PLUS POWER BATTERY AND TEMPORARY POWER OPTIONS
CASE CARRYS ON HOW CASE IS GETTING AHEAD
BOBCAT DEMO DAYS
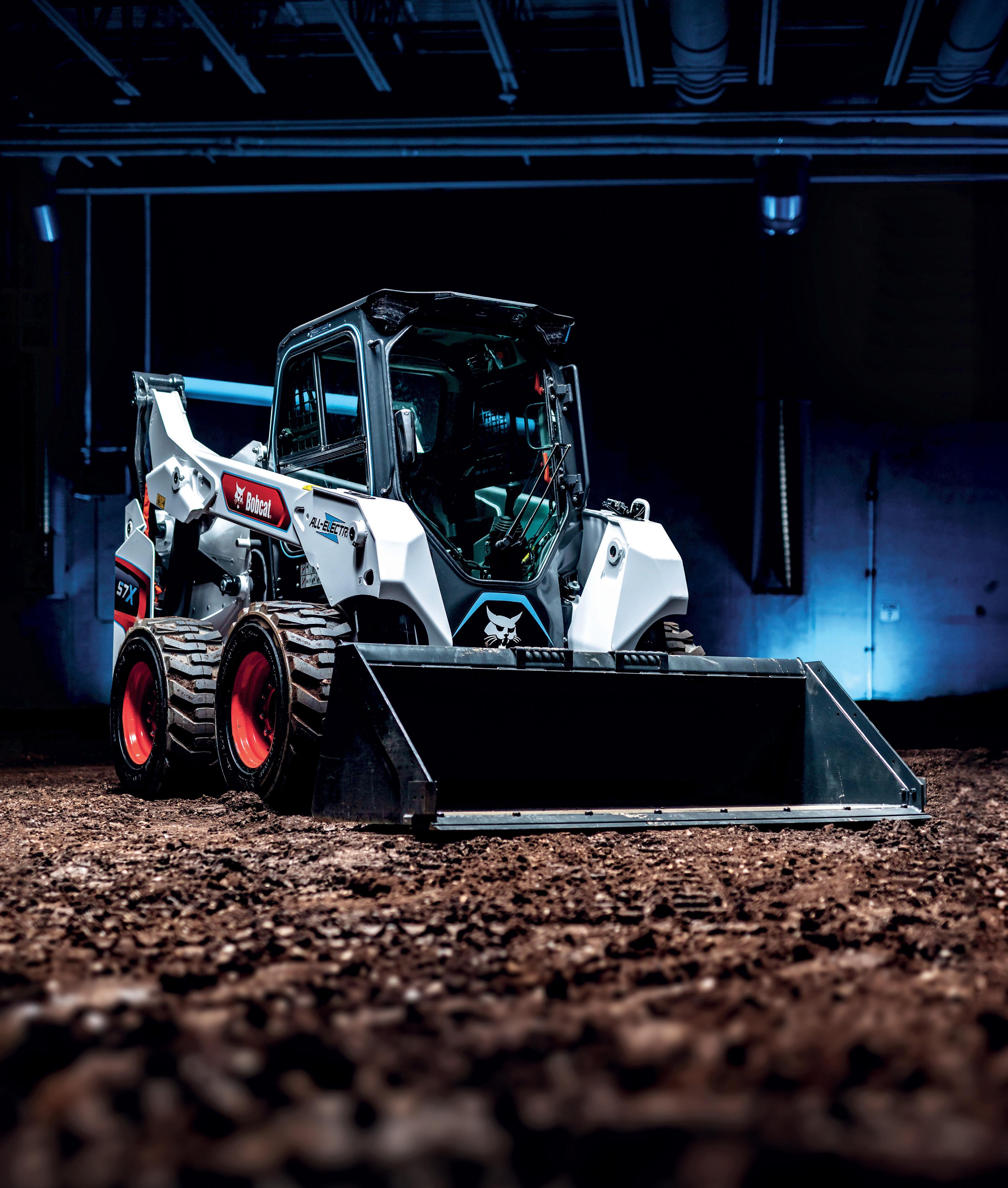
PLUS POWER BATTERY AND TEMPORARY POWER OPTIONS
CASE CARRYS ON HOW CASE IS GETTING AHEAD
BOBCAT DEMO DAYS
CMME TRAVELS TO PRAGUE TO TAKE A TRIP THROUGH BOBCAT’S PAST AND ITS FUTURE
Upgrade your fleet of on-road heavy-duty vehicles to a high performance fully synthetic engine oil with over 200 approvals
totalenergies.ae
totalenergies.ae
6_NEWS
The latest news from across the region and further afield.
12_FRONT LOADING THE FUTURE
CMME is in the Czech Republic for the Bobcat Demo Days event and a preview of its upcoming line-up.
CMME visits CASE CE’s plant in central India to learn how it is preparing for further international growth.
20_POWERED UP
CMME looks Volvo Penta’s development of new battery and power solutions for the region and beyond.
28_TOP TEN TIPS: MOBILE CRANES
How to get the most of the popular crane option and how to do it safely on site.
30_FEELING ELECTRIC
CMME looks at how the electric machinery market continues to grow in importance.
Liebherr’s electric hammer proves its worth in Sweden.
20 32
16
The Construction Machinery Awards take place next month – I really hope that you had a chance to get your vote in, it really does matter! – and one of the words that kept on coming up, was a word that I spent most of my career avoiding: innovation.
As many of you now, I’ve just moved back to Dubai after a few years of being based back in Europe and it’s been a good time to reflect on my first adventure here a decade and a half ago (time really does fly, doesn’t it!). Innovation was one of the first issues to address in one of my first meetings.
My group editor at the time, hated the word with a passion.
To him innovation was the worst type of catch-all words. It means nothing, he would fume whenever one of the staff writers or editors would dare to put it down on the page. Cue a firm line through all ten letters and a frantic search through a dictionary for the poor scribe that deemed to use it.
Seeing him angered by it was really something. This was a mild mannered and considered person who kept his cool despite what was clearly a stress-ridden job. Innovation it seemed was his way of raging back at a system that had chosen him to be in charge just when publishing switched from being about integrity to engineering ways to monetise content.
I’m sure you don’t read my comments for brief histories on media and publishing, so I won’t dwell on why that was happening, but suffice to say innovation, for him, summed up everything that had gone with his vocation. It left so many questions unanswered and unsaid about what the ‘thing’ that was innovating, it was a long word and a long way to say nothing. And what was the point of dedicating
your life to something so empty?
In the intervening years, I’ve taken a more lenient attitude towards it. Surely if someone is genuinely coming up with something new and fresh to the market, why can’t they be described as innovating? Or at least be able to bring a truly innovative product to market?
Also, the last ten years have seen remarkable progress in a huge amount of areas relating to technology. A quick whizz through this issue and you will find dozens of examples where companies are creating new machines and bringing them to market.
Often this has been done at great cost in terms of time and money, and manpower. The advent of practical electric and hydrogen power means almost every new application could be described as innovative. Thinking of the amount of effort and risk involved, I would argue that in most cases – not all – they earned the right to have the BIG I given to them. So where it is appropriate, I feel more comfortable than ever in using the word.
BUT! All revolution must come to an end. All ideas will eventually be shared and re-done. I suspect that there still may be a time when I feel the need to put the word back on the ban list. But now is not that time.
GROUP MANAGING DIRECTOR
RAZ ISLAM
raz.islam@cpitrademedia.com
+971 4 375 5471
MANAGING PARTNER
VIJAYA CHERIAN vijaya.cherian@cpitrademedia.com
+971 4 375 5713
DIRECTOR OF FINANCE & BUSINESS OPERATIONS
SHIYAS KAREEM shiyas.kareem@cpitrademedia.com
+971 4 375 5474
PUBLISHING DIRECTOR ANDY PITOIS andy.pitois@cpitrademedia.com
+971 4 375 5473
EDITORIAL EDITOR
STEPHEN WHITE stephen.white@cpitrademedia.com
+44 7541 244 377
ADVERTISING
SALES MANAGER
BRIAN FERNANDES brian.fernandes@cpitrademedia.com
+971 4 375 5479
DESIGN
ART DIRECTOR SIMON COBON simon.cobon@cpitrademedia.com
DESIGNER PERCIVAL MANALAYSAY percival.manalaysay@cpitrademedia.com
MARKETING
EVENTS EXECUTIVE MINARA SALAKHI minara.s@cpitrademedia.com
+971 4 433 2856
SOCIAL MEDIA EXECUTIVE DARA RASHWAN dara.rashwan@cpitrademedia.com
CIRCULATION & PRODUCTION
DATA & PRODUCTION MANAGER
PHINSON MATHEW GEORGE phinson.george@cpitrademedia.com +971 4 375 5476
WEB DEVELOPMENT
ABDUL BAEIS UMAIR KHAN
FOUNDER
DOMINIC DE SOUSA (1959-2015)
PUBLISHED BY The
Stephen White Editor, CMMEJCB have used their experience in designing tough, hardworking equipment to ensure their electric scissors range are also built to higher standards. With high quality paint finish and many unique features, the machines have higher levels of safety, ease of use, reliability and serviceability. Industry standard components across the range allow seamless integration into existing rental fleets. JCB also offer higher levels of support through an unrivalled dealer network with quick start guides, good parts availability, finance and technical advice.
