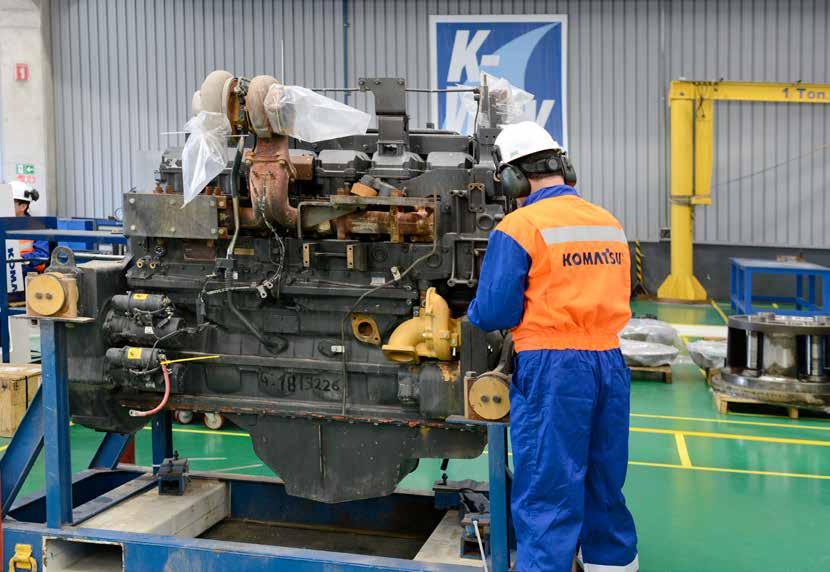
10 minute read
Informe Técnico
Ala hora de renovar o adquirir maquinaria, la remanufactura resulta una opción de interés para las compañías mineras, al ser una alternativa que se alinea con su búsqueda de productividad y la reducción costos y de impacto en la huella ambiental. Respecto de los alcances de este proceso, Álvaro Orellana, gerente de Ingeniería e Innovación de Komatsu Reman Center, explica que la remanufactura “consiste al recuperar parte del elemento usado. De manera adicional, presenta mejoras de los tiempos de respuesta en comparación con la adquisición de un componente nuevo en el extranjero, potenciando la industrialización local”. Su visión es complementada por Enrique Mancilla, gerente de Proyectos de Crecimiento Product Support de Finning, quien considera que la remanufactura “es un proceso que contribuye mente reutilizables, etc.” Para ello, en el caso de esta firma “se aplican procedimientos de recuperación que suministra Caterpillar, que aseguran que dichos componentes pueden dar una segunda vida al equipo que pasa por el proceso de remanufactura. Esta oferta es cada vez más solicitada por clientes que desean tener un buen impacto medio ambiental, pero además un ahorro de costos significativos en la renovación o
Foto: Gentileza Komatsu
Equipos mineros Remanufactura: Oportunidad de eficiencia y sostenibilidad
en maximizar el reciclado y recuperación de los componentes desgastados de un equipo minero, mediante un proceso que permite que estas unidades adquieran una condición equivalente a la de un producto nuevo. De esta forma se genera un efecto positivo múltiple: se disminuye la generación de desechos por descarte de componentes usados; se evita el uso tanto de materias primas como de energía, al no fabricar un componente desde cero y, además, se genera un ahorro en costo, de forma muy significativa al desarrollo sostenible y a la productividad, ya que ahorra recursos de toda clase, desde los hidrocarburos quemados por los buques para transportar equipos nuevos desde otras latitudes, ahorro de energías usadas en la fabricación, reciclando chasis y partes que son perfectaadquisición de maquinaria reconstruida propia o provista desde terceros”, señala el ejecutivo. Destaca que “la reconstrucción permite que el equipo se vea, rinda y opere como una máquina nueva, con el máximo de actualizaciones de ingeniería disponibles. Entregando confiabilidad, disponibilidad y aumentando la producción”. Mancilla agrega que llevar el equipo a condición “reconstruido a cero horas” permite reducir considerablemente los costos de mantención”, y contribuye a disminuir la huella de carbono, por su mayor eficiencia de consumo de energía, de agua y
Una serie de ahorros, tanto en materia de costos, productividad y ambiental, conlleva la decisión de optar por equipos reconstruidos.
