three times greater. Seventy new farm-based projects came online in 2023, contributing 21,000 SCFM of additional biogas output, with capital investments exceeding $700 million.
Tidewater Renewables Ltd.’s 3,000-barrel-per-day renewable diesel facility in Prince George, British Columbia, is currently operating near nameplate capacity. Work is also progressing toward proposed plans to produce sustainable aviation fuel (SAF). Tidewater CEO Jeremy Bains discussed both the plant’s current operations and plans for future SAF production during a fourth quarter earnings call held March 14. The company commenced commercial operations at its renewable diesel and renewable hydrogen complex during the final quarter of last year, he said.
U.S. wood pellet producer Enviva Inc. on March 12 filed a voluntary Chapter 11 bankruptcy petition with the U.S. Bank-
ruptcy Court for the Eastern District of Virginia in hopes of restructuring its approximately $1 billion in debt. The company currently has 10 operational wood pellet plants spanning areas in North Carolina, Mississippi, Florida, South Carolina, Virginia and Georgia with a combined capacity of approximately 5 million metric tons. In addition, a 1.1 million-metric-ton-per-year (MMTPY) pellet plant is under construction in Epes, Alabama, with a 1.1 MMTPY facility proposed for development in Bond, Mississippi. Enviva also operates six deep-water ports in the U.S. South. The company began facing financial troubles last year, following some bad bets on future pellet prices. In its third quarter 2023 financial report, released on Nov. 9, 2023, Enviva described how sales contracts that it entered in late 2022 “have had a significant negative impact on the company’s profitability, cash flows and liquidity due to the negative current spread between the sale and purchase prices of the agreements and the anticipated loss on resale of those volumes within an unfavorable pricing environment in the wood pellet spot market.” Absent a significant and near-term increase in wood pellet market pricing, the company said it expected 2022 transactions to continue to have a negative impact on profitability, cash flows and liquidity through 2025, ultimately causing it to be in breach of certain covenants under its senior secured credit facility.
The restructuring is targeted to be complete during the fourth quarter of 2024. Throughout the process, Enviva said it plans to continue construction of the Epes plant, with an in-service date expected to be during the first half of 2025. Enviva also said it plans to pause development of the proposed Bond plant and intends to consider resuming development of the facility once the company emerges from its in-court restructuring process, depending on the level of customer contracting.
On March 15, Enviva announced that the U.S. Bankruptcy Court for the Eastern District of Virginia had approved $500 million in debtor-in-possession financing related to its Chapter 11 bankruptcy filing.
Drax Group plc released 2023 financial results on Feb. 29, reporting that its pellet production segment achieved robust performance in a challenging market environment. The company also discussed progress it has made on its bioenergy with carbon capture and storage (BECCS) projects in the United States and United Kingdom. Drax’s pellet segment reported adjusted EBITDA of approx. $113 million last year, down from about $171 million in 2022. The company said the reduction reflects lower levels of production, an increased proportion of sales to third parties under legacy contracts and higher operating expenditure due to maintenance costs arising from unplanned outages and increased staff costs. Drax noted it is continuing to progress development opportunities with the expansion of its Aliceville, Alabama, plant and the newly built Longview, Washington plant. Development of the Longview project includes a colocated port facility. The new projects and existing operations will give Drax a network of 18 pellet plants with a combined capacity of approximately
5.4 million metric tons as well as access to five deep water ports in the U.S. South and North American West Coast. In the short term, Drax said it is focused on managing risks to its supply chain while remaining alert to the opportunities this might create. Long-term, the company said it is fundamentally positive on the outlook for biomass demand and expects it to grow, citing the increasing use of biomass for BECCS, carbon removal and as a feedstock for sustainable aviation fuel.
Rep. John Garamendi, D-California, and Sen. Angus King, I-Maine, on March 11 each introduced legislation that aims to allow facilities generating renewable electricity from forest biomass such as woodchips or sawdust to participate in the Renewable Fuel Standard.
The bill, titled the “Biomass for Transportation Fuel Act,” would fully implement the eligibility for electricity generated from renewable biomass, including biogas, to participate in the RFS. The legislation directs the U.S. EPA to approve an RFS pathway for renewable electricity for biomass, but only for feedstocks already eligible under the program, such as agricultural waste, forest byproducts and municipal and commercial food waste. The bill would make biomass removed from federal forestlands as part of wildfire hazard reduction efforts to be eligible under the RFS. Currently, only biomass collected from nonfederal lands is considered eligible RFS feedstock.
Garamendi introduced the House version of the bill, H.R. 7609, on March 11. The bill was referred to the House Committee on Energy and Commerce. To date, Reps. Jared Golden, D-Maine, and Ann Kuster, D-New Hampshire, have signed on to cosponsor the House bill. King also introduced the Senate version of the bill, S. 3899, on March 11. That bill is being cosponsored by Sen. Jeanne Sha heen, D-N.H., and was referred to the Sen ate Committee on Environment and Public Works.
The U.S. Department of Energy has released its 2023 Billion-Ton Report (BT23), which shows that the U.S. could sustainably triple its production of bio mass to more than 1 billion tons per year. The report—the fourth in a series of assess ments of potential biomass resources in the United States since 2005—finds that 1 billion tons of biomass could satisfy over 100% of the projected demand for airplane fuel in the country, allowing the U.S. to fully decarbonize
the aviation industry with sustainable aviation fuel (SAF). Highlights from the report include, but aren’t limited to, the following:
-The U.S. currently uses about 342 million tons of biomass, including corn grain for ethanol and wood/wood waste for heat and power, to meet roughly 5% of America’s annual energy demand.
-The U.S. can triple the production of biomass, producing an estimated 60 billion gallons of low greenhouse gas liquid fuels while still meeting the projected demand for food, feed, fiber, conventional forest products and exports.
-Currently available but unused biomass resources can add around 350 million tons of additional biomass per year above current uses and double the U.S. bioeconomy.
The BT23 report analyzes the biomass production capacity of approximately 60 resources, several of which have never been the subject of a DOE Billion-Ton assessment, including winter oilseed crops, trees and brush harvested from forests to prevent wildfires, macroalgae such as seaweed cultivated in ocean farms and carbon dioxide from industrial plants.
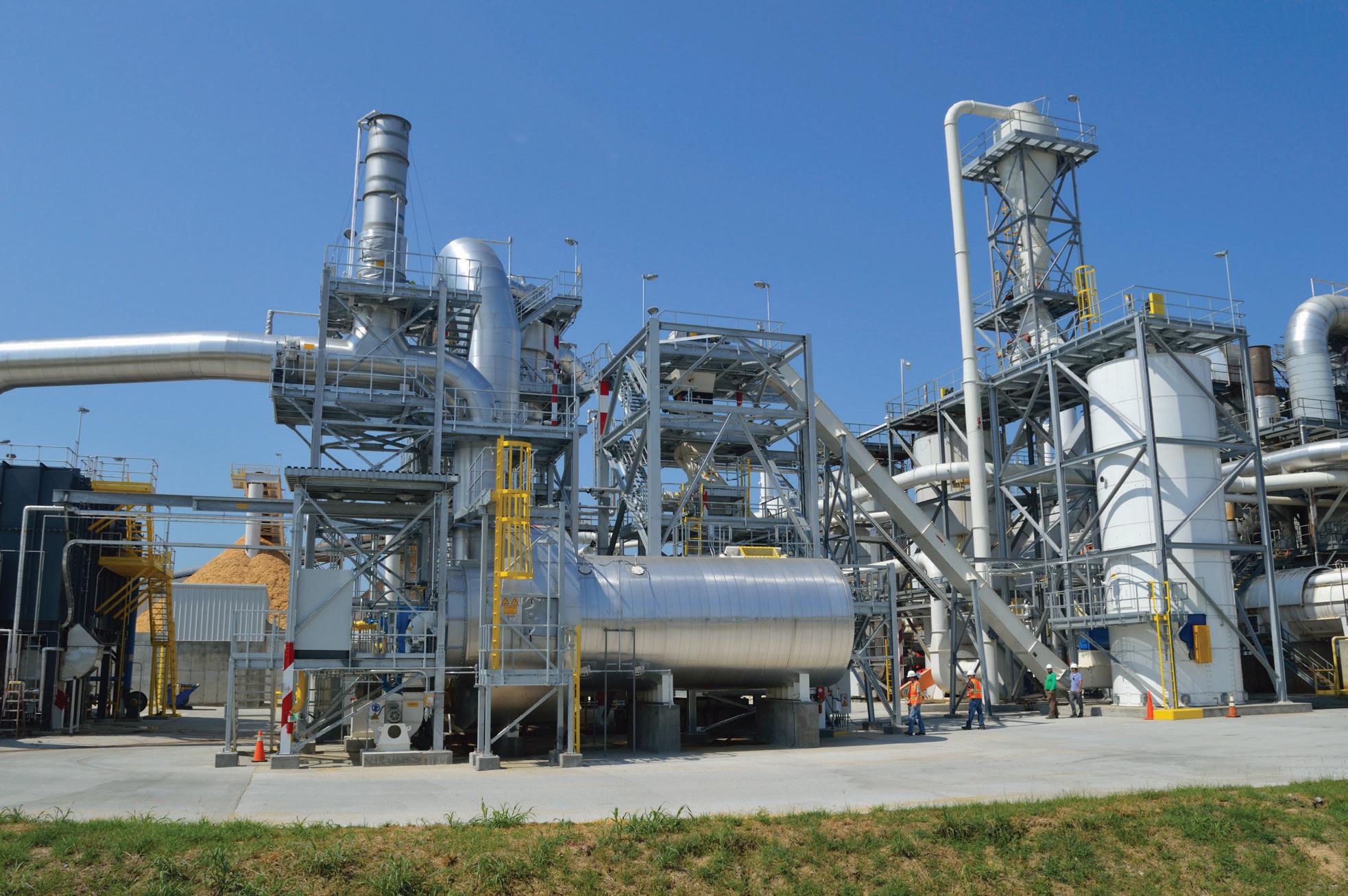
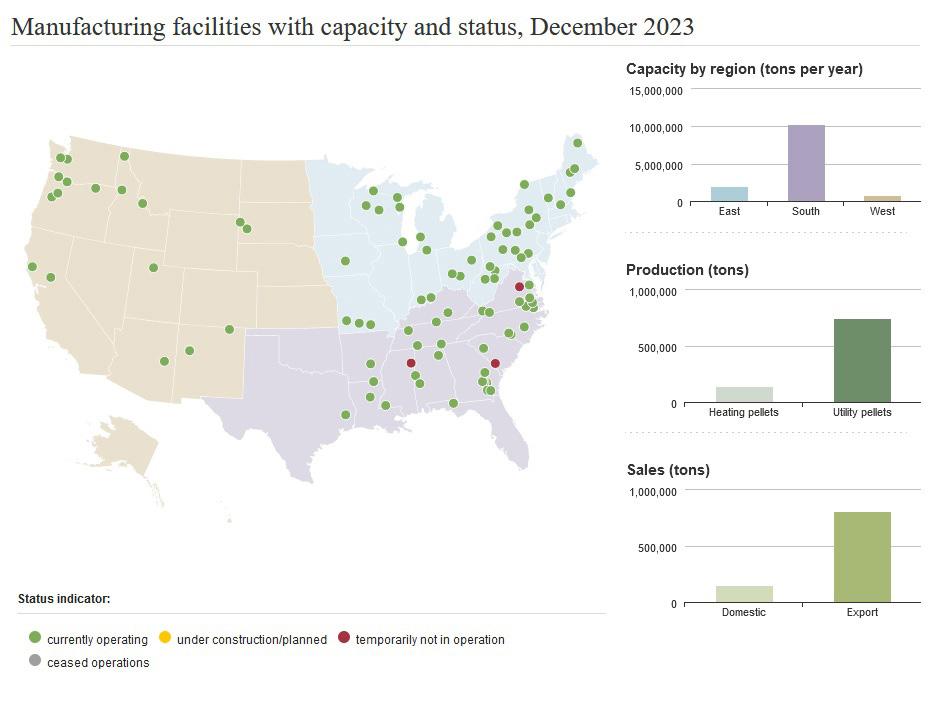
The U.S. Energy Information Administration is providing an opportunity for U.S. densified biomass industry stakeholders such as wood pellet producers to comment on ways to improve its monthly data collection efforts. In February, the agency opened a public comment period on a proposed three-year extension to Form EIA-63C Densified Biomass Fuel Report, which is part of the EIA’s comprehensive energy data program.
Form EIA-63C collects monthly data on the manufacture, shipment, exports, energy characteristics and sales of densified biomass fuels and other densified biomass fuel products from facilities that manufacture densified biomass fuel products such as wood pellets, for use in energy applications. Data collected via the form is used to compile the EIA’s Monthly Densified Fuel Report, which includes data
Viridi Energy announced it has acquired a legacy biosolids digester plant in Brunswick, Maine, with plans to transform the site into a waste-to-renewable natural gas facility. In connection with the acquisition, Casella Waste Systems Inc. will manage feedstock collection and delivery logistics for an estimated 85,000 tons of biosolids per year from a network of wastewater treatment plants. At Viridi’s overhauled Brunswick anaerobic digestion facility, the biosolids will be transformed into enough energy to heat more than 3,000 homes for a year, according to the company. The facility will also supply electricity directly to Brunswick Landing, the 3,300-acre campus featuring more than 1.6 million square feet of commercial, industrial and professional office space that is home to both the Brunswick facility and more than 160 other companies.
on wood pellet manufacturing facilities, capacity, production volumes, sales volumes and prices, inventories and several other metrics. The EIA is specifically inviting comments on whether the proposed collection of information is necessary for the proper performance of agency functions, including whether the information will have practical utility; EIA’s estimate of the burden of the proposed collection information, including the validity of the methodology and assumptions used, is accurate; if EIA can improve the quality, utility and clarity of the information it will collect; and whether EIA can minimize the burden of the collection of information on respondents, such as through automated collection techniques or other forms of information technology.
The public comment period is open through April 22. Additional information is available on the Federal Register website.
Drax Group has agreed to a memorandum of understanding with Viking CCS, a Humber-based CO2 transportation and storage network led by Harbour Energy, together with non-operated partner bp, to assess options to transport and store CO2 in the Humber region.
The MOU will see the companies work together on an early pipeline study to explore options that could connect Drax Power Station to the depleted Viking gas fields in the southern North Sea.
Once operational, and subject to a final investment decision, the Viking CCS cluster could capture and store up to 10 million metric tons of United Kingdom emissions per year by 2030 and up to 15 million metric tons by 2035.
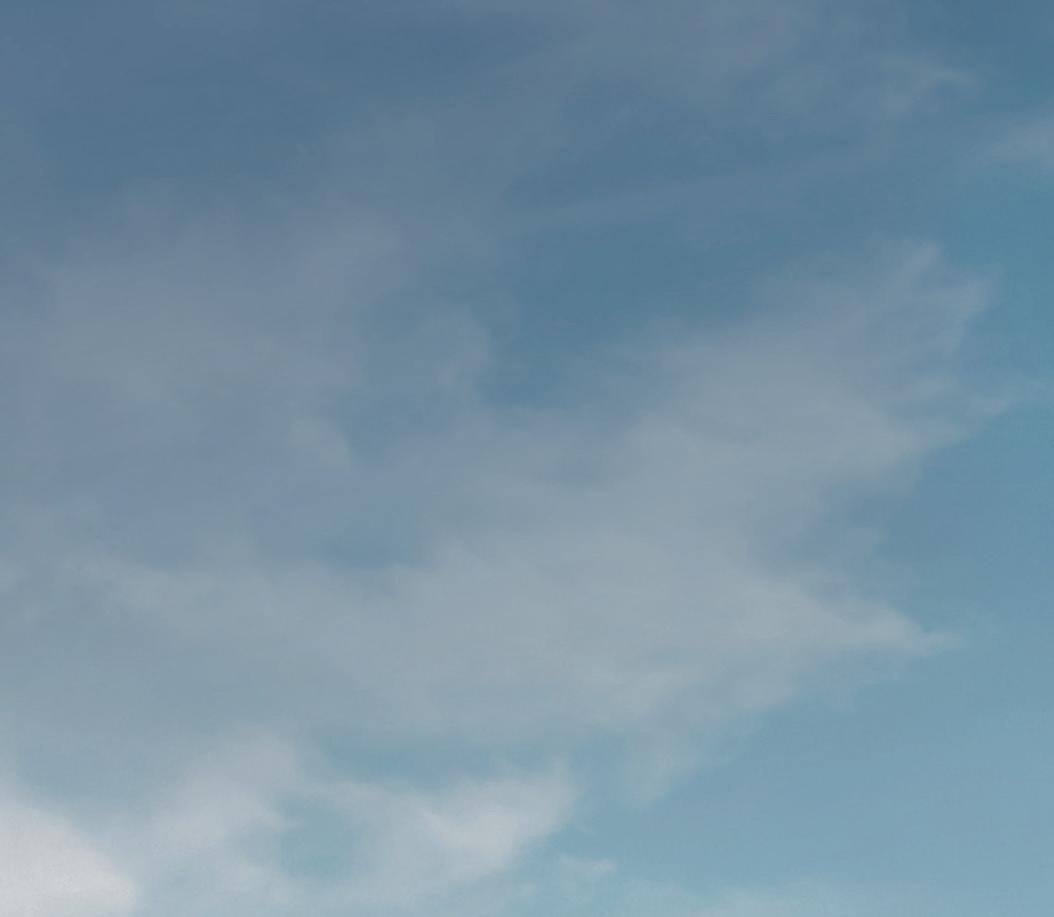
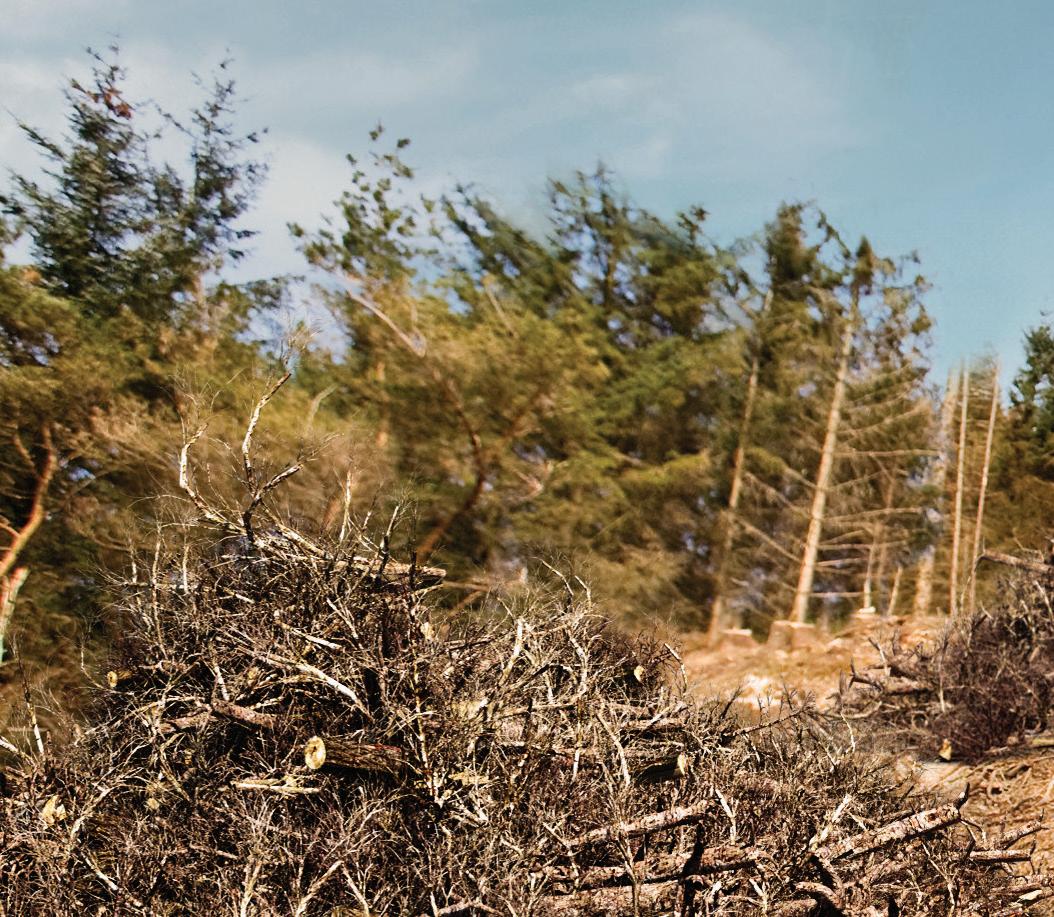
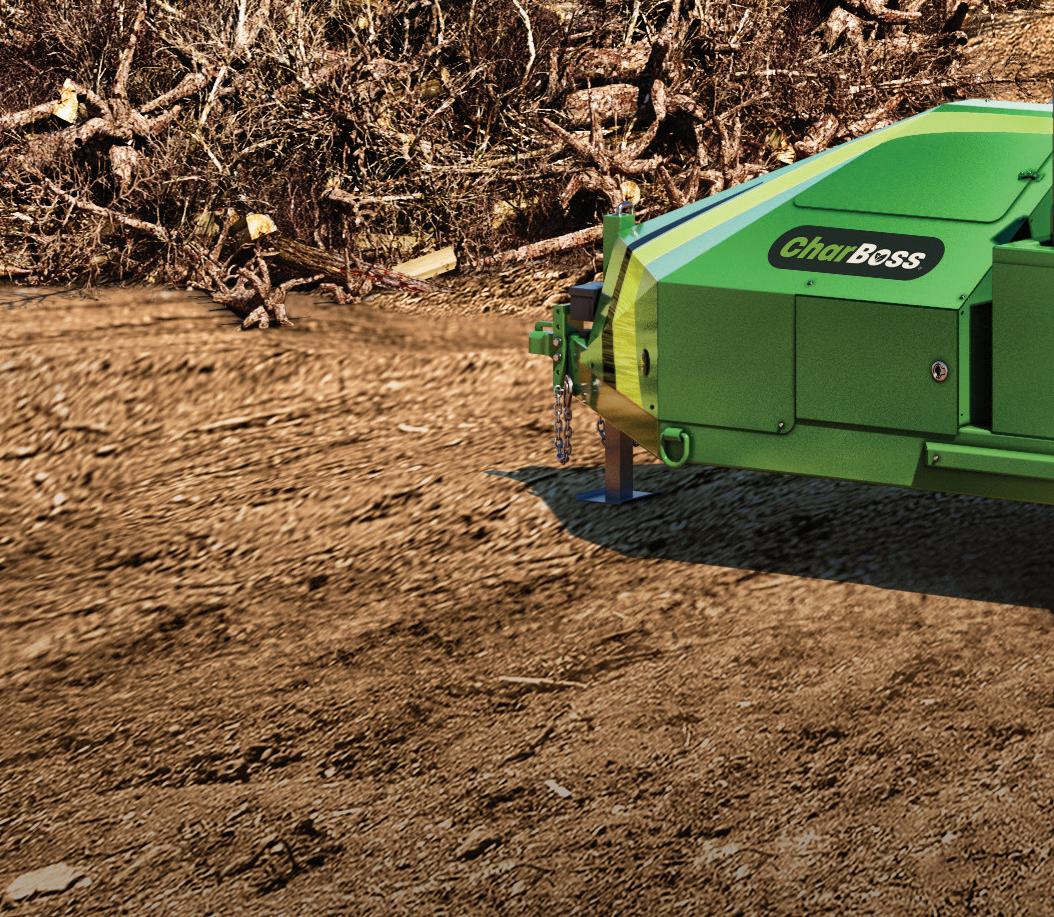
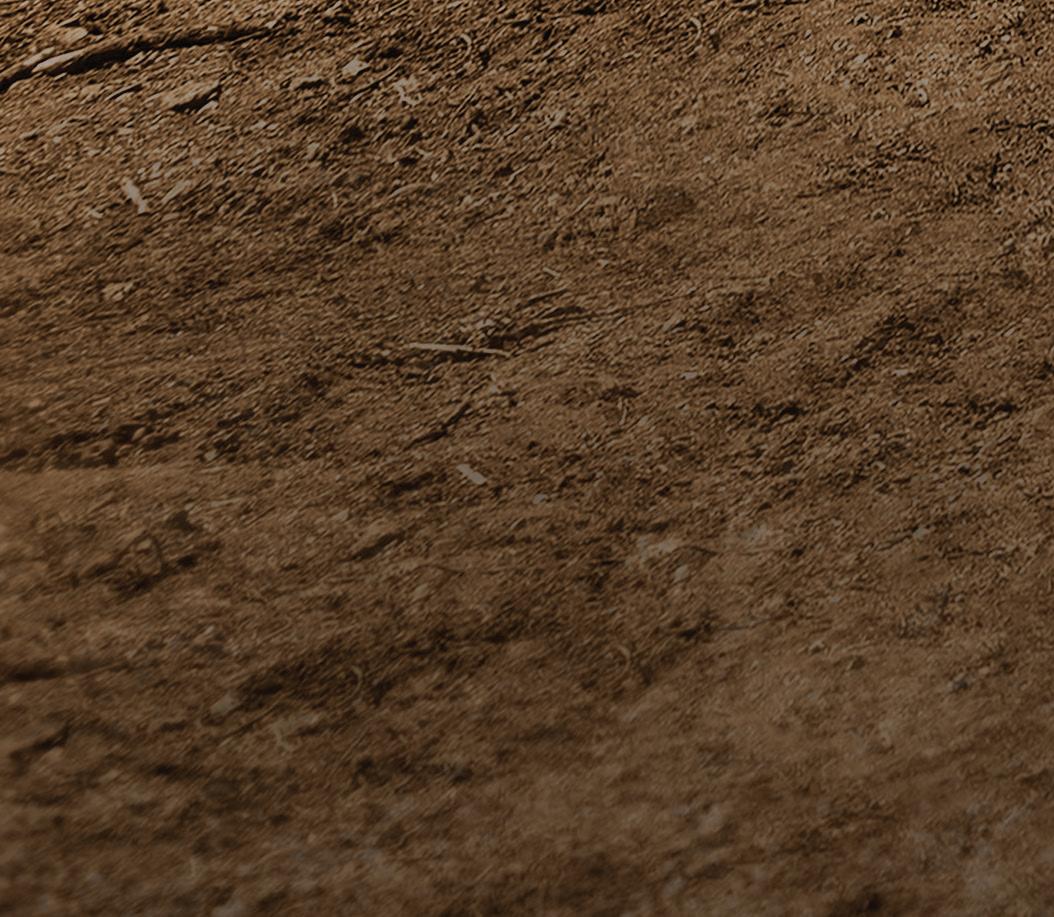
CharBoss®

