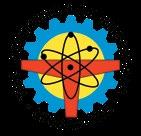
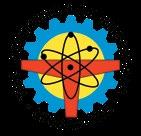
THE SINGAPORE ENGINEER
BUILT ENVIRONMENT INDUSTRY: Targets and initiatives to support transformation
MARINE INDUSTRY INNOVATION: Facilitating sustainable and efficient marine travel
STRUCTURAL ENGINEERING: Reaching new heights in timber-hybrid design
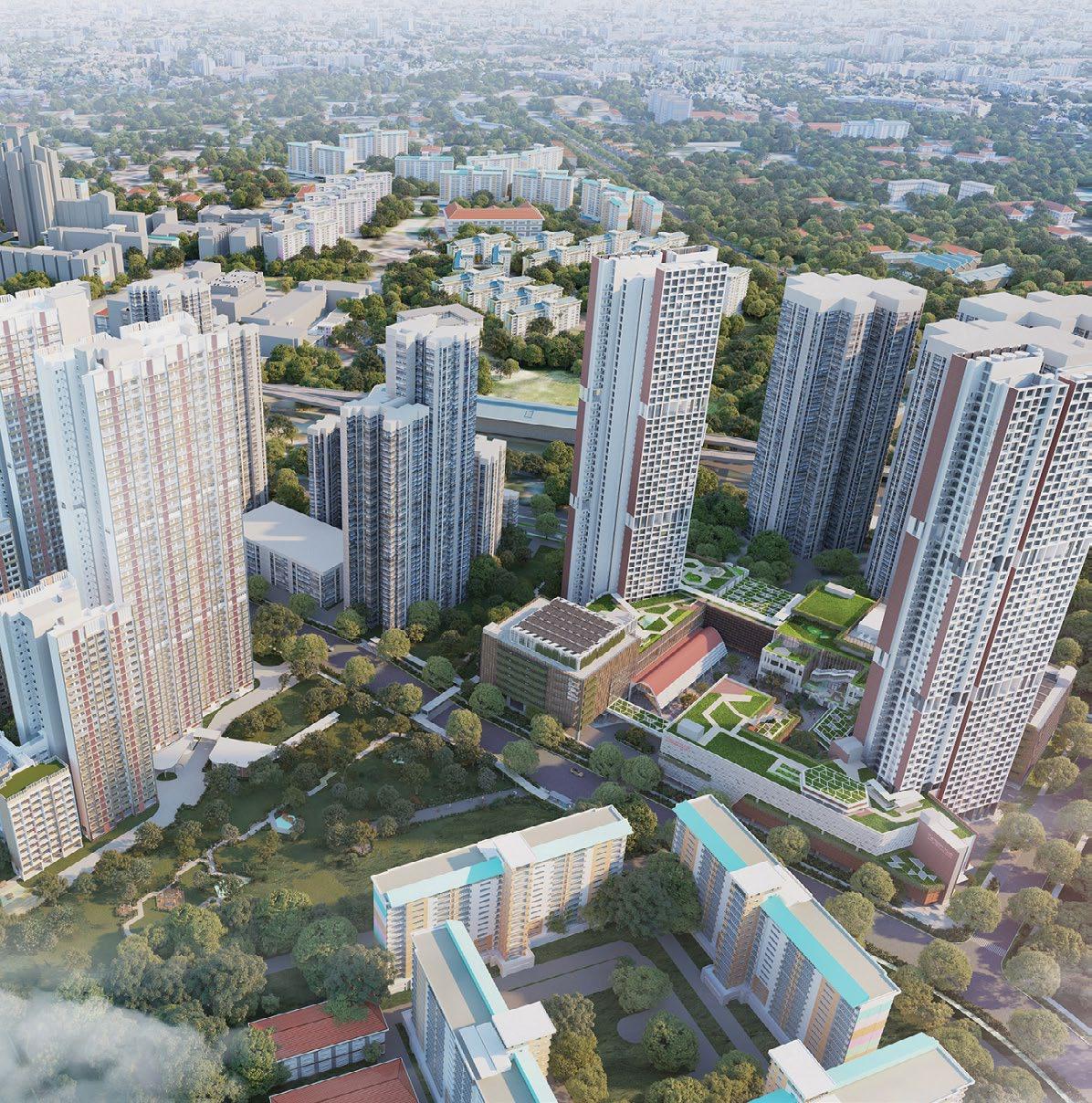
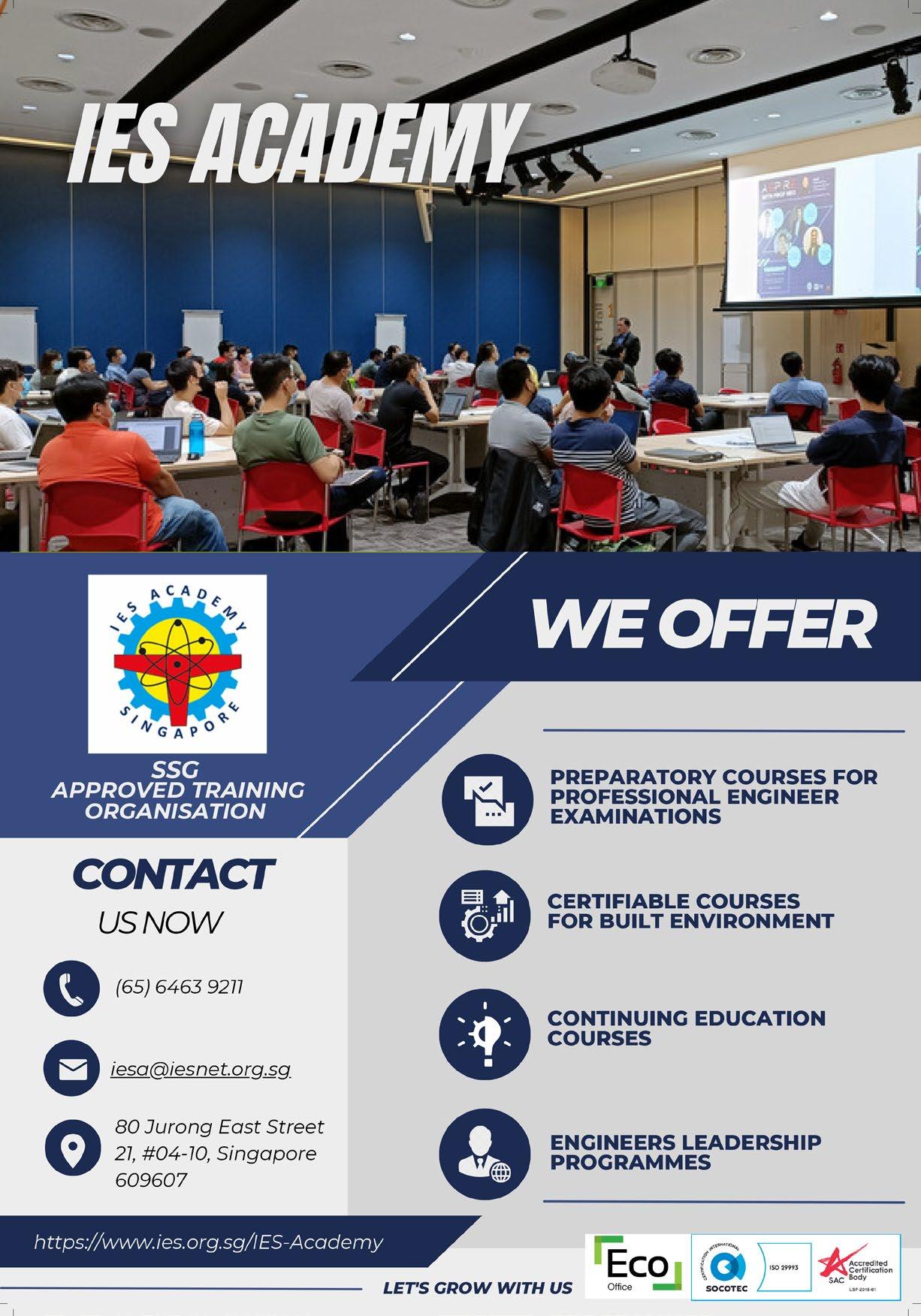
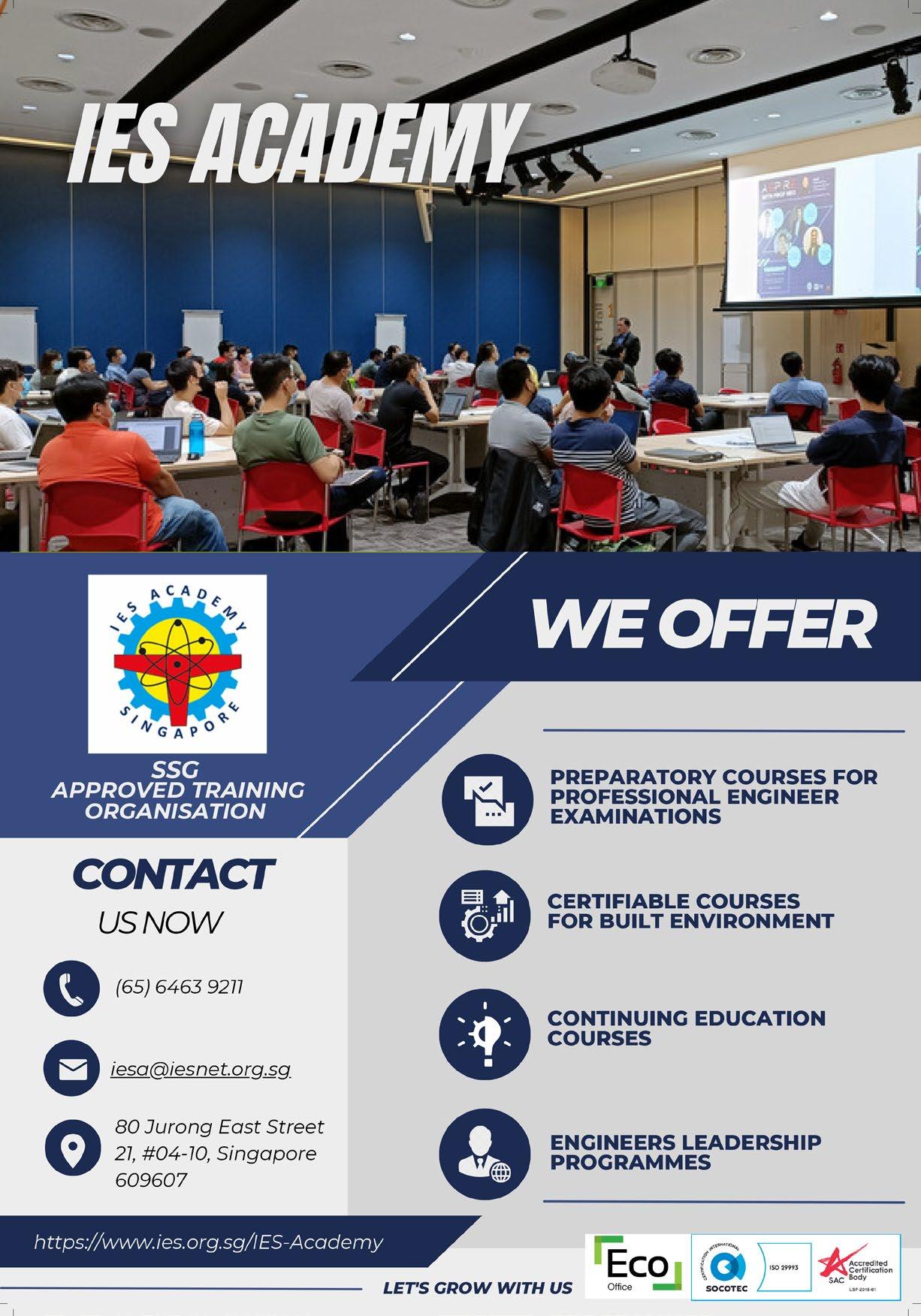
An Ode to Wing-in-Ground
Across the Ocean how she Glides
With Grace and Beauty on Air she Rides
While Wind Whips up the Symphony
As Waves Embellish the Rhapsody
Fast and Safe her Wing-In-Ground Effect Promises
Boundless the Ocean's Runway she Optimises
Comfort and Convenience belie true Sustainability Maintainability, Dependability, Extraordinary Ability
Communities she easily Connects
Coast-to-Coast she leaves no Tracks Transport, Logistics, Tourism, Surveillance - whatever the Mission Destination Splendid Beach, Craggy Berth or Bewitching Sea with no Question
Flies like a Plane, Floats like a Ship, Drives like a Car
Clearly, there is no Avatar
Bird, Plane, Ship or Car, let run Wild your Imagination Come, Join us on our Magni cent Journey of Finest Orchestration

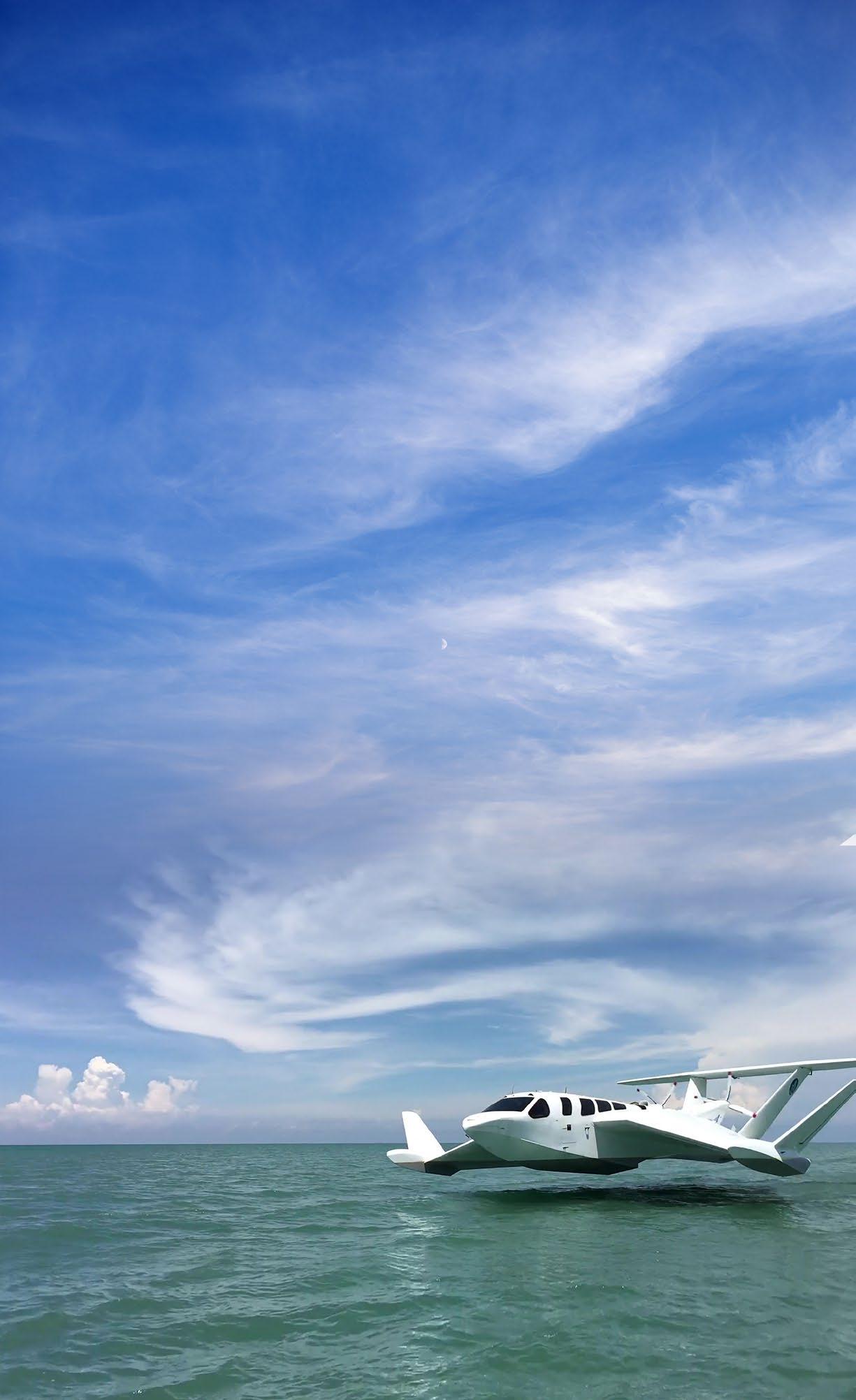

MARINE INDUSTRY INNOVATION
DIGITALISATION
20 Leveraging technology to overcome construction challenges in 2024
The use of digital tools is the solution.
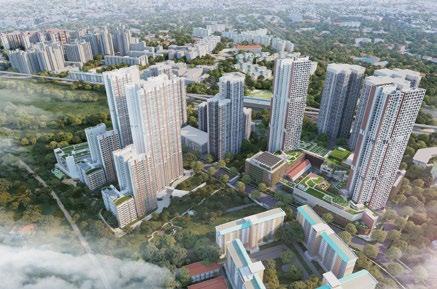
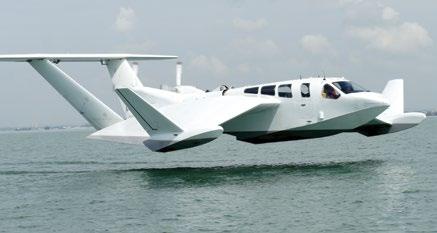
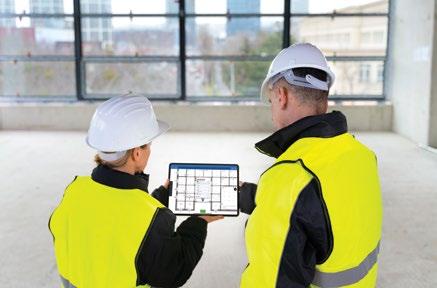
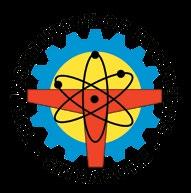
PROJECT MANAGEMENT
22 Understanding the demand for project manager competencies in the Singapore construction industry: a data mining approach
The findings of a study are presented.
STRUCTURAL ENGINEERING
27 Reaching new heights in timber-hybrid design Designing the Netherlands’ tallest timber-hybrid residential building.
PROJECT APPLICATION
34 Formwork and scaffolding for VIENNA TWENTYTWO
The solutions ensure a fast construction sequence, a safe working environment and flexibility.
35 Renovation of a historic building in Italy A specific binder was developed to restore the exterior surfaces of the Torre Velasca in Milan.
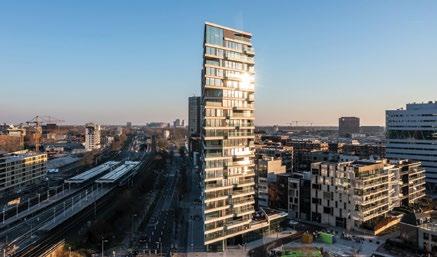
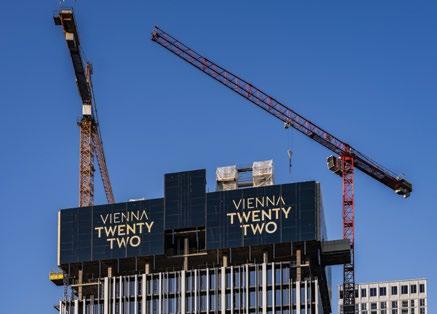
REGULAR SECTIONS
04 NEWS & EVENTS
40 PRODUCTS & SOLUTIONS

