Accelerating the use of modern methods of construction
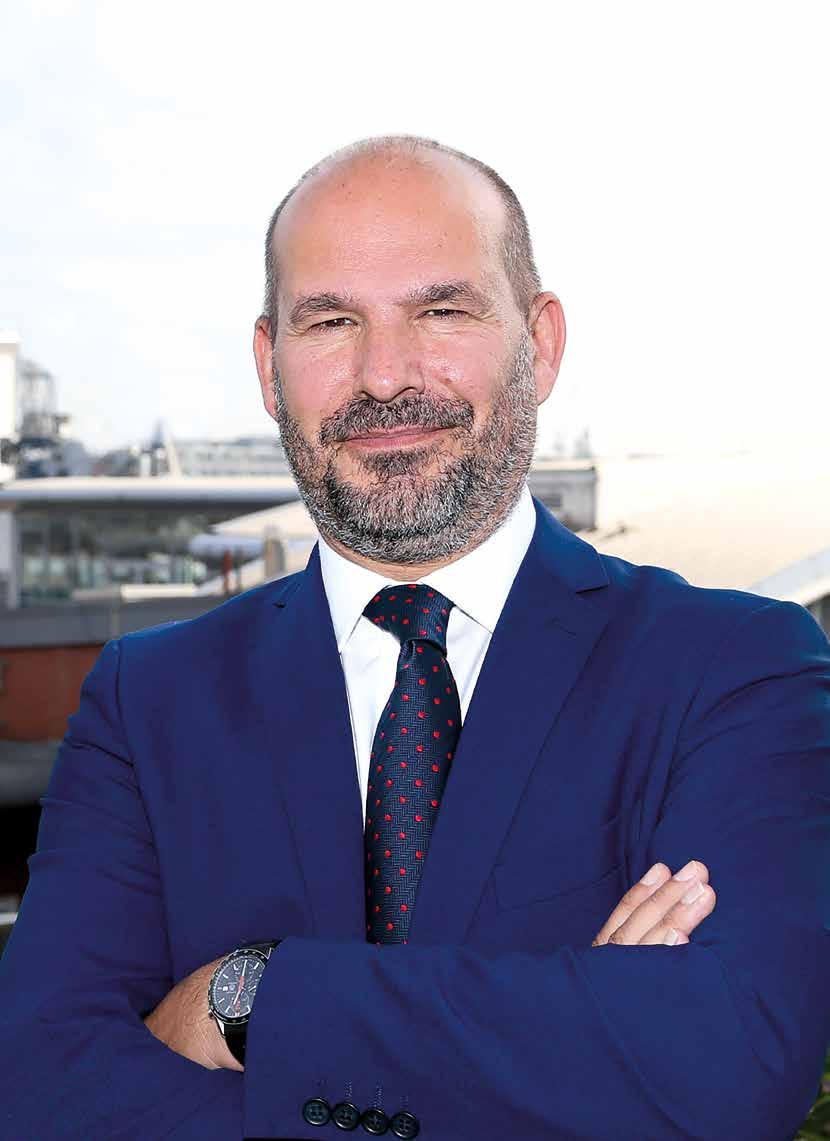
Mandatory whole-life carbon assessment moves one step closer
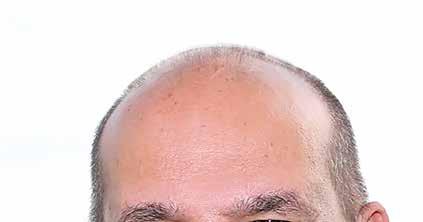
Mandatory whole-life carbon assessment moves one step closer
Firestone roofing, wall and lining systems are becoming Elevate. Our name may be changing, but the same people, products and standards you trust will remain.
Go to HolcimElevate.com for more information.
NEWS
MAGAZINE DIGITAL SOCIAL constructionnews.ie April/May 2023
5 Development levies temporarily waived in bid to boost housing activity
7 Government announces actions to enhance the delivery of NDP projects
8 Planning backlog delays delivery of 65,000 homes
10 Taoiseach turns sod on new €190m Bon Secours Hospital Limerick
10 LDA launches affordable homes in Waterford
11 Key appointments announced for Construct Innovate Technology Centre
12 John Paul Construction appoints Helen Forbes as HR director
12 Aengus Consulting Ltd announces the appointment of two new directors
13 Ken Aherne appointed managing director of Sisk Ireland East
13 Kieran Holohan appointed managing director of Saint-Gobain Ireland
16 Unlocking the value of MMC for Irish construction – Mark Farmer, CEO, Cast Consultancy
22 Respond aims to deliver 1,000 social homes and 250 cost-rental homes annually from the end of 2024 – Parag Joglekar, Director of Investment and Development, Respond
26 “The prohibition on the use of timber for buildings of heights above 10 metres needs to be brought in line with EU building regulations” – John Casey, Managing Director, CORA Consulting Engineers
29 Learnings from Ireland’s growing MMC sector – Dick Clerkin, Managing Director, Clerkin Consulting.
22 INTERVIEW
34 Kingspan Quadcore LEC panels reduce embodied carbon emissions by over 20%
37 Uisce Éireann introduces a new brand identity
37 Construction Professionals Skillnet launches ‘Return with Confidence’ 2023 industry programme
38 SETU launches MSc in Building Regulatory Compliance to ensure safe and sustainable buildings into the future
38 Hardware sector welcomes government vacant homes package
39 Lean solution for duplex construction – IJM Timber Engineering
42 Inaugural MMC Ireland National Conference set for Croke Park in June
43 Construct Innovative aims to build a better construction sector in Ireland
45 Irish Cement celebrates 85 years of making high-quality cement
42 SECTOR FOCUS
46 If a contractor has based its pricing on a client’s consultant designs that are wrong, what can they do? – Henry Hathaway, Principal, Henry Hathaway Solicitors
49 NTA to brief construction sector on sustainable transport plans
49 Allianz Ireland launches Climate Safe Homes initiative to futureproof Irish homes
51 Mandatory whole-life carbon assessment of buildings moves one step closer –Stephen Barrett, Irish Green Building Council
55 Building a Sustainable Future: How the latest UN Climate Report impacts housing delivery
51 SUSTAINABILITY
50 All the latest products and services news
PUBLISHER
Foundation Media Ltd
1 Northumberland Place, Dún Laoghaire, Co Dublin.
Tel: +353 (0)1 677 3157
EDITOR
Robbie Cousins robbie@foundationmedia.ie
DESIGN
Joanne Birmingham
CONTRIBUTORS
Henry Hathaway, Carol Tallon, Stephen Barrett
PRINTER
WG Baird Ltd
ADVERTISING SALES
Joe Connolly joe@foundationmedai.ie
Tel: +353 (0)86 396 6158
ADVERTISING AND PROMOTIONAL OPPORTUNITIES
To advertise in Irish Construction News or on www.constructionnews.ie, or to request a ratecard or details of promotional opportunities, contact Joe Connolly at joe@foundationmedia.ie
CONNECT WITH US ON SOCIAL MEDIA
Twitter: @constructionnews.ie
Linkedin: Constructionnews.ie
Facebook: Constructionnews.ie
COVER IMAGE: MARK FARMER, CEO, CAST CONSULTANCY
SIGN UP FOR OUR E-NEWSLETTER
To get the latest news, articles and offers related to the Irish construction industry to your inbox sign up to our free e-newsletter at www.constructionnews.ie
While every effort has been made to ensure that the information contained in this publication is correct, the publisher cannot not accept responsibility for any errors, omissions or discrepancies. Views expressed in this publication are not necessarily those of the publisher.
The contents of this publication are copyright. No part of this publication may be reproduced or transmitted in any form or by any means mechanical, electronic (including photocopying) or digital without the prior consent of the publisher.
With its latest Housing for All measures, the government aims to increase housing completions to 35,000 units annually, with social housing a key part of that figure. Also, stipulating an increase in the use of off-site manufacturing for public homes should speed up delivery, as well as help address labour challenges and improve quality and efficiency.
One of the most significant barriers to housing roll-out is the general shortage of skilled labour. According to the Central Statistics Office figures, there were 163,200 people employed in construction in Q4 2023, a drop of 7,800 people from the 171,000 employed in the previous quarter.
In this issue of Irish Construction News, we look at some of the solutions being presented to increase output. In addition to looking at the latest government plans to support the industry, we talk to industry experts on the critical issues involved in bringing MMC centre stage for the delivery of new housing and building in a more sustainable way.
Our interviewees in this issue include internationally respected UK MMC champion Mark Farmer, who discusses the lessons learnt since the publication of his 2016 Farmer Report on the survival of the UK construction industry and growth strategies MMC producers should be pursuing.
Former Monaghan footballer turned MMC business consultant Dick Clerkin discusses the barriers MMC producers face and the need for developers and contractors to be more collaborative in their dealings with offsite manufacturers.
Parag Joglekar, Director of Investment and Development, Respond, discusses what Housing for All has meant for the AHB’s
ability to deliver social housing.
Engineer John Casey, founder of CORA Consulting Engineers, explains what needs to happen for timber frame and mass timber to become a solution for delivering more houses and apartments in Ireland.
The recasting of the Energy Performance of Buildings Directive recently received the support of the European Parliament. This means that mandatory whole-life carbon assessment of buildings has moved one step closer. The IGBC’s Stephen Barrett outlines how the construction sector should approach addressing whole-life carbon measurement in a consistent manner.
In Opinion, solicitor Henry Hathaway outlines the principle behind a Deed of Novation and suggests that when it comes to projects where design obligations are being transferred to the contractor, the appropriate instrument must be implemented from the start.
Elsewhere, we have all the latest construction, engineering and sustainability news and analysis.
Please take a moment to scan the QR code below and sign up for our free e-newsletter. And, if there are any issues or stories you would like to see featured in Irish Construction News, email me at robbie@foundationmedia.ie
Regards
Robbie CousinsReduce your lighting costs by up to 80% with
Save time and money by upgrading your old lighting now
Our Lighting Solution is an upgrade to your current lighting system using high quality, energy efficient LEDs. This will guarantee savings on your monthly bill, reduce your energy consumption and improve the lighting in your business. The savings you make finance the project so there is no upfront cost.
Find out more at energia.ie/business/lighting-solutions
The government has agreed on a number of measures under the Housing for All Plan to make it cheaper to build and refurbish homes, speed up home building and drive down building costs across the board.
The Cabinet has signed off on three measures at a cost of €1bn, which are aimed at encouraging the construction of homes in the near term.
These include a 12-month exemption on development levies for new homes; a subvention of up to €150,000 on the cost of constructing cost-rental units, and a €20,000 increase in grants available under the Croi Conaithe scheme to help renovate vacant and derelict homes.
For a 12 month period, developers and builders will not have to pay development levies to build houses and apartments required to connect new homes with roads, water and other services.
The levies are used to connect new homes with roads, water and other services, such as footpaths. The government estimates this will save an average of €12,650 on the cost of building a new home.
This measure comes at a cost of €380m, and builders can only avail of the waived fees if they begin projects this year and finish them by 2025. Government officials hope this supply measure will send a message to the construction industry to activate building permissions.
The government hopes to build between an extra 4,000 to 6,000 apartments under a major €750m subsidy, which will be administered through the Land Development Agency (LDA) and other providers as part of this initiative to complete additional affordable apartments under the Cost Rental system.
The subsidy will see a payment of up to €150,000 per apartment to builders of cost-rental apartments. These homes are delivered by approved housing bodies (AHBs), local authorities and the LDA.
The government has also agreed to increase the value of grants for renovating vacant and derelict homes. The Vacant Property Refurbishment Grant will be increased from €30,000 to €50,000 for vacant properties and from €50,000 to €70,000 for derelict properties, extended to cover houses built up to 2007, and will be available for properties intended for rental as well as owner-occupied.
Speaking at the announcement of the measures, Taoiseach Leo Varadkar said, “Housing for All is working. At the moment, about 400 people are buying their first home every week, which is the highest since the Celtic Tiger. We have the best social housing output since the 1970s. After a slowdown, commencements are bouncing back. And we are likely to meet our overall target again this year. But we need to do more.”
The Minister for Housing, Local Government and Heritage, Darragh O’Brien, said, “The greatest security anyone can have is to own the roof over their heads. That is why increasing home ownership is a priority for the government. We’ve introduced a range of major innovations through Housing for All, including the First Home Scheme, which has granted support to 1,336 buyers during its short existence, and the new – and very popular - vacancy grant. We’ve also made a strong start to delivering affordable housing under Housing for All. This year will see more homes delivered for affordable purchase or rent as the pace of delivery quickens.”
The government has also published a Progress Report on Housing for All for the first three months of 2023, with the year off to a good start and work starting on a record number of homes in the first quarter.
Progress has also continued across a range of important measures, including continued take-up of the First Homes Scheme, LDA grant of planning permission for over 1,100 homes, additional capacity for An Bord Pleanála and €41m in capital funding approved for student accommodation.
The report states that there is a strong pipeline of social and affordable housing, with over 19,000 social homes at various stages of construction and over 2,700 more affordable homes already approved for funding.
The Minister for Public Expenditure, National Development Plan Delivery and Reform, Paschal Donohoe, has announced a package of significant actions to enhance project delivery for the National Development Plan (NDP). The actions include significant changes to reduce the administrative burden in delivering major capital projects.
Under the reforms, the Public Spending Code, which sets out the approvals process for new projects, will be replaced by a set of Infrastructure Guidelines. The effect of this will be to reduce the number of approval stages prior to the implementation of projects from five to three.
The level of cost at which a new proposal is considered a major project is also raised from €100m to €200m. This will allow projects below this limit to proceed more speedily through the appraisal and evaluation process compared to those of greater scale and complexity.
This will allow departments that are responsible, greater freedom to pursue the delivery of their priority projects.
Further changes include additional reforms to the Capital Works Management Framework, which sets out the contracts used for public capital projects.
Minister Donohoe will also take a direct role in overseeing the delivery of the NDP by chairing the Project Ireland 2040 Delivery Board, which will meet on a quarterly basis. Capacity reviews of departments and agencies with significant delivery programmes will be carried out, where appropriate, to ensure that adequate resources for project delivery are in place.
Direct reporting to the government on NDP delivery quarterly throughout 2023 and 2024 will now also take place.
Finally, an independent evaluation of NDP priorities and capacity will be conducted over the coming months.
Commenting on the actions to enhance NDP delivery, Minister Donohoe said, “The government’s €165bn investment through the NDP is already providing homes, schools, and primary healthcare centres across the country. However, no one is any doubt that we need to ensure timely delivery is part of the government’s focus to respond
effectively to the pressing challenges of our time, particularly in areas like housing, health and climate.”
Paul Sheridan, Director of Main Contracting, Construction Industry Federation (CIF), speaking on behalf of the CIF, welcomed the announcement. “The industry needs a visible pipeline of work to support investment in innovation
and talent,” Paul Sheridan commented. “It is critical that the NDP processes under the administrative control of the government are resourced effectively to speed up the commencement of the construction phase on projects, and there are equitable price variation clauses and fair balancing of risk. This will support the construction of the necessary infrastructure to support Housing for All and climate action.”
The following priority actions have been identified for 2023 to support and improve delivery under the NDP, including:
• Action 1: The Public Spending Code will be replaced by a set of Infrastructure Guidelines. The level of cost at which a new proposal is considered a major project is raised from €100m to €200m, and major projects will be subject to review by the Department of Public Expenditure NDP Delivery and Reform (PENDR) and Major Projects Advisory Group (MPAG) at the preliminary business case stage only. All major projects will go to the Cabinet for approval.
• Action 2: The Capital Works Management Framework will continue to work on rebalancing risk in the Public Works Contract while maintaining expenditure control. The focus on lifecycle costs in tender documentation as opposed to construction costs will allow public clients to focus on quality over cheapest bid. Action 3: The Project Ireland 2040 Delivery Board will be reconstituted and be chaired by the Minister for Public Expenditure, NDP Delivery and Reform, and comprise the existing independent members and key secretaries general.
• Action 4: Review of capacity in major departments and agencies to deliver on NDP priorities with a particular focus on significant capital projects to ensure appropriate resourcing to assist delivery.
• Action 5: An independent mid-term evaluation of investment priorities and capacity of the NDP, focusing on the capacity to deliver current government priorities to utilise sectoral capital allocations and to estimate the impact of the NDP on key economic indicators.
• Action 6: Reporting to the government on NDP delivery throughout 2023 and 2024 will take place on a quarterly basis.
New data from Construction Information Services (CIS) has identified that circa 65,000 new residential units are tied up within planning appeals, judicial reviews, and Strategic Housing Development processes.
The Irish planning system has been identified as one of the primary factors in the delay of housing delivery across Ireland. While blame is often directed at individual planning departments and processes, the full scale of the issues plaguing each administrative process hasn’t been understood until now.
New data from Construction Information Services (CIS) identifies that circa 65,000 new residential units are tied up within planning appeals, judicial reviews, and Strategic Housing Development (SHD) processes. The data also identifies the volume of units held in limbo under each administrative process:
• The appeals process: Circa 18,000 awaiting approval
• Judicial review process: Circa 15,000 units in the courts pending a decision
• Strategic Housing Developments (SHD) initiative: Circa 32,000 await an initial decision from An Bord Pleanala (ABP). Planning appeals and judicial reviews are two legal processes that can have a significant impact on the housing market in Ireland.
Planning appeals allow parties to appeal planning decisions made by local authorities or An Bord Pleanála.
CIS analysed over 700 projects on appeal as of March 2023. In total, there are over 18,000 units which are currently on appeal and awaiting a decision. Just over 13,000 of these 18,000 residential units’ appeal decision due date has now passed.
Dublin has the highest number of residential schemes currently on appeal with 151, followed by Cork with 63, and Wicklow with 31. These three counties have the most significant number of total residential units attributed to these appeals, with Dublin leading the way with 7,512 units, followed by Cork with 3,084, and Wicklow with 1,276.
Judicial reviews are legal challenges to decisions made by bodies such as local authorities or government agencies, and residents and local community groups opposed to developments.
These reviews focus on issues such as inadequate infrastructure, environmental concerns, and overdevelopment. In recent years, there has been a significant increase in the number of housing schemes in
Ireland under judicial review.
As of March 2023, there were 105 judicial reviews relating to largescale residential development sites in Ireland. The development sites that have gone through the judicial review process comprise a total of just under 34,000 units and just over 2,000 student bed spaces.
