www.biomassmagazine.com/pellet PLUS: Material Flow Impacts on Plant Performance Page 26 US, ProjectCanadaRoundup Page 12 Tips to Reduce Costs, Downtime Page PRESSING22 EFFICIENCYFOR Issue 3, 2022
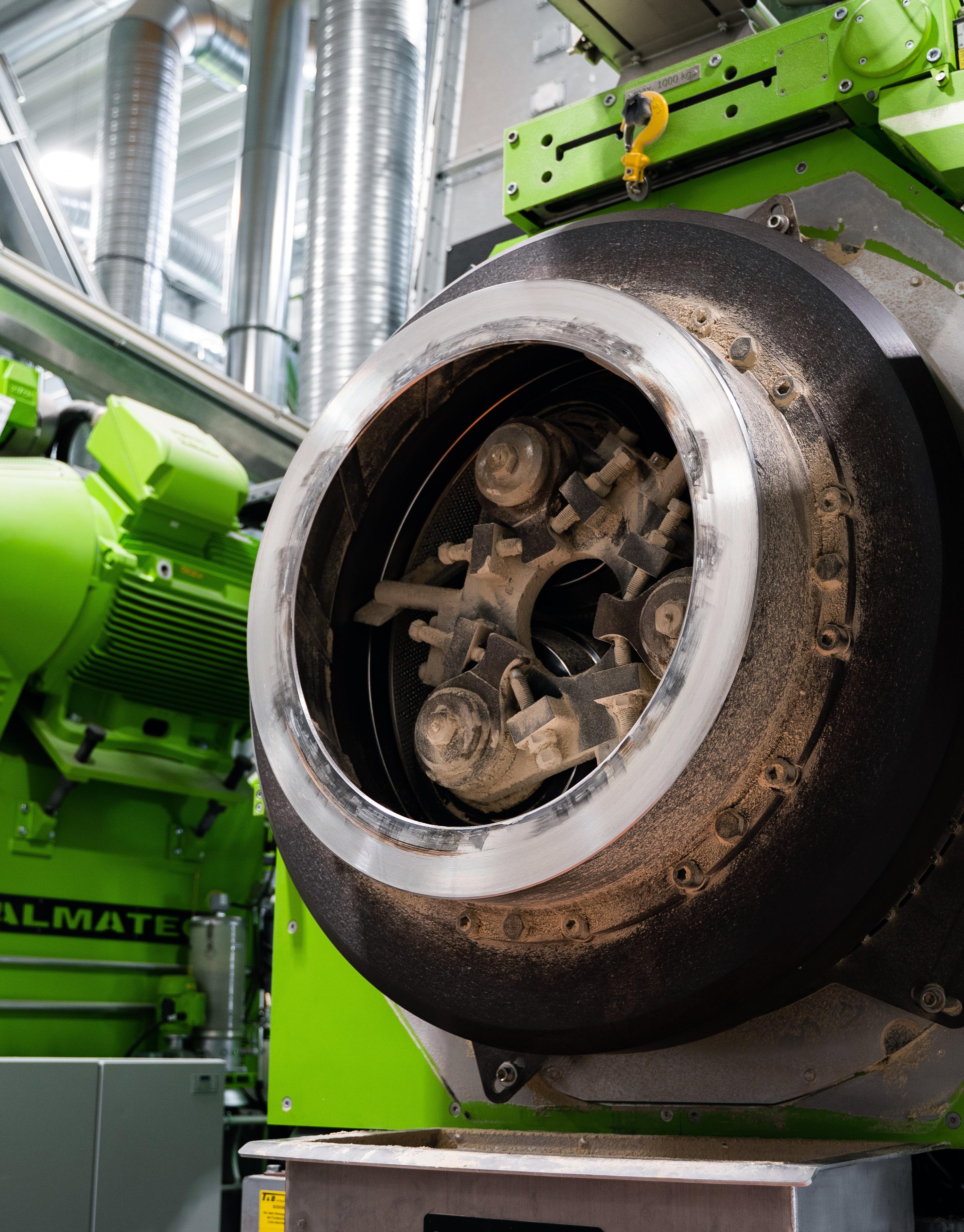
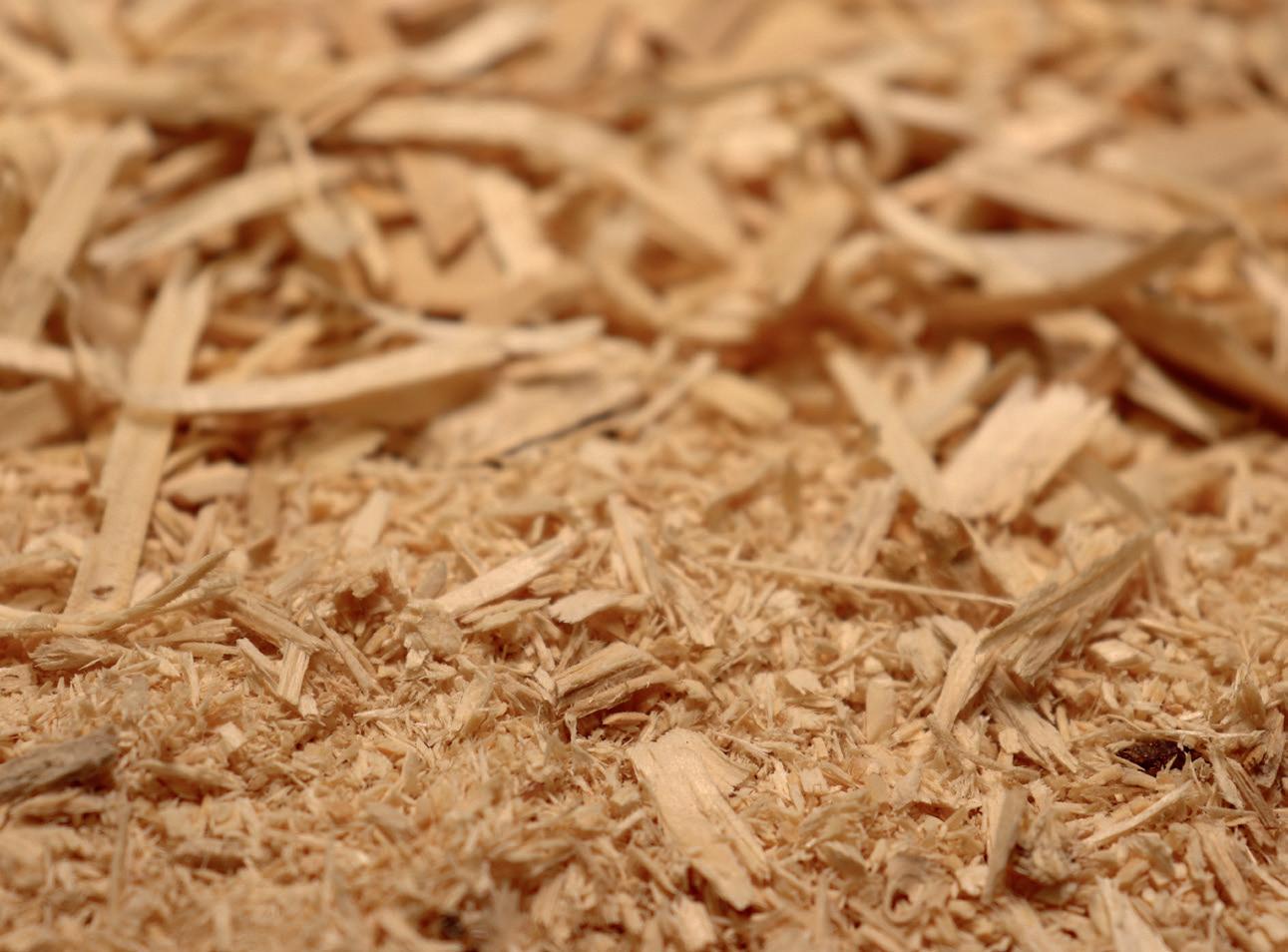
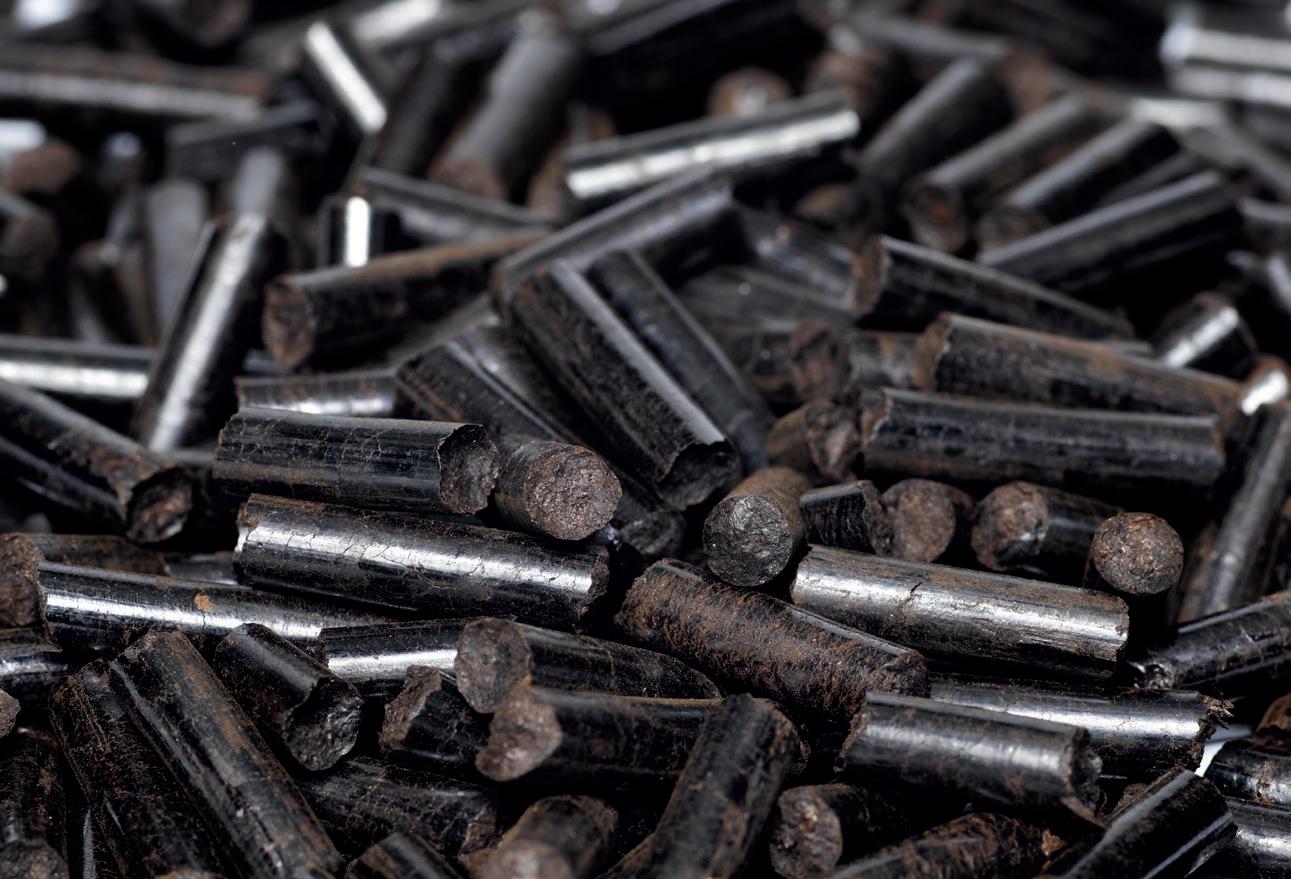
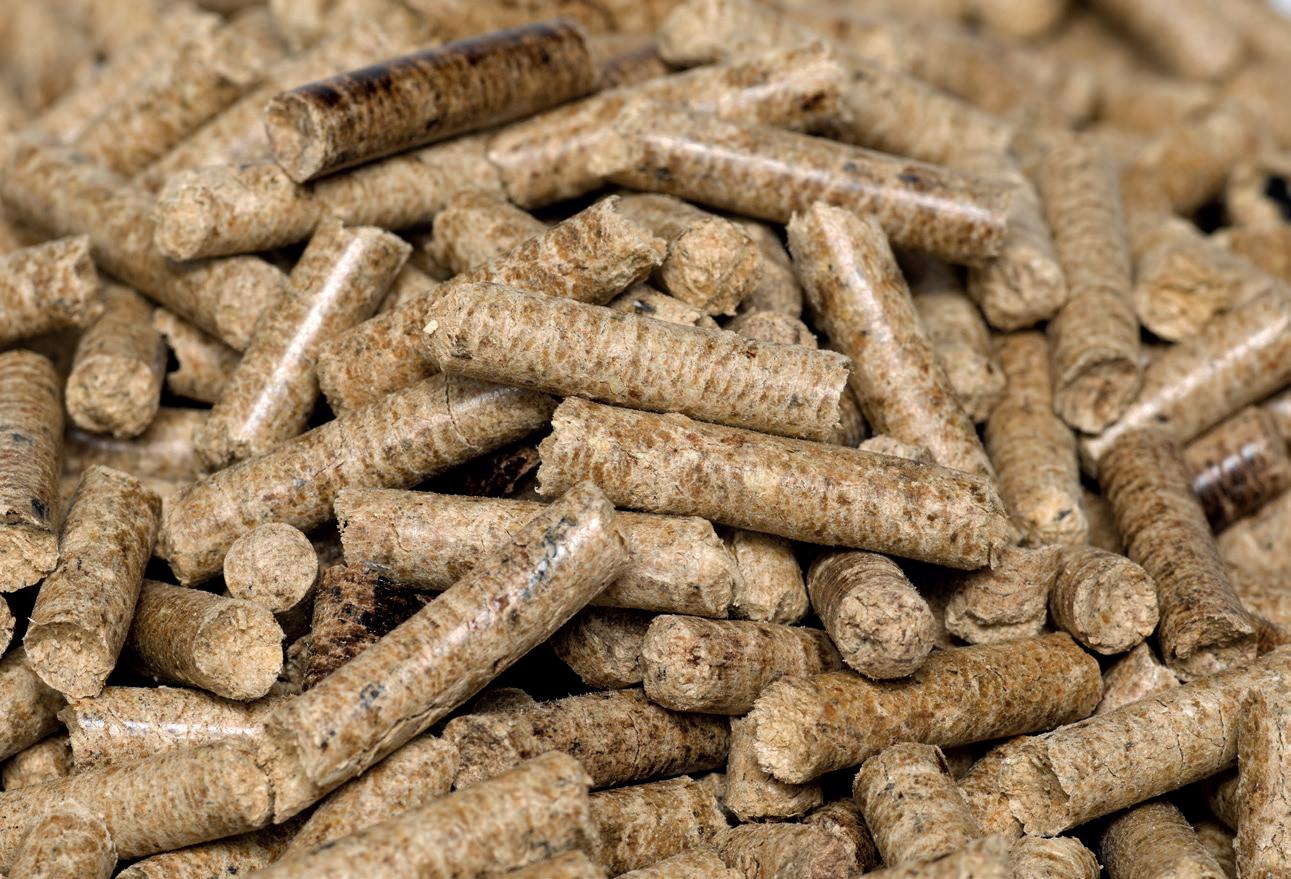

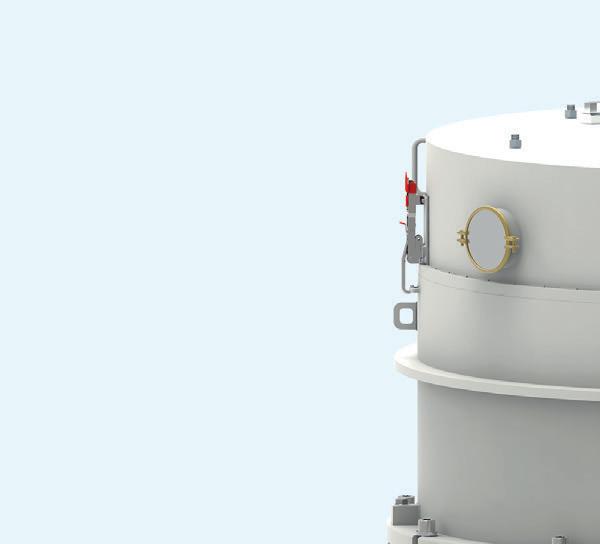
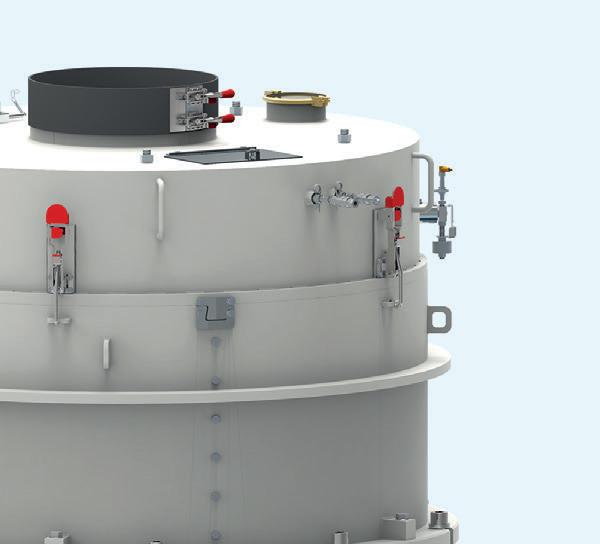

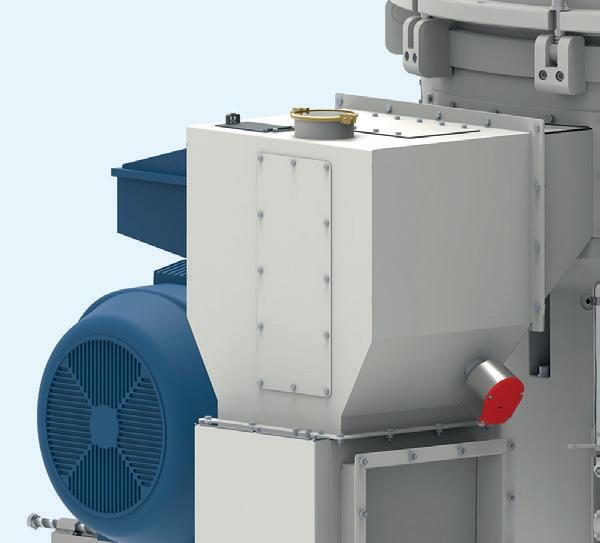
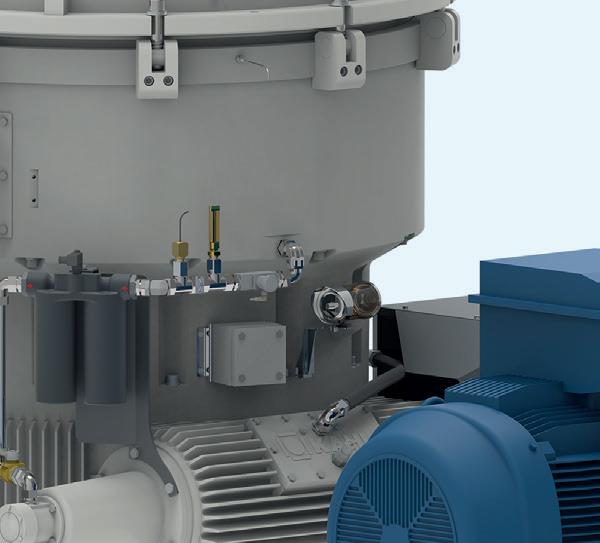

BIOMASSMAGAZINE.COM/PELLET 3 Pellet Mill Magazine Advertiser Index 29 2023 U.S. & Canada Fuel Pellet Production Map 14 Agra Industries 11 Airoflex Equipment 2 AMANDUS KAHL GmbH & Co. KG 28 Benetech 32 CPM Global Biomass Group 16 Evergreen Engineering 19 IEP Technologies 10 Jacobs Corporation 15 KEITH Manufacturing Company 27 KESCO, Inc. 23 Mid-South Engineering Company 17 MoistTech 22 PAL s.r.l. 25 Screw Conveyor Corporation 18 Timber Products Inspection / Biomass Energy Laboratories 30 USIPA C ontents » 2022 | VOLUME 12 | ISSUE 3 04 EDITOR'S NOTE Turning to Wood Heat Amidst an Energy Crisis By Anna Simet 05 EVENTS 06COLUMNSTheBTUAct Breaks Out By Tim Portz 07 Celebrating National Forest Week By Thomas Meth 08 NEWS ROUNDUP 10 PODCAST PREVIEW 12FEATURESPROJECTDEVELOPMENTBuildingOutCapacity Pellet Mill Magazine provides a roundup of U.S. and Canada pellet plants under development and construction, as well as closures and acquisitions. By Anna Simet 18 CARBONCutting Carbon Via Sails A new sail technology and environmentally friendly bulk carrier development has attracted the interests of Drax Group and Enviva. By Katie Schroeder 22CONTRIBUTIONSOPERATIONS&MAINTENANCEO&MTipsforEfficientPelletProduction Each hour that a pellet operation is not in production equates to lost money. By Timo Müller 26 EFFICIENCYTheInfluence of Material Flow on Pellet Mill Performance The topic of dust control and management is not limited to safety, as it can impact other aspects of production. By Holger Streetz SPONSOR SPOTLIGHT 28 MATERIAL BENETECHHANDLING A Low-Cost Solution to Combat Off-Center Loading PHOTO: CM BIOMASS ON THE COVER The press chamber of a three-roller pelletizer with a 900-millimeter ring die, by Salmatec PHOTO: SALMATEC
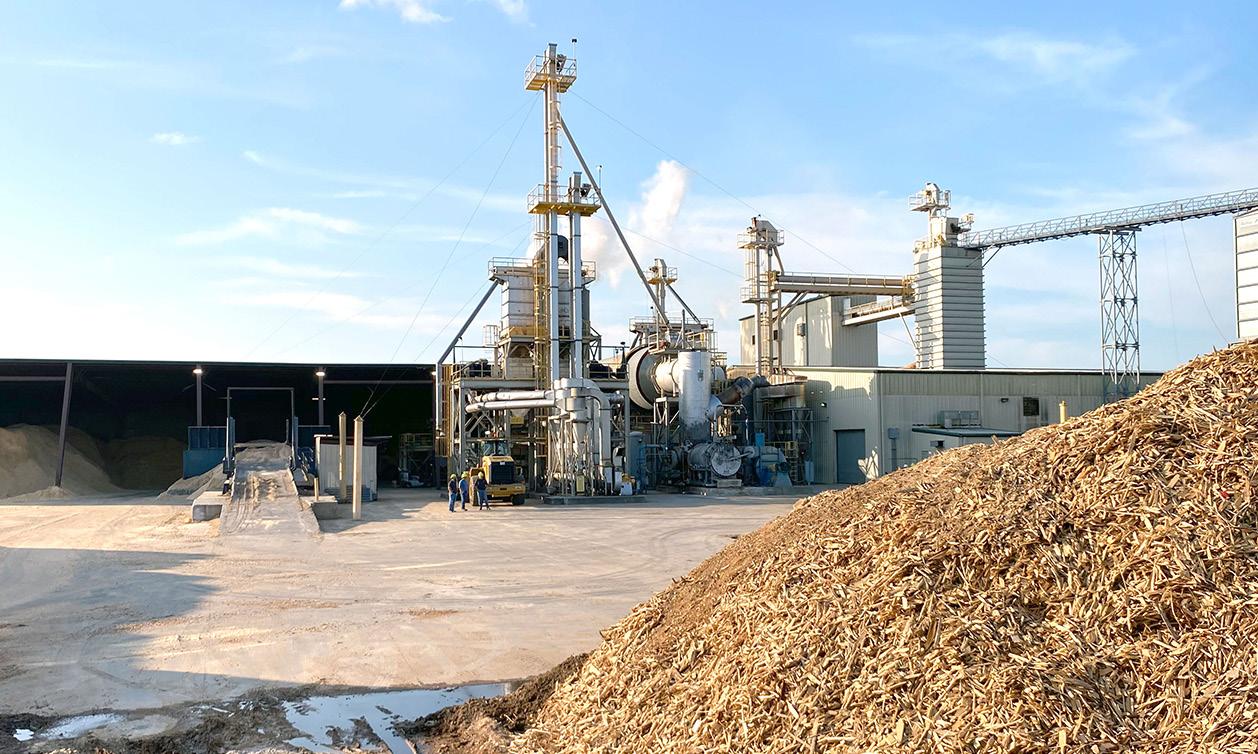
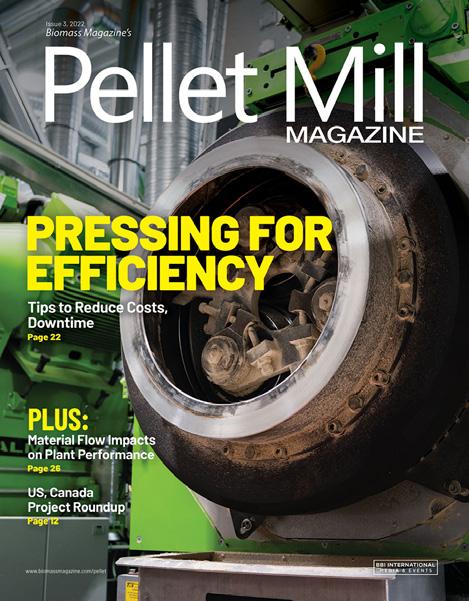
Subscriptions to Pellet Mill Magazine are free of charge distributed 4 times/year to Biomass Magazine subscribers.To subscribe, visit www.BiomassMagazine.com or you can send your mailing address to Pellet Mill Magazine Subscriptions, 308 Second Ave. N., Suite 304, Grand Forks, ND 58203. You can also fax a subscription form to 701-746-5367. Back Issues & Reprints Select back issues are available for $3.95 each, plus shipping. Article reprints are also available for a fee. For more information, contact us at 866-746-8385 or service@bbiinternational.com. Advertising Pellet Mill Magazine provides a specific topic delivered to a highly targeted audience. We are committed to editorial excellence and high-quality print production. To find out more about Pellet Mill Magazine advertising opportunities, please contact us at 866-746-8385 or service@bbiinternational.com. Letters to the Editor We welcome letters to the editor. Send to Pellet Mill Magazine Letters to the Editor, 308 2nd Ave. N., Suite 304, Grand Forks, ND 58203 or email to asimet@ bbiinternational.com. Please include your name, address and phone number. Letters may be edited for clarity and/or space.
4 PELLET MILL MAGAZINE | ISSUE 3 2022
The other feature in this issue, “Cutting Carbon Via Sails,” page 18, goes into detail about Drax’s partnership with MOL Drybulk, which has developed a cutting-edge sail technology that is expected to reduce carbon emissions of Drax’s wood pellet exports. Enviva has also partnered with MOL for a similar initiative, and a long-term goal of both us to integrate the use of alterna tive fuels as well. On the operations and maintenance side of the equation, be sure to read “O&M Tips for Efficient Pellet Production,” on page 22, well as “The Influence of Material Flow on Pellet Mill Performance,” on page 26. The latter is focused on dust control and management, but emphasizes that this isn’t just a safety topic—it can have big influence on the pelletization process and product quality.Finally, Pellet Mill Magazine will be heading to Miami in October for the U.S. Industrial Pellet Association’s annual Exporting Pellets Conference. Hope to see you there—be sure to stop by our booth.
Much of the world is facing daunting challenges when it comes to energy, due to a number of influences that include rocketing prices, supply chain disruptions, lingering pandemic effects, inflation and an ongoing war. While the U.S. has not remained unscathed by any means, the severity in some other countries is of a much deeper extent. National media outlets report that Germany is rationing hot water, dimming street lights, reducing heating during the night, etc.—all measures aimed at minimizing an unprecedented energy shortage this upcoming winter. Firewood and wood pellet sales have been soaring—to the point of some suppliers rationing sales, too. Deutsche Bank issued a notice on the energy supply situation in mid-June, advising that if further disruptions of Russian natural gas supply to western Europe occur, German households will need to turn to wood heat. Here in the U.S., consumers face steep energy costs, with homeowners using fossil fuels pro jected to spend thousands more this year than in previous years. In Maine, for example, one of the most heating oil-dependent states in the country, the cost of wood pellets per MMBtu as of Aug. 1 was $18.91—for heating oil, it was $34.97 per MMBtu. While the savings alone may be a motivator for some consumers to seriously consider a heating fuel switch, the current tax credit via the BTU Act may just seal the deal. Currently, it is at 26% and is set to expire next year, but the Inflation Reduction Act—which was just passed by the Senate and is headed to the House for a vote—reups the credit to 30% and extends it for 10 years, although it does cap the credit at $2,000.As for expanding pellet production capacity in the U.S. and Canada to meet growing de mand, much of what’s currently under construction or expansion will be funneled into the export market, though there are some domestic producers making investments in modest capacity ex pansions. While we work to update our 2023 U.S. and Canada Fuel Pellet Production Map, I put together a list of developing and active projects in our page-12 feature, “Building Out Capacity,” which also includes some closures and acquisitions (this is not an exhaustive list, however). The next map will be mailed out with Q1 2023 issues.
Editor's
Turning to Wood Heat Amidst an Energy Crisis
« Note Anna Simet asimet@bbiinternational.comEDITOR

