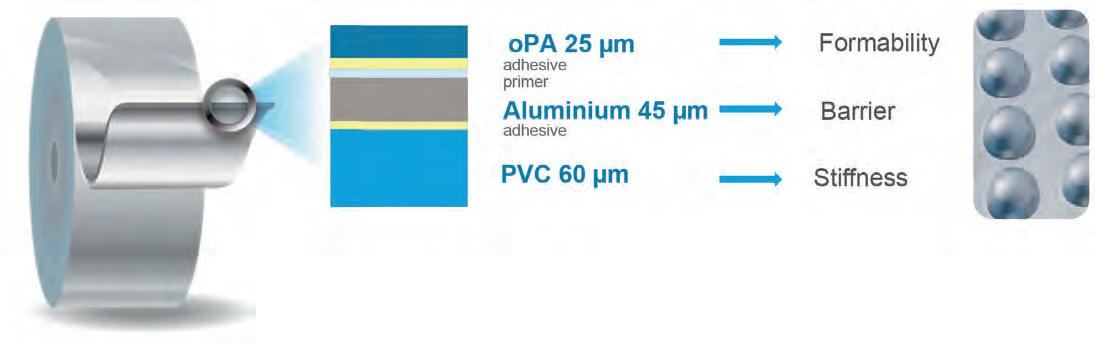
9 minute read
BLISTER COLD FORM IN ALLUMINIO MONOMATERIALE
Dalla R&D di Laminazione Sottile, una soluzione innovativa e tecnologica per il confezionamento in blister di medicinali. Chiaro esempio di economia circolare, il nuovo packaging non solo risponde a tutti i criteri di igiene e sicurezza richiesti dal mercato farmaceutico ma è totalmente riciclabile ed è quindi destinato a stabilire nuovi standard in fatto di sostenibilità.
In questa sede documentiamo l’iter progettuale seguito da Laminazione Sottile per arrivare alla produzione di un blister alveolare per il settore pharma, passando attraverso le prove sul materiale più idoneo e la sua successiva ottimizzazione.
Advertisement
Dallo studio del mercato alla ricerca… e ritorno
Da molti anni il mercato farmaceutico usa sistemi alveolari in materiale plastico per confezionare medicinali sotto forma di compresse, capsule, confetti e similari. Se il farmaco teme l’umidità, l’ossigeno o la luce, per creare gli alveoli si usa un multimateriale complesso che unisce, per incollaggio, poliammide/alluminio/PVC saldante.
La struttura alveolare viene chiusa con laminati di alluminio, di spessore compreso tra i 20 e i 25 micron, verniciati internamente con lacche termosaldabili viniliche, che sigillano il blister.
Tali strutture sono definite “cold form”, perché gli alveoli vengono formati a freddo con una semplice operazione di deformazione meccanica.
Tuttavia, pur essendo un’ottima e collaudata soluzione di packaging, i blister multimateriale presentano un problema: a fine vita, sono infatti “praticamente” non smaltibili, dato che è difficilissimo separare i materiali plastici incollati indissolubilmente al metallo.
Da questa considerazione è nata l’idea del gruppo di ricerca di Laminazione Sottile: studiare una lega di alluminio, successivamente verniciata con pochi g/m2 di polimeri, che consentisse da sola la deformazione meccanica sempre a freddo degli alveoli, nonché la perfetta sigillatura per termosaldatura con il tradizionale film di alluminio di chiusura.
I vantaggi di una soluzione del genere sono molteplici, a partire dalla barriera assoluta a ossigeno, vapor d’acqua (ovvero zero WVTR e OTR) e luce. Inoltre, a differenza di quanto accade oggi, il proces- so consentirebbe di verniciare esternamente con qualsiasi colore la struttura alveolare (che oggi è esclusivamente di color alluminio).
Al proposito, in funzione della tipologia di farmaco, la farmacopea potrebbe per esempio indicare un colore caratteristico che aiuterebbe i pazienti (costretti magari ad assumere giornalmente farmaci differenti per curare diverse patologie) a non sbagliare il medicinale da assumere.
