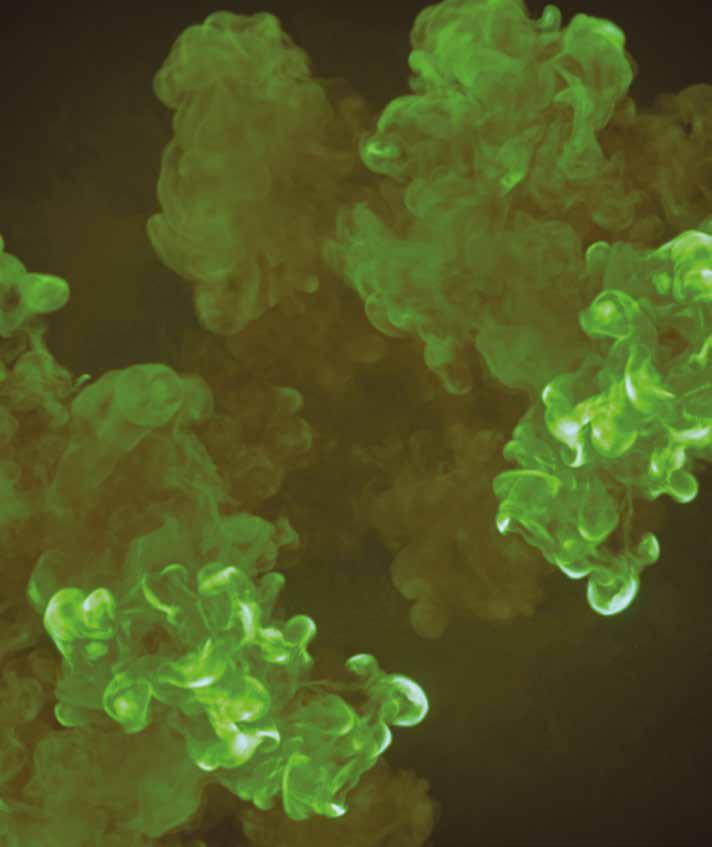
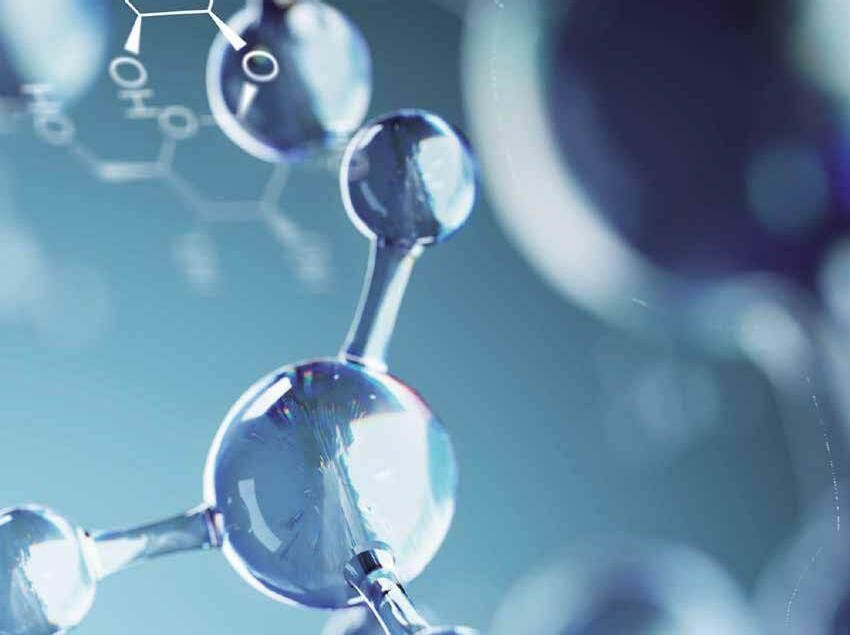


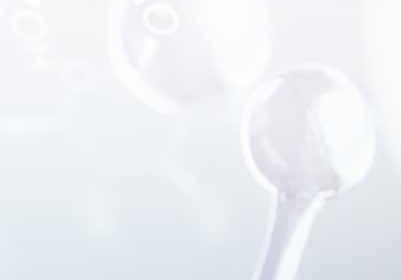

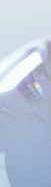


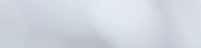
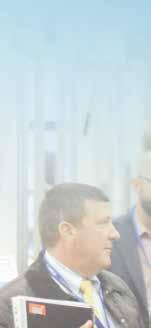
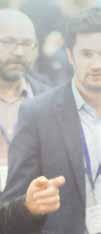
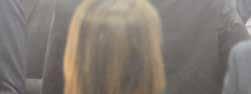
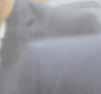
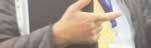
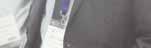
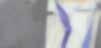
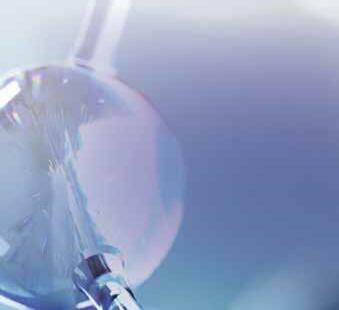

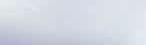


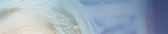
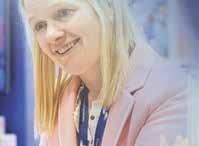
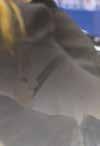
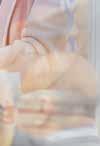




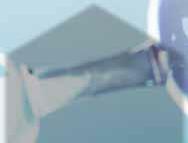
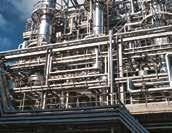
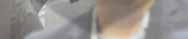
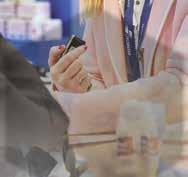
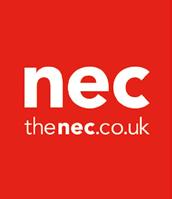




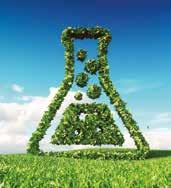
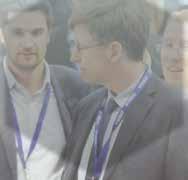




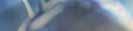
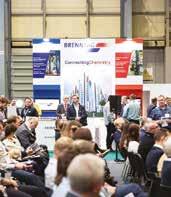

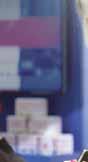


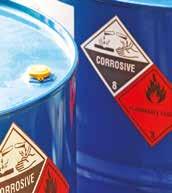
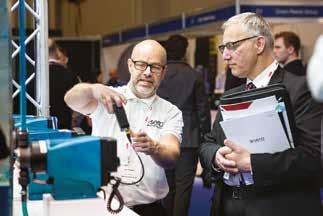



