INNOVATION Asia
Serving Printing, Packaging and Publishing Industries across Asia Pacific since 1985 Issue 11 2022
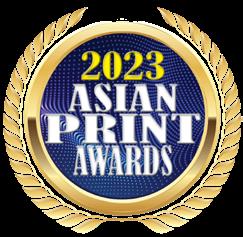
Details of the winners on pages 4-6 of this issue
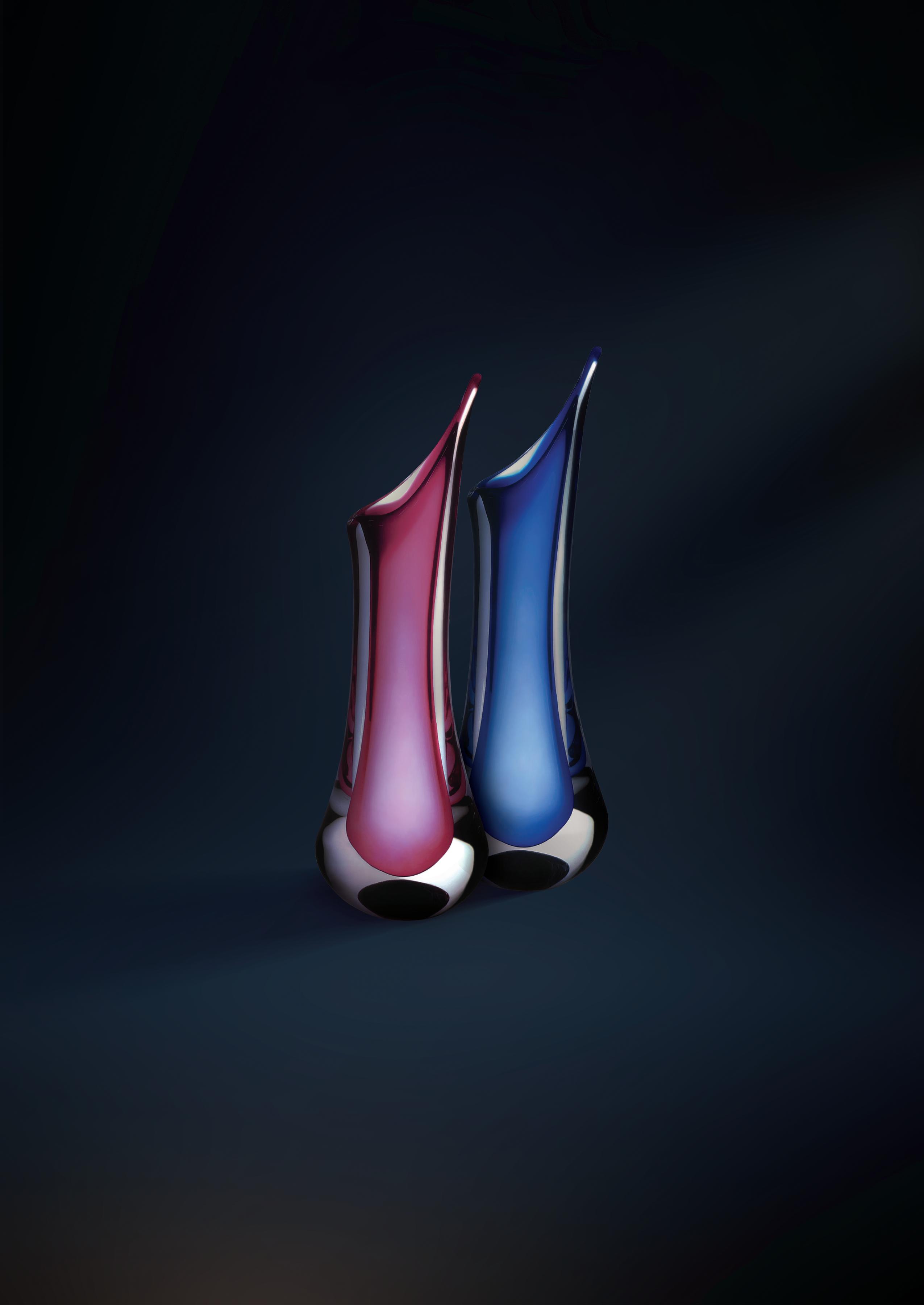
Serving Printing, Packaging and Publishing Industries across Asia Pacific since 1985 Issue 11 2022
Details of the winners on pages 4-6 of this issue
Whatever kind of packaging business you’re in, BOBST offers the connectivity, sustainability, digitalization, and automation you need to move your quality and productivity forward. Interested? Find your local BOBST representative at www.bobst.com/contact
FUJIFILM Business Innovation Asia Pacific announced today the winners of the Innovation Print Awards (IPA) 2022. In its 15th year, IPA is congratulating 47 winners from 10 countries across the Asia Pacific region for winning this prestigious award. The annual competition is open to all users of FUJIFILM Business Innovation graphic communications solutions across the region.
There was a total of 193 (single) submission for 25 categories -- with the most competitive categories in Brochure, Catalogues & Leaflets and
Packaging & Labels -- over 40 entries were received for each of the category.
The entries under Brochures, Catalogues & Leaflets and Packaging & Labels categories grew more than
double of last year and it demonstrated an upcoming trend and demand for short run packaging and labels. Brands not only seek for more impactful appeal on their packaging to entice customers, but to reach them quickly
as well. The current digital print packaging allows shorter run length, just-in-time delivery, and a reduced minimum order quantity (MOQ) requirement as product lifecycle becomes shorter.
“What we saw, what is trending and what we noticed this year -- digital packaging in this competition has taken off and was one of the most significant categories we judged,” said Paul Callaghan*1, head judge for IPA 2022. “In fact, we had to split into two sub-categories, Rigid Packaging and Carton Packaging. If you think digital packaging was lagging in any way, I can assure you, it is here and has come of age.”
Innovation Print Awards 2022 – “Best Innovation Award’ Winner
“The Voyage of Life” using Fujifilm digital press by Winson Enterprise (H.K.) Limited, Hong Kong
Out of 47 winning entries, 34 were printed on Iridesse™ Production Press or Revoria Press™ PC1120, including the winner of the “Best Innovation Award”, Winson Enterprise (H.K.) Limited from Hong Kong. Entitled “The Voyage of Life”, the submission is inspired by a series of four paintings created by Thomas Cole*2, representing an allegory of
the four stages of human life. Winson Enterprise applied the same idea and tells the life story of a couple. Each page showcases a different type of paper and effect, intricately representing the changes in life, exuding a multitude of feelings and experience to the reader.
“The immense technology and speed in digital printing enables brands to be more explorative in their designs and totally think out of the box, especially with the availability of different specialty colours,” said Scott Mackie, General Manager, Graphic Communication Business Group at FUJIFILM Business Innovation Asia Pacific. “We are thrilled to be part of this trendsetting journey with our
customers in communicating their brand story to their customers via our print technology. Through IPA, it is heartening to see quick and strong adoption of digital printing technologies as businesses embrace digital transformation.”
The winning applications will be showcased in FUJIFILM Business Innovation Graphic Communication showroom in Tokyo, Japan and in regional Graphic Communication industry events.
To further profile these talents, FUJIFILM Business Innovation Asia Pacific Pte. Ltd. will submit all entries*3 to the Asian Print Awards, a competition for printers in the region.
Over the course of the two days, close to 400 people attended both the SHIFT 22 conference, the Packaging Excellence Awards dinner and as a special treat for the 2022 event, a winners private dinner river cruise by invitation only to finish 2022 in style!
Over the two days, close to 400 people attended the SHIFT 22 conference and the Packaging Excellence Awards dinner. And as a special treat for the 2022 event, a winner's private dinner river cruise by invitation only to finish 2022 in style!
The packaging event of 2022 was held at the Royal Orchid Sheraton Hotel Bangkok at the start of December. After the judging, the gold, silver and bronze winners were notified that they had successfully won “something”. They were invited to a private river cruise on Thailand's most famous river, the Chao Phraya River. They were welcomed by the sponsors of this event - Miracoln, Glunz and Jensen, XSYS, UTECO, CGS ORIS, Windmöller & Hölscher, Tesa Tape, PackPrint International, Corrutec Asia, DRUPA, HP, IST, MPS, The Thai Corrugated Packaging Association, The Thai Packaging Association, and the Thai Print Association.