En un equipo remanufacturado conviven elementos nuevos y usados.
otros recursos, reduciendo la generación de residuos y de las emisiones de CO2.
Cuándo optar por la remanufactura
La adquisición de un equipo reconstruido se ve condicionada tanto por sus características técnicas como por los requerimientos de la compañía. Álvaro Orellana menciona que los equipos remanufacturados “cumplen con altos estándares, al punto que cuentan con especificaciones iguales, equivalentes, y en algunos casos incluso mayores que los equipos que usan componentes nuevos. En un equipo remanufacturado conviven elementos nuevos y usados, por lo que su proyección de vida se sitúa comúnmente entre el 80% e inclusive más del 100% de la vida de uno nuevo. Sin embargo, al cabo de ese tiempo, los componentes pueden volver a remanufacturarse, extendiendo la vida de éstos varias veces. Con ello se reduce drásticamente el costo por hora para la compañía minera, en comparación con la adquisición de nuevos componentes o equipos”. En tanto, Enrique Mancilla explica que “normalmente, un equipo nuevo de última generación provee de la máxima productividad disponible y los avances tecnológicos de vanguardia. Estos diferenciadores podrían tener un impacto mayor en la productividad de la mina; si estos aspectos son importantes, lo mejor es optar por un equipo nuevo. Sin embargo, si los diferenciales para la aplicación minera en cuestión son menores y además existen restricciones de CAPEX para viabilizar los proyectos o extender la vida de la mina a un costo razonable, la alternativa de remanufactura resulta muy atractiva. Existen compañías mineras que basan toda su propuesta de unidades móviles con equipos reconstruidos, con bastante éxito en términos de disponibilidad y confiabilidad”. En la visión del profesional de Finning, en los siguientes casos se debe pensar en una reconstrucción: • Existe la necesidad de renovar el equipo o flota, pero no se dispone de CA-
PEX suficiente. • El equipo será detenido por un periodo de tiempo extenso producto de una reparación mayor u otro motivo (accidente, etc.) • La confiabilidad y/o costo de mantención del equipo no es la esperada y el estado del chasis permite una segunda vida. • La vida útil proyectada del equipo se puede hacer
nuevo es menor que el promedio del segundo tramo de 30.000 horas”.

Izq.: Álvaro Orellana, gerente de Ingeniería e Innovación de Komatsu Reman Center.

Der.: Enrique Mancilla, gerente de Proyectos de Crecimiento Product Support de Finning
Foto: Gentileza Komatsu
coincidir con el cierre de la operación de la mina. • Para mantener estandarizada la flota a un único modelo, facilitando la mantención. • Para viabilizar proyectos greenfields con alto requerimientos iniciales de
CAPEX.
Foto: Gentileza Finning
Además, menciona que “cuando se evalúa una reconstrucción se debe tener en consideración los beneficios directos de contar con un equipo reconstruido a cero horas en faena. El promedio de la tarifa de mantención las primeras 30.000 horas de un equipo
Impulso a la remanufactura
Las empresas que proveen equipos reconstruidos han ido ampliando su catálogo, y la propuesta de valor que entregar a sus clientes. Es así como Finning promueve la remanufactura “a través del programa de fábrica de reconstrucción certificada CAT, el cual consiste en diferentes opciones. Por ejemplo, la certificación total de la maquina con garantía de equipo nuevo y número de serie renovado e inscrito como máquina reconstruida a cero horas en la fábrica.

