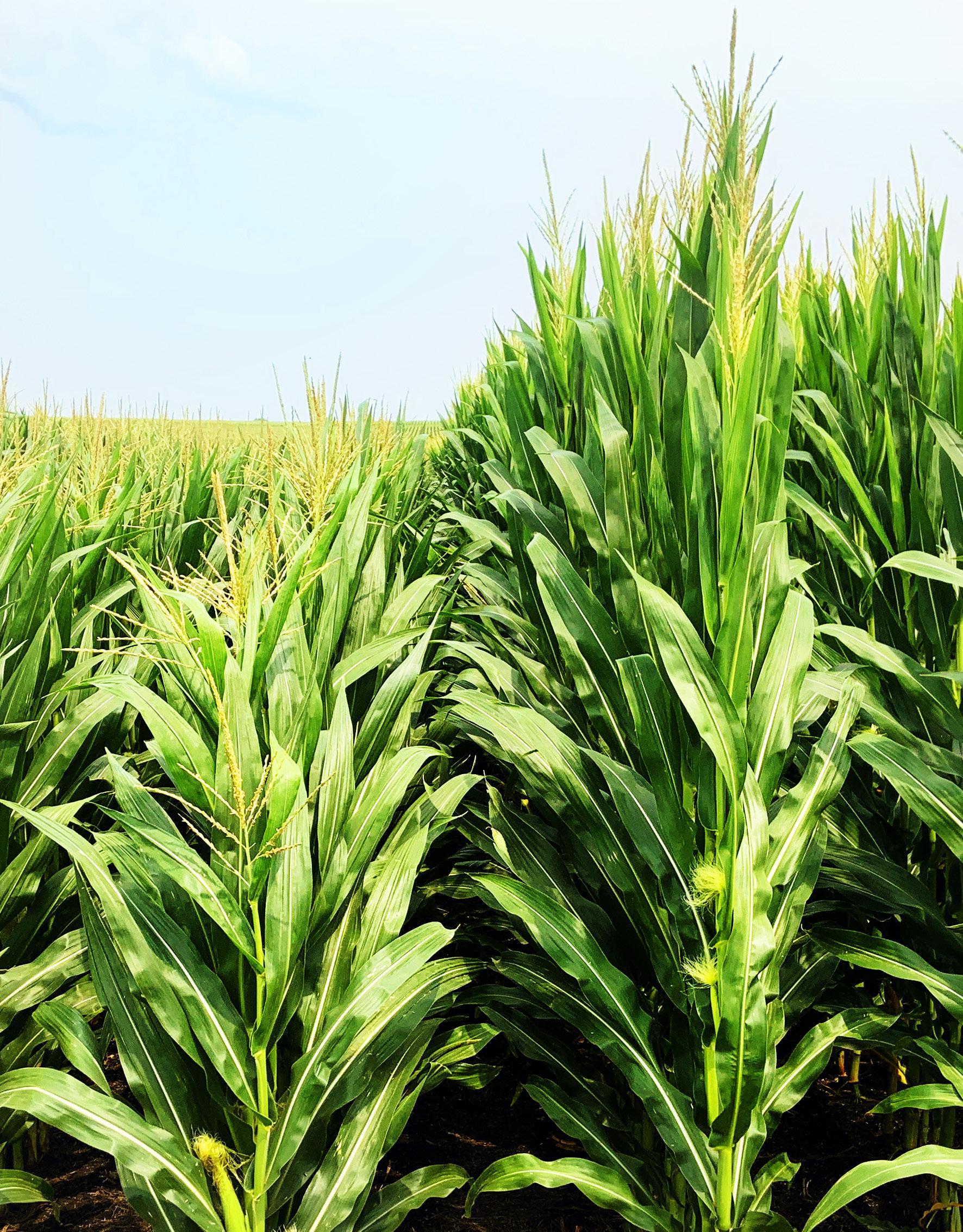


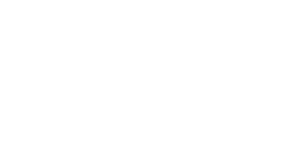

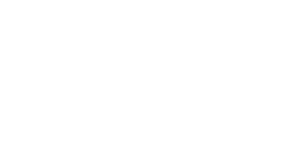
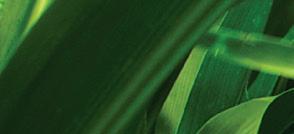
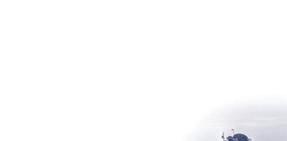
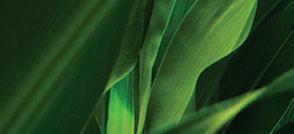
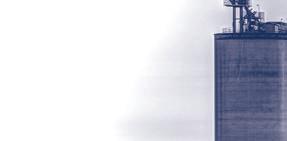
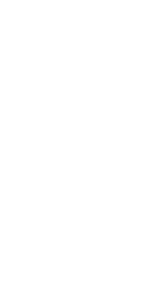
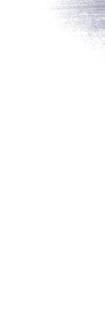

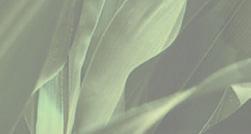
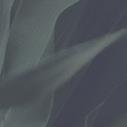
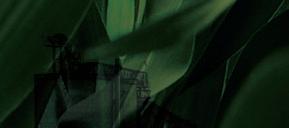
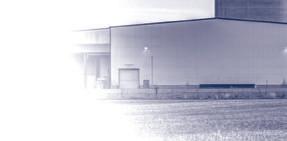


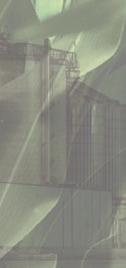
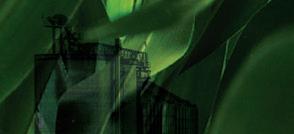
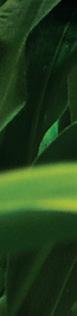

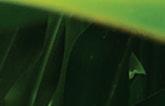
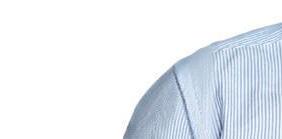

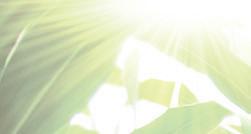


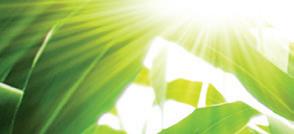

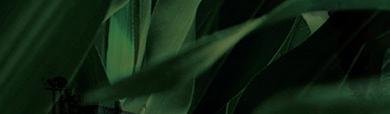

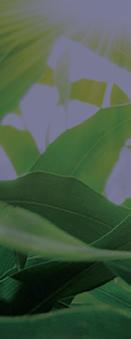
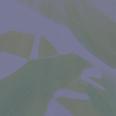



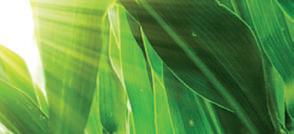

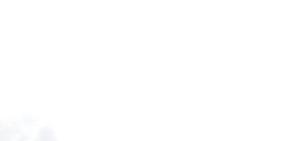


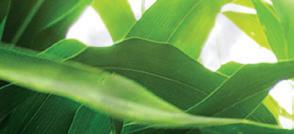
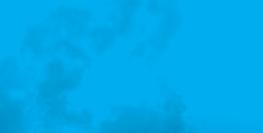
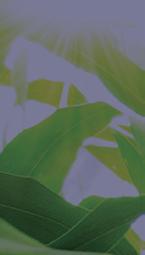
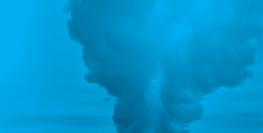

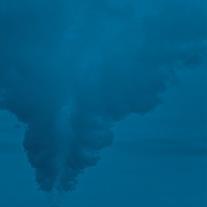
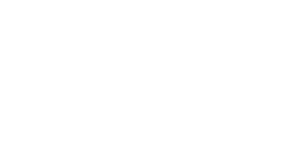
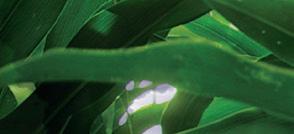
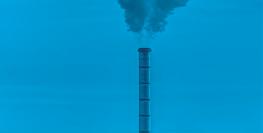
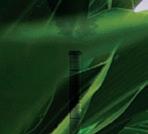

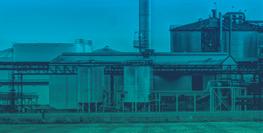
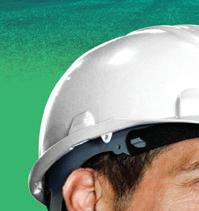
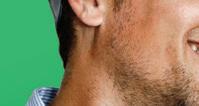
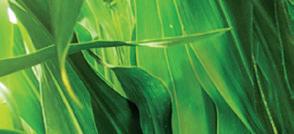
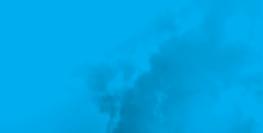

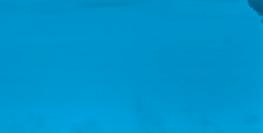
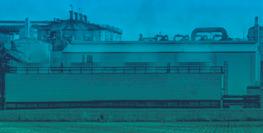
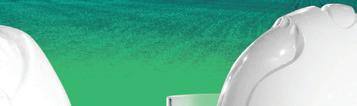
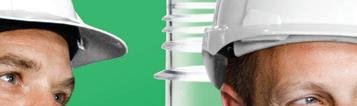

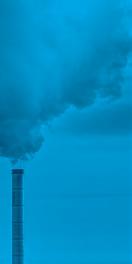
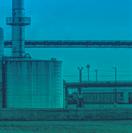
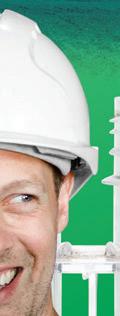
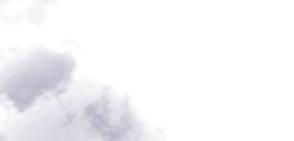
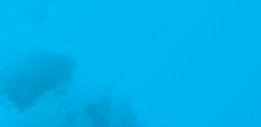
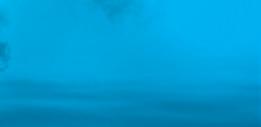
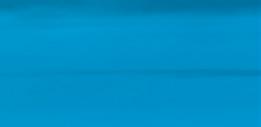

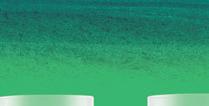
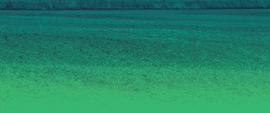
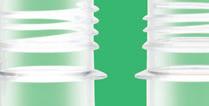




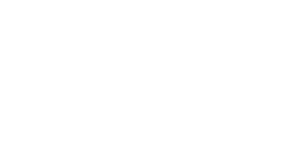
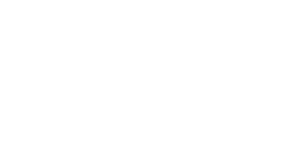
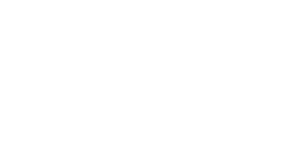