Collaboration to develop integrated CCUS and lower carbon hydrogen value chains
Chevron Singapore Pte Ltd, Keppel, Pan-United Corporation, Surbana Jurong, Air Liquide Singapore, Osaka Gas Singapore, and Pavilion Energy (together referred to as the Parties) have signed a Memorandum of Understanding (MoU) to collaborate on opportunities to lower the carbon footprint and thereby support Singapore’s aspiration of achieving net-zero emissions by 2050.
Through the Low Carbon Technology Industry Consortium (LCTIC), the Parties will explore the advancement of technology, to accelerate the development of cost-effective Carbon Capture, Utilisation and Sequestration (CCUS) as well as the production, transportation, distribution and utilisation of lower carbon hydrogen and its derivatives at scale. This is with the aim of commercialising new lower carbon technology pathways in Singapore.
The MoU is an extension of a previous MoU signed in July 2020, which aimed to accelerate the development of integrated and energy-efficient CCUS systems that lead to industrially scalable solutions and a lower carbon economy for Singapore. The MoU now welcomes Air Liquide Singapore, Osaka Gas Singapore, and Pavilion Energy as new members to the LCT-IC.
Under the MoU, the LCT-IC members will seek to partner, exchange ideas, share technical insights and develop lower carbon research, development and demonstration projects guided by the following framework:
Research in lower carbon technology – Develop research and development projects on lower carbon energy technology solutions, together with various Institutes of Higher Learning (IHLs) and Research Institutes (RIs). Other industry collaborators could also be involved.
Technology Translation – Partner technology scale-up platforms
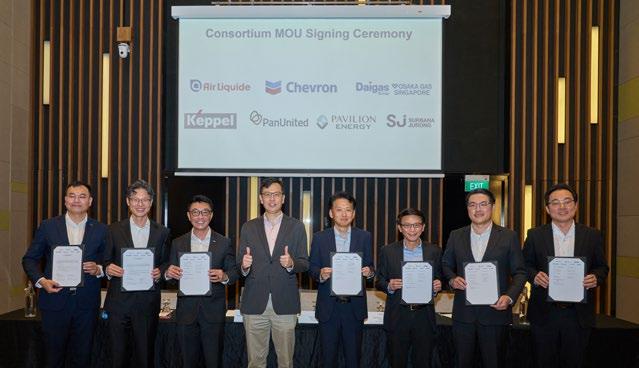
to translate and advance lab-scale research and technologies of lower Technology Readiness Levels to technology test-beds for scale-up.
Scalable Solutions – Establish scalable industrial solutions to realise lower carbon value chains, including first-of-its-kind, pre-commercialisation demonstration projects.
As a consortium, members regularly engage with technology startups, academia, and research institutes to keep abreast of developments in lower carbon technology in Singapore, which have the potential to scale into commercially viable solutions. This consortium and its members have participated in earlier relevant research grant calls from government agencies.
The consortium was also invited to contribute towards developing new industry standards related to energy transition, e.g. for CCUS.
Areas of partnership include:
• Collaboration with the National University of Singapore (NUS) to propose innovative solutions in combating rising seawater levels as part of a Marine Climate Change Science (MCCS) grant call.
• Participation in the Low Carbon Energy Research (LCER) Grant Call – Chevron and Surbana Jurong part-
nered with NUS and Nanyang Technological University (NTU) on the development and validation of novel hollow fibre membranes for carbon dioxide (CO2) capture, a project awarded under the LCER Grant Call.
Encouraged by the progress and fruitful discussions, the seven Parties of the consortium are keen to build on these efforts and broaden the partnership and scope of the MoU to include, but not be limited to, CCUS and lower carbon hydrogen and its derivatives, in end-toend value chains.
In the area of Carbon Capture and Utilisation, parties are currently exploring opportunities around CO2 mineralisation, for use within the building and construction sector.
Carbon dioxide sequestered in concrete has the potential to lower the embodied carbon of buildings and other structures where concrete could be utilised. Consortium members are expected to be involved at various points within this value chain to jointly study feedstock availability, potential market demand within Singapore and new product qualification requirements. This could be followed by a techno-economic analysis and product life cycle assessment.
Thomson – East Coast Line 4 to welcome commuters from 23 June 2024
As announced at the Ministry of Transport’s Committee of Supply debate recently, the Thomson-East Coast Line Stage 4 (TEL4) will commence passenger service on 23 June this year. TEL4 will improve accessibility for commuters by linking Singapore’s newest rail line with the East Coast region.
Spanning 10.8 km, the seven TEL4 stations – Tanjong Rhu, Katong Park, Tanjong Katong, Marine Parade, Marine Terrace, Siglap and Bayshore – will provide commuters along the East Coast area with alternative travel options. Commuters can expect travel time savings of up to 50% when using TEL. For example, a Marine Parade resident travelling to Shenton Way will take 20 minutes via TEL compared to the current 40 minutes by bus and train.
TEL4 also extends the reach of the rail network, providing commuters along the TEL with better access to work and play options along the East Coast area. With the opening of TEL4, around 235,000 households will be within a 10-minute walk from an existing TEL station (Woodlands North to Bayshore).
To get familiarised with TEL4 stations, commuters can preview and travel for free, along the seven new TEL4 stations during the opening event on 21 June 2024 from 10 am to 9 pm. A series of activities will also be held to mark the opening of the newest stage of the TEL.
Residents in the east of Singapore can look forward to the opening of four other stations – Bedok South, Sungei Bedok interchange and Xilin – in 2026, when TEL5 and the Downtown Line extension (DTLe) projects are completed. The East Coast Integrated Depot, which has connecting tunnels to both TEL and DTL as well as viaducts from the East-West Line, will also open in 2026.
Updates on other major rail projects
North East Line extension (NELe) –Works on the Punggol Coast station
on the North East Line extension (NELe) are progressing well. Civil and structural works have been completed and fitting-out works are progressing as planned. Testing and commissioning activities are ongoing. The station is on track to open by the end of this year.
Bukit Panjang LRT (BPLRT) renewal works – Since 1 December 2019, BPLRT has been operating on one loop (counter-clockwise loop on Service B via Petir Station) during off-peak hours to facilitate BPLRT renewal works, which began in 2018 to enhance the line’s reliability. Dual loop operations were scheduled to resume on Saturdays at selected hours, from 16 March 2024.
LTA will monitor the performance of the BPLRT network closely after the resumption, before deciding on further extensions to more off-peak hours, while continuing to run full dual loop services during peak hours on weekday mornings and evenings.
In addition, two new trains for BPLRT have arrived and will begin passenger service in the third quarter of this year after testing and commissioning works. These are among the 19 new trains which will replace the first-generation vehicles that have been in service since 1999.
Upgrading works for the second-generation vehicles, in tandem with the new Communications Based Train Control (CBTC) signalling system, are also progressing well. More trains are expected to
complete the upgrade and re-enter passenger service later this year.
Sengkang-Punggol LRT (SPLRT) enhancements – Works will enhance the platforms of Sengkang LRT station to improve commuter flow, with dedicated stopping locations for each of the four routes plying the station. New signs and queue markings, as well as a new tactile guiding system will also be implemented to facilitate boarding and alighting.
In addition, the first of the 25 new two-car trains for the SPLRT is expected to arrive in Singapore by the end of the year. The new trains will undergo testing upon arrival, before being progressively deployed for passenger service. They will replace the existing one-car trains and some of the existing two-car trains, increasing the overall passenger capacity of SPLRT.
Hume Station – Construction is progressing well and the station is on track for opening in 2025. In addition to serving existing residential developments along Hume Avenue, the station will also provide more convenient access for commuters to the Rail Corridor (Central).
The country is on track to reach the goal of expanding the rail network to about 360 km by the 2030s, with eight in 10 households located within 10 minutes of a train station. The ongoing rail expansion projects will strengthen the connectivity and resilience of the land transport network.
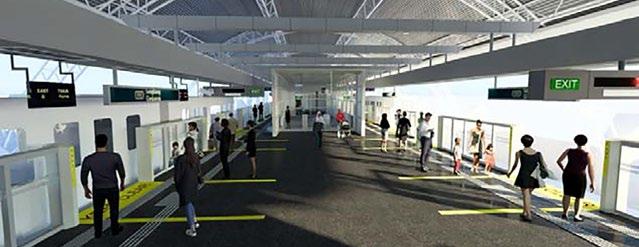
Hyster-Yale Group enhances aftermarket capabilities in Asia-Pacific
Hyster-Yale Group, a leading integrated full-line lift truck manufacturer, is strengthening its aftermarket fulfilment capabilities in Asia-Pacific by relocating its parts distribution centre (PDC) to Johor Bahru, Malaysia.
This new distribution centre will further anchor Hyster-Yale’s activities in the region, as it will serve as a logistics hub for all regional distribution of genuine parts manufactured by the company.
Supported by global 3PL provider, Geodis, the PDC offers customers good first-fill rates and next-day deliveries to dealers within the region. As part of the relocation, Hyster-Yale will also introduce new streamlined approaches for parts and dealers’ identification, enabling dealers and customers to have quick access to information such as pricing, availability and technical specifications.
Tony Unsworth, Vice President ofAftermarket, Service and Fleet, Asia Pacific, India & China, Hyster-Yale Group, said, “As Hyster-Yale becomes the choice material handling equipment provider regionally, the new location of our parts distribution centre enables our dealers and customers to have direct and more efficient access to the parts they need.”
“Our continued investment in logistics and services underscores our commitment to provide better service and support at reduced costs. This relocation and increase in inventory capacity is essential to our strategic growth, and we are very excited about the opportunities that lie ahead,” he added.
Hyster-Yale will maintain an extensive inventory of readily available parts at the newly relocated PDC, allowing dealers to reduce inventory costs and decrease time between ordering and receiving parts.
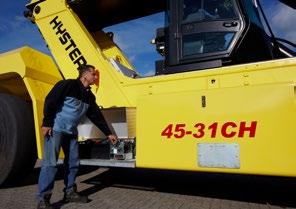
Additionally, Hyster-Yale will use a single part number for each of its genuine parts, regardless of where it is manufactured or shipped from. This makes it easy for all dealers to order and track parts.
The company has also introduced a new Parts Selector portal, a convenient source for competitively priced parts. All Hyster-Yale dealers will have 24/7 access to the web-based tool for parts availability checks and order status information.
Enhanced measures to reduce heat stress risks for outdoor workers
Outdoor workers have less discretion over their work activities and may be more exposed to heat stress. The Ministry of Manpower (MOM), in consultation with the Ministry of Health (MOH)’s Heat Stress Expert Panel, has introduced an enhanced set of measures to reduce the risks of heat stress for outdoor workers.
A combination of measures focusing on the four aspects of acclimatise, drink, rest, and shade, will provide protection to outdoor workers across various industries.
New workers must be given time to gradually adjust to outdoor work and all outdoor workers must hydrate at least hourly, and take regular rest breaks under shaded areas to dissipate accumulated body heat.
Employers are required to monitor the Wet Bulb Globe Tem-
perature (WBGT) for every hour of outdoor work performed, especially during the hotter periods of the day. WBGT is an internationally recognised measurement that takes into account the main environmental factors contributing to heat stress, including air temperature, humidity, wind speed and solar radiation.
Construction sites with a contract sum of SGD 5 million or more, shipyards and the process industry, will be required to have a WBGT meter on-site, for localised measurements, as these workplaces are likely to have prolonged outdoor activities. The requirement of a WBGT meter on-site for localised measurements has become effective from 1 January 2024.
Other workplaces can use NEA’s myENV app to monitor
WBGT readings.
When the WBGT is 32° C or higher, a minimum rest break of 10 minutes hourly, under shade, has to be provided to workers carrying out heavy physical activities. For workers with pre-existing health conditions, the rest duration should be longer or as advised by their doctors.
Workplaces are also encouraged to effect a buddy system for early recognition of heat injury symptoms and implement prompt interventions when any worker shows signs of excessive heat exposure.
Employers will be required to implement these measures to reduce heat stress risks for outdoor workers and MOM will conduct inspections at workplaces to ensure that these measures are adequately implemented.
Singapore International Water Week 2024 sets the stage for global water industry collaboration
As one of the leading global water events focused on innovation and solutions, the 10th Singapore International Water Week (SIWW), to be held from 18 to 22 June 2024 at the Sands Expo and Convention Centre in Singapore, will once again play host to global leaders, experts and practitioners, from governments, cities, water utilities, agencies, industry and academia, to share and co-create innovative solutions to solve the world’s urban water and associated climate challenges.
The event is expected to attract 500 global water leaders, 2000 delegates, 500 exhibitors and more than 30,000 trade visitors.
SIWW2024 is organised by PUB, Singapore’s National Water Agency, and Singapore’s Ministry of Sustainability and the Environment.
Key themes such as climate mitigation, water sustainability, net zero and decarbonisation, resource circularity, digitalisation, and a new pillar on climate adaptation, will be featured across SIWW flagship pro-
grammes including the Lee Kuan Yew Water Prize, Leaders Roundtable and Summit, Water Convention, and Water Expo.
A cornerstone of SIWW, the Water Expo, taking place from 19 to 21 June 2024 at the Sands Expo and Convention Centre in Singapore, is the pre-eminent marketplace for the international water, as well as coastal protection and flood resilience communities to converge and find opportunities in business. Exhibitors from all over the world will showcase their latest urban water technologies, innovations, and solutions for municipal and industrial water users in Southeast Asia.
Attendees can view innovative exhibits in the areas of water and sewage treatment, mechanical engineering and plant engineering in water management, flood and coastal protection, water digitalisation, water financing, water insurance, and more.
A key highlight for the SIWW2024 Water Expo is a new thematic zone featuring innovations in coastal pro-
IFAT Munich 2024 expected to set new standards
IFAT Munich 2024 will be held from 13 to 17 May 2024 in Munich, Germany. The event will feature top-class speakers, more international exhibitors, and a varied programme.
The world’s leading trade fair for water, sewage, waste and raw materials management, will present innovative environmental technologies, flanked by panel discussions, expert lectures, and live demonstrations.
“More than ever, IFAT Munich is seen as the central solution platform and knowledge hub for all aspects of the circular economy. In addition to the many
national and international experts, we also welcome many high-ranking politicians to IFAT Munich, who are looking for an exchange with the industry,” said Stefan Rummel, CEO of Messe München GmbH, organisers of the event.
IFAT Munich 2024 will feature a top-level talk on the circular economy as well as the ‘Day of Resilient Municipalities’ which will include lectures, expert panels, and guided tours, organised in collaboration with the German Technical and Scientific Association for Gas and Water (DVGW), the German Association for Wa-
tection and flood resilience.
The Water Expo is held in cooperation with IFAT, the world’s leading trade fair for environmental technologies, organised by Messe Munich.
In anticipation of the event, SIWW2024 kicked off its first roadshow in Malaysia recently, which was attended by more than 60 local senior utility and industry leaders, distributors, industrial water end-users, as well as trade associations and chambers.
Ryan Yuen, Managing Director of Singapore International Water Week said, “Amidst water challenges brought about by climate change, SIWW2024 offers an ideal platform to connect Asian municipal and industrial water stakeholders with global experts and leaders who are at the forefront of innovation. Through the myriad of programmes presented at the show, SIWW2024 will facilitate new business partnerships and spur action to build a more sustainable water future for all.”
ter Management (DWA), and the Association of Municipal Enterprises (VKU), for representatives of the municipal sector.
The event will also host a panel discussion on the ‘Future of Living – Adapting to the results of climate change’, featuring star architect Daniel Libeskind and Ian Goldin, Professor of Globalization and Development at Oxford University, and Founding Director of the world-leading Oxford Martin School research group.
In addition, IFAT Munich will offer visitors more than 25 guided solution tours.
Redevelopment of Tanglin Halt Estate
As part of the transformation, about 5,500 new flats will be built.
Tanglin Halt Estate, one of Singapore’s oldest public housing estates in Queenstown will be redeveloped and transformed into an attractive housing estate with new amenities designed to benefit both existing and future residents. Plans will include a new development that integrates housing with a hawker centre, market and polyclinic, all under one roof. When fully redeveloped, Tanglin Halt is expected to offer up to 5,500 new flats, providing more housing options for Singaporeans.
The redevelopment plans for Tanglin Halt estate were officially announced by Senior Minister of State, Ministry of National Development and Ministry of Communications & Information, Mr Tan Kiat How at the HDB Professional Engagement and Knowledge-sharing (PEAK) Forum on 19 October 2023.
A CELEBRATION OF OLD AND NEW
Tanglin Halt Estate was identified for the Selective En bloc Redevelopment Scheme (SERS) in 2014, the largest SERS exercise to-date, involving some 3,480 households. Residents were offered new flats in the nearby Dawson estate, and have since moved into their new home.
The Housing & Development Board (HDB) will progressively redevelop Tanglin Halt to ensure that it stays vibrant and attractive. The redevelopment plans will focus on introducing new amenities and facilities for existing and future residents, and improving connectivity for pedestrians and cyclists between Commonwealth MRT Station and the Rail Corridor. Additionally, the greenery will be enhanced and as much of Tanglin Halt’s history and heritage will be retained as possible.
New Tanglin Halt Integrated Development
A key feature of the redevelopment plans is the new Tanglin Halt Integrated Development that will be located on the site of the former Tanglin Halt Neighbourhood Centre which housed the former Commonwealth Drive Food Centre and the existing Tanglin Halt Market. Most stallholders from the former Commonwealth Drive Food Centre have relocated to the new Margaret Drive Hawker Centre sited within the SkyResidence @ Dawson development, while Tanglin Halt Market is still in operation.
To minimise disruption to stallholders in the Tanglin Halt Market, the Tanglin Halt Integrated Development will be constructed in two phases. Phase 1, which includes the new hawker centre and mar-
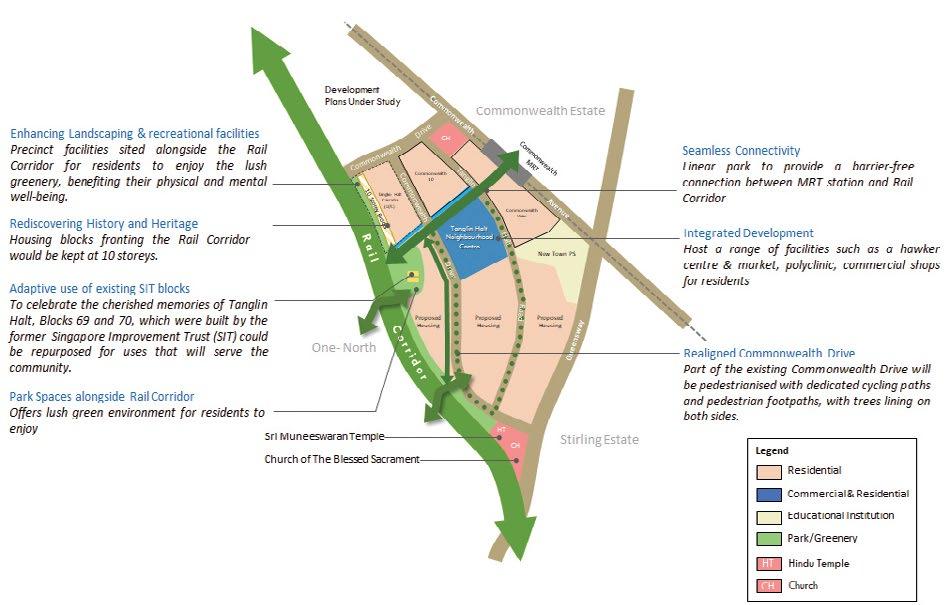
ket, will commence in 2024 on the site of the former Commonwealth Drive Food Centre. Once Phase 1 is complete and the stall owners have moved to the new integrated development, construction for Phase 2 will begin on the site of the existing Tanglin Halt Market.
When completed, the new landmark development will integrate public housing with a hawker centre and market, and also house the redeveloped Queenstown Polyclinic. In addition, there will be shops and social communal facilities to cater to the daily needs of residents.
These amenities were suggested by
former Tanglin Halt residents, shop tenants and stallholders, during interviews conducted by HDB. These
interviews allowed HDB to document residents’ memories of their estate and understand the enhance-


