
16 minute read
EQUIPPED FOR INLAND TRANSPORTATION: RAIL & BARGE HANDLING SYSTEMS
ENGINEERING & EQUIPMENT Equipped for inland transportation
rail & barge handling systems
Using iLoadout, Teck Resources has been able to cut its railcar unloading time by half.
Louise Dodds-Ely
indurad’s systems halve rail loadout time, vastly increasing throughput
indurad is a German company that has made a sizeable impact in the world of dry bulk handling. Its products are used with a wide range of commodities, from metallic ore to agricultural products.
Since its founding in Aachen in 2008, indurad has branched off into all major markets and counts some of the world’s largest mines, ports and terminals as its customers.
CASE STUDIES
TECK RESOURCES
Copper and coal miner Teck Resources operates Fording River mine in southeastern British Columbia in Canada. The mine produces nine million tonnes of metallurgical coal annually, which is shipped by rail to Vancouver for export.
In 2020, indurad commissioned its iLoadout solution at one of the mine’s two train loadouts and in the following month, railcar underloading was reduced by half and tonnes shipped was increased dramatically.
The system uses indurad’s radars to determine exactly how and when to operate the chutes so that the load is maximized for each car while at the same time ensuring that no car gets overloaded and ensuring an optimal load distribution
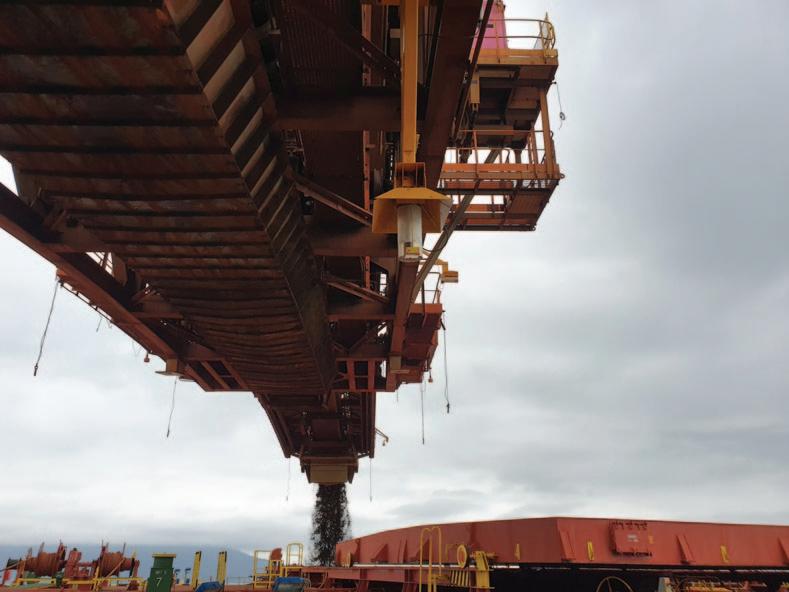
between bogies.
The speed with which a car can now be loaded has been increased by 41.5%, reducing the total time to load a train to only two and a half hours.
Nick Himmelman is the Director of Technical Sales for indurad Corp. in Montreal and was responsible for the iLoadout deployment at Fording River.
“It’s quite astonishing how large the untapped potential in train loadout stations can be. We find that they are often handling far less material than what they were designed for due to the lack of real-time operational insight.”
Himmelman said that several radars have been installed in the loadout to measure train speed, identify car types and to execute real-time volumetric scans of the cars as they are being loaded.
“Because the radars can see through dust, steam, rain, and snow, they can be mounted right next to the chutes. And when you move a sensor closer to what needs to be measured, you shorten the control loop which enables a much faster correction to the process. In the case of Fording River, they are now able to correct a deviation from normal in the very moment it occurs,” Himmelman continued.
“Compare that to more traditional measurement methods that often take place at a weigh station that could be quite a distance from the loadout. In those cases, you could have 20 cars to correct by the time a deviation makes itself known.”
Teck Resources is now planning to deploy iLoadout at other company-owned train loadouts.

VALE ILHA GUAÍBA TERMINAL
Another important market turning to indurad for solutions is Brazilian iron ore. Vale is the world’s largest iron ore miner and chose indurad’s iShiploader solution for its Ilha Guaíba terminal (TIG), in Rio de Janeiro when modernizing the facility.
Utilizing sensor fusion and advanced artificial intelligence (AI) software, iShiploader can help significantly reduce the time to load a ship while also reducing risk of harm through a sophisticated human-tomachine and machine-to-machine collision avoidance system.
Fabian Riedel, VP Sales at indurad GmbH, explains what makes indurad’s solutions unique. “In the case of Vale, reliability was everything. Traditional methods of monitoring the shiploading process were neither dependable, nor could they scale to meet the demands of a modern operation.”
