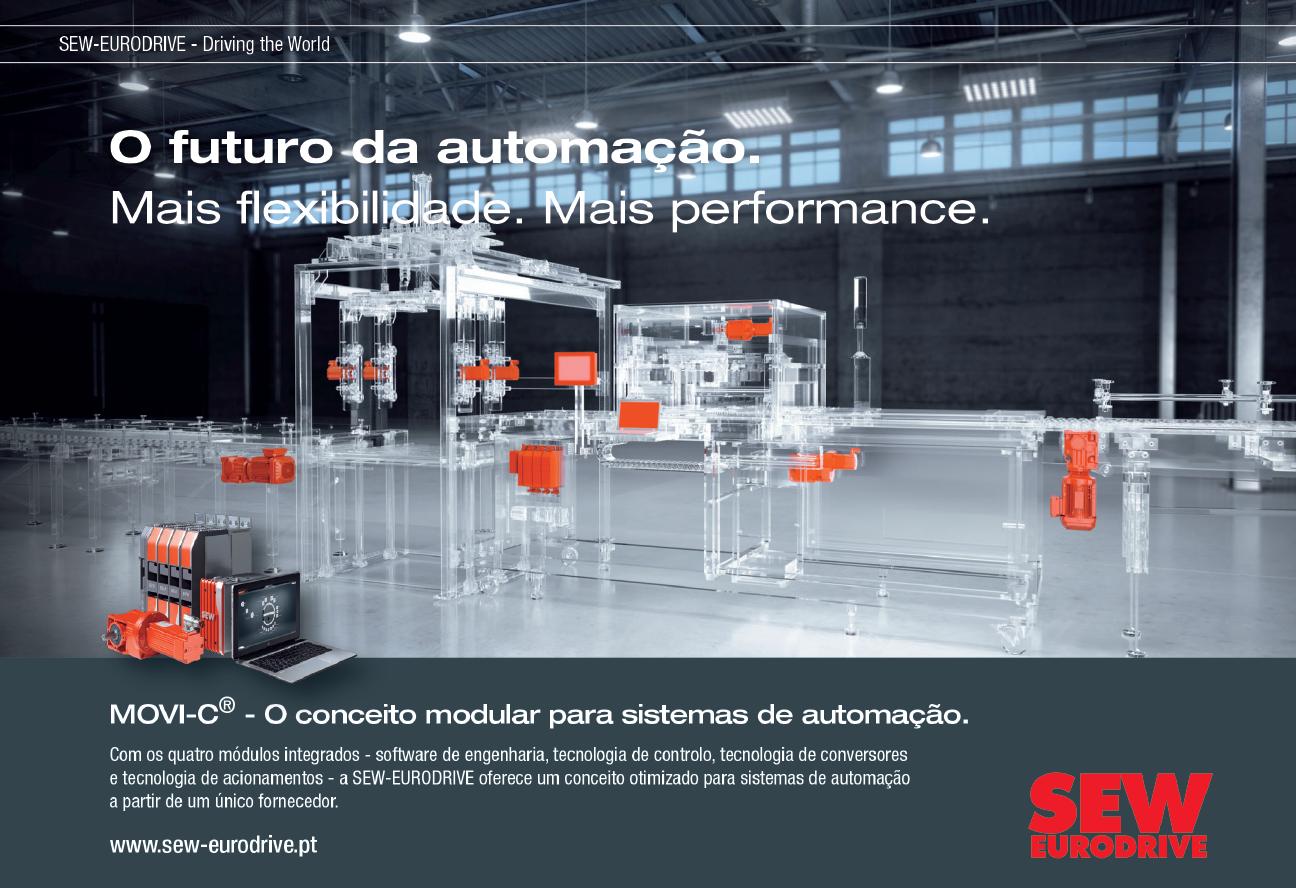
15 minute read
Notícias dos Associados
FLEXCRAFT - INVESTIMENTO DA SETSA NO I&DI GERA RESULTADOS E PRÉMIOS
09
A SETsa considera a Investigação, Desenvolvimento e a Inovação (I&DI) como um dos pilares estratégicos da empresa dirigido à satisfação contínua da expectativa dos clientes e cuja missão principal é acompanhar tendências e apresentar soluções inovadoras que potenciem a extensão da sua oferta no mercado como uma filosofia da empresa.
Na continuidade dos projetos na área aeronáutica, Life (2009), ‘newFace’ (2012) e Xaerostructures (2012), a empresa SETsa, do Grupo IBEROMOLDES, conciliando a sua experiência ao conhecimento adquirido na área de desenvolvimento de produto, coordenou o projeto “Flexcraft - Flexible Aircraft” (2016).
O projeto “LIFE, Lighter, Integrated, Friendly and Eco-efficient Aicraft Cabin”, que decorreu entre 2009 e 2010, e vencedor do prémio Crystal Cabin Award, em 2012, na categoria de Conceitos Visionários, teve igual enquadramento no desenvolvimento do produto e produção de ferramentas inovadoras para a remodelação de cabines de aeronaves executivas e orientado para a sustentabilidade. Este projeto recorreu a materiais naturais, como o couro e cortiça para apresentar uma cabine sofisticada, confortável e com uma baixa pegada ecológica.
Seguiu-se o projeto Xaerostructures (2012) com o propósito de desenvolver competências em diferentes áreas tecnológicas (engenharia aeroespacial, engenharia mecânica, engenharia de materiais, gestão de projetos de I&D) que permitam a evolução de métodos de desenvolvimento e ensaios de aeroestruturas, como os macro componentes (asas, fuselagem e superfícies de controlo de voo) ou subcomponentes estruturais internos segundo uma premissa de certificação aeronáutica. Em 2014, foi executado o projeto de moldes para compósitos (produção de fuselagem em fibras compósitas).