Of the 100 or so judicial reviews, 42% are still ongoing, 5% were won by An Bord Pleanála, 37% were lost or conceded by An Bord Pleanála, and 16% were withdrawn.
The 42% of cases which are currently ongoing equate to close to 15,000 units and over 200 student-bed spaces.
The 5% of cases that were won and upheld by An Bord Pleanála equate to 1,200 units. The 37% of cases that the Bord lost or conceded equate to just under 13,000 units and just over 1,000 student bed spaces. While 16% of judicial reviews that were subsequently withdrawn equated to 5,100 units and just under 700 student bed spaces.
The now-defunct SHD process aimed to expedite the planning process for large-scale housing developments. SHDs include residential projects with 100 or more housing units, mixed-use developments with a majority of residential units, and large-scale student accommodation projects with at least 200 bed spaces.
By mid-March 2023, a total of 488 SHDs had been lodged through the fast-track process, of which 243 applications were granted. There are currently 91 SHD applications awaiting a planning decision from An Bord Pleanála.
These 91 schemes equate to nearly 32,000 residential units, with just over 7,000 houses and just under 25,000 apartments. Of the 91 schemes, 4% were lodged in 2021, 94% in 2022 and 2% in 2023. As expected, Dublin has the highest volume of units, which are awaiting a planning decision, with over 21,000 units still with the Bord. County Clare has the lowest volume of units, which are awaiting a planning decision, with just under 300 units still with the Bord.
As of late March 2023, CIS understood that the Department of Housing had granted An Bord Pleanála permission to dissolve its Strategic Housing Division, the unit within the planning body that oversees the controversial fast-track housing scheme.
+ Innovative, world-class products that enhance performance, speed installation and reduce risk
+ End-to-end drainage solutions, certified to work together
+ Wavin Hep2O is 4x faster to install a joint than copper with an installed cost saving of 30%
+ Wavin AS+ is the world’s best performing and most installed acoustic soil system
Game-changing BIM that + boasts productivity and reduces costs
+ No. 1 commercial partner across Europe
+ Wavin Tigris is Europe’s No. 1 press-fit plumbing system
+ Industry-leading sustainability, unmatched support services and strong supply chain
+ Wavin Compact Soil features tighter waste connections than any other soil system
provided to add to the 96 new beds being provided at UHL.”
Marcus Carne, Regional Director, John Sisk & Son, said, “John Sisk & Son is excited to mark the official ground-breaking of BSHS’s new hospital in Limerick. The project has been an aspiration for clinicians, health planners and local people for many years, and this is another milestone in its delivery. The Sisk team and our local supply chain partners have been actively on site for the last six weeks. We look forward to continuing our valued relationship with BSHS and collaborating on the delivery of a state-of-the-art medical facility for the people of Limerick and the greater mid-west region.”
The Taoiseach, Leo Varadkar, has welcomed the development of a new €190m Bon Secours hospital in Ballysimon, Limerick, to be opened in 2025, which will create 250 new jobs and greatly expand services offered to all patients in the mid-west.
Part of a wider €300m national investment by Bon Secours Health System (BSHS) in line with its 2025 strategic plan, the Limerick hospital, being delivered
by John Sisk & Son, expects to be able to treat more than 50,000 patients annually through a wide range of services and technologically advanced care offered by the new facilities.
Turning the sod for the development in Limerick, the Taoiseach said, “This is an extremely welcome healthcare development for the Limerick and mid-west region. In addition to creating 250 new high-skilled jobs, 150 additional hospital beds are being
Bill Maher, Group Chief Executive, BSHS, added, “This new facility will transform day-care surgical and oncology treatments available in Limerick, provide new services such as general medicine, a new cath lab and cardiology, and widen patient-centred services to a growing local population.”
The hospital is being built on a sustainable site with access to public transport, provision for EV parking and facilities for cyclists. The buildings will be equipped with heat pump technology for heating and cooling, green roof technology and natural daylight and ventilation will be used where appropriate.
The Land Development Agency (LDA) has announced the launch of 92 affordable purchase homes in Summerfields, Kilbarry, Co Waterford, under the Project Tosaigh programme.
The homes are being made available under the Local Authority Affordable Purchase Scheme to eligible buyers in partnership with Waterford City and County Council. The new homes, developed by the Whitebox Group, are located in Elder Walk, Summerfields, Kilbarry, Co Waterford.
Summerfields is Waterford’s newest planned ‘urban village’ and is within walking distance of the city’s main educational and employment centres, SETU and the IDA Industrial Park. The homes include a mix of three- and four-bed semi-detached houses with private gardens set in a well-designed and landscaped estate.
Waterford City and County Council is managing the application process for prospective purchasers. The council will provide an ‘Affordable Dwelling
Contribution’ or equity share arrangement to reduce the upfront purchase price payable by successful applicants. Affordable Housing funding will be available depending on the income of successful applicants, their deposit and their savings. Buyers can avail of support through the Help to Buy scheme.
John Coleman, Chief Executive, LDA, said, “We are delighted to announce the launch of these affordable purchase homes in Kilbarry under the Project Tosaigh initiative.
This scheme, in partnership with Waterford City and County Council, offers eligible buyers a wonderful opportunity to secure their own home at an affordable price.”
Project Tosaigh is the government initiative in which the State steps in to purchase housing in cases where developers have planning permission, but delivery has either not commenced or stalled. Under this scheme, the LDA is due to deliver at least 5,000 homes by 2026.
Paul Keogh has been selected, following an expressions of interest process managed by Enterprise Ireland, as the inaugural Chair of the centre’s steering committee.
Keogh is a business leader with experience spanning a wide range of industries, including entertainment, hospitality, construction equipment, construction development, and healthcare.
He has considerable international experience in the US, the UK, Central Europe, and Australia. He runs his own management consultancy advising large family-owned businesses, many of whom are in the construction sector. He has worked for well-known bluechip brands such as Guinness, Budweiser, JCB and Ballymore.
Colm McHugh joins the Construct Innovate team as Centre Manager following a competitive recruitment process managed by the centre.
McHugh, a chartered mechanical engineer with over 17 years’ national and international experience as an engineering consultant, main contractor, and equipment supplier, has seen the industry from most sides and brings a deep understanding of the needs of stakeholders at all levels. His leadership and strategic and operational experience will be critical in ensuring Construct Innovate will be as impactful as possible in supporting the continued transition of the Irish construction industry into a modern, efficient, and sustainable sector.
Construct Innovate, Ireland’s national research centre for construction technology and innovation, is the newest addition to Enterprise Ireland’s industry-led Technology Centres programme. It was launched by the then Tánaiste Leo Varadkar T.D. in December 2022 with initial funding of €5M over five years. Hosted at the University of Galway, the centre leverages the capabilities, facilities and high levels of expertise available across the consortium partners of Trinity College Dublin, University College Dublin, University College Cork and the Irish Green Building Council.
To ensure that it delivers for housing, the centre will be focused on key industry challenges and innovation in residential construction in its first three years of operation. Construct Innovate will be at the forefront of initiatives to meet the demands of major building and investment programmes as part of Project Ireland 2040 and the National Development Plan 2021-2030; Housing for All; and the Climate Action Plan.
with 1,433 homes in construction
building homes, improving lives
In a move aimed at further strengthening its senior leadership team, John Paul Construction has appointed Helen Forbes as its human resources (HR) director.
In a career that includes senior HR roles with large multinationals such as Aviva Ireland and General Electric (GE), Helen Forbes has established a strong track record for sustaining trusted business relationships. Importantly for John Paul Construction, which has diversity and inclusion at its heart, she is focused on nurturing talent in ways that empower people to play to their strengths.
Commenting on Forbes’ appointment, Liam Kenny, Managing Director, John Paul Construction, said, “I am delighted to welcome Helen to the company. She will work with our senior leaders to deliver on our strategic objectives with respect to our number one asset: Our people. These objectives include enhanced employee engagement and wellbeing initiatives, professional development and performance management and talent attraction and retention in what is a very competitive market. We’re excited to have Helen join us, and we wish her every success.”
Most recently, as people director at Aviva Ireland, Forbes led the company’s People & Culture strategy.
At John Paul Construction, which in 2022 grew its workforce to over 500 employees, she will focus on aligning and consolidating the company’s people development and leadership development practices while equipping the fast-growing workforce with the skills to develop both professionally and personally. The past few years have seen strong growth at the company despite the challenges of the Covid-19 pandemic and, most recently, the war in Ukraine. Liam Kenny attributes much of this success to the company’s robust culture,
which has supported people to remain agile and resilient through a period of significant growth and change.
Commenting on her new role, Helen Forbes said, “I’m so excited to be working with John Paul Construction. This is a company and a leadership team that really understands that people are the most important factor in their success.”
Aengus Consulting Ltd (ACL), founded by P J Rudden in 2020, has announced the appointment of Eleanor Boland (CEng, BA, BAI, Dip Const Law) as Director of Engineering and Carol Connery (BSc, MSc, MCIWM) as Director of Environment.
Rudden, Boland and Connery have many decades of strategic infrastructural and stakeholder experience and have worked together for some 15 years.
Commenting on the appointments and the challenges facing Irish engineering and construction firms, PJ Rubdden,
Managing Director, ACL, said, “Ireland is now challenged to build at greater scale with a lower carbon footprint, using more sustainable materials and producing less waste. In addition, we continue to have significant skill shortages, particularly in the newer digital and modern methods of construction, including off-site manufacturing skills.
“To meet the current significant infrastructural deficit in Ireland, many new projects need to be delivered in the National Development Plan 2021-2030 and the Climate Action Plan 2023. A wider national ambition is Project Ireland 2040 to accommodate another one million people living on our island by 2040.”
ACL’s current portfolio of work is greatly assisted by the three directors’ previous delivery track record. They include national strategic projects in renewable energy, sustainability, circular economy, resource management, stakeholder engagement, infrastructural planning and development across both public and private sectors in Ireland and UK, among their achievements.
John Sisk & Son has announced the appointment of Ken Aherne as Managing Director for its Ireland East business.
Ken Aherne, an engineer, joined Sisk in 1988 and has a wealth of experience across all aspects of its business. He is a strong advocate of Sisk’s company values of Care, Integrity and Excellence and takes pride in supporting his team in developing fulfilling careers and delivering complex construction projects.
Aherne is known to many within the industry and can be relied on for an insightful perspective on subjects relating to the industry, Sisk and people development.
He has played an instrumental role in many projects with Sisk, not least some of its more challenging projects such as Croke Park, Dundrum Town Centre, Grangegorman and Fibonacci Square, as well as developing a suite of projects in Sisk’s healthcare portfolio.
Ken Aherne’s vision and ability to translate strategy into practice leave him well-placed to deliver in this key role for the company.
Speaking about the appointmenta, Steven McGee, COO, Ireland, John Sisk & Son, said, “I offer my congratulations to Ken in achieving this position and look forward to working closely with him to deliver his business unit’s strategic plan for 2023 and beyond. I am particularly pleased that an internal promotion for such an important role demonstrates our commitment to our People & Culture strategic priority.”
Saint-Gobain has announced the appointment of Kieran Holohan as its new managing director as of 01 May. He succeeds Pádraig Barry who has retired.
Kieran Holohan joined Saint-Gobain in 2007 and has spent the past nine years as marketing director for SaintGobain Ireland. Prior to this, he held the positions of marketing manager with Moy Isover and strategy manager for Saint-Gobain Ireland. During this time, he has been instrumental in the development of Saint-Gobain’s Gyproc and Isover businesses and played a pivotal role in the organisation’s wider success. Throughout his career at SaintGobain, Holohan has been an integral part of the leadership team and has amassed extensive experience of the Irish construction market and the competitive dynamics that shape it.
As managing director, he will be responsible for developing and executing business strategies for the Saint-Gobain brands Gyproc and Isover in Ireland. He will oversee the company’s executive team, manage the company’s business
operations, as well as continuing to grow and enhance Saint-Gobain’s brand profile as a leader in the Irish building materials market.
Speaking on his appointment as managing director of Saint-Gobain Ireland, Kieran Holohan commented, “I am delighted to be appointed managing director of Saint-Gobain Ireland. I want to thank Pádraig [Barry] for for the stellar work done under his leadership and the substantial contribution he has made to this organisation during his 16 years of service.
“As a key contributor to the construction of safe and sustainable buildings in Ireland, I have a huge passion for our organisation and its ability to do an enormous power for good. As a worldwide leader in light and sustainable construction, we have a pivotal role to play in building a carbon-neutral economy in Ireland. I look forward to leading our exceptionally talented team to continued success and further growth as we play our part to ensure Irish buildings are efficient, safe, sustainable and great places to live and work.”
Pannually. The Pipelife Eco team works with homeowners, contractors, architects & consulting engineers nationwide in projects ranging from residential homes, offices, hospitals and nursing homes to warehouses, car showrooms and other commercial &
videos the different heating systems in the simplest way possible so homeowners and installers can make the most informed decision about the system that will work best for their needs.
Padjoe Barry, National Sales Manager, commented, “Building a house can be quite daunting. Within that, the heating system chosen for a home is one of the most important investment decisions a homeowner will make. Heating your home represents the largest annual running cost you will have in ensuring your family’s comfort over many years. The heating system you choose and the supplier you choose to provide it are decisions that will impact you for decades.”
The purpose of the website is to give homeowners and installers a point of reference that they can send their customers to learn about the different heating systems available, the pitfalls to watch out for, the quality of all the components used in your heating solution is critical to its long successful operation and the recommended system the Pipelife would recommend.
At Pipelife Eco, we believe in providing our customers with a one-stop shop for complete package solutions, from market-leading products and free initial advice through to bespoke design, final commissioning, and technical support, allowing you to purchase with confidence.
Multiple Package Solutions Design Service
Pipelife has a team of Design Engineers ready to assist in the design, sale and
installation of a variety of water-/energyefficient systems. Our Renewables Division covers every aspect of underfloor heating and integrated renewables and delivers fully designed, energy-efficient systems to a range of Installers, Developers, Builders, Engineers & Architects. We have a proven track record of 20 years of service and commitment to the industry, backed by exceptionally trained staff and dedicated technical backup service.
Whether you’re building a new house, adding an extension or renovating your home, we can help you find the right system for your project
As Underfloor Heating is now the most common method of heating homes in Ireland today, it is important to note that the most critical component of an underfloor heating system is the pipework that will be buried in the concrete floor of your home. Once installed, this pipework will be encased and inaccessible for the lifetime of your home. Any problems associated with this pipework would entail the floor of your home being dug up, causing massive disruption.
It is critical that all components used, but especially the pipework, are top quality and fully backed by reputable manufacturers. Pipelife is the only supplier that manufactures its own specialised underfloor heating pipe in Ireland. We offer our Guaranteed Irish Qual-Pex Plus+ ‘Easy-Lay’ Multilayer Pipe with a 50-year guarantee! We provide full design indemnity insurance on all our heating solution
systems, so you can rest assured our system will deliver on what we promise, providing you with a home heating solution you can rely on for decades to come, safe in the knowledge we will always be there to support you if the need ever arises.
The nationwide Pipelife Eco team of experienced design and technical service engineers always provides complete support to installers to ensure the successful completion of Pipelife ECO projects.
Pipelife is a company with annual revenues of €1bn a year, and we operate in 28 countries and employ 3,000 employees in 28 manufacturing locations. Pipelife is a wholly owned subsidiary of the Wienerberger Group, with group revenues of over €4bn per year and 16,000 employees worldwide.
This long history plus the financial strength of Pipelife is the best guarantee we can offer you that we will be there to support our products over the long lifetimes expected of those products.
For more information and to talk to our team, call us on 021 488 4700 or e-mail us at ireland@pipelife.com and check out our website www.pipelifeeco.ie
Put your trust in Pipelife – 50 years of proud Irish manufacturing & serving the Irish plumbing & Heating industry.
Our Reputation…Your Peace of Mind!
E-mail – Ireland@pipelife.com
Phone - +353 21 4884700
In 2016, Mark Farmer, CEO of UK-based specialist construction consultancy Cast, authored the Farmer Review, an influential independent government review of the UK’s construction labour model, which he entitled ‘Modernise or Die’. In 2019, he was appointed the UK government’s Champion for Modern Methods of Construction in Housebuilding.
Farmer is an internationally-respected commentator on construction technology and how MMC, in particular, can significantly improve productivity and reduce carbon emissions. He has also been a regular contributor to the MMC dialogue in Ireland over the past few years.
In his 2016 review of the UK construction industry, Farmer set out what he saw as the obvious steps that the industry needed to take if it was to remain fit for purpose. It was clear to him that one of the biggest threats to the sector was workforce size and demographics. An ageing and much-
depleted workforce has since been further impacted by the knock-on impacts of Brexit and Covid-19.
In 2016, Farmer saw a huge productivity challenge coming, and he said that the sector needed to look at alternatives to traditional methods of construction to be able to deliver and achieve levels of efficiency not previously considered possible.
Today, Mark Farmer says that progress has been made, but it has been slow.
“Many things have changed in the UK construction sector since 2016, and they continue to change. But the transition from less efficient traditional construction methods has been a slow journey, which I had anticipated would be the case. It was a huge ask to expect the construction industry to change from its established and embedded building practices, but it became clear in time to the sector that it needed to move to more modern ways of building if it was to be productive and sustainable.
The report received a positive reaction from the UK government and the
construction sector.
“Some of my recommendations related to policies and initiatives the government could introduce as a policy maker and as a client of the industry to drive positive change.
“Homebuilding is one area that has benefitted from government programmes. In terms of the actions that have been taken, various initiatives and programmes are now in train, including the UK Affordable Homes Programme 2021-2026, which is linked to the need to use MMC as part of new home building delivery.
“This has been a stimulating activity in the market and has been a catalyst in getting the sector to move to more innovative construction techniques, MMC usage and digital technology,” he adds. “I think what’s really interesting is that the initial period of government-led interventions to try and push the industry to a different place has moved to a new phase where the industry is increasingly recognising the need to be proactive in that transition.
“Irrespective of the government prodding
it towards a different place, we now have contractors, house builders and trade subcontractors in the UK addressing the big challenges, particularly around its workforce.”
The Covid-19 pandemic has also had a significant impact on that journey and was quite a big interruption. Farmer comments that the Covid-19 pandemic resulted in contractors pivoting to more lean practices and rolling out digital construction technologies. Previously bustling sites with trades and construction workers trying to work around each other were replaced with socially-distanced task-at-hand focused operations. Greater efficiency was one of the early gains from the pivot in response to the start of the Covid-19 pandemic.
