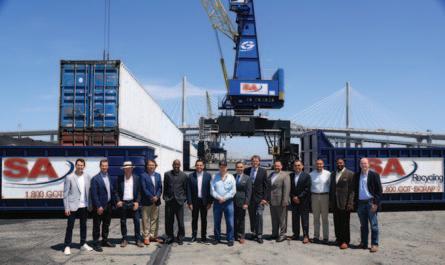
17 minute read
Milestone: TBA Group and Peel Ports Group extend 23-year relationship
Celebrating a milestone: TBA Group and Peel Ports Group extend 23-year relationship
TBA Group has announced that Peel Ports Group has signed a framework agreement that will see its Terminal Management Software, CommTrac V4, deployed across four key bulk terminals in Liverpool, UK.
The upgrade to CommTrac V4 will significantly reduce the demand of manual data input across Peel Ports’ operational activities whilst providing improved functionalities, such as standardized and enhanced reporting, comparative multiterminal data, and improved planning capabilities.
“CommTrac gives us quick and easy access to the information we depend on to make critical operational decisions. The software allows us to manage our day-today operations efficiently and effectively and gives us with the ability to plan and react to the evolving needs of our customers,” says Lance Weissenborn, Operations and Trading Director at Peel Ports.
The longevity and technological advancements of the relationship has facilitated a partnership focused on efficiency, process optimization and valueadded solutions to meet the commercial objectives across Peel Ports’ bulk terminal portfolio.
David Trueman, Managing Director at TBA Doncaster Limited, stated: “Peel Ports was our first CommTrac customer in 1999 and continues to be a valued client. CommTrac has continued to prove itself as a strategic and robust solution to Peel’s operations with the latest deployment offering increasingly advanced function alities to enhance the performance of Peel’s terminals.”
Weissenborn further stated: “TBA are integral to Peel Ports journey of growth and development. As a trusted partner they share our vision, our values, and importantly understand our business. I’m delighted we are able to continue our collaborative relationship through the release of CommTrac V4.”
Peel Ports, the second-largest port group in the UK and one of the largest in Europe, handles over 70 million tonnes of cargo and 26,000 vessel movements a year with a diverse portfolio of commodities including agri-bulks, biomass, containers, metals, and steel.
SA Recycling hits milestone in iron ore exports
PORT OF LONG BEACH BULK TERMINAL’S SUCCESS POWERS LOCAL ECONOMY The SA Recycling terminal in the Port of Long Beach has topped a total of 2.5mt (million tonnes) in exports of iron ore since October 2020, showing strong growth in the shipment of a resource once added to diversify the terminal’s business beyond the processing and export of recyclable metal.
The company has operated a marine terminal at the Port of Long Beach’s Pier T on Terminal Island since 1998. Starting in 2013, it has received iron ore mined in the western United States via railroad. The material is loaded onto bulk cargo ships that sail to ports in East Asia.
The company directly employs about 1,000 people at various Los Angeles County operations. Factoring in indirect and induced employment, the company’s operations generate 3,300 jobs, according to a 2019 economic report by the Los Angeles County Economic Development Corporation.
“I want to congratulate SA Recycling on this achievement,” said Mayor Robert Garcia. “Thank you to all the workers across our region who have made this milestone possible.”
“We congratulate the team at SA Recycling for growing its business and thriving throughout the pandemic,” said Steven Neal, President of the Long Beach Board of Harbor Commissioners. “This is a company that has shown its ability to innovate and adapt. Their hard work is a huge benefit to the community.”
“We are proud to partner with SA Recycling, which excels at generating jobs and economic opportunities, all while serving as a steward of the environment,” said Port of Long Beach Executive Director Mario Cordero. “We applaud SA Recycling for achieving this milestone in iron ore exports and we look forward to many more years of working together.”
SA Recycling has more than 75 facilities located across eight states in the US, with more than 30 facilities located in California.
The Port of Long Beach is one of the world’s premier seaports, a gateway for trans-Pacific trade and a trailblazer in goods movement and environmental stewardship. As the secondbusiest container seaport in the United States, the port handles trade valued at more than $200 billion annually and supports 2.6 million trade-related jobs across the nation, including 575,000 in Southern California.