Having been awarded the project, indurad deployed several of its nextgeneration scanning radars to monitor the shiploader’s movements complementing the collision avoidance system.
“When we set out to solve a problem in dry bulk handling, there are two fundamental principles that we apply to the engineering and development processes,” said Riedel. “The first is that the sensing technology must excel in the environment in which it will be deployed. Nextgeneration scanning radars have shown themselves to be far and beyond the best option as they are unaffected by airborne dust, water spray, fog or precipitation and they even operate to within specification when covered by a layer of dirt or other material.”
Riedel continues: “The other design principle is that our solutions must be able to withstand the extreme conditions that they will be exposed to when in service. We make sensor housings from billet material and put them through a rigorous battery of tests to make sure they perform as expected whether deployed in the Brazilian jungle or on the Canadian prairie.”
FUTURE FOCUSED When asked about what lies ahead for indurad, Riedel said that the company is increasingly focusing on helping customers reach their sustainability and safety goals: “The most efficient use of resources and zero harm are central to everything we do. Whether that means improving the utilization of existing assets or improving the safety of humans who work on or around machinery, we will continue to apply best-in-breed technology and best practices to help make it happen.”
Shiploading at Ilha Guaíba terminal has been made safer and more efficient with indurad’s iShiploader.
GB Railfreight names new locomotive in support of Ukraine
(Left to right) Adam Barber, Arlington Fleet Services, Gary Woodman, Arlington Fleet Services, Bob Tiller, GB Railfreight, Jim Nickman, Arlington Fleet Services, Christian Sganca, Arlington Fleet Services.
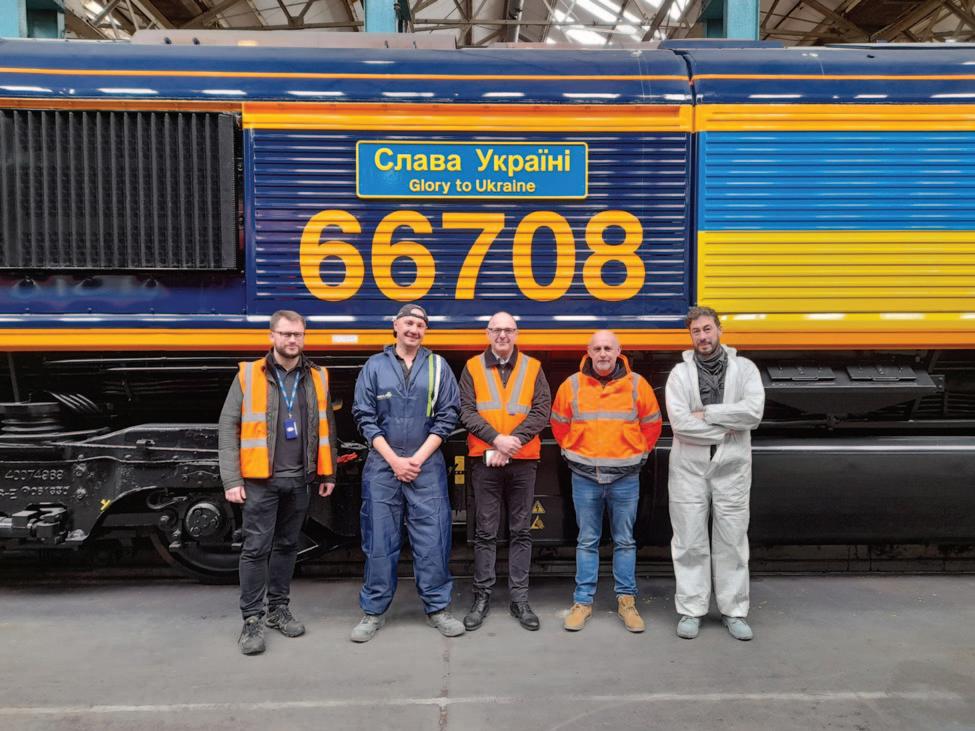
On 6 April, GB Railfreight (GBRf) unveiled its latest Class 66 locomotive named Glory to Ukraine, outshopped in a special Ukrainian livery.
GBRf stands with Ukraine and this newly painted locomotive honours the people affected by the conflict as they continue to courageously defend their homeland.
ABOUT GB RAILFREIGHT Founded in 1999 and headquartered in London, United Kingdom, GB Railfreight (GBRf) is one of the fastest-growing companies in the rail industry, transporting goods for a wide range of customers across the country.
GBRf operates a reliable, safe, and sustainable portfolio of rail freight services for customers working in intermodal, energy generation, infrastructure, waste, construction, and rail services.