90 people were hosted to a feast, with food and drinks flowing for 3 hours.
It was a great networking opportunity, finishing with brilliant fireworks display before heading back to the hotel.
The second day started with the annual SHIFT Packaging Conference, where a line-up of world-class presenters shared trends, developments, and insights into where the industry is heading. Suppliers, Packaging companies, Associations, Label companies and brand owners shared the stage for the full-day conference event, finishing with ample time to catch up before the region's only Labels and Packaging Awards dinner commenced with cocktails at 6pm and then followed by the award gala dinner.
The ballroom for the awards dinner was full, with many more companies booking tables as well as industry people arriving to see first-hand what the best in Packaging looks like, and with many new categories such as Security print, Packaging Innovation seeing stunning work be rewarded with Gold Silver and Bronze. It was great to see so much networking,
laughing, and socializing again after the impact covid played over the last few years. The awards will continue to expand with new categories for the 2023 event such as Hybrid Printing Category being added along with some other new categories. A full list of the winners with photos are below and on the following pages.
If you would like to download the conference presentations, please go to https://www.printinnovationasia. com/copy-of-asian-packagingconference
If you would like to download the photos (500) of the event and awards dinner presentations, please go to https://www.printinnovationasia. com/copy-of-asian-packagingexcellence-aw
Shenzen Sunrise Technology China
Job Title: Red Star Wine Box Press: Mutoh VJ628MP Sunrise iDo enhance platformInk: Toyo Ink Colour Management: CGS ORIS
Silver Hoang Ha Label Co QLM Vietnam Vietnam Bronze Color Press Pakistan Pvt Ltd Pakistan
Rigid Packaging Winner
Printcare PLC Sri Lanka
Job Title: MNASA Premium Quality Gift Box Press: Heidelberg - Hongming - Bobst
Ink: DIC Lanka Paper: Matt Art Paper, 2.5mm & 1.5mm Chip Board
Silver Cyberprint Group Thailand
TPN Food Packaging Co., Ltd Thailand
Job Title: Charcoal Grilled Chicken Skewer Press: Windmöller & Hölscher Ink: Siegwerk Co Ltd Plate: XSYS Tape: Tesa Tape Substrate: Nylon / LDPE
Silver Cyberprint Group Thailand
Silver Liksin Packaging Enterprise Vietnam
Bronze SB Packagings Pvt Ltd India
GS Paperboard & Packaging Sdn Bhd Malaysia
Job Title: Roland Press: Bobst – Masterflex PrePress: Eye Graphic Sdn Bhd Ink: Swan Coatings (M) Sdn Bhd Plate: XSYS - Nyloflex
Silver Harta Packaging Industries (Cambodia) Limited Cambodia
Mega Label (Malaysia) Sdn Bhd Malaysia
Job Title: Ajax Fabuloso Lavender Fresh 3L Press: Gallus Ink: Siegwerk Substrate: White PE
Silver Fastroll Labels (M) Sdn Bhd Malaysia
Bronze Hoang Ha Label Co QLM Vietnam Vietnam
Kwality Offset Printers
India
Job Title: Kamet Whisky Press: Mark Andy
In 2024, the international print industry will once again meet at drupa, the world’s leading trade show for printing technologies. drupa stands for inspiration, innovation, first-class knowledge-transfer, and intense networking. drupa is where top international decision makers meet and discuss the latest technological trends and groundbreaking developments.
May 28 – June 7, 2024 Düsseldorf/ Germany
#drupa2024 www.drupa.com blog.drupa.com
Messe Düsseldorf Asia Pte Ltd
Messe Düsseldorf Asia Pte. Ltd.
3 HarbourFront Place
3 HarbourFront Place
#09-02 HarbourFront Tower Two Singapore 099254
#09-02 HarbourFront Tower Two Singapore 099254
Phone: (65) 6332 9620 mdrep@mda.com.sg
Tel. +65 6332 9643 / 6332 9620 Fax +65 6337 4633 / 6332 9655 mdrep@mda.com.sg http://mda.messe-dusseldorf.com/
Pre-Press: In House Plates: Miraclon Ink: Siegwerk Tape: Tesa Tape Paper: Vamet Chromo Metallised 120gsm
Silver Hoang Ha Label Co QLM Vietnam Vietnam
Cyberprint Group Thailand
Job Title: Red Bull Box Set Press: HP Indigo 10000 Design/PrePress: The Best One Co., Ltd Ink: HP Ink Stock: Art Card Paper 350gsm
Silver Printcare PLC Sri Lanka
Bronze Hoang Ha Label Co QLM Vietnam Vietnam
SB Packagings Pvt Ltd India
Job Title: Pushti Dried Blueberry 250g Press: Expert Pre-Press: Uflex Ink: Sakata Stock: Matt BOPP + Met PET + Natural
Uflex Limited India
Job Title: Purina Friskies
Junior 10kg Press: Comexi Pre-Press: Uflex Ink: Toyo - Water Base Stock: BOPP Plates: Miraclon Tape: Tesa Tape
Scientex Great Wall (Ipoh) Sdn Bhd
Malaysia
Job Title: Huggies Airsoft Pants M56 Press: Windmöller & Hölscher - Miraflex PrePress: SGK Substrate: PE White
Silver SB Packagings Pvt Ltd India
Bronze
Multiflex Polybags Pvt Ltd India
Letra Graphix Pvt Ltd India
Job Title: Sticker Me with Security Code Label Press: Gallus EM 280 Pre-Press: Pin Mark Pvt Ltd Ink: Siegwerk Stock: PP White Film + Sp. Lamination + 80 gsm Pharma Chromo
SIAM TOPPAN PACKAGING Co Ltd Thailand
Job Title: The Next Normal Store Press: Komori
Silver
TPN Packaging Co., Ltd Thailand
Bronze Printcare PLC Sri Lanka
Color Press Pakistan Pvt Ltd Pakistan
Job Title: Spices Press: Omet Evolution Series Pre-Press: In House Paper: Century Paper Ink: DIC Pakistan Tape: Tesa Tape
QLM Label Makers Sdn Bhd Malaysia
Job Title: Hammered Head Whisky Press: HP Silver
Mega Label (Malaysia) Sdn Bhd Malaysia
Bronze Kwality Offset Printers India
Print Master Co., Ltd Thailand
Job Title: Ovaltine Finest Cocoa 5 sticks
Mid Web Flexo Winner
SB Packagings Pvt Ltd India
Job Title: BG Pampers Pants XXL Press: Uteco Ink: DIC Tape: 3M Pre Press: Creative
Silver Scientex Great Wall (Ipoh) Sdn Bhd Malaysia
Bronze Multiflex Polybags Pvt Ltd India
EAN Label Industry Sdn Bhd
Malaysia
Job Title: Hammered Head Whisky Press: HP Indigo 6800 Ink: DIC (Malaysia)
Silver Hoang Ha Label Co QLM Vietnam Vietnam
Silver Printcare PLC Sri Lanka
Bronze
QLM Label Makers Sdn Bhd Malaysia
Labels Flexo Winner
Letra Graphix Pvt Ltd India
Job Title: Fabessentials Cocoa Butter Body Lotion 250ml Press: Gallus EMS 340Ink: Siegwerk Stock: PP Clear on Clear Film - 95 Micron Pre Press: Pin Mark Pvt Ltd
Silver Mega Label (Malaysia) Sdn Bhd Malaysia Silver Kwality Offset Printers India
Bronze Hoang Ha Label Co Ltd (QLM) Vietnam
Gravure Film Surface Print Winner
Liksin Packaging Enterprise Vietnam
Job Title: Roasted Whole Cashew Sea Salt Press: Windmöller & Hölscher Plate Supplier: Donyun Ink: Sakata
Silver SB Packagings Pvt Ltd India
Narrow Web Film Flexo Winner
Multiflex Polybags Pvt Ltd India
Job Title: Bella Ultra 7 XXL Pads Press: SOMA
Stock: LDPE White Opaque LDPE Film Pre Press: Veepee Graphics Tape: Tesa Tape
Fastroll Labels (M) Sdn Bhd Malaysia
Job Title: Everyday Head To Toe Cleanser Sachet Press: HP Indigo Substrate: PET12/ALU6/ LLDPE60 & BOPP Matt LAM Ink: HP Ink
Silver Printcare PLC Sri Lanka
Hoang Ha Label Co
QLM Vietnam
Job Title: Sampan Cellar Series Press: HP Indigo Ink: HP Substrate: Antique Linen Tape: 3M CMYK + Matt Varnish + Spot Gloss + Emboss + Copper Foil+ Variable Data
Silver Letra Graphix Pvt Ltd India
Bronze Kwality Offset Printers India
Thung Hua Sinn Co., Ltd Thailand
Job Title: Sweet Chili Sauce 700ml Press: Heidelberg Stock: Art Coated Paper Ink: Flint Silver
Kwality Offset Printers India
Neolt Asia Pte Ltd
Singapore
Job Title: Metallica Beverages Press: Quantix Pre-Press: In House
The FLEX PACK system is the ideal solution for packaging customers for virtually any type of packaging prototype – from design agency to converter.