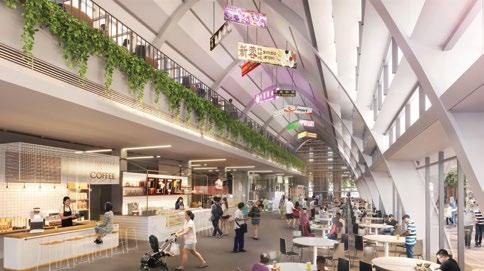
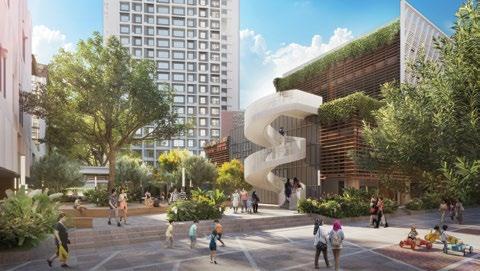
ments that residents hoped the redevelopment would bring.
The new Tanglin Halt Integrated Development will be designed to incorporate elements of well-remembered spaces. These include the iconic hexagonal shape of the former Commonwealth Drive Food Centre that was built to house roadside hawkers, the barrel vault shape of the existing Tanglin Halt Market at Blk 48A Tanglin Halt Road, and the open community atmosphere of the courtyard spaces of the former Tanglin Halt Neighbourhood Centre.
New public housing developments at Tanglin Halt
HDB will progressively offer up to 5,500 new flats in Tanglin Halt Estate to provide more housing options for Singaporeans. The first public housing project, Tanglin Halt
Cascadia, was launched in the October 2023 sales exercise. In 2024, HDB expects to launch additional new flats as part of the new Tanglin Halt Integrated Development. Besides offering new and younger families the opportunity of living in Tanglin Halt, these housing developments will also introduce new commercial amenities as well as social and communal facilities in the estate, benefitting all residents in the surrounding Queenstown area.
Linear park to provide greater connectivity
In the longer term, to enhance connectivity, a linear park will be built between the Commonwealth MRT Station and the Rail Corridor, providing residents with a more convenient and pleasant pathway to walk and cycle on, amidst lush greenery. Commonwealth Drive will also be
Commonwealth 10
Tanglin Halt Cascadia
realigned, with the existing road being transformed into a pedestrian-friendly zone equipped with dedicated cycling and pedestrian footpaths.
Preserving Tanglin Halt’s heritage
In carrying out the redevelopment plans, special efforts will be made to preserve as much of Tanglin Halt’s history and heritage as possible. This includes keeping the 10-storey height for new housing blocks near the Rail Corridor, in homage to the old ‘chap lau chu’ (or 10-storey house in Hokkien). Additionally, key heritage elements that residents cherish will be integrated into the redeveloped communal spaces via street furniture and murals.
Agencies are also exploring the adaptive use of some of the residential blocks in Tanglin Halt, that hold historical significance. For

