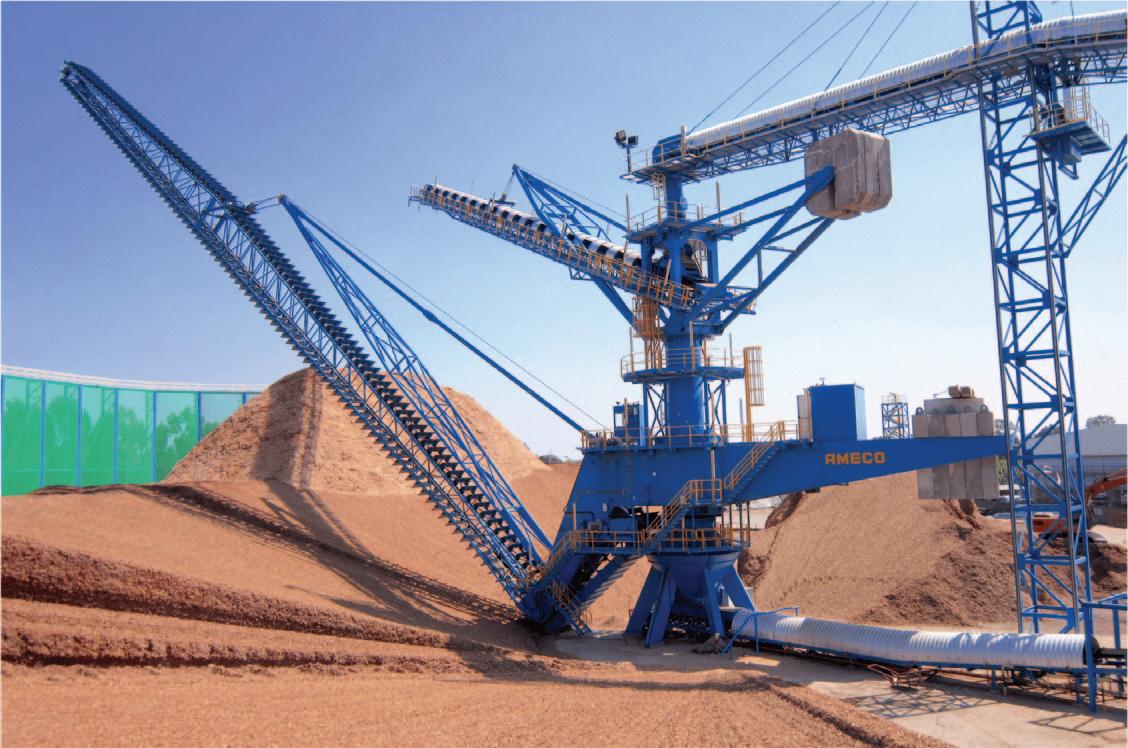
32 minute read
ENGINEERING CONSULTANTS: WHEN PROPER PLANNING MAKES ALL THE DIFFERENCE
ENGINEERING & EQUIPMENT Engineering consultants
when proper planning makes all the difference
The best first step for a bulk handling project
Picking a vendor to design, engineer, manufacture, and service fit-for-purpose bulk material handling equipment is an investment in a long-term professional partnership. It’s a big job, but it doesn’t have to be a painful experience. Clients can simplify pricing requests by asking themselves the right questions before approaching potential vendors. The scope of the project shouldn’t prevent clients from taking the time to get it right. Spending the time at the outset of the project pays off in future returns.
Industrial equipment lasts a long time. An investment in machinery is an investment in a relationship that can be leveraged for years to come. It is important to start new partnerships off on the right foot with clear communication.
IDENTIFY ‘NEED-TO-KNOWS’ A solid working relationship should start with direct and open communication from the start, setting the tone for all future dealings. Price is one of a client’s most immediate concerns. To provide the client with what they need to know, potential vendors require specific details about the context of the project that is being planned. Aside from application details regarding what bulk materials the client’s company handles and how these materials should be handled (e.g., storage, shipping, reclamation, etc.), vendors also need: v technical specifications; v space requirements and limitations; and v relevant environmental factors.
Gathering all this information before reaching out to vendors has two distinct benefits. First, it clarifies the project’s
Louise Dodds-Ely
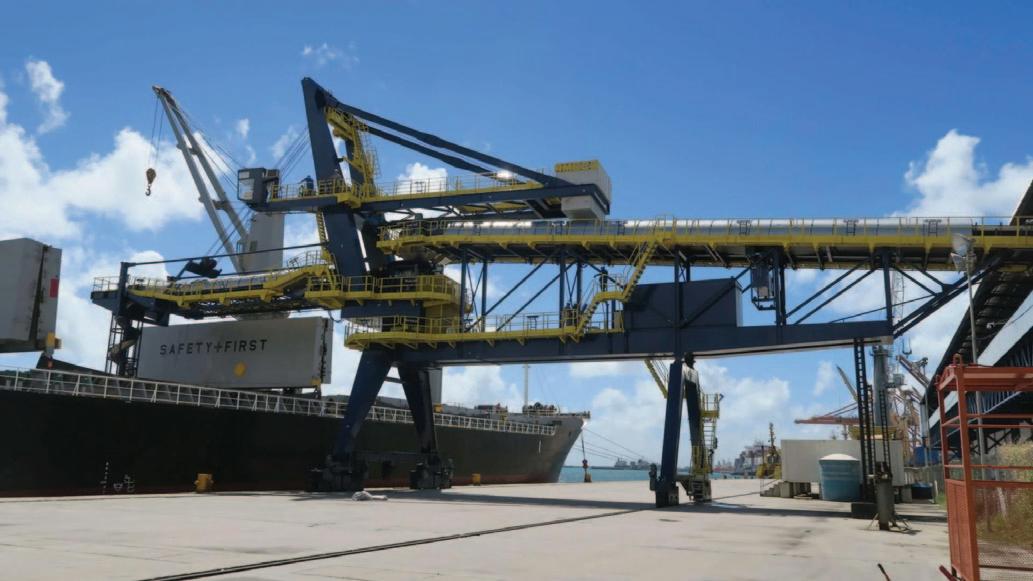
scope for the client and its stakeholders. Second, it streamlines a fit-for-purpose equipment pricing process.
KEEP IT SIMPLE It is vital to set everyone’s expectations early with clear, precise, and simple communication. What follows is the best email ever written . . . regarding a bulk material handling equipment vendor search.