What makes FLEX PACK truly unique, however, is the flexibility to prototype a color-accurate mockup that is true to life and accurately represents the final produced package. Once a new packaging design innovation is production-ready, FLEX PACK utilizes CGS ORIS’ 4D color management to provide the very best in color accuracy in the shortest possible time. Paired with a custom interface for CGS ORIS supported Eco-Solvent series printers, FLEX PACK is easy to use and all printer features, such as multipass printing and print-and-cut, are supported.
Unique to FLEX PACK, the Varnish & Emboss and the Cold Foil packages are available for high-end finishing effects. Expanding your color accurate prototyping capabilities even further.
Only FLEX PACK users enjoy both the financial and time-saving benefits of proofing with an all- in-one prototyping solution.
FLEX PACK is a comprehensive proofing and prototyping system based on the proven CGS ORIS 4D iterative color management process, making use of the print device’s entire color gamut. This allows for the system to optimize the lowest possible Delta E relative to its target. The entire Pantone® library as well as packaging-specific spot color management are included, which supports native CxF/4 spectral data,
achieving perfect spot color overprints. Completing the package, the FLEX PACK software offers integrated soft proofing, proof certification and halftone support.
An absolute requirement when bringing your package design to life, spot color accuracy is critical when creating package proofs and prototypes.
FLEX PACK delivers a variety of tool sets for enabling the most accurate spot colors on your proofs. Leverage CxF and our unique Spectral Color Engine to achieve the most color-accurate brand colors.
Eco-Solvent
The revolutionary eco-solvent printers available from Roland work harmoniously with CGS ORIS’ Expanded Gamut XG Inks to provide the complete solution for your brand colors. In addition to White and Metallic ink, the system features unique Orange and Green inks, developed exclusively by CGS ORIS.
This expanded gamut XG Ink set allows for the production of color accurate, contract-quality proofs and prototypes heat transferred to actual press substrate or a wide range of direct imaged medias – from adhesive film to shrink film and foils. The printer hardware has been customized with several components developed by CGS ORIS, such as a pre-heater, add-on dryers and special media feed systems, for our customer’s convenience. Other hardware options, including custom
laminators, punch and register units, are also available.
Not all substrates for Eco-solvent printers are created equal. CGS ORIS has developed a wide range of specialty proofing substrates to fit your operation’s needs. This extensive media portfolio has been developed with the needs of packaging professionals in mind. In addition to, a high ink limit and quick drying characteristics, the latest coating technology paired with extensive quality control guarantees consistent results and maximizes quality.
The PackPROOF Transfer Film is on the forefront of innovation when it comes to producing packaging prototypes or proofs on actual production stock. The Transfer Film is an open-pored synthetic mesh, which can be thermal-transferred at low temperatures onto almost any production stock using a standard laminator. Because the Transfer Film is only a few microns thick, it is colorneutral and undetectable.
This equips customers with the ability to produce proofs and prototypes that precisely match the press output, whether it is laminated to PE film, aluminum or fluted board. The film is also extremely flexible – allowing it to be deep-drawn in metal printing or inmold processes.
PackPROOF Transfer Film can be complimented with the use of PackPROOF Embossing Foils. The
original gloss surface can be modified to match your original stock, with a semi-matte or matte finish.
CGS ORIS
Clear Shrink Foil
Like all CGS ORIS media, quality is of the utmost importance. That is why we have created a shrink film with a high-quality emulsion layer and PET base. Coupled with significantly faster dry times than the competition, the media allows for greater ink laydown capacity and, therefore, lending the largest achievable color gamut. Finally, what differentiates the CGS ORIS PackPROOF Clear Shrink Foil is the 90% unidirectional shrink ratio and linear shrink reaction, making the shrink process more controllable and easier to avoid flaws such as wrinkles and distortions.
For your convenience, CGS ORIS has created the CGS ORIS Shrink Sleeve Solution. This solution includes the necessary components best recommended to properly seam PackPROOF Clear Shrink Foil, including a custom seaming table, glue and seaming tools.
A key benefit of FLEX PACK is its ability to print designs in the same laydown order as your production printing process. With FLEX PACKS’s multi-pass printing feature you have complete control over the separation sequence of your printed job. Double hits of white… No problem!
Modern packaging increasingly features complex finishing effects like spot varnishes, cold foils or embossing. As these packages become more complex, proofing and prototyping them becomes increasingly more difficult. These finishing effects not only have a significant impact on the appearance of a product but can also lead to color shifts in production print processes.
With the CGS ORIS Varnish & Emboss expanded capabilities package, it is possible to not only produce stunning, color accurate packaging prototypes, but also to apply spot varnishes and embosses with pin- point accuracy. Using a custom punch and precision register system, FLEX PACK prototypes can then be finished on a Roland VersaUV printer, controlled by FLEX PACK.
Even delicate matte or gloss spot varnishes can be produced, as well as embossing or textured effects.
To elevate a package even further, the FLEX PACK system now offers the ability to apply production-grade cold foil to your prototypes. Using the CGS ORIS Cold Foil expanded capabilities package, you are able to achieve intricately applied cold foils with the same pin-point precision.
Connect to Grow. That is your key to stay ahead in a demanding market. By connecting with MPSConnect, you ensure the best in reliability and productivity from your printing press. You will increase competitive advantages and maximize profits.
To improve productivity and profi tability, it’s critical to increase the understanding of your overall label print operation. With MPSConnect, you get real-time insights in the operator activities. You dive into the printing press and see exactly what’s happening.
mps-printing.com/connect-to-grow
mps-printing.com
• Uematsu Installed the sixth Speedmaster XL106-4-P within five years.
• Push to Stop and Internal project “IJIGEN” to address the growing shorter job run segment.
• Continuous Improvement in internal workflow and process to increase output and profitability.
Since its foundation in 1958, Uematsu Corporation has specialised in the fields of plate-making, printing and finishing. Uematsu is one of the most productive prin-ting companies in Japan as a contract manufacturer specialising in sheet-fed offset printing.
In the previous years Heidelberg Polar cutting and Stahl folding machi-nes had previously been installed by Heidelberg Japan, however 2017 was the first time a Heidelberg Speedmas-ter was installed.
Masao Tsuchiyama, the Head of Sales at Heidelberg Japan, said: ‚President Fukuda, who came from the financial industry, has very high expectations on cost-effectiveness, and this has been instilled into the management team of Uematsu. This is the reason why it is a great pleasure for us that he decided to install the first printing machine five years ago and has added several machines since then, and now five
years later, Heidelberg Japan recently installed a sixth machine, including a further two machines for one of the groups company Smart Graphics Co. “It gives all of us a great pleasure and confidence that Uematsu see’s Heidelberg Japan as a first choice partner” adds Tsuchiyama.
Before the first installation of the XL106, Uematsu had been proactively adopting the concept of “Digital transformation” through the adoption of digitalisation and automation of all processes.
This Is also aligned with Heidelberg’s strategy of the autonomous Smart print shop, an area which has been seeing a huge adoption and success globally within the commercial printing segment, and The new Speedmas-ter XL 106 is also equipped with all of the high automa-tion devices to eliminate
unnecessary manual interven-tion during the production process.
Our production is now conducted with a clear separati-on between what should be done by machines and what should be done by people.
Push to Stop and Internal project “IJIGEN” to cover the growing market demand for short production run lengths
Mr Fukuda, President of the Uematsu Corporation, states “In the course of our efforts to improve producti-vity, we were able to visit the most productive printing company in the world in 2014 by arrangement with Hei-delberg. It was a company called ESP in the UK, and the president, Anthony Thirlby, who today is a visionary within the Printing industry with a production philoso-phy thoroughly committed to high productivity.
