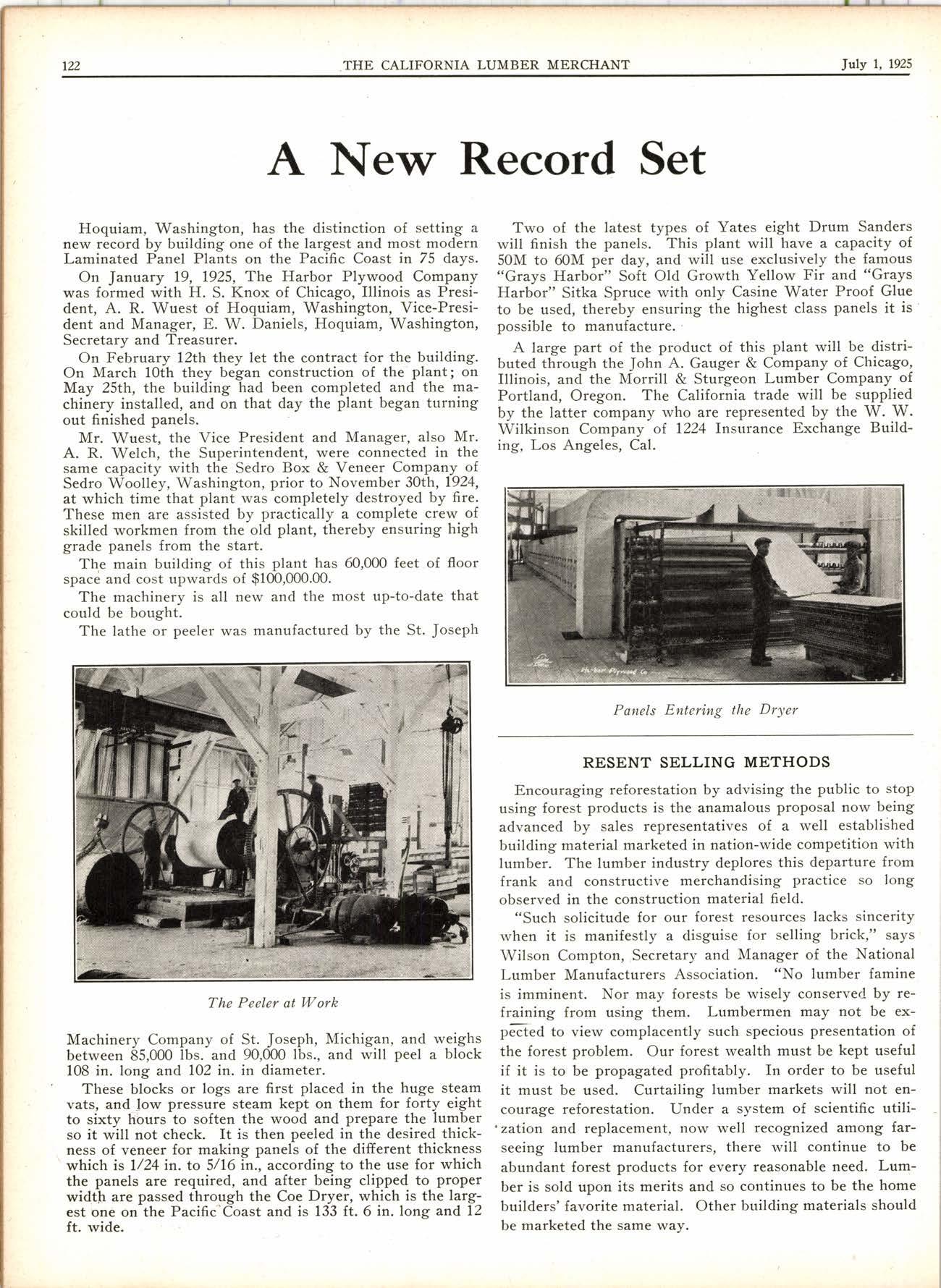
2 minute read
A New Record Set
Hoquiam, Washington, has the distinction of setting a new record by building one of the largest and most modern Laminated Panel Plants on the Pacific Coast in 75 days.
On January 19, 1925, The Harbor Plywood Company was formed with H. S. Knox of Chicago, Illinois as President, A. R. Wuest of Hoquiam, Washington, Vice-President and Manager, E. W. Daniels, Hoquiam, Washington, Secretary and Treasurer.
On February l2th they let the contract for the building. On March 10th they began construction of the plant; on May 25th, the building had been completed and the machinery installed, and on that day the plant began turning out finished panels.
Mr. Wuest, the Vice President and Manager, also Mr. A. R. Welch, the Superintendent, were connecteC in the same capacity with the Sedro Box & Veneer Company of Sedro Woolley, Washington, prior to November 30th, 1924, at which time that plant was completely destroyed by fire. These men are assisted by practically a complete crew of skilled workmen from the old plant, thereby ensuring high grade panels from the start.
The main building of this plant has 60,000 feet of floor space and cost upwards of $100,000.00.
The machinery is all new and the most up-to-date that could be bought.
The lathe
Machinery Company of St. Joseph, Michigan, and weighs between 85,000 lbs. and 90,000 lbs., and will peel a block 108 in. long and IO2 in. in diameter.
These blocks or logs are first placed in the huge steam vats, and low pressure steam kept on them for forty eight to sixty hours to soften the wood and prepare the lumber so it will not check. It is then peeled in the desired thickness of veneer for making panels of the difierent thickness which Is I/24 in. to 5/16 in., according to the use for which the panels are required, and after being clipped to proper width are passed through the Coe Dryer, which is the largest one on the Pacific'Coast and is 133 ft. 6 in. long and 12 ft. wide.
Two of the latest types of Yates eight Drum Sanders will finish the panels. This plant will have a capacity of 50M to 60M per day, and will use exclusively the famous "Grays Harbor" Soft Old Growth Yellow Fir and "Grays Harbor" Sitka Spruce with only Casine Water Proof Glue to be used, thereby ensuring the highest class panels it is possible to manufacture.'
A large part of the product of this plant will be distributed through the John A. Gauger & Company of Chicago, Illinois, and the Morrill & Sturgeon Lumber Company of Portland, Oregon. The California trade will be supplied by the latter company who are represented by the W. W. Wilkinson Company of 1224 Insurance Exchange Building, Los Angeles, Cal.
Panels Entering tke Dryer
Resent Selling Methods
Encouraging reforestation by advising the public to stop using forest products is the anamalous proposal now being advanced by sales representatives of a well establiihed building material marketed in nation-wide competition with lumber. The lumber industry deplores this departure from frank and constructive merchandising practice so long observed in the construction material field.
"Such solicitude for our forest resources lacks sincerity when it is manifestly a disguise for selling brick," says Wilson Compton, Secretary and Manager of the National Lumber Manufacturers Association. "No lumber famine is imminent. Nor may forests be wisely conserved by refraining from using them. Lumbermen may not be exp6Ted to view complacently such specious presentation of the forest problem. Our forest wealth must be kept useful if it is to be propagated profitably. In order to be useful it must be used. Curtailing lumber markets will not encourage reforestation. Under a system of scientific utili 'zation and replacement, now well recognized among farseeing lumber manufacturers, there will continue to be abundant forest products for every reasonable need. Lumber is sold upon its merits and so continues to be the home builders' favorite material. Other building materials should be marketed the same way.