For more information, please contact your local dealer.
www.jcb.com/access-platforms
TECHNOLOGY
Omnix to distribute structural detailing software across the GCC
ANALYSIS: Saudi Arabia is ‘single biggest hospitality opportunity’
INDUSTRY
Diyar Al Muharraq begins third phase of its internship programme
PROPERTY
Benoy unveils designs for Konoz in Riyadh
EXPERTS: Enabling the airports of tomorrow with digital twins
CONSTRUCTION
Azizi’s Park Avenue II set for Q2 completion
EXPERTS: Think globally, act locally: Delivering projects across borders
INDUSTRY
Sobha Realty announces new Co-Chairman
ENERGY
Lhyfe announces start of construction of green hydrogen facility
The plant will be located in the Triangle business park in Bessières, 40km from Toulouse
CONSTRUCTION
NBK reveals project awards in Q1 2023 in Kuwait reached $1.71bn
The acceleration was mainly due to projects in the power and water sectors, a report by NBK revealed
CONSTRUCTION
Arada announces handover of 114 homes in Aljada
The developer says that over 5,500 homes have now been completed within the megaproject
MACHINERY
Construction equipment rentals set to exceed $225bn
Innovation and growth in construction methodologies are pushing need for high-end, AI-led equipment
PROPERTY
PROPERTY
Knight Frank achieves highest-ever price for single land plot in Dubai
The company said the deal is a significant milestone for the UAE’s real estate market
INFRASTRUCTURE
Saudi’s NCP approves 200 projects under PPP model
CONSTRUCTION
Kuwait Arab Contractors wins $367mn contract for infrastructure services
INFRASTRUCTURE
RTA begins second phase of Smart Pedestrian Signals project
Sobha Realty launches ‘Sobha Reserve’ in Dubailand INFRASTRUCTURE
CUMMINS APPOINTS NEW GLOBAL OFFHIGHWAY SUPPORT OFFICER
Diriyah Company says it has witnessed its largest ever volume concrete pour in a single location to date this week at its $63bn project in Saudi Arabia.
“As the development of the Diriyah project moves forward, infrastructure progress is yielding significant success,” said the firm in a statement.
Located in the southern portion of the development contractor El Seif Engineering Construction and China State Construction joint venture poured 6100m³ of reinforced concrete for the underground Main Spine Tunnel roundabout base slab, which further connects to four adjacent tunnels.
Diriyah is set to become Saudi Arabia’s foremost historical, cultural and lifestyle destination. As part of the Kingdom’s 2030 Vision, 14 square kilometres of Diriyah will be transformed into one of the world’s foremost historic tourism destinations. Diriyah is located within Riyadh province, just 15 minutes north-west of Riyadh’s city centre.
Utilising a fleet of 75-plus concrete trucks, from five separate batching plants on site and seven pumps, the pour was completed in 21 hours, ahead of schedule due to seamless coordination between the batching plants and logistics teams.
Whilst the initial phase of the pour used external sources for concrete, the remainder was drawn from the internal batching plants on site, including those owned by other contractors, representing a truly collaborative operational partnership. The scale of this single-location pour of reinforced concrete in the Diriyah project is something that is rarely seen, demonstrating the technical capabilities of the teams involved, said Diriyah Company.
“To witness a concrete pour of this size in one location is a marvel,” says Jerry Inzerillo, group CEO, Diriyah Company.
“The scale of the infrastructure works underway across Diriyah are a reflection of the ambition and transformative power of Vision 2030’s programme for KSA.”
Cummins has appointed two new senior executives in its off-highway engine business. David Atkinson has taken on the role of global off-highway support with Phil Dawson, also UKbased replacing Annie Schmelzer as Cummins’ global agriculture segment leader. Atkinson, a veteran in the off-highway space, now has ultimate responsibility for the delivery of best-in-class customer support to Cummins’ agriculture and construction clients, said the engine-maker. A significant part of his new role will be working closely with regional teams to deliver tailored sales and post-sales support for Cummins.
ACCIONA will reduce by 40% the carbon footprint using low-emissions circular steel in the renovation and expansion of Son Sant Joan airport in Palma de Mallorca (Spain), awarded to the company last year.
One of the main materials for this project is corrugated steel, of which 7,000 tonnes will be required. ACCIONA regarded the ability to offer a low-emissions product, in line with the company’s sustainability commitments, as a decisive criterion in the selection of the supplier. CELSA Group was the chosen company to supply this material, which will have a circular and low-emissions origin.
The entire process to ensure the material’s sustainability consists of several phases. Firstly, the authorised manager in charge of the demolition and management of the ferrous waste from the old Palma airport terminal will process these metals at its facilities in the Ses Veles industrial park and supply them to CELSA Group.
Once this material has been received, CELSA Group will produce the corrugated steel using electric arc furnace technology, powered exclusively by electricity from renewable sources. Finally, ACCIONA will receive this steel and use it in the construction of reinforced concrete structural elements in the refurbishment and expansion of the new terminal. It advances circularity in the use of materials, as the steel that is obtained during demolition will return to the airport in the form of material to be used in its renovation and reduces of more than 40% of emissions in production.
Galfar Al Misnad has added a pair of Grove GMK4100L-2 all-terrain cranes through local Manitowoc dealer Mannai Trading. Galfar Al Misnad has been using Grove cranes for over 18 years, with its fleet already featuring an array of all-terrain and roughterrain cranes, said the US manufacturer in a statement. The first of the GMK4100L-2 cranes was handed over in March 2023 at Grove’s facility in Wilhelmshaven, Germany.
Anwar Sadath, head of the plant department at Galfar Al Misnad, and Kareem Ramadan, sales manager at Mannai Trading, both traveled to Wilhelmshaven to receive the new crane. After handover, the crane began its journey to Galfar Al Misnad’s newly-built plant and equipment workshop in Doha, Qatar, before deployment on its first job at Ras Laffan, assisting in the construction of a gas pipeline as part of the local
North Field Expansion Project. The second GMK4100L-2 from the order will also be sent to the same project once it reaches Qatar. The GMK4100L-2 allterrain crane is a four-axle, 100 t capacity crane that delivers both compact size and power. It has a width of only 2.55m and MEGATRAK suspension, “allowing it to manoeuvre well into and out of position on jobsites.” It also boasts the best load charts in its class, capable of carrying 6.8t of counterweight in its taxi configuration, with overall vehicle weight at 12t per axle, says Grove: “The crane is designed for efficiency, with low fuel consumption and the capability to run entirely on HVO fuel. A 60 m main boom offers a 16.0 m swingaway jib for further reach.”
“We choose Grove cranes for their reliability and durability, as well as their strong after-sales service, excellent resale value, and operator-friendly designs,” said Anwar Sadath, head of the plant department, Galfar Al Misnad.
Landscaping works at Port de La Mer have been successfully concluded according to contractor Akar Technical Services. The project is a part of the 9.5m sqft comprehensive development across Dubai’s beachfront district of Jumeirah.
According to the landscaping contractor, soft landscaping work included more than thousand trees (large and small) planted to form a green belt along the roadsides of the area, while more than 40,000 shrubs were planted across the four district zones. Approximately 50,000 ground covers and nearly 5,000 climbers/grasses were used to transform sparse spaces.
Hardscaping encompassed elements like the installation of precast concrete kerbs; porcelain paver, clay paver, clay paver banding, clay paver banding, granite banding, precast concrete pavers, precast concrete banding, granite banding, decomposed gravel, play area surface (sand), pots, shade structure and water feature.
DEYAAR APPOINTS
NEW GM FOR ITS FM BUSINESS
Adnan Jabri has been appointed as the new General Manager for Deyaar Facilities Management (Deyaar FM). The move comes as Deyaar FM expands its project portfolio and strives to set new benchmarks in service delivery, it said.
