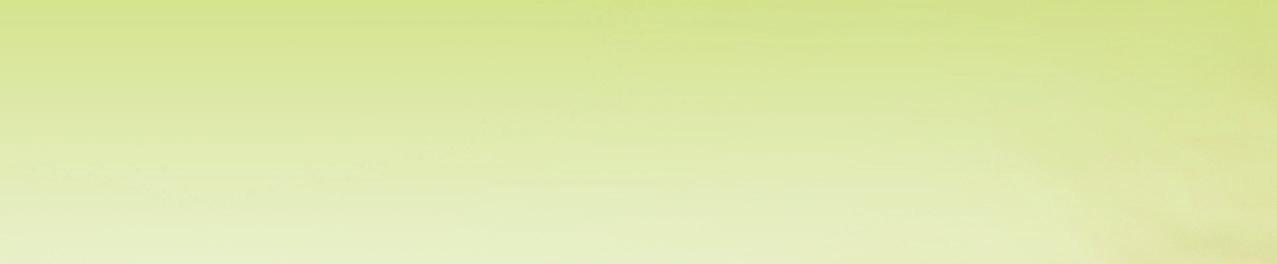
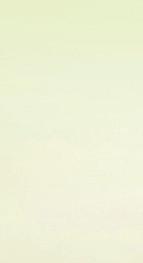

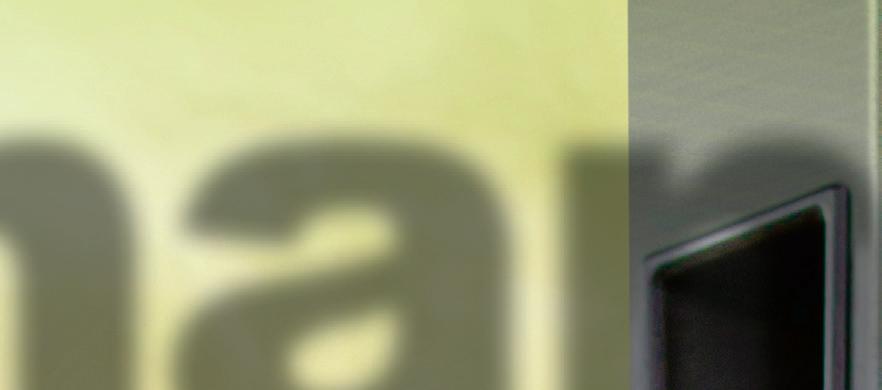
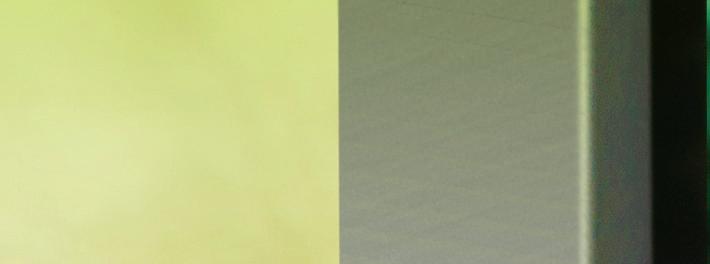
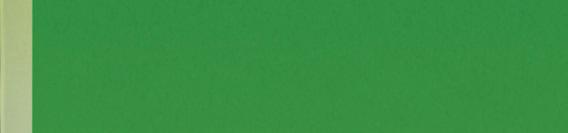

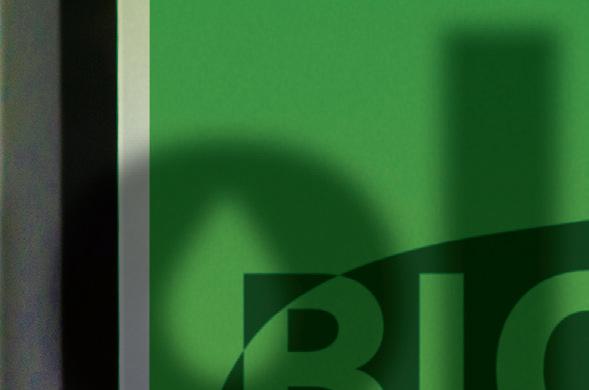
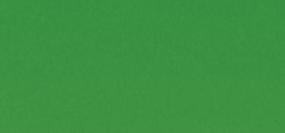




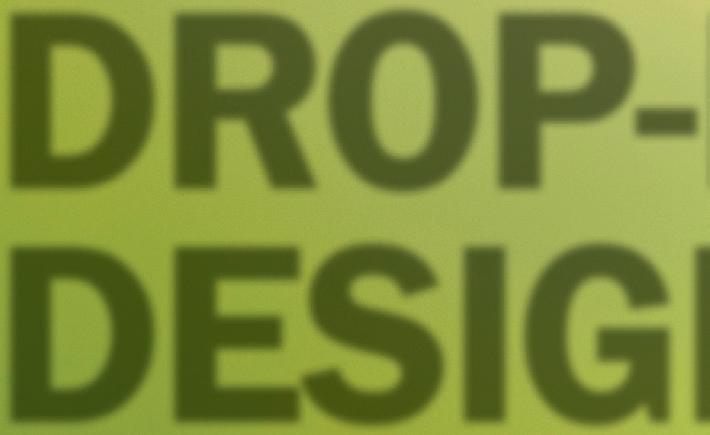

Ethanol’s Potential As A Green Gasoline, JP-8, SAF Blendstock
PAGE 32
PLUS
Turning DCO Into A Diesel Additive
PAGE 28
Tech with Ancillary CI-Reduction Upside
PAGE 12
to boost corn oil's value
realizing longtime quest for drop-in biofuel
President & Editor Tom Bryan tbryan@bbiinternational.com
Online News Editor Erin Voegele evoegele@bbiinternational.com
Associate Editor Katie Schroeder katie.schroeder@bbiinternational.com
Vice President of Production & Design Jaci Satterlund jsatterlund@bbiinternational.com
Graphic Designer Raquel Boushee rboushee@bbiinternational.com
PUBLISHING & SALES
CEO Joe Bryan jbryan@bbiinternational.com
Vice President of Operations/Marketing & Sales John Nelson jnelson@bbiinternational.com
Senior Account Manager/Bioenergy Team Leader Chip Shereck cshereck@bbiinternational.com
Account Manager Bob Brown bbrown@bbiinternational.com
Circulation Manager Jessica Tiller jtiller@bbiinternational.com
Marketing & Advertising Manager Marla DeFoe mdefoe@bbiinternational.com
Ringneck Energy Walter Wendland Little Sioux Corn Processors Steve Roe Commonwealth Agri-Energy Mick Henderson Western Plains Energy Derek Peine Front Range Energy Dan Sanders Jr.
Saint Paul, MN (866) 746-8385 | www.safconference.com
The North American SAF Conference & Expo, produced by SAF Magazine, in collaboration with the Commercial Aviation Alternative Fuels Initiative (CAAFI) will showcase the latest strategies for aviation fuel decarbonization, solutions for key industry challenges, and highlight the current opportunities for airlines, corporations and fuel producers. The North American SAF Conference & Expo is designed to promote the development and adoption of practical solutions to produce SAF and decarbonize the aviation sector.
Atlanta, GA (866) 746-8385 | www.biomassconference.com
Now in its 18th year, the International Biomass Conference & Expo is expected to bring together more than 900 attendees, 160 exhibitors and 65 speakers from more than 25 countries. It is the largest gathering of biomass professionals and academics in the world. Powered by Biomass Magazine, the conference provides relevant content and unparalleled networking opportunities in a dynamic business-to-business environment. In addition to abundant networking opportunities, the largest biomass conference in the world is renowned for its outstanding programming, maintaining a strong focus on commercial-scale biomass production, new technology, and near-term research and development. Join us at the International Biomass Conference & Expo as we enter this new and exciting era in biomass energy.
Omaha, NE (866) 746-8385 | www.fuelethanolworkshop.com
Please recycle this magazine and remove inserts or samples before recycling
Customer Service Please call 1-866-746-8385 or email us at service@bbiinternational.com. Subscriptions Subscriptions to Ethanol Producer Magazine are free of charge to everyone with the exception of a shipping and handling charge for anyone outside the United States. To subscribe, visit www.EthanolProducer.com or you can send your mailing address and payment (checks made out to BBI International) to: Ethanol Producer Magazine Subscriptions, 308 Second Ave. N., Suite 304, Grand Forks, ND 58203. Back Issues, Reprints and Permissions Select back issues are available for $3.95 each, plus shipping. Article reprints are also available for a fee. For more information, contact us at 866-7468385 or service@bbiinternational.com. Advertising Ethanol Producer Magazine provides a specific topic delivered to a highly targeted audience. We are committed to editorial excellence and high-quality print production. To find out more about Ethanol Producer Magazine advertising opportunities, please contact us at 866-746-8385 or service@bbiinternational.com. Letters to the Editor We welcome letters to the editor. Send to Ethanol Producer Magazine Letters to the Editor, 308 2nd Ave. N., Suite 304, Grand Forks, ND 58203 or email to editor@bbiinternational.com. Please include your name, address and phone number. Letters may be edited for clarity and/or space. TM
Now in its 41st year, the FEW provides the ethanol industry with cutting-edge content and unparalleled networking opportunities in a dynamic business-to-business environment. As the largest, longest running ethanol conference in the world, the FEW is renowned for its superb programming—powered by Ethanol Producer Magazine —that maintains a strong focus on commercialscale ethanol production, new technology, and near-term research and development. The event draws more than 2,300 people from over 31 countries and from nearly every ethanol plant in the United States and Canada.