Good morning,
At XYZ-Corp., an XYZ manufacturing company, located in XYZ City, we are working on a project for the bulk handling and storage of XYZ material. We want to know what solutions you can offer considering the following data:
Storage capacity: XX tonne(s) Storage indoor: Longitudinal/ Circular Product: XYZ Bulk density: XXkg/m3 Angle of repose: XX° Particle size: XXmm Reclaim capacity: XX tonne/h Moisture content: XX% Average temperature: XX°C Design ambient temperature: XX°C Humidity: XX%
Best regards,
Mr. XYZ
What makes this email the best is what it does well. It is polite, direct, and provides all the necessary information in both precise and straightforward terms. In short, it is the perfect opening communication for a potential long-term vendor relationship. This type of message sets both sides of a project up for success by demonstrating the client’s thorough preparation for your project and inviting the vendor to contribute their knowledge and expertise. While not poetic, this is industry communication at its finest: proactive details and efficient presentation. And ideally, the response the client receives will follow a similar form.
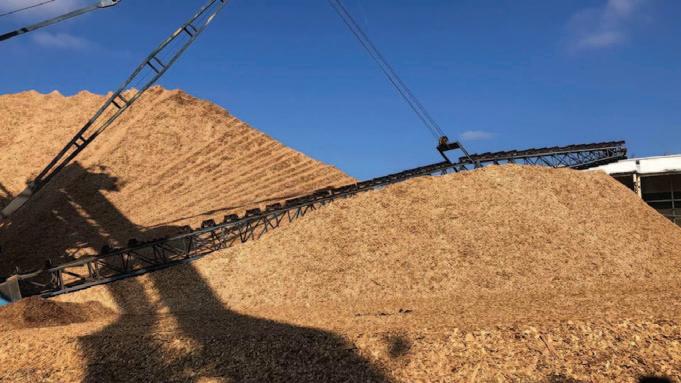
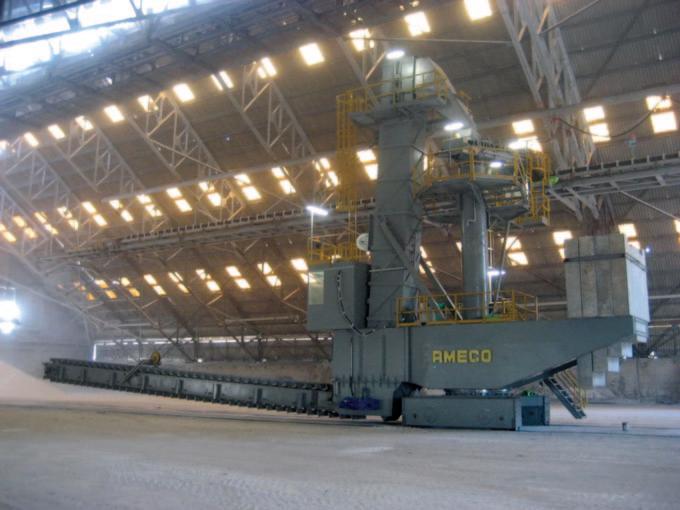
BUILDING VENDOR RELATIONSHIPS Relationships take effort, and vendor partnerships are no exception. Building a solid business relationship with a vendor is an investment in the long-term success of any bulk materials handling machine. Industrial machines are designed and constructed for extended wear life. A strong partnership with the vendor ensures ongoing support for the life of the client’s fit-for-purpose machine. These relationships are the key to mutual success — which brings us to one final question.
Once the client has gathered its project details, how do they decide which vendors to approach? The best route is to look for industry experience and expertise, an extensive machine portfolio, comprehens ive after-sales service, and a value proposition worth investment.
AMECO Group has nearly 90 years of experience crafting custom bulk materials handling equipment. With 400+ machines in its portfolio, and half of them in continuous operation for 20 years or more, AMECO Group’s experience is at its clients’ service. Its six-point value proposition includes: v robust design; v safety and connectivity; v continuous improvement; v sourcing and manufacture of highquality spare parts; v end-to-end partnership from design and manufacture to delivery and aftersales support; and v onsite expertise to augment the client’s team.
AMECO Group’s unique approach to value-added service protects its customers’ machines from unplanned downtime, extending operating life, and providing with the same source of reliable expertise for its entire lifecycle
ABOUT AMECO
Founded in 1932, the company went from providing maintenance services to potash mines in the region where German, Swiss, and French borders meet to supplying conveyors for the fertilizer and mining industry and delivering robust material handling equipment to fulfill new specific needs from its existing customer base. These successful experiences allowed AMECO Group to expand into different markets, such as cement plants and electricity power Plants where bigger storage facilities were required at the time. In the 1950s, AMECO Group was one of the few companies from its region providing machinery internationally. This early international vocation is the origin of the company’s global presence today. With over 400 references around the globe, this proud business now operates in the cement, commodity food, fertilizer, mining, power generation as well as pulp & paper industry.
AMECO Group’s HQ is located in Germany in a thriving area where the borders of Germany, Switzerland, and France meet. AMECO Group also has offices in the USA and Malaysia as well as a strong network of agents worldwide to best serve AMECO Group’s customers.
Equipment designed and supplied by AMECO includes: v reclaimers; v circular stockyards; v shiploaders; v rotary scrapers; and v stackers.

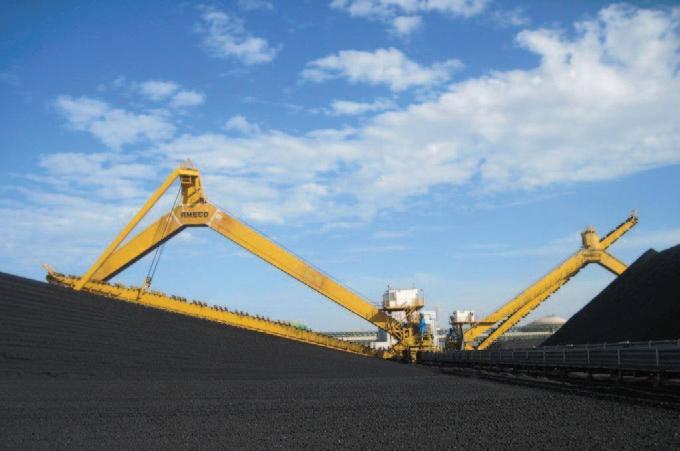
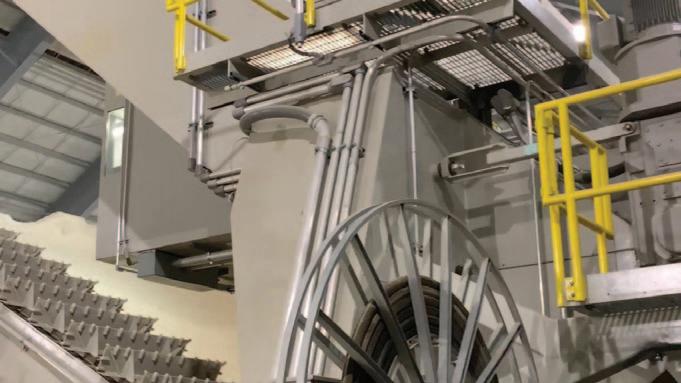
A new research study yields significant improvements in the lifetime of the vertical screw conveyor and its wear parts, delivering substantially lower total maintenance costs for operators, writes Per Hansson.
