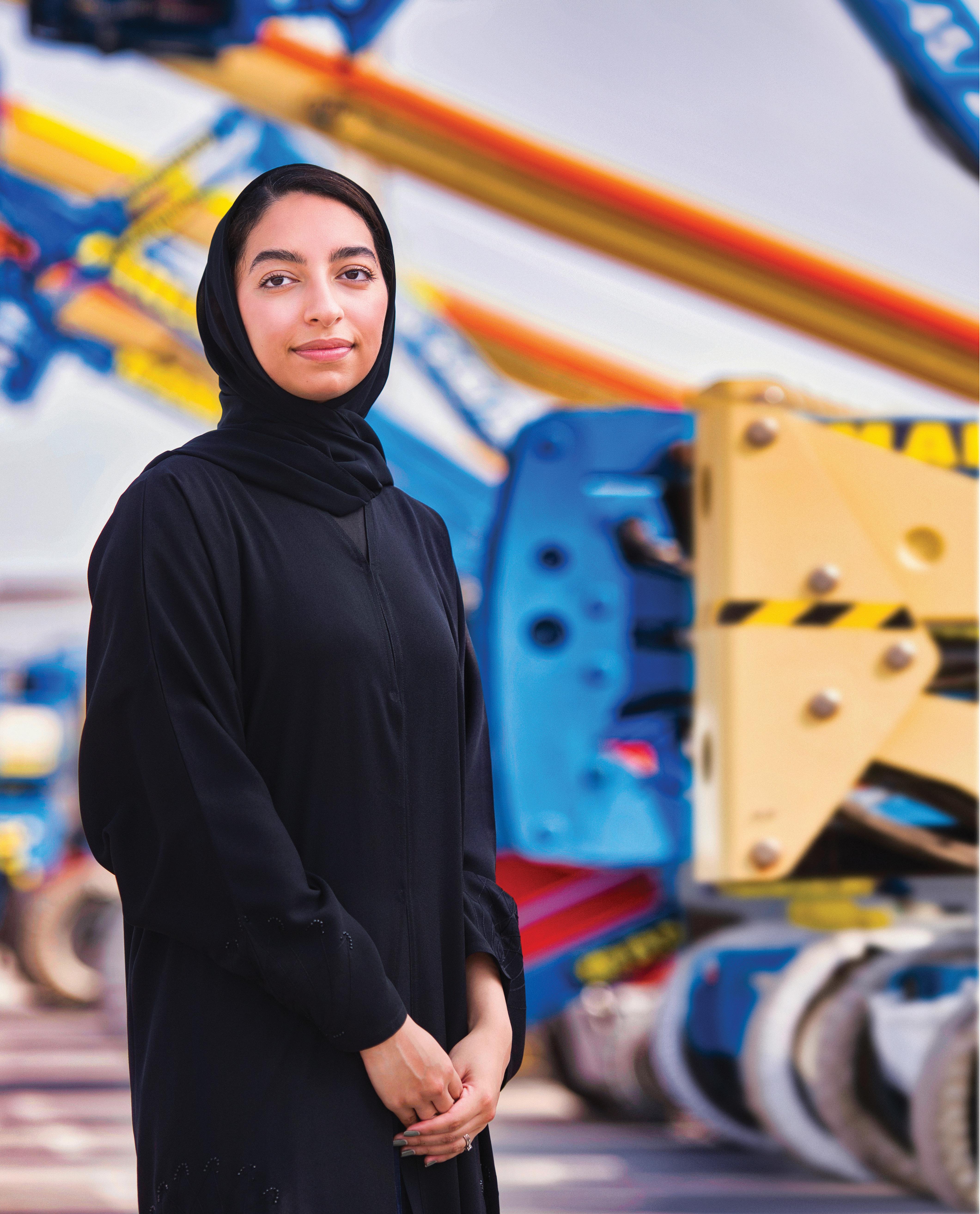
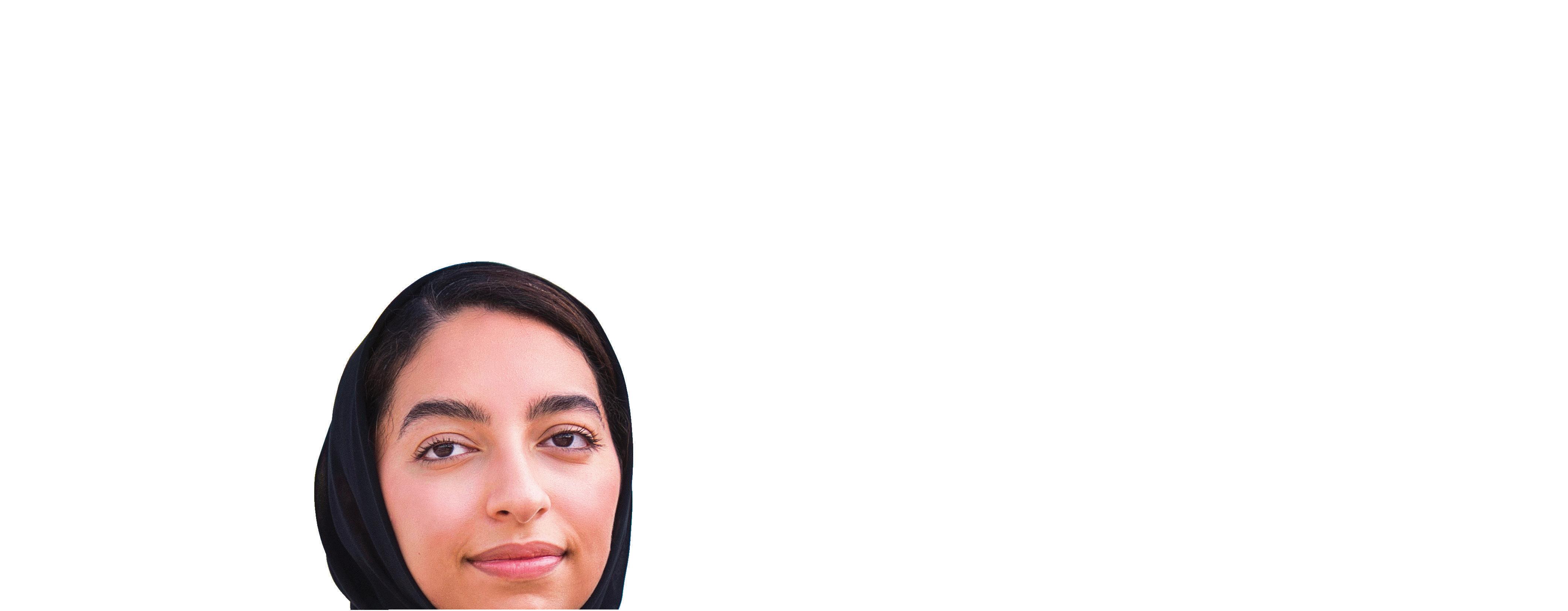
The LTM 1110-5.2 with 3 new core features: the crane control system, the driver’s cab and the gearbox. The new LICCON3 crane control system comes with large touch displays and is prepared for fleet management and tele matics. The ZF TraXon gearbox with DynamicPerform offers wear-free manoeuvring. Plus a modern crane design
the future of the all-terrain series.
By any standards a lot has happened in the three years since the world’s biggest machinery trade fair last took place. At times, during the swell of a certain pandemic I’m sure many of us questioned how long the wait would be before an event of such global appeal and mass logistical movement could again take place. Yet, the countdown has started and by now the set up of Bauma 2022 is well underway. Although the look and feel of the event this year may represent a slight separation from the norm, with the event moved from April to October and certain manufacturers choosing to stay away, the overall figures show that what hasn’t changed is the enormity of the event that makes it incomparable to anything else in this industry. In this issue, we give you a taste of what you can expect by previewing the fair through the lens of roadmaking, cranes and heavy lifting, earthmoving, access & handling, and technology and innovation. When it comes to the latter three years is a sizeable gap given the rapid advancements that technology has made in the last several years. Not to mention that this can also be considered the year that many of us have just come back down from the stay-at-home tech boom that swept us all these past couple of years. Things in the digital space have been moving quickly in all industries lately and it makes me even more excited to see how certain things have evolved from events of yesteryear. Aside from the machines themselves, new launches and a raft of new features, I am looking forward to hearing several perespectives at Bauma’s new Innovation Hall Bauma LAB0, which through keynotes, presentations and panel discussions, will provide an overview of the
trends moving the construction machinery and mining industry today.
The interesting parallel of this issue is the shift from one of the biggest shows on earth to another. Expo City Dubai officially launched this month continuing the legacy of Expo 2020 and as the transition takes shape what better time to look at another legacy; that of Expo’s High Access operations team which successfully used a new first-ofits-kind smart system for managing MEWPS on site. The superlatives of this event and this operation are wide ranging. Not only was this the largest MEWP access-controlled project in the world but playing a key role was the world’s first female Emirati IPAF operator. Having the right machine that is capable of doing the job is always supremely important but how the operation of these machines is managed and co-ordinated is just as vital, especially in such a vast operation. On this special project there were a number of lessons that could be learned and it gives me great pleasure to not only highlight these lessons but to make CMME history with our first woman to feature on the front cover.
