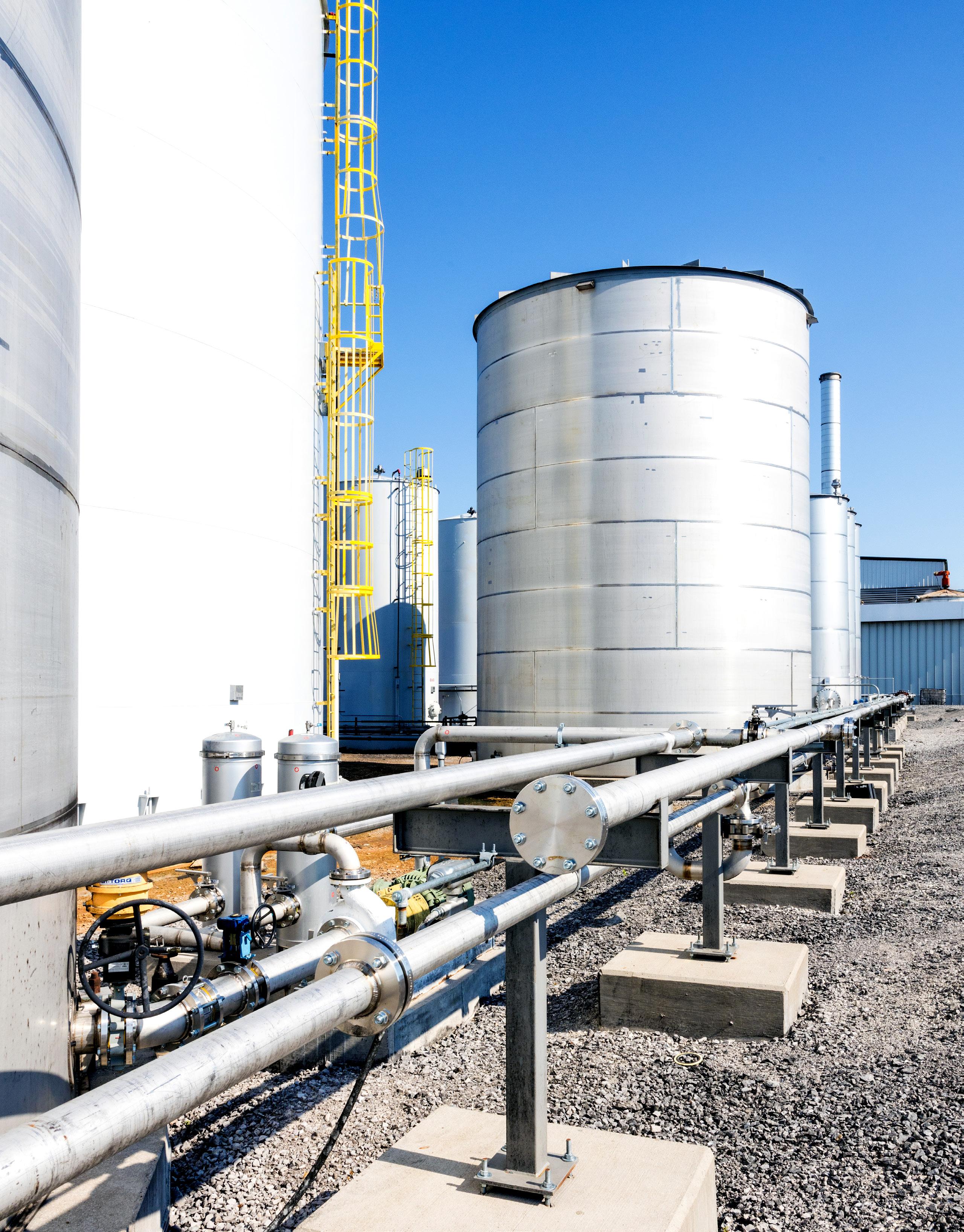
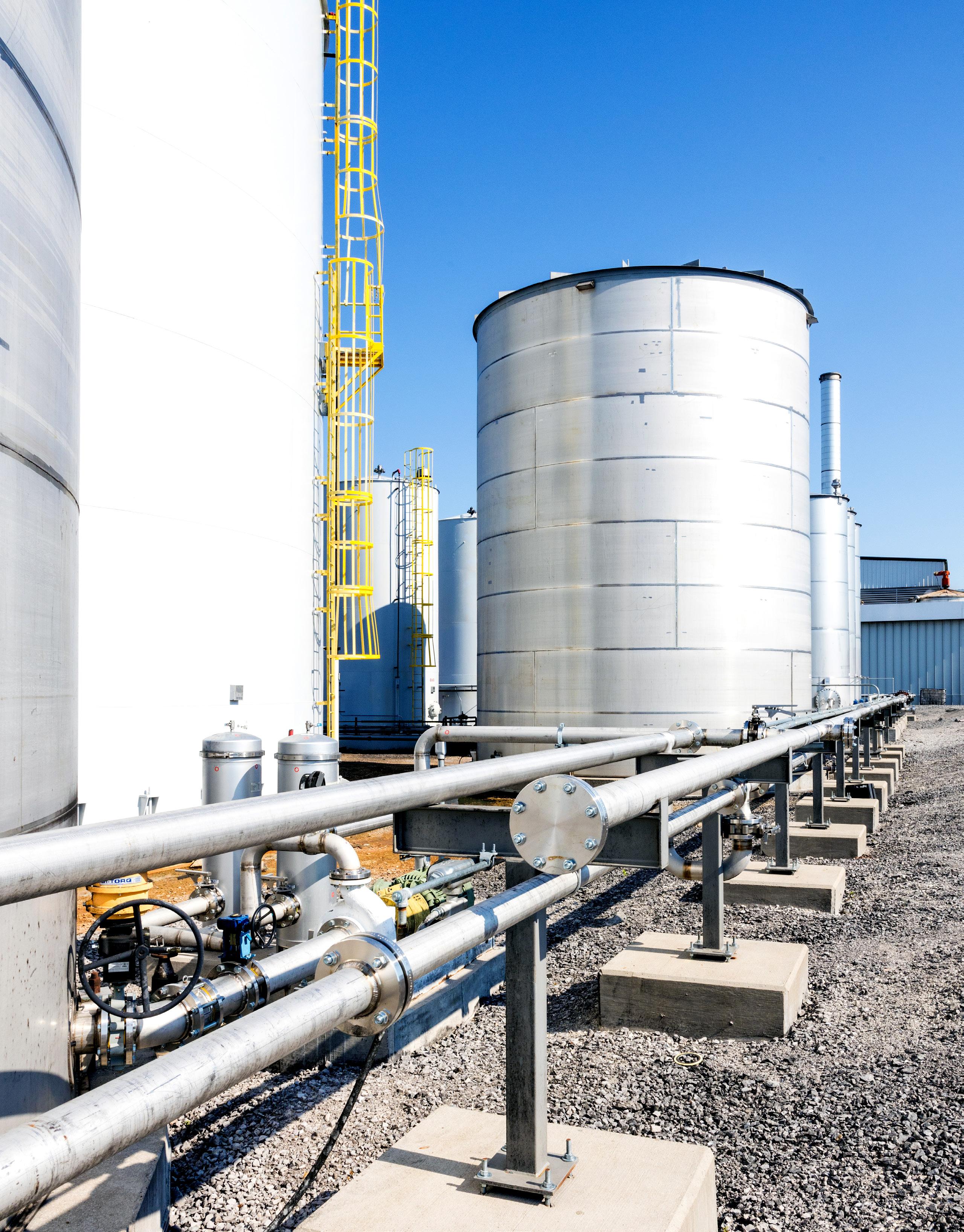
GUIDEPOSTS OF GROWTH


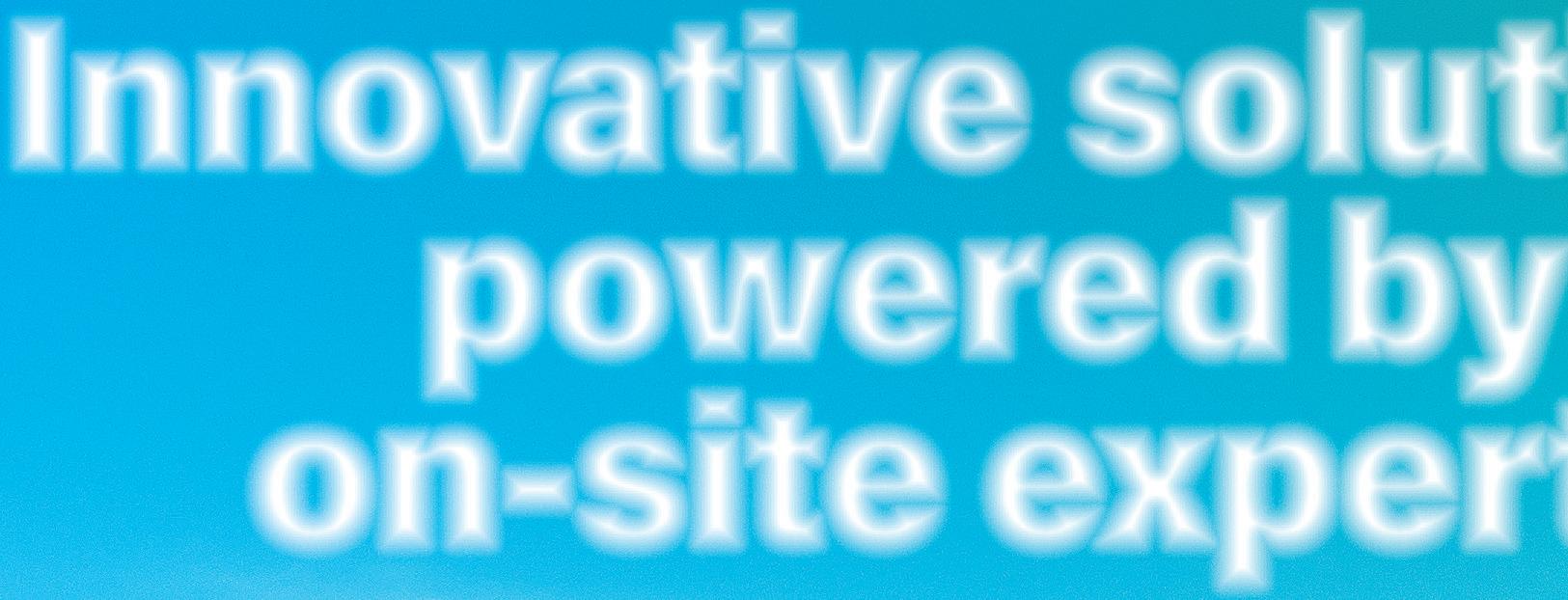

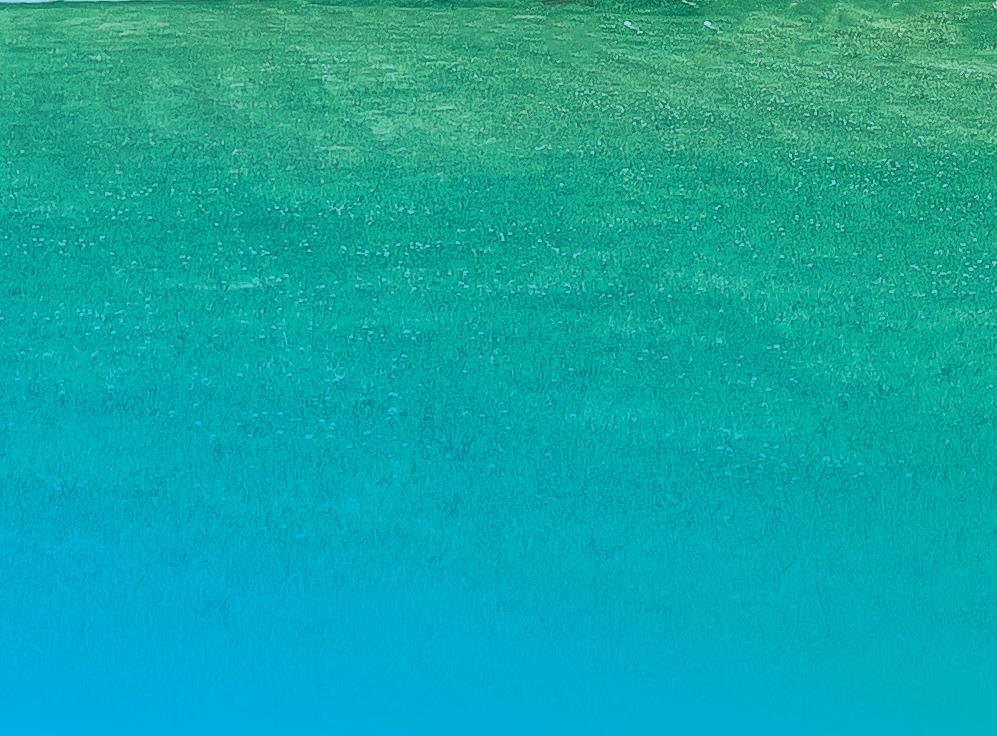
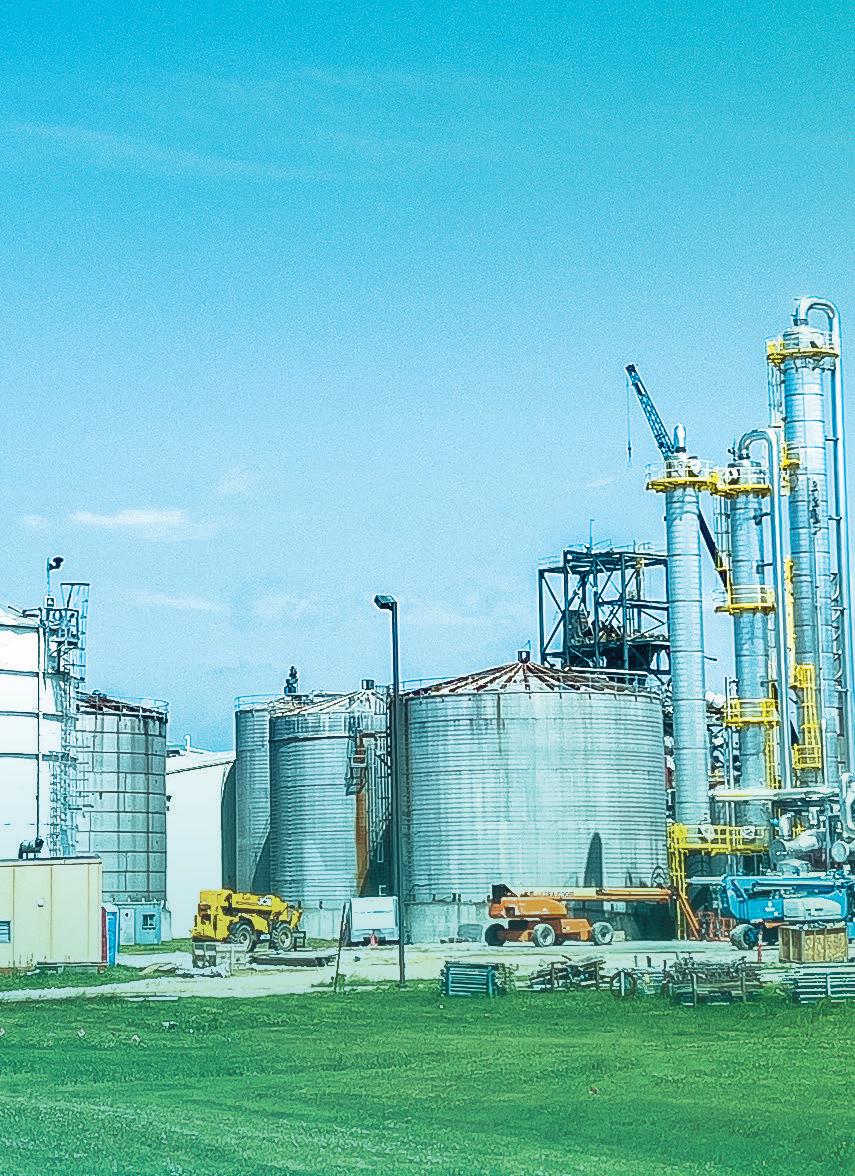

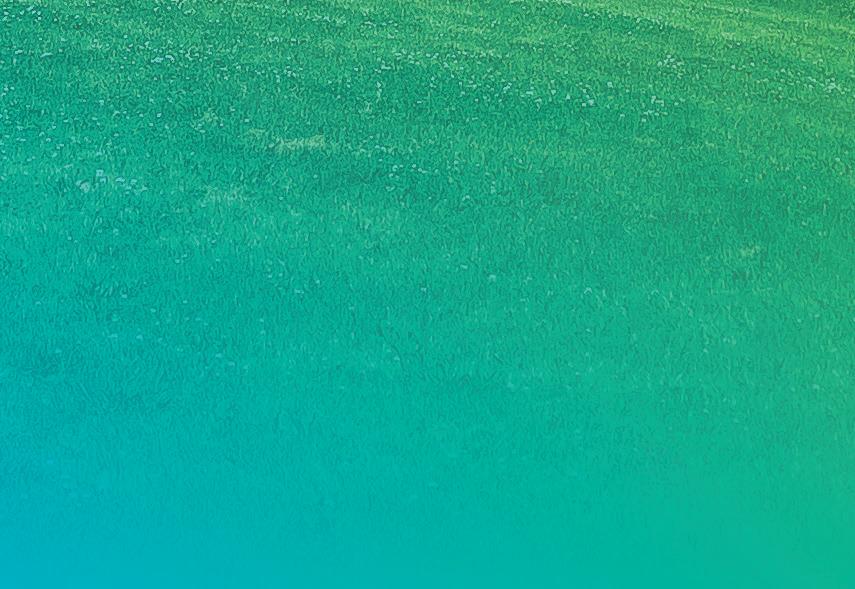
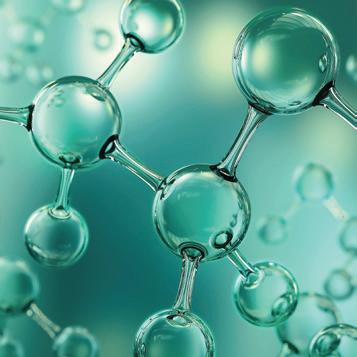

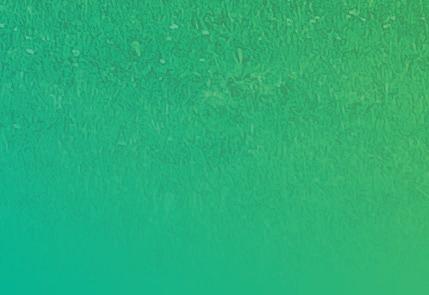
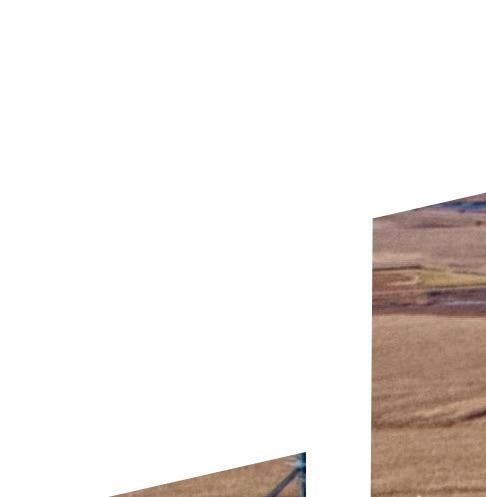
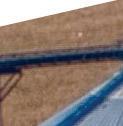
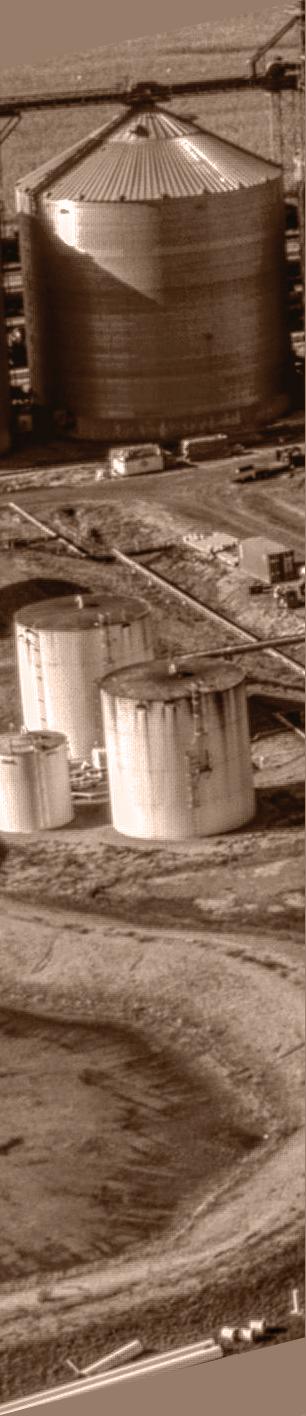
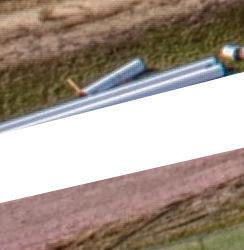
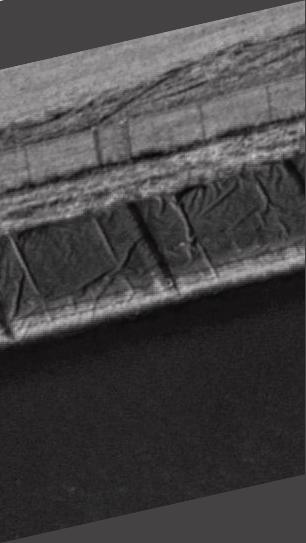
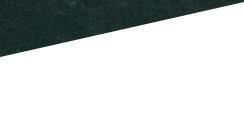
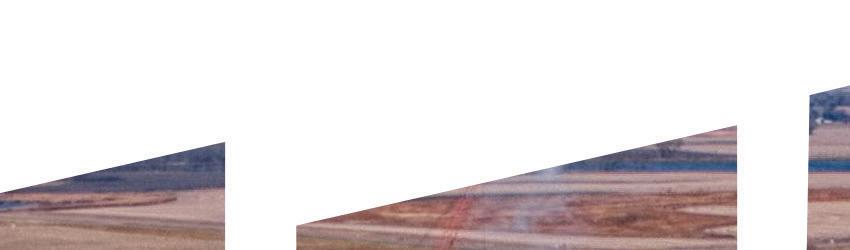

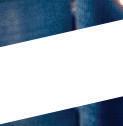
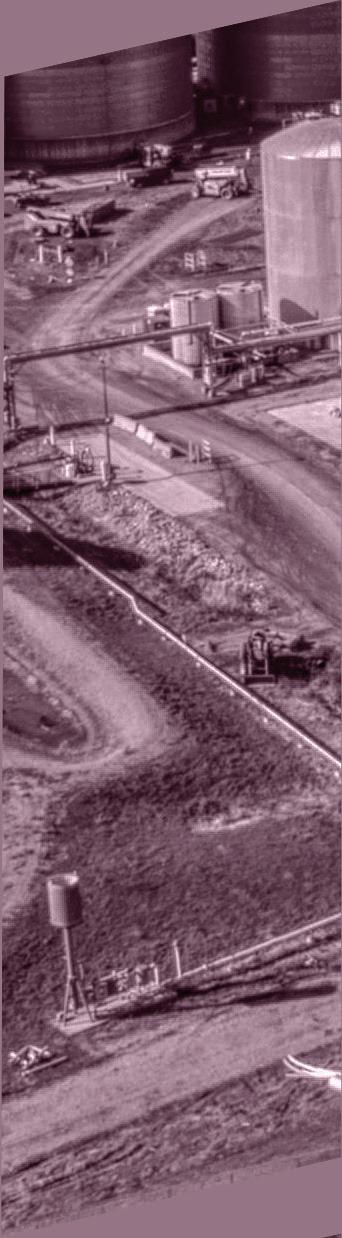
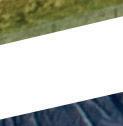


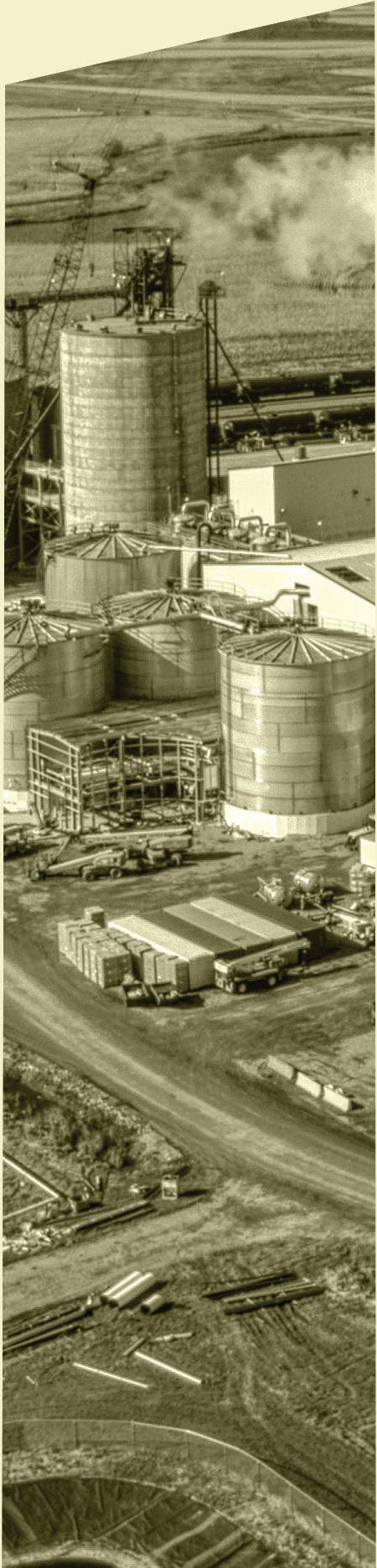
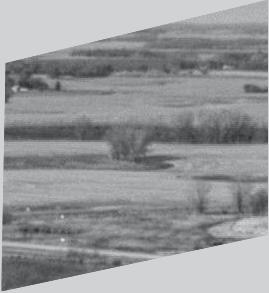
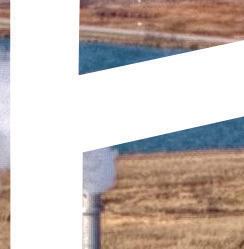
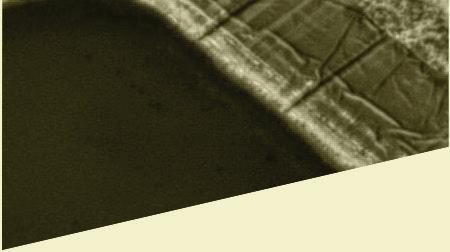
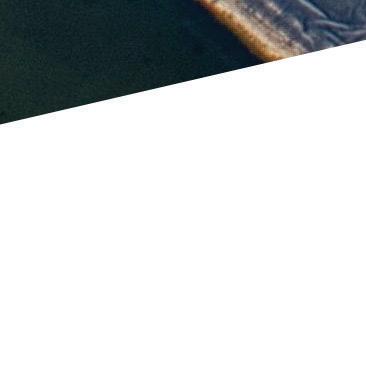



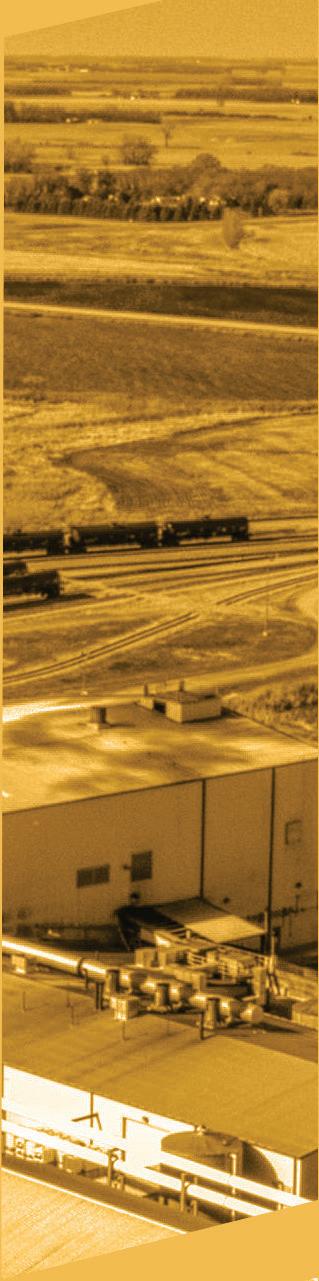
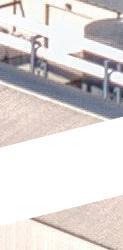
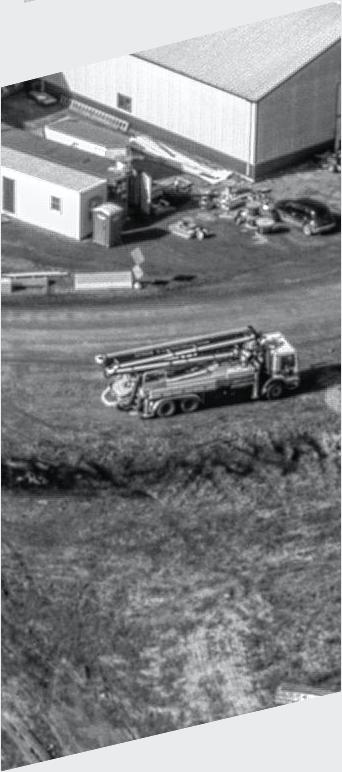
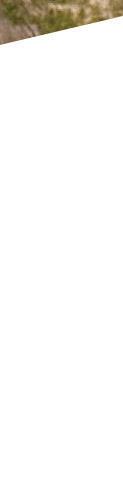
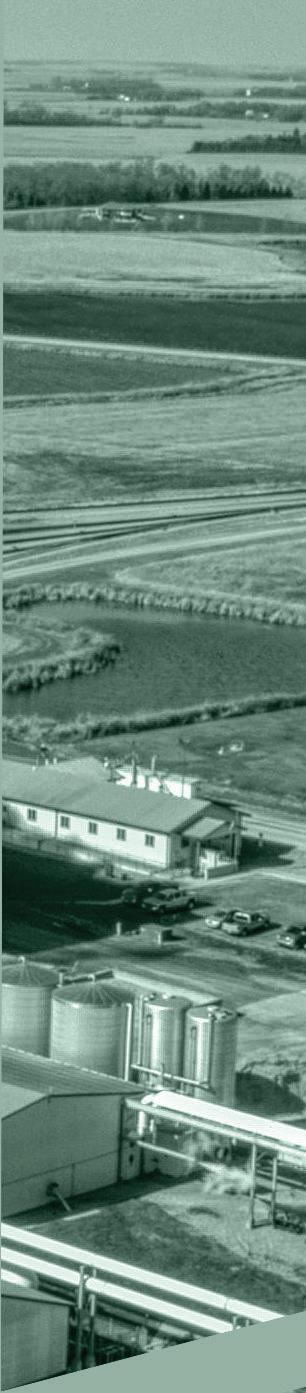
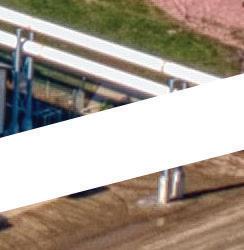

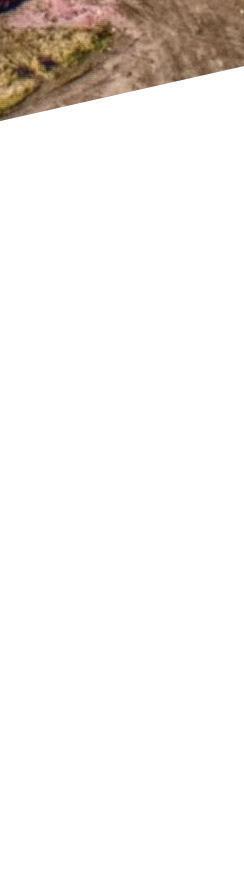

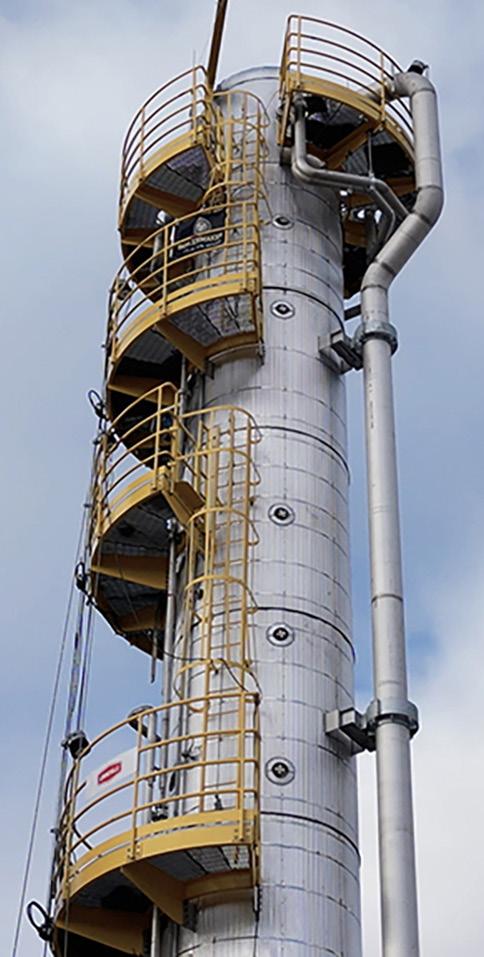
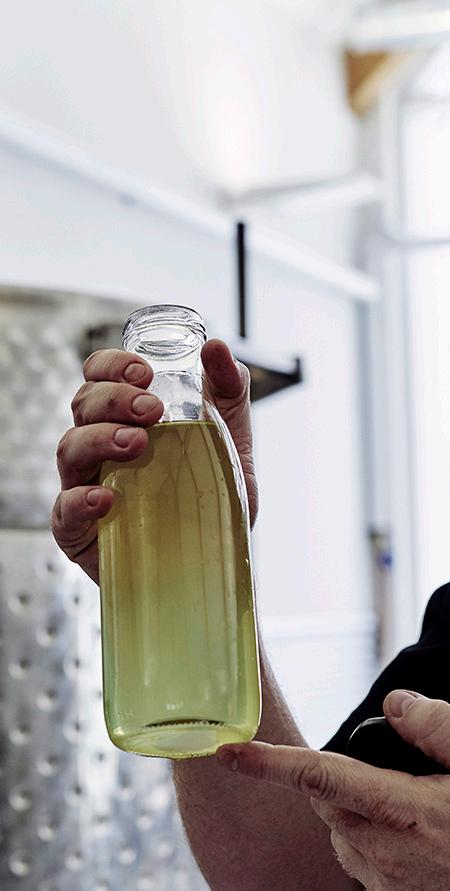
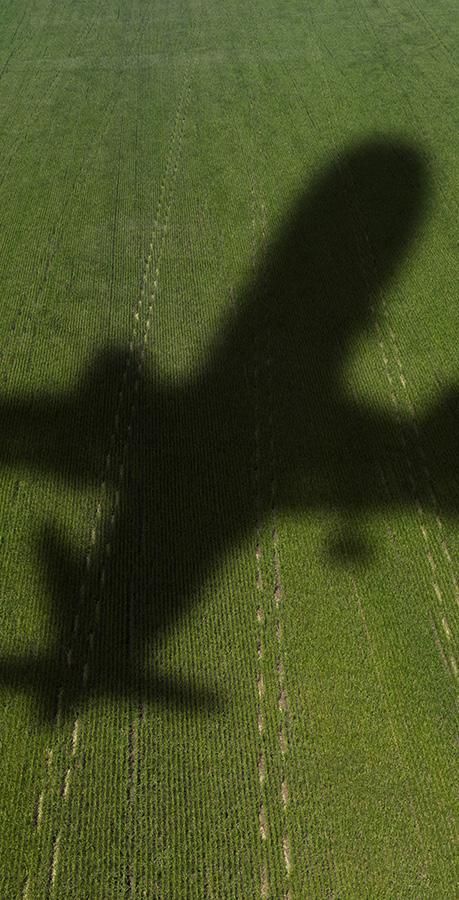

EDITORIAL
President & Editor Tom Bryan tbryan@bbiinternational.com
Online News Editor Erin Voegele evoegele@bbiinternational.com
Associate Editor Katie Schroeder katie.schroeder@bbiinternational.com
DESIGN
Vice President of Production & Design Jaci Satterlund jsatterlund@bbiinternational.com
Graphic Designer Raquel Boushee rboushee@bbiinternational.com
PUBLISHING & SALES
CEO Joe Bryan jbryan@bbiinternational.com
Vice President of Operations/Marketing & Sales John Nelson jnelson@bbiinternational.com
Senior Account Manager/Bioenergy Team Leader Chip Shereck cshereck@bbiinternational.com
Account Manager Bob Brown bbrown@bbiinternational.com
Circulation Manager Jessica Tiller jtiller@bbiinternational.com
Marketing & Advertising Manager Marla DeFoe mdefoe@bbiinternational.com
EDITORIAL BOARD
Ringneck Energy Walter Wendland Little Sioux Corn Processors Steve Roe Commonwealth Agri-Energy Mick Henderson
Aemetis Advanced Fuels Eric McAfee Western Plains Energy Derek Peine Front Range Energy Dan Sanders Jr.
Advertiser Index
Upcoming Events
2024 North American SAF Conference & Expo September 11-13, 2024
Saint Paul, MN (866) 746-8385 | www.safconference.com
The North American SAF Conference & Expo, produced by SAF Magazine, in collaboration with the Commercial Aviation Alternative Fuels Initiative (CAAFI) will showcase the latest strategies for aviation fuel decarbonization, solutions for key industry challenges, and highlight the current opportunities for airlines, corporations and fuel producers. The North American SAF Conference & Expo is designed to promote the development and adoption of practical solutions to produce SAF and decarbonize the aviation sector.
2025 International Biomass Conference & Expo MARCH 18-20, 2025
Atlanta, GA (866) 746-8385 | www.biomassconference.com
Now in its 18th year, the International Biomass Conference & Expo is expected to bring together more than 900 attendees, 160 exhibitors and 65 speakers from more than 25 countries. It is the largest gathering of biomass professionals and academics in the world. Powered by Biomass Magazine, the conference provides relevant content and unparalleled networking opportunities in a dynamic business-to-business environment. In addition to abundant networking opportunities, the largest biomass conference in the world is renowned for its outstanding programming, maintaining a strong focus on commercial-scale biomass production, new technology, and near-term research and development. Join us at the International Biomass Conference & Expo as we enter this new and exciting era in biomass energy.
2025 Carbon Capture & Storage Summit June 9-11, 2025
Omaha, NE (866) 746-8385 | www.fuelethanolworkshop.com
Please recycle this magazine and remove inserts or samples before recycling
Customer Service Please call 1-866-746-8385 or email us at service@bbiinternational.com. Subscriptions Subscriptions to Ethanol Producer Magazine are free of charge to everyone with the exception of a shipping and handling charge for anyone outside the United States. To subscribe, visit www.EthanolProducer.com or you can send your mailing address and payment (checks made out to BBI International) to: Ethanol Producer Magazine Subscriptions, 308 Second Ave. N., Suite 304, Grand Forks, ND 58203. Back Issues, Reprints and Permissions Select back issues are available for $3.95 each, plus shipping. Article reprints are also available for a fee. For more information, contact us at 866-7468385 or service@bbiinternational.com. Advertising Ethanol Producer Magazine provides a specific topic delivered to a highly targeted audience. We are committed to editorial excellence and high-quality print production. To find out more about Ethanol Producer Magazine advertising opportunities, please contact us at 866-746-8385 or service@bbiinternational.com. Letters to the Editor We welcome letters to the editor. Send to Ethanol Producer Magazine Letters to the Editor, 308 2nd Ave. N., Suite 304, Grand Forks, ND 58203 or email to editor@bbiinternational.com. Please include your name, address and phone number. Letters may be edited for clarity and/or space. TM
Capturing and storing carbon dioxide in underground wells has the potential to become the most consequential technological deployment in the history of the broader biofuels industry. Deploying effective carbon capture and storage at biofuels plants will cement ethanol and biodiesel as the lowest carbon liquid fuels commercially available in the marketplace. The Carbon Capture & Storage Summit will offer attendees a comprehensive look at the economics of carbon capture and storage, the infrastructure required to make it possible and the financial and marketplace impacts to participating producers.
COPYRIGHT © 2024 by BBI International
Novel Feedstock, Niche Markets and High-Purity Plays
We value opportunities to report on ethanol producers whenever possible, and earlier this summer we were fortunate to visit with three of them—each having some connection to high-purity alcohol.
Our cover story, “Lessons to Celebrate,” on page 16, offers a unique look at Commonwealth Agri-Energy’s 20year journey of adaptation and growth. As the plant’s longtime general manager, Mick Henderson, says, it’s easy to keep a plant online when everything is going great; it’s how you make decisions when things aren’t ideal that define your plant’s long-term success. Operating on the southern fringe of the U.S. Corn Belt could have been a problem for Commonwealth, but it never really has been. The 50 MMgy corn ethanol plant in Hopkinsville, Kentucky, about 70-miles northwest of Nashville, has always found a way to succeed in a state known more for bluegrass and horse racing than corn and cattle. But then again, the area is certainly no stranger to alcohol.
This autumn, Commonwealth’s staff will gather with the 2,300-plus members of the Hopkinsville Elevator Co.— which owns the plant—to officially celebrate 20-years of ethanol production. It will be a time for celebration, yes, but also a chance to reflect on lessons learned during its two-decade-long (and counting) journey of perseverance and success. We share some of those lessons, including prioritizing regional markets, being ready for the unpredictable, being creative about plant upgrades and staying focused on the future.
Next, in “Higher Alcohols, Broader Reach,” on page 24, we look at how Canada’s, Greenfield Global is steadily expanding the capacity of its high-purity alcohol (HPA) production in North America and Europe, with a focus on transparency and scale. Greenfield has been supplying alcohol, specialty solvents and custom-blended solutions to businesses across more than 50 countries worldwide for over three decades. As we report, its network now includes three high-purity alcohol distilleries, five blending and packaging facilities and eight warehouses. Its global footprint includes facilities in Canada, the U.S. and Ireland. As the HPA space continues to grow, supporting the needs of customers in myriad industries, the Greenfield team has a strategy in motion to ensure its aspirations continue to mirror the “green” and “global” parts of its corporate name.
On page 30, you’ll find a story about a niche alcohol production pursuit, this one being ethanol production from a milk processing byproduct. In “Low-CI Ethanol Made from Milk,” we share the story of a dairy producer in Michigan that’s partnering with a vodka manufacturer to make low-carbon ethanol from milk permeate. It’s another example of our industry’s incredible breadth.
Finally, be sure to check out this month’s eclectic contributions section, including “Alcohol to Jet: A Lifeline for Corn Ethanol,” on page 36; “Navigating Complexities,” on page 44; “Fractionation and Efficiency,” on page 48; and “Evaluating Carbon Content,” on page 52.
There is truly something for everyone in this issue. Enjoy the read!
You already set the standard. Let’s raise it again.
“ The Gold Standard”
Omaha Marriot Downtown at the Capitol District
Omaha, Nebraska
August 14 — 16, 2024
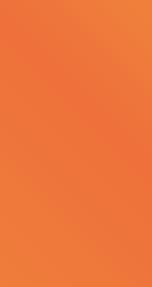
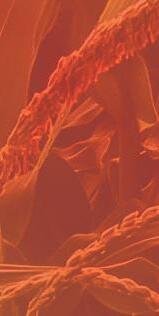
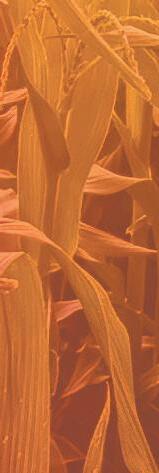
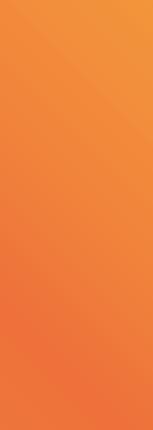
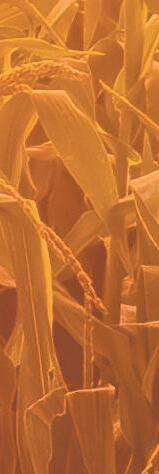
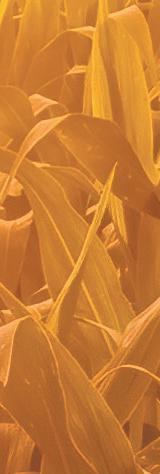

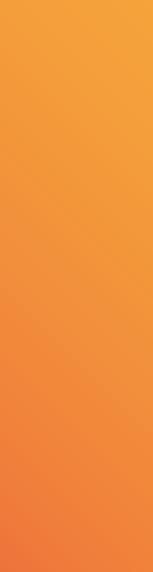
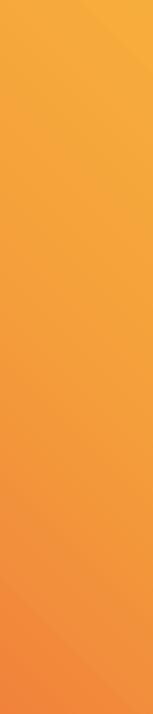
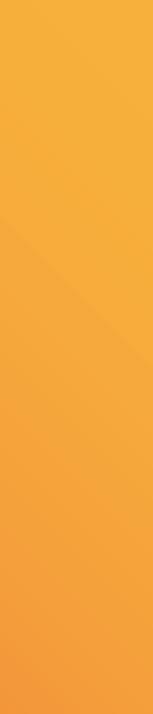

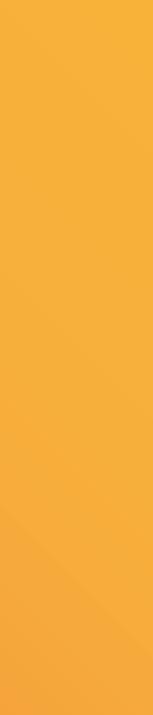
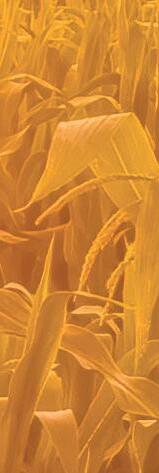

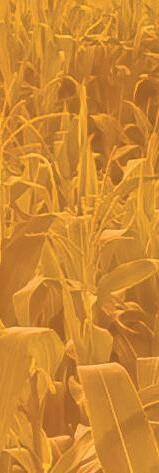
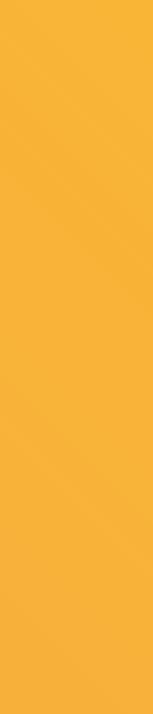
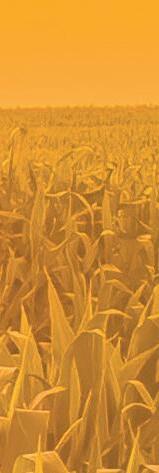

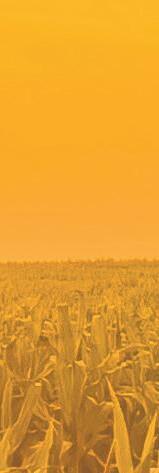

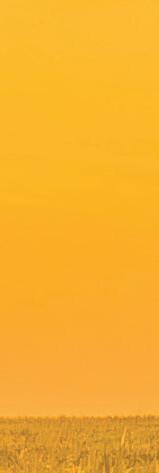

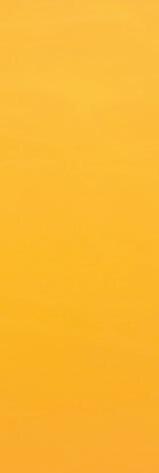
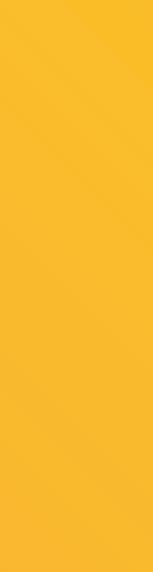
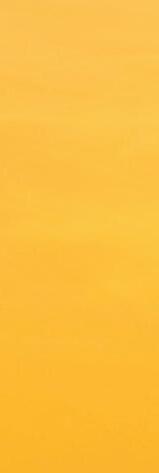
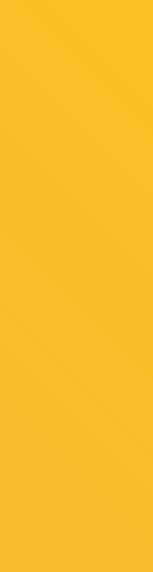
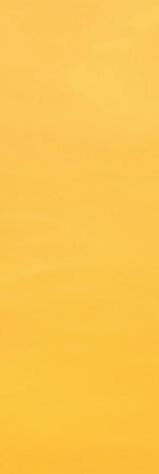
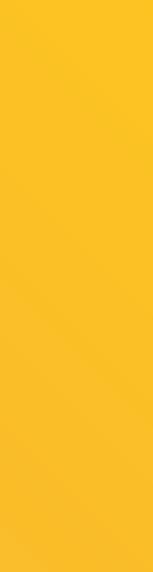
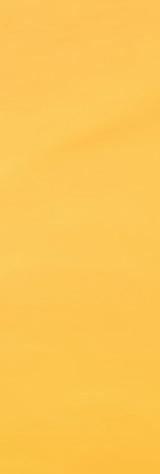

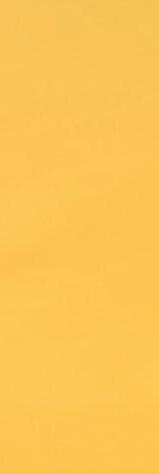
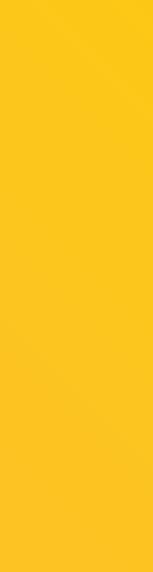
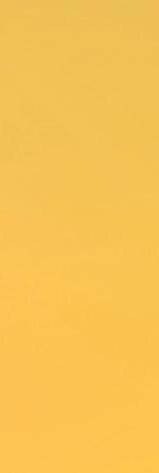
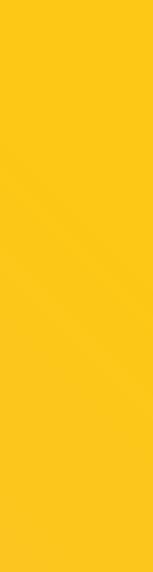

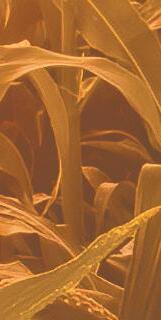


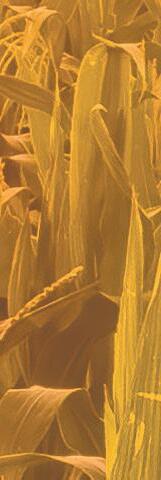

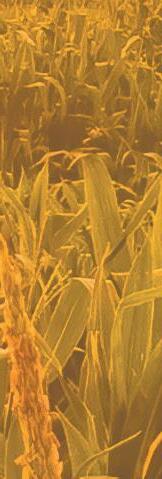
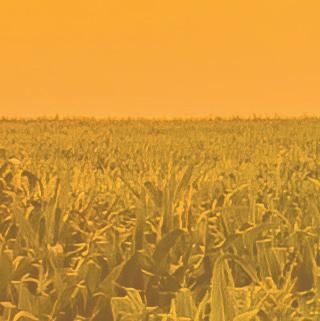
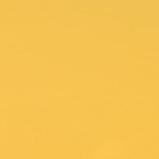