A collective fine of US $37.32mn has been imposed on 14 cement companies in the Kingdom by Saudi Arabia’s General Authority for Competition (GAC). The antitrust authority imposed a $2.66mn fine on each of the cement firms for manipulating cement prices for their own benefit, infringing Article 4 of the Competition Law. The law prohibits practices, agreements, or contracts among competing firms that lead to controlling the prices of goods and services intended for sale by increasing or decreasing them to harm the market, the authority explained.
UD Trucks MEENA and its Abu Dhabi importer Al Masaood say they have recorded a significant achievement in the UAE by ‘winning’ the Abu Dhabi Waste management Project. A highly competitive tender process supervised by Abu Dhabi municipality, Tadweer, and three subcontractors, Averda, Lavajet, and BEEAH, saw UD Trucks securing 300 out of the 420 trucks specified.
The Abu Dhabi Waste Management Project was divided into four lots, with the primary objective of improving the waste management infrastructure and services in the region. With rapid urbanisation and increasing population, waste management became important for environmental care and sustainability.
UD Trucks said it impressed the authorities meeting the highest
specifications and standards required for the project and with the most competitive value proposition. The Quester HDE11 Euro 5 with ESCOT and Croner Euro 5 with Allison gearbox with highest specifications will be used in the deal, added the Japanese manufacturer.
The firm said the victory is
significant as historically, the waste management sector in the UAE has been dominated by European brands: “UD Trucks’ success shows that our vehicles can compete with the best in the world and that they are the ideal partner for largescale infrastructure projects in our region,” it added in a statement.
Mourad Hedna, president of UD Trucks MEENA said it wants to establish itself as a leading player in the waste management sector in the GCC.
“It is a game changer for UD Trucks in the region. We are definitely growing in all segments and Euro 5 will enable us to take more space from European manufacturers. I would like to thank all functions for the fantastic cross functional collaboration: UD MEENA and Al Masaood teams, S&OP, Logistic, manufacturing, and Engineering, who supported us, because, in the challenging supply and freight situation and the diverse variants of applications, such achievement would not have been possible if it wasn’t for the true collaboration with an Extra Mile Mindset.”
The piling rig LRH 100.1 unplugged is one of the latest models in the electrically driven unplugged series from Liebherr. Fitted with a hammer H 6 of the latest generation, it has found its first jobsite in Sweden. The company Hercules Grundläggning AB is using this model to drive nearly 300 concrete piles into the ground and is very satisfied with the first performance.
“I am retiring in two years. It is very nice to operate such a machine for the last few years.” Mats Andersson operates the piling rig LRH 100.1 unplugged on the jobsite in Karlstad, Sweden and is pleased to “avoid exhaust and noise emissions, and vibrations” with it. It is the first application and endurance test for the battery-powered piling rig from Liebherr. A building complex with flats, offices and shops on the ground floor is being built in Karlstad. In order to transfer the load of the building into load-bearing soil layers, Hercules Grundläggning AB is driving piles into the ground with the LRH 100.1 unplugged. “We are installing 284 piles with sizes of 270 x 270mm and lengths between 15 and 20m.”
The LRH 100.1 unplugged excels with its large working range. A radius of up to 8.7m has the advantage that
the machine does not have to be constantly moved. The design of the leader enables inclinations of up to 18° in all directions. Furthermore, it is also possible to raise or lower the leader by 4m which makes the machine even more flexible.
For the piling work, Hercules Grundläggning used a Liebherr hammer type H 6. The hammer is modular and can be used with drop weights of between 3,000 and 6,000t, depending on requirements.
At the jobsite in Karlstad, Mats Andersson drives the piles into the soil with a 5,000t weight from a drop height of 40cm. Depending on the length of the pile, between 800 and 1,500 strokes of the hammer are necessary for each one. In only 10 to 20 minutes, Mats Andersson can lift the pile and drive it into the soil. The unplugged machines of this series do not produce any exhaust fumes and are extremely quiet. This strikes the right note especially in noisesensitive regions and finds favour with construction site personnel.
The battery is charged using a conventional jobsite electric supply. “That was no problem at all,” Andersson is pleased to say.
Operation can continue as normal while charging, the performance and range of application remains unchanged.
Kanoo Cranes offers engineered solutions for any lifting requirements with knowledgeable experts engaged in the field of lifting with Mobile cranes,Crawler cranes, Tower cranes and passenger hoists with a combined experience of more than 50 years and we continue to retain an excellent reputation alliance agreements with:
• JASO
• SMIE-Anti collision
• MEADA
• SPIERINGS
• ALBA
Our Focus is to provide engineered crane solutions to the Construction, Oil and Gas and Industrial markets.
KANOO CRANES L.L.C
P.O.Box: 290, Dubai, United Arab Emirates
info@kanoocranes.com www.kanoocranes.com
T: +971 4 446 5532 F: +971 4 446 5538
The Demo Days was a chance to try out the full range of Bobcat wheeled and tracked loaders, mini-excavators, telehandlers, light compaction products in working conditions.
“Demo Days also provides our dealers and customers with an exclusive first look at the new L35 and L40 concept machines that enables them to participate in the development process as well as provide us with their valued assessments and feedback”
This year’s Bobcat Demo Days event played host to customers, dealers and the press from all over Europe, the Middle East and Africa (EMEA), who had come to see the latest that Bobcat has to offer.
CMME was there last month to look at the US brand’s latest technology and will be digging into more detail in the coming issue, including the first look at Bobcat’s S7X, the world’s first allelectric skid-steer loader.
The event was also an opportunity to meet Joe Keller, the son of one of the two brothers that invented the original four wheel skid steer loader – which followed their even earlier threewheelers – back in the 1950s.
The event, then, was both an opportunity to get a feel for how the popular compact brand is growing and expanding – there are now more Bobcat-branded machines and equipment than ever before – but also step back into its history through the display of its first machines and by sitting for an afternoon with a man who was born the same year as his family designed and built their first loader.
But for the moment, let’s look at the here and now. Blending established products with new developments, Demo Days 2023 provided an industry unique opportunity to try out the full range of Bobcat wheeled and tracked loaders, mini-excavators, telehandlers, light compaction
products and attachments in working conditions. Bobcat was also showing how the recently acquired Doosan Industrial Vehicle forklifts and Doosan Portable Power products will look in signature Bobcat white and orange branding.
Bobcat loader portfolio expands Bobcat is showing both smaller and larger sized models in line with the company‘s commitment to become a compact wheel loader full liner in the near-future.
The new Bobcat L95 model that was previewed at Demo Days will be the next addition to the Bobcat compact wheel loader line-up, following on from the original L85 machine launched in 2021. The L95 is powered by a powerful Bobcat 75 HP engine and offers a top speed of 40 km/h and an increased lift capacity.
Like the L85, there are multiple Bobcat loader attachments approved for use on the L95. Among the new attachments are a 1.0 m3 general purpose bucket and a 1.5 m3 light material bucket and new grapple bucket and tines attachments for agriculture. Other new features include an air-ride heated seat; DAB+ radio with phone connectivity and improved automatic ride control, high flow and quick tach systems.
Alongside the L95, Bobcat was also keen to test market interest in two new concepts for its wheel loader portfolio.
At the smaller end of the range, the company was displaying a new concept machine - the
L40 – in the 2-3 tonne category. The L40 weighs less than 2.5 tonne and is designed as a powerful load and carry, applicationfocused machine. Whilst it is simple, robust, and easy to operate, the L40 is designed for heavy duty applications such as road maintenance and construction.
Bobcat was also showing the L35, a new small articulated loader (SAL) concept machine, which is an extension of the existing SAL portfolio to cover the market segment for high performance machines which are easy to transport on a trailer. The machine weight is again below 2.5 tonne, which allows easy transportation and a high lift capacity. The engine power on the L35 is 57 HP, which allows for higher travel speeds and pushing power. The L35 is designed to be a tool carrier machine with high hydraulic power available for demanding attachments such as snow blowers, sweepers or angle brooms and it is equipped with a telescopic boom as standard to ensure a higher working range.
“With the new L95 loader and the smaller wheeled loader concepts, we are once again demonstrating our commitment to offer the most complete loader portfolio in the world,” said Jaroslav Fiser, product line directorloaders for Doosan Bobcat EMEA.
“Demo Days also provides our dealers and customers with an exclusive first look at the new L35 and L40 concept machines that enables them to participate in the development process as well as provide us with their valued assessments and feedback.“
The company was also demonstrating an industry with the Super Flow system on its T86 Compact Track Loader.
One of the most exciting aspects of the
new top-of-the-range T86 compact track and S86 skid-steer loaders is that both machines have for the first time three different auxiliary flow outputs, including a new, industry unique Super Flow function taking auxiliary flow to 159 l/min.