With that being said, it’s time to get ready for the only show in town this month, which promises more broken records as manufacturers continue to push the boundaries of what is possible.
MANAGING DIRECTOR
RAZ ISLAM raz.islam@cpitrademedia.com +971 4 375 5471
VIJAYA CHERIAN vijaya.cherian@cpitrademedia.com +971 4 375 5713
SHIYAS KAREEM shiyas.kareem@cpitrademedia.com +971 4 375 5474
ANDY PITOIS andy.pitois@cpitrademedia.com +971 4 375 5473
EDITOR
MARK DOWDALL mark.dowdall@cpitrademedia.com +971 4 375 5496
SALES MANAGER BRIAN FERNANDES brian.fernandes@cpitrademedia.com +971 4 375 5479
ART DIRECTOR SIMON COBON simon.cobon@cpitrademedia.com
DESIGNER PERCIVAL MANALAYSAY percival.manalaysay@cpitrademedia.com
EVENTS EXECUTIVE MINARA SALAKHI minara.s@cpitrademedia.com +971 4 433 2856
DATA & PRODUCTION MANAGER
PHINSON MATHEW GEORGE phinson.george@cpitrademedia.com +971 4 375 5476
ABDUL BAEIS
UMAIR KHAN
FOUNDER DOMINIC DE SOUSA (1959-2015)
The publisher of this magazine has made every effort to ensure the content is accurate on the date of publication. The opinions and views expressed in the articles do not necessarily reflect the publisher and editor. The published material, adverts, editorials and all other content are published in good faith. No part of this publication or any part of the contents thereof may be reproduced, stored or transmitted in any form without the permission of the publisher in writing. Publication licensed by Dubai Development Authority to CPI Trade Publishing FZ LLC. Printed by Printwell Printing Press LLC. CPI Trade Media. PO Box 13700, Dubai, UAE. +971 4 375 5470 cpitrademedia.com
© Copyright 2022. All rights reserved.
QatarEnergy
HH Sheikh Hamdan launches Dubai Robotics and Automation Program
The development of the sector will support the diversification of Dubai’s future economy
UAE hotel development pipeline to grow to 48,000 keys by 2030
Continental launches LD-Master L5 Traction construction tyre
The LD-Master ensures high traction and durability for loaders with demanding load requirements, company says
Zāzen Properties announces new sustainability and wellness project The announcement of the project follows the handover of the developer’s flagship development – Zāzen ONE –in JVT earlier this year
CONSULTANT
“Wellness initiatives deliver commercial benefits and there are studies to demonstrate ROI for the business”
According to McKinsey & Company the global wellness market is worth about $1.5tn, with annual growth of 5% to 10%
Arada launches Masaar Discovery Centre
The new offering serves as a multiactivity community hub for the forested development project
Union Coop announces completion of Nad Al Hammar Mall
TRSDC unveils design for Red Sea Marine Life Institute at AMAALA
PROPERTY Nakheel unveils new brand focus in line with Dubai 2040 Urban Master Plan
Honouring the champions of the truck and fleet sectors, rewarding outstanding performance
Nominate now!
MACHINERY Komatsu to focus on future technologies at Bauma 2022
This summer came with a lot of surprises for the Johnson Arabia team. As the business grows a range of new battery-powered equipment was added to its fleet, enhancing both the customer service and experience the company says.
The investments included a Liebherr – LTM 1450-8.1, two MAN tractors, electric scissors (R1932, R2632, R3246, R4045), booms (450AJ, 660SJ, 860SJ, 1200SJP) and also equipment, which is new to region such as the EC600, EC450 and EC520 electric booms.
The new electric booms, which are said to have long battery life and the capability of a diesel equivalent, are in line with the rental company’s aim of having environmentally conscious machinery for projects that are trying to get LEED accreditation.
“As market leaders we constantly evaluate what our clients are hiring on a larger scale from us and what will have long term benefit to our
fleet and that is why we have decided to invest in so many new machines,” says Managing Director Martin Kirby.
Joe Keely, AWP Executive Manager adds, “As Dubai moved towards a more sustainable approach a lot of our clients were becoming conscious of emissions generated and we found out electrical AWPS were being sent out a lot more, so we had to ensure we improved our existing fleet to meet the market needs.”
The Manlift fleet expansion which includes new machinery like the E600, EC450 AND EC 520 was facilitated due to Johnson Arabia’s long-standing relationship with JLG. According to Johnson Arabia, the purchase of the Liebherr LTM 1450-8.1 was made for a similar reason of efficiency.
Mohammad Fareed, Crane Executive Manager, adds “We are pleased with our 450 tonne Liebherr which has ECOmode so that the mobile crane’s fuel consumption is reduced by up to 10% in addition to its lifting capabilities.
DAVID KOHLER AS CHAIR AND CHIEF EXECUTIVE OFFICER Kohler Co. has elected President and CEO David Kohler to the additional role of Chair of the Board, following the passing of Executive Chairman Herbert V. Kohler, Jr. on September 3rd at age 83. David will Chair the Board of Directors and Executive Committee, in addition to his role as CEO, which will include full scope responsibility for the three business groups of Kohler Co., including its power division which specialises in engines and generators.
The appointee has been with Kohler Co. for over 31 years and was elected to the role of President and Chief Executive Officer in 2015.
Weir Group will integrate vertical stirred grinding mills technology into the business as part of a new alliance with Swiss Tower Mills Minerals AG (STM), the company has announced.
Designed to improve throughput and energy efficiency, STM’s vertical stirred grinding mills for coarse grinding applications offers a low energy alternative to traditional high energy consuming tumbling mills. According to Weir, it will be integrated into a single flow sheet, delivering significant reductions in energy use, driving down costs and carbon emissions.
The technology is already well-known for energy efficient comminution in the mining market with more than 80 units currently operating in the hard rock mineral processing industry globally. It is used within the comminution segment of the minerals processing circuit as part of a series of crushing and grinding processes that create the fine particles from which minerals can be extracted through floatation.
Comminution is one of the most energy intensive parts of the mine, accounting for 25% of the final energy consumption of an average mine site. The vertical stirred grinding mills further complement Weir’s existing comminution technologies, such as Enduron® HPGRs. In a statement announcing the new alliance, Ricardo Garib, Weir Minerals Divisional President said. “Weir and STM share the same vision of enabling primary resource providers to produce resources in the most sustainable manner.”
He added: Integrating STM mills with Weir’s comminution products, which includes Enduron® high pressure grinding rolls (HPGRs) and Enduron® screens, will improve throughput and help bring substantial reductions in carbon emissions. This is a real win-win.”
NEW MACHINES, NEW OFFICES, NEW PROJECTS, NEW INITIATIVES – WE LOOK AROUND THE REGION AT WHAT’S NEW THIS MONTH
a beeping sound, the White Noise Alarm makes more of a whooshing sound which can be heard by personnel who are in direct proximity to the MEWP, but which dissipates quicker than a tonal alarm if further away, due to the technical acoustical differences in the alarm.
Show organisers Messe München have announced that the Bauma China trade show, due to be held on November 2225, 2022, has been postponed to 2024, due to the ongoing impact of Covid-19.
Genie has introduced a new White Noise Alarm that detects movement on mobile elevating work platforms (MEWPs) and is an optional fitting for Genie equipment.
The new Genie Lift Guard White Noise Alarm provides an alternative to a traditional tonal
alarm and can reduce noise emissions on jobsites by up to 45%, the manufacturer says.
Like a traditional tonal alarm, the new White Noise Alarm sounds when a MEWP travels forward or in reverse, or moves up or down.
However, instead of making
InDro Robotics has announced it has completed trials using T-Mobile 5G to remotely connect and operate its groundbased industrial inspection robots, testing security and inspection capabilities.
“On busy jobsites, personnel can become desensitised to competing warning alarms coming from a variety of equipment. However, because the White Noise Alarm makes a sound that is directional and not penetrating, it is more obvious from where the sound is coming. As a result, it is audible only to people who are near the equipment and serves as an immediate reminder to watch out,” says Bryan Williams, Genie Product Manager.
In addition to crowded job sites, the alarm can be beneficial for environmentally sensitive work areas, or for after-hours work in locations where it is important to minimise public disturbances.
It comes on the back of several lockdowns across the country in recent months as fears persist about the spread of the virus. Although global travel has opened back up, the government has continued to take a strict approach, recently encouraging people to stay put during its National Day holidays.
Bauma China, which was first held in 2002 and has grown to attract more than 3,000 exhibitors was due to be held at the Shanghai New International Exhibition Centre.
“A successful bauma CHINA with certainty for planning is our primary concern. Due to the still unforeseeable circumstances, this objective is unfortunately no longer feasible,” said Ms. Xu Jia, CEO of Messe Muenchen Shanghai Co., Ltd, in a statement.
