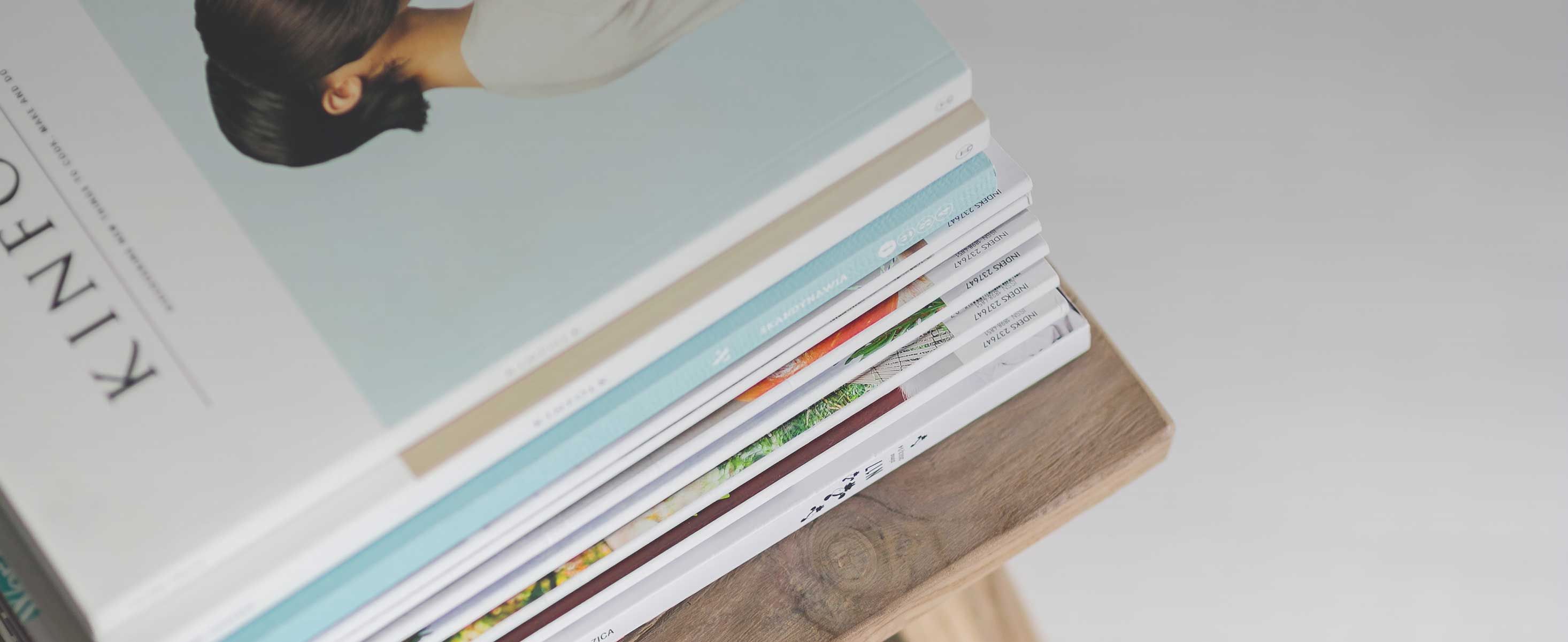
10 minute read
TABLE 21: Site Specific Environmental Impacts
9.2. Site Specific Environmental Impacts
WBS #
Advertisement
Environmental Aspect Description Environmental Impact Description Env. Risk Rating (H,M,L) Environmental Controls
2.1; 2.3; 2.5Air pollution Site work, concrete and masonry will release high levels of dust in the air, causing distress and potential health issues to the community
2.1; 2.3; 2.4; 2.5; 2.6; 2.7; 2.8 Waste pollution Construction activities produce large amounts of waste, some of them non degradable
2.1; 2.3; 2.4; 2.5; 2.6; 2.7; 2.8 Noise pollution and vibration
Construction as a whole Traffic issues
Construction as a whole Pedestrian experience risk
2.2; 2.3; 2.13 Discharge of waste water Several different activities will produce high levels of noise and vibration, causing distress to the community Roads will need to be blocked for different activities, parking spots will be occupied with construction related personnel, delivery and pick up trucks will circulate in the area, affecting the traffic Sidewalks will need to be blocked for different activities, affecting the circulation of pedestrians. Construction work could damage sidewalks and produce hazards. Sheltered walkways are a necessary The site was previously occupied by a factory. Therefore, the sanitary main line and other utilities could be old and hard to connect to, potentially provoking leaks
Construction as a whole Street storm inlet - risk of flash floods
2.3; 2.4 Material source and waste - Renewability risk Waste and debri from construction could block nearby gutters and provoke flash floods during rainy seasons Large amounts of natural resources (wood and steel) utilized in the project
All exterior activities Visual pollution Construction will possibly cause aggressive visuals to nearby community H Periodic air monitoring; special equipment; isolation of critical areas; water sprays; adequate PPE
H
H
H
M Selective collection and sorting of waste to be performed previously to the removal from the site. Each type of material to be addressed to appropriate recycling facility. Limit loud noise activities to business hours with no exceptions; adequate equipment with periodic maintenance Traffic control staff on site at rush hours when street blockage is occuring; additional signage indicating construction areas and reroutes; community communication regarding scheduled work Site Superintendent will inspect sidewalks periodically for potential hazards and coordinate repairs; additional signage indicating reroutes; additional sensorial warning signs for visually disabled people
L Plumber subcontractor should perform a survey previously to utility connection and repairs should be made as required
L
L
L Site Superintendent will instruct subcontractors to leave exterior of the site free from waste and debri at all times Should be well planned ahead to avoid waste and purchased from sustainability certified Opaque fencing and temporary gates; daily clean up of sidewalk from debri and waste; communication with community to inform schedule and construction end date
9.3. Management Plans for the ‘Top Five’ Environmental Aspects
9.3.1. Air Pollution
Description of the Environmental Aspect & Impact: The release of dust in the air is the most common environmental hazard during construction activities. In the 620 N 3rd St project, the three activities that are the most concerning when it comes to air pollution are site work, concrete and masonry. The particles released in the air provoke pollution and cause not only discomfort, but also potential health issues, especially for the construction workers who are the closest to the critical areas. There is a tolerance for temporary air pollution levels, but controlling this environmental risk is critical for a healthy community.
