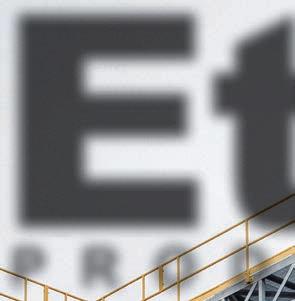

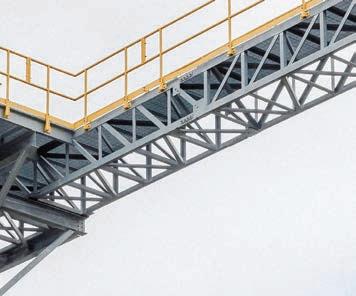
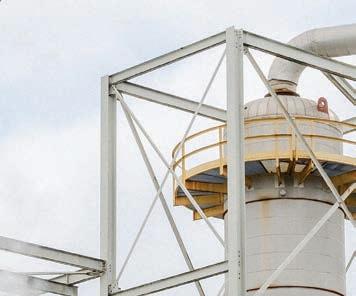
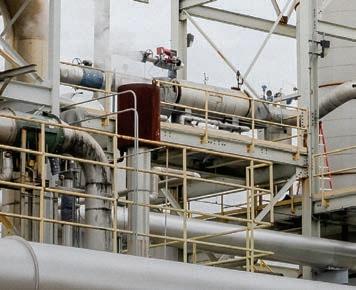
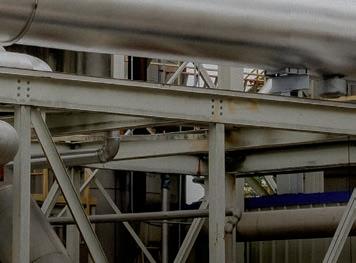

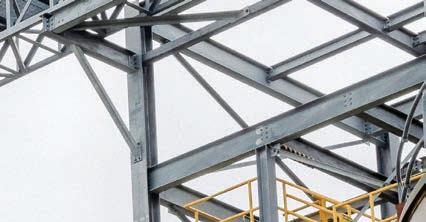


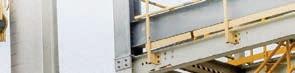
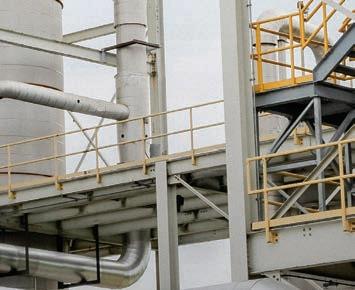
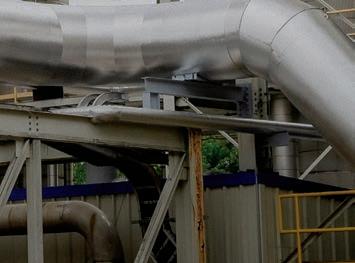

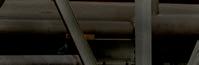
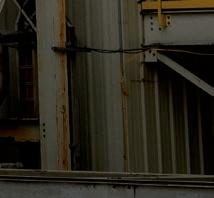
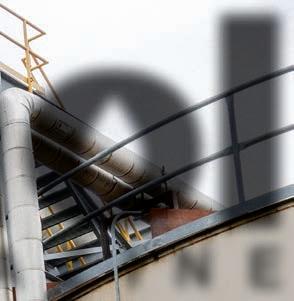
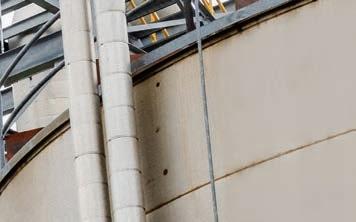
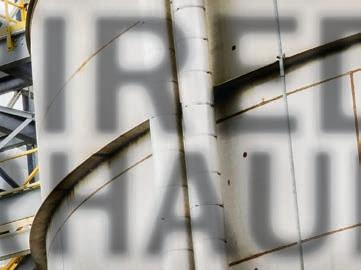
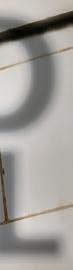

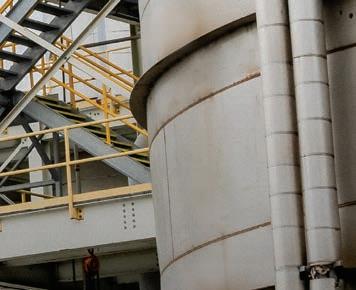

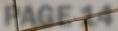


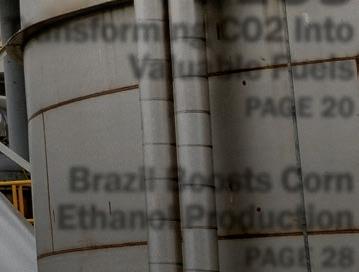
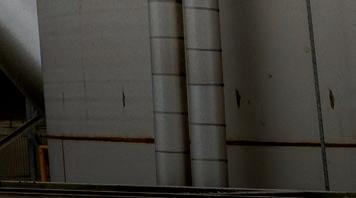


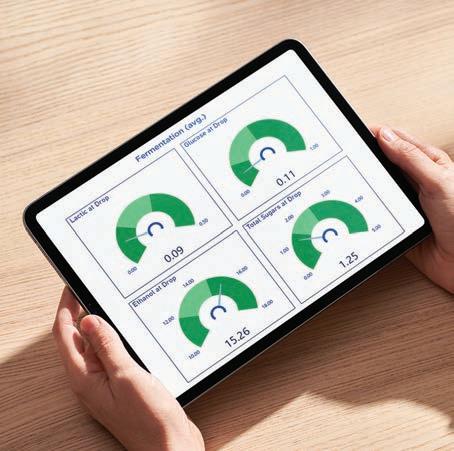


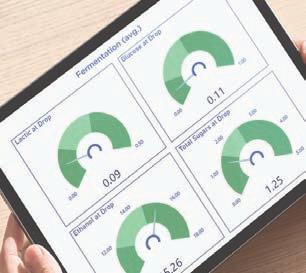
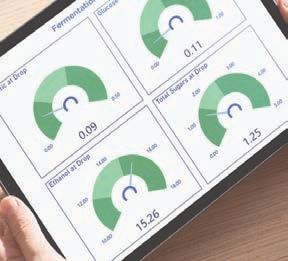

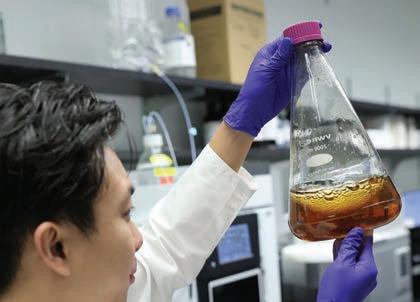
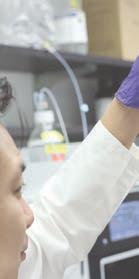


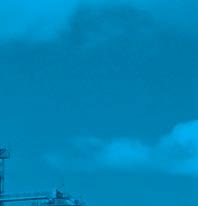
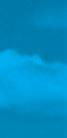
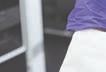


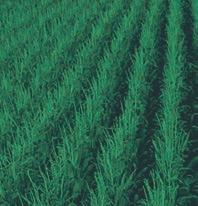

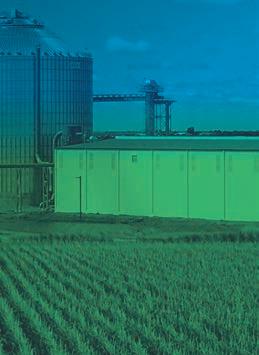
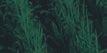