At Demo Days, Bobcat was presenting the T86 in a forestry application that amply demonstrates the Super Flow function by equipping the machine with the new XT FRC extra torque forestry cutter. Supplied as a plug and play solution, the new forestry
cutter with 2 m width is perfect for mulching tree sections into smaller chips.
The XT FRC can even operate below grade to process mulch into the soil. Despite the power of the attachment, the compact size and manoeuvrability of the T86 allow the operator to easily move between trees and surgically cut only the damaged/unwanted tree sections.
Like the T7X, the world’s first all-electric compact track loader unveiled last year, the S7X prototype is all electric, as it is powered by a 60.5-kWh, lithium-ion battery, features electric drive motors and utilises ball screw actuators for lift and tilt functions.
Together, the battery and electrical powertrain generate incredible performance characteristics, with instantaneous torque that is as much as three times greater than traditional loaders. The powerful loader balances sustainability and performance with zero emissions and is equipped to outperform its diesel-powered equivalent.
This all-electric skid-steer loader offers operators a smooth and comfortable experience with minimal vibration and nearly silent operation.
“The S7X can operate for up to 8 hours on a single charge depending on the application, giving most operators more than a full day’s work when breaks and downtime are considered. A full charge takes approximately 10 hours,” added Joel Honeyman, VP Global Innovation, Doosan Bobcat.
In the Innovation Display at the event, Bobcat’s R&D team were showing off the Bobcat MaxControl, a system that uses the new Razer Kishi gaming controller to operate machines.
Bobcat MaxControl Remote Operation provides convenient, easily accessible remote-control operation using an app on an iPhone. As was being demonstrated at Demo Days, Bobcat has combined MaxControl with the universal Razer Kishi mobile gaming controller designed to bring console-level comfort in controlling the machine.
“At Bobcat, we like packaging complex solutions into simple and easy to use products. With this solution, one can simply enable physical joysticks for Bobcat MaxControl Remote Operation by plugging the phone into the Razer Kishi mobile gaming controller,” said Vijay Nerva, head of Innovation, Bobcat EMEA.
Arguably even more impressive was a system that seems ideal for operators that spend a lot of time in the cabin or want to full transparency on the jobsite.
“The S7X can operate for up to 8 hours on a single charge depending on the application”
Mounted on a compact loader, Bobcat showcased its T-OLED touchscreen, an advance in transparent display technology developed together with LG that gives operators the ability to touch and customise their user interface with smart widgets and interactive applications. This transparent, multifunction set-up, delivers jobsite-specific data, providing vital information and machine insights for users in real-time. Moreover, thanks to its transparent nature, operators can simply refocus their vision to see everything that is going on around them on site.
It is also obvious that the system could be used to do anything that a tablet or a phone could do assuming there is connectivity on site. The screen makes it possible to hold Zoom Meetings remotely, for example. After you’ve caught up with your latest episode of Ted Lasso.
At Demo Days, visitors could also see the Bobcat E35z electro-hydraulic miniexcavator in combination for the first time with the company’s MaxControl remote operation system. Bobcat MaxControl enables operators to control their Bobcat excavator from outside of the cab at a variety of distances using their iPhone to maximize versatility on the jobsite.
The 3.5-tonne E35z features an electrohydraulic control system rather than conventional hydraulic joysticks, meaning it can be customized and programmed to suit all levels of operator skill. Thanks to its integrated sensors, the model can perform a variety of semi-automated
tasks, helping users to conduct precise grading, levelling and trenching activities in addition to other repetitive operations such as return-to-dig movements.
While there was genuine innovation on display, perhaps the most profound session was the talk on Doosan Bobcat’s global brand expansion.
Bobcat has broadened its product portfolio significantly within the past five years, launching more machines and attachments during this period than previously in its entire
history. The brand has successfully expanded its offerings with new technologies and innovations and expanded product lines, such as compact wheel loaders, light compaction or ground maintenance equipment, including compact tractors, mowers and turf equipment.
Doosan Bobcat recently announced a new global branding strategy to create business and growth opportunities for the Bobcat product portfolio. This initiative includes rebranding of the product offering of Doosan Industrial Vehicle (DIV), a supplier of quality material handling equipment, including forklifts and Doosan Portable Power (DPP), an industry-leading global manufacturer of air compressors, mobile generators and light towers under the Bobcat brand. At Demo Days 2023, visitors could see the first products with new Bobcat trade dress that will enter the market in the near future.
The Bobcat branded forklifts were represented by the D30S-9 model, part of the 9-Series of high performance and fuel-efficient premium diesel forklifts. The ergonomic operator compartment ensures control, productivity and reduced fatigue.
Doosan Portable Power products on display at Demo Days included the new PG100 100 kVA Stage V Generator and the PL01 and PL40 lighting towers. All displayed DPP products are already using the new, simplified product naming - Compressors use the designation PA (Portable Air), Generators will use the designation PG (Portable Generator) and Lighting Systems will use the designation PL (Portable Light).
HIGHLIGHTS OF THE PRODUCT ARRAY AT THE 2023 BOBCAT DEMO DAYS
• Preview: L95 compact wheel loader
• Material handling and Portable Power products with first view of Bobcat branding
• L35 Small articulated loader
• L40 Compact wheel loader
• MaxControl with new Kishi physical remote
• S7X - The World’s First All-Electric Skid-Steer Loader
• T-OLED (Transparent Touch OLED Display) mounted on a loader cab
• E35z Electro-hydraulic MiniExcavator with MaxControl remote operation
“With the new L95 loader, we are demonstrating our commitment to offer the most complete loader portfolio in the world”
CMME was in the sultry confines of Indore last month to visit CASE Construction Equipment’s impressive and sprawling Pithampur plant. Close enough to the city to plug into all the travel links a major manufacturer needs, it is also nestled in an area with a rich agricultural heritage, much like CASE, the world’s second largest maker of farm equipment, itself.
However, this was a trip to look forwards with CASE and the perfect opportunity to find out why the state-of-the-art manufacturing facility in the heart of Madhya Pradesh is at the centre of its plans to revamp and renew its ranges and global operation.
The CNH Industrial-owned powerhouse machinery-maker is clearly confident that its 8 plants in India can help position itself in a number of segments where it is traditionally not the strongest player. During the event, CASE revealed that it has invested $6.5 million to move 4,000 of its 15,000 units annual production of skid steer production to the plant. Models moving to India cover the skid steer loader range from SR130B up to its SR210B models to cover Tier-3, including the Middle East, and Tier-5 markets.
The CMME team was also treated to firsthand experience of the advanced manufacturing processes and technologies used at the facility to produce construction equipment ranges for the global markets. Throughout, CASE presented an array of products catering to various markets with demonstrations of the 1110EX compactor, and the
newly launched V-Series backhoe loader and the CX220C LC HD crawler excavator.
“Our state-of-the-art facility in Pithampur operates to the high manufacturing standards of CNH Industrial plants across the world,” said Satendra Tiwari, Plant Head – CNH Industrial, India. “With its range of high-quality construction equipment that stands out for the reliability and durability that are the hallmarks of the CASE brand, it serves the Indian domestic market and exports to more than 75 countries. India is a global manufacturing hub and a strategically important market for CASE Construction Equipment’s growth in the region.”
The Pithampur manufacturing facility was built in 1989 and is one of the brand’s eight manufacturing hubs. Spread across 40 acres of land, the facility operates according to the company’s CNH Business
System (CBS), which involves all employees across the entire organisation to drive “greater accountability, agility, efficiency and safety.”
The plant achieves consistently high quality with its class-leading and automated production technologies, including robotic welding, laser cutting and high-precision machining. CMME saw first-hand how workers are also trained using VR and AR technologies for key jobs like welding and machine spraying. This enables CASE to skill-up its workforce before they even touch a tool.
In 2022, the plant achieved the significant milestone of manufacturing 50,000 loader backhoes. It produces a wide range of products for the global markets including India, Africa, the Middle East, the Asia Pacific region, North and Latin America. The plant also houses an important Research and Development facility to ensure that
machines go through regular upgrades and are future ready.
CMME was told on several occasions that CASE is keen to be see as not using sustainability as just a word. On product level you can see this on its electric machinery development, where it is focusing principally in the mini, compact and lighter applications, but it is also examining the way it is making its machines, often by engaging with the local construction communities in sustainable projects.
As part of its efforts to contribute to CNH Industrial’s wider sustainability goals and its aims to reduce carbon emission, the company has also installed solar panels at its Pithampur plant which helps provide up to 25% of the facility’s energy through renewable sources, CMME was told. The high-tech and high production methods being
ingrained into the workforce at Pithampur are part of gearing up at global level to prepare CASE for the challenges ahead.