COPYRIGHT © 2024 by BBI International
With decarbonization at the forefront of everything happening in biofuels today, this issue of Ethanol Producer Magazine looks at how various process and energy center enhancements—bolt-on tech, retrofits and replacements— can help producers lower their carbon intensity (CI) scores—even while some of the systems are designed more for yield maximization than energy reduction. Carbon capture and sequestration is generally regarded as the most impactful way to lower an ethanol plant’s CI, but other solutions—energy storage, CHP, electrification and more—can make a big difference, too. In “CI Score Solutions,” on page 12, we look at a handful of unique plant investments ranging in complexity, cost and purpose, and offering CI reductions ranging from one point to as much as 27.
Of course, getting energy-reducing projects to the finish line starts with project development—and well before that, questions. Ethanol producers know their own plants better than anyone else, of course, but it takes outside help to vet big projects and tailor them to the unique requirements of a given facility. And, of course, the financing component of a big project can be daunting. In “Partnering to Scale,” on page 20, we visit with Saola Energy, an engineering and project development group out of Kansas that recently partnered with Nexus PMG to help ethanol producers achieve their next-gen, low-CI aspirations—from feasibility studies to financial completion. “We are facing an inflection point in the renewable fuels sector,” Chirs Hart, president of Nexus PMG, tells us, explaining the timing of the company’s decision to go all-in on low-carbon energy, and Saola.
While leading distillers corn oil (DCO) yield optimization platforms double as CI-reducing strategies, there are an abundance of end-use drivers keeping DCO values relatively high. Biodiesel, renewable diesel and sustainable aviation fuel (SAF) have created unprecedented demand for the darling coproduct of corn ethanol production, and new opportunities seem to keep coming. In “DCO Turned Diesel Additive,” on page 28, we examine a simple process that could offer ethanol producers a low-cost opportunity to boost the value of their DCO even more—right on sight. A company called InSitu DS, in collaboration with BetaTec, has received an EPA pathway approval to generate D4 RINs—1.7 of them per gallon, in fact—for an additive approved to be blended with low-sulfur diesel. It’s a simple value-added process that could give ethanol producers an option to engage more directly in the clean diesel market.
We stay focused on new market opportunities in “Ethanol Blendstock Ready to Flow,” on page 32, a story about turning ethanol into a drop-in biofuel for renewable gasoline, JP-8 military fuel or SAF. The story chronicles the 15year history of Vertimass’ CADO process, developed by Oak Ridge National Lab scientists, which converts ethanol into a hydrocarbon duplicate that’s, in essence, biobased gasoline. The company has big plans with commercialization footprints in both Europe and the U.S., where an affiliate joint-venture, VertiBlue LLC, is pursuing SAF production in Florida. It’s a peripheral, distant opportunity, but ethanol as a drop-in gasoline blendstock—with virtually no market limitations—provides yet another fascinating example of the endless applications for our coveted, low-carbon product.
Enjoy the read!
Enter a new era of ethanol production with FermaCore™ Propel, the LATEST INNOVATION IN LIQUID YEAST OFFERINGS. Featuring extreme robustness and the fastest fermentation kinetics we’ve ever o ered, FermaCore™ Propel is a true breakthrough designed to MAXIMIZE ETHANOL YIELDS AND INCREASE ENZYME REPLACEMENT — leading to LOWER CARBON INTENSITY. Whatever form you need it to take, you can expect more from FermaCore™ Propel. Because at LBDS, fermentation is at our core.
START SHAPING THE FUTURE OF ETHANOL PRODUCTION
For years, Growth Energy has highlighted the expertise of the nation’s top GHG lifecycle scientists to counter misinformation about American biofuels. Sound science is the bedrock of our legal strategy, which aims to protect the Renewable Fuel Standard against misguided challenges lodged year after year by certain critics of renewable fuels. Now, experts in the fields of biomass and agricultural economics are taking on the challenge directly by filing their own amicus brief challenging claims offered by plaintiffs in Center for Biological Diversity (CBD) v. EPA et al. (Case No. 23-1177), in the U.S. Court of Appeals for the District of Columbia Circuit.
In CBD’s case, plaintiffs argue that the climate benefits of biofuels are undermined by the negative impacts of cutting into previously undisturbed land—an argument we know is based on debunked research.
In response, researchers from the University of Illinois Chicago, University of Illinois UrbanaChampaign, University of Idaho, Oak Ridge National Laboratory, South Dakota State University, University of California-Davis and other institutions are setting the record straight and putting the best science before the D.C. Circuit.
Specifically, they point out, “When the RFS was first adopted in 2007, some analysts predicted its targets for producing ethanol in the United States would generate major land-use changes and that emissions associated with the conversion of ‘natural land’ to ‘cropland’ would result in higher GHG emissions than gasoline.” They continued, “Experts in the field of biomass and agricultural economics have demonstrated that much of the outlier research was based on flawed assumptions and methods related to land use.”
For example, they note, the “satellite imagery at the resolution used in those early studies failed to accurately distinguish between land that has never been tilled and cropland that was temporarily fallow ... outlier researchers have also erroneously treated ‘cropland pasture’ as ‘natural’ land not previously tilled.”
Now, they explain, real-world data is available showing, “In research examining farmland over a 36-year period, only 1.8 percent of the 1,000 land parcels outlier researchers described as 'converted' appeared to fall into the category of untilled grassland, while 98.2 percent was in agriculture and toggled between crop and non-crop uses.” They added, “For the small percentage of previously untilled lands described as ‘converted,’ there is no causal evidence linking the RFS or biofuels to any such change in use.”
In short, they write, “Analyses based on more complete, updated data found that the average carbon intensity of biofuels is significantly less than conventional gasoline. Over time, as technologies and practices advance, and with various incentives the federal government has put into place, that benefit is expected to continue growing at an accelerated pace.”
Certainly, they aren’t the first experts to correct the record on biofuels. In 2022, the U.S. Department of Energy (DOE) even sent a letter to Growth Energy sharing concerns “about the methods and assumptions used” by Tyler Lark, who has authored numerous discredited studies contradicting mainstream science on biofuels.
The new amicus brief takes peer review to the next level, with top academic experts explaining directly to the courts why—when it comes to ethanol’s environmental benefits—there is no longer any genuine debate. Hopefully, those backing misleading challenges to the RFS will take note and join us as we continue to expand access to low-carbon biofuels at the gas pump.
I’m writing this column on the 12th anniversary of my entry into the Canadian biofuels industry—a total coincidence but one that inevitably prompts reflection. Such milestones offer an almost irresistible opportunity to pause and consider the journey, and (apologies in advance) this column will be no exception.
I am still impressed and amazed daily by the progress made over the last dozen years, not to mention since Canada’s first renewable fuels regulations in 2009. When I began at the Canadian Renewable Fuels Association (now Renewable Industries Canada), the biofuels industry was primarily driven by volume-based mandates. Today, we stand at the forefront of a sector defined by a new and growing global commodity: carbon. Back then, many fossil fuel producers and suppliers opposed ethanol blending in every possible jurisdiction. Today, many fossil fuel producers are themselves adopters and financial backers of low-carbon fuel production and technologies. Then, national ethanol blending in Canada was set at an average minimum blend rate of 5%. Today, under its Clean Fuel Regulations (CFR), national ethanol blending is projected to reach 15% by 2030.
This evolution has been driven by two major forces over the years. First, our industry helped shape landmark policies like Canada’s CFR and the U.S. Inflation Reduction Act (IRA), which focus on reducing the carbon intensity of fuels. Second, forward-thinking and, in many cases, blue-chip companies are creating a “voluntary” market aimed at reducing the carbon impact of their global logistics, transportation and operations that rely on low-carbon fuels and technologies. However, one briding factor is an honest and cost-quantifiable assessment of fuel on a lifecycle carbon basis.
While not yet a household name, Lifecycle Assessment (LCA) is a rigorous, scientific and equitable method for evaluating carbon emissions across the entire value chain. Embedded in the Canadian CFR and U.S. IRA, LCA helps policymakers assess performance. It also enables companies and investors exploring decarbonization projects and capital investments to assess risks, rewards and costs.