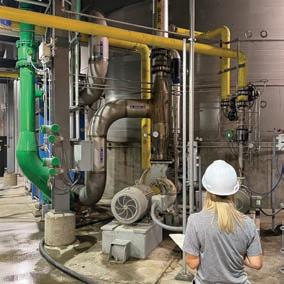


CTE Complete is uniquely innovative. Combining the strengths of our Technology Center with our Technical Services and Operational Support teams, we provide on-site expert guidance beyond our enzyme and yeast solutions. Ready to elevate your plant’s performance?
ClonBio
Replicating Success Hungarian biorefinery inspires retrofits at Wisconsin ethanol plant
The Case for Carbon Utilization
New technologies transform fermentation CO2 into green fuels
Grain Ethanol Grows Amidst the Cane Brazil's corn ethanol production is booming as its blending mandate increases By Lisa Gibson
Enhancing Every Batch
Modern plant hygiene isn't just about fermentation bacteria anymore By
Biofuels
President & Editor Tom Bryan tbryan@bbiinternational.com
Online News Editor Erin Voegele evoegele@bbiinternational.com
Associate Editor Katie Schroeder katie.schroeder@bbiinternational.com
Features Editor Lisa Gibson lisa.gibson@sageandstonestrategies.com
Vice President of Production & Design Jaci Satterlund jsatterlund@bbiinternational.com
Graphic Designer Raquel Boushee rboushee@bbiinternational.com
PUBLISHING & SALES
CEO Joe Bryan jbryan@bbiinternational.com
Vice President of Operations/Marketing & Sales John Nelson jnelson@bbiinternational.com
Director of Sales Chip Shereck cshereck@bbiinternational.com
Account Manager Bob Brown bbrown@bbiinternational.com
Circulation Manager Jessica Tiller jtiller@bbiinternational.com
Marketing & Advertising Manager Marla DeFoe mdefoe@bbiinternational.com
Ringneck Energy Walter Wendland Little Sioux Corn Processors Steve Roe Commonwealth Agri-Energy Mick Henderson Western Plains Energy Derek Peine Front Range Energy Dan Sanders Jr.
Atlanta, GA (866) 746-8385 | www.biomassconference.com
Now in its 18th year, the International Biomass Conference & Expo is expected to bring together more than 900 attendees, 160 exhibitors and 65 speakers from more than 25 countries. It is the largest gathering of biomass professionals and academics in the world. Powered by Biomass Magazine, the conference provides relevant content and unparalleled networking opportunities in a dynamic business-to-business environment. In addition to abundant networking opportunities, the largest biomass conference in the world is renowned for its outstanding programming, maintaining a strong focus on commercial-scale biomass production, new technology, and near-term research and development. Join us at the International Biomass Conference & Expo as we enter this new and exciting era in biomass energy.
Omaha, NE (866) 746-8385 | www.fuelethanolworkshop.com
Now in its 41st year, the FEW provides the ethanol industry with cutting-edge content and unparalleled networking opportunities in a dynamic business-to-business environment. As the largest, longest running ethanol conference in the world, the FEW is renowned for its superb programming—powered by Ethanol Producer Magazine —that maintains a strong focus on commercialscale ethanol production, new technology, and near-term research and development. The event draws more than 2,300 people from over 31 countries and from nearly every ethanol plant in the United States and Canada.
Omaha, NE (866) 746-8385 | www.sustainablefuelssummit.com
Customer Service Please call 1-866-746-8385 or email us at service@bbiinternational.com. Subscriptions Subscriptions to Ethanol Producer Magazine are free of charge to everyone with the exception of a shipping and handling charge for anyone outside the United States. To subscribe, visit www.EthanolProducer.com or you can send your mailing address and payment (checks made out to BBI International) to: Ethanol Producer Magazine Subscriptions, 308 Second Ave. N., Suite 304, Grand Forks, ND 58203. Back Issues, Reprints and Permissions Select back issues are available for $3.95 each, plus shipping. Article reprints are also available for a fee. For more information, contact us at 866-7468385 or service@bbiinternational.com. Advertising Ethanol Producer Magazine provides a specific topic delivered to a highly targeted audience. We are committed to editorial excellence and high-quality print production. To find out more about Ethanol Producer Magazine advertising opportunities, please contact us at 866-746-8385 or service@bbiinternational.com. Letters to the Editor We welcome letters to the editor. Send to Ethanol Producer Magazine Letters to the Editor, 308 2nd Ave. N., Suite 304, Grand Forks, ND 58203 or email to editor@bbiinternational.com. Please include your name, address and phone number. Letters may be edited for clarity and/or space. TM
Please recycle this magazine and remove inserts or samples before recycling
The Sustainable Fuels Summit: SAF, Renewable Diesel, and Biodiesel is a premier forum designed for producers of biodiesel, renewable diesel, and sustainable aviation fuel (SAF) to learn about cutting-edge process technologies, innovative techniques, and equipment to optimize existing production. Attendees will discover efficiencies that save money while increasing throughput and fuel quality. Produced by Biodiesel Magazine and SAF Magazine, this world-class event features premium content from technology providers, equipment vendors, consultants, engineers, and producers to advance discussions and foster an environment of collaboration and networking. Through engaging presentations, fruitful discussions, and compelling exhibitions, the summit aims to push the biomass-based diesel sector beyond its current limitations. Co-located with the International Fuel Ethanol Workshop & Expo, the Sustainable Fuels Summit conveniently harnesses the full potential of the integrated biofuels industries while providing a laser-like focus on processing methods that deliver tangible advantages to producers. Registration is free of charge for all employees of current biodiesel, renewable diesel, and SAF production facilities, from operators and maintenance personnel to board members and executives.
In our cover story this month, Jeff Oestmann, chair of the Renewable Fuels Association, offers a statement that defines both the reporting in this issue and the state of our industry right now. He says, “Technology is unlocking new ways to harness the power of grains, enabling us to make greater strides towards sustainability … [while] our industry is navigating new economic, regulatory and environmental terrain.”
Oestmann’s words couldn’t be more fitting in early 2025 as the U.S. ethanol industry simultaneously faces broad policy uncertainty and unprecedented opportunities for growth, efficiency gains and product enhancement. The biorefinery Oestmann oversees, Aztalan Bio in Jefferson, Wisconsin, is the subject of our page-14 story, “Replicating Success.” The plant was acquired in 2022 by ClonBio, the parent company of Europe’s largest single-site ethanol plant, Pannonia Bio in Hungary. ClonBio’s plan is to reshape the Wisconsin plant in the image of its flagship biorefinery, via a $450 million investment. The vision includes a suite of enhancements hinging around front-end dry fractionation, which separates the components of corn up front to make higher-end coproducts downstream. And that’s just the start. Aztalan might fold in RNG production and other tech down the road. This bold, multi-stage reimagining of an existing U.S. asset is a must read.
Next, we look at the most progressive branch of coproduct diversification—CO2 transformation. While many ethanol producers are pursuing, or waiting on, permanent underground storage, others are exploring ways to transform their fermentation CO2 into valuable fuels and chemicals. In “The Case for Carbon Utilization,” on page 20, we learn how these potentially zero-CI products range from green methanol and sustainable aviation fuel to syngas and low-CI hydrocarbon fuels and chemicals. Ethanol plants are, indeed, the “low-hanging fruit” of carbon capture and utilization because their high-purity CO2 is ideal for conversion.
We trek south to report on the continued rise of corn ethanol production in Brazil, the second-largest ethanolproducing nation in the world—the U.S. being first. In the past five years, Brazil’s corn ethanol production has grown from 2% of its total volume to nearly 20%, thanks in part to one facility with an output of 555 million gallons (2.1 billion liters) per year, which may be the largest corn dry mill in the world. This expansion doesn’t help U.S. producers that compete with Brazil on the international stage, but it does benefit our industry’s product, equipment and technology providers that serve dry mill corn ethanol plants globally. What’s happening down there is worth understanding, and we do a good job explaining it in “Grain Ethanol Grows Amidst the Cane,” on page 28.
We delve into bacterial control in “Enhancing Every Batch,” on page 36, a look at production hygiene products and strategies helping ethanol producers avoid upsets and achieve yield gains. That’s followed by a Spotlight on BASF’s new tool for tracking low-CI feedstock and, finally, an insightful piece from CoBank about the months ahead.
Enjoy the read!
LED™ (Low Energy Distillation) allows facilities to expand production while lowering energy and carbon intensity per gallon. This patented Fluid Quip Technologies’ solution uses less energy than existing distillation designs, reduces downtime, and lowers CI scores. In fact, we’ve designed and engineered one of the lowest CI score ethanol plants in the world.
Expand your plant without expanding your CI. Talk to FQT today and start planning for tomorrow.
This year the ethanol industry will celebrate the 20-year anniversary of the Renewable Fuel Standard, the most transformative and influential public policy in our industry’s long and storied history. But we’ll do more than simply commemorate the successes of the RFS over the past two decades. We will also use this milestone to remind a new administration and new Congress that the health and welfare of America’s family farms is directly and inextricably tied to the health and welfare of America’s biofuels industry.
Indeed, the RFS program’s platinum anniversary could not have come at a more important time. Many of the farm economy challenges that led Congress to adopt the RFS in 2005 are resurfacing today across rural America. As growth in the supply of agricultural commodities is again outpacing demand, farm income has plummeted 23% since peaking in 2022 and the total value of U.S. crops is down $37 billion—or nearly $20,000 per family farm. Agricultural exports are down, interest rates remain stubbornly elevated, farm debt is rising, cropland values are falling, and ag machinery sales are slumping. Moreover, expenses for seed, fertilizer, fuels and labor have all hit record highs in recent years.