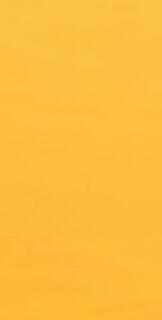
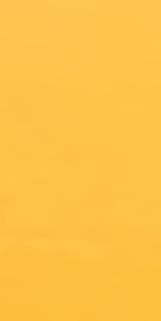
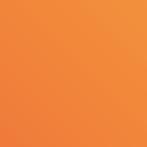

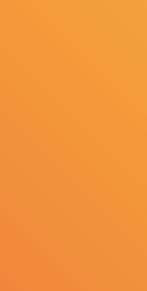
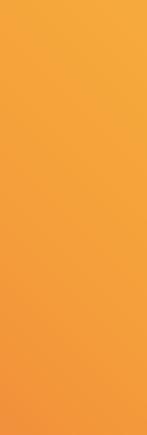
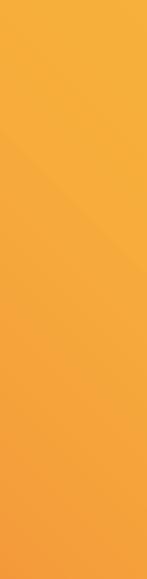
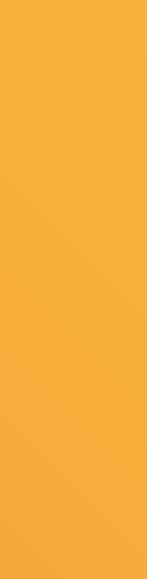
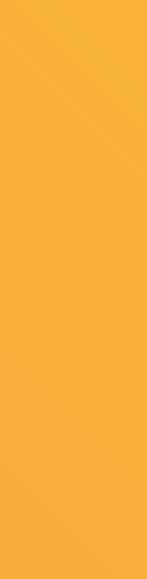
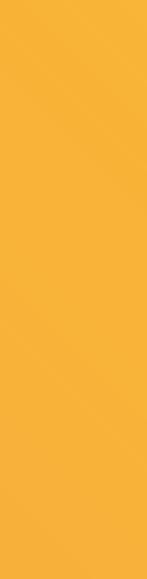
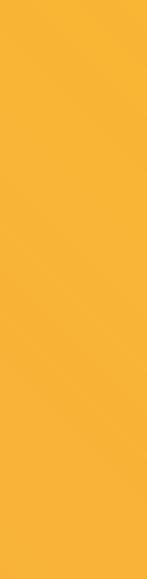
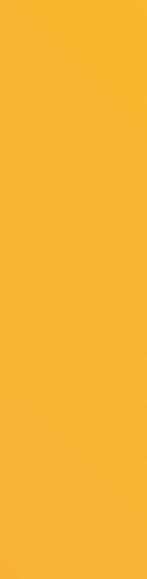

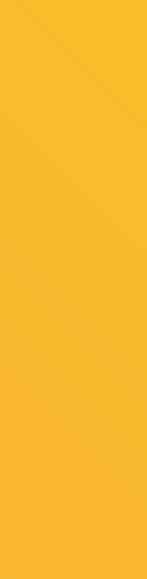
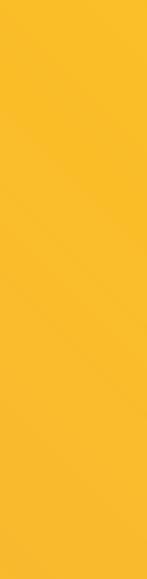
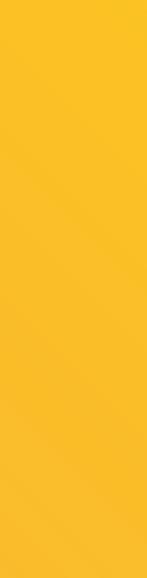
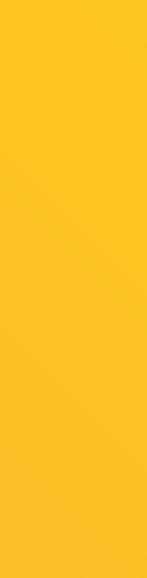
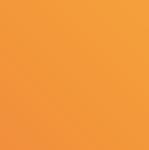
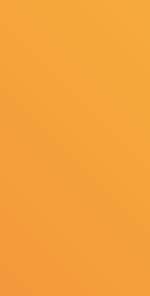
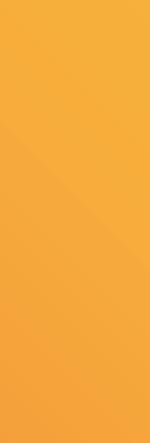
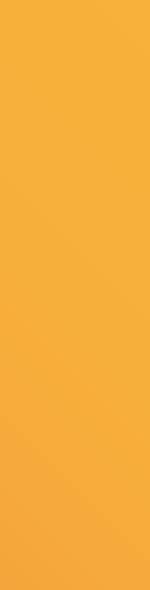
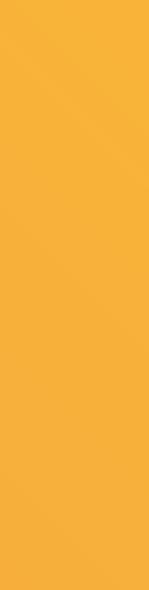
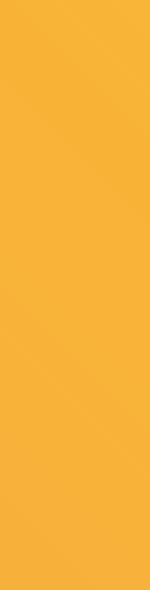
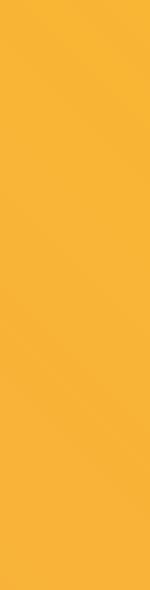
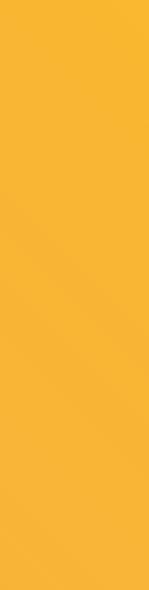
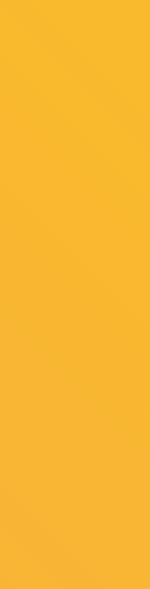
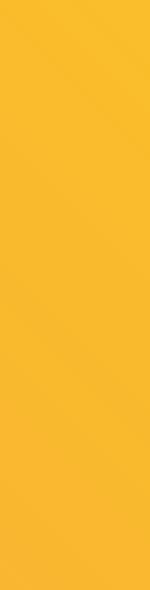
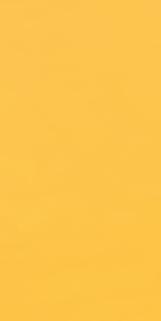

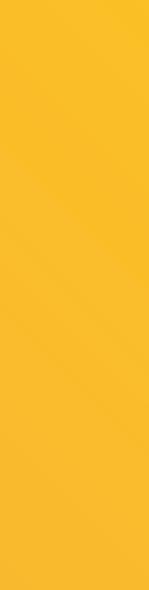
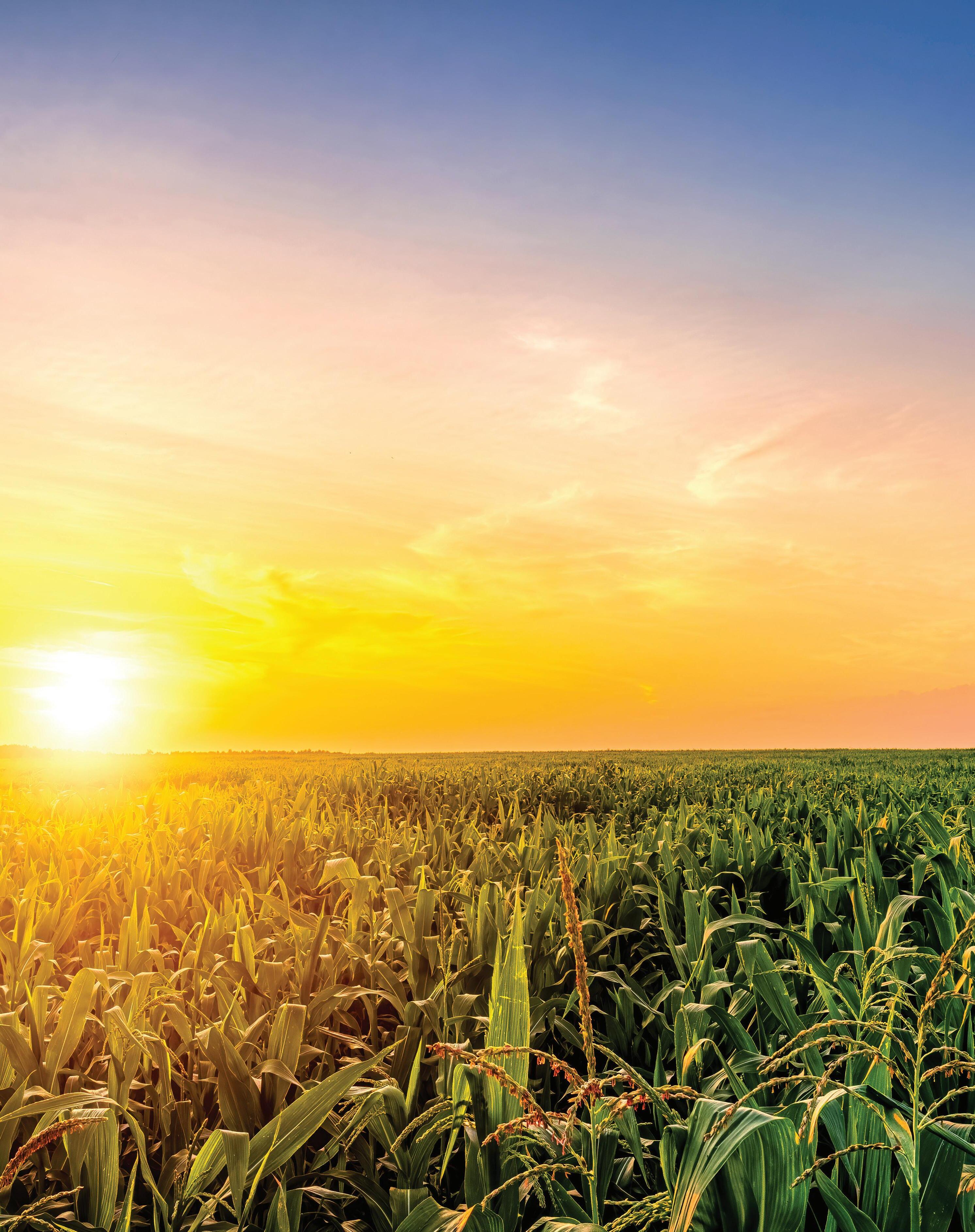
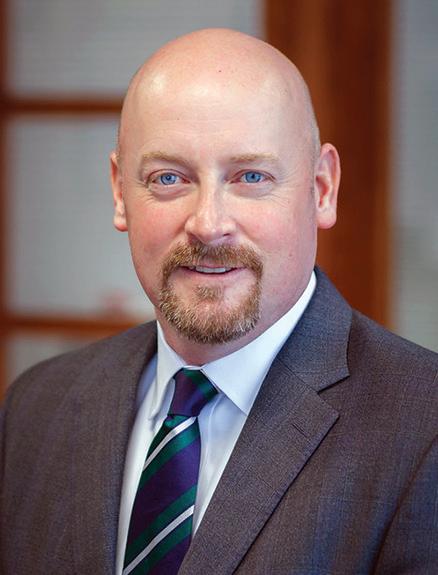
Court Ruling Sets Important Precedents for Future of RFS
For more than 18 years, the Renewable Fuel Standard has faced unrelenting legal assaults from oil refiners, poultry producers, grocery manufacturers, environmental extremists and others who oppose the expanded use of low-carbon renewable liquid fuels. Since Day One, RFA has vigorously protected the RFS from these attacks; and overall, the program has faithfully withstood the steady barrage of courtroom sieges and emerged with flying colors.
In May, yet another high-stakes legal challenge to the RFS was rebuffed, establishing some important precedents and putting the program on solid footing for the future. A decision from the D.C. Circuit Court upheld EPA’s RFS volumes for 2020-2022 (known widely as the “reset rule”) and rejected the oil refining industry’s challenges to the rule. The Court found that EPA exercised its discretion appropriately in setting RFS standards for those years, including a supplemental volume requirement to comply with a separate D.C. Circuit Court decision from 2016.
The American Fuel & Petroleum Manufacturers and individual refiners had sued EPA over the 2020-2022 standards, arguing that 1) the volumes were set too high, 2) EPA lacked the authority to prospectively reallocate projected small refinery exemptions (SREs), and 3) EPA should not have restored the 500-million-gallon remanded volume that was illegally waived from the 2016 RFS volumes. RFA intervened in this litigation on EPA’s behalf, arguing that the Agency validly exercised its authority in each instance.
Ultimately, the court agreed with us and found in our favor on all the issues raised, denying the refiners’ request to vacate the 2020-2022 standards.
Notably, this decision will have ramifications beyond the 2020-2022 volumes. It sets three important precedents that help solidify the RFS program’s foundation for the future.
First, the court afforded EPA substantial discretion to set volumes, as long as the agency could show it properly considered certain statutory factors specified by Congress in 2007. Since these are the same factors that EPA considered in the newer “set rule” for 2023-2025 volumes, this is extremely precedential and has favorable implications for litigation already underway on the “set rule” volumes.
Second, the court found EPA acted appropriately in projecting volumes affected by expected small refinery exemptions and creating a mechanism to reallocate exempted volumes. Although EPA’s recent approach to SREs has been to deny petitions because there is no showing of “disproportionate economic harm”—thus, zero exemptions have been projected—this decision affirms that EPA can indeed reallocate expected exempted volumes if its approach to adjudicating SRE petitions changes in the future.
Finally, the court confirmed that EPA acted within its statutory authority by restoring the 500 million gallons of illegally waived volume from 2016, per the same court’s earlier ruling in litigation brought against the agency by RFA and others eight years ago. This affirms that EPA has the authority to restore past volumes that are determined to be illegally lowered or waived.
Overall, this is a very positive result for the ethanol industry that could have important positive implications for administration of the RFS moving forward. Also, it proves once again why we must continue to protect and defend the program from the onslaught of baseless legal attacks.
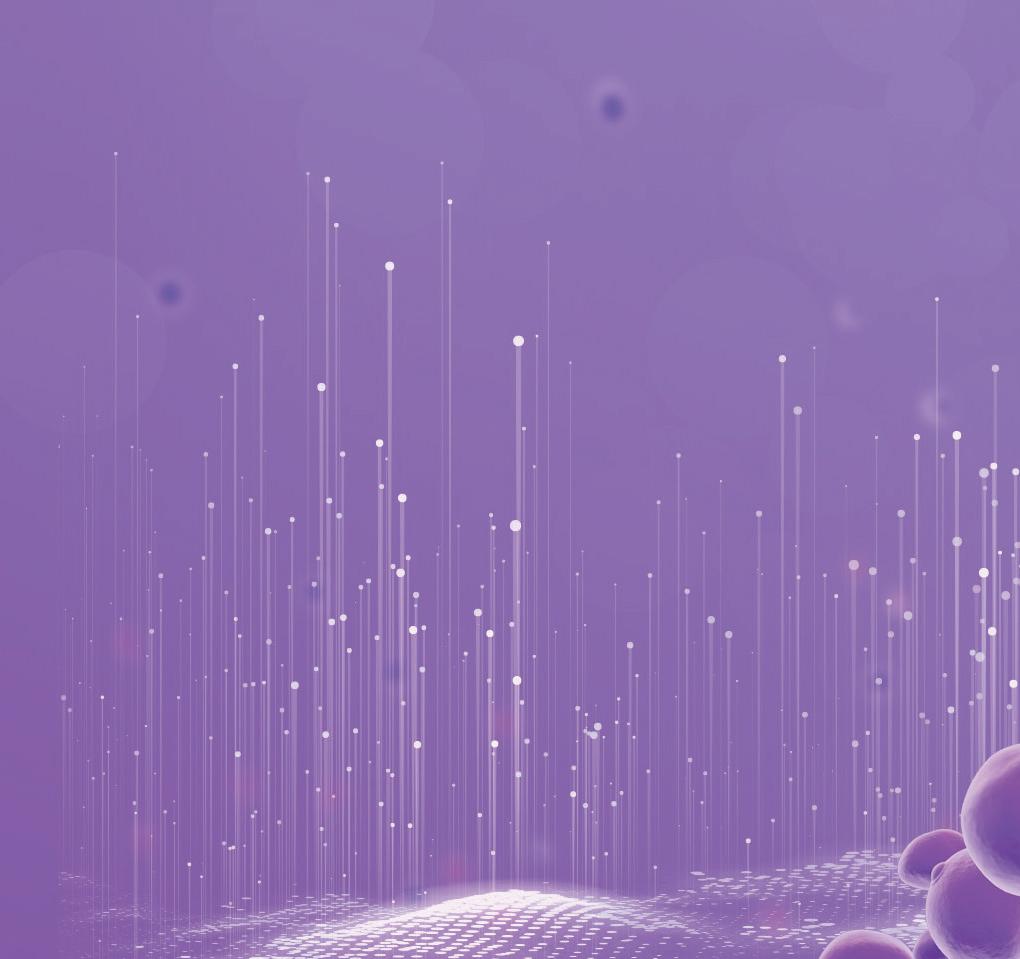
S YNERXIA ® GEMS T ONE C OLLE CTION
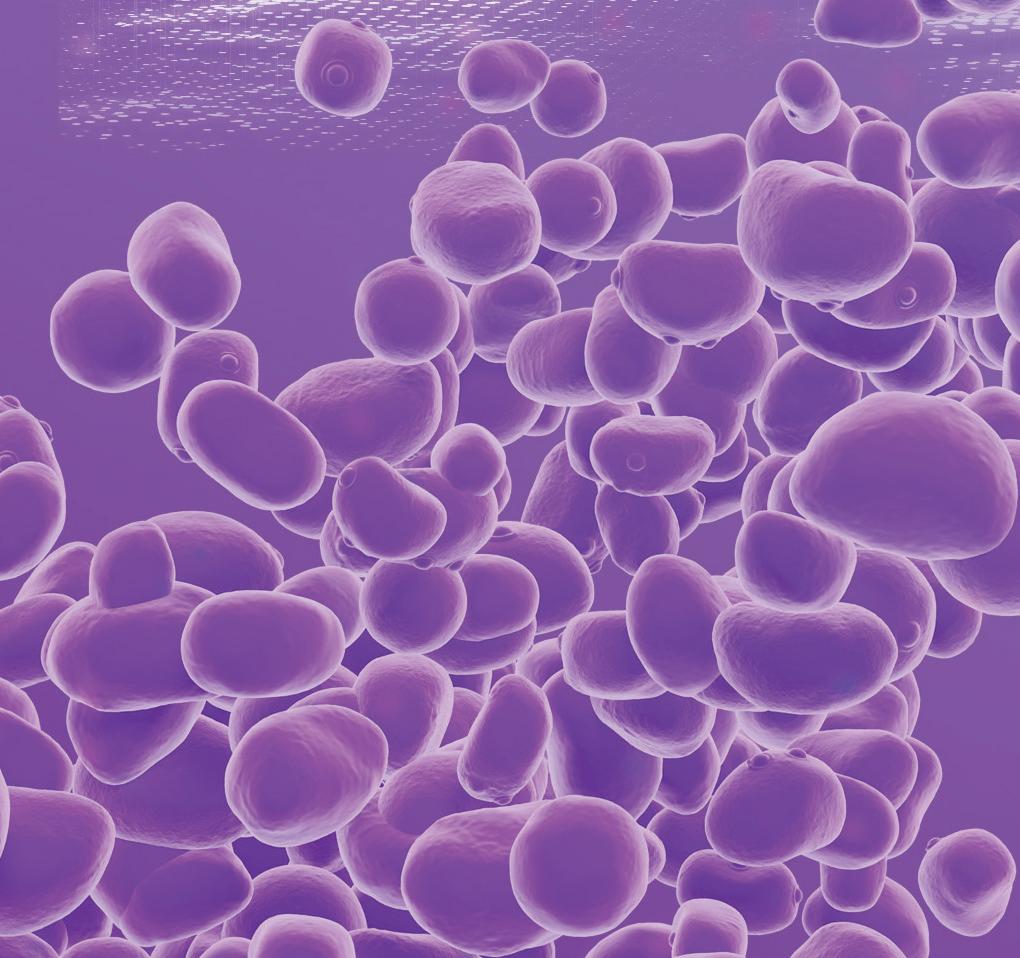

THE RIGHT YEAS T S, A T THE RIGHT TIME, F OR THE RIGHT PURPOSE
Yeast blends are often greater than the sum of their parts. Achieve the perfect synergy of fermentation yield, speed and robustness with the SYNERXIA® Gemstone Collection.
Our broad portfolio of yeasts and yeast blends offers greater flexibility to tailor solutions based on shifting process requirements or market conditions.

Powered by XCELIS® AI, our proprietary data analytics and predictive modelling tool, the SYNERXIA® Gemstone Collection helps de-risk decision making with custom yeast blends that take your ethanol production process to the next level.
Learn more at bioscience.iff.com/synerxia-gemstone
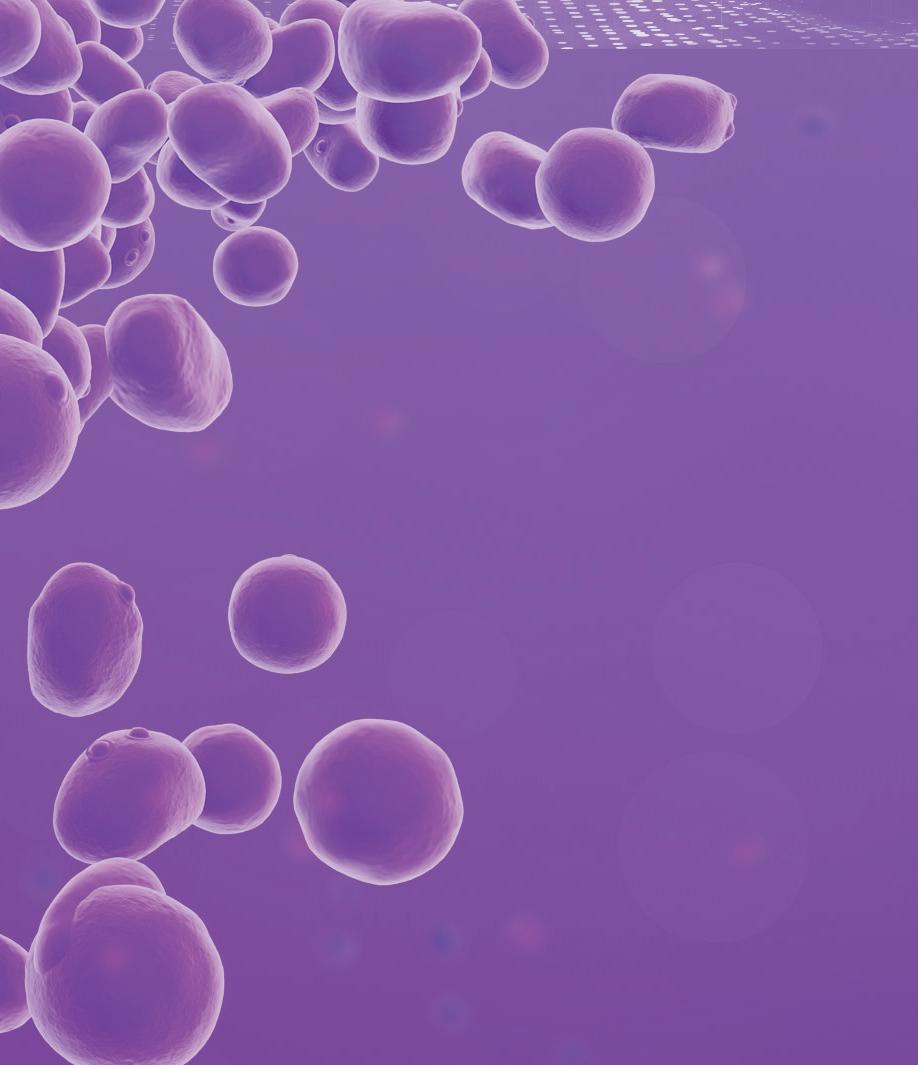
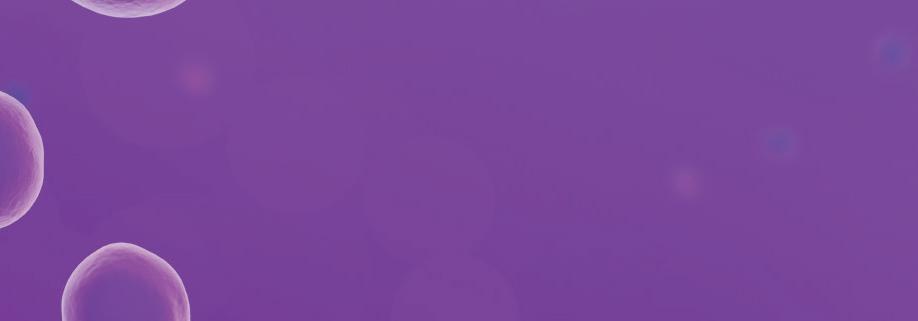
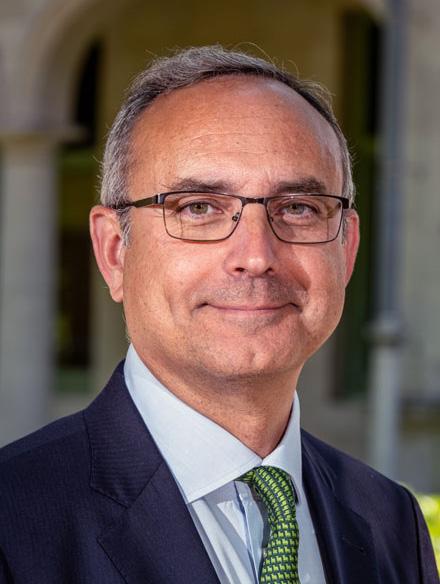
A Food, Feed and Fuel Manifesto
The EU is entering a new political era, with European voters electing a new Parliament and Member States sending new commissioners to Brussels. However, some of the key challenges facing the Union— fighting climate change, ensuring energy independence and boosting food security—remain as daunting as ever.
In the coming months and years, the European renewable ethanol industry will be working alongside stakeholders in the biofuels, food and feed value chains to help build awareness of the strategic importance of renewable ethanol production in addressing these challenges.
Crucial to this effort will be raising awareness in Europe, and globally, about the benefits of EU ethanol biorefineries, including reducing CO2 emissions in transport, supporting European farmers, boosting food security and lessening Europe’s dependence on imported oil.
Here are just a few ways the EU can act now to better achieve Green Deal ambitions:
The EU approach to emissions-reduction should be open to all technologies
Europe can’t afford to bet on electrification as the only solution for reducing emissions from cars. That’s not just common sense, it’s also the finding by the European Court of Auditors that in a 2023 report, warned against the current EU strategy of focusing only on electric vehicles, which, will lead to overreliance on scarce resources needed for batteries. A more pragmatic approach would make the best use of existing technologies that reduce emissions now, work in existing infrastructure, and preserve citizens’ purchasing power and freedom of mobility.
All CO2-neutral fuels should be recognized for current and new vehicles after 2035
In the coming months, the EU will clarify its definition of CO2-neutral fuels. This is important because even with the recent market growth in sales of battery-electric vehicles, Europeans continue to buy mostly petrol and hybrid cars. De-fossilizing these cars with carbon-neutral liquid fuels is vital. Innovations in production are already increasing the GHG-savings score of renewable ethanol, in some cases to more than 90% compared to fossil fuel. All renewable ethanol that is compliant with the Renewable Energy Directive (RED) should be included in the definition of CO2-neutral fuels.
The EU approach to bioethanol should be consistent and coherent in all legislation
The revised RED II confirms the sustainability of bioethanol; however, other EU legislation in ‘Fit for 55’—such as ReFuelEU Aviation, FuelEU Maritime and the Energy Taxation Directive—marginalizes, or even prohibits, the contribution of these sustainable biofuels to achieving climate goals. Instead of this patchwork approach to biofuels, Europe needs a coherent and consistent EU policy approach that promotes investor confidence. Otherwise, the EU risks losing out on innovation and investment to other countries with more pragmatic approaches to biofuels legislation.
The EU’s Protein Strategy should recognize the potential contribution of biorefineries
The European Commission is planning to unveil a new EU Protein Strategy aimed at amplifying the domestic production of protein for food and animal feed and reducing Europe’s dependence on imports such as GMO-based soybean meal. Fortunately, the EU has a domestic source of high-protein feed production from European agriculture: ethanol biorefineries. In 2022, ePURE members’ biorefineries produced 5.9 million tonnes of food and feed coproducts along with 4.5 million tonnes of renewable ethanol—more food than fuel.
Now is the time to realize the potential of renewable ethanol biorefineries for a more autonomous Europe.

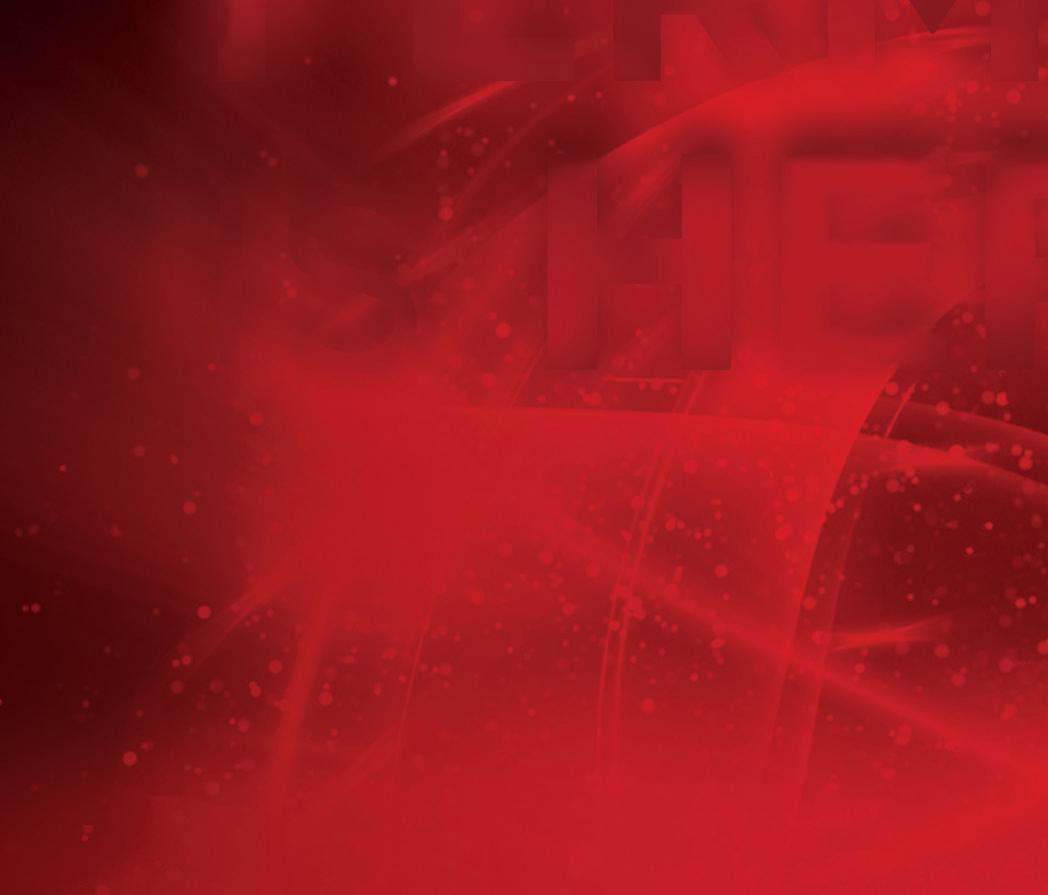
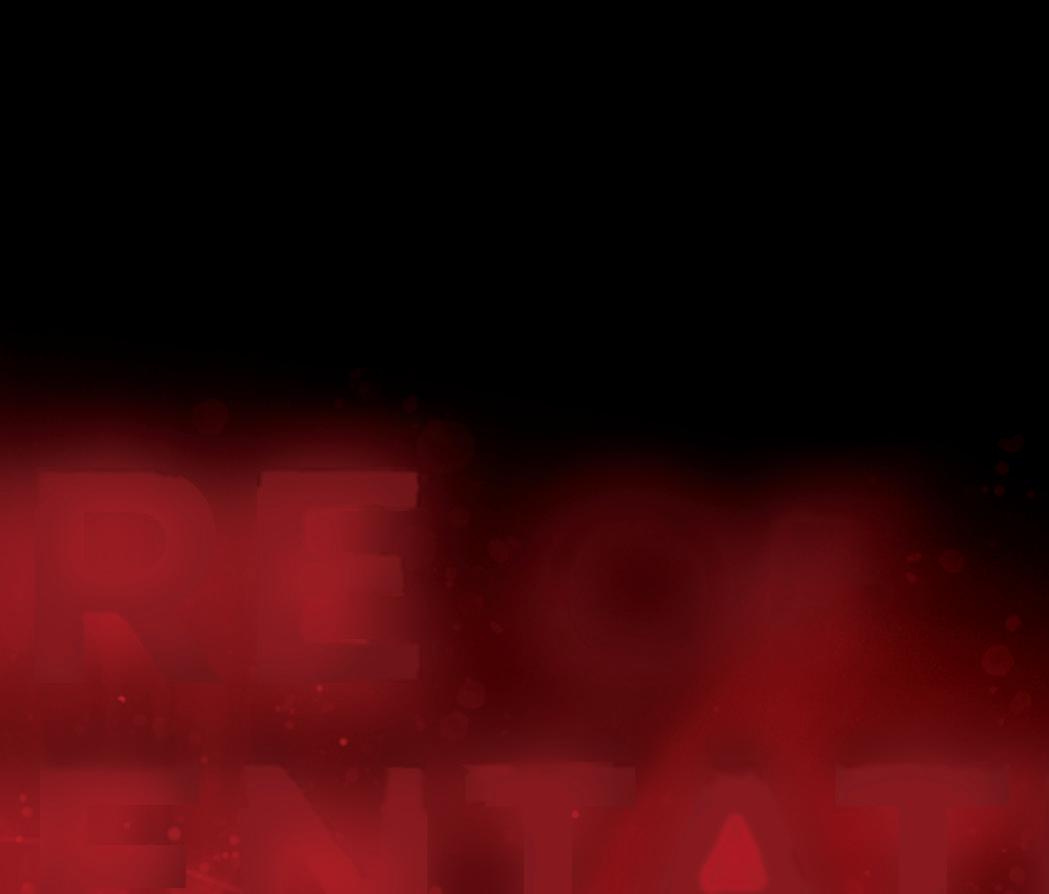
THE FUTURE OF FERMENTATION IS HERE
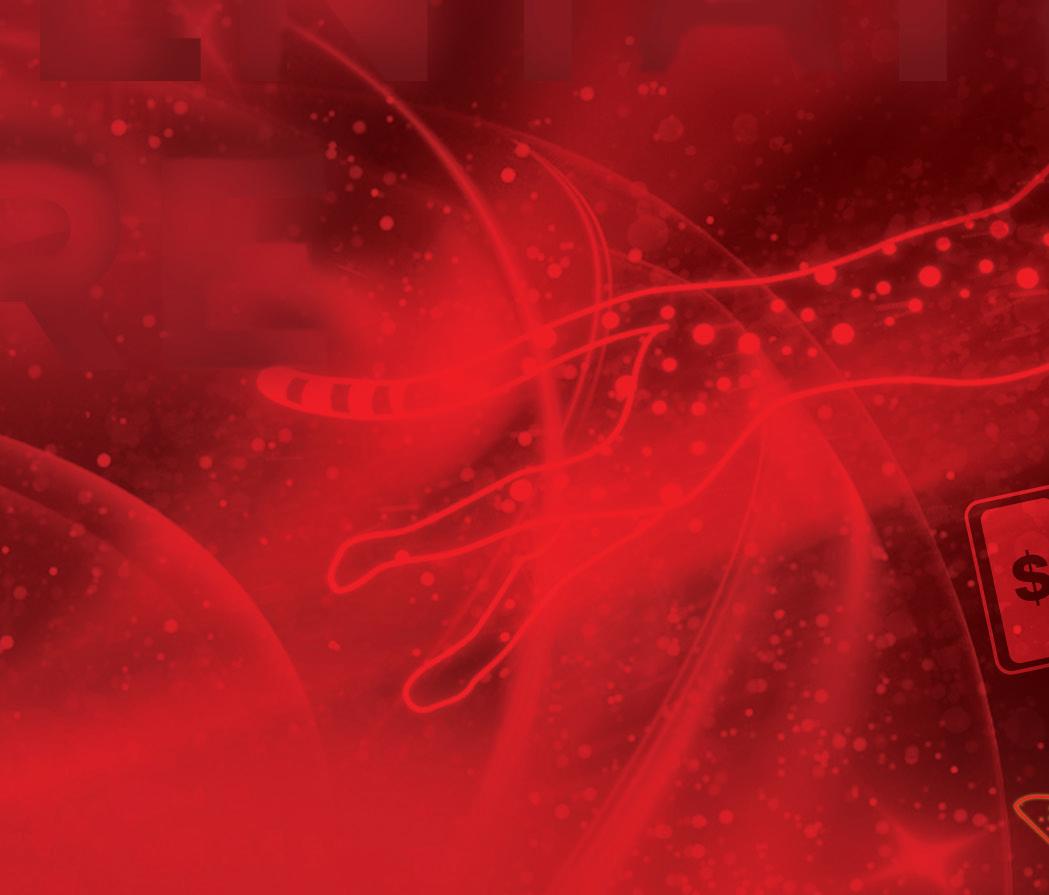
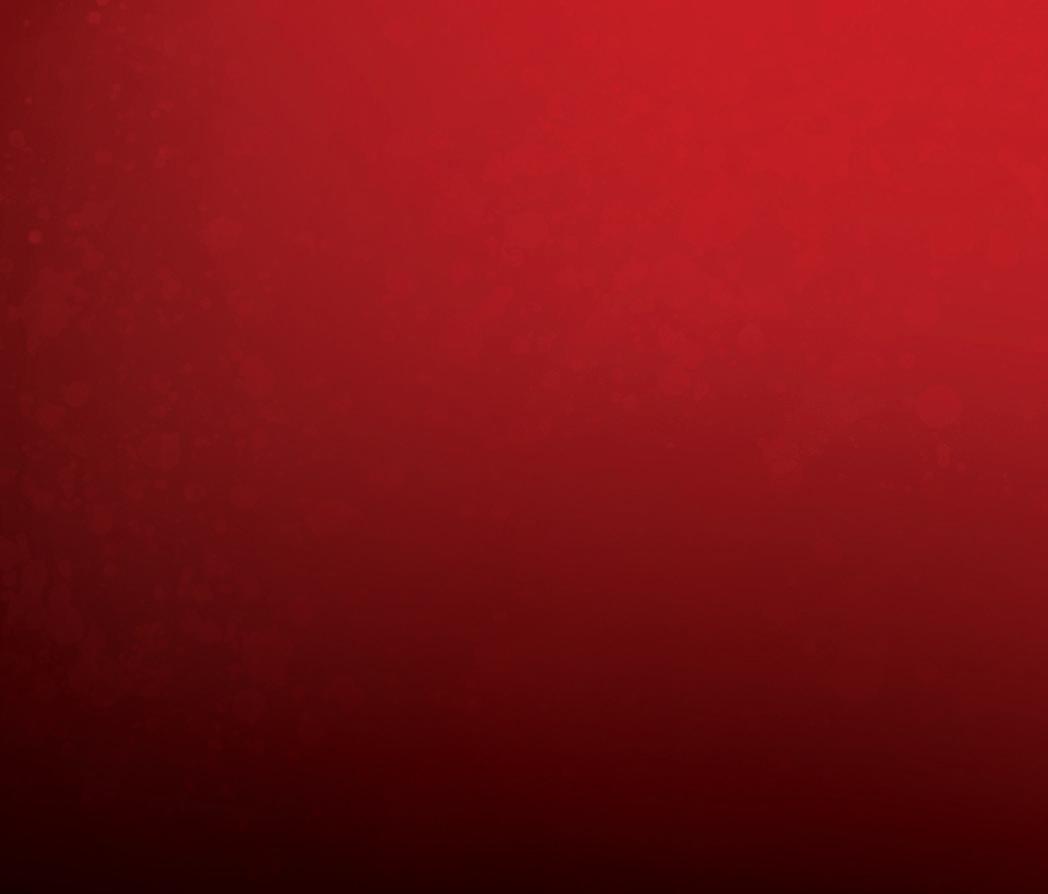
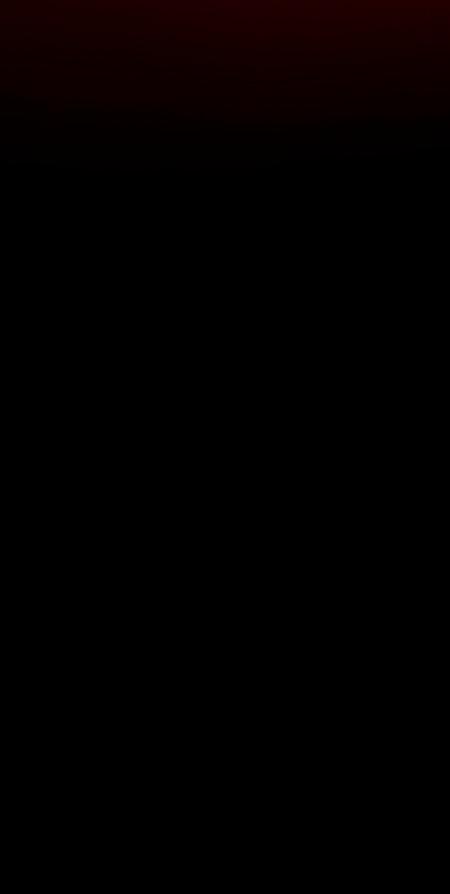
Enter a new era of ethanol production with FermaCore™ Propel, the LATEST INNOVATION IN LIQUID YEAST OFFERINGS. Featuring extreme robustness and the fastest fermentation kinetics we’ve ever o ered, FermaCore™ Propel is a true breakthrough designed to MAXIMIZE ETHANOL YIELDS AND INCREASE ENZYME REPLACEMENT — leading to LOWER CARBON INTENSITY. Whatever form you need it to take, you can expect more from FermaCore™ Propel. Because at LBDS, fermentation is at our core.
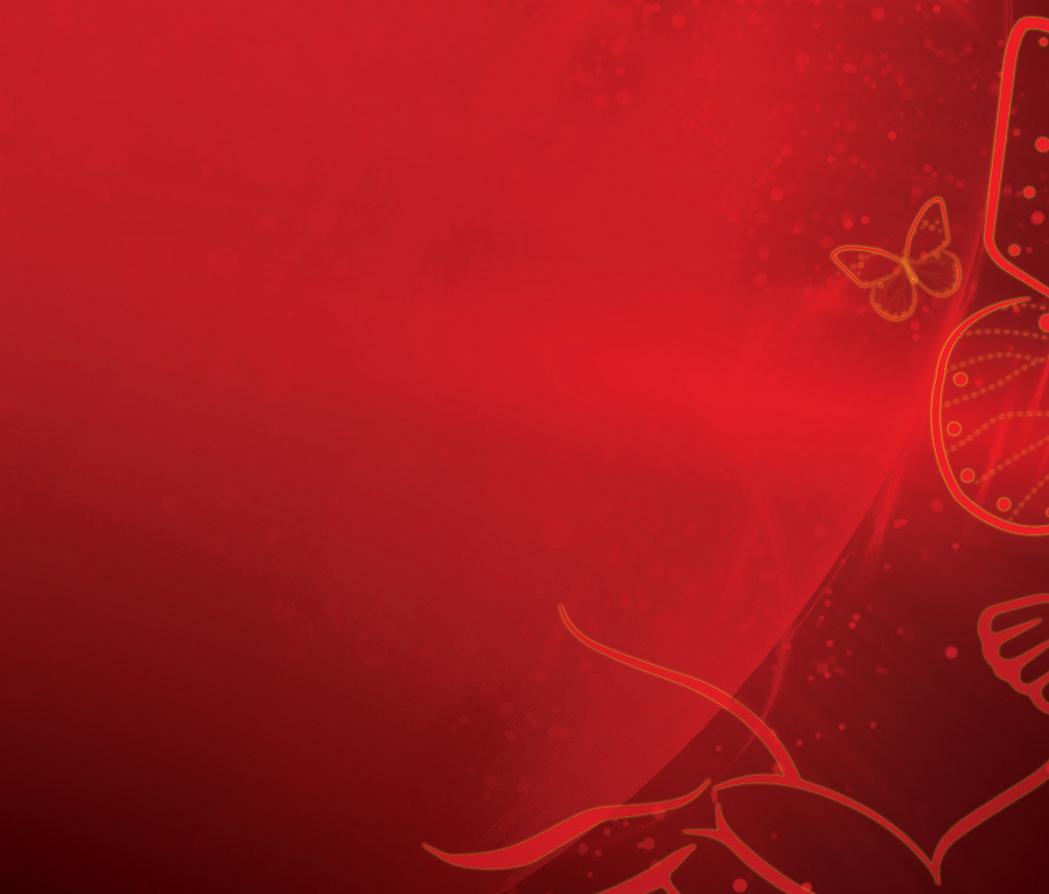


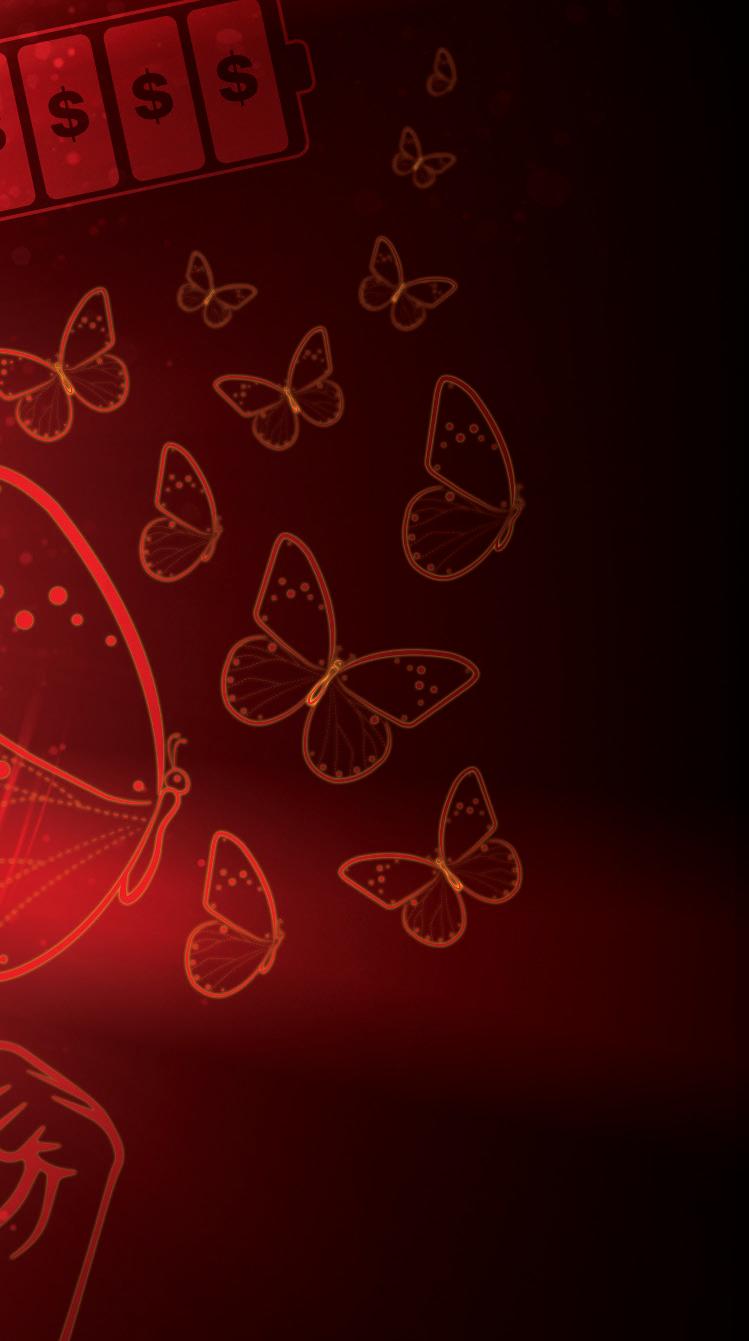
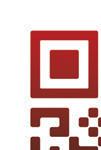
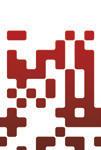

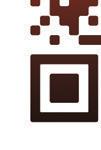


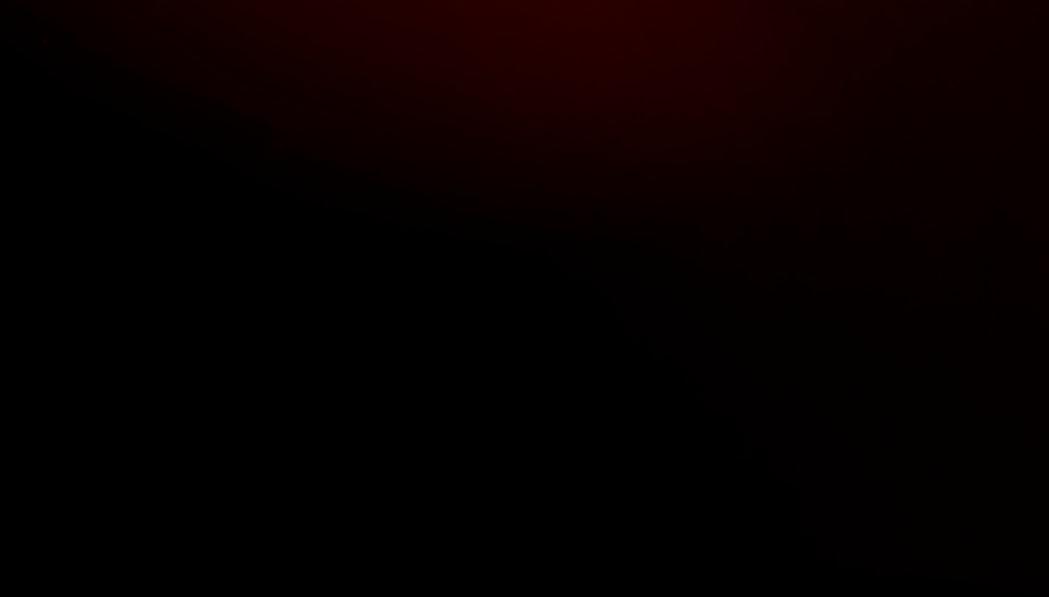
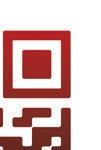
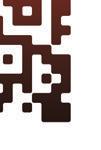
START SHAPING THE FUTURE OF ETHANOL PRODUCTION


SHOW US YOUR SAVI NGS
BUSINESS BRIEFS
PEOPLE, PARTNERSHIPS & PROJECTS
United Cooperative acquires Marquis’ Wisconsin ethanol plant
In April, Marquis and United Cooperative announced the sale of Marquis’ Necedah, Wisconsin, ethanol facility to United Cooperative. The facility will operate under the new name of United Energy Necedah LLC. The asset sale will be effective May 31, ensuring a seamless transition for grain customers and staff.
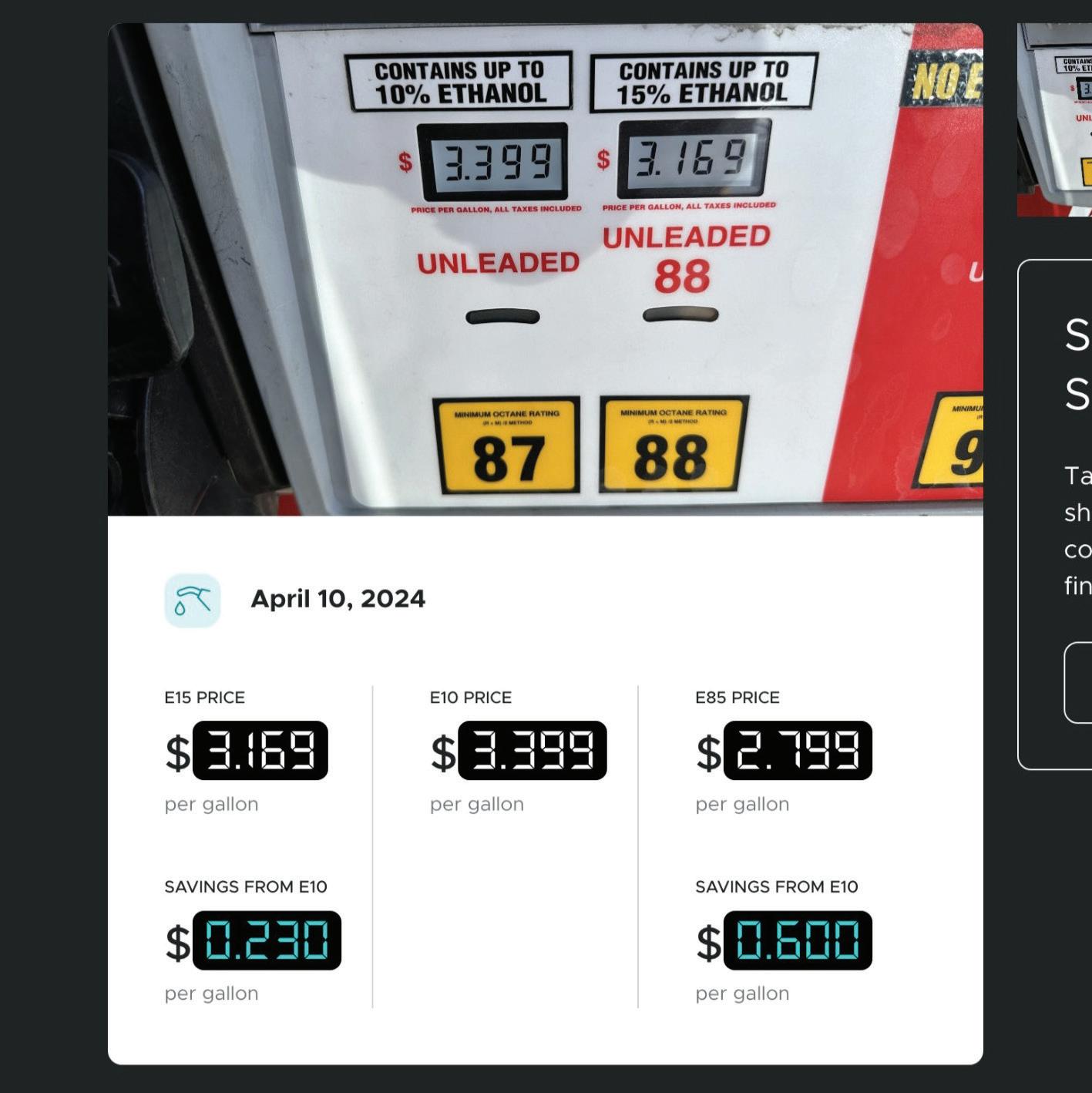
The Necedah facility, which consumes 36,000,000 bushels of regionally grown corn annually, is a vital asset to the local community’s agricultural landscape. With an annual production capacity of 100 mil-
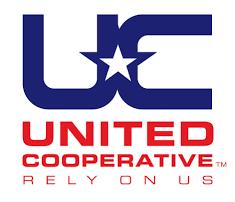
lion gallons of ethanol, along with DDGS, high-protein animal feed and corn oil, the facility plays a vital role in supporting regional economies and meeting market demand. The ethanol facility employs more than 50 staff members and will continue to provide exceptional market access and service within the trade territory.
Marquis will continue to own and operate its 400 MMgy corn ethanol plant in Hennepin, Illinois, the largest ethanol plant in the country.
Redfern joins USGC as global ethanol program coordinator
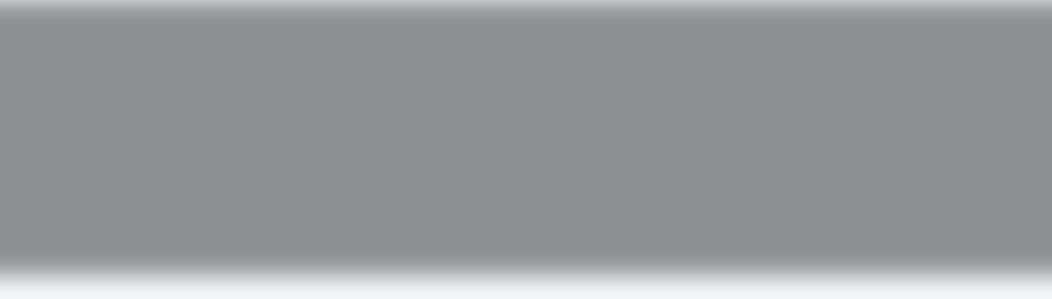
Samantha Redfern has joined the U.S. Grains Council as global ethanol program coordinator. In this role, Redfern is responsible for providing support to the global ethanol market development team, organizing staff and member travel, making arrangements for visiting teams, facilitating program planning, handling correspondence, reports, data and information management, in addition to being responsible for invoice compliance tracking and contracting.