With a workforce totalling more than 1,000 staff from across the UK, GBRf’s unique people-focused culture has won the acclaim of the sector, achieving the Great Place to Work award at the National Rail Awards 2020.
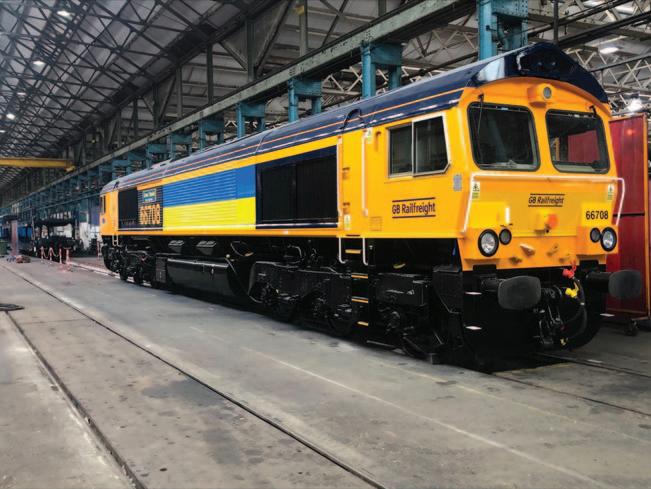
ENGINEERING & EQUIPMENT The VIGAN rivers of unloading
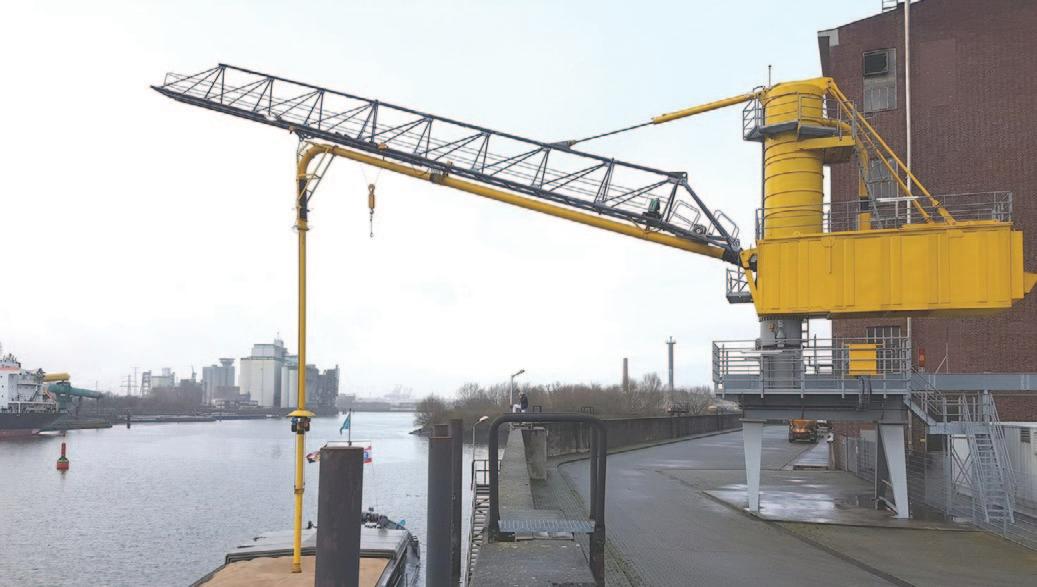
Hamburg Germany, one 150tph/110kW NIV with a stationary gantry.
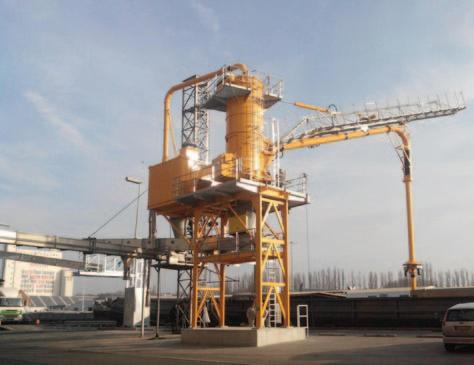
In the past decade, fluvial transport has been intensively promoted throughout Europe. The goal has been to get more trucks from the continent’s heavily congested road network. The recent jump in energy prices will only further increase this tendency.
To further promote fluvial transport and facilitate the unloading of the typical barge ship sizes from 500dwt to 4,000dwt, almost 30 years ago VIGAN developed its pneumatic barge unloader concept and has not stopped further improving it ever since. A lot of those machines are located on Western Europe’s rivers. VIGAN’S PNEUMATIC BARGE UNLOADER, A POWERFUL UNLOADING SYSTEM This type of machine is fully compatible with the scope above. It is generally mounted on a fixed gantry, although mobile systems are possible, whereas capacities can range from 100tph (tonnes per hour) to 600tph of grain, oil seeds, soyabean meal, or other types of cargo.