We’ve been here before. There was the devastating farm crisis of the 1980s, which saw the collapse of commodity prices and mass farm foreclosures and bankruptcies. Then there was the late 1990s and early 2000s, when crop production again outpaced demand, crop prices fell to levels below the farmer’s cost of production, farm bill safety net payments surged, and farm consolidation accelerated.
Everything began to change in 2005 when Congress overwhelmingly passed legislation establishing the RFS, requiring oil refiners to blend increasing volumes of biofuels like corn ethanol into our nation’s fuel supply. The RFS, which was greatly expanded by Congress two years later in 2007, ushered in a golden era of demand-driven market dynamics and value creation for America’s farm sector. Farmers and their neighbors pooled their resources to build ethanol biorefineries in their communities. Rapid expansion in ethanol production created a growing market for corn and added significant value to farm commodities. Good-paying jobs, prosperity and wealth returned to small towns across rural America, and a new generation came home to the family farm.
It is not an exaggeration to say that growth in biofuels, driven by the RFS, helped rescue the farm economy and save rural America.
It can do so again.
Cutting away the red tape that restricts ethanol consumption will not only reduce fuel costs for consumers, but it can also help stave off a looming farm crisis by winnowing down the mountains of grain piling up across the Midwest. President Trump, his new cabinet and the new Congress can support and protect farmers, boost American energy production, decrease reliance on trade with undependable partners and create new manufacturing jobs in the heartland, simply by doubling down on the power of renewable fuels.
Two decades ago, passage of the RFS and the creation of a robust market for ethanol lifted family farmers out of economic peril and kicked off the most prosperous run in the history of American agriculture. Now, with farmers facing a new round of severe financial challenges, it’s time to go back to our roots. It’s time to turn to renewable fuels once again to lift up rural America and secure our energy future.
Linda Schmid
U.S. Grains Council Manager of Ethanol Policy and Sustainability
While at the 29th United Nations Climate Change Conference (COP29) in Baku, Azerbaijan, I promoted ethanol as a way to help countries meet their climate commitments, including keeping the global temperature rise below 2.7 degrees Fahrenheit.
During the conference, developed countries committed to offering $300 billion annually to help low- and medium-income countries transition to more sustainable options, and completed the rulebook on carbon credit trading under Article 6 of the 2015 Paris Agreement. COP29 outcomes on finance offer opportunities for the expansion of bioethanol blending rates and cross-border trade while governments increasingly adopt climate mitigation policies.
COP29 financing commitments can help governments evaluate their current bioethanol blending policies, assess carbon intensity savings from biobased fuels and incorporate bioethanol in their energy transition plans. It’s a win-win for ethanol producers and developing countries with greater access to financing for renewable resources. The governments in these countries can explore why most highincome countries maintain a bioethanol blend rate of 10% as a floor, and countries in the global south pursue rates as high as 27%.
In preparation for COP30 in Belem, Brazil, in 2025, governments around the world are formulating Nationally Determined Contributions (NDCs) to plan their energy transitions, and the Council is working to ensure U.S. ethanol is considered as a part of the solution. In 2025, bioethanol proponents can help governments shape their NDCs to obtain carbon intensity savings over fossil fuels.
Farmers and producers have responded to climate mitigation policies with smart climate practices, investment in carbon capture and storage, and increasing corn and bioethanol yields. Policymakers can increase private sector investment and accelerate the energy transition with stable and harmonized climate mitigation policies underpinned by international cooperation.
The council believes that through climate-smart action including the expanded export of U.S. ethanol globally, developed and developing countries can take another step closer in the quest for a cleaner environment and a healthier climate that improves the lives of those around the world.
• Delivers up to 15% increased corn oil recovery
• Enables pathway to produce low-CI cellulosic gallons
• Dewaters corn kernel fiber for reduced natural gas consumption
• Maximizes plant operability
To learn more, contact your account manager.
POET has donated over $629,000 through its 2024 Community Impact Grant Program. The program, established by POET Founder and CEO Jeff Broin, offers individuals and organizations operating in POET’s home communities an opportunity to apply for funding to support projects that create a positive impact. Each grant is awarded to causes that fall under one of three categories: the earth, the community and the next generation.
The 2024 POET Community Impact Grant Program—which included its Sioux Falls headquarters, all 34 POET bioprocessing locations and its Savannah, Georgia, terminal—received nearly 1,400 applications. POET ultimately awarded nearly 150 grants, totaling $629,000, across its footprint.
Eligible parties apply online for a chance to receive a grant from their local POET location. Team members at each respective location then select and award
The Renewable Fuels Association congratulated Erik Huschitt and Bill Couser for their appointments to the U.S. Environmental Protection Agency’s Farm, Ranch and Rural Communities Federal Advisory Committee, which provides independent policy advice and recommendations to the
EPA administrator on environmental issues affecting agriculture and rural communities. Huschitt is the CEO and general manager of Badger State Ethanol in Wisconsin and is RFA’s immediate past chairman. Couser is a founder of Lincolnway Energy in Nevada, Iowa. Couser is a returning
Alicia Koch has joined the U.S. Grains Council as its new director of global ethanol export development. As director, Koch will be based in the Council’s Washington, D.C. headquarters and oversee the development and execution of the Council’s global ethanol program, including program implementation, public affairs and strategic partnerships.
Koch previously served as executive director at Pivot Clean Energy Co., a nonprofit biofuels industry coalition, and spent more than nine years across a variety of roles at POET.
“Alicia’s wealth of experience in the U.S. ethanol industry will be an outstanding benefit to the Council’s ethanol market development efforts, especially at a key time
grant recipients. This year’s recipients included local fire departments, schools, libraries, parks, food pantries and a variety of youth programs, among many others.
POET is the world's largest ethanol producer, exceeding 3 billion gallons in annual output. The company has an integrated business model that combines research and development with expertise in design and construction, technology, operations, public affairs, and marketing.
member to the committee, and Huschitt is a new appointee.
“Erik and Bill bring a lot of practical experience to the table when it comes to agriculture, renewable fuels, and the environment,” said RFA President and CEO Geoff Cooper.
when additional biofuel applications like sustainable aviation fuel (SAF) and clean cooking are becoming more prevalent,” said Ryan LeGrand, USGC president and CEO.
Operating in over 50 countries, the USGC develops export markets for U.S. barley, corn, sorghum and related products including distillers grains and ethanol.
Dakota Spirit, a Harvestone Low Carbon Partners company, recently announced the successful installation and operation of Alfa Laval’s Prodec Oil Plus centrifuge technology, designed to optimize oil recovery at the plant. After two months of operation, the results have met expectations, achieving an approximate 25% increase in oil recov-
The Japanese government has announced its intention for the country’s gasoline to be blended with 10% ethanol (E10) by 2030 and E20 by 2040, a move that will have significant benefits for the economic, environmental and human health of Japan and its consumers.
The Council is a longstanding supporter of biofuel growth in Japan, including
ery yield. This technology has positioned us as a leader in adopting innovative ideas and solutions to improve plant efficiency.
“We’ve sharpened our sustainability profile with this partnership,” said Gunner Greene, Chief Operations Officer at Harvestone Low Carbon Partners. “Alfa Laval’s technology helps us meet the growing de-
mand for biofuel feedstocks in an increasingly competitive market and assists us in advancing toward achieving Vision Carbon Zero—a multi-phase initiative aimed at making our facilities net carbon zero.”
recent steps like witnessing the opening of the first E7 fuel pump in Japan and Council President and CEO Ryan LeGrand’s participation in a USGC and U.S. Department of Agriculture conference on sustainable aviation fuel.
The Japanese Ministry of Economy, Trade and Industry spearheaded the effort as part of its goal for the country to be
Summit Carbon Solutions announced that it has received three Class VI sequestration permits from the North Dakota Industrial Commission, marking a critical step forward in the Midwest Carbon Express project. These permits authorize the safe and permanent storage of CO2 in North Dakota’s deep saline geologic formations.
In Minnesota, the Minnesota Public Utilities Commission has granted a permit for the company’s 28-mile pipeline route through Otter Tail and Wilkin Counties. The company also announced the submission of its permit application to the South Dakota Public Utilities Commission. The company’s 2,500-mile pipeline,
carbon neutral by 2050. METI noted that because of Japan’s relatively low domestic production of ethanol, imports will drastically increase from the U.S. and other countries; infrastructure improvements will be required as most of Japan’s fuel stations are only equipped for E3 blends.
which includes 700 miles in South Dakota, will transport CO2 from 57 ethanol plants across five states, including 14 in South Dakota and Gevo’s planned SAF plant near Lake Preston.