“We are delighted to have Samantha become a part of the USGC staff as she brings a plethora of project facilitation and coordination experience,” said Mackenzie Boubin, USGC director of global ethanol export development. “Samantha’s eagerness to learn, approachable demeanor, organizational abilities and robust communication skills will serve the Council and the ethanol team well in our future programmatic efforts.”
NREL highlights role in SAFFiRE Renewables SAF platform
On its path to opening a facility designed to turn agriculture residue into a scalable biofuel business, SAFFiRE Renewables LLC plans to break ground on its pilot plant near Liberal, Kansas, in late 2024.
Last year, the company negotiated a license agreement for the National Renewable Energy Laboratory’s deacetylation and mechanical refining (DMR) process, a technology seen as important for sidestepping challenges with cellulosic biofuel
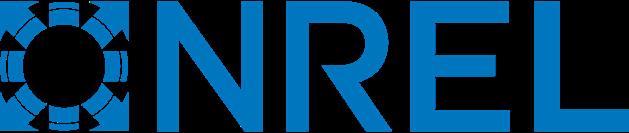
facilities in the past. DMR uses a gentle alkaline bath and a mechanical shredder to prepare corn stover for ethanol fermentation—essential steps for accessing the energy-dense sugars locked inside.
Ultimately, ethanol made at the plant, which will be operated by Conestoga Energy, will be upgraded into sustainable aviation fuel (SAF). Estimates suggest the resulting SAF will have a carbon footprint at least 83% lower than conventional jet fuel.
LanzaTech: Freedom Pines Fuels to begin SAF production in Q2
LanzaTech Global Inc. has announced that LanzaJet’s 10 MMgy ethanol-to-sustainable aviation fuel plant in Soperton, Georgia, is on track to begin producing fuel during the second quarter. LanzaJet celebrated the grand opening and mechanical completion of the Freedom Pines Fuels facility in January.
In the first quarter earnings release, the company addressed the project, saying its cellulosic ethanol will be a critical feedstock for SAF production. When coupled

with LanzaJet’s technology, LanzaTech’s ethanol enables production of SAF from a variety of waste inputs and residues, including municipal solid waste and e-fuels.
LanzaTech also provided an update of its project development pipeline, noting that it added nine new net qualified project opportunities into the first phase and one net addition into the advanced engineering phase of its project pipeline during the first quarter.

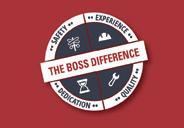
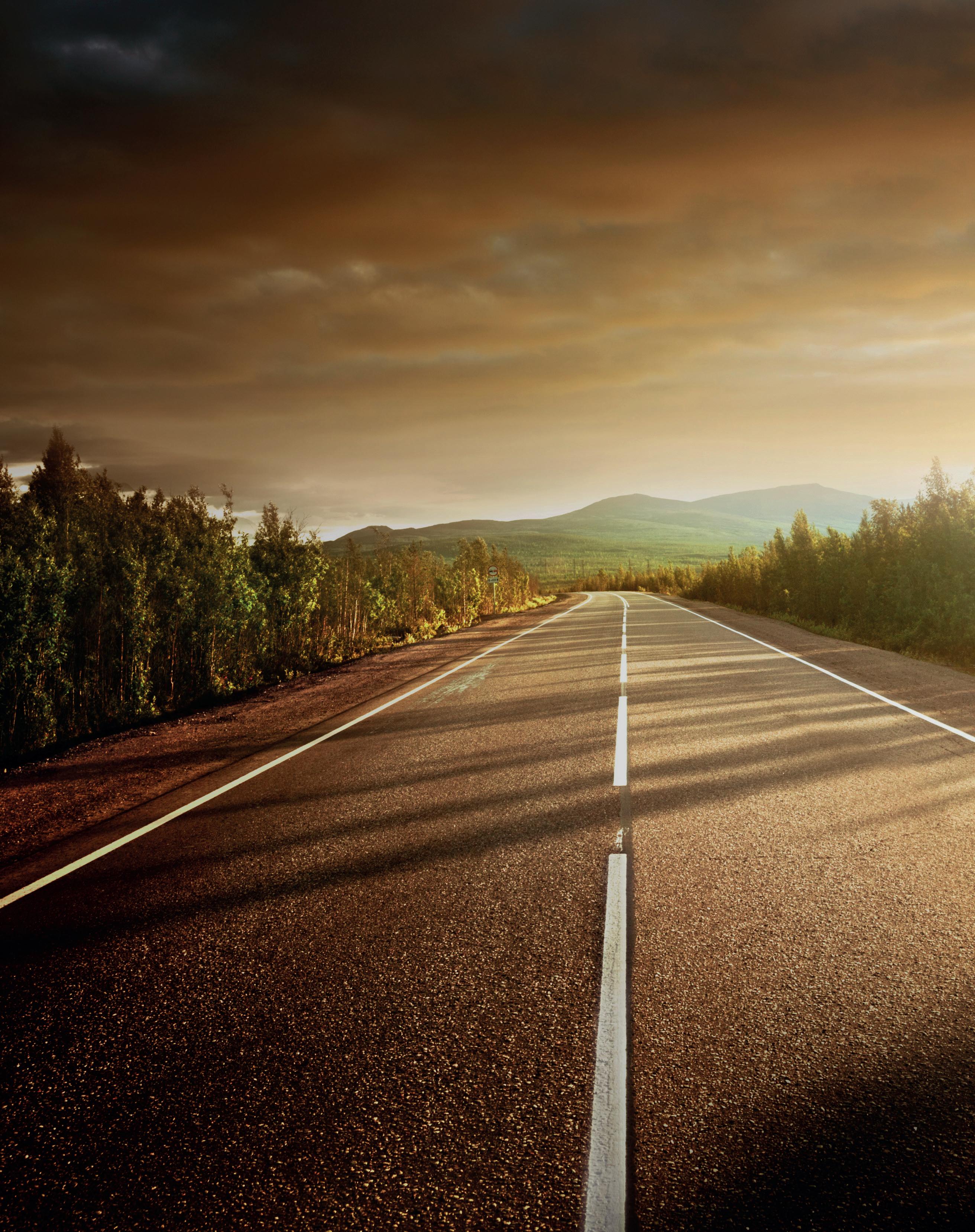
Chart your path
The future of the ethanol industry depends on decarbonization.

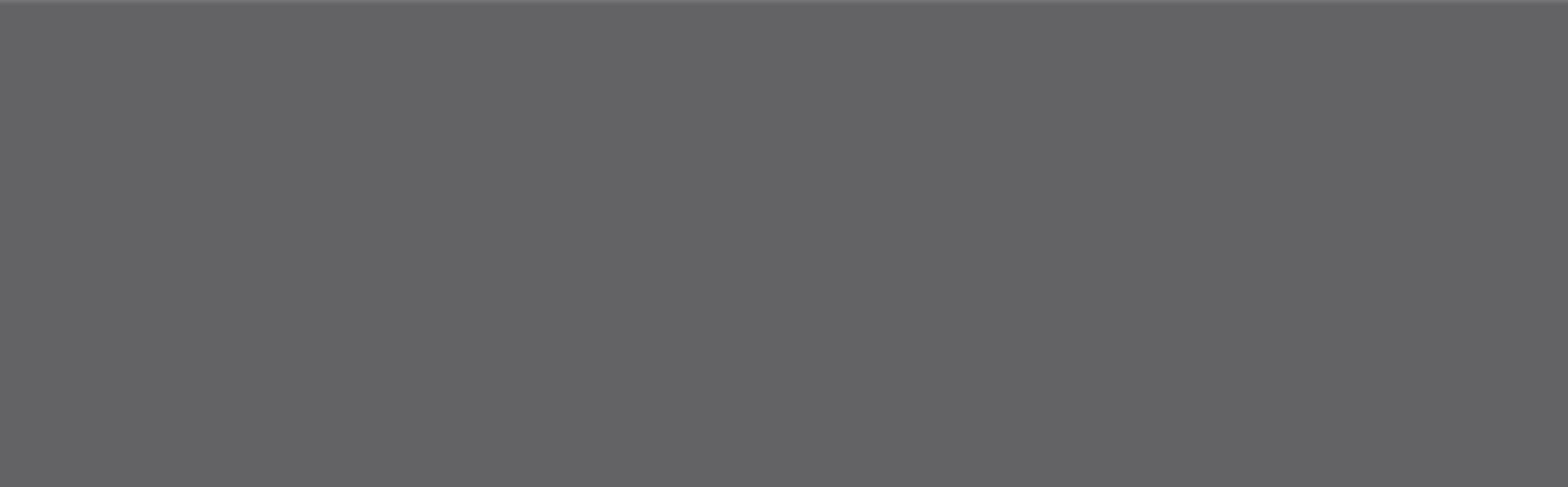
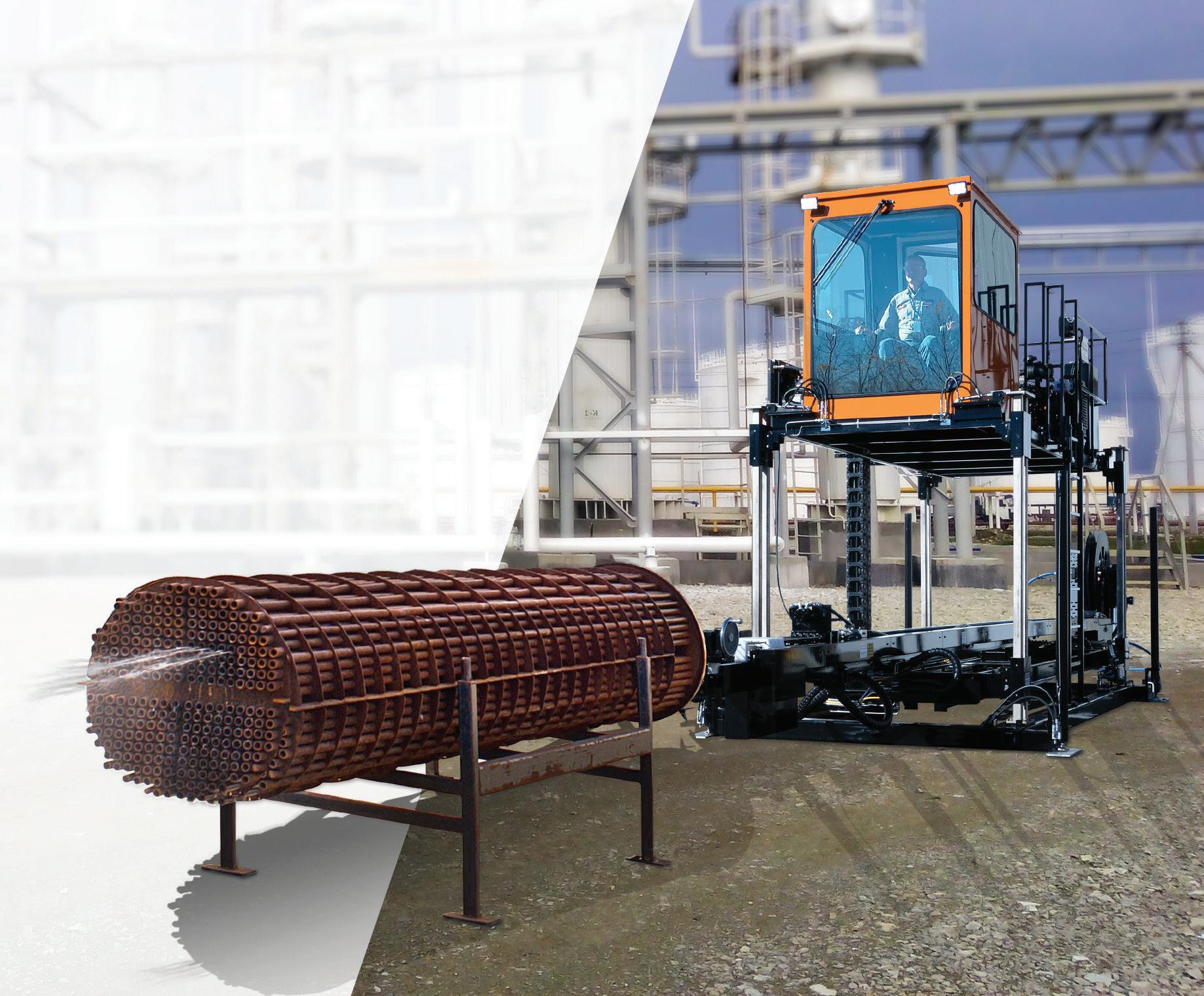
NEW! ATL-5022 AUTOMATED TUBE LANCER
NLB’s ATL-5022 tube lancer cuts downtime and expense, delivering high -pressure water to five rotating lances from a single hose . Fewer hoses m eans fewer tangles , and rotating the lances ins tead of the nozzles m eans fewer nozzle replacements.
All movements are directed from the cab, with remote troubleshooting . And the system operates with smaller, more economical pumps than other models.
With the ATL-5022, NLB s ets a new standard for pro ductivit y and cost- e ec tiveness
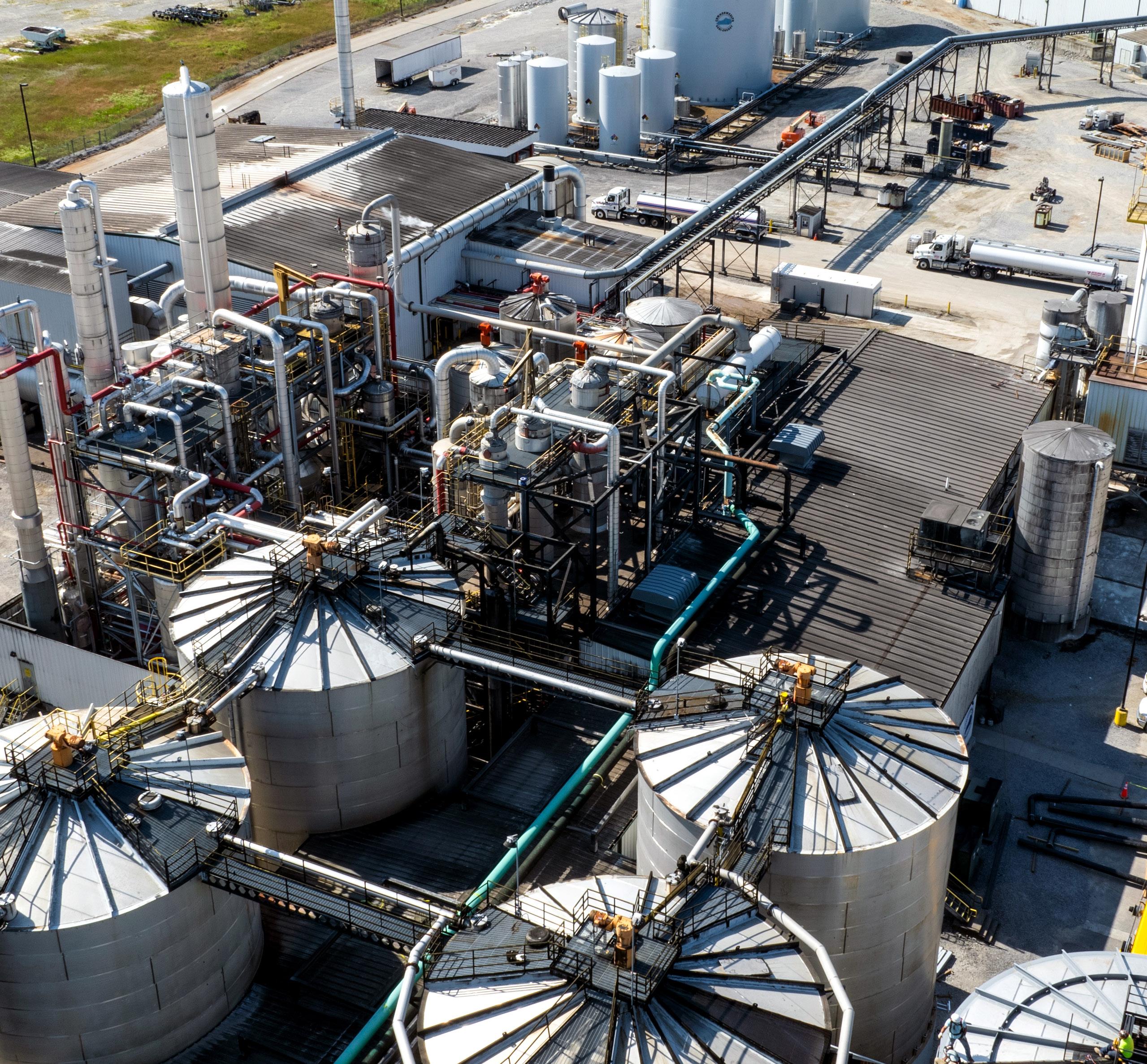
GROWTH GUIDEPOSTS: Commonwealth has always approached plant upgrades with a two-prong strategy. The first goal is to add efficiency. The second is to expand.
LESSONS TO CELEBRATE
Commonwealth Agri-Energy will hit its 20-year production milestone this fall. The plant has succeeded in Kentucky by being resilient, ready and creative.
By Luke GeiverOperating on the southern fringe of the U.S. Corn Belt has never been an issue for Commonwealth Agri-Energy LLC. The 50 MMgy corn ethanol plant, brought online in 2004, exists a few miles southeast of Hopkinsville, Kentucky, about 70-miles northwest of Nashville. The plant has always found a way to succeed in a state known more for bluegrass and horse racing than corn varieties and harvesting combines, according to Mick Henderson, long-time general manager of the plant. “But there’s an advantage of being southeast of everybody else,” he says.
There’s also a lot to learn from Commonwealth that has little to do with the plant’s geographical location, Henderson explains. And there’s reason for celebration. In the fall, the ethanol plant’s team will gather with many of the 2,300-plus members of the Hopkinsville Elevator Co.—which owns the plant—to officially celebrate 20-years of ethanol production. Henderson says it will be a time for celebration, for sure, but also a time to reflect on lessons learned on a two-decade-long, non-linear path to success.
Lesson 1: Compete In Nearby Markets
From its inception, the vision for Commonwealth was rooted in a local strategy. “Like most things in commodity processing,” Henderson says, “logistics is everything.”
The Commonwealth plant does well because its corn supply—roughly 15 million bushels per year—is almost entirely local. All of the plant's 45 million gallons of ethanol goes to Nashville by truck. Between 80 and 95 percent (or 129,000 tons) of the plant's distillers grains goes to the regional poultry industry by truck. Roughly 7,000 tons of feed-grade distillers corn oil also goes to the local poultry industry. A commercial 110,000-ton CO2 offtake agreement, which began when the plant started, supplies CO2 for food-grade liquid and dry ice production locally. The only product the plant rails out is its high-purity alcohol.
“Build and operate a plant that supplies customers with consistent quality and delivers to contract volumes, especially to nearby markets,” Henderson says, “and you can compete with anyone.”
Lesson 2: Prepare To Remain Running In Challenging Times
It’s easy to keep a plant online when everything is running right, Henderson says, but it’s how you make decisions when things aren’t going perfectly that will in some ways define your plant’s long-term success.
Over the past 20 years, the biggest challenges for Commonwealth have been regional drought impacting the local corn crop and navigating the continuous challenge of equipment replacement or upgrades. Within the last five years, for example, the team had to figure out how to stay running when gasoline demand and prices plummeted—taking ethanol with it—due to the global pandemic. Like others, they produced high-purity alcohol. It was a period of “handsanity,” Henderson riffs. The plant started making 190-proof at low impurity and neutral odor in 2021. While others stayed in the high-purity game only for a while, Commonwealth remained in it with the goal of establishing additional sales in the industrial, food and beverage alcohol markets. The plant can now produce roughly 5 MMgy of high-purity alcohol.
On the regulatory side of the ethanol business, Henderson and his team have to constantly stay up to date on changes that may impact near- and short-term business. He says he works to keep his board of directors informed on the regulatory landscape because they want the plant to be able to operate in any regulatory environment, regardless of which party is in office. To do that, Henderson travels to ethanol events—regularly attending a number of them—and stays tapped into the pulse of the policies that can alter ethanol production for good or bad. In some cases, he says, that means doing more listening than talking in order to absorb and interpret what’s on the horizon.
“I’ve got to have a better crystal ball than everyone else,” he says with a wry chuckle.
Managing through tough times is only possible with the right team in place, a sentiment Henderson says almost all businesses espouse but not all commit too. For Commonwealth, the internal team has been key, he says. The plant has eight employees that have been with the company for 20 years, along
with a couple of early employees that left and have since returned. “Their plant knowledge and experience have carried us through tough times,” he says.
The same could be said for some of the local contractors for maintenance support and new construction, he adds. The plant has also kept up good relations with major industry ingredient, engineering and equipment suppliers.
“They have always provided the innovations we need to compete in the fuels and feeds markets,” he says.
Physical catastrophes—however unlikely—are something Henderson and his team constantly train for. Certain events can cause significant downtime, and plant personnel have to be trained for myriad scenarios. The day Henderson was interviewed for this story, his team was wrapping up a training scenario involving a hypothetical offsite (but nearby) anhydrous ammonia leak. The team not only went over all the possibilities and how to react, but also came up with a way to maintain some level of production at the plant safely. “You need to have your crew trained to handle things when times are good and when they’re difficult,” he says.
Lesson 3: Embrace Plant Upgrade Creativity
Commonwealth was originally an ICM Inc./Fagen Inc. design-build project, breaking ground in 2003. Since then, the plant has been improved in stages, including the addition of DCO extraction in 2006. The plant relies on a dry mill process, using semi-continuous yeast propagation with an RTO addition with stack heat recovery. Commonwealth has a flexible wet feed production system that helps with dryer and centrifuge maintenance, along with spare bowls for wet cake and oil machine quick turnarounds, Henderson says.
“Today we are investigating plant efficiency projects, new product projects, major equipment replacement projects and capacity expansion in all processes with better quality,” he says.
This year in particular, some of the major pieces of equipment at the plant are needing replacement after 20 years in operation. “We have some fully depreciating equipment that will require more than just upgrading,” he
says. “Some will need to be changed out and retired completely.”
Ahead of this predicted work, the team is going through a rigorous examination of its personnel—skillsets, experience, bandwidth—to help define how each can contribute. They want to be sure that forthcoming jobs are done efficiently, safely and in optimal sequence.
Commonwealth has always approached plant upgrades with a two-prong strategy. The first goal is to add efficiency. The second is to expand. The plant performed major efficiency upgrades interwoven with expansions in 2006, 2012 and 2017, followed by a highpurity install in 2021. Now, it's time for another round.
Henderson will apply his “efficiency first, expansion second” strategy again. The idea is that increasing plant efficiency first allows the plant to be competitive in any market (both physical and political). Adding efficiency prior to expansion also allows return-on-investment dollars to become realized through the money spent on efficiency upgrades, before the expansion dollars are ever spent. “Doing it that way lowers the cost of the plant expansion,” Henderson explains.
The commitment to such a strategy is linked to the way Commonwealth pays for
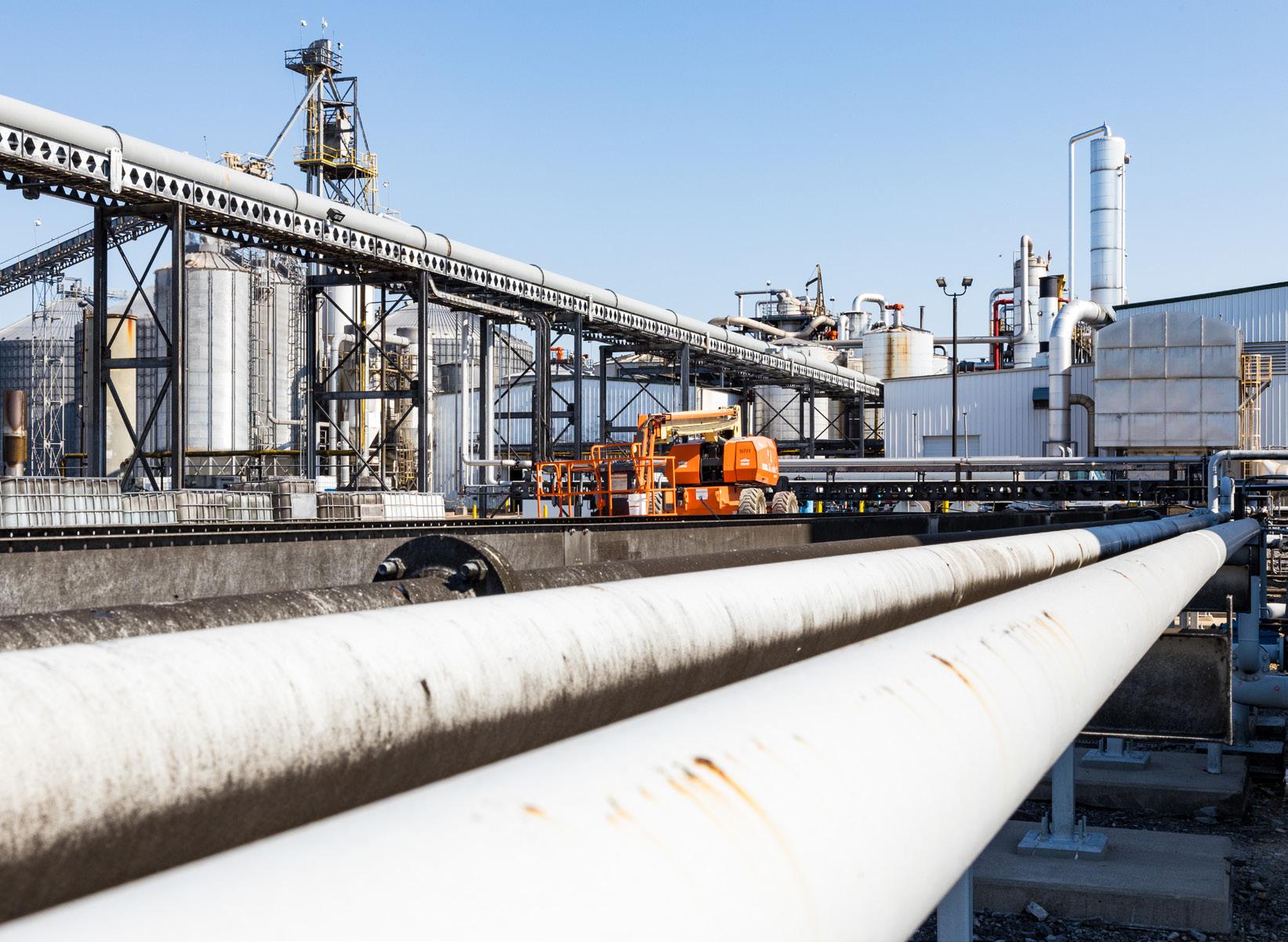
projects. “All of our expansions have been completed with our own cash,” he says. “We haven’t borrowed any outside money.” That has required a commitment to be different or, as Henderson puts it, “creative.”
Lesson 4: Look Forward, Not Back
Henderson and his team are confident that they’ve earned the right to celebrate the


plant’s 20-year anniversary. Look at 2022, for example. The plant’s profits feed into the Hopkinsville Elevator’s balance sheet before finding their way to its members via patronage dividends, a total that reached $40 million in 2022. But that doesn’t mean they spend inordinate time waxing poetic about the past or thinking about how they should plan a party.
Just before Henderson took our call, he was up high on the ladders of the distillation towers. He was still catching his breath when
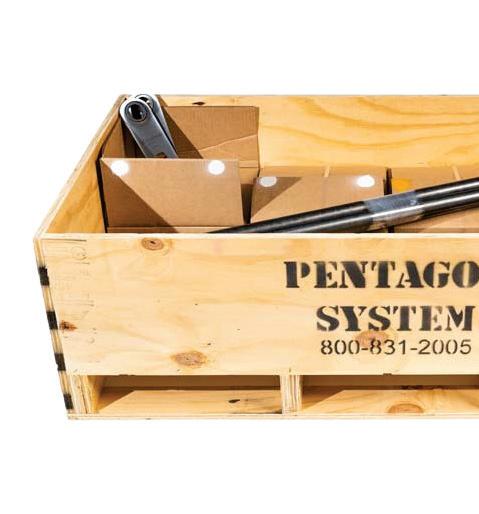
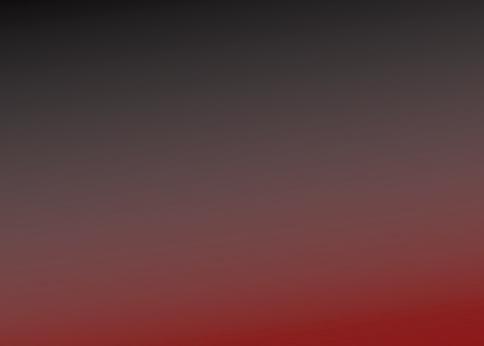
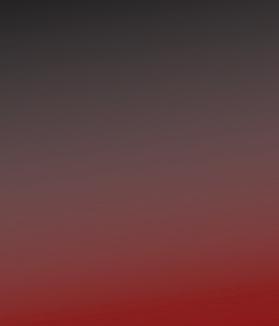
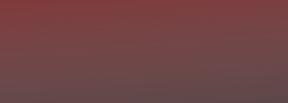
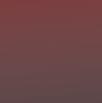
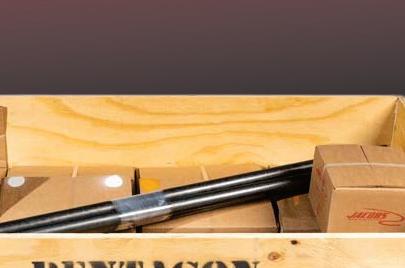
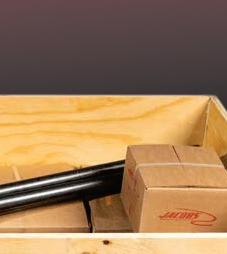
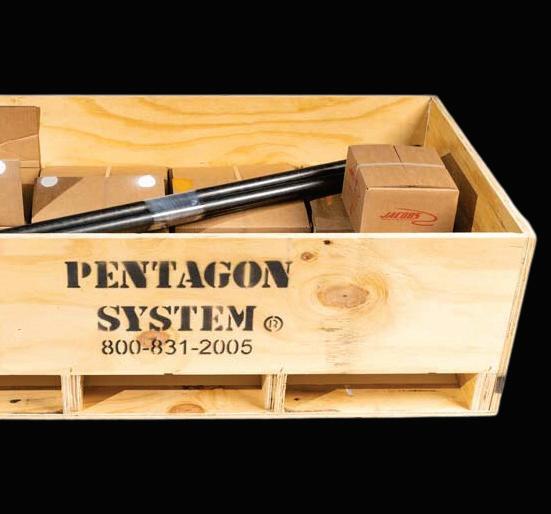
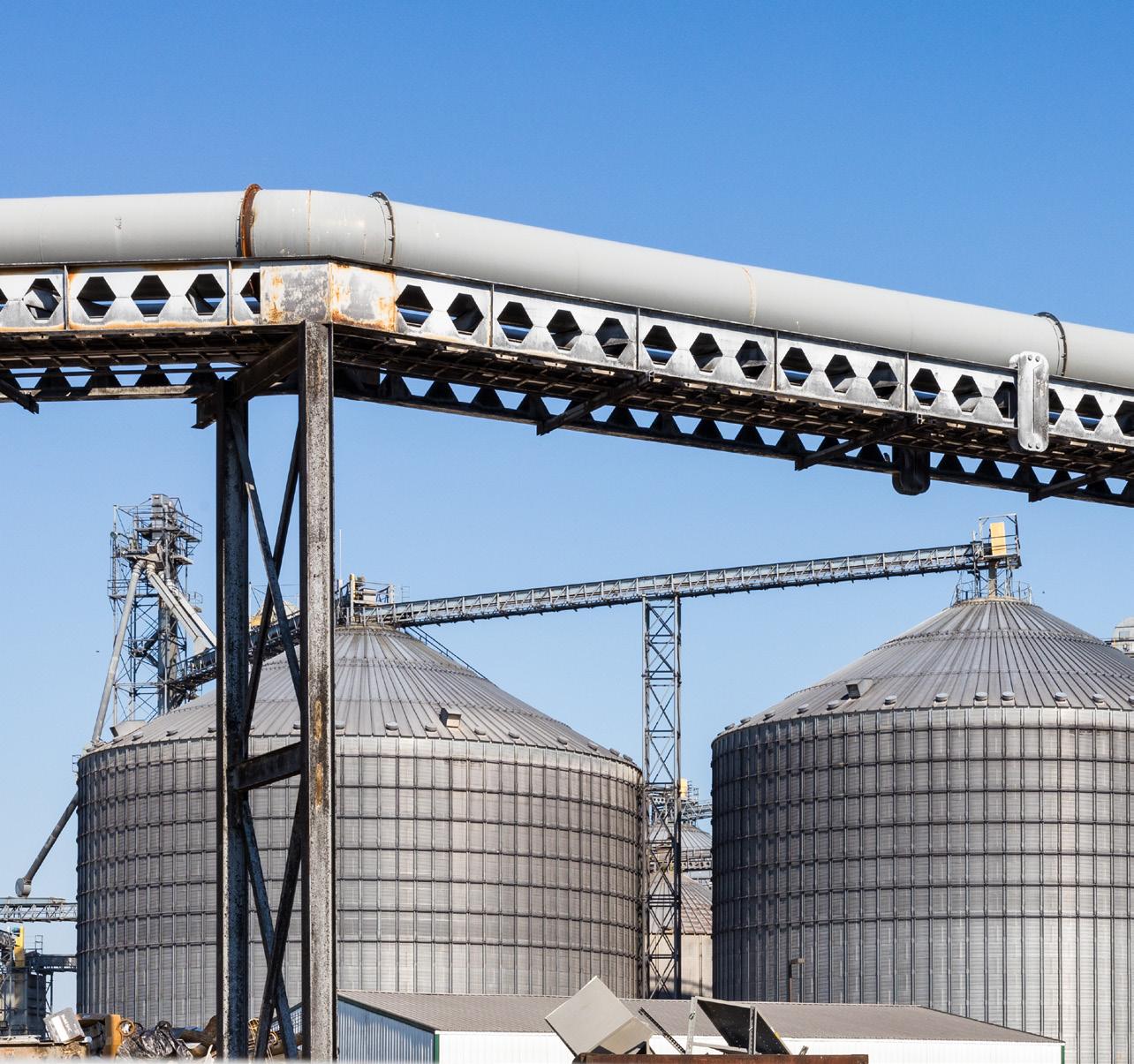
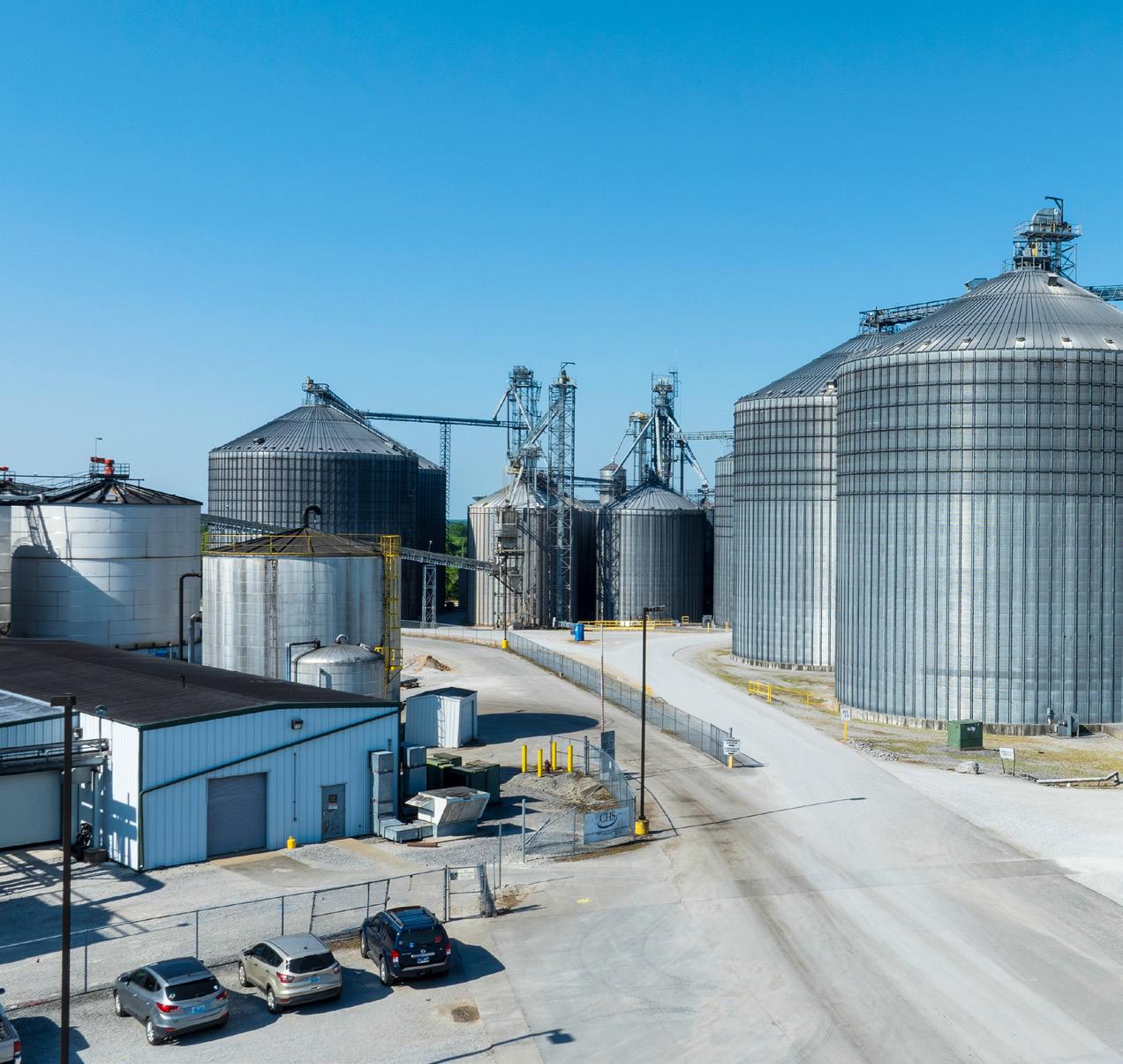
he picked up the phone. Most days, Henderson says he walks about 2.5 miles around the plant. That’s just normal. At night, in the morning, or any time he’s not contemplating something else plant related, he’s thinking about corn prices or weather. When he’s not at the plant, he’s probably thinking about it. And when he’s at work, he’s often thinking about external factors that could impact the business.
According to Henderson, much of his team operates that way—thinking about the plant and the variables that will impact its success in the days, weeks and months to come.
Right now, the team is focused on improving its carbon intensity score along with ethanol yield and the amount of Btu’s per gallon used.
“When the regulatory environment is assured, we will look at bigger projects too,” he says, including the possibility of multi-million-dol-
Continous,






lar projects with outside investment and other partners to help.
They may be committed to succeeding locally, but that doesn’t mean they don’t have an eye towards expansion into new markets.
The biggest reason for the success of Commonwealth during the past 20 years comes down to two things, Henderson says: how they view challenges and approach them.
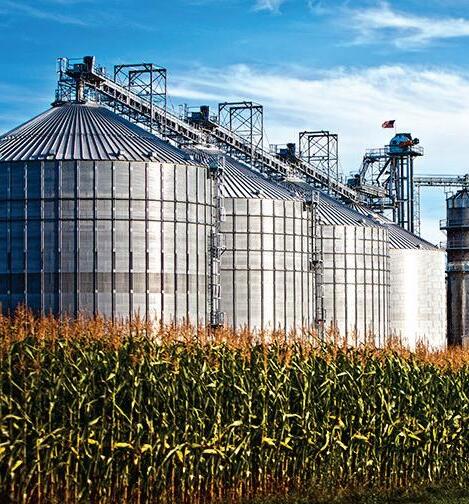
Thoughts On 20-Years At Commonwealth
As told by 20-year Plant General Manager Mick Henderson.
What are the biggest challenges the plant has faced in the past 20 years?
Regional drought is the biggest. We’ve gone through two in twenty years. Also, keeping the plant supplied with corn at a reasonable cost. Then, 20-year old equipment. We need upgrades.
How has the ethanol sector changed in the past 20 years?
It’s changed the most with the acceptance of ethanol in the fuel supply. E10 is now regular. E15 should be accepted soon. DDGS has also been accepted in most animal feed markets, along with distillers corn oil.
After 20 years, what is important to your plant?
I always need to thank our farmers. Farming practices and CI score will have a huge impact on our ability to sell into new markets. Ethanol is an integral part of valueadded agriculture.
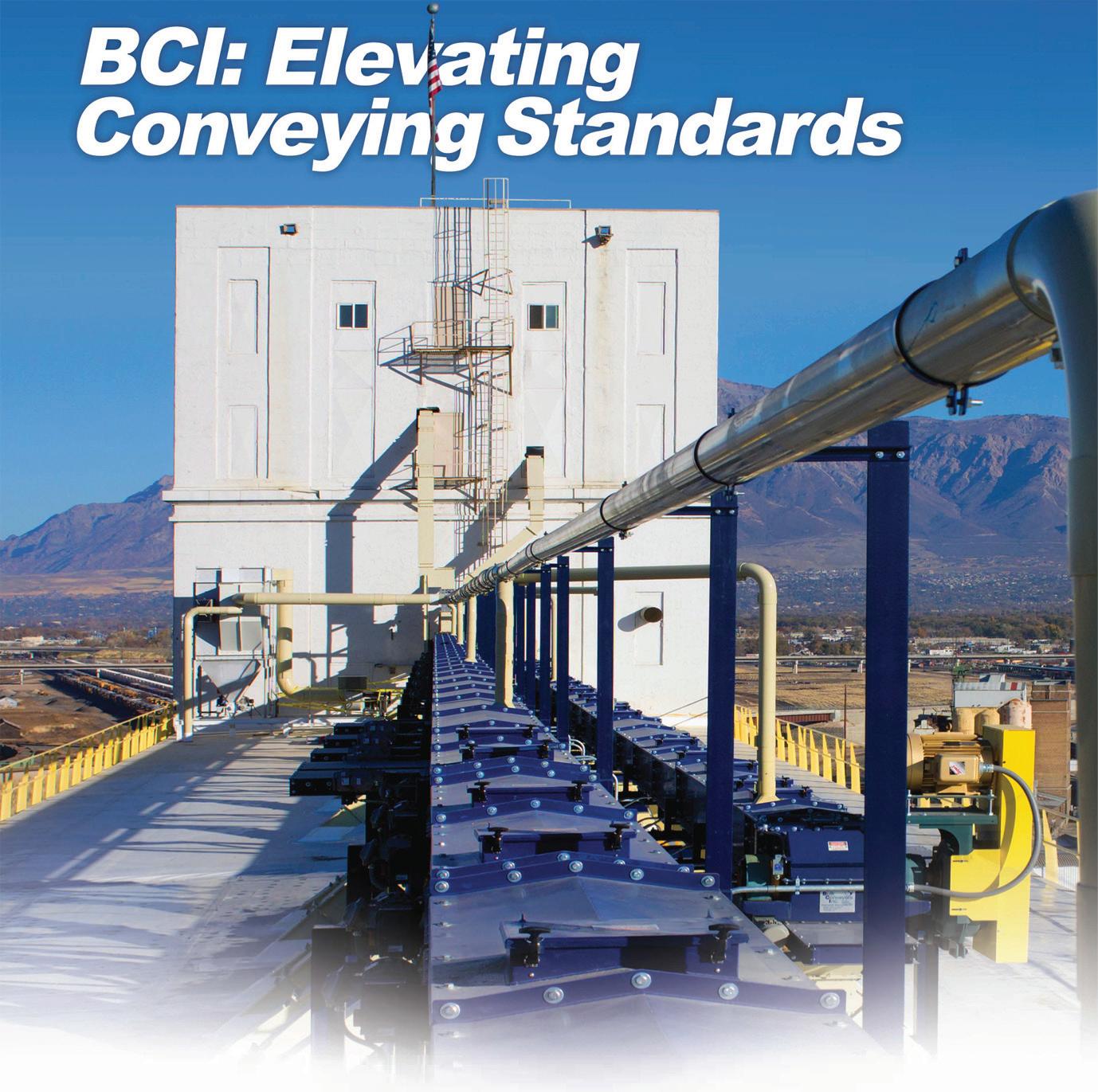
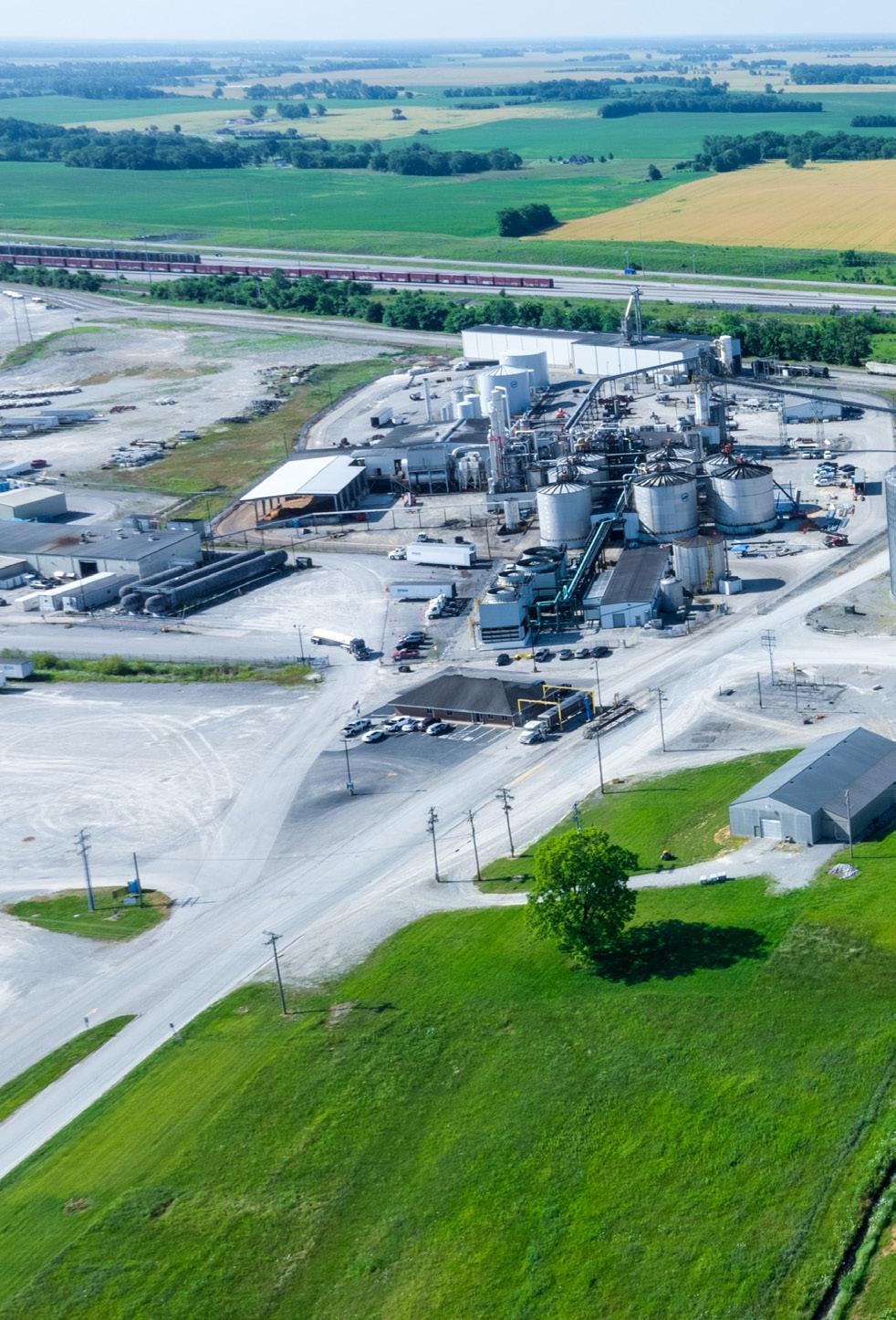
BCI equipment is built to last, one piece at a time, by a team that still believes quality matters.
From custom design, to fabrication, to service & support...
BCI is Elevating Conveying Standards
• Chain Conveyors
• Bucket Elevators
• Parts & Accessories for all makes/models of conveying equipment
Over 200 Years of Combined Experience. Made in the USA.
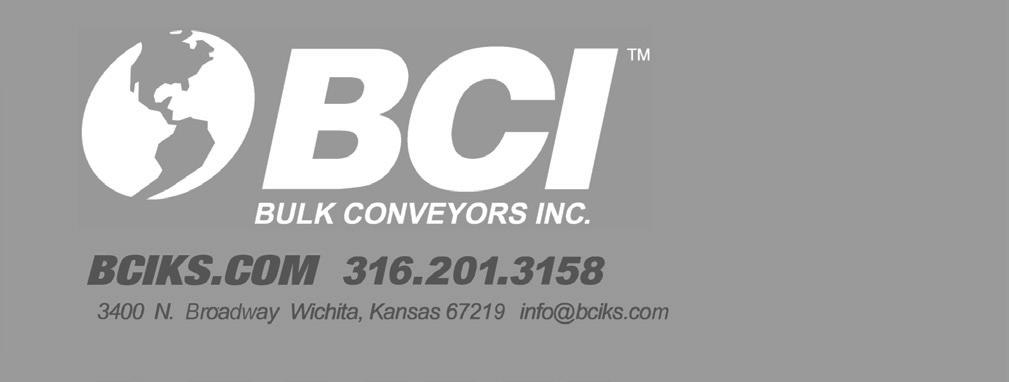