The heart of the system is the multistage VIGAN-designed turbine. The turbine is directly driven by a high-speed electrical motor with frequency inverter control. Thanks to this configuration, the energy consumption is kept low — recent systems have energy consumption records as low as 0.65kW/tonne grain unloaded.
The powerful vacuum created by the turbine sucks in the cargo at impressive tonnages per hour. To unload ships in the most versatile way, the barge unloaders consist of a horizontal and a vertical telescopic tube system.
At the near end of the vertical telescopic tube is the suction nozzle. It is an ingeniously designed coaxial tube system allowing air to come in from the outer ring above the cargo, making a turn in the cargo to the inner tube, thereby transporting the cargo through airlift into the vertical and subsequently horizontal telescopic tube.
The elbow between the vertical and horizontal tube is of the highest wearing resistance (records of more than ten million tonnes of grain with one elbow have been reported by VIGAN customers). Both the vertical and horizontal tubes are moved
by electrical hoists. The boom Merksem carrying the suction tube system is Belgium mounted on a receiving bin with a 200tph/132kW powerful self-regenerating filter: on fixed gantry no dust emissions possible. (cereals). To maximize reach when unloading the hatches on the barge, the receiving bin is mounted on a slewing ring. The boom can be elevated by an ultra-safe hydraulic jack: no risk of breaking. By gravity, the grain is finally channeled through the air-lock system into a conveyor system, ready to be stored or processed directly by the customer. This very versatile concept offers excellent wear durability. v its operating height is adjustable through the mounting on a fixed or mobile gantry; v the sucking capacity is adaptable to the need of the customer; v good reach is provided through: o a range of boom lengths up to a maximum of 17.5m; o a rotating bin/filter cabin on a slewing ring; o a set of telescopic tubes that consist out of two or three segments, adapted to the boom length for maximum reach; o the use of specific alloys and/or steel finishing in the suction tubes; o the mounting of an extremely durable elbow in NI-Hard;
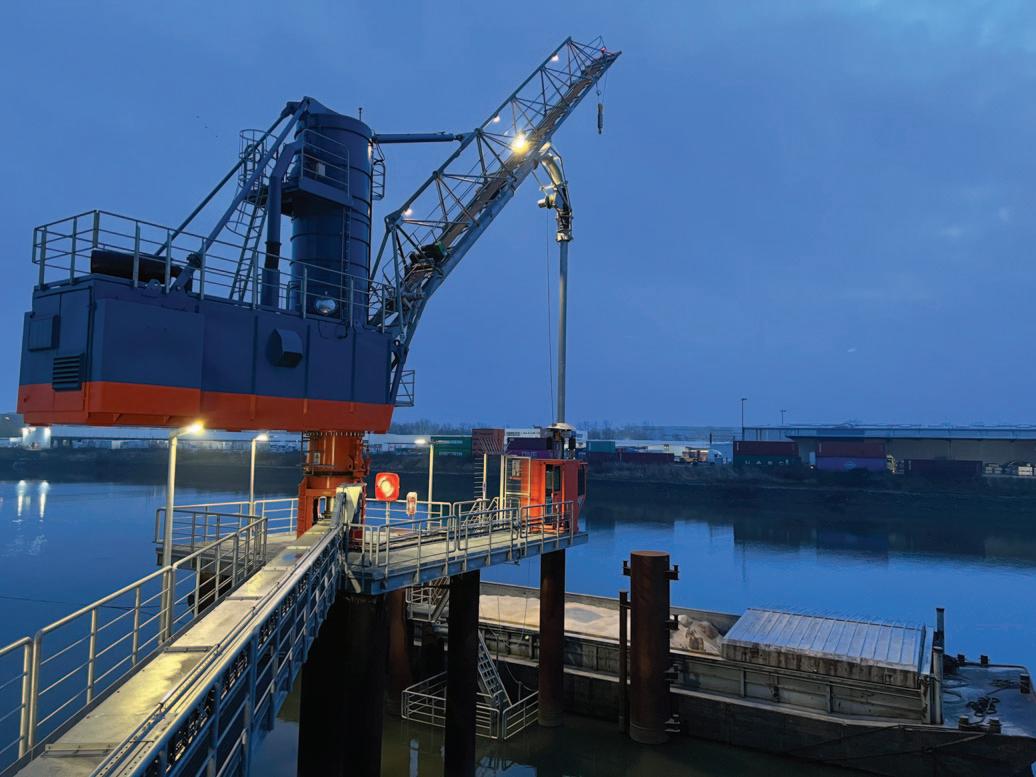
o smooth operation from a radio command control panel with one operator; and o the possible use of an extra hoist on the boom to facilitate the use of a bobcat with the bottom cleaning of the ship.