Volvo Construction Equipment (Volvo CE) has added a host of upgrades to its zero-emissions L25 Electric wheel loader, increasing versatility, operator comfort and uptime, the company has announced. Among the new enhancements, a parallel linkage, especially suited for medium-duty cycles and pallet-handling applications, will serve as a compliment to the existing Z-type, delivering high breakout torque with the maximum speed of the L25 Electric increasing up to 20 kph. According to Volvo, noise emissions have been reduced inside and outside the cab due to a new hydraulic pump and the relocation of the main control valve to the front frame. Also on offer is a pre-warmed and defrosted cab with the new programmable cab heater option.
Two Potain MR 295 luffing jib cranes are leading the con struction of a major new building in Marseille, France, designed to transform the city’s skyline and help regen erate the waterfront area with 21,800 m² of modern office space.
Work began on the Mirabeau Tower in July 2020 and, once complete, the 85m high, 21-story office block will become one of the city’s tallest skyscrapers.
The first Potain MR 295 crane was erected on a Y800 chassis at a freestanding height of 55.8m. It will climb every month until it reaches its final working height of 85.8m, with three anchor points securing it to the building.
The second MR 295 was erected on a ZY854 chassis, which is mounted on a 15m concrete portal to give an initial free-standing height of over 31m. This crane will also climb throughout construction, eventually reaching 79.45m with four anchor points securing it to the building.
The cranes’ configuration includes AK801 anchor frames, which are being used for the first time in France on this project. According to Manitowoc, these latest generation connectors boost performance by increasing the free-standing height of the crane and minimising the number of anchor points that are required.
Léon Grosse, the contractor leading work on the Mirabeau Tower project, is a long-time user of Potain cranes. The family-owned business even owns a
fleet of around 30 topless Potain cranes with capacities ranging from 150 to 400mt, although the two MR 295 cranes the company is using on this project are on loan from Loga.
Given the particularly confined nature of the jobsite, Léon Grosse’s lifting advisor Damien Le Huec felt the Potain MR 295 luffing jib crane was the rmost suitable model for the work.
“This model has already proven itself on many construction sites,” he said. “It has a strong load curve and is adapted to the team’s needs on this specific site.”
Léon Gosse was founded in Savoie and is now a promminent player in the French construction industry. It employs 2,000 people and recorded revenue of €650m in 2021. Throughout its 140 years in business, the company has faced a range of technical and envrionmental challenges, gaining experience and skills which it will once again will use on the Mirabeau Tower project.
As part of the project and its sustainability ambitions, glass and aluminum panel facades have been desgined to change position according to the trajectory of the sun, while opaque awnings are expected to control light and noise levels to help maintaiin comfort levels inside the building. The Mirabeau Tower will also feature a marine geothermal energy cooling system, which promises 70% lower emissions than conventional cooling technology. The project is due for completion at the end of 2023.
“This model has already proven itself on many construction sites. It has a strong load curve and is adapted to the team’s needs on this specific site”
MACHINES OFFER A SAFE AND PRACTICAL APPROACH TO SOME OF CONSTRUCTION’S MOST DANGEROUS MISSIONS. CMME SPEAKS TO JOHAN EKSTROM, SENIOR
AND
SPECIALIST AT HUSQVARNA CONSTRUCTION ABOUT THE
IMPACT OF
Can you describe the trend toward remote demolition robots? How common is this becoming compared to more traditional methods and how does this improve the industry?
In the Middle East market, we are competing with old manual handheld technologyelectric, pneumatic jackhammers that are hard on the operator and extremely unproductive. In addition, these manual types of technology can cause damage to the wider structure causing issues around structural integrity and water tightness. With hi-tech productive, modern equipment such as a Husqvarna DXR demolition robot, the contractor can achieve in one hour, what 20 men could do.
As the labor cost is low it’s hard sometimes to justify expensive demolition machines, however, if you look at productivity, safety and precision it becomes a clear reason for investing in this technology. There are several benefits to using a Husqvarna DXR Demolition Robot, for example:
• Safer work environment, with the user being away from the danger zone due to the bluetooth operated remote control
• Increased Operator Health and safety due to no vibration impact as well as limited dust exposure by being away from the demolition point
• Increased speed and productivity
• Precise demolition
• No emissions, suitable for indoor applications
• Low machine weight and compact size
Our remote-controlled demolition robots are the very latest in demolition machines, featuring high power, low weight, and functional design. They are the obvious choice for users who want maneuverable yet highly powerful, stable machines with a long reach. Our DXR machines have a modern and easy-to-use remote control, with unrivalled user-friendliness and design. All this, combined with our experience, know-how, and global presence, means you are also assured of highly accessible and competent service and support.
The most popular are the DXR 305 and 145 with a hydraulic breaker enabling fast and productive demolition. As an alternative we also supply a crushing tool (DCR 300) that is used to enable silent demolition which is 50% less productive however in some applications the crushing tool is the perfect solution for demolition in areas where there are restrictions on vibration and sound.
The project types we are currently seeing are hotel re-fits, commercial repurposing to bring a more collaborative and efficient workspace and large upgrades to infrastructure projects such as airports and universities.
Can you describe the role of data and making demolition tools more connected on-site?
Husqvarna Fleet Services™ is a system that collects and presents data regarding your machine fleet. It enables you to make better decisions and unleash the full potential of your company’s productivity.
What kind of demolition projects are you seeing most of in the Middle East region in 2022?
There is a growing need for controlled demolition given that there are a large number of facilities going through renovation or re-purposing. Our DXR enables controlled demolition inside buildings given its size, enabling it to enter rooms or even climb stairs. This brings huge efficiency to the project as well as reduces the impact on the overall building or structure.
Your fleet data is generated by digitally tracking each machine’s performance, runtime and job location. All data is displayed in your Husqvarna Fleet Services™ portal for further analysis.
What are some of the most notable things that demolition clients are asking for?
• Safety – They want to be able to execute demolition work in a safe manner. We are operating the machine from distance, so the operator is safe from falling debris, dust, or other safety hassles
• No emission – This is a significant topic. In some situations, the main reason for customers buying our DXR is that they can operate with low emissions in indoor locations.
• Size – They want to be able to access tight areas where no other machinery can access. A width of just 78 cm, and the ability to run on stairs makes the DXR unique and able to access the toughest locations.
• Weight – This is an important factor when demolishing a structure. For example, when work should be done in an area that has weight restrictions, it is important for the site engineers to know the surface load per m2 and Husqvarna demolition robots are often perfect for those applications.
• Power (efficiency) – Performance is something that demolition contractors look for to ensure they have the right tools for this aggressive environment.
• Serviceability – It is very important for the operator to be able to troubleshoot on-site when technical issues happen.
Husqvarna has developed a world-class software where the operator can read on the remote control the status of the machine in easy-to-understand prompts. Furthermore, Husqvarna has a fully equipped service centre located in Dubai with trained technicians able to service all mechanical and electrical components in the machine.
Lissmac floor saws range from 10hp to 140hp and have been used for several bridge demolition jobs in the past eighteen months.
“For any demolition project, whether it be a high-rise building, villa, or bridge, the major quantum of work lies on the horizontal arrangement, - ‘The floor’”
With any new demoli tion project there are a range of challenges that determine the feasibility of the job, both commercial ly and technically. In public or priority areas restrictions on sound, vibration, and dust commonly prevent the use of
explosives forcing contractors to consider more contained methods. Controlled demolition by dia mond cutting provides an effective way to carry out tricky jobs with extremely high levels of precision and is an art that German manufacturer, Lissmac has perfected over the years, both in terms of the expertise it provides and the highly specialised dem olition equipment it produces.
“For any demolition project, whether it be a highrise building, villa, or bridge, the major quantum of work lies on the horizontal arrangement, - ‘The floor’,” says Johnson Pereira, Lissmac’s Regional Manager, Middle East and Africa. “
“We have the biggest fleet of floor saws, ranging from 10hp to 140hp to capture any extent of controlled demolition projects. In addition, our latest high-frequency wall saw and wire saw complete the turnkey project supply to demolition contractors.
The list of projects that Lissmac has worked on in the region in the last twelve months is extensive including major airport refurbishment in Dubai and several bridge demolition jobs in Abu Dhabi that required a surgical demolition method in a fast-track manner.
Although a bridge can be cut down in many ways wire sawing is one of the easiest and most efficient. Yet, as it is also one of the most expensive diamonds contractors will often choose to use a combination of wire saws, wall saws and floor saws instead, dismantling the bridge in different stages. For any job of this nature the contractor needs a structural engineer to ensure the demolition is carried out as safely and efficiently as possible. Providing
consultation on the technicalities of the operation is an important part of the service Lissmac provides.
“One of our main benefits is the experience of our people where we can go into deep detail,” says Pereira. “We don’t just sell the machine and go but we help our customer by servicing the machines if they need it, we consult with them on their projects and we make sure we have specialist people in different segments of the business.”