Il blister concepito da Laminazione Sottile potrebbe essere ottimale anche per confezionare lenti a contatto: vernici sterilizzabili in vapor d’acqua a 121 °C per 30’ o anche a raggi γ potrebbero essere utilizzate per consentire la sterilizzazione dei pozzetti contenenti lenti e soluzione salina sterile con pH normalmente compreso tra 7.2 e 7.6.
L’idea progettuale
Attualmente la struttura alveolare prodotta per contenere farmaci in compresse, capsule e formati similari, che deve garantire un effetto barriera verso luce, vapor d’acqua e ossigeno, ha una struttura come quella indicata in figura 1 (stratigrafia tipo). Anche il ciclo produttivo di questo multimateriale è alquanto complesso. Per garantire un buon incollaggio tra i materiali bisogna infatti:
- realizzare l’accoppiamento dei film di OPA e PVC con adesivi normalmente poliuretanici, mediante tecnologia conosciuta con il nome di “secco a solvente”;
- effettuare un processo di cura termica dei coils dopo accoppiamento in camera climatica e a umidità controllata per minimo 3 giorni. Infatti, l’adesivo termina la sua polimerizzazione dopo molte ore dall’incollaggio;
- tagliare in nastri nella larghezza richiesta dal cliente.
L’idea progettuale è stata dunque di realizzare un laminato di alluminio con spessore inferiore rispet-
2 to ai 135 micron (spessore totale del laminato accoppiato OPA/Adesivo/Al/Adesivo/PVC), mettendo a punto un sistema monomateriale che, a fine vita, potesse essere smaltito nell’alluminio come una comunissima lattina, per poi essere recuperato e riciclato in pochi mesi. Si ricorda che in Italia nel 2022 è stato recuperato e avviato al riciclo il 73,6% dei packaging in alluminio immessi sul mercato e il 91,6% delle lattine (dati ufficiali CIAL).
Ottimizzare il ciclo di produzione dei laminati
La difficoltà principale è stata creare un laminato in una lega capace di resistere agli stress meccanici nella formatura a freddo degli alveoli.
La sperimentazione effettuata ha consentito di ottenere una struttura metallografica particolarmente fine, per massimizzare l’allungamento a rottura del laminato realizzato a spessore tra i 70 e i 100 micron. Lo spessore, infatti, potrà essere determinato in funzione della geometria degli alveoli da realizzare.
Controllo della struttura metallografica del laminato. Mediante metallografia si è provveduto a caratterizzare il laminato in termini di dimensione dei grani, dispersione e taglia dei composti intermetallici.
I campioni, dopo lucidatura, sono stati attaccati con soluzione fluoborica e osservati al microscopio metallografico con luce polarizzata (figure 3 e 4).
1. Tipica stratigrafia di un materiale cold form. * Typical stratigraphy of a cold form material.*
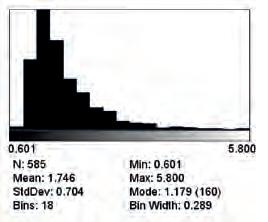

* From Simone Hermann, Amcor Product Development Manager Pharma, in Amcor, Innovative HochbarrierefolienHerstellung, Design und neueste Anwendungen, 17 May 2017.
Prove di formatura degli alveoli su stampo pilota: a) lato esterno; b) lato interno.
Tests on the forming of cells on a pilot mould: a) external side; b) internal side.