|
Now in its 16th year, the International Biomass Conference & Expo is expected to bring together more than 800 attendees, 140 exhibitors and 65 speakers from more than 21 countries. It is the largest gathering of biomass professionals and academics in the world. The conference provides relevant content and unparalleled networking opportunities in a dynamic business-to-business environment. In addition to abundant networking opportunities, the largest biomass conference in the world is renowned for its outstanding programming—powered by Biomass Magazine—that maintains a strong focus on commercialscale biomass production, new technology, and near-term research and development. (866) 746-8385
BiomassConference.com
Please check our website for upcoming webinars Please recycle this magazine and remove inserts or samples before recycling © 2022 by BBI International
| NationalCarbonCaptureConference.com
www.biomassmagazine.com/pages/webinar TM
2023 Int’l Fuel Ethanol Workshop & Expo JUNE 12-14, 2023 CHI Health Center, Omaha, Nebraska
COPYRIGHT
From its inception, the mission of this event has remained constant: The FEW delivers timely presentations with a strong focus on commercial-scale ethanol production—from quality control and yield maximization to regulatory compliance and fiscal management. The FEW is the ethanol industry’s premier forum for unveiling new technologies and research findings. The program is primarily focused on optimizing grain ethanol operations while also covering cellulosic and advanced ethanol technologies. (866) 746-8385
| FuelEthanolWorkshop.com
2023 Int’l Biomass Conference & Expo FEBRUARY 28 - MARCH 2, 2023 Cobb Galleria Centre, Atlanta, GA
BIOMASSMAGAZINE.COM/PELLET 5 EDITORIALEDITOR Anna Simet asimet@bbiinternational.comONLINENEWSEDITOR Erin Voegele evoegele@bbiinternational.comSTAFFWRITER Katie Schroeder kschroeder@bbiinternational.comDESIGNVICEPRESIDENT,PRODUCTION&DESIGN Jaci Satterlund jsatterlund@bbiinternational.comGRAPHICDESIGNER Raquel Boushee PUBLISHINGrboushee@bbiinternational.com&SALESCEO Joe Bryan jbryan@bbiinternational.comPRESIDENT Tom Bryan VICEtbryan@bbiinternational.comPRESIDENT,OPERATIONS/MARKETING&SALES John Nelson jnelson@bbiinternational.comSENIORACCOUNTMANAGER/BIOENERGYTEAMLEADER Chip Shereck cshereck@bbiinternational.comACCOUNTMANAGER Bob Brown bbrown@bbiinternational.comCIRCULATIONMANAGER Jessica Tiller MARKETINGjtiller@bbiinternational.com&ADVERTISINGMANAGER Marla DeFoe mdefoe@bbiinternational.comMARKETING&SOCIALMEDIACOORDINATOR Dayna Bastian dbastian@bbiinternational.com Industry Events » 2022 National Carbon Capture Conference & Expo NOVEMBER 8-9, 2022 Iowa Events Center, Des Moines, IA Produced by Carbon Capture Magazine and BBI International, the National Carbon Capture Conference & Expo is a two-day event designed specifically for companies and organizations advancing technologies and policy that support the removal of carbon dioxide (CO2) from all sources, including fossil fuel-based power plants, ethanol plants and industrial processes, as well as directly from the atmosphere. The program will focus on research, data, trends and information on all aspects of CCUS with the goal to help companies build knowledge, connect with others, and better understand the market and carbon (866)746-8385utilization.
Author: Tim Portz Executive Director, Pellet Fuels www.pelletheat.orgtim@pelletheat.orgInstitute
6 PELLET MILL MAGAZINE | ISSUE 3 2022
The BTU Act Breaks Out BY TIM PORTZ As this edition of Pellet Mill Magazine goes to press, the Inflation Reduction Act of 2022 sits in limbo, passed by the Senate but awaiting a vote by the House of Repre sentatives and a signature from President Joe Biden. This feels largely like a formality as the Democrats look toward the midterm elections and delivering some tangible action on key pieces of their agenda, including investments in clean energy. The legislation includes over $350 billion in clean energy programs, including tax credits for everything from electric vehicles to hydrogen fuels cells to wood pellet stoves and boilers. Close observers of federal policy fully expect this legislation to pass through the House in an en tirely party line vote, be signed into law and hailed as a sig nificant victory for the Biden Administration. Supposing the predictions of a swift passage through the House and a signature by Biden play out, the domestic wood pellet will have achieved its most significant federal policy victory before this issue lands in industry mailboxes. A short history lesson in industry efforts to establish provisions of the Biomass Thermal Utilization Act in the right policy vehicle are warranted to illustrate the long and winding road this market-boosting policy has traveled. The act was introduced in February 2015 by Sen. Angus King, I-Maine, and Congressman Peter Welch, D-Vermont, in a move hailed by both the Pellet Fuels Institute and the Bio mass Thermal Energy Council. The policy chugged along in fits and starts for nearly five years before portions of it were included in the Consolidated Appropriations Act of 2021, signed into law by former President Donald Trump in December 2020. The policy included a tax credit for qualifying pellet appliances installed in residences for three years, starting out at a 26% credit (with no cap on the credit generated) and ratcheting down to 22% for 2022 and 2023. The Inflation Reduction Act of 2022 extends those same provisions with three notable changes. First, the tax credit has been raised to 30% of cost of the appliance and installation. Second, a $2,000 cap has been introduced to the tax credit. There was no cap on the tax credit passed in 2020. For manufacturers of large, whole-home pelletheating solutions, this cap dilutes the impact of a 30% tax credit. A consumer selecting an appliance and installation with a total cost of $10,000 would be capped at a $2,000 tax credit, effectively reducing the tax credit percentage to 20%. Finally, the tax credit has been extended through 2032, giving our industry and appliance manufacturers a much longer runway to capture the opportunities provided by the legislation. The tax credit on commercial installa tions of wood pellet appliances was not included in the legislation.Taken as a whole, the membership at the PFI sees this as a significant federal policy achievement that we’ve been actively working toward for a decade. With a 10-year runway, the tax credit is arguably the biggest policy win in the industry’s history. Getting more appliances installed in American homes is fundamental to growing the market for wood pellets, and this tax credit puts another arrow in the quiver of the hearth retailers we rely on to promote, sell and install the appliances that burn wood pellets. For the wood pellet sector to grow, either the number of installed appliances needs to increase, or the home heat ing season needs to deepen and lengthen. Anyone tracking heating degree days (HDD) knows that the current trend is toward shorter, milder winters and the marketplace im pact of those conditions is felt immediately. The 2021-‘22 heating season was largely a disappointment for wood pel let producers, as HDD numbers lagged well behind longterm averages, and pellet sales suffered as a result. A 30% tax credit on qualifying appliances is a tailwind for the wood pellet sector. Now, the work of maximizing its marketplace impact falls to industry participants. The Pellet Fuels Institute looks forward to working with our customers and partners in the space to capture the full op portunity this policy victory has provided.

BIOMASSMAGAZINE.COM/PELLET 7
Celebrating National Forest Week BY THOMAS METH
In honor of National Forest Week, we thank the dedicated men and women that serve in the USDA Forest Service. We appreciate the research that is conducted to advance wood science and applications that drive a circular economy, diversify wood applications and markets, keep manufacturing jobs in the U.S., and contribute to the pros perity of rural communities. We look forward to working together to continue our global efforts to maintain healthy, growing forests and to mitigate the effects of climate change this century and for generations to come.
Author: Thomas Meth President, www.envivabiomass.comEnviva
From July 11-17, we celebrated nearly 55 years of what is known today as National Forest Week, an annual celebration of the National Forest System, and all it pro vides and has to offer. I am humbled to be leading a com pany for the past 18 years that is dedicated to displacing coal, growing more trees and fighting climate change.
Climate change—the greatest challenge of our time—begins and ends with the forest. Whether through preservation, conservation, adhering to forestry best management practices, or overseeing a healthy, working, growing forest—we all play a role in sustaining and pro tecting the U.S. landscape. While national parks are highly vested in preservation, national forests are managed for many purposes—timber, recreation, grazing, wildlife and more. The USDA Forest Service was created to sustain the health, diversity and productivity of the nation’s forests and grasslands to meet the needs of present and future generations.Today,about 37% of all the land in the U.S. is cov ered in forests. In fact, our country has more than 751 mil lion acres of forest, 245 million acres of which are in the Southeast U.S. This region alone provides approximately one-fifth of the timber that is used globally each year to make long-lived wood products such as telephone poles, houses, furniture, books, diapers and more. U.S. forests are thriving and growing in inventory, according to the USDA Forest Service. For instance, in the U.S. Southeast alone, forests are growing at a rate nearly two times greater than they are being harvested. That is primarily driven by mod ern-day, sustainable forestry management practices and a robust wood products industry, including wood bioenergy, that incentivizes forest landowners to continue to grow forests instead of converting their land to nonforest use. Working forests in the U.S. Southeast, where Enviva’s operations are located, are a thriving ecosystem, provid ing value for both the environment and people. Wood is a renewable resource and sustainable material when it is harvested from responsibly managed forests. The robust market for forest products drives forest growth, green jobs and economic activity. According to Forest2Market, the forest products industry in the U.S. supports nearly 3 mil lion jobs, providing over $125 billion in payroll. According to the American Forest and Paper Association, the U.S. forest products industry is among the top 10 manufactur ing sector employers in 45 states. The industry accounts for approximately 4% of the total U.S. manufacturing gross domestic product, producing nearly $300 billion in products. Enviva supports over 4,200 jobs across the U.S. Southeast and creates over $3 billion in positive economic value in the areas in which we operate. Although Enviva does not own any forests, we play an important role in helping U.S. forests thrive and grow. For instance, Enviva produces wood pellets using an array of sustainable practices that protect environmentally sensitive areas and conserve working forests. To put our industry in perspective, only 3% of forests in the U.S. Southeast are harvested annually. From this, approximately 3% (of that harvest) is used for the biomass industry each year. As the data shows, these removals are more than offset by con tinual forest growth year over year. Additionally, sustain ably sourced biomass has been proven to reduce lifecycle greenhouse gas emissions by more than 85% compared to coal, and by more than 70% compared to natural gas. For this reason, sustainably sourced wood bioenergy is recog nized by leading scientific authorities around the world as an effective, renewable energy solution to mitigate the ef fects of climate change.

Pellet
The U.S. EIA has released the July edition of its U.S. Monthly Densified Biomass Fuel Report, which contains data for April from 80 operating manufacturers. These fuel pellet producers had a total production capacity of 13.27 million tons per year and collective ly had an equivalent of 2,463 full-time employees. In April 2022, monthly respondents purchased 1.72 million tons of raw biomass feedstock, compared to 770,000 tons in April 2021. Manufacturers produced 850,000 tons of densified biomass fuel, and sold 680,000 tons of densified biomass fuel. Domestic sales of densified bio mass fuel in April 2022 were 80,000 tons and averaged $200.34 per ton, compared to 110,000 tons sold at $184.19 per ton in 2021. Exports in April 2022 were 600,000 tons and averaged $160.83 per ton, compared to 580,000 tons averaging $177.52 in April 2021.
The U.S. exported 832,092.2 metric tons (MT) of wood pel lets in June, up from both 740,605 MT in May and 603,794.9 MT in June 2021, according to data released by the USDA Foreign Agricultural Service on Aug. 4. The U.S. exported wood pellets to more than a dozen countries in June. The U.K. was the top destina tion for U.S. wood pellets at 518,904.3 MT, followed by the Neth erlands at 249,065 MT and the French West Indies at 36,019.5 MT. The value of U.S. wood pellet exports reached $141.32 million in June, up from both $131.78 million the previous month and $82.97 million in June of last year.
Blackwood Technology B.V. and TTCL Public Company Ltd. reported the inauguration of a torrefaction demonstration plant in the Lampang province of Thailand. The demo plant is using Blackwood’s proprietary FlashTor torrefaction technology to turn low-grade plant biomass into a torrefied pellets, black pel lets or biocoal, according to the companies. Beyond the successful launch of the demo plant, Blackwood and TTCL state they have started engineering work for a commercial-scale FlashTor torrefac tion plant in Thailand. The partners plan to roll out more plants in Thailand and other Southeast Asian countries.
News Roundup
8 PELLET MILL MAGAZINE | ISSUE 3 2022
The European Union consumed a record 23.1 million met ric tons (MT) of wood pellets in 2021, according to a new report filed with the USDA Foreign Agricultural Service Global Agricultural Information Network. Demand is expected to expand to 24.3 million MT this year. The report primarily attributes the record-breaking 2021 consumption to increased residential use in Germany and cofiring of wood pellets with coal in the Nether lands. Increased consumption this year is expected to result from the expansion of EU residential markets, mainly in Germany and France, boosted by support programs for the installation of bio mass boilers and the high price of fossil fuels. The report notes that EU demand for pellets has significantly outpaced domestic pro duction for the past 10 years, resulting in increased imports from Russia, the U.S., Belarus and Ukraine. The EU, however, in April 2022 banned the import of Russian wood pellets in response to the country’s invasion of Ukraine.
Drax Group plc experienced significant increases in both op erating profit and wood pellet production when compared to the same six-month period of 2021, according to the company’s finan cial and operational results for the first half of 2022. Drax pro duced approximately 2 million metric tons (MT) of wood pellets during the first half of this year and shipped 2.4 million MT. The company produced and shipped 1.3 million MT of pellets during the same period of 2021. An estimated 1 million MT of wood pel lets were sold to third parties during the first half of 2022, up from 400,000 MT during the same period of last year. Drax also recently announced the expansion of its operations into Japan. To celebrate the launch of Drax Asia and the opening of a new office in Japan, more than 160 that included government officials, major trading houses, energy businesses and shipping companies, attended a reception at the British Ambassador’s resi dence in Tokyo.
Ecostrat Inc. announced that Airex Energy has joined the BDO Zone Strategic Alliance as a partner in the technology group. Ecostrat describes its BDO Zone Strategic Alliance Partners as some of the leading companies in the bioenergy industry that help de-risk biobased project development in BDO Zones. Airex En ergy’s biomass carbonization systems enable large-scale production of biocoal pellets and biochar, according to the company, via its proprietary CarbonFX technology. Airex Energy has operated an industrial-scale biocarbon plant in Canada since 2016. The plant, in operation 24/7, is located in Bécancour, Québec.
Denmark-based energy company Orsted A/S plans to establish carbon capture at two of its biomass-fired power sta tions and utilize surplus heat to reduce the long-term consump tion of wood pellets for district heating. According to the July 5 announcement, the company plans to establish carbon capture at its Avedore Power station’s straw-fired boiler and at its Asn aes Power Station. The Avedore facility, located near Copenha gen, is primarily fueled with wood pellets and straw and has the capacity to generate 806 MW of heat and 953 megajoules per second (MJ/s) of heat. The Asnaes facility is located in Kalun dborg, Denmark. It is primarily fueled with wood chips and has the capacity to produce 26 MW of electricity and 125 MJ/s of heat. If implemented, planned carbon capture and storage and green fuels projects would create large amounts of surplus heat that can be utilized by the district heating system served by the Avedore Power Station. Use of the surplus heat would reduce the long-term demand for wood pellet heating fuel, according to Orsted.
BIOMASSMAGAZINE.COM/PELLET 9 PELLET & POWER ROUNDUP ¦
PHOTO: ASNAES POWER STATION/ ØRSTED
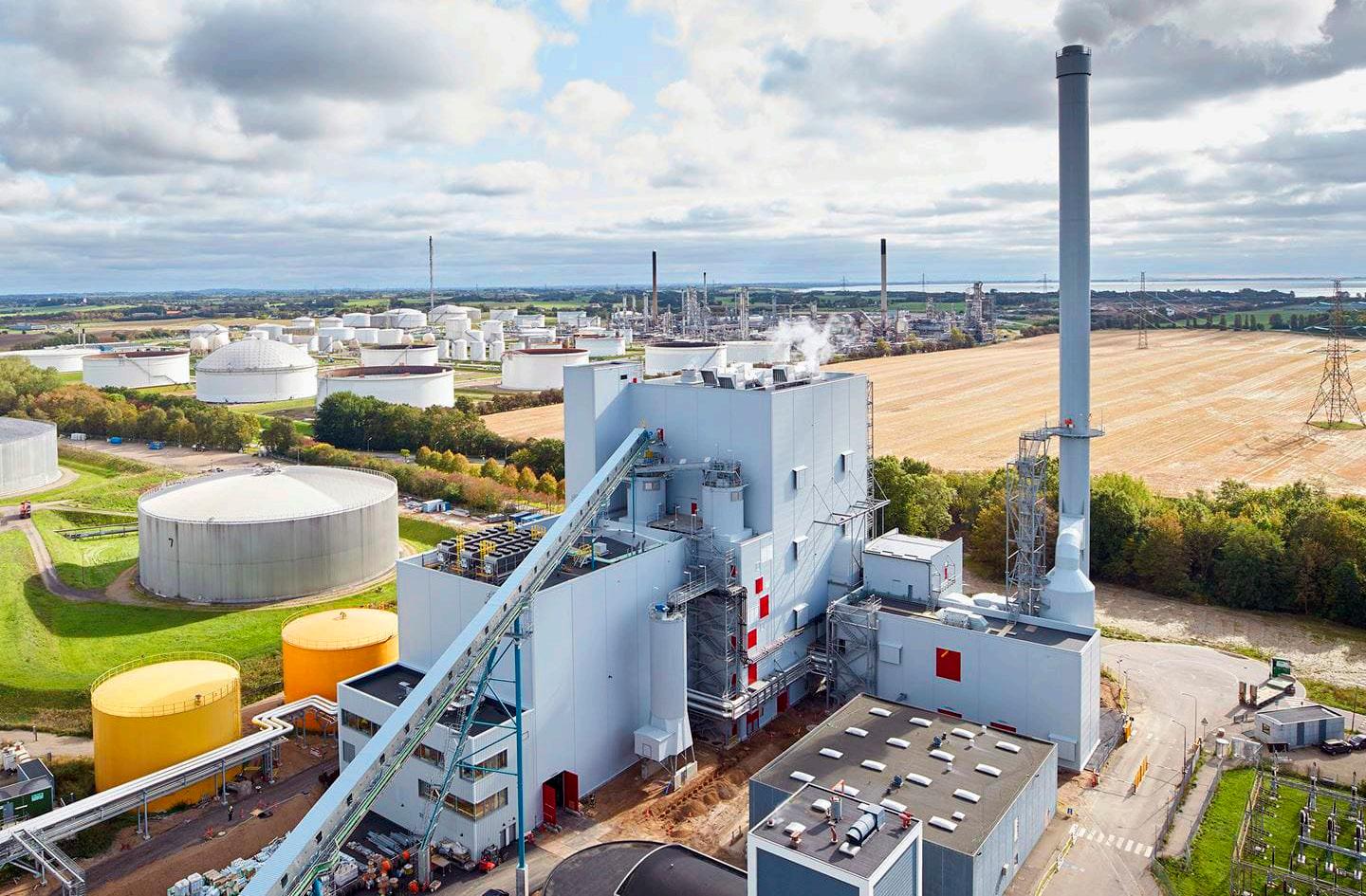
A significant proportion of that 3.4 million tons is challenged—a lot of it won’t make its way into Europe, because the certifications from SBP (Sustainable Biomass Partnership) have been withdrawn, as well the other major certification agencies, which means eastern European and U.K. utilities would not get the credits that they need
PREVIEW WITH WILLIAMSTRAUSS STRAUSS
PODCAST
William Strauss, president of wood pellet consultancy firm FutureMetrics Inc., was Biomass Magazine’s first guest on its newly launched podcast series. If you’re active in the wood pellet industry, you likely know or have at least heard of William, who goes by Bill. He is a wellrespected, widely recognized industry expert, and for Volume 1, Episode 1, he shared some insight on the current state of the global pellet market, with a focus about the current challenges—and right now, there are quite a few.
10 PELLET MILL MAGAZINE | ISSUE 3 2022
PMM: The Russian attack on the Ukraine, as well as other market forces, are really straining global wood pellet supply. Can you provide a high-level view of what’s going on in the markets right now? W.S. The industrial pellet markets have grown tremendous ly over the past 10 years or so—actually over the past 20 years, from almost nothing. One of my colleagues at FutureMetrics, John Swaan, filled and shipped the first vessel of industrial pellets to ever leave North America in bulk, back in 1998 ... so that is just how young his industry is; it didn’t exist before that first shipment, out of western Canada to Sweden. In 2021, total exports in the indus trial market were almost 23 million tons. The average growth rate over the past 10 years in the market has been close to 17% for an nualized growth rate, so the market is large and has grown tremen dously—we expect it to continue to grow, especially among Asian countries, specifically Japan. So, it’s already turning into something of a mature market with a 23 million-metric-ton volume, but as you suggested in your question, recent events have really turned things upside down—it’s a highly disruptive period of time in the com modity markets, including wood pellets. So, for Russia, Belarus and the Ukraine, in 2021, total exports from those three countries were about 3.4 million tons, and that was about 15% of the total global market for industrial wood pellets.
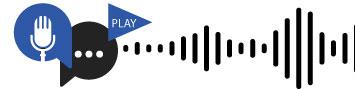

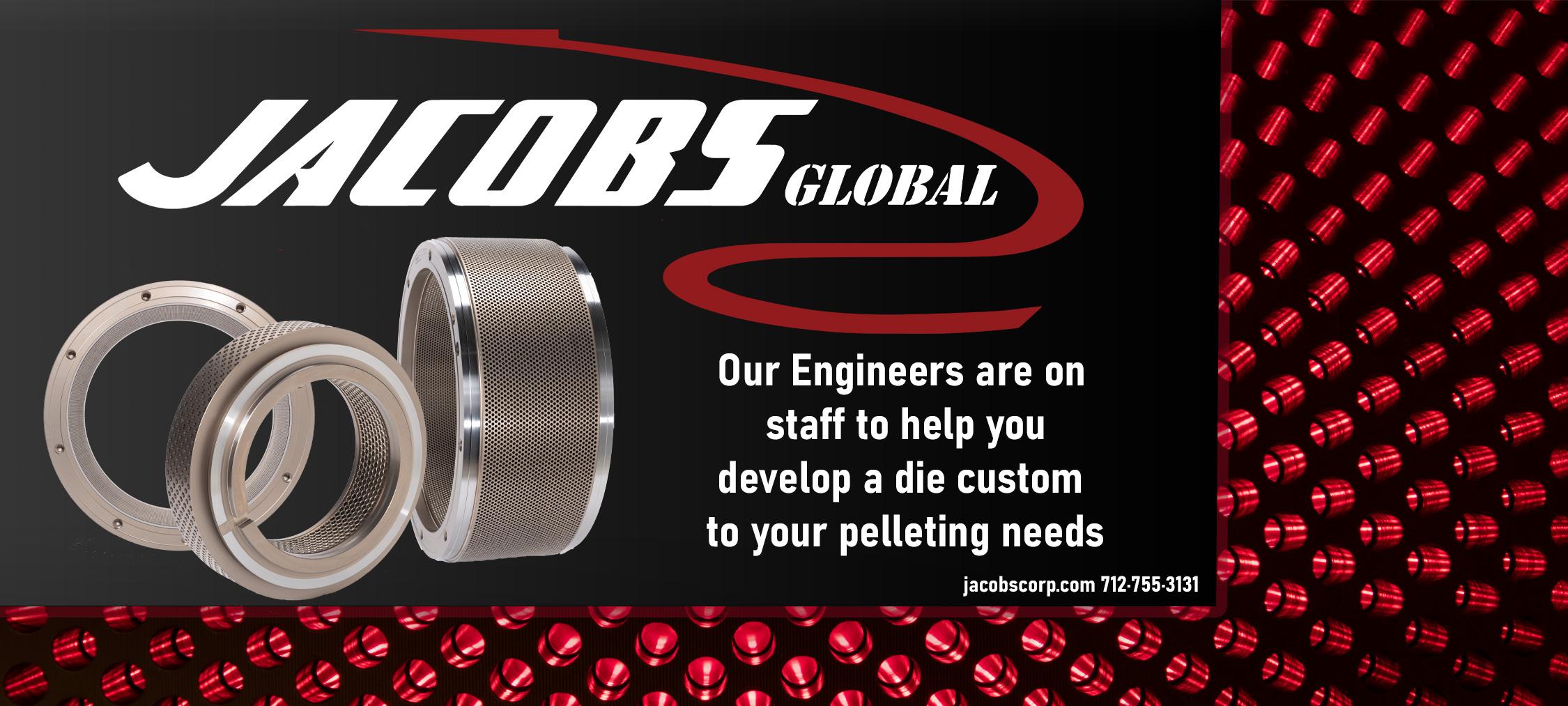
BIOMASSMAGAZINE.COM/PELLET 11 to get for using those pellets. Add to that very high energy prices in Europe—there is a strong demand for heating pellets, as natural gas and heating oil prices are crazy high—and the market is super short right now. Spot prices are well over $300 per ton in western Europe—if you go back a year and a half to two years ago, the average spot price was about $165 per metric ton, so it’s almost doubled. And about inflation, it’s obviously driving up prices for the end user, as well as alternatives to wood pellets, such as coal for power generation. Today (July 27), the price of coal was almost $400 per ton, and a year or two ago it was $60, so it’s about five times higher—it’s crazy. Inflation is also impacting the supply side. High diesel fuel prices are causing the delivered price of wood to pellet factories to go up, and quite significantly in some places ... in some locations, diesel fuel is 60% of the delivered cost of wood, and diesel fuel prices have essentially doubled in the past year and a half, so we’re seeing delivered wood prices increase pretty dramati cally across the board. Listen to the rest of the podcast: www.biomassmagazine.com/pages/podcasts PODCAST PREVIEW ¦ PELLE TS WOODCHIPS BIOMASS 5 63-26 4 -8066 | airof le x. co m Truck Dumpers Trailer Tippers Portable Trailer Tippers Receiving Hoppers YO UR SOLUTION FOR BULK MATERIALHANDLING Don't Miss an Episode: Pellet Mill Magazine's next podcast to air on Aug. 17, talking pellet plant design with KESCO Inc. President and Founder Jason Kessler. Interested in being a guest? Contact Danielle Piekarski at dpiekarski@bbiinternational.com