The manufacturer serves the region through a huge warehouse established to provide different diamonds quickly to contractors in the region. For particularly unique projects it can also design machines to do a specific job, a good example being its chimney saw, which was specially designed to demolish a 200-metre-high chimney within eight weeks. Demolition using traditional methods would have taken approximately six months.
“Lissmac machine reliability and productivity diminish and reduce idle time during project timelines. The faster the cutting machines continue to go, the more often you will see such projects in the region,” Pereira explains
“Wherever they need speed and progress our tools and machines fit in. Last year our premium range diamond wire went into a prestigious marine project in Layyah port to demolish and remove retaining seawalls and underwater piles, which was a very critical project where the cutting speed of the wire was significant to meet the deadline for the combined cycle power plant project for SEWA.”
Daniel Keller, Managing Director of Lissmac, agrees, telling CMME, “There are two trends I am seeing. First clients are looking for more efficiency so increased speed and less dust. Second is everything to do with battery and electric forward speed and drive,”
With that in mind, the company, which prides itself on its German roots and values, has been busy working on a range of battery driven floor solutions which it will showcase at Bauma, this month, reflecting the greater shift to electrification in this segment.
Keller adds: “Although it is not here at the moment we are going more and more towards a self-driven machine. Our new machines which are developed
HIGH-RISK DEMOLITION JOBS REQUIRE EXTREMELY HIGH LEVELS OF PRECISION ALONG WITH EQUIPMENT THAT CAN COMPLETE THESE TASKS IN A CONTAINED, SECURE WAY. IT IS AN ART THAT GERMAN MANUFACTURER LISSMAC CONTINUES TO PERFECT
example, a 55KW floor saw machine or a 20KW wall or wire saw can easily lead to overcrowding and unsafe situations with one or two cutting machines managed by multiple crews. A highly productive floor saw, on the other hand, can do the same job safely, and productively with one person saving health, time and money. When the user is cutting a lot of water must be used to cool the diamonds resulting in lots of slurry going everywhere. To counteract this, Lissmac have developed a live vacuum system that can suck the slurry out while cutting. In addition, it has a filtration system that is mostly used in Europe. The water goes into the filtration system and the filtered water can be pumped back into the machine six times.
“Most of our customers who use our MULTICUT range, their machine has lasted for years,” says Pereira referring to an engineering technology in Germany that considers the need to build a machine that can keep going in the long term.
and will be presented at Bauma will have all electrics inside. We can only go up to 5kw at the moment but at Bauma we will show how we can go up to 7.5kw. With battery driven we can have smaller cuts inside the building as it’s easier to come in, cut and then go as you are no longer relying on long distance cable.”
The latest developments reflect another step for Lissmac along the road of electric driven operation. Three years ago, at Bauma, Lissmac presented a prototype hybrid 3-tonne machine which normally would run on 136 horsepower but the manufacturer brought it down to 75 horsepower because the engine was able to produce electrics for the full machine – just like a generator.
“Although this was only a prototype, we learned how to sensitively steer the machine with forward speed. And what we have done now is have an automatic forward speed drive. So that means that you cut and if you come against the steel, normally you must push the machine a little harder because harder material is coming. Now the machine does that automatically. With the hydraulic machine that reaction time is often too slow but if the forward speed happens automatically, you can be a lot more efficient after that,” Keller says.
One of the other notable points, especially for specialist contractors is the weight of not just hydraulic machines but the powerpacks too. In many cases, the electric equivalent is more than half the weight vastly improving mobility, especially when contractors are working across different stories or levels. Of course, the company says it will not just focus on demolition equipment at Bauma. It also has a number of new grinding machines
which it will present for the first-time along with a range of equipment across its other core divisions of metal processing, material handling and plant engineering.
Right from the very beginning of building any new demolition machine there are various safety considerations that Lissmac says it takes into account, such as emergency stop buttons, clutches and gears. This is all for the safety of the machine and safety of the user as well.
As Pereira points out, there is also an essence of safety involved when building machines that are highly productive. For
“Not only do we have strong machines, but we come with a know-how. When a customer comes with an enquiry, we first ask what are you doing and is there any way we can help you? Finally, on the application side we are the only people in the market who have dust control systems in our floor saw machines.”
“These are our specialties,” Pereira adds, “good machines so you don’t spend money trying to fix them, technical know-how, and finally producing accessories that improves both safety and the environment.”
C M Y CM MY CY CMY K“Not only do we have strong machines, but we come with a know-how”
It was about two months in at the biggest show on earth when Lamya Alaydaroos realised that High Access was the thing she most wanted to do. Up until then she had been combining her duties of High Access Manager with that of a Facilities Maintenance (FM) manager in the Expo’s Mobility & Jubilee zones. Yet the sheer volume of requests and different operations she was responsible for was rising at such a rate that soon she would find herself at a crossroads.
The High Access team, which had a small group of three, including Lamya, John Hyatt and Darren Williams, would eventually be responsible for more than 126 machines, over 20 contractors and 500 individuals across Expo making it the largest, longest-running and most comprehensive access-controlled MEWP project in the world. And Lamya knew that to run such a vast operation successfully she needed to be all in.
“At that moment my vision was clear that High Access required a dedicated person when tasks were overwhelming and I realised we were only three people. I needed to put all my effort and time into
that. So I made a tough decision and spoke to the heads of department and said that High Access was what I wanted to do,” she explains.
Although a turning point, it was also the result of several months of preparation having joined the High Access Team as its third member in 2020 and undertaking a series of training courses such as IPAF’s MEWPS for Managers and MEWP Operator Training. It was during this time that she became the world’s first female Emirati IPAF operator, gaining the knowledge to run and manage a range of access equipment but also getting an understanding of what was required to manage a fleet operation from health and safety right down to basic communication techniques and overcoming language barriers.
“Only after that I was able to jump in to manage this team. And that took time. I remember it was only once the event had started that I was fully on board with being the manager of High Access,” Alaydaroos says.
She adds: “When I joined Expo it was 2018 in the planning phase. I joined the cleaning and waste operation, which was mainly project planning. Including policies, procedures, development of operational plans, working with the service providers
WITH THE TRANSITION FROM EXPO 2020 TO EXPO CITY TAKING SHAPE THE EVENT’S HIGH ACCESS OPERATIONS TEAM LEAVES THE LEGACY OF HAVING SUCCESSFULLY USED A NEW FIRSTOF-ITS-KIND SMART SYSTEM FOR MANAGING MEWPS ON SITE.
PLAYING A KEY ROLE WAS THE WORLD’S FIRST FEMALE EMIRATI IPAF OPERATOR, MARK DOWDALL REPORTS
“Working in fleet management and events in particular, I believe adaptability is so important because of the time restrictions we had, the manpower we had and the multiple co-ordinations we had. If there is any change in plan, we just look at the situation again and find another solution”
to deliver these plans. I never expected to get into the high access field.”
Once the team had been put in place, one of the key contributions to the overall success of the project was an idea that Hyatt had with Manlift regarding an RFID chip in the IPAF PAL card. Traditionally a PAL card is a Powered Access License for operating Mobile Elevating Work Platforms (MEWPs), Mast Climbing Work Platforms (MCWPs) or Construction Hoists (CHs). To qualify for this, operators must complete an IPAF training course and pass a test at an IPAF-accredited training centre.
Introducing the chip allowed the High Access team to separate access between the 3A, 3B and 1B equipment categories and provide a very clear means of identification of which machines could be used, in certain places on site, and by predefined groups.
Under the system, a card reader is fit to MEWPs so when an operator swipes their PAL card a green light shows up if the machine is active. Alternatively, a red flash means the machine is outside the operator’s designated group, so use is prohibited. What it doesn’t mean, as Alaydaroos points out, is that the operator is not qualified.
“We had multiple users and each user had to work in a certain zone on site. Even if they had the qualification for a machine type, if it wasn’t in their zone and machine group, they could not use it. The zones came after working with the technical
The High Access team would eventually be responsible for over 126 machines, 20 contractors and 500 individuals makiing it the world’s largest access-controlled MEWP project.
service provider. Each one of them had a zone and I had to provide each of these service providers in each of these zones. Having this system meant we could easily keep track of all our machines in each zone, and track machine utilisation. That made life easier for them as well,” she says.
With a project of this scale just getting the machines into place often involved a high volume of activity. Again, the team relied on the innovative tracking system to manage the logistics and movement of the
machines to be around their corresponding zones with four compounds on site allowing the machines to always be close to users. In fact, at its peak, High Access had about 30 different operator groups across site in its bespoke trackunit programme supplied by Manlift who were instrumental in ensuring the machines were always looked after and available to the team at a moment’s notice.
When asked to explain the importance of the aerial work platform (AWP) specialist to the project, Alaydaroos pauses for a moment, searching for the words to sufficiently describe Manlift’s continued support throughout the event.
“We are so thankful that with our agreement with Manlift we always had technicians on site and on call during the event. I think the flexibility of Manlift in meeting our demands even at the last minute was significant. We had situations where we needed a machine and would ask Manlift to assist and they always came up with a solution.”