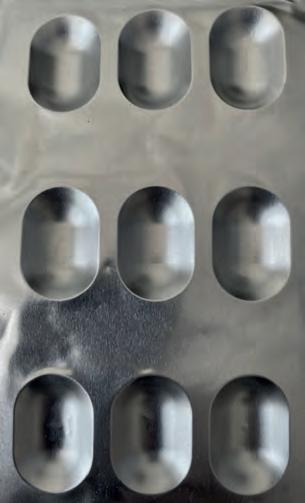
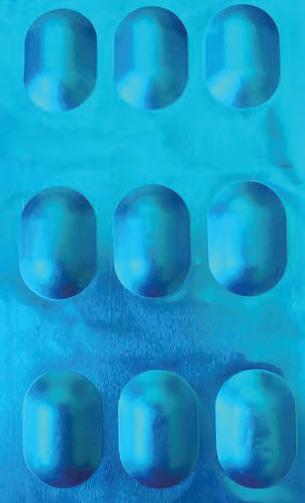
Anche l’isotropia dei materiali è stata attentamente studiata, per far sì che le caratteristiche meccaniche, misurate mediante prove di trazione con provini realizzati parallelamente al senso di laminazione e a 90° e 45° rispetto alla rolling direction, minimizzassero le differenze in termini di carico di rottura, snervamento e allungamento.
Uno stampo “pilota” prototipale da laboratorio è servito per verificare la fattibilità degli alveoli (figura 2).

5. Esempio di imbutitura a bicchierino su campione marcato con cerchi mediante laser e analisi dimensionale con microscopio confocale. Example of deep drawing on a sample marked with circles using laser and dimensional analyses with confocal microscope.

Controllo indice di anisotropia del materiale. Le misure di anisotropia sono state calcolate sia mediante prove di trazione in piano del laminato a spessore finito su provini a 0°, 45° e a 90° rispetto al senso di laminazione, effettuando anche misure sperimentali dei coefficienti di Lankford, sia su campioni sottoposti a imbutitura a bicchierino. Per valutare la deformazione sugli imbutiti, i lamierini sono stati preventivamente incisi con un laser di precisione (Marcatore Laser Yb:YAG - Costruttore: IPG Photonics) e si è analizzata l’incidenza del fascio laser sulla superficie dell’alluminio laccato mediante un microscopio confocale (figura 5).
Le prove su stampo pilota. È stato costruito un piccolo stampo da laboratorio, per fare le prime prove di imbutitura su un’impronta considerata abbastanza critica. In figura 6 alcune immagini dello stampo prototipale.
Cold form blisters in monomaterial aluminium
An innovative and technological solution for medicinal blister packaging from Laminazione Sottile’s R&D team. A clear example of circular economy, the new packaging not only responds to all the hygiene and safety criteria required by the pharmaceutical market, but is totally recyclable and therefore destined to set new sustainability standards.
Ciro Sinagra, Anthony W. Ipock - Laminazione Sottile Group
In this article we describe the design process followed by Laminazione Sottile in order to arrive at the production of an alveolar blister for the pharma sector, involving tests on the most suitable material and its subsequent optimisation.

From the study of materials to research… and back again
The pharmaceutical market has been using plastic alveolar systems for years to package medicines in the form of tablets, capsules, dragees and the like. If the medicine is sensitive to humidity, oxygen or light, a complex multi-material that glues together polyamide/ aluminium/sealing PVC is used to create the cells.
The alveolar structure is closed with aluminium laminates, of 20 to 25-micron thickness, fully coated with vinyl heat-sealable lacquers, which seal the blister.
These structures are defined as “cold form” because the cells are cold-formed
In conclusione with a simple mechanical deformation operation.
La soluzione monomateriale studiata - un laminato in lega di alluminio verniciato, specifico per la produzione di blister alveolari per il settore farma - potrebbe rappresentare una rivoluzione nel packaging farmaceutico.
Il Dipartimento R&D del Gruppo Laminazione Sottile è aperto alla collaborazione con i costruttori di macchine automatiche, convinto che il progetto di questo packaging innovativo, igienico, ermetico, con barriera totale a luce e gas, perfettamente e facilmente riciclabile possa rappresentare nel prossimo futuro una soluzione ottimale per le case farmaceutiche più sensibili ai concetti di economia circolare. In questo modo, un prodotto che oggi, a fine vita, diventa un rifiuto potrà facilmente trasformarsi in una risorsa. Un concetto, questo, che il mondo dell’alluminio ha peraltro introiettato da tempo, superando l’ottica tradizionale del ciclo di vita “dalla culla alla tomba”, e progettando ormai le soluzioni di packaging secondo il criterio “dalla culla alla culla”.