Commonwealth View
Tanglin Halt Integrated Development
example, Blocks 69 and 70, which were built by the former Singapore Improvement Trust (SIT), could be repurposed for other social-communal uses.
The redevelopment plans aim to retain and enhance as much of the existing greenery as possible, to enable residents to enjoy the benefits of living close to nature. Along the segment of the Rail Corridor that runs along the edge of Tanglin Halt, landscaping and recreational
facilities will be introduced, letting residents connect with nature while bonding with family and friends. There will also be a new park near the Rail Corridor to serve as a community space and pit-stop for residents and visitors.
KEEPING OLDER ESTATES VIBRANT AND LIVEABLE
The redevelopment plans for Tanglin Halt estate will complement the broader rejuvenation plans for
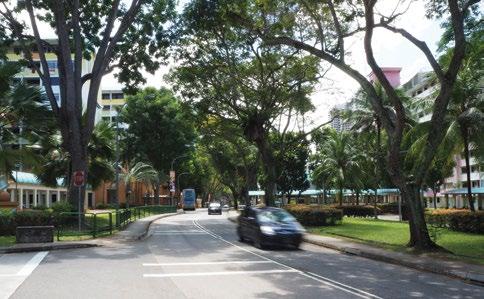
Queenstown. As part of these plans, more housing, greenery, new amenities and facilities will be injected into the estate, while preserving as much of Tanglin Halt’s history and heritage as possible. This will ensure that the future Tanglin Halt continues to be vibrant, liveable and resilient, to meet the evolving needs of its residents.
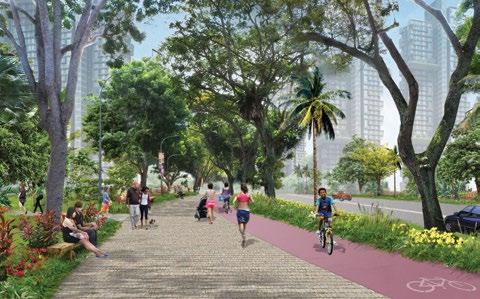
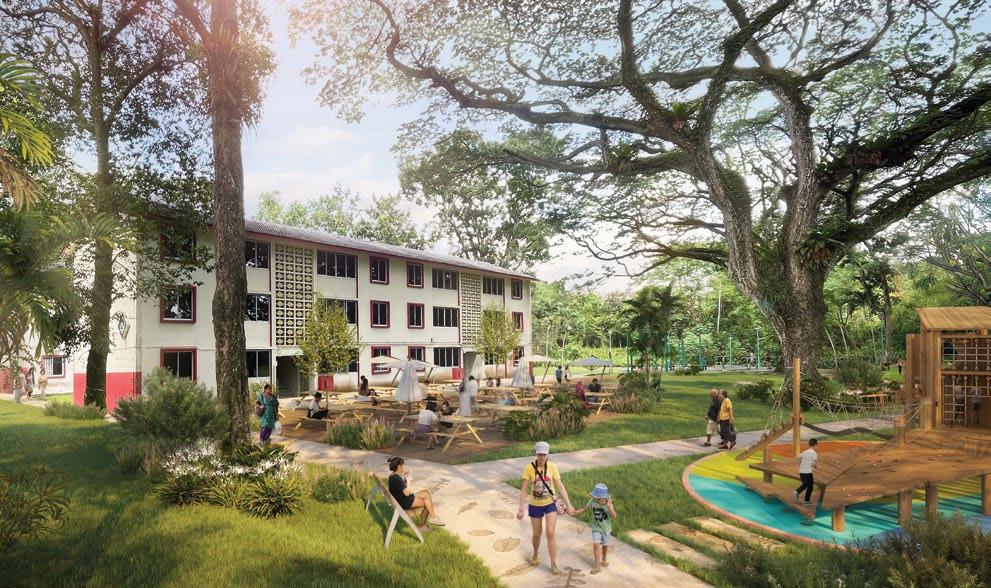
Targets and initiatives to support transformation
An update on the progress.
The Building and Construction Authority (BCA) has been working closely with the Built Environment (BE) sector on its transformation efforts under the BE Industry Transformation Map (ITM).
THE BUILT ENVIRONMENT INDUSTRY TRANSFORMATION MAP
The refreshed Built Environment (BE) Industry Transformation Map (ITM) was launched on 9 September 2022 at the International Built Environment Week 2022. The ITM integrates the transformation plans for the Construction and Facilities Management (FM) industries under one BE umbrella, as part of a building lifecycle approach towards transformation. The three key transformation areas are Integrated Planning and Design (IPD), Advanced Manufacturing and Assembly (AMA), and Sustainable Urban Systems (SUS).
The BE ITM was developed in conjunction with industry stakeholders through the Future Economy Council (FEC) Urban Systems (US) Cluster Sub-Committee. The FEC US Sub-Committee was co-chaired by SMS Tan Kiat How and Mr Liam Wee Sin (Group CEO, UOL Group Ltd), and comprised representatives from government agencies, Trade Associations and Chambers (TACs) and stakeholders from across the BE value chain.
INTEGRATED PLANNING AND DESIGN
Building on the efforts towards Integrated Digital Delivery (IDD) under the Construction ITM, IPD aims to optimise the planning and design of a building/district for its entire lifecycle where downstream considerations are incorporated upfront. This will help to minimise the downstream wastage of resources for construction and maintenance, which could result in unnecessary reworks and retrofits.
With regard to achieving the target of 70% IDD adoption for all new developments, by Gross Floor Area (GFA), by 2025, the IDD adoption rate for new developments, by GFA, has increased from about 45% in 2022 to 58% in 2023.
ADVANCED MANUFACTURING AND ASSEMBLY
Building on the efforts to drive Design for Manufacturing and Assembly (DfMA) (i.e. a continuum of technologies which shifts construction activities off-site into more productive factory-like settings), Advanced Manufacturing and Assembly (AMA) seeks to encourage the adoption of robotics and automation (R&A) to enhance construction productivity both on-site and off-site. This will also provide a better work environment and better jobs for the workforce. The construction supply ecosystem will also be strengthened by developing Integrated Construction Parks (ICPs).
Examples of DfMA technologies include Prefabricated Prefinished Volumetric Construction (PPVC), structural steel, Advanced Precast Concrete System (APCS) and Prefabricated Mechanical, Electrical and Plumbing (Prefab MEP) System.
With regard to achieving the target of 70% DfMA adoption for all new developments, by GFA, by 2025, the DfMA adoption rate for all new developments, by GFA, has increased from about 51% in 2022 to 61% in 2023.
SUSTAINABLE URBAN SYSTEMS
Building on existing efforts under the Singapore Green Building Masterplan (SGBMP) launched in 2021, Sustainable Urban Systems (SUS) seeks to drive best-in-class sustainability standards to achieve a low-carbon BE sector. In particular, efforts will be ramped up at the operations and maintenance
stage, through smart solutions and integrated and aggregated facilities management (FM) services.
GREEN BUILDINGS
There are three key targets under the SGBMP, or ‘80-80-80 in 2030’:
• With regard to achieving the target of greening 80% of the buildings, by GFA, by 2030, as of December 2023, about 58% of the buildings, by GFA, have been greened.
The new Mandatory Energy Improvement (MEI) regime, which will be introduced by end-2024, will require owners of energy-intensive buildings to carry out energy audits and implement measures to improve their building energy use intensity (EUI).
EUI measures the annual energy consumption of a building over the GFA, in terms of kWh/m2
• With regard to achieving the target of 80% of new developments (by GFA) to be Super Low Energy (SLE) buildings from 2030, in 2023, more than 7% of new developments, by GFA, have been certified as SLE buildings – these are buildings that have achieved at least 60% improvement in energy efficiency, compared to 2005 levels.
One effort to drive this is the Built Environment Transformation GFA Incentive Scheme which encourages new private developments to achieve GM Platinum SLE certification, among other requirements. There have been nine approved applications as of December 2023.
• With regard to achieving 80% improvement in energy efficiency, compared to 2005 levels, for bestin-class green buildings by 2030, as of December 2023, the best-inclass buildings have achieved 71% improvement in energy efficiency, over 2005 levels.
Best-in-class buildings refer to buildings that achieve the highest possible energy efficiency standards
with the technology available at the time.
The Green Buildings Innovation Cluster (GBIC) programme continues to push the boundaries of energy efficiency through technology development and demonstration. The first thematic challenge call was launched in February 2023 to encourage hotels and high-rise office buildings to achieve a 75% improvement in energy efficiency, from 2005 levels, by adopting innovative energy-efficient solutions.
FACILITIES MANAGEMENT
There are three key thrusts of Facilities Management (FM) transformation under the BE ITM:
• Design for Maintainability (DfM) which involves upstream collaboration between the developers/ building owners, designers, and FM companies (FMCs) to incorporate maintainability and Smart FM considerations upfront at the design stage.
• Smart FM which is the digitalisation of systems, processes, technologies and personnel to enhance the management of a building’s facilities and raise productivity for FMCs. With regard to achieving the target of 80% of public buildings and 40% of private buildings, by GFA, adopting Smart FM by 2030, the Smart FM adoption rate for public buildings, by GFA, has increased from 33% in 2022 to 85% in 2023. The adoption rate for private buildings, by GFA, has increased from 28% in 2022 to 43% in 2023.
• Integrated FM (IFM) and Aggregated FM (AFM). FMCs can harness efficiencies from managing different FM services on an integrated platform, and aggregating FM services across many buildings.
IFM and AFM are still nascent in Singapore. BCA opened applications for a SGD 30 million grant in September 2022 to kickstart their adoption. As of December 2023, 18 potential projects (by over 20 companies) have engaged BCA through pre-consultations to apply for the grant. One project has since been awarded funding under the grant.
FURTHER INITIATIVES
As challenges will continue to remain in the horizon, efforts must be made to collectively press on towards a more productive, digitalised and sustainable sector. BCA will partner the BE sector to implement several initiatives.
EXPANSION OF THE CONTRACTORS REGISTRATION SYSTEM
To enable transformation to be driven more effectively across the construction industry, BCA will expand the scope of its Contractors Registration System (CRS) from a public sector registry to a nation-wide registry of construction firms. This will be done by requiring all firms hiring foreign construction workers to register under the CRS.
BCA will also raise the CRS entry requirements to keep pace with the current market conditions to ensure that firms hiring foreign construction workers have the minimum financial capabilities and experience to sustain their operations and deliver projects.
Currently, BCA administers the CRS to facilitate Government procurement of construction services. Firms that want to participate in Government tenders or to be engaged as first-level subcontractors in public sector projects will need to register under the relevant workheads in CRS.
CRS is also one of the three gateways for firms to access foreign construction workers. The other two gateways are BCA’s Builders Licensing Scheme (BLS) and Singapore List of Trade Sub-contractors (SLOTS) administered by The Singapore Contractors Association Ltd (SCAL).
BLS aims to ensure building safety by only allowing firms that meet certain standards to undertake high-impact building works that are regulated under the Building Control Act (BC Act).
SLOTS is used as a reference for main contractors to identify competent sub-contractors.
Entry-level requirements for paidup capital and track record across these gateways are different (as
shown in Table 1). This means that some firms may find it easier to access foreign construction workers under certain gateways. At the same time, there are also firms that only hire certain foreign construction workers that do not need to go through any of the three gateways, or are not subject to any requirements set by BCA or SCAL.
To ensure that the same minimum standards are applied equally to all firms hiring foreign construction workers, BCA will make CRS the sole gateway for firms to access foreign construction workers. This means that all firms hiring foreign construction workers will need to be registered under the CRS and meet the same entry-level Paid-Up Capital (PUC) and Track Record (TR) requirements.
Effectively, CRS will expand its scope from a public sector registry to a nation-wide registry of construction firms. This will enable the implementation of quality, manpower, productivity, and innovation measures across the construction industry more effectively, but it will be done in a calibrated manner to minimise disruption to the industry.
As a start, BCA will raise the CRS minimum PUC and TR entry requirements to keep pace with the current market conditions (as shown in Table 2). This is to ensure that the registered firms have the minimum financial capability and experience to sustain their operations and deliver projects.
Firms will be given time to meet these entry requirements. BCA will announce further details on the changes later this year.
BCA has engaged the industry, including key Trade Associations and Chambers (TACs), such as SCAL, SIFMA and STAS, on these moves. The industry supports the upcoming changes to CRS.
“SIFMA is supportive of the CRS enhancements as part of the transformation efforts in the Built Environment (BE) sector,” said Mr Frank Ngoh, President, Singapore International Facility Management Association (SIFMA).
“SCAL has always been a partner of BCA in transforming the Built Environment sector. SCAL is supportive of raising the standards for the whole industry and SLOTS members are well-positioned to meet the new requirements,” said Mr Lee Kay Chai, President, Singapore Contractors Association Ltd (SCAL).
EXPANSION OF THE ENERGY EFFICIENCY GRANT
The Government will be expanding the Energy Efficiency Grant (EEG) to new sectors, including construction. EEG aims to support businesses in their sustainability journey by co-funding investments in energy-efficient equipment.
For the construction industry, the grant will support the cost of energy efficient construction equipment. Companies registered and operating in Singapore with at least 30% local shareholding, at least one local employee and group annual sales turnover of not more than SGD 500 million, will be eligible for support under the EEG.
The EEG will provide two tiers of support – a Base Tier where eligible
local construction firms will be able to receive up to 70% of funding support for pre-approved energy-efficient construction equipment, up to SGD 30,000; and an Advanced Tier to support companies that wish to make larger investments to drive greater energy efficiency, up to SGD 350,000.
The energy-efficient equipment supported under the Advanced Tier need not be pre-approved, but must demonstrate energy savings above 350 t lifetime carbon abatement. The grant amount for this will be based on committed energy savings or up to 70% of the equipment cost, whichever is lower. The EEG for the construction industry is expected to be launched by the end of 2024. More details will follow.
EXTENSION OF THE PRODUCTIVITY INNOVATION PROJECT SCHEME
The Productivity Innovation Project (PIP) scheme supports investments in automation and productive technologies in the Built Environment (BE) sector. This includes Integrated Digital Delivery (IDD) systems, Robotics & Automation (R&A) and
Design for Manufacturing and Assembly (DfMA) technologies. The PIP co-funds up to 70% of the costs of adopting these solutions, capped at SGD 10 million.
Since 2018, the PIP has helped 78 firms, including local SMEs, adopt productive and labour-efficient technologies.
One of the firms that has benefited is Techniques Air Conditioning and Engineering Pte Ltd. The Mechanical, Electrical and Plumbing (MEP) subcontractor set up four production lines to automate the cutting and welding of pipes in its off-site factory. The off-site automation has helped to increase its productivity by at least 40% compared to manual cutting, welding and quality inspection processes.
Another example is Great Resources M&E Contractor Pte Ltd, a builder who has tapped on the PIP and will deploy an automated drilling and anchoring robot onsite, replacing manual drilling and anchoring processes. This will enable the firm to increase productivity by at least 30%, with one-third less workers. With less manual work and fewer workers on-site, the company can also carry out this work more safely.
To continue the support for firms in their productivity and digitalisation efforts, the PIP will be extended until 31 March 2025. This will give firms more opportunities to invest in transformative technologies.
Applicants must meet the following eligibility criteria at the point of application:
• They are construction-related companies that are registered and located in Singapore.
• The solutions must meet a minimum productivity improvement of 30% for the trade activity and/or process.
Also, the applicant must not have signed or confirmed a contract with, or made payment to, a supplier, vendor or third party, in relation to the purchase/subscription of the solutions before the application.
The submission of application does not automatically entitle the
Firm Description
CapitaLand Development Pte Ltd (CLD)
Surbana Jurong Architecture (SJ)
CapitaLand Development is the development arm of CapitaLand Group, one of Asia’s largest diversified real estate groups. Its well-established real estate development capabilities span across various asset classes, including integrated developments, retail, office, lodging, residential, business parks, industrial, logistics and data centres.
Surbana Jurong Group employs over 1000 employees in its architecture and design practice worldwide, including 639 architects. With a track record of over 70 years in successful project delivery, SJ provides multidisciplinary consultancy services across a diverse range of sectors such as hospitality, healthcare, and aviation.
Threesixty Cost Management Pte Ltd
Woh Hup (Private) Limited (WH)
Threesixty is a subsidiary of Surbana Jurong Group. It helps clients manage the associated costs and contracts of their projects in an independent, efficient, and responsible manner. Threesixty provides in-depth cost and commercial management, and contractual advice from project inception to completion.
WH is one of the largest privately owned civil engineering and construction companies in Singapore that consistently delivers a high standard of quality in its projects. As a forward-looking company, WH seeks to spearhead cutting-edge, innovative building and engineering solutions. This has led to their market expansion regionally.
CapitaLand Development-led Alliance Firms.
applicant to funding. All applications will be subject to evaluation and approval. Applicants may be required to submit additional supporting documents to facilitate evaluation of the application.
THE GROWTH AND TRANSFORMATION SCHEME
The Growth and Transformation Scheme (GTS) supports initiatives that build best-in-class capabilities and enable holistic transformation for BE value chains. These initiatives are undertaken by groups of firms –each led by a progressive developer and includes consultants, builders and subcontractors – to achieve mutually beneficial transformation outcomes.
The key objectives of the GTS are:
• To groom a core group of strong industry leaders to drive industry transformation.
• To push the boundaries for bestin-class capabilities and spearhead adoption of advanced technologies such as Advanced Manufacturing and Assembly (AMA), Integrated Planning and Design (IPD) and Sustainable Urban Systems (SUS).
• To achieve transformative workforce development and business growth / strategic collaboration goals.
At Committee of Supply (COS) 2023, it was announced that SGD 90 million had been set aside under the GTS to co-fund up to 70% of qualifying costs in areas such as equipment, software and training.
Since then, the CapitaLand Development-led and CDL-led alliances have made good progress.
CapitaLand Development (CLD) and its partners are focusing on collaborative contracting, where they will be amongst the first to pilot this contracting approach for the private sector. CapitaLand will also establish and maintain a Common Data Environment (CDE) platform that connects value chain partners working on their projects. The CDE platform will allow value chain partners to refer to a single reference point for key project information and BIM models, and create a conducive environment for upfront collaboration.
Ms Goh Ah Moi, Chief Development Officer, CapitaLand Development (Singapore), said, “By co-funding our efforts, the GTS has
accelerated the digitalisation goals of CapitaLand Development and those of our Alliance Partners. Through our CDE platform supported by the GTS, we can enhance data sharing and deepen collaboration with our partners, which will enable us to improve productivity and deliver better products for our customers.”
Woh Hup, one of the partners in the CDL-led Alliance, is implementing an IDD app, which will compile and analyse key metrics from project sites with near real-time tracking, on a digital dashboard. With the IDD app, Woh Hup will be able to generate detailed reports such as on material wastage, manpower productivity and progress tracking, for different stakeholders. This is expected to improve productivity by 88% at the use case level, in the data collection, analysis and reporting processes.
Woh Hup is also implementing the Purchasing Order, Delivery Order, Invoice, Payment Certificate (PDIP) App. This will integrate their contracts, procurement and finance teams, and allow them to track approvals and payment statuses, with
Firm Description
ADDP Architects Pte Ltd (ADDP)
City Developments Limited (CDL)
Woh Hup (Private) Limited (WH)
CDL-led
ADDP is an architectural design firm based in Singapore, providing consultancy services for a wide spectrum of projects in architecture, interior, and urban planning. ADDP also pioneered the use of prefabricated construction and sustainability design in Singapore.
As Singapore’s property pioneer with a heritage spanning six decades, CDL has shaped the Singapore skyline with numerous architectural icons such as Amber Park, CanningHill Piers, Republic Plaza, South Beach, The Sail @ Marina Bay, The Oceanfront @ Sentosa Cove and Tree House, many of which are award-winning green buildings. Since 1995, CDL has embraced its ethos of ‘Conserving as we Construct’, investing in green building innovation and game-changing technology to drive resource efficiency and productivity.
WH is one of the largest privately owned civil engineering and construction companies in Singapore that consistently delivers a high standard of quality in its projects. As a forwardlooking company, WH seeks to spearhead cutting-edge, innovative building and engineering solutions. This has led to their market expansion regionally.
a new, single digital workflow. This is expected to reduce the time taken for approvals and facilitate prompt payments to Woh Hup’s subcontractors and suppliers. To further streamline processes, Woh Hup is exploring uplifting the digital capabilities of its supply chain via direct integration with its suppliers’ payment systems.
“As part of our focus on digitalisation and innovation, we are aligned with BCA’s vision to drive value-chain transformation for a future-ready built environment. The Growth and Transformation Scheme (GTS) has enabled us to tap on funding to support our capability-building efforts,” said Ms Lee Mei Ling, Executive Vice President and Head, Property Development of City Developments Limited (CDL).
“By leveraging on digital tools such as the Common Data Environment (CDE) to enhance collaboration and communication among project stakeholders, we have been able to boost project outcomes, increase efficiency and achieve cost savings. We have embarked on the CDE pilot for our upcoming Central Mall / Central Square redevelopment project and expect to achieve productivity improvements and other beneficial outcomes during the development process,” Ms Lee added.
Streamlining building design and construction
Autodesk Inc recently unveiled Autodesk Informed Design, a cloudbased solution that connects design and manufacturing workflows to streamline the building design and construction process.
Informed Design allows architects to work with customisable, pre-defined building products that yield valid results, and allows manufacturers to share their products with design stakeholders.
Informed Design unlocks industrialised construction – the application of manufacturing principles to the built environment – and is expected help transform the architecture, engineering, construction and operations (AECO) industry.
The AECO industry is facing rising pressure to accommodate growing populations, urbanisation and a global housing crisis. For example, nearly 100,000 new affordable homes need to be built every day to house an estimated 3 billion people by 2030. Additionally, the industry faces pressure to improve its sustainability.
“The way the AECO industry works today is not sustainable or scalable. For the industry to keep
pace, it needs to build more, faster and more sustainably. The answer is industrialised construction,” said Mr Ryan McMahon, Director and General Manager, Informed Design at Autodesk.
“Autodesk Informed Design connects design and make from day one and brings industrialised construction workflows to reality. Our solution is unique because it empowers architects to design with certainty and validate their plans in real-time, while product managers and engineers can share accurate manufacturing information with design teams,” he added.
“As a result, projects are completed quicker, with higher quality, and generate less waste,” Mr McMahon continued.
Informed Design is part of Autodesk’s Design and Make Platform environment which includes cloud-connected software solutions that unite teams, data and workflows across entire project lifecycles to deliver better results.
Informed Design is available globally as a free add-in for two of Autodesk’s industry solutions –Revit and Inventor.
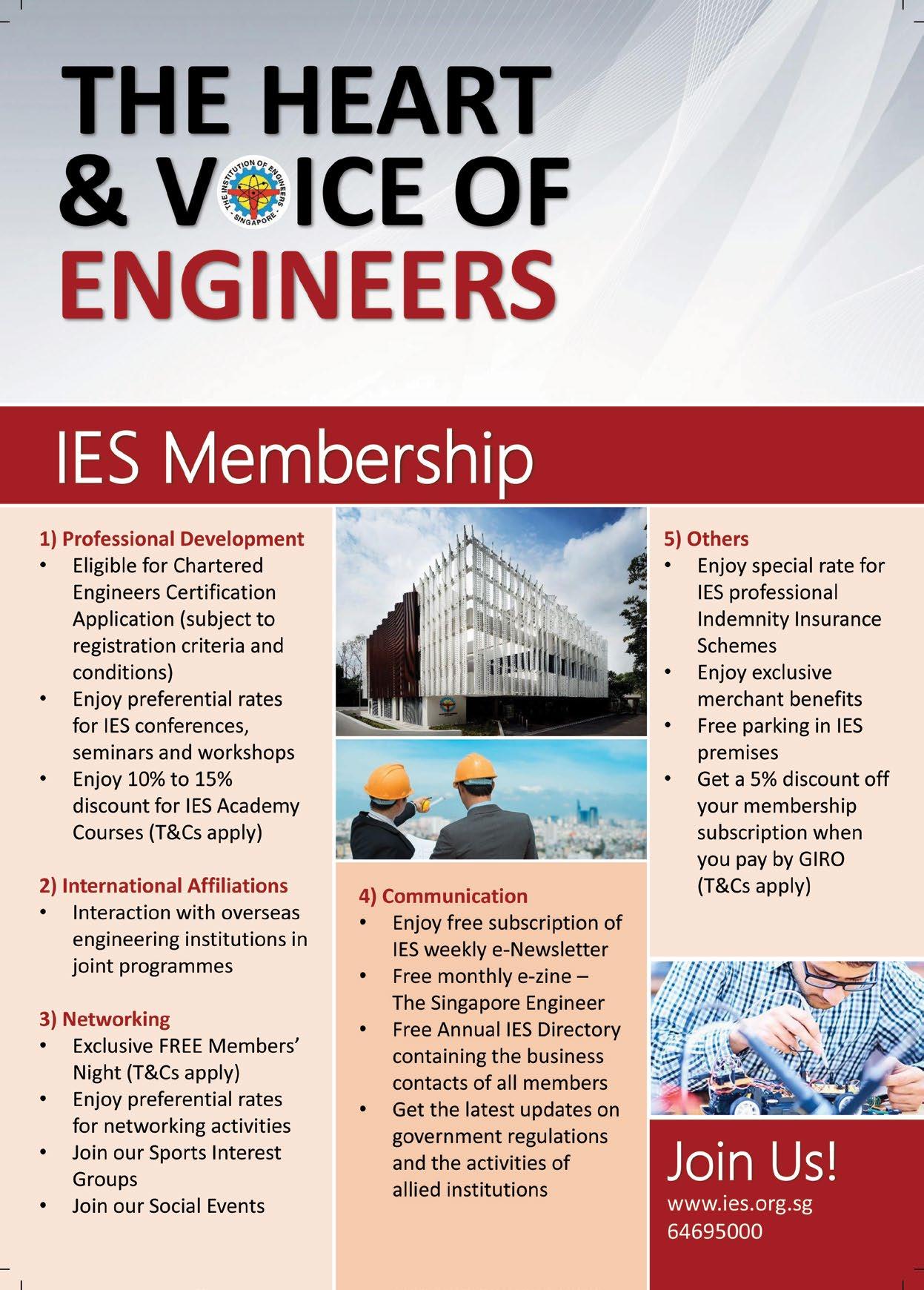
Facilitating sustainable and efficient marine travel
Convergence of aviation and marine technologies.
ST Engineering AirX, a subsidiary of ST Engineering and Peluca (formerly known as Wigetworks), has combined various disciplines in aviation, marine and wing-in-ground effect technologies to form a centre of excellence for WIG craft in Singapore, that can effectively serve transportation and logistics needs in coastal areas.
The company’s portfolio comprises the AirFish family of WIG craft, which includes the two-seater AirFish 3 and the 10-seater AirFish 8, and in time to come, new AirFish platforms with greater seat capacity.
The goal of ST Engineering AirX is not to just get the AirFish flying safely, but to enable a sustainable future in the maritime travel industry.
Mr Jeffrey Lam, President of Commercial Aerospace at ST Engineering, said, “We are excited to be working with the maritime community to introduce our new WIG platform which has the potential to reinvent marine transportation and provide multiple applications and use cases for the maritime sector.”
The AirFish Wing-in-Ground craft
The AirFish Wing-in-Ground (WIG) craft is a marine craft that utilises aerodynamic forces and air pressure generated between itself and the water surface, to reduce induced drag and achieve high fuel-efficiency and travel speed.
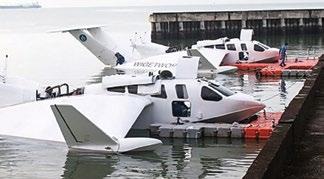
This is the same principle of flight used by large-bodied birds such as the albatross to conserve energy while staying in the air.
Gliding above the waves, the WIG craft does not experience any hydrodynamic drag like other marine vessels such as ferries, high-speed boats or hydrofoil craft. It can therefore operate at up to three times the speed of these vessels.
This significantly reduces downtimes and increases the convenience of travellers.
Furthermore, the increased aerodynamic efficiency and absence of hydrodynamic drag leads to a strong reduction in required engine power, fuel consumption and greenhouse gas emissions during operations.
Designed to take off and land on water, AirFish WIG Craft also avoids the need for major infrastructure such as an airfield, making it a more convenient option.
While the AirFish WIG craft has been developed to provide maritime public transport, parapublic services and luxury transport, it can also support military missions, with potential applications being amphibious operations, movement of special forces during operations and sensor payload deployments.
ST Engineering
ST Engineering is a global technology, defence and engineering group with a diverse portfolio of businesses across the aerospace, smart city, defence and public security segments. The group harnesses technology and innovation to solve real-world problems, enabling a more secure and sustainable world. Headquartered in Singapore, it has operations spanning Asia, Europe, the Middle East and the US, serving customers in more than 100 countries.


