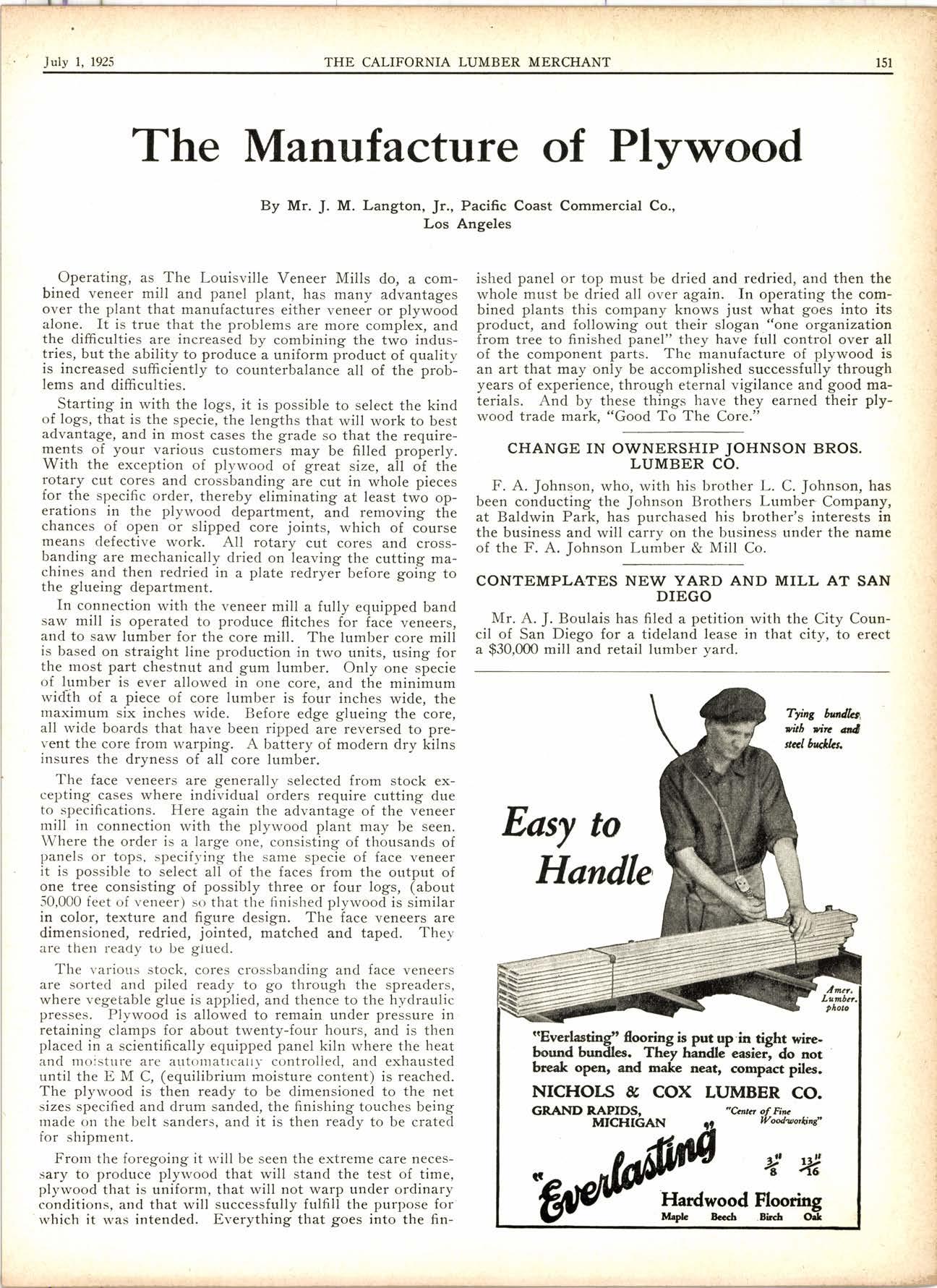
3 minute read
The Manufacture of Plywood
By Mr. J. M. Langton, Jr., Pacific Coast Commercial Co., Los Angeles
Operating, as The Louisville Veneer Mills do, a combined veneer mill and panel plant, has many advantages over the plant that manufactures either veneer or plywood alone. It is true that the problems are more complex, and the difficulties are increased by combining the two industries, but the ability to produce a uniform product of quality is increased sufficiently to counterbalance all of the problems and difficulties.