LOW DUST AND NOISE EMISSIONS Next to VIGAN pioneering its unloaders towards technical excellence, other tendencies also became clear over the last decade: people live closer to urban areas, move into former industrial areas or become more demanding in terms of quality of life.
Quality of life means the air that we breathe, the noise we hear and the view from our windows. VIGAN has worked hard to also reduce environmental impact of its equipment further: v its auto regenerated filter system to prevent dust emission has extremely low dust permission specifications; v its mounting of engine and turbine in an acoustically isolated (baffles) cabin and the use of acoustically insulated suction tubes minimizes noise emission to acceptable levels nearby urban areas.
All these aspects together have combined to put VIGAN among the preferred suppliers of barge unloading systems. In Germany, the Netherlands, France, and Belgium, together, VIGAN unloads an excess of ten million tonnes of cargo a year — with a combination of wheat, barley, corn, malt, rapeseed, soybean meal and even fertilizer. That is 330,000 truck transports annually counted at 30 tonnes each, versus 4,000 vessels annually at 2,500 tonnes each. Don’t blame us for the traffic jams, we did our best!
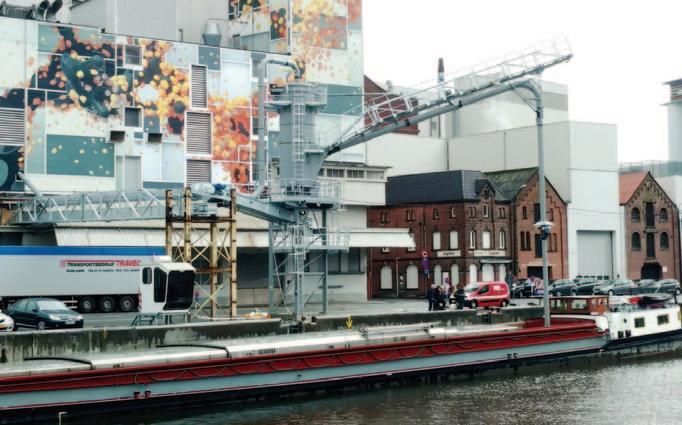
VIGAN machines in Germany, The Netherlands, Belgium and France. Roeselare Belgium 200tph/132kW (cereals).
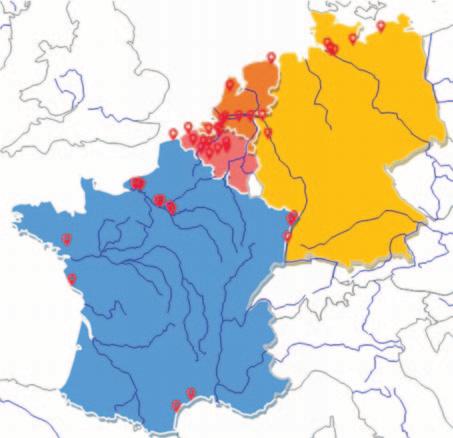
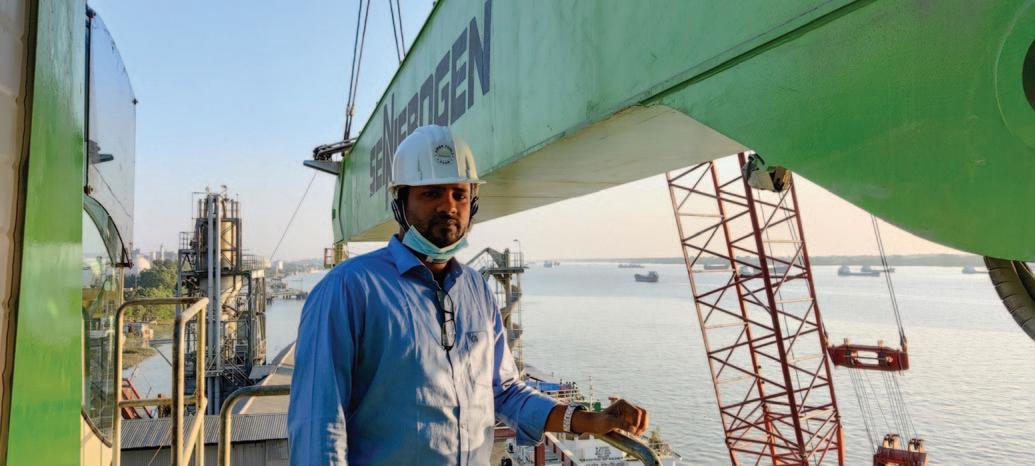
As Asia Pacific continues to grow, so does the demand for better-built machines for faster return on investment and sustainable practices. Major equipment manufacturer SENNEBOGEN has its own company in Singapore and has established over 20 distributors strategically covering the AsiaPacific region. Thanks to its tightly knit sales and service network, customers can rely on an excellent supply chain, good advice and reliable service.