It's worth mentioning that writing this column also coincides with a politically charged time in July. The U.S. elections are just around the corner this fall, and Canada is expected to have an election in 2025. In this heated political climate, the demand for transparency and accountability is paramount, particularly regarding significant policies and taxpayer-funded clean fuel initiatives.
For the ethanol industry, LCA is not just a rule we have to follow; it’s key to unlocking new ideas and investing back into the industry. For instance, alcohol-to-jet tech for eco-friendly aviation fuel, along with carbon capture and storage, can make ethanol production almost zero carbon or even carbon-negative. LCA will be crucial to verify this and help form the business case for needed capital investments.
Reflection is satisfying, but looking ahead is where the real excitement lies. Every marker of past success and every milestone reached in the future underscores the need to continually advocate for and advance the biofuel agenda. Today, low carbon fuel isn’t just preventive climate policy; it is proactive economic policy. Designing and using LCA correctly makes a strong case for ethanol and helps create sustainable and cost-effective policies that voters can measure, investors can trust, and consumers can rely on for many years—and elections—to come.
ZFS Riga LLC, a new affiliate of Michigan-based Zeeland Farm Services Inc., has purchased an idle 55 MMgy corn ethanol plant located in Riga Township, Michigan, from Valero Energy. There are no immediate plans to resume ethanol production.
According to ZFS Riga, the site comprises 137 acres and can store approximately 2.3 million bushels of grain. It also contains a cold-idled ethanol production facility
that historically crushed 19 million bushels of corn annually to produce ethanol, distillers grains, corn oil and CO2.
“ZFS Riga has begun rehabilitating the grain receiving, storage and shipping areas of the site,” said Gary Brower, ZFS Riga spokesperson. “The corn processing portion of the facility has not operated in about five years and is obsolete without rehabilitation.”
Green Plains Inc. and joint venture partner Tharaldson Ethanol announced that the world’s largest MSC system to date at Tharaldson’s 175 million-gallon biorefinery in Casselton, North Dakota, is producing and shipping on-spec product. Leveraging MSC technology from Fluid Quip Technologies, it expands the production of Ultra-High Protein, a high-quality protein
ingredient, providing superior nutrition solutions for pet, aquaculture and other animal feed markets with up to a 40% lower carbon-intensity than competing products.
In addition to producing higher protein ingredients, the MSC system has allowed Tharaldson to achieve record renewable corn oil yields. Green Plains is dedicated to maximizing the value of every kernel
Kemin Industries, a global ingredient manufacturer, has acquired Archangel Inc., a company specializing in antimicrobials for fermentative biofuel production. The acquisition expands Kemin’s product offerings for the U.S. biofuel industry.
Founded in 2015 by Allen Ziegler, Archangel Inc. has focused on develop-
ing advanced bacterial control solutions tailored specifically to the fermentation of biofuels for the renewable energy industry. Leveraging over 30 years of experience in the biofuels sector, Ziegler has led the development of innovative technologies and customer service offerings to address the unique challenges of bacterial control in
of corn, contributing more low-carbon intensity feedstocks for advanced biofuels including renewable diesel, biodiesel and sustainable aviation fuel.
biofuel production processes. With this acquisition, he joins Kemin as a principal sales manager for the Kemin Bio Solutions business unit.
LanzaTech Global Inc., the carbon recycling company transforming waste carbon into sustainable fuels, chemicals and materials, and LanzaJet Inc., a leading sustainable fuels technology company and fuels producer, are launching CirculAir, a new joint offering to convert waste, carbon and renewable power into sustainable aviation fuel and immediately accelerate decarbonization of the aviation industry globally.
CirculAir provides an economical and commercialized alternative to Fischer-Tropsch technology to create e-fuels, power-toliquids, and waste-to-fuels leveraging the already ASTM-approved SAF production pathway that uses ethanol as the biointermediate and alcohol-to-jet technology to produce SAF and renewable diesel.
CirculAir is a formalized joint offering and end-to-end technology solution
ePURE, the European renewable ethanol association, elected Antonio Vallespir as its new president for a two-year term. Vallespir, the CEO of Vertex Bioenergy, had previously served as ePURE’s vice-president.
In his new role, Vallespir takes over from Stephan Meeder, who had served as ePURE president since 2023 but has taken
on new duties as CFO of Südzucker AG.
“With a new European Parliament and European Commission, the need to raise awareness about the strategic value of EU ethanol biorefineries is more important than ever,” said Vallespir. “As ePURE president, I will work with policymakers and stakeholders to help ensure that the European renewable ethanol sector can continue
The American Carbon Alliance recently announced that Dakota Ethanol has joined the growing organization. To date, this marks 28 ethanol plants and 11 companies that have joined the ACA.
Dakota Ethanol, located in Wentworth, South Dakota, produces 90 million gallons of ethanol annually along with distillers corn oil and distillers grains.
Dakota Ethanol joins other biofuel producers and several industry trade groups, including Growth Energy, the Renewable Fuels Association, the American Coalition for Ethanol, the Iowa Renewable Fuels Association, the Iowa Corn Growers Association, the Renew Kansas Biofuels Association, and the North and South Dakota Ethanol Producers Associations as members of the American Carbon Alliance.
that turns nearly any waste source including municipal solid waste, agricultural residues, carbon emissions from industrial and refining processes, carbon dioxide through direct air capture, and renewable power into SAF.
to be part of the solution to climate change, energy independence, food security and industrial and agricultural autonomy.”
ePURE members also elected Alarik Sandrup, director public and regulatory affairs of Lantmännen, as the association’s new vice president.
“Dakota Ethanol is a wonderful addition to our coalition as we work to promote initiatives to ensure the long-term sustainability and resilience of our agriculture sector,” said Tom Buis, CEO of the American Carbon Alliance. “Dakota Ethanol is dedicated to producing clean, homegrown energy.”
Although ethanol producers are looking ahead to carbon capture and storage as the predominant means of lowering their carbon intensity scores, measures such as energy storage, CHP and electrification can have a substantial impact on CI scores now.
By Lisa Gibson
As the ethanol industry waits for significant carbon intensityreducing measures to come to fruition, such as carbon capture and storage (CCS)—already happening for some—and regenerative farming practices, multiple strategies exist today that, when deployed together, can substantially decrease CI scores.
While CCS is often considered the most powerful and immediate way to lower CI— with reductions as high as 30 points in some cases—energy efficiency retrofits combined with process heat and power decarbonization can achieve meaningful results as well.
There are numerous ways to lower your CI today—outside of CCS—with ancillary operational and financial benefits. Here are just some of the compelling solutions to consider.
Through the addition of a simple box with brick, ceramic insulation and iron, California-based Rondo Energy can help ethanol plants store energy onsite, for a CI-point re-
duction of between 22 and 27, depending on the geographical location and existing electricity profile of an ethanol plant.
“Rondo heat batteries take that zero-carbon power and [harness it] with the same kind of heating elements that are in your toaster, to store energy and ... uniformly heat up a big surface area of a brick material that the steel industry has been using for 200 years in blast furnaces to store heat,” says John O’Donnell, Rondo founder and chief innovation officer. “We found a way to use that material, which is exciting because it’s cheap, it’s safe, and it’s available at million-ton scale.”
The bricks contain electrical heaters that reach around 2,000 degrees Fahrenheit when air is circulated through them, O’Donnell explains. “That superheated air can be used for a lot of different things, including mash and distillation—among the largest steam needs at at a biorefinery.”
In addition, the system can accommodate a standard heat recovery steam generator that many ethanol plants already have installed for their combined heat and power systems.
O’Donnell says the system is truly bolton, similar to existing boilers, and doesn’t require a single change to the facility. In fact, a recent installation at Calgren Renewable Fuels in Pixley, California, caused no downtime.
“With some technologies you’re going to tear the plant apart to put in new process equipment. We’re not one of those,” O’Donnell adds. “This is something that can be done pretty quickly.”
A CI reduction of 22 to 27 points is very significant and even approaches the 30-point reduction estimated through CCS. “The big dog is the primary energy, and if I can capture intermittent electricity, I can build new generation that’s absolutely zero CI, no matter whose analysis you look at.”
He continues, “We are the big hammer as far as we understand, and we are pretty excited about what else is there.”
With Rondo’s system alone, an ethanol plant could reach or even dip below CI scores of soybean pathways for sustainable
aviation fuel, O’Donnell emphasizes. Stacked with CCS, the CI score dips to near or below zero, he says. “That’s lower than cooking oil. There’s no lower-CI fuel source.”
ICM’s FOT Oil Recovery Technology is a two-state washing system that uses counterflow wash water to remove oil from the cake coming out of the whole stillage decanters. “This technology ensures the oil doesn’t leave with the cake,” says Chuck Gallop, director of innovation for ICM.