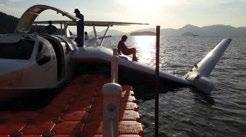
ST Engineering signs Letter of Intent for delivery of Wing-in-Ground craft
ST Engineering recently announced that its joint-venture company, ST Engineering AirX, has signed a Letter of Intent (LOI) with Eurasia Mobility Solutions for an order of up to 10 AirFish Wing-in-Ground (WIG) craft, with options for 10 more.
Eurasia Mobility Solutions (EMS), founded by Mr Kubilay Ilgin in 2023, is a smart urban mobility solutions provider headquartered in Istanbul, Turkey. EMS is dedicated to implementing transportation modes that enable individuals to utilise intelligent, cost-effective, and time-efficient options while prioritising safety.
Under the agreement, ST Engineering AirX, original equipment manufacturer of the AirFish family of WIG craft, will customise and deliver the 10-seater AirFish 8 to Eurasia Mobility Solutions, progressively from 2025, to serve Turkey’s tourism and private transportation sectors.
AirFish 8 can carry up to 10 passengers including crew members or 1,000 kg of logistics, and can travel up to 90 knots, making it one of the fastest marine craft operating in the seas. Integrated with state-of-the-art aerospace and marine technologies, the marine craft serves as a viable
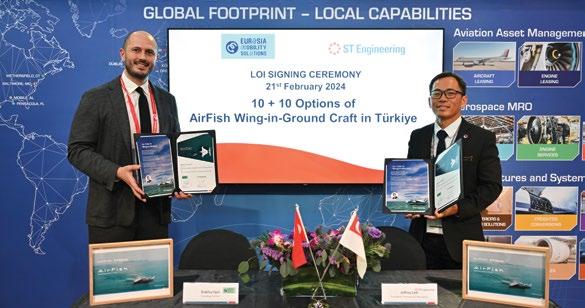
and attractive alternative to ferries, helicopters and seaplanes, and is slated for certification and entry into market by 2025.
“We are happy to introduce an innovative transportation model using a brand-new technology to Turkey, a country surrounded by the sea on three sides,” said Mr Kubilay Ilgin, Founder of Eurasia Mobility Solutions.
“As an alternative mode of transportation, AirFish 8 offers a safe, sustainable and faster solution to conveniently reach places without any port or runway. Faster than existing air and marine travel options, this new technology will change the rules of marine trans-
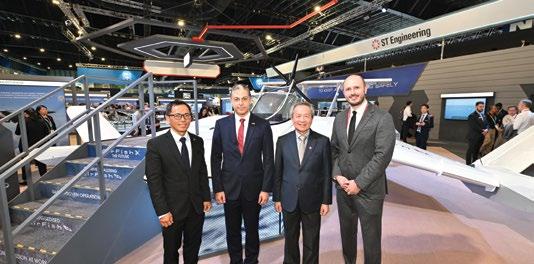
portation and create new trends in Turkey,” he added.
“We are excited to be working with Eurasia Mobility Solutions to introduce our new WIG platform which has the potential to reinvent marine transportation for Turkey’s maritime sector,” said Mr Jeffrey Lam, President of Commercial Aerospace at ST Engineering.
“This is a significant milestone for ST Engineering’s Commercial Aerospace business as we scale up our engineering and original manufacturing capabilities to develop more innovative and sustainable solutions that connect people and goods along some of the earth’s vast coastal areas,” he added.
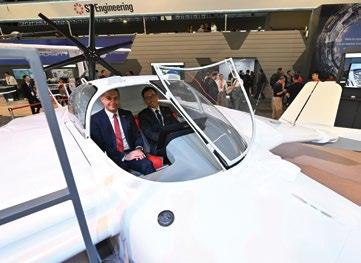
Leveraging technology to overcome construction challenges in 2024
by Vitaly Berezka, Head of Sales, Central Asia, MENA and APAC, PlanRadarThe use of digital tools is the solution.
As Singapore continues its rapid urbanisation, a tech-driven approach is paramount to meeting the escalating demands for infrastructure development, and digitalisation is increasingly crucial for the Built Environment (BE) sector. Regulatory bodies such as the Building and Construction Authority (BCA) have also been strongly advocating digitalisation and collaborating with partners within the BE sector to push Integrated Digital Delivery (IDD) in their projects.
With pressure from challenges like rising costs, labour shortages and tight project timelines, the industry needs to look to innovation for problem-solving, and fast. Here are a few ways to leverage technology to meet key challenges in 2024.
SEVEN KEY CHALLENGES AND THE WAY TO ADDRESS THEM
• Resource constraints
To tackle resource constraints in Singapore’s construction sector, Construction Management Software (CMS) tools can optimise resource allocation and scheduling, thereby mitigating shortages of skilled labour, materials and equipment. Robotics and automation fill labour gaps, while 3D printing aids efficient construction and helps reduce project delays and errors. They also enhance collaboration and communication, streamlining processes to address resource and manpower challenges.
• Project delays and overruns Singapore’s construction industry is well-known for its fast-paced and dynamic nature. To address delays, the adoption of Building Informa-

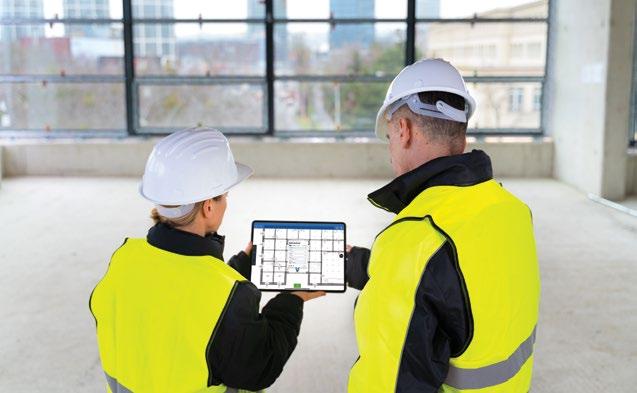
tion Modelling (BIM) is crucial. BIM provides a digital representation of project characteristics, using 3D models for accurate planning and clash detection. It helps in identifying and preventing issues early on, automates scheduling and resource allocation, and empowers project managers to make critical decisions, while monitoring key performance indicators (KPIs) to keep projects on track.
• Regulatory complexity
With the ever-changing regulatory landscape, it can prove challenging for companies to keep up with compliance, approvals and permits. Using digital tools for regulatory compliance enhances efficiency by automating processes, effectively managing documents and providing real-time updates on regulations.
This saves time, reduces errors and improves compliance. When used for safety analysis and risk assessment, data on safety regula-
tions, guidelines and best practices can be integrated. For example, to comply with Singapore’s latest regulations on video surveillance for safety, high-risk areas can be identified and safety measures integrated into the design and construction phases, including where and how to install video surveillance systems.
Technology solutions also offer transparency and accountability –which allow teams to access, review and track all necessary documents on one platform.
• Environmental and social impact concerns
It is also important for the construction sector in Singapore to consider and address issues that have potential environmental and social impact – from noise pollution and air quality to long-term effects on ecosystems and communities. Recent advancements in technology have streamlined environmental impact monitoring for construction companies.
Real-time data from monitoring tools aids in early problem identification and allows for proactive mitigation. Sustainable construction methods can also be devised with the right data at hand, with eco-friendly materials sourced and allocated, while renewable energy resources can further reduce environmental impact.
• Global supply chain disruptions
Supply chain disruptions can have a significant impact on businesses of all sizes. From delays in production and delivery to increased costs, these disruptions can cause cost and schedule overruns, impacting a company’s reputation. Tech solutions such as IoT sensors can track shipments and inventory in real-time, aiding informed decisions and minimising disruptions.
Digital twin technology creates virtual replicas of physical assets and streamlines supply chain monitoring, reducing delays and enhancing efficiency. Alongside technology solutions, a robust risk management plan is vital for handling supply chain disruptions. This involves identify-
ing risks and developing contingency plans accordingly.
• Technological skills gaps
IDD plays a crucial role in the Built Environment Industry Transformation Map (BEITM) and supports Singapore's efforts to revolutionise the built environment sector. It aims to develop a highly skilled workforce proficient in utilising cutting-edge technologies in architecture, engineering, construction and operations. To meet the increasing need for workers with digital construction skills, companies must proactively upgrade their workforce through training programmes.
Online training platforms can offer flexible and efficient learning opportunities, with interactive modules that enable workers to build practical experience, upskill rapidly, and foster knowledge and skills retention.
• Infrastructure resilience
Technology plays a vital role in enhancing infrastructure resilience through advanced tools like BIM software. BIM enables engineers to anticipate and address climate
change, disasters and unforeseen events, during design, and plan accordingly. Real-time collaboration, data analytics and sensors ensure seamless communication among stakeholders, facilitating quick decision-making for fast-response action, thereby enhancing predictive maintenance and adaptive responses to challenges.
A SMARTER AND MORE CONNECTED WAY OF WORKING
As the demand for infrastructure continues to rise, the Singapore construction industry must look to innovation to achieve sustainability, efficiency and cost-effectiveness. In 2024, it is essential that we continue to push boundaries and embrace new technologies to stay ahead.
PlanRadar
PlanRadar is an award-winning digital B2B platform that creates timeand cost-savings in construction and real estate projects by digitising task management, documentation and communication for over 120,000+ users in 75+ countries worldwide.
Trimble introduces roadworks paving control platform for mills and cold planers
Trimble recently announced the availability of the Trimble Roadworks Paving Control Platform for Mills and Cold Planers, extending the functionality of Trimble’s next-generation, 3D paving control system. Trimble Roadworks for Mills and Cold Planers runs on an Android operating system and enables operators to precisely control cutting depth of the mill or cold planer. The intuitive system allows operators to meet demanding specifications on complex projects, minimising over-cutting and creating a smoother surface, on airport runways, highways, racetracks and other projects that require smoothness. The 3D design is displayed to the machine operator, showing areas
that are on, above or below ideal grade, and comparing the actual drum position and slope with the digital design. The platform automatically guides the milling drum to cut the ideal depth and slope, without string lines or manual adjustments.
“Complex paving projects such as airport runways and heavily-travelled highways have some of the tightest specifications in the construction industry. Trimble Roadworks for milling and cold planing takes both the guesswork and the re-work out of milling, making it easy for operators to mill precisely to a 3D design elevation. The benefits of this extend throughout the entire paving process, creating less work for pavers, decreasing asphalt usage
and increasing overall surface smoothness,” said Kevin Garcia, General Manager of Civil Specialty Solutions at Trimble.
The milling and cold planing software features the same user interface as existing Trimble Roadworks applications, with intuitive graphics, natural interactions and gestures, and self-discovery features, reducing operators' training time.
The system is compatible with Trimble WorksManager software which manages data transfer and tracks construction technology equipment across jobsites, and with Trimble Business Center software which is used to create 3D milling plans and comprehensive quality and production reports.
Understanding the demand for project
manager competencies in the Singapore construction
industry: a data mining approach
by Chen Chen, Nathanael Foo Song Ern, Lee Woo Bin, Zheng Qing and Robert Tiong, School of Civil and Environmental Engineering, College of Engineering, Nanyang Technological University, SingaporeConstruction Project Managers (CPMs) are vital to the success of construction projects, but the required core competencies for CPMs are not well-defined, despite high expectations from them. To address this issue, we collected job advertisements from the Singapore market and used data mining techniques to identify the core competencies required for CPMs.
We classified competencies into five major categories – knowledge, skills, self-concept, traits, and motives – based on McClelland's system. We analysed the results using qualitative data analysis software. Finally, we revealed 12 core competencies that recruiters expect from CPMs.
The study's findings shed light on the great demand for skilled CPMs in the real world and provided a theoretical implementation for developing a competency model that can meet these demands. These insights help construction companies and practitioners understand industry needs and develop strategies. CPM practitioners can benchmark their competencies to industry demands and enhance their skills to be more effective.
Introduction
The key figure in any construction project team is the construction project manager (CPM). Successful construction projects require appropriate project managers who possess adequate competency. Competency is a person-related concept that refers to personal attributes underlying competent performance. The word ‘competency’ was coined by David McClelland, an American management expert, in 1953. He broke down competency into five key components – knowledge, skills, self-concept, traits, and motives [1].
Demonstrating competency is not just about meeting the minimum standards of functional performance but rather about exhibiting underlying behavioural characteristics that lead to effective performance [2].
There are several books about construction project management
[3, 4, 5, 6] as well as numerous project management standards [7, 8, 9]. These resources provide guidance on managing construction projects and developing competencies but lack uniform definitions and methodologies, which may deter building core competencies. The competency profiles of generic managers and those of construction managers differ significantly due to the challenges of complex and dynamic construction project environments.
Additionally, local cultures have a significant influence on the project environment, requiring bespoke competency models for accurate performance prediction.
This study aims to develop a competency model for CPMs in Singapore's construction industry through data mining of job advertisements. It will answer the research question ‘What core competencies do CPMs need in the era of Industry 4.0?’
Literature review
The modern construction industry requires qualified CPMs with a thorough understanding of real-world demands. Significant interest has been shown in developing competency models for CPMs since the early 1970s. Research has focused on identifying core competencies needed by CPMs and assessing the readiness of existing practitioners.
Accreditation bodies have established requirements for project management certification, but experts argue that more technical expertise and interpersonal skills are necessary for effective communication with diverse stakeholders.
Standards like the PMBOK Guide [10], Construction Project Management Skills [11], Achieving Excellence in Construction Procurement Guide [12], and Code of Practice for Project Management for Construction and Development [13], offer guidance for construction project
management. As projects become more complex, ongoing research is necessary to keep up with changes and identify core competencies for CPMs.
Likert scale questionnaires are commonly used to understand demand in construction [14, 15, 16, 18, 19, 20, 21]. Survey data can be analysed using different methods, such as descriptive statistics, exploratory factor analysis, partial least squares, clustering and semi-structured interviews. However, the sample size must meet minimum requirements for meaningful results.
Alternatively, a literature review method that includes both empirical and review studies can be used [17, 22, 23]. Data mining of online job advertisements has also become popular [24, 25]. These job postings reflect real-time industry needs.
Table 1 summarises the competencies required for CPMs based on existing literature. The competencies are diverse and wide-ranging, and we have grouped them into five categories using McClelland’s system – knowledge, skills, selfconcept, traits, and motives.
Research method
Data mining is an automated process of analysing large sets of data to extract useful information. We scraped job advertisements from LinkedIn, using in-house web crawlers, with LinkedIn's permission. We used Beautiful Soup, a Python library, to parse HTML and XML documents and extract data. We saved the data in an Excel format and removed duplicates using VBA codes. We then used NVivo software for data analysis.
Figure 1 shows the data mining procedure and Figure 2 shows the qualitative data analysis procedure in NVivo.
Results
We collected 116 job advertisements seeking project managers or directors, from 1783 LinkedIn postings, after removing duplicates.
Figures 3 and 4 represent the keywords identified manually and via auto-coding, respectively. The word
Categories Code Constructs
Knowledge
A1 Experience
A2 Expertise
A3 General knowledge Skills
B1 Problem-solving
B2 Coordination and communication
B3 Leadership
B4 Teambuilding
B5 Motivation
B6 Interpersonal skills
B7 Planning
B8 Resource management
B9 Digital skills
B10 Conflict and crisis management
B11 Impact and influence
B12 Scope, cost, and time
B13 Control and report
B14 Diversity
B15 Risk management
B16 Quality management
B17 Change management
B18 Organizational management
B19 Environmental awareness
Self-concept
C1 Charisma
C2 Innovation
C3 Ethics Traits
D1 Mentality
D2 Emotional intelligence
D3 Learning
Motives
E1 Strategic perspective
E2 Customer orientation
E3 Project success
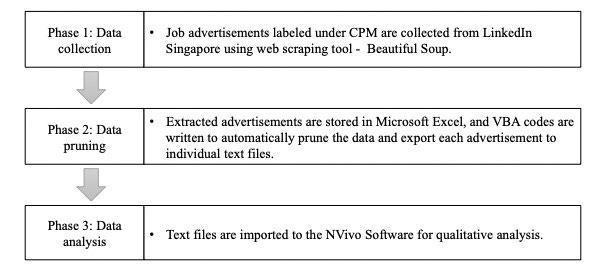
cloud highlights frequently used words by making them larger and clearer.
We linked keywords from manual and auto coding to Table 1's competency items. Table 2 compares the top 10 competencies from both methods, which we combined into one list representing core employer requirements.
Conclusions
This paper used data mining to identify 12 core competencies for skilled CPMs in the Singapore construction market. The findings provide valuable insights to construction companies and practitioners, helping them to better understand industry needs and develop strategies accordingly.
Future research will include surveying employees to determine core competencies sought by job seekers and evaluate the effectiveness of current job advertisements.
Funding statement
This work was supported by IESWong Yui Cheong Research in Construction Project Management Fund, funding number 04FOP000066C120EOM01.
References
[1] L M Spencer and S M Spencer: ‘Competence at work: models for superior performance’, Wiley, 1993.
[2] R Mansfield: ‘What is 'competence' all about?’, Competency, vol 6, no 3, pp 24-28, 1999.
[3] P Netscher: ‘Successful construction project management: the practical guide’, Kindle, 2014.
[4] F L Bennett: ‘The management of construction: a project lifecycle approach’, Rouledge, 2007.
[5] M Chris: ‘Construction management: theory and practice’, Taylor and Francis, 2017.
[6] L Dennis: ‘Project management in construction’, Taylor and Francis, 2016.
[7] Project Management Institute: ‘A guide to the project management body of knowledge’, 2021.
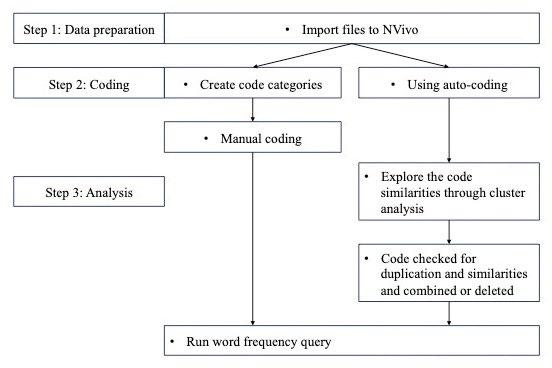
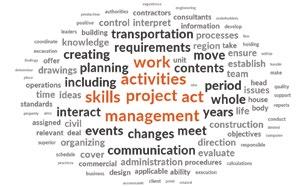
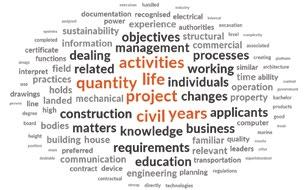
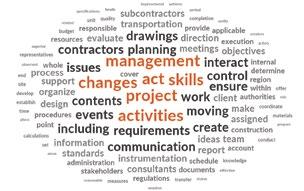
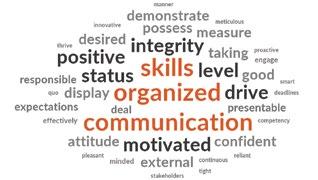
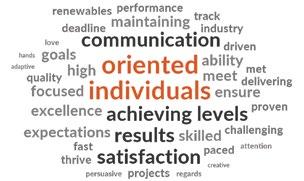