SENNEBOGEN’s machines are used in ports, recycling plants, scrap yards, sawmills, industrial plants and construction sites and in the extraction industry and for problem tree felling throughout Asia Pacific. They show that energy efficiency and high performance are not contradictory. SENNEBOGEN focuses on durability and reliability in the construction of its machines, uses robust materials and avoids over-engineering. Users benefit from high uptime and low total costs of ownership.
SENNEBOGEN established its Asia Pacific headquarters, SENNEBOGEN Asia Pacific, in Singapore due to the country’s unique position in the global economy and its central role as a business epicenter in the heart of Asia.
This further affirms SENNEBOGEN’s commitment to sharing expertise knowledge, sales and service support for its existing and future customers in the Asia Pacific region.
The Asia-Pacific region is characterized by great diversity. As diverse as the individual countries are, so are the operations in which SENNEBOGEN’s machines operate every day. The company’s unique selling proposition is that it has a finely tuned product range and manufactures its machines to customer specifications, so that they exactly meet operational requirements.
Customers using SENNEBOGEN machinery in Asia Pacific can expect industrial grade machinery to weather through harsh working environment with minimum work disruption. The region has one of the largest daily temperature ranges and heaviest rainfall occurring in the world. This can greatly affect machinery and components if it is not carefully considered at the design stage.
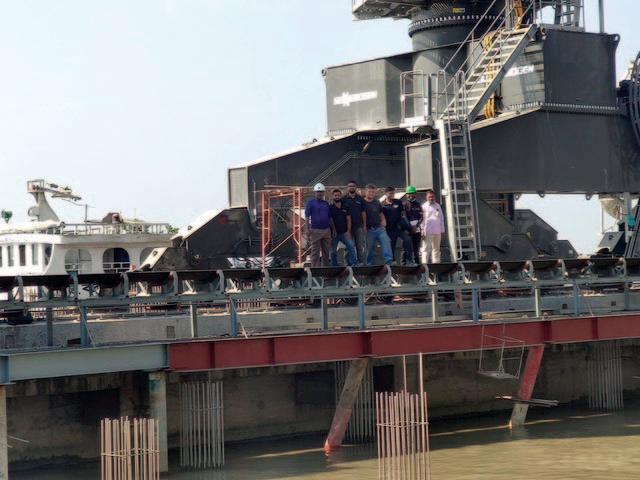
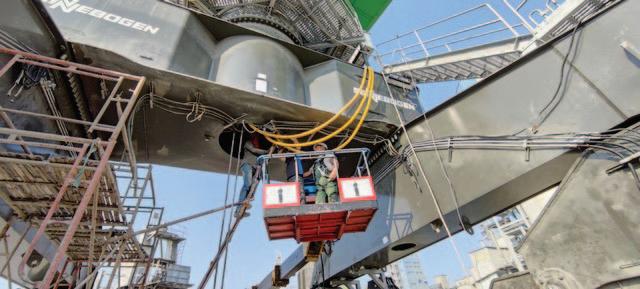
RECENT BARGE-UNLOADING CONTRACT SENNEBOGEN recently commissioned a SENNEBOGEN 8400 EQ, a balanced material handler, in Bangladesh. The SENNEBOGEN 8400 EQ is rail-mounted, and handles clinker (cement products) by offloading from barges and loading onto hoppers that lead directly to storage silos via conveyor belt.
The SENNEBOGEN 8400 EQ was sold and is serviced by SENNEBOGEN Asia Pacific’s local dealer, Banglamark, for use by the Bashundhara Group to handle cement and clinker. The Bashundhara Group’s needed an unloader that could offload clinker at a rate of 650 tonnes per hour. The SENNEBOGEN 8400 EQ is able to exceed expectations.
The SENNEBOGEN 8400 EQ is equipped with a boom that can reach up to 32m, and is able to reach below ground to a depth of –11m.
The SENNEBOGEN 8400 EQ is balanced in any work position by the counterweight, which is directly connected to the equipment. This means that only a small amount of energy is needed to power the equipment — even when large operating ranges and heavy loads are involved. Because of that, the unit offers an energy saving of up to 50% compared with conventional material handlers — there is no simpler way of lowering the operating costs.
ABOUT SENNEBOGEN: A GLOBAL CLASS MANUFACTURER v 69+ years of machinery manufacturing; v 85% output is exported to over 100 countries on all five continents; v four manufacturing plants and a fully automated spare part centre; and Fahad Rahman Bhuiyan, Deputy Chief Engineer, Supply Chain Division (imports) of Bashundhara Group, attends the commissioning of the SENNEBOGEN 8400 EQ.