Being on the fringe of corn country and outside the main ethanol production region hasn’t been something the team has taken as a challenge, but rather as an opportunity to embrace. Their local strategies have proven effective. And their willingness to operate how they see fit has helped. The fact that the plant hasn’t yet financed a project with outside money is a prime example of their commitment to creativity, Henderson says. However, being creative and flexible also means staying open to the possibility of outside investment for future growth.
Their view of what’s right in front of them and what might be coming in the future, has also been a major factor in their success. Like Henderson says, he’s always trying to improve his crystal ball.
“The 20-year milestone celebration is great. But none of us look back very well,” he says. “We look at what we have to do today, and what we have to get done for the future.”
Author: Luke Geiver Contact: writer@bbiinternational.com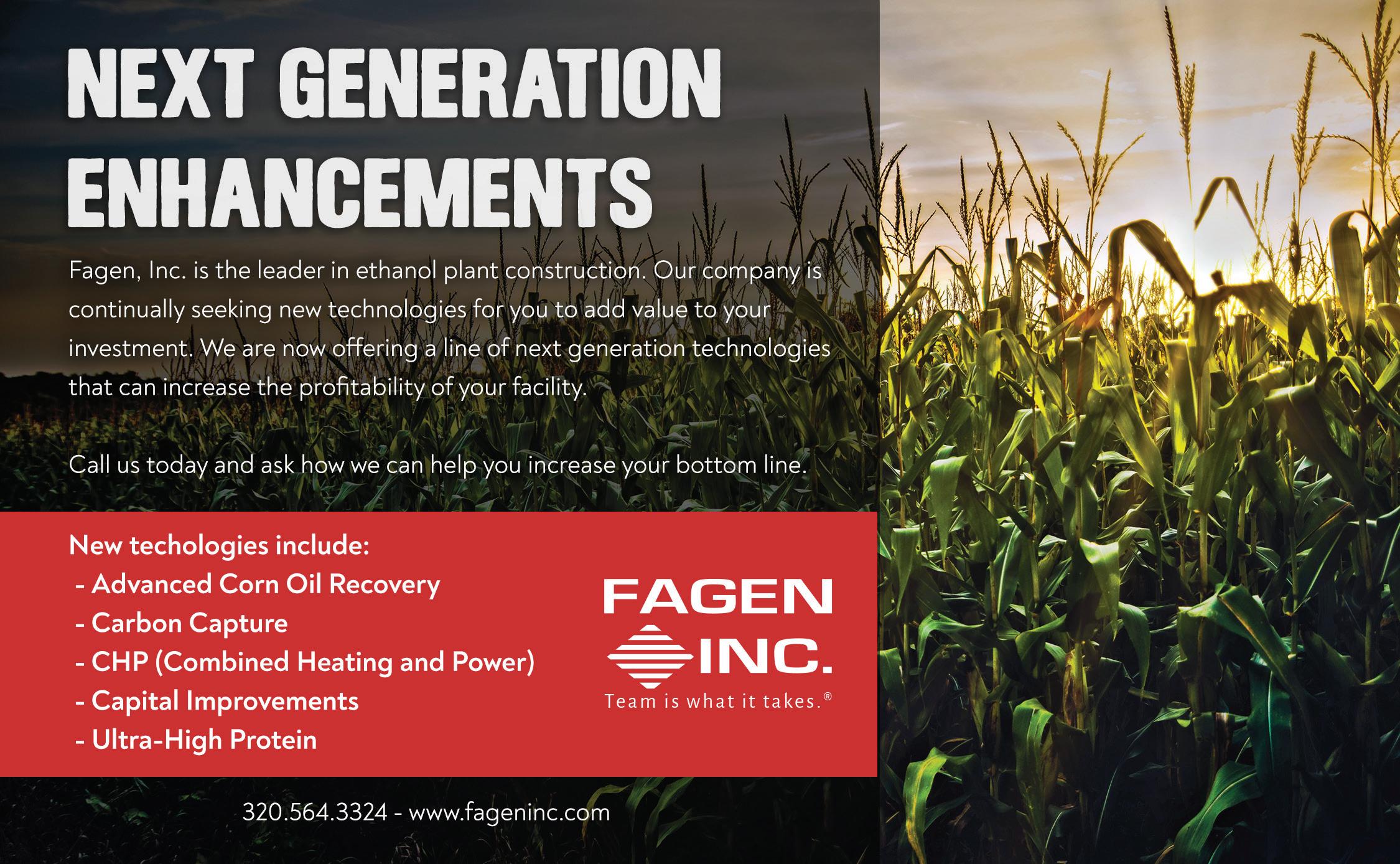


HIGHER ALCOHOLS, BROADER REACH
Greenfield Global is expanding the capacity of its high-purity alcohol production in North America and Europe, focusing on transparency and scale.
By Luke GeiverGreenfield Global may not be the largest global supplier of high-purity alcohol (HPA), but the Toronto-based producer— with facilities in North America and Europe—competes well with the biggest. According to Heather Hayes, director of marketing, the familyowned company, which formed in 1989 with a Tiverton, Ontario, industrial alcohol plant, is unique in its “kernel-to-glass” supply chain transparency and its ability to “punch above its weight.” And don’t let the term “familyowned” characterize the size of the company. Greenfield is a well-known and for-
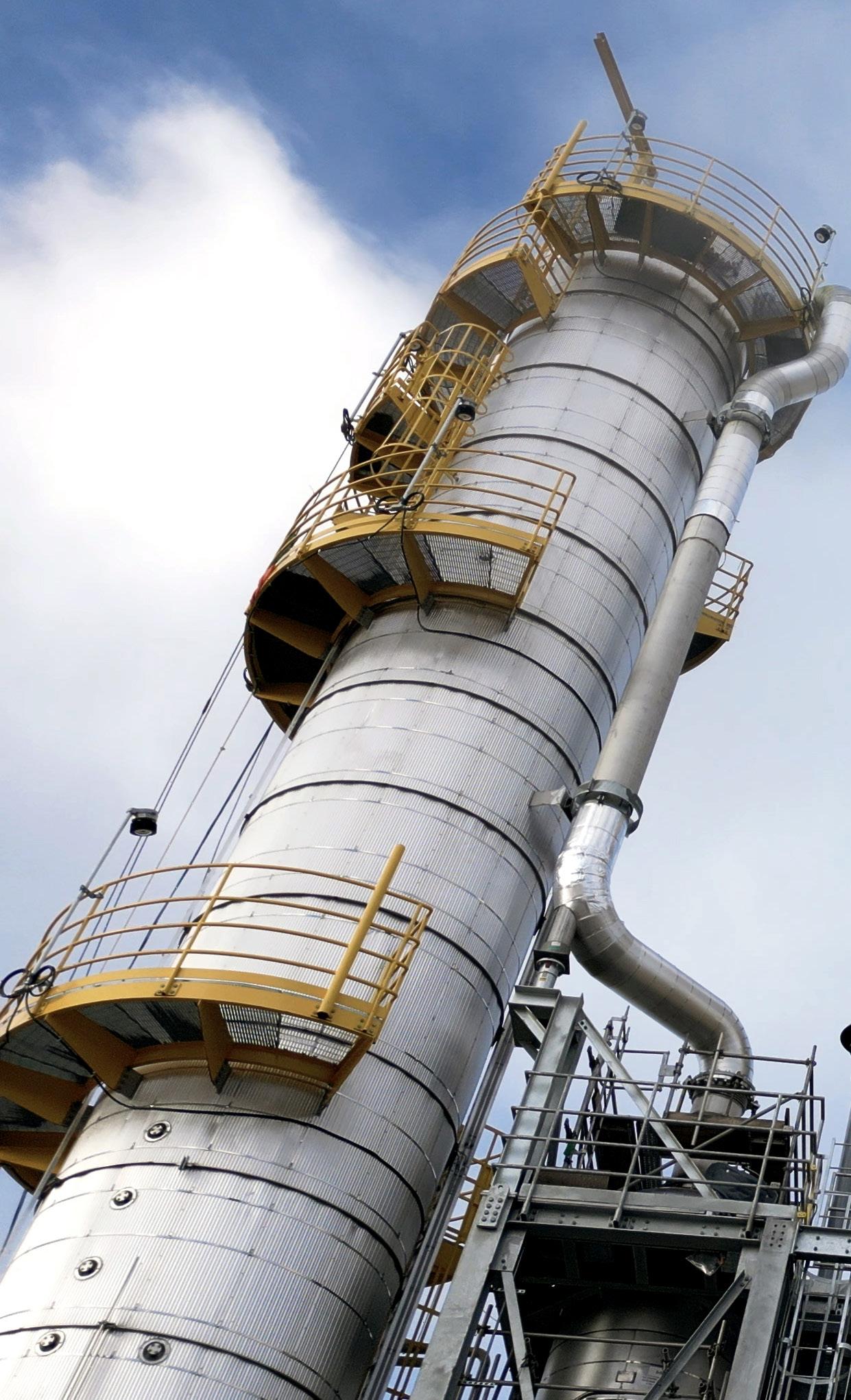
midable international player in the specialty alcohols sector.
The company launched its current corporate brand in 2017, But has been supplying HPAs, specialty solvents and customblended solutions to businesses across more than 50 countries worldwide for over three decades. Greenfield’s network includes three high-purity alcohol distilleries, five blending and packaging facilities and eight warehouses. Its global footprint includes facilities in Canada, the U.S. and, as of 2020, Ireland.
“We are vertically integrated from production to downstream processing,” Hayes says.
As the HPA space continues to grow, supporting the needs of customers in the life
sciences, flavor/fragrance, personal care and other industries like the aerospace and chip manufacturing sectors, the Greenfield team has a strategy in motion to ensure its aspirations continue to match the reach inferred by both the “green” and “global” parts of its corporate name.
Fuel Ethanol's Connection to HPA
“At our core, we produce ethanol,” Hayes says. “Our constant improvements to our distilleries and added production capacity means we are here, now and in the future, to support the demands of [customers seeking] quality and reliable HPA while continu-
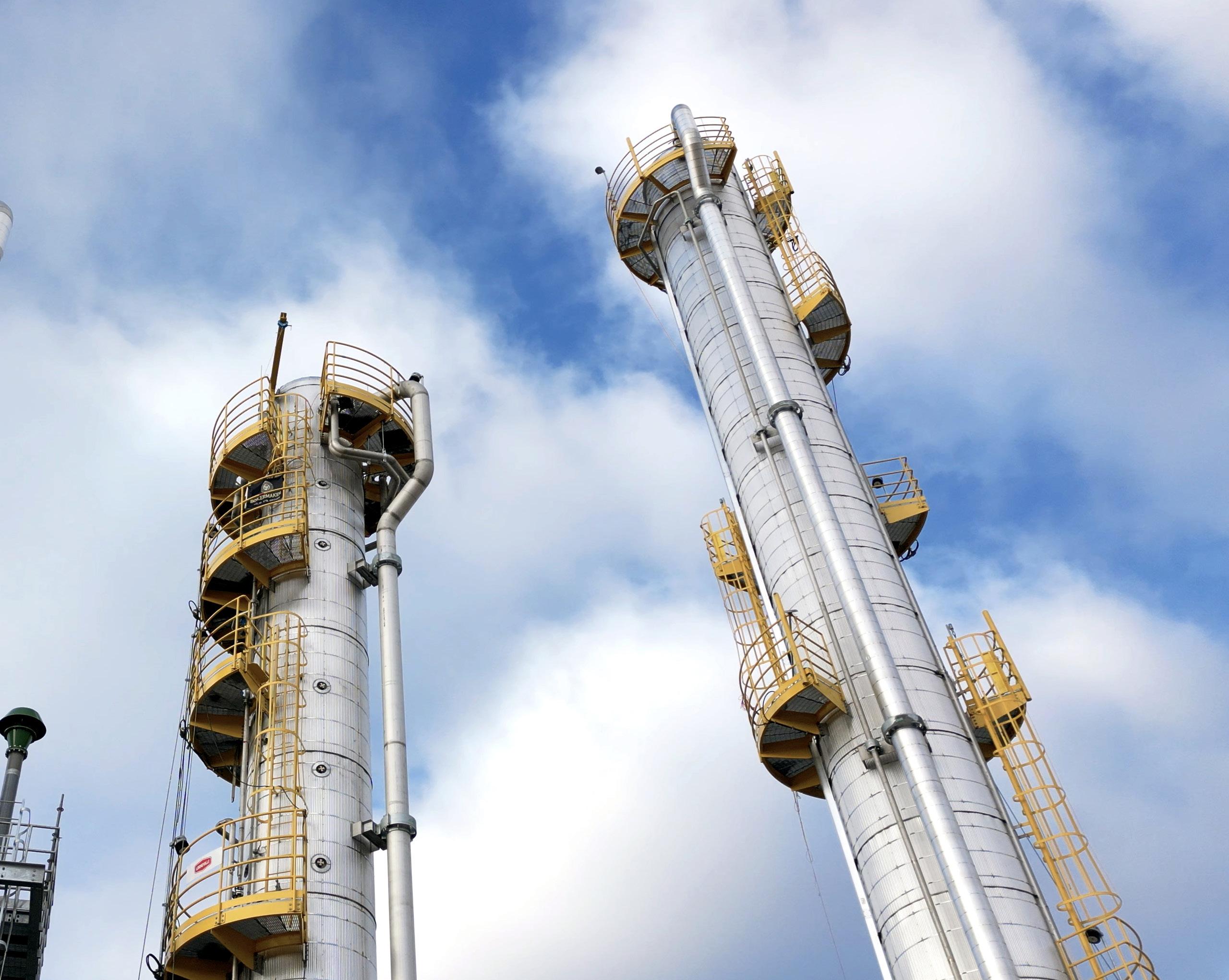
ing to be a leader in reducing our environmental impact.”
In addition to HPA, Greenfield is the largest fuel ethanol producer in Canada and runs four plants in Ontario and Quebec.
From start to finish, the company’s hallmark is its ability to convert grain into highquality, value-added products, Hayes says. In addition to fuel ethanol, Greenfield supplies grain neutral spirits, flavor blenders and a variety of specialty products to customers— in the exact quantities and packaging they need. In most cases, the company can deliver within one to three days, even during peak seasonal demand.
In the HPA space, Hayes says, customers are relying on Greenfield more and more
to not only provide raw-material alcohol products, but to create blends and solutions that a client may have formerly produced in house. “Because they can rely on our quality systems, they are willing to outsource some of their internal processes to [us],” she says. So, as the industry has become more integrated, the customer process and quality systems have become more important than ever.
Transparency and Sustainable Offerings
Part of the allure of Greenfield is its ability to provide supply chain clarity, or as its management team calls it, kernel-to-glass
transparency. Creating a reliable supply chain means providing full product documentation, regulatory expertise and scalable packaging solutions.
Greenfield maintains the chain of custody from its distilleries to its GMP manufacturing facilities. Doing so allows for full quality control and supply chain transparency at every step. The company deploys onsite quality control and microbial labs with state-of-the-art instrumentation, along with onsite generation and storage for USP (U.S. pharmacopeia-grade) purified water and water for injection. Plus, they provide certificates of analysis on raw materials as well as finished goods.
“This is important to the customers because it means a reliable partnership can grow with them in terms of R&D,” Hayes says. “We can meet them and serve them wherever they are in the procurement process.”
Transparency also applies to product and supply chain sustainability, something Greenfield’s customers are increasingly looking for. “We continue to see customers seeking vendors that have sustainable product offerings and sustainability platforms,” Hayes says.
According to the Greenfield team, they were working on sustainability before it ever became a buzzword. “We have been doing this for 30 years, and our ability to help navigate the regulatory landscape can help mitigate the risk in handling certain raw materials,” she adds. As sustainability programs continue to evolve, introducing ways to compensate farmers or product suppliers for sustainable practices, Greenfield seems to be positioned well for the push for clean, low-carbon intensity products. That push all
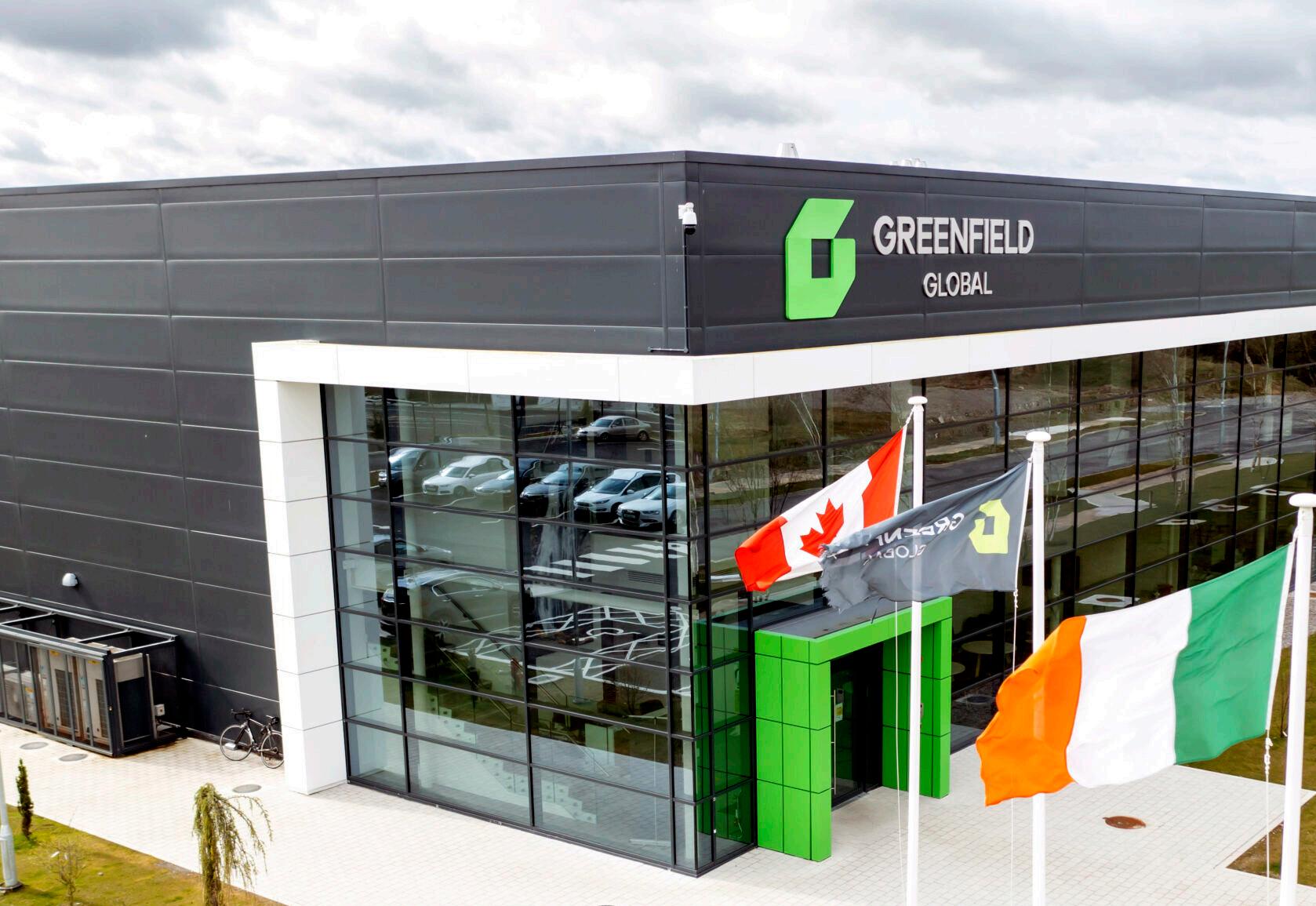
starts with the ability to track and source materials from beginning to end. The ability to track inputs and include transparency in its processes allows Greenfield to ensure that whatever product or process being touted as sustainable, whether that input is its supplier’s or its own, is actually true.
Expanding the HPA Footprint
Greenfield has steadily grown since its inception, but in the past three years, the growth of its HPA and specialty solvents production capacity has been especially pro-
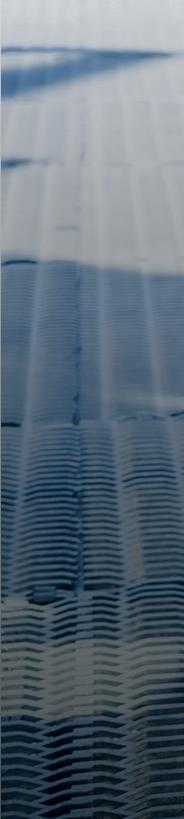
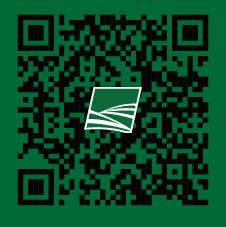

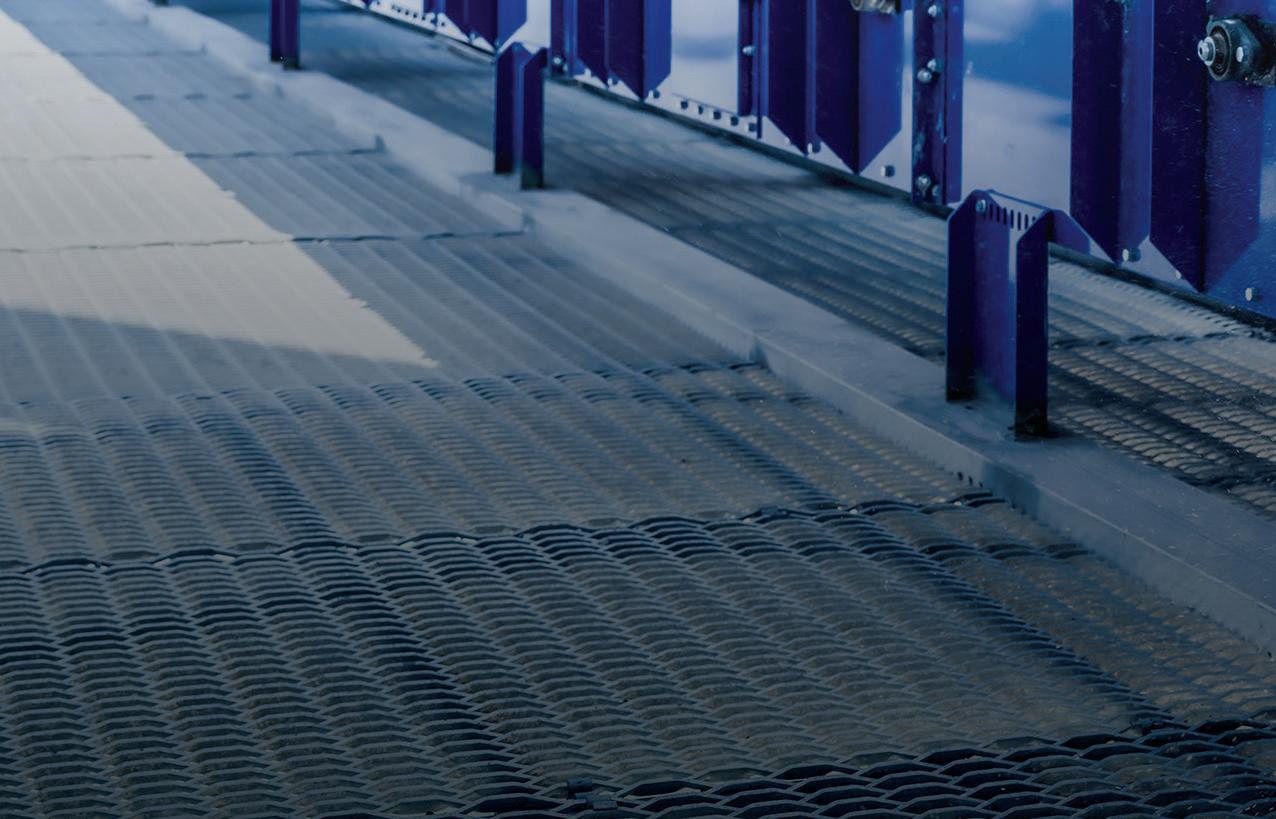
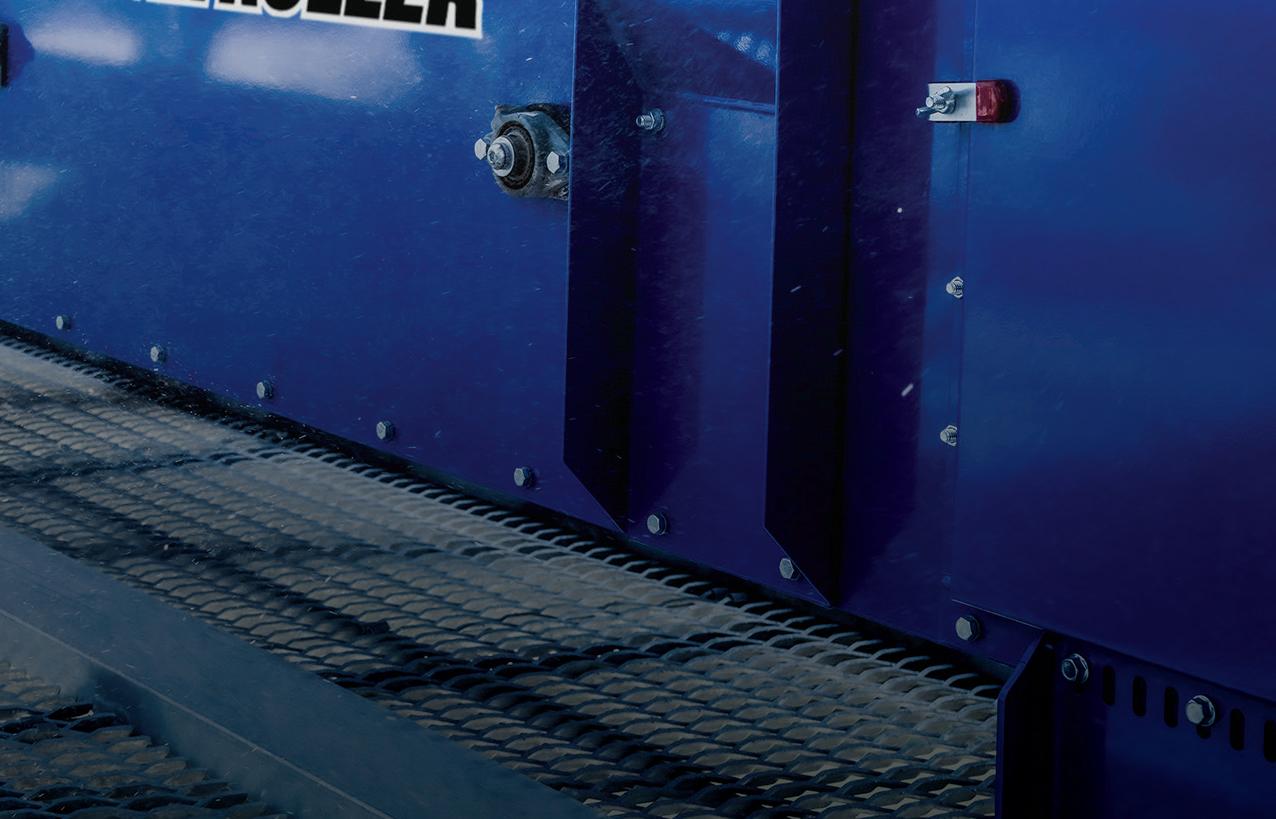

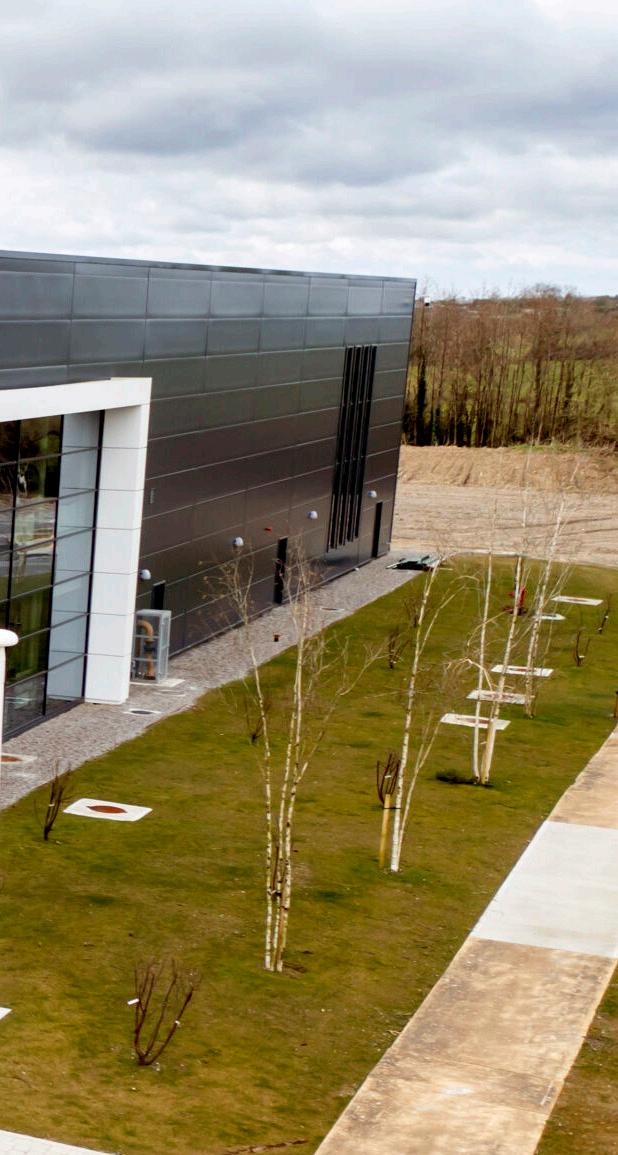
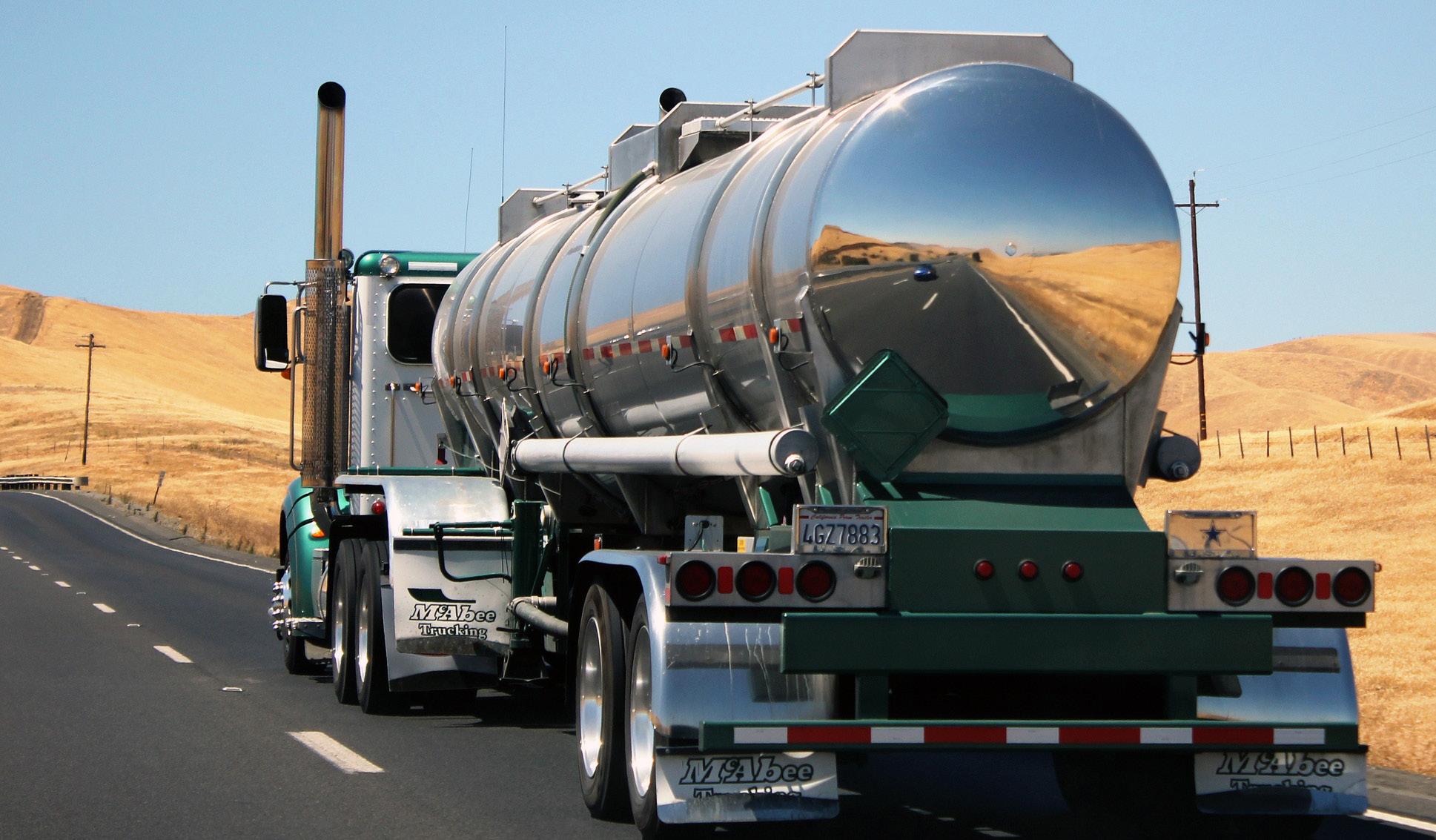
nounced. In 2022, the company tripled its production of ethanol blends with waterfor-injection at its Connecticut plant. The capacity increase subsequently provided greater confidence to labs, medical device makers and pharmaceutical companies, large and small, around the globe—knowing they could get product when they needed it.
Prior to the Connecticut expansion, Greenfield opened a facility in Ireland to serve life science customers there and throughout Europe. The Ireland facility
sources both ethanol and isopropyl alcohol from dedicated storage tanks. The ethanol is distilled at a Canadian plant before being shipped to Portlaoise in central Ireland.
In August 2023, Greenfield expanded its supply chain capabilities with a new ware-
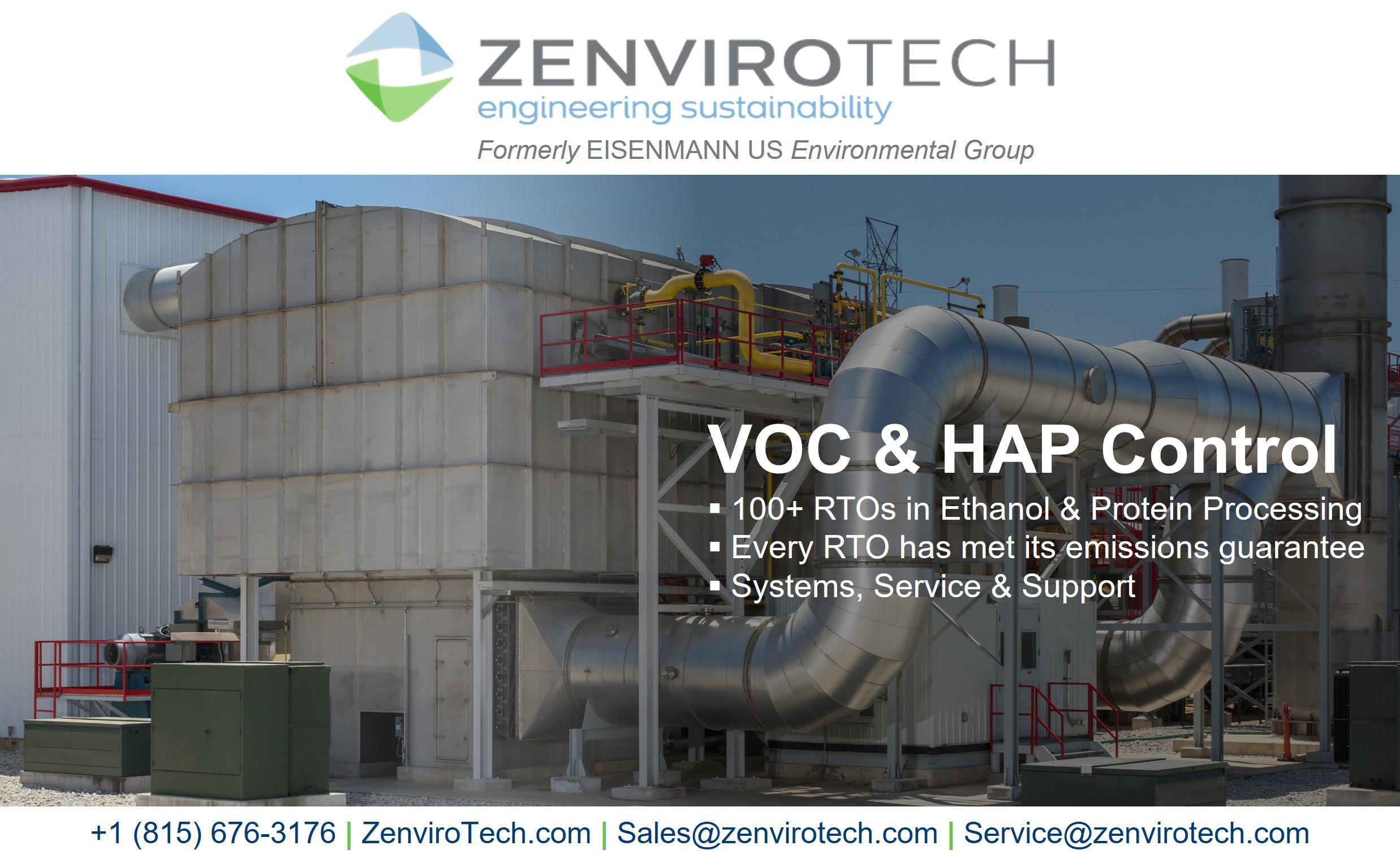
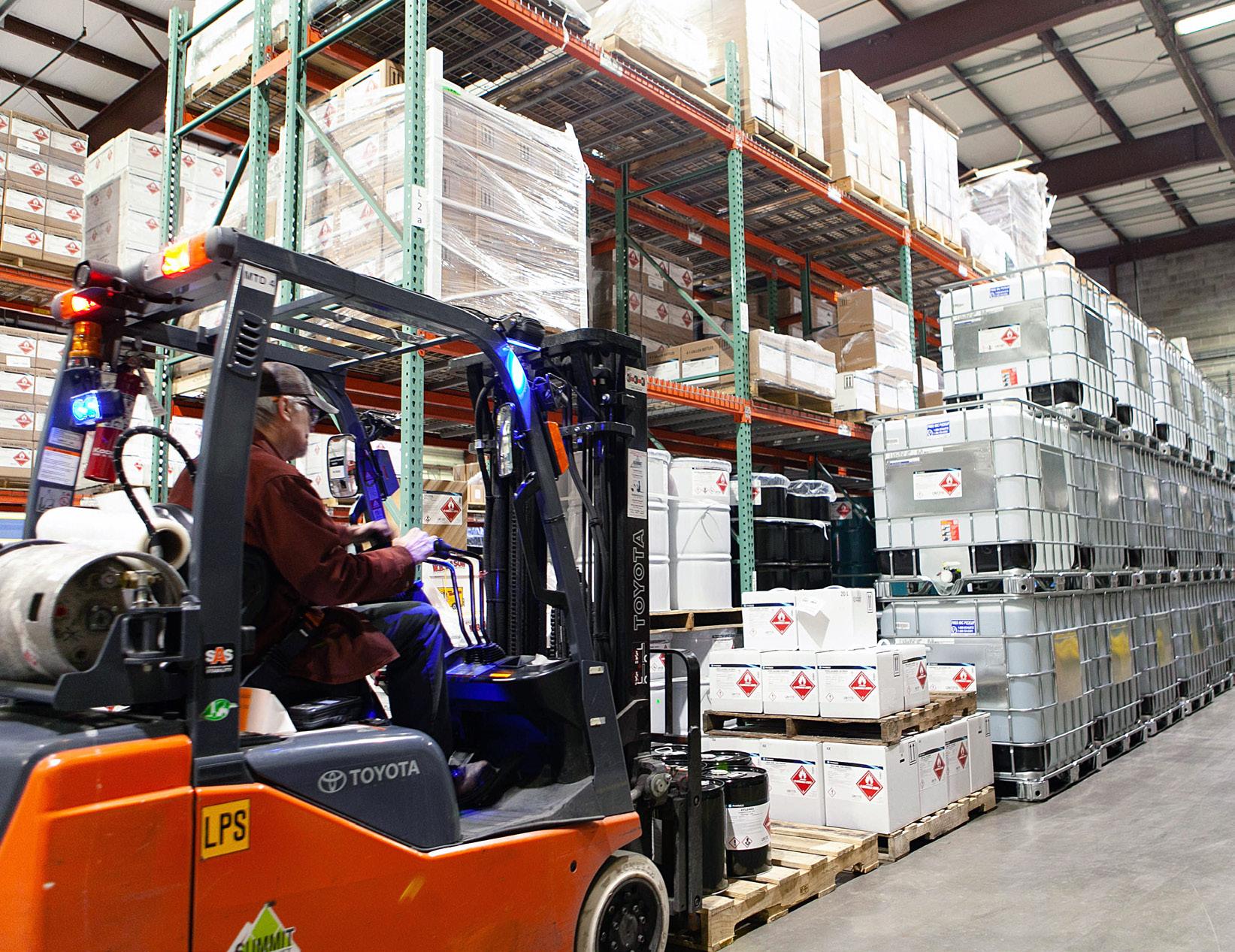
house for supplying methanol, acetone and acetonitrile for hospitals, labs, universities and pharmaceutical companies.
Last September, the comapny made a 30-million-gallon HPA upgrade to its Johnstown, Ontario, distillery to be able to ship 190- and 200-proof alcohol by tanker truck
and rail to blending facilities in Canada, the U.S. and Europe.
Howard Field, president and CEO, said the expansion would ensure greater security of supply across three HPA distilleries, “especially at a time when older, less economically viable distilleries in the industry are
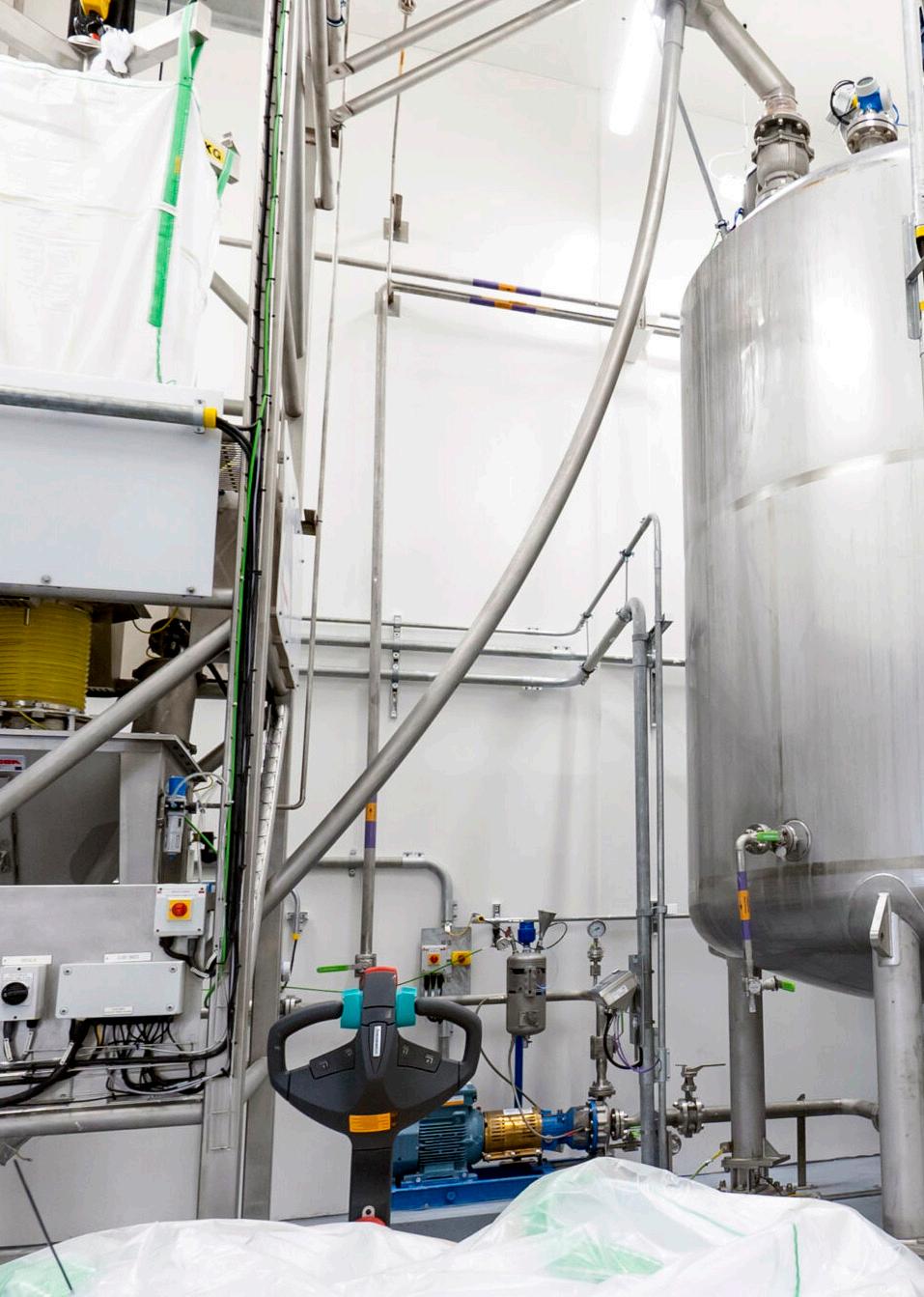
shuttering,” he explained at the time. Just four days after the expansion announcement, Greenfield announced a strategic partnership with REMET Alcohols Inc. to supply HPA to California and the western U.S. John Paraszczak, president and CEO of REMET, said the agreement was a win-
Inside Greenfield’s Specialty Chemicals and Ingredients Business
The HPA expansion work of Greenfield isn’t the only reason why the company is growing. Its Specialty Chemical and Ingredients business is also thriving.
Greenfield Global’s Growth at a Glance:
• Packaging facilities in Ontario, Connecticut, Kentucky and Ireland
• Bulk ethanol, solvents and other raw materials received by railcar or truck then packaged as pure or blended forms
• Customers include: beverage, pharma, hospitals, universities, food and flavor, fragrance, extraction, industrial solvents
• Packaging options: pint, gallon, pail, drum, one-way tote, returnable totes, pressurized returnable containers, bulk tanker truck
Basic Processes Performed
• Packaging in various configurations
• Formulation blending
• Clean room packaging
• Quality control analysis and product quality certification
• Quality system certification
• Warehouse distribution management (U.S. and Canada)
• Logistics management (global)