Já no projeto NewFACE - Future Aircraft Configurations for Eco- Efficiency, (2012), a SETsa participou na definição e desenvolvimento de três conceitos diferentes de aviões para utilização comercial: avião de transportes de pequenas cargas; avião de pequenas dimensões para transporte até 75 passageiros e avião de grande dimensão.
Dos três conceitos criados no projeto “NewFACE” (V-Tail, Box-Wing e o Utility), o conceito Utility foi considerado o mais promissor, tendo dado origem ao projeto “Flexcraft – Flexible Aircraft” (2016), o qual teve grande impacto devido à sua inovação tecnológica e complexidade. Com este projeto pretendeu-se criar/melhorar novas configurações de aeronaves, desenvolver novos processos de produção e integrar novos materiais, de forma a criar soluções sustentáveis, eficientes, flexíveis e adaptáveis a diferentes tipologias de utilização. É uma aeronave inovadora e que conjuga a ideia de modularidade, permitindo uma reconfiguração da cabine para diferentes missões (comerciais e de lazer, de socorro de populações) para competir com soluções de asa rotativa, através de uma operação em pistas curtas, melhorando o desempenho global.
Além dos projetos na área aeronáutica, a SETsa apresenta experiência na área da engenharia e construção de interiores para protótipos de veículos de transporte, como por exemplo, autocarros e comboios, como é o caso dos projetos IBUS e Modseat.
O projeto IBUS (2009) teve em vista o desenvolvimento e a integração de componentes e sistemas para a construção de uma secção transversal (interior e exterior), designado por mock-up, para aplicação em carroçaria de autocarros de turismo, sob o mote: Integrado, Mais Leve, Mais Ecológico e Mais Confortável. O projeto MODSEAT - Modular Light Rail Seat (2016), que foi apresentado na INNOTRANS 2018, em Berlim, teve como objetivo o desenvolvimento e a construção de um protótipo de banco ferroviário com uma conceção inovadora, modular, versátil e customizável, utilizando novos processos e materiais e integrando novas funcionalidades para comboios de classe regional/ intercidades.
A experiência e o histórico da SETsa na área de desenvolvimento de interiores para protótipos de veículos de transporte foram fundamentais para a participação da empresa, em 2018, no desenvolvimento de todo o interior do primeiro avião 100% elétrico do mundo, da empresa israelita Eviation. Esta aeronave, de nome Alice, poderá transportar nove passageiros numa viagem de até 1.040 km de distância e a 440 km/h. Para a produção do interior, a SETsa utilizou processos de engenharia diversos e produziu todos os componentes nas mais diversas tecnologias que integrou o modelo à escala real da mockup. Em 2019, o projeto ALICE, foi apresentado na exposição da indústria aeronáutica de Le Bourget, que decorreu em Paris. CONCEITUADO CONCURSO INTERNACIONAL IDA PREMEIA PROJETO FLEXCRAFT
Foi distinguido com o galardão ‘Ouro’, o Projeto FlexCraft, uma aeronave modular que tem como promotor líder a empresa SETsa. O prémio atribuído pelo IDA - International Design Awards, na categoria Product Design dedicado aos projetos de aeronáutica.
O FlexCraft conjuga a ideia de modularidade e flexibilidade, permitindo uma reconfiguração da cabine para diferentes missões (comerciais e de lazer, de socorro, entre outras) para competir com soluções de asa rotativa, através de uma operação em pistas curtas, melhorando o desempenho global. Esta distinção vem reconhecer o trabalho e dedicação do consórcio que, para além da SETsa, é constituído pela empresa Almadesign, pelo Instituto Superior Técnico, a Embraer Portugal e o Instituto de Ciência e Inovação em Engenharia (INEGI).
Uma aposta inequívoca na inovação e desenvolvimento de tecnologia foi, desde sempre, o objetivo do FlexCraft, explica Leonel de Jesus, da SETsa, adiantando que, ao aliar estas duas condições, o projeto pretende “fazer a diferença no mundo atual”.
Foi neste pressuposto que os responsáveis pelo desenvolvimento desta aeronave decidiram candidatá-la, após três anos de trabalho intensivo, a um dos prémios mais reconhecidos a nível internacional, na área do design e desenvolvimento de produto. E, concorrendo com mais de mil trabalhos submetidos a concurso, provenientes de mais de 40 países, o FlexCraft acabou distinguido e com o galardão ‘Gold’, na 15ª edição do concurso, na categoria de Product Design | Transportation / Aircraft/Aerospace.
A importância desta distinção é assinalável: os International Design Awards (IDA), criados em 2007, são um prémio anual interdisciplinar que reconhece, celebra e promove soluções visionárias nos campos da Arquitetura e do Design. Salientando que o júri inclui os mais importantes especialistas a nível mundial, Leonel de Jesus considera que o prémio vem “reconhecer o trabalho, numa área pioneira, a nível internacional e da excelência das empresas e instituições que fizeram parte do Projeto Flexcraft”, como é o caso da SETsa (promotor líder), Almadesign, Instituto Superior Técnico, Embraer Portugal e Instituto de Ciência e Inovação em Engenharia (INEGI).

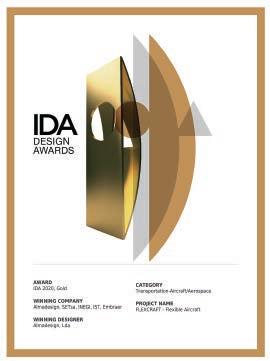
Recorde-se que esta inovadora aeronave, desenvolvida entre 2016 e 2020, teve como principal objetivo dar resposta a diferentes missões civis, nomeadamente, serviços de logística, missões de busca e salvamento, transporte de passageiros e carga em trajetos urbanos e suburbanos, entre outros.