HOW LONG DOES NEW EQUIPMENT LAST? Businesses often pay much more attention to the answer to this question than their end consumers might. Considering through-life costs, when machinery is earmarked for decades of operation, is a very wise strategy, as this could mean vast cost savings for a terminal over equipment lifetimes.
Siwertell unloaders have a global reputation for reliability and service longevity, and their component screw conveyors offer some of the market’s longest wear times.
The programme, which began in 2021, involved analysing key elements of the vertical screw conveyor; given its critical role in Siwertell dry bulk handling technology. The results are extremely positive, extending its service life even further. Bruks Siwertell’s entire portfolio of new and existing screw-type equipment including Siwertell ship-unloaders, loaders and conveyors, can now benefit.
The vertical screw conveyor is totally enclosed and built up from screw sections, outer tubes and intermediate bearings. In ship unloaders, the vertical screw conveyor elevates bulk material from below the cargo level in the hold up to the horizontal conveyor.
Screw-type conveyors have minimal energy consumption demands, and already provide excellent through-life efficiencies, as they have few moving parts, and freeflowing cargo throughput under continuous torque loads. This generates predictable patterns of wear-and-tear.
NEW WAYS OF THINKING “Although these are already great products, the starting point of this R&D project was to not assume anything; we really questioned already proven designs and processes to see if they could be improved and updated, and invariably they could,” says Per Hansson, Sales Director, Bruks Siwertell.
“Throughout the programme, several different configurations of vertical screw unloading were tested, incorporating variations in production methods and materials used to make the parts. The aim: to provide a major increase in the length of maintenance intervals, based on the circumstances they face in real-world conditions, and without a corresponding increase in costs for customers. The testing leveraged the latest breakthroughs in materials science.
“Every element has been
carefully considered and verified, prior to products being available on the market,” Hansson continues. “The result is an advanced solution that offers the best of previous generations in a more resilient package, with lower operator costs. It also benefits the environment. The very concept of ‘sustainability’ encompasses keeping existing equipment and components running for longer and therefore not incurring the requirement for machinery to be replaced as often. “As well as considering alternative production methods and techniques, we reviewed the entire supply chain. This has enabled shorter lead times and has resulted in making the entire chain more effective and environmentfriendly as well,” he highlights.
A TOUGH SECTOR TO CHOOSE The grain handling market was taken as the program’s core segment for analysis. “This was for numerous reasons,” Hansson explains. “Thanks to the tremendous growth in the agri-bulk segment over the last few years, grain is now the third largest cargo that Bruks Siwertell machines handle, so we have a lot of knowledge in this area.
“The grain handling sector demands an incredible amount from its dry bulk handling equipment, not only in terms of intensity, but it is also an extremely competitive market that places substantial expectations on component lifetimes and
Longer screw lifetimes ensures a better balance between cost and component longevity. Per Hansson, Sales Director, Bruks Siwertell

through-life costs. What better sector, then, to use as a basis?”
Siwertell screw-type ship unloaders can discharge grain and other agri-bulk commodities at rated capacities up to 1,800tph (tonnes per hour). Its grainhandling attributes also include the highest continuous rated loading capacities, which are in excess of 3,000tph.
“We have grain, soya bean and soya meal handling systems operating in Brazil that run up to 4,000 hours per year,”Hansson notes. “These systems work to some of the agri-bulk industry’s tightest seasonal schedules, with import and export terminals subject to massive surges in intake from the seasonality of crop harvests. There is no capacity for any unplanned downtime.
“In this region, many of our customers are dependent on their Siwertell screwtype ship unloaders being able to handle one year’s full intake of grain,” he stresses. “Several customers do not have any other equipment to unload incoming material or their supplementary equipment is simply not suitable, as grain unloading has to happen so quickly and frequently, only their Siwertell unloader is up to the task.
“These very high-use conditions naturally have an inevitable impact on wear parts. When combined with the remoteness of some of these operations, many of these customers often carry a large stock of critical spare parts, minimizing the risk of unexpected stoppages. However, being able to offer longer screw conveyor lifetimes ensures a better balance between cost and component longevity, so we can meet the needs of this sector in a more effective way,” Hansson says.
THE ADVANTAGES OF ORIGINAL The R&D programme, and the significant advantages offered by these longer component lifetimes, highlight the substantial rewards of choosing original equipment manufacturer (OEM) parts, in particular.
Decades of investment, expertise and knowledge are channeled into Bruks Siwertell’s product development, and this is a continuous process, delivering truly compatible wear components that are guaranteed to offer the very best reliability, longevity and operational performance.
OEM parts are intrinsically valuable along with OEM labour, service support, and tailored training programmes.
As the Siwertell operators in Brazil highlight, a robust service strategy pays dividends. They can plan for the availability, purchase and budgeting of any spare parts that are needed and have it available at these service intervals; planned maintenance is almost always less expensive than emergency support.
SIMPLIFIED SCREW REPLACEMENTS The enhanced durability and wear resistance means that screw components do not have to be replaced so often. This delivers longer, reliable equipment availability, and longer periods between servicing, so fewer services are required.
When it is time to replace screwcomponents, Bruks Siwertell has already made this easier with the introduction of a new self-supporting service tower that substantially simplifies and lowers the cost of fitting replacement screws on its renowned Siwertell ship-unloaders.
Principally, it eliminates the need for cranes, which are traditionally used to lift the screws. This reduces costs and improves the overall safety of the operation. Also, because the tower is specifically designed for the task, the whole process is faster.
OEM wear components are guaranteed to offer the very best reliability, longevity and operational performance
A replacement screw is placed and fitted into the tower’s lowered screw-holding cradle, specifically matched to the dimensions of the screw. A winch raises the cradle and screw into an upright position. When in place, the new screw is locked into position and the outer diameter bearing wings are assembled. The same procedure is repeated with the next screw section. Removal and disassembly of the screws is achieved using the same equipment, but in reverse.
By using adaptors, the service tower can accommodate the various screw lengths and sizes of the Siwertell product range. Also, although specifically designed for screw replacements, it can be built with additional levels to service and inspect other areas of the vertical conveyor.
R&D OFFERS WIDE BENEFITS Bruks Siwertell’s commitment to improve owner benefits, set ever higher standards for intelligent solutions, and drive positive, sustainable change, mean that this R&D programme is one of many that are under way.