Además, existen opciones que incluyen sólo componentes o soluciones intermedias customizadas a la necesidad de cada cliente”, detalla Enrique Mancilla Resalta, además, que “todas estas opciones permiten al cliente maximizar el beneficio de la reconstrucción”, y consideran la reparación de máquina propia. Adicionalmente, “podemos ofrecer la búsqueda de equipos usados de terceros, candidatos a ser reconstruidos y puestos en el mercado, reciclando y reactivando flotas de operaciones que han terminado su actividad o han cambiado el tamaño de sus equipos, dando una segunda vida al activo”. Álvaro Orellana asegura que el Grupo Komatsu Cummins, a través de su planta de remanufactura Komatsu Reman Center Chile, “fue pionero en la materia y a causa de ello se mantiene como una industria líder en el uso de remanufactura para equipos mineros. Entre los procesos más importantes de su historia destaca la recuperación de bobinas y rebobinado de motores de tracción para camiones eléctricos; trabajos que comenzaron hace más de 25 años, en torno a 1995. La compañía además ha ampliado la remanufactura a generadores a bordo de camiones eléctricos, enfriadores de resistencias de frenado, cilindros y baldes de palas mineras de gran tonelaje, sistemas de
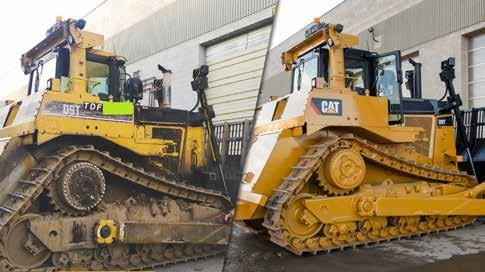
Foto: Gentileza Finning
control electrónicos. Es un trabajo que en la actualidad está cubriendo toda la gama de equipos mineros móviles y que sigue ampliando su abanico de soluciones hacia aplicaciones estacionarias industriales”. El ejecutivo añade que esta experiencia acumulada ha permitido que Komatsu Reman Center Chile se posicione como una planta referente a nivel global, dando soporte a más de 20 distintos centros de rede las mejores prácticas de remanufactura de equipos mineros. Adicionalmente, Komatsu Reman Center Chile “está comprometido con el desarrollo de las nuevas generaciones, compartiendo conocimientos bidireccionalmente con instituciones académicas, trabajando en proyectos de Innovación y desarrollo, para continuar avanzando en la mejora continua y nuevos procesos. De hecho, junto con potenciar la formación
La remanufactura contribuye al desarrollo sostenible y a la productividad en la minería.
Álvaro Orellana explica que la remanufactura “consiste en maximizar el reciclado y recuperación de los componentes desgastados de un equipo minero, mediante un proceso que permite que estas unidades adquieran una condición equivalente a la de un producto nuevo”.
manufactura Komatsu en el mundo. Afirma que entre los focos que han mantenido su consolidación se encuentra el traspaso de conocimientos y estandarización global de especialistas dedicados a la remanufactura, también estamos generando espacio para el conocimiento de procesos e industrialización del país”, indica Orellana.