Leonel de Jesus conta que o projeto “já concluiu os objetivos propostos para os três anos, que se cumpriram em março de 2020”, enfatizando que “deste projeto resultaram um demonstrador de processo, um modelo VRP (Veículo Remotamente Pilotado) e uma mockup à escala real do módulo de passageiros, apresentados no dia 28 de janeiro de 2020 no Instituto Superior Técnico, em Lisboa”.
O FlexCraft seria, após esta apresentação nacional, dado a conhecer a nível internacional, entre 31 de março e 2 de abril, em Hamburgo, na Alemanha. Contudo, sublinha, a pandemia de Covid-19 impediu que tal sucedesse. Este projeto foi financiado pelo Portugal 2020, no âmbito do Programa Operacional Competitividade e Internacionalização através do Fundo Europeu de Desenvolvimento Regional.
O FUTURO
Mas a pandemia não impediu, contudo, que os criadores do FlexCraft continuassem a trabalhar em novas soluções, de forma a melhorálo e prepará-lo para o futuro. “Os consorciados já candidataram um novo projeto de desenvolvimento para levar mais longe os resultados alcançados, com uma duração de 36 meses, igualmente inovador e ainda mais sustentável e amigo do ambiente”, explica o responsável. Deste modo, adianta, “pretendemos continuar a apostar numa área em ascensão, em que os consumidores, tendo estilos de vida cada vez mais atribulados, querem viajar da maneira mais rápida e eficiente possível”.
Leonel de Jesus enfatiza que, no seu entender, “a mobilidade, nos próximos anos, tenderá a ser personalizada, eficiente e ininterrupta”.
No âmbito do consórcio do projeto FlexCraf, a SETsa assumiu o papel de coordenador responsável por todas as atividades de desenvolvimento de ferramentas de produção, bem como todas as atividades de integração de todos os componentes que incluem os protótipos desenvolvidos (mockups). Mas para além da componente técnica e tecnológica, a empresa da Marinha Grande teve ainda a seu cargo a responsabilidade de coordenação técnica do projeto, tendo sido o seu promotor líder.
O consórcio Flexcraft teve início em dezembro de 2016 e o término em março de 2020, perfazendo um total de 40 meses de trabalho conjunto.
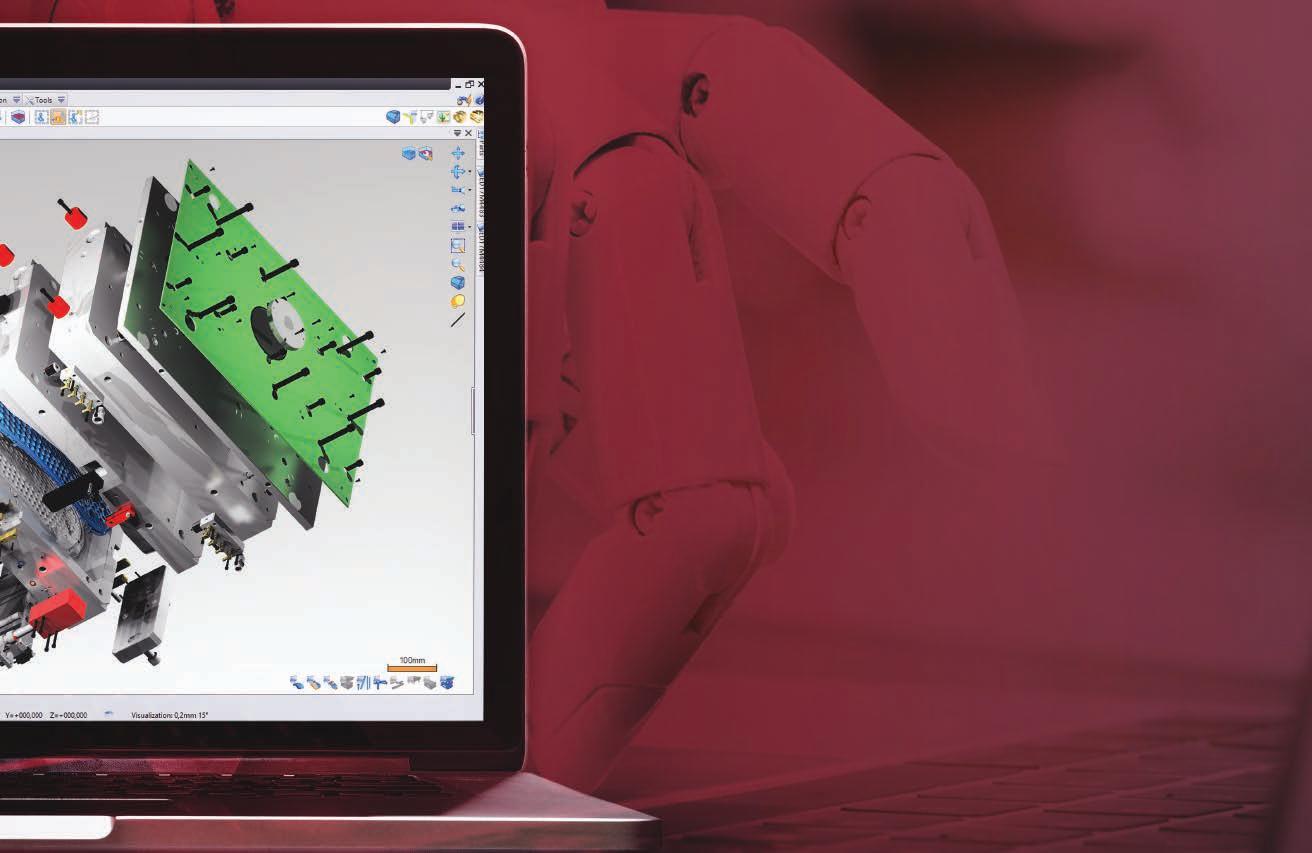
12 AES MOLDES: MUDANÇA PARA NOVAS INSTALAÇÕES CELEBRA 20 ANOS DE ATIVIDADE
O grupo AES vai passar a funcionar, até final do primeiro semestre deste ano, em novas instalações, na zona da Barosa (Leiria). O espaço, criado de raiz, permite ampliar a capacidade instalada da organização que, este ano, celebra duas décadas de atividade. A mudança permite, também, avançar para novos desafios e aumentar o número de colaboradores que ascende, neste momento, a 55 pessoas.