“It is exciting to think of all these progressive changes, and how research, science and innovative thinking through collaborations, can result in tangible product advances that not only have a direct positive impact on our customers, but also the environment,” concludes Hansson.
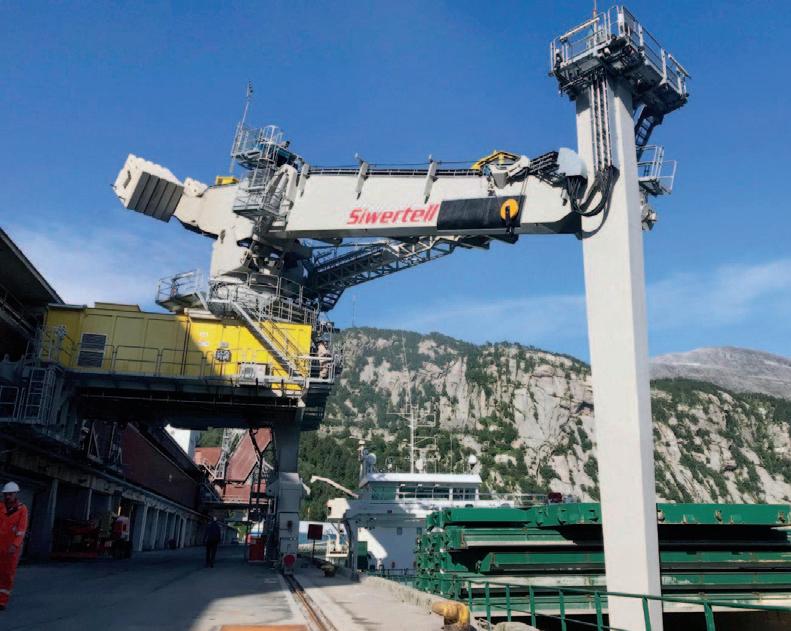
ENGINEERING & EQUIPMENT AAL’S Asia to Australia East & West Coast Liner Services provide solution for shiploader & berth replacement in Queensland brownfields project

AAL’s longstanding ‘Asia to Australia East & West Coast Liner Services’ successfully delivered a series of five project cargo shipments from China to Eastern Australia for a major brownfields coal project in Mackay, Queensland.
5AAL Shipping’s (AAL) longstanding ‘Asia to Australia East & West Coast Liner Services’ successfully delivered a series of five project cargo shipments from China to Eastern Australia for a major brownfields coal project in Mackay, Queensland. Harnessing several of AAL’s 19,000dwt S-class fleet of heavy lift vessels and commissioned by global logistics provider Geodis Australia, the shipments transported berth components of varying sizes from Shanghai and discharged in Mackay.
The brownfields project involves the disassembly and replacement of one of the existing berth and shiploaders to improve cyclonic wave immunity to terminal operations. The site is located within the lease boundaries of the Hay Point Coal Terminal, approximately 38 kilometres south of Mackay, Central Queensland.
Shipment one carried heavy lift components from China to Mackay, to facilitate the on-site installation of new berth modules. The cargo comprised temporary steelworks including walkways, platforms, huts and piles — the latter between 2m and 53m in length. Shipments two, four and five from China transported components in support of preparatory works including modification of existing concrete caisson berth foundations, disassembly and removal of the existing

The brownfields project involves the disassembly and replacement of one of the existing berth and shiploaders to improve cyclonic wave immunity to terminal operations.
berth and shiploader and on-site installation, tie-in and commissioning of new berth modules. Shipment three, from China to Henderson on the Australian West Coast, comprised 86 frames and walkways and enabled the off-site fabrication of new berth topside modules (decking, shiploader rail beams, conveyor galleries and sections) and the new shiploader (SL2A).
Frank Mueller, General Manager of AAL Australia, explained, “We have worked extensively with Geodis Australia over the years, and they know the experience of our local team and the regularity and flexibility that our Asia to East and West Coast Australia Liner Services have delivered for 27 years. The Australian market has been experiencing significant terminal congestion issues, extended waiting times and increased port charges. The success of our operations involves the careful handling of these challenges — either mitigation of potential port congestion and detention charges, or schedule optimization by remaining flexible and having the ability to add inducement ports, when required. This is why AAL has maintained its reputation and standing when other carriers have either reduced their local presence or pulled out of the trade altogether.”
Nicola Pacifico, Global Head of Engineering at AAL and speaking on behalf of the engineering team at AAL Shanghai who planned most of the shipments into Mackay, added, “Cargo components were loaded in Shanghai from barge, truck and wharf — depending on their unit size — and carefully stacked and secured these on deck into tiers of three and four units high to ensure as much cargo as possible could be safely stowed on each sailing. Local Covid-19 restrictions in China meant that our Cargo Super intendent could not physically attend loading; instead, we monitored activity via live video feed and online comms with our Master and crew. Before the pandemic, remote supervision of such operations was rare. Today, it is a fact of life and all our teams have been extensively cross-trained to execute work under these forced conditions.” Harnessing several of AAL’s 19,000dwt S-class fleet of heavy lift vessels and commissioned by global logistics provider Geodis Australia, the shipments transported berth components of varying sizes from Shanghai and discharged in Mackay. ENGINEERING & EQUIPMENT


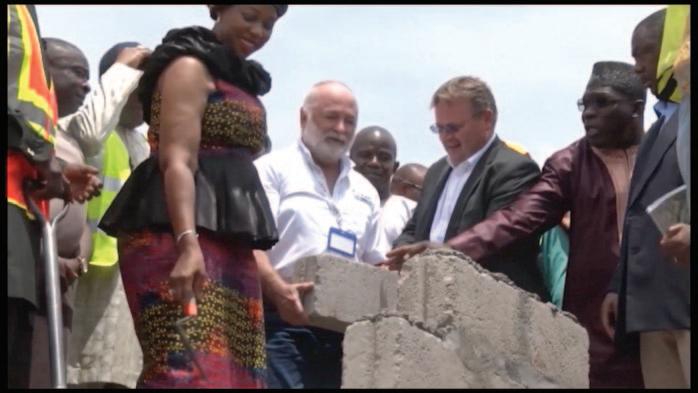
Groundbreaking event to mark the launch of NSBT’s Berth Expansion Project in Freetown, Sierra Leone
Nectar Sierra Leone Bulk Terminal (NSBT) has announced the successful groundbreaking ceremony for the newly launched Berth Expansion Project at Queen Elizabeth II Port in Freetown.
The special day welcomed an impressive number of dignitaries and partners, marking the commencement of this new venture with the Guest of Honour at the event, First Lady Dr. Fatima Maada Bio, turning the sod.