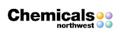

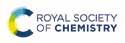

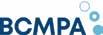


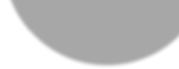

costs of energy in Europe, and uncertainty on supply of natural gas from Russia, are making BASF consider expanding involvement in China. BASF is investing $10bn in Zhangjiang in southern China and has no alternative to expansion in China – the world’s largest chemical market – if it wants to remain the world’s No.1 chemical company.
Across all sectors of industry – but chemicals in particular – supply chain strategy evolved from ‘just-intime’ to ‘just-in-case’ in the 2020s.
In a relatively short space of time, chemicals procurement progressed from ordering products and feedstock to meet customer demand to stockpiling surplus in case of a large, sudden increase in demand.
That progression typified industry response to several factors impacting value chain integrity in recent years. Negative factors range from the world’s first pandemic in almost a century to an unprecedented Suez Canal incident which prevented passage for 50-plus cargo ships daily. This highlighted logistics vulnerability on the one hand; and on the other hand, the world’s workshop – China – significantly reducing output as per governmental zero-Covid restrictions. Then followed Russia’s (alleged) sabotage of Europe-bound gas output amid customers’ increasing dismay at the Ukraine invasion.
On both the supply and demand side of global chemicals trading, there has been much to contend with.
The issues began to sow seeds of strategy shifts away from China as a supply source. Concepts such as on-shoring and near-shoring were raised in boardrooms across the globe: bringing operations and supplies closer to home; dual and multiple sourcing tactics; and regionalised supply chains. That new thinking was fast reflected in financial markets with Chinese shares in Hong Kong and New York losing $21trn in a year. Investment groups grew wary of China’s increased regulation and slowing growth.
Many companies, however, have worked for decades to establish themselves in China and are still expanding, hoping the present slowdown is temporary. BASF has invested time and treasure in building its manufacturing base in China. Now, increasing
But still, a live audience at the 2022 World Economic Forum Annual Meeting in Davos, Switzerland – entitled History at a Turning Point: Government Policies and Business Strategies – indicated overwhelmingly that globalisation was retreating, not advancing.
Then energy issues hit the headlines hard. Since then, chemical industry conversations – as in the wider economic arena – are increasingly focused on natural gas price hikes, the RussoUkraine war impacts, the Chinese economy’s sustained down-trending, and how to survive in markets flooded with Asian and Chinese imports. Whilst global buyers and traders perhaps envisioned a new trading table as China Plus One, circumstance suddenly made the country’s cheap surpluses irresistible again.
Procurement leaders and purchasers are asking, ‘how will Opec+ oil production cuts play out?’ and ‘how deep might a global recession penetrate?’ They want to hear that plants key to their chemical value chains can continue to run. But already, closures have been announced by Italian-headquartered Polynt, force majeure cover is set for Germanyheadquartered Covestro’s chlorine, caustic soda and hydrochloric output and there are production halts at Polish producer Grupa Azoty’s caprolactam and Nylon 6 plants.
Even before Q4, the German Chemical Industry Association said more than one in three North Rhine-Westphalia-located producers had cut back production, with 13% offshoring operations. Over half of the companies surveyed had reduced planned investments for the coming year.
Largely, industry contacts say that a chemical supply buyer’s market exists today – with epoxy resin purchasers claiming discounts of up to 10% for October – and discounts available elsewhere in the chemicals value chain. But nuance around exactly who is setting the market becomes immaterial if plants shut – or scale down – as energy costs make operation economically unviable.
Meanwhile, a fall in the cost of shipping from last year’s highs of $15,000 per
container has boosted the attractiveness of Asian imports. This year’s average freight cost for a 40ft container from China to Europe is $7,402 according to maritime and shipping industry consultancy Drewry. While still double the five-year average, the reduction could be just enough to render the country’s chemicals cost effective to European buyers. And since the port issues which triggered gridlock at Hamburg – and problems at other European ports – appear to have eased as October progressed, another significant obstacle to an import strategy has been removed too.
Not only did Europe’s energy crisis create opportunity for Chinese and Northeast Asian sellers to undercut European domestic suppliers, the Russo-Ukraine war disrupted many markets, including PVC and unsaturated polyester resin (UPR).
With Russian-origin raw material subject to European sanctions, Tecnon OrbiChem consultants reported whispers of cheaper materials and end products reaching Europe via Turkey. With Russian-origin PVC helping to meet Turkey’s domestic needs, competitively priced Turkish-made PVC was being exported to Europe. Similarly, raw material for UPR production was coming from Russia to Turkey before sale to European buyers in the form of end product.
The issue of security of supply has also not gone away. Many buyers are exploring new relationships with US producers for 2023. Supply from here has its attractions – it’s assessed to be more reliable than Asia, which has a tendency to disappear whenever demand in China picks up, and to be not as expensive as European produced material. But discussions here too have quickly dried up as volume commitments remain ever elusive.
All markets agree there is one known unknown – demand for 2023 remains unclear. Buyers face the following conundrum: Pay almost double for secure domestic supply; or increase their exposure to a cheap Asian spot market and risk being subjected to violent swings in supply and pricing next year.
Buyers have already been warned that if they turn their backs on their domestic suppliers, they will be heavily penalised if they come back looking for help during a future supply crunch – a real possibility as run rates continue to be lowered. Suppliers and buyers may have to come to an agreement that will allow a greater degree of flexibility, but this will be limited as plant production cannot quickly adapt to market peaks and troughs.
Collaboration is key to scaling up low carbon hydrogen output
Maersk: accelerating the transition from fossil fuel follower to green industry leader
UK’s hydrogen powerhouse leads the way to clean growth for process industries
www.chemicalindustryjournal.co.uk
4-5 Contents
14-15
Sustainability underpins A.P. Møller-Maersk’s pledge to be the responsible logistics partner of choice for the chemical industry. Global Vertical Head of Chemicals, Patrick Hore, explains how the end-to-end international freight services partner is leading by example.
22-25
NEPIC recently hosted a Clean Growth Conference about decarbonisation opportunities and challenges for local process industries. Chris Holt, clean growth manager, talks to Chemical Industry Journal about how ‘super hub’ status could shape the future for its 320 member companies.
30-40
Bruno Roche, Global Head of Energy Transition, ABB Process Automation, Energy Industries, explains how ongoing technological innovation and collaboration can make a world of difference in scaling up green hydrogen production to decarbonise industry.
Lithium-ion batteries (LIBs) are at the forefront of energy storage solutions thanks to their high storage capacity, superior energy density, and relatively low cost.
Thermal storage is the key to powering industrial processes in a sustainable, reliable, and affordable way, says Christian Thiel, CEO, ENERGYNEST.
42-43
The ‘holy grail of catalysis’ — turning methane into methanol under ambient conditions using light.
Taking the reins of an established, successful, family-owned British manufacturing company is not for the fainthearted.
Following secondary school was a trip to university to work on my business degree before returning to the hustle and bustle of manufacturing.
As you would expect, my daily focus is working on the business and taking the lead role in our ongoing tier-one product development program.
NPI and NPD are my professional nourishment, especially when working with the petrochemical and industrial chemical industries, because the specifications are exacting with the slimmest of tolerances. The specifications often include temperature control, insulation, agitators, PH control, and intricate fluid distribution rates with tank integrity and security front and centre.
Professionally, I thrive on the demands of Tuffa’s bespoke work.
Southern EditorKaren Southern karen.southern@distinctivegroup.co.uk
Distinctive Media Group Ltd, 3rd Floor, Tru Knit House, 9-11 Carliol Square, Newcastle, NE1 6UF Tel: 0191 580 5990 distinctivegroup.co.uk
Distinctive Media Group Ltd, 3rd Floor, Tru Knit House, 9-11 Carliol Square, Newcastle, NE1 6UF Tel: 0191 5805990
Business Development Manager email: david.perratt@distinctivegroup.co.uk Tel: 0191 5805471 distinctivegroup.co.uk
LAUDA – Empowering Excellence For A Better Future As Experts In Thermal Control And Measurement Providing Innovative Solutions For Thermal Process Control, Chilled Water Applications, Water Baths, Freezers, Incubators, Shakers, Stills, Tensiometers, Viscometers And Contact Angle Measurement.
LAUDA continues to provide an expanding range of feature-rich, future proof solutions with energy efficiency and connectivity front of mind, serving a diverse range of industries including chemical, pharmaceutical, biotechnology, energy, composites, automotive, aerospace food & beverage, brewing, digital printing, laser and beyond.
Specific to the needs of the Chemical industry LAUDA has a proven set of solutions applicable to small scale, bench scale and pilot/full production stages of the product development process. Our process circulators and chillers are frequently coupled to multi-use, single-use, and microreactors, condenser coils, rotary evaporators, and cooling of a diverse range of analytical instruments such as mass spectrometers. Additionally, our powerful range of water chillers, rated for indoor or outdoor use, are frequently used to provide cooling for entire laboratory cooling circuits, to counter the rising costs of water-to-waste.
LAUDA’s new range of water chillers has been designed not only to comply with the new Eco-design directive, but to surpass it through the innovative use of variable speed modules that automatically reduce their duty cycle in line with the cooling demand hence reducing energy consumption and running costs, giving a tangible return on investment for the user, whilst ensuring full compliance with the latest regulations on refrigerant (fluorinated) gases.
Further portfolio expansion delivers the new LAUDA ‘Versafreeze’ ultra-freezers, (deep-freeze storage down to -85°), and higher power ‘Integral’ process circulators, (process control from -90 to 320°C with >25kW of cooling @20°C), with pressure overlay options to increase the working range of water / glycol up to 140°C.
Furthermore, for applications requiring customised
solutions tailored to individual requirements, we offer a made-to-measure design service using a long-established and highly skilled team. Project engineering is a core competence of LAUDA and using the modular engineering approach we can design and scale a system specifically matched to the application needs.
With the capability to provide accurate heating and cooling in the range -150 to +550 °C using a variety of proven modules including heat transfer systems, process cooling systems, secondary circuit systems, fired heaters and molten salt plants, we are able to provide unique, costeffective solutions unparalleled by others.
Beyond temperature control, LAUDA has a well-established suite of solutions for measuring viscosity and surface/ interfacial tension aimed at the development of polymers, oils, and surfactants.
In order to remain connected the new ‘LAUDA.LIVE’ digital platform enables the user to achieve fleet management of their specific devices, but also provides the option for remote diagnostics support directly from LAUDA via trained personnel, maximising uptime of the equipment and process.
We look forward to hearing from you.
Contact details:
T: +44 (0)1780 243118
E: info@lauda-technology.co.uk www.lauda-technology.co.uk www.linkedin.com/company/lauda-technology-ltd www.facebook.com/LAUDA.UK/ https://twitter.com/lauda_uk
Queen Mary scientists have created a new type of nanomembrane that presents a less energy intensive way to fractionate hydrocarbons from crude oil.
The global production of crude oil is currently around 80 million barrels per day. Hydrocarbons extracted from crude oil are the main ingredients for manufacturing fossil fuels, plastics, and polymers. The process by which they are extracted is extremely energy intensive.
Most refineries process crude oil using atmospheric and vacuum distillation, in which crude oil is heated to separate compounds according to their boiling points. Typical refineries process 100,000-250,000 barrels/day – there are some processing over 1 million. The maximum temperature for the distillation varies based on the quality of the crude, but the distillation temperatures can exceed 500 °C. This process consumes 1100 terawatt-hours per year – nearly 1% of global energy use.*
Membrane technology that can separate the molecules in crude oil by their different sizes and classes could be a far more energy efficient process, consuming 90% less energy than distillation columns. Exceptionally thin nanomembranes have proved successful for extracting fresh water from sea water by rejecting the salt while allowing the water to permeate through reverse osmosis (RO) process. The researchers sought to separate hydrocarbons from crude oil by a parallel method.
This requires nanomembranes to be hydrophobic, which can provide high affinity and rapid pathways for processing hydrocarbons. However, conventional nanomembranes used for RO are hydrophilic in nature and exhibit limited permeance of hydrocarbon liquids, remaining too low for industrial crude separation.
A team led by Professor Andrew Livingston at Queen Mary University of London used multiblock oligomer amines to create hydrophobic polyamide nanofilms that provide100
times faster permeance than that of hydrophilic nanofilms.
By reducing the membrane thickness to approximately 10 nanometers, they achieved permeance one order of magnitude higher than the current state-of-the-art hydrophobic membranes, with a comparable selectivity in fractionation of real crude oil. As a result, the membranes developed by the team could markedly reduce the energy consumption of processing crude oil. The analysis of the fractionation was performed by ExxonMobil in a laboratory in the United States.
Andrew Livingston, Professor of Chemical Engineering at Queen Mary University of London, said: ‘A vast amount of energy is consumed in industry separating molecules. The aim of our research is to provide low energy alternatives to these processes. Due to the innovations in the chemistry we used to make these membranes, we can achieve molecular architectures that achieve exquisite separations, and provide less resource intensive techniques for the separation of molecules.’
Study co-corresponding author Dr Zhiwei Jiang, Research Associate at Queen Mary University of London, said ‘Thinner is better - the liquid passes through the membranes much more quickly, rapidly speeding up the process, and therefore reducing the plant footprint while processing same quantity of liquids’.
This work was funded by ExxonMobil; the European Research Council; King Abdullah University of Science and Technology; and the Engineering and Physical Sciences Research Council.
Paper: ‘Hydrophobic polyamide nanofilms provide rapid transport for crude oil separation’, in Science.
Authors: Siyah Li, Ruijiao Dong, Valentina-Elena Musteata, Jinoon Kim, Neel D. Rangnekar, J.R. Johnson, Bennett D. Marshall, Stefan Chisca, Jia Xu, Scott Hoy, Benjamin A. McCool, Suzana P. Nunes, Zhiwei Jiang, Andrew G. Livingston.
unmet recently, this time due to shortages in stocks of chlorphenamine maleate.
Current trade tensions have only exacerbated the issue. Raw materials and active pharmaceutical ingredients sourced from countries like China can be caught in log jams due to international disputes. Meanwhile, some believe that Brexit has created importation complexity, significantly slowing down the entry of externally sourced drugs.
In some cases, pharma manufacturing sites have had to be closed for periods of time due to non-compliance with regulatory requirements. This was recently seen in the US when Abbott Laboratories shut down its Michigan plant in February. Unsanitary, non-compliant conditions had led to the contamination of Abbott’s baby formula, worsening national shortages of the product. These business interruptions can have substantial and long-lasting downstream effects.
Inevitably, questions of profitability can also come into play. Pharmaceutical companies often prioritise patent protected drugs, where profit margins are high, over drugs with generic competition, where profit margins are much lower. This does little to help tackle shortages of non-patented painkillers, blood pressure pills, and antidepressants.
performance, says Allen Jacques, Industry Thought Leader at Kinaxis.
The pharmaceutical industry fared relatively well through the pandemic, with few manufacturing sites being closed due to infections. It may come as some surprise, then, that the sector has recently hit rockier ground. A supply chain shortage has come to light, leaving many patients struggling to access pain relief, oncology medication, antihistamines, hormone replacement therapy, anticlotting agents, and other important drugs.