“In the UK, as in Ireland, we restarted construction quickly with social distancing rules and a new standard operating procedure, and productivity improved.
“Site productivity improved because work was carried out in a more structured, orderly and efficient way. Workers were not crawling all over each other to get in to complete their individual tasks. Better planning and lean became part of the process.
“Unfortunately, post-lockdown, we seem to be back to square one. Evidence suggests that our productivity has tailed off dramatically from where we were preCovid. It’s difficult to work out why this is the case. But anecdotal evidence suggests that construction has a bigger productivity issue now. We need to look at this to regain
momentum, otherwise, the efficiencies temporarily gained during the pandemic will become wasted opportunities.”
Irish construction has also been going through a metamorphosis in recent years, with the Construction Sector Group’s Innovation and Digital Adoption SubGroup bringing together stakeholders from private and public sectors to transform Ireland’s construction sector into a modern, efficient and sustainable industry.
Mark Farmer has been a regular visitor to Ireland since the publication of his UK review and is very much aware of how the sector is tackling the challenge.
Most recently, in February, he attended a forum of industry stakeholders where he had the opportunity to speak with Enterprise Minister Simon Coveney.
“I have been collaborating with the Irish construction sector for the past five or so years and have spoken at a number of conferences, and I value the links I have made.
“Recently, I was at a stakeholder event in Trinity College that looked at how the Housing for All plan can be mobilised through a different approach to housing delivery. I had the pleasure of meeting Minster Coveney, and we discussed the importance of reforming and modernising home-building delivery in the face of the challenges that Ireland is facing. The challenges are very similar to those being faced by the UK sector in relation to workforce productivity, efficiency and
quality issues, and, of course, reducing carbon.
Farmer notes that the Irish government has been very proactive by consulting with the sector on what needs to happen and setting out long terms plans such as Project Ireland 2040 and Housing for All. It has also been supportive in incentivising the sector to modernise.
“The Irish government has changed policies and incentivised change by providing resources such as funding and land. But the industry as a whole must want to change, and this also means changing culture.
“From what I have seen, many developers and contractors are making decisions for their own businesses’ health to pivot towards more modern, innovative construction techniques. But they also need to bring their subcontractors along with them and recognise that if they are using MMC, offsite factories require upfront funding and pipeline surety in order to be viable.
“Government programmes such as Project Ireland 2040 and Housing for All show the Irish government’s determination to drive change, and the industry is also starting to make progress in working through the challenges.”
Mark Farmer is passionate about the benefits that can be gained from developing an indigenous off-site manufacturing industry but adds that it is essential that contractors and developers understand
that manufacturing facilities require a lot of up-front investment and pipeline security to survive and mature.
“MMC is a basic manufacturing model with the fixed costs of a factory, plant and machinery as well as full-time labour. It requires a lot of investment before anything makes it onto the production line.
“This does not sit well with an industry that’s used to a cyclical boom and bust profile of demand and the indeterminate nature of the planning system,” he adds. “Committing resources and investment to assets without necessarily knowing that you have continuity of demand is counter-intuitive.
“To survive and thrive, MMC requires a different business model to traditional construction. Investment has to be linked to diversified end demand. Setting up a factory on a speculative basis and hoping someone will consistently buy your product at a constant rate is an extremely high-risk strategy. Over the past few years, there have been failures in the UK, where people set up factories and haven’t linked investment to surety of demand, and, as a result, they have failed.
He continues. “Many offsite firms are still in start-up mode. It can take years to become a mature business. So, deep pockets are required. There are players in the UK who have made significant investments of tens of
millions of pounds and have still not reached profit-making maturity.”
He says that the business model has to be linked to client investment with sufficient continuous demand to de-risk the investment.
“It should also be noted that creating a mega-factory with centralised production isn’t always necessary. Small is agile and carries less risk.”
Mark Farmer says that vertically integrated delivery is the most insulated business model for an MMC manufacturer. “A developer with land and planning permission has the building and selling/renting element of their business in-house.
“The next stage of taking more control of the business is moving from building to manufacturing the product, creating an end-to-end process. When the developer or builder decides to manufacture their buildings, they are effectively taking a vertically integrated approach, whereby they can also control the quality of production, reduce embodied and operational carbon and align what is required to the end customer.”
He continues, “A manufacturer who sells their product to a third-party house builder,
developer or housing association bears the risk of being a commoditised transaction and may not know where the next job is coming from or at what price. Survival and maturing as a business is about resiliency.
“If a manufacturing business is not part of a vertically integrated chain, they are by necessity marketing and selling their product externally. The best strategy in this scenario is to have a diverse client base with as many clients as possible, preferably with some being counter-cyclical.
“Some manufacturers work across different sectors, such as housing, education, health, etc. This is particularly popular with modular manufacturers whose product is adaptable if economies of scale can be reached. This can be a very resilient business if a good client base is in place.”
He adds that manufacturers can often also provide a rental offer, which ensures there is cash generation in the business. “This has been working particularly well in the UK in the education and health sectors, where rented units garner a monthly income for manufacturers.
“The vertically integrated model, in my experience, tends to be the most resilient, and most successful businesses to date tend to be SMEs, not mega-factories. Larger plants are cash hungry and must produce thousands of units to survive. There is a role
for this centrally-industrialised model in the housebuilding market, but we are not yet at that level of acceptance and maturity, so we need alternative pathways as well.”
Whatever form of MMC is incorporated into a project, there will always be a need for some level of traditional building activity on site, particularly where panels, pods and component sub-assemblies are being brought to site.
Mark Farmer explains, “MMC is nuanced in that there is a hybrid element to it where factory production and traditional building are combined. Panels, pods, and component subassemblies are delivered to site, construction workers prepare the site, install them and build traditionally around them. There will always be some level of modern and traditional crossover.”
Farmer sees a gradual move towards what he calls “pre-manufactured value (PMV). This is the financial proportion of a construction project’s gross construction cost derived through pre-manufacturing.
His consultancy, Cast, has pioneered the use of PMV as a key industry metric for measuring progress towards modernisation. The use of a PMV proxy measure enables construction project teams to adapt designs, supply chain, logistics and site-based construction and assembly choices to deliver improvements against the following criteria:
• Predictability of outcome
• Productivity improvement and waste reduction
• Quality & performance
• On-site delivery speed and site overheads
• Transactional costs
• Community disruption
• Site health and safety risk. He comments that PMV is a strong proxy for multiple industry performance measures, and its use in early target setting and gauging projects is a vital element of driving behavioural change, albeit it should be used
alongside more qualitative measures for the best effect.
Expanding on the establishment of a sustainable MMC sector, Mark Farmer says that clients need to understand that, unlike traditional construction methods, manufacturing plants have upfront costs and need pipeline security to invest in production.
“There are a lot of challenges entering the construction market with a different approach to how you physically design and build your product. The construction industry is notoriously traditional, and anyone doing anything different is up against it.
“Manufacturing models need upfront investment. They need equity or access to funding, which is not always easy, particularly for an SME.
“It is critically important to think about the execution and delivery model. The significant bit in all of this is that you can have a good plan on paper, but I’ve seen many businesses fail because they have a poorly-executed business plan in practice. Either the business model linked to demand has been wrong, or the physical product hasn’t been good enough.
“Then, you have to combine manufacturing technologies and plant and equipment with people. To this end, we have a whole new part of our industry that has not existed up to now. We have had trades – bricklayers, carpenters, electricians, plumbers, and the like. However, apprenticeship models for hybrid trade/manufacturing skills and for outright manufacturing technicians or construction and assembly technicians is a new idea, and governments have a role to play in supporting the creation of these new apprenticeship streams. These apprenticeships then need to give people real qualifications recognised industry-wide so that they can move jobs.
“The employment model for manufacturing is also different to traditional construction. Traditional construction is very much self-employment-led. It’s all about casual labour. To run a factory, you need to have permanently employed staff that are properly trained and have good working conditions. To attract the right people, you must create a better working environment and offer better packages and security.
“Anyone starting out in an MMC business has to think about their workforce. Where are you going to get it from? How are you going to train it? How are you going to keep it? How are you going to attract others to come to your business? And, ultimately, how will you physically manufacture products in a way that is to a quality level that the clients want?
“It’s all common sense, but you’d be surprised how many people don’t think through some of those common steps, those basic steps to running a business. But there are examples of people who have cracked and continue to crack the MMC nut. So it’s not impossible.”
So back to the challenge at hand as Mark Farmer sees it for the construction industry to modernise or die.
“I have travelled a lot over the past few years and observed the appetite for change in construction industries across the world. I have been working with various parties in Ireland and am aware of all the plans and initiatives in place to change how things are done.
“Forward-looking construction sectors are looking to evolve. Ireland has been very innovative in its approach to addressing the challenge, changing house-building and other construction models and developing more integrated supply chain arrangements. Combine this with the government’s interest and desire to change how things are built, particularly in relation to Housing for All, and I think there is a real willingness to do things differently.
“It doesn’t mean the challenges will disappear because they won’t, or that the government can’t do more because it can. But no one wants to repeat the mistakes of the past. Ireland has gone through a lot of boom and bust cycles over the years. The Celtic Tiger experience damaged the property and construction sector, and there has been a real appetite to repair the industry long-term so it can provide proper sustainable, high-quality jobs for people, better wages, better productivity and ultimately cheaper but high-quality buildings. This will benefit everyone economically, and I sense that Ireland is an exciting hotbed of thinking on the subject at this time,” Mark Farmer concludes.
Respond’s recently-appointed Director of Investment and Development, Parag Joglekar, oversees over €1.5bn in housing under construction. Having been with the AHB for over 20 years, he is well acquainted with the complexities of delivering social housing at scale.
Established in 1982, the approved housing body (AHB) Respond has built more than 7,000 units nationwide over the years, providing homes for families and individuals who need them. The organisation also provides community services, such as learning and school-age care, day care for older people, family support, refugee resettlement and family homeless services.
Over the past five years, Respond has commenced 3,347 homes with a value of just over €1.03bn. It currently has 1,433 new homes under construction, with construction schemes ranging in value from €15m to €65m and total programme value in excess of €1.5bn.
As a direct response to Housing for All, the Respond board, in a mid-term review of its strategic plan, set out an increased delivery target. This included aiming to deliver up to 1,000 social homes and 250 cost-rental homes annually from the end of 2024.
Respond’s recently appointed Director of Investment and Development, Parag Joglekar, joined the AHB in 2001. He is a registered architect in Ireland and the UK. He has over 25 years of experience in urban design, private and public housing, regeneration, commercial projects and risk and asset management, in addition to managing design and construction contracts across Ireland, the UK and India.
Joglekar leads Respond’s multidisciplinary development team of 20 construction professionals, responsible for
its social and cost rental homes building programme.
He explains that Respond’s core goal is to create a positive future for people by alleviating poverty and creating vibrant, socially integrated communities.
“We achieve this by providing access to education, childcare, community development programmes, family support, early learning and school-age care, day care for older people, family homeless services and refugee resettlement,” Parag Joglekar comments. “When people receive the keys to their new home from Respond, this marks the start of a life-long relationship that they will have with us. Each of our developments is assigned a tenant relations officer who works with tenants so they become part of a community. The Respond housing team oversees asset management services, addressing maintenance and other related issues.”
Joglekar notes that being a large social housing provider allows the Respond team to get involved in some really innovative work.
“We are, for instance, partnering with the Global Brain Health Institute (GBHI) to deliver what we believe is a first – a Brain Health Village. This is a pilot project from which we hope to use the learnings for all our tenants.”
Parag Joglekar believes that the biggest opportunity to come out of Housing for All for AHBs is the provision of multi-annual
funding with a substantial government investment of €4bn per year until 2030.
“Providing everyone is operating in a stable economic environment, such an investment by the State has the potential to address the core objective of Housing for All.
“As a result of Housing for All, we have an opportunity for innovation and greater collaboration between the private, voluntary and public sectors to deliver real change through planning and procurement reform, addressing the need for multiple models for housing demand-access-affordability, investment in communities, social inclusion, climate agenda, social and physical infrastructure.
“As an AHB, Respond has a central role to play to support the delivery of the Housing for All plan, including the development of cost rental homes.”
Joglekar acknowledges that Housing for All also presents several challenges for AHBs.
“Aside from the essential aspect of financing, the delivery of Housing for All will depend on the commitment and collaboration of its key stakeholders,” he comments. “The ambition of Housing for All means it will require continuous monitoring of its targets. As with any plan, flexibility is important to facilitate agility and adaptability in an ever-changing economic context. This must be supported through legislative and financial interventions, as and when required.”
He continues, “It will be critical to balance the various facets of planning measures,
Respond aims to deliver 1,000 social homes and 250 cost-rental homes annually from the end of 2024
St Doolagh’s Oaks, Malahide Road, Dublin.
development viability and facilitating physical infrastructure. This is the biggest challenge in the midst of high inflation and the overall context we are operating within.”
He believes that aligning objectives between the National Development Plan (NDP) and National Planning Framework (NPF) will also be critical, as the focus should not be on housing delivery and targets alone.
“In Respond, we firmly believe that the success and sustainability of any development depend on access to key social and physical infrastructure and, in particular, transport, utilities, schools, hospitals and local economic and commercial zones, which in turn contribute to the sustainability and climate agenda.”
Parag Joglekar recognises that the private sector, developers and builders have a central role to play in helping deliver various social housing.
Respond’s housing investment programme includes various models for the delivery of social and cost-rental housing. One of these strands is engagement with the private sector to deliver homes.
“We partner with the Irish Home Builders Association (IHBA), Construction Industry Federation (CIF) and other stakeholders, which accounts for just over 80% of our delivery programme,” he explains. “The majority of our delivery is new construction where Respond acquires the site and facilitates financing of construction stage payments in accordance with specified deliverables. This forward funding model has unlocked sites to deliver new housing, which otherwise would have been unviable because of financing costs. Developers and builders submit proposals for new housing schemes in response to our Request for Tenders. This tender process is advertised through the eTenders portal. Following the assessment of proposals, including support from the
relevant local authority in terms of housing need and demand, tenders are put forward for review and approval by the Respond executive, development board subcommittee and finally, our board.
“Once Heads of Terms are issued, we commence contract and funding stages with a view to begin construction and deliver schemes based on agreed programmes.
“In addition to our own technical team, we engage the services of external registered architects, planners, chartered quantity surveyors for cost validation, chartered fire engineers and building surveyors and any other specialist consultants through various project stages.”
Joglekar says that the Capital Advance Leasing Facility (CALF) continues to be the primary source of facilitating the delivery of social housing, with the remainder of funding, in the case of Respond, coming from the Housing Finance Agency plc (HFA).
“Respond recognises the vital role that the HFA plays in facilitating the delivery of new housing for local authorities and AHBs through its lending. CALF is currently undergoing refinements to facilitate some of the current risks and challenges in the market pertaining to viability, such as inflation and interest rate increases.
“96% of Respond’s development pipeline is funded through CALF and 2% through Cost Rental Equity Loans (CRELs), with the remainder funding coming from the HFA.
“This is debt finance over periods ranging from 20 to 30 years. Only 2% of our development pipeline is funded through a grant under the Capital Assistance Scheme (CAS), which facilitates housing for specific tenures such as older persons, persons with disabilities, homelessness, etc.”
Joglekar notes that providing access to public
land is a key aim of Housing for All, but it also needs to be serviced land.
“While it aims to make public land available for building new homes, there are measures set out for zoning of serviced land that allow housing demand and need in the local area to be met. Respond is currently involved in developing projects on land made available through local authorities and the Housing Agency.
“Access to land has either been through local authority Expressions of Interest (EOI) or existing sites in land aggregation schemes where Respond was previously involved.
“Across these sites/land parcels, Respond is working with relevant local authorities to secure planning grants either through a standard planning permission or through a Part VIII planning process.
“Upon securing of planning permission, Respond undertakes further detailed design development, tenders schemes under public works contracts and progresses delivery by securing funding through CALF-PAA, CREL and HFA funding or grant under CAS funding.”
In addition to the current 1,433 homes on various sites, Respond is hoping to commence a number of new schemes throughout 2023 and 2024. Its development team is working to initiate the construction of an additional 1,350 homes with planning in its existing development pipeline.
Housing for All has increased engagement between Respond, developers and builders.
“Respond’s engagement with the private sector – developers/builders and main contractors has increased significantly since the launch of Housing for All,” Joglekar notes. “Our development team is involved in many projects in urban and non-urban areas with developers and builders of varying size and capacity. The projects can range from complex schemes involving varied housing
typologies and tenures to straightforward housing schemes on greenfield or brownfield sites and/or regeneration areas. Respond has also been involved in repurposing existing buildings into new homes.
“We are working on viability assessments on several new schemes nationwide that can potentially deliver social and cost rental homes. All of this work is through the support of local authorities, the Department of Housing, the Housing Agency, HFA, IHBA, CIF and other stakeholders.
“As Respond works to add to the national housing stock, our focus remains on new construction to deliver cost rental and social housing.”
Over the past few years, Parag Joglekar says that he has noted an increased awareness and desire by various stakeholders to engage in modern methods of construction (MMC).
“This has been most notable in urban areas across larger sites involving apartments and, in some instances, standard houses,” he comments. “We have seen early engagement, from planning stage, between developer, design teams and main contractors, as well as specialist subcontractors. This engagement or collaboration focuses on the speed of delivery of new homes, quality control, health and safety and environmental performance.
“Some of the schemes developed for Respond have included the use of prefabricated wall panels, balcony systems for apartments and bathroom pods,” he adds. ”Some traditional housing units we have developed have also been manufactured offsite utilising timber frame. We are currently working on a large apartment scheme where composite architectural wall panels are being used. These wall panels are being designed and manufactured in a coordinated approach using BIM. This requires collaboration between our design team, the main contractor and specialist subcontractors. “In addition, the scheme incorporates bathroom pods, currently in production.”
Joglekar believes that while MMC has many benefits, several challenges exist, including perceptions of build types, the
need for scale/volume, understanding the maintenance of such buildings and contribution to placemaking.
“Procurement methodologies also need to be further refined to allow the adoption of MMC from an early design stage. An appropriate procurement methodology and securing relevant warranties must be facilitators and not hinder adoption of new construction technologies.”