The photo above shows officials marking SA Recycling's 2.5mt in exports milestone on 29 June. From left: Mike Adams, Vice President of Engineering, SA Recycling; Terry Adams, Director, SA Recycling; George Adams Jr., CEO, SA Recycling; Mario Cordero, Executive Director, Port of Long Beach; Steven Neal, President, Long Beach Board of Harbor Commissioners; Long Beach Mayor Robert Garcia; Steve Gilbert, President, Utah Iron; Dr. Noel Hacegaba, Deputy Executive Director/COO, Port of Long Beach; Thomas Jacobsen, President/CEO, Jacobsen Pilot Service; Joe Gregorio Jr., CEO, Pacific Crane Maintenance Company; Moises Figueroa, Regional General Manager, SA Recycling; Brian Leslie, Superintendent-Train Operations, Union Pacific; Otis Cliatt II, President, Pacific Harbor Line; Mark Sweetman, CFO, SA Recycling.
Associated British Ports (ABP), the UK’s leading ports group, welcomed its first shipment of conditioned pulverized fly ash (CPFA) at the Port of Immingham.
The raw material is used in other products to produce components for road or ground bases, in concrete and cement, or tile and brick manufacturing.
The shipment was brought in by Power Minerals Ltd (PML), the UK’s leading supplier of Power Station Ash products. PML supplies millions of tonnes of quality ash each year contributing a major ingredient to the construction industry. This first cargo of around 25,000 tonnes arrived on the Loyalty last month.
Simon Bird, Regional Director for the Humber ports said: “Immingham plays a key role in bringing in components for the construction industry and we’re delighted to welcome this first shipment of conditioned pulverized fly ash. The strength of the Humber Ports is in the diversity of the markets and commercial sectors that we support, so it is great to be adding another new product to that range.”
Ivan Skidmore, Sales & Technical Director of Power Minerals said: “This is the largest single shipment that we have arranged of ash, and working with ABP was very straightforward and clear, in terms of the process and delivery. They have been very supportive throughout the process and implementation.
“This significant shipment of ash illustrates the strength of PML as part of our international group — EP Power Minerals — and shows our ability to source ash, invest in delivery and ensure a robust, continuity of ash supply when needed.
“We always go above and beyond to meet our customer’s needs and this shipment, with the support of ABP, is a great example of that ethos.” ABOUT ABP HUMBER ABP Humber Ports complex form the UK’s busiest trading gateway. The four ports of Immingham, Grimsby, Goole, and Hull handle more than 58 million tonnes of cargo between them each year worth approximately £75 billion.
Across the Humber, the ports support 34,900 jobs and contribute £2.5 billion to the UK economy.
ABP Humber’s major investment programme ensures the ports offer state-of the-art cargo handling infrastructure and equipment, alongside a highly skilled team who can handle a vast array of cargo safely, efficiently and sustainably.
ABP Humber works collaboratively to build long-term partnerships and deliver the right supply chain solutions for customers, including value-added services and new facilities tailored to suit their business needs.
Port Operations are complemented by ABP Humber’s Pilotage Service and Vessel Traffic Service which ensure vessels are safely navigated through the Humber Estuary.
ABP Humber offers 364 hectares of development land across its port locations capable of attracting investment and delivering transformational benefits for the economy both locally and nationally.
The ports are all part of the new Humber Freeport, which offers three tax sites with an exceptionally business-friendly tax and regulatory environment for potential manufacturing investors.
ABP Humber supports its local
The discharge of the conditioned pulverized fly ash (CPFA). communities. The ABP Humber Coastal Half Marathon and 5k is now in its sixth year and complements ABP’s race sponsorship across the country.
