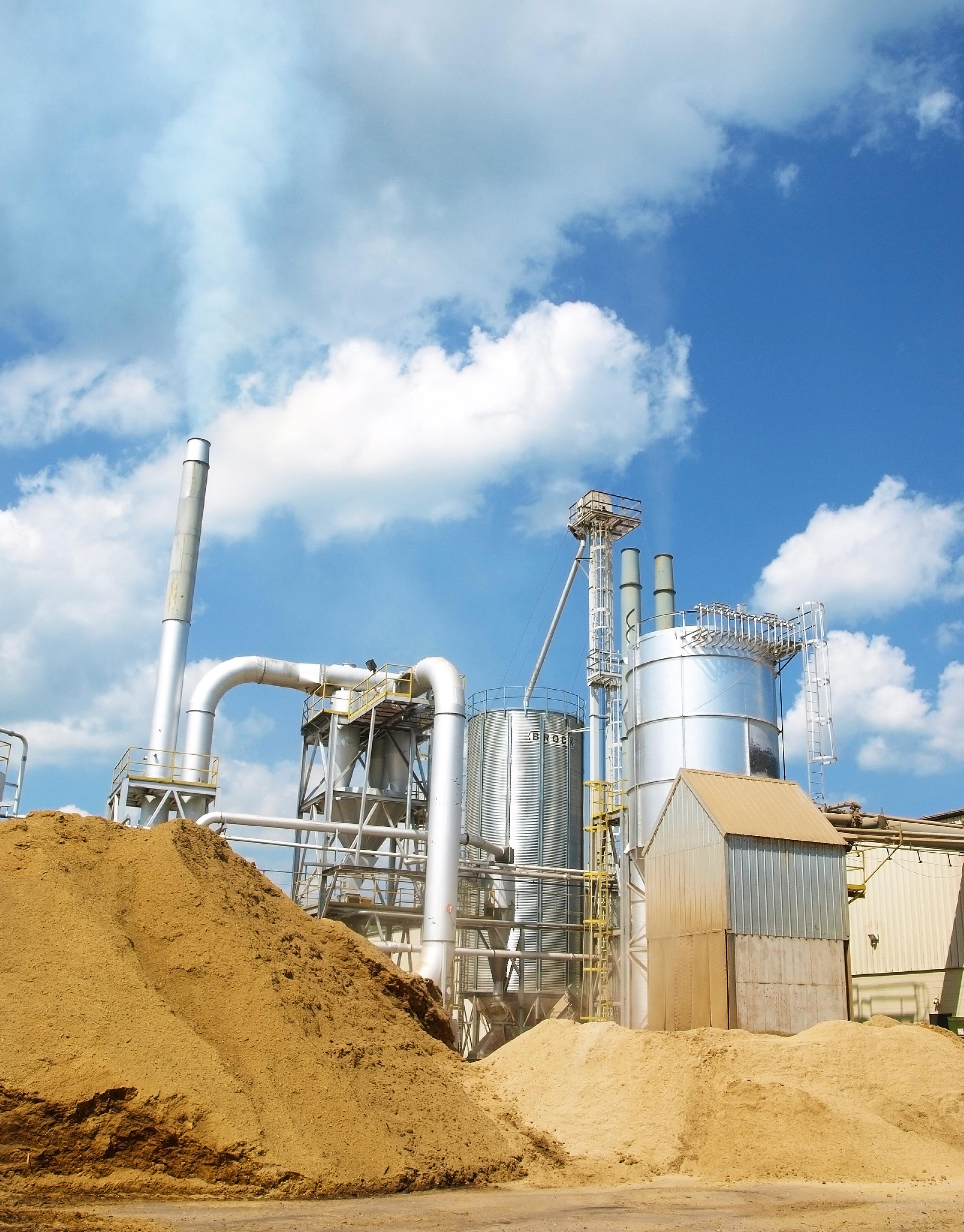

By Anna Simet
By Katie SchroederBy Anna Simet
By Katie Schroeder22 PROJECT DEVELOPMENT Start Well, End Well Successfully managing a pellet project requires an organized start that begins with a business case.
By Joel Dulin
PROJECT MANAGEMENT Project Talk Good project oversight comes at a cost but more than pays for itself by keeping a project on track.
By Sven Swenson
Clean, sustainable wood fiber awaits processing into wood pellets at a plant in Georgia.
PHOTO: BBI INTERNATIONAL
asimet@bbiinternational.com
In early October, the U.S. Industrial Pellet Association’s annual Exporting Pellets Conference returned to Miami after a pandemic-induced, two-year hiatus. This year was different than years past, with topics of discussion broadening to much more than wood pellets for heat and power. In fact, I moderated a panel that focused on sustainably sourcing and transporting all kinds of biomass for the very fast-growing renewable transportation fuels market, and what was discussed during that hour was just the tip of the iceberg. The global wood pellet industry is evolving and is poised to play a critical role in global decarbonization efforts. Find a summary of the event’s opening session, as well as photos, on our page-12 event review, “Mission Biomass Mobilization.”
Appropriately, sustainability was an underlining theme at the conference, and on that note, be sure to check out “Affirming Sustainability,” on page 18. In the story, staff writer Katie Schroeder details the results of a British Columbia fiber-sourcing study commissioned by the Wood Pellet As sociation of Canada. The province is home to roughly 65% of the country’s wood pellet production, with producers there manufacturing upward of 2 million metric tons annually. One of the main findings of the study was that 85% of the biomass material used for wood pellet production is mill residue, with 15% being forest residue. Not only do these plants provide an outlet for this waste material, but the wood pellet industry has a huge impact on the provincial economy—check out the story to learn more.