The ramifications of this supply chain issue could be severe. Already, over half (54%) of UK pharmacists surveyed fear that patients have been put at risk in the past six months due to shortages. With the government now urging hospitals to ration stocks of certain drugs, action must be taken to minimise the impact on end consumers needing medicines. However, the picture is not all bleak. The pharmaceutical industry is robust enough to heal its supply chains – if it leverages the right tools. By using technology to improve supply chain visibility and transparency, companies can plan for volatility and identify potential disruption before it occurs, thereby restoring consumer wellbeing and trust.
Supply chain shortages have been a recurring problem over recent months, leaving very few industries unscathed. But for pharma, a number of factors have combined to create a unique challenge. Firstly, demand for hormone replacement therapy has doubled over the last five years – largely due to increased awareness of the menopause – while capacity has failed to keep up. Seasonal demand for certain hay fever medications was similarly left
Of course, some factors – like Brexit and geopolitical trade tensions – are outside of the pharmaceutical industry’s control. But the time has come for companies to focus on what they can control – and they can do this by bolstering the resiliency of their supply chains. Technological solutions have now come to the fore as key enablers of supply chain performance and agility.
The pharma supply chains that are in the best current shape are those that can see and assess events quickly and drive actions to mitigate any ensuing disruption. This involves having consistent visibility and transparency, not only internally but also into suppliers, contract manufacturers, and downstream distribution. While this may initially sound complex, innovations in technology mean that companies can now work from a single platform to intuitively manage, link, align, share, and collaborate with data insights across the supply chain network.
Having this capability allows companies to respond much more quickly to potential disruptions in the pharmaceutical supply chain. For example, the visibility provided by data analytics will help the industry to anticipate and pre-empt changes in consumer demand, so that a targeted, timely response can be put into motion. Technology can also facilitate better planning for factors such as manufacturing problems, late supply of raw materials and components, and compliance issues.
Everybody benefits from greater supply chain visibility, transparency, and resilience. For pharmaceutical companies, the agility to make fast, confident decisions across the entire supply chain will undoubtedly drive business growth and help to protect revenues. But even more importantly, it ensures that end consumers can get the medicines they need, exactly when they need them. With technology, the pharma industry can futureproof its supply chains to better serve the needs of companies, healthcare providers, and the public at large.
“The time has come for companies to focus on what they can control”
Allen Jacques Industry Thought Leader at Kinaxis
Drug molecules and biofuels can be made to order by living cell factories, where biological enzymes do the job. Now researchers at Chalmers University of Technology have developed a computer model that can predict how fast enzymes work, making it possible to find the most efficient living factories, as well as to study difficult diseases.
Enzymes are proteins found in all living cells. Their job is to act as catalysts that increase the rate of specific chemical reactions that take place in the cells. The enzymes thus play a crucial role in making life on earth work and can be compared to nature’s small factories. They are also used in detergents, and to manufacture, among other things, sweeteners, dyes and medicines. The potential uses are almost endless but are hindered by the fact that it is expensive and time-consuming to study the enzymes.
“To study every natural enzyme with experiments in a laboratory would be impossible, they are simply too many. But with our algorithm, we can predict which enzymes are most promising just by looking at the sequence of amino acids they are made up of,” says Eduard Kerkhoven, researcher in systems biology at Chalmers University of Technology and the study’s lead author.
The enzyme turnover number or kcat value, describes how fast and efficient an enzyme works and is essential for understanding a cell’s metabolism. In the new study, Chalmers researchers have developed a computer model that can quickly calculate the kcat value. The only information needed is the order of the amino acids that build up the enzyme - something that is often widely available in open databases. After the model makes a first selection, only the most promising enzymes need to be tested in the lab.
Given the number of naturally occurring enzymes, the researchers believe that the new calculation model may be of great importance.
“We see many possible biotechnological applications. As an example, biofuels can be produced when enzymes break down biomass in a sustainable manufacturing process. The algorithm can also be used to study diseases in the metabolism, where mutations can lead to defects in how enzymes in the human body work”, says Eduard Kerkhoven.
More possible applications are more efficient production of products made from natural organisms, as opposed to industrial processes. Penicillin extracted from a mould is one such example, as well as the cancer drug taxol from yew and the sweetener stevia. They are typically produced in low amounts by natural organisms.
“The development and manufacture of new natural products can be greatly helped by knowledge of which enzymes can be used”, says Eduard Kerkhoven.
The researchers tested their model by simulating metabolism in more than 300 types of
When compared with measured, pre-existing knowledge, the researchers
predicted kcat values could accurately simulate metabolism. The image
Saccharomyces cerevisiae
The calculation model can also point out the changes in kcat value that occur if enzymes mutate and identify unwanted amino acids that can have a major impact on an enzyme’s efficiency. The model can also predict whether the enzymes produce more than one “product”.
“We can reveal if the enzymes have any ‘moonlighting’ activities and produce metabolites that are not desirable. It is useful in industries where you often want to manufacture a single pure product.”
The researchers tested their model by using 3 million kcat values to simulate metabolism in more than 300 types of yeasts. They created computer models of how fast the yeasts could grow or produce certain products, like ethanol. When compared with measured, pre-existing knowledge, the researchers concluded that models with predicted kcat values could accurately simulate metabolism.
The study Deep learning based kcat prediction enables improved enzyme constrained model reconstruction has been published in Nature Catalysis. The authors are Feiran Li, Le Yuan, Hongzhong Lu, Gang Li, Yu Chen, Martin Engqvist, Eduard Kerkhoven and Jens Nielsen. The researchers are active at Chalmers University of Technology.
“To study every natural enzyme with experiments in a laboratory would be impossible, they are simply too many. But with our algorithm, we can predict which enzymes are most promising just by looking at the sequence of amino acids they are made up of.”
The past two years have been a combination of bizarre, exciting, challenging and professionally nourishing at Tuffa HQ.
Historically our business success has been built around turnkey storage and distribution solutions. Still, over the past 24 months or so, we saw a significant shift, especially where the demands of the chemical industry are concerned.
We are a British manufacturer with a proud history and culture, working from a world-class ISO9001 FPC factory with proven production control systems guaranteeing Quality Control, lead times and compliance.
As you would expect, my daily focus is working on the business and taking the lead role in our ongoing tier-one product development program.
NPI and NPD provide my professional nourishment, especially when working with the petrochemical and industrial chemical industries because of their unique applications and challenges. They demand well-thought-out, well-planned, and well-executed engineered solutions. The specifications often include temperature control, insulation, agitators, PH control, and intricate fluid distribution with tank integrity and security front and centre.
Our world is going through a significant shift, with the status quo no longer an acceptable option. We are on board with this shift and are now looking at the benefits of hydrogen storage and distribution, carbon capture and industrial filtration, to name just a few.
My colleagues and I attended the Bremen hydrogen and carbon capture exhibition in October. It was inspiring to see so many great and unique approaches to fundamentally the same problems. Hydrogen, as you know, needs to be stored under tremendous pressure to be functional, and that alone requires significant design effort and an understanding of the demands placed on any storage vessel.
It was great to speak to so many forward-thinking, intelligent people from a broad spectrum of companies vying to provide the best products, services, and efficient means to resolve a global and growing problem.
We must acknowledge that technology will play a fundamental role in rescuing our planet. Still, we should keep in mind proven technology, systems, and processes. An example would be the differing approaches between mainland Europe being earlier adopters of B100 fuel rather than the UK’s continued HVO and B20 biofuel approach.
France, in particular, appears to be adopting B100, pure crop oil such as rapeseed, rather than HVO, which refines a waste oil product. The decision to adopt the pure crop route is a little surprising, especially as you consider the concerns around food production not meeting global demand.
According to the GLEC framework, HVO offers around a 64 per cent reduction in emissions. Still, Neste, a company that appears to provide the majority of HVO in Europe, and Prema Energy in the UK can achieve up to 90% emissions reduction compared to fossil diesel with their HVO.
According to a report by the well-respected Ecoinvent Association, CFRP technology is an option for several industries and OEMs. Carbon fibre offers the highest tensile strength with a low coefficient of thermal expansion and EMI shielding, making it robust and fit for its purpose for high-pressure applications. CFRP is a technology we continually investigate and will almost certainly become an inherent factor in our bespoke activity.
James Shenton managing Director, tuffa uk ltdBespoke solutions, an overly abused term to give hubris to the smallest of projects, now represent a significant part of our business in the steel and the large rotomoulded landscapes with storage capacities as high as 100,000 litres. More and more of our bespoke work utilises our seamless rotomoulded plastics because of their designs’ inherent quality and integrity. Factor in the tier-one ancillaries, long-life engineering materials and security; you can see why the rotomoulded option makes sense for many of our customers.
Specifications, as you will appreciate better than most demand that we manufacture precision storage & distribution systems. Our bespoke solutions can incorporate temperature control & agitation with complex control and monitoring systems designed to integrate seamlessly with your people, project, plant & equipment, factoring in its application, environment and, importantly, your budget.
We have a unique and collaborative approach to the work we proudly do within the petrochemical sector. We offer all the design and modelling in-house, removing previous points of failure and unforeseen design errors before manufacturing and reducing lead times significantly. The time savings notwithstanding, our design approach allows us to work with the specialist customer rather than for them.
An in-house project manager is assigned to work with you through every stage of the process, gathering all the intelligence and a granular understanding of the project’s purpose.
With this information, we build a project plan, carefully selecting best-in-class materials and supply chains, giving an entire audit trail and the most efficient manufacturing plan. We produce seamless rotomoulded vessels with bestin-class polymers, tier-one ancillaries, and a concept-tocompletion strategy.
With the skills, technology, and scientific approach we enjoy in the UK, we can achieve great things together. I look forward to working with you soon. tuffa.co.uk
customers who are either embarking on - or have reached a critical stage - of their own decarbonisation journeys. Currently, the global transport and logistics industry produces approximately 3.5 billion tonnes of Greenhouse Gas (GHG) emissions per year. Maersk has been very transparent about its own contribution to the issue, with a share of around 1% of the total transport and logistics emissions recorded.
With Maersk’s ambitious Environmental, Social, and Governance (ESG) goals feeding directly into their end-toend (E2E) integrator strategy, the company already offers several innovative solutions to support its customers with emissions insights and ways to decarbonise their supply chains (Scope 3), from low emissions shipping solutions such as Maersk ECO Delivery to electric trucks and low emission warehouses.
Patrick Hore Global Vertical Head of ChemicalS for A.P. Møller-Maersk © Peter C. Harry/MaerskAdditionally, sustainable aviation fuels will power 30% of Maersk’s air freight by 2030, and orders have been placed for 19 dual-fuel container ships capable of running on green methanol.
The first of these green methanol compatible vessels is due to launch on Scandinavian routes as early as next year. Once all 19 ships are operating on international trade routes, an estimated 2.3 million metric tonnes of CO2 emissions will be saved annually.
Sustainability underpins A.P. Møller-Maersk’s pledge to be the responsible logistics partner of choice for the chemical industry. Global Vertical Head of Chemicals, Patrick Hore, explains how the end-to-end international freight services partner is leading by example.
Maersk has pledged to decarbonise its entire business by 2040. This updated commitment coincides with Maersk’s aim to become the end-to-end integrator of container logistics and follows a series of investments to stay at the forefront of sustainable logistics; including new technologies, new fuels, and new vessels.
Global Vertical Head of Chemicals for A.P. Møller-Maersk, Patrick Hore, explains that sustainable partnerships built on collaboration and trust are key to the success of this ambitious mission.
Maersk’s bold transition to environmentally sustainable logistics and supply chain management will cover all areas of operations: from sea and air to rail and road. This transition will offer solid, strength-in-depth support to
Hore elucidates, “Back in 2018, we set up a goal to decarbonise our shipping operations by 2050, an ambitious target at that time. It became very clear early on that while decarbonising ocean freight was key to our strategy, we needed to expand our target to other parts of the business to align with our business strategy and go hand in hand with our positioning as a leading partner in sustainability.
“At the same time, science is telling us that we cannot wait to limit global warming and temperature rise to 1.5 °C and we have seen interest from our customers to join forces in that challenging and yet necessary journey. That’s why our net zero target has been brought forward from 2050 to 2040. We aim to offer 100% green solutions by that date.”
He adds, “We know this will not be an easy target to achieve, and we certainly need close collaboration with customers, suppliers and other actors to make it happen. We really mean business and are very clear about the need to make radical, far-reaching change for the better. We want to be part of the solution, not the problem.
“Maersk has already invested heavily in digitalisation and decarbonisation projects and made big decisions to be at
the head of the discussion. For instance, we completed the order for the dual-fuel vessels when it wasn’t clear if there would be enough ‘green’ fuels available to power them.”
Patrick points out that this investment in new sustainable vessels has helped start addressing the “chicken or the egg” dilemma in the shipping industry. The availability and costs of green fuels is one of the challenges the industry must address to meet its targets. What comes first – the green fuel availability or the capital investments at scale?
He explains, “Our initial investments made fuel suppliers come forward to develop strategic partnerships with Maersk. They saw it as good for their industry and good for ours too, so it’s been a win-win all-round.”
“It made a real statement to the market. If I use the analogy of looking in our rear-view mirror, we are seeing other carriers and suppliers coming in behind us in a solid show of support, which is fantastic.
“That’s just one example of the partnerships we are seeking to build. We are very open to collaboration and co-innovation, and there’s already been a hugely positive response from both customers and suppliers.”
Even ongoing economic turmoil hasn’t tempered Maersk’s appetite for change. Hore explains, “We know our customers have conflicting priorities, but in our experience, it hasn’t changed their approach to sustainability.