win to connect REMET’s bulk blending and distribution service with “Greenfield’s gold standard quality in ethanol production.”
One of the main communities that REMET serves is Los Angeles.
HPA IN ALL SIZES: To serve customers across several industries, Greenfield Global will package HPA products in sizes ranging from pints to totes (left) to bulk tankers. Right, a big part of what makes the company unique is its strict adherence to transparency and quality testing during every part of the HPA production process.
PHOTOS: GREENFIELD GLOBAL
Hayes says the partnership with REMET solidifies Greenfield’s position as the only grain alcohol producer in North America with manufacturing, packaging and distribution capabilities nationwide serving key industries.
“This expansion not only enhances supply chain efficiency but also ensures greater accessibility to customers in fast-growing markets across California and neighboring states like Nevada, Utah, Oregon, Washington and Arizona,” she says.
The family-owned company that began nearly 35 years ago with a single alcohol plant in southern Ontario has embarked on a strategy of international growth and product
diversity that has clearly worked. It now has 18 HPA, ethanol and packaging sites across North America and beyond, shipping products to more than 5,000 customers in almost 50 countries worldwide. Producing HPA from grain-based ethanol, along with specialty ingredients, has helped Greenfield reach customers in several industries, all of which exist globally at a large scale (pharma, healthcare, universities and even aerospace). It’s always been apparent that Greenfield has been on a growth journey across Canada and the U.S. Today, it’s increasingly clear that it’s also a leading HPA supplier with global reach and an uncompromising commitment to quality.
Author: Luke Geiver Contact: writer@bbiinternational.com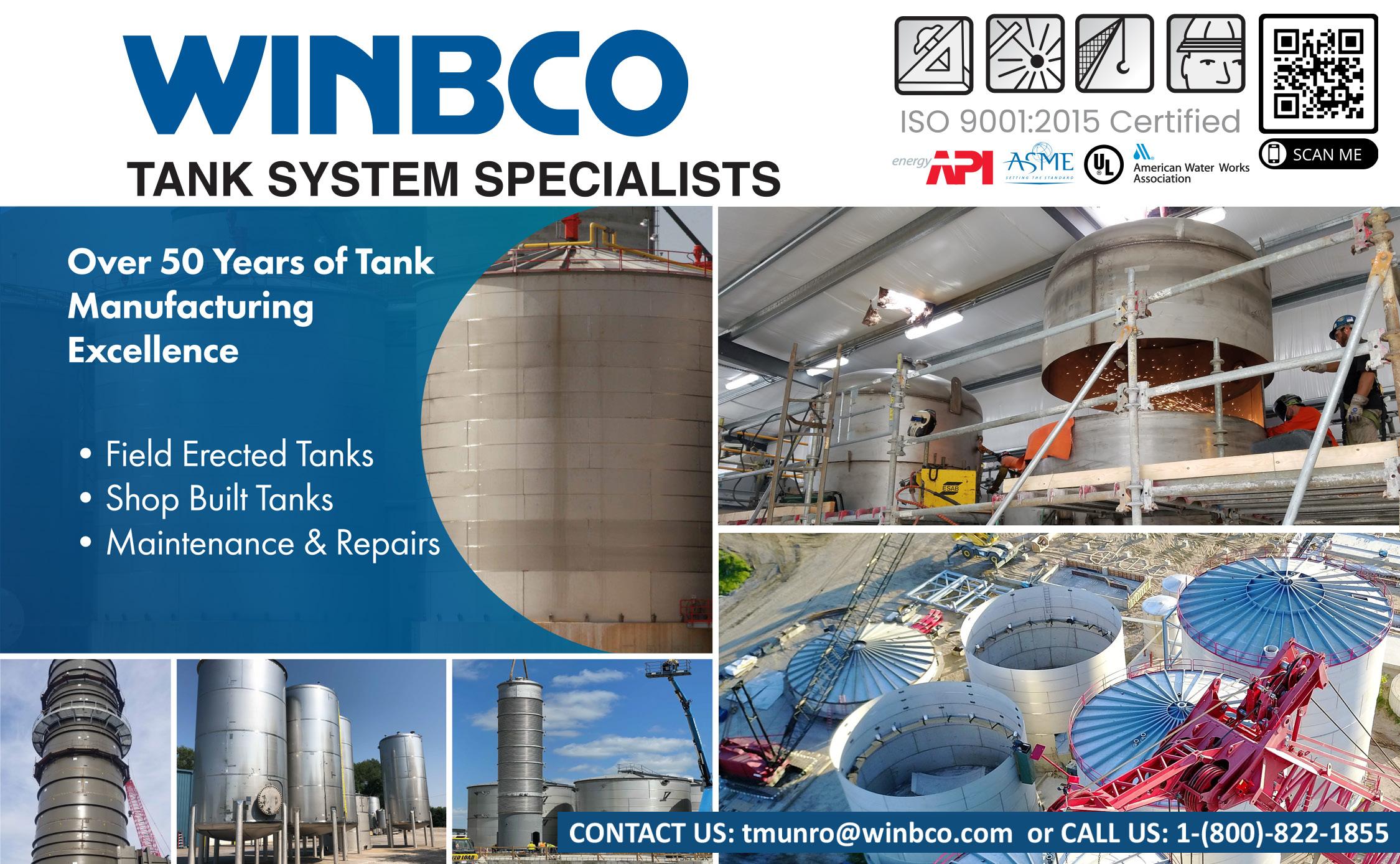
LOW-CI ETHANOL MADE FROM MILK
A dairy producer in Michigan is partnering with a vodka manufacturer to make low-carbon ethanol out of a dairy byproduct.By Katie Schroeder
Corn starch is far and away the most common ethanol feedstock in the United States—94%, according to the U.S. Department of Energy—however, throughout the years, a variety of other feedstocks, ranging from corn stover to wheat straw to milo, have been used. One distillery is utilizing an unusual feedstock, one experimented with during the 1970s oil crisis, to make ethanol.
Milk permeate is a byproduct made when milk is filtered for a variety of products. The process begins with removing fats for butter and ice cream production, leaving behind skim milk. To make it efficient for cheese and yogurt manufacturers, some dairies concentrate the remaining skim milk even further, retaining the proteins and separating out the milk permeate, a mixture of water and lactose. Although it is typically disposed of through animal feed, the sugar content in lactose makes it a great feedstock for alcohol production, explains Omid McDonald, founder of Dairy Distillery. He originally founded the company to use milk permeate as a feedstock for vodka, making a product branded Vodkow.
“The way we got into this was my cousin had come back from his local dairy farm, and they were talking about excess milk being dumped, and I said, ‘Whoa, can that be turned into alcohol?’ And the idea was to do a craft distillery to make vodka, but very early on I learned just how much of this byproduct is out there, and how it’s a problem for the dairy industry as a whole,” McDonald explains.
McDonald turned to David Geros, a process engineer with experience in cellulosic ethanol production, to explore the economic business model of turning milk permeate into ethanol. In 2021, the Michigan Milk Producers Association, the tenth largest dairy farmer-owned cooperative in the United States, reached out to McDonald about utilizing milk permeate to make vodka. In this case, the feedstock would be a variety of permeate produced via ultra-filtration (UF) at the co-op’s Constantine, Michigan, plant. After realizing that the amount of milk permeate made at the plant would create 47 million bottles of vodka—a volume that would be difficult to sell into the market—Dairy Distillery and MMPA pivoted to ethanol production. Planned to come online in Q1 of 2025, the Constantine facility will make 2.3 MMgy of low-carbon ethanol.

Profitability and Sustainability
Currently, the facility sells the milk permeate to local pig farmers at a very low value—essentially giving it away—explains Joe Diglio, president and CEO of MMPA. “Because we represent dairy farmers, and we take their milk to the marketplace, it was important for us to find an alternative solution,” he says. With consumers’ increased interest in the proteins found in milk, UF
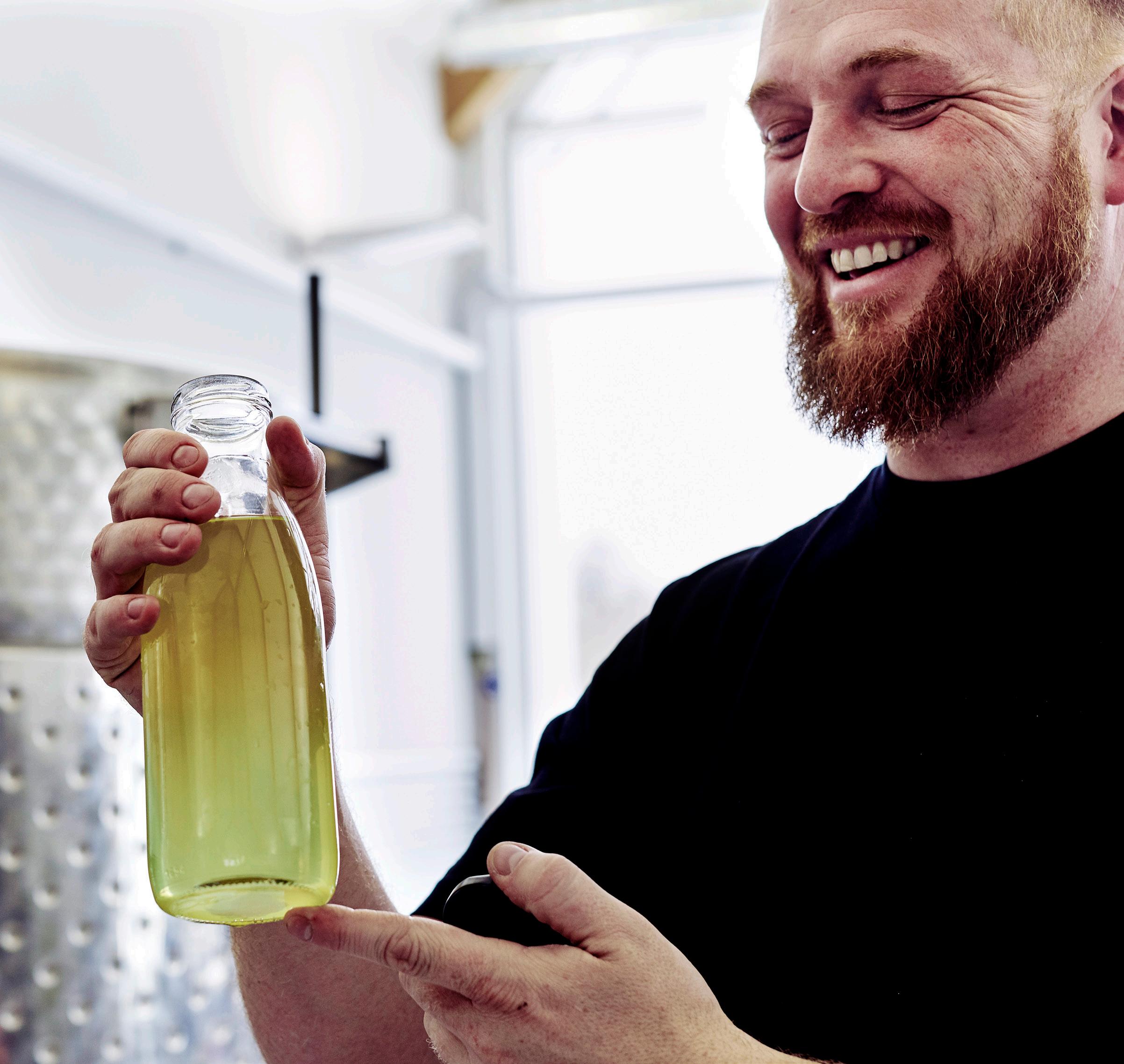
systems are becoming more common, and more left-over milk permeate is being made as a result. McDonald explains that it is not necessarily an ideal ingredient for pig farmers: a limited amount of it can be fed to the pig, and it is a challenge for farmers to handle the byproduct in its liquid form. “This is not a huge amount of ethanol like the corn guys [produce],” McDonald says. “We’re not going after corn ethanol; this is a way for dairy to be able to get into a new market and diversify their portfolio. As Joe [says], it’s about
finding value, but also resiliency. It allows them to have a revenue stream that’s totally independent from the dairy side, which just provides more resiliency and safety for their members.”
Turning the milk permeate into lowcarbon ethanol is a great opportunity for MMPA to advance its decarbonization efforts. As the project was being designed, Dairy Distillery commissioned EcoEngineers to do the carbon accounting for the project; an important step for determining
the carbon intensity of the fuel and the profitability of the project. Completing this step has been time consuming due to the amount of paperwork involved, Diglio explains.
MMPA started pursuing this project before the Inflation Reduction Act became a reality, but it was “lucky” timing for the project developers. Half of the project’s cost is attributed to the biogas production process that is eligible for IRA investment tax credit support, McDonald says. The ethanol’s low CI number of 15 gives it opportunities in
READY TO GET MORE OIL?

What can 5% more oil mean to your operation?
Contact us today to learn more about how Overdrive™ can help you turn oil production all the way up
several markets, from the SAF industry to the low-carbon fuel programs in California, Canada and other areas. “A lot of the folks that [will] utilize the product coming off of Constantine’s … production [are] looking to attach themselves to a project like this to get the creditability established with the sustainable message that we’re creating,” Diglio says.
Process Design
Lactose fermentation is an unusual process, but it has been done before, McDonald explains. In the ’70s and ’80s, dairy producing countries like Ireland and New Zealand experimented with the process to make ethanol to help ease the supply pressure caused by oil shortages. However, many of those facilities shut down because they were unable to compete with corn-based ethanol production. Dairy Distillery started working with the University of Ottawa to research lactose fermentation in 2017 and has spent the last five years developing the process.
McDonald outlines the steps involved in moving milk permeate from the milk producer to the distillery, and the processing needed to turn it into ethanol. First, the milk permeate will be piped from the dairy under the road over to the distillery. Then, it will be pumped into fermentation tanks, and yeast will be added to ferment the lactose into ethanol. After that, the ethanol is sent to the stills to be concentrated and separated, and finally, purified for use as an on-road fuel or SAF feedstock. The waste stream will be sent to an anerobic digester that turns it into biogas used to power the stills. After it is run through the aerobic digester, the water is then treated and discharged into the river.
There are several advantages of using milk permeate as a feedstock; for example, it already contains all the water needed for fermentation and there is no milling step required, explains McDonald. This means feedstock processing requires only a small amount of energy, keeping the carbon intensity of the final product low. However, the biggest benefit is the fact that the byproduct is a waste stream, so the ethanol production does not need to account for
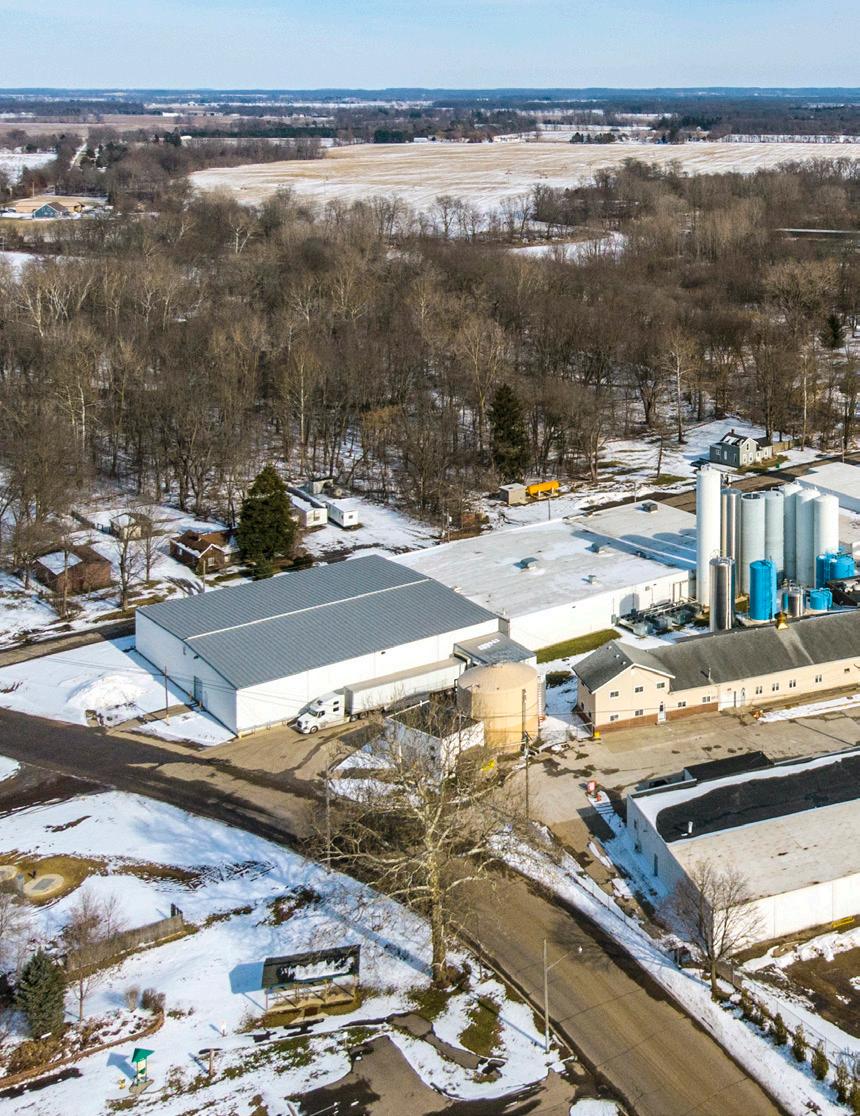
any upstream carbon impact coming from producing the milk permeate. “Another advantage is after we finish our fermentation [and] distillation process, our waste stream is put into a digester that generates biogas to power all the energy needed for the stills to further reduce the carbon intensity,” McDonald says. “So … it's actually a carbonneutral sugar, and a very efficient production process that gets our CI so low.” According to calculations, the ethanol produced at the Constantine plant will be 15 grams of CO2 per megajoule, most of that number comes

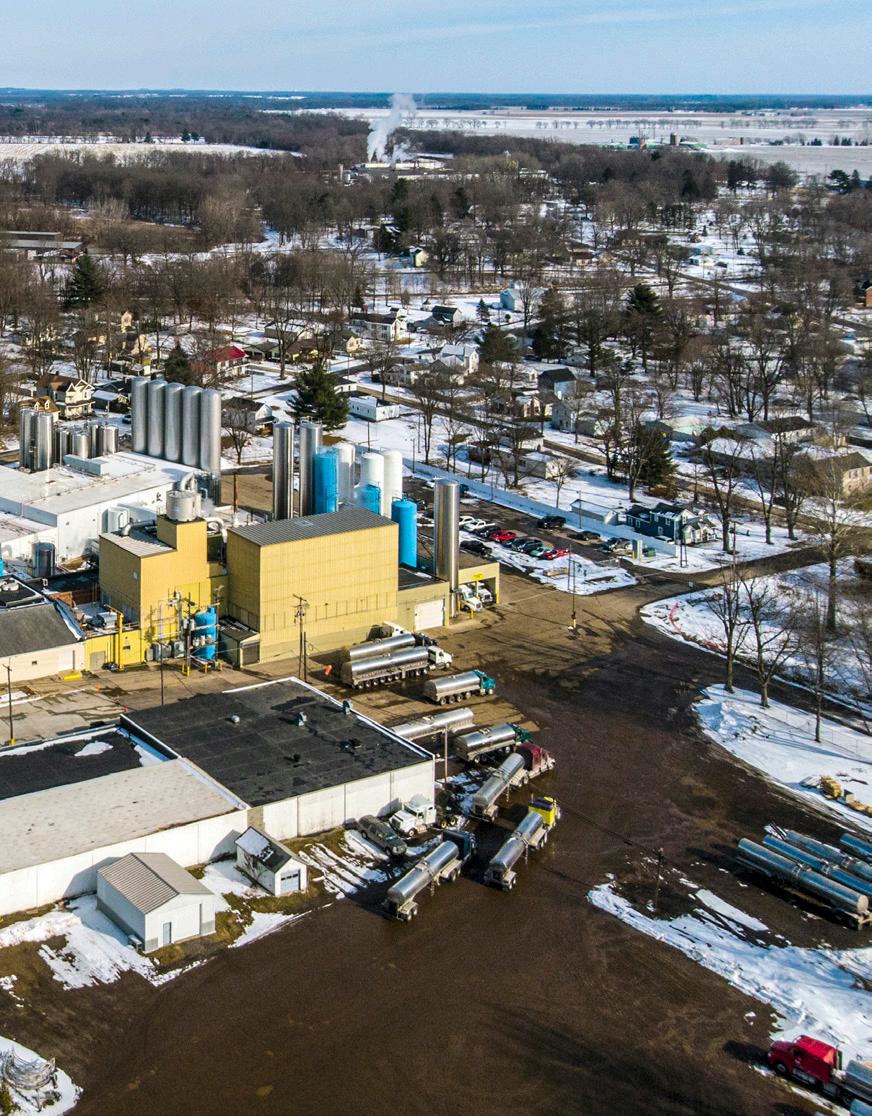
from Michigan’s electrical grid, which is not as clean as some other states.
The disadvantage of using a waste feedstock is that the volume of feedstock available is typically finite. However, the Constantine facility is a great fit for the technology because, due to its ultrafiltration system, the plant produces a good amount of accessible, continuously available byproduct.
Although the volume of ethanol produced is limited, the decarbonization potential made this project an important step toward achieving MMPA’s sustainability goals.
BYPRODUCT REMOVAL: The Constantine, Michigan plant produces 16,000 tons of permeate each year. Currently, the permeate is sold as a feed component to nearby pig farmers.
PRODUCERS ASSOCIATIONEvery ton of permeate that gets converted to ethanol displaces a ton of carbon, Mc Donald says. “Constantine produces about 16,000 tons of permeate that will create a displacement of [in the end] 16,000 tons of carbon, which represents about 10% of the carbon footprint of the milk that’s produced at Constantine,” he continues. “So, that’s sizeable, maybe one of the largest dairy decarbonization projects out there, and MMPA has a lot to be proud of leading that charge.”
Community Impact
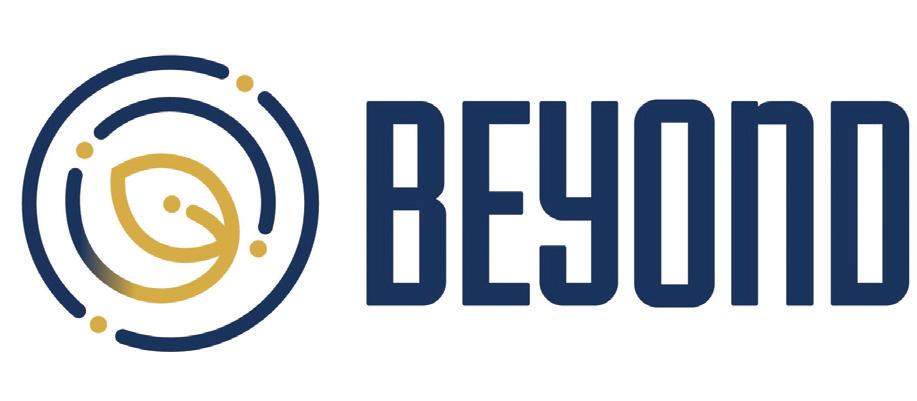
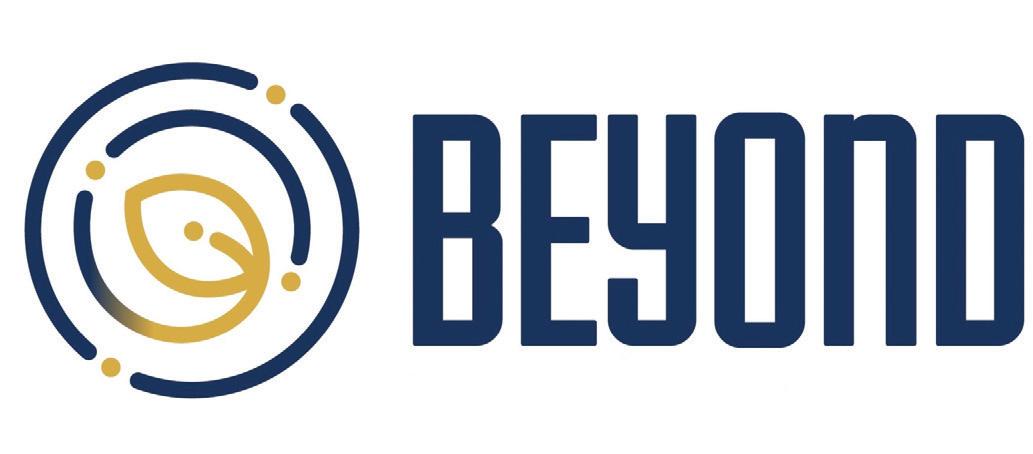
As part of this project, MMPA will leave the Constantine municipality’s wastewater system, instead combining the ethanol plant and dairy facility’s wastewater to produce natural gas, cleaning the remaining water and pumping it back to the river afterward. “We built one single system that takes our distillation waste and the waste from the dairy, produces biogas, which powers the stills, and then cleans the water to river qual-
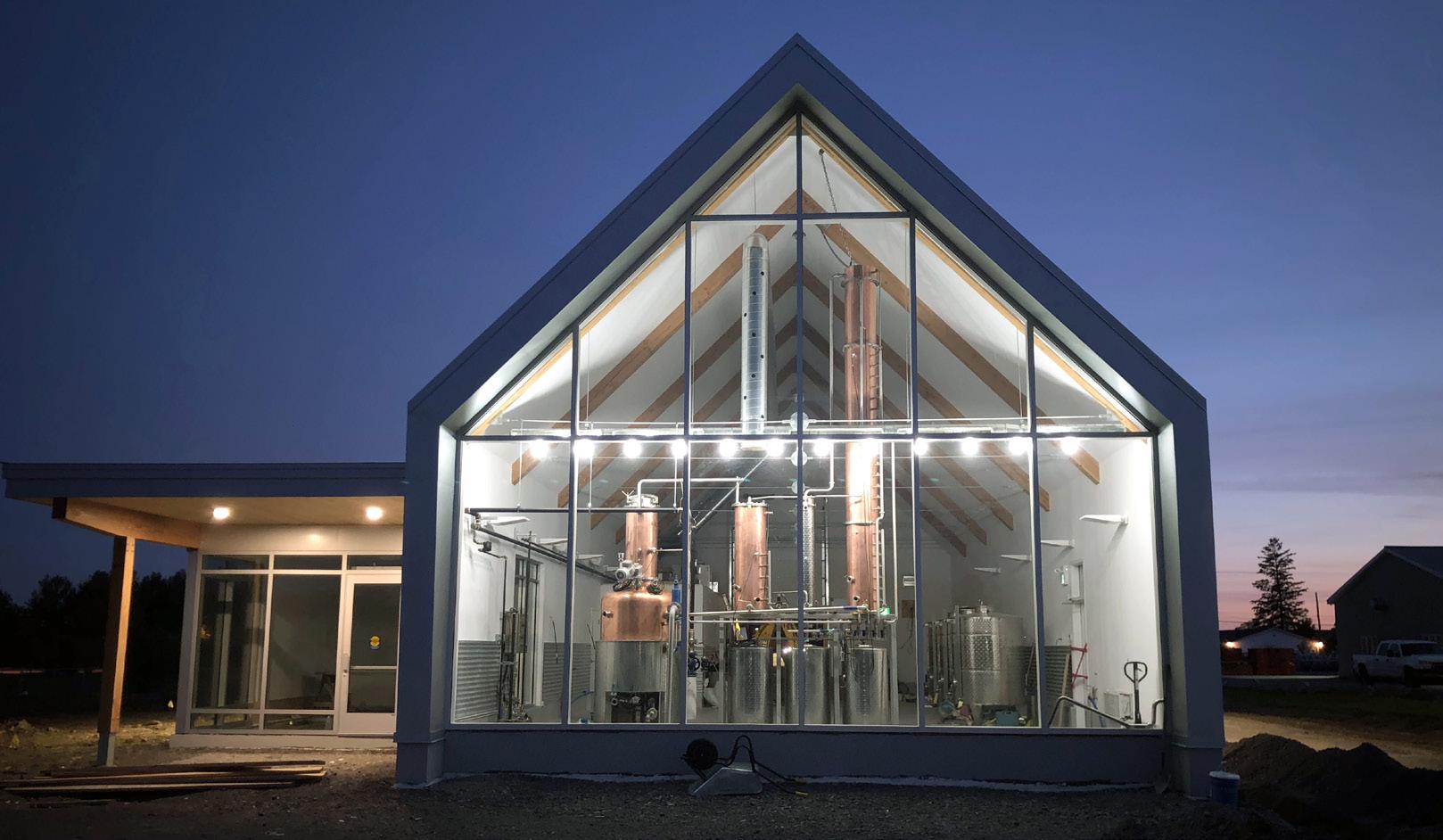

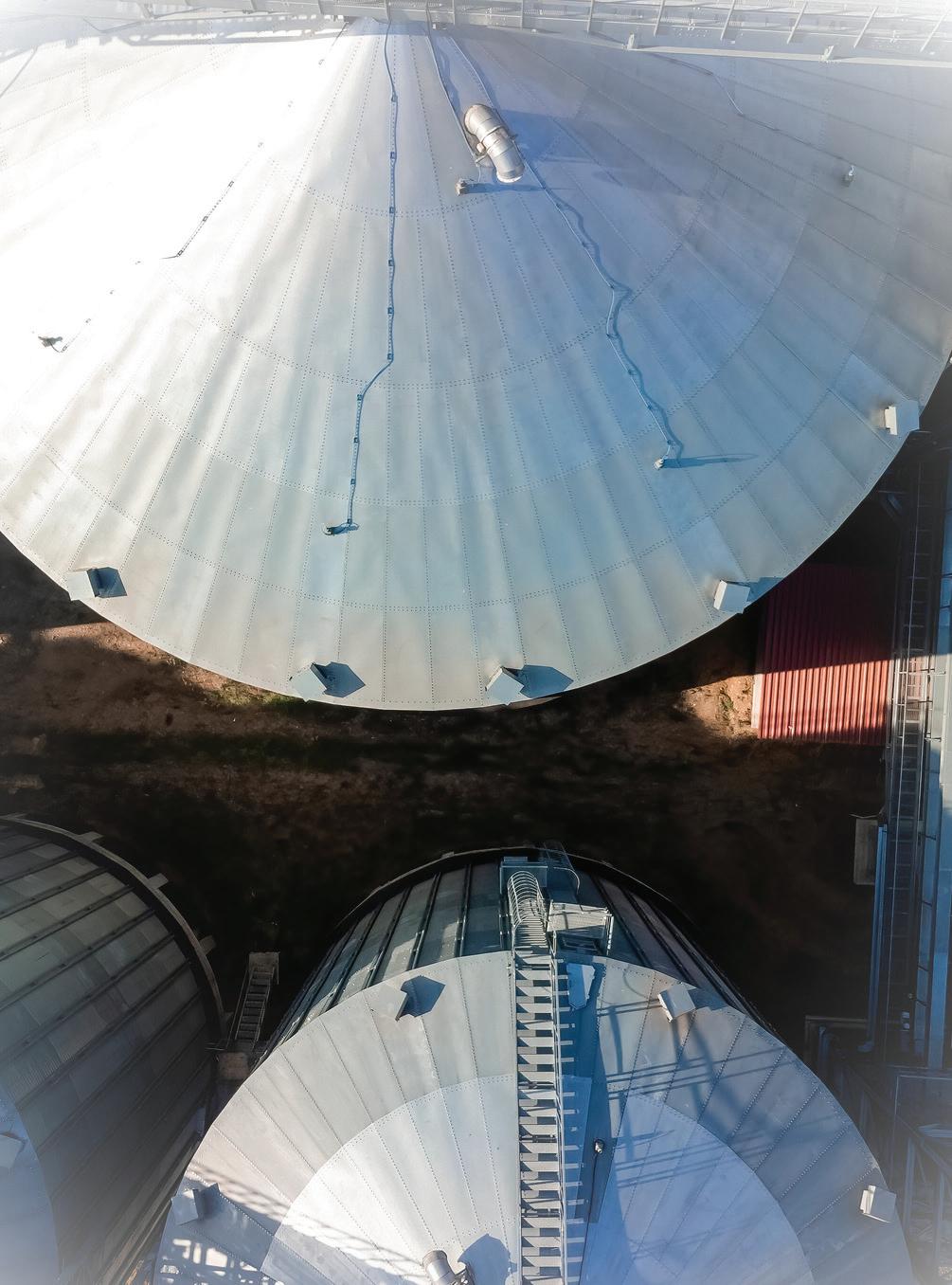
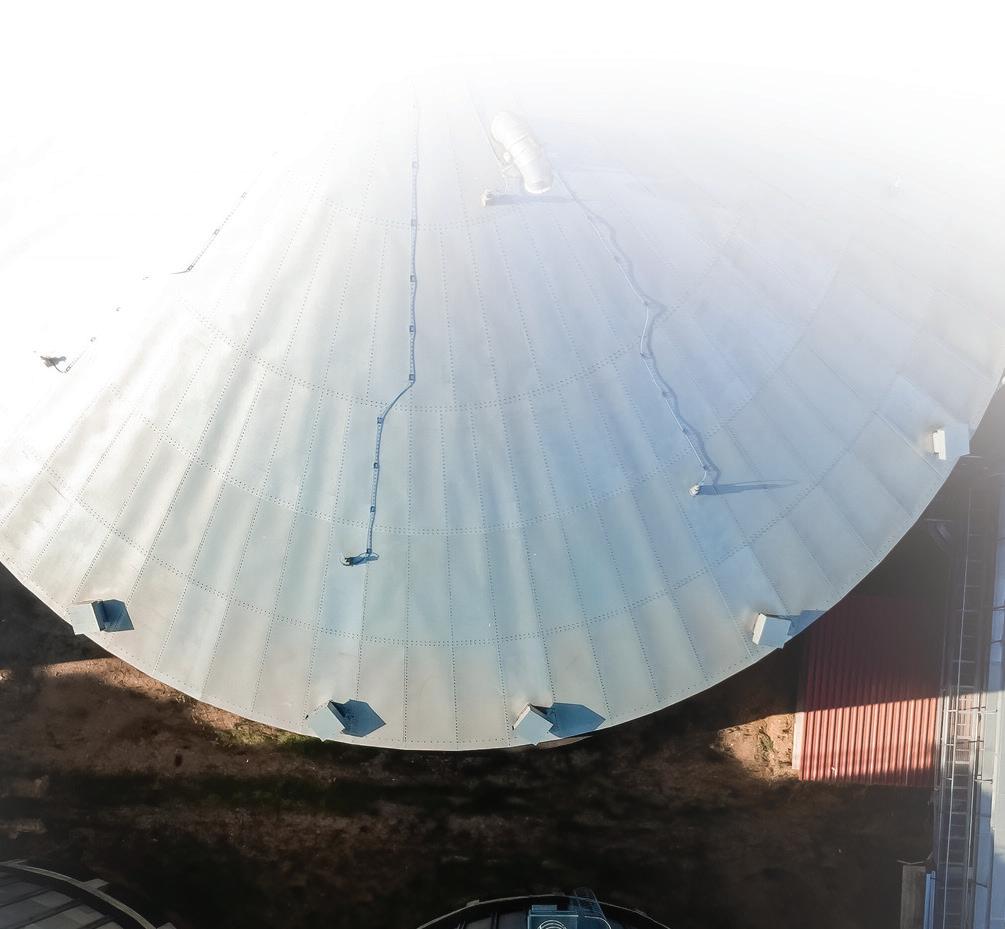
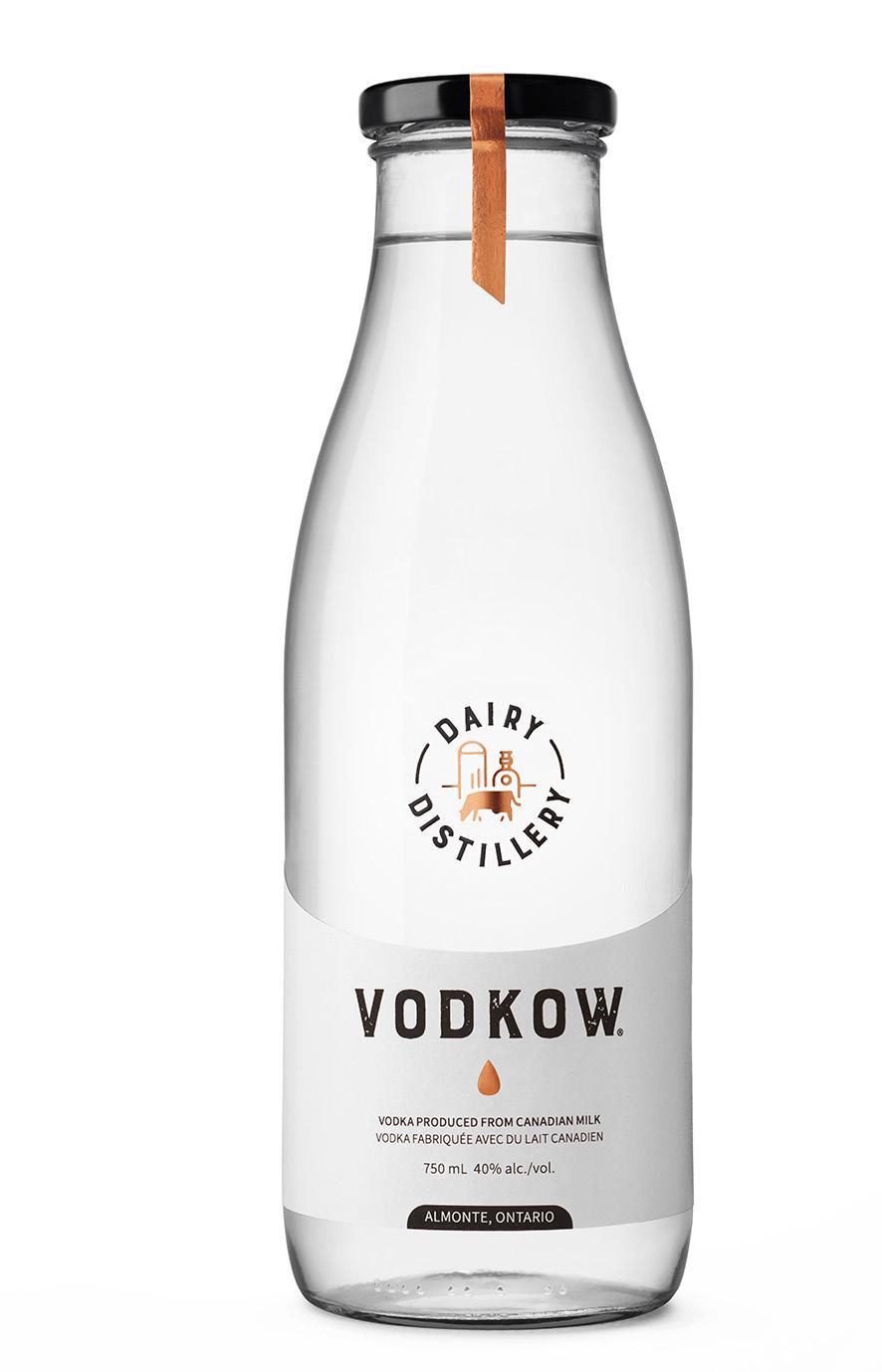
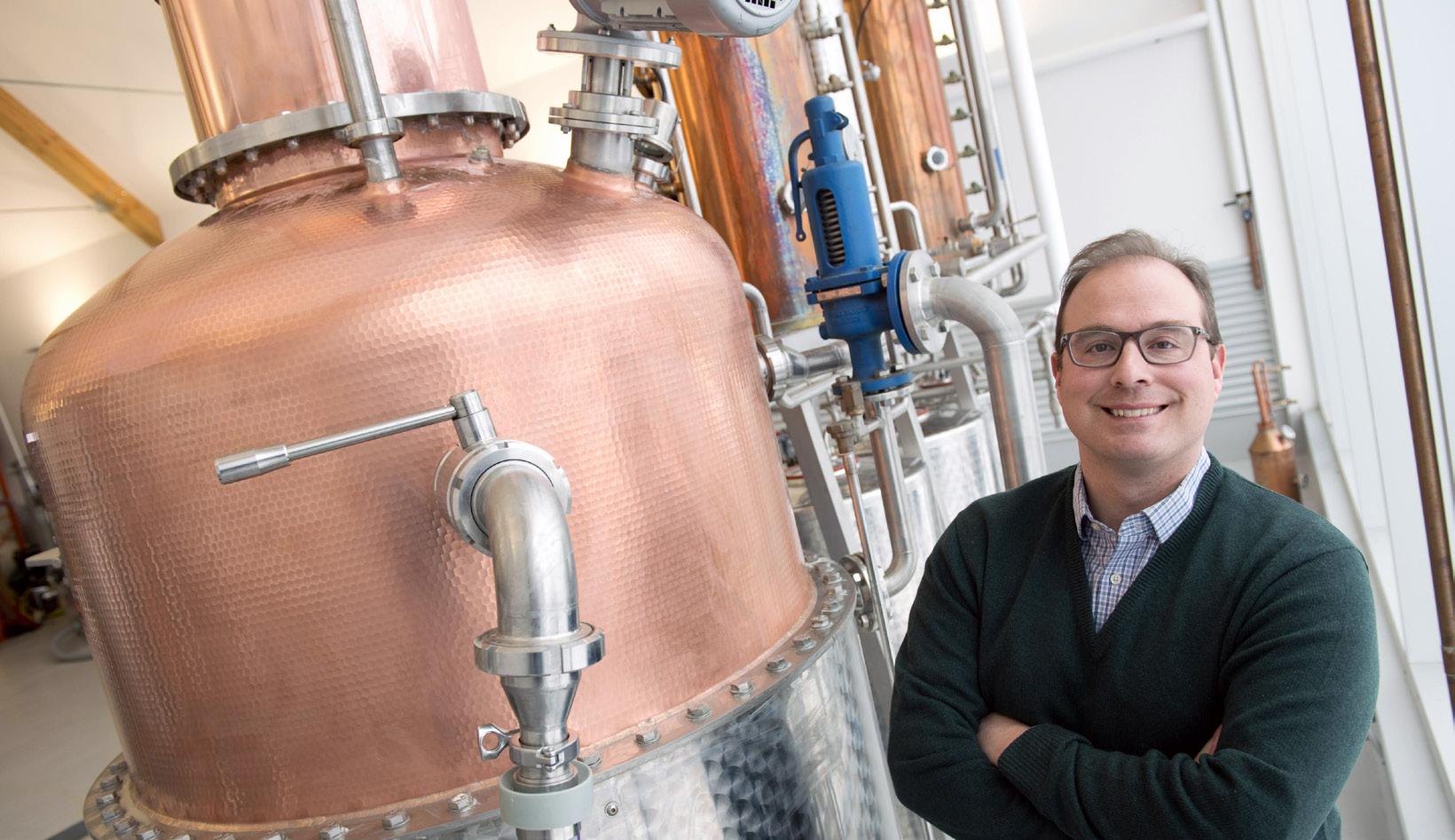
ity,” McDonald says. “And it just discharges to the local river. So, truly it [works like this]: permeate comes in with waste from the dairy and out comes low-carbon ethanol and water to discharge to the river.
The plant has several community impacts, including new local jobs, decreased traffic and decarbonization. It will create 12 full-time jobs and remove the truck traffic
that was needed to send the milk permeate to local farmers. “You’re having basically two plants side by side, which gives this plant the opportunity to continue to expand, continue to innovate, and I think that adds an element to the community as a good steward of a business operation that can generate opportunities for those that live around the area,” Diglio says.
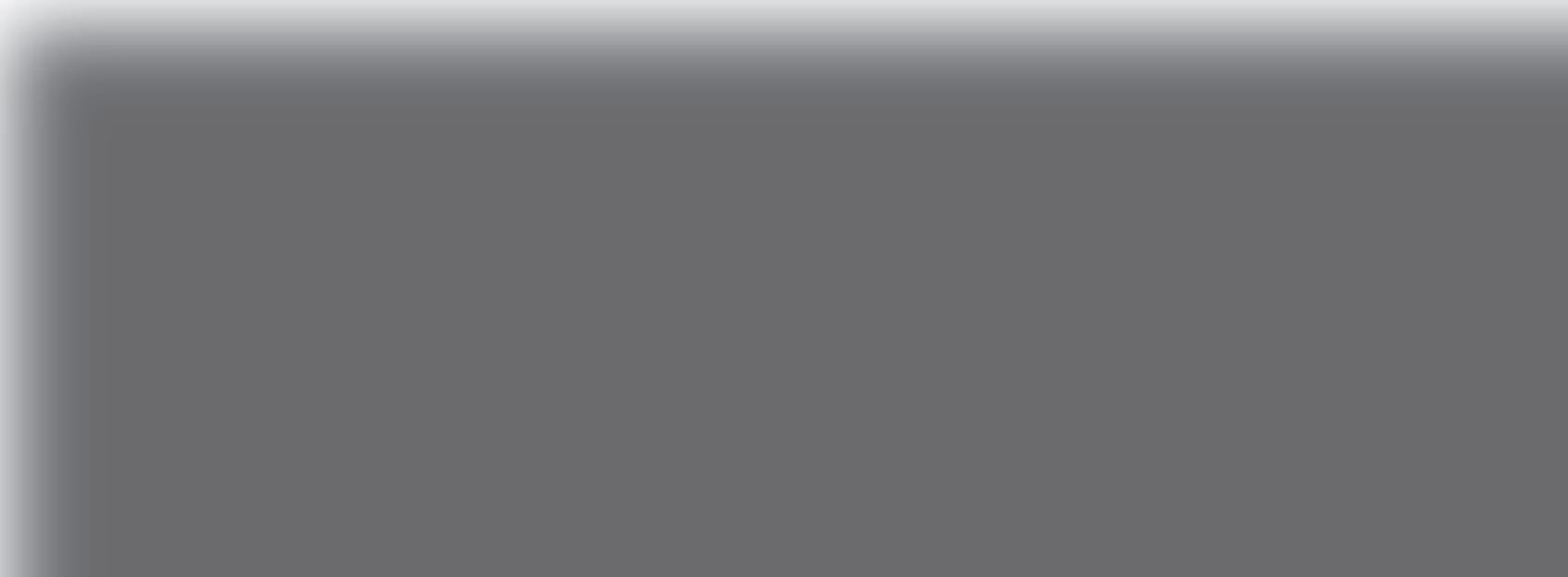
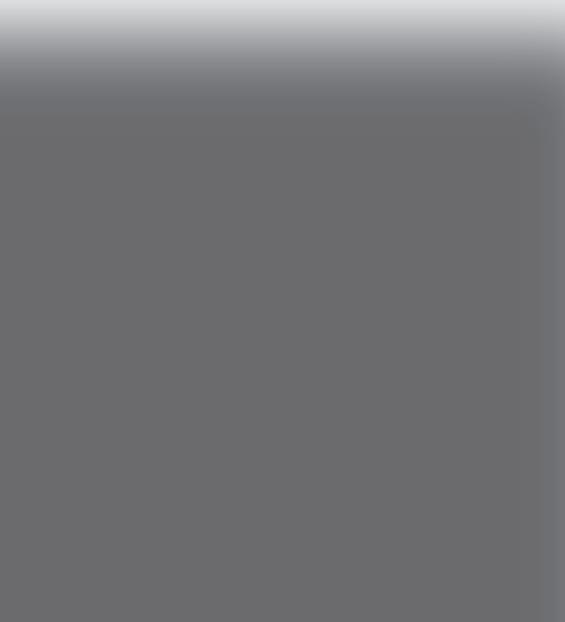
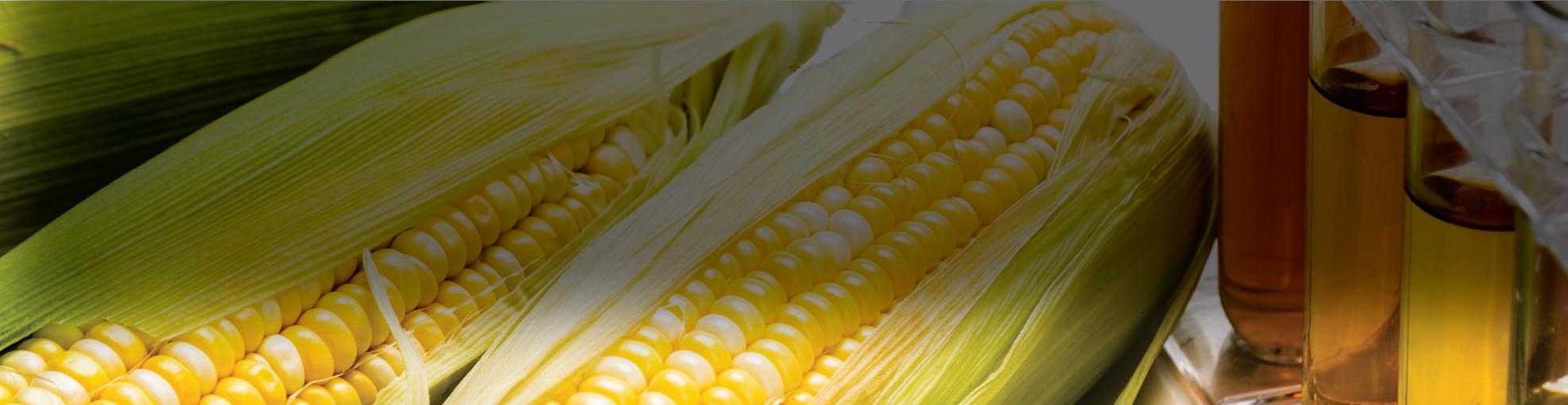
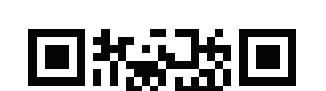
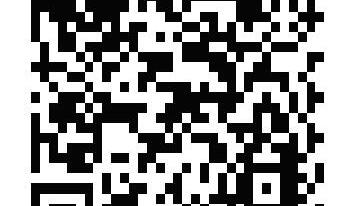
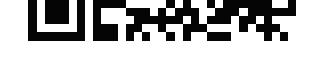