Uematsu Corporation President Hiroshi Fukuda and Heidelberg Japan President Jorg Bauer exchange elbow touches in front of the sixth Speed-master XL 106-4-P.They were producing as much volume and more printed sheets as our whole company was with just two prin-ting presses. While we had 18 various offset machines at the time. Although there were differences in their printing business compared to ours, such as our use of proofs and manual press checks, I thought there was something extraordinary to be learnt from ESP and Anthony.
So I launched our internal “IJIGEN project (Different Dimension)” as soon as I returned to Japan. The idea was to dramatically improve productivity by reducing the press set up and make ready time to the ultimate levels Heidelberg, on the other hand, also
the XL 106 with the highest levels of automation and speed.
These are machines have features such as full job data set up and color control, fully automatic plate chan-ging and job preparation this eliminates the need for manual operation and therefore reduce the make ready times significantly. That‘s exactly what the times demanded, the IJIGEN project we are working on together with Heidelberg‘s ability to realise Push to Stop Autonomous print production is a gutsy match.“ He stated.
“We believe that the Heidelberg Speedmaster machines being more productive in turn generate vastly more
be productive and profitab-le, such as 1/1 and 2/2 and special spot colour printing.” He also expressed.
Continued strong support, end to end for the best per-formance and success Jorg Bauer, the managing director of Heidelberg Japan said: “We are very grateful to President Fukuda, who has held many important positions in the industry, including Chairman of HDF21, and who understands the value of Heidelberg’s solutions and is committed to DX, productivity improvement and execution. I am very grateful to him for understanding the value of the Heidelberg solution and for investing with Heidelberg for six machines over five years.
had the ‘Push to Stop concept”, which aimed for automation by elimi-nating as many of the manual processes that we were all too familiar with in our way of work.
In this sense, we thought that we could take on the challenge of our internal process Improvement “IJIGEN project” together with Heidelberg, so we decided to form a partnership with the aim of improving nume-rous predefined KPI’s .“ Explains Mr Fukada. As for why the Speedmaster XL 106 was chosen, he ad-ded: ”The decrease in production run lengths has been extraordinary since 2017. No matter how much the number of individual job orders increases, the decrease in run lengths outweighs it.
If that happens, it‘s easy to choose the right machine to invest in. For us it was
sa-les are better for the company’s profits Even the initial investment was significantly higher than our previ-ous acquisitions, the Heidelberg Presses are far more profitable in the long-term. In reality, the data we are recording proves how far more productive Heidelberg machines are.” Mr Fukada added.
Two specific and unique Heidelberg technology’s equip-ment that were decisive in our decision to choose Heidelberg as our project partner were the Prinect Produc-tion Manager Prinect Inpress Control, which reduces manual touch points to an absolute minimum, and the Hi-Color Multi Drive, which allows the preparation of units during production, among other things, this has a tremendous effect on reducing make ready time. He added: “With these new features, we are able to expand into new business areas and
I was shown the Uematsu production site today and all of the machines were running at maximum production speed with various paper substrates, bringing out the best performance of our machines.
We are very pleased and Heidelberg Japan will continue to provide the best in class end to end sales and service support for the success of Uematsu Co.“We are com-mitted to working together in a strong partnership to achieve success,” he said.
1. Speedmaster XL 106-6, in May 2017
2. Speedmaster XL 106-5, in Jan 2018
3. Speedmaster XL 106-6, in Jan 2019
4. Speedmaster XL 106-8-P*, in October 2019
5. Speedmaster XL 106-8-P*, in October 2019
6. Speedmaster XL 106-4-P, in December 2021
*Machines supplied to Group company Smart Graphics Inc.
Glunz& Jensen A/S (Headquarters) Selandia Park 1 4100 Ringsted, Denmark +45 5768 8181 gj@glunz-jensen.com
Glunz& Jensen s.r.o Kosicka, 50 08001 Prešov, Slovakia +421 51 7563811 gj@glunz-jensen.com
Glunz& Jensen Inc 2185 Hwy 292 Inman, SC 23349, USA +1 864 568 4638 gj-americas@glunz-jensen.com
Since Fujifilm launched the original Jet Press 720 in 2011, upgraded models and enhanced functionality have been a continual feature of its development. From the launch of the Jet Press 720S in 2014, to the arrival of the Jet Press 750S in 2018 and the Jet Press 750S High Speed Model in 2021. More than ten years after the first iteration of Fujifilm’s flagship B2 inkjet press, Fujifilm has continued to listen to market demands and the needs of its customers to make the Jet Press even more versatile and flexible so that it can be used for a greater number of print jobs, in addition to its well-known ability to produce the ultimate industryleading print quality.
As a result, the company is introducing a new High Value mode which offers a third production option in addition to the High Quality and High Performance modes already available. The new High Value mode sits in between Jet Press High Quality and High Performance
modes. It prints at the same resolution as High Quality mode (1200 x 1200 dpi native resolution), but without the need for the rapid coagulation primer (RCP). This intermediate level will be ideal for applications that do not require the ultimate highest quality that the Jet Press High Quality mode can produce, and as it uses no RCP, running costs are reduced, offering even greater flexibility to users.
Increased feed and delivery stack height benefits packaging converters
In addition to the new High Value mode, Fujifilm is also now introducing the option of increased feed and delivery stack heights to the Jet Press 750S, bringing multiple production benefits to both commercial and folding carton packaging print businesses. The additional 300mm height means 1,000 extra sheets of 300μm folding carton board (an increase of 37%) can be used. This also has the added benefit of increasing non-stop running time to
over an hour for folding carton stock, and to more than two hours for thinner commercial stocks.
Both the High Value Mode and the increased capacity options will be available from early 2023.
Print businesses need flexibility. They need to be able to adapt, from one day to the next, to rapidly changing and often unpredictable market demands. With the addition of the High Performance mode to the Jet Press last year, we were effectively able to offer the benefits of two presses in one, allowing users to pivot between very high quality, short run work, to more mass market longer run jobs. Now, with a third High Value mode, and the ability to handle higher volumes of non-stop printing, FUJIFILM bring yet more flexibility to our customers, all within one machine.”
Jet Press 750S evolution continues with the addition of a new “High Value” mode and increased feed and delivery stack height
Kato Shiko Ltd., which celebrates 51 years in business in 2022, has focused mainly on postpress processing of commercial printed materials such as catalogs, pamphlets, and flyers. In recent years, the company has also strengthened its publication-related processing business.
Since its founding, the company has maintained production by an elite crew with around 10 employees. In order to build an efficient production system, the company has now installed an MBO K70 (B1 size Combi Folder) with an MBO SBAP signature stacker. As a result, the company has increased the number of multi-skilled workers and improved efficiency, leading to reduced outsourcing costs due to a significant increase in production volume. We asked President Fumito Kato and operators Sakie Kato and Mayumi Hayashi about the background of the installation and the effects after the machine began operation.
"As a paper processing company, we have few opportunities to get work by ourselves, and most of our business is managed in partnership with customers who work in the front line," says Mr. Kato, president of Kato Shiko Ltd. He advocates laborsaving as the axis of management.
As a paper processor with a wide range of equipment such as folders, cutting systems, and binding machines, the company promotes a multi-skilled workforce, where one person is in charge of multiple types of equipment.
"In order to improve efficiency with a small number of first-class workers, laborsaving is the first priority. It is important to create an environment in
which the production system can be maintained with the current staff.
With this in mind, we are switching to new efficient machines that reduce the workload of each worker and we are making equipment investments accordingly," says Kato. With this background, the company installed an MBO K70 (B1 size Combi Folder) to replace two obsolescent machines in 2021.
Kato explains the reason for the selection: "We asked a company in Kyoto that had installed an MBO K80 to run tests of folding on various types of paper. The tests showed that there were no papers that could not be folded, and the performance and quality were so high that we were very impressed with the machine. We consulted with Komori about a machine that would give us the best performance at the lowest possible installation cost and finally selected the manual specification MBO K70," he says. The installation was made after considering both performance and cost.
In 2016 the company installed an Apressia CT137 Programmable Hydraulic Clamp Cutting System. One of the reasons for the decision to follow this up with a folder was Komori's service system. "Komori has a great service system for printing companies, and this is amazing. We trust Komori the most since we are a company working around the clock at times," he says.