ClonBio Group Ltd. is taking its biorefinery build-out strategies proven in Tolna County, Hungary, and applying them in Jefferson County, Wisconsin. The European Union’s largest ethanol producer acquired a former Valero corn ethanol production facility in Jefferson in 2022 and has already made progress in reshaping the 100-year-old site through more than $450 million in investments. More progress is on the way, the company says, in years, not decades. Pannonia Bio, a subsidiary of ClonBio, officially restarted operations in October 2024 at the 120 MMgy Wisconsin facility.
“ClonBio invested in transforming the Aztalan facility into a cutting-edge biorefinery, drawing on the same principles that propelled Pannonia Bio to global leadership,” says György Tamaska, communications manager for ClonBio, an agribusiness based out of Dublin, Ireland.
Through Pannonia, ClonBio was able to turn an ethanol production site in Hungary into a modern biorefinery that just keeps growing. Since 2012, the Hungary facility, located adjacent to the Danube River, has tripled in size and become a multi-product facility. The site is the largest in Europe and produces for multiple end-users in nutrition, health, biochemical and biofuels.
The Hungary site utilizes front-end dry fractionation to separate the components of corn. The process utilizes the germ, starch, protein and oils for separate products, in addition to producing biofuel.
ClonBio believes it can reproduce its unique, biorefinery-based approach proven in Hungary at the new facility in Wisconsin. To achieve its global goals, the team has invested in—and will rely on—powerful technology and experienced leadership with strong connections.
ClonBio has renamed the Wisconsin facility Aztalan Bio. Upgrades already performed or ongoing include state-of-the-art process au-
After restarting a former Valero plant in Wisconsin, ClonBio is retrofitting it in the image of the largest biorefinery in Europe.
By Luke Geiver
tomation, energy efficient production systems and the integration of technologies designed to maximize yield while minimizing waste, Tamaska says.
“The focus was not just on restarting the plant, but elevating it to a new standard of operational excellence,” he says.
ClonBio chose the Wisconsin facility to recreate its Hungary success largely because it was already equipped with dry front-end fractionation. The combination of existing infrastructure, a skilled workforce and access to grain presented the company with what it calls an “unparalleled opportunity to replicate and adapt ClonBio’s European success in the U.S. market.”
In Wisconsin, the goal for Aztalan is to become a leading biorefinery capable of producing multiple products for multiple industries, many of which traditional ethanol plants in the U.S. aren’t currently serving.
“The project is an excellent example of the fact that the industry is moving away from the ‘ethanol plant’ model and fully embracing the ‘integrated biorefinery model’,” says Geoff Cooper, president and CEO of the Renewable Fuels Association. According to Cooper, the future of the industry is more than just being a supplier of ethanol as an additive for E10 and E15.
“Projects like this are significant in two ways: as a symbol of continuing overall growth in the industry, and as a way to promote new
technologies for better production efficiencies,” he says.
In addition to ethanol, the plant will eventually produce coproducts that will range from high-protein animal feed to distillers grains to food-grade corn oil and more. The team there is already looking at anaerobic digestion to produce renewable natural gas and fertilizer products as well.
The Hungary plant currently doesn’t use antibiotics at any stage of production, instead relying on alternative means to control infection. Throughout the facility, a zero-effluent design produces no solid or liquid waste. And all process contact waters are fully recycled and reused.
ClonBio says the Wisconsin plant’s retrofit is a testament to its philosophy of thinking outside the box, consistently reinvesting in research and development, and prioritizing innovation. “Unlike conventional retrofits, this project reflects a vision for creating a true biorefinery, where ethanol production is just one element of a broader ecosystem that includes high-value coproducts like protein concentrates and fibers,” Tamaska says. “It embodies a progressive and sustainable approach to ethanol production, setting a new standard in the U.S. market.”
To lead the establishment and expansion of its U.S. facility, ClonBio has tapped Jeff Oestmann as the CEO of Aztalan. Oestmann has previous leadership roles at Granite Falls Energy, Syngenta’s Biofuels division and East Kansas Agri-Energy. A 30-year veteran in the biofuels and agriculture sectors, Oestmann has overseen multiple plants globally and led operations, strategy and sales in diverse markets. In addition to his extensive background in managing the function and strategy of largescale operations, Oestmann has also been successful working with policymakers and industry groups to navigate complex regulatory landscapes while advocating for the industries he’s served.
“Our goal is to position Aztalan Bio at the forefront of ethanol production and biorefinery innovation, much like Pannonia Bio has achieved in Europe,” Oestmann says. “To
achieve this, we require continued investment in technology, strong partnerships with local stakeholders and a clear focus on sustainability and operational excellence.”
The Jefferson plant is working with growers in a 40-to-50-mile radius for its corn supply.
Aztalan Bio will bring as much knowhow from the Pannonia plant as possible. Oestmann says his early strategies include leveraging advanced fermentation techniques, streamlining operations for minimal waste and integrating sustainability into every aspect of production.
In 2021, Pannonia Bio won an IChemE (Institution of Chemical Engineers) Energy award in Europe for its work to install a unique mechanical vapor recompression system designed by U.S.-based Energy Integration Inc. The system was recognized for its ability to reroute Btus that would normally go into cooling towers. By installing EII’s system, the Hungary plant was able to put heat destined for the cooling towers into blowers or condensers that raise the heat of compression. The process ultimately allowed the plant to avoid diverting energy to water for use in the cooling towers.
Aztalan announced in 2023 that it would use the same mechanical vapor recompression technology.
In 2017, ClonBio began working with Buhler when it was looking at further separation processes prior to fermentation. Buhler helped the company design and build a cornfiber separation plant on-site. Corn fiber is used to make animal feed or converted into biogas through anaerobic digestion. The Pannonia Bio plant will use the natural gas on-site or sell the biomethane to customers. The company makes a fertilizer product out of the nitrogen, phosphorus and potassium in the AD residues and sells it to the same growers that supply the site with corn.
When ClonBio added barley to its list of feedstocks used at its European plants, the company used Buhler again to design another system.
“We were impressed by our first interaction,” says Mark Turley, ClonBio founder and CEO. “When Buhler built our corn-fiber extraction plant, nothing existed anywhere else in the world, so it was a learning curve.”
The barley processing system has two parts, wet and dry. The process includes intake, cleaning, handling and removal of particles.
Similarly, Aztalan has a fractionation system designed by U.S.-based Cereal Process Technologies, which has been operating since 2007.
In addition to his leadership role at Aztalan, Oestmann has already made an impact on the U.S. biofuels industry. In September 2024,
Oestmann was elected as the chairman of the board for the Renewable Fuels Association after previously serving as vice chairman.
At the time of the election, Cooper called Oestmann a “big-picture thinker with a compelling vision for the industry’s future.”
“He brings energy and plenty of experience to this role,” Cooper says. “He has shown a real talent for bringing people together to tackle complex challenges.”
Oestmann says his leadership comes at an exciting yet transformative time for the industry. “Technology is unlocking new ways to harness the power of grains, enabling us to make greater strides towards sustainability,” he says. “Our industry is navigating new economic, regulatory and environmental terrain.”
The focus remains on the Renewable Fuel Standard, along with the evolving landscape of carbon markets, “as these factors will greatly influence our strategic decisions,” he says, adding that expanding the U.S. market for E15 continues to be another top priority as it helps grow ethanol demand.
Also on the demand side, the RFA sees the increasing interest in sustainable aviation fuel as a compelling growth avenue that aligns with a global energy transition. And ensuring clarity and stability in energy tax policies, particularly regarding the Inflation Reduction Act’s clean fuel tax credits, is critical.
“We’re actively engaging with federal and state biofuel policymakers,” Oestmann says.
Cooper says 2024 was a good year for ethanol with records set or nearly reached for ethanol production, distillers corn oil and CO2 capture. Going into 2025, the goals will
Our team of experts haveover 20 years of ethanol plant maintenance expertise. We o er full service and parts for all Fluid Quip equipment to ensure peak performance.
•OEM Parts Warehouse
•$2 million+ inventory on-hand
•Factory Trained & Certified Techs
•MZSA™ Screens
•Paddle Screens
•Grind Mills
•Centrifuges
•Gap Adjusters
be to expand in existing markets, create new opportunities and work with the new Congress and White House. “There will be many in Washington who will need to be brought up to speed on the current state of the ethanol industry and our coproducts,” Cooper says.
Pannonia Bio and ClonBio are setting their sights globally. In the summer of 2024, the companies helped form the Climate Ethanol Alliance to represent interests in Europe, the U.S. and Asia. The CEA brings together and represents ethanol producers, service pro-
viders and input suppliers in an effort to accelerate the transportation sector’s transition to lower carbon emissions. Eco-Energy, IFF, Lallemand, Murex and Praj are supporting the effort as well.
The CEA is looking to introduce highoctane fuels produced, in part, with ethanol as a necessary component of delivering on global climate goals. Part of that achievement will come from standardizing E20 globally. In addition to that, the CEA will push to get fermentation carbon capture and storage recognized as a vital policy framework to address climate change concerns around the world.
