
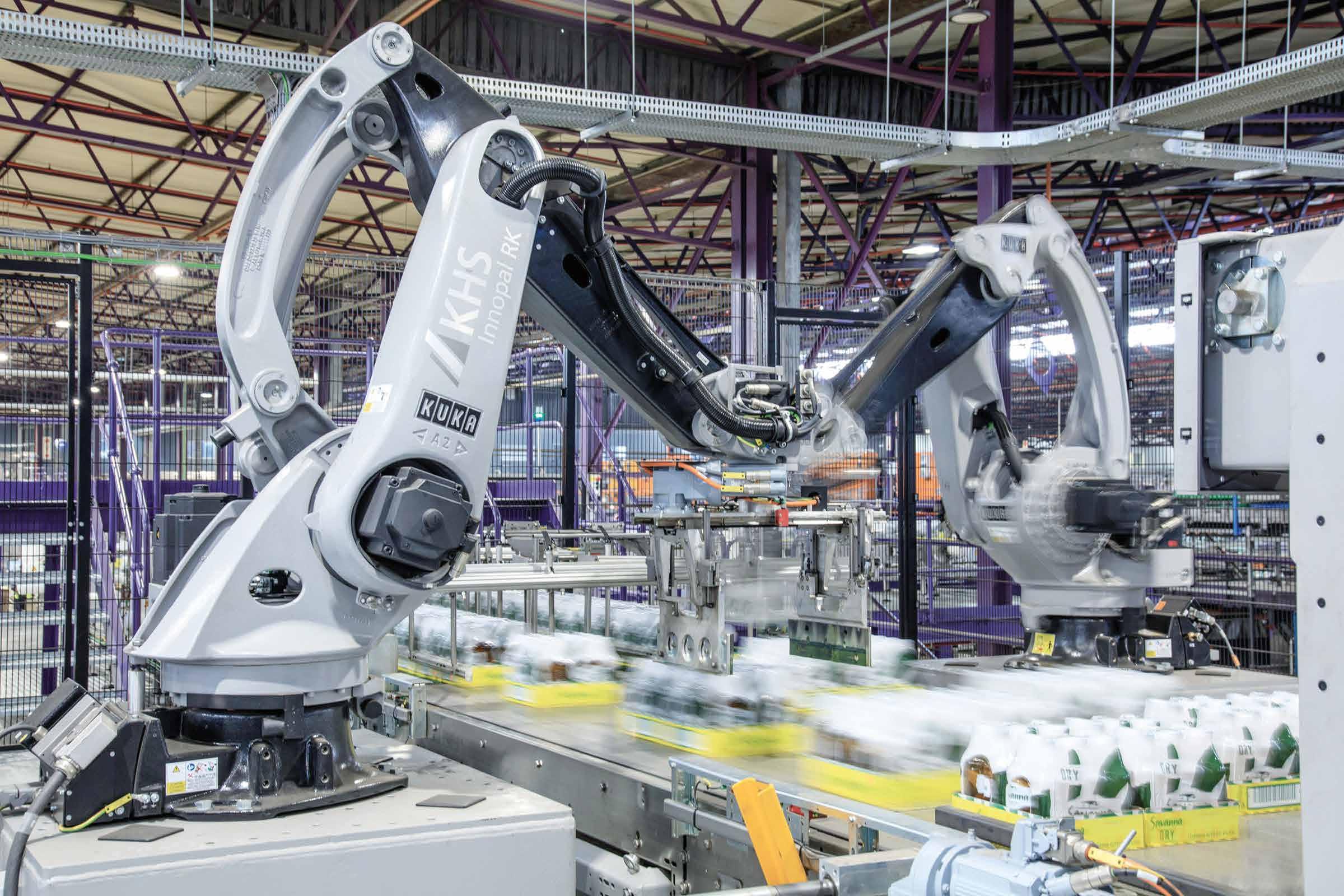
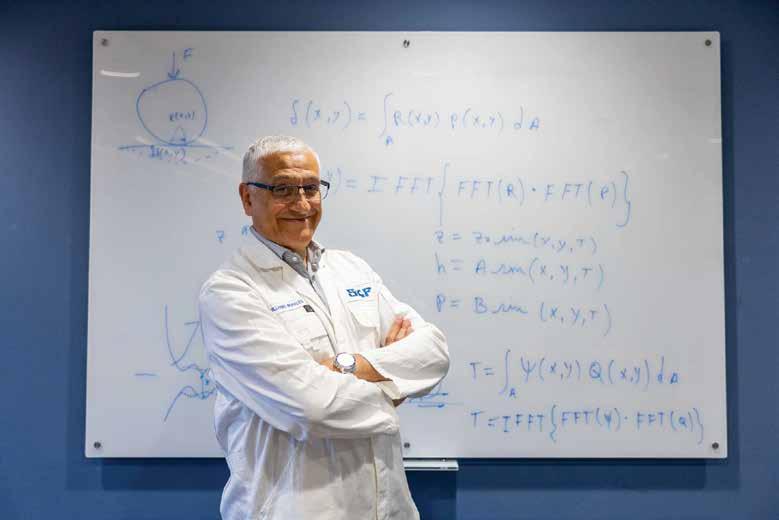
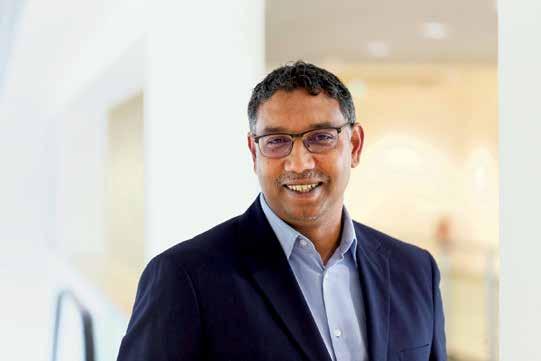


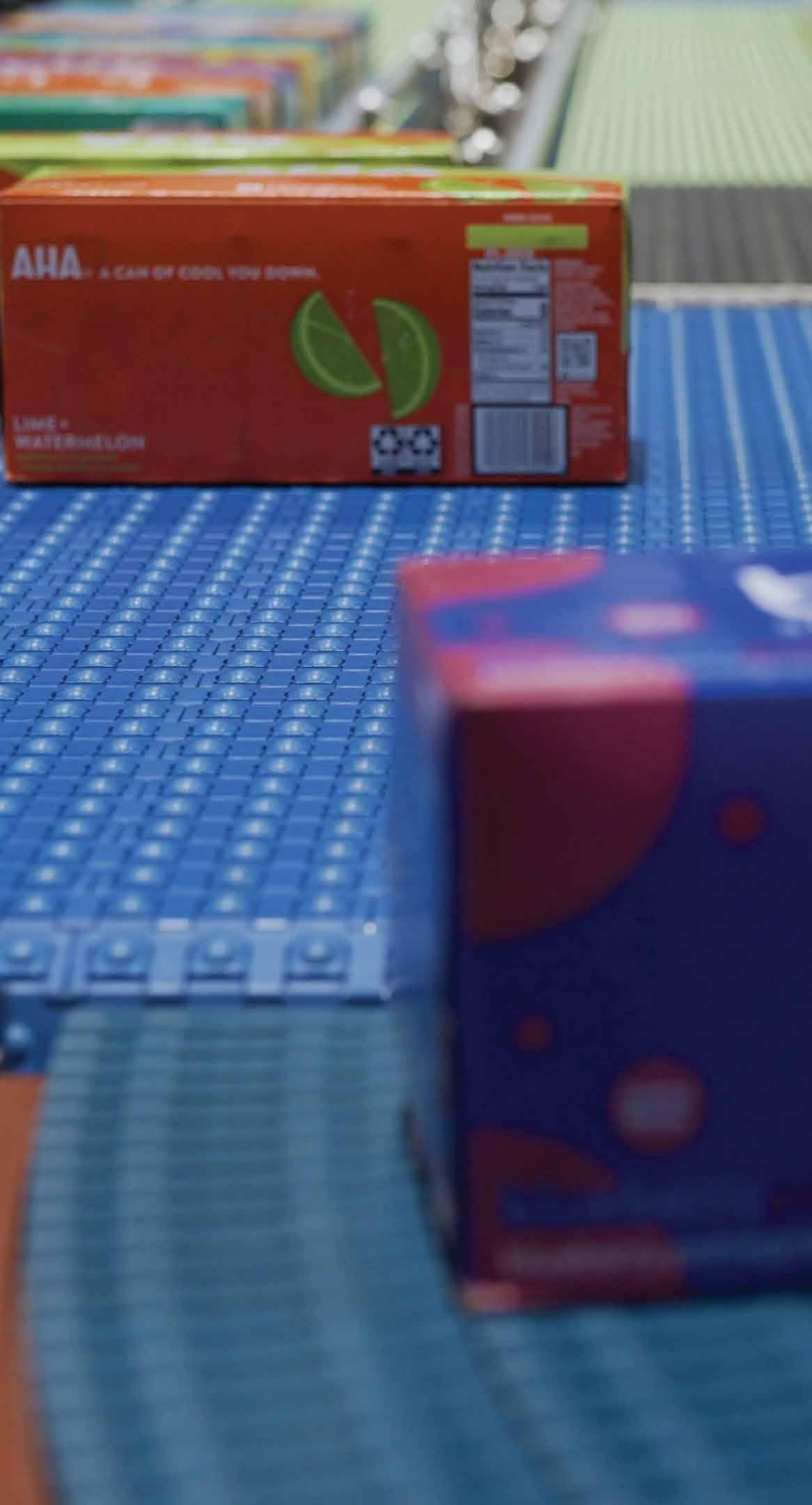

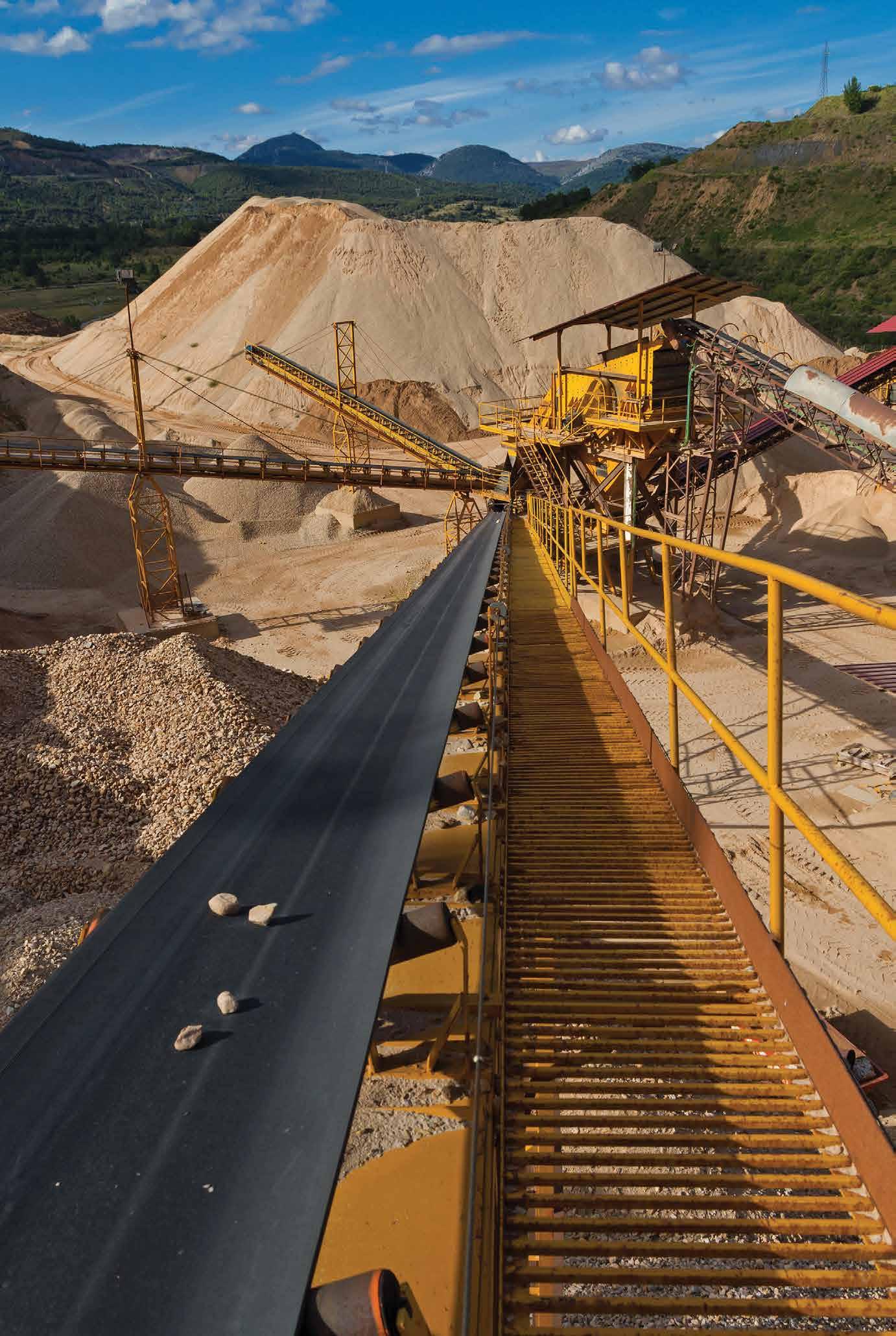
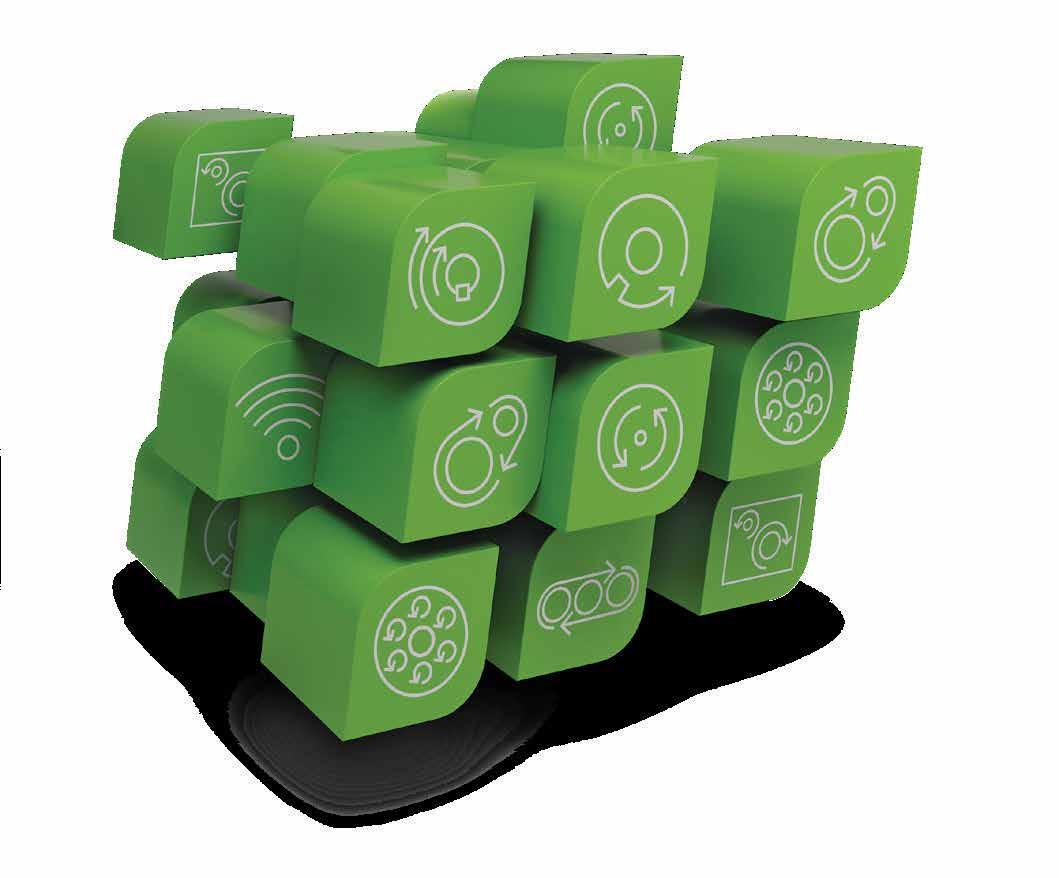
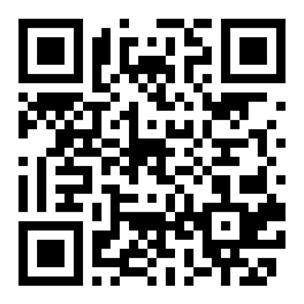
FDA-compliant AISI 420 and AISI 304 stainless steel.