Jumping to our contribution articles, both are focused on one of the subthemes of this issue, which is project management. There is some solid, real world experience-based advice in these stories, which emphasize just how crucial good planning and project oversight are. A good summa rizing point for page-22 “Start Well, End Well,” by Joel Dulin, Biomass Engineering & Equipment: “Getting a project done right, on budget, and on time requires the project managers to develop it fully from the outset, a feat that requires good development even before the project starts.”
On a different note, we have been closely following what’s happening in Europe (on top of the evolving renewable energy directive) in regard to an anticipated pellet shortage. Recently, the U.K. Department of Business, Energy and Industrial Strategy announced it would temporarily suspend ENplus requirements for one year, as of now. The intentions behind this are to help ease challenges stemming from Russia’s invasion of Ukraine, and this temporary rule change applies to both the domestic and nondomestic RHI schemes. While it won’t eliminate the shortfall and surging prices (Europe imported more than 2 million tons of Russian wood pellets in 2021), it will allow for some producers that do not traditionally serve these markets to get a foot in the door and contribute to Europe’s supply—at least for now. Adding insult to injury, there are widespread reports of wood pellet, firewood and other fuel scams occurring right now. Not only are consumers getting duped online, being enticed by much lower-than-average prices for product they never end up receiving, but scammers are impersonating wood pellet manufacturers and even copying websites. Buyers and sellers beware.
Finally, we just closed the abstract submission portal for the International Biomass Conference & Expo, which will be in Atlanta, Georgia, Feb. 28-March 2. The agenda is shaping up nicely, so be sure to be on the lookout. Pellet manufacturers get into the event for free—I hope to see you there.
Subscriptions to Pellet Mill Magazine are free of charge distributed 4 times/year to Biomass Magazine subscribers.To subscribe, visit www.BiomassMagazine.com or you can send your mailing address to Pellet Mill Magazine Subscriptions, 308 Second Ave. N., Suite 304, Grand Forks, ND 58203. You can also fax a subscription form to 701-746-5367. Back Issues & Reprints Select back issues are available for $3.95 each, plus shipping. Article reprints are also available for a fee. For more information, contact us at 866-746-8385 or service@bbiinternational.com. Advertising Pellet Mill Magazine provides a specific topic delivered to a highly targeted audience. We are committed to editorial excellence and high-quality print production. To find out more about Pellet Mill Magazine advertising opportunities, please contact us at 866-746-8385 or service@bbiinternational.com. Letters to the Editor We welcome letters to the editor. Send to Pellet Mill Magazine Letters to the Editor, 308 2nd Ave. N., Suite 304, Grand Forks, ND 58203 or email to asimet@ bbiinternational.com. Please include your name, address and phone number. Letters may be edited for clarity and/or space.
EDITOR
Anna Simet | asimet@bbiinternational.com
ONLINE NEWS EDITOR
Erin Voegele | evoegele@bbiinternational.com
STAFF WRITER
Katie Schroeder | kschroeder@bbiinternational.com
VICE PRESIDENT, PRODUCTION & DESIGN
Jaci Satterlund | jsatterlund@bbiinternational.com
GRAPHIC DESIGNER
Raquel Boushee | rboushee@bbiinternational.com
CEO
Joe Bryan | jbryan@bbiinternational.com
PRESIDENT Tom Bryan | tbryan@bbiinternational.com
VICE PRESIDENT, OPERATIONS/MARKETING & SALES
John Nelson | jnelson@bbiinternational.com
SENIOR ACCOUNT MANAGER/BIOENERGY TEAM LEADER
Chip Shereck | cshereck@bbiinternational.com
ACCOUNT MANAGER
Bob Brown | bbrown@bbiinternational.com
CIRCULATION MANAGER
Jessica Tiller | jtiller@bbiinternational.com
MARKETING & ADVERTISING MANAGER
Marla DeFoe | mdefoe@bbiinternational.com
2023
FEBRUARY 28 - MARCH 2, 2023
Cobb Galleria Centre, Atlanta, GA
Now in its 16th year, the International Biomass Conference & Expo is expected to bring together more than 800 attendees, 140 exhibitors and 65 speakers from more than 21 countries. It is the largest gathering of biomass professionals and academics in the world. The conference provides relevant content and unparalleled networking opportunities in a dynamic business-to-business environment. In addition to abundant networking opportunities, the largest biomass conference in the world is renowned for its outstanding programming—powered by Biomass Magazine—that maintains a strong focus on commercial-scale biomass production, new technology, and near-term research and development.