“[Looking at the industry], we have identified that the plants have done a tremendous
job of recovering the oil from the syrup, [but] essentially forgetting about the oil leaving with the cake,” he says. “So we’ve pivoted and started removing the oil from the cake and forcing it toward the syrup.”
The FOT system allows up to 25 percent more oil recovery, but comes with another, timely benefit: it presents a much drier cake to the dryer. “When we remove the water from that cake, the dryer then uses less natural gas to produce a dried distillers grains with or without solubles,” Gallop says.
The savings could range from 600 to 1,900 Btu per gallon, depending on centrifugation, which can vary by plant. Older centrifuges produce a wetter cake that requires more natural gas to dry, Gallop explains. “Each plant over the last 20 years has gone
through some level of improvement or adaptation of newer techs, so each plant will need its own individual appraisal and engineering study.”
As a general rule of thumb, Gallop says, a carbon intensity score reduction could be calculated assigning 0.9 points to every 1,000 Btu. On the high end (1,900 Btu at 0.9 per 1,000), that CI reduction is nearly two points.
The primary benefit would be for plants that dry DDGs, but even plants that don’t will gain an advantage, Gallop says. “There’s a financial benefit from mixing all of that syrup onto the wet distillers grains and selling it as a wet distillers grains with solubles rather than the lower-value product coming from the plant in the form of a syrup or condensed distillers solubles.”
Deploying Whitefox’s ICE membrane technology in lieu of molecular sieves for dehydration automatically results in a savings of 1,000 to 1,500 Btu per gallon, says Jackie Hayes, business development manager for Whitefox. “First and foremost: membrane tech is the most efficient way to dehydrate on the market today for both fuel and industrialgrade ethanol,” she says. “We provide continuous dehydration, so there is no regenerative step, and that automatically provides natural gas savings.”
In addition, ICE can recycle or reintegrate heat streams within the facility, providing even more Btu savings.
Whitefox has a new version of ICE— ICE XL—that offers up to 50 percent natural gas savings. The first installation is in precommissioning at Western Plains Energy in Kansas and will offer upwards of 7,000-Btuper-gallon savings, Hayes says. “In many cases, that is about half of what their energy consumption is in (dehydration, distillation and evap), so that’s really sizable, resulting in a six to seven CI-point reduction.”
ICE XL is a more holistic approach to DD&E that reconfigures the entire system, whereas the original ICE is a bolt-on technology. “We’re taking the energy-conscious
allow us to maximize the benefits of our integrated processes.”
The CHP systems installed by Minneapolis-based McGough Construction in the past few years have lowered ethanol producers’ CI scores by between two and four points, says Ben Juhnke, industrial preconstruction manager for McGough.
“The plant’s electrical consumption drops substantially when you have on-site generation, which lowers carbon emissions there,” Juhnke says. “Secondly, that energy has to come from somewhere, so you’ll see an increase in natural gas consumption on site, but with those things combined ... you net a 10 to 15% savings on carbon emissions.”
McGough has installed multiple 5MW and larger CHP systems in the past decade, predominantly gas turbine and heat recovery steam. While McGough isn’t a technology provider, the company partners closely with turbine and boiler manufacturers and can either procure all equipment for its customers and roll it all into a large project finance structure, or operate in an owner-furnished contractor-installed capacity, Juhnke says.
Either way, the efficiency benefits of CHP are undeniable, he adds. “It is really done holistically. Onsite power generation and waste heat recovery from that power generation really shifts fossil power generation [away from] far-off utilities with centralized, economy-of-scale power plants. It brings that generation onsite, and we can recover that waste heat and apply it to the process.”
UNDENIABLE EFFICIENCY: McGough Construction has a decade of experience installing combined heat and power systems and shaving points off of CI scores. This system is installed at Heartland Corn Products in Winthrop, Minnesota.
PHOTO: MCGOUGH CONSTRUCTION
And that’s where the heat recovery steam generator comes in, Juhnke adds. “We can tap into the high temperature exhaust and make steam with it for the ethanol plant.”
ICM is developing a technology that recovers waste energy from the cooling tower and uses a refrigerant-based heat pump to generate either steam to power the plant, or hot air to offset natural gas use in the dryers.
“We want to pull the heat out of the cooling tower water to the refrigerant, then there’s a handoff between the heat in the refrigerant and water to generate steam or air going into the dryer to make hot air. Essentially, it gives us the ability to connect something like a cooling tower to evap or distillation and exchange that heat,” Gallop says.
The system’s physical footprint and thermodynamic cycle depends upon the use case for the system—steam or hot air—but both employ a heat pump and refrigerant. ICM’s refrigerant-based compressor does not require the heat to already be in vapor form, in contrast with other compressors on the market. “We are taking heat that is not in a vapor state—heat that is very low grade— such as the heat that’s in the cooling tower water, and transferring it to refrigerant and
then compressing that refrigerant and then transferring that intensified heat to another medium such as air or water or alcohol to vaporize that product.”
The refrigeration cycle also sends supercooled air to the fermentors. “During hot days of summer when most plants have to rent chillers to cool the water going to ferm or slow down their plant, we won’t have to do that,” Gallop says. “We will have supercooled water going to fermentation so the plant can run the same rate all year round and not suffer synergistic stresses to the yeast from high temps. And that supercooled water now can be used in distillation condensers, making them more efficient.” The process can reduce energy requirements for distillation by 10%.
The CI reduction depends on geographical location, as electricity CI varies by regional resources and proximity to them. The technology is still new, but Gallop estimates it could lower a CI score by between five and nine points.
The largest energy pull from the plant to the cooling tower is the 190-proof condenser, Gallop says. The second is the fermentors. He says if all that energy was captured and used, it could power a 70 MMgy plant expansion. “It’s phenomenal, the amount of energy that is wasted to the cooling tower.”
Gallop says ICM is looking to partner with innovative first adopters in the industry.
When it comes to CI reduction, some technology providers are delivering not just one, but multiple offerings to producers. Fluid Quip Technologies (FQT) provides a variety of efficiency-enhancing, decarbonization technologies for ethanol plants. Neal Jakel, president of FQT, has seen the interest in decarbonization grow intensely since the passage of the Inflation Reduction Act in 2022.
Jakel highlights two of FQT’s decarbonization technologies: Low Energy Distillation (LED) and DCO Technology. LED systems have been installed in several ethanol plants already, with more projects underway. The systems have been shown to increase distillation, dehydration and evaporation efficiency, reducing energy consumption by over 40%
More than 35 years of tackling the most dif cult silo cleanout projects in 30+ countries worldwide.
Safety
Professional service technicians are MSHA and OSHA-certi ed and adhere to a rigorous continuing education program.
We conquer the most dif cult cleanout projects in the world with our proprietary silo cleaning technology.
and dropping a plant’s CI score by four to six points by cascading the heat throughout the evaporation and distillation steps, reducing the amount of phase changes the liquid goes through. “You have the highest temperature with the cleanest fluids and more of the dirty fluids with the lower temperature, which also prevents fouling,” Jakel explains. “It mitigates some of those other historical downtime challenges. The technology really is about utilizing energy more effectively and utilizing energy multiple times.”
The value of FQT’s LED technology is the monetary return available to the ethanol producer through the 45Z Clean Fuel Production Tax Credit and accessing LCFS markets; the focus is not on increasing product yields. Jakel explains that, over the past several years, many different process improvements were simply hard to justify from a return-on-investment perspective because of the low cost of natural gas and electricity throughout most of the United States. However, the IRA tax incentives have opened the door to an increased opportunity for producers to seek out every available option to decarbonize, providing a route to achieving that goal in a financially sustainable manner.
DCO Technology reduces CI score by around one point while maximizing oil production, thereby reducing the mass going through the dryers. The technology typically increases oil recovery by 0.2 pounds per bushel of corn; the removal of that amount of mass from the dryers is important because the dryer is one of the most energy intensive elements of a corn ethanol dry mill.
“You’ve got to keep in mind that every little half point, quarter point, three-quarters of a point, one point of CI reduction substantially starts making a lot of economic sense, especially as you get below 50 on your CI score,” Jakel says. “And as all these little technologies add up, not only can they give you a primary benefit of an oil enhancement, or throughput gain, but a secondary or tertiary benefit of a lower CI and driving that down, because that will also allow you to participate in the LCFS markets (e.g. California, Oregon, Washington, Canada, etc.).”
Some ethanol plants located near carbon sequestration opportunities are looking at expansion, building greenfield LED systems to produce more low-carbon ethanol and capture more biogenic CO2 for sequestration. Ethanol producers are increasingly prioritizing opportunities to lower their energy costs. “If I’m on a pipeline, and I can sequester, I’m getting paid to make and capture more CO2 in a sense, so I’m not only an ethanol producer, … I’m a carbon-sequestering producer,” Jakel says. “Or, even if I’m not able to sequester, I’m highly incentivized now to drive my energy costs super low.”