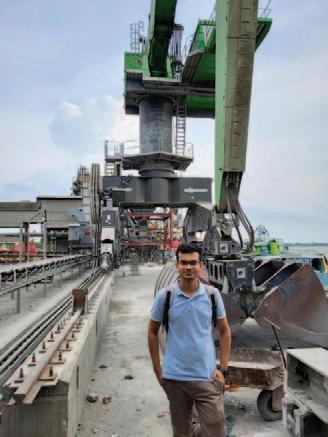
v 1,800 employees worldwide.
SENNEBOGEN is located in Straubing, a city in Lower Bavaria of Southern Germany. It is a family-owned machinery manufacturing company fully committed and inspired to be the leader in many sectors of crane technology and demanding material handling.
The company is proud that its quality machines are made in Germany v efficient and user-friendly machinery; v no over-engineering from meticulous design; v ease of maintenance by well-planned machinery system; v extremely robust components for continuous operation; v engines and hydraulics system; and energy efficiency and environment friendly in machine performance
PRODUCT RANGE SENNEBOGEN offers a wide range of robust machinery with easy-to-understand technology catering for broad multi languages and operator classes. SENNEBOGEN machinery is designed to meet the demanding environment and fastchanging weather in the Asia Pacific region.
The company’s machines include: telescopic cranes, crawler cranes, duty cycle cranes, material handlers, electric material handlers, demolition machinery, balance material handlers, port cranes and telehandlers. There are more than 16,000 options for different applications and industries. SENNEBOGEN is also the manufacturer of the biggest material handler (SENNEBOGEN 895 E) in the world.
SENNEBOGEN’s equipment can handle almost every type of commodity, from dry bulk (feeds, cement and other raw material) to steal beams to full containers. The customer base includes port companies, raw material companies, steel mills, and so forth.
SENNEBOGEN is able to remain competitive in the market, with its up-todate customized solutions. The company stays in constant contact with both its direct customers and the authorities to introduce, provide custom solutions and update latest solutions from its success case studies to tackle and improve productivity.
Recently, SENNEBOGEN has launched its SENNEBOGEN 817 E, a fully batterypowered material handling.
Safe and dust-free railway systems with coatings from Instral
In nearly every country, railway is pivotal in the infrastructure both for passenger transport as for cargo. In the Netherlands, the railway system stretches for 7,000 kilometres (4,350 miles). Nearly everywhere in the world, track ballast is used to stabilize the railway tracks. These ballast stones provide stability, damping vibrations of the trains and allow the drainage of excess rainwater. The Netherlands needs approximately 500,000 tonnes of ballast per year for the renewal and/or replacement of the railway.
Not just any kind of stone is suitable for use as ballast. The ballast used in the railway mainly consists of crushed stone, crushed slag, and improved gravel, etc.
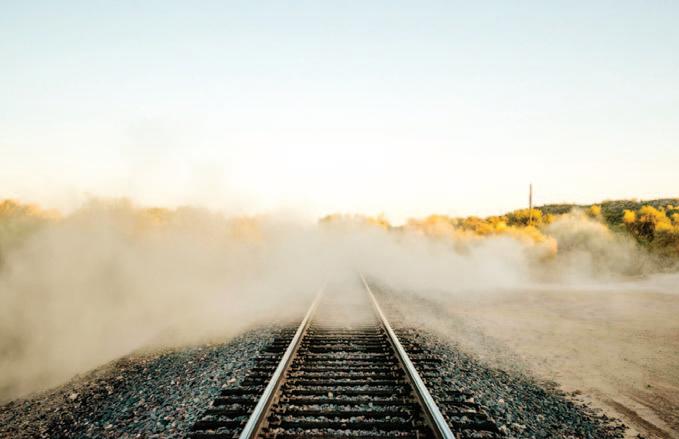
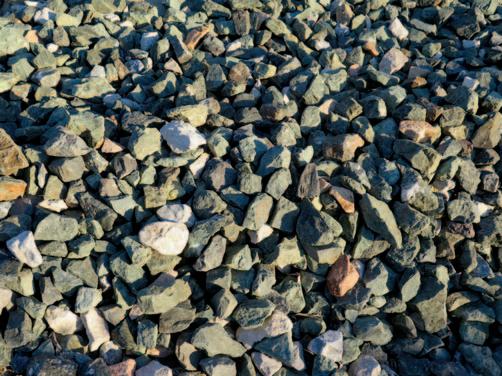
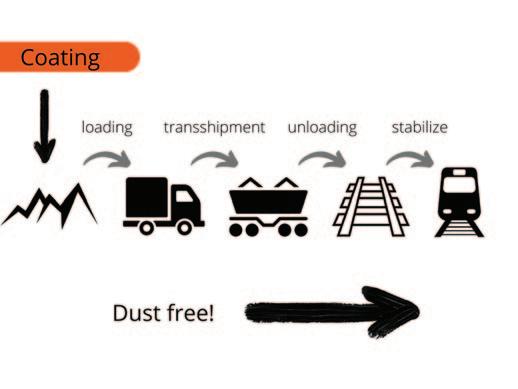
Among them, the improved gravel is generally not used except for branch lines or station lines with minimal volume. The most widely used are broken rocks such as igneous rock and hard limestone. granite, quartzite, basalt, and limestone are four kinds of rocks widely used.