“If anything, there is an increased sense of urgency. Decarbonisation targets aren’t being ‘grandfathered’ in. They are real and they need to be achieved. Some of our customers are also linked into their origin country’s national
targets and need to demonstrate how they can achieve those too.”
To date, the chemical industry has primarily focused on reducing Scope 1 and 2 emissions – those that are directly controlled by the company itself, such as production and operation emissions. Looking forward, it is clear that the industry is shifting focus to also include Scope 3 emissions (i.e. company supply chains) and that involves supply chain management. Maersk has been honing its offerings so that the company can be integral to the reduction of Scope 3 emissions for their partners.
Hore continues, “We can share our solutions with customers approaching Scope 3, while those already working on these targets have possibly reached the stage where partnerships are needed to help them reach the next level.
“Very difficult issues must be tackled, and we are acutely aware that neither we, nor our customers, can do this alone.
“By working together, we can identify links in the supply chain which fall short of decarbonisation goals. For instance, Maersk has invested in over 400 electric trucks in North America, but the current charging infrastructure is limited. So, we are looking at ways to make best use of biofuels and short shuttle journeys, for example.
“Maersk will continue to invest in green solutions and invite our partners in the chemical industry to collaborate and coinnovate to achieve these common goals.”
To start achieving your supply chain management sustainability goals with Maersk, email Patrick Hore at patrick.hore@maersk.com.
“Our initial investments made fuel suppliers cOme forward to develop strategic partnerships with Maersk. They saw it as good for their industry and good for ours too, so it’s been a win-win all-round.”
The chemical industry faces many major and complex challenges as it moves towards a sustainable future. Reducing carbon emissions necessitates a balance between investment and access to reliable, validated data; all while maintaining healthy profit margins.
This is where end-to-end integrated logistics partner A.P. Møller-Maersk’s sustainable solutions can help.
Cutting your carbon footprint can only be achieved by making informed decisions. That is why Maersk has collaborated with one of their major customers, Syngenta, to create their Emissions Dashboard, a powerful tool to track and measure your company’s supply chain emissions.
This one-stop-shop consolidates all of your company’s emissions data and offers proactive solutions to help optimise your operations.
Patrick Hore, Global Vertical Head of Chemicals at Maersk, explains, “We have taken the lead in democratising solutions like the Dashboard for the benefit of all our customers, with immeasurable help from Syngenta… “Together we created Emissions Dashboard to calculate and measure all emissions across all modes of transport and carrier on the end-to-end journey. It’s a simple, transparent process providing accurate, reliable data which can then be used to set targets and in formal reporting.”
“The tool can be utilised in several ways. For example, some companies may wish to analyse their supply chain as a whole, while others may choose to measure only discrete parts, allowing for in-depth visibility wherever it is needed.
“Aligned with the leading industry methodology of the Global Logistics Emissions Council (GLEC)1, the data will allow companies to make informed decisions about their supply chain.”
Hore illustrates, “The data can then be used to take decisive action. For example, could your company move its shipping cargo while emitting less CO2? Could an order be sourced from a closer warehouse? Could air freight switch to a sea/ air solution, or travel by ocean only? Is it possible to swap a diesel truck for an intermodal train?
“As a digital platform solution, it allows informed decisions to be made quickly, efficiently and very effectively.”
Ai May Ong, Global Logistics Capacity Manager for Syngenta, sums up the Emissions Dashboard collaboration perfectly. “Maersk and Syngenta have a joint vision to significantly reduce our carbon footprint for transport/ logistics.
“Maersk’s new Emissions Dashboard is a key enabler towards that success and represents a step in the right direction. We know that to succeed, we will need highquality emissions data.
“The clear visuals and insights provided by Emissions Dashboard offer an accurate picture of our emissions, guide our decision-making, and help us identify the most impactful changes we can make. Our collaboration with Maersk makes a difference and moves us towards a more sustainable future, together.”
Maersk ECO Delivery offers a highly cost-effective solution to cut carbon emissions in your ocean logistics. This innovative product replaces fossil fuels with green fuels, while also measuring carbon emissions savings according to GLEC methodologies.
Hore explains: “Maersk ECO Delivery offers immediate emissions reductions in our customers’ supply chains. That is because green fuels, as opposed to fossil fuels, are injected into the vessel network moving the cargo. Compared to carbon offsetting, this offers faster carbon reduction results.”
“Maersk then issues a certificate which can be used in company reports to verify that the shipment meets regulatory, market and social requirements. It shows how much green fuel was used, FFEs shipped, and most importantly how many tonnes of CO2 emissions have been saved by your company in a year.”
Maersk ECO Delivery has many advantages:
It offers immediate reductions in carbon emissions, delivering green fuels directly to Maersk’s Ocean network.
Delivery is easy and flexible. There is no commitment to a long-term investment, and carbon reductions can be applied to specific geographies and products to align properly with your sustainability strategy. ECO -Delivery can simply be added to your contract, providing complete transparency of all costs.
Credibility for your carbon-cutting initiative is assured through adherence to GLEC methodologies, using ISCC2 certified fuels and feedstocks with proof of sustainability (POS).
Calculations are based on Clean Cargo methodology, with independent audits carried out by PWC on emission savings according to ISAE 3410.
Find out how Maersk can help your company thrive and grow in a future built on green logistics at Maersk.com/sustainability.
1 Global Logistics Emissions Council (GLEC) is a universal method developed for calculating logistics emissions across all transport mediums from road, rail, air and sea to inland waterways and transshipment centres.
2 The ISCC (International Sustainability and Carbon Certification) system is for all sustainable raw materials and markets. ICSS ensures the entire supply chain from raw material to end product is certified and traceable through proof of sustainability documentation.
Having brought forward its climate ambitions by 10 years, Maersk has made a number of industryleading commitments.
Maersk aims to be net zero across their business and value by 2040 with 100% green solutions for customers.
Maersk has set a new 2030 target to align with a Science Based Targets initiative (SBTi) 1.5C pathway.
By 2030, Maersk also aims to offer customers:
• 25% of ocean cargo transported with green fuels
• 90% green operations for contract logistics and cold chain
• At least 30% of air cargo transported with sustainable aviation fuels (SAF).
Maersk knows these targets won’t be easy to achieve, but believe they are ‘doable’ because, since setting the first target in 2018, Maersk has consistently found that green solutions are available. Maersk acknowledges that no one can do it alone, but together much more can be achieved! Maersk welcomes long term partnerships with customers to co-create and drive the sustainability transformation of logistics at scale.
Maersk has also taken a major step in aligning their finance strategy with their decarbonisation strategy through a Green Finance Framework, which has attracted a high level of interest from investors.
See Maersk’s 2021 Sustainability Report for full details.
The Novaflex Group is a market leader through excellence in product innovation and a commitment to continuous advancement in hose and connector solutions.
Novaflex offer a wide range of ducting products for air and dust control, light material handling and wet or dry fume control, and many other applications.
Novaflex ducting is lightweight, flexible and economical.
Novaflex composite hoses are manufactured to meet British and European standards BS5842, BS3492, and BS EN 13765.
Novaflex composite hoses and assemblies hold Lloyd’s Register Certified Type Approval for BS EN 13765:2018.
Novaflex have manufactured composite hoses in the UK since 2008 and supply thermoplastic composite hoses in diameters ranging from 1” to 12” in lengths of up to 40 metres.
Hoses are made to a wide range of specifications for a wide range of chemical, application, and customer requirements.
The Novaflex rubber hose range includes material handling, chemical, food grade, and mining hoses, as well as a range of expansion joints and connectors. Novaflex rubber hoses are available in a wide range of diameters in EPDM, UHMWP, Teflon, Nitrile, and Viton, for resistance to chemicals, abrasion, heat and corrosive conditions.
Hoses are manufactured in North America and comply with FDA, 3A, USDA, and REACH standards.
Drawing on decades of real world application experience, the NovaFlex® Hi-Flow™ Dry-Release™ ‘HDC®’ Couplings optimise every area of function and design to deliver a truly innovative and reliable safety product.
Safety Breakaway Couplings by Novaflex® provide the highest standard of safety technology to protect personnel, critical assets and the environment.
Fittings are also available in a range of threaded and flanged designs specifically designed to work with our range of Novaflex hoses.
www.novaflex.com
Rollinson, Managing Director of Dachser UK, examines the overarching trends in the global economy and how they may impact on logistics needs in the European chemical industry over the years to come. He recounts how his own organization is responding through its dedicated DACHSER Chem Logistics industry solution.
The megatrends that the world faces today are, of course, complex. They range from a slowing in globalization to changes in the mobility of both labour and goods. It is a truism to say there is nothing more constant than change itself and it is within this environment that more detailed changes must be examined.
The first is very clear, the establishment of new business models through harnessing digital technologies such as artificial intelligence (AI) - the importance of digitalization in the transformation of logistics is growing. A number of logistics companies are now offering integrated digital concepts that are designed to improve productivity—either by automating processes, or by enhancing usability and transparency for customers and employees. Dachser itself is aiming to become a leader in the adoption of digitized solutions.
Big data will make logistics work more efficiently along the entire supply chain. The main advantages of such technologies are that they can support people in the decision-making process and relieve them of routine tasks. Transparency along the supply chain is also improved. Smart, connected sensors collect and transmit data on position, temperature, environmental conditions, and vibration. This is particularly useful when transporting chemicals, many of which require specific conditions. In the future, digitalization will help make it possible to monitor and secure these even better while in transit.
In the UK those in the chemical sector are seeking to utilize digital technology to assist with the other significant trend in the demands of the market – that of sustainability. Industry ambitions to become carbon neutral over the next two decades requires significant changes in energy resourcing. And, although the country leads in the use of renewables, particularly wind power there are still enormous challenges ahead to further diminish reliance on fossil fuel power generation. Suppliers and manufacturers of chemical product will naturally also turn to supply chain partners to achieve these tough goals. Once more logistics operators must turn to digital technology to help create efficiencies and effect the changes required.
Changes to global supply chains have been accelerated by the pandemic and the war in Ukraine. Other factors include the lack of drivers and other qualified personnel as well as digitalization and climate change. It is important to clearly establish that these changes to the supply chains are not fleeting—they are here to stay. The major challenge
facing logistics providers lies in the stability of production networks.
Rapidly evolving customer requirements mean that new business models and sales channels are being created all the time, which in turn alters the supply chains. In the past, logistics was often regarded as a mere “cost factor.” This has changed considerably to the point where logistics has taken a place on the executive board agenda, and the results of these partnerships between companies and their logistics providers are integrated, end-to-end solutions from a single source. This adds a new, forward-thinking dimension to the relationship.
Such end-to-end solutions work only when paired with close-knit, integrated networks. Logistics service suppliers must invest in dovetailing multimodal offerings by expanding their overland transport networks, while also sustainably strengthening air and sea freight options. Efficient network management and intelligent supply chain management also involve capacity demand forecasts that are as accurate as possible. The application of AI and analysis of big data provide the necessary conditions for this.
In addition, logistics companies must ramp up their climate action efforts with the focus shifting more and more toward carbon emissions. For chemical producers, emissions generated by third parties also play a major role. Lowering emissions for the entire product chain requires all partners in the value network – manufacturers, distributors, and logistics providers – to work together.
Climate-friendly logistics brought about through a shift toward low- and zero-emissions technologies will, however, inevitably lead to an increase in transport costs. It is also debatable how close the technology is to making zeroemissions vehicles a viable option for long-haul routes. As the future unfolds, logistics companies and players in the chemical industry will face some major challenges, which will not be overcome by going it alone. It’s the job of logistics providers to understand the many simultaneous processes in their full complexity and to consider every angle when developing their own solutions. A group effort is required to actively shape upcoming changes and megatrends, and the opportunities this approach creates should vastly outweigh the risks and justify disrupting the status quo. dachser.co.uk
The North East is the UK’s leading hydrogen hub, with two major blue hydrogen projects shortlisted for support from the government’s £1bn Infrastructure Fund.
The large-scale projects - both in Tees Valley - are Kellas Midstream’s H2NorthEast development and bp’s H2Teesside, part of The Northern Endurance Partnership’s East Coast Cluster.
They are included in Phase-2 of the Carbon Capture Usage and Storage Cluster (CCUS) Sequencing Process, announced by the Department for Business, Energy & Industrial Strategy.
This means the North East now has considerably more hydrogen projects than anywhere else in the country. It’s the only cluster shortlisted for two blue hydrogen projects,
and is also home to the UK’s largest independently owned hydrogen production plant operated by BOC, along with several ongoing green hydrogen projects.
Philip Aldridge, CEO of The North East of England Process Industry Cluster (NEPIC), praised the news, saying: “The BEIS Phase-2 announcement is excellent news for our region and really cements the North East as the hydrogen hub of the UK and a global ‘Super Place’ for hydrogen.”
“Almost half of the UK’s Carbon Capture Storage (CCS) projects are based in the North East, which demonstrates our commitment to lead on CCUS initiatives.
“Not only will this create thousands of jobs and attract investment across the local landscape, but it’s also a huge step in the future distribution of low-carbon power that will be essential to the long-term sustainability of many businesses throughout the area.”
“Teesside is already the UK ‘super place’ for hydrogen with BOC producing over half of the UK’s total hydrogen.”
NEPIC recently hosted a Clean Growth Conference about decarbonisation opportunities and challenges for local process industries. Chris Holt, clean growth manager, talks to Chemical Industry Journal about how ‘super hub’ status could shape the future for its 320 member companies.
The North East of England Process Industry Cluster is a cluster organisation that represents and supports the process industries in the North East. NEPIC does this by networking its members together to create meaningful partnerships that deliver growth. NEPIC also helps drive forward the transition to Net Zero by collaborating to produce regional decarbonisation roadmaps, facilitating knowledge transfer, and by launching technical projects to construct new sustainable supply chains on Teesside.
Teesside is already the UK ‘super place’ for hydrogen with BOC producing over half of the UK’s total hydrogen. Currently, it is the only industrial cluster within the UK that has a hydrogen pipeline. Teesside is also a highly concentrated cluster, with the main industrial operations taking place within a five-mile radius. Due to the density of energy-intensive industrial assets, existing supporting infrastructure, and a skilled industrial workforce, Teesside is an excellent place for large-scale industrial decarbonisation. This is especially true for blue hydrogen which is akin to outsourced carbon capture, which would likely have limited economic or environmental viability outside of an industrial cluster.