Starting in with the logs, it is possible to select the kind of logs, that is the specie, the lengths that will work to best advantage, and in most cases the grade so that the requireTg.n_ts of your various customers may be filled properly. With the exception of plywood of great size, all of tlie rotary cut cores and crossbanding are cut in whole pieces for the specific order, thereby eliminating at least two op- erations in the plywood department, and removing the chances of open or slipped core joints, which of cburse means defective work. All rotary cut cores and crossbanding are mechanically dried on'leaving the cutting machines and then redried in a plate redryei before going to the glueing d€partment.
In connection with the veneer mill a fully equipped band saw mill is operated to produce flitches for faci- veneers, and to saw lumber for the core mill. The lumber core mill is based on straight line production in two units, using for the most part chestnut and gum lumber. Only one specie of lumber is ever allowed in one core. and the minimum widih of a piece of core lumber is four inches wide, the maximum six inches wide. Before edge glueing the core, all wide boards that have been ripped are reversed to prevent the core from warping. A baltery of modern drv kilns insures the dryness of all core lumber.
The face veneers are generally selected from stock excepting cases where individual orders require cutting due to specifications. Here again the advantage of the veneer mill in connection with the plyrvood plant may be seen. Where the order is a large one, consisting of thousands of panels or tops, specifving the same specie of face veneer it is possible to select all of the faces from the output of one tree consisting of possibly three or four logs, (about 50,000 feet of veneer) so that tl-re finished plywood is similar in color, texture and figure design. The face veneers are dimensioned, redried, jointed, matched and taped. They are then ready to be glued.
The r.arions stock, cores crossbanding and face veneers are sorted and piled ready to go through the spreaders, where vegetable glue is applied, and thence to the hydraulic presses. Plywood is allowed to remain under pressure in retaining clamps for about twenty-four hours, and is then placed in a scientifically equipped panel kiln where the heat and moistute are autolratlcalt_v controllecl, and exhausted until the E M C, (equilibrium moisture content) is reachecl. The plywood is then ready to be dimensioned to the net sizes specified and drum sanded, the finishing touches being rnade on the belt sanders, and it is then ready to be crated for shipment.
Frorn the foregoing it ivill be seen the extreme care necessary to produce plywood that will stand the test of time, plylvood that is uniform, that will not warp under ordinary conditions, and that will successfully fulfill the purpose for rvhich it u'as intended. Everything that goes into the fin- ished panel or top must be dried and redried, and then the whole must be dried all over again. In operating the combined plants this company knows just what goes into its product, and following out their slogan "one organization from tree to finished panel" they have full control over all of the component parts. The manufacture of plywood is an art that may only be accomplished successfully through years of experience, through eternal vigilance and good materials. And by these things have they earned their plywood trade mark, "Good To The Core."
CHANGE rN OWNERSHTP JOHNSON BROS. LUMBER CO.
F. A. Johnson, who, with his brother I-. C. Johnson, has been conducting the Johnson Brothers Lumber Company, at Baldwin Park, has purchased his brother's interests in the business and will carry on the business under the name of the F. A. Johnson Lumber & Mill Co.
Contemplates New Yard And Mill At San Diego
Mr. A. J. Boulais has filed a petition with the City Council of San Diego for a tideland lease in that city, to erect a $30,000 mill and retail lumber yard.
Eoty to Handle
"Everlasting' fooring ig put up in tieht wirebound buniiles. Th+ handte easier] do not break open, and make neat, compact piles.
NICHOIS & COX LUMBER CO.
GRAND RAPIDS' "Anm gf-Fiu MICIIIGAN .. woduo*itrll
Flandwood Flooring lllryL