É uma mudança pensada e muito desejada. A AES celebra este ano o seu vigésimo aniversário nas novas instalações. Foi criada em 2001, dedicando-se na primeira década exclusivamente ao projeto e engenharia. Em 2011, estendeu a sua ação à área do fabrico de moldes, criando a AES Manufacturing. O grupo deixa a Marinha Grande para passar a laborar na zona da Barosa.
A mudança teve início em setembro de 2020, com a passagem da AES Manufacturing. Desde então, é na nova localização que são produzidos os moldes. E é também aí que já está em funcionamento a mais recente aposta: a injeção. A área da engenharia (AES Moldes) mudará este ano, até final do primeiro semestre. Rui Marques e Ana Paula Marques, administradores, explicam que a criação das novas instalações se insere, por um lado, numa “estratégia de crescimento da empresa” e, por outro, na criação de um melhor local de trabalho para a equipa, que são a espinha dorsal do projeto. “Nas instalações antigas, estávamos com uma ocupação de 150%”, referem.
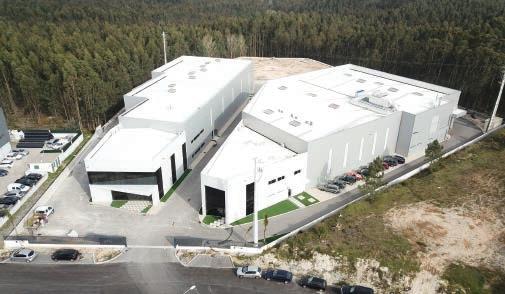
O novo espaço permitirá ao grupo consolidar a sua estratégia, mas também crescer. Para já, com a mudança, foram adquiridos novos equipamentos, que permitiram fortalecer os departamentos de CNC, de maquinação de elétrodos, erosão e medição. As novas instalações possibilitaram também o fortalecimento dos processos e projetos para novos desafios.
EXCELÊNCIA E INOVAÇÃO
E a AES cresceu também em número de colaboradores. O novo espaço acolheu mais sete pessoas, aumentando o quadro de pessoal que é, hoje, de 55 pessoas. Uma equipa jovem, dinâmica e altamente qualificada.
Tendo nas indústrias automóvel, médica e eletrónica os seus principais mercados sectoriais, a AES exporta os seus produtos, essencialmente, para a América do Norte e a Europa Central. Projeta e fabrica cerca de 100 moldes por ano.
Desde a sua fundação que a empresa tem conseguido afirmar-se pela excelência do seu serviço, conquistando e consolidando a sua posição junto dos clientes e mercados mais exigentes.
Uma das prioridades do grupo tem sido a promoção de uma cultura de melhoria contínua, inovando nos processos e mantendo a vanguarda nas tecnologias.