The East Coast Cluster has the Northern Endurance Partnership at its core, which involves the sequestration, transport and storage of carbon dioxide produced by the Teesside and Humberside industrial clusters. Within this, it contains projects for carbon capture with low-carbon power production, blue hydrogen manufacturing and existing industrial assets.
On Teesside, Kellas Midstream and bp’s blue hydrogen projects were shortlisted as part of the BEIS Phase-2 cluster sequencing process, twice as many as any other industrial cluster in the UK. BOC were also successful with their application to convert their existing grey hydrogen plant to
produce blue hydrogen via the East Coast Cluster. Teesside will also be a green hydrogen hub with companies such as bp, EDF Renewables UK and Protium all having projects to manufacture green hydrogen.
Many projects aim to decarbonise existing assets and operations, which will be done as soon as they can connect with the carbon capture infrastructure or access blue hydrogen. A good example of this is the BOC hydrogen plant that is already producing grey hydrogen and will switch to blue hydrogen once the plant is integrated with the carbon capture infrastructure.
Blue hydrogen production will start at the bp and Kellas Midstream sites in 2027, with the ambition for each site to scale to 1 GW at around 2030. The timelines for the green hydrogen sites differ and so do the final planned scales of operation.
For example, the Protium green hydrogen project aims to produce ~70 MW of green hydrogen by 2026, with the first phase of the project taking place in 2025. There is also more flexibility regarding scale, for example the bp HyGreen Teesside could scale to 500 MW in the future. Regarding CCS power projects, the Whitetail Clean Energy project will produce around 350 MW of power and the Net Zero Teesside Power project will produce up to 860 MW of power.
Given the number of different projects it is difficult to accurately estimate the total number of jobs that could be created, the Net Zero Teesside project alone could create 5,500 direct jobs during construction. Sourcing the skilled workforce necessary to deliver large and transformative projects is always a challenge but Teesside is already very well placed in this area due to its already significant industrial operations. NEPIC have also been working to
support the cluster to meet the challenge of skills, most recently via skills surveys to understand the training needs of industry.
I’m very optimistic. Decarbonisation is a massive challenge for industry, but it has proven to be an opportunity to grow industrial operations and create jobs. A multitude of new manufacturing sites have been announced on Teesside over the past year or so including Tees Valley Lithium, Alfanar’s Lighthouse Green Fuels plant, Circular Fuels and Peak Resources. There are also many more sites within the pipeline for Teesside. The need to decarbonise has also helped secure existing industrial assets; for instance, the opportunity to operate the world’s first decarbonised cracker is often cited as the reason that SABIC’s UK operations were secured.
It is an understatement to say that the road to Net Zero will be long, complex, and challenging. It is essential that decarbonisation initiatives maintain strong support from key stakeholders and government to deliver Net Zero. Commercial viability is at the heart of this and utilising economics as a tool to drive forwards Net Zero is the single biggest challenge and opportunity. A decrease in government support for decarbonisation is a substantial risk that would severely reduce the ability of industry to meet this challenge.
For me, the key message was the unprecedented demand to attend from delegates and exhibitors, which highlighted the level of interest there is to take advantage of decarbonisation as an opportunity to achieve Clean Growth. The level of discussion and engagement between talks also showed the interest and willingness to collaborate to achieve this.
nepic.co.uk
Natechs (Natural Hazards Triggering Technological Accidents) refers to accidents initiated by natural causes, including earthquakes, lightning and flooding, all of which have the potential to impact high hazard industrial sites.
Major accidents have the potential for catastrophic consequences to people and the environment as well as business reputation and sustainability. Such natural hazards can both trigger major accidents and weaken safeguards in place to prevent, control and mitigate them. For this reason, the risk posed by Natechs needs careful consideration.
Natural hazards can be broadly categorised as seismic, hydrological and meteorological (e.g. earthquakes, flooding and wind storms respectively) and will have different likelihoods, severities, warning times and consequences. Generally, natural hazards will impact widespread areas. Climate change also plays a role, typically increasing the likelihood and severity of hydrological and meteorological events.
An example of a Natech accident in recent history is the floods that occurred in Central Europe in August 2002. In total, 232 lives were lost and one site, in the Czech Republic, was struck particularly hard. Large volumes of chlorine gas were released from pressurised storage tanks. The flood itself was a one in five hundred year event and as such, the severity was unprecedented, with the hundred year water level of the site being exceeded by 1.3 metres. Whilst it may not be practicable or justified to implement safeguards for events of unprecedented scale and severity, consequences involving the loss of containment of hazardous substances are still possible during lesser events, highlighting the importance of robust safety measures. Since the consequences of Natech events are often severe, just being aware of them is not enough and the duty holders of hazardous sites must be proactive in their approach to understanding, assessing and managing the risk.
Risk reduction and preparedness for natural hazards is something which is often overlooked. There is a requirement under the COMAH Regulations and the Seveso directive for sites to understand their risks from natural hazards, with some other countries having specific laws/ programs regarding the protection of people from earthquakes and/or tsunamis. There is however a shortage
of dedicated methodologies and guidance for assessing and managing Natech risks. In addition, for some natural hazards there is a limitation to the measures which can be implemented, and other measures may be deemed too costly, especially if considering the likelihood of the natural hazard event at the site versus a non-Natech major accident hazard event. Many measures in place to prevent a major accident hazard may not work in a Natech incident, meaning that crediting these barriers needs to be done with caution.
The use of hazard mapping, such as flood maps, may be useful for understanding the current risk, and can include inundation areas in the event of sea level rise and climate change. In New Zealand, GNS Science have provided vulnerability and evacuation maps to the government, authorities and private industry which focus on the possibility of a tsunami. The maps show the areas in the most danger and provide vital information for evacuation planning. These types of maps can also be available for other natural hazards such as volcanoes and can be used to help inform site emergency response plans, as well as the emergency response plans for the local authorities. It should be noted however that in a Natech event, there is a reasonable chance that emergency response teams would not be able to reach the site(s) requiring support. This may be due to damaged access roads, services being overwhelmed by the public, or the services themselves being affected by the hazard. This may reduce the resources available to sites in an emergency and should be considered in response planning.
There is no ‘one size fits all’ when it comes to specific sites and hazards. Therefore, duty holders need to understand the risks posed by Natech events to their specific site and then ensure they are informed of what equipment may be impacted, how, and what to do in the event of a natural hazard. Although there may be a low likelihood, natural hazard events can often be a case of ‘when’ not ‘if’, and so we must be prepared for their eventuality.
Rob Ritchie and Carolyn Nicholls enquiries@ras.ltd.ukOnly when the risk facing an organisation is well understood can it be effectively managed. Key to the successful identification, assessment and management of risk is engagement with the right people, using the right processes at the right time. We believe we are different to many of our competitors and our approach is distinctive, we don’t always walk the well-trodden path but look at each client’s particular risk context and develop a tailored solution, working in partnership with our client.
We work across all aspects of risk, from Quantitative Risk Assessments and Predictive & Consequence modelling, through to the ‘softer’ risks which may affect an organisation’s reputation.
Cogent assured providers –Process Safety Management for Operations (PSMO)
Authorized distributor for Wolters Kluwer – BowTieXP software
Understanding and facilitating the effective management of risk is our core business. Our expertise covers the full range of risk assessment and management services.
E Coli strain MC4100 is known to be poor at forming biofilms. The researchers monitored the biomass and biocatalytic activity of MC4100 and E. Coli strain PHL644 (a good biofilm former) incubated in the presence of the polymers. They found MC4100 matched and even outperformed PHL644.
Birmingham scientists have revealed a new method to increase efficiency in biocatalysis, in a paper published in Materials Horizons.
Biocatalysis uses enzymes, cells or microbes to catalyse chemical reactions, and is used in settings such as the food and chemical industries to make products that are not accessible by chemical synthesis. It can produce pharmaceuticals, fine chemicals, or food ingredients on an industrial scale.
However a major challenge in biocatalysis is that the most commonly used microbes, such as probiotics and nonpathogenic strains of Escherichia coli, are not necessarily good at forming biofilms, the growth promoting ecosystems that form a protective micro-environment around communities of microbes and increase their resilience and so boost productivity.
This problem is normally solved by genetic engineering, but researchers Dr Tim Overton from the university’s School of Chemical Engineering, and Dr Francisco Fernández Trillo from the School of Chemistry*, both of whom are members of the Institute of Microbiology and Infection, set out to create an alternative method to bypass this costly and timeconsuming process.
The researchers identified a library of synthetic polymers and screened them for their ability to induce biofilm formation in E. coli, a bacterium that is one of the most widely studied micro-organisms, and commonly used in biocatalysis.
This screening used a strain of E. coli (MC4100) that is widely used in fundamental science to study genes and proteins and is known to be poor at forming biofilms, and compared it to another E. coli strain PHL644, an isogenic strain obtained through evolution that is a good biofilm former.
This screening revealed the chemistries that are best suited to stimulating biofilm formation. Hydrophobic polymers outperformed mildly cationic polymers, with aromatic and
heteroaromatic derivatives performing much better than the equivalent aliphatic polymers.
The researchers then monitored the biomass and biocatalytic activity of both strains incubated the presence of these polymers, and found that MC4100 matched and even outperformed PHL644.
Further studies examined how the polymers stimulate these profound increases in activity. Here the research indicated that the polymers precipitate in solution, and act as coagulants, stimulating a natural process called flocculation that triggers bacteria to form biofilms.
Dr Fernandez-Trillo said: “We explored a broad chemical space and identified the best performing chemistries and polymers that increase the biocatalytic activity of E. coli, a workhorse in biotechnology. This has resulted in a small library of synthetic polymers that increase biofilm formation when used as simple additives to microbial culture. To the best of our knowledge, currently there are no methods that provide this simplicity and versatility when promoting biofilms for beneficial bacteria.”
“These synthetic polymers may bypass the need to introduce the traits for biofilm formation through gene editing, which is costly, time-consuming, non-reversible and requires a skilled person in microbiology to implement it. We believe this approach has an impact beyond biofilms for biocatalysis. A similar strategy could be employed to identify candidate polymers for other microorganisms such as probiotics or yeasts, and develop new applications in food science, agriculture, bioremediation or health.”
University of Birmingham Enterprise has filed a patent application for the method and polymer additives, and is now seeking commercial partners for licensing.
*Dr Fernandez-Trillo is now at the Universidade da Coruña, Spain.
Polymer-Induced Biofilms for Enhanced Biocatalysis, P. Adoni, A. Romanyuk, T. W. Overton and P. Fernandez-Trillo, Mater. Horiz., 2022, is available at https://doi.org/10.1039/ D2MH00607C
We help businesses get the most from their assets by developing people, plant, and management processes to drive sustainable improvements in safety, environmental protection and productivity.
Find out more about how we can help improve your performance safetyadvisoryeu@slrconsulting.com www.slrconsulting.com
A global leader in environmental and advisory solutions
Hydrogen has a significant role to play in decarbonising hard-to-abate industries as part of efforts to reduce greenhouse gas (GHG) emissions and limit global temperature rises, helping to achieve the goals of global treaties such as the Paris Agreement. When produced through electrolysis powered by renewable energy – known as renewable or ‘green’ hydrogen – it produces only energy and water with zero carbon.
Scaling up production to meet rising demand for renewable energy is perhaps the greatest challenge currently facing the nascent hydrogen industry – and the sector.
Although green, low carbon hydrogen can and will play a vital role in decarbonising industry, there are two big problems: supply volumes are too low and costs are too high. Scaling up hydrogen production inevitably requires significant capital investment (CAPEX), as well as operating costs (OPEX). The electricity costs to run a hydrogen plant are significant. In fact, more than 70% of the total operating costs to make 1kg of hydrogen could come from the electricity costs, used to split the water molecule in the electrolysis process.
To succeed, the world’s industrial operations will likely depend on multi-gigawatt-scale electrolysis plants, and of course the necessary supply of fossil-free electricity, to produce the required quantities of low carbon hydrogen
at an affordable cost. If we are to enable green hydrogen to scale-up to the needed GW levels in line with expected growth, we will need to drive these costs down.
Given that 70 percent of operating costs are spent on the electricity used to split the water into H2 and O2 in the electrolysis process, Energy management will be particularly important. In addition, in the new energy ecosystem, proactive energy balancing performed by energy management systems will be critical in deciding which energy flows and sources to use when, where and at the best price.
Much of what is involved in undertaking this massive scaleup of electrolyzer capacity is uncharted territory – including all the other necessary infrastructure and technology such as the electrical supply for AC-DC conversion, and automation and digitalization to get the highest efficiency in producing green hydrogen at the lowest cost. Companies must collaborate to undertake such large pioneering projects.
Using a combination of automation and control systems, along with expert digitalisation solutions and strategies, efficient power apparatus for motors and pumps, and dedicated sensor portfolio for pressures, temperatures and concentrations enables the whole operation to work at far higher efficiencies than ever before.
It is also vital to recognize that there are safety risks and dangers involved with hydrogen. For any professional company, the safety of its people, equipment and environment is the number one priority. When handling flammable and potentially explosive hydrogen in the presence of electrical equipment, sensing and monitoring flows and leaks, are key areas that must be thoroughly assessed and addressed as part of any scale-up.
Finally, as hydrogen starts to be fed into pipelines, control and monitoring using sensors and leakage detection will be an extremely important aspect of the system, especially since hydrogen is a powerful GHG if it escapes into the atmosphere.1
To fast-track and standardise the production of green hydrogen, an end-to-end templatised approach needs to be adopted to make the design, build and operation of green hydrogen facilities more efficient. As an industry collective, we must join forces and expertise to help customers overcome the challenges associated with green hydrogen production.
To truly achieve low costs – and continuously reduce them over time – the complex scale-up of green hydrogen-based electrical energy systems will require superior project execution. Through early engagement in the design process,
Using