[8] Chartered Insitute of Building: ‘Code of practice for project management for construction and development’, Wiley-Blackwell, 2014.
[9] International Project Management Association: ‘Individual competence baseline for project, programme & portfolio management’, 2015.
[10] Project Management Institute: ‘Construction Extension to the PMBOK Guide’, Newton Square: Project Management Institute, USA, 2007.
[11] Construction Industry Council: ‘Construction Project Management Skills’, UK, 2000.
[12] Office of Government Commerce: ‘Achieving excellence in construction procurement guide no 2. Project organization roles and responsibilities’, The UK Office of Government Commerce, UK, 2007.
[13] Chartered Insitute of Building: ‘Code of Practice for Project Management for Construction and Development’, Wiley Blackwell, UK, 2014.
[14] F T Edum-Fotwe and R McCaffer: ‘Developing project management competency: perspectives from the construction industry’, International Journal of Project Management, vol 18, pp 111-124, 2000.
[15] A R J Dainty, M-I Cheng and D R Moore: ‘Competency-based model for predicting construction project managers' performance’, Journal of Management in Engineering, vol 21, no 1, pp 2-9, 2005.
[16] S Moradi, K Kahkonen and K Aaltonen: ‘Project managers' competencies in collaborative construction projects’, Buildings, vol 10, no 50, 2020.
[17] M Ershadi and F Goodarzi: ‘Core capabilities for achieving sustainable construction project management’, Sustainable Production and Consumption, vol 28, pp 13961410, 2021.
[18] A A Tabassi, K M Roufechaei, M Ramli, A H Abu Bakar, R Ismail and
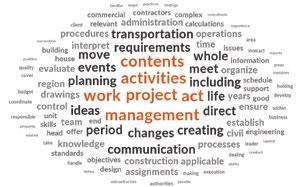

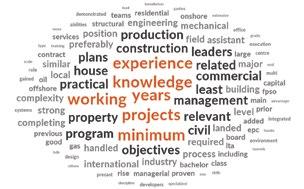
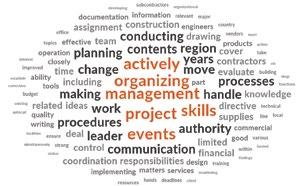
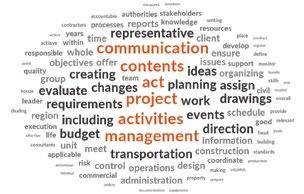

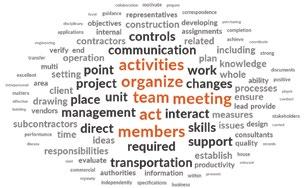
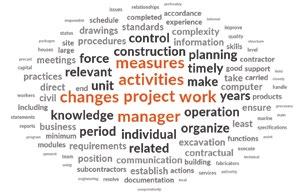
H K Pakir: ‘Leadership competences of sustainable construction project managers’, Journal of Cleaner Production, vol 124, pp 339-349, 2016.
[19] K Dziekonski: ‘Project managers' competencies model for construction industry in Poland’, Procedia Engineering, vol 182, pp 174-181, 2017.
[20] F Zamora-Polo, M M Sanchez-Cortes, A M Reyes-Rodriguez and J G Sanz-Calcedo: ‘Developing
project managers' transversal competences using building information modeling’, Applied Science, vol 9, no 4006, 2019.
[21] T A Amri, K P Khetani and M Marey-Perez: ‘Towards sustainable I4.0: key skill areas for project managers in GCC construction industry’, Sustainability, vol 13, no 8121, 2021.
[22] F Alshammari, K Yahya and Z B Haron: ‘Project manager's skills for improving the performance of com-
plex projects in Kuwait construction industry: a review’, IOP Conference Series: Materials Science and Engineering, vol 713, 2020.
[23] F Pariafsai and A H Behzadan: ‘Core competencies for construction project management: literature review and content analysis’, Journal of Civil Engineering Education, vol 147, no 4, p 04021010, 2021.
[24] H Liu, H Zhang, R Zhang, H Jiang and Q Ju: ‘Competence model of construction project manager in the digital era - the case from China’, Buildings, vol 12, no 1385, 2022.
[25] J Zheng, Q Wen and M Qiang: ‘Understanding demand for project manager competences in the construction industry: data mining approach’, Journal of Construction Engineering and Management, vol 148, no 8, p 04020083, 2020.
[This article is based on a paper presented at the World Engineers Summit (WES) 2023, held in Singapore, from 8 to 10 November 2023. WES 2023 was organised by the Institution of Engineers, Singapore (IES).]
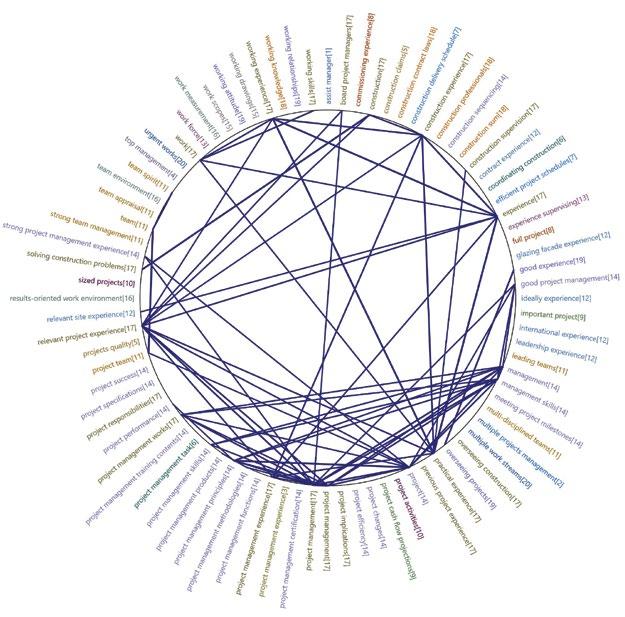
Manual Auto
Keywords Competencies
Contents Scope, cost, and time (B12)
Changes Change management (B17)
Communication Coordination and communication (B2)
Planning Planning (B7)
Direction Leadership (B3)
Whole, objectives Strategic perspective (E1)
Keywords Competencies
Contents Scope, cost, and time (B12)
Communication Coordination and communication (B2)
Direct Leadership (B3)
Planning Planning (B7)
Interpret, drawings Control and report (B13)
Changes Change management (B17)
Drawings, control Control and report (B13) Whole Strategic perspective (E1)
Instrumentation Digital skills (B9) Evaluate Problem-solving (B1)
Issues Conflicts and crisis management (B10)
Evaluate Problem-solving (B1)
Table
Knowledge Expertise (A2)
Assignments Teambuilding (B4)
Reaching new heights in timber-hybrid design
by Pascal Steenbakkers, Babette Verheggen and Mathew Vola, ArupDesigning the Netherlands’ tallest timber-hybrid residential building.
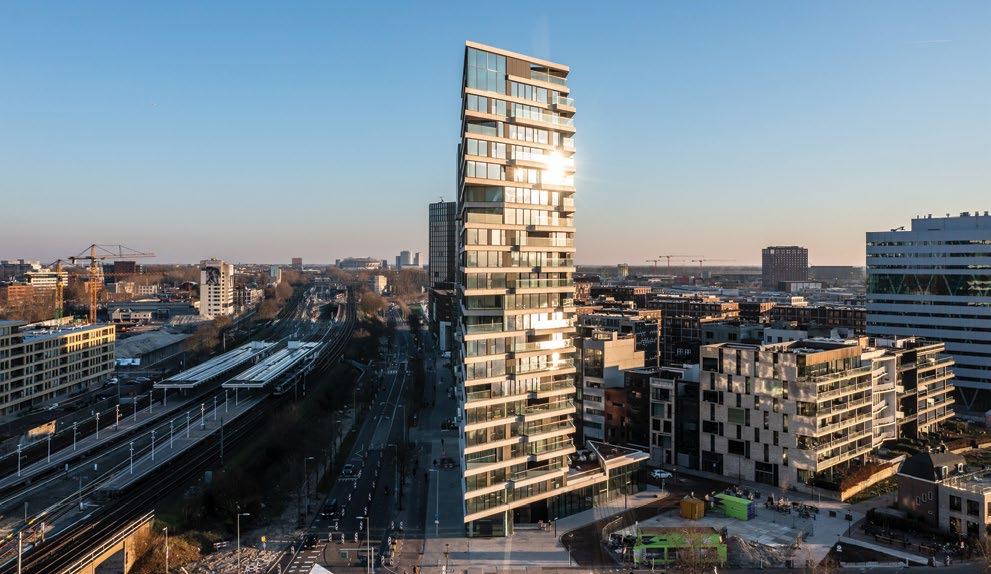
INTRODUCTION
Standing 21 floors tall, HAUT is one of the tallest timber-hybrid buildings in the world. The name of the building is a play on the Dutch words for timber (hout), on the French word for high (haute), and on ‘haute couture’, befitting this ‘high end’ building in Amstelkwartier – a new district on the edge of Amsterdam’s city centre.
When the city’s municipality launched a design competition in 2016 for the building plot adjacent to the Amstel river, they emphasised the importance of the design being both sustainable and of high architectural quality. Together with developer Lingotto and Team V Architecture, Arup’s multi-disciplined approach has delivered on that intent with a revolutionary timber-hy-
brid residential tower, reaching an impressive 73 m above the river. To engineer this bio-based, high-rise 14,500 m2 residential building, the firm’s team of specialists delivered the sustainable, structural and technical design, including building physics, building services, acoustics and fire safety engineering.
GROUNDBREAKING ACHIEVEMENTS
With its focus on reducing carbon footprint even before it was built, HAUT won the International BREEAM Award 2018.
Following its opening, it won the Dutch Timber Construction Award (Het Houtblad), which recognises the best timber building in the Netherlands. In addition, it was certified BREEAM Outstanding – an acknowledgement awarded to only
a handful of high-rise residential buildings globally. HAUT is also the first residential project in the Netherlands to achieve this sustainability certification.
In November 2023, HAUT received the ‘Award for the development of a novel timber-concrete-composite solution in high-rise residential design’, at Structural Awards 2023, presented by the Institution of Structural Engineers (IStructE).
CARBON REDUCTION
To achieve its climate goals, the Netherlands has committed to becoming carbon neutral by 2050. Using timber as a building material is one of the most effective ways of accelerating decarbonisation, as the associated carbon footprint is much lower, compared to construction
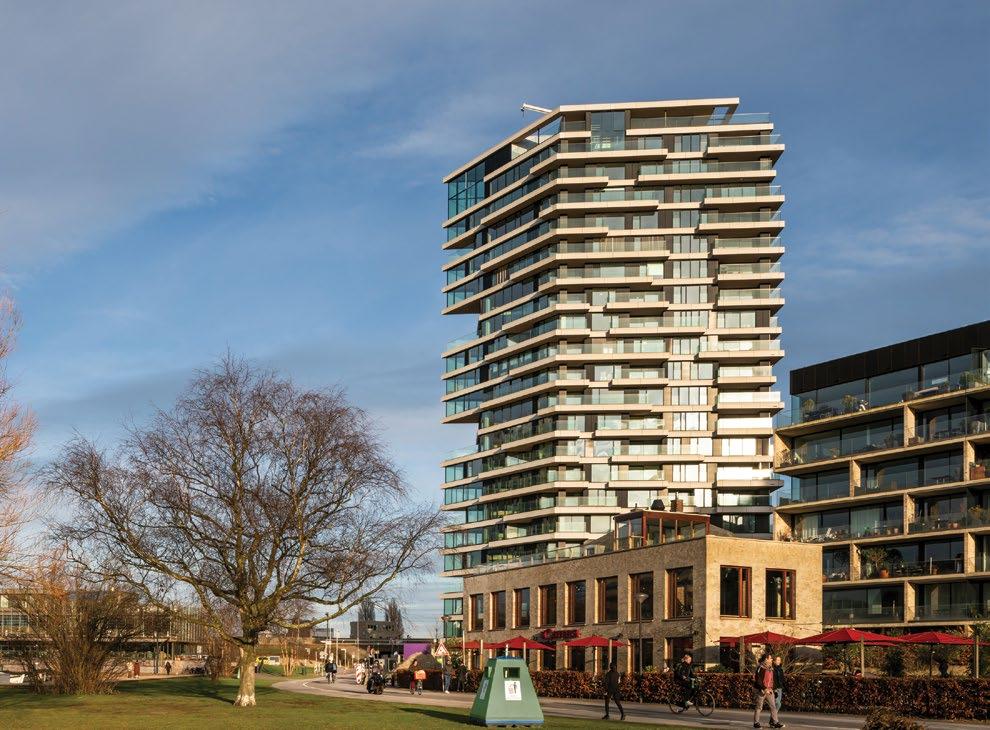
with concrete or steel. In addition, the timber acts as carbon storage for decades to come and is a regenerative material.
In 2021, more than 80 Dutch companies signed a Green Deal covenant, ‘Houtbouw of the Metropoolregio Amsterdam’. With this covenant, Amsterdam is committing to the goal of building at least one in five residential buildings using timber as the main structural material, from 2025 onwards.
Bio-based building is gaining momentum all over the world, as more and more people embrace the natural qualities of timber. While the natural material’s enhanced atmospheric, acoustic and health qualities are a factor, the most important driver for the growing use of timber is the potential to significantly reduce carbon emissions. In HAUT, more than 2,800 m3 of timber was used in the structure alone, bring-
ing the total reduction in embodied carbon to half of a conventional high-rise structure. When including sequestration, some 1,800 tonnes of CO2 is stored in the structure.
SUSTAINABLE AND INNOVATIVE
In recent years, Arup has designed and delivered a number of timber and concrete/timber hybrid framed buildings, including the sevenstorey H7 timber-hybrid building in Münster in Germany; Sydney’s Macquarie University Incubator and adjacent four-storey Ainsworth Building; and 80 M, the first mass-timber overbuild in Washington DC. The firm was able to tap into its global experience for HAUT, in particular on the fire engineering aspects, where integrated fire safety provisions played a key part in enabling the overall sustainable timber design.
The architectural aim was for the
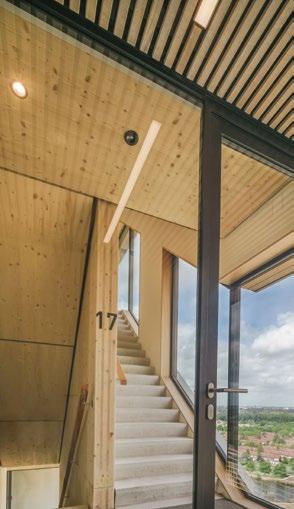
tower to have a transparent appearance, with lots of sunlight supplying the building with natural heating and optimal lighting conditions. The team designed a façade that consists largely of (triple) glass, with custom photovoltaics (PV) panels that were fully integrated into the façade attached to non-combustible panels and with fire stops at floor levels.
Combined with the rooftop panels, the 1,250 m2 of PV provides an energy-positive exterior that generates a large portion of the building’s electricity. The tower features an aquifer thermal energy storage system, sensor-controlled installations and low temperature underfloor heating, making it one of the most climate-friendly high-rise residential buildings in Europe. A rooftop garden and nest boxes for birds and bats add to the biodiversity on site, with the rainwater collected at roof level used to irrigate the garden.
STRUCTURAL SCHEME
With 21 levels, HAUT needed to be easily constructed while satisfying structural, acoustic and fire safety requirements. The design had to consider various site constraints, including the plot orientation, proximity to the river embankment, railway and
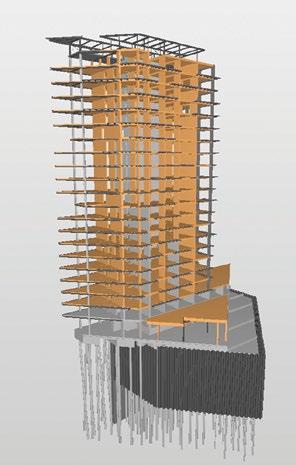
existing buried data cabling, and the soft soil conditions. The foundations included 104 ground-displacing steel screw grout injection (Tubex) piles and 54 tension anchors. In addition, a load-bearing diaphragm wall was utilised along the edge of the building plot.
The design principle for HAUT was to use timber where possible, and concrete and steel only when necessary. While the foundations, two-level basement, core, and ground and first floor were constructed in concrete, for the 20 levels above that, timber was predominantly used. Looking for ways to maximise the use of timber as much as technically possible, Arup
developed an innovative and affordable technical solution for the upper levels.
The result was a custom-designed precast timber-concrete composite floor plate developed in close collaboration with Lingotto, Team V Architecture, contractor J.P. van Eesteren and the German timber specialist Brüninghoff.
HYBRID CONSTRUCTION
The floor build-up consists of a 160 mm deep cross-laminated timber (CLT) plate with an 80 mm concrete top layer, supported on CLT load-bearing walls and glued laminated (glulam) timber columns. In this floor build-up, the two horizon-
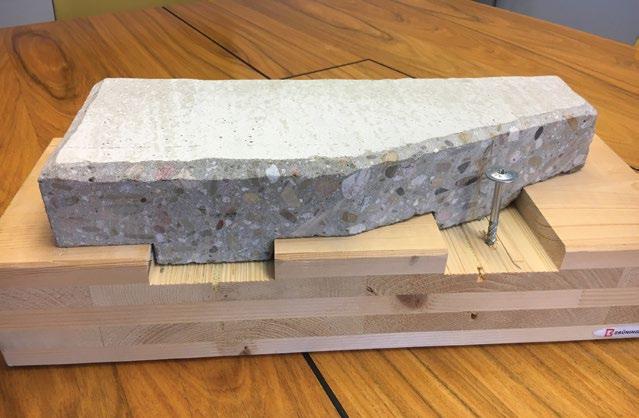