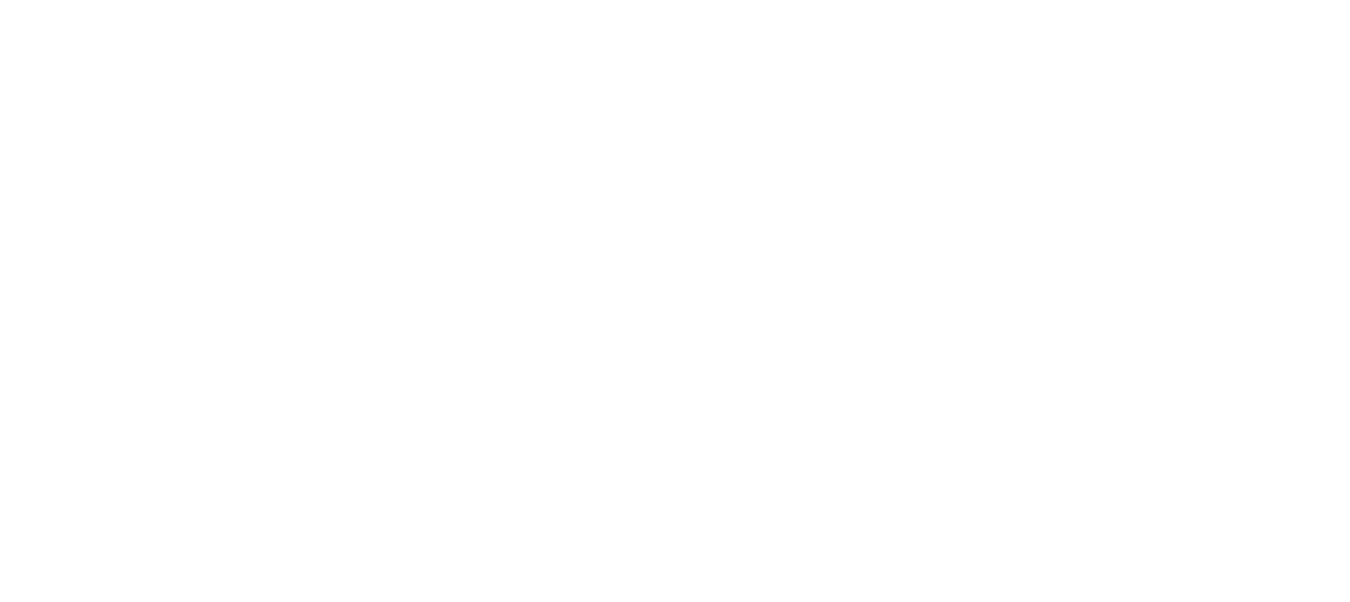
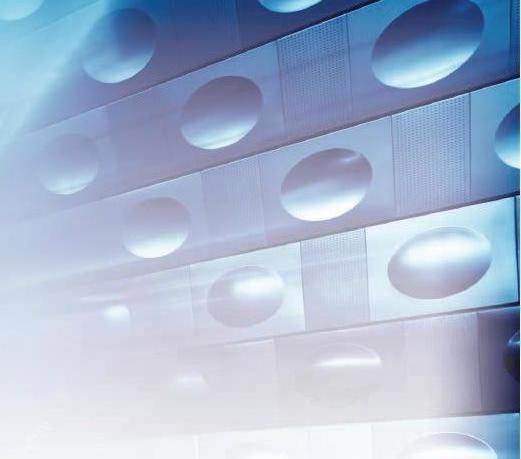
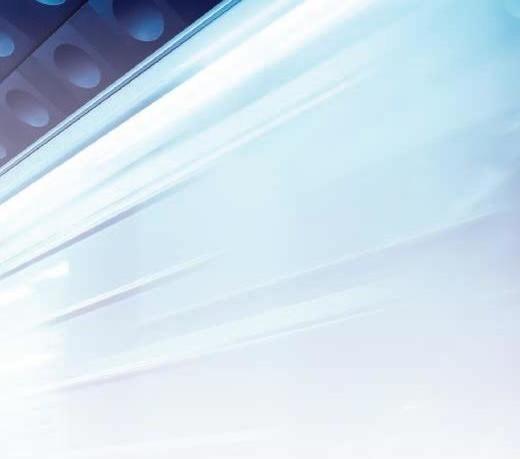
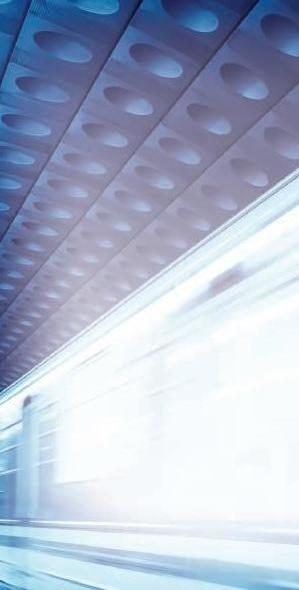
EDIFÍCIO NOMEADO PARA PRÉMIO INTERNACIONAL ACOLHE NOVA EMPRESA DO GRUPO JR MOLDES
13
O edifício da STEELFORM, a mais recente empresa de moldes do grupo JR Moldes, de Oliveira de Azeméis, foi nomeado para ‘Building oftheYear2021’, na categoria de arquitetura industrial. O concurso internacional, promovido pela Arch Daily, tem como objetivo premiar os melhores projetos arquitetónicos do mundo, colocando as instalações da STEELFORM na corrida a este prémio do melhor edifício do ano. Este foi o único projeto português a receber uma nomeação nesta categoria.
Foi com “muito orgulho e satisfação” que a JR Moldesviuoedifício dasua mais recente aposta, a empresa de moldes STEELFORM, nomeado para melhor edifício industrial internacional. O mérito, adianta a empresa-mãe, é do Arquiteto Lopes da Costa, responsável por este projeto arquitetónico único, e da Construtora de Loureiro que lhe deu forma, tendo como requisitos fundamentais o bom funcionamento da empresa, maximizando o aproveitamento da área do terreno e a integração do edifício na zona envolvente. Saliente-se que este projeto foi o único edifício industrial português nomeado nesta categoria.

A STEELFORM tem know-how para produzir moldes de 10 a 40 toneladas, para todas as indústrias.Amplia, desta forma, a capacidade do grupo para a produção de moldes de maior dimensão.Atualmente conta com uma equipa de 17 colaboradores e equipamentos com tecnologia de ponta para prestar um serviço de excelência.
Da engenharia à produção e aos testes, este grupo – composto pela JR Moldes, STEELFORM e Platec (testes e produções) – assegura um serviço completo, respondendo com qualidade e eficácia às cada vez mais elevadas exigências dos mercados onde opera. O grupo desenvolve e produz moldes para a injeção de plásticos, magnésio e alumínio.
A sua evolução deve-se à dedicação de toda a equipa e ao constante investimento em equipamentos com tecnologia de ponta.