For Aztalan, Oestmann says he will focus on helping the Wisconsin plant shape the policies and narratives that will impact the ethanol industry in the Badger State.
Simultaneously, Oestmann and his team are bringing new tech, millions of dollars in investments and a proven biorefinery mindset from Hungary.
“ClonBio’s commitment to partnering with stakeholders—be it farmers, regulators or customers—will also be central to our approach here in Wisconsin,” Oestmann says. “To put it simply, we are going to build the world’s most advanced grain biorefinery right here in the U.S.”
Author: Luke Geiver writer@bbiinternational.com
While many companies are developing ways to remove carbon emissions from the atmosphere and sequester them deep underground, other innovators are exploring ways to use carbon emissions, turning them into valuable fuels and chemicals.
For decades, many ethanol producers have been selling their CO2 on the merchant market for uses such as freezing meat and carbonating beverages, but new processes and technologies are enabling producers to find even more attractive outlets for their CO2.
When Carbon Sink was founded in 2019, there were no green methanol-powered ships
in the world’s oceans, explains Randy Roy, co-founder and chief strategy officer of Carbon Sink. Still, the company’s founders acted on the momentum toward a green fuel they identified in the marketplace. “We saw an opportunity to build a business around capturing very pure, abundant CO2 from ethanol plants in the Midwestern U.S. and combining that with hydrogen manufactured using relatively inexpensive renewable electricity, also located in the Midwest,” Roy says.
With the passage of legislation like the Inflation Reduction Act as well as the presence of over 400 dual-fueled ships capable of burning green methanol and increasing demand for sustainable aviation fuel (SAF), the market has developed as Carbon Sink’s founders expected. “We believed the landscape would change in a way that would make our business model more viable when we embarked on his
journey,” Roy says. “The shipping industry has embraced methanol as a replacement for diesel, and the airline industry has also embraced SAF as a replacement for fossil-based jet fuel. In addition, there is increased state and federal support for renewable energy and carbon capture and utilization.”
The company has signed letters of intent with five ethanol plants to build green methanol facilities. Currently, the only publicly announced project is located at Red River Energy in Rosholt, South Dakota. Carbon Sink serves the role of a project developer, primarily using technologies created by other companies.
Every 50 MMgy ethanol plant produces enough CO2 to make roughly 100,000 metric tons of methanol each year, Roy explains. The amount of methanol produced is equivalent to about two-thirds the volume of ethanol produced at the nearby ethanol plant.
New technologies are emerging with creative solutions that put carbon emissions to work for ethanol producers.
By Katie Schroeder
The project development process starts with negotiations with the ethanol plant on supplying CO2 and, in some cases, water and land. Negotiations are also made with technology developers for the various plant components, and terms for offtake agreements must be negotiated with the parties receiving the green methanol or SAF. After negotiations are completed and technology vendors are selected, the next phase can begin.
“At that point, we would hire a third party to complete the engineering work and then raise the capital we need to construct the project,” Roy says. “Our typical project, which would be co-located with a 50 MMgy ethanol plant, would cost in the range of $150 million to construct.” Because Carbon Sink’s first facility is a “fairly early stage project,” and there are not many facilities like it in the world, Roy
anticipates that the $150 million price tag will come down by nearly 25% over time after the first project is completed, reaching approximately $100 million by year seven. Carbon Sink’s first project is planned for completion in 2029.
“As you can imagine, we are all for [CO2] transformation,” he says. “Because we know we can create a zero-CI score product, a real zero-CI score product, a form of SAF or methanol, and you can’t do that by putting CO2 in the ground.”
HYCO1 uses its proprietary catalyst to convert carbon dioxide and natural gas into syngas (carbon monoxide and hydrogen). Kurt Dieker, co-founder and chief development officer of HYCO1, explains that the company’s
SHIPPING APPLICATIONS: Technology developers are increasingly looking to carbon transformation over sequestration. CO2 from ethanol plants can be used in a variety of value-added applications, including green methanol in lieu of diesel for marine fuel.
name was born out of its technology’s capability to produce hydrogen and carbon monoxide at a one-to-one ratio. Greg Carr, Jeff Brimhall and Dieker launched the company in February 2021. The technology’s resulting syngas can be utilized to make a variety of downstream products via Fischer Tropsch technology, including low-CI hydrocarbon fuels and chemicals.
Traditional hydrogen is made by steam methane reformers using more steam than is necessary for the chemical reaction to make the hydrogen. This “steam cleaning” of the catalyst prevents the reformer from coking—filling up with carbon. “The catalyst for HYCO1, that is the innovation … it’s a noncoking catalyst,” Dieker says. “That allows us to do … what’s called dry methane reforming or methane reforming without water at all. That’s been the Holy Grail reaction because
it’s the most efficient reaction—the historical problem is coking.” The catalyst can be used for both dry methane reforming and steam methane reforming, or a blend of the two, improving the operator’s efficiency and flexibility in operations.
Since HYCO1’s technology recognizes “carbon as carbon,” it converts CO2 into syngas at the same rate as methane, making CO2 an equivalent feedstock to RNG from a chemistry standpoint. The ethanol industry is “low-hanging fruit” for the company because, as Dieker explains, the industry is among the “most mature” in carbon market knowledge and produces biogenic, high-purity CO2 that is easy to capture.
In July 2024, HYCO1 announced a 20year CO2 supplier agreement with Kansas Ethanol in Lyons, Kansas. Dieker explains that HYCO1 plans to build a facility capable of making 5,000 barrels per day or 80 MMgy of synthetics using natural gas and CO2 as the feedstock. Currently, Dieker and his team are in the detailed design phase of project devel-
opment, working with multiple technology providers for downstream refining of products. “There are actually four technologies on site—the first is ours, syngas which enables everything else to be more efficient, lower carbon intensity and therefore more sustainable,” he says. “The second is a Fischer Tropsch technology, and then there’s a refining section, or we’ll call it a distillation and isomerization
section, to polish the molecules, and separating the products is what you’re doing on the back end.” HYCO1 plans to capture all emitted CO2 and use it as a low-cost feedstock in the production process.
HYCO1 has three different vertical paths to profitability, explains Dieker. First, swapping out existing catalysts in small modular reactors (SMR) within the syngas industry for
to the gas,” he says. “You can add [low] carbon attributes, you can add renewable natural gas or landfill gas or others to that to even further improve it. What we’ve found is users really don’t want to pay for that premium.”
HYCO1’s catalyst offers a significant increase in efficiency and allows for CO2 to be used as an efficient feedstock with HYCO1’s CUBE technology.
The second vertical is licensing of the carbon utilization catalyst technology to nextgeneration facilities by adding carbon capture technology or building new facilities with third-party project developers. “Then you can actually use that CO2 as part of your feedstock and offset your natural gas or fossil fuel usage into that reformer,” Dieker says.
Third, HYCO1 is exploring production of high-value specialty products through internal projects—like the one sited near Kansas Ethanol—making jet fuels, base oils (group IV alternatives) and light alkanes.
The HYCO1 team keeps the economics in mind when designing their facilities, targeting low CI scores while keeping their products affordable for consumers. “If you’re looking at CI with renewable diesel or jet or base oils, base oils are 110 grams per megajoule—we’re under 30 without adding any carbon attributes
The main goal for Jeff Bonar, CEO of CapCO2 Solutions, is to make a positive impact in addressing climate change while also supporting rural communities and bringing biofuels into the next generation. Through his company, he intends to take CO2 from ethanol plants and turn it into green methanol using low-cost renewable energy. CapCO2’s “capture as a service” business model captures and utilizes ethanol producers’ CO2, but owns and operates the equipment, giving the ethanol producer a share of the profits as well as tax incentives. Producers can also choose to invest in the infrastructure to get an increased share of the profits. Integrating CapCO2’s utilization into an ethanol producer’s system grants them an estimated 25-point CI reduction under the GREET model.
CapCO2’s disruptive technology allows green methanol to be made in relatively small and compact units, explains Bonar. “Roughly nine or 10 feet in diameter, 25 to 28 feet long reactor vessels—you can put it on a skid and that is the unit of work,” he says. “It’s 1/20th the size of conventional methanol equipment and you can do it modularly, so we can manufacture them, deliver them on-site and hook them up.” The footprint for the green methanol equipment is roughly equivalent to 30 to 40 shipping crates, and the design is intentionally straightforward. “We’re not trying to build a whole new chemical factory next door,” Bonar says.
The equipment can be run intermittently, optimizing the process for when purchasing green energy is most cost effective. “Our equipment works just fine if you turn it on and off, and in fact, we’ll see as we scale up the plants, but we think we can make green methanol for roughly the same price as regular methanol because we will take advantage of electricity when no one else wants it,” Bonar