Exceptional corrosion & temperature resistance.
Endures frequent high-pressure washing and chemicals.
Non-toxic, easy to clean, and non-porous.
Supplied with FDA-compliant Mobilgrease™ FM (NSF H1 Registered, Kosher/Parve, and Halal compliant).
FDA approved NBR seals that resist oils, fats, mould, and water, maintaining food integrity.
Mike Brandt Editor-in-Chief
Welcome to the latest issue of Motion+Drives Magazine! This edition is a celebration of cutting-edge advancements and transformative solutions in the world of motion control and drive technologies. Whether your focus is on sustainability, customized industrial solutions, or groundbreaking conveyor designs, this issue has something for everyone.
In our first feature, "Redefining the Future of Sustainable Logistics," we explore how the industry leader is championing sustainability through energy-efficient power transmission solutions. With innovations aimed at reducing carbon emissions and enhancing resource efficiency, Megadyne is paving the way for a greener, more responsible logistics sector.
Next, we spotlight "Engineered Timing Belts: Custom Solutions for Industry." Discover how tailored belts, designed with specialized coatings and machining, are addressing the unique challenges of industries ranging from food production to automation. With a focus on efficiency and precision, Ydins exemplifies how customization can revolutionize industrial processes.
Finally, the how-to guide, "Designing Conveyors with Plastic Modular Belts," delves into the advantages of this innovative alternative to traditional conveyor systems. Learn how these lightweight, durable, and energy-efficient belts are transforming production lines while minimizing maintenance and operational costs.
What’s in Motion…
What’s in motion for the PT industry? Learn further more about key companies, investments, trends, and advanced product solutions specifically for high precision bearings, belts, gearboxes, collars, couplings, and material handling solutions. Read about new energy-efficient drive systems, state-of-the-art repair tooling, and AI-infused remanufacturing strategies. We invite you to dive into this issue and explore how these advancements can inspire your projects and propel your business forward.
Thank you for joining us in this journey through the latest in Motion+Drives magazine.
I hope that you will enjoy it.
Editor-in-Chief Mike Brandt
: www.linkedin.com/company/motion-drives : www.facebook.com/MotionDrivesmagazine : www.twitter.com/motion_drives : www.youtube.com/channel/ UChCnbcmjFPbLEkLZGdjEXIw
12
Research & Development
The deep science of imperfect surfaces
Belts & Belting
Megadyne: Redefining the Future of Sustainable Logistics
23
Belts & Belting
Ydins Engineered Timing Belts Custom Made Belts For Specific Industrial Needs
26
Conveyor Systems How-to Guide: Designing Conveyors with Plastic Modular Belts
Fasteners
Fastener leader BUMAX goes even greener
Gearboxes Flender One: the next chapter
Condition Monitoring Testimonies from the LUBExpert Implementation Master Class
32
Bearings RKB bearings for gearboxes
Bearings
NES and The Art of Reverse Engineering
Lubrication 30 years of simalube: a success story in industrial lubrication 51 55
Gearboxes How bulk material is set in motion
Couplings
Ruland introduces new bellows couplings with enhanced misalignment capabilities
67
Motors & Drives
OCT: one cable for servo and motor connection
59 61 63
Couplings Spidex elastic jaw couplings for high-temperature applications
69
Motors & Drives Functional Safety certified servomotor brakes from Nexen
Bearings
Bearings Play Pivotal Role In Todays Landing Gear Systems
73
Pump Motors 50-year-old pump motor replaced
74
Lubrication perma STAR VARIO LONG RANG automatic Lubrication System
87
Food & Beverage Growth spurt
Food & Beverage More reliability in coding & marking for the food industry
Automation
Automation: Deep code automation and RPA in comparison
Steel Industry
World-first Trial of New Technology to Recycle CO2 Emissions from Steel Production Begins at ArcelorMittal Gent, Belgium
97 Equipment
How to avoid damage during mounting and optimally align machines
Powertrain
Motion Control Solutions from Regal Rexnords
99
Lifting Sarens, awarded for enabling and accelerating the energy transition in the port of Antwerp
93
Metrology
Inficon launches three extensions for more efficient helium leak detection
103
Ultrasound Technology
Case Study: Assessing bearing health with ultrasound-assisted lubrication
Sustainability GoGreen
We would like you to take advantage of our design co-operation service from initial application appraisal, through costing and prototypes, to ISIR and PPAP approval and production supply of your rod based Linkage assemblies. They can be supplied loose for final adjustment at the point of fit, alternatively, where required, by using length setting gauges and tooling, linkages can be supplied to pre-determined fixed centres. The flexible manufacturing techniques used in the production of linkage components allow non-standard derivatives to be readily manufactured. We produce hundreds of customer specials with varying dimensions, thread forms and features. We welcome your enquiries - please contact us at sales@btl-uk.com
BTL-UK is proud to be a committed European manufacturer of Dunlop brand Bearings, Power Transmission and Linkage components. We believe in the future of European manufacturing and will continue to focus and further enhance the requirements and expectations of our customers globally. As a proud manufacturer we want to help Europe’s industry flourish and to meet the world’s evolving appetite for innovative designs and responsibly produced quality manufactured products.
Dunlop linkage components such as Rod Ends, Spherical Bearings & Ball Joints are proudly manufactured in the UK and are used to transfer mechanical motion. Whether that motion is shifting the cutting height in a lawnmower or controlling the exhaust valve on an articulated lorry, we specialise in the supply of these products to bearing distributors and to some of the World’s most well-known original equipment manufacturers.
A wide range of materials are available, steel, stainless steel, plastic, bodies with options of bronze, nylon, PU and PTFE liners and with over 100 plating specifications we are sure to meet your customers heat or corrosion resistant requirements.
We believe our range of Dunlop rod ends, spherical bearings & ball joints are the largest range available throughout Europe.
Please visit www.btl-uk.com for further information.
BTL-UK LTD - Head office & European Distribution Centre MPT House, Brunswick Road, Cobbs Wood Industrial Estate, Ashford, Kent, TN23 1EL United Kingdom
BTL-UK LTD - Production Site Units 6&7 Hilton Road, Cobbs Wood Industrial Estate, Ashford, Kent, TN23 1EW United Kingdom
BTL-UK LTD - Production Site Unit 22, Albert Drive, Burgess Hill, West Sussex, RH15 9TN United Kingdom
SKF principal scientist Guillermo Morales-Espejel was the driving force behind a radical new approach to bearing life prediction, which has important implications for design engineers, equipment makers, and end users.
The role of fatigue in bearing life is something engineers have known for a long time, but the development of models that could account for that fatigue has taken generations. "You can't predict bearing life in a deterministic way," says Guillermo Morales, Principal Scientist at SKF. "You have to combine statistics with physics to make useful predictions."
The first models that took this combined approach to bearing life prediction were published in the mid20th century, with SKF scientists at the forefront of their development. "Those early papers introduced basic concepts that we still use today," says Morales. "Things like the difference between the static and dynamic capacity of a bearing."
You can't predict bearing life in a deterministic way. You have to combine statistics with physics to make useful predictions.
Guillermo Morales, Principal Scientist at SKF
Over the next 50 years, advances in theoretical understanding and practical experience, paved the way for more sophisticated models. In the 1980s, for example, engineers figured out how to account for the fatigue limit in predicting bearing life - a stress level below which very little fatigue accumulates in the material.
"All these 20th century models were based mainly on subsurface fatigue," Morales explains. “But thanks to advances in manufacturing technology, such as the introduction of very clean steels, the subsurface fatigue challenge has been largely solved.” Today, most bearing failures are triggered by a problem on the surface, such as including poor lubrication, contamination, frictional heat, or electrical damage.
And the surface was something Guillermo Morales knew a lot about. After earning bachelor's and master's degrees in mechanical engineering in his native Mexico, he traveled to the University of Cambridge, UK, to pursue a Ph.D. in tribology: the science of friction, lubrication, and wear.
"My Ph.D. work was trying to model the effect and behavior of roughness in lubricated contacts," he says. "In tribology, 'roughness' is a general way of describing any microgeometric feature. It can be a scratch, an indentation, or a texture on the surface." Such surface patterns are a headache for tribologists because they disrupt the thin films of lubricant that allow mechanical components to move smoothly over long periods of time.
But roughness is difficult to model. "People used to do numerical work to model roughness," recalls Morales, "but it's a very hard, time-consuming problem for a computer. You need a system of five equations with five unknowns distributed in time and space."
The key to Morales' dissertation was to find a simpler, faster way to tackle the complex mathematics of roughness. He did so by breaking it down into sinusoidal "waves". This dramatically simplified the calculations required, while still allowing any type of surface imperfection to be modeled as a collection of different waves.
Morales joined SKF’s research laboratory in January 2000 and immediately began to study the impact of surface issues in bearings. One early project simulated bearing performance in mixed lubrication environments, where contamination or lack of lubricant creates areas of direct metal-to-metal contact within a bearing. Another evaluated the effect on bearing life of the small indentations that can occur if a bearing is mishandled during manufacturing, shipping, or assembly.
Fast forward a few years, Morales and his colleagues were successfully applying mixed lubrication and surface damage models to a wide range of problems within SKF and for its customers. In 2012, a new technical director approached Morales with a bigger challenge. "He said our bearing life models were useful, but they were too rigid," recalls Morales. "It takes too much effort to adapt the model to a different problem or to integrate new knowledge."
The technical director's request was simple, but daunting. Could Morales and his team take what they had learned about the effect of surface conditions on
bearing life and build a general-purpose model that would better predict bearing life in the real world?
Their answer to this challenge was two years in the making. "We already had some of the key ingredients," says Morales. "To build a generalpurpose bearing life prediction model, you have to simulate the operation of different bearings, under different conditions, over millions of cycles. Without a fast solver, that would have been impossible."
Other parts of the model required the team to break new ground. In particular, Morales says, they had to develop an approach that combined their new surface damage models with traditional methods for estimating subsurface fatigue.
The first iteration of the SKF Generalized Bearing Life Model (GBLM) for conventional steel bearings was introduced as a concept to customers at the 2015 Hannover Messe. It offered the promise of an immediate solution to many challenges faced by design engineers every day. "With a better life prediction model, you can design better machines," says Morales. "Our model helps designers select the optimal size and type of bearing for their application, and allows companies to provide more reliable advice on maintenance and replacement intervals." The result is more efficient use of resources, with fewer breakdowns and less premature replacement of parts that still have life left in them.
Over the past decade, Morales and his colleagues have expanded the GBLM to include new types of bearings, notably adding models for the hybrid bearings now used in demanding applications ranging from turbomachinery to electric vehicle transmissions. They have also updated the approach to reflect ongoing improvements in conventional bearing technology, including new steels, and better heat treatment techniques.
GBLM is also helping SKF respond to other major industry trends. For example, as companies look for ways to further reduce their consumption of resources, users are increasingly turning to remanufacturing to extend the life of large bearings. The GBLM helps these users make informed decisions about remanufacturing intervals based on the likely rate at which surface damage will accumulate in their applications.
Is there more to come? As principal scientist, Guillermo Morales now has much more on his plate than bearing life models, but he maintains a strong interest in the development of the GBLM. "We have developed a flexible and extensible way to model different bearings, operating conditions and failure modes," he says, "but all such models need to be validated with data from experiments and tests. Advanced sensors are now giving us better insight into the conditions inside our bearings, and these insights will help us extend and improve our modeling approach.
FLUID COUPLINGS
Power rating up to 3.700 kW E-MAGNETIC BRAKES
Braking Torque up to 12.450 Nm E-HYDRAULIC BRAKES
Braking torque up to 400.000 Nm
Braking torque up to 29.900 Nm HYDRAULIC BRAKES
Clamping force up to 400.000 N BACKSTOPS Torque up to 578.000 Nm
VULKAN Kupplungs- und Getriebebau
Bernhard Hackforth GmbH & Co. KG
Heerstraße 66 | 44653 Herne/Germany
Phone + 49 23 25 922-0
info.vdt@vulkan.com
As global industries increasingly prioritise sustainability, the logistics sector finds itself at the forefront of this movement. Reducing environmental impact, particularly in terms of energy consumption, is essential for companies aiming to remain competitive and socially responsible.
Megadyne, a leading provider of power transmission solutions, is deeply committed to supporting industries in their quest for sustainability through innovative, energy-efficient technologies.
Sustainability is a core value at Megadyne, a member of the AMMEGA Group, and a key element of our business strategy. Our dedication is outlined in the latest AMMEGA Sustainability Report, a cornerstone of our environmental responsibility.
Key highlights from our sustainability report:
+ Carbon emission reduction: rigorous processes are in place to drastically cut carbon emissions, enabling businesses to make a significant impact on global climate action.
+ Resource efficiency: our innovative products and processes are designed to use resources more efficiently, reducing waste and energy consumption, and leading to substantial savings in both time and cost.
+ Sustainable product development: Megadyne
high-performing solutions support sustainability goals, ensuring environmental targets are achieved without compromising quality.
The Sustainability Report is more than just a document; it is a testament to our ongoing commitment to making a positive impact on the environment.
Energy efficiency is vital in logistics. Inefficient power transmission can lead to substantial energy loss, higher operational costs, and a larger carbon footprint.
Megadyne tackles these challenges with innovative belting solutions, engineered to enhance energy efficiency and help customers achieve their sustainability goals.