Finally, much has changed in the social housing sustainability space in more recent times. “The Respond development team have a heightened awareness of reducing carbon emissions throughout a building’s life cycle from the initial design to the refurbishment or eventual disposal of a building,” Parag Joglekar explains. “On all of our projects, we now work with designers, contractors and other stakeholders to assess the carbon footprint of our buildings. This is then used to plan an effective reduction strategy through all stages of the building life cycle.”
The sustainability assessments are carried out across the following categories:
• Product stage,
• Construction stage
• Use stage (includes maintenance, repair, refurbishment and replacement),
• End of life stage, and
• Beyond building life cycle (Promoting circular economy).
“As an organisation operating for over 40 years, a significant proportion of Respond’s stock is over 25 years old. It is essential that we maintain and improve these homes so that our tenants can continue to enjoy them.
“Energy efficiency and providing warm and affordable homes continues to be a priority for Respond. In 2022, we invested another €1.5m in our energy retrofit programme, utilising matching funding from the Sustainable Energy Authority Ireland (SEAI), raising the overall investment in the year to over €3m. Our total energy retrofit investment over the past 10 years is in excess of €34m. Improvements in our retrofit programmes included renewable heating, windows, doors and insulation upgrades,” he concludes.
Woodside, Enniskerry Road, Dún Laoghaire-Rathdown.
First purpose-built cost-rental homes
– Woodside, Enniskerry Road, Dún Laoghaire-Rathdown
Respond delivered the first purposebuilt cost-rental homes in Ireland as part of a mixed tenure development on Enniskerry Road in Dún LaoghaireRathdown.
This project resulted from an innovative collaboration between Dún Laoghaire-Rathdown County Council, the Housing Agency, the Housing Finance Agency, the Department of Housing, Planning and Local Government, Respond and Tuath Housing Association. Respond was the main employer of the scheme, and it worked with the stakeholder partners to deliver 155 social and affordable homes and is now managing the homes for tenants, together with Tuath.
The scheme won awards at the National Property Awards 2022 and the Chartered Institute of Housing Working in Partnership Awards 2022.
St Doolagh’s
– St Doolagh’s Oaks, Malahide Road, Dublin
The St Doolagh’s Oaks housing scheme comprises 29 homes in a mix of one-, two- and three-bedroom apartments. The scheme is located close to retail and public facilities, including schools, health services and sports venues. All 59 units have air-to-water heating systems installed along with photovoltaic (PV) panels on the roof, green roof structures and heat recovery heating.
This development is an exemplar scheme showing that sustainability does not have to be beyond the realm of social housing.
Construction Sales
Carlow, Dublin, Kildare, Kilkenny, Laois, Louth, Meath, Monaghan, Offaly, Tipperary, Waterford, Westmeath, Wexford, Wicklow
Shane Leavy 087 091 7184 shane leavy@liffeyd com
Construction Sales Cavan, Clare, Cork, Donegal, Galway, Kerry, Leitrim, Limerick, Longford, Mayo, Roscommon, Sligo
Paul Burke 087 640 0811
paul burke@liffeyd com
Mass timber is a category of engineered wood products typically comprising large, solid wood panels, columns or beams, often manufactured off-site for load-bearing wall, floor, and roof construction. Mass timber includes cross-laminated timber (CLT), naillaminated timber (NLT), dowel-laminated timber (DLT) and glue-laminated timber (glulam or GLT).
Developed in the 1990s, CLT is a popular mass timber material for residential and commercial structures across much of mainland Europe and North America. It comprises several layers of structural grade timber arranged crosswise and glued together.
CLT is a CO2 reservoir and, therefore, a zero-carbon alternative to concrete to form the walls, roofs, floors and ceilings of a building. It is particularly well-suited to multi-storey taller wood construction and can include pre-insulated wall and roof sections.
In Ireland, under current regulations, timber or, more specifically, timber frame and CLT is only used to construct buildings of up to 10 metres in height or three storeys. While planning applications have been made
to use CLT for buildings above 10 metres, it has only featured as an elemental part of non-complex buildings or single-storey extensions.
The Irish Green Building Council (IGBC) construction sector decarbonisation roadmap Building a Zero Carbon Ireland: A Roadmap to decarbonise Ireland’s Built Environment across its Whole Life Cycle calls for greater use of bio-based materials, such as timber, to reduce the embodied carbon emissions of the built environment. More specifically, the roadmap includes a number of recommendations on mass timber and CLT.
These include:
- Reviewing Technical Guidance Document (TGD) Part B (Fire Safety) to reflect international research and developments in mass timber construction and best practice, and:
- Providing financial incentives or directly funding research and production facilities for biobased construction materials (eg, CLT, sheep’s wool, hemp, mycelium, and straw) such as through an accelerator scheme. A review of TGD Part B of the building
John Casey, Managing Director, CORA Consulting Engineers, outlines to ROBBIE COUSINS why he believes a major opportunity to meet housing needs while reducing the embodied carbon of our building stock is being missed due to prohibitions on mass timber construction in Ireland.
“The prohibition on the use of timber for buildings of heights above 10 metres needs to be brought in line with EU building regulations”
regulations was due to complete its public consultation stage at the end of April 2023.
In parallel, much out of the necessity to address the shortfall in housing output as well as meeting commitments as set out in the government’s Climate Action Plan 2023, namely, reduce carbon emissions by 51% by 2030, a number of government ministers and senior civil servants are now considering various additional solutions to meet housing targets and carbon emission reduction goals.
CLT is one of the solutions currently under review. However, a couple of substantial stumbling blocks need to be addressed if the full potential of CLT is to be realised.
John Casey, founder and Managing Director of CORA Consulting Engineers, has a long record of working with timber, steel and concrete as structural elements in buildings. Two of his firm’s most notable projects are the VHI building exoskeleton frame on Abbey Street in Dublin, and the 6,500-sq-foot Barretstown Gang Camp glulam pavilion with dining hall, kitchens, office space and rest-rooms in Co Kildare.
Casey is a member of the IGBC Mass Timber Construction Committee and has been part of recent discussions with various government departments on the impediments to its use in the construction of more complex buildings.
Casey believes that if the way was cleared for CLT to become a mainstream building material in Ireland as it is in Europe, it would have an immediate impact on increasing housing output, particularly apartment construction. It would also dramatically reduce the embodied carbon of our new building stock.
“CLT is a commonly accepted building material in many countries across Europe where it is used to construct buildings of up to and over 10 storeys in height,” John Casey explains.
“In Ireland, off-site construction techniques, such as precast concrete manufacturing, have producers at maximum output at this time. We understand that precast concrete products cannot be supplied quickly enough to meet the needs of the industry. The timber in CLT has sequestered carbon dioxide as it grew, and this is locked into the timber while used as CLT. From examples of buildings both in Europe and North America, it has proven structural alternative to concrete, but Irish regulators have been slow to warm to it.”
In recent discussions with government departments, the issue of requiring an Agrément certificate for CLT has been raised as a stipulation for its use. John Casey does not agree that an Agrément certificate is necessary. He believes that the material just
needs to be CE marked.
“CE marking indicates that a product has been assessed in accordance with a European technical assessment, which enables a declaration of performance to be drawn up and the CE mark affixed by the manufacturer. It is required for products manufactured in Europe and other parts of the world that are then marketed in the EU.”
Agrément certification is designed specifically for new building materials, products and processes in Ireland that do not yet have a long history of use and for which published national standards do not yet exist. NSAI Agrément assesses, specifies testing, and, where appropriate, issues Agrément certificates for such products.
“CLT has been in use since the early 1990s,” Casey explains. There are 71 largescale CLT manufacturing facilities operating across Europe, requiring investments of up to €50m to build. It is an established building system for all types of buildings, including taller buildings in many EU countries.
“Despite this, civil servants and fire officers involved in construction regulation in Ireland refer to CLT as an innovative product. To get Agrément certification, a CLT manufacturer would have to submit their product to the NSAI for Agrément assessment, which could take up to a year or more with a significant costs attached. But, then, at the end of this process, if successful, the certificate will permit access to the Irish market, where building regulations don’t allow timber buildings over 10 metres.
“This process would have to be undertaken separately by each manufacturer. So, no manufacturer will spend money on
the assessment because even if they get an Agrément certificate, they will only have access to a market where their product can be used up to three stories.”
“There are a number of Irish companies supplying mass timber products, including CLT, which is imported, but not at a scale that would be required to deliver large-scale housing.
“It should be noted that a number of the international developers operating in Ireland are experienced in building with CLT in other parts of Europe and North America and would have a ready supply chain to deliver the product. It should also be noted that there is a ready supply of raw material if a manufacturing plant were ever to be constructed, as the timber grown in Ireland is ideal for the production of CLT.
He continues, “Timber frame construction has been a mainstay of Irish construction for many years. Irish Standard IS EN 440 covers the design, manufacture, supply and installation and certification of timber frame buildings. It can comprise many parts, including insulation, membranes, etc. These are put together in a factory and brought to site on the back of a truck, then put together, and the entire assembly is certified.
“Mass timber is a simpler product. It is a direct zero-carbon replacement for traditional concrete, blockwork and precast concrete. You replace the concrete elements with mass timber. All other elements, such as insulation, membranes, brick, etc, are separate and are incorporated afterwards.”
TGD B has been under review for revision for the past two years, and a public consultation process concludes at the end of April.
“The revised draft for TGD B hasn’t changed very much in terms of mass timber,” John Casey explains. “One of the proposed clauses advises that no combustible material shall be used in compartment floors above 11 metres in height, previously 10 metres. That means that any building above three storeys still can’t use timber or other mass timber elements.
“But other clauses in the fire regulations allow a ‘prescriptive approach’ to be taken. This means that if a fire consultant could demonstrate how the building would behave in a fire and demonstrate that it would pass all the necessary criteria, it would be acceptable for a fire officer to grant a fire certificate for the proposed building. But, to date, no fire officer has granted a fire certificate to any timber building above 10
metres because they are holding fast on the height clause.
“Anyone who submits a fire certificate application for a mass timber building in Ireland is going to struggle to receive a grant because there is little or no relevant experience with the product, and fire officers remain conservative in their thinking on this.”
He adds, “The restrictions on mass timber usage are due to the interpretation of regulations. This means despite the knowhow and supply chain being in place, we are missing out on a huge opportunity with mass timber construction.”
Through the IGBC Mass Timber Construction Committee, John Casey and several like-minded technical experts have combined their resources with the IGBC to engage with the government on the benefits of mass timber and CLT.
“A small group of like-minded people for the industry came together to look at the barriers to CLT in Ireland and decided that
the best route forward was to engage with the government under the auspices of IGBC, providing IGBC with technical back-up in any meetings that took place.”
This has led to a number of high-level meetings with ministers and senior civil servants to see if there is a way to break the impasse on the use of the material. Casey says that the Agrément certification requirement is a massive impediment to opening up the market. Also, Ireland needs to address the prohibition of the use of timber for buildings over three storeys.
“If the requirement for Agrément certification is confirmed, there will be no interest among regulators in allowing CLT to be used for the construction, and nothing will change. The longer this issue is not addressed, the harder it will be to achieve housing output and carbon reduction targets.
“The prohibition on the use of timber for buildings of heights above 10 metres also needs to be brought in line with EU building regulations.”
John Casey has been actively involved in trying to open up the CLT market in Ireland for the past five years. And while it is a slow process, he says that in the past few months, the mass timber and CLT movement is gaining momentum.
“Mass timber is a sustainable and highly efficient building material. It is an established building system, and we have the technical skills to build with it.
“We have finally started to address the issues around its usage, and I am optimistic that we will soon reach a stage where civil servants and fire officers who make the decisions about its usage will have greater confidence about its many merits,” he concludes.
John Casey founded CORA in 2006. The consultancy has a staff of 28. CORA promotes a culture of creativity, innovation and quality in the firm, always striving to produce a better, more innovative and economical structural solution.
Low-carbon design solutions are an integral part of its service offering, and it has enabled many clients to achieve substantial carbon reductions in their developments. One project, currently on site, is reusing original steelwork from a building for a new extension.
Its portfolio includes the VHI extension on Abbey Street, Dublin; Barretstown Camp Pavilion, Co Kildare; Saint Luke’s Church office conversion, Dublin; West Cork Arts Centre, Skibbereen; and Windmill Quarter development in Dublin.
Its recent clients include Google, Facebook and DAA, as well as several blue-chip property development companies.
From brilliant manoeuvres on the pitch to smart plays on the manufacturing floor, former Monaghan football stalwart Dick Clerkin is a consummate strategist. The specialist management consultant discusses the changes needed for Irish offsite manufacturers to achieve their full potential.
Dick Clerkin and his associates at Clerkin Consulting work with clients in the construction products manufacturing and modern methods of construction (MMC) industries, driving productivity, profitability and sustainability improvements. He believes that when it comes to identifying the cause - or indeed causes - of profit or productivity losses within an MMC business, people tend to be both the problem and the solution.
Over a 21-year career, with a background in process engineering and an MSc in Business and Management, Clerkin has worked with many leading brands in the construction products manufacturing and MCC industries across Ireland and the UK. Having faced recurring productivity challenges, he and his team have developed a number of effective frameworks that can first identify and then drive sustainable improvements in their clients’ businesses.
“We are finding a common trend of problems that in one way is good because it allows us to quickly identify them,” Dick Clerkin comments. “We don’t have to spend needless time and potential costs
doing lengthy diagnostics. We can get in quickly and have a good sense of what will get a quick return. It is about quickly identifying the main constraints in their operations. Very often, it doesn’t require a huge amount of investment; but it does require a change in mindset. Traditional thinking is not going to win in the emerging MMC sector.”
The transition from traditional construction to offsite manufacturing and other MMC is relatively new. It is still very much an emerging industry in Ireland, so even the leaders are learning as they grow.
“Everyone is talking about digitalisation, industrialisation, robotics, all the hot topics,” he continues. “But the reality on the ground is that most companies are failing to optimise their business with the assets and resources they already have. There can be many reasons for this, but it generally comes back to the people. From the leadership team and frontline management right through to operatives on the shop floor people, if people are not working at the best level they can, there is an opportunity to unlock a quick upturn in the business of anywhere between 15 to 20% productivity just by getting people working better or working smarter. Again, that doesn’t require a huge level of investment. But it does require a commitment from the senior leaders to recognise the value of their people.”
Dick Clerkin believes that one of the biggest challenges is facility owners not necessarily seeing their people as assets. In his experience, people are sometimes seen as commodities, causing facility operators to rely too heavily on agency workers to scale up or down the workforce as and when needed.
However, he argues that, unlike more established industries, these MMC businesses are simply not mature enough, nor do they have the established and stable systems and processes in place to bring people in or to lose people, with such regularity, without a significant impact on productivity.
He is adamant that the delivery of offsite and other MMC outputs is not low-skilled work; it requires semi-skilled or skilled/trained people. “This thinking is important to reducing the currently high level of turnover at shopfloor level, which results in huge losses for a business and gives rise to quality control issues.”
As the industry is well aware, quality defects have a massive cost on a business. Unlike traditional manufacturing, delivering commoditytype small units, MMC facilities are making large, expensive frames and pieces/packs, so the cost of on-site reworks required due to quality issues can be excessive and very often can eliminate the margin out of a complete job.
“Too many companies are only slowly starting to realise the importance of having stable, well-trained teams in place, and then committing to their future through more robust onboarding, training and development, proper remuneration, with better frontline management on the shop floor. Committing to your people is to invest in them in much the same way a company might invest in a
new factory or automation. Investing in your people and the systems to train and retain them is critical for the industry. The companies we have seen do this unlock good, quick returns in terms of productivity and overall profitability.”
He emphasises the need for a good onboarding or induction process.
“Every facility needs to have a good frontline manager to guide new team members and to ensure they have the necessary tools and training on the standard operating procedure, delivered clearly and concisely, through multiple languages, where appropriate.
He cites a company’s inability to communicate with new hires as a significant barrier. He surmises that this is a symptom of the early stage of maturity of Ireland’s offsite manufacturing sector. “Most MMC companies are not yet at this level. They are deeply focused on their product, which is understandable. So, while they have the capacity to make a really good product, they may not have the stable systems and structures in place to do it repeatedly to a consistently high level of quality and at scale.”
Dick Clerkin says that MMC in Ireland is facing an identity crisis right now in the eyes of the end-user or buyers.
He explains, “It is seen as a solution that can be rapidly rolled out for temporary housing in response to the refugee housing shortage and to the broader homeless crisis, which gives the impression that it is a lower-quality product when the very opposite is true.”
So, does offsite manufacturing automatically lead to better buildings?
He continues, “That depends on what you assign value to. If it is better because you can make it and install it on-site in less time and at less cost, then it’s better because MMC can do that.
“It is also sustainable in terms of energy efficiency, from production right through to building performance over its lifetime.
“While some people value more traditionally built buildings, that is their perspective. It is naïve for anyone involved in MMC to think they can shout down traditional methods to lift the profile of their own product or system.
“The reality is that the future will see a combination of building solutions in the marketplace, all sharing a common goal. All
indicators point towards construction demand significantly outstripping what traditional build methods can deliver. So, MMC simply has to grow its market share in order to meet society’s growing needs. At the end of the day, value should be judged and experienced by the client and by the end user. MMC can deliver safe and sustainable buildings at scale, and I believe this is an outstanding proposition.”
Reflecting on his everyday work, Dick Clerkin paints a picture of two worlds colliding; the traditional construction industry made up of people and leaders who have been in that game for a long time, and on the other side, manufacturing.
“Offsite and other MMC products represent a meeting in the middle. Bringing these two distinct worlds, or industries, together brings a necessary element of conflict – healthy tension.
“For many projects, there is a traditional procurer who might not fully understand benefits and key frameworks that manufacturing can deliver, or, equally, people who are coming from a solid manufacturing background might not understand or appreciate the nuances of construction.
According to Clerkin, “For MMC to thrive, there needs to be a meeting in the middle. For example, when we, as consultants, go into an established manufacturing facility, there are robust frameworks to enable benchmarking based on a number of KPIs and triggers across a number of areas of the business. Our associates can put it on a sliding scale, whereby the performance generally tallies with that across health and safety, profitability, quality defects, whatever it may be; one follows the same.
“Traditional thinking is not going to win in the emerging MMC sector.”
“In MMC facilities, particularly those only recently established, their compliance systems and standards with respect to health and safety, and quality would often be towards the lower end of that scale when benchmarked against manufacturing best practices. What can be referred to as an ‘agricultural’ approach to health and safety, stemming from the prevailing onsite construction culture, is not sustainable in a factory environment.