says. The other vital ingredient needed for making green methanol is water, roughly 25% the volume needed by an ethanol plant. Bonar explains that CapCO2 plans to look for ethanol producer partners in places where the local water supply will not be stressed by adding their facility.
As of print time, CapCO2 had not yet announced an ongoing project, but Bonar explains that the company has identified some good candidates and anticipates a forthcoming announcement. A pilot plant currently under development will have one reactor, costing a total of $15 million. In comparison, a full-scale facility will cost $200 million to $300 million and be 30 to 35 times larger. The costs may vary depending on how consistently the plant is turned on and off, explains Bonar. If the producer takes the approach of running intermittently, a larger investment into CO2 storage infrastructure will be needed. A 100 MMgy
Bonar explains that, hypothetically, “we may only want to build it to handle 25% of the CO2 because there’s a new wind farm being put in, but it’s not going to be ready for another two years,” he says. “We’re going to have to kind of layer it into whatever else is being developed in the area, but, again, it’s modular so there’s no real significant cost to doing it a piece at a time.”
As these new technologies gain a foothold, the options grow for ethanol producers to lower their CI scores while increasing their profit margins. With various providers and cost structures available, it has perhaps never been easier for producers to explore a new approach to CO2 utilization.
Author: Katie Schroeder katie.schroeder@bbiinternational.com
When it comes to fermentation, why settle for anything less than Lallemand Biofuels & Distilled Spirits? With our industry-leading lineup of yeast and yeast nutrition, plus our newly added Spartec® enzymes, you get the best tools available to optimize your ethanol production. And that’s just the beginning. Our renowned educational programs and handson services complete the package, delivering a winning combination to maximize your results.
WITH LBDS, BETTER ISN’T JUST POSSIBLE — IT’S GUARANTEED.
Brazil’s ethanol production—both sugarcane and corn— is expanding significantly, predominantly to fulfill the demands of the country’s increasing blending mandate.
By Lisa Gibson
In 2018, Brazil produced 431 million liters (113.9 million gallons) of corn ethanol. For the 2024’25 crop year (April to March), the country is expected to produce north of 6 billion liters (1.6 billion gallons). Corn ethanol now accounts for 18% to 20% of Brazil’s total ethanol production, up from about 2% in 2018.
“It’s a remarkable growth—stunning growth,” says Hagan Rose, director of international sales and marketing for EcoEnergy.
The expansion is not relegated to just corn ethanol, as Brazil has also increased its sugarcane ethanol production from 25 billion liters (6.6 billion gallons) to 33.5 billion (8.8 billion gallons) in the same time period. Rose says that’s also “good growth.”
Brazil’s Ministry of Mines and Energy says the country saw a 48% increase in production capacity between 2018 and 2023 alone. “With the approval by the National Congress of the RenovaBio Law, the receptivity on the part of the productive agents and the expectation of an increase in market share brought the favorable environment
for new investments in the expansion of the production capacity of biofuels in the country,” the MME wrote in a response to questions from Ethanol Producer Magazine Rose has theories for ethanol’s growth in Brazil, as does David Lococo, president and CEO of Katzen, a U.S.-based technology design and engineering firm that recently completed the world’s largest dry mill corn ethanol plant for Brazil’s largest corn ethanol producer, INPASA (Industria Paraguaya de Alcoholes S.A.). Both emphasize agricultural prowess and volatile sugarcane prices.
All that increased production will be necessary, as Brazil boosts its blending mandate to 35% under RenovaBio. Still, both Rose and Lococo say they remain bullish on U.S. ethanol for world exports, with no concerns that Brazil’s new supply will edge the U.S. out of the world market in the near-term.
INPASA’s new production came online at its Sinop, Mato Grosso, location in 2024, boosting its capacity to more than 6,000 cubic meters per day, 2.1 billion liters annually
(554.7 MMgy), Lococo says. “That makes it the largest dry mill corn ethanol plant that we know of, anywhere.”
Katzen initially began working with INPASA in Paraguay a few years ago to help design a retrofit for its distillation system, to include a molecular sieve. “That project was very successful, they were pleased with our performance and they asked us to build a brand new standalone plant in Paraguay. From that, we co-developed a strategy for fermentation and distillation and evaporation that was very profitable and worked very well. And they decided that the future
of ethanol was bright for them, but the future of ethanol in the short-term was Brazil, so they opened operations in Brazil.”
INPASA has 14 plants in Brazil and accounts for more than 50% of the country’s corn ethanol production capacity. Katzen has three more corn ethanol projects in the works with INPASA, as well as a project with a company out of southern Brazil named 3tentos that is expected to come online in November 2025. Even new producers are reaching out to Katzen, interested in traditional corn ethanol.
“We’re actively pursuing expansion in Brazil because Brazil is definitely growing its market for corn ethanol,” Lococo says. “The market is growing tremendously.”
In addition, the Brazilian Development Bank (BNDES) recently announced financial support for two corn ethanol plants, together boosting production capacity by 130 MMgy. BNDES will contribute R$500 million ($87.86 million) to a project under development by Alvorada Bioenergia, part of the Alvorada Agricultural Group, in Canarana, Mato Grosso. Another R$500 million will go toward a Campo Mourão, Paraná, facility under development by Coamo Agroindustrial Cooperativa.
“I think RenovaBio is having an impact,” Lococo says of ethanol expansion in Brazil. “It’s driving dollars into that marketplace.”
Brazil’s RenovaBio legislation was implemented in 2017, a result of the Paris Agreement. The initial goal was to reduce greenhouse gas emission by 37% in 2025, 43% in 2030, from a 2005 baseline.
“The policy takes into account the relationship between energy efficiency and the reduction of GHG emissions in order to assist in the decarbonization of the Brazilian transport matrix, also contributing to energy security, market predictability and the development of the green economy in Brazil,” MME wrote to EPM.
“It should be noted that, after the institution of RenovaBio, the Brazilian government increased its ambitions in relation to decarbonization,” MME added. “The latest commitment, signed in Baku (Azerbaijan) during COP29 provides for the reduction of emissions between 59% and 67% in 2035, taking into account 2005 emissions, which reinforces the role of biofuels in the decarbonization of the transport sector.”
During the COVID-19 pandemic, adverse prices and reduction in ethanol consumption prompted a decrease in blending biodiesel with mineral diesel, MME added. “With the resumption of normality in agricultural markets, the production and consumption of biofuels grew again in 2023 and we are back on the trajectory necessary to meet the goals set for 2030.”
While RenovaBio might be helping to drive development, Rose says Brazil’s corn ethanol boom is largely a “two-fold story:” year-round opportunity for ethanol from corn; and pressure on the sugarcane/ethanol mix based on weather, crop conditions and prices.
Brazil now does a two-crop rotation each year—largely soybeans and corn. “It’s a real success story for Brazilian agriculture to find that second crop over soybeans—find a use for the material to keep it domestic.”
The construction of traditional U.S. ethanol plants in Brazil allows year-round processing of corn. “Without ethanol, it would be very difficult to grow the corn and move the corn on its own,” Rose says, adding the agricultural infrastructure there is challenging, with high costs to move corn to port and export.
Corn is also stable as an ethanol feedstock. “The price of sugar overrides the market in determining what you’re going to make,” Rose says of sugarcane as a feedstock. “Most processors make the decision at the beginning of the season.
“What stands out to me is sugar ethanol has always been the baseload in Brazil and is still by far the largest production of ethanol in Brazil. However, the crop changes,” he adds. “The conditions change and provide more or less sugarcane for ethanol every year.”
The consistent supply of corn ethanol lends confidence to support the higher blend.
“They have the most aggressive blend in the world and certainly want to support their ag community and become more selfsufficient for their energy,” Rose says.
Lococo also emphasizes the traditional U.S. corn ethanol plants in Brazil gaining a foothold and showing profitability, as well as the benefit of a two-crop rotation. “Their productivity is greater compared to U.S. plants supported by the same amount of land. It also drives down their carbon intensity score, so their corn ethanol plants look better when evaluated against global carbon intensity metrics.”
Rose avoids the word “better” when discussing Brazil’s corn ethanol CI. “The fact that Brazil runs two crops in a year does allow them to provide some opportunity for the feedstock for corn ethanol to have a sharp score. I won’t say that it’s better.”
But neither Rose nor Lococo anticipate Brazil’s corn ethanol will move to the world market in significant quantities.
Only recently has the world market seen Brazilian corn ethanol, headed to the European Union, Rose says. “We have seen that happen over the last two crop years.” Brazil’s main markets for its sugarcane ethanol have been the U.S. and the EU.
“We do anticipate that Brazil will be less of an exporter to the world,” Rose says.
“The U.S. market has found cheap feedstock and lower prices on ethanol than we’ve seen in the last several years. … I think the U.S. is in a great position for the next crop year as Brazil sees a challenged sugar crop, a smaller sugar crop, and still has a growing corn market.”
Lococo agrees. “I’m bullish on U.S. ethanol still. I think, depending on administra-
tion and politics, I think the U.S. demand is going to go up for ethanol, especially as there’s more pressure to use E15 throughout the year. … I don't see Brazil’s exports going up for a while anyway, because of their new legislation and future law increasing ethanol blending to 35%, which is going to increase their internal demand.”