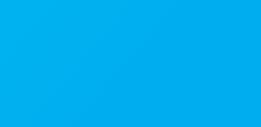

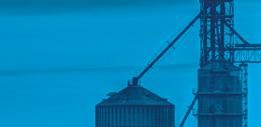
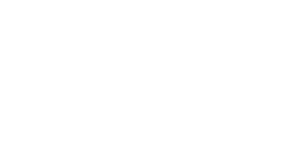
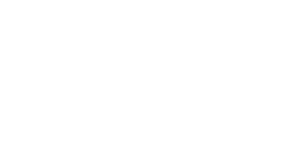

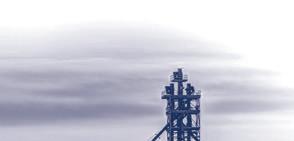
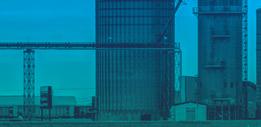
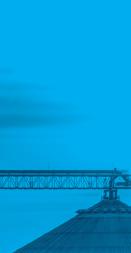
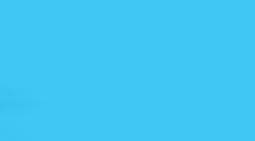
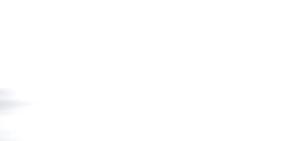

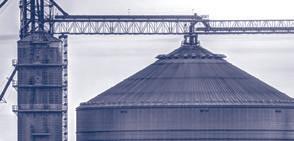

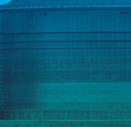
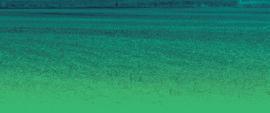

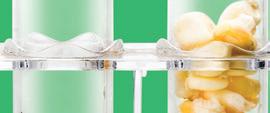

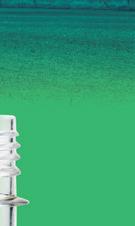
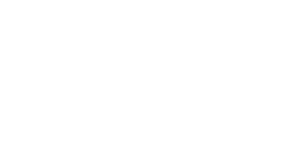

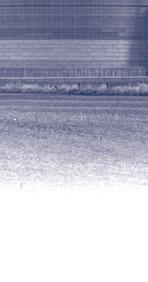
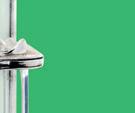




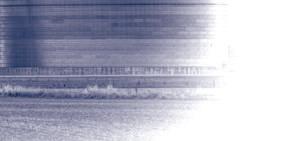
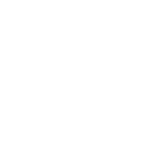
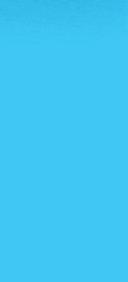
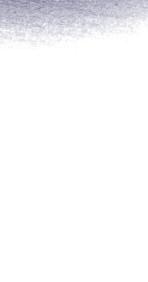
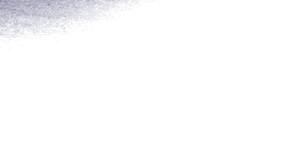
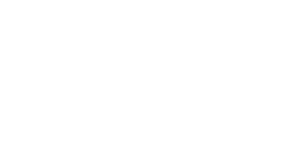
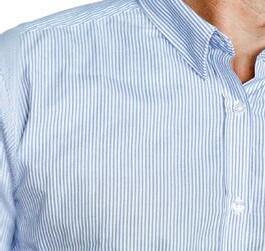
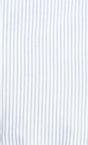
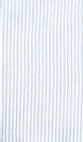



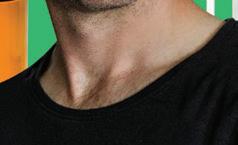
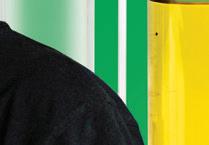

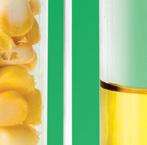
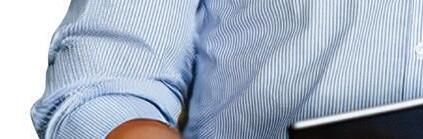
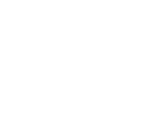
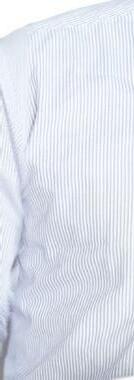

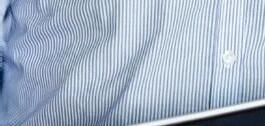
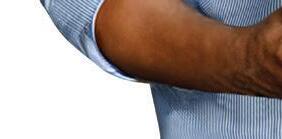
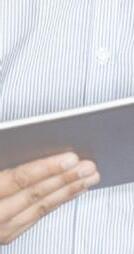
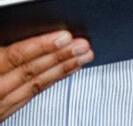

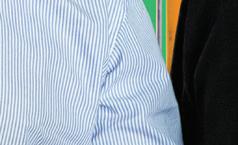
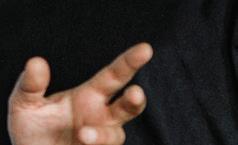


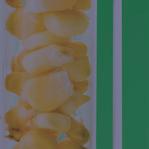
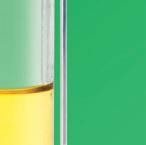


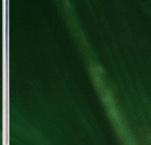

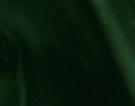
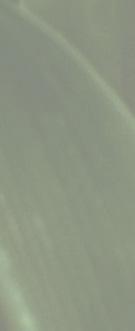
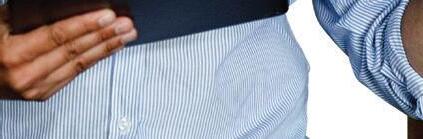
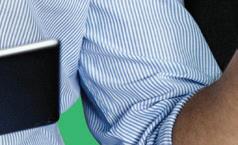

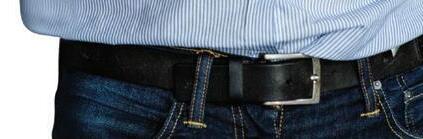
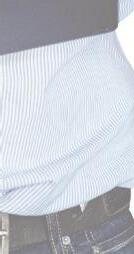



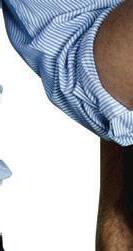
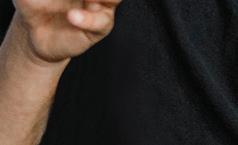
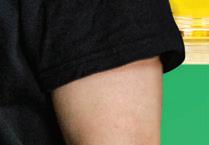


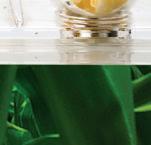
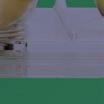
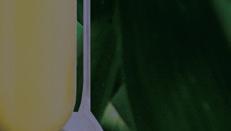
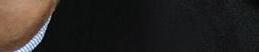


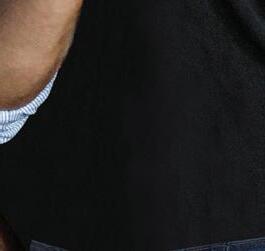


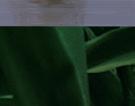

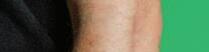


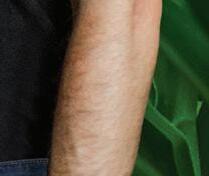
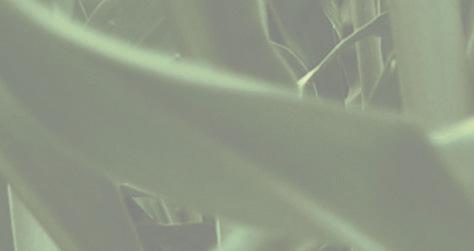