Author: Lisa Gibson
Embrace the benefits of both truck and rail transportation with TRANSFLO – the Eastern U.S. leader in bulk-commodity transloading. Our team of logistics experts are standing by, ready to grow your business with innovative transportation solutions and best-in-class environmental stewardship.
Commodities We Move: • Chemicals • Plastics • Energy
Food Grade Products • Dry Bulk
• Waste Materials transflo.net
Nexus PMG has invested in Saola Energy, making a bold entrance into ethanol production by coupling its unique finance offerings with the capabilities of a proven project development firm.
By Luke Geiver
To enter the ethanol sector, Nexus PMG chose to invest in Saola Energy of Wichita, Kansas. Although Nexus PMG is already well known and respected for its work in engineering, project finance, project development and infrastructure decarbonization services in several low-carbon-related industries ranging from biomass to solar, the South Carolinafirm wanted to partner with a proven ethanol and renewables engineering company that would complement what it could bring to the ethanol side.
“We are facing an inflection point in the renewable fuels sector as the industry continues to see rising interest in ethanol, and as more producers seek opportunities to reduce their carbon intensity,” says Chris Hart, president of project development at Nexus PMG. “Ethanol in particular is really growing as a key focus area for our business given its domestic availability, readily available feedstock and lower greenhouse gas emissions.”
Nexus PMG’s investment and commitment to work with Saola will enable the Wichita team to add engineers and take-on bigger projects. According to Ben Root, one of the cofounders of Saola and the company’s current general manager, the Saola team and their
counterparts at Nexus PMG already talk every day. And, the additional workforce is not only welcome, but needed.
Both Root and Adam Belyamani, cofounder and COO of Saola, share the same perspective on the norms now seen throughout most plants considering systems upgrades or CI reduction investments. “A lot of the low-hanging fruit has already been taken,” Root says of the bolt-ons, process additions or other things that most ethanol plants have done in the past few years to stay as competitive and efficient as possible. “The projects now will be intensive and expensive,” he adds.
While there will always be small changes a plant can make, those looking to take advantage of tax credits like the 45Z and 45Q awarded for certain CI-related metrics will have to look at the type of project that Root describes as the new norm. In the era of CI reduction, the teams at Saola and Nexus PMG believe their newly formed partnership combines their complementary areas of expertise for the benefit of their clients in ethanol produc-
tion. Both companies also believe that their new partnership means the ethanol industry now has a resource that can create custom engineering solutions and CI-reduction options able to help low-carbon ethanol production in the U.S. scale.
Root and Belyamani are both curious by nature, they say. And both are also high-level, experienced engineers. In fact, most at Saola are, Root says. When Root or Belyamani walk through an ethanol plant, they look for every detail or area where something could be improved. While they often meet with plant CEOs or board members, they also spend time with ground-level personnel, managers and anyone else willing to talk with them and tell them what they are seeing. Their team has engineered projects start to finish using existing tech, jumped into already-started projects to assist, saved projects and even created new tech in-house for clients in ethanol and renewable diesel.
“We stay up to date on the changes happening across the industry,” Root says. “We are nimble, and we know technologies.” When asked what he’s most eager to see unfold over the next few years across the industry, Root smiles before saying it is technology integration that he enjoys most. Finding solutions for ethanol plants is what he gets excited about.
Most at Saola spend time daily looking at new technologies or potential new ways of integrating those technologies, Belyamani says. The team also designs new options as well.
There is no shortage of new tech on the market, they add, but there are always challenges in how an ethanol plant brings that tech into existing footprints and operations. Saola has built a reputation for finding ways to integrate new tech or new ideas into a plant. As Belyamani explains, they can always do small projects and anything considered standard. However, increasingly, producers want customized options. They want insight into new technology. When they call or email Saola, a
common question for the team is how a technology can be added into a particular system. The producers are mostly up to date on what’s out there for tech, Root says, they just don’t have the specialized experience of a team like Saola to know how to add it.
“Most producers we talk to have their eyes open and they just like to hear another technical perspective,” Root says.
While both Saola and Nexus PMG can provide constructive answers to questions like those, Root says Nexus PMG will be the better resource for plants needing help with project finance or project assessments. A big part of Nexus PMG’s success has been built on its ability to perform technical, operational and financial due diligence during the pre-financial and post-financial close of a project. The company has helped to advise debt and equity investors throughout the project finance and M&A process, and also has access to investor capital.
“The Nexus PMG team collectively has decades of experience working in emerging
low-carbon sectors—including advising some of the biggest names at the intersection of low-carbon infrastructure, engineering and finance,” Hart says, “And we truly understand what it takes to successfully scale projects.”
Nexus PMG is actually part of a larger Nexus family of services that also includes
Nexus PDS, Nexus OS and Nexus OPI. The Nexus PDS team does financial modeling, offtakes, permitting, FEED studies and EPC contracts. The Nexus OS team performs “operational-readiness audits” to baseline operational health and identify areas of opportunity.” And the Nexus OS team provides
real-time reporting, analytics and key performance indicator dashboards via its own system.
Starting in 2018, the Nexus leadership team pivoted from its roots in metals and mining, oil and gas and fossil-based power generation to only carbon reduction type
projects. According to Ben Hubbard, CEO of Nexus, investors using Nexus for its advisory services at the time kept asking about renewable-based projects. Biogas, woody biomass and other projects kept coming up. Some investors began moving away from more traditional renewable projects
like wind and solar, according to Hubbard, as their returns diminished from the teens to the single digits. That shift was part of the reason why the Nexus leadership team went all-in on low-carbon infrastructure projects. Today, Hubbard and his team believe they will play a very large role in helping a lot of the low-carbon companies achieve scale through engineering and design, due diligence and operational readiness. The partnership with Saola shows that Nexus believes ethanol producers are a part of that low-carbon future they themselves are so heavily invested in.
Hubbard explained his views on decarbonized infrastructure during an April talk with Evercore ISI, a global independent investment banking advisory firm. “There is a tremendous amount of infrastructure capital waiting on the sidelines,” Hubbard said during the talk.
Now that Saola has the backing to expand thanks to Nexus PMG, Root and Balyamani believe things will change, but also stay the same. When they started the company back in 2016, the team
brought an approach centered around custom solutions for its ethanol clients. That approach has helped the team grow its presence in the past few years, especially with the push to lower CI scores. Producers want to improve their efficiency as always, Root says, but they also want to take advantage of a lowered CI score.
“Before, producers would just ship their ethanol to the West Coast to take advantage of CI scoring,” he says. “Now, they know there are other options to be found and new markets to participate in.”
One of the biggest projects the Saola team has performed to date was a steam turbine installation project at Mid-Missouri Energy. The project helped to show Saola’s depth of competence and creativity on challenging projects. According to their team, Saola was asked to come in mid-project and provide some much-needed help on the project that seemed to be heading in the wrong direction on time, budget and effectiveness.
Root and his team stepped in and drove the project to completion ahead of schedule and, most importantly, helped to reduce the
CI score of the plant. The steam turbine now powers one-third of the plant’s operations.
The technology itself transforms highpressure steam, typically 120 to 160 psig generated during ethanol production, into electricity. The turbines help to convert steam let-down for evaporation into a big value for the plant, including a reduced CI score.
The team has also worked on other ethanol power related projects and helped customize installations to the exact needs of its producer clients. As Belyamani explains it, a combined heat and power project being handled by the power company almost left Saola’s ethanol client without the right type of steam. Saolo was able to help match the particular steam needs of the plant to the output of the system, a big detail that would have gone overlooked had the ethanol plant not taken the step to bring Saola in and have the work checked.
“We pay attention to the intricacies at our ethanol plants in terms of integration,” Belyamani says. “We are always looking at the details.”
Sometimes equipment manufacturing teams change mid-project. Other times the needs of an ethanol plant that only an experienced engineer would notice can go unchecked. And often, with a big project, the kind that can reduce a plant’s CI score in a big way or help it enter a new market, requires a team with more than just an engineer’s touch. In today’s ethanol era, projects that bear fruit will most likely not be of the lowhanging variety in scope or price, as Root and Belyamani say. The term bolt-on has become common but that doesn’t mean it is simple, the engineers add. The push for CI reduction is here, and with it there are now proven— and strengthened—players entering the sector ready to help the industry reach a new scale. Nexus PMG is one of them, and its experienced team believes that, with Saola, it has all the right tools to help the industry expand, improve and transform.
Author: Luke Geiver Contact: writer@bbiinternational.com
A simple process offers corn ethanol producers a low-cost opportunity to enhance the value of their distillers corn oil right at the plant.