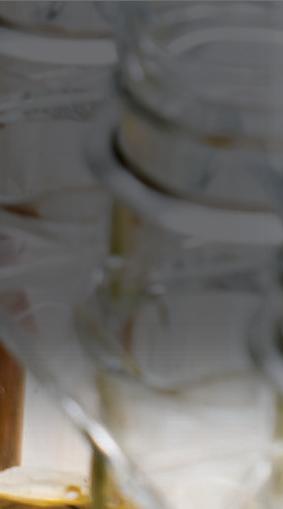
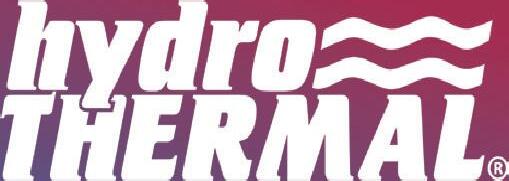

The project has received support from the local government because of the benefits it brings to the community, being granted $2 million by the Michigan Business Development Program along with a 15-year State Essential Services Assessment exemption worth $682,500, according to a press release from the Michigan Economic Development Corporation.
Demand for milk and other dairy products free of lactose has increased in recent years, Diglio says. Although it remains to be seen whether that trend is here to stay, UF systems’ are a valuable efficiency improvement, helping dairy processors produce cheese and other products that don’t need the water in the milk. As these systems are being implemented in the U.S. and Canada,
Dairy Distillery’s lactose fermentation process is an opportunity for dairy farmers to find new value from this waste stream. Moving forward, McDonald hopes to expand Dairy Distillery to dairies across the U.S. and Canada, helping dairy producers maximize value.
“There’s an opportunity for this technology, which has been pioneered through the leadership of MMPA, to be bolted onto dairies across the U.S. [and] here in Canada,” McDonald says. “MMPA’s leadership has gotten the attention of Canadian dairies who often look to the U.S. for guidance, and so to provide both value and decarbonization, which are both central to what all dairy processors need to do.”
Author: Katie SchroederContact: katie.schroeder@bbiinternational.com
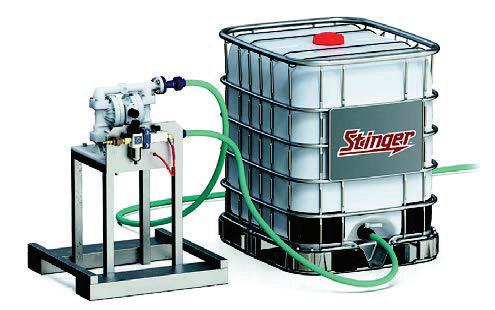
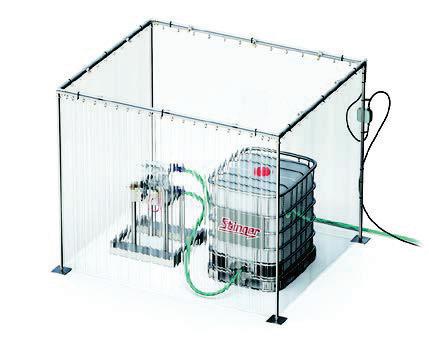
Alcohol to Jet: A Lifeline for Corn Ethanol
ATJ has the potential to provide more than a fourth of the U.S. government’s total SAF target, eventually eclipsing HEFA-based SAF.
By Dave CollingsThe U.S. corn ethanol industry is at a crossroads. According to the U.S. Department of Agriculture, ethanol production has largely flattened since 2017. The industry is no longer experiencing rapid growth like it did between 2000 to 2009. This is due in part to the so-called “blend wall,” which has historically limited ethanol content in gasoline to approximately 10%. The use of higher ethanol blends, namely E85 and E15, is growing, but perhaps not at the pace or scale necessary to sustain the U.S. ethanol industry’s current size amidst projected electric vehicle (EV) sales.
Gasoline production in the U.S. has also been flat since 2005. This is more the result of increases in fuel efficiency and driving behaviors than the nation’s still nascent transition to electric vehicles. Nonetheless, for the ethanol industry to maintain long-term profitability, it must pursue other growth opportunities.
The ethanol lobby is promoting 15% ethanol-gasoline blends (E15) as a primary growth/hold solution. While this is a logi-
cal step and consistent with the 20%-25% ethanol-gasoline blends in Brazil, it doesn’t address the elephant in the room: the automotive market is expected to steadily move away from internal combustion engines (ICE). Gasoline, the carrier for ethanol, is widely viewed as a gradually shrinking market. Therefore, even with the growth of E15 and E85, the ethanol industry may be chasing a larger share of a smaller overall market.
Sustainable aviation fuel (SAF), on the other hand, may be the most promising growth opportunity for corn ethanol in years. The airline industry consumes 18 billion gallons of jet fuel per year. Incentive programs like the 2022 Inflation Reduction Act, or IRA, are also incentivizing SAF blending with a $1.25 per gallon tax credit for fuels that meet a 50% greenhouse gas reduction threshold.
For U.S. corn ethanol producers, this could be a much-needed lifeline as the industry faces headwinds from emerging technologies and policies.
A Need to Adapt
The U.S. corn ethanol industry needs to prepare for change. In January, Bloomberg-
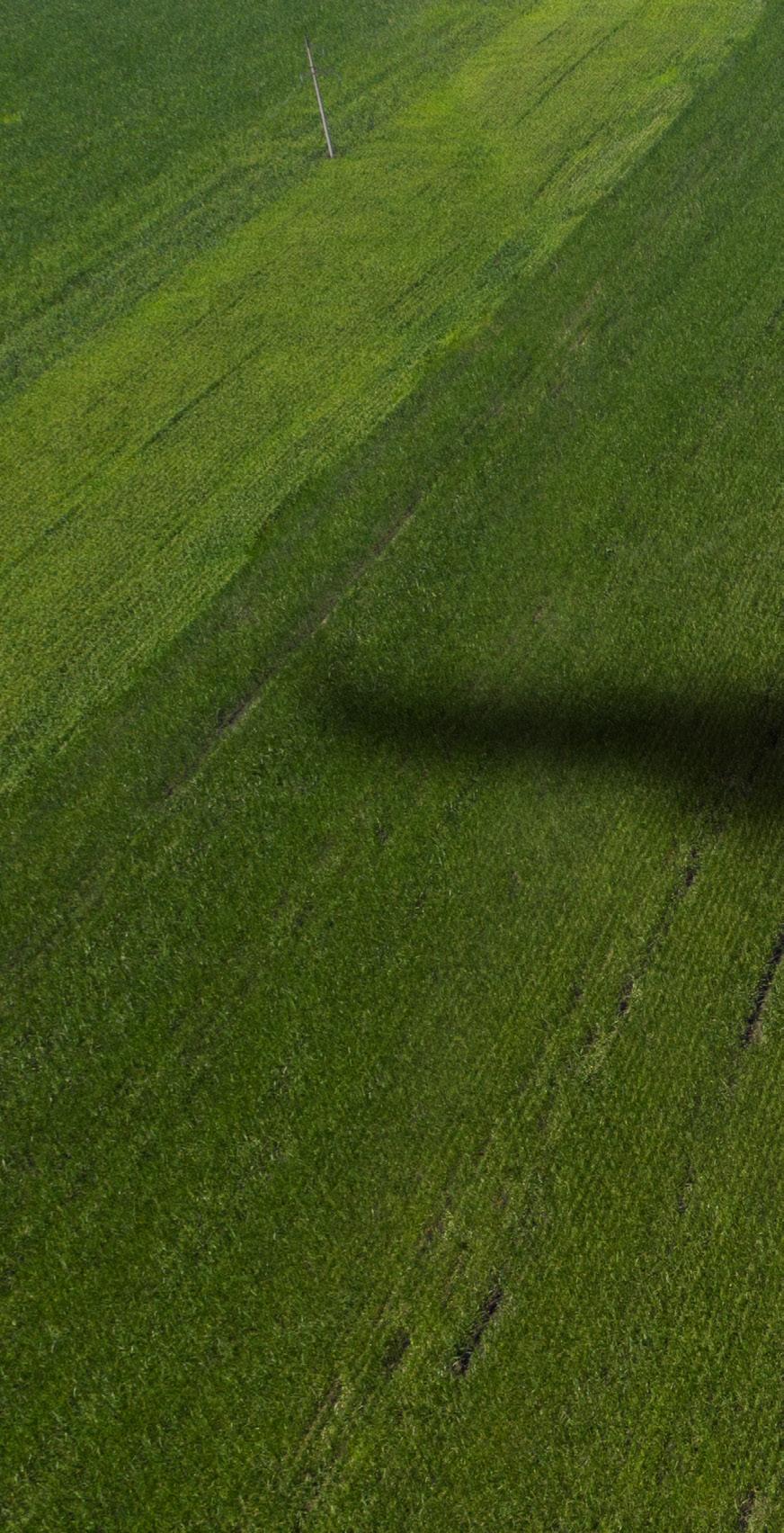
NEF published an aggressive forecast of gasoline decline, which would have a dramatic negative impact the viability U.S. corn ethanol production over the next 20 to 30 years.
Even with widespread E15 sales, ethanol blending in gasoline would be far less than it is today. Although the ethanol industry should keep chasing E15, it may not be an adequate solution in the face of a steep decline in gasoline usage.
So, what is behind this anticipated decline?
A Reduction in Government Incentives
For a long time, the U.S. corn ethanol industry was a recipient of government incentives to support agriculture and reduce transportation related emissions. However, the ethanol blender’s tax credit expired in 2012. The latest Renewable Volume Obligations (RVOs) of the Renewable Fuel Standard maintain the conventional ethanol blending mandate to 15 billion gallons, while advanced biofuels blending obligations have increased.
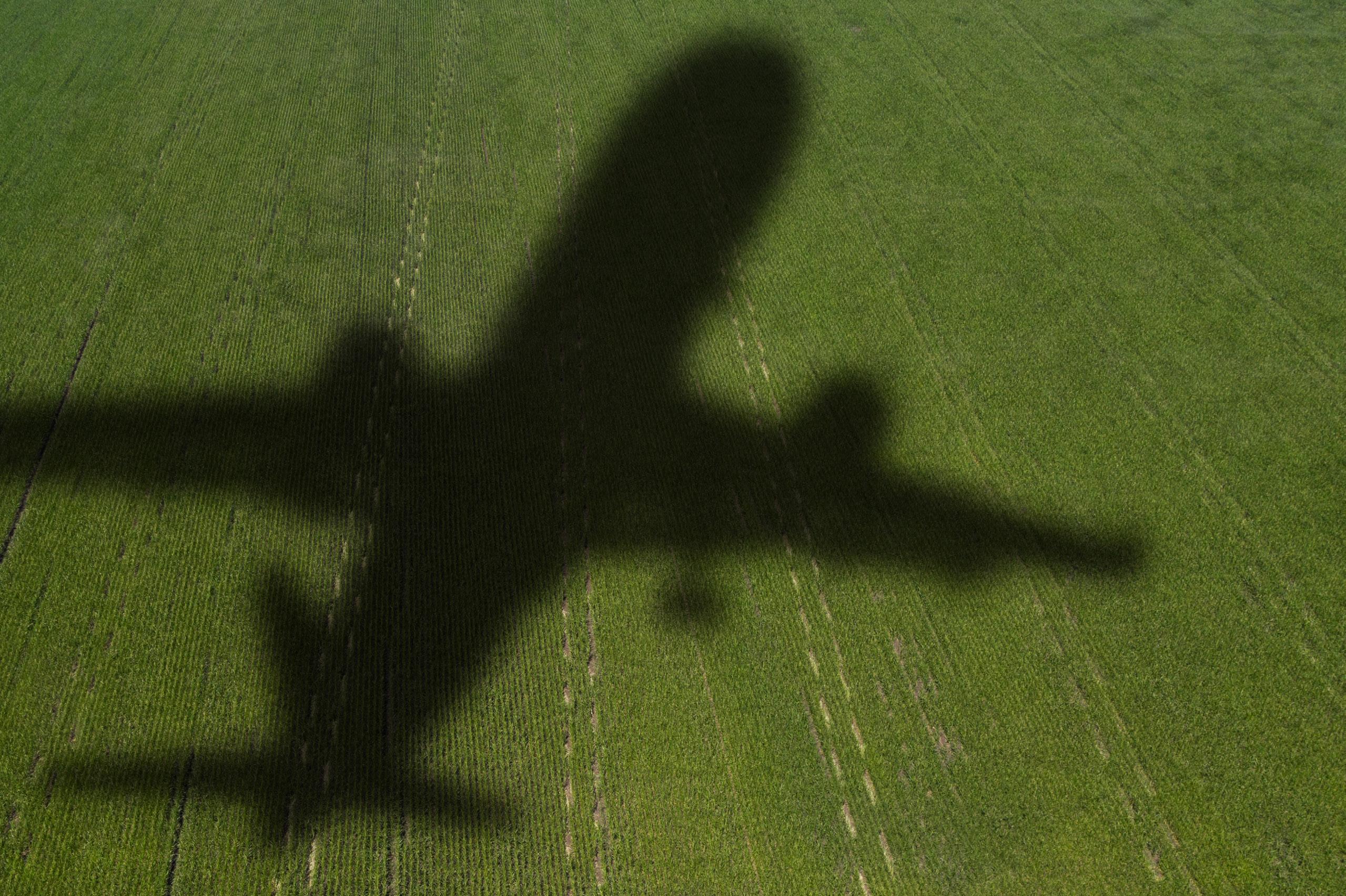
This update implies that the U.S. Environmental Protection Agency is more focused on the growth of renewable natural gas, renewable diesel and other fuels that have lower carbon intensity (CI) than corn ethanol. Corn ethanol also faces challenges from the Low Carbon Fuel Standard (LCFS) credit generation due to its higher CI.
The Emergence of Electric Vehicles
In contrast to corn ethanol, EVs have experienced tremendous support from federal and some state governments. The IRA offers up to $7,500 in tax credits per vehicle, while the Infrastructure Investment and Jobs Act of 2022 is investing up to $7.5 billion in EV charging infrastructure.
Additionally, California intends to phase out ICE vehicles by 2035. Other states such as New York and Massachusetts plan to follow suit. Furthermore, the EPA anticipates that the market share for EVs will reach 67%
by 2032 as compared to 7.6% in 2023. These predictions may be ambitious, but there is momentum in government support and the EV market.
The continued growth of EVs is relevant to the ethanol industry because it reduces gasoline demand, which in turn reduces ethanol demand. The consistent support of EVs at the federal, state and local levels suggests that this trend will continue.
SAF Offers A Long-Term Opportunity
SAF production may offer long-term and sustainable growth prospects for U.S. corn ethanol producers. Apart from incentive programs spurring growth, such as the Inflation Reduction Act, global SAF mandates are also pressuring the airline industry to adopt more SAF. By 2050, the U.S. aims to scale up SAF production to 35 billion gallons through its SAF Grand Challenge. In the E.U., airlines are expected to adopt a 20% SAF blend by 2035.
These factors are each likely to increase SAF demand.
There are several SAF pathways, including hydrotreated esters and fatty acids (HEFA), alcohol-to-jet, Fischer-Tropsch and e-SAF. The HEFA process has proven to be the most readily available technology to produce SAF from fats and oils. While the HEFA process is an effective technology, it won’t be sufficient to meet the anticipated demand of SAF due to lack of feedstock availability. So, the ATJ pathway may help the SAF industry achieve its ambitions.
An advantage that ethanol has over fats and oils is its availability at a lower cost and in much larger volumes. By utilizing the ATJ pathway, ethanol can be converted to ethylene and then oligomerized into longer-chain molecules in the jet fuel boiling point range.
While there are other pathways besides ATJ that can support the growth of SAF beyond the capabilities of HEFA, Worley Consulting’s analysis suggests ATJ is one of the most viable and economical. Other potential
pathways are arguably more constrained by their level of technical readiness, product yield or feedstock energy density.
Assessing the Viability of ATJ to Meet SAF Ambitions
When considering producing SAF from corn ethanol, there are several factors to consider. These factors include CI, carbon capture potential, crop yields, ATJ yields, feedstock cost, technology maturity, HEFA outlook and potential volume of SAF produced.
Corn ethanol’s high CI can hinder producers from qualifying for IRA-related tax credits. To qualify, corn ethanol needs to have a CI that is less than 50% of the oil industry. ATJ may fall short as a result, but various pathways can help reduce its CI. Figure 3 illustrates several pathways of improving the carbon footprint of ethanol-based jet fuel.
Implementing carbon capture on the CO2 stream from the ethanol plant can have the largest impact on CI. This pathway reduces ATJ’s CI from approximately 72 g CO2e/MJ to 38 g/CO2e MJ. According to Figure 3, this improvement alone is enough to drop corn ethanol to below the 50% greenhouse gas (GHG) reduction threshold.
Therefore, integrating carbon capture with ethanol production is critical to help corn ethanol-based SAF qualify for IRA tax credits.
To reduce ATJ’s CI even further, ethanol producers can introduce additional technological pathways. This can involve fuel switching, supplying renewable energy, gasification of biomass and changing agricultural practices.
Carbon Capture for ATJ is Economically Challenging
While carbon capture can significantly reduce corn ethanol’s CI, its adoption has been slow. Recent Midwest carbon capture projects have also faced challenges.
For example, the Navigator CO2 pipeline was cancelled after several years of campaigning for support in the Midwest. Separately, the Summit and Wolf pipelines have both faced permitting challenges. However, there are some promising developments, including Tallgrass Energy’s Trailblazer pipeline. It has Federal Energy Regulatory Commission (FERC) approval to convert its natural gas pipeline to transport CO2 instead.
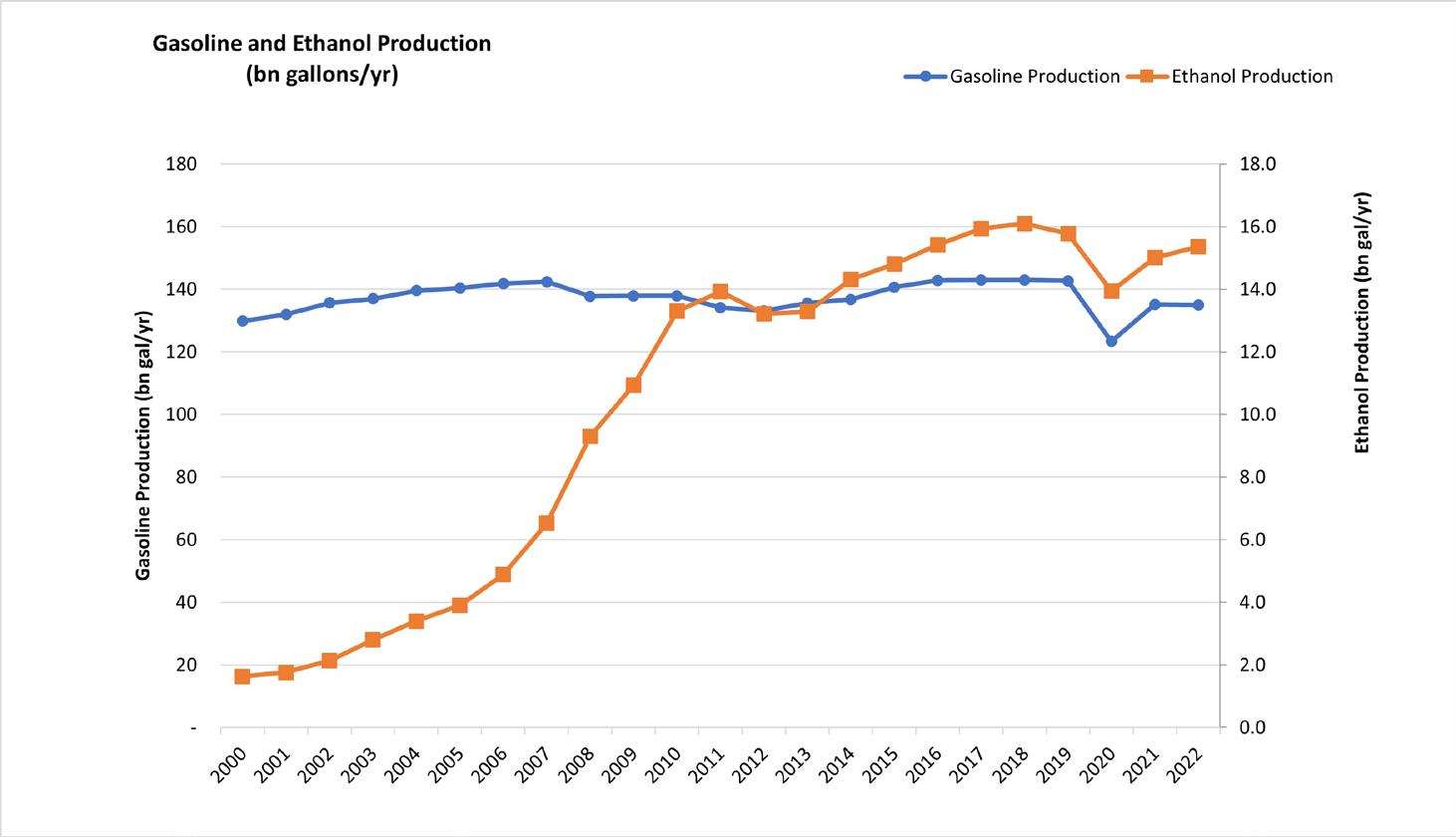
SOURCE: EIA

SOURCE: EPA
Yields of ATJ Process Are Low
One challenge for corn ethanol is product yield. While corn ethanol is more abundant than soybean oil, ethanol only yields about 52% jet fuel in the ATJ process. In comparison, soybean oil yields about 80% jet fuel in the HEFA process.
This would seem like a clear victory for the HEFA process over ATJ. However, corn yields about 9,800 pounds per acre producing 507 gallons of ethanol. On the other hand, soybean yields 3,000 pounds per acre to produce 76 gallons of soybean oil.
The result is that an acre of corn can produce 4.4 times as much jet fuel per acre than an acre of soybeans.
Ethanol Has a Feedstock Cost Advantage
Another advantage for corn ethanol over fats and oils is feedstock cost.
Soybean oil has a history of being more costly than corn ethanol, presumably because corn yields 175 bushels/acre vs. 50 bushels/ acre for soybeans. Corn ethanol is also available in greater quantities, producing 2.9 gal/ bushel whereas soybean oil produces 1.5 gal/ bushel.
At the time of authoring this paper, the price of ethanol was $1.60/gal. In contrast, the price of soybean oil was $3.70/gal. Looking back at the history of corn ethanol and soybean oil prices, soybean oil is regularly almost double the price in our review of long-term trends.
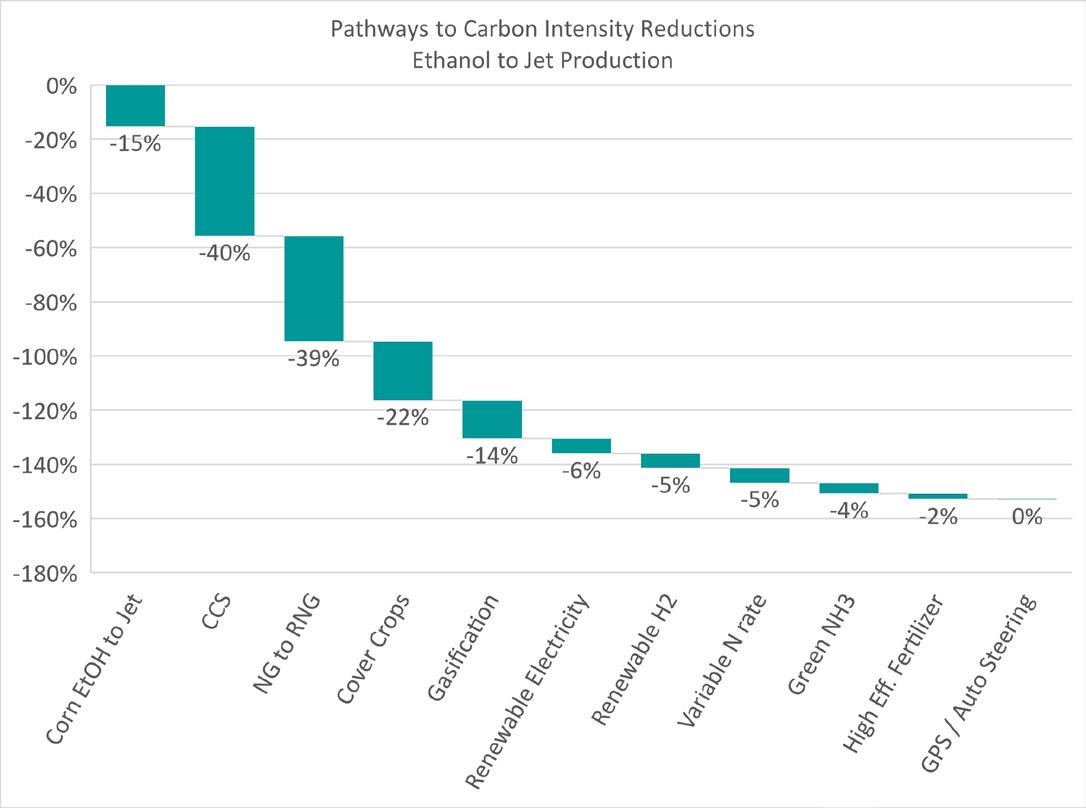
SOURCE: EIA
HEFA Technology Is More Mature
When it comes to commercial experience, the HEFA process has a significant advantage compared to ATJ. In the past few years, there has been rapid growth in the production of renewable diesel from fats and oils. Some SAF can be fractionated from renewable diesel, and the renewable diesel process can be modified to produce even more SAF via established hydrocracking technology.
The HEFA process involves pretreating the feed using technologies by Alfa Laval, ARA and Crown. Hydrotreatment is the next step, using technology from Axens, Haldor Topsoe, Sulzer, UOP and others. The end product is either renewable diesel or SAF.
ATJ technology is a work in progress. However, the technology is the sum of existing mature technologies as described below:
• Dehydration to ethanol for the purpose of ethylene production has been commercialized by Braskem.
• The oligomerization process is well understood and has been widely commercialized in the oil refining industry. It’s used for converting propylene and butylenes into naphtha molecules. Ethylene is not typically the reactant and naphtha molecules are typically the product, but the technology is similar and, therefore, could be expanded to jet fuel production. In April, Next Wave Energy Partners announced the completion of an ethylene-to-alkylate plant that employs this technology.
• The oligomerization product is 100% olefinic and must be saturated via well-understood hydrogenation technology.
Licensors working on the development of this technology have a long history of successful technology commercialization. They include Axens, LanzaJet, Lummus and UOP.
LanzaJet has recently commissioned its 10 MMgy commercial demonstration plant in Soperton, Georgia, using sugarcane ethanol as feedstock. This is a step towards wider commercialization of the technology.
Although ATJ is trailing HEFA in terms of commercialization, it’s arguably ahead of other options under consideration, such as the Fischer-Tropsch production pathway that uses lignocellulosic feedstocks. It’s also more likely to achieve wider adoption ahead of e-fuel pathways, such as CO2-to-jet via methanol as an intermediate.
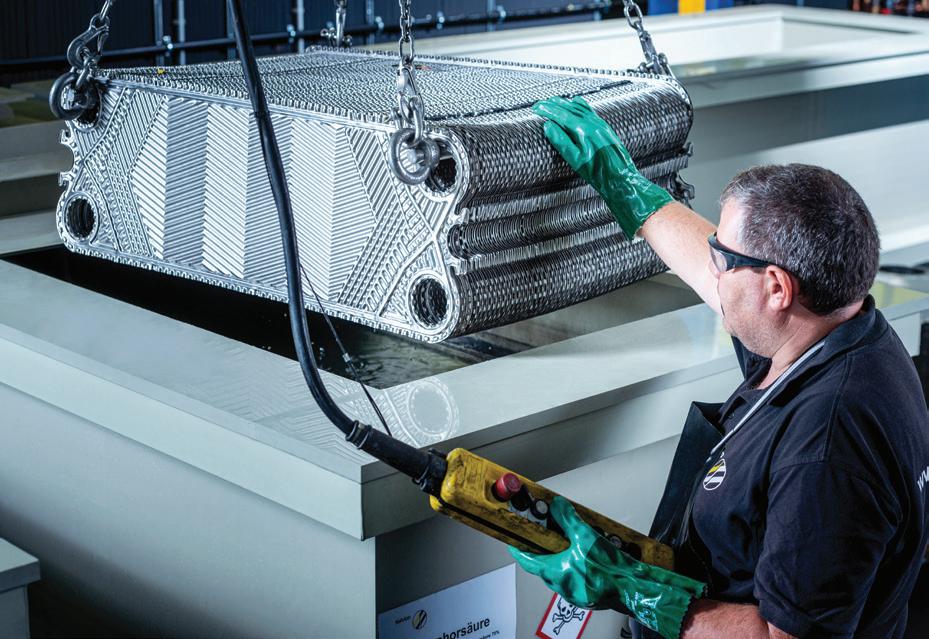
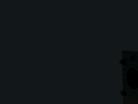

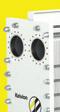
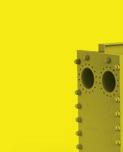
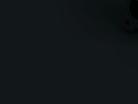
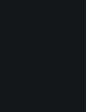
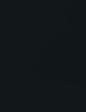
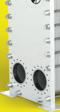

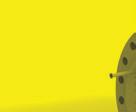
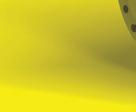
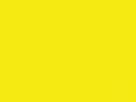
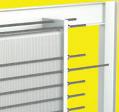
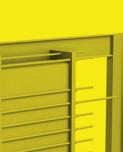
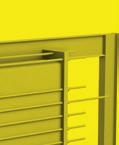
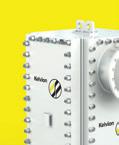
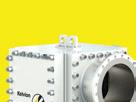
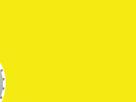

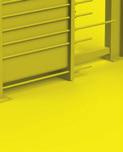
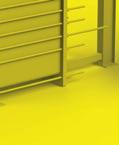

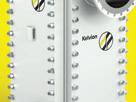
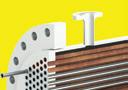
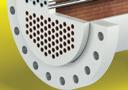
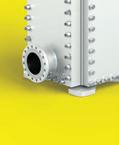
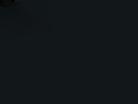
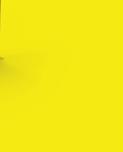
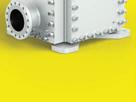

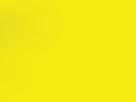
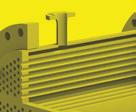
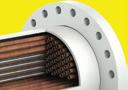

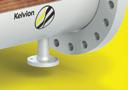
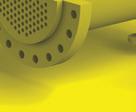
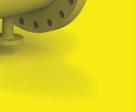

Potential Future Market and Technological Trends
Like corn ethanol, soybean oil faces challenges in achieving 50% greenhouse gas reduction. In the future, low-CI feedstock such as used cooking oil, animal fats and distillers corn oil might be diverted from renewable diesel to SAF. Higher-CI soybean oil feedstock, in turn, may be routed to renewable diesel, which does not have a 50% GHG reduction requirement.

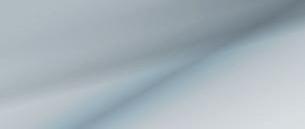
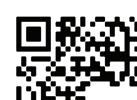

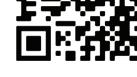
For corn ethanol, BloombergNEF suggests most of the 15 billion gallons will be available for SAF production. If 85% of ethanol production is available for SAF by 2050, it would be an additional 6.6 billion gallons of SAF, or 2.6 times the potential contribution of soybean oil.
Combined, the growth of soybean oil from new crushing facilities—and the displacement of corn ethanol from gasoline to SAF— could contribute to as much as 9.2 billion gal-
lons of SAF. However, this is well below the SAF Grand Challenge laid out by the DOE, the Department of Transportation and the USDA, which targets 35 billion gallons by 2050.
Other sources such as imports, FischerTropsch, or e-fuels would have to come into play to meet the 2050 target. However, the technical maturity of these technologies and the cost of production of these pathways exceeds HEFA and ETJ (ethanol-to-jet).
Growth Opportunity


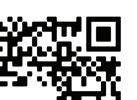
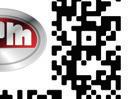







Corn ethanol producers need to consider sustainable aviation fuel as a growth opportunity. The corn ethanol industry has had to confront several challenges, such as disappearing tax credits, volatile RINS prices, the pandemic, and competition from the oil industry over E15 and small refinery exemptions.
Through it faces uncertainty, the industry has proven its resilience. As it faces new challenges from factors like the emerging EV market, steps the industry takes today will determine its growth trajectory in the coming decades.
ATJ is emerging as a compelling growth opportunity for the corn ethanol market, especially because existing ethanol plants can remain productive, reducing the capital cost associated with ethanol production. Compared to HEFA, it has the advantages of low feedstock cost, higher crop yields and high feedstock availability. Although corn ethanol on its own is not enough to meet the SAF Grand Challenge, it can contribute more than double what HEFA can.
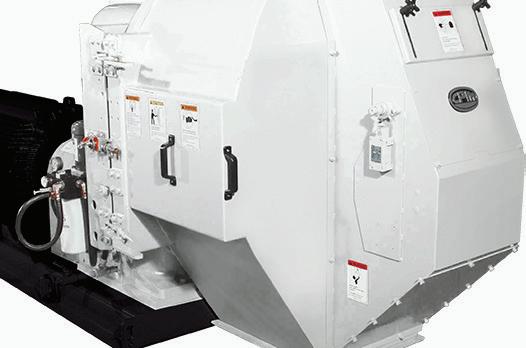
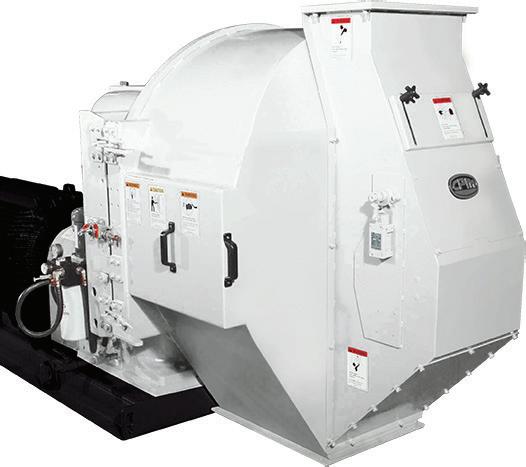
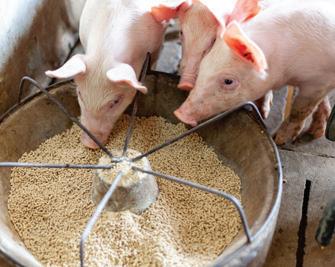
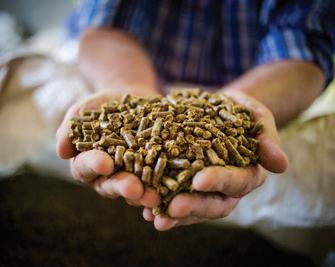
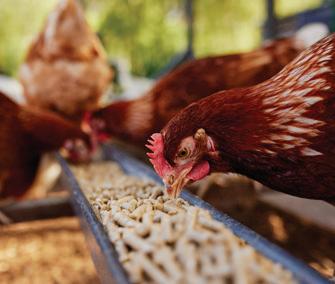
ATJ technology may not be as mature as HEFA, and it has challenges to overcome. But several industries have commercially demonstrated the components of the technology.
As more production plants like LanzaJet’s come online, the case for ATJ will strengthen. Alongside ongoing incentive programs and policy support, ATJ may provide a stronger future for corn ethanol and overcome its uncertainties today.
Author: Dave Collings Group Manager, Fuels and Chemicals, WorleyContact: Dave.Collings@Worley.com

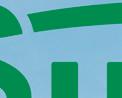
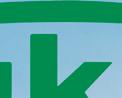
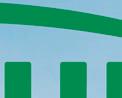
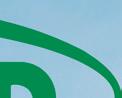
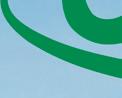
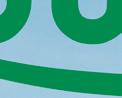
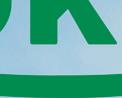

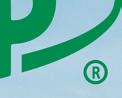


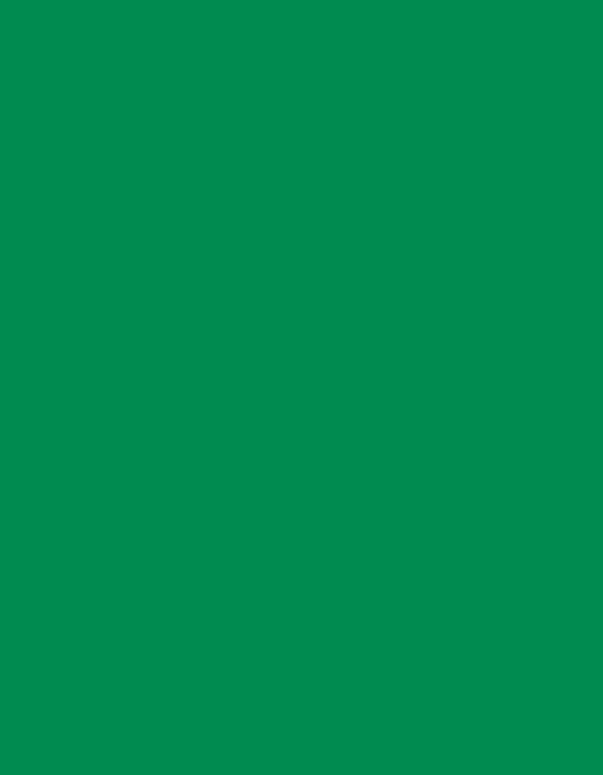

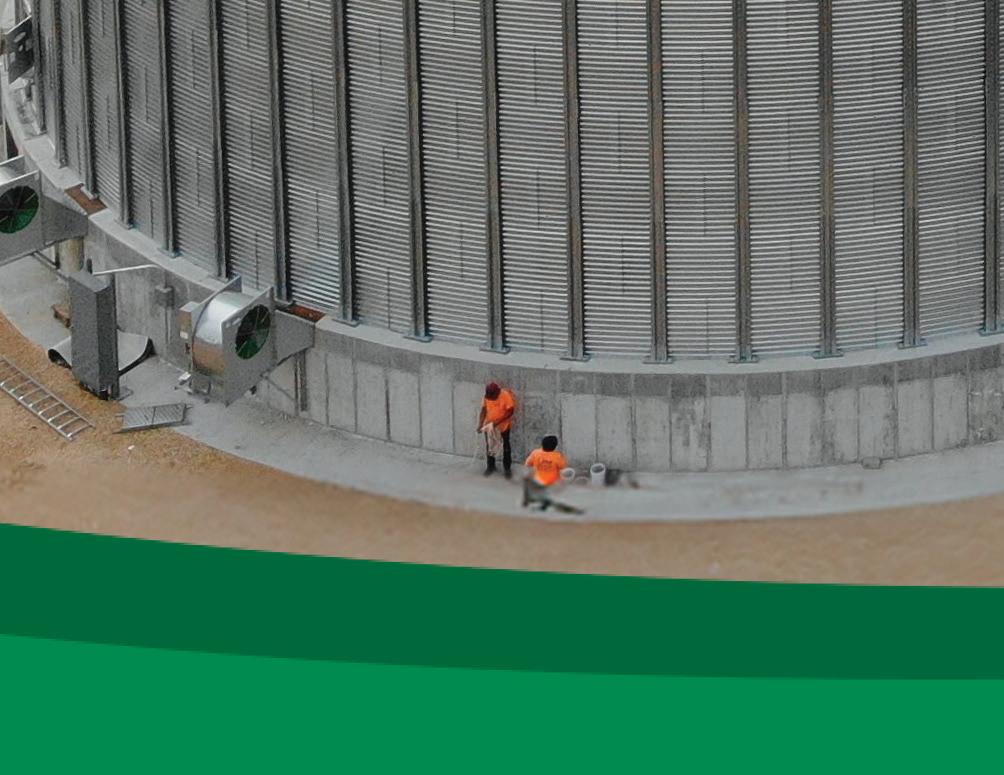
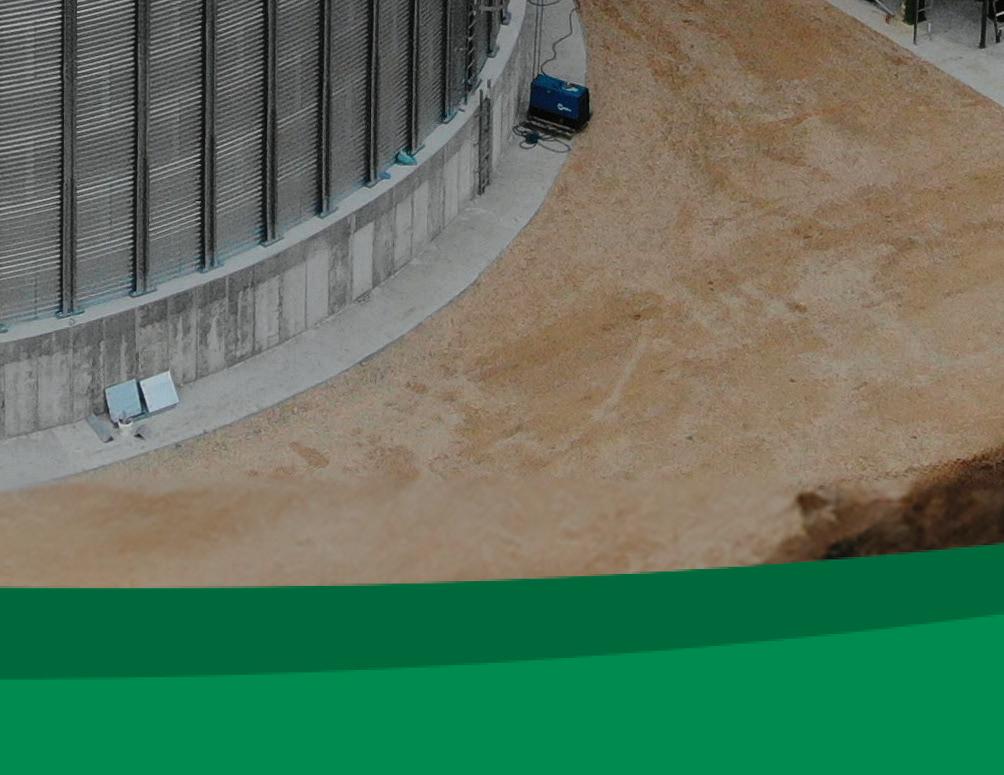
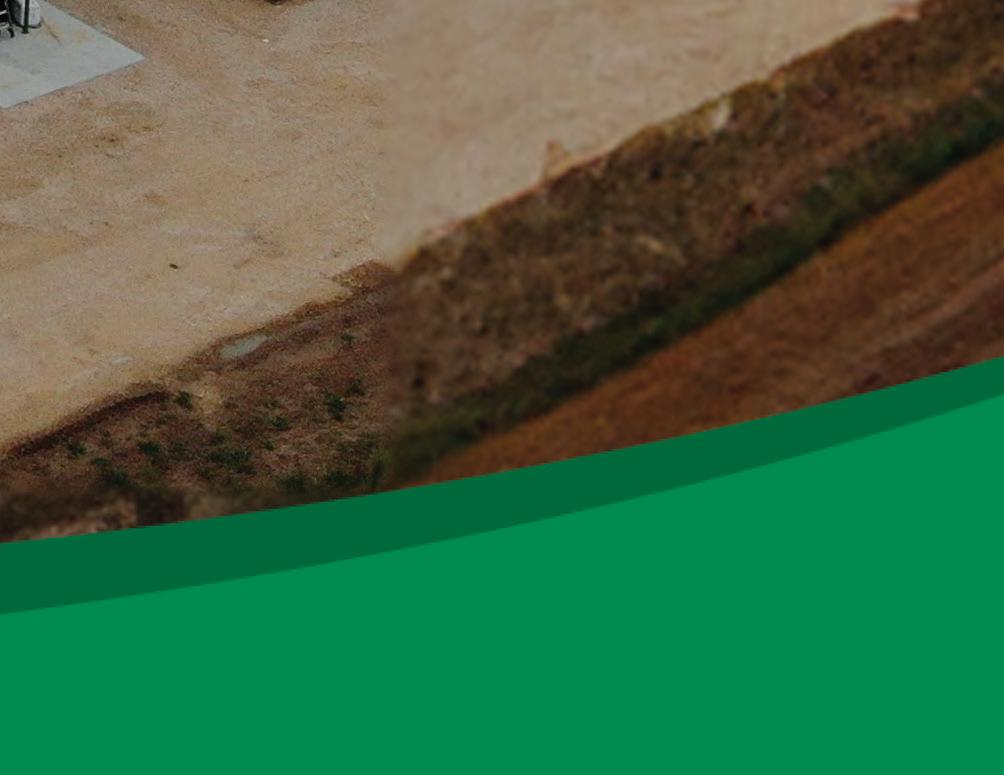
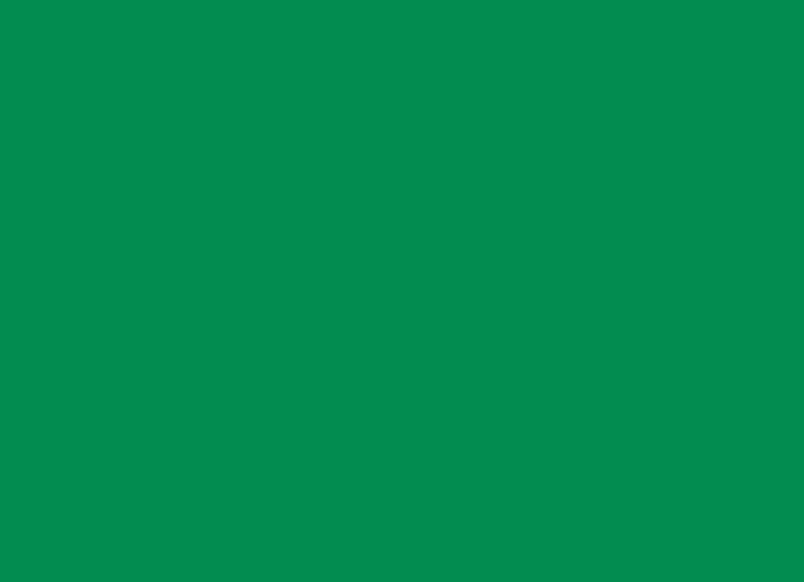

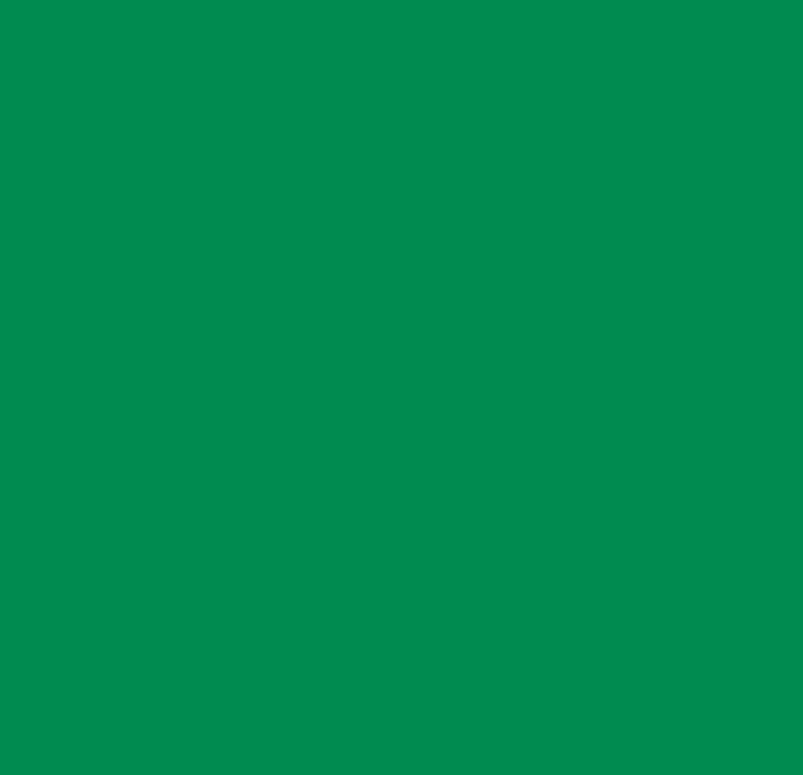
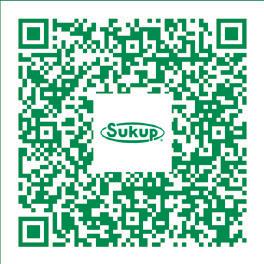