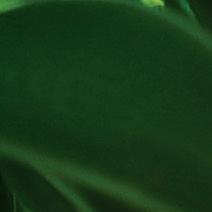

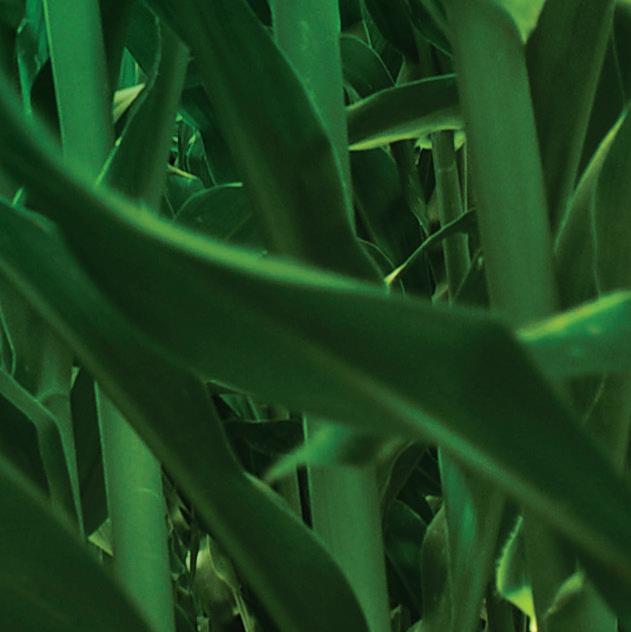


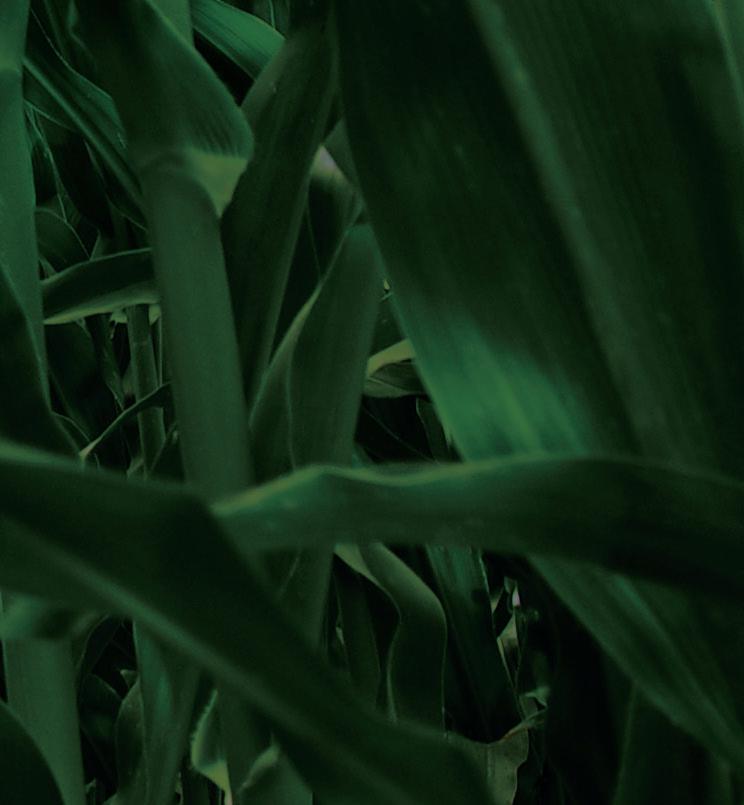
OK, so our IRmadillo™ may have a long nose and a funny look.
But that nose can sni out exactly what’s going on inside every one of your processes. Every single second of the day.
And if you know the precise chemical composition inside all your lines and tanks, there’s virtually nothing you can’t improve
Filled with ground-breaking new technology, IRmadillo™ helps keep yeast happy, eliminates failed batches, reduces enzyme use, and much, much more.
So while you’re sitting around waiting for your next set of HPLC results, why not visit our website, and read up on the whole amazing IRmadillo™ story?
starts up ethanol, RNG coproduction in Iowa
President & Editor Tom Bryan tbryan@bbiinternational.com
Online News Editor Erin Voegele evoegele@bbiinternational.com
Associate Editor Katie Schroeder katie.schroeder@bbiinternational.com
Features Editor Lisa Gibson lisa.gibson@sageandstonestrategies.com
Vice President of Production & Design Jaci Satterlund jsatterlund@bbiinternational.com
Graphic Designer Raquel Boushee rboushee@bbiinternational.com
PUBLISHING
CEO Joe Bryan jbryan@bbiinternational.com
Vice President of Operations/Marketing & Sales John Nelson jnelson@bbiinternational.com
Director of Sales Chip Shereck cshereck@bbiinternational.com
Account Manager Bob Brown bbrown@bbiinternational.com
Circulation Manager Jessica Tiller jtiller@bbiinternational.com
Marketing & Advertising Manager Marla DeFoe mdefoe@bbiinternational.com
Ringneck Energy Walter Wendland Little Sioux Corn Processors Steve Roe Commonwealth Agri-Energy Mick Henderson Western Plains Energy Derek Peine Front Range Energy Dan Sanders Jr.
Atlanta, GA (866) 746-8385 | www.biomassconference.com
Now in its 18th year, the International Biomass Conference & Expo is expected to bring together more than 900 attendees, 160 exhibitors and 65 speakers from more than 25 countries. It is the largest gathering of biomass professionals and academics in the world. Powered by Biomass Magazine, the conference provides relevant content and unparalleled networking opportunities in a dynamic business-to-business environment. In addition to abundant networking opportunities, the largest biomass conference in the world is renowned for its outstanding programming, maintaining a strong focus on commercial-scale biomass production, new technology, and near-term research and development. Join us at the International Biomass Conference & Expo as we enter this new and exciting era in biomass energy.
Omaha, NE (866) 746-8385 | www.fuelethanolworkshop.com
Now in its 41st year, the FEW provides the ethanol industry with cutting-edge content and unparalleled networking opportunities in a dynamic business-to-business environment. As the largest, longest running ethanol conference in the world, the FEW is renowned for its superb programming—powered by Ethanol Producer Magazine —that maintains a strong focus on commercialscale ethanol production, new technology, and near-term research and development. The event draws more than 2,300 people from over 31 countries and from nearly every ethanol plant in the United States and Canada.
Omaha, NE (866) 746-8385 | www.sustainablefuelssummit.com
Please recycle this magazine and remove inserts or samples before recycling
Customer Service Please call 1-866-746-8385 or email us at service@bbiinternational.com. Subscriptions Subscriptions to Ethanol Producer Magazine are free of charge to everyone with the exception of a shipping and handling charge for anyone outside the United States. To subscribe, visit www.EthanolProducer.com or you can send your mailing address and payment (checks made out to BBI International) to: Ethanol Producer Magazine Subscriptions, 308 Second Ave. N., Suite 304, Grand Forks, ND 58203. Back Issues, Reprints and Permissions Select back issues are available for $3.95 each, plus shipping. Article reprints are also available for a fee. For more information, contact us at 866-7468385 or service@bbiinternational.com. Advertising Ethanol Producer Magazine provides a specific topic delivered to a highly targeted audience. We are committed to editorial excellence and high-quality print production. To find out more about Ethanol Producer Magazine advertising opportunities, please contact us at 866-746-8385 or service@bbiinternational.com. Letters to the Editor We welcome letters to the editor. Send to Ethanol Producer Magazine Letters to the Editor, 308 2nd Ave. N., Suite 304, Grand Forks, ND 58203 or email to editor@bbiinternational.com. Please include your name, address and phone number. Letters may be edited for clarity and/or space. TM
COPYRIGHT © 2024 by BBI International
The Sustainable Fuels Summit: SAF, Renewable Diesel, and Biodiesel is a premier forum designed for producers of biodiesel, renewable diesel, and sustainable aviation fuel (SAF) to learn about cutting-edge process technologies, innovative techniques, and equipment to optimize existing production. Attendees will discover efficiencies that save money while increasing throughput and fuel quality. Produced by Biodiesel Magazine and SAF Magazine, this world-class event features premium content from technology providers, equipment vendors, consultants, engineers, and producers to advance discussions and foster an environment of collaboration and networking. Through engaging presentations, fruitful discussions, and compelling exhibitions, the summit aims to push the biomass-based diesel sector beyond its current limitations. Co-located with the International Fuel Ethanol Workshop & Expo, the Sustainable Fuels Summit conveniently harnesses the full potential of the integrated biofuels industries while providing a laser-like focus on processing methods that deliver tangible advantages to producers. Registration is free of charge for all employees of current biodiesel, renewable diesel, and SAF production facilities, from operators and maintenance personnel to board members and executives.
This issue is, to say the least, eclectic—we’ve got pieces on crop science, yeast engineering, sustainable aviation fuel (SAF) and the coproduction of ethanol and renewable natural gas (RNG). Wide-ranging for sure, but together these stories represent the interconnected layers of evolution taking place across our industry.
Our cover story, “Corn’s Next Step Change,” on page 14, looks at how corn researchers are identifying and predicting corn trait performance with greater speed and accuracy, leading to new hybrids that are more sustainable, weather tolerant and versatile—without giving up yield. No longer confined to DNA science, crop designers are now deploying RNA-based processes that enable them to better predict research outcomes. The result: scientists are making breakthroughs much faster and, along the way, building transformative models and gene expression data sets that stand to revolutionize the entire field. Meanwhile, crop scientists are also producing novel crop varieties like high-oil, low-CI corn that will benefit U.S. farmers as demand for SAF feedstock soars; and they’re designing physically different crops like “short corn,” which better withstands extreme weather while offering season-long ground-spraying access and the same yield as its taller counterpart due to a higher planted density.
Next, we look at how major yeast suppliers are offering new products with enhanced benefits, and how these commercial breakthroughs parallel academic yeast science. “In Unceasing Innovation,” on page 18, we catch up with suppliers that are rolling out new products in step with a changing industry—highly robust yeast products with better kinetics and lower resultant glycerol levels, for example. A few of them have unveiled high-performance yeasts with built-in enzymes—a potential gamechanger for fermentation efficiency. Meanwhile, university researchers are also moving the needle on yeast science, in one case unveiling a product that is encased in an anti-microbial shell.
In “The Case for Conversion,” on page 26, we jump into SAF, capturing a possible trend in the alcohol-to-jet segment: the acquisition of existing ethanol plants to serve as the foundations for SAF production. Longtime biofuel player Gevo Inc. is expected to soon close on the acquisition of Red Trail Energy LLC in Richardton, North Dakota, an ethanol plant with operational CCS. Gevo intends to use RTE to accelerate its ambitious SAF plans. And while RTE is a vibrant, healthy business leading the industry with carbon storage, Crysalis Biosciences Inc. is transforming a shuttered ethanol plant near St. Louis for a similar purpose. While anecdotal, the two acquisitions—different as they may be—highlight the growing value of existing biorefineries in the context of prioritizing speed-to-market in the SAF space.
Finally, we provide a timely update on Verbio, a European company that owns two U.S. biorefineries—one already doing ethanol and RNG coproduction, and the other pursuing it. Verbio integrates corn starch-based ethanol production and RNG processing by utilizing both corn stillage and corn stover. Getting the first project up and running in central Iowa was not achieved without meeting certain challenges, but those tests will only help the company graft its unique platform onto its other plant in Indiana. It’s a strategy worth reading about.
A new day is dawning for ethanol production. Our industr y-leading lineup of yeasts and yeast nutrition, plus our newly added Spar tec® enz ymes, are pushing the limits of fermentation and reaching levels of performance never achieved before. Paired with our renowned educational programs and expert ser vices, we’re setting a course for even greater yields and performance.
With LBDS,
ACE’s Hybrid Electric Flex Fuel (HEFF) demonstration project began by logging 3,688 miles on regular gasoline to establish a baseline mileage number in August 2021, and then our used 2019 Ford Fusion Hybrid vehicle became “HEFF” after installing an eflexfuel.com converter, which allowed it to use ethanol blends up to E85. In addition to proving a standard vehicle could safely run on the highest ethanol blends, the HEFF project aimed to find out how low the real-world, on-road emissions could be for a hybrid electric vehicle (EV) when that hybrid’s internal combustion engine runs, and battery is charged, using flex fuel.
Forty thousand miles became our target after Car and Driver published a 40,000-mile road test of a 2019 Tesla Model 3 LR (long range) in April 2022. The test caught our attention because we devised the HEFF project after seeing EV tailpipe and upstream greenhouse gas (GHG) emissions between 100-150 grams per mile (g/mi) on fueleconomy.gov, and full-sized hybrids, like the Fusion, emitting around 250 g/mi total GHGs using regular gas. We calculated that the hybrid’s emissions could drop to EV levels running on E85 instead of gas, and the vehicle we compared HEFF to was 2019’s best-selling EV—you guessed it—the 2019 Tesla Model 3 LR. The dumb luck of Car and Driver doing a 40,000-mile road test on that exact vehicle meant we would be dumb if we didn’t use this stroke of luck by extending our HEFF test a few weeks beyond the original three-year time frame, so we could reach a total of 40,000 miles to more readily compare to their Tesla study.
In mid-October, HEFF had travelled 40,007 miles using flex fuel averaging 71.4% ethanol over the life of the demonstration project. We had zero maintenance issues (not the case with Car and Driver’s Tesla), and the 1,518 gallons of E71 divided over those miles works out to just over 200 g/mi tailpipe CO2. However, had we been able to consistently use E85, that number would drop to about 176 g/mi. E85 made with California Air Resources Board (CARB)-certified, low-carbon-intensity (CI) ethanol (sold in California today) would emit around 112 g/mi CO2, and HEFF fueled by E85 made with low-CI ethanol and renewable naphtha instead of gas (also available in California) would drop HEFF’s tailpipe emissions to approximately 75 g/mi CO2.
All but the last of those numbers are still higher than the fueleconomy.gov estimate of 111 g/mi GHGs for the 2019 Tesla Model 3 LR using the average U.S. electricity mix — but they’re similar or lower than emissions in higher-CI electricity markets like St. Louis or central Wisconsin, where fueleconomy.gov estimates the Tesla lifecycle emissions at 194 and 201 g/mi, respectively. This is where the Car and Driver test results become even more interesting. Since fueleconomy.gov GHG estimates are based on Tesla's “long range” being 310 miles per full charge, while Car and Driver’s range was consistently 80 miles lower throughout their road test, at 230 miles per full charge, the Tesla U.S. average electric mix number goes up to nearly 150 g/mi, and more than 260 g/mi in the Wisconsin and Missouri markets mentioned.
Demonstrating E85 in general, and E85 in a flex-fuel hybrid in particular, as viable and readily available tools in the fight to reduce carbon pollution, was the goal of the HEFF project, but it was only part of what we discovered. You can “HEFF around and find out” what the data looks like at ethanol.org, but the bottom line is this: HEFF shows that anyone truly interested in reducing carbon pollution should be interested in flex fuel hybrids.
• Delivers up to 15% increased corn oil recovery
• Enables pathway to produce low-CI cellulosic gallons
