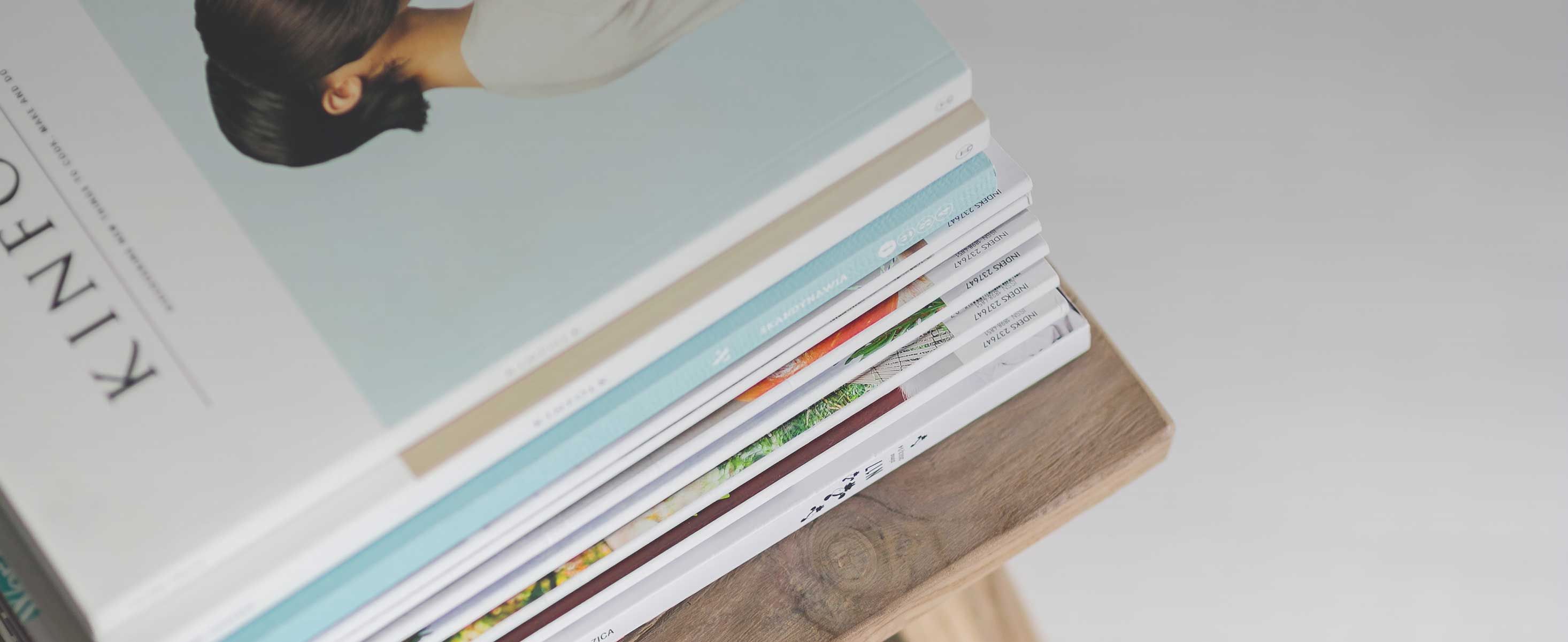
15 minute read
TABLE 20: Site Specific Safety Hazard Analysis - Pages 145 to
Work Package / Activity #
Work Package / Activity Description Hazards
Advertisement
Inherent Risk Rating Before Controls Controls Residual Risk Rating After Controls
184, 189, 194 Rough carpentry Falls 184, 189, 194 Rough carpentry Falls 20 Tie-in PPE 10 20 Tie-in PPE 10
184, 189, 194 Rough carpentry Muscular injury 10 Training on lifting 3
184, 189, 194 Rough carpentry Overheating 5 Shorter shifts 3 392, 397, 402, 407 6Gypsum board (prime) Toxic fume inhaling 10 Breathing mask PPE 6392, 397, 402, 407 Gypsum board (prime) Toxic fume inhaling 10 Breathing mask PPE
247, 248, 257 247, 248, 257 Install exterior Install exterior openings (façade openings (façade windows) windows) Electrocution 12 Electrocution 12 Adequate Adequate PPE, PPE, supervision, supervision, aereal line aereal line protection protection 8 8
232 232 Exterior finishes Exterior finishes (façade) (façade)
247, 248, 257 247, 248, 257 Install exterior Install exterior openings (façade openings (façade windows) windows)
232 232 Exterior finishes Exterior finishes (façade) (façade)
382 382
Roofing Roofing 343, 344 Insulation
465 Mechanical final Electrocution 12 Electrocution 12 Adequate Adequate PPE, PPE, supervision, supervision, aereal line aereal line protection protection 8 8
Falls Falls
Falls Falls
Falls Falls 20 20 Tie-in PPE, Tie-in PPE, adequate adequate equipment equipment (lift) (lift) 10 10
20 20 Tie-in PPE, Tie-in PPE, adequate adequate equipment equipment (lift) (lift) 10 10
20 Tie-in PPE 10 20 Tie-in PPE 10
Toxic fume inhaling Injury by material drop 8
8 Breathing mask PPE Steel boots, adequate PPE 4
5
473, 479, 485, 491 Electrical final Injury by material drop 8 Steel boots, adequate PPE 5
412 Kitchen countertops Injury by material drop 8 Steel boots, adequate PPE 5
457 457
508 508 Plumbing final - RoofFalls Plumbing final - RoofFalls 20 Tie-in PPE 10 20 Tie-in PPE 10
Commissioning Electrocution 20 Commissioning Electrocution 20 Adequate Adequate PPE, PPE, supervision, supervision, disconnection disconnection of systems of systems 10 10
8.3. Management Plans for the ‘Top Five’ Safety Hazards
8.3.1. Falls
Description of the hazard or risk: Falls are statistically among the number one cause of serious accidents in construction. In 620 N 3rd St project it’s no different. A number of work packages will include height exposure and therefore the possibility of falls. These work packages are rough carpentry, steel erection, install of exterior openings and finishes, roofing and other activities to occur on the roof like final plumbing. In this project, falls can occur when vertical elements are being installed or connected to horizontal ones, such as welded connections between columns and beams, from facade work or from activities on the roof.
Objective or goal: The objective of this item of the Safety Analysis is to prevent falls from happening.