BUSINESS IS GREEN BUSINESS
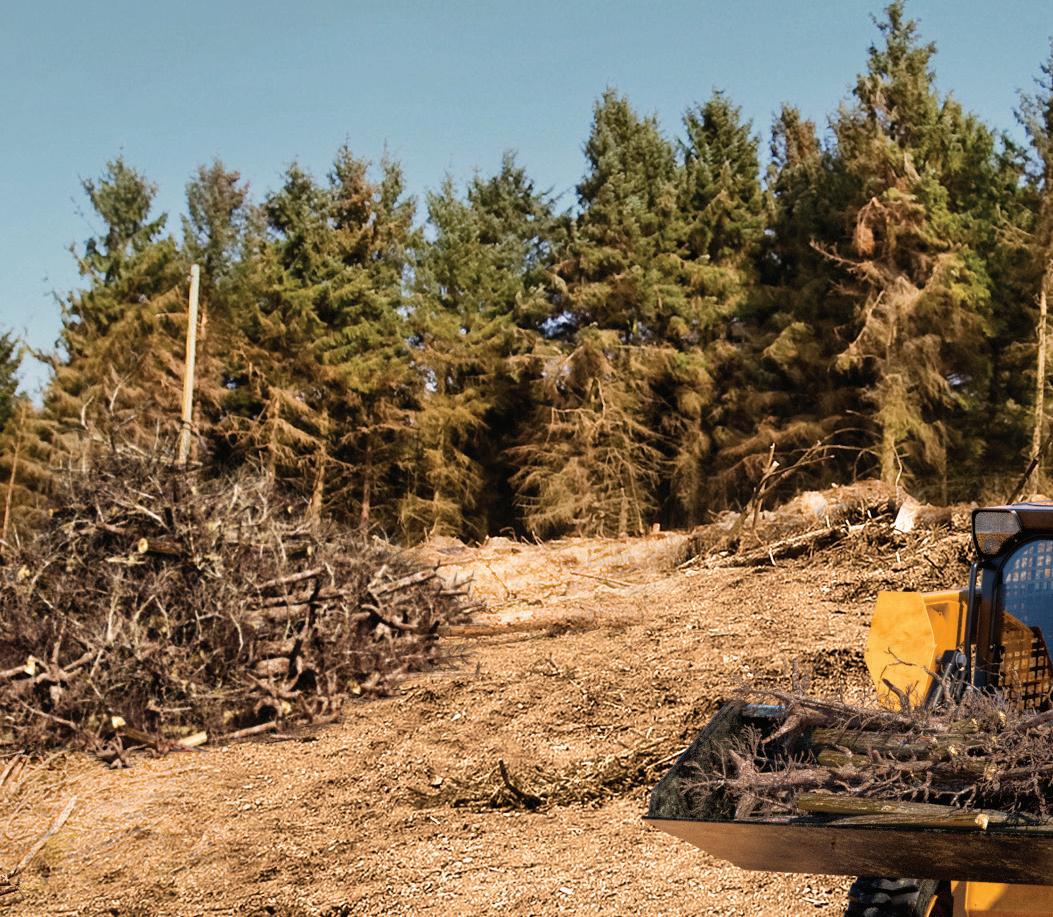
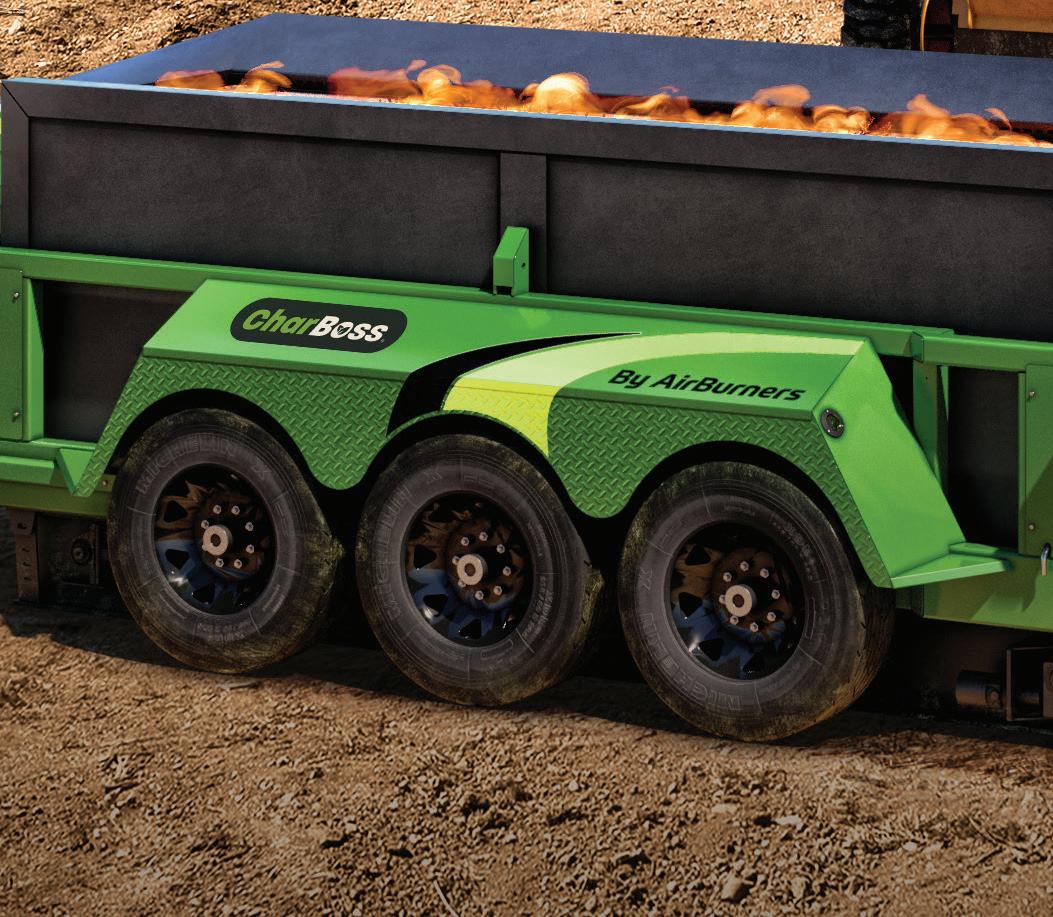
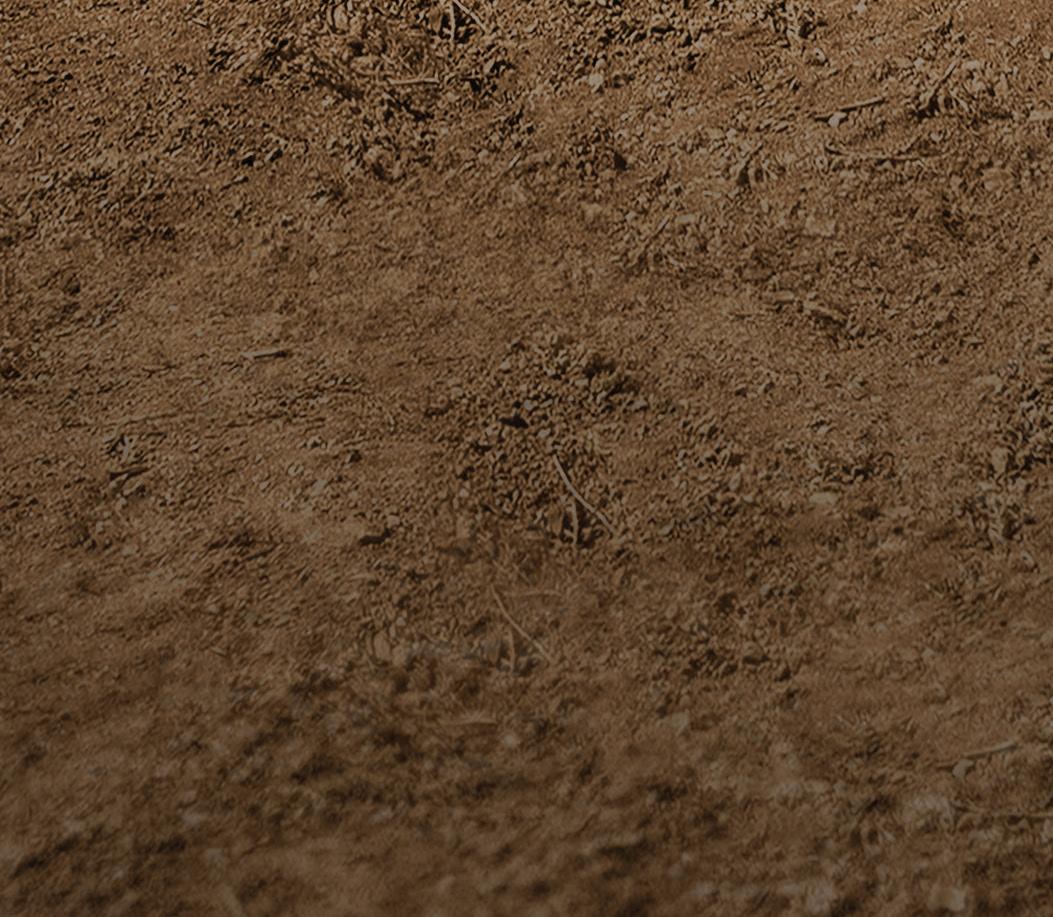
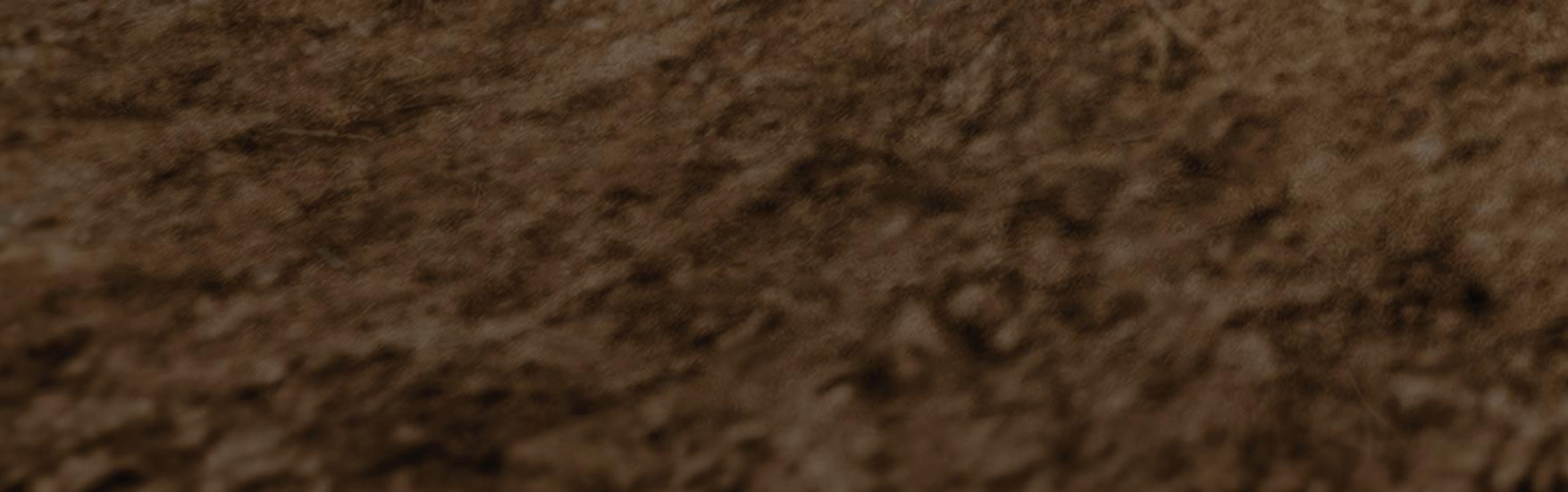
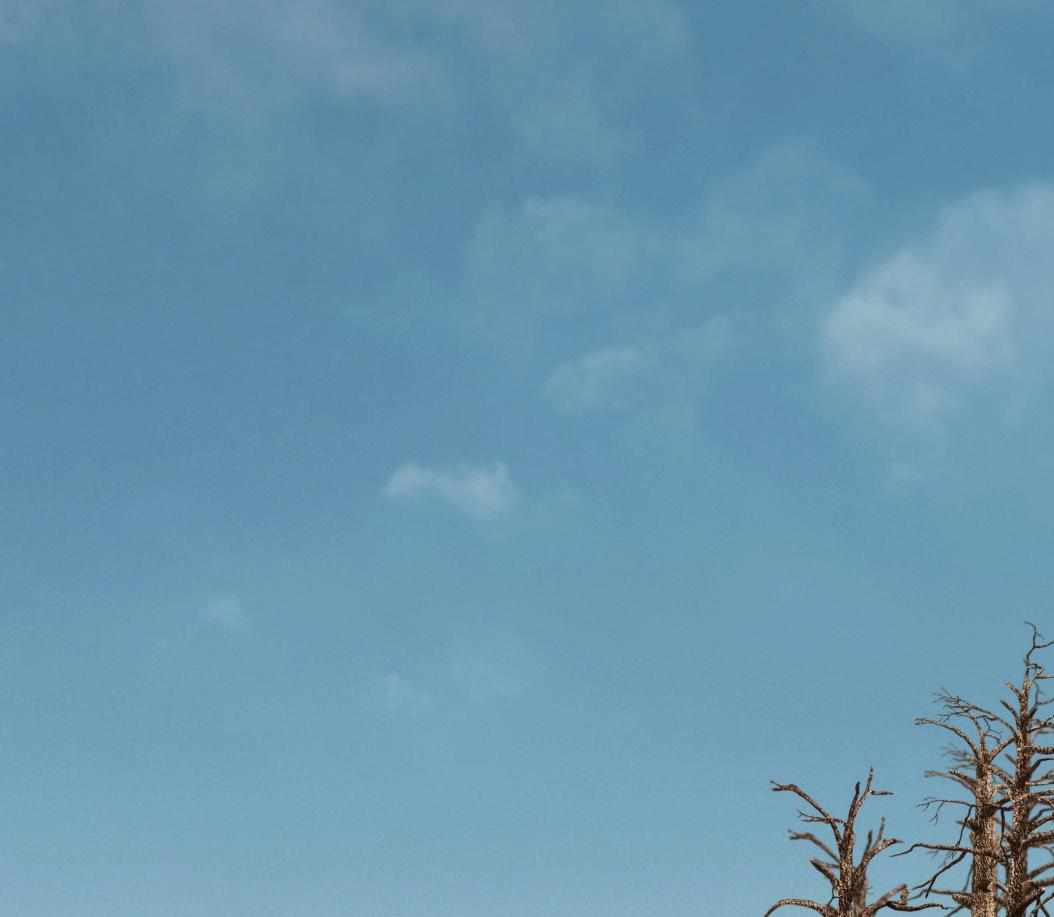
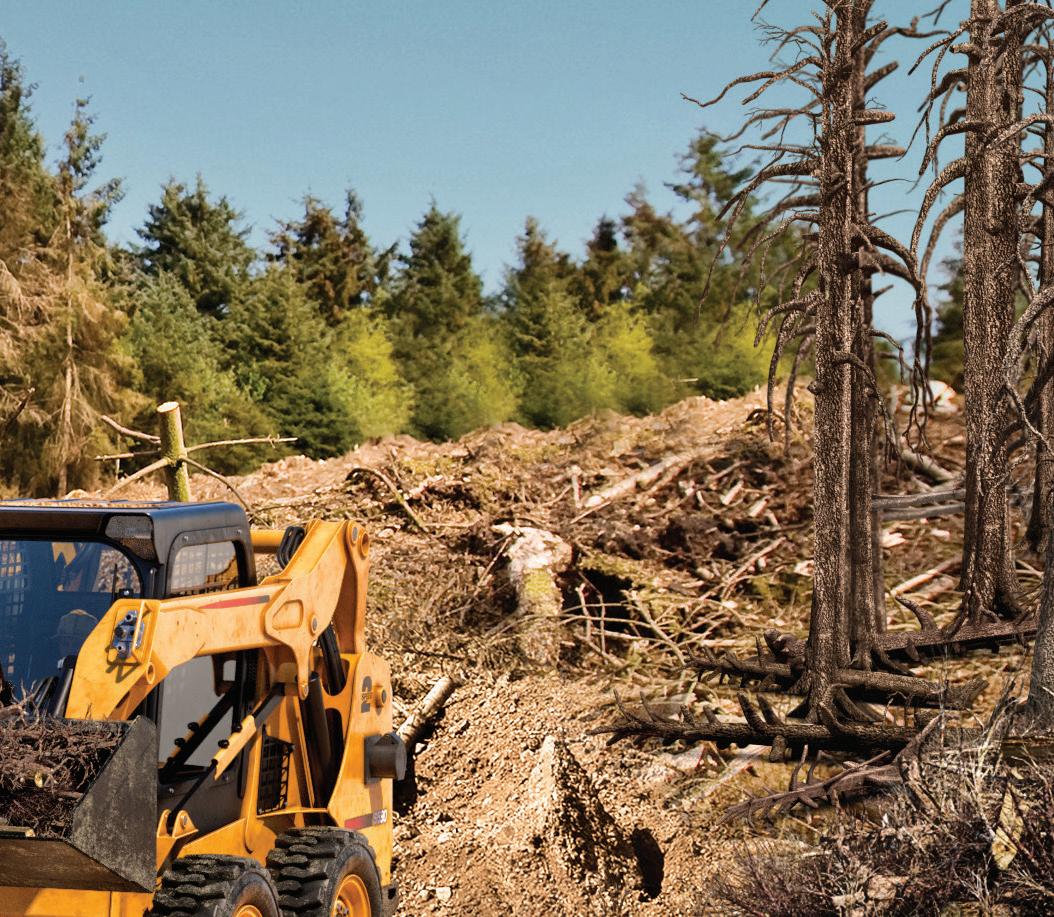

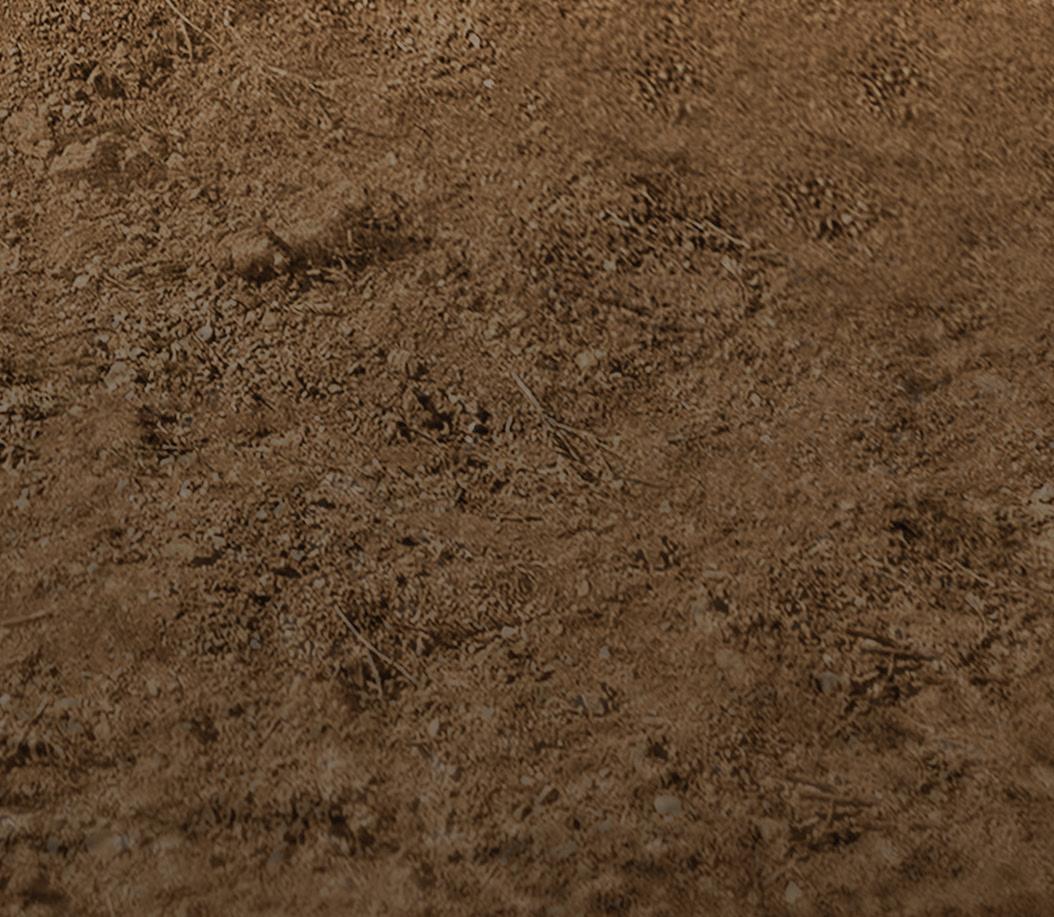
Managing forest health takes time and money, but the alternative is even more costly to our environment. The CharBoss, the world’s first mobile biochar production system, can help on both fronts and turn unwanted wood waste into nutrient-rich biochar. This valuable soil amendment can either be recycled onsite, enriching soils, or bagged as a product for sales. Go deep into the woods to manage forest growth and mitigate wildfire safely. The self-contained CharBoss is easy to maneuver, eliminates wood waste 40x faster than open burns while reducing the particulate matter released significantly. Air Burners® o ers the most cost-e ective, earth-conscious solution for organizations to sustainably manage biomass and reduce waste. Contact us for a quote today.
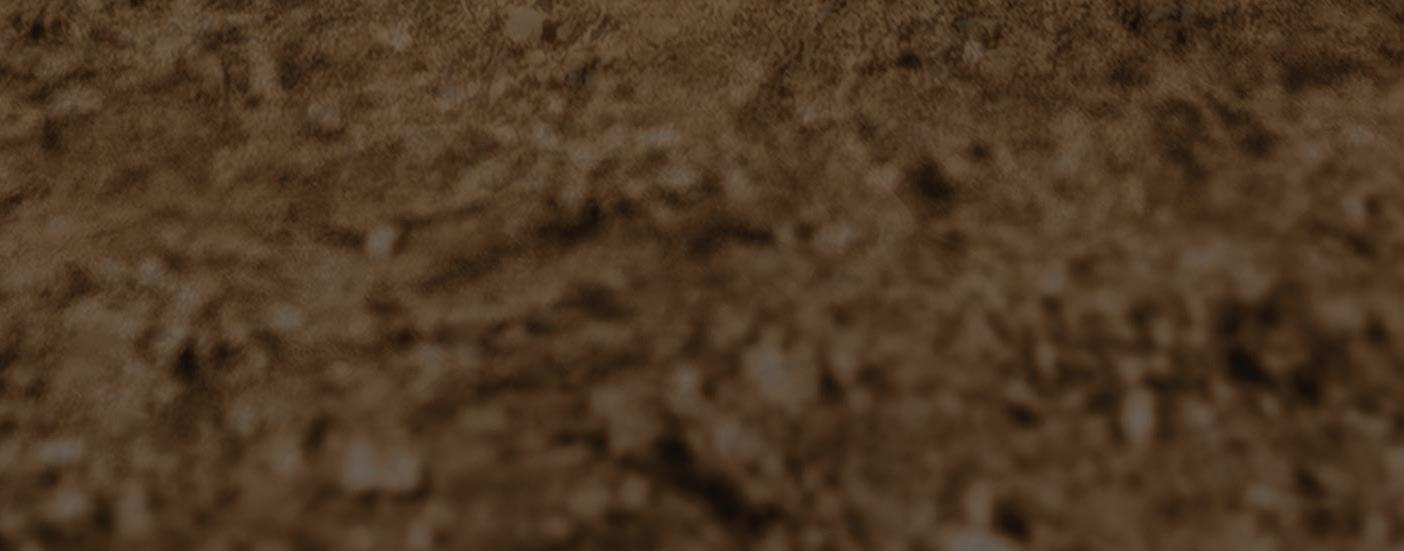
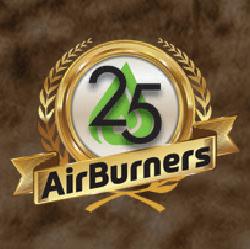
A SUSTAINABLE STRATEGY
A new player in the wood pellet industry, Peak Renewables has fired up its Dothan, Alabama, plant, with more projects in the works.
BY MARIA CHURCHNew kid on the block in the North American wood pellet world Peak Renewables has bid farewell to the quiet planning phase and is kicking things into high gear. The company’s flagship pellet plant in Dothan, Alabama—a joint venture with Rex Lumber— is in the late stages of commissioning. With a 150,000 tons-per-year nameplate capacity, the plant will run 100% on dry shavings.
Peak Renewables’ unique ownership structure as one of six vertically integrated companies owned by the Brian Fehr Group, as well as its ability to refurbish and relocate equipment from other acquired assets, resulted in an impressive turnaround. Groundbreaking to start-up took just nine months.
CEO Corey Woolard couldn’t be happier with the speed and quality of start-up. Having worked previously at Drax as senior vice president of operations, Woolard went into the project with high expectations. “It’s been an excellent start-up from the perspective of turnaround time and bringing assets up methodically to ensure safe operation and quality of the product being made,” he says. “I’ve been [involved] in numerous startups, so I fully understand the pressures of getting up to full capacity as quickly as possible. This plant should be at full capacity before the end of Q2 this year.”
Dothan Dealings
Dothan is nestled in the southeast corner of Alabama, a state where more than 90% of its timberland is privately owned. The pellet plant is a joint venture with partner Rex Lumber, which owns the majority and supplies dry shavings from its sawmills within the area. Peak Renewables is responsible for staffing and plant operations.
The joint venture with Rex Lumber is both in the company’s ethos of partnering locally and a practicality of today’s market, Woolard says. Rising capital costs, fiber costs, transportation costs—the list goes on to whittle away at the bottom line for pellet producers.
“If you are able to partner with a sawmill that already has dried fiber and you don’t have to incur the capital costs of installing and operating a dryer, you’re much more economical in the pellet manufacturing process,” Woolard says.
Beyond the economics, skipping the drying process eliminates a plant’s major source of environmental emissions. “Our GHG [greenhouse gas] footprint is extremely low,” Woolard says. “For example, a plant that’s 500,000 tons per year where [it’s] processing round wood, running several front-end loaders, a rotary drum dryer and other equipment, then you’re going to have to start exploring carbon capture
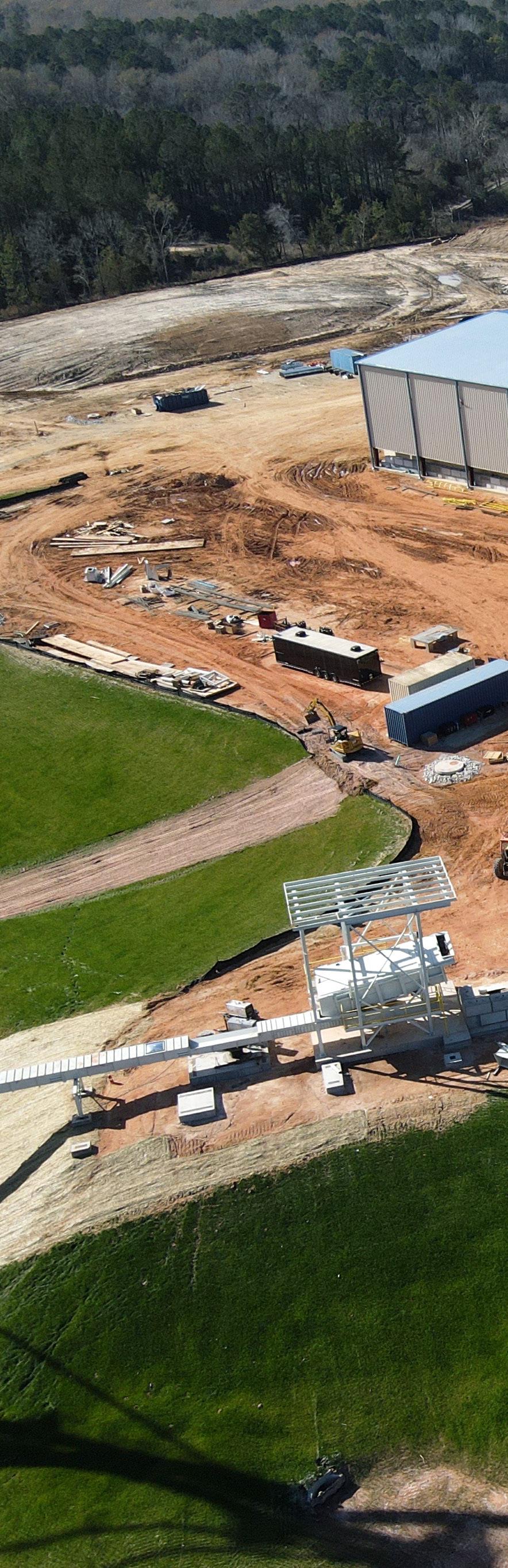
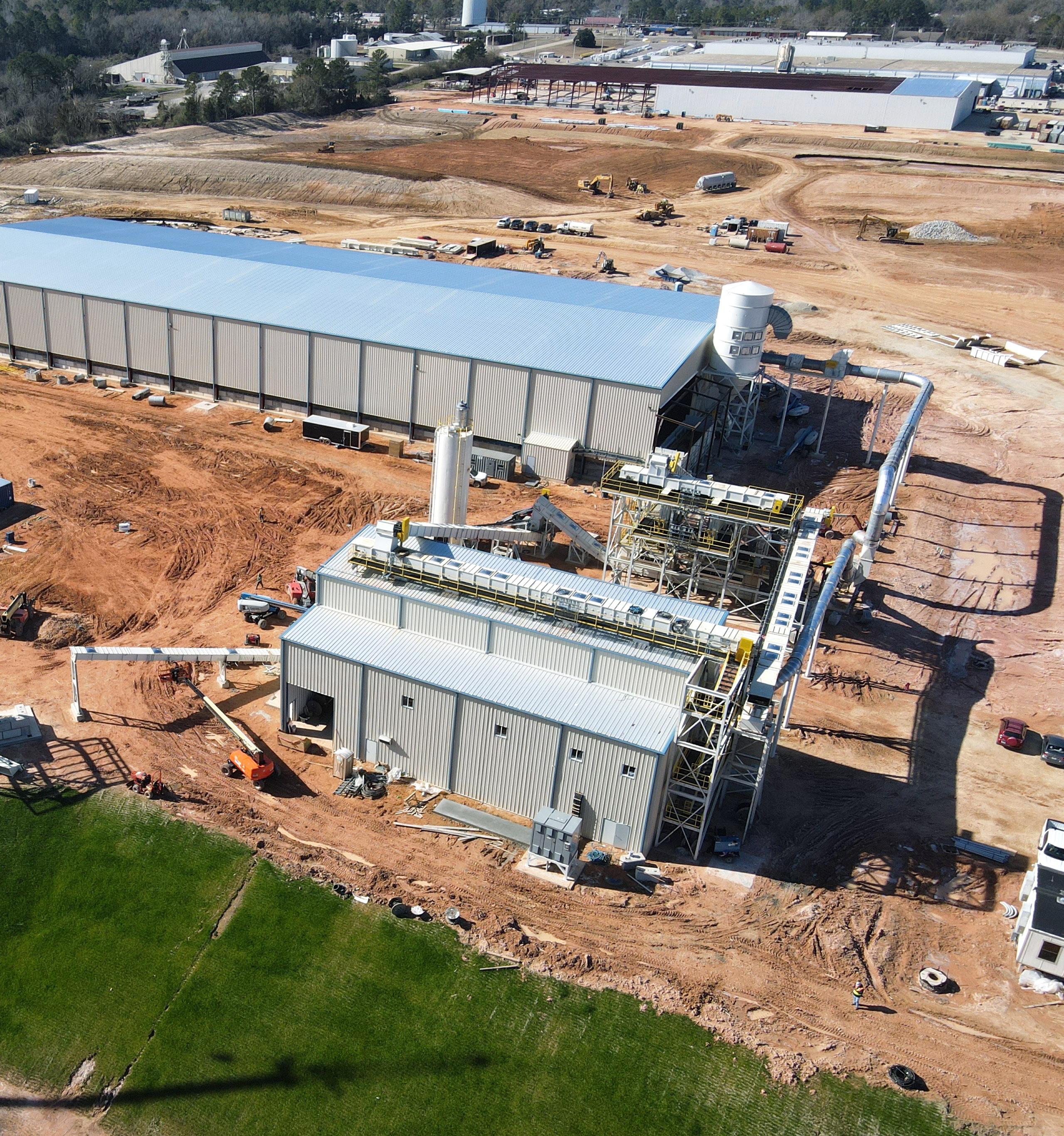
reduction technologies. At smaller-scale operations, our emissions are much lower, making sustainability initiatives readily attainable and aligning with the company’s overarching goals.”
With their Sustainable Biomass Program certification and Europe’s Programme for the Endorsement of Forest Certification in hand, Dothan’s wood pellets will soon be heading overseas. Peak signed an offtake agreement with CM Biomass, which distributes worldwide. While exports will get their feet under them, Woolard says the company’s end goal is much bigger than third-party sales.
“We envision the need for domestic supply in the U.S. to grow exponentially over the next ten years in part due to the Inflation Reduction Act and other regulatory acts that are coming into play,” he says. “Peak Renewables will be positioned to partner with other green energy companies as they progress their carbon reduction initiatives.”
Power generation through pellets or wood chips is another option the company is enthusiastic about, particularly in Canada, where some regions don’t have access to cheap, dispatchable power. Hydrogen production through wood gasification is anoth-