“The strategy company is now to be the first to reach the places where the other competitors will arrive later,” says CASE CE’s Andrea Bernasconi. “At the beginning of 2022, we went through a very important operation, the spin-off of Iveco company from the rest of the brands. Now we have, a single company that is composed of 10 brands.
“We can say that we have four global brands that are two for agriculture, and two for construction New Holland and CASE. On top of that, we have some regional brands. The strategy of the company is to identify leaders in some sectors, often very small companies and acquire them. The most important one for the construction brand is Eurocomach (a compact equipment specialist) and we more
“India is a global manufacturing hub and a strategically important market for CASE Construction Equipment”
detail about this company. We have three segments, agricultural, construction, and financial. We can say agriculture is the big brother of the company, but in the last year, the construction business is growing. It’s progressing in terms of the number of sales, but also in terms of new products and innovation.”
Last year, collectively the group earned over $20 billion in revenue. Of it’s 42 plants, eight are located in the Africa, Middle East, and APAC region. And one of these eight is the plant in Pithampur.
“This is a key plant for our region. Here, we produce for the domestic market, but we are also exporting modern machines all over the world to more than 75 countries.”
With 2022 seeing revenue increase by 20%, Mateo Calo, head of product marketing, APAC and AMEA, CASE, adds that innovation is one of three main pillars for the brand going forwards.
“You cannot do a 20% revenue increase, if you keep doing, the same product you were doing in the past. So innovation is the key now for every company. Carbon fossil fuel is a problem going through the future. And our company has for many years worked on alternative fuel. From the CNHI family we have a FIAT powertrain and a very close relationship with the engine manufacturer for our machines. In agriculture we have products running on LNG but that’s not the only alternative fuel. We have also have products running on batteries and replacing the diesel engine. And we are the first in the world, as a construction manufacturer,
to have developed an electric back loader.”
Being the first to produce an electric back loader is clearly seen as a coup for CASE, although it is stressed it was one of the first to make the iconic machine back in 1957. Since first electric model was revealed in 2018, development has been rapid, despite the challenges it represented.
“But still, this was a big challenge because one that machine does two different applications, the front loader and the back hoe. It’s quite a complicated
machine but we have taken the challenge and succeeded,” stresses Calo, adding that the machine is the first step in a ‘journey’ towards electrification.
“It was only the first step,“ he adds. “At ConExpo in Las Vegas in March, we just launch two mini excavators alongside the electric back loaders, compact loaders and a small articulated loader. These are four different products, platforms, where we are working on electric..and already in the market and in standard production. These are not prototypes. Development is closed. It’s done.”
According to Calo, many of the brands acquired by CASE will help it take a leap in other ways beyond the drivelines of the electric equipment.
“Those brands are working to the digitalisation, as well as electrification. We understand that we cannot win the evolution or the innovation game alone. So the company is heavily investing in acquiring expertise which were not part of our family. And that’s the way we can deliver. It’s an internal process plus emerging acquisition strategy combined,” he explains. “It’s a big effort from our company. There is a lot of investment, but if you want to be committed in the industry, that’s the only way. There’s no alternative to investment and that’s what we’re doing.”
Not all of its moves have been a success, but the experience learned from them are still used to help guide other product innovations.
“We introduced the electric back loader
Designed for heavy and demanding applications, the CASE 1110EX is equally at home in road and building construction jobsites, as in mining operations. It features the proven S8000 engine developed by FPT Industrial, which has recently been upgraded to deliver more performance with a power increase of 110 hp and a massive 430 Nm of torque. The turbocharged engine delivers power with excellent fuel economy. The 1110EX is equipped with a class leading 32mm thick drum, which provides a higher weight and robustness which guarantees
maximum productivity and reliability. The 1110EX delivers an outstanding compaction applied force of 33 375 kgf: this reduces the number of compaction passes, in turn reducing fuel cost and work hours. The EX-Series compactor delivers an effective performance on every surface with its two configurations: the CASE 1110EX-D with drum drive and increased traction is ideal for slopes and landfills, while the CASE 1110EX-PD featuring drum drive and clamp-on pad foot is the perfect solution for compacting more cohesive materials such as clay and silt.
“The strategy is now to be the first to reach the places where the other competitors will arrive later”
to the US in 2018 as that was our most advanced market. And then in 2019 at Bauma we demonstrated a revolutionary wheeled loader using methane. But we didn’t bring it into the market because the space required for the tanks on the front was not working for the customers. So there are good ideas which don’t always see the light of implantation for good reason,” continues Calo.
Fortunately for CASE it is able to rely on a steady stream of innovative ideas from
its team like the so-called CASE Minotaur DL550 hybrid. The Minotaur’s C-frame blade is as big as the blade on Case’s 650M dozer. It’s a chassis-integrated six-way dozer blade, and it attaches to the DL550 via two C-shaped metal hooks. The DL550 can be outfitted with a five-shank ripper on the back for tearing up tough terrain. The new first-of-its-kind machine delivers true dozing and grading performance, as well as powerful site loading capabilities and compatibility with hundreds of
The newly launched 570V and 570SV backhoe loaders feature a brand-new cab, which is one of the largest in their class. The ROPS/ FOPS cab equipped with air conditioning (optional) and best-in-class internal storage capacity raises operator comfort and ergonomics to a new level, while retaining the excellent performance, reliability and versatility of the range. The range includes models with power of 86hp and 97hp, that can be equipped with either 2WD or 4WD axles. Both machines are fitted with a four-speed
Power Shuttle transmission that delivers great speed and drive power suitable for any worksite. Adding versatility to the mix, the backhoe loader can have either a fixed or extendable dipper arm, increasing digging reach and depth. Up front both machines are equipped with a straight loader arm providing great breakout force and excellent dump height. All these features combined with a full range of general and multipurpose buckets and forks, make the new 570V and 570SV the tools of choice.
The CX220C LC HD crawler excavator has been designed with stronger boom and arms and undercarriage structures, with increased thickness to make it suitable for the harshest application. The machine is equipped with a 6-cylinder 6.7-liter engine which delivers outstanding torque that ensures maximum power with the best fuel efficiency. This electronic engine from FPT is the perfect match with the CASE Intelligent Hydraulic
System that features 5 automatic energy saving functions that further improve machine efficiency. These functions constantly adjust the engine rpm and the hydraulic pump displacement to match the actual power requirement at any time. The powerful and reliable industrial engine ensures high productivity with low fuel consumption making the machine suitable for stone quarry, general and road construction, earthworks and mining applications.
attachments. The C-frame then can be dropped with a few easy steps, and then the machine serves as a loader with a 1.25-cubic-yard bucket — or it can be run with any of the hundreds of attachments equipment owners already have for their current loader.
“Our solution provides possibilities to store energy from and add resiliency to renewable solar or wind-powered sources, opening new business models that appeal to end customers on their road to net-zero emissions”
Volvo Penta recently announced it was targeting OEMS with its steadily evolving battery energy storage systems (BESS). A new modular and scalable update has emerged with the intention of powering manufacturers’ own BESS applications to accelerate market entry. The firm firmly believes BESS represents a step towards the company’s road to net-zero ambitions.
In a strategic move to supplement its power generation business and tap into new segments, Volvo Penta is launching a new offer – a high-performance subsystem based on the Volvo Group’s electromobility platform, optimised for OEMs’ BESS applications.
“Battery energy storage is increasingly in demand for a variety of applications including utilities, factories, decentralised microgrids and mobile charging stations,” says Hannes Norrgren, President of Volvo Penta Industrial. “As our solution is application agnostic, we see huge potential for its adoption. Together with OEMs, our solution provides possibilities to store energy from and add resiliency to renewable solar or windpowered sources, opening new business models that appeal to end customers on their road to net-zero emissions.”
The signature attribute in Volvo Penta’s modular and scalable BESS subsystem is a high-energy-density and high-power battery system with a favourable C-rating – which ensures quick and substantial charge and discharge, in response to sudden demand.
These battery systems are energy and power-optimized to meet business and operational needs. From just one, to as many units as are required for the OEM’s BESS applications, Volvo Penta’s solution is scalable up to hundreds of mega-watt hours (MWh) in energy.
Volvo Penta’s value-added systems-supplier approach ensures that its offer is deployed in a holistic way to manufacturers. The value chain, which spans from the design of the battery packs to meet safety, industry and performance standards for repeat operation, all the way to its transportability and integration into turnkey BESS applications, is secured.
“BESS will enable highly flexible energy solutions, making low to no emissions a far more viable proposition for mobile and stationary use,” adds Hannes. “We’re starting by introducing the solution to customers in North America and Europe, followed by other markets, and are eager to begin collaborating with OEMs to kickstart new projects in BESS.”