With the expansion now under way, the project highlights will comprise the design and construction of a new deep-water berth of 190m and enhanced quay space of 1.2 hectares (12,000m2) to facilitate a largerclass of vessel size to call at QEII terminal at Freetown (the largest natural harbour on the African Continent) as well as incorporating refurbishment of the existing berths; in partnership with Marine Consulting Engineers, Beckett Rankine and Civil Engineering firm, Eiffage Génie Civil.
The collaboration is part of steps being taken to meet international standards of the terminal in every operational aspect, with NSBT significantly investing in equipment and infrastructure at Sierra Leone’s primary multi-user bulk and breakbulk port.
“The berth extension project marks the commitment, belief, and trust that Nectar and NSBT have in the future of Sierra Leone and its people. We are proud to partner with the Sierra Leone Port Authority to expand the capacity of the port and ensure that generations to come will benefit from it,” General Manager of NSBT, Jim Page commented.
“Nectar Group is proud to invest in Sierra Leone in this strategic project that will be of benefit to the local community, the people of Sierra Leone and the economy in general for years to come. The berth expansion project has been two years in development, and it is a proud moment to see this project move to the next stage of construction. We would like to thank all our local and international partners on the work done to get to this point and for their ongoing support and trust in us and the work we do and look forward to handling new business when the berth is completed,” said Chief Operating Officer, Chris Leonard.
Nectar Group handles over 10 million tonnes of cargo each year, proudly employing over 400 people around the world, having operated in 156 different locations in 75 countries to date.
As a global market expert in specialist bulk cargo handling services at ports and terminals across the world, Nectar Group’s historical connection in Sierra Leone can be traced back to the late 1980s, when the company founded bulk/bagging operations at Freetown under the USAID’s Title II (Food for Peace) initiative, pioneered logistical savings for importers of rice and other basic commodities.
Since 2015, Nectar Group has supported the Freetown Port with substantial investment to develop the
Guest of Honour at the event, First Lady Dr. Fatima Maada Bio, turning the sod.

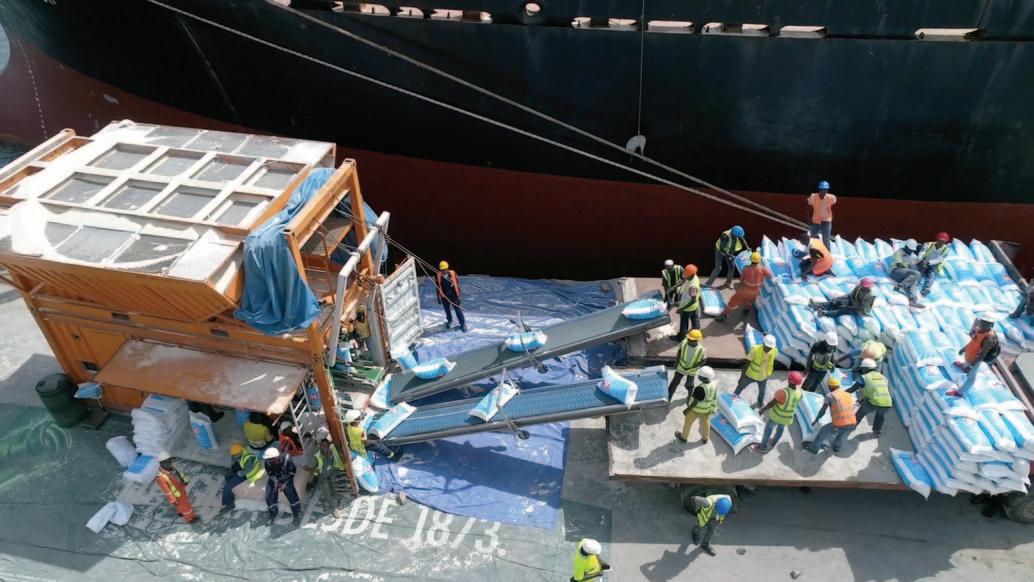
logistical capabilities, helping drive economic prosperity and noteworthy commercial advantages. Nectar Group and the Government of Sierra Leone have a partnership agreement of 21 years + sevenyear option concession to further realize the area’s full potential.
This ambitious project will not only strengthen the Nectar Group’s enterprise with Sierra Leone Ports Authority (SLPA) in relation to competitiveness and growth; it will additionally provide positive environmental and sustainability improve ments following the berth expansion. The new berth will increase vessel discharging speeds and enable enhanced cargo handling capabilities.
Nectar Group and NSBT are fully committed to supporting and promoting new technologies and sustainability within shipping and port management; as they jointly drive innovation and future development to Freetown, Sierra Leone. This third berth expansion programme promotes the country’s aims and vision to advance the local economy into a major logistical hub for imports and exports in West Africa.
NSBT is pleased to announce and kindly thank the many participants of the groundbreaking ceremony including: First Lady of the Republic of Sierra Leone, Dr. Fatima Maada Bio; Minister of Trade and Industry, Dr Hinga Sandy; British High Commis sioner to Sierra Leone, HE Lisa Cheney; the Deputy Minister of Transport and Aviation, Rex Bonapha; the Member of Parliament of Constituency 121 (where the project is implemented) Hon. Miniru Lansan; General Manager of the Sierra Leone Ports Authority (SLPA) and his Deputy, Dr Abdulai Fofana and Yakuba Askia Bio, respectively; SLPA Board Chairman, Manso Dumbuya; Beckett Rankine, Project Consultant, Gordon Rankine; Eiffage Génie Civil, Deputy CEO, Laurent Guilbaud; The National Commission for Privatization, Saffura Rogers; Event Chairman, Dr Julius Spenser; Nectar Group, Director, Guy Wilkes; and General Manager of NSBT, Jim Page.
This was a very proud occasion for the local NSBT team, Nectar Group, partners, and most importantly, the wider Freetown community. The Nectar Group extends its sincere gratitude to all those who participate on 9 June, during the co-operative launch of this exciting project, which strengthens the relationship between Sierra Leone, the UK and promotes a future of longevity.