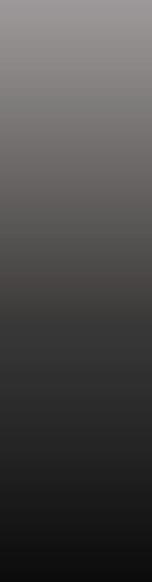
er project on the horizon. “Yes, the export market is the beginning, but our long-term play is in North America,” Woolard says.
Plant Design
Nearly all equipment in Dothan is refurbished from shuttered assets that closed their doors a few years ago in Prince George, B.C.
Peak Renewables’ general manager Mark Cunningham has overseen all interfacing with the construction team for the Dothan startup. Working with refurbished equipment shipped from a single site forced the construction company to be nimble, swiftly installing equipment as it arrived, Cunningham says. “They took a clear site with no civil done, and they’ve done a ton of work to beat the timelines and provide exceptional service,” he says.
As of early March, the company hired and trained around 25 operators and the plant has produced more than 2,000 tons of wood pellets. Training employees during a startup is not without its challenges, Cunningham says, but staff can learn more during a ramp-up than they can at a plant that has been running smoothly for many years.
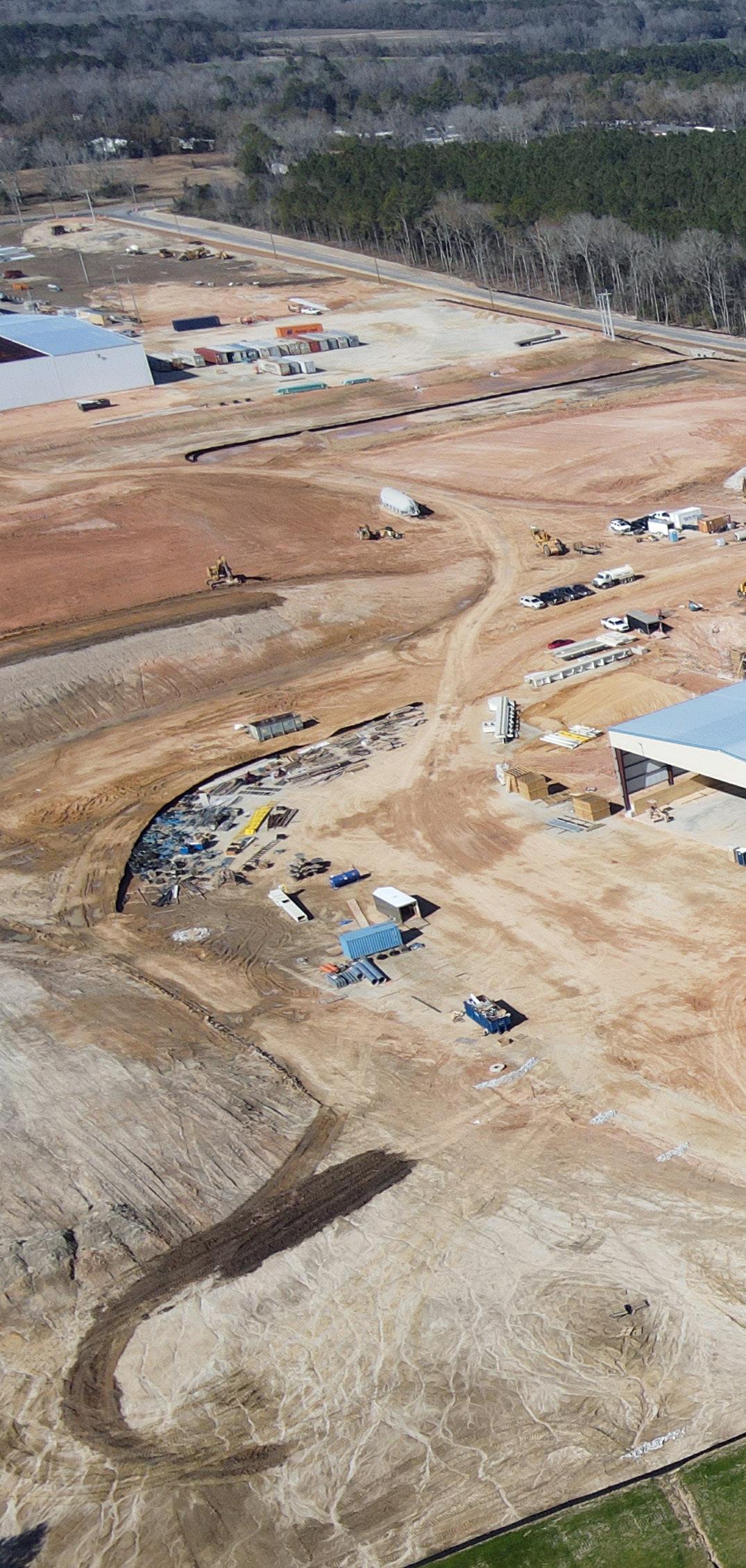

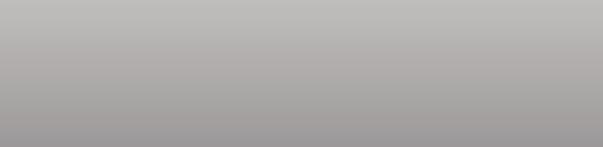




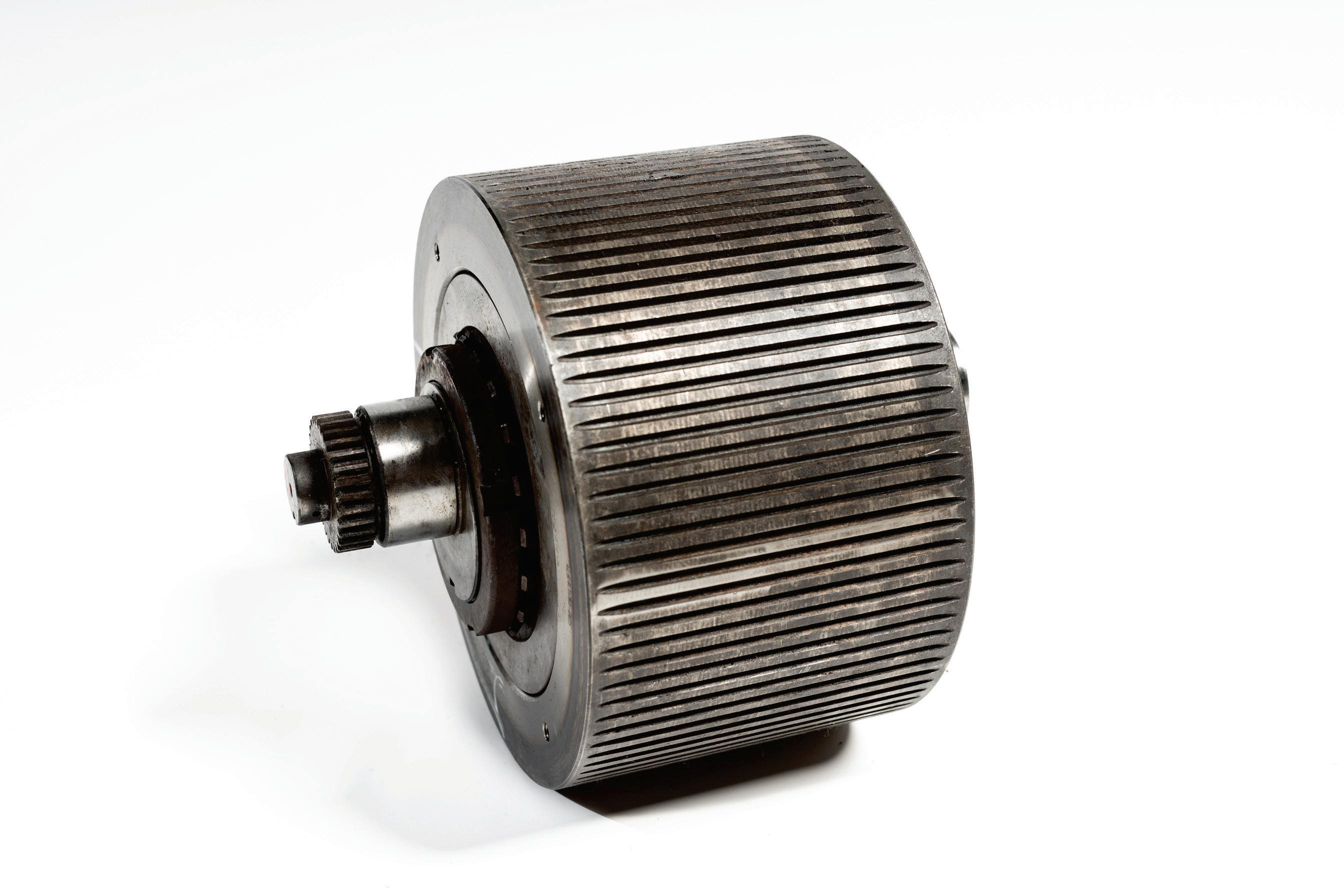
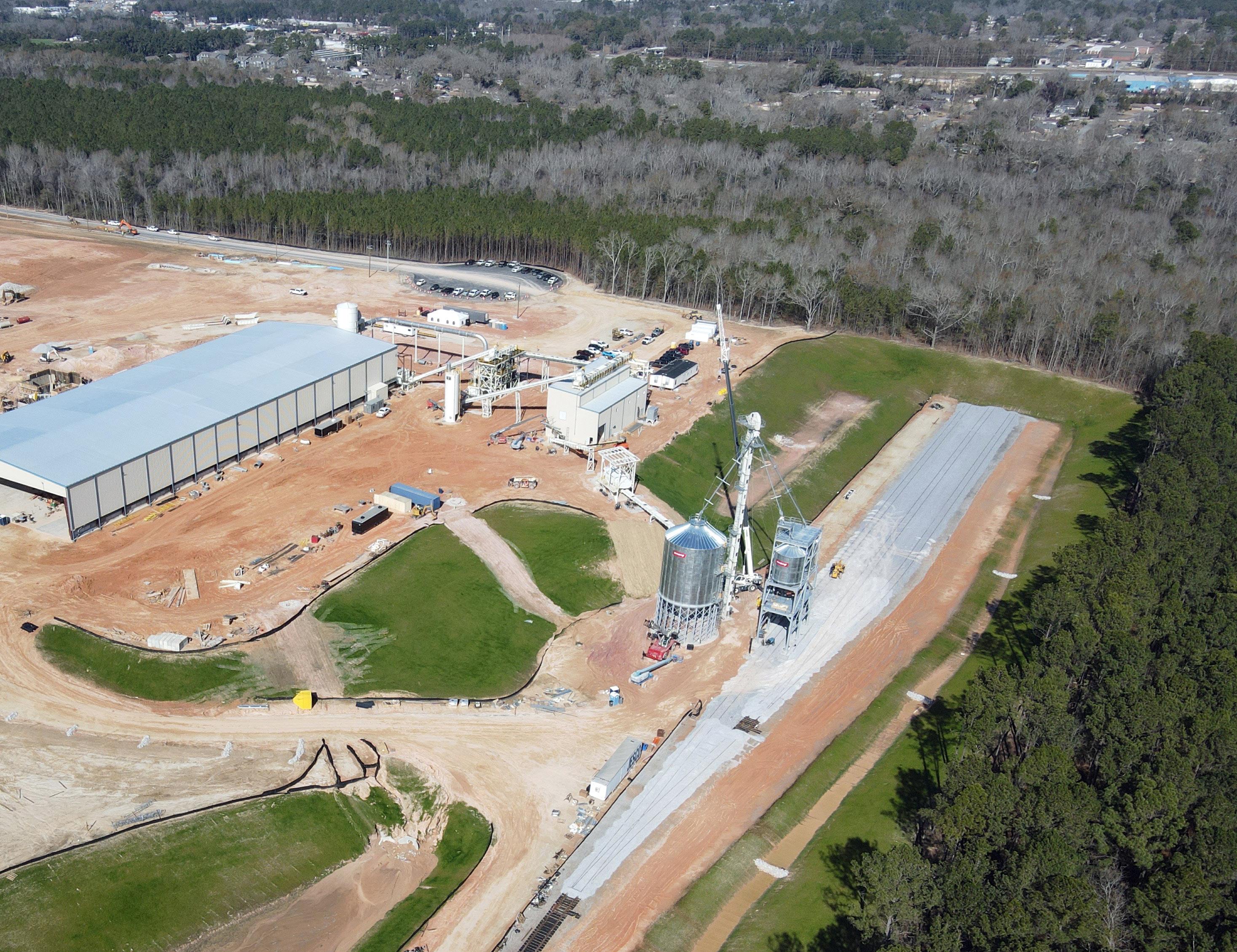
At the Dothan plant, dry shavings are conveyed from a covered building to two hammer mills. Conveyors then bring material to one of five pellet mills. A shared conveyor under the mills brings pellets to finished goods storage or directly to loadout silos.
IMAGE: PEAK RENEWABLES
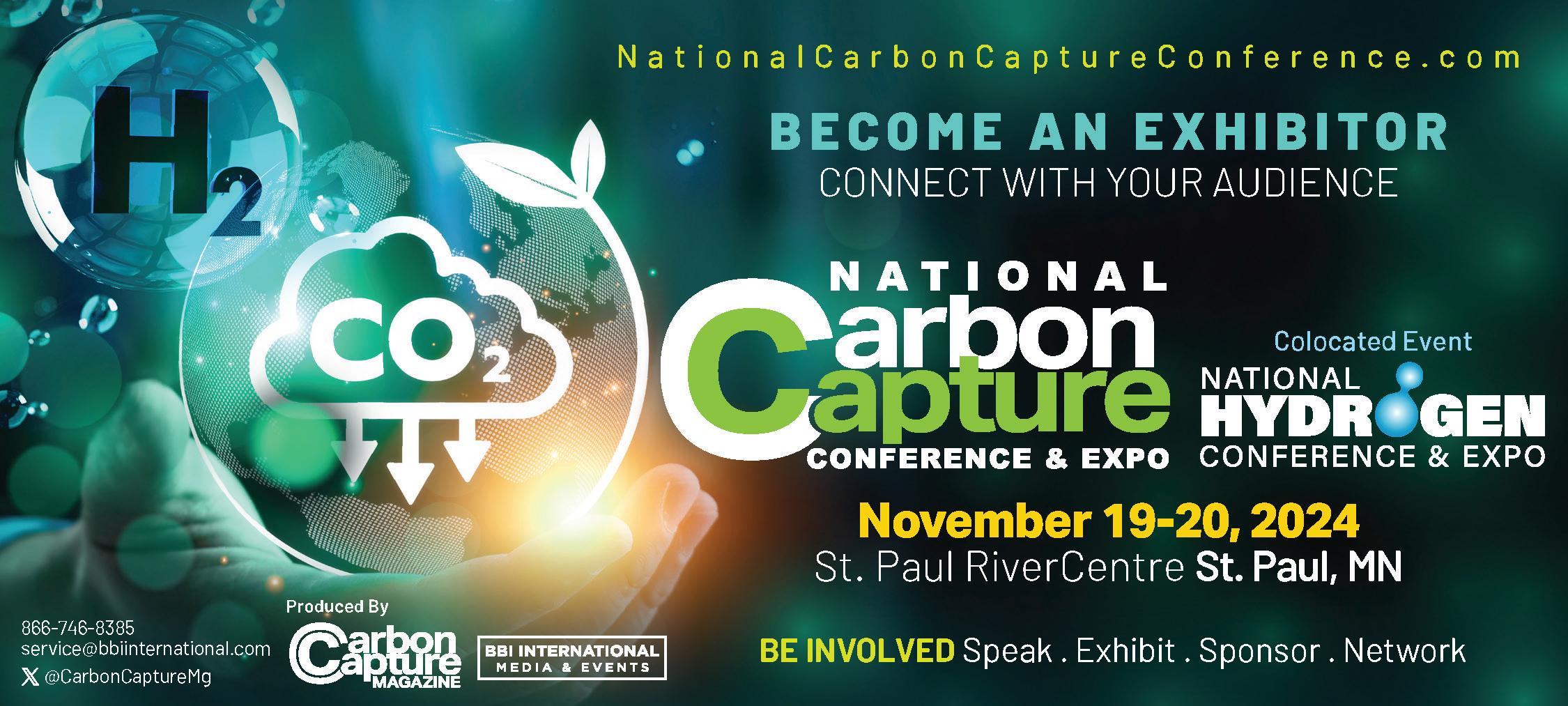
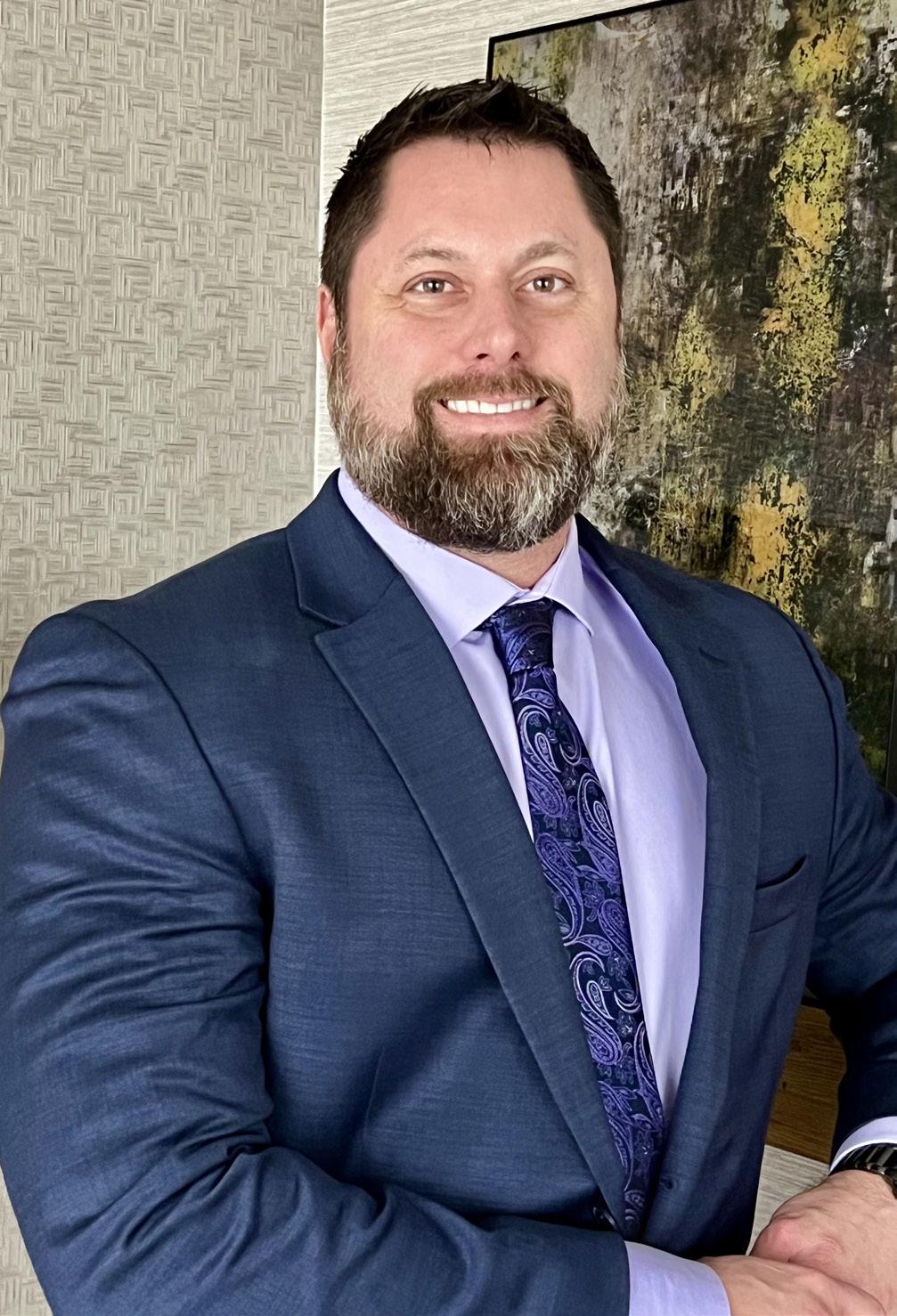
The Dothan plant is a simple, flexible design. Dry shavings are conveyed from a covered building to two hammer mills. Conveyors then bring material to one of five pellet mills. A shared conveyor under the mills brings pellets to finished goods storage or directly to loadout silos where railcars or trucks can be loaded. “We have a great layout that would enable us to expand to add a drying system if we wanted to add roundwood and chipping to our process,” Woolard explains. “We made it very flexible and adaptive. That adaptability includes the footprint to double the equipment, which would effectively bring capacity into the 400,000 tons per year range.”
While running exclusively on dry shavings, the Dothan plant will be testing all incoming shavings loads to both source the material and determine moisture content, which is required to support its certification schemes and to ensure the right fiber mix for pellets.
“A supply of dry shavings is inherent with some variability in moisture content,” Cunningham says. “That is different than a lot of plants. You have to be very focused on how you receive the fiber and how you mix and feed it into the plant to make pellets.”
Cunningham also credits strong OEM partnerships for the smooth startup. Andritz, being the main vendor, was on site several times to support the used equipment installations, reacting to the site’s changing needs.
Peak’s Priorities
With Dothan expected at full capacity in early summer, Woolard and the company are turning attention to other wood pellet projects in North America. Two facilities are in the works in British Columbia, Canada, specifically one in Fort Nelson and the other in Chetwynd. Key to both projects is for Peak to lock in local partners, especially with local First Nations.
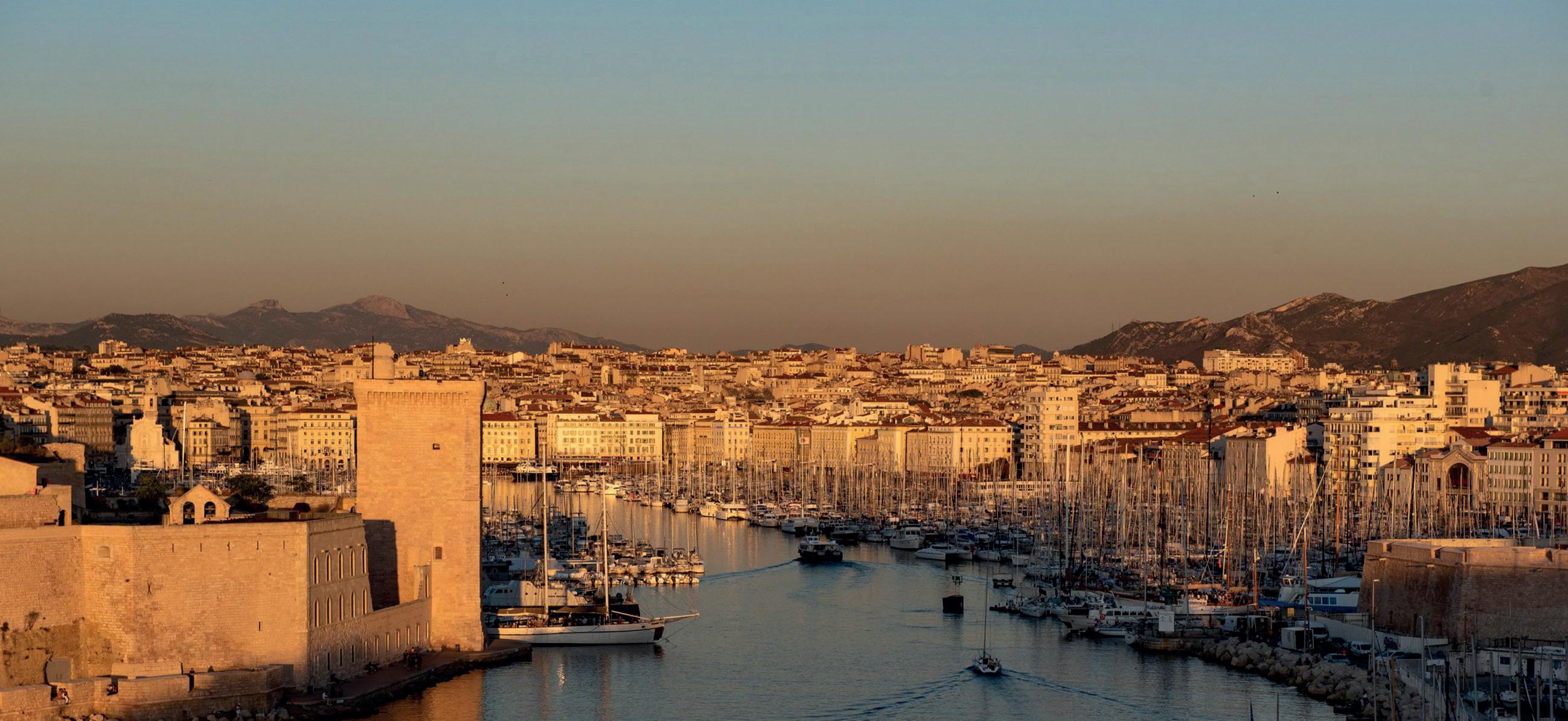
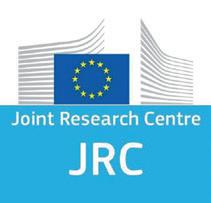
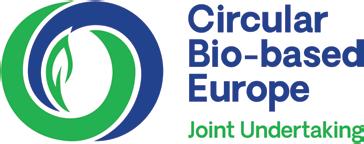
Even though some challenges exist regarding infrastructure at both sites, Woolard says collaborative conversations are ongoing with key stakeholders and the First Nations groups involved to advance the projects. “Indigenous partnerships are very important,” he says. “We want to supply jobs and revitalize communities that industry has left. The key to that is engaging provincial government and First Nations to ensure availability of fiber supply and generate longstanding business opportunities.”
Although Peak Renewables has turned the ignition on pellets so far, the company is open to exploring other wood products project as well. Oriented strand board (OSB) is another focus, and, with the right partner, the company is poised to expand its portfolio across North America. “We’re currently focused on our next project, which is OSB-related and will have excellent positioning to deliver jobs and economic performance in the southeast U.S.,” Woolard says. “Our focus isn’t just in one area of bioenergy and wood products but
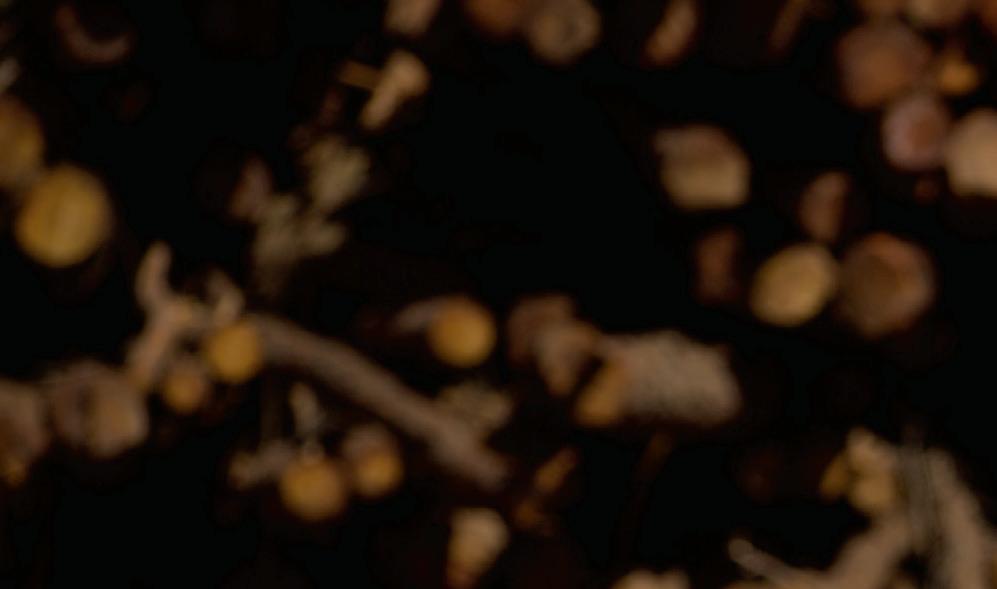
in several areas to ensure the longevity of our company.”
Company Connections
Peak Renewables Ltd. as a wood products entity came onto the scene in 2020 as an arm of the Brian Fehr Group. “Brian’s name is highly reputable. He has so many connections in wood products,” Woolard says. “His network of relationships has enabled him to grow a new business in different arenas.”
Fehr’s companies include Peak North America, a construction and fabrication company; Peak Renewables Kootenays, overseeing projects in B.C.’s Kootenay region; Formula Contractors, a Prince George, B.C.-based heavy construction company; SmartLam, a mass timber manufacturer with facilities in Montana and Alabama; and Hydrogen Naturally, a joint venture with Northwest Capital to produce hydrogen from low-value waste wood.
The companies are uniquely linked in the industry. Peak North America con-
structed the Dothan pellet facility, which Cunningham attributes in no small part to the swift startup.
“As we started the construction and worked together for where different components were going to be, it enabled us to adjust quickly and hit very tight timelines,” Cunningham says.
Colocation of assets is another perk of the integration. The Dothan pellet plant sits adjacent to the SmartLam mass timber facility in Alabama. “The vertical integration of the Brian Fehr Group provides a competitive advantage when constructing and operating new projects, whether it be green energy or wood products,” Woolard adds. “It’s a visionary approach that allows for a bright future and opportunity to strategically grow Peak Renewables into a very profitable company.”
Author: Maria Church Freelance Writer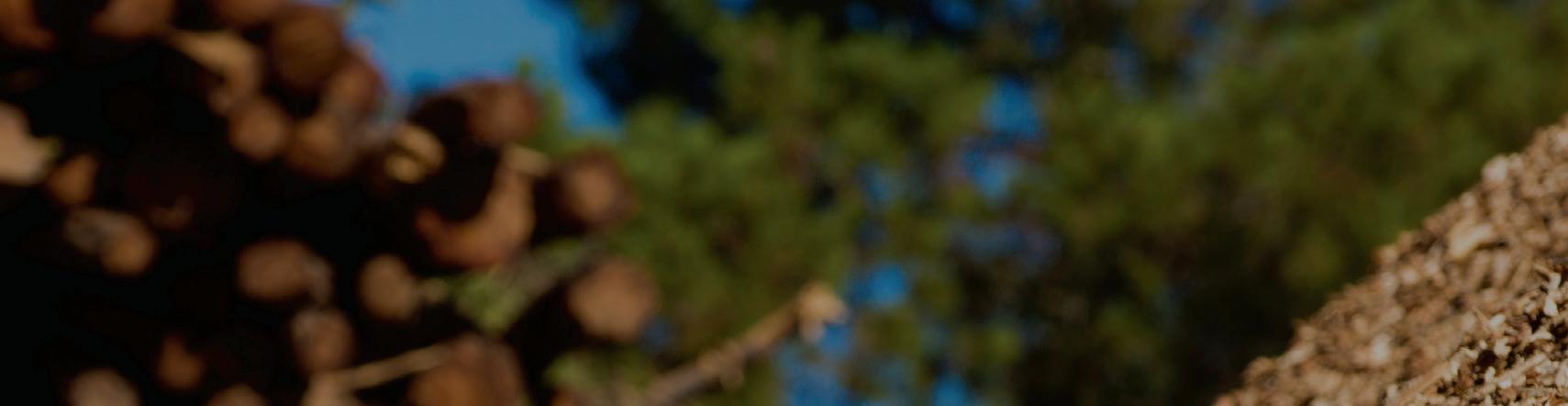