Legal and other requirements: Generally, by the minimum OSHA standard, an employee needs fall protection when working from 6 feet high above the floor. The full OSHA rules on fall protection is extensive and consists of the 29 CFR 1926 regulation.
List of Resource Requirements: For heights up to 6 feet, metal, sturdy ladders should be utilized for the work. These ladders should be maintained and checked for safety every week. When working above 6’ high, the employee should utilize tie-in PPE and a scaffolding should be utilized. The scaffolding should have a 42” high handrail all around. When working in heights over 10 feet, the scaffolding should also include a kickplate all around. When working on a roof, a temporary support structure should be built in order to allow the employees to connect their tie-in equipment. If working anywhere less than 6 feet from the edge of the building, employees are required to be tied-in. When working on the facade, a lift with 42” double guardrail and a kickplate is required.
Monitoring Methods: All people at the site have the duty and authority to verify if an employee performing work in a high level is doing so securely. The infraction should be called out immediately and the work should be stopped until the safety rules are followed.
Responsibilities: All people on site have the duty and authority to check on one another. The Site Superintendent is the responsible contact point on site full time for safety, followed by the Field Engineer. The Safety Engineer visits the site on a periodic basis and has the authority to provide the safety plans and reports.
Emergency Response: In case a fall does occur, the employee should be kept immobile and an ambulance should be called.
Documents and Records: A record of infractions will be kept by the Site Superintendent even if it doesn’t become an OSHA violation. These records will contribute to the subcontractor qualification in future projects, as well as to assessments of the work in general.
8.3.2. Electrocution
Description of the hazard or risk: Another frequent safety hazard in construction sites is electricity. In the 620 N 3rd St project, the high density of power outlets, low voltage items and lighting, due to the residential nature of the building, cause the work to be electricity intensive. It’s important to note that low voltage doesn’t imply low risk, and that electricity hazards have a high fatality rate, therefore should be treated with the required attention. Electrocution is a constant hazard in this project and can happen during the entire construction period. Starting with the utilities connection, then electrical rough work, electrical final, low voltage and ending with commissioning, all electrical work includes a risk. In addition to that, the proximity of the building’s facade with PECO aerial cabling imposes one more serious hazard.
Objective or goal: To eliminate the occurrence of serious electrocutions during the construction of the 620 N 3rd St project.