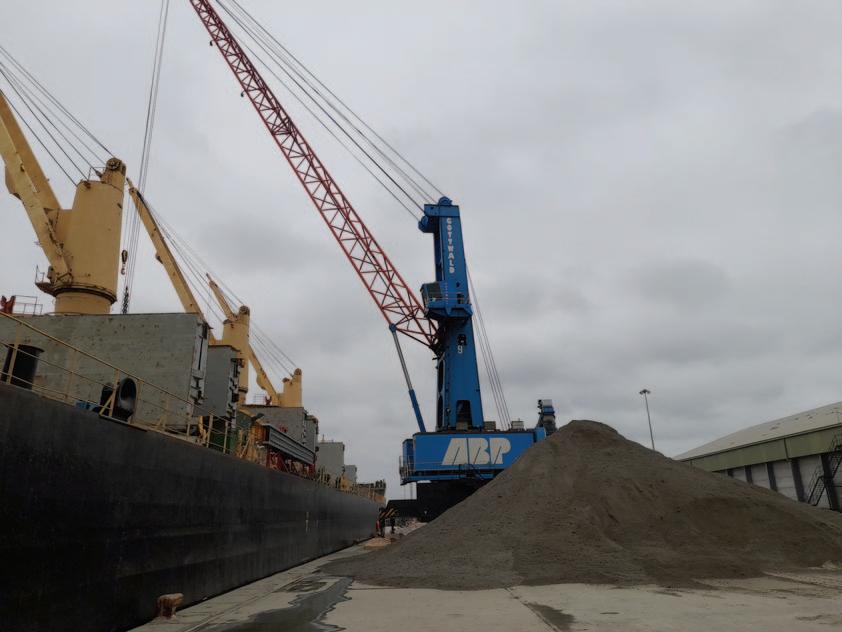
ABOUT ABP
ABP, the UK’s leading ports group is Keeping Britain Trading with 21 ports and other transport-related businesses, creating a unique national network capable of handling a vast array of cargo. The group is driving growth, contributing £7.5 billion to the UK economy every year and supporting over 119,000 jobs. Its current investment programme promises to further increase its contribution to regional economies around the UK.
ABP is also an essential partner for the offshore wind industry, providing operations and maintenance (O&M) for over 50% of the sector’s activity, as well as investing in infrastructure to realize future renewable energy generation.
ABP in numbers: v ~ 90 million tonnes of cargo handled each year; v 5,000 hectares of port estate owned; v 1,000 hectares of open storage; v 1.4 million square metres of covered storage; v 87km of quay; v >1.5 million vehicles every year; v > £55 million investment made in low emission and renewable energy generation technologies.

The international shipping and materials handling industries are growing enormously, as new ports and terminals continue to be built globally. This means operations and vehicle technology are evolving rapidly, and understanding the new fire risks accompanying this has never been more important.
Holger Pfriem, business manager – Asia and Australasia, Dafo Vehicle Fire Protection, reviews the rising fire risks associated with the port industry’s technological development and delves into how accommodating these risks can help to cut costs, save lives and minimize downtime.
Protecting material handling at dry bulk ports is incredibly important, as they facilitate around 50% of the global trade transported by ocean shipping. With an estimated 200 million containers — some carrying dry bulk — shipped by ports globally each year, minimizing downtime is essential to meet tight deadlines.
Vehicle technology in dry bulk terminals is evolving to reach sustainability targets and keep up with rising demand. However, this is seeing fire risks increase. If not addressed effectively, these risks have the potential to bring about additional downtime and even suspend the transportation of certain goods. For example, after a fire, the Port of Shanghai, the busiest container port in the world, was recently suspended from transporting high-risk goods by the Shanghai authorities for two weeks.
AN EVOLVING INDUSTRY The dry bulk industry continued to operate at the height of the coronavirus pandemic. Naturally, keeping individual workers safe from Covid-19 became a crucial priority — which accelerated the sectors adoption of automated vehicles. These modern, autonomous vehicles enabled a large portion of port workers to work from home or at remote workstations, while staying safe from Covid-19.
Even after the world has returned to work, automated vehicles in ports are here to stay – with a combination of these automated cranes and automated port vehicles now the norm for many port businesses. However, maximizing uptime to meet tight schedules is a key priority, and understanding this new technology to address its associated risks is a necessity.
Against this autonomous background, the port industry’s drive for greater sustainability is seeing the global electrification of vehicles and machinery, as many businesses are moving from traditional combustion engines to modern hybrid and fully electric motors.
RECOGNIZING RISING RISKS These developments are supporting the growth of the dry bulk sector, however it’s also important to consider the new risks brought about by electrification and automation. Whenever you introduce new technology to your operations, your site’s risks will change — so you first need to gain a new understanding of these. There are a range of different risks associated with autonomation and electrification, including:
1. INCREASED RESPONSE TIME
As the number of autonomous vehicles increases on site, drivers will be located at remote workspaces. This means there will be a reduced number of staff on site at any given time to manually detect the early signs of a fire, by seeing or smelling smoke, for example.
In turn, this can cause significant delays in the activation of manual fire suppression systems, where these systems are being used, exacerbating damage and safety risks. Even though drivers may be able to activate the system remotely, there will still be a delay in the system’s activation, as the distance between the vehicle and operator (and vice versa) will cause a time lag.