By selecting Megadyne as your partner, you are choosing a company that prioritises sustainability at every level. Our advanced belting solutions are not only designed to meet the highest standards of efficiency and durability but also to support your company's sustainability initiatives.
Reduce your environmental impact, lower operational costs, and ensure that your operations are as efficient and sustainable as possible.
Contact us here https://info.ammega.com/ mdsustainabilityadv to learn more!
Rated Excellent
“
Very fast service & shipping, much less expensive than ordering locally. Very happy with my orders from ACORN!”
- Myles B, Export Customer
Improved quick search functionality
More support to help you reach Product Experts
Product alternatives feature to enhance user experience
Enhanced keyworddriven search with improved imagery and filters
Quicker ‘add to basket’ functionality for faster check-out
Ydins belts are designed to adapt to specific processes and applications, ensuring optimal performance and contributing to increased industrial efficiency. The flexibility in design and manufacturing, paired with extensive technical expertise, enables Ydins to provide tailored solutions across various industrial sectors.
+ Specialized machining including perforations, grooves, and other modifications designed to enhance belt functionality across a variety of applications.
+ Wide range of coatings to meet diverse requirements for grip, resistance (wear resistance, chemical resistance, hydrolysis resistance, UV-C radiation resistance), and food safety (FDA compliant). These finishes allow the belt to adapt to specific working conditions, thus improving process performance.
+ Custom-made cleats designed for transportation processes that require increased precision. Ydins customises cleat shapes and sizes to ensure more controlled product transport.
+ The welding options include Pin-Joint, belt fasteners, and endless.
Ydins serves sectors like food, pharmacy, automotion, and packaging, with designs suited to each industry’s challenges.
Ydins offers expert consultation, customized solutions, and rapid delivery to meet the tight schedules essential in industrial settings.
For more information about Ydins, please visit our website at www.ydins.es
In the fast-paced world of industrial automation, conveyor systems are the backbone of production lines, ensuring smooth and efficient transportation of goods. However, designing the right belt conveyor involves more than just choosing the components; it’s about understanding the nuances that make a system both functional and durable.
When designing a belt conveyor, there are several factors to keep in mind to ensure the system runs efficiently. These include:
+ Motor and gearbox selection: Choosing the right power source is essential for smooth operation.
+ Belt speed: The speed at which the belt moves can impact both efficiency and energy consumption.
+ Tension and take-up: Proper tensioning ensures the belt remains aligned and reduces wear.
+ Material handling: Different materials require different belt types for optimal transportation.
+ Distance and working environment: Environmental factors such as temperature and humidity can affect performance.
While these considerations lay the foundation for a functional conveyor system, advancements in technology have introduced superior alternatives to traditional designs, such as plastic modular belts.
Traditional roller and cloth belt conveyors, widely used in various industries, come with their own set of challenges. Over time, roller conveyors suffer from chain pitch alterations due to metal fatigue, and bearings wear out quickly, increasing downtime for repairs and maintenance. This not only affects productivity but also leads to higher operational costs.
Plastic modular belts offer a revolutionary alternative. Unlike roller conveyors, plastic modular belts incorporate transmission and conveying into a single plane, eliminating the need for chains, bearings, and additional heavy components. They are lightweight, require minimal maintenance, and are significantly more energy-efficient. These belts can be installed and dismantled easily, require no lubrication, and last much longer, making them a smart choice for businesses looking to reduce downtime and energy costs.
While PVC and rubberized cloth belts may appear more affordable initially, their long-term costs can outweigh their benefits. These belts lack a gear drive, leading to issues like belt wobbling and skidding over time. Additionally, they are prone to wear, with the fabric beneath the belt becoming exposed after minimal use.
On the other hand, plastic modular belts allow for localized repairs and are designed for durability. Their unique geometry ensures they last longer and can be repaired with ease, minimizing operational interruptions.
Designing a conveyor system isn’t always straightforward, and there are a few common missteps that can affect performance and longevity:
1. Over-engineering the structure: Designers often make the mistake of adding unnecessary weight to the conveyor, believing it will improve durability. However, this increases friction, accelerates wear, and heightens energy consumption.
2. Prioritizing price over quality: Selecting a conveyor solely based on its price without considering lifecycle and maintenance costs can lead to higher long-term expenses.
3. Sticking to outdated technology: Decisionmakers may resist adopting new, more
efficient technologies due to unfamiliarity or perceived risks.
4. Allowing customer specifications to dictate design: Often, designers follow client requests without questioning whether the specification is up-to-date or aligns with the latest advancements in conveyor technology.
Stainless steel belts have long been a staple in heavy industries such as bottling, glass processing, and forestry. However, since the introduction of plastic modular belts in the late 20th century, these traditional stainless-steel systems are gradually being replaced by lighter, more efficient plastic alternatives.
Plastic belts weigh significantly less than their metal counterparts, reducing energy consumption and wear. Stainless steel, while durable, is prone to rust and is not as resistant to chemicals as plastic belts, which can withstand a wide range of substances due to their hydrocarbon structure. Additionally, the modular design of plastic belts ensures that the system can stop safely if a failure occurs, preventing extensive damage.
In contrast, stainless steel chains do not offer this level of protection and can continue running even when malfunctioning, leading to costly repairs.
Durability and Longevity
Maintenance and Repair
+ Made from high-quality plastics such as polypropylene, polyethylene, and acetal, these belts offer excellent resistance to wear and tear.
+ They are less susceptible to cracking or fraying, leading to a longer lifespan.
+ Designed with interlocking segments, which allow for easy maintenance and repair.
+ Damaged sections can be replaced quickly without the need to replace the entire belt, reducing downtime and costs.
+ While generally durable, these belts can experience issues like cracking, stretching, or deterioration over time.
+ Exposure to harsh chemicals or extreme temperatures may shorten their lifespan.
Hygiene and Cleanliness
Flexibility and Versatility
+ Feature smooth surfaces and open hinge designs, making them easier to clean and minimizing bacterial buildup.
+ Ideal for industries where hygiene is a priority, such as food processing and pharmaceuticals.
+ Highly customizable to fit different conveyor systems and applications.
+ Available in various configurations, such as straight-running, radius, and spiral designs, to meet diverse operational requirements.
As industries continue to modernize, the benefits of plastic modular belts are becoming increasingly clear. They offer improved durability, lower maintenance costs, and superior energy efficiency compared to traditional roller, cloth, and stainless-steel conveyors. These advancements reflect a broader trend towards adopting lightweight, high-performance materials that deliver cost savings and reliability.
With conveyor systems being the lifeblood of
+ Repairs are often more complex and time-consuming, requiring specialized tools or expertise.
+ In some cases, the entire belt may need to be replaced if a section is damaged, leading to higher maintenance expenses.
+ May have more crevices where dirt and bacteria can accumulate.
+ Cleaning can be more labor-intensive, requiring more frequent maintenance to meet hygiene standards.
+ Offer less flexibility in customization and may not provide the same range of configurations as plastic modular belts.
+ Limited in their ability to handle more complex or varied conveyor layouts.
production lines, selecting the right design—one that prioritizes both technology and functionality—will play a key role in driving productivity and maintaining a competitive edge in today’s industrial landscape.
This article is provided by ÇAĞRI® ENDÜSTRI A.S.
For more information, contact the company at info@alhan-cagri.com or visit the website at www.alhan-cagri.com.
An increasing number of tested samples per hour and zero failures are the most important factors in bioscience analysers. Nowadays, linear motion mechanism is an indispensable part in these devices which are used widely in medical and researching facilities. Though dozens of linear bearing manufactures provides small size linear guides in the market, IKO Nippon Thompson brings unique technology and solutions to these high-end devices with our unique technology and the solution we offer:
- Excellent and accurate repeatability
- Maintenance-free
- Made from corrosion resistant stainless steel
The engineer from one of IKO’s Miniature Linear Way ML users who is responsible for designing the precision scanners for their medical devices explains: “Smooth and stable linear movement without a mechanical clearance is absolutely a crucial factor for our device performance. A linear motor-driven table must have zero-compromise speed stability in order to achieve a high quality scanning of the biological membrane. IKO Linear Way brought the solution to our high demands.” During the prototype designing, the engineer and IKO discussed numerous factors and finalized the specification. In addition, the end users or maintenance engineers of the devices are free from a re-lubrication thanks to IKO C-Lube technology. In addition to providing the above mentioned technical solutions, IKO worked together with the customer to plan and arrange optimized delivery control in a recently problematic supply chains system, successfully securing the customer’s on-schedule production.
IKO Miniature Linear Way ML does not stop in the field of mechanical parts, but has evolved to IKO linear motor tables by incorporating their excellent performances. IKO provides the extremely thin and compact structured linear motor tables that are suitable for bio-medical, semiconductor, small automation devices. These positioning tables achieve quick positioning from A to B with more than 80% reduction of the settling time compared to the ball screw driven mechanism.
IKO provides the following size range
Miniature Linear Way ML : 1mm to 42mm in width
Linear Motor Table NT : 38mm to 88mm in width
Linear Motor Table LT : 100mm to 170mm in width
For more information on how IKO can support your new and current projects, visit www.ikont.eu or email nte@ikonet.co.jp, Phone +31 (0)10 462 68 68
IKO Nippon Thompson Europe B.V. Keersopstraat 35, 3044EX Rotterdam, the Netherlands
Swedish premium fastener manufacturer BUMAX makes further energy, water and cost savings in its ambitious long term effort to reduce the company’s environmental impact.
After more than halving its electricity use between 2007 and 2019, the latest investments at the BUMAX factory in Åshammar in central Sweden annually save an additional 90 MWh of electricity. It is part of the company’s work to strive for cleaner, greener and more efficient stainless steel fastener manufacturing.
“We have sourced 100 percent renewable electricity for our operations at Åshammar since 2011 and we continuously work to optimize energy efficiency,” explained Anders Sjölund, Manager Production Projects & Production IT at BUMAX. “Two of our recent investments have not only significantly reduced our electricity use, but also made water and cost savings.”
The 90 MWh electricity savings from these two investments are equivalent to around 7 percent of the site’s total electricity use in 2023 and are enough to power four and a half typical Swedish family homes each year.
BUMAX installed a new fastener carrier coating bath in the autumn of 2022 that is super insulated to reduce heating demand and is fully enclosed to minimize evaporation. The investment is part of ongoing improvements in its operations. In its first full year in operation in 2023, the bath saved BUMAX
around 50 MWh and more than 70,000 liters of water compared with its old bath.
The carrier coating bath has fully automated heating and ventilation systems with energy saving modes. A pump stirs the bath solution, which is much more energy efficient than the pressurized air circulation system in the old bath.
BUMAX also replaced its central domestic hot water electric boiler with four smaller boilers that produce hot water close to where it is consumed. The hot water is used for the kitchen, washrooms and showers at the BUMAX factory in Åshammar, Sweden. The new boilers save around 40 MWh of electricity per year compared with the old central boiler.
In a competitive market, the RKB Group has invested heavily in R&D to meet the power transmission industry's growing demands for performance and cost-effectiveness.
Essential components and the most common devices in the power transmission sector, gearboxes are critical for transmitting power and maintaining operational efficiency in various industrial applications.
The RKB bearings installed in gearboxes are not only important for efficiency but also for longevity. This is why we produce bearings with a long service life, specifically designed for the harsh operating conditions associated with the power transmission sector, including heavy loads, changing speeds, misalignment, and temperature requirements, which generic or low-quality bearings may be unable to handle.
With almost 90 years of experience and an amazing team of engineers (RKB TTU), we can offer bearing selection guidance for specific gearbox configurations, installation and maintenance training, troubleshooting and failure analysis services. This expertise can prevent errors during installation and ensure optimal performance.
The use of high-quality, application-specific RKB bearings ensures uninterrupted operation across a wide range of applications:
General applications: Helical gearboxes, planetary gearboxes, worm gearboxes, pinion stand gearboxes, and central drive gearboxes.
Metals industry: Gearboxes for forging groups, speed reducers for hot strip rolling mill stands, and tube drawing mill gearboxes.
Where there is a gearbox, there is an RKB bearing, no matter the industry, whether in cement, marine, green energy, aluminium, steel, or others. From concrete mixers to rolling mills, we are there.
Iulian Grigore, Customer Relationship Manager
Mines & minerals: Gearboxes for crushers, screeners, and presses; dual tandem gearboxes; bucket wheel drives and slew drives; main hoist drive gearboxes for ladle cranes; and concrete mixer gearboxes.
Additional sectors: Marine gearboxes, wind turbine gearboxes, recycling machine gearboxes, propulsion gearboxes, mixer drive gearboxes, shafts and couplings, brakes and clutches, and sugar mill gearboxes.
The demands of every gearbox application are different, and we tailor our solutions accordingly. By ensuring quality, customization, and support, RKB helps prevent failures, improve efficiency, and ultimately save costs.
The RKB Bearing Industries Group, a Swiss-based manufacturing organization, has been a key player in the bearing industry since 1936. Leveraging decades of experience, RKB possesses the specialized knowledge and skills required to design and produce industrial bearings from 1 mm bore diameter to over 2.000 mm outer diameter.
With a global distribution footprint reaching over 70 countries, RKB provides value-driven solutions characterized by impressive operational adaptability, top-tier services, huge stock reserves, quick shipping times, and the hallmark quality expected of a premium bearing provider.
The easiest way to build a conveyor!
Alhan Bipods and Tripods
Alhan Adjustable Bracket, Clamps, and Photocell Connection Equipments
+ Flender One expands to over one hundred new applications
+ Tailored solutions through configuration process with just three parameters
+ +
+ Smart gearbox technology AIQ decreases service costs by up to 40 percent
“We are reinventing the standard.” That were the words of CEO Andreas Evertz when Flender introduced the Flender One single stage version to the market last year. Now, this reinvention enters the next chapter. Flender announces the global launch of the next extension of Flender One gearboxes. After the models for pumps and paper applications, Flender One expands its reach, offering versatile solutions for over one hundred different applications.
The new gear units are designed to meet a wide range of application needs, including bucket elevators, belt conveyors, and hoisting applications. With a broad spectrum of power classes, sizes, and designs, these gear units ensure optimal coverage of various industrial requirements.
Flender One stands out with its tailored solutions. Customers only purchase what they need, eliminating unnecessary components and maximizing efficiency. This customization reduces operating expenses and enhances performance, providing a perfect fit for each specific application.
Additionally, the gearboxes offer a wide range of add-on parts and customizable output shafts.
The Flender One design saves both time and money in planning and plant operations. The new configuration process can be completed in minutes with just three parameters. Combined with instantly accessible 3-D data, prompt quotations, and shorter delivery times due to automated manufacturing processes, project timelines are accelerated from the planning phase. Overall, plant operators can achieve up to 25 percent time savings in planning through simplified processes.
In operation, the Flender One platform reduces operating expenses. All gearboxes are equipped with performance-optimized Metaperform® gearing, reducing power dissipation by up to 20 percent compared to previous models and a 30 percent higher thermal capacity. Also, the bearing lifetime increases by 80 percent. This results in faster cost amortization for industrial gearboxes from Flender than ever before.