we can maximize the efficiencies. By using simulation to not only simulate the future process (and thereby maximizing efficiencies in design, build and operate), but also this simulation helps later as a benchmark and for training.
In addition, by integrating expert teams, new technologies, agile processes, shared learnings and proven methodologies, we can drive better cost, material and resource efficiencies.
The scale up is clearly starting, and evolving rapidly. Every six months, the number of green hydrolysis projects is doubling. Three years ago, hydrogen pilots were appearing at kilowatt scale; two years ago, the first megawatt (MW) plants arrived; then, last year, tens of MWs. Today, in 2022, plants are already executing at hundreds of MWs and gigawatt (GW)-scale plants on the horizon. Obviously, the market and investment activity is growing, but this is only the beginning of what is needed.
Economically viable green hydrogen is critical in the move towards a low carbon world. It is only through collaboration, Energy management, agile processes and new technology that it will be possible to drive down the cost of green hydrogen production and enable a thriving hydrogen economy - making hydrogen a key part of our world’s low/ no carbon future.
1. Hydrogen ‘twice as powerful a greenhouse gas as previously thought’: UK government study - https://www.rechargenews.com/energy-transition/ hydrogen-twice-as-powerful-a-greenhouse-gas-as-previously-thought-ukgovernment-study/2-1-1200115
a combination of automation and control systems, along with expert digitalisation solutions and strategies, efficient power apparatus for motors and pumps, and dedicated sensor portfolio for pressures, temperatures and concentrations enables the whole operation to work at far higher efficiencies than ever before.
As societies grow and advance, interest in hygiene and cleanliness rises, which also increases the use of detergents. Worldwide consumption of these products has grown exponentially in recent decades in both personal and industrial sectors. The surge of Covid-19 gave a new impulse as well to asepsis and disinfection and offered the detergent industry a leading role in the fight against the pandemic. Undoubtedly, this increased consumption of detergents has an impact on the environment.
The chemical industry has been concerned for more than half a century with producing sustainable and environmentally friendly detergents. This trend has turned into a need in the last decade, with the development of stricter environmental regulations driven by a more sensitive society towards the protection of the natural environment and the aim to fight climate change.
With this goal in mind, researchers in the detergency sector are working to achieve a 100% sustainable detergent which has a neutral impact on the environment and whose production does not lead to CO2 emissions into the atmosphere.
The growing demand for environmentally friendly cleaning products means that environmental certifications are increasingly sought after by manufacturers of household products. In this context, the world’s largest detergent producers have gone a step further in their environmental protection policies and demand increasingly sustainable raw materials.
In order to provide an adequate response to the growing market demand for “zero emission” products, manufacturers of the raw materials used in detergent production have multiplied their R&D efforts in order to obtain increasingly sustainable products. The main product used in the manufacture of detergents is linear alkylbenzene (LAB), which, once sulphonated, is converted into LAS, the surfactant currently used as the main ingredient in most biodegradable detergents.
So far, only one company - Cepsa Química - has succeeded in producing a more environmentally friendly biodegradable LAB. This environmentally improved version of LAB includes vegetable oils in its formula and reduces CO2 emissions by 60% in the product’s life cycle, compared to its counterpart of fossil origin.
And the research continues. In recent years we have managed to significantly reduce the CO2 emissions produced in the manufacture of the new sustainable LAB - called NextLab – while keeping the same attributes as the one currently produced but making it much more environmentally friendly. We are a world leader in the use of Detal technology, which means greater water savings, greater energy efficiency, more safety in the manufacturing process and lower CO2 emissions.
We are developing new formulas to produce a more sustainable LAB in the coming years and to make our commitment, and that of our customers, to achieve a detergent with recycled materials and zero emissions a
reality. This commitment to research is in line with the decarbonisation and the circular economy objectives set by the UN Agenda 2030 for Sustainable Development and the Green Deal set by the EU.
Achieving a zero-emission detergent is a further step in the quest for sustainability in the detergency sector. This search began in the 1960s with the development of a biodegradable formula that would eliminate the severe environmental problems caused by the uncontrolled dumping of nondegradable detergents.
LAS, the most widely used biodegradable surfactant in detergents worldwide, was developed in this context. More than 60% of these products use LAS as a surfactant in their formulations. Its excellent properties, its washing efficiency, as well as its processability and compatibility with other ingredients, make it a very useful element in the washing process both in traditional formats (powder or detergent bars) and in more sophisticated products (single-dose capsules or highly concentrated liquid detergents).
LAS is produced in roughly four stages. The first focuses on obtaining raw material, the linear paraffins (n-paraffins), from kerosene. The second phase is the transformation of the n-paraffins into olefins; the third is the alkylation of benzene through monolefins to produce LAB and, finally, LAB is subjected to a sulphonation process to obtain LAS.
Once a biodegradable detergent has been achieved, the next natural step is the manufacture of a product that is neutral in terms of CO2 emissions into the atmosphere.
With the achievement of a sustainable origin product that, in turn, means lower emissions into the atmosphere, but that retains the same characteristics as the current LAB (in fact, it is the same molecule) a fundamental step has been taken in the sustainability of the detergent sector.
Now the next goal is to achieve a CO2-neutral LAB. A big challenge for the detergency chemical industry. I am optimistic that this will be achieved in a few years´ time.
Eleanor MacIver and Jeremy Webster, partners at IP firm Mewburn Ellis, look at the issues inherent in patenting Green Chemical innovation, and the importance of a clear IP strategy to achieve commercially valuable protection.
Research into and development of Green Chemicals is being carried out in all parts of the chemical industry.
The interest in Green Chemicals provides a wealth of new technologies, know-how and marketing potential. In turn, the sector provides opportunities for businesses in terms of partnering, collaboration and investment. Combine this with emerging regulation, legislation, incentives and powerful public opinion, and it seems certain that Green Chemicals will play a key role in the chemical industry going forward.
As businesses, customers and nations move towards a net zero future, the chemical industry (and chemicals themselves) must become more sustainable for parties to achieve their net-zero aims. With all the valuable innovation in Green Chemicals, it is important to consider how they can be protected and exploited using Intellectual Property (IP).
Having a well-thought-out IP strategy is important for any business. This doesn’t mean lots of patent filings are a must; rather it’s important to think about your plans and how IP can help with them (and equally, or possibly more, importantly how to avoid IP issues that might hinder them). For Green Chemical innovations, all these things are true and more so.
The technology itself is most likely to be protected by patents, although trade secrets may play a role in some cases. Branding will also be important, particular for consumer goods, with designs and trademarks playing a key role in distinguishing Green Chemicals from less sustainable alternatives.
Green Chemical innovations are moving at a relatively fast pace as is the commercial landscape. It is possible to accelerate the patenting process for green technologies in a number of countries (e.g., UK, Australian, Japan, Canada and Brazil) based on its green potential. Acceleration might be commercially valuable by providing a granted patent quickly to facilitate licencing or other deals around the technology.
There’s no exact definition of what the term ‘Green Chemicals’ means but, at least for the purpose of this article, we use it to mean any chemical that is produced in a (more) sustainable manner.
Making chemicals more sustainable can be done in a variety of ways, each way having a unique IP potential
and strategy. For example, the technology making traditional polymers more sustainable requires a different patenting approach to technologies developing alternative materials to replace traditional polymers. The same is true for the technology being developed to make Green Graphene or efforts to make the pharmaceutical industry more sustainable.
Broadly speaking, some Green Chemical innovations can be protected by patents in similar ways to traditional chemical inventions. However, in lots of cases it can be more difficult to capture Green Chemical innovations using traditional patent strategies.
Some Green Chemicals might not match or improve over traditional products in terms of physical characteristics. These physical characteristics (and their improvement) are often used traditionally to demonstrate non obviousness which is required for patentability.
In some such cases, encouraging patent examiners to take a more holistic view of the technology can be key to success. For example, it is helpful to explain at the outset that the invention lies in the balance of properties between the improved sustainability and physical characteristics.
The balance of properties is also often commercially valuable as consumers are keen to see credible sustainability claims for the products they buy and are potentially willing to accommodate some change in physical characteristics.
In other cases, the use of functional definitions in combination with physical features can be employed to effectively protect Green Chemicals by putting us in a better position to persuade a patent office that our patent claims are limited to only those compositions that are effective.
Finally, some Green Chemical innovations might, on paper, seem like obvious modifications compared to known technologies to reach the goal of sustainability.
A relevant example is the switch from fossil fuel derived monomers to the same monomer from bio sources for producing traditional polymers. This might at first sight seem obvious given that bio monomers are now relatively well known. Telling the right story in such cases can be key to success.
For example, it is helpful to explain any difficulties encountered in developing the technology. These “difficulties” – and an explanation as to how they were overcome - can stop an examiner saying the modification is obvious because you have explained that it was not routine to make the change.
In our experience, with the right approach from the outset – especially when grounded in a clear IP strategy - it is possible to provide commercially valuable patent protection for Green Chemical innovations.
More details at mewburn.com.
Lithium-ion batteries (LIBs) are at the forefront of energy storage solutions thanks to their high storage capacity, superior energy density, and relatively low cost. Over the past three decades, demand for LIBs has grown at an astonishing rate, driven by a combination of ground-breaking scientific advances and consumer product power needs. The rapid and accelerating rise of electric vehicles over the past decade is fuelling even greater demand: by 2050, more than 300 million electric vehicles (EVs) are expected to be on the road, massively reducing gas emissions.1
By Simon Nelms Product Marketing ManagerICP-MS,Thermo Fisher ScientificDespite the popularity of LIBs, their development and production face numerous challenges. Most notably, all components of LIBs require rigorous analysis and quality control: this includes lithium salts, electrodes, and electrolytes. Without these thorough checks, safety and quality can be compromised.
Inductively coupled plasma optical emission spectroscopy (ICP-OES) is the gold standard for LIB material analysis, delivering accurate results with fast sample turnaround.
Gas chromatography-mass spectrometry (GC-MS), another powerful technique, enables effective electrolyte composition analysis. When used together, these two highly complementary tools provide a multidimensional approach to support the stringent analysis and quality controls in LIB development. Here we explore how these techniques can improve LIB component examination by delivering detailed analysis of lithium salts and electrolytes.
Lithium is most commonly traded in the form of two salts, Li2CO3 and LiOH, which are used to manufacture the cathode materials in LIBs. These starting lithium salts must be analysed for any elemental impurities, including transition metals, and alkaline and alkaline earth metals. This insight is vital to ensure the performance of the final cathode products, which themselves also need to be analysed to validate their composition and purity.
Two approved standards exist for lithium salt analysis: Chinese Standard GB/T-11064.16-2013, and International Electrotechnical Commission (IEC) 62321. In both these methods, ICP-OES is the suggested technique: not only can it perform multi-elemental analysis in a short time, but it also handles a variety of sample types.
A recent study demonstrating the power of ICP-OES looked at 45 trace elements present in three samples, including two Li2CO3 and one hydrated LiOH salt, with compelling results. The method used had the following advantages:
Fast: sample run time was 144 seconds.
Sensitive: of the 45 elements, 43 had method detection limits well below 1 mg/L.
Robust: After 12 hours continuous measurements, no significant drift or QC failures were found throughout the duration of the experiment.
The internal standard recovery remained within 90-100%, as seen in Figure 1 (opposite).
The results clearly demonstrate the suitability of ICPOES for lithium salt analysis. Not only does it show the high accuracy and sensitivity needed for thorough characterisation, but it is robust enough to withstand the continuous testing demands of the analytical laboratory.
The LIB electrolyte significantly affects the battery’s charging and discharging performance and must also be well understood. Lithium hexafluorophosphate (LiPF6) is the most commonly used salt in electrolyte solutions. To make the electrolyte, LiPF6 is dissolved in an organic carbonate solvent mixture, containing, for example, dimethyl carbonate, ethyl methyl carbonate, and/or diethyl carbonate.
Several factors influence the performance of an electrolyte and it therefore needs careful analysis. Crucially, any elemental or organic impurities must be determined. What’s more, the composition of the electrolyte needs to be characterised and validated to enable the required battery performance to be achieved. For these analyses, ICP-OES and GC-MS can be used as complementary techniques to gather the detailed insights needed.
Analysing impurities in electrolytes provides a wealth of information. Significantly, impurities offer insight into ageing processes as degradation products accumulate in the electrolyte. This knowledge supports the development of better batteries in the future. It is also essential to understand components at their end of life, not only for recycling and potential environmental contamination concerns, but also to minimise risks to personnel disassembling the batteries.
The standard method for electrolyte impurity analysis is detailed in Chinese Standard HGT/ 4067-2015. It is demanding in that it requires method detection limits of 1 mg/L in the final LiPF6 electrolyte samples. Furthermore, analysing LiPF6 in organic solvents over long measurement periods can be challenging, as the high carbon content in the samples may lead to high background signals, injector blockage, and high plasma load.
ICP-OES helps overcome such challenges to deliver effective electrolyte impurity analysis, offering detection limit performance well within the required range for analysis. In addition, its robust set-up enables effective characterisation of the materials involved.
A recent study showed the strength of ICP-OES analysis, investigating three different samples of fresh, unused LiPF6 containing electrolyte solutions. The results of determining the trace elemental composition of these solutions are shown in Table 1 (opposite).
Figure 1: The internal standard recovery over 12 hours, with calibration solutions matrix matched to real samples.
Table 1: Trace elemental composition of the fresh electrolyte samples (dilution corrected), showing elements detected in the quantifiable range.
The linearity of the method was tested up to concentrations of 1000 mg/L for all elements, with the calibration curves giving an R2 value of between 0.9991 and >0.9999. The method also showed excellent accuracy and precision: recovery was 80 to 120% for all elements, with most being >90%. What’s more, the method is robust. Internal standard recovery of between 85 and 90% was found for measurements obtained over 6 hours, demonstrating its suitability for large-scale applications.