ENGINEERING & EQUIPMENT Kinder Australia solves conveyor issue at Queensland fertilizer facility
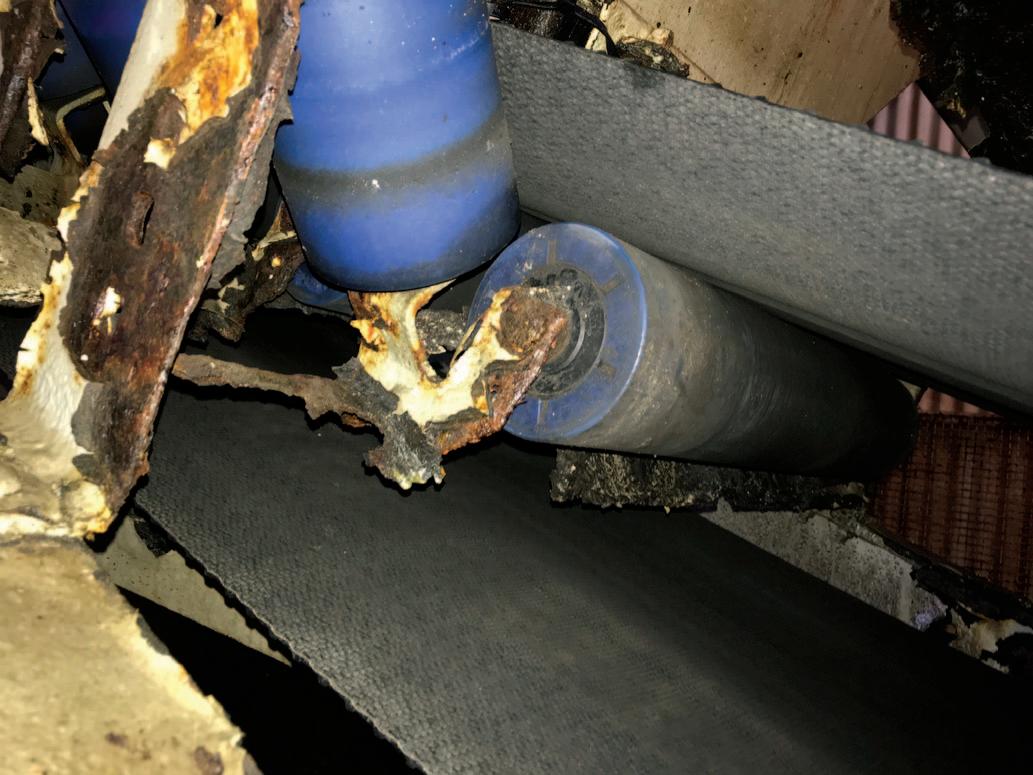
The presence of corrosive rust caused conveyor componentry damage; idler frames were on the verge of collapse.
CASE STUDY: K-SURE® BELT SUPPORT & K-SNAP-LOC® DUST SEAL SYSTEM Kinder Australia was contracted to resolve the issue of corrosive rust in a conveying system, which was damaging idler frames. The challenge was to resolve belt edge sag between idlers, and thus fix material spillage and product loss, which was leading to escalating maintenance/housekeeping costs due to OHS hazards.
The client is a major supplier of fertilizer blended products, servicing primarily the agricultural sector within Toowoomba and surrounding regions. Its core business relies on various material blends such as phosphate and calcium being processed and mixed in the plant’s hopper; the finished fertilizer product is then bagged and ready for shipping to nearby retail outlets.
Steel idler frames with plain rubber soft skirting was mostly used as the plant’s primary line of support within the transfer point areas. It was clear from site inspections that high humidity environment and atmosphere generated within the hopper from blended materials was a key contributor to significant rust and corrosion damaging critical plant and equipment.
After installation of K-Sure® & K-Snap-Loc®.
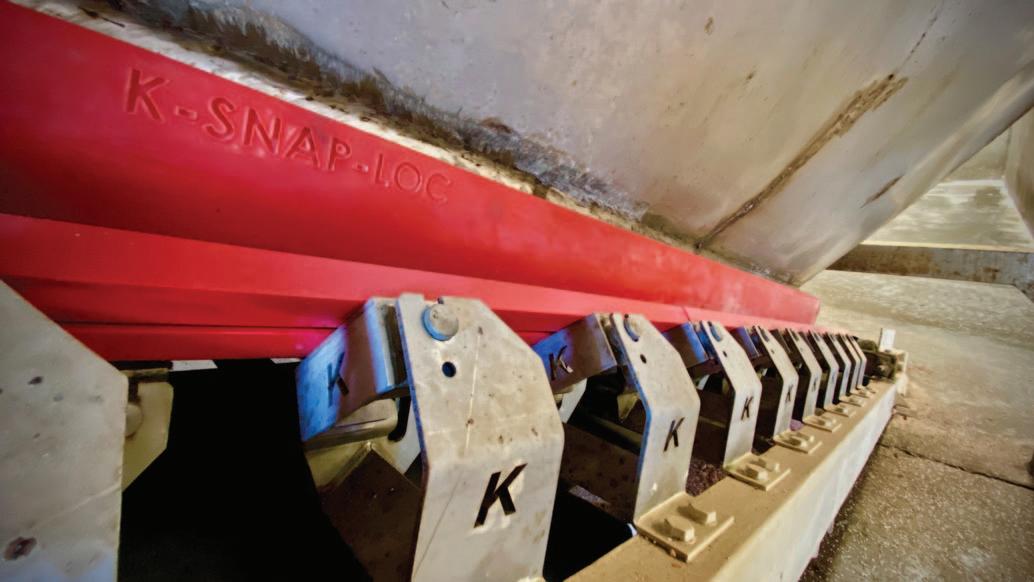
Corrosive rust present on the idler frames was so severe the frames were ready to collapse; the potential to cause production havoc and short-term shutdowns was a constant concern for the operator. Belt sag between the idlers was also identified as a key area for rectification. The material being loaded was not adequately supported. This caused skirting to lift away from the belt line resulting in major spillage and product loss.
One tonne of product each season was written off, plus additional maintenance and cleaning up costs was factored in to remove material spillage.
From an OHS perspective, the combination of humidity and conveyed material spillage led to a toxic and dangerous work environment with false floors posing a major slipping and tripping hazard.
Kinder Australia installed its K-Sure® belt support & K-Snap-Loc® dust seal system, with the result that: v material spillage has been slashed from one tonne to 1/2kg per season. v product loss and cleaning up costs are now contained; there has been overwhelming positive
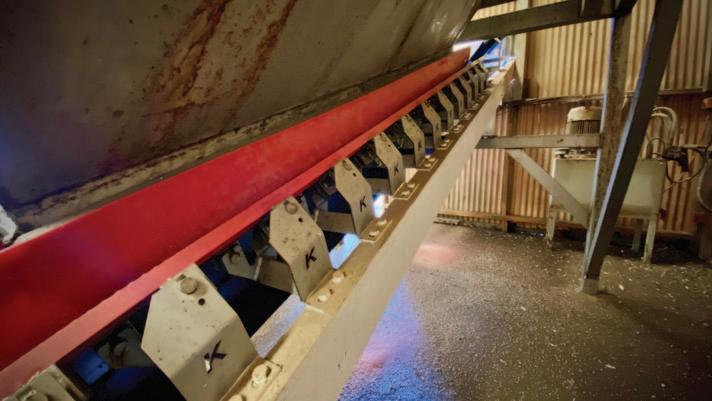
Installing the K-Sure® belt support & K-Snap-Loc® dust seal system has slashed product loss per season from one tonne to 0.5kg.
v
v feedback and excellent product performance; and there is potential to upgrade other areas of the plant.