(866) 746-8385 | BiomassConference.com
2023
JUNE 12-14, 2023
CHI Health Center, Omaha, Nebraska
From its inception, the mission of this event has remained constant: The FEW delivers timely presentations with a strong focus on commercial-scale ethanol production—from quality control and yield maximization to regulatory compliance and fiscal management. The FEW is the ethanol industry’s premier forum for unveiling new technologies and research findings. The program is primarily focused on optimizing grain ethanol operations while also covering cellulosic and advanced ethanol technologies. (866) 746-8385 | FuelEthanolWorkshop.com
2023 Biodiesel Summit: Sustainable Aviation Fuel & Re newable Diesel
June 12-14, 2023
CHI Health Center, Omaha, Nebraska
The Biodiesel Summit: Sustainable Aviation Fuel & Renewable Diesel is a forum designed for biodiesel and renewable diesel producers to learn about cutting-edge process technologies, new techniques and equipment to optimize existing production, and efficiencies to save money while increasing throughput and fuel quality. Produced by Biodiesel Magazine, this world-class event features premium content from technology providers, equipment vendors, consultants, engineers and producers to advance discussion and foster an environment of collaboration and networking through engaging presentations, fruitful discussion and compelling exhibitions with one purpose, to further the biomass-based diesel sector beyond its current limitations. (866) 746-8385 | BiodieselSummit.com
CHI Health Center, Omaha, Nebraska
Capturing and storing carbon dioxide in underground resivoirs has the potential to become the most consequential technological deployment in the history of the broader biofuels industry. Deploying effective carbon capture and storage at biofuels plants will cement ethanol and biodiesel as the lowest carbon liquid fuels commercially available in the marketplace. The Carbon Capture & Storage Summit will offer attendees a comprehensive look at the economics of carbon capture and storage, the infrastructure required to make it possible and the financial and marketplace impacts to participating producers. (866) 746-8385 | FuelEthanolWorkshop.com
Earlier this year, in Issue 2 of Pellet Mill Magazine, I authored a column titled “Filling a 2-Million Ton Hole.” In the article, I offered some back-of-the-envelope calcula tions to frame up how North American wood pellet pro ducers who serve the domestic heating and BBQ market might contribute to easing the European supply shock cre ated by the Russian invasion of Ukraine, and the result ing sanctions on Russian goods—wood pellets included. I closed the column by noting that stateside producers would have to perform some tricky calculus and make some bets on the length and depth of winter when making decisions about how much, if any, of their production they would be willing to commit to opportunities overseas. As the industry plunges headlong into the heart of the home heating season and consumers fire up their pellet appli ances, we are being reminded that despite the year’s unique marketplace dynamics, it is the weather that drives demand.
The industry has successfully increased early pellet buying with its end users. By the end of summer, most pellet users have purchased some, but likely not all, the pel lets they will need for the season. Instead, consumers delay the purchase of the remainder of their supply until later in heating season, buying as necessary. It is this late season “top off” that separates the years with strong sales num bers from those with disappointing results. The back half of the 2021- ‘22 heating season offers a stark illustration of the impact of mild temperatures on pellet demand. U.S. heating pellet sales for February through April were just 250,000 tons, well off the February through April average of 345,000 tons. Consumers with one eye on their remain ing pellets and the other on unseasonably warm forecasts simply skipped or significantly curtailed their late season top off. Compare those numbers to the second half of the 2018- ‘19 heating season, when the February through April top off yielded pellet sales of 437,000 tons, nearly 75% more than the lackluster top off the industry just ex perienced. Interestingly, pellet sales in the first half of the following heating season were brisk as well. The reason for that, retailers have shared with me, is pellet buyers re
member running short the prior year, and beefed up their first purchase the following year. In October 2019, pellet sales were an eye-popping 283,000 tons, just short of the 289,000 highwater mark for pellet sales in any month since the U.S. Energy Information Administration started col lecting the sales data in 2016.
Last year, the Pellet Fuels Institute launched its PFI Heating Degree Day Index to provide producers and re tailers alike with an at-a-glance snapshot of how the winter is shaping up when compared to the year prior and longterm averages. This year, the PFI HDD Index reveals that winter got off to a colder start than last year in all pelletburning regions, with the exception of the Pacific North west. That said, pellet-burning regions are lagging longterm, accumulated HDD averages, all by more than 20%.
Lackluster heating seasons impact the sales totals of two calendar years. Last heating season’s soft sales resulted in annualized pellet sales of just 1.7 million tons for 2021, the lowest annual total in the report’s history. The back half of the 2021- ‘22 heating season was slower than the front half. Through July, pellet sales total just 774,000 tons, well off an average of 915,000 tons through the same period.
While the heating season will be all but over before a clear picture of how the year unfolded emerges, I suspect that producers—hoping to avoid two consecutive years where sales fizzled—are taking opportunities to move pel let volume overseas when and where they can. The indus try exited July with an inventory position of over 300,000 tons, the most since 2018. Paired with a trend toward warmer winters, it isn’t surprising that the question for producers with access to ocean freight egress has moved beyond “Should we take opportunities in the export mar ket?,” and toward “How much volume should we commit to export opportunities?”
tim@pelletheat.org www.pelletheat.org
Following a public consultation, on Oct. 25, the U.K. Department for Business, Energy and Industrial Strategy announced it will implement a 12-month suspension of certain fuel quality re quirements for domestic and nondomestic Renewable Heat Incen tive scheme participants using wood pellets, in order to help ensure adequate fuel supplies this winter
The BEIS estimates that up to 40% of the ENplus pellets used in the U.K are imported from Russia and Belarus. The agency said that the ban of wood pellets imported from these countries is likely to impact the availability and price of wood pellets in the coming months and through the winter of 2022-’23. Most consultation re spondents expressed overall support for a temporary suspension of the fuel quality requirement for RHI participants using wood pellets, the BEIS said, and while the use of non-ENplus pellets could have short-term negative impact on fuel efficiency and air quality in some cases, those impacts have been deemed as accept able so that homes heated by biomass do not experience significant price rises or a lack of fuel supply this winter. The BEIS noted the 12-month suspension could be extended in the future.
Drax Group plc released financial and operational results for the first half of 2022, reporting significant increases in both op erating profit and wood pellet production when compared to the same six-month period of 2021. Drax produced approximately 2 million metric tons (MT) of wood pellets during the first half of this year and shipped 2.4 million MT. The company produced and shipped 1.3 million MT of pellets during the same period of 2021. An estimated 1 million MT of wood pellets were sold to third par ties during the first half of 2022, up from 400,000 MT during the same period of last year. According to Drax, its cost to produce wood pellets and transfer them to a port in North America for onward transit was at $146 per ton during the first half of 2022, up 2% when compared to last year. The company primarily attributed the increase to the inflationary impact on utilities and bunker fuel.