The productivity of the MBO K70 is
Fumito Kato, President
"We have run two lines of saddle stitchers with one folder many times.
unparalleled."
Per-person production volume has increased dramatically and profitability has also improved due to in-house production "Our company's main business is saddle stitching binding, and in the past each of our two folders had its own operator for folding, which is the prior process. Therefore, since two operators were occupied with folding for a large volume of work, we had no choice but to outsource some jobs. With the installation of the MBO K70, we are now able to do about twice as much folding as before with only one person working, and we are now producing all work in-house.
As a result, we are about twice as profitable as before. Moreover, we can schedule our work more easily. For example, we can run three-fold jobs at speeds of up to 210 m/min, which enables us to produce 24,000 sheets per hour. For normal eight-page saddlestitched folding jobs, we can process approximately 100,000 products per day without overtime," he says, noting that the company has achieved overwhelming results, especially for large-lot jobs.
Medium and large lots are done on the MBO K70, taking advantage of its high productivity. "We regularly have washi paper jobs that sometimes caused folding wrinkles with conventional folders. The MBO K70 folds them with no problem. For special paper, we definitely use the MBO K70," says Kato.
The delivery this time is using the MBO SBAP stacker, which can discharge signatures vertically. "With a conventional machine, the signatures would pile up in a shingle stream and remain in the delivery, making it difficult to collect and inspect, and often forcing the machine to slow down.
With the MBO SBAP, signatures come
out in vertically aligned bunches, so work can be done without slowing down the machine. Also, the work can now be done by anyone since there is no heavy lifting," he says.
of procedure manual to standardize high-quality, largelot production
This time, the company chose to use manual operation instead of a fully automatic machine. "With manual machines, things are not left to the machine, so we are aware of the need to check and work on our own every day, and we are able to quickly notice any problems that may occur. We also notice various things through trial and error, which in turn improves our skills and experience," he says, describing the new growth as a company specializing in processing.
He continues, "In the past, we needed dedicated operators who were familiar with the machine's peculiarities, but this machine works exactly according to the setting, so anyone can make adjustments if they have our procedure manual. Since the potential of the machine itself is high, once it is set, the settings do not change during operation, which is the most reliable aspect of this machine."
Now is the time to set targets and create the working environment Kato comments on the future outlook: "Previously, the processing industry tended to install multiple machines in preparation for busy periods and problems, but this was costly and required maintenance for each machine. By consolidating the production of multiple machines into a single machine, space can be used more effectively and maintenance costs can be reduced.
When we thought about what kind of environment would provide the best balance of profitability throughout the year, including peak and off-peak periods, installation of the MBO K70 was the best choice for our company. Our decision that now was the time to eliminate waste and change our way of thinking led to success. We will continue to innovate with our production system to improve QCD (quality, cost, and delivery) in the future."
He also expressed his hope for the development of the Japanese market since MBO is now part of the Komori Group, saying, "I also believe that the opportunity to learn about MBO's folders has expanded greatly in the Japanese market."
Curious to know who has won the awards? Stay tune to our announcement in November.
Innovation Print Award (IPA) is an annual competition that seek to recognise FUJIFILM Business Innovation’s customers creativity and innovation in print.
Push the creativity and technical boundaries of print with FUIFILM Business Innovation technologies – the only limit is your imagination!
An EXPERT K5 3650 installed at PT Polyplex Indonesia at the end of last year has enabled the company to meet their customers’
The new machine complements the existing EXPERT K5 3300mm which was installed in 2019 and together the two machines incorporate a host of BOBST unique process innovations including AluBond, AlOx and DarkNight.
PT Polyplex Indonesia is part of the Polyplex Corporation which has had a relationship with BOBST since 2015 and has 4 EXPERT K5’s across their production sites in Indonesia, India and USA. The Indian multinational company which started in 1988 has 7 manufacturing locations in 5 different countries and is a leading PET Film manufacturer and supplies customers across the globe. PT Polyplex Indonesia incorporated in 2017 has an annual turnover of 160 million USD, nearly 600 staff and operates primarily in the Flexible Packaging sector.
Both machines at the Indonesia site incorporate a 700mm coating drum, which is unique to the EXPERT K5 and the largest in the industry resulting in less aluminium consumption and maximum productivity and production cost savings.
Also unique to BOBST is the AluBond process which is on both machines and was initially developed to increase metal adhesion and dyne level on the most commonly used film substrates but is now fast becoming the standard metallizing process for polyolefin based PP substrates due to its ability to increase barrier levels on these film types.
The DarkNight® process which is installed on Polyplex’s latest metallizer is designed to achieve high barrier metallized films at a lower cost due to the fact that it eliminates the need to
use high Optical Density levels which is usually required for high barrier applications. An enhanced barrier performance is achieved by reducing defects during the metallization process. Working in conjunction with BOBST Hawkeye, the process provides a new approach to defect reduction and is a major step forward in the journey towards full aluminium foil replacement with high barrier metallized films.
Commenting on the investment, Amit Prakash. Managing Director & PCH for Thailand/Turkey/Indonesia Operations Unit at Polyplex said “We originally chose the EXPERT K5 due to the large capacity and fast speed with good output quality. The BOBST machines provide higher production with less defects giving better quality metallized film and when we needed to increase capacity, we didn’t hesitate to purchase a second EXPERT K5. We had good support from local BOBST experts for installation and start-up and our operators are well-trained on the machine. We look forward to continuing our relationship with BOBST in the future”.
demand and support new applications
A. Yes. I just had a phone conversation with a client who had a familiar story to tell. He had built his business on the model of an entrepreneurial sales force –give them a territory, pay them straight commission, and tell them they are in business for themselves, free to develop the customers they chose with the products they wanted.
And for a couple decades it had worked well. The business grew and expanded. More entrepreneurial salespeople were added, and the model was duplicated over and over again.
So far so good. But then the growth in sales began to slow down. Three flat or declining years in a row has caused
this company president to question the status quo. Not only is business flat, but he’s unable to get his sales force to promote the lines that he wants to promote, he’s unable to get them to use some of the new technology that the company wants them to use, and he’s unable to get them to prospect for new customers. Now he’s faced with an experienced sales force, who for the most part, are unmanageable.
The culprit? A sales model that was built on the concept of the entrepreneurial salesperson. There was a time when this model was effective, but in today’s competitive economy, there are serious difficulties with the entrepreneurial model.
This model works best when the market is growing. As long as there is more and more business out there to be had, the focus of most companies is to grab as much as they can, without caring a whole lot as to which customers and which products make up the business. Employing a group of entrepreneurial salespeople reduces the demands on sales management so that the company’s executives can focus on building the infrastructure necessary to keep up with the consistent growth.
As we all know, this was the case for most of the previous decade. By shifting the responsibility for sales management onto the salespeople, however, you give up much of your management influence. In effect, you cede management of the sales force to the salespeople. And they generally make decisions that are in their own self interest, not yours.
The very concept of an entrepreneurial salesperson is that he/she will manage himself. By definition, you abdicate your managerial role and cede management to the salesperson.
Is it any wonder that you can’t direct the salesperson?
As long as business was consistently growing, this wasn’t an issue. But now it is a concern. Most distributors have experienced a reduction in sales volume at least once in the last decade. Many have come to the conclusion that they have to initiate significant changes in their sales organizations if they are going to be profitable and growing.
Now, instead of just more business,
Q. I’m frustrated. My sales force just doesn’t seem to be motivated. They agree with me at sales meetings, but then don’t follow through. Any ideas?
progressive distributors want to expand the business in target accounts, emphasize key product lines, and acquire new accounts. In other words, they want to direct the sales force more precisely, to focus them on the behaviors that further the company’s strategic objectives.
At just the time that they want to more precisely focus the sales force, they are faced with a group of experienced salespeople who have become satisfied and content.
These salespeople would rather not move out of their comfort zones of established customers and established products. They have no desire to do the hard work of prospecting for new accounts. And many are content with the diminished incomes of the past few years.
The culprit in this difficult situation is the entrepreneurial model. This is not to say that there are no entrepreneurial salespeople. Certainly a certain percentage of every large group of sales people will turn out to be highly motivated, constantly improving, driven to succeed and willing to accept your direction. From my experience,
this is about one of 20 salespeople. The chances of your entire group fitting this mold are slight. The issue is not the occasional exception to the rule; the issue is the model that no longer supports your strategic interests.