She adds, “When we had a machine breakdown and machines had to go back to the Manlift yard they always brought back a replacement machine for operations to still go ahead. Other than that, there was the logistical aspect of machine delivery. Manlift also helped us with the truck movement across site. We had a fleet of vehicles. Around event time we had nine recovery trucks. Their job was to go to the
compound pick up a machine, drop it off and then come back and do this trip four times at least.”
During event time the High Access team always had a range of scissor lifts and boom lifts to choose from as well as the spider lifts, which were popular in certain areas because of restrictions on access and weight. For the booms, the wide scope of reach made these a highly efficient choice for most jobs. Over half the fleet was made up of electric powered machines which were charged at set points in all of the compounds for maximum utilisation.
“Because of the utilisation it was the best approach to have electric machines. As well as being more sustainable. They were less noisy and they came with non-marking tyres which prevented tyre marks on the concourses. That’s why all diesel machines had tyre covers. It’s always better to go electric,” says Alaydaroos.
Six months on from the event, Alaydaroos’ role has shifted from looking after operations to more management and audit such as adjusting the fleet according to current requirements. This month sees the official launch of Expo City Dubai as a hub for sustainability, innovation, education and entertainment, and as the transition begins to take shape there has been a noticeable reduction in the frequency of use of the MEWPS on site which has naturally led to a reduction in fleet as well. It has also given Alaydaroos some time to reflect on some of the key takeaways from running the largest accesscontrolled MEWP project in the world.
“Working in fleet management and events in particular, I believe adaptability is so important because of the time restrictions we had, the manpower we had and the multiple co-ordinations we had. If there is any change in plan, we just look at the situation again and find another solution.”
“You need patience,” she adds. “Training takes time. And then practice is as
important to be a good operator. Agility and problem solving, too. Because you may think you have a solution to every problem but when you speak to other people you realise there are better solutions to the same problem. Especially when it comes to machine selection.”
Another on-site challenge she is quick to list is communication and having clear lines of dialogue was vital to the team during event time. “We were lucky to have a team that was actually a team even
Alaydaroos says one of the key on-site challenges was communication and always having clear lines of dialogue to the team on the ground during event time.
though there were multiple companies. So at event time we worked with three sub-contractors to provide manpower. The three of them had managers and supervisors that spoke English, Urdu and Arabic too. And when needed they translated to the workers on ground.”
As technology continues to evolve there is no reason to believe that equipment tracking won’t become even more refined in the future not only allowing fleet managers to monitor with greater accuracy than ever but further improving access to the machines at almost any time.
As for her own future, she knows it will be difficult to match the experience of managing high access at the world’s premier event, but she is keen to move forward and is always searching for the next challenge.
“I have spent four years here and it has been a great growth journey and that’s just from a career perspective. It’s easy that you get comfortable in a space or environment that you are very familiar, so I am always looking to challenge myself and I look forward to seeing what the next project holds.”
“I think the flexibility of Manlift in meeting our demands even at the last minute was significant. We had situations where we needed a machine and would ask Manlift to assist and they always came up with a solution”
The Trelleborg EMR range is designed to improve productivity in critical construction applicatons through enhanced damage protection and durability.
“With heavy duty working conditions, high temperature and tough soil conditions, construction operators need to take care of every aspect of their machines, including tyres”
Firstly Yasin, can you tell us a little bit about the company and your presence both globally and in the Middle East?
Trelleborg Wheel Systems is one of the key designers and producers of innovative tyre solutions and services for agriculture, materials handling, construction and two-wheelers with a differentiated multi-brand offer and operations across five continents. Its brands portfolio includes Trelleborg, Mitas, Maximo, Cultor and Interfit as a service brand.
Boasting fourteen state-of-the-art manufacturing facilities, advanced research and development labs, field tests and sustainable product sourcing, Trelleborg Wheel Systems offers highly specialised solutions to create added value for customers and it is a partner of the leading Original Equipment Manufacturers.
Within the earthmoving industry, it is important that the tyres of the machines can withstand different surfaces. For example, rocky to soft terrain and muddy to hard terrain. In what way do you adapt your tyres specifically to the needs of each of the different types of machines that are used on these different surfaces?
Product development is driven by our customer needs and the Trelleborg brand is synonymous
with advanced technology and tyre expertise. In particular the Trelleborg EMR (Earthmover Radial) tyre range is a good example of how we adapt to a range of applications. Designed for loader, dumper and grader work, the EMR range is suitable for open pits and quarries, underground mines, landscaping, haulage as well as general construction applications. It is easily adaptable because of its multi surface tread design which delivers control and perfect grip when it’s needed the most, whether on sand, rock, gravel or soil.
In addition to this, the Trelleborg EMR range is designed to enhance productivity in critical construction applications, delivering both enhanced damage protection and durability. There are several other benefits we focus on such as longer tyre life, equal load distribution for a comfortable drive and maintaining low fuel consumption, all of which is achieved thanks to a strong radial carcass and state of the art compound.
When it comes to earthmoving tyres, it is important to understand the global classification of the different patterns and structures. Can you explain how this works and how your tyres are classified to make them more easily identifiable? Yes, we take an approach that helps our
customers immediately identify our tyres with ease. For instance, our “L“ series type tyres are categorised by number code, type and tread depth and the letter designation and number code is found on the sidewalls of tires. These are used on all size loaders and dozers in off-road applications. Most loader type tyres, because of their extremely heavy construction, are limited to very low speeds and very short haul distances, 10 km/h and 250m maximum.
In our series, the L-2 traction design tyre gives maximum traction in sand and soft soil conditions. The L-3 rock design offers good traction and rock resistance in general purpose loader operations while the L-4 rock deep tread offers excellent tyre life. Our final tyre in the series is the L-5 extra rock deep tread which offers high resistance to cutting.
When it comes to “E” Series Type Tyres, these are referred to as haulage tyres in offroad earthmoving applications. These tyres transport material over uneven surfaces at speeds under 65 km/h and short distances, up to 40km one way. The machine then returns unloaded to the loading point. These “E” series tyres are also categorised by number code, type and tread depth. The EMR range consists of eight sizes from 24 to 33 inch in ten tread pattern designs and is suitable for open pits and quarries, underground mines, as well as general construction.
Can you describe a couple of the key features of this range that make these tyres such a good fit for earthmoving machinery in the Middle East?
At Trelleborg we are continuously innovating
and exploiting cutting edge technology to anticipate customers’ needs and face new market challenges. Earthmoving machinery in the Middle East is an extremely demanding environment. With heavy duty working conditions, high temperature and tough soil conditions, construction operators need to take care of every aspect of their machines, including tyres. To face with the various type of application, our EMR range offers ten different patterns from L2 to L5, from E2 to E4 and from G2 to G5.
A good example is our recently launched EMR 1031. Here, we took on the challenge to improve earthmoving operations with the release of our newest radial tyre, the EMR1031, designed to perform on the most demanding terrain, from sand to rock or extra hard surfaces. Not only is this manufactured using a cut-resistant compound but the tyre features a premium sidewall protector for damage protection and longer tyre life, alongside a multi-surface tread design for superior traction.
In particular we developed another specific compound for haulage operation tyres: High TKPH. This compound enables all construction professionals to safely work in high temperature environments over long working cycles.
When it comes to the maintenance of equipment and parts one of the reasons this is so important is so that machine downtime is minimised which also results in increased levels of productivity. What is the most notable feature or technology in these tyres that helps maximise uptime and reduce operator costs in the long run?
The EMR1031 tyre lets earthmoving operators that work in quarries or open pits, construction or landscaping, get a firm grip on the ground, especially when they need it most. It’s just one of our premium solutions that help our customers do the heavy lifting, with ease, comfort and less downtime.
It also has a wide tread contact area which provides up to 7% more stability, with less vibration when compared to a premium competitor. Its cut-resistant compound is 20% more resistant to cuts and wear compared to standard compounds, reducing machine downtime and resulting in lower operating costs. The deep tread pattern ensures longer tyre life, enhanced grip, and boasts a selfcleaning action during use, even on sandy or muddy terrain.
To reduce environmental impact, the EMR1031 tyre comes with a retreadable casing, maximising customers’ investment in a sustainable way. Long lasting performance, firm grip, superior control and tyre damage prevention all adds up to operators improved productivity, excellent stability, and comfort they can count on in the most demanding applications.
What are some notable improvements to tyre technology in the last five to ten years and how is Trelleborg leading this change?
In recent years, tyre technology has evolved to the extent that vibration from tyres especially on rough terrain is now lower than ever. This is another area in which we have
been leading the way. In our Brawler HPS Soft Ride, for example, the new version of the Brawler solid tyre offers reduced vibration, significantly improving operator comfort and equipment-life, yet it retains the signature Brawler life performance in the most difficult of applications.
I would describe this as a solid tyre that is very tough, yet much less stiff. What this means is that users gain all the benefits of a premium solid tyre with a more comfortable ride for operators. Even at higher operating speeds it offers no loss of load-index and increased efficiency.
