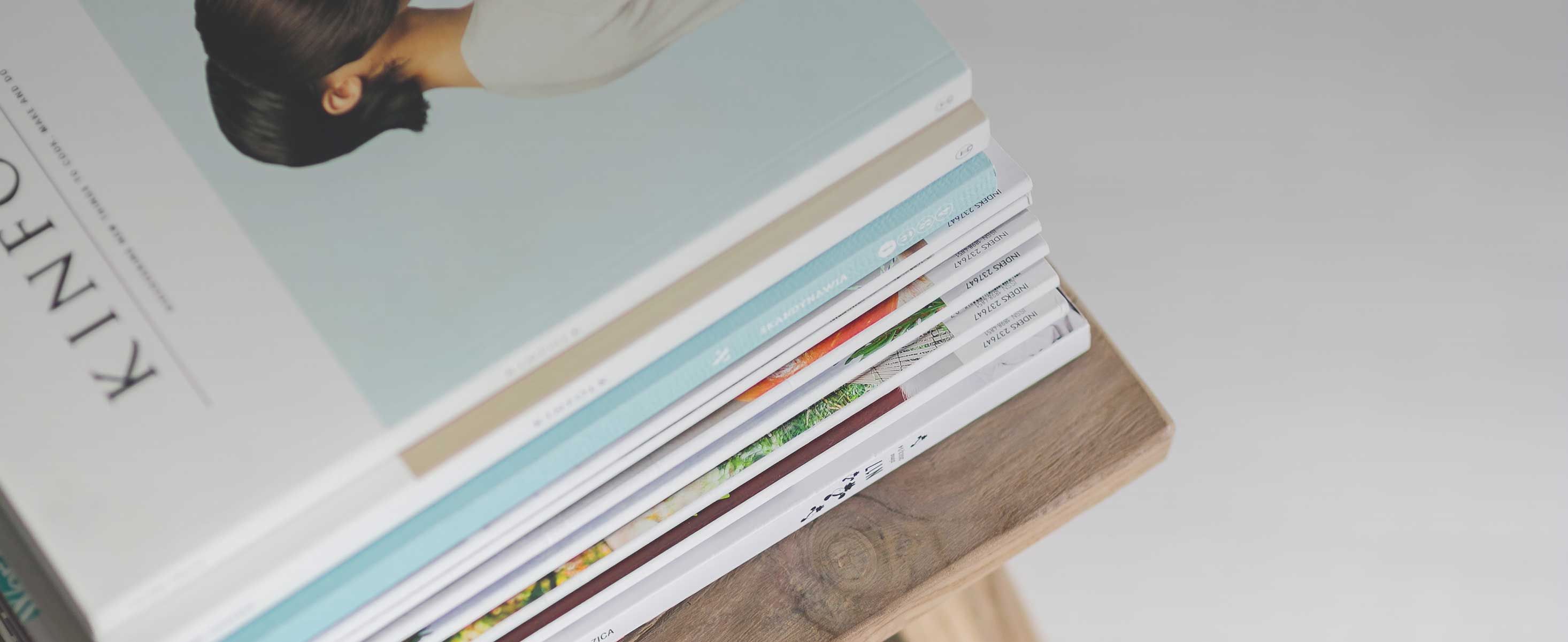
15 minute read
TABLE 22: Contract Quality Requirements - Pages 161 to
Spec Section / Paragraph
8.1. Doors
Advertisement
8.2. Glass and Glazing 8.2. Glass and Glazing 9.1. Gypsum Board Assemblies 9.1. Gypsum Board Assemblies
9.3. Painting
11. Equipment
QA / QC Requirement
Where fire-rated door assemblies are required, provide fire-rated door and frame assemblies that comply with NFPA80 Standard for Fire Doors and Windows and have been tested, listed and labeled in accordance with ASTME 152 Standard Methods of Fire Testes of Door Assemblies. Comply with the recommendations of the Flat Glass Marketing Association (FGMA)Glazing Manual and Sealant Manual except where more stringent requirements are indicated. Where safety glass in required, provide tempered glass cerified by the Safety Glazing Certification Council (SCCC) Gypsum wallboard shall be finished with a Level 5 finish as described by the Gypsum Association, AWCI, Painting and Decorating Contractors of America, and CISCA's recommendation GA-214-96 Install steel framing members to comply with ASTM C754 and C645 requirements that apply to framing installation. Install as recommended in the Gypsum Construction Handbook published by USG. A level 5 paint finish shall be provided as described by the Drywall Finishing Council, Inc Energy rating: Provide Energy Guide labels with energy cost analysis and efficiency information as required by the Federal Trade Commission. -UL Standards: Provide Residential Equipment with AUL Labels.