MSG Group inks a deal for a cement plant in Berbera, Somaliland
MSG Group of Companies, through its DIFC Dubai-based subsidiary company Horn Holding Group ltd (HHG), has signed an agreement with Bedeschi SPA for the construction of Phase 1 of a full cement plant. This will take about 18 months, with installed production capacity of 700,000 tonnes of cement per annum.
The entire full plant project will take three years to complete, with a production capacity of 3,300 tonnes of cement and 3,000 tonnes of clinker per day. The agreement is as a result of negotiations lasting over a year, led by Bergs & More — a leading law, tax and financial advisory firm with a well-established presence in Europe, Middle East and Africa.
Somaliland is a net importer of cement, hence this facility will put on the maps of a cement-producing nation. It is also an exporter of cement, earning the country much-needed revenues as well as boosting exports with a long-term positive effect on the country’s balance of trade. The Phase 1 of the project is expected to translate to employment opportunities for locals during both the construction phase as well as once the factory comes to life.
An estimated 300 Somalilanders are expected to benefit directly from this project by way of employment and a further 200+ citizens will benefit indirectly. To the region, the project will spur economic growth through opening infrastructural development as well as trading opportunities for both wholesale and retail businesses.
Proximity to the Berbera port will be key to the export of the cement which will, in the long run, lower shipping costs to Berbera since the freight companies would have a range of cement products to ship outbound.
Speaking at the signing ceremony, Mohamed Said Guedi, the group Chairman, expressed high confidence that the project would be a success, and will be one whose economic benefits will not only flow back to the MSG group but also to the government of Somaliland and its citizens.
MSG group is widely known for its appetite for undertaking huge complex projects — recently, it successfully deployed fibre-optic cable across Somaliland linking Djibouti, Ethiopia and Somalia.
The general public believes that the project will be a success owing to the past successes as well as the experience of the Group Management team, which is a blend of different multinationals tapping the diverse talent abilities within its work force.
With a population of about six million inhabitants an area of about 177,000km2 , and a strategic location in the Horn of Africa facing the coast of the Arabian Peninsula, Somaliland needs to accelerate its growth in terms of both infrastructure and as well as planned urban development. “Building a cement plant is therefore a strategic operation which will be of benefit to the country,” stresses Ahmed Said (Director HHG). “In addition, the agreement may pave the way for further forms of collaboration and brings an Italian company that is a leader in its own sector to a new, unprecedented, complex and at the same time concrete untapped market,” added Rita Ricciardi, partner at Bergs & More.
“We are very proud of this project; it will be a state-of-the-art installation particularly from the environmental impact and power consumption point of view. Our R&D Department is constantly working to improve the efficiency and sustainability of our solutions as main focus of our development strategy.” commented the President Rino Bedeschi.
Founded in 1908, Bedeschi SpA is today one of Europe’s oldest companies specializing in the creation of turnkey solution for bulk material handling, container logistics and bricks.
Horn Holding Group Ltd, founded and headquartered in Dubai with a branch in Somaliland, is headed by Mohamed Said Guedi (Chairman and Founder of MSG group of companies). The group is diverse with specialization in: telecommunications, fibre optic cables and internet provision; manufacturing; oil and gas exploration; construction; energy generation and distribution; logistics; shipping; transit services; and real estate and property management. It employs over 700 employees with headquarters in Dubai and Djibouti.
The groundbreaking has been earmarked for July 2022 at the proposed project site in Berbera Somaliland.
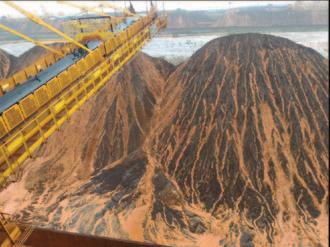
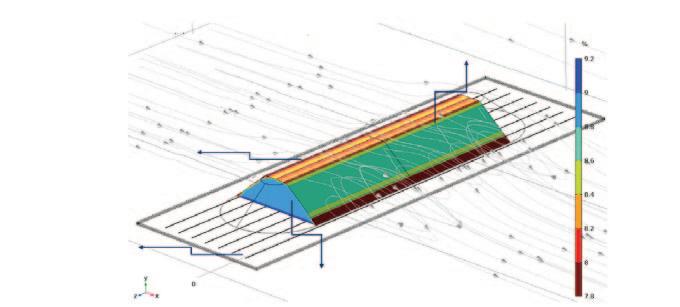
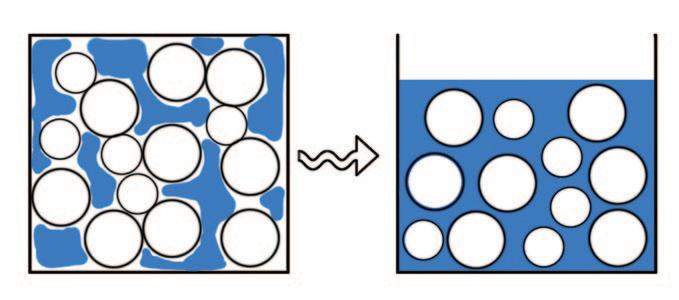
Some core capabilities from Jenike & Johanson to support bulk cargo handling
Anyone who deals with the handling and transportation of bulk cargos knows that these tasks come with a variety of challenges that need to be mastered in order to ensure a safe and unproblematic outcome. As a renowned bulk material engineering firm, Jenike & Johanson (Jenike) offers solutions to the toughest bulk material handling issues.
This article will provide a quick overview of some of the challenges that Jenike helps to overcome every day, such as stockpile drainage, caking of cargoes, fluidization, vessel stability, and more.
STOCKPILE MOISTURE MIGRATION: WATER EVAPORATION, SEEPAGE AND DRAINAGE Ores in a mine operation or port facility are often required to be stacked in stockyards prior to handling or shipping since the arrival time is usually much shorter compared to their consumption time. Buffer storage and homogenization Severe seepage and moisture migration from a stockpile.
Time = 7191 min Streamline: velocity field. Contour: moisture content by wet basis (%)
Wind, ambient T/RH, solar irradiation, precipitation Surface evaporation
Ore stockpile geometry v
v moisture evaporation from stockpile surface coupled with drainage (when important). Computational model validation (when necessary): o drainage columns; and o wind tunnel and surface evaporation.
STABILITY OF VESSELS The global economy relies heavily on the large-scale dry bulk solids transport in shipping vessel holds. The transported materials include raw and processed mineral ores, such as iron, coal, potash, metal concentrates and finished products such as Portland cement, sugar, and grains. To facilitate the safe stowage and shipment of solid bulk cargoes the International Maritime Solid Bulk Cargoes (IMSBC) Code, provides guidance for handling cargoes. The code also outlines testing requirements and methods and dictates responsibilities for the shipper and the ship’s masters.