Flender One offers built-in gear unit intelligence straight from the factory. Each unit comes with an integrated AIQ Core sensor, providing digital monitoring and intelligent onboard analytical functions. This allows for increased plant availability and process optimization, reducing unplanned downtime by up to 70 percent. Data- and needbased maintenance intervals can decrease service costs by up to 40 percent and service-related downtime by up to 50 percent. The optional torque measurement function allows for process and operating point optimization. The AIQ Core torque can be easily selected via the configurator.
Rouven Daniel, President Industrial Gear Units at Flender, also once again stresses the fact that with the help of collected data and AI models, Flender is now able to size the gearboxes only as large as needed for the respective application. “Most industrial gearboxes from all manufacturers in the field, including Flender, are oversized by up to 50 percent. With Flender One and AIQ, we have the right tools to continuously eliminate this oversizing together with our customers. As a result, we will realize massive savings in raw materials, energy consumption, delivery times and installation space. Any waste is eliminated in terms of the environment and costs.”
In the future, further expansions of the Flender One platform will make it possible to configure
gearboxes tailored to the respective application and the associated requirements. Despite maximum individuality, customers will benefit from the advantages of series production: Process efficiency in production and thus fast delivery times and low costs.
This is made possible by a real milestone in transmission manufacturing: the complete digitization of the engineering process. It triggers the design exactly according to customer requirements and translates it into a fully automated manufacturing and delivery process.
Flender CEO Andreas Evertz states, "Flender One represents a significant shift in how we think about gearboxes. It is not just a mechanical iteration of its predecessor FSG but an entirely new solution from the first customer inquiry to operation in the plant.”
Rouven Daniel adds, "Flender One stands for being more individual, efficient, and smarter. With an easyto-understand configuration process, automated manufacturing, and comprehensive 3-D data and documentation in the cloud, it saves our customers valuable time. In operation, Flender One excels with improved power dissipation and AIQ optimization, making it the most efficient Flender gearbox solution we have ever introduced."
Flender One succeeds the renowned standard industrial gearbox range, FSG, with over 500,000 units in the field. As the most successful standard industrial gearbox range to date, FSG sets a high bar, but Flender One is ready to surpass it with its innovative features and superior performance.
The LUBExpert Implementation Master Class is a training program designed to improve lubrication practices thanks to advanced ultrasound technology. Delivered by experts in the field, this course equips participants with the knowledge and tools to develop their lubrication strategies, using SDT’s LUBExpert ultrasound detection device. Thanks to really positive feedback from participants in previous sessions, this course has proved to be a significant step forward for companies hoping to improve their lubrication management and overall equipment performance.
What the training offers
The LUBExpert Implementation Master Class provides a comprehensive understanding of how to implement efficient lubrication strategies using ultrasound technology. Participants learn the importance of precise lubrication, reducing machine failures due to over- or under-lubrication. The course covers
everything from the fundamentals of lubrication theory to hands-on use of SDT’s LUBExpert system, enabling attendees to immediately apply these concepts to their daily maintenance activities. It also places a strong emphasis on best practices, giving participants a deeper understanding of lubrication’s very important role in the health of industrial equipment.
One attendee mentioned, "the course made me look at lubrication from a different perspective," highlighting the useful nature of the training. Others shared similar sentiments, with one stating, "it made a positive contribution to our approaches to lubrication," while another participant shared how the training helped them "put into practice knowledge and perspectives that could really improve performance."
Attendees praised the training for "redelivering the basics of lubrication—why, how, and best practices." The combination of technical knowledge and practical application ensured that participants walked away with a comprehensive understanding of how to improve lubrication strategies in their respective organizations.
Participants appreciated the hands-on approach to learning. The course allowed them to familiarize themselves with the LUBExpert device and UAS3 software, giving them the confidence to use these tools in the field. "I discovered many features of the device," noted one attendee, while another explained how the training "helped with mastering the device, software, and the necessary technical knowledge."
The training also provided a thorough introduction to SDT’s technology, with one participant stating, "the precise explanation of the lubrication system and its functionality was incredibly useful." This
comprehensive approach allowed participants to leave the class ready to implement new lubrication plans and preventive maintenance strategies immediately.
The LUBExpert Implementation Master Class is not just for lubrication specialists, as it has broader applications across multiple departments. Feedback from participants highlighted the potential for mechanical maintenance teams, workshop technicians, and even managers to benefit from the course. As one participant noted, "it would be beneficial if mechanical maintenance managers of large factories participated," recognizing the value this training could offer at various organizational levels.
Other participants shared similar thoughts, with some recommending that "all individuals involved in rotating machines and partners performing lubrication tasks" attend the training. This feedback
highlights the importance of spreading this knowledge across departments to ensure a cohesive, company-wide approach to lubrication management.
Participants widely agreed on the value of the course's practical content. One aspect that stood out was the UAS3 software presentation, which allowed participants to see how data could be effectively managed and used to optimize lubrication processes. "The presentation of the UAS3 software was incredibly useful," one participant said, underlining the importance of integrating technology into lubrication strategies.
Moreover, many participants appreciated the overall course flow, with one stating, "the training in its entirety was extremely beneficial." This reflects the thorough nature of the program, which combines theory with real-world application.
Participants saw clear benefits for a wide range of colleagues in their organizations. Suggestions included "workshop technicians, methodologists, and SEM management," as well as "all individuals involved in mechanical maintenance." Another participant pointed out the broader applicability of the training, stating, "the more people trained, the more reliable and sustainable services will become." This highlights the widespread impact that this training can have, not just for individuals, but for entire maintenance teams and organizations.
The feedback regarding the trainers was very positive. Participants appreciated the depth of knowledge and the ability of the trainers to respond to questions with precision. One participant commented on the overall positivity of the training experience, stating that
the trainer was "one of the few experts in this field, making the session highly informative." The trainers' ability to engage and impart knowledge effectively played a significant role in the course's success.
The LUBExpert Implementation Master Class has clearly proven to be a valuable asset to companies seeking to enhance their lubrication management through innovative approaches and advanced technology. The hands-on experience, coupled with expert instruction, left participants feeling capable of implementing what they had learned. The course not only imparted technical skills, it also helped participants to see lubrication from a new angle, with one participant concluding: “This training has been useful on several levels, as it has enabled me to apply my knowledge and create radical improvements." The overwhelmingly positive feedback reflects the program's success in delivering actionable insights that participants can apply immediately to improve equipment reliability and maintenance practices. As lubrication is a cornerstone of industrial maintenance, the skills gained from this training will undoubtedly contribute to longer equipment life, reduced maintenance costs, and increased operational efficiency. With such strong endorsements from participants, the LUBExpert Implementation Master Class proves to be a key training program for organizations looking to optimize their lubrication strategies and ensure sustainable success.
Have a look at our agenda to take part in the 2025 training courses:
BY
NES Bearing Co.’s place as a U.S. bearing reverse engineering leader, and the recipe for a successful RE
OLEAN, N.Y. – In late October, a leading provider of advanced engine repairs walked into Napoleon Engineering Services (NES) with a question.
Four years earlier, NES performed a reverse engineering (RE) for this company on a legacy component for a gas turbine engine. NES was so successful in this undertaking, providing a detailed report that expressed professionalism and authority along with the appropriate pictures, data and drawings, that it returned with a similar request this
fall – this time on replaceable components for a different batch of bearings.
Reverse engineering plays a critical role in sustaining the aerospace industry – the aircraft sector, in particular – through helping to maintain the bearing supply for legacy aircraft. And over the last 27 years, NES has established itself as a national leader in this service, conducting RE jobs for hundreds of satisfied customers.
“We’ve hung our hat on being able to help our customers out of a jam,” Chris Napoleon, NES’ president and chief engineer, noted.
Yes, NES, for nearly the last three decades, has only sharpened its bearing reverse engineering capabilities for Parts Manufacturer Approval (PMA) by the Federal Aviation Administration. This, however, is a process that can also be applied to the industrial market, specifically by OEMs in need of truly thorough reverse engineering support that’s punctuated with a comprehensive requirement drawing.
This kind of RE work, however, is easier said than done. A seemingly simple procedure on the surface, it actually requires a broad skillset of knowledge and proficiency to achieve the desired outcome. It’s an admittedly painstaking process, even for an operation
as experienced as NES. Napoleon Engineering, however, possesses the recipe needed to attain those results. And it details those actions in this piece.
THE GENERAL key to executing a quality reverse engineering job is to apply all available knowledge and information. For NES, that includes the following 10 foundational elements: dimensional, visual, metallurgy/chemistry, part number, government sites, overhaul manuals, bearing engineering handbooks, customer-supplied information, application engineering knowledge and product design/ manufacturing standards.
Essential to the latter two items is knowing how to properly merge them into the manufacturing process. And that means finding a harmonious common ground.
On the application engineering side, one must understand the design strategies of the application itself. Since, in most cases, we’re not redesigning for the application, it’s incumbent upon an engineering team to have a grasp on what the bearing is going into. “So, there’s a need for broad-based application engineering experience as well as intuitive knowledge about the role that the bearing plays within the application,” Napoleon said.
However, product design in support of manufacturing is also crucial.
Oftentimes, the tolerances associated with a specific target value for a design characteristic are a function of manufacturing capability. Knowing the limits of modern manufacturing techniques is critical to offering an RE solution that meets application needs, manufacturing capability and agreed-upon costs.
“You have to come to an agreement as to what is most reasonable because it has to work in the application,” Napoleon went on. “There’s a lot of scaffolding involved; you need a solid foundation of knowledge to do an RE job the right way.”
A THOROUGH reverse engineering also incorporates all inspection capabilities specific to bearings, from dimensional and visual to chemical and metallurgical. For this, one must have both good eyes and ears, Napoleon insisted.
Measurements can “speak to us,” about what we need to be focusing on from a dimensional standpoint. Certain physical characteristics can inform us as to how critical a certain feature is. “So, it’s important to be a good listener and really be willing to look at a bearing,” Napoleon said. “That’s a huge part of it.”
Additionally, an engineering team must be willing to implement various standards, from both a quality and industry standpoint.
A good RE typically defines a bearing’s critical characteristics and the control plan associated with them. This includes dimensional traits, but also material quality, non-destructive testing requirements, marking and packaging specifications. The use of bearing standards and catalogs, engineering handbooks, overhaul manuals and customer-supplied materials, meanwhile, greatly enhances the quality of the overall reverse engineering project by defining the characteristics that control the collective quality of workmanship of the completed bearing while ensuring its success within the application.
AFTER UTILIZING all available resources, engineers must capture that data, ensure its accuracy and relevancy and, finally, create a logical link between
the part and its drawing. In the end, everything needs to add up.
“We need to look at a part and, through our visual inspection, be able to understand how it’s being manufactured,” Napoleon began of the overarching process. “What are the techniques, what’s the equipment that’s being used and how does that drive the tolerances of certain characteristics and the criticality of those characteristics, which then drive the tolerances? And that’s validated by the dimensional measurements, what the targets are and how tightly controlled they are.
“Then, you have to marry that with your understanding of manufacturing capability and typical application engineering practices for design of those characteristics for particular industries.”
Reaching this point, however, is far from easy. Some traits are more critical than others depending on the industry or application. What’s important to a bearing in a food processing plant might be different from that on a main-shaft gas turbine engine. The difference between NES’ Source Qualification Inspection program, an industrial reverse engineering initiative, and an aerospace bearing RE is being mindful and observant of what is critical to each application for the appropriate addition into the process.
But even that’s an inherently difficult step, “because you’re putting yourself out there.”
“Pulling all of this together is a monumental task,” Napoleon concluded. “It takes an organization that has all of these skills and capabilities and is able to communicate effectively across all areas of specialty to create a clear and concise finished requirements package.” (Courtesy of J.P. Butler, Marketing Coordinator, Napoleon Engineering Services)
+ NORD’s powerful MAXXDRIVE® XT is equipped with a heavily-ribbed axial fan. Image: NORD DRIVESYSTEMS
Robust industrial gear units with NORD modular products
Whether dusty grain or heavy rocks: Bulk material is conveyed vertically or horizontally, upwards or downwards – also over long distances. NORD DRIVESYSTEMS offers individual drive solutions that enable smooth operation and meet the industry’s special requirements. The industrial gear units of the MAXXDRIVE® series are particularly advantageous here.
For storing and conveying, weighing and metering as well as loading and unloading bulk material, NORD’s portfolio features robust industrial gear units whose characteristics precisely cover the industry’s requirements. They are characterised by their modular design, high performance and longevity as well as low maintenance effort.
NORD always designs industrial gear units based on the respective application and ambient conditions. In combination with motors, frequency inverters, couplings and brakes, this creates flexible and reliable drive systems for the bulk goods industry. The system provider relies on its modular products and provides tailor- made solutions from a single source.
NORD’s robust and powerful industrial gear units feature high-quality, low-friction bearings and the especially torsionally rigid, one-piece UNICASE housing. MAXXDRIVE® XT is also equipped with a heavily-ribbed housing and an axial fan. This way, it achieves a very high thermal limit power.
Large roller bearings and optimised geometries ensure excellent load capacity, long life and high operational reliability. Optimum sealing concepts against water and dust allow for long deployment times without leakage, and thus significantly reduce maintenance effort. If required, the drive experts equip your gear units with a corrosion-resistant surface treatment for use in harsh environments.
NORD customers benefit from the manufacturer’s comprehensive industry expertise in the field of bulk goods handling. “From the initial concept onwards, we assist our customers from the design phase up to commissioning”, says Jörg Niermann, Head of Marketing at NORD DRIVESYSTEMS. “In addition, we provide worldwide service which is based on a network of partners that covers more than 80 countries.” The system manufacturer thus implements worldwide availability and short delivery times for its products.
The Mighty Heart of Vehicles’ Suspension System
• Best-in-class automatic forging line • CNC turning machines organized in work cells • Heat treatment by Aichelin technology
• Automatic grinding lines
• Patented full-scale inspection lines, with sorting accuracy of 1 micron for all the main dimensions
30 years ago, the introduction of the simalube lubricator set a milestone in industrial maintenance and servicing. Since then, this automatic lubricant dispenser has become an indispensable component in many industrial applications. In this article, we take a look at the history, the technical innovations and the significant benefits that simalube has brought over the last three decades.
The beginnings: A revolution in lubrication
In 1994, the Swiss company simatec launched the first simalube lubricator on the market. The concept was simple but revolutionary: an automatic dispenser that continuously and precisely delivers lubricant to machines and systems. Based on the unique technology of the gas development cell, the simalube set new standards in terms of functionality, reliability and sustainability. This solved many of the problems of manual lubrication, such as irregular lubrication intervals, over- or underdosing and the high amount of work involved.
innovations and development
The simalube lubricator impresses with the following features, some of which have been unique since its launch:
+ Stepless adjustment of the running times from 1 - 12 months
+ Environmentally friendly and reusable, which reduces the ecological footprint
+ Transparent housing thanks to which the function can be easily monitored visually
+ Compact size
+ Easy disposal
Over the years, simatec has continuously developed the simalube lubricant dispenser and adapted it to the needs of the industry. Here are some of the remarkable technological advances:
1998: The 60 ml simalube is launched under the name “shorty”
2005: The simalube family grows, the 30 and 250 ml sizes are added
2008: simalube lubricators receive Ex approval for zones 0, 20 and M1 and thus meet the highest requirements for explosion protection
2013: simatec presents another world first. The simalube 15 ml is still the smallest single-point lubricant dispenser in the world today.