The solution is going to require strenuous work.
Wipe the slate clean and start over. Begin with the definition of what you would like the salespeople to do. What do you really want your sales force to do? Noodle your ideas onto a blank sheet of paper and review it for a couple of days. When you have a wellarticulated full page of detail, you will have taken a major step forward.
Once you have a clear and specific idea of what you want them to do, then start dealing with implications of that. For example, does you compensation plan support the behavior you want? If not, then change it.
Does your training and development program equip the sales people with the skills that support your vision? If not, it’s time to revise it.
Does your infrastructure support your idea of what the salespeople should be doing? In other words, does customer service, purchasing, delivery, operations, sales management, etc., all support the revised job description? If not, make some refinements.
Finally, do you have the kind of people who will whole-heartedly embrace your new vision? If not, then it’s time to begin the process of recruiting new salespeople.
Each of these is a difficult and challenging issue that speaks to the heart of how you have your sales force structured. Designing and implementing these changes can take the better part of a year or two. Each of these initiatives will be met with resistance from some. It won’t be easy. Before you rush into the fray, however, make sure you count the cost. You may decide that you are not up for the task and that it is easier to continue to cede management to your salespeople.
Should you decide to revise your sales force, you can anticipate arriving at a focused and directable sales force –an enormously powerful asset for any company.
Amcor, a global leader in responsible packaging solutions, has announced the opening of its new state-of-the-art manufacturing plant in Huizhou, China.
China. With an investment of almost $100 million, the 590,000-square-foot plant is the largest flexible packaging plant by production capacity in China, further strengthening Amcor’s ability to meet growing customer demand throughout Asia Pacific.
The new facility is expected to employ more than 550 people, who will produce flexible packaging solutions for food and personal-care products. The plant comes equipped with the first automated packaging production line in China. This, along with high-speed printing presses, laminators, and bagmaking machines, can deliver doubledigit reductions in manufacturing cycle times.
Amcor is also deploying the first smart production and operation system in the Chinese flexible packaging industry, which includes smart laser scanners, light curtains, high-standard machine guarding and multiple quality-control points. All key process equipment is also CE-certified to stringent European Union health, safety and environmental requirements. Other benefits of
the new state-of-the-art facility are traceability throughout the production cycle, a climate-controlled production environment and low-carbon emission production.
“This investment is testament to our commitment to grow with our customers in China and throughout Asia Pacific by bringing the best of Amcor’s global expertise closer to them,” said Xin She, Vice President and
General Manager of Amcor Greater China. “The world-class capabilities of our new plant are designed to enable us to exceed our customers’ expectations of quality, responsiveness and innovation.”
The plant features three labs with innovative testing and analytical capabilities to fully leverage the expertise from the recently opened Amcor Asia Pacific Innovation Center in Jiangyin, China, helping to accelerate the development of responsible packaging solutions. The new Huizhou site also includes a number of sustainability features, including the latest regenerative thermal oxidizers (RTO) system to reduce harmful emissions, as well as a number of energy-reduction, heat-recovery, lowpower consumption and rainwater harvesting systems to help reduce its carbon footprint and environmental impact.
The German electrical engineering company has digitalized the imaging process with the installation of an XSYS ThermoFlexX 30 for the production of pad printing plates. The conversion from analogue to digital has drastically reduced the throughput time and increased consistency and quality thanks to the highly innovative technical characteristics of the new solution.
DEHN is a global specialist in the fields of surge and lightning protection as well as safety equipment. In production, the company works with many types of printing technologies including inkjet, laser, direct thermal and pad printing to make components for a wide variety of devices and systems.
Having in-house printing facilities not only speeds up production and controls cost, it improves supply chain traceability and facilitates the implementation of product design changes very quickly.
Until recently, the company relied on time-consuming analogue photopolymer plates for their pad printing operation. This involved a number of manual steps, including positioning the print image by hand, while the plate imaging was performed with traditional tube exposure.
“The analogue process we had in place before was a real bottleneck in our workflow,” said Willibald Fink, Head of Special Projects at DEHN SE. “It involved getting the artwork created externally, before making the plate in-house using mechanical processes and exposures. Altogether, this took about a week. In addition, the in-house processing tied-up the platemaking for as long as an hour.”
Wanting to streamline and optimize the workflow while removing the risk
of human error, DEHN decided it was time to go digital and invest in an imager that would allow them to improve the print resolution and quality, whilst also reducing waste of plate materials and energy consumption for improved sustainability and lower costs. Once DEHN was convinced of the high accuracy of the laser and the speed at which plates could be produced, they placed an order with XSYS for a ThermoFlexX30.
“We are known for our consistently high product quality but that doesn’t stop us from striving to improve further with innovative and future-oriented logistics and production technologies combined with modern ergonomics. As we move to digital platemaking, choosing the ThermoFlexX imager is a small but very important piece of the puzzle that will help DEHN be even more successful,” added Harald Daffner, Head of SPD assembly at DEHN SE.
The ThermoFlexX 30 Imager from XSYS is designed for the imaging of photopolymer plates for flexographic and letterpress printing as well as direct engraving of pad printing plates as part of a digital workflow. At DEHN, the imager is used with the XSYS nyloprint® DLE S 30 pad printing plates – a combination of best-inclass technologies that offers superior printing quality at a resolution of up to 5080 dpi.
The ThermoFlexX imager operates a fibre laser with the option of simultaneously imaging multiple plates at different resolutions which significantly lowers waste and increases efficiency. To handle the steel-backed nyloprint® plates, the device has been fitted with the hybrid drum option and customized register pins.
“The conversion from analogue to digital processes has not only reduced the throughput time to about 10 minutes (from digital template to imaged plate), but the repeatability is also much higher; in part thanks to the register pins incorporated on the drum which correspond precisely to the holes in the plate,” said Harald Daffner. All in all, the new device contributes to process optimization and, as a result, to better product availability and increased sustainability.
Although the partnership with XSYS was only established very recently with the purchase of the new imager, this addition to the platemaking department has certainly impressed the team at DEHN.
Furthermore, the comprehensive service and support offered by XSYS facilitated a smoother set up phase allowing DEHN to progress rapidly with the switchover to digital.
Bearing all the hallmarks of innovation, productivity and quality now synonymous with the Evolution name, the ROLAND 900 Evolution offers a wealth of automation technology to deliver cost & energy savings for printers, along with ever faster makeready times.
Among these are Autoprint, providing uninterrupted productivity from prepress to post press at the touch of a button and InLine ColorPilot 3.0 –the fastest, most efficient and most accurate color measurement technology available, measuring densitometrical and colorimetric values in a single pass.
New Triple Flow inking technology addresses specific challenges for large format print, providing three separate inker running modes, while the AC Drive promises annual savings of up to 10,000 kWh – or 8 years over the lifetime of the press.
With its host of complementary, innovative technologies, the ROLAND 900 Evolution pushes the boundaries for what is possible in large format offset printing.
Commenting on the ROLAND 900 Evolution, Krzysztof Pietrzak, Managing Director, Manroland Polska Sp. z.o.o. said:
“Our quest to deliver value to our customers is an ongoing mission which guides everything we do. We were immensely proud to have launched the ROLAND 900 Evolution because it breaks new ground and opened a new world of possibilities for our customers”
We are strong in this sector of the market, and this was a natural next
step in the development of the product line using the proven ROLAND 700 Evolution platform and going to the larger format. We have already installed ROLAND 900 Evolution presses globally which includes Poland, Italy, USA, China, Mexico, South Africa and others”
Manroland also introduced two new 700 additions to the Manroland Evolution family. One is a high-speed model, the 700 Evolution Speed, rated at 20,000sph and aimed at longer run applications. The other is a more stripped-down model for those who do not need the level of technology that comes with the 700 Evolution Elite.
This is the 700 Evolution Lite, configured as a standard machine and priced to appeal to those wanting a new press, with the fast make-ready benefits
of
Heidelberg continues to lead the way in productivity throughout the entire production process. Whether it be prepress, printing, cutting, folding, or packaging requirements, Heidelberg is there to assist our partners with the latest technology, OEE, service & support.
As our partners have adapted to new technology in the pressroom over the last few years, bottlenecks then occur in different areas of production such as postpress. Polar, Stahl and our OEM partner MK Masterworks have several innovative solutions in this area, which we examine a little further below¬¬.