This delayed response time can mean a fire is more likely to take hold, resulting in greater safety risks, more extensive vehicle or machinery damage and a greater likelihood of operational downtime.
2. INCREASED NUMBER OF LI-ION BATTERIES
The worldwide change to electric vehicles is seeing an increased number of lithiumion (li-ion) batteries in ports and various high-risk environments. These batteries are rechargeable, and sustainable energy is created as lithium ions move between negative and positive electrodes.
Although a much more sustainable energy source, these batteries also pose new fire risks. Due to the large volume of energy stored in li-ion batteries, increased heat, mechanical failure, physical damage or overcharging can all result in an internal short circuit, which can lead to a process called ‘thermal runaway’.
Thermal runaway is an extremely dangerous state, which can lead to poisonous gas emissions, in addition to large explosions, if not controlled quickly. In this state, a battery can also produce its own source of oxygen, reducing the effectiveness of traditional suppression techniques.
PROTECTING OPERATIONS As the dry bulk terminal industry evolves and risks change, protecting your site to ensure maximum safety and minimal downtime is paramount. To fully understand your site, you can use the following steps:
1. UPDATE YOUR RISK ASSESSMENT MAP
You should create a risk assessment map before considering how you might change your fire detection and suppression systems. This assessment should include sources of fire, emergency routes, location of current firefighting equipment and how emergency services can enter your site, for example.
Your site may already have one of these maps, but it’s important to update this as
you acquire new equipment or machinery, as it will help you to identify specific areas of risk and consider how you can make the area safer.
2. CHOOSE YOUR EQUIPMENT
If you’re protecting new, autonomous vehicles, automatic detection and suppression systems are extremely important to ensure fires are controlled quickly and safely. It’s important to ensure the system you choose is a good match for the vehicle it will be installed on to reduce false activations and unnecessary downtime.
If you’re protecting electric vehicles or machinery, it’s also important to consider the battery chemistry, so you know the potential risks and the necessary fire suppression system to address these. For instance, the Research Institutes of Sweden (RISE) and Dafo Vehicle Fire Protection found that an early fire warning system and spot cooling is often the most effective way to prevent a li-ion battery from reaching thermal runaway.
3. CONSIDER YOUR SITE AS A WHOLE
When protecting new technology, it’s important to grasp how this sits within your whole site’s safety measures. For example, the risks of older, combustion engine vehicles may need to be looked at, and could require an alternative protection solution. There is still no ‘one-size-fits-all’ approach to fire suppression — as different vehicles, machinery and sites all carry different risks.
The first step is to install fire detection and suppression equipment to increase the safety of your site. However, to ensure it’s effective, take the time to train your teams, so they can use the equipment safely. Your teams need training in how to respond in the case of an autonomous vehicle fire, an electric vehicle fire and a traditional combustion engine fire. This will ensure their personal safety and the safety of the site and its equipment.
As the dry bulk terminal industry is growing and evolving, understanding the fire risks brought about by new technology is crucial when safeguarding site operations and ensuring maximum safety and maximize operational uptime.