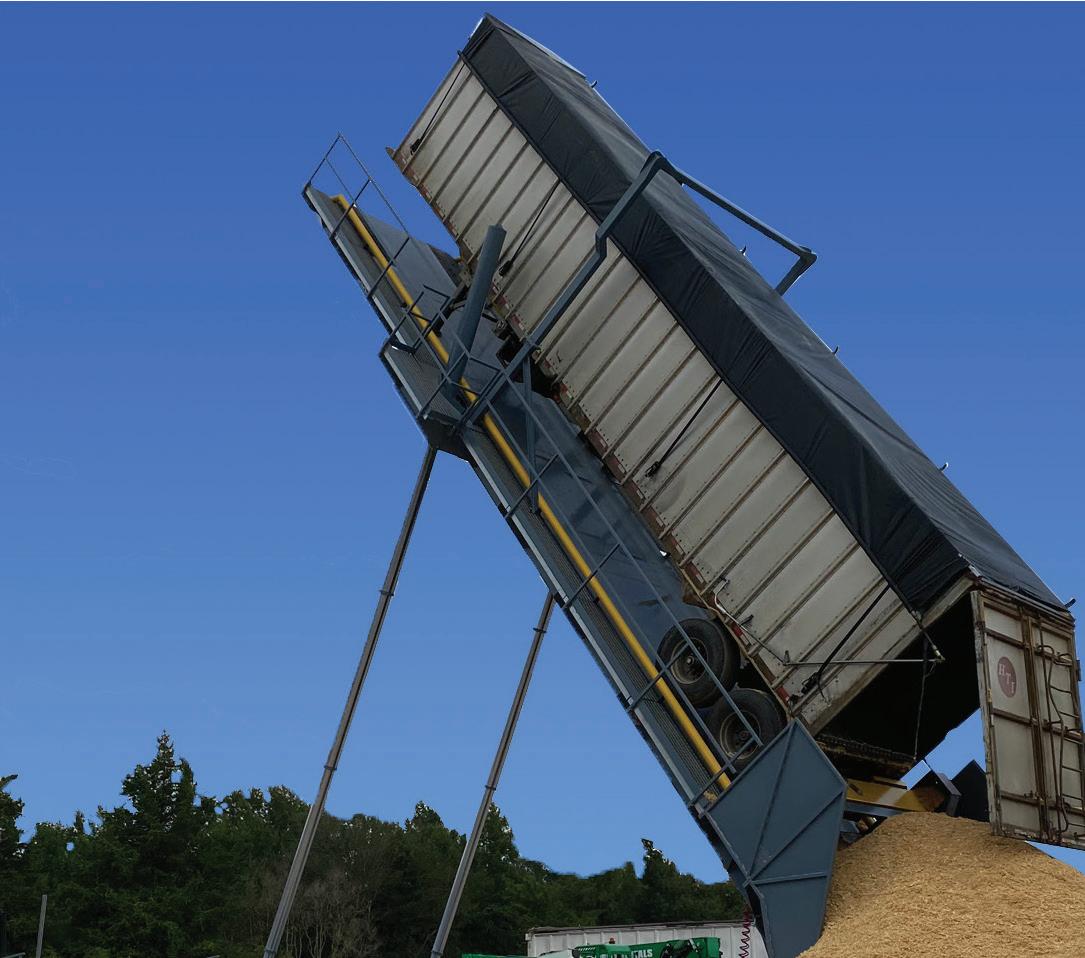


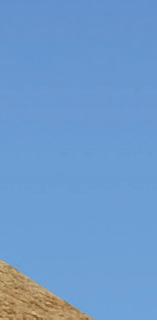

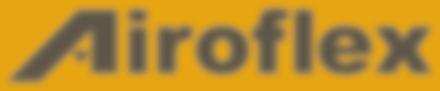
12 PELLET MILL MAGAZINE | ISSUE 3 2022 « Project Development BUILDING OUT
Summary: Drax completed commissioning of its 360,000-ton-per-year pellet plant in Demopolis, Alabama, and its 40,000-ton-per-year satellite plant in Leola, Arkansas, earlier this year, both expected to reach full production ca pacity by 2023. Like the Demopolis plant, the satellite plant under construction in Russellville is a containerized plant being delivered by Prodesa. A third satellite plant, at an Arkansas location that Drax has not yet disclosed, is planned. During a July 26 financial and operational results update, Drax CEO Will Gardiner said the company plans to make a final investment decision on up to 500,000 metric tons of additional wood pel let production capacity before the end of 2022. Drax’s Leola plant began operations in February. It is the first of three 40,000-ton satellite plants Drax is building in Arkansas.
CAPACITY
PHOTO: CM BIOMASS
BY ANNA SIMET G lobal wood pellet demand continues to soar, with tight market conditions likely to spur significant invest ments in new production facilities around the world. Demand growth from 2020-’21 outpaced supply growth by approx. 10% (18.2% versus 8.4%, respectively), accord ing to market intelligence firm Hawkins Wright, a trend that is likely to continue. Global demand in 2021 was approx. 45 mil lion metric tons (MT), with an additional 5 million MT in additional demand expected in 2022.As for pellet production capacity in the U.S. and Canada, Pellet Mill Magazine’s 2022 U.S. and Canada Fuel Pellet Produc tion Map included approx. 12.8 million MT of operational capacity in the U.S., with roughly 1.7 million tons proposed or under construction. Data for Canada indicated approx. 4.9 million MT of operating capac ity, with an additional 865,000 proposed. These numbers will be updated in the up coming 2023 map, which will be mailed with issues of the 2023 Issue 1 edition. The following are some of the active projects in both countries, as well as acqui sitions and closures.
PHOTO: DRAX CM Biomass recently acquired Mohegan Renewable Energy's three pellet production facilities, including the pictured plant in Crossville, Alabama.
Status: Under Construction Capacity: 40,000 metric tons (MT)
Pellet Mill Magazine provides a roundup of pellet production capacity that is under development, active construction or recently acquired.
Company: Drax Plant: Drax Russelville Location: Russellville, Arkansas

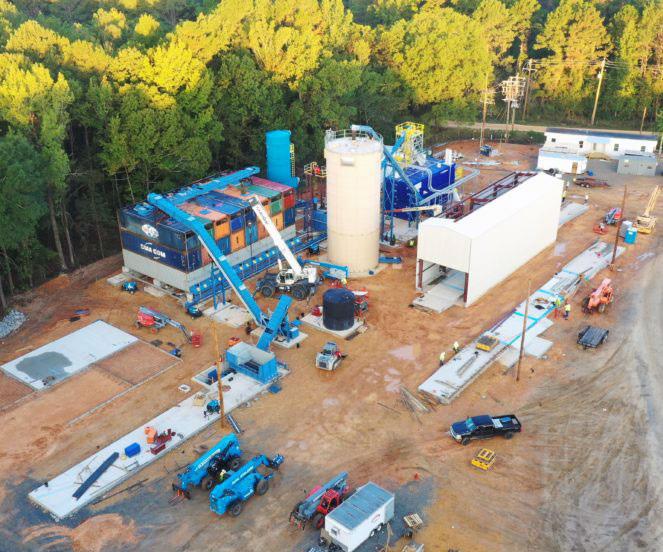
Company: Enviva Plant: Enviva Pellets Epes Location: Epes, Alabama Status: Under Construction Capacity: 1.1 million MT
BIOMASSMAGAZINE.COM/PELLET 13
Completion of the Epes plant, the second in Enviva’s Pascagoula cluster, is slated for the second half of 2023.
PHOTO: ENVIVA
Directly employing about 100, the company estimates it will invest approximately $300 million in the plant and surrounding infra structure, and will generate approximately $265 million in annual economic impact in the region. The plant’s location will allow the use of barges to carry the pellets approximately 200 miles down the Tombigbee River to Enviva's newly opened terminal at the Port of Pascagoula, Mississippi, to be shipped to overseas customers.
Construction of Enviva’s Epes plant—expected to be the largest fuel pellet manufacturing plant in the world—began in early July, Pellet Mill Magazine confirmed with Enviva. In mid-July, United Bank Community Development announced $42.5 million in New Markets Tax Credit funds for the project, which will be lo cated at the former Mannington Mills wood flooring plant in Epes.
Installation of temporary power to Enviva’s forthcoming wood pellet production site in Epes.

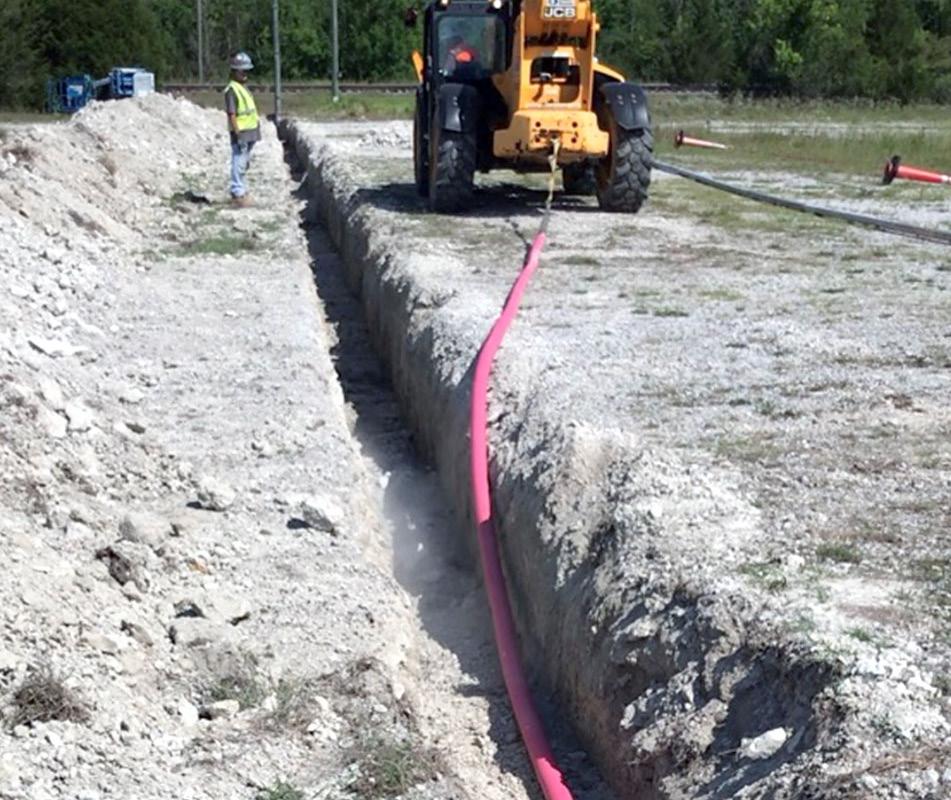
Enviva’s previously announced “multiplant expansion” project is expected to be complete by the end of the year. The $50 million investment was made to debottleneck manufacturing processes, reduce greenhouse gases, eliminate certain costs and increase production capacity. The Hamlet plant production capacity will ex pand from approx. 545,000 MT to 600,000; Sampson from 500,000 MT to 600,000, and Cottondale from 750,000 MT to 780,000 MT. According to the application, some of the permitted revisions for the Hamlet plant include revisions to potential emissions for the dryer, green hammermills, dry hammermills, pellet mills and cool ers, and dried wood handling; the addition of two natural gas-fired burners to heat the dryer system ducts to prevent wood tar con densation/coating in the duct walls; updating green wood handling throughputs and increasing maximum annual throughput for bark hog.
Location: Hamlet, North Carolina; Sampson, North Carolina; Cottondale, Florida
14 PELLET MILL MAGAZINE | ISSUE 3 2022
« Project Development Company: Peak Fort Nelson Properties Ltd. Plant: Peak Renewables Location: Fort Nelson, British Columbia Status: Under Construction Capacity: 600,000 MT In late 2020, Canfor announced it had reached multiyear, $30 million agreements with Peak Renew ables involving the sale of its forest tenure in the Fort Nelson region of British Columbia, which were ap proved by the British Columbia government in August 2021. The agreement followed Peak Renewables’ pur chase of Canfor’s Fort Nelson mill assets in the third quarter of 2020. The mill had been shuttered for more than a decade, and the company is transitioning the site into a pellet manufacturing plant. Peak Renew ables’ CEO is Scott Bax, formerly chief operating of ficer at Pinnacle Renewable Energy. Pellet Mill Maga zine was able to confirm the project is underway, but unable to get a specific update by press time.
Company: Enviva Plants: Enviva Hamlet, Enviva Sampson, Enviva Cottondale
Status: Expansions/Under Construction Added Capacity: Approx. 185,000 MT
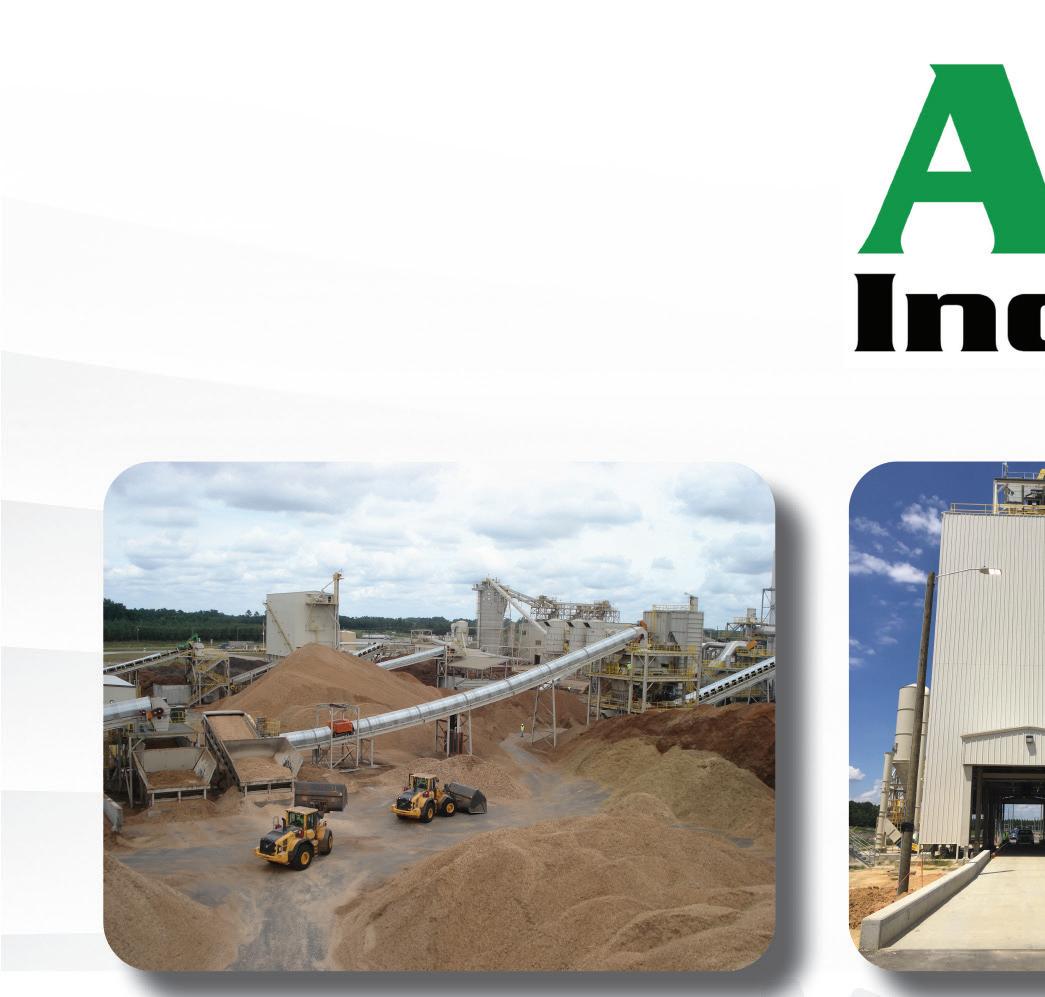
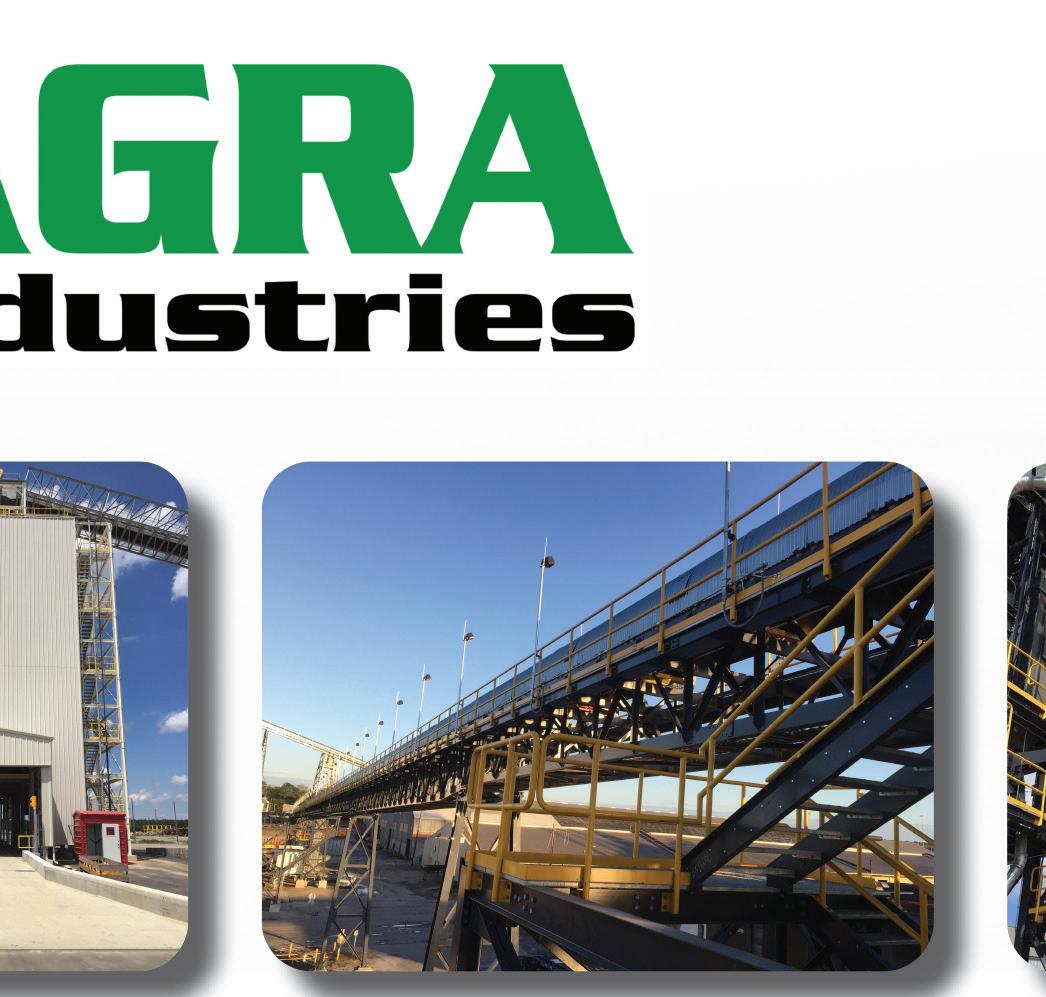
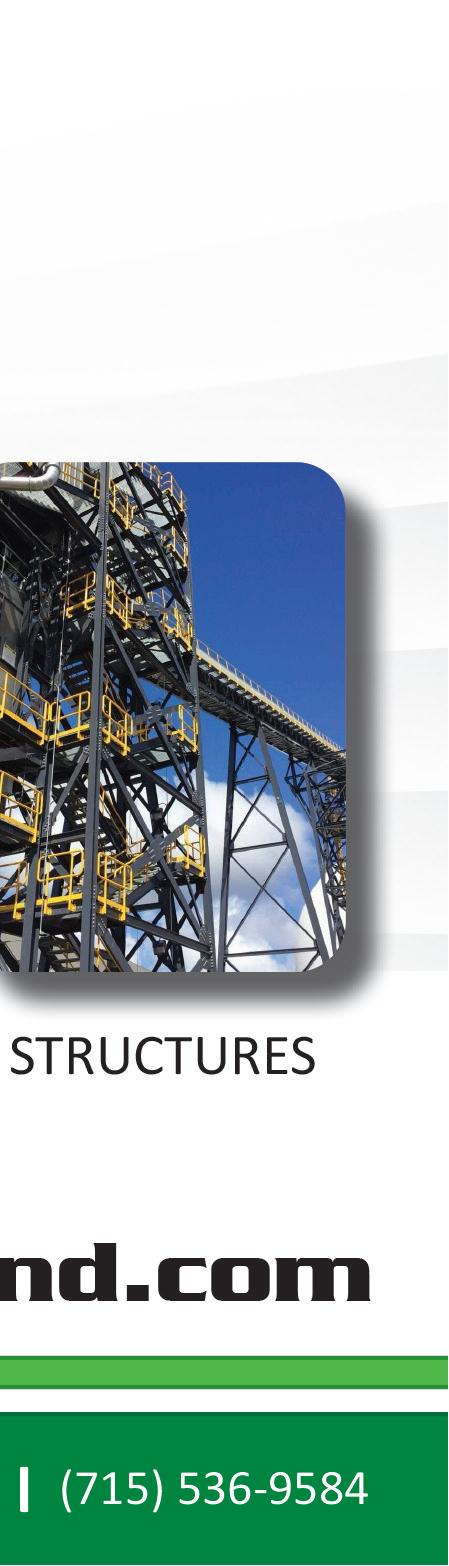
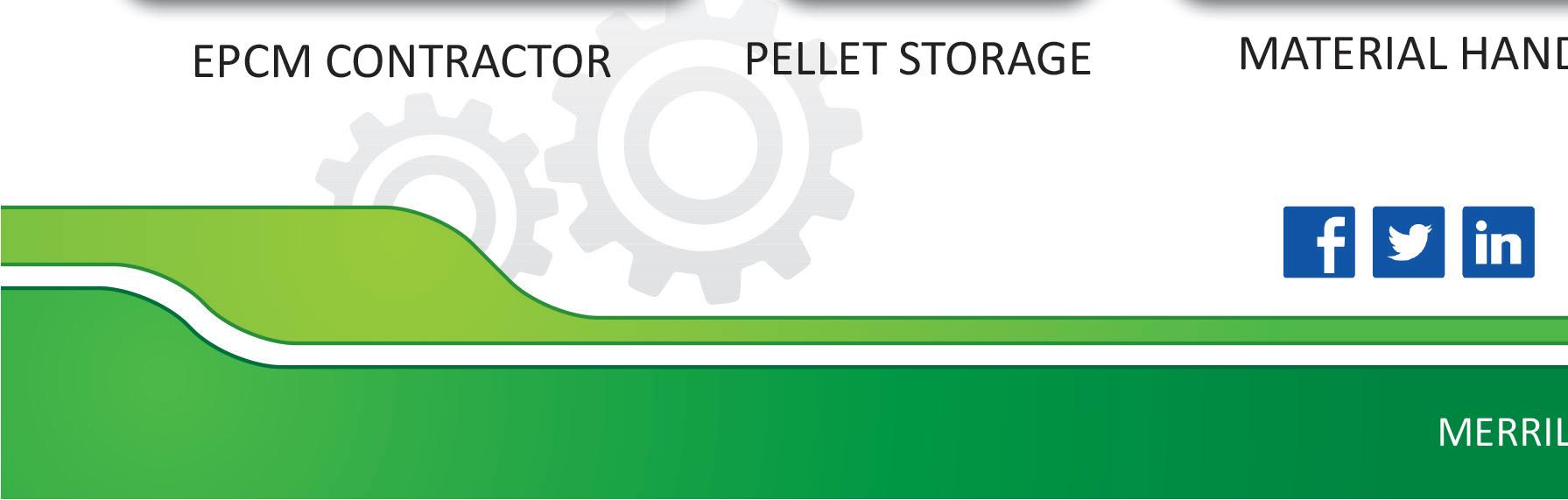
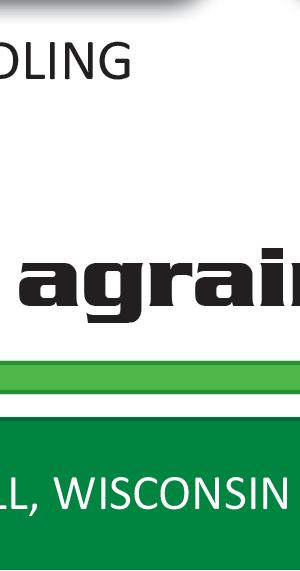
Location: Vanderhoof, British Columbia
Status: Expansion/Under Construction Capacity: 176,000 to 240,000 MT Premium Pellet began operating in 2011, and is wholly owned and operated by Nechako Lumber Co. The vast ma jority of pellets produced are sold in bulk to overseas mar kets (150,000 MT) but a small amount is packaged in 40-lb bags for the local home heating market. The plant supplies RWE Supply and Trading with pellet fuel, as it has for the past 10 years. Phase 1 of Premium Pellets expansion is complete with the installation a new Brunette BioSizer, MEC 12x60 dryer, Kinedizer 14-inch, 40-MBtu gas burner and a Fisher Klosterman multi-cyclone system, according to David Her zig, general manager of lumber operations at Sinclar group. Premium Pellet is currently waiting for permit approval to be gin full dryer production. "Phase 2 of the project is well un derway and is focused on increasing pelletizing capacity," Herzig says. "Inside the plant, we’ve had to add some expan sions on to fit some of the equipment coming in. We’ve had to break into the concrete, reinforcing the footings for the roof supports for everything coming in and hanging off of it. We’ve had to put in new transformers, electrical rooms, power distribution center rooms, and run power to feed all of the equipment." A third dry hammermill and four additional Bliss Pioneer 200 pellet mills, bringing the plant’s total up to nine, have been installed, Herzig reports. "The teams are fin ishing off the building expansion before beginning the instal lation of the pellet feed bins, associated conveyors and pellet cooling equipment. Outside, we’ve installed additional pellet storage that tied into the current shaker screen. Phase 2 also saw the relocation of the Hamer packaging system to fit in with the new equipment." Phase 3 of the project has also begun, with engineering work underway for a wet electrostatic precipitator, which will reduce the plant’s air emissions, Herzig adds.
-
BIOMASSMAGAZINE.COM/PELLET 15
Company: Sinclar Group Forest Products Plant: Premium Pellet
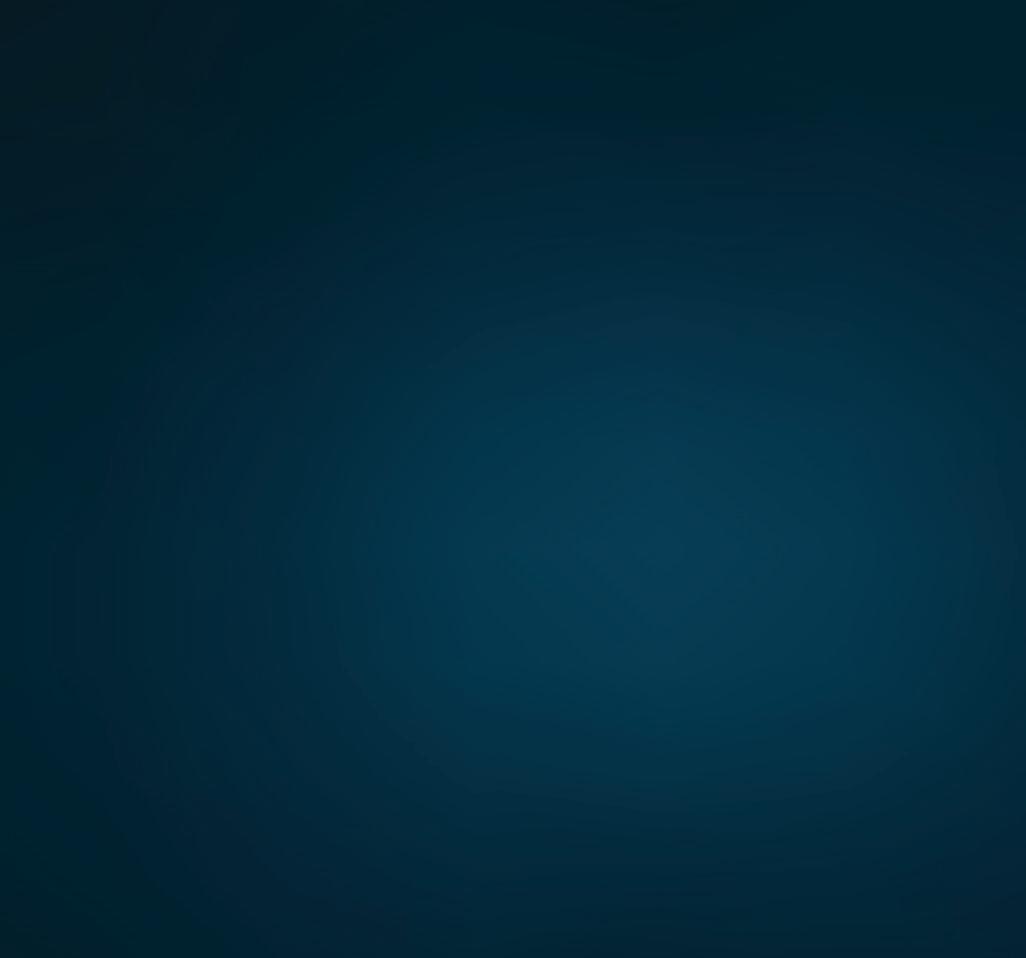
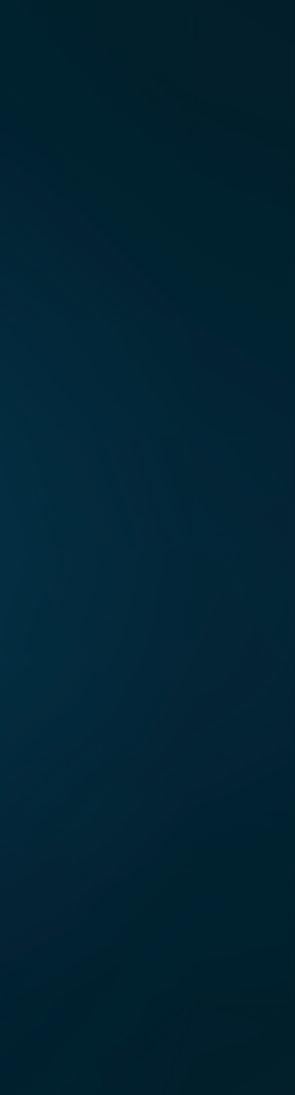

