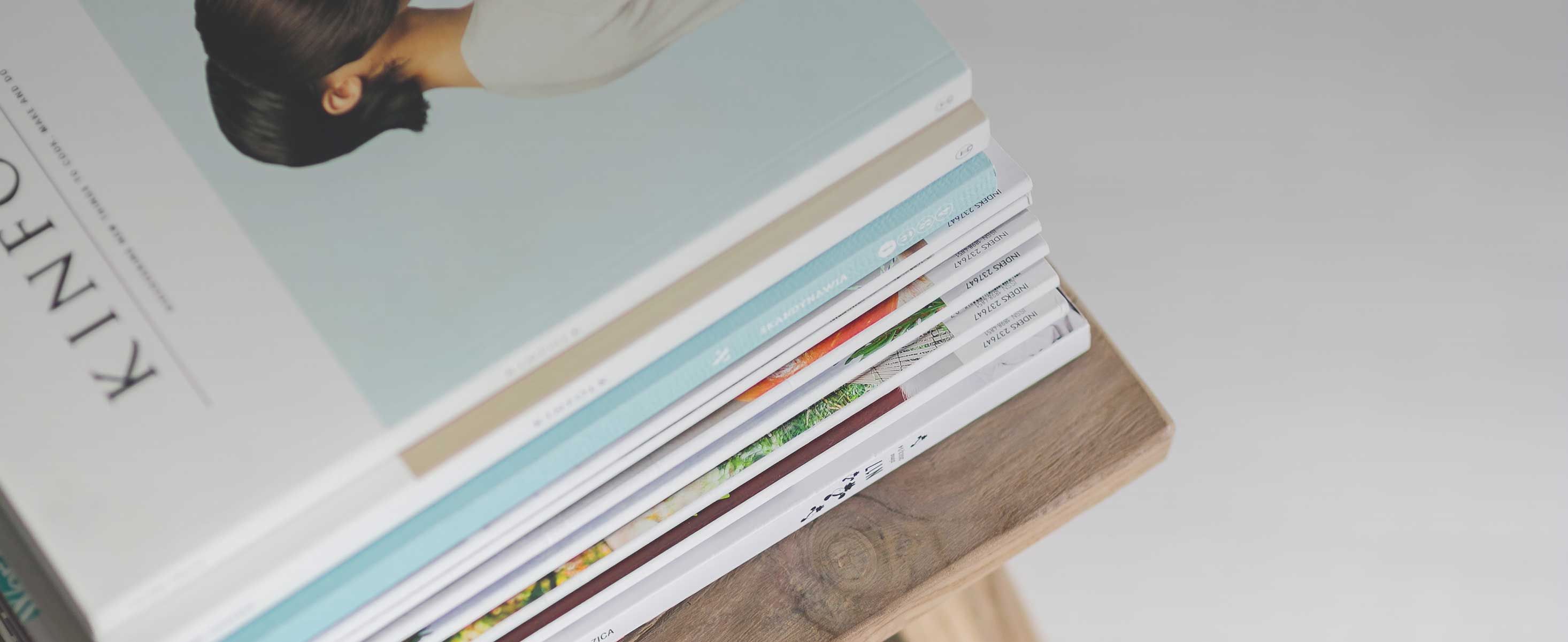
7 minute read
TABLE 17: Project Team Risk Responsibility Matrix
7.4. Management Plans for the ‘Top Five’ Risks
7.4.1. Material delivery and storage difficulty - impact to schedule
Advertisement
Category: Construction
Risk Owner: CM/Subs
Risk Statement: Due to the site’s location and project layout, logistics will be challenging in different ways.
Risk response: Mitigate. The access to the site itself will be restricted, since it is situated in a densely populated residential area, with plenty other construction sites around. Material deliveries will have to be done in restricted hours of the day, week days planned ahead and often communicated or negotiated with the community to avoid disturbance. Material storage will also require a lot of planning, as the entire property area corresponds to the construction area. Specific issues can be identified during the layout of the Logistics Plan and therefore can be efficiently approached. A detailed schedule will be developed with the input of the subcontractors on the material quantity/volume and the equipment required to perform their work. The schedule will foresee specific dates and locations where each subcontractor will lay their materials before installation. Coordination between subcontractors is also essential, as the following top 5 risk will demonstrate.
7.4.2. Need for highly efficient coordination
Category: Technical
Risk Owner: CM
Trigger: Identification of issues during meetings with subs and during Logistics Plan
Risk Statement: The limited space inside of the construction site will need to be shared between construction work, GC staff, mobilization items such as portable toilets and dumpsters and also multiple subcontractor’s teams performing different tasks. Such high density workload can potentially causes serious schedule and cost problems, in addition of safety related issues.
Risk response: Mitigate. The subcontractor’s tasks, if coordinated properly, can provide for the share of resources and auxiliary action. That can boost construction productivity by decreasing the work time and reducing waste, improving the budget and overall project results. Again, a highly detailed schedule, with the addition of illustrative phasing plans showing each subcontractor’s area of work and durations can provide for the required coordination. On top of that, the CM will gather subcontractors for an “all staff” action plan revision on early morning, before shift starts, as required per each phase, possibly multiple times in one week. It’s crucial that the subcontractor’s learn to communicate with each other, even when the responsibility and final word comes from the CM team.