Lococo says Brazil is projected to have 50 billion liters (13.2 billion gallons) of internal demand, with production hovering around 35 billion to 40 billion liters (10.6 billion gallons) for this crop year.
In addition, Brazil’s Chamber of Foreign Trade in October rejected a request from the U.S. Grains Council and Brazilian Association of Fuel Importers to remove an 18% import tariff on U.S. ethanol, further encouraging use of domestic ethanol to satisfy the increased blend mandate.
“Corn ethanol continues to grow and will continue to grow in Brazil,” Rose says. “The economics make sense and the market can absorb to a great extent the ethanol being produced in Brazil. I expect to see this continue to grow.”
Lococo adds, “I think the government is recognizing the benefit ethanol is having for farmers and for Brazil to have its own energy source and agricultural support, and that’s kind of the story of ethanol wherever it goes.”
Brazil’s ethanol sector will face its own challenges as it expands, but Lococo sees potential there. “It represents exciting opportunities for companies like Katzen, because we get to figure out the solutions to those problems.”
“Do I think that the growth of Brazilian corn could eventually pressure world exports? I believe world demand will grow to keep both the U.S. and Brazil in the game,” Rose says.
Author: Lisa Gibson lisa.gibson@sageandstonestrategies.com
Traditional cleaning methods expose your team to serious risks like injuries and heatstroke in hot, confined spaces. Automated tube cleaning keeps operators safe, using dual-direction high-pressure cleaning for better performance and heat transfer. Operators can remotely control the cleaning speed, ensuring consistent, thorough results. Protect your team and improve e ciency—contact NLB today to transform your operations!
Remove the operator from the blast zone. Increase tube heat transfer.
Enhanced operator control produces better results.
our future
By Luke Geiver
Effective plant hygiene practices aren’t just about maintaining production levels by attempting to control bacteria anymore. From highly strategic clean-in-place strategies to new bacteria control products, an ethanol plant’s approach to hygiene can create opportunities to enhance total production per batch and the quality or type of end products.
Eric Sumner has been working in the ethanol hygiene space for more than a decade for some of the biggest names in the industry. In the early 2000s, Sumner was part of a team that created and patented a unique fermentation additive used to control bacteria. The product provided an option that didn’t rely on the tried-and-true usage of antibiotic cocktails to mitigate the harmful effects of bacteria on yeast productivity during fermentation runs.
In 2021, Sumner formed a new team and a new company—ArrowUp—to build on his previous experience designing and deploying fermentation additives.
“ArrowUp has a vision of creating new value for our ethanol customers by helping them make more money from what they are already doing,” Sumner says. In essence, Sumner and his team believe they can help producers increase production by creating a better environment for the yeast strains to do their job.
With multiple patents already held, the company is working with many ethanol clients across North America, providing them with their trademarked ArrowUp Stinger package.
The first-generation liquid Stinger product (there’s already a new gel version in the works) does more than maintain, control or destroy bacteria. Stinger can promote greater batch production efficiency, which results in greater production volumes. The product
maximizes ethanol conversion by minimizing the production of organic lactic or acetic acids. Both acids are the root cause of lower production. Stinger can also eliminate process upsets created by bacteria outbreaks, Sumner says.
“Ultimately, it allows ethanol producers to see greater yields and efficiency by supporting stronger yeast prop, fermentation and storage performance, even with specialized and sensitive yeast strains,” he says.
Stinger is not an antibiotic-based product. According to Sumner, it works through oxidation and chemical destruction of bacteria cells at a microbial level. There is no risk of resistance from the bacteria, as the oxidation process kills all the bacteria.
Antibiotics work differently. Typically, an antibiotic strain or cocktail version of several strains will poison the bacteria and create a harsh environment before, during or after a yeast strain is deployed. Sumner explains that a ferm tank, beer well or other area in con-
tact with the bacteria can eventually develop and house an antibiotic-resistant strain that can survive from batch to batch. Antibiotic providers can and do rotate their products to avoid that problem, but if resistance occurs, the strains can survive from one batch to the next. This means production volumes in consecutive batches can be negatively altered until a new antibiotic is used, Sumner says.
“Our process controls a chemical reaction versus making the fermentation environment toxic to bacteria,” Sumner says.
Stinger deploys chlorine dioxide, a product also used in wastewater treatment facilities, drinking water facilities, pulp and paper mills and other established industries. Chlorine dioxide, not handled or used properly, can be highly reactive—almost like a match head when the right energy encounters the liquid product. Thus, since his early days developing and deploying Stinger, Sumner has had to find ways to stabilize it. ArrowUp has created an effective and safe deployment sys-
tem to combine a full enclosure around the product and an irrigation timer that ensures even the smallest drop of the product will be washed away and cleaned safely. The process is also certified GRAS (generally recognized as safe).
ArrowUp’s Stinger can be used during yeast propagation, yeast fermentation and with product storage inside the beer well. Before a yeast is introduced to a fermentation tank, it must be propagated to grow into more yeast at a volume that will achieve full production of the mash. Sumner and his team will help every plant customize the addition of its Stinger product into the propagation process to ensure the yeast responds favorably and isn’t compromised.
But it’s the fermentation process where the ArrowUp option offers the most production enhancement potential, Sumner says.
“The best yields I’ve ever seen have not come from antibiotics, they have come from using chlorine dioxide technology,” he says.
According to Sumner, Stinger has already helped plants increase productivity by a couple percentage points. “That presence of bacteria is a value going out of the door,” he says. “They are losing money on their acids.” Sumner says, in some cases, there could be a 3% to 4% difference in yield between a chlorine dioxide product and an antibiotic mix.
ArrowUp provides its products in totes at a 32% solution or via trunk tankers that can fill an on-site tank monthly. For every client that wants to explore or even switch to the Stinger approach, ArrowUp will run batch trials to ensure its effectiveness and prove the enhanced results will be reproducible for the yeasts chosen by each plant.
The Stinger approach is more expensive than antibiotics, but it is not an apples-toapples comparison, Sumner says. The team brings its own equipment to install the safety deployment systems, and they only charge for the product itself.
“The ROI is better than antibiotics,” he says.
Sumner urges producers to constantly think about the yeast environment. A 2024 study published in the widely read journal Nature, highlights the important interplay between yeast performance, yeast environment and overall production yield.
In “Strain Dynamics of Contaminating Bacteria Modulate the Yield of Ethanol Biorefineries,” the study’s authors point out how important it is to control bacteria during fermentation.
“Improved microbial management strategies could unlock environmental and economic gains in the U.S. ethanol industry,” the authors write. The concept is no secret to producers, but Sumner says many in the industry have yet to grasp the idea of controlling the environment as a means to enhance production.
Yield levels are always hampered by factors intrinsic to the production process, the study points out, including continual changes in oxygen levels, temperature, pH, ethanol concentration and others. All those factors create a less-than-ideal environment for yeast.
There are several ways to improve the environment or rid it of unwanted bacteria including, but not limited to, antibiotics, additives like Stinger or even acid-wash steps.
Regardless of the approach, controlling the bacteria or hygiene of the process can maintain or even improve the bottom line of every batch.
Today, producers looking to modernize plant hygiene can go beyond fermentation. Companies like Polar Clean provide dry ice blasting to remove dust and dried distillers grain residue from electrical, thermal and facility equipment to help plants save on energy costs. Other firms, like Lakos, provide
separators that ensure CIP runs don’t create an accumulation of solids in holding tanks or other areas where backed-up material could create a build-up of bacteria.
Some plant hygiene practices are free, according to Lallemand Biofuels and Distilled Spirits. Any plant manager can establish and maintain a plant cleaning schedule, inspect lines, monitor spray balls or temperatures and check samples on HPLC, according to the company, whereas practices like bleaching sumps or beer wells cost money. Companies like Ecolab believe plant hygiene isn’t a one-size-fits-all approach and that truly optimizing a plant should require a full assessment of measures to clean more effectively, while also auditing the process to ensure optimal performance.
Kemin Bio Solutions out of Des Moines, Iowa, has taken a big step in its commitment to plant hygiene. In June of 2024, Kemin acquired Archangel, a company specializing in antimicrobial solutions for fermentative biofuel production. Lau-
ren Hurt, company spokesperson and the head of global corporate affairs, says the acquisition was significant because it gives Kemin an antimicrobial product line with multiple antibiotic-free products that “align with industry trends toward sustainable and residue-free biofuel production,” she says.
Kemin’s newly purchased and trademarked Nova EZP is a concentrated ethyl lauroyl arginate-based powder that is effective against both gram-negative and grampositive bacteria strains. Gram-positive strains are built with a singular cell wall, while gram-negative strains feature a dual