2015: With the simalube IMPULSE pressure booster, simatec opens up applications in which the lubricant is supplied via longer lines.
2021: The simalube IMPULSE connect, combined with the simatec World of Maintenance app, marks simatec's move towards digitalized products and services.
2023: The simalube family is being completely redesigned; the design and drive head are new.
Make the world move forward*
LUBSOLIDTM is the outcome of our unparalleled proficiency in lubrication development. Through an extensive battery of tests conducted on bearings in the most stringent conditions, this French technology represents the most effective method to combat the causes of premature bearing failure. The solid lubricant solution is highly recommended for numerous industry. It is compatible with most articulated bearings and ensures safety and longevity.
*At NTN, efficiency hinges on a sustainable product life cycle
Explore the next level of automatic lubrication: simalube IMPULSE connect
The «simatec World of Maintenance» app is the overarching digital simatec platform: simatec products can be controlled by the app, taking simatec another step into the
Features
Monitoring of lubrication points
Creation of electronic lubrication schedules in Lubechart (available in the App)
Digital ordering process
Calculation Pro: Calculation programme for the correct setting of your lubricators. Available in the app «simatec World of Maintenance» only Download the simatec app now:
Ruland continues to expand its motion control coupling product line by introducing bellows couplings with increased misalignment capabilities. These new bellows couplings complement Ruland’s existing high-stiffness line by offering equivalent torque with greater misalignment flexibility.
Ruland's bellows couplings are lightweight, have low inertia, and can reach speeds up to 10,000 rpm due to the combination of anodized aluminum hubs and stainless steel bellows. The thin walls of the bellows flex easily while remaining rigid under torsional loads, allowing the coupling to accommodate all forms of misalignment. The new increased misalignment style features more convolutions than the high-stiffness style, meeting the desired misalignment requirements.
"Designers who require a high-torque, highmisalignment coupling can now come to Ruland if a bellows coupling is their preferred choice," says Bill Hewitson, President of Ruland Manufacturing. "Our rigorous design and physical testing process ensures these couplings exceed market standards. This marks the second expansion of our bellows coupling line in 2024 and reinforces why Ruland is the first choice for OEM coupling designers and our distribution partners.”
The new bellows couplings with increased misalignment are available in clamp style designs, with or without keyways, in bore sizes from 3/16 in (4 mm) to 3/4 in (20 mm). A planned increase to 1-1/4 in (32 mm) will be available before the end of 2024. Ruland manufactures bellows couplings from meticulously selected North American bar stock in the ISO 9001:2015 certified advanced manufacturing facility in Marlborough, Massachusetts. The couplings are RoHS3, REACH, and Conflict Minerals compliant.
Summary:
+ Increased misalignment due to more convolutions than high-stiffness styles
+ Reduced vibration at speeds up to 10,000 rpm because of a balanced design
+ Low inertia for use in precision systems due to the use of high-grade lightweight 2024-T351 aluminum
+ Ratings validated through thorough physical testing
+ Carefully manufactured in Ruland’s advanced manufacturing facility in Marlborough, Massachusetts, USA
Welcome to the Megadyne world, a place of innovative power transmission solutions. Megadyne is a group of talented people supporting their customers in achieving operational perfection. The company invests in skilled designers and engineers, who are the key factor in providing the most innovative Megadyne power transmission belt systems. As field experts, they thoroughly analyse and study industrial processes to develop new solutions and upgrades to the already existing ones.
Sustainability is as important as ever at Megadyne. The group consists of like-minded people cherishing the beauty of the world, focused on preserving it for generations to come. For that reason, they produce solutions which last longer, save energy, emit less noise and limit the overall carbon footprint of customers. Contact us. Welcome to Megadyne power transmission solutions.
R+L Hydraulics GmbH presents the new Spidex couplings of the HighTemp and UltraTemp series, developed especially for high-temperature applications. These elastic jaw couplings are durable and resistant to wear and tear while boasting high temperature and hydrolysis resistance.
“Spidex elastic jaw couplings provide reliable performance, even under extreme conditions,” says Detlef Peick, Business Development Manager at R+L Hydraulics. “They are the result of many years of experience and continuous further development.” The exceptional temperature and hydrolysis resistance of the UltraTemp series allows for the application of these couplings at long-term operating temperatures of up to 180°C. “This is a unique feature within the industry,“ says Peick. The three-part couplings are axially pluggable, fail-safe and maintenance-free, making them an ideal choice for demanding environments in steel mills, lime kilns, drying plants or marine applications.
By using high-temperature resistant elastomeric inserts called spiders, Spidex couplings are particularly durable and resistant to frequent temperature variations. This reduces downtimes and leads to longer maintenance intervals, providing higher system availability and resulting in both economic and ecological benefits.
“The enhanced temperature resistance of our elastomer spiders allows for the reliable use of Spidex couplings in processes involving thermal processing steps,” Peick explains. “The HighTemp and UltraTemp spiders’
resistance to wear and tear applications with frequent temperature changes contributes significantly to the durability and reliability of the system.”
Another benefit of Spidex couplings with UltraTemp spiders is their superior hydrolysis resistance. This means the couplings can be used in humid environments including sea water, making them suitable for marine applications as well as for environments with high humidity.
Depending on their size and the application, Spidex couplings are designed for use with up to 11,000 Nm nominal torque and a maximum torque of 22,000 Nm, which makes them ideal for difficult tasks. “This superior performance combined with excellent damping properties and the ability to compensate for high radial misalignment sets new standards in the industry,” says Peick.
“R+L Hydraulics provides transparent and comprehensible specifications regarding the temperature range within which the HighTemp and UltraTemp series can be used,” Peick emphasizes. “Our clients can rely on our products to deliver the promised properties.”
R+L Hydraulics, headquartered in Germany, engineers and produces a wide range of couplings and hydraulic accessories. R+L Hydraulics is a subsidiary of the USbased coupling specialist Lovejoy LLC; both companies are owned by The Timken Company.
• Simple operation via perma CONNECT
• Configuration, control and maintenance from a distance
• Management of up to 2,000 lubrication points via Gateway LONG RANGE
• LED visible all round signals functioning and errors
• Backlit LCD display
Aircraft landing gear has critical engineering requirements due to the demanding and varied forces it must withstand during take-off, landing and ground operations. Regarded as a ‘mechanical marvel’ by some aviation experts, it is certainly a big deal with the world’s top airline manufacturers considering the fact that it accounts for around 20% of total aircraft maintenance and around 7% of the total weight of today’s commercial aircraft.
When an aircraft lands, the landing gear has to absorb the entire weight of the aircraft, which can range from around 64,500kg for an Airbus A320 and up to around 201,800kg for a Boeing 777. Clearly the landing gear must be robust enough to handle not only the vertical load, but also the horizontal forces generated by the forward motion of the aircraft. Additionally, during landing, the gear must absorb the impact energy which can be substantial, especially during hard or emergency landings. Therefore, the key requirements demand designs and materials that can dissipate energy effectively, while avoiding structural failure.
Today landing gear is typically manufactured by specialist suppliers to the aviation industry, who then supply to the major aircraft manufacturers. This is because the landing gear and shock absorption technologies are recognised as specialist, separate fields of science when compared to other aspects of aviation technology. Beyond impact absorption landing gear must also provide optimum stability and control on the ground as aircraft often encounter varying ground conditions, including uneven and slippery surfaces and crosswinds. The design must ensure that the aircraft maintains directional control during taxiing, take-off and landing, even under adverse weather conditions.
To achieve this today’s landing gear systems incorporate features such as shock absorbers, antiskid braking systems and steering mechanisms.
These components must work together seamlessly to prevent the aircraft from veering off the runway or skidding, ensuring passenger safety whilst minimising wear on the aircraft’s tyres and other components. The landing gear must also be designed with considerations for weight and space constraints because fuel efficiency as part of overall aircraft performance, has never been more important than it is today. Therefore, the landing gear must be lightweight yet strong, utilising advanced materials such as titanium alloys, or high strength composites. Also the landing gear must be retractable to reduce aerodynamic drag during flight which means complex mechanical systems are needed to ensure reliable extension and retraction. Balancing these requirements; strength, stability and weight efficiency, while also integrating the landing gear into the aircraft’s overall design, makes it one of the
most challenging aspects of aircraft engineering.
Specialist bearings are an essential component of innovative landing gear systems particularly when applications involve landing gear struts and actuators and precision bearing and tooling specialists
CARTER MANUFACTURING are approved aerospace bearing suppliers to industry leading landing gear manufacturers. Carter’s key focus is high quality and customer satisfaction illustrated by the accreditations to ISO9001, incorporating the requirements of AS9120, with flow down to AS9100. Carter also specialises in the custom design and manufacture of Aerospace Bearing Tools, because your application could have clearance restrictions, such as blocker door, or flight control MRO repair. Or maybe you’d like to streamline your production with a custom tooling package and Carter has an impressive back catalogue of thousands of proven custom tool designs and world-class tooling engineers ready to design innovative, bespoke solutions for any application.
Carter’s swaging tools are precision engineered to fit specific landing gear bearings, reducing operational risks and costs by reducing the likelihood of damaging expensive bearings and housings. When a specific application requires a different approach, or the customer doesn’t wish to use portable tools, the drill press style swaging tools are a much better alternative to anvil staking tools. This is because the required swaging force is just a fraction of the overall staking force and will significantly improve the quality of the swage.
Finally, Carter also offer a comprehensive range of tool training services and technical support ranging from trouble-shooting to multi-day training packages. This means that every one of our customers can rest assured they will have the necessary skills required to utilise our tools to the highest performance standards.
Bearings, more at: www.carterbearings.co.uk/industries/aerospace
Tools, more at: www.carterbearings.co.uk/aerospace-bearing-tools
www.carterbearings.co.uk email: sales@carterbearings.co.uk
In view of growing data volumes in automation and drive technology, the trend is towards so-called One Cable Technology (OCT). SAB Bröckskes, one of the technology leaders in industrial Ethernet cabling, has developed several application-specific product series for hybrid and OCT cabling. The special cable manufacturer offers SL 875 C low-capacity hybrid motor cables as connection solutions for SICK HIPERFACE DSL and HEIDENHAIN HMC6. Adaptations to other standards are available on request. Cables specified for HIPERFACE are available in 10 standard versions with outer diameters from 9.8 mm to 24.4 mm. In addition, there are four specifications in the HEIDENHAIN standard with diameters ranging from 10.8 mm to 15.4 mm. Robust, hard-wearing cable sheaths ensure that the cables are sufficiently flexible and durable
to withstand narrow bending angles over the long term, even with minimal core cross-sections down to AWG 30, corresponding to a core crosssection of 0.057 mm². To achieve the lowest possible capacity, SAB Bröckskes has replaced the conventional PVC insulation with low-capacity insulation materials made of PE or PP. Additional small shield capacities ensure low-loss transmission. For optimal EMI protection, SAB Bröckskes motor and servo cables feature double shielding made of shielding braid and an aluminum-laminated PE film. The double shielding ensures interferencefree operation of frequency inverters. Symmetrical stranding with a split protective conductor reduces inductive couplings and improves EMC properties.
Detect early bearing failures | Lubricate bearings with precision | Easily monitor & trend bearing condition | Suitable for slow speed bearings
CONDITION-BASED LUBRICATION
Listen to your bearings and know when to stop lubricating
Avoid over-lubrication: the cause of 60% of failures
Be alerted when bearings need lubrication
Create lubrication routes
Easily create inspection routes
Trend bearing condition
Setup alarms for early failures
Record bearing sounds for deeper analysis
+ NexSafe servomotor brakes can include up to three sensors to monitor disengagement, engagement, and wear.
Nexen Group, Inc. provides servomotor brakes with Functional Safety Certification to international safety standard ISO 13849-1.
Nexen’s NexSafe servomotor brakes offer bidirectional braking capabilities and are Industry
4.0 compatible. The full line of NexSafe servomotor brakes is Functional Safety certified to comply with the international safety standard ISO 13849-1. Category Level up to 4 and Performance Level up to e can be achieved using Nexsafe products in recommended configuration.
NexSafe servomotor brakes have multiple engagement springs and an integrated clamp collar with backup keyways. Up to three operating mode sensors for feedback ensure confident, safe emergency stopping, holding and positioning. The sensors provide feedback and information to maximize machine efficiency and aid with motor and drive programming, predictive maintenance, and operational feedback.
Servomotor brakes are part of Nexen's line of Functional Safety certified products, including rail brakes and rod locks. Nexen engineers and manufactures advanced motion control components
for a wide variety of industrial applications. Headquartered in the USA and with its European office based in Belgium, Nexen supplies products to customers through a global network of local distributors and representatives.
Summary of key features and benefits:
+ Functional Safety certified to CAT4/PLe
+ Integral clamp collar with backup keyway
+ Three operating mode sensors available
+ Multiple engagement springs
+ Default to lock
Menzel Elektromotoren manufactures identical replacements for old motors, thus ensuring the smooth running of industrial plants without long downtimes and elaborate construction work. Recently, a 50-year-old pump motor in a combined heat and power (CHP) plant was to be replaced. While the original motor had still been performing reliably, the utility company already looked for a future-proof replacement as a preemptive measure and found no suitable standard motor on the market. The German manufacturer Menzel has a more flexible offer and is set up to provide all electrical and mechanical modifications to suit the individual application requirements. Menzel configured a three-phase squirrel cage motor in size 630 for the cooling tower pump of a CHP plant in Cologne, equipping it for vertical flange mounting and implementing protection class IP23
and cooling type IC 01 (open-circuit ventilation). The design boasts high power density, a low weight and low purchase and operating costs. The MEBKSD-type squirrel cage motor features 1650 kW rated power, 6000 V rated voltage and a rated torque of 31897 Nm. Menzel copied all the main connection dimensions, terminal box locations and instrumentation of the original motor in its own custom-configuration, which meets the latest standards and offers higher efficiency. In addition, Menzel installed the coupling supplied by the customer, thus ensuring an easy motor replacement and speedy recommissioning of the cooling tower pump. As with this follow-up order from an existing customer, the motor manufacturer has already served many electric companies to their full satisfaction.
The new generation with long range wireless connection
Large-scale operations pose a special challenge when it comes to maintenance. The perma STAR VARIO LONG RANGE automatic Lubrication System provides an effective solution to this problem.
The new perma STAR VARIO LONG RANGE has been specifically designed for use in extensivefacilities and is ideally suited for this purpose. This product innovation combines the functionality of the perma STAR VARIO with the advantages of LoRa®WAN wireless technology, elevating automated lubrication to a new level.