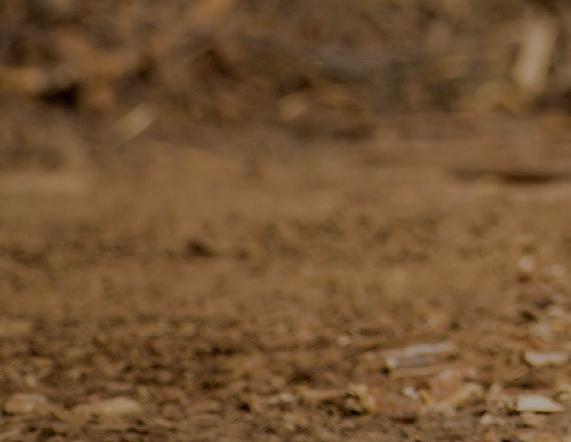

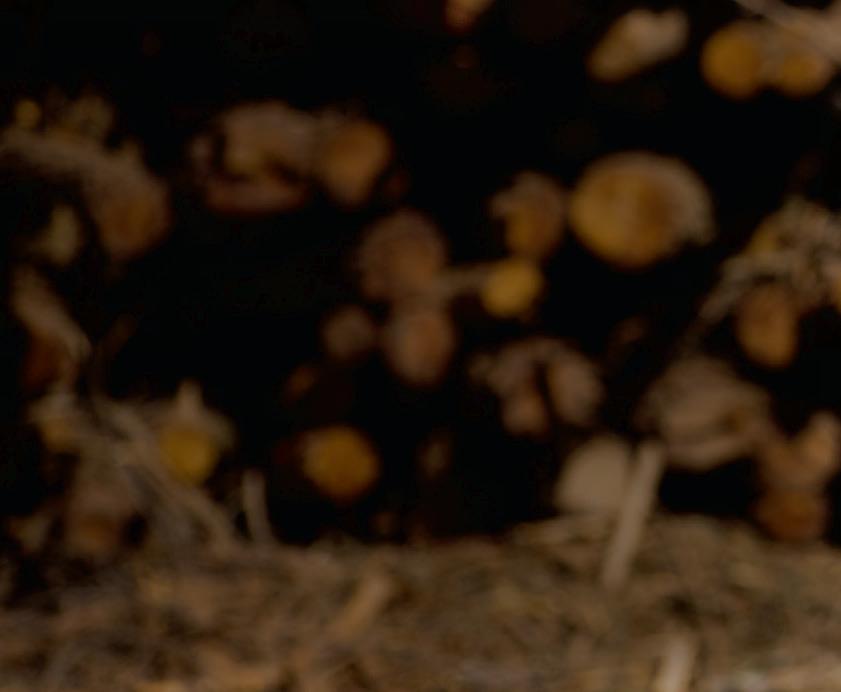
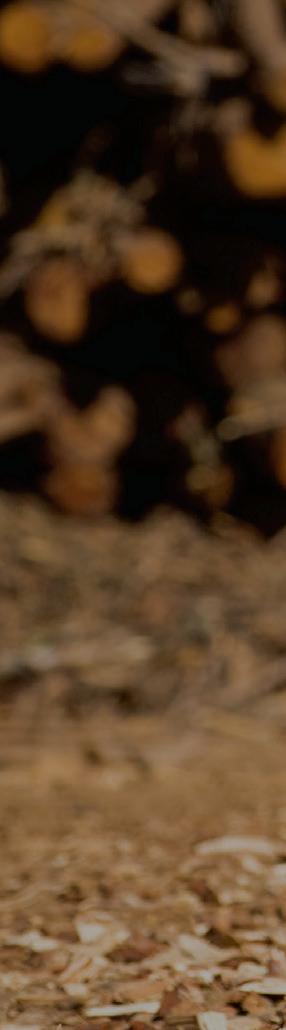
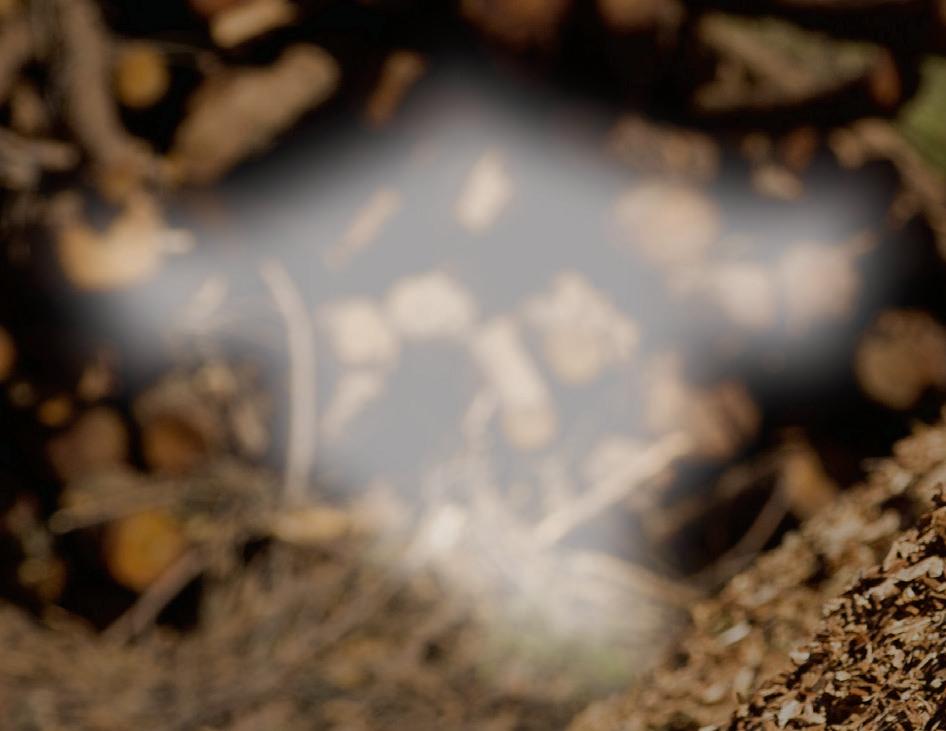
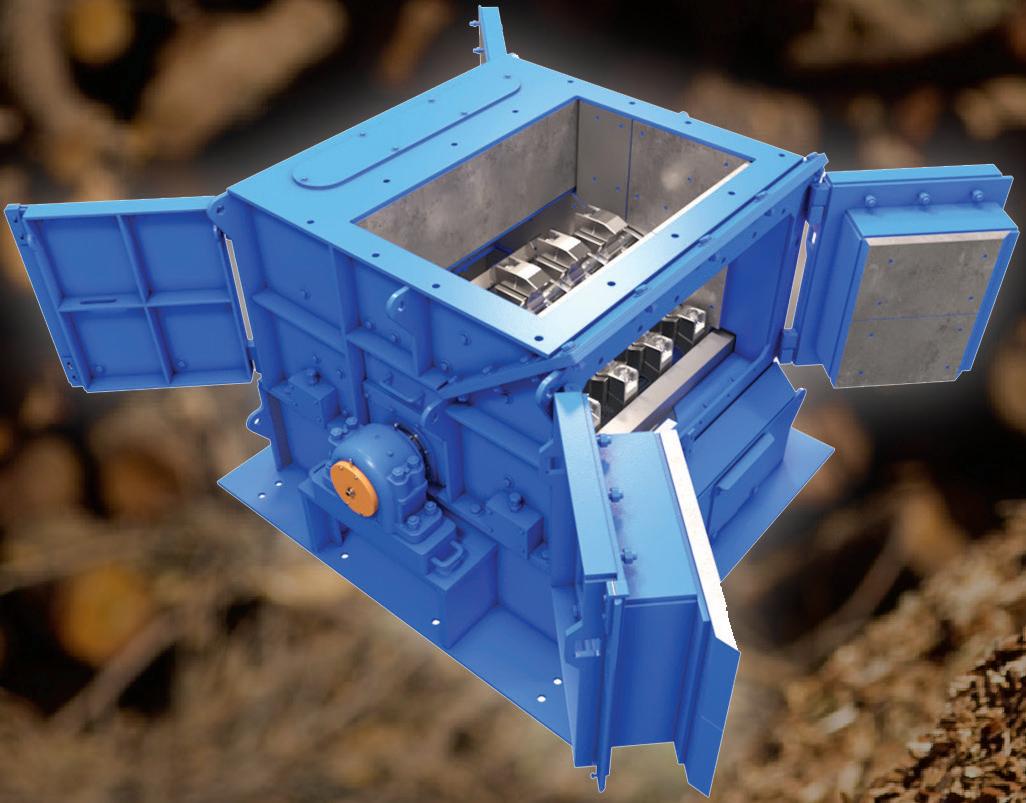
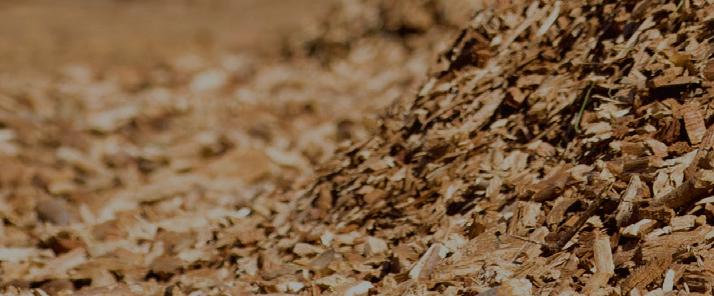

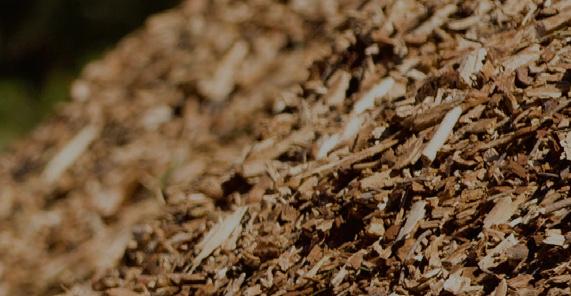
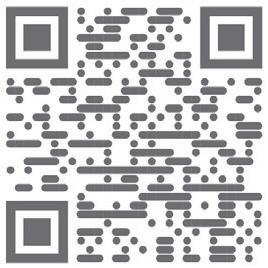
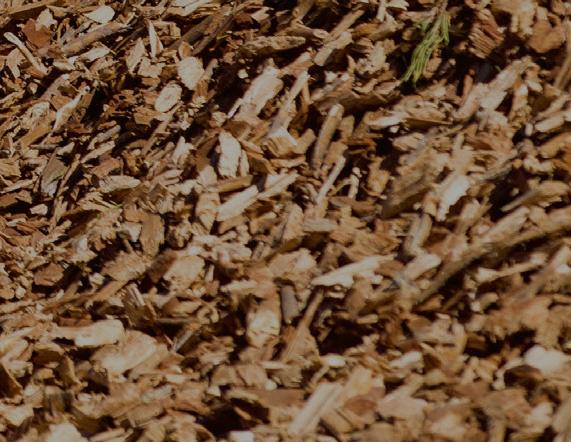
BEACON OF THE BIOMASS WORLD
The International Biomass Conference & Expo was held in Richmond, Virginia, in early March.
BY KATIE SCHROEDER Images by Digital Images HouseIndustry leaders at the 17th Annual International Biomass Conference and Expo shared highlights from the past year for their respective sectors, discussed policy victories and priorities and cautioned of the potential hurdles ahead. The event was held in Richmond, Virginia, March 4-6. Nearly 950 attendees and 172 exhibitors were registered, hailing from 45 nations, 44 U.S. states and nine Canadian provinces. Attendees included 250 producers alongside policymakers, academics, technology providers, utility providers, equipment manufacturers and project developers. John Nelson, vice president of BBI International, opened the conference’s general session by sharing these statistics with the audience and called the conference “a beacon of progress, innovation and collaboration,” citing the diverse programming of the conference and the addition of Pitch
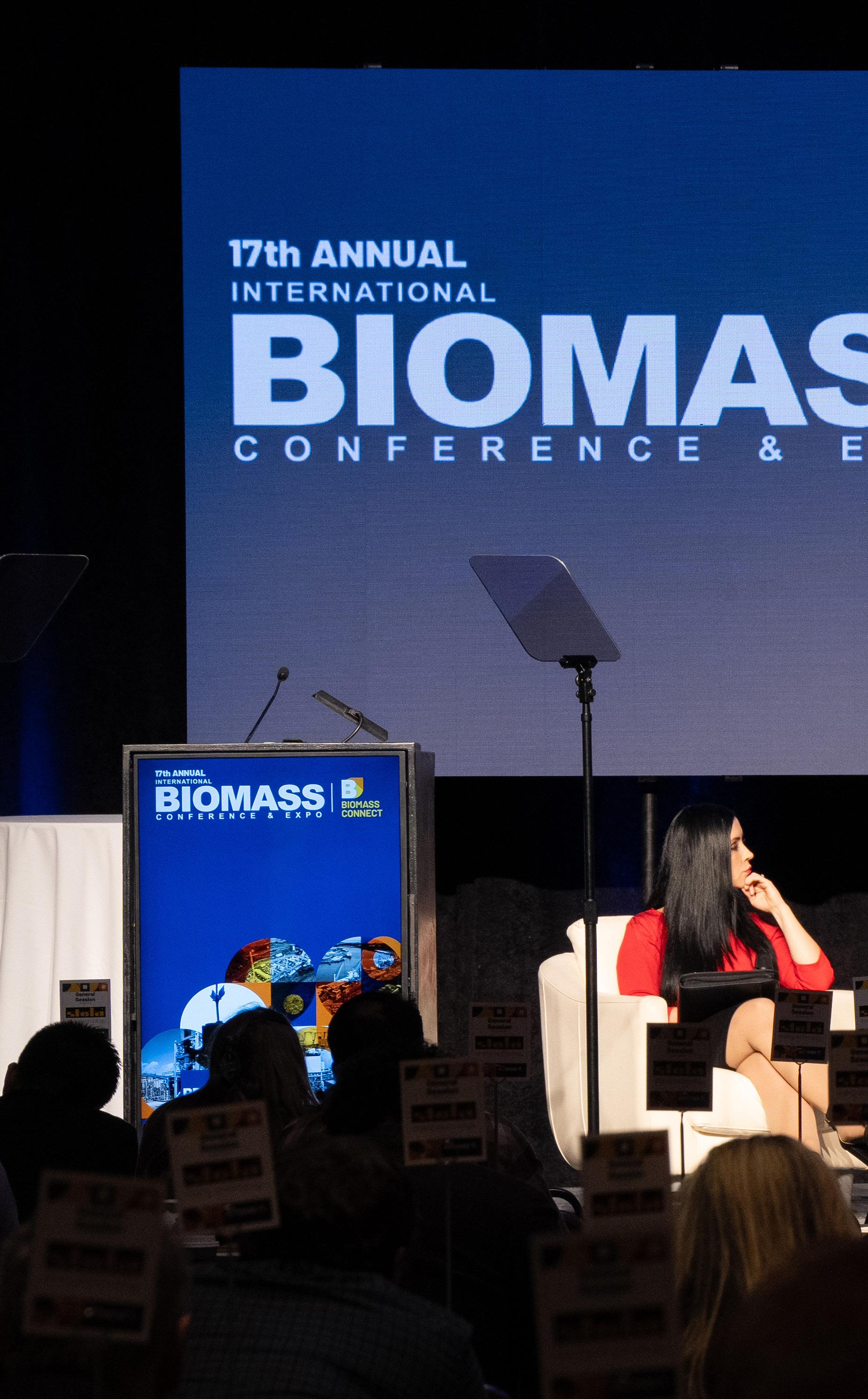
Day, an opportunity for startups to share their visions with investors.
Anna Simet, editor of Biomass Magazine, presented the two awards in recognition of achievements in the biomass industry. Jason Kessler, president and owner of KESCO Inc., received the Excellence in Bioenergy award. “To be recognized by my peers for helping this industry grow is extremely humbling,” he said during his acceptance speech.
North America’s largest sustainable aviation fuel (SAF) producer, Montana Renewables, was recognized with the Groundbreaker of the Year award. Greg Staiti accepted the award on behalf of the biorefinery, speaking about the company’s journey of transforming the plant from a traditional petroleum refinery to a producer of SAF and biodiesel. A subsidiary of Calumet Specialty Products LP, Montana Renewables is an expres-
sion of Calumet’s efforts to transition part of the company’s Great Falls refinery away from petroleum and toward production of renewable fuels. “We [have] a hundred-yearold facility [and this cycle] of investments has positioned it to thrive for the next hundred years,” Staiti said.
Following the awards, representatives from the diverse sectors that make up the biomass industry delivered individual presentations prior to a group Q&A with the audience. The speakers covered topics including the importance of educating voters on biomass use, tax credit advantages and hurdles, and industry growth.
Domestic and Industrial Pellets
Tim Portz, executive director of the Pellet Fuels Institute, provided a snapshot of the domestic U.S. pellet market. A total
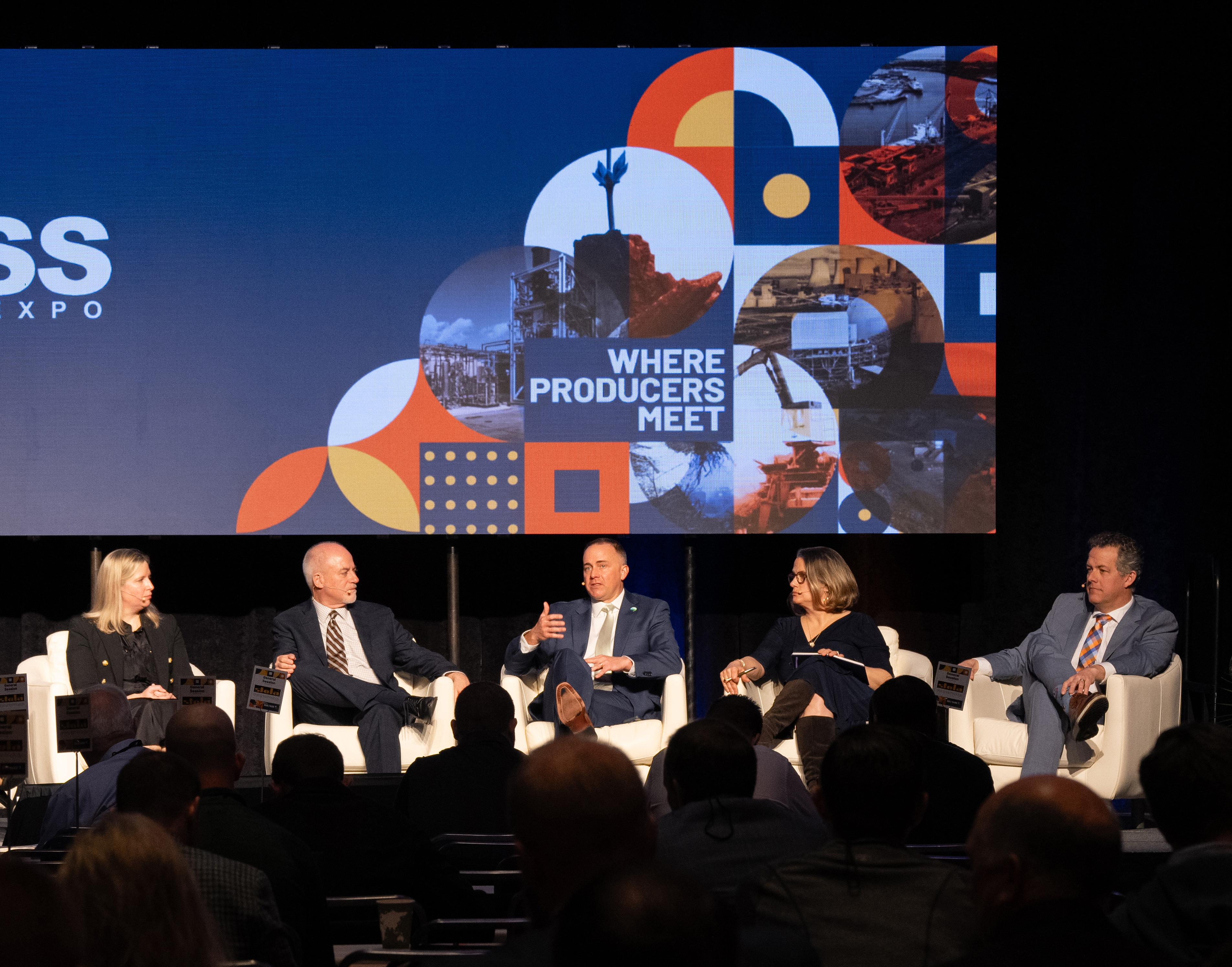
of 1.79 million tons of pellets were sold in the domestic market in 2023, slightly less than in 2022. Portz explained that this reduced volume—significantly lower than the most recent peak in 2017—is due to the unusually warm winter throughout the U.S. “All across the upper Midwest, including the whole Great Lakes region, up into New York State, it has been the warmest winter ever,” he says. “That doesn’t bode well for wood pellet sales, which is why we saw a relatively soft year.”
Portz emphasized the importance of pellet producers sharing their industry’s value and message with policymakers and expanding their support amongst forestry product interests and environmental organizations. Wood residuals are the “lifeblood” of the wood pellet industry, and their use is key to the industry’s value proposition, he ex-
plained. Wood pellet producers paid sawmills and wood processing facilities $270 million to purchase 7.7 million tons of wood residuals in 2023. “We pay for those materials, because we recognize their inherent value as a Btu,” he said. “We manufacture and engineer heating fuel from those wood residues; we recognize the value in it. We pass some of that value upstream to our partners in sawmills and wood-processing sites.”
Portz also outlined risks the wood pellet industry faces, including shifts in the clean energy landscape. He explained that since 2008 and 2009, words like “renewable” and “combustion” have been replaced with “low carbon” or “zero carbon,” and the priority has shifted to pursuing electrification first. Policymakers are prioritizing a net-zero narrative and want different things than they did several years ago, and pellet producers need
to be mindful of this when they present and defend their value proposition to policymakers. “This comes into some of our big objectives in Washington, D.C., making sure that the federal government recognizes that biomass is carbon-neutral,” he said. “We’re taking materials that are biogenic in nature— the carbon’s already there—and we’re just recycling it and capturing the Btus from it; it’s a virtuous zero-carbon [process].”
Accusations of deforestation and causing land use change are lodged at the pellet industry frequently, Portz explained, and the industry needs to be wary of statements from government bodies such as the White House and the United Nations as well as environmental groups that recommend avoiding the usage of biomass in favor of electrifying everything, even if it means doing it before the grid is green.
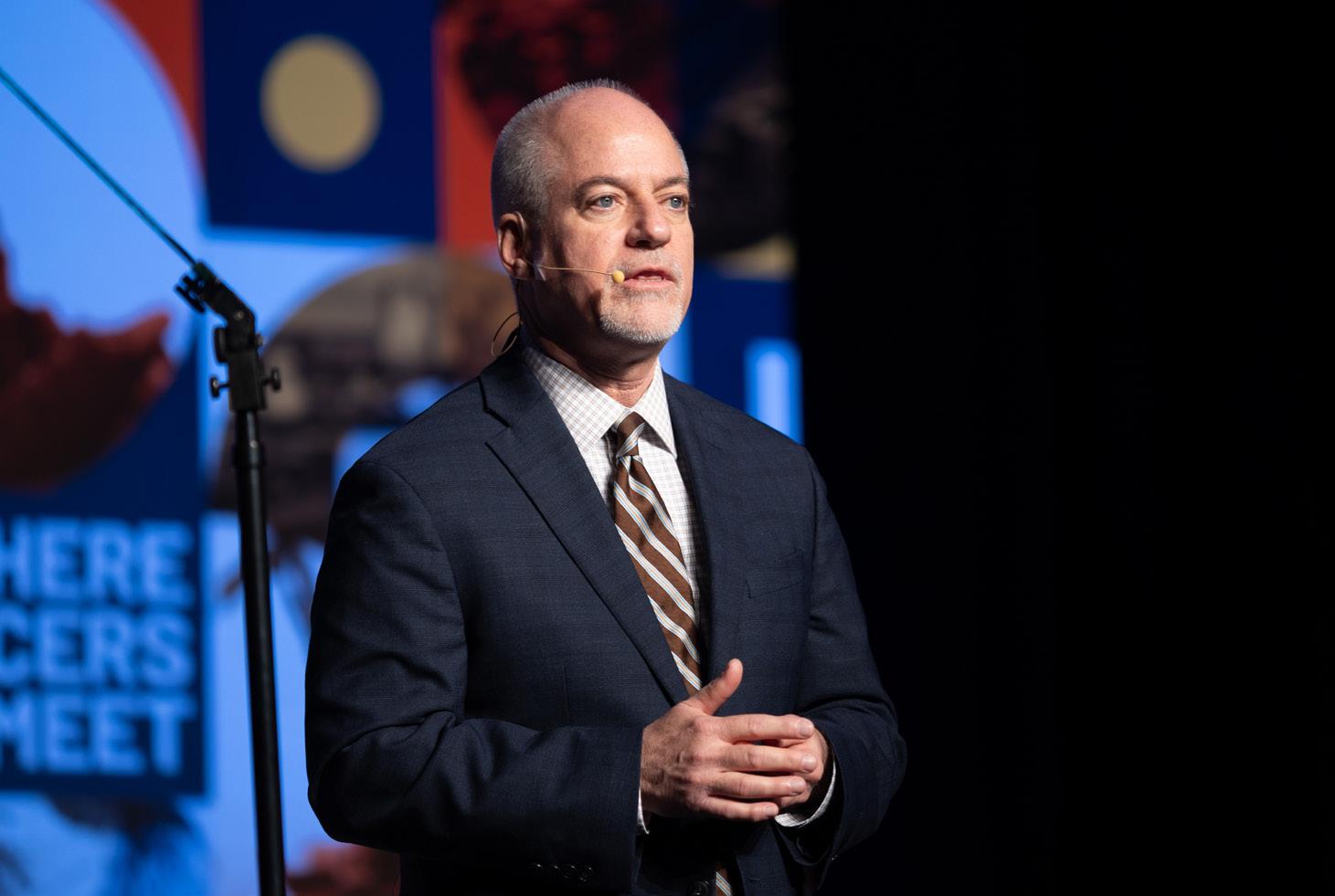