We can also be seen to be at the forefront of change through our Pit Stop Line which is a revolutionary solution to one of the industry’s most elusive and critical questions – how to know, with 100% certainty, when a forklift tyre is worn out and needs replacing?
We achieve this by incorporating an orange line which is embedded into the tire. It serves as an indicator that is visible on the tyre wall and is designed to reveal itself across the surface of the tyre when the rubber has reached the end of its lifetime. The new Pit Stop Line completely encompasses the European Tyre and Rim Technical Organisation (ETRTO) manual recommendations on tyre safety and enables 100% accurate tyre safety checks: a huge first for the industry. Delivering more than just better value for spend; its sophisticated design will help improve machine uptime
Range include longer tyre life, equal load distribution and the ability to maintain low fuel consumption.
and service planning. With the Pit Stop Line appearing 100 hours or five to fifteen working days before the tyre needs replacing, operators are able to plan their tyre changes in advance, totally eradicating unplanned downtime.
Pit Stop Line also offers a strong environmental benefit, enabling a dramatic reduction in waste, raw material as well as the carbon footprint associated with packaging and transportation. Replacing tyres less often means a reduced environmental impact.
Is Trelleborg planning any new updates/ additions to this series?
We are always looking at ways we can enhance the series and our latest update, the TPMS system does just that. The latest Trelleborg TPMS system, engineered for construction applications, is a cloud-based system which integrates tyre sensors with a central gateway on the machine and an online platform to fully monitor fleet operations and guarantee machine uptime.
In a competitive segment what has been the overall reception to your EMR series so far? In terms of the reaction to these tires I think you just have to look at Trelleborg’s EMR 1051 tire, which was awarded the 2021 Hevea award in the Best OTR (Off-the-Road) Tyre Category, during the closing gala for the awards organized by Europneus, at the Ifema fairgrounds in Madrid, Spain. Designed specifically for wheel loaders, the EMR 1051 tire received almost 30% of the votes from the public and judges and we are proud to once again receive a Hevea award, this time in the OTR category.
We really feel this award recognizes the excellence of our products and the continuous effort we invest in the research and innovation for all our products. This recognition of our EMR range underlines Trelleborg’s commitment to the construction sector, which requires high quality solutions and high expertise, both of which our customers have come to expect.
“Product development is driven by our customer needs and the Trelleborg brand is synonymous with advanced technology”
The
from
world
See some of the machines and technology to be highlighted at the event as the world’s largest machinery trade fair returns.
The
For the 33rd time, the world’s construction equipment manufacturers and cus tomers from all quarters will descend on Munich for a week, this month, to experience a display of dazzling innovation on a truly grand scale. Given the challenges of the last cou ple of years the return of Bauma 2022 from October 24-30, is particularly pertinent with more than 3,000 exhibitors from 58 countries and nearly 630,000 visitors from 217 countries, expected to again take part in moving for ward the needle in the global construction, building materials and mining industries.
The sheer size of the event makes it incomparable to anything else in the industry, set across a colossal 200,000 square metres of hall space and 414,000 square metres of space outdoors. The exhibition will again have 18 halls, five of which (B5, B6, C4, C5, C6) will be dedicated to construction machinery and attachments. In addition, there will be further space for this in the outdoor area north and middle. Lifting equipment is again in hall C4 and the outdoor area south while other halls have been divided into categories such as road construction, sensor technology, mining inside, construction equipment and tools, and mineral processing.
With global travel having opened up, the figures have been encouraging with 97 percent of available space for exhibition companies confirmed since the start of the year.
The numbers have given Klaus Dittrich, Chairman and CEO of show organisers, Messe München, a reason to be optimistic about the upcoming fair: “This feedback is a clear signal of our customers’ intention to take part in Bauma. In the personal conversations we have with exhibitors and visitors, we hear one thing over and over again: They are really looking forward to having face-to-face discussions and, of course, to experiencing the special atmosphere that only bauma can create.”
Although the look, and even feel, may be different to previous events having been postponed from April to October, yet again it promises to be full of exciting product development.
This year’s bauma will focus on digitalisation and sustainability, trends that are reflected in the five key topics that have been defined for bauma 2022:
• Construction methods and materials of tomorrow
• The way to autonomous machines
• Mining – sustainable, efficient, reliable
• Digital construction site
• The way to Zero Emission
“In the personal conversations we have with exhibitors and visitors, we hear one thing over and over again: They are really looking forward to having face-to-face discussions and, of course, to experiencing the special atmosphere that only Bauma can create”
In Munich, Bauma’s second-largest exhibitor, the Wirtgen Group will focus on sustainable solutions for the road construction industry while it is once again appearing at the event together with John Deere, sharing the motto: ‘The Future in Roadbuilding –Smart. Safe. Sustainable.’
Recognising that digitisation and connected system solutions are important drivers in the development of the overall road construction process chain, in the Technology Zone, the Wirtgen Group says it will be showing application-specific core “technologies of tomorrow that are already available today,” while its commitment to sustainability will be apparent in the world premieres of new products and innovations by its popular brands such as Wirtgen, Vögele and Hamm.
The Mill Assist machine control system, for example, will give an insight into sustainable and efficient machine operation in the new generation of compact milling machines from Wirtgen. With the KMA 240i cold recycling mixing plant, it is now not only possible to produce high-quality mixes from recycled construction materials, but also cement-treated base layers.
That Vögele sees green as much more than the colour of the paintwork of its machines, is clearly demonstrated by the
company’s new Dash 5 generation of road pavers. Also on show are the SUPER 1900-5(i) and SUPER 2100-5(i) Highway Class pavers and the latest generation of the AB 500 and AB 600 extending screeds.
In the future, electrically-powered HD CompactLine tandem rollers from Hamm are likely to be required whenever a contract demands zero-emission compaction. According to Wirtgen, the e-tandem rollers are the ideal solution in all areas where compaction work must be particularly quiet.
As, in many cases, low vibration levels are also specified, the compaction specialist is also presenting an e-combination roller with oscillation alongside e-vibration and e-oscillation rollers.
Ammann says their presence at Bauma 2022 in Munich recognises this new world, which is reflected in the company’s show theme of, “Sustainability. Productivity. Connectivity.”
“That is not only our focus at Bauma 2022, but our commitment on a daily basis,” says Hans-Christian Schneider, CEO of Ammann.
“Our customers increasingly need products that are more sustainable. There also is an industry need for improved digital tools and connectivity between machines and the office.”
Ammann’s large array of road-making equipment from light and heavy compaction equipment to pavers, will be showing off technologies at the fair such as digital telematic data management tool, Service Link, and the new, highly advanced continuous compaction control system for soil and asphalt compactors. ACEpro.
Notably, its new 3D Drive Compactor is a finalist for the Bauma Innovation Award. According to Ammann, this is the first vibratory plate on the market that can go in an arc, circle or turn on the spot. The number of shafts has been doubled, from two to four and are newly arranged in an X shape. The compactor also features an e-drive for sustainability with a low centre of gravity and an electronic control system.
Currently being tested in markets in the USA, Bobcat’s Quad Track concept allows the wheels of selected Bobcat skid-steer loaders to be easily replaced with four individual track pods, effectively converting them into tracked loaders.
Chosen as one of the finalists in the Mechanical Engineering category of the Bauma 2022 Innovation Awards, Bobcat quad tracks add considerable versatility to skid-steer loaders, allowing them to easily adapt to different environments. According to the manufacturer, its benefits include increased flotation, reduced ground pressure and better traction on wet ground, compared to traditional wheeled skid-steer loaders, with a smoother ride compared to two-track compact track loaders. The machine can easily be converted back to a wheeled loader, when desired.
Whilst quad tracks are a known technology, they have not been used before on skid-steer loaders, which require a track system that can withstand side-to-side movements, as well as forward and backward, which is introduced in skid-steering.
With its innovative haptic collision avoidance system, another nominee for the Bauma Innovation Award 2022, Bosch
Rexroth warns operators of excavators, wheeled loaders and other construction machinery about imminent collisions. It does this intuitively on the basis of precise surround sensing using ultrasound with the assistance function allowing for vibration on the operators’ joystick.
The type and intensity of the haptic feedback provide information regarding the distance to the object. If the machine is operated with two joysticks, the system can even indicate the direction from which
the object is approaching on the basis of which joystick is vibrating. Unlike with purely visual or acoustic feedback, the operator’s attention is virtually unaffected while working, the company says, which helps to save valuable reaction time
For higher automation levels, there is also the option of automatic braking via the electro-hydraulically controlled power brake valve from Bosch Rexroth. If the warning is not reacted to in good time, the necessary brake pressure builds up automatically. In addition, so-called “virtual walls” allow situation-specific workspace monitoring so that excavators, wheeled loaders and other construction machinery can work much more safely and productively, the company adds. Visitors to Bauma can experience haptic collision avoidance firsthand at the event further reflecting the rise of autonomy in the construction machinery industry.