Connecting without boundaries
Equipped with integrated LoRa® WAN communication technology, perma products are redefining industry standards for remote control.
Using the Gateway LONG RANGE, up to 2000 perma STAR VARIO LONG RANGE lubrication systems at a single site can now be centrally managed. It enables
convenient remote monitoring and control over distances of up to 2 km. The signal strength, stability and security of the wireless connection ensures a highly reliable and almost unlimited connectivity.
The system consistently transmits updates to the perma CONNECT app, providing essential information such as operational status, timestamps, ambient temperature, and the fill level of the STAR VARIO LC. This functionality not only saves valuable time but also enhances efficiency, productivity, and workplace safety.
The perma SERVICES Offer – Support during every step of the way
The perma SERVICES team consists of highly qualified professionals who support you from the very start of the project. It's responsible for lubrication system surveys, assessing the optimal location for the Gateway LONG RANGE, and verifying network coverage. The Gateway LONG RANGE is delivered pre-configured and fully operational. The service offering also includes system installation, onboarding of the perma STAR VARIO LONG RANGE lubrication systems, instructions and user trainings for perma
CONNECT, and comprehensive application training for the entire system. perma is dedicated to ensuring the successful realisation of every project.
perma STAR VARIO LONG RANGE operates fully automatically, independent of temperature and pressure with a very precise discharge. The system consists of an electromechanical drive, a LC (Lubricant Cardrige) with 60, 120, 250 or 500 cm3 lubricant and a battery pack.
perma STAR VARIO LONG RANGE provides pressure build-up of 7.5 bar. The lubrication system is used for single-point lubrication of roller and sliding bearings, sliding guides, open gears, gear racks, spindles, shaft seals and chains and is ideal for lubricating electric motors with specified lubricant quantities thanks to extremely precise lubricant metering. Thanks to LoRa® wireless technology, up to 2,000 lubrication systems in a facility can be conveniently managed via perma CONNECT over a distance of up to 2 km, using the Gateway LONG RANGE.
Visit www.perma-tec.com to learn more about perma products.
Companies whose growth rates run into two figures like to associate themselves with a technological partner who can reliably deliver the required capacities. This applies in particular to South African cider record-holder Distell who enjoys a long-term cooperation with KHS.
While some regions are only just discovering cider as a trend beverage, in other countries this fermented, alcoholic apple juice looks back on a long tradition. In Great Britain and Ireland especially, this specialty has been extremely popular since the time of Julius Caesar. On his retreat from the land of the AngloSaxons the imperator took the refreshing potable back to Rome with him and was subsequently responsible for its distribution to many parts of Europe. Cider thus developed lots of different regional variations: the French, for example, took sweet dessert apples as the main ingredient and used them to make weak alcoholic cidre. The English, on the other hand, preferred cider apples that were too bitter, sharp or sour to be eaten without further processing. When it comes to the tart dryness of the beverage, Germany wins hands down: in the federal state of Hesse in particular a veritable Ebbelwoi or ‘apple wine’ culture has grown up around a cider that contains 5–8% alcohol by volume and in 2022 was added to UNESCO’s Representative List of the Intangible Cultural Heritage of Humanity. In our modern era it was the Brits who again precipitated the beverage’s march of triumph around the globe, however; in the 19th and 20th centuries cider spread from England
throughout the British Empire to its most remote colonies and the later Commonwealth – to India, Canada, Australia and South Africa, where it’s now one of the country’s most popular thirst-quenchers.
The market leader in South Africa is Distell, one of the premier beverage producers on the entire continent and, according to the company, the second-largest cider producer worldwide. Formed at the end of 2000 when Stellenbosch Farmers’ Winery merged with the Distillers Corporation, the group makes wine, spirits, cider and RTDs. The last two categories alone made up around 55% of the quantities of beverage produced in 2021 and thus accounted for more than a third of a turnover of over €1.2 billion.
The portfolio includes several brand names: besides Hunter’s, Extreme and Bernini, premium product line Savanna in particular is exceedingly popular with local consumers and on various international markets. It comes as Savanna Dry, in an alcohol-free and a light variant and flavored with lemon or chili, and is filled into 330- and 500-milliliter glass bottles with crown
corks that are retailed singularly or in packs of up to six containers.
The brand language is spritely and witty to communicate the beverage’s fresh character. For example, at the peak of the corona pandemic, when the people in South Africa were confronted with closed restaurants and bars, curfews and a ban on the sale of alcohol lasting months, the idea of the Savanna Virtual Comedy Bar was born; here you could meet up weekly with friends on Zoom and interact with comedians together with a bottle of cider. Comedy Specials were also held every two weeks that were streamed on Savanna’s social media channels. On the one hand, the measure supported entertainers made redundant by the closure of cultural venues; on the other, it soon became a huge cult that cheered the South Africans up during these difficult times and helped the brand to double its sales volume within the space of a year.
The campaign was largely borne by the non-alcoholic version of Savanna launched just a few months before the onslaught of Covid-19, with lots of consumers of other beverage categories turning to this particular product as it was impossible to tell it from the original. Once they’d acquired a taste for it, they remained loyal, with Savanna now the most popular brand of all in South Africa.
Distell generally believes in practicing social responsibility, as shown by a number of other examples; above and beyond the financial goals of its stakeholders, various CSR* activities are a fixed feature of its corporate strategy. It runs programs aimed at reducing the harmful consumption of alcohol, warns of the consequences of drunk driving, launches vaccination campaigns, helps young people to
develop their skills and engages in the empowerment of women. Together with its innovative marketing concepts and high-quality products, this commitment has earned the company wide acceptance and high recognition among consumers. In turn, this all translates into hard cash – and means that sometimes production can hardly keep up with demand.
It’s thus all the more important to have a technological partner to hand whom you can fully rely on when capacities desperately need expanding. Distell has enjoyed a relationship like this with Dortmund systems supplier KHS for around 20 years now; during this time a good number of KHS lines and machines have been installed in both
Stellenbosch near Cape Town and in Wadeville and Springs not far from Johannesburg, including most recently two turnkey can and three glass lines, plus countless fillers, packers and process technology units. Of the total of 36 lines the beverage producer now operates in South Africa a third is reserved for Savanna, the majority of which are situated at the plant in Springs.
Vital partner
“We haven’t merely established ourselves as a vital partner to Distell with our first-class machines and seamless installation and commissioning processes,” says Leroy Thangamuthu, managing director of KHS
South Africa. “For as long as we’ve been working together, it’s chiefly been our service engineers who’ve always ensured that the lines continue to produce with their customary reliability and standard of quality. It’s thanks to them that our equipment can be used with a degree of availability that’s always at an optimum. This is what’s earned us our status of first choice among the providers of plant technology.”
The most recent milestone in the Distell/KHS cooperation is a direct result of the growing demand for the Savanna brand: a glass line with an output of up to 60,000 330-milliliter bottles an hour. “We
needed to be able to expand our capacity by 30% within a very short time indeed,” explains Sharief Gallie, who as head of Manufacturing South Africa is responsible for production throughout the entire country. “It’s the height of summer here in December and therefore the high season for cider. KHS was the only supplier who could promise to hand over turnkey machines to us on time within a period of sevenand-a-half months. All other manufacturers would’ve needed at least five months more.” The industry had previously considered the proposed speed of delivery to be practically impossible, Gallie remembers. It’s thus no surprise to learn that the company’s top management experienced a moment of disbelief when the plans were submitted for decision and approval. The long-term trust in and reliability of the Dortmund company ultimately dispelled all doubts, however. Distell is thus all the more pleased that the project was completed within the given time frame and that the agreed performance figures were even exceeded. The only real challenge lay outside KHS’ sphere of influence: owing to industrial disruptions caused by corona and problems with the supply chain, there were temporary shortfalls in the replenishment of glass bottles, meaning that alternatives had to be found on site; 15 million liters were then filled into cans. When the number of new cases of Covid infections in South Africa fell significantly at the end of 2021 and everything could then continue according to plan, 25 million liters of cider were filled in December alone –more than ever before within the space of one month.
The line includes a depalletizer, a rinser, the filler, flash pasteurizer, warmer, two packaging machines – a shrink and a tray packer – and a robot palletizer,
The constant optimum availability of our equipment makes us first choice among plant technology providers for Distell
Leroy Thangamuthu, Managing director of KHS South Africa.
among other equipment. However, Gallie is especially delighted with the performance of the two KHS Innoket Neo Flex labeling machines. “We’ve been used to having KHS provide us with sophisticated top technology and absolute reliability for many years. What we’re seeing in speed and reliability with these two machines, however, has really left a lasting impression on me. I could go on about the fantastic design for hours! However, what always holds the most significance is the feedback we get from the operators on their experience with the technology. And if this is as positive as it is in this case, then you know you’ve
purchased a really good machine.”
Despite his immense satisfaction with his procurement, Gallie sees no reason to sit back and take it easy. By no means does the new non-returnable glass line indicate that the company’s maximum filling and packaging capacity has been reached. Far from it: the steep rise in demand has prompted the planning of further projects with KHS that include a ninth line for Springs and a canning line for Stellenbosch which together will mark a further chapter in the success story of Savanna and the joint partnership of the two companies.
Packaging leader SÜDPACK and industrial printing specialist LEIBINGER have joined forces to meet the growing demand for sustainable packaging solutions. The first joint project is testing the suitability of CIJ inks for printing on recyclable films for packaging food that is sterilised following the packaging process. The tested system combination of packaging and printing solution saves food manufacturers time and ensures investment security.
Today, packaging films are expected to be resourcesaving and recyclable to support a circular economy. The EU Packaging Regulation requires all packaging on the EU market to be recyclable by 2030. As a result, composite materials are being increasingly replaced by monomaterials. If these monomaterials are not equipped with a barrier function that prevents ink components from migrating to food, they may only be printed with harmless ink. This raises the requirements for the production, coding & marking of packaging films.
The packaging market is experiencing very fundamental changes. And it is with this in mind that SÜDPACK is continuously expanding its portfolio of recyclable film solutions. The company is developing monomaterials that are very much on par with previous composite materials – both in terms of convenience and protection. For printing and coding this type of food packaging, LEIBINGER offers industrial inkjet printers and develops special
continuous inkjet (CIJ) inks together with SIS Ink Solution, a LEIBINGER Group company. The interaction of these components is the focus of the joint project between SÜDPACK and LEIBINGER.
In test: Sterilisation resistance of CIJ ink for marking food packaging
Are continuous inkjet inks suitable for printing on and subsequently sterilising recyclable food packaging? Specialists from both companies investigated this very question at SÜDPACK’s technical centre. The team printed the innovative single-material solutions based on PE and PP with advanced CIJ ink. During the subsequent steam sterilisation, the printed films were heated at 121°C for 30 minutes. Assessment of the print samples before and after sterilisation showed that the print was still perfectly legible. The inks used are suitable for printing on food contact materials. This means that they only contain raw materials that are approved in compliance with the German Printing Inks Ordinance and the Swiss Commodities Ordinance.
The idea for the joint project between the two familyrun Swabian companies SÜDPACK and LEIBINGER originated at a meeting at the PackExpo trade fair in Chicago in 2022. Together, the two companies set themselves the goal of providing food manufacturers with a packaging and printing solution that had already been tested for key customer requirements.
“The sterilisation resistance of ink is always a major challenge. I am delighted that we have succeeded in developing a food-approved CIJ ink that is this effective when printing on monomaterials,” explains Dr Thomas Paul, ink expert and Managing Director at SIS Ink Solution, a LEIBINGER Group company.
High-performance films and packaging solutions from SÜDPACK have been winning over customers in various industries worldwide for more than 50 years. With some 1,800 employees at 10 production sites
worldwide, SÜDPACK distinguishes itself through its high level of innovation, quality and reliability.
Printers and inks from LEIBINGER in Tuttlingen, Germany, are also used worldwide. For about 75 years, the company has been an expert in industrial printing systems that are used to print expiry dates on packaging, among many other things. LEIBINGER is ideally positioned globally with 150 partners and 300 employees.
Would you like to learn more about the cooperation between LEIBINGER and SÜDPACK? Visit us at booth 7-550, hall 7 at the Fachpack in Nuremberg and experience the printing on the sustainable films live.
If you are interested in finding out more about the collaboration project or the tested packaging and marking solution, we would be delighted to hear from you. Further information about the company can be found on the LEIBINGER website: www.leibinger-group.com
Engineering, Bearings, Technology.
Headquartered in Fort Worth, Texas, EBT Bearings showcases a 20,000 sq. ft., ISO Certified warehouse, an in-house quality control (QC) department complete with Zeiss CMM, a complete line of bearings ready for immediate shipment, and humbly speaking, the best team of employees in the industry. In addition to their Fort Worth facility, EBT Bearings, has a global manufacturing footprint which also adheres to the same ISO Quality Management System and allows for a level of customization, flexibility, and control rarely found anywhere else in the marketplace. In addition to manufacturing their own bearings, EBT is also an authorized distributor for many leading bearing manufacturers, including URB.
There are several options for automation: deep code automation, off-the-shelf automation with robot process automation (RPA) and, of course, automation with the help of generative AI. Each of these options has its own advantages and disadvantages that need to be considered when planning a solution.
Automation is rightly one of the current trend topics in the business world, as the digitalisation, optimisation and ultimately automation of business processes holds great potential for companies. In this context, the activities of specialised departments are automated, which leads to cost savings, the acceleration of processes and an increase in quality. Relieving employees of routine tasks through automation offers a great opportunity in dealing with the shortage of skilled labour. On the one hand, the workload of staff can be reduced. On the other hand, employee productivity can be increased if they can concentrate on value-adding activities instead of filling their working day with routine tasks.
Deep code automation and RPA are presented below.
Deep code automation describes the classic approach to automation using programming (PowerShell, Python, HTML / CSS and C#, etc.) and scripting. Here, solutions are programmed from scratch and precisely tailored by using existing interfaces and infrastructures.
Individual activities can often be automated in a sensible and cost-saving way using a script. For more complex activities, however, this approach can also involve a high level of development effort. This means that there is little certainty in terms of effort and costs. In addition, maintenance must be ensured after development, which requires a deep technical understanding of the solution. Professional process changes can also entail complex technical changes.
For this reason, this approach should always be carried out with an experienced team in order to limit the aforementioned risks. An experienced team of consultants can significantly limit the risks, e.g. through precise analysis of the process to be automated, modularized development of the code and a well thought-out IT architecture. The transfer of knowledge to internal staff during the course of implementation is also essential in order to minimize future dependence on external support.
The major advantage of this approach is the ability to tailor solutions. As there are hardly any technical limits to the complexity of the developed solution, the requirements of a specialist department or a company can be implemented precisely - regardless of whether they are extensive regulatory requirements or very individual requirements.
A high degree of automation can be achieved for a large proportion of common business processes using simple means. Repetitive activities with defined processes can be automated cost-effectively and very often completely with Robot Process Automation (RPA). If RPA platforms such as UiPath, Power Platform or Automation Anywhere are used, cost-effective "off-the-shelf" automation is possible.