By Susanne Retka Schill
New business opportunities present themselves in many ways, but Bob Miller never expected to get one through social media. A semi-retired, long-time consultant for BetaTec living in Vero Beach, Florida, Miller is a frequent poster on LinkedIn where he was found in mid-2021 by Florida businessmen.
“In 2011, a company in south Florida, Sunshine Go Inc., started making a biofuel out of used cooking oil,” Miller explains. “By mid-2015 they had grown to a production capacity of about 5 million gallons a year. Unfortunately, their business operations came to a halt in 2020 due to a combination of factors, including COVID-related diesel demand destruction and challenges with feedstock cost and availability.”
He continues, “The people involved in that reached out to me via LinkedIn, saying, ‘It looks like you could be interested in doing
something with diesel stuff.’ I said, ‘Not really, I’m more of an ethanol guy, but I’d be happy to take a peek at it.’”
Miller drove down to Lake Worth near Ft. Lauderdale, Florida, to look at Sunshine Go’s operation. “I agreed with them that it makes no sense to do this in south Florida, but what might make sense is to take it where the feedstock is readily available. The ethanol process has corn oil that will work as a feedstock, and there might be an opportunity for ethanol plants to capture some additional value.”
Miller, in turn, reached out to John Forte, president of BetaTec, to help with analyzing the project and begin conversations with potential plant customers. InSitu DS (the DS stands for diesel supplement) was incorporated in 2023 by the Florida busi-
ness partners who then formed a collaborative partnership with BetaTec. The first step, they decided, was to get a pathway approved to generate RINs, the renewable identification numbers used by obligated parties to demonstrate compliance with the Renewable Fuel Standard. Being able to generate D4 RINs and getting 1.7 RINs per gallon is a big part of the InSitu DS value proposition.
“We engaged EcoEngineers to shepherd us through the EPA pathway petition process. It was submitted, and over a year
later, EPA came back and said we’re good to go,” Miller says. Since EPA only gives singlesite pathway approvals, the InSitu DS team used one of the plants they’d been talking to, CHS Rochelle, in its petition. The Rochelle plant supplied the DCO used in the demonstration unit built by a BetaTec engineer to manufacture samples for testing.
Getting the EPA pathway in April was the critical first step coming in time for Miller and Forte to introduce their idea informally at the 2024 International Fuel Eth-
anol Workshop & Expo, hoping to recruit producers interested in exploring the opportunity. Miller points out that plants already have relationships with fuel marketers, many of which blend biofuels with diesel as well as gasoline. The process itself is simple and the risk is low.
The InSitu DS process involves a twostep filtration and two proprietary additives, Miller explains. “We tie into the existing corn oil separation at the end of the process because we want the cleanest oil we can get.
We run it through a filter so it’s particulate free. Then we run it through resin beds, add a couple of proprietary chemicals and run it into a storage vessel. The CAPEX is primarily in the resin beds and storage vessel—it’s not much.” The resin beds filter out sulfur compounds to ensure the additive meets ASTM standards for ultra-low sulfur diesel. The other chemicals help with factors such as oxidation.
“The opportunity can be substantial,” he continues, “depending on the selling
SIMPLE BUT EFFECTIVE: InSitu DS is a two-step filtration process augmented with a couple of proprietary additives. The process ties into an ethanol plant's existing corn oil separation at the end of the process in order to get the cleanest oil possible. After filtration, the oil goes through a resin bed before the proprietary chemicals are added in advance of storage.
SOURCE: INSITU DS
price, the value of the RINs and the tax rate. Plus, ethanol producers would retain the option to sell their oil as they do now if the market switches.” Running the numbers for the 40 million pounds of DCO produced annually by a 130 MMgy plant, Miller says a 45 cent RIN value, $1 per gallon tax credit and an estimated $2.75 per gallon selling price would result in $5 million additional value for a plant, compared to simply selling the DCO at 45 cents.
InSitu DS’ biofuel is neither a biodiesel nor a distilled renewable diesel, but rather a treated straight vegetable oil. The developers of the process, Sunshine Go, targeted marine applications along the Florida coast, with a sister company, Green My Fleet, modifying boats to preheat the Sunshine BioFuel so it could be used at 100% in diesel engines. In April 2017, the company’s Facebook page announced EPA’s approval of its biofuel for use as a diesel additive, which still appears on the EPA’s list of approved diesel additives today.
To be able to generate a D4 RIN for their fuel, Miller explains that a plant would need to petition EPA for its own pathway
and develop a Quality Assurance Plan that will need to be audited by an independent third party. With one pathway approved and EcoEngineers standing by to help with others, Miller expects the process to be straightforward. EPA’s letter on the first pathway affirms InSitu DS’ biofuel is classified as a non-ester renewable diesel that can generate D4 RINs and be blended with diesel as a 5% additive.
InSitu’s carbon intensity rating is impressive. EPA found a 79% greenhouse gas reduction compared to the diesel baseline (80% for heating oil), or 20.4 kgCO2e/ mmBtu. Energy used in the process itself contributes less than 2 points, while livestock sector impacts contribute just under 18 points, and the remainder is fuel transport and use. EPA explains the livestock sector impacts are from the corn needed to replace the DCO no longer available for feed use.
Miller believes InSitu DS will provide a viable alternative to biodiesel because of its low cost. “Biodiesel runs through the transesterification process with a production cost that is much higher than ours. They’ve got to add methanol or ethanol in a process that
is a lot more complicated, and you end up with a product that EPA assigns less RINs [to].” Many biodiesel producers are struggling right now because of high feedstock costs and the erosion in RIN value due to EPA’s current low renewable volume obligation levels for biomass-based diesel.
InSitu DS’ low cost compares even more favorably with renewable diesel, he adds, which requires feedstock pretreatment and a refinery. “Those are mega-milliondollar ventures, and the cost is much higher. We’re coming in at a much lower cost with the opportunity to blend in with diesel [at] a value that is more than biodiesel. While not a drop-in fuel, there are RIN values.”
BetaTec’s role in the new venture is to supply the business infrastructure, Miller says. “BetaTec will be the primary contact for an ethanol plant to participate in InSitu DS.”
“We’re excited about the opportunity,” says Forte. “We have [been] talking about this for a long time and have been waiting for approval to come through. We’re all-in on this project with Bob and the team. The timing is perfect.”
Forte says InSitu DS is complementary to BetaTec’s primary business in supplying hops-based antimicrobials and yeast nutrition to the ethanol industry. “Hops will always be our lifeblood,” he says, “but we are looking at other products to bring to the market that are complementary to what we do, and who we already service.”
“It’s a great opportunity, a great technology,” Forte says. “I’m looking forward to the launch going forward this year—we’ve got one plant to do the trial and going from there to 10 or 20.” Introducing an unknown product and developing a niche is familiar to BetaTec’s team, he adds, “We’ve taken small ideas—I’m thinking natural antimicrobial or yeast health back in the day—and making them mainstream topics. Everybody knows hops now in ethanol.”
For Miller, the venture puts him into the fuel side of ethanol plants after years of working on the fermentation side. After a decade working at a Florida distillery, he was considering retirement when the opportunity came to manage a newly built ethanol plant. Shortly after startup in 2008, he arrived at E Energy Adams in Adams,
Nebraska. “I made more alcohol in a month there than I did in a year in Florida,” he says. In his four years there, he was instrumental in starting a popular plant managers group to help mostly independent plants network and learn from each other. When he and his wife moved back to her native state of Florida, he began consulting for BetaTec. “The exposure from the ethanol plant managers group was very helpful, as it allowed me to learn the
many different approaches, requirements and constraints ethanol plant management has.”
The new venture with InSitu DS, he says, “represents a continuing effort to create yet another [advancement] in driving growth and innovation in the industry.”
Author: Susanne Retka Schill Contact: writer@bbiinternational.com
From an idea in the lab to a commercial product now approved by the EPA, ethanol-based blendstocks for drop-in fuels have arrived.
By Luke Geiver
From the beginning, the CADO technology developed by scientists at Oak Ridge National Laboratory was meant to be an ethanol blend-wall breaker. CADO stands for conventional alcohol deoxygenation and oligomerization—a process that ORNL first studied in its Tennessee labs about 15 years ago.
“I got challenged by management,” says Brian Davison, ORNL’s chief scientist for systems biology and biotechnology. “They asked what we could do to deal with the etha-
nol blend wall (i.e., to get past 10% ethanol in the U.S. gasoline pool).”
Davison and other scientists working with him explored the idea of converting ethanol into other things. On their list of must-have characteristics, the team agreed that a product that was water stable and didn’t require the use of hydrogen during production would be ideal. It was the work of a catalytic chemist that set their early effort in the right direction and helped them discover a novel catalyst capable of producing a drop-in blendstock suitable for gasoline, diesel or jet fuel. The blendstock, they determined, could
be made from any form of pure alcohol, including the most ubiquitous, commercial type—corn ethanol.