The U.S. exported 880,876 MT of wood pellets in August, up from 649,185 MT the previous month and 647,922 MT in August 2021, according to data released by the USDA Foreign Agricul tural Service on Oct. 5. The U.S. exported wood pellets to ap proximately 20 countries in August. The U.K. was the top destina tion for U.S. wood pellet exports at 484,637 MT, followed by the Netherlands at 243,397 MT and Belgium-Luxembourg at 49,500 MT. The value of U.S. wood pellet exports reached $150.74 million in August, up from both $119.89 million in July and $90.43 million in August of last year.
Total U.S. wood pellet exports for the first eight months of 2022 reached 5.85 million MT at a value of $1 billion, compared to 4.77 million MT exported during the same period of 2021 at a value of $687.13 million.
The U.S. Energy Information Administration recently re leased the September edition of its Monthly Densified Biomass Fu els Report, which indicates 80 operating manufacturers produced approximately 930,000 tons of densified biomass fuel in June, with sales reaching 1.07 million tons. Combined production capacity was approximately 13.27 million tons per year. Collectively, producers had the equivalent of 2,479 full-time employees.
Respondents purchased 2.16 million tons of raw biomass feedstock in June, produced 930,000 tons of densified biomass fuel and sold 1.07 million tons of densified biomass fuel. Production included 138,544 tons of heating pellets and 800,845 tons of utility pellets. Domestic sales of densified biomass fuel in June reached 140,340 tons at an average price of $203.48 per ton. Exports in June reached 933,554 tons at an average price of $192.49 per ton. Inventories of premium/standard pellets increased to 310,998 tons in June, up from 300,511 tons in May. Inventories of utility pellets fell to 352,243 tons in June, down from 393,803 tons in May.
In late October, FutureMetrics published a new white paper that focuses on how reduced pellet supplies in Western Europe and the U.K.—resulting from sanctions on Russia—has produced a supply shock that has vastly increased prices. According to the consulting firm, global pellet supply has historically been, on av erage, sufficient to meet demand. Local seasonal shortages have occurred during unusually long, cold winters, but aggregate supply has been sufficient to meet aggregate demand. With Russian sanc tions now in place, a significant portion of the 3.5 million metric tons of wood pellets exported from these regions last year are no longer entering European markets. As a result, prices for pellet fuel have risen to previously unseen levels in every country that uses pellet fuels for heat and power generation. The white paper cites data indicating that industrial pellets are trading on the spot market at more than $453 per metric ton. The price for heating pellets has risen even higher in many European markets in recent months, with the German bulk price surpassing $760 per ton earlier this fall.
‘Na Aksa Gyilak’yoo School in Terrace, British Co lumbia, received a boost to its educational initiatives with a $2,000 contribution from the Wood Pellet Association of Canada, Skeena Bioenergy and the Prince Rupert Port Authority. The announcement was made at a luncheon host ed by the Kitsumkalum Economic Development Group It was the last stop in a series of events that began with WPAC’s annual conference in Vancouver, then onto Prince Rupert and ending in Terrace, with a tour of the Nation’s lo cal forest operations and logistics park.
An independent analysis by Oxford Economics shows that last year, renewable energy leader Drax contributed ap proximately $744.6 million toward the Canadian economy and supported 10,400 jobs across the U.K. The analysis measured the economic impact of Drax Group’s Canadian operations, which includes 10 wood pellet plants across Brit ish Columbia and Alberta. Drax spent $548 million with Ca nadian suppliers last year, with more than half of this total (58%) spent with businesses located in British Columbia. A further 13% was spent with businesses in Alberta and 12% with firms in Montreal.
Enviva Inc. held a ceremonial ribbon cutting at its recently constructed wood pellet manufacturing facility in George County, Mississippi. The Lucedale plant is Enviva’s second operating plant in the state, and the first plant in its newly formed Pascagoula cluster. The Lucedale plant began its production ramp-up at the beginning of 2022, with a goal of reaching an annual permitted production capacity
of 750,000 metric tons per year. Construction of the plant represented an investment of more than $215 million in the county, according to Enviva. The company said now that the plant is fully operational, it has hired approximately 90 full-time employees for the facility, which supports nearly 300 jobs across the George County community.
Scott Bax, CEO at Peak Renewables, was the guest on Season 1, Episode 9 of the Biomass Magazine/Pellet Mill Magazine podcast. Most recent to joining Peak Re newables, Bax served as chief operating officer at Pinnacle Renewable Energy (now Drax), where he grew the business threefold, to over 2.5 million metric tons of annual wood pellet production. Bax exudes passion for sustainable forestry, the environment and giving back, and he gave us all the details about Peak’s business model and developing projects.
PMM: Tell us a little about your background.
Bax: Early on in my life, I had the opportunity to work in the for est products industry, and during those experiences, it became clear that I wanted to channel my passion for trees into a career. That led me to the University of Alberta, where I got my master’s in business administration and master’s in forestry. From that point forward, I focused on trying to work in as many aspects of the
forest industry as possible. So, over the next two decades, I worked in areas from reforestation and forest management to harvesting, to continuous improvement and consulting in the forest products industry, for sawmills and value-added products, and then finally to wood pellets. Those opportunities had me working and living both across Canada and the U.S., and I’m incredibly grateful for them.
PMM: You’re at Peak Renewables now. Can you give our listeners a high-level rundown of what your company is all about?