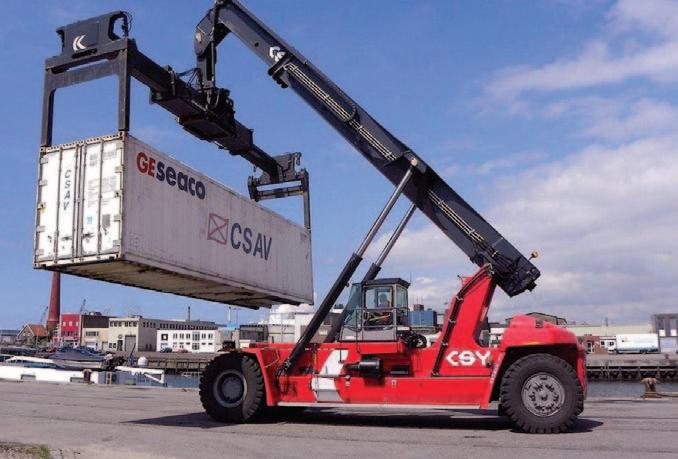
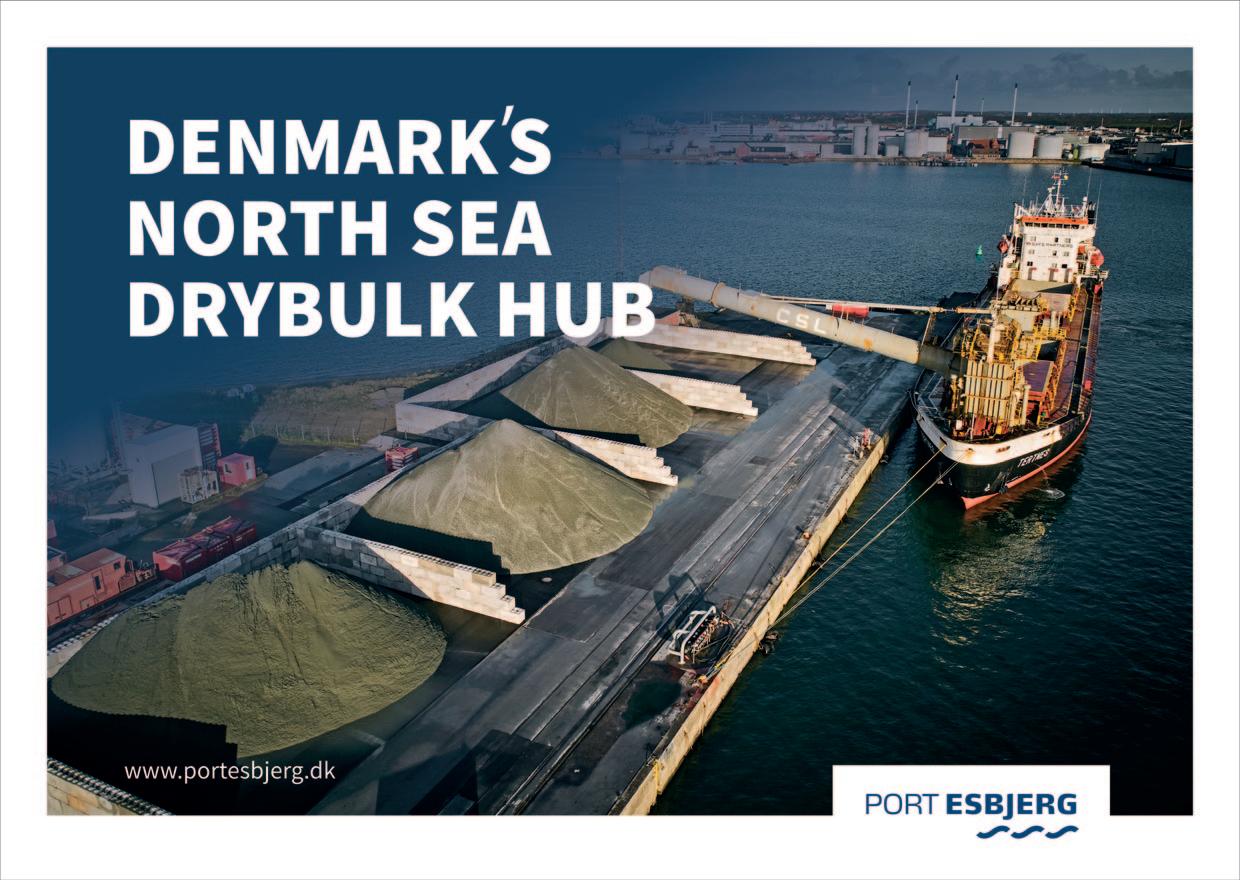
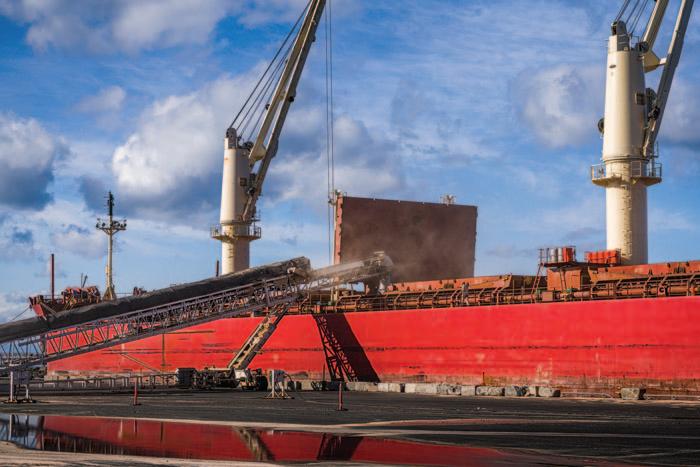
$1.6 MILLION NET PROFIT FOR 2021 FISCAL YEAR The Belledune Port Authority continues to be a strong economic contributor to northern New Brunswick, reporting a second consecutive year of profitable operations despite the global supply chain slowdown.