• Dewaters corn kernel fiber for reduced natural gas consumption
• Maximizes plant operability
To learn more, contact your account manager.
Even before the U.S. presidential election significantly altered the political landscape on both sides of the Atlantic, Europe was already talking about how to improve its competitiveness while still achieving much-needed goals for climate change mitigation, energy independence and food security.
Now that this drive for strategic autonomy and economic resilience is becoming even more vital, it’s clear that the European Union will have to make better use of domestic assets such as ethanol biorefineries.
These biorefineries convert raw materials from European farmers—multipurpose crops, waste and residues—into food, feed, renewable fuel, biogenic CO2 and other important coproducts.
This contribution goes way beyond simply helping the EU reduce its dependence on fossil fuels —even though that contribution is significant. In 2023, bioethanol from ePURE members reduced greenhouse gas emissions by more than 79% compared to fossil fuels—a figure that only rises year by year.
It also includes contributing to food security by offsetting Europe’s protein deficit. In fact, European ethanol biorefineries produced more food and feed than fuel in 2023—a statistic that often goes overlooked in EU policy debates over biofuels. In fact, EU ethanol biorefineries are one of the main sources of vegetable protein in Europe.
Using a small fraction of arable land without danger of deforestation, European biorefineries produce food, feed and renewable fuel that complies with strict EU legislation.
These biorefineries also create thousands of jobs across the EU, supporting farmers, strengthening local communities and fostering rural economies. Every year, the production of crop-based biofuels, including bioethanol, generates over €6.6 billion in revenue for farmers—boosting Europe’s selfsufficiency and improving its food supply.
ePURE unites around 50 bioethanol plants across Europe, accounting for about 85% of EU renewable ethanol production. Our members across the continent harness innovation, sustainability and socially inclusive change in the fight for a more resilient, carbon-neutral Europe.
This issue of social inclusiveness was underlined in the recent European elections, in which voters made it clear they want a more pragmatic approach that combines important climate goals with policies that support consumer choice and freedom of mobility.
Fortunately, some important EU political figures have begun to notice. Consider the recent report to the European Commission from former European Central Bank President Mario Draghi, who said the EU should take a more pragmatic, technology-open approach to achieving its climate goals and unleash the potential of sustainable low-carbon alternative fuels such as renewable ethanol.
The Draghi report also notes that while the EU has been a world leader in developing renewable energy—thanks in part to the use of sustainable biofuels—its recent policy choices put it at a competitive disadvantage against the rest of the world going forward.
But there’s a better way, one that valorizes local farmers, encourages local production, creates local jobs and produces local benefits with a global impact. This is how to help build a more resilient and strategically autonomous Europe.
Redshaw Advisors, a leading environmental markets risk management company, has entered into a marketing agreement with Summit Carbon Solutions, a prominent global biogenic carbon capture and storage project developer.
Summit Carbon Solutions’ Biomass with Carbon Removal and Storage (BiCRS) project aims to capture biogenic carbon dioxide before it is released into the at-
mosphere from ethanol plants across the Midwest United States and transport it to North Dakota for permanent and secure underground storage.
Redshaw Advisors will play a key role in marketing the carbon dioxide removal (CDR) credits generated by this groundbreaking project and will make them available to environmentally conscious businesses in Europe seeking to procure high-quality
Green Plains Inc. announced that Phil Boggs, formerly EVP of investor relations and finance, took over as chief financial officer of Green Plains on Nov 1, 2024. Outgoing CFO Jim Stark will retire from Green Plains by the end of the year.
“As part of a predetermined succession planning, Jim became CFO in 2022 with the intent to prepare Phil to take over the position when Jim was ready to retire from Green Plains,” said Todd Becker, president and chief executive officer of Green Plains.
Whitefox Technologies announced the successful installation of the Whitefox ICE XL membrane dehydration system at Western Plains Energy LLC in Oakley, Kansas.
Whitefox is at the forefront of advanced dehydration technology, and this
is the first installation of the new ICE XL membrane solution in the United States.
The solution enables Western Plains to achieve a 50% reduction in natural gas and steam, a 25% increase in production capacity and improved overall operational cost efficiency.
carbon removals as part of their net zero strategy.
This project will adhere to the Gold Standard for the Global Goals’ new, robust methodology to ensure the integrity and long-term permanence of its climate impact. With over $1 billion already raised and deployed, Summit anticipates the first issuance of CDRs for vintage year 2026.
Phil Boggs has served in multiple areas of increasing responsibilities since joining the company in 2009, most recently as head of investor relations since 2019 and treasurer from 2014 to 2021. He will lead all aspects of finance, accounting and investor relations.
The system advances Western Plains towards its goal of net zero carbon emissions by reducing its carbon intensity score by more than a 10%.
New Energy Risk, a wholly owned division of Paragon Insurance Group, and Ecostrat, a leader in assessing, developing, optimizing and managing biomass supply chains, have announced a partnership to develop Feedstock Supply Insurance, an insurance offering that aims to mitigate risk in biomass feedstock supply chains. It will do this by effectively capping feedstock costs
and securing long-term project debt repayment obligations.
A key barrier to the rapid scaling of the trillion-dollar global bioeconomy is the fragmented nature of biomass supply chains, which often comprise small- and mediumsize suppliers such as forestry companies, sawmills, farmers and truckers.
LanzaTech Global Inc., the carbon recycling company transforming aboveground carbon into sustainable fuels, chemicals, materials, and proteins, announced plans to develop a commercial-scale carbon capture and utilization (CCU) facility at Herøya Industrial Park in Porsgrunn, Norway. The plant will produce ethanol and is expected to begin operations in 2028.
Eramet will supply furnace gas as feedstock to the facility from the Porsgrunn Manganese Alloys smelter but will not participate in its financing.
To unlock further emissions reductions, the two companies also intend to build upon the CCU infrastructure and, if demonstrated to be feasible, integrate carbon capture and storage (CCS) technology
Technip Energies and Enerkem Inc. have announced the official signing of their collaboration agreement, solidifying their commitment to accelerating deployment of Enerkem’s technology converting non-recyclable waste and residues into sustainable fuels and circular chemical products.
Enerkem’s gasification technology caters to hard-to-abate sectors such as avia-
tion and marine fuels. Under the terms of the agreement, Technip Energies and Enerkem will provide everything from strategic plant design and modularized project delivery services to clients.
As Enerkem’s strategic partner, Technip Energies will contribute its expertise in engineering, technology integration (hydrogen, carbon capture, etc.) and project deliv-
Through the partnership between Ecostrat and NER, FSI aims to transform non-investment grade supply chains into bankable, investment-grade ones by transferring risk from project developers and capital providers to A-rated insurance markets.
as part of a second phase of the project. The integration of LanzaTech’s CCU technology with CCS, two commercially proven carbon management solutions, is expected to establish a first-of-a-kind, integrated facility that drives leading-edge carbon abatement metrics.
ery to support joint development of such projects. The collaboration will focus on strategic efforts to further optimize design elements and industrialize the approach, offering a cost-effective solution.
Breakthrough research seeks to better pinpoint and predict corn trait performance, while new hybrids enhance inherent sustainability, reduce yield loss and improve accessibility.
By Lisa Gibson
When James Schnable, professor of agronomy and horticulture, began his career at the University of Nebraska Lincoln a decade ago, the ability to measure DNA differences among hundreds of varieties of corn was a breakthrough technology. But the science is moving fast, and Schnable’s UNL team is on the cutting edge with an RNA-based process that shows promise at better predicting performance of corn hybrids.
“By looking at the RNA, we think, and so far initial results confirm, we do a better job of predicting how different corn hybrids perform in different environments, which is a really cool thing,” Schnable says. “We want to match hybrids to environment, and as we’re developing new hybrids, we want to be aiming for the environments that we know they’re going to grow in.”
The research looks so promising, in fact, that the U.S. Department of Energy’s Advanced Research Projects Agency-Energy contributed a $650,000 grant to its expansion.
Meanwhile, corn hybrid developers are discovering their own innovative scientific processes that could revolutionize how we grow corn.
Both DNA and RNA are present in cells. “RNA is made from the DNA—the interme-
diate that allows our genome to turn into proteins, that allows the cell to do what it does,” Schnable explains. “It’s very dynamic—it can change from one cell to another, whereas the DNA remains stable.”
That variability in RNA, even within the same hybrid varieties, applies to location and time of day—a sample collected in the morning will show different RNA than one collected in the evening in the same field. “We can actually look at differences in the RNA between environments, whereas we don’t have that additional layer of information for genetics,” Schnable says. “With corn, every plant DNA is identical for each hybrid strain, whether in Omaha, Lincoln or South Carolina. But that RNA produced from that DNA will be variable.”
And those differences in RNA are more likely to be meaningful than the DNA variances among different strains currently used to predict behaviors, Schnable adds. But equally important, the corn genome has about 204 billion nucleotides and 10s to 100s of millions of genetic differences, whereas RNA consists of around 30,000 variables to analyze.
“We have on the order of 1,000x fewer variables we need to look at in the RNA data than the DNA data,” Schnable says. “And having fewer, more informative variables makes it easier to build a good predictive model. ... “In the past four or five years, we have gotten to the point where we really can measure the RNA differences in hundreds of varieties of corn,” Schnable says.
But sampling does present a challenge. While DNA remains stable, RNA is susceptible to changes, even after the sample (a leaf punch) is taken. The removal of material is much more traumatic for RNA than for DNA, so measures must be taken immediately to preserve the sample. Schnable’s team uses liquid ice in styrofoam cases to preserve their samples during collection. “Instead of being able to take our time sampling everything, we get 20 people out in the field and they’re all running around,” Schnable says.
Analyzing RNA instead of DNA is not a brand-new idea. “Lots of people had thought about this idea conceptually,” Schnable says. “But we were able to figure out how to generate and collect the data.”
Schnable’s team completed a first phase of this research, and in doing so produced what they believe is the world’s largest data set of corn gene expression measurements. But to produce a useful process for seed suppliers to change their methods, a much larger database will be necessary. And that’s what
the follow-up research with the DOE grant is about. “We showed in two environments, two fields. But that’s not a scalable solution. We need to be able to go out to any field in the country, collect the data and make the predictions to figure out how the plants will perform.”
The team needs to determine whether the model will work across environments. “If one sample is taken at a certain date and time in Nebraska, and another at another date and time in Michigan, does it still translate? I think it’s going to work, but we do need to test it and that’s why I’m really glad we have this funding from the government.
“When you are designing research projects, it’s always good if you can design a project where if it works or doesn’t work, you still get an interesting result. This was something where,
if it didn’t work, we were going to spend a huge amount of money and have nothing to show for it. So we’re very fortunate that the DOE was willing to roll the dice on that.”