Bax: Fundamentally, Peak is a renewables company focused on partnering with other companies, organizations and indigenous groups, to make sustainable, renewable products that reduce the carbon footprint of today through the utilization of marginalized trees, forest and mill residuals, as well as other biomass that would typically go to waste. Today, we’re working on various projects in cluding industrial pellets, black pellets, biocoal, biochemicals, as well as carbon sequestration and hydrogen. We have a very broad sphere of potential products, with a number of projects in the que. And we have been very fortunate that we have a chairman and individ ual who is an exceptionally visionary leader, by the name of Brian
Fehr. Brian spent many decades effectively revolutionizing the sawmill industry with his company, the BID Group, which he sold a number of years ago. In that transition, he started a new series of companies with a vision of making a difference—reinvesting in communities, and partner ing with First Nations and likeminded organizations trying to make the world a better place. That vison inspired me and brought me to Peak, and really, it’s an exciting time to grow an organization …
PMM: You have been in the wood pellet business for a decade. What are a couple of key takeaways for someone considering starting a new company?
Bax: That’s a great question. I would have to say … one is that you don’t know what you don’t know. Wood pellet production, by many standards, is a young industry—decades younger than the internet … Collectively, we’re still evolving. I would say that industry experts are rare, and there have been many good companies that have failed. So engage and partner with organizations and people in ways that can ultimately reduce your risk. Another takeaway is…
Tune in for the rest of the podcast at www.biomassmagazine.com/pages/podcasts
The annual Exporting Pellets Conference left no stone unturned in discussions about the ever-expanding applications for sustainable biomass.
The 2022 Exporting Pellets Conference returned to Miami Beach in Oc tober, drawing a diverse mix of bioenergy industry stakeholders from all over the world. At the famous Fontainebleau resort, attendees con vened in the afternoon on Oct. 2. The World Bioenergy Association’ s Christian Rakos, master of ceremonies, opened the event, describing the present as “a decisive time in this sector. I think it’s a time to keep our eyes and ears wide open to be well connected, and to hear any different views of the world in this respect,” he said. After a brief welcome, Rakos introduced Thomas Meth, chair man of USIPA and president of Enviva, for a state-of-the-industry discussion that emphasized how some of the most significant current events—whether directly are indirectly—are related to critical discussion topics at the conference. “I have been doing this for 20 years, but until two or three years ago, this was really about manufacturing wood pellets for the power and heat sector,” Meth said. “And now, it’s an entirely different world. We’ve had the pandemic, we’ve had supply disrup
tions, we’ve had regulatory confusion, we have the war in Ukraine—which of course is unbelievably sad—and we had a hurricane just a few days ago, on the outside of Florida. You have to stop and think about the devastation; it’s deeply troubling and saddening. And at the same time, it reminds us that we are really here to fight for a better outcome for climate change. And that has motivated and been a great passion for me … and I know that’s why all of you have come back here, to this conference, in 2022.”
At the annual event—which took a hiatus in 2020 and 2021, due to the pandemic—one of USIPA’s goals is to create a snapshot of where the industry is, Meth said. “Of course, that means we’ll talk about the elements that have allowed us to grow to what we’ve become so far, but we’re also going to have all sorts of variables—liquid [biofuels] and other industries that we historically haven’t dealt with.”
But whatever the technology or end product, it always comes down to one point, Meth emphasized. “And that is, where will the feedstock come from, and how do we ensure it’s sustainable, that it will be there tomorrow? How can we scale it in a way that matters? How do we bring it from place A to place B? [Place] A being where it available in large quantities in a sustainable manner, to B, where it’s most useful. Those places are typically not in the same spot. That’s the basis of why we exist.”
From biochemicals to green hydrogen, energy from woody biomass isn’t something of the past, from Meth’s perspective.
“In fact, it’s quite the opposite.”
Fiona Matthews, associate director at Hawkins Wright, provided a global wood pellet market overview with a focus on demand and how it has evolved over the past 18 months. Fossil fuel prices—coal and gas—are at levels that were previously unimaginable, she said, which has completely shifted the picture for biomass power generation economics, resulting in higher industrial biomass demand in Europe.
For the past 10 years, USIPA has been a successful, true force when it comes to educating stakeholders and en suring that a backbone is in place for the industry to do business, Meth said. “And the role of USIPA has never been more important,” he added. “When you think about the discussions in Europe and the European parliament, if we don’t make our case—particularly the noise of ideol ogy versus national security driven by en ergy—the case will be made for us. It has never been more important that we sup port industry associations like USIPA, to allow them to put our best foot forward.”
Meth reiterated how imperative it is that as much sustainable biomass as possible is mobilized for the many dif ferent potential applications available to day. “It’s not only sustainability—though without it, the rest doesn’t matter—we also have to make the case for the good outcomes it creates … for the concepts of national security and energy shortag es—this has never been more prominent in our industry than it is today. When we
think about the discussion in the U.S., how the government can help Europe more quickly decrease its dependence on Russian gas, wood pellets do play a role. This isn’t just about gas—this is about biomass mobilization.”
From biochemicals to green hydro gen, energy from woody biomass isn’t something of the past, from Meth’s per spective. “In fact, it’s quite the opposite.”
Author: Anna Simet Editor, Pellet Mill Magazine asimet@bbiinternational.com 701-738-4961
A new study demonstrates the British Columbia wood pellet sector’s responsible care for forests and communities.