“In 2010, we knew it was going to work,” Davison says.
Now, a decade-and-a-half later—a timeframe Davison says is respectable for bringing new biotechnology to market—the ORNL team has another reason to celebrate their work. It all started as a simple idea initially meant to give ethanol producers a way to break through the perceived production limit created by the E10 maximum volume policy of the time. Today, the idea is on the
precipice of becoming a market-ready technology that companies and ethanol producers alike may soon be able to tap into.
In May, the U.S. Environmental Protection Agency approved the registration of a renewable gasoline blendstock that is produced through a process based on that original work at ORNL by Davison and others. It’s welcome news to Vertimass LLC, a company that has licensed the ORNL CADO technology process and catalyst, positioning the platform at the center of its growth plan.
At the heart of the ORNL and Vertimass technology is a unique catalyst made from low-cost metals and zeolite. The mineral zeolite contains aluminum and silicon compounds that are used for many things ranging from dry agents to air purifiers. In some instances, zeolite products are used for personal health purposes like balancing pH to remove heavy metals in the body.
The zeolite catalyst chosen by the original ORNL team was porous and absorbent. From an ethanol feedstock, the catalyst is able
to produce a longer hydrocarbon chain. Because the zeolite catalyst can produce lengthier hydrocarbon chains, the need for some of the traditional production steps were eliminated. “Contrary to long-held assumptions,” the ORNL team says, “an energy-consuming, separate intermediary dehydration step converting ethanol to ethylene was not required for the conversion.”
From the very beginning of their work, Davison and his team were achieving a neartotal conversion of the ethanol feedstock into hydrocarbons, he says. “But it wasn’t always the hydrocarbons you wanted.”
In the early days, the blendstock created via ethanol would create a significant amount of ethylene. Although the byproduct was valuable, the researchers knew it wouldn’t be an easy product for ethanol producers to manage.
Over time, the research team was able to dial in their catalyst choice to feature what they call a “hydrocarbon pooling effect.” According to Davison, inside the catalysts are pores that create this pooling once the liquid enters. “We think the pore size and the mouth size of the catalysts play a role in that [pooling] process,” he says.
Because the pooling effect is so important to the process, the ORNL researchers performed labeling experiments using a hydrogen isotope to track the molecular transition. In simple terms, they were able to test and confirm that the hydrocarbon pooling mechanism was in fact working and crucial to the process.
Once the catalysts permeate another porous support surface that provides stability and keeps the catalysts from washing out with the liquid products, substantive production can be achieved. “This is a onetime, one-place reaction,” Davison says, explaining that the environment created by the process “lowers the energetics” of the transactions to the right level, making a one-step
reaction possible. In an overly simplified explanation of the process, he says, ethanol goes in and renewable blendstock comes out. The product looks similar to gasoline. When tweaked, it can also be made to look like diesel or JP-8 (military fuel).
The renewable blendstock production approach is able to operate at lower temperatures. While reaction temperatures for ethanol are generally in the 350 degree Celsius and above range, the CADO process only requires a range that can start at 250 degrees Celsius. In addition, the process does not require hydrogen. And dehydration is not required to upgrade the ethanol into the blendstock.
“One of the things we found early on was that by having a water-stable catalyst, we could eliminate the molecular sieve,” Davison says. “We could run a 90% ethanol, 10% water solution through.”
In a scientific paper the team published early on, they noted that fermentation streams at any stage of purification can be converted into blendstock. Impurities in the ethanol stream, they said, did not impact the performance of the catalyst, meaning partially concentrated ethanol streams can be used for upgrading to blendstock—and expensive dewatering is not necessary.
One of the many challenges faced by Davison and his team was getting buy in, not necessarily from their ORNL colleagues and others working directly on the project, but from outside researchers and ethanol experts. Internally, the research was continuously supported financially by the Center for Bioenergy Innovation at ORNL and the DOE Office of Science. The DOE Office of Energy Efficiency and Renewable Energy was also a big supporter. Outside institutions and research labs eventually played a part in further testing and verification of the process before and after Vertimass licensed the process in 2014.
The real issue for the team was getting others to believe in the one-step process. “People didn’t believe it [was valid and realistic] because it [wasn’t performed] using a traditional multi-step process,” he says, explaining that the technology simply didn’t fit traditional thinking in the late 2000s.
“It challenges a long-held but incorrect assumption,” says ORNL scientist Chaitanya
Narula. “It has been assumed that you must go from ethanol to ethylene, which is endothermic and requires energy. We showed [that] this step doesn’t occur, and that the overall reaction is slightly exothermic.”
Eventually, Davison and his team say the liquid fuels research community—including those with funding ability—began to realize that if the cellulosic ethanol movement was going to work, there had to be a way to get more ethanol into the market. The blend wall had to be broken through, one way or another, he says.
The EPA’s decision to approve the renewable gasoline blendstock this year means that the process is proven and everything is, as Davison puts it, ready to go. “The EPA announcement hits the mark that there is a market for this,” he says.
To get the renewable gasoline blendstock into the market, Davison and the team at Vertimass believe ethanol plants currently in production can add bolt-on technology to diversify their ethanol into two streams. One stream of ethanol will go into the traditional gasoline blending market and the other will become a feedstock for renewable gasoline.
Vertimass is ready to fully commercialize the technology. Several entities from around the world have shown interest, including UGI Corp., which entered into an agreement with Vertimass to produce SAF from an ethanol feedstock for sustainable aviation fuel (SAF). The goal of the joint venture is to build 20 plants over 15 years.
“Starting with technology developed at a national lab—with the foundation of that scientific expertise—gave us an excellent starting point for refining and commercializing the technology,” says John Hannon, COO of Vertimass. “Having that initial technology verification and intellectual property has been essential.”
Since obtaining the intellectual property for the process a decade ago, Davison says Vertimass has substantially improved the selectivity and stability of the catalysts. Blue Biofuels Inc., another advanced biofuels production company looking to become an early adopter of the process, formed a partnership
Our team of experts have over 20 years of ethanol plant maintenance expertise. We o er full service and parts for all Fluid Quip equipment to ensure peak performance.
• OEM Parts Warehouse
•$2 million+ inventory on-hand
•Factory Trained & Certified Techs
•MZSA™ Screens
•Paddle Screens
•Grind Mills
•Centrifuges
•Gap Adjusters
with Vertimass early this year. Their new company, VertiBlue Fuels LLC, is owned equally by both. The goal for VertiBlue is to build an SAF plant in Florida using sugarcane as a feedstock to produce ethanol.
Vertimass also has plans to take its CADO approach outside the U.S. Last year the company purchased Ekobenz, a Polandbased company that was one of the first biorefineries in Europe. The Ekobenz facility
provides Vertimass with a commercial-scale site to deploy its CADO tech to produce SAF for the European market.
Davison, who is a patent holder for the original process and a cofounder of Vertimass, is excited about the recent EPA approval. He’s also pleased with the attention Vertimass and the CADO process are now receiving, a sort of validation of his longtime work.
It has taken a lot to get the original idea from that challenge about breaking the blend wall back in 2009 to a real bolt-on possibility at operational ethanol plants. It’s been a long road to success made possible by many collaborators: scientists, post-docs, students, legal professionals and more. And even though the first eight years of the work was performed at ORNL, several other entities have played a hand.
“As a scientist, I’m happy to see the excitement around this, and also for others to see the arc it takes to get a process like this
moving forward,” he says. “It takes an original idea and people that don’t take no for an answer.”
Without getting into specific numbers on the cost of installation and potential ROI, Davison says the economics of adding a CADO-based bolt-on technology to an existing ethanol plant look favorable. CADO-derived blendstocks could potentially be blended at 20 percent with petroleum-based jet fuel, he explains, based on the aromatics limits currently in place. For gasoline it could be more. The process now offered by Vertimass has made it possible for the use of more ethanol in the general fuel mix. It’s also given cellulosic ethanol another route to market once it is developed at scale. And either way, the research and commercialization efforts, including everything that may result from it, Davison says, just shows there is always another way for ethanol and science to breakthrough.
Author: Luke Geiver Contact: writer@bbiinternational.com
Vertimass seeks to diversify ethanol market opportunities for ethanol producers by commercializing its unique single-step CADO technology for making SAF, gasoline, LPG and chemicals.
By Katie Schroeder
Technology developer Vertimass provides ethanol producers with the opportunity to diversify their product portfolio through bolt-on of a novel one-step process for transforming ethanol and other alcohols into jet fuel, gasoline, LPG and other hydrocarbon products.
“Vertimass’ mission is to commercialize breakthrough technologies for low-cost production of sustainable transportation fuels that can quickly cut greenhouse gas emissions and improve energy security and domestic economies,” notes Charles Wyman, Vertimass CEO and president. “We believe
the Vertimass Consolidated Alcohol Deoxygenation and Oligomerization (CADO) technology provides the lowest cost route to make low-carbon liquid transportation fuels that are compatible with the existing fuel infrastructure and can thereby reduce greenhouse gas emissions now.” This perspective is based on Wyman’s 40-plus years of leadership in advancing and developing biofuels technologies and processes.