“The same can be said for quality, as the cost of retrofit and repairs on site can be significant in MMC. These are often under-appreciated risks. In my experience, a safe plant is an efficient plant. A safe working environment is more likely to be well organised and well laid out in terms of equipment locations, flow, materials, and vehiclepedestrian interaction, along with a more engaged and committed workforce who recognise the efforts and investment being made towards their well-being.”
He adds, “Another indicator of sector maturity is how well MMC operators know their numbers. Too often, we find that operators have no idea how much it costs them to make a frame or to make a finished pack. They know the individual price of the components and raw materials and their selling price to the customer, but very often, they lack the cost measurement and tracking systems during the manufacturing and dispatch phases. They don’t know in real-time how much they are spending on labour, materials, machinery, energy, etc, to ensure that they maintain a healthy margin for their output. This is a key challenge that we are helping our clients in the sector address.”
In recent weeks, the government acknowledged a shortfall in housing exceeding a quarter of a million homes, and the only solution is to build more homes. The traditional construction industry does not have the capacity to ramp up delivery by 250,000+. Clerkin points out that MMC has a critical and, frankly, urgent role to play in addressing this challenge.
“This is a huge opportunity for the sector,” he explains. “But there are many shared challenges and obstacles to MMC delivery at scale. Overcoming these obstacles will require public sector intervention and a mindset shift by the private sector.
“The State needs to figure out how to support the people, the businesses, and the institutions that can deliver housing. There is work to be done on the funding models to ensure the viability of building. One of the big risks that MMC has over traditional construction sites is the capital cost. So, that’s the capital cost of the facility, cost of equipment, cranage, forklifts, automated lanes, and pre-bought raw materials such as steel coils and or timber, insulations etc. Both primary contractors and State agencies need to solve that problem because MMC companies will struggle to sustain that level of cost and risk alone.”
A recently published study in the UK highlighted the number of MMC companies that have gone out of business due to their inability to withstand such losses without a secure pipeline of work and a more sustainable funding model.
Dick Clerkin cites the example of an Irish MMC manufacturing client with a full order book that achieved 20% productivity through efficiency measures they implemented.
“That additional capacity was then built into the company’s commercial forecasts, which led to a significant order with a large home builder. Due to market and price volatility, this large client pushed out site delivery schedules by six months. This left a hole in the factory’s order book that couldn’t be filled in the short term, with plant, equipment and labour costs all needing to be maintained throughout. While in the traditional construction world, a contractor could take the team off-site and not buy the building materials until needed, the offsite construction manufacturer incurs the cost in terms of their reduced factory output levels. This is not just a problem for the facility operator, in real terms, this is a problem for the entire industry and the broader economy. MMC operators cannot be left to shoulder this burden. State policies and private sector project owners need to educate themselves on the realities of MMC delivery and work towards a marketplace with sustainable and reliable pipelines.
“Private entities will build when it is most profitable to do so, and that is their responsibility to shareholders. The State does not have the same modus operandi, and they can play a huge role in ensuring a steady pipeline of projects for MMC suppliers to both invest towards and successfully deliver. Doing so will both lift and sustain our overall house-building capacity this country urgently requires to meet the needs of its growing population.”
Ireland’s MMC sector is still an emerging industry and, as such, is facing various challenges, from a lack of investment in people to funding models and sustainable pipelines. However, according to Dick Clerkin, there is hope.
“As more players enter the market, there is an opportunity to learn from each other and to share best practices. The key to success lies in recognising the value of people, investing in stable systems, and committing to their future.
“With a mindset shift, public sector intervention, and private sector support, MMC can deliver safe, sustainable, and cost-effective buildings at scale. Let us redraw the blueprint for the factory, keep the MMC pipeline flowing and growing, and build the homes that Ireland urgently needs,” Dick Clerkin concludes.
“Delivering MMC is not lowskilled work. Too often, MMC operators view their people as commodities, rather than assets that, with investment, will drive value.”
360 Degree Underwriting adds value to the construction and development space by consistently delivering bespoke quality insurance solutions to developers and contractors.
Significant construction cost inflation in recent years, combined with the growth in high-density construction, has created greater demand for comprehensive “A-rated” insurance capacity on large-scale capital projects in the Irish market.
360 Degree Underwriting dac (360) is a managing general agent (MGA) specialising in the provision of fully rounded insurance solutions.
Operating in the construction space since 2019, 360 was established in direct response to demands from its broker partners for better service and better products -
backed up by empowered underwriters.
The joint managing directors of the company are Paul Sherry and Tommy Byrne. Each has over 25 years of experience nationally and internationally in the construction sector.
Paul Sherry comments, “At 360, we are well positioned to meet our clients’ risk management needs. Our experience has shown that developers, lenders, investors and future purchasers are heavily focused on ensuring that their assets are adequately protected now and in the future. Because our capacity is A-rated, and our claims service is managed locally in ROI, we are well positioned to assist. We can also present Preventative Maintenance options to clients to protect their assets from Water Damage losses post PC – the introduction of leak detection systems can attract premium and T&C concessions during the build phase and on into operational insurances, delivering premium savings year on year.”
360 PRODUCTS
360 offers protection with capacity levels of up to €250m in respect of its core products.
360’s core construction insurance solutions include:
• Commercial Latent Defects Insurance –10/12 Year Structural Warranty
• Residential Latent Defects Insurance –10/12 Year Structural Warranty
• Mechanical and Electrical Defects Insurance – 10/12 Year M&E Warranty
• Construction Project Insurance – OCIP Insurance (Contractors ‘All Risks’, Delay in Start Up, Public Liability and NonNegligence Insurance)
360 Degree Underwriting, in partnership with its A-rated Insurer partners, offers the above insurance solutions to developers and builders of:
360 Degree Underwriting gets your project covered quickly and with minimal fuss
• Apartment and office blocks
• Mixed-use commercial developments
• Warehousing/logistics centres
• Pharmaceutical developments
• Data centres
• Mixed PDH/apartment block residential schemes
• Hotels
• Hospitals
360 products are approved by leading lender and investor entities, law firms and local and international brokers.
Citing an example of a growing side of the business, Tommy Byrne explains that the latent defects/warranty business in Ireland has seen a dramatic uptake in recent years.
“Clients are more aware than ever of the need to future-proof their investment to meet the demands of future purchasers and prospective tenants – many of whom expect a structural warranty on the completed building as standard now. With flexible solutions and a modest deposit premium option upfront, clients are choosing to activate warranties to maintain the option at PC without incurring full premium outlay initially.”
Over the past four years, 360 has been entrusted with insuring over €4bn of construction assets by such marquee clients as Cairn Homes, Marlet Property Group, Lioncor Developments Limited, Hibernia
Commercial Latent Defects Insurance – 10/12
Year Structural Warranty
• €250m+ capacity
• Structural Defects
• Ingress of Water
• Loss of Rental Income
Real Estate Group, Bartra, Ardstone and Ballymore Group.
360 offers a tailoring service, striving to customise insurance solutions that meet the needs of project developers, financiers and legal teams first time, every time.
Paul Sherry adds, “Much time can be lost debating trivia, so our focus is on providing proven solutions to satisfy the respective interests of the parties and progress to contract signing and project commencement at the earliest possible opportunity. If a request can be facilitated, it will be.”
The claims function is key to 360’s ongoing successful relationship with repeat clients.
Tommy Byrne explains, “The high standards we demand of ourselves ensures that the claims function is also managed to the highest of standards. With the agreement of our capacity providers, we outsource the claims function to provide a comprehensive claims-handling service, on the ground and to site locally, within 24 hours of incident notification – 365 days a year.”
360 has access to cost-effective leak detection solutions with both new build and minimally invasive retrofit options available. Water
Residential Latent Defects Insurance – 10/12
Year Structural Warranty
• €200m+ capacity
• Structural IDI for Apartment Blocks with associated PDH or Duplex Units
• Minimum SI €20m
• Ratio of PDH to Apartment Block Values must be < 25% of the Total Sum Insured
damage losses can be costly and recurring. Our solution provider can install ‘plug and play’ kit (without a need for extensive opening up works) to monitor and report on leaks as they occur in real time, enabling the asset owner to protect their interests quickly before serious costs accrue. The introduction of water leak detection systems can attract premium and T&C concessions during the build phase and post PC for each insurance renewal thereafter, offering a return on investment and peace of mind in protecting assets from serious water damage disruption.
Mindful of onerous contractual conditions and the construction regulatory environment imposed by BCAR and the HSA, the 360 risk engineering approach is a collaborative one. Its team of professional engineers and surveyors work with its broker partners and clients to identify and manage risk in a manner designed not to stifle progress with the works schedule but rather to support on-time delivery of that schedule and to help protect the asset – both during the build phase and on into operational ownership. Working closely with the Assigned Certifier, Design Certifier and Professional Team, 360 risk engineering is a value-added service that its partners appreciate.
To learn more about 360 Degree Underwriting, visit www.360uw.ie or scan the QR code
Alternatively, contact your broker or get in touch directly and the 360 team can put you in touch with an approved construction broker to manage your placement.
Machinery Inherent Defects Insurance – 10/12
Year M&E Warranty
• Damage caused by defects which result from poor design, materials and workmanship, which manifest in the machinery
• Limits of up to €15m “any one loss”
• Loss of Rental Income –max indemnity period 36 months
Construction Project Insurance – OCIP ‘Wrap Up’ Insurance (Contractors ‘All Risks’, Delay in Start Up, Public Liability and NonNegligence Insurance)
• €250m+ capacity
• Contractors ‘All Risks’/ Erection ‘All Risks’
• Delay in Start Up / Advanced Loss of Profits Insurance
• Public/Products Liability
– limits of up to €75m available
• Non-Negligence – limit of up to €75m available
Kingspan’s QuadCore LEC product range, launched earlier this year, is the next generation in Quadcore sustainable technology.
QuadCore LEC has been developed specifically to help reduce the carbon footprint of buildings.
Utilising comparative life cycle assessment (LCA) data to the EN15804-A2 standard, Kingspan’s new QuadCore LEC (lower embodied carbon) breakthrough insulated panel technology demonstrates a 21% reduction in embodied carbon in modules A1-A3 (product stage) for QuadCore AWP in 100mm thickness.
The original QuadCore product is one of the highest-performing insulation technologies in terms of thermal efficiency, which can enable higher energy and carbon savings through the operational life of a building.
Quadcore LEC takes the product to a new sustainability level and, according to Kingspan Insulated Panels Divisional Head of Sustainability Lizzie Young, is the next stage in Kingspan’s journey to lowering the embodied carbon of its products.
She explains, “Quadcore LEC is a lower embodied carbon variation of our Quadcore product. The range currently includes the Quadcore KS1000RW LEC Wall Panel, Quadcore AWP LEC Wall Panel, QuadCore KS1000RW LEC Roof Panel and the Quadcore Coldstore LEC Panel.
“According to recent research, 15% of the upfront carbon of a building is in its facade or its envelope. The Quadcore AWP LEC Wall Panel, for instance, shows a 21% reduction in LCA modules A1 – A3 (product stage) when compared to our original Quadcore AWP LCA to the EN15804-A2 standard for a 100mm thickness. So, this
one-fifth reduction in envelope carbon emissions, across these modules by using LEC wall panels can offer substantial overall carbon reduction at a total building level.”
The development of the Quadcore and Quadcore LEC range has come about as a result of Kingspan’s Planet Passionate programme. Through Planet Passionate, Kingspan works with its supply chain, clients and other construction industry stakeholders to integrate whole life thinking into all aspects of construction that its operations touch.
In 2019, it opened its IKON Innovation Centre in Kingscourt, Co Cavan. The goal of IKON is to research and develop advanced materials and digital technologies that will achieve a net-zero-emissions future, with any products developed in the centre being designed to ensure higher lifetime energy and carbon savings.
In 2022, Kingspan Limited was certified ‘Gold’ under Ecovadis, a sustainability management platform that helps it monitor and track its suppliers’ ESG performance, promote transparency, reduce risk and identify areas for improvement.
Lizzie Young explains that the next steps, through quarterly supplier briefings at IKON, is to onboard suppliers across the Kingspan group onto Ecovadis, a project that began in 2021.
“This ensures that suppliers can align their targets with our targets and more broadly, EU targets for decarbonisation,” Young explains. “Our suppliers are also developing net-zero strategies and are working to
provide biobased, higher-recycled content, lower-carbon materials that we can then use in our products.”
Before Planet Passionate, Kingspan had a net-zero policy in place since 2011. Its objective was to save more energy and generate more energy from renewable sources, with the rest purchased renewables from the grid.
“Under Planet Passionate, we moved to another level, setting targets for the percentage of energy we generate from renewables onsite and targets for the percentage of renewables directly procured from the grid. We also have zero waste to landfill and packaging reduction programmes, whereby we have targets for the percentage of recycled content in our packaging as well as taking back waste through take-back schemes on sites where it’s practical and can be facilitated.”
Lizzie Young explains that environmental product declarations (EPDs) are a core part of Kingspan’s product offering, as these detail the exact embodied carbon reductions it has been achieving.
“At this point in time, we still do not have a good understanding of what buildings consume with non-regulated energy and how occupants truly use them.” says Young. “EPDs show how a product performs a function on a building and exactly what upfront carbon is going into a building. We can present scenarios for digital twins
of buildings and provide an indicative impact of post-occupancy contributions, refurbishment and disposal of building materials at end of life. This data, presented holistically in the EPD, helps customers make informed product choices.”
She advises, “It should be noted that it is essential not to look at a product in isolation.
QUADCORE KS1000RW
LEC WALL PANEL
QuadCore KS1000RW
LEC Wall Panel has a life cycle assessment (LCA) that shows an 18.82% reduction in embodied carbon (measured by the Global Warming Potential ‘GWP’ kgCO2e) between life cycle modules A1-A3, and a 13% reduction in embodied carbon between life cycle modules A-C.
The reduction percentage is created by comparing standard QuadCore with QuadCore LEC to the EN15804-A2 standard.
Taking a holistic approach is essential when considering embodied carbon. Specifiers should be considering installation, technical performance, refurbishment and end-of-life criteria when considering their options.”
One of the biggest sustainability challenges
QUADCORE
AWP LEC
WALL PANEL
QuadCore AWP
LEC Wall Panel has an LCA that shows a 21.17% reduction in embodied carbon (measured by the Global Warming Potential ‘GWP’ kgCO2e) between life cycle modules A1-A3, and a 15% reduction in embodied carbon between life cycle modules A-C. The reduction percentage is created by comparing standard QuadCore with QuadCore LEC to the EN15804-A2 standard.
facing specifiers and designers looking to reduce embodied carbon in developments is getting reliable data. Lizzie Young explains, “You can’t carry out a reliable whole-life carbon analysis of a building if you don’t have good data. It is the responsibility of manufacturers and suppliers to ensure that the data that is being provided is comprehensive and accurate in order to support customers.
“We are working to ensure that all Kingspan products have good, accessible environmental product data available, and are utilising ESG criteria such as BES 6001 responsible sourcing”.
Further reductions in the embodied carbon of the QuadCore LEC range are expected between now and 2030, and these are underpinned by the business commitment to net zero carbon manufacturing by 2030, the introduction of an internal carbon charge, and an investment in H2 Green Steel - a company pioneering the manufacture of steel using hydrogen instead of fossil fuels.
In closing, Lizzie Young comments, “The important thing is to reduce emissions materially through science-based targets. All of this relies on having good data and a better understanding of how buildings operate in terms of how people use them.
“The Kingspan team is really proud of the Quadcore LEC product range, the decrease in embodied carbon and the increase in recycled content, Quadcore LEC comprises nearly 50% recycled content. We think that coupled with the certification and its technical performance, this makes Quadcore LEC an exciting addition to the Kingspan portfolio of products,” she concludes.
QUADCORE COLDSTORE
LEC PANEL
QuadCore
QUADCORE KS1000RW
LEC ROOF PANEL
QuadCore KS1000RW LEC Roof Panel has an LCA that shows an 18.82% reduction in embodied carbon (measured by the Global Warming Potential ‘GWP’ kgCO2e) between life cycle modules A1-A3, and a 13% reduction in embodied carbon between life cycle modules A-C. The reduction percentage is created by comparing standard QuadCore with QuadCore LEC to the EN15804-A2 standard.
Coldstore LEC Panel has an LCA that shows a 22.35% reduction in embodied carbon (measured by the Global Warming Potential ‘GWP’ kgCO2e) between life cycle modules A1-A3, and a 17% reduction in embodied carbon between life cycle modules A-C. The reduction percentage is created by comparing standard QuadCore with QuadCore LEC to the EN15804-A2 standard.
Are you looking for the most innovative, sustainable, and cost-effective foundation system in Ireland? Look no further than Geocell Foam Glass Gravel! Our product is made from 100% recycled glass, making it the perfect choice for environmentally conscious builders and developers. When it comes to Environmental, Social, and Governance (ESG) practices, Geocell Foam Glass Gravel is leading the way. With our product, you can significantly reduce your carbon footprint across the entire lifecycle of your building.
Here are just a few reasons why Geocell Foam Glass Gravel is the perfect choice for your next project:
• Less excavation from the land, which can result in up to 50% reduced muck-away costs.
• Guaranteed 100% Pyrite free material
• Lightweight material: Density (dry bulk) approx. 150kg/m3
• Granular size 10-60mm
• Excellent insulation: Thermal Conductivity 0.08 W/mK
• Durability: Compressive Strength 570 kN/m2 (10% Compression)
• Non-Capillary: Internal Water Absorption 0%
• Inert and essentially pH-Neutral
• Resistance to insects and rodents
• Save on Concrete (one pour only)
• No requirement for Insulation Boards anymore
• Fewer trades are required to bring your build to floor level (no blocks required)
With Geocell Foam Glass Gravel, you can save time, money, and the environment.
Uisce Éireann is the new name for Irish Water, Ireland’s public water authority dedicated to helping communities to thrive by delivering water services for Ireland. The name change came into effect in January, in line with the provisions of the Water Services Amendment Act 2022, which confirmed Uisce Éireann as the standalone publicly-owned utility with full responsibility for the delivery of all public water services in Ireland.
The new brand identity reflects Uisce Éireann’s vision of a sustainable Ireland where water is respected and protected and offers a new opportunity to communicate with the public about the vital services it provides.