Legal and other requirements: When employees are working with exterior openings and finishes, they’ll be very close to the electrical lines. PECO requires by law that owners apply to require aerial line protection when these conditions occur. PECO installs their own protection equipment on the lines for the period of time determined by the project. That dramatically reduces electrocution hazard from this scenario, but employees are still required to take the same measures designated for other types of electrical hazard exposure
List of Resource Requirements: The most common electrical hazards arise from unsafe equipment, environment or bad practices. To reduce and eliminate these hazards we will invest on periodic equipment maintenance and utilize strategies including insulation, electrical protective devices, guarding and safe work practices. The insulation should be in accordance with the type of work being performed, like voltage, presence of oil or other easily burning material and weather conditions. Electrical protective devices consists of a mechanism that automatically shuts the circuits down in case of higher than regular electrical discharges. Guarding means to protect high voltage equipment by installing guardrails all around it to prevent people from coming to close. Safe work practices include training, the use of proper PPE, equipment maintenance and the de-energizing of equipment during activities to which it isn’t required.
Responsibilities: All people on site have the duty and authority to check on one another. The Site Superintendent is the responsible contact point on site full time for safety, followed by the Field Engineer. The Safety Engineer visits the site on a periodic basis and has the authority to provide the safety plans and reports.
Emergency Response: In case of emergency, other people around the victim need to be extremely careful to avoid also being electrocuted. A highly insulating material, like rubber or wood needs
to be utilized to disconnect the person being electrocuted from the electricity source and an ambulance should be immediately called.
8.3.3. Impalement
Description of the hazard or risk: The impalement hazard can be closely related to falls, described under item one of this section. Consists of the risk of an employee’s body being perforated by a construction element. This hazard is often connected to unprotected sharp protruding structures incorporated in structure and masonry partitions. In the 620N 3rd project, the entire first floor exterior walls are concrete reinforced with rebar. Due to the fact that the schedule foresees the install of structural steel concomitant with the construction of the concrete walls and the CMU elevator shaft, falls risk includes impalement hazard.
Objective or goal: To dramatically reduce the risk of impalement from the construction work.
Legal and other requirements: By OSHA’s 29 CFR 1926.701(b) requirement, “all protruding reinforcing steel, onto and into which employees could fall, shall be guarded to eliminate the hazard of impalement”.
List of Resource Requirements: Utilization of rebar caps, as well as investing in falls protection further described under 8.3.1.
Responsibilities: All people on site have the duty and authority to check on one another. The Site Superintendent is the responsible contact point on site full time for safety, followed by the Field Engineer. The Safety Engineer visits the site on a periodic basis and has the authority to provide the safety plans and reports.
Emergency Response: If impaled by a foreign object, the object should not be removed and medical attention should be provided immediately.
8.3.4. Structure collapsing
Description of the hazard or risk: The collapsing of structures is a critical hazard during excavation and especially underpinning, but also a possibility during the pour of the foundations. At the 620 N 3rd St project, one entire side of the building, which extends the length from one
street to another, will need to be excavated and underpinning in order to provide the existing neighbor building structural support previously provided by the ground. That process exposes structures and has to be done in portions, in a way that only these portions are treated at once.
Objective or goal: To reduce the likelihood and consequences of a collapsing structure accident.
List of Resource Requirements: The first measure taken to prevent this hazard is the design in itself. An underground specific survey is performed during preconstruction to identify the existing structure. The design is made accordingly, but subsurface unknown conditions are a constant in construction, making underpinning a risky activity. The second measure would be to follow the design meticulously and not underpin larger portions than what is provided in the drawings. Lastly, the neighbor building should be braced, a minimum amount of staff should be at the site while underpinning is happening, the sidewalks should be closed and the neighbor building should be advised that underpinning is occurring. Ideally, the building should be empty during excavation. A clear emergency exit path has to be defined previously to the start of the work and all staff members should be made aware of it.
Monitoring Methods: The Site Superintendent is in charge of imposing safety rules to the subcontractors. Anyone at the job site can and should point out when an unsafe practice is taking place, that should then be informed to the Site Superintendent. The Safety Engineer is responsible for compiling this information into a comprehensive report.
Responsibilities: All people on site have the duty and authority to check on one another. The Site Superintendent is the responsible contact point on site full time for safety, followed by the Field Engineer. The Safety Engineer visits the site on a periodic basis and has the authority to provide the safety plans and reports. The Site Superintendent has the authority to stop the work if he/she finds the circumstances to be unsafe.