German compaction specialist Weber MT will use Bauma to launch Weber Smart Assist (WSA), a system to prevent damage to machines and provide troubleshooting guidance. The system analyses signals from sensors in the machine and warns the operator of possible issues. It includes an upgraded version of the COMPATROL compaction control tool and provides useful guidance for users on cleaning and replacing air filters. The system will be launched as an option on its reversible soil compactors, the CR 6, CR 7, CR 8 and CR 9, which are in the 400 to 700 kg weight capacity range..
While a significant number of major European and North American access equipment manufacturers have pulled out of the first Bauma since the start of the Covid pandemic, including JLG, Genie, Skyjack, Haulotte, Snorkel and Niftylift, the leading Chinese access equipment manufacturers will all be at the show
Sinoboom will participate in the event with its largest-ever Bauma stand, featuring a wide range of electric MEWPs from its diverse product portfolio as well as new and upgraded slab and RT scissor lifts, articulating and telescopic boom lifts and vertical mast lifts. Its flagship vertical mast lift, the ML10EJ, is suitable for logistics, warehousing and other narrow-aisle applications. It has an 8.3 m platform height, 10.3 m working height, and 200 kg loading capacity. Its key characteristics include a retractable pothole guard, zero tailswing and almost-zero turning radius plus a removable mast assembly to allow for more convenient maintenance.
Another of the big Chinese players, Zoomlion will present a comprehensive lineup of aerial work platforms (AWP) in addition to an extensive portfolio of earthmoving, hoisting and concrete equipment. This will include
scissor lifts, straight boom and crank-type models as with multiple new energy AWPs with lithium batteries, the company says.
The manufacturer has also developed an intelligent remote monitoring and rental management system for exhibited models, providing real-time, remote monitoring of equipment conditions which according to the company enables better customer support in improving both management and operation efficiency.
One of its most popular equipment
launches is expected to be the new ZT58J Ultra telescopic boom lift. Boasting a working height of 58.8m, the four-wheeldrive unit, which can handle rough terrain will be presented alongside three new lithium-battery powered MEWPS.
From the wider access sector, Bauma 2022 is also expected to reflect the growing influence of spider lifts and low-level access Italian spider lift manufacturer, Easy Lift, for example, will launch what the company claims is the highest spider lift in the world. It’s tracked platform RA53 features a double telescopic boom and jib and has a working height of 52.4metres with a maximum outreach of 20metres, the company says.
Meanwhile, Global IoT solutions provider Trackunit will introduce its new 5G-ready, battery-powered device to connect and monitor non-powered construction equipment and accessories. The company says its new Spot 2 device offers increased connectivity and visibility of the full fleet, significantly reducing operating costs and increasing the utilisation of each machine in real-time.
“This is very much in alignment with the Eliminate Downtime movement, as it cuts down on inefficiency and contributes to making construction a better, more useful industry,” said Lærke Ullerup, Chief Marketing Officer in a statement announcing the launch its latest technology.
At Bauma 2022, heavy-haul specialist Goldhofer will be aiming to provide next generation solutions on how a wide range of heavy haul operations can be handled reliably, sustainably and on a cost-effective basis. The highlights from a cross-section of its exhibits will be a completely new vehicle concept: the FT SERIES, which the company says provides “outstanding operational flexibility,” combining “simple handling with the versatility needed to meet a wide variety of transportation needs.”
In Munich, Goldhofer will also present the latest addition to its STAR family: the TRAILSTAR, which was recently unveiled at IAA Transportation while another big attraction will be a further model from the STEPSTAR line: the new force-steered STEPSTAR Z.
“This much can be revealed: With our FT SERIES all customers will get exactly the transportation solution they need. What’s more, a retrofit-friendly design is the key to extremely flexible and future-proof working, so that customers can configure their fleets on a variable basis for many years to come,” says Goldhofer CEO, Matthias Ruppel.
In the run-up to Bauma 2022, Tadano has announced a large-scale innovation campaign with a wide range of products and offerings that is in line with its One Tadano strategy which started with the integration of Demag into the Tadano Group in 2019.
One of the major initiatives that Tadano has taken since then was the recent launch of the Tadano AC 2.040-1 all-terrain crane, which is the first all-terrain crane jointly developed by Tadano’s Lauf and
Zweibrücken locations in Germany and the very first member of the future Tadano AC family.
“That’s why this market launch is really special for us – after all, the new AC 2.0401 is the first crane to combine the best of our two worlds with the know-how from Zweibrücken and Lauf,” says Dr. Frank Schröder All Terrain Crane Product Line VP.
All future models will share the same DNA with a standardised crane control system, cab, on board diagnostics, telematics, and
Goldhofer will display a crosssection of exhibits including the FT SERIES which has been designed to meet increased versatility needs in heavy transportation.
many other technologies, Tadano says. Tadano says it is on schedule to fulfill its 2021 announcement that it would be launching 15 new cranes in the coming years, with its exhibit at Bauma planning to reflect this rapid progress.
“Our OneTadano transformation process is going as planned, and it’s something we’ll get the chance to show everyone at Bauma,” says Tadano Faun GmbH and Tadano Demag GmbH CEO Jens Ennen.
Visitors to Bauma 2022 will see several new Grove all-terrain cranes in public for the first time. Both the GMK5150XL and Grove GMK5120L are expected to be popular exhibits at the Manitowoc booth.
“In recent years, Grove has led the way in the five-axle all-terrain class and these two new models raise the bar. Their outstanding taxi crane features, strength, and reach redefine what’s possible with a five-axle machine in the capacity classes of 120 t and 150 t,” says Andreas Cremer, vice president of product management for mobile cranes at Manitowoc.
The GMK6400-1 all-terrain crane, which was launched virtually at Conexpo 2020, will also be introduced as an upgraded version of the GMK6400. Like its predecessor, it has a 60-metre main boom but comes with new technological features such as increased hydraulic oil flow for faster operation and smoother movements and Crane Control System (CCS) to help optimise performance.
Comansa, meanwhile, has announced it is expanding its range of luffing jib cranes with the launch of the LCH300, its first hydraulic model, at the machinery trade fair. According to the manufacturer, the new addition has a maximum load capacity of 16t and reach of 60m, and is available in several versions: embedded, supported on bases of six or eight metres and movable.
Easily the most recognisable machinery in any construction site because of their size and significance, earthmoving equipment can be found across a whole host of applications in the construction industry. This segment will have some notable absentees at Bauma, this year, as some of the major manufacturers have decided not to travel while Caterpillar will be represented at the trade fair by its local German dealer, Zeppelin. Yet, throughout the week there will be several exciting product developments on display across a range of earthworks including laying foundations, grading soil, removing dirt and rocks, digging trenches and demolition works.
A true heavyweight in the earthmoving sector, Komatsu will be using Bauma to focus on future technologies in response to the rising concern for global climate change, the manufacturer says.
According to the manufacturer, event attendees will get a first look at upcoming innovations in Komatsu wheel loaders through an exclusive virtual stand while its Earthbrain technology will show a new way of working, with unique solutions to support companies in the construction sector.
As part of its line-up at the event, Komatsu will display a range of electrified machines
Caterpillar will be represented by its German dealer Zeppelin and will feature more than 70 pieces of Cat equipment and attachments.
including a fully electric, remote-controlled mini excavator that was announced as a concept machine last year. Among the other highlights will be the PC01E-1 electric micro excavator introduced to the Japanese market, earlier this year, as well as a threetonne class electric mini excavator, which is a model change of the PC30E-5 introduced to the Japanese market in March 2021.
With Caterpillar not travelling it will be
represented by its German dealer, Zeppelin, in an exhibit under the theme “Let’s Do The Work,” which will feature more than 70 pieces of Cat equipment and attachments inside and outside hall B6 at the venue.
The manufacturer has said that several different model platforms will be on display – from XE models built for performance with the latest technologies and advanced drive systems to GC models designed to deliver rugged reliability and value. Other highlights include nine next generation Cat mini hydraulic excavators for increased performance and higher breakout forces compared to prior models.
Among the exhibited compact wheel loaders, attendees will see the recently introduced Cat 906, 907 and 908 (in a highlift configuration) models. These feature a re-engineered operator’s station that leverages exclusive Caterpillar technologies to improve operator experience and the new Cat 2.8 engine with an upgraded drive and powertrain for faster roading speeds and drivetrain performance.
Bauma will be one of the highlights of Hitachi’s 50th anniversary celebrations at which the company will present a specially selected line-up of new machines to showcase its leading technology. The new models on display at the trade fair will include amongst
others: the first Hitachi zero-emission batterypowered excavator in Europe (the ZX55U6EB); the smallest Hitachi wheeled excavator (the ZX95W-7); a special ZX210LC-7 medium excavator customised with 3D machine control system and new machines (a ZX390TC-7 and a ZX400MC-7) that are specifically customised for demanding demolition projects.
At Bauma 2022, the manufacturer will also be shining a spotlight on its lifecycle offerings as a first-choice solutions provider, highlighting its range of after-sales services that help to reduce lifecycle costs, improve safety and increase productivity on site.
In addition, further representing the shift to digitalisation HCME will showcase its suite of digital construction solutions which the company says, “combine to lower the total cost of ownership” of a machinery fleet.