Category: Technical
Risk Owner: Designers
Risk Statement: Prior to the bid, during the estimating phase, several information gaps and conflicting information between design parties were identified. Multiple RFIs were issued, but that fact yells the necessity of a thorough Constructibility Review, to be followed by a value engineering analysis, prioritizing critical items. All efforts must be made to prevent scope surprises and to protect schedule, budget and relationships.
Risk response: Mitigate. In addition to the above mentioned measures, two other measures will be taken. The first consists in a part of the weekly meetings being dedicated to review and plan ahead the work to be performed three weeks in advance, including all major participants such as important subcontractors and vendors. The second measure will be the development of a realistic and complete BIM model to help identify clashes, design gaps and conflicting information.
7.4.4. Scarcity of qualified subcontractors due to high season
Category: Project Management
Risk Owner: CM
Trigger: Low quantity of subs bidding the job
Risk Statement: The construction market is booming and it’s a possibility that there might be more work than workers. Several GCs and CMs are facing difficulties in contracting with a full set of reliable, well known subcontractors. The risks involved directly impact schedule and budget. The work could be severely delayed, harming logistics, sequencing and coordination with other trades. At the same time, the lack of competition is recognized to drive the prices up high.
Risk response: Mitigate. The response strategy, in that case, consists of addressing both sides of the situation from two different perspective. The first is to plan early, perform a market research to identify critical trader and prequalify enough bidders to open the possibilities as much as possible. The second perspective is to play with allowances and contingencies in the original project budget to foresee a complicated situation and try to contain damage on only the financial side This is important since, as stated before, the delay of the award can delay the entire work and potentially cause further loss than one overpriced subcontractor.
7.4.5. Disputes over budget due to delivery system (IDP)
Category: Project Management
Risk Owner: All parties
Trigger: Frequent discussions about scope
Risk Statement: The decision to perform an IDP hybrid delivery system comes from an intention to remedy incomplete set of drawings. With the fast tracking of the project, decisions can be made on-the-go and the project budget is not completely restricted to the bid. This flexibility is intended to improve final schedule and quality results, as changes in scope can be approached as something simpler than a change order. The same scenario, due to its unpredictable and risky nature, could likely set the stage for disputes over scope.
Risk response: Accept. These disputes, being the “intended result”, must still be closely tracked, analyzed and controlled. In addition to the detailed weekly meetings, when budget is also discussed, the production of the BIM model will be developed with the input and participation of each major subcontractor, who then has the ability to view, in 3D, the almost exact scope they should include in their base prices. The original contracts might include a written description of the scope and images of the 3D model to further illustrate and define the boundaries of the contracted work. That approach would help arise deeper questions, which then would become solid answers with the capability of decreasing disputes.
SECTION EIGHT
SITE SPECIFIC SAFETY PLAN
As mentioned in the summary of Section Seven, Fit Construction produces a Project Risk Management Analysis, a Safety, an Environmental and a Quality plan for all of our projects deriving from the Plan - Do - Check - Act - Review approach.
Section Eight identifies potential hazards during construction. These hazards are specific to the 620 n 3rd St project and categorized by their probability and severity calculated through the Boston Square. For each of the top five hazards, descriptive information is provided on the nature of the risk, the Safety Plan’s main goal, the legal requirements, the monitoring methods, the responsibility structure, the training requirements, the emergency response and the documenting process.
The greatest objective of the Site Specific Safety Plan is the elimination of serious accidents at Fit Construction’s sites through the documentation and analysis of the information and results achieved by each project.
8.1. Site Specific Safety Management System
The Site Specific Safety Management System is structured to have the OSHA standards as a minimum. This Safety System does not replace, it rather complements OSHA directions. It is composed by three parts: 1) Fit Construction Safety Guidelines, a complete publication with all the company’s safety preferred methods that will guide subcontractors as how to act in the company’s job sites and also demonstrate to Owners how we address the subject; 2) The identification of the main hazards in the 620 N 3rd St project specifically with the listing of the controls and hazard ranking before and after them; 3) The detailed description of plans to address the top 5 identified hazards.
Fit Construction collects and documents data from all projects and combines it into a comprehensive system which then allows us to process that information and foresee the main activities that need to be closely tracked, as well as the subcontractors that are a better fit with our safety culture.
A Safety Engineer works exclusively on the identification of hazards, application of controls and collection of data on Fit Construction projects, including 620 N 3rd St. This employee will periodically visit the site and perform reports which will then be analyzed and applied as controls during construction.
In the field, the Site Superintendent and the Field Engineer have the authority to monitor safety at all times and to stop the work if an unsafe activity is identified. They are the main contact points on site to address all subjects related to safety, including emergencies. They will also provide specific directions to subcontractors when required. However, all people working or visiting the site are strongly encouraged to watch out for each other’s work and to point out if they see something which isn’t correct or safe.
The Fit Construction Safety Guidelines is a document which has been carefully tailored by years of experience in the construction field. This publication is also periodically updated in accordance with the latest trends presented in the projects. Fit Construction utilizes the Plan - Do - Check - Act - Review approach when it comes to safety and believes that this process provides continuous learning and improvement.