cell-wall, construction. The dual mode of action present in the product acts on the cell membrane and the cell cytoplasm of the bacteria, which ultimately inhibits bacterial resistance no matter its electron formation.
The antimicrobial products are made of natural raw materials. L-arginine is a non-essential amino acid, present in many foods like cheese, poultry and nuts. Lauric acid, another component in the powder, is present in coconut and palm kernel oil.
The Nova EZP product works best in the propagation and fermentation stages, according to Hurt, and is effective in pH ranges of 3 to 7. Like the ArrowUp products, Nova EZP is certified GRAS and non-GMO. For ethanol plants that prefer automated dosing and the use of totes, Kemin offers a liquid form of its antimicrobial product through the Nova EZL line.
Kemin also provides in-house fermentation capabilities so it can replicate fermentation conditions and provide reliable data to its customers, Hurt says. And, like Sumner, Ke-
ai172122621117_ICM4602 FOT Oil Recovery Ad_EPM_7.5x4.625 with .25 bleed .pdf 4 7/17/2024 9:23:32 AM
min knows the industry wants alternatives to antibiotics.
Kemin’s mineral-based Kallsil supports the quality of end products like dried distillers grains. Enhanced zeolite-based Kallsil reduces the harmful effects of naturally occurring fungal metabolites in livestock and poultry feeds. It has the potential to reduce caking caused by mold growth, Hurt says.
New products from Hurt’s team or others across the industry show that from fermentation to feed, producers have new tools, options and products that align with the current trends of the industry, all offered to not only maintain, but enhance what they’re already producing.
Author: Luke Geiver writer@bbiinternational.com
BASF offers ethanol producers an innovative tool for tracking low CI feedstocks, enabling them to access potential tax credits and partner with farmers and their trusted agronomic advisors.
By Katie Schroeder
Entering the new year, ethanol producers may have questions about the logistics of utilizing low carbon intensity (CI) corn as a feedstock to access lucrative tax credits. The Low Carbon Intensity Crop program (LCIC) is an integrated service from BASF and Anew that offers ethanol producers a way to source low CI corn directly from the farmer, utilizing the ecosystem of the retailer and trusted retail agronomist to work directly with farmers to gather the documentation needed to access tax credits, explains Jeff Carver, commercial and technical service manager with BASF.
BASF has expanded the xarvioFM (Field Manager) platform with a new interface for ethanol producers—titled xarvio Bioenergy—which offers a straightforward solution to accessing and managing documentation of sustainable agricultural practices.
“[Xarvio Bioenergy] interfaces with xarvioFM that the ag retail agronomist uses with the farmer to help track the low carbon intensity crop practices that farmer is doing on that farm and documents it throughout the growing season, and then upon delivery of that corn provides a final CI score as well as all the documentation,” says Carver.
The platform enables the trusted agronomist to be a vital go-between, helping educate farmers on the ag practices needed to qualify for tax credit programs and giving ethanol producers the data needed to offer the best premium for the high quality, low-CI corn that the farmers provide.
By Jacqui Fatka
The biofuels sector embarks on 2025 facing several headwinds from political and regulatory uncertainty, while tailwinds could continue from strong exports and higher biofuel mandates from countries around the world.
Renewable diesel (RD) expansion, driven by California’s Low Carbon Fuel Standard, and the world’s growing appetite for ethanol boost the biofuels outlook in 2025. The U.S. Energy Information Administration projects a modest increase in biofuel production over the course of the year, although ethanol supplies will maintain 2024 production levels of 1.05 million barrels per day (b/d). Biodiesel supplies will drop nominally, while renewable diesel will increase from 210,000 b/d to 230,000 b/d (figure). Renewable naphtha and renewable propane are byproducts of a growing RD industry, helping double production of “other biofuels.”
How the incoming administration and Republican-controlled House and Senate finalizes the Inflation Reduction Act’s Clean Fuel Production Tax credit 45Z will be a major driver of expanded biofuel production with lower emissions. The completion of regulations that account for climate-smart agricultural practices and adequately reward corn and soybean producers will be the lynchpin for future revenue opportunities. Ethanol producers have the most to gain if lower carbon intensity corn can help plants qualify for the 45Z tax credit.
Year-round E15 adoption can see a renewed push under the incoming Trump administration and offset some of the reduced domestic ethanol gasoline consumption due to lower consumer use, as well as the presence of more electric and hybrid vehicles on the road. The shift to E15 from E10 can provide cost savings for consumers but will face logistical challenges of blending and distributing another grade of gasoline as retailers will need to update infrastructure. Ethanol producer margins turned lower in 2024 as excess capacity came online, and
it may take much of 2025, or possibly longer, to better align capacity with demand.
U.S. ethanol exports set new records in 2024 with Canada as the top destination. USDA anticipates 2025 ethanol exports to reach $4.2 billion in value, tying the 2023 record value. Falling ethanol export unit values may slightly offset higher volumes, likely hitting above last year’s record of 1.8 billion gallons. Private estimates indicate ethanol exports could surpass 2 billion gal/yr. Expanded renewable blending requirements around the world help build global demand. Indonesia is working toward instituting a 5% blend of fuel ethanol into gasoline for retail use (E5) in 2025, while Vietnam is expanding is current E5 mandate.
The impact of potential tariffs on world trading partners and retaliatory tariffs on U.S. agricultural products, including ethanol and DDGs, could limit ethanol export growth. Brazil’s increasing corn production supported the country’s own domestic growth of corn ethanol facilities, which may increase ethanol competition in the world market.
Statutorily, the U.S. Environmental Protection Agency was to propose new renewable volume obligations in the Renewable Fuels Standard last November, but the Biden administration chose to punt that until 2025. The incoming administration is not apt to quickly propose new 2026-2029 RVO levels but will instead wait, making decisions on pending small refinery exemptions (SREs) first. During the previous Trump term, EPA granted 34 SREs from the 2017 compliance year. Under the Biden administration, the EPA did not approve any SREs and instead denied 79 requests. Now the EPA will need to reevaluate those earlier denials and more, totaling 129 exemption petitions from 2018 and later.
The biodiesel industry criticized EPA for setting the 2023-2025 RVO biomass-based diesel (BBD) levels too low and underestimating the capacity potential from the industry’s $6 billion capacity expansion investments. In 2023, domestic and imported feedstocks supported the production of 4.3 billion gallons of BBD, which surpassed the yearly
CONTRIBUTION: The claims and statements made in this article belong exclusively to the author(s) and do not necessarily reflect the views of Ethanol Producer Magazine or its advertisers. All questions pertaining to this article should be directed to the author(s).
PRODUCTION PROJECTIONS: This graph from the Energy Information Administration shows the capacities of various biofuels, as well as the projected capacity for 2025.
SOURCE: EIA
renewable volume targets for 2023, 2024 and 2025. In 2024, additional blending of soy oil and imported tallow and used cooking oil (UCO) pushed levels above mandated volumes. Soy oil could recapture blending market share if tariffs or regulatory action limit the imports of UCO and tallow, as well as the domestic build out of renewable fuels in China and Brazil where these imported oils originate. China already eliminated its 13% export tax rebate for UCO which will incentivize more Chinese use of its UCO supplies rather than export.
Renewable diesel production capacity will grow just 100 million gallons from 2024 to 2025, reach a total of 5.2 billion and remain steady through 2026, according to an updated analysis from University of Illinois. Despite the recent boom in RD production and a predicted expansion of 20% or more per year, the latest outlook reveals the industry is temporarily plateauing. Beyond the RVO mandates, California and other states’ low carbon fuel programs encourage the continued shift from conventional diesel to RD. California’s 20% limit on vegetable oil feedstocks in its low carbon fuel standard puts downward pressure on the use of soy and canola oil in RD production.
Federal and state tax incentives and low carbon fuel policies will drive the future viability of sustainable aviation fuel (SAF) as most hydrotreated esters and fatty acids (HEFA) plants today can produce either RD or SAF based on market economics. Alcohol-to-jet SAFl has the potential to expand in the longer term, but small pilot and pre-pilot projects will provide minimal supplies in 2025. Airlines including United, Delta and Southwest secured a small amount of domestically produced SAF to fuel planes, but costs remain two to three times as expensive when compared to conventional airline fuel. EIA projects SAF production to expand to 50,000 b/d in 2025 if all announced capacity additions come online. However, today’s SAF use domestically, including some imported fuel, represents a drop in the bucket of the total domestic aviation fuel market.
At Growth Energy, we’re reimagining what’s possible with crops.
We’re the leading voice of America’s biofuel industry, who are helping transform abundant supplies of grain into a cleaner, healthier future for us all.
The promise of SAF may not be realized in the near term, despite the need to continue to find a new demand base to support struggling corn and soybean prices domestically. Potential expansion of SAF is limited by a short tax credit runway for the 45Z, as well as delayed regulatory guidance and uncertain political actions. Illinois’ $1.50 tax credit incentive for SAF limit soy oil’s use but makes the state a potential hub for SAF growth.
Author: Jacqui Fatka, CoBank farm supply and biofuels lead economist JFatka@cobank.com