Action Description
Submittal
Submittal
Submittal
Inspection
Submittal
Inspection
Submittal
Quality Risk Rating (H,M,L) QA / QC Controls
M QA: Subcontractors shall submit shop drawings to Designers for approval. QC: Superintendent on site will inspect work.
L
L
L
M
L
M QA: Subcontractors shall submit shop drawings to Designers for approval. QC: Superintendent on site will inspect work. QA: Subcontractors shall submit shop drawings to Designers for approval. QC: Superintendent on site will inspect work. QA: Subcontractors are contractually obligated to comply with requirements. QC: Superintendent on site will inspect work.
QA: Subcontractors shall submit shop drawings to Designers for approval. QC: Superintendent on site will inspect work. QA: Subcontractors are contractually obligated to comply with requirements. QC: Superintendent on site will inspect work. QA: Subcontractors are contractually obligated to submit documentation atesting all work is in compliance with requirements. QC: Superintendent on site will inspect work.
10.3. Management Plans for the ‘Top Five’ Quality Issues
10.3.1. Concrete
Description of the QA / QC Issue: Concrete work must comply with latest editions of American Concrete Institute ACI 301 ‘Specification for Structural Concrete for Buildings”, ACI 318 “Building Code Requirements for Structural Concrete”, ACI 305 “Hot Weather Concreting” and ACI 306 “Cold Weather Concreting”.
Operational Controls: Subcontractors to submit legally binding report of how the work to be performed in is compliance with requirements. The ACI 301 Standard doesn’t include specific required strength of concrete and types and grades of reinforcing steel and other supplemental requirements, to be defined by Designer. For hot weather and cold weather concreting, per ACI 305 and ACI 306, subcontractors are required to submit production procedures for the Designer’s approval previously to the start of the work.
List of Resource Requirements: Designers to include in specs the required strength of concrete and types and grades of reinforcing steel (ACI 301) and revise subcontractor’s shop drawings.
10.3.2. Steel
Description of the QA / QC Issue: Structural steel must comply with latest editions of American Institute of Steel Construction “AISC Specification for the Design, Fabrication and Erection of Structural Steel for Buildings” and “AISC Code of Standard Practice”.
Operational Controls: Subcontractors to submit legally binding report of how the work to be performed in is compliance with requirements. The “AISC Specification for the Design, Fabrication and Erection of Structural Steel for Buildings” confirms that, while the publication is accurate, specifications and approval from the responsible licensed professional is imperative.
List of Resource Requirements: Designers to include in specs all required information on structural work to be performed and responsibly revise and approve shop drawings. Subcontractors to submit shop drawings. Fit Construction to perform additional revising of shop drawings.
10.3.3. Wood Framing
Description of the QA / QC Issue: Wood framing must comply with 2009 IBC Chapter 23 or National Design Specification for Wood Construction (NDS), latest edition.
Operational Controls: Designer to develop wood framing design in accordance to National Design Specification for Wood Construction (NDS), under penalty of professional liability. Subcontractors to submit legally binding report of how the work to be performed in is compliance with the requirements included in 2009 IBC Chapter 23.
List of Resource Requirements: Subcontractor to provide shop drawings and report in accordance with 2009 IBC Chapter 23, Designer to review and approve. Fit Construction to perform additional revising of shop drawings.