Operational Controls: When possible, activities that could release high levels of particles into the air should be isolated. Water sprays should be utilized as considered required by the Site Superintendent. The air should be periodically tested and the subcontractor’s equipment should be properly maintained.
List of Resource Requirements: Fit Construction will provide water spray equipment to contribute with dust control inside the premises. In addition, the company will provide masks for their own staff and for visitors. There will be an equipment to measure air pollution levels on site during the entire pre-shell phase.
Monitoring Methods: The level of air pollution will be periodically tested. During the most critical activities, the air should be tested as considered required by the Site Superintendent. The subcontractor’s equipment should be periodically checked for performance.
Responsibilities: Each subcontractor is responsible for the maintenance of their own equipment. The Site Superintendent is in charge of the environmental risk controls on site full time and has the authority to direct subcontractors and to supervise their equipment and work. The Environmental Engineer performs periodical site visits, provides the main guidelines of what should be done in order to control environmental hazards, collects information from the Site Superintendent, documents and generates reports for improvement of the plans.
Training Requirements: The Site Superintendent should receive specific training on how to measure air pollution levels.
Emergency Response: If air pollution levels become critical, the work should be stopped until the Environmental Engineer issues a new plan and considers the conditions safe again.
9.3.2. Waste pollution
Description of the Environmental Aspect & Impact: This hazard concerns pollution on a scale larger then the construction project, but the measures to be taken start on site.
Operational Controls: Selective waste management with the objective of encouraging recycling to the fullest extent.
List of Resource Requirements: A third party company will run the educational workshop about construction waste management on site. Fit Construction will provide the required separate dumpsters to allow for the appropriate process.
Monitoring Methods: Selective dumpsters will be verified at the end of each day.
Responsibilities: Each subcontractor is responsible for the proper selective collection of their own waste. The Site Superintendent is in charge of supervising the subcontractors waste management outcome. Subcontractors are obligated by contract to perform the required waste sort to the penalty of backcharge.
Training Requirements: Fit Construction’s staff and subcontractors will participate on a workshop on site to learn how to properly sort construction waste.
Emergency Response: Not applicable.
9.3.3. Noise Pollution and Vibration
Description of the Environmental Aspect & Impact: As air pollution, noise and vibration are very common construction environmental hazards. Long exposure to loud noise can cause hearing problems to construction workers in the long run. Construction noise and vibration are often motives for community discomfort and consequent disputes.
Operational Controls: Considering Northern Liberties as a densely populated residential area, Fit Construction determines that high noise activities will be strictly restricted to business hours, no exceptions. The loudest activities will be mapped and scheduled in advance and the community will be previously communicated of it. Additionally, subcontractors are required to utilize low noise and vibration equipment, which should be properly maintained.