Developing a corn hybrid traditionally takes seven to 10 years, simply because of the nature of scalability generation to generation— it takes two generations to plant just one acre, Schnable says. But the enormous database his team will create through its research will be a boon to seed hybrid developers everywhere. The database will be available online for all.
“That’s why we’re doing this. We want this to actually have impact and if it’s going to have impact, people have to be able to find it and use it.
“That’s also a good thing for farmers and ethanol producers,” he adds. “If there is more competition in this space, if there are more companies that can stand up competitive breeding programs, that creates a wider range of options for farmers.”
It’s a similar goal to that of ZeaCal and its developing PhotoSeed variety. PhotoSeed, according to a recently released independent analysis, reduces soybean oil’s carbon intensity score by 4.6 points, while increasing oil production without impacting yields. The company believes those results will translate to corn as well, once ongoing studies are complete. “We believe this tech can help decarbonize agriculture and energy at the same time and hopefully uplift growers away from a commodity market.” says Han Chen, co-founder and CEO of ZeaCal.
Chen likens the PhotoSeed technology to Schnable’s team’s research, in that it came about not only through a genomics approach. “It was protein engineering, understanding the biochemistry of the plant, understanding the plant physiology.
“If research is becoming more integrative looking beyond genetics at the DNA level, that’s going to be very important for our research to translate into commercial outcomes,” Chen adds.
PhotoSeed works by changing the way the plant conducts photosynthesis, Chen explains. “I call PhotoSeed a technology of serendipity—we didn’t originally set out to change photosynthesis. But through our research, we inadvertently figured out that we were changing the way plants use carbon and sunlight.
“We knew, with extra carbon capture and extra energy, we could get that plant to store more of that energy. We were curious if we could produce a high oil corn variety.”
High oil corn varieties on the market now tend to sacrifice yields, as corn is not genetically ideal for oil production. But PhotoSeed expands that oil production through adding it to the endosperm, increasing biomass.
“Already, in elite hybrids, we’re seeing yield stability but with 44% more oil on average,” Chen says. “Whether it goes into food, feed or fuels, it’s important because what we want is more of that energy.
[Plant oils are] very much in high demand, especially for end uses in jet fuel where other areas don’t exist for decarbonization, and those oils are direct drop-ins. We’re going to uplift profitability and improve sustainability.”
PhotoSeed represents the first sustainability-imbedded trait that is not subject to agronomic practices, Chen says. The CI reduction would come from that seed composition.
“In corn, farmers will be not just growing bushels, but growing oil and carbon reduction,” he adds. “Those are two other forms of revenues with local markets that are not as correlated to commodities.”
Chen anticipates PhotoSeed corn will be ready for market in 2027 or 2028.
Bayer Crop Science’s short stature corn hybrids are also aimed at preserving, and even improving, yield. Short varieties of the past have sacrificed yield, but Bayer’s varieties hold promise for improved management practices and an actual increase in yield, says Denise Bouvrette, North America Smart Corn Systems strategy and launch lead for Bayer Crop Science.
“We’re doing a lot of things differently with this launch,” Bouvrette says. The only other short corn variety she is aware of is not developed using a breeding trait, but simply is a consequence of traditional breeding selection for plants that are responsive to ultra-high populations and ultra-narrow rows. “Bayer is the only entity that I’m aware of that has commercially available short-stature plants that are developed through breeding with a shortstature trait.” Previously, the short-stature trait
was not one that could be displayed in the elite corn varieties.
“It takes the elite varieties with all the agronomic traits you’re looking for and makes a shorter plant,” Bouvrette says of Bayer’s short-stature corn. “The introduction of this trait into our elite varieties shortens the plant by about 30%, so it’s between 5 and 7 feet tall. The ear is around 2 feet, to make sure we can still harvest that using traditional equipment. ... The farmers can take the full benefit of that shorter stature plant, but also expect similar yields to what they see in commercial tall varieties today.”
The main benefits of Bayer’s short-stature hybrid are protection against yield loss as a result of tolerance to lodging and green snap during high winds; physically shorter stature of less than 7 feet, allowing access all season long; and yield potential in the ability to explore more soil volume than traditional hybrids.
“Because these plants have that inherent stability or standability from a lodging or green snap perspective, you can add more plants to that acre,” Bouvrette explains. “So plants at higher populations, closer together, with less risk of falling over. Farmers have been looking to increase yields by adding more plants to the acre for years, but you can only push so far with those standard varieties.” The short stature presents a sturdier stalk and a shorter architecture—basic physics, she says.
Jason Wistehuff, global crop strategy lead for BASF, which owns portions of Bayer’s seed businesses, adds, “Growers are super excited about the application flexibility you get late season.” Flying over a field for a late-season fungicide application is costly and difficult. “If you can get in later in the season with your ground rigs, more specifically where you need it, at the right time, that’s a huge benefit.”
Bayer is releasing two short corn technologies under its branded Preceon Smart Corn system—a bred variety and a biotech variety. The bred variety uses a recessive trait to impact a hormone pathway that brings the nodes below the ears closer together. It’s on the market as of this season, in about 30,000 acres and jumping to about 100,000 next year.
The biotech variety, expected on the market toward the end of the decade, impacts a different hormonal pathway that shortens all the nodes on the plant, from top to bottom.
But the benefits of Bayer’s process is not just in the height of the mature field. “What Bayer has been able to do is speed up the breeding cycle through our use of AI and advanced analytics,” Bouvrette says, explaining the company has shortened that breeding life cycle from seven years to just four.
“We can do a lot of this work in silica in the lab and the algorithms can very quickly determine which hybrids have the best likelihood of getting the different attributes that we’re looking for,” says Brian Leake, director of external communications for Bayer. Then, field testing is more targeted than in traditional hybrid development, Bouvrette adds.
“In certain situations, what we’re breeding for today may not be what growers need seven years from now,” Leake says. “We can be more agile in reacting to the farmer’s needs and be more responsive.”
“The faster you can respond to those market needs and get those products out there, the better,” Bouvrette adds. “Having that ability to target that and identify it up front and then rapidly get to the field to validate is really important and that’s the shift we’ve been making towards precision breeding.”
Beyond short corn, the Preceon Smart Corn System is a true partnership with farmers that can unlock even more yield potential by maximizing the technology for each field and farmer.
This technology represents a first for Bayer, Bouvrette says, in the process of creating a community of select farmers and working directly with them to test and learn in their fields. “The response has been incredible,” she says. “Farmers love having the ability to see this in a commercial environment, see this on the farm scale and be able to provide that feedback for us about what they love, what could be better.
“Our participating farmers say if we had enough volume and products for them tomorrow, they would swap almost half their acres to short corn tomorrow.”
American corn has seen a few major step changes in its history, Bouvrette says, including the evolution from inbreds to hybrids, and the introduction of advanced genomics. “We think this will be that next step change for farmers,” she says. “We think this product concept is really transformative, and we really think it’s going to change corn production.”
Author: Lisa Gibson lisa.gibson@sageandstonestrategies.com
Major yeast suppliers are offering new products, enhanced benefits and strain characteristics that reveal how the industry continues to evolve.
By Luke Geiver
Yeast suppliers to the ethanol sector have steadily released new and improved products to better match the needs and wants of the industry. Using third-party yeast developers capable of selecting, testing or altering strains with cutting-edge research and modification technology, some of the big names in ethanol yeast supply continue to enhance their offerings, giving producers a lot to consider.
There are, of course, single yeast products to choose from. There are also entire yeast product lines to search. Some options are selected and offered for a single characteristic, such as superior tolerance to heat or an increase in yield or the ability to reduce the need for additional fermentation inputs like glucoamylase. Many strains offer all of these characteristics in a single product.
Need a custom consult to find the perfect yeast product, a nutritional supplement or a quality control program? That is also part of the standard offering from many of the yeast suppliers working in ethanol today.
Global enzyme and yeast provider Novonesis offers 11 yeast products for ethanol production through its Innova platform. Producers can select products for biomass conversion, fermentation, fiber conversion, liquefaction or saccharification. The fermentation category consists of nine options, eight of which offer the following benefits: fermentation at high dry solids levels, high temperature tolerance, high organic acid tolerance, reduction in need for additional yeast nutrients, expression of enzymes and maximum starch conversion to improve ethanol yield.
In 2022, the Innova product line consisted of only three products: Apex, Quantum and Turbo. Each product was customdesigned to provide different benefits to help producers with everything from bulk production to longer fermentation times to ramping up output without upsetting the overall operations of a plant. In only two years, Novonesis has increased its offerings significantly, through research and development and industry-specific surveys.
BETTER THAN ONE:
Researchers at Georgia Tech University are proving that a mix of yeasts that targets glucose and xylose might provide better fermentation outcomes than single strains. In the yeast sector, both companies and institutions continuously make improvements to products offered in the ethanol industry.
PHOTO: GEORGIA INSTITUTE OF TECHNOLOGY
When it comes to choosing the best yeast products, data is the key, says Pedro Peña, vice president of technology and innovation for CTE Global, which now offers Innova yeast products to its clients. Peña says the company combines lessons learned during on-site visits and data obtained through collaboration to help producers find the right products.
Matthew Ben, director of technical services for CTE Global, says his team provides a complete package of products and services to ensure ethanol plants get the best results and their products or recommendations are always well-researched. That package includes Innova Eclipse, the newest offering from Novonesis.
With Innova Eclipse, CTE Global believes it can help producers “push past fermentation limits, significantly reduce glycerol levels and increase ethanol yields.”
Alex Shifman, president and CEO of CTE, says his team is pushing Innova Eclipse particularly because of its ability to help producers’ bottom lines. Innova Eclipse offers fast fermentation kinetics, reduced fermentation times and a robust stress tolerance.
For ethanol producers looking for a nonGMO yeast option, Novonesis now has Innova Delta.
“For 20 years, ethanol producers required to use non-genetically modified yeasts
have been forced to run their operations to cater to their yeast performance,” said Jens Kolind, vice president of planetary health for Novonesis Europe, in early 2024 when the new non-GMO yeast was announced. Innova Delta can increase yield by 2%, reduce fermentation times by 25% and reduce exogenous nitrogen demand for urea or ammonia by up to 9%, according to the company.
The yeast product was developed through a research and development collaboration between Novonesis and MicroBioGen, an Australia-based biotech company with a library of elite yeast genetics for improving Saccharomyces cerevisiae. Geoff Bell, Mi-
croBioGen CEO, says decades of work and thousands of hours went into the development of Innova Delta.