From the industrial wood pellet perspective, the challenges the industry faces are similar. Elizabeth Woodworth, interim executive director at the U.S. Industrial Pellet Association, stressed the importance of U.S. forests as the source of its “No. 1 and only raw material” and emphasized the value that forest education and the pellet industry’s role in caring for them brings to combating misinformation. In the U.S., 800 million acres of forest are responsible for absorbing 14% of the country’s annual greenhouse gas emissions. The majority of U.S. forests—57%— are privately owned, and most of that private ownership consists of property owners with a hundred acres or less. The pellet industry
works alongside logging companies, sawmills, pulp processing and other forest product industries to use the entire tree. “A lot of the misinformation you often see is when people take pictures of log carts going into a pellet mill and saying, ‘You’re cutting down whole forests, and [that’s] deforestation, and why are you using whole trees to burn in boilers?’ I just want to pick that apart because there’s nothing further from the truth, honestly, in terms of what the wood pellet industry is using as raw material,” Woodworth says.
When a tree is cut down, different parts of it go to different industries, she explains. Pellet mills help utilize waste and ensure that
the entire tree is used, everything from treetops, limbs, thinnings, wood chips and sawmill residuals. The industry has a particular synergy with sawmills, consistently sourcing some of their feedstock to make wood pellets. The percentage of residuals used in the industry varies depending on the demand for lumber in a given year.
Although the carbon used in wood pellets is renewable, detractors of the industry struggle to understand that cutting down a tree does not necessarily have a negative impact on the environment when done responsibly. Woodworth said that she sees “defossilization” as a better term to use when championing the pellet industry. She
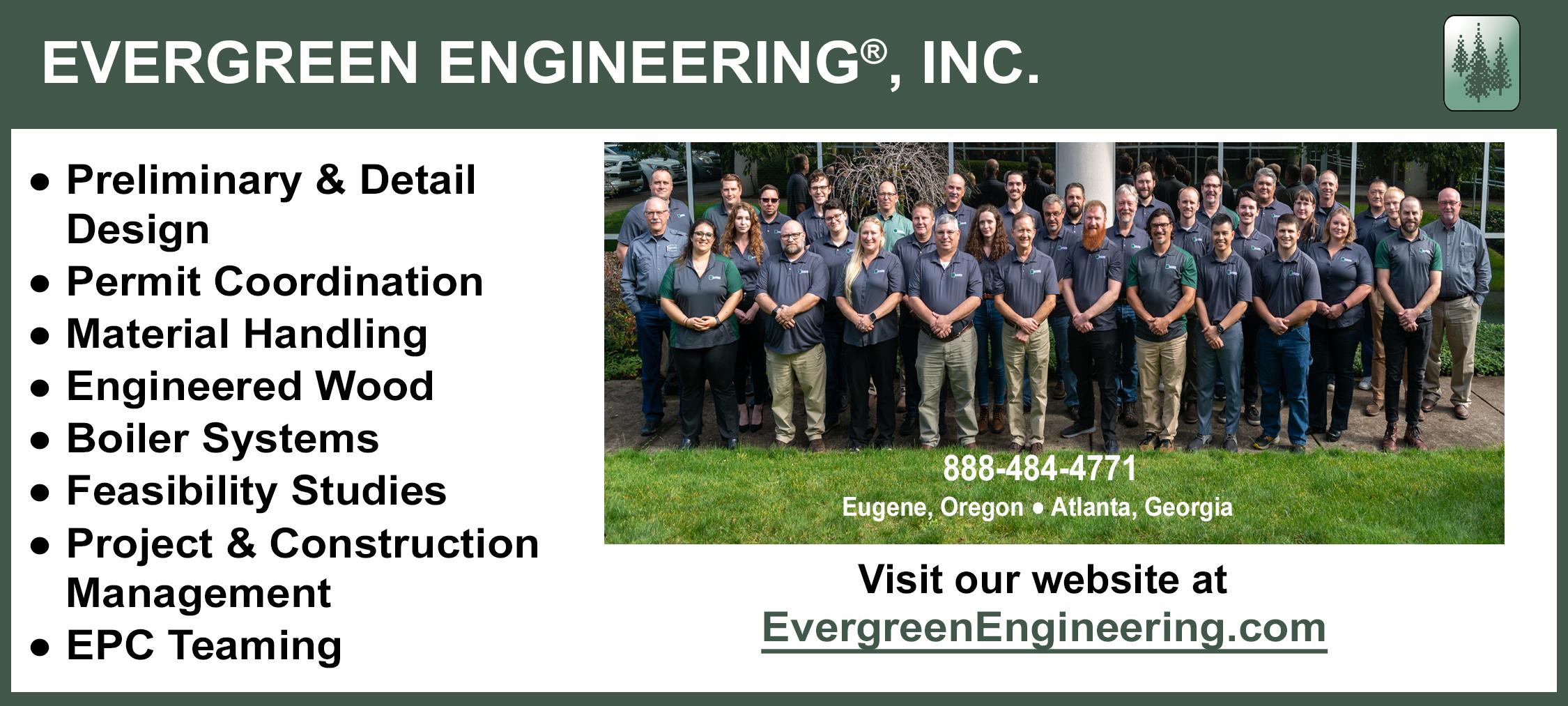
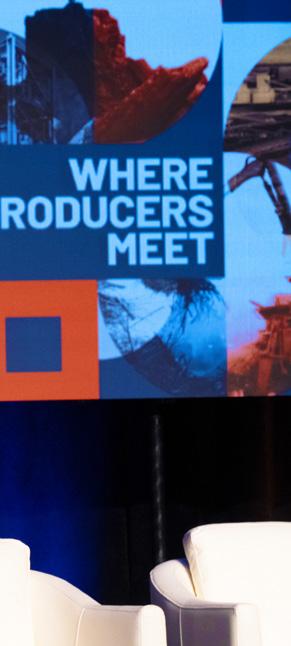
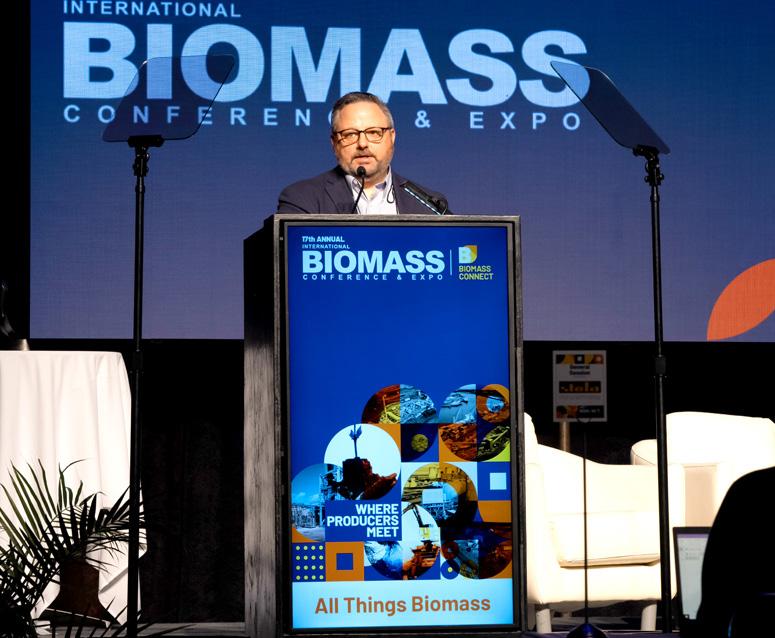
explained pellets are made up of carbon, but they are a renewable and biogenic carbon that can help reduce reliance on fossil-based fuels like coal and petroleum.
Biogas/RNG, Biomass-Based Diesel
The biogas sector has seen significant progress in the past few years, explained Patrick Serfass, executive director of the
erating systems at a total of 1,901, but the fastest-growing sector is the RNG sector, currently at a total of 350. “The RNG projects have been growing much, much faster than the electricity projects to the point now where the number of projects coming online as RNG projects are an order of magnitude greater than those coming online as electricity projects,” he said.
Serfass said, “[Fuels] like ethanol, hydrogen, even gasoline and SAF, and others are using biogas now to decarbonize their fuels.”
RNG was not alone in its significant build-out and growth across the United States. The biomass-based diesel industry is having “a moment,” explained Paul Winters, director of public affairs and federal communications with Clean Fuels Alliance America. The volume of renewable diesel, biodiesel and SAF produced in the U.S. grew by a billion gallons in 2023. This growth was called impossible by the U.S. EPA, along with other naysayers from the world of economics. “There was a number of economists with international banking groups, the University of Illinois in particular, who are continuing to tell us that we’re going to go bankrupt because we’re feeding more biomass-based diesel into the market than it can handle, according to their economic models,” Winters said. “Nonetheless, we’re still having our moment, and we anticipate that production will increase by another bil
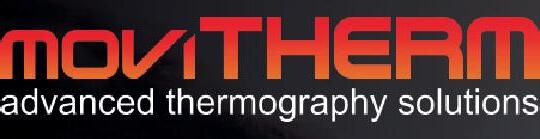

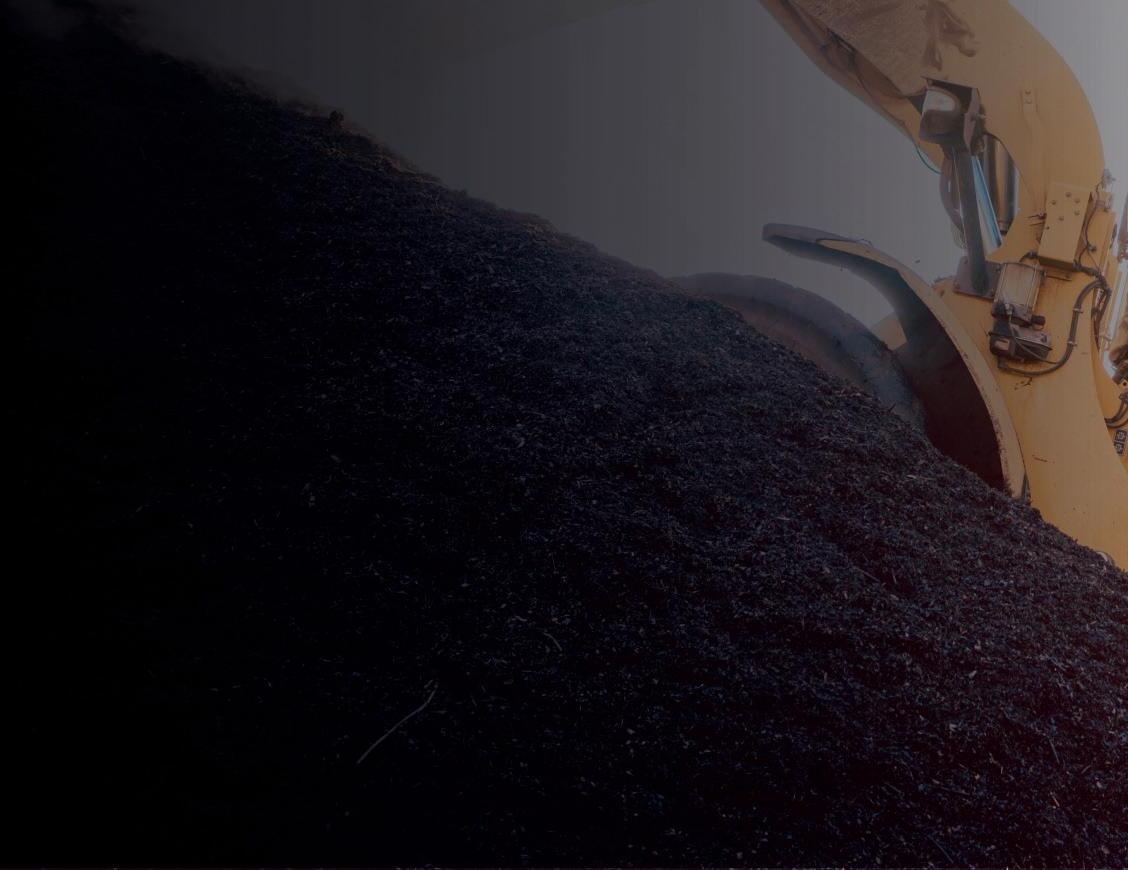
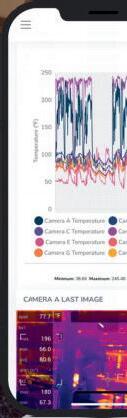


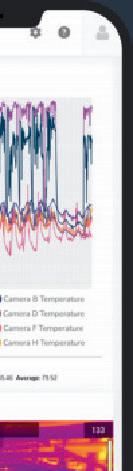
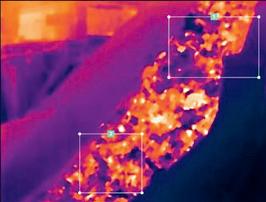
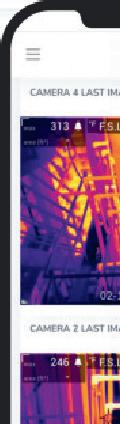
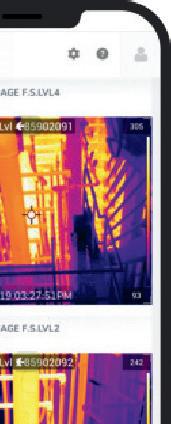
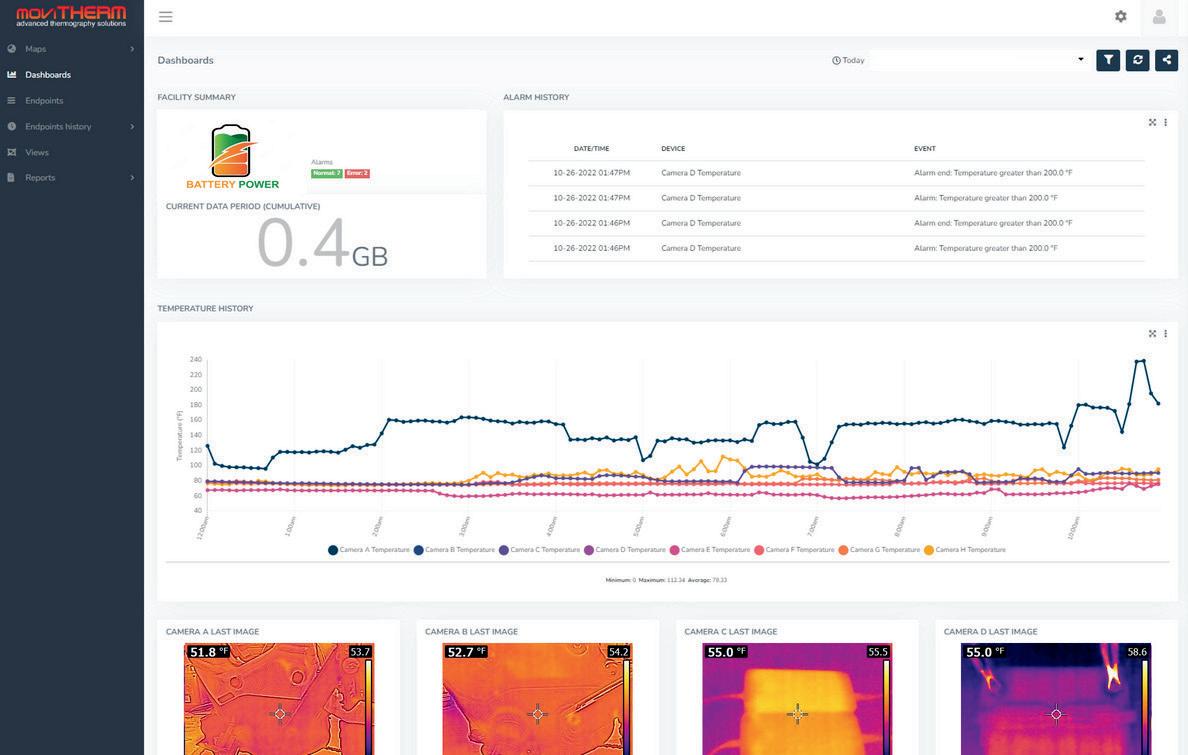
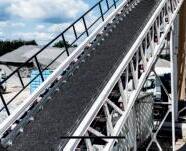
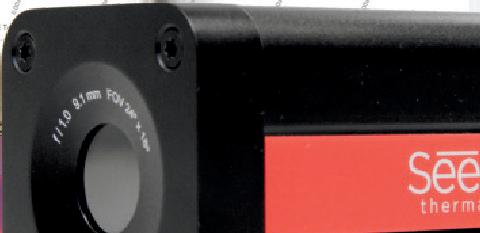
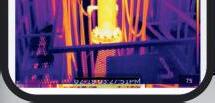



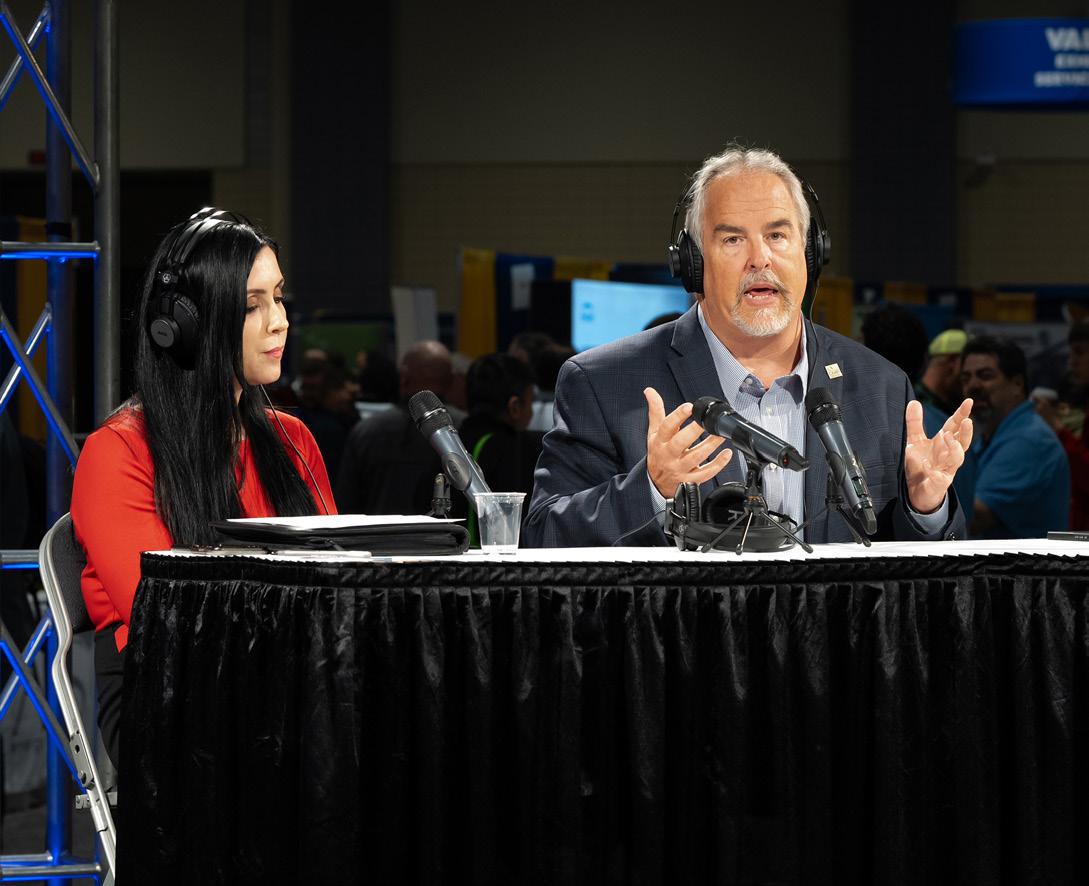
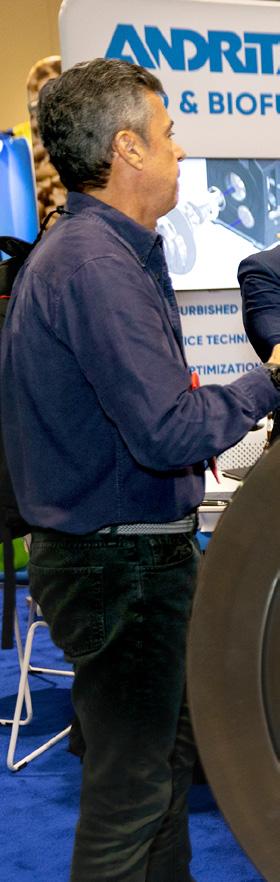
lina and increased supply chain efficiency allow growth to continue.
The primary feedstocks for renewable diesel and biodiesel are include agricultural oilseed crops such as soybeans, camelina, canola and others. Farmers are responding to the demand, with the soybean industry investing $6 billion into soybean processing.
The industry’s secondary feedstock source is used cooking oil and other waste greases. Recycled greases are a growing feedstock, which was unexpected, Winters explained. The market’s use of greases does not directly respond to demand; however, the collection of these greases for recycling and the global supply chains for them do respond. “On the
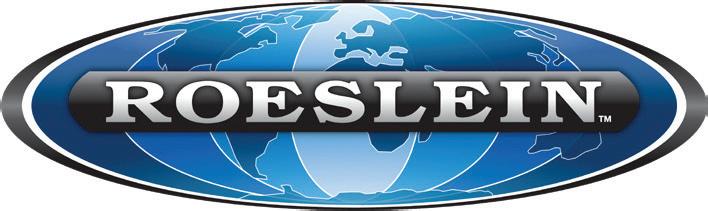
policy front, we’ve kind of faced mixed results—the EPA didn’t just tell us that growth was impossible; they actually wrote that into the Renewable Fuels Standard. I think the actual regulatory language was just ‘pfft,’” he said. “The low volumes they set really pushed RIN prices off a cliff, and that’s impacting a number of small producers.”