The pellet industry is no stranger to accusations from environmentalists that the fi ber it uses is not sustainable or is handled irresponsibly. Recently, the Wood Pellet Association of Canada took action to prove these claims are false and combat misinformation with the facts. Gordon Murray, executive director of WPAC, explains that organization com missioned the study in response to ar ticles in environmental publications with photos of logs at pellet plants, accusing the industry of turning whole logs into fuel. “They were also accusing us of do ing dedicated harvesting on a large scale of forests in order to make wood pellets,” he says. “And both of those were false, but we knew that people would suspect whatever the industry would say. So, we wanted to get an independent group to report on what we are actually doing.”
Bull & Bull Consultants performed the study, which entailed a combination of examining and cross-checking data as well as conducting interviews. “They ex amined log scaling data from all across British Columbia, essentially looking at every load that had been taken into pellet plants over a period of time, and then an alyzed and compared it with audit reports from the Sustainable Biomass Program. They did a bunch of cross-checking and then came to report conclusions,” Mur ray says.
The study analyzed the feedstock source of sawmills in British Columbia for a few reasons, Murray explains. Brit ish Columbia has the highest concentra tion of pellet mill plants in all of Canada, containing 60 to 70% of the country’s production capacity. The second reason was that the accusations were targeted at plants in that area. And finally, the data in that province was all in the same format and was easily accessible. The research ers found that 85% of the biomass ma
Operational (2,214,800 MT)
Proposed (600,000 MT)
Under Construction (64,000 MT)
As of Januar y 2022, there were 12 operating pellet plants in British Columbia, with a capacity of about 2 million ODTs, a 500% increase from 2005
terial was mill residue and 15% was forest residue, with the for est residue breaking down into 11% lowquality roundwood and 4% bush grind. “Essentially, we confirmed that all the fiber being consumed by the province comes from residues produced by either other mills or from leftover wood from forests,” Murray says. “It confirmed that we work in cooperation with indigenous and other communities to improve forest health and support the local economy, and that our fiber sourcing creates an extra revenue stream for sawmills, so it helps the viability of the sawmill industry.” Demonstrating that everything harvested from the forest is important for sawmills, he explains. The pellet industry also provides economic op portunities and employment, contributes to fossil fuel substitution and helps manage fire and wildfire risk.
“As an industry, we want to be respon sible using the low-end, what’s left behind material, that no other industry can use,” Murray says. “And if by doing that we can create a renewable product, lower green house gas emissions and offset the use of fossil fuels by replacing coal, for example, then we think we’re being an environmen tally responsible sector.”
Gary Bull, forestry professor and one of the study’s lead authors, explains that one of the study’s surprising findings was the amount of dead biomass in the forest that accumulates due to natural disasters such as fire and insect disease. “While you leave some on the ground for biodiversity reasons … there is still this huge surplus of biomass on the landscape, and if you don’t find an industrial way to use it and generate economic activity, the current regulations force you to burn it on-site and create a lot of emissions,” Bull says. “So, these emis sions are a huge problem from a societal point of view in terms of dealing with the climate change problem.”
The researchers did three case stud ies throughout the province, Bull explains. One plant was a Drax facility located near Burns Lake, which has a community for est partially owned by First Nations com munities that receive a share in the revenue from harvesting the forest. “The commu nity had no option to try and get that wood or forest residue to a pulp mill. It’s just too far away, so the economics don’t work,” he explains. “So, the community was very supportive of installing a pellet plant.”
The second case study was a smaller op eration—Skeena Bioenergy near Terrace, British Columbia, where the study found that First Nations communities worked with the sawmills to dispose of residues in the remote location. The third case study was of Drax Meadowbank, a larger facility.
Utilization of sustainable biomass provides remote and indigenous commu nities with a way to decarbonize, Bull ex plains. “Frankly, I’ve been in conversations with several indigenous communities that want more, rather than less, use of pel lets or chips—biomass used—because in remote communities, they’re most inter ested in getting off diesel. Biomass is the most logical way for them to get off die sel power plants in these northern remote communities,” he says. One challenge he believes the pellet industry must work through is engaging civil society, especially indigenous people, in conversations about complex problems. “I’m particularly con
• The wood pellet industr y in B.C. has created about 2,500 direct and indirect jobs throughout the province.
• The industry provides about $750 million in economic activity and has made more than $500 million in capital investments over the past decade
• Wood pellet facilities create an additional revenue stream for sawmills and other facilities that they purchase residuals from.
• The wood pellet industr y creates more viable economic opportunities and employment, especially in remote communities that are too far to supply ber to pulp mills.
cerned about the role of indigenous people and how that plays into their land ethic,” Bull says.
Murray believes the main takeaway from this study is that the wood pellet in dustry is responsible and concerned about forest health, ensuring complete utilization by turning previously difficult-to-get-rid-of forest and mill residues into a renewable energy product that helps lower GHG emis
sions around the world. “All in all, I think [for] the pellet industry, it’s a good news story,” he adds. “By doing this study, we’ve had third parties verify that we’re sourcing responsibly.”
Screw Conveyor Corporation has provided engineered material handling solutions since 1932. We focus on Screw Conveyors, Screw Feeders, Round and Flat Bottom Drag Conveyors, as well as Centrifugal and Continuous Bucket Elevators (both belt and chain).
Visit screwconveyor.com to learn more about our capabilities. We look forward to working with you on your next engineered material handling solution!
®
screwconveyor.com
® ®
700 Ho man St., Hammond, IN 46327-1894 Phone 219-931-1450
Winona, MS P: 662-283-3142 Visalia, CA P: 559-651-2131
Guadalajara, México P: 333-645-7110
Successfully managing a project successfully requires an organized start.