LIQUEFACTION Cargoes are split into three groups (A, B, and C). To avoid the loss (or reduction) of stability resulting from cargo shifting, a cargo that falls into Group A can only be loaded onto a ship if its moisture content is less than the transportable moisture limit (TML) value determined by testing using one of the following methods: Flow Table, Penetration, Procter/Fagerberg, or Modified Proctor/Fagerberg. Jenike understands the many complexities such as how to obtain representative samples especially of materials that have a wide range of particle
Stockyard pad pervious/impervious
Moisture seepage/drainage: Liquid
Main components for moisture migration analysis in stockpiles.
piles are also necessary to take care of disruptions and/or variability of the operation. These stockpiles typically range from a seven- to 45-day capacity. An important disadvantage is moisture migration and infiltration into the stockpile as a result of long-lasting and continuous rainfall. This affects flowability of the ore and, in some cases, slope stability.
Ores with high moisture contents can face significant problems in processing steps downstream of the stockpile, such as flow blockages, liquefaction and flooding, and safety of cargo due to MC (Moisture Content) above TML (Transportable Moisture Limit). On the other hand, very low moisture contents in ores can cause problems as well, such as dusting in stockpiles.
A study on moisture migration analysis in stockpiles is a valuable tool to provide insights into the mine operations. It should cover the necessary drainage time and size of the stockyard, stockpile geometry for improvement of stability and water drainage while reducing rainfall infiltration, and the optimal use of agents and/ or water resources to prevent dusting.
Jenike conducts effective and thorough moisture migration analyses for stockpiles that include: v Material testing to determine intrinsic
hydraulic properties of the ore and other important physical properties. Computational analysis of drainage inv
stockpile to determine: o moisture profile in stockpile as a function of storage time; o analysis of different stockpile
configurations and its effect on drainage; o water infiltration due to rainfall; and o effectiveness of subsurface drainage systems. Computational analysis to determine
Liquefaction effect.
sizes and can segregate, inconsistencies in test timing protocols around the world, difficulties in testing at ports, awareness/ education/training, and maintenance/ calibration of test equipment.
Jenike conducts flow property testing, including TML, which done sufficiently early in a project that anticipates shipping its bulk solid product by bulk carrier can help identify the potential for liquefaction and Jenike can help you work through what options may be available to prevent it (stockpile drainage, drying sheds, particle size distribution control).
FLUIDIZATION In the case of fine powders, the IMSBC code provides no specific rules governing the safe shipment of fine, dry, dense powders such as non-ferrous metal concentrates. The source of potential instability comes because in the loading process, the fine material can become aerated, especially if pneumatically conveyed from the load out storage, and this condition could remain even long after the loading is complete. Aerated material has reduced internal friction and consequently — in extreme cases — behaves like a liquid. After sufficient time at rest, the material will de-aerate in the hold and eventually become sufficiently stable to set sail. The settlement time needed for a material resulting from air escape to a bed surface depends on permeability, compressibility, wall friction, bed confined cross-sectional area and height, fill rate, and the Janssen coefficient.
Jenike’s approach to determining required settlement time includes a number of laboratory tests, such as measurement of flow properties, and the calculation of the stabilization time. For the latter, Jenike uses SETTLE, internally developed computer software, as well as a series of fully instrumented laboratoryscale tests with samples of the cargo.
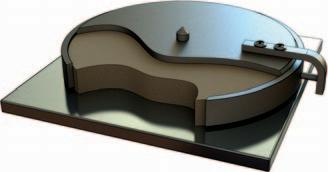
CAKING OF CARGOES Caking refers to the state of a bulk solid that has agglomerated or lumped due to the formation of strong bonds between particles. It can severely affect the quality of products in several industries, such as food, fertilizers, chemicals, pharmaceuticals, mining, and others. It is not uncommon to receive the following and similar complaints in association with caking of products: v “Some bulk bags are caked so hard that we cannot unload the material; we have to break them up by ramming them against a wall.” v “Some bulk containers are taking excessive time to unload. This is costing us too much money.” “Some batches are full of agglomerates
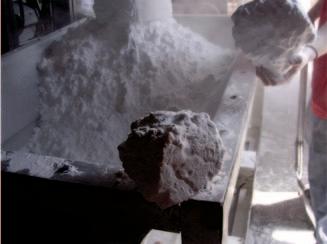
Caking of an organic compound powder – as received from shipment.
Caking evaluated in Jenike Direct Shear Tester.
Caking evaluated in uniaxial compression tester.
v
that don’t dissolve.” There are several mechanisms that can be responsible for the caking of a product, but the most common one is the presence of sufficient moisture. In moisture caking, liquid interparticle bridges (with some moisture-related particle surface dissolution) form and solidify under dry conditions.
A material’s sensitivity to caking can be determined by performing bench-scale tests on representative samples of the product, with consideration to the expected storage conditions including temperature, relative humidity, moisture contents and storage pressures.
Unfortunately, these tests alone may not be sufficient to prevent or remedy moisture caking problems entirely. This proves to be especially true when caking is caused by moisture migration due to temperature gradients during storage or transportation. One example would be extreme variations in diurnal temperature and relative humidity that can be experienced inside shipping containers. Therefore, bench scale testing in combination with the ambient conditions and potential moisture migration phenomena during storage can provide a good understanding on a material’s caking behaviour and ultimately help prevent caking by identifying acceptable ranges of storage variables.
DEM ON CHUTE TRANSFERS The industry applications and research areas using discrete element methods (DEM) are vast.
Undoubtedly the most common application of DEM is chute design. Whether chutes are employed to direct the flow of material from one conveyor belt to another, or into a ship or railcar, chute failures can be costly. It is widely accepted that DEM is a reasonable and effective tool for solving chute problems associated with plugging, wear, and particle attrition. A well-designed chute must prevent plugging at impact points to keep material in motion and wear to a minimum. It should ensure sufficient cross-sectional area where material can accelerate and decelerate as the chute crosssectional area changes.
By modelling particle-particle and particle-wall collisions, DEM is well suited to computing chute trajectories and wear patterns. The results can show the effect of transferring dry versus cohesive materials, the effect of converging or diverging a stream, the effect of the stream’s impact angle on wear and much more. A DEM simulation can show the effectiveness of a chute design to control the velocity of the material stream, its impact angle, and the concentration of the stream. All are important parameters in minimizing wear, attrition of friable product, and controlling dust generation.

Bulk solid Ring Shear stress = F/A
Jenike shear test cell used in caking analysis.
Stationary base