Volvo Penta’s offer is built on the Volvo Group’s electromobility platform which has seen real-world success in applications such as trucks, buses and construction equipment. In parallel, the Volvo Group is also investing in battery cell and pack manufacturing around the world to secure capacity and large-scale series production. The Volvo Penta BESS offer demonstrates high-power output from an energy-dense and small footprint. With its origins in heavyduty design, and being optimized for tough environmental conditions, the battery system is an excellent option for BESS applications.
“Volvo Penta’s engineering expertise, together with knowledge from the Volvo
Group, will be key in guiding our OEMs in developing a battery energy storage solution to meet new segment and application needs as we jointly navigate this energy transition,” says Heléne Mellquist, CEO of Volvo Penta. “The company has taken an exciting next step in its journey to visualizing and realizing an ecosystem of road-to-net-zero solutions that not only strengthen our power generation business but go well beyond into new segments.”
This ensures rapid and significant charging and discharging in response to sudden demand. These BESS subsystems are energy and power optimised to meet operational and business requirements. The solution from Volvo Penta can be scaled from a single unit to as many units as required for the OEM’s BESS applications, up to hundreds of mega-watt hours (MWh).
Norrgren, added: “Our BESS subsystems have immense potential for widespread adoption, offering OEMs the opportunity to store energy and increase resiliency from renewable sources like solar and wind. This paves the way for new business models that align with customers’ aspirations of achieving net-zero emissions. Being represented by Al Masood Power Division at Middle East Energy gave us an invaluable opportunity to showcase the evolution of our power generation business and the strength of our portfolio.”
Al Masaood Power Division recently exhibited Volvo Penta’s modular and system at the Middle East Energy (MEE) event in Dubai.
At the event, Al Masaood Power Division also showcased Volvo Penta’s latest addition to their industrial genset product line, the 200 kVA D8 Stage II engine. Combined with low noise levels, this 8-liter power generation engine strengthens the company’s robust range of industrial genset engines and boasts up to 8% reduction in fuel consumption per kWh, compared to the D7 model it replaces. The D8 is available in four power nodes: 200, 253, 303 and 326 kVA at 1,500 rpm (50 Hz) at prime power to
meet different application configurations.
“At Al Masaood Power Division, we are committed to promoting sustainable solutions and delivering optimum performance with lower emissions,” affirmed Rasso Bartenschlager, General Manager, Al Masaood Power Division.
Al Masaood Power Division has for some time been exploring a range of power options for the market, including its much-vaunted Shams+, an off-the-grid solar powered charging solution for electric equipment and vehicles. On the sidelines of MEE, Bartenschlager said that although the BESS system is an exciting new addition to its ability to offer continuous power in applications like data centres, the group is also sure that it will need to offer a wide selection of options in the market. If a fully renewable option isn’t appropriate than it is seeking to provide cleaner greener and cleaner fossil-fuel power while the market develops.
“During the three-day show, we showcased Volvo Penta’s solutions that are known for their low fuel consumption, low emissions, and low noise levels. With this, we are taking another step towards our goal of a cleaner and more sustainable power supply in Abu Dhabi and the UAE. Our focus is on outstanding service operations and the relentless efforts to address the demands of the industry and our commitment to sustainability.”
Returning to Volvo Penta, it is also continuing its work in electrifying the machinery sector. At CONEXPO it demonstrated an electrified version of Gradall’s XL 4100 V highway speed wheeled excavator. The zero-emissions
“We see Volvo Penta as a power partner rather than an engine supplier –this is a turnkey solution to them”
concept machine, named EL41H4, is on display at the Gradall Booth, W41500.
The concept machine is powered entirely by two Volvo Penta batteries, matched to the duty cycle of the excavator, which fit neatly into the existing engine bay. The electric driveline system from Volvo Penta also includes the complete high voltage system — electric motors, gearboxes, inverters, junction boxes and cabling. The partnership began in 2014 when Volvo Penta became the exclusive supplier of 5 and 8-liter Tier 4 Final engines for Gradall’s diesel-powered telescopic boom excavators. This nearly decade-long partnership made Volvo Penta the obvious choice for the company’s first step into electromobility.
“We were looking for a major power solutions provider with a good track record to partner with,” said Mike Popovich, president of Gradall. “We see Volvo Penta as a power partner rather than an engine supplier – this is a turnkey solution to them. We didn’t want to be in a situation where we’re mixing and matching from 10 different suppliers and trying to make it all work seamlessly. Volvo Penta’s full systems approach and expertise, together with proven Volvo Group technology, was the ideal solution for us. This is a natural progression of our existing partnership towards where we’re both heading in the future.”
With growing interest from Gradall’s municipality customers for quieter, cleaner solutions that meet intensifying sustainability demands and regulations, collaborative discussions between Gradall and Volvo Penta began in spring 2022.
Al Masaood Power Division exhibited some new technologies and sustainable power solutions during its participation at Dubai International Boat Show (DIBS) earlier in the year.
As the authorised distributor of MTU, a Rolls Royce Solution, and Volvo Penta in the UAE and Bahrain, the division showcased its extensive product portfolio, inhouse application and aftersales capabilities, future propulsion trends, and sustainable and green power solutions, including its MTU Yacht Propulsion Solution, which provides an end-to-end hybrid solution and Selective Catalytic Reduction (SCR) technology for the Aftertreatment
“Expanding our partnership with Gradall into electromobility is an exciting development for us,” said Hannes Norrgren. “This is our first electrification project in a construction application, representing another milestone in Volvo Penta’s electromobility journey and aligning with our sustainability ambitions.”
Unlike a traditional hydraulic excavator, Gradall’s highway speed solution features a telescopic boom mounted next to a separate cab sitting to the rear of a road-going chassis that allows the machine to be independently
System, essential for meeting the IMO Tier III regulations.
“In response to the global drive to decrease carbon emissions, we have embedded sustainability at the core of our operations by adopting innovative strategies.
dispatched to many locations throughout the workday, rather than requiring a low loader for transport.
With a hydraulic system powered by a Volvo Penta-supplied electric machine power take-off (EM PTO), this concept machine can effectively use battery power to transport its own excavator. The system will deliver 94 kWh of energy, and with the increased likelihood of the EL41H4 operator returning to the yard between jobs or for lunch, the potential is high for opportunity charging, or reaching full capacity in under 45 minutes from a 150kW charger. The unique highway speed design – and its suitability for work in environments where knuckle boom models may not be the ideal fit for operation, such as under overhead obstructions like power lines – means the concept has huge potential for application to other designs in the Gradall portfolio. Currently, the EL41H4 is still a concept machine and further testing and development is required before the next steps can be decided.
Following its appearance at CONEXPO and at the Association of Equipment Manufacturers (AEM) display in Washington, DC last month, the EL41H4 will undergo extensive testing and verification.
“At Volvo Penta, we partner with our customers and collaborate to optimize the design and adapt the complete electric driveline system for a specific vehicle, allowing us to deliver a tailored solution based on their exact usage requirements,” concludes Fredrik Högberg, president of Volvo Penta North America.”
During DIBS 2023, the division is pleased to announce the MTU in-house developed and supplied Aftertreatment systems (SCR) for diesel engines,” said Rasso Bartenschlager, GM, Al Masaood Power Division. This additional system helps to decrease harmful emissions to meet the latest IMO and EPA standards. Alongside our global partners MTU and Volvo Penta, both leading companies in the marine engine and propulsion systems industry, we are dedicated to achieving the IMO2050 Goals by exploring and creating sustainable and eco-friendly power solutions with low-carbon/ zero carbon fuels and innovative
emission reduction mechanisms.”
The division also displayed the MTU 16V2000 M96L engine with ICFN rated power of 2600 bhp @ 2450 rpm, a suitable engine for fast vessels with low load factors in applications such as fast yachts, fast patrol boats, police crafts, and firefighting vessels. The engine boasts the highest power-to-weight ratio, providing unmatched advantages.
Al Masaood invited people to experience the Volvo Penta Joystick Simulator during the show, which attracts the world’s leading yacht builders, with the yachts on display covering all shapes, styles, and genres. The event is renowned for its extravagance from seainspired art to luxury watches.
The need for power is global and it is growing. From dense urban cities to remote communities, operations and industries of all types require robust, reliable, flexible and fully integrated power systems, that are available on demand.
Cummins Power Generation has looked beyond today’s challenges to help you meet your future needs by developing the next generation of power – an ever-expanding range of power system solutions that are reliable, flexible and user friendly. Supported by next-level global Cummins sales and service support that ensures you’re covered no matter where your business takes you.