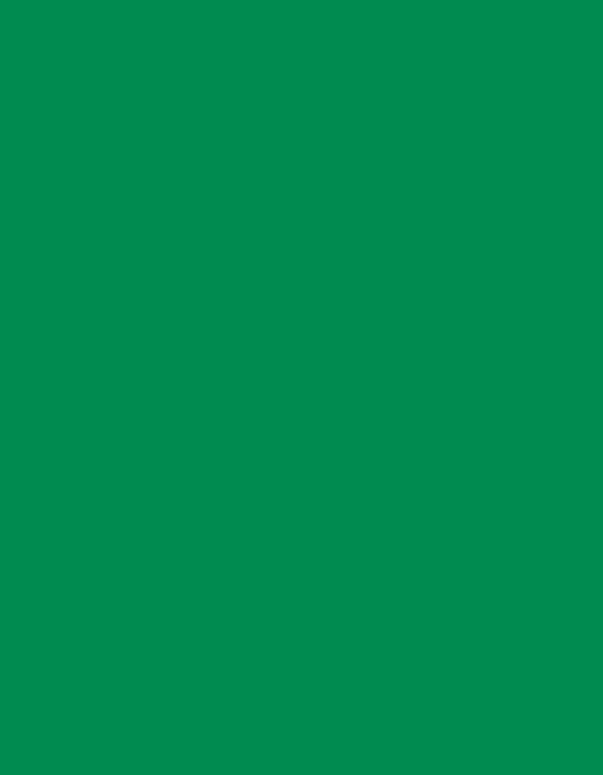

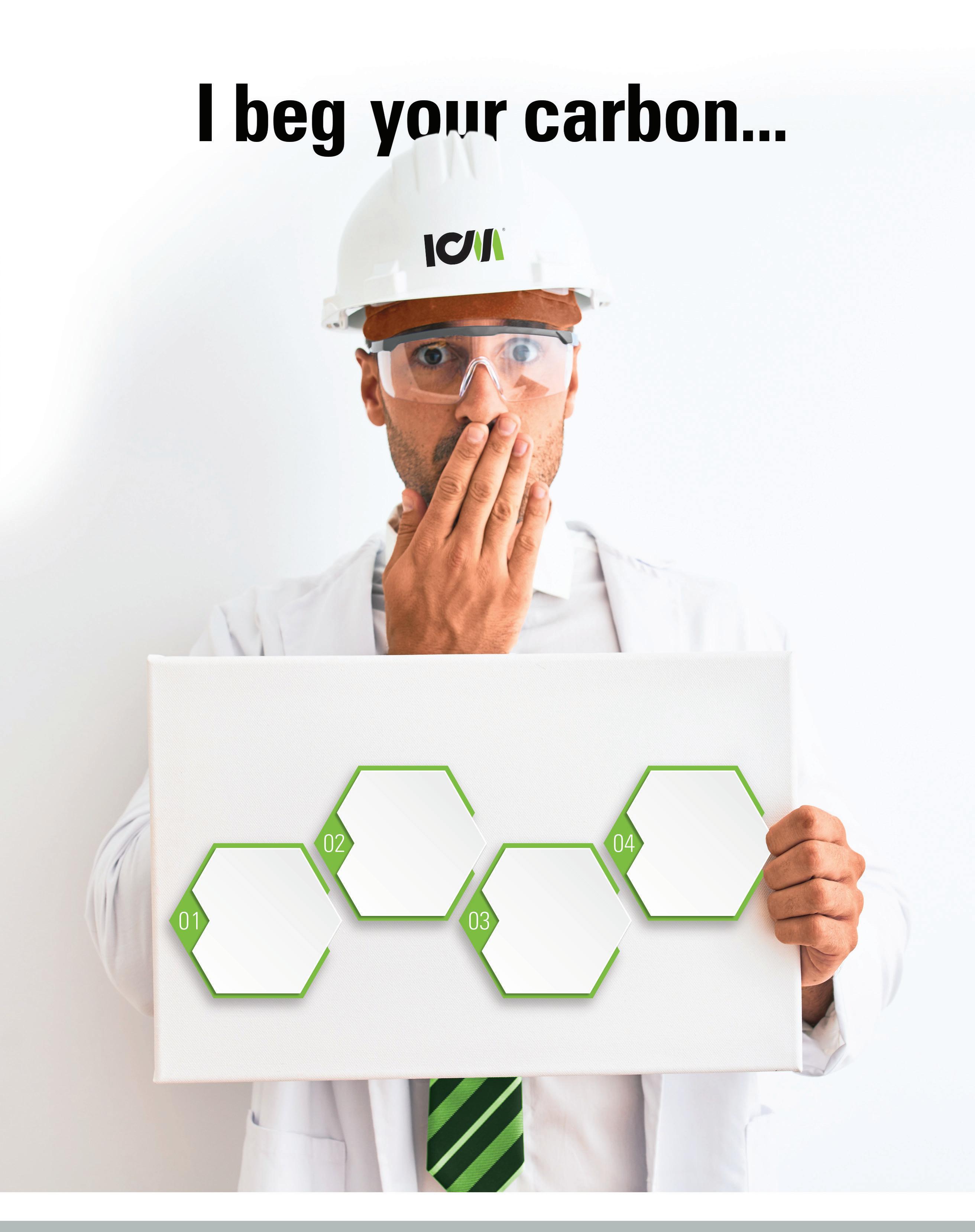
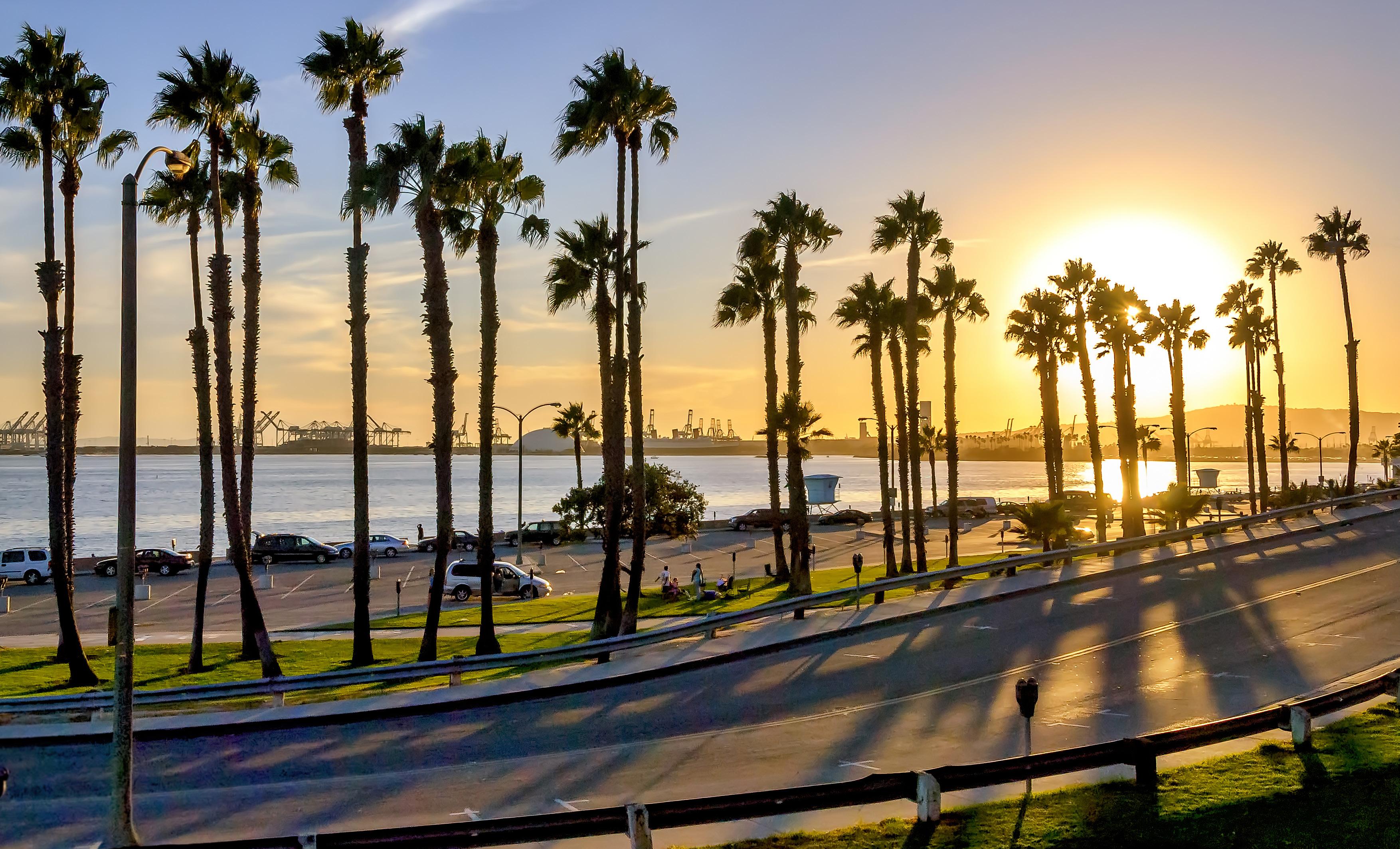
Navigating Complexities
The top concerns for third-party verification bodies in state low carbon fuel programs. By Danielle Anderson and Kari Buttenhoff
As a third-party verification body in the renewable fuels sector, Christianson PLLP’s mission is to ensure the integrity and compliance of the various state low-carbon fuel programs and fulfill biofuel producers' required fuel pathway application validation, as well as verifying ongoing carbon intensity calculations reporting and documentation.
This critical role includes navigating numerous challenges and complexities to keep ethanol, biodiesel, renewable diesel and other renewable fuel producers informed about
key concerns affecting the validation and verification process.
Currently, California, Oregon and Washington have their own clean fuel programs, and New Mexico's legislature has recently passed a bill to establish a similar program. Each of these state programs are undergoing changes through a rulemaking process. It is crucial for verification bodies to participate in these discussions to ensure that the process is streamlined and efficient for both our firm and the renewable fuel producers we represent.
As the rulemaking processes in these states progress, we anticipate changes will be finalized either late this year or early next year. Below are some of the top concerns verification bodies have regarding the cur-
rent state low-carbon fuel programs, the amendments they are making and suggestions for improvement.
Streamlined U.S. Accreditation Process
Throughout our company’s years of experience as an accredited validation and verification body, we have seen an increasing number of states, and even other countries, implementing their own clean fuel programs; we find it important to streamline the process of accreditation for verification bodies.
We currently advocate for U.S. state programs to adopt a reciprocal accreditation process, so if a verification body is accredited in one state, it can go through a simplified process of registration and not have to
CONTRIBUTION: The claims and statements made in this article belong exclusively to the author(s) and do not necessarily reflect the views of Ethanol Producer Magazine or its advertisers. All questions pertaining to this article should be directed to the author(s).
duplicate efforts, or pass through additional barriers, in another state.
Granting reciprocity streamlines administrative processes, reduces regulatory complexity and minimizes compliance burdens. It also ensures that a biofuel producer’s chosen verification body can easily enter into additional verification systems to allow everyone to take advantage of audit efficiencies between programs.
Verification Body Rotation
Rotation requirements for verification body firms are included in many of the state low carbon fuel programs. Numerous public comments have been made by several parties asking the governing agencies to consider a lead verifier rotation. A lead verifier rotation would allow the verification body firm to retain its client, instead switching out the lead verifier. This would allow for the retention of the verification team’s knowledge built from extensive time spent understanding the regulated party's processes, contributing to an efficient and effective audit for the biofuel producer.
A firm rotation rather than a partner rotation is highly disruptive and costly to regulated parties, especially when there is a small pool of accredited verification bodies available. This problem is further exacerbated with lookback periods in place in many states, making it more difficult for producers to find a quality verification body who has also not been utilized in previous verifications or in a consulting capacity.
Once an audit team becomes familiar with the various aspects of the client and their documentation, it allows the auditor to find problem areas or unusual activity more easily for the client, resulting in a more effective audit.
Currently, financial auditors serving public companies in the U.S. are required to rotate only the lead engagement partner for financial audits every five years. There is no requirement for a whole firm rotation. In fact, the American Institute of Certified Public Accountants (AICPA) stands against an audit firm rotation, stating that a mandatory firm rotation comes at a great expense to audit quality.
Our company has communicated through various public comment opportunities that if there is a desire to implement rotation requirements, it should be a partner rotation rather than a firm rotation, meaning the person leading the verification organization’s services for a client is rotated every six to ten years, not the entire verification firm.
Benefits of Less Intensive Verification
Site visits to each renewable fuel producer’s facility are required by verification bodies in the process. In California, these site visits are required for each validation or verification engagement for all regulated parties. An amendment being proposed in California would allow only electric transportation verifications to skip site visits, also known as less intensive verification.
Less intensive verification allows for verification bodies to skip site visits if they visited the site in the last two years and issued a positive verification statement.
California’s rationale for this proposed change on electric transportation states, “there is little change of operation from reporting period to reporting period, thus reducing the benefit of annual site visits.” Additionally, staff rationale states, “there is no or little risk to the integrity of the LCFS program to allow for less intensive verification services without a site visit in the annual verifications for the following two years. This should reduce the cost of verification services which is often passed on to program participants.”
Christianson agrees with the staff’s stated rationale, and we have communicated through public comment opportunities that less intensive verification should be extended as an option for verification bodies on all validations and annual verifications for any reporting entities, not just for electric vehicles.
Both the California Mandatory Reporting Rule, Cap and Trade Program, and Oregon’s verification regulations already include provisions for less intensive verification. California’s LCFS is the only program that does not allow less intensive verifications. This difference is preventing less intensive verifi-
cations in the programs that do allow them, when the regulated entity is participating in multiple jurisdictions.
We agree with staff that less intensive verification leads to little to no risk to the integrity of the LCFS program, and that there is little change in operation from reporting period to reporting period, while also providing cost savings to verification providers that are passed on to program participants.
Pathway Validation Process Timeline
Proposed amendments to the current Low Carbon Fuel Standard (LCFS) regulations in California aim to refine the validation process for submitted carbon intensity pathway applications. Currently, validations must occur within six months of the submission date, which often may expire before the verification body even receives the application to begin procedures. The California Air Resources Board (CARB) has recognized this, and in its current proposed amendment initiates the six-month timeline from the moment the verification body receives the application from CARB, following the staff’s application review.
This revised timeline allows the verification body a full six months to meticulously verify data and complete the validation, instead of requiring both staff review and third-party validation within the initial sixmonth period.
Additionally, the proposed amendments introduce new requirements regarding the timeliness of data within the application, stipulating that data must be current within one quarter of the submission date.
These changes to the validation process ensure a process with a defined timeline and the most current carbon intensity calculations in establishing new pathways, while allowing verification bodies and producers adequate time to complete the application. This is a welcome change, and all state programs would benefit by implementing similar timelines for new pathways entering their programs.
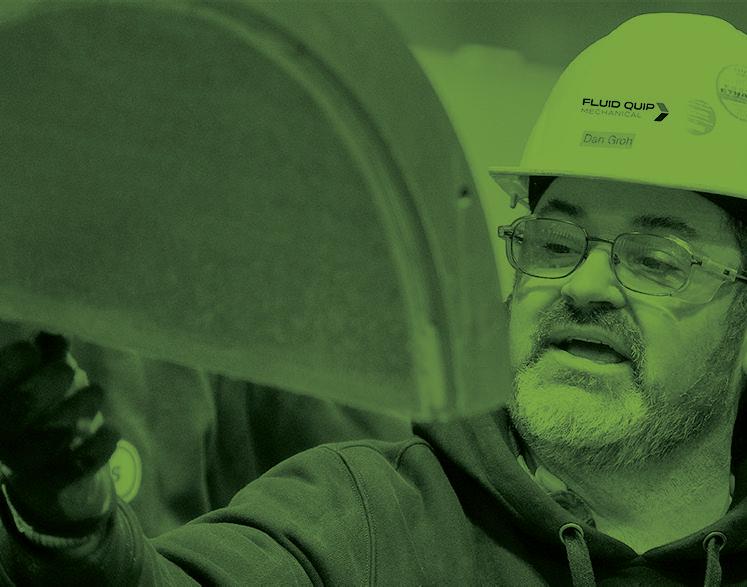
Verification
Sustainability Requirements
Our team of experts have over 20 years of ethanol plant maintenance expertise. We o er full service and parts for all Fluid Quip equipment to ensure peak performance.
• OEM Parts Warehouse
•$2 million+ inventory on-hand
•Factory Trained & Certified Techs
•MZSA™ Screens
•Paddle Screens
•Grind Mills
•Centrifuges
•Gap Adjusters
The concept of sustainability requirements for biofuels has recently emerged in state clean fuel programs as a potential safeguard against land conversion to farmland. A similar initiative was introduced and implemented into Canada’s Clean Fuel Regulations (CFR) program, which imposes stringent criteria for land use changes.
It is important to highlight that U.S. feedstock is exempted from Canada’s Crops-Excluded land criteria based on the U.S. Environmental Protection Agency’s (EPA) aggregate compliance approach, citing that “the U.S. Code of Federal Regulations provides a sufficient level of environmental protection with respect to the land on which the feedstock is harvested.”
Furthermore, the USDA released its 2022 Census of Agriculture in February, revealing a 14 million-acre (4%) decrease in cropland across the U.S. since 2017. This decline reflects a longstanding trend in the U.S., rendering the argument of additional safeguards for cropland irrelevant to U.S. crop producers.
Considering the limited availability of accredited third-party verification bodies and the fact that renewable fuel producers already must qualify through the U.S. EPA’s Renewable Fuel Standard aggregate compliance, imposing additional sustainability guardrails on biofuels produced in the U.S. is unwarranted.
Verifier Shortages
The last, and one of the largest and most overarching areas of concern, is the number of available verifiers for the evergrowing regulatory programs. Currently, there are only 30 verification bodies registered under the California LCFS program, which has the largest verification body listing. Oregon’s verification regulation requires a California LCFS accreditation to apply for accreditation in its program, and Washington is expected to implement similar requirements.
As noted in the beginning of this article, reciprocity is very helpful to ensure
easy access for verification bodies to work in multiple jurisdictions. Canada’s Clean Fuels Program is not compatible with the U.S. West Coast programs, but rather requires an ISO accredited firm to perform the verifications. To date, this has resulted in fewer verification body participants due to the additional hurdles to become accredited under the Clean Fuels Program.
While reciprocity is a good thing, it still means that the same small set of verification bodies is handling all the work in multiple programs. In addition, another subset of these verifiers is serving the voluntary markets or are one of the only three Quality Assurance Program (QAP) auditors serving the RFS program. The RFS program has also implemented certain rules that make QAP mandatory rather than voluntary, increasing the number of biofuel producers utilizing this program. With additional audit requirements in new and existing programs, along with the difficulties finding employees in the current workforce environment, we are headed into an even more strained verification pool.
As a third-party verification body, we play a crucial role in ensuring the integrity and success of state low carbon fuel programs. By addressing these top concerns and advocating for adjustments to streamline processes and align with evolving regulations, we uphold the credibility of low carbon fuel initiatives, relieve some of the strain on the existing verification body pool and contribute to a more sustainable energy future. Collaboration, innovation and stakeholder engagement remain essential in overcoming challenges and advocating for the best outcome for our nation’s renewable fuel producers.
Authors: Danielle Anderson, Senior Government Policy and Advocacy Manager Christianson PLLP danderson@christiansoncpa.com
Kari Buttenhoff, CPA, Partner Christianson PLLP kbuttenhoff@christiansoncpa.com
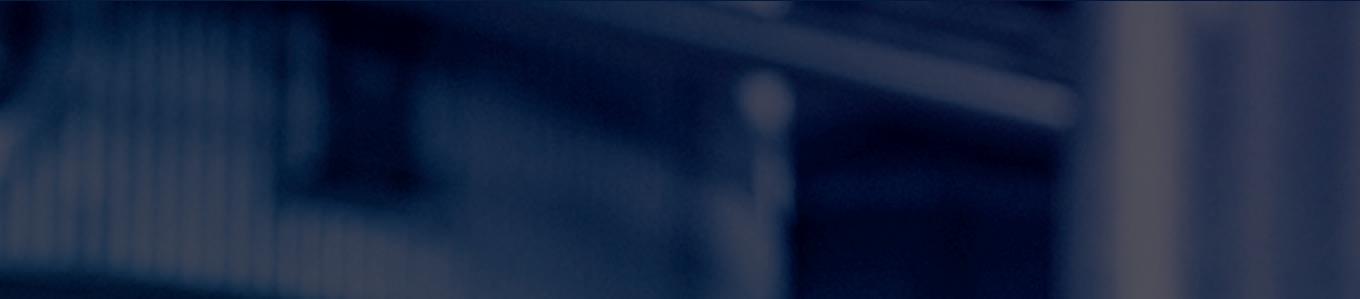










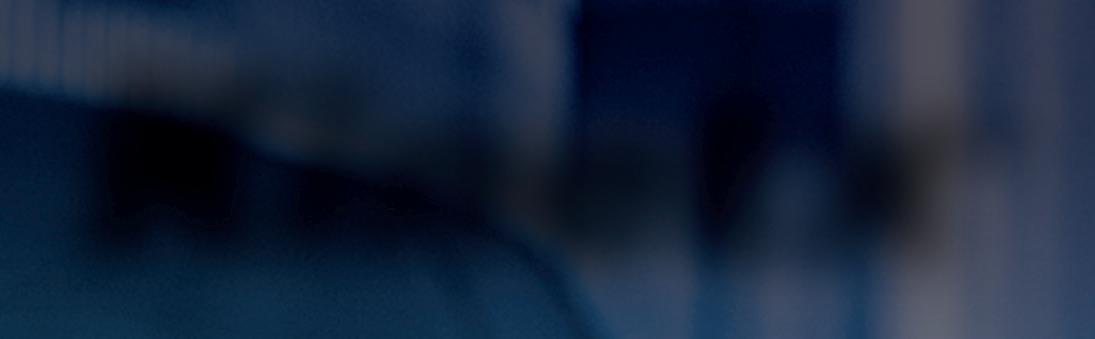
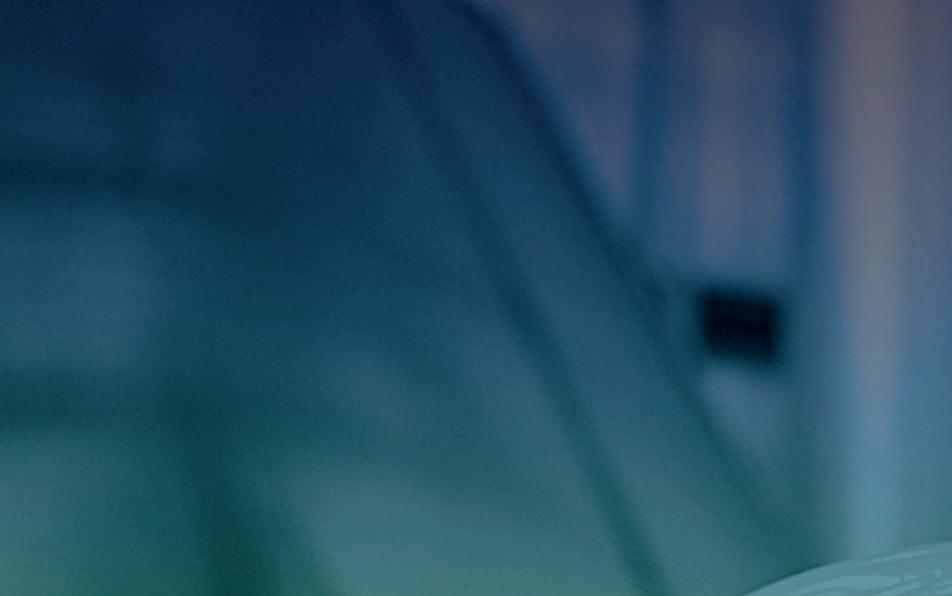
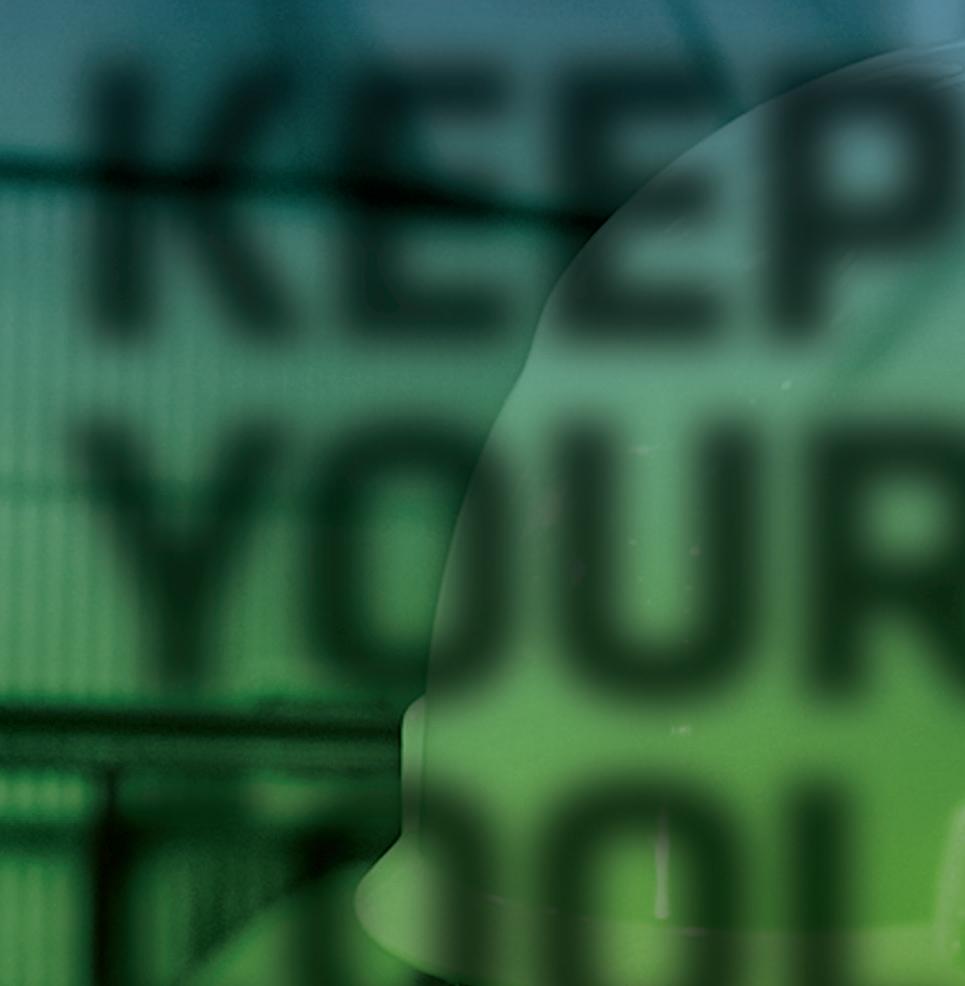

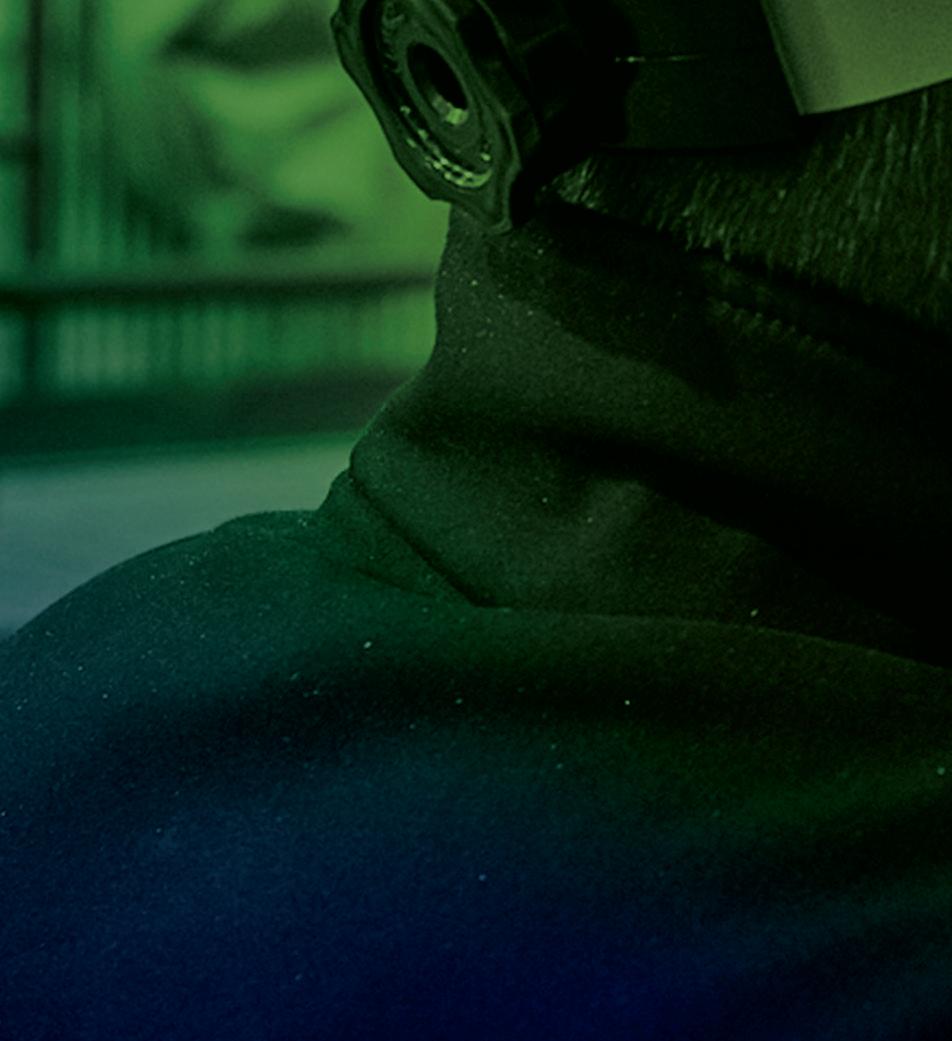


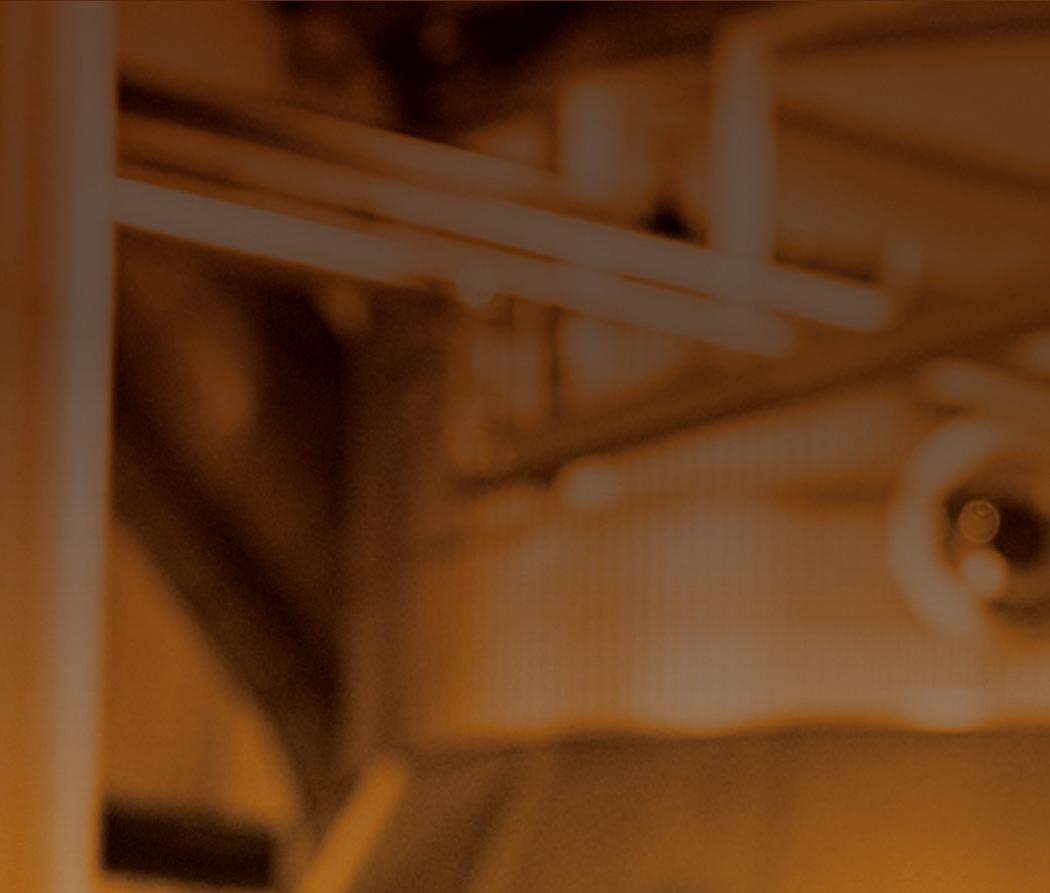
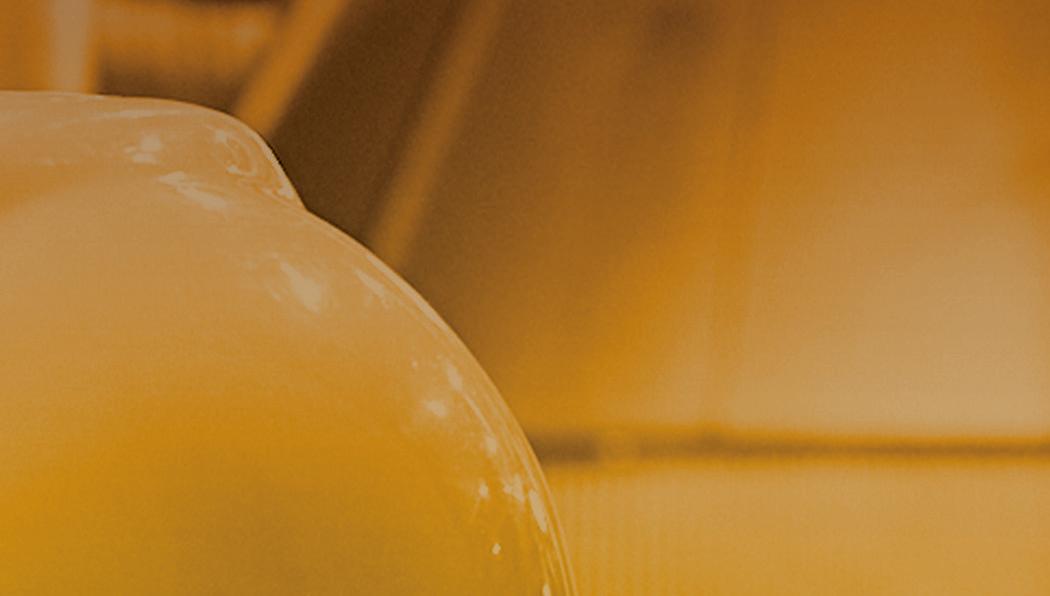
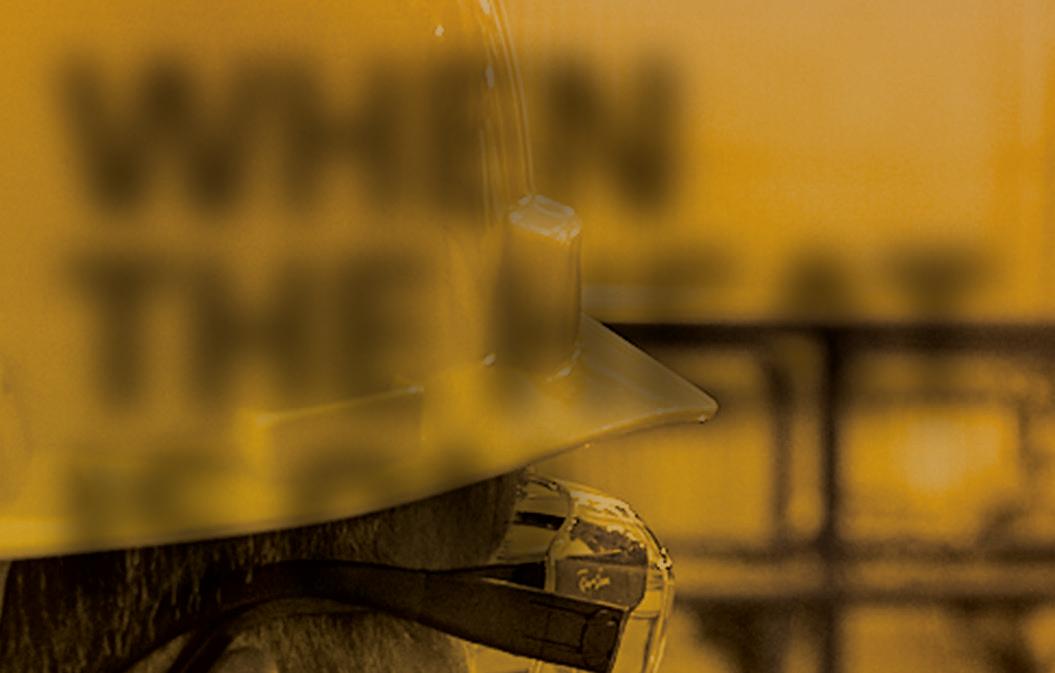
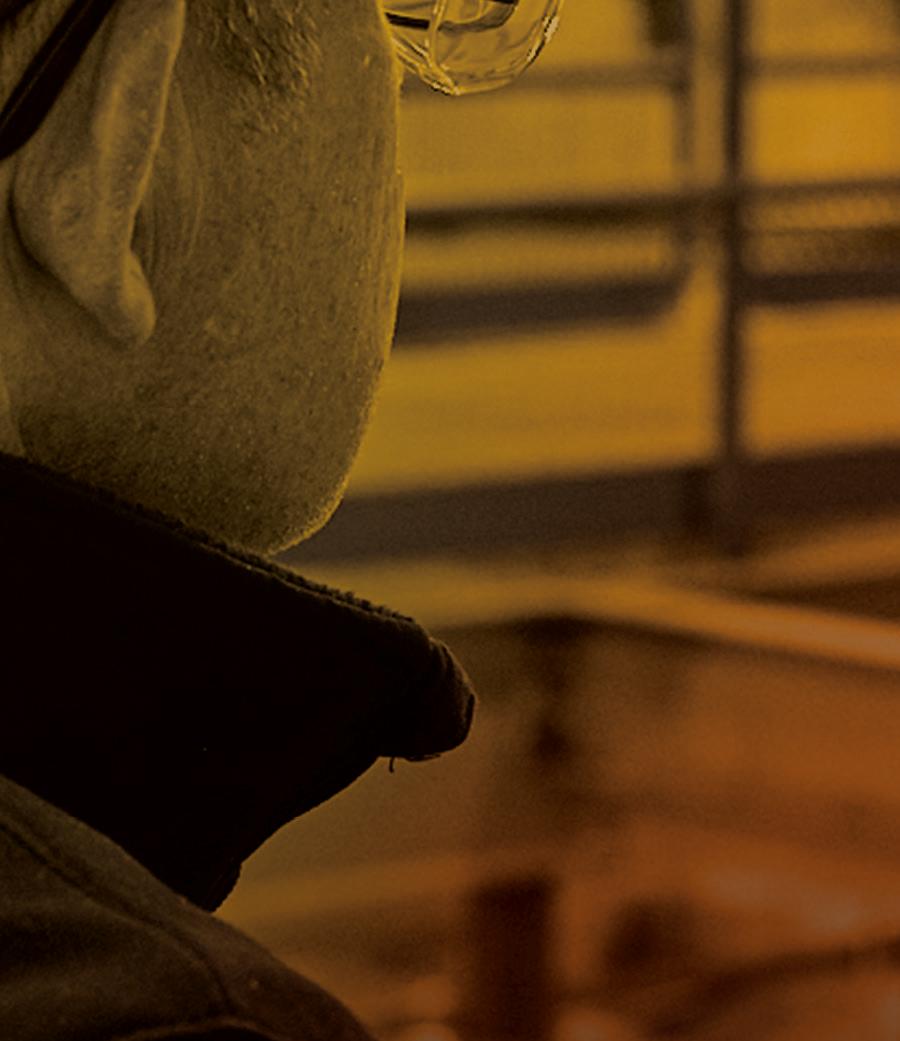


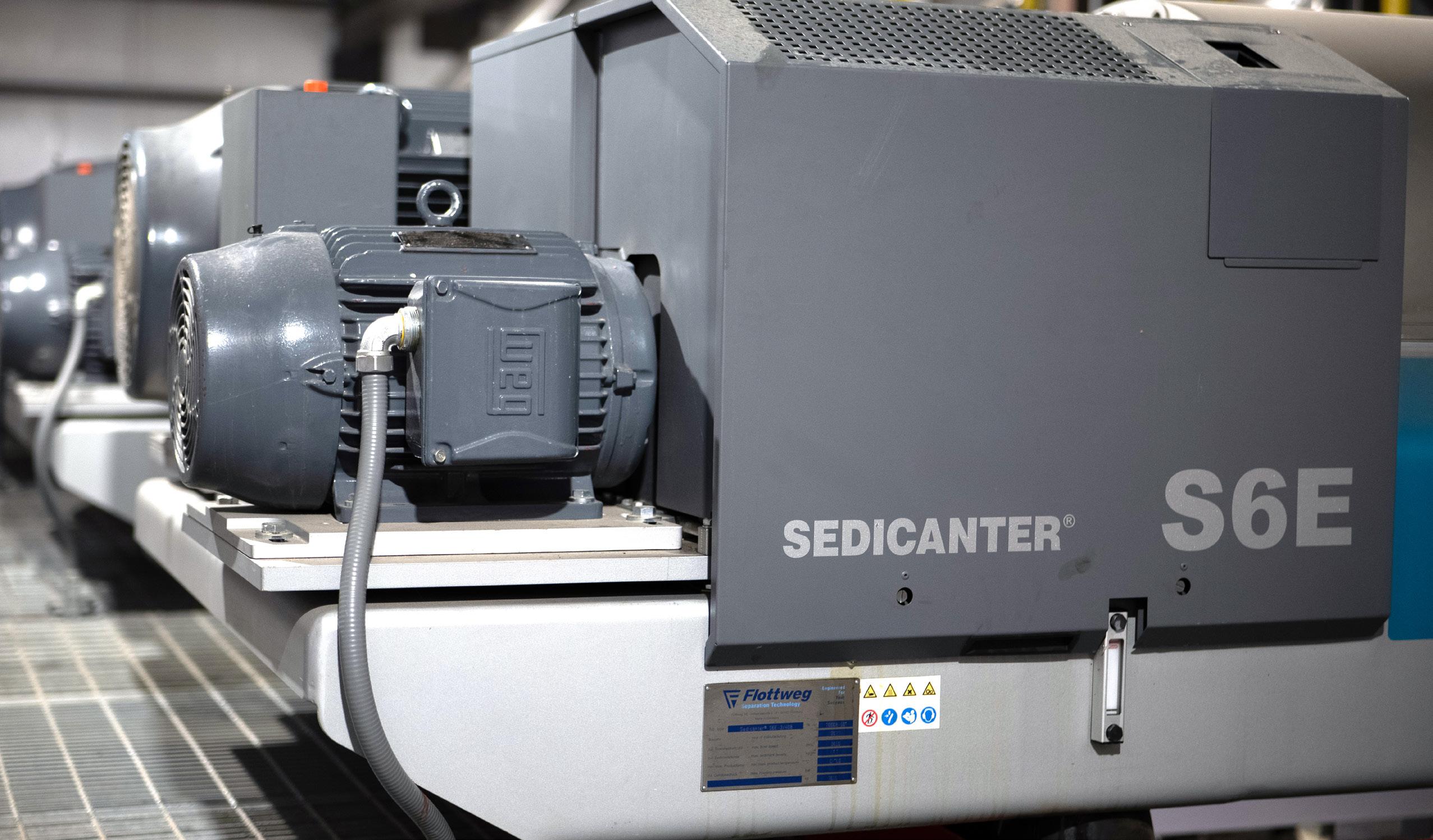
Fractionation and Efficiency
Ethanol plants use Advanced Processing Package to produce high protein feeds and increase plant capacity while lowering CI scores.
By Daniel LakovicUsing ICM’s Advanced Processing Package, several ethanol plants have been upgraded to utilize a new technology that enables the fractionation of a traditional distiller’s grains into two different piles—a high-energy pile and a yeast enriched high-protein pile, Protomax. With a combined ethanol production of 300 million gallons per year, these enhanced ethanol plants consume around 100 million bushels of corn annually. Located in the middle of the Corn Belt, the plants provide ethanol, CO2 and animal feed throughout the United States.
Advanced Processing Package and Centrifugation
Chuck Gallop, Director of Innovation for ICM, explains that ICM’s approach to this technology has been refined in recent years. ICM offers a range of biofuel industry products and services designed to maximize productivity, diversify revenue and yield valuable feed products.
“We roller mill the corn to control the particle size more accurately, and then it is slurried and liquefied,” Gallop says. “The next step is to remove components of that slurry through a fractionation process called Selective Milling Technology and Fiber Separation Technology. These two technologies combined to separate the solids from the liquids,
re-mill the solids in a wet state, and then multiple stages of counter-flow washing of those solids to produce a clean fiber product.”
The solids are separated and dewatered with a rotary press to create a low-protein, low-starch, high-fiber product. The fiber sidesteps the entire ethanol process, freeing up fermentation and distillation capacity and optimizes pump, heat exchanger and centrifuge efficiencies.
After the fiber is removed, high-protein, starch-rich liquid is processed through fermentation and distillation. The de-fibered beer is processed through optimized decanters.
“We use a Flottweg decanter that's been optimized for high-protein processing and high fat removal,” Gallop says.
CONTRIBUTION: The claims and statements made in this article belong exclusively to the author(s) and do not necessarily reflect the views of Ethanol Producer Magazine or its advertisers. All questions pertaining to this article should be directed to the author(s).
This process is called FOT (Feed Optimization Technology), a two-stage process that uses several decanter enhancements— including a proprietary open body scroll—to increase the decanter capacity and the cake’s dryness.
“After processing through FOT, the washed wetcake out of the second-pass decanter is now much higher in protein than traditional wetcake,” Gallop explains. “It's somewhere between 55% and 57% protein on a dry matter basis. The centrate from the first-pass decanters, which would normally go directly to the evaporators, goes through a Sedicanter, which is Flottweg’s high G-force decanter-style centrifuge. This removes fine suspended solids to include the yeast from the decanter centrate. The yeast cake is then mixed with the decanter cake to make Protomax. At that point we have a clarified stillage, which goes to evaporation.”
With the use of Sedicanters in ICM’s TS4 process, the suspended solids are removed, the evaporators become more efficient, and the total solids in the syrup can cycle up to much higher levels. This produces anywhere from seven to ten concentrations of solids in the syrup.
Traditionally, ethanol plants have made dry distiller’s grains with solubles: a large pile of the most imperfect blend of materials. ICM’s approach is to take the dried distiller’s grains and solubles pile and fractionate it into individual piles or components, making it marketable for specific animals or pets.
For example, the fiber and syrup are blended, which is a great, high-energy feed for livestock. The protein is then concentrated, making it perfect for dairy cattle, swine, poultry, aquaculture and pets. When the distillers corn oil is removed, it is perfect for biodiesel, renewable diesel, sustainable aviation fuel, and for increasing energy content in animal feeds.
In addition, DCO is used in a growing segment of renewable fuels—specifically renewable diesel and sustainable aviation fuel. Vegetable oils, specifically distiller’s corn oil, are a low CI feedstock that's perfect for those renewable diesel and sustainable aviation fuels.
Why Separation Equipment is Needed in the FOT Process
In the past 20 to 25 years of the ethanol process, there has been an evolution that includes the enhancement of solid-liquid separation post distillation.
“Without this enhancement, we would consume a tremendous amount of energy used to dry the solids and evaporate the water,” Gallop explains. “In fact, if we take a step back, and I were to describe the ethanol process in very basic steps, the first step would be to mix grain with water. The second step
would be to distill the ethanol from the grain and water. The third step would be to separate the remaining grain from the water. To do this, we use centrifuges.”
ICM uses Flottweg centrifuges to separate the suspended solids from the water. The water at that point goes to the evaporators to be concentrated into condensed distillers solubles or, more commonly known as, syrup. The solids go to the dryers. “Without that centrifuge step, there would be too many solids in the water for the evaporators and too much water in the solids for the dryers. The centrifugation step is essential to the success of every ethanol plant,” Gallop says.
Since 2005, ICM and Flottweg have de-
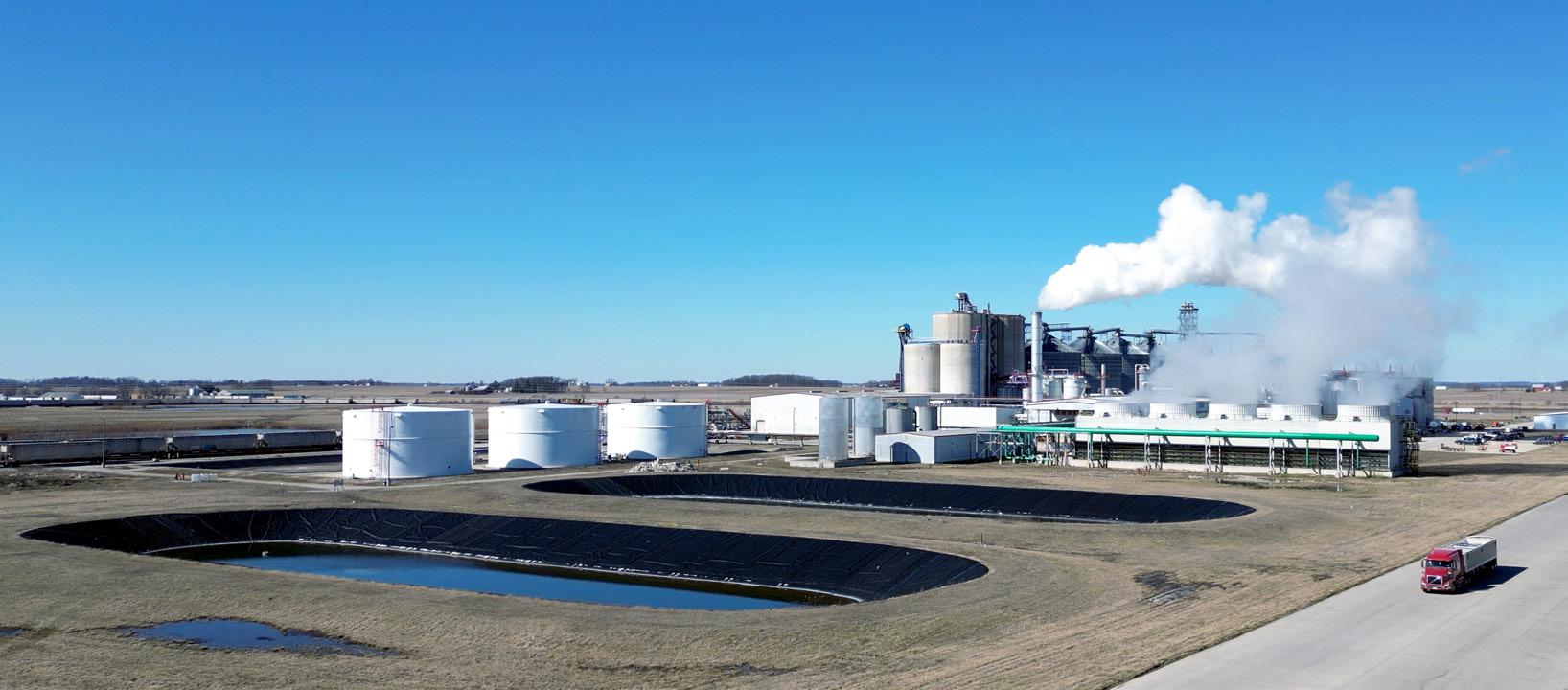
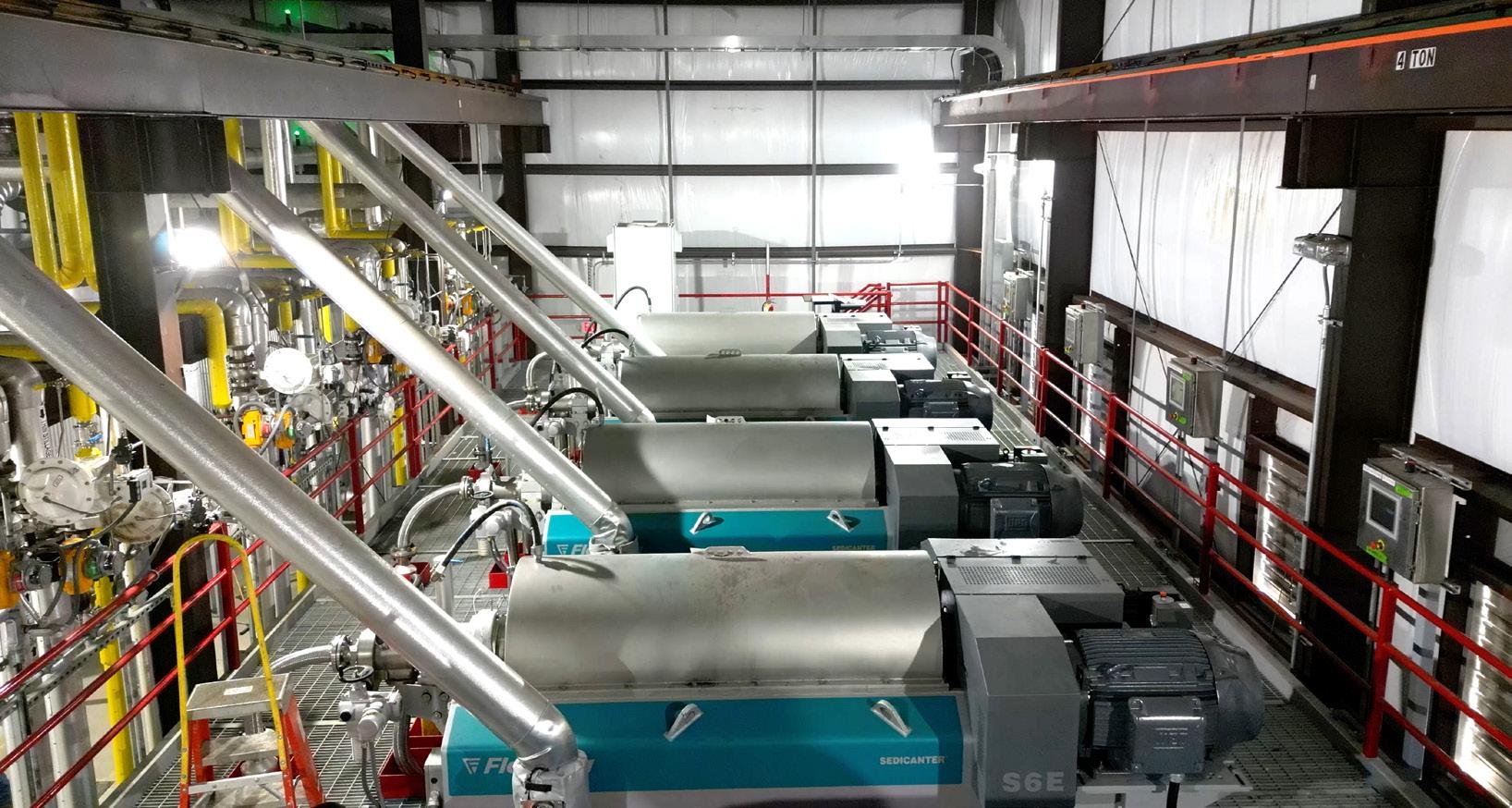

veloped a growing partnership. It started with installing decanters into the ethanol process. Flottweg decanters were capable of processing twice as much of the of the whole stillage on a per-machine basis than other previously used centrifuges.
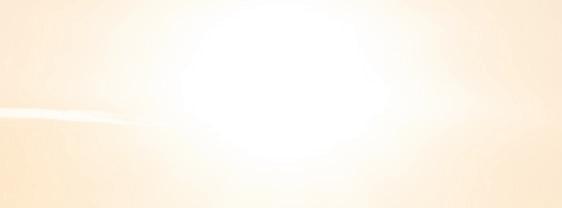
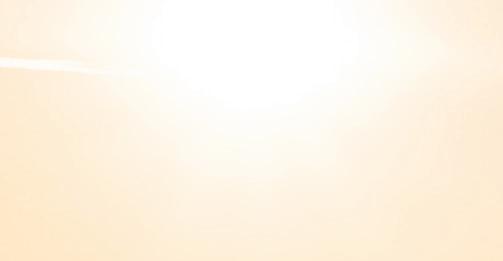
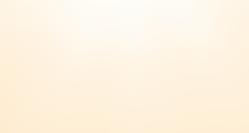