By accessing applications that were previously operated by humans, RPA bots take over rule-based human screen activities. In concrete terms, this means that the RPA robots access existing IT systems via the front end in a similar way to the actions of a human and type, copy, paste, extract or merge. As these platforms place low demands on the IT infrastructure and access existing interfaces or user interfaces, implementation is usually possible quickly and interaction with practically any software is possible.
As a result, surprisingly fast ROIs (return on investment) are regularly achieved in RPA projects. Particularly if the automated process (step) is frequent or involves a high volume of work, this can save a great deal of time. An increase in quality and savings in opportunity costs are also typical results of process automation with RPA.
This type of automation requires significantly less effort than automation through programming. Once the automated process has matured, changes are usually only necessary if a user interface of an application without an interface is changed.
Before automating with RPA, it is essential to take a proper look at the process in question. If it is not mature enough, incompletely defined or even defective, it cannot be optimized by pure automation. Automation is often carried out by a team with exclusively technical skills. Unfortunately, in practice, the repair of the poor process is often neglected before the automation is carried out. We therefore always recommend prior process optimization before implementing RPA.
The new Regal Rexnord introduces engineered-to-order industrial powertrains, delivering power for the most demanding of applications
It took the combined strengths of our new company to develop complete industrial powertrain solutions, custom designed and built for applications across the full spectrum of horsepower and torque. From start to finish, Regal Rexnord™ electromechanical industrial powertrains are designed, configured, integrated and optimized for your unique applications, opening the door to new ideas and unlimited possibilities. Read about Regal Rexnord and our prominent brands. Go to regalrexnord.com.
Creating a better tomorrow™...
+ ArcelorMittal Gent is hosting the first industrial trial of D-CRBN’s technology
+ Unit was connected on 1 July 2024
+ MHI’s carbon capture unit, being tested in Gent, provides high-purity CO2 for the D-CRBN unit
ArcelorMittal and Mitsubishi Heavy Industries, Ltd. (MHI) are working with a climate tech company, D-CRBN, to trial a new technology to convert carbon dioxide (CO2) captured at ArcelorMittal’s plant in Gent, Belgium into carbon monoxide which can be used in steel and chemical production.
This is the first industrial testing of D-CRBN’s plasma technology, making ArcelorMittal Gent the first steel plant in the world to trial the process, which has been designed to reduce CO2 emissions.
This new trial expands the current multi-year carbon capture pilot taking place at the site to test the feasibility of full-scale deployment of MHI's carbon capture technology (Advanced KM CDR Process™).
D-CRBN, an Antwerp-based company, has developed
a technology that uses plasma to convert carbon dioxide into carbon monoxide. Using renewable electricity, the plasma is used to break the carbonoxygen bond, thereby converting CO2 into carbon monoxide. The carbon monoxide can be used as a reductant in the steelmaking process – replacing part of the coke or metallurgical coal used in the blast furnace – or as a basic ingredient in Gent’s Steelanol plant, for chemicals or alternative fuel production.
The D-CRBN process requires high-purity CO2, which can be provided by MHI’s carbon capture unit, currently being used to capture blast furnace offgases, and off-gases from the hot strip mill reheating furnace, in Gent.
A pipeline between MHI’s carbon capture unit and D-CRBN’s unit was connected on July 1st, to test
the feasibility of using the CO2 captured by the MHI technology as a feedstock for D-CRBN. The industrial pilot is an important stage of testing D-CRBN’s technology, to make sure that any impurities that accompany the CO2 produced during steelmaking do not have a detrimental effect on the process and product gas.
ArcelorMittal is pursuing a number of decarbonization routes in order to achieve its climate targets, which include a 35% reduction in CO2 emissions from ArcelorMittal Europe, by 2030. One of these routes is Smart Carbon steelmaking, which uses circular carbon in the blast furnace, carbon capture and storage (CCS) or utilization (CCU).
Manfred Van Vlierberghe, CEO, ArcelorMittal Belgium, said, “We are proud to be part of this unique carbon capture and usage trial in Gent, which is part of our strategy to develop the Smart Carbon steelmaking route in ArcelorMittal Belgium. Our team of engineers has worked hard with our partners to reach this stage – and we are thrilled that our new partner, D-CRBN, have created this new CCU technology here in Belgium.”.
Gill Scheltjens, CEO at D-CRBN, said, “D-CRBN is thrilled to partner with ArcelorMittal and Mitsubishi Heavy Industries on this innovative carbon capture and utilization (CCU) pilot project. Electrifying steel production is challenging, but D-CRBN's process,
which recycles CO2 emissions back into CO, offers a cost-effective and scalable solution. Our technology can electrify and decarbonize existing blast furnaces and significantly reduce their coal use. The conversion of CO2 back into CO for steel production will limit the need for green hydrogen in the future and reduce the costs of emission-free products. Moreover, some of the CO produced can be supplied to neighboring chemical companies as feedstock.”
MHI's Senior Vice President (CCUS) of GX (Green Transformation) Solutions, Tatsuto Nagayasu, said, “CCUS will play a critical role in decarbonizing existing assets in the steel industry. Our collaboration with ArcelorMittal and D-CRBN in Belgium provides another tool for the industry to reduce its carbon footprint — capturing emissions, converting them into a valuable feedstock, and feeding them back into the process. This initiative demonstrates our commitment to sustainable practices and innovative solutions for a greener future.”
ArcelorMittal, MHI, BHP and Mitsubishi Development Pty Ltd (Mitsubishi Development) announced in May 2024 that they had successfully started operating a pilot carbon capture unit on the blast furnace off-gas at ArcelorMittal Gent in Belgium. In October 2022, the four parties announced their collaboration on a multi-year trial of MHI’s carbon capture technology (Advanced KM CDR ProcessTM) at multiple CO2 emission points, starting at the Gent steelmaking site.
Only bearing manufacturer in the world to win Deming Grand Prize
Bearings for wide range of applications: from 20 mm to 2000 mm
Exports to 30+ countries worldwide
Major suppliers to Global Automotive OEMs and Railways
R&D and technology centres in Germany, Slovakia and India
Leak tests are essential in semiconductor factories and in the manufacture of solar cells and flat panel displays. Identifying the smallest leaks with helium leak detection is important for maintaining the required purity, avoiding defects and ultimately for product quality. To enhance the UL family of leak testers, INFICON has therefore launched the three intelligent additions SMART-Spray, I·BOOST and SPRAY-Check. The specialist in measurement technology, sensor technology and control software thus ensures easier handling, faster response times, shorter test cycles and more reliable measurement results.
SMART-Spray: fast, simple and reliable
INFICON is offering a new helium spray gun with
the SMART-Spray. The hose-bound handling of large helium cylinders and the error-prone adjustment of the spray volume are a thing of the past with SMARTSpray. "The handy device, which is designed for over 1,000 sprays per helium filling, replaces a remote control and combines its functions with those of a manual helium spray gun," says Product Manager Markus Schwambera, summarising the advantages. Equipped with an illuminated colour display, it makes leak detection on complex semiconductor systems with many test points and potential leaks easier. These applications are characterised by limit leak rates of less than 1 x 10-9 mbar x l/s. In these applications, the battery-operated, portable device makes leak testing more flexible, simpler and more efficient.
I·BOOST: short response time, precise measurement result
With the signal processing filter I·BOOST software update, INFICON accelerates the leak rate signal. This shortens the response and test times, especially for the UL3000 Fab and UL6000 Fab series, because the test points can be sprayed at shorter intervals. "The bottom line is that this results in a time saving up to 50 % in leak detection in all measuring ranges," says Product Manager Markus Schwambera, outlining the leap in efficiency. "Users who purchase the licence achieve faster and more precise measurement results for different chamber volumes," assures Schwambera. The benefits of I·BOOST are also particularly effective in complex semiconductor systems. "The lower the limit leakage rates, the longer the test cycles usually take – and this is where the higher sensitivity and time savings of I·BOOST have the greatest impact," argues Schwambera.
With the SPRAY-Check, INFICON offers an easy-toinstall test leak. "The tool is based on quartz windows that are only permeable to light gases such as helium and hydrogen. This increases safety and extends the functionality of leak detection," explains Markus Schwambera. SPRAY-Check allows the measurement set-up and test method to be checked in the relevant leak rate range. It can also be attached directly to the system to carry out dead-time checks. "Sometimes a certain amount of time elapses between the spray shot and the indication on the display," says Markus Schwambera. This allows users to better estimate how long the pause between spraying points should last so that potential leaks can be clearly assigned. The
exclusion procedure applies: If there is no indication after the dead time has elapsed, there is no leak. "Because SPRAY-Check is impermeable to gases that are harmful to the process, such as water or oxygen, it can also remain mounted on the semiconductor system," explains the product manager. Important areas of application are systems with limit leakage rates below 10-9 mbar x l/s.
These smart essentials are available worldwide
SMART-Spray, I·BOOST and SPRAY-Check are suitable for all mobile INFICON helium leak detectors of the UL family, whereby I·BOOST is limited to the latest generation of UL devices (UL3000 Fab/UL6000 Fab series). The UL6000 Fab is the most powerful and best device on the market for larger test volumes in modern semiconductor factories and coating systems with very large chamber volumes. It offers the fastest response times and shortest test times in all measuring ranges. Its compact design makes it easy to maneuver even in tight spaces. The UL3000 Fab series was also developed for leak detection in semiconductor factories. "It is characterised by flexibility, mobility, fast commissioning and high sensitivity. Users also receive their precise test results very quickly" and are the standard in modern semiconductor factories," emphasises Product Manager Markus Schwambera. The UL3000 Fab also requires only a small footprint and can be easily and maneuvered through narrow spaces. The UL1000 Fab series covers a wide range of applications when it comes to economical helium vacuum leak tests in industrial or semiconductor environments - especially for smaller chamber volumes. The main advantages: The device is very powerful, robust and inexpensive to purchase.
31 MAY - 04 APRIL 2024
+ Incorrect mounting and dismounting of rolling bearings, as well as imbalances in machine shafts, can result in damage to the bearings and other components
+ Schaeffler’s new white paper provides all you need to know about the correct preparation, installation and removal of rolling bearings, and how to ensure machine shafts are properly aligned.
+ The paper includes basic knowledge, expert tips and guidance, as well as case studies showing how customers are profiting from using the right tools for the job.
Global motion technology company Schaeffler has published a white paper on the mounting and dismounting of rolling bearings and shaft alignment.
Learn from the experts on how to avoid damage during bearing mounting and dismounting, how to simplify mounting work, how to save time and ultimately money by protecting the bearing and optimally aligning your machines. Schaeffler’s practical white paper contains valuable knowledge that you can incorporate directly into your maintenance process.
Our 10-point checklist for safe mounting work will help you avoid premature bearing failures in the future:
+ Protect your workspace and the rolling bearing from dust, dirt, and moisture.
+ Use drawings to familiarise yourself with the design.
+ Make sure that your bearing matches the specifications on the drawing.
+ Check the housing bore and the shaft seat for dimensional, shape and positional accuracy, as well as cleanliness.
+ Ensure that the mounting of the bearing rings on the shaft or in the housing bore cannot be impaired by edges. A slip angle of 10° to 15° is helpful.
+ Wipe off any corrosion protection on the seat and contact surfaces.
+ Apply a very thin layer of suitable mounting paste to the cylindrical seating surfaces of the bearing rings.
+ Do not cool the bearings. Condensation can lead to corrosion in the bearings and bearing seats.
+ After installation, apply a suitable lubricant to the rolling bearings.
+ Check the bearing to make sure it’s working properly.
The port of Antwerp recently highlighted the work of Sarens in sustainability by updating and expanding the fleet towards greener machinery like the electric cranes.
Sarens has recently added to its fleet 80 all-terrain cranes that meet the latest EUROMOT Stage V standards, building a greener fleet of trucks as each new truck to join its European fleet complies with the latest EURO 6 emissions standards.
The crane industry is constantly investing in innovative solutions in order to reduce emissions and noise pollution and Sarens is taking actions and efforts to commit to sustainability. The heavy lifting crane specialist, based in Wolvertem, continues updating and developing the fleet towards greener machinery like the electric cranes, while investing in the belgian industry to support the development in the country.
Sarens, world leader in heavy lifting, engineered transport and crane rental services, first developed the SGC-90 (Sarens Giant Crane), the world’s first green giant crane, followed by the HLTC (Heavy Luffing Tower Cranes) and most recently the E-Pack for telescopic cranes. The motor control system of these telescopic ring cranes not only runs on electricity, but it also puts electricity back into the grid while the cranes are in operation. These cranes are becoming very popular at ports that need to lift cargo for offshore wind projects. The operations
reduce emissions and operating costs in comparison to diesel-operated cranes.
Sarens also recently announced the expansion of its Spierings eLift fleet with the acquisition of two additional battery-powered self-erecting mobile tower cranes. This order, which includes the SK597-AT4 eLift and the SK1265-AT6 eLift, increases its eLift fleet to a total of eight units. This strategic investment aligns with Sarens’ commitment to reducing the carbon footprint and enhancing sustainable operations.
Sarens has been at the forefront of innovation with a strong focus on sustainability and for the past 2.5 years they have successfully utilised Spierings’ battery-powered eLift cranes. The eLift concept has impressed with its efficiency and environmental benefits. The eLift cranes operate 63% of the time on electricity and 37% in hybrid mode, achieving a 90% reduction in fuel consumption compared to conventional mobile tower cranes. The demand for these cranes continues to grow, and their clients are increasingly adopting this green technology.
The SK597-AT4 eLift, the latest addition to Spierings’ tower crane range, features a seven-ton maximum capacity, a 48-metre jib, and a compact chassis. It provides a maximum lifting height of 58.1 meters with the jib luffed to 45 degrees, or 28 meters with the jib in a horizontal position. This model will be the fifth four-axle Spierings crane in the Sarens fleet.
The SK1265-AT6 eLift boasts a 10-ton maximum capacity, capable of handling this load at a radius of over 13 meters. Its 60-meter jib offers a 1,700-kilogram jib tip capacity at a 37-meter horizontal jib height, with a maximum lift height of 66 meters when the jib is luffed to 30 degrees.
Sarens has received many awards in the last few years, like the Environmental Award at Heavy Lift Awards in 2022, and keeps its intention to continue to collaborate in renewable energy projects around the world. As today there is a global call for action towards the transition to green energies and with international and national strategies in place that will accelerate the transition, Sarens wants to stay in the frontrunner as in the past 10 years in the construction and industrial green industry projects.
After building the world’s first green giant crane, the SGC-90, and the investment in the hybrid cranes, some other environmental initiatives Sarens carry out are, for example, always prioritising low emissions technology by actively choosing cranes with the latest low-emissions technology, and adding over 80 all-terrain cranes that meet the latest EUROMOT Stage V standards, building a greener fleet of trucks as each new truck to join its European fleet complies with the latest EURO 6 emissions standards.