10.3.4. Plumbing
Documents and Records: Documents and Records: Quality Engineer to develop report on work completed, document it to Fit Construction’s records and continual learning process. These records will contribute to shape better quality solutions and to evaluate subcontractor’s performance, influencing future bids.
10.3.5. Mechanical
Operational Controls: According to NFPA, the state of Pennsylvania requires compliance with the International Mechanical Code (IMC), the International Building Code (IBC) and the International Fuel Gas Code (IFGC), all provided by the International Code Council (ICC), in addition of the local codes. Subcontractors to submit legally binding report of how the work to be performed in is compliance with requirements.
SECTION ELEVEN
LEED
Section Eleven’s objective is to provide PRDC with an insight on how and what can be achieve through a LEED Silver certification. It consists of the LEED scorecard with the options considered by Fit Construction. For each of these options, there is a written description of the minimum requirements and the project specific solutions suggested to 620 N 3rd St. The information under this section correlates with the LEED estimate option shown in Section Four for a better holistic understanding of the pros and cons of pursuing a LEED Silver certification.
11.1. Minimum Program Requirements (MPRs)
11.1.1. Location and Transportation
• Surrounding Density and Diverse Uses (5 points): This item refers to the residential and nonresidential separate or combined density values regarding the one quarter of a mile radius concerning the site. Northern Liberties is a highly dense neighborhood with a strong commercial scene, which guarantees that people can move less and utilizing non-motorized means to get to places.
• Access to Quality Transit (5 points): This items refers to the accessibility to multi-modal transportation options from the site, especially those that are non motorized. Being close to
Center City, Northern Liberties has abundant access to public transportation, including buses and subway. In addition, it offers bike lanes and mostly decent sidewalks for those who prefer to walk or bike to and from work.
• Bicycle Facilities (1 point): The original project already includes a storage space on the basement, ideal to store bicycles. Every residential unit has it’s own storage and inside of it both residents’ and visitors’ bikes can be stored. In addition to that, Philadelphia’s shared bicycle system has several stations located close by to the 620 N 3rd St site.
• Reduced Parking Footprint (1 point): This item consists of not exceeding the minimum local code requirements for parking capacity. Despite of the fact that the 620 N 3rd St has nine parking spaces on the first floor, these slots do not belong to the home owners automatically.
Rather, they can be purchased additionally to the homes, which indicates that parking is not offered as included with the residential units.
11.1.2. Sustainable Sites
• Rainwater Management (3 points): This item refers to the commitment of replicating the natural site hydrology process by managing at least 95% of the rainfall poured on the site by using green infrastructure or low impact development. We will address this item by implementing rainwater harvesting, which will consist of a cistern located in the basement that’s used to captured rain water to be later used for gardening purposes. In addition, we will utilize downspout disconnections, which basically consists of a downspout on the building facade that connects the stormwater pipe coming from the roof and flows the water adjacently to a street gutter, where the water can then directly drain into the main stormwater system without running off the streets and collecting pollution. This will only occur on the N
Galloway St facade and if approved by the Building Department.
11.1.3. Water Efficiency
• Outdoor Water Use Reduction ((2 points): This item concerns the reduction or elimination of the necessity for irrigation in outdoor facilities such as planters and lawns. In the 620 N 3Rd
St project, the water utilized to irrigate the planters will be provided by the cistern filled with rainwater, demonstrated under “Rainwater Management” above. Philadelphia is a location where rain is abundant all throughout the year, making this plan actually feasible. In addition to that, highly resilient, low water necessity plants will be placed in the planters in order to assure the cistern will supply enough water for this use. The goal is to eliminate the need for an irrigation system that is connected to the main water supply lines.
• Indoor Water Use Reduction (6 points): This item concerns the reduction of the indoor water consumption. To address this, we have specified high efficiency plumbing fixtures in accordance with the LEED requirement, which can be seen in full in the Appendix of this manual. As an example, we are specifying toilets (water closets) with a maximum of 6 liters per flush and shower heads that use 9.5 liters per minute. See specs in the Appendix.