tal layers act as a hybrid system, in which the timber takes tension forces and the concrete takes the compression.
In certain areas, where the floor edges are not supported by a load-bearing wall, glulam downstand beams were introduced. These beams transfer façade and balcony loads, and provide additional stiffness to the floor. They also double as a tension ring around the perimeter of the floor, transferring diaphragm forces and acting as a structural tie.
The choice of a hybrid floor plate had big advantages for footfall performance (reducing vibration), acoustic performance, construction sequence and detailing. Due to the low self-weight of the floor plates, delivery vehicles could also be loaded more efficiently, resulting in fewer deliveries to the building site.
STABILITY SYSTEM
A concrete-timber lateral stability system was used, consisting of a concrete core and two full-height CLT shear walls. The eccentric positioning of the core (for architectural reasons) introduced torsional effects under wind loads, increasing lateral deflections and wind-induced vibrations.
To determine the expected maximum lateral deflections and perform sensitivity studies, two
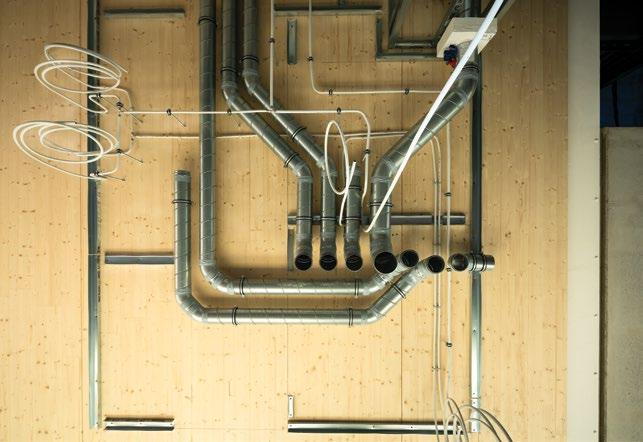
finite element models were created. The first was a 3D model of the entire lateral load-bearing system, including the concrete ground floor, basement and foundations elements. This was predominantly used as a means of assessing total deflections and the sensitivity to stiffness of individual structural elements, including the foundations.
The second model consisted of a 2D model of the CLT wall, including specific wall openings, orthotropic material behaviour and locally reduced stiffness to allow for acoustical decoupling and connection
details. The model was subjected to gravity loads and lateral loads taken from the 3D model. Subsequently, the resulting deflection in the 2D model was compared to the deflection in the 3D model, allowing for a check on the initially assumed stiffness.
The concrete core is also used as a fire brigade entrance and provides the fire escape routes. Risers were used for the building services, which were then distributed horizontally at a high level into each apartment. The distribution of the services required careful coordina-
tion to meet the structural, acoustic and fire safety requirements. In the apartments, the air ducting system was distributed in the ceiling zone in the non-living spaces, e.g. corridor, kitchen and bathroom zones.
VIBRATION CONTROL
As HAUT’s hybrid structure is a lot lighter than an equivalent concrete building, wind-induced vibrations were considered a risk, and were investigated in detail to ensure compliance with the code. To calculate the expected maximum accelerations, a modal analysis was performed on the previously developed 3D model of the structure. The calculated vibrations were sensitive to the mass of the building. This was one of the most important motivations for choosing the specific floor build-up that is used in HAUT.
The additional mass of timber-hybrid floor (compared with a full CLT plate) provides additional benefits, improving acoustic performance, reducing footfall-induced vibrations and increasing performance against wind-induced vibrations. Several floor elements are supported by the concrete core wall on one side and a timber wall or beam on the other.
The difference in mechanical properties between these supporting elements will cause differential movements between the two, and careful design considerations were given to ensure this would not create architectural or functional issues. To take into account creep and shrinkage effects, the concrete core was constructed using in situ concrete, rather than assembled from prefabricated concrete elements.
A wind tunnel test of a physical model of the building was carried out, along with on-site testing with building-mounted sensors, during construction. The analysis and results from the sensors on site compared favourably.
ACOUSTIC DESIGN
Laboratory and on-site testing were completed to ensure that the acoustic design limited any crossover of sound between the apartments. This is an elevated risk for this type
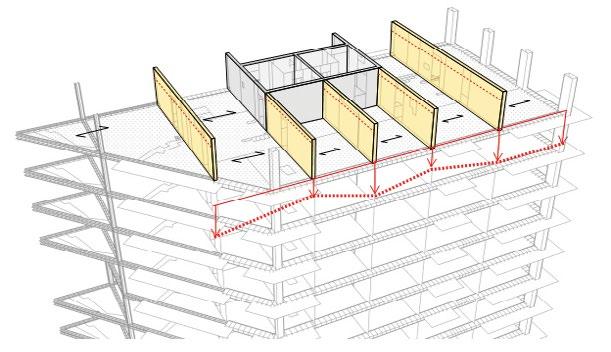
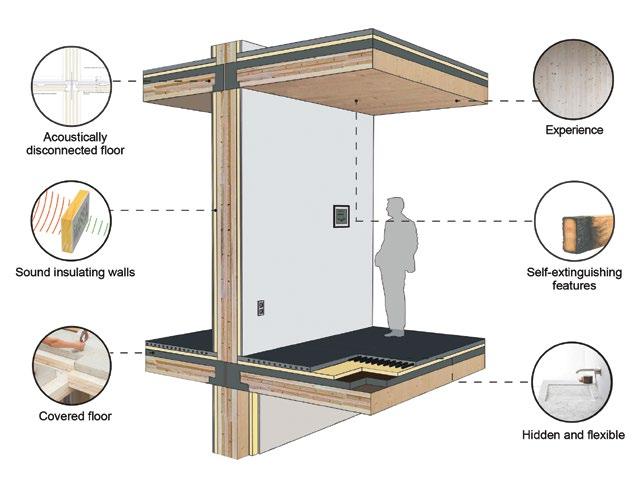
of project because of the extensive exposed timber elements – particularly in the living spaces, where there are no ceilings. Arup went beyond the existing acoustic requirements for residential projects in the Netherlands, which are some of the most stringent in Europe.
To determine acoustic performance in those high-risk areas, a section of the floor build-up was tested for both airborne and impact sound isolation. With the low-
er mass of the hybrid floor system, low frequency sound isolation was the determining factor in overall acoustic performance. During construction, further tests were carried out on site to provide additional reassurance on the acoustic performance of the system.
FIRE SAFETY
HAUT pushes the boundaries of what is possible with high-rise timber design. Local building codes do
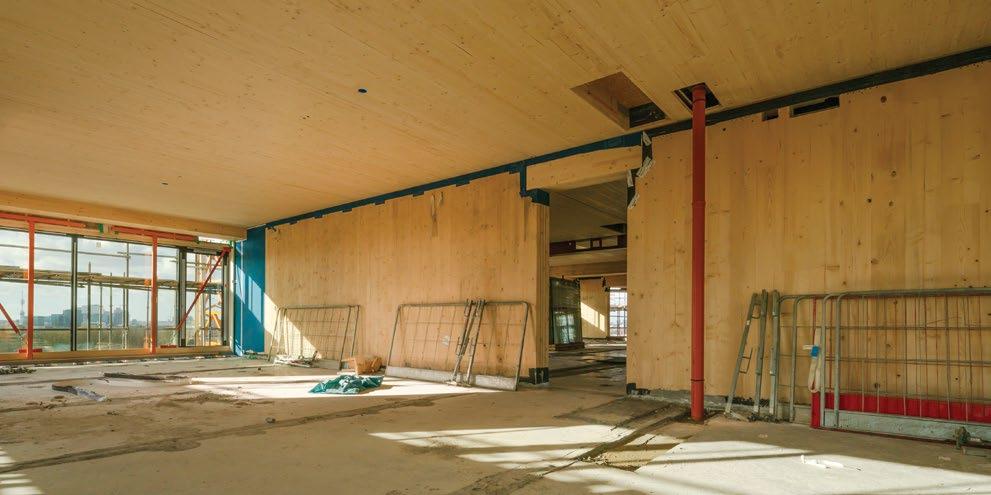
not address the additional fire risks inherent in tall timber buildings. The bespoke fire engineering design needed to address those fire risks, ensuring adequate means of escape and structural stability in fire situations, and mitigating the risk of fire spread.
Arup called on its global expertise to carry out a rigorous review of the project, developing solutions that brought the design in line with international best practice. This led to additional fire safety measures being implemented in the building.
The fire risks that needed to be addressed in the bespoke fire safety design revolved around the height of the building, and the use of load-bearing CLT walls and exposed timber ceilings in the apartments. As timber is a combustible material and the architectural intent was to expose the timber at the ceiling, this fire hazard had to be addressed.
The fire safety engineering assessed the likelihood and consequences of an extended fire duration and fire spreading beyond the compartment of origin. The performance-based fire strategy identified and managed those risks.
The Dutch building code does not require sprinkler protection in resi-
dential buildings of this height, but to contribute to a robust design, sprinklers were included. Also, to reduce the volume of exposed timber, a double layer of fire-resistant panels was installed to protect the CLT walls. The panels also improved the acoustic performances and are an example of an integrated design approach which enhanced the building redundancy and its quality.
Laboratory fire testing was carried out in Belgium on the fire-resistant wall panels, with furnace tests providing both data and giving a practical demonstration of the compliance. Additional fire tests were carried out in Vienna to demonstrate the charring rate of the exposed CLT floor system.
The tests determined the extent to which CLT panels burn over time, and helped determine the type of adhesive used.
The choice of adhesive was critical to reduce the risk of CLT adhesive bond line failure in fire (so called char delamination) and to control the charring rate of the timber. Excessive charring could result in an unpredictable fire outcome and additional fire load.
By engaging Arup’s international global fire safety engineering
network and its extensive global research, the firm used the project to develop and formulate design solutions that can now also be used to enable the sustainable design of other mass timber high-rise projects.
As a result of this global knowledge sharing, Arup has now been asked to support the development of additional guidelines to aid with amendments to local building codes. The firm is also influencing changes to regulations around the use of timber in construction in the Netherlands, particularly for large scale and mid-rise to tall timber buildings.
THE AUTHORS
Pascal Steenbakkers was the fire safety discipline lead. He is an Associate Director in the Amsterdam office of Arup.
Babette Verheggen was the acoustics and building physics discipline lead. She is an Associate and leads the acoustic team in the Amsterdam office of Arup.
Mathew Vola was the Project Director and is Arup’s global computational design skill leader. He leads the structures team in the Amsterdam office, where he is a Director.
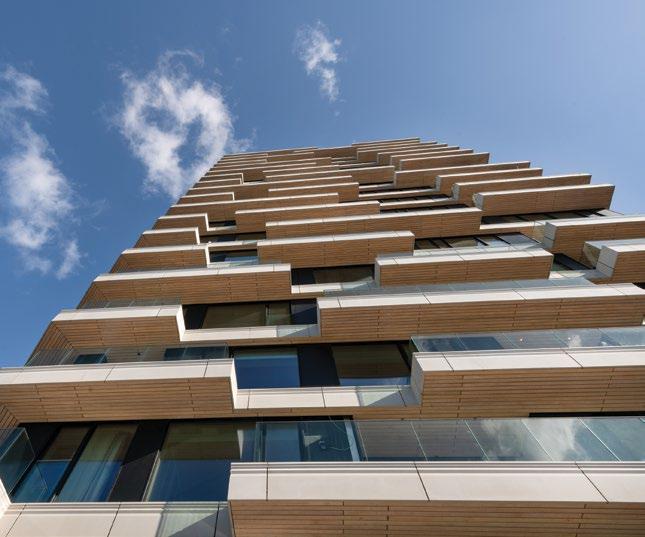
PROJECT CREDITS
Developer
Lingotto
Architect
Team V Architecture
Timber engineering
Assmann beraten + planen and RWT Plus
Contractor
J.P. van Eesteren
Timber sub-contractor
Brüninghoff
Acoustic consulting, building physics, building services, fire safety, structural engineering, sustainable building design
Arup
(Adapted from an article in ‘The Arup Journal’, 1/2023)
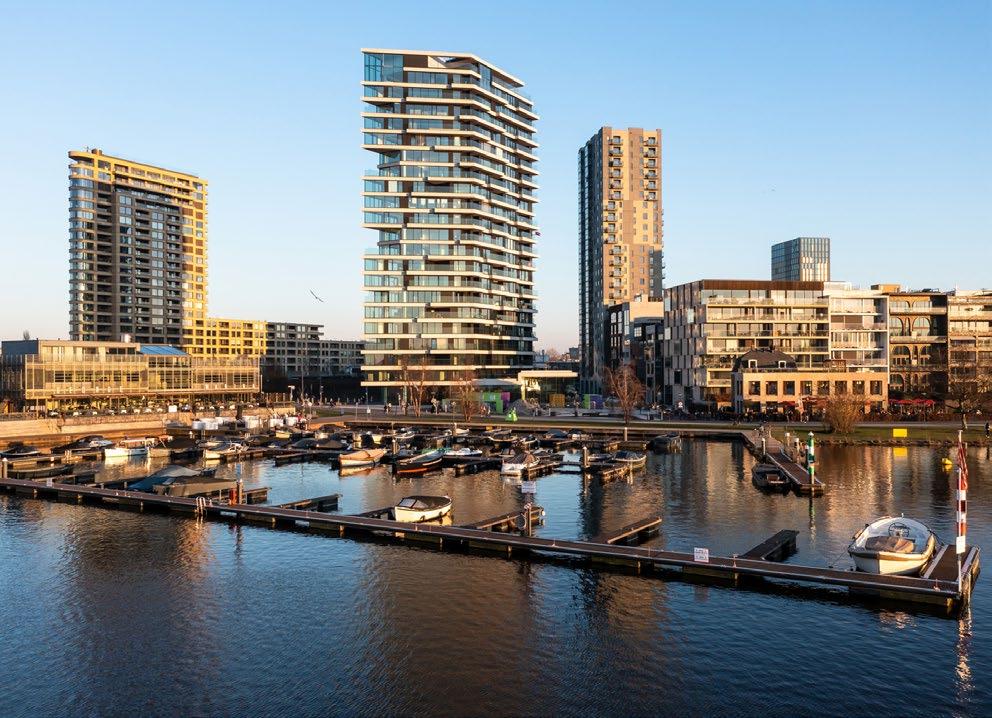
Formwork and scaffolding for VIENNA TWENTYTWO
The solutions ensure a fast construction sequence, a safe working environment and flexibility.
VIENNA TWENTYTWO, one of the largest urban development projects in Vienna, Austria, is being built in the 22nd district of Donaustadt. Two diagonally positioned tower blocks and four low-rise buildings form a varied ensemble. Tried-andtested formwork and scaffolding solutions for the project were provided by Doka.
The 15,000 m² site includes apartments and offices, as well as two hotels, shops and restaurants. VIENNA TWENTYTWO owes its distinctive look and striking skyline to internationally renowned Viennese architects, Delugan Meissl Associated Architects.
Proven formwork solutions
The design of the project, developed by ARE Austrian Real Estate, includes several modern details – from generous open spaces to fine-tuned wind optimisation. Once completed, the tallest tower in the VIENNA TWENTYTWO multi-purpose ensemble will have a height of 153 m.
In addition to high-quality formwork solutions from Doka, the V22 HABAU-DYWIDAG consortium is also using Doka’s Ringlock modular scaffolding for the steel construction.
With the help of the field-proven, pre-assembled Xclimb 60 protection screen from Doka, the tallest tower in the ensemble is growing upwards safely and quickly. The hydraulic climbing system with the Xbright frame enclosure protects against the effects of weather at great heights, thus ensuring stable working conditions.
Ringlock modular scaffolding
Outriggers, a set of structural steel trusses to provide stability and connect the building core to vertical components while concealed from the outside, were installed on levels 16/17.
Doka’s Ringlock serves as the working scaffolding around them, capitalising on its flexibility to fit around the steel structure. This scaffolding offered optimal support for the site team during assembly, welding, and weld seam inspection of the outriggers. Access for workers between levels was facilitated through a combination of staircases and ladder hatch decks, prioritising a secure working environment.
Upon completing the first outrigger, the scaffolding tower seamlessly transitioned to support the second one. Leveraging Ringlock’s strong node connection and features like the jack retainer and locking pins, the entire scaffolding unit could be relocated with minimal crane lifts, significantly reducing downtime in disassembly and re-assembly.
VIENNA TWENTYTWO is an inspiring project that embodies the dynamic spirit of optimism in the city on the Danube and benefits
from proven Doka solutions. The completion of the 153 m tallest part of the building is scheduled for the end of 2025.