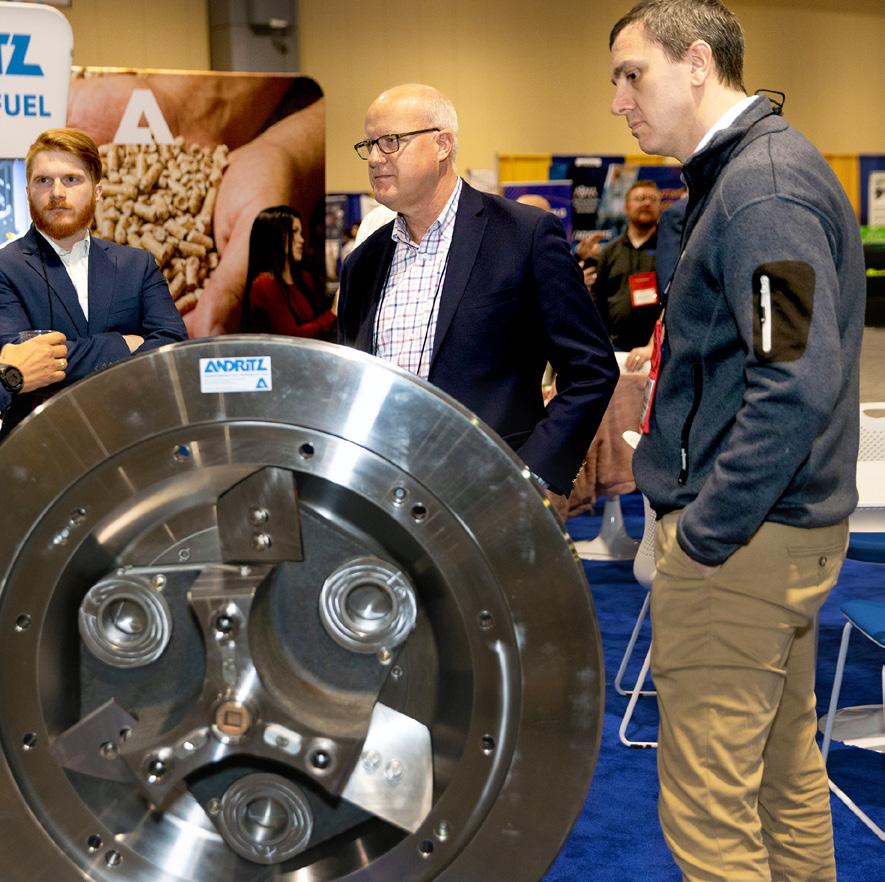
From Biomass Power to Energy
Carrie Annand, executive director of the American Biomass Energy Association, announced the organization’s change from the Biomass Power Association. Annand discussed the process that ABEA went through in changing its name and the organization’s focus group findings about voters’ educa-
tion—and the lack thereof—on bioenergy. The ABEA engaged a PR firm to assemble focus groups of standard voters and climate-concerned voters, she explained. The firm’s findings were that most voters did not know what biomass power was or had very little knowledge about it, which presents an excellent opportunity for education. She explained that when biomass is introduced with “the five Rs”—recover, recycle, repurpose, renewable and reliable—voters had a positive response.
One of the focuses of ABEA’s policy agenda is advocating for eRINs, or electric renewable identification numbers, Annand explained. “One thing EPA’s proposal did was [to stipulate] that car companies will be the ones—call them OEMs, original equipment manufacturers—those entities will be the generators of the RINs, which was maybe a little frustrating to hear that it wouldn’t be the renewable fuel producers like how the program works for the ethanol industry,” she said.
Additional topics discussed during the general session included a focus on education and thoughtful communication with the general public, the importance of firmly combating misinformation with facts, the exciting expansion of the RNG and biomass-based diesel industries, and the impact of advocating for the biomass industry’s many sectors with policymakers.
The conference continued with innovation stage presentations and live podcasts on the trade show floor as well as two days of breakout panels with categories including biomass power and thermal, pellets and densified biomass, biogas and RNG, and advanced biofuels and chemicals.
The 18th annual International Biomass Conference & Expo will be held in Atlanta, March 18-20.
Author: Katie Schroeder Katie.schroeder@bbiinternational.com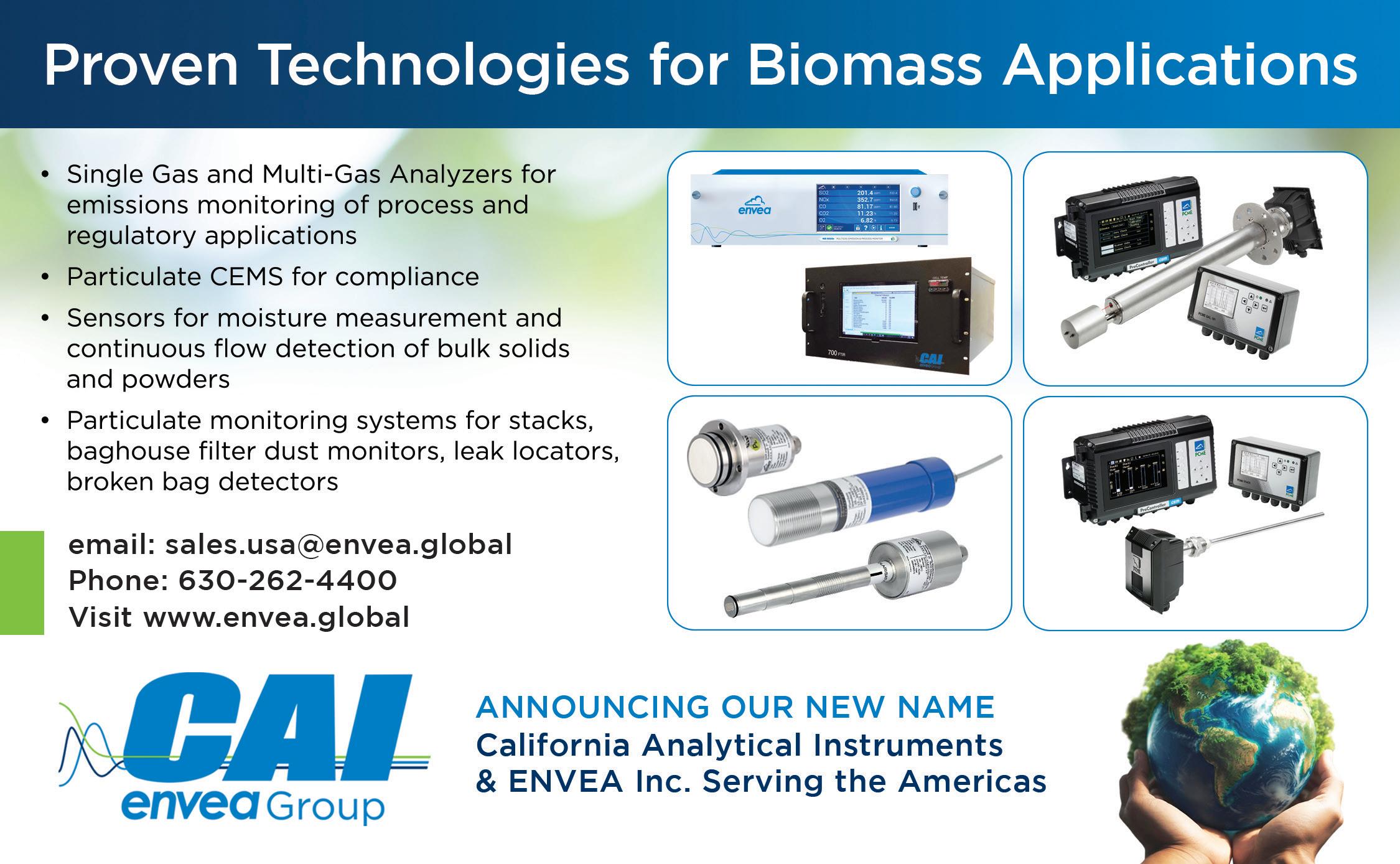
DECARBONIZING WOOD PELLET PRODUCTION VIA MOVING BED HEAT
EXCHANGE TECHNOLOGY
Meeting net-zero objectives will require operators to increasingly leverage modern technologies and adopt innovative processes.
BY JILL CASKEYIn efforts to effectively tackle the climate crisis and reach net-zero emissions by 2050, operators across multiple industries have adopted highly deliberate strategies to decarbonize their processes.
Yet, as many have discovered, these endeavors have frequently encountered formidable barriers such as high capital costs, regulatory approvals and long implementation timelines. In the meantime, operators need access to low-cost, high-ROI, carbon-reducing solutions now.
The wood pellet industry is no exception. Raw material sourcing, transportation and waste management all heavily contribute to a carbon footprint that is no longer sustainable. The industry’s conventional approach to wood pellet production has also been very energy-intensive and required extensive equipment to clean emissions before being released into the atmosphere.
While many efforts are already underway within the wood pellet industry to increase efficiencies at the manufacturing stage, meeting net-zero objectives will require operators to increasingly leverage modern technologies and adopt innovative processes.
Wood Pellet Process Traditional Technology
Before delving into decarbonization solutions, it is important to understand the wood pellet manufacturing process and technologies that are currently in use. Wood pellets are created by first removing moisture from incoming wood fiber. That fiber is then
ground into dust and compressed into small pellets measuring between 6 and 8 millimeters in diameter and up to 40 millimeters in length.
During the process, the pellets are heated up so the lignin in the wood acts as an adhesive to keep the compressed particles together. Once discharged, the pellets range in temperature from 70 degrees Celsius (158 degrees Fahrenheit) to 100 C, making them too hot for storage and transport. The preferred option is to cool the pellets to approximately 3 C to 5 C above ambient temperatures.
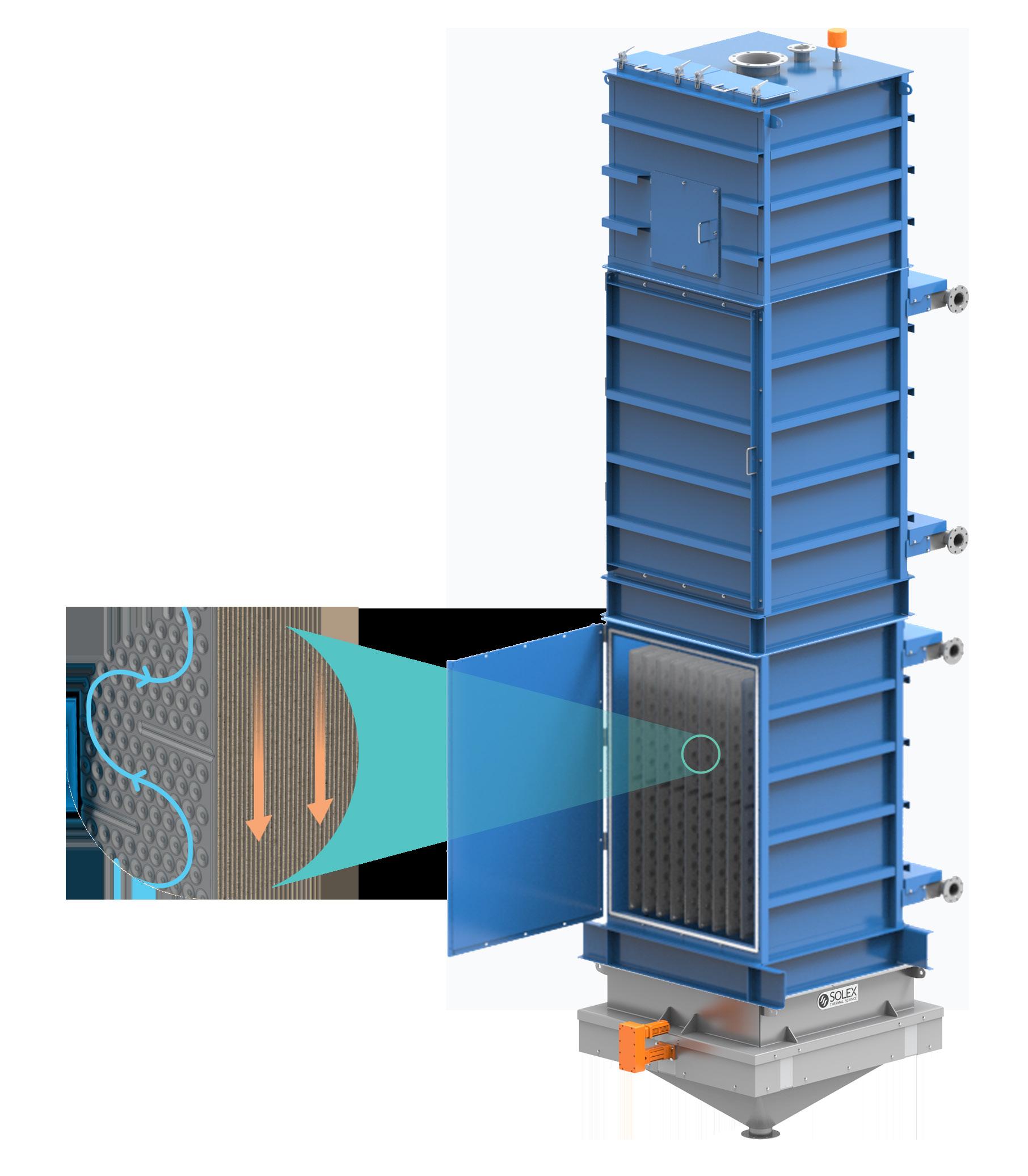
Moving Bed Heat Exchangers
Conventional counterflow air pellet coolers use chilled or ambient air to cool the pellets. The pellets enter a cooling bin, typically through a rotary valve, and are leveled off by a distributor. Cold air is then injected into an isolated bin under the bed of pellets, thereby indirectly cooling the product from the bottom up. A level sensor inside the bin determines when the pellets are discharged.
This traditional cooling method has the disadvantage of requiring large energy inputs (e.g., high horsepower fans) to get the job done—a challenge for pellet producers who are already facing high energy costs.
Alternatives such as plate-based moving bed heat exchangers (MBHE) at the cooling step of production offer pellet producers the opportunity to improve the energy efficiency of their existing processes, with the added benefit of significantly improved heat transfer efficiency.
Plate-based MBHEs blend the thermal efficiency of plate heat exchange design with the science of uniform mass flow to cool pelletized bulk solids such as wood pellets. In an MBHE, the solids flow by gravity between a series of vertically oriented, hollow stainless-steel plates—typically made of SS304L for the wood pellet industry. The plates are cooled by a working fluid that flows through the plates’ internal channels countercurrent to the product flow.
The cooling medium is often a cooling water source or chiller water. In some cases, brine, river water or seawater can be used by incorpo-
rating a closed-loop fluid temperature control module. The system can also operate as a stand-alone system via a dedicated closedloop circuit using a dry cooler and chiller.
The MBHE has a discharge device at the bottom that controls the flow of product, usually by a variable frequency drive or pneumatic actuator, before it exits to the downstream conveyance system.
Typical Wood Pellet Cooling System
After the pelletizing process, the wood pellets enter the inlet hopper of the MBHE at temperatures typically around 70 C to 100 C. The bed of product, ranging from 1 to 200 metric tons per hour, then flows at a controlled speed through the heat exchanger bank(s)—usually 0.3 meters per minute— while cooling water at 20 C to 30 C flows countercurrently within the plates’ internal channels. The number of heat exchanger banks required depends on the duty of the process conditions and necessary surface area to meet the cooling temperature target.
The flow of pellets is controlled by a sliding ladder feeder equipped with a pneumatic actuator positioner that ensures uniform mass flow and even product temperatures at the outlet. A level probe or transmitter in the inlet hopper maintains the proper level as it controls the instrumentation on the feeder.
The MBHE is static, with the only moving part being the feeder at the outlet. It is isolated from the rest of the installation to avoid any transmission of vibrations.
If the MBHE is installed in a hot, humid location, a small amount (less than 1,500 standard cubic feet per minute) of dehumidified purge air may be injected between the heat exchanger banks to prevent condensation from forming inside the column.
MBHEs can easily be retrofitted into existing processing facilities, as they have a small installation footprint (less than seven feet by seven feet) and can be used in conjunction with current equipment. As the heat exchanger banks are modular, additional banks can be added in the future when a plant considers increasing capacity.
How MBHEs Help Decarbonize
Reduce primary energy consumption: Water is a more effective cooling medium than air, absorbing up to 24 times as much heat, resulting in lower power requirements to circulate the much lower volume of
cooling medium. While air coolers typically consume around 4 to 5 kilowatt hours per metric ton (kWh/mt) of pellets, an MBHE consumes, on average, just 0.4 kWh/mt of pellets.
Eliminates emissions: Because air is not being used as the heat transfer media, emissions are reduced to near zero. An MBHE will emit approximately 0.42 kilograms per 1 kWh, which is approximately eight times less than traditional cooling technologies.
Waste heat recovery: With advances in heat pump technology, it is now feasible to recover the heat extracted from wood pellet cooling rather than discharging it to the environment. The heat pump system extracts the thermal energy from the cooling water to a refrigerant via a plate-and-frame heat exchanger. Then, a small pump will move the refrigerant through a refrigerant cycle, resulting in an amplification of the heat. Typically, the heat amplification is three to four times the power input of the pump.
This heat is then extracted from the refrigerant—for example, to air using a finnedtube, air-to-liquid heat exchanger. This heated air can be sent to the dryer burner to displace a material amount of fossil fuel energy needed to produce the hot drying air. Alternatively, the recovered heat can be transferred to water, and the heated water can be used in other processes such as steam production.
Conclusion
The path to greener wood pellet production requires a comprehensive approach that involves making sure each stage aligns with broader sustainability goals. The cooling stage has always been an essential part of ensuring a quality finished product. Yet the technology employed at this stage must now do more.
Plate-based MBHEs provide wood pellet producers with an energy-efficient, near-zero emissions solution. By combining plate heat exchange design with uniform mass flow to indirectly cool pellets, the technology avoids having to rely on energy-intensive ancillary equipment to get the job done while virtually eliminating emissions and opening the door to additional waste heat recovery options.
Author: Jill Caskey Global Sales Director, Solex Thermal Science Jill.caskey@solexthermal.com www.solexthermal.com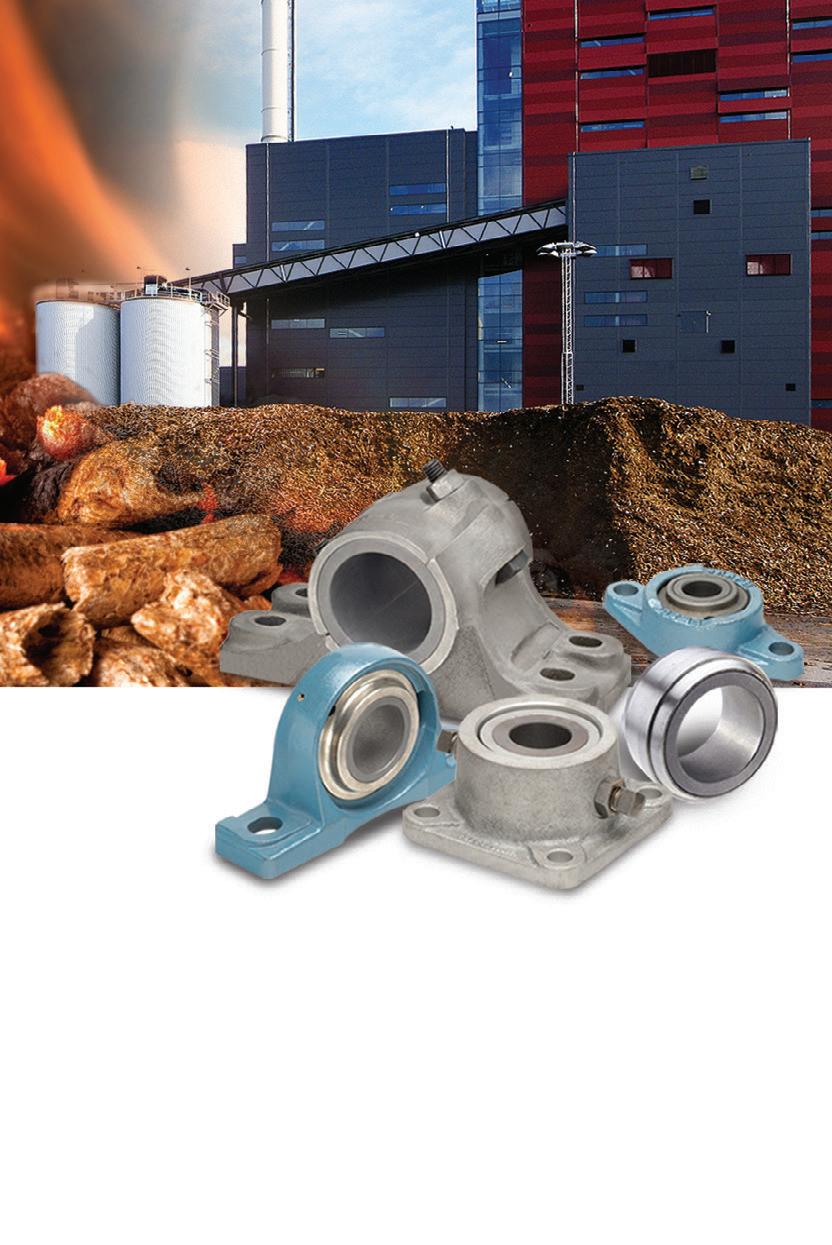
• Works Where Others Won’t
• Run hot, cold, wet or dry
• Corrosion resistant
• Self-lubricating
• Low maintenance
• -400˚F to 1000˚F (-240˚C to 535˚C)
• Ovens, furnaces,
conveyors,mixers, damper,
augers,agitators, pyrolysis chambers, traveling grates and drag chain conveyors
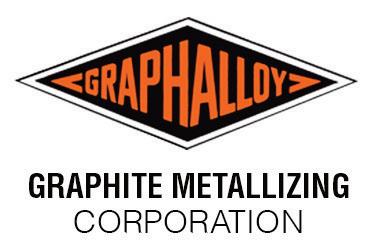
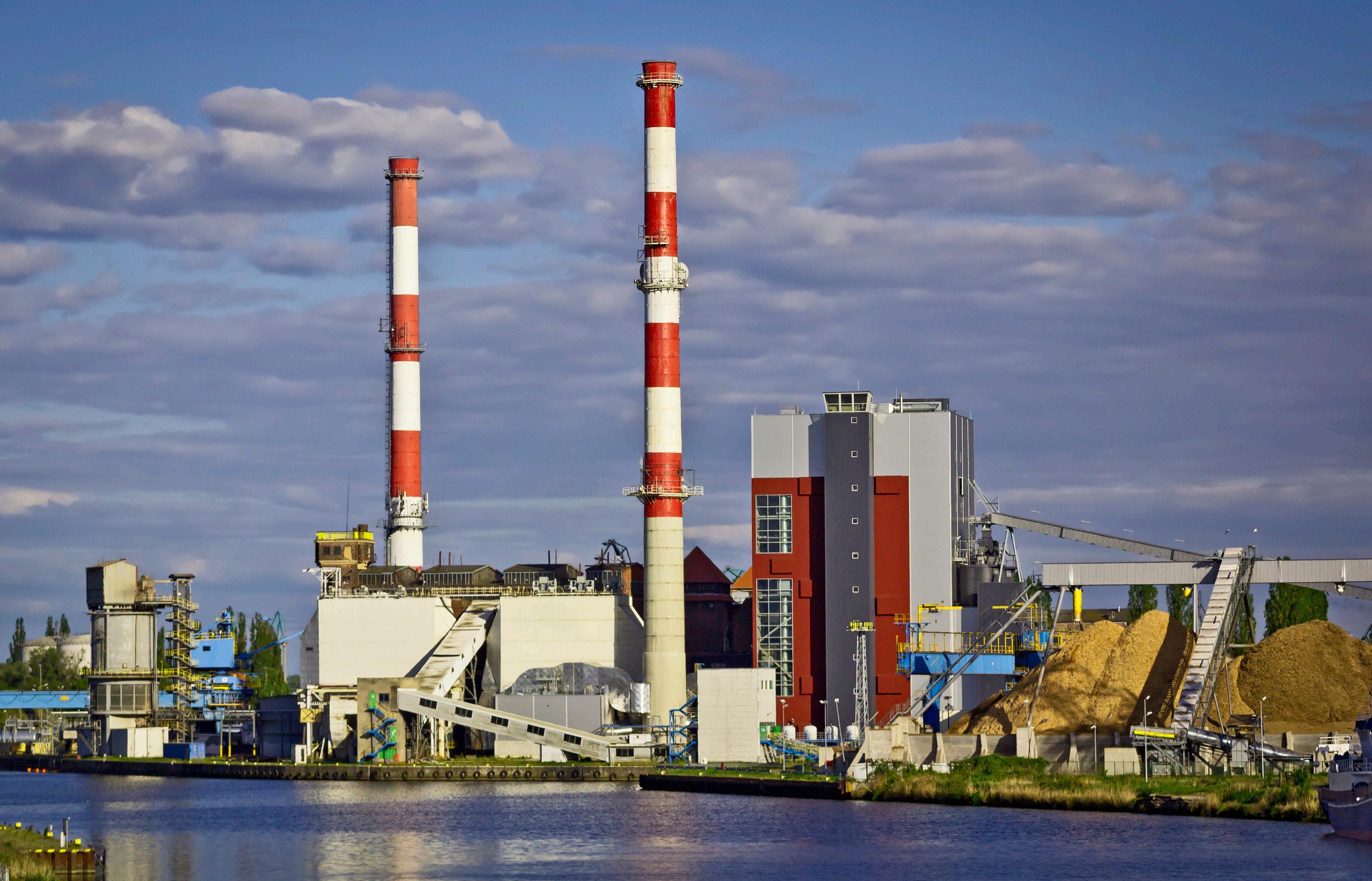
OPERATION AND MAINTENANCE OF CERAMIC FILTER SYSTEMS
With a well-executed operation and maintenance program, ceramic filter systems are robust, maintaining consistent uptime at low OpEx.
BY JOHN WILSONSuccessful operation and maintenance of ceramic filter systems requires a proactive approach. The original design parameters for ceramic filter systems should be correlated to experienced parameters in operation. This exercise will help outline opportunities for system improvements. Operating a ceramic filter system outside of its intended design parameters (e.g., higher static pressure than
intended to draw from a furnace) may result in costly operations and maintenance (O&M). The following sections describe key segments of a ceramic filter system and present suggestions for proper O&M.
Key Components for O&M Fans
Fans for ceramic filter systems operate in high temperatures and static pressures, expounding the requirement for well-executed design and O&M. Fans developed
advertisers. All questions pertaining to this article should be directed to the author(s).
for high temperatures and static pressures have a smaller band of adjustment, oftentimes requiring multiple fans to operate in parallel when high flows and pressures are present and in single-fan operations during lower production ranges. It is paramount to align the fan curves to system flow, temperature and static pressures. This ensures fans do not operate within the stall region of the curve, which is detrimental to fan health and will
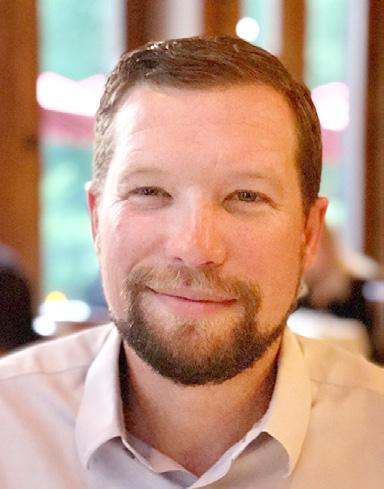
cause premature failure in fan components along with instruments and equipment connected within proximity to the fans.
Hot fans require astute attention to preventative maintenance procedures, including fan bearing and motor greasing, impeller and shaft inspections for debris buildup and corrosion, and periodic vibration analysis. It is suggested to utilize ultrasonic monitors to perform fan bearing greasing. Ultrasonic monitors provide an easily trainable, highly successful way to ensure the correct amount of grease is applied at the correct rates while observing the response of the bearings. It is recommended to be mindful of automatic greasing solutions on the hot fans, as when not designed or operated correctly, they can cause premature and unpredictable failure of fan bearings and components. Grease utilized in the fan bearings should also be reviewed for effectiveness in the application, and grease lubrication amounts and schedules should be developed with respect to the specific lubricant selected. High-temperature synthetic greases can be helpful in elongating the fan bearings’ lifespan, but very detrimental if utilized incorrectly.
Ceramic Filters
High-temperature, multipollutant control is placed into a neat and easy-to-maintain package in ceramic filters. When operated and maintained correctly, ceramic filters have proven themselves to be a robust solution requiring minimal maintenance, and they’re able to maintain deNOx catalyst life and differential pressure performance over many years.
Ceramic filters capture particulate in the nano range, often capturing a variety of particulate that was unexpected and missed in the clients’ specifications. It is recommended to perform waste analysis during the infancy of a system’s operations. This allows for periodic comparisons throughout the life of the system and is an effective tool for root cause analysis when changes occur.
Proper design and O&M of reverse-pulse cleaning of ceramic filters are crucial. Pulse cleaning should not be specifically triggered by system differential pressure,
but the sequence should pay regard to the development of particulate buildup on the filters (i.e., filter cake). Pulsing too often, not allowing an effective filter cake to develop, can lead to higher system differential pressures overall. The effectiveness of reverse-pulse systems can change drastically in conjunction with changes in production rates. Higher production rates may result in a less powerful reverse-pulse system due to increased face velocity and pressure across the filters. It is advised not to adjust reverse-pulse cleaning parameters without fully understanding the interaction between reverse-pulse design, sorbent injection, process constituents, waste constituents and system flow and temperatures.
Periodic ceramic filter testing is recommended annually to plot life expectancy and develop a plan for when the filters should be replaced.
Sorbent Injection Systems
Operation temperatures of ceramic filter systems correlate directly to peak efficiency ranges of performance hydrated limes, facilitating high removal rates of acid gases. The performance of hydrated limes is highly reactive by design and tends to scale in the storage and transport systems if not well managed. These difficulties can be overcome with proper design and O&M practices. Reward can be found in the following ways:
• Operate with minimal velocities to maintain entrainment of the material without fallout. Variable-speed transport blowers and flow sensors shine in this aspect.
• Operate with low transport temperatures. High temperatures increase the reactivity of the material and promote scaling in the transport lines prior to injection. Consider heat exchangers after pressure blowers.
• Maintain low moisture content in the storage and transport air. All compressed air should be clean and dry. Convey air should be considered for dehumidification.
• A sensor for relative humidity in the convey air can help correlate operational experiences to better understand whether humidity control will be beneficial.
Preventative maintenance goes a long way in maintaining high uptime and reducing overall maintenance in a hydrated lime transport system. Sensors on the convey system for flow, pressure, temperature and humidity can be integrated with proactive warnings and alarms. Baseline transport pressures and flows of the system with clean transport lines should be recorded. If these pressures and flows are not met, it indicates that there is a clog or scaling of the transport line that needs to be resolved. Failure to resolve plugging as soon as detected will lead to more severe clogging. Severe clogging of hydrated lime transport systems is difficult and time-consuming to resolve.
Waste Handling Systems
Robust waste handling systems are integral to a ceramic filter system’s success. Process particulate and injected hydrated lime need to be removed from the ceramic filter houses smoothly and without bridging in the housings or clogging in the transport and collection systems. The waste material may still contain reactivity from performance hydrated lime that can cause clogging similar to the sorbent injection system. Airlocks must be designed properly to remove the ingress and egress of air to or from the filter housing to the waste transport system. Air moving to the housings will make it difficult to collect the waste material, potentially creating a condensation point within the housing. Air moving into the waste transport system will bring heat and moisture, which can condense and corrode or plug the system. It is good practice to implement a mass balance tracking system to understand the amount of waste leaving the system relative to sorbents being injected into the system. This mass balance can provide early warnings to trigger reviews before critical damage occurs in the system. Failure of waste transport systems is the leading cause of critical filter breakages.
Ammonia/Urea Injection
Proper atomization and mixing of the ammonia are important to ensure high deNOx performance. Leading causes of ob-