11.1.4. Energy and Atmosphere
• Enhanced Commissioning (6 points): This item addresses the requirement for a specialized commissioning party which could be an independent consultant, an employee of the owner or a subcontractor. This entity has to have proved experience in commissioning buildings of the same type. The enhanced commissioning consists of 1) reviewing contractor’s submittals; 2) verifying if construction documents have manual requirements and their respective updates and delivery; 3) verifying if construction documents have operator and occupant training guidelines, as well as their effectiveness; 4) verifying periodic testing; 5) reviewing buildings operations after ten months of turnover; 6) establishing a continuous commissioning plan to assure the system’s best performance throughout the time. Fit Construction will hire a specialized third party company to perform these services.
• Optimize Energy Performance (10 points): This item addresses the reduction of energy consumption, beyond the minimum ASHRAE standard requirements, to try to minimize the environmental impact imposed by energy production. We will address this item by adopting several different approaches. Energy Star appliances will be furnished by the Owner. The electrical and mechanical devices such as the Air Handling Units, chillers and water heaters will be highly energy efficient, which, in addition to the Enhanced Commissioning, will provide an optimized system. The building itself will exceed the minimum requirements of insulation, including SunGuard Advanced Architectural Glass glazing, compliant with
ASHRAE Advanced Energy Design Guide, ANSI and IESNA standards, reducing the necessity for artificial heating and cooling. Daylighting strategies and high efficiency artificial lighting will be further described under the “Indoor Environmental Quality” section. Please see specs on this manual’s Appendix.
11.1.5. Materials and Resources
• Building Product Disclosure and Optimization - Sourcing of Raw Materials (2 points): This item concerns the rewarding of the choice for raw materials due to the fact that their life cycles are limited and recognizable. In the 620 N 3rd St project, the entire upper structure and interior
framing is primarily wood and wood based. To achieve this requirement, we will purchase the materials from five different accredited manufacturers who have released verified Corporate Sustainability Reports (CSRs) regarding their raw material supply and production. These manufacturers are also directly responsible for replenishing the resources utilized for their production. Lastly, all wood materials must be certified by the Forest Stewardship Council.
• Construction and Demolition Waste Management (2 points): This item regards the reduction of construction waste, as well as the recycling of that waste. We will address this item by diverting at least 75% of the total construction waste and separating this waste into at least four material categories and send it to recycling. A third party, specialized company will be subcontracted to perform this work. In addition to the recycling, LEAN methods will be incorporated to the construction practices at the 620 N 3rd St to reduce the amount of produced waste overall.
11.1.6. Indoor Environmental Quality
• Interior Lighting (2 points): This item addresses the use of artificial lighting to promote human comfort for occupants, while still achieving low energy consumption in order to do so. For that, we will utilize only LED, high efficiency lighting with a luminance of less than 2,500cd/m2 distributed between different work planes such as the ceiling and walls. Specs for these lighting fixtures and bulbs are attached on the Appendix of this manual.
• Daylight (2 points): This item regards both human comfort and energy efficiency by the utilization of daylighting to promote biophilia by connecting the occupant with the exterior, while reducing the need for electricity to light the interior of the building. Daylighting efficiency was thought throughout the design process and was addressed from the beginning by the presence of large windows on all high occupancy rooms in the building. In addition to that, the glass specified (see specs in Appendix) offers high visual transmittance while still providing efficient insulation.
• Acoustic Performance (1 point): This item has the goal to ensure comfort through acoustic performance, using as a minimum standard the ASHARAE 2011 Applications Handbook. In the 620 N 3rd St project, all walls between units are acoustically insulated, as well as the floors.
The floors also received sound reduction mat layers, in order to minimize sound and vibration travel between residential units.
11.1.7. Innovation
• Brownfield redevelopment (5 points): The innovation subsection regards items that are not listed on the scorecard but are related to sustainability. The 620 N 3rd St site, previously a part of an industrious facility which left the soil contaminated, is now redeveloped into housing and returned to community usage.
• LEED Accredited Professional: All of Fit Construction’s Project Managers are LEED AP.