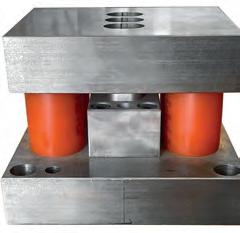
6. Realizzazione di uno stampo prototipale per test di imbutitura. Creation of a prototype mould for deep drawing tests.
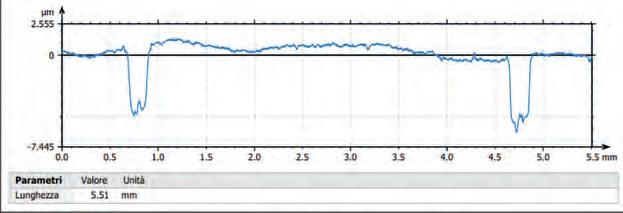
Although this is an excellent tried-andtested packaging solution, multimaterial blisters, however, have a problem: at end-of-life, they are “practically” non-disposable, given that it is very difficult to separate the plastic materials which are inextricably glued to the metal.
This situation gave Laminazione Sottile’s research group an idea: to research an aluminium alloy, subsequently coated with a few g/m2 of polymers, which alone allows for the cold mechanical deformation of the cells, as well as perfect sealing through heat sealing with traditional closing aluminium foil. The advantages of such a solution are numerous, starting from the perfect barrier against oxygen, water vapour (that is, zero WVTR and OTR) and light. In addition, in contrast with what happens today, the process would make it possible to externally coat the alveolar structure with any colour (which is today exclusively the colour of aluminium). In this regard, depending on the type of medicine, the pharmacopoeia could, for example, indicate a characteristic colour which would help patients (perhaps obliged to consume different medicines every day to treat different pathologies) take the right medicine.
The blister developed by Laminazione Sottile could also be perfect for packaging contact lenses: coatings sterilised in steam at 121 °C for 30’ or also by gamma rays could be used to allow for sterilisation of the cells containing lenses and a saline solution with pH normally between 7.2 and 7.6.
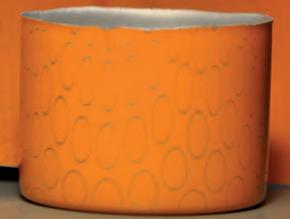
The design idea
The alveolar structure produced to contain medicines in the form of tablets, capsules and similar forms, which have to guarantee a barrier against light, water vapour and oxygen, has a structure as shown in figure 1 (standard stratigraphy).
The production cycle of the multi- material is also somewhat complex. To guarantee effective adhesion between the materials, it is necessary, in fact, to:
- obtain the lamination of OPA and PVC film with normally polyurethane adhesives, using technology known with the name of “solvent dry”;
- carry out a thermal treatment process of the coils after lamination in a climatic chamber with controlled humidity for a minimum of 3 days. The adhesive finishes its polymerisation many hours after gluing;
- cut into strips in the width requested by the customer.
The design idea was, therefore, to create an aluminium laminate with a thickness below 135 microns (total thickness of the coupled OPA/Adhesive/Al/ Adhesive/PVC laminate), developing a mono-material system which, at end-of-life, can be disposed with aluminium like a normal can, to be then recovered and recycled in a few months.
It is worth noting that in Italy in 2022
73.6% of aluminium packaging and 91.6% of cans were recovered and sent to recycling (official CIAL data)..
Optimising the laminates production cycle observed under a metallographic microscope with polarized light (figures 3 and 4).
The main problem was creating a laminate in an alloy able to resist the mechanical stresses in the cold forming of the cells.
The experimentation carried out made it possible to obtain a particularly fine metallographic structure to maximise the elongation at break of the laminate developed at a thickness between 70 and 100 microns. The thickness, in fact, can be established according to the geometry of the cells to be made. The isotropy of the materials was carefully studied, to ensure that the mechanical characteristics, measured with tensile tests with specimens carried out parallel to the rolling direction and at 90° and 45° with respect to the rolling direction, minimised differences in terms of breakage load, yield strength and elongation.