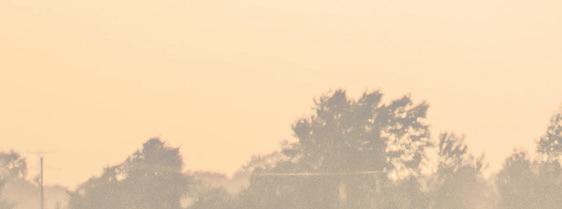
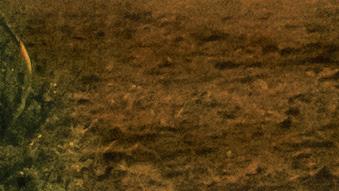
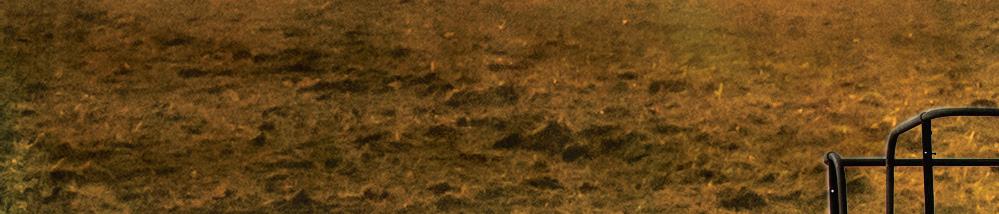
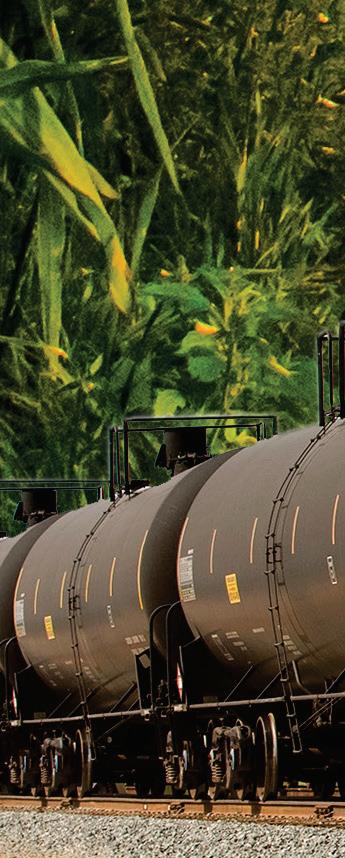
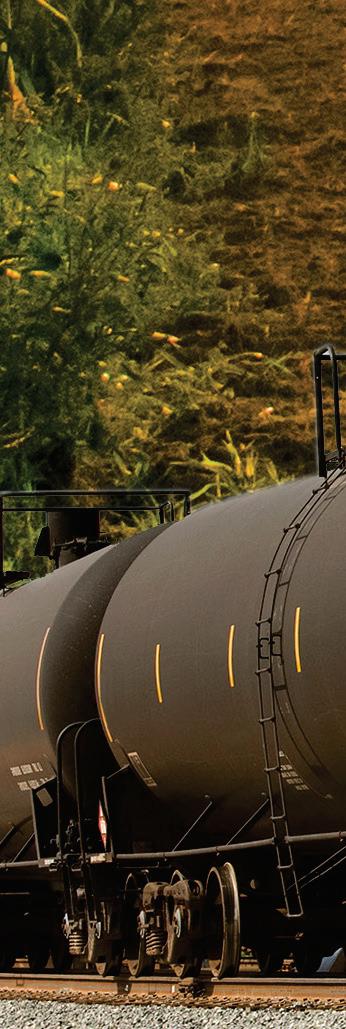
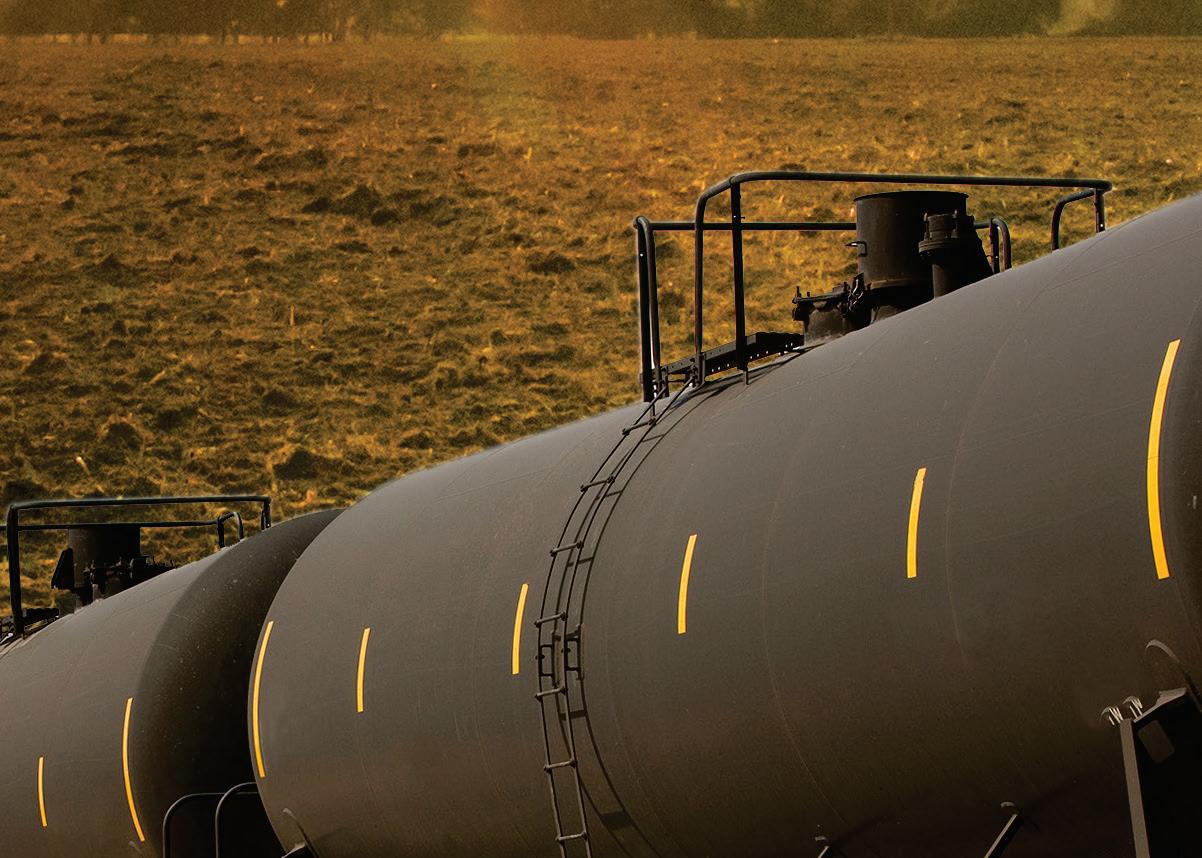
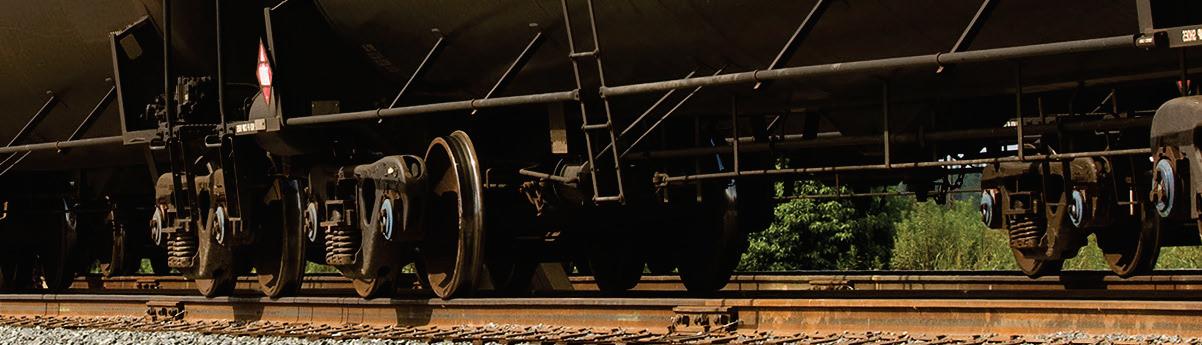
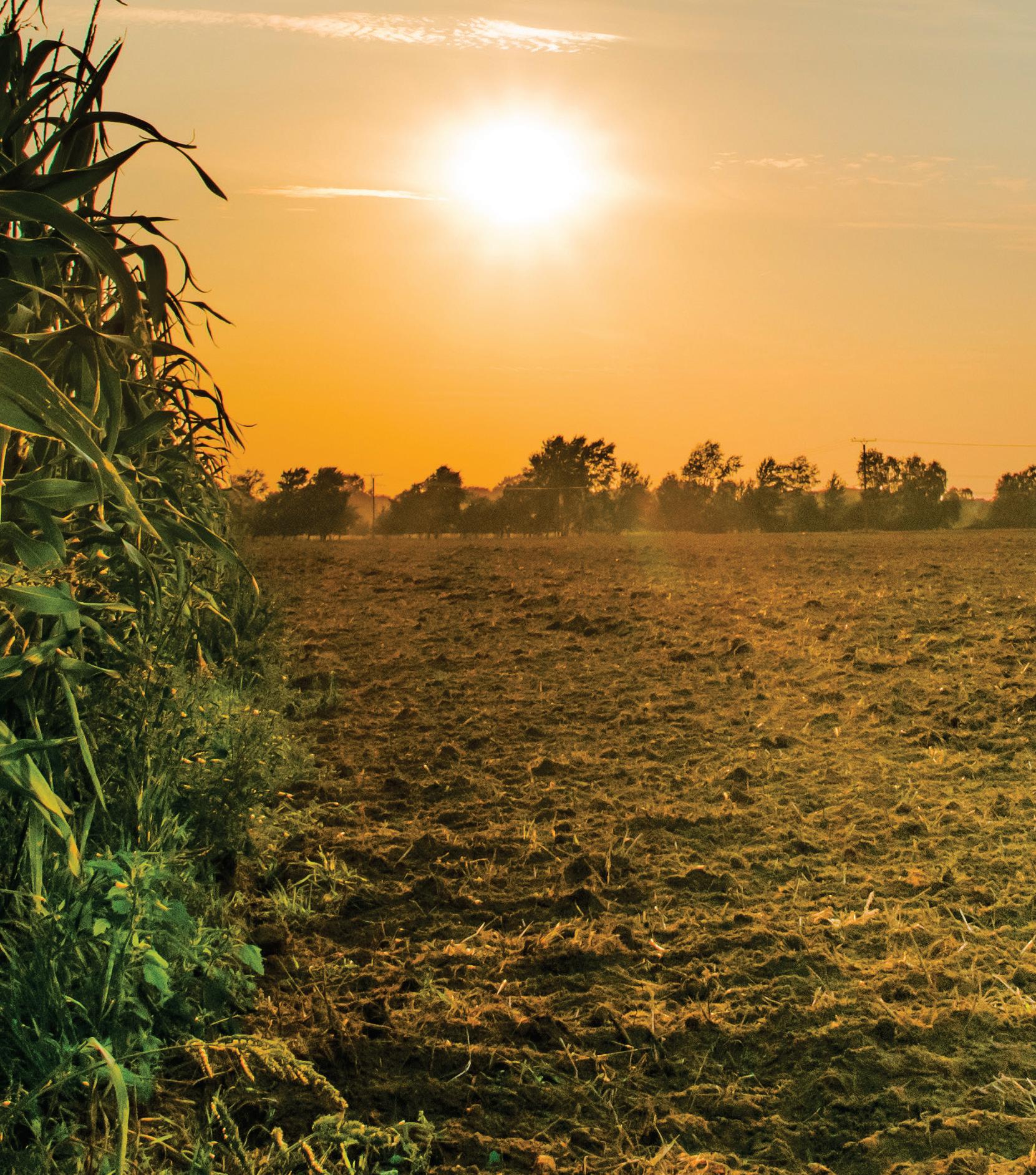

“ICM and Flottweg have continued to collaborate into an exclusive partnership where we developed an oil recovery system utilizing Flottweg’s Tricanter,” Gallop says. “ICM calls it Base Tricanter System or BTS. We then developed TS4, which is the Thin Stillage Solid Separation System, using Flottweg’s Sedicanters, which are a pressurized high G-force decanter. It’s a decanterstyle centrifuge that performs equally or slightly better than a stack disk centrifuge for stillage clarification. And then most recently, we developed the Feed Optimization Technology or FOT, which uses the enhanced scroll design in concert with several additional improvements to the Flottweg decanters to increase the throughput and cake dryness of each decanter.”
With the increased throughput, it is possible to split the decanters into two passes. The primary separation step is followed by a re-wetting of the cake solids and then a secondary decanting step. “Without those improvements to the internals of the decanters, this technology would not have been financially plausible,” Gallop explains.
Through innovative and robust plant design, ICM focuses on profitably adding value to local agriculture and feeding the world.
“We recognize that the world is starch long and protein short,” Gallop says. “So, the way we can address this is taking those feedstocks that have too much starch and too little protein, and concentrate that protein into a feed, going to our livestock, and then that becomes a food source. ICM partners with companies that have the same mindset, and the same drive to enhance humanity. By working together, we are developing technologies and solutions that enhance every one of these plants.”
Author: Daniel Lakovic, Business Development Manager for Flottweg Separation Technology Inc. dlakovic@flottweg.net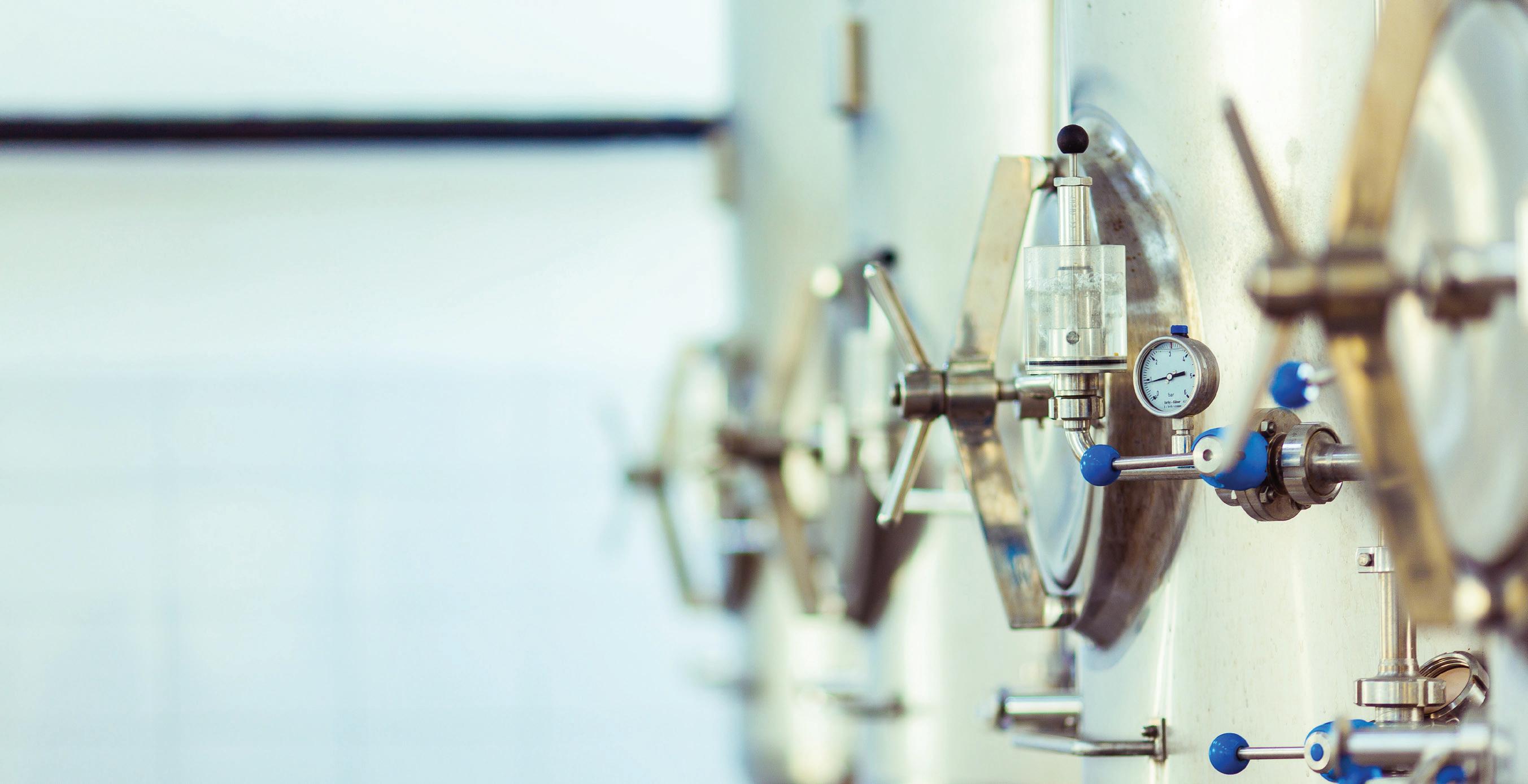
YOUR PLANT IS UNIQUE

Evaluating Carbon Content
The use of carbon-14 analysis for measuring the biogenic carbon content of biomass-derived fuels.
By Jordan TurnerCurrently, the global fuel industry continues to experience a growing trend in favor of the production and use of biomassbased alternatives to fossil fuels as interest in renewable-sourced products drives consumer behaviors and governmental regulations. Bioethanol in particular is experiencing significant product growth among transportation fuels, followed closely by biodiesel.1 In order to ensure biofuel formulations are evolving toward sustainability goals, and so industry professionals can continue to monitor compliance with ever-developing regulations, a reliable third-party verification tool for measuring the biomass-derived – or biogenic – content of biofuel formulations and blends is vital. One such tool is ASTM D6866 standardized biogenic carbon content testing via carbon-14 (or radiocarbon) analysis. Carbon-14 testing is applicable to biofuels, municipal solid waste (MSW) and other renewable fuels.
Radiocarbon Analysis: Not Just For Archaeologists
The term “biogenic” defines a product or material that contains organic or inorganic carbon from renewable sources such as plants, animals, agricultural materials and other forms of biomass. Biogenic content testing harnesses the scientific methodology of carbon-14 analysis, also known as radiocarbon, based on the ASTM D6866 test method.2 Although this method may come to mind as the wheelhouse of archaeologists and geologists for dating artifacts and soils, carbon-14 has a number of applications beyond the scientific realms it’s most known for.
Carbon-14 analysis is applicable to various samples such as biofuels. Biomass-derived fuels, such as bioethanol and biodiesel,
CONTRIBUTION: The claims and statements made in this article belong exclusively to the author(s) and do not necessarily reflect the views of Ethanol Producer Magazine or its advertisers. All questions pertaining to this article should be directed to the author(s).
are processed from plants, animals and other sources that contain the radioactive isotope carbon-14. Over the course of the life cycle of the plant or animal, carbon dioxide is exchanged with the atmosphere via photosynthesis and the food chain. Carbon-14 is concentrated within the atmosphere at known levels, allowing it to be precisely measured and keeping it in balance in biomass. When the biomass is harvested or otherwise ceases interaction with the atmosphere, the remaining carbon-14 begins the process of radioactive decay. The detection limit of carbon-14 analysis is approximately 43,500 years and, once complete, a material will no longer contain carbon–14.3 Thus, the carbon-14 method is an ideal and highly accurate tool for verifying biogenic content as fossil-derived fuel sources will not contain any carbon-14.4
Analysis is performed using an Accelerator Mass Spectrometer (AMS) instrument. Results yield a percentage of biogenic content representing the fraction of biomass-derived and fossil-fuel derived carbon present in the sample. A sample that is wholly formulated from biomass will result in 100% biogenic content, whereas a traditional fossil fuel will have 0% biogenic content. Measurements of mixtures formulated with a fraction of biomass can also be accurately obtained.
Carbon-14 testing is a well-trusted verification method for fuel industry producers, distillers and plant personnel to measure the biogenic carbon content of biofuel blends. It is often applied during the research and
development phases of biofuel formulation to obtain reliable data regarding the biogenic carbon content of a fuel mixture to ensure goals are being met. Refineries can also benefit from the precision of carbon-14 analysis for determining the ratio of their biofuel blends that originate from bio-oil as opposed to petroleum feedstocks. Furthermore, one primary use of biogenic testing results is for monitoring carbon intensity reduction and regulatory compliance.
Reducing Carbon Intensity and Regulatory Compliance
Biogenic carbon testing via the ASTM D6866 method is required by several industry regulations and recommended by others. Compliance allows manufacturers to stay up to date with current regulations and certifications, as well as to qualify for tax or carbon credits as an incentive for carbon intensity reduction. Testing is applicable to a number of mandatory regulations worldwide.
The U.S. EPA Renewable Fuel Standard (RFS) requires ASTM D6866 testing for certain fuels, such as municipal solid waste (MSW) and co-processing fuels, and allows producers to generate Renewable Identification Numbers (RINs).5 In the state of California, the Air Resources Board Low Carbon Fuel Standards (LCFS) requires or recommends ASTM D6866 testing for fuels produced by co-processing and MSW. The Oregon Department of Environmental Quality Clean Fuels Program
(CFP) also requires testing for fuels derived from MSW and co-processing.6 Similarly, Canada’s Clean Fuel Regulation (CFR) program requires ASTM D6866 testing for fuels produced by co-processing and their co-products.
Beyond North America, several European standards also call for ASTM D6866 testing including the Roundtable on Sustainable Biomaterials (RSB)’s Standard for Advanced Fuels, the Renewable Energy Directive (RED), and the Dutch Emissions Authority’s Hydrotreated Vegetable Oil (HVO) Regulation.
Overall, biogenic content testing using the ASTM D6866 carbon-14 method is an accurate third-party verification tool for biofuel formulations and blends. Such a tool is a key resource as efforts toward sustainability continue to progress in future decades. Results provide vital data that can be used for research and development, and to aid in meeting carbon neutrality milestones and goals. Additionally, these results are often required by programs and mandatory regulations to confirm compliance and qualify for tax incentives.
Author: Jordan Turner, Beta Analytic www.betalabservices.com info@betalabservices.com
1. https://www.grandviewresearch.com/industry-analysis/biofuelsmarket
2. https://www.betalabservices.com/biofuels/astm-d6866.html
3. https://www.betalabservices.com/radiocarbon-ams-dating.html
4. https://www.betalabservices.com/biofuels.html
5. https://www.epa.gov/renewable-fuel-standard-program/overview-renewable-fuel-standard
6. https://www.oregon.gov/deq/ghgp/cfp/Pages/CFP-Overview.aspx
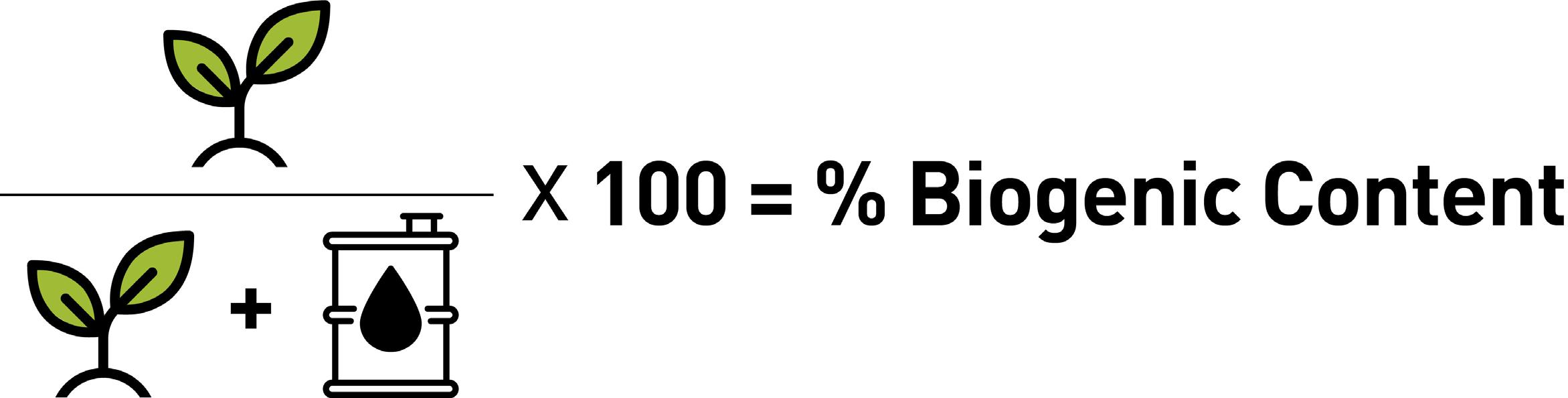
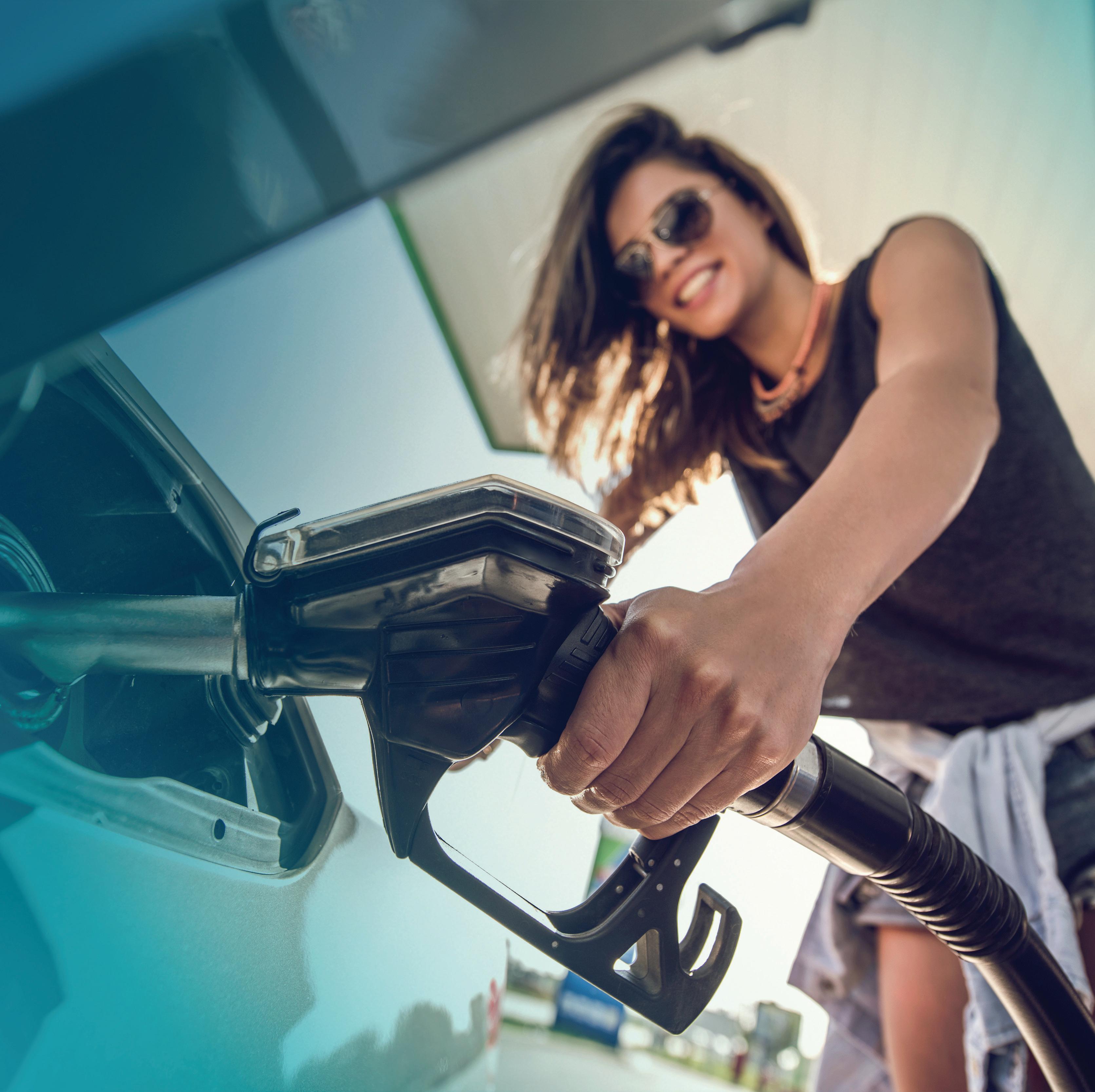
in rh ythm with natur e
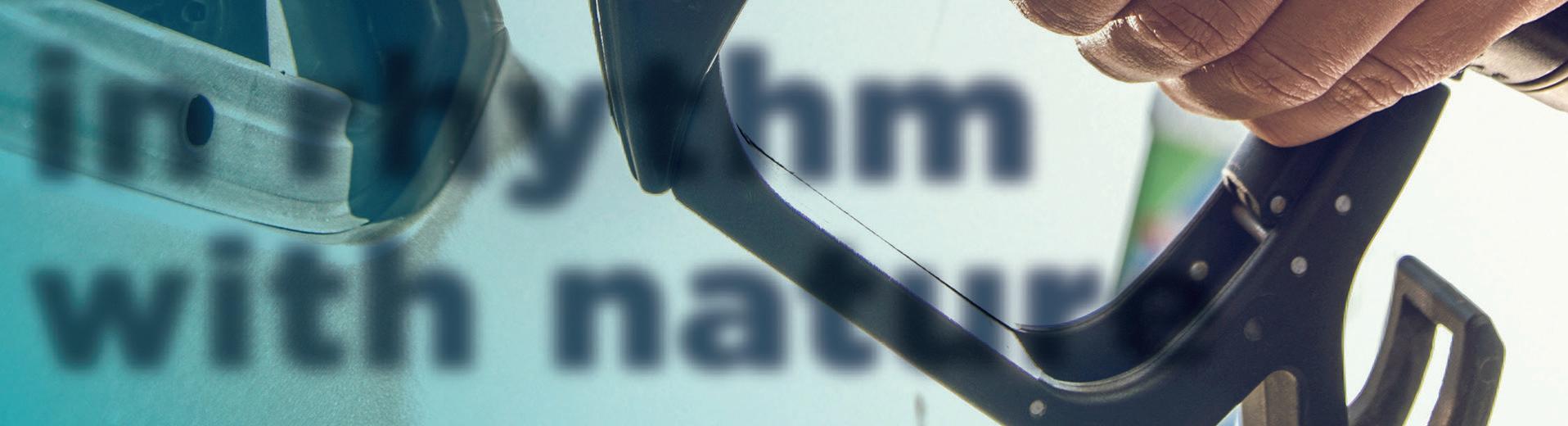
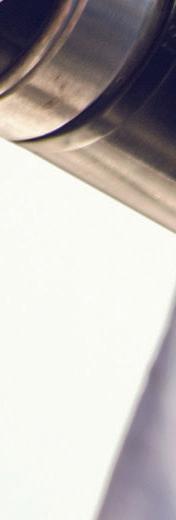
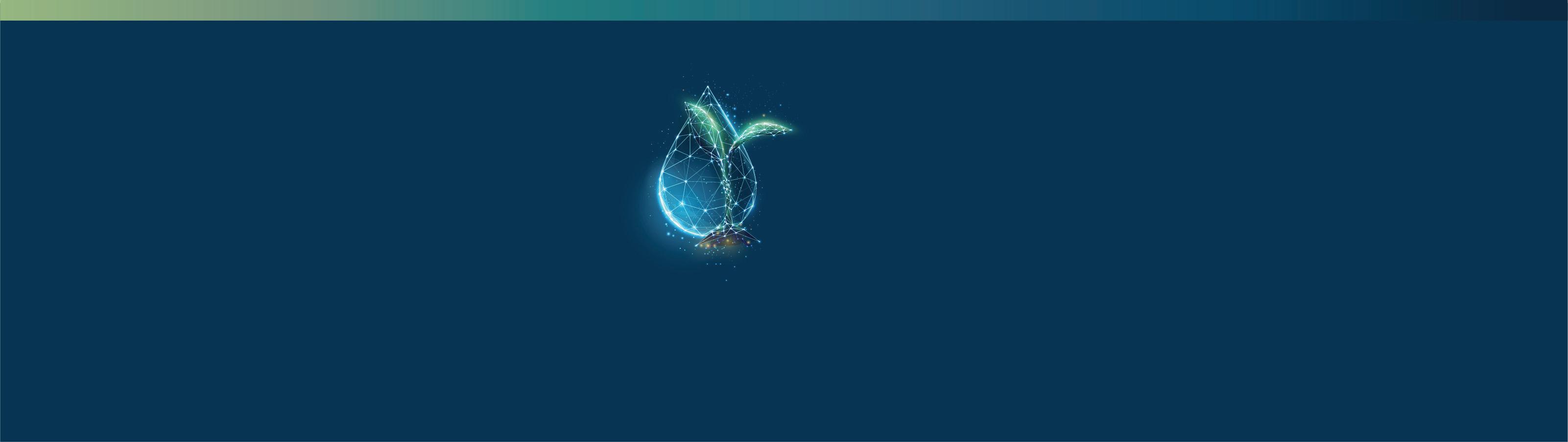
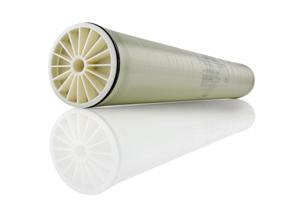

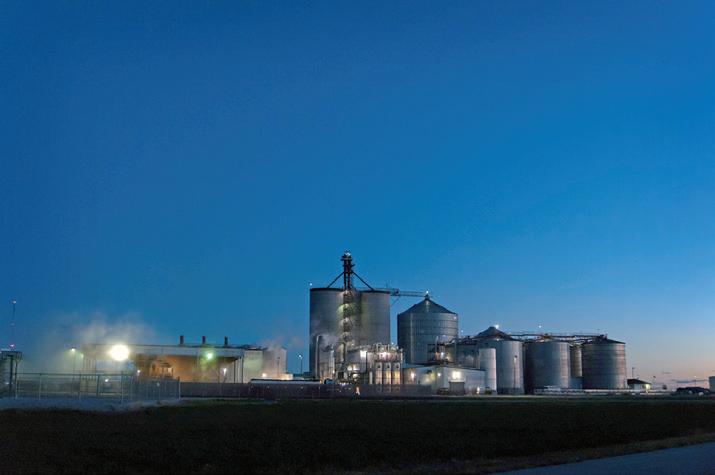
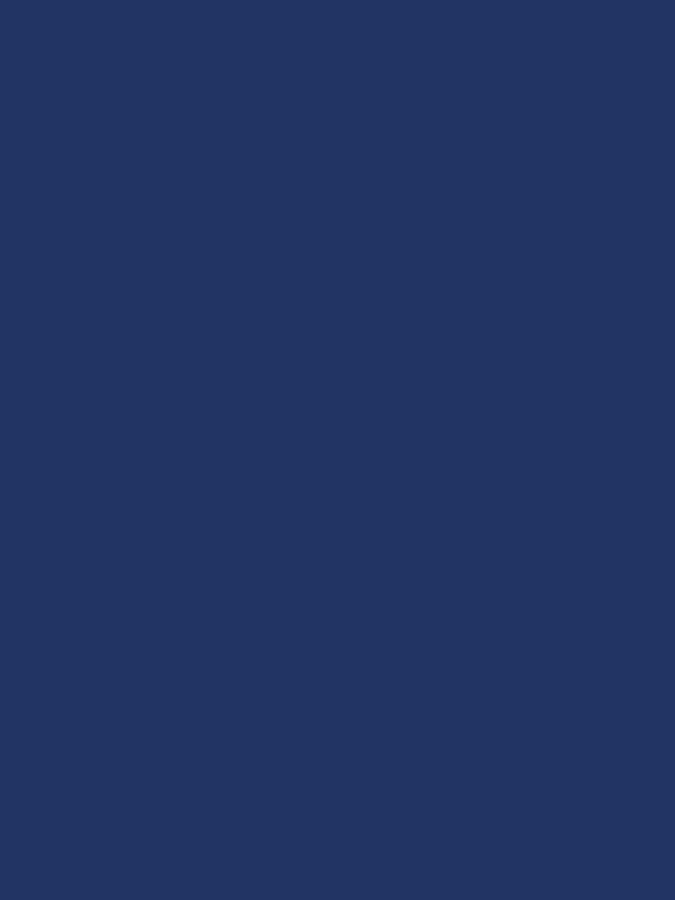

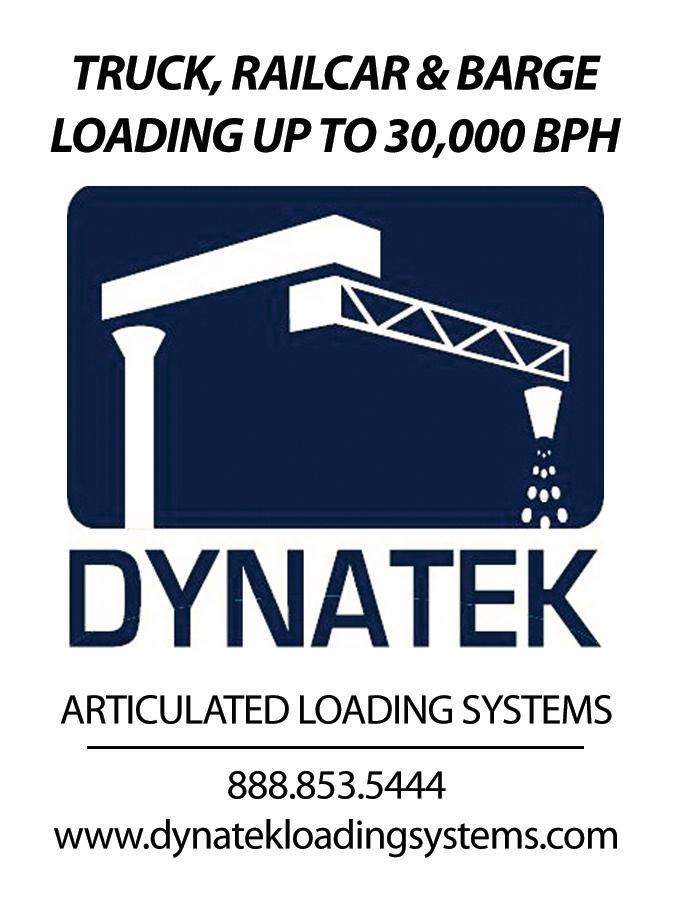
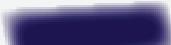
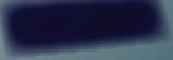


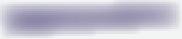

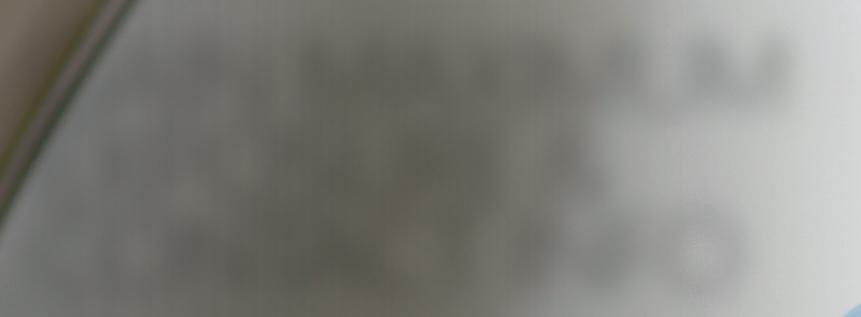



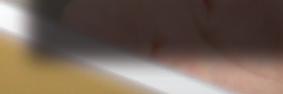
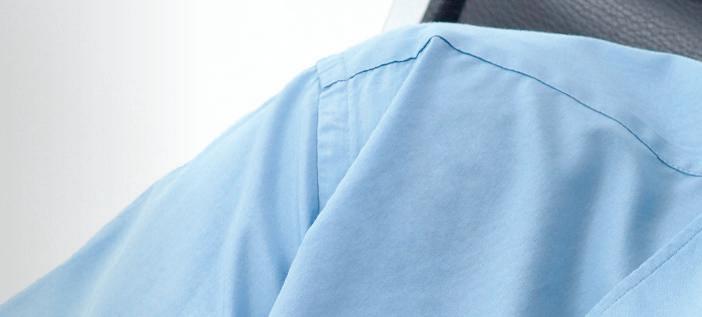

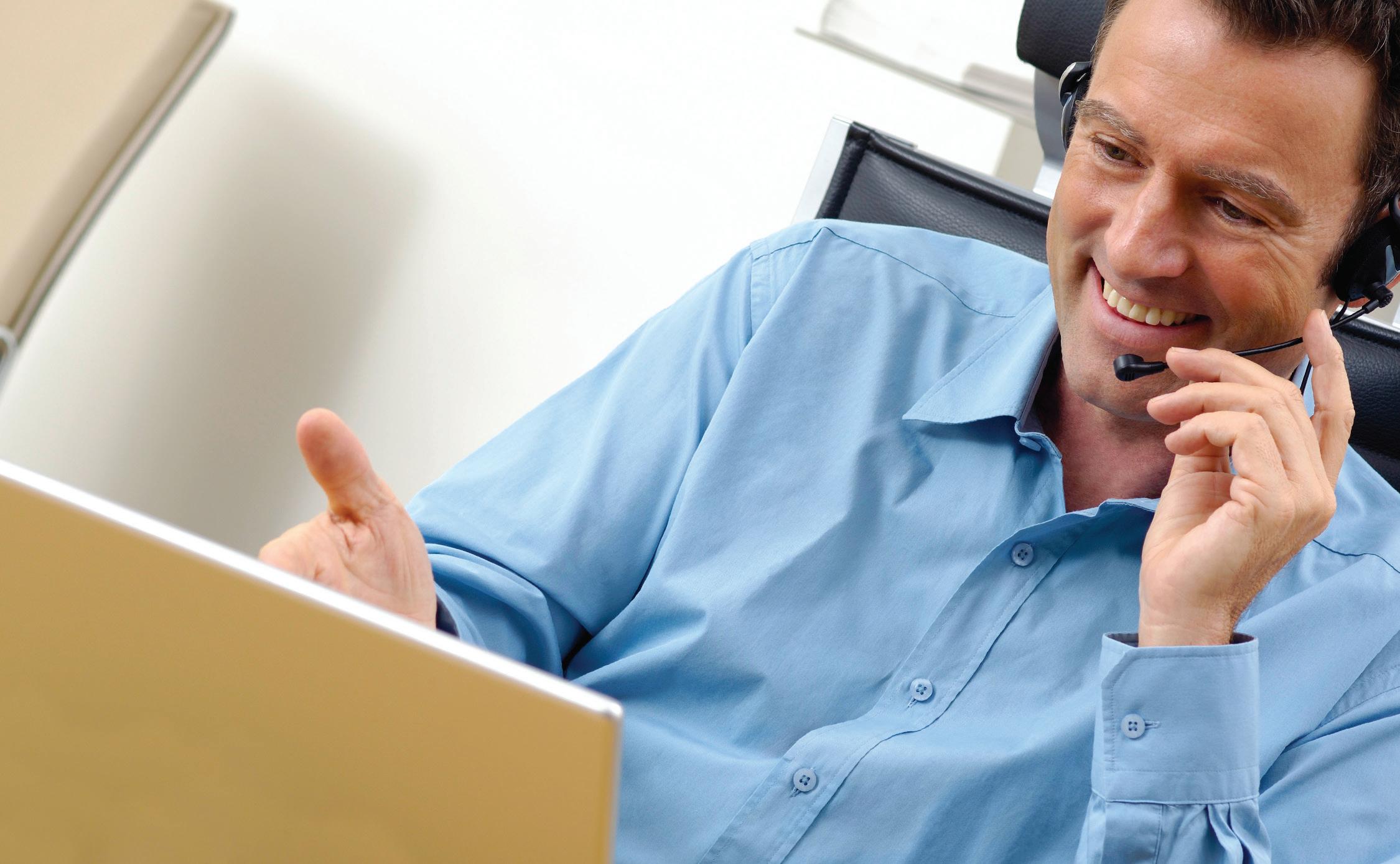
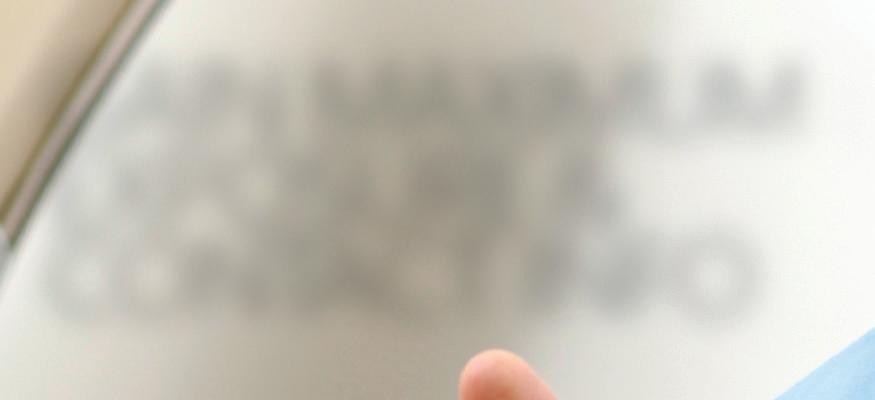

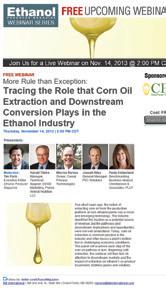







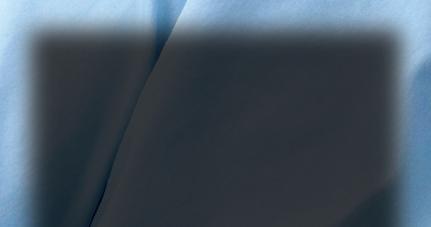
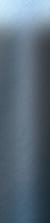
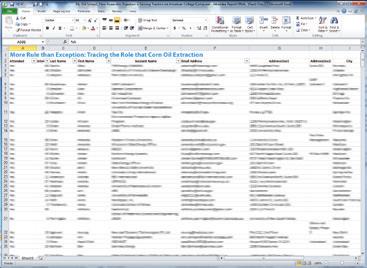
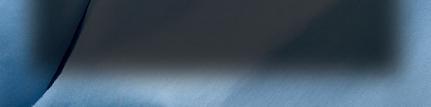



308 2nd Ave. N., Suite 304
Grand Forks, ND 58203

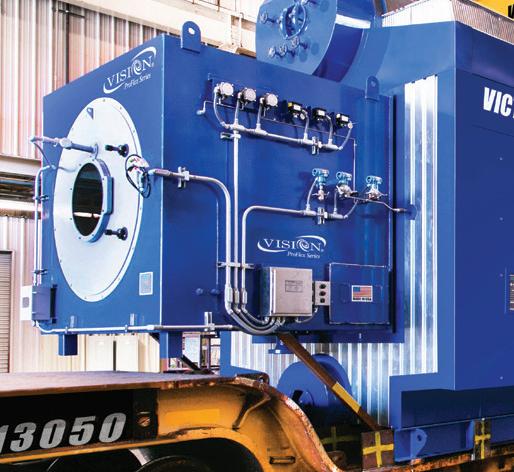
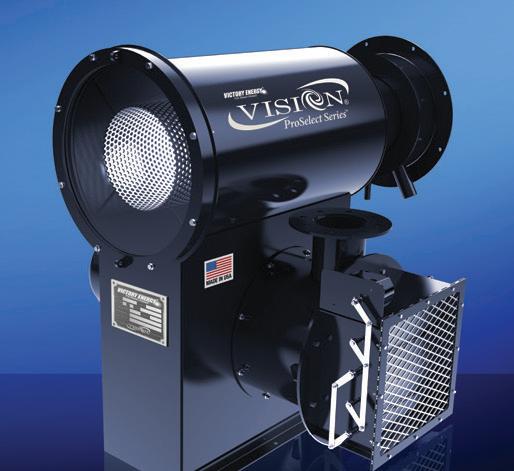
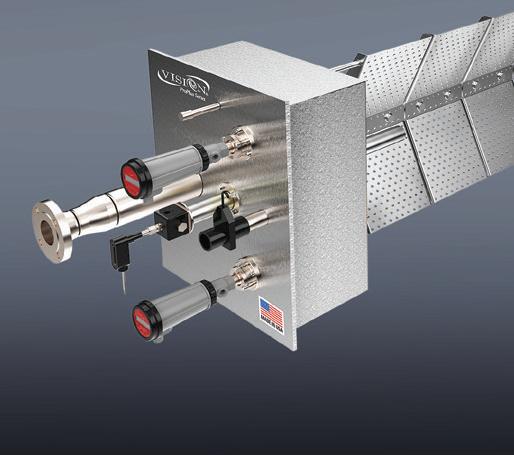

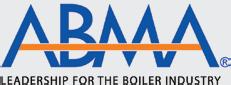