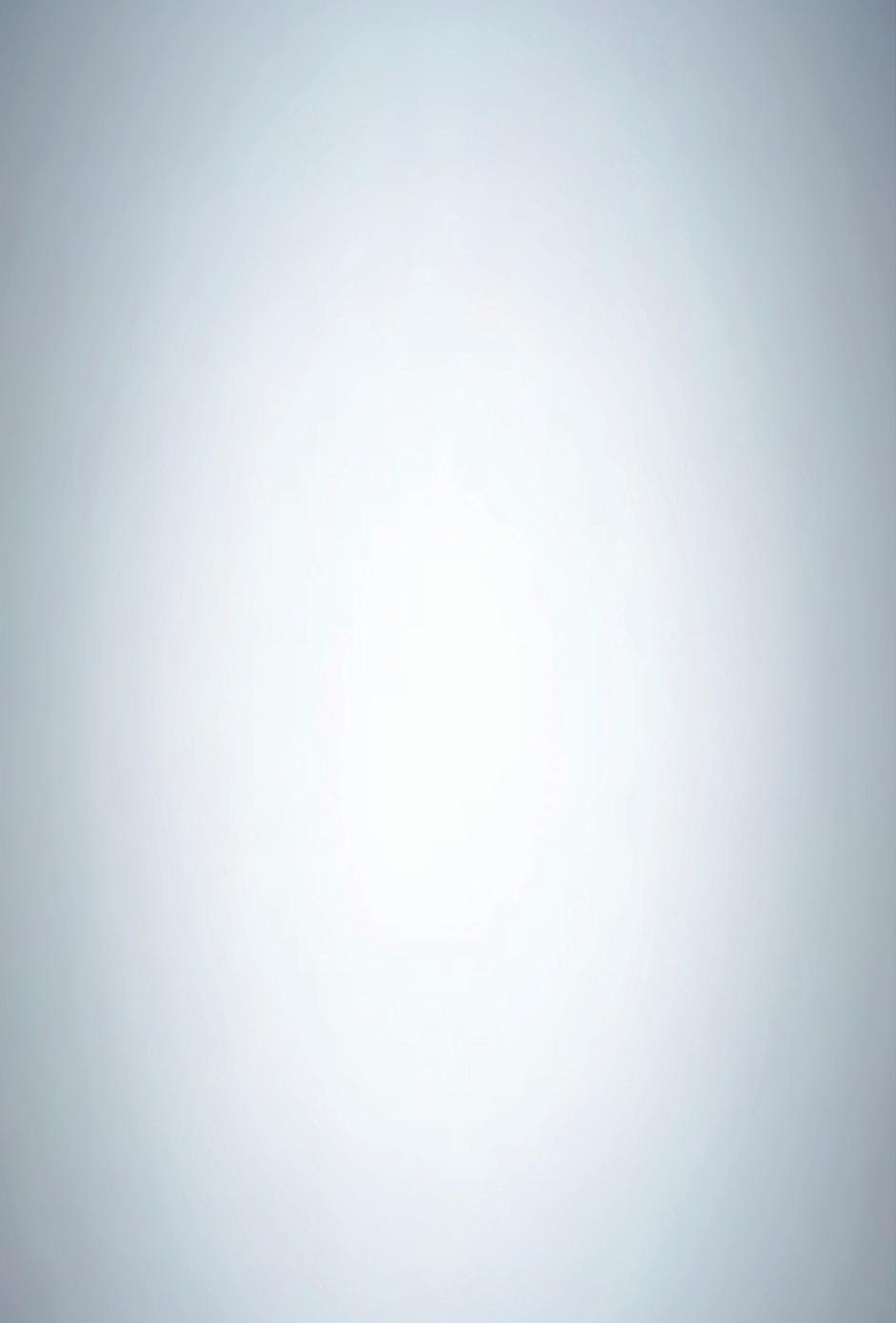
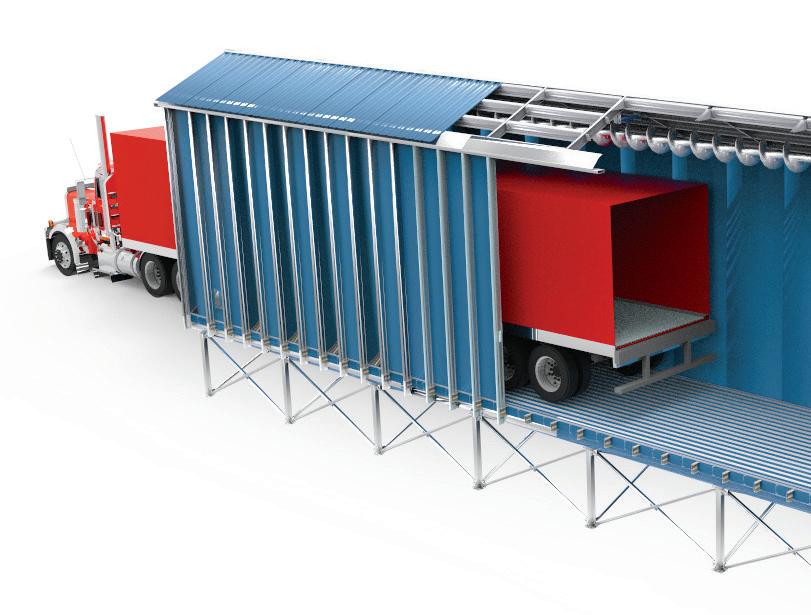

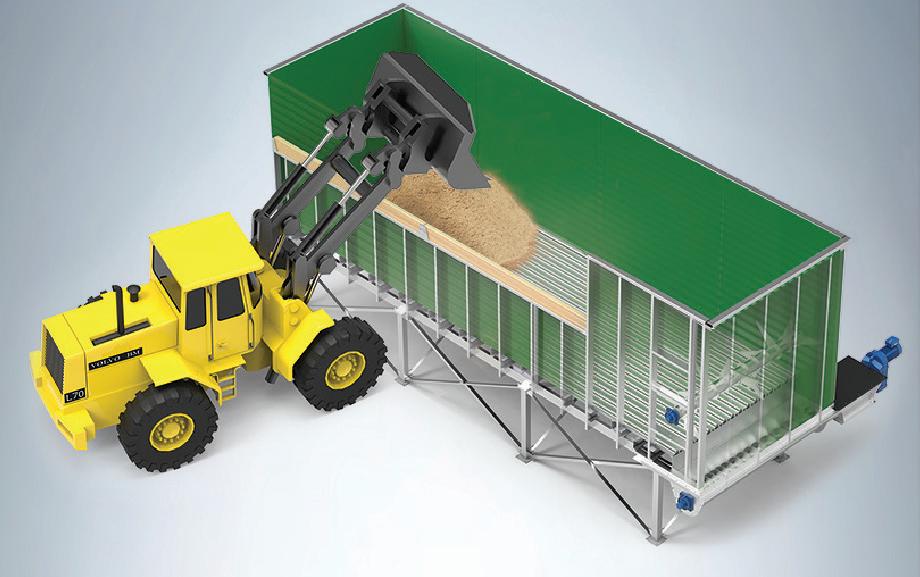
Pending permit approval, Enviva plans to expand capacity at Ahoskie from approx. 436,000 MT to 571,000 MT ODT per year.
«
-
Some of the proposed changes on the application include: reconfig uring of the wood yard, addition of three green hammermills, adding an regenerative thermal oxidizer to the existing dryer following the existing WESP; addition of two dry hammermills and two associated material collection cyclones; addition of two pellet mills, one pellet cooler and one supple cyclone, and addition of two natural gas-fired boilers to provide steam to the pelletizing process.
Company: Enviva Plant: Enviva Lucedale Location: Lucedale, Mississippi Status: Planned Expansion Added Capacity: 250,000 MT
During a recent earnings and results presentation, CEO John Keppler said Enviva plans to acceler ate the timing of a fourth wood pellet production plant in the Pascagoula cluster. “We continue to make progress in our evaluation of site location op tions, and anticipate making a decision by year-end 2022,” he stated. Enviva has also indicated that, given the quality and size of its current customer sales pipeline, the company “believes it will be able to support the addition of six new fully contracted wood pellet production plants and several highly accretive expansion projects, which, over approximately the next five years, would roughly double our current production capacity.”
Project Development Company: Enviva Plant: Enviva Pellets Bond Location: Bond, Mississippi Status: Planned/Under Development Capacity: 1 million MT Enviva’s Bond, Mississippi plant is the third plant in its Pascagoula cluster. Construction is scheduled to begin in early 2023. According to the company, the plant is fully contracted under long-term takeor-pay supply contracts with customers around the world. With a corporate investment of $250 million, the Bond plant will generate more than $1 million in taxes per year for the county and school district and deliver over $250 million annually in economic impact in the region, according to Enviva. Production is expected to commence in 2024.
According to recent statements, Enviva plans to commence and complete a fully-permitted 300,000 MTPY expansion of its Lucedale plant during 2023, which will increase its nameplate production ca pacity from the current 750,000 MT to approximately 1 million MT.
16 PELLET MILL MAGAZINE | ISSUE 3 2022
Company: Enviva Plant: Enviva Ahoskie Location: Ahoskie, North Carolina Status: Planned Expansion Added Capacity: Approx. 135,000 MT
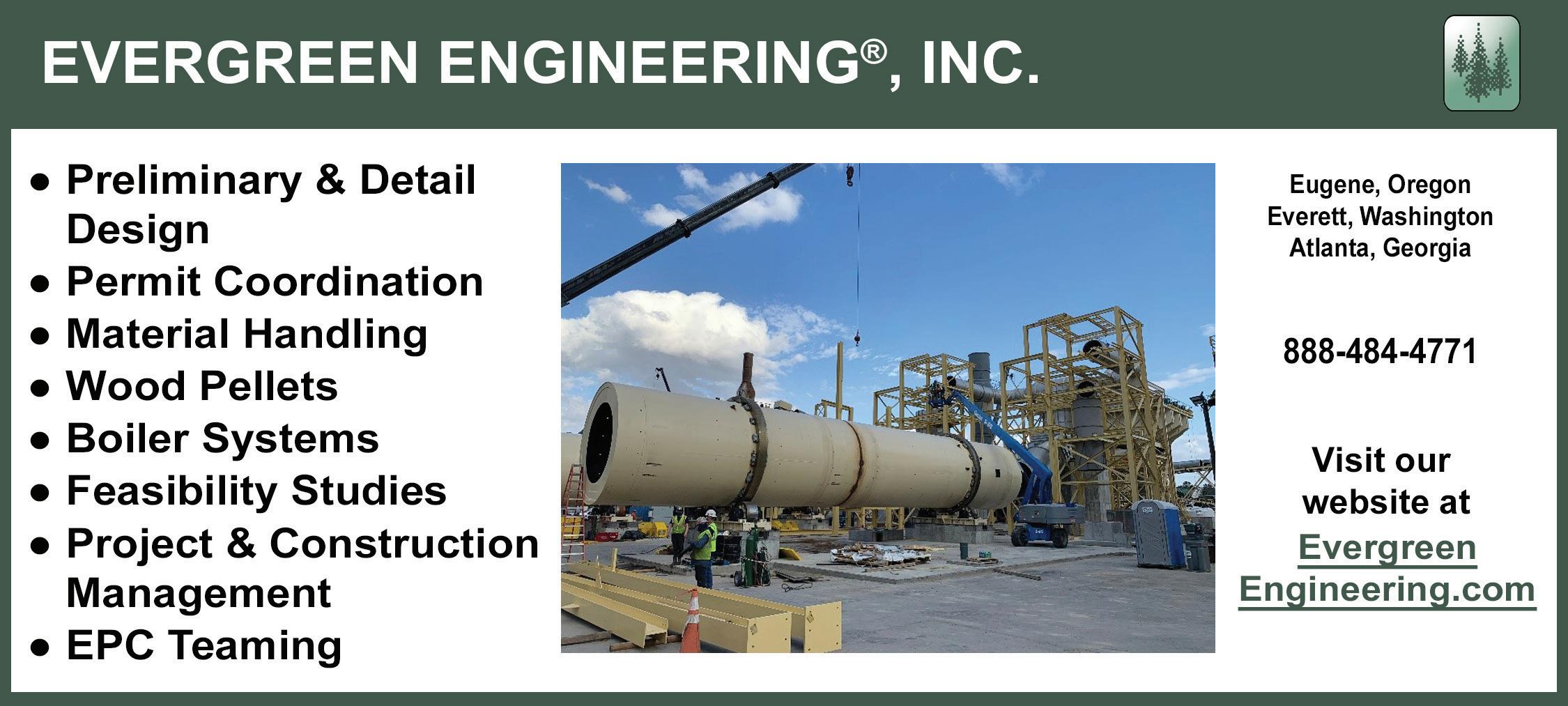
BIOMASSMAGAZINE.COM/PELLET 17
A groundbreaking ceremony was held by Groupe Lebel on April 4, for construction of a pellet plant in Cacouna, Quebec.
Company: Groupe Lebel Plant: Groupe Lebel Pellet Plant Location: Cacouna, Quebec Status: Planned/Under Development Capacity: 100,000 MT In April, Groupe Lebel announced it would build a pellet plant at its Cacouna, Quebec, site. The first phase of the plant’s operations is scheduled for 2023, with an annual capacity of nearly 100,000 MT of wood pellets. Groupe Lebel aims to ship the majority of its production to growing international mar kets. CEO Frédéric Lebel said engineering and project execu tion has been awarded to Prodesa. The $40 million project received $15 million in backing from key partners, including the Quebec Ministry of Economy and Innovation, the Quebec Department of Energy and Natural Resources and the Quebec Ministry of Forests, Wildlife and Parks.
Company: Pacific Coast Fiber Fuels Plant: Pacific Coast Pellets Location: Shelton, Washington Status: Under Expansion Added Capacity: Approx. 9,100 MT Built in 2008, Pacific Coast Pellets has over 300 deal ers and produces three different lines of heating pellets using 100% Douglas fir: Sierra Supreme, Olympus and Cascade. President Stan Elliot confirmed the modest increase in capacity. "We have added a third Andritz pellet mill, but because of electrical capacity limits, the mill we purchased will only add 10,000 tons to our annual capac ity," he says.
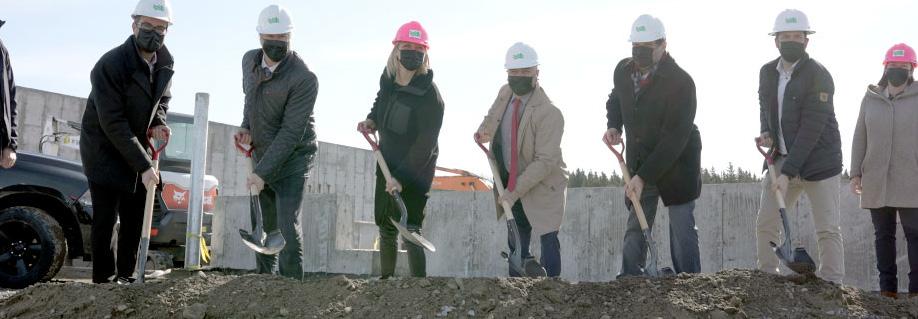
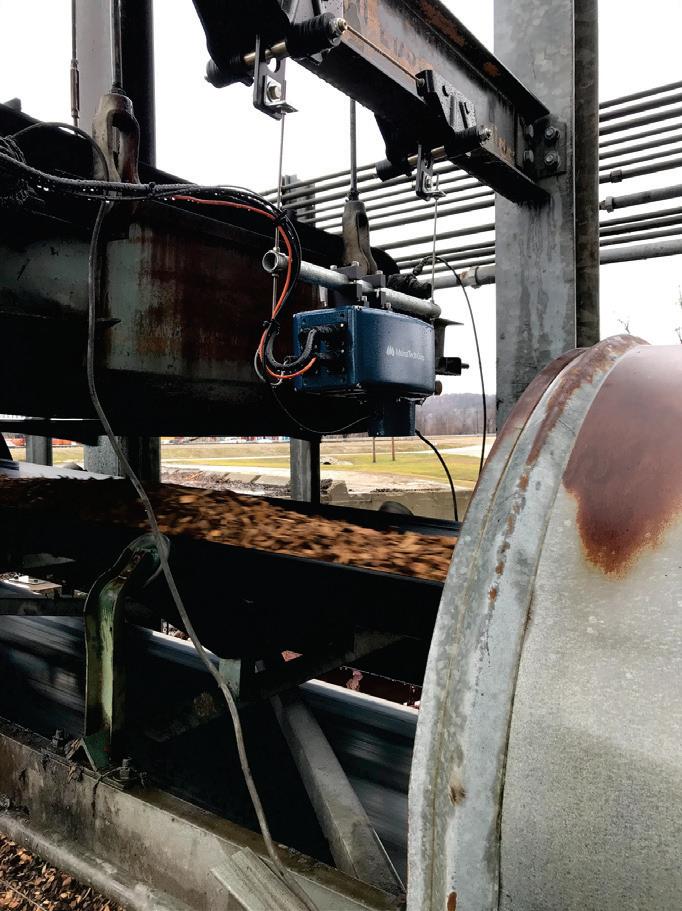
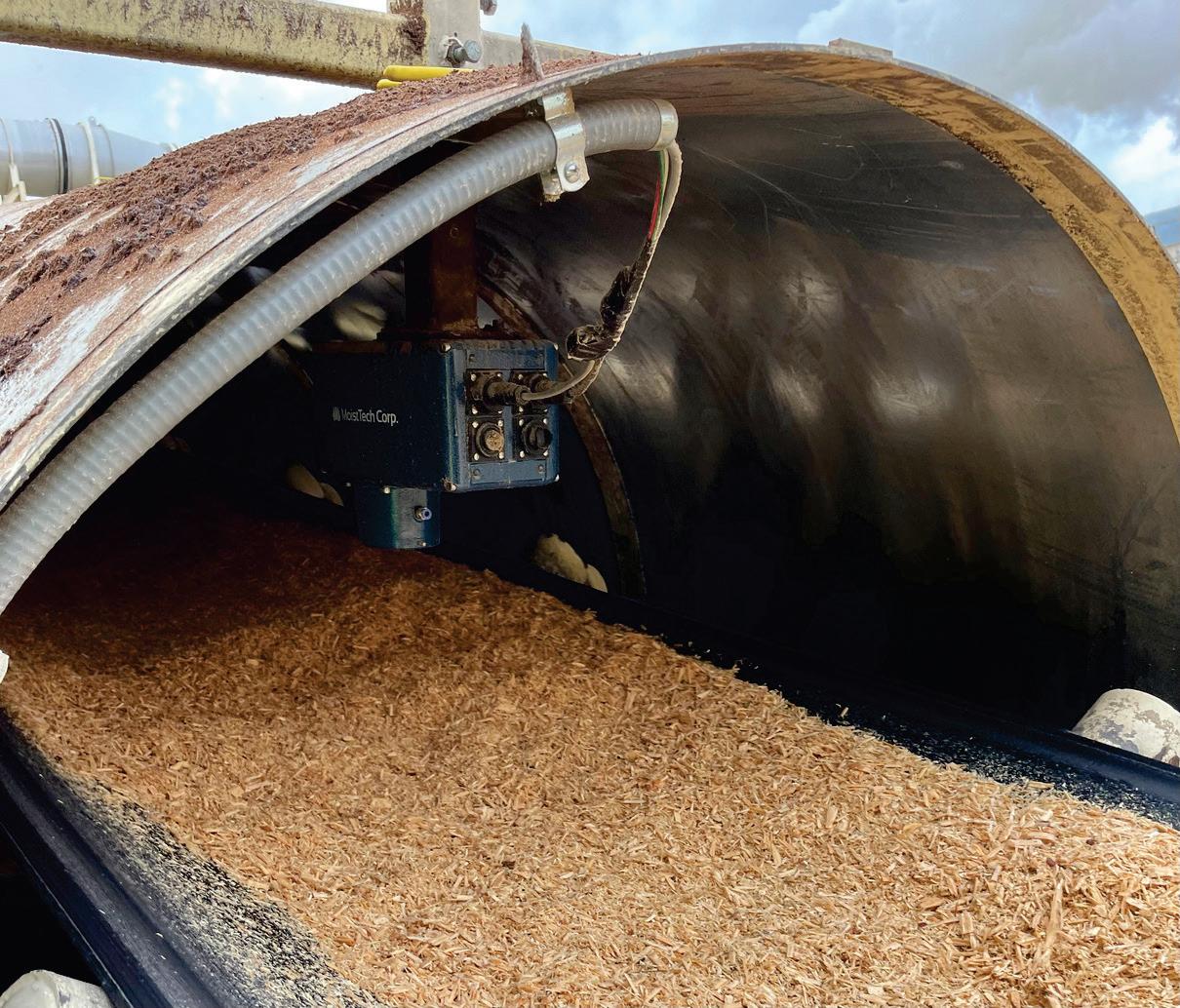
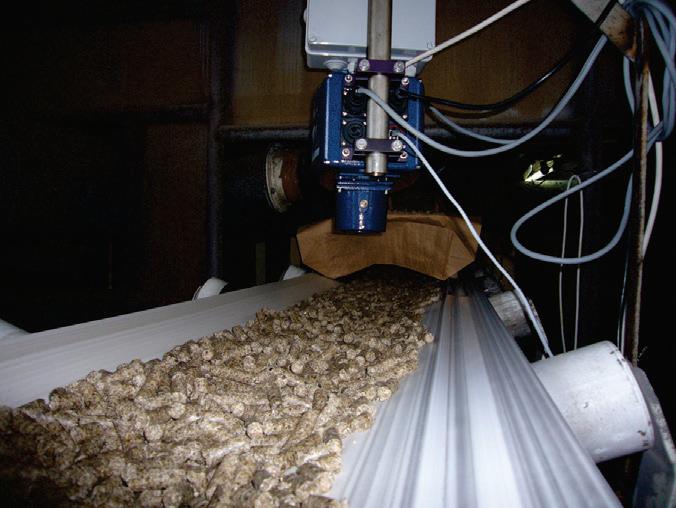
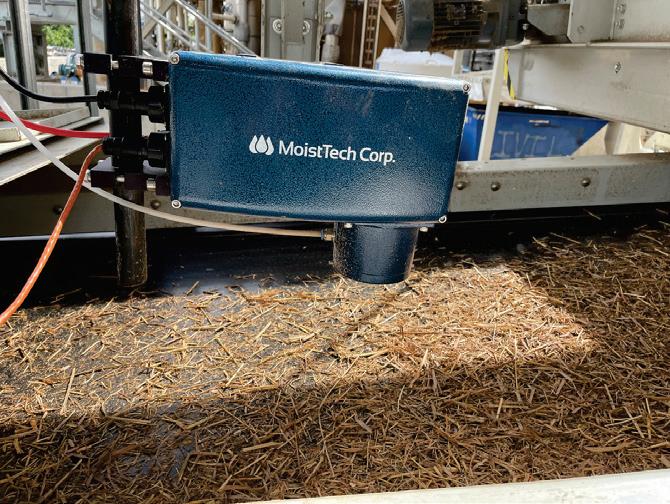