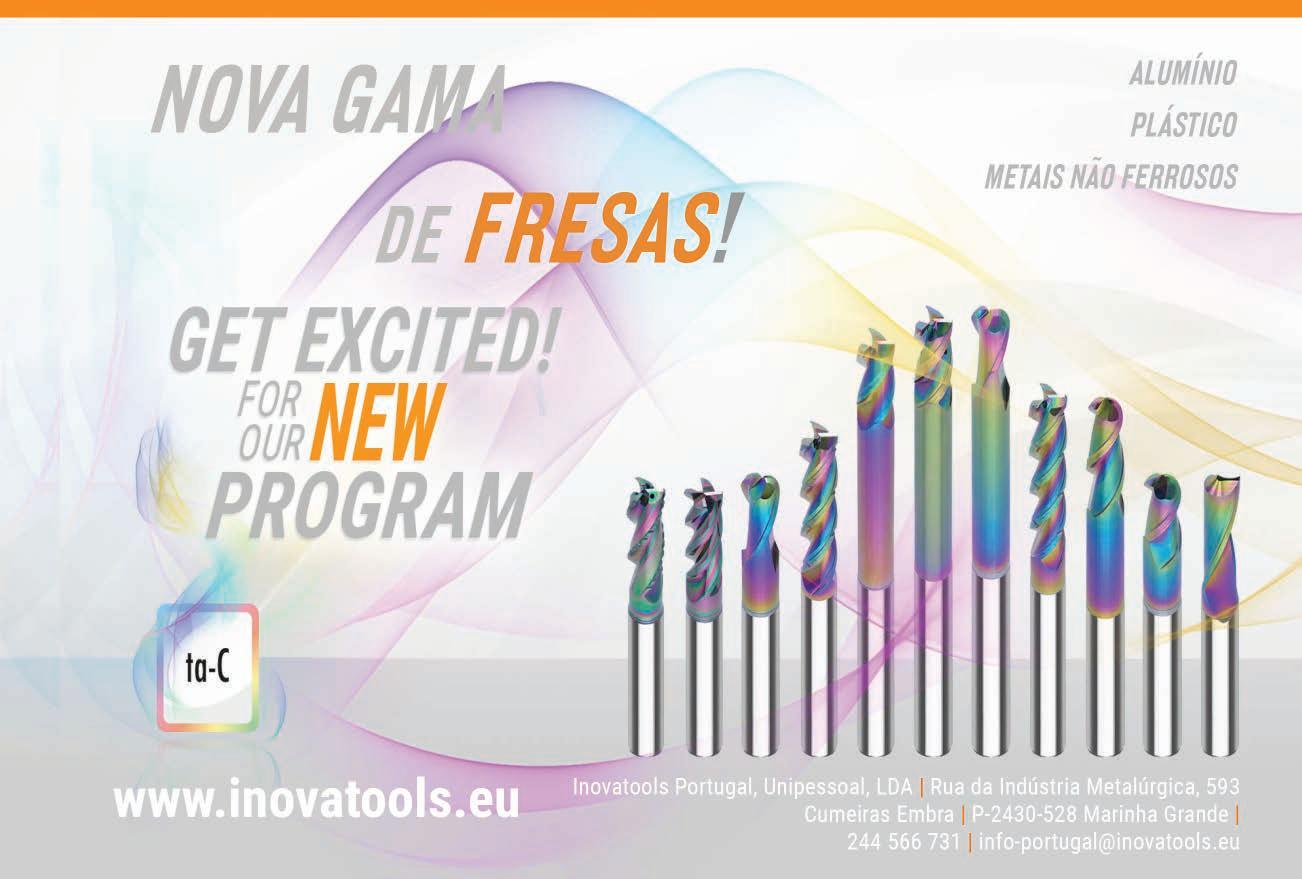
14 STEELPLUS: HÁ DUAS DÉCADAS A APOSTAR NO PROGRESSO DE FORMA PROFISSIONAL E EXIGENTE


Vinte anos após a sua criação, em 2001, em Vale de Cambra, a SteelPlus impressiona pela dinâmica da sua produção: conta até hoje com 1.500 moldes realizados, para 13 países, em quatro continentes. Tem, atualmente, 32 colaboradores e segue como prioridade o aperfeiçoamento diário de tarefas e processos, de forma a alcançar a satisfação dos clientes e mercados mais exigentes.
Fundada a 6 de março de 2001, a SteelPlus passou, logo nesse primeiro ano, por um momento extremo de exigência: o atentado que mudou o mundo, a 11 de setembro, nos Estados Unidos. Terá sido esse um dos fatores que ajudou a empresa a criar a resiliência necessária para ultrapassar os momentos de dificuldade que, nos anos seguintes, atingiram a indústria de moldes e chegar, hoje, aos 20 anos, como um dos fabricantes de referência da indústria nacional de moldes.
Com 32 colaboradores, tem como principais mercados o Leste Europeu, Espanha, França, Bélgica, Alemanha, Suécia, Magreb, México e EUA. Mas até chegar a esta diversidade, a empresa foi caminhando passo a passo, de forma ponderada e consistente. Até 2008, dedicou-se essencialmente a pequenos clientes do mercado ibérico.
Já depois de 2014, devido aos requisitos de qualidade do mercado e dos novos clientes, a empresa apostou na otimização dos recursos internos, quer a nível de tecnologia, quer a nível de especialização dos seus colaboradores.
A aposta mostrou resultados e, em 2019, a SteelPlus alcançou o melhor ano da sua história. E aos 20 anos, sublinham os seus responsáveis, a vida da empresa pauta-se por “centenas de exemplos de sucesso no desenvolvimento de moldes para as indústrias Automóvel, Aeronáutica e Medicina, entre outras”. FOCO NA QUALIDADE
A satisfação dos seus clientes é o principal foco da empresa que, apesar do período conturbado por que passa o mundo, devido à pandemia de Covid-19, não descura aquilo que sempre foi a sua prioridade: a excelência do que produz.
Para isso, contribui o auxílio inevitável da tecnologia, na qual tem investido e continuará a fazê-lo à medida das suas capacidades: centros de maquinação paletizados e robotizados, sistemas rápidos de aperto e centramento, controlo dimensional em todas as fases da produção e monitorização para o cliente.