Lallemand’s role in the global yeast and enzyme sector is only getting bigger. In June 2024, BASF sold its enzyme business to Lallemand in a move that Angus Ballard, president and general manager of Lallemand Biofuels & Distilled Spirits, says will help the company meet the needs of its global customer base. Lallemand’s portfolio was already wellestablished before the BASF deal. But the deal did help Lallemand build out its trademarked
Convergence fermentation platform to combine high-performance yeast with enzymes.
For more than 10 years, Lallemand has offered the Transferm yeast product line. Now, it has the FermaCore platform, a novel approach borne from new research and engineering.
The FermaCore portfolio includes 10 products for dry, liquid and cellulosic applications. In addition to yeast options, Lallemand has developed five antimicrobial options and five yeast nutrition products, many of which are proven solutions for producers’ current needs, and well-suited for anticipated future needs.
The newest yeast product from Lallemand is FermaCore Propel. Craig Pilgrim, vice president of marketing and product development, calls the product a gamechanger because of its ability to “radically reduce fermentation time, allowing producers to process more fermentations per year with more ethanol going out the door.
“Fermentation efficiency is where it’s at,” Pilgrim says.
Propel yeast is highly efficient and completely converts sugars into ethanol while producing less glycerol, according to Lallemand. Because the product expresses high amounts of glucoamylase, supplemental glucoamylase and other inputs are reduced. And, because the yeast is extremely robust, according to Ballard, the product performs well in elevated temperatures or periods of bacterial contamination.
Jim Miers, technical service manager for Lallemand, says fermentation isn’t just about fuel ethanol anymore—now it’s also about oil recovery and protein capture. Lallemand has developed products to specifically capture more yield and greater protein through more cell mass in fermentation with its new yeast options.
“Yield is always king in the ethanol industry,” Miers says. “But in today’s marketplace, ethanol plants are more like biorefineries, trying to get every penny they can out of a small kernel of corn.”
Most producers prefer liquid yeast over dry because it is easier to introduce a liquid
into the system, as it’s already hydrated and accessible by the fermenter. Yeast nutrients are also more popular with producers than they have been in the past, as they improve performance.
No matter what yeast product the Lallemand biofuels team offers to the industry, Pilgrim and Ballard agree, the company will always work with ethanol producers to develop tailored solutions through a commitment to customer service (the team spends a lot of time at their clients’ plants) and experience in the industry.
Phibro Ethanol provides non-GMO offerings under its trademarked platform Kinetx, as well as PhibroADY, its GM option. In addition to its yeast strains, Phibro provides two unique services: Phibro CertiPhied and FortiPhi.
The Kinetx lineup was released in 2023, designed to secrete glucoamylase during fer-
mentation, through a collaboration with U.K.based yeast strain developer Ingenza.
While the company says its products have a variety of positive impacts, Jenny Forbes, vice president of sales and services North America, says Kinetx Spark is likely of particular interest to producers. It has an extremely clean profile that results in low hydrogen sulfide, acetaldehyde and other off-product.
“Producers interested in grain neutral spirits production and CO2 sequestration have solved problems by adopting Kinetx Spark,” she says.
Phibro CertiPhied is a quality control program that tests every lot of products and ensures they meet key product indicators (similar
to performance-based KPIs). The program relies on a three-tiered commitment. The first tier includes live yeast, fungal, bacterial contamination counts and sensory measurements. The second tier tests for lot-to-lot consistency. And the third tier includes periodic stress testing to ensure performance under high temperatures and in the presence of organic acids.
Phibro emphasizes quality control as a differentiator. “The services offered include total plant optimization, not simply yeast trial support,” says Rogerio Prata, senior director of global innovation for Phibro.
“Products do not leave a Phibro facility without a full battery of rigorous quality tests,” says Forbes. “Producers should not worry about product performance and should be assured that all products come with our guarantee.”
FortiPhi is a broad nutritional supplement line that includes inactivated yeast cultures, essential minerals, vitamins and micronutrients to support yeast health, all to protect against unseen stressors.
The trademarked Evolve Evergreen yeast product from Leaf, a Lesaffre business
Our team of experts have over 20 years of ethanol plant maintenance expertise. We o er full service and parts for all Fluid Quip equipment to ensure peak performance.
• OEM Parts Warehouse
•$2 million+ inventory on-hand
•Factory Trained & Certified Techs
•MZSA™ Screens
•Paddle Screens
•Grind Mills
•Centrifuges
•Gap Adjusters
We’re the leading voice of America’s biofuel industry, who are helping transform abundant supplies of grain into a cleaner, healthier future for us all.
unit, was developed to maximize efficiency and yields, minimize costs and reduce environmental footprint. The product was developed with the help of Recombia Biosciences, a synthetic biology developer. While Evolve Evergreen is Leaf’s newest and most advanced product, the company also offers Ethanol Red for industrial ethanol production from corn and Safdistil Plus for ethanol produced from beet substrates.
Evolve Evergreen is also suitable with cassava as a feedstock. In early 2023, Leaf released a case study involving an Asian-based starch and sugar operation using the strain for ethanol production. After trialing the new yeast product from Leaf, PSC Starch Products received a yield improvement of 2%, a 40% reduction in glycerol production and a 50% reduction in exogenous glucoamylase needs, all results Leaf says will be reproduced in corn-based ethanol production. The company believes the Evolve strain, is “the future of fuel ethanol fermentation.”
At the Georgia Institute of Technology School of Biological Sciences, researchers are working on a yeast strain that is “happier with the lights on.” Such a yeast could be more suitable and robust for biofuels production. The Georgia Tech team is looking at ways to introduce rhodopsins, a protein found on trees that converts light into energy. The addition of the rhodopsins to a yeast strain on the cellular level could help the strain grow up to 2% faster when exposed to light, which would benefit the evolution of the yeast. The studies are still ongoing.
At the University of Chicago IllinoisUrbana, researchers are looking at how yeast strains with differing capabilities can work together within a community of microbes in the fermenter. Researchers from a lab working on a synthetic yeast capable of breaking down xylose joined forces with researchers from another lab working to find a more efficient yeast strain capable of breaking down glucose.
As the private sector deploys new research methods for new yeast strain capabilities, the public sector is doing the same.
The researchers tested and collected data on a process that introduced the two yeast strains at different times.
At the USDA’s Agricultural Research Service, a team of scientists is developing a yeast that can stop bacteria strains from “bullying” yeast strains used in ethanol plants. The ARS research team is genetically modifying baker’s yeast with an outer enzyme shell that helps kill or inhibit bacteria. The problem bacteria act as a microbial rival by releasing acetic and lactic acid during fermentation, which the researchers say hinders peak ethanol production capabilities.
The bacteria the researchers are fighting are common in products such as sauerkraut and pickles, according to Shao-Yeh Lu, a research microbiologist working on the new yeast strain. It feeds on the glucose in the corn mash. The coated yeast is upgraded with endolysin, an enzyme that can reduce the presence of bacteria by 85%. To date, only lab-scale trials have been performed. But, according to ARS, if the trials are proven at a larger scale, the need for antibiotics or other chemical cleansers could be greatly reduced.
The researchers discovered that adding the xylose-fermenting yeast strain to the mixture first, followed by the glucose specialist 14 to 29 hours later, dramatically boosted ethanol production, more than doubling the yield. The work helped them see how a division of labor in bioprocessing might help create a better design for the fermentation process.
Lallemand’s Ballard says the future of the yeast sector in the ethanol industry is extremely bright.
“We are close to a new era with more ethanol producers making more products,” he says. “In the next two years, we will see some very exciting developments.”
Author: Luke Geiver writer@bbiinternational.com
Alcohol-to-jet hopefuls are buying up both healthy and shuttered ethanol plants, drawing up their business blueprints while state and federal funding mechanisms expand to allow for the SAF sector's rise.
By Luke Geiver
Gevo Inc. expects to close early this year on a deal to acquire the ethanol production and carbon capture and storage assets of Red Trail Energy LLC in Richardton, North Dakota, for $210 million. Gevo intends to transform the RTE facility into an operation that produces transportation fuels and chemicals with net-zero emissions.
In Illinois, Crysalis Biosciences Inc. announced plans in October 2024 to retrofit a shuttered ethanol plant into a firstof-its-kind SAF plant. Crysalis intends to produce 5,000 to 10,000 gallons per day of low carbon-intensity sustainable aviation fuel (SAF), or the feedstock needed for its production.
Although the conversion, utilization and long-term plans of Gevo and Crysa-
lis differ in many ways, there are common themes between the projects—they illustrate the growing trend in producers, investors and even state organizations entering the SAF market. These parties want to play a part in carbon intensity score reduction and job creation and to establish their place in a new, financially appealing opportunity that links ethanol production to SAF production.
Patrick Gruber, CEO of Gevo Inc., believes RTE will help the company reach its near- and long-term goals. “We have been looking for years for an existing ethanol plant,” he says.
Gruber and Chris Ryan, president and chief operating officer, share five main reasons for the purchase and conversion of RTE to a SAF facility.
• The revenue gained from RTE operations will combine with Gevo’s operations to make the company’s adjusted EBITDA positive in 2025.
• Gevo will have the ability to market carbon abatement while also delivering advanced biofuel, enhancing Gevo’s value to shareholders.
• The value of Gevo’s RTE operations in conjunction with its goals for creating
what it calls Net-Zero carbon sites capable of producing SAF are well-suited to serve U.S. and Canadian markets.
• The Net-Zero 1 SAF project that Gevo is developing near Lake Preston, South Dakota, will also benefit from the CCS capabilities of the Richardton site, as well as the additional supply of low carbonintensity ethanol that could be used on site or elsewhere.
• And finally, the CCS assets of RTE present a major opportunity for future CCS
work. Of the 1 million metric tons available for capture and sequestration per year at the site in North Dakota, only 160,000 metric tons are currently being utilized.
“When we first visited Red Trail, we could see that their vision for reducing carbon was very much in line with ours,” says Ryan. For the ethanol industry, he adds, “it is ahead of the game.”
The CCS asset pursued and created by RTE was a multi-year, multi-million-dollar effort that involved many organizations,
permits and exploratory growing pains. Since 2022, the capture and sequestration operation has been running without incident and today is generating 45Q tax credits.
“Even though the Red Trail board was open to selling the asset, they wanted someone that could take the next step,” Ryan says.
Gruber is eager to point out that his team is committed to taking the next steps at RTE and beyond. While committed to
producing SAF, Gevo is also admittedly on a mission to change the narrative about renewable energy such as SAF and other biobased products. Gruber wants the industry to focus on a net-zero outcome—he believes it should be the ultimate goal, from the agriculture practices used to grow corn, to the end products such as ethanol for fuel or SAF feedstock. SAF presents an exciting future for Gevo and ethanol producers alike, he says, but no one cares about SAF with a high CI score. “That is the message the ethanol industry needs to remember,” Gruber says.
Gruber enthusiastically explains the math behind the net-zero scenario at RTE. “We are pushing the envelope,” he says. “Red Trail is where it will work.”
Ryan says Gevo will be able to go fast and accomplish a lot at the RTE facility, in part because of the work Gevo has already done in South Dakota. The company will use plans initially geared for its proposed Lake Preston biorefinery to update the RTE operation. Gevo creates modularized systems that are pre-tested at fabrication yards before they are shipped, Ryan says. The tech in the modularized units relies on corn-based ethanol as a feedstock to produce SAF and other products.