18 PELLET MILL MAGAZINE | ISSUE 3 2022
Company: Pacific Bioenergy Plant: Pacific BioEnergy Location: Prince George, British Columbia Status: Permanently closed Capacity: 175,000 MT In late March, PacBio President John Stirling confirmed to Pellet Mill Magazine that the plant was idle and would be sold. Some of its assets, in cluding long-term wood pellet sales contracts, were sold to Drax Group and transferred offsite. Certain assets owned by PacBio were assigned to Pin nacle Renewable Energy Inc., part of Drax Group. In statements announcing the closure, the company said “PacBio is proud to have been a part of the Prince George community for over 25 years and we want to thank the community for its support. Our employees have been dedicated to our business and we want to thank them and their families for their contributions.”
Pursuant to an order by the United States Bankruptcy Court for the Southern District of Alabama, the Zilkha Biomass Plant was put up for auction, available for purchase or by the piece, which included all assets as well as hundreds of tons of finished product. The plant began operations in 2015, utilizing the patented Zilkha Black Pel let technology. The plant site has a his tory of bankruptcy—it opened as Dixie Pellets in 2008, closed in 2009 and was purchased out of bankruptcy by Zilkha in May 2010. Zilkha Biomass went up for auction in the fall of last year.
PHOTO: ZILKHA BIOMASS
« Project Development
Company: Zilhka Biomass Fuels Plant: Zilkha Selma Location: Selma, Alabama Status: Permanently closed Capacity: 240,000 MT (black pellets)

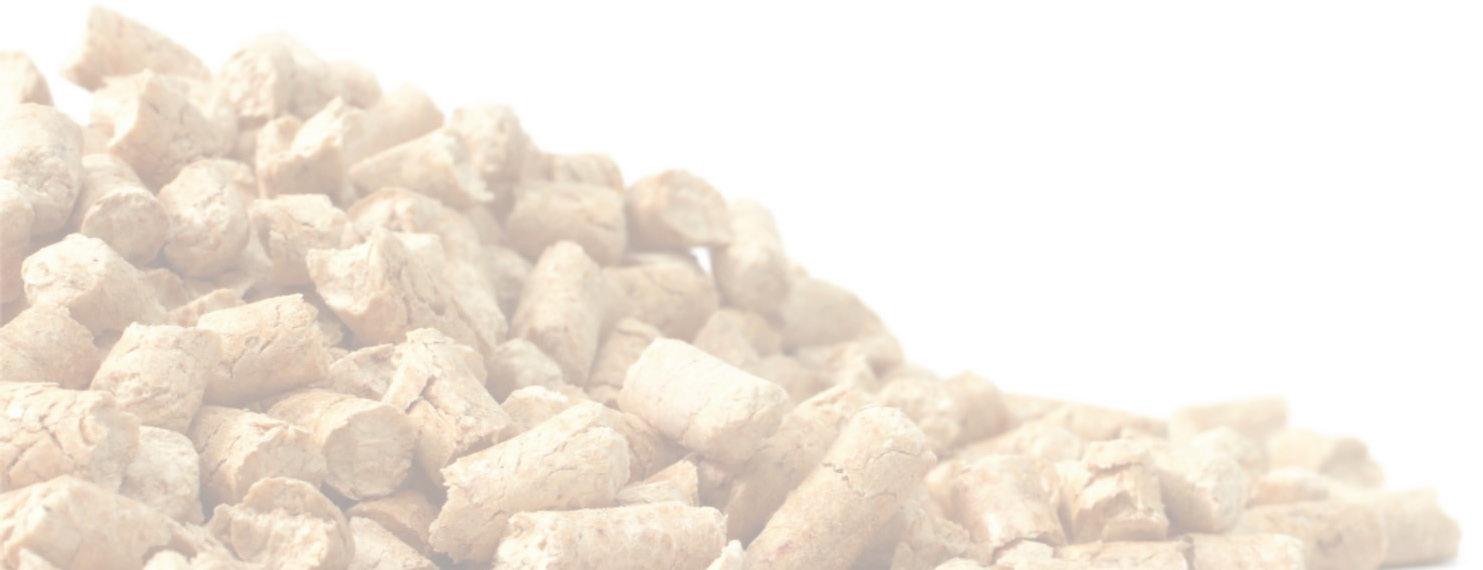
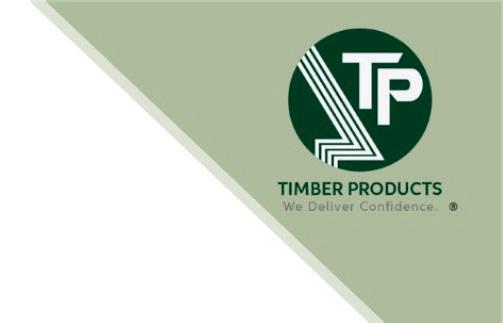
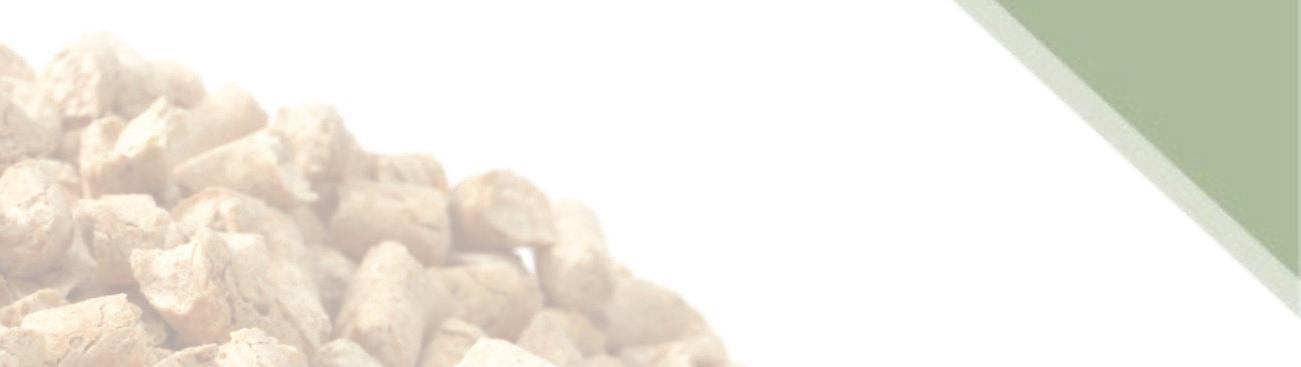
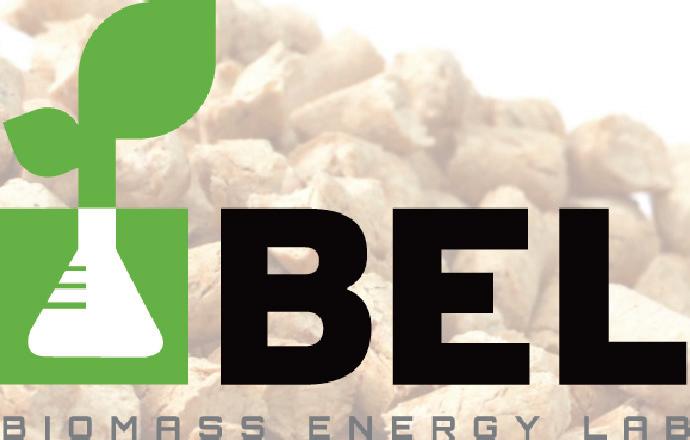
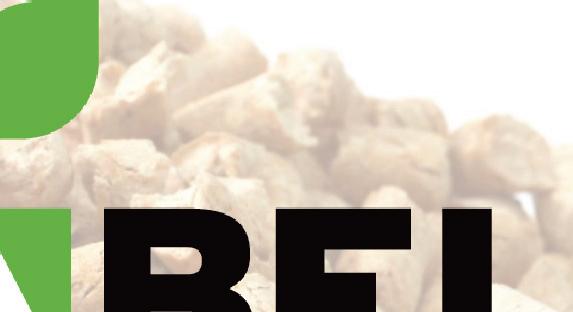
BIOMASSMAGAZINE.COM/PELLET 19 PROTECTING YOUR PROCESS AGAINST EXPLOSIONS +1-855-793-8407 IEPTechnologies.com
SupprVentingessionFlamelessVentingIsolation
Company: Albioma Plant: La Granaudière Location: Saint-Michel-des-Saints, Québec Status: Capacity:Acquired/Operational 200,000 MT The La Granaudiere plant was commis sioned in the fall of 2020, then shuttered in July 2021. It was purchased by Albioma in early 2022, which said the operation was ideally positioned to supply the company’s Caribbean biomass power plants. The trans action also included a long-term agreement granting access to a 45,000-MT pellet stor age facility in the Port of Quebec, as well as raw material supply guarantees issued by Quebec's Ministry of Forests, Wildlife and Parks. Recommissioning of the plant began in the second quarter of this year. Albioma acquired the La Granaudière wood pellet plant earlier this year.
PHOTO: ALBIOMA
Company: CM Biomass Plants: Mohegan Renewable Energy (3) Location: Crossville, Alabama; Quitman, Mississippi; Jasper, Tennessee Status: Capacity:Acquired/Operational 350,000 tons CM Biomass made its pellet producer debut in Huntsville, Texas, in December 2019 at Huntsville Pellets, and with the acquisition of MRE in Feb ruary—350,000 tons of capacity—the company doubled its production ca pacity to over 700,000 tons. In a press release, the company said its expecta tion is to achieve a capacity of 1 million tons by 2023-‘24, based on already decided projects and expansions of existing facilities. CM Biomass, the second largest seller of wood pellets worldwide, has a distribution system of more than 50 storage hubs and sold 3.5 million tons of wood pellets in 2021, primarily in Europe.
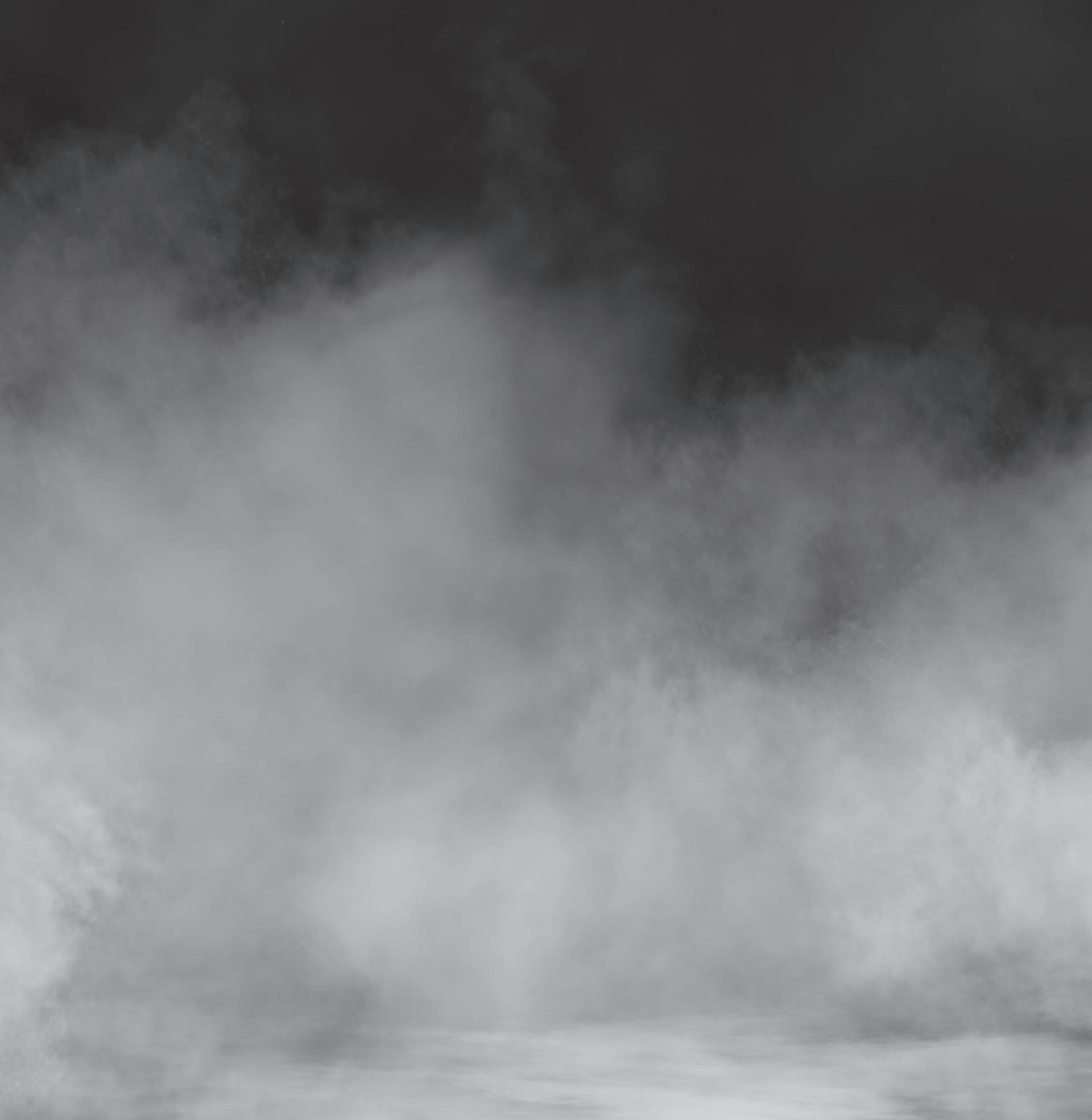

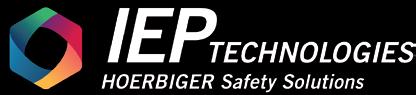

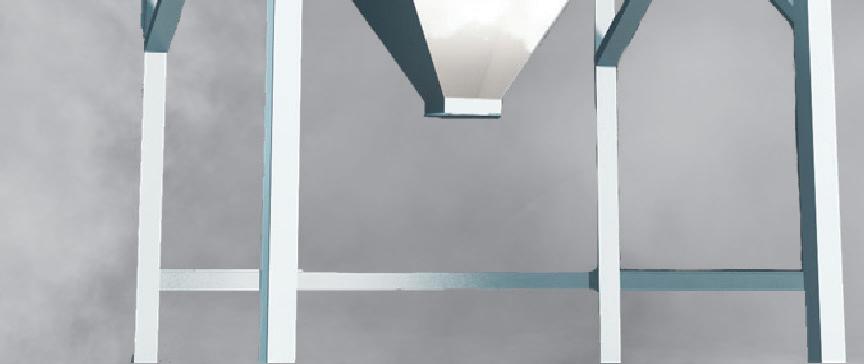
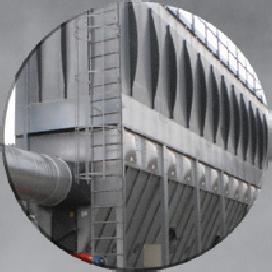
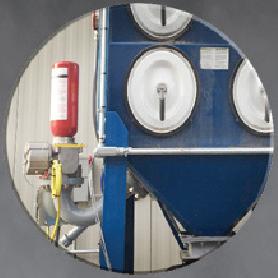



In a bid to further reduce its carbon footprint, Drax Group plans to work with MOL Drybulk to deploy environmentally friendly bulk carriers to transport product overseas.
The Wind Challenger sail technology has been in develop ment for well over a decade, mainly by MOL and Oshima Ship building, as an industry-academia joint research project led by the University of Tokyo. MOL took over in 2018, and has been work ing on the technology since. It received Approval in Principle from ClassNK for the design of the hard sail system in 2019, and Sails
« Carbon
Drax Group has the goal of becoming carbon negative by 2030 and is aggressively pursuing this ambition through a variety of endeavors. Most recently announced is a memoran dum of understanding with Japanese company MOL Drybulk, to deploy what they have dubbed Environmentally Friendly Bulk Carriers, which will be developed in two generations. The first EFBC generation would deploy MOL’s Wind Challenger technol ogy, shipping pellets to Drax’s overseas customers. In develop ment since 2009, debut of the Wind Challenger technology is imminent—in fact, equipment for the first vessel, a 99,000-deadweight-ton (DWT) ship, is currently being fabricated and assem bled at Oshima Shipbuilding. The result of a deal with Tohoku Electric Power Co. Inc., it is scheduled for delivery in October, according to MOL. Ross McKenzie, Drax Group director of international affairs, says use of MOL Drybulk’s technology aligns well with Drax’s zero carbon goals, adding that the company has already reduced its emissions by more than 99% through converting its Drax Pow er Station in North Yorkshire from coal to biomass. Doing so has made the company one of the lowest-carbon-intensity power generators in Europe, supplying 11% of the U.K.’s electricity. On top of that are the company’s carbon capture and storage (CCS) efforts, the most recent of which are the submission of plans to build the world’s largest CCS project at its power station, after piloting technologies for the past several years. The green shipping initiative provides Drax with an opportu nity to decarbonize even further, McKenzie says. He explains that the pilot of the project could deliver a 20% reduction in emis sions and costs related to shipping Drax’s biomass from Canada to Japan, all while providing potential for decarbonization in the maritime industry. “International shipping is the backbone of the global economy, transporting about 90% of global trade vol umes,” he says. “Shipping produces around 2.5% of the world’s total CO2 emissions. Reducing these emissions, while still having a vibrant global trading economy, is the goal, and green shipping initiatives like ours could play a significant role in achieving that.”
Cutting Carbon Via
BY KATIE SCHROEDER I ndustries across the globe have set goals to reduce their carbon footprint, and the pellet industry is no exception.
Wind Challenger Technology
20 PELLET MILL MAGAZINE | ISSUE 3 2022
The first vessel fitted with MOL Drybulk’s Wind Challenger Technology, which harnesses wind as a propulsive force
PHOTO: MOL DRYBULK
was certified by Japan’s Ministry of Land, Infrastructure, Trans port and Tourism earlier this year. The hard sails can be fitted onto a variety of ships and are made from fiber-reinforced plastic, a light but strong composite material. The first challenger is being built with four sail tiers, each of which is approximately 15 meters (49 feet) wide and 20 meters high. The sails convert wind energy directly to a vessel propulsion force, automatically expanding, contracting or rotat ing in response to the situation—for example, contracting when entering or leaving a port and while berthed, without obstructing loading and unloading of cargo. Information and communica tions technology (ICT)-enabled, the Wind Challenger sails catch the wind in the most efficient way, according to conditions. They use Big Data to analyze sea conditions, weather information and a variety of other data to predict wind direction, saving energy by sailing along the most optimal route, choosing areas with the best MOLwind. expects a vessel equipped with a Wind Challenger sail to reduce GHG emissions by about 8% on a route from Japan to A rear view of a four-tier Wind Challenger sail
PHOTO: MOL DRYBULK
BIOMASSMAGAZINE.COM/PELLET 21
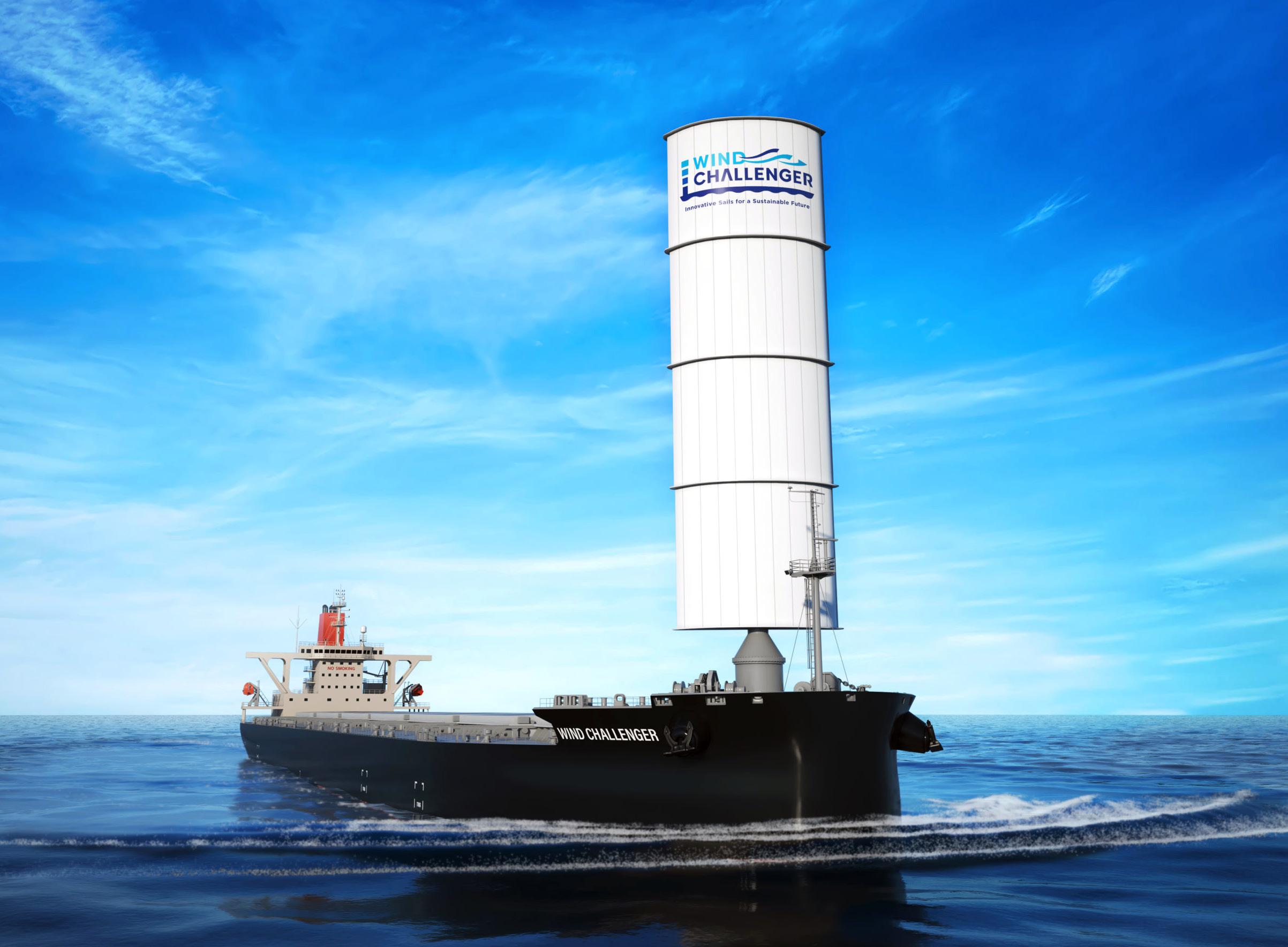
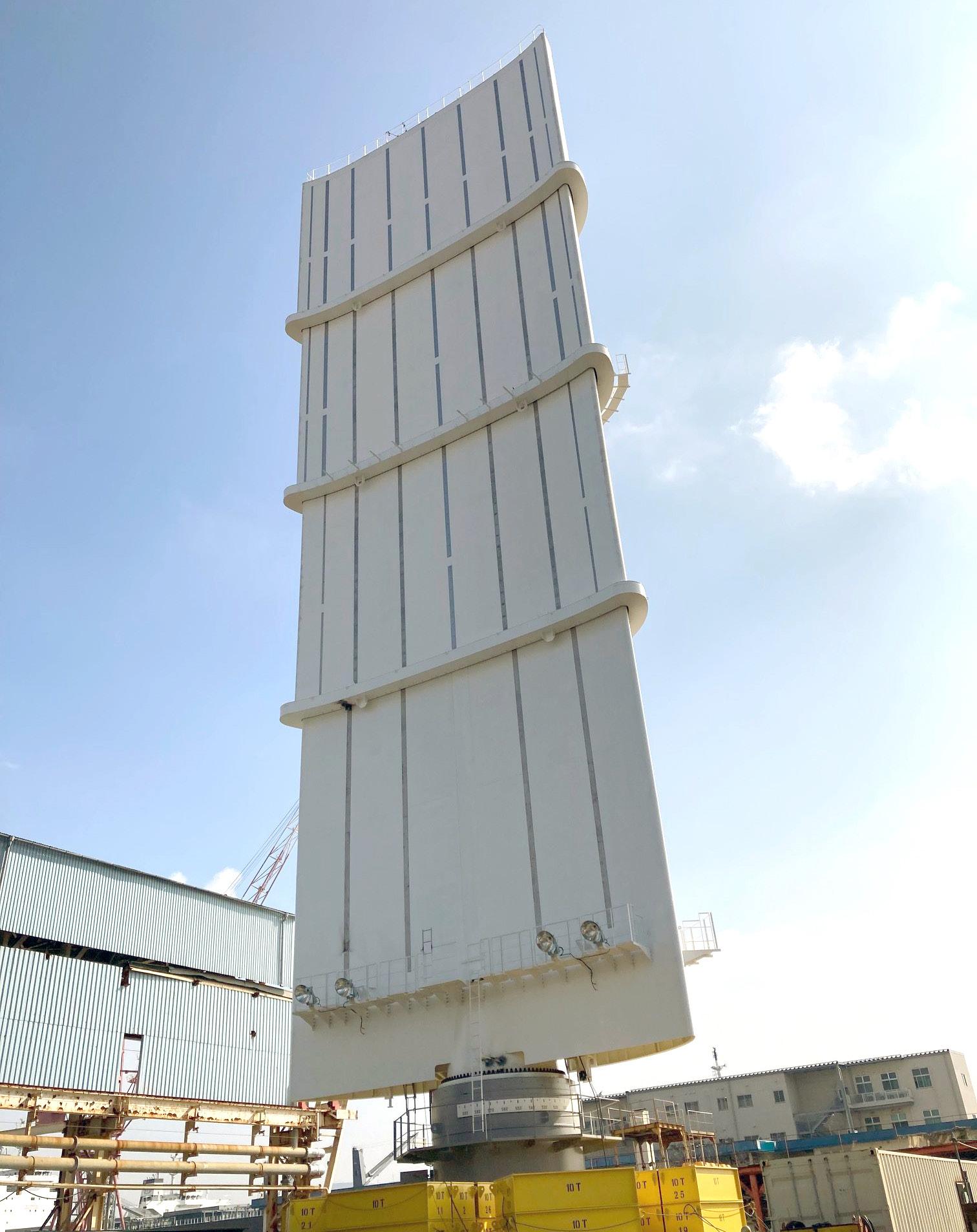
« Carbon ai165884424121_IMALPALGroup_PelletMill_2022_Sep-Oct.pdf 1 26/07/2022 16:04:09 the North American West Coast. However, with multiple sails combined with alternative fuels—the second generation of the EFBCs—emissions could be much further reduced. These vessels would be used to transport Drax’s wood pellets to Ja pan, estimated to decrease the carbon intensity of biomass shipping by a fifth, with the goal of putting the first vessel in the water in Alongside2025.its efforts in green shipping initiatives, Drax is looking to reduce carbon emissions throughout the supply chain with the development of the company’s Biomass Car bon Calculator, McKenzie explains. The tool is being used by other end users and biomass producers, and Drax expects it to become the most widely used tool across the industry. “[The calculator] allows companies to measure their supply chain emissions more accurately by using actual supply chain data,” McKenzie says. “This helps raise the quality of carbon accounting for the biomass supply chain and enables the in dustry to identify where emissions reductions can be made so the supply chain is as low carbon as possible.”
Construction of the Wind Challenger sail at Oshima Shipbuilding Yard PHOTO: MOL DRYBULK
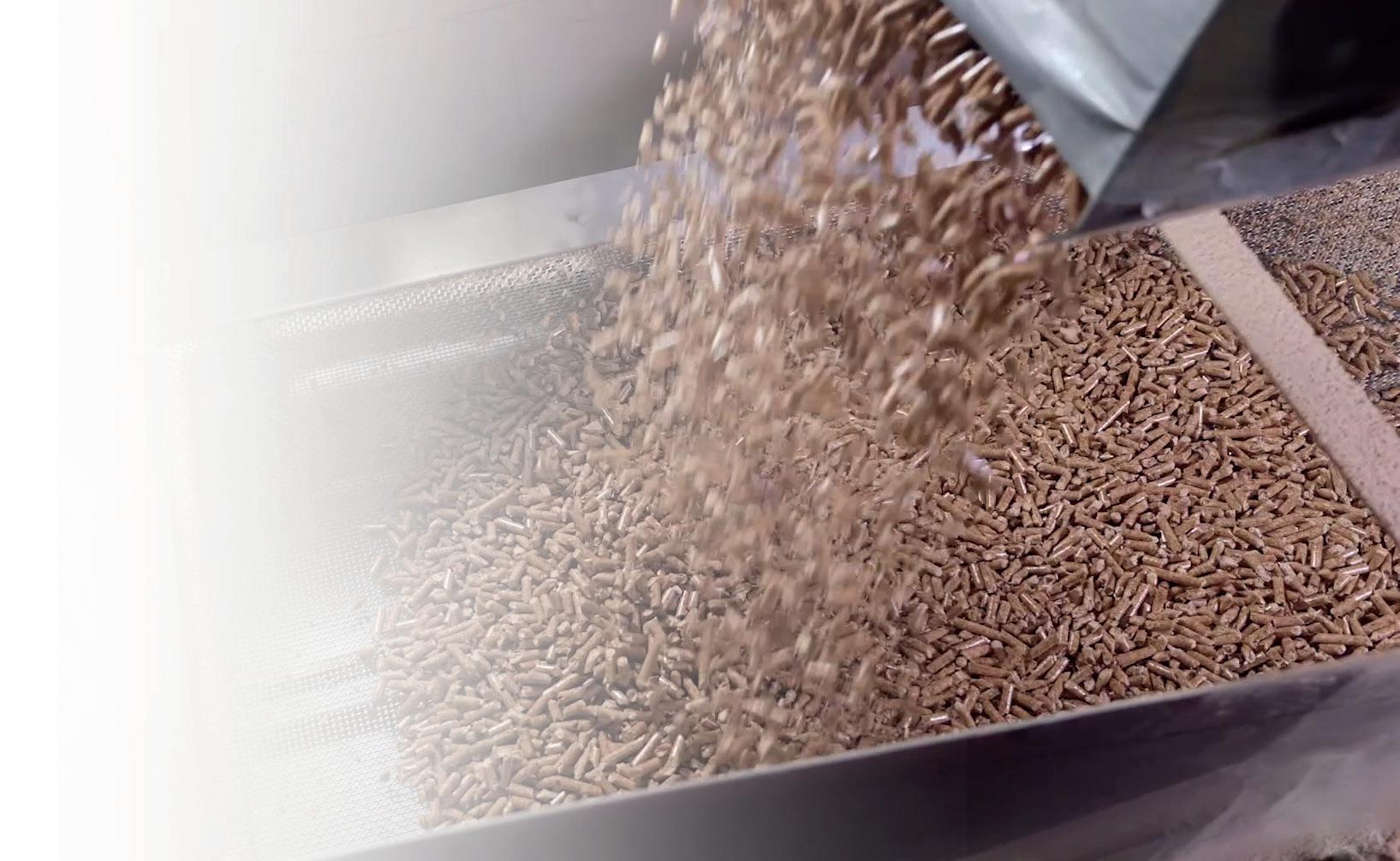
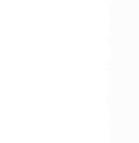