The port is reporting a $1.6 million net profit for the fiscal year of 2021-2022, supported by revenues of $8.2 million with a return on revenue of 19.8 per cent. Total tonnage handled by the Port in 2021 was 1,837,766 mega tonnes.
“We are very pleased and proud of our financial results this year, which is thanks to the hard work of our team and the many tenants and suppliers who partner with us at the port,” said President & CEO, Denis Caron. “This strong performance continues our proud history of bringing prosperity to the region.”
The BPA’s financial results were shared publicly in early June, at the Annual General Meeting, along with highlights from the year’s activities.
The 2021 profits are due in part to a 63% increase in wood pellet and wood chips exported through the BPA’s marine terminals compared to the previous year, making the BPA Atlantic Canada’s top biomass exporter. The port is supporting efforts to transition away from fossil fuels to biomass, and with its partner QSL –Eastern Division, has constructed a new wood pellet storage facility on the port’s Terminal 3. With this expansion, the port and QSL are projecting another increase in exports in 2022.
“All in all, 2021 was a great year and one that laid the foundation for better things to come,” said Chair of the Board of Directors, Hermel Vienneau. “Board colleagues and I are confident that we are on the cusp of major economic development progress at the port.”
Other highlights from 2021 that the BPA shared include: v the BPA Master Development Plan and Green Energy Hub: the BPA, with help from Hatch Consulting, is finalizing a long-term vision to expand the BPA’s existing capacity while seeking out clean energy projects with the potential to kick off a green economic transition for the region.
Stakeholder, public and rights holder engagement is being completed with a final report anticipated for autumn 2022. v First Nations Tripartite Committee
for Smelter Decommissioning:
coming together in the spirit of partnership and good faith, the BPA, Pabineau First Nation, and Eel River Bar First Nation have created a tripartite group to actively engage and work with Glencore Canada Ltd. on the current decommissioning of the Brunswick Smelter in Belledune, NB, adjacent to the Port of Belledune. Grounded in proactive sharing of information and working collaborat ively, the Tripartite Committee is actively continuing to move this project forward.
Proactive Underwater Noise Study:
Exporting wood pellets at the Port of Belledune.
v
v The BPA in 2021 undertook a voluntary study to survey and report on underwater noise in the area around the port and the impact it can potentially have on wildlife. This was a proactive project and will help to assess risks and identify areas to improve. This work falls under the port’s Green Marine Certification efforts and the results will be reported to stakeholders, rights holders, and the community in 2022.
Terminals 3 and 4 Expansion and
Upgrade Project: work on this important expansion project continued in 2021 the construction of additional cribs to expand the terminals footprint and build a new tug wharf. Rock and fill were moved between Terminals 3 and 4, creating in a safer operating area, and stabilization of a section of Terminal 4 for additional laydown area. As a part of this work, a habitat compensation project was carried out in 2021. Habitat locations were chosen in consultation with First Nations’ fishers and much of the work was carried out by fishers from the surrounding communities and Eel River Bar First Nation. Monitoring of the work will commence in 2023 to assess the success of the habitat locations.
The BPA’s complete financial results are available for viewing by visiting the administration office during normal business hours.
The Port of Belledune is a world-class deep-water facility with four marine terminals, offering exceptional year-round cargo handling capacity. Comprising of ultra-modern facilities and equipment and situated in a strategic location for accessing large North American markets, the port has continued to grow and evolve over its 50+ year history.
Generating great economic spinoffs in the region, the port continues to hold a strong role in supporting the local job market and continues to reinvest profits back into the community in the form of donations and sponsorships. In recent years, the port has increased tonnage, profits, and revenue, and diversified its product mix, now handling a total of 27 different bulk commodities as of 2017.
The BPA is an equal opportunity employer and offers competitive compensation packages, as well as a unique and flexible work environment where employees are supported through teamwork and professional development opportunities. The BPA prides itself on its innovative and proactive approach to both employee relations and port operations.