SOLUCIÓN DE TEGA WEARTEC DISMINUYE COSTOS Y
AUMENTA SEGURIDAD EN MANTENCIONES DE CHUTES
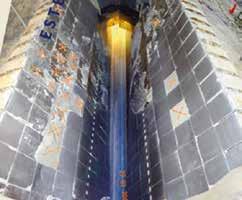
Cambio diseño revestimiento Interior
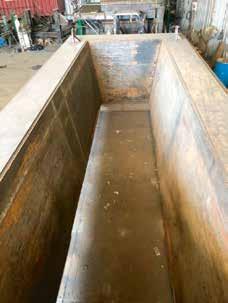
Disminuir la acumulación de material al interior del chute, al mejorar el flujo dentro del mismo; y reducir tanto la frecuencia de sus mantenciones como el tiempo que toma efectuarlas, son las principales ventajas que ofrece una solución creada por el área Weartec de Tega Industries. La firma de origen indio desarrolló una solución de ingeniería con el soporte de un equipo multidisciplinario, que combinó diseño y pruebas técnicas. “Una buena Ingeniería, entendiendo claramente la necesidad del cliente, en conjunto con un correcto cálculo y selección de material puede mejorar la operación, disminuir los costos asociados a la misma y reducir el número y tiempo de las mantenciones de los chutes”, destaca Cristian Duran, Product Manager de WearTec. Esto último, dice el ejecutivo, ocasiona beneficios importantes desde el punto de vista de la seguridad, ya que se reduce la cantidad de personas necesarias en cada reparación y, además, baja el tiempo de exposición de los operarios durante las maniobras de cambio de revestimiento. “Desde la llegada a Chile de Tega, el área de Weartec ha trabajado en solucionar los problemas del cliente, logrando tener un crecimiento sostenido y que este año podría alcanzar un 65% en comparación a 2020”, resalta. EL PROVEEDOR DE ORIGEN INDIO MARCA LA DIFERENCIA CON FLEXIBILIDAD, DISEÑOS PERSONALIZADOS Y RESPUESTAS RÁPIDAS PARA DAR SOLUCIÓN A LOS REQUERIMIENTOS DE SUS CLIENTES.
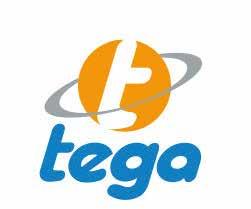
DESAFÍO
Duran recuerda que en 2019 Tega fue invitado para dar solución a una problemática existente en un chute bajo stockpile, donde los desafíos apuntaban, en primer lugar, a disminuir la acumulación de material al interior del mismo, la que se generaba por velocidades distintas entre las correas de alimentación y descarga. Además, se debía mejorar el flujo ya que el material se adhería a sus paredes; reducir los tiempos de mantención asociados al cambio de revestimientos interiores y, por último, bajar la frecuencia de las mantenciones, evitando la caída de los mismos durante la operación. “Un equipo multidisciplinario, conformado por personal de Tega Chile e India inicia los procesos de diseño y desarrollo para hacer frente a la problemática. Se generaron varios diseños y pruebas hasta lograr dar con la solución final”, asevera.
Rediseño interior del Chute

FENÓMENOS
El proceso se inició con el diseño 3D de las condiciones que presentaba en ese minuto el chute y una simulación de elementos discretos, con la finalidad de determinar de manera correcta los fenómenos que ocurrían en su interior. Con esto se pudo constatar que el chute presentaba un ángulo variable, lo que generaba una disminución del volumen interno, por lo cual la altura de la pila del material al interior de éste se incrementaba. También se constató gran cantidad de revestimientos, lo que ocasionaba que en cada unión de los mismos el material se acumulara y se adhiriera a las paredes. Ese mismo diseño influía en los altos tiempos requeridos para la mantención, mientras que el ángulo de contacto del material con las paredes del chute propiciaba la caída de los revestimientos interiores.
PROPUESTA EFECTIVA
Duran sostiene que “la solución propuesta por Tega se basó en un rediseño estructural del chute, donde se trabajó en una propuesta de ángulo único, que trajo como consecuencia un aumento de volumen en su interior de 5% y un mejor flujo de material, lo cual evita grandes pilas de material al interior del equipo”. Además, agrega, se efectuó un diseño único de revestimientos de gran tamaño y con sistema de instalación, que permite disminuir en 70% los tiempos de mantención asociados a su cambio y que evita la caída de éstos durante la operación, lo cual incrementa la confiabilidad y disponibilidad de este equipo, reduciendo la frecuencia de las reparaciones.
TEGA INDUSTRIES
Raúl Morales O. Sales Manager Chile-Perú - Fono: +569 3404 1220. Email: Raul.morales@tegaindustries.cl ventas@tegaindustries.cl