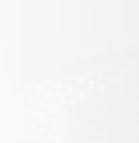
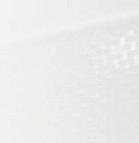

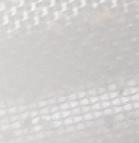

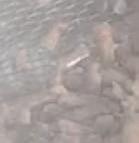


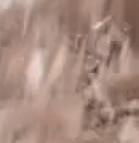
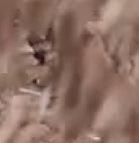
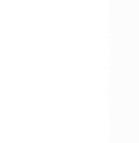
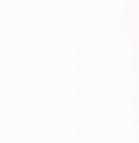
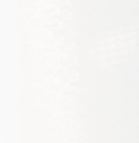
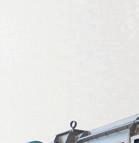
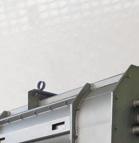
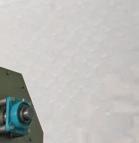

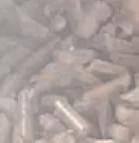
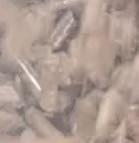
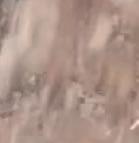
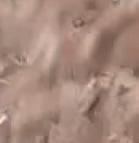
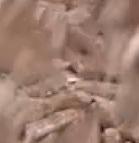
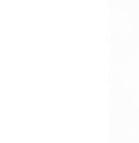
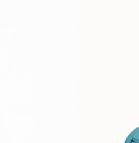
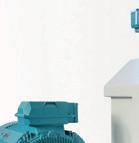
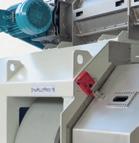
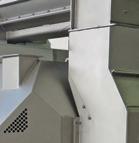
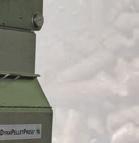

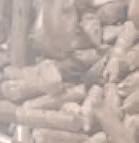


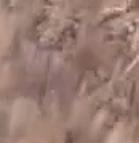
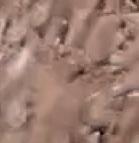
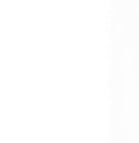
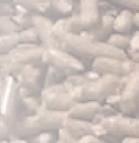
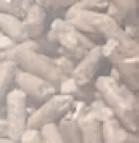

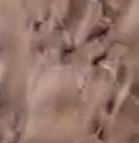
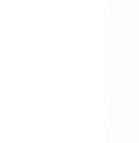

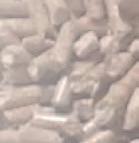


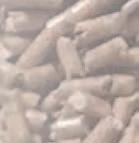


















































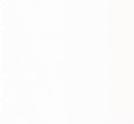
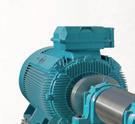
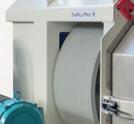
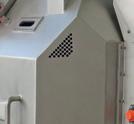
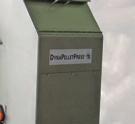
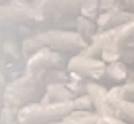


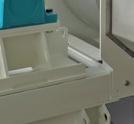
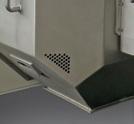


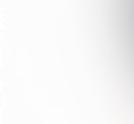


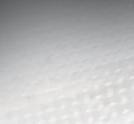
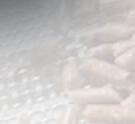
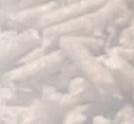
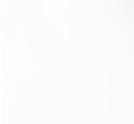
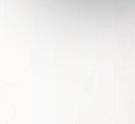
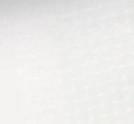
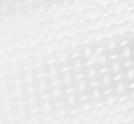
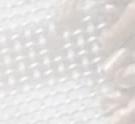
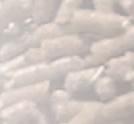


























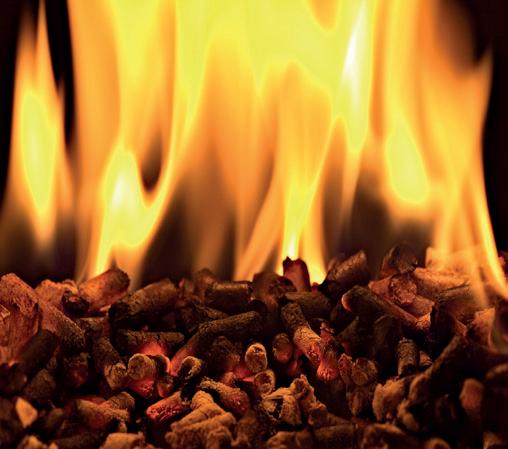

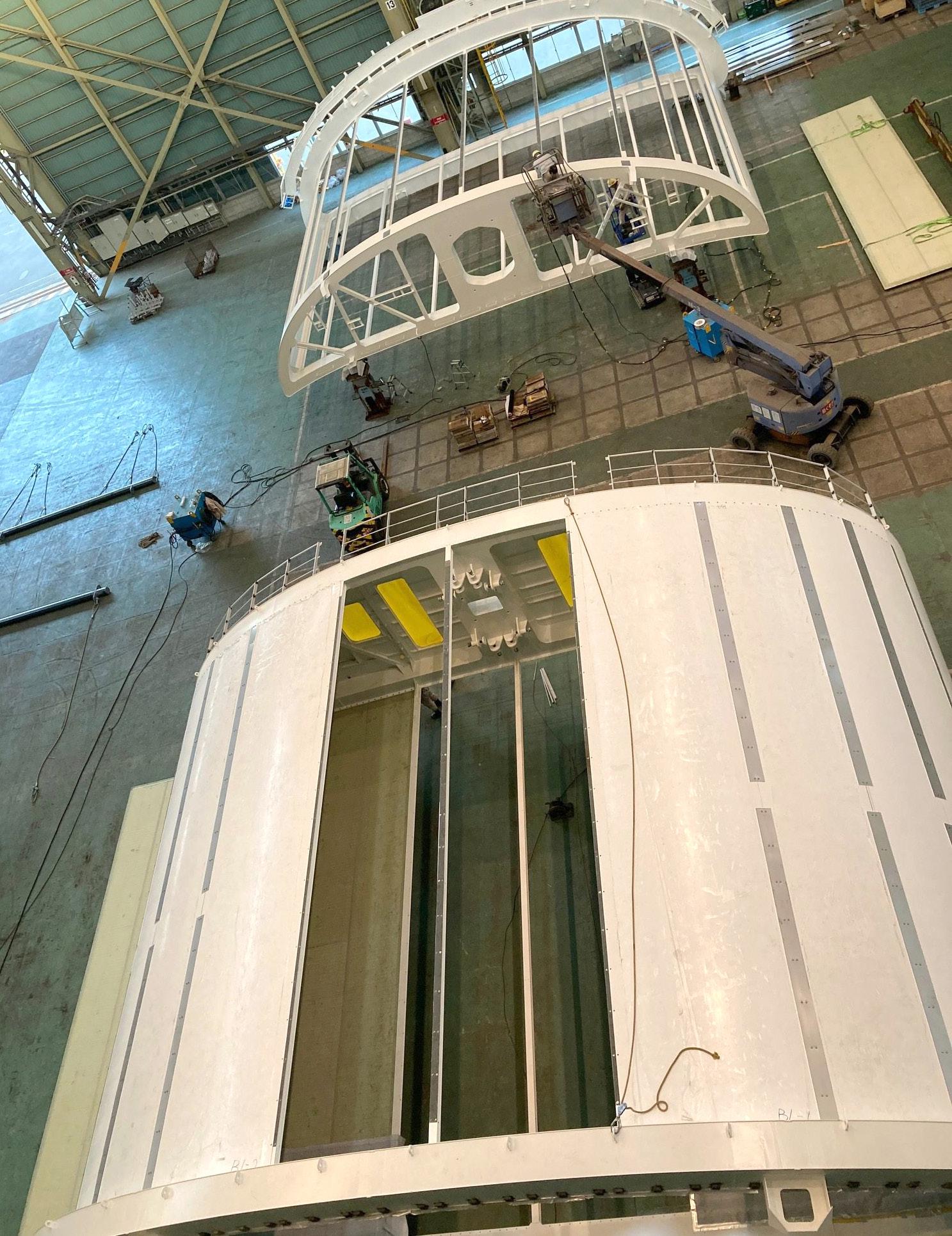
Author: Katie Schroeder Staff Writer, Pellet Mill Magazine kschroeder@bbiinternational.com
PHOTO: ENVIVA
Not only is Drax exploring options for low-carbon transportation in the Pacific Ocean, but McKenzie tells Pellet Mill Maga zine that the company has also been part of a 12-month feasibility study to find out how Smart Green Shipping’s wind-assisted sail technology could reduce the carbon emissions in shipping across the Atlantic Ocean. “The analysis, supported by the In novate U.K. program, of retrofitting ‘Fas tRigs’ to an existing 83,000-metric-ton bulk carrier showed annual fuel and emissions savings of at least 20% per annum at the ship’s usual operating speed,” he says. With carbon reduction being at the forefront of the climate change conversa tion, Drax's initiatives are a great example of taking action. The company’s methods to bring down its CI throughout both its supply chain and operations demonstrate how producers can view CI reduction ho listically, rather than going all-in.
Enviva Partners with MOL Enviva has also partnered up with MOL Drybulk, in May announc ing an MOU to deploy EFBCs. Fol lowing a successful joint study phase, the EFBC is scheduled for launch in 2024. It will aim to utilize rotor sail technology developed by Anemoi Marine Technologies Ltd. alongside MOL’s Wind Challenger technology, according to Enviva, which would both reduce emis sions by harnessing wind energy, for an expected average GHG sav ings of about 20% in total. The 62,900-DWT vessel will be built by Oshima Shipbuilding. Enviva, MOL Drybulk and Anemoi Martine Technologies have teamed up for development of a carboncutting vessel.
BIOMASSMAGAZINE.COM/PELLET 23


In the current market situation with fuel shortages and pellet prices going through the roof, it is more important than ever to reduce downtime to the absolute minimum. In ad dition, increasing energy costs and material scarcity requires pellet producers to optimize their processes. The following are some op erations and maintenance guidelines that will help producers stay online maximize their bottom lines. Roller and Die Lifetime Rollers are one of the main wear parts in every pellet mill. Extending their lifespan means saved maintenance time and lower operating costs. The main reason a roller needs to be changed is a worn down surface. In fact, the inner components of a roller can often be reused up to three times. A major accelerator of the roller’s surface wear is a high mineral content (e.g., sand). Therefore, it is advisable to keep the material input as clean as possible. This can be achieved through cleaning processes and a monitoring system of the raw material. It is also important to keep the rollers at the right temperature, roughly 194 to 212 degrees Fahrenheit (90 to 100 degrees Cel sius) in order to ensure a smooth operation and protect the components. Many mod ern pellet mills have integrated sensors that constantly monitor the heat within the press chamber. Based on this data, the rollers can then, during operation, be automatically or manually cooled from the inside with grease or oil.If the material input is too high, rollers can slow down, and the press chamber may eventually become clogged. To prevent this early on, the roller RPM, or revolutions per minute, should be monitored as well. Some machines have this feature integrated as well. When the roller speed slows down, the mate rial input rate should be decreased. However, even the best treatment will eventually require a roller change. After a couple thousand hours of operation, the roller surface loses friction and efficiency de creases. If that is the case, it is advisable to
CONTRIBUTION: The claims and statements made in this article belong exclusively to the author(s) and do not necessarily reflect the views of Pellet Mill Magazine or its advertisers. All questions pertaining to this article should be directed to the author(s).
24 PELLET MILL MAGAZINE | ISSUE 3 2022 « Operations &
O&M Tips for Efficient Pellet Production
MaintenanceBYTIMOMÜLLER
A pellet mill is built to pelletize. Each hour that it is not in operation equals to lost money.
PHOTO: SALMATEC
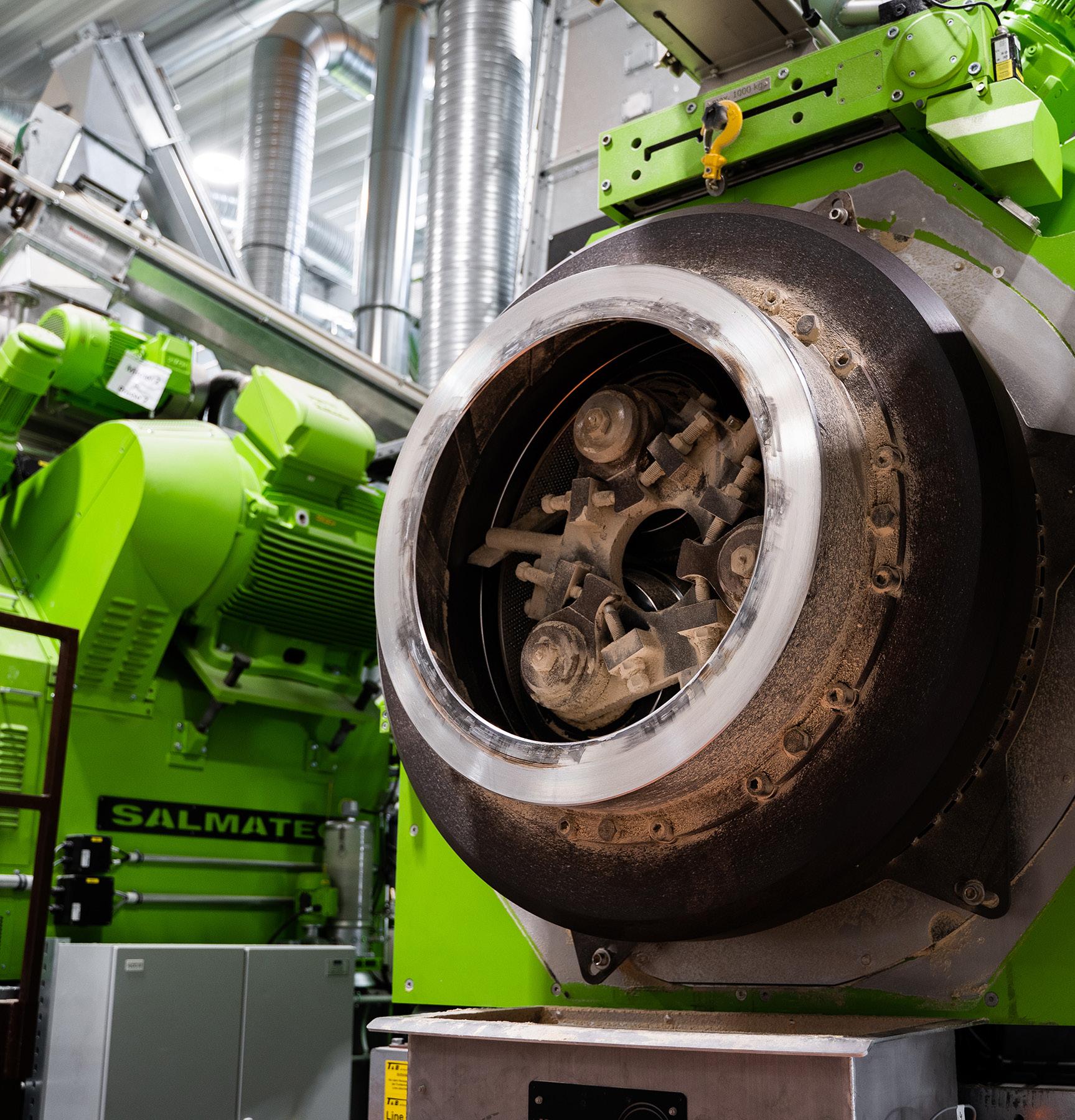
Lubrication and Safety Every pellet mill requires sufficient lu brication in order to run smoothly and pro tect its components. Many pellet mills come with a central lubrication system that can be automated to a high degree. There are also big differences between lubricants. Where as traditional greases require high amounts, special lubricants such as ceramic-based greases can reduce the volume significant ly, by up to 95%, while also extending the bearingFinally,lifetime.safety should be the highest priority at every pellet operation. Ignoring important safety measures does not only bring the risk of sudden and long-lasting production stops, but also puts machine operators in danger. Therefore, protective devices and features installed by the ma chine manufacturer should not, under any circumstances, be bypassed. There are no shortcuts when it comes to safety. This in cludes dust formation, too. The production facility should be kept clean with a power ful extraction system and regular cleanups. Too much dust can not only lead to danger ous explosions but have negative effects on workers’ health. In conclusion, there are several aspects that need to be kept in mind when produc ing high-quality wood pellets in large quan tities. Regular checkups are the key to pre vent major damages and production stops, and to keep downtime as short as possible, critical wear and spare parts such as rollers and dies should be kept in stock.
Screw Conveyor Corporation has provided engineered material handling solutions since 1932. We focus on Screw Conveyors, Screw Feeders, Round and Flat Bottom Drag Conveyors, as well as Centrifugal and Continuous Bucket Elevators (both belt and chain). Visit screwconveyor.com to learn more about our capabilities. We look forward to working with you on your next engineered material handling solution! Feeding, Conveying and Elevating Solutions ® ® ® screwconveyor.com 700 Ho man St., Hammond, IN 46327-1894 Phone 219-931-1450 Winona, MS P: 662-283-3142 Visalia, CA P: 559-651-2131 Guadalajara, México P: 333-645-7110 For the Wood Pellet Industr y
BIOMASSMAGAZINE.COM/PELLET 25 use a spare set of rollers and refurbish the used ones. When taken apart with care, the inner components can often be used again. This reduces the amount of metal waste and saves costs for new parts. As well as roller lifetime, pellet die lifetime also heavily depends on the mate rial input. If holes become clogged, chanc es of the die breaking increases, especially if there are clusters of clogged holes. If the machine operator notices this soon enough, the die can be changed in order to prevent breakage and possible damages to other press components. To do this, pro duction should schedule routine inspec tions. Afterward, the affected holes can be cleared through a combination of highpressure water cleaning and heat treating. If this does not work, it sometimes makes sense to drill the holes free. A common cause of hole clogging is foreign objects falling into the press chamber. If the percentage gets too high, it not only risks the die, but also decreases overall pellet quality. Filtering systems are a solution for this. Magnets installed be tween the conditioner and the pellet mill can detect and sort out metal parts that would otherwise cause major damage in the press chamber. Those parts might be nails or saw parts that came from the raw material, or pieces of tools that got into the material flow during transportation or pretreatment (e.g., truck parts, screws, hammer mill components, etc.). Key to a long die lifetime and a high material throughput is the correct die con figuration. With high capacities of several tons per hour, the slightest change can have a big impact. Therefore, it is of great importance to find the best configuration regarding the die’s thickness, width and press length. The best parameters depend on the characteristics of the input material. With longer delivery times, it makes more and more sense to keep the most essential wear parts in stock. It is advis able to keep one extra set of rollers (two or three individual rollers) and one die per pellet mill in stock. These components are custom-made and require several weeks of production and shipping during peak times.
Author: Timo Müller Salmatec timo.mueller@salmatec.deGmbH

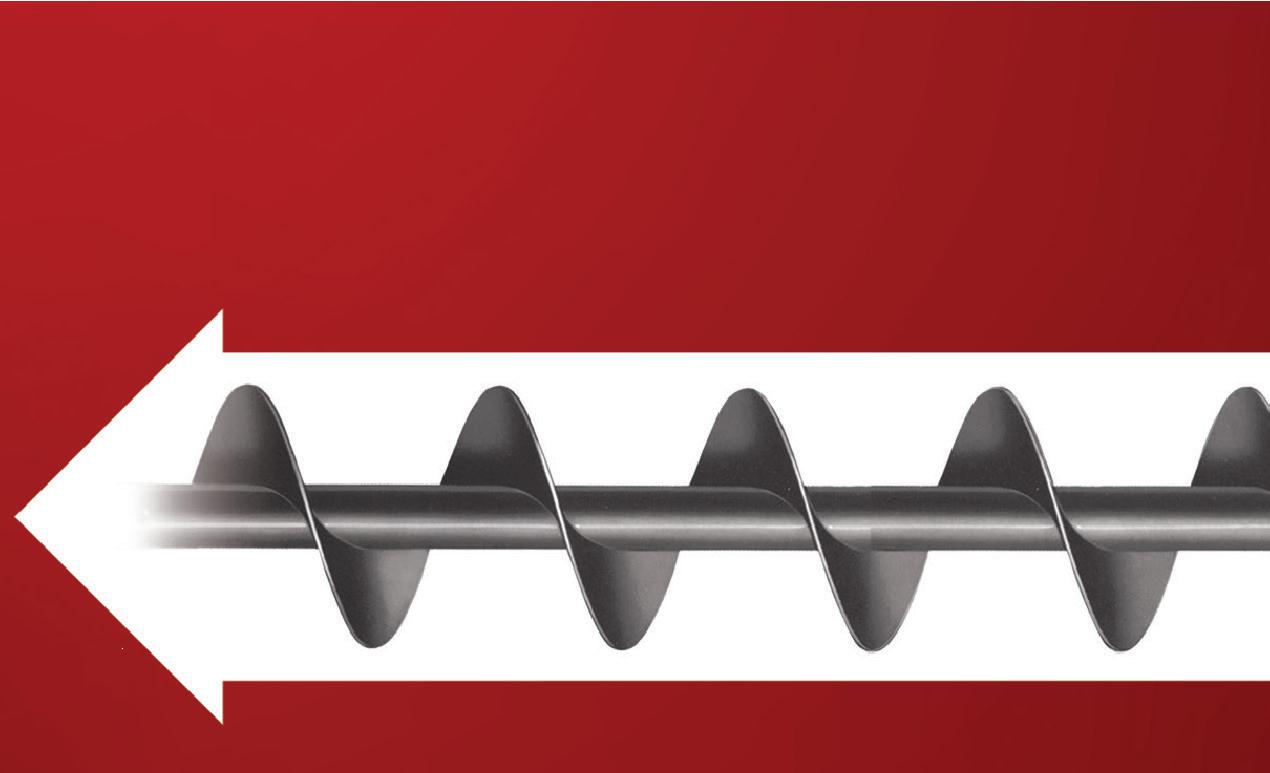


Operations
Fine saw dust as raw material PHOTO: JÖRG LANGENHUYSEN, BATHAN AG «
26 PELLET MILL MAGAZINE | ISSUE 3 2022 BY HOLGER STREETZ
The Influence of Material Flow on Pellet PerformanceMill
CONTRIBUTION:
Dust control and dust management is not only a safety topic. Wood dust is a byproduct of all wood manufac turing. Thus, all wood processors have dust manage ment for safety reasons in common. For a dust ex plosion to happen, all that is required is a single spark from a hot surface or an electrical device. When the dust disperses and mixes with atmospheric oxygen, ignition in an enclosed or contained area causes an explosion. However, it is often not the first reaction that is devastating, but the much larger amount of dust aroused by the blast wave. This can ultimately lead to a chain reaction that can potentially destroy The claims and statements made in this article belong exclusively to the author(s) and do not necessarily reflect the views of Pellet Mill Magazine or its advertisers. All questions pertaining to this article should be directed to the author(s).