List of Resource Requirements: Fit Construction will provide signage to be hung on gates to provide information of scheduled loud work activities. An equipment to measure sound intensity will be provided and kept at the site all throughout the construction project.
Monitoring Methods: The Site Superintendent will perform sound intensity measurement as required, as well as the periodic checking of the subcontractor’s equipment maintenance proof.
The Site Superintendent is in charge of the environmental risk controls on site full time and has the authority to direct subcontractors and to supervise their equipment and work. The Environmental Engineer performs periodical site visits, provides the main guidelines of what should be done in order to control environmental hazards, collects information from the Site Superintendent, documents and generates reports for improvement of the plans.
Emergency Response: If construction activities exceed the maximum allowed for that time and day, the work should be stopped.
9.3.4.Traffic Issues
Description of the Environmental Aspect & Impact: The main access to the site is the N 3rd St, a local, fairly busy street which provides access to many residential units nearby. Even though material deliveries and waste pick-ups will occur on N Galloway St, it is undeniable that the 620 N 3rd St project will increase vehicle flow and provoke disruptions in the area, especially when the streets will need to be partially or fully blocked for certain construction activities. That scenario will likely cause traffic and disturbance to the nearby community.
Operational Controls: All work blockages have to be previously scheduled and a specific permit needs to be issued, allowing the work. In that occasion, Fit Construction will notify the community of the upcoming blockage and, during these activities, a traffic controller will work at the site to help orient the traffic. Additional temporary traffic signage will be placed to provide safe directions.
List of Resource Requirements: Fit Construction will provide one staff members to control traffic during the hours when road blockage will happen. Additional traffic signage will be provided. Specific permits will be gathered.
Monitoring Methods: The Site Superintendent will coordinate the traffic controller and stay in touch for updates.
Responsibilities: Each subcontractor is responsible for the maintenance of their own equipment. The Site Superintendent is in charge of the environmental risk controls on site full time and has the authority to direct subcontractors and to supervise their equipment and work. The Environmental Engineer performs periodical site visits, provides the main guidelines of what should be done in order to control environmental hazards, collects information from the Site Superintendent, documents and generates reports for improvement of the plans.
Emergency Response: Not applicable.
9.3.5. Pedestrian Experience Risk
Description of the Environmental Aspect & Impact: During the construction project, the sidewalks adjacent to the site on both N 3rd St and N Galloway St will be exposed to damage due to material and equipment transportation, working in the surrounding areas, etc. Additionally, these sidewalks will need to be blocked to allow for specific construction activities, disturbing pedestrian circulation.
Operational Controls: Additional signage, sheltered walkaway, specific tactile floor as a warning sign for visually disabled people.
List of Resource Requirements: Additional signage, sheltered walkaway, tactile floor.
Monitoring Methods: The Field Engineer will personally verify sidewalk conditions periodically.
Responsibilities: Fit Construction is responsible for the maintenance of the sidewalks. If a subcontractor is responsible for sidewalk damages, they will be backcharged for the repair but the work will be provided by Fit Construction. The Site Superintendent is in charge of the environmental risk controls on site full time and has the authority to direct subcontractors and to supervise their equipment and work. The Environmental Engineer performs periodical site visits, provides the main guidelines of what should be done in order to control environmental hazards, collects information from the Site Superintendent, documents and generates reports for improvement of the plans.
Emergency Response: If the sidewalk presents serious hazards, it should be immediately blocked and urgently repaired. If a pedestrian suffers an accident arisen from unsafe sidewalk conditions, the authorities, Fit Construction insurance and medical assistance should be contacted as required.
SECTION TEN
SITE SPECIFIC QA/QC PLAN
Section Ten is dedicated to the Site Specific Quality Control and Quality Assurance Plan. According to ISO-9000, Quality Control relates to the nature of the final product achieved. Quality Assurance, however, relates to the processes which are utilized to orient the final product towards what it should be.
The QA/QC plan lists the 620 N 3rd St main specs and their specific requirements, actions, rating and environmental controls. Then, the top five quality risks are deeper demonstrated. The standards for the description of each of the five risks are: the description of the issue, their operational controls, the list of the required resources, the monitoring methods, the responsibility ownership, the training requirements and the documentation process.
Through the monitoring of the process of planning for these issues, implementing a plan, placing the plan in action and then analyzing the results Fit Construction is able to provide valuable insight for the next projects, accumulating experience exponentially.