Renovation of a historic building in Italy
A specific binder was developed to restore the exterior surfaces of the Torre Velasca in Milan and bring them back to their original colours.
“The Tower proposes to culturally summarise that ineffable yet perceptible characteristic atmosphere of the city of Milan without following the language of any of its buildings”, is how Ernesto Nathan Rogers described the thought process that led to the BBPR design studio’s conception of Torre Velasca, one of the city’s most iconic buildings.
Built between 1955 and 1957, the tower is the result of a dialogue with the surrounding space. Its vertical momentum is in contrast, firstly, with the small square at its base, but also with the rest of the city centre, that the designers believed would be able to welcome a new tall building which, at first sight, may seem out of place with the urban fabric.
“The continuous vertical growth of current building stock from the start of the century had flattened the profile of the city landscape and almost submerged traditional landmarks such as towers, cupolas and bell towers, the gables of buildings. To us, creating new, architecturally relevant elevations, including in city centres, seems to be a sustainable proposition, I would even say desirable,” explained Lodovico Barbiano Di Belgioioso from BBPR.
Torre Velasca is a modern building that transforms the skyline of the old city centre, evoking, however, some of the features of the surrounding historic buildings, first and foremost, the Milan Cathedral, with a take on its flying buttresses, but also the architecture of the medieval Lombardy era.
Its ‘mushroom’ structure is, in fact, a clear homage to Torre di Bona di Savoia at Castello Sforzesco in the centre of Milan. Torre Velasca was the subject of heated discussions in the world of architecture, but also amongst the inhabitants of Milan, who soon nicknamed the building the ‘skyscraper with braces’.
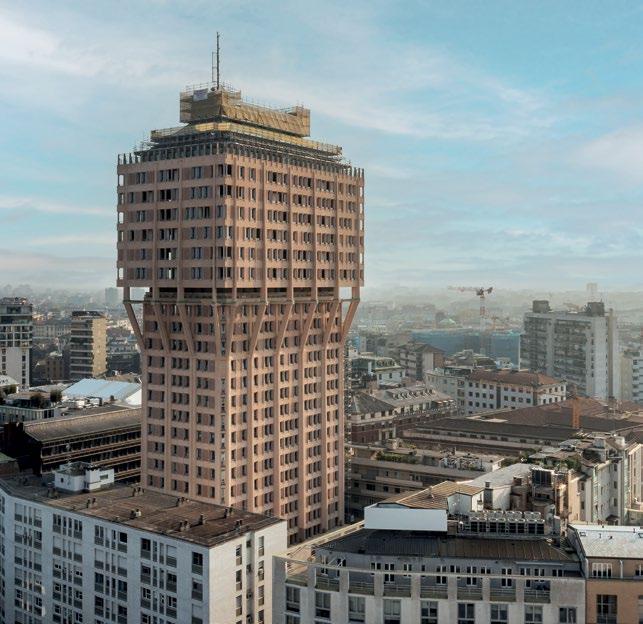
The building has a height of 106 m and 28 floors, two of which are below ground level. The structure is made up of reinforced concrete pillars and beams. The reinforced concrete structural elements made on site (columns, parapet beams, tie-rods and link points) are covered with a double layer of render containing granulates of pink Verona marble applied at different thicknesses and with a floated textured finish.
The external closure elements incorporating the windows, on the other hand, are made up of a series of precast elements which, positioned together in an irregular pattern, generate a characteristic decorative layout for the façade of the
tower. The small pillars are precast monolithic elements with a variable section made from granules of red Verona marble in white cementitious mortar.
The most characteristic structural feature of the building is clearly visible between the 15th and 18th floors – a load-bearing structure designed to support the overhanging upper module containing the remaining eight floors. Twenty oblique beams emerge from the external prospects in correspondence with the 18th floor and are then grafted to the perpendicular upper pillars and the large link points.
The upper module, in fact, has a larger footprint. According to the designers, the private dwellings located between the 19th and the
25th floors needed to have more depth to the main body than the offices below and, at the same time, create a sort of formal detachment to clearly define the two areas of the building.
Redevelopment work
In 2020, Hines, Development Manager and an investor in the HEVF Milan 1 fund managed by Prelios SGR SpA, signed an agreement with the Local Heritage Authority and Milan City Council to redevelop Torre Velasca, which also included transforming the piazza into a pedestrian zone. Work is scheduled to be completed in 2024.
Designed by Studio Asti Architetti, in partnership with CEAS (for masonry renovation works), the redevelopment work included the complete restoration and consolidation of its original exteriors to maintain the iconic façade and bring it back to its original colour. The internal spaces, on the other hand, have been given a new layout and are divided into different functional areas to include shops, restaurants, a spa centre, offices and apartments.
To restore the original colour of the building’s façades, which had been exposed, for more than 60 years, to pollutants and all types of atmospheric conditions, the design studio reached out to Mapei who developed a special binder for a render specifically for this site.
The decorative, white, cementitious render with specific polymers was mixed with the aggregates to match the type and grain size of the original render of that era, until a formula as close as possible to the authentic colour of the render used for the façades of the tower was obtained. Mapei also supplied products for structural strengthening work on the tie-rods in the upper floors of the building.
Preparation of surfaces and concrete repair
The first phase of the work was the removal of the old render and preparation of the surfaces, removing the part of the reinforcement rods that had become carbonat-
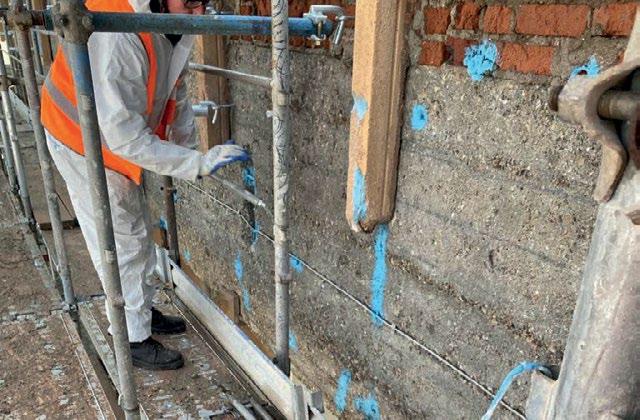
ed, by hydro-scarifying, to leave a rough, compact surface free of dust.
The reinforcement rods, left exposed after removing the cementitious conglomerate, were thoroughly cleaned to remove all the rust, again by hydro-scarifying, and then treated with MAPEFER 1K one-component, anti-corrosion, protective cementitious mortar – a product applied by brush in layers at least 2 mm thick.
The sections from which the carbonated concrete had been removed were reintegrated by applying MAPEGROUT 430 fibre-reinforced, compensated-shrinkage, thixotropic mortar which can be applied in layers from 5 mm to 35 mm thick.
MAPEGROUT 430 was chosen not only for its mechanical characteristics that made it suitable for the concrete substrate, but also due to its workability and ease of pumping with a worm-crew rendering machine or with a continuous-feed rendering machine. Electro-welded 0.8 mm diameter AISI 304 non-magnetic stainless-steel mesh (mesh size: 24 mm x 24 mm) was embedded in the mortar by fastening it to the substrate with fasteners made from pieces of AISI 304 stainless steel bar shaped to suit.
Restoring the colour
After restoring and reconstructing the concrete, an intermedi-
ate scratch-coat needed to be applied over the entire surface with a notched trowel so that the next layer, in this case, the new LEGANTE INTONACO VELASCA render, would mesh mechanically and form a strong bond. This scratchcoat was created by applying PLANITOP HDM MAXI, a two-component, ready-mixed, fibre-reinforced, pozzolan-reaction cementitious mortar.
Mapei was also involved in restoring the façades to their original colour. This part of the work required an in-depth scientific analysis of the original render, in the R&D laboratories and, through a series of laboratory tests, the most appropriate aggregates and colours were identified in order to develop a bespoke binder specifically designed for Torre Velasca, from which it takes its name.
The new, white cementitious LEGANTE INTONACO VELASCA was formulated, in order for it to be mixed with aggregates from the Bellamoli and Ferrari quarries, in a granulometric curve, until a ‘mix design’, as similar as possible to the original render used on the façades, was obtained.
LEGANTE INTONACO VELASCA was modified with specific polymers to create a highly adhesive, water-repellent and crack-free product to guarantee the maximum level of durability possible for the surface
exposed to aggressive atmospheric agents and the urban environment.
FRP strengthening package for the tie-rods
Since the chain/tie-rod package has an important structural function in the overall static capacity of the upper floors of the building, it was deemed necessary to add further structural strengthening to increase the tensile strength of these structural elements.
Because of the particular geometry of the external elements, an FRP strengthening package, with carbon fibre fabric, the MAPEWRAP C UNIAX SYSTEM, and special connectors (also made of carbon fibre) from the MAPEWRAP C FIOCCO line, was designed.
The system guarantees the following:
• Very little intrusion from an aesthetic and architectural perspective, so there is no interference with the architectural constraints of the tower.
• An increase in the structural capacity of the elements, while maintaining the same mass and stiffness of the existing structure.
• High durability of the building/ structure through the use of a certified, tried and tested, scientifically valid system.
Due to their low thickness, carbon fibre fabrics from the MAPEWRAP line were applied to both the inside and outside of the floor and followed exactly the same layout as the chains embedded in the floor slab and the external tie-rods.
Water-repellent treatment for the rendered surfaces
The cycle was completed by treating all the façades with PLANISEAL WR 100, a protective hydrophobising product which, thanks to its particular composition, penetrates deep down into the render and protects it from degradation, without affecting the aesthetics or colour of the surface. Thanks to a considerable reduction in the absorption of surfaces treated with PLANISEAL WR 100, degradation due to freezethaw cycles is prevented and, as a result, they are much more durable.
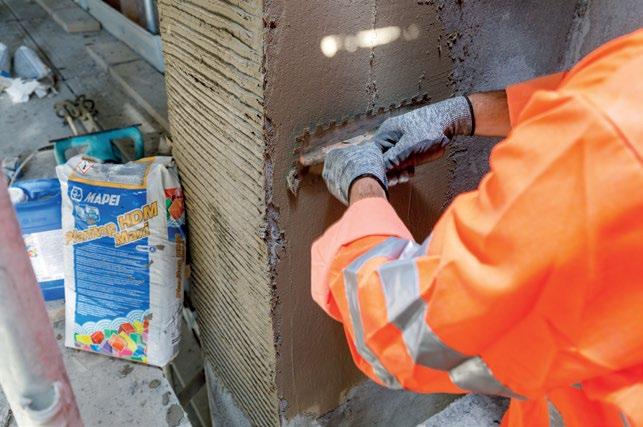


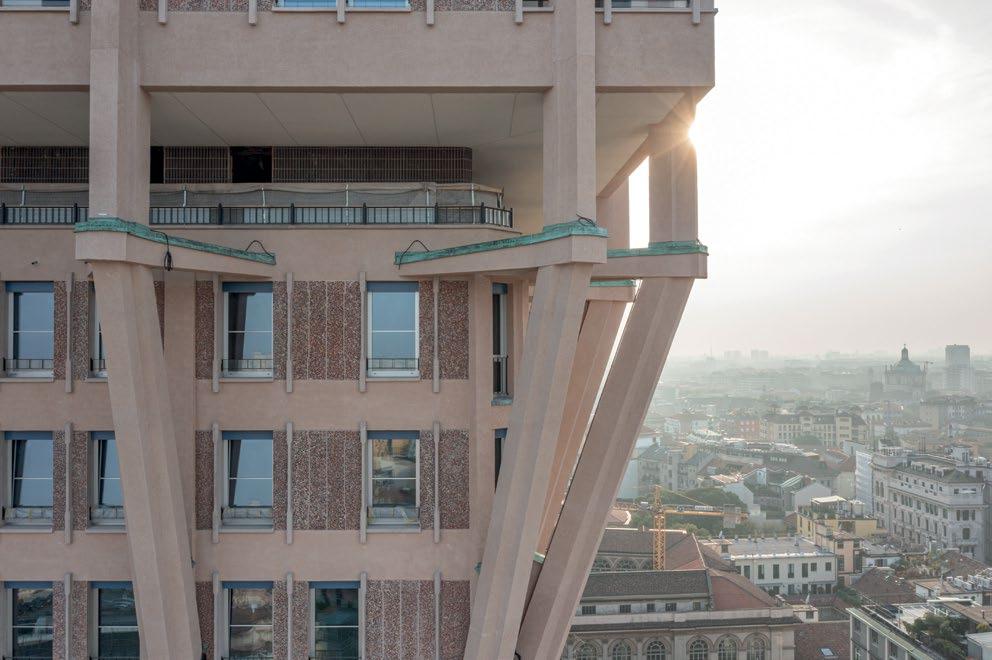

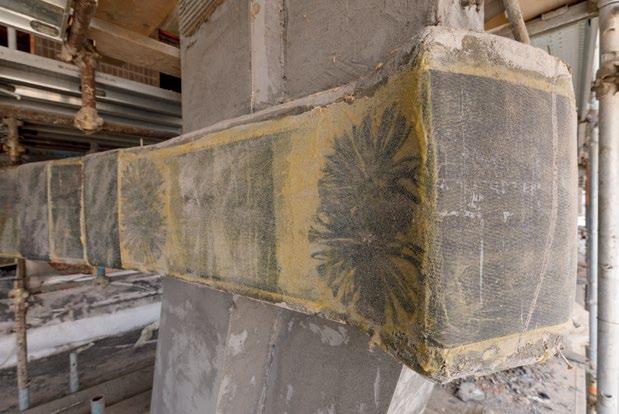

PROJECT DATA
Project Torre Velasca
Location Milan, Italy
Original designers
Studio BBPR
Period of original construction 1955-1957
Period of redevelopment work 2020-2024
Owners
Hines and Prelios sgr
Redevelopment work
designers
Studio Asti Architetti CEAS srl
Main contractors
Ars Aedificandi SpA
Gasparoli Srl
Works Management
Fontana Architetti
ESA engineering
INTERVENTION BY MAPEI
Period of intervention
2021-2022
Contribution by Mapei
Supply of products for concrete repair, protection and structural strengthening, and restoration of facades
Mapei distributor
Bild Distribuzione srl
Application of Mapei products
Concrete repair –MAPEGROUT 430
Protection for steel reinforcement – MAPEFER 1K
Surface preparation –PLANITOP HDM MAXI
Structural strengthening – MAPEWRAP C UNI-AX SYSTEM, MAPEWRAP C FIOCCO
Protection of surfaces –PLANISEAL WR 100
Restoring the render – LEGANTE INTONACO VELASCA (the product was specifically developed for the restoration of the Velasca Tower)
Website for further information
www.mapei.com/sg utt.mapei.com
(Some products mentioned in this article are available in Singapore. Please contact customer service at Mapei Far East for the available products).
This editorial feature is based on an article from Realtà MAPEI INTERNATIONAL ISSUE 99. Images by Mapei, unless otherwise stated.
New vibration crusher drum for compactors
Hamm is offering compactor models for countries with exhaust emission standard EU Stage V/EPA Tier 4f, which have been designed specifically to crush and compact rock and stone. The new models are available in countries with Tier 3 exhaust emission standard, from the autumn of 2024.
The benefits to construction companies are plain to see. Processes on the construction site can be streamlined by deploying VC compactors, which reduce the work and expense needed for material preparation and transport. For customers, this means time, cost and CO₂ emissions are reduced.
The HC 250 C VC (Tier 3) and HC 250i C VC (EU Stage V/EPA Tier 4f) compactors are able to crush and compact mixed soils, stones such as basalt and granite, and other construction materials with comparable pressure resistance, in a single step.
Featuring powerful Deutz engines and reinforced components around the front frame, 3-point articulation and the underbody, the new compactors are well-equipped for tough applications. The separate ‘C’ in the type designation also symbolises a reinforced drum drive, capable of inclines of up to 60%.
The 25 t machines are supplied with heavy-duty tyres for rocky terrain, driver's cab and the Easy Drive operating concept, all as standard. When it comes to comfort, operators will appreciate the seat with ex-
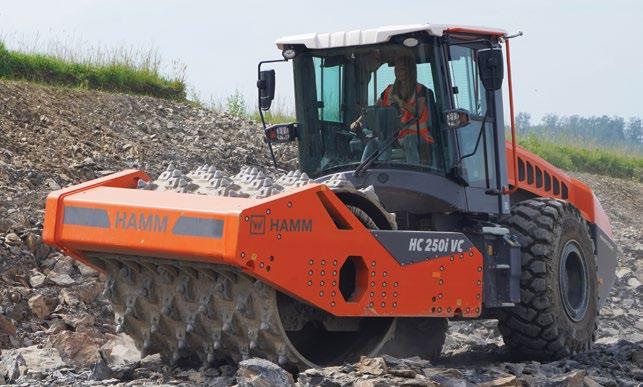
tended backrest, especially during tougher applications. An air-sprung driver's seat can be selected as an optional extra.
A highlight of the new VC compactors is the newly designed tool holder system. This is compatible with round-shank cutting tools for stone, as well as wear-resistant heavy-duty cutting tools with carbide tips and hard facing for abrasive stone or hard stone.
The configuration of the tool holder system and the way the tool inserts are attached ensure that assembly and removal are quick and easy, with no need for specialist tools.
This keeps maintenance and servicing costs low. Existing machines
(H 25i VC/3625 VC) can also be fitted with the new-design tool holder system by switching the drum. Transport rings are available for easy transport.
The new VC compactors are suitable for a wide range of applications. In addition to the customary crushing and compacting of geological material to create a stable substrate, the machines are also utilised to level rubble in landfill sites.
The VC compactor can also be called upon for road planing works in tunnel building and surface mining sectors or to pre-crush and loosen stone. This takes a lot of hard work out of subsequent processes, such as layer-by-layer milling off.

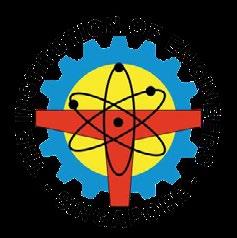
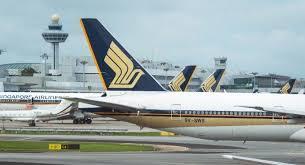


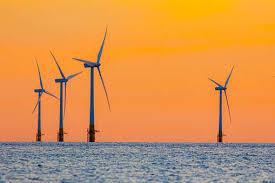
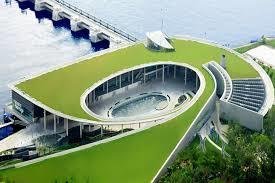
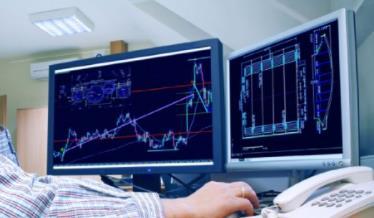
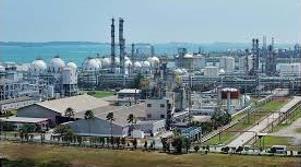
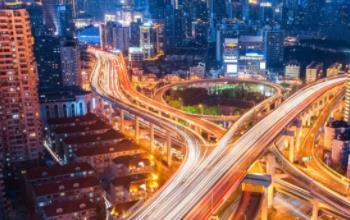
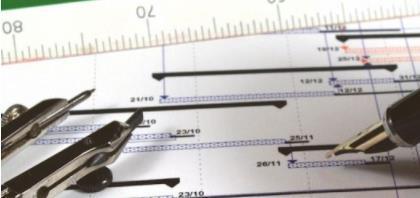