• Increase load toward current maxi mum, while adjusting effective press chan nel length and other parameters.
EXPERIENCE
• Correct measurement of KPIs, espe cially power consumption.
Most pellet producers are well aware of explosion risks. However, wood dust has an enormous effect on the pelleting process and plant performance, too. For instance, a high amount of wood dust leads to increased maintenance on filters and a heightened risk for filter fires. Additionally, when raw material management in the silo is not considering the wood dust properly, the material flow is inhomogeneous. An un even material mix will lead to high variances in power consumption and pellet quality. A German wood pellet plant with four pellet mills (4-ton-per-hour capacity each) recent ly upgraded its pelleting process with a dry hammer mill with a higher capacity. With the installation, the plant has been able to reach a higher material flow. The dust content is greater than 50%. With such a large amount of small particles and wood dust, the effective press channel length for a high-quality residential heating ENplus wood pellet is just 35 millimeters (mm), or 1.378 inches. The dry hammer mill sifters have a size of 5.5 to 6 mm and the pellet mills are producing approximately 3.6 tons of wood pellets at 420 amps. The power consumption of 75 kilowatt-hours per ton (kWh/t) is very high, compared to the in dustry average for this equipment of 55 to 60 kWh/t. Potential reasons for the high power consumption include particle size, incoming material humidity, and the dwell time in the ripening bunker. In general, the material should ripen for 10 to 15 minutes and have a moisture content of 10 to 12% when entering the pellet mill. At a status quo assessment that we witnessed, the pellet producer had been operating the pellet mills with caution. The plant was not running at full capacity. The motors of the pellet mill were oper ating at 75% of maximum current (motor power in kW x2 -10%). Due to the low load, the product in the die longer, which causes overrunning of material. Addition ally, the key performance indicator (KPI) power consumption measured in kWh/t was metered at the flapper scale. The ideal measurement for the power consumption and the according kWh/t KPI is directly behind the press, including debris and dust from abrasion. The pellet mill should be operated with an open pellet chute for one minute at 70 to 80% load and collect the pellets, dust and debris. The weighed material translates into kWh/t. The per formance is also measurable by the feeder screwThespeed.plant desires to improve on per formance toward nameplate capacity. Our recommendations from the assessment are:
Author: Holger Streetz Chief Operating Officer, Bathan h.streetz@bathan.chAG
MATTERSLEARNMORE@
Celebrating 20 Years of kescosolutions.comService 803-802-1718
In conclusion, the amount of dust in the process has an impact on quality and pelletizing performance. Get in touch with us to discuss performance optimization in pellet production.
The Effects of Wood Dust
BIOMASSMAGAZINE.COM/PELLET 27
a whole plant. If there is a risk of accu mulating wood dust, the main hazard con trol measures are good housekeeping, well maintained equipment to reduce any igni tion risk, and existing controls to reduce the effects of an explosion, such as vents or dust collectors.
• Improve material management in the silo for a more even mixture. In the following months, we will help increase production toward nameplate ca pacity while also ensuring other KPIs are met. Power consumption is especially of importance. Now more than ever, prices for power are increasing significantly.
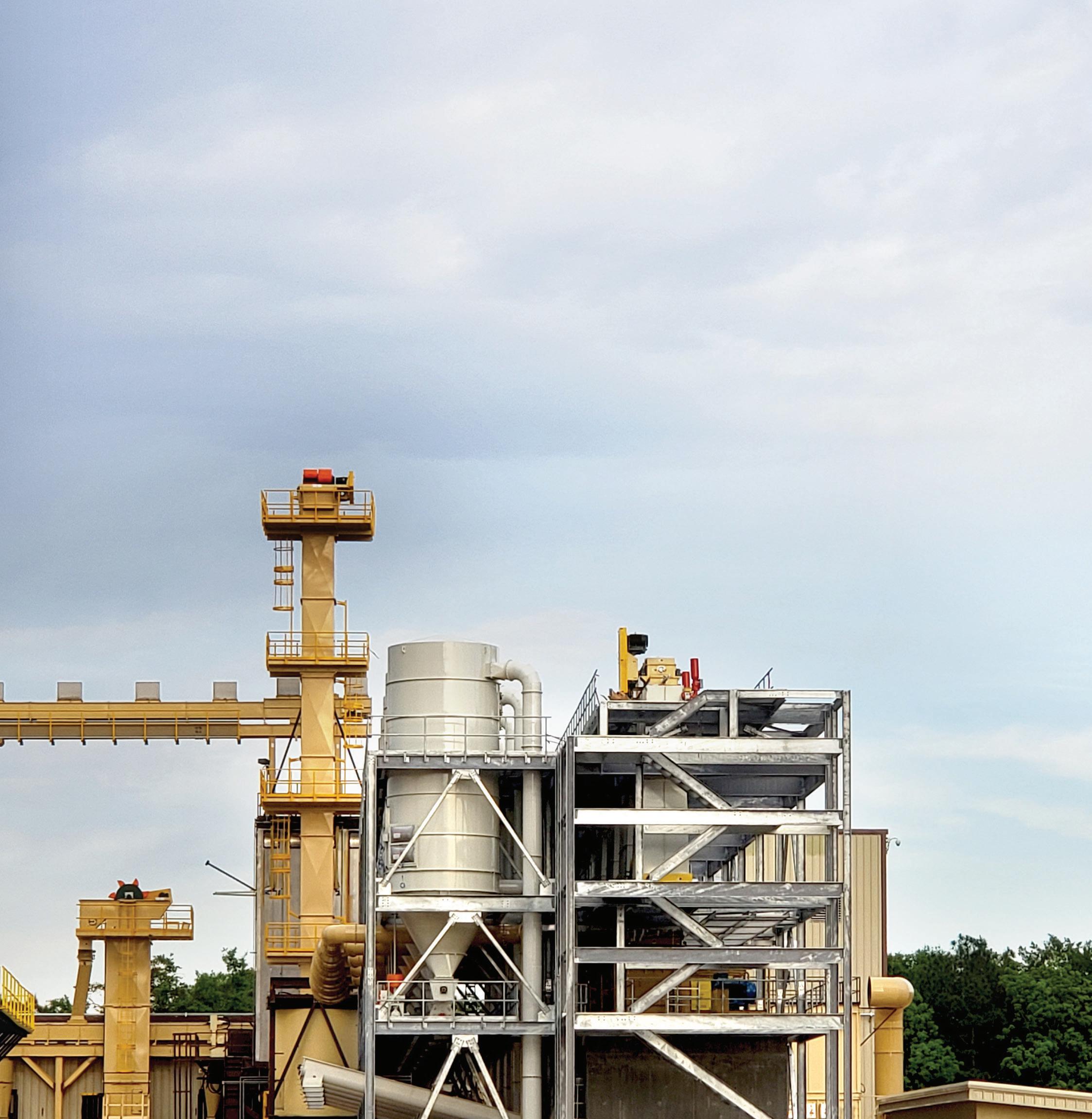


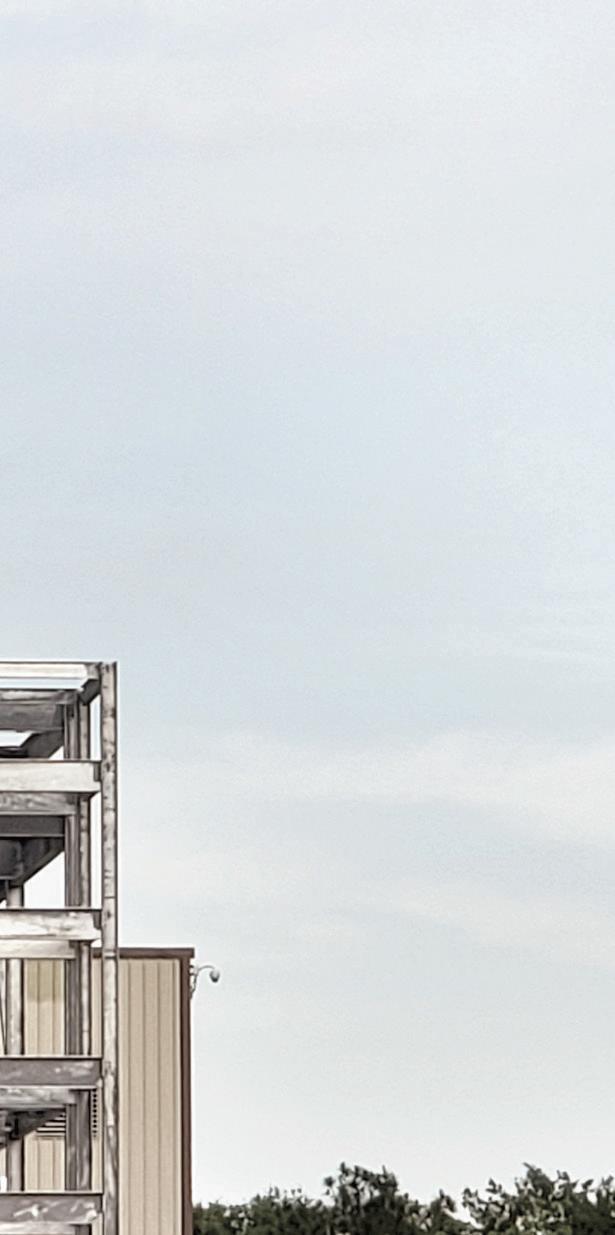
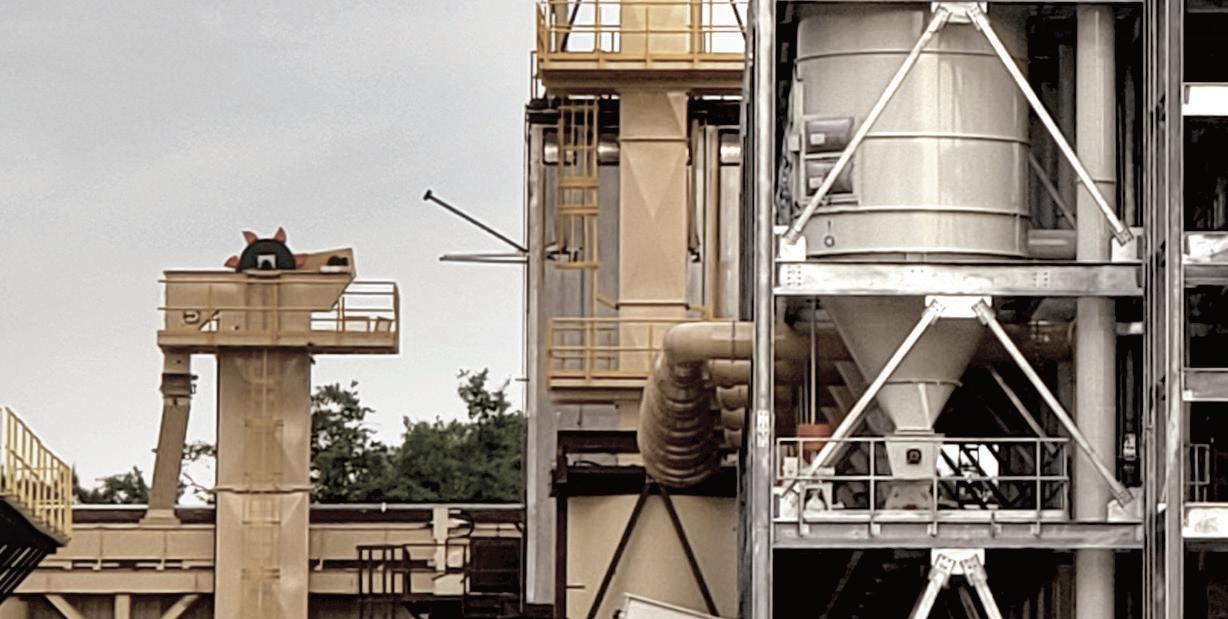
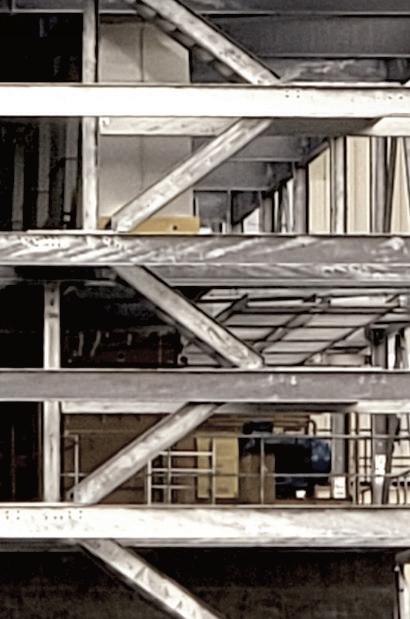
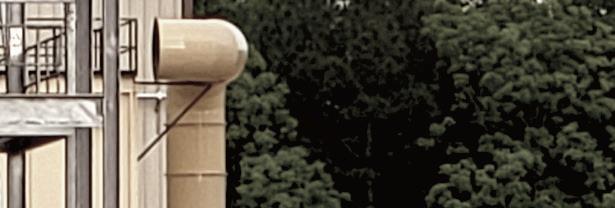
PELLET MILL MAGAZINE | ISSUE 3 2022 « Spotlight: BENETECH A Low-Cost Solution to Combat Off-Center Loading
In addition to reducing dust in fragile pellet production, the Max Zone Plus helps keep product intact through the flow correction in a directed manner, reducing dust from the loading area. Benetech has nu merous installations at pellet manufacturing plants and other bulk mate rial handling facilities. "We have installed these systems in a number of places, and they're performing extremely well,” Jasin adds. “They direct material flow, limit product degradation, and decrease dust simultane ously, and at a cost that is nowhere near it would be for an entire transfer system."
The MaxZone system is a modular, heavy-duty skirt system with an externally adjustable wear liner. This system is installed in four-foot sections, as many as required to achieve the desired length and height to create a stilling or chamber where dust can settle before it exits the skirt system. "The MaxZone is built in modular sections, and it's extremely robust for any application," Jasin says. "As Benetech moved forward, we designed our related skirt systems in a modular fashion, which can be bolted directly onto the MaxZone system. The idea was to offer a series of products to fit every skirt system need." Typically, transfer system installations may be two or three systems high from a head pulley or head section of a conveyor down to the receiving conveyor, which can be anywhere from a 20- to 50-foot drop, Jasin explains. “In many cases, we found the most dust was generated at the loading point—the very bottom of these transfers, by how the ma terial was loading onto the belt. In determining the easiest way to correct this, we took our MaxZone system and integrated a small rear deflector and side deflectors that correct the material flow right before it hits the conveyor. This led us to the development of the MaxZone Plus."
The MaxZone Plus deflectors limit the dust generated at the load ing point and secure center loading onto the receiving conveyor belt so that once material leaves the skirt system, it does not spill off the belt.
Material handling is arguably one of the biggest challenges in wood pellet production. Oftentimes, problematic load zones result in spillage and excess dust, stymieing operational goals. Recognizing this problem, Benetech designed its MaxZone and MaxZone Plus systems. In addi tion to addressing spillage and dust issues, they enable extended perfor mance, require less frequent maintenance, prolong equipment life and allow for greater safety—all at an affordable price. "Through experi ence, we found that many material handling facilities have issues, but funding isn't there to replace entire transfer systems or chutes within their facilities” says Kevin Jasin, Benetech technology manager. "Our goal was to offer a low-cost alternative."
The MaxZone Plus system has a simple design that bolts onto the existing MaxZone or can be retrofitted to other containment systems. "The side wings and rear deflector are the guts of MaxZone Plus and can be adjusted to conditions from outside of the system to correctly center load material,” Jasin says. “For example, if the material flow came in aggressively from one side of the loading center, the material would likely fall to one side, resulting in uneven loading and dusting. Without any means to control the material, the material is free to hit and bounce off surfaces, creating additional dust. "

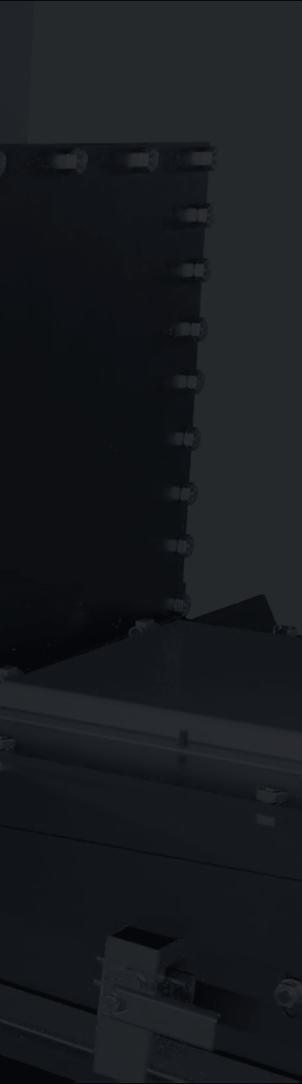



Reach Producers Book Your Ad AD SPOTS LIMITED Ad Deadline: Oct. 19, 2022 Mailed with the Quarter 1 issue of Pellet Mill Magazine Need more info on advertising opportunities? service@bbiinternational.com - 866-746-8385 - BiomassMagazine.com REACH AUDIENCETARGETYOUR Fuel Pellet Plant Map Fuel Pellet Plant Map PURCHASE A SPOT ON THE U.S. & CANADA FUEL PELLET PLANT MAP Receive 12 Months FREE Online Advertising! Advertise now on Pellet Mill Magazine’s U.S. & Canada Fuel Pellet Plant Map. It is the easiest and most cost-effective way to get your name, product and/or service in front of Pellet Producers, as well as other industry professionals for 12 months at a time. REACH 8,000 PROFESSIONALS All Biomass Magazine subscribers All Pellet Mill Magazine subscribers Pellet mill owners, operators & management All major related conferences