Polar - The postpress area of cutting offers a great deal of potential for improvement in production.
A solo high-speed cutter reaches its limits above a certain press output. The high-speed cutter is at a standstill during manual loading and unloading of cut material, hence valuable production time is lost. A typical cutting operation consists of the following processes: Loading, manual programming, cutting, unloading.
In the case of a Solo high-speed cutter, it can be assumed that approximately 35% of the time of the cutting process must be spent on loading material. 15% on programming with only about 25% of the time spent on the actual cutting. The last step in the process chain, unloading the cutting material, also takes about 25% of the time.
The time taken by the supporting processes can be significantly reduced with a POLAR Cutting System 200, which includes a stack lift, an automatic jogger and a Transomat unloader. Existing high-speed cutters can easily be retrofitted with peripheral equipment.
The stack lift moves the cutting material to an ergonomic working height. This not only speeds up loading, but also reduces the strain on personnel. From there, the material can be fed to the automatic jogger, which precisely aligns the material. Parallel cutting is possible during the automatic jogging and spreading process. After cutting, the Transomat unloader unloads the cut products onto a pallet with edge accuracy. During the unloading process, the next cutting layer can be prepared or cut.
A POLAR Cutting System 200 increases productivity by up to 100%
compared to a stand-alone high-speed cutter, improves quality and thanks to its ergonomic arrangement is easy on personnel, thus providing a solution that can prevent finishing from continuing to be a bottleneck.
Stahlfolder TH / KH82-P range of folders carry forward peak performance
The Stahlfolder TH82 -P folding machines set the benchmark for productivity and quality. Since 2016 we have placed over 180 such units in the marketplace, whilst a further 70 units of the KH 82-P model can also be found worldwide.
The PFX feeder introduces the flat sheets into the folding system shingled, which helps achieve a folding output of up to 18,000 sheets per hour. This means that the Stahlfolder TH 82-P can keep pace with production on the Speedmaster XL 106, so that the peak performance in sheetfed offset printing
can be carried seamlessly through to postpress. A P-Stacker installed at the output of the folding machine will take the stacks of signatures and automatically set them down on pallets. Besides safeguarding excellent process stability at high speeds, the robot also takes care of heavy physical work that would otherwise be left to staff. This means employees can apply their skills to other production tasks instead.
As of today, the operator of one of our Peak Performance folding machines in industrial signature folding, moves up to 7 tons of paper per shift from the delivery to the pallet. This is equivalent to the weight of a large, full-grown elephant. The P- stacker increases the productivity and profitability of the folding machine, as it can produce at full speed, without interruption. Personnel costs fall and the attractiveness of the workplace increases.
This makes it easier to recruit skilled personnel for the finishing department in the future.
With the Stahlfolder P-Stacker, postpress is taking another major step towards operator-independent productivity and its demand has exceeded our expectations with the factory being fully booked until mid-
2023 for delivery. Together with our Stahlfolder TH/KH 82-P and autonomous signature production, the result is a coherent overall concept in line with Heidelberg's Push to Stop philosophy.
Heidelberg's total solution including Postpress packaging solution
Heidelberg offers products along the complete value chain of packaging
production: starting with Prinect software solutions for structural design, digital workflow with solutions for color management, nesting, layout, separation and rendering, thus offering a complete software suite for converters.
We excel with our CX & XL range of presses in complex applications for high-end folding cartons, as well as in efficient manufacturing. For finishing,
we have worked for 8 years exclusively with products from MK Masterwork. That gives us access to more than 20 products for a wide range of finishing applications like foil-stamping, diecutting, inspection and folding carton gluing.
Beyond the products, Heidelberg also maintains the largest service network of any supplier to the folding carton industry. But our system service offerings go far beyond the traditional support after an incident has happened: Video Call, one of our latest products, enables the service engineers to look directly into a machine for a live diagnosis.
We might even be able to advise a work around to keep your machine in production. Another highlight of our service products is “Predictive Monitoring”: this service detects anomalies in our printing presses before malfunctions and related downtime occur – with the help of big data analysis and our experts we can plan countermeasures before the worst case is happening.
Once printed, a carton needs to be diecut and processed on a folder gluer. In many converting operations, the finishing side has not enjoyed the same level of investment activity than the printing side. It seems that both diecutting and folding gluing haven’t moved in several years – yet nothing could be further from the truth: options that were once considered high-end only are today available in more affordable
segments (for instance auto non-stop feeding with a pallet logistics system, optical sheet alignment, and even the blanking station itself). Standardized tools and quick-locks functions in all stations are speeding up make-readies. Another option is to combine two processes in one machine – for instance hot-foiling and die-cutting.
Heidelberg and MK Masterwork offer the unique Duopress with two cutting stations for this requirement. The first platen station allows for instance for hot-foiling or embossing across the complete blank, the second station is used for die-cutting and creasing, stripping and blanking stations follow. This machine reduces inventory and speeds up significantly the manufacturing of high-end folding cartons.
For folder gluers, the machine development has been one of specialization on the one hand and efficient high-speed manufacturing on the other hand. For pharma cartons, an inline braille system plus inspection helps to comply with all compliance regulations, including 100% braille and print inspection. Luxury cartons can now be finished in one pass on a folding carton gluer, thanks to a turning station.
And for high-speed straight line carton manufacturing, we offer even the complete logistics system around the folder gluer, including robotic depalletizing and feeding to automatic blank packing in several rows and layers. The packers can even be equipped with a carton erector, tie-
sheet inserter, a labeling system and a palletizing robot – completing the fully automatic features.
The collaboration between Heidelberg and MK Masterwork started in 2014 – and has grown stronger in many dimensions over the years. To date, more than 850 machines have been sold through Heidelberg – and with MK Masterwork as the exclusive OEM partner more growth is in the forecast. Since 2019 MK is also the largest single shareholder of Heidelberg, underlining that the partnership between the two companies runs deeper than the standard OEM relationship.
With the successful launch of the Mastermatrix in 2021, Heidelberg has now a complete product lineup available – for shorter runs with lower volumes all the way to our peak performance machines. The last 12 months have been the strongest 12 months ever in order intake for Heidelberg’s postpress packaging products – the post COVID recovery of our customers drove our success to new heights.
It was through flexo lamination that Lakshman first entered the printing industry 30 years ago, before building ALFT into a major force in packaging production for the food industry.
“At that time, gravure was the preferred choice of brands for quality tonal reproduction, so that was the direction we took, and where we stayed for the next 25 years or so. But it’s a different story today. In terms of quality, we see no difference between gravure and flexo, thanks almost exclusively to the advances in plate imaging that FLEXCEL NX Technology has made possible. The new production facility is a sign of our confidence in flexo’s future.”
In-house production for total control To bring plate production in-house,
ALFT has installed a FLEXCEL NX 4260 System at the new production facility, providing plates for their new Windmöller & Hölscher Miraflex II press. “Investing in in-house flexo platemaking and printing gives us total control of production and delivers a host of benefits that are relevant to our customers,” says Lakshman. “The faster turnaround with flexo is a particular advantage, enabling packaging design changes — to color or for regional variations — to be expedited.
With gravure, we’re talking about lead times of three to four weeks for cylinders, which all have to be imported. And if a cylinder gets damaged during production, you wait ten to 12 days for a replacement. Compare that to the 90 minutes to make new FLEXCEL NX
Plates, and the advantages are obvious. “We can also guarantee brands the confidentiality that matters when they’re launching new products and designs — something that can be an issue with gravure, given the time between releasing artwork and receiving cylinders.”
Brands welcome investment in “best and latest technology”
Many of ALFT’s brand owner customers were in the audience at the opening ceremony, along with local business and political leaders and ALFT’s technology partners. Welcoming ALFT’s investment in “the best and latest technology”, Mrs Hajar Alafifi, chairperson and MD of Unilever Sri Lanka, predicted that “having such a facility will make Sri Lanka a prime partner for countries in South and Southeast Asia.”
She also described vividly what moving to flexo from gravure means to all brand owners. “Currently we have to go to places like Dubai for this work, which can take six weeks. Because we can now do it in Sri Lanka, we are more agile, more flexible, and faster to market.”