Training Requirements: All workers on site on a regular basis should be OSHA-30 certified. All site visitors, with the exclusion of the Owner and authorities, should be OSHA-10 certified. The subcontractors should be specialized in performing this type of work (underpinning), so no special training is required.
Emergency Response: If the structures start to crack, shift or present any kind of change whatsoever, the entire area, especially the building, need to be evacuated immediately.
8.3.5. Toxic fume inhaling
Description of the hazard or risk: Inhaling toxic fumes can be identified in a number of different activities, the two main ones being painting and gypsum board priming. This is a hazard that can be easily underestimated and frequently neglected by employees, but that could cause serious health damages. In the 620 N 3rd St project, large areas of gypsum board partitions will
be primed and painted in an enclosed, dense space, amplifying this hazard’s impact. Sprayed insulation can also release fumes.
Objective or goal: To protect all project participants from inhaling harmful toxic fumes and therefore prevent long term consequences.
List of Resource Requirements: As ways to prevent it, firstly, the areas where toxic fumes could be being spread should be isolated with plastic and the entrance should be controlled. Only people wearing the require mask as PPE should be allowed inside of these areas during these activities. Subcontractors who are exposed during full shifts or considerable amounts of time are required to provide their own respiratory protection in accordance to OSHA, at a minimum. Fit Construction will provide its own staff’s PPE, as well as three extra sets for visitors available at the trailer or site office, which should be used only for quick visits.
Monitoring Methods: The Site Superintendent is in charge of imposing safety rules to the subcontractors. Anyone at the job site can and should point out when an unsafe practice is taking place, that should then be informed to the Site Superintendent. The Safety Engineer is responsible for compiling this information into a comprehensive report.
Responsibilities: All people on site have the duty and authority to check on one another. The Site Superintendent is the responsible contact point on site full time for safety, followed by the Field Engineer. The Safety Engineer visits the site on a periodic basis and has the authority to provide the safety plans and reports. The Site Superintendent and the Field Engineer have the authority to command subcontractors to utilize the required PPE and, if they don’t, to stop the work. In addition, other subcontractors can also help supervise each other and contact the Site Superintendent if they see something wrong.
Training Requirements: All workers on site on a regular basis should be OSHA-30 certified. All site visitors, with the exclusion of the Owner and authorities, should be OSHA-10 certified. The subcontractors should be specialized in performing this type of work (priming, painting and insulating), so no special training is required.
Emergency Response: If anyone enters an area where toxic fumes are being released (these areas will be isolated), that person should be immediately removed from the isolated perimeter. If large amounts of fume are inhaled, immediate medical assistance is required.
Documents and Records: The same documenting process used for falls described under the previous item should be used to track the job’s safety conditions. All these internal infractions will be documented and kept in Fit Construction’s records. These will later be utilized to assess subcontractor’s performance, likelihood of future bidding and also bonuses provided by the Incentives Program.
SECTION NINE
SITE SPECIFIC ENVIRONMENTAL PLAN
Section Nine dedicates to identify and prepare for potential environmental risks to be faced during the 620 N 3rd St project. The main risks are listed and categorized by severity and probability through the Boston Square. After that, the five top environmental risks are studied in depth.
Each one of these five risks are analyzed in their nature and impact potential, the organizational controls to be utilized to respond to these events, the list of the required resources in order to prevent and control the risks, monitoring methods, the responsibility structure demonstrating which project members own the risk, training requirements and emergency responses.
Fit Construction believes that this exercise allows for learning and improvement in a continuous process to be built project after project.
Before the 620 N 3rd St Environmental Management System is developed, Fit Construction’s top management engages and establishes the overall policies that guide all the company’s work. Only after that, the actual plan is composed and then implemented. In accordance with ISO-9001, the process then moves on to comparison and evaluation of the foreseen results versus the actual achieved ones. The last step is the revision of the system according to the processed data. This information is documented at Fit Construction, helping to improve the initial overall policies and becoming available to the following projects.
The Environmental Plan will list the major risks regarding 1) the identification of areas potentially affected by construction; 2) the mapping of the involved community; 3) the monitoring and assessment of the air quality, noise and soil conditions before, during and after construction.
The environmental risk evaluation is pivotal to the maintenance of comfort levels to the nearby community, the future tenants and to construction itself. The data provided will help protect budget and schedule, protecting not only the construction work, but everyone directly or indirectly involved with it as well. Fit Construction’s management will closely observe and allocate the required resources in order to prevent undesirable events, reversing the crisis management mentality and investing in prevention.