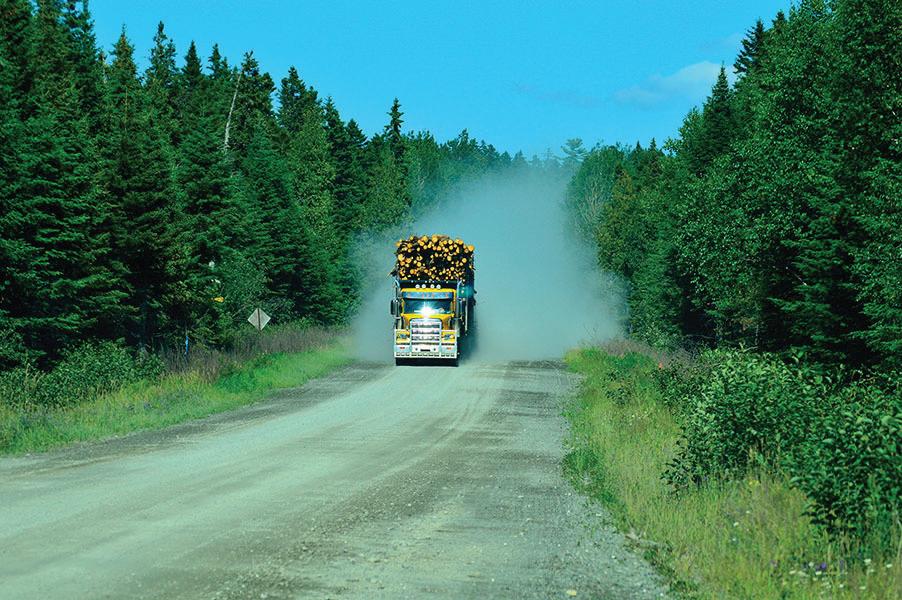
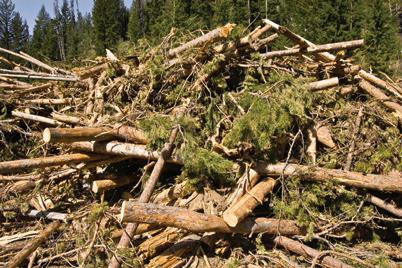
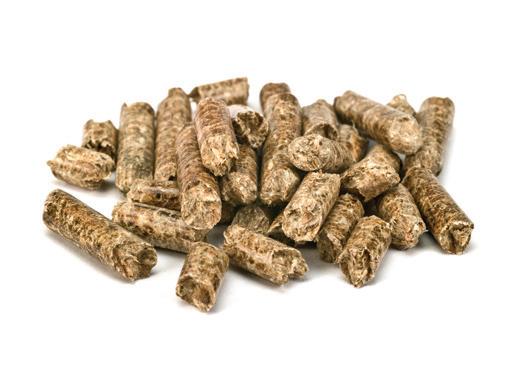
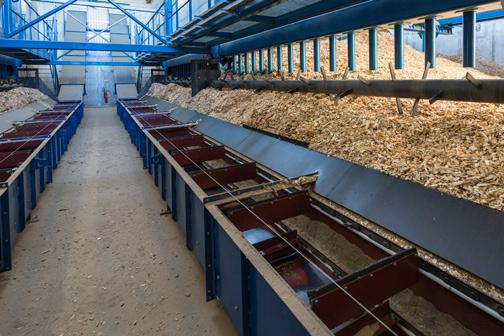
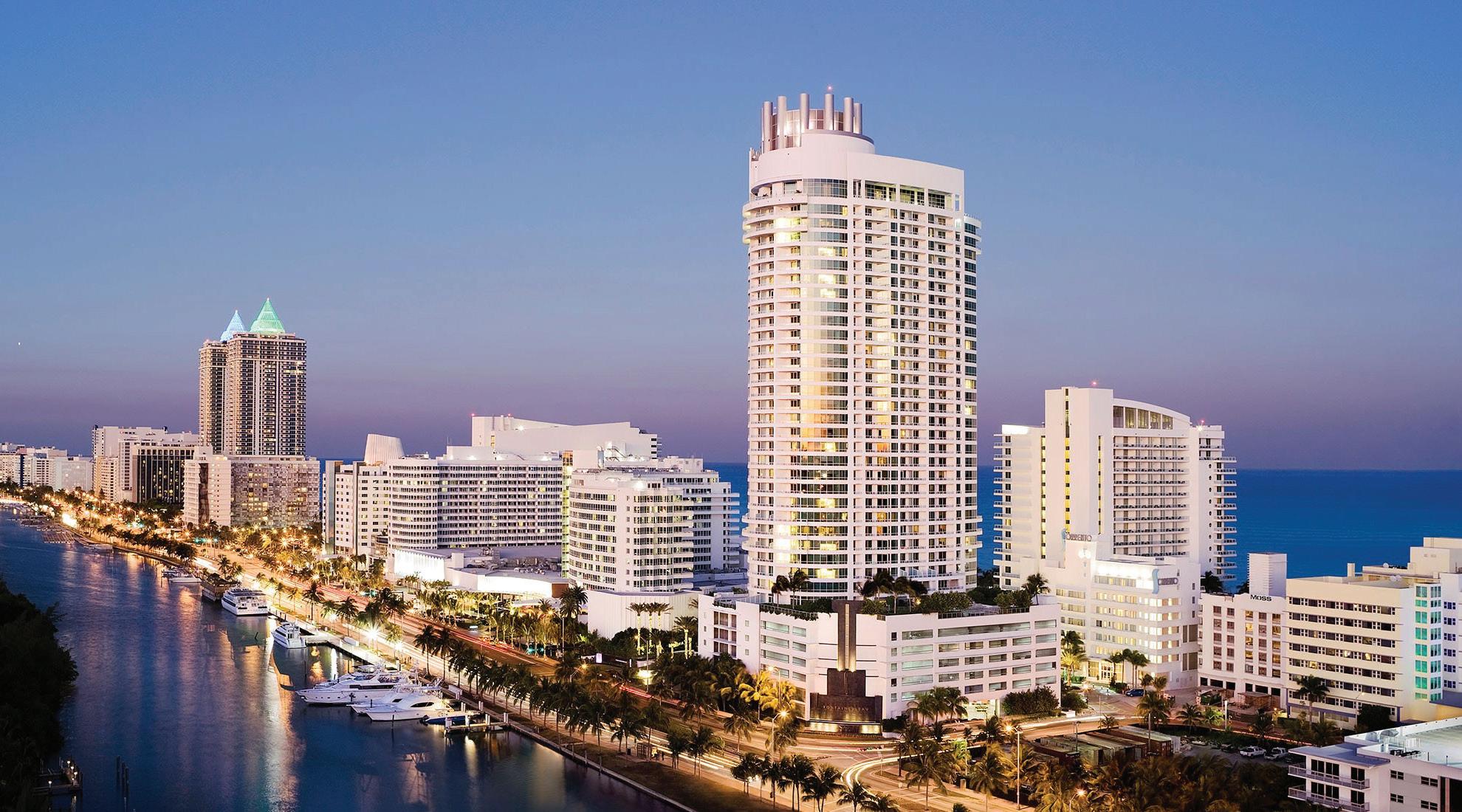
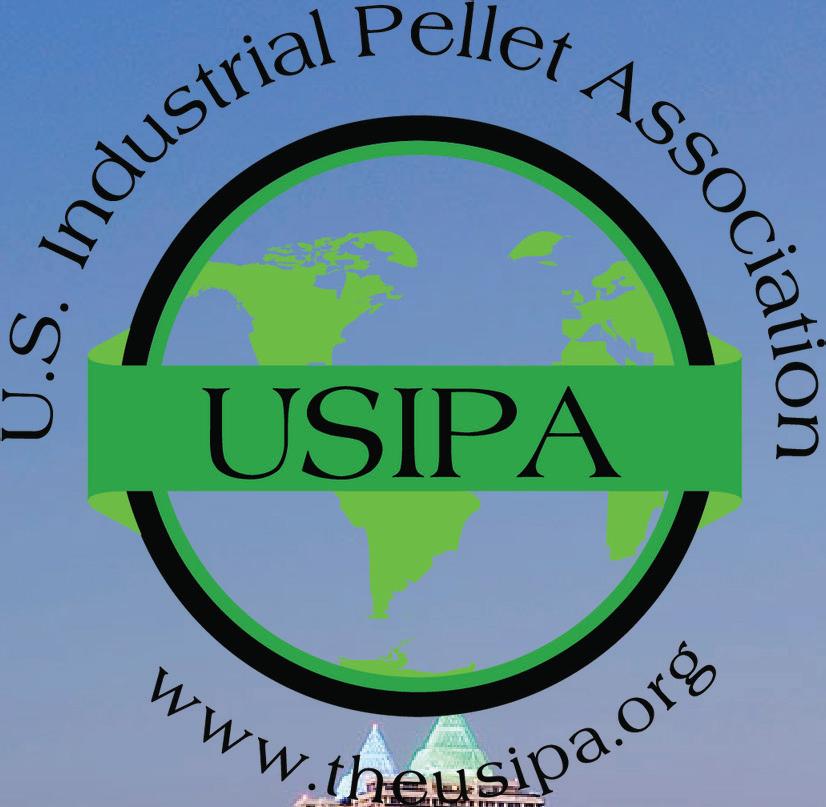
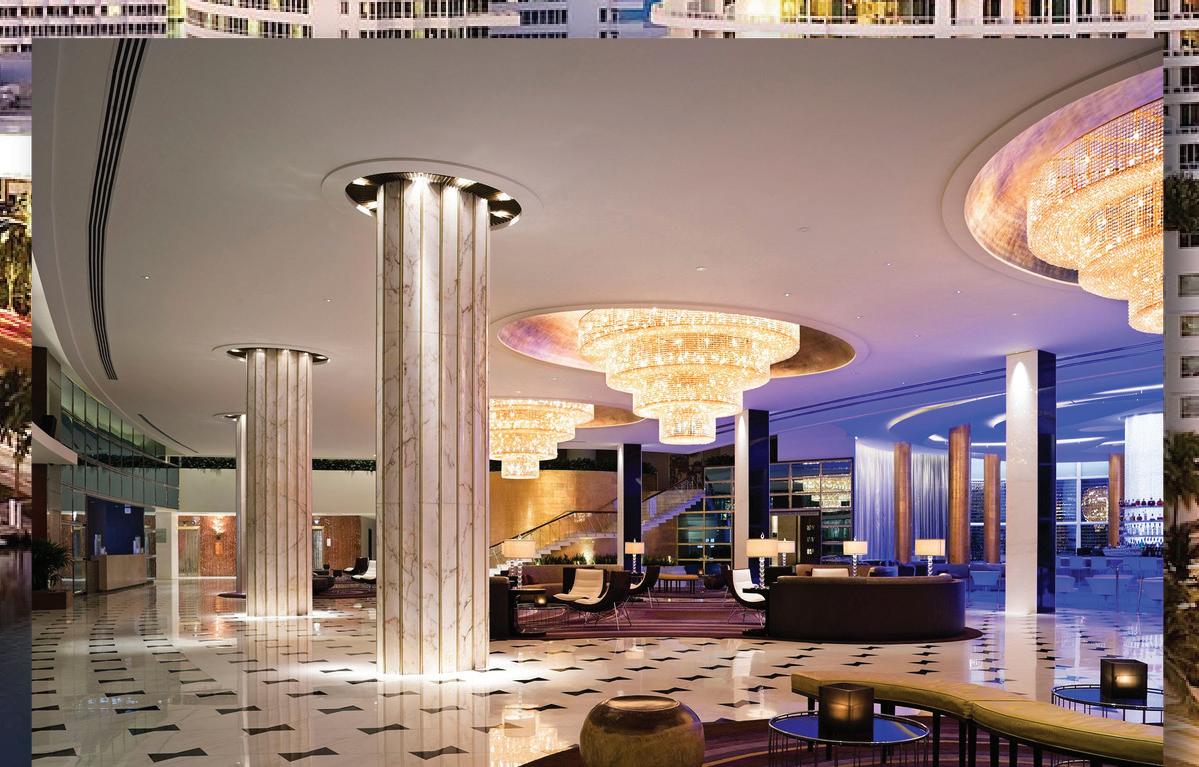
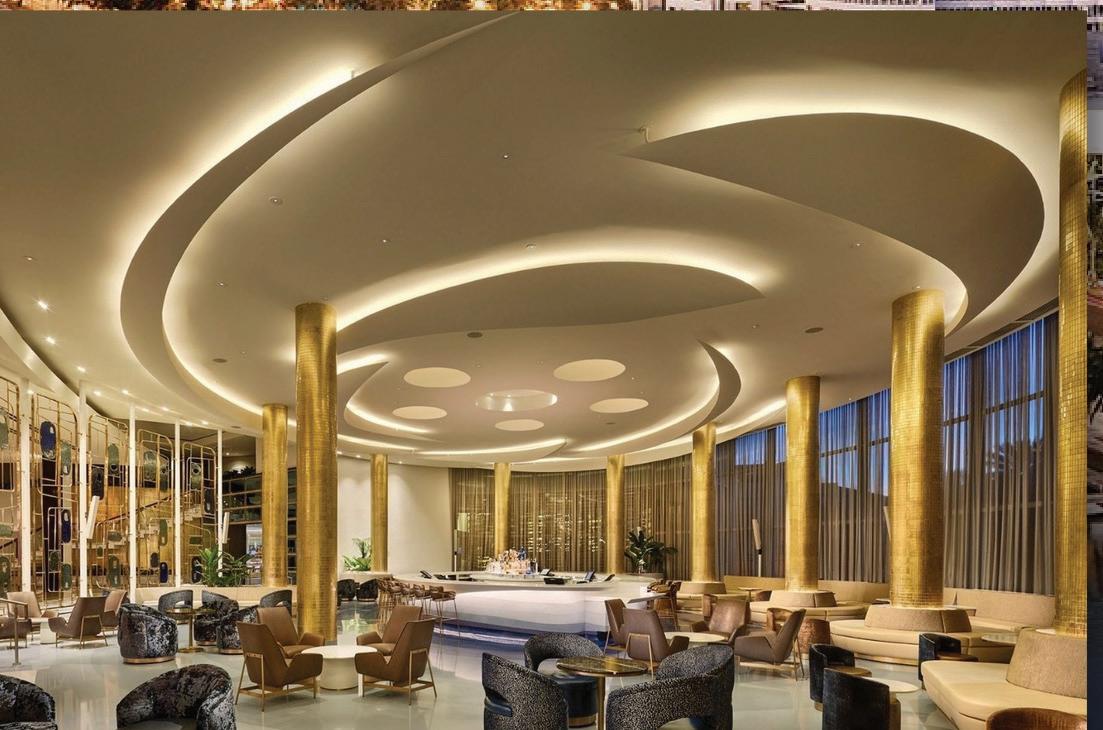
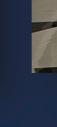
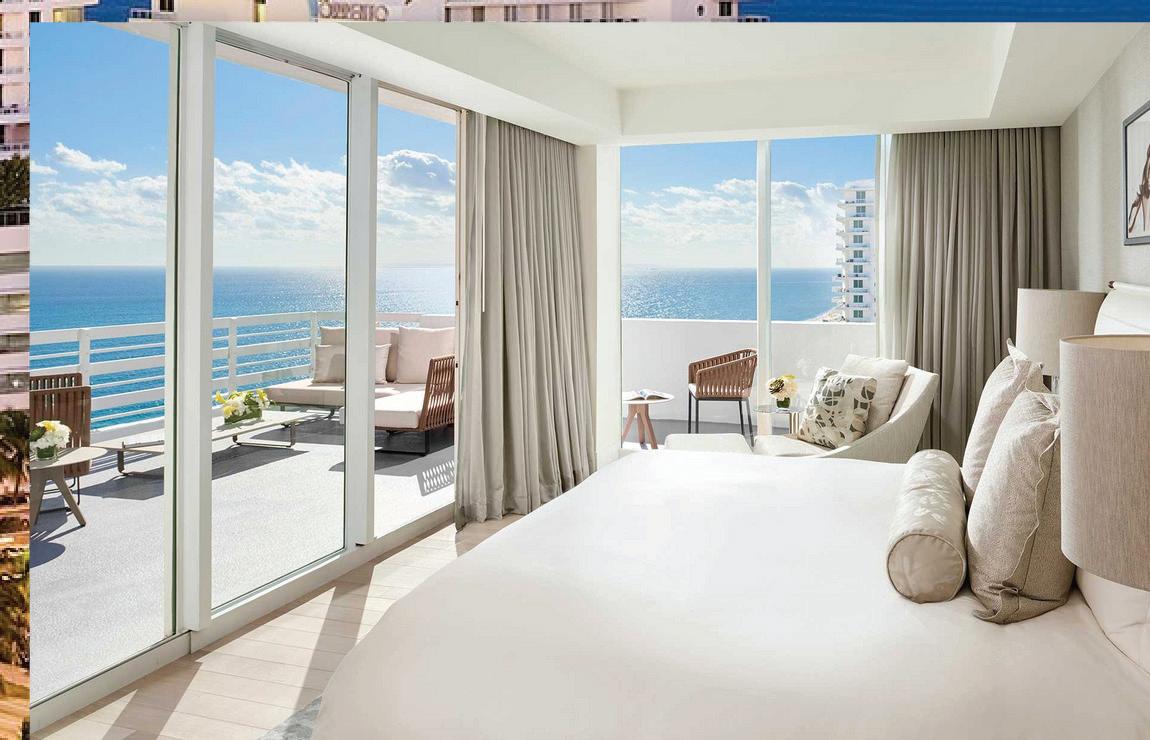
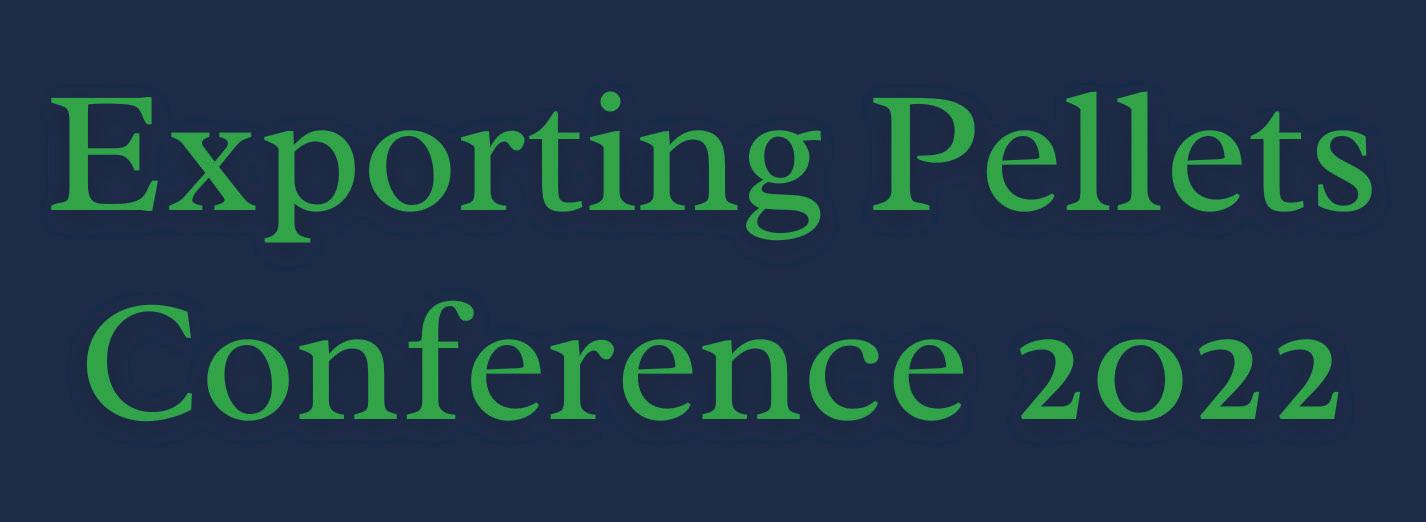
BIOMASSMAGAZINE.COM/PELLET 31
www.dryer-one.cominfo@dryer-one.com+1-443-204-4885
Conference &
International Biomass Expo in its 16th year, national Biomass Conference conference world renowned
for its service@bbiinternational.comwww.biomassconference.com866-746-8385development.ogy,biomassstrongmassprogramming—poweredoutstandingbyBioMagazine–thatmaintainsafocusoncommercial-scaleproduction,newtechnolandnear-termresearchand BIOMASS JOBS Let Biomass Jobs showcase your open position(s) to the renewable fuels industry. Post a Job - Reach Workers Post unlimited jobs for one year (jobs will expire after 30 days) All job posts include a company Joblogoposts will be visible: - Biomass Jobs website - Biomass Magazine's homepage - Biomass Magazine's Biomass Week E-Newsletter - Biomass Magazine's social media -channelsIncluded in a monthly jobs email sent to Biomass Magazine sub www.bbiprojectdevelopment.comservice@bbiinternational.com866-746-8385scribers Biomass DirectoryIndustry Biomass Magazine’s Biomass Industry Directory is the most comprehensive list of industry sup pliers, producers, researchers and government agencies available in the world. The directory is an invaluable resource to help find the contact information you are look ing for, and help others find you. directory.biomassmagazine.com service@bbiinternational.com866-746-8385 Pellet Mill Magazine Marketplace 1 6th Annual Feb. 28 - Mar. 2, 2023 | ATL ANTA, GA TECHNOLLATESTOGY innovations & policies Post unlimited 30-day online listings for 1 year with a Jobs Package POST UNLIMITED JOBS FUELING CAREERS Jobs.BiomassMagazine.com
Now
DRYER ONE™ DRYER ONE™ is a revolutionary drying machine that uses low tem perature air (~90°C/194°F), flowing through the product, which is distributed on two discs, rotating around a central chimney. This unique technology allows massive energy savings, outstand ing safety, a great flexibility, and low dust and VOC emissions.
the Inter
& Expo provides relevant content and unparalleled network ing opportunities in a dynamic business-to-business environment. In addition to abundant network ing opportunities, the largest biomass
DRYER ONE™ dryers can easily adapt to all situations and can be paired with a gas burner, biomass burner or cogeneration unit.
in the
is
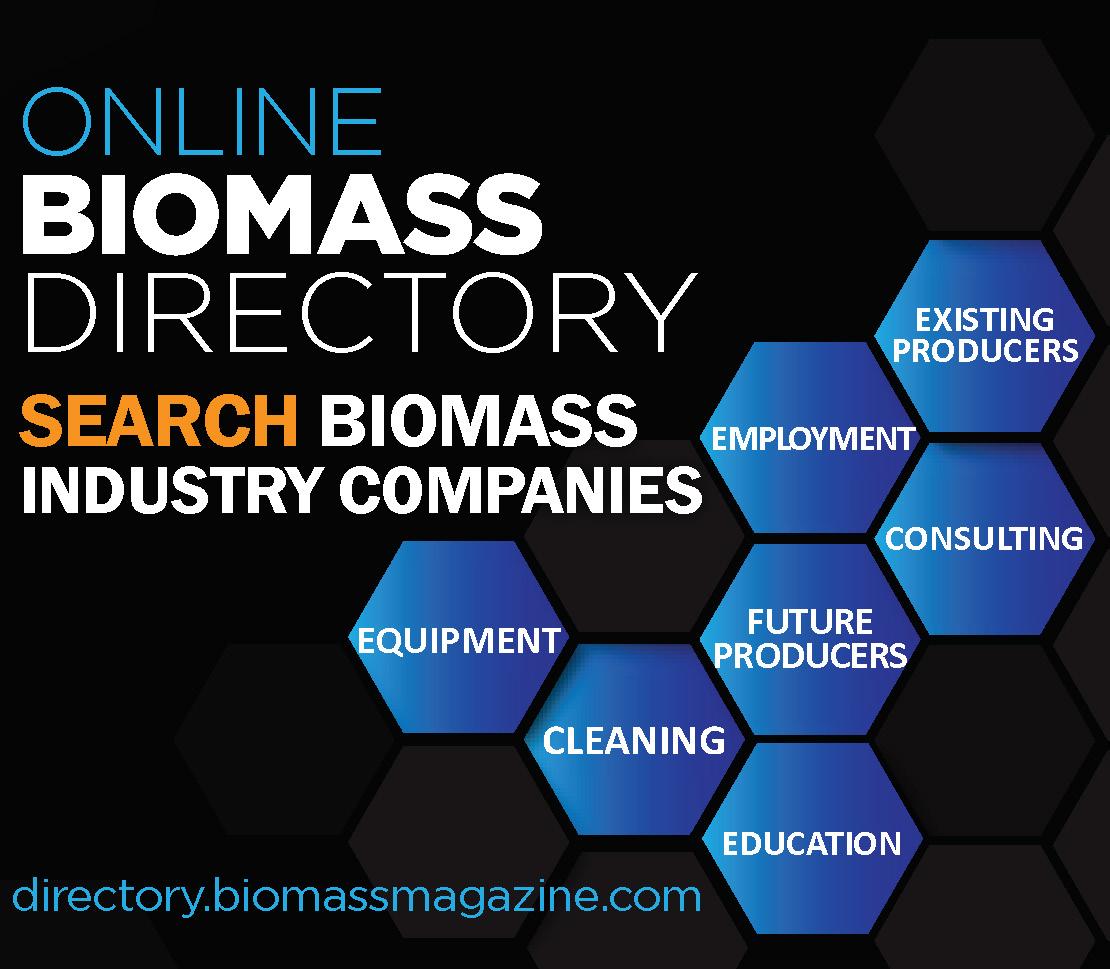
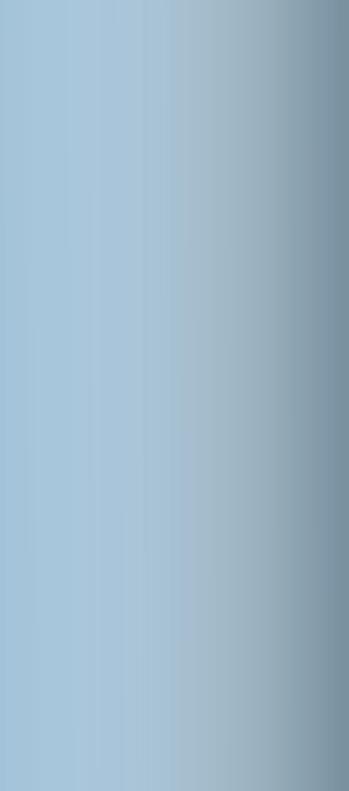
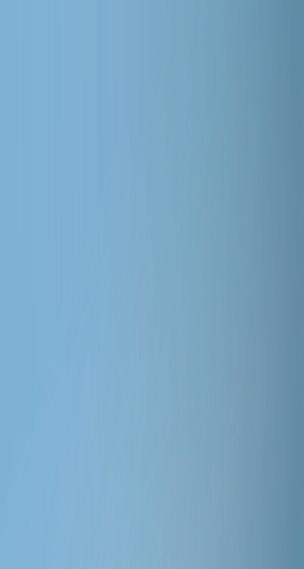
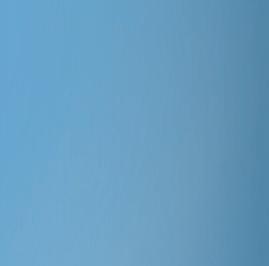

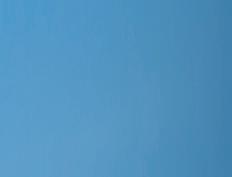
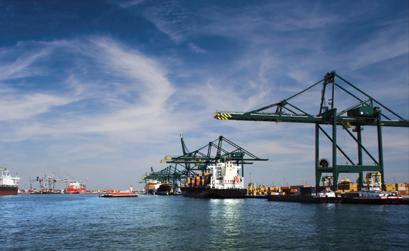
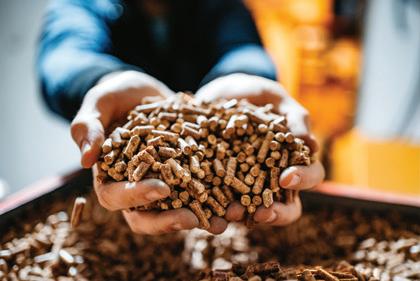

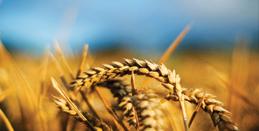
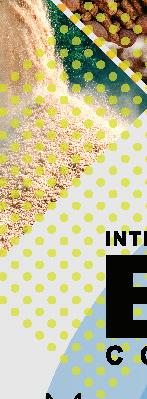

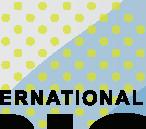

BBI International 308 2nd Ave. N., Suite 304 Grand Forks, ND 58203 Change Service Requested
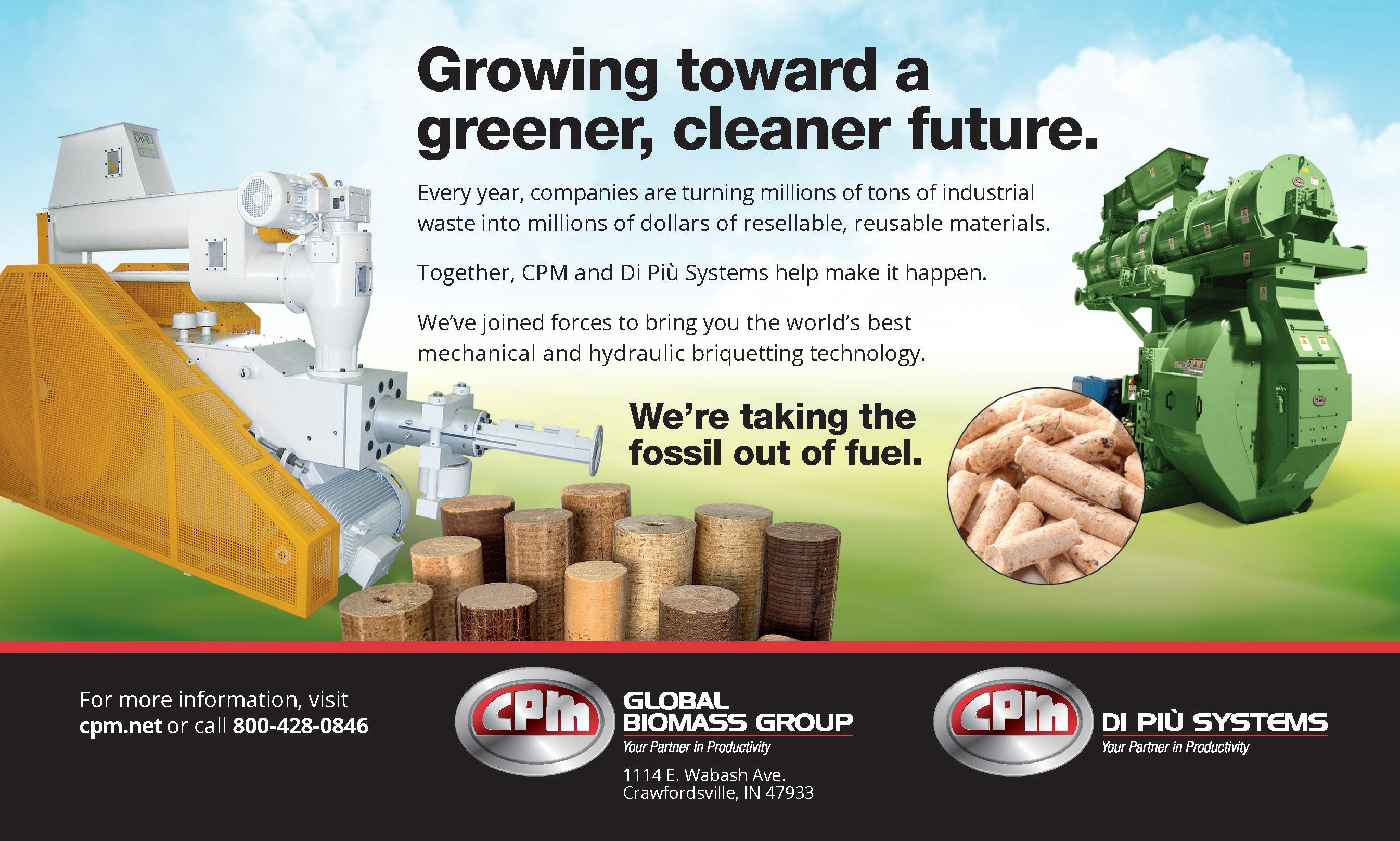