“Tentamos dentro da nossa organização, e apesar de ser uma pequena estrutura, prestar um serviço como uma média/grande empresa”, explicam. Por isso, consideram “estar ‘condenados’ ao progresso de uma forma profissional e exigente”.
A SteelPlus afirma ainda não temer a competitividade do mercado, uma vez que esta sempre existiu ao longo da sua história. “Esta (competitividade) sempre vai existir e vai mesmo acentuar-se, sem qualquer dúvida, por isso as nossas energias centralizam-se no aperfeiçoamento diário de tarefas e processos”, consideram os seus responsáveis, mostrando-se determinados a manter a sua rota.
“Como fator externo de reputação da nossa indústria de moldes é importante continuarmos a reforçar o nome de Portugal como fabricante de moldes de grande qualidade”, defende a Steelplus.
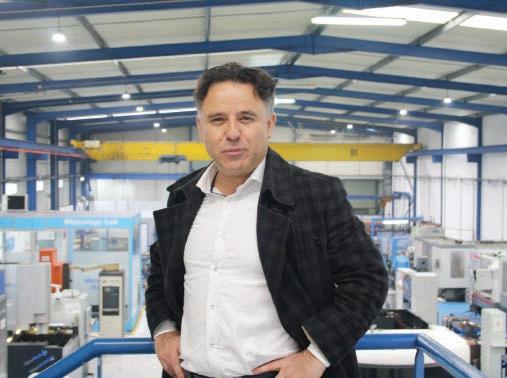
/ / Luís Lima - SteelPlus
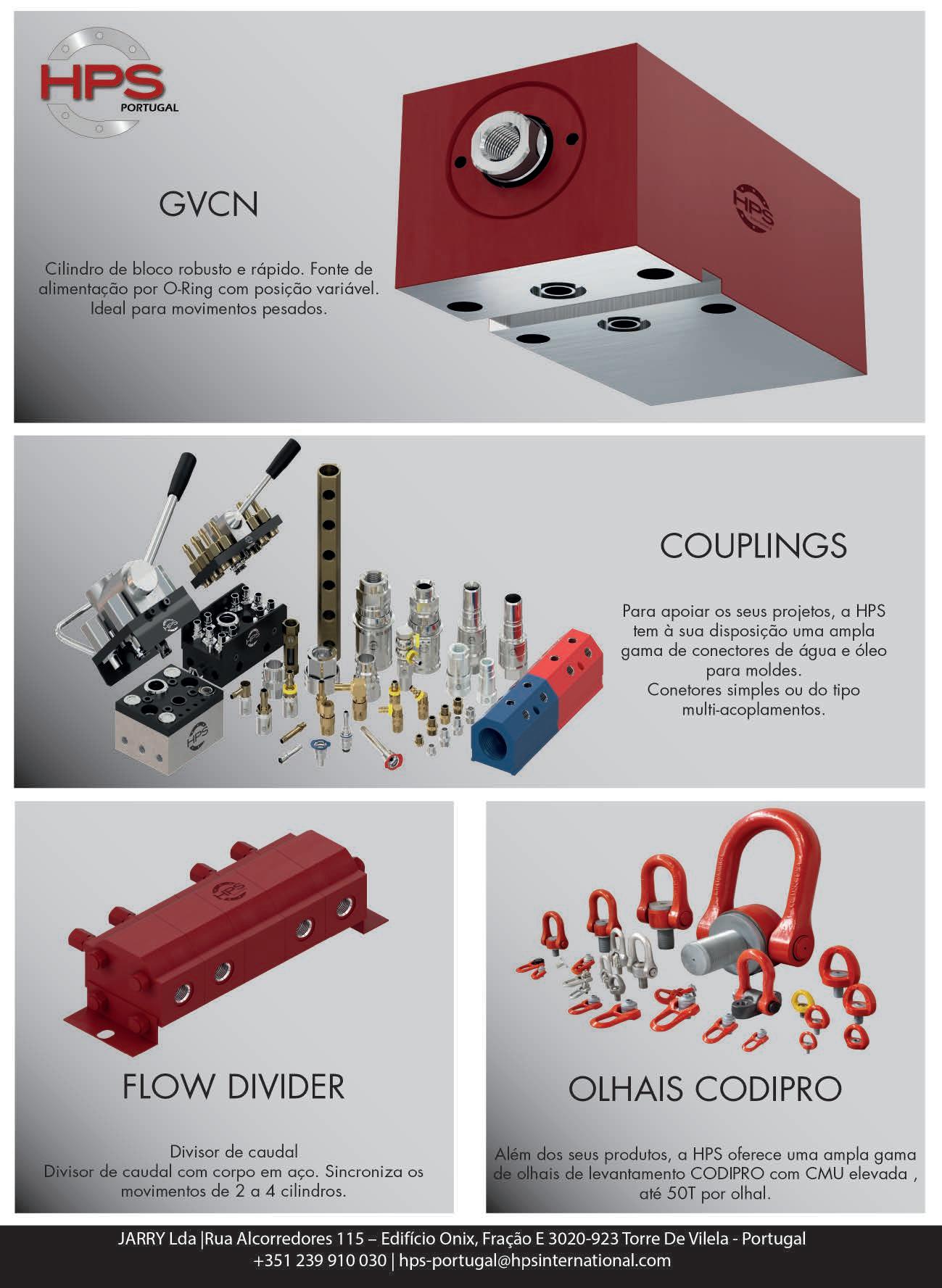
16 LEOMÁVEL APOSTA EM MATERIAIS DE ALTA PERFORMANCE
A Leomável Moldes. Lda., em sintonia com as novas tecnologias, adiantou-se às necessidades do mercado na crescente procura do cliente por novos materiais plásticos. Materiais, que possam atender aos pedidos de um exigente segmento de peças injetadas e de extrema precisão.