HEALTH RISKS TO BALLAST During mining, transport and processing of these stones, (construction) dust is always released, specifically harmful quartz dust. Some particles are so small that they can cause health problems when inhaled. At high concentrations of this so-called respirable substance and with prolonged exposure, serious lung problems can arise. Quartz dust is also associated with the development of cancer.
DUST SUPPRESSION COATINGS The C-Force® dust suppression coatings of Instral can prevent these health risks by ensuring a dust-free maintenance workenvironment. Instral B.V. specializes in dust control, and is a major presence in the market. Since 2014, the company has been active in using its products to develop solutions to reduce the liberation of dust in many different global applications, such as those during mining, bulk cargo handling and transport, agriculture, steel industry and civil engineering.
However, Instral does not aim to deliver a product, it aims to deliver an answer. In this case the solution to the dust problem in railway maintenance would ideally be to apply the product as a coating at the quarry using spraying nozzles on a conveyor belt, in a chute or a fall between two conveyor belts. This would cover most stones on most sides with the dust suppressing product/coating.
Since the C-Force® coatings are weatherproof, the entire process of transporting and positioning the ballast stones will remain dust-free. Alternative dust control methods and products such as mist cannons, foam coatings, polymers (latex/polyvinyl acetate) do not have this feature and only work ‘on the spot’.
BALLAST MAINTAINS ITS FUNCTION The C-Force® coatings do not have a negative influence on the function of the ballast. The influence on water absorption of the ballast stones can be influenced as desired. The ballast bed remains permeable to water, thus keeping its drainage function intact.
DUST-FREE CARGO Besides the dust suppression at the railway tracks, various types of C-Force® coatings can also prevent dust issues in cargo such as iron ore, fertilizers and others. DCi
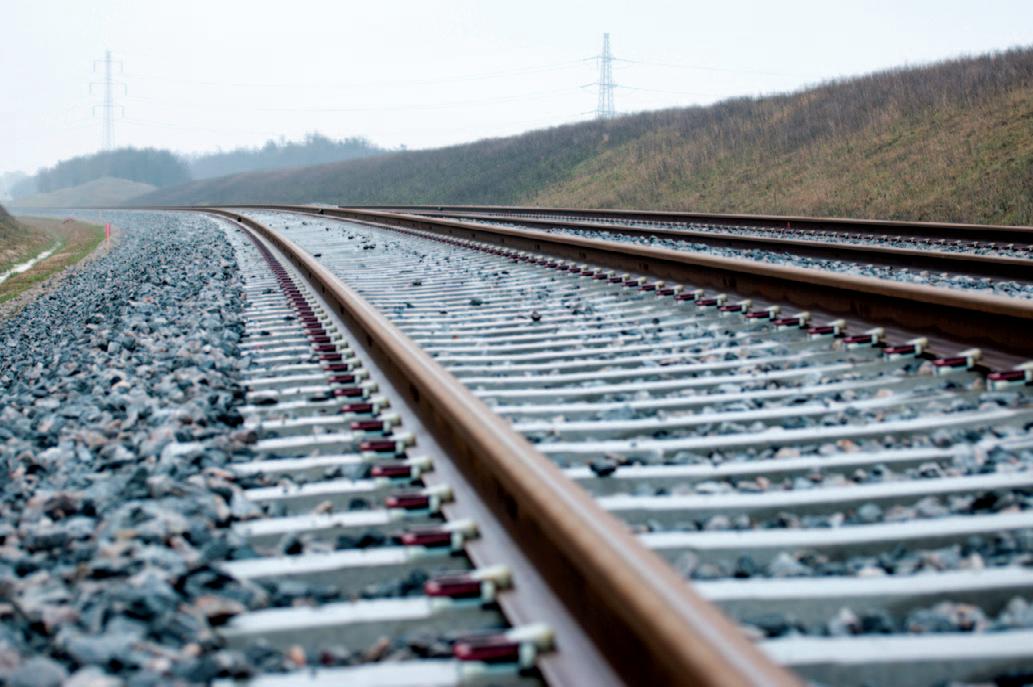