Efficient production is a key focus for ALFT. For example, when it was setting up its gravure operation the company took key staff to Japan to study that country’s approach to efficient production. Their learnings inspired ALFT to replicate and implement
the same approach, which saw them building a state-of-the art facility with stringent hygiene and cleaning standards.
This also enabled it to become the only packaging facility with an A+ rating in their BRC Global Food Safety Standards Certification in Sri Lanka today. So, how FLEXCEL NX Plates perform on-press is especially important. “The consistency of the plates means we can standardize the production process and get the maximum efficiency and productivity from the new press. It’s also enabling us to move into Extended Color Gamut for certain brands, which is another huge efficiency gain. FLEXCEL NX Plates are also very durable, so we have fewer machine stops.”
“Always choose the Number One product”
Lakshman is gratified that his early enthusiasm for flexo has now been vindicated, with the technology widely acknowledged as a premium production method for flexible packaging. He credits the FLEXCEL NX System for the change: “The basic concept and design of the flexo CI press hasn’t changed. What has changed is the prepress and platemaking upstream of the press, and this evolution has been supported by the anilox and ink manufacturers. So everything is now at the right level and going in the right direction.”
Asked why ALFT chose the FLEXCEL NX System, he says simply, “The FLEXCEL NX System is a brilliant piece of equipment”, adding that “our philosophy is always to buy the best. If you choose anything other than the Number One solution you’re compromising, and you won’t get the best out of the set-up. It’s for this reason that we invested in the W&H Miraflex II press and FLEXCEL NX System. Recognized as some of the flexo industry’s best-in-class equipment, they work beautifully together, ensure fast changeovers and enable faster turnaround times.”
Moving from gravure to flexo While Lakshman acknowledges that gravure is still the dominant process in the South and Southeast Asian markets, in the future he foresees the steady migration to flexo. “It’s just a question of changing customers’ mindsets, and the best way to do that is to show them the results. So, we are gradually moving work previously gravure printed to flexo, with our customers’ consent of course.
Our approach is that whenever there’s a change to a product, we take the opportunity to propose a flexo version. In our experience, as long as we can show brand owners that flexo quality is every bit as good as the gravure, they’re very comfortable with the change. Especially when they get all the additional efficiency benefits that come with flexo.”
Gallus Group today announces the appointment of Dario Urbinati to the role of Chief Executive Officer, succeeding Dr. Frank Schaum, who will now head HEIDELBERG’s Print Segment. With 17 years of experience in the graphic arts industry and as its previous Chief Sales & Service Officer, Urbinati will continue to drive Gallus’ mission to turn the narrow web market towards a more sustainable and profitable future – providing revolutionary new technologies to achieve it, such as the recently launched Gallus One.
Urbinati comes to the role with significant experience of running label businesses, having served in senior positions with leading manufacturers around the world. Urbinati first joined Gallus in 2007, where he served nine years with the company – latterly as its Managing Director for Southeast Asia – driving growth and transforming the business and its culture. He then joined OMET China as its narrow/ mid web Managing Director, before becoming Chief Sales and Marketing Officer for ACTEGA Metal Print, where he was instrumental in launching and then commercializing its breakthrough sustainable metallization technology.
Commenting on his new role, Dario Urbinati said: “I am honored to take up the role of Gallus CEO. This is a fantastic, growing business with incredibly talented and committed people and, with the might of
HEIDELBERG behind us, an exciting trajectory for the future. While our ongoing mission is to support the success of our customers in the field, our wider ambition is to provide dynamic technologies and services to secure the future of the narrow web industry.”
Dr. Ludwin Monz, HEIDELBERG CEO, comments, “Dario has been responsible for refocusing the business against a very clear vision for the future of labels. This has meant resetting the business in important areas by increasing customer service and support, boosting sales and marketing activities and much more.
He has also introduced an ambitious sustainability program, with a landmark pledge to make our products carbon neutral by the end of 2022. Gallus is an important pillar in the Heidelberg Group’s packaging business, which offers long term growth potential and, importantly, shares our commitment to quality –and we are delighted to have Dario lead this business. I would also like to thank Dr. Frank Schaum, previously the Gallus Group CEO, for his excellent leadership to date, and we are pleased that he will remain as Chairman of the Gallus board.”
Under Urbinati’s stewardship, the business is also building a ‘Gallus Experience Center’ in St. Gallen, Switzerland. Expected to open in Spring 2023, the new facility is part of his vision for realizing ‘the label industry of the future’. The new facility has been specifically designed to aid collaboration across the
industry, inviting customers, brands and suppliers from throughout the entire ecosystem to meet and share solutions, as well as develop new ideas to help solve key industry issues and create new opportunities.
New chuck technology for winding and unwinding operations of paper and board manufacturers Sonoco, a global leader in diversified packaging, developed a new chuck technology for winding and unwinding operations of paper and board manufacturers. The new technology offers significant runnability improvements for paper and board reels in the most demanding winding operations, especially in centre drum winders and special unwinding stands like sheeters as well as corrugators.
“To meet today’s challenges of paper and board manufacturers and to offer significant productivity improvements in a cost inflation environment, we developed a new generation of chucks exclusively with our partner,” said Markku Ronnila, Product Manager Paper Mill Cores in Europe. “Our new chuck technology is a step change in paper and board winding and eliminates typical problems such as vibration, torque transmission issues and chew-out. We called this innovative technology ViPer Chucks in reference to the improved VIbration PERformance.”
ViPer Chucks offer significant process improvements during winding runs, less vibration leading to reduced web-breaks or web-tension, overall faster winding speeds and reduced chew-out causing less abrasive dirt.
with optical systems for UV curing and drying
Consequently, this avoids frequent chuck cleaning and saves employees’ working time.
The chucks also provide better torque transmission for heavy reel weights. The result allows for higher productivity due to significantly reduced process interruptions coming along with an improvement on process safety. Existing chucks can be easily replaced in a plug-and-play solution.
Are you ready to embrace the transformative tone of an unconventional shade?
Vibrating with vim and vigour is how Pantone has described its colour of the year, Viva Magenta 18-750. The unconventional shade for an unconventional time is ‘powerful and empowering’. Rooted in nature it descends from the red family and is expressive of a new signal of strength. Viva Magenta is brave and fearless, a pulsating colour whose exuberance promotes a joyous and optimistic celebration, writing a new narrative.
Pantone goes on to say it is an assertive, but not aggressive, carmine red that does not boldly dominate but instead takes a ‘fist in a velvet glove’ approach. Exuding dynamism, the transformative red tone is capable of driving design to create a more positive future.
The strong colour echoes Pantone’s
forecasted spring and summer 2023 top ten standout colours for London Fashion Week including Cherry Tomato, Blazing Yellow, Electric Blue Lemonade and Pink Cosmos. They integrate tradition and innovation marrying the need for brightness and vibrant positivity with quieting tinted tones. They embrace the freedom to colourfully express individuality without constraint.
Vivid colours form the foundations of some key trends set to dominate 2023. Among the ones that caught my eye are the following with their descriptions:
This is not just about bright, sharp colours, it’s about colours that hurt your eyes. They are arresting and striking. They grab your attention.
It is a trend rooted in science. It takes inspiration from testing acidic substances. The more acidic a substance, the brighter the colour gets.
2. Colourful Retro
Bright colour pallets will combine with idyllic retro imagery as the 1990s revival and vintage visual trends of 2022 continue. Everything from posters to packaging will be imbued with a sense of nostalgia.
This moody and dark trend subverts the status quo with its distorted,
melted metallic look. The shade of silver can range from a dark or dull tone to a shiny silver metal. This colour trend is about stirring antiestablishment expression and pushing back on norms.
The rich jewel colours of 2023 are elegant, tonal and sensual. They are ushering in an interesting and chic era for colour in graphic design. Inspired by 1930s palettes, rich crimson, burnt orange, forest green or powdery lavender, offer a cosseting and indulgent quality. They allow colour to do the talking for high end branding or luxury packaging design.
Simple neutral colour schemes or black and neon can be combined with condensed typography to create two very different results – to temper drama or escalate it. In 2023, in line with the move towards metaverse and futuristic styling, condensed fonts and compact typography will take centre stage.
Strong, vibrant colours that stir emotions are shaping the palette for 2023. Combined with the leading design trends they deliver an energised tone for the coming year. For Print Service Providers the accurate recreation of the shade, depth, and nuances of a colour is vital. Consistent repeatability is essential.