Nesse sentido, a empresa lançou-se, de forma pioneira, em projetos de fabrico de moldes para materiais de alta performance, como o LCP. Um polímero de cristal líquido de alto desempenho, desenvolvido e utilizado em peças de elevada precisão, como, por exemplo, em engrenagens, nos quais se requerem detalhes mínimos, com variações extremamente apertadas, alta repetibilidade e extrema resistência ao desgaste que, até então, só eram possíveis de se atingir com materiais metálicos por processos de maquinação. Devido a estas características, que se devem ao seu elevado grau de cristalinidade e também à sua estrutura molecular altamente orientada, o LCP está a ganhar espaço no mercado de polímeros de engenharia. No entanto, apresenta particularidades no seu processamento e os requisitos para os moldes são elevados. Por consequência, a expertise necessária na execução de um molde robusto, com qualidade e precisão com a exigência de processamento deste polímero, é elevada.
A Leomável antecipou-se nesta vertente e, graças ao seu know-how técnico, já desenvolve e fabrica moldes para injeção com LCP. Uma competência reservada apenas aos que já estão no mercado há várias décadas, atendendo, desta forma, à necessidade dos seus clientes, que se tem demonstrado muito satisfeitos com o nível de resultados atingido.
O futuro dos moldes passará também pela capacidade das empresas se adaptarem aos novos polímeros, com características complexas. Nos próximos anos, o leque de materiais com especificações cada vez mais precisas irá aumentar significativamente. Nesta perspetiva, a empresa fomenta a formação e o desenvolvimento, também para este segmento, considerando crucial para a sua competitividade no mercado.

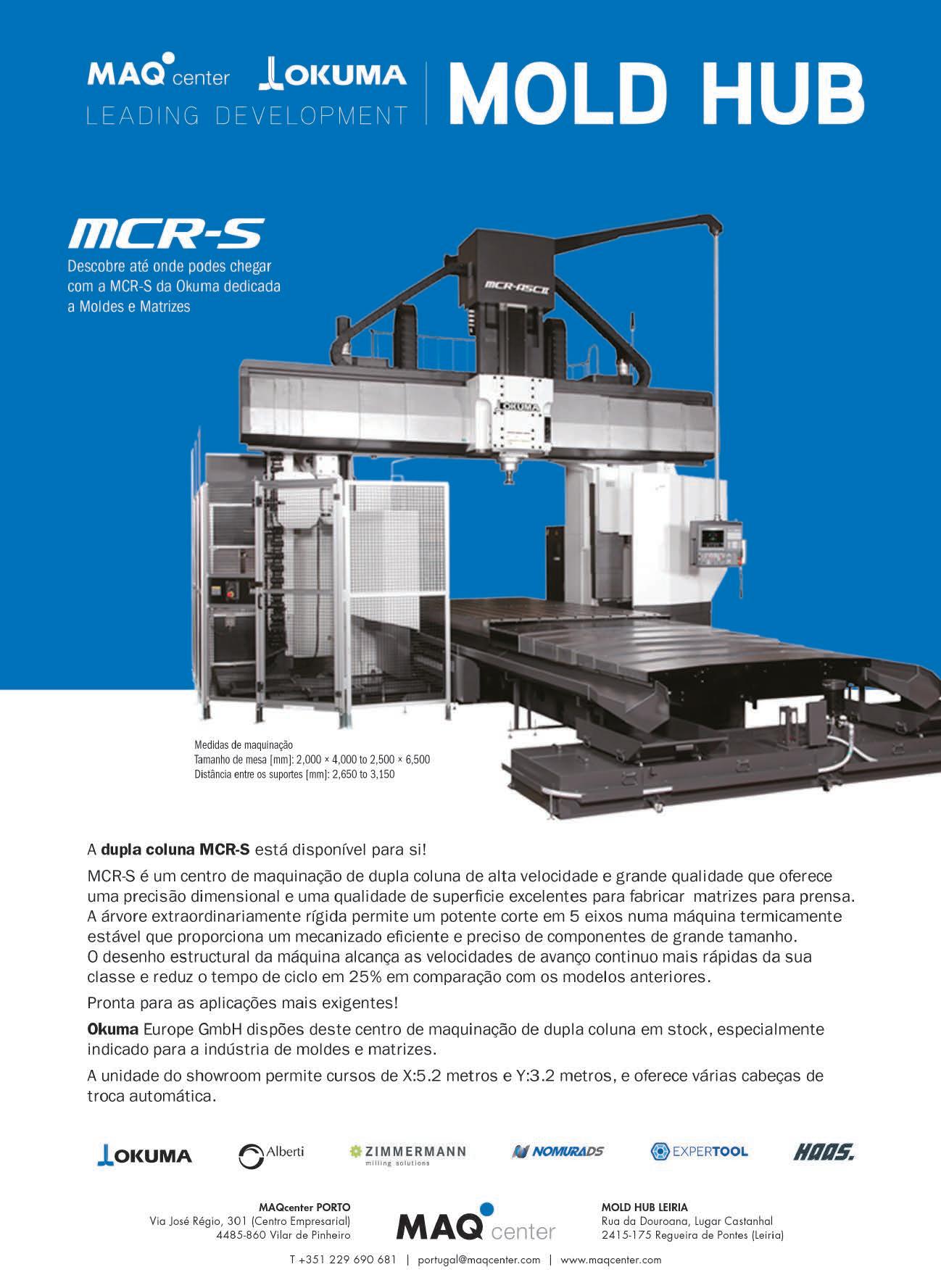