The new S86 R-Series Skid-Steer Loader and T86 R-Series Compact Track Loader will be on show for Bobcat replacing the previous 700 and 800 M-Series loaders and completing the current R-Series loader lineup. Delivering a higher engine and hydraulic output, the company says that the Bobcat S86 and T86 are the most powerful compact loaders the company has ever built. The machines both use a well-proven Stage V compliant 3.4 l Bobcat engine – producing 78 kW (105 HP) at 2600 RPM.
One of the most exciting new aspects of the S86 and T86 is that both machines have for the first time three different auxiliary flow outputs. There is a standard flow configuration providing 87 l/min for applications such as load and carry, or where low hydraulic flow attachments are used. Bobcat also offers two additional hydraulic performance functions using the new Electronic Displacement Control (EDC) Pump: a High Flow function giving 138 l/ min and a new, industry unique Super Flow function taking auxiliary flow to 159 l/min.
SANY will be another one to focus on electric technology when it debuts its new electric mini excavator in the 1.8t class at the trade fair. The company has announced that in addition to the traditional excavator portfolio, SANY will have wheel-loaders, telescopic handlers, road construction machinery and cranes all on display. The exhibit will include both its SW305 heavy-duty wheel loader as well its STH1440 and STH1840 telescopic handlers.
The SY19E mini excavator comes equipped
with an electric motor that delivers a peak output of 15 kW and a battery pack said to last one working day on a single charge. According to the company, it impresses with its high-power density and long service life, plus permanent charging to 100% does not affect its longevity. Other highlights are the short charging times and flexibility as charging is possible at either a fast-charging station via DC (direct current) in 1.5 hours, at a public AC charging station in 2.5 hours, or overnight at a 220-volt socket.
Doosan will launch its new 4x4 articulated dump truck (ADT), as part of several world premieres at Bauma 2022, the company has announced.
Complementing the company’s standard range of 6x6 ADT models, the company says the new 4x4 version of the DA45-7 ADT is intended to compete with rigid dump trucks (RDTs) in the 40-tonne class. The current market-leading range of Stage V compliant 6x6 ADTs from Doosan includes the DA30-7 and DA45-7 models with payloads of 28 and 41 tonnes, respectively.
In the new 4x4 ADT, the front truck and cab unit is the same as in the original 6x6 model, with modifications being made on the rear dumper unit only. Featuring a ZF EP8-420 transmission, the 4x4 DA45-7 is a two-axle ADT with twin wheels at the rear, and with a dumper section similar to that on RDTs in the 40-tonne class.
According to the manufacturer, the new 4x4 DA45-7 ADT has a width of less than four metres to avoid the need
for special transportation and offers a better turning radius than a comparable RDT, providing particular advantages in the mining and tunnelling industries.
“With superior operation on poorer roads, smoother surfaces and steeper terrain, the aim of our new 4x4 machine is to challenge RDTs in the 40-tonne class, by providing a dumper product that delivers much more than RDTs,” says Beka Nemstsveridze, ADT Product Manager at Doosan.
He adds, “The development of our 4x4 ADT was inspired by customer demand and the new 4x4 ADT can meet the needs of markets around the world by offering a compelling advantage to customers with specific requirements. For example, a machine like this might be able to extend the season for a mine that normally has to be stopped for a certain period due to the rainy season,”
in southern Africa, the UK and Australia. Construction and bulk earthmoving contractors involved in roads, dams, airports, landfills and development projects are also large users of ADTs. Together these areas make the ADT market a wide and varied one, ensuring a large customer base in this segment.
The new 4x4 DA45-7 ADT has been developed at the Doosan ADT plant located in Elnesvågen, near Molde in Norway.
41According to Doosan, its key advantages include having the ability to climb up bigger inclinations than equivalent RDTs, performing better than RDTs in wet and slippery conditions, working without stop in heavy rain, operating effectively on compact sites and causing less ground disturbance than 6x6 configurations.
The DA45-7 model has a payload of 41 tonnes
The tunnelling industries are growing markets for ADTs, and include pioneering, short-term mining projects, quarrying and contract mining industries, especially those
In addition, the company says the new Doosan Stage V 4x4 ADT provides excellent load carrying performance, fuel efficiency, controllability and high operator comfort together with improved reliability, durability and reduced maintenance and servicing costs.
For the first time TML will present at Bauma the new, fully remotely controlled mobile machine UNIDACHS 430RK.
The special kinematics of its 360° endlessly rotating telescopic boom and its compact dimensions allows the machine to work in confined spaces or in areas with difficult access, the company says, while the operator works at a safe distance using the radio remote control.
TML has developed the new UNIDACHS 430RK for job sites where the available space, surrounding structures or dangerous conditions make work difficult. The “RK” in the product name stands for “Remote” and “Knickgelenk” (articulated joint): all the machine’s functions are remotely controlled,
the additional cradle mount for the telescopic boom makes it possible to work over a particularly large working area even in a confined space.
The attachments such as pneumatic or hydraulic hammers, ripper tips, rotary drum cutters as well as various types of excavator buckets can be moved in up to five axes simultaneously.
According to the company, they can be used in the roof and side wall areas, underneath the machine or in confined spaces, at almost any angle.
Typical applications are profiling tunnel cross-sections, the excavation of caverns and galleries, the precise linear scaling of roofs and walls in mines and tunnels. The telescopic arm can also be fitted, for instance, with spray nozzles for liquid concrete as well as drilling attachments and tools for setting arches and anchors.
Thorsten Bolender, Sales Manager Tunnel & Mining at TML, says, “With the compact design and its unique kinematics, the new UNIDACHS 430RK makes it possible to work safely in places that standard hydraulic excavators cannot reach. The telescopic arm covers a vertical slewing range of +45° to -108°; with a telescopic stroke of 3,000 mm the attachment reaches heights of more than 10 m. At the same time, the telescopic arm provides a torque of 14.8 kNm as well as a maximum breakout force of 73 kN.”
Auger Torque will use this year’s Bauma to launch the Cone Crusher Bucket and InSite Range, the company has announced.
Suitable for parent machines in the 3-10T bracket, the Cone Crusher Bucket is designed to quickly and efficiently repurpose rubble into usable hardcore of approximately 40-70mm in size. It has been tried and tested on excavators, telehandlers, skid steers and mini loaders, the company says.
In-Site will also be introduced displaying Auger Torque’s new range of data driven tools designed to give operators knowledge and insight whilst out in the field. A plug and play tool, with one power cable, sensor plugs and a handled touchscreen device, the InSite range offers high levels of accuracy and precision, says the company.
As part of the range In-Site Align ensures accurate alignment when drilling holes, preventing the need for an additional person to help align drilling. In-Site Data has pressure sensors in addition to the alignment functionality so the operator can be sure the correct torque parameters are being met while In-Site Data Plus, suitable for 13T machines and above, has all the functionality of the first two models with the addition of temperature and speed sensors.
“Goodnight, Goodnight Construction Site,” Caterpillar has released its latest Trial series video which tells the story of Crane Truck, Cement Mixer, Dump Truck, Bulldozer and Excavator as they spend an action-packed day in the dirt.
The Cat Trials have taken on multiple tasks over several years, including playing a giant game of Jenga and lighting up a Chinese mountain side, which have racked up millions of views. Cat Trial 13 is the second trials video to be released this year. In this case, the manufacturer brings the children’s story to life with special guest appearances from three Cat dealer service trucks whose motto is “when you go to bed, we go to work!”
protection features, hoist-assist system, advanced automatic traction control system, stability-assist machine rollover warning system and a fuel saving ECO mode.
Finally, Excavator is a 349 Hydraulic Excavator that comes with simple to use technologies like Cat GRADE with 2D, Grade Assist and Payload, helping to “boost your operating efficiency up to 45 percent,” the company says.
The three Cat dealer service trucks that feature in the video are intended to emphasise the work Cat dealers do around the world and around the clock to ensure maximum uptime is maintained.
Crane Truck is a Cat TL642 Telehandler which can handle any task and “offers stability, maneuverability, speed and power in any application,” Caterpillar says. Bulldozer is a Cat D6 Track Type Tractor with an integrated engine and power train designed and built by Caterpillar to work together for “maximum productivity, efficiency and reliability.”
Cement Mixer is powered by a Cat On-Highway Truck Engine, built “to have multiple lives,” while Dump Truck is a Cat 745 Articulated Truck, reenhanced with new controls, transmission-
“We take pride in providing you unparalleled support. It’s about extending the life of your machines and minimising your operating costs. And we do our best to be proactive instead of reactive,” the manufacturer says.
Authored by Sherri Dusker Rinker, Goodnight, Goodnight, Construction Site is a New York Times bestseller and a favourite children’s bedtime book while it has a successful sequel called Mighty, Mighty Construction Site. Cat Trial 13 was enacted to celebrate the work operators do every single day and the commitment Caterpillar’s dealers make to provide support any time, day or night.
Cat dealer service trucks feature in the video