LiPF6 is thermodynamically unstable at higher temperatures (above 60°C) and it degrades. This degradation leads to a thicker and more resistive solid-electrolyte interface (SEI), thereby limiting current flow and the LIB’s charging capacity. Additives can reduce degradation, but their structures affect the properties of the SEI. Understanding electrolyte composition and the by-products formed is essential to develop more efficient and higher performing LIBs.
Complete composition analysis can be challenging, particularly as electrolytes contain many different components over wide concentration ranges. Organic carbonate solvents are present at high concentration, but the concentrations of additives and side reaction products are much lower, making thorough analysis difficult.
GC-MS can measure all components of the electrolyte over a wide range of concentrations. One study investigated LIB electrolytes for 16 different electrolyte solvent, additive and degradation compounds. The method showed high linear correlation from 0.1 – 200 mg/L for all compounds except fluoroethylene carbonate and triethyl phosphate. The GCMS method is also highly sensitive, giving an instrument detection level (IDL) and instrument quantification level (IQL) of 0.021 and 0.07 mg/L respectively, or lower, for all compounds (Table 2).
Table 2: IDL and IQL limits for electrolyte solvents and additives. Relative standard deviation (% RSD) based on replicate injection (n = 10) of 0.1 mg∙L-1 standard.
Rigorous quality control and detailed analysis of LIB components not only ensures safety, quality, and value, but is also vital in driving the development of increasingly effective batteries. ICP-OES and GC-MS are indispensable techniques to enable faster and more accurate analysis of lithium salts and electrolytes. With these in the toolkit, researchers and developers have the power in their hands to unleash the full potential of LIBs for next generation EVs.
1 Electric Vehicles, IEA Report, November 2021, https://www.iea.org/reports/electric-vehicles
Industrial heat is a critical input in many processes that the chemical industry depends on. It is also a large source of emissions, with fuel combustion accounting for three quarters of the sector’s CO2 emissions, according to the International Energy Agency (IEA). In fact, it is one of the most underestimated problems we face in the fight against climate change – and a stumbling block in decarbonising industry and cutting fossil fuel dependencies.
If the current geopolitical situation has taught us one lesson, it’s that we must accelerate our transition away from fossil fuels – not only to avoid the devastating effects of climate change but to ensure stability, energy security and affordable energy prices.
Cutting the chemical industry’s dependency on fossil fuels is also critical for its survival and enduring competitiveness. Adopting low carbon production methods and enabling a more circular economy is vital to retaining and winning new customers as pressure to reduce carbon footprints across the supply chain continues to mount and is front of mind for investors, consumers and the public.
As the UK is preparing for a difficult winter, with warnings of blackouts and soaring energy prices, it is a critical time to employ all solutions at our disposal to ensure industry and businesses continue to operate without disruption. Thermal storage is one proven solution and can be integrated into plants within less than twelve months – it makes industry less dependent on natural gas by electrifying process heat from fossil sources and storing it for later use. Using this technology, companies can quickly take control of their heat and steam supply and maintain manufacturing processes with significantly reduced use of fossil fuels. In essence, it addresses all aspects of the so-called ‘energy trilemma’ – it boosts security of supply by enabling green heat and steam production from local renewable energy generation, it reduces the cost of energy and lowers the carbon intensity of production.
Thermal battery technology can be used in almost all industries and works particularly well when used in the chemical industry. The technology can address a range of industrial applications – electrification, waste heat recovery and steam grid balancing.
Electrification through thermal batteries can completely eliminate the need for fossil fuels. The thermal batteries
can be connected to on-site renewable energy installations to take off-peak electricity from renewables, ensuring that energy reserves last longer. It can provide high-grade, low carbon steam (saturated or superheated) to all industrial processes for manufacturing as the thermal batteries allow companies to buy large quantities of renewable energy when costs are low and store it until needed – enabling the use of heat-on-demand.
In addition to electrification, thermal storage can also leverage the untapped potential of waste heat. Quite often, valuable high temperature heat from industrial processes cannot be re-used and needs to be released as waste heat. Thermal storage batteries can store heat and store it for later reuse, increasing independence from the grid and limiting exposure to fluctuations in the energy market.
In a typical chemicals plant, heating of endothermal- or cooling of exothermal processes must continue round the clock – adding major cost and resource burdens. And more often than not, batch processes or interruptions lead to imbalances between supply and demand which require back-up boilers to start or steam to be let to go to waste. Thermal storage can also facilitate a steam-to-steam process for steam grid balancing by storing, time-shifting and balancing high- or medium pressure steam to make it available on demand to the local steam grid.
At a time when energy efficiency is of utmost priority, all these use cases can make a significant difference to energy security and affordability in the chemical industry. These modes of operation are examples of applications that are already being implemented today by ENERGYNEST, a manufacturer of thermal batteries with locations in Germany, Norway and Spain.
ENERGYNEST’s technology uses a steel and concrete mix called Heatcrete© - a high performance concrete, which is composed of 75% quartz aggregates and 25% additives, which can be manufactured at low cost and has excellent thermal properties. A steel carrier structure encloses HEATCRETE®-embedded carbon steel pipes, through which a heat transfer fluid is charging and discharging the storage system at a pressure of up to 160 bar. A single module, fitting into a standard 40-foot container, provides an energy capacity of up to two megawatt hours thermal.
ENERGYNEST’s ThermalBattery™ system is modular, scalable and purpose-built for industrial applications. It is made from abundant, recyclable and non-hazardous
Thermal storage is the key to powering industrial processes in a sustainable, reliable, and affordable way, says Christian Thiel, CEO, ENERGYNEST.
geomaterials that are easy to acquire, which means local workforces and materials can be used for its manufacture and transportation can be kept to a minimum. Due to its modular structure, this system can be scaled up into the gigawatt hour range.
At the world’s largest fertilizer manufacturer Yara International’s plant in Porsgrunn, Norway, ENERGYNEST is demonstrating how the technology works in practice by integrating a 4 MWh thermal battery and directly connecting it to the steam grid at the production facility.
This renewable storage system now provides increased flexibility to the plant by balancing local steam production and reducing the amount of excess steam. This form of steam grid balancing ensures that fewer fossil fuels need to be used to generate additional steam and that fluctuations in production and energy feed-in can be balanced out.
Current price pressures and increases in CO2 prices mean industry must act swiftly: rapid implementation and scaling of climate-friendly storage technologies is essential. Which means one thing – there is no better time than the present to start the conversation about industrial heat at your company. Thermal storage is commercially viable and ready. It is sustainable, economical, quickly implemented and scalable. The batteries can therefore play a central role in securing industrial heat supply in the current energy crisis and become a core component of low carbon production processes. Thermal storage should be on the agenda of every chemicals company – why not put it on the agenda for your next management meeting?
Saving energy and dispatching on demand is going to be crucial to get us through the next two winters – and on our way to a world without fossil fuels.
More details at energy-nest.com.
Bio-Sep, a sustainable startup converting low-value sawdust into high-value biochemicals, has secured $1.7 million in an oversubscribed seed round led by London Business School’s Enterprise 100 Club (E100 Club) and ACF Investors, with additional participation from a hedge fund that specialises in climate and clean energy technology.
The startup was founded by Stephen Brooks, a sugar chemist, who was trying to find a solution to the waste from sugar cane production, where 30% of the plant is waste woody biomass which is generally burned or left to rot. Brooks developed and patented a cleaner, low-energy solution that uses ultrasound to help break down woody biomass into high-value biochemical products.
Bio-Sep has built on this technology and is currently upcycling sawdust, which is the most widely available woody biomass in the UK, from forestry partners. Each £1 of sawdust from sawmills is transformed into £6 of biochemicals with a broad range of potential uses. These biochemicals can often be used to replace petrochemicals, contributing to the decarbonisation of the chemicals industry.
These include:
Microcrystalline cellulose – a well-known speciality chemical found in medications, cosmetics, composites and 3D printing
Hemicellulose hydrolysate – a mixed sugar syrup extracted from softwood that can either be used as a syrup or further processed into sugar alcohols, such as xylitol and sorbitol frequently found in dental products, pharmaceuticals, food and beverages
Natural lignin – a complex aromatic polymer that is the only natural substitute for a petroleum-sourced chemical known as phenol which offers a huge number
of business opportunities to be used for bio-based resins, composites, coatings, polyurethane foams, bioplastics and more.
The funding will be used to recruit staff to operate the firm’s pilot plant and design the first scaled-up, commercial plant planned for development in heavily forested Scotland. Construction of the commercial plant, which will be able to process 13,000 tonnes of wood a year, is set to begin in 2023.
Adrian Black, CEO at Bio-Sep, said: “Our technology takes a low-value forestry co-product and turns it into essential chemical building blocks, with all manner of applications across the chemical industry and beyond, delivering significant environmental and economic benefits. This investment will enable us to push on and commercialise the technology and is a fantastic show of support for what we believe to be a world-changing innovation.”
22 years and injecting new blood into the School’s ecosystem. I look forward to seeing Bio-Sep reaching new heights with this funding.”
Sam Fennell, Partner at ACF Investors added: “As a society, we rely heavily on the chemicals industry. Products produced by chemical companies afford us high quality of life – they’re the backbone of everything from modern healthcare to technology. But it’s also an industry that’s notoriously polluting. Cleaning up and decarbonising the chemicals industry will be absolutely key if we are to meet climate goals like the Paris Agreement, and the technology provided by Bio-Sep is well-placed to play a central role.”
“Our technology takes a low-value forestry co-product and turns it into essential chemical building blocks, with all manner of applications across the chemical industry and beyond, delivering significant environmental and economic benefits.”Adrian Black, CEO at Bio-Sep
An international team of researchers, led by scientists at the University of Manchester, has developed a fast and economical method of converting methane, or natural gas, into liquid methanol at ambient temperature and pressure. The method takes place under continuous flow over a photo-catalytic material using visible light to drive the conversion.
To help observe how the process works and how selective it is, the researchers used neutron scattering at the VISION instrument at Oak Ridge National Laboratory’s Spallation Neutron Source.
The method involves a continuous flow of methane/ oxygen-saturated water over a novel metal-organic framework (MOF) catalyst. The MOF is porous and contains different components that each have a role in absorbing light, transferring electrons and activating and bringing together methane and oxygen. The liquid methanol is easily extracted from the water. Such a process has commonly been considered “a holy grail of catalysis” and is an area of focus for research supported by the U.S. Department of Energy. Details of the team’s findings, titled “Direct photooxidation of methane to methanol over a mono-iron hydroxyl site,” are published in Nature Materials.
Naturally occurring methane is an abundant and valuable fuel, used for ovens, furnaces, water heaters, kilns, automobiles and turbines. However, methane can also be dangerous due to the difficulty of extracting, transporting and storing it.
Methane gas is also harmful to the environment when it is released or leaks into the atmosphere, where it is a potent greenhouse gas. Leading sources of atmospheric methane include fossil fuel production and use, rotting or burning biomass such as forest fires, agricultural waste products, landfills and melting permafrost.
Excess methane is commonly burned off, or flared, to reduce its environmental impact. However, this combustion process produces carbon dioxide, which itself is a greenhouse gas.
Industry has long sought an economical and efficient way to convert methane into methanol, a highly marketable
and versatile feedstock used to make a variety of consumer and industrial products. This would not only help reduce methane emissions, but it would also provide an economic incentive to do so.
Methanol is a more versatile carbon source than methane and is a readily transportable liquid. It can be used to make thousands of products such as solvents, antifreeze and acrylic plastics; synthetic fabrics and fibers; adhesives, paint and plywood; and chemical agents used in pharmaceuticals and agrichemicals. The conversion of methane into a high-value fuel such as methanol is also becoming more attractive as petroleum reserves dwindle.
A primary challenge of converting methane (CH4) to methanol (CH3OH) has been the difficulty of weakening or breaking the carbon-hydrogen (C-H) chemical bond in order to insert an oxygen (O) atom to form a C-OH bond. Conventional methane conversion methods typically involve two stages, steam reforming followed by syngas oxidation, which are energy intensive, costly and inefficient as they require high temperatures and pressures.
The fast and economical methane-to-methanol process developed by the research team uses a multicomponent MOF material and visible light to drive the conversion. A flow of CH4 and O2 saturated water is passed through a layer of the MOF granules while exposed to the light. The MOF contains different designed components that are located and held in fixed positions within the porous superstructure. They work together to absorb light to generate electrons which are passed to oxygen and methane within the pores to form methanol.
“To greatly simplify the process, when methane gas is exposed to the functional MOF material containing monoiron-hydroxyl sites, the activated oxygen molecules and energy from the light promote the activation of the C-H bond in methane to form methanol,” said Sihai Yang, a professor of chemistry at Manchester and corresponding author. “The process is 100% selective – meaning there is no undesirable by-product – comparable with methane monooxygenase, which is the enzyme in nature for this process.”
The experiments demonstrated that the solid catalyst can be isolated, washed, dried and reused for at least 10 cycles, or approximately 200 hours of reaction time, without any loss of performance.
The new photocatalytic process is analogous to how plants convert light energy to chemical energy during
This process has been termed the ‘holy grail of catalysis.’ Instead of burning methane, it may now be possible to convert the gas directly to methanol, a high-value chemical that can be used to produce biofuels, solvents, pesticides and fuel additives for vehiclesMartin Schröder, vice president and dean of faculty of science and engineering at
Manchester
photosynthesis. Plants absorb sunlight and carbon dioxide through their leaves. A photocatalytic process then converts these elements into sugars, oxygen and water vapor.
“This process has been termed the ‘holy grail of catalysis.’ Instead of burning methane, it may now be possible to convert the gas directly to methanol, a high-value chemical that can be used to produce biofuels, solvents, pesticides and fuel additives for vehicles,” said Martin Schröder, vice president and dean of faculty of science and engineering at Manchester and corresponding author. “This new MOF material may also be capable of facilitating other types of chemical reactions by serving as a sort of test tube in which we can combine different substances to see how they react.”
“Using neutron scattering to take ‘pictures’ at the VISION instrument initially confirmed the strong interactions between CH4 and the mono-iron-hydroxyl sites in the MOF that weaken the C-H bonds,” said Yongqiang Cheng, instrument scientist at the ORNL Neutron Sciences Directorate.