BY JOEL DULINWe could cite a dozen tropes about the importance of starting well, from get ting off on the right foot to getting up on the wrong side of the bed. And we’ve all heard about (or been involved in) projects that have gone awry because someone failed to plan (and thus, planned to fail). Unfortu nately, people mismanage projects regularly. The resulting delays, out-of-control expens es, lost production time and angry contrac tors are all too familiar. So it goes, when you work with humans. Yet, it is possible to avoid gross mistakes when managing a proj ect. It simply takes good preparation during the project’s development.
First, understand that the earlier mis steps occur in a project’s development, the
more extensive the damage. A tool for un derstanding this relationship is the 1-10-100 rule, which states that a dollar’s worth of time spent preparing is worth $10 in time processing change orders and $100 in fix ing a problem after equipment has been in stalled. Such exponential costs are how $150 million greenfield plants end up costing $2 billion by the time the lights turn on, as what happened at the former Katerra CLT plant in Washington state. Getting a project done right, on budget, and on time requires project managers to develop it fully from the outset, a feat that requires good devel opment even before the project starts. This primary development comes in the form of a business case.
A business case is a document that lays out a project’s objectives, benefits and costs, explaining why the project should take place and providing an overarching scope. Too many projects go forward without the clear picture a business case provides. While there are many reasons this may happen, it’s usually because those driving the project believe they have a developed case, when in reality, they’re ignorant of critical chal lenges. For example, someone has an asset like a forest, and they’re trying to monetize the timber coming off the land. They know they can make lumber, so they plan to build a sawmill and move forward with the proj
CONTRIBUTION: The claims and statements made in this article belong exclusively to the author(s) and do not necessarily reflect the views of Pellet Mill Magazine or its advertisers. All questions pertaining to this article should be directed to the author(s).
Biomass
Joe’s Wired Electrical Corp.
Joe’s Wired Electrical Corp.
Nancy’s Structural Design Ser vices, Inc.
Silverdale Civil Work and Silviculture Nonexplosive
ect. However, they’ve failed to consider how they’ll dispose of the residuals.
For this reason, managers working on front-end endeavors must first help their customers think through the challenges to them to the point of knowing what ques tions to ask for an accurate picture of what it will take to fulfill their ambition. The landowner, for example, needs to ask, “What will I do with the residuals? Is there a market for green chips in my area? For shavings? What are the consequences of piling up the waste on site?”
Those asking such questions often need help answering them, too, as they tend to think there are too many options or that none exist for their situation. In such cases, the stakeholders must complete more high-level development work before the project can proceed. Of course, many projects revolve around specific problems at brownfield sites, such as poor uptime or too many pellets crumbling into fines. The project is at a particular facility with specific operational challenges that the team there is looking to address. In these scenarios, the business case isn’t the issue; it’s how well the manager organizes the nuts and bolts of the project as it gets underway.
The effort should begin with a process flow diagram (PFD). The PFD is a critical document, as it describes the flow of inputs through a system and the relationships be tween subsystems. It also ensures there’s an energy balance, and it dictates the size of components like conveyors.
Being such an important document, the manager overseeing the PFD should not base it on guesswork (though informed guesswork must sometimes occur). Yet, this does happen. BE&E recently had a customer provide a PFD for a pellet plant devoid of tenable engineering. The project manager tried to pull together the elements of his customer’s process from a patch work of information and what he knew about pelleting systems. Fortunately, our team recognized this and was unwilling to perform work until the project manager had gathered accurate data. Any engineer ing completed using the PFD would have been wasted. Worse, it could have resulted in purchase orders worth tens to hundreds of thousands of dollars for equipment built to incorrect specifications.
Only from an accurate PFD and de fined scope can project managers establish dependencies that allow the management team to drive a schedule. Depending on how much the client has done, this step may require managers to start way back in the process. Say the landowner we referenced decides to make pellets from his sawmill residuals. He aims to produce 36,000 tons of white pellets annually, which will require 72,000 tons of fiber. The project manager, in turn, will start by identifying fiber sourc es, only one of which is the landowner’s sawmill.
Once the project manager has defined the PFD, they can create a work breakdown document, which maps out who is in charge
of what tasks and provides a timeline. Completing such a document is yet another critical step that can prove detrimental to the project if mismanaged. For example, the landowner’s project calls for a silo, for which there are mechanical, civil, structural and electrical components. The manager’s breakdown document will divide the re sponsibilities related to the silo into these manageable pieces, as shown in Figure 1.
Only after the business case is com piled and the project manager has created the PFD and breakdown documents should they specify components and issue pur chase orders for equipment. Without these controlling documents, the project will in evitably blunder. Imagine that the project manager overseeing the landowner’s pellet mill forgets to delineate who is responsible for the conveyors’ structural supports. The oversight results in a months-long delay and adds thousands of dollars of costs related to change orders and rush fees. But such blunders aren’t inevitable. Just as people regularly mismanage projects, people regu larly manage projects well. Careful planning and well-thought-out documentation are what make it happen.
In a previous edition edition of Project Talk, I caught up with Ugo Santone, a project management aficionado and partner at PTAG, a project management services firm. We ex plored the wise concept of “Inspect what you expect,” which Ronald Regan fans may remem ber as “Trust, but verify.” Whatever you call it, nothing should be taken for granted when dealing with large capital projects. Proper proj ect controls should be in place to alert you if things are going off the rails, but one problem is that project controls and their associated met rics provide largely high-level lagging indicators. These are fantastic for many purposes and very useful for keeping a project steered in the right direction, but they don’t tell you what’s going on in real time. For some issues, by the time you see it in feedback from project controls, you may not be able to prevent going off the rails. For real time feedback and intelligence to pro tect a project from issues that may be difficult or impossible to recover from, eyes in the field are needed. Those eyes are called oversight.