Vertimass’ renewable gasoline made from ethanol was recently registered with the EPA for up to 20% blends, thus opening a potential market for up to about 56
billion gallons of additional ethanol production to make 28 billion gallons, per year of renewable gasoline. Vertimass is now working to certify CADO SAF for blending in jet fuel. Vertimass seeks to commercialize this unique technology through joint ventures, partnerships with ethanol producers, and Vertimass-owned-and-operated production facilities.
Wyman adds that “a driving goal for Vertimass is to work with ethanol producers to broaden their market range while addressing the vital need to reduce greenhouse gas emissions as soon as possible.”
•Groundbreaking CADO catalyst offers low capital and operating costs
•Single stage reactor bolt-on completely converts ethanol into hydrocarbons for established and new ethanol plants
•CADO offers flexibility to favor jet, high octane gasoline, and LPG blendstocks plus BTEX
•EPA registration of 20% blends of Vertimass fuel in gasoline: VertiGas20
•Compatibility with wet ethanol can reduce costs and debottleneck ethanol production
•Successful demonstration reactor operation positions Vertimass for immediate scale up
•SAF certification in process
Seeking new opportunities to add profits to your Ethanol Plant?
Contact Us Today: info@vertimass.com Vertimass.com
An IFF scientist outlines how enzymes can help producers maximize distillers corn oil extraction in fermentation.
By Katie Schroeder
Maximizing distillers corn oil (DCO) yields is a goal for many ethanol producers as they seek to get the most out of every corn kernel. Reaching DCO production’s full potential entails the utilization of a variety of solutions throughout the production process, including biotechnology, chemical and mechanical means, explains Jaclyn DeMartini, lead scientist with IFF. Enzymes are one of the valuable allies for ethanol producers in their pursuit of higher oil yields.
Unlike ethanol, where optimizing yields largely focuses on the fermenter, corn oil maximization requires producers to examine the entire process, DeMartini explains. “All the way from corn quality, grind and liquefaction to whole stillage decanting, syrup evaporation and corn oil centrifuge performance. Literally every single step along the way can impact corn oil recovery,” she says. Ethanol producers have the potential to extract up to 85-90% of the crude fat content found in a corn kernel, but in reality most plants extract less than 60-65%.
That 20% difference in yield represents a significant margin difference for a producer. Although corn oil prices are not at the record highs of 2020, when they reached 80 to 90 cents per pound, they are still at 40 to 50 cents per pound, significantly higher than the 20 to 30 cents per pound that producers were seeing a decade ago. “[That price is] still higher than it was ten years ago, and at that level, really a valuable
coproduct for ethanol producers to extract,” DeMartini says.
DeMartini has spent over 15 years working with enzymes. She explains that cellulases and xylanases are two classes of enzymes that can play a key role in reducing the amount of oil that leaves the plant with the wet cake, instead directing it to the centrate and oil recovery system.
“You add cellulases and xylanases into fermentation typically, and their main role is to disrupt the interaction between fiber and corn oil,” she says. “The fiber in wet cake can act like a sponge, and soak up free oil, and as a result, instead of oil going with your centrate at the decanter, the oil gets stuck to the wet cake and goes out with the feed, that’s basically lost value. Cellulases and xylanases, they disrupt that interaction between the oil and the fiber, [allowing] the oil [to] go with the centrate, as opposed to with the wet cake.”
However, one of the potential issues with adding these enzymes, particularly xylanases, is that they can increase the amount of suspended solids in the centrate, and potentially cause viscosity issues, explains DeMartini. “It’s really critical to understand the baseline conditions of a plant, understanding where they’re running in terms of
their centrate solids, their syrup solids, their syrup viscosity,” she says. “That type of information will impact what dosages and ratios of ... cellulases and xylanases are the right fit for a given plant.”
IFF offers producers an experienced perspective when considering what biotechnology options will be the optimal fit for their unique process conditions.
THE RIGHT YEAS T S, A T THE RIGHT TIME, F OR THE RIGHT PURPOSE
Yeast blends are often greater than the sum of their parts. Achieve the perfect synergy of fermentation yield, speed and robustness with the SYNERXIA® Gemstone Collection.
Our broad portfolio of yeasts and yeast blends offers greater flexibility to tailor solutions based on shifting process requirements or market conditions.
Powered by XCELIS® AI, our proprietary data analytics and predictive modelling tool, the SYNERXIA® Gemstone Collection helps de-risk decision making with custom yeast blends that take your ethanol production process to the next level.
Learn more at bioscience.iff.com/synerxia-gemstone
With minimal investment, NCERC’s validated process doubles the conversion of corn fiber cellulose in the feedstock from 20% to 40%, delivering a 2% total ethanol increase.
By Yanhong Zhang
CONTRIBUTION:
First-generation ethanol production (1G) is based on yeast fermentation using corn starch, but when cellulase is added at the beginning of the 1G fermentation, the processing turns into in situ 1.5G ethanol production, where the coproduction of corn starch and cellulosic ethanol can occur. It is critical to use accurate analytical methods to quantify the starch and cellulose content in the pre-conversion samples (liquefied corn mash), and post-conversion samples (dried final beer at low temperature). Ethanol producers must demonstrate to the U.S. EPA what fraction of the total ethanol produced is cellulosic, made as a result of the in situ 1.5G processing. The cellulosic ethanol production from corn flour is eligible for D3 Renewable Identification Numbers (RINs), financially benefiting the ethanol producer.
The major carbohydrates in corn matrix are starch, cellulose and hemicellulose, with both starch and cellulose being naturally occurring glucose-containing polymers with different linked structure. Traditionally, the analytical assays to quantify each polymer involve converting them to glucose, making it extremely challenging to accurately identify whether the converted glucose came from starch or cellulose. Therefore, it is hard to obtain accurate data on starch and cellulose contents in corn matrix.
The National Corn-to-Ethanol Research Center of Southern Illinois University Edwardsville (NCERC) tackled this challenge by optimizing the total starch testing method first. NCERC modified the AOAC 996.11 method for the measurement of total starch in cereal matrix by improving the conversion of starch in the corn matrix to glucose. Another modification was implementing strict quality control criteria for data quality, such as using high quality calibration standards, in-house check standards, and a recovery acceptance range for those check standards. The method was validated for precision and accuracy in various sample formats, such as pre- and post-conversion samples, as well as corn flour.
Next, NCERC developed the total cellulose method based on the method of NREL LAP on cellulose in biomass, but with modification. Through acid hydrolysis, NCERC can convert both starch, cellulose and yeast cell wall (for post-conversion samples) to glucose. By using two check standards made freshly with each batch—one with starch only in corn matrix and the other with both starch and cellulose—its possible to monitor both starch and cellulose conversion rates and calculate the total cellulose level
(within acceptable error bar) after the consideration of the contribution from total starch. In addition, the yeast cell wall contribution in the post-conversion samples can be estimated by testing the cellulose level in fermented yeast biomass and assuming 15% yeast biomass in the sample. The accuracy of the total cellulose method is between 85% to 115% recovery with a spiked standard in the corn matrix, and the precision is lower than 10% relative standard deviation.
After the validation of the total starch and total cellulose methods in corn matrix, NCERC used the methods to build sound scientific data for various contractual projects and selfinitiated projects. The success of each project provides the best testimonial for the high quality of the NCERC starch and cellulose methods:
1. We built mass balance within a single bioreactor, from flask to 1,000 L size, between the production of ethanol, carbon dioxide, and the conversion of starch and cellulose from feedstock to DDGS. The independent lines of evidence related to mass balance from the in situ 1.5G trials have demonstrated the accuracy of the analytical methods within acceptable error bar.
2. NCERC worked with multiple ethanol plants on samples related to in situ 1.5G processes and observed an average of 1% total ethanol production increase. Of that percentage, 50% was cellulosic ethanol, however, less than 20% of the cellulose in the
corn flour was used in the conversion.
Optimizing the in situ 1.5G processing can help increase cellulosic ethanol yields. In order to increase the cellulose conversion from less than 20% through the in situ 1.5G, NCERC has modified the front-end processing by adding one liquefaction tank and other processing steps. As a result, with minimal investment on CAPEX, NCERC is able to double the cellulose conversion from 20% to 40%, which leads to 2% total ethanol increase and more than 50% of the ethanol increase belongs to cellulosic ethanol. NCERC’s Boost in situ 1.5G Technology has been validated using a 1,000 L bioreactor with accurate mass balance data.
Author: Yanhong Zhang, Interim Executive Director/ Director of Research at NCERC YZhang@ethanolresearch.com
rh