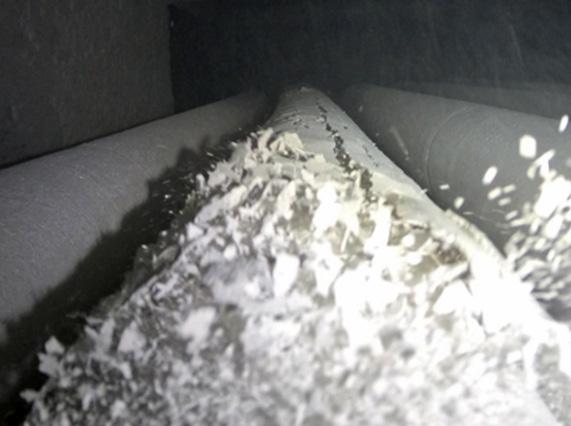
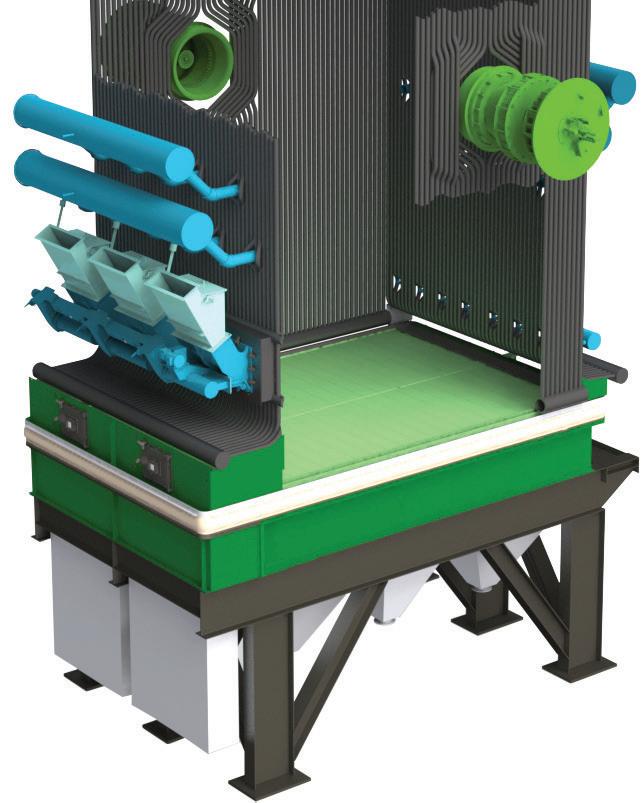
served ammonia slip or low deNOx performance include eroded injection nozzles, improper ammonia or compressed air pressures, improper mixing in the flue gas and degraded catalyst in the ceramic filters. Injection control loops can also be a concern for deNOx performance. Extractive NOx measurement equipment can delay the response for changes in NOx loading, delaying timely adjustments for ammonia injection. Integrating instruments that can provide instantaneous NOx measurements on the inlet or outlet of the system is a leading solution for proactively controlling and maintaining ammonia injection systems.
Control System
It is imperative to have a clear and concise graphical control system that utilizes sensors throughout the system for proactive alarms. The control system should include trending features to allow for reviews of the system’s health. Trends are also a leading tool for root cause analysis. With current technology, control systems should be continuously reviewed for improvement. Sensors provide information that can be used in proactive alarms and further expanded with powerful predictive analysis tools to improve the operation and upkeep of a system.
Conclusion
Ceramic filter systems are a proven method of multipollutant control in biomass and many other markets. With a well-executed operation and maintenance program, these systems are robust, maintaining consistent uptime at low OpEx. If you have a ceramic filter system that is not achieving your expectations, we can work together to resolve the problem.
Author: John Wilson Director of Field Operations, Precision Partners john.wilson@ppidg.com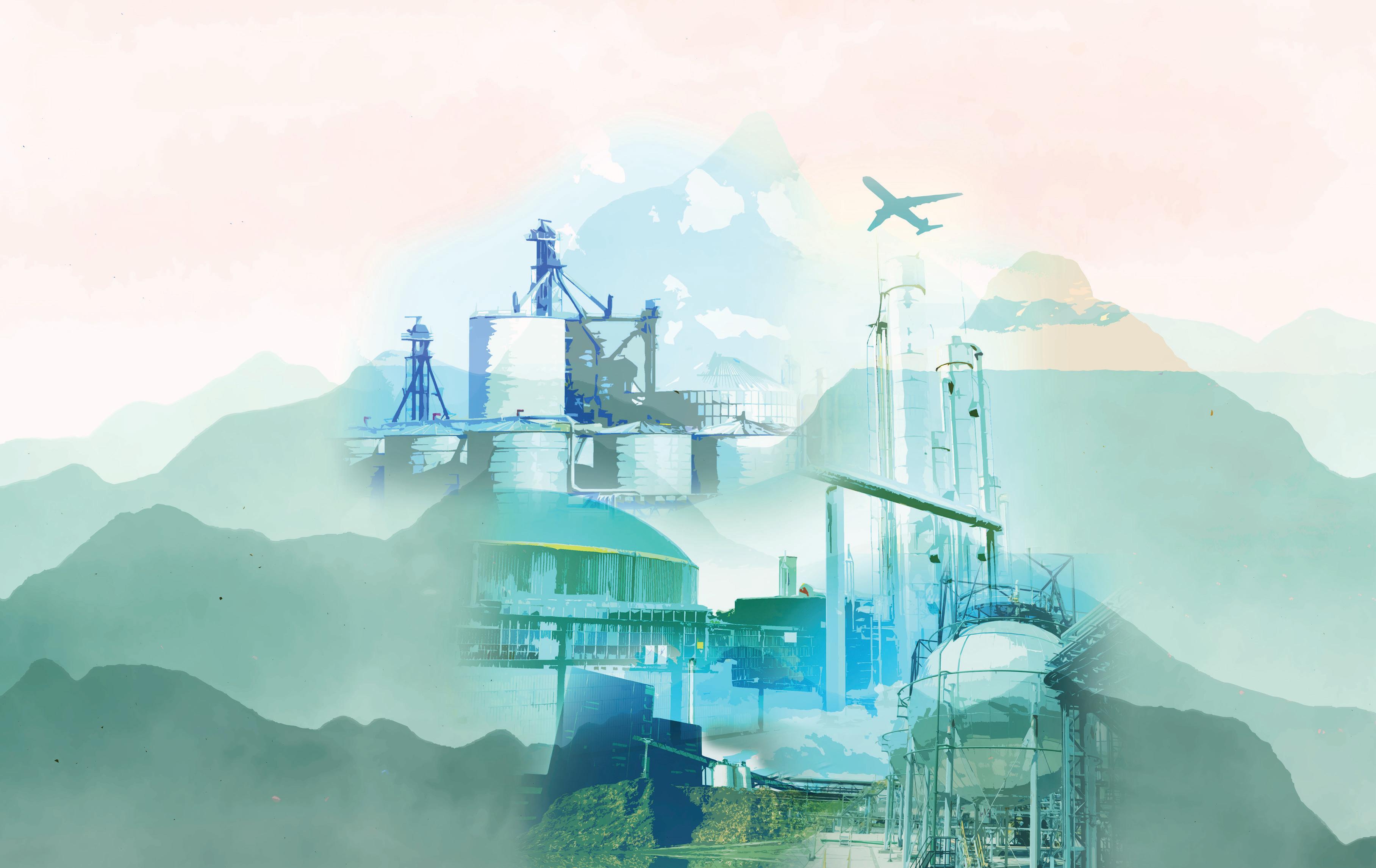
18th ANNUAL
The Int’l Biomass Conference & Expo is where future and existing producers of biobased power, fuels and thermal energy products go to network with waste generators and other industry suppliers and technology providers.
Largest Biomass Event in North America
BiomassConference.com
The Int’l Biomass Conference & Expo is the largest, fastest-growing event of its kind, the conference is expected to draw nearly 1,000 attendees in 2025. In 2024, the event drew 160 exhibitors and more than 900+ attendees, with 29% of attendees being producers. This growth is fueled by a world-class expo and an acclaimed program.
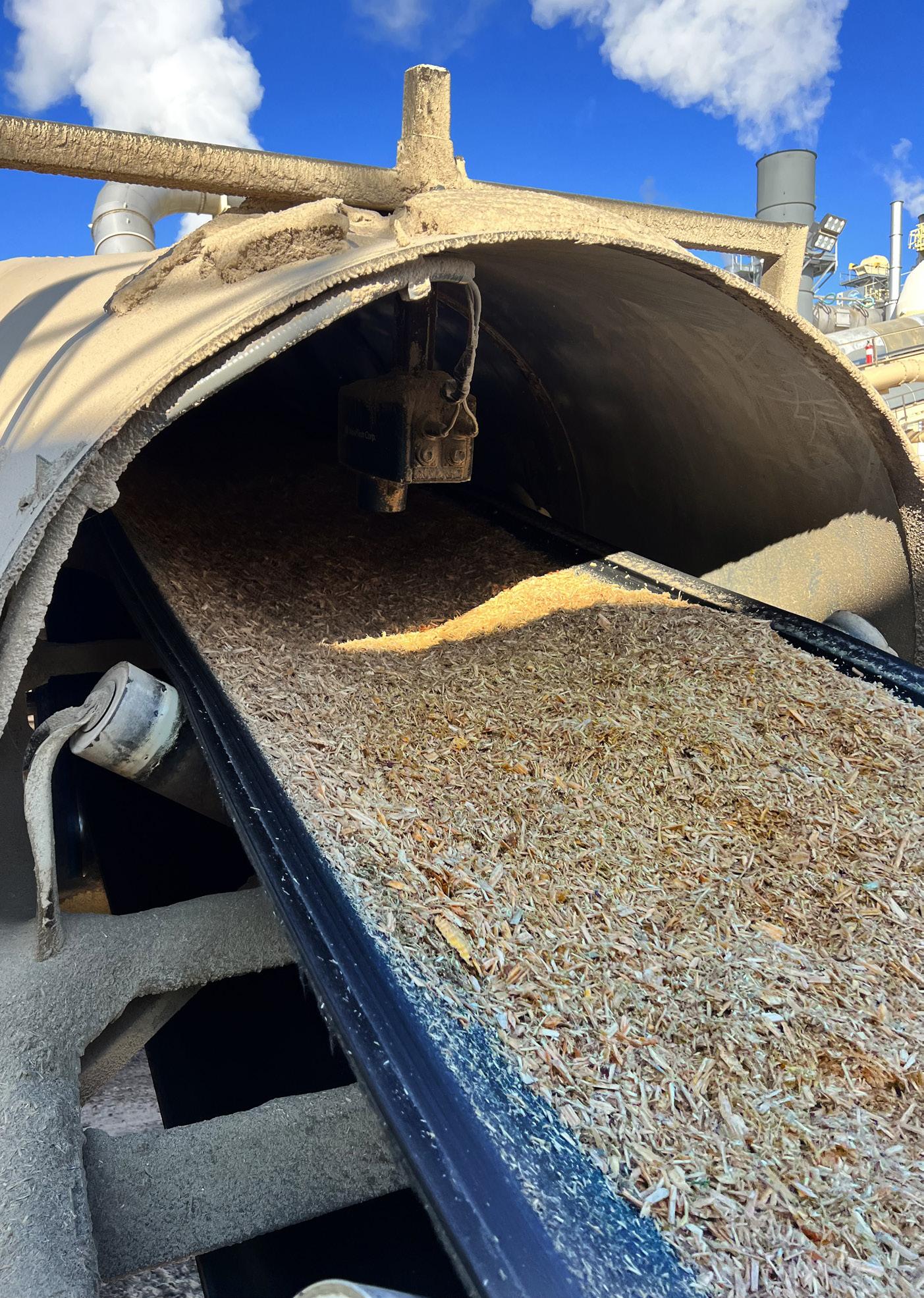
INCREASING PLANT EFFICIENCY THROUGH REDUCED MOISTURE
Moisture in wood and biomass operations impacts product as well as equipment, energy usage, production efficiency, downtime and more.
BY SARAH HAMMONDMinimize cost and increase efficiency. Both manufacturers and producers have this at the forefront of their agenda, especially in today’s economy. Knowing where improvements can be made and implementing increasingly lean operating procedures creates immediate process line results.
Moisture and wood fuel biomass are vital to each other for minimizing cost, proper operation of biomass boilers, and genuine fuel load assessment. Near-infrared (NIR) technology is a great noncontact way to measure moisture content, immediately improving the product and overall efficiency of the plant.
Moisture control is crucial in wood and biomass operations, as excess moisture can have wide-ranging impacts that affect not only the product, but also the equipment, energy usage, production efficiency, downtime and more. Wood fuel boilers are optimally designed to operate within a limited moisture content range. When the fuel exceeds this range, it can result in various inefficiencies, increased emissions and control system errors. Therefore, understanding and maintaining the moisture content is essential for production efficiency, yielding many immediate benefits.
Minimizing costs is a top priority for producers, and thoroughly evaluating methods of reducing waste can reduce wasted efforts, wasted product and wasted energy.
Proactive Avoidance
Continuous monitoring of moisture content enables proactive prevention of potential issues caused by out-of-tolerance moisture levels. Delivering the highest quality product by utilizing the diamond standard in NIR moisture detection systems ensures the highest accuracy and repeatability. The sensors are insensitive to material variations such as particle size and material height and color, providing continuous, reliable readings with zero maintenance requirements. With one-time calibration, noncontact operation and a nondrift optical design, adjustments can be made on the fly, producing instant measurements while improving performance, reliability and consistency.
Dry products create avoidable risk, as do products that are too wet. Pelletizers require a specific moisture range to ensure the efficient operation of the machine. Excess moisture can cause
the pelletizer to malfunction, resulting in significant product loss and downtime on the production line.
Moisture control provides immediate benefits such as reduced transportation costs stemming from excess water, decreased wear and tear on equipment caused by ash and dust buildup, and prevention of blockages on the conveyor that can lead to boiler shutdown. When it comes to addressing the challenges faced by plant operators, moisture detection and control are among the most crucial steps. If there are no current methods of moisture measurement in the production process, significant opportunities for increased efficiencies are being missed.
Ultimate Efficiency
Do you currently have the ability to consistently measure 100% of the product being produced? Installing NIR moisture sensors throughout the process makes this easily achievable. Proactive, immediate adjustments are easily made to ensure optimal manufacturing by line personnel while monitoring the process anywhere in the facility.
Maximizing automation and increasing reliability through reduced costs is of significant importance for operating personnel, and this goal is easily achieved through moisture monitoring. Moisture levels outside of tolerance can unravel important facets of the
process, each phase of which runs more efficiently with accurate moisture content. Identifying and using the best methods can minimize common problems, including warping, claims, check and excessive transportation costs.
Near-Infrared
Multiple moisture detection methods exist for industrial processing, but not all technology is created the same. Radio-frequency (RF), weight loss and probe methods involve various factors to be considered, as they can sometimes provide more of an educated guess than a reliable measurement that can be repeated.
NIR technology differs from others in that it does not require being in contact with the product at all—in fact, it is measured approximately four to 12 inches away from the product. Nondestructive and precise accuracy also make NIR a superior choice for moisture detection. Simply put, NIR spectroscopy and imaging provide fast, nondestructive analysis of the chemical and physical information in the product. When light hits a product, it interacts in various ways; transmitted light will pass through while backscattered light will reflect from the product back to the sensor. Absorption is key to the NIR analysis.
By implementing an NIR moisture sensor, wood and wood fuel product users and
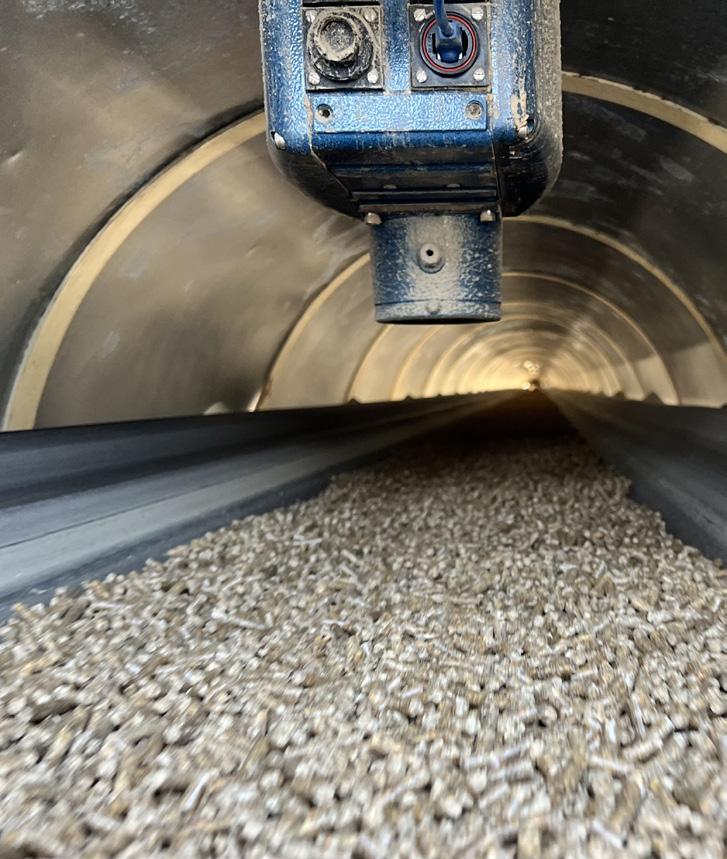
In pellet manufacturing, moisture sensors are recommended to be installed in multiple locations throughout the production process to achieve maximum efficiency.
manufacturers can adjust moisture levels based on real-time information, lowering raw material and fuel costs and resulting in higher yields and more uniform products. NIR offers advantages over the traditional methods, the most important being ease of use, elimination of hazardous chemicals and increased efficiency of product testing.
Author: Sarah Hammond shammond@moisttech.com MoistTech Corp. www.moisttech.com