Orlaith Blaney, Director of Corporate Affairs, Uisce Éireann, commented, “We are proud to be taking the next steps in our journey as Ireland’s standalone public water authority. We know from our own surveys, and also in research carried out by the Water Advisory Body, that there is still work to be done in informing the public about our critical role in providing safe drinking water, protecting the environment and supporting Ireland’s economic growth and development. Our priority is public health, and in order to ensure the public know who to contact in the event of an issue about their water, we will be communicating more
proactively on radio and on television in June this year.
“Uisce Éireann is leading the delivery of water services for Ireland and all this entails. We are investing €1.2bn in 2023 to address water and wastewater infrastructure deficits to bring our water services up to standard for a modern growing economy and to ensure a sustainable supply of water in the future.”
The new brand identity features a dynamic “stream” reflecting the flow of water and the circularity of nature, and it re-enforces visually Uisce Éireann’s stated vision for a sustainable Ireland, where water is respected and protected, for the planet and all the lives it supports.
confidence and succeed in their careers. The Return with Confidence programme will provide participants with the essential skills and support they need to excel in the construction industry and secure employment.”
The programme will cover a range of topics, including job-finding skills, soft skills and industry-specific software, among others. Participants will also network with industry professionals and receive one-to-one career mentoring and support in addition to a placement in one of the businesses signed up to support the programme.
Construction Professionals Skillnet, the leading provider of upskilling programmes for the construction industry in Ireland, has announced the launch of its 2023 ‘Return with Confidence’ programme, aimed at upskilling workers who have left the construction industry for various reasons and helping them re-enter the industry.
The 2023 programme commences on 15 May and is open to those who have left the
construction industry. The programme is designed to provide participants with the necessary skills and knowledge to return to the industry with confidence and is delivered virtually.
Liz Carroll, Spokesperson for Construction Professionals Skillnet, said, “We understand that many people have left the construction industry due to various circumstances, and we are committed to helping them return with
The Return with Confidence programme has limited places available and is subject to eligibility criteria. Interested parties are encouraged to apply as soon as possible to secure their place. The previous 2022 programme saw several of the participants obtaining permanent contracts within the industry following their placements as part of the programme.
For more information on the programme, contact Liz at CPSkillnet@CIF.ie
Industry leaders and representative organisations recently joined South East Technological University (SETU) faculty for the official launch of its Master of Science in Building Regulatory Compliance, a programme focusing on how regulations and standards affect a positive, healthy and safe environment where peoples’ best interests are at heart.
The Building Regulatory Compliance Masters programme is designed to meet the growing demand for qualified professionals who can ensure compliance with building regulations to deliver high-quality and sustainable buildings.
The postgraduate programme is ideal for a wide variety of professionals seeking to enhance their skills and knowledge in the areas of building control, regulation and compliance, including fire service professionals, architects, engineers, construction managers, building surveyors and regulatory officers. It will also be of interest to recent graduates who wish to specialise in this rapidly growing field.
The Masters degree is designed to give participants the knowledge and skills to interpret and apply building regulations, conduct site inspections, and evaluate compliance. Students will learn how to navigate the complex legal and technical aspects of building regulation and how to communicate effectively with stakeholders, including clients, contractors, and
regulatory authorities.
Dr Ken Thomas, Dean of Engineering, SETU Waterford, said, “We are delighted to announce the launch of our new MSc in Building Regulatory Compliance. With the construction industry experiencing significant growth, there is a need for qualified professionals who can support compliance with building regulations, standards, and performance. This programme will equip students to excel in this exciting and rewarding field”.
Hubert Fitzpatrick, Director General Designate, Construction Industry Federation (CIF), said, “The CIF is delighted
to support the launch of the Building Regulatory Compliance programme at SETU. We believe this programme will play a vital role in developing the skills and knowledge required to ensure that our built environment is safe, sustainable and fit for purpose.”
The programme starts in September 2023 and is offered as a one-year full-time programme or over two years in blended mode.
More information on the programme can be found at www.setu.ie/courses. Applications can be made through www.pac.ie
Hardware Association Ireland has welcomed the government’s announcement of major changes to the Croí Cónaithe vacant property grant scheme.
The grant will be available for renovations to all homes built before 2007, where previously, it was only available to homes built before 1993.
Another significant change sees the grant becoming available for people renovating vacant homes to be used as rental properties, whereas it is only available to owneroccupied houses under current rules. The grant rates are also going to be increased to meet inflation in the cost of building materials.
Welcoming the government’s announcement, Hardware Association Ireland Chief Executive Martin Markey commented, ‘’This is excellent news from the government and Minister for Housing Darragh O’Brien. These are very sensible and substantial changes that will give a major
boost to getting more empty homes back into use. We are delighted that the minister and his department are being proactive on the issue of vacant homes, as it has the potential to free up a lot of housing stock, create a lot of jobs, transform rural towns and villages and tackle dereliction in urban areas.’’
Hardware Association Ireland has been intensively campaigning for greater supports for renovating empty homes for the past three years, and many of its proposals were adopted by the government last year. The association is currently preparing to launch revised empty homes proposals in the coming weeks.
Hardware Association Ireland is the representative body for Irish hardware and DIY retailers, builders’ merchants, distributors and manufacturers. It represents over 400 members nationwide and 26,000 staff in the sector.
Ireland’s longest-established timber frame company, IJM Timber Engineering, has been providing timber frame solutions to its customers since 1965. IJM has recognised recent trends in planning for increased density, with developments veering towards a greater need for duplexes to be built. While exploring various methods to try and address this with an off-site solution, IJM identified light gauge steel framing (LGSF) could be utilised similarly to timber frame while providing a concrete slab over the ground floor apartment.
Having delivered numerous timber frame units to its customers who have been building the ground floor in masonry to date and have always struggled to adhere to programme dates, this solution allowed them to control programme and achieve deadlines.
Killross Properties Ltd completed a four-block duplex unit with IJM and their connected-partner Frameform Steel Systems earlier this year.
Lar McKenna, Director, Killross Properties, commented, “Using this hybrid approach enabled us to have the building
watertight in under five weeks versus in excess of 12 weeks had we used a block and precast system. Once watertight, we could allow access for other trades to commence on site. It was also highly advantageous to have one ancillary certifier sign off on the complete design of the duplex structure.
“From order, through design process to certification, we found everything happened as per programme provided by IJM at order stage, alleviating the hassles associated with organising various trades to get to the same stage of building.”
Peter McCaughey, who leads both IJM Timber Engineering and Frameform Steel Systems, commented, “I am excited about the synergistic nature of both systems, and I truly believe this will transform the construction process of duplexes for our customers. The connection between these companies encourages a shared approach, which ensures that we continue to work together to develop a combined system of timber frame and LGSF that solves all of the technical issues, with our respective teams thinking as one.”
This LGSF system is available from IJM Timber Engineering and Frameform Steel Systems.
To learn more, phone 047 74500.
Tekla once again raises the bar for construction productivity, efficiency and quality with its 2023 software releases. Learn about our 2023 user-experience improvements and feature updates that transform the way you work with reliable and data-rich structural software.
www.tekla.com/2023
Appointed to deliver the roof steel package on the new National Children’s Hospital, automation and collaboration was critical to Struccie Design Associates’ work - both facilitated by BIM and cloud-based tools.
Once completed, the new National Children’s Hospital (NCH) in Dublin will offer a world-class paediatric medical facility, combining the services currently provided at three hospitals into the one, modern and custom-designed hospital.
Appointed by lead steel fabricator KH Engineering, Struccie Design Associates was responsible for delivering the steel detailing for the NCH roof package. With a curved and oval form, the structure alludes to the architecture of Dublin’s best-known civic spaces and buildings, most notably the Royal Hospital at Kilmainham (Irelands oldest hospital).
Speaking about the project, Lee Chitty, Director at Struccie Design Associates, said: “There were numerous challenges on this project, many of which presented themselves very early on. The first was the complexity of the roof package details. Given the oval form, the rafters were curved with transverse purlins spanning onto the curved rafters, creating a faceted framework, which was very challenging both to detail and set out. It was also an Execution Class 4 project, each assembly and part were able to be traced by splitting the steelwork into smaller phases which meant easier control of the steelwork when being issued for fabrication.
“The use of intelligent 3D modelling software proved key in helping us to overcome these challenges, particularly through the use of custom components. Using Tekla Structures, we were able to utilise the modelling software to create our own project specific custom components and apply pre-defined settings in our assembly drawings, with the automation helping us to minimise repetitive tasks.
“A great example of this in action relates to the steelwork weep holes, required in all beams and columns to aid the discharge of moisture. The galv-holes tool, available in Tekla Warehouse, was brilliant and an absolute gamechanger. Once you’ve pre-defined the settings for specific section sizes and connections, you can reduce your workflow times, as opposed to having to manually detail every single one.”
Understandably, coordination was also critical when it came to considering and detailing the NCH roof package, particularly when it came to the steel-to-concrete connections. With four sloping concrete cores on the project and a large number of steel connections to consider, accuracy was essential.
Lee explained: “Working in partnership with our client KH Engineering, they carried out a survey of the concrete cores whilst the build was going on, on site. We were then able to import the survey data directly into the 3D modelling environment within Tekla Structures and use this to accurately detail and set out our steel connections. Without this survey data and the ability to import it directly into our model, there would have definitely been issues on site further down the line.”
In addition to Tekla Structures, Struccie Design Associates also utilised the cloud-based Trimble Connect tool to aid collaboration, both internally and externally.
Lee said: “Collaboration on a project of this scale was critical and is somewhere that digital technology and a cloud-based system can really add value. Trimble Connect was a big tool for us on the NCH project. We had two ‘projects’ within Trimble Connect; one of which contained all our steelwork detailing. Using the ‘To Do’ action tool, we were able to tag design team members and keep a live diary of what actions were required and what actions had been taken, making the internal communication process far more streamlined.
“The second ‘project’ was one that we shared externally. We were able to import all other design team models, giving us an accurate, consolidated and multi-discipline model to work from and refer to. Used as a focal collaboration point, sharing our data and models enabled effective coordination and the ability to easily highlight any potential clashes.”
Struccie Design Associates’ work on the National Children’s Hospital saw the team win the ‘Public Vote’ category in the 2022 UK Tekla Awards, with people praising the level of complexity and detail involved.
For more information, please visit: www.tekla.com/uk.
The inaugural MMC Ireland National Conference at Croke Park on 06 June will include presentations on volumetric modular high-rise buildings and look at the role of offsite construction and modern methods of construction in making Irish construction more sustainable.
The MMC Ireland National Conference 2023, in association with Explore Offsite, is set to be a unique event that will bring together experts from across Ireland, the UK, and beyond to showcase best practices in offsite and modern methods of construction (MMC). The conference will be held on 06 June at Croke Park, Dublin, and it is expected to attract a large audience of industry leaders, academics, and policymakers.
The conference will feature a range of project case studies that will demonstrate the latest developments, innovations, and investments in the MMC sector.
Attendees will learn about the MMC Ireland Framework, which is aimed at promoting the use of MMC across the country. The framework focuses on encouraging the use of offsite manufacturing, digitalisation, and other innovative approaches to construction.
One of the highlights of the conference will be a presentation on moving volumetric modular high-rise buildings into Ireland. This will showcase the potential of this construction method for addressing the housing crisis in the country.
Volumetric modular construction involves manufacturing entire building units in a factory setting before being transported to the site for assembly. This method can
significantly reduce construction time and costs while improving quality and safety.
There will also be a panel debate led by MMC Ireland, focused on how the housing sector can be further advanced using MMC. The panel will feature industry experts who will discuss the challenges and opportunities for adopting MMC in the housing sector.
Sustainability will be a key focus of the conference, with a presentation on the MMC journey to energy efficiency.
Attendees will learn about the latest innovations in sustainable construction and gain insights into the latest trends and best practices in this area. A case study will also be presented on Energy House 2.0, which is an innovative project that explores the use of energy-efficient materials and construction methods in building design.
Another important topic that will be discussed at the conference is upcoming national legislation related to climate and energy plans. Attendees will gain insights into the latest policy developments and learn about the impact of these changes on the MMC sector.
The conference will feature several interactive and dynamic panel discussions, including a session on ‘Digital Platforms Leading the way in MMC’. This will provide
attendees with an opportunity to learn about the latest digital platforms that are driving innovation in the MMC sector. The panels will feature experts who will discuss the latest trends in digitalisation and provide insights into how digital platforms are transforming the construction industry.
With new speakers being announced weekly, the MMC Ireland National Conference 2023 is a must-attend event for anyone interested in the latest developments in offsite and modern methods of construction in Ireland. It will provide attendees with the opportunity to learn from industry leaders, network with peers, and gain valuable insights into the future of the MMC sector.
Register now to secure your place at this exciting event at https://www.eventbrite.co.uk/e/mmc-irelandnational-conference-tickets-590007417067 or scan the QR code
MMC Ireland is a representative body that strives to promote and advance the use of MMC in Ireland by building knowledge and awareness, advocating for regulatory change, and fostering access to the MMC market.
Construct Innovate, Ireland’s Research Centre for Construction Technology based at the University of Galway, has started to onboard new members and is working to develop new advanced processes and harness innovative thinking in the Irish construction sector.
Construct Innovate, Ireland’s Research Centre for Construction Technology and Innovation, brings together multidisciplinary research groups in five partner institutions (University of Galway, University College Dublin, Trinity College Dublin, University College Cork and the Irish Green Building Council). Researchers and academics work together with Construct Innovate members under the five pillars:
1. Productivity, affordability & cost
2. Quality & safety
3. Sustainability
4. Skills & training
5. Collaboration.
Construct Innovate aims to empower the construction industry to directly influence and participate in the research, development and innovation process. The working groups within Construct Innovate are formed by stakeholders in the construction/built environment sector (eg, SMEs, start-ups, research-performing organisations (RPOs), universities, associations, professional bodies, government agencies, etc) to carry out cooperative activities of general interest for the sector and promote large R&D projects on a collaborative basis. This will drive partnerships on research proposals and the development of major innovation projects that otherwise would not have been possible to carry out individually. It will reduce barriers for the industry to access innovation due to research being led by industry needs.
Furthermore, the proposed governance and management structures of Construct Innovate drive cooperation between RPOs and member companies and provide an international perspective.
On 26 October 2022, Construct Innovate hosted a webinar on the opportunities and challenges of modern methods of construction (MMC) and their adoption in Ireland. The event started with the introduction and background from the Department of Enterprise, Trade and Employment. Representatives from industry (Evolusion Innovation, Vision Built), the National Standards Authority of Ireland (NSAI), HomeBond and the Building Research Establishment UK then presented their perspectives on MMC. A Q&A session with participants followed the presentations.
A report from the webinar was published and includes the key findings from the presentations and a summary of the discussions. This report is available at www.constructinnovate.ie/resources
Construct Innovate helped to facilitate a construction stakeholder event on accelerating MMC, which took place in Trinity College Dublin on 22 February 2023. The event was organised by the Department of Enterprise, Trade and Employment. Many insights and practical steps were discussed that industry and government could take together to accelerate the adoption of MMC in housing.
Construct Innovate is currently onboarding its first 30 members. The
next deadline for applications is July/August.
Members will actively participate in working groups, as well as in the creation of new project definitions and calls for proposals. The working groups are the fundamental part of Construct Innovate and will be led by the members, who will decide which activities are beneficial to the sector.
Membership of Construct Innovate is open to all stakeholders with interest in developing research and innovation expertise in the area of construction and built environment technology.
If your company or organisation is interested in applying for membership of Construct Innovate, full details can be found at www.constructinnovate.ie/resources/ or scan the QR code.
Irish Cement is tremendously proud its unique heritage and the work done by previous generations. It also recognises the responsibility of this current generation to ramp up further the pace of change and address industry carbon emissions.
The world has transformed over the past 85 years. Think back to Ireland of the 1930s, when our grandparents tell tales of walking to school barefoot, ponies and traps, black bicycles, and very few cars on the roads. By and large, they recall simpler times when the pace of life seemed more relaxed. There were very few telephones, let alone smartphones. Instead, there were telegrams, letters, and messenger boys, no urgent emails demanding an immediate response. Farming was as vital in Ireland then as it is now, and the Electricity Supply Board had been established just a decade earlier. Rural electrification was transforming communities throughout Ireland, and today we all recognise the important role electricity plays in our daily lives. There is something else from that era, which is vital to our daily lives but is often overlooked.
On 23 May 1938, Sean Lemass, then Minister for Industry and Commerce, surrounded by other dignitaries, pushed an oversized red button and two cement factories, one on the banks of the Boyne in Drogheda, the other in Mungret outside Limerick, sprang into life. The location of the Cement Ltd (later to become Irish Cement) factories had been carefully chosen to be
close to abundant supplies of limestone, ports for the importation of fuel, and centres of the population for the sale of its product. From that day on, cement used in concrete and mortar has been one of the key ingredients in the foundations of the Irish State. Irish Cement has been at the forefront of manufacturing high-quality cement since 1938, and cement continues to be a critical ingredient in our modern economy. During those eight and a half decades, Irish Cement has transformed its operations through upgrades and continuous investment in the most energy-efficient cement manufacturing technology.
Today’s workforce in Irish Cement is tremendously proud of that unique heritage and the work done by previous generations. They also recognise the responsibility of this current generation to ramp up further the pace of change. That change is to address the carbon emissions from the cement industry and to further improve the resource efficiency of its operations. The cement sector has committed to being carbon neutral by 2050, and progress is well underway. Already, a typical bag of Irish Cement has a 20% lower carbon footprint compared to the 1990s. It is still the same great cement that delivers the same great
performance, but you can have confidence knowing its production had less impact on our environment, both in terms of climate change and circular economy.
These reductions have been achieved through energy efficient investments, which need less energy to make each tonne of cement; the introduction of lower carbon CEM II cements, Ireland’s most popular cement; and the replacement of imported fossil fuels using locally sourced alternative fuels. Continuous investment in training and development of the workforce has underpinned these developments.
Maintaining quality and cement performance for customers remains the top priority as the company innovates and becomes more sustainable in the way it makes cement. In 15 years, when Irish Cement will celebrate 100 years in business, the way cement is manufactured will be radically different from today. To achieve those improvements, further investment will be made to reduce fossil fuel consumption and make operations more resource efficient. Irish Cement is committed to maintaining its leadership position as Ireland’s highquality cement maker through innovation, collaboration and a recognition of its unique heritage.