Learn more at cummins.com/generators
FOR A WORLD THAT’S ALWAYS ONTM
The latest releases from the world of construction machinery.
Ten tips to lower risks and improve safety on site. 30
Jaytrac looks at the potential for unplugging on site.
H ow the Chinese giant is using leading edge technology to find the cutting edge.
THE CRANE FOLLOWS THE LAUNCH AT BAUMA LAST YEAR OF THE 60 TONNE XCA60 EV THREE AXLE HYBRID ATC.
Chinese manufacturer XCMG has launched a new European All-Terrain crane, the 120 tonne four axle XCA120_E. The new model will be officially unveiled at the 2023 JDL Expo in France. The new crane boasts a seven section 66 metre main boom, topped by an 11.65 to 18.5 metre bi-fold swingaway extension, which can offset by up to 40 degrees.
Two 7.1 metre lattice extension sections can be added between the boom nose and the swingaway to achieve the maximum tip height of just over 96m. while the maximum working radius is 60m. The 120t nominal capacity is achieved at a theoretical 2.5m radius, at three metres radius the crane can handle 80t.
Power comes from an MTU diesel driving a 12 forward – two reverse speed ZF 12 TraXon transmission, with the three rear axles all driven, while all wheel steering is standard as is a retarder. The independent suspension system avoids the need for full width axles and is similar in overall concept to that used by Grove. The new crane has an overall width of 2.75m, depending on tyres, while the overall length is just over 14.3m.
The outriggers have up to five working widths, from fully retracted to 3.83, 5.0m, 5.9m or a fully extended seven metres. The maximum counterweight is 33 tonnes, built up from eight slabs allow for a variety of configurations.
THIS SKID-STEER LOADER OFFERS OPERATORS A SMOOTH AND COMFORTABLE EXPERIENCE WITH MINIMAL VIBRATION AND NEARLY SILENT OPERATION
Following the 2022 release of the Bobcat T7X, the world’s first all-electric compact track loader, Bobcat has now unveiled the world’s first all-electric skid-steer loader, the Bobcat S7X. Bobcat has also stepped beyond industry expectations with the unveiling of its new concept track loader, the Bobcat RogueX. This next-generation concept machine explores the capabilities of electric power, autonomous operation and dual lift-arm geometry.
“At Bobcat, we are always pushing the boundaries to explore the next leading advancements that help our customers accomplish more and propel the industry forward,” said Scott Park, Doosan Bobcat CEO and Vice Chairman. “As an organisation,
we are committed to innovating for our customers’ needs first and foremost, so that they can become more efficient, more productive and more successful.”
Like the T7X, the S7X is all electric, as it is powered by a 60.5-kWh, lithium-ion battery, features electric drive motors and utilizes ball screw actuators for lift and tilt functions. Together, the battery and electrical powertrain generate incredible performance characteristics, with instantaneous torque that is as much as three times greater than traditional loaders. The powerful loader balances sustainability and performance with zero emissions and is equipped to outperform its diesel-powered equivalent. This skid-steer loader offers operators a smooth and comfortable experience with minimal vibration and nearly silent operation. The S7X can operate for up to 8 hours on a single charge depending on the application, giving most operators more than a full day’s work when breaks and downtime are considered. A full charge takes approximately 10 hours.
8“As the inventor of the original skid-steer loader, we are excited to take the machine that created the industry and reinvent it all over again,” said Joel Honeyman, Doosan Bobcat Vice President of Global Innovation. “The S7X is an incredible product with real-world application that can support operators to the customers’ needs makes them the premier choice for a growing and evolving business.”
The S7X can operate for up to 8 hours on a single charge depending on the application
UNRIVALLED LOAD CAPACITIES AND LIFTING HEIGHTS, THE LR 1700-1.0W IS THE SUCCESSOR TO THE LR 1600/2-W
Just as the LR 1700-1.0 replaced the LR 1600/2 in Liebherr’s line-up almost two years ago, the narrow track version of the 600-tonner is now also being replaced by the new 700t LR 1700-1.0W. The company’s successful crane concept has thus been continued: Liebherr has designed a narrow crawler travel gear and a new centre section with star support for the existing slewing platform. The boom systems from the standard crane can be adopted to a large extent. At 5.9m, the crawler travel gear is only 10cm wider than its predecessor. When driving, the supports are folded forwards and backwards.
The biggest differences to the predecessor model, the LR 1600/2-W, are the new crane’s significantly higher lifting capacities and greater lifting heights. The basis for this is a more powerful basic machine as well as the 3.5m-wide H-lattice type sections in the
lower area of the main boom, which increase the lateral stability of the entire system. Comparing the longest wind-turbine boom with the derrick system on the predecessor model (156-metre main boom plus 12m lattice type fixed jib) with the new crane with the same boom length results in a 64% increase in lifting capacity (from 73 to 120t). In addition, the new LR 1700-1.0W can be built up higher: with derrick system plus 15m, without derrick system plus 6m. The new crane thus meets the more challenging requirements of working on modern wind turbines with hub heights reaching 170 metres. Liebherr also offers the LR 1700-1.0W with a luffing jib. This option was not available for its predecessor.
system is a hydraulically adjustable folding frame that allows the ballast radius of the crawler crane to be adjusted continuously between 13 and 21m. A rigid ballasting system is thus no longer required for large radii. These innovations offer great advantages, especially for wind turbine assembly. The modern lattice type fixed jib which can lift up to 170t is designed for both single and parallel operation.
Crawler travel gear with a particularly powerful and lowwear drive train
The “VarioTray” is a small counterweight frame that can be unbolted quickly and easily as required. This eliminates the need for tiresome stacking and unstacking of counterweight plates. The V-Frame ballasting
Limited rope length is no longer an issue because two winches can work simultaneously over the jib. A particularly wide hook block prevents twisting. To save weight, the whip line is integrated on the head section. Since crawler cranes – and especially narrow track models – have to cope with longer distances and inclines on wind farms, Liebherr’s designers have placed a special focus on maximising the performance of the new LR 1700-1.0W’s drive train.
SELECT THE RIGHT CRANE FOR THE JOB
Ensuring safe crane operation begins with choosing the correct crane. Cranes are either mobile or fixed, with fixed cranes generally being used in industrial settings or in complex or tall construction projects. There are dozens of crane types to choose from, including truly massive cranes, and safety starts with picking the right crane for each unique job site.
MAKE THE MOST OF QUALIFIED PERSONNEL
Safe operation of cranes demands trained personnel for setting up, rigging, signaling, and operation. Some makets have regulations in place that require only trained, certified and properly evaluated individuals to operate cranes on job sites. Make sure to adhere to all regulations to be certain that qualified personnel are being used to operate cranes at all times.
Complex lifts are any lifts that involve loads greater than 80% of crane capacity — or greater than 50% of crane capacity. It’s imperative to have a complex lift plan in place for any such scenario.
READ THE OPERATOR MANUALS
Even when employing qualified personnel, it’s important to remember that cranes from different manufacturers have unique controls, failsafe devices, and features. Anyone operating or working with cranes should have a detailed understanding of the specific crane being used. Be sure to read the operator’s manual in full before operating any crane.
A crane operator must use a daily inspection checklist to ensure the crane is safe prior to operation. These checks include pre-start checks, engine start-up checks, and safety system checks. Before starting the crane, the operator should check tyre condition, oil levels, seat belts, air reservoir, and the battery, among other things. As daily work begins, the operator should start the engine, and check the pressure gauge, fuel level, turn signals, horn, suspension, and brain system, among other things. Make sure to evaluate the anti-two block, the rated capacity limiter, and the outriggers.
Proper rigging of loads prevents objects from falling and potentially striking workers on the site. When rigging a load, take note of the hitching as it’s possible to attach slings to a load in a variety of ways, so consider the object being lifted as well as the weight distribution of the object. Whenever an angle other than vertical is used, additional forces are induced on the slings, reducing their overall weight capacity. Make sure to use slings that are properly rated.
Mobile cranes use outriggers or other stabilizing features to prevent the crane from tipping over during operation. Many crane accidents and tip-overs occur due to improper outrigger setup, so be certain that you’ve made a solid safety assessment of outrigger placement.
Prior to crane travel, it’s essential that a path is planned and cleared of all obstacles. Hazards that can’t be moved, like power lines or other permanent features, should be avoided, and the operator should keep a safe distance at all times. For instance, regulations require that cranes stay at least 10 feet away from power lines up to 50,000 volts.
Although many modern cranes include load moment indicators and rated capacity limiters, crane operators should still know how to read load charts in order to prepare for a safe lift. Load charts are the most essential tool for planning a safe lift and preventing crane failure or tip-over.