“VISION is a high-throughput neutron vibrational spectrometer optimized to provide information about molecular structure, chemical bonding and intermolecular interactions,” said Anibal “Timmy” Ramirez Cuesta, who leads the Chemical Spectroscopy Group at SNS. “Methane molecules produce strong and characteristic neutron scattering signals from their rotation and vibration, which are also sensitive to the local environment. This enables us to reveal unambiguously the bond-weakening interactions between CH4 and the MOF with advanced neutron spectroscopy techniques.”
By eliminating the need for high temperatures or pressures, and using the energy from sunlight to drive the photooxidation process, the new conversion method could substantially lower equipment and operating costs. The higher speed of the process and its ability to convert methane to methanol with no undesirable byproducts will facilitate the development of in-line processing that minimizes costs.
Funding and resources were provided by the Royal Society; the University of Manchester; the EPSRC National Service for EPR Spectroscopy at Manchester; the European Research Council under the European Union’s Horizon 2020 research and innovation program; the Diamond Light Source at the Harwell Science and Innovation Campus in Oxfordshire; the U.S. Department of Energy’s Spallation Neutron Source at Oak Ridge National Laboratory and the Advanced Photon Source at Argonne National Laboratory; and the Aichi Synchrotron Radiation Centre in Seto City. Computing resources at ORNL were made available through the VirtuES and ICE-MAN projects funded by ORNL’s Laboratory Directed Research and Development program and Compute and Data Environment for Science.
SNS is a DOE Office of Science user facility. UT-Battelle manages ORNL for the DOE Office of Science. The Office of Science is the single largest supporter of basic research in the physical sciences in the United States and is working to address some of the most pressing challenges of our time.
For more information, please visit energy.gov/science
The age-old discussion between print technologies for labelling, do I purchase a laser printer, or an inkjet printer? The decision may seem simple for some, but others may need a little more guidance on the issue and that’s where Dura-ID can help.
There are several things you need to take in to consideration when it comes to making the best decision for your business to bring your printing in-house.
Is my printer going to be solely a label printer or do I need it to perform other functions such as printing documents in the office? If your answer is the latter, a desktop or larger format laser printer is probably the option you need to consider. If you have a separate printer for your documents and need a dedicated label printer, inkjet could be a better choice.
The GHS regulation stipulates that you must include signal words, hazard pictograms and statements, product identifiers, precautionary statements and manufacturer information. These can be produced on either a laser or inkjet printer. If you need a 3-part fully BS5609 approved solution, backed up with certification, Dura-ID offer both laser and inkjet machines that are capable of producing full 3-part BS5609 solutions. This includes the adhesive, the face material and the print and our experts can provide you with the relevant information to ensure you are compliant with the by sea export regulation.
If you’re going to need lots of different sizes of labels, either an inkjet or laser printer could work for you. There are benefits to both technologies. With a laser printer, the media is sheet-fed and you can opt for several media trays that all hold a different format or size of sheet, allowing for the least intervention from yourself during the printing process. However, this can be a wasteful approach, particularly if you only need one or two labels and use a full sheet of 8 labels as that correlates with he size you need. An inkjet label can be supplied in so many formats and sizes, to suit the printer of course, and with the media being on a roll, it allows for easy small batch label printing. However, the media being on rolls also presents a downfall, the need for human
intervention when changing label size as the reel itself will need to be removed and replaced.
Laser printers are great at producing crisp black text and barcodes, it’s where they come in to their own, particularly for multi-lingual labels in the smallest possible point size. When it comes to inkjet printers, these are unrivalled when printing graphically heavy designs. If you need your product to stand out against your competitors on a shelf in a retail environment, then an inkjet is definitely for you.
Speed varies within the ranges of available laser and inkjet machines, and this is where your budget needs to start speaking. Generally when it comes to inkjet printers, the slower the print time, the cheaper the machine. With laser printers, the main time to consider is the warm up time for the fuser unit, which is minimal. These machines can output a large number of sheets very quickly.
There are limitations when it comes to all print technology, but the big one for us is that industry 4.0 within the chemical sector is moving to the forefront and we’re seeing it more. Ensuring your printer can be added in-line to your manufacturing process is essential to moving towards digitisation. Inkjet printers with their various options such as peel units will allow you to introduce this in to your business. With laser printers, the vast majority are sheet-fed, meaning that manual handling is required.
Discuss your label requirements and start your journey with the team at Dura-ID today by calling 0114 242 2111 or email at info@dura-id.com.
SIEF communications have increased over the past few weeks as more EU Consortia decided on their data sharing actions for Turkey’s upcoming KKDIK registration deadline (31st of December 2023). On October 11, The Ministry of Environment, Climate, and Urbanization (MoECC) convened in Ankara a short notice meeting, exclusively for the Lead Registrants and the Only Representative companies to hear about the problems they are experiencing during the registration processes and to exchange views about solution suggestions.
During the meeting attended by about 100 participants, the striking news concerning the registrations was the announcement of the Ministry representatives concerning a circular note they will share soon with the industry. The circular sounds promising as it will include several topics that the registrants are keen to learn, such as amendments on data sharing, clarification on supplier information that is shared via the registration dossiers, enforcement, and monitoring, regulation on training and certification bodies and more.
Companies were still having hopes on a possible postponement of the 2023 registration deadline. Though the Ministry declared once again that they are not planning on changing this deadline. In fact, with the above mentioned circular there will be crucial changes impacting the lead registrants. It is now expected to have interim deadlines, such as March 2023, June 2023 for different tonnage bands.
The Ministry is trying to encourage the industry as much as possible, as there are only about 500 dossiers that have been submitted until now, in spite of the 7000 substances they have in their database for final registration. This resulted in another decision they announced at the meeting: since there are thousands of SIEFs without any Lead Registrant, the Ministry would designate the lead registrants amongst the potential co-registrants if they are unable to do so. Following this decisive explanation, the Ministry added that they are waiting for 5 days before starting to assess a dossier’s completeness check. Thus the Ministry will make sure that there is no objection from the SIEF members for that particular company to be the lead registrant and that no other co-registrant is challenging the accuracy of the submitted data by the LR.
There have been some discussions on how the coregistrants can act when they have a higher tonnage band than the lead registrant and what the lead registrant can do if they do not have all the relevant data for the dossier. In such scenarios a communication should be initiated within the SIEF to see if any other company do have the missing data.
Another critical new information was the confirmation by the Ministry that they will be looking for data content reflecting and referring to EU REACH dossiers. Where needed, companies will be able to discuss testing proposals with the MoEUCC as well.
Having a hybrid system of REACH-IT and IUCLID in Turkish language with a different IT infrastructure, Turkey is struggling with flaws especially in Chemical Safety Report (CSR) generation as the companies are unable to use the
outcomes for dossier submittals. The Ministry is aware of these dysfunctionalities and it was confirmed that they are working at the highest level with the IT team to resolve these issues.
There were a lot of discussions on the section for collecting Downstream User information which may enable more audits in the future. On the other hand, there will be soon enforcement for restricted substances at customs authorities level.
We will hear more from the Ministry soon on their roadmap for having a comprehensive laboratory infrastructure in Turkey to analyze KKDIK data and keep costs at a minimum.
RGS Group based in Brussels, Belgium with a subsidiary in Istanbul, Turkey is representing global companies located in over 55 countries as a local Only representative through its Turkish subsidiary based in Istanbul. As a leading company, RGS also transfers 14 years of intensive regulatory experience in EU REACH to its operations in Turkey. Do not hesitate to contact RGS, if you need compliance with Turkish Chemicals Regulations or more details on our services.
This investment will allow CatSci to offer “more and better” support to customers while adding strategic value to their pharmaceutical pipeline.
The news comes following CatSci’s significant investment from Keensight Capital to support their ambitious and strategic growth plans.
Oligonucleotides are an emerging modality and an innovative technology offering new therapeutics opportunities to treat previously unmet patients’ needs. CatSci’s investment will further accelerate the development and manufacture of these complex molecules.
Oligonucleotides are traditionally used to treat rare diseases; they represent a broad class of different moieties, including microRNAs, small-interfering RNAs (siRNAs), antisense oligonucleotides (ASOs) and aptamers.
With the growth of genomics providing detailed insights into the genetic basis of many diseases, it is now possible to identify sections of the gene that are amenable to interference by synthetic oligonucleotides. These new mechanisms have the potential to deliver new RNA medicines for previously undruggable targets.
The investment into CatSci’s oligonucleotide capability will commence at their Cardiff site, led by Dr Nigel Richardson, CatSci’s Director of New Modalities. Nigel has decades of experience in the oligonucleotides space, having previously led GSK’s oligonucleotide therapy for Duchenne Muscular Dystrophy into the final stages of development and regulatory submission. This capability will allow CatSci to make oligos from nanomole quantities up to 30 grams using solid phase synthesis.
This investment will also allow CatSci to carry out unique research into new manufacturing approaches as they explore a new technology platform that aligns to their green chemistry commitments. The firm adds it will “enable CatSci to continue meeting the ever-evolving needs of the pharmaceutical world by leveraging their customerfocused attitude and superlative understanding of both the CMC landscape and the requirements of oligonucleotides development.”
Dr Nigel Richardson, CatSci’s Director of New Modalities, said: “I am thrilled that CatSci are investing into oligonucleotides; this is an exciting development and will allow us to offer even more to our customers and get even more life-changing medicines into the hands of patients in need.
“RNA medicines are greatly expanding and moving into more mainstream therapy areas, while they are also crucial for addressing unmet disease needs. I am excited to be able to offer our oligonucleotides capability to our customers while driving the paradigm shift needed for their manufacturing process, using our expertise and innovative multi-disciplinary solutions to combat patients’ needs.”
Dr Jerome Théobald, CatSci’s Chief Operating Officer, added: “It is great news for CatSci and our customers alike that CatSci are entering further into the oligonucleotide space.
“Our expert team will leverage their decades of CMC experience to speed up the development and delivery of oligonucleotide therapeutics that meet the requisite quality standards. I am excited for what the future holds; we will enhance our GMP capability to support our customers’ pre-clinical and clinical needs, while embarking on our journey to become a fully integrated partner for innovative medicines development. I am thrilled to be part of CatSci’s growth journey powered by Keensight’s continuous support.”
Dr Nigel Richardson Director of New Modalities, CatSci
“I am thrilled that CatSci are investing into oligonucleotides; this is an exciting development and will allow us to offer even more to our customers and get even more life-changing medicines into the hands of patients in need.”
At Yokogawa our purpose is clear, ‘Utilising our ability to measure and connect, we fulfil our responsibilities for the future of our planet.’
Contact Us to learn more:
+44 (0)1928 597100
www.yokogawa.com/uk uk.marketing@uk.yokogawa.com
Swiss pharmaceutical company Bachem has invested in extended capacity for largescale production of oligonucleotide active pharmaceutical ingredients (APIs).
Several new processes have been introduced to deliver highest-quality products and increase sustainability, including:
To ensure only the highest-quality oligonucleotide is supplied to customers, Bachem designed a large-scale oligonucleotide synthesiser. This synthesiser optimises the process of oligonucleotide synthesis and has been qualified for GMP batches from a 0.2 mol to 2 mol scale.
One of the engineering solutions used for the innovative synthesiser is in-line mixing of dichloroacetic acid (DCA) and toluene. This solution is used as the initial step for all coupling cycles of oligonucleotide synthesis, deprotecting the 5’-dimethoxytrityl (DMT) group and releasing the 5’-hydroxy group to ensure the coupling reaction takes place.
For the majority of synthesisers, the percentage of DCA in toluene is fixed, whereas Bachem’s new skid has a possibility to change the ratio of DCA (usually between 3% to 10%). This ability to change the concentration is highly beneficial, since using too much DCA can cause undesired side reactions and decrease API quality.
In addition, Bachem has also introduced further innovative customisations to optimise oligonucleotide synthesis. These new customisations aim to provide a more efficient process that will consistently produce high-quality crude API. Firstly, a heat exchanger has been added to enable full temperature control, maintaining the optimal conditions for deprotection and coupling. The synthesiser also features dynamic axial columns (DAC) which contain a piston that moves throughout each synthesis cycle of the process. This piston allows full control of the column’s volume, avoiding dead volume and optimising the amount of solvent required.
After synthesis has taken place, an oligonucleotide has to undergo a process of cleaving and deprotection (C&D). To improve efficiency, Bachem has equipped their oligonucleotide production line with an automated, largescale C&D system which uses a two-step process.
Once the synthesis is complete, and the same column has been installed onto the C&D skid, the first step is to deprotect the cyanoethyl groups before the cleavage of the oligonucleotide from its solid support. Importantly, a solution of room temperature ammonia is able to circulate throughout the column of a given volume. This solution carries the released oligonucleotide to the collector vessel, which is made from Hastelloy®, providing resistance against highly-corrosive solutions.
The second step of the process is the deprotection of the protecting groups from the oligonucleotide. Once the ammonia solution has recirculated several times between the vessel and the column, all the oligonucleotide is cleaved from its support before it’s collected in the vessel. The vessel
is then closed and heated under pressure with the ammonia solution, using a unique automated temperature feature. And if other deprotection solutions are required, Bachem’s C&D machine is also equipped with a multi-port inlet.
After the C&D step has been completed, the oligonucleotide is free from the support and protecting groups, meaning the crude API is ready for ultrafiltration.
To further optimise the process of oligonucleotide manufacturing, Bachem has set up the first continuous chromatography equipment for use at an industrial scale. Through enabling continuous recycling of side-cuts (mixed fractions of impurities and API), solvent consumption can be decreased by more than 30% compared to singlecolumn batch purification. This innovative Multicolumn Countercurrent Solvent Gradient Purification (MCSGP) technology therefore improves sustainability during this important step.
In addition, this technology is also cost-effective and substantially reduces waste. MCSGP runs continuously, providing high product yield without negatively impacting purity, whilst allowing room for additional savings in cycle time. These savings in cycle time can reach up to 70%, compared to other batch chromatography methods.
The unique, custom-built synthesiser, C&D system and MCSGP equipment will all enhance the quality, sustainability and cost-effectiveness of oligonucleotide API production.
Bachem has extended production of oligonucleotide active pharmaceutical ingredients (APIs)