This article will delve a bit deeper into “In spect what you expect,” and include input from Herb Marshall, the man who literally wrote the book on project oversight. The book is called The Project Oversight Guide, and his company is Oversight Advantage. Marshall would argue
that, just like project controls, which can pro vide a 10% overall cost improvement for a 3% investment, good oversight is something that costs hard cash in the project budget. But it more than pays for itself by keeping the project on the rails and improving the predictability of the project’s outcome.
I caught up with Marshall virtually from his fortress of solitude in an undisclosed loca tion, and we discussed how he got to be such an expert on oversight. He offered that he went through many years of on-the-job training in Naval Reactors, an organization that spent the past 75 years developing a culture of oversight. Oversight was just something done because it provided for well-informed—and thus, wellrun—projects. As for me, I started directly out of college as a yardbird at Mare Island Naval Shipyard, and was introduced to the culture of oversight from the beginning of my career. (A yardbird is one of the more euphemistic terms for a civilian shipyard worker.)
Marshall rose from the ranks to lead the reactor servicing team at Puget Sound Naval Shipyard, which, at the time, was doing more refueling and reactor servicing work than any other facility in the world. This team included
dozens of oversight personnel digging into not only the typical complement of four or five ves sels from the nuclear fleet undergoing overhaul, but also the shipyard itself, including the dry docks and other equipment and systems used to perform the work. When he was asked to help a private utility with a large project that was fail ing (which he did with great success), Marshall recognized that there was simply no legitimate information available regarding how to oversee a large complex capital project—thus, the book.
The concept may seem simple: Eyes in the field providing feedback and intelligence to the owner allows for self-correction. The execution, however, can have interesting results if not ap proached with the right mentality. Marshall rec ognizes the need for emotional intelligence, and likes to use an example of building an extension on your house. If you’re paying someone to do it, everyone who’s been down that path knows that you have to watch the contractor “a little bit.” You can’t just sit back and drink piña co ladas, waiting for the contractor to tell you it’s done. At the same time, if you’re out there in the contractor’s business, redirecting his work ers and interfering with his self-governance, you can end up in litigation. Good project oversight advocates for the owner’s interests for a winwin, identifying underperforming contractors
CONTRIBUTION: The claims and statements made in this article belong exclusively to the author(s) and do not necessarily reflect the views of Pellet Mill Magazine or its advertisers. All questions pertaining to this article should be directed to the author(s).
or hidden issues sooner than later, while at the same time allowing the project team to do its job unencumbered. Underperforming contrac tors can improve performance based upon this feedback, and the now-revealed issues can be corrected in the field before horribly impacting downstream activities. And this is all done with out telling anyone what to do. Rather, it simply exposes these issues to light.
Another important takeaway is that over sight does not direct. Oversight’s role is to step back, look at the big picture and recognize things that those who are too close to the action may not, and also delve deep into issues to en sure records support quality completion. Fail ing to recognize that the foundation the addi tion is built upon is substandard until after it is complete and starts cracking is not happy times. Oversight can and often does look at the con crete mix records for just that reason, as well as weld records, examination and testing results, and other important documentation that may be available. For important equipment, they can also perform receipt inspection or site surveil lance to ensure what was ordered is made the way that is expected.
So, oversight needs to step back and look closely, which is why Marshall’s company logo is a combination of a telescope and a magnifying glass. It’s all about seeing what’s coming down the pike, assessing risks and how they are being mitigated, and whether or not the contractor gets it. It’s also digging into critical details in a way that cannot be provided by standard proj
ect controls. Even things like body language at the production meeting, or scuttlebutt about the latest people to drag up and leave the proj ect, provide good inputs to oversight, painting a picture long before an issue becomes evident by other means.
Oversight is a two-way process, though, and how one approaches oversight and the re sults can be ineffective if social intelligence is not in play. This is why Marshall trains all his oversight people. If he was king for a day, Mar shall says that he would create an oversight cre dential similar to the project management pro fessional certification, providing initial training and certification followed by periodic refresher training. As that does not exist, Marshall cre ated it for his projects. Personality, as well as social and emotional intelligence, are certainly included.
Because human interaction is really where the rubber meets the road, Marshall dedicated two chapters in his book to oversight behaviors. He offers that oftentimes—far too often—large capital projects result in litigation, and a lot of it boils down to personalities. When some or ganizations assign the typical alpha-personality project manager to oversight, it initially seems like a good fit (you want someone intelligent, who understands the project). Project managers usually fit that bill nicely, but in reality, it doesn’t always work out, since the interface is likely with the contractor’s own alpha-personality project
manager. As issues arise, so does conflict, typi cally, as those alpha-personalities battle each other to the detriment of the message.
To counteract this tendency, Marshall uses a five-rung ladder to describe the methods and overall tone of providing feedback. The most organic and pleasant is the lowest rung: referent power, where one is able to get people to fol low them based upon their personality and cha risma. The highest rung is coercive power: “I’m not going to pay you unless you do it my way.”
The second rung is “expert power,” where a book is cracked open to get technical. Reward power is the third rung, where the contractor has a chance to save face if he’s not exactly right, and show empathy when he runs into is sues beyond his control. The goal is to stay in those first three rungs. Oftentimes, improperly performed oversight jumps right to the top two rungs: legitimate authority (I’m the owner, do what I say), and coercive power (I’m not going to pay you, unless you do what I say).
There are a host of subtleties with great oversight, and although Marshall and I had a lengthy discussion, we just scratched the sur face. Keep in mind that the goal of oversight is for everybody to win, especially the owner.
Delta Energy Services LLC sven@workdelta.com 352-201-984