In order to safely operate a crane, it’s vital to understand how a crane works and what forces are working against it. One of the most important concepts to understand is load radius, which essentially states that the further away the load is from the center of the crane, the less weight the crane can manage without tipping over or collapsing.
Lithium-ion batteries work by a process of charging and discharging, generating an electrical current. They consist of an anode, a cathode, positive and negative current collectors, an electrolyte and a separator.
The electrolyte is conductive gel or liquid which carries positively charged lithium ions from the anode to the cathode, and vice versa. This movement takes place through the separator, a porous plastic film that separates both electrodes. Free electrons generate a charge at the positive current collector, which then flows through the machinery or appliance to the negative current collector. When all ions have been received by the cathode, the battery needs to be recharged, whereby the opposite process happens: ions are released by the negative electrode and received by the positive.
Electrical heavy machinery without a doubt offers a range of benefits, for contractors, the environment and for local people.
Equipment noise is a big factor to consider when planning your project, particularly when working in busier commercial or residential areas. Consider the fact that Volvo’s ECR25 electric excavator reduces noise levels from 93 dB to 84dB, a massive decrease in noise disruption when a 10 dB increase represents a tenfold increase in sound intensity. Diesel engines are much louder and affect not only those operating them, but also the environment and local people.
The advantage of quieter electrical construction equipment is that, while also safer and reducing the likelihood of tinnitus among users, operating hours can potentially be extended, or moved to more convenient times, such as earlier starts on hot summer days. Less noise pollution also has a positive effect on local wildlife and minimises disruption to populated habitats in both urban and rural areas.
Another benefit of electrical construction machinery over diesel counterparts is the reduction in vibration. Extreme vibration over extended periods of time can result in headaches, fatigue and back pain, leading to discomfort. By using battery powered heavy
machinery, working conditions can be optimised to offer greater comfort and increased productivity.
Battery powered construction machinery delivers a 100% reduction in exhaust emissions when compared to traditional diesel powered engines. As the only requirement is electricity, these greener alternatives contribute to international decarbonisation efforts and address the push for more sustainable industry practices from both the public and private sectors. The World Green Building Council’s 2019 report suggests that the building and construction industry can reduce carbon emissions by 40% by 2030, and can reach zero emissions by 2050. Of course, this is not a simple task, however it does highlight the potential of lithium-ion batteries as at least one solution to consider.
While battery powered heavy machinery technology is looking promising, globally it seems we are not quite ready for a full scale electricrevolution. Companies such as Volvo and Komatsu are making leaps and bounds within the industry, reflecting the fact that battery powered equipment certainly has great potential. Volvo’s well-received
‘Add Silence’ campaign, for example, highlights the comparable performance of electric equipment to the original diesel powered options, with the added benefits we have already mentioned. Coming from a slightly different angle, Komatsu are focusing their technological efforts on hybrid systems for excavators. However, the question as to whether these industry advancements are ready for a larger scale roll-out is not a simple one.
Industry wide considerations have to be made for the practicality of such machinery; where it seems that smaller machinery is headed in the right direction, larger equipment isn’t quite there yet.
While these innovations are looking encouraging, it’s only when battery powered options are as consistently accessible and reliable as traditional diesel engines that they can be confidently considered the future of heavy machinery.
Another hope are hydrogen fuel cells and their own ‘zero emissions’ properties. No harmful emissions are released by the generation of energy through hydrogen fuel cell technology; the only by products are heat and water. Cited as the ‘clean fuel of the future’, hydrogen fuel cells offer a potentially cleaner way forward within the heavy duty machinery industry, and the costs associated with handling and storing diesel fuel or toxic battery acid would not apply.
Hydrogen fuel cell technology, where used, is very reliable. It can operate at temperatures as low as -40°c with ease, not to mention its applications across all different climates. Hydrogen fuel cells can also be reliably used at scale too, whereas the likes of lithium powered batteries are limited with regards to
increasing battery capacity due to structural issues.
Hydrogen fuel cells are 40-60% energy efficient, according to US Department of Energy. Compare that to the typical internal combustion engine of a vehicle, running at typically around 25% efficiency. Hydrogen also has an energy density of 120MJ/kg,
three times greater than diesel. This means that more energy is generated per kilogram of hydrogen fuel than that of diesel, ultimately leading to cost savings down the line.
So, why aren’t we seeing more hydrogen-fuelcell-powered heavy duty machinery?
Despite the proposed advantages of hydrogen fuel cells for heavy duty machinery, the technology does have its drawbacks.
Firstly, there is the fallacy that hydrogen fuel is completely clean. While a heavy duty machine running on hydrogen fuel cell power will not release any polluting gases into the atmosphere, the cost to the environment is not free. Hydrogen is, by and large, not harvested using renewables and the process emits significant amounts of carbon dioxide.
‘Grey hydrogen’ is a term used to describe nonclean hydrogen sources, and currently fossil fuels account for 96% of hydrogen production, while ‘green hydrogen’, made using electrolysis and renewable energy only, makes up a mere 5% of hydrogen production.
Storage issues are another one of the large drawbacks concerning hydrogen-fuel-cell-powered heavy duty equipment. Hydrogen is very reactive, and ‘hydrogen embrittlement’ corrodes metals over time. This makes storage both heavy and expensive, reducing its practicality for some within the industry.
What this tells us is that hydrogen technology is far from being a perfect solution to energy within the heavy-duty machinery sector, and industry experts question whether hydrogen fuel cells are really worth it, when other options like reliable low emission diesel or battery powered options exist.
“Hydrogen fuel cells offer a potentially cleaner way forward within the heavy duty machinery industry”
In XCMG’s production base, the days of welding dust flying everywhere are long gone. Robots have replaced humans in welding operations, exemplifying the beginning of XCMG’s green manufacturing movement
Under the company’s long-term intelligent manufacturing plan, the production of XCMG loaders took the lead in the industry as early as 2012, introducing technologies such as robotic welding and automatic machine coating while integrating cloud computing, big data, and other information technologies into production. Internet access has covered 85% of production machinery and equipment.
XCMG has continued to apply big data in production, creating many industrial examples. Modern production methods, especially the application of big data, have led to significant improvements in product quality and production efficiency.
85%
Internet access coverage has reached 85% of XCMG’s production line
The core of intelligent manufacturing is to reduce costs, increase efficiency, and improve quality to improve overall production with less raw material waste, thereby reducing carbon emissions. XCMG aims to integrate people, machines, and materials; connect all aspects of production to collect data; apply the results to self-diagnose and improve production lines; and reduce waste. Access is the primary link in sustainable supply chain management.“The current market competition has changed from competition among enterprises to supply chain competition, and truly sustainable development is the only way to create a differentiated competitive advantage,” says Yang Xi, head of XCMG’s supplier inspection team. XCMG is taking the initiative to create differentiation in supply chain competition by setting green access thresholds and green procurement standards to enforce the green production of enterprises in the chain. To.achieve the goal of carbon neutrality, XCMG has formulated a series of plans, including the ‘Supply Chain Allies Emission Reduction Action’ pla. In the last five years, XCMG has cooperated with suppliers to solve the 72 issues of green production since it launched the initiative of building a green supply chain. It has achieved more than 50 million yuan in energy-saving results while motivating suppliers to recycle and reuse resources, saving more than 3 million yuan on average per year.
The smart meters for collecting data on energy-consuming equipment revealed that the instantaneous standby power of the robot is 3.13 kW, with an energy consumption ratio of 15%. We improved the automation control system and reduced it to 0.83 kW. Meanwhile, it strengthened the management of abnormal use of production power on the equipment and achieved a 17% reduction in unit energy consumption, saving over 6 million yuan per year.
With its compact design and light weight the applicators reach challenging project sites with ease. The improved LWSE hi-frequency motor and the compact control unit are also suitable for expanding to wire sawing and core drilling units, handing out a wide range of applications to construction sites.
The Demag AC 450‑7 is in a class of its own: With a carrier length of 15.99 m and an outrigger base of 8.45 m, it is as compact as a six axle crane, and yet is as powerful as some eight axle cranes. In fact, the Demag AC 450‑7 can reach lifting capacities of up to 23.7 tonnes when its 80 m main boom is fully extended, and that is without even using the SSL system. Bring in SSL, and the lifting capacity goes up to an unbeatable 37.3 tonnes.
In addition, Demag is using a new Sideways Superlift design for the first time ever in the AC 450 7 – one that makes handling and setup easier. The system can be extended with an 81 m luffing jib, and the sections of this jib can also be used to assemble fixed extensions.
Above. Ahead. Always.