HENRY HATHAWAY outlines the principle behind a Deed of Novation and suggests that when it comes to projects where design obligations are being transferred to the contractor, the appropriate instrument must be implemented.
Ausual feature of construction projects is a scenario where the employing party will undertake designs and then generate the specifications for a project with the consultant team prior to engaging with contractors for tendering.
Generally, the consultant team will set out the performance specifications and take the design to a developed stage according to its agreement. Contractors will then tender on the designs and specifications that have been produced. Where the contractor is to take responsibility for further design or implementation, it then has a choice, it may employ its own design teams directly, or it may decide, usually through agreement with the employer, that it will retain the original design team given the fact that there is a familiarity with the scheme or that it is convenient to carry through with the designs that are in development.
One particular way to facilitate this mechanism is to proceed with a ‘Deed of Novation’. Essentially, a novation is the transfer of all obligations under one agreement between two initial parties
(employer and consultant) to an incoming party (the contractor) and allows for the designs to continue. The incoming party takes the place of the original party, usually the employer, and so the process of design development continues, hopefully seamlessly.
A question then arises. If a contractor that had based its entire tender pricing on the designs and specifications by the consultant when it was retained during the time with the employer later finds out that the design was wrong or perhaps negligently performed, then what can the contractor do about this scenario?
To explain further, a contractor who costed its tender against drawings and specifications that were either not developed correctly or are unworkable might turn to the employer and set out that the contractor merely followed the designs and specifications at the time of tendering and relied upon the information that was provided at the time but later found to be wrong.
This is a scenario that was evident in the
Scottish case of ‘Blyth & Blyth Limited v Carillion Construction Limited’ in 2001. Carillion was the design and build contractor and agreed to enter into a novation agreement of the engineer’s appointment that was originally with the employer. Carillion subsequently found that the tender drawings were wrongly prepared for the employer prior to the novation. If Carillion were to return to the employer, the employer would certainly have stated that it no longer was a contracting party with the engineer and that redress should be direct from the consultant. Carillion then pursued Blyth & Blyth, the engineer and stated that the engineer had underestimated the scope and quantity of work and suffered loss, having caused Carillion to undervalue the works. Carillion relied on broad wording of the novation, but the court found that the wording was insufficient to give Carillion a right to pursue for losses pre-novation. It found that no greater loss had been suffered by Carillion than the employer, and given the fact that the employer had not, in fact, suffered any loss (it was released from the contract and arguably was in benefit because Carillion had under-priced the works),
If a contractor has based its pricing on a client’s consultant designs that are wrong, what can they do?
then no greater loss could be claimed by Carillion above what the employer had suffered. It is known as the no-loss principle.
If the above sounds difficult, it is because it was a difficult position. It emerged to be a “black hole” but essentially derives from loss.
In my previous articles and lectures, I will have spoken about a claim requiring a coincidence of breach and loss with the required factual and legal causation.
Since this case, the remedy was in drafting and organising the transfer of obligations. There are, in essence, two types of novation generally accepted, ab-initio, where an imaginary scenario is provided that the incoming party was always the contracting party or a switch agreement. The above scenario in Blyth & Blyth is catered for through a “no loss clause” in drafting.
The key takeaway is to ensure that the appropriate instrument is implemented where obligations are, in effect, being transferred.
However, pragmatically, many other issues arise for all of the parties, be they consultants, employers or contractors and need to be considered.
In the first instance, where there is a transfer, and the contractor has relied upon the developed design to that point in order
to provide a cost, it ought to be identifiable to what extent the design has been progressed to and whether the employer’s requirements can be adequately met.
A further point arises as to payment and to consider what scope of the original services have been undertaken by the consultant, whether payments are up to date and what scope of services are required to be completed. A consultant can find itself in difficulty when an incoming contractor may seek to value engineer or make changes, and the consultant must be alive to this in terms of its own previous work and whether or not adequate sums have been allowed for to carry out any further designs.
At the outset of any such agreement, a developed set of schedules are required to be incorporated, which set out the performed scope and detailed costs as well as prospective work and fees along with the programme development. Any deviations or methods to be proposed by the contractor at this point should be contained within its proposals and the underlying construction contract.
Given the complexity of the case in Blyth & Blyth and the theories related to the underlying problems that can arise, it is best advised to stay clear of such arguments.
The case of Blyth & Blyth is examined and discussed in detail in training and development courses offered by Henry Hathaway Solicitors and pragmatic steps provided to assist in avoiding the circumstances that can arise.
Henry Hathaway is a solicitor who practices in both Ireland and England and Wales and specialises in construction law. He is a qualified civil engineer and spent 12 years working in the industry. He regularly advises on contract formation and provides practical advice when entering construction contracts and regularly provides training and seminar days to companies to assist knowledge and application in order to assist them in avoiding disputes in construction.
If you require further information in relation to contract formation or would like to discuss training and development in this area, contact henry.hathaway@hathawaysolicitors.ie
“Ensure that the appropriate instrument is implemented where obligations are, in effect, being transferred.”Henry Hathaway, Principal, Henry Hathaway Solicitors.
We offer years of experience shaping concrete and cutting holes and conduits in solid floors and walls
Diamond Core Drilling
Wire Sawing
Concrete Cutting Walls
Concrete Cutting Floors
Wall Chasing
Brokk Remote Demolition
Ralkore Ltd is a company specialist in core drilling and concrete cutting services
Based in Dublin, Ireland, we are able to provide nationwide services, including the North of Ireland, and also UK, 24 hours a day and 7 days per week.
The National Transport Authority (NTA) is to brief contractors and consultants in Ireland and abroad on opportunities that will arise as a result of National Development Plan (NDP) investment in sustainable transport over the next decade.
The briefing will take place via a two-hour Zoom webinar on 26 May.
The meeting will be chaired by NTA CEO Anne Graham and addressed by Minister for Transport Eamon Ryan along with Minister for Public Expenditure, NDP Delivery and Reform Paschal Donohoe.
Iarnród Éireann and Transport Infrastructure Ireland representatives will also participate in the event.
The meeting will hear of NDP plans to invest in public transport, active travel and the connectivity of communities to the tune of €35bn, including €15.3bn allocated to the NTA between now and 2030.
Sustainable transport programmes earmarked for funding in the NDP include BusConnects, MetroLink and DART+, along with an ambitious programme of active travel schemes around the country.
NTA CEO Anne Graham commented, “Thanks to the NDP, we are facing into a period of unprecedented levels of investment in sustainable transport. But to deliver this portfolio, engagement is required with the market, particularly with construction interests that have the capacity to deliver large-scale capital programmes,” Ann Graham said. “We’re looking to hear from contractors, designers, consultants, and any other interested parties involved in the construction supply chain. Attendees will be encouraged to
message NTA facilitators to schedule one-to-one follow-up sessions with ourselves or with some of the other key stakeholders, either for later that day or in the following days or weeks.”
Minister for Transport Eamon Ryan said: “This Government is firmly committed to investing in sustainable mobility to realise our 2030 carbon-reduction and 2050 net-zero targets. Under our 10-year capital investment programme, €35bn will be invested in the transport system between 2021 and 2030. In the coming years, we will commence construction of some of the largest and most ambitious public transport projects in the history of the state, such as MetroLink, DART+ and BusConnects in our five cities.
“Alongside this historic investment, we are spending €1m every day on active travel to bring our cycling infrastructure up to worldclass standards.”
Allianz Ireland has launched a new Climate Safe Homes initiative to accelerate climate adaptive home building in Ireland. The programme is a firstof-its-kind for the Irish insurance industry and includes a new €1m investment to help drive sustainable solutions and collaborative innovation across the financial services and home construction sectors.
As part of Climate Safe Homes, Allianz Ireland will bring together key stakeholders across construction, engineering, and architecture to pioneer and develop a new home-building model designed specifically to withstand the effects of Ireland’s changing climate. The project will initially focus on developing a climate-resilient threebed semi-detached home, ensuring that affordability is taken into account. This approach will also ensure that climate adaptive solutions identified by the project can be retrofitted to existing housing stock.
In addition, solutions developed through Climate Safe Homes aim to align with future approaches to housing in Ireland, such as climate adaption for higher-density housing.
Ursula Murphy, Chief Transformation
Officer, Allianz Ireland, said that climate change is one of the main challenges facing our society, and while every effort must be
taken to mitigate future climate change, we are already seeing the effects of changing weather patterns
“At Allianz Ireland, protection that gives people confidence in tomorrow is at the core of what we do. Climate Safe Homes will allow us to help provide that by helping to transform Irish homes through climateadaptive building.”
Allianz Ireland is partnering with the Irish Green Building Council (IGBC) and others to establish a cross-industry working group to provide a home-grown solution for building and renovating sustainable, climateready homes in Ireland.
Speaking on the announcement Pat Barry, CEO, IGBC, said, “In Ireland, we are currently facing a dual crisis – housing supply and climate change. By working collaboratively through initiatives such as Climate Safe Homes with Allianz, we have the opportunity to influence the construction of thousands of climateadaptive homes for the future while also safeguarding Ireland’s existing housing stock, hence contributing to a reduction in our carbon emissions.”
Solicitors specialising in:
Construction Law
The Build Environment
Dispute Resolution
Corporate Training & Seminars
Contract Reviews and Drafting
a: Osprey Business Centre, Naas, Co Kildare
p: +353 01 639 2911
e: henry.hathaway@hathawaysolicitors.ie
w: www.hathawaysolicitors.ie
Henry Hathaway Solicitors is a niche law firm that is tailored and designed to cater specifically to the construction industry.
Henry Hathaway qualified originally as a Civil & Structural Engineer and has previously spent twelve years in the construction industry representing both Contractors and Engineering Clients. He is a practising solicitor in both Ireland and England and Wales. He acts for clients in relation to disputes and litigation as well as regularly advising on dispute avoidance and alternative dispute resolution. He also acts on non-contentious matters on smalland large-scale construction projects using his
extensive knowledge of the industry both in Ireland and the UK.
Henry Hathaway Solicitors provides bespoke training and development progammes for construction companies, which cover areas of contract formation and interpretation, claims in loss expense, and interim and final account disputes. These programmes are suitable for companies that require advice on the compiling of claims, that have payment disputes and to support those who require legal assistance in the process of administering their contracts.
With mandatory carbon assessments on the horizon, STEPHEN BARRETT, Whole Life Carbon Lead, Irish Green Building Council, outlines how the construction sector should approach addressing whole-life carbon measurement in a consistent manner.
The recasting of the Energy Performance of Buildings Directive (EPBD) has just received the support of the European Parliament in a plenary vote on 14 March.
This means that the mandatory requirement for whole-life carbon assessments (WLCAs) of buildings just took another step closer to becoming a reality. Many investors already require WLCAs to provide evidence of green investments in line with the EU Taxonomy and for access to better funding terms.
Regulations on WLCA are already in place in some countries and cities – Denmark, the Netherlands, France and London – and are being progressed in others, such as Finland, Sweden and Norway.
Research carried out by UCD found that the built environment is responsible for 37% of Ireland’s annual emissions – 23% from operating buildings and 14% from materials manufacture. BER assessments help us consider and reduce energy use in buildings, which is useful but not if the reduction is achieved by shifting the emissions from the operational stage of the building’s lifecycle to the production stage by requiring more materials to be manufactured, which is arguably worse as it increases emissions in production plants to reduce them in buildings later.
This is an important point, as we need to halve our total emissions in this decade in order to have a chance of staying under the target of a 1.5-degree increase.
WLCA looks at emissions from the beginning of a building’s lifetime right through to the end and beyond. It quantifies the emissions from the mining, processing and transporting of material used in a building – embodied carbon; emissions from energy used over the building’s lifetime – operational carbon; and the usefulness the materials may have in the future when the building is decommissioned – its ‘circularity’.
Currently, in Ireland, there are no building regulations aimed at reducing embodied carbon, and, where WLCA is being carried out, it is not being done in a consistent way. This means results from any two assessments are not comparable since they may be based on differing parameters and assumptions on things like the electricity grid’s carbon intensity in the future or the amount of greenhouse gases emitted in producing certain materials.
We need a standard WLCA methodology so all our building designs, both new-build and renovation, are comparable from a carbon perspective. This will allow us to make better design decisions, draw conclusions fairly and decide what does and does not get built.
Figure 5 (below) shows the annual emissions from a notional new 5,000 sq m building modelled using the IGBC methodology. The high emissions in red in year zero represent the emissions incurred in the production of materials and the construction process in that year – the upfront embodied carbon. The annual emissions in grey represent day-to-day electricity from a decarbonising grid as forecast by the SEAI, and the figures in blue show likely renovation and refurbishment emissions during the building’s lifetime (lifetime embodied carbon).
While we have regulations around operational energy and, therefore, carbon, there are currently no regulations that address the carbon intensity of the production of materials and components. This means the most carbon-intensive year of a typical building’s lifetime – year 0 - has no carbon regulation around it at all.
Historically, operational emissions of buildings were the most significant contributor to global warming, but as we build higher performing, more insulated buildings, this has reduced, and the demand for materials has increased, meaning the emissions from the production of materials for a building is now roughly the same as that of operating that building for 50 years – in short, both have to be considered to produce the lowest possible carbon intensity of a building over its lifetime.
There is a growing interest in embodied carbon at all levels, including among investors and legislators. The Irish government recognises the need to address whole-life carbon consistently and has made provisions to do this in the Climate Action Plan (CAP).
Action 13.4 in the 2023 CAP and Action 198 in the 2021 CAP highlight the need for a national methodology to calculate the emissions from Irish buildings at each stage in their lifecycle.
With funding from the SEAI, the Irish Green Building Council (IGBC) launched the UpfrontC02 Project in order to develop and test this national methodology. The methodology we developed is based on the European Standard EN 15978 and indicator 1.2 of the EU Level(s) framework for measuring the sustainability of buildings. This is the same framework and indicator used for EU Taxonomy investment decisions and underpinning the EPBD recast mentioned above.
A consistent methodology allows for a fairer comparison of buildings in Ireland and across the EU.
So far, our project partners include the Land Development Agency (LDA), the Health & Safety Executive (HSE), the Department of Education, Dublin City Council, and numerous architects and developers – who are currently applying the methodology to realworld projects in order to understand the impacts of their tenders and designs and how they might mitigate them. They are also learning about how a significant requirement like this will fit into their workflows and feed back ideas and suggestions.
The methodology is evolving as we learn and will be offered back to the Sustainable Energy Authority of Ireland (SEAI) with the recommendation that it be the single methodology for quantifying the WLC of all building projects – thus ensuring fairness and comparability of all building plans.
To minimise a building’s impact, we need data on its likely carbon footprint over its whole life, and we need this as early as possible to guide how it will be designed and built. This kind of data is challenging to create as decisions on how to build have not been taken yet, and manufacturing processes vary greatly across materials and manufacturers.
To help with this, the methodology provides generic average data – like a rate card for cost estimation, only providing carbon instead of price figures. In the same way as a cost analysis can be done for different design approaches, this can be used for a carbon analysis, at least for Stage A of the building’s lifetime. We can apply the SEAI’s forecast carbon intensity of the energy grid to understand the balance between this upfront embodied carbon and the emissions from Stage B - the use phase of the building’s life. It helps us optimise our design decisions from a carbon perspective, considering both the quantity of emissions and their timing.
We need case studies to understand our current position and plan for the future. Current case studies are hard to compare with one
another as they are assessed using different methodologies. We need a set of consistently assessed case studies so we can better understand the carbon intensity of our different building typologies today. This will help us to:
• Identify our most impactful decisions – the carbon hotspots
• Rethink them in the light of a need to reduce emissions
• Measure the differences we can make
• Design out waste
• Design in circularity
The volunteer partners in the UpfrontCO2 project are currently;
• Learning about the future of EU legislation
• Learning about the balance between Operational and Embodied Carbon
• Learning how to use the WLC calculation methodology
• Discussing problems and sharing their results as they learn
• Understanding how they can embed this process in their workflows
We are starting to see case studies completed using the methodology with plausible results, but we want to see many more; We need to make a concerted effort where all actors in the industry get involved, contribute and learn because legislation in this area is coming.
The IGBC can supply the methodology, but it is up to the teams themselves to implement it. The benefits of this are:
• Gaining an understanding of the methodology, which will be a requirement in some form in the future
• Influencing the development of the methodology – it is a
prototype, and we are trying to understand how best to include this vital aspect of building design into current working patterns
• Reduce the emissions from your building designs –understanding the hotspots is the first step in understanding where to focus your attention. The earlier this is done, the greater the difference you can make as the design evolves. It is not too late to get involved and join us. Through Construct Innovate, Ireland’s new national centre for construction research, we are calling for more case studies to support and verify the initial findings of UpfrontCO2. This new project, called INDICATE, has been set up to find 50 more case studies across all typologies to build a picture of the whole life carbon of the industry in Ireland today. Cases do not have to be low energy or particularly green – we want to understand what is our business as usual today so we can all learn and improve. This will only work if we collaborate and share our learning. This is an opportunity to upskill for free, with national and European experts on hand to guide and advise on the methodology and provide guidance on possible design ideas that may help us all move in the right direction.
If you have a project in development or one recently finished and you are curious about how it could be optimised to reduce its carbon footprint, please get in touch – email stephen@igbc.ie. He will share the methodology and welcome you to the team.
Stephen Barrett is the Whole Life Carbon Lead at the Irish Green Building Council. He is managing the UPFRONTCO2 project to establish the methodology for WLCA in Ireland and the INDICATE project to test and verify results across a greater sample of case studies.
The latest report from the Intergovernmental Panel on Climate Change (IPCC) warns of the increasing devastation caused by climate breakdown, including millions of deaths, destroyed homes, hunger, and losses to vital ecosystems. The report also highlights that more than three billion people already live in areas highly vulnerable to climate breakdown, with half of the global population experiencing severe water scarcity for at least part of the year. The Climate Change 2023: Synthesis Report is almost certain to be the last such assessment while the world still has a chance of limiting global temperature rises to 1.5°C above preindustrial levels.
The Climate Change 2023: Synthesis Report, based on years of work by hundreds of scientists during the IPCC’s sixth assessment cycle, reiterates that humans are responsible for all global heating over the past 200 years, leading to a current temperature rise of 1.1°C above pre-industrial levels, causing increasing destruction to people and the planet.