A significant volume of their work today is with clients in offshore/onshore wind, nuclear, and hydrogen. So far Sarens has installed over 1.000 wind turbines on solid ground and continues to do more. Sarens has created valuable alliances with World Forum Offshore Wind on floating offshore wind (FLOW) projects; PSG Marine and Logistics Ltd. to service the offshore wind market in Scotland; and Tugdock to service the FLOAT offshore wind market. And is partnering in Small Modular Reactor (SMR) technology to engage in clean nuclear energy projects across the United States.
To protect marine ecosystems everywhere they operate, Sarens is switching to biodegradable oil for all barge hydraulic systems. All ballasting systems are being converted to use Biohydran TMP hydraulic fluid, which contains none of the harmful zinc used in commercial hydraulic oils.
And lastly, their Belgian headquarters boasts over 3.000 solar panels and is setting a precedent for further solar energy installations at their offices across Europe.
www.sonotec.eu
Proper lubrication is fundamental for bearing health. Applying too much or too little lubricant will drastically reduce the life of bearings and, even worse, cause production halts and unplanned downtime. Using ultrasound instruments to precisely lubricate bearings is an established, well-known and reliable method to assure proper lubrication. This method also allows maintenance teams to have a first level of bearing health assessment, as we will see in these examples.
Ultrasound-assisted lubrication & bearing monitoring: How does it work?
By using ultrasound, we measure bearing friction levels in real time, translated into decibel (dB) levels. It enables lubrication problems and requirements to be detected at an early stage, well before the bearings are damaged.
By using bearing friction as a guide, this enables bearings that require lubrication to be precisely lubricated with the right amount of lubricant, avoiding over- and under-lubrication. As the friction level is measured in real time, during lubrication, we can stop lubricating as soon as the friction level has dropped to its reference value, or baseline.
By establishing a bearing baseline in dB and comparing the baseline with the current reading, we can have a good idea on the bearings’ health. Generally speaking, we will consider the dB reading against the baseline as the following:
+ +8dB above baseline indicates lack of lubrication
+ +12dB above baseline indicates microscopic damage
+ +16dB above baseline indicates visible damage to the bearing
+ +35dB above baseline indicates critical failure This is an easy process to implement and follow, but of course, there are always nuances. For example, how can we assess if a bearing simply needs lubrication or is also damaged?
Let’s look at the case study below.
The act of lubricating a bearing with the assistance of an ultrasound instrument will gives us some clues about its health, but there are a couple more steps we can take to more accurately assess its condition:
+ Evaluate sound quality: Ultrasound instruments allow you to listen to what the bearing sounds like. A uniform smooth sound normally indicates no issues, while a rough sound where crackling or popping sounds may be present will indicate bearing damage.
+ Check sound spectrum: Some ultrasound instruments allow you to record the sound from the bearing and further analyse it on a sound spectrum software. By looking at the time wave form we can have a better idea of what’s going on with the bearing by checking sound wave amplitude and eventual peaks.
+ Take regular readings: taking regular dB readings, especially when you suspect the bearing might be damaged, is good practice.
The more readings you take the more data you have to work with.
This is a good example of all these steps in use: on a steel plant, we carried on an inspection on 2 bearings from a combustion fan. They were called East bearing and West bearing.
To determine a baseline for this bearing, we have lubricated it while watching the dB levels and the sound recording. While lubricating, we could observe how the dB levels dropped to and stayed consistent at 60dB. We can also observe below, in the sound recording, what happens as we apply lubricant – the amplitude drops as the lubricant gets in the bearing, thus lowering the friction levels.
If this bearing is in good condition, the 60 dB we established as baseline will remain for some time. However, if the bearing presents issues beyond a lack of lubrication, the dB levels will go up and the sound quality will worsen in the short term.
Thus, on the following day, we took another reading and sound recording of the West Bearing. The reading showed 69 dB: that’s 9db above baseline, in just one day.
We decided to lubricate the bearing once again, and immediately noticed an improvement in sound quality as well as a drop in the dB levels, to 64 dB.
We waited 8 minutes and took another reading and sound recording and we could observe that the 69dB reading was back, as well the previous sound quality we got before this second round of lubrication. Thus, we conclude that lubricating the bearing is not bringing it back to baseline and is not enough for it to keep a uniform and smooth sound quality. This bearing needs to be regularly monitored, as it is possible it has already some microscopic damage.
We used the same method to evaluate the East bearing of this combustion fan. After a first round of lubrication, we got to 60db, which corresponds to our baseline. The screenshot from the sound file clearly shows the drop in amplitude when lubricant is applied.
Again, we took the same measurement and sound recording one day after, only to realize the bearing went way above baseline, by displaying a reading of 72dB. Sound quality showed some signs of concern, with pops and sputtering. After a 2nd round of lubrication, we were able to get the bearing to 67db and noted a quick sound quality improvement but retaining some tones of damage.
Just like with the West bearing, we waited 8 minutes before taking another reading and observed that the 72dB and the prior lubrication sound quality had returned.
Both bearings show clear signs of damage, even though still on an early stage (microscopic damage). Normally, healthy bearings will respond well to lubricating and will stay longer on their dB baseline, while presenting a smooth and uniform sound.
We can see how useful ultrasound technology is when assessing what’s going on with a bearing, and how easy it is to do so. Even though ultrasound may not be able to indicate the root cause of the issue, it provides an effective, easy and quick way to understand which bearings need more attention.
For this combustion fan, regular monitoring is advised, as well as including other predictive maintenance technologies to determine the root cause of the additional friction occurring with the bearings. While we cannot make a prognosis as to the underlying issue, we are able to observe that there is an issue causing strain on the bearings that will eventually lead to damage and/or failure.
Regal RexnordTM Corporation is a global leader in the engineering and manufacturing of industrial powertrain solutions and power transmission components, serving customers throughout the world. Our solutions are found in cement, food and beverage, intralogistics, agriculture, material handling, construction, mining, automotive, forestry, and more. Our essential products help keep systems running in mission-critical applications worldwide, while being sustainable and energy efficient.
Our teams of expert engineers have years of industry knowledge and experience, ensuring innovative solutions that target your most specific needs. We know the ins and outs of these applications, from the
Rex® high performance roller, leaf, and engineered chain exhibit outstanding performance in challenging conditions. Rex RN Series metric mounted spherical roller bearings with SHURLOK tapered adapter were designed shaft-ready for ease of use and durability.
smallest bearing to the largest belt. Regal Rexnord partners with our customers to carefully select the products that solve their toughest challenges. Our flagship brands have amassed billions of hours of reliable operation and are well-known throughout the industry for their high quality.
CENTA® is the world’s leading manufacturer of torsionally soft couplings, primarily used in marine, industrial, and wind.
Euroflex™ has a strong reputation of high-performance disc couplings, used in power generation, gas compression, and industrial process machinery.
Jaure™ family of flexible couplings and transmission elements include the LAMIDISC, MT, and BAREFLEX European brand leaders since 1958.
McGill® Metric Camrol® cam followers feature LUBRI-DISC® seals that provide positive protection against contamination and loss of lubricant.
Rollway® bearings play a significant role in the open ball and roller bearing industry, providing high quality bearings to OEM and end users for over 100 years.
Link-Belt® mounted spherical roller bearings prove their performance with outstanding misalignment capabilities, field adjustable clearance, and excellent sealing options.
Sealmaster® mounted ball bearings are engineered to reduce downtime. The IP69K-rated PN Gold™ offers corrosion resistant solutions for washdown environments.
System Plast® is a global leader in high quality plastic conveyor chains, modular plastic belts, and industry-leading conveying components.
Rexnord® KleanTop® belts provide a plastic modular belting solution for conveyor applications requiring adherence to strict hygiene regulations.
Rexnord MatTop® & TableTop® chains are engineered to satisfy a wide range of conveyor applications, with straight running and side-flexing chain designed to convey flawlessly.
Perceptiv™ condition monitoring enables our customers to improve productivity, increase uptime, and enhance safety by monitoring equipment from a distance.
With manufacturing, service centers, and engineering support across the world, Regal Rexnord can meet you where you are. We maintain stock in Europe to ensure our customers have what they need. Our global reach ensures that wherever our customers are in the world, they receive the same expert level of service and reliability.
Regal Rexnord designs and manufactures the products that keep your applications running. Our expertise and our strong portfolio of brands make us a trusted source for sustainable, durable, problem-solving solutions. Our brands and products have the longevity needed to maintain industries around the world.
More information about Regal Rexnord™ can be found at www.regalrexnord.com
From Machine Tool, Injection Molding, Medical & Measuring to General Machinery applications, NSK offers the best technical solutions and a full range of engineering services. Every NSK Linear Guide, Ball Screw, Support Bearing and Super Precision Bearing is tailored to your specific needs. NSK, the only comprehensive engineering service supplier on the market, will take your business a step ahead. Find out more at www.nskeurope-motionsolutions.com.
The Bearing & Power Transmission World Meetings is a B2B meet up, exhibition and forum at global level attended by professionals from 40+ countries. Key distributors, manufacturers, solution providers and end-users from the bearing and power transmission industry will come together for three days during the B2B table meetings, Expo, lunches, dinners, and many more networking activities.
• Global Participation: Expecting 450+ delegates from 42+ countries in 2025 edition,
• Unity in Diversity: Distributors, Manufacturers, and Industrial Solution Providers convened, crafting connections and fostering partnerships.
• Beyond Meetings: Beyond the core B2B meetings, the event includes an exhibition area to showcase innovative products and solutions.
• Networking Perfected: Our gala dinner, networking lunches, farewell dinner, and other activities proved that business thrives not just in meetings but in shared moments of interaction.
• World Power Transmission Association: The upcoming 2025 edition will host the annual meeting of the World Power Transmission Association (WorldPTA). This association aims to foster global collaboration and networking within the power transmission industries, aligning with current and future industry standards, the Net Zero strategies and mutual goals on a global scale.
Secure Your Spot Today!
✓ Distributors
✓ Manufacturers
✓ Service & Solution providers
✓ OEM, MRO & End-Users
✓ Service & Solution providers
✓ Procurement prefessionals
✓ Engineering companies
✓ Organizations & Associations
✓ Universities & Students
The global B2B Meet-Up, Exhibition, and Forum for the entire PT/MC supply chain, from raw materials to finished products and distribution. " "
Bearing & Power offers a unique opportunity to expand your professional network and boost your brand's visibility on a global scale. With exclusive access to B2B meetings, exhibition and forum, you'll connect with industry peers and gain valuable insights.
✓ NETWORK with peers from all around the world
✓ EXPAND sales and distributors network
✓ Join the B2B SPEED DATING & B2B TABLE MEETINGS
✓ Increase your BRAND VISIBILITY
✓ CONNECT with potential suppliers
✓ Participate to the “DISTRIBUTORSHIP program”
✓ Gain market and product insights at the FORUM
64 Countries Participated Participants
Pullman Istanbul Hotel & Convention Center is 30min. from Istanbul Airport and easily accessible through highway connections. The 16.000m2 convention centre enables the event guests to enjoy a variety of lunch, dinner, meeting, seminar and exhibition facilities. The 3500 m2 spa offers relaxation areas and treatment along with a fitness centre. You will also enjoy the delicacies of Turkish and International cuisine that will rejoice your tastebuds along with special cocktails from around the world that is served in our enjoyable bar areas. With its 750 rooms, Pullman Istanbul offers its guests the luxury and comfort that they deserve. This and many more awaits you at the Pullman Istanbul Hotel.
Istanbul is today with its 20 million large population, a critical business hub who does direct business with 200 different countries in the world. For centuries Istanbul has been a key trading point, connecting the east and west, thanks to its prime location between two continents. The market stalls of the Silk Road may have been replaced by gleaming skyscrapers and major banks, the city remains one of the world’s premier business destinations. This prime location helped the city to grow rapidly into a cross-continental trading hub, paving the way for its distinction as the premier international business destination it is today. Now, still thanks in part to its thriving port, Istanbul is responsible for over a half of the regional trade, making it an important meeting point for representatives from all industries.
Find new Distributors and Suppliers. The Distributorship Program allows distributors to connect with alternative suppliers and helps manufacturers expand their network in new markets globally.
Beside the classic B2B table meetings, an additional B2B Speed Dating program will be organized with the start of the event to meet max. number of delegates and attendees.
The 2025 edition will host the World Power Transmission Association's annual meeting, focused on global collaboration, networking, and aligning with industry standards and Net Zero strategies.
The Bearing & Power event will host a Forum designed for the PT/MC industry. The
✓ Supply Chain stragegies from raw material to finished products
✓ Innovative models for Procurement and Supplier Development
✓ How to expand into New Markets
✓ Use of AI and how AI will transform the PT/MC industries
✓ How to find Investments for your PT/MC projects
✓ Technical Workshops for End-Users
✓ Industry and application presentations
Do you have any bearing and power transmission solution, research, workshop or insights to share? Feel free to contact us
To ensure that BearingNews and Motion+Drives magazines are doing their part to protect the environment, the parent company, iMotion Media, has developed a strategy to offset the carbon footprint of its printed magazines. The twofold approach includes a fully supported tree planting campaign in conjunction with each newly released edition, and the use of recycled paper in the printing process.
Sustainability is no longer just a buzzword. Members of the globalcommunity have become increasingly aware of human impact on the environment. As a result, a massive movement is driving private sector companies to responsibly manage their environmental, economic, and social resources to safeguard the well-being of future generations.
The term ‘sustainability’ encompasses a large swath of efficiency objectives that aim to go beyond the thresholds of carbon neutrality. Companies must fulfill further economic and social obligations by devising less wasteful practices. When discussing the printing of magazines, there is long-term value achieved by responsibly implementing environmentally friendly solutions associated with the use of paper. The paper industry has focused its efforts on the sustainability of raw materials, processes, and products. Highlighted
within the industry’s strategy is the promotion of sustainable forestry practices and responsibly harvesting renewable raw materials. Tree planting is considered one of the most effective ways to combat global warming, as forests naturally reduce atmospheric carbon dioxide (CO2) by removing it from the air through photosynthesis. In line with this strategy, iMotion Media has adopted ‘tree planting for reforestation’ as the most effective method to reduce the carbon footprint associated with the printing and distribution of Bearing News and Motion+Drives magazines. In careful coordination with the release of each printed edition, a tree planting campaign will be launched to help restore forests and offset the use of natural wood materials used in paper production. In addition, iMotion Media is supporting the use of recycled paper in the printing process to reduce dependence on new materials. It will also continue to promote the currently available digital magazine options.
Thanks to the use of recycled paper and certified companies dedicated to carefully managing wood harvesting, there has been a decline in global deforestation. And while there are positives to both recycled paper and the responsible production of new paper, recycled material contributes significantly more to global social and economic sustainability goals.
iMotion Media is happy to be a part of a forward-thinking movement with ambitions for a greener future. Through its broad reach within the Bearing. Power Transmission, and Motion Control Industries, iMotion Media intends to create an infectious optimism that will compound progress towards greater sustainability.