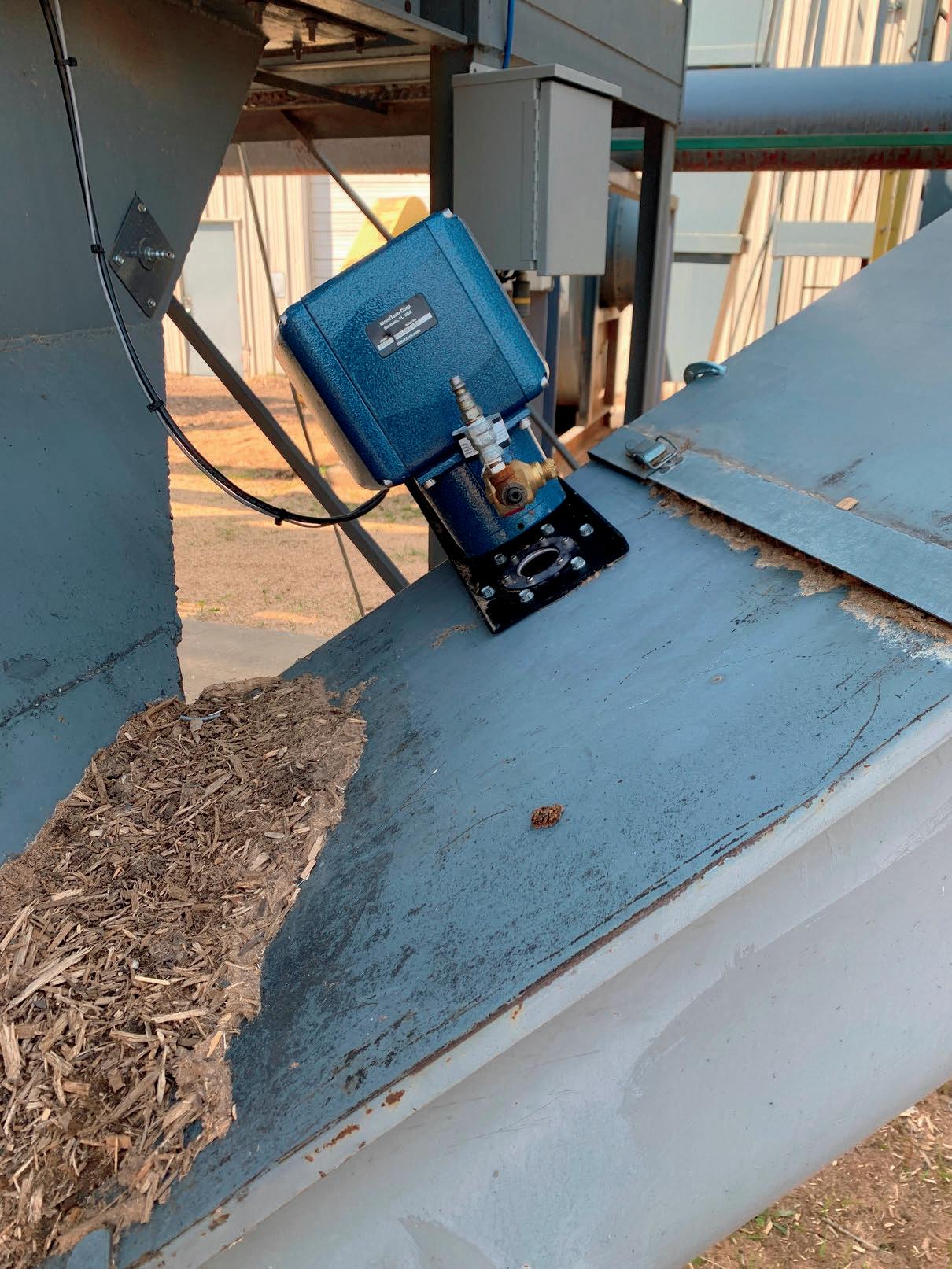

Kompogas SLO recently reached five years of operations.
AN ORGANIC WASTE DIVERSION SUCCESS STORY
Hitachi Zosen Inova’s Kompogas SLO anaerobic digestion facility diverts up to 30,000 tons of local organic waste per year while producing electricity, compost and fertilizer.
BY LEANNE FRISBIEAsunny beachside town in California might seem like the last place you’d find one of the most advanced waste-to-resource facilities in the United States, but in San Luis Obispo, against the backdrop of this popular vacation spot, this is exactly what was built in 2018 by global waste-to-energy company
Hitachi Zosen Inova.
Kompogas SLO is the name of the plant, a reference to HZI’s proprietary anaerobic digestion system that is at the core of the facility, which takes in the county’s organic waste and turns it into electricity that is fed into the local grid. The resulting compost and fertilizer go back onto the land, making it a closed-loop, circular economy initiative.
When Kompogas SLO reached its fiveyear milestone last year, HZI took stock of the facility’s successes to date. The results are impressive—as of the end of December 2023, the plant had diverted over 140,000 tons of organic waste from the local community, including residents, businesses and agriculture. From this waste, the plant produced over 10 million cubic meters of biogas, fed over 11 million kilowatt hours of electricity into the grid and produced over 30,000 tons of compost and 6.5 million gallons of liquid fertilizer.
Heath Jones, managing director of HZI North America, attributes the success of the facility down to the quality of the operation. HZI built the Kompogas plant in San Luis
Obispo as a finance, design, build, own and operate model, along with the cooperation and support of the local community, San Luis Obispo County Integrated Waste Management Authority, local waste hauler Waste Connections and funding assistance from state programs.
Regulatory Support
“California’s regulatory and legislative environment makes it easier to build organic waste diversion facilities like Kompogas, in support of the state’s goals of diverting 75% of organics from landfills by 2025,” Jones says. “And because our facility is helping California reach its climate goals, CalRecycle contributed $4 million to the project, making the Kompogas SLO facility part of California Climate Investments. The California Energy Commission also provided $4 million for development under the Electric Program Investment Charge Program.”
Jones adds that this is the kind of support needed at a state level for facilities like Kompogas to become commonplace around the U.S. “The state of California has world-leading climate goals, including an ambitious goal of net-zero carbon emissions and 100% clean electricity by 2045,” he says. “Establishing waste-to-resource facilities like Kompogas SLO that are not only reducing methane emissions from landfill, but also harnessing biogas for reuse as clean, renewable energy, are going to help California achieve these goals. By producing compost and fertilizer from the residual waste after we’ve harnessed the energy, we’re helping California get to a zero-waste future as well.”
State-of-the-Art Innovation
The Kompogas facility is designed to process up to 36,500 short tons of source-separated organics and green waste as well as fats, oils and greases from the county’s residential collection program. After pretreatment, the organic waste is fed into the plug-flow digester, where the thermophilic anaerobic digestion process ensures complete sanitation of the organic matter while its gas potential is fully exploited. The resulting biogas is utilized in an on-site combined-heat-and-power unit to produce electricity that is exported to the local power grid.
CONTRIBUTION: The claims and statements made in this article belong exclusively to the author(s) and do not necessarily reflect the views of Biomass Magazine or its advertisers. All questions pertaining to this article should be directed to the author(s).
BIOGAS ¦
The HZI KOM+Press separates the discharge into a solid and a liquid fraction. The solid digestate is aerated and, like the liquid digestate, produces nutrient-rich compost and fertilizer for local agriculture.
A state-of-the-art supervisory control and data acquisition system supervises all facility controls, monitoring processes and performance tracking of the plant. For odor control, all processing at the facility is enclosed within negative air pressure buildings. The subsequent biofilter assures natural and efficient cleaning of the collected waste air. Therefore, no emissions are released into the surrounding environment.
Community Involvement
Also crucial to the success of Kompogas SLO is the support and cooperation of the local community. Jones says that thanks to local publicity and education initiatives, SLO County residents and businesses have gotten behind separating their organic waste and have also enjoyed the free annual compost giveaway days, when they get to see their efforts turned into a valuable resource. “To date, we have given away more than 800 tons of compost on our giveaway days,” Jones says. “Local residents get a real thrill out of turning up to the plant with a trailer and loading it up with free compost that came from the organic waste they provided. It’s a very tangible giveback.”
He also points out that Kompogas SLO is an example of a waste-to-resource facility “done right,” which has enabled the operation to be situated literally in SLO’s backyard, with full support from the community who live alongside it. “A pivotal aspect to the success of this facility and the entire project from start to finish is that a highly experienced waste-to-energy company was enlisted to build and operate the plant,” he says. “HZI has been around for over 100 years, and our innovative and reliable solutions have been part of more than 1,600 reference projects worldwide. We take a completely integrated approach to everything we do.”
Jones adds that HZI’s Kompogas system operates in a completely contained environment so that emissions are captured and there are no issues with odor—something that is very important to maintaining good relations with the locals. HZI also works closely with Waste Connections and is located on-site with the company, making the process of transferring organic waste to the Kompogas facility seamless.
As a local SLO resident, HZI sales manager Tom Gratz, who frequently runs tours of the Kompogas facility, knows firsthand how effective the Kompogas plant is. “We have nurtured strong relationships with our community through education and open, friendly engagement with the locals,” Gratz says. “We are proud to show off our operation, and it helps to keep the community support going, because without their organic waste, we would not have a consistent feedstock to turn into the energy, compost and fertilizer that we produce, which in turn goes back to the community.” Contact:
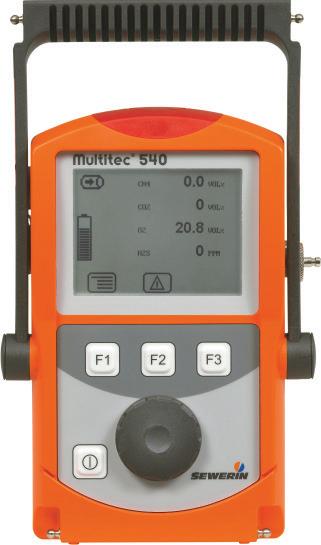
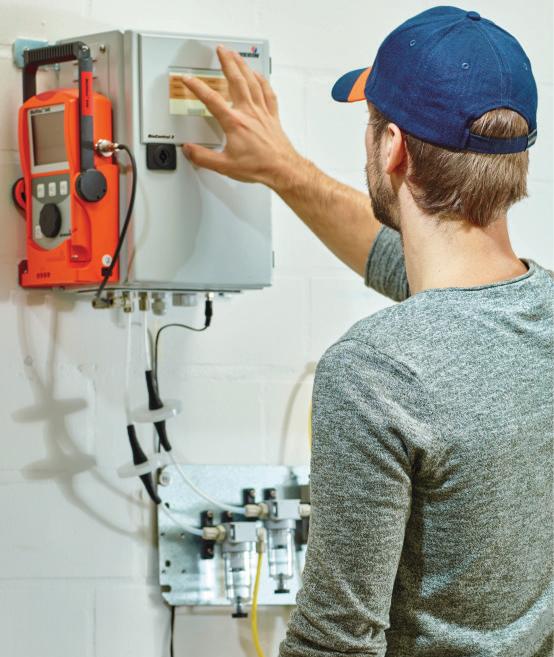
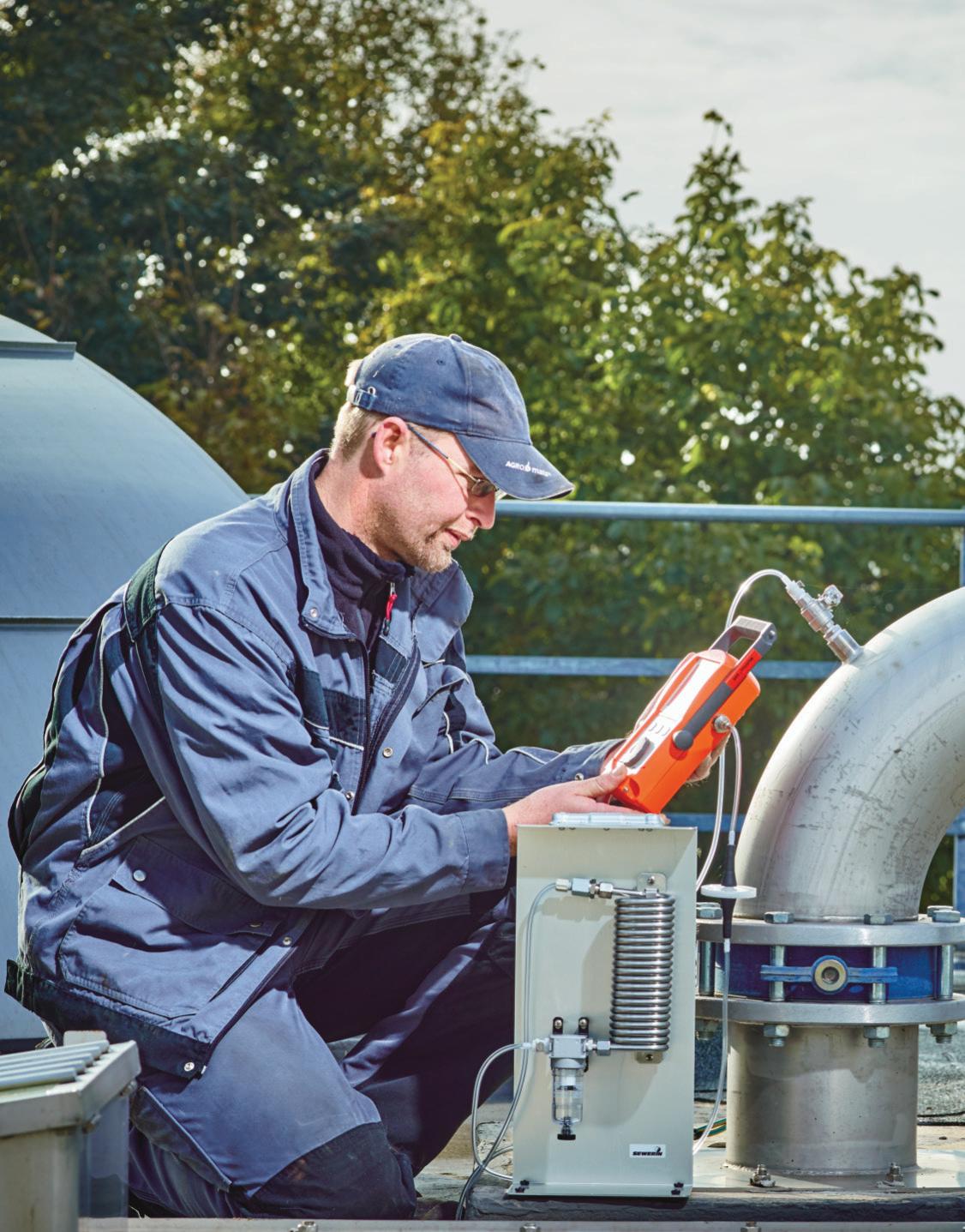
Biomass Magazine Marketplace
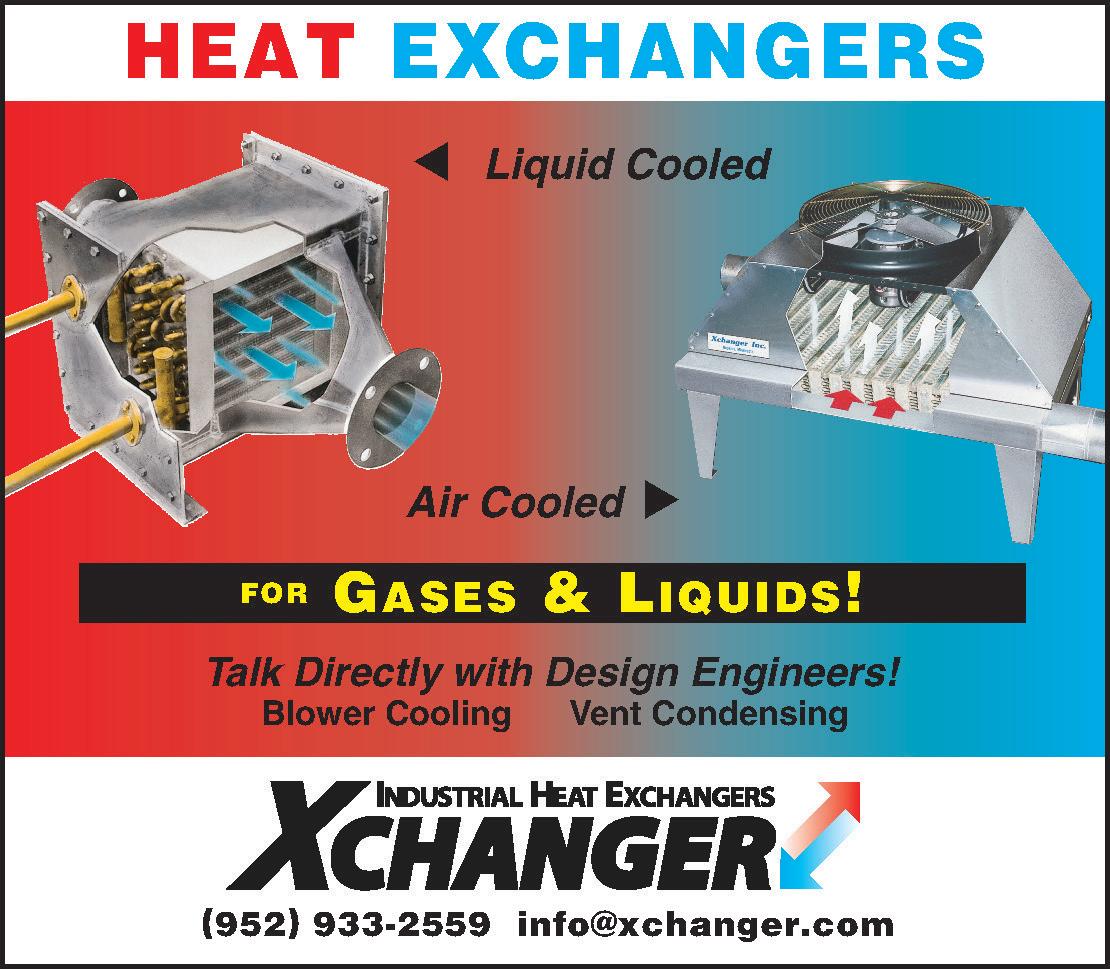
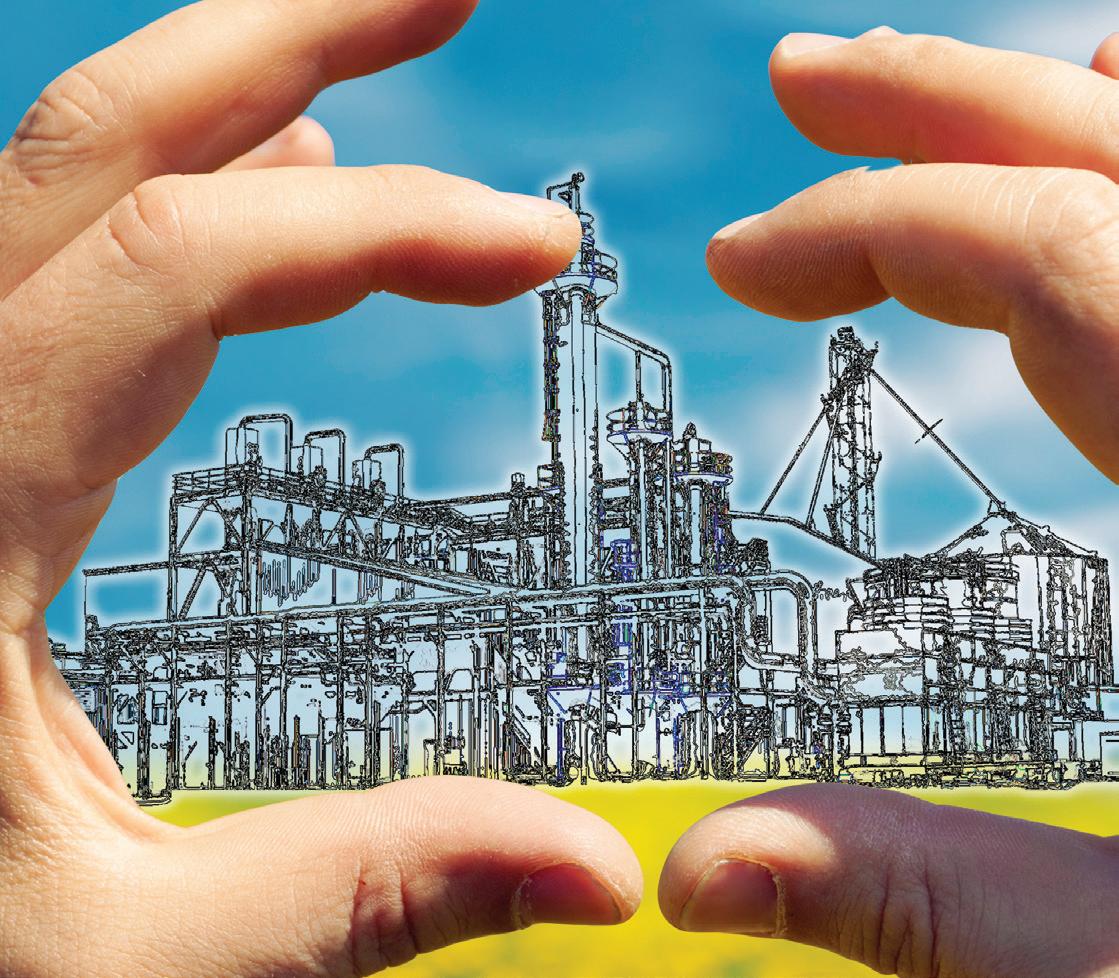
BBI Project Development
Heat Transfer Solutions
Since 1972
Xchanger is a leading manufacturer of custom heat exchangers and blower aftercoolers, with over 25,000 units installed worldwide. We can optimize any of our 10 standard product models to control temperature and humidity in almost any application. By making simple changes to our standard models, our Mechanical Engineers are able to provide custom designs at a fraction of the cost.
Xchanger
952-933-2559
xchanger.com
David Wangensteen
david.wangensteen@xchanger.com
BBI Project Development
BBI’s technical experts provide feasibility studies and project development for new biomass power facilities as well as pellet mill facilities. In many countries power generation through anaerobic digestion addresses waste management and power needs and its application continues to expand. BBI’s experts are able to perform engineering studies, perform technology assessments and evaluate the economic impacts of these projects.
866-746-8385
service@bbiinternational.com
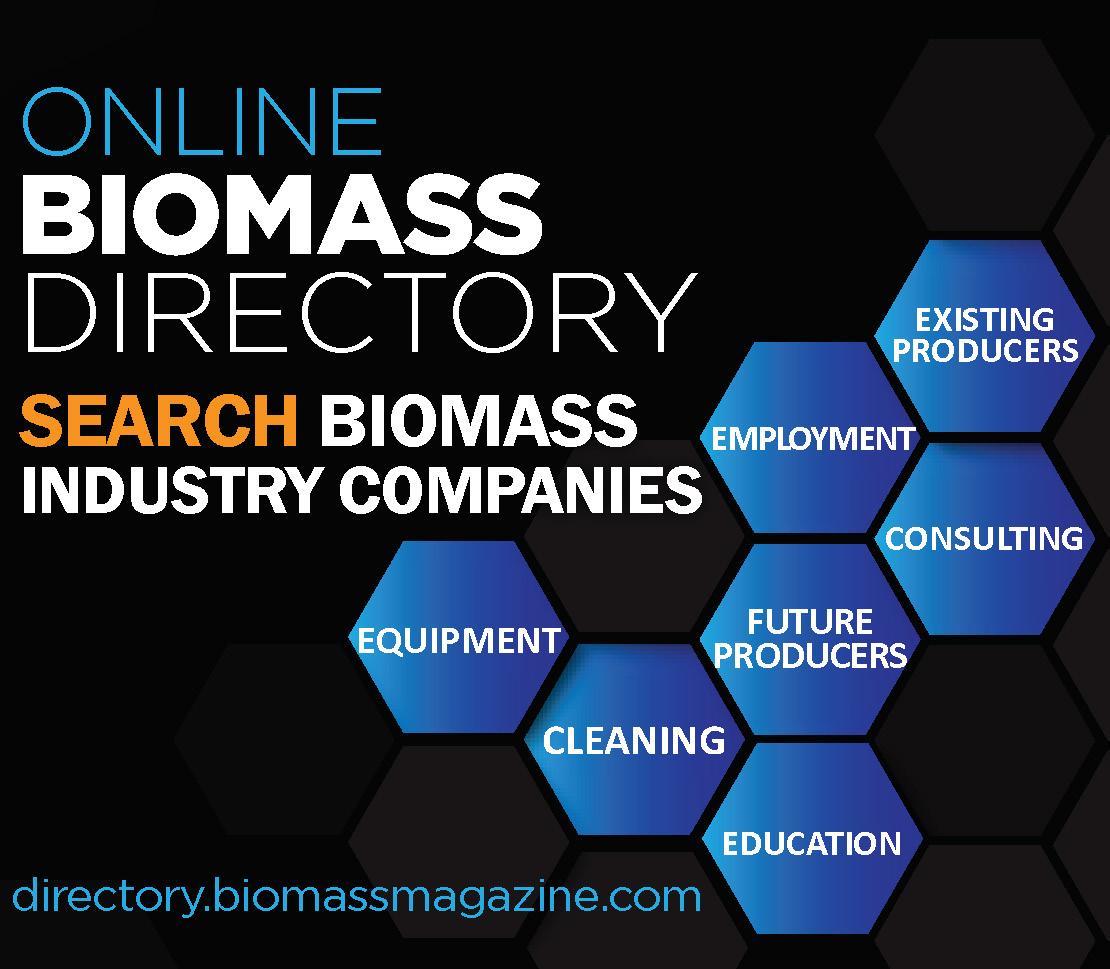
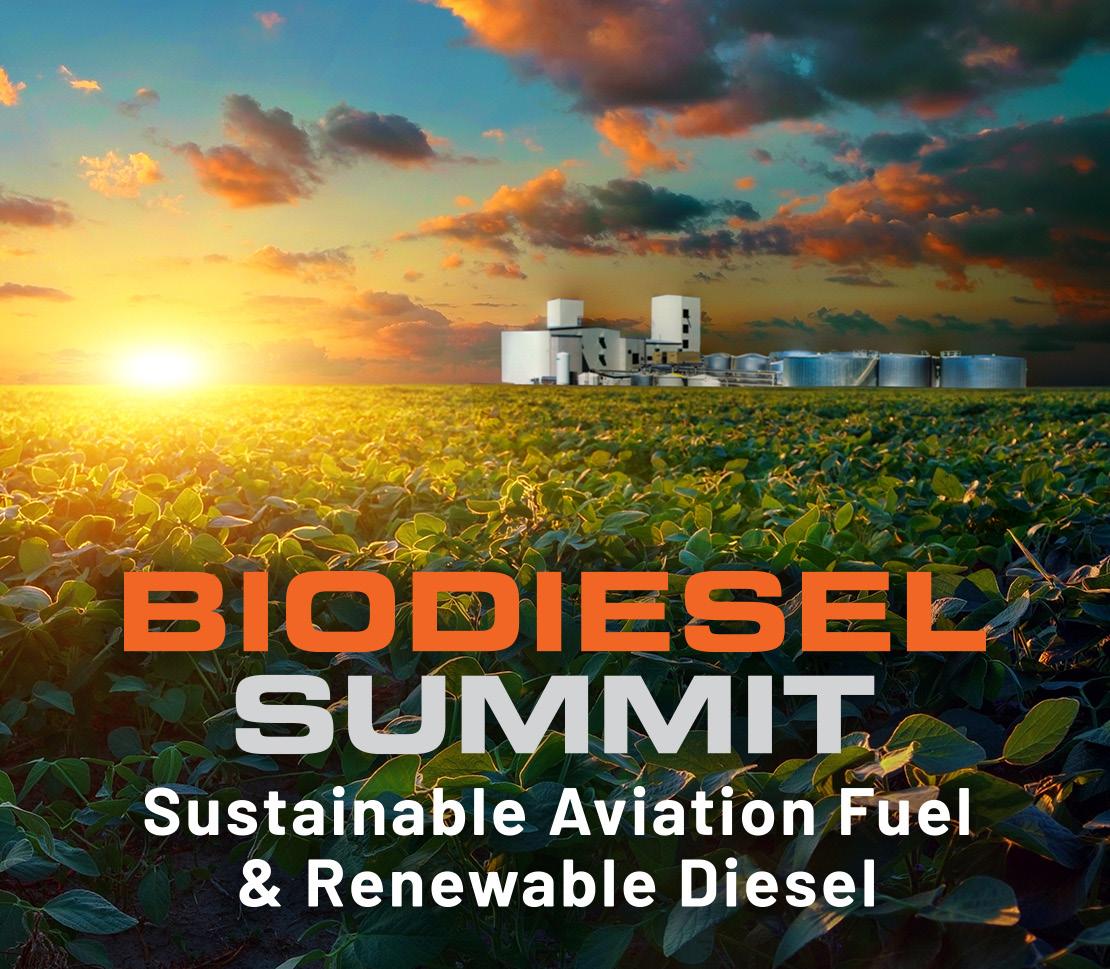
Biomass Industry Directory
Biomass Magazine’s Biomass Industry Directory is the most comprehensive list of industry suppliers, producers, researchers and government agencies available in the world. The directory is an invaluable resource to help find the contact information you are looking for, and help others find you.
directory.biomassmagazine.com
866-746-8385
service@bbiinternational.com
Biodiesel Summit: Sustainable Avaition Fuel & Renewable Diesel
The Biodiesel Summit: Sustainable Aviation Fuel & Renewable Diesel is a forum designed for biodiesel and renewable diesel producers to learn about cutting-edge process technologies, new techniques and equipment to optimize existing production, and efficiencies to save money while increasing throughput and fuel quality.
Colocated with Int’l Fuel Ethanol Workshop & Expo
June 10-12, 2024, Minneapolis
866-746-8385
service@bbiinternational.com
BiodieselSummit.com
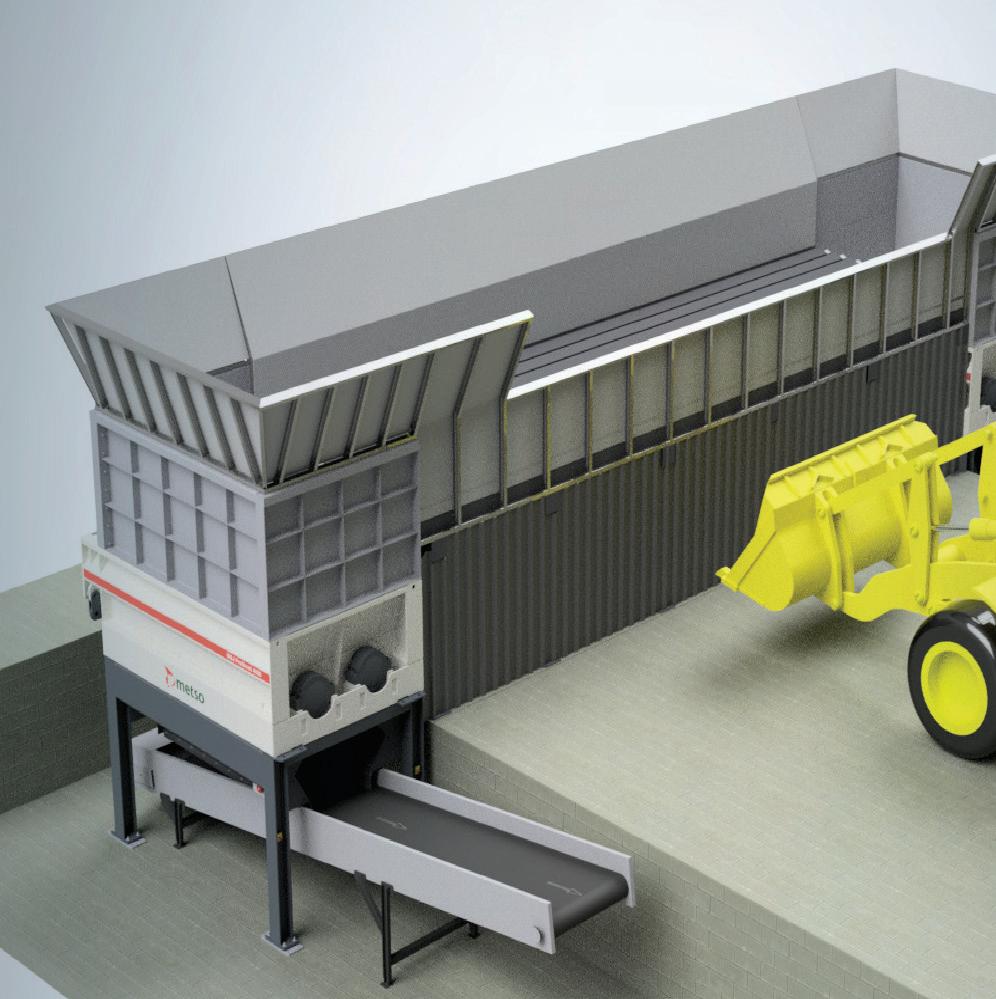

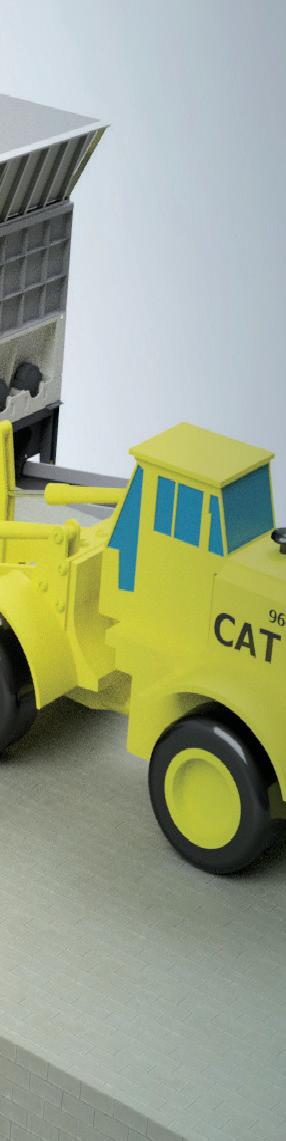
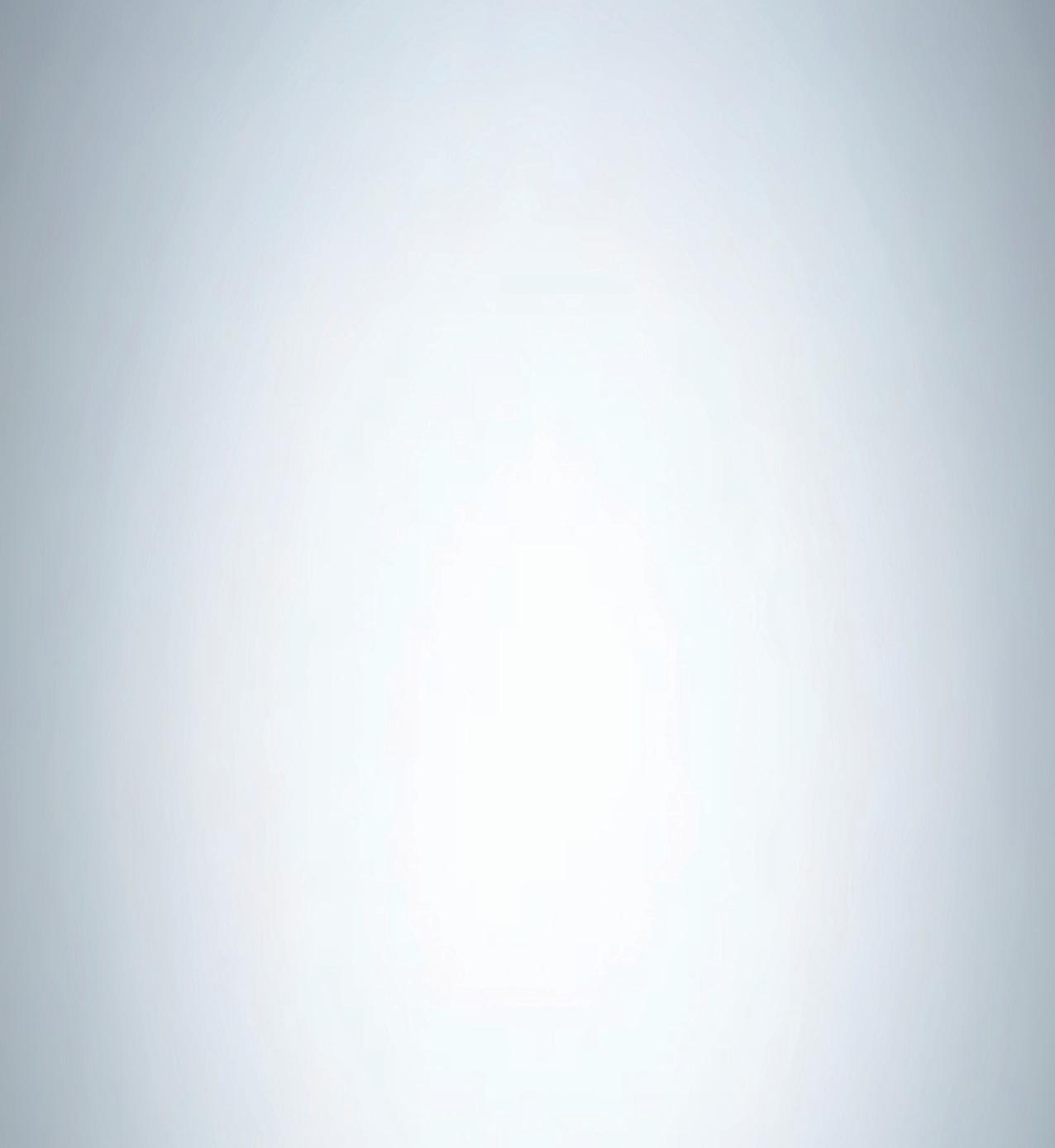

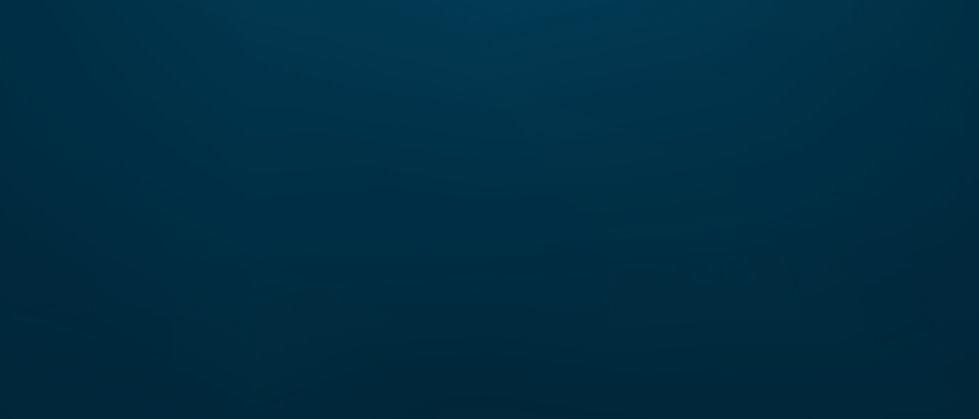