It suggests sharing best practices, technology, effective policy measures, and mobilising sufficient finance to decrease or prevent the usage of carbon-intensive consumption methods, prioritising climate risk reduction for low-income and
marginalised communities for the biggest gains in wellbeing.
The latest report from the IPCC highlights that there are multiple feasible and effective options available now to reduce greenhouse gas emissions and adapt to human-caused climate change. The report emphasises the urgency of taking more ambitious climate action and underscores the need for effective and equitable climate action that will reduce losses and damages for nature and people. The report also highlights that climate justice is crucial because those who have contributed least to climate change are being disproportionately affected. The solution lies in climate-resilient development, which involves integrating measures to adapt to climate change with actions to reduce or avoid greenhouse gas emissions in ways that provide wider benefits.
The report calls for political commitment, coordinated policies, international cooperation, ecosystem stewardship, and inclusive governance to achieve effective and equitable climate action.
Finally, the report emphasises the need for significant investment in adaptation, conservation of approximately 30-50% of the earth’s land, freshwater, and ocean, and
transformational changes in the food sector, electricity, transport, industry, buildings, and land use to reduce greenhouse gas emissions.
Real estate is responsible for approximately 39% of total global emissions. Approximately 11% of these emissions are generated by manufacturing materials used in buildings (including steel and cement), while the rest is emitted from buildings themselves and by generating the energy that powers buildings. The housing sector has a crucial role to play in reducing emissions and addressing the climate crisis. Housing delivery is a crucial aspect of the sector, and the latest IPCC report will undoubtedly impact how we approach it. The report highlights the need for more sustainable building practices, including increasing the use of MMC, which can significantly reduce emissions while improving the quality and affordability of homes.
MMC involves the use of innovative construction techniques and materials, such as modular building systems, offsite construction, and 3D printing, which reduce waste and energy consumption while improving the quality and efficiency of
In light of the publication of the most recent UN Climate Report, CAROL TALLON looks at the role modern methods of construction could play in the fight against climate change.
construction. These methods have several benefits over traditional construction methods, including reduced construction times, lower labour costs, and fewer emissions. For example, offsite construction can significantly reduce the amount of waste generated during construction, as materials are measured and cut to precise specifications, resulting in less waste.
The use of MMC in housing delivery can help reduce the carbon footprint of the sector while providing more sustainable and affordable homes. By reducing waste and energy consumption, MMC can significantly reduce the emissions associated with housing construction, making it a crucial tool in the fight against climate change. MMC can also improve the quality and efficiency of construction, leading to more durable and energy-efficient homes, which require less maintenance and provide a better quality of life for residents.
The adoption of MMC in Ireland’s housing sector is still relatively low, and there are several barriers to its widespread adoption, including a lack of awareness, resistance to change, and the perception that MMC is more expensive than traditional construction methods. However, with the urgent need to reduce carbon emissions and create sustainable housing, the benefits of MMC are becoming increasingly evident.
MMC can significantly reduce the carbon footprint of construction projects by minimising waste, reducing energy consumption during the construction process, and using sustainable building materials. Moreover, MMC allows for more efficient and streamlined construction processes, reducing construction time and costs while improving the quality of the finished product. This can be particularly
beneficial in addressing Ireland’s current housing crisis, where there is a significant shortage of affordable, high-quality housing.
To overcome the barriers to adoption, the Irish government has implemented a range of policies and initiatives to promote the use of MMC in the housing sector.
For example, the State’s Climate Action Plan sets a target of achieving a 51% reduction in carbon emissions from new buildings by 2030, with a strong focus on the use of low-carbon construction methods such as offsite and other modern methods of construction.
MMC Ireland, along with several national initiatives including the Modern Methods of Construction Taskforce, is developing a roadmap for the adoption of MMC in the Irish construction sector. By bringing together key stakeholders from across the industry, the organisation is working to identify and address the barriers to adoption and to promote the holistic benefits of MMC.
In support of this, the government has introduced a range of financial incentives to encourage the use of MMC in housing construction, such as grants and tax incentives for developers who use sustainable construction methods. This has helped to increase awareness and adoption of MMC in the industry, contributing to the development of best practices and encouraging investment in research and development of new MMC technologies and methods.
Policymakers can continue to drive progress through the development of policies and incentives that encourage the increased use of offsite and other MMC. This can include funding for research
and development, investment in training and skills development, and regulatory frameworks that promote sustainable construction practices.
Despite the progress made in promoting the use of MMC in Ireland’s housing sector, there is still much work to be done. The State and industry stakeholders must continue to work together to address the remaining barriers to adoption, such as a lack of skilled labour and the reputation of the sector, specifically, raising awareness about the durability and longevity of MMC buildings. Moreover, the benefits of MMC extend beyond the construction phase and into the operational phase of buildings. Energyefficient and sustainable building designs can significantly reduce energy consumption and associated costs, leading to long-term cost savings for homeowners and reducing the carbon footprint of the housing sector.
The latest UN climate report serves as a stark reminder of the urgent need to reduce carbon emissions and mitigate the effects of climate change. The housing sector has a significant role to play in achieving this, and the adoption of MMC can help to significantly reduce the carbon footprint of construction projects while improving the quality and efficiency of housing delivery.
MMC Ireland is a representative body that strives to promote and advance the use of modern methods of construction (MMC) in Ireland by building knowledge and awareness, advocating for regulatory change, and fostering access to the MMC market. Join MMC Ireland to transform the construction industry through innovation and excellence: https://mmcireland.ie/
Firestone Building Products has announced that its iconic Firestone brand in roofing, wall and lining systems, will now become ‘Elevate’.
The new Elevate brand name comes as the company adopts the Holcim name, becoming the Holcim Building Envelope division of its Solutions & Products business unit.
The new Elevate brand name for Firestone Building Products roofing, wall and lining systems “symbolises Holcim’s continued commitment to deliver superior quality and innovation with advanced building solutions,” the company says.
Holcim’s range of building envelope brands now encompasses Gaco, GenFlex and Malarkey roofing products, as well as Elevate, the new brand name for Firestone roofing systems.
“Over the past 40 years, Firestone has built a reputation as a leader and innovator in the commercial roofing sector. And now we are making it official; we are uniting Firestone Building Products’ iconic legacy with Holcim’s future focus on accelerating green growth,” said Jamie Gentoso, Global Head, Solutions & Products, Holcim.
“As we open this new chapter of growth with star brands from Elevate to Malarkey, I am committed to contributing to our customers’ success with a rigorous focus on advanced solutions, superior quality and innovation.”
Under the new brand, the people, products and standards in the industry will remain the same. Sales representatives and distribution networks will continue to provide the same customer
service and product support. Customers will now see Elevate as the brand name on products including RubberCover, RubberGutter, PondGard, PondEasy, GeoGard and Geosmart, RubberGard EPDM and UltraPly TPO, all of which will remain in the market. The network of licensed applicators and warranties will also remain unchanged.
Holcim’s other brands in the construction industry include ACC, Aggregate Industries, Ambuja Cement, Disensa, Geocycle, Holcim, Lafarge and Malarkey Roofing Products.
Holcim employs 70,000 people globally through four business segments: Cement, Ready-Mix Concrete, Aggregates, and Solutions & Products.
Wavin has launched environmental product declarations (EPD) for its suite of products sold in the Irish and UK markets.
Based on third-party verified life cycle assessments (LCAs), EPDs transparently map production processes to resource impacts. Providing details on the environmental impact across the entire life cycle, EPDs enable building designers, planners, contractors and developers to choose more sustainable products and solutions.
Customers in the construction sector are increasingly asking for EPDs, and Wavin is one of the first companies in the sector to be able to provide these.
Commenting on the announcement, Michael O’Donohoe, Country Director, Wavin Ireland, said, “We’re delighted to be able to provide EPDs across our product portfolio to make things easier for specifiers when selecting more sustainable solutions for their projects. Our project teams are always ready to provide technical and
practical advice, and having these EPDs in place further enhances this service providing reassurance to the customer around their specification.”
Anneleen Veldhuizen, Sustainability Manager, Wavin EMEA, said that as a global business, Wavin aims to make a difference and become a worldwide leader in sustainability. By monitoring, measuring and communicating emissions and process
impacts for its products based on LCAs and EPD disclosures, Wavin can initiate continuous product improvements and production measures that contribute to lower greenhouse gas emissions.
“Providing detailed environmental information for each Wavin product marks an important milestone in realising a sustainable value chain for the European construction industry,” commented Anneleen Veldhuizen. “LCAs and EPDs offer our customers transparency and insight into the environmental impact of their construction projects. With these EPDs, we have supported various customers in selecting the best products for their projects that also have the lowest footprints.”
The EPDs that are currently available cover the majority of Wavin’s product portfolio in Ireland and the UK. EPDs for the remaining products are expected in the near future.
If you’re looking to use EPDs on your project, email projects.ie@wavin.com
requirements. Whether designing a new commercial office, assessing the impact of noise on the environment, or undertaking acoustic commissioning testing, we are committed to providing effective and innovative solutions.
“Our ethos focuses on innovation, sustainability, collaboration and knowledge,” James Cousins adds. “Our experienced consultants are committed to delivering tailored solutions. As a result, we have quickly established a foothold in the market.” Wave Dynamics’ range of services includes:
• Building acoustic design
Wave Dynamics, a consultancy specialising in acoustic consultancy, planning assessments, testing and monitoring solutions, provides services to industries that include architecture, engineering, construction, life sciences and environmental fields.
The company is led by James Cousins and Sean Rocks. They have previously worked on projects that include Cleary’s, One Lime Street, Qualtrics, AIB HSQ, Tourism Ireland HQ, HEA PPP Bundle 2, One and Two Three North as part of their portfolio.
Wave Dynamics have offices in Dublin and Wexford which service Ireland and the UK. The company’s current portfolio includes commercial office, residential, industrial, and environmental projects in Ireland, Northern Ireland, and London.
Managing Director, James Cousins says the company’s mission is to deliver highquality acoustic engineering solutions tailored to meet its clients’ individual needs.
“We achieve this by combining our technical expertise with the latest equipment and software, and we work closely with clients to understand their specific
• Acoustic testing (commercial and residential)
• Planning stage acoustic assessments
• Noise, dust and vibration monitoring
• Environmental noise assessments
• Building services noise modelling
• Industrial noise assessments
• Acoustic assessments for LEED, BREEAM and WELL
To find out more about Wave Dynamics, phone 01 912 5070, visit www.wdacoustics. com or email james.cousins@wdacoustics.com or sean.rocks@wdacoustics.com
In recent years there has been a rise in awareness of the importance of ‘building tight and ventilating right’. Ventilation goes hand-in-hand with airtightness and is particularly important when you look at the huge number of traditional buildings dotted across the country in need of repair. Older buildings with solid masonry walls often present challenges in terms of moisture and uncontrolled airflow, which can damage the building fabric and potentially lead to respiratory complications.
For Ecological Building Systems, the addition of a ventilation system to complement its range of Pro Clima Airtightness solutions was an obvious choice within its portfolio.
Ecological has partnered with Inventer, based in Germany, a pioneer in decentralised heat recovery ventilation systems since 1999.
Decentralised heat recovery ventilation systems offer many of the same benefits of a centralised system without the complexity of installing ductwork throughout the building fabric and the resulting cost and upheaval this can cause.
What sets Inventer apart from its competitors is its unique ceramic heat recovery core. The intelligent honeycomb-structured design of the core means the internal surface area consists of 80% air. As ceramic accumulates and stores heat very easily, less energy is required to warm the incoming fresh air. The result is an extremely effective low-energy method of heat recovery ventilation with an efficiency of up to 90%.
Niall Crosson, Group Technical Manager, Ecological Building Systems, comments, “As a company, we have spent many years evaluating the range of ventilation system manufacturers on the
market, and we are confident that Inventer offers the same high standard of quality products, backed up with world-class technical support. Inventer ventilation systems are perfectly suited for new builds and particularly for the retrofit market.”
The innovative technology from Inventer includes the Xenion® fan, which helps prevent the passage of external noise, as well as a patented acoustic insulation system. The IV-14 Zero, which won ‘Best Interior Product’ at the Architect’s Choice Awards, runs on a whisper-quiet fan of 10-31 dB (A). This makes it ideal for bedrooms and areas where noise is a concern.
To find out more about Inventer ventilation solutions, visit www. ecologicalbuildingsystems.com/shop-by-brand/inventer
Three new sales appointments have been made at McHale Plant Sales, appointments that chairman Michael McHale says will add significantly to the company’s sales force, with an additional appointment planned at its Birdhill headquarters.
The newcomers are Pat Egan, from Thurles, who has taken up the role of area sales manager with a countrywide brief for Komatsu forestry equipment, including harvesters and forwarder machinery sales, coupled with sales of other McHale products in counties Tipperary, Offaly and Laois.
From Carlow, Michael Doyle joined the company’s Rathcoole office on the Greenogue Industrial Estate, his role covering all products with a focus on walkin customers and used equipment sales, nationally and globally.
Niall Barry, from Kilmacthomas, has joined the company as area sales manager with a countrywide brief for sales of machine control systems and machine
attachment products that include tiltrotators and others, coupled with other product sales in Wexford, Waterford and East Cork.
McHale Plant Sales also recently announced the appointment of its business
development manager Darragh O’Driscoll to the board of directors of the company. Driscoll will be responsible for multiple projects including the company’s launch in the UK and other key projects in the business development area.
Energia has supported Fitzgeralds of Sandycove’s efforts to become more sustainable with a lighting upgrade, helping to reduce the carbon footprint of the well-known south county Dublin pub. By availing of Energia’s Lighting Solutions offering, Fitzgerald’s has replaced outdated lighting with more energy-efficient options, all while maintaining the atmosphere and character of the building. This has resulted in estimated lighting savings of 82%.
As a part of this process, Energia arranged
for an energy audit to assess light levels in place and to capture the consumption data of the business. This data helps to prepare the upgraded lighting design, as well as to calculate the predicted savings.
This upgrade is one of many steps for the team at Fitzgeralds as part of its Go Green initiative, which has included adding solar panels to the roof, developing their own herb garden for the kitchen, renewing the emphasis on recycling waste and upgrading the cold room.
Ross Sheridan from Energia said, “Fitzgeralds of Sandycove has a long history dating back to the Edwardian era, but now they are looking to the future and the steps they can take to help protect the environment for generations to come. Energia is committed to climate action, but we know that for some businesses it can be difficult to know where to start. Our lighting upgrades help businesses to find the best solution for them as well as offering encouragement to those who are taking steps towards sustainability and becoming more energy efficient.”
Fitzgerald’s manager Will Agar said, “When we bought the bar in February, one of our big priorities was to make the business more environmentally friendly. Joining Energia has helped us to do that, not only with the lighting upgrade but through the support and guidance we have received from them. The whole process was so quick and has made a big difference. We knew it would make the pub brighter, but it was important to us to have the option to dim the lights for a nice atmosphere. Energia worked with us to make sure that was a priority.”
For more information about Energia’s Lighting Solutions, visit:
www.energia.ie/business/lighting-solutions
The Murdock Builders Merchants Group has announced the appointment of Kieran Burke as CEO of Brooks Group.
With full responsibility for the leadership of the Brooks business, Kieran Burke will play a vital role in the next stage of developing the Brooks business following the acquisition of the Brooks Group by the Murdock Builders Merchants Group in August 2021.
Commenting on the appointment, James Higgins, Group CEO, Murdock Builders Merchants, said, “We are delighted that Kieran is taking up this position. Kieran’s incredibly strong knowledge and over 40 years of builders merchanting experience in Ireland, the UK and Europe will be vital as we continue our ambitious plans to grow and develop the iconic Brooks business.”
Murdock had appointed Eddie Kelly as chairman of Brooks following the completion of its acquisition in 2021.
James Higgins thanked Eddie Kelly for his interim management of the Brooks business following its acquisition. “Eddie will continue to work with our business in a non-executive role as chairman of Brooks, primarily involved in identifying strategic
opportunities for both the Brooks business and the wider Murdock Builders Merchants Group.”
Headquartered in Newry, Northern Ireland, the Murdock Builders Merchants Group was founded in 1982 by the Murdock family. As suppliers of building and related products to the construction sector, the group has continued to grow through an organic and acquisitive strategy. The group has a turnover in excess of €225m and is now the second largest builders merchanting group on the island of Ireland.
The group operates from 25 locations in Northern Ireland and the Republic of Ireland. It includes the brands Murdock Builders Merchants, Brooks Timber and Building Supplies and Kildare Building Supplies.
Brooks Group has been an institution in the Irish construction industry since its inception in the late 1700s. It returned to Irish ownership in 2021 when it was purchased by Murdock Builders Merchants. Brooks Group employs 195 people across nine branches in Ireland.
Ecocem has announced the appointment of Jennifer Dolan as its Head of People and Culture. In this role, Dolan’s responsibilities will include oversight of the company’s people strategy and objectives and evolving Ecocem’s workplace ethos and culture to support the business’ ambitious mission.
Jennifer Dolan brings over 15 years of experience in the HR industry. Prior to joining Ecocem, she held various roles leading HR programmes at technology companies, including a decade-long tenure at IT service provider Version 1.
The newly created role at Ecocem will see her develop and oversee Ecocem’s people and talent strategy, employee experience and engagement.
Jennifer Dolan’s arrival follows a series of senior appointments over the past 18 months, including Jean-Christophe Trassard as Ecocem France’s Director of Marketing Sustainable Innovation, Pat Cox as Chair, and Christian Clergue as European Standards Manager.
Donal O’Riain, founder and Group Managing Director, Ecocem, said, “As our business continues to evolve, finding and keeping the right talent and maintaining the strong yet flexible culture that has brought us this far is critical if we are to fulfil our ambition of delivering substantial reductions in cement industry CO2 emissions by 2030. Having Jennifer and her expertise on board will enable us to sustain and evolve our culture and, in turn, build a better, more sustainable future for all.”
Commenting on her appointment, Jennifer Dolan said, “This is a hugely exciting time for Ecocem. The role offers a unique opportunity to build a workplace culture centred around innovation, collaboration and changing the world for the better. As the company grows, harnessing the energy and commitment of our people and ensuring they have a clear understanding of the critical part they play in this mission is essential.”
We have a strong proven track record in the transport sector for public and private clients.
Our wide range of construction experience includes frameworks, early contractor involvement, design and build traditional works.
Projects ranging in size have been successfully delivered including motorways, local road improvements, structures, tunnels, harbours and rail work.