A laboratory prototype “pilot” mould was used to verify the feasibility of the cells (figure 2).
Material anisotropy index control. Anisotropy measurements were calculated both with flat tensile tests of laminates at final thickness on specimens at 0°, 45° and 90° with respect to the rolling direction, carrying out also experimental measurements of Lankford coefficients, and on samples subjected to deep drawing. To evaluate the deformation on the drawn parts, the strips were previously engraved with a precision laser (Yb:YAG Laser Marker - Manufacturer: IPG Photonics) and the incidence of the laser beam on the lacquered aluminium surface was analysed using a confocal microscope (figure 5).
Pilot mould tests. A small laboratory mould was constructed to carry out initial deep drawing tests on an impression considered sufficiently critical.
In conclusion
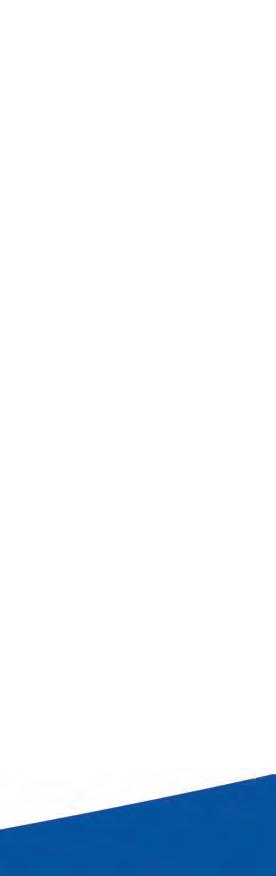
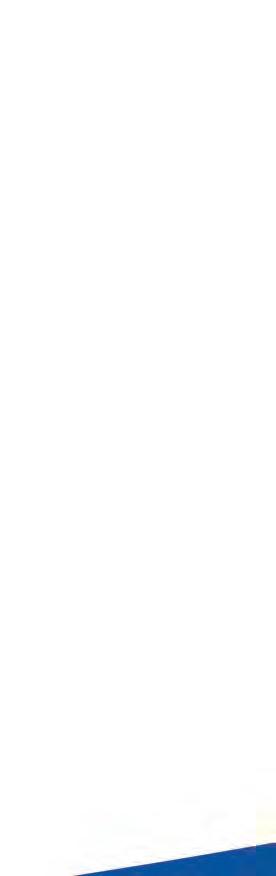
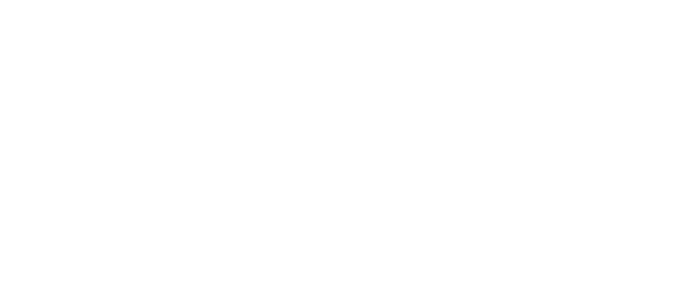
The mono-material solution studied - a coated aluminium alloy laminate, specific for the production of alveolar blisters for the pharma sector - could represent a revolution in pharmaceutical packaging.
Laminazione Sottile Group’s R&D department is open to partnerships with automatic machine manufacturers, convinced that this innovative, hygienic hermetic packaging design, with a total light and gas barrier, perfectly and easily recyclable, could represent in the near future an excellent solution for pharmaceutical companies more sensitive to the concepts of the circular economy.
In this way, a product which today, at end-of-life, becomes an item of waste, could easily turn into a resource. It’s a concept which the aluminium world has already embraced for some time, overcoming the traditional “from cradle to grave” view, and designing today packaging solutions according to “from cradle to cradle”.