The main hurdle for Gevo will be in permitting, but overall, Ryan and his team have several improvements planned for RTE. The company will retain the current employee base. One of the immediate goals is to add a combined heat and power system to lower the CI score even further.
Jodi Johnson, RTE CEO, says the team is excited for its future under Gevo’s leadership. “Gevo’s vision for a sustainable future aligns with our philosophy of ‘our farms, our fuel, our future,’” she says.
Meanwhile, Gevo has secured a conditional commitment from the U.S. DOE Loan Programs Office for a loan guarantee of roughly $1.46 billion, to be used for the Net-Zero 1 facility in South Dakota. The plant could represent the largest-ever economic development project in the state’s his-
tory, according to Lindsay Fitzgerald, senior vice president of public affairs for Gevo.
The loan guarantee could also be important for the growth of the SAF industry overall, Gruber says.
“This valuable commitment to help finance NZ1, if finalized, should also attract
other capital investments to unlock SAF commercialization, given the robust due diligence conducted by the agency,” Gruber says. “The due diligence work by the DOE has been incredibly detailed and thorough, and the benefit is a substantially reduced execution risk profile for the project.”
Gruber says he knows everyone is watching Gevo and that the RTE deal will draw even more attention. He and Ryan are enthusiastic about the future and undeterred by forging a path no one else has taken before, he says, especially with their goal of investing in and bringing to life the concept of carbon abatement reaching net zero.
Crysalis Biosciences is a biochemicals maker that, like Gevo, has invested in an ethanol plant to fulfill its true SAF vision. In early 2024, the company acquired and began renovation of a 55 MMgy ethanol plant shuttered in 2019 near Sauget, Illinois, a mostly industrial area adjacent to the Mississippi River in greater St. Louis. The original plant, run by Center Ethanol, included four fermentation tanks, four distillation tanks, a beer well and other field-erected tanks across a 57-acre campus.
Crysalis, with help from the National Renewable Energy Lab, developed its biorefinery tech that converts plant-derived raw materials into various chemicals through microbial fermentation with catalytic upgrading. The company has used a variety of funding and backing to make the initial purchase and subsequent upgrades to the plant, including investments from the Sustainable Aviation Fuel Financing Alliance Fund (SAFFA Fund I) that counts Airbus as its anchor investor.
The ethanol plant conversion will create new jobs and maintain existing positions, according to the company. Crysalis is in the process of hiring a new maintenance manager, process operator and plant trainer, along with plant engineers, lab technicians, logistics personnel, general office help and maintenance mechanics. Existing positions such as plant manager, EHS manager, operations manager, office manager, maintenance techs and process operators will all need to be retained.
Recently, Crysalis was awarded $239.5 million in funding from the Illinois Department of Commerce and Economic Oppor-
tunity office through a Reimagining Energy and Vehicles in Illinois (REV Illinois) agreement.
“It’s an exciting project that will support the decarbonization of the St. Louis airport and create more good-paying jobs in the Metro East,” says Eliza Glezer, assistant deputy director of communications for DCEO.
According to Glezer, Illinois is competing with other states and countries for com-
panies like Crysalis and winning for several reasons. Site Selection Magazine ranked Illinois as the No. 2 state for corporate expansions or relocations as of 2023. The state has embraced a “Team Illinois” approach to helping businesses like Crysalis navigate the exploration or application process for funding, including the funding it received from REV.
“There is no cap on the number of companies that can benefit from the REV program,” Glezer says. “While the REV
LED™ from FQT allows you to expand your base plant while lowering your CI score.
LED™ Proven, Reliable, Trusted.
SCAN TO LEARN MORE
program does have stipulations for meeting investment and hiring goals, as well as annual reporting requirements, the barriers to entry are low.”
An eligible company looking to establish or expand its operations in Illinois could qualify with a capital investment starting at $2.5 million and creation of at least 50 new jobs (or 10% of their statewide employment, whichever is less) within four years. REV benefits include payroll withholding, credits and exemptions.
To be eligible, companies must either be manufacturing products in the supply chain for electric vehicles (including batteries and other EV components) or for renewables. The second criterion is that the company must meet minimum job creation and capital investment thresholds. Team Illinois is available to explain the full benefits and requirements to any company, as well as to assist in site selection and market analysis, Glezer says.
Illinois is also creating benefits for SAF users. In 2023, the state passed a SAF purchase credit. Through 2032, SAF sold to or used by an aircraft in Illinois would earn a credit of $1.50 per whole gallon purchased.
REV provides funding opportunities to EV, solar, renewable and energy storage manufacturers that move or expand, to Illinois. Crysalis is the first-ever SAF producer to earn the funding.
REV was initially part of the Reimagining Electric Vehicles Act passed by the Illinois General Assembly in 2021, according to Glezer. REV was then updated and renamed in 2022 to include SAF and other renewable energy projects because of their potential impacts to the regions where they are produced or consumed.
It’s how Glezer explains the renewed goal of REV that helps reveal why projects and deals by companies like Gevo or Crysalis are meaningful now, and why more might be on the way in the future.
The goal of REV is to create incentives that support well-paying jobs, she says, “in these newer, fiercely competitive industries, while localizing the supply chain for products that reduce carbon emissions.”
Author: Luke Geiver writer@bbiinternational.com
Germany-based Verbio overcomes challenges in applying its novel ethanol and RNG coproduction process in the U.S.
By Katie Schroeder
Verbio made the decision to coproduce ethanol and RNG two decades ago. At the time, it was risky—a decision between the energy-intensive method of using stillage for DDGS or developing a complex system using the stillage leftover from ethanol production to make renewable natural gas and fertilizer. Out of a desire to avoid reliance on fossil fuels, Verbio ultimately decided to take the risky route.
Claus Sauter, CEO of Verbio, set out to reduce energy’s climate impact by partnering with farmers to make energy—both liquid fuels and RNG. Since its founding in Germany back in 2005, Verbio has grown and developed biorefineries across three continents, transforming organic material into energy.
“Our approach is to achieve the best margin per ton of CO2 that is saved,” Sauter
says. “And that’s for everything—it applies not only to vegetable oil and grains as feedstocks, but also to the use of all residues.” Whether processing corn, corn stover or other cereals, Verbio’s goal is to maximize profitability and maintain sustainable production.
In 2017, the company started considering entrance into the North American market following increased European skepticism toward crop-based biofuels. In 2022, Verbio held a grand opening for its first plant in the United States, located in Nevada, Iowa. Verbio Nevada utilizes the company’s proprietary biorefinery process, which integrates corn starch-based ethanol production and RNG processing by fermenting the stillage leftover from ethanol production, along with corn stover.
The first of its kind in the U.S., the plant promised a unique approach to extracting value and fuel from Iowan corn, producing 60 MMgy of ethanol and 2.3 MMbtu of RNG. However, being the first of a kind comes with a number of unique challenges, ranging from market and policymaker education to processing hiccups. The Verbio team has worked to overcome each of these challenges at its Nevada facility and continues to grow in the U.S. through its purchase of an ethanol plant in Indiana.
The engineering steps of Verbio’s proprietary process are well-established, Sauter explains. The company has been operating several such plants in Europe for over 10 years. However, applying it to a new location and navigating the complexities of a different country’s regulatory landscape changed
the timeline for getting the ethanol side of the facility up and running. In August 2024—two years after the biorefinery started injecting RNG from corn stover into the grid—the Nevada plant started up the ethanol production side of its process. “The first plant is always the most complicated and challenging, but you know, that’s not the first plant from us,” Sauter says. “We know the technology works, we know the yields, we know the flexibility.”
There are three major technological challenges at the facility, according to Oliver Lüdtke, Verbio’s chief technology officer and vice chairman of its management board. First, corn stover for RNG production has a high moisture content, and Verbio targets less than 25%. The stover needs to be harvested and covered by a roof or tarp as soon as possible to prevent feedstock degradation, which could cause pro-
cess problems. If the stover gets wet and degrades during storage, it will disrupt the RNG production process and prevent Verbio from achieving maximum throughput. To prevent that from happening, Verbio’s team works to remove stover from the field before rain. “They’ll have a lot of organizational discussion with the farmers, with the local companies which are supporting us, [such as] certain companies which are supporting us in the baling,” he says. “That’s a big challenge to get this quality on the ground and get this to our storage location.” Each fall, Nevada’s team works with 80 to 100 local farmers and gathers the 135,000 stover bales needed for full production throughout the year, according to the company.
Another problem causing production issues has been the subpar quality of certain components supplied to the Nevada
plant. When components do not reach required specifications, Lüdtke and his team must find a way to get the process into the correct performance range. And Verbio’s process is uniquely complex, so personnel training is a challenge, too. It is crucial that the team has thorough knowledge of the system, empowering them to run the unit, he explains. “This ethanol and RNG biorefinery that’s based on our own technology and basically the knowledge ... only [exists] in our teams and where we developed it,” Lüdtke says. “But it’s a complex interconnection of the different process steps between each.”
The third challenge is the biological processes used in the facility. Developing yeast and bacteria populations takes at least 12 months, meaning Verbio biorefineries need more time to complete the startup process. The RNG side of the process of-
PHOTO: VERBIO
fers its own array of unique challenges, as well, Sauter explains. “RNG goes into the gird, but at the very beginning, when we started the process, we had a lot of challenges because it was not stable,” he says. “It [is] a biological process, and a lot of digesters just died, so Oliver and his team had to find out what [was] harming the process and what kind of technologies we need to keep the process stable. As part of the stabilization of the process, we are extracting some components where we are producing biofertilizer.”
The soil conditioner Verbio offers— also known as humus—is derived from the material remaining after anerobic digestion, which is recycled for use as soil conditioner by local farmers. Sauter explains that it contains potassium and nitrogen at a quality comparable to fossil-based fertilizers. Verbio wants to build two-way relationships with farmers, where the company can buy local corn and corn stover and sell liquid fertilizer and soil conditioner for nearby fields. The humus has similar characteristics to peat moss and serves a similar purpose in improving the fertility of the soil by increasing the amount of moisture it can hold.
Verbio Nevada is working with Iowa State University to determine how much CO2 is stored in the soil when humus is
applied to a field each year. Humus must be applied yearly to achieve visible results, Lüdtke explains. The novelty of products such as humus in the U.S. agricultural community means that there is work to be done in educating policymakers about the carbon storage benefits of humus as well as its value as a soil conditioner. These unique strategies to decarbonization are not recognized under tax credit frameworks such as 45Z, but are a simple, yet effective solution, Sauter argues. “You don’t have to drill a hole and make CCS; you can also store the carbon in the soil.”
Lüdtke expects it to take time for farmers to recognize the value of humus as a soil conditioner. Farmers are conservative when it comes to change, and they prefer to see the results before using a new product. “We’ve already got a couple of farmers [who] really like our material,” he says. “[It’s] really developing, and they are spreading the information to the community basically.”
Verbio continues to move forward with project development at other locations, even while problem-solving in Nevada, embarking on a new ethanol plant retrofit in South Bend, Indiana. Formerly known as South Bend Ethanol, the operating ethanol plant was purchased by Verbio from Mercuria Investments in May 2023. An estimated total
of $230 million will be spent on upgrading the plant into Verbio’s biorefinery model—coproduction of ethanol and RNG, along with liquid fertilizer and humus.
The production goals for the facility are currently estimated at 90 MMgy of
ethanol and 3.5 MMbtus of RNG, Sauter and Lüdtke explain. Verbio South Bend currently sells its CO2 to the beverage market. “From a commercial perspective, it’s a good location,” Sauter says. It’s an old plant, he adds, and the former owner
would have needed to invest in the DDGS line to be competitive in the ethanol industry. “So, that is a good target for us because we don’t need a DDGS line.”
In May 2024, construction began to convert the facility to Verbio’s biorefinery model and improve production. The technology additions include a total of 16 anerobic digestion tanks, process equipment for energy efficiency optimization, equipment for upgrading methane gas to pipeline-quality natural gas, 10 new buildings, updated IT operating systems and flares. Injection of RNG is expected to begin in 2026.
The “why” behind Verbio’s innovative biorefinery model is simple, according to Sauter. It all boils down to finding a way to make the most energy possible in an environmentally responsible way. Coproducing RNG and ethanol has the benefit of removing the most energy intensive element of ethanol produc-
tion: drying DDGS. Excluding the dryer helps lower the CI of the fuels by directing stillage into RNG production. “To have stillage with 90% water and 10% protein, cellulose to evaporate this water to make a product like DDGS takes a lot of energy and destroys your CI,” Sauter says. The top priority for Verbio has always been CI reduction, he explains. For that reason, the amount of natural gas needed to produce DDGS was a nonstarter.
“It was already 20 years ago we made this decision,” Lüdtke says, adding Verbio’s management board discussed at length whether to produce DDGS or go with the riskier RNG solution. But the environmental advantages tipped the scales.
Sauter entered the ethanol market from a different perspective. Even in the early 2000s, the European framework prioritized climate impact, followed by farmer support, then energy security. “With this approach, our focus was always CI,” he says. When the ethanol industry started booming in the U.S. during the same time, the top priority was energy security, then helping the Midwestern farmer, with environmental benefits as a lower priority, Sauter explains.
Lower energy usage, as well as innovative carbon sequestration through humus,
has the potential to contribute to a lower CI score, too. Currently, Verbio is gathering data to determine the carbon intensity of the Nevada facility’s fuel. The score that Verbio’s process has received under the EU’s model is at 10 to 12 grams of CO2 per megajoule. Although the model differs from GREET, Sauter expects that the U.S. CI score for the facility will be well below 50 kg per MMbtu.
Not long after Verbio entered the U.S. market, the Inflation Reduction Act was passed in 2022. The legislation’s focus on decarbonization is a “home run” for Ver-
bio, Sauter explains. “We came at the right time to the right location.” For Sauter, replacing 1.1 million barrels of fossil fuels each day with ethanol produced across the Midwest—including Verbio Nevada’s 60 million gallons, and soon, 90 million gallons from the South Bend plant—is a perfect solution.
Author: Katie Schroeder katie.schroeder@bbiinternational.com
Novonesis’ Innova® Eclipse yeast enhances yields and shortens fermentation times for ethanol producers.
By Katie Schroeder
Ethanol producers are always striving for the next level and developing their plant’s process to its full potential. Novonesis, the company born out of a merger between Novozymes and Denmark-based bioscience company, Chr. Hansen, continually innovates and identifies products to assist producers in their pursuit of ever-improving yields and process efficiency. Innova® Eclipse, Novonesis’ new yeast strain, offers the benefits of the company’s yield and robustness platforms, explains Tom Kortuem, head of sales, Bioenergy for Novonesis in North America.
Innova Eclipse offers a 1-2% increase in ethanol yields, while reducing glycerol up to 40% compared to their leading yeasts, Innova Apex and Innova Quantum.
“I think the key differentiator is trying to squeeze out that extra ethanol,” says Amanda Moser, senior research and development manager with Novonesis. “Modifying the yeast ensuring we maintain the robustness we know our customers want and demand, while also reducing glycerol by utilizing that carbon for ethanol yield instead.”
It is all about getting the most of what you want out of the process—ethanol—and the least of what you don’t want — glycerol
and organic acids — while achieving “fast fermentation kinetics,” explains Moser. Innova Eclipse is a fast-fermenting yeast, reducing overall fermentation times by up to 18% and offering higher throughput potential.
This yeast does not demand producers adjust their process to maximize its potential, but rather works well with however the plant is run. “We’re not saying, ‘you have to run this way in order to make our yeast work,’” Moser says. “We’re saying, ‘let our yeast work in your plant the way you want to run your plant.’ Because we know ethanol producers are different, and we know that they have their own processes and their own needs for their customer base, they have customers that they’re serving as well.”
Customer centricity drives everything Novonesis does, she explains, and an early stage of each project is devoted to ensuring the product is something that fulfills customers’ needs or addresses problems producers are facing. Prior to launch, Novonesis ran
Innova Eclipse through multiple trials at different ethanol plants.
“Ethanol producers are prioritizing efficiency, which plays a key role in achieving a lower carbon intensity score. Innova Eclipse can assist in this regard by reducing the amount of water needed for the process by enabling the fermentation to run with higher solids throughput,” explains Kortuem.
“When you look at producers today, they are trying to maximize the capital in their plants and trying to produce as much ethanol as possible and not be bound by the one thing in the plant which isn’t mechanical or capital related, it’s the biologics,” says Kortuem. “And yeast is that limiting factor from a biological standpoint in the plant. We want to make sure that biology isn’t a limitation [on] what the producers are able to achieve in the plant.”
October 2014 – December 2022.
SOURCE: IRWIN, S. "TRENDS IN THE OPERATIONAL EFFICIENCY OF THE U.S. ETHANOL INDUSTRY: 2023 UPDATE." FARMDOC DAILY (14):28, DEPARTMENT OF AGRICULTURAL AND CONSUMER ECONOMICS, UNIVERSITY OF ILLINOIS AT URBANA-CHAMPAIGN, FEBRUARY 9, 2024.
By Keit Industrial Analytics
Yields have been edging up towards 3 gallons per bushel for years (Figure 1). But for many plants, such a milestone must seem a pretty challenging target.
So, what will it take to raise your yields that high? The efficiency of your fermentation process is probably top of the list.
But fermentation can be difficult to control – certainly once the process has started, and particularly after the 15-hour mark. Many ethanol plants face issues like bacterial contamination or stressed-out yeast, and sometimes it is as simple as someone forgetting to add glucoamylase (hey, it happens!). But with the right tools, you can spot problems like these early on and intervene to save both time and money.
That is where an advanced new monitoring system like the IRmadillo comes in, providing a continuous stream of real-time data to catch problems before they start to spiral.
The old way to monitor fermentation, via HPLC analysis, is not exactly foolproof. Most plants take about seven samples throughout a batch, which is like trying to understand what is going on in a movie by only looking at a few snapshots. You are bound to miss the key moments.
For instance, consider a lactobacillus infection kicking in around the 10-hour mark, but the next sample is not until hour 20. Any reme-
CONTRIBUTION: The claims and statements made in this article belong exclusively to the author(s) and do not necessarily reflect the views of Ethanol Producer Magazine or its advertisers. All questions pertaining to this article should be directed to the author(s).
dial action taken, the addition of antibiotics or hops acid, this late after the initial spike is not likely to be as effective, if at all. Or, say yeast health takes a nosedive because of high glycerol production or insufficient nitrogen availability. Small adjustments made in time can prevent a lot of hassle.
With continuous monitoring, your operators get instant feedback on what is really going on inside the fermentation tanks, giving them a chance to respond in real time.
The IRmadillo does not just give snapshots; it continuously tracks everything, from the different types of sugars and their levels to organic acids, ethanol and glycerol concentrations.
It’s so robust, you can place it in-line almost anywhere in your production process. And it captures subtle shifts early on, letting operators jump in with the right response.
Continuous data from the IRmadillo also opens up new opportunities for fine-tuning. When trying new yeast strains or tweaking enzyme doses, you get instant feedback, so there is no more guesswork. Over time, this means more efficient batches, healthier margins, and higher yields. Suddenly, that 3 gallons per bushel seems achievable.
The ongoing developments on designing and implementing simple graphical interfaces will be capable of signaling deviations from “ideal” batch profiles, providing live alerts, end of batch reports and retrospective batch data visualization tools to help troubleshoot substandard runs. This is a great deal of information for ethanol producers, allowing them to delve deeper into understanding how to achieve the optimal fermentation every time.
UWGP runs a robust fermentation process that consistently deliv-
ers high yields. The plant recently tested the IRmadillo and saw the value of real-time monitoring for themselves. They installed one unit on the recirculation line of one of their fermenters to track sugar consumption, glycerol, and organic acids:
• Sugars (DP1, DP2, DP3, DP4+): These species allow UWGP to track how fermentation is progressing, and they are critical to optimize enzyme dosing.
• Glycerol: High levels are a symptom of unhealthy yeast (due to excessive glucose) and can lead to loss of ethanol yield.
• Lactic and acetic acids: These are key species to identify bacterial contaminations early on.
• Ethanol: The main event! Monitoring ethanol concentration helps ensure optimal conversion and shows overall fermentation performance.
Since installation, the IRmadillo has proven to be an impressive tool for process monitoring at UWGP – they can see changes early, which gives them a head start on fixing issues before they hit hard.
While full operational integration is still in progress, the early results are promising. UWGP is currently developing an interface that will allow operators to interact more easily with the real-time data provided by the IRmadillo. They expect even greater operational feedback and benefits in terms of yield optimization and fermentation infection detection!
The IRmadillo usefulness is not limited to fermentation. It can improve efficiency across many other parts of the plant, including:
• Distillation: the IRmadillo can track ethanol levels in beer bottoms to control the balance between overdriving the column and sustaining a certain ethanol loss, to minimize energy usage and reduce risk.
• Propagation: the IRmadillo monitors sugars, nitrogen and ethanol, to keep yeast in tip-top shape and optimize cell growth.
• Liquefaction: the IRmadillo allows you to fine-tune enzyme and nitrogen levels to maintain quality without overdosing.
All in all, real-time insights from the IRmadillo have the potential to boost ethanol yield like never before, all while cutting down on waste and improving overall efficiency.
The IRmadillo is a robust real-time monitoring device that uses FTIR spectroscopy. It has no moving parts and can withstand vibrations, impacts and general movement, so it can be installed into any manufacturing line. But the results it produces are laboratory grade, giving you continuous and accurate measurements of the concentrations of a huge range of chemical substances.
The device and the unique technology within it were actually developed for use on Mars, as part of the UK’s contribution to the Mars space program. But the IRmadillo seems to have found an even more perfect niche in industrial ethanol production!
Author: Keit Industrial Analytics info@IRmadillo.com
By Ethanol Producer Magazine
308 2nd Ave. N., Suite 304 Grand Forks, ND 58203
ai172122621117_ICM4602 FOT Oil Recovery Ad_EPM_7.5x4.625 with .25 bleed .